压铸基本概念之压铸模具设计
压铸模具设计范文

压铸模具设计范文压铸模具设计是指为了生产压铸件而设计的模具,其主要任务是将液态金属注入模具中,并在模具中冷却、凝固,最终得到所需形状的金属零件。
压铸模具设计的主要工作包括设计模具的结构、选材、计算模具的合理尺寸和形状等。
一、压铸模具结构设计1.模具整体结构设计:根据压铸件的形状和尺寸,确定模具的整体结构。
一般情况下,压铸模具采用上下模结构,上模为固定模,下模为活动模。
针对复杂形状的压铸件,可能需要设计多个滑模和拉杆。
2.模腔设计:根据压铸件的形状和尺寸,确定模腔的几何形状和尺寸。
模腔的设计应保证在模具关闭时,模腔中的液态金属能够充满整个腔体,并且在冷却凝固过程中,金属能够均匀收缩,避免产生缩孔和其他缺陷。
3.浇口和导流系统设计:浇口和导流系统的设计对于压铸件的质量和生产效率有着重要的影响。
浇口的设计应尽量避免金属的湍流流动,避免气泡的产生。
导流系统的设计应考虑金属的顺序填充和排气,以及冷却和凝固过程中的温度控制。
二、压铸模具选材压铸模具的选材应根据金属的性能和压铸工艺的要求来确定。
通常情况下,模具会选用高强度和耐磨损的合金钢作为材料,以保证模具的使用寿命和精度。
同时,还需要考虑模具的热传导性能,以确保压铸件能够快速冷却、凝固。
三、压铸模具尺寸和形状计算1.模具尺寸计算:模具尺寸的计算包括模腔尺寸、模板尺寸、滑模尺寸、导流系统尺寸等。
模具尺寸的计算需要考虑压铸件的最终尺寸、缩孔和收缩率等因素。
2.模具形状计算:模具的形状计算主要是指模腔内部的曲面和棱角的设计。
对于复杂形状的压铸件,需要使用CAD软件进行三维建模和形状优化,以确保模具的制造精度和压铸件的质量。
压铸模具设计需要充分考虑压铸件的形状和尺寸、材料的性能、压铸工艺要求等因素,通过合理的结构设计、选材和计算,能够提升压铸件的质量和生产效率。
在设计过程中,还需要考虑模具的制造难度和制造成本,以确保模具的可行性和经济性。
压铸工艺与模具设计

压铸工艺与模具设计压铸是一种常见的金属成型工艺,通过将熔融金属注入到预先设计的模具中,经过冷却与固化,得到所需形状的金属制品。
压铸工艺具有高效、精度高、生产周期短等优点,广泛应用于汽车、机械、电子等领域。
而模具设计是实现压铸工艺的关键环节,决定了产品的质量和生产效率。
下面将从压铸工艺和模具设计两个方面进行详细阐述。
一、压铸工艺1.压铸工艺流程:首先,将金属加热至熔点,并注入到模具中;然后,通过高压注射机构,将熔融金属迅速注入模具中,并保持一段时间;待金属冷却并固化后,打开模具,取出成品。
2.压铸工艺特点:①高效、精度高:压铸通过模具的高速填充和快速冷却,能够实现高效率、高精度的生产;②生产周期短:相比其他金属成型工艺,压铸生产周期较短,适用于大批量生产;③生产成本低:压铸可以实现自动化生产,减少人工成本;④可复杂成型:压铸可以实现复杂形状、薄壁、高强度的金属制品成型。
二、模具设计模具设计是实现压铸工艺的关键环节,影响产品的质量和生产效率的重要因素。
以下是模具设计的主要考虑因素:1.模具材料选择:模具材料要具有耐磨性、耐腐蚀性、热传导性和高温强度,常用的模具材料包括铸钢、合金钢等。
2.模具结构设计:模具结构设计要考虑产品的形状、尺寸及要求,尽可能减少产品缺陷和铸件结构应力,提高生产效率和产品质量。
3.模具冷却系统设计:模具冷却系统的设计直接影响到成品的质量和生产效率。
合理的冷却系统设计可以加快铸件凝固速度,减少缺陷的产生。
4.模具排气系统设计:排气系统的设计对于排除铸件中的气体孔洞和缺陷非常重要,合理的排气系统设计能够提高产品质量。
5.模具表面处理:模具表面处理可以提高成品的表面质量和延长模具寿命,常见的表面处理方式包括硬镀铬、熔融硬化、电镀等。
总结:综上所述,压铸工艺与模具设计是密切相关的。
压铸工艺具有高效、精度高、生产周期短等优点,模具设计是实现压铸工艺的关键环节,包括模具材料选择、模具结构设计、模具冷却系统设计、模具排气系统设计和模具表面处理。
压铸模具的设计与制造

压铸模具的设计与制造摘要本文介绍了压铸模具的设计与制造的基本原理和步骤。
首先,通过分析压铸工艺的特点和要求,确定压铸模具的设计准则和选材原则。
然后,介绍了压铸模具的结构和主要部件,并详细阐述了压铸模具设计的关键要素,如模具尺寸、浇口设计、冷却系统等。
最后,介绍了压铸模具的制造过程和注意事项,包括模具加工工艺、表面处理和模具试模等。
1. 引言压铸是一种常用的金属件成型工艺,广泛应用于汽车、电器、航空航天等领域。
而压铸模具作为压铸工艺的核心部件,直接影响产品的质量和生产效率。
因此,设计和制造高质量的压铸模具对于压铸工艺的成功应用至关重要。
2. 压铸模具设计的准则和选材原则2.1 压铸模具设计准则 - 模具的结构要易于制造和装卸。
- 模具的结构要满足产品的要求,确保产品的尺寸和表面质量。
- 模具的结构要考虑生产的连续性,尽量减少生产过程中不必要的停机时间。
2.2 压铸模具选材原则 - 模具材料应具有足够的强度和耐磨性。
常用的模具材料有H13、5CrNiMo等。
- 模具材料的热稳定性要好,能够承受高温和热冷交替的工作环境。
- 模具材料的导热性要好,以便快速散热,降低模具温度。
3. 压铸模具结构和主要部件3.1 压铸模具结构 - 模具底座:承载模具的主要部件,负责固定模具和提供支撑。
- 固定板:固定模具的位置,具有高度和平面度要求。
- 移动板:用于模具的开合动作,实现铸件的脱模。
- 滑块:用于在模具开合过程中加快铸件的脱模速度。
-缩水板:用于控制铸件在冷却过程中的收缩变形。
3.2 压铸模具主要部件 - 模具腔:用于形成铸件的空腔部分,需要考虑产品的尺寸和形状。
- 浇杆系统:用于将熔融金属注入模腔中的系统,包括浇杆、浇口和溢流槽等。
- 冷却系统:用于控制模具温度的系统,可以通过冷却水或其他介质实现。
4. 压铸模具设计的关键要素4.1 模具尺寸 - 模具尺寸的确定要考虑产品的尺寸和结构要求,确保产品的尺寸和形状的准确性。
压铸成型工艺与模具设计

压铸成型工艺与模具设计一、引言压铸成型工艺是一种常见的金属零件制造方法,它通过将熔融金属注入模具中,经过冷却凝固后获得所需形状的零件。
模具设计是压铸成型工艺的关键环节,合理的模具设计可以保证产品质量和生产效率。
本文将介绍压铸成型工艺的基本原理以及模具设计的要点。
二、压铸成型工艺原理压铸成型工艺是将金属材料加热至液态,然后通过高压将熔融金属注入模具中,待冷却后获得所需形状的零件。
压铸成型工艺具有以下特点:1. 精度高:压铸成型工艺可以制造出形状复杂、尺寸精确的零件,满足不同行业的需求。
2. 生产效率高:压铸成型工艺具有高度自动化的特点,可以实现连续生产,提高生产效率。
3. 材料利用率高:压铸成型工艺可以减少废料产生,提高材料利用率。
4. 表面质量好:压铸成型工艺可以制造出光滑平整的表面,减少后续加工工序。
三、模具设计要点1. 材料选择:模具的材料应具有良好的热导性和耐磨性,常用的材料有冷作工具钢、热作工具钢和硬质合金等。
根据零件的要求,选择合适的模具材料。
2. 模具结构设计:模具的结构设计应考虑到零件的形状、尺寸和工艺要求,确保零件的成型质量。
模具的结构主要包括模腔、模芯、导向机构和冷却系统等。
3. 浇注系统设计:浇注系统的设计直接影响到熔融金属的流动和充填情况,应合理布置浇口、冲压头和溢流槽等。
同时,应考虑熔融金属的冷却和凝固过程,避免产生缺陷。
4. 铸件脱模设计:铸件脱模设计应考虑到零件的形状、表面质量和模具的结构,以确保零件的完整性和光洁度。
可以采用顶出机构、斜顶和分模等方式来实现铸件的脱模。
5. 冷却系统设计:冷却系统的设计对于模具寿命和零件质量有着重要影响。
应根据零件的形状和厚度,在模具中设置合适的冷却水路,以加快冷却速度,避免产生缺陷。
6. 模具加工工艺:模具的加工工艺应选用适当的加工方法和工艺参数,以确保模具的精度和表面质量。
常用的加工方法包括数控加工、电火花加工和线切割等。
7. 模具试模调试:模具制造完成后,需要进行试模调试,以验证模具的性能和调整工艺参数。
压铸模具设计基础知识

熱室壓鑄鋅合金中的合金元素
---雜質元素-鐵
鋅合金中鐵元素含不能>0.02%,鐵 元素可:
☺ 增加合金的硬度
但同時
增加合金的脆性
和合金中的鋁發生反應形成Al5Fe2金屬間化合物, 造成鋁元素的損耗並形成浮渣
在壓鑄件中出現硬點
2024/2/1
压铸模具设计基础知识
五.壓鑄合金及其性能
熱室壓鑄鋅合金中的合金元素 ---雜質元素-硅
t1:F1為克服磨擦力(壓室中)
壓
t2:開始進入型腔﹐因澆口急減﹐阻力 力
F
增大﹐F2>F1,達到高速充填
t3:(快速增壓階段)快速充填直止充滿
型腔最大值F3為壓射壓力
t4:F4靜壓力﹐對鑄件壓實
時間t
(壓射力與時間關係曲線見右圖)
2024/2/1
压铸模具设计基础知识
六.壓鑄工藝
定義2﹕壓射壓力就是在充模剛結束時壓射沖頭作用在金屬液面上的力。 定義3﹕壓射壓力是以壓射比壓來表示﹐壓射比壓就是充模結束時﹐壓射
沖頭作用于單位面積金屬液面上的壓力。
P ﹕壓射比壓( Pa ) P= F 4F F: 壓射壓力(N)
A πd 2 d ﹕壓室直徑 (m) A﹕沖頭截面積( m 2 )
壓射比壓與壓射壓力成正比﹐與壓射沖頭的截面積成反比。
鋅合金的 壓射比壓
壁厚 =<3mm 30MPa 簡單 40MPa 復雜
壁厚 >3mm 50MPa 簡單 60MPa 復雜
有害雜質元素:鐵(Fe),硅(Si),鉛(Pb),鎘(Gd),錫(Sn)
來源於鋁
來源於鋅
2024/2/1
压铸模具设计基础知识
五.壓鑄合金及其性能
2024/2/1
压铸模具设计基础知识

压铸模具设计基础知识一、概述压铸模具是用于压铸工艺的模具,在金属、塑料等材料的制品生产过程中起到关键作用。
压铸模具的设计质量直接影响产品的质量和生产效率。
本文将介绍压铸模具设计的基础知识,包括设计原则、材料选择、结构设计等内容。
二、设计原则1.功能性原则压铸模具应该符合产品的设计要求,能够满足产品的结构、尺寸、表面质量等要求。
设计过程中需要充分考虑产品的功能性需求,确保模具能够满足生产要求。
2.可制造性原则在设计压铸模具时,需要考虑到模具的加工工艺和生产成本。
设计应尽量简化,避免复杂的结构和加工工艺,以降低生产成本。
3.可靠性原则压铸模具在长期使用中需要具有稳定可靠的性能。
设计中需要考虑模具的寿命、耐磨性等因素,确保模具能够长时间稳定运行。
4.易维护性原则模具在使用过程中可能会有损坏或磨损,设计时需要考虑模具的易维护性,便于维修和更换受损部件。
三、材料选择压铸模具的材料选择直接影响模具的寿命和性能。
常用的模具材料包括工具钢、合金钢、硬质合金等。
在选择材料时需要考虑以下因素:1.硬度模具材料应具有足够的硬度和强度,能够抵抗压力和磨损,确保模具的稳定性和寿命。
2.热稳定性压铸过程中温度较高,模具材料需要具有良好的热稳定性,不易变形或烧损。
3.耐磨性压铸模具在长期使用中会有磨损,需要选择耐磨性好的材料,延长模具的使用寿命。
4.耐蚀性部分压铸过程中会有化学物质接触,模具材料需要具有良好的耐腐蚀性,避免腐蚀损坏。
四、结构设计压铸模具的结构设计直接影响产品质量和生产效率。
在设计时需要考虑以下因素:1.分型设计合理的分型设计能够提高产品的成型效率和质量,减少缺陷产生。
分型设计应考虑产品的结构特点和成型过程中的收缩变形。
2.冷却系统设计冷却系统设计影响压铸过程中的温度控制和冷却速度,直接影响产品的组织和性能。
设计时应考虑冷却系统的布局和冷却介质的选择。
3.排气系统设计在压铸过程中需要排除模具内的气体,避免气泡和气孔产生。
压铸工艺及模具设计

压铸工艺及模具设计在工业生产中,压铸工艺及模具设计是常见且重要的工艺制造方法。
压铸工艺以其高效、高质量和高精度的特点,被广泛应用于汽车、摩托车、电子、机械和家电等行业。
压铸工艺是指将金属材料经过加热熔化后,通过高压注入模具中,使金属凝固成型的工艺过程。
压铸工艺的主要特点是能够快速、高效地生产复杂形状、高精度的零部件。
压铸工艺通常分为冷室压铸和热室压铸两种方式。
冷室压铸适用于铝合金、镁合金和铜合金等高熔点金属的铸造,而热室压铸适用于低熔点金属如锌合金、铅合金和锡合金等的铸造。
模具设计在压铸工艺中起到了至关重要的作用。
模具设计的质量直接影响到产品的质量、生产效率和成本。
压铸模具通常包括上模、下模、模芯和顶针等零件组成。
对于复杂形状的产品,还需要考虑模具的结构、冷却系统和顶出机构等技术要求。
模具设计要考虑到产品的材料、几何复杂度、尺寸精度和表面质量等因素,充分利用材料的力学性能和热传导性能,以满足产品的工程要求。
1.材料选择:压铸工艺适用于铝合金、镁合金、铜合金、锌合金等多种金属材料。
不同的材料有不同的熔点、流动性和固化速度等特点,需要根据产品的要求选择合适的材料。
2.模具结构:模具的结构包括上模、下模和模芯等组成部分,需要考虑产品的几何形状、尺寸精度和表面质量等工程要求。
同时,模具还要具备良好的刚性和稳定性,以确保产品的精度和质量。
3.冷却系统:在压铸过程中,金属材料需要快速冷却和固化,以保证产品的密实性和准确性。
因此,模具中需要设置合理的冷却系统,以提高铸件的冷却速度和冷却效果。
4.顶出机构:对于出模困难的产品,需要设计合适的顶出机构,以确保产品能够顺利脱模。
顶出机构通常包括顶针、顶杆和顶出板等部件。
5.加工工艺:压铸工艺需要考虑金属材料的熔化温度、注射压力和注射速度等因素。
在模具设计中要合理设置熔化炉、喷嘴和压机等设备,确保加工工艺的可行性和稳定性。
在压铸工艺及模具设计中,需要综合考虑产品的功能要求、表面效果、生产批量和成本等因素,以找到最优的工艺和设计方案。
压铸工艺及压铸模具设计要点

压铸工艺及压铸模具设计要点压铸工艺及压铸模具设计要点压铸是一种利用压力将液态金属注入模具中,通过冷却凝固形成定形零件的制造方法。
压铸产品在重量、强度、尺寸方面都有非常高的准确性和稳定性,被广泛应用于汽车、摩托车、电子、通讯设备、家电等产业中,成为目前工业生产中不可或缺的一种制造技术。
下面将从压铸工艺及压铸模具设计要点两个方面进行阐述。
一、压铸工艺1. 材料准备:首先需要准备液态金属,一般使用的是微量合金钢、铝合金、镁合金、铜合金等牌号。
材料的纯度、质量直接影响产品的质量。
2. 模具设计:由于压铸的成形过程主要依靠模具的形状和大小,所以模具设计非常重要。
模具一般由流道、高压室、模腔等主要部分组成,需要用CAD 设计软件绘制出预想的产品三维模型,然后进行分析预测。
3. 夹具安装:很多压铸厂家采用自动化流水线作业,这样可以让夹具自动加载模具。
夹具的准确安装和保持最佳状态对产品稳定的尺寸和质量有着至关重要的作用。
4. 液态金属注入:注入过程需要注意金属温度的控制,因为如果注入过热的金属会造成热缩,也会加快金属与模具接触面损耗的速度。
注入金属的速度和压力也需要掌握恰当的水平。
5. 压力保持和冷却:完成注入后,需要将模具保持一定的压力,通常设置的保持时间在15-20秒之间,直到金属凝固成型,然后通过水冷却或空气冷却来加速金属的冷却,降低模腔温度,以便后续顺利脱模。
6. 脱模:经过强制冷却后,模具表面的金属固化成型,可以脱模取出。
如果模具内存在脱模困难的产品,则采用震动或喷水技术来辅助脱模。
二、压铸模具设计要点1. 模具材料:模具材料的决定因素是金属的特性和成本。
有些材料具有良好的抗磨损性和耐腐蚀能力,例如CrMoV 钢,有些材料则具有良好的导热性和导电性能,例如铝合金。
选用模具材料需要考虑两方面因素:一、材料的使用寿命;二、成本。
2. 模具结构:模具结构需要考虑到成品的尺寸、线条、强度和表面质量等因素。
通常情况下,模具结构应该是四侧对称的,以确保在生产过程中的稳定性和成品准确性。
压铸基本概念压铸模具设计
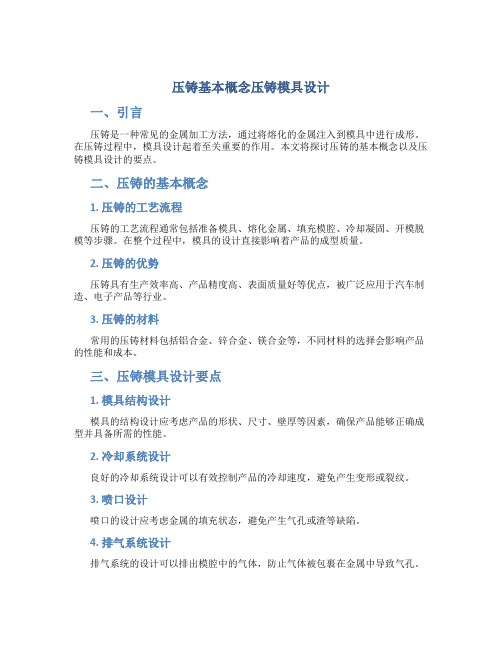
压铸基本概念压铸模具设计
一、引言
压铸是一种常见的金属加工方法,通过将熔化的金属注入到模具中进行成形。
在压铸过程中,模具设计起着至关重要的作用。
本文将探讨压铸的基本概念以及压铸模具设计的要点。
二、压铸的基本概念
1. 压铸的工艺流程
压铸的工艺流程通常包括准备模具、熔化金属、填充模腔、冷却凝固、开模脱模等步骤。
在整个过程中,模具的设计直接影响着产品的成型质量。
2. 压铸的优势
压铸具有生产效率高、产品精度高、表面质量好等优点,被广泛应用于汽车制造、电子产品等行业。
3. 压铸的材料
常用的压铸材料包括铝合金、锌合金、镁合金等,不同材料的选择会影响产品的性能和成本。
三、压铸模具设计要点
1. 模具结构设计
模具的结构设计应考虑产品的形状、尺寸、壁厚等因素,确保产品能够正确成型并具备所需的性能。
2. 冷却系统设计
良好的冷却系统设计可以有效控制产品的冷却速度,避免产生变形或裂纹。
3. 喷口设计
喷口的设计应考虑金属的填充状态,避免产生气孔或渣等缺陷。
4. 排气系统设计
排气系统的设计可以排出模腔中的气体,防止气体被包裹在金属中导致气孔。
5. 浇口设计
浇口设计应考虑金属的流动路径,避免产生气孔或短裂纹。
四、总结
压铸是一种重要的金属加工方法,模具设计是保证产品质量的关键。
通过合理的模具设计,可以有效提高产品的生产效率和质量。
希望本文对压铸基本概念和压铸模具设计有所帮助。
以上内容为压铸基本概念和压铸模具设计的相关内容,涉及了压铸的优势、材料、模具结构设计、冷却系统设计等方面。
压铸成型工艺与模具设计
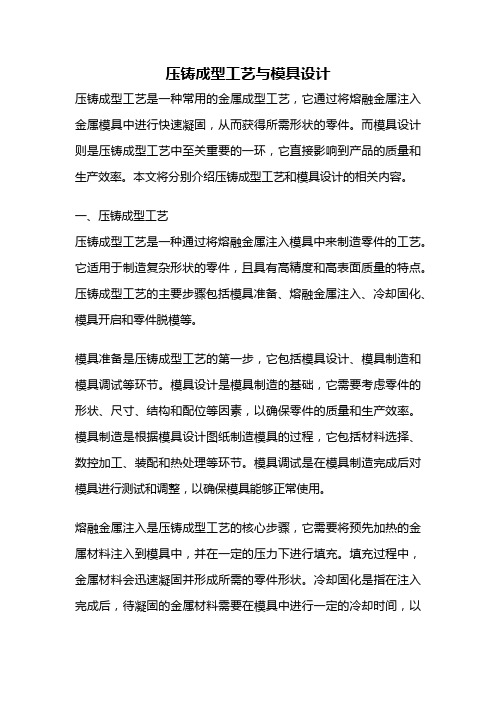
压铸成型工艺与模具设计压铸成型工艺是一种常用的金属成型工艺,它通过将熔融金属注入金属模具中进行快速凝固,从而获得所需形状的零件。
而模具设计则是压铸成型工艺中至关重要的一环,它直接影响到产品的质量和生产效率。
本文将分别介绍压铸成型工艺和模具设计的相关内容。
一、压铸成型工艺压铸成型工艺是一种通过将熔融金属注入模具中来制造零件的工艺。
它适用于制造复杂形状的零件,且具有高精度和高表面质量的特点。
压铸成型工艺的主要步骤包括模具准备、熔融金属注入、冷却固化、模具开启和零件脱模等。
模具准备是压铸成型工艺的第一步,它包括模具设计、模具制造和模具调试等环节。
模具设计是模具制造的基础,它需要考虑零件的形状、尺寸、结构和配位等因素,以确保零件的质量和生产效率。
模具制造是根据模具设计图纸制造模具的过程,它包括材料选择、数控加工、装配和热处理等环节。
模具调试是在模具制造完成后对模具进行测试和调整,以确保模具能够正常使用。
熔融金属注入是压铸成型工艺的核心步骤,它需要将预先加热的金属材料注入到模具中,并在一定的压力下进行填充。
填充过程中,金属材料会迅速凝固并形成所需的零件形状。
冷却固化是指在注入完成后,待凝固的金属材料需要在模具中进行一定的冷却时间,以确保零件的质量。
模具开启是指在冷却固化完成后,将模具开启,并将形成的零件从模具中取出。
零件脱模是指将零件从模具中取出的过程,通常需要使用专用的工具。
二、模具设计模具设计是压铸成型工艺中至关重要的一环,它直接影响到产品的质量和生产效率。
模具设计的主要目标是实现零件的准确成型和高效生产。
模具设计需要考虑以下几个方面的因素。
模具设计需要考虑零件的形状和尺寸。
根据零件的形状和尺寸,确定模具的结构和形状,以确保零件能够准确地成型。
同时,还需要考虑到零件的配位和装配要求,以便在成型过程中能够满足零件的功能需求。
模具设计需要考虑材料的选择和加工工艺。
根据零件的材料和加工要求,选择合适的模具材料,并确定相应的加工工艺。
压铸工艺及压铸模具设计
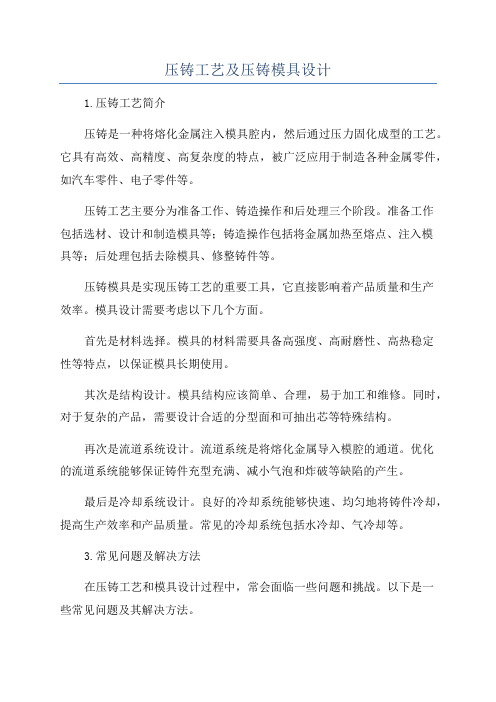
压铸工艺及压铸模具设计1.压铸工艺简介压铸是一种将熔化金属注入模具腔内,然后通过压力固化成型的工艺。
它具有高效、高精度、高复杂度的特点,被广泛应用于制造各种金属零件,如汽车零件、电子零件等。
压铸工艺主要分为准备工作、铸造操作和后处理三个阶段。
准备工作包括选材、设计和制造模具等;铸造操作包括将金属加热至熔点、注入模具等;后处理包括去除模具、修整铸件等。
压铸模具是实现压铸工艺的重要工具,它直接影响着产品质量和生产效率。
模具设计需要考虑以下几个方面。
首先是材料选择。
模具的材料需要具备高强度、高耐磨性、高热稳定性等特点,以保证模具长期使用。
其次是结构设计。
模具结构应该简单、合理,易于加工和维修。
同时,对于复杂的产品,需要设计合适的分型面和可抽出芯等特殊结构。
再次是流道系统设计。
流道系统是将熔化金属导入模腔的通道。
优化的流道系统能够保证铸件充型充满、减小气泡和炸破等缺陷的产生。
最后是冷却系统设计。
良好的冷却系统能够快速、均匀地将铸件冷却,提高生产效率和产品质量。
常见的冷却系统包括水冷却、气冷却等。
3.常见问题及解决方法在压铸工艺和模具设计过程中,常会面临一些问题和挑战。
以下是一些常见问题及其解决方法。
首先是翘曲和变形问题。
由于金属在冷却过程中会有收缩和变形,容易导致铸件产生翘曲和变形。
解决方法可以是增加冷却系统,控制金属温度等。
其次是气孔和缺陷问题。
气孔和缺陷是常见的铸件质量问题,可能是由于金属中的气体未能完全排出或模具内部有不完全填充的区域导致。
解决方法可以是优化流道和冷却系统,增加压力等。
最后是模具使用寿命问题。
模具在使用过程中会受到磨损、冲击和热应力等的影响,容易损坏。
解决方法可以是选用高耐磨材料、增加模具表面硬度等。
4.发展趋势随着科技的发展和需求的变化,压铸工艺和模具设计也在不断发展和改进。
未来的发展趋势主要包括以下几个方面。
首先是数字化和智能化。
通过数字化技术和智能化设备,可以实现对压铸工艺和模具设计的更精确和高效的控制。
压铸工艺与模具设计

压铸工艺与模具设计压铸是一种将熔化的金属,通过模具施加高压力注入到模具腔中,然后在熔融金属冷却硬化后,得到所需形状和尺寸的零件的工艺过程。
压铸工艺通常适用于生产大批量、高精度、复杂形状的零件。
本文将探讨压铸工艺和模具设计的相关内容。
首先,压铸工艺的步骤通常包括以下几个环节:模具准备、熔化金属、注射过程、冷却固化和模具开合。
在模具准备阶段,需要设计和制造出合适的模具来满足产品的形状和尺寸要求。
模具通常由两部分组成,上模和下模,通过模具腔来形成零件的形状。
熔化金属通常使用锌合金、铝合金或镁合金等。
在注射过程中,熔化金属被注入到模具腔中,并施加高压力以保证充满整个腔体。
随后,冷却固化过程中,熔化金属冷却变硬,形成所需的零件形状。
最后,模具开合以取出成品零件,准备进行后续的加工和表面处理。
在模具设计方面,需要考虑以下几个关键因素:零件的形状和尺寸、模具材料的选择、模具结构设计和冷却系统设计。
首先,要根据产品的形状和尺寸要求,设计出相应的模具腔。
模具腔的设计需要保证零件的形状完整、尺寸精确,并能满足产品的功能要求。
其次,模具材料的选择非常重要。
常用的模具材料包括工具钢、热作钢和硬质合金等。
模具材料需要具有足够的强度和韧性,以承受高压力和高温的影响,并具有良好的耐磨性。
然后,模具结构设计需要考虑模具的刚度和稳定性。
模具结构应该合理布置,以减少零件变形和缩孔等缺陷。
最后,冷却系统的设计对于压铸工艺的质量和效率都有很大的影响。
冷却系统通常包括冷却通道和冷却剂。
冷却通道的布置应合理,以实现均匀的冷却效果。
冷却剂的选择需要考虑其散热性能和耐腐蚀性能,以确保模具的冷却效果。
在实际应用中,压铸工艺和模具设计都面临着一些挑战。
首先,零件的形状和尺寸越复杂,模具设计的难度就越大。
一些复杂形状的零件可能需要设计多个活动模块和滑动芯来实现。
这对模具制造和使用都提出了更高的要求。
其次,模具材料的选择和模具结构的设计都会影响到产品的质量和寿命。
压铸模设计压铸件结构设计及压铸工艺

压铸模设计、压铸件结构设计及压铸工艺引言压铸是一种常用的金属零件制造方法,其通过将熔化的金属注入到预先加工好的模具中,通过压力将金属冷却固化成型。
在压铸过程中,压铸模具的设计、压铸件结构的设计以及压铸工艺的选择都是至关重要的。
本文将分别介绍压铸模设计的相关要点、压铸件结构设计的原则以及压铸工艺的选择。
压铸模设计要点压铸模具是进行压铸加工的关键工具,其设计的合理与否直接影响到产品质量和生产效率。
下面是一些压铸模设计的要点:1.模具材料选择:常见的模具材料有钢、铝合金等,根据压铸件的要求和使用场景选择合适的模具材料,以确保模具具有足够的强度和耐磨性。
2.结构设计:模具的结构要合理,与压铸件的形状相匹配,避免出现脱模困难、变形等问题。
同时,要考虑到模具的拆卸和维护,方便进行清理和更换模具零部件。
3.冷却系统设计:在模具中设置合适的冷却系统,以提高压铸件的凝固速度并避免产生缺陷。
冷却系统的设计要考虑到冷却介质的流动性、冷却效果以及与压铸件形状的匹配等因素。
4.压铸模表面处理:对模具表面进行适当的处理,如喷涂涂层、表面硬化等,以延长模具的使用寿命和提高模具的抗腐蚀性能。
压铸件结构设计原则压铸件结构设计的目标是在满足产品功能和外观要求的前提下,尽量减少结构复杂性和提高生产效率。
以下是一些常用的压铸件结构设计原则:1.壁厚均匀:保持压铸件的壁厚均匀,避免厚度过大或过薄导致不均匀收缩和应力集中。
2.避免尖角和过度薄壁结构:减少压铸件中的尖角和过度薄壁结构,因为这些部分容易引起变形和缺陷。
3.引导放料设计:在压铸件结构中设置合适的引导放料设计,以确保熔融金属能够充分填充整个模腔,并避免产生气孔和冷却不均。
4.滑动方向和出料设计:考虑到模具的拆卸和压铸件的出料,结构中应合理设置滑动方向和出料设计,以方便模具的安装和压铸件的脱模。
压铸工艺选择在确定了压铸模具设计和压铸件结构设计后,还需要选择适合的压铸工艺。
以下是一些常用的压铸工艺选择要点:1.压铸机选择:根据压铸件的尺寸和形状,选择合适的压铸机型号和规格。
压铸基本概念压铸模具设计2.pptx
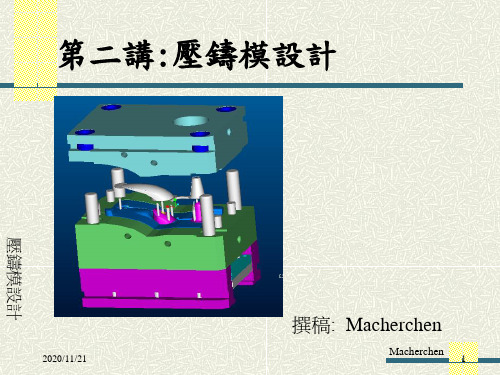
(1) 分型後壓鑄件能從模具型腔內取出來 (2) 開模後壓鑄件應留在動模上 (3) 分型面選擇應保証壓鑄件的尺寸精度
和表面質量(產品的要求) (4) 有利於澆注系統和排氣系統的布置 (5) 應便於模具加工,模具加工工藝的
可行性,可靠性及方便性
壓鑄模設計
2020/11/21
壓鑄模設計
2020/11/21
Macherchen
3
壓鑄模設計
二. 壓鑄模的結構組成
二). 壓鑄模結構根據作用分類
(一)成型零件
型腔:外表面 型芯:內表面
(二)澆注系統
直澆道(澆口套) 模澆道(鑲塊) 內澆口 余料
(三)導準零件: 導柱;導套
2020/11/21
Macherchen
4
二. 壓鑄模的結構組成
Macherchen
10
壓鑄模零部件設計
二.成型零部件的結構設計與尺寸計算
(一)熱交變應力 除承受金屬液的高速沖刷
外,還吸收金屬凝固過程中 的熱量,產生熱量交換,表 面高溫膨脹,其它相對較小 激冷產生拉應力, 交變應 力增強,超過疲勞極限,產生 塑性變形,在晶界處產生裂紋.
熱膨脹
壓應力
拉應力
2020/11/21
壓鑄模零部件設計
(三)成型零部件工作尺寸計算
1. 定義:成型零部件中直接決定壓鑄件幾何形狀的尺寸稱為工作尺寸.
分為:型腔尺寸,型芯尺寸,中心距尺寸.
徑向尺寸
型腔尺寸
包容尺寸,磨損變大
深度尺寸
徑向尺寸 型芯尺寸
高度尺寸
被包容尺寸,磨損變小
壓鑄模設計
2020/11/21
Macherchen
压铸工艺及模具设计

2003年
2004年
23
2005年我国压铸件主要用户行业需求量和比
81400 t例
一般机械及其
101900 t
他领域 9.40%
电器、电子
和电脑
11.80%
138200 t 五金、玩具
、车模 16.00%
542700 t 汽车和摩
托车, 62.80%
24
25
26
27
28
2、发展展望
➢自主开发先进压铸机、熔炼设备和其他 辅助装备; ➢压铸模CAD/CAM/CAE技术; ➢注重薄壁、复杂形状和高性能铝合金压 铸技术的开发与应用; ➢镁合金压铸的发展及应用; ➢半固态成形技术。
20
(二)国内压铸的发展
21
1、发展现状
中国模具行业发展迅猛,1996年~2004年其 产量年均增长率为14%,2003年压铸模行业的 产值达38亿元。
目前,国产模具只能满足市场需求的80%左 右,其中又以中、低档模具为主;在生产大型、 复杂的精密模具方面,其工艺技术、模具质量、 使用寿命以及生产能力等均不能满足国民经济发 展的需要。
22
2000年至2004年全国压铸件总产量与汽车 产量增长情况
5000000 4500000 4000000 3500000 3000000 2500000 2000000 1500000 1000000 500000
0
汽车总产量/辆 其中轿车产量/辆 压铸件总产量/t
2000年 2001年
2002年
4
压铸工艺过程演示
5
产品图 工艺设计 模具设计 模具制造
模具安装
模具预热
喷刷涂料 合模 浇注
压铸成形 开模取件
压铸模具设计基础知识

压铸模具设计基础知识压铸模具是制造压铸件的关键设备,它直接影响着压铸产品的质量和生产效率。
下面将详细介绍压铸模具设计的基础知识。
一、压铸模具的分类压铸模具一般可分为冷室压铸模具和热室压铸模具两大类。
冷室压铸模具适用于铝合金和铜合金的压铸生产,相对简单,但适用于高温熔融的压铸合金。
热室压铸模具适用高熔点压铸合金,具有较高的耐热性和抗高温挤压性能。
二、压铸模具的结构1.压铸模具主要由模架、模座、模芯、出料系统和冷却系统等组成。
2.模架是模具的主架构,起着支撑模具部件和固定模具部件的作用。
3.模座是连接模具与注射机的部件,将模具安装在注射机上,保证注射过程的稳定性。
4.模芯是模具中用来形成产品内部空洞的零件,它通常由多段组成,可以根据产品的形状进行组装。
5.出料系统是将熔融的金属注入模腔的路径,通常由进料口、浇口和溢流槽等组成。
6.冷却系统是保证模具持续工作的关键部分,它能够快速降温和加热模具,确保产品冷却时间的缩短和生产效率的提高。
三、压铸模具设计的基本原则1.单向释放原则:保证产品易于从模具中脱模,避免产品损坏。
2.对称设计原则:尽量保证模具零件左右对称,以降低模具零部件制造和装配的难度。
3.预防变形原则:通过模具结构设计和冷却系统的合理布局来降低模具零件的变形,确保产品的尺寸精度。
4.合理浇注和冷却系统原则:通过优化浇注系统设计和加强冷却系统的作用,提高压铸产品表面质量,并缩短冷却时间。
5.合理安装和调整原则:确保模具零件的安装和调整精度,提高模具的使用寿命和产品的质量。
四、压铸模具设计的步骤1.确定产品的设计要求和材料性能,进行产品分析和模具选型。
2.进行模具结构设计,包括模腔结构、模芯结构、冷却系统和出料系统等设计。
3.进行模具零部件设计,包括模板、模座、模芯、冷却水口等零部件的形状和尺寸设计。
4.进行模具零部件的制造和装配,进行试模和测试,及时修复和调整模具零部件。
5.进行模具的调试和优化,包括调整出料系统、冷却系统等,确保模具的正常工作。
压铸基本概念之压铸模具设计

压铸基本概念之压铸模具设计一、引言压铸是一种工业生产中常用的金属加工方法,其核心是利用高压将熔化的金属注入模具中进行塑性变形,从而得到所需的零件或产品。
在压铸过程中,压铸模具的设计是至关重要的环节。
本文将深入探讨压铸模具设计中的基本概念和要点。
二、压铸模具设计的基本原理1.压铸模具的作用–压铸模具是实现压铸工艺的关键设备,其主要作用是将熔化的金属注入模具腔体,使其形成预定形状和尺寸的零件或制品。
2.压铸模具设计的目标–实现零件的精确成形–提高生产效率–增加模具的使用寿命三、压铸模具设计的要点1.模具结构设计–模具应具有合理的结构,便于金属的顺利充填和零件的脱模。
常见的模具结构有冷室型模具、热室型模具等。
2.材料选用–模具应具有良好的硬度、韧性和耐磨性。
常用的模具材料有铝合金、钢等。
3.流道设计–流道设计直接影响金属的充填情况和零件的质量。
合理设计的流道可以减少气泡、冷隔等缺陷的产生,提高产品的一致性。
4.散热设计–快速散热有助于减少生产周期,并提高生产效率。
模具的散热设计包括散热通道、冷却系统等。
5.脱模设计–脱模是压铸过程中关键的一步,脱模不畅容易导致产品变形、表面缺陷等问题。
因此,模具设计时应考虑脱模的便捷性和稳定性。
四、模具设计的优化方法1.CAE仿真–使用计算机辅助工程(CAE)仿真技术,可以模拟压铸过程中的各种影响因素,帮助优化模具设计,提前发现潜在问题。
2.CAD设计–利用计算机辅助设计(CAD)软件,可以精确绘制模具结构和流道设计,提高设计效率和精度。
五、结论压铸模具设计是压铸工艺中至关重要的一环,优化的模具设计可以提高产品质量,降低生产成本,提高生产效率。
通过深入了解压铸模具设计的基本概念和要点,可以帮助工程师们更好地设计出符合需求的模具,推动压铸工艺的发展。
以上是关于压铸模具设计的基本概念和要点的详细介绍,希望对压铸行业从业人员有所帮助。
压铸模具设计
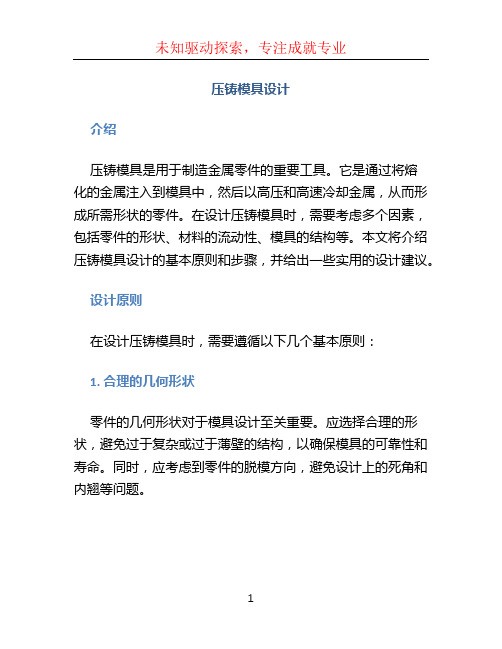
压铸模具设计介绍压铸模具是用于制造金属零件的重要工具。
它是通过将熔化的金属注入到模具中,然后以高压和高速冷却金属,从而形成所需形状的零件。
在设计压铸模具时,需要考虑多个因素,包括零件的形状、材料的流动性、模具的结构等。
本文将介绍压铸模具设计的基本原则和步骤,并给出一些实用的设计建议。
设计原则在设计压铸模具时,需要遵循以下几个基本原则:1. 合理的几何形状零件的几何形状对于模具设计至关重要。
应选择合理的形状,避免过于复杂或过于薄壁的结构,以确保模具的可靠性和寿命。
同时,应考虑到零件的脱模方向,避免设计上的死角和内翘等问题。
2. 流线型设计在注入熔融金属时,要确保金属流动的顺畅和均匀。
因此,模具的设计应尽量避免死角和锐角,采用流线型的设计,以提高金属的流动性和充填性。
3. 强度和稳定性模具需要承受高压和高温的工作环境,因此需要具备足够的强度和稳定性。
结构设计应合理,考虑到模具的受力情况和热膨胀等因素,以确保模具在工作过程中不会出现变形和损坏。
4. 易于制造和维修模具的制造和维修是一个复杂的过程,因此设计时应考虑到制造和维修的可行性。
模具的结构应尽量简化,并采用易于加工和替换的零部件,以便在需要时进行维修和更换。
设计步骤1. 零件分析在进行压铸模具设计之前,首先需要对待生产的零件进行全面的分析。
分析包括材料的性质、几何形状和尺寸、工艺要求等方面的内容。
通过这些分析,可以初步确定模具的类型和结构。
2. 模具类型选择根据零件的性质和生产要求,选择合适的模具类型。
常见的模具类型包括单腔模、多腔模和滑动模等。
选择模具类型时,需要综合考虑生产效率、成本和质量等因素。
3. 模具结构设计根据选择的模具类型,进行具体的模具结构设计。
设计包括模具的核心和型腔结构、冷却系统、进气系统等。
设计时应考虑到零件的几何形状、材料的流动性和冷却要求等因素,以提高生产效率和零件质量。
4. 模具材料选择模具的材料需要具备一定的硬度、强度和耐磨性。
- 1、下载文档前请自行甄别文档内容的完整性,平台不提供额外的编辑、内容补充、找答案等附加服务。
- 2、"仅部分预览"的文档,不可在线预览部分如存在完整性等问题,可反馈申请退款(可完整预览的文档不适用该条件!)。
- 3、如文档侵犯您的权益,请联系客服反馈,我们会尽快为您处理(人工客服工作时间:9:00-18:30)。
壓鑄模設計
2020/10/24
Macherchen
17
壓鑄模零部件設計
圓形小型芯的固定形式如圖所示:
壓鑄模設計
a)一般式通孔台肩 b)階梯式(固定長) c)壓塊式
3 凹模鑲塊和型芯的止轉
形式有﹕ (1)圓柱銷 (2)平鍵
(3)平面式
2020/10/24
d)螺塞固定
e)螺柱聯接
Macherchen
18
谢谢大家!
Macherchen
壓鑄模設計
壓鑄模設計
2020/10/24
Macherchen
3
壓鑄模設計
二. 壓鑄模的結構組成
二). 壓鑄模結構根據作用分類
(一)成型零件
型腔:外表面 型芯:內表面
(二)澆注系統
直澆道(澆口套) 模澆道(鑲塊) 內澆口 余料
(三)導準零件: 導柱;導套
2020/10/24
Macherchen
4
二. 壓鑄模的結構組成
(1) 凸模是成型壓件整體內形的零部件,所以也稱為主型芯. 主型芯的結構形式有:整體式,通孔台肩式,通孔無台肩 (螺絲固定)式及非通孔.
壓鑄模設計
2020/10/24
利於加工
利於加工
Macherchen
16
壓鑄模零部件設計
(2)小型芯的結構形式 a.小型芯要有起導流作用的圓角弧或倒角過渡,如圖a)所示。通 常 台階c的大小為1~2mm,最小0.3mm。如果制成直通式﹐如 圖B)所示﹐則金屬易進入配合間隙﹐常期使用會侵蝕該處 (圖中A處)﹐嚴重時影響脫模。 b. 如果型芯雖有台階但制成清角而不是圓弧過渡﹐過小的型 芯在熱處理時會產生應力集中而折斷。
Macherchen
2
二. 壓鑄模的結構組成
一). 壓鑄模結構組成 定模:固定在壓鑄機定模安裝板上,有直澆道與噴嘴或壓室聯接 動模:固定在壓鑄機動模安裝板上,並隨動模安裝板作開合模移動 合模時,閉合構成型腔與澆鑄系統,液體金屬在高壓下充滿型 腔;開模時,動模與定模分開,借助於設在動模上的推出機構將鑄件 推出.
二).壓鑄模結構根據作用分類 (四)推出機搆:推杆(頂針),复位杆,推杆固定板,推板,
推板導柱,推板導套. (五)側向抽芯機搆:凸台&孔穴(側面),鍥緊塊,限位彈簧,螺杆. (六)排溢系統:溢澆槽,排氣槽.
(八)支承零件:定模&動模座板﹐墊塊(裝配,定位,安裝作用)
壓鑄模設計
20பைடு நூலகம்0/10/24
Macherchen
壓鑄模設計
2020/10/24
Macherchen
20
树立质量法制观念、提高全员质量意 识。20. 10.2420 .10.24Saturday , October 24, 2020 人生得意须尽欢,莫使金樽空对月。1 0:47:55 10:47:5 510:47 10/24/2 020 10:47:55 AM 安全象只弓,不拉它就松,要想保安 全,常 把弓弦 绷。20. 10.2410 :47:551 0:47Oc t-2024- Oct-20 加强交通建设管理,确保工程建设质 量。10:47:5510 :47:551 0:47Saturday , October 24, 2020 安全在于心细,事故出在麻痹。20.10. 2420.1 0.2410:47:5510 :47:55 October 24, 2020 踏实肯干,努力奋斗。2020年10月24 日上午1 0时47 分20.10. 2420.1 0.24 追求至善凭技术开拓市场,凭管理增 创效益 ,凭服 务树立 形象。2 020年1 0月24 日星期 六上午1 0时47 分55秒1 0:47:55 20.10.2 4 严格把控质量关,让生产更加有保障 。2020 年10月 上午10 时47分2 0.10.24 10:47O ctober 24, 2020 作业标准记得牢,驾轻就熟除烦恼。2 020年1 0月24 日星期 六10时4 7分55 秒10:47:5524 October 2020 好的事情马上就会到来,一切都是最 好的安 排。上 午10时4 7分55 秒上午1 0时47 分10:47:5520.1 0.24 专注今天,好好努力,剩下的交给时 间。20. 10.2420 .10.241 0:4710:47:551 0:47:55 Oct-20 牢记安全之责,善谋安全之策,力务 安全之 实。202 0年10 月24日 星期六1 0时47 分55秒Saturday , October 24, 2020 相信相信得力量。20.10.242020年10月 24日星 期六10 时47分 55秒20 .10.24
5
二. 壓鑄模的結構組成
二).壓鑄模結構根據作用分類
壓鑄模設計
2020/10/24
Macherchen
6
二. 壓鑄模的結構組成
二).壓鑄模結構根據作用分類
壓鑄模設計
2020/10/24
Macherchen
7
壓鑄模零部件設計
定義:1. 成型零部件:構成模腔的所有零部件的統稱. 2.結構零部件:保証模具有足夠的剛度,強度及正確安裝和模具 正常工作.
Macherchen
11
壓鑄模設計
壓鑄模零部件設計
(二)成型零部件結構形式 1. 凹模
凹模常用的結構形式有整體式﹐整體鑲入式﹐鑲拼組 合式﹐瓣合式。 凹模鑲拼的例子: (1)便於機械加工的鑲拼
壓鑄模設計
2020/10/24
Macherchen
12
壓鑄模零部件設計
(2)有利於脫模的鑲拼
A處橫向毛邊,不利脫模,且產生飛邊後型腔很難清理. B處形成的飛邊與脫模方向一致有利於脫模.
注意事項(分型面選擇的原則)﹕
(1) 分型後壓鑄件能從模具型腔內取出來 (2) 開模後壓鑄件應留在動模上 (3) 分型面選擇應保証壓鑄件的尺寸精度
和表面質量(產品的要求) (4) 有利於澆注系統和排氣系統的布置 (5) 應便於模具加工,模具加工工藝的
可行性,可靠性及方便性
壓鑄模設計
2020/10/24
2.尺寸標注規定:
1)壓鑄件上的外形尺寸采用單向負偏差,基本尺寸為最大值,與 壓鑄件外形尺寸相應的模具上型腔類尺寸采用單向正偏差,基 本尺寸為最小值.
2)壓鑄件上的內形尺寸采用單向正偏差,基本尺寸為最小值,與 壓鑄件內形尺寸相應的模具上型芯類尺寸采用單向負偏差,基 本尺寸為最大值.
3)壓鑄件上和模具上的中心距尺寸均采用雙向等值正負偏差,它 們的基本尺寸為平均值.
一. 分型面的類型 二. (一)分型面型腔的相對位置分類
動模
定模
動模
定模
動模
定模
壓鑄模設計
2020/10/24
Macherchen
8
壓鑄模零部件設計
(二)按分型面的形狀分類 1 平直分型 2. 傾斜分型
3. 階梯分型
4 曲面分型
壓鑄模設計
2020/10/24
Macherchen
9
壓鑄模零部件設計
8.
選定壓鑄機
9.
繪製壓鑄毛胚圖
10. 三). 設計壓鑄模的基本要求
11. 符合壓鑄毛胚技術要求
12. 適合壓鑄生產工藝要求
13. 滿足模具加工工藝要求,結構
14.
簡單合理,標準通用
15. 四). 設計壓鑄模
16. 模具結構的擬定與比較
17. 繪製模具總裝圖及零件圖
18. 模具圖樣的修正與定型
2020/10/24
第二講:壓鑄模設計
壓鑄模設計
2020/10/24
撰稿: Macherchen
Macherchen
1
壓鑄模設計
一. 壓鑄模的設計過程
一). 設計前的基礎性準備
1.
研究產品對象
2.
熟悉壓鑄機
3.
模具制造知識
4.
現場壓鑄工藝知識
5. 二).壓鑄模設計的工藝準備
6.
對零件圖進行工藝性分析
7.
對模具結構的初步分析
壓鑄模零部件設計
(三)成型零部件工作尺寸計算
1. 定義:成型零部件中直接決定壓鑄件幾何形狀的尺寸稱為工作尺寸.
分為:型腔尺寸,型芯尺寸,中心距尺寸.
徑向尺寸
型腔尺寸
包容尺寸,磨損變大
深度尺寸
徑向尺寸 型芯尺寸
高度尺寸
被包容尺寸,磨損變小
壓鑄模設計
2020/10/24
Macherchen
19
壓鑄模零部件設計
壓鑄模設計
2020/10/24
Macherchen
13
壓鑄模零部件設計
(3)避免銳角的鑲拼
壓鑄模設計
2020/10/24
Macherchen
14
壓鑄模零部件設計
(4)防止熱處理變形的鑲拼
壓鑄模設計
(5)便於更換維修的鑲拼
2020/10/24
Macherchen
15
壓鑄模零部件設計
2. 凸模和型芯
Macherchen
10
壓鑄模零部件設計
二.成型零部件的結構設計與尺寸計算
(一)熱交變應力 除承受金屬液的高速沖刷
外,還吸收金屬凝固過程中 的熱量,產生熱量交換,表 面高溫膨脹,其它相對較小 激冷產生拉應力, 交變應 力增強,超過疲勞極限,產生 塑性變形,在晶界處產生裂紋.
熱膨脹
壓應力
拉應力
2020/10/24