erp课件 第5章 物料需求计划
物料需求计划MRP与企业资源计划ERP课件(87页){修}89页PPT

61、奢侈是舒适的,否则就不是奢侈 。——CocoCha nel 62、少而好学,如日出之阳;壮而好学 ,如日 中之光 ;志而 好学, 如炳烛 之光。 ——刘 向 63、三军可夺帅也,匹夫不可夺志也。 ——孔 丘 64、人生就是学校。在那里,与其说好 的教师 是幸福 ,不如 说好的 教师是 不幸。 ——海 贝尔 65、接受挑战,就可以享受胜利的喜悦 。——杰纳勒 尔·乔治·S·巴顿
物料需求计划MRP与企业资源计划 ERP课件(87页){修}
1、纪律是管理关系的形式。——阿法 纳西耶 夫 2、改革如果不讲纪律,就难以成功。
3、道德行为训练,不是通过语言影响 ,而是 让儿童 练习良 好道德 行为, 克服懒 惰、轻 率、不 守纪律 、颓废 等不良 行为。 4、学校没有纪律便
ERP原理及应用教程(第二版) 第五章-物料需求计划
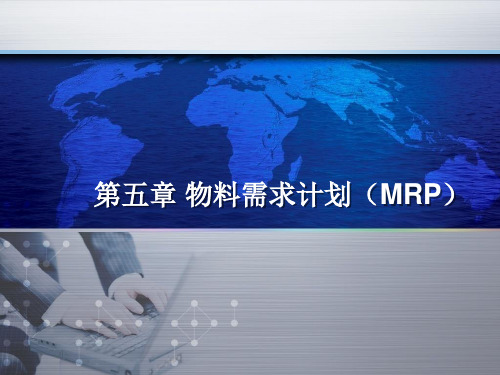
父的利期项用末的批库相量存关规量需则。 求,生=父成项订的单计
划2计)订划确单(定净数计需量划求订×量单项入目库用)量,因 子如于包果零括在,计某则划个产产时生出间净段需量上求和的量产预:出计的库存量小 净时需间求。量=预计可用库存的相反数
否则,净需求量为零,此时表明对该
物料无实际需求量。
2021/11/24
2021/11/24
4
5.1 物料需求计划的作用和特点
1.物料需求计划概念
什么时间生产多少数量 的产品?
MRP要回答的问题是:
需要那些物料? 物料现有多少?
还缺什么?何时需要?
2021/11/24
5
MRP?
5.1 物料需求计划(M的at作eria用l R和eq特uire点ment Planning)
开始 准备MRP输入数据 把MPS传送给MRP
订单计划包括制造订 单计划和采购计划, 有关物料究竟属于制 造订单计划范畴,还 是属于采购订单计划 范畴,则由该物料的 制造/采购标识码确 定。
2021/11/24
计算毛需求量
计算净需求量
净需求>0? 否
是 生产订单计划
下达订单计划
是 处理其他项目 否 结束
第五章 物料需求计划(MRP)
本章知识要点
物料需求计划的相关概念 物料需求计划的作用 物料需求计划的工作原理 物料需求计划的处理过程
2021/11/24
2
本章主要内容
5.1 物料需求计划的作用和特点 5.2 物料需求计划的工作原理 5.3 物料需求计划的工作步骤 5.4 MRP的调整方法 5.5 MRP的编制案例
3.物料需求计划的二项输出数据
① 采购订单 ② 制造订单
《ERP》Unit_05_物料需求计划与能力需求计划
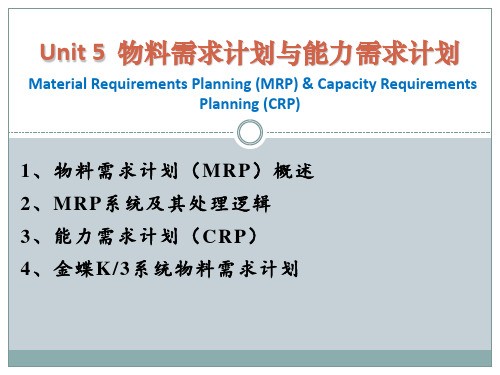
举例:表上作业法
21
准备 MRP 处理所需的各种输入,将 MPS 作为确认的生产订单
下达传给MRP。
根据产品的BOM,从第一层项目起,逐层处理各个项目直至
最低层处理完毕为止。
A
LT=2
0层
低位码处理
A
LT=2
0层
LT=1
B(1)
C(2)
LT=2
1层
LT=1
B(1)
1层
C(2)
1.00 1.00 1.00
M-----自制件
《ERP原理与应用》
B-----外购件
15
16
A B(1) C(2) D(2)
0层 1层 2层 3层 4层
低层码 / 低位码: 相同的元件出现 在不同的层次 上——采用低层 码技术处理,即 取其最低层次号,
D(3) G(3kg)
C(2)
E(3)
D(3)
A 2 (0 层)周
B 1 (1 层)周
C 2 (2 层)周
总需要量 预计到货量 0 现有数 净需要量 计划发出订货量 总需要量 预计到货量 2 现有数 净需要量 计划发出订货量 总需要量 预计到货量 5 现有数 净需要量 计划发出订货量
20 5 10 15 15 15 5
22
15
-5 5 26
《ERP原理与应用》
Unit 5 物料需求计划与能力需求计划
Material Requirements Planning (MRP) & Capacity Requirements Planning (CRP)
1 、物料需求计划 ( MRP )概述 2 、 MRP 系统及其处理逻辑 3 、能力需求计划 ( CRP )
ERP物料需求计划

ERP物料需求计划什么是ERP物料需求计划?ERP(企业资源规划)物料需求计划是指通过企业资源规划系统来进行物料需求预测和计划的一个过程。
它是一种基于生产和销售计划的方法,通过分析企业生产过程中所需的物料,预测未来的需求,并制定相关的计划以确保物料供应的准确性和及时性。
ERP物料需求计划的目标和重要性ERP物料需求计划的主要目标是在减少库存成本的同时,确保所需物料的及时供应。
它的重要性体现在以下几个方面:1.减少库存风险:通过预测和计划物料需求,企业可以避免过高或者过低的库存水平,减少库存持有成本和库存过期的风险。
2.提高客户满意度:准确的物料需求计划可以确保及时满足客户需求,提供高质量的产品和服务,从而提高客户满意度。
3.优化生产计划:物料需求计划与生产计划之间的关联紧密,通过提前预测物料需求并与生产计划相结合,可以实现生产过程的优化和最大化利用资源。
4.降低供应链风险:物料需求计划可以帮助企业及时发现并应对供应链中的风险和挑战,如供应延迟或者供应商故障等,从而保证供应链的稳定性。
ERP物料需求计划的基本步骤ERP物料需求计划通常包括以下几个基本步骤:1.物料需求预测:根据历史销售数据、市场需求趋势和其他相关因素,对未来一段时间内的物料需求进行预测和估算。
2.物料需求计划的编制:基于物料需求的预测结果,制定具体的物料需求计划表,明确需要采购的物料种类、数量和采购时间等信息。
3.物料供应商选择和采购:根据物料需求计划,选择合适的供应商,并与其进行合作进行物料的采购和供应。
4.物料需求计划的执行与控制:监控物料需求计划的执行情况,确保采购和供应的及时性和准确性。
5.物料需求计划的调整与优化:根据实际情况对物料需求计划进行调整和优化,以适应市场的变化和企业内外部环境的变化。
ERP物料需求计划的实施要点在实施ERP物料需求计划过程中,需要注意以下几个要点:1.数据的准确性:准确的数据是物料需求计划的基础,企业需要确保采集和分析的数据准确可靠,避免过于主观的估算和预测。
ERP系统物料需求计划演示教学

2020/6/9
第17页
再生式MRP
在再生式MRP运算中,MPS中列出的每一个最终 产品项目的需求都进行分解,每一个需要的BOM 文件都被访问,每一个相关物料的库存状态记录 都要更新,每一个物料的毛需求量和净需求量都 要重新计算,每一项作业计划的日程需要重新安 排,系统输出大量的相关报告。
在传统的手工管理方式下,由于计算效率 低、计算误差大等原因,某些物料的缺乏 往往在生产加工过程和装配过程中才能被 发现和记录。
缺料表往往是这种缺料现象的具体表现形 式。根据缺料表来进行采购作业安排和生 产作业安排的计划被称为缺料计划。
2020/6/9
第8页
MRP应该回答的问题
[A] 生产什么?生产多少?何时生产? [B] 要用到什么?用到多少?何时用到? [C] 已经有了什么?有多少?何时使用? [D] 还缺少什么?缺少多少?何时需要? [E] 何时安排?
2020/6/9
第6页
分时段的优先计划管理方式
MRP是一种分时段的优先计划管理方式。 为了理解这个概念,需要理解以下两点:
– 第一,物料需求量和物料需求时间之间的关系; – 第二,传统生产计划管理方式中采用的缺料计
划。
2020/6/9
第7页
缺料表
缺料表是传统手工管理方式下的缺料计划 的表现形式。
净改变式MRP的运行既可以每天运行,也可以实时运行。 净改变式MRP的优点在于对状态变化能够及时做出反应。
但是,这种方法也存在诸多缺点,例如,系统的自清理能 力差、数据处理的效率相对比较低以及对于各种变化过于 敏感等。
物料需求计划【共49张PPT】
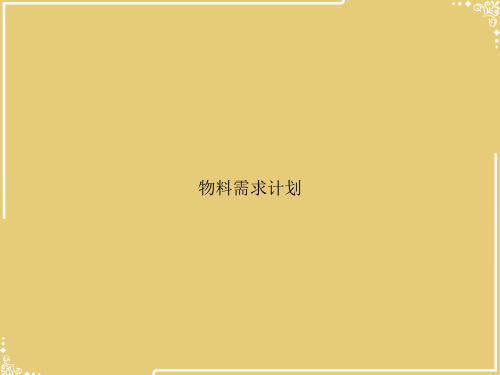
采购供应计划
每一项加工件的建议计划 • 需求数量 • 开始日期和完工日期
每一项采购件的建议计划 • 需求数量 • 订货日期和到货日期
MRP 的基本逻辑
四、MRPII的输入信息
MRP的输入有3个部分: • 主生产计划(产品出产计划MPS)
• 物料清单(产品结构文件,BOM) • 库存状态文件
物料清单(产品结构文件,BOM)
净需求=总需求—(预计到货量+现有量)+安全库存 于是,人们便思考:怎样才能在需要的时间,按需要的数量得到真正需用的物料?从而消除盲目性,实现低库存与高服务水平并存。 ERP是在MRP基础上发展起来的,以供应链思想为基础,融现代管理思想为一身,以现代化的计算机及网络通信技术为运行平台,集企业的各项管理功能为一身,并能对供应链上所有资源进行有效控 制的计算机管理系统。
件;要加工各种零件,就必须提前一定时间准备所需
数量的各种毛坯,直至提前一定时间准备各种原材料 。
其主要功能及运算依据为:
处 理 的 问 题 1. 生 产 什 么 ?生 产 多 少 ? 2. 要 用 到 什 么 ? 3. 已 具 备 什 么 ? 4. 还 缺 什 么 ? 何 时 需 要 ?
所 需 信 息 1. 切 实 可 行 的 主 生 产 计 划 ( M PS) 2. 准 确 的 物 料 清 单 ( BOM表 ) 3. 准 确 的 物 料 库 存 数 据 4. M RP的 计 算 结 果 ( 生 产 计 划 和 采 购 计 划 )
物料需求计划
本章学习目标
• 物料需求计划(MRP):
– Material Requirements Planning
• 制造资源计划(MRPⅡ ):
– Manufacturing Resource Planning
物料需求计划MRP与企业资源计划ERP课件38693

2024/7/29
10
POM
MRP的产生和发展(续)-小结
• 90年代,市场需求瞬息万变,竞争空间迅速扩大, 企业管理从面向内部资源管理转向面向社会一切 市场资源的有效利用。从而促进了ERP的出现。
一、MRP在企业经营系统中的地位和作用
– 在制定生产计划的过程中要进行任务与能力平衡。 这种平衡是粗略的,是以假定产品或代表产品为计 划单位核算的
– 将生产计划细化到具体产品,明确每种产品的出产 数量与出产时间,就得到了产品出产预计划
– 确定产品出产预计划时,要进行任务与能力的粗略 平衡,就得到了产品出产计划,也称主生产计划。
• 高库存,低服务水平
– 相关需求 – 95%服务水平,5个配件,总体服务水平0.774
• 形成块状需求
2024/7/29
7
POM
四、MRP的产生和发展
1) MRP阶段
– 六十年代初发展起来的MRP仅是一种物料需求计算器, 它根据对产品的需求、产品结构和物料库存数据来计算 各种物料的需求,将产品出产计划变成零部件投入出产 计划和外购件、原材料的需求计划,从而解决了生产过 程中需要什么,何时需要,需要多少的问题。它是开环 的,没有信息反馈,也谈不上控制。
处理的问题 1.生产什么?生产多少? 2. 要用到什么? 3. 已具备什么? 4. 还缺什么?何时需要?
所需信息 1. 切实可行的主生产计划(MPS) 2. 准确的物料清单(BOM) 3. 准确的物料库存数据 4. MRP的计算结果(生产计划和采购计划)
第5章物料需求ERP

3. 应用最先进的计算机技术,更加快速获取和 处理信息,为企业决策和运作提供更准确的 依据。
复习思考题
5-1 5-2 试述MRP与MRPⅡ的异同点。 简述MRPⅡ的组成及其特点。
5-3
5-4 5-5 5-6
ERP有哪些功能模块?
准时生产的基本思想是什么? 试述精良生产的特点和体系结构。 敏捷制造需要研究哪些关键技术?
第五章 先进管理理念与技术
5.1 物料需求计划(MRP)和制造资源计 划(MRPⅡ) 5.2 企业资源计划(ERP)
5.3 产品数据管理
5.1 物料需求计划和制造资源计 划
离散制造面临的问题:零部件繁多,需求提前期差
异大,由此造成物料供应非常复杂。因此,如何实
现各零部件协调生产,做到“在需要的时候提供需
4.人力资源管理模块
以往的ERPห้องสมุดไป่ตู้统基本上都是以生产制造及销售过程
(供应链)为中心的。因此,长期以来一直把与制造资源
企业内部的人力资源开始越来越受到企业的关注,被视 为企业的资源之本。在这种情况下,人力资源管理作为 一个独立的模块被加入到了ERP的系统中来,和ERP中
有关的资源作为企业的核心资源来进行管理。但近年来,
购件的采购和零部件的生产,以期将在制品、原材
料及成品控制在最优的水平。此外,根据物料需求 计划的结果可对生产能力进行核算,调整主生产计 划,尽量维持生产的平衡。
(2) 物流管理子系统。物流管理子系统包括库存
管理、物料的采购供应、市场营销等部分。物流管
理系统将向采购、销售和库房管理部门提供灵活的 日常业务处理功能,并能自动将物料执行信息反馈 给生产计划部门和财务部门。 (3)财务管理子系统。财务管理系统除对各类往 来账目和日常发生的货币支付账目进行处理外,根 据销售部门的销售单、发票、采购单、库存资金还
erp课件_第5章_物料需求计划(2015-4)详解

D(1)
E(2)
1
C(1)
D(1)
D(1)
F(1)
2
5.1.4 MRP的生成与更新方法
再生法:将对整个MRP系统进行重新计算与更新,是现行的 ERP系统大多采取的一种方法。
主生产计划的每一个最终产品的需求都加以分解 对每一个BOM文件进行访问 每一个库存状态记录都要刷新 只对主生产计划改变而影响MRP的部分物料清单进行MRP的局 部生成与更新。 该方法只适用于环境变化较大,而MRP计算复杂、耗时很长 的企业,通过局部的作业方式来取代全面分解的作业方式。
5.1.3 MRP报表与计算流程
MRP报表
MRP计算流程 MRP报表计算示例
批 提 现 已 分 前 有 配 量 期 量 量 1 1 0 1 2 0
安 低 物 全 库 层 料 存 量 码 号 MPS 计划产出 MPS 计划投入 MPS 计划产出 MPS 计划投入
时 段(周) 当 期 1 2 10 3 4 10 20 20 20 20 0 0 20 20 10 40 45 55 5 50 55 0 5 6 20 10 20 10 0 10 10 0 7 8 10
5.2.2 能力需求计划的分类
无限能力计划
无限能力计划是在作物料需求计划时暂时不考虑生产能力 的限制,而后对各个工作中心的能力、负荷进行计算得出 工作中心的负荷情况,产生能力报告。 当负荷>能力时,对超负荷的的工作中心进行负荷调整。 尽量平衡与调整能力,发挥最大能力。
超负荷
工作中心平均可用能力 交 货 期 日 一 二 三 四 五 六 日 一 二 三 四 五 ( 星期 )
可行、有效的计划管理方法。
MRP-ERP管理技术第5章 物料需求规划(MRP)

第五章 物料需求规划(MRP )本章内容在说明[物料需求规划(MRP )]的基本逻辑,以及它在管理上的功能。
重点在:我们为什么需要像MRP 这样的管理工具。
■共用料件引发的问题假设我们有两个成品,甲和乙,它们各自的BOM 如下所示:料品B 是甲的子件,同时也是D 的子件;料件c1是C 的子件,同时也是E 的子件。
因此,我们说B 和c1均是[共用件(Common Parts )].如果甲和乙均有客户订单量各100个,而现在我们要用在上一章中所说明的BOM 展开方式来计算各料品的供应数量。
当我们将甲的BOM 逐层展开后,再接着将乙的BOM 也展开时,B 的毛需求量为200,库存(可用)量为50个吗?当然不行,这50个已经预备给甲生产用了,如果再扣一次,将来生产乙时必会缺料,这种[一屋两卖]的现象,正是共同料件无法靠BOM 展开来计算需求量的原因。
该如何做才对呢?我们必须借助一个称作[低阶码]的技巧。
a2 (2) E (1)D (1) c1 (2) c3 (2)乙B (2)b1 (2)b2 (3)a1 (2) b2 (3) b1 (2) C (1) B (2) c1 (1) c2 (2)甲■低阶码与BOM 展开的顺序B 在甲的BOM 中,其阶码(Level Code)为1,但它在乙的BOM 中,阶码为2。
我们定义B 的低阶码(Low Level Code, LLC )为2,也就是B 在各BOM 中最[低]的那个[阶码]。
依照这个LLC 的定义,可以逐一计算各料品的LLC 如下示: LLC=0的有甲、乙LLC=1的有a1、a2、C 、D 、E LLC=2的有B 、c1、c2、c3 LLC=3的有b1、b2LLC 的计算是由电脑自动计算的,不能单由手工来计算,否则要是产品和料件一多,势必发生错误。
接着我们将要“同时”计算甲和乙所需各料品的净需求量,列表如5.1所示,依循的规则是:依照LLC 的顺序(由小到大)计算:步序 料品毛需求量(GR) X库存可用量(A V) Y 净需求量(NR)Z=X-Y读BOM 带出其下属子件的毛需求量1 甲 100 0100 a1 B C200(*3)200(*8-1) 100(*5)2 乙 100 40 60 a2 D E120(*4)60(*6) 60(*7)3 a1 200 120 804 a2 120 30 905 C100100c1 c2100(*9-1) 200(*10)6 D 60 0 60 B 120(*8-2)7 E6060c1 c3120(*9-2) 120(*11){表5.1 依低阶码展开BOM}{注:*符号为各步序计算时,毛需求的依据}到目前为止,已经完成LLC=0和1所有料品的净需求计算,依步序1~7的顺序,每次计算时都将毛需求量的来源予以注记,以免重复或漏失。
- 1、下载文档前请自行甄别文档内容的完整性,平台不提供额外的编辑、内容补充、找答案等附加服务。
- 2、"仅部分预览"的文档,不可在线预览部分如存在完整性等问题,可反馈申请退款(可完整预览的文档不适用该条件!)。
- 3、如文档侵犯您的权益,请联系客服反馈,我们会尽快为您处理(人工客服工作时间:9:00-18:30)。
低层码
A的低层码是 的低层码是1 的低层码是
0层 X MPS MRP Y
1层
A(1)
B(1)
C(1)
E(1)
2层
C(2)
D(1
F(1)
G(1)
C的低层码是 的低层码是2 的低层码是 计算时从上到下,需求累加 计算时从上到下 需求累加
5.1.3 MRP报表与计算流程 报表与计算流程
MRP报表 报表 MRP计算流程 计算流程 MRP报表计算示例 报表计算示例 报表
MRP的运算结果 MRP的运算结果
提出每个加工件和采购件的建议计划。 提出每个加工件和采购件的建议计划。
每种物料的需求 量 MRP运算 运算 每种物料的需求 时间
每一个加工件的开始 每一个加工件的开始 加工件 日期(计划投入期) 日期(计划投入期)和 完成日期(计划产出 完成日期( 期)
每一个采购件的订货 每一个采购件的订货 采购件 日期和入库日期
的主要问题
5 物料需求计划与能力需求计划
5.1 物料需求计划
5.1.1 MRP定义与作用 5.1.2 MRP的相关概念 5.1.3 MRP报表与计算流程 5.1.4 MRP MRP的生成与更新方法
5.2 能力需求计划
5.2.1 能力需求计划概述 5.2.2 能力需求计划的分类 5.2.3 能力需求计划的计算方法 5.2.4 能力需求计划的平衡
5.1.1 MRP的定义与作用 的定义与作用
MRP的作用 MRP的作用 编制零件的生产计划和采购计划. 生产计划和采购计划. 生产计划和采购计划 1
要用到什么? 要用到什么?
主生产计划 MPS
要生产什么? 要生产什么? 生产多少? 生产多少? 已经有了什么? 已经有了什么?
2
产品信息 物料清单) (物料清单) 工艺路线) (工艺路线)
计划接收量 预计可用库存量 35 50 2 40 5 10 2 C 净需求 计划产出量 计划投入量
55
55
MRP计算逻辑 计算逻辑
MRP的处理逻辑 的处理逻辑
先计算上层物料的需求,依次计算下层物料的需求。 先计算上层物料的需求,依次计算下层物料的需求。 每一层物料的计算项目与MPS计算类似, 每一层物料的计算项目与MPS计算类似,先计算第一时 MPS计算类似 段的项目,逐步计算未来时段。 段的项目,逐步计算未来时段。
X
时 段
提前期=1
批量=1 批量
现有量=0
1
2 10
MPS
计划产出量 计划投入量
3 10
4 10
5 10
6 10
7 10
9 10 11 12 10 10 10 10 5 8 10 9 10 11 12 10 5 10 5 9 10 11 12 20 20 10 10 10
8
物料需求计算
(逐级展开)
4
5
6
7
8
期 2/03 2/10 2/17 2/24 3/03 3/10 3/17 3/24 10 10 20 10 15 5 5 30 50 55 50 5 10 20 20 10 0 5 5 20 60 55 45 15 50 50 0 10 20 20 20 20 0 20 20 10 40 45 55 55 55 55 5 50 0 20 10 20 10 0 10 10 0 10
批 提 现 已 分 前 有 配 量 期 量 量 1 1 0 1 2 0
安 低 物 全 库 层 料 存 量 码 号 MPS 计划产出 MPS 计划投入 ቤተ መጻሕፍቲ ባይዱPS 计划产出 MPS 计划投入
时 段(周) 当 期
1
2 10
3
4 10
5
6 20
7
8 10
MRP的输入 的输入
10 20 10 10 20 20 10 0 5 5 20 60 45 15 50 50 50
20 3 4 20 5
20 6 20 7
采 购 计 划
O
时 段 毛 需 求 计划接收量 预计库存量 净 需 求 计划产出量 计划投入量
批量=40 现有量=10 批量
1
2 20
8 20
9 10 11 12 10 10 0 30 10 40
40 50 30 30 10 10 30 30 10 10 0 10 40 40 40
MRP与CRP的关系 与 的关系
物料需求计划: 物料需求计划: 对象:物料
物料1
物料2
物料3
工艺路线1
工序10 工序20 工序10 工序30
工艺路线2
工序10
工艺路线3
工序20 工序30 工序20 工序40
能力需求计划: 能力需求计划: 对象:工作中心
工作中心1
工作中心2
工作中心3
工作中心4
5.2.1 能力需求计划概述
A
时 段 计划产出量 计划投入量
提前期=1
批量=1
现有量=0
MRP
1 10
2 10
3 10
4 10
批量=1
5 10
6 10
7 10
X A (1) C (2) O (2)
加 工 C 计 时 段 划 计划接收量
计划产出量 计划投入量
提前期=1
现有量=0
1 20
2
3 20
4
5 20
6
7 20
8
20
提前期=2
观
3
4 个计划层次
总 帐
成本中心 会计科目 库存信息 物料清单 工作中心 工艺路线
微 观
4
1 个执行 控制 层次 个执行(控制 控制)层次
应 付 帐
供应商信息
5
成本会计 业绩评价
5.1.1 MRP的定义与作用 的定义与作用
MRP的定义 MRP的定义
MRP是对主生产计划的各个项目所需的全部制造件和全部 采购件的网络支持计划和时间进度计划。
结果1:还缺什 结果1:还缺什 1: 么?
4 物料需求计划 MRP
3 库存信息
(物料可用量) 物料可用量) 结果2:何时安 结果2:何时安 2: 排?
采购计划
生产计划
5.1.2 MRP的相关概念 的相关概念
物料清单BOM的概念 的概念 物料清单
物料清单BOM(Bill of Materials):是产品结构的技 物料清单 术性描述文件,它表明了产品组件、子件、零件直到 原材料之间的结构关系,以及每个组装件所需要的各 下属部件的数量 物料清单是一种树型结构,又称为产品结构树.
物流工程学院-陈敏
产品BOM 产品
1-指的是数 指的是数 0 层 量关系
X
MPS MRP
Y
1层
A(1)
B(1)
C(1)
E(1)
2层
C(2)
D(1
F(1)
G(1)
5.1.2 制定 制定MRP时需用的几个概念 时需用的几个概念
低层码的概念
物料的低层码是分配给物料清单上的每个物品一个从0 至N的数字码 在产品结构的物料清单中,最上层的低层码为0,下一 层则为1,依次类推 一个物品只能有一个MRP低层码。当一个物品在多个产 品中出现,或在同一个产品结构的不同层次出现时, 则取处在最低层的低层码为该物品的低层码。
2 能力需求计划解决如下问题: 能力需求计划解决如下问题:
2 2 2
各个物料经过哪些工作中心加工? 各工作中心的可用能力是多少,负荷是多少? 各工作中心的各个时段的可用能力与负荷是多少?
CRP与RCCP的区别 与 的区别
能力需求计划 运行流程图
加工任务
准备下达/已下达定单 需用 负荷 需用 能力 可用 能力
Y
1
2
15
0
0
1
A
毛需求 计划接收量 预计可用库存量 净需求 计划产出量 计划投入量
50
2
40
5
10
2
C
毛需求 ╳2+20╳1=30 5 计划接收量 35 预计可用库存量 净需求 计划产出量 计划投入量
5.1.4 MRP的生成与更新方法 的生成与更新方法
再生法:将对整个MRP系统进行重新计算与更新, 再生法:将对整个MRP系统进行重新计算与更新,是现行的 MRP系统进行重新计算与更新 ERP系统大多采取的一种方法。 ERP系统大多采取的一种方法。 系统大多采取的一种方法
MRP子系统与其他子系统的关系图 子系统与其他子系统的关系图
制造标准 BOM 独立需求
MPS 计划信息 生成 平衡
库存管理 库存信息
销售管理
MRP 生成
CRP
采购管理
车间管理
JIT管理 管理
5.2 能力需求计划
本节主要介绍能力需求计划及其运算
5.2.1 能力需求计划概述
CRP是一种将 是一种将MRP输出的对物料的分时段需求计划转 输出的对物料的分时段需求计划 是一种将 输出的对物料的分时段需求计划转 变成对企业各个工作中心的分时段需求计划的管理工具 变成对企业各个工作中心的分时段需求计划的管理工具 各个工作中心的分时段需求计划 ,同时协调MRP的计划内容和确保MRP在现有生产环境中 同时协调MRP的计划内容和确保MRP在现有生产环境中 MRP的计划内容和确保MRP 可行、有效的计划管理方法。 可行、有效的计划管理方法。 CRP是对于 是对于MRP包含的产品结构中每一级项目,分时 包含的产品结构中每一级项目, 是对于 包含的产品结构中每一级项目 段对各工作中心所需的各种资源进行计算, 段对各工作中心所需的各种资源进行计算,得到设备负 荷、人力负荷等资源负荷情况,进行生产能力与生产负 人力负荷等资源负荷情况, 荷的平衡,制订出能力需求计划。 荷的平衡,制订出能力需求计划。