长流程钢铁生产工艺规范导引
钢铁生产工艺流程DOC知识讲解
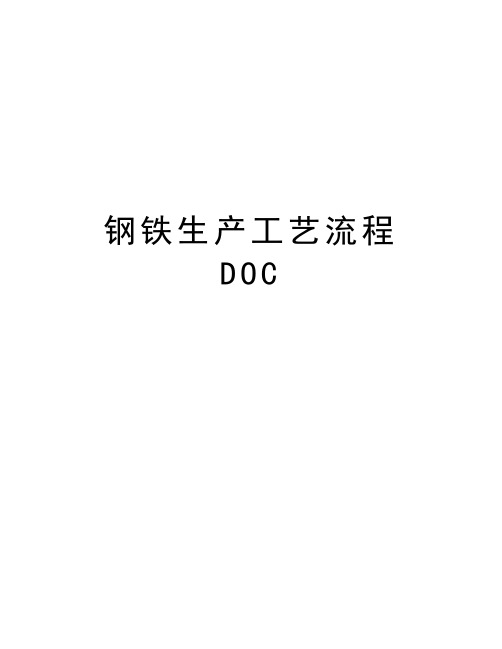
钢铁生产工艺流程D O C钢铁生产工艺流程炼焦生产流程:炼焦作业是将焦煤经混合,破碎后加入炼焦炉内经干馏后产生热焦碳及粗焦炉气之制程。
资源来源:台湾中钢公司网站。
烧结生产流程:烧结作业系将粉铁矿,各类助熔剂及细焦炭经由混拌、造粒后,经由布料系统加入烧结机,由点火炉点燃细焦炭,经由抽气风车抽风完成烧结反应,高热之烧结矿经破碎冷却、筛选后,送往高炉作为冶炼铁水之主要原料。
资源来源:台湾中钢公司网站。
高炉生产流程:高炉作业是将铁矿石、焦炭及助熔剂由高炉顶部加入炉内,再由炉下部鼓风嘴鼓入高温热风,产生还原气体,还原铁矿石,产生熔融铁水与熔渣之炼铁制程。
资源来源:台湾中钢公司网站。
转炉生产流程:炼钢厂先将熔铣送前处理站作脱硫脱磷处理,经转炉吹炼后,再依订单钢种特性及品质需求,送二次精炼处理站(RH真空脱气处理站、Ladle Injection盛桶吹射处理站、VOD真空吹氧脱碳处理站、STN搅拌站等)进行各种处理,调整钢液成份,最后送大钢胚及扁钢胚连续铸造机,浇铸成红热钢胚半成品,经检验、研磨或烧除表面缺陷,或直接送下游轧制成条钢、线材、钢板、钢卷及钢片等成品。
资源来源:台湾中钢公司网站。
连铸生产流程:连续铸造作业乃是将钢液转变成钢胚之过程。
上游处理完成之钢液,以盛钢桶运送到转台,经由钢液分配器分成数股,分别注入特定形状之铸模内,开始冷却凝固成形,生成外为凝固壳、内为钢液之铸胚,接着铸胚被引拔到弧状铸道中,经二次冷却继续凝固到完全凝固。
经矫直后再依订单长度切割成块,方块形即为大钢胚,板状形即为扁钢胚。
此半成品视需要经钢胚表面处理后,再送轧钢厂轧延。
资源来源:台湾中钢公司网站。
热轧生产流程。
热轧生产流程。
资源来源:台湾中钢公司网站。
热轧生产流程>第一热轧钢带生产流程:热轧钢带工场主要制程是将扁钢胚加热后,经粗轧机及精轧机轧延成钢带,并以层流冷却系统喷水冷却至适当温度,再由盘卷机卷成粗钢卷。
资源来源:台湾中钢公司网站。
炼钢的生产流程及原理

级论文题目:炼钢的生产流程及原理专业班级姓名学号指导教师日期炼钢的生产流程及原理摘要本文概述了炼钢生产的现状及发展趋势,介绍了炼钢生产的流程、原理及现代炼钢方法。
炼钢生产之初的造渣对钢的冶炼起到决定性作用,而碳、磷、硫、氧等成分的含量对钢的冶炼起着关键性作用,除此之外,钢中所含的气体和夹杂物对钢的质量也有影响。
本文就造渣过程及脱碳、脱磷、脱硫、脱氧过程进行了详细的阐述。
总之,炼钢的生产过程可归纳为:“四脱”(脱碳、脱磷、脱硫、脱氧),“二去”(去气和去夹杂)“二调整”(调整成分和温度)。
关键词:目录摘要第一章引言 (1)第二章现代炼钢方法简介 (3)2.1 氧气转炉炼钢 (3)2.1.1 氧气顶吹转炉炼钢法特点 (3)2.1.2 氧气底吹转炉炼钢法特点 (3)2.1.3 复合炼钢法特点 (4)2.2电弧炉炼钢 (4)第三章炼钢的生产流程及原理 (6)3.1炼钢的基本任务 (6)3.2 炼钢原材料的来源 (7)3.3 装料 (7)3.4 炼钢炉渣 (7)3.4.1 造渣 (8)3.4.2 炼钢炉渣的作用 (10)3.4.3 炼钢炉渣的来源 (11)3.4.4 炼钢炉渣的分类与组成 (11)3.4.5 炼钢炉渣的主要性质 (11)3.5 炼钢过程的基本反应 (13)3.5.1 碳的氧化 (13)3.5.2 硅的氧化和还原 (14)3.5.3 锰的氧化和还原 (15)3.5.4 脱磷反应 (15)3.5.5 脱硫反应 (17)3.5.6 脱氧 (18)3.6 去除钢中的气体 (21)3.7降低钢中的非金属夹杂物 (22)3.8 出钢 (24)结论 (25)参考文献 (26)致谢 (27)第一章引言(三号黑体)我国有丰富的铁矿石、有色金属、煤炭和水力资源等,是发展钢铁工业的基本条件。
我国是世界上钢铁冶金起源最早的国家之一,早在春秋战国时代(公元前8世纪~5世纪)就出现了生铁冶炼,制造出了很锋利的宝剑和其他用具,在历史上有着极其辉煌的成就。
钢铁生产工艺流程简介
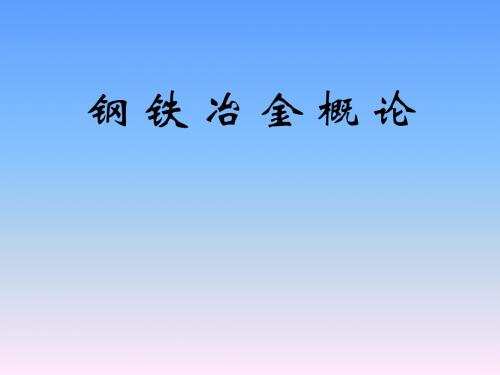
选矿工艺流程
原 矿
αβγθ
• 2.3.2 选矿的工艺指标 • (1)精矿品位。即产品中改金属的重量 与产品中两笔,用百分数表示。如铁精矿 品位为65%,就是一精矿中含0.65吨金属铁。 • (2)精矿产率。 是指精矿与入选原矿 重量之比,用百分数表示。通过选矿前后 金属平衡来计算: • 100×α/100= γ×β/100+(100-γ)×θ/100
• (3)杂质元素。有害元素如:S、P、K、F、Na、 Zn等。有益元素如:Mn、Cr、Ni、V、Ti、Nb等 。 • (4)矿石的还原性。矿石中与铁结合的氧被 还原剂夺取的难易程度,称为还愿性。冶炼易还 原的矿石,可降低碳素燃料的消耗量。它与矿物 组成、致密程度、气孔率等有关。 • (5)矿石的高温性能。要求矿石具有较高的 荷重软化温度和熔融滴下温度,且两者的温差 要 小。 • (6)矿石的强度与粒度组成。 • (7)矿石成分的稳定性。
• 2.1.2 铁矿石分类及对其评价 • 目前铁矿石主要有磁铁矿石、赤铁矿石、褐铁 矿石和菱铁矿石等 。各种矿石的组成见表2-1 (课本22页)。 • 对铁矿石的评价: • (1)铁矿石品位(含铁量)。他决定着冶炼 的经济性,是衡量铁矿石质量的重要指标。矿石 品位越高,脉石含量越少,冶炼时所需熔剂量和 形成渣两就少,因而能耗相应降低,产量增加。 • (2)脉石成分。 •
• 主要冶金过程
• 干燥:除去水份,干燥温度400~600°C。 • 焙烧:将矿山置于适当的气氛下,加热至低于它 的熔点温度,发生氧化、还原或其它化学变化的 过程。 • 煅烧: • 烧结和球团:将粉矿经加热焙烧,固结成多孔块 状或球状的物料。 • 熔炼:在高温下通过氧化还原反应使矿山中金属 和杂质分离为两个液相,即金属液和熔渣的过程, 也叫冶炼。 • 精练:进一步处理所得到含有少量杂质的粗金属, 以提高其纯度。
钢铁厂生产和主要工艺流程

钢铁厂生产和主要工艺流程钢铁生产工艺主要包括:炼铁、炼钢、铸钢、轧钢等流程。
1. 炼铁铁矿石的品种分为磁铁矿Fe3O4、赤铁矿Fe2O3、褐铁矿2Fe2O3.3H2O、菱铁矿FeCO3。
铁矿石中除铁的化合物外,还含有硅、锰、磷、硫等的化合物(统称为脉石)。
铁矿石刚开采出来时无法直接用于冶炼,必须经过粉碎、选矿、洗矿等工序处理,变成铁精矿、粉矿,才能作为冶炼生铁的主要原料。
将铁精矿、粉矿,配加焦炭、熔剂,烧结后,放在100米高的高炉中,吹入1200摄氏度的热风。
焦炭燃烧释放热量,6个小时后温度达到1500度,将铁矿融化成铁水,不完全燃烧产生的CO将氧从铁水(氧化铁)中分离出来,换句话说CO作为还原剂将铁从铁水(氧化铁)中还原出来。
熔剂,包括石灰石CaCO3、荧石CaF2,其作用是与铁矿石中的脉石结合形成低熔点、密度小、流动性好的熔渣,使之与铁液分离,以便获得较纯净的铁水。
铁水即生铁液,然后被送往炼钢厂作为炼钢的原料。
宝钢炼铁车间由两座4063立米大型高炉组成,预留有第三座高炉的建设场地。
全车间年产生铁600万吨(最终产量可达650万吨)。
向炼钢车间热送576.6万吨铁水,钢锭模铸造车间热送6.78万吨,其余16.62万吨铁水送铸铁机铸块。
全车间分两期建设,1号高炉计划1982年4季度投产,2号高炉计划1984年投产。
全车间约占地572,000平米,采用半岛式布置,1、2高炉中心距370米,原料、燃料均用胶带运输机分别由原料场,烧结车间,炼焦车间送入矿槽、焦槽。
筛下粉矿、碎焦亦由胶带运输机运出,转送烧结车间。
铁水输送采用320吨鱼雷式混铁车。
高炉煤气灰、垃圾、废铁的…2. 炼钢炼钢就是把原料(铁水)里过多的碳及硫、磷等杂质去掉并加入适量的合金成分。
最早的炼钢方法出现在1740 年,将生铁装入坩锅中,用火焰加热溶化炉料,之后将溶化的炉料浇铸成钢锭。
1856 年,英国人亨利-贝塞麦发明了酸性空气底吹转炉炼钢法,第一次解决了铁水直接冶炼钢水的难题,从而使钢的质量得到提高,但此法不能脱硫,目前己被淘汰。
钢铁生产工艺流程图

钢铁生产工艺流程炼焦生产流程:炼焦作业是将焦煤经混合,破碎后加入炼焦炉内经干馏后产生热焦碳及粗焦炉气之制程。
资源来源:台湾中钢公司网站。
烧结生产流程:烧结作业系将粉铁矿,各类助熔剂及细焦炭经由混拌、造粒后,经由布料系统加入烧结机,由点火炉点燃细焦炭,经由抽气风车抽风完成烧结反应,高热之烧结矿经破碎冷却、筛选后,送往高炉作为冶炼铁水之主要原料。
资源来源:台湾中钢公司网站。
高炉生产流程:高炉作业是将铁矿石、焦炭及助熔剂由高炉顶部加入炉内,再由炉下部鼓风嘴鼓入高温热风,产生还原气体,还原铁矿石,产生熔融铁水与熔渣之炼铁制程。
资源来源:台湾中钢公司网站。
转炉生产流程:炼钢厂先将熔铣送前处理站作脱硫脱磷处理,经转炉吹炼后,再依订单钢种特性及品质需求,送二次精炼处理站(RH真空脱气处理站、Ladle Injection盛桶吹射处理站、VOD真空吹氧脱碳处理站、STN搅拌站等)进行各种处理,调整钢液成份,最后送大钢胚及扁钢胚连续铸造机,浇铸成红热钢胚半成品,经检验、研磨或烧除表面缺陷,或直接送下游轧制成条钢、线材、钢板、钢卷及钢片等成品。
资源来源:台湾中钢公司网站。
连铸生产流程:连续铸造作业乃是将钢液转变成钢胚之过程。
上游处理完成之钢液,以盛钢桶运送到转台,经由钢液分配器分成数股,分别注入特定形状之铸模内,开始冷却凝固成形,生成外为凝固壳、内为钢液之铸胚,接着铸胚被引拔到弧状铸道中,经二次冷却继续凝固到完全凝固。
经矫直后再依订单长度切割成块,方块形即为大钢胚,板状形即为扁钢胚。
此半成品视需要经钢胚表面处理后,再送轧钢厂轧延。
资源来源:台湾中钢公司网站。
热轧生产流程。
热轧生产流程。
资源来源:台湾中钢公司网站。
热轧生产流程>第一热轧钢带生产流程:热轧钢带工场主要制程是将扁钢胚加热后,经粗轧机及精轧机轧延成钢带,并以层流冷却系统喷水冷却至适当温度,再由盘卷机卷成粗钢卷。
资源来源:台湾中钢公司网站。
热轧生产流程>一号调质重卷线布置图:主要功能为将原料钢卷上线解卷、调质轧延、分切、重卷及包装为成品H.R COIL 或H.R BAND〔HR BAND 未调质轧延〕。
长流程钢铁——生态环境部重污染天气重点行业绩效分级及减排措施
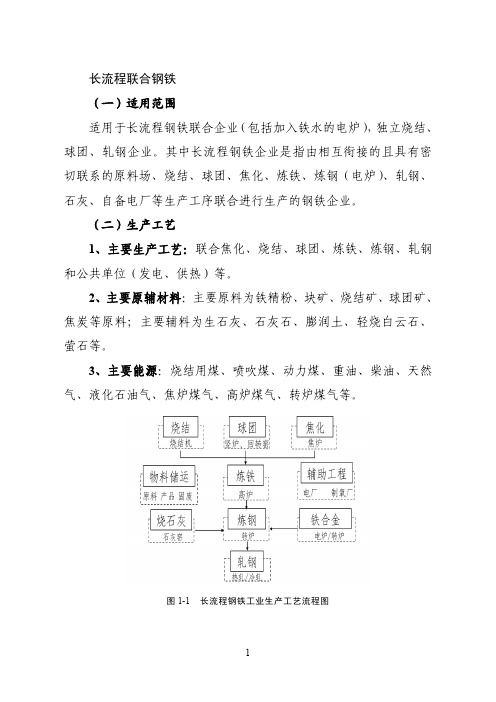
三及以上排放标准或使用新能
械全部达到国三及以上
源机械
排放标准或使用新能源
机械
参照《重污染天气重点行业移动源应急管理技术指南》
运输监管 建立门禁系统和电子台账
未达到 A、B 级要求
注 1:a 是指《排污许可证申请与核发技术规范 钢铁工业》(HJ846-2017)中规定的主要排放口
6
(五)减排措施 1、A 级企业: 鼓励结合实际,自主采取减排措施。 2、B 级企业: 黄色预警期间:停止使用国四及以下重型载货车辆(含燃气) 进行运输。 橙色预警期间:每座转炉(电炉)日出钢数不大于 36 炉, 带动整体降低生产负荷,其中烧结机、球团设备限产 10%(含) 以上,石灰窑限产 30%(含)以上,以“环评批复产能、排污许 可载明产能、前一年正常生产实际产量”三者日均值的最小值为 基准核算;停止使用国四及以下重型载货车辆(含燃气)进行运 输。 红色预警期间:每座转炉(电炉)日出钢数不大于 32 炉, 带动铁前工序、高炉和轧钢工序减产,整体降低生产负荷,其中 烧结机、球团设备限产 20%(含)以上,石灰窑限产 30%(含) 以上,以“环评批复产能、排污许可载明产能、前一年正常生产 实际产量”三者日均值的最小值为基准核算;停止使用国四及以 下重型载货车辆(含燃气)进行运输。 3、B-级企业: 黄色预警期间:焦炉负荷降至设计生产负荷的 80%以内,以 延迟出焦时间计;停止使用国四及以下重型载货车辆(含燃气) 进行运输。 橙色预警期间:每座转炉(电炉)日出钢数不大于 30 炉, 带动整体降低生产负荷,其中烧结机、球团设备,石灰窑停限产
1、按照《关于做好钢铁企业超低 焦运输满足:(1)在封闭车间内装卸物料,并设
排放评估监测工作的通知》开展无 置集尘罩等集尘装置,(2)运输车辆封闭;各料
钢铁生产工艺流程
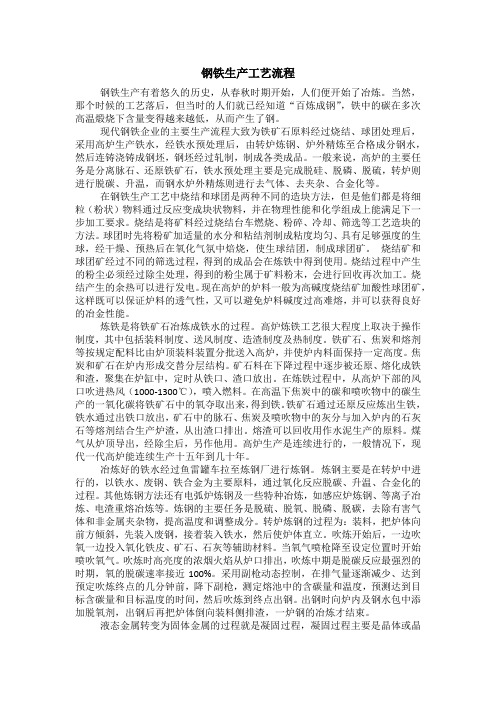
钢铁生产工艺流程钢铁生产有着悠久的历史,从春秋时期开始,人们便开始了冶炼。
当然,那个时候的工艺落后,但当时的人们就已经知道“百炼成钢”,铁中的碳在多次高温煅烧下含量变得越来越低,从而产生了钢。
现代钢铁企业的主要生产流程大致为铁矿石原料经过烧结、球团处理后,采用高炉生产铁水,经铁水预处理后,由转炉炼钢、炉外精炼至合格成分钢水,然后连铸浇铸成钢坯,钢坯经过轧制,制成各类成品。
一般来说,高炉的主要任务是分离脉石、还原铁矿石,铁水预处理主要是完成脱硅、脱磷、脱硫,转炉则进行脱碳、升温,而钢水炉外精炼则进行去气体、去夹杂、合金化等。
在钢铁生产工艺中烧结和球团是两种不同的造块方法,但是他们都是将细粒(粉状)物料通过反应变成块状物料,并在物理性能和化学组成上能满足下一步加工要求。
烧结是将矿料经过烧结台车燃烧、粉碎、冷却、筛选等工艺造块的方法。
球团时先将粉矿加适量的水分和粘结剂制成粘度均匀、具有足够强度的生球,经干燥、预热后在氧化气氛中焙烧,使生球结团,制成球团矿。
烧结矿和球团矿经过不同的筛选过程,得到的成品会在炼铁中得到使用。
烧结过程中产生的粉尘必须经过除尘处理,得到的粉尘属于矿料粉末,会进行回收再次加工。
烧结产生的余热可以进行发电。
现在高炉的炉料一般为高碱度烧结矿加酸性球团矿,这样既可以保证炉料的透气性,又可以避免炉料碱度过高难熔,并可以获得良好的冶金性能。
炼铁是将铁矿石冶炼成铁水的过程。
高炉炼铁工艺很大程度上取决于操作制度,其中包括装料制度、送风制度、造渣制度及热制度。
铁矿石、焦炭和熔剂等按规定配料比由炉顶装料装置分批送入高炉,并使炉内料面保持一定高度。
焦炭和矿石在炉内形成交替分层结构。
矿石料在下降过程中逐步被还原、熔化成铁和渣,聚集在炉缸中,定时从铁口、渣口放出。
在炼铁过程中,从高炉下部的风口吹进热风(1000-1300℃),喷入燃料。
在高温下焦炭中的碳和喷吹物中的碳生产的一氧化碳将铁矿石中的氧夺取出来,得到铁。
炼钢简单工艺流程

炼钢的工艺流程7月8日上午听了苏教授给我们讲的关于炼钢的工艺流程,我对我们的专业课有了初步的了解与认识。
炼钢就是将铁水冶炼成钢水,而钢与铁的区别就在于含碳量不同,只要将铁里边的含碳量降低到一定程度就是我们所需要的钢了,所以要想炼钢首先便要炼铁。
这里一般有两个流程:长流程:选矿→烧结(球团)→高炉→铁水预处理→转炉→精炼→连铸→轧钢短流程:废钢→电炉→精炼→连铸→轧钢这里说的选矿,烧结,球团,是高炉冶炼的原料准备阶段,当完成烧结,造球后进入高炉利用高炉内的还原性环境将铁水从铁矿石从还原出来,为下一阶段的炼钢提供原料供给。
而接下来的铁水预处理就是脱去硫等杂质。
接着就是利用转炉内的氧化性环境将铁水中过量的碳氧化成一氧化碳和二氧化碳,达到钢水要求的碳含量。
转炉出钢后的钢水精炼(LF或LF+RH或LF+VD,VOD等),完成精炼后用行车调运至连铸机的大包回转台,进行连铸浇铸的工序环节,为后续的轧钢厂提供钢坯原料。
实际中,整个联合钢铁厂的工艺流程为:原料码头(各种原料集中卸载存放区域)——烧结(矿石造块或造球团)——高炉(炼铁)——炼钢(铁水预处理-转炉或电炉-精炼-连铸)-轧钢。
其流程图如下:现在普遍使用的是转炉炼钢法,这种炼钢法使用的氧化剂是氧气。
把空气鼓入熔融的生铁里,使杂质硅、锰等氧化。
在氧化的过程中放出大量的热量(含1%的硅可使生铁的温度升高200摄氏度),可使炉内达到足够高的温度。
因此转炉炼钢不需要另外使用燃料。
转炉炼钢是在转炉里进行。
转炉的外形就像个梨,内壁有耐火砖,炉侧有许多小孔(风口),压缩空气从这些小孔里吹炉内,又叫做侧吹转炉。
开始时,转炉处于水平,向内注入1300摄氏度的液态生铁,并加入一定量的生石灰,然后鼓入空气并转动转炉使它直立起来。
这时液态生铁表面剧烈的反应,使铁、硅、锰氧化(FeO,SiO2 , MnO,) 生成炉渣,利用熔化的钢铁和炉渣的对流作用,使反应遍及整个炉内。
几分钟后,当钢液中只剩下少量的硅与锰时,碳开始氧化,生成一氧化碳(放热)使钢液剧烈沸腾。
最全钢铁企业制造流程

§1964年我国第1家氧气顶吹转炉炼钢厂在首钢建成投产,与 此同时我国太钢从奥钢联引进了2台50 t氧气顶吹转炉,使我 国的氧气顶吹转炉炼钢进入了发展的初始阶段。
PPT文档演模板
2020/11/17
最全钢铁企业制造流程
转炉炼钢
PPT文档演模板
2020/11/17
最全钢铁企业制造流程
将高温钢液连续地浇铸到一个或多个强制水冷的金属型腔内。凝 固成形后,再经二次冷却,使之凝固,且成一定形状(规格)铸坯的 工艺方法,其典型特征是生产过程的连续化。
PPT文档演模板
2020/11/17
最全钢铁企业制造流程
连铸工艺——设备
PPT文档演模板
2020/11/17
最全钢铁企业制造流程
连铸工艺——相关技术
– 振动装置 采用小振幅高频率的结晶器振动,一般频率可达0~360次/min, 振幅<10mm(有的为±4mm)。
– 二冷控制 精确控制二次喷水冷却。按不同钢种、不同拉速自动调节,均 匀冷却。尽管气-水雾冷却会增加控制上的困难、价格较高,但对特殊钢 连铸来说仍是十分必要的。
– 自动控制 采用计算机控制对稳定铸坯质量非常重要。
§看炉口的火,听声音。看火亮度--加第二批(渣料)--提 枪化渣,控制“返干”。
§降枪控制终点(FeO),倒炉取样测温,出钢。 §技术水平高的炉长,一次命中率高。50%。(宝钢是付枪)
根据分析取样结果--决定出钢(或补吹)--脱氧、合金化。
不要补吹的就是通常说的一次命中。
PPT文档演模板
2020/11/17
§ 铁水脱硫预处理的工艺方法
– 投掷法: 将脱硫剂投入铁水中 – 喷吹法: 将脱硫剂喷入铁水中 – 搅拌法(KB法): 将通过中空机械搅拌器向铁水内加入脱硫剂,搅拌脱硫。
长流程钢铁流程介绍
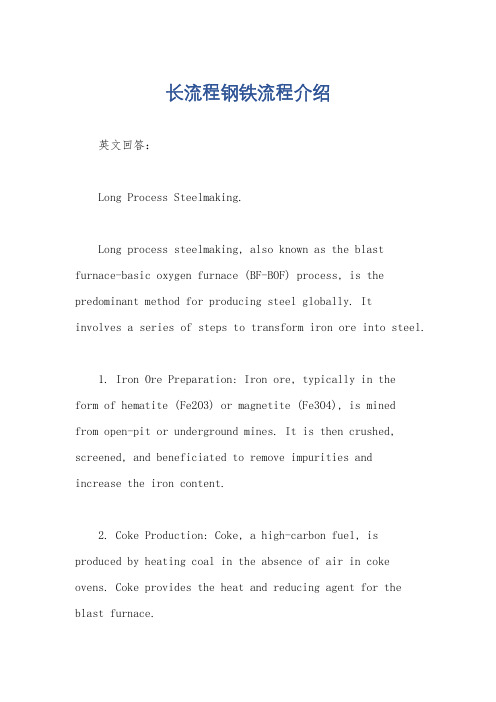
长流程钢铁流程介绍英文回答:Long Process Steelmaking.Long process steelmaking, also known as the blast furnace-basic oxygen furnace (BF-BOF) process, is the predominant method for producing steel globally. Itinvolves a series of steps to transform iron ore into steel.1. Iron Ore Preparation: Iron ore, typically in theform of hematite (Fe2O3) or magnetite (Fe3O4), is minedfrom open-pit or underground mines. It is then crushed, screened, and beneficiated to remove impurities andincrease the iron content.2. Coke Production: Coke, a high-carbon fuel, is produced by heating coal in the absence of air in coke ovens. Coke provides the heat and reducing agent for the blast furnace.3. Sintering: Iron ore fines, along with coke and flux materials (e.g., limestone), are sintered in a sintering machine to form agglomerates called sinter. Sintering enhances the strength and porosity of the iron ore, making it more suitable for the blast furnace.4. Blast Furnace Operation: The blast furnace is a large cylindrical furnace lined with refractory materials. It is charged with iron ore, sinter, coke, and flux materials. Hot air is blown into the furnace from the bottom, which reacts with the coke to produce carbon monoxide (CO). The CO gas reduces the iron oxides in the ore to form molten iron, which collects at the bottom of the furnace.5. Basic Oxygen Furnace (BOF) Operation: Molten iron from the blast furnace is transferred to the BOF, which is a pear-shaped vessel lined with refractory bricks. Oxygen gas is blown into the molten iron, which oxidizesimpurities such as carbon, silicon, and manganese. These oxides form a foamy slag, which floats on top of the moltenmetal. The process produces low-carbon steel that can be used to make a variety of products.6. Continuous Casting: The molten steel from the BOF is poured into a tundish and then into a continuous casting machine. The steel is solidified and formed into slabs, blooms, or billets. These semi-finished products are usedas input materials for rolling mills.7. Rolling: Slabs, blooms, or billets are heated in reheating furnaces and then rolled into various shapes, including bars, rods, wires, and flat rolled products (e.g., sheets, coils).8. Finishing: After rolling, the steel products may undergo further processing, such as heat treatment, coating, or galvanizing, to enhance their properties and meetspecific requirements.中文回答:长流程钢铁工艺。
钢铁企业工艺流程

钢铁企业工艺流程钢铁生产的工艺流程大致分为:选矿,烧结,焦化,炼铁,炼钢,连铸,轧钢等过程;辅助系统有:制氧/制氮,循环水系统,烟气除尘及煤气回收等。
原煤粉状含铁原料铁矿原料物料流线能源流线钢成品1选矿1.1工艺介绍选矿是冶炼前的准备工作,从矿山开采下来矿石以后,首先需要将含铁、铜、铝、锰等金属元素高的矿石甄选出来,为下一步的冶炼活动做准备.1.2工艺流程选矿一般分为破碎、磨矿、选别三部分。
其中,破碎又分为:粗破、中破和细破;选别依方式不同也可分为:磁选、重选、浮选等。
1.3原料原矿石。
1.4产物铁精矿。
1.5设备矿石破碎设备:颚式破碎机、锤式破碎机。
磨矿工艺设备:球磨机、螺旋分级机。
选别工艺设备:浮选机、磁选机。
2烧结2.1工艺介绍为了保证供给高炉的铁矿石中铁含量均匀,并且保证高炉的透气性,需要把选矿工艺产出的铁精矿制成10-25mm的块状原料。
铁矿粉造块目前主要有两种方法:烧结法和球团法。
铁矿粉造块的目的:◆去除有害杂质,回收有益元素,保护环境;◆综合利用资源,扩大炼铁用的原料种类;◆改善矿石的冶金性能,适应高炉冶炼对铁矿石的质量要求.2.2工艺流程2.2.1烧结法烧结是钢铁生产工艺中的一个重要环节,它是将铁矿粉、粉(无烟煤)和石灰、高炉炉尘、轧钢皮、钢渣按一定配比混匀。
经烧结而成的有足够强度和粒度的烧结矿可作为炼铁的熟料。
烧结矿生产流程:烧结料的准备,配料与混合,烧结和产品处理。
精矿粉石灰石碎焦高炉灰结矿热烧结矿电2.2.2 球团法球团是把细磨铁精矿粉或其他含铁粉料添加少量添加剂混合后,在加水润湿的条件下,通过造球机滚动成球,再经过干燥焙烧,固结成为具有一定强度和冶金性能的球型含铁原料。
球团矿生产流程:原料准备、配料、混合、造球、干燥和焙烧、冷却、成品和返矿处理铁精粉精矿粉膨润土电2.3原料含铁原料:含铁量较高、粒度〈5mm的矿粉,铁精矿,高炉炉尘,轧钢皮,钢渣等。
一般要求含铁原料品位高,成分稳定,杂质少。
电冶金专题:钢铁工业长流程和短流程的比较分析

电冶金专题:钢铁工业长流程和短流程的比较分析电冶金专题钢铁行业的生产有三个流程即:高炉-转炉流程、电弧炉流程及特种熔炼。
高炉-转炉流程又称为长流程,生产的钢被称为转炉钢,它是以铁矿石和焦炭为主要原料冶炼成铁水,再由转炉冶炼成钢;电弧炉流程被称为短流程,生产的钢称为电炉钢,它以废钢为主要原料冶炼成钢。
1工艺技术的比较分析转炉流程和电弧炉流程是钢铁冶金行业两个主要生产工艺,其在炼钢方面的主要差别体现在以下几个方面:1)所用主要钢铁料不同。
转炉炼钢主要以铁水为原料,还有15%左右的废钢,近一年多时间,由于废钢价格较低,吨钢利润较高,为转炉炼钢用高比例废钢提供了条件,废钢消耗比例大幅提高,有的甚至高达40%,但存在转炉内热量不足的问题,解决转炉内热量问题是提高废钢比的关键。
电弧炉炼钢主要以废钢为原料,还有铁水(生铁)、直接还原铁,脱碳粒铁、碳化铁及复合金属料等废钢替代品。
2)主要能源不同。
转炉炼钢主要是铁水的物理热和化学热,电弧炉炼钢主要是电弧的物理热、原料物理热和化学热、辅助化学热及回收的烟气余能。
辅助化学热主要指吹氧喷碳粉和燃气烧嘴,烟气余能包括物理热和烟气中的化学热。
3)主要操作目标不同。
转炉炼钢是在给定的时间内完成脱碳、脱磷及温度控制的冶金操作,实现成分(碳、磷)及温度的命中;电弧炉炼钢是在全废钢的条件下,在给定的时间内,完成废钢的升温、熔化和过热等,在加铁水等废钢替代品的情况下,也有部分脱碳的要求。
另外,电弧炉炼钢可分别控制成分和温度。
4)工艺发展方向不同。
转炉炼钢主要是通过包括提高供氧强度的高效吹炼技术、碳及温度命中率的全自动化吹炼技术、不倒炉出钢的快速出钢技术、采用炉外处理和铁水预处理减轻转炉冶金负荷等措施,实现转炉生产高效化,通过接近平衡的冶炼工艺、高效脱磷工艺、出钢挡渣技术,实现产品的洁净化,通过少渣冶炼与炉渣返回,使用合金元素熔融还原(Cr、Mn)矿,干法除尘用水减量化,煤气余热回收等技术,实现低成本及负能炼钢。
钢铁制造流程

将炼钢分两步进行的好处是: 可提高钢的质量, 缩短冶炼时间,简化工艺过程并降低生产成本;
炉外精炼的种类很多,大致可分为常压下炉外精 炼和真空下炉外精炼两 类。按处理方式的不同, 又可分为钢包处理型炉外精炼及钢包精炼型炉
2024/8/3
精炼——常用方法与设备
2024/8/3
精炼——工艺路径
以钢种为中心,正确选择精炼设备 CAS-OB是最简单的非真空精炼设备,多适用于 普碳钢、低合金钢等以化学成分交货的钢种; LF有很强的清洗精炼和加热功能,适宜冶炼低氧 钢、低硫钢和高合金钢;
2024/8/3
铁水预处理——脱硫
铁水在进入转炉冶炼前进行脱硫具备最佳的反应条件 铁水中含有大量Si、C.Mn等还原性好的元素,其还原性
有利于脱硫 反应,(强脱硫剂Ca、Mg等烧损少); 铁水中C.Si能大大提高S在铁水中的活度系数,致使硫较
易脱到低的 水平; 铁水中氧含量低,硫的分配系数相应有所提高,有利于
2024/8/3
转炉炼钢过程
上一炉出钢--倒完炉渣(或加添加剂)-- 补炉或溅渣--堵 出钢口--兑铁水--装废钢--下枪--加渣料(石灰、铁皮)- 点火-- 熔池升温--脱P、Si 、Mn----降枪脱碳。
看炉口的火, 听声音。看火亮度--加第二批(渣料)--提 枪化渣, 控制“返干”。
降枪控制终点(FeO), 倒炉取样测温, 出钢。 技术水平高的炉长, 一次命中率高。50%。(宝钢是付枪
2024/8/3
转炉炼钢的技术发展
1855-1856年英国人亨利.贝塞麦(Henly)开发了酸性底吹 空气转炉炼钢法;
1878年英国人托马斯(S.G.Thomas)碱性底吹空气转炉炼 钢法;
1940年廉价获得氧气后, 瑞士、奥地利开发了顶吹氧气转 炉, 1952年在奥地利林茨(Linz)和多纳维茨城(Donawitz)建 成第一座30吨碱性顶吹氧气转炉(LD转炉);或称BOF (Basic Oxygen Furnace);
- 1、下载文档前请自行甄别文档内容的完整性,平台不提供额外的编辑、内容补充、找答案等附加服务。
- 2、"仅部分预览"的文档,不可在线预览部分如存在完整性等问题,可反馈申请退款(可完整预览的文档不适用该条件!)。
- 3、如文档侵犯您的权益,请联系客服反馈,我们会尽快为您处理(人工客服工作时间:9:00-18:30)。
附件1:
长流程钢铁生产工艺规范导引
一般长流程钢铁公司所采用主要生产工艺流程为:
焦化、烧结、炼铁、炼钢、轧钢等主要生产工序。
1、长流程钢铁生产所采用主要生产工艺流程(见附图1)
2、主要生产工序工艺技术文件目录见表1:
3长流程钢铁生产主要工艺流程:
3.1焦化工序工艺流程:
将无烟煤预破碎至1mm以下,与主焦煤、肥煤、1/3焦煤按一定比例配合,送至锤式粉碎机破碎混均后,进JN43-80型65孔焦炉干馏,主产品焦炭经筛分处理后,送炼铁厂使用;副产品荒煤气经煤化工公司处理,提取其中的化产品后,供后道工序(如轧钢加热炉加热钢坯)使用。
该工序中应用直接配无烟煤炼焦工艺,取代配合煤中部分烟煤,在不降低焦炭总体质量的前提下,充分利用福建省内的白煤资源,对于降低成本,解决紧张资源具有现实的战略意义。
该工序的主要经济技术指标控制要求:①吨焦精煤耗≤1280kg/t、
②冶金焦率≥94%。
3.2 烧结工序工艺流程:
将精矿、澳矿、印矿、烧结粉、富矿及回收的轧钢氧化铁皮、钢渣进行预配料,并进行中和平铺堆取,得到混合均匀的各种带铁原料。
加入生石灰及预先破碎的煤粉进行混合,送至造球系统配入水及外滚焦粉进行造球,而后送入烧结机进行布料、点火烧结,成品烧结矿经破碎及筛分冷却后送入炼铁高炉使用,一小部分筛下物即返矿返回配料系统回收再行配料循环使用。
该工序中运用的小球、低温热风烧结技术,通过造球改善烧结的状态,对提高烧结矿性能,降低固体燃料耗具有实用价值。
该工序的主要经济技术指标控制要求:①固体燃料耗≤45kg标煤/t、②烧结矿平均品位≥55%、③转鼓指数≥64%、④返矿率≤17%。
3.3炼铁工序工艺流程:
将破碎筛分好的冶金焦炭(除自产外,尚有一部分外购焦)、烧
结矿,及配加一定的球团矿、块矿或焦丁、煤块、废铁按一定的比例顺序送入高炉,在前述中的燃料及喷煤、富氧、鼓风的燃烧作用下,在高炉内发生分解还原反应,分离出铁水及高炉渣,产生高炉煤气,铁水除一小部分铸为铸造用生铁外,绝大部分作为炼钢用铁水送入炼钢厂混铁炉备用;高炉炉渣经冲渣后的水渣可作为水泥厂的配料外售;高炉煤气净化后供焦化厂焦炉加热及炼铁热风炉等用户使用。
该工序的主要经济技术指标控制要求:①铁矿石耗≤1660kg/t、
②高炉入炉焦比≤420kg/t、③高炉喷煤比≥100 kg/t。
3.4 炼钢工序工艺流程:
将预先处理的废钢铁加入转炉,从混铁炉取出铁水兑入,加入石灰等造渣材料并予以吹氧冶炼,经出钢配加各类铁合金,成分合格后送至吹氩站进行吹氩、吹氮调温或喂丝,合格的钢水送至连铸机进行浇注成连铸坯送至轧钢厂轧制。
对于特殊要求的钢种还需配备铁水预处理设施及LF精炼炉等工序并结合上述的转炉及连铸工序来生产合格连铸坯。
在冶炼过程产生的转炉煤气,经净化处理后供炼钢内部烘钢包及并网使用,转炉污泥水及钢渣经处理后,返回烧结工序中配入循环使用。
该工序中应用转炉溅渣护炉技术、小方坯全连铸技术等先进技术提高炉衬寿命及金属收得率等。
该工序的主要经济技术指标控制要求:①转炉钢铁料耗≤1075kg/t、②氧气耗≤70m3/t、③石灰耗≤80 kg /t 。
3.5轧钢工艺流程
a)棒材轧钢厂工艺流程:
将热送坯或冷坯送入步进式加热炉进行加热,进入架小型全连轧
机组的粗轧、中轧、精轧道次进行轧制(包括飞剪切头、尾),后经倍尺飞剪切成倍尺上冷床进行冷却,经定尺剪切后,定尺材经支数计数后自动打捆称重标牌后入库;非定尺材经手动打包称重标牌入库。
轧制中产生的切头、尾及中间冷条废钢经处理后回收至炼钢转炉使用,产生的氧化铁皮回收至烧结工序中配加循环使用。
b)高速线材轧钢厂工艺流程:
将连铸坯送入步进式加热炉进行加热,进入高架式机组的粗轧、中轧、预精轧、精轧道次进行轧制(包括飞剪切头、尾),中间穿水冷却,经吐丝机形成线圈,经风冷辊道运输机冷却和集卷,P&F线输送冷却,压紧自动打包,称重、标牌后入库。
轧制中产生的切头、尾及中间冷条废钢经处理后回收至炼钢转炉使用,产生的氧化铁皮回收至烧结工序中配加循环使用。
该工序的主要经济技术指标控制要求:①棒材厂的成材率(含负偏差率)≥100%、②棒材厂的定尺率≥97%、③高线厂的成材率≥96%。
3.6 最终产品的工艺水平要求
为保证最终产品的工艺水平及特色,要求采用转炉炼钢静态控制技术、钢包底吹氩技术、转炉-----小方坯全连铸技术、连铸全过程保护浇注,氢氧火焰切割技术,热送热装技术的等一系列冶炼、连铸技术的推广应用,以确保提供了化学成分稳定、尺寸、外观优良的连铸坯。
主要成品棒材、高速线材轧钢作业线应实现连续化、自动化,使其生产具有高效、低耗的特色。
加热采用步进底式加热炉,棒材轧钢厂采用全连续式轧机,并设有轧后穿水冷却系统,采用高精度倍尺飞剪和齿条步进式冷床,可进行6-12米不等的成品定尺剪切及自动计
数、自动打捆,从而确保产品的质量指标达标准要求,生产出化学成分稳定、性能优良、外形尺寸,表面质量、定尺可靠、外观打包整齐的棒材产品。
低碳热轧圆盘条采用全连续式轧机轧制,采用控轧、控冷技术、设有轧后穿水冷却系统及散卷冷却、P—F冷却系统,机械自动打包,确保按标准组织生产的产品质量指标,提供化学成分稳定、通条力学、工艺性能均匀、稳定,外形尺寸、表面质量等品质优良、大盘重、外观打包整齐的高速线材盘条产品。