高副接触摩擦学设计模型的构建
摩擦学第三章表面接触

1 2
1 2
A
' i
R
1 3
(3-14) (3-15)
3 2
9 '2 16 E R
pi
'
2 3
a 已知 R
2
a
3 3Pi R 4 E'
pi
4 3
E R
1 2
(3-13)
二、理想粗糙表面的接触计算
研究粗糙表面时,n 个微凸体按某些特定规律处理
4E 3
3 2
n
R
Ar
3 2
(3-15)
上述结果表明在弹性变形情况下接触面积与载荷成正比
2、完全塑性接触
假设载荷使微凸体在一恒定流动压力 p下发生塑性变形,材料作垂直 向下的位移而不作水平扩展。此时应力达到屈服应力 s y ' 已知微凸体接触面积等于2π Rδ ,若单个微凸体接触面积 A ' ,作用载荷 p i
当两圆柱体均为钢时
E1 = E 2 = E
1 = 2 =0.3
m ax
0 .4 1 8
qE R
(3-11)
三、球面与平面的接触(HZ)
令接触两球中的一球半径R2趋于无穷大设圆球面积为R0
P
max
0 . 388 3
pE R0
2
弹性压入面积
2
2a
压缩应力
四、圆球面与凹球面的接触(HZ)
表面1
1
h
2
表面2 若两个表面的粗糙度均方根值分别为Rq1( 1)、 Rq2( 2 ) ,且参考中线之间 距离为 h 。他们的接触可转化为一个光滑刚性平面和另一个具有均方根值为:
机械摩擦学特性分析与摩擦副优化设计
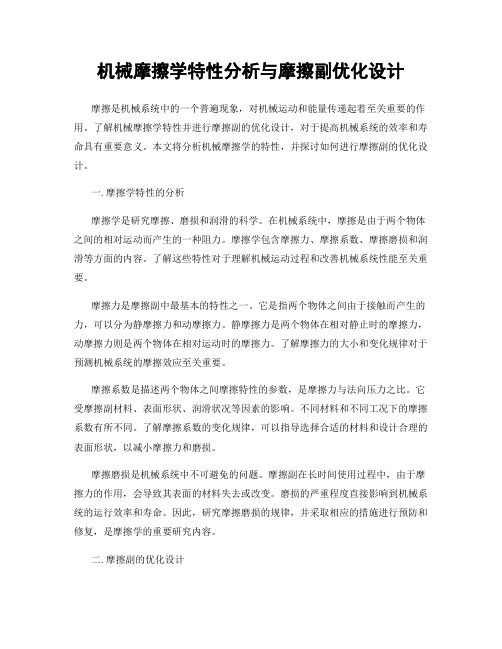
机械摩擦学特性分析与摩擦副优化设计摩擦是机械系统中的一个普遍现象,对机械运动和能量传递起着至关重要的作用。
了解机械摩擦学特性并进行摩擦副的优化设计,对于提高机械系统的效率和寿命具有重要意义。
本文将分析机械摩擦学的特性,并探讨如何进行摩擦副的优化设计。
一. 摩擦学特性的分析摩擦学是研究摩擦、磨损和润滑的科学。
在机械系统中,摩擦是由于两个物体之间的相对运动而产生的一种阻力。
摩擦学包含摩擦力、摩擦系数、摩擦磨损和润滑等方面的内容。
了解这些特性对于理解机械运动过程和改善机械系统性能至关重要。
摩擦力是摩擦副中最基本的特性之一。
它是指两个物体之间由于接触而产生的力,可以分为静摩擦力和动摩擦力。
静摩擦力是两个物体在相对静止时的摩擦力,动摩擦力则是两个物体在相对运动时的摩擦力。
了解摩擦力的大小和变化规律对于预测机械系统的摩擦效应至关重要。
摩擦系数是描述两个物体之间摩擦特性的参数,是摩擦力与法向压力之比。
它受摩擦副材料、表面形状、润滑状况等因素的影响。
不同材料和不同工况下的摩擦系数有所不同。
了解摩擦系数的变化规律,可以指导选择合适的材料和设计合理的表面形状,以减小摩擦力和磨损。
摩擦磨损是机械系统中不可避免的问题。
摩擦副在长时间使用过程中,由于摩擦力的作用,会导致其表面的材料失去或改变。
磨损的严重程度直接影响到机械系统的运行效率和寿命。
因此,研究摩擦磨损的规律,并采取相应的措施进行预防和修复,是摩擦学的重要研究内容。
二. 摩擦副的优化设计在机械系统中,摩擦副的设计是摩擦学研究的核心问题之一。
通过合理的摩擦副设计,可以减小摩擦力和磨损,提高机械系统的性能。
以下是摩擦副优化设计的几个关键方面:1. 材料选择:不同材料的表面性质和耐磨性不同,选择合适的材料对于减小摩擦力和延长摩擦副寿命至关重要。
在选择材料时,需要考虑材料的硬度、热导率、热膨胀系数等因素。
2. 表面处理:通过表面处理,可以改变摩擦副的摩擦系数和润滑性能,减小摩擦力和磨损。
摩擦学设计PPT教案学习
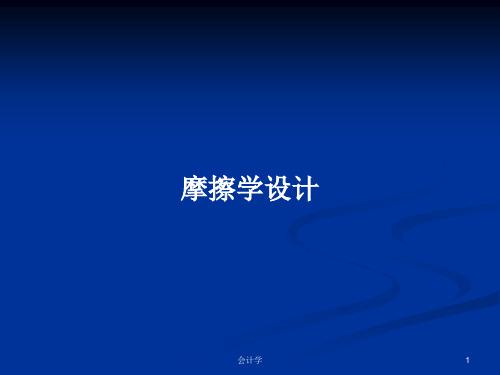
第4页/共85页
2.边界摩擦
边界摩擦又称为边界润滑。当运动副的 摩擦表 面被吸 附在表 面的边 界膜隔 开,摩 擦性质 取决于 边界膜 和表面 的吸附 性能时 的摩擦 称为边 界摩擦 (图 8.1 b)。润滑油中的脂肪酸是一种极性化合 物,它 的极性 分子能 牢固地 吸附在 金属表 面上。 吸附在 金属表 面上的 分子膜 ,称为 边界膜 。
v
(b)边界润滑
第5页/共85页
按边界膜形成机理,边界膜分为吸附膜 (物理 吸附膜 及化学 吸附膜 )和反 应膜。 润滑剂 中脂肪 酸的极 性分子 牢固地 吸附在 金属表 面上, 就形成 物理吸 附膜; 润滑剂 中分子 受化学 键力作 用而贴 附在金 属表面 上所形 成的吸 附膜则 称为化 学吸附 膜。吸 附膜的 吸附强 度随温 度升高 而下降 ,达到 一定温 度后, 吸附膜 发生软 化、失 向和脱 吸现象 ,从而 使润滑 作用降 低,磨 损率和 摩擦系 数都将 迅速增 加。
第13页/共85页
摩擦系数
1 50
1 0. 5 0.1 0.05
0.0 0.0015
纯净金
氧化膜
属
干摩擦状态
边界润 边界润滑 流体润
滑
和流体润滑
滑
图8.3 摩擦系数的典型值
第14页/共85页
随着工况参数的改变可能导致润滑状态 的转化 。图 8.4 是典型的 S t r i b e c k 曲线,它表示润滑状态转化过程以及摩 擦系数 随润滑 油粘度 、滑 动速度 v 和轴承单位面积载荷 p 变化的规律。
合理选择摩擦副材料和润滑剂,降低表 面粗糙 度值, 在润滑 剂中加 入适量 的油性 添加剂 和极压 添加剂 ,都能 提高边 界膜强 度。
重载丝杠螺母副的摩擦学系统模型的建立

第 1 8卷第 5期
20 年 1 02 0月
机 械 设 计 与 研 究
M a hne De i n s a c c i sgn a d Re e rh
VO 1 NO l 8 5
0c .. 02 t 20
文 章 编 号 :0 62 4 (0 2 0 —0 80 10 3 3 2 0 ) 50 3 —3
2 重 载 丝杠 螺 母 的力 学 分 析 及 失 效 分 析
2 丝 杠 一 螺 母 副 的 受 力 分 析 1
在 钢制 板 材 的制 造 中 , 般 采 用 轧 机 系 统 , 系 统 的 主 一 该
要 装 置 称 动 它 丝杠作定轴 转动 , 母作往 复运动来实 现的 。 螺
式 中 Q—— 轴 向 载 荷 或 工 作 阻 力 由 于 A很 小 , 母 牙 齿 正 压 力 P 可 认 为 与 轴 向 载 荷 相 螺
等,
即 : = Q P
的 摩擦 学 研 究 ~ , 把 这 个 范 围 的 研 究 称 为 选 择 性 转 移 研 并
究 我 国 从 八 十 年 代 初 以 来 也 一 直 在 进 行 着 这 一 特 殊 领 域 的研 究 , 目前 , 这 一 域 中 做 了 大 量 的 实 验 研 究 和 理 论 探 在 领 讨 ’ 但 由 于 技 术 上 的某 些 原 因 , 直 没 有 建 立 完 善 的 摩 。 一
重 载 丝 杠 螺 母 副 的 摩 擦 学 系 统 模 型 的 建 立
吴 保 群 。 建 生 徐 ( 汉 化工 学 院 札械 系 , 汉 4 0 7 ) 武 武 3 0 3
摘 要 :在 基 本 摩 擦 学理 论 和 实验 的 基 础 上 , 析 了 某种 选 定 的 摩 擦 副 在 某 种 选 定 的 摩 擦 学 工 况 条 件 下 的 摩 分 擦 学 系统 特 性 , 立 了 轧 机 压 下 装 置 中重 载 丝 螺 母 副 的 摩 擦 学 特 性 与 载 荷 之 间 关 系的 数 学 模 型 , 导 出相 对 准 确 建 推 的摩 擦 系数 一 载 荷 , 损 率 一 栽 荷 计 算 公 式 , 实 验 结 果 比 较 有 较 好 的 吻 合 性 。 该 数 学 模 型 可 为 摩 擦 学 系统 特 性 磨 与 转 化 的 研 究提 供 研 究参 照 体 , 亦可 为 工程 设 计 人 员在 摩 擦 学设 计 时提 供 有 效 的 计 算 工具 。
机械密封摩擦副端面接触分形模型的修正

area
fractal dimension,and for only
a
decreased with the increase of characteristic length scale.The real
part of the nominal contact
area
accounts
small
under normal operating conditions.
area
Key words:mechanical seal;fractal model;asperity bearing
ratio;face pressure
引
言
研究机械密封摩擦副端面间的接触特性对分析
载荷P。与量纲1真实接触面积A?之间的关系。
第64卷第5期 2013年5月
化工学报
CIESC
Vol・64
No・5
Journal
May
2013
机械密封摩擦副端面接触分形模型的修正
魏
龙1,顾伯勤2,刘其和1,张鹏高1’2,房桂芳1
(1南京化工职业技术学院,江苏省流体密封与测控工程技术研究开发中心,江苏南京210048; 2南京工业大学机械与动力工程学院。江苏南京211816)
WEI
Lon91,GU Boqin2,LIU Qibel,ZHANG Pengga01”。FANG Guifan91
(1 Fluid Sealing Measurement and Control Engineering Research and Development Center of Jiangsu Province,
口。=等
a,=n:
(1) (2)
11摩擦学设计方法
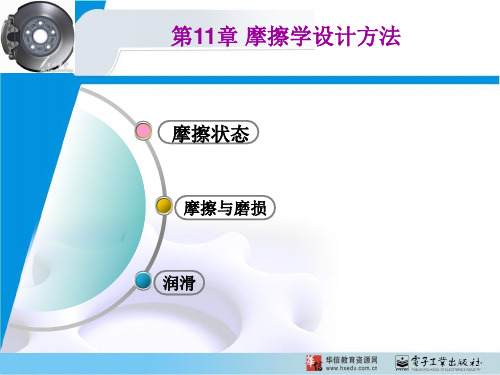
第11章 摩擦学设计方法
6.微动磨损(微动损伤) 这是一种由黏附磨损、磨粒磨损、机械化 学磨损和疲劳磨损共同形成的复合磨损形式。 它发生在宏观上相对静止,微观上存在微 幅相对滑动的两个紧密接触的表面上,如轴与 孔的过盈配合面、滚动轴承套圈的配合面、旋 合螺纹的工作面、铆钉的工作面等。
第11章 摩擦学设计方法
第11章 摩擦学设计方法
边界摩擦又称为边界润滑,是指当运动 副的摩擦表面被吸附在表面的边界膜隔开, 摩擦性质取决于边界膜和表面的吸附性能时 的摩擦。 润滑油中的脂肪酸是一种极性化合物, 其分子的一端带有强电荷的极性团,对金属 表面有垂直取向的特性,能牢固地吸附在金 属表面上。
第11章 摩擦学设计方法
第11章 摩擦学设计方法
当摩擦表面之间处于边界摩擦与流体摩擦 的混合状态时称为混合摩擦。混合摩擦也称为 混合润滑。混合润滑及流体润滑可以用膜厚比 来大致估计。
hmin R R
2 q1 2 q2
式中,hmin为两个表面之间的最小公称油膜厚度(μm);Rq1、 Rq2为两表面的轮廓均方根偏差(μm)。Rq=(1.20~1.25) Ra,Ra为表面轮廓的表面粗糙度值(μm)。
第11章 摩擦学设计方法
设计者思维
作为工程师,就需要利用摩擦学的知识与技术,使所设 计的零部件有良好的摩擦学性能,以延长其工作寿命。 需要考虑的是机械零部件在哪些部位容易产生摩擦? 摩擦状态分为哪几类? 摩擦一定会产生磨损吗? 磨损分为哪几类? 有效降低磨损的方法有哪些? 如何通过选择材料来降低磨损? 如何确定和选用润滑方式? 要如何来选择润滑油?
第11章 摩擦学设计方法
为了减小黏附磨损,可采取以下措施 (1)合理选择配对材料。相同的金属互溶性 强,比不同的金属黏附倾向大;多相金属比单 相金属黏附倾向小;脆性材料比塑性材料的抗 黏附能力强;进行表面处理(如表面热处理、 电镀、喷涂等)可防止黏附磨损的发生。 (2)限制摩擦表面的温度,采取合适的散热 措施,防止油膜破裂及金属发生熔焊。 (3)采用含油性和极压添加剂的润设计方法
微型滚珠丝杠副摩擦力矩模型的建立与实验验证

微型滚珠丝杠副摩擦力矩模型的建立与实验验证陈勇将;汤文成【摘要】Being capable of predicting the friction torque of micro-type ball screw accurately allows the designer to correctly determine the energy loss and heat generation rate. Since the calculation of traction force is complex and requires much computer time, the forces and moments equilibrium are used for deriving the rolling element-race sliding force. Take into account the influence of spin sliding and helix angle, the final friction torque of micro-type ball screw can be calculated. The micro-type ball screw tests were conducted on a special machine for verification. It is found that good a-greement is held between the predictions of the new analytic torque model and the test results obtained with the micro-type ball screw torque rig. Analysis indicates that the performance parameters of lubricant and friction coefficient in ball-races contacts are the main factor to influence the friction torque of micro-type ball screws.%为了可以快速且准确地预测微型滚珠丝杠副的能量损耗与温升速率,建立了新的摩擦力矩模型.首先基于微型滚珠丝杠副的摩擦机理,利用力与力矩平衡的方法求得滚珠与滚道接触界面间的摩擦力,该方法比通过对接触区域上的切应力积分求解摩擦力的方法更简单方便,易于编程实现;其次考虑自旋滑动摩擦及螺旋升角的影响,推导出微型滚珠丝杠副的摩擦力矩模型;最后在微型滚珠丝杠副综合测试实验台上进行了实验验证.分析结果发现,在不同转速下,微型滚珠丝杠副摩擦力矩模型的预测值与实验值都有较好的吻合,表明摩擦力矩主要受润滑介质的性能参数及滚珠与滚道接触的滑动摩擦系数的影响.【期刊名称】《东南大学学报(自然科学版)》【年(卷),期】2011(041)005【总页数】5页(P982-986)【关键词】微型滚珠丝杠副;摩擦力矩;摩擦机理;滑动摩擦【作者】陈勇将;汤文成【作者单位】东南大学机械工程学院,南京,210096;东南大学机械工程学院,南京,210096【正文语种】中文【中图分类】TH132.1;TH117微型滚珠丝杠副的摩擦力矩是指各种摩擦因素对微型滚珠丝杠副运动构成的阻力矩,其带来的能量损耗降低了传动效率,引起的温升产生热变形影响了定位精度[1-2].对于广泛应用于高精度小型机电一体化设备的微型滚珠丝杠副来说[3],摩擦力矩模型的建立十分必要,可以快速且准确地预测能量损耗与温升速率.文献[4]建立了一个估计滚珠丝杠副摩擦力矩的模型,主要参考了滚动轴承建立摩擦力矩模型的方法,没有考虑自旋滑动摩擦及滚珠丝杠副独有的螺旋结构对摩擦力矩的影响,且没有进行实验验证.文献[5]将文献[4]建立的滚珠丝杠副摩擦力矩模型计算结果与文献[6]测量到的滚珠丝杠副摩擦特性数据进行了比较,发现文献[4]建立的摩擦力矩模型计算结果与实验数据存在较大差异.本文从微型滚珠丝杠副的摩擦机理出发,得出影响摩擦力矩的各种阻力与阻力矩;考虑自旋滑动摩擦及螺旋升角的影响,推导出适用于微型滚珠丝杠副的摩擦力矩模型;通过实验对模型进行验证.1 微型滚珠丝杠副的摩擦机理微型滚珠丝杠副中接触面虽为滚动界面,但滚动接触所引起的摩擦损耗很少,损耗主要来自于滚动过程中发生的滑动行为.这些滑动产生于滚珠与丝杠滚道接触界面间、滚珠与螺母滚道接触界面间、滚珠与返向器滚道接触界面间和滚珠与滚珠接触界面间(见图1),其中滚珠与丝杠滚道、滚珠与螺母滚道及滚珠与返向器滚道接触界面间的滑动摩擦为损耗的主要来源.返向器是螺母的一部分,所以滚珠与返向器滚道接触可看作滚珠与螺母滚道接触的特例,将这3个接触界面间的滑动摩擦统称为滚珠与滚道接触界面间的滑动摩擦.图1 微型滚珠丝杠副的摩擦机理分解图1.1 滚珠与滚道接触产生的摩擦微型滚珠丝杠副中滚珠与滚道间的纯滚动与滑动一样也会发生能量损耗,主要是接触表面的应力循环引起的黏着损失和弹性滞后损耗.虽然滚动接触发生在离散的微凸体上,但由于滚动表面的微凸体沿着法向接近和分离,不像滑动接触那样沿着切线方向,因而滚动接触面积变化不大;滚动接触区的黏着力主要来自范德华力,黏着力将在滚动接触区末端以拉伸形式被分离,而不像滑动接触那样以剪切形式产生分离,所以滚动接触所引起的摩擦损耗较滑动摩擦相比很少.滚动摩擦的弹性滞后损耗源于消耗功与复原功之差,单个接触点处由弹性滞后所形成的摩擦力矩为[7]式中,Dw为滚珠直径;Qi为滚珠与滚道间的法向载荷;k为滚珠与滚道接触的椭圆率.滑动摩擦主要包括楔紧滑动、差动滑动和自旋滑动.楔紧滑动源于滚珠丝杠副的螺旋结构,是滚珠丝杠副特有的运动,而滚珠与滚道间的接触变形引起的差动滑动,仅在2条窄带上不发生滑动,同时由于接触角的存在,滚珠丝杠副中还将引起绕纯滚动点的自旋滑动.当滚珠与滚道接触区域上存在2条纯滚动线时,差动滑动摩擦力矩MCi和自旋滑动摩擦力矩MPi的计算公式为[8]式中,μ为滑动摩擦系数;l为接触椭圆的长半径;ri为滚珠与滚道间接触变形后的半径;fc,fp分别为差动滑动MCi和自旋滑动MPi计算系数.1.2 滚珠在返向器中产生的摩擦滚珠在返向器中的摩擦主要为滚珠进出返向器时碰撞力产生的摩擦和滚珠在返向器滚道内的滑动摩擦[9].由于滚珠在返向器中不承受载荷,所以滚珠中心的线速度不高,相对于滚珠与丝杠滚道及滚珠与螺母滚道产生的滑动摩擦而言,这一部分摩擦很小,通常情况下可以忽略.碰撞力产生的摩擦与丝杠转速成正比,高速下这一部分摩擦较大[10-11],但微型滚珠丝杠副的应用领域对转速要求不高,因此这一部分摩擦也不作考虑.1.3 润滑剂产生的阻力及滚珠间的滑动摩擦在流体润滑微型滚珠丝杠副中,滚珠必须克服润滑剂产生的黏性摩擦力.润滑剂产生的阻力取决于散布在滚珠丝杠副内部润滑剂的量.运用弹流润滑理论求得润滑剂引起的滚动阻力为[7]式中,E为等效弹性模量;Li为滚珠与滚道间接触点法向平面内的综合曲率半径;G 为材料参数;U无纲量速度参数;W为载荷参数.微型滚珠丝杠副的螺旋传动难以实现在滚珠间加上类似于轴承的保持架,所以滚珠间的滑动摩擦力无法避免,滚珠间摩擦产生的摩擦力矩可表示为式中,μb为滚珠间摩擦系数;FB为滚珠间摩擦力.2 摩擦力矩模型的建立2.1 滚珠与滚道接触的摩擦力微型滚珠丝杠副中滚珠与滚道接触的摩擦力FSi可以通过滚珠上力与力矩的平衡关系式求得.由微型滚珠丝杠副摩擦机理可知,作用于滚珠滚动方向的阻力除了滚珠与滚道间摩擦力FSi外,还有滚珠间接触力FB及润滑剂引起的滚动阻力FRi和压力FPi;而作用于滚珠上沿运动方向绕滚珠球心的阻力矩主要为差动滑动摩擦力矩MCi、弹性滞后阻力矩Mi及滚珠间摩擦力矩MB(见图2),由力和力矩平衡可得式中,FSS为滚珠与丝杠滚道间的摩擦力;FSN为滚珠与螺母滚道间的摩擦力;FPN 为滚珠与螺母滚道间的润滑剂引起的压力;FPS为滚珠与丝杠滚道间的润滑剂引起的压力;MCN为滚珠与螺母滚道间的差动滑动摩擦力矩;MCS为滚珠与丝杠滚道间的差动滑动摩擦力矩;MN为滚珠与螺母滚道间的弹性滞后阻力矩;MS为滚珠与丝杠滚道间的弹性滞后阻力矩.图2 单个滚珠所受力与力矩平衡关系图由式(6)和(7)解得FSS和FSN的表达式为润滑剂作用于滚珠球心的压力FP可以表示成以FR为变量的函数,即式中,d0为微型滚珠丝杠副的公称直径;aS为滚珠与丝杠滚道的接触角;aN为滚珠与螺母滚道的接触角.将式(10)和(11)代入式(8)和(9)可得滚珠与滚道接触界面间摩擦力的最终表达式为2.2 滚珠与滚道接触的摩擦力矩模型对于微型滚珠丝杠副中单个滚珠的摩擦力矩,除了包含滚珠与滚道间摩擦力与力臂之积外,还应将自旋滑动摩擦力矩MPi投影至旋转轴上(见图2),其分量应为MPisinaicosβ,因此单个滚珠与滚道接触的摩擦力矩表达式为式中,RS为滚珠与丝杠滚道接触点至丝杠轴心的距离;RN为滚珠与螺母滚道接触点至丝杠轴心的距离;β为螺旋升角.因此,对于滚珠数为Z的微型滚珠丝杠副,其摩擦力矩最终表达式为3 摩擦力矩模型的实验验证3.1 试验设备及方法微型滚珠丝杠副摩擦力矩的测量是在微型丝杠综合测试实验台上进行的,测量实验台结构如图3所示.由安装在工作台上的驱动电机与滚珠丝杠副的一端连接带动旋转,另一端用尾座顶尖限制,通过摩擦力矩测量装置的悬臂与安装在螺母上连接杆相配合,来约束滚珠丝杠副的周向与轴向运动.当丝杠旋转时,螺母旋转运动被限制只能带动摩擦力矩测量装置在滑动导轨上作轴向运动,在此方向上由气压缸施加轴向载荷给滚珠丝杠副,此轴向力的大小由拉压式力传感器测得.而限制周向运动的阻力由压力传感器测得,转换成数字信号后,乘以力臂因子即可得到所测量的微型滚珠丝杠副的摩擦力矩.图3 微型滚珠丝杠副综合测试实验台结构示意图试验产品为FF型微型滚珠丝杠副(南京工艺装备制造有限公司),具体结构参数及性能参数如表1所示.被测试的微型滚珠丝杠副首先以400 r/min的转速跑合5 min后停转,然后保持轴向载荷恒定,再调节驱动电机转速从零增加到800r/min.在这期间测量螺母移动方向与轴向载荷方向相反时的摩擦力矩,为验证试验结果的准确性和可重复性,同一转速下重复测量多次.试验时测量参数的采集频率设置为100,力臂直径为38 mm.表1 FF1605型微型滚珠丝杠副结构与性能参数16公称导程/mm 5滚珠直径/mm 3.5弹性模量/GPa 210泊松比 0.3滚珠数 40动力黏度/GPa 0.04黏压系数/(nm·N-1)参数数值公称直径/mm 223.2 结果与讨论图4所示为FF1605型微型滚珠丝杠副在不同转速下测得的摩擦力矩值及其变化范围,摩擦力矩是在同一转速下螺母移动方向与轴向载荷方向相反时重复试验多次所取的平均值.由图4可知,在较低转速(n=400 r/min)下,摩擦力矩的变化幅度较大,随着转速的增加,摩擦力矩的变化速度有所放缓;微型滚珠丝杠副的摩擦力矩极不平稳,存在较大的波动,且波动范围的大小与转速没有明显关联,这主要是由于影响微型滚珠丝杠副的因素较多,因而摩擦力矩特性具有随机性和复杂性.图4 不同转速下微型滚珠丝杠副的摩擦力矩实验值及变化范围由不同转速下摩擦力矩实验值与模型值对比可知(见图5),不同转速下微型滚珠丝杠副的摩擦力矩模型值与实验值都有较好的吻合.随转速的提高,摩擦力矩模型值一直以较大的速度上升,而实验值在n=400 r/min以下与模型值上升速度相近,尤其当转速为400 r/min时两值误差几乎为零.但随着转速进一步升高,实验值的上升速度慢于模型值,但上升趋势不变.图5 不同转速下微型滚珠丝杠副的摩擦力矩模型值与实验值对比图4 结论在拟静力学分析基础上,考虑了微型滚珠丝杠副螺旋升角及自旋滑动摩擦的影响,利用力与力矩平衡的方法,推导出了微型珠丝杠副摩擦力矩模型,实验证明所建立的新摩擦力矩模型基本符合实际情况.由依据微型滚珠丝杠副摩擦机理建立的新模型可知,润滑介质的性能参数及滚珠与滚道接触的滑动摩擦系数对摩擦力矩影响较大,实验也表明摩擦力矩的变化主要是转速影响了滚珠所受的润滑剂黏性阻力,因此要减小微型珠丝杠副摩擦力矩、提高摩擦力矩的平稳性,需要特别重视润滑的研究.参考文献(References)[1] Brecher C,Witt S,Yagmur T.Infuence of oil additives on the wear behavior of bal screws[J].Production Engineering,2009,3(3):323-327. [2] Wei C W,Lin J F.Kinematic analysis of the ball screw mechanism considering variable contact angles and elastic deformations[J].Journalof Mechanical Design,2003,125(4):717-733.[3]严虎勤,闫笃政,田茂林.HJ微型滚珠丝杠副的设计与制造[J].制造技术与机床,2006,4(9):109-110.Yan Huqin,Yan Duzheng,Tian Maolin.Design and manufacture of micro-type ball screw[J].Manufacturing Technology & Machine Tool,2006,4(9):109-110.(in Chinese)[4] Olaru D,Puiu G C,Balan L C,et al.A new model to estimate friction torque in a ball screw system[C]//Advanced Computer Aided Design of Ecological Products.Brasov,Romania,2004:333-346.[5]苏益德.滚珠导螺杠之摩擦力分析研究[D].中国台湾:中兴大学机械工程系,2009.[6] Kamalzadeh A.Precision control of high speed ball screw drives [D].Waterloo,Canada:Department of Mechanical Engineering,University of Waterloo,2008.[7] Houpert L.Ball bearing and tapered roller bearing torque:analytical,numerical and experimental results[C]//Proc of STLE AnnualMeeting.Houston,USA,2002:19-23.[8] Houpert L.Numerical and analtical calculations in ball bearing[C]//Proc of Congres Roulements.Toulouse,France,1999:1-15.[9]Braccesi C,Landi L.A general elastic-plastic approach to impactanalysis for stress state limit evaluation in ball screw bearing return system [J].International Journal of Impact Engineering,2007,34(7):1272-1285. [10] Hung J P,Wu J S S,Chiu J Y.Impact failure analysis of re-circulating mechanism in ball screw [J].Engineering Failure Analysis,2004,11(4):561-573.[11]张佐营,宋现春,姜洪奎,等.滚珠丝杠副中滚珠与返向器的碰撞研究[J].中国机械工程,2008,19(7):850-881.Zhang Zuoyin,Song Xianchun,Jiang Hongkui,et al.Research on the impact between balls and re-circulating mechanism in ball screw [J].China Mechanical Engineering,2008,19(7):850-881.(in Chinese)。
高温高速摩擦副的摩擦学特性研究

高温高速摩擦副的摩擦学特性研究摩擦学是研究在两个物体表面接触过程中产生的相互耗散能量和接触特性的学科。
在高温高速条件下,摩擦学特性的研究尤为重要,因为这种环境下的摩擦会导致严重的摩擦磨损和热衰减现象。
本文将探讨高温高速摩擦副的摩擦学特性研究进展及其应用。
首先,我们来了解高温高速条件下摩擦学特性的变化。
在高温高速环境下,摩擦副的表面温度迅速上升,导致润滑剂的挥发和降解,使摩擦阻力和磨损显著增加。
同时,高速运动也使得接触面的摩擦热迅速扩散,导致局部高温区域的形成,增加了摩擦副的摩擦热和热应变。
这些因素都对摩擦副的摩擦学性能产生了巨大影响。
其次,我们来分析高温高速摩擦副的摩擦学特性研究进展。
研究者们通过实验和模拟手段,对高温高速摩擦副的摩擦学性能进行了广泛研究。
例如,他们通过设计不同材料的摩擦副,并在实验中控制温度和速度,来模拟高温高速工况。
同时,他们还利用纳米材料和新型润滑剂来改善摩擦副的性能。
通过这些研究,我们可以更好地理解高温高速摩擦副的摩擦学特性,并为实际应用提供参考依据。
另外,高温高速摩擦副的摩擦学特性的研究也对应用产生了积极的影响。
首先,它有助于提高摩擦副的工作效率和寿命,在高温高速工况下减少摩擦磨损。
其次,它可以为摩擦材料的选用提供指导,以提高工程设备的可靠性和安全性。
最后,研究高温高速摩擦副的摩擦学特性,还有助于开发新型摩擦材料和润滑剂,推动摩擦学技术的发展和应用。
在实际应用中,高温高速摩擦副的摩擦学特性研究还存在一些挑战和需要进一步解决的问题。
首先,如何准确地模拟高温高速工况下的摩擦副行为,以及如何获取真实可靠的实验数据。
其次,如何设计更有效的润滑系统,以提供足够的润滑剂并减少摩擦热的产生。
最后,如何开发出新型的高耐热高耐磨摩擦材料,以适应高温高速工况下的需求。
综上所述,高温高速摩擦副的摩擦学特性研究对于提高工程设备的可靠性和安全性有着重要意义。
通过深入了解摩擦学特性的变化,并进行研究和实践,我们可以更好地应对高温高速条件下的摩擦问题,并为实际应用提供有效的解决方案。
高速摩擦副的磨损与摩擦学特性分析

高速摩擦副的磨损与摩擦学特性分析摩擦学是研究摩擦、磨损和润滑的学科,广泛应用于机械工程、材料科学和电子工程等领域。
在高速摩擦副中,摩擦学特性的分析对于提高摩擦副的性能和寿命至关重要。
本文将从摩擦副的磨损机制和摩擦学特性两个方面进行分析。
一、摩擦副的磨损机制摩擦副的磨损机制是指在摩擦副工作过程中,零件表面因相互之间的接触与摩擦而发生的材料的损耗和变化。
磨损机制是多种多样的,主要包括磨粒磨损、表面疲劳磨损、磨粒掠过等。
1. 磨粒磨损磨粒磨损是指外来硬颗粒在摩擦副中的接触与摩擦下导致零件表面的磨损。
这些磨粒可以是灰尘、颗粒或金属碎屑等。
当磨粒与零件表面接触时,会形成微小的凹坑和划痕,进而导致摩擦副的磨损加剧。
2. 表面疲劳磨损表面疲劳磨损是指由于零件在高速摩擦副中经受连续循环应力作用,从而引起轻微的塑性变形和疲劳破坏现象。
这种磨损通常表现为微小的裂纹和微观断层,进而导致零件表面的颗粒脱落。
3. 砂粒掠过砂粒掠过是指由于砂粒在摩擦副中的运动和颗粒与零件表面的接触与摩擦而导致的磨损。
当砂粒在高速中掠过零件表面时,会造成颗粒的嵌入和划伤,进而导致零件表面的磨损。
二、摩擦学特性的分析摩擦学特性是指摩擦副在摩擦过程中所表现出的性质和行为。
具体而言,摩擦学特性包括摩擦系数、摩擦热和磨损率等。
1. 摩擦系数摩擦系数是反映摩擦副表面之间摩擦阻力大小的物理量。
摩擦系数的大小受到多种因素的影响,例如表面粗糙度、润滑状态和温度等。
在高速摩擦副中,摩擦系数的减小可以降低能量损耗和摩擦副的磨损。
2. 摩擦热摩擦热是指在摩擦副工作过程中由于摩擦而产生的热量。
摩擦热的大小与摩擦系数和摩擦副的速度有关。
过高的摩擦热可能会导致摩擦副的脱离和热变形,因此在摩擦副设计中,必须考虑摩擦热的有效散热方式。
3. 磨损率磨损率是指单位时间内摩擦副表面的磨损量。
高速摩擦副的磨损率通常较大,因此在摩擦副设计中,应选择耐磨性好的材料和合适的润滑方式以降低磨损率。
摩擦学原理及其在摩擦副设计中的应用研究
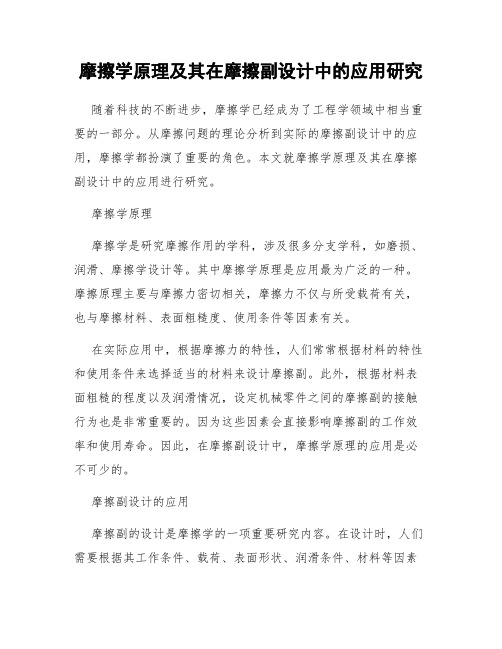
摩擦学原理及其在摩擦副设计中的应用研究随着科技的不断进步,摩擦学已经成为了工程学领域中相当重要的一部分。
从摩擦问题的理论分析到实际的摩擦副设计中的应用,摩擦学都扮演了重要的角色。
本文就摩擦学原理及其在摩擦副设计中的应用进行研究。
摩擦学原理摩擦学是研究摩擦作用的学科,涉及很多分支学科,如磨损、润滑、摩擦学设计等。
其中摩擦学原理是应用最为广泛的一种。
摩擦原理主要与摩擦力密切相关,摩擦力不仅与所受载荷有关,也与摩擦材料、表面粗糙度、使用条件等因素有关。
在实际应用中,根据摩擦力的特性,人们常常根据材料的特性和使用条件来选择适当的材料来设计摩擦副。
此外,根据材料表面粗糙的程度以及润滑情况,设定机械零件之间的摩擦副的接触行为也是非常重要的。
因为这些因素会直接影响摩擦副的工作效率和使用寿命。
因此,在摩擦副设计中,摩擦学原理的应用是必不可少的。
摩擦副设计的应用摩擦副的设计是摩擦学的一项重要研究内容。
在设计时,人们需要根据其工作条件、载荷、表面形状、润滑条件、材料等因素来选择合适的摩擦材料。
设计中重要的一步就是要根据摩擦副材料的特性来分析和计算其工作过程中的摩擦力。
利用摩擦力计算公式可以计算出摩擦力和摩擦副中的摩擦系数。
在摩擦副设计中,摩擦系数的大小很大程度上决定着摩擦副的工作寿命和使用效果。
因此,在设计时,必须充分考虑这一因素。
不同的工作条件会对摩擦副的工作方式及长期使用产生影响。
例如,在润滑薄膜足够厚的情况下,滚动、滑动的摩擦系数都会变小,从而降低摩擦力,提高摩擦副的使用寿命。
如果长期工作的条件恶劣,需要重复高负荷的工作,那么选择摩擦副材料时需要考虑材料的磨损和其他方面的问题,使摩擦副能够长期稳定地工作。
而在摩擦副设计中,还有一个非常重要的因素:表面形状。
表面形状对摩擦副工作的摩擦力、摩擦系数以及接触应力等都有非常重要的影响。
在一定程度上,形状决定了工作面的实际接触面积,因此设计摩擦副时,必须考虑表面的粗糙度、硬度和摩擦材料的厚度。
摩擦学研究中的实验技术及装置设计

摩擦学研究中的实验技术及装置设计随着现代科技的不断发展,人类对于材料的摩擦学性能研究越来越深入,对于提高材料的性能及寿命有着日益重要的意义。
而实验技术及装置设计是这一领域中必不可少的一环,为摩擦学研究的深入发展提供了坚实的基础。
下面将对摩擦学研究中的实验技术及装置设计进行探讨。
一、摩擦测试技术摩擦测试技术是摩擦学研究中不可或缺的一部分,是了解各种材料的摩擦特性、磨损规律以及润滑性能的关键。
目前常用的摩擦测试技术有以下几种:1. 平面双摩擦试验平面双摩擦试验是比较常用的摩擦测试技术之一,其主要原理是通过磨擦两个平面对材料进行测试,测试中可以测量材料的摩擦力、磨损量等参数,进而分析材料的摩擦特性。
2. 旋转摩擦试验旋转摩擦试验是一种简单而直观的摩擦测试技术,其原理是通过旋转装置对材料进行测试。
常用于测试一些采用旋转零件的设备的摩擦特性,如发动机、水泵等。
3. 弧形摩擦试验弧形摩擦试验是一种测试材料磨损性能的摩擦测试技术,其测试原理是通过在弧形试样上施加应力,测量弧形试样表面的磨损量,进而分析材料的磨损性能。
二、摩擦测试装置设计摩擦测试装置的设计是落实摩擦测试技术的重要手段,针对不同的测试要求和目的需要设计不同的测试装置。
下面介绍几种常见的测试装置设计。
1. 摩擦试验机摩擦试验机是一种专门用于进行材料摩擦测试的装置,可以用于进行平面双摩擦试验、旋转摩擦试验、弧形摩擦试验等,具有多种测试模式,测试数据准确性高,实验成本低等优点。
不同型号的摩擦试验机能够测试不同范围的摩擦系数以及磨损量。
2. 高温摩擦磨损试验机高温摩擦磨损试验机是一种专门用于高温下进行磨损测试的装置,能够稳定控制高温环境下的测试参数,如磨擦系数、磨损量等。
适用于研究高温下材料的摩擦特性、磨损规律以及耐磨性能等。
3. 压电陶瓷摩擦试验装置压电陶瓷材料的摩擦性能是研究的热点问题,为了研究压电陶瓷材料的摩擦性能,需要设计一种专门的测试装置,如压电陶瓷摩擦试验装置。
材料的摩擦学行为与摩擦副设计

材料的摩擦学行为与摩擦副设计摩擦是指物体表面之间的相互阻力,其产生与材料的摩擦学行为有着密切关系。
摩擦学行为是指材料在与其他物体表面接触时所表现出的力学性质。
而摩擦副设计则是指在摩擦副的选择和设计方面进行的一系列工程问题的分析和解决。
在工程实践中,摩擦学行为的特性对于设计和选择合适的摩擦副具有重要的意义。
材料的摩擦学行为通常包括摩擦系数、磨损、热效应等方面。
摩擦系数是指在给定条件下,表征材料界面间摩擦性能的系数。
磨损是指摩擦副表面的物质流失或变形,这会引起摩擦副的性能丧失和使用寿命的减少。
热效应是摩擦过程中会产生热量,并可能导致摩擦副温度升高。
不同材料之间的摩擦学行为具有显著的差异。
例如,金属材料通常具有较高的摩擦系数和磨损率,而聚合物材料则具有较低的摩擦系数和磨损率。
这些差异主要是由于不同材料的化学、物理性质以及微观结构所决定的。
因此,选择和设计摩擦副时需要综合考虑材料的摩擦学行为。
摩擦副设计的主要目标是降低摩擦磨损、提高摩擦性能和延长使用寿命。
在进行摩擦副设计时,需要考虑以下几个方面的问题。
首先是材料的选择。
根据材料的性质和使用条件的不同,选用不同的材料来构成摩擦副。
常见的材料包括金属、聚合物、陶瓷等。
在选择材料时,应综合考虑其摩擦系数、磨损率、耐热性、耐蚀性等方面的性能。
其次是表面处理。
通过表面处理可以改变材料的表面性质,提高材料的摩擦性能和耐磨性。
常用的表面处理方法包括镀层、高能束流处理、化学处理等。
此外,还需要考虑润滑剂的选择和使用。
润滑剂可以降低摩擦系数、减少热效应和磨损。
常用的润滑剂有液体润滑剂和固体润滑剂。
在选择润滑剂时需要考虑其温度范围、使用环境和性能要求等因素。
最后,需要进行适当的摩擦副设计的实验验证。
通过实验可以评价摩擦副的性能,调整设计参数,并验证设计的可行性和有效性。
综上所述,材料的摩擦学行为与摩擦副设计密切相关。
通过选择合适的材料、进行表面处理、使用适当的润滑剂,并进行实验验证,可以有效地改善摩擦副的性能,延长其使用寿命。
工程摩擦学9 摩擦学的设计共48页文档
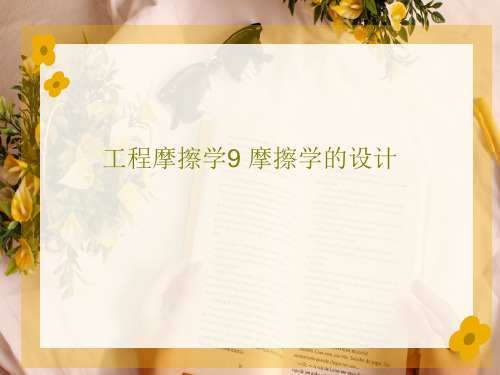
耐磨性与金属的显微组织有关。马氏体耐磨性优于珠光体,珠 光体优于铁素体。对珠光体的形态,片状的比球状的耐磨,细片的 比粗片的耐磨。回火马氏体常常比不回火的耐磨,这是因为未回火 的组织硬而脆。
2021/3/31
9. Tr考虑的因素 2)结构设计
磨损率受结构的影响很大,包括整机的结构和零件的形状尺 寸。例如:4M3电铲斗齿寿命较低,首钢公司迁安煤矿通过改善 斗齿形状,即把斗齿上下面上挖一长槽,将这部分材料放在齿尖 部位,加长了斗齿长度,改变了矿石与零件表面接触时的力流状 况,从而增加了耐磨性。
摩擦学系统是机器系统的一种抽象,它由机器中的全体摩擦 副和必要的支持系统组成。设计一个能经济而可靠地实现运动并 保证功能的摩擦学系统就是摩擦学设计的任务,所以,摩擦学设 计必须理解为摩擦学系统的设计,它不仅仅只是一个摩擦副或其 中一个摩擦学元素的设计。
2021/3/31
9. Tribology Design
2021/3/31
9.2 耐 磨 设 计
9. Tribology Design
9.2.1 考虑的因素 4)使用与维护
经常维护保养使用设备也是提高零件使用寿命的一项重要措施,
同样的机械产品,不同技术素养的工人操作,设备会有不同的寿命。
2021/3/31
9. Tribology Design
9.2 耐 磨 设 计 9.2.2 防止和减少磨损的方法 1)润 滑
9.2 耐 磨 设 计
9.2.1 考虑的因素 1)选 材
要提高机器的耐磨性,最重要的问题就是要合理选择符合该 工况条件的最佳性能材料,不同类型的磨损方式,选择的方向也 不同。
摩擦系数对高副接触磨损影响的有限元模拟

摩擦系数对高副接触磨损影响的有限元模拟张优云;陈朝;朱永生;蒋翔俊【摘要】为研究摩擦系数对高副接触磨损的影响,利用有限元方法,采用ANSYS软件建立了圆柱和平板相接触的磨损预测模型.根据改进的Archard磨损模型计算磨损量,采用移动接触边界节点的方法来模拟材料的去除过程,并与实验数据进行了对比,证明了模型的合理性.利用该模型,研究不同的摩擦系数对磨损量、接触压力、滑移量、正应力、剪应力的影响.仿真结果表明,较小的摩擦系数会产生较大的接触压力和滑移量,从而使磨损量增大.较大的摩擦系数会加速疲劳的产生.【期刊名称】《哈尔滨工业大学学报》【年(卷),期】2013(045)009【总页数】6页(P64-69)【关键词】磨损;Archard模型;有限元方法;摩擦系数;接触压力;滑移量【作者】张优云;陈朝;朱永生;蒋翔俊【作者单位】西安交通大学现代设计与轴承转子系统教育部重点实验室,710049西安;西安交通大学现代设计与轴承转子系统教育部重点实验室,710049西安;西安交通大学现代设计与轴承转子系统教育部重点实验室,710049西安;西安交通大学现代设计与轴承转子系统教育部重点实验室,710049西安【正文语种】中文【中图分类】TH117.1磨损占机械零件失效的60%~80%[1],因此,研究磨损具有非常重要的意义.随着计算机技术的发展,数值仿真技术已经成为磨损研究的一种非常重要的手段.蒋翔俊等[2]利用数值仿真方法研究了不同交变载荷力作用下燃机端面齿的磨损规律.在数值仿真研究方法中,有限元仿真分析已经在工程中得到了广泛的应用,并且在磨损分析方面具有很强的实用性[3].冯伟[4]利用有限元方法进行滑动磨损试验的摩擦学仿真研究.Sfantos等[5]、Andersson等[6]提出了应用边界元法及有限元方法的磨损预测方法.Rezaei等[7]利用有限元方法和Archard方程,建立了径向滑动轴承磨损过程的模型.Cruzado等[8]利用商用有限元软件ABAQUS,研究了钢丝绳的微动磨损,并且进行了试验验证.宿月文[9]利用有限元方法进行了滑动磨损过程的仿真研究,对销轴的磨损进行了预测.但是上述研究只能对长距离的滑动磨损进行仿真,而不能对小幅振动下的磨损进行有效的仿真.摩擦系数、接触压力和滑移量等特征参数是影响磨损的主要因素[10].在磨损过程中,摩擦系数并不是一个恒定的值,而是随着磨损循环次数的增加而逐渐增大,最终在一个较小的范围内波动[11].在目前的磨损有限元仿真中,针对变化的摩擦系数的影响研究并不多见.本文建立了一种基于有限元方法的磨损预测模型,利用有限元软件ANSYS12.1对圆柱和平板相接触的小幅振动磨损过程进行了仿真分析,将仿真结果与文献[11]中的实验数据进行了对比验证,并利用该模型分析了摩擦系数的变化对磨损量、接触压力、滑移量、正应力、剪应力的影响.1 磨损分析的有限元建模1.1 接触分析圆柱和平板的接触问题广泛应用于磨损的研究中,其接触情况如图1所示.根据赫兹接触计算公式,可以得到接触压力的分布为式中,接触区域半宽度a为最大接触压力p0为其中式中,E1和E2、ν1和ν2、R1和R2分别为两个接触体的弹性模量、泊松比和曲率半径.图1 圆柱和平板的接触在有切向力T(t)的作用下,两个接触表面间会出现相对滑动.在整体滑移的情况下,切向力的最大值Tmax和摩擦力μp相等(μ为摩擦系数).如果Tmax<μp,则会产生局部滑移.此时,接触区域的中心会产生一个半宽度为c的粘着区,而在c≤|x|≤a的区域则会产生一个局部滑移区.瞬时时刻的粘着区的宽度c*可以表示为1.2 有限元模型本文针对的材料与文献[11]相同,为高强度合金钢.由于圆柱和平板的接触属于线接触,因此可以将接触模型简化成二维模型.图2是磨损仿真的有限元模型.图2 圆柱和平板接触的有限元模型半圆和矩形的单元类型均为PLANE42,弹性模量为200 GPa,泊松比为0.3,摩擦系数为0.8.接触区域的半宽度设置为0.3 mm,这一宽度是根据赫兹接触计算所确定的.为了得到比较精确的计算结果并尽可能的减少节点数量,划分网格时只将接触区域的网格细化(网格宽度为5 μm).为了使网格划分较细的区域和网格划分较粗的区域能够平稳的过渡,该模型在两个区域之间增加了一个过渡区.节点总数为24 004个.本模型使用接触单元CONTA172和目标单元TARGE169来定义接触对.但是ANSYS只能保存接触单元的计算结果.为了能将相互接触的两个面的数据都提取出来,该模型定义了两个接触对,即以接触区域中上方的圆弧为接触面、下方的直线为目标面的接触对,和以直线为接触面、圆弧为目标面的接触对.圆柱在平板上的运动方式与文献[11]中的实验相同,即以坐标原点为中心,沿x方向作往复运动,幅值为25 μm.1.3 磨损计算模型Archard磨损模型是一种经典且应用非常广泛的磨损计算模型.该模型可表述如下:式中:V为总的体积磨损量,m3;P为法相载荷,单位为N;S为总的滑动距离,m;H 为材料的布氏硬度,Pa;K为磨损系数,是一个无量纲的比例常数.为了体现两接触表面的轮廓随磨损循环进行的变化,研究磨损深度更具实际意义.假设在一个极小的接触区域dA内,有一段较小的滑动距离dS,此时应用式(1)可以得到方程两边同时除以dA可以得到式中,dP/dA为局部的接触压力,它是一个接触点水平位置的函数,记为p(x);dV/dA为局部磨损深度,记为dh;将K/H记为k1,则式(2)可写为如果将磨损过程离散为若干个子步来计算磨损量,则第i个节点在第j次磨损循环时的磨损增量为式中,k1与材料属性、运行工况等因素有关;Δsi,j是接触区域的滑移量,通常小于实际的滑动距离;接触压力pi,j可通过数值方法,如有限元方法来得到.1.4 磨损仿真过程磨损仿真的过程是十分缓慢的,如果完全仿真实际磨损过程的每一步,将耗费大量的资源和时间,而计算精度却不会有太大的提高.本文采用的磨损计算流程见图3.为了提高磨损计算的效率,本文主要采用两种方法:其一,如果将半圆往复运动1次视为1个磨损循环,并且假定n(本文的模型中n=20)次磨损循环内的磨损量都是相等的,这样n次磨损循环的磨损量就可以用1次磨损循环的磨损量的n倍得到;其二,1个磨损循环内半圆滑动的距离是原点到右极限位置距离的4倍,假设1个磨损循环内产生的磨损量是半圆动到右极限位置所产生的磨损量的4倍,这样也可以在保证计算精度的情况下提高计算效率.在施加y方向向下的载荷时,如果直接将一个集中力施加在A点位置的节点上,则会导致受集中力作用的区域产生变形,且受力情况与实际不符.为了避免这一情况,本文用CERGID命令将A点处的节点和y坐标值与其相等的节点耦合,形成一个刚性区域,这样在半圆圆心的节点处施加集中力载荷时,就是通过整个刚性区域来传递载荷了.平板的底部和两边都添加了x和y方向上的位移约束,使之在仿真过程中固定不动.图3 磨损计算流程图在添加好约束,并在A点施加了y方向向下的载荷后,进入后处理器,将接触区节点的数据提取出来.提取的数据主要包括节点的x坐标、y坐标、压力和滑移量.然后再在A点对圆柱施加x方向向右的位移载荷.为了提高计算结果的精度,这里不是直接将半圆移动到右极限位置,而是将这个过程分成若干个子步,每进行一个子步之后,提取节点的压力和滑移量,根据Archard方程计算这一子步的磨损量.在所有的子步都进行完之后,将计算的磨损量叠加,就可以得到将圆柱从原点位置移动到右极限位置这一过程的磨损量.如前所述,将这一结果乘以4就可以得到一个磨损循环内的磨损量.再乘以n,即可得到n次磨损循环的磨损量.然后用节点在经历磨损循环前的y坐标值减去其对应的磨损量,得到其磨损后的位置,再将节点移动到各自的新位置,就可以得到磨损后的表面轮廓.最后卸掉所有的载荷.使用循环命令反复进行上述求解操作,就可以得到指定循环次数后的磨损量和磨损后的表面轮廓.2 有限元仿真结果图4是在185 N的载荷下,本文的有限元预测模型与赫兹接触理论分别计算出的压力分布.从图中可以看出,这两种计算方法所得到的压力分布很接近,最大压力值的误差为4.67%.图4 有限元模型与赫兹接触分别计算的压力分布(载荷:185 N)图5是有限元预测模型在载荷为185 N,往复运动的幅值为25 μm的条件下,不同磨损循环次数后,圆柱和平板的表面轮廓.从图中可以看出,随着磨损次数的增加,两接触表面的磨损深度逐渐增加,接触区域逐渐增大,并且两个表面的接触区的宽度非常接近.图5 不同磨损循环次数后的表面轮廓(载荷:185 N,幅值:25 μm)图6是在载荷为185 N,往复运动幅值为25 μm的条件下,文献[11]的实验数据与有限元磨损模型的计算结果对比图.从图中可以看出,在载荷为185 N的条件下,实验结果和有限元模型计算的结果非常接近.图6 参考文献实验数据与本文的有限元磨损模型计算结果对比(载荷:185 N,磨损次数:18 000次)图7是文献[11]的实验所测得的摩擦系数.从图中可以看出,在磨损过程中,摩擦系数并不是一个恒定的值,而是由初期一个较小的值逐渐增大并最终在一个小的范围内波动.因此,本文就不同的摩擦系数对磨损的影响进行了讨论.图7 摩擦系数随磨损次数的变化(往复运动幅值:25 μm,频率:20 Hz)图8是有限元预测模型在载荷为500 N,往复运动幅值为25 μm的条件下,在不同的摩擦系数下磨损5 000次后圆柱的表面轮廓.从图中可以看出,随着摩擦系数的增大,磨损量呈现出减小的趋势.根据本文的Archard模型,磨损量是接触压力和滑移量的函数.从图9中可以看出,摩擦系数对接触压力的影响并不是很明显,但放大后仍可发现接触压力随摩擦系数的增大而减小.而随着摩擦系数增大,滑移量亦随之减小(如图10所示),这都是导致磨损量随摩擦系数增大而减小的原因.从图10还可以看出,在500 N的载荷下的滑移均为整体滑移,并且滑移量均小于实际的滑动距离.越靠近中心区域,滑移量越小.在磨损的过程中,往往同时也伴随着疲劳.在疲劳的产生过程中,正应力和剪应力的变化是非常重要的现象[12].图11是有限元预测模型在载荷为500 N,往复运动幅值为25 μm的条件下,在不同的摩擦系数下磨损5 000次后的x方向正应力和剪应力分布.从图中可以看出,不同摩擦系数下的x方向正应力和剪应力均在磨损边界处出现峰值,并且随着摩擦系数的增大,这个峰值也逐渐增大.因此,在其他条件相同的情况下,较大的摩擦系数会比较容易导致疲劳的发生.图8 不同的摩擦系数下磨损5 000次后圆柱的表面轮廓(载荷:500 N,幅值:25 μm)图9 不同摩擦系数的压力分布(载荷:500 N)图10 不同摩擦系数下移动2.5 μm后的滑移量(载荷:500 N)图11 不同摩擦系数下磨损5 000次后应力分布(载荷:500 N,幅值:25 μm)3 结论1)利用有限元的方法,将连续的磨损过程离散化,选取适当的磨损放大因子来缩短计算时间,采用有限元分析软件来进行磨损过程的仿真,可以为实际工程应用提供一种摩擦磨损分析工具.2)由仿真计算结果发现,较大的摩擦系数会降低接触面滑移量和接触压力,从而降低磨损量.较大的摩擦系数同时也会导致接触区域正应力和剪应力上升,进而加速接触疲劳的产生.参考文献[1]温诗铸,黄平.摩擦学原理[M].第2版.北京:清华大学出版社,2002:301-302.[2]蒋翔俊,张优云,袁淑霞.燃机端面齿微动磨损分析及数值仿真[J].哈尔滨工业大学学报,2011,43(3):75-79.[3]汪选国.销盘滑动磨损试验的仿真方法研究[D].武汉:武汉理工大学能源与动力工程学院,2009:1-7.[4]冯伟.滑动磨损试验的有限元法数字仿真研究[D].武汉:武汉理工大学能源与动力工程学院,2005:25-33.[5]SFANTOS G K,ALIABADI M H.Wear simulation using an incremental sliding boundary element method[J].Wear,2006,260(9/10):1119-1128. [6]PODRA P,ANDERSSON S.Finite element analysis wear simulation ofa conical spinning contact considering surface topography[J].Wear,1999,224(1):13-21.[7]REZAEI A,VAN PAEPEGEM W,DE BAETS P,et al.Adaptive finite element simulation of wear evolution in radial sliding bearings[J].Wear,2012,196(1/2):660-671.[8]CRUZADO A,URCHEGUI MA,GOMEZ X.Finite element modeling and experimental validation of fretting wear scars in thin steel wires [J].Wear,2012,289:26-38.[9]宿月文,陈渭,朱爱斌,等.滑动磨损过程有限元分析及销磨损预测[J].中国机械工程,2009,20(13):1573-1581.[10]MOHD TOBI A L,DING J,BANDAK G,et al.A study on the interaction between fretting wear and cyclic plasticity for Ti-6Al-4V[J].Wear,2009,267(1/2/3/4):270-282.[11]MCCOLL IR,DING J,LEEN SB.Finite element simulation and experimental validation of fretting wear[J].Wear,2004,256(11/12):1114-1127.[12]DING J,LEEN S B,MCCOLL I R.The effect of slip regime on fretting wear-induced stress evolution[J].International Journal of Fatigue,2004,26(5):521-531.。
北京理工大学高等机构学第六章-外接触瞬心线高副机构-共轭高副机构

b)
18
n1 1, n2 2, 0 180
n1 1, n2 3, 0 180
n1 1, n2 4, 0 180
n1 2, n2 3, 0 90
n1 2, n2 4, 0 90
n1 2, n2 5, 0 90
n1 3, n2 4, 0 60
靠曲线接触点处之间的推动力传递动力的共轭曲线的 应用日益广泛。 轭 两头牛背上的架子称为轭,轭使两头牛同步行走。 共轭即为按一定规律相配的一对。
22
共轭曲线的形成
共轭曲线的相对滑动
23
1、共轭曲线的性质
2、共轭曲线的方程
1. 微分几何法 2. 法线法
24
常用非圆齿轮传动机
椭圆齿轮机构
40
谐波齿轮传动
41
双波传动 双波传动最常用
三波传动
42
§7-6 其它高副机构
43
不完全齿轮机构
内啮合 外啮合
齿轮齿条啮合
44
12
13
14
15
4、瞬心线方程
16
1
2
电动机
3
4
泵体
5
a)
6
6 7
1
2
3
4
4
5
Ⅰ
6
Ⅱ
12
3
Ⅳ Ⅲ
5
1,2—偏心圆齿轮
3,4—非圆齿轮 5,6—叶轮 7—泵壳
17
偏心圆——非圆齿轮驱动系统运动方案
1
2
3
4
5
6 7
8
9
10
11
10 9 8 7 6 5 4 3 2 1
高性能陶瓷关节摩擦副材料设计与制备关键技术研究
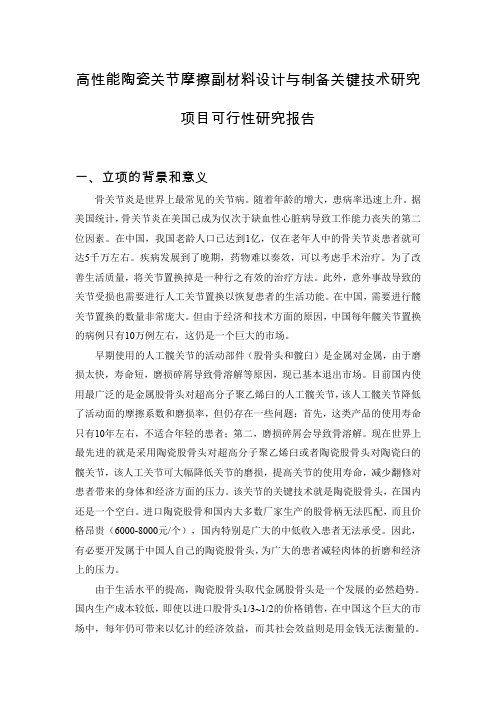
高性能陶瓷关节摩擦副材料设计与制备关键技术研究项目可行性研究报告一、立项的背景和意义骨关节炎是世界上最常见的关节病。
随着年龄的增大,患病率迅速上升。
据美国统计,骨关节炎在美国已成为仅次于缺血性心脏病导致工作能力丧失的第二位因素。
在中国,我国老龄人口已达到1亿,仅在老年人中的骨关节炎患者就可达5千万左右。
疾病发展到了晚期,药物难以奏效,可以考虑手术治疗。
为了改善生活质量,将关节置换掉是一种行之有效的治疗方法。
此外,意外事故导致的关节受损也需要进行人工关节置换以恢复患者的生活功能。
在中国,需要进行髋关节置换的数量非常庞大。
但由于经济和技术方面的原因,中国每年髋关节置换的病例只有10万例左右,这仍是一个巨大的市场。
早期使用的人工髋关节的活动部件(股骨头和髋臼)是金属对金属,由于磨损太快,寿命短,磨损碎屑导致骨溶解等原因,现已基本退出市场。
目前国内使用最广泛的是金属股骨头对超高分子聚乙烯臼的人工髋关节,该人工髋关节降低了活动面的摩擦系数和磨损率,但仍存在一些问题:首先,这类产品的使用寿命只有10年左右,不适合年轻的患者;第二,磨损碎屑会导致骨溶解。
现在世界上最先进的就是采用陶瓷股骨头对超高分子聚乙烯臼或者陶瓷股骨头对陶瓷臼的髋关节,该人工关节可大幅降低关节的磨损,提高关节的使用寿命,减少翻修对患者带来的身体和经济方面的压力。
该关节的关键技术就是陶瓷股骨头,在国内还是一个空白。
进口陶瓷股骨和国内大多数厂家生产的股骨柄无法匹配,而且价格昂贵(6000-8000元/个),国内特别是广大的中低收入患者无法承受。
因此,有必要开发属于中国人自己的陶瓷股骨头,为广大的患者减轻肉体的折磨和经济上的压力。
由于生活水平的提高,陶瓷股骨头取代金属股骨头是一个发展的必然趋势。
国内生产成本较低,即使以进口股骨头1/3~1/2的价格销售,在中国这个巨大的市场中,每年仍可带来以亿计的经济效益,而其社会效益则是用金钱无法衡量的。
本项目通过分析氧化铝粉体的纯度、形貌、颗粒尺寸分布对氧化铝陶瓷烧结性能和强度的影响,系统研究氧化铝陶瓷烧结和陶瓷球带锥孔成型关键技术,自主创新开发高精度耐磨损陶瓷关节摩擦副材料,可顶替进口,降低医疗成本,为国家和患者带来了福音。
- 1、下载文档前请自行甄别文档内容的完整性,平台不提供额外的编辑、内容补充、找答案等附加服务。
- 2、"仅部分预览"的文档,不可在线预览部分如存在完整性等问题,可反馈申请退款(可完整预览的文档不适用该条件!)。
- 3、如文档侵犯您的权益,请联系客服反馈,我们会尽快为您处理(人工客服工作时间:9:00-18:30)。
摩擦 学设 计是 以润 滑设计 为 中心 , 以形成 机 器 的润 滑状 态 为 目的进 行 的设 计 .由于 摩擦 学 设计 系
统 的特 性 , 擦学 设 计 中存在 着大 量 问题 有 待解 决 .国内外 的摩 擦 学设 计 者在 摩 擦学 设 计 上作 了大 量 摩 工作 , 但是 基本 上还 是停 留在 摩擦 学设 计 的演算 阶段 , 然其 演算 方法 逐渐 科学 化 、 理 化 , 把一 些现 虽 合 也 代 方 法 引入设 计 中 , 但没 有把 摩擦 学设 计 提到 主 动地 位 .笔 者提 出将传 统 的强 度 设计 与润 滑设 计相 结 合 , 出 了强度 设计模 型 , 滑设 计 模型 , 而建 立摩 擦学 设计 模 型 . 除 完整 的摩擦 学演 算 , 给 润 进 抛 变被 动 为
润 滑判剧 准则
厶
= —
兰兰 ≥[ _ n
() 4
√ 十盯 ;
式 中 ^ 为最 小 油膜厚 度 ;;I 用膜厚 比 ; , 分 别为 两表 面的 均方根 偏差 . E 许
3 直 齿 圆柱 齿 轮 的 摩擦 学设 计 模 型
由齿 面 接触 疲 劳 强度 条件 与润 滑设 计 准 则 相结 合 , 以得 出摩 擦学 设 计 模 型 , 可 在保 证 润 滑 的前 提 下, 又具有 一定 的疲 劳强 度 .由润 滑判 断准 则( ) 4 式得
一
√ 鲁 [] ・≤
一 ;
式 中 F 为 两轮齿 的法 向力 . 一 一 L 为轮 齿 的接触 线总 长 , 一 L一
Z, F
E 综合 弹 性模 量 , 一 1一
■ ■ 1
±
■ ,
;
综合 曲率半 径 , 1一
2 ・ 五
.
计 入 载 荷 系 数 K ,一 ・ 以 匕 数 代 入 ( ) 得 6 d 将 参 1式
第 2 期
陈 海 真 等 : 副 接 触 摩擦 学 设 计 模 型 的 构 建 高
其中
应力 .
重 合度 系数 ’ 虑 重合度 对 靴 考
载 荷 的影 响 ’
厚 端重度 一用触 面厶; 许接
2 润滑设计模型[ z
道森 ( o o ) 希金森 ( g isn 1 5 D w sn 和 Hi no ) 9 9年用 电子计 算机 成功 地证实 了弹 性流 体动 压润 滑理论 的 g
计 算公式 . 9 1年和 1 6 16 9 7年又 进行 了两 次修 正 , 据理 论分 析和计 算结果 得 出最小 油膜 厚度 的拟 合指 根 数方 程 , 方 程应 用于 线接触 , 此 压粘 效应 及 弹性 变形 均有显 著影 响 的情况下 , 算结 果与 实验结 果一 致 计
^ i 2 6 口 (o ) E.。 。 lW _ = . 5 。 yU _。 R 3 。 。 。 () 3
hm [] m≥
由 () () 3 和 5得 式 中各参数 :
:3 7 .5
.1— Os
() 5
() 6
取 ] 3a . 5 R 为表 面的算术 平 均偏差 . 一 ,=1 2 R , 。 0 7 . 0.。 ・(o ) . -・ . 3W . ≥ [ 口 . 1 1 。口 yU 。 R 4 ∞ . 。。 R ]
f1z zc az K}- E o n 2 u ̄. 1 、 s d .・ a Z - ・ + ] / ̄ T l 1
%
收 稿 日期 :2 0 一 ll 0 1l —6
( 2)
作 者简 介 :陈海 真 (9 3) 女 、 东 菏 泽 人 , 16一, 山 山东 理 工 大 学 交 通 与 车 辆工 程 学 院讲 师 , 事 机 械 设 计 教 学 与 研 究 从
主动 .
1 直 齿 圆柱 齿 轮 的强 度 设 计 模 型 [ ]
应用 H r et z理论 得 出的两 圆柱 体接触 应力 的计算 公式 .为此 须将 两 渐 开线 曲 面的接 触 转化 为两 当 量 圆柱 体 的接触 .
计 算点 : 点 . 节
由于节 点处Βιβλιοθήκη 一 般 只有 一对齿 啮 合 , 点蚀 也 往往 发生 在 节点 附 近 的齿根 面上 .所 以将节 点 处两 渐 开 线 曲面 的接触 视 为两 圆柱 体 的接 触 . 在 预期 使用 期 限内不 发生疲 劳点 蚀 的强 度条 件为
高 副接触摩擦学 设计模 型的构建
陈 海 真 , 秀 清 ,曲庆 文 郝
( 山东理 工 大 学 , 山东 淄博 2 5 9 ) 5 0 1
摘 要 :给 出 了直 齿 圆柱 齿 轮传 动 的强度 设计 模 型 , 立 了润 滑设 计 准则 , 进 而建立 了直齿 圆 建 并
柱 齿轮传 动 的摩擦 学 设计模 型 . 关键 词 :强度设 计 ;润滑 设计 ;摩擦 学设 计 中 图分类 号 : TH1 7 1 文献标 识 码 : A
103 1。 ・ ) }。E o cs s tn. ・ ・7 ・0 (。 ・ 卜 3 0 6 aos . a 4
由强度 条件 ( ) 得 2式
第1卷 第 2 6 期
20 0 2年 6月
山
东
工
程
学
院
学
报
V o .1 .No. 1 6 2
J u n l fS a d n n t ueo c n lg o r a h n o g I si t fTeh oo y o t
Jn 2 0 u .,0 2
文章编 号 :0 71 5 ( 0 2 0 — 0 20 1 0 — 8 7 2 0 ) 20 7 — 3
单长载 位度荷
许 术平 偏差 用算 均
综合 曲率 半径
卷 吸速度
w = ・= = 器
[口 R] :√
R=
=
( rm) N/ a
(m)
, R=d cst nd , aa o
z
U
一
百
( m) a r
=
( s m/ )
将 以上各式 代入 ( ) 6 式得