棘爪离合器的原理及故障分析
爪形离合器工作原理_概述说明以及解释
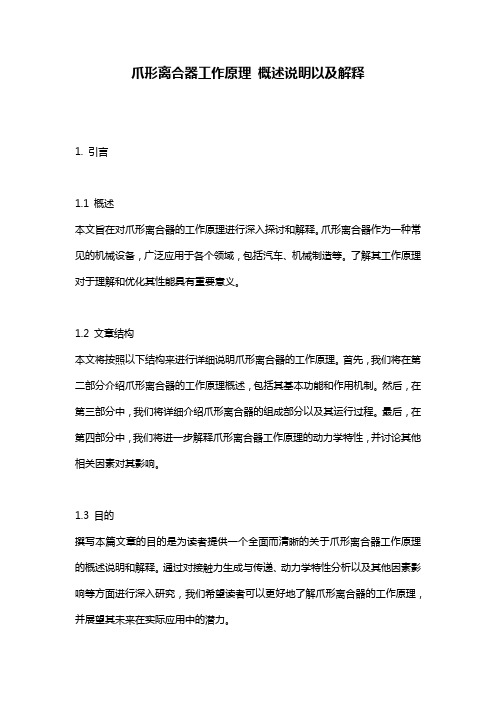
爪形离合器工作原理概述说明以及解释1. 引言1.1 概述本文旨在对爪形离合器的工作原理进行深入探讨和解释。
爪形离合器作为一种常见的机械设备,广泛应用于各个领域,包括汽车、机械制造等。
了解其工作原理对于理解和优化其性能具有重要意义。
1.2 文章结构本文将按照以下结构来进行详细说明爪形离合器的工作原理。
首先,我们将在第二部分介绍爪形离合器的工作原理概述,包括其基本功能和作用机制。
然后,在第三部分中,我们将详细介绍爪形离合器的组成部分以及其运行过程。
最后,在第四部分中,我们将进一步解释爪形离合器工作原理的动力学特性,并讨论其他相关因素对其影响。
1.3 目的撰写本篇文章的目的是为读者提供一个全面而清晰的关于爪形离合器工作原理的概述说明和解释。
通过对接触力生成与传递、动力学特性分析以及其他因素影响等方面进行深入研究,我们希望读者可以更好地了解爪形离合器的工作原理,并展望其未来在实际应用中的潜力。
2. 爪形离合器工作原理2.1 工作原理概述爪形离合器是一种常用的离合器类型,主要用于传递动力和断开动力传输。
它由两个主要组成部分构成:一个固定在主轴上的外爪和一个与之配对的内爪。
当两个爪相互嵌入时,它们能够通过牙齿间的摩擦产生接触力,并传递扭矩。
2.2 爪形离合器的组成部分爪形离合器由外爪、内爪、轴和弹簧等几个关键部件组成。
外爪是固定在主轴上的,通常具有一个或多个牙齿以提供更好的摩擦力。
内爪则是螺栓式连接到另一个动力传输装置上,如飞轮。
这样,在需要时可以将内部装置与主轴连接起来。
2.3 爪形离合器的运行过程当驱动装置启动时,外爪与内爪开始接触并插入到其牙齿之间。
随着引擎转速增加,摩擦力也会增加,从而使外爪和内爪之间产生足够的接触力来传递扭矩。
当需要断开动力传输时,例如换挡或停车时,内爪会与外爪分离,并停止牙齿间的摩擦接触。
这种设计使得离合器具有可靠的传输能力和快速切换功能。
3. 解释爪形离合器工作原理3.1 接触力的生成与传递在工作过程中,爪形离合器通过摩擦力产生足够的接触力来传递扭矩。
叉车离合器常见问题及维修方法
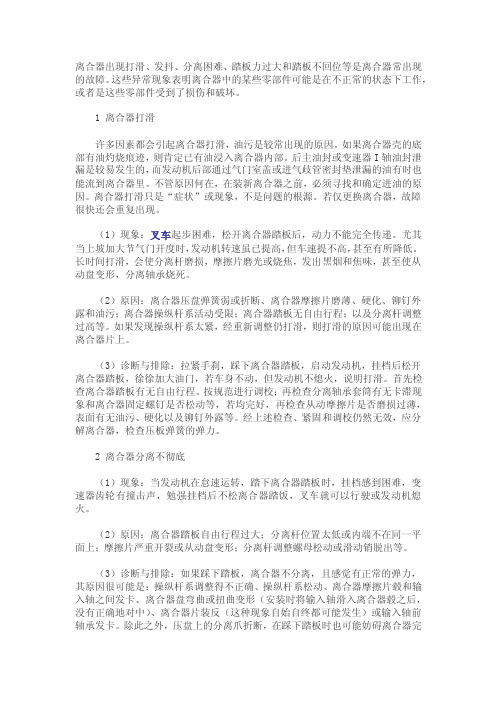
离合器出现打滑、发抖、分离困难、踏板力过大和踏板不回位等是离合器常出现的故障。
这些异常现象表明离合器中的某些零部件可能是在不正常的状态下工作,或者是这些零部件受到了损伤和破坏。
1 离合器打滑许多因素都会引起离合器打滑,油污是较常出现的原因。
如果离合器壳的底部有油灼烧痕迹,则肯定已有油浸入离合器内部。
后主油封或变速器I轴油封泄漏是较易发生的,而发动机后部通过气门室盖或进气歧管密封垫泄漏的油有时也能流到离合器里。
不管原因何在,在装新离合器之前,必须寻找和确定进油的原因。
离合器打滑只是“症状”或现象,不是问题的根源。
若仅更换离合器,故障很快还会重复出现。
(1)现象:叉车起步困难,松开离合器踏板后,动力不能完全传递。
尤其当上坡加大节气门开度时,发动机转速虽已提高,但车速提不高,甚至有所降低。
长时间打滑,会使分离杆磨损,摩擦片磨光或烧焦,发出黑烟和焦味,甚至使从动盘变形,分离轴承烧死。
(2)原因:离合器压盘弹簧弱或折断、离合器摩擦片磨薄、硬化、铆钉外露和油污;离合器操纵杆系活动受限;离合器踏板无自由行程;以及分离杆调整过高等。
如果发现操纵杆系太紧,经重新调整仍打滑,则打滑的原因可能出现在离合器片上。
(3)诊断与排除:拉紧手刹,踩下离合器踏板,启动发动机,挂档后松开离合器踏板,徐徐加大油门,若车身不动,但发动机不熄火,说明打滑。
首先检查离合器踏板有无自由行程。
按规范进行调校;再检查分离轴承套筒有无卡滞现象和离合器固定螺钉是否松动等,若均完好,再检查从动摩擦片是否磨损过薄,表面有无油污、硬化以及铆钉外露等。
经上述检查、紧固和调校仍然无效,应分解离合器,检查压板弹簧的弹力。
2 离合器分离不彻底(1)现象:当发动机在怠速运转,踏下离合器踏板时,挂档感到困难,变速器齿轮有撞击声,勉强挂档后不松离合器踏饭,叉车就可以行驶或发动机熄火。
(2)原因:离合器踏板自由行程过大;分离杆位置太低或内端不在同一平面上;摩擦片严重开裂或从动盘变形;分离杆调整螺母松动或滑动销脱出等。
自行车变速器离合器的工作原理
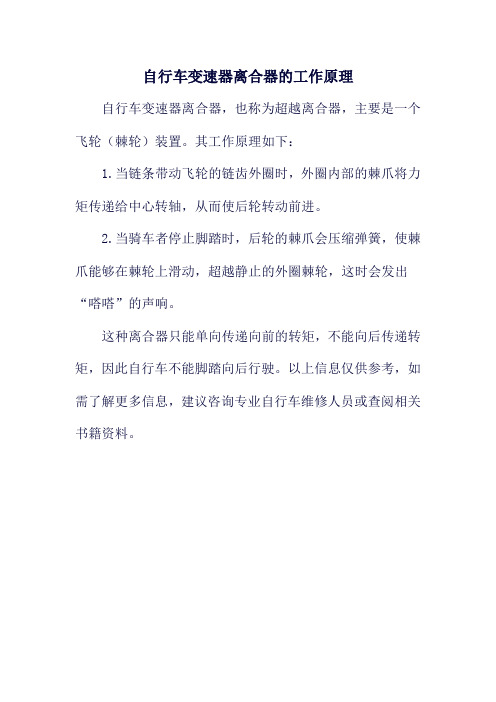
自行车变速器离合器的工作原理
自行车变速器离合器,也称为超越离合器,主要是一个飞轮(棘轮)装置。
其工作原理如下:
1.当链条带动飞轮的链齿外圈时,外圈内部的棘爪将力矩传递给中心转轴,从而使后轮转动前进。
2.当骑车者停止脚踏时,后轮的棘爪会压缩弹簧,使棘爪能够在棘轮上滑动,超越静止的外圈棘轮,这时会发出“嗒嗒”的声响。
这种离合器只能单向传递向前的转矩,不能向后传递转矩,因此自行车不能脚踏向后行驶。
以上信息仅供参考,如需了解更多信息,建议咨询专业自行车维修人员或查阅相关书籍资料。
棘轮棘爪原理

棘轮棘爪原理
棘轮是一种具有齿轮形状的零件,其特点是只能在一个方向上
旋转,而在另一个方向上则会被锁死。
这种特性使得棘轮可以用于
控制机械装置的旋转方向,使其只能朝着需要的方向进行旋转。
同时,棘轮的齿轮形状也可以用来传递力,使得机械装置可以更加稳
定地工作。
而棘爪则是与棘轮配合使用的零件,其特点是可以在棘轮上来
回移动,并且可以与棘轮的齿轮相互咬合。
通过棘爪的移动,可以
使得棘轮在需要的时候被释放,从而改变机械装置的旋转方向或者
传递更大的力。
棘轮棘爪原理在机械传动中有着广泛的应用,例如在汽车变速
箱中,就使用了棘轮棘爪原理来实现换挡功能。
当驾驶员需要改变
车速时,通过操作变速杆,可以使得棘爪与不同的棘轮齿轮相互咬合,从而改变传动比,实现换挡的功能。
在这个过程中,棘轮棘爪
原理起到了至关重要的作用,使得汽车可以顺利地完成换挡操作。
除此之外,棘轮棘爪原理还可以应用在各种不同的机械装置中,例如工业生产中的输送带系统、机械手臂的控制系统等等。
通过合
理地设计和利用棘轮棘爪原理,可以使得这些机械装置更加稳定、高效地工作,从而提高生产效率和降低成本。
总的来说,棘轮棘爪原理是一种非常重要的机械传动原理,它通过棘轮和棘爪的相互作用,实现了机械装置的转向控制和力的传递。
在现代工业生产中,棘轮棘爪原理有着广泛的应用,为各种机械装置的稳定运行和高效工作提供了重要的支持。
离合器的常见故障诊断及案例分析
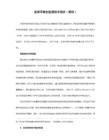
目录1.离合器的构造 (2)2.离合器故障诊断 (3)3.离合器的维修 (9)4.离合器故障案例分析 (10)5.总结 (14)离合器的常见故障诊断及案例分析摘要:本文对离合器的几种常见故障用分析比较的方法进行了论述,阐述了离合器的功用、要求、类型、结构及其常见故障,其中重点论述了离合器的常见故障的原因及其维修方法,并且结合实例进行了分析,指出了离合器的日常维护方法,对实际维修有一定的参考价值。
关键词:打滑分离不彻底结合不稳异响案例分析一、离合器的构造(一)离合器的功用离合器的基本功能是按照需要,适时地切断或结合发动机与传动系之间的动力传递。
在此基础上,它还应具备以下功用:1、保证汽车平稳起步。
2、保证传动系换挡时工作平顺。
3、限制传动系所承受的最大扭矩,防止传动系过载。
(二)对离合器的要求根据离合器的功用,它应满足以下主要要求:1、既能保证传递发动机最大扭矩,且具备有合适的储备能力,又能防止传动系过载。
2、结合平顺柔和,以保证汽车平稳起步。
3、分离迅速彻底,便于发动机启动和变速器换挡。
4、具备良好的散热能力。
5、操纵轻便,以减轻驾驶员的疲劳。
6、从动部分的转动惯量应尽量小,以减小换挡时的冲击。
(三)离合器的类型机械式传动系汽车,主要采用摩擦式离合器,根据分类方法不同,其类型也不相同。
1、按从动盘的数目不同,可以分为单片式离合器、双片式离合器和多片式离合器。
2、按压紧弹簧的结构及布置形式不同,可分为周布螺旋弹簧式离合器、中央弹簧式离合器、膜片弹簧式离合器和斜置弹簧式离合器。
3、按操纵机构不同,可分为机械操纵式(杆式和绳式)、液压操纵式、气压操纵式和空气助力式等。
(四)离合器的典型结构常见的离合器有使用螺旋弹簧的周布弹簧离合器或中央弹簧离合器和使用膜片弹簧的膜片弹簧离合器。
膜片弹簧离合器由于结构简单,磨损均匀,操作轻便,在汽车尤其是乘用车得到广泛使用。
其组成及操纵机构如图3.3所示。
图3.3 膜片弹簧离合器及操纵机构的一般组成1—从动盘;2—膜片弹簧—压板组;3—分离轴承;4—衬套;5—分离轴;6—离合器拉索;7—轴承套及密封件;8—卡簧;9—回位弹簧;10—分离轴传动杆;11—分离套筒二、离合器故障诊断离合器的常见故障部位主要有:飞轮与从动盘接触面、从动盘、压盘、膜片弹簧、分离叉、分离套筒、工作行程等。
离合器的修理及故障排除
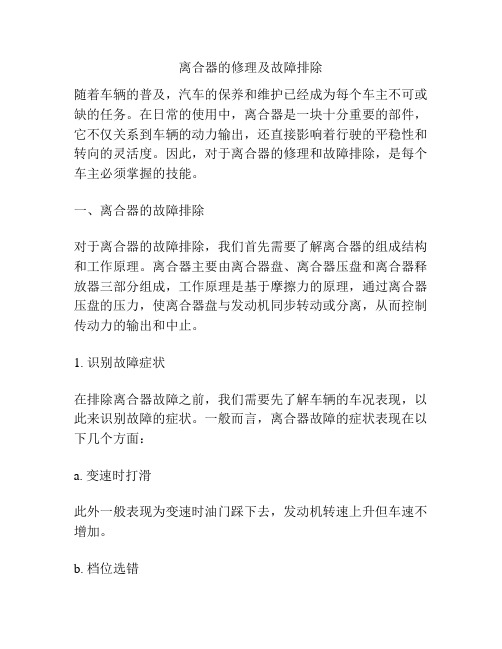
离合器的修理及故障排除随着车辆的普及,汽车的保养和维护已经成为每个车主不可或缺的任务。
在日常的使用中,离合器是一块十分重要的部件,它不仅关系到车辆的动力输出,还直接影响着行驶的平稳性和转向的灵活度。
因此,对于离合器的修理和故障排除,是每个车主必须掌握的技能。
一、离合器的故障排除对于离合器的故障排除,我们首先需要了解离合器的组成结构和工作原理。
离合器主要由离合器盘、离合器压盘和离合器释放器三部分组成,工作原理是基于摩擦力的原理,通过离合器压盘的压力,使离合器盘与发动机同步转动或分离,从而控制传动力的输出和中止。
1. 识别故障症状在排除离合器故障之前,我们需要先了解车辆的车况表现,以此来识别故障的症状。
一般而言,离合器故障的症状表现在以下几个方面:a. 变速时打滑此外一般表现为变速时油门踩下去,发动机转速上升但车速不增加。
b. 档位选错选挡时轻轻挂上,挂不进去,或者就算挂上也进不了档,甚至有时候驾驶员感觉挂上了,实际上却没有挂上。
c. 离合器抖动离合器出现抖动,主要表现在启动车辆、换挡、加速等过程中,会有明显的抖动现象。
2. 排除离合器故障综合以上症状,我们需要结合实际情况,对离合器故障进行排除。
一般而言,可以从以下几个方面入手:a. 检查离合器盘检查离合器盘的磨损情况。
如果离合器盘磨损过度,会导致离合器失效,需要更换新的离合器盘。
b. 检查离合器压盘和离合器释放器检查离合器压盘和离合器释放器的松紧情况。
如果离合器压盘或离合器释放器松动或损坏,也会导致离合器失效,需更换新的离合器压盘或离合器释放器。
c. 检查离合器液检查离合器液的充盈情况。
如果离合器液不足或液压系统有堵塞,也会导致离合器故障,需添加或更换离合器液。
二、离合器的修理当出现离合器故障时,如果没有及时排除,会进一步影响车辆的行驶表现。
在一般情况下,简单的离合器故障可以在自己家中就可以维修和更换。
如果需要更换整个离合器,可以寻找专业的汽车维修站来进行更换。
离合器常见的故障现象及原因

离合器常见的故障现象及原因离合器是汽车传动系统中重要的部件之一,负责连接发动机和变速器,实现动力传递和换挡操作。
然而,由于长时间使用和外部因素的影响,离合器常常会出现故障。
本文将介绍离合器常见的故障现象及其原因。
1. 离合器打滑离合器打滑是指离合器片无法有效地传递动力,导致发动机转速上升,而车速不增加或增加缓慢。
离合器打滑的原因主要有以下几点:(1)离合器片磨损严重:长时间使用后,离合器片会因摩擦磨损而变薄,降低了离合器片的摩擦系数,导致离合器打滑。
(2)离合器片油污:离合器片表面沾有油脂或润滑剂,会减少摩擦力,造成离合器打滑。
(3)离合器压盘失效:离合器压盘失效会导致离合器片无法紧密贴合,造成离合器打滑。
2. 离合器抖动离合器抖动是指离合器操作时出现抖动或震动的现象。
离合器抖动的原因可以有以下几点:(1)离合器片磨损不均匀:离合器片磨损不均匀会导致其与飞轮不平行,在离合器操作时产生抖动。
(2)离合器片变形:长时间使用后,离合器片可能会因高温或负载过大而变形,造成离合器抖动。
(3)离合器轴承故障:离合器轴承损坏或磨损会导致离合器抖动。
3. 离合器磨损离合器磨损是指离合器片磨损严重,无法正常传递动力的现象。
离合器磨损的原因主要有以下几点:(1)长时间使用:离合器片在长时间高速摩擦下会磨损,特别是在频繁的起步和换挡操作时。
(2)操作不当:不正确的离合器操作方式,如猛踩离合器、长时间踩离合器等,会导致离合器磨损加剧。
(3)润滑不足:离合器轴承部位缺乏润滑会加速磨损。
4. 离合器失灵离合器失灵是指离合器无法正常工作,无法连接发动机和变速器的现象。
离合器失灵的原因可能有以下几点:(1)离合器压盘故障:离合器压盘失效、变形或损坏会导致离合器无法紧密贴合,从而无法传递动力。
(2)离合器齿轮损坏:离合器齿轮损坏会导致离合器无法正常工作,无法实现换挡操作。
(3)离合器泵故障:某些车型的离合器采用液压控制,如果离合器泵故障,会导致离合器无法正常工作。
安全带棘爪原理

安全带棘爪原理一、什么是安全带棘爪?安全带棘爪是一种安全装置,它能够有效地固定乘坐者在车辆或其他交通工具中,以降低在碰撞或急刹车时的伤害风险。
二、安全带棘爪的工作原理安全带棘爪的工作原理是通过一系列机制实现的,下面我们将深入探讨几个关键的工作原理。
2.1 惯性锁安全带棘爪中的惯性锁是核心部件之一,它能够根据乘坐者的惯性力来调整安全带的松紧程度。
当车辆突然加速或急刹车时,乘坐者的身体会发生惯性,惯性锁会自动将安全带拉紧,从而保护乘坐者不被甩出座位。
2.2 摩擦力调节器为了提供合适的摩擦力,安全带棘爪中还配备了摩擦力调节器。
摩擦力调节器可以通过改变旋钮的位置来调整安全带拉力的大小,使得安全带能够紧固在乘坐者身上,但又不至于过于紧绷,影响乘坐舒适度。
2.3 弹簧收卷器安全带棘爪还采用了弹簧收卷器来实现安全带的回卷功能。
当乘坐者需要离开座位时,安全带会自动松弛,并通过弹簧的收卷作用,将安全带快速回卷,确保安全带不会缠绕乘坐者或者其他部件。
三、安全带棘爪的优势相比传统的安全带,安全带棘爪具有以下几个明显的优势:3.1 灵活性更高安全带棘爪可以根据乘坐者的实际需求进行调整,既保证了乘坐者的安全,又提供了更高的舒适性。
乘坐者可以通过调整摩擦力调节器来控制安全带的紧绷程度,以适应不同的身材和乘坐姿势。
3.2 自动保护安全带棘爪在发生碰撞或急刹车时会自动拉紧,为乘坐者提供更有效的保护。
传统的安全带需要乘坐者自己拉紧,容易因为忘记或操作不当而降低了安全性。
3.3 便于使用安全带棘爪的使用非常简便,乘坐者只需要将安全带插入扣环,并听到“咔嗒”声后即可,无需额外的操作。
而传统的安全带则需要乘坐者自己调节拉紧度和扣紧扣环,操作相对繁琐。
四、如何正确使用安全带棘爪为了充分发挥安全带棘爪的保护作用,我们需要正确使用安全带。
以下是正确使用安全带棘爪的步骤:1.根据身材和乘坐姿势调整摩擦力调节器,使安全带紧贴身体但又不至于过紧。
浅析离合器常见故障诊断与分析

浅析离合器常见故障诊断与分析
离合器是汽车传动系统的一个重要组成部分。
它主要起到分离和接合发动机与变速器之间传递的动力,使车辆可以平滑地加速和换挡。
由于离合器长期处于高强度工作状态,它的寿命受到重大影响。
经常出现故障甚至完全失灵,对车辆安全和驾驶体验产生负面影响。
下面我们就来简单分析一下离合器常见故障的诊断和分析方法。
1.异响故障
异响故障是离合器最常见的一种故障类型。
一般来说,离合器出现异响主要是离合器压盘或副离合器轴承损坏引起的。
我们可以以下两个方法来判断具体原因。
方法一:行车中打离合故障消失。
如果在行驶过程中,在离合踏板踩下时杂音消失,这表明离合器压盘已经损坏,需要进行更换。
2.失效故障
离合器失效是指离合器传递动力的能力不足或完全没有传递动力现象。
这种故障的主要原因是离合器片、压盘或离合器副处于磨损过度或结构不良的状态。
失效故障的最明显的表现是发动机转速的急剧上升,而车辆前进速度却几乎没有变化。
为了判断原因,我们需要进行以下步骤:
首先,排除气压和离合器的压力是否正常。
其次,检查离合器压盘和片是否磨损过度或损坏。
如果发现离合器片磨损过度,就需要进行更换。
如果离合器压盘变形,也需要更换解决。
3.打滑现象
综上所述,离合器故障的诊断和维修需要根据具体情况进行分析,慎重判断,并采取相应的解决措施,这是确保车辆行驶安全和延长离合器寿命的关键。
简述离合器的工作原理

简述离合器的工作原理离合器是汽车等机械设备中的一个重要部件,它的作用是将发动机的动力传递到变速器中,同时在换挡时将动力中断,以保证换挡的平稳性。
本文将简述离合器的工作原理及其结构组成。
一、离合器的工作原理离合器是由摩擦片和压盘组成的。
摩擦片固定在离合器盘上,压盘则固定在发动机的飞轮上。
当离合器踏板松开时,压盘和摩擦片之间没有接触,发动机的动力不会传递到变速器中。
当离合器踏板踩下时,压盘与摩擦片之间接触,摩擦片受到摩擦力的作用,将发动机的动力传递到变速器中。
离合器的工作原理可以用以下公式表示:T1 = T2 x e^-μθ其中,T1为发动机输出的力矩,T2为变速器输入的力矩,μ为摩擦系数,θ为接触角度。
当离合器完全接触时,θ为90度,此时T1等于T2。
当离合器完全分离时,θ为0度,此时T1等于0。
二、离合器的结构组成离合器主要由以下部分组成:1.离合器盘离合器盘是离合器的主要部分,它由钢板、摩擦片和弹簧组成。
钢板是离合器盘的主体,摩擦片贴在钢板上,弹簧则用于固定摩擦片。
离合器盘的作用是将发动机的动力传递到变速器中。
2.压盘压盘是离合器的另一个重要部分,它由钢板、弹簧和压盘指针组成。
压盘与发动机的飞轮相连,当离合器踏板踩下时,压盘会向离合器盘施加压力,使离合器盘与发动机的飞轮之间接触。
3.离合器轴承离合器轴承是用于连接离合器盘和压盘的组件,它可以使离合器盘和压盘相对运动,以实现离合器的工作。
4.离合器踏板离合器踏板是用于控制离合器的开合的组件,当踏板松开时,离合器分离,当踏板踩下时,离合器接合。
5.离合器分泵离合器分泵是用于分离离合器盘和压盘的组件,它可以使离合器盘和压盘之间脱离接触,以实现换挡。
三、离合器的维护保养离合器作为汽车的重要部件,需要定期进行维护保养。
以下是一些常见的维护保养方法:1.定期更换离合器盘离合器盘是离合器的主要部分,其磨损情况会影响离合器的工作效果。
一般来说,离合器盘的寿命为3-5万公里,需要定期更换。
离合器的常见故障现象、原因及故障诊断方法

离合器的常见故障现象、原因及故障诊断方法卡车 /客车 /工程车维修 /卡车人频道离合器打滑故障现象① 起步或重载上坡时动力不足② 行驶中发动机加速无力。
严重打滑时,离合器摩擦片处冒烟,有焦臭味,甚至烧坏摩擦片故障原因① 离合器踏板自由行程过小或没有② 摩擦片表面性质发生变化,如油污、烧蚀、硬化、破裂、铆钉外露等③ 离合器压紧弹簧弹力减弱或折断,使压紧力不足造成打滑④ 压盘磨损过薄使压簧伸长过多⑤ 主、从动盘翘曲不平使接触不良故障诊断方法①启动车辆,拉紧驻车制动,挂上低挡,使车辆正常起步,若车身不动而发动机不熄火说明离合器打滑② 不启动车辆,挂上低挡,拉紧驻车制动,在不踩离合器踏板的情况下用手柄摇动发动机,如能摇动,说明离合器打滑。
离合器分离不彻底故障现象① 启动车辆,挂低挡,松开驻车制动,不松开离合器时,车辆就行驶或熄火②发动机怠速时,踩下离合器踏板,挂挡感到困难,并伴有变速器齿轮撞击声故障原因① 踏板自由行程过大,导致分离时压盘行程不足② 分离杠杆高度不一致③ 主、从动盘翘曲不平④压盘弹簧弹力不一致或折断故障诊断方法:在汽车未启动时两人配合判断,一人将变速器挂入1挡,踩下离合器踏板,另一人用手柄摇动发动机,若摇不动或车辆有前移趋势,证明离合器分离不彻底。
离合器发抖故障现象汽车挂挡起步时,离合器断续冲击,整个车身发抖故障原因① 分离杠杆高度不一致② 压紧弹簧弹力分布不均或个别折断,摩擦片铆钉松动③ 主、从动盘翘曲变形④从动盘毂花键严重磨损故障诊断方法让发动机低速运转,挂上低挡慢慢起步,此时若汽车发生连续冲击即为离合器发抖。
离合器发响故障现象离合器分离和接合时有异响故障原因① 分离轴承缺油发响② 分离轴承损坏发响③ 双盘离合器中压盘与传动销配合间隙过大④ 从动盘毂键齿与一轴键齿配合间隙过大⑤从动盘毂铆钉松动故障诊断方法将变速器放到空挡位置,使发动机怠速运转,踩下或放松离合器踏板(分离或接合),汽车不移动的情况下响声比较明显。
离合器常见原因和故障大全

离合器常见原因和故障大全无论新手还是开车多年有驾驶经验的老司机来说,离合器的使用磨损以及如何自行检测是驾驶员非常关注的一件事情,以下就是店铺整理的常见的离合器故障原因,希望对你有用。
一、离合器打滑现象汽车在起步时,离合器踏板抬得很高才能勉强起步;行驶中加速时,车速却不能随之提高。
这些都属离合器打滑现象。
1、液压操纵式离合器打滑,多数是因为离合器踏板自由行程不够从而造成分离轴承压在分离杠杆或膜片上而随之转动。
可调节离合器踏板的返回位置,并调整总泵推杆长度,将推杆调长并与活塞顶住,再将推干倒转半圈,使总泵推杆与活塞之间留有间隙。
然后再调整分泵调节杆长度使其伸长,感到分离轴承与分离杠杆或膜片顶住以后,再把调整螺钉调口到二者间隙为2mm左右。
2、对于机械操纵式离合器,离合器踏板自由行程不够,可调整踏板拉杆的工作长度,使分离轴承与分离杠杆或膜片之间的间隙达到规定的值。
3、如因离合器摩擦片沾有油污而打滑,可将分离杠杆或膜片调高,增大分离间隙,用绳索或硬木将离合器踏板固定在分离位置上,之后用螺丝刀缠上一层浸过汽油的擦布,插进分开的一面,转动飞轮,将油污擦掉,再换用干擦布彻底清洁一次。
然后用螺丝刀撬开摩擦片的另一面,进行上述操作。
洗净后,重新调整分离杠杆高度即可。
4、因离合器片烧蚀而打滑时,如摩擦片较厚,可将烧蚀部分打磨掉,并调整分离杠杆高度。
二、离合器分离不彻底,挂挡困难故障现象发动机怠速运转时,离合器踏板虽已踩到底,但挂挡困难,变速齿轮有撞击声。
勉强挂上挡后,尚未放松离合器踏板,汽车已行驶或熄火。
检查:拆下离合器底盖,将变速器挂入空挡,将离合器踩到底。
然后,用起子拨动从动盘。
如果能轻松拨转,说明离合器分离良好;如果拨不动,说明离合器分离不彻底。
排除方法:1、检查离合器踏板自由行程是否过大,并调整。
2、检查分离杠杆高度是否一致、是否过低。
在车下拨动分离拨叉,使分离轴承前端轻轻地靠在分离杠杆内端面上,转动离合器一周进行查看,如果分离杠杆的内端能同时和分离轴承接触不上,说明分离杠杆的高度不一致,应进行调整。
棘轮棘爪

棘轮棘爪情况介绍
根据国家机械工业局发布的冶金起重机技术条件(JB/T7688.15-1999)铸造起重机主起升机构应有两套驱动系统,当其中一套驱动系统发生故障时,另一套驱动系统应能保证在额定起重量下完成一个工作循环。
应此,两套驱动系统应通过刚性联接联接在一起。
在驱动系统正常工作时应保证两个卷筒组同步。
因此,在减速器中加装棘轮棘爪装置以消除由于两个输入电动机转速不同带来的影响,保证两个卷筒组同步。
(如下图所示)
棘轮棘爪装置工作原理介绍:
棘轮棘爪装置属于棘轮停止器,一般用来作为机械中防止逆转的制逆装置或供间歇传动用。
一、当两套驱动系统正常工作时:
1、当主起升机构起升时,电动机逆时针旋转驱动减速
器高速轴,通过齿轮副驱动棘轮顺时针旋转,棘轮通过棘爪驱动减速器第一中间轴,在通过齿轮副驱动卷筒组顺时针旋转以提升重物。
2、当主起升机构下降时,电动机顺时针旋转驱动减速器高速轴,通过齿轮副驱动棘轮,由于重物自身的质量作用,驱动卷筒组逆时针旋转,通过齿轮副驱动减速器第一中间轴及棘爪逆时针旋转;电动机顺时针旋转驱动减速器高速轴,通过齿轮副驱动棘轮逆时针旋转。
当由重物下降引起的棘爪逆时针旋转速度大于由电动机驱动的棘轮逆时针旋转速度时,棘爪与棘轮相啮合,重物的下降速度由电动机所控制。
二、当一套驱动系统工作时:
1、当发生故障的电动机端不制动时,系统工作同两套驱动系统正常工作时一样。
2、当发生故障的电动机端制动时,制动端棘轮停止不转,棘爪只能单方向旋转。
因此起升机构在电动机的作用下只能起升不能下降。
下降时需将制动端制动器打开,通过另一端电动机驱动使重物下降。
棘轮离合器工作原理
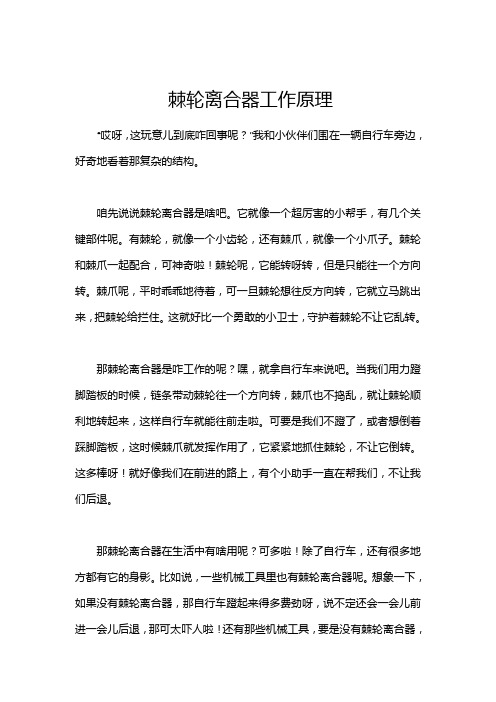
棘轮离合器工作原理
“哎呀,这玩意儿到底咋回事呢?”我和小伙伴们围在一辆自行车旁边,好奇地看着那复杂的结构。
咱先说说棘轮离合器是啥吧。
它就像一个超厉害的小帮手,有几个关键部件呢。
有棘轮,就像一个小齿轮,还有棘爪,就像一个小爪子。
棘轮和棘爪一起配合,可神奇啦!棘轮呢,它能转呀转,但是只能往一个方向转。
棘爪呢,平时乖乖地待着,可一旦棘轮想往反方向转,它就立马跳出来,把棘轮给拦住。
这就好比一个勇敢的小卫士,守护着棘轮不让它乱转。
那棘轮离合器是咋工作的呢?嘿,就拿自行车来说吧。
当我们用力蹬脚踏板的时候,链条带动棘轮往一个方向转,棘爪也不捣乱,就让棘轮顺利地转起来,这样自行车就能往前走啦。
可要是我们不蹬了,或者想倒着踩脚踏板,这时候棘爪就发挥作用了,它紧紧地抓住棘轮,不让它倒转。
这多棒呀!就好像我们在前进的路上,有个小助手一直在帮我们,不让我们后退。
那棘轮离合器在生活中有啥用呢?可多啦!除了自行车,还有很多地方都有它的身影。
比如说,一些机械工具里也有棘轮离合器呢。
想象一下,如果没有棘轮离合器,那自行车蹬起来得多费劲呀,说不定还会一会儿前进一会儿后退,那可太吓人啦!还有那些机械工具,要是没有棘轮离合器,
可能就没法好好工作了。
棘轮离合器可真是个了不起的小发明呀!它让我们的生活变得更加方便,更加有趣。
我觉得它就像一个默默无闻的小英雄,虽然不显眼,但是却发挥着巨大的作用。
爪型离合器工作原理

爪型离合器工作原理
爪型离合器是一种常见的机械传动装置,它的工作原理如下:
1. 基本结构,爪型离合器由两个主要部分组成,分别是驱动轴
和从动轴。
驱动轴和从动轴之间通过爪形齿轮(也称为爪状摩擦片)进行连接。
当爪型离合器处于工作状态时,爪形齿轮会将驱动轴和
从动轴连接起来,使它们一起旋转;而在离合状态下,爪形齿轮则
会分离驱动轴和从动轴,使它们停止旋转。
2. 工作原理,当驱动轴旋转时,爪型离合器的工作原理是基于
摩擦的。
当爪形齿轮受到一定的压力,它会与从动轴产生摩擦力,
从而传递动力并使从动轴开始旋转。
而当不需要传递动力时,通过
操纵离合器的控制机构,可以使爪形齿轮脱离从动轴,从而实现离
合状态。
3. 应用,爪型离合器广泛应用于各种机械传动系统中,如汽车
变速箱、摩托车变速箱、工程机械等。
它的工作原理简单可靠,操
作方便,能够有效地实现驱动轴和从动轴的连接和分离,从而控制
动力传递和变速。
总的来说,爪型离合器通过爪形齿轮的摩擦连接和分离驱动轴和从动轴,从而实现机械传动系统的工作状态控制,是一种常见且有效的传动装置。
棘轮棘爪原理

棘轮棘爪原理
棘轮棘爪原理是一种机械传动原理,常见于各种机械设备中,特别是在需要实现定向传动和防逆转的场合。
它通过棘轮和棘爪的结合,实现了在一个方向上的传动,而在反方向上则能够阻止传动,具有很高的实用价值。
棘轮棘爪原理的核心在于棘轮和棘爪的结合。
棘轮是一种齿轮,其齿形呈现出一个或多个斜面,而棘爪则是一个能够在棘轮齿面上移动的机构。
当棘轮沿着一个方向旋转时,棘爪能够顺利地滑过棘轮的斜面,实现传动。
而一旦棘轮发生反向旋转,棘爪就会立即卡住,阻止棘轮的反向运动,从而实现了单向传动的目的。
棘轮棘爪原理在实际应用中有着广泛的用途。
比如,在自行车的后轮上,就常常使用了棘轮棘爪原理,使得踏板在向前踩的时候能够顺利传动,而在向后踩的时候则能够防止后轮的反向转动。
这种设计不仅简单实用,而且能够有效地提高自行车的传动效率和安全性。
除了自行车之外,棘轮棘爪原理还被广泛应用于各种机械设备中。
在工业生产中,许多需要定向传动和防逆转的场合都可以看到棘轮棘爪原理的身影。
比如在起重机、输送带、机床等设备中,都可以看到棘轮棘爪原理的应用,这些设备能够在保证传动效率的同时,避免了因为反向传动而导致的安全隐患。
总的来说,棘轮棘爪原理作为一种机械传动原理,具有简单可靠、实用高效的特点,在各种机械设备中有着广泛的应用。
它通过巧妙的结构设计,实现了单向传动和防逆转的功能,为机械设备的安全运行提供了有力的保障。
相信随着科技的不断发展,棘轮棘爪原理在更多领域中将会发挥出更大的作用,为人们的生活和生产带来更多便利和安全。
棘爪和棘轮工作原理

棘爪和棘轮工作原理
棘爪和棘轮都是机械学中常用的传动装置,它们主要用于实现转矩传递和定位。
棘爪和棘轮的工作原理十分简单,它们都利用了机械原理中的“挂钩定理”。
棘爪通常由一个或多个垂直于轴线方向的“爪子”组成,和一个可以转动的环形零件相配合。
在传动过程中,当环形零件转动时,爪子会自动弹出并与环形零件的齿轮相咬合,从而实现转矩的传递。
由于爪子只在一个方向上能够移动,因此棘爪只能实现单向传动。
棘轮则由一个齿轮和一个可以转动的齿轮盘相组合。
与棘爪相似,棘轮的齿轮盘上也有一些凸起的齿轮,这些齿轮与齿轮盘上的凹槽相对应。
在传动过程中,当齿轮盘转动时,凸起的齿轮会自动弹出并咬合凹槽,从而实现转矩的传递。
与棘爪不同的是,棘轮能够实现双向传动。
总的来说,棘爪和棘轮是机械学中非常常用的传动装置,它们能够实现转矩传递和定位,应用范围非常广泛。
同时,由于它们的工作原理十分简单,因此制造成本也比较低廉。
- 1 -。
棘爪和棘轮工作原理
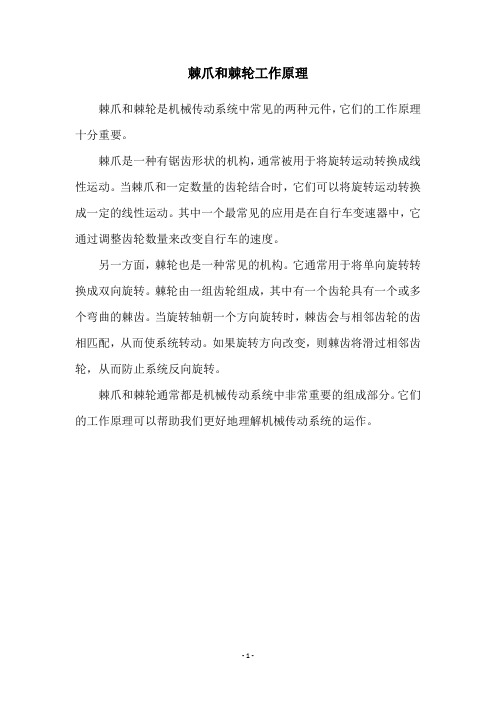
棘爪和棘轮工作原理
棘爪和棘轮是机械传动系统中常见的两种元件,它们的工作原理十分重要。
棘爪是一种有锯齿形状的机构,通常被用于将旋转运动转换成线性运动。
当棘爪和一定数量的齿轮结合时,它们可以将旋转运动转换成一定的线性运动。
其中一个最常见的应用是在自行车变速器中,它通过调整齿轮数量来改变自行车的速度。
另一方面,棘轮也是一种常见的机构。
它通常用于将单向旋转转换成双向旋转。
棘轮由一组齿轮组成,其中有一个齿轮具有一个或多个弯曲的棘齿。
当旋转轴朝一个方向旋转时,棘齿会与相邻齿轮的齿相匹配,从而使系统转动。
如果旋转方向改变,则棘齿将滑过相邻齿轮,从而防止系统反向旋转。
棘爪和棘轮通常都是机械传动系统中非常重要的组成部分。
它们的工作原理可以帮助我们更好地理解机械传动系统的运作。
- 1 -。
- 1、下载文档前请自行甄别文档内容的完整性,平台不提供额外的编辑、内容补充、找答案等附加服务。
- 2、"仅部分预览"的文档,不可在线预览部分如存在完整性等问题,可反馈申请退款(可完整预览的文档不适用该条件!)。
- 3、如文档侵犯您的权益,请联系客服反馈,我们会尽快为您处理(人工客服工作时间:9:00-18:30)。
棘爪离合器的原理及故障分析
李 艳 苏 宁
(沈阳黎明航空发动机〈集团〉有限责任公司 辽宁 沈阳 110043)
摘 要: 发动机等机构中的棘爪离合器结构作为重要的超越离合器的一种被广泛应用于航空、汽车、工业等行业中。
就在于浅谈几点棘爪离合器原理及故障分析。
关键词: 离合器;棘爪;分析
中图分类号:TH133 文献标识码:A 文章编号:1671-7597(2012)1210009-02
解决问题。
1 棘爪离合器的原理
3.2 结构
棘爪离合器就是许多人俗称的“三爪离合器”,它是超越内啮合形式的棘爪离合器是最常见的离合器,它分别包含离合器(overrunning-clutch)的一种,即嵌合式离合器。
因棘轮、弹簧、棘爪、离合器拨轮、止动销和定位销六部分,如为它的特殊结构,许多教科书上也把它称之为棘爪式超越离合下图2。
器。
其主要的原因有两条:第一是为了区别于摩擦式工作原理的离合器,如我们俗称的“滚棒离合器”(学名为滚柱离合器)等;第二个原因就是因为它有三个楔形的小“爪”。
说起棘爪离合器的原理其实就是超越离合器的原理,离合
器由主、动从动轮组成,主动带动从动,当转速 时,二者保持传递扭矩,称为结合状态;一段时间后 ,离合器脱开转速,变为超越状态。
对于超越离合器来说,主动轮的形式变化较多,如内星轮、组件外圈等。
结合状态下又分为动态楔合与静态楔合两个阶段,而超越状态也分为解楔与自锁——脱离过程,和空转状态。
2 棘爪不是“三爪”
其实棘爪离合器不能等同于“三爪离合器”,当离合器大径 <80时,棘爪数J=3,当 ≥80时,根据需要J={3、5或者其它的数字}。
我们常见的棘爪离合器都是J=3的情况,因此我们习惯称它为三爪离合器。
1.棘轮
2.止动销
3.弹簧
4.棘爪
5.定位销
6.离合器拨轮
3 棘爪离合器的结合与脱开原理及结构
图2
3.1 原理
当发动机未工作时,由于弹簧的弹力作用棘爪贴合在棘轮由于超越离合器的结合与脱开原理较为相似,所以我们选的齿槽里。
发动机工作初期,离合器拔轮带动棘轮与棘爪一起取最为简单的滚柱离合器的方式来简单说明(如下图1)。
旋转,处于结合状态;当离合器达到一定转速时,由于离心力
的作用 ,棘爪的末端以止动销为圆心运动,而前端克服弹簧力与齿槽脱离,两者互不干涉的以自己的转速旋转。
3.2.1 棘轮。
棘轮是棘爪离合器中比较关键,它与棘爪配合,传递稳定的载荷及转速,但是与此同时,它也是最为变化多端的结构,比如在双速传动机构中,棘轮是依托齿轮的结构,在直齿端面呈现多个棘齿。
根据《中国机械通用零部件工业年鉴——传动联结件产品分类标准与名词术语》可知,目前制造齿数是12~20范围内的棘轮是国家标准化推荐使用的,因为一般啮合时的冲击力与齿数有关,增加齿数可以有效的减小啮合冲击,使传动平稳可靠。
不过,与齿轮公式D=mz类似,齿1.外壳 2.滚柱 3.星轮
数越多相应的棘轮直径也越大。
这就需要设计员充分考虑合理图1
的空间结构,尽可能选取较多齿数的棘轮,提高整机稳定性。
离合器能够顺利的的结合与脱离,必须由 3.2.2 棘爪。
棘爪是棘轮离合器中较为关键的零件,同时它作为与棘轮重要的配合部件,其结构也与棘轮有密切的关系,一般设计棘爪时需要棘轮的尺寸确定后,根据棘爪长度L=2倍的棘轮齿距P( ,其中m为棘轮的模数)。
上文说到了棘轮离合器的脱开依靠的是离心力的作用下使具体要求,通常许多情况下选择大约7度是比较好的。
,那么如何设计离合器结合状态下的 呢?离合由此可知,当离合器出现打滑情况时,可以减小摩擦角а器又是如何确保在规定的转速状态下脱开的呢?所有的答案都防止打滑,可以采用加大 的方式;反之,如果脱开困难的情在于弹簧的选择和设计的综合考虑上了。
举个例子,比如我们况下,适当增大摩擦角а,采用加大D的方法就可以简单快速的
要求离合器在50r/min时顺利脱开,而实际上发现在45r/min时
、表面直径 、滚柱外径尺寸 及摩擦角а四个要素共同作用完成,
就已经脱开,不满足我们预期的目标,这就说明了脱开时的离心力需要降低。
这时候,我们过销子装配-制动爪装配-磨加工工作面-弹簧安装-离合器拔轮
就应该对棘爪适当的进行减重处扩口-脱开转速试验(验证其脱开转速需要在模拟发动机工作状理,而对弹簧的结构尺寸相应的减小。
态的试验台上进行)-弹簧选配(考虑到零件的装配误差和制造在离合器棘爪的频繁结合与脱开(也有的教材称之为合闸精度等因素的影响,需要选择弹簧C值不同的组别)-选配后试与脱开状态转换)过程中,应该尽量提高棘爪的抗疲劳强度和验-修正组件等步骤。
静强度安全系数。
这就严格的要求了在加工中棘爪的倒圆、倒在弹簧选配过程中,可以根据不同的转速要求,为保证弹角处尺寸一定要符合设计图要求,同时零件的表面完整性也是簧能够方便地更换,允许不铆死离合器销子,待试验完成后再抗疲劳强度提高的一个重要方面,应该尽量避免电加工法和手铆死止动销。
应该注意的是在装配中不允许使弹簧变形来修合工打磨齿槽结合处及零件设计减轻窗口处倒R等。
弹簧。
棘爪的材料应具有高硬度、强度高、抗热冲击、热膨涨系为了得到较为准确的试验结论,需要重复五次测量得到最数低,适宜于高温条件,不易磨损。
因此,HRC63左右的耐热小转速值作为脱开转速。
然而单次试验,每个棘爪的脱开转速材料,如镍钼/铬钼/锰钼合金或者常用发动机缸体及活塞类零差不能大于200r/min。
在装配时,更换弹簧时不能破坏组件的件材料较为适合。
同时,对于棘爪部件应该采用材料热处理中成套性,制动爪的两面可以均匀的挫修。
三个制动爪的工作面氮化的方法,使零件被一层硬度值达HRC 77的良好耐磨表面的沿着圆周的不均布度不大于0.03mm,若变化时可按整个平面均氮化扩散物渗透,保持零件0.3mm深度都具有较好的抗疲劳和匀研修。
研修时去除重量要保证棘爪尾部两侧面对称,为了保抗超越磨损的寿命。
证棘爪离合器强度,每面切除深度一般不超过1.5mm。
止动销棘爪部件的工作面也应该采用化学气相沉积(CVD),如装配时不允许有轴向活动,局部透光可以允许单不得大于发蓝或物理气相沉积(PVD),如电离子喷涂等方法,针对不0.03mm。
在装配试验依然不合格但装配完成或者装机件返修同材料的表面提高部件的抗氧化性、抗剥离性、耐磨性、韧性时,可以采用钻头钻去制动爪拔轮定位销,扩口部分深度保证及热震抗性。
同时8~10Lm精度的薄膜厚度,不仅能将其耐磨损 1.2~1.5mm。
性能提高10倍以上,还能显著改善部件的表面粗糙度,防止疲 4 离合器故障分析
劳断裂。
4.1 棘爪的断裂分析
3.2.3 弹簧。
圆柱扭转弹簧为棘爪超越离合器的普遍形棘爪离合器在材料选择上有较为苛刻的要求,材料中尤其式,它一般受到设计脱开转速和棘爪末端产生的离心力两个方面以硫化物的最为不好,国家标准中材料硫化物的含量要求在影响。
但是由于装配间隙和制造误差等影响因素,如前文提过的0.03%以下,当硫化物杂质超标时,部件内基体与夹杂比较容表面直径 和摩擦角а,棘爪在脱开时的力会有一定的差别,因易分离,材料内部组织结合力差。
在反复结合与脱开的大扭矩此多采用分组弹簧的形式,(如图3)将弹簧角C加以分组。
传动中易导致了微裂纹得发生,在反复的疲劳冲击作用下微裂
纹受到疲劳扩展,以材料韧窝截面处发生不断的过载瞬断裂。
因此棘爪离合器的失效原因多半是材料成分不合格及加工中未
注意抗疲劳加工造成。
4.2 弹簧的断裂分析
离合器装配中,明确规定不允许采用弹簧变形的方法。
因
为弹簧断裂部位多数发生在零件的直线段与圆弧段的交结处,
采用变形方法的弹簧,更容易在形变尖角过渡处产生应力集
中。
尤其在弹簧直线段位置的根部处,出现疲劳应力集中。
同时,热处理的调质对弹簧也是至关重要的,在热处理
时,弹簧直径产生收缩量,同时其出现氧化、脱炭等因素,未
经过调质的弹簧直径不回弹,疲劳寿命降低。
在装配中,弹簧
的内径同止动销之间的间隙减小。
工作状态下,离合器以较高图3频率运动,产生较大的疲劳源。
3.2.4 装配结构。
棘爪超越离合器在装配时,必须保证棘
爪安装轴的轴心线与棘轮完全重合才能使棘轮受载荷轮齿平面参考文献:
[1]工程材料,哈尔滨工程大学出版社[M].2001,1.
通过棘轮轴心,否则棘轮轮齿平面就不能与棘爪充分,载荷传
[2]发动机的故障分析,国防科技大学出版社[M].2000,9.
递不均匀。
因此装配中对于棘爪工作面和棘轮工作齿面进行着
色检查是至关重要的。
该着色面积相比其它零件的着色要求
(不低于70~75%)也要严格很多,需要沿轴向不小于90%,沿作者简介:
径向不小于80%。
因为离合器安装时棘轮齿槽必须保证与每个李艳,女,毕业于沈阳航空学院,机电一体化,现任沈阳黎明航空棘爪都能够完美啮合,沿周向均匀分布。
以避免频繁工作状态发动机(集团)有限责任公司质量技术员,工程师,致力于技术服务和因为传动不平稳对弹簧等的疲劳损伤。
在装配过程中也应该尽质量管理工作;苏宁,男,毕业于哈尔滨工程大学,机械设计制造及其量避免划伤或碰伤弹簧。
自动化专业,现任黎航部件公司作动筒工段技术工长,助理工程师,致
3.2.5 组件装配及实验。
棘轮离合器在装配过程中需要经力于作动筒齿轮类零件的加工和装配。