通用汽车公司关于前期样件及样件材料供应商程序GP11
通用汽车供应商管理16步法【最新版】

通用汽车供应商管理16步法1.初级评估广告积分制管理全新的管理方法,打破传统管理思维,一切以人为本,员工乐于接受.^^积分制管理被国内越来越多的单位引进实施,在国...定义:在进行潜在供应商评估之前,对新的潜在的供应商做一个初步的现场评估,或让供应商自我评估以确定供应商是否具有基本的质量体系,合适的技术能力和良好的管理水平。
目的:通过评估以确认一个新的潜在供应商是否有资格至少能进行潜在供应商评估范围:这个初步评估的过程适用于所有被认作是潜在来源的新的供应商。
程序:a.通用汽车公司的采购人员,经理或工程师进行现场评估b.供应商自我评估只能在通用汽车公司的要求下进行所有要素与现场评估的要素一致。
评分体系用以确定供应商是否有资格至少能进行潜在供应商评估。
2.潜在供应商评估定义:现场评估供应商是否能达到对管理体系的最基本要求目的:进行为期一至二天的评估以验证新的潜在供应商是否有能力达到与上汽通用五菱公司开展业务的最基本要求范围:在推荐某一供应商来开拓新的业务之前,如果该供应商未具备QS-9000认证,并且在以下任一状况成立的情形下,必须进行潜在供应商评审:1.潜在供应商的制造场所不是上海GM的现有供货源。
2.该项技术/零部件对此供应商的制造场所而言是全新的。
另外,当采购部门认为具有高度风险时,也将进行潜在供应商评审。
程序:1.采取根据QS-9000制定的潜在供应商评审文件形式。
2.必须在选定供应商只之前完成。
3.选定供应商定义:供应商评选委员会批准合格厂商的程序。
目的:选定在质量,服务及价格方面都具有竞争力的厂商来提供产品范围:全球范围内的供应商。
程序:由上海GM的供应商开发几供应商质量部门来:1.审核潜在供应商评审结果2.评估各候选供货来源3.批准或否决建议4.在必要的情形下批准整改计划5.签署决议文本4.产品质量先期策划和控制计划定义:为确保产品能满足客户的要求而建立一套完整的质量计划。
目的:此程序要求供应商开发并实施产品质量计划来:•利用资源,满足客户要求•近早发现所需的更改•保证全部必要步骤按期完成•促进双方信息交流•以具有竞争性的价格按时提供合格产品适用范围:所有为GM供货的供应商都必须针对每一个新零部件执行“产品质量先期策划和控制计划”程序。
各大主机厂整车开发流程解析(附:采购和主机厂打交道不可不知的英文缩写(通用篇))

各大主机厂整车开发流程解析(附:采购和主机厂打交道不可不知的英文缩写(通用篇))汽车(整车、零部件)的开发是相当复杂的项目工程,众所周知,项目的三要素:时间、质量与成本,那么如何在大量的设计和验证过程中保证项目质量的同时,确保项目进度?每家公司都有自己的项目管理方式,今天梳理几家OEM的项目管理流程供大家参考。
所有汽车新项目的开发和管理,都会把质量放在第一,质量广义上代表一种能力,包含了一家品牌汽车厂的制造能力、管理能力、研发能力与业务能力,其实统统都可以叫质量能力,汽车行业内部称之为新项目流程管理和开发,这个流程和汽车最终成品下线的整体质量息息相关。
大众集团大众集团对于新项目的开发流程就如上图所示,整个项目节点划分非常细,其中最关键点分别是:PF项目确认、B认可、0S零批量以及SOP量产。
B认可后,所有零部件供应商必须要进行开模,相当于实物制造启动指令;0S交样也是大众非常关键的一点,这个时候大众质保部门会全力介入,比如产线试装、各路况路试、供应商首批样件检验和认可,供应商产能评审2TP等等。
沃尔沃沃尔沃的节点名称和描述较大众而言更为详细,造车理念也是贯彻了欧洲人的精细,有意思的是,沃尔沃在MP1批量投产后,会进行为期6个月的量产全检,用通用体系的术语叫GP12,GP12全检对新项目刚投产的质量不稳定现象能够有效防范和隔离。
日产日产的流程是分为从Phase1~Phase5,初看让人觉得日系的项目很简单,其实只是化繁为简,可以看看图二,每个阶段中有小的任务和里程碑,只有将所有任务验证完成并且合格,才能进入到下一个大阶段,其中一些关键字:1、VC lot代表试装样件,主机厂试验和实车试装;2、PT1预批量生产,需要完成量产流程和产品尺寸过程能力验证;3、PT2预批量生产,需要完成制造过程能力审核;日系这种地图指导式的项目开发流程,让人觉得非常可靠,一环扣一环的感觉。
通用通用汽车是贯彻先期质量策划的先驱,其流程和体系被业界广为效仿,甚至很多零部件供应商直接照搬通用的流程体系,这个流程对于文件、订单方式、造车区域有了明确的定义,让初学者和新手可以一目了然,正式物流订单分为小批量、中批量、大批量。
通用汽车前期样件及样件材料供应商程序
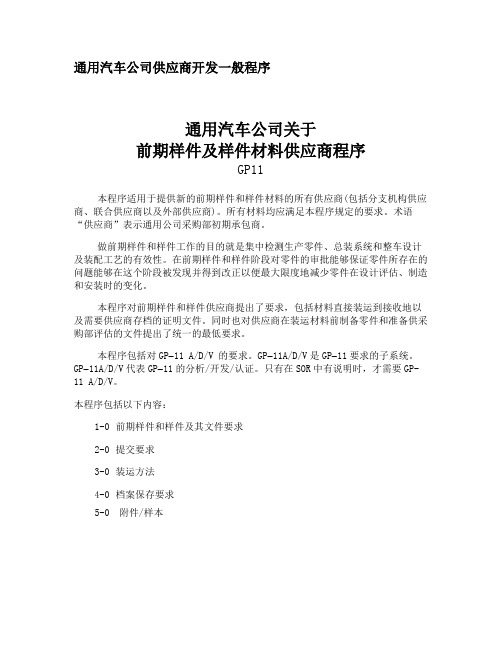
通用汽车公司供应商开发一般程序通用汽车公司关于前期样件及样件材料供应商程序GP11本程序适用于提供新的前期样件和样件材料的所有供应商(包括分支机构供应商、联合供应商以及外部供应商)。
所有材料均应满足本程序规定的要求。
术语“供应商”表示通用公司采购部初期承包商。
做前期样件和样件工作的目的就是集中检测生产零件、总装系统和整车设计及装配工艺的有效性。
在前期样件和样件阶段对零件的审批能够保证零件所存在的问题能够在这个阶段被发现并得到改正以便最大限度地减少零件在设计评估、制造和安装时的变化。
本程序对前期样件和样件供应商提出了要求,包括材料直接装运到接收地以及需要供应商存档的证明文件。
同时也对供应商在装运材料前制备零件和准备供采购部评估的文件提出了统一的最低要求。
本程序包括对GP-11 A/D/V 的要求。
GP-11A/D/V是GP-11要求的子系统。
GP-11A/D/V代表GP-11的分析/开发/认证。
只有在SOR中有说明时,才需要GP-11 A/D/V。
本程序包括以下内容:1-0前期样件和样件及其文件要求2-0提交要求3-0装运方法4-0档案保存要求5-0 附件/样本前期样件和样件的要求GP-111-0前期样件和样件及其文件要求零件应按照通用公司授权的图纸、样板、模型和/或其它设计文件所规定的材料制做。
若与设计有偏差,请与采购部联系以获得正式的授权。
所有的前期样件及样件供应商均需要具有下文所列的完整的、成文的、有效的文件以供评审。
规定年型的样件的存档应保存到该样件开始正常生产后的两个月。
1.通用公司前期样件及样件材料供应商保证书(样本A)2.设计档案3.检查结果和检查和/或检测工具4.材料证明5.零件重量(质量)6.排序信息7.生产材料及工艺8.分析/开发/认证(若需要的话)1-1.通用公司前期样件及样件材料供应商保证书通用公司前期样件及样件材料供应商保证书应由负责制备和装运零件的供应商授权的官员完成并签字。
上海通用汽车对供应商质量要求的规定 2.4E
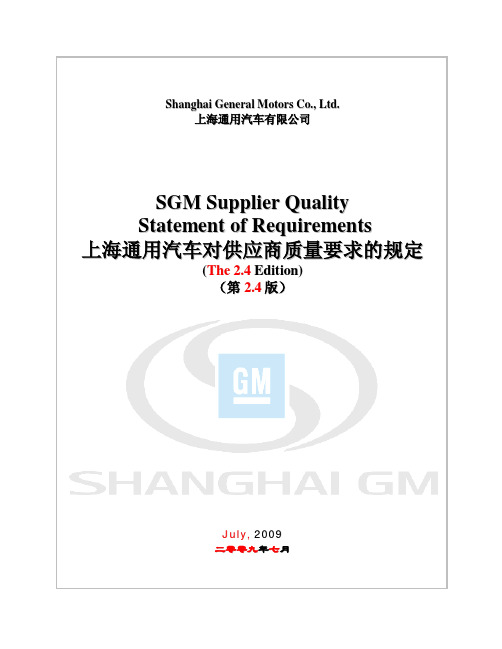
S h a n g h a i G e n e r a l M o t o r s C o.,L t d.上海通用汽车有限公司S G M S u p p l i e r Q u a l i t yS t a t e m e n t o f R e q u i r e m e n t s上海通用汽车对供应商质量要求的规定(T h e2.4E d i t i o n)(第2.4版)J u l y,2009二零零九年七月(第2.4版)前言SGM要求其供应商满足最新版ISO/TS16949及相关参考手册的要求,并适用所有通用汽车的相关顾客特殊要求(明确不适用于通用汽车亚太区的部分除外)。
要求供应商满足通用汽车供应商质量SOR的要求及通用汽车一般程序的适用部分(如GP5,GP9,GP10,GP11,GP12等)。
本文件概述了上海通用汽车对供应商质量方面的基本要求,是有关SGM供应商质量工作相关的程序和规定的节录,目的是为了帮助供应商更好地了解和执行SGM的相关要求。
欲了解相关具体要求和规定,请参考ISO/TS16949系列、GM Global APQP等文件及SGM其他有关程序文件。
如有任何问题,请与相关主管SQE联系。
欢迎各位SQE、供应商或其他使用人员反馈您的修改意见,有关意见请反馈至上海通用汽车采购部SDE小组。
第二版制订说明:针对GM Global APQP的更新内容以及SGM当前业务发展的需要,同时结合SGM电子采购E-Procurement系统的相关操作要求,SGM采购部对《上海通用汽车对供应商质量要求的规定》进行了相关内容的修订,并于2008年1月发布第二版。
欢迎各位SQE、供应商或其他使用人员反馈您的意见或建议,有关意见或建议请反馈至上海通用汽车采购部SDE小组。
上海通用汽车采购部供应商质量与开发科2008年1月1日(第2.4版)PREFACESGM requires that all suppliers must meet all requirements, which include TS16949 (the latest Edition), related reference manuals and GM Customer Specifics (except for inapplicability at GM AP). SGM suppliers must also follow GM Supplier Quality Statement of Requirements and applicable items of GM General Procedures (for example GP5, GP9, GP10, GP11, GP12, etc...)This SQ SOR, which is part of SGM supplier quality procedures and regulations, summarizes SGM’s basic requirements for supplier quality, aiming to help SGM suppliers understand and perform more effectively SGM related requirements.For more details, please refer to ISO/TS 16949 series, GM Global APQP related documents and other SGM procedures accordingly.Any question, please contact the related SQE.We welcome all SQE, suppliers and other people feed back any modification advices to SGM SDE GROUP.2nd Edition ExplanationFor meeting the latest edition of GM Global APQP requirements and SGM current business development, SGM Purchasing Department revises “SGM Supplier Quality Statement of Requirements”based on SGM E-Procurement System and releases 2nd edition of SGM SQ SOR in Jan. 2008.Welcome any SQE, suppliers or other people feed back any modification suggestion or comments to SGM SDE GROUP.Supplier Quality & Development SectionPurchasing Department, SGMJan. 1st, 2008(第2.4版)Major Revisions主要修订记录Oct., 2004, the first edition2004年10月,第一版制订Jun., 2005, the major revisions:2005年6月主要修订内容:1. SGM SOR is updated refer to GM SGM SOR, Mar., 2005 version. Add SGM requirements forconsignment supplier.SGM供应商质量声明参考GM2005年3月版本更新,并增补SGM对Consignment(集成供货)供应商的要求2. For APQP, add requirements for vehicle body welding assembly supplier.APQP增补对车身焊接总成供应商的要求3. FE is updated according to SGM related procedure (Feb., 2005 version).FE按SGM有关程序(2005年2月版)改版4. PPAP canceled the detailed define of interim approval for fitting the new class standard of GMinterim approval.PPAP删除对临时批准的具体定义,以适应GM临时批准的新分类标准5. Definitude procedure that if Control Shipping I can’t be closed in time, supplier will enter ControlShipping II directly.受控发运明确对一级发运不及时关闭时,直接进入二级受控发运的规定6. Add GP9 procedure.增加GP9的具体规定May, 2006, the major revisions:2006年5月主要修订内容:1. Edit GM Automotive special requirement according to ISO/TS16949 GM Automotive specialrequirement (Mar,2006 version).按ISO/TS16949通用汽车特殊要求2006年3月版修订补充通用汽车的特殊要求2. Edit the related requirement according to PPAP 4.0.按PPAP 4.0修订相关要求3. Updated GM SQ SOR.GM SQ SOR的最新更新4. Edit and list the requirement for SGM consignment supplier.修订并单列SGM对集成供货供应商的要求。
SGM通用公司常用名称术语缩写
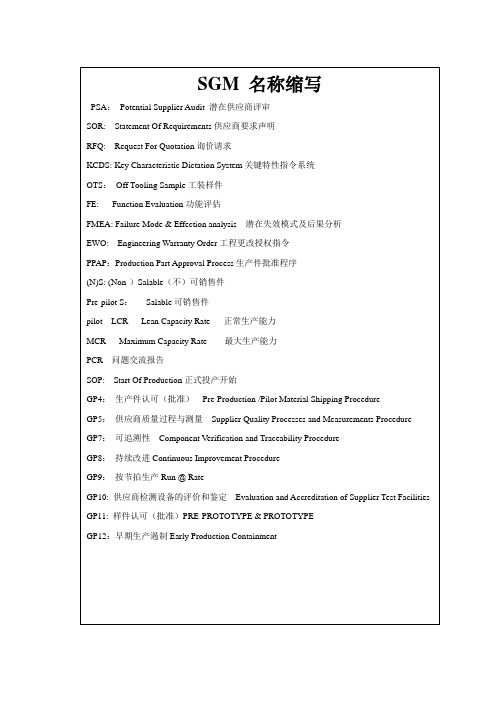
GM术语词汇GP-4 生产件批准程序GP-5 供应商质量过程和测量(问题回复及解决)GP-8 持续改进GP-9 按节拍生产GP-10 试验室认可程序GP-11 样件批准GP-12 早期生产遏制AAR 外观件批准报告ADV 分析/开发/验证ADV-DV ADV设计验证ADV P&R ADV计划和报告ADV-PV ADV产品验证AIAG 汽车工业行为集团AP 先期采购APQP 产品质量先期策划APQP Project Plan APQP项目策划APO 亚太分部AQC 属性质量特性ASQE 先期供应商质量工程师BIW 白车身BOM 材料清单BOP 过程清单Brownfield Site 扩建场地CMM 三坐标测试仪M complex system/subassembly M复杂系统/分总成Consignment 集成供货(外协供应商)CPK 过程能力指数CTC 零部件时间表(DRE)文件CTS 零件技术规范CVER 概念车工程发布DC 设计完成Defect outflow detection 缺陷检测DFM/DFA 可制造性/可装配性设计DFMEA 设计失效模式分析DPV 每辆车缺陷数DR DR特性DRE 设计释放工程师DV 设计验证E&APSP 工程&先期采购定点程序EP 电子采购流程Error Occurrence Prevention 防错EWO 工程更改指令FE1,2,3 1,2,3功能评估FMEA 失效模式和后果分析(DFMEA设计; PFMEA生产;MFMEA设备维护)FTQ 一次通过质量GA 总装GD&T 几何公差&尺寸GM 通用汽车公司GMAP 通用汽车亚太GME 通用汽车欧洲GMNA 通用汽车欧洲GP 通用程序GPDS 全球产品描述系统GPS 全球采购系统GPSC 全球采购及供应链GQTS 全球质量跟踪系统GR&R 量具的重复性与再现性Greenfield Site 新建工厂GVDP 全球整车开发流程IPTV 每千辆车缺陷数IVEP 集成车工程发布KCC 关键控制特性KCDS 关键特性指示系统Kick-off Meeting 启动会议(第一次APQP供应商项目评审)KPC 关键产品特性LAAM (通用汽车)拉丁美洲、非洲及中东LAO 拉丁美洲分部Layered Process Audit 分层审核LCR 正常生产能力MC 匹配MCR 最大生产能力MOP 制造/采购MPC 物料生产控制MPCE 欧洲物料生产控制MRD 物料需求日期(首次正式交样)MSA 测量系统分析MVBns(原:NS) 非销售车制造验证MVBs(原: S) 销售车制造验证NAO 北美分部NBH 停止新业务N.O.D. 决议通知OEM 主机客户OTS 外购国产化零部件和/或系统工程认可程序PAD 生产装配文件PC&L 生产控制&物流PDT 产品开发小组PFMEA 过程失效模式和后果分析PPAP 生产件批准程序PPM (1)项目经理(2)每百万件的产品缺陷数PPK 过程能力指数PPV 产品及过程验证PQC 产品质量特性PR/R 问题报告及解决PSA 潜在供应商评审PTR 零件试生产QSA 质量体系评审QSB 质量体系基础QTC 工装报价能力RASIC 负责,批准,支持,通知,讨论RFQ 报价要求RPN 风险顺序数RPN reduction plan 降低RPN值计划R@R 按节拍生产SDE 供应商开发工程师SFMEA 系统失效模式分析SMT 系统管理小组SOA 加速开始SORP 正式生产SOR (供应商质量)要求声明SPC 统计过程控制SPO (通用汽车)零件与服务分部SQ 供应商质量SQE 供应商质量工程师SQIP 供应商质量改进过程SSF 系统填充开始SSTS 分系统技术规范S.T.E.P 采购定点小组评估过程Sub-Assembly/Sub-System Subcontractor 分供方SVE 子系统验证工程师SVER 结构车工程车Team feasibility commitment 小组可行性承诺TKO 模具启动会议UG UG工程绘图造型系统V AP 每辆车开发过程VLE 车辆平台负责人VTC 验证试验完成WO 工程工作指令WWP 全球采购旧称呼IV2 新称呼OTS旧称呼PVV 新称呼Trgout旧称呼MC1 新称呼FE2旧称呼MC2 新称呼FE3旧称呼MCB 新称呼FE1Layered Process Audit 分层审核通用汽车一般程序下载: 或: 备注: 绿色为通用程序对照黑色为09年06月01日培训发放的术语资料红色为结合以前版本术语资料。
上海通用供应商质量管理6步程序

——质量方面有12个要素
——技术方面有7个要素
——管理方面有6个要素
B 供应商自我评估(只能在客户的要求下进行,所有要素与现场
评估的要素一致。
评分体系用以确定新的潜在供应商是否有资格进行潜在供应商评估。
任务:确定供应商是否有资格进行潜在供应商评估
潜在供应商评估(PSA)
定义: 现场评估供应商是否能达到对管理体系的最基本要求。
目的: 进行为期一至二天的评估以验证新的潜在供应商是否有能力达
到与上汽通用五菱汽车股分有限公司开展业务的最基本要求。
范围: 在推荐某一供应商来开拓新的业务之前,如果该供应商未具备
QS9000认证,并且在以下任一状态成立的情形之下,必须进
行潜在供应商评审:
1. 潜在供应商的制造场所不是上汽通用五菱的现有供货源。
目的:保证所有质量要求在供应商及客户负责供应商的部门之间得到
确切的交流。
范围:建议对所有需要进行PPAP的新部件或新材料行使本程序,依
照其风险程度之不同来确定先后。(这是先期质量策划的一个部
分)
程序:通过供应商与客户有关人员在产品开发小组会议上进行密切的
交流以对质量,生产能力和进度等要求进行研讨并取得认同。
定义:在潜在供应商评估之前,对新的潜在供应商作一个初步评估,或
让供应商自我评估以确定其是否具备基本的质量体系、合适的技
术能力和良好的管理水平。
目的:通过半天的评估以确认新的潜在供应商是否有资格进行潜在供应
商评估。
范围:适用于所有被认作是潜在来源的新的供应商。
程序:A 采购员、经理或工程师进行现场评估
-工程样品(OTS)文件的提交
生产件批准程序PPAP
Hale Waihona Puke 定义: 关于正式生产件得以审批的一般产业程序。
通用汽车公司的供应商评估报告

三、范围: 建议对所有需要进行PPAP的新部件或新材料行使本
程序,依照其风险程度之不同来确定先后(这是前期 质量规划的一部分)
五、投产前会议(续)
四、程序 通过供应商与客户有关人员在产品开发小组会议上进 行密切交流对以下方面的要求进行研讨并取得认同:
一、初级评估(续)
四、程序: a、通用汽车公司的采购人员,经理或工程师进行现场 评估 ---质量方面有12个要素 ---技术方面有7个要素 ---管理方面有6个要素 b、供应商自我评估只能在通用汽车公司的要求下进行 所有要素与现场评估的要素一致。 评分体系用以确定供应商是否有资格至少能进行潜 在供应商评估。
七、正式生产件审批程序
一、定义: 关于正式生产件得以审批的一般产业程序。
二、目的: 验证某供应商的生产工艺是否具备生产满足客户要求 的产品的潜能。
三、范围: 在新产品投产前,或当现有产品在技术、工艺上有改 动,或供应商情况发生变化,都必须通过此“正式生 产件审批”程序
四、程序 供应商严格按照正式生产件审批程序(PPAP)中规
二、潜在供应商评估
一、定义: 现场评估供应商是否能达到对管理体系的最基本要求
二、目的: 进行为期一至二天的评估以验证新的潜在供应商是否 有能力达到与上汽通用五菱公司开展业务的最基本要求
三、范围: 在推荐某一供应商来开拓新的业务之前,如果该供应商 未具备QS-9000认证,并且在以下任一状况成立的情形 下,必须进行潜在供应商评审:
一、初级评估
一、定义: 在进行潜在供应商评估之前,对新的潜在的供应商做
一个初步的现场评估,或让供应商自我评估以确定供 应商是否具有基本的质量体系,合适的技术能力和良 好的管理水平。 二、目的:
通用汽车APQP供应商质量声明

通用汽车APQP供应商质量声明1. 所有的供应商应该向通用公司提供零缺陷的产品。
在首次报价和其后的报价中,供应商商需要说明为检测缺陷(防错装置等)和防止缺陷流至客户所需要的预算。
供应商以后追加的控制手段,费用由供应商承担。
2. ISO/TS 16949 或QS-9000 –质量体系要求∙GM 所有的供应商必须通过其中之一的质量体系认证,并且取得相应的证书.这些标准要求对供应商质量做广泛的,正式地审核并且型式可操作。
这个评价应得到第三方的认证注册。
∙供应商如果没有通过ISO/TS 16949 或QS-9000的认证,或者这些供应商新建或采购设备来制造报价的零件,供应商在报价时必须包括通过认证的时间。
3. 通用汽车的程序和参考文件●供应商必须遵守以下文件:质量先期策划和控制计划参考手册(AIAG)潜在失效模式和影响分析(FMEA)参考手册(AIAG)统计过程控制(SPC)参考手册(AIAG)测量系统分析(MSA)参考手册(AIAG)生产件批准程序(PPAP)手册(AIAG)关键特性指示系统(KCDS )GM-1805QNGP-5 供应商质量过程和测量程序. GM-1746GP-7 总成件确认和可追溯程序.GM-1730GP-8 持续改进程序. GM-1747GP-9 按节拍生产. GM-1960GP-10 供应商检测设备的评价和鉴定.GM-1796GP-11 预样件和样件物料综合程序. GM-1820GP-12 早期生产遏制 .GM-1920GM-供应商技术信息GM-1825追溯性标识的要求TIR-15-300. GM-1731供应商焊接质量支持手册发运零件的证明标签标准. GM-*1724检具要求标准GM-1925供应商样件物料的操作指南NAO-0065GMNA 和LAAM规范)—供应商发送零件到GM 南北美洲工厂GP-4 预试生产/试生产物料发运程序. GM-1407GP-6 供应商检查物料相应的让步接受标准零件和成品的条形码ECV/VCVS. GM-1737包装和生产产品的鉴定要求。
通用汽车供应商管理十六步法(下)
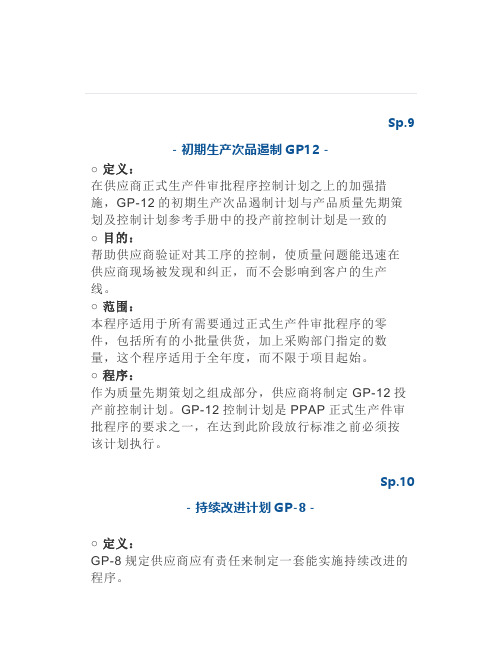
Sp.9- 初期生产次品遏制GP12 -○定义:在供应商正式生产件审批程序控制计划之上的加强措施,GP-12的初期生产次品遏制计划与产品质量先期策划及控制计划参考手册中的投产前控制计划是一致的○目的:帮助供应商验证对其工序的控制,使质量问题能迅速在供应商现场被发现和纠正,而不会影响到客户的生产线。
○范围:本程序适用于所有需要通过正式生产件审批程序的零件,包括所有的小批量供货,加上采购部门指定的数量,这个程序适用于全年度,而不限于项目起始。
○程序:作为质量先期策划之组成部分,供应商将制定GP-12投产前控制计划。
GP-12控制计划是PPAP正式生产件审批程序的要求之一,在达到此阶段放行标准之前必须按该计划执行。
Sp.10- 持续改进计划GP-8-○定义:GP-8规定供应商应有责任来制定一套能实施持续改进的程序。
○目的:GP-8概述了在通过正式生产件审批程序(PPAP)和初期生产次品遏制(GP-12)程序之后,客户对供应商的持续改进的要求。
○范围:该程序适用于所有生产零部件及材料的供应商,即使在客户没有规定具体要求时依然适用。
○程序:所有供应商必须监测其所有零件的质量工作情况并致力于持续改进,持续改进程序目标在于减少生产加工的偏差和提高产品的质量。
供应商应着重于通过听取用户用户的意见和工序的反馈,以努力减少工序波动。
Sp.11- 成本监控-○定义:一个监测供应商质量成效,促进相互交流和促使有针对性的改进的程序。
○目的:提供质量成效反馈,以促使重大质量问题的改进。
○范围:适用于所有的供应商。
○程序:采用批量生产的百万分不合格率(R/RPPM)来监控供应商质量成效并将信息反馈于供应商和有关部门人员,以便:• 与每一供应商一起确认主要问题• 通过着眼于主要质量问题的整改措施来促进产品质量的持续改进• 加强对质量目标,期望及成效等信息的交流作为定点供应商和年度优秀供应商的选择依据。
Sp.12- 问题通报与解决-○定义:为促进解决已确定的供应商的质量问题而进行交流的程序。
上海通用汽车有限公司对供应商APQP的要求

宝岛优品—倾心为你打造精品文档上海通用汽车有限公司上海通用汽车有限公司对供应商A P Q P的要求上海通用汽车有限公司采购部前言为了进一步协调和规范上海通用各供应商的APQP过程,降低产品和过程开发中的风险,上海通用汽车有限公司采购部供应商质量和开发科根据通用汽车全球先期产品质量策划手册(2002.10 第二版),并结合国内供应商的实际情况,修订而成。
本程序作为标准要求, 以向上海通用SQE 以及供应商提供一种通用的格式,以推进APQP的各个步骤的实施。
本程序的解释权归上海通用汽车有限公司采购部供应商开发小组所有。
附:与AIAG APQP手册相比,本要求的主要变化:1、强调了各家供应商在APQP过程中的统一性和严密性。
2、对APQP各阶段工作明确定义为17项任务(对1-3项任务要求,SGM已与其它任务合并),对各项任务的责任人、时间、任务输入输出、实施方法、SQE责任、供应商责任、参考资料等明确定义,以规范项目的开展。
3、在RFQ中增加供应商质量SOR,明确质量要求、体系要求、适用程序、质量策划、分供方要求等。
对PT零件供应商,还对KPC过程能力、PFMEA风险顺序数等明确要求。
4、供应商报价时应同时提交“要求的质量信息”和相应的质量计划,SQE最迟于APQP启动会议评审。
5、由SQE、采购员、PE等对各家供应商进行详细风险评估(有打分表),降低定点风险,并针对选定供应商的弱点,制定相应的APQP控制策略,以降低系统风险。
6、通过APQP问题清单程序,对APQP项目进展中的所有问题,及时发现并加以跟踪和解决,以降低项目风险。
7、APQP过程中的4个重要阶段,要进行供应商项目评审,从而保证及时评估项目状态和解决问题。
8、APQP不同阶段中,供应商要分别就其项目能力、设计能力、制造能力和产能进行4次评估,并分别向SGM作出书面承诺。
9、在项目的各个阶段,提供了详细的检查表或指导文件,以规范项目的开展并确保任务的完成。
APQP(上海通用汽车培训教材)
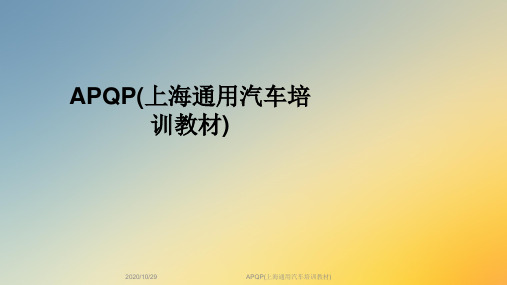
目的 促进参与各方相互信任和支持,并 充分联系
求的步骤 按时完成。
以确保所要
范围 适用于所有新零件
优点
有 效 利 用 资 源 ,使 顾 客 满 意 促 进 对 所 需 更 改 进 行 早 期 识 别 并 实 施 ,避 免 后 保证在满足所需能力和项目进度要求下交付合
期更 改 格产品
供 应 商 高 级 管 理 层 的 支 持 是 APQP 成 功 实 施 的 关 键 !
• 输出:设计目标;可靠性目标; 质量目标; 初始原材料和分供方清 单;初始过程流程图; 初始特殊特性清单; 政府安全、环保法规等 。
APQP(上海通用汽车培训教材)
Product & Process Development-
2.0 Product Design & Development产品设计和开发
预生产会议
经验
零件生命期
GM 全 球 APQP
先 期 产 品 质 量 策 划 (APQP) 选点ቤተ መጻሕፍቲ ባይዱ定
潜在供应商评审
开始生产
APQP(上海通用汽车培训教材)
Primary
背景
定义
产 品 质 量 先 期 策 划 -- APQP
采用系统化方法确定和建立必要的步骤,明确 相关方职责,以 确保满足顾客对产品的要求
• Engineering drawings including CAD data • Engineering specifications • Material specifications
• 7. New equipment, tooling & facilities (included in overall timing plan)新设备、工装和设施 • 8. Finalization of special characteristics特殊特性 • 9.Any new inspection, measuring and test equipment device 检测、测量设备 • 10. Team feasibility statement(compulsory as per QS9000) 小组可行性承诺
浅谈汽车零部件供应商管理的样件审批(GP—11)

浅谈汽车零部件供应商管理的样件审批(GP—11)作者:梁彩倩覃俊来源:《科学与财富》2018年第20期摘要:汽车是我们现在生活中使用最多的交通工具,人们对汽车的质量和使用安全性要求也越来越高,而汽车的各种各样零部件的质量直接决定了汽车的整体质量和使用安全性。
俗话说,千里之堤,溃于蚁穴,因此汽车零部件的质量管控至关重要,本文就通用公司供应商管理16步法的样件审批(GP-11)对供应商的零部件质量管理进行了阐述,希望可以给读者带来新的认识。
关键词:样件审批GP-11;供应商质量;供应商现场审核2017年我国汽车市场需求达到2915万辆,同比增长3.5%。
人们对于汽车需求量越来越多,对汽车产品质量和使用安全性要求也越来越高。
近年来,汽车市场竞争也将着重围绕质量展开,构成汽车的各种各样零部件的质量直接决定了汽车的整体质量和使用安全性。
从狭义的角度来说质量仅仅是一个产品符合规定的标准这个结果,但是从广义上来说质量却是一个过程,比如汽车的一颗螺栓,從前期策划到进料到成型再热处理最后到成品出货,无时无刻都离不开质量,这个质量过程不是某个人某个部门能够独自完成,要使我们的产品质量达到卓越水平,它需要每个涉及制造产品的成员积极配合,在这个产品质量过程应以预防为主,控制为辅。
汽车零部件在样件制作阶段,主机厂应做样件审批(GP-11),对供应商的零部件质量进行前期的质量预防和管控。
1、GP-11的定义及目的GP-11是通用公司规定关于前期样件及样件材料供应商程序,是工装样品审批规程,是试生产前样件质量保证流程,是通用第11个全球程序文件。
在前期样件和样件阶段通过对产品零件GP-11资料及生产现场的审批,测试供应商提供的100%正式工装零部件是否符合原设计的工程要求,保证零件所存在的问题能够在这个阶段被发现并得到改正,以及最大限度地减少零件不合标准对设计评估、制造和装配的影响。
2、GP-11的应用主机厂产品工程师(简称PE)将零部件开发要求书SOR发给供应商,供应商质量管理工程师(简称SQE)根据SOR要求书,需对关键零部件开展GP-11审批。
通用汽车全球产品质量先期策划

Supplier Monitored
APQP
Supplier
GM
N/A
R
S
R
N/A
R
R
I
R
A
R
I
R
I*
R
I*
R
I
R
I
R
A
R
I*
R
I*
R
I*
R
A
R
A
R
I
R Responsible (GM or Supplier) A Approve - GM approves deliverables S Support completion of deliverables (GM or Supplier) I Inform – GM reviews deliverables at discretion of SQE C Consult
o---------------------------------------------------------------------------------------------------------
15 PPAP
PR-4
Plan
16 Run @ Rate (GP-9)
PR-1,4
o
o
17 Lessons Learned
o------------------------------------------------------------------------------------------------------------o
Plan
Complete/Status
o----- ----------------o
GP-11(中文)

通用汽车公司程序文件预样品(Pre-Prototype)和样品(Prototype)材料GP11本程序适用于所有提供新的预样品和样品材料的供应商,(无论是内部的,合作的或外部的)。
所有材料都应满足本程序中提出的要求。
术语“供应商”应指明是GM采购部门总承包人。
预样品(Pre-Prototype)和样品(Prototype)工作的目的是为了组装和测试生产用的零部件,总成系统和汽车,以便确认设计和组装过程。
预样品和样品阶段的零件认可确保对零件的问题的确定和纠正,减少零件偏差对设计评估、制造和组装的影响本程序规定了对供应商在预样品和样品零件上的要求,包括把材料直接运到接收地点和供应商应完成的记录文件的要求。
在供应商把材料运往接收地点之前应准备的供采购部门评估的零件和文件,本程序还规定了统一的最低要求。
本程序包括对GP-11 ADV的要求,GP-11 ADV是GP-11 要求的一部分。
GP-11 ADV就是GP-11 分析/开发/验证的意思。
当GP-11 ADV在SOR规定时才要求时提交GP-11 ADV文件。
本程序含如下内容:1-0 预样品和样品零件和文件的要求2-0 提交要求3-0 运输方式4-0 记录保存要求5-0附录/示例(注释:对于GMPT的GP-11文件的提交,GMPT的DRE负责GMVE的工作。
)1-0 预样品和样品零件和文件的要求:零件将按照GM授权的图纸,模板,模具和/或其它工程设计记录,指定材料制作。
如果与工程要求相偏离,请与你的采购部门来联系取得正式授权许可。
所有提供预样品和样品材料的供应商,都应该有完整的、文件化的和可供检查的如下所列的项目:1. 通用汽车供应商对预样品和样品材料的保证书(例子A)2. 设计记录3. 检验结果和检验与/或测试设备4. 材料合格证5. 零件重量 (质量)6. 系列化信息7. 生产材料和工艺8.分析/开发/验证文件(当要求)1-1 通用汽车的供应商对预样品和样品材料的保证书《通用汽车供应商对预样品和样品材料保证书》应填制完整并由授权的,负责准备零件发货的供应商负责人签字。
通用汽车公司关于前期样件及样件材料供应商程序 GP11
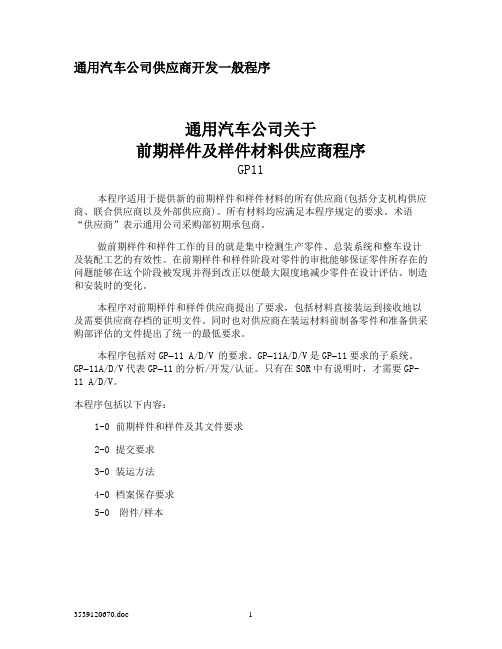
通用汽车公司供应商开发一般程序通用汽车公司关于前期样件及样件材料供应商程序GP11本程序适用于提供新的前期样件和样件材料的所有供应商(包括分支机构供应商、联合供应商以及外部供应商)。
所有材料均应满足本程序规定的要求。
术语“供应商”表示通用公司采购部初期承包商。
做前期样件和样件工作的目的就是集中检测生产零件、总装系统和整车设计及装配工艺的有效性。
在前期样件和样件阶段对零件的审批能够保证零件所存在的问题能够在这个阶段被发现并得到改正以便最大限度地减少零件在设计评估、制造和安装时的变化。
本程序对前期样件和样件供应商提出了要求,包括材料直接装运到接收地以及需要供应商存档的证明文件。
同时也对供应商在装运材料前制备零件和准备供采购部评估的文件提出了统一的最低要求。
本程序包括对GP-11 A/D/V 的要求。
GP-11A/D/V是GP-11要求的子系统。
GP-11A/D/V代表GP-11的分析/开发/认证。
只有在SOR中有说明时,才需要GP-11 A/D/V。
本程序包括以下内容:1-0前期样件和样件及其文件要求2-0提交要求3-0装运方法4-0档案保存要求5-0 附件/样本前期样件和样件的要求GP-111-0前期样件和样件及其文件要求零件应按照通用公司授权的图纸、样板、模型和/或其它设计文件所规定的材料制做。
若与设计有偏差,请与采购部联系以获得正式的授权。
所有的前期样件及样件供应商均需要具有下文所列的完整的、成文的、有效的文件以供评审。
规定年型的样件的存档应保存到该样件开始正常生产后的两个月。
1.通用公司前期样件及样件材料供应商保证书(样本A)2.设计档案3.检查结果和检查和/或检测工具4.材料证明5.零件重量(质量)6.排序信息7.生产材料及工艺8.分析/开发/认证(若需要的话)1-1.通用公司前期样件及样件材料供应商保证书通用公司前期样件及样件材料供应商保证书应由负责制备和装运零件的供应商授权的官员完成并签字。
- 1、下载文档前请自行甄别文档内容的完整性,平台不提供额外的编辑、内容补充、找答案等附加服务。
- 2、"仅部分预览"的文档,不可在线预览部分如存在完整性等问题,可反馈申请退款(可完整预览的文档不适用该条件!)。
- 3、如文档侵犯您的权益,请联系客服反馈,我们会尽快为您处理(人工客服工作时间:9:00-18:30)。
通用汽车公司供应商开发一般程序通用汽车公司关于前期样件及样件材料供应商程序GP11本程序适用于提供新的前期样件和样件材料的所有供应商(包括分支机构供应商、联合供应商以及外部供应商)。
所有材料均应满足本程序规定的要求。
术语“供应商”表示通用公司采购部初期承包商。
做前期样件和样件工作的目的就是集中检测生产零件、总装系统和整车设计及装配工艺的有效性。
在前期样件和样件阶段对零件的审批能够保证零件所存在的问题能够在这个阶段被发现并得到改正以便最大限度地减少零件在设计评估、制造和安装时的变化。
本程序对前期样件和样件供应商提出了要求,包括材料直接装运到接收地以及需要供应商存档的证明文件。
同时也对供应商在装运材料前制备零件和准备供采购部评估的文件提出了统一的最低要求。
本程序包括对GP-11 A/D/V 的要求。
GP-11A/D/V是GP-11要求的子系统。
GP-11A/D/V代表GP-11的分析/开发/认证。
只有在SOR中有说明时,才需要GP-11 A/D/V。
本程序包括以下内容:1-0 前期样件和样件及其文件要求2-0 提交要求3-0 装运方法4-0 档案保存要求5-0 附件/样本前期样件和样件的要求GP-111-0前期样件和样件及其文件要求零件应按照通用公司授权的图纸、样板、模型和/或其它设计文件所规定的材料制做。
若与设计有偏差,请与采购部联系以获得正式的授权。
所有的前期样件及样件供应商均需要具有下文所列的完整的、成文的、有效的文件以供评审。
规定年型的样件的存档应保存到该样件开始正常生产后的两个月。
1.通用公司前期样件及样件材料供应商保证书(样本A)2.设计档案3.检查结果和检查和/或检测工具4.材料证明5.零件重量(质量)6.排序信息7.生产材料及工艺8.分析/开发/认证(若需要的话)1-1.通用公司前期样件及样件材料供应商保证书通用公司前期样件及样件材料供应商保证书应由负责制备和装运零件的供应商授权的官员完成并签字。
对于每一种零件编号和每一种装运到通用公司的零件应有单独的保证书。
当采购部批准后,一组仅颜色不同的零件编号或同一零件的左手方或右手方可以贴上一张保证书。
如果零件不满足技术要求,但通用的工程师认为它对于前期样件和样件有用,则在提交前应由通用公司的工程师在保证书的后面完整地填写改正措施计划并签字。
请参考附件II和样本I 的步骤说明来完成保证书。
1-2设计档案设计档案包括但并不仅限于简图、图纸、数据、兰图和其它辅助图纸(如GDT图)。
零件编号、设计档案编号,设计存档日期,变更版本编号以及采购部负责工程师的签字均应在上面体现(除电子输出工艺外)。
1-3检验结果、检验和/或检测工具供应商负责做检查和或检测以证明其是否与设计档案、坐标测量仪(CMM) 输出结果一致。
这些实际测理结果必须与用户提供的设计资料或用来检查材料的设计资料相互参照。
检查零件所得到的CMM三维结果将参考本文件的附件II、样本2记录下来。
对于仅颜色不同的零件,只需对一种颜色做完整的检查。
并且应以已经做过完整检查的零件的零件编号相同的编号(但无检查完成号码)为所有其它颜色的零件做附注。
1-3A 完整的特性检查1-3B 主要产品特性检查1-3C 设计变更检查1-3D 组装元件及详细零件1-3E 检查和/或检测工具(若需要的话)1-3A 完整特性检查一般情况下,应对三个零件做完整的特性检查,除非采购部另有规定。
1-3B 主要产品特性检查对于生产出的数量超过1 3A所规定数量的所有零件,如果设计档案中对其主要产品特性的测量有规定,则应检查其主要产品特性测量结果是否与要求一致。
1-3C 设计变更检查因设计变化或对原来零件有修改,仅需要对变化部分和受变化影响的部分进行检查。
检查结果应由通用公司采购部审查。
如果需要的话,还需要呈交。
1-3D 组装元件和详细零件检查和或/检测组装零件时,记录在组装设计档案上和所有详细设计档案上所有尺寸及技术要求均应检查。
供应商负责对每种详细元件的可接受性做评估,如果采购部有要求的话,请提供满足要求的证据。
1-3E 检查和/或检测工具当使用诸如计量仪表、卡具,检查辅助器或模板等检查或检测零件时,供应商负责检查和证实这些检查装置是按照相同的设计发布和变更号安装的。
供应商要利用合适的方法来检查零件。
按照采购部的指示也许需要做CMM 检查。
补充检查表应包括零件编号、设计存档标准、设计存档日期及供应商名字。
1-4材料证明材料证明是材料生产商的文件,它标明了生产地址,批号、产品识别号、产品名称,检测日期及需要的与通用公司产品技术要求一致的检测数据。
供应商应将材料证明存档以供采购部评审时使用。
若有必要的话,还要呈交。
1-5零件单位重量(质量)供应商要把供应给通用公司的每种零件编号的零件的单位重量提供给通用公司。
零件重量(质量)应以公斤表示并保留到小数点后面第三位,这些内容要在供应商前期样件和样件材料保证书上体现。
一般情况下至少要对十个零件进行称量并将结果平均。
例如,称量重量小于0.1公斤的零件,如紧固件等,十个零件将一起称重并将结果除以10以获得所需数字。
如果定单上定的零件数少于10件,则称量所定购的全部零件重量再进行平均。
零件应在无润滑油、冷却剂等的情况下称量。
1-6顺序排列信息零件应参考检测/检验结果按顺序进行编号。
编号应从S-0001开始并按顺序直到装运的最后一个零件。
每个零件的编号布置应不影响零件的处观、装配或功能。
设计记录、设计结果及补充检查结果必须清晰地标明其顺序号。
零件均应编顺序号除非采购部另有要求。
1-7生产材料和工艺如果生产材料和整个生产工艺被采用时,供应商应开始执行PPAP的要求。
这方面事宜请向采购部咨询。
1-8分析/开发/认证(A/D/V)采购部必须决定是否需要设计认证和产品认证。
样件采购定单上必须包含这些信息。
详细的要求反映在SOR上或其它工程资料上。
所需的说明产品认证和设计认证的结果是SOR的一部分内容。
在某些情况下,SOR需要供应商确定所需的结果。
1-8A1 认证是通过分析、说明、检查和检测确认产品满足全部要求的正式过程。
1-8A2 设计认证(DV)是通过分析、说明、检查和/或检测确认产品的设计满足全部技术要求。
它不包括制造所引发的变化的影响。
1-8A3 产品认证(PV)是通过分析、说明、检查和/或检测确认产品设计满足了全部技术要求。
它包括制造引发的变化的影响。
1-8A4 按照GP-11,设计认证通常是在硬件阶段需要。
有时,产品认证也在这个阶段需要。
当产品认证是为前期样件和样件服务时,将需要使用GP-11/A/D/V。
如果产品认证出现在前期样件和样件设计之后,将需要除1-8B1以外所有以1-8命名的文件。
提交时间将在SOR中确定。
1-8B 在批准GP-11 A/D/V之前,认证工程师至少要审查下面的文件:1-8B1 表明A/D/V状态的GP-11保证书1-8B2 到提交之日,认证不能顺利完成的情况下带有时间进度的改正措施计划1-8B3 反映最新认证结果的完整的DFMEA。
1-8B4 用分析/开发/认证计划和报告 (ADV&R) 描述的A/D/V计划和结果,请参考样本B1-8B5 详细的计划和结果。
采用GM NAO 的评估格式。
一般信息生产批准件通过生产件批准过程(PPAP)批准的零件应直接装运到接收地以满足采购部的装运计划,并且可以不执行本程序列出的证明文件要求。
这些零件必须用前期样件和样件材料标签(附件1,样本2)和用前期样件和样件材料装运集装箱标签(附件1,样本3)标识. 按照 GP – 5 程序,不满足设计文件要求的零件需经问题报告和解决程序(PR/R)处理。
2-0 提交要求采购部应规定呈交要求。
没接到呈交要求通知的供应商应按2-1,标准B 规定的程序执行。
对于所有的提交要求,当零件不满足设计要求和/或认证要求(如果需要GP-11A/D/V)时,带有完整改正措施计划并经通用工程师签字的完整的通用公司前期样件和样件供应商保证书应直接发到采购部指定的地点。
如果需要GP-11A/D/V,保证书还要包括完整的认证结果(ADVP&R)。
下文将把通用公司前期样件和样件材料供应商保证书描述为“保证书”。
不符合要求的零件还需要额外的文件。
关于这方面问题请向采购部咨询。
当结果没有被完全批准时,改正措施计划应被用于标准的GP-11要求和认证总结上。
认证结果的改正措施计划必须要有通用公司认证工程师的签字。
所有其它的发布则需要通用公司负责发布工程师的签字。
注:∙参考附上的样本(附件1,样本1)∙不论提交标准如何,所有前期样件和样件供应商均需要按照1.0 部分列出的要求完成、记录和存档。
2.1 样件直接装运到接收地标准A 零件直接装运到规定的接收地。
保证书直接发到采购部指定的地点。
按照3.2和3.3部分所描述的、已贴上标签的零件应由供应商装运到采购定单上注明的接收地。
保证书应直接发到采购部规定的地点。
标准B 零件直接运到规定的接收地。
完整的文件直接发到采购部规定的接收地。
如果需要GP-11A/D/V ,那么还要包括认证总结(PR/R)。
按照3.2和3.3部分所描述的,贴上标签的零件应由供应商直接运送到采购定单上所规定的接收地。
保证书、设计文件和检查结果应直接发到采购部指定的地点。
如果零件不满足要求,供应商必须在材料装运前与前期样件和样件协调员联系要求对零件进行处理。
没有经过处理的由供应商运送的不满足要求的零件将按照GP-5程序被拒收并记录到问题报告及解决系统(PR/R)。
2.2 装运到接收地前采购部的评估和授权标准C 带有改正措施计划(若需要的话)的保证书,若需要GP-11A/D/V,则还要包括认证总结零件装运到接收地前,保证书应直接发到由采购部指定的地点。
采购部还要发布零件处理结果,这是关于零件装运的授权。
按照3.2和3.3的描述,已贴好标签的零件(不包括文件),由供应商装运到采购定单指定的接收地。
标准D 具有完整的证明文件和检查/检测工具(若需要的话)的零件。
如果需要GP-11A/D/V的话,还包括认证结果(ADVP&R)在装运到接收地之前,保证书、设计记录、检查结果、检查工具(若需要的话)以及采购部规定的零件数量等文件应直接发到由采购部规定的地点。
零件的装运应在采购部对问题做出处理后才能授权。
按照3.2和3.3部分贴了标签的零件 (不包括文件),由供应商装运到采购定单所规定的接收地。
零件分类—采购部应通知供应商提交的处理结果。
A。
前期样件和样件的批准这表示供应商已生产出完全符合技术要求的材料。
但这不是生产批准。
如果需要GP-11A/D/V,那么,当零件即通过了三维要求又通过了设计/产品认证要求时,才能被批准。
B。
前期样件和样件的可用性这种情况是表示允许使用不满足要求的零件。