船舶薄板焊接防变形技术
论船舶薄板焊接的变形问题及控制方法
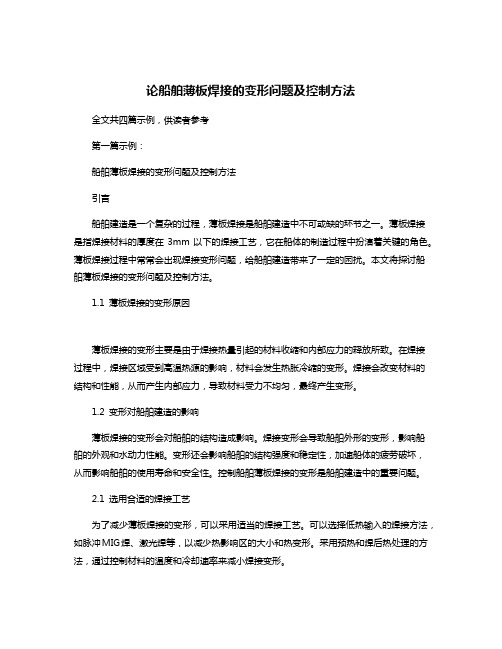
论船舶薄板焊接的变形问题及控制方法全文共四篇示例,供读者参考第一篇示例:船舶薄板焊接的变形问题及控制方法引言船舶建造是一个复杂的过程,薄板焊接是船舶建造中不可或缺的环节之一。
薄板焊接是指焊接材料的厚度在3mm以下的焊接工艺,它在船体的制造过程中扮演着关键的角色。
薄板焊接过程中常常会出现焊接变形问题,给船舶建造带来了一定的困扰。
本文将探讨船舶薄板焊接的变形问题及控制方法。
1.1 薄板焊接的变形原因薄板焊接的变形主要是由于焊接热量引起的材料收缩和内部应力的释放所致。
在焊接过程中,焊接区域受到高温热源的影响,材料会发生热胀冷缩的变形。
焊接会改变材料的结构和性能,从而产生内部应力,导致材料受力不均匀,最终产生变形。
1.2 变形对船舶建造的影响薄板焊接的变形会对船舶的结构造成影响。
焊接变形会导致船舶外形的变形,影响船舶的外观和水动力性能。
变形还会影响船舶的结构强度和稳定性,加速船体的疲劳破坏,从而影响船舶的使用寿命和安全性。
控制船舶薄板焊接的变形是船舶建造中的重要问题。
2.1 选用合适的焊接工艺为了减少薄板焊接的变形,可以采用适当的焊接工艺。
可以选择低热输入的焊接方法,如脉冲MIG焊、激光焊等,以减少热影响区的大小和热变形。
采用预热和焊后热处理的方法,通过控制材料的温度和冷却速率来减小焊接变形。
2.2 采用预制配合和辅助支撑装置对于大型船舶薄板的焊接,可以采用预制配合和辅助支撑装置的方法来控制焊接变形。
预制配合是在焊接前就进行材料的加工和拼焊,通过预先控制材料的形状和尺寸,来减小焊接变形。
在焊接过程中,可以使用辅助支撑装置来支撑和固定焊接区域,从而减小焊接变形的影响。
2.3 采用适当的尺寸设计和工艺控制2.4 对变形进行补偿和调整在薄板焊接后,可以对焊接变形进行补偿和调整。
这主要包括局部加热、局部拉伸和修正焊接接头等方法,来恢复材料原本的形状和尺寸,减小焊接变形的影响。
结论船舶薄板焊接的变形问题是船舶建造中的重要问题,对船舶的外观、水动力性能、结构强度和稳定性等都会产生影响。
论船舶薄板焊接的变形问题及控制方法
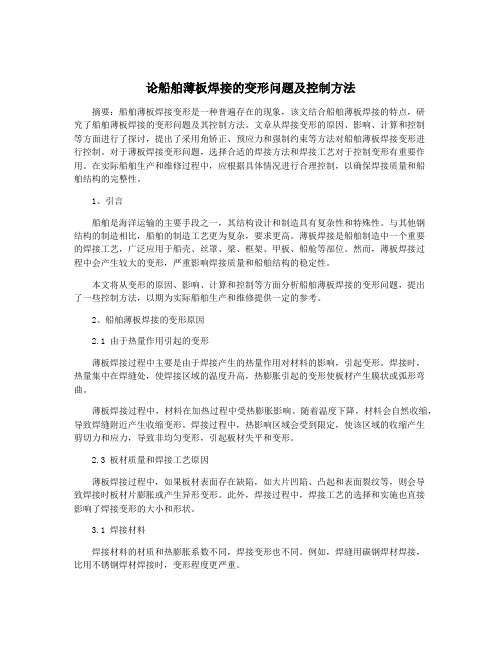
论船舶薄板焊接的变形问题及控制方法摘要:船舶薄板焊接变形是一种普遍存在的现象,该文结合船舶薄板焊接的特点,研究了船舶薄板焊接的变形问题及其控制方法。
文章从焊接变形的原因、影响、计算和控制等方面进行了探讨,提出了采用角矫正、预应力和强制约束等方法对船舶薄板焊接变形进行控制。
对于薄板焊接变形问题,选择合适的焊接方法和焊接工艺对于控制变形有重要作用。
在实际船舶生产和维修过程中,应根据具体情况进行合理控制,以确保焊接质量和船舶结构的完整性。
1、引言船舶是海洋运输的主要手段之一,其结构设计和制造具有复杂性和特殊性。
与其他钢结构的制造相比,船舶的制造工艺更为复杂,要求更高。
薄板焊接是船舶制造中一个重要的焊接工艺,广泛应用于船壳、丝罩、梁、框架、甲板、船舱等部位。
然而,薄板焊接过程中会产生较大的变形,严重影响焊接质量和船舶结构的稳定性。
本文将从变形的原因、影响、计算和控制等方面分析船舶薄板焊接的变形问题,提出了一些控制方法,以期为实际船舶生产和维修提供一定的参考。
2、船舶薄板焊接的变形原因2.1 由于热量作用引起的变形薄板焊接过程中主要是由于焊接产生的热量作用对材料的影响,引起变形。
焊接时,热量集中在焊缝处,使焊接区域的温度升高,热膨胀引起的变形使板材产生膜状或弧形弯曲。
薄板焊接过程中,材料在加热过程中受热膨胀影响。
随着温度下降,材料会自然收缩,导致焊缝附近产生收缩变形。
焊接过程中,热影响区域会受到限定,使该区域的收缩产生剪切力和应力,导致非均匀变形,引起板材失平和变形。
2.3 板材质量和焊接工艺原因薄板焊接过程中,如果板材表面存在缺陷,如大片凹陷、凸起和表面裂纹等,则会导致焊接时板材片膨胀或产生异形变形。
此外,焊接过程中,焊接工艺的选择和实施也直接影响了焊接变形的大小和形状。
3.1 焊接材料焊接材料的材质和热膨胀系数不同,焊接变形也不同。
例如,焊缝用碳钢焊材焊接,比用不锈钢焊材焊接时,变形程度更严重。
不同的焊接方式和工艺对焊接变形有很大影响。
论船舶薄板焊接的变形问题及控制方法
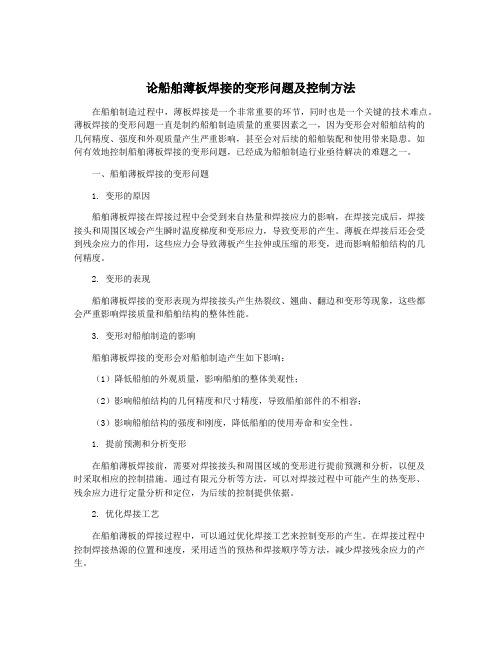
论船舶薄板焊接的变形问题及控制方法在船舶制造过程中,薄板焊接是一个非常重要的环节,同时也是一个关键的技术难点。
薄板焊接的变形问题一直是制约船舶制造质量的重要因素之一,因为变形会对船舶结构的几何精度、强度和外观质量产生严重影响,甚至会对后续的船舶装配和使用带来隐患。
如何有效地控制船舶薄板焊接的变形问题,已经成为船舶制造行业亟待解决的难题之一。
一、船舶薄板焊接的变形问题1. 变形的原因船舶薄板焊接在焊接过程中会受到来自热量和焊接应力的影响,在焊接完成后,焊接接头和周围区域会产生瞬时温度梯度和变形应力,导致变形的产生。
薄板在焊接后还会受到残余应力的作用,这些应力会导致薄板产生拉伸或压缩的形变,进而影响船舶结构的几何精度。
2. 变形的表现船舶薄板焊接的变形表现为焊接接头产生热裂纹、翘曲、翻边和变形等现象,这些都会严重影响焊接质量和船舶结构的整体性能。
3. 变形对船舶制造的影响船舶薄板焊接的变形会对船舶制造产生如下影响:(1)降低船舶的外观质量,影响船舶的整体美观性;(2)影响船舶结构的几何精度和尺寸精度,导致船舶部件的不相容;(3)影响船舶结构的强度和刚度,降低船舶的使用寿命和安全性。
1. 提前预测和分析变形在船舶薄板焊接前,需要对焊接接头和周围区域的变形进行提前预测和分析,以便及时采取相应的控制措施。
通过有限元分析等方法,可以对焊接过程中可能产生的热变形、残余应力进行定量分析和定位,为后续的控制提供依据。
2. 优化焊接工艺在船舶薄板的焊接过程中,可以通过优化焊接工艺来控制变形的产生。
在焊接过程中控制焊接热源的位置和速度,采用适当的预热和焊接顺序等方法,减少焊接残余应力的产生。
3. 使用辅助固定和支撑设备在船舶薄板焊接过程中,可以使用辅助固定和支撑设备,以减少焊接接头和周围区域的变形。
可以采用焊接变形补偿装置、支撑架和外部夹具等设备,来防止焊接过程中的翘曲和变形现象。
4. 采用预变形和后处理在船舶薄板焊接后,可以通过采用预变形和后处理等方法来控制残余应力和减少变形。
论船舶薄板焊接的变形问题及控制方法
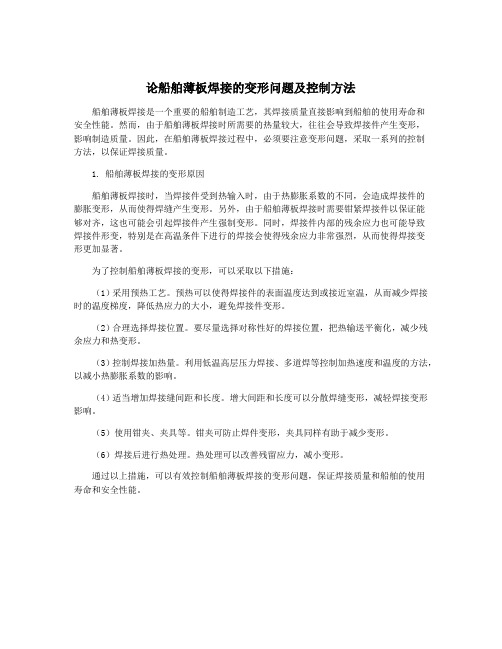
论船舶薄板焊接的变形问题及控制方法船舶薄板焊接是一个重要的船舶制造工艺,其焊接质量直接影响到船舶的使用寿命和安全性能。
然而,由于船舶薄板焊接时所需要的热量较大,往往会导致焊接件产生变形,影响制造质量。
因此,在船舶薄板焊接过程中,必须要注意变形问题,采取一系列的控制方法,以保证焊接质量。
1. 船舶薄板焊接的变形原因船舶薄板焊接时,当焊接件受到热输入时,由于热膨胀系数的不同,会造成焊接件的膨胀变形,从而使得焊缝产生变形。
另外,由于船舶薄板焊接时需要钳紧焊接件以保证能够对齐,这也可能会引起焊接件产生强制变形。
同时,焊接件内部的残余应力也可能导致焊接件形变,特别是在高温条件下进行的焊接会使得残余应力非常强烈,从而使得焊接变形更加显著。
为了控制船舶薄板焊接的变形,可以采取以下措施:(1)采用预热工艺。
预热可以使得焊接件的表面温度达到或接近室温,从而减少焊接时的温度梯度,降低热应力的大小,避免焊接件变形。
(2)合理选择焊接位置。
要尽量选择对称性好的焊接位置,把热输送平衡化,减少残余应力和热变形。
(3)控制焊接加热量。
利用低温高层压力焊接、多道焊等控制加热速度和温度的方法,以减小热膨胀系数的影响。
(4)适当增加焊接缝间距和长度。
增大间距和长度可以分散焊缝变形,减轻焊接变形影响。
(5)使用钳夹、夹具等。
钳夹可防止焊件变形,夹具同样有助于减少变形。
(6)焊接后进行热处理。
热处理可以改善残留应力,减小变形。
通过以上措施,可以有效控制船舶薄板焊接的变形问题,保证焊接质量和船舶的使用寿命和安全性能。
论船舶薄板焊接的变形问题及控制方法
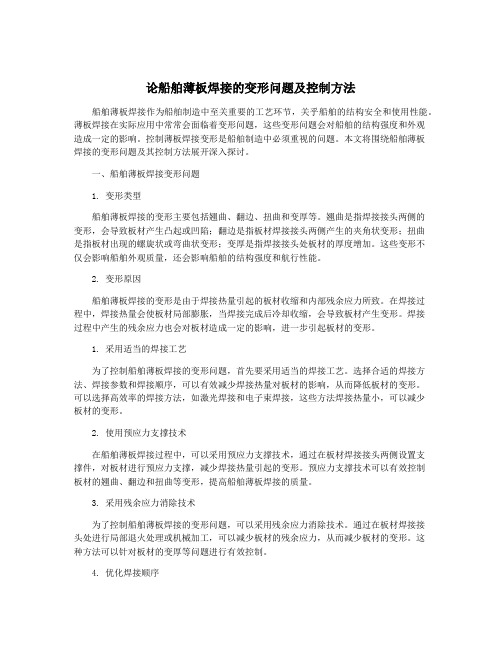
论船舶薄板焊接的变形问题及控制方法船舶薄板焊接作为船舶制造中至关重要的工艺环节,关乎船舶的结构安全和使用性能。
薄板焊接在实际应用中常常会面临着变形问题,这些变形问题会对船舶的结构强度和外观造成一定的影响。
控制薄板焊接变形是船舶制造中必须重视的问题。
本文将围绕船舶薄板焊接的变形问题及其控制方法展开深入探讨。
一、船舶薄板焊接变形问题1. 变形类型船舶薄板焊接的变形主要包括翘曲、翻边、扭曲和变厚等。
翘曲是指焊接接头两侧的变形,会导致板材产生凸起或凹陷;翻边是指板材焊接接头两侧产生的夹角状变形;扭曲是指板材出现的螺旋状或弯曲状变形;变厚是指焊接接头处板材的厚度增加。
这些变形不仅会影响船舶外观质量,还会影响船舶的结构强度和航行性能。
2. 变形原因船舶薄板焊接的变形是由于焊接热量引起的板材收缩和内部残余应力所致。
在焊接过程中,焊接热量会使板材局部膨胀,当焊接完成后冷却收缩,会导致板材产生变形。
焊接过程中产生的残余应力也会对板材造成一定的影响,进一步引起板材的变形。
1. 采用适当的焊接工艺为了控制船舶薄板焊接的变形问题,首先要采用适当的焊接工艺。
选择合适的焊接方法、焊接参数和焊接顺序,可以有效减少焊接热量对板材的影响,从而降低板材的变形。
可以选择高效率的焊接方法,如激光焊接和电子束焊接,这些方法焊接热量小,可以减少板材的变形。
2. 使用预应力支撑技术在船舶薄板焊接过程中,可以采用预应力支撑技术,通过在板材焊接接头两侧设置支撑件,对板材进行预应力支撑,减少焊接热量引起的变形。
预应力支撑技术可以有效控制板材的翘曲、翻边和扭曲等变形,提高船舶薄板焊接的质量。
3. 采用残余应力消除技术为了控制船舶薄板焊接的变形问题,可以采用残余应力消除技术。
通过在板材焊接接头处进行局部退火处理或机械加工,可以减少板材的残余应力,从而减少板材的变形。
这种方法可以针对板材的变厚等问题进行有效控制。
4. 优化焊接顺序在船舶薄板焊接过程中,要合理选择焊接顺序,优化焊接顺序可以减少板材的变形。
论船舶薄板焊接的变形问题及控制方法

论船舶薄板焊接的变形问题及控制方法船舶薄板焊接是船舶制造中非常重要的工艺之一,它主要用于船体结构的拼接和加强,因此焊接质量和变形控制是非常关键的问题。
在船舶薄板焊接过程中,会产生各种变形问题,如焊接变形、热变形和残余应力等,这些问题会对船舶结构的是否安全和合格产生重要影响。
控制船舶薄板焊接的变形问题是至关重要的,本文将从变形问题的原因出发,探讨船舶薄板焊接的变形问题及其控制方法。
一、船舶薄板焊接变形问题的原因1. 焊接过程中的热变形船舶薄板焊接过程中,焊缝区域受到高温作用,会引起局部的膨胀膨胀和收缩,从而导致热变形。
热变形是船舶薄板焊接中最主要的变形方式,尤其是对于较大尺寸的焊接组件来说,热变形会对结构产生重要的影响。
2. 焊接残余应力在船舶薄板焊接完成后,焊接区域残留有残余应力,这些残余应力会对船舶结构产生重要的影响。
焊接残余应力的大小和分布会直接影响船舶的结构安全和船舶的使用寿命。
3. 材料变形船舶薄板焊接时,焊接区域的材料会受到各种变形的影响,如拉伸变形、弯曲变形等,这些材料变形也会对船舶的结构产生重要的影响。
二、船舶薄板焊接变形问题的控制方法1. 焊接工艺的优化在船舶薄板焊接过程中,可以通过优化焊接工艺来控制焊接变形。
在焊接参数选择时,可以选择合适的焊接电流、电压和焊接速度,来减小焊接区域的热影响区和热输入,从而减小焊接变形。
2. 预应力控制通过预应力控制来减小船舶薄板焊接的残余应力,预应力控制主要有拉伸预应力和压缩预应力两种方式。
通过预应力控制,可以有效减小船舶薄板焊接的残余应力和变形。
4. 改善材料的变形性能在船舶薄板焊接中,可以通过改善焊接材料的变形性能来减小焊接变形。
可以选择具有较好变形性能的船舶焊接材料,从而减小船舶薄板焊接的变形。
5. 使用变形补偿装置在船舶薄板焊接中,可以使用变形补偿装置来减小焊接变形。
可以采用板材夹具、气垫和拉伸装置等来减小船舶薄板焊接的变形。
船舶薄板焊接变形问题的控制是一个非常复杂的工程问题,需要综合考虑焊接工艺、预应力控制、温度控制、材料变形性能和变形补偿装置等多种因素。
论船舶薄板焊接的变形问题及控制方法

论船舶薄板焊接的变形问题及控制方法船舶薄板焊接是船舶建造中不可或缺的工艺,其焊接质量及变形控制对船舶的安全性和性能影响极大。
但由于薄板焊接过程中受到的热应力和冷却收缩等因素的影响,容易导致薄板变形,影响船体的几何精度和结构牢固性。
本文将探讨船舶薄板焊接的变形问题及控制方法。
一、船舶薄板焊接的变形原因(一)热应力引起的变形焊接过程中,局部区域受到高温作用,由于板材的热膨胀系数大于熔池的热膨胀系数,使板材受到了横向的压力,导致局部变形。
焊接完毕后,横向压力消失,板材受到冷却收缩的作用,引起纵向收缩等变形。
焊接过程中,为了保持板材的平整度,在焊接区域周围设有支撑架或底板等,但在完成焊接后,这些辅助支撑并不会完全消失,板材自身重力作用下,容易发生塌陷、变形等现象。
(三)板材接口的变形在船舶薄板焊接中,通常采用间隙填充的方式,即在板材连接面上留下一定间隙,用焊丝或焊条填充连接。
但是填充过程中很难保证板材的对齐度,所以在填充后会对板材的形状和尺寸产生影响,容易导致板材的变形。
(一)控制焊接温度采用合适的焊接参数和焊接序列,低温高速度的焊接方式有助于减小局部高温区域的影响,降低热应力和变形程度。
另外,还可以采用预热的方式在焊接前加热板材,降低焊接应力和变形程度。
(二)采用合适的支撑结构在焊接过程中采用合适的支撑结构能够有效地控制板材的塌陷和变形。
在支撑结构的设计中应充分考虑板材的自重和焊接后的收缩变形,尽可能减小对板材的影响,保持板材的平整度。
(三)调整间隙尺寸在焊接前测量板材间隙的大小,对间隙进行适当调整,可以减小填充时对板材造成的影响,保证填充后板材的几何尺寸和形状。
(四)采用机器人焊接机器人焊接具有高精度、高速度、高可靠性的优点,可通过程序和工艺参数的优化来控制薄板的变形程度。
(五)使用补偿焊接补偿焊接是一种通过反向补焊来抵消轻微变形的方法。
采用补偿焊接有助于让板材恢复其原有的形态和尺寸,保证焊接连接及时得到补偿和修正。
论船舶薄板焊接的变形问题及控制方法

论船舶薄板焊接的变形问题及控制方法1. 引言1.1 背景介绍船舶薄板焊接是造船行业中常见的焊接工艺之一,通过焊接各种薄板材料来构建船体结构。
在焊接过程中,常常会出现焊接变形问题,这对船舶的质量和性能都会产生负面影响。
研究如何控制船舶薄板焊接的变形问题成为当前的研究热点之一。
焊接变形是指在焊接过程中,由于热量集中引起的材料膨胀和收缩而产生的变形现象。
船舶薄板在焊接过程中,由于受到热影响区的热膨胀和残余应力的影响,容易出现各种形式的变形,比如翘曲、扭曲等。
这不仅会影响船体的外观美观,还可能影响船舶的结构强度和航行性能。
研究船舶薄板焊接的变形问题,分析变形的原因,寻求有效的控制方法是当前研究的重点。
只有通过深入探讨和实验验证,找到有效的变形控制方法,才能确保船舶的质量和性能,提高船舶的竞争力和市场占有率。
部分完毕。
1.2 研究目的船舶薄板焊接作为船舶制造过程中不可或缺的环节,其变形问题一直是制约船舶建造质量的关键因素之一。
本文旨在深入探讨船舶薄板焊接的变形问题及其控制方法,为船舶制造行业提供更有效的解决方案。
研究目的主要包括以下几个方面:了解船舶薄板焊接变形问题的实际情况及现状,分析目前存在的主要问题和挑战;探讨船舶薄板焊接变形的原因,通过对相关机理和影响因素的分析,寻找出实质性的解决途径;总结和归纳当前变形控制方法的优缺点,提出改进与完善的建议;结合实际案例和结构优化设计的理论,探讨船舶薄板焊接变形问题的最佳解决方案,为相关行业提供参考和借鉴。
通过本文的研究,旨在为船舶薄板焊接变形问题的解决提供更全面、科学和实用的方法,推动船舶制造技术的不断进步和提高。
2. 正文2.1 船舶薄板焊接变形问题船舶薄板焊接是船舶制造中常见的一种工艺,但在焊接过程中往往会产生较大的变形问题。
这些变形问题主要表现为板材弯曲、翘曲、扭曲等,严重影响了船舶整体结构的精度和质量。
造成船舶薄板焊接变形问题的主要原因包括焊接引起的热应力、板材受热和冷却不均匀导致的内部应力、焊接顺序和方式不当引起的应力集中等。
论船舶薄板焊接的变形问题及控制方法
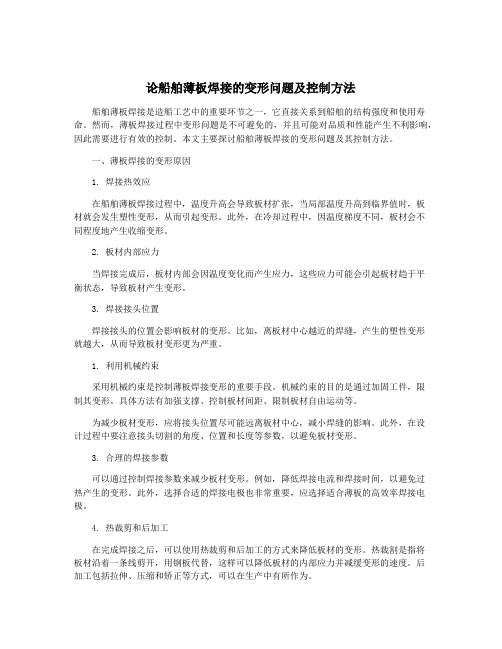
论船舶薄板焊接的变形问题及控制方法船舶薄板焊接是造船工艺中的重要环节之一,它直接关系到船舶的结构强度和使用寿命。
然而,薄板焊接过程中变形问题是不可避免的,并且可能对品质和性能产生不利影响,因此需要进行有效的控制。
本文主要探讨船舶薄板焊接的变形问题及其控制方法。
一、薄板焊接的变形原因1. 焊接热效应在船舶薄板焊接过程中,温度升高会导致板材扩张,当局部温度升高到临界值时,板材就会发生塑性变形,从而引起变形。
此外,在冷却过程中,因温度梯度不同,板材会不同程度地产生收缩变形。
2. 板材内部应力当焊接完成后,板材内部会因温度变化而产生应力,这些应力可能会引起板材趋于平衡状态,导致板材产生变形。
3. 焊接接头位置焊接接头的位置会影响板材的变形。
比如,离板材中心越近的焊缝,产生的塑性变形就越大,从而导致板材变形更为严重。
1. 利用机械约束采用机械约束是控制薄板焊接变形的重要手段。
机械约束的目的是通过加固工件,限制其变形。
具体方法有加强支撑、控制板材间距、限制板材自由运动等。
为减少板材变形,应将接头位置尽可能远离板材中心,减小焊缝的影响。
此外,在设计过程中要注意接头切割的角度、位置和长度等参数,以避免板材变形。
3. 合理的焊接参数可以通过控制焊接参数来减少板材变形。
例如,降低焊接电流和焊接时间,以避免过热产生的变形。
此外,选择合适的焊接电极也非常重要,应选择适合薄板的高效率焊接电极。
4. 热裁剪和后加工在完成焊接之后,可以使用热裁剪和后加工的方式来降低板材的变形。
热裁割是指将板材沿着一条线剪开,用钢板代替,这样可以降低板材的内部应力并减缓变形的速度。
后加工包括拉伸、压缩和矫正等方式,可以在生产中有所作为。
总之,船舶薄板焊接的变形控制是一个复杂的问题,需要综合考虑许多因素并采取相应措施来降低变形影响。
在实践中,需要根据具体情况采取不同的措施,以确保船舶结构的安全和可靠性。
船舶薄板焊接变形的控制
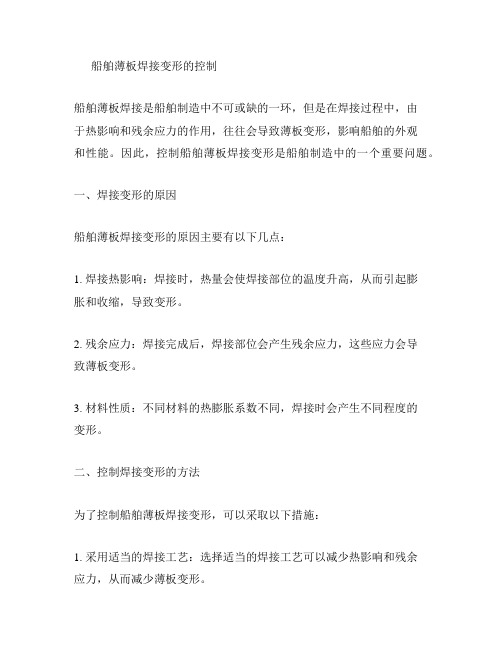
船舶薄板焊接变形的控制
船舶薄板焊接是船舶制造中不可或缺的一环,但是在焊接过程中,由
于热影响和残余应力的作用,往往会导致薄板变形,影响船舶的外观
和性能。
因此,控制船舶薄板焊接变形是船舶制造中的一个重要问题。
一、焊接变形的原因
船舶薄板焊接变形的原因主要有以下几点:
1. 焊接热影响:焊接时,热量会使焊接部位的温度升高,从而引起膨
胀和收缩,导致变形。
2. 残余应力:焊接完成后,焊接部位会产生残余应力,这些应力会导
致薄板变形。
3. 材料性质:不同材料的热膨胀系数不同,焊接时会产生不同程度的
变形。
二、控制焊接变形的方法
为了控制船舶薄板焊接变形,可以采取以下措施:
1. 采用适当的焊接工艺:选择适当的焊接工艺可以减少热影响和残余
应力,从而减少薄板变形。
2. 控制焊接温度:控制焊接温度可以减少热影响和残余应力,从而减少薄板变形。
3. 采用预应力技术:预应力技术可以在焊接前施加一定的应力,从而减少焊接后的残余应力,减少薄板变形。
4. 采用补偿焊接:补偿焊接可以在焊接前预留一定的余量,焊接后再进行修整,从而减少薄板变形。
三、总结
船舶薄板焊接变形是船舶制造中的一个重要问题,需要采取适当的措施进行控制。
在实际操作中,应根据具体情况选择适当的焊接工艺和控制方法,从而减少薄板变形,提高船舶的外观和性能。
论船舶薄板焊接的变形问题及控制方法

论船舶薄板焊接的变形问题及控制方法船舶薄板焊接的变形问题是指在船舶制造过程中,由于焊接引起的板材变形现象。
船舶薄板焊接的变形主要有以下几个方面:焊接接头区域的局部收缩变形、板材整体弯曲变形、板材局部扭曲变形和板材表面变形等。
这些变形不仅会影响船舶的外观质量,还会对船舶的性能、稳定性和安全性产生影响。
必须采取有效的控制方法来减少船舶薄板焊接的变形。
1.采用预留焊接变形量的方法:在板材焊接前,对板材进行预留,通过计算和试验确定合适的焊接变形量,然后在焊接过程中通过适当的补焊和拉伸方法来达到预留变形量。
这种方法可以将变形分散到整个板材上,减少焊接接头区域的局部变形。
2.采用焊接顺序控制:在焊接过程中,可以合理安排焊接的顺序,先从板材中心区域开始焊接,再逐渐向两侧进行焊接。
这样可以避免板材整体弯曲变形,使变形集中在板材中心区域,减少局部变形。
3.采用焊接参数优化控制:合理选择焊接参数,如焊接速度、焊接电流、焊接温度等,通过调整焊接参数来控制焊接变形。
可以使用辅助装置,如加热装置或加压装置,来控制板材的温度和形变。
4.采用焊接残余应力调控方法:通过在焊接过程中施加外部应力或者局部加热来调节焊接残余应力的分布,从而减少板材的变形。
5.采用焊接后矫正变形的方法:在焊接完成后,通过机械矫正、矫直或加热矫正等方法来纠正板材的变形。
这种方法可以在保证焊接质量的修复已经产生的变形。
船舶薄板焊接的变形问题是一个复杂而严重的问题,需要采取多种控制方法来减少变形的发生。
需要综合考虑板材材料特性、焊接工艺、焊接参数和焊接设备等因素,并通过合理的设计和工程实践来解决变形问题,以提高船舶焊接质量和性能。
船舶薄板焊接防变形
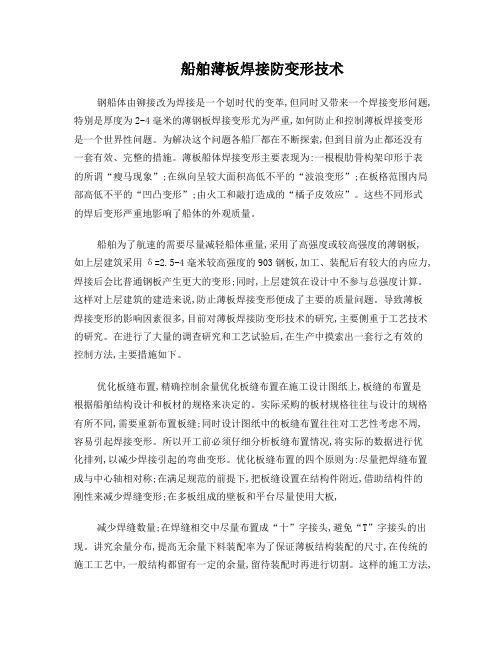
船舶薄板焊接防变形技术钢船体由铆接改为焊接是一个划时代的变革,但同时又带来一个焊接变形问题,特别是厚度为2-4毫米的薄钢板焊接变形尤为严重,如何防止和控制薄板焊接变形是一个世界性问题。
为解决这个问题各船厂都在不断探索,但到目前为止都还没有一套有效、完整的措施。
薄板船体焊接变形主要表现为:一根根肋骨构架印形于表的所谓“瘦马现象”;在纵向呈较大面积高低不平的“波浪变形”;在板格范围内局部高低不平的“凹凸变形”;由火工和敲打造成的“橘子皮效应”。
这些不同形式的焊后变形严重地影响了船体的外观质量。
船舶为了航速的需要尽量减轻船体重量,采用了高强度或较高强度的薄钢板,如上层建筑采用δ=2.5-4毫米较高强度的903钢板,加工、装配后有较大的内应力,焊接后会比普通钢板产生更大的变形;同时,上层建筑在设计中不参与总强度计算。
这样对上层建筑的建造来说,防止薄板焊接变形便成了主要的质量问题。
导致薄板焊接变形的影响因素很多,目前对薄板焊接防变形技术的研究,主要侧重于工艺技术的研究。
在进行了大量的调查研究和工艺试验后,在生产中摸索出一套行之有效的控制方法,主要措施如下。
优化板缝布置,精确控制余量优化板缝布置在施工设计图纸上,板缝的布置是根据船舶结构设计和板材的规格来决定的。
实际采购的板材规格往往与设计的规格有所不同,需要重新布置板缝;同时设计图纸中的板缝布置往往对工艺性考虑不周,容易引起焊接变形。
所以开工前必须仔细分析板缝布置情况,将实际的数据进行优化排列,以减少焊接引起的弯曲变形。
优化板缝布置的四个原则为:尽量把焊缝布置成与中心轴相对称;在满足规范的前提下,把板缝设置在结构件附近,借助结构件的刚性来减少焊缝变形;在多板组成的壁板和平台尽量使用大板,减少焊缝数量;在焊缝相交中尽量布置成“十”字接头,避免“T”字接头的出现。
讲究余量分布,提高无余量下料装配率为了保证薄板结构装配的尺寸,在传统的施工工艺中,一般结构都留有一定的余量,留待装配时再进行切割。
论船舶薄板焊接的变形问题及控制方法

论船舶薄板焊接的变形问题及控制方法船舶薄板焊接是船舶制造过程中的重要环节,其焊接质量直接影响到船舶的使用安全和性能。
在船舶薄板焊接过程中,常常会出现焊接变形问题,给船舶制造带来了诸多困扰。
本文将从船舶薄板焊接的变形问题及控制方法进行探讨。
一、船舶薄板焊接的变形问题在船舶薄板焊接过程中,由于焊接热量对板材的影响,往往会导致薄板产生变形。
主要表现为以下几个方面:1. 变形形式多样船舶薄板焊接变形的形式主要有翘曲、翻边、弯曲等多种形式。
这些变形不仅影响了焊接质量,同时也对后续的工艺制造和船舶使用带来了一定的隐患。
2. 影响船舶装配焊接变形会导致薄板尺寸和形状的变化,从而影响到船舶其他部件的装配。
严重的焊接变形会导致相邻板材之间无法对接,严重影响船舶整体结构的装配质量。
3. 降低焊接质量焊接变形会影响到焊缝的形成和质量,导致焊接接头质量下降,从而加剧了船舶的潜在安全隐患。
二、船舶薄板焊接变形的控制方法为了解决船舶薄板焊接变形问题,需要采取一系列的控制方法来加以解决。
主要包括以下几个方面:1. 采用合理的焊接工艺在船舶薄板焊接过程中,应根据板材的厚度、材质和形状等因素,合理选择焊接工艺,包括焊接电流、焊接速度和焊接顺序等。
通过合理的焊接工艺能够减少焊接变形的产生。
2. 使用适当的焊接顺序在焊接薄板时,应采取合理的焊接顺序,避免集中焊接或跨度过大的焊接,通过适当的焊接顺序来减少焊接热量对板材的影响,从而降低焊接变形的产生。
4. 使用辅助设备和固定夹具在焊接薄板时,可以使用合适的辅助设备和固定夹具来固定和支撑板材,以减少焊接变形的产生。
同时可以采用适当的预压和支撑来保持板材的形状稳定。
5. 焊接变形的仿真分析利用计算机仿真技术对焊接过程进行模拟分析,通过仿真结果来指导实际焊接操作,从而降低焊接变形的产生。
船舶薄板焊接的变形问题是制约船舶制造质量的重要因素,针对这一问题需要采取一系列的控制方法。
通过合理的焊接工艺、适当的焊接顺序、预热和焊后处理、辅助设备和固定夹具、以及仿真分析等措施来减少焊接变形的产生,提高船舶薄板焊接的质量和效率。
浅谈船舶薄板焊接变形问题与控制对策
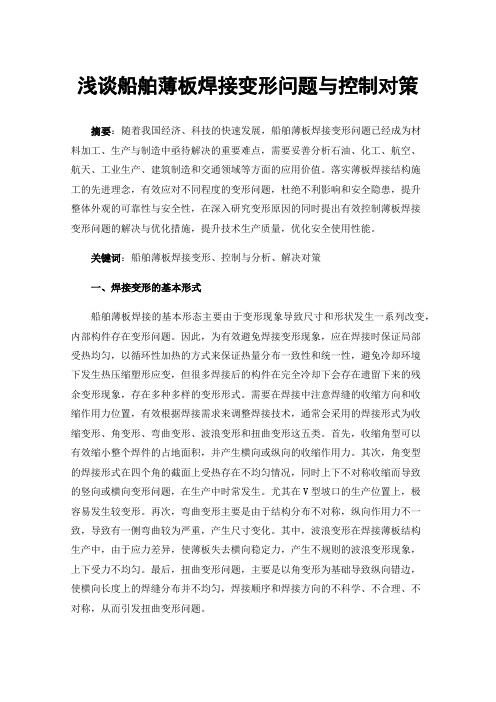
浅谈船舶薄板焊接变形问题与控制对策摘要:随着我国经济、科技的快速发展,船舶薄板焊接变形问题已经成为材料加工、生产与制造中亟待解决的重要难点,需要妥善分析石油、化工、航空、航天、工业生产、建筑制造和交通领域等方面的应用价值。
落实薄板焊接结构施工的先进理念,有效应对不同程度的变形问题,杜绝不利影响和安全隐患,提升整体外观的可靠性与安全性,在深入研究变形原因的同时提出有效控制薄板焊接变形问题的解决与优化措施,提升技术生产质量,优化安全使用性能。
关键词:船舶薄板焊接变形、控制与分析、解决对策一、焊接变形的基本形式船舶薄板焊接的基本形态主要由于变形现象导致尺寸和形状发生一系列改变,内部构件存在变形问题。
因此,为有效避免焊接变形现象,应在焊接时保证局部受热均匀,以循环性加热的方式来保证热量分布一致性和统一性,避免冷却环境下发生热压缩塑形应变,但很多焊接后的构件在完全冷却下会存在遗留下来的残余变形现象,存在多种多样的变形形式。
需要在焊接中注意焊缝的收缩方向和收缩作用力位置,有效根据焊接需求来调整焊接技术,通常会采用的焊接形式为收缩变形、角变形、弯曲变形、波浪变形和扭曲变形这五类。
首先,收缩角型可以有效缩小整个焊件的占地面积,并产生横向或纵向的收缩作用力。
其次,角变型的焊接形式在四个角的截面上受热存在不均匀情况,同时上下不对称收缩而导致的竖向或横向变形问题,在生产中时常发生。
尤其在V型坡口的生产位置上,极容易发生较变形。
再次,弯曲变形主要是由于结构分布不对称,纵向作用力不一致,导致有一侧弯曲较为严重,产生尺寸变化。
其中,波浪变形在焊接薄板结构生产中,由于应力差异,使薄板失去横向稳定力,产生不规则的波浪变形现象,上下受力不均匀。
最后,扭曲变形问题,主要是以角变形为基础导致纵向错边,使横向长度上的焊缝分布并不均匀,焊接顺序和焊接方向的不科学、不合理、不对称,从而引发扭曲变形问题。
二、影响薄板焊接变形的主要因素导致薄板焊接变形的原因有很多,尤其是焊接过程中的刚度条件或温度条件不均,会引发变形现象。
论船舶薄板焊接的变形问题及控制方法
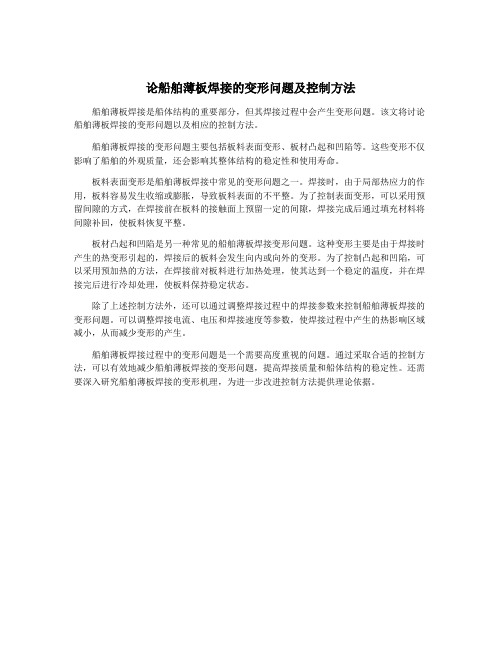
论船舶薄板焊接的变形问题及控制方法
船舶薄板焊接是船体结构的重要部分,但其焊接过程中会产生变形问题。
该文将讨论船舶薄板焊接的变形问题以及相应的控制方法。
船舶薄板焊接的变形问题主要包括板料表面变形、板材凸起和凹陷等。
这些变形不仅影响了船舶的外观质量,还会影响其整体结构的稳定性和使用寿命。
板料表面变形是船舶薄板焊接中常见的变形问题之一。
焊接时,由于局部热应力的作用,板料容易发生收缩或膨胀,导致板料表面的不平整。
为了控制表面变形,可以采用预留间隙的方式,在焊接前在板料的接触面上预留一定的间隙,焊接完成后通过填充材料将间隙补回,使板料恢复平整。
板材凸起和凹陷是另一种常见的船舶薄板焊接变形问题。
这种变形主要是由于焊接时产生的热变形引起的,焊接后的板料会发生向内或向外的变形。
为了控制凸起和凹陷,可以采用预加热的方法,在焊接前对板料进行加热处理,使其达到一个稳定的温度,并在焊接完后进行冷却处理,使板料保持稳定状态。
除了上述控制方法外,还可以通过调整焊接过程中的焊接参数来控制船舶薄板焊接的变形问题。
可以调整焊接电流、电压和焊接速度等参数,使焊接过程中产生的热影响区域减小,从而减少变形的产生。
船舶薄板焊接过程中的变形问题是一个需要高度重视的问题。
通过采取合适的控制方法,可以有效地减少船舶薄板焊接的变形问题,提高焊接质量和船体结构的稳定性。
还需要深入研究船舶薄板焊接的变形机理,为进一步改进控制方法提供理论依据。
薄板焊接变形控制技术

薄板焊接变形控制技术在国外先进的军事强国如美国、俄罗斯等国在建造大型水面舰艇时普遍采用强度高的船体钢材,板厚减薄,从而使舰艇的自身重量减轻,可以使舰艇的战斗威力提高,具有航速加快等优点,图1为美国廿世纪90年代以来在舰艇制造中薄板钢材的使用情况及将来薄板在舰艇制造中所占比例的趋势。
然而,由于板厚的减薄也带来了薄板焊接变形控制难题,在国外先进国家均采用专门的焊接工装及装配夹具,同时大胆采用先进的焊接方法和开发新的焊接变形控制工艺。
在我国由于工艺方法的局限性,造成了舰艇在制造过程中存在焊接变形大,舰艇性能差、性能差、外观不美等缺点,不但影响了舰艇的机动性能,而且经火工矫正,增加了建造周期,降低了钢板的力学性能和耐蚀性,影响舰船寿命。
这一问题同样也存在于国外先进国家的舰艇制造中,比如在美国DDG-51导弹舰制造过程中变形控制成本中火工矫正就占相当大的比例(见图2)。
薄板焊接变形具有复杂性、多元性,从而严重影响了焊接质量,是国内外薄板焊接制造的一个技术难题。
本文主要针对焊接变形产生的理论基础、影响因素、预测技术及先进的焊接方法和工艺进行了综述。
图1 薄板在美国舰艇制造中的使用情况图 2 美国导弹舰制造过程中火工矫正在变形控制成本中所占的比例1.薄板变形的数学物理模型按照板壳理论的观点,薄板焊接发生的压曲变形实质就是薄板的屈曲问题。
焊接薄板构件时,在远离焊缝的区域中产生残余压应力(见图3),该残余压应力的平均值大于薄板构件产生变形的临界压应力时就会产生压曲变形(也称挠曲变形)。
薄板结构主要承受两种载荷,一种是作用在中面内的拉、压或剪力,总称为中面力;另一种是垂直于中面的力,称为横向力。
对于中面力,可以认为它们沿板厚均匀分布,由此产生的应力和形变可按弹性力学中的平面问题计算;而横向力使薄板发生弯曲,由此产生的应力和形变可按薄板弯曲问题来处理。
对于薄板焊接的压曲变形而言属于中面力的载荷问题。
薄板焊接发生的压曲变形属于薄板的小挠度问题。
薄板焊缝防变形措施方案
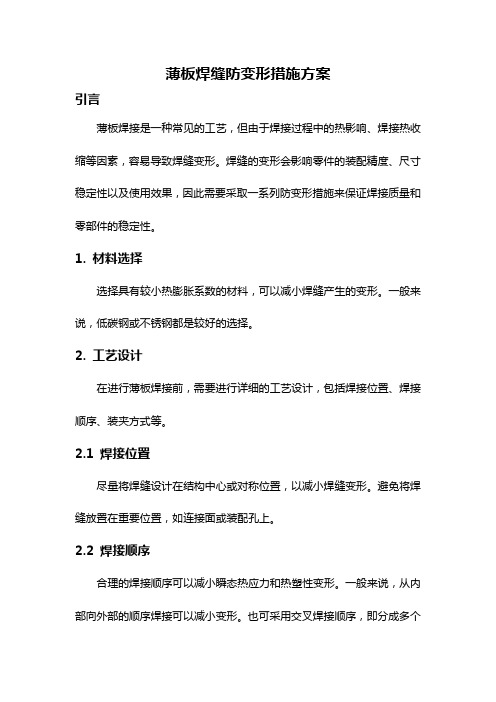
薄板焊缝防变形措施方案引言薄板焊接是一种常见的工艺,但由于焊接过程中的热影响、焊接热收缩等因素,容易导致焊缝变形。
焊缝的变形会影响零件的装配精度、尺寸稳定性以及使用效果,因此需要采取一系列防变形措施来保证焊接质量和零部件的稳定性。
1. 材料选择选择具有较小热膨胀系数的材料,可以减小焊缝产生的变形。
一般来说,低碳钢或不锈钢都是较好的选择。
2. 工艺设计在进行薄板焊接前,需要进行详细的工艺设计,包括焊接位置、焊接顺序、装夹方式等。
2.1 焊接位置尽量将焊缝设计在结构中心或对称位置,以减小焊缝变形。
避免将焊缝放置在重要位置,如连接面或装配孔上。
2.2 焊接顺序合理的焊接顺序可以减小瞬态热应力和热塑性变形。
一般来说,从内部向外部的顺序焊接可以减小变形。
也可采用交叉焊接顺序,即分成多个小区域交错焊接。
2.3 装夹方式适当的装夹方式可以减小焊缝的变形,主要有以下几种方式:- 使用适当的夹具和固定支撑,使焊件受力均衡,减小变形。
- 采用气动夹具,通过内部气压来固定焊件,减小变形。
3. 焊接参数控制合理的焊接参数可以控制焊缝的变形。
3.1 焊接电流和电压合理选择焊接电流和电压可以控制焊缝的热输入量,从而减小热变形。
3.2 焊速控制合适的焊接速度可以减少热影响区的面积,减小变形。
太快的焊接速度会增加焊接热输入,太慢的焊接速度则会增加变形风险。
3.3 焊接顺序将焊缝分成多个局部区域进行焊接,并遵循逆时针或顺时针的焊接顺序,可以减小变形。
4. 临时固定和支撑采用合适的临时固定和支撑方式,可以有效减小焊缝变形。
4.1 用临时支撑支撑构件在进行焊接之前,可以在焊缝附近使用临时支撑件来支撑构件,从而减小变形。
4.2 采用临时固定件夹紧焊缝在焊接过程中,使用临时固定件夹紧焊缝,以减小受热部位的变形。
5. 焊后处理焊后处理可以进一步减小焊缝的变形。
5.1 热处理采用热处理方法,例如退火或回火处理,可以减小焊接残余应力,进一步减小焊缝变形。
论船舶薄板焊接的变形问题及控制方法
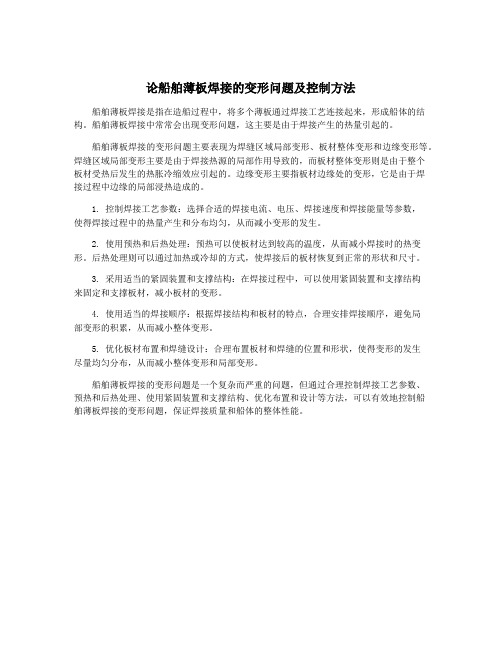
论船舶薄板焊接的变形问题及控制方法
船舶薄板焊接是指在造船过程中,将多个薄板通过焊接工艺连接起来,形成船体的结构。
船舶薄板焊接中常常会出现变形问题,这主要是由于焊接产生的热量引起的。
船舶薄板焊接的变形问题主要表现为焊缝区域局部变形、板材整体变形和边缘变形等。
焊缝区域局部变形主要是由于焊接热源的局部作用导致的,而板材整体变形则是由于整个
板材受热后发生的热胀冷缩效应引起的。
边缘变形主要指板材边缘处的变形,它是由于焊
接过程中边缘的局部浸热造成的。
1. 控制焊接工艺参数:选择合适的焊接电流、电压、焊接速度和焊接能量等参数,
使得焊接过程中的热量产生和分布均匀,从而减小变形的发生。
2. 使用预热和后热处理:预热可以使板材达到较高的温度,从而减小焊接时的热变形。
后热处理则可以通过加热或冷却的方式,使焊接后的板材恢复到正常的形状和尺寸。
3. 采用适当的紧固装置和支撑结构:在焊接过程中,可以使用紧固装置和支撑结构
来固定和支撑板材,减小板材的变形。
4. 使用适当的焊接顺序:根据焊接结构和板材的特点,合理安排焊接顺序,避免局
部变形的积累,从而减小整体变形。
5. 优化板材布置和焊缝设计:合理布置板材和焊缝的位置和形状,使得变形的发生
尽量均匀分布,从而减小整体变形和局部变形。
船舶薄板焊接的变形问题是一个复杂而严重的问题,但通过合理控制焊接工艺参数、
预热和后热处理、使用紧固装置和支撑结构、优化布置和设计等方法,可以有效地控制船
舶薄板焊接的变形问题,保证焊接质量和船体的整体性能。
滚装货船薄板焊接变形及对策分析

滚装货船薄板焊接变形及对策分析0 前言随着造船技术的提升,船舶逐渐趋于大型化,货物装载量不断提升。
以国内商品汽车滚装船为例,普遍载车量在800辆以上,载车甲板包括底舱、主甲板、上甲板和多层上层建筑甲板。
由于船舶载车楼层数量多,船舶重心上移,船舶稳性受到考验,因此薄板加筋结构的应用显得尤为重要。
焊接作为一种重要的工业制造手段,正被广泛应用于船舶建造中。
宋娓娓等人[1]通过建立薄板焊接有限元模型,对薄板焊接温度场分布、应力场分布和变形规律进行了分析,结果表明焊接过程中薄板的平均温度逐渐升高并趋于准稳态状态,焊缝区域产生了拉应力,焊缝区域周边的母材金属则产生压应力。
陈怀忠等人[2]对薄板加强筋结构焊接过程进行了有限元模拟,结果显示薄板加强筋结构焊后残余应力主要沿着焊缝分布,在远离焊缝处残余应力迅速减小,最大残余应力位于横向筋板与底板焊缝处。
宗小彦等人[3]分析了薄板焊接烧穿和失稳变形的原因及影响因素。
对于如何控制薄板焊接变形,石小清等人[4]结合薄板焊接的影响因素,从焊接顺序方面进行了梳理;李忠明等人[5]阐述了在作业中薄板焊接变形的控制措施,并从焊接工艺设计方面入手进行了实践验证;王顺俊等人[6]重点探讨了薄板箱体的焊接变形及其控制方法。
薄板焊接变形后的校正难度较大,即使顺利校正,亦会影响其几何精度和装配性能,杜小明等人[7]、齐伟等人[8]和冯伟等人[9]从薄板变形矫正的方法进行了分析,归纳了几种有利于控制薄板焊接变形的矫正方法。
然而,很多工作者大多从有限元模拟或者汽车、船舶的局部变形进行了分析,很少从整个船舶的建造角度去考虑如何控制薄板焊接变形。
文中主要基于多艘国内大型商品汽车滚装船建造中薄板焊接变形情况,将产生的焊接变形位置和种类进行了梳理。
针对不同变形采取了相应的控制方案和纠正措施,包括对船舶图纸设计的优化和现场施工工艺的控制,通过不断总结,后续船薄板变形得到有效控制,船舶整体质量水平进一步提升。
- 1、下载文档前请自行甄别文档内容的完整性,平台不提供额外的编辑、内容补充、找答案等附加服务。
- 2、"仅部分预览"的文档,不可在线预览部分如存在完整性等问题,可反馈申请退款(可完整预览的文档不适用该条件!)。
- 3、如文档侵犯您的权益,请联系客服反馈,我们会尽快为您处理(人工客服工作时间:9:00-18:30)。
船舶薄板焊接防变形技术Anti-deforming welding techniques for thin ship plates陈奇For the same horse power of the marine desiel, tominimizethe hull weight is the key factor in order to raisethe steelship speed. At present, thin high and highertensile steelplates are widely used for hull structures. In suchcase, howto deal with the plate welding deform has becomea headachetechnical problem. The auther made a full study onthisproblem and finally summarized a series ofpractical weldingtechniques for the thin hull plates. The newtechniques havebeen justified successfully during the shipconstruction.钢船体由铆接改为焊接是一个划时代的变革,但同时又带来一个焊接变形问题,特别是厚度为2-4毫米的薄钢板焊接变形尤为严重,如何防止和控制薄板焊接变形是一个世界性问题。
为解决这个问题各船厂都在不断探索,但到目前为止都还没有一套有效、完整的措施。
薄板船体焊接变形主要表现为:一根根肋骨构架印形于表的所谓“瘦马现象”;在纵向呈较大面积高低不平的“波浪变形”;在板格范围内局部高低不平的“凹凸变形”;由火工和敲打造成的“橘子皮效应”。
这些不同形式的焊后变形严重地影响了船体的外观质量。
船舶为了航速的需要尽量减轻船体重量,采用了高强度或较高强度的薄钢板,如上层建筑采用δ=2.5-4毫米较高强度的903钢板,加工、装配后有较大的内应力,焊接后会比普通钢板产生更大的变形;同时,上层建筑在设计中不参与总强度计算。
这样对上层建筑的建造来说,防止薄板焊接变形便成了主要的质量问题。
导致薄板焊接变形的影响因素很多,目前对薄板焊接防变形技术的研究,主要侧重于工艺技术的研究。
在进行了大量的调查研究和工艺试验后,在生产中摸索出一套行之有效的控制方法,主要措施如下。
优化板缝布置,精确控制余量优化板缝布置在施工设计图纸上,板缝的布置是根据船舶结构设计和板材的规格来决定的。
实际采购的板材规格往往与设计的规格有所不同,需要重新布置板缝;同时设计图纸中的板缝布置往往对工艺性考虑不周,容易引起焊接变形。
所以开工前必须仔细分析板缝布置情况,将实际的数据进行优化排列,以减少焊接引起的弯曲变形。
优化板缝布置的四个原则为:尽量把焊缝布置成与中心轴相对称;在满足规范的前提下,把板缝设置在结构件附近,借助结构件的刚性来减少焊缝变形;在多板组成的壁板和平台尽量使用大板,减少焊缝数量;在焊缝相交中尽量布置成“十”字接头,避免“T”字接头的出现。
讲究余量分布,提高无余量下料装配率为了保证薄板结构装配的尺寸,在传统的施工工艺中,一般结构都留有一定的余量,留待装配时再进行切割。
这样的施工方法,虽然能保证分段尺寸的质量,但由于在装配过程中的二次切割,增加了受热的变形和内应力,对分段变形的控制和后续工序的施工都带来了不利的影响。
经分析确定,改变传统做法,采取在分段接头处单边留有余量,其它位置一律改为不留下料余量,使大部分板材下料剪切一次成功。
采取这样的措施,在施工中可减少加热次数和加热量,有效控制装配过程薄板的变形。
实行焊后滚平和无码焊接技术板缝焊后滚平薄板焊接无论事前采取何种预防措施都只能减少变形量而不能消除变形,焊接后变形是难免的。
按传统工序拼板焊后安装构架,这样板部位变形很难处理,靠火工校正,一方面很难收到理想效果,另一方面火工多了又会出现橘子皮现象。
采取构架安装前先消除拼板焊接变形的措施,把切割好的薄板放在固定平台上装焊,焊后用十三星滚平机滚压消除焊接变形。
由于用机械的方法消除焊缝的焊接变形,减少了火工工作量,也为构架安装和最终减少总体变形打下了基础。
推行无码焊接在以往的造船中,焊了许多拉码把钢板固定于胎架上是保证线型和防止变形的主要工艺,这种方法给薄板带来的码脚印和弧坑,需进行大量的割、批、补、磨等工作。
既增加了变形又损伤了钢板,为改变这一状况,采用无码焊接技术,可有效控制薄板焊接变形。
现行施工工艺采用的无码焊接工艺是:使用磁吸码,用磁力把钢板固定于胎架上,不至损伤钢板,也避免了繁杂的修补工作。
以压代拉,在平台或胎架上安装板材时采用压铁压紧来实现线型吻合和防止变形。
先装构架后焊板缝,确实需要在胎架上焊接的板缝,也要改变传统的先焊板缝后装构架的做法,采用拼板后先进行构架安装,装好构架后一起烧焊,利用构架来限制板的焊接变形。
限制使用工艺拉条,在上层建筑分段、总段装配中不轻易采用焊拉条和支撑,尽量利用纵横壁板自身相互的支持来实现定位,必须要焊支撑或拉条时也只能焊在构架上,绝不允许焊在板中。
实施全方位CO2气体保护焊薄板的焊接变形是因为板材受到不均匀的局部加热和冷却的影响,内部产生了不均衡应力所引起的,变形的大小与输入的热量有密切的关系,减少热量的输入是控制变形的有效措施。
采用下面公式计算手工焊和CO2保护焊的能量输入,分析对比发现,采用CO2气体保护焊可大大地减少热量的输入。
Q=0.2ηUI/V式中:Q为焊缝焊接线能量;η为电弧热利用系数;U为电弧电压;I为焊接电流;V焊接速度。
经计算对2-4毫米的薄板采用CO2气体保护焊的线能量仅为手工焊的30-40%,可见用CO2气体保护焊对控制焊接变形是十分有效的。
根据理论和试验研究成果,自行改造MZ-400型自动焊机控制箱,改进电压负反馈电路,减少车间电网波动对焊接的影响,解决埋弧自动焊在4毫米板的平对接焊,达到美观平整,熔深达到焊接规定。
改造CO2焊机解决小于3毫米板的平对接和平角焊,也达到理想的效果。
选用KS—1型(日产)CO2全方位垂直自动焊机解决分段对接自动焊。
在进行了充分工艺试验的基础上,确定了不同部位/不同板厚选用不同型号焊机以及用不同的参数,解决上层建筑全方位使用CO2气体保护焊,对上层建筑薄板防变形起了关键的作用。
严格控制和准确使用火工技术火工校正是薄板防变形技术的最后一道措施,但火工校正是一理论性强、技术复杂的工作,用得不好反而给薄板带来新变形和新问题。
对船上上层建筑薄板使用火工校正技术,在做了大量模拟变形火工试验研究,并做了几十种火工技术预案后,明确火工技术实施的控制原则,改变传统使用火工校正工艺选用较低热值的DKL工业气体。
经过试验研究和建造实践,摸索出一套对903薄板变形矫正行之有效的办法。
明确了不同的变形要选择不同的加热方法(主要用条形法、圆圈法、链状法和“十字法”)来解决,不同结构和不同部位要采用不同的方式处理,同时其操作方法和选择工作参数也要不同,不同板厚的903板选择不同工作参数如下表:采用火工校正方法的原则如下:下料和构件组装所产生的变形必须校正后再上分段安装;在分段建造完成后只对骨材吊装接口边缘的变形进行火工校正,减少火工加热次数;在校正施工中要严格执行规定的工作程序和选定的火工参数,特别是要严格控制加热温度不得随意更改;绝对禁止用铁锤敲击,必须锤击时只能用木锤和塑料锤;903钢板温度在200-350℃区间为兰脆区,在该温度内禁止任何形式的锤击,以免产生微裂纹;对板的局部凹凸变形采用小火圈加热形式,火圈直径为20毫米,从外到内,火圈疏密视情况而定;板的纵向波浪在加强材两侧边缘条形加热火路距离构架5毫米,采用隔档加热的办法控制总体变形;构架变形可采用加外力和烧火结合的办法,用外力帮助校正变形; 板缝角变形用条形加热法;同一部位加热次数不得超过3次。
前面提及的四个方面是解决903薄板焊接防变形的主要措施。
实际生产中还应采取其他措施:如采用先滚平再剪切下料;对扭曲变形的板,先火工校正再滚平下料,下料后再次滚平,最后送去装配。
考虑到薄板从下料到装配、焊接成型需要多次吊运,以往吊运引起变形也相当严重,所以必须改进吊运方法和条件,在薄板加工全过程吊运采用磁吸吊机,对加工后尺寸大小不一或有形的工件采用专制钢板吊 架床转运。
采取这些措施,可有效控制吊运环节产生变形。
在上层建筑分段制作中还采用预舾装工艺等,这些都是有效控制薄板焊接变形的措施。
采用上述综合措施后,最终质量结果达到:上层建筑、壁板平台光顺平直,没有瘦马现象,没有橘子皮出现,没有明显的波浪变形,没有码脚印痕和电弧坑。
经过实船测量两肋间的局部变形几乎为零,不管焊缝部位还是非焊缝部位,只有个别位置有局部变形,其最大值都没有超过规范的要求。
(见图1)。
在火工后对整幅壁板的变形测试,所有内外纵横壁板从头到尾整幅直线度最大偏差也只有5毫米左右(见图2)。
图2 纵横壁板从头到尾整幅直线度。