渣油加氢催化剂全蜡油硫化
渣油加氢工艺流程

渣油加氢工艺流程渣油加氢工艺是一种将高硫、高含蜡的渣油通过加氢反应降低硫含量和提高产品质量的工艺。
该工艺的主要流程包括预处理、加氢反应和分离三个步骤。
首先是预处理步骤。
在这一步骤中,渣油经过加热后进入预加热器,以达到合适的反应温度。
然后,预加热后的渣油进入加工器,在这个设备中与一定量的催化剂进行接触。
接触时间的长短和温度的高低可以根据实际需求进行调整。
在接触过程中,催化剂能够去除渣油中的杂质,如硫、氮和有机蜡,从而减少对后续催化剂的影响,并提高反应效率。
接下来是加氢反应步骤。
预处理后的渣油进入加氢反应器,与高效加氢催化剂接触,进行加氢反应。
在加氢反应中,渣油中的硫、氮和重蜡等杂质会与催化剂发生作用,从而被还原、分解或结构改变,生成较少含硫、含氮和较轻的石蜡等反应产物。
加氢反应的条件通常包括反应温度、压力和催化剂的加载量。
较低的反应温度和较高的压力可以提高催化剂的活性,加速杂质的去除。
此外,催化剂的特性也会对反应结果产生一定影响。
最后是分离步骤。
在加氢反应后,反应物进入分离器进行相应的处理。
分离过程主要通过不同组分的沸点差异实现,包括气液分离和液液分离。
液相分离主要是通过凝固和冷凝的方式,使较重的组分凝结成液体,而较轻的组分则通过冷凝回收。
气相分离则利用分析和纯化设备,对气体中的各种组分进行分别处理,从而得到高纯度的产品。
总的来说,渣油加氢工艺流程包括预处理、加氢反应和分离三个步骤。
通过预处理可以去除渣油中的杂质,提高反应效率;加氢反应则通过与催化剂的作用,将渣油中的硫、氮和重蜡等杂质转化为较少含硫、含氮和较轻的石蜡等反应产物;最后的分离步骤则通过不同组分的沸点差异,将反应产物进行分离和纯化,得到高质量的产品。
渣油加氢工艺在石油化工行业中具有重要的应用价值,能够有效改善石油产品的质量,并满足环保要求。
上海石化3.9Mt/a渣油加氢装置采用全蜡油硫化方案
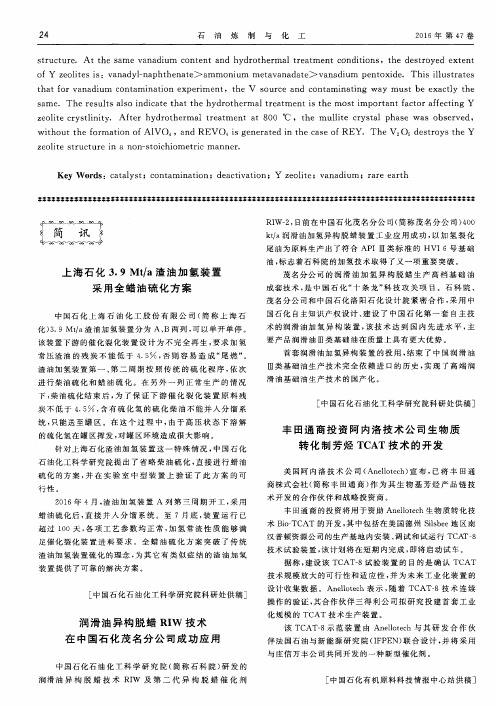
~
Ke y Wo r ds :c a t a l ys t ;c o nt a mi n a t i on;de a c t i v a t i o n;Y z e ol i t e;v a n a d i um ;r a r e e a r t h
要 产 品润 滑油 Ⅲ类 基 础 油在 质量 上具 有更 大优 势 。
化) 3 . 9 Mt / a 渣 油 加 氢 装 置 分 为 A、 B两 列 , 可以单开单停 。
该装置下游的催化裂化装置设 计为不 完全再 生 , 要 求 加 氢
常压渣油 的残 炭 不能 低 于 4 . 5 , 否则 容 易造 成 “ 尾燃” 。
: :::;:::; :; ;::::
ቤተ መጻሕፍቲ ባይዱ
: ::::::;::: :::::::: :: :::::::: :::::::::: ・ b , - ::::::::: :::::::: :: :::::::::
R I W一 2 , 日前 在 中 国 石 化茂 名 分 公 司 ( 简称茂 名分公 司) 4 0 0 k t / a 润滑油加氢异构脱蜡 装置工 业应用 成功 , 以 加 氢 裂 化
2 4
石
油
炼
制
与
化
工
2 0 1 6 年 第 4 7卷
s t r u c t ur e . At t h e s a me v a na di u m c o nt e nt a nd hy d r ot h e r ma l t r e a t me nt c o nd i t i on s, t he d e s t r o ye d e xt e nt
炼油“三剂”汇总

三剂名称
作用
催
化
重
整
1)加氢脱硅剂
硅是焦化石脑油加氢精制过程中的毒物,可造成催化剂孔容和比表面损失,使催化剂永久失活。加氢脱硅剂可用于石脑油加氢催化剂之前进行脱硅和捕硅,有利于保护加氢催化剂免收硅污染,延长加氢催化剂的使用周期。
2)预加氢催化剂
重整预加氢精制目的主要是除去重整原料油中的含硫、 氧化合物和其他重整催化剂的毒物, 以保护重整催化剂
5)金属钝化剂
金属钝化剂是利用某些金属的有机或无机化合物,以液体状态注入催化裂化反再系统并使之沉淀在催化剂上与催化剂上的重金属发生作用,抑制其对催化剂的污染。
6)油浆阻垢剂
催化裂化油浆阻垢剂主要用于催化裂化装置油浆及换热系统。加入该剂后,可减少分馏塔底、油浆及换热系统的结垢,改善油浆系统工况提高换热效率、抑制结焦、延长操作周期。
12)低磁剂
利用磁选的方法对催化裂化平衡剂进行回收,把污染重、性能差的催化剂从平衡剂中分离出去,将污染相对较轻、性能相对较好的催化剂加以回收利用,达到催化剂再利用的目的。
装置名称
三剂名称)汽油选择性加氢脱硫催化剂
用于加氢装置反应器,可脱除原料中的硫、氮、氧及金属杂质,同时还使烯烃、二烯烃、芳烃及稠环芳烃选择性加氢饱和,从而改善原料及产品的品质与使用性能。
10)高压空冷缓蚀剂
高压空冷缓蚀剂一方面具有阻垢功能,可阻止铵盐低温析出,避免硫氢化铵沉积造成垢下腐蚀;另一方面具有缓蚀作用,在空冷器表面能够形成致密、稳定的保护膜,在一定程度上避免管束受硫氢化铵溶液冲蚀。
11)蜡油阻垢剂
加氢装置原料油结垢,可引起原料油换热器传热系数迅速下降,导致反应流出物冷却负荷及反应加热炉负荷增加,从而缩短装置运行周期,在原料油中注入阻垢剂,可减缓原料油的结垢程度,提高换热效率。
300万吨渣油加氢工艺流程简述
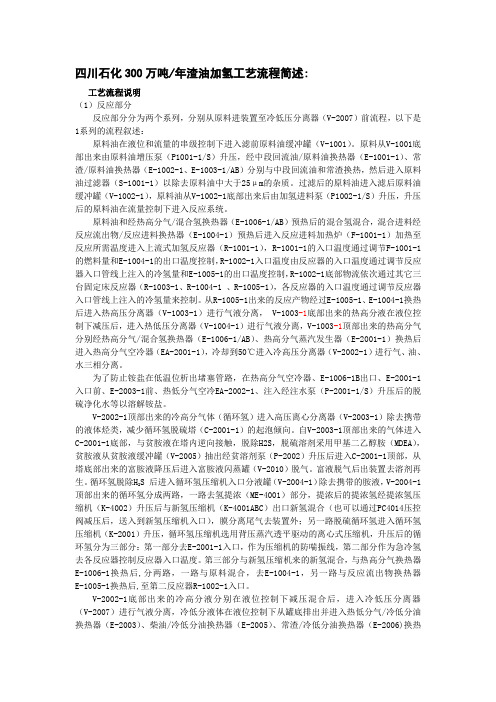
四川石化300万吨/年渣油加氢工艺流程简述:工艺流程说明(1)反应部分反应部分分为两个系列,分别从原料进装置至冷低压分离器(V-2007)前流程,以下是1系列的流程叙述:原料油在液位和流量的串级控制下进入滤前原料油缓冲罐(V-1001)。
原料从V-1001底部出来由原料油增压泵(P1001-1/S)升压,经中段回流油/原料油换热器(E-1001-1)、常渣/原料油换热器(E-1002-1、E-1003-1/AB)分别与中段回流油和常渣换热,然后进入原料油过滤器(S-1001-1)以除去原料油中大于25μm的杂质。
过滤后的原料油进入滤后原料油缓冲罐(V-1002-1),原料油从V-1002-1底部出来后由加氢进料泵(P1002-1/S)升压,升压后的原料油在流量控制下进入反应系统。
原料油和经热高分气/混合氢换热器(E-1006-1/AB)预热后的混合氢混合,混合进料经反应流出物/反应进料换热器(E-1004-1)预热后进入反应进料加热炉(F-1001-1)加热至反应所需温度进入上流式加氢反应器(R-1001-1),R-1001-1的入口温度通过调节F-1001-1的燃料量和E-1004-1的出口温度控制,R-1002-1入口温度由反应器的入口温度通过调节反应器入口管线上注入的冷氢量和E-1005-1的出口温度控制,R-1002-1底部物流依次通过其它三台固定床反应器(R-1003-1、R-1004-1 、R-1005-1),各反应器的入口温度通过调节反应器入口管线上注入的冷氢量来控制。
从R-1005-1出来的反应产物经过E-1005-1、E-1004-1换热后进入热高压分离器(V-1003-1)进行气液分离, V-1003-1底部出来的热高分液在液位控制下减压后,进入热低压分离器(V-1004-1)进行气液分离,V-1003-1顶部出来的热高分气分别经热高分气/混合氢换热器(E-1006-1/AB)、热高分气蒸汽发生器(E-2001-1)换热后进入热高分气空冷器(EA-2001-1),冷却到50℃进入冷高压分离器(V-2002-1)进行气、油、水三相分离。
渣油加氢处理-催化裂化双向组合(RICP)技术

渣油加氢处理-催化裂化双向组合(RICP)技术中国石化石油化工科学硏究院开发的渣油加氢-催化裂化双向组合(RICP)技术是将催化裂化装置中回炼的重循环油(HCO)掺入渣油加氢原料中,作为渣油加氢原料的稀释油,和渣油一起加氢后作为催化裂化原料。
RICP技术对渣油加氢和催化裂化两套装置均有改善效果:对渣油加氢装置,高芳香性的HCO促进了渣油加氢反应;对催化裂化装置,因HCO加氢后再作为催化裂化原料,轻油收率可提高1~3百分点,焦炭收率下降。
本技术已获授权专利13件。
♦RICP技术将传统工艺中RFCC装置原本自身回炼的HCO改为输送到渣油加氢装置,和渣油一起加氢后再作为RFCC原料。
高芳香性的HCO掺入到渣油加氢原料中,促进了渣油加氢反应并抑制了渣油加氢催化剂结焦;加氢后的HCO再回催化裂化装置作为原料,提高了催化裂化处理量和轻油收率。
♦通过改变HCO抽出位置并增设精密过滤器除去HCO中催化剂颗粒,避免了HCO中催化剂颗粒对渣油加氢装置的影响。
♦装置改造费用低,工业上易实施。
氢气减压渣油固定床渣油加氢>350°C加氢渣油渣油催化裂化―干气―液化气―汽油―柴油HCO▲RICP技术工艺流程示意4气体»石脑油»柴油4油浆主要技术指标:♦渣油加氢装置进料中可掺入5%〜30%的HCO作为稀释油,相应可顶替同样比例的直馏蜡油。
♦RICP技术与常规渣油加氢-重油催化裂化组合工艺相比,催化裂化装置处理能力可提高4%〜5%,轻质油收率增加1〜3百分点,油浆产率下降1〜3百分点,焦炭产率降低0.1〜0.5百分点。
▲中国石化齐鲁分公司1.5Mt/a年渣油加氢和0.8Mt/a催化裂化装置与传统的渣油加氢-催化裂化单向组合技术(现有技术)相比,RICP技术的轻油收率高1〜3百分点,催化裂化处理量和掺渣量也有所提高,因此具有更高的经济和社会效益。
RICP技术于2006年5月在中国石化齐鲁分公司1.5Mt/a渣油加氢装置和0.8Mt/a催化裂化装置进行了工业应用试验。
关于渣油加氢处理催化剂及工艺技术

关于渣油加氢处理催化剂及工艺技术关于渣油加氢处理催化剂及工艺技术一、渣油加氢处理技术概况当今世界,石油资源逐渐变劣、变重,使轻质油品收率下降,而世界经济的快速发展对轻质油品的需求却日益增长。
如何合理利用和深度加工劣质或重质原油,是炼油工业面临的一个迫切需要解决的难题。
在国内,原油资源满足不了我国国民经济快速发展的需要,进口中东原油以增加我国的能源供给势在必行。
中东原油加工的主要技术难点是高硫原油的合理利用,从当今炼油技术水平来看,渣油固定床加氢处理是合理利用含硫渣油的最为有效的手段之一二、渣油加氢处理过程的化学反应及催化剂1、渣油加氢处理过程的化学反应在重油加氢处理过程中,主要的化学反应有:加氢脱金属(HDM);加氢脱硫(HDS);加氢脱氮(HDN);加氢裂化(HC);不饱和键的加氢(如芳烃饱和-HDA)等。
针对这些反应,渣油加氢处理催化剂主要包括渣油加氢保护剂,脱金属催化剂,脱硫催化剂和脱氮催化剂四大类。
2、减压渣油加氢处理系列催化剂(FZC-XX系列)该系列催化剂自1986年开始研制以来,现已研究开发成功四大类共十六个牌号的催化剂。
研究开发过程中共申请国内外专利六十余项,有效地保护了我国自力更生开发的渣油固定床加氢处理技术(简称S-RHT技术)。
FZC-XX系列催化剂特点和作用类别第一代第二代特点作用保护剂FZC-10FZC-10Q大孔容(>1.0ml/g),大孔径(有400nm以上大孔)脱金属杂质及垢物,保护下游催化剂,防止床层压力降快速升高FZC-11FZC-11QFZC-12FZC-12QFZC-13FZC-13QFZC-14FZC-14QFZC-15FZC-10UFZC-16FZC-11UFZC-17FZC-18脱金属剂FZC-20FZC-23大孔容(≥0.7 ml/g),大孔径(有100nm以上大孔)最大限度地脱镍、钒FZC-21FZC-24FZC-22FZC-25FZC-26FZC-27脱硫剂FZC-30FZC-33较强的酸性,较小的孔径,较大的比表面积脱硫、部分脱氮FZC-31FZC-34FZC-32FZC-35FZC-36脱氮剂FZC-40FZC-41强酸性,小孔径,大比表面积,高金属含量高活性脱氮、转化3、常压渣油加氢处理系列催化剂(FZC-XXX系列)1995年我国开始针对进口高硫原油开展了常压渣油加氢处理系列催化剂的研究开发工作。
渣油加氢工艺流程

渣油加氢工艺流程
《渣油加氢工艺流程》
渣油加氢是一种重油加工工艺,用于将含硫、含氮和重金属的渣油转化为符合环保标准的产品。
渣油加氢工艺流程主要包括加氢裂化、脱硫、脱氮和脱金属等步骤。
首先,渣油被送入加氢裂化装置,通过高温和高压下,使渣油中的大分子链烃裂解成小分子链烃,提高了产品的燃烧性能和稳定性。
然后,经过加氢裂化后的产品进入脱硫装置,通过催化剂的作用,将其中的硫化合物转化为硫化氢,并且去除掉。
接着,产品进入脱氮装置,通过脱氮剂的作用,将其中的氮化合物去除。
最后,产品进入脱金属装置,通过催化剂的作用,将其中的重金属去除,提高了产品的质量。
整个渣油加氢工艺流程,不仅可以得到高质量的产品,而且还能大幅减少渣油中的有害物质对环境的影响。
因此,渣油加氢工艺已经成为炼油厂的重要工艺之一,对于改善大气环墮境质量起到了积极的作用。
渣油加氢
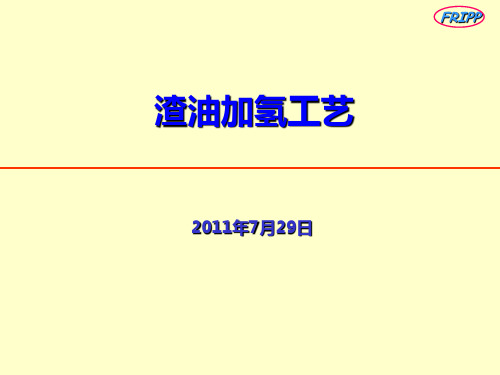
FRIPP
渣油加氢设计
FRIPP
渣油加氢工艺控制
• 一反入口氢分压 • 催化剂体积空速 • 反应器入口氢油体积比 • 循环氢纯度 • 反应温度 • 总压降
≮16.0MPa 0.18h-1 ≮600:1
≮85v% 380℃
1.58/2.88
渣油加氢设计
渣油加氢物料平衡
项目
收率
入方
原料油
100
化学耗氢
FRIPP
渣油加氢设计
FRIPP
渣油加氢催化剂
• 渣油加氢处理催化剂共四大类9个牌号, 其中保护剂4个牌号(FZC-11A, FZC-12A, FZC-13A,FZC-103E)共计61.01t;脱金 属催化剂2个牌号(FZC-28A, FZC-204) 共 计242.143t,脱硫催化剂2个牌号(FZC-33 【改进型】,FZC-34【改进型】) 共计 178.31t,脱氮残炭转化催化剂1个牌号 (FZC-41A) 共计234.425t (Mo-Ni)
渣油加氢催化剂
FRIPP
颗粒尺寸 孔径
大
大
活性 低
小
小
高
渣油加氢
FRIPP
渣油加氢处理装置长周期运转关键:
• 提高催化剂的脱金属和容金属等杂质能力,即 催化剂体系要提供足够的容杂质的空间;
• 使沥青质等大分子物质进入催化剂孔道内部进 行反应。
渣油加氢
FRIPP
• 渣油加氢脱硫催化剂:
– 提高催化剂的容金属能力 – 进一步提高脱硫性能和脱金属及脱残炭性能 – 提高催化剂的孔径和孔容
FRIPP
渣油加氢工艺
2011年7月29日
目录
• 渣油加氢催化剂 • 渣油加氢工艺流程简介 • 渣油加氢设计数据 • 开停工 • 首次开车 • 相互配合内容 • 建设期安装
固定床渣油加氢催化剂失活的原因分析及对策

固定床渣油加氢催化剂失活的原因分析及对策曾松【摘要】固定床渣油加氢技术是重油改质的重要手段,是优化重油催化裂化装置原料的主要措施,而固定床渣油加氢装置催化剂的价格昂贵、使用周期短且不具再生使用性,因此探讨固定床渣油加氢催化剂失活的原因并采取相应的对策,对延长催化剂的使用周期有积极的意义.通过对固定床渣油加氢装置催化剂末期运行的现象、废旧催化剂化学组成等方面的分析,发现导致固定床渣油加氢装置催化剂失活的主要原因是积炭和金属沉积.同时分析催化剂级配装填的比例、催化剂硫化、原料油的性质和反应温度的分布等因素对固定床渣油加氢催化剂失活的影响,提出了采用抗积炭和容垢能力高的催化剂,进行合理的催化剂级配装填,控制好原料的性质,调整各床层反应温度的匹配分布和控制好催化剂开工条件等措施,可有效延长催化剂的使用寿命.%Fixed-bed residue hydrogenation is an important process to upgrade heavy oil and a major measure to optimize feedstock of heavy oil fluidized catalytic cracking units. However, the catalysts for the said process are expensive in addition to the short service life as well as the non-regenerative nature, which makes it worthy to study the causes of fixed-bed residue hydrogenation catalyst deactivation and to take corresponding countermeasures to extend the catalysts life. The analysis of EOR performances of fixed-bed residue hydrotreating catalysts and chemical compositions of spent catalysts has found out that the main causes of cata lyst deactivation are carbon and metal depositions. The impacts of proportion of catalyst graded loading, cata lyst pre-sulfiding, feedstock properties and distribution of reaction temperatures on catalystdeactivation are studied. The use of coke-deposition-resistant catalystswith good deposition capacity, appropriate graded load ing of catalysts, good control of feedstocks, good adjustment of bed temperature distribution and good control of catalyst start-up conditions are recommended to extend the service life of catalysts.【期刊名称】《炼油技术与工程》【年(卷),期】2011(041)009【总页数】5页(P39-43)【关键词】渣油加氢;催化剂;失活;级配;硫化【作者】曾松【作者单位】中国石油化工股份有限公司茂名分公司,广东省茂名市525011【正文语种】中文随着原油日益重质化、劣质化和轻油需求量的不断增加,提高原油加工深度已是企业提高经济效益的必由之路。
渣油加氢技术工艺原理

渣油加氢技术工艺原理由于石油资源有限、原油变重变劣、中间馏分油的需求量增加及环保法规越来越严格等因素,渣油轻质化技术不断发展,通过渣油加氢处理后的渣油,送到催化裂化装置处理,生产出大量的合格轻质油。
减压渣油是原油经过加工后密度最大、杂质组分含量最高的油品,含有相当多的金属、硫、氮、及残炭等物质,杂质金属、氮会使下游装置催化剂失去活性,严重影响下游装置的生产周期;硫化物会腐蚀生产装置的设备及管线;残炭在下游装置催化裂化装置深加工过程中,极不稳定,很容易结焦,影响催化裂化装置的长周期运行;在装置原料中掺入减压重蜡油与焦化蜡油,有效降低渣油进料的粘度与杂质含量,利于催化加氢反应的进行,利于装置的操作与长周期运行。
本装置采用固定床加氢工艺,在适当的温度、压力、氢油比和空速条件下,原料油和氢气在催化剂的作用下进行反应,使油品中的杂质,即硫、氮、氧化物转化成为相应的易于除去的H2S、NH3和H2O而脱除,重金属杂质与H2S反应生成金属硫化物沉积在催化剂上,稠环芳烃及一部分不饱和烃得到加氢饱和,为下游装置生产出合格的原料油,同时副产出部分柴油及石脑油。
在渣油加氢处理过程中,所发生的化学反应很多,也非常复杂,但主要有以下几种反应发生:1)加氢脱硫反应2)加氢脱金属反应3)加氢脱氮反应4)加氢脱残碳反应5)加氢脱氧反应6)芳烃饱和反应7)烯烃饱和反应8)加氢裂化反应9)缩合生焦反应2.1加氢脱硫反应(HDS)渣油加氢脱硫反应是渣油加氢处理过程中所发生的最主要的化学反应,在催化剂和氢气的作用下,通过加氢脱硫反应,各种含硫化合物转化为不含硫的烃类和H 2S 。
烃类留在产品中,而H 2S 从反应物中脱除。
原油中大部分的硫存在于渣油中,渣油中的硫主要分布在芳烃、胶质和沥青质中,其中绝大部分的硫以噻吩和噻吩衍生物的形式存在。
通过氢解反应将这种大分子的C -S 键断开,使S 转化为H 2S 。
以噻吩和苯并噻吩为例,加氢脱硫反应式为:存在于非沥青质中的硫,在加氢条件下较容易脱除,可达到较高的转化深度,但存在于沥青质中的硫,由于沥青质的大分子结构,则很难脱除,因此,渣油加氢脱硫过程的脱硫率是有一定限度的。
加氢催化剂硫化阶段的操作原则

加氢催化剂硫化阶段的操作原则
1.硫化期间,严格执行操作规程中的不得、严禁、必须等字样的内
容;严格执行开工方案及工艺指标;
2.硫化前必须确认高压系统氧含量≤0.1%(体积);
3.硫化期间,高分压力必须≤12.5MPa,为10.5~12.5 MPa;
4.硫化期间,高分气H2纯度≥75%(V),为75~97%(V);
5.硫化期间,高压系统静压降速度≤0.1 MPa / h.
6.硫化期间,只能通过调行程调节注硫量,严禁使用高压注硫泵的
出口阀调节注硫量;
7.硫化启动后注硫量的调整幅度,任何时刻不能单次大幅度,而只
能多次、小幅调整;
8.硫化期间,任一催化剂床层总温升必须控制在≤25℃;
9.硫化期间,R15301第一冷氢阀阀前后压差大于0.4 MPa;R15311
第一冷氢阀前后压差大于0.4 MPa;
10.、硫化期间,“F15301出口温度─R15301第一床层顶温差≤5℃”;
F15311出口温度─R15311第一床层顶温差≤5℃。
12.硫化启动时条件:反应器入口温度175~190℃,反应器入口H2S
含量为3000ppm(V),预期温升≤25℃。
硫化开始后按照硫化方案执行。
渣油加氢催化剂全蜡油硫化
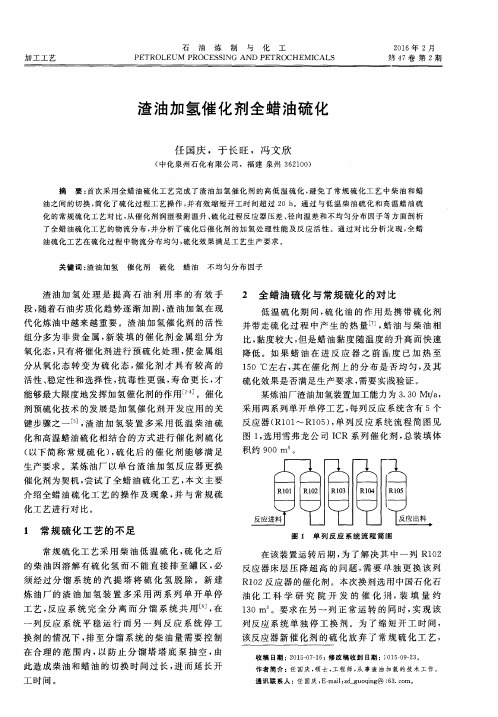
2 全 蜡 油 硫 化 与 常规 硫 化 的对 J:匕
低 温 硫 化 期 间 ,硫 化 油 的作 用 是 携 带硫 化 剂 并带 走硫 化 过 程 中 产 生 的热 量 I7],蜡 油 与柴 油 相 比 ,黏度较 大 ,但是 蜡 油黏 度 随温 度 的 升高 而 快 速 降低 。如 果 蜡 油 在 进 反 应 器 之 前 温 度 已 加 热 至 150。C左 右 ,其 在 催 化 剂 上 的 分 布是 否均 匀 ,及 其 硫化 效果 是否 满足 生产要 求 ,需 要 实践验 证 。
1 常规 硫 化 工 艺 的不 足
常 规硫 化 工 艺 采 用 柴 油 低 温 硫 化 ,硫 化 之 后 的 柴油 因溶 解有 硫 化 氢 而 不 能 直 接 排 至 罐 区 ,必 须经 过 分 馏 系 统 的 汽 提 塔 将 硫 化 氢 脱 除 。新 建 炼 油厂 的渣 油 加 氢 装 置 多 采 用 两 系 列 单 开 单 停 工艺 ,反 应 系 统 完 全 分 离 而 分 馏 系 统 共 用 [6],在 一 列 反 应 系 统 平 稳 运 行 而 另 一 列 反 应 系 统 停 工 换 剂 的情 况下 ,排 至 分 馏 系 统 的柴 油 量 需 要 控 制 在合 理 的 范 围 内 ,以 防止 分 馏 塔 塔 底 泵 抽 空 ,由 此造 成 柴 油 和蜡 油 的切 换 时 间过 长 ,进 而 延 长 开 工 时 间 。
关于减压渣油掺减压蜡油加氢处理(DVHT)技术的应用分析

关于减压渣油掺减压蜡油加氢处理(DVHT)技术的应用分析【摘要】减压渣油掺减压蜡油加氢处理(DVHT)技术是一种在炼油行业中被广泛应用的技术。
本文首先介绍了该技术的工艺原理,通过掺入减压蜡油实现渣油加氢处理,进一步提高产品质量。
接着分析了该技术的优势,包括提高产品收率、降低能耗等方面。
通过实际应用案例分析和效果评价,进一步验证了该技术在炼油行业中的价值和效果。
展望了DVHT技术在未来的应用前景,指出其具有广阔的发展空间和潜力。
综合分析了DVHT技术的应用前景,总结了该技术的优势和展望,为炼油行业的发展提供了有益的参考。
【关键词】减压渣油、减压蜡油、加氢处理、DVHT技术、工艺原理、实际应用、效果评价、应用前景、炼油行业、优势、案例分析、总结展望、应用分析。
1. 引言1.1 研究背景石油加工工业是我国能源工业的重要组成部分,而炼油工艺中一直存在着减压渣油的处理难题。
减压渣油是炼油过程中产生的一种重质残留油,含有大量的蜡质和沥青质,其中蜡质含量高达10%以上。
传统的炼油工艺中,减压渣油往往会造成设备堵塞、能耗高、产品质量低等问题,给生产带来不小的困扰。
为了提高减压渣油的加工利用率,降低生产成本,炼油行业开始研究掺减压蜡油加氢处理(DVHT)技术。
这项技术通过将减压渣油与减压蜡油进行掺合,再进行加氢处理,可以有效降低蜡质和沥青质的含量,提高产品的质量,增加产品的附加值。
本文旨在深入探讨DVHT技术在炼油工业中的应用情况,分析其工艺原理、优势、应用案例以及效果评价,同时展望该技术在未来的应用前景。
通过研究和实践,不断推动我国炼油工业的转型升级,提高生产效率,降低成本,推动能源工业的可持续发展。
1.2 研究目的研究目的是对减压渣油掺减压蜡油加氢处理(DVHT)技术的应用进行深入分析,探讨其在炼油行业中的实际效果和应用前景。
通过研究,我们希望能够全面了解该技术的工艺原理和优势,分析其在实际生产中的应用案例,评价掺减压蜡油加氢处理的效果,并对DVHT技术在未来的应用前景进行展望和总结。
渣油加氢装置催化剂全蜡油硫化技术应用总结

渣油加氢装置催化剂全蜡油硫化技术应用总结
杨勤
【期刊名称】《炼油技术与工程》
【年(卷),期】2024(54)3
【摘要】分析了固定床渣油加氢装置开工全部使用蜡油硫化方案的可行性。
某公司首次采用全蜡油硫化对新鲜催化剂进行预硫化,全蜡油硫化可节省装置开工时间16 h,减少装置开工柴油使用量,减少产生不合格蜡油720 t,在低温硫化阶段蜡油硫化的上硫率更高,硫化更均匀。
对比分析了全蜡油硫化与分阶段硫化的催化剂性能,在工艺条件、原料性质基本相同的条件下,两种不同方式硫化后的催化剂杂质脱除率同样高,活性相当。
使用全蜡油硫化的催化剂运行周期相对较长,说明全蜡油硫化催化剂的稳定性较高。
全蜡油硫化具有操作简单、节约资源、还原活性好等优点,对于其他同类装置具有借鉴意义,为今后同类装置开工优化预硫化操作提供了宝贵经验。
【总页数】6页(P14-19)
【作者】杨勤
【作者单位】中石化湖南石油化工有限公司
【正文语种】中文
【中图分类】TE624.9
【相关文献】
1.渣油加氢催化剂全蜡油硫化
2.渣油加氢技术的研究Ⅰ.RHT固定床渣油加氢催化剂的开发及应用
3.蜡油加氢装置停工催化剂卸剂步骤总结
4.渣油加氢蜡油加氢装置原料直供料节能改造技术方案
5.上海石化3.9Mt/a渣油加氢装置采用全蜡油硫化方案
因版权原因,仅展示原文概要,查看原文内容请购买。
渣油加氢催化剂全蜡油硫化技术与应用
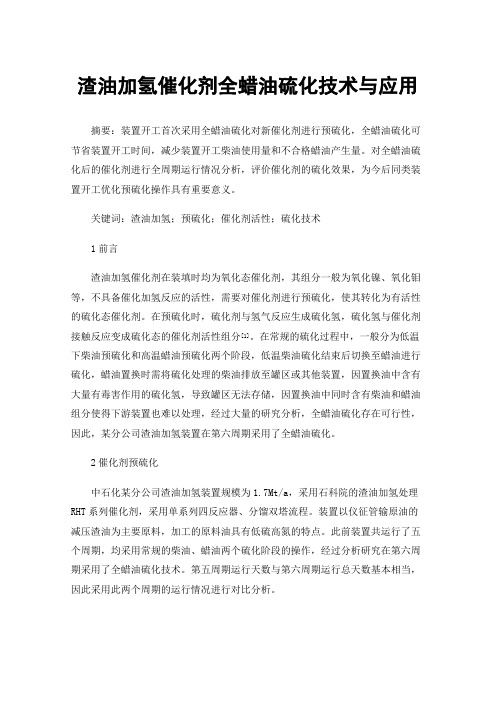
渣油加氢催化剂全蜡油硫化技术与应用摘要:装置开工首次采用全蜡油硫化对新催化剂进行预硫化,全蜡油硫化可节省装置开工时间,减少装置开工柴油使用量和不合格蜡油产生量。
对全蜡油硫化后的催化剂进行全周期运行情况分析,评价催化剂的硫化效果,为今后同类装置开工优化预硫化操作具有重要意义。
关键词:渣油加氢;预硫化;催化剂活性;硫化技术1前言渣油加氢催化剂在装填时均为氧化态催化剂,其组分一般为氧化镍、氧化钼等,不具备催化加氢反应的活性,需要对催化剂进行预硫化,使其转化为有活性的硫化态催化剂。
在预硫化时,硫化剂与氢气反应生成硫化氢,硫化氢与催化剂接触反应变成硫化态的催化剂活性组分[1]。
在常规的硫化过程中,一般分为低温下柴油预硫化和高温蜡油预硫化两个阶段,低温柴油硫化结束后切换至蜡油进行硫化,蜡油置换时需将硫化处理的柴油排放至罐区或其他装置,因置换油中含有大量有毒害作用的硫化氢,导致罐区无法存储,因置换油中同时含有柴油和蜡油组分使得下游装置也难以处理,经过大量的研究分析,全蜡油硫化存在可行性,因此,某分公司渣油加氢装置在第六周期采用了全蜡油硫化。
2催化剂预硫化中石化某分公司渣油加氢装置规模为1.7Mt/a,采用石科院的渣油加氢处理RHT系列催化剂,采用单系列四反应器、分馏双塔流程。
装置以仪征管输原油的减压渣油为主要原料,加工的原料油具有低硫高氮的特点。
此前装置共运行了五个周期,均采用常规的柴油、蜡油两个硫化阶段的操作,经过分析研究在第六周期采用了全蜡油硫化技术。
第五周期运行天数与第六周期运行总天数基本相当,因此采用此两个周期的运行情况进行对比分析。
第六周期于2019年4月17日开进料泵进行催化剂预硫化,第五周期于2017年5月30日开进料泵进行催化剂预硫化,采用柴油与蜡油硫化的方式,在硫化过程中,蜡油置换柴油理论上只需要4小时,但实际上因置换油含硫化氢只能由下游装置接收处理,置换油中同时含有柴油和蜡油组分,导致下游的催化裂化装置的处理能力有限,大幅降低了置换速率,置换时间大幅延长,而全蜡油硫化没有油品置换步骤,因此实际上全蜡油硫化可节约16小时。
渣油悬浮床加氢水溶性催化剂预硫化研究 Ⅱ 钼酸盐硫化产物的XPS分析

!1 #! $ ! #! %$! ’ #! & & & $O ( ’ !! $ 1 #1 #1 %$1 #1 据光电效应理论有
(!)
对于 % $ , 根 在本研究所用的仪器中有 ’ S 1# $ , % $ & )"*%+, (") 2 2 )" 即 光 子 能 量, 在本研究所用仪器中是 1 !$E %&, %+ 即作为 ./0 谱图横坐标的结合能。由 式可知, !!,# - %& 发射峰所对应的 %$ 为 1 -!$ %&, !"!# $ %& 发射峰所对应的 % $ 为 1-!1# $ %&, 代入式 (!) 后得相对比例系数 $ O S 1# --$ 。 上述各式中 # 为某一化学环境下的某元素的 绝对量, 本研究只需求取其相对质量分数即可。四 价钼相对质量分数为 , ’( )& & ! ’( )& # ’( )& 1 & , (E) # ’( )& - # ’( &) $O ! ’( )& - ! ’( &)
2 2 由此可以求得在上述三种情况下硫化产物表 面 上四价钼在全部钼元素中所占的比例分别为
关于减压渣油掺减压蜡油加氢处理(DVHT)技术的应用分析
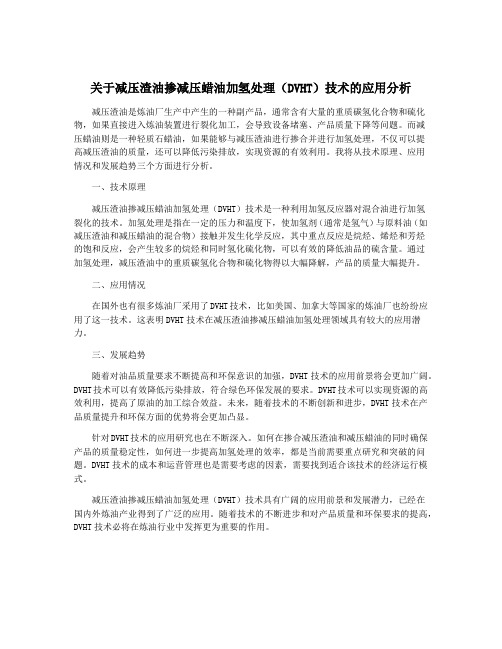
关于减压渣油掺减压蜡油加氢处理(DVHT)技术的应用分析减压渣油是炼油厂生产中产生的一种副产品,通常含有大量的重质碳氢化合物和硫化物,如果直接进入炼油装置进行裂化加工,会导致设备堵塞、产品质量下降等问题。
而减压蜡油则是一种轻质石蜡油,如果能够与减压渣油进行掺合并进行加氢处理,不仅可以提高减压渣油的质量,还可以降低污染排放,实现资源的有效利用。
我将从技术原理、应用情况和发展趋势三个方面进行分析。
一、技术原理减压渣油掺减压蜡油加氢处理(DVHT)技术是一种利用加氢反应器对混合油进行加氢裂化的技术。
加氢处理是指在一定的压力和温度下,使加氢剂(通常是氢气)与原料油(如减压渣油和减压蜡油的混合物)接触并发生化学反应,其中重点反应是烷烃、烯烃和芳烃的饱和反应,会产生较多的烷烃和同时氢化硫化物,可以有效的降低油品的硫含量。
通过加氢处理,减压渣油中的重质碳氢化合物和硫化物得以大幅降解,产品的质量大幅提升。
二、应用情况在国外也有很多炼油厂采用了DVHT技术,比如美国、加拿大等国家的炼油厂也纷纷应用了这一技术。
这表明DVHT技术在减压渣油掺减压蜡油加氢处理领域具有较大的应用潜力。
三、发展趋势随着对油品质量要求不断提高和环保意识的加强,DVHT技术的应用前景将会更加广阔。
DVHT技术可以有效降低污染排放,符合绿色环保发展的要求。
DVHT技术可以实现资源的高效利用,提高了原油的加工综合效益。
未来,随着技术的不断创新和进步,DVHT技术在产品质量提升和环保方面的优势将会更加凸显。
针对DVHT技术的应用研究也在不断深入。
如何在掺合减压渣油和减压蜡油的同时确保产品的质量稳定性,如何进一步提高加氢处理的效率,都是当前需要重点研究和突破的问题。
DVHT技术的成本和运营管理也是需要考虑的因素,需要找到适合该技术的经济运行模式。
减压渣油掺减压蜡油加氢处理(DVHT)技术具有广阔的应用前景和发展潜力,已经在国内外炼油产业得到了广泛的应用。
- 1、下载文档前请自行甄别文档内容的完整性,平台不提供额外的编辑、内容补充、找答案等附加服务。
- 2、"仅部分预览"的文档,不可在线预览部分如存在完整性等问题,可反馈申请退款(可完整预览的文档不适用该条件!)。
- 3、如文档侵犯您的权益,请联系客服反馈,我们会尽快为您处理(人工客服工作时间:9:00-18:30)。
渣油加氢催化剂全蜡油硫化
作者:王静
来源:《中国科技博览》2017年第12期
[摘要]本文开创性地使用了全蜡油硫化的工艺对渣油的加氢催化剂分别进行高低温的催化反应,从而使得在常规的硫化工艺过程中的柴油与蜡油的转换得以避免,同时也将工艺时间缩短了20小时。
此外,本文还通过对照低温环境下柴油的硫化过程和高温条件下蜡油的硫化过程,对其硫化工艺工程中的反应容器的直径方向的温差、催化剂润湿过程中的吸附温升以及反应器的不均匀分布因子进行分析。
通过研究得出,全蜡油硫化的工艺可以使物流在硫化过程中在空间均匀分布,从而达到相关工艺标准。
[关键词]全蜡油硫化、径向温差、不均匀分布因子、反应器压差、催化剂润湿吸附温升
中图分类号:TM173 文献标识码:A 文章编号:1009-914X(2017)12-0068-01
0 引言
随着全球石油能源开采利用的效率逐渐达到上限,在现代化的炼油企业中也不得不对炼油过程中的劣质石油进行处理,而渣油加氢无疑是一种较好的提升石油利用效率的方法。
在渣油加氢处理过程中使用的催化剂,其主要的活性组分是非贵金属,刚装填进去的催化剂中,其活性组分主要以氧化态金属的形式存在。
要让催化剂在工艺过程中保持良好的活性以及稳定性,提高其抗毒性和寿命,就需要将催化剂中金属由氧化态转化为硫化态,这样才能使加氢催化剂的效能最大化。
在加氢催化剂的开发过程中,对催化剂进行预硫化处理是最重要的瓶颈。
在常规的硫化过程中,一般是将低温下柴油的硫化处理和高温下的蜡油硫化处理组合在一起进行。
本文旨在将常规的硫化处理与全蜡油硫化处理工艺进行比较,分析讨论全蜡油硫化处理加氢催化剂的优势。
一、常规的硫化处理工艺的缺点
在常规的硫化处理过程中,一般是使用柴油去进行低温的硫化处理,但是经过硫化处理的柴油不能直接排放到罐区,因为柴油里面含有硫化氢等有害物质。
因此,需要对常规的硫化工艺进行脱氢处理。
在新建的炼油厂,一般会选择两系列单开单停的渣油加氢设备,两列反应系统是分开的,而其两列的分馏系统是共用的。
当其中一列反应系统正常工作,但是另一列反应系统需要停机换剂时,需要对蒸馏系统里面的柴油的用量进行调整,从而预防分馏系统塔底的泵被抽空,进一步导致柴油和蜡油的切换时间太长而使工艺时间延长。
二、比较常规硫化工艺与全蜡油硫化工艺
1.硫化过程的工艺、硫化时间对比
在低温硫化反应过程中,需要在硫化油中添加硫化剂并且将硫化过程产生的热量带走[1]。
一般情况下,蜡油与柴油相比,其黏度更大,但是在升温过程中,蜡油的黏度会随着温度的升高而迅速降低,因此采用全蜡油硫化工艺的效果如何需要通过实验进行验证。
本文在渣油加氢装置中将采取常规硫化工艺得到的数据与采用全蜡油工艺得到的数据进行比较和分析。
在二者的比较分析过程中,无论是采用哪一种工艺,其硫化过程的反应步骤都是差不多的。
通过实验对比可以得出:全蜡油硫化过程的进油量大约是120t/h,低于常规硫化过程的150t/h;同时全蜡油硫化的低温硫化时间和高温硫化时间分别为4h和2h,而常规硫化工艺的时间分别为8h和2h。
通过比较可得知:在排除反应过程中催化剂及硫化层穿透的因素对硫化过程的影响以后,全蜡油硫化过程大约可以节省20h的反应时间。
2.硫化过程中的各种影响因素
在硫化过程中,硫化油对硫化工艺的影响是很大的。
蜡油的黏度在常温下比柴油大,可是蜡油的黏度对温度十分敏感,因此,如果硫化油中的催化剂在硫化早期没有均匀地分布的话,就会导致偏流的形成,从而影响硫化过程中催化剂的加氢能力以及催化剂的使用时长。
一般而言,我们可以采用反应器压差对黏度进行表征,可以用反应器在直径方向的温度差(径向温差)以及不均匀分布因子对流体的分布进行表征。
3.径向温差对反应器硫化过程的影响
在反应器的上部及下部的同一水平面分别放置4个对称的测温点,可将径向温差定义为剔除异常的温度测量之后,在同一个水平面上的最高温度和最低温度的差值。
通过实验可知,常规硫化和全蜡硫化过程中的径向温差都没有超过2℃,说明两种硫化过程中催化剂都是均匀分布在反应器内部空间的。
4.不均匀分布因子对硫化过程的影响
在硫化过程中,反应器的温度分布不是很均匀,这是由于在反应器中气相和液相的不均匀分布,同时液相和气相的流速过低以及以及硫化油的黏度过高等因素导致的。
不均匀分布因子的定义是指反应器中的床层顶部与底部的热电偶的温差的最大值和最小值之比[2]。
在硫化过程中,可以采用不均匀分布因子去判断反应器的温度分布是否均匀。
5.反应器压差对硫化过程的影响
通过实验可知,在低温硫化过程中,采用全蜡油硫化工艺的反应器的压差要比采用常规硫化工艺的反应器压差略高,大约是0.01MPa;而在高温硫化时,结果却刚好相反,二者的压差相差也不是很大,也小于0.1MPa。
因此可以知道;在两种硫化工艺中,硫化油的黏度对于反应器的压差影响不大。
6.催化剂的润湿吸附产生的温差对硫化过程的影响
在硫化过程中,催化剂由于润湿吸附作用,会放出部分热量,使反应器内的温度升高。
通过实验可知:在常规硫化过程中,催化剂润湿吸附导致的温升比较高,甚至最大温差达到45℃,同时存在温差的时间较长,可达50分钟;在全蜡油硫化过程中,催化剂润湿吸附产生的温升较小,最大温升仅有20℃,温差存在的时间只有15分钟左右。
通过比较可知,全蜡油硫化过程中的催化剂润湿吸附温升比常规硫化过程中的温升少,因此对催化剂的使用性能和使用寿命的保护更好。
三、结论
常规硫化过程相比,全蜡油硫化可节省约20h的反应时间。
两种硫化工艺工程中的径向温差、不均匀分布因子以及反应器压差的区别都不大。
全蜡油硫化过程中的催化剂润湿吸附温差比常规硫化工艺中的温差要小,持续时间也更短,更有利于保护催化剂。
参考文献
[1] 佚名.上海石化3.9Mt/a渣油加氢装置采用全蜡油硫化方案[J].石油炼制与化工,2016.12(11):0012-0012.
[2] 吕振辉,薛冬,彭绍忠,等.介孔氧化铝制备方法对其载体及催化剂性能的影响[J].石油化工,2017.2(1):17-26.。