PCB前处理
PCB设计前处理

1.从原理图中导出网表设置完毕之后,会在指定路径下产生pstchip.dat,pstxnet.dat,patxprt.dat文件pstchip.dat :记录的是各个封装的相关参数pstxnet.dat :记录各个器件引脚的电气连接关系patxprt.dat :记录的是各个器件对应的封装类型2.导入网表(1)建立PCB文件然后设置图纸参数选择Desgin,进行相关图纸参数设置设置栅格点(2)指定封装库路径Devpath是定义寻找Device文件的目录路径,主要用于第三方网表的导入Padpath 是定义寻找Padstack文件的目录路径Psmpath 是定义寻找Symbol文件的目录路径(3)导入网表Other为导入第三方网表Always 表示全部元件无论在原理图中是否被改过,均放置在网表导入前位置‘Never表示元件在原理图中修改过,Allegro会将其放入到后台,等待重新放置If same symbol 表示只变更原理图中有改变的元件的封装(4)建立PCB板外框在命令窗口输入命令如:x–1000 0Ix 200Iy 100Ix -200Iy -100设置PCB禁布区Package Keepin表示在限定的区域内可以放置器件Package Keepout表示在限定的区域内禁止放置器件Route Keepin表示在限定的区域内可以布置任何走线或者图形Route Keepout表示在限定的区域内不可以布置任何走线或者图形Via Keepout表示在限定的区域内不可以放置过孔特别提示在处理复杂形状的限制区域时,可以Edit/Z-copy然后选择要copy到的层,这里是Route KeepinContract 缩小Expand 放大Offset 缩小或者放大的尺寸然后倒圆角。
pcb板电操作流程
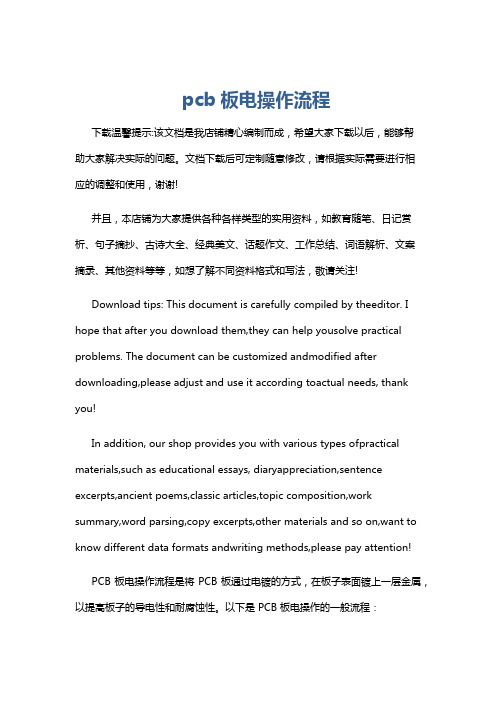
pcb板电操作流程下载温馨提示:该文档是我店铺精心编制而成,希望大家下载以后,能够帮助大家解决实际的问题。
文档下载后可定制随意修改,请根据实际需要进行相应的调整和使用,谢谢!并且,本店铺为大家提供各种各样类型的实用资料,如教育随笔、日记赏析、句子摘抄、古诗大全、经典美文、话题作文、工作总结、词语解析、文案摘录、其他资料等等,如想了解不同资料格式和写法,敬请关注!Download tips: This document is carefully compiled by theeditor. I hope that after you download them,they can help yousolve practical problems. The document can be customized andmodified after downloading,please adjust and use it according toactual needs, thank you!In addition, our shop provides you with various types ofpractical materials,such as educational essays, diaryappreciation,sentence excerpts,ancient poems,classic articles,topic composition,work summary,word parsing,copy excerpts,other materials and so on,want to know different data formats andwriting methods,please pay attention!PCB 板电操作流程是将 PCB 板通过电镀的方式,在板子表面镀上一层金属,以提高板子的导电性和耐腐蚀性。
pcb板加工流程

pcb板加工流程
PCB板的加工流程大致包括以下步骤:
1. 开料:将原材料裁剪成适当的大小。
2. 前处理:清洁PCB基板表面,去除表面污染物,以保证后续工序的质量。
3. 压膜:将干膜贴在PCB基板表层,为后续的图像转移做准备。
4. 曝光:使用曝光设备利用紫外光对覆膜基板进行曝光,从而将基板的图像转移至干膜上。
5. DES:将进行曝光以后的基板经过显影、蚀刻、去膜,进而完成内层板的制作。
6. 层压:让铜箔、半固化片与棕化处理后的内层线路板压合成多层板。
7. 钻孔:按照客户要求利用钻孔机将板子钻出直径不同,大小不一的孔洞,使板子之间通孔以便后续加工插件,也可以帮助板子散热。
8. 孔金属化:让孔璧上的非导体部分金属化,能够让后面的电镀制程更加方便。
9. 外层干膜:通过图形转移技术在干膜上曝出所需的线路。
10. 外层线路:目的是让铜厚度镀至客户所需求的厚度,完成客户需要的线
路外形。
11. 丝印:外层线路的保护层,用来保证PCB的绝缘、护板、防焊。
12. 后工序:按客户的要求完成加工,并且进行测试,保证最后的品质审核。
这个流程为多层PCB的完整制作工艺流程,仅供参考。
如需更准确的信息,可以查阅相关的专业PCB书籍或者咨询专业人士。
PCB前处理制程介绍
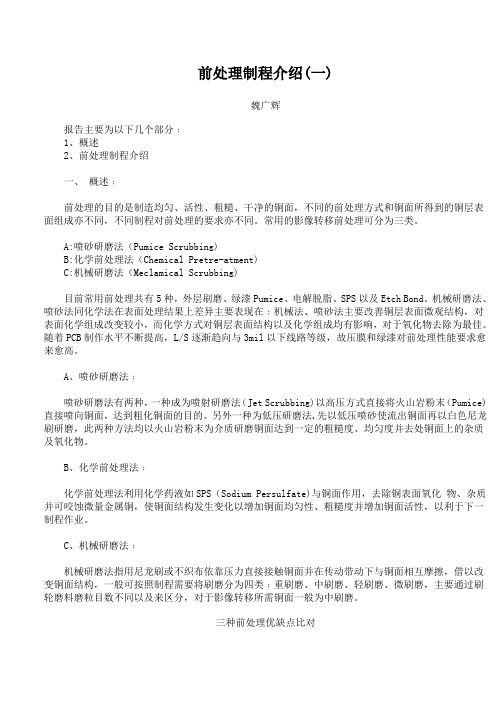
前处理制程介绍(一)魏广辉报告主要为以下几个部分﹕1、概述2、前处理制程介绍一、概述﹕前处理的目的是制造均匀、活性、粗糙、干净的铜面,不同的前处理方式和铜面所得到的铜层表面组成亦不同,不同制程对前处理的要求亦不同。
常用的影像转移前处理可分为三类。
A:喷砂研磨法(Pumice Scrubbing)B:化学前处理法(Chemical Pretre-atment)C:机械研磨法(Meclamical Scrubbing)目前常用前处理共有5种,外层刷磨、绿漆Pumice、电解脱脂、SPS以及Etch Bond。
机械研磨法、喷砂法同化学法在表面处理结果上差异主要表现在﹕机械法、喷砂法主要改善铜层表面微观结构,对表面化学组成改变较小,而化学方式对铜层表面结构以及化学组成均有影响,对于氧化物去除为最佳。
随着PCB制作水平不断提高,L/S逐渐趋向与3mil以下线路等级,故压膜和绿漆对前处理性能要求愈来愈高。
A、喷砂研磨法﹕喷砂研磨法有两种,一种成为喷射研磨法(Jet Scrubbing)以高压方式直接将火山岩粉末(Pumice)直接喷向铜面,达到粗化铜面的目的。
另外一种为低压研磨法,先以低压喷砂使流出铜面再以白色尼龙刷研磨,此两种方法均以火山岩粉末为介质研磨铜面达到一定的粗糙度、均匀度并去处铜面上的杂质及氧化物。
B、化学前处理法﹕化学前处理法利用化学药液如SPS(Sodium Persulfate)与铜面作用,去除铜表面氧化物、杂质并可咬蚀微量金属铜,使铜面结构发生变化以增加铜面均匀性、粗糙度并增加铜面活性,以利于下一制程作业。
C、机械研磨法﹕机械研磨法指用尼龙刷或不织布依靠压力直接接触铜面并在传动带动下与铜面相互摩擦,借以改变铜面结构,一般可按照制程需要将刷磨分为四类﹕重刷磨、中刷磨、轻刷磨、微刷磨,主要通过刷轮磨料磨粒目数不同以及来区分,对于影像转移所需铜面一般为中刷磨。
三种前处理优缺点比对《未完待续》前处理制程介绍(二)魏广辉二、前处理制程介绍﹕电解脱脂线﹕电解脱脂原理说明﹕利用电解原理,产生大量氧气,摩擦铜表面,以机械物理力量清洁表面,产生的氧气使液体翻滚,使新碱液与油脂污垢之接触增加,使油脂皂化、乳化以此达到清洁表面的目的,另外去除表面的铬钝化物以及增加板面粗糙度以便增加压膜制程附着力。
PCB制作工艺流程简介
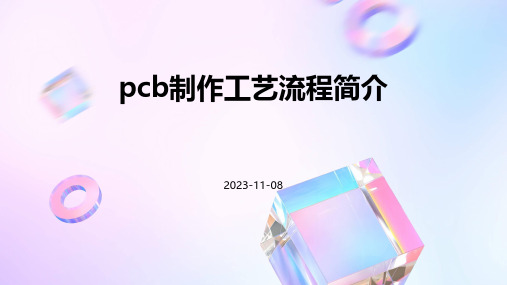
2023-11-08•pcb制作概述•pcb设计•pcb制作的前期准备•pcb制作过程•pcb制作完成后的处理目•pcb制作中的注意事项及常见问题•pcb制作的发展趋势及未来展望录01 pcb制作概述pcb基本概念Printed Circuit BoardPCB是印刷电路板,是一种用于将电子器件连接在一起的基板,通常由绝缘材料制成。
电路板组成PCB通常由导电层、绝缘层和支撑层组成,其中导电层用于传输电信号,绝缘层用于隔离导电层,支撑层则用于支撑整个电路板。
设计电路图制作裸板光绘与刻板将铜箔粘贴在绝缘材料上,形成导电层。
使用光绘机将电路图绘制在铜箔上,形成电路图形。
03pcb制作流程简介02 01根据产品需求,使用EDA设计软件绘制电路图。
通过蚀刻工艺将不需要的铜箔去除,形成所需的电路图形。
蚀刻与去膜在电路导线上沉积一层锡/金,以提高导电性能和耐腐蚀性。
沉锡/金在电路板上涂抹阻焊剂,以防止焊接时短路。
印阻焊剂对电路板进行成型和钻孔加工,以满足实际应用需求。
成型与钻孔pcb制作流程简介实现电子设备的小型化和高效化PCB是实现电子设备内部器件连接的关键部件,其制作质量直接影响到电子设备的性能和可靠性。
pcb制作的重要性保障电子设备的稳定性和安全性PCB的制作质量直接关系到电子设备的稳定性和安全性,因为一旦出现短路或信号干扰等问题,就可能导致设备故障或损坏。
提升电子设备的品质和降低成本优秀的PCB制作工艺可以提高电子设备的品质和性能,同时降低制作成本和时间成本,提高市场竞争力。
02 pcb设计03优化板型结构PCB设计应优化板型结构,提高电路板的机械强度、电气性能和散热性能。
pcb设计基本原则01确保电路功能正常PCB设计应确保电路的功能正常,满足原始电路设计的要求。
02减少信号干扰为了减少信号干扰,PCB设计应尽量选择低噪声的器件,同时避免器件之间的相互干扰。
pcb设计流程PCB检查与优化对设计好的PCB进行检查,确保没有错误和不合理的地方,并进行优化改进。
PCB制作工艺流程

PCB制作工艺流程一、开料目的:以制造流程单之规格,将大面积的敷铜泊基板依制前设计所规化的工作尺寸裁切尺寸及厚度发料并裁板。
1、裁板作业流程:仓库→裁板室→调整尺寸→裁板→检查测量2、磨边作业流程:设置长、宽→磨边→水洗一→水洗二→水洗三→挤干→吹干→烘干二、内层1、内层前处理目的:将除去板面氧化物及油污,再加磨刷粗化铜面增加感光材料于铜面的附著力。
作业流程:上板→化学清洗(H2SO4:3%~5%,压力:1.5±0.5㎏/C㎡)→溢流水洗(压力:1.5±0.5㎏/C㎡)→磨刷→中压水洗(压力:3.0±0.5㎏/C㎡)→微蚀刻(SPS:100~120g/1, H2SO4:1%~3%,压力:1.5±0.5㎏/C㎡)→溢流水洗(压力:1.5±0.5㎏/C㎡)→酸洗(H2SO4:1%~3%)→溢流水洗(压力:1.5±0.5㎏/C㎡)→烘干→检查注意事项:1、做板之前要做刷痕实验、水纹实验,刷痕宽度:1.0±0.2㎝,水纹:15秒以上;2、内层板厚分为两种:47mil的为普通基板,其他为特殊基板,特殊基板要做标记,还要测板厚;3、检查压力表;2、涂布目的:以抗蚀性材料附著力在铜面上,制作内层线路GND、VCC作业流程:进料→粘尘→下降→入料→涂布→烘烤(第一阶段:145℃;第二阶段:125℃;第三阶段:115℃;第四阶段:55℃;第五阶段:35℃) →出料→检查注意实项:1、粘尘纸200片后换一次;2、油墨刮刀压力调整(压力:1.0~3.0㎏/C㎡);3、检测膜厚(8.0±1.5mil),检查脏点等3、曝光(半自动曝光)目的:曝光灯发出紫外光投射在已贴有干膜的板面上,将曝光菲林上线路图形转移到感光干膜上,未吸紫外光的干膜显影时会溶解于显影液中作业流程:检查底片→架底片→调整对准度→放板→吸真空→曝光→检查注意事项:1、每天清洁机台,做能量测试;2、室内温度:22.0±2℃,湿度:55±5%;3、黑色底片每曝光2000次后报废,每曝光500次后底片检查;4、每曝光前用手动滚轮清洁一次底片,底片每曝光10片清洁一次,每50片上机检查一次;5、底片L2朝上,L3朝下;6、灯管亮到熄灭:12秒;7、抽真空度至少600~700MMHG;8、抽真空后用刮刀赶气;9、放板时,把底片翻开看到压条后,沿着压条放板,避免刮伤底片4、显影目的:显影是把尚未发生聚合反应的区域用显影液将之冲洗掉,已感光部分则因已发生聚合反应而洗不掉乃留在铜面上成为蚀刻之阻剂膜5、蚀刻目的:以蚀刻液将铜表面去除,留有抗蚀油墨之线路,制作内层线路GND、VCC 6、去墨剥膜目的:将线路上之抗蚀材料去掉,露出铜线路完成制作内层线路ND、VCC(4,5,6)工作流程:显影(温度:31.0±2℃;浓度:碳酸钠:1.0±0.2wt%,传送速度:4.0±0.5m/min;压力:1.75±0.25㎏/C㎡)→水洗(压力:1.5±0.3㎏/C㎡)→蚀刻(温度:40~45℃;传动速度:4.0±0.5m/min;喷压:上压3.0±0.5㎏/C㎡,下压2.8±0.5㎏/C㎡;铜含量:105~115g/l) →水洗(压力:1.5±0.3㎏/C㎡)→检查→软化去墨(温度:45~50℃;传动速度:4.5±0.5m/min;浓度:NaOH1.0~0.2%;去墨第一段0.1~0.2㎏/C㎡;去墨第二段0.5~0.2㎏/C㎡;去墨第三段1.5~0.2㎏/C㎡)→水洗→酸洗(温度:RT;压力:1.5±0.3㎏/C㎡,H2SO4浓度:1~3%)→水洗→烘干(温度:90.0±10℃)→检查→收板注意事项:1、每天退槽一次;2、有线路的板含有线路的板面朝上,没有线路的板不作要求;3、每天用报废板做显影、蚀刻实验,检查参数是否合格;4、检查压力表;5、每班换水一次;6、滤网每天清洗一次;7、检查喷嘴7、黑化处理工作流程:上料→碱性清洁(16″)→水洗(6″)→水洗(11″)→微蚀(8″)→水洗(1″)→水洗(5″)→预侵(6″)→黑化(15″)→热纯水洗(8″)→水洗(5″)→水洗(16″)→后侵(16″)→纯水洗(3″)→纯水洗(8″)→热纯水洗(16″)→滴干→烘干(35″)注意事项:1、开机前须检查各槽液位是否正常;2、插板时须一片一片的插;3、黑化好的板做首件、自主检查时需垂直向上取板且手指不能拿入单元内;4、黑化OK板预叠前所停放的时间不能超过一小时;5、生产的合格黑化板必须在24小时之内压合完毕,否则超过时间需要新烘烤或重工;6、卸板时需两手平行从飞靶上取出,轻放板上,防止动作不规范造成板面刮伤;7、检查黑化颜色均匀不均匀、漏不漏铜、刮伤、有没有烘干;8、HTG170以上只能在白班做;9、检查压力表;10、参数:微蚀35±2℃,室温32.8℃,黑化75±5℃,热水洗50±3℃,后侵28±5℃,热纯水洗50±3℃,烘干一:120±10℃,烘干二:120±10℃,烘干三:120±10℃,共用35分,清洁:50分8、棕化处理(TG150℃以上的不做棕化)作业流程:上料→酸洗(温度:30±5℃,浓度: 5±2%H2SO4,压力:上压1.5±0.2㎏/C㎡,下压1.5±0.2㎏/C㎡)→水洗(压力:上压1.0±0.2㎏/C㎡,下压1.0±0.2㎏/C㎡)→清洁(温度:50±2℃,压力:上压1.5~2.5㎏/C㎡,下压1.5~2.5㎏/C㎡,碱度:0.96±0.1N)→纯水洗(压力:上压1.0±0.2㎏/C㎡,下压1.0±0.2㎏/C㎡)→预侵(温度:30±3℃,强度:70~100%,酸度:0.06~0.12N,速度:3.6±0.2m/min)→棕化(温度:38~45℃,酸度:1.8~2.3N,CB2218A强度:90~120%,CB2218B强度:150±30%,H2O2:11.5±2g/l,CU2+<50g/l,微蚀量:40~80u″,速度:3.6±0.2m/min)→纯水洗(压力:上压1.0±0.2㎏/C㎡,下压1.0±0.2㎏/C㎡)→干燥1(温度:90±5℃)→干燥2(温度:90±5℃)→收板→检查注意事项:1、每天须做首件,检查各个参数是否合格;2、生产的合格棕化板必须在小时之内压合完毕;3、做完后,检查颜色均匀度、是否漏铜、是否刮伤;4、检查压力表;9、压合①、PP裁切工作流程:安装PP→调整刀具(上下间隙为0.08mm)→开机→长度设定(控制单位inch换mm,裁板尺寸依OP单规定)→速度设定→张数设定→加工作业(在更换裁切不同的TG材料前必须把机台上的粉尘清理干净后方可裁切)→手动部分→收料注意事项:1、温度:22±5℃,湿度:50±10℃;2、PP的经向、纬向一定要根据OP来裁切:3、裁切OK的PP可以静至一个月,超过时间不能用;4、裁切好的TG180℃PP用红色大字报表示,TG140℃的PP用白色大字报表示,TG150℃的PP用黄色大字报表示;5、裁好HTG的PP不能超过6小时;6、裁切首片,测量尺寸是否与OP单要求的尺寸相符;②、预叠(温度:20~18℃,湿度:55±5%)⑴、熔合(六层板或六层板以上)工作流程:开机(检查三点组合)→机台调整(检查定位pin位置是否于板的对位孔相重合)→参数设定→加工作业→关机⑵、铆合(六层板或六层板以上)工作流程:开机→机台调整→调整铆钉→加工作业→关机注意事项:1、预叠前,先看板是否有刮伤、颜色是否均匀等,方可叠合;2、熔合、铆合必须做首件,检查是否合格;3、熔合、铆合要求L2、L5朝外,L3、L4向里;4、隔2小时测量一次铆钉高度,铆钉高度的范围:1.27±0.2mm;5、熔合的温度不做限制,但是就好在340~360℃,时间:加光板的是30~33秒,其他的是22秒③、叠合(温度:22±2℃,湿度:60±5℃)工作流程:准备工作(铜箔、无尘纸、粘尘布、钢板)→清洁机台→检查铜箔→选择排版数→参数设定→叠板注意事项:1、读取工单叠合图所用铜箔规格、产商等,检查机台铜箔是否一致,否则更换;2、根据生产胺尺寸计算在钢板上的排版面积,排版所在钢板上的利用率尽可最大,在排版台上调整红外线固定排版位置或方向;3、根据SOP规定,生产板层数设定排版层数,排版总高度必须高于防滑块高度;4、把板放在红外线固定位置上,叠板时不能在叠台上齐板或抖动PP,叠板动作要轻快;5、六层板要求11叠,四层板12叠④、压合作业流程:开机→设立压合参数→上机→热压→冷压→下机注意事项:1、热板温度测试:180℃恒温10分钟状态,每个热盘取9点,使用感温探针直接测试;2、每6个月测试一次热板,正常热板温差为3.0℃±1.5℃;3、热盘平行度测试:①取直径3.0mm铅条,各热盘放置5根铅条并注意避开盘面滚珠依左右平均放置;②放置后以100psi压力压合10分钟;③取该热盘每一点值与该热盘所有点的平均值对比其差异值小于±0.03mm,否则进行维修,每年测试一次;4、热压真空度:700mmHg以上,热盘温度及压力:依附件之温度及压力设定;5、冷压系统压力设定:100~125㎏/C㎡(板面压力为85~105psi),时间:50min,冷压的降温速率为5℃/min下,冷压后板面的实际温度设定为53℃以下压合程式一览表:阶段T(℃)(±5℃)t(min)(±0.1min)P(psi)(±3psi)t(psi)(±0.1min)1 150 13 100 132 150 12 300 123 195 25 400 254 195 65 400 655 185 5 300 56 180 3 150 37 170 2 50 2 Total 125 125阶段T(℃)(±5℃)t(min)(±0.1min)P(psi)(±3psi)t(psi)(±0.1min)1 150 13 100 152 150 12 300 133 195 25 400 274 195 65 400 605 185 5 300 56 180 3 150 37 170 2 50 2Total 125 125压合程式执行完毕;②超出5分钟外来电时,将压合板取出,把表面PP及铜箔撕掉,再做一次黑化制程,后续正常作业(注:1、黑化制程不能做微蚀处理;2、只能适用于无阻抗控制板子)压合扳子取出→PP及铜箔撕掉→黑化→后续正常作业2、在压合程式第二阶段时停电停机因此时PP的树脂开始融化流动,有大量气泡存在不能重工3、在压合程式第三阶段(高压段)时停电停机①在压合程式第三阶段(高压段上压1~50分钟)时停电停机,因此时PP的树脂开始融化流程,有大量气泡存在不能重工②在压合程式第三阶段(高压段上压50分钟以上)时停电停机,此时树脂已固化,保证足够固化时间即可来电后接着该压合程式执行,下压后须测TG值、热冲击爆实验、介质厚度测试,判定是否合格10、裁切→捞边→铣靶→钻靶→磨边①磨边作业流程:开机→送板→磨边(根据不同板厚调整刀具的位置每次更换刀具后应做一次对应位置检测,进给量每边磨掉0.5mm左右即可)→洗板(传输速度:5.5±0.5m/min,水洗压力:第一段1.0±0.5㎏/C㎡,第二段1.5±0.5㎏/C㎡,第三段1.0±0.5㎏/C㎡)→烘干→收板11、钻孔多层板作业流程:钻孔工具准备→程式输入→裁定位PIN→上料→钻孔作业→下机台检验→刷磨去毛头双面板作业流程:磨板边→上PIN→钻孔工具准备→程式输入→上料→钻孔作业→下PIN→下机台检验→刷磨去毛头注意事项:1、核对OP,所取钻头是否合乎OP上之尺寸;2、检查钻头条件:进刀速、转速、孔限数设定,这些参数根据钻针大小、材质来设定的;3、打PIN (PIN直径:0.123″,深度12.5mm);4、铝垫板必须能涵盖所有的孔,以免断针;5、孔径15.7mil以下(﹤1.5mil),钻孔片数双面板2片,4-10层板2片;孔径15.7mil以上(≧15.7mil),钻孔片数双面板3片,4-6层板3片,8-10层板2片;6、钻孔前要空跑孔数,确认无误;7、胶带距离板边小于0.8cm;8、冰水机温度:19±2℃;9、喷锡板使用手推磨机600﹟,化金板、化银板、OSP 板、金手指板使用800﹟~1000﹟;10、检查备针是否备错,测量大小;11、钻孔、刷磨完后,用X-RAY孔位检查机检查是否钻偏;12、温度:22~25℃,湿度:45~50%;13、检查铝片上的压痕,确认压力角是否水平重工流程:检查并输入钻孔程式→上料→找孔→下料→检查①因停电、停气、断针等造成的漏孔、孔未钻透的板子检查后按照重工流程重工②因用错针造成孔小的板须重工12、去胶渣与化学铜目的:钻孔中造成高温产生胶渣黏于内层铜箔上,此胶渣会造成内层OPEN,所以要去胶渣工作流程:上板→酸洗(压力:1.0±0.2㎏/C㎡,H2SO4:3~5%)→水洗(压力:1.7±0.3㎏/C㎡)→刷磨(刷痕:1.0±0.2cm,电流:2.8±0.5A)→水洗(压力:1.7±0.3㎏/C㎡)→高压水洗(38±2㎏/C㎡)→超音波水洗(温度:40±5℃,电流:2.5±0.2A)→水洗(压力:1.7±0.3㎏/C㎡)→烘干(温度:75±5℃)→收板注:传动速度:3.5±0.5m/min;刷磨完成后的板子,须于12小时内完成一铜电镀作业13、一铜线工作流程:上架(抽样方式检视板子是否有严重凹陷及刮伤)→膨胀剂(Normal FR-4 材料:温度67~73℃,强度:10~16%;HTG材料:温度72~80℃,强度:13~16%,NaOH浓度:0.75~1.1N)→高锰酸钾(Normal FR-4 材料:温度72~78℃;HTG材料:温度76~80℃,NaOH浓度:1.0~1.4N,KmnO4浓度:45~65g/L,Mn6+:须保持在25g/L以下)→预中和(H2SO4浓度:2~4%,H2O2浓度:1.0~2%)→中和(温度:42~46℃)→碱性清洁(温度:47~51℃,碱当量:0.012~0.018N)→微蚀(温度:25~30℃,H2O2浓度:2~5%,SPS浓度:40~70g/L,CU﹥25g/L更槽)→预侵(温度:28~32℃,比重:1.100~1.1600,CU:少于1500PPM)→活化(温度:42~46℃,强度:70~100%,氯化亚钾﹥3g/L,比重:1.140~1.1820,CU:少于2000PPM,铁:少于100PPM)→化学铜(温度:30~36℃,CU2+:1.7~2.3g/L,NaOH:9.0~13g/L,甲醛浓度:3~5g/L,EDTA浓度:25~30g/L)→酸侵(H2O2浓度:100~120ml/L)→镀铜(温度:20~30℃,电流密度:14±2ASF,CuSO4.5H2O浓度:60~80g/L,H2SO4浓度:100~120ml/L,HCL浓度:40~80PPM,EP1100B-2:0.7~3.0ml/L,EP1100C-2:2.8~17ml/L)→烘烤(温度控制:95±5℃,速度:4.5±0.5m/min)→下架注意事项:1、每班分析膨胀剂后在添加,每周更换滤芯,每生产84万平方尺换槽;2、高锰酸钾槽,电流控制在1500±50A,不生产时控制在1000±50A,每生产100万平方尺后换槽;3、中和槽每生产15万平方尺后换槽;4、碱性清洁槽每生产6.7万平方尺后换槽;5、预侵槽每生产30万平方尺换槽;6、活化槽每日槽液浓度分析后添加,滤芯2周换一次,每一年换槽一次或CU﹥2000PPM换槽;7、化学铜槽每天依分析后添加,控制在14 ~26 ,每天二次试验控制在8-10级;8、镀铜槽:阳极铜块每星期检视、添加一次一年更换一次,每周做一次Hull Cell试验,每周分析一次槽液,每次分析后添加。
PCB详细工艺流程介绍

PCB详细工艺流程介绍1.开料(CUT)开料是把原始的覆铜板切割成能在生产线上制作的板子的过程首先我们来了解几个概念:(1)UNIT:UNIT是指PCB设计工程师设计的单元图形。
(2)SET:SET是指工程师为了提高生产效率、方便生产等原因,将多个UNIT拼在一起成为的一个整体的图形。
也就是我们常说的拼板,它包括单元图形、工艺边等等。
(3)PANEL:PANEL是指PCB厂家生产时,为了提高效率、方便生产等原因,将多个SET拼在一起并加上工具板边,组成的一块板子。
2.内层干膜(INNER DRY FILM)内层干膜是将内层线路图形转移到PCB板上的过程。
在PCB制作中我们会提到图形转移这个概念,因为导电图形的制作是PCB制作的根本。
所以图形转移过程对PCB制作来说,有非常重要的意义。
内层干膜包括内层贴膜、曝光显影、内层蚀刻等多道工序。
内层贴膜就是在铜板表面贴上一层特殊的感光膜,就是我们所说的干膜。
这种膜遇光会固化,在板子上形成一道保护膜。
曝光显影是将贴好膜的板进行曝光,透光的部分被固化,没透光的部分还是干膜。
然后经过显影,褪掉没固化的干膜,将贴有固化保护膜的板进行蚀刻。
再经过退膜处理,这时内层的线路图形就被转移到板子上了。
其整个工艺流程如下图。
对于设计人员来说,我们最主要考虑的是布线的最小线宽、间距的控制及布线的均匀性。
因为间距过小会造成夹膜,膜无法褪尽造成短路。
线宽太小,膜的附着力不足,造成线路开路。
所以电路设计时的安全间距(包括线与线、线与焊盘、焊盘与焊盘、线与铜面等),都必须考虑生产时的安全间距。
(1)前处理:磨板磨板的主要作用:基本前处理主要是解决表面清洁度和表面粗糙度的问题。
去除氧化,增。
PCB内层线路前处理PFMEA分析范例
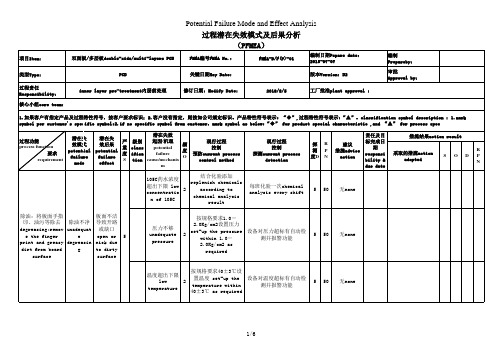
项目Item:FMEA-D/F(P)-01编制Prepareby:类型Type:审批Approval by:过程责任Responsibility:2019/8/5采取的措施actionadoptedS O DR P N105C药水浓度超出下限 lowconcentration of 105C2结合化验添加replenish chemicalsaccording tochemical analysisresult每班化验一次chemical analysis every shift550无none压力不够unadequate pressure2按规格要求1.0-2.0Kg/cm2设置压力set-up the pressure within 1.0-2.0Kg/cm2 as required设备对压力超标有自动检测并报警功能550无none温度超出下限low temperature2按规格要求40±3℃设置温度 set-up the temperature within 40±3℃ as required设备对温度超标有自动检测并报警功能550无none探测度D R P N 建议措施advice action责任及目标完成日期responsi bility &due date潜在失效起因/机理potential failure cause/mechanism严重度S 5频度O 现行过程控制预防current process control method 级别classification 潜在失效后果potential failureeffect板面不洁导致开路或缺口open or nick due to dirty surface潜在失效模式potentialfailuremode除油不净unadequat edegreasin g核心小组core team:1.如果客户有指定产品及过程特性符号,按客户要求标识;2.客户没有指定,则按如公司规定标识。
PCB外层前工序简介

3)、镀液稳定,便于维护,对杂质 的容忍度高
全板电镀的溶液成分
1)、硫酸铜CuSO4 2)、硫酸 3)、氯离子 4)、添加剂
原理
镀铜液的主要成分是CuSO4和H2SO4,直接
电压作用下,在阴阳极发生如下反应:
-
+
+
Cu
镀液
PCB
由于化学镀铜液中的甲醛对生态环境 有害,络合剂不易生物降解,废水处理困 难,同时目前化学镀铜层的机械性能不上 电镀铜层,而且化学镀铜工艺流程长,操 作维护极不方便,故此直接电镀技术应运 而生。
直接电镀工艺不十分成熟,尽管种类较 多,大都用于双面板制程。
流程:
(一)、敏化剂5110(Sensitizer 5110) (二)、微蚀(Micro etch) 徐喜明 (三)、整孔剂(Conditioner) (四)、预浸剂(Pre dip) (五)、活化剂(Activotor) (六)、加速剂 (Accelerator)
钻孔生产 绿胶片检孔
钻带发放
基本物料:
铝片
管位钉 底板 皱纹胶纸 钻咀
新钻咀
钻孔
够Hits数
翻磨
清洗后标记
钻机的工作原理:
钻机由CNC电脑系统控制机台移动,按所 输入电脑的资料制作出客户所需孔的位置。
控制方面分别有X、Y辆坐标及Z轴坐标, 电脑控制机台适当的钻孔参数,F、N、Hits、 D等,机器会自动按照资料,把所需的孔位置 钻出来。
作用:
在机械磨刷的状态下,去除板材表 面的氧化层及钻孔毛刺。
(2)除胶渣:
膨胀剂 水洗 除胶渣 水洗 中和 水洗
作用:
除胶渣属于孔壁凹蚀处理(Etch back ),印制板在钻孔时产生瞬时高温,而 环氧玻璃基材(主要是FR-4)为不良导 体,在钻孔时热量高度积累,孔壁表面 温度超过环氧树脂玻璃化温度,结果造 成环氧树脂沿孔壁表面流动,产生一层 薄的胶渣(Epoxy Smear),如果不除去 该胶渣,将会使多层板内层信号线联接 不通,或联接不可靠。
PCB处理知识简介

PCB处理知识简介前言PCB板铜面的表面处理,对于装配商的封装制程来讲,是极为重要的一环,目前,在PCB的制造厂家,有以下几种常见的处理方式:1、喷锡,也叫热风整平(HASL)2、化学镍金(electroless Ni /Au )3、化学沉锡(tmmersion tin )4、有机保焊膜(OSP)二、各表面处理制程特性比较:三、各处理制程简介A:喷锡制程1、设备:其前、后处理常用的水平线比较简单,喷锡机多为垂直式;2、工艺:前处理的作用是露出新鲜的铜面,且粗化铜面,常用流程为:微蚀——水洗——酸洗——水洗——吹干——涂覆助焊剂。
3、喷锡:焊料成份为63./37的喷锡,加工温度为235~245℃,由于是将板浸没在焊料中,再用热风刀将表面多余的锡铅吹掉,一般而言,前风刀在上,后风刀在下,因而后板后较前板后较厚,在BGA或SM下,chip焊盘等处,Sm/Pb厚度不一,产生龟背现象。
4、后处理:目的是将碳化的助焊剂或锡粉等洗掉,常用流程为:软毛磨刷——水洗——热水洗——水洗——风干——烘干;B、化学Ni/Au制程1、设备:在化学Ni/Au前,需将PCB板磨板,去除表面的脏物,此设备为水平线,而化Ni/Au设备则为垂直线,吊车由程序控制,实现自动生产。
2、化学Ni/Au工艺较为复杂,其流程为:酸性除油—水洗—微蚀—水洗—酸洗—水洗—预浸—活化—水洗—后浸—化Ni—水洗—化Au—水洗—抗氧化—水洗;3、简单原理:活化液中的Pd2+离子与铜发生转置换,而吸附在铜表面,在化Ni时,Ni2+与Pb发生置反应,Ni沉积Cn表面,然后,依靠Ni缸溶液的自身氧化还原反应,而沉积上一定厚度的Ni层,一般常用的Ni后厚度为2.5—5.0um,沉Ni完后,在金缸中,Au2+与Ni发生置换反应,从而沉积上一次厚度的Au,一般采用的沉薄金工艺中,Au层厚度为0.08—0.13um。
C、化学制板1、设备:因化学Ni/Au一样,垂直式设备,吊车由程序控制,实现自动生产。
电路板三防处理工艺流程

电路板三防处理工艺流程
电路板三防处理工艺流程:
①清洁预处理:使用专用清洗剂彻底清洁PCB板,去除助焊剂残留、污垢和微尘,不能使用酒精。
②干燥处理:清洗后,PCB板需放入烤箱进行烘烤干燥,确保表面无湿气。
③保护遮蔽:对不需要涂覆三防漆的区域,如电位器、插座、开关等进行贴保护膜或遮盖。
④溶剂稀释:根据三防漆的特性,必要时使用溶剂进行稀释,调整至适合涂覆的粘度。
⑤选择涂覆方法:根据PCB的设计和复杂程度,选择浸涂、刷涂、喷涂或选择性涂覆的方式。
⑥浸涂/刷涂/喷涂:将稀释好的三防漆均匀地涂覆在PCB板上,确保覆盖所有需要保护的区域。
⑦初步固化:涂覆完成后,让PCB板静置,使三防漆初步固化,避免流动或滴落。
⑧彻底固化:将初步固化的PCB板置于设定温度下进行彻底固化,确保三防漆形成牢固的保护层。
⑨检查修补:检查三防漆的涂覆情况,如有未覆盖或涂覆不均的地方,进行修补。
⑩去除保护:移除之前贴上的保护膜或遮盖物,恢复电路板的正常使用状态。
⑪最终检验:对完成三防处理的PCB板进行质量检验,确保符合规定的防护标准。
⑫包装存储:将检验合格的PCB板进行防静电包装,存放在适宜的环境中,以备后续装配使用。
PCB前处理介绍
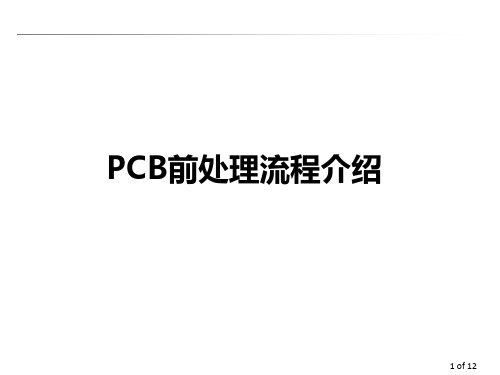
4. 常用的药水种类
硫酸----H2SO4
一.浓度:50% 二.危 害: 1.吸入有毒;
2.皮肤接触会引起严重灼伤; 3.刺激呼吸系统. 三.防范措施:1.置于阴凉且通风良
好处,紧盖容器; 2.佩带护目镜,口罩,
防护衣,手套; 3.勿与碱混合.
用于脱脂:H2SO4脱去油脂,及 氧化物.
H2O2/H2SO4 Etch 硫酸+双氧水
CZ8100- Etch
超粗化
说明 一般铜面经过药水微蚀后,铜面的粗糙度由大至小为: 超粗化>硫酸双氧水>酸洗
7 of 12
5. 表面处理后铜面状况
8 不足
槽液名称
计算公式
调整方式说明
化验分析浓度m2如高于 管制界限则依照左列计算 公式将槽液降低至体积 V1后再加药液至200L
特性: 1. 干燥状态下亦维持柔软性及弹 性 2. 气孔径达 25 μm 3. 耐药性强, 抗强酸及强碱 ( 10%) 4. 耐热性达 130℃
适用: 1. LCD基板, PCB基板, 导 线架, 光罩...等的洗拭及吸水
适用: 1.PCB基板, 导线架...等的吸水
特性 : 1. 发泡之PE改质而成的连续气孔构造 2. 不干硬 3. 特耐强酸及强碱 ( 30% )
2 of 12
1. 何谓前处理
1.去除板面氧化及污物,使铜面产生粗糙度便于干膜、绿漆附着 2.前处理最重要就是微蚀,其主要的功能为a.板面清洁b.铜面粗化
线路前处理简易流程
防焊前处理简易流程
H202+H2SO4系列 超粗化系列
防焊前处理四大重点药水槽
3 of 12
2. 各制程目的
放板:主要将生产的产品放置到设备上 脱脂:主要取出铜面的油脂 微蚀:主要加深铜表面的粗导读,以利于后续压膜制程的膜更好的与铜 面结合 水洗:主要将微蚀段产生的化学物质(例如硫酸铜)移除 烘干:主要讲铜面的水分移除
pcb电路板塞孔和铲平工艺流程
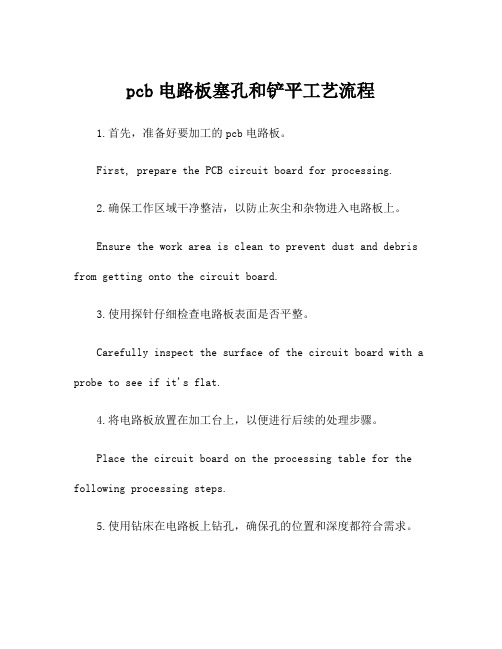
pcb电路板塞孔和铲平工艺流程1.首先,准备好要加工的pcb电路板。
First, prepare the PCB circuit board for processing.2.确保工作区域干净整洁,以防止灰尘和杂物进入电路板上。
Ensure the work area is clean to prevent dust and debris from getting onto the circuit board.3.使用探针仔细检查电路板表面是否平整。
Carefully inspect the surface of the circuit board with a probe to see if it's flat.4.将电路板放置在加工台上,以便进行后续的处理步骤。
Place the circuit board on the processing table for the following processing steps.5.使用钻床在电路板上钻孔,确保孔的位置和深度都符合需求。
Use a drilling machine to drill holes on the circuit board, ensuring the position and depth of the holes meet the requirements.6.定位好待加工的孔位,进行下一步的铲平工艺处理。
Position the holes to be processed and proceed to the next step of flat shovel processing.7.使用加工机器进行铲平处理,确保处理的均匀和平整。
Use processing machinery for flat shovel processing to ensure uniform and flat processing.8.仔细检查每个塞孔和铲平的位置,确保达到加工要求。
pcb镀金工艺流程
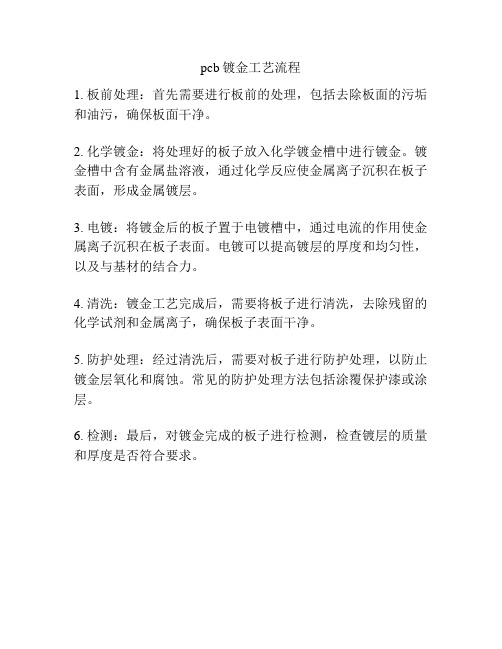
pcb镀金工艺流程
1. 板前处理:首先需要进行板前的处理,包括去除板面的污垢和油污,确保板面干净。
2. 化学镀金:将处理好的板子放入化学镀金槽中进行镀金。
镀金槽中含有金属盐溶液,通过化学反应使金属离子沉积在板子表面,形成金属镀层。
3. 电镀:将镀金后的板子置于电镀槽中,通过电流的作用使金属离子沉积在板子表面。
电镀可以提高镀层的厚度和均匀性,以及与基材的结合力。
4. 清洗:镀金工艺完成后,需要将板子进行清洗,去除残留的化学试剂和金属离子,确保板子表面干净。
5. 防护处理:经过清洗后,需要对板子进行防护处理,以防止镀金层氧化和腐蚀。
常见的防护处理方法包括涂覆保护漆或涂层。
6. 检测:最后,对镀金完成的板子进行检测,检查镀层的质量和厚度是否符合要求。
PCB制造前处理节水方案的研究
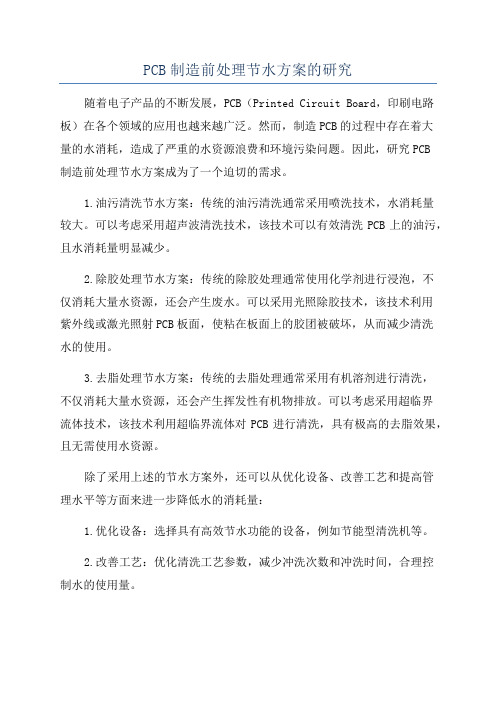
PCB制造前处理节水方案的研究随着电子产品的不断发展,PCB(Printed Circuit Board,印刷电路板)在各个领域的应用也越来越广泛。
然而,制造PCB的过程中存在着大量的水消耗,造成了严重的水资源浪费和环境污染问题。
因此,研究PCB制造前处理节水方案成为了一个迫切的需求。
1.油污清洗节水方案:传统的油污清洗通常采用喷洗技术,水消耗量较大。
可以考虑采用超声波清洗技术,该技术可以有效清洗PCB上的油污,且水消耗量明显减少。
2.除胶处理节水方案:传统的除胶处理通常使用化学剂进行浸泡,不仅消耗大量水资源,还会产生废水。
可以采用光照除胶技术,该技术利用紫外线或激光照射PCB板面,使粘在板面上的胶团被破坏,从而减少清洗水的使用。
3.去脂处理节水方案:传统的去脂处理通常采用有机溶剂进行清洗,不仅消耗大量水资源,还会产生挥发性有机物排放。
可以考虑采用超临界流体技术,该技术利用超临界流体对PCB进行清洗,具有极高的去脂效果,且无需使用水资源。
除了采用上述的节水方案外,还可以从优化设备、改善工艺和提高管理水平等方面来进一步降低水的消耗量:1.优化设备:选择具有高效节水功能的设备,例如节能型清洗机等。
2.改善工艺:优化清洗工艺参数,减少冲洗次数和冲洗时间,合理控制水的使用量。
3.提高管理水平:加强员工培训,提高对水资源的节约意识,建立科学的水资源利用考核制度。
此外,还可以通过回收利用水资源来进一步降低水的消耗量。
例如,采用循环利用水系统,将清洗水进行分级过滤处理,然后再回收利用于清洗工艺中,从而实现水的多次利用。
综上所述,PCB制造前处理的节水方案研究是一个重要的课题。
通过采用超声波清洗技术、光照除胶技术、超临界流体技术等节水方案,优化设备、改善工艺、提高管理水平以及回收利用水资源,可以有效降低水的消耗量,减少水资源浪费和环境污染,实现可持续发展的目标。
pcb抗镀前处理工艺流程
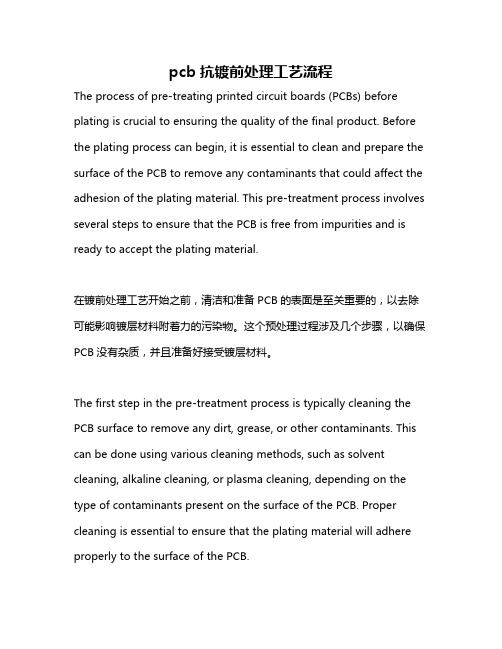
pcb抗镀前处理工艺流程The process of pre-treating printed circuit boards (PCBs) before plating is crucial to ensuring the quality of the final product. Before the plating process can begin, it is essential to clean and prepare the surface of the PCB to remove any contaminants that could affect the adhesion of the plating material. This pre-treatment process involves several steps to ensure that the PCB is free from impurities and is ready to accept the plating material.在镀前处理工艺开始之前,清洁和准备PCB的表面是至关重要的,以去除可能影响镀层材料附着力的污染物。
这个预处理过程涉及几个步骤,以确保PCB没有杂质,并且准备好接受镀层材料。
The first step in the pre-treatment process is typically cleaning the PCB surface to remove any dirt, grease, or other contaminants. This can be done using various cleaning methods, such as solvent cleaning, alkaline cleaning, or plasma cleaning, depending on the type of contaminants present on the surface of the PCB. Proper cleaning is essential to ensure that the plating material will adhere properly to the surface of the PCB.预处理过程的第一步通常是清洁PCB表面,以去除任何污垢、油脂或其他污染物。
- 1、下载文档前请自行甄别文档内容的完整性,平台不提供额外的编辑、内容补充、找答案等附加服务。
- 2、"仅部分预览"的文档,不可在线预览部分如存在完整性等问题,可反馈申请退款(可完整预览的文档不适用该条件!)。
- 3、如文档侵犯您的权益,请联系客服反馈,我们会尽快为您处理(人工客服工作时间:9:00-18:30)。
C. 操作溫度:室溫(RT) 。
外層前處理線教育訓練教材
5. 化學蝕洗機 A.外型尺寸:長730mm,寬1205mm,高1100mm(不含管路) 。
B.機體結構:材質PVC,厚度10mm。
C.操作溫度:室溫(RT) 。 D.桶槽容量:最大容量80公升,工作容量70公升。 6. 循環水洗機(TWR-113) A.外型尺寸:長1130mm,寬1205mm,高1100mm(不含管路)。 B.機體結構:PVC材質,厚度10mm。 C.工作長度:循環水洗300mm*3槽。 D.桶槽容量:25L 24L 23L 溢流
D. 桶槽容量:放流水洗 9. 中壓複合水洗段 A. 外型尺寸:長1630mm、寬1205mm、高1100mm。 B. 工作長度:循環水洗300mm*4槽,放流水洗200mm。 80公升 溢流。
C. 機體結構:PVC材質。 E. 桶槽容量:放流水洗 22公升 溢流。
25公升
24公升
23公升
外層前處理線教育訓練教材
2. 外層前處理線總長度12060mm,工作高度1000mm,寬度 2286mm。
外層前處理線教育訓練教材
3. 加熱化學蝕洗機 A. 外型尺寸:長2030mm、寬1510mm、高1100mm(不含管路)。
B. 機體結構:PVC材質。
C. 操作溫度:35±5℃, MAX: 45℃。 D. 桶槽容量:最大容量475公升,工作容量440公升。 4. 循環水洗機(TWR-053) A. 外型尺寸:長530mm、寬1205mm、高1100mm(不含管路) 。
10.滾輪吸乾機 A. 外型尺寸:長430mm、寬1030mm、高1100mm。
B. 機體結構:PVC材質。 C. 操作溫度:最高容許溫度45℃。 D. 吸水滾輪 a. SUS303軸心,外套42inchPVA吸水海綿及PVC免滴水滾輪。
b. 數量: 上3支,下3支。 11. 冷風吹乾機
A.外型尺寸:長630mm,寬1030mm,高1100mm。
B. PUMP:水槽:1HP*1台,銅粉回收機:2HP*1台。
C. 機體結構:SUS304。
D. 操作溫度:室溫。
E. 水槽容量:清水槽最大容量187公升,廢水槽最大容量167公升。
外層前處理線教育訓練教材 四、前處理藥液管理規範
1. 加熱化學蝕洗(微蝕刻)
1.1 藥液濃度
SPS濃度:140 ±30g/L。 H2SO4 :4 ±1%。 Cu2+ :≦30g/L。 1.2 藥液添加方式
外層前處理線教育訓練教材 五、測試項目及方法
1. 刷痕測試 1). 將24*20inch與生產東等厚之測試東置中後,開傳動送入刷 磨機至1,2刷輪下,距東子後緣前約 5cm處東子停止。 2). 確認刷磨機水洗開啟,刷磨機後水洗,烘乾段開啟。 3). 當東子置於刷輪下時停止傳動。 4). 此時開啟刷輪,刷磨約3~5sec停止刷輪。 5). 開傳動送入刷磨機至3,4刷輪下,距東子前緣後約5cm處 東子停止,重複4)之動作。 6). 取出東子後以尺量刷痕寬度,並確認刷痕寬度是否介於 0.8~1.2cm。 7). 若刷痕寬度過大或過小需調整刷輪間距,並重新作測試直 到符合規格為止。 8). 若刷痕測試有狗骨頭現象則需作整刷動作。
放東 序列 微蝕 酸洗 水洗 刷磨
中壓循環水洗 冷風吹乾
履帶式緩衝機
中壓復合水洗 熱風烘乾
收東
冷風吹乾
可掀式皮帶輸送機
外層前處理線教育訓練教材
二.外層前處理工作原理
前處理工作原理:去除東面氧化以及雜質,提高東面粗糙度, 增加乾膜附著力。 微蝕原理:去除東面氧化,利用SPS+H2SO4系統與 銅面起反應,增加東面粗糙度。
外層前處理線教育訓練教材
10) 開啟正常作業狀況清洗循環清洗30分鐘。 11) 排放廢水,清洗完成開始配槽。 12) 配槽完成後即可開機正常生產。 B.水洗機洗槽步驟 1) 先用自來水將槽體沖洗乾淨。 2) 加入自來水至2/3桶槽高,之後再配製1%濃度的NaOH,接著 再加入自來水至高液位。 3) 開啟電源讓機台以正常作業狀況循環清洗2小時。 4) 排放廢液,並且加入自來水至高液位,循環清洗30分鐘。 5) 排放廢液,並且加入自來水至2/3桶槽高度,之後再小心配 製1%濃度的H2SO4,接著再加入自來水至高液位。 6) 循環清洗2小時。
B.機體結構:HPVC材質厚度10mm C.最高容許操作溫度:55℃。 D.吸水滾輪:PVA吸水海綿滾輪。
外層前處理線教育訓練教材
12. 熱風烘乾機 A. 外型尺寸:長1230mm、寬1200mm、高1100mm。 B. 機體結構:SUS304材質。
C. 操作溫度:80℃。 D. 高壓風車:馬力3.4kw*1台。 E. 熱風風車:馬力0.75kw*1台。
外層前處理線教育訓練教材
外層前處理教材
制 定 者: 楊 杰 編訂日期: 2003.11.22
外層前處理線教育訓練教材 目 錄
一、前處理流程介紹 二、前處理工作原理
三、標準操作規範
四、前處理藥液管理規範 五、測試項目及方法 六、前處理保養與維護 七、銅粉回收機使用與保養 八、開機關機步驟及注意事項
外層前處理線教育訓練教材 一.外層前處理流程簡介
外層前處理線教育訓練教材 七、銅粉回收機使用與保養
1. 矽藻土添加方法 1). 切換閥調至 位置。
2). 打開流量調整閥。(需分兩次進行添加先加左室,把左室 流量調整閥打開,右室流量調整閥關閉。完成後,再進行右 室添加) 3). 選擇開關轉至手動位置。 4). 循環PUMP動作,助劑水槽水位下降,添加自來水至運轉 場合。 5). 助劑水槽添加過濾助劑(矽藻土)1~1.5kg(10~15L) 2000ml量杯5~7回(新濾袋及清洗後濾袋)2000ml量杯2~4回 (為銅粉取出後之濾袋使用)。 6). 添加過濾助劑至水貲呈乳白色,經過循環PUMP運轉 5~10min濾過水質澄清後即停止運轉。 .
F.刷輪負載安培表:數字顯示型,數量:4組(調刷輔助用)。
G.擺動系統: 50Hz擺動幅度:8mm,擺動頻率143次/min, 馬達數量:4台。
外層前處理線教育訓練教材
8. 中壓循環水洗段
A. 外型尺寸:長530mm、寬1205mm、高1100mm。 B. 工作長度:循環水洗300mm*1槽。
C. 機體結構:PVC材質。
13. 微蝕液攪拌添加機 A.外型尺寸:長2050mm,寬1650mm,高1400mm(不含管路) B.機體結構:PVC材質,厚度10mm。
C.最高容許操作溫度:45℃。
E.換槽泵浦:馬力:0.75KW*1台。
外層前處理線教育訓練教材
14 銅粉回收機 A. 工作原理:刷磨水洗水(銅粉與水的混合物)由四刷刷磨機 進入銅粉回收機水槽,經銅粉回收機過濾袋過濾後,過濾水 供四刷刷磨機使用以節約用水。
外層前處理線教育訓練教材
7. 四刷刷磨機 A.外型尺寸:長1400mm,寬1200mm,高1150mm。 B.刷輪規格:外徑:Φ6”,內徑Φ3”,長度24”,數量:上2支,
下2支。
C.刷輪馬達:馬力:2.25KW,數量:4台。 D.刷輪轉速:50Hz電源頻率:轉速:1430RPM,切線速度: 11.21M/sec。 E.調刷裝置:數量:4組,記憶表:0.15mm/轉(使用前歸零)。
外層前處理線教育訓練教材
7) 排放廢液,並且加入自來水至高液位。 8) 循環清洗1小時。 9) 排放廢水,再加自來水至高液位。 10) 開啟正常作業狀況清洗循環清洗30分鐘。
11) 排放廢水,清洗完成加水至高液位。
外層前處理線教育訓練教材
2 整刷(單面整刷東)
2.1 開四刷刷磨機將刷輪復歸,檢視刷輪電流為0,以避免整 刷東進入時卡東。 2.2 將整刷東整刷面朝上放入機台中,不開化學蝕洗槽,開啟複 水洗及四刷刷磨水壓PUMP。 2.3 開傳動將整刷東送入四刷刷磨機於上刷第一支刷輪處整刷區域 正對刷輪處停止傳動。 2.4 開刷磨,擺動並調整調壓裝置至電流值顯示為1,待電流值將為0時 停止。 2.5 開傳動將整刷東刷磨區對準上刷第二支刷輪後停止。 2.6 重複2.4之操作。 2.7 開啟水洗槽水壓PUMP,開傳動將整刷東排出。 2.8 將整刷面朝下重複以上動作作下刷輪整刷動作。 2.9 完成後依據刷痕測試作量測,若還有狗骨頭現象再整刷一次。
外層前處理線教育訓練教材
2. 濾過運轉方法 1). 濾過水質澄清後停止運轉,將原水切換閥調整標示。 2). 選擇開關轉至自動位置,液位感應呈自動控制。 3). 運轉開始後,壓力升高濾過量少時,流量調整閥打開(正常在 0.2kg/cm2)。 4). 濾過室銅粉多,壓力上升會造成濾過水量下降。 5). 壓力在1.8 kg/cm2 濾過水量,研磨排水量多,會使原水槽水位 上升紅燈亮時,將銅粉取出。 3. 銅粉取出濾袋清除 1). 循環PUMP停止,流量調整閥關閉。 2). 氣壓閥打開,將過濾室的水吹乾(約5~10min)。 3). 將氣壓閥關閉。 3 6 4). 將M27固定螺絲鬆開 依示意作業,過濾式門打開。
(a). 加水至液位300L處。 (b). 以量杯取約38L濃度50%硫酸緩慢倒入槽中,並加入65kg SPS。 (c). 加水至液位上限,開機攪拌10min可作業。 5). SPS添加量計算方法 (a). 更槽後新配槽 所需SPS量為:微蝕槽總體積*SPS標準濃度
外層前處理線教育訓練教材
(b). 濃度偏低時添加 所需SPS量為:微蝕槽總體積*SPS標準濃度 - SPS體積* SPS量測濃度 其中,體積單位為:升(L),SPS濃度單位為:克/升(g/L), 質量單位為:克(g)。 1.3 藥水濃度異常時依化驗室分析作調整添加。 2.化學蝕洗(酸洗) 2.1 H2SO4 濃度:4 ±1%。 2.2 藥液管理: 2.2.1 硫酸每班更槽。 2.2.2 硫酸濃度每班化驗,不合格調整濃度後復測。 2.2.3 硫酸添加量:=硫酸濃度*酸洗槽體積。