生产流程及维修指导1
生产工艺流程作业指导书

湖北普龙消防设备有限公司Q/PL3---2014生产工艺流程作业指导书第A 版编制:审核:批准:2014 年月日发布2014 年月日实施工艺作业指导书目录自动制管生产线作业指导书Q/PL3-011.适用范围:本作业指导书适用于3、4 型手提式灭火器筒体自动制管生产线的作业指导。
2.使用设备:自动制管机、焊机、无屑切管机组成的成套生产线。
3.检测器具:0-500游标卡尺4.使用材料:厚1.20mm、宽404.8mm 钢带5.作业程序5.1作业准备5.1.1设备检查5.1.1.1空载检查行吊是否能前后、左右、上下正常运转。
5.1.1.2将制管、切管设备启动空载运行,检查电、气管路和设备是否运转正常,有无不正常动作和异常音响。
发现问题及时排除。
严禁带病运转。
5.1.1.3对设备中应润滑的部位应加注润滑油,检查切管刀片是否应该更换,进刀是否合适。
5.1.1.4设定切管机切割工件的长度。
5.1.2备料5.1.2.1将整件卷材用五吨行吊移至吊装工位,用电动葫芦将其吊起安放在开平机料架主轴适当位置上,并安装两侧固定架,顶紧中心固定块,使钢圈不致晃动,又能灵活转动。
在吊装过程中,注意不使钢带两侧受损。
同时注意钢带方向,钢带从上部抽出开平为正确,反之错误。
5.1.3清理作业现场5.1.3.1将行吊钩升高至2m 以上,并移至非制管线上方位置。
5.1.3.2将所有工具、材料、杂物撤离工作区域,保证工作区域整洁、干净,不妨碍行走。
5.2装机调试5.2.1去除钢卷包装,剪断去除钢卷包装钢带。
5.2.2将电机调速旋钮调到最低档后开机,并将钢带一端从上部抽出,对准挤管模进口处的导引模中,并根据实际情况调整压力,使钢板产生纵向弧状形变,并逐渐对后面的模具进行调整,使钢板纵向形变逐渐扩大,最终成圆筒状。
5.2.3检查成形后的钢管是否符合焊接要求,焊接处两侧既无间隙又不重叠为最佳焊接工况。
如达不到最佳焊接工况要求,可采取调整模具压力、调整电机转速,或调整电机转动方向,使主机反转进行重复旋压。
FT维修过程管理指南11.4.14
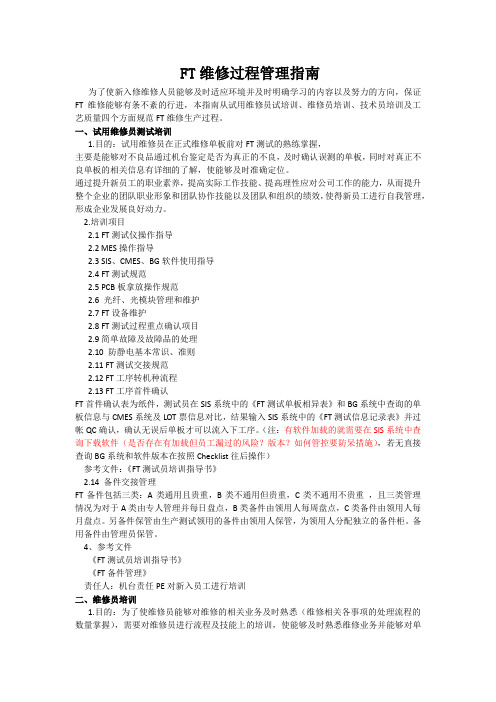
FT维修过程管理指南为了使新入修维修人员能够及时适应环境并及时明确学习的内容以及努力的方向,保证FT维修能够有条不紊的行进,本指南从试用维修员试培训、维修员培训、技术员培训及工艺质量四个方面规范FT维修生产过程。
一、试用维修员测试培训1.目的:试用维修员在正式维修单板前对FT测试的熟练掌握,主要是能够对不良品通过机台鉴定是否为真正的不良,及时确认误测的单板,同时对真正不良单板的相关信息有详细的了解,使能够及时准确定位。
通过提升新员工的职业素养,提高实际工作技能、提高理性应对公司工作的能力,从而提升整个企业的团队职业形象和团队协作技能以及团队和组织的绩效,使得新员工进行自我管理,形成企业发展良好动力。
2.培训项目2.1 FT测试仪操作指导2.2 MES操作指导2.3 SIS、CMES、BG软件使用指导2.4 FT测试规范2.5 PCB板拿放操作规范2.6 光纤、光模块管理和维护2.7 FT设备维护2.8 FT测试过程重点确认项目2.9简单故障及故障品的处理2.10 防静电基本常识、准则2.11 FT测试交接规范2.12 FT工序转机种流程2.13 FT工序首件确认FT首件确认表为纸件,测试员在SIS系统中的《FT测试单板相异表》和BG系统中查询的单板信息与CMES系统及LOT票信息对比,结果输入SIS系统中的《FT测试信息记录表》并过帐QC确认,确认无误后单板才可以流入下工序。
(注:有软件加载的就需要在SIS系统中查询下载软件(是否存在有加载但员工漏过的风险?版本?如何管控要防呆措施),若无直接查询BG系统和软件版本在按照Checklist往后操作)参考文件:《FT测试员培训指导书》2.14 备件交接管理FT备件包括三类:A类通用且贵重,B类不通用但贵重,C类不通用不贵重,且三类管理情况为对于A类由专人管理并每日盘点,B类备件由领用人每周盘点,C类备件由领用人每月盘点。
另备件保管由生产测试领用的备件由领用人保管,为领用人分配独立的备件柜。
蒸汽管道维修方案1

蒸汽管道维修方案1背景蒸汽管道是工业生产中常见的设备之一,用于输送蒸汽到不同的工艺设备中。
然而,蒸汽管道在使用过程中可能会出现损坏或故障,这就需要进行维修和修复。
因此,制定一套合理有效的蒸汽管道维修方案非常重要。
目标本方案的目标是为了提供一套简单易行且没有法律复杂性的蒸汽管道维修方案。
维修流程以下是蒸汽管道维修的基本流程:1. 检查和诊断:首先,对蒸汽管道进行检查和诊断,确定出现的问题和损坏程度。
这可以通过使用传感器和检测设备来实现。
检查和诊断:首先,对蒸汽管道进行检查和诊断,确定出现的问题和损坏程度。
这可以通过使用传感器和检测设备来实现。
2. 确定维修方案:根据检查和诊断结果,确定合适的维修方案。
维修方案可能涉及更换损坏的部件、修复漏损或加固管道等。
确定维修方案:根据检查和诊断结果,确定合适的维修方案。
维修方案可能涉及更换损坏的部件、修复漏损或加固管道等。
3. 准备工具和材料:根据维修方案,准备必要的工具和材料。
这可能包括替换零件、焊接设备、密封材料等。
准备工具和材料:根据维修方案,准备必要的工具和材料。
这可能包括替换零件、焊接设备、密封材料等。
4. 执行维修:根据维修方案和准备的工具材料,进行蒸汽管道的维修工作。
确保操作者具备相关技能和经验,以确保安全和质量。
执行维修:根据维修方案和准备的工具材料,进行蒸汽管道的维修工作。
确保操作者具备相关技能和经验,以确保安全和质量。
5. 测试和验证:在维修完成后,对蒸汽管道进行测试和验证,以确保修复效果符合要求。
这可以包括检测管道是否有漏损、恢复正常工作等。
测试和验证:在维修完成后,对蒸汽管道进行测试和验证,以确保修复效果符合要求。
这可以包括检测管道是否有漏损、恢复正常工作等。
安全措施在进行蒸汽管道维修时,必须采取适当的安全措施,以保护操作者和周围环境。
以下是一些常见的安全措施:- 使用个人防护装备,如安全帽、手套、护目镜等。
- 在维修区域设置警示标志,以提醒其他人员注意。
味精的生产工艺流程简介

1味精的生产工艺流程简介味精的生产一般分为制糖、谷氨酸发酵、中和提取及精制等4个主要工序。
1.1液化和糖化因为大米涨价,目前大多数味精厂都使用淀粉作为原材料。
淀粉先要经过液化阶段。
然后在与B一淀粉酶作用进入糖化阶段。
首先利用一淀粉酶将淀粉浆液化,降低淀粉粘度并将其水解成糊精和低聚糖,应为淀粉中蛋白质的含量低于原来的大米,所以经过液化的混合液可直接加入糖化酶进入糖化阶段,而不用像以大米为原材料那样液化后需经过板筐压滤机滤去大量蛋白质沉淀。
液化过程中除了加淀粉酶还要加氯化钙,整个液化时间约30min。
一定温度下液化后的糊精及低聚糖在糖化罐内进一步水解为葡萄糖。
淀粉浆液化后,通过冷却器降温至60℃进入糖化罐,加入糖化酶进行糖化。
糖化温度控制在60℃左右,PH值4.5,糖化时间18-32h。
糖化结束后,将糖化罐加热至80 85℃,灭酶30min。
过滤得葡萄糖液,经过压滤机后进行油水分离(一冷分离,二冷分离),再经过滤后连续消毒后进入发酵罐。
1.2谷氨酸发酵发酵谷氨酸发酵过程消毒后的谷氨酸培养液在流量监控下进入谷氨酸发酵罐,经过罐内冷却蛇管将温度冷却至32℃,置入菌种,氯化钾、硫酸锰、消泡剂及维生素等,通入消毒空气,经一段时间适应后,发酵过程即开始缓慢进行。
谷氨酸发酵是一个复杂的微生物生长过程,谷氨酸菌摄取原料的营养,并通过体内特定的酶进行复杂的生化反应。
培养液中的反应物透过细胞壁和细胞膜进入细胞体内,将反应物转化为谷氨酸产物。
整个发酵过程一般要经历3个时期,即适应期、对数增长期和衰亡期。
每个时期对培养液浓度、温度、PH值及供风量都有不同的要求。
因此,在发酵过程中,必须为菌体的生长代谢提供适宜的生长环境。
经过大约34小时的培养,当产酸、残糖、光密度等指标均达到一定要求时即可放罐。
1.3 谷氨酸提取与谷氨酸钠生产工艺该过程在提取罐中进行。
利用氨基酸两性的性质,谷氨酸的等电点在为pH3.0处,谷氨酸在此酸碱度时溶解度最低,可经长时间的沉淀得到谷氨酸。
1、简述 pcb 双面板和多层板生产流程。

【主题】:PCB双面板和多层板生产流程一、引言PCB(Printed Circuit Board,印刷电路板)是现代电子产品中不可或缺的一部分,它承载着电子元器件并提供电气连接。
在不同的电子产品中,我们经常会听到双面板和多层板的概念。
那么,它们的生产流程究竟是怎样的呢?二、双面板生产流程1. 设计与布局:双面板的生产流程首先要进行电路设计和布局,包括元件布局和线路走向的设计。
2. 制作内层板:将玻璃纤维布浸渍树脂,然后在铜箔上覆盖光敏胶,通过曝光、显影、蚀刻等步骤形成线路和铜箔残留的区域。
3. 复板:将内层板与预制好的介质层板及铜箔层板复合,并通过热压技术将其加以固化。
4. 外层图形化:在外层板铜箔表面上覆盖一层光敏胶,然后按照设计图形进行曝光、显影、蚀刻,形成外层线路及铜箔残留的区域。
5. 孔位铆合:利用机械或激光技术在板面上打孔(冲压孔位)。
6. 表面化学镀镍金:对板面进行化学镍金处理,以增强其与焊盘的附着力。
7. 色素沉积:在板面上形成阻焊油墨或者焊盘油墨图形。
8. 表面喷镘:将表面喷上喷锡层,构成铅(锡)粘接的表面。
三、多层板生产流程1. 设计与布局:多层板的设计和布局要比双面板更为复杂,需要考虑多层板间的互连关系和信号传输。
2. 制作内层板:多层板同样需要制作内层板,但在此之前需要将设计好的电路图分层布局,并使用铜箔、介质等材料进行层压。
3. 复合与预压:通过预压机将内层板与预制好的介质层板及铜箔层板复合,并进行热压处理。
4. 钻孔:利用高精度数控钻孔机对多层板进行钻孔处理,确保孔位的精确性。
5. 表面处理:在板面进行化学镀铜处理,以增强其导电性。
6. 外层图形化:进行外层线路的图形化处理,包括曝光、显影、蚀刻等步骤。
7. 色素沉积:形成阻焊油墨或者焊盘油墨图形。
8. 表面处理:喷镘或者喷锡等表面处理工艺,以增强焊盘的焊接性能。
四、总结从以上的生产流程可以看出,双面板和多层板的生产流程都是需要经过多道工艺步骤的复杂过程。
微通道换热器安装及维修手册 Version1 1

最小推荐折弯半径
mm
in
90
3.5
110
4.3
903.5Fra bibliotek140
5.5
170
6.7
200
7.87
170
6.7
>220
>8.7
190
7.5
110
4.3
125
5.0
3
MAKING LIVES MORE COMFORTABLE THRU INNOVATION
R
折弯过程中请注意如下事项;
• 微通道换热器是由相对软的金属铝制造而成,在搬运过程中很容易弯曲变形。在折弯之前,请确认微 通道换热器是方正平整而无损坏的。可以考虑通过整平工序确保上述要求。
2
MAKING LIVES MORE COMFORTABLE THRU INNOVATION
R
手柄的胶合板或塑料板)轻轻敲击进行整平。这种方法仅适用于翅片平齐的弯曲换热器,不适用于局部 翅片突出的情况。
3. 折弯程序
用于翅片管换热器的折弯机也可应用于微通道换热器的折弯。为方便包装及运输,我们建议微通道换热 器平板运输,在客户端进行折弯。
或弯曲进出口连接管。
铜管和铝管结合在一起,会产生电化学腐蚀。为了防止电化学腐蚀,可以在结合处喷涂油漆或套上一个 塑料的热缩管,阻止湿空气进入结合处发生电化学腐蚀。
6
MAKING LIVES MORE COMFORTABLE THRU INNOVATION
R
为了防止铜-铝钎焊点和热缩管在随后的焊接中过热,进出口接管上的钎焊点后面的铜管长度应大于 70mm。焊接过程中,可以采取额外的保护,如用干燥的氮气吹扫或者用湿布裹住接头处。微通道换热器 如果采用的是铝质出入口接管,集流管上的焊接点后的铝管长度也应当大于 70mm。
1.菊花生产流程

菊花栽培技术规范一、目的:对菊花生产流程规范操作,确保切花质量。
二、范围:适用于菊花繁殖、栽培、田间管理、采收、包装全套管理过程。
三、使用设备:保温大棚、供肥、药、水系统、加温(加温机)等设备。
一、菊花种苗繁殖栽培技术规范1、种苗的繁殖材料质量控制:种苗繁殖材料质量的好坏,直接影响最终切花生产切穗,为确保品种纯正,品质优良,健康无病害,应重视以下几个方面:1.1.1生产出高品质的种苗繁殖材料(切条),应坚持不懈的选择最佳品种,并定期更新繁殖母株,从而能保证种苗品质的稳定性和优秀性。
1.1.2对每一批母株的生产过程进行记录,使用好品质的母株,标明各个品种的情况,从母株下切条时,应记录好采穗日期,采穗人,品种、数量,以便有效追溯。
1.2母本定植前的准备工作1.2.1选择土质疏松、排水良好、肥沃、易于整理,土壤PH植在5.8—6.5最佳,对于较粘重的土壤适量添加谷壳,有机肥等,以改善土壤的通透性、质地及肥力。
1.2.2施基肥:每10平方米撒施15—15—15复合肥1千克+钙镁磷肥1千克+硝酸钙1千克,均匀施撒后用施耕机均匀施耕,并深翻土壤。
1.2.3土壤消毒:采用蒸气消毒或采用1平方米撒98%必速灭30克,后盖膜1周后拉开薄膜再做土壤整理。
1.2.4种植方式方法1.2.4.1按株行距10CM×12CM栽植。
1.2.4.2定植时注意:在定植前一天浇适当的水,第二天定植时根系和土壤尽量紧密粘在一起,不要让根系露于外面,防止根系脱水现象,植株定植深度为3-5cm。
1.2.4.3定植后浇充足的定根水。
1.2.4.4定植后用遮荫网根据天气遮光一周左右,同时保持昼温在20—250C之间,夜温不低于180C。
1.2.4.5母株处于长期的营养生长期,需补足光照,时间不少于16小时。
1.3水份管理:当苗定植后浇充足的定根水,苗在幼苗期间,水应特别注意,水量不要太多,也不要太少,保持土壤表面湿润即可,当定植3周后,根据天气情况来给水,一般正常情况下(晴天),每隔1—2天给一次水,给水的量一般根据土壤干湿度来决定,土壤湿润保持在20CM土层深度左右,不能积水。
氮肥工业生产工艺流程及主要产污环节、工业产污环节及污染物浓度水平(一)
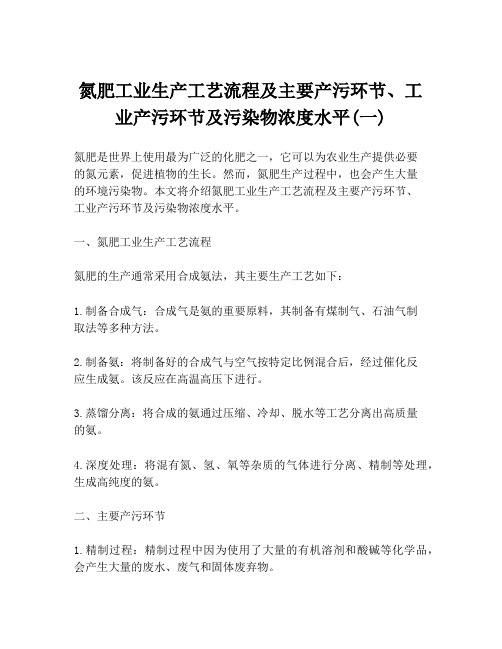
氮肥工业生产工艺流程及主要产污环节、工业产污环节及污染物浓度水平(一)氮肥是世界上使用最为广泛的化肥之一,它可以为农业生产提供必要的氮元素,促进植物的生长。
然而,氮肥生产过程中,也会产生大量的环境污染物。
本文将介绍氮肥工业生产工艺流程及主要产污环节、工业产污环节及污染物浓度水平。
一、氮肥工业生产工艺流程氮肥的生产通常采用合成氨法,其主要生产工艺如下:1.制备合成气:合成气是氨的重要原料,其制备有煤制气、石油气制取法等多种方法。
2.制备氨:将制备好的合成气与空气按特定比例混合后,经过催化反应生成氨。
该反应在高温高压下进行。
3.蒸馏分离:将合成的氨通过压缩、冷却、脱水等工艺分离出高质量的氨。
4.深度处理:将混有氮、氢、氧等杂质的气体进行分离、精制等处理,生成高纯度的氨。
二、主要产污环节1.精制过程:精制过程中因为使用了大量的有机溶剂和酸碱等化学品,会产生大量的废水、废气和固体废弃物。
2.化肥生产过程:制造氮肥过程中,废水和废气的排放量极大。
其中,产生的废水多含有高浓度的氨氮和固体颗粒物,废气则多含有氨气和氮氧化物。
三、工业产污环节及污染物浓度水平1.废水处理:氮肥废水中氨化氢、氨、尿素等浓度较高,难以降解,若直接排放会污染环境。
因此,废水必须进行处理。
经过处理后,NH3-N的浓度一般应低于50mg/L,COD应低于100mg/L。
2.废气治理:氮肥废气中氨气、氮气化合物、硫化物、烟气等浓度很高,是大气污染的主要来源之一。
因此,废气必须进行处理。
处理后,废气的NH3、NOx、SO2、烟尘等污染物浓度要达到国家要求的排放标准。
综上所述,氮肥工业生产中的主要产污环节包括精制过程和化肥生产过程。
废水和废气的产生量很大,其中氨气、氮氧化物等污染物的浓度也很高。
为了保护环境,氮肥厂必须科学规划、有序生产,并对污染物的排放进行科学控制和治理。
参考文献:1. 李玉霞. 氮肥工业行业分析[J]. 青年学者(学术版), 2020,2(4):186-187.2. 马平, 石凤珍. 氮肥生产主要环境问题及对策[J]. 中国工程科学, 2008(9):118-120.。
服装制衣厂基本生产流程与检验标准(1)
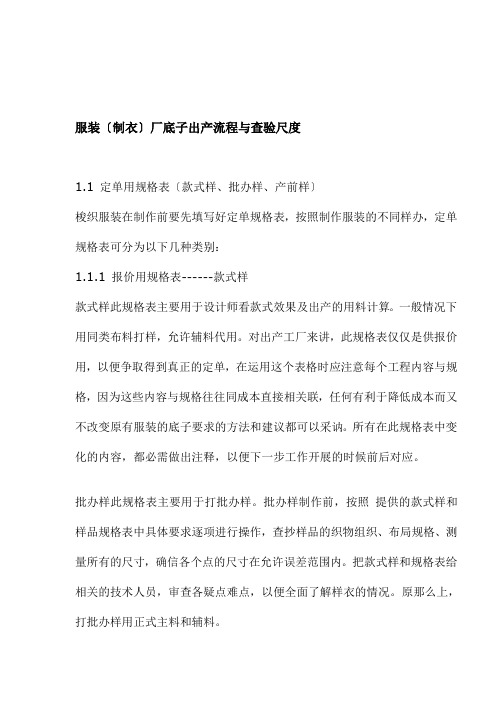
服装〔制衣〕厂底子出产流程与查验尺度1.1 定单用规格表〔款式样、批办样、产前样〕梭织服装在制作前要先填写好定单规格表,按照制作服装的不同样办,定单规格表可分为以下几种类别:1.1.1 报价用规格表------款式样款式样此规格表主要用于设计师看款式效果及出产的用料计算。
一般情况下用同类布料打样,允许辅料代用。
对出产工厂来讲,此规格表仅仅是供报价用,以便争取得到真正的定单,在运用这个表格时应注意每个工程内容与规格,因为这些内容与规格往往同成本直接相关联,任何有利于降低成本而又不改变原有服装的底子要求的方法和建议都可以采讷。
所有在此规格表中变化的内容,都必需做出注释,以便下一步工作开展的时候前后对应。
批办样此规格表主要用于打批办样。
批办样制作前,按照提供的款式样和样品规格表中具体要求逐项进行操作,查抄样品的织物组织、布局规格、测量所有的尺寸,确信各个点的尺寸在允许误差范围内。
把款式样和规格表给相关的技术人员,审查各疑点难点,以便全面了解样衣的情况。
原那么上,打批办样用正式主料和辅料。
产前表此规格表主要是批办样被客户批准后客户才提供的表格。
只有这个产物规格表才是供工厂大货出产用。
如果用以前的规格表代替,经常会发生过掉,因为颠末打样后,客户常更改原有的尺寸,而这个尺寸的更改又往往是不起眼的,在多量出产经营之前,还须打一次样,叫做产前样,在制作这个样衣中,所有的主料和辅料都必需用以后出产中要用的料,客户完全承认前方可多量开裁。
服装出产底子工艺流程包罗布料物料进厂查验、裁剪、缝制、锁眼钉扣、整烫、裁缝查验、包装入库等八个工序。
布料进厂后要进行数量清点以及外不雅和内在质量的查验,符合出产要求的才能投产使用。
把好面料质量关是控制成品质量重要的一环。
通过对进厂面料的查验和测定可有效地提高服装的正品率。
物料查验包罗松紧带缩水率,粘合衬粘合牢度,拉链顺滑程度等等。
对不克不及符合要求的物料不予投产使用。
技术筹办是确保批量出产顺利进行以及最终成品符合客户要求的重要手段。
维修安全生产规程范文

维修安全生产规程范文一、总则为了保障维修工作的安全进行,有效预防事故的发生,确保员工身心健康,提高工作效率,特制定本维修安全生产规程。
二、维修前的准备工作1. 维修人员在接到任务后,应先查阅设备的相关资料,了解设备的工作原理、维修方法和安全注意事项。
2. 维修人员应穿戴必要的个人防护装备,包括安全帽、防护眼镜、防护手套、防护鞋等,确保自身的安全。
3. 维修人员应确保维修所需工具的完好性,检查工具是否损坏或缺失,如有问题应及时更换或修理。
4. 维修人员应对维修区域进行安全检查,清除可能造成绊倒或撞击的障碍物,确保工作环境的安全。
三、维修现场安全管理1. 维修人员应按照安全操作规程进行维修工作,严禁违反规章制度和操作规程。
2. 维修人员应注意工作现场的通风状况,必要时应开启通风设备或戴上防护口罩,防止因有害气体产生而造成中毒。
3. 维修人员在进行高空维修时,应使用稳固的脚手架和安全绳,严禁擅自攀爬或站在不稳定的物体上工作。
4. 维修人员应遵守禁止吸烟和明火作业的规定,严禁在易燃易爆环境下进行维修工作。
5. 维修人员在进行电气维修时,应切断电源并使用绝缘工具,严禁在带电条件下操作,以免触电事故发生。
四、维修工具和设备管理1. 维修工具应定期检查,发现损坏或故障的工具需及时维修或更换。
2. 维修设备应经过定期检修,保证设备的正常工作,严禁使用未经检修或有缺陷的设备。
3. 维修人员在使用工具和设备时,应严格按照操作说明进行,避免操作失误或不当使用造成事故。
五、维修员安全意识培训与考核1. 新进维修人员应接受安全意识培训,了解维修工作的风险和防范措施。
2. 维修人员应定期进行安全知识培训,提高安全意识和应急处理能力。
3. 对维修人员进行安全考核,确保其具备必要的安全操作技能和知识。
六、维修事故的处理与上报1. 若在维修过程中发生事故或事故隐患,维修人员应立即采取必要的紧急措施,确保人员的安全。
2. 维修人员应按照规定的程序和时限上报事故,提供详细的事故经过、原因和处理措施,并及时进行事故的调查和分析,以避免类似事故再次发生。
成品生产控制程序(1)

台州市丝丝席业有限公司成品生产控制程序运作流程图:1.0目的:为了更好的控制成品生产数量,控制物料损耗及成本,明确各生产环节的实际数量及追溯成品的异常数量及品质,以便得到更有效的控制整个生产环节,使生产流程更顺畅,确保客户交期。
2.0范围:适用于所有成品生产的各车间及仓库,包括裁床车间、席子车间、枕套车间、包装车间、辅料仓库、成品仓库等。
3.0运作流程:3.1销售部收到客户订单后结合客户的工艺图纸、品质标准、包装要求和打样记录制定《成品订单评审表》直接下给成品生产厂长。
3.2成品生产厂长根据客户订单的数量、花型、规格、交期,辅料到厂周期、半成品生产周期、以及生产车间的实际产能和人员配备、设备状况、工艺成熟度、场地空间等编制《成品生产计划》,并下发各生产车间及仓库。
3.3裁剪车间主任按成品生产厂长所编制的《成品生产计划》进行跟进半成品的生产情况,对所需之半成品向半成品厂仓库领用或交接,并填写《半成品转接单》后,进行配套安排本车间每日生产任务,开裁以前核对样板、生产工艺、作业指导书等,由品质部检验员做好首件检验合格后方可开始批量裁剪,裁好之裁片由质检部检验员全检合格后(席子10条/困,枕套100片/困)按类型规则放在指定的区域,由指定的点数统计人员清点好数量,方可由送料员送至席子或枕套车间。
裁剪车间还担当夹里布和盖头秀布料的裁剪工作,而且对移交到缝纫车间的半成品以及布料都必须有准确的数据记录。
3.4席子或枕套车间在接收到裁床车间所送的裁片后必须核对样板、作业指导书,核对准确无误后发料给车工生产。
并详细告知车工生产时的注意事项(包含布料的搭配和正反面、开线颜色、水洗标的位臵和型号等),如有必要还应生产一个首件样板由品质部检验员做好首件检验合格后开始批量生产。
3.5质检部全检(包含外观检验、线头、摘除工号等)合格后将产品规则的放臵在指定的区域,由包装车间人员进行包装。
3.6包装车间领回已生产好的席子或枕套以及所需之包装辅助材料后,先核对包装样板或包装以前核对客户的包装指示,由质检部检验员确认首件合格后方可进行批量包装(有客户跟单员跟单的产品必须取得对方的认可或书面文件认可后方可开始批量包装)。
镀锡板生产工艺流程及关键工序

镀锡板⽣产⼯艺流程及关键⼯序镀锡板⽣产⼯艺流程及关键⼯序1.⽣产⼯艺流程原板卷开卷切头尾焊接剪边碱洗酸洗电镀锡软熔钝化静电涂油镀层测厚净⾯检查针孔检测剪切卷取镀锡板带卷堆放2.镀锡机组的⽣产过程吊车将原料钢卷吊到镀锡机组的上料台架上,由上料⼩车将带钢尾卷送到开卷机的悬臂卷筒上,然后带钢送到夹送辊,送⼊双层剪切机切头,再送到窄缝焊机进⾏焊接,成为连续带钢卷。
焊后的带钢卷必须经过纠偏装置进⾏对中,再进⼊到圆盘剪剪切,剪后带钢边缘有压⽑刺机压⽑刺。
压⽑刺后的带钢通过张⼒辊再进⼊活套塔,由活套塔储存⼀定的带钢量,带钢从⼊⼝活套塔出来后,由张⼒矫直机对带钢进⾏弯曲和拉伸,以改善带钢板形,然后进⼊电解清洗段,经过电解脱脂冲洗,接着进⾏电解酸洗冲洗,把带钢表⾯氧化物去除,然后再进⼊电镀槽,电镀是将锡条作为阳极作为阳极,带钢作为阴极,通过电流、镀液的作⽤将锡镀到带钢表⾯上,镀层厚度可以⾃动控制。
带钢出镀液回收槽烘⼲后再进⾏软熔,软熔是通过电阻将带钢加热到⾼于锡熔点温度,然后淬⽔冷却,使镀锡板形成光亮的表⾯并改善耐腐蚀性。
机组中还安装有打印机,在带钢表⾯上印上条形码标记。
软熔后的带钢进⼊钝化处理,然后烘⼲、涂油、镀层测厚,再经过张紧辊进⼊出⼝活套塔,带钢出活套塔后,经过镜⾯检查、针孔检查、带钢光电检测,由导向辊、输送平台将带钢送⼊卷取机液压浮动齐边活错边卷取。
卷取后卸道下料台架上,由吊车⾦爱那个镀锌钢卷吊到剪切线中间仓库堆放。
3.镀锡机组的主要特点3.1窄缝焊机在镀锡机组中,可选⽤先进的窄缝焊机、焊缝厚度为焊接前单⽚带钢厚度的130-170%,塔接量为0.8-4.0mm,焊缝强度为带钢本体强度的100%,焊接时间为18s。
带钢镀锡后卷取,焊缝不需要切除。
3.2拉伸矫直机拉伸矫直机位于镀锡机组⼯艺段中,为了保证带钢的镀锡质量,为机组⽣产均匀⼀致的产品提供恒定速度,在张⼒辊的轴承座下装有压⼒传感器,通过传感器来反应张⼒⼤⼩。
生产工艺流程培训
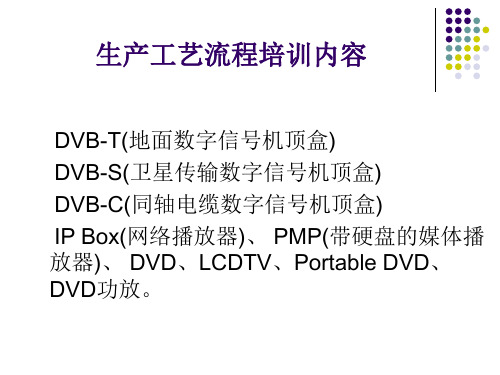
生产工艺流程培训内容DVB-T(地面数字信号机顶盒)DVB-S(卫星传输数字信号机顶盒)DVB-C(同轴电缆数字信号机顶盒)IP Box(网络播放器)、PMP(带硬盘的媒体播放器)、DVD、LCDTV、Portable DVD、DVD功放。
生产工艺制程策划:(删除、简化、重组)一.原则:人、机、料、法二.步骤:1. 产品分解;2. 人力配置;3. 设备工具的评估;4. 生产产能的核算;5. 材料需求的评估。
SMT车间生产流程●SMTSMT表面贴装技术,实现电路板的高密度、高可靠性、小型化以及低成本。
●流程:烘板—印刷锡膏—贴装—检正—回流焊接—清洗—测试—返修。
●1.烘板a.温度:120℃时间:4小时;b.作用:①除潮;②防氧化,便于锡膏附着。
●2.印刷锡膏●1)钢网:a.厚度0.12mm—0.15mm;b.钢网开口大小=焊盘大小×2/3●2)无铅锡膏<ROHS>:a.无铅锡膏熔点:217℃;b.成分:锡Sn、银Ag、铜Cu、助焊剂、添加剂;c.比例:Sn:Ag:Cu = 96.5% :3.0%:0.5%;d.各成分作用:Ag 防氧化;Cu 增强导电性;助焊剂:去氧化;添加剂:增强粘性等;e.储存温度:储存于2℃—10℃冰箱中。
●3)刮刀:a.常用类型:拖裙形、菱形;b.压力:0.5Kg/25mm²;c.速度:与板的厚度和2C脚的密度有关,当板的厚度≦0.5mm时速度为20mm-30mm/s。
●3.贴装●1) 贴片机型号:高速贴片机YG200(气动)、YG300(电动):适用于较小的贴片元件;泛用贴片机YG100:适用于较大的贴片元件。
产线配置:YG200+YG200+YG100 时产5.5万YG300+YG100 时产5.5万。
●2)贴装八大原则:一.元件形状要求适合自动化表面贴装;二.尺寸、形状在标准化具有互换性;三.具有良好的尺寸精度;四.适应流水或非流水作业;五.具有一定的机械强度、能承受有机溶液的洗涤;六.可执行零散包装,有适应于边带包装;七.具有电性能及机械性的互换性;八.耐焊接热度应符合相应规定。
MI资料制作指导书1
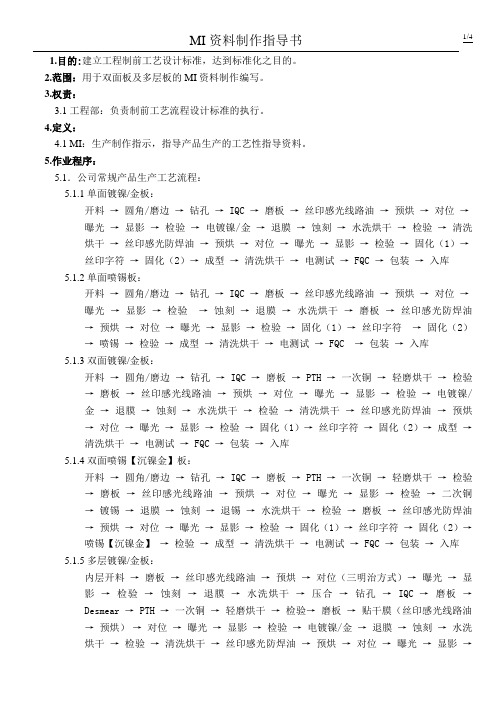
1.目的:建立工程制前工艺设计标准,达到标准化之目的。
2.范围:用于双面板及多层板的MI资料制作编写。
3.权责:3.1工程部:负责制前工艺流程设计标准的执行。
4.定义:4.1 MI:生产制作指示,指导产品生产的工艺性指导资料。
5.作业程序:5.1.公司常规产品生产工艺流程:5.1.1单面镀镍/金板:开料→圆角/磨边→钻孔→ IQC →磨板→丝印感光线路油→预烘→对位→曝光→显影→检验→电镀镍/金→退膜→蚀刻→水洗烘干→检验→清洗烘干→丝印感光防焊油→预烘→对位→曝光→显影→检验→固化(1)→丝印字符→固化(2)→成型→清洗烘干→电测试→ FQC →包装→入库5.1.2单面喷锡板:开料→圆角/磨边→钻孔→ IQC →磨板→丝印感光线路油→预烘→对位→曝光→显影→检验→蚀刻→退膜→水洗烘干→磨板→丝印感光防焊油→预烘→对位→曝光→显影→检验→固化(1)→丝印字符→固化(2)→喷锡→检验→成型→清洗烘干→电测试→ FQC →包装→入库5.1.3双面镀镍/金板:开料→圆角/磨边→钻孔→ IQC →磨板→ PTH →一次铜→轻磨烘干→检验→磨板→丝印感光线路油→预烘→对位→曝光→显影→检验→电镀镍/金→退膜→蚀刻→水洗烘干→检验→清洗烘干→丝印感光防焊油→预烘→对位→曝光→显影→检验→固化(1)→丝印字符→固化(2)→成型→清洗烘干→电测试→ FQC →包装→入库5.1.4双面喷锡【沉镍金】板:开料→圆角/磨边→钻孔→ IQC →磨板→ PTH →一次铜→轻磨烘干→检验→磨板→丝印感光线路油→预烘→对位→曝光→显影→检验→二次铜→镀锡→退膜→蚀刻→退锡→水洗烘干→检验→磨板→丝印感光防焊油→预烘→对位→曝光→显影→检验→固化(1)→丝印字符→固化(2)→喷锡【沉镍金】→检验→成型→清洗烘干→电测试→ FQC →包装→入库5.1.5多层镀镍/金板:内层开料→磨板→丝印感光线路油→预烘→对位(三明治方式)→曝光→显影→检验→蚀刻→退膜→水洗烘干→压合→钻孔→ IQC →磨板→Desmear → PTH →一次铜→轻磨烘干→检验→磨板→贴干膜(丝印感光线路油→预烘)→对位→曝光→显影→检验→电镀镍/金→退膜→蚀刻→水洗烘干→检验→清洗烘干→丝印感光防焊油→预烘→对位→曝光→显影→检验→固化(1)→丝印字符→固化(2)→成型→清洗烘干→电测试→ FQC →包装→入库5.1.6多层喷锡【沉镍金】板:内层开料→磨板→丝印感光线路油→预烘→对位(三明治方式)→曝光→显影→检验→蚀刻→退膜→水洗烘干→压合→钻孔→ IQC →磨板→Desmear → PTH →一次铜→轻磨烘干→检验→磨板→贴干膜/(丝印感光线路油→预烘)→对位→曝光→显影→检验→二次铜→镀锡→退膜→蚀刻→退锡→水洗烘干→检验→磨板→丝印感光防焊油→预烘→对位→曝光→显影→检验→固化(1)→丝印字符→固化(2)→喷锡【沉镍金】→检验→成型→清洗烘干→电测试→ FQC →包装→入库5.2.厂内产品编号方法:版本号流水号工艺类别样/量代号层数说明:(1)版本号---以两个字位表示,前一个英文字母,表示客户版本号,以A开始,按英文字母顺序排序,代表客户资料版本;后一个为阿拉伯数字,从“0”开始,按数字升序表示本厂修改次数。
工程机械维修生产制度

工程机械维修生产制度一、总则为规范工程机械维修生产行为,提高维修质量,降低维修风险,保障职工安全,制定本制度。
二、适用范围本制度适用于公司内所有从事工程机械维修生产的人员,包括维修工人、工程师、管理人员等。
三、维修流程1.维修接单阶段(1)接到客户报修电话后,维修员应核实机械型号、故障情况,并填写报修单。
(2)管理员工程师分析故障原因,确定维修方案,分派维修工人进行处理。
2.维修过程阶段(1)维修过程中,维修工人应根据维修方案,仔细分解、清洗、检修、更换零部件等。
(2)任何更换零部件都需经过管理员工程师确认和签字。
3.维修完成阶段(1)维修完工后,维修工人应进行维修记录,详细记录机械型号、维修内容、更换零部件等。
(2)管理员工程师进行维修验收,确认维修质量符合标准后,签署验收单交予报修用户。
四、维修安全1.工具使用(1)使用维修工具时应按照说明书操作,严禁乱用、擅自拆卸。
(2)操作完毕后,应及时清理工具,确保工作环境整洁。
2.劳动保护(1)维修期间,应佩戴工作手套、安全帽等劳动保护用品,确保人身安全。
(2)禁止在维修时穿戴松散衣物,以及长发等会危害安全的物品。
3.作业环境(1)工作场所应保持干净整洁,严禁乱堆乱放。
(2)设备故障处需设置明显的安全标识,以示警示。
五、维修质量1.维修工人需具备相应的技术资格和经验,经过公司培训合格后方可上岗。
2.维修过程中要认真对待每一个细节,确保维修质量达到标准,并定期进行维修质量检查。
3.维修过程中发现新问题需立即上报管理员工程师,进行解决处理。
六、维修责任1.维修工人应对自己的操作负责,确保不出现差错。
2.管理员工程师应对维修过程进行监督管理,确保维修质量符合标准。
3.如因维修不当导致机械再次故障,维修人员需承担相应的责任。
七、维修保养1.定期对维修设备进行保养,确保设备运行稳定。
2.保养过程中,应根据实际情况更换润滑油、清洁过滤器等。
八、维修记录1.工程机械维修过程中的每一个细节都需进行记录,包括故障情况、维修措施、更换零部件等。
腐植酸生产工艺流程
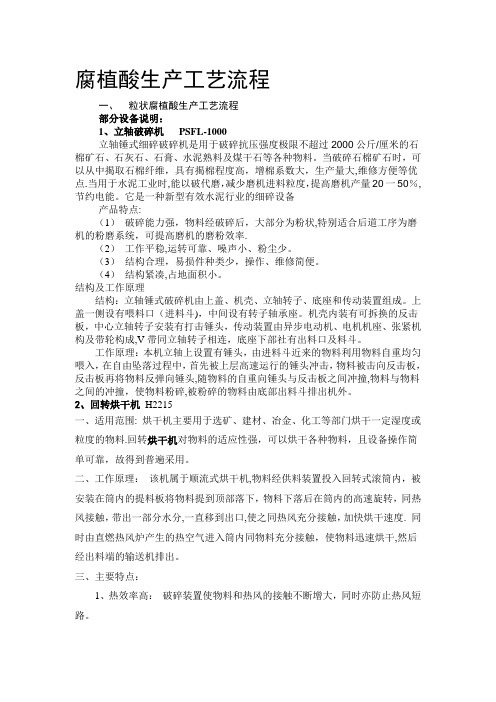
腐植酸生产工艺流程一、粒状腐植酸生产工艺流程部分设备说明:1、立轴破碎机PSFL-1000立轴锤式细碎破碎机是用于破碎抗压强度极限不超过2000公斤/厘米的石棉矿石、石灰石、石膏、水泥熟料及煤干石等各种物料。
当破碎石棉矿石时,可以从中揭取石棉纤维,具有揭棉程度高,增棉系数大,生产量大,维修方便等优点.当用于水泥工业时,能以破代磨,减少磨机进料粒度,提高磨机产量20一50%,节约电能。
它是一种新型有效水泥行业的细碎设备产品特点:(1)破碎能力强,物料经破碎后,大部分为粉状,特别适合后道工序为磨机的粉磨系统,可提高磨机的磨粉效率.(2)工作平稳,运转可靠、噪声小、粉尘少。
(3)结构合理,易损件种类少,操作、维修简便。
(4)结构紧凑,占地面积小。
结构及工作原理结构:立轴锤式破碎机由上盖、机壳、立轴转子、底座和传动装置组成。
上盖一侧设有喂料口(进料斗),中间设有转子轴承座。
机壳内装有可拆换的反击板,中心立轴转子安装有打击锤头,传动装置由异步电动机、电机机座、张紧机构及带轮构成,V带同立轴转子相连,底座下部社有出料口及料斗。
工作原理:本机立轴上设置有锤头,由进料斗近来的物料利用物料自重均匀喂入,在自由坠落过程中,首先被上层高速运行的锤头冲击,物料被击向反击板,反击板再将物料反弹向锤头,随物料的自重向锤头与反击板之间冲撞,物料与物料之间的冲撞,使物料粉碎,被粉碎的物料由底部出料斗排出机外。
2、回转烘干机H2215一、适用范围:烘干机主要用于选矿、建材、冶金、化工等部门烘干一定湿度或粒度的物料.回转烘干机对物料的适应性强,可以烘干各种物料,且设备操作简单可靠,故得到普遍采用。
二、工作原理:该机属于顺流式烘干机,物料经供料装置投入回转式滚筒内,被安装在筒内的提料板将物料提到顶部落下,物料下落后在筒内的高速旋转,同热风接触,带出一部分水分,一直移到出口,使之同热风充分接触,加快烘干速度.同时由直燃热风炉产生的热空气进入筒内同物料充分接触,使物料迅速烘干,然后经出料端的输送机排出。
现代高端装备的维护与维修方案(一)
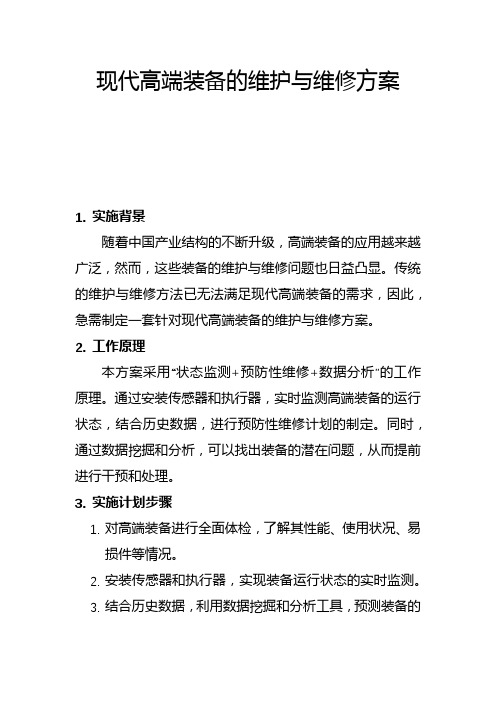
现代高端装备的维护与维修方案1. 实施背景随着中国产业结构的不断升级,高端装备的应用越来越广泛,然而,这些装备的维护与维修问题也日益凸显。
传统的维护与维修方法已无法满足现代高端装备的需求,因此,急需制定一套针对现代高端装备的维护与维修方案。
2. 工作原理本方案采用“状态监测+预防性维修+数据分析”的工作原理。
通过安装传感器和执行器,实时监测高端装备的运行状态,结合历史数据,进行预防性维修计划的制定。
同时,通过数据挖掘和分析,可以找出装备的潜在问题,从而提前进行干预和处理。
3. 实施计划步骤1.对高端装备进行全面体检,了解其性能、使用状况、易损件等情况。
2.安装传感器和执行器,实现装备运行状态的实时监测。
3.结合历史数据,利用数据挖掘和分析工具,预测装备的维修需求。
4.制定预防性维修计划,包括维修时间、维修内容等。
5.实施维修计划,对装备进行预防性维修和保养。
6.持续监测装备的运行状态,根据实际情况调整维修计划。
4. 适用范围本方案适用于各种现代高端装备,如数控机床、精密仪器、石油化工设备等。
通过本方案的实施,可以大大提高设备的运行效率和使用寿命。
5. 创新要点1.采用大数据和人工智能技术进行数据分析和预测,提高了维修计划的准确性和及时性。
2.通过实时监测和预防性维修,避免了设备突发故障对生产的影响,提高了设备的稳定性和可靠性。
3.通过持续的数据积累和分析,可以找出设备的潜在问题,提前进行处理,减少了设备的停机时间。
6. 预期效果1.降低设备故障率:通过预防性维修和实时监测,可以及时发现并处理设备的潜在问题,从而降低设备故障率。
2.提高设备运行效率:通过提前处理设备问题,可以避免设备突发故障对生产的影响,从而提高设备的运行效率。
3.延长设备使用寿命:通过预防性维修和保养,可以延长设备的使用寿命。
4.降低维修成本:通过大数据和人工智能技术进行数据分析和预测,可以更准确地制定维修计划,从而降低维修成本。
生产厂长的日常工作流程范文(通用3篇)_1
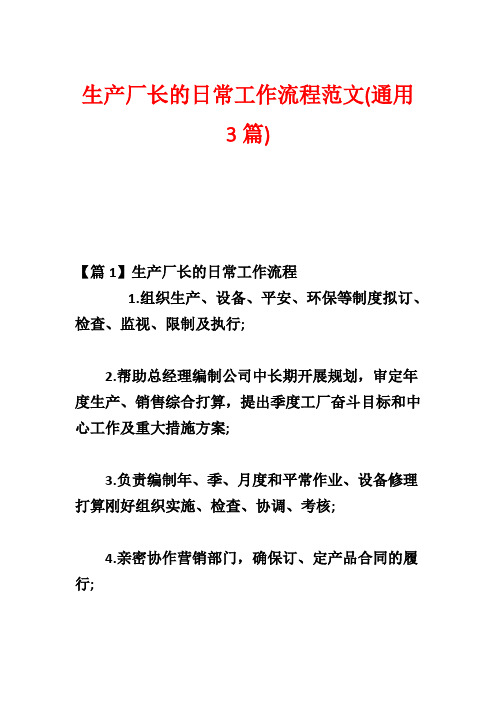
生产厂长的日常工作流程范文(通用3篇)【篇1】生产厂长的日常工作流程1.组织生产、设备、平安、环保等制度拟订、检查、监视、限制及执行;2.帮助总经理编制公司中长期开展规划,审定年度生产、销售综合打算,提出季度工厂奋斗目标和中心工作及重大措施方案;3.负责编制年、季、月度和平常作业、设备修理打算刚好组织实施、检查、协调、考核;4.亲密协作营销部门,确保订、定产品合同的履行;5.协作组织审定技术管理标准,编制生产工艺流程,审核新产品开发方案,并组织试生产,不断提高产品的市场竞争力;6.负责抓好生产平安教育,加强平安生产的限制、实施、严格执行平安法规、生产操作规程,即时监视检查,确保平安生产,杜绝重大火灾、设备、人身伤亡事故的发生;7.负责组织生产现场管理工作,重视环境爱护工作,抓好劳动防护管理和制订环保措施打算;8.加强管理,确保工厂各部门和各类人员职责、权限标准化,建立质量管理体系;9.做好生产统计核算根底管理工作,重视原始记录、台账、统计报表管理工作,确保统计核算标准化、统计数据的正确性;10.督导工厂各部门的日常生产活动,定期召开有关会议,发觉问题、分析缘由,采纳有效措施,确保生产线正常运转;11.抓好生产统计分析报告。
定期进展生产统计分析、经济活动分析报告会,总结经历、找出存在的`问题,提出改良工作的看法和建议,为公司领导决策供应专题分析报告或综合分析资料;12.负责做好生产设备、计量器具维护检修工作。
结合生产任务,合理的支配生产设备、计量器具打算,确保设备维护保修所须的正常时间;13.负责做好生产调度管理工作。
强化调度管理、肃穆调度纪律,提高一线管理人员生产专业学问和业务管理水平,平衡综合生产实力,合理支配生产作业时间,平衡用电、节约能源;14.抓好生产管理人员的专业培训工作。
负责组织质检员、车间管理人员、统计员、车工等的业务指导和培训工作,并对其业务水平和工作实力定期检查、考核、评比;15.贯彻、执行公司的本钱限制目标,踊跃削减厂区的各种本钱,确保在提高产量、保证质量的前提下不断降低生产本钱;16.谨慎抓好超领物料的损耗统计。
- 1、下载文档前请自行甄别文档内容的完整性,平台不提供额外的编辑、内容补充、找答案等附加服务。
- 2、"仅部分预览"的文档,不可在线预览部分如存在完整性等问题,可反馈申请退款(可完整预览的文档不适用该条件!)。
- 3、如文档侵犯您的权益,请联系客服反馈,我们会尽快为您处理(人工客服工作时间:9:00-18:30)。
DCRS-7600系列生产流程及维修指导版本:V2.0适用产品:MRS-7600-CPU8245MRS-7604-M12GBMRS-7604-M4GX24TXMRS-7600-12GTMRS-7600-12GBMRS-7608-MI修改记录目录1.MRS-7604-M12GB。
5 2.MRS-7604-M4GX24TX。
6 3.MRS-7600-12GT。
7 4.MRS-7600-CPU8245。
10 5.MRS-7600-12GB。
11 6.MRS-7608-MI。
13一. 概述:76系列的所有板卡生产的生产流程基本相同,但每一块板的生产都必须走完这一流程才能算该块板的生产结束。
而在生产流程中难免会有不良品的出现,本维修指导需依赖于产测程序的判断来进行,指导中写入了主要地方的电压,时钟等的标准参考值,以及整块板的工作方框图。
维修时可根据方框图来找到区域,然后测量该区域的各个点的参数是否这。
二. 生产流程图:Array三. 不良维修:在测试时分为了几个区域的测试,并且屏幕上都有直接的显示当前的测试区域。
维修时看程序在测某区域时出错,并依据出错的提示在板上找到该区域。
1.不良问题排出顺序1)拿到不良的板后找到提示错误的区域。
2)目检本区域有无焊接问题,比如:空焊,缺件,短路等。
3)如看不出问题再跟据方框图检查与本区域有直接连联,通讯的有无焊接问题。
4)测试有没有工作起来,比如最基本的电压,时钟。
5)作芯片级维修,更换相应的不良器件。
2.功能框架图和测量参考值2.1 MRS-7604-M12GB(EM4612-SX-FLF-CO)1)上电前电源对地电阻测量板上总共有四种电源,分别是1.25V,3.3V,2.5V, 1.8V。
上电之前分别需要测试四个电源和GND之间的电阻值。
3.3V的测试如下:电容C77两端的电阻在12欧姆左右为正常。
1.25V的测试如下:电容C199两端的电阻在37欧姆左右为正常。
2.5V的测试如下:电容C64两端的电阻在221欧姆左右为正常。
1.8V的测试如下:电容C62两端的电阻在348欧姆左右为正常。
以上的电阻值为一参考值,实际操作过程中,测量值在参考值左右浮动视为正常。
2)通电中的电压值测量点每组电压的测量点就为上面测电阻时的电容处,每组电压值偏差不超过±5%为正常。
3)时钟信号测量点157M参考时钟测试点为X3的3脚;127M参考时钟测试点为X1的3脚;156.25M差分参考时钟测试点为U16的4脚,5脚;(测试时要用差分探头)33M参考时钟测试点为X4的3脚;25M参考时钟测试点为X2的3脚;4)复位信号测量点板上总的复位信号测试点为U17的4脚;BCM5671的复位信号测试点为U17的6脚;BCM5690的复位信号测试点为U17的3脚;BCM5325的复位信号测试点为U17的8脚;CPLD的复位信号测试点为U17的11脚;2.2 MRS-7604-M4GX24TX(EM4628-FLF-CO)1)上电前电源对地电阻测量板上总共有五种电源,分别是1.25V,1.25AV,3.3V,2.5V, 1.8V。
上电之前分别需要测试五个电源和GND之间的电阻值。
3.3V的测试如下:电容C819两端的电阻在14欧姆左右。
1.25V的测试如下:电容C820两端的电阻在32欧姆左右。
1.25AV的测试如下:电容C645两端的电阻在600欧姆左右。
2.5V的测试如下:电容C706两端的电阻在133欧姆左右。
1.8V的测试如下:电容C821两端的电阻在3.8k欧姆左右。
以上的电阻值均为参考值,实际操作过程中,测量值在参考值左右浮动视为正常。
2)通电中的电压值测量点3.3V R282两端电压1.25V R284两端电压2.5V R276两端电压1.8V R286两端电压1.25A V R289两端电压3)时钟信号测量点157M参考时钟测试点为X5的3脚;127M参考时钟测试点为X1的3脚;156.25M差分参考时钟测试点为U21的4脚,U21的5脚;(测试时要用差分探头)33M参考时钟测试点为X2的3脚;25M参考时钟测试点为X3的3脚,X7的3脚;125M参考时钟测试点为X4的3脚;4)复位信号测量点板上总的复位信号测试点为U33的1脚;BCM5671的复位信号测试点为U33的3脚;BCM5665的复位信号测试点为U33的13脚;BCM5325的复位信号测试点为U33的8脚;CPLD的复位信号测试点为U33的11脚;BCM5248的复位信号测试点为U34的6脚;BCM5464的复位信号测试点为U34的8脚;2.3 MRS-7600-12GT(EM4012-FLF-CO)1)上电前电源对地电阻测量板上总共有四种电源,分别是1.25V,3.3V,2.5V, 1.2V,1.2V_A。
上电之前分别需要测试四个电源和GND之间的电阻值。
3.3V的测试如下:电容C165两端的电阻在11欧姆左右为正常。
1.25V的测试如下:电容C166两端的电阻在37欧姆左右为正常。
2.5V的测试如下:电容C163两端的电阻在219欧姆左右为正常。
1.2V的测试如下:电容C680两端的电阻在92欧姆左右为正常。
1.2V_A的测试如下:电容C682两端的电阻在165欧姆左右为正常。
以上的电阻值为一参考值,实际操作过程中,测量值在参考值左右浮动视为正常。
再查上面5个电容(C163, C165, C166, C680, C682)正极之间的电阻,两两之间没有0欧姆表示电源之间没有短路;2)通电中的电压值测量点3.3V C165两端电压1.25V C166两端电压2.5V C163两端电压1.2V C680两端电压1.2V_A C682两端电压电压值偏差不超过±5%为正常。
3)时钟信号测量点157M参考时钟测试点为X5的3脚;127M参考时钟测试点为X1的3脚;156.25M差分参考时钟测试点为U13的4脚,U13的5脚;(测试时要用差分探头)33M参考时钟测试点为X2的3脚;25M参考时钟测试点为X3的3脚,X6的3脚;4)复位信号测量点单板上总的复位信号测试点为U17的4脚;BCM5671,BCM5690, CPLD的复位信号测试点为U17的11脚;BCM5464S的复位信号测试点为U17的8脚;PCI2050, AM79C973的复位信号测试点为U17的3脚;2.4MRS-7600-CPU82451)上电前电源对地电阻测量板上总共有三种电源,分别是5V,3.3V,1.8V。
上电之前分别需要测试几个电源和GND之间的电阻值。
5V的测试如下:J12的第2脚对地电阻应为1M欧以上。
3.3V的测试如下:J12的第1脚或U35的第5脚对地电阻应在600欧以上。
1.8V因是U35由3.3V转换而来,不便测量阻值,3.3V正常即可。
2)通电中的电压值测量点5V量J12的第2脚。
3.3V 量U35的第5或J12的第一脚。
1.8V 量U35的第1脚或第3对。
(J12的第3脚为GND)电压值偏差不超过±5%为正常。
3)时钟信号测量点33M时钟X1的第3脚25M时钟X2的第3脚133M的SDRAM同步时钟,U5,U6,U7,U8的第38脚。
以上时钟信号都是TTL电平,电压范围是-0.6~+4.0V;时钟占空比50±5%以内即可。
正常情况下时钟波形完整,电压动态范围符合要求,频率准确。
4)复位信号测量点硬件复位是指:系统正常工作时,MPC8245定时发送脉冲信号来清空WDT芯片内的计数器,若系统锁死,则计数器超时溢出,则由WDT芯片ADM706产生复位信号强制cpu复位。
此功能可以通过软件设置打开和关闭。
AMD706(U15)的P7管脚输出复位信号,测量复位脉冲宽度是否符合要求,一般是要求大于200ms,以及复位脉冲低电平是否小于400mV,上升沿是否平滑,有没有台阶,否则都会影响复位可靠性。
5)数据信号测量点若时钟信号和电压正常,并且CPLD加载成功,可以手工按复位键重启动,之后可以看到串口打印信息。
如果没有串口输出,重点检测SDRAM的数据信号。
U5,U6,U7,U8这四个芯片分别有16根数据线,分别是Pin2,4,5,7,8,10,11,13,42,44,45,47,48,50,51,53。
测量其中的任意几根,看波形是否正常,其电压范围应该在-0.6~+4.0V左右,TTL电平,低电平输出小于0.4V,高电平大于2.4V2.5MRS-7600-12GB(EM4012-SX-FLF-CO)1) 上电前电源的电阻测量点3.3V的测试如下:电容C165两端的电阻在12欧姆左右为正常。
2.5V的测试如下:电容C90两端的电阻在261欧姆左右为正常。
1.25V的测试如下:电容C166两端的电阻在34欧姆左右为正常。
各组电源之间的短路测量:检查上面4个电容(C165, C90, C166)正极之间的电阻,两两之间没有0欧姆表示电源之间没有短路;2) 通电中的电源值测量3.3V C165两端电压2.5V C90两端电压1.25V C166两端电压电压值偏差不超过±5%为正常。
3) 时钟信号测量157M参考时钟测试点为X5.3;127M参考时钟测试点为X1.3;156.25M差分参考时钟测试点为U13.4,U13.5;(测试时要用差分探头)33M参考时钟测试点为X2.3;25M参考时钟测试点为X3.3,X4.3 ;5)复位信号测量单板上总的复位信号测试点为U17第4脚;BCM5671,BCM5690, CPLD的复位信号测试点为U17第11脚;PCI2050, AM79C973的复位信号测试点为U17第3脚;6)常见维修点6.1 单板某芯片出问题:首先,确定此芯片的电源、时钟输入是否正常,如不正常则查找出原因并解决;再次,确定此芯片的各信号输入是否正常,如不正常则查找出原因并解决;然后,确定此芯片的输出管脚的后端电路对芯片的输出没有影响;最后,如果前面几步的问题都确定接决的情况下,输出还是不正常,这确定为该芯片已经坏了,更换芯片;通常情况下,我们查芯片问题都是从上面几方面看其输入、输出信号从而定位问题原因。
6.2 单板出问题:A.电源灯不亮:线卡用VDD3V3来点电源灯,根据如下电源的整体框图:2.5V 1.25V3.3V图:电源逻辑功能框图根据“单板某芯片出问题”可知,先确定DC/DC 模块(U5)是否有问题,然后确定热拔插电路中的MOS 管(Q1)是否有问题、还有热拔插芯片(U12)是否有问题,然后应该已经定位出问题的原因;电源DC/DC 模块U5、U11经常出的问题为模块上的大电感焊接后脱落;另外,也容易被静电击坏;注意:如电源有问题一定要立刻断电,重新确定是否有短路现象,以免烧坏芯片;B.前面板灯全亮察看CPU 扣板是否扣好和两者之间的接插件是否正常,有时出现接插件的针弯曲在里面;察看CPLD 逻辑是否烧录正确,焊接是否有问题,焊接有虚焊情况; 察看复位芯片(U17.11)是否正常;C.与主控板通讯的HG 口不通一般情况下,BCM5671不会有问题,但是,给它提供156.25M 差分时钟的BUFFER 芯片MC100LVEP111(U3)较容易出问题,可以察看其输入输出,来确定问题;D.100M 调试端口不通一般AM79C973存在虚焊或短路的现象,排除了此两项之后,如果还是不通,则要查此芯片的输入输出,看看芯片AM79C973是否坏了;在调试时这些情况都出现过;E.部分光口不通(或不link )运行产测程序,一些光口link不上,特别是ge7-10这四个端口,这种情况一般为bcm5690虚焊导致,可以用接绝缘体轻轻压bcm6595的定位端(管脚a1),如果此时能link上,则可确定为芯片虚焊问题;另外,察看bcm5695下面(BOTTOM层)的电阻电容等器件是否在焊接时有脱落现象;F.串口不打印信息mini USB(J4)接插件是否焊接好,焊接易出现短路情况;2.6MRS-7608-MI(EM0602-FLF-CO)1)上电前电源的电阻测量点3.3V的测试如下:电容C276两端的电阻在12欧姆左右为正常。