毕业设计英语翻译
毕业设计中英文翻译【范本模板】
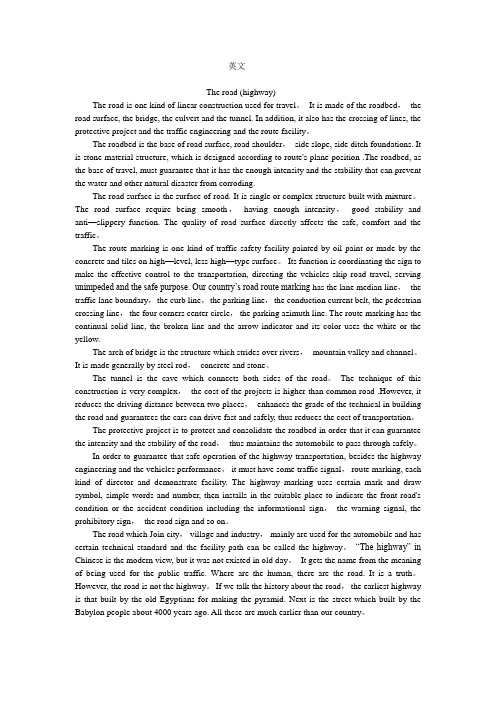
英文The road (highway)The road is one kind of linear construction used for travel。
It is made of the roadbed,the road surface, the bridge, the culvert and the tunnel. In addition, it also has the crossing of lines, the protective project and the traffic engineering and the route facility。
The roadbed is the base of road surface, road shoulder,side slope, side ditch foundations. It is stone material structure, which is designed according to route's plane position .The roadbed, as the base of travel, must guarantee that it has the enough intensity and the stability that can prevent the water and other natural disaster from corroding.The road surface is the surface of road. It is single or complex structure built with mixture。
The road surface require being smooth,having enough intensity,good stability and anti—slippery function. The quality of road surface directly affects the safe, comfort and the traffic。
毕业设计外文翻译译文

1 工程概论1.1 工程专业1.2 工业和技术1.3 现代制造业工程专业1 工程行业是历史上最古老的行业之一。
如果没有在广阔工程领域中应用的那些技术,我们现在的文明绝不会前进。
第一位把岩石凿削成箭和矛的工具匠是现代机械工程师的鼻祖。
那些发现地球上的金属并找到冶炼和使用金属的方法的工匠们是采矿和冶金工程师的先祖。
那些发明了灌溉系统并建造了远古世纪非凡的建筑物的技师是他们那个时代的土木工程师。
2 工程一般被定义为理论科学的实际应用,例如物理和数学。
许多早期的工程设计分支不是基于科学而是经验信息,这些经验信息取决于观察和经历,而不是理论知识。
这是一个倾斜面实际应用的例子,虽然这个概念没有被确切的理解,但是它可以被量化或者数字化的表达出来。
3 从16、17世纪当代初期,量化就已经成为科学知识大爆炸的首要原因之一。
另外一个重要因素是实验法验证理论的发展。
量化包含了把来源于实验的数据和信息转变成确切的数学术语。
这更加强调了数学是现代工程学的语言。
4 从19世纪开始,它的结果的实际而科学的应用已经逐步上升。
机械工程师现在有精确的能力去计算来源于许多不同机构之间错综复杂的相互作用的机械优势。
他拥有能一起工作的既新型又强硬的材料和巨大的新能源。
工业革命开始于使用水和蒸汽一起工作。
从此使用电、汽油和其他能源作动力的机器变得如此广泛以至于它们承担了世界上很大比例的工作。
5 科学知识迅速膨胀的结果之一就是科学和工程专业的数量的增加。
到19世纪末不仅机械、土木、矿业、冶金工程被建立而且更新的化学和电气工程专业出现了。
这种膨胀现象一直持续到现在。
我们现在拥有了核能、石油、航天航空空间以及电气工程等。
每种工程领域之内都有细分。
6 例如,土木工程自身领域之内有如下细分:涉及永久性结构的建筑工程、涉及水或其他液体流动与控制系统的水利工程、涉及供水、净化、排水系统的研究的环境工程。
机械工程主要的细分是工业工程,它涉及的是错综复杂的机械系统,这些系统是工业上的,而非单独的机器。
毕业设计论文外文文献翻译
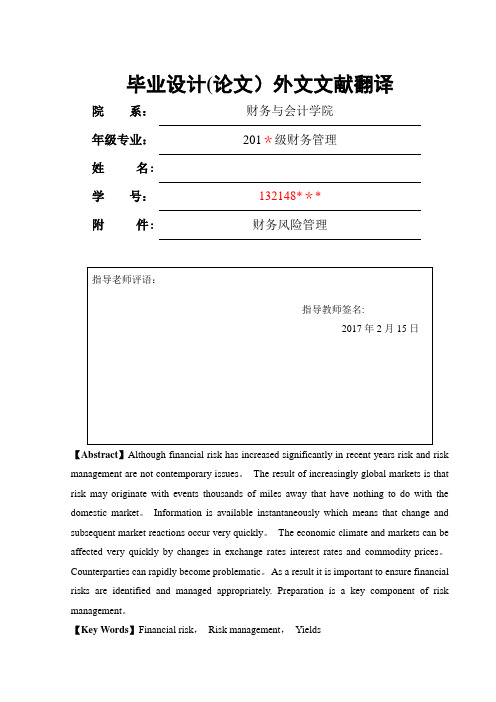
毕业设计(论文)外文文献翻译院系:财务与会计学院年级专业:201*级财务管理姓名:学号:132148***附件: 财务风险管理【Abstract】Although financial risk has increased significantly in recent years risk and risk management are not contemporary issues。
The result of increasingly global markets is that risk may originate with events thousands of miles away that have nothing to do with the domestic market。
Information is available instantaneously which means that change and subsequent market reactions occur very quickly。
The economic climate and markets can be affected very quickly by changes in exchange rates interest rates and commodity prices。
Counterparties can rapidly become problematic。
As a result it is important to ensure financial risks are identified and managed appropriately. Preparation is a key component of risk management。
【Key Words】Financial risk,Risk management,YieldsI. Financial risks arising1.1What Is Risk1.1.1The concept of riskRisk provides the basis for opportunity. The terms risk and exposure have subtle differences in their meaning. Risk refers to the probability of loss while exposure is the possibility of loss although they are often used interchangeably。
毕业设计中英文翻译
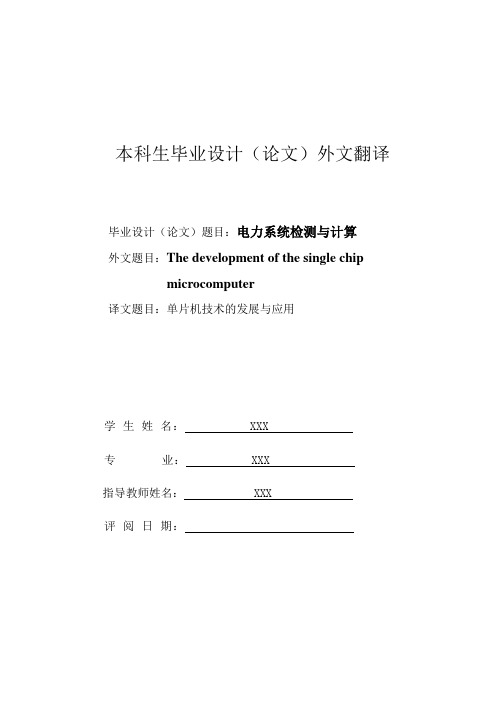
本科生毕业设计(论文)外文翻译毕业设计(论文)题目:电力系统检测与计算外文题目:The development of the single chipmicrocomputer译文题目:单片机技术的发展与应用学生姓名: XXX专业: XXX指导教师姓名: XXX评阅日期:单片机技术的发展与应用从无线电世界到单片机世界现代计算机技术的产业革命,将世界经济从资本经济带入到知识经济时代。
在电子世界领域,从 20 世纪中的无线电时代也进入到 21 世纪以计算机技术为中心的智能化现代电子系统时代。
现代电子系统的基本核心是嵌入式计算机系统(简称嵌入式系统),而单片机是最典型、最广泛、最普及的嵌入式系统。
一、无线电世界造就了几代英才。
在 20 世纪五六十年代,最具代表的先进的电子技术就是无线电技术,包括无线电广播,收音,无线通信(电报),业余无线电台,无线电定位,导航等遥测、遥控、遥信技术。
早期就是这些电子技术带领着许多青少年步入了奇妙的电子世界,无线电技术展示了当时科技生活美妙的前景。
电子科学开始形成了一门新兴学科。
无线电电子学,无线通信开始了电子世界的历程。
无线电技术不仅成为了当时先进科学技术的代表,而且从普及到专业的科学领域,吸引了广大青少年,并使他们从中找到了无穷的乐趣。
从床头的矿石收音机到超外差收音机;从无线电发报到业余无线电台;从电话,电铃到无线电操纵模型。
无线电技术成为当时青少年科普、科技教育最普及,最广泛的内容。
至今,许多老一辈的工程师、专家、教授当年都是无线电爱好者。
无线电技术的无穷乐趣,无线电技术的全面训练,从电子学基本原理,电子元器件基础到无线电遥控、遥测、遥信电子系统制作,培养出了几代科技英才。
二、从无线电时代到电子技术普及时代。
早期的无线电技术推动了电子技术的发展,其中最主要的是真空管电子技术向半导体电子技术的发展。
半导体电子技术使有源器件实现了微小型化和低成本,使无线电技术有了更大普及和创新,并大大地开阔了许多非无线电的控制领域。
毕业设计外文文献翻译范文
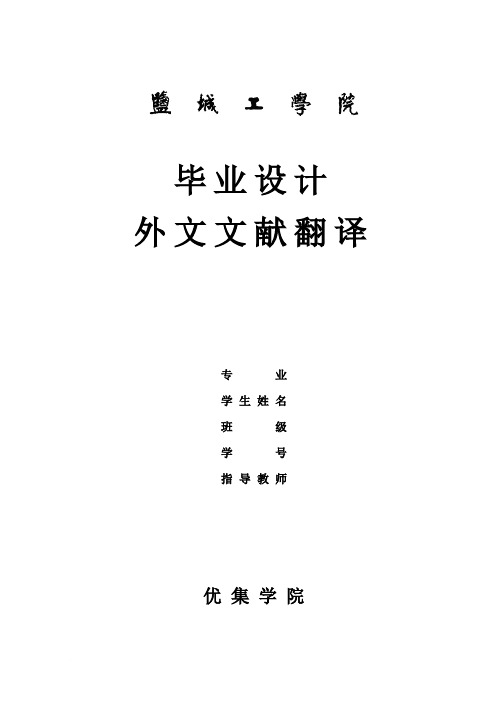
毕业设计外文文献翻译专业学生姓名班级学号指导教师优集学院外文资料名称:Knowledge-Based Engineeri--ng Design Methodology外文资料出处:Int.J.Engng Ed.Vol.16.No.1附件: 1.外文资料翻译译文2.外文原文基于知识工程(KBE)设计方法D. E. CALKINS1.背景复杂系统的发展需要很多工程和管理方面的知识、决策,它要满足很多竞争性的要求。
设计被认为是决定产品最终形态、成本、可靠性、市场接受程度的首要因素。
高级别的工程设计和分析过程(概念设计阶段)特别重要,因为大多数的生命周期成本和整体系统的质量都在这个阶段。
产品成本的压缩最可能发生在产品设计的最初阶段。
整个生命周期阶段大约百分之七十的成本花费在概念设计阶段结束时,缩短设计周期的关键是缩短概念设计阶段,这样同时也减少了工程的重新设计工作量。
工程权衡过程中采用良好的估计和非正式的启发进行概念设计。
传统CAD工具对概念设计阶段的支持非常有限。
有必要,进行涉及多个学科的交流合作来快速进行设计分析(包括性能,成本,可靠性等)。
最后,必须能够管理大量的特定领域的知识。
解决方案是在概念设计阶段包含进更过资源,通过消除重新设计来缩短整个产品的时间。
所有这些因素都主张采取综合设计工具和环境,以在早期的综合设计阶段提供帮助。
这种集成设计工具能够使由不同学科的工程师、设计者在面对复杂的需求和约束时能够对设计意图达成共识。
那个设计工具可以让设计团队研究在更高级别上的更多配置细节。
问题就是架构一个设计工具,以满足所有这些要求。
2.虚拟(数字)原型模型现在需要是一种代表产品设计为得到一将允许一产品的早发展和评价的真实事实上原型的过程的方式。
虚拟样机将取代传统的物理样机,并允许设计工程师,研究“假设”的情况,同时反复更新他们的设计。
真正的虚拟原型,不仅代表形状和形式,即几何形状,它也代表如重量,材料,性能和制造工艺的非几何属性。
本科毕业设计外文文献翻译
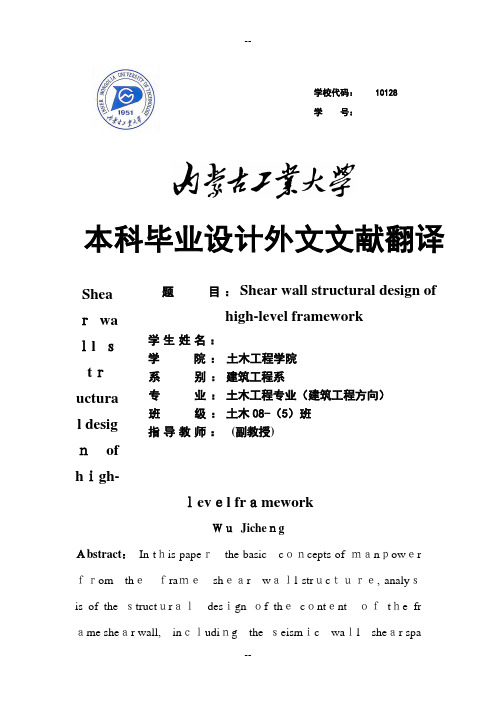
(Shear wall st ructural design ofh igh-lev el fr ameworkWu Jiche ngAbstract : In t his pape r the basic c oncepts of man pow er from th e fra me sh ear w all str uc ture, analy sis of the struct ur al des ign of th e c ont ent of t he fr ame she ar wall, in cludi ng the seism ic wa ll she ar spa本科毕业设计外文文献翻译学校代码: 10128学 号:题 目:Shear wall structural design of high-level framework 学生姓名: 学 院:土木工程学院 系 别:建筑工程系 专 业:土木工程专业(建筑工程方向) 班 级:土木08-(5)班 指导教师: (副教授)nratiodesign, and a concretestructure in themost co mmonly usedframe shear wallstructurethedesign of p oints to note.Keywords: concrete; frameshearwall structure;high-risebuildingsThe wall is amodern high-rise buildings is an impo rtant buildingcontent, the size of theframe shear wall must comply with building regulations. The principle is that the largersizebut the thicknessmust besmaller geometric featuresshouldbe presented to the plate,the force is close to cylindrical.The wall shear wa ll structure is a flatcomponent. Itsexposure to the force along the plane level of therole ofshear and moment, must also take intoaccountthe vertical pressure.Operate under thecombined action ofbending moments and axial force andshear forcebythe cantilever deep beam under the action of the force levelto loo kinto the bottom mounted on the basis of. Shearwall isdividedinto a whole walland theassociated shear wall in theactual project,a wholewallfor exampl e, such as generalhousingconstruction in the gableor fish bone structure filmwalls and small openingswall.Coupled Shear walls are connected bythecoupling beam shear wall.Butbecause thegeneralcoupling beamstiffness is less thanthe wall stiffnessof the limbs,so. Walllimb aloneis obvious.The central beam of theinflection pointtopay attentionto thewall pressure than the limits of the limb axis. Will forma shortwide beams,widecolumn wall limbshear wall openings toolarge component atbothen ds with just the domain of variable cross-section ro din the internalforcesunder theactionof many Walllimb inflection point Therefore, the calcula tions and construction shouldAccordingtoapproximate the framestructure to consider.The designof shear walls shouldbe based on the characteristics of avariety ofwall itself,and differentmechanical ch aracteristicsand requirements,wall oftheinternalforcedistribution and failuremodes of specific and comprehensive consideration of the design reinforcement and structural measures. Frame shear wall structure design is to consider the structure of the overall analysis for both directionsofthehorizontal and verticaleffects. Obtain theinternal force is required in accordancewiththe bias or partial pull normal section forcecalculation.The wall structure oftheframe shear wall structural design of the content frame high-rise buildings, in the actual projectintheuse of themost seismic walls have sufficient quantitiesto meet thelimitsof the layer displacement, the location isrelatively flexible. Seismic wall for continuous layout,full-length through.Should bedesigned to avoid the wall mutations in limb length and alignment is notupand down the hole. The sametime.The inside of the hole marginscolumnshould not belessthan300mm inordertoguaranteethelengthof the column as the edgeof the component and constraint edgecomponents.Thebi-direc tional lateral force resisting structural form of vertical andhorizontalwallconnected.Each other as the affinityof the shear wall. For one, two seismic frame she ar walls,even beam highratio should notgreaterthan 5 and a height of not less than400mm.Midline columnand beams,wall midline shouldnotbe greater tha nthe columnwidthof1/4,in order toreduce thetorsional effect of the seismicaction onthecolumn.Otherwisecan be taken tostrengthen thestirrupratio inthe column tomake up.If theshear wall shearspan thanthe big two. Eventhe beamcro ss-height ratiogreaterthan 2.5, then the design pressure of thecut shouldnotmakeabig 0.2. However, if the shearwallshear spanratioof less than two couplingbeams span of less than 2.5, then the shear compres sion ratiois notgreater than 0.15. Theother hand,the bottom ofthe frame shear wallstructure to enhance thedesign should notbe less than200mmand notlessthanstorey 1/16,otherpartsshouldnot be less than 160mm and not less thanstorey 1/20. Aroundthe wall of the frame shear wall structure shouldbe set to the beam or dark beamand the side columntoform a border. Horizontal distributionofshear walls can from the shear effect,this design when building higher longeror framestructure reinforcement should be appropriatelyincreased, especially in the sensitiveparts of the beam position or temperature, stiffnesschange is bestappropriately increased, thenconsideration shouldbe givento the wallverticalreinforcement,because it is mainly from the bending effect, andtake in some multi-storeyshearwall structurereinforcedreinforcement rate -likelessconstrained edgeofthecomponent or components reinforcement of theedge component.References: [1 sad Hayashi,He Yaming. On the shortshear wall high-rise buildingdesign [J].Keyuan, 2008, (O2).高层框架剪力墙结构设计吴继成摘要: 本文从框架剪力墙结构设计的基本概念人手, 分析了框架剪力墙的构造设计内容, 包括抗震墙、剪跨比等的设计, 并出混凝土结构中最常用的框架剪力墙结构设计的注意要点。
毕业设计用英语怎么说

毕业设计用英语怎么说毕业设计是教学过程的最后阶段采用的一种总结性的实践教学环节。
仅对大专以上学校要求在毕业前根据专业的不同进行毕业设计,对中等专业学校的学生不作要求。
那么你知道毕业设计用英语怎么说吗?下面店铺为大家带来毕业设计的英语说法,欢迎各位同学们学习!毕业设计的英语说法:graduation project毕业设计相关英语表达:毕业设计大赛 Graduation Design Competition毕业设计作品 Graduation Design Works毕业设计指导 graduation-project guidance毕业设计论文质量 qualities of graduation design毕业设计模式 graduate design modes毕业设计的英语例句:1. This article introduced the customer system management system realization method.本文介绍了客户管理毕业设计的实现方法.2. Andworked at an insurance company my graduation field work.我在家保险公司进行我毕业设计.3. This project is my graduation design. a sub - item of my tutor's.此项目为本人的毕业设计. 是导师项目下的子项目.4. This graduation design is about project management's new critical chain method. "本毕业设计是对项目进度管理新技术关键链法的研究.5. This graduation project's topic is on - line auto sale management system management system.本次毕业设计的题目就是网上汽车销售管理系统.6. The traveling website construction is faces the realistic demand an utility system.旅游网站建设是面向现实需求的一个实用毕业设计.7. The whole design procedure consists of the architectural and the structural design.此次毕业设计包括两部分:建筑设计,结构设计.8. This graduation project's topic is on - line books management system management system.本次毕业设计的题目就是网络订餐系统.9. During a metalworking and machine tool plant internships, courses and graduate design.其间进行了金工及机床厂实习, 课程及毕业设计.10. This project belongs to reseachful new task, and is of a assignment.本毕业设计是一个属于研究型的新课题, 工程浩大.11. The study are the design of the logistics and transport systems.本毕业设计的研究内容是物流运输的系统.12. My graduation project is about the origin and regulation of stem cells.我的毕业设计是关于干细胞调节的起源的.13. After the graduation project and found a lot of accumulated several more.毕业设计做完了,发现好多,积累了好更.14. Ninety percent of my class is already working on the final project.我们班百分之九十的同学都已经开始做毕业设计了.15. This paper analyzes the Web - based e - commerce platform -- Automobile Sales Management System.本文研究分析了基于的电子商务的平台开发汽车销售管理毕业设计.。
关于毕业设计的英文翻译

Development of polymer-based sensors for integration into a wireless data acquisition system suitable for monitoring environmental and physiological processesBiomolecular Engineering Volume 23, Issue 5, October 2006, Pages 253-257AbstractIn this work, the pressure sensing properties of polyethylene (PE) and polyvinylidene fluoride (PVDF) polymer films were evaluated by integrating them with a wireless data acquisition system. Each device was connected to an integrated interface circuit, which includes a capacitance to frequency converter (C/F) and an internal voltage regulator to suppress supply voltage fluctuations on the transponder side. The system was tested under hydrostatic pressures ranging from 0 to 17 kPa. Results show PE to be the more sensitive to pressure changes, indicating that it is useful for the accurate measurement of pressure over a small range. On the other hand PVDF devices could be used for measurement over a wider range and should be considered due to the low hysteresis and good repeatability displayed during testing. It is thought that this arrangement could form the basis of a cost-effective wireless monitoring system for the evaluation of environmental or physiological processes.Keywords: Pressure; Thick film; Polymers; Sensor; Wireless1. IntroductionIn many professions and industries, the ability to make measurements in difficult to reach or dangerous environments without risking the health of an individual is now a necessity. A way of wirelessly transmitting data from the sensor, which is at the point of interest, to a remote receiver is required. Using this approach, sensors can be implanted in a difficult to reach or harsh environment and left there for a period of time. Sensors designed to measure any number of parameters including pressure, conductivity and pH could be used (Barrie, 1992, Astaras, 2002and Flick and Orglmeister, 2000). Data transfer is typically achieved using radio frequencies to send information to a receiver, which is remote from the area of interest.Apart from industrial and environmental applications, these acquisition systems could revolutionise the healthcare system in a number of areas. They could find applications in the treatment of patients which have experienced extreme traumas by monitoring critical parameters such as intra-cranial pressure (Flick and Orglmeister, 2000). However, in a more routine setting they could also be used to make long term measurements of biological fluid pressure for clinical studies in several areas, such as cardiology, pulmonology and gastroenterology (Yang et al., 2003). In the future, it may even be possible to monitor patients while they reside in their home or continue to work (Budinger, 2003).With these applications in mind, a wireless data acquisition system, including a capacitance to frequency converter (C/F) and an internal voltage regulator to provide a stable operation has been developed. The circuitry was developed to minimise power consumption, as power will not be randomly available in the test environment. The system was developed specifically for the measurement of pressure. Two capacitive structures were formed using polyethylene (PE) and polyvinylidene fluoride (PVDF) for the sensing layer. These materials were chosen for their biocompatibleand mechanical properties. Capacitive structures are preferred as they lead to lower power consumption and higher sensitivity than their piezoelectric counterparts (Puers, 1993).PVDF is a low-density semi-crystalline material, consisting of longrepeating chains of CF2CH2molecules. The crystalline regionconsists of a number of polymorphs, of which the α- and β-phase are most common. The β-phase is piezoelectric and has many advantages including its mechanical strength, wide dynamic range, flexibility and ease of fabrication (Payne and Chen, 1990). Poled PVDF films have been employed in the development of devices, which can be used in a wide range of applications, for example, providing robots with tactile sensors and the measurement of explosive forces (Payne et al., 1990and Bauer, 1999). In a medical context, poled PVDF films have been popular in the development of plantar pressure-measurement systems, where their flexibility and the ease with which electrode patterns can be attached has been a particular advantage (Lee and Sung, 1999). Micromachined devices using PVDF as a flexible element in the system have also been developed for use in an endoscopic grasper because of its high force sensitivity, large dynamic range and good linearity (Dargahi et al., 1998).Polyethylene is a cost effective and versatile semi-crystalline polymerconsisting of repeating CH2CH2units. The most common forms arelow-density polyethylene (LDPE) and high-density polyethylene (HDPE), where the density is related to the degree of chain branching. It is a material which is useful in pressure-sensing applications and has been popular for use in the development of flexible electronics (Harsanyi, 1995 and Domenech et al., 2005). PE is particularly popular in the fabrication of polymer/carbon-black composites for pressure measurement (Zheng et al., 1999 and Xu et al., 2005). Furthermore, polyethylene terephtalate (PET)has been identified as an electret material with possible dynamic pressure sensing applications (Paajanen et al., 2000).In this work, both PE and PVDF films were formed into a sandwich capacitor, which was then subjected to changing hydrostatic pressures. The films deformed under pressure and the resulting change in capacitance was transmitted wirelessly through the liquid to an external receiver, which converts the signal to a corresponding voltage.2. Experimental procedureThe sensing layers were in the form of films with thickness of approximately 100 μm. The PVDF film has a dominant β-phase and was purchased from Precision Acoustics Ltd. The LDPE film was supplied from Goodfellow Cambridge Ltd. The Young's modulus of each material is an indication of how likely the material is to deform under applied pressure and is quoted to be 8.3 GPa and 0.1–0.3 GPa for PVDF and PE, respectively. To form the capacitors, DuPont 4929 silver paste was deposited using a DEK RS 1202 automatic screen-printer to form electrodes measuring15 mm × 10 mm. The sensor structure is shown in Fig. 1. This approach was used as difficulties in depositing other electrode materials on PVDF have been recorded (Payne and Chen, 1990). After deposition, the electrodes were dried in air and cured at 100 °C for 30 min. The electrical properties of each device were measured, from 1 Hz to 1 MHz, using a Solatron S1 1260 Impedance Gain/Phase Analyser.Fig. 1. Structure of the PVDF and PE capacitor.To evaluate the performance of each material under pressure, capacitors were individually connected to the interface and transmitter circuit. The sensor was protected using a thin, flexible waterproof membrane. The circuit was contained in a weatherproof housing. This was a rigid structure of dimensions 54 × 59 mm2 and was necessary to protect the electronics from the liquid environment. To connect the sensor to the interface an opening was drilled into the housing and the connections were made waterproof.The change in capacitance with increasing depth in a liquid environment was then recorded.The pressure in this case ranged from 0 to 17 kPa. The change in capacitance was converted to a frequency, which was wirelessly transmitted to an external receiver. The transmitter and receiver are battery powered. A comparison of the power requirements, this circuit (marked with an asterisk) is compared to other standard interface circuits is shown in Table 1. A block diagram of the transmitter and receiver system can be seen in Fig. 2.Table 1.Power consumption for sensor interface circuitsThe main element of the sensor interface circuit is an integrated capacitance to frequency converter, which is used to link the sensoris the sensor capacitance,converted to voltage levels using phase locked loop (PLL) unit. This IC is a micro-power device since it typically draws 20 μA. The relationship between the frequency (f) and the voltage (V) has been measured to bef=V×13.1kHz/V (2)The value of 13.1 kHz/V was found by measuring the slope of the change in frequency with voltage for the voltage-controlled oscillator as shown in Fig. 3. It should be noted that while the PLL unit reduces power supply, it creates a non-linear output signal. Therefore the sensor response will appear to be non-linear.Fig. 3. Measured F/V characteristics of the VCO.Finally, a Lloyd Instruments LR50k was used to evaluate the sensitivity of the PVDF material over a wider pressure range. The LR50k is commonly used to place materials under tension or compression. In this work, it was used in compression mode, increasing the load on the capacitor over time. The change in sensor output was measured using a HP 4192 A LF Impedance Analyser at a frequency of 100 kHz. The capacitor was repeatedly tested in the range 0–560 kPa.3. Results and discussionWhen parallel plate capacitors, such as those formed in this study, are placed under pressure, the thickness of the sensing layer changes, resulting in an alteration of the distance, d, between the electrodes or plates. When the pressure is applied uniformly, there is a correspondingly uniform change in d, which leads to a change in the overall capacitance, according to Eq. (3)(3)where, C is the capacitance, r, is the relative permittivity of the , is the permittivity of free space and A is the area of dielectric,othe capacitor plates. The capacitance was found to be 40 pF and 140 pF for the PE and PVDF sensors, respectively. The relative permittivity was measured to be 3.45 for PE and 9.27 for PVDF at a frequency of 1 MHz. The capacitance of both materials showed a high stability over a wide range of frequencies, as shown in Fig. 4, making them well suited for integration into the wireless data acquisition system. Previous work on thick film capacitors using a PZT and PVDF dielectric layer have shown that device sensitivity is affected by operating frequency (Arshak et al., 2000). The differences are attributed to changes in dissipation factor. The PE sensor showed a stable response, however there is some variation the capacitance of the PVDF sensor at higher frequencies. Therefore, operating frequency could be used to optimize the sensor response.Fig. 4. Variation of capacitance with frequency for PE and PVDF devices.Fig. 5shows the response of the PE and PVDF sensors to pressure in the range 0–17 kPa. It was observed that PE shows a higher sensitivity to pressure changes than the PVDF film. The change in voltage is related to the capacitance change, which is a direct result of deformation of the dielectric layer under pressure. For the PE sensor, the voltage changes by 20 mV over the entire range. For the PVDF sensor the change is 5 mV. The relationship between capacitance and voltage is shown in Eqs. (1)and (2). Therefore, it can be seen from the results that PE sensors show the highest sensitivity, and are well suited to pressure measurement over the range tested. On the other hand PVDF devices may be more useful for measurements over larger ranges. For example, shock sensors based on PVDF are used to measure impact pressures up to 12 GPa (Bauer, 1999).Fig. 5. Change in voltage with pressure in the range 0–17 kPa for the PE and PVDF sensors.In order to investigate the behaviour of the PVDF over a large pressure range, it was tested using an LR50k and the results are shown in Fig. 6. It can be seen that the material showed a high sensitivity, particularly for pressures up to 100 kPa. It is thought that the dissimilarity in Young's modulus can explain their different behaviour under pressure. PVDF is a tougher, more resilient material that PE and so it requires higher pressures, to achieve a measurable change in capacitance. Alternatively, PE will deform more easily, resulting in larger changes in capacitance over a reduced pressure range.Fig. 6. Relative change in capacitance for PVDF sensors, tested using a Lloyd Instruments LR50k.The maximum difference between loading and unloading cycles was measured and expressed as a percentage of the full-scale deviation in order to calculate the hysteresis. Values ranging from 6 to 30% have previously been calculated for polymer thick film devices (Arshak et al., 1995 and Arshak et al., 2000). In this work, the hysteresis was calculated to be 5% and 6% for the PE and PVDF sensors, respectively, as shown in Fig.7. This corresponds well with the values quoted above.Fig. 7. Hysteresis of (a) the PE sensor and (b) the PVDF sensor as measured for one loading and unloading cycle.Each device was also subjected to repeated cycling, in order to establish its repeatability (the maximum difference between output readings as determined by two calibrating cycles). Five cycles are shown for PE in Fig. 8(a) and PVDF in Fig. 8 (b). The repeatability was calculated to be 10% and 6% for PE and PVDF, respectively. This can be attributed to movement of the polymer chains while they are under pressure (Arshak et al., 1995). The more rigid nature of the PVDF can explain the lower percentage repeatability, as it does not suffer the same degree of slippage.Fig. 8. Repeatability of (a) the PE sensor and (b) the PVDF sensor as measured for five loading cycles.From the results shown above, it can be seen that both PE and PVDF have shown a good sensitivity to pressure. The measured levels of hysteresis and repeatability are similar to that previously measured for polymer devices (Arshak et al., 1995and Arshak et al., 2000). PVDF is best suited to the measurement of pressure in the range 0–100 kPa. PE could also be used over this range, but it is expected that because of its lower Young's modulus, the sensor would experience a high level of hysteresis and slippage of the polymer chains during its operation. However, for medical purposes, it is not likely, that measurements over a pressure of 40 kPa will be required. In this respect, PE is more suited for the measurement of physiological processes.4. ConclusionIn this work, the pressure sensing properties of sandwich capacitors based on PE and PVDF were evaluated using a specially constructed data acquisition system. It was seen that each material displayed a high sensitivity to pressure changes in the range 0–17 kPa. It was found that the PE sensors were the most sensitive, but each device displayed low hysteresis and repeatability. It can be concluded that PE is the most sensitive to pressures over a small range, however PVDF could find applications in systems where pressures measurements over a large range are required. Further evidence for this was found by testing the PVDF samples using an LR50k where they showed a high sensitivity to pressures from 0 to 100 kPa.AcknowledgementsThis research was supported by the Enterprise Ireland Commercialization Fund 2003, under the technology development phase, as part of the MIAPS project, reference No. CFTD/03/425. Funding was also received from theIrish Research Council for Science, Engineering and Technology: funded by the National Development Plan.ReferencesArshak et al., 2000K.I. Arshak, D. McDonagh and M.A. Durcan, Development of new capacitive strain sensors based on thick film polymer and cermet technologies., Sens. Acutators A-Phys.79(2000), pp. 102–114. Article | PDF (662 K) | View Record in Scopus | Cited By in Scopus (27) Arshak et al., 1995K.I. Arshak, A.K. Ray, C.A. Hogarth, D.G. Collins and F. Ansari, An analysis of polymeric thick-film resistors as pressure sensors,Sens. Acutators A-Phys.49 (1995), pp. 41–45. Abstract | PDF (346 K) | View Record in Scopus | Cited By in Scopus (18)Astaras, 2002Astaras, A., Ahmadian, M., Aydin, N., Cui, L., Johannessen, E., Tang, T.-B., Wang, L., Arslan, T., Beaumont, S.P., Flynn, B.W., Murray, A.F., Reid, S.W., Yam, P., Cooper, J.M., Cumming, R.S., 2002. A miniature integrated electronics sensor capsule for real-time monitoring of the gastrointestinal tract (IDEAS). IEEE ICBME conference: The Bio-Era: New Challenges, New Frontiers, Singapore.Barrie, 1992 S.A. Barrie, A Textbook of Natural Medicine: Heidelberg pH Capsule Gastric Analysis, Churchill Livingstone, New York (1992). Bauer, 1999 Bauer, F., 1999. Advances in Piezoelectric PVDF Shock Compression Sensors. 10th International Symposium on Electrets, 1999, ISE 10, Delphi, Greece, 647–650.。
毕业设计英文怎么说
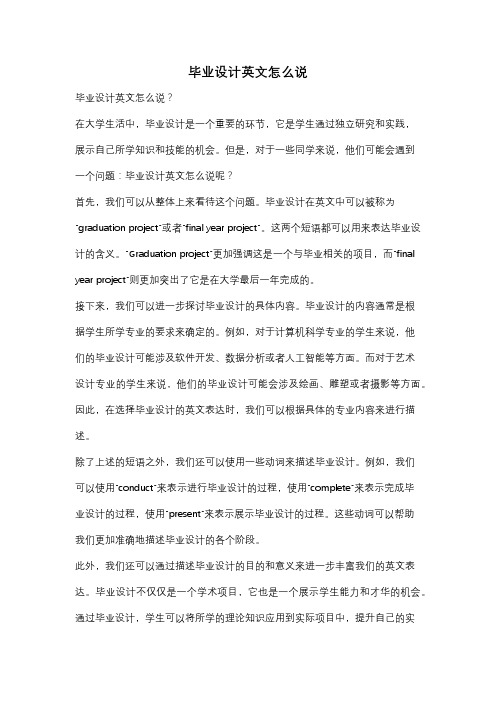
毕业设计英文怎么说毕业设计英文怎么说?在大学生活中,毕业设计是一个重要的环节,它是学生通过独立研究和实践,展示自己所学知识和技能的机会。
但是,对于一些同学来说,他们可能会遇到一个问题:毕业设计英文怎么说呢?首先,我们可以从整体上来看待这个问题。
毕业设计在英文中可以被称为"graduation project"或者"final year project"。
这两个短语都可以用来表达毕业设计的含义。
"Graduation project"更加强调这是一个与毕业相关的项目,而"final year project"则更加突出了它是在大学最后一年完成的。
接下来,我们可以进一步探讨毕业设计的具体内容。
毕业设计的内容通常是根据学生所学专业的要求来确定的。
例如,对于计算机科学专业的学生来说,他们的毕业设计可能涉及软件开发、数据分析或者人工智能等方面。
而对于艺术设计专业的学生来说,他们的毕业设计可能会涉及绘画、雕塑或者摄影等方面。
因此,在选择毕业设计的英文表达时,我们可以根据具体的专业内容来进行描述。
除了上述的短语之外,我们还可以使用一些动词来描述毕业设计。
例如,我们可以使用"conduct"来表示进行毕业设计的过程,使用"complete"来表示完成毕业设计的过程,使用"present"来表示展示毕业设计的过程。
这些动词可以帮助我们更加准确地描述毕业设计的各个阶段。
此外,我们还可以通过描述毕业设计的目的和意义来进一步丰富我们的英文表达。
毕业设计不仅仅是一个学术项目,它也是一个展示学生能力和才华的机会。
通过毕业设计,学生可以将所学的理论知识应用到实际项目中,提升自己的实践能力和解决问题的能力。
因此,我们可以使用一些形容词来描述毕业设计的目的和意义,例如"meaningful"、"challenging"、"rewarding"等。
毕业设计英语翻译

毕业设计英语翻译【篇一:毕业设计中英文翻译】英文资料翻译题目基于网络信息的自动化控制系别专业班级学生姓名学号指导教师2012年4月con trol based on n etwork andin formatio na automation networking application areas networking is used in all areas of automation. in factory automation, process automati on and buildi ng automati on n etworks perform diverse tasks. likewise, there are dist inct differe nces betwee n tasks performed for applicati ons in differe nt in dustry sectors that all have unique characteristics and con seque ntly vary ing requireme nts. the way devices are conn ected, con figured, and excha nge data also differ.there is no on e-size-fits-all for in dustrial n etworks; rather, buses are optimized foter differe nt characteristics. for example, factory automati on and process automati on are ofte n used in harsh and hazardous en viro nments where a producti on in terrupti on is costly. these requireme nts con trast sig nifica ntly with build ing automati on, for example, where keep ing costs low is a main driving force.factory automatio nfactories with assembly-l ine manu facturi ng, as in the automotive, bottli ng, and mach inery in dustries, are predo minan tly con trolled using discrete logic and sen sors that sense whether or not, for example, a process mach ine has a box standing in front of it. the network types ideal for simple discrete i/o focus on low overhead and small data packets, but they are un suitable for larger, messages like con figurati on download and the like. examples of this network type are seriplex, i nterbus-s, and as-i (as-in terface), which are sometimes called sen sor buses or bit level buses. other more adva need protocols orie nted toward discrete logic in clude device net, con troln et, and profibus (dp and fms applicati on profiles). these buses are sometimes referred to as devicebuses or byte-level buses. factory automati on in volves fast-moving mach inery and therefore requires quicker resp onse than slower processes. traditi on ally, these tasks have bee n han dled by plcs.process automati onprocess plants in industry segments like refining, pulp paper, power, and chemicals are dominated by continuous regulatory con trol. measureme nt is an alog (here meaning scalar values tran smitted digitally), and actuatio n is modulat ing. of course, process industries also use some discrete control and the predo minan tly discrete manu facturi ng in dustries use some modulating. fieldbus on/off valves are already available in the market, as are small remotely moun ted i/o modules for discrete sen sors .in the past, a dcs or sin gle-loop con troller did this.process-related n etwork in clude foun dati on fieldbus, profibus (pa application profile), and hart. all these buses as a category are now typically referred to as fieldbus (without the capital f), though some would argue that one or the other does not bel ong. these three protocols were specifically desig ned for bus-powered field in strume nts with predefi ned parameters and comma nds for asset man ageme nt in formatio n like iden tificati on, diag no stics, materials of con structi on, and fun cti ons for calibratio n and commissi onin g. i n term of size, the n etworks used in in dustrial automati on are con sidered to con stitute local area n etworks (la n) spa nning areas no greater tha n a kilometer or two in diameter and typically confined to a sin gle build ing or a group of build in gs. n etworks that exte nd only a few meters are in sufficie nt, and n etworks that spa n cities or eve n the globe are overkill.field and host tier networkseven within control systems for the process sector there is a n eed for differe nt n etwork characteristics at each tier of the control system hierarchy. at the field and there are instruments such as tran smitters and valve positti oners that have their specific needs, and valve positioners that have their specific n eeds (fig.5-1a-1). whe n fieldbus bega n to evolve, the process in dustry put a large nu mber of requireme nts on the field-level n etwork that were not met by other types of n etworks. many new desig n con sideratio ns n eeded to be take n into acco unt.on the upper tier, data from all the field-level networks have to be marshaled on to a si ngle host-leveln etwork that also serves any tasks the pla nt may have that seem related to factory automatio n.fig.5-1a-1 field level at the field level, the dominant protocols for process instrument are hart, foundation fieldbus h1, and profibus pa.hart is significantly different from the other two in that it is a so-called smart protocol, that is a comb in atio n of digital com muni cati on simulta neously superimposed on a conven tio nal 4-20ma sig nal. as such, the hart protocol has bee n an ideal in termediate solutio n in the tran siti on from an alog. hart is compatible with exist ing an alog recorders, controllers, and indicators while at the same time it makes possible remote configuration and diagnostics using digital com mun icatio n. the hart protocol does allow several devices to be multidropped on a sin gle pair of wires, but this is a capability in freque ntly explored because of the low update speed, typically half a sec ond per device. for a vast majority of in stallati ons hart devices are conn ected point to point, that is, one pair of wires for each device and a han dheld conn ected temporarily from time to time for configuration and maintenance. both foundation fieldbus h1 and profibus pa are completely digital and even use identical wiri ng, follow the iec 61158-2 sta ndard. however, bey ond that there are major differe nces betwee n these two protocols, and depe nding on the desired system architecture one may be more suitable than the other.at the field level, i nstrume nts appear in large qua ntities, ofte n in the hundreds or thousands. the wire run are very long, as the network cable must run from the control room all the way into the field, up towers, and the n branching out to devices scattered throughout the site. because there is a limit to the nu mber of devices that can be multidropped on each n etwork, eve n a medium-sized pla nt may have many n etwork cables running into the field, although substantially fewer than if poi nt-to-poi nt wiri ng was used. the field-level n etworks were therefore desig ned to en able very long wire runs and to allow field devices to take their power from the network. only asin gle pair of wires carries both the device powera s d thedigital com muni cati ons sig nal. this elimi nates the n eed for a separate power cable, thus keep ing the wiri ng simple and in expe nsive.as ano ther measure to keep costs dow n, desig ners chose a moderate field-level n etwork speed so no rmal in strume nt- grade cable could be used in stead of special data cable. no special conn ectors, couplers, or hubs are required either, which makes it possible to use rugged and weatherproof conn ecti ons.the grade of cable used for conven tio nal in strume nt conn ecti ons on most sites is more tha n sufficie nt for fieldbus n etwork ing. as a result, it is possible to reuse that cable when an existing plant is migrated to fieldbus. in hazardous process en vir onments where flammable fluids are prese nt in tri nsic safety is many times the preferred protecti on method. the field-level n etworks were therefore desig ned to allow safety barriers to be in stalled on the bus.because desig ners chose a moderate field-level n etwork speed the devices conn ected to it do not require a great deal of cpu process ing power to han dle the com muni cati on quickly. as a result, they also con sume very little power. because the low power con sumpti on results inlow voltage drop along the wire, it is therefore【篇二:毕业设计英文翻译模板】都信业设系别姓名专业班级学号息工程学院计英文翻译论文标题****学院大气探测、信***处、两个专业填写电子信息*******工程。
毕设翻译原文
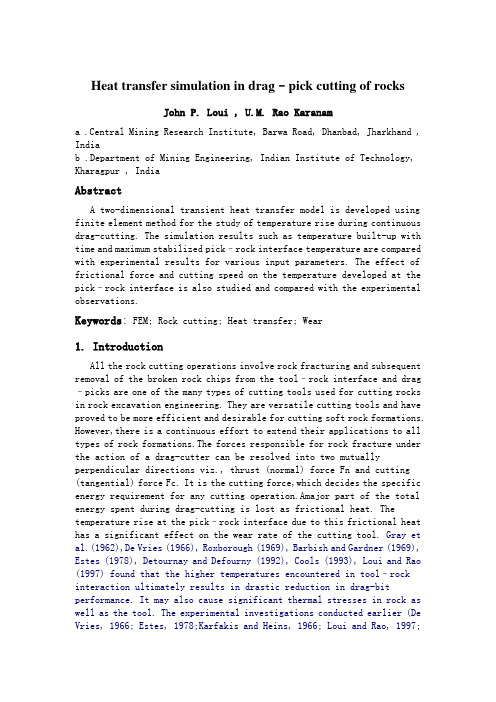
Heat transfer simulation in drag–pick cutting of rocksJohn P. Loui , U.M. Rao Karanama .Central Mining Research Institute, Barwa Road, Dhanbad, Jharkhand , Indiab .Department of Mining Engineering, Indian Institute of Technology, Kharagpur , IndiaAbstractA two-dimensional transient heat transfer model is developed using finite element method for the study of temperature rise during continuous drag-cutting. The simulation results such as temperature built-up with time and maximum stabilized pick–rock interface temperature are compared with experimental results for various input parameters. The effect of frictional force and cutting speed on the temperature developed at the pick–rock interface is also studied and compared with the experimental observations.Keywords: FEM; Rock cutting; Heat transfer; Wear1. IntroductionAll the rock cutting operations involve rock fracturing and subsequent removal of the broken rock chips from the tool–rock interface and drag –picks are one of the many types of cutting tools used for cutting rocks in rock excavation engineering. They are versatile cutting tools and have proved to be more efficient and desirable for cutting soft rock formations. However,there is a continuous effort to extend their applications to all types of rock formations.The forces responsible for rock fracture under the action of a drag-cutter can be resolved into two mutually perpendicular directions viz., thrust (normal) force Fn and cutting (tangential) force Fc. It is the cutting force,which decides the specific energy requirement for any cutting operation.Amajor part of the total energy spent during drag-cutting is lost as frictional heat. The temperature rise at the pick–rock interface due to this frictional heat has a significant effect on the wear rate of the cutting tool. Gray et al.(1962),De Vries (1966), Roxborough (1969), Barbish and Gardner (1969), Estes (1978), Detournay and Defourny (1992), Cools (1993), Loui and Rao (1997) found that the higher temperatures encountered in tool–rock interaction ultimately results in drastic reduction in drag-bit performance. It may also cause significant thermal stresses in rock as well as the tool. The experimental investigations conducted earlier (De Vries, 1966; Estes, 1978;Karfakis and Heins, 1966; Loui and Rao, 1997;Martin and Fowell, 1997) could only measure pick–rock interface temperatures at 2–3 locations on the cutting tool.Most of the temperature measurements during laboratory experiments were done by thermocouples placed within the tool. Conducting such experiments is not onlytime consuming and costly but also provide inadequate information if the objective is to study the temperature distribution in the pick–rock system.Analytical modelling for predicting the temperature during rock cutting requires major simplification of the problem and this may not be able to provide accurate results for the complicated real life situation of drag-cutting.Therefore, a numerical modelling technique viz., the finite element method is used in the current study to develop a two dimensional transient heat transfer model to solve for the temperature profile in the pick –rock system.The present paper discusses the development of this transient heat transfer model and its experimental validation.2.Theoretical heat transfer analysis in drag-cuttingPrior to the finite element solution of the problem,theoretical analysis has been done to evaluate input parameters for the finite element program. These parameters include velocity field in the pick–rock system,forces acting on the rake and flank face of the drag-cutter and the heat generated due to the interfacial friction while cutting.2.1. Velocity fieldsFor simplicity, the drag-cutting process is simulated as the pick remaining stationary against the rock moving past the cutter at a cutting velocity Vc. The resulting velocity fields in the uncut rock and fully formed chip are evaluated theoretically as input parameters for the numerical model.Though the researchers in the past have postulated linear (Nishmatsu, 1972) and curvilinear (Loui, 1998)paths of rock failure during the process of chip formation,for simplicity, it is assumed to be linear for the evaluation of velocity fields in the chip and the uncut rock. Fig. 1 illustrates this process of chipping under the action of a drag-cutter. The failure path is linear and at an angle / with respect to the cutting velocity as shown in Fig. 1. The inter-relationships between the cutting velocity Vc, shear velocity along the shear plane Vs, and chip velocity along the rake face Vr are represented in Fig. 2. These velocity fields in the rock areevaluated relative to the pick and thus the pick domain is assumed to be stationary against a moving rock domain.It has been found from chip-formation simulation studies (Loui, 1998) that the fracture plane (shear plane)exists at an angle of 30–35 with respect to the cutting velocity.From the velocity diagram (Fig. 2), the velocity components,u and v in x and y directions respectively, for the uncut rock and fullyformed chip are given by the following Eqs. (1) and (2), respectively. Uncut rocku =V c and v =0 (1)Fully formed chipu =γsin r V and v =γcos r V (2)2.2. ForcesThe forces acting on an orthogonal drag-cutter are representeddiagrammatically in Fig. 1. The cutting force Fc and the thrust force Fn were measured experimentallyand are related to the normal and frictional forces at the rake face and flank face (N and F, and /N and /F , respectively) as shown below: ,sin cos /c F F F F ++=γγ (3),sin cos /n N N F F +-=γγ (4)If μ is the tool –rock interface friction,//NF N F ==μ, (5)Solving for N and /N , we get,γμγμμsin ,2cos )1(2+--=N C F F N (6) γμγμγγμγμγsin 2cos )1()sin cos ()sin cos (2/+---+=C N F F N , (7) 2.3. Heat generationHeat generation during drag-cutting is mainly caused by friction at the interface between the pick and the rock (at flank and rake faces) as the cutter is dragged againstthe rock surface at a certain cutting velocity.It requires large or repeated plastic deformations to result in heat generation as in the case of metal cutting.Though elasto-plastic deformations take place in certainrock types before their failure and the formation of chips, suchdeformations are not large enough in rocks to result in the generation of heat. Therefore, for the purpose of estimating the heat generation during dragcutting,the rock chipping can be assumed to be caused by brittle failure and the heat generation limited to frictional heating. )(c f r V N NV Q Q Q /r tot +=+=μ, (8)where Qr and Qf are the frictional heat generated per second (watts) at the rake and flank faces, respectively,and Vr and Vc are the interfacial chip velocity at the rake face and flank face respectively.The velocity at which rock slides along the rake face of the tool (Vr) after rock chipping is difficult to assess.A fully formed chip does not offer a force against the rake face of the tool since it is completely detached from the rock mass and gets thrown away during the process of cutting. It has been observed by researchers in the past that drag tools undergo severe flank wear (wear land) and insignificant wear of the cutting face (Pliset al., 1988). Hence, for all practical purposes, the heat generated due to tool –rock friction at the rake face could be ignored and Eq. (8) reduces toV N Q Q f /tot μ==, (9)3. Discretization of pick –rock systemSince a simple orthogonal cutting tool is considered,heat transfer in the pick –rock system is treated as a two-dimensional problem by ignoringthe end effects.The whole domain has been discretized and analyzed in a two-dimensional Cartesian coordinate system. In the finite element solution of the problem, the domain is discretized into four-noded isoparametric elements as shown in Fig. 3. In the cutting simulations the pick is assumed to be stationary, thus the spatial discretizationof the pick does not change with time. However,since the rock is assumed to move past the pick at a constant velocity Vc, the discretized domain in the rock changes with time as per the velocity fields evaluated above.4. Finite element formulationGalerkin s approach has been used for converting the thermal energy equation (Eq. (10)) into a set of equivalent integral equations,tT C Q y T V X T C y T T K P P ∂∂=+∂∂+∂∂-∂∂+∂∂ )()x (2222μ, (10) where k is the coefficient of thermal conductivity, q is the density and Cp is the specific heat capacity at constant pressure.Let T be the approximate solution temperature and Rfem the finite element residue. Then, fem 2222-)()x (R tT C Q y T V X T C y T T K P P =∂∂+∂∂+∂∂-∂∂+∂∂ μ, (11) The approximate temperature solution T can be represented over the solution domain by[][]n T N T = , (12)where [N] is the overall shape function vector and {Tn} is the nodal temperature vector. With the use of Eq. (12), Eq. (11) can be discretized (Shih, 1984) yielding,5. Laboratory micro-pick experimentsThe cutting action was simulated using laboratory scale micro-picks and the rotary drag-cutting was carried out against an applied vertical thrust force. The applied thrust levels (Fn) were in the range of 230–750 N and the cutting speeds (Vc) were 0.01, 0.16 and 0.25m/s, which are within the practical drag-cutting ranges.The experiments were conducted on a vertical drill machine. A schematic diagram of the complete experimental setup is shown in Fig. 4. Laboratory scale micro-picks used for rotary cutting had tungsten carbide inserts as the cutting edge. The inserts were 12 mm in length, 10 mm in width and 3.5 mm in thickness and was designed to have a wedge angle of 80 and a rake angle of 10. For the measurement of temperature developed during cutting, copper–constantan thermocouple was introduced into a 1-mm diameter hole drilled at a distance of 2 mm from the cutting edge within the tungsten carbide insert and blazed with silver to secure a good holding. The micro-picks along with thermocouple are given in Fig. 5.A pre-calibrated milli-voltmeter of the range 0.1–1000 mV was used to record the difference of voltage across the thermocouple. Torque generated at the pick–rock interface is measured using a spoked wheelTorque generated at the pick–rock interface is measured using a spoked wheel dynamometer (Rao and Misra, 1994) in line with arecorder.In all these experiments, the drag–pick cutter was held stationary between the plates of the dynamometer and the rock core samples were held in a holder. The rock sample holder is designed to hold samples at one end, while the other end is provided with a taper, which fits into the drill shank. With this arrangement, rock core sample rotates against the stationary drag –pick during the cutting process. The pick-holder and rockholder are shown in Fig. 6. The experimental results have been discussed, in details, in Loui and Rao(1997). However, only a few of the experimental results are used in this paper for validation of the numerical model.6. Results and discussionThe numerical model developed in the current study has the ability to predict the pick–rock interfacial temperature and the temperature profiles in the pick–rock system. The main input parameters, which influence the temperature development at the pick–rock interface, are the cutting speed and the interfacial friction at the flank face ofthe pick. Eq. (9) shows they are linearly related to the quantity of heat generated at the pick–rock interface. The results obtained from the numerical model are compared with those observed from the experimental observations.6.1. Temperature built-upAll the simulation runs indicated that after 6 minute of pick–rock contact time, the temperature through out the domain stabilizes.Pick-rock interface temperature is defined as the average interface temperature observed along the flank face of the tool and is evaluated using Eq. (23). The temperature rise with time at the pick–rock interface for the rock type sandstone at a cutting speed of 0.25 m/s, thrust force of 230 N, and for a depth of cut of 1 mm is shown in Fig. 7. A comparison is also made with the experimental observation of the pick–rock interface temperature for the same input parameters used for the numerical model. The trend by which temperature builds up and further stabilizes has been found to be in a good agreement with the experimental observations. This trend is due to the fact that the amount of the heat generated being much higher during the onset of the cutting process compared to the dissipation of heat. As the cutting proceeds, the temperature builds up in the pick –rock system. When the temperature attains higher regimes, the heat dissipation due to convection and conduction also increases and eventually equals the heat generation due to friction. As the rate of heat generation remains constant, provided the machine operating parameters are unaltered, the temperature in the pick–rock system tends to stabilize after a few minutes of cutting.6.2 Stabilized interface temperatureThe stabilized pick–rock interface temperature at the end of 6 min of continuous cutting is termed as the stabilized interface temperaturefor that particular simulationor experiment. The variation of the stabilized pick–rock interface temperature has been studied against some of the input parameters, which directly influence the temperature such as the cutting speed and the frictional force. Other parameters like depth of cut, rake angle, etc. influence the frictional force at the interface and therefore, have only indirect effect on the temperature developed.Fig. 9 shows the variation of stabilised interfacial temperature with the cutting speed and its comparison with the experimental observation. The input parametersfor the numerical model were taken corresponding to the operating parameters used for the experiments. The predicted values by FEM analysis show a linear variation(Fig. 9) since the cutting speed is directly proportional to the quantity of heat generated (Eq. (9)).The other parameter, which directly influences the heat generation at the pick–rock interface, is the frictional force at the flank face of the pick and therefore,it has been plotted against the pick rock interface temperature for numerical and experimental results (Fig.10). As observed from Fig. 10, both the results show aLineartrend.In general, from all the temperature prediction runs,the numerical results showed a higher temperature values(up to approximately 25%) compared to their experimentalcounterparts. In the numerical model it has been assumed that all of the frictional heat generated at the flank face of the tool has been converted into frictional heat which may be the reason for an over estimation. However, the errors incurred in the experimental dragcutting and also during observation using thermo-couple type of temperature measurement system cannot totally be ignored. Martin and Fowell (1997) has measured the pick–rock interface temperature using thermocouples as well as infra-red gun and found that the latter recorded higher temperature values. The error incurred may be partly due to the two-dimensional approximation of drag-cutting.6.3. Temperature variation along rake face and flankfaceFigure 11 shows the temperature variation at its stabilized state (after 6 min of continuous cutting period) along rake face and flank face of the tool. Both the curves (flank and rake faces) are plotted simultaneouslystarting from the tip of the cutter, which is the intersection point for both the forces. As frictional heat is generate at the wear-land of the flank face of the tool,temperature rises along the wear land reaches a maximum approximately at the mid point of the wear land (hf), and drops rapidly towards the flank side of the cutter as show in Fig. 11. Since at the rake face of the tool no heat is being generated during cutting, temperature falls along the rake face from the tool edge.This indicates that the temperature concentration takes place at the worn-out portion of the flank face of the cutting tool (wear land), which comes in direct contact with the rock.7.ConclusionsA general purpose finite element program has been developed to study the temperature attained during pick–rock interaction. The model has been used forthe prediction of pick–rock interface temperatures as well as temperature profile of the whole pick–rock System.The transient heat transfer modelling showed that the temperature builds up steeply during the onset of cutting and stabilizes within a few minutes of continuous pick–rock contact. This trend has been validated from experimentalobservations.The results obtained from the numerical model proves direct effect of the rock cutting parameters viz., frictional force and cutting velocity on the temperaturerise at the pick–rock interface. This has been validated by linearly increasing trends observed between the stabilized interface temperature and the rock cuttingParameters.The current study has dealt with continuous dragcutting,both numerically and experimentally. However,the transient finite element program developed can bemodified to predict the temperature rise in the pick during intermittent cutting, which mostly occurs in real life cutter picks used in road headers and shearers. With theprior knowledge of frictional forces acting in the pick–rock system during intermittent cutting, this modification can be done by suppressing the heat generationterms and adding convective heat transfer terms at the pick–rock interface nodes when the pick leaves the contact with the rock; and by initialization of rock domaintemperatures and re-introduction of heat generation terms duringre-contact. Since the experimental setup used in the current study was not designed for intermittentcutting, experimental data could not be obtained for validation and therefore, intermittent cutting was not dealt in this paper. Further, it may require a moredetailed three-dimensional modelling to reduce the errors and to get the results closer to the realistic temperature values.ReferencesBarbish, A.B., Gardner, G.H.F., 1969. The effect of heat on some mechanical properties of igneous rocks. ASME J. Soc. Petr. Eng. 9,395–402.Cools, P.C.B.M., 1993. Temperature measurements upon the chisel surface during rock cutting. Int. J. Rock Mech. Min. Sci. Geomech.30, 25–35.De Vries, M.F., 1966. Investigation of drill temperature as a drilling performance criterion. Ph.D. thesis, University of Wisconsin, USA.Detournay, E., Defourny, P., 1992. A phenomenological model for the drilling action of drag bits. Int. J. Rock. Mech. Min. Sci. 29, 13–23. Estes, J.C., 1978. Techniques of pilot scale drilling research. ASME J. Pressure Vessels Technol. 100, 188–193.Gray, K.E., Armstrong, F., Gatlin, C., 1962. Two-dimensional study of rock breakage in drag-bit drilling at atmospheric pressure. J. Pertol. Technol., 93–98.Karfakis, M.G., Heins, R.W., 1966. Laboratory investigation of bit bearing temperatures in rotary drilling. ASME J. Energy Resourc.Tech. 108, 221–227.Loui, J.P., Rao, K.U.M., 1997. Experimental investigations of pick –rock interface temperature in drag–pick cutting. Indian J. Eng.Mater. Sci. 4, 63–66.Loui, J.P., 1998. Finite element simulation and experimental investigationof drag-cutting in rocks. Ph.D. thesis, Indian Institute of Technology, Kharagpur, India.Martin, J.A., Fowell, R.J., 1997. Factors governing the onset of severe drag tool wear in rock cutting. Int. J. RockMech. Min. Sci. 34, 59–69. Nishmatsu, Y., 1972. The mechanics of rock cutting. Int. J. Rock Mech. Min. Sci. 9, 261–272.Plis, M.N., Wingquist, C.F., Roepke, W.W., 1988. Preliminary Evaluation of the Relationship of Bit Wear to Cutting Distance, Forces and Dust Using Selected Commercial and ExperimentalCoal and Rock Cutting Tools. USBM, RI-9193, p. 63.Rao, K.U.M., Misra, B., 1994. Design of a spooked wheel dynamometer. Int. J. Surf. Mining Recl. 8, 146–147.Roxborough, F.F., 1969. Rock cutting research. Tunnels Tunnelling 1, 125–128.Shih, T.M., 1984. Numerical Heat Transfer. Hemisphere/Springer, Washington/New York, p. 563.。
毕业设计英文翻译中英文对照版
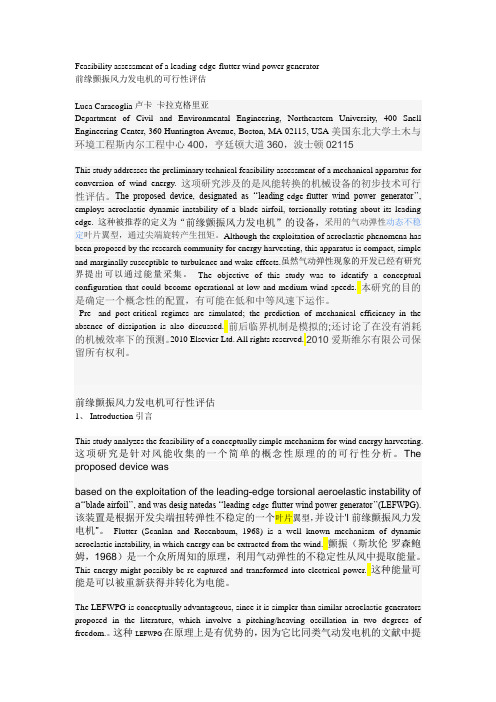
Feasibility assessment of a leading-edge-flutter wind power generator前缘颤振风力发电机的可行性评估Luca Caracoglia卢卡卡拉克格里亚Department of Civil and Environmental Engineering, Northeastern University, 400 Snell Engineering Center, 360 Huntington A venue, Boston, MA 02115, USA美国东北大学土木与环境工程斯内尔工程中心400,亨廷顿大道360,波士顿02115This study addresses the preliminary technical feasibility assessment of a mechanical apparatus for conversion of wind energy. 这项研究涉及的是风能转换的机械设备的初步技术可行性评估。
The proposed device, designated as ‘‘leading-edge-fl utter wind power generator’’, employs aeroelastic dynamic instability of a blade airfoil, torsionally rotating about its leading edge. 这种被推荐的定义为“前缘颤振风力发电机”的设备,采用的气动弹性动态不稳定叶片翼型,通过尖端旋转产生扭矩。
Although the exploitation of aeroelastic phenomena has been proposed by the research community for energy harvesting, this apparatus is compact, simple and marginally susceptible to turbulence and wake effects.虽然气动弹性现象的开发已经有研究界提出可以通过能量采集。
本科毕业设计翻译英文

( 1. Faculty of Civil Engineering & Geosciences, Delft University of Technology , P. O. Box 5048,2600 GA Delft, t he Nether lands; 2. Key Laboratory of Silicate Materials Science and Engineering of the Ministry of Education, Wuhan University of Technology, Wuhan 430070, China)Abstract: Coal tar, a by- product from the destructive distillation of coal in co king oven, is widely used in road engineering for its excellent adhesion and fuel resistance properties, especially for pavement surface treatments in gas stations and airports.However, coal tar has a high Poly cyclic Aromatic Hydro carbons ( or PAHs) content, which makes it toxic.I n 1985, the International Agency for Research on Cancer ( IARC) has proved that coal tar is carcinogenic to humans. Research showed that Coal Tar- based Sealers ( CTS) contribute to the majority of PAHs pollution in the water environment. Because of this environmental concern, CT S are not allowed in many dev eloped countries in the USA and Europe. In contrast, coal tar is still used for road engineering in China and is even used increasingly .This paper gives a literature review on the general information and research about environmental concern of using coal tar in road engineering. Based on the review , some possible alternatives to replace coal tar are described. These alternatives include nanoclay/ epoxy modified bitumen/ bitumen emulsion and waterborne polyuret hane/ epoxy resin, which are environmental friendly. They have the potential to perform as w ell as CTS, and even better in some special applications.Key words:coal tar; pavement surface treatment; adhesion property; poly cyclic aromatic hydrocarbons; modified bitumen emulsionCLC number: U 416 Document code: A Article ID: 1671- 4431( 2010) 17- 0001- 07Received date: 2010- 05- 07.Biography : Xiao Y( 1986- ) , Ph D Candidate. E-mail: yue. xiao@1 introductionTwo basic types of binders are currently used in the pavement surface treatment market: coal tar-based and bitumen-based. At some places like g as stat ions and airports, coal tar-based surface sealers performed much better than bitumen-based sealers with regards to adhesion properties and chemical resistance. Coal tar-based have better resistance to petroleum oils and inorganic acids, and have better moisture resistance[ Austin, 2005] .Because of these out standing properties, CTS are widely used in road engineering for pavement surfacetreatment for many years. However, coal tar is a complex hydrocarbon mixture consisting of hundred of PAH[SCHER, 2008] . These PAHs are toxic and considered human carcinogens. Because of it s environmental unfriendly properties, coal tar is not allowed in most of the developed counties like the Netherlands. In the Netherlands,use of tar containing product s is not allowed since 20 years, with one temporary except ion for antiskid runways in airfields [ van Leest , 2005] . But after 2010, it w ill not be allowed for airport pavement application anymore. Compared to these bans, coal tar is still used for road engineering in China. China Coal Tar Industry Report mentioned that the coal tar consumption w ill be on the upward t rend [CCTIR, 2008] .Based on new technologies like nano technology and two-component technology, other materials are developed for pavement surface treatment and they perform w ell. Modified bitumen emulsions, which can be applied at low temperatures, were successfully used in South Africa, Australia and many other countries. Additives such as polymers ( SBS, SBR and EVA ) , clays ( illite, kaolinite and montmorillonite ) are known to improve the properties of bitumen emulsions in special road applications [ TRB-EC102, 2006;Xiao, 2010] . With the waterborne two-component technology, coating manufacturers can producehigh-performance sealers and achieve the same or better properties than solvent-based sealers. Furthermore, waterborne resins for coating s usually do not contain or just contain a small amounts of other solvent s, indicating that waterborne two component systems are environmental friendly. Epoxy modified bitumen w as originally developed in the late 1950s by Shell Oil Company as a material designed to withstand fuel exposure [ Thom, 2006] . After full curing , epoxy modified bitumen mixture has high temperature stability and strength, excellent fatigue, superior adhesion and rutting resistance.In this paper, a short literature review is given on the use and properties of CTS for pavement surface treatment and its environmental concern. After that several possible alternatives are discussed, such as nanoclay modified bitumen emulsion, epoxy modified bitumen, waterborne polyurethane/ epoxy resin. These alternatives may have good properties and are environmental friendly.2 Use and Advantages of Coal Tar Based SealersCoal tar-based products are used in many industries, for example pavement engineering, the building industry and medical treatment s. In pavement engineering , one of the largest applications is CTS.Coal tar can be used as a binder and filler in surface treatment formulations, and as a modifier for epoxyresin surface coating s. T he streets of Baghdad w ere the first to be paved with tar from the 8th century AD. Tar was a vital component of the first sealed, or tarmac roads. The first tar macadam road with a tar-bound surface was placed in 1848 out side Nottingham, England. In Washington D. C. some of thetar-bound surface courses have a service life of about 30 years.Coal tar is a very complex mixture of chemicals. It s molecular structure is quite different from bitumen.Some of the constituents are described as PAHs. Being stable in molecular structure, these chemicals are incompatible with oil and gas, and provide a barrier coat to protect asphalt surfaces against the destructive effects of petroleum based products and chemicals [Aust in, 2005] . CTS have a better chemical resistance than bitumen based, extremely low permeability to moisture and a high resistance to ultraviolet radiation. These properties make it ideally suited for parking areas w here concentrations of oil and gasoline leaks are prevalent, like gas stations, truck and bus terminals and airport s. CTS are used to extend the life and reduce maintenance cost associated with asphalt pavements, primarily in asphalt road pavement. They are typically used at airports for aprons, taxiways and runways. The Federal Aviation Administration Advisory Circular 150/ 5370-10A Standards for Specifying Construction of Airports include a requirement for pavement sealers that they should contain at least 35% coal tar in runway asphalt pavement.The reason for this requirement is that CTS have a much better resistance to jet fuel than bitumen-based sealers [Austin, 2005].3 Environmental ConcernGenerally, coal tars consist of a mixture of many organic compounds, like benzene, toluene, phenol, naphthalene, anthracite , and others. The risk assessment of coal tar is largely based on PAHs, especially on Benzo (a) pyrene . PAHs are the most relevant component s in terms of toxicity in coal tarproducts[ SCHER, 2008] .3. 1 Polycyclic aromatic hydrocarbonsPolycyclic aromatic hydrocarbons are also known as polycyclic aromatic compounds, polyaromatic hydrocarbons or as polynuclear aromatics. PAHs are a group of over 100 different chemicals consisting of carbon and hydrogen in fused-ring structures. T able 1 shows several typical chemical structures of PAHs. PAHs are highly toxic and harmful to human and ecosystem health [Austin, 2005] . The content of PAHs in coal tar increases as the carbonization temperature increases.3.2 Environmental riskIn 1985, IARC has pointed out that coal tar pitches are carcinogenic in humans [IARC, 1985] . In 2008,three scientific commit tees ( SCCP, the Scientific Commit -tee on Consumer Products; SCHER, the Scientific Committee on Health and Environmental Risks; SCEN IHR, the Scientific Commit tee on Emerging and NewlyIdentified Health Risks) concluded that cancer risk was the most serious point of coal tar s risk characterizations [ SCHER, 2008] . Occupational exposure to coal tar increases the risk of developing skin cancer and other tissue sites , like lung, bladder, kidney and digestive tract . According to the IARC, products that include more than 5 percent of crude coal tar are Group 1 carcinogen which has sufficient evidence of carcinogenicity in humans. So, many countries all over the world have eliminated it s usage.In 2003, scientist s from the city of Austin ( USA ) identified CTS as a significant source of PAHs contamination. The United States Geological Survey and Austin City have conducted additional research that corroborates this finding, concluding that coal tar sealants are responsible for the majority of PAHs pollution in water environment in the Austin area. Coal tar-based pavement sealers are considered as a source of urban water pollution. These are long-lasting substances that can build up in the food chain to harmful levels to humans. Based on their investigations, Austin became the first city in the USA to ban the use of CTS for pavements [ Austin,2005; Mahler, 2005] .As a precaution, in Germany, manufacturers have voluntarily agreed to ban coal tar from their product s. In the Netherlands, coal tar containing products did not meet the Dutch Environmental Standards and w ill not be allowed for airport pavement after 2010.4 Possible AlternativesAccording to these environmental concerns, alternatives are required. These alternatives should have atleast comparable or better properties than CTS. At the same time, they should be environmental friendly. In this section, the possible use of modified bitumen emulsions, epoxy modified bitumen and waterborne resins are discussed.4. 1 Modified bitumen emulsionsBitumen emulsions are heterogeneous systems with two or more liquid phases, consisting of a continuous liquid phase ( water ) and at least one second liquid phase ( bitumen) dispersed in the former as fine droplets [ TRB-EC102, 2006] . Standard bitumen emulsions are normally considered to be of the oil in water type and contain from 40% to 75% bitumen, 0. 1% to 2. 5% emulsifier, 25% to 60% water plus some minor components. The bitumen droplets rang e from 0. 1 to 20 micron in diameter.4. 1. 1 Properties of modified bitumen emulsionsUnlike bitumen, bitumen emulsions do not need to be heated at high temperatures before application. Temperature storage and application at ambient temperature can avoid the use of energy and emissions associated with heating and drying [Kennedy, 1997]. This makes bitumen emulsions more economic and environmental friendl , compared to coal tar-based products.Additives are used to improve the properties of bitumen emulsions in special road applications. Polymer( SBS, SBR and EVA) , clay illite , kaolinite and montmorillonite and epoxy modified bitumen/ bitumen emulsions were successfully used in South Africa and Australia [ TRB-EC102, 2006; Xiao, 2010] .During the application of bitumen emulsion, the water must be separated from the bitumen phase and evaporate.This separation is called breaking. After complete evaporation of the water, the bitumen particles will coalesce and bond together to develop mechanical properties. This strength development is curing.4. 1.2 nanoclay modified bitumen emulsionThe most preferred and widely used nanoclays are organically modified smectite clays with a 2: 1-type layey structure such as montmorillonite, saponite, etc [ Ammala , 2007] . All these layered silicates have the same crystalline structure and normally have a thickness of about 1 nanometer and a length of about 50 ~ 1 000 nanometers.In nanoclay modified bitumen emulsion, three possible particle dispersions can be distinguished as Fig. 1 shows [Xiao, 2010]. In the case of type one (see Fig. 1( a) ) , all the nanoclay particles are dispersed in the bitumen droplets. In this case, after breaking and curing the particles are dispersed in the binder between the aggregates. In the second type (see Fig. 1( b) ) , all of the nanoclay particles are dispersed in the water phase. After breaking and full curing, the particles are surrounding at the boundaries of the bitumen droplet s. The third type( see Fig. 1( c) ) is a combination of the first two types. Some of the particles are dispersed in the bitumen droplets while the others are dispersed in the water phase. In this condition, after breaking and curing the nanoclay particles both occur in the binder and between the bitumen droplets.These dispersion types have a significant influence on the properties of bitumen residues. Further investigations need to be carried on for checking these dispersions.Fig . 2 shows the possible outstanding properties of nanoclay modified bitumen emulsion on outside chemical resistance [Xiao, 2010] . With the unmodified bitumen emulsion after curing on the pavement surface, fuel, moisture and ultraviolet radiation can affect the binder directly. These can decrease the performance and cause raveling and ageing problems. When nanoclay modified bitumen emulsions are used for surface treatment, four steps can be dist inguished during breaking and curing. First, nanoclay modified bitumen emulsion consist s mainly of water, bitumen drop and nanoclay layers. Second, the water phase evaporates during the breaking and curing process. Then, bitumen droplets adhere to nanoclay particles, causing clusters to form the binder. At the last, binder is formed with nanoclay layers inside.The dispersed nanoclay particles can decrease surface damages due to fuel, moisture, air, etc. to a certain extent, resulting in better chemical and ageing resistance.4.2 Epoxy modified bitumensThe epoxy modified bitumen binder is a two phase chemical system in which the continuous phase is an acid cured epoxy and the discontinuous phase is a mixture of specialized bitumens, which makes the mixture performdifferent from a traditional asphalt mixture.4. 2. 1 Properties of epoxy modified bitumensEpoxy modified bitumen was used for pavement treatment long time ago and has achieved better properties than unmodified bitumen. In 1967, it was used to strengthen the surface of San Francisco Bay smile-long San Mateo-Hay ward Bridge. After more than 40 years, the bridge surface is reported to be in excellent condition.The special structure of epoxy modified bitumen makes it perform different from traditional bitumen. It does not become brittle at low temperature and does not melt at high temperature. Epoxy modified bitumen is a flexible material that can be applied in thin surface layers. When used on roads, it sets quickly enough to allow early traffic even before full curing, which enables the road to be reopened withintwo hours [ Xiao, 2010] .Epoxy modified bitumen is reported to be extremely durable as w ell as flexible. Surfaces with epoxy modified bitumen obtained better skid resistance and produce less noise than bitumen based sealers. Epoxy modified bitumen has extremely high temperature stability and strength, superior rutting resistance, excellent adhesion properties, high resistance to surface abrasion and is sufficiently fuel resistance [ Elliot t, 2008; Xiao, 2010] .4.2.2 Two-component epoxy modifiedbitumenTwo-component epoxy modified bitumen is acold mix application material. It is a two componentreactive material based on two components. One is amix of bitumen, bitumen-compatible epoxides andadditives. The other one is a mix of hardeners. After mixing of these two component s, there will be a fast react ion leading to epoxy resin within a bitumen based matrix.The tensile strength of Esha Seal 2C, which is a kind of two-component epoxy modified bitumen, obtained from ICOPAL BV, was evaluated using the Direct T ensile Test . Fig. 3 shows the tensile strengthafter different curing times and temperatures.Results indicate that the curing rate of epoxy modified bitumen emulsion depends on the curing temperature. The tensile strength increases with increasing curing time temperature . The tensile strength after full curing is higher than thetensile strength of bitumen, which implies that roads can be reopened for traffic very quickly w hen epoxy modified bitumens are applied in the surface layer.4. 3 Waterborne resinsWaterborne resins use water as the main volatile liquid component . It always shows good adhesion and the resistance to fuel, water and chemical is good. New technologies in waterborne systems provide unique technical solutions to get good properties, such as good adhesion to concrete and acidic resistance. With the waterborne two-component technology, coating manufacturers can formulate high-performance coatings without a cosolvent and achieve the same or better properties. Here waterborne polyurethane and epoxy resins will be discussed.4. 3. 1 Waterborne polyurethane resinsPolyurethane is a polymer consisting of a chain of organic units joined by urethane carbamate links. Polyurethane resins are formed from the reaction of an isocyanate with compounds containing active hydrogen, as Fig.4 shows. When the two components are mixed the hydroxyl groups ( - OH) in the resin react with the isocyanate groups ( N=C=O) in the hardener and a three dimensional molecular structure is produced[Weiss, 1997] .Because only one isocyanate group can react with one hydroxyl group, it is possible to vary the ratio of hydroxyl groups and isocyanate groups slightly either w ay in order to modify the mechanical properties of the system.Basically, waterbornepolyurethanes can be described asreactive or non-reactive polymerscontaining urethane and urea groupswhich are stabilized in water byinternal or external emulsifiers. Thesedifferent hydrophilic modify cationsallow the production of stablewaterborne polyurethanes with average particle sizes between 10 nm and 200 nm. Waterborne polyurethane resin is a water-based aliphatic polyurethane emulsion.Waterborne polyurethanes are environmental friendly. They provide a tough, durable and highly flexible binder. The advantages associated with polyurethane coatings are their high tensile strength, excellent adhesion properties and chemical/ mechanical resistance. Properties of waterborne polyurethanes can be improved by adding modifiers, such as organoclay layers [ Kim, 2003; Xiao, 2010] .Addagrip 1000 System resin is a two-component polyurethane resin designed by Addagrip Surface Treatments UK Ltd. It can be used for sealing to protect asphalt surfaces from erosion caused by frostdamage, chemical at tack and aviation fuel spillage. Areas treated over the last twenty years at military and civil air fields have prevented further deterioration and increased the service life of the concrete pavement by an estimated 10~ 15 years. Table 2 show s the properties of the samples before and after surface treatment with Addagrip 1000 System resin. 10 cm x 10 cmx10 cm blocks w ere used. The sample surfaces w ere heated and dried by a hot compressedair system before the resin w as sprayed onto the surface [Addagrip Ltd. ] . After surface reatment with this kind of polyurethane resin, the water and fuel resistance can be improved significantly.4. 3. 2 Waterborne epoxy resinsEpoxy is a copolymer. It is formed from two different chemicals, the resin and the hardener. Most common epoxy resins are produced from a reaction between Epichlorhydrin and bispheno-l A, see Fig.5[Weiss,1997] .Waterborne epoxy resin, with excellent adhesion properties, is another possible alternative. Waterborne epoxy resin is a stable resin material prepared by dispersing epoxy resin in the form of particles or droplet s into the dispersion medium based on water as a continuous phase.Application ofwaterborne epoxy resinsis not onlyconvenient but alsocauses no pollution tothe environmentand no harm to thehuman body. Afteradding a properamount of curing/ solidifying agent, advantages like high strength ,high-temperature resistance, chemical resistance, fatigue resistance, and high antiaging ability can be achieved [ Xiao, 2010; Weiss, 1997]5 ConclusionCTS are widely used for pavement surface treatments because of their excellent adhesion properties and good fuel resistance. How ever, because of their high PAHs content s, which are considered as human carcinogens, CTS are not allowed anymore in some of the developed counties. In order to eliminate the significant threat of pollution to our environment, w e should stop using CTS. Instead, modified bitumen emulsions, epoxy modified bitumen, waterborne polyurethanes and waterborne epoxy resins could achievecomparable or better properties than CTS. All of them have good adhesion, excellent chemical and ageing resistance. Epoxy modified bitumen has extremely high temperature stability and strength. Application of waterborne resins is convenient and the curing rate can be easily adjusted by changing the ratio of chemical components. And, the most important, these alternatives are environmental friendly.AcknowledgementsThe scholarship from the China Scholarship Council is acknowledged. T he authors would like to express thanks to ICOPAL BV for their materials and technical supports.References[1] AddagripLtd.www .adda grip [2] Ammala A, Hill A J.Poly( M-Xylene Adipamide)-Kaolinite and Poly( M-XyleneAdipamide)-Montmorillonite Nanocomposites [J] . Journal of Applied Polymer Science, 2007(104):1377- 1381.[3] Austin. http: / /www .ci. austin. tx . us/ watershed/ coaltar- ban. htm. Austin Bans Use of Coal Tar Sealants-first in Nation,2005.[4] CCTIR.China Coal Tar Industry Report 2006-2010.[R],2008.[5] Elliott R. 2008. Epoxy Asphalt: Concept and Properties. Workshop of TRB 2008.[6] IARC. Polynuclear Aromatic 4 Bitumens , Coal Tars and Der ived Products,Shale Oils and Soots. IARC Monographs on the Evaluation of Carcinogenic Risk of Chemicals to Humans,Vol. 35. Lyon, France:International Agency for Research on Cancer,1985.[7] Kennedy J. Alter native Materials and Techniques for Road Pavement Construction[R] . London: DOE Energy Efficiency Office,1997.[8] Kim B K, Seo J W, Jeong H M. Morphology and Properties of Waterborne Polyurethane/ clay Nanocomposite [J]. European[9] SCHER. Scientific Committee on Health and Environmental Risks. Coal tar pitch, high temperature Human Health Part. CAS No: 65996- 93- 2. EINECS No: 266- 028-2.[10] Thom N H. Asphalt Cracking: A Nottingham Perspective [J].Engenaria Civil/ Civil Engineering, 2006(26) : 75- 84.[11] TRB-EC102. Asphalt Emulsion Technology. Transportation Research Board[S], 2006.[12] Van Leest A J, Gaar keuken G. The F O D. Resistance of Sur face Layers on Airfields in the Netherlands; in Situ and Laboratory Testing [R] . 2005 European Airport Pavement Workshop, 2005. [13] Van Metre P C, Mahler B J. Trends in Hydrophobic Organic Contaminants in Urban and Reference Lake Sediments Across the United States, 1970- 2001[J]. Environmental Science and Technology,2005, 39( 15) : 5567- 5574.[14] Weiss K D. Paint and Coatings: A Mature Industry in Transition [J].Progress in Polymer Science, 1997, 22(2):203- 245.[15] Xiao Y. Literature Review on Possible Alternatives to Tar for Antiskid Layers . Delft University o f Technology, Road and Railway Engineering Section[R] . Report No.7-10-185-1,the Nether lands.。
本科毕业设计(论文)外文翻译译文
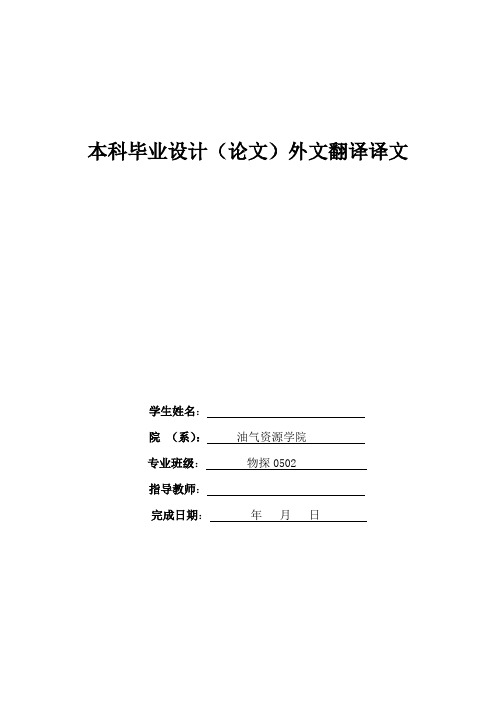
本科毕业设计(论文)外文翻译译文学生姓名:院(系):油气资源学院专业班级:物探0502指导教师:完成日期:年月日地震驱动评价与发展:以玻利维亚冲积盆地的研究为例起止页码:1099——1108出版日期:NOVEMBER 2005THE LEADING EDGE出版单位:PanYAmericanYEnergyvBuenosYAiresvYArgentinaJPYBLANGYvYBPYExplorationvYHoustonvYUSAJ.C.YCORDOVAandYE.YMARTINEZvYChacoYS.A.vYSantaYCruzvYBolivia 通过整合多种地球物理地质技术,在玻利维亚冲积盆地,我们可以减少许多与白垩纪储集层勘探有关的地质技术风险。
通过对这些远景区进行成功钻探我们可以验证我们的解释。
这些方法包括盆地模拟,联井及地震叠前同时反演,岩石性质及地震属性解释,A VO/A V A,水平地震同相轴,光谱分解。
联合解释能够得到构造和沉积模式的微笑校正。
迄今为止,在新区有七口井已经进行了成功钻探。
基质和区域地质。
Tarija/Chaco盆地的subandean 褶皱和冲断带山麓的中部和南部,部分扩展到玻利维亚的Boomerange地区经历了集中的成功的开采。
许多深大的泥盆纪气田已经被发现,目前正在生产。
另外在山麓发现的规模较小较浅的天然气和凝析气田和大的油田进行价格竞争,如果他们能产出较快的油流而且成本低。
最近发现气田就是这种情况。
接下来,我们赋予Aguja的虚假名字就是为了讲述这些油田的成功例子。
图1 Aguja油田位于玻利维亚中部Chaco盆地的西北角。
基底构造图显示了Isarzama背斜的相对位置。
地层柱状图显示了主要的储集层和源岩。
该油田在Trija和冲积盆地附近的益背斜基底上,该背斜将油田和Ben i盆地分开(图1),圈闭类型是上盘背斜,它存在于连续冲断层上,Aguja有两个主要结构:Aguja中部和Aguja Norte,通过重要的转换压缩断层将较早开发的“Sur”油田分开Yantata Centro结构是一个三路闭合对低角度逆冲断层并伴随有小的摆幅。
毕业设计英语

毕业设计英语Graduation ProjectFor my graduation project, I have chosen to design and create a smart home system. The aim of this project is to design and develop a home automation system that can control and monitor various appliances and devices within a home.The smart home system will be able to control appliances such as lights, air conditioning, heating, and security systems. It will also be able to monitor various sensors throughout the house, such as temperature, humidity, and motion sensors. The system will have a user-friendly interface that can be accessed from a smartphone or computer, allowing the user to easily control and monitor their home.To design and create this system, I will first research and study existing smart home technologies and systems. I will then select the most suitable hardware and software components to build the system. This will involve selecting microcontrollers, sensors, actuators, and communication modules.Once the hardware components are selected, I will design the system architecture and develop the software. This will involve programming the microcontrollers to control the appliances and sensors, as well as developing the user interface for the smartphone or computer.To test the system, I will set up a prototype in a simulated home environment. I will then conduct various tests to ensure that thesystem functions properly and meets the design requirements. This will involve testing the control and monitoring capabilities of the system, as well as testing its reliability and security measures.Once the system is fully developed and tested, I will document the design process and create a user manual that explains how to set up and use the smart home system. I will also evaluate the system's performance and discuss any potential improvements or enhancements that could be made in the future.Overall, this graduation project will allow me to gain knowledge and experience in the field of home automation and smart home technologies. It will also provide a practical solution for controlling and monitoring a home's appliances and devices. I am excited to undertake this project and look forward to the challenges and rewards it will bring.。
毕业设计英文 翻译(原文)
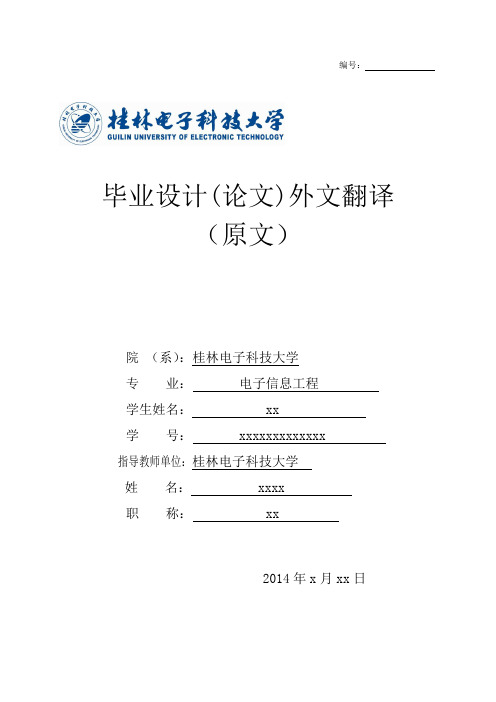
编号:毕业设计(论文)外文翻译(原文)院(系):桂林电子科技大学专业:电子信息工程学生姓名: xx学号: xxxxxxxxxxxxx 指导教师单位:桂林电子科技大学姓名: xxxx职称: xx2014年x月xx日Timing on and off power supplyusesThe switching power supply products are widely used in industrial automation and control, military equipment, scientific equipment, LED lighting, industrial equipment,communications equipment,electrical equipment,instrumentation, medical equipment, semiconductor cooling and heating, air purifiers, electronic refrigerator, LCD monitor, LED lighting, communications equipment, audio-visual products, security, computer chassis, digital products and equipment and other fields.IntroductionWith the rapid development of power electronics technology, power electronics equipment and people's work, the relationship of life become increasingly close, and electronic equipment without reliable power, into the 1980s, computer power and the full realization of the switching power supply, the first to complete the computer Power new generation to enter the switching power supply in the 1990s have entered into a variety of electronic, electrical devices, program-controlled switchboards, communications, electronic testing equipment power control equipment, power supply, etc. have been widely used in switching power supply, but also to promote the rapid development of the switching power supply technology .Switching power supply is the use of modern power electronics technology to control the ratio of the switching transistor to turn on and off to maintain a stable output voltage power supply, switching power supply is generally controlled by pulse width modulation (PWM) ICs and switching devices (MOSFET, BJT) composition. Switching power supply and linear power compared to both the cost and growth with the increase of output power, but the two different growth rates. A power point, linear power supply costs, but higher than the switching power supply. With the development of power electronics technology and innovation, making the switching power supply technology to continue to innovate, the turning points of this cost is increasingly move to the low output power side, the switching power supply provides a broad space for development.The direction of its development is the high-frequency switching power supply, high frequency switching power supply miniaturization, and switching power supply into a wider range of application areas, especially in high-tech fields, and promote the miniaturization of high-tech products, light of. In addition, the development and application of the switching power supply in terms of energy conservation, resource conservation and environmental protection are of great significance.classificationModern switching power supply, there are two: one is the DC switching power supply; the other is the AC switching power supply. Introduces only DC switching power supply and its function is poor power quality of the original eco-power (coarse) - such as mains power or battery power, converted to meet the equipment requirements of high-quality DC voltage (Varitronix) . The core of the DC switching power supply DC / DC converter. DC switching power supply classification is dependent on the classification of DC / DC converter. In other words, the classification of the classification of the DC switching power supply and DC/DC converter is the classification of essentially the same, the DC / DC converter is basically a classification of the DC switching power supply.DC /DC converter between the input and output electrical isolation can be divided into two categories: one is isolated called isolated DC/DC converter; the other is not isolated as non-isolated DC / DC converter.Isolated DC / DC converter can also be classified by the number of active power devices. The single tube of DC / DC converter Forward (Forward), Feedback (Feedback) two. The double-barreled double-barreled DC/ DC converter Forward (Double Transistor Forward Converter), twin-tube feedback (Double Transistor Feedback Converter), Push-Pull (Push the Pull Converter) and half-bridge (Half-Bridge Converter) four. Four DC / DC converter is the full-bridge DC / DC converter (Full-Bridge Converter).Non-isolated DC / DC converter, according to the number of active power devices can be divided into single-tube, double pipe, and four three categories. Single tube to a total of six of the DC / DC converter, step-down (Buck) DC / DC converter, step-up (Boost) DC / DC converters, DC / DC converter, boost buck (Buck Boost) device of Cuk the DC / DC converter, the Zeta DC / DC converter and SEPIC, the DC / DC converter. DC / DC converters, the Buck and Boost type DC / DC converter is the basic buck-boost of Cuk, Zeta, SEPIC, type DC / DC converter is derived from a single tube in this six. The twin-tube cascaded double-barreled boost (buck-boost) DC / DC converter DC / DC converter. Four DC / DC converter is used, the full-bridge DC / DC converter (Full-Bridge Converter).Isolated DC / DC converter input and output electrical isolation is usually transformer to achieve the function of the transformer has a transformer, so conducive to the expansion of the converter output range of applications, but also easy to achieve different voltage output , or a variety of the same voltage output.Power switch voltage and current rating, the converter's output power is usually proportional to the number of switch. The more the number of switch, the greater the output power of the DC / DC converter, four type than the two output power is twice as large,single-tube output power of only four 1/4.A combination of non-isolated converters and isolated converters can be a single converter does not have their own characteristics. Energy transmission points, one-way transmission and two-way transmission of two DC / DC converter. DC / DC converter with bi-directional transmission function, either side of the transmission power from the power of lateral load power from the load-lateral side of the transmission power.DC / DC converter can be divided into self-excited and separately controlled. With the positive feedback signal converter to switch to self-sustaining periodic switching converter, called self-excited converter, such as the the Luo Yeer (Royer,) converter is a typical push-pull self-oscillating converter. Controlled DC / DC converter switching device control signal is generated by specialized external control circuit.the switching power supply.People in the field of switching power supply technology side of the development of power electronic devices, while the development of the switching inverter technology, the two promote each other to promote the switching power supply annual growth rate of more than two digits toward the light, small, thin, low-noise, high reliability, the direction of development of anti-jamming. Switching power supply can be divided into AC / DC and DC / DC two categories, AC / AC DC / AC, such as inverters, DC / DC converter is now modular design technology and production processes at home and abroad have already matured and standardization, and has been recognized by the user, but AC / DC modular, its own characteristics make the modular process, encounter more complex technology and manufacturing process. Hereinafter to illustrate the structure and characteristics of the two types of switching power supply.Self-excited: no external signal source can be self-oscillation, completely self-excited to see it as feedback oscillation circuit of a transformer.Separate excitation: entirely dependent on external sustain oscillations, excited used widely in practical applications. According to the excitation signal structure classification; can be divided into pulse-width-modulated and pulse amplitude modulated two pulse width modulated control the width of the signal is frequency, pulse amplitude modulation control signal amplitude between the same effect are the oscillation frequency to maintain within a certain range to achieve the effect of voltage stability. The winding of the transformer can generally be divided into three types, one group is involved in the oscillation of the primary winding, a group of sustained oscillations in the feedback winding, there is a group of load winding. Such as Shanghai is used in household appliances art technological production of switching power supply, 220V AC bridge rectifier, changing to about 300V DC filter added tothe collector of the switch into the transformer for high frequency oscillation, the feedback winding feedback to the base to maintain the circuit oscillating load winding induction signal, the DC voltage by the rectifier, filter, regulator to provide power to the load. Load winding to provide power at the same time, take up the ability to voltage stability, the principle is the voltage output circuit connected to a voltage sampling device to monitor the output voltage changes, and timely feedback to the oscillator circuit to adjust the oscillation frequency, so as to achieve stable voltage purposes, in order to avoid the interference of the circuit, the feedback voltage back to the oscillator circuit with optocoupler isolation.technology developmentsThe high-frequency switching power supply is the direction of its development, high-frequency switching power supply miniaturization, and switching power supply into the broader field of application, especially in high-tech fields, and promote the development and advancement of the switching power supply, an annual more than two-digit growth rate toward the light, small, thin, low noise, high reliability, the direction of the anti-jamming. Switching power supply can be divided into AC / DC and DC / DC two categories, the DC / DC converter is now modular design technology and production processes at home and abroad have already matured and standardized, and has been recognized by the user, but modular AC / DC, because of its own characteristics makes the modular process, encounter more complex technology and manufacturing process. In addition, the development and application of the switching power supply in terms of energy conservation, resource conservation and environmental protection are of great significance.The switching power supply applications in power electronic devices as diodes, IGBT and MOSFET.SCR switching power supply input rectifier circuit and soft start circuit, a small amount of applications, the GTR drive difficult, low switching frequency, gradually replace the IGBT and MOSFET.Direction of development of the switching power supply is a high-frequency, high reliability, low power, low noise, jamming and modular. Small, thin, and the key technology is the high frequency switching power supply light, so foreign major switching power supply manufacturers have committed to synchronize the development of new intelligent components, in particular, is to improve the secondary rectifier loss, and the power of iron Oxygen materials to increase scientific and technological innovation in order to improve the magnetic properties of high frequency and large magnetic flux density (Bs), and capacitor miniaturization is a key technology. SMT technology allows the switching power supply has made considerable progress, the arrangement of the components in the circuit board on bothsides, to ensure that the light of the switching power supply, a small, thin. High-frequency switching power supply is bound to the traditional PWM switching technology innovation, realization of ZVS, ZCS soft-switching technology has become the mainstream technology of the switching power supply, and a substantial increase in the efficiency of the switching power supply. Indicators for high reliability, switching power supply manufacturers in the United States by reducing the operating current, reducing the junction temperature and other measures to reduce the stress of the device, greatly improve the reliability of products.Modularity is the overall trend of switching power supply, distributed power systems can be composed of modular power supply, can be designed to N +1 redundant power system, and the parallel capacity expansion. For this shortcoming of the switching power supply running noise, separate the pursuit of high frequency noise will also increase, while the use of part of the resonant converter circuit technology to achieve high frequency, in theory, but also reduce noise, but some The practical application of the resonant converter technology, there are still technical problems, it is still a lot of work in this field, so that the technology to be practical.Power electronics technology innovation, switching power supply industry has broad prospects for development. To accelerate the pace of development of the switching power supply industry in China, it must take the road of technological innovation, out of joint production and research development path with Chinese characteristics and contribute to the rapid development of China's national economy.Developments and trends of the switching power supply1955 U.S. Royer (Roger) invented the self-oscillating push-pull transistor single-transformer DC-DC converter is the beginning of the high-frequency conversion control circuit 1957 check race Jen, Sen, invented a self-oscillating push-pull dual transformers, 1964, U.S. scientists canceled frequency transformer in series the idea of switching power supply, the power supply to the size and weight of the decline in a fundamental way. 1969 increased due to the pressure of the high-power silicon transistor, diode reverse recovery time shortened and other components to improve, and finally made a 25-kHz switching power supply.At present, the switching power supply to the small, lightweight and high efficiency characteristics are widely used in a variety of computer-oriented terminal equipment, communications equipment, etc. Almost all electronic equipment is indispensable for a rapid development of today's electronic information industry power mode. Bipolar transistor made of 100kHz, 500kHz power MOS-FET made, though already the practical switching power supply is currently available on the market, but its frequency to be further improved. Toimprove the switching frequency, it is necessary to reduce the switching losses, and to reduce the switching losses, the need for high-speed switch components. However, the switching speed will be affected by the distribution of the charge stored in the inductance and capacitance, or diode circuit to produce a surge or noise. This will not only affect the surrounding electronic equipment, but also greatly reduce the reliability of the power supply itself. Which, in order to prevent the switching Kai - closed the voltage surge, RC or LC buffers can be used, and the current surge can be caused by the diode stored charge of amorphous and other core made of magnetic buffer . However, the high frequency more than 1MHz, the resonant circuit to make the switch on the voltage or current through the switch was a sine wave, which can reduce switching losses, but also to control the occurrence of surges. This switch is called the resonant switch. Of this switching power supply is active, you can, in theory, because in this way do not need to greatly improve the switching speed of the switching losses reduced to zero, and the noise is expected to become one of the high-frequency switching power supply The main ways. At present, many countries in the world are committed to several trillion Hz converter utility.the principle of IntroductionThe switching power supply of the process is quite easy to understand, linear power supplies, power transistors operating in the linear mode and linear power, the PWM switching power supply to the power transistor turns on and off state, in both states, on the power transistor V - security product is very small (conduction, low voltage, large current; shutdown, voltage, current) V oltammetric product / power device is power semiconductor devices on the loss.Compared with the linear power supply, the PWM switching power supply more efficient process is achieved by "chopping", that is cut into the amplitude of the input DC voltage equal to the input voltage amplitude of the pulse voltage. The pulse duty cycle is adjusted by the switching power supply controller. Once the input voltage is cut into the AC square wave, its amplitude through the transformer to raise or lower. Number of groups of output voltage can be increased by increasing the number of primary and secondary windings of the transformer. After the last AC waveform after the rectifier filter the DC output voltage.The main purpose of the controller is to maintain the stability of the output voltage, the course of their work is very similar to the linear form of the controller. That is the function blocks of the controller, the voltage reference and error amplifier can be designed the same as the linear regulator. Their difference lies in the error amplifier output (error voltage) in the drive before the power tube to go through a voltage / pulse-width conversion unit.Switching power supply There are two main ways of working: Forward transformand boost transformation. Although they are all part of the layout difference is small, but the course of their work vary greatly, have advantages in specific applications.the circuit schematicThe so-called switching power supply, as the name implies, is a door, a door power through a closed power to stop by, then what is the door, the switching power supply using SCR, some switch, these two component performance is similar, are relying on the base switch control pole (SCR), coupled with the pulse signal to complete the on and off, the pulse signal is half attentive to control the pole voltage increases, the switch or transistor conduction, the filter output voltage of 300V, 220V rectifier conduction, transmitted through the switching transformer secondary through the transformer to the voltage increase or decrease for each circuit work. Oscillation pulse of negative semi-attentive to the power regulator, base, or SCR control voltage lower than the original set voltage power regulator cut-off, 300V power is off, switch the transformer secondary no voltage, then each circuit The required operating voltage, depends on this secondary road rectifier filter capacitor discharge to maintain. Repeat the process until the next pulse cycle is a half weeks when the signal arrival. This switch transformer is called the high-frequency transformer, because the operating frequency is higher than the 50HZ low frequency. Then promote the pulse of the switch or SCR, which requires the oscillator circuit, we know, the transistor has a characteristic, is the base-emitter voltage is 0.65-0.7V is the zoom state, 0.7V These are the saturated hydraulic conductivity state-0.1V-0.3V in the oscillatory state, then the operating point after a good tune, to rely on the deep negative feedback to generate a negative pressure, so that the oscillating tube onset, the frequency of the oscillating tube capacitor charging and discharging of the length of time from the base to determine the oscillation frequency of the output pulse amplitude, and vice versa on the small, which determines the size of the output voltage of the power regulator. Transformer secondary output voltage regulator, usually switching transformer, single around a set of coils, the voltage at its upper end, as the reference voltage after the rectifier filter, then through the optocoupler, this benchmark voltage return to the base of the oscillating tube pole to adjust the level of the oscillation frequency, if the transformer secondary voltage is increased, the sampling coil output voltage increases, the positive feedback voltage obtained through the optocoupler is also increased, this voltage is applied oscillating tube base, so that oscillation frequency is reduced, played a stable secondary output voltage stability, too small do not have to go into detail, nor it is necessary to understand the fine, such a high-power voltage transformer by switching transmission, separated and after the class returned by sampling the voltage from the opto-coupler pass separated after class, so before the mains voltage, and after the classseparation, which is called cold plate, it is safe, transformers before power is independent, which is called switching power supply.the DC / DC conversionDC / DC converter is a fixed DC voltage transformation into a variable DC voltage, also known as the DC chopper. There are two ways of working chopper, one Ts constant pulse width modulation mode, change the ton (General), the second is the frequency modulation, the same ton to change the Ts, (easy to produce interference). Circuit by the following categories:Buck circuit - the step-down chopper, the average output voltage U0 is less than the input voltage Ui, the same polarity.Boost Circuit - step-up chopper, the average output voltage switching power supply schematic U0 is greater than the input voltage Ui, the same polarity.Buck-Boost circuit - buck or boost chopper, the output average voltage U0 is greater than or less than the input voltage Ui, the opposite polarity, the inductance transmission.Cuk circuit - a buck or boost chopper, the output average voltage U0 is greater than or less than the input voltage Ui, the opposite polarity, capacitance transmission.The above-mentioned non-isolated circuit, the isolation circuit forward circuits, feedback circuit, the half-bridge circuit, the full bridge circuit, push-pull circuit. Today's soft-switching technology makes a qualitative leap in the DC / DC the U.S. VICOR company design and manufacture a variety of ECI soft-switching DC / DC converter, the maximum output power 300W, 600W, 800W, etc., the corresponding power density (6.2 , 10,17) W/cm3 efficiency (80-90)%. A the Japanese Nemic Lambda latest using soft-switching technology, high frequency switching power supply module RM Series, its switching frequency (200 to 300) kHz, power density has reached 27W/cm3 with synchronous rectifier (MOSFETs instead of Schottky diodes ), so that the whole circuit efficiency by up to 90%.AC / DC conversionAC / DC conversion will transform AC to DC, the power flow can be bi-directional power flow by the power flow to load known as the "rectification", referred to as "active inverter power flow returned by the load power. AC / DC converter input 50/60Hz AC due must be rectified, filtered, so the volume is relatively large filter capacitor is essential, while experiencing safety standards (such as UL, CCEE, etc.) and EMC Directive restrictions (such as IEC, FCC, CSA) in the AC input side must be added to the EMC filter and use meets the safety standards of the components, thus limiting the miniaturization of the volume of AC / DC power, In addition, due to internal frequency, high voltage, current switching, making the problem difficult to solve EMC also high demands on the internal high-density mountingcircuit design, for the same reason, the high voltage, high current switch makes power supply loss increases, limiting the AC / DC converter modular process, and therefore must be used to power system optimal design method to make it work efficiency to reach a certain level of satisfaction.AC / DC conversion circuit wiring can be divided into half-wave circuit, full-wave circuit. Press the power phase can be divided into single-phase three-phase, multiphase. Can be divided into a quadrant, two quadrant, three quadrants, four-quadrant circuit work quadrant.he selection of the switching power supplySwitching power supply input on the anti-jamming performance, compared to its circuit structure characteristics (multi-level series), the input disturbances, such as surge voltage is difficult to pass on the stability of the output voltage of the technical indicators and linear power have greater advantages, the output voltage stability up to (0.5)%. Switching power supply module as an integrated power electronic devices should be selected。
毕业设计英文翻译

沈阳工业大学化工装备学院毕业设计(论文)外文翻译毕业设计(论文)题目:含硫氨污水冷却器外文题目:Head processing technology译文题目:封头加工工艺院(系):化工装备学院专业班级:过控0802班学生姓名:孙鹏博指导教师:闫小波2012年3月11日Head processing technology1.welding process1.1welding operationOur factory common welding methods are: manual welding, argon arc welding, submerged arc welding.(1) manual welding is mainly used for carbon steel 3-6mm plate welding.(2) submerged arc welding to more than 8mm carbon steel stainless steel sheet welding mainly.(3)3-6mm stainless steel argon arc welding with welding mainly. Commonly used stainless steel wire ER304and ER316L steel wire, commonly used to J422and J507and J426and J427low-temperature welding consumables. Flux of carbon steel used is the HJ431, stainless steel commonly used is HJ260,.As a result of welding wire flux can be easily affected with damp, stored in the infrared drying machine, flux HJ431and HJ260drying temperature is 250-300℃. Welding wire J422and J350drying temperature were 150℃ and 300 ℃Welding process is completely in accordance with the" welding" execution, sheet thickness determines the welding to welding or double sided arc welding in welding, after the weld seam inspection ( RT X ray ) judgment without pores, cracks and other defects, such as found in the above deficiencies, to the repair, until the filming.1.2 welding operation standard(1) welding procedure card after receiving process, affirm the process card and physical material, quantity, unit number, specifications, size instruction number is consistent, whether there is debris around the wafer, wafer splashes whether clean removal, such as treatment is not clean, will use the grinding clean.(2) there is no welding test plate, groove cutting quality can meet the requirement, material surface without obvious defects, such as abnormal response.(3) according to the" Regulations" welding procedure card check of welding groove type and dimensions correspond to.(4) on each side of groove surface grinding, butt edge offset is not greater than the10% thickness, and not more than1.5mm.(5) point fixed the first weld layer terminal welding length not less than 50mm, arc board specifications should be 150*150mm and a mask having R arc, team rounds should be given within 8 hours of welding, or to use flame to the moisture inside the baking groove.(6) the welder holds" welding" and" welding records" for welding consumables, welding two class library for registration, using flux field volume should not exceed 4 hours, or to continue to back into the oven drying.(7) a, preheating plate thickness not less than 30mm carbon steel, low alloy steel, the preheating temperature of welding process by" card"," standard" provisions of the welding technology.B, preheating range width not less than 4mm and no less than 100mm. C, in the process of welding groove at any time temperature shall not be less than the prescribed temperature.D, when welding temperature is below 0 ℃( arbitrary thickness) must be heated to 15 ℃or above in order to welding.(8) a before welding, welding to welding equipment inspection, examination was normal before welding facilities.According to B,"" the requirements of welding process welding, welding and fill in the recordsC, welding, welding layers shall be in accordance with" welding" requirements, welding shall not be a large current, less layers. (9) removal of the root a, stainless steel cleaning before the root groove sides, within the range of 300mm, splashing paint coating.B, using carbon arc air gouging, should be selected according to the request carbon rod diameter.C, root cleaning, grinding cleaning groove and two side the existence of carburized layer, oxide, slag and other sundries. Grinding width: manual welding, rust, oxide above 20mm, oil30mm above, automatic welding, rust, grease, oxides 25mm50mm groove inner grinding requirements, carbon steel, low alloy steelδn ≤10mm weld, its two ends within the range of 300mm carburized layer must be completely removed, the rest part allows the removal of more than 50%. Other non-ferrous metals must be completely clear. [3]D, root cleaning, composite steel Cr-Mo, manual welding and the thicknessofδn ≥30mm welds shall be examined by PT.(10) during the process of welding defect repair by welding repair welding repair monitor instruction experienced welders as. Repair welding process should eliminate soldering phenomenon, or polished after welding, the following defects must be removed before welding to welding crack,①partial②③pits the stomaA shall not be lower than the parent material, weld.B, there shall be no undercutting.C, without removing the residual high seam. The surface shall not have cracks, pores, crater, undercut and slag inclusions, and may not retain the slag and spatter.D, removal of residual high weld inspection shall not have any defect display PT.E, such as the defects of carbon steel, low-alloy steel repair procedures: a grinding wheel or a carbon arc gouging polishing cleaning→ PT check grinder grinding out the welding groove, welding, PT, stainless steel repair procedures: a grinding wheel or a carbon arc gouging polishing cleaning→PT (δ n≥ 2mm need )→grinder polished to a welding groove welding→ PT examination. [4](12) welded internal rework, repair procedures: location of defect, defect removal→ PT→→removal check welding weld→ PT examination. [5] (13) according to RT film, RT staff and the welders in welding seam together determine the location of defects, including the following requirements when using UT to determine the defect position, the first repairδ n≥ 30mm use UT to determine the location of defects, two or three repairδ n≥ 20mm using UT to determine the defect position, UT positioning by RT after class. The position and depth of defect ( calibration side shall be the depth of defect≤1/2 side).(14) after the welding inspector or monitor by confirmed, in the process card signed your name and object together with transfer to the next process, by the next process responsibility recognition can.2.stamping process2.1stamping operationStamping operation is small head forming an important operation. The same stamping is also head of the cracking, thinning appeared most processsection.2.2punching machine.(1) the master cylinder is mainly used to connect the die head, is the head forming the necessary parts.(2) side cylinder used for pressing die ring, fixing the upper and lower mold ring of head disk. The head in the pressing process is to prevent the crease, as an important part of the drum kit.(3) the overflow valve used for controlling the compressor overall pressure, prevent the wafer during the pressing process of tears. (4) stamping valve in pressure, stamping valve on pressure relief, achieve average pressure effect.In addition, circuit boards, motors, circuit boards, storage tank, operation platform, pedestal are stamping machine components.2.3.3 stamping operation steps(1) first of all to undertake a blanking process card, find a good wafer.(2) the control process card on the technological requirements, put ona set of corresponding die, and with the use of gauges to determine the selected die size and to suppress the wafer size.(3) the wafer is clamped on the upper and lower mold inside the circle, and determine the die head of the center point and the center point of the wafer in a straight line.(4) the operation ring mold and die relative motion, pressure test, according to the control rod rebound to judge the size of the pressure, thereby regulating pressure size.(5) pressure test end, pressed wafer, stamping.2.3the stamping operation standard(1) the control task orders, confirm physical and process card is consistent, according to the process card confirming workpiece number, material, specification, batch number and other factors, at the same time check wafer end there is no crack, burr, polished wafer whether it meets the requirements, whether chamfer, is facing the good, there are special requirements when the problem is found, in time to contact.(2) according to the process card correct selection of die mold surface, inspection, found bruises and serious injury must be polished, but must be clean mold surface corrosion and dirt.(3) according to the technology card size, shape, texture, straight edge higher to suppress.(4) the warm-stamping ( according to requirement sheet property is heated to a certain temperature, and then stamping process ), to prepare a baking gun, gas, oxygen, percussion with head shall prepare the corresponding template, double-sided film to the wafer edge of both sides in a range of about 200-300mm template removal, and clear the film surface. [6] (5) mounted on the lower die, as the case to join the die pad, the wafer inside and outside surface coated with oil, applied range of top to200-300mm, smear should be uniform, the upper and lower mold are evenly coated.(6) the first gold stamping head, hanging out with a model head, check section shape, at the same time, check whether the drum kit, and there is no thinning, and check the surface has no scratch, hoop printing, such as none of the above abnormalities can continue to stamping, head forming, sealing surfaces such as scratches are timely grinding, and confirm the minimum board thickness, confirm whether a scratch, strain, curved peel, orange peel, drum kits, wrinkle, hoop printing etc..(7) such as a head drum kit fold phenomenon should be together with the card with the move to rework process technology.(8) each head should be able to see the instruction, piece number, material, or to transplantation, each product specifications after testing, the process card ( to sign the name ) together to the next process, by the next process validation.3.pressure drum process3.1pressure drum operationPressure drum process and stamping processes are the same steps in the process, stamping process range of φ 159- φ1900mm and pressure drum process is in the range of φ 1600- φ4800mm. And stamping is different pressure drum mostly the head generally forming, eventually forming is completed by spinning, stamping without the special requirements of customers, eventually forming step is not required. φ 1600- φ1900mm heads the two processes is needed.3.2pressure drum machine.(1) the main cylinder is provided with an upper die head is pressed drumexecution as long as part of.(2) supporting seat fixed lower die and upper die head center in a straight line.(3) supporting frame1is provided with a rolling wheel, a position adjusting before and after.(4) supporting frame is provided with a rolling wheel rotating disk II. In addition, there are hydraulic system, the motor, oil pump, oil tank, and a control console.3.3pressure drum machine operation steps(1) first of all to undertake a blanking process card, find a good wafer.(2) the control process card on the technological requirements, put ona set of corresponding die, and with the use of gauges to determine the selected die size and to suppress the wafer size.(3) and stamping machine is different from the original film is not pressure drum center began to suppress, but from the wafer edge, as long as the die and wafer alignment on the line.(4) the pressing process is continuously by controlling the rotation wheel is driven by the rotation of a wafer rotating, according to a certain order to suppress.(5) in after the pressing process, prepared template matching. If a deviation to make further adjustments.3.4pressure drum operation standard(1) die on the quality of the products and the smooth pressure drum forming crucial. Therefore, require that the operator must according to the processing situation of choice for mold and timely adjust shim plate.(2) the operator receives the process card, see process card, according to the process card check objects, to confirm the real instruction, one-piece, material. Number, batch number etc.. According to the choice of mold process card.(3) for EHA, EHB head shapes have adopted the 0.82*D standard selection, for DHB, PSH, MD and other special products according to technology card selection of mold, but in principle according to P*0.82/1.15or P*0.82/1.2 standard selection. [1](4) pressing carefully before inspection wafer quality, no seam wafer end is smooth, there is no gap, surface has no cutting slag and defects.(5) a weld in addition to carefully check the end of the wafer wafer defects, at the same time should be checked for weld seam is higher than that of base metal, weld ends of are welding spatter, weld end grinding smooth, there is no crack notch.(6) two or two or more superimposed when pressed, each slice of the joint surface should be clean, according to the circumstances must entrust welding class, the wafer is welded together to suppress.(7) detection of wafer thickness ( the thickest, most thin, whether and process card, measurement of wafer size and process card.(8) suppression must be removed before the inside and outside surface of all debris, to prevent pitting appeared.(9) for general stainless steel materials ( more than 5mm plate ) using Teflon plate mold and the lower mold dressing on surface polished smooth ( necessary nowadays mold to Teflon plate. ) to ensure the surface quality of the workpiece, while in the process of the pressing need to avoid debris into molds and semi-finished products. [6](10) the pressing process, when the wafer is a R shape, must use the corresponding R model measurement, the pressing process should be considered to adjust the pressure deformation degree.(11) pressing is finished, the measurement of plate thickness, measuring arc length. Check surface quality, check end and weld end is smooth ( necessary to polish out the ceremony ).(12) to check the semi-finished product with process card is on the move to the next process ( and sign the name ) by the next process to confirm acceptance before.4.spinning process4.1spinning operationThe spinning process is pressed after the drum head molding process, mainly for large head R and straight edge formation.4.2spinning machine.(1) forming wheel is connected to the corresponding mold, forming in the head inside, mold top with half formed head R and straight edge is tangent to tangent.(2) supporting wheel is also connected and molded wheel mold, forming in the head outside, and a forming wheel tangent.(3) base for fixing head, and the bottom according to head size before and after moving, the head should be installed so that the center of the base and the head of the center in a straight line.(4) the center rod is used for fixing head, and the center and the center of the base is in a straight line.In addition to the motor, a circuit board, is connected to the shaft, anda control console.4.3spinning procedure(1) to undertake pressure drum process card, according to the card to determine the corresponding head spinning.(2) according to the head of the diameter, select the corresponding upper and lower mold.(3) the clamping head, ensure that the head of the center point and the center of the base point in a straight line.(4) to adjust the molding wheel and the head of tangent, then according to the forming wheel position adjustment roller.(5) in the spinning process to observe the forming roller and the supporting roller relative position, and continue to use the template on the line alignment. Until the R reaches the requirements.4.4spinning operation standard(1) spinning wheel material for steel bearings or ductile iron, mold on the quality of the products and can spin forming closely related, therefore the operator must be processed according to choose suitable mold, at the same time, because of the shape of the mold and the surface condition of the quality of the workpiece has a great influence, therefore, before processing and machining process must on the mold for full inspection.(2) according to the process card requirements, confirm wafer, pressure drum or preload semi-finished instruction number, specifications, quantity of material, compliance, and check the quality of surface and end with no defect, abnormal timely and on the procedures of contact, and in a timely manner(3) check the semi-finished end is smooth, with or without notch, crack, surface has no cutting or welding slag, and shall inspect the weld seam is higher than that of base metal, weld ends whether spatter, weld end grinding smooth, there is no crack. [7](4) pressure drum or to the press after the finished product, must checkfor folding, cracking, crack is not conducive to the spinning processing defects.(5) for stainless steel workpiece, through to the pickling method of decontamination.(6) according to the process card selection of mold, general small arc r size requirements as a basis for selecting the internal wheel. (7) according to the different material, thickness of plate and sheet rebound, selection is slightly smaller than the internal wheel circular arc R.(8) for the special requirements of the product, according to its shape design inside the wheel, confirm the mold surface, good polishing processing.(9) spinning processing, in order to prevent scratching and improve the processing performance, suitable lubricant ( grease ) to prevent process heating head appears on the surface of hot cracks and scratches, can also prolong the service life of die.(10) the spinning process, should be considered a workpiece shaping and timely for pressure adjustment.(11) after the molding process, deal with the size, shape, thickness, surface quality inspections, confirmation.(12) molded product with the card with the transfer process to the next process ( in the process card signed their name ) by the procedures under the inspector or monitor check before.5.groove processThe 5.1groove Essentials(1) groove process is a head of the data ( including circumference, total height) to achieve JB/T4746 standard key process. [1](2) groove is in order and cylinder head connection time, make welding more thoroughly.(3) the main groove cutting process and cutting process tools, is the use of plasma cutting.(4) cutting, according to the card on the technological requirements, determine groove type ( inner groove, outside the mouth, X groove ) and determine the groove angle.(5) the groove before the head splashing agent applicator.(6) groove when the first test slope, then a protractor measuring angle, identified in the tolerance range, after adjustment, the whole slope. The 5.2groove operation standard(1) according to the process card to find real, order confirmation No., specification, material, batch number, quantity and check whether the workpiece has a drum kit, crack, delamination, wrinkle, and whether the loss of a round, found problems in a timely manner to contact, processing, the plate thickness of more than 8mm, is suggested to lose the round groove, the following 6mm, tooling plate pressure is groove.(2) stainless steel head, should be in the groove wall smearing splash front head agent, prevent groove, slag spout to head on the wall. (3) head onto the beveling machine before, first confirm the head weight, based on the weight of suitable sling, sling safety inspection.(4) head onto the groove machine, beveling rotary table adjustment screw rod, with a center adjusting position, rotating table, is aligned to the center.(5) groove, according to technology card height and height tolerance groove height ruler to draw lines, confirm the high line, the slope slope, should first slope flat groove, and then the slope groove.(6) outside the mouth or the inner groove angle should be controlled within ± 2.5 tolerance.(7) groove after, should check the head circumference, height, straight edge, angle, if not qualified to repair process, repair.(8) qualified head will remove and clean the slag grinding head internal slag, together with card transfer to the next process ( and sign their name ) by the next process inspector confirmation can be.6.polishing process6.1 polishing process steps(1) according to the card process requirements, identify the need for polishing head.(2) the head rotating table, determine the level of, the clamping head.(3) polishing from edge to center, or from the center to the edge; according to the diameter size determine the head beam, lower speed and working stage, after moving speed.(4) check the polishing condition, appropriate for rework.The 6.2polishing operation standard(1) according to the process card and materials to confirm the product instruction number, specifications, material, batch number, quantity, and check whether the workpiece has a drum kit, crack, delamination defects, and whether the loss of a round, found problems in a timely manner to contact, processing, check the appearance, to determine the need for manual processing, the polishing before hook head to mark.(2) according to the requirements of the choice of using a polishing, polishing pads, and the necessary auxiliary tool.(3) confirm the head weight, based on the weight of suitable sling, and check whether the safety hanger.(4) the head hanging onto a work table, adjust the center, at the same time to ensure that the head is in the basic level (0-5 deviations ).(5) people in the scene when polishing polishing, attention, especially the left centre, speed fast, or outward from a center left, a little pressure to increase, from the edge to the center of pressure during polishing, to a little decrease in polishing head, thin wall, as the case may be mounted shockproof wheel, at the same time attention to mechanical work has no abnormal.(6) after the completion of inspection head polishing, with or without defect, and the necessary contact.(7) the Polish well head with coated packaging, in the process card signed their names, together with the head and process the card with the circulation storage, and by the next inspection approval.封头加工工艺1.焊接工序1.1 焊接操作我们厂常用的焊接方法有:手工焊、氩弧焊、埋弧焊。
- 1、下载文档前请自行甄别文档内容的完整性,平台不提供额外的编辑、内容补充、找答案等附加服务。
- 2、"仅部分预览"的文档,不可在线预览部分如存在完整性等问题,可反馈申请退款(可完整预览的文档不适用该条件!)。
- 3、如文档侵犯您的权益,请联系客服反馈,我们会尽快为您处理(人工客服工作时间:9:00-18:30)。
水解胶原蛋白:一种用在棉花和皮革染色新的添加剂摘要:本文介绍了水解胶原蛋白在对棉花和皮革染色上的影响。
首先,概括了将水解胶原蛋白与直接或阴离子染料在不同pH值下的配伍性研究。
利用被染色的棉花和皮革各种组分进行了水解胶原蛋白实验,其中pH值也非常重要,实验结果表明,在有水解胶原蛋白的协同效应下对皮革进行染色,而以棉花为例效果不太明显,另外也介绍了有一种可能避免使用盐和重用的残余浴染色。
关键词:水解胶原蛋白、棉和皮革、染色1. 介绍无论是纺织和皮革行业都面临着显着的环境问题。
主要是在湿处理部分,传统的棉花和皮革染色过程中产生的巨大的废水,其中残存的染料和盐的量较大。
这个问题是主要是由于染料的低亲和力的基板。
此外,在盐浴中流失染料的量意味着可能不仅仅是环境问题的经济损失。
胶原蛋白是一种天然的皮革的工业副产品,在化妆品和护肤品有很多应用。
可以从皮革的不同步骤产生的废物中获得。
它是以其非凡的保湿能力而备受注意[ 1,2 ]。
胶原蛋白,一旦水解就变成一种混合物肽。
为了从制革中获得水解胶原蛋白垃圾,水解过程是实现通过酸,碱或酶。
在工业,化学和酶的方法主要用于获得蛋白质水解物。
碱处理比的酸是更柔和,更适合获得工业水解产物。
在碱性环境中的酶水解在温和的温度是强烈建议,因为它允许为了得到的产品具有不同的化学反应控制功能特性。
肽键的可达性酶解是非常重要的,由于蛋白质的结构这些可能无法进入。
一种变性预处理可以促进后续的酶攻击[ 3 ]。
不同的过程是在参考文献[ 4 ]描述获取蛋白质水解牛皮废料,主要是基于氢氧化钙的化学过程。
隐藏的废物也可以碱蛋白酶下水解[ 5,6 ]。
酶法优于化学因为它是更环保的过程。
研究了在动物的皮肤组织的水提取在40e70 C在不同pH [ 7 ]酶处理。
水解胶原蛋白是用于洗涤剂配方提供纺织品保护和整理效果。
但实际上在水解胶原蛋白在没有参考应用纺织品和皮革染色。
用直接染料染棉涉及到大量的盐的使用。
同时,它是很难在皮革染色获得均匀的色调。
这些变化在颜色和音调是由于原料的性质,它在矩阵[ 8e10 ]的变化。
在这种情况下,它是将知道棉花和皮革染色效率过程可以通过将胶原蛋白的改进。
2. 实验2.1 材料平纹织物漂白,无荧光增白剂,180克/平方米重量值的电子探针(参考210),原产于西班牙羊皮制成的镀铬的绵羊皮革,直接染料天狼星黄k-cf(C.I.直接yellow86),小天狼星的蓝色s-brr(C.I.直接蓝71)和天狼星红k-be(C.I.直接红243),阴离子皮革染料鞍快速黄R(C.I.直接黄11),蝶鞍快速红E(C.I.直接红239)和蝶鞍快速蓝BBN(C.I.酸性蓝83),用于商业细菌来源的碱性蛋白酶2.2 水解胶原蛋白的制备牛皮废料的装饰是一种使酶作用的热处理。
酶水解是在生物统计学的 B反应器进行监测微生物燃料电池(布劳恩生物科技国际公司)。
发现0.1% o.w.f.的最佳条件碱性蛋白酶酶在pH 9.5和50e60 C ,作用2小时后,酶失活提高到20分钟90个,用温度进一步调节至pH值为4.5节约水解蛋白。
得到的肽混合的各种分子量。
完整的分数一样从三个不同的组分(高,中,低)的基础上得到的分子量。
2.3 相容性的研究相容性的完整的部分水解所有选定的直接和阴离子dyeswas研究胶原细节。
研究是由溶液制备的95:05进行水的比例:水解胶原蛋白在不同的pH值3,5,7,9,和1% o.w.f.各种染料混合。
样品保持24 h和兼容性是直观地观察。
一个空白的研究还没有进行水解胶原蛋白,为了比较的结果。
2.4 常规棉的染色工艺棉花样品与红色的直接染料染色,天狼星红k-be(1% o.w.f.)。
20 g / L的钠氯德瓦斯加入染浴在染色过程中[11,12]开始。
染色用在染色机80 C 30分钟40转的速度和材料白酒类比固定为1:20。
2.5 水解胶原蛋白的染色工艺初步筛选试验表明,90∶10的比例水:胶原蛋白是直接染料的情况下最好的。
因此,棉花样品与天狼星红k-be染色(1% o.w.f.)使用这个比例和pH调节至4.7,用盐酸。
本研究使用完整的进行,高,中水解胶原蛋白低分数。
染色进行了一个在染色机80 ℃30 min的速度在每分钟40转与材料固定在白酒类比1:20。
在染色水解胶原蛋白,没有加入盐和与对照样品,按常规方法染。
2.6 残余浴重用在常规和水解胶原蛋白的结束过程,残余染液量与水和棉花样品调整增加。
染色的进行上面的程序。
常规染色(1% o.w.f.)是镀铬的进行利用红阴离子染料皮革,蝶鞍快速红E染色开始在pH 5.5和后来增加至pH 6.5和最后结束pH值3以固定的颜色。
在并行改进染色工艺将水解胶原蛋白进行。
基于的初步研究结果,各组分的重量进行了调整,使重量含量E水解活性胶原蛋白E 5%浴中。
此外,染料水解胶原蛋白是分两批加入被发现比单独添加。
2.7 表征水解胶原蛋白的各种组分进行了分析在变性的聚丙烯酰胺凝胶电泳SDS-PAGE条件。
在相容性研究,样本直观地分析以确定水解的影响在不同pH 对染料的胶原蛋白。
样品被评为上一个规模0e4。
染色棉样品进行5次在40 C 国内洗涤后,程序6A标准,EN ISO 6330,使用清洁剂iec-a *在一个国际标准缩水试验机洗衣机。
然后将样品在一个平坦的表面干燥,根据标准的C程序。
皮革样品进行5个循环洗涤每IUF 423,用十二烷基硫酸钠硫酸在邦博simplex-4洗衣桶洗涤剂。
的未洗和水洗的样品进行了分析,用分光光度法测量的K/S值(颜色)。
染色棉的样品也进行水洗牢度测试根据EN ISO 105-c06,采用ECE磷酸盐洗涤剂无荧光增白剂在gyrowash FOM 71 MP的实验室设备。
评估了皮革样品的耐洗牢度邦博simplex-4,按IUF 423和灰度评价根据IUF 131。
干、湿摩擦牢度以每UNE-EN ISO染色棉和皮革样品105-x12 IUF和450,分别3. 结果与讨论3.1 水解胶原蛋白的制备水解胶原蛋白得到混合各种不同分子量的组分。
这完全分数超滤得到的高,中,低分子量分数。
含有高分数的分子量高于15000大,介质中含有5000分子量15000大和低分数有分子量小于5000大。
这些组分的化学特性,给出了表1。
据观察,在干物质明显减少重量,从高到低的组分有机和蛋白质含量。
图1显示通过SDS-PAGE分析蛋白条带分析完整的(CF),高(HF),中等(MF)和低(LF)馏分。
蛋白质凝胶的分子标记,“万花筒染标准的“伯乐(P)被用来确定确切的的馏分的分子量。
13和15 kDa的特异性条带观察到完整的分数,13,15和20 kDa的高分数,13和15 kDa的中等分数和不带对低分子组分在这个范围。
3.2 相容性的研究据称,水解胶原蛋白的相容性在不同pH各种染料,以确定最佳的染色条件。
水的95:05比例:水解猪皮选择为了确定是否固定染料是一个非常小的浓度的水解更好胶原蛋白。
一个空白的研究还没有进行水解胶原蛋白,为了比较的结果。
空白样品研究了编码如表2所示,样品中含有水解胶原蛋白在表3。
该解决方案进行了分析,直观地知道效果水解胶原蛋白在染料通过观察是否有任何沉淀,沉淀,结块或相分离。
此外,该参考期间的颜色以下的样品规模:0:透明的溶液,但小打火机;1:透明溶液,但小暗;2:透明的溶液,但暗;3:混浊4:非常浑浊。
表4显示的相容性研究的结果基于水的直接和阴离子染料的视觉观察和水解胶原蛋白溶液在不同pH。
结果表明,在一般的染料是兼容的除了与水解胶原蛋白在pH 3所有小灵通。
的水解胶原蛋白,等电点为5.2,所以它成为阳离子在较低的pH,从而与阴离子染料静电产生沉淀或沉降颜色变化。
在黄色的阴离子染料的情况下,溶解度随着水解胶原蛋白加普遍增加。
它也看来,水解胶原蛋白可以作为表面活性剂的降低表面张力。
3.3 棉的染色工艺棉花的传统直接染色进行了高量的盐和碱性pH在初步研究中,我们进行了以水解胶原蛋白棉治疗在酸性pH值,其次是在碱性pH值。
结果盐染色从这个染色工艺结合水解胶原蛋白被认为是常规工艺差多了。
在为了解释的结果,其作用机制的水解在不同pH胶原的阐明和展示表5。
如前所述,等电点的水解胶原蛋白是在5.2。
棉花,一旦注入水总是表明阴离子字符[ 13 ],而离子电荷的水解胶原可能取决于pH值。
在pH低于其变化等电点表明阳离子性质和在较高的pH它阴离子字符显示。
所以我们认为水解在酸性pH胶原蛋白可以在染色盐相同的作用的过程,从而降低染料与棉之间的斥力。
但在更高的小灵通,水解胶原蛋白在本质上是阴离子将提高染料与棉,因此之间的斥力在染色具有有害的影响。
pH值对离子的影响水解胶原蛋白收费,但没有盐的加入。
一些方法如阳离子化化学预处理已被提出,为了避免使用盐在棉印染过程[ 12 ]。
我们试图使棉通过将胶原蛋白水解的阳离子,这是一种天然的生态产品。
为了确定最佳的稀释水解胶原蛋白在水,我们首先研究了染色不同稀释95:05一样,90:10,80:20和发现90:10被示出最好的结果。
因此,固定在90:10与样品是在表6中的描述。
每一个分数是不同的分子的重量和全馏分的混合物的所有。
传统的染色也进行了比较。
3.4 染色棉颜色的评价棉花样品的K / S值染色使用在LMAX 530相比,常规染色的胶原水解各种馏分。
从图中观察到,样本用常规方法染出最高的K / S值和胶原蛋白的使用降低了颜色的强度。
在所有的样品染色采用水解胶原蛋白,低分子分数给最好的结果。
类似的趋势持续,洗涤5次后。
即使我们已经取得了较低的染料的吸收值与水解胶原蛋白比在传统的过程中,我们取得了无盐染色。
如表5所示,在pH<5之间有水解胶原蛋白和棉花的协调。
的水解胶原蛋白得到固定的静电,减少棉花的负电荷。
此外,与水解的染色工艺胶原蛋白可以避免染浴中加入盐。
在另一方面,很明显,染料不会固定在pH对棉花> 7有一个电荷相斥的棉花,染料和水解胶原蛋白。
但要注意,有可能染棉有趣直接染料在酸性pH值而不使用盐。
因此,胶原蛋白可以发挥盐作用减少相同的电荷相斥,有助于固定导致染料不含盐废水。
水解胶原蛋白是一种天然的产品可生物降解,不提出任何环境关注。
3.5 棉花的牢度性能表7显示了洗涤和摩擦牢度的棉花样品染色采用水解胶原蛋白各种馏分与传统的染色工艺。
正如从表中观察到的样品,采用水解胶原表现出类似的洗涤牢度的传统样品。
这证明水解胶原蛋白在加染浴洗上没有任何负面影响的样品色牢度。
此外,干、湿摩擦牢度测试已经实现了每个样本。
在场的所有样品在干摩擦牢度和湿好结果的平均结果摩擦牢度。
因此,胶原蛋白水解不影响样品的摩擦牢度。
3.6 残余浴重用作为染液废水会造成重大环境问题,利用剩余浴可以解决。