轧制过程中的宽展
项目05 轧制过程中的横变形-宽展
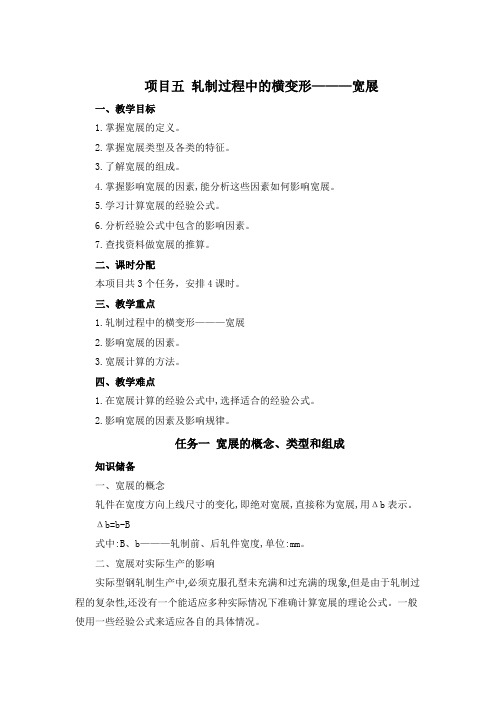
项目五轧制过程中的横变形———宽展一、教学目标1.掌握宽展的定义。
2.掌握宽展类型及各类的特征。
3.了解宽展的组成。
4.掌握影响宽展的因素,能分析这些因素如何影响宽展。
5.学习计算宽展的经验公式。
6.分析经验公式中包含的影响因素。
7.查找资料做宽展的推算。
二、课时分配本项目共3个任务,安排4课时。
三、教学重点1.轧制过程中的横变形———宽展2.影响宽展的因素。
3.宽展计算的方法。
四、教学难点1.在宽展计算的经验公式中,选择适合的经验公式。
2.影响宽展的因素及影响规律。
任务一宽展的概念、类型和组成知识储备一、宽展的概念轧件在宽度方向上线尺寸的变化,即绝对宽展,直接称为宽展,用Δb表示。
Δb=b-B式中:B、b———轧制前、后轧件宽度,单位:mm。
二、宽展对实际生产的影响实际型钢轧制生产中,必须克服孔型未充满和过充满的现象,但是由于轧制过程的复杂性,还没有一个能适应多种实际情况下准确计算宽展的理论公式。
一般使用一些经验公式来适应各自的具体情况。
三、宽展种类1.自由宽展2.限制宽展3.强制宽展四、宽展的分布1.双鼓形2.单鼓形3.平直形4.实际意义任务二影响宽展的因素知识储备影响宽展的因素及影响规律1.压下量Δh基本规律:随着压下量的增加,宽展也增加。
2.轧辊直径基本规律:随着轧辊直径增大,宽展量增大。
3.轧件宽度基本规律:轧件宽度增大,即变形区平均宽度增加,横向流动阻力增大,宽展减小。
4.摩擦系数基本规律一般情况(短变形区),宽展随摩擦系数的增大而增大;对长变形区,随摩擦系数的增大,宽展可能保持不变。
5.轧制道次在总压下量相同的条件下,轧制道次越多,总的宽展量越小。
6.后张力基本规律:在后张力作用下,延伸增大,宽展减小,且宽展量随后张力的增大成线性。
7.工具形状工具形状对宽展的影响分为两方面,一方面是指轧制时所用的工具(圆柱形轧辊有利于轧件的延伸)形状不同于其他加工方式;另一方面是指孔型形状的不同对宽展所产生的影响也不同。
塑性变形与轧制技术:宽展的概念及种类

限制宽展
在斜配孔型内的宽展
三、宽展的种类
3、强迫宽展
坯料在轧制过程中,被压下的金属体积受轧辊凸峰的切展而强制金属横向流 动,使轧件的宽度增加,这种变形叫做强制宽展。
例如:立轧孔内轧制钢轨、轧制扁钢时采用的“切展”孔型。 特点:可以用宽度较小的钢坯,轧制成宽度较大的成品。 注意:强迫宽展在剧烈的不均匀变形条件下产生。
宽展的概念及种类
一、宽展的概念 二、宽展的意义 三、宽展的种类
主要内容
一、宽展的概念
金属在轧制过程中,由于轧制力的作用,轧件在高度方 向上被压缩的金属体积将流向纵向和横向,流向横向的金 属使轧件产生横向变形,产生宽展。
图1-1 轧制示意图
一、宽展的概念
轧制前、后轧件横向尺寸的绝对差值,称为绝对宽展,简
济指标亦有着重要的保证。
三、宽展的种类
根据金属沿横向流动的自由程度,宽展可分为: 自由宽展,限制宽展和强迫宽展。
图4-12 自由宽展
图4-13 限制宽展 展
图4-14 在斜配孔型内的宽
图4-15 强迫宽展 a)-钢轨底层的强迫宽展;b)-切展孔型的强迫宽展
三、宽展的种类
1、自由宽展 轧件在轧制过程中,金属高度受到压缩而可以自由横向展
称为宽展。以Δb表示。即 b b B
a)
b)
图4-1 矩形断面工件轧制前后的尺寸
a)加工前矩形坯料;b)加工后矩形轧件
二、研究宽展的意义
1)给定坯料尺寸、压下量可以确定轧后产品的尺寸; 或已知轧后轧件尺寸、压下量,可以确定坯料尺寸。 2)在孔型设计中,可以利用轧后产品要求,反推出轧件
孔型设计尺寸; 也可以利用宽展确定孔型是恰好充满、未充满还是过充满。 3)正确估计宽展值,对于实现负公差轧制,改善技术经
塑性变形与轧制技术-轧制过程中的横变形-宽展
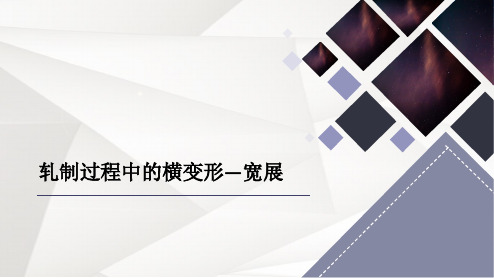
图 5-9 轧件宽度对宽展影响
二 影响宽展的因素
实施
实施
二 影响宽展的因素
二 影响宽展的因素
实施
Байду номын сангаас
二 影响宽展的因素
实施
二 影响宽展的因素
实施
三
计算宽展
学习目标
1. 学习计算宽展的经验公式。 2.分析经验公式中包含的影响因素。 3.查找资料做宽展的推算。
描述
三 计算宽展
依据实际轧制条件,在宽展计算的经验公式中,选择适合的经 验公式。借助资料确定公式参数,应用于得出这些公式或系数的 条件中,估算出很接近于实际情况的宽展值。
轧制过程中的横变形—宽展
项目导入
轧制过程中,轧件的高度受到压缩而减小,变形金属将沿着纵向流动而 产生延伸变形,同时,也沿着横向流动而产生宽展。研究并掌握宽展的变化 规律,正确估计宽展的大小,在制定轧制工艺制度时,确定轧制后的尺寸以及 根据用户品种规格需求选择坯料尺寸,都具有重要意义。若对宽展量计算不 正确,将会导致轧制废品。在此项目中,我们就来分析宽展的变形规律和确 定方法。
实施
三 计算宽展
宽展的计算公式 影响宽展的因素也很多,只有在深入分析轧制过程的基础上,正确考虑主要因素
对宽展的影响后,才能获得比较完善的公式。 一、若兹公式
二、艾克隆得公式
实施
三 计算宽展
三、在孔型中轧制时计算宽展的简化方法 【例5-1】 已知轧制前轧件断面尺寸H×B=100mm×200mm ,轧件厚度h=70mm , 轧辊材质为铸钢,工作直径为650mm,轧制速度v=4m/s,轧制温度t=1100℃,轧件 材质为Q235,依据给出的资料,试计算该道次的宽展量。
实施
图 5-1 由于宽展计算产生的缺陷
宽展
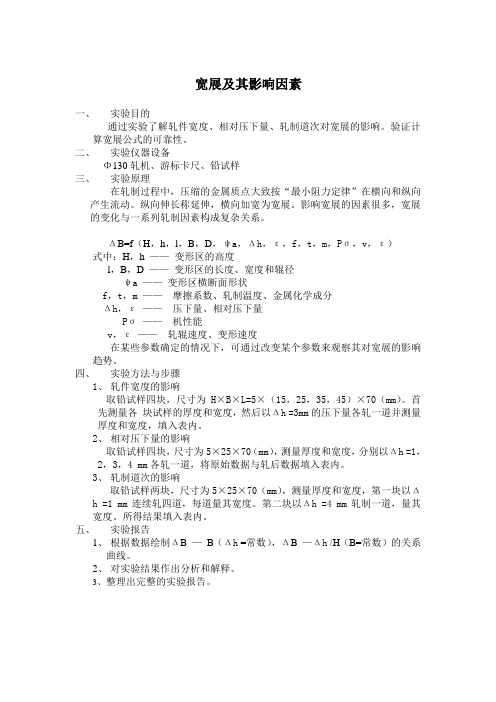
宽展及其影响因素一、实验目的通过实验了解轧件宽度、相对压下量、轧制道次对宽展的影响。
验证计算宽展公式的可靠性。
二、实验仪器设备Φ130轧机、游标卡尺、铅试样三、实验原理在轧制过程中,压缩的金属质点大致按“最小阻力定律”在横向和纵向产生流动。
纵向伸长称延伸,横向加宽为宽展。
影响宽展的因素很多,宽展的变化与一系列轧制因素构成复杂关系。
ΔB=f(H,h,l,B,D,ψa,Δh,ε,f,t,m,Pσ,v,ε)式中:H,h ——变形区的高度l,B,D ——变形区的长度、宽度和辊径ψa ——变形区横断面形状f,t,m ——摩擦系数、轧制温度、金属化学成分Δh,ε——压下量、相对压下量Pσ——机性能v,ε——轧辊速度、变形速度在某些参数确定的情况下,可通过改变某个参数来观察其对宽展的影响趋势。
四、实验方法与步骤1、轧件宽度的影响取铅试样四块,尺寸为H×B×L=5×(15,25,35,45)×70(mm)。
首先测量各块试样的厚度和宽度,然后以Δh =3mm的压下量各轧一道并测量厚度和宽度,填入表内。
2、相对压下量的影响取铅试样四块,尺寸为5×25×70(mm),测量厚度和宽度,分别以Δh =1,2,3,4 mm各轧一道,将原始数据与轧后数据填入表内。
3、轧制道次的影响取铅试样两块,尺寸为5×25×70(mm),测量厚度和宽度,第一块以Δh =1 mm连续轧四道,每道量其宽度。
第二块以Δh =4 mm轧制一道,量其宽度。
所得结果填入表内。
五、实验报告1、根据数据绘制ΔB —B(Δh =常数),ΔB —Δh /H(B=常数)的关系曲线。
2、对实验结果作出分析和解释。
3、整理出完整的实验报告。
单位(mm)。
011 轧制过程宽展
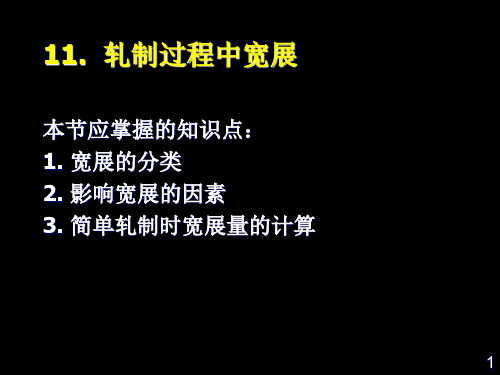
BH C = 1.34 − 0.15 ⋅ e R ⋅ ∆h
0.15−
BH R⋅∆h
+ 0.5
28
2)巴赫契诺夫公式
根据移动体积与其消耗功成正比的关系: 根据移动体积与其消耗功成正比的关系:
V∆b Ab = ∆ V∆h Ah ∆
V∆b、A∆b向宽度方向移动的体积与其所消耗功; 向宽度方向移动的体积与其所消耗功; V∆h、 ∆h 高度方向移动体积与其所消耗的功。 A 高度方向移动体积与其所消耗的功。
a-凹形孔型
b-两侧金属受强烈压缩时 5
3) 宽展的组成
滑动宽展∆ 滑动宽展∆B1:
变形金属与轧辊的接触面产生相对滑动所 增加的宽展量。 增加的宽展量。 由于接触摩擦阻力的作用, 由于接触摩擦阻力的作用,使得轧件两侧 的金属在变形过程中翻转到接触表面上, 的金属在变形过程中翻转到接触表面上, 使得轧件宽度增加。 使得轧件宽度增加。 由于摩擦阻力的作用, 由于摩擦阻力的作用,轧件两侧变为鼓形而造成的宽展
依据: 依据: 宽展决定于压下量及轧件与轧辊接触面上纵横阻力的大小。 宽展决定于压下量及轧件与轧辊接触面上纵横阻力的大小。 假设条件: 假设条件: • 接触面范围内,横向及纵向的单位面积上的单位功相同; 接触面范围内,横向及纵向的单位面积上的单位功相同; • 在延伸方向上,滑动区为接触弧长的2/3,粘着区为接触 在延伸方向上,滑动区为接触弧长的2/3, 1/3。 弧长的 1/3。
11. 轧制过程中宽展
本节应掌握的知识点: 本节应掌握的知识点: 1. 宽展的分类 2. 影响宽展的因素 3. 简单轧制时宽展量的计算
1
11.1 宽展及分类 宽展及分类 1) 宽展及其实际意义
轧制过程中的宽展
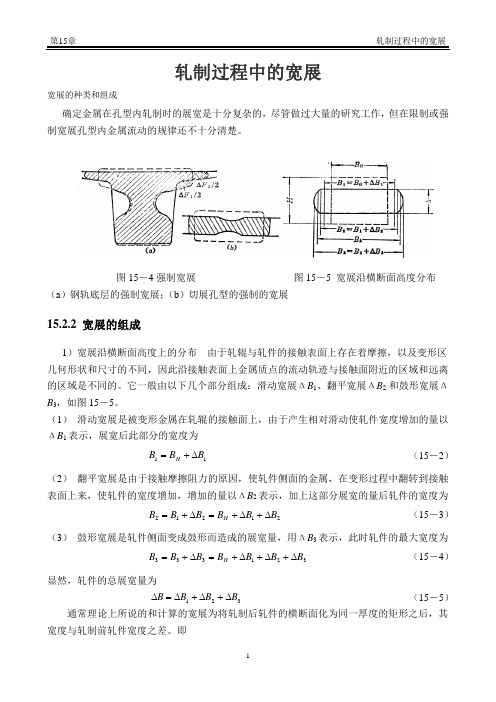
轧制过程中的宽展宽展的种类和组成确定金属在孔型内轧制时的展宽是十分复杂的,尽管做过大量的研究工作,但在限制或强 制宽展孔型内金属流动的规律还不十分清楚。
15.2.2 宽展的组成1)宽展沿横断面高度上的分布 由于轧辊与轧件的接触表面上存在着摩擦,以及变形区 几何形状和尺寸的不同,因此沿接触表面上金属质点的流动轨迹与接触面附近的区域和远离的区域是不同的。
它一般由以下几个部分组成:滑动宽展ΔB 1、翻平宽展ΔB 2和鼓形宽展ΔB 3,如图15-5。
(1) 滑动宽展是被变形金属在轧辊的接触面上,由于产生相对滑动使轧件宽度增加的量以ΔB 1表示,展宽后此部分的宽度为11B B B H ∆+= (15-2)(2) 翻平宽展是由于接触摩擦阻力的原因,使轧件侧面的金属,在变形过程中翻转到接触表面上来,使轧件的宽度增加,增加的量以ΔB 2表示,加上这部分展宽的量后轧件的宽度为 21212B B B B B B H ∆+∆+=∆+= (15-3)(3) 鼓形宽展是轧件侧面变成鼓形而造成的展宽量,用ΔB 3表示,此时轧件的最大宽度为321333B B B B B B B H ∆+∆+∆+=∆+= (15-4)显然,轧件的总展宽量为321B B B B ∆+∆+∆=∆(15-5)通常理论上所说的和计算的宽展为将轧制后轧件的横断面化为同一厚度的矩形之后,其宽度与轧制前轧件宽度之差。
即H h B B B -=∆ (15-6)因此,轧后宽度b h 是一个理想值,但便于工程计算,必须注意这一点。
上述宽展的组成及其相互的关系,由图15-5可以清楚地表示出来。
滑动宽展ΔB 1、翻平宽展ΔB 2和鼓形宽展ΔB 3的数值,依赖于摩擦系数和变形区的几何参数的变化而不同。
它们有一定的变化规律,但至今定量的规律尚未掌握。
只能依赖实验和初步的理论分析了解它们之间的一些定性关系 。
例如摩擦系数f 值越大,不均匀变形就越严重,此时翻平宽展和鼓形宽展的值就越大,滑动宽窄越小。
轧件的宽展系数

轧件的宽展系数轧件的宽展系数是衡量金属材料在轧制过程中宽度拉伸程度的一个重要指标。
通过掌握宽展系数,可以有效预测和控制轧件的变形,提高生产效率和成品质量。
宽展系数是指材料在轧机中被拉伸的宽度与初始宽度的比值。
宽展系数越大,说明材料在轧制过程中容易发生宽度拉伸,而宽展系数较小则说明材料较难拉伸。
因此,宽展系数对于设计合适的轧制工艺和选择适合的轧制机械设备至关重要。
对于不同种类的金属材料,其宽展系数不尽相同。
一般来说,冷轧钢板的宽展系数较高,而铝及其合金材料的宽展系数较低。
这是由于材料的晶粒结构、成分和热处理等因素决定的。
在实际生产中,要根据不同材料的宽展系数特性来选择合适的轧制工艺,并且在机械设备的设计过程中充分考虑宽展系数对轧制过程的影响。
了解宽展系数的重要性,不仅可以帮助我们设计出更加合理的轧制工艺,还能引导生产操作者在实际操作中做出正确的判断和决策。
在轧制过程中,如果宽展系数较大,操作者可以适当提高轧制速度,加快材料的宽度拉伸过程,提高生产效率。
而当宽展系数较小时,应采取合适的控制措施,如降低轧制速度、增加辊缝之间的摩擦力等,以确保材料的宽度拉伸均匀,避免产生变形缺陷。
此外,了解宽展系数还可以帮助我们评估材料的可加工性。
宽展系数较大的材料通常具有较好的塑性和可加工性,更容易形成复杂的形状和结构。
这对于一些需要较高加工精度和复杂形状要求的行业,如汽车制造、航空航天等,具有重要的意义。
总而言之,轧件的宽展系数是一个重要的工程参数,对于轧制生产过程中的变形控制和产品质量提升起到关键作用。
我们应该深入了解不同材料的宽展系数特性,灵活运用合适的工艺和设备,以提高生产效率和产品质量。
塑性变形与轧制技术:宽展的分布及组成
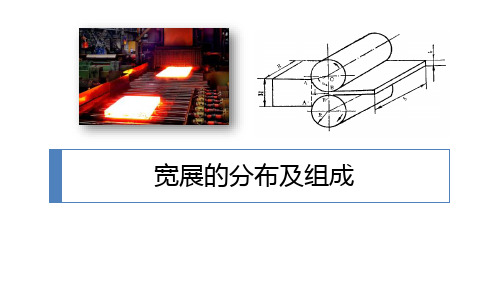
实验要求:当轧件咬入后再减小轧辊辊缝,使轧
件在α>β条件下轧制时。
实验结果:变形区中后滑区靠近轧件入口处有拉
应力区存在。
在α≤β条件下轧制时,无此拉应力区。
结论:宽展主要集中在后滑区的非拉应力区,拉
应力区和前滑区都很小。
谢谢大家!
轧件,不符合实际。
宽展沿宽度均匀分布的假说
二 宽展沿轧件宽度上的分布假说
第二种假说:变形区分为四个区域:两
边的区域为宽展区,中间为前后两个延
伸区。
这种假说不完全准确:变形区中金属质
点的流动轨迹,并不严格按所画的区间
流动。但可以定性描述变形时金属沿横
纵向流动的总趋势。
轧制示意图
变形区分区图示
三、宽展沿变形区长度的分布
滑动使轧件宽度增加的部分,称滑动宽展。Δb1=B1-B
图4-16 宽展沿轧件断面高度的分布
图4-17 各种宽展与值的关系
一、宽展沿横断面高度上的分布
2、翻平宽展:由于接触面摩擦阻力的原因,使轧件侧面的金属在变
形过程中翻转到接触表面上来,称为翻平宽展。Δb2=B2-B1
图4-16 宽展沿轧件断面高度的分布
图4-17 各种宽展与值的关系
一、宽展沿横断面高度上的分布
3、鼓形宽展:轧件侧面变为鼓形而产生的宽度增加量,
称为鼓形宽展。Δb3=B3-B2
图4-16 宽展沿轧件断面高度的分布
图4-17 各种宽展与值的关系
显然,轧件的总宽展量为Δb=Δb1+Δb2+Δb3。
三种宽展分布的变化规律:
ത
度b与轧前宽度B之差,称为平均宽展。
宽厚板轧制过程中的宽展浅析
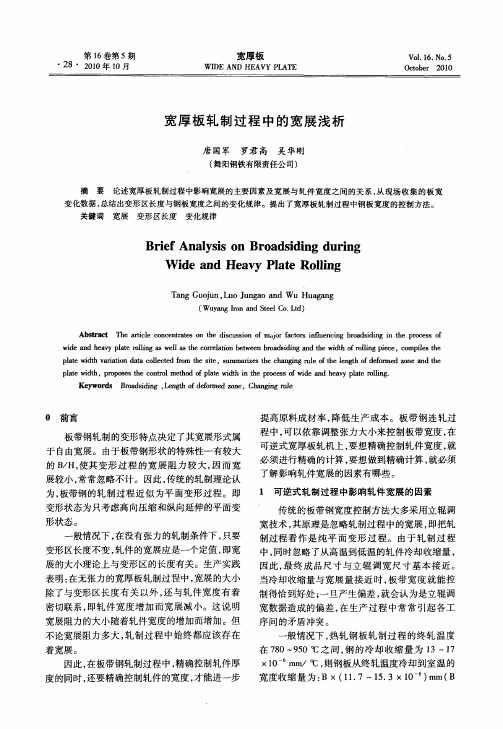
摘 要 论述宽厚 板轧制过 程中影响宽展的主要 因素及 宽展与轧件宽度之 间的关系 , 从现场 收集 的板宽
宽展 变形 区长度 变化规律
变化数据 , 总结 出变形区长度与钢板宽度之 间的变化规律。提出了宽厚板轧制过程中钢板宽度 的控制方法 。 关键词
Bre ay i n Br a sd n u i g ifAn lsso o d i i g d rn W i e a d He v a e Rol g d n a y Pl t l n i
般情 况下 , 在没有 张力 的轧制条 件下 , 只要
变形 区长度 不变 , 轧件 的宽展应 是一个 定值 , 即宽 展的大小理 论上与 变形 区的长度 有关 。生产实践 表明 : 在无 张力 的宽 厚板 轧制过 程 中, 展的大小 宽 除了与变形 区长 度有 关 以外 , 与 轧 件宽 度 有着 还 密切 联系 , 即轧 件 宽度 增 加 而宽 展 减小 。这 说 明 宽展阻力 的大小 随着 轧件 宽度 的增加 而增 加 。但
pae w d 。p p s st e c nr lme o fp ae w d h i e p o e so i ea d h a y pa e rl n . lt t i h o r o e h o t t d o lt t n t rc s f ( e v lt ol o h i h w 1n i g Ke wo d B a s i y rs o r di n dg ,  ̄ t fd fr e o e L n h o eo g m d z n ,C a gn ue h n i g r l
Tn ujn L oJ na n aa g agG o ,u goadWuHugn u u
轧制过程的宽展
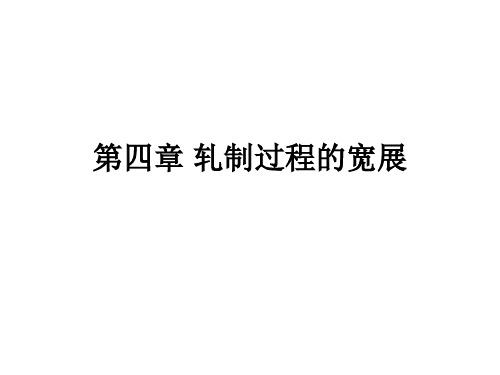
未入孔型前轧件的平均高度: 未入孔型前轧件的平均高度: H=F0/B = 轧制后轧件的平均高度: 轧制后轧件的平均高度: h1=F/b 轧件的压下量: 轧件的压下量: △h=H- h1 = - 轧辊工作直径: 轧辊工作直径: Dp=D0-h1
将孔型内轧制条件简化成平辊轧制,即用同面积、 将孔型内轧制条件简化成平辊轧制,即用同面积、同宽度的矩形代替曲 线边的轧件。 线边的轧件。 孔型轧制时要先计算轧件和孔型的等效断面。 孔型轧制时要先计算轧件和孔型的等效断面。 等效断面:宽度及面积与原轧件或孔型的宽度、面积相等的矩形断面。 等效断面:宽度及面积与原轧件或孔型的宽度、面积相等的矩形断面。
• 1)轧制温度的影响 • 一般规律T↑ ,△B↑,但达到一定程度后, 随T↑, △B ↓。 • 分析:轧件变形温度对宽展的影响,是通 过温度影响氧化皮的状态(氧化皮的厚薄, 软硬等)影响f,从而影响B的。
(4)轧制速度的影响
4.3 宽展计算公式
4.4 孔型轧制时宽展的特点
速度差导致孔型磨损不均匀
第四章 轧制过程的宽展
4.1宽展的研究意义及种类 宽展的研究意义及种类
沿横向移动的体积所引起的轧件宽度的变化称为宽展
• 4.1.1研究宽展的意义 研究宽展的意义 • 1.保证孔型轧制的正常生产 保证孔型轧制的正常生产 • 2.保证产品质量(尺寸精度) 保证产品质量(尺寸精度) 保证产品质量
由宽展估计错误产生的缺陷
宽展沿宽度均匀分布的假说
变形区分区图示
4.2影响宽展的因素 影响宽展的因素
• • • • 4.2.1体积不变关系 体积不变关系 V=HBL=hbl=常数 常数 dv=BLdh+HLdb+HBdl=0 即△VH+ △VB+ △Vl=0 高
《材料成型工艺学 下》课件:第三章 轧制过程中的横变形-宽展
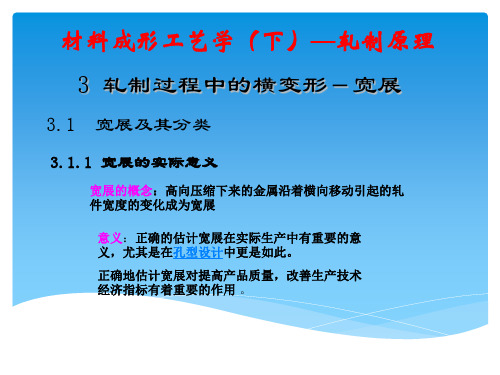
1(
h D
)
2(
h D
,f )
K
I G
( h ,
D
f
)
材料成形工艺学(下)—轧制原理
3 轧制过程中的横变形-宽展
3.2 影响宽展的因素
3.2.1 影响轧件变形的基本因素分析
3.2.1.2 轧辊形状的影响
0
K
I G
1
由于轧辊形状的影响,使纵向阻力 一般小于横向阻力,而极限情况是 二者相等,即 KG 1
钢轧辊取1.0 铸铁轧辊取0.8
轧制速度影 响系数
轧件化学成分对摩擦 系数的影响系数
如果取 ln b b 1 BB
当 b 1.2 时,简化为 B
b A A2 b2 4m R h(3H h)
A 2m(H h) R h b
材料成形工艺学(下)—轧制原理
3 轧制过程中的横变形-宽展
材料成形工艺学(下)—轧制原理
3 轧制过程中的横变形-宽展
3.2 影响宽展的因素
3.2.2 各种因素对轧件宽展的影响
1.相对压下量的影响
相对压下量越大,宽展越大。
增加压下率有不同的方式,使Δ b的 变化方式也不同。
H=c
Δh
h=c
增加
压下体积增 加
L增加,纵向 阻力增加
Δ h=C
(1)压下量增加时,变形区 长度增加,变形区水平投 影 形状 l/b 增大,因而使 纵向塑性流动阻力增加, 纵向压缩主应力值加大。 根据最小阻力定律,金属 沿横向运动的趋势增大, 因而使宽展加大。 (2) Δh/H增加高向压下的金属
3.3 宽展的计算
3.3.4 C.N.古布金公式
b
1
h H
f
轧制过程的宽展
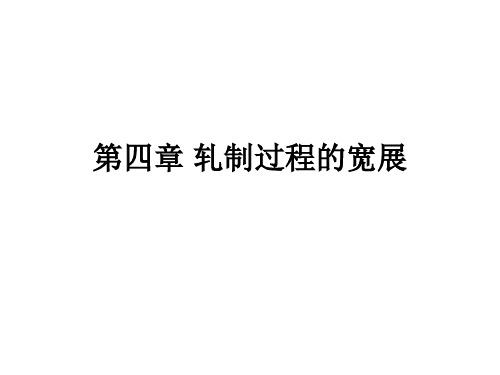
有接触摩擦条件下变形图示
• 4.2.3 纵向阻力 • 影响宽展的因素可以归纳两方面: 影响宽展的因素可以归纳两方面:
(1)高向移动体积(2)变形区内轧件变形的纵横阻力比 )高向移动体积( )
分析后滑区的受力: 分析后滑区的受力: 设后滑区的合力作用点在后滑区的中点, 设后滑区的合力作用点在后滑区的中点 后滑区的纵向阻力: 后滑区的纵向阻力:T1x-P1x 后滑区的横向阻力: 后滑区的横向阻力:T1=fP1 后滑区纵横向阻力比公式: 后滑区纵横向阻力比公式:
4.1.3 宽展的组成
滑动宽展
翻平宽展 计算宽展 鼓形宽展
宽展沿轧件横断面高度分布
各种宽展与变形区几何参数之间的关系
l/h越小,粘 着区越大, 摩擦系数越 大
摩擦系数越大,不均匀变形越严重,则翻平和鼓形越大,滑动宽展越小
4.1.4 宽展沿轧件宽度上的分布
均匀分布假说及变形区分区假说 轧制宽而 薄的薄板, 宽展很小 甚至可以 忽略时的 变形
4.1.2 宽展的种类
• 1.自由宽展:变形区中,金属质点横向流动, 自由宽展:变形区中,金属质点横向流动, 自由宽展 仅受摩擦阻力的影响。 仅受摩擦阻力的影响。
发生在变形比较均匀的条件下,如平辊轧制矩形断面, 发生在变形比较均匀的条件下,如平辊轧制矩形断面,或宽度富裕的扁平孔 型内轧制。 型内轧制。
413宽展的组成宽展沿轧件横断面高度分布滑动宽展翻平宽展鼓形宽展计算宽展各种宽展与变形区几何参数之间的关系摩擦系数越大不均匀变形越严重则翻平和鼓形越大滑动宽展越小lh越小粘着区越大摩擦系数越414宽展沿宽度均匀分布的假说均匀分布假说及变形区分区假说变形区分区图示轧制宽而薄的薄板宽展很小甚至可以忽略时的变形42影响因素都建立在最小阻力定律和体积不变定律基础上的
(整理)轧制过程中的宽展
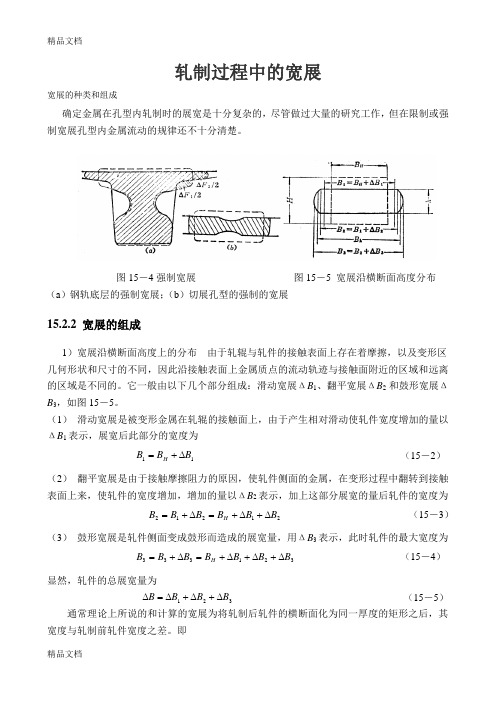
快。而Δh=常数时,增加 是依靠减少H来达到的。这时变形区长度l不增加,所以ΔB的增加较上一种情形慢些。
Ю.M.齐日柯夫作出 有宽展指数 之间关系曲线的三条实验曲线(图15-11),根据上述的道理可以完满地加以解释。当 增加时,ΔB增加,故 增加。在Δh=常数时,增加 时显然 会直线增加,当h或H=常数时,增加 时,是靠增加Δh来实现的,所以 增加的缓慢,而且到一定数值以后即Δh增加超过了ΔB的增大时,会出现 下降的现象。
一方面, 增加,高方向压下来的金属体积也增加,所以使ΔB也增加。
应当指出,宽展ΔB随压下率的增加而增加的状况,由于 的变换方法不同,使ΔB的变化也有所不同(图15-10 a),当H=常数或h=常数时,压下率 增加,ΔB的增加速度快;而Δh=常数时,ΔB增加的速度次之。这是因为,当H或h=常数时,欲增加 ,需增
从相对量来说,则随着宽展区FB和前、后滑区F1的FB/Fl比值不断减小,而ΔB/B逐渐减小。同样若B保持不变,而l增加时,则前、后滑区先增加,而后接近不变;而宽展区的绝对量和相对量均不断增加。
一般来说,当l/B增加时,宽展增加,亦即宽展与变形区长度l成正比,而与其宽度 成反比。轧制过程中变形区尺寸的比,可用下式来表示
(15-7)
此比值越大,宽展亦越大。l/ 的变化,实际上反映了纵向阻力及横向阻力的变化,轧件宽度 增加,ΔB减小,当 很大时,ΔB趋近于零,即BH/Bh=1即出现平面变形形态。如前述,此时表示横向阻力的横向压缩主应力 。在轧制时,通常认为,在变形区的纵向长度为横向长度的二倍时(l/ )=2,会出现纵横变形相等的条件。为什么不在二者相等时(l/ =1)时出现呢?这是因为前面所说的工具形状影响。此外,在变形区前后轧件都具有外端,外端将起着妨碍金属质点向横向移动的作用,因此,也使宽展减小。
【技术专题】轧制时候的宽展计算
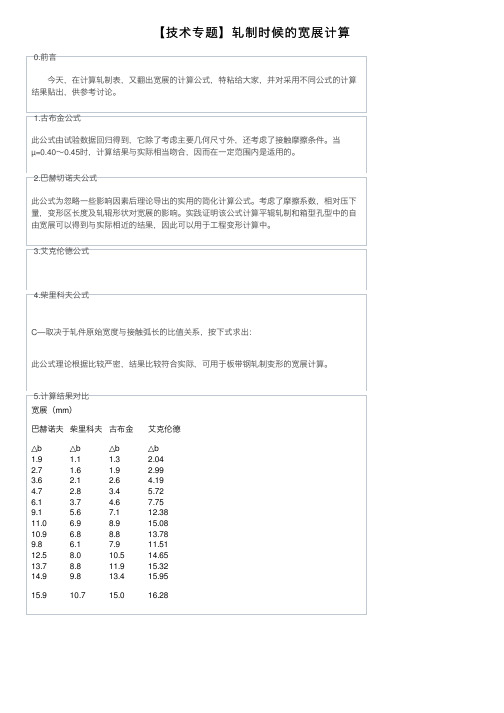
【技术专题】轧制时候的宽展计算0.前⾔
今天,在计算轧制表,⼜翻出宽展的计算公式,特粘给⼤家,并对采⽤不同公式的计算结果贴出,供参考讨论。
1.古布⾦公式
此公式由试验数据回归得到,它除了考虑主要⼏何尺⼨外,还考虑了接触摩擦条件。
当
µ=0.40~0.45时,计算结果与实际相当吻合,因⽽在⼀定范围内是适⽤的。
2.巴赫切诺夫公式
此公式为忽略⼀些影响因素后理论导出的实⽤的简化计算公式。
考虑了摩擦系数,相对压下量,变形区长度及轧辊形状对宽展的影响。
实践证明该公式计算平辊轧制和箱型孔型中的⾃由宽展可以得到与实际相近的结果,因此可以⽤于⼯程变形计算中。
3.艾克伦德公式
4.柴⾥科夫公式
C—取决于轧件原始宽度与接触弧长的⽐值关系,按下式求出:
此公式理论根据⽐较严密,结果⽐较符合实际,可⽤于板带钢轧制变形的宽展计算。
5.计算结果对⽐
宽展(mm)
巴赫诺夫柴⾥科夫古布⾦艾克伦德
△b△b△b△b
1.9 1.1 1.3
2.04
2.7 1.6 1.9 2.99
3.6 2.1 2.6
4.19
4.7 2.8 3.4
5.72
6.1 3.7 4.6
7.75
9.1 5.67.112.38
11.0 6.98.915.08
10.9 6.88.813.78
9.8 6.17.911.51
12.58.010.514.65
13.78.811.915.32
14.99.813.415.95
15.910.715.016.28。
薄板冷轧过程中宽展的变化规律及其影响因素

薄板冷轧过程中宽展的变化规律及其影响因素下载提示:该文档是本店铺精心编制而成的,希望大家下载后,能够帮助大家解决实际问题。
文档下载后可定制修改,请根据实际需要进行调整和使用,谢谢!本店铺为大家提供各种类型的实用资料,如教育随笔、日记赏析、句子摘抄、古诗大全、经典美文、话题作文、工作总结、词语解析、文案摘录、其他资料等等,想了解不同资料格式和写法,敬请关注!Download tips: This document is carefully compiled by this editor. I hope that after you download it, it can help you solve practical problems. The document can be customized and modified after downloading, please adjust and use it according to actual needs, thank you! In addition, this shop provides you with various types of practical materials, such as educational essays, diary appreciation, sentence excerpts, ancient poems, classic articles, topic composition, work summary, word parsing, copy excerpts, other materials and so on, want to know different data formats and writing methods, please pay attention!Certainly! Here’s a structured demonstration article on the topic "Variation Characteristics and Influencing Factors of Width Expansion in Thin Sheet Cold Rolling Process":薄板冷轧过程中宽展的变化规律及其影响因素。
【材料课件】材料成型工程第三讲宽展

l f 、 t、 m、 p、和υ是物理因素,它们影响到变形区内的作 用力,尤其是对于摩擦力。
l 几何因素和物理因素的综合影响不仅限于变形区的应力状态, PPT文档演模同板 时涉及到轧件的纵向和横向变形的特【征材料。课件】材料展成型工程第三讲宽
金属体积如何分配延伸和宽展
l 轧制时高向压下的金属体积如何分配延伸和宽展 受体积不变条件和最小阻力定律来支配。
【材料课件】材料成型 工程第三讲宽展
PPT文档演模板
2020/10/30
【材料课件】材料成型工程第三讲宽 展
2)研究宽展的意义
l 研究轧制过程中宽展的规律具有很大的实际意义,具体讲 为:
l (1)拟订轧制工艺时需要确定轧件宽展. (给
定坯料尺寸和压下量,确定轧制后产品的尺寸,
或者已知轧制后轧件的尺寸和压下量,要求定出 所需坯料的尺寸)
压下增加宽展增加的原因
l (1)因为压下量增加时,变形区长度增加, 变形区形状参数 增大,因而使纵向塑性流动
阻力增加,纵向压缩主应力数值加大。根据最
小阻力定律,金属沿横向运动的趋势增大,因 而使宽展加大。
l (2)压下增加,高方向压下来的金属体积也增加, 所以使ΔB 也增加。
l
PPT文档演模板
【材料课件】材料成型工程第三讲宽 展
PPT文档演模板
【材料课件】材料成型工程第三讲宽 展
1)滑动宽展
l 滑动宽展变形金属在轧辊的接触面上,由于产 生相对滑动使轧件宽度增加的量以ΔB1 表示, 展宽后此部分的宽度为 :
l
B1 =BH+ΔB1
l 2)翻平宽展
l 由于接触磨擦阻力,轧件侧面的金属在变形过 程中翻转到接触表面,使轧件的宽度增加,增 加的量以 ΔB 2表示,展宽的后轧件的宽度为
轧制原理的第三讲_宽展.

❖ 3.1塑性变形的不均匀性 ❖ 3.2 金属在变形区的流动规律 ❖ 3.3 宽展及其分类 ❖ 3.4 影响宽展的因素 ❖ 3.5 宽展计算公式 ❖ 3.6 孔型轧制的宽展
3.1金属塑性变形的不均匀性
3.1.1 金属的流动规律 一.体积不变定律
变形前后,材料的体积保持不变。 H·B·L=h·b·l 用真变形表示:ε1+ε2+ε3=0 ①忽略了弹性变形引起的体积变化 ②忽略了密度变化引起的体积变化
1
A
2
② f≠0 假如接触面上f=0 ,即理想情况??
此时,物体产生均匀变形,质点流动呈放射状。
f 各向同性,f 较大,A→D f 较小,A→B
f=0,理想情况,A→C
f↑,AB靠近AD
f↓, AB靠近AC
•A DB C
3.1.2均匀变形和不均匀变形
若变形区内金属各质点的应变状态相同,即它们相 应的各个轴向上变形的发生情况,发展方向及应变量 的大小都相同,这个体积的变形可视为均匀的。
3.1.5 变形不均匀的后果 及预防措施
一.后果 1.使变形抗力↑ 2.使塑性↓ 3.使产品质量↓ ①ε不同,产品组织
性能不同, 质量↓
② 产生σ附(+),材料发生断裂,废品 4.使技术操作复杂
① 使工具使用寿命↓ 工具设计、制造、维护复杂
② 使导卫装置复杂化 ③ 使热处理工艺复杂 组织性能不均
二.最小阻力定律 定义:变形过程中,金属质点有向各个方向移动
的可能时,它向阻力最小的方向移动。 如果满足以下条件: ① 接触摩擦各向同性 ② 摩擦系数较高 f≠0 则最小阻力方向就是:
离周边距离最短的法线方向。
对矩形断面的金属,随ε↑: 矩形→椭圆形→圆形
3.4轧制时金属的横变形-宽展

图9-8 宽展沿宽度均匀分布的假说
图9-9 变形区分区图示
9.3 影响宽展的因素
一 压下量的影响
实验表明,随压下量增加,宽展量也增加如图9—10 所示。 二 轧辊直径的影响 如图9-12的实验曲线表明,随轧辊直径增大, 宽展量增大。
图9-10 宽展与压下量之间的关系 (a)当Δh、H、h为常数、低碳钢在=900℃、v=1.1m/s时, Δb与Δh/H的关系; (b)当H、h为常数,条件同(a)时Δb与Δh/H的关系
课程引入 :
1. 拟定轧制工艺时要确定宽展 。
2. 宽展在生产实际中影响产品质量 。
3.4 轧制时金属的横变形——宽展
9.1 宽展与研究宽展的意义
一、宽展的概念
通常把轧制前、后轧件横向尺寸的绝对差值,称 为绝对宽展,简称为宽展。
二、研究宽展的意义
1 根据给定的坯料尺寸和压下量,来确定轧制
后产品的尺寸,或已知轧制后轧件的尺寸和压 下量,要求定出所需坯料的尺寸。 2 宽展在实际生产中和孔型设计时得到了广泛的 应用。在孔型设计中,必须正确计算出宽展量。 否则,孔型不是欠充满就是过充满。
值范围如表15—1所示。
表9-1 宽展系数表
二、巴赫契诺夫公式
b 1.15 h h ( Rh ) 2H 2f
三、彼德诺夫—齐别尔公式
h b Rh H
四、采里柯夫公式 五、艾克伦德公式
小结:
1.掌握影响宽展的主要因素 2.了解宽展的计算公式。
图9-11 宽展系数与轧辊直径的关系
图9-12 轧辊直径对宽展的影响
三 轧件宽度的影响 实验证明,轧件宽度小于某一定值时,随轧件宽 度的增加宽展增加;超过此一定宽度之后,随轧
件宽度的继续增加而宽展减小,且以后不再对宽
塑性变形与轧制技术:宽展的影响因素(二)
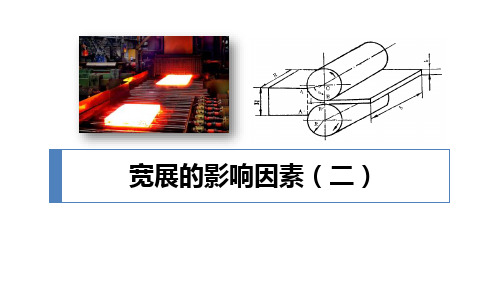
五、轧制道次的影响
结论:总压下量相同时,轧制道次越多,总的宽展量越小。 公式表示:Δb>Δb1+Δb2+……Δbn
轧制道次和宽展
五、轧制道次的影响
根据M·A·扎罗辛斯基的研究,得出: Δb=c(Δh)2
绝对宽展Δb与绝对压下量Δh的平方成正比。
图4-29 轧制道次对宽展的影响
五、轧制道次的影响
结论:宽展随摩擦系数的增加而增加。
四、摩擦系数的影响
影响摩擦的因素同样影响宽展。 1、轧辊材质及辊面状态 2、轧制温度 3、轧制速度 4、化学成分
四、摩擦系数的影响
1、轧辊材质及辊面状态 辊面状态粗糙要比辊面状态光洁摩擦系数高。 淬火比未淬火的钢轧辊摩擦系数低20%; 铸铁轧辊比钢轧辊轧钢摩擦系数低15%~20%,因为前者
宽展的影响因素(二)
宽展的影响因素
一、压下量的影响 二、轧辊直径的影响 三、轧件宽度的影响 四、摩擦系数f的影响 五、轧制道次n的影响 六、张力的影响 七、工具形状的影响
四、摩擦系数的影响
摩擦对宽展的影响可以归结为摩擦对纵横方向塑性流动阻力 比的影响。
变形区塑性流动阻力
宽展与压下量,辊面状况的关系 实线-光面辊;虚线-粗糙表面轧辊
原因:在后张力作用下使金属质点纵向 塑性流动阻力减小,必然使延伸增大、 宽展减小。
七、工具形状的影响
轧制时所用的工具形状不同:圆柱形辊促进延伸。 孔型形状的不同,对宽展的影响:凹形孔限制宽展,凸性
孔促进宽展。
图4-31 在不同形状的孔型内轧制
谢谢大家!
图中的纵坐标C=Δb/Δb0,Δb为有后张力时 的实际宽展量,Δb0为无后张力时的宽展量 。横坐标为qH/K,其中qH为作用在入口断面 上单位后张力,K为平面变形抗力
- 1、下载文档前请自行甄别文档内容的完整性,平台不提供额外的编辑、内容补充、找答案等附加服务。
- 2、"仅部分预览"的文档,不可在线预览部分如存在完整性等问题,可反馈申请退款(可完整预览的文档不适用该条件!)。
- 3、如文档侵犯您的权益,请联系客服反馈,我们会尽快为您处理(人工客服工作时间:9:00-18:30)。
一般来说,当l/B增加时,宽展增加,亦即宽展与变形区长度l成正比,而与其宽度 成反比。轧制过程中变形区尺寸的比,可用下式来表示
2)宽展沿宽度上的分布关于宽展沿宽度分布的理论,基本上有两种假说:第一种假说,
认为宽展沿轧件宽度均匀分布。这种假说主要以均匀变形和外区作用做为理论的基础。因为变形区内金属与前后外区彼此是同一整体紧密联系在一起的。因此对变形起着均匀的作用。使沿长度方向上各部分金属延伸相同。宽展沿宽度分布自然是均匀的。它用图15-7来说明。
1.29
1.33
1.35
1.35
1.25~1.32
Ⅲ
奥氏体钢
4Cr14Ni14W2Mo
2Cr13Ni4Mn9(不锈耐热钢)
1.36
1.42
1.35~1.40
Ⅳ
带残余相的奥氏体(铁素体、莱氏体)钢
1Cr18Ni9Ti(不锈耐热钢)
3Cr18Ni25Si2(不锈耐热钢)
1Cr23Ni13(不锈耐热钢)
1.44
图15-17是轧制温度对ΔB影响的曲线。轧制温度对ΔB的影响是通过摩擦系数起作用的,假如没有氧化铁皮时,随着温度的升高,摩擦系数增大,故ΔB呈虚线所示的样子增大;在有氧化铁皮时,由于在高温下氧化铁皮变成润滑剂,故ΔB急剧下降。
轧制速度对ΔB的影响也是通过摩擦系数起作用的。有人曾作过这种实验,其条件是,在轧辊直径为340mm的二辊轧机上,轧制速度在0.3~7m/s的范围内,轧后高度h=10mm,轧件宽度为40mm。试件在套管中加热,并一起拿到轧机前,去掉套管,进行一道轧制。每次变化压下量,轧件的轧制温度是相同的,都是在1000℃左右。根据所测数据,当压下量一定时,轧制速度与宽展的关系曲线,如图15-18所示。从图中可以看出,在所有压下量条件下,轧制速度由1m/s到2m/s,宽展量ΔB有最大值,当轧制速度大于3m/s时,曲线保持水平位置,即轧制速度提高,宽展保持恒定。这与轧制速度对摩擦系数的影响的变化趋势一致。
轧制时高压下的金属体积如何分配延伸和宽展,受体积不变条件和最小阻力定律来支配。所以,在未分析具体因素对宽展的影响之前须先了解最小阻力定律的概念。
最小阻力定律是阐明变形物体质点流动规律的。如果物体在变形过程中其质点有向各种方向流动的可能时,则物体各质点将是向着阻力最小的方向流动。
(1)如变形在两个主两个主轴方向是给定的,则质点只有在第三主轴一个方向流动的可能性。金属挤压变形就是这种变形过程。
变形区分区假说,也不完全准确,许多实验证明变形区中金属表面质点流动的轨迹,并非严格地按所画的区间进行流动。但是它能定性地描述宽展发生时变形区内金属质点流动的总趋势,便于说明宽展现象的性质和作为计算宽展的根据。
总之,宽展是一个极其复杂的轧制现象,它受许多因素的影响。
15.23
宽展的变化ቤተ መጻሕፍቲ ባይዱ一系列轧制因素构成复杂的关系
1.44
1.53
1.4~1.5
Ⅴ
铁素体钢
1Cr17Al5(不锈耐热钢)
1.55
Ⅵ
带有碳化物的奥氏体钢
Cr15Ni60(不锈耐热合金)
1.62
按一般公式计算出来的宽展,很少考虑合金元素的影响。为了确定合金钢的宽展,必须按一般公式计算所求得的宽展值乘上表15-1的系数m,也就是
表15-1钢的化学成分对宽展的影响系数
组别
钢种
钢号
影响系数
(m)
平均数
Ⅰ
普碳钢
10号钢
1.0
Ⅱ
珠光体-马氏体钢(珠光体钢、珠光体-马氏体钢、马氏体钢)
T7A(碳钢)
GCr15(轴承钢)
16Mn(结构钢)
4Cr13(不锈钢)
38CrMoAl(合金结构钢)
4Cr10Si2Mo(不锈耐热钢)
1.24
1.29
轧制过程中的宽展
宽展的种类和组成
确定金属在孔型内轧制时的展宽是十分复杂的,尽管做过大量的研究工作,但在限制或强
制宽展孔型内金属流动的规律还不十分清楚。
15.2.2
1)宽展沿横断面高度上的分布由于轧辊与轧件的接触表面上存在着摩擦,以及变形区
几何形状和尺寸的不同,因此沿接触表面上金属质点的流动轨迹与接触面附近的区域和远离的区域是不同的。它一般由以下几个部分组成:滑动宽展ΔB1、翻平宽展ΔB2和鼓形宽展ΔB3,如图15-5。
15.3.2
由实验得知,其它条件不变时,宽展△B随轧辊直径D的增加而增加。这是因为当D增加时变形区长度加大,使纵向的阻力增加,根据最小阻力定律,金属更容易向宽度方向流动(图15-12)。
研究辊径对宽展的影响时,应当注意到轧辊为圆柱体这一特点,沿轧制方向由于是圆弧形的,必然产生有利于延伸变形的水平分力,它使纵向摩擦阻力减少,有利于纵向变形,即增大延伸。所以,即使变形区长度与轧件宽度相等时,延伸与宽展的量也并不相等,而由于工具形状的影响,延伸总是大于宽展。
15.3.3
如前所述,可将接触表面金属流动分成四个区域:即前、后滑区和左、右宽展区。用它说明轧件宽度对宽展的影响。假如变形区长度l一定,当轧件宽度B逐渐增加时,由l1>B1到l2=B2如图15-13所示,宽展区是逐渐增加的,因而宽展也逐渐增加,当由l2=B2到l3<B3时,宽展区变化不大,而延伸区逐渐增加,因此从绝对量上来说,宽展的变化也是先增加,后来趋于不变,这也为实验所证实(图15-14)
式中H、h——变形区的高度;
l、B、D——变形区的长度、宽度和轧辊直径;
——变形区的横断面形状;
Δh、 ——压下量和压下率;
f、t、m——摩擦系数、轧制温度、金属的化学成分;
——金属的机械性能;
v、ε——轧辊线速度和变形速度。
H、h、l、B、D和 是表示变形区特征的几何因素。f、t、m、 、ε和v是物理因素,它们影响到变形区内的作用力,尤其是对于摩擦力。几何因素和物理因素的综合影响不仅限于变形区的应力状态,同时涉及到轧件的纵向和横向变形的特征。
一方面, 增加,高方向压下来的金属体积也增加,所以使ΔB也增加。
应当指出,宽展ΔB随压下率的增加而增加的状况,由于 的变换方法不同,使ΔB的变化也有所不同(图15-10 a),当H=常数或h=常数时,压下率 增加,ΔB的增加速度快;而Δh=常数时,ΔB增加的速度次之。这是因为,当H或h=常数时,欲增加 ,需增
(15-4)
显然,轧件的总展宽量为
(15-5)
通常理论上所说的和计算的宽展为将轧制后轧件的横断面化为同一厚度的矩形之后,其宽度与轧制前轧件宽度之差。即
(15-6)
因此,轧后宽度bh是一个理想值,但便于工程计算,必须注意这一点。上述宽展的组成及其相互的关系,由图15-5可以清楚地表示出来。
滑动宽展ΔB1、翻平宽展ΔB2和鼓形宽展ΔB3的数值,依赖于摩擦系数和变形区的几何参数的变化而不同。它们有一定的变化规律,但至今定量的规律尚未掌握。只能依赖实验和初步的理论分析了解它们之间的一些定性关系。例如摩擦系数f值越大,不均匀变形就越严重,此时翻平宽展和鼓形宽展的值就越大,滑动宽窄越小。各种宽展与变形区几何参数之间有如图15-6所示的关系。由图中的曲线可见当 越小时,则滑动宽展越小,而翻平和鼓形宽展占主导地位。这是 越小,粘着区越大,故宽展主要是由翻平和鼓形宽展组成。而不是由滑动宽展组成。
(15-7)
此比值越大,宽展亦越大。l/ 的变化,实际上反映了纵向阻力及横向阻力的变化,轧件宽度 增加,ΔB减小,当 很大时,ΔB趋近于零,即BH/Bh=1即出现平面变形形态。如前述,此时表示横向阻力的横向压缩主应力 。在轧制时,通常认为,在变形区的纵向长度为横向长度的二倍时(l/ )=2,会出现纵横变形相等的条件。为什么不在二者相等时(l/ =1)时出现呢?这是因为前面所说的工具形状影响。此外,在变形区前后轧件都具有外端,外端将起着妨碍金属质点向横向移动的作用,因此,也使宽展减小。
加Δh,这样就使变形区长度l增加,因而纵向阻力增加,延伸减小,宽度ΔB增加。同时Δh增加,将使金属压下体积增加,也促使ΔB增加,二者综合作用的结果,将使ΔB增加的较
快。而Δh=常数时,增加 是依靠减少H来达到的。这时变形区长度l不增加,所以ΔB的增加较上一种情形慢些。
Ю.M.齐日柯夫作出 有宽展指数 之间关系曲线的三条实验曲线(图15-11),根据上述的道理可以完满地加以解释。当 增加时,ΔB增加,故 增加。在Δh=常数时,增加 时显然 会直线增加,当h或H=常数时,增加 时,是靠增加Δh来实现的,所以 增加的缓慢,而且到一定数值以后即Δh增加超过了ΔB的增大时,会出现 下降的现象。
15.3.5
金属性质对宽展的影响主要是化学成分对摩擦系数的影响,一般是通过轧制时所产生的氧化铁皮的多少及其性质对摩擦系数的影响。这种影响是比较复杂的。为了确定轧件的化学成分和组织对宽展的影响。ю.M.齐日可夫做了具有各种化学成分和各种组织的大量钢种的宽展试验。所得结果列入表15-1中。从这个表中可以看出来,合金钢的宽展比碳素钢大些。
(2)如变形在一个主轴方向是给定了的,而在第二个主轴方向受阻;此时,在第三个主轴方向正反两方面流动的多少由这两方面阻力而定,阻力小者流动的多。在封闭孔型中轧制就属于这种情况。
(3)如变形在一个主轴方向是给定了的,而在另外两个主轴方向上,物体有自由流动的可能性,此时向阻力小的主轴方向流的多。自由镦粗和平辊轧矩形件就属于这种变形过程。
最小阻力定律常近似表达为最短法线定律,即金属受压变形时,若接触摩擦较大其质点近似沿最短法线方向流动。如宽度、压下量和接触摩擦等相同的条件下,由于变形区长l1增至l2,按最短法线定律,则宽度方向流动区域将增大,即FB2/Fl2>FB1/Fl1(图15-9),因而使宽度增加。
很多实验表明,随着压下量的增加,宽展量也增加。如图15-10b所示。这是因为压下量增加时,变形区长度增加,变形区形状参数 增大,因而使纵向塑性流动阻力增加,纵向压缩主应力数值加大。根据最小阻力定律,金属沿横向运动的趋势增大,因而使宽展加大。另