TPS5改善的原点IE手法概述
19学习丰田的方法论实践TPS的五个阶段
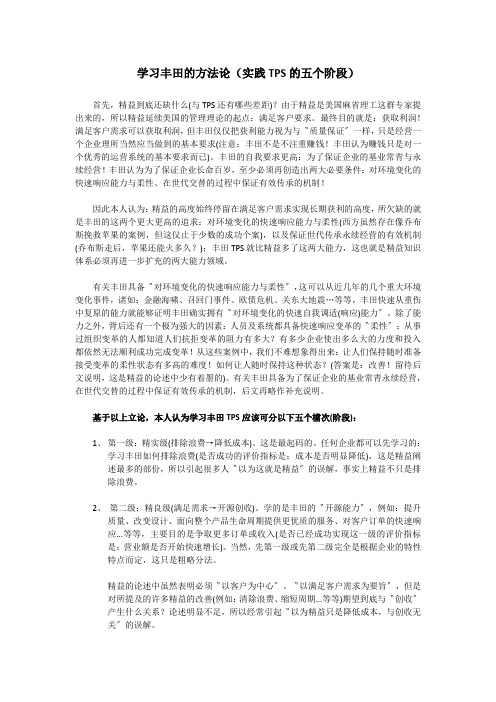
学习丰田的方法论(实践TPS的五个阶段)首先,精益到底还缺什么(与TPS还有哪些差距)?由于精益是美国麻省理工这群专家提出来的,所以精益延续美国的管理理论的起点:满足客户要求。
最终目的就是:获取利润!满足客户需求可以获取利润,但丰田仅仅把获利能力视为与〝质量保证〞一样,只是经营一个企业理所当然应当做到的基本要求(注意:丰田不是不注重赚钱!丰田认为赚钱只是对一个优秀的运营系统的基本要求而已)。
丰田的自我要求更高:为了保证企业的基业常青与永续经营!丰田认为为了保证企业长命百岁,至少必须再创造出两大必要条件:对环境变化的快速响应能力与柔性、在世代交替的过程中保证有效传承的机制!因此本人认为:精益的高度始终停留在满足客户需求实现长期获利的高度,所欠缺的就是丰田的这两个更大更高的追求:对环境变化的快速响应能力与柔性(西方虽然存在像乔布斯挽救苹果的案例,但这仅止于少数的成功个案),以及保证世代传承永续经营的有效机制(乔布斯走后,苹果还能火多久?);丰田TPS就比精益多了这两大能力,这也就是精益知识体系必须再进一步扩充的两大能力领域。
有关丰田具备〝对环境变化的快速响应能力与柔性〞,这可以从近几年的几个重大环境变化事件,诸如:金融海啸、召回门事件、欧债危机、关东大地震…等等,丰田快速从重伤中复原的能力就能够证明丰田确实拥有〝对环境变化的快速自我调适(响应)能力〞。
除了能力之外,背后还有一个极为强大的因素:人员及系统都具备快速响应变革的〝柔性〞;从事过组织变革的人都知道人们抗拒变革的阻力有多大?有多少企业使出多么大的力度和投入都依然无法顺利成功完成变革!从这些案例中,我们不难想象得出来:让人们保持随时准备接受变革的柔性状态有多高的难度!如何让人随时保持这种状态?(答案是:改善!留待后文说明,这是精益的论述中少有着墨的)。
有关丰田具备为了保证企业的基业常青永续经营,在世代交替的过程中保证有效传承的机制,后文再略作补充说明。
IE七大手法 四 5×5WIH(5X5何法) 标杆精益
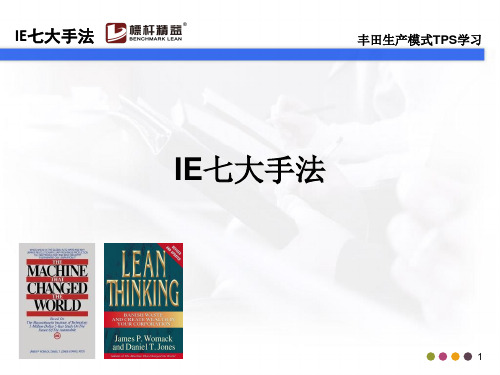
33
IE七大手法
丰田生产模式TPS学习
为协助大家产生创意,我们收集了一些实际上的改善创 意经验,归纳成十二种创意思考法则,都是经过很多改善专 家的丰富经验整理升华而得到的结晶,可提供给大家作为改 善的提示。
34
IE七大手法
丰田生产模式TPS学习
五五法应用12法则:创意思考法则
创意思考法则:产生创意的方法或技巧。这些方法、技巧可
学贵有疑,小疑则小进,大疑则大进;疑者, 觉悟之机也。
——陈献(明代学者)
18
IE七大手法
丰田生产模式TPS学习
质问的技巧:
质问的一般对象: ➢ 对“目的”(what)的质问; ➢ 对有关“人”(man)的方面的问题; ➢ 对“工作顺序”(when)的质问; ➢ 对“地点”(where)的质疑。
19
只要有问题存在,就可以运用5W1H去发掘问题的根本原 因(n次因)。
10
IE七大手法
丰田生产模式TPS学习
五五法实例:黎叔家的电视
话说在黎叔的家人在看电视节目兴运现场实况转播,正 看得津津有味,浑然忘我的时候,突然电视机坏了,没办法 只好请了维修中心的人来修理,维修人员检查了半天,终于 发现原来毛病是有一个电子零件 —— 电阻坏了。于是维修 人员就拿了一个新的电阻换上,黎叔很高兴他们一家人又可 以享受看电视的乐趣。
27
IE七大手法
丰田生产模式TPS学习
质问的技巧:对“工作顺序”(when)的质问
变更时间的顺序,包括操作发生时刻、时期、耗费时间, 是不是可以启发改善的头绪?一般有以下的质问方式:
➢ 在何时做的? ➢ 为何要在当时做? ➢ 改在别的时候做是否更有利? ➢ 在何时做最好?何时要完成?需要几天才算合理? ➢ 何时最切时宜?将来有何转变?等等。 这一质问的目的是在寻求可能的“合并”,“重组/变更” 的改善方向。
生产管理之-5M1E分析法

3.主要工序都有工艺规程或作业指导书,工艺文件对人员、工装、设备、 操作方法、生产环境、过程参数等提出具体的技术要求。
4.工艺文件重要的过程参数和特性值经过工艺评定或工艺验证;特殊工序 主要工艺参数的变更,必须经过充分试验验证合格后,方可更改文件。
控制措施:
(1)加强工序操作技能培训,使操作人员熟悉工艺标准;
(2)积极推行控制图管理,以便及时采取措施调整;
(3)严肃工艺纪律,对贯彻执行操作规程进行检查和监督。
(4)加强工具工装和计量器具管理,切实做好工装模具的周期
检查和计量器具的周期校准工作。
生产管理之-5M1E分析法
工序管理(法)标准化
3、5M1E的简介:物料
控制措施:
(1)在原材料采购合同中明确规定质量要求;
பைடு நூலகம்
(2)加强原材料的进厂检验和厂内各工序半成品和成品检验;
(3)合理选择供应商(包括“外协厂”);
生产管理之-5M1E分析法
(4)搞好协作厂间的协作关系,督促、帮助供应商做好质量控 制和质量保证工作。
生产物料(料)标准化
1.有明确可行的物料采购、仓储、运输、质检等
设备维护和保养(机)标准化
1.有完整的设备管理办法,包括设备的购置、流转、维护、 保养、检定等均有明确规定。
2.设备管理办法各项规定均有效实施,有设备台账、设备履 历档案、维修检定计划、有相关记录,记录内容完整准确。
生产管理之-5M1E分析法
3.生产设备、检验设备、工装工具、计量器具等均符合工艺 规程要求,能满足工序能力要求,加工条件若随时间变化能 及时采取调整和补偿,保证质量要求。 4.生产设备、检验设备、工装工具、计量器具等处于完好状 态和受控状态。
IE基础知识介绍

S30起身坐下
4、代码中第二个数字代表所需MOD单位时间值的多少, 例:M2代表手腕
动作需要2个MOD时间.
NPS
N=New P=Production S=System
衍生自日本的丰田生产方式(Toyota Production
System,简称TPS),是一种先进的生产管理技术。 利润公式的三种形式:v售价=成本+利润 成本主义卖方市场v 利
防错法:又称防愚法, 也就是说,连愚笨的人也不会做错事的设计
方法.
狭义: 如何设计一个东西(一套方法),使错误绝不会发生.
广义: 如何设计一个东西(一套方法),而使错误发生的机会减至最
低的程度
防误设计的种类:
控制法:
1.定位插座法 定位凹凸槽正确装置
2.光电开关法 光电照射带动某些动作
3.通过法
GO,NO GO 量规
1) Total Productivity’s Improvement 『全体的生产性改善』
2) Totally Process Improvement 『工程全部改善』
3) Towards Process-yield Increasing 『目标工程良品率』
4) Taking Personal Intelligence 『活用人的智慧』
润=售价-成本 售价主义 v 成本=售价-利润 利润主义
NPS的具体内容: n 心----- 意识 n 技----- 技法 (a. 流线化生产
b. 安定化生产 c. 平稳化生
产 d. 超市化生产) n 体----- 实践(自主研究会)
TPI
1.TPI =Total Production Innovation 『総合生产革新』
IE基础知识介绍
IE概论_
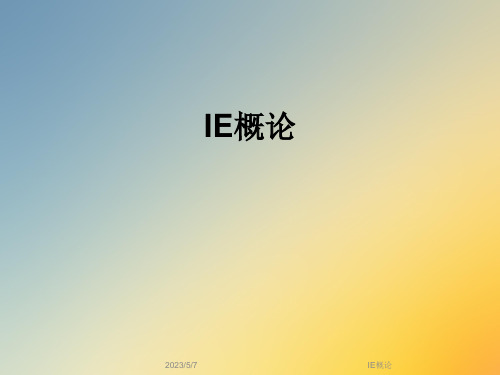
▪ 埃默森(Emerson,1853~1931)美国早期的科学管理专家,创立
了“奖励工资制”(Emerson Premium System),对当时公认的 劳动生产率提高具有重要作用,并提出了“效率十二原则”,被后 人尊称为“效率的大教长” 。
IE概论
二:工作研究概述
IE概论
工作研究的概念
工作研究的定义:
工作研究是是IE中最重要的基础技术,以提高生产率和整体效益 为目的.利用方法研究和作业测定两大技术,分析影响工作效率 的各种因素,以挖掘,革新,消除人力,物力,财力和时间的浪费,减 轻劳动强度,合理安排作业,用新的工作方法来代替现行的方法, 并制定该项工作所需的时间,从而提高劳动生产率和经济效益的 一种科学管理技术.
——英国工业工程视察团
IE概论
IE的起源
IE基础知识介绍
泰勒(Taylor, 1856~1915)“科学管理之父”“工业工程之父”
1898年,泰勒氏工作于伯斯利恒(Bethlehem) 钢铁厂,当时该厂雇有铲手工人400~600名,每日于 一长约2哩,宽约1/4哩之广场上,铲动各种不同之物 料。这些铲手,不用工场所准备的铲子,很多人自己 从家中带来铲子,铲煤时,每铲重仅3.5磅,而铲矿砂 时每铲竟重达38磅。此种自备铲子的情形与每铲重量 之差额,颇引起泰氏之好奇。他想:「铲子的形状、
▪ 运筹学影响的时期( 20世纪40年代中期~20世纪70年代)
IE进入成熟时期。运筹学和计算机的出现解决了IE长期缺乏理 论基础的问题。运筹学用于产品和市场决策,而计算机为处理 数据和对大系统进行数学模拟提供里有力的手段。同时,1955 年 美国工业工程师学会制定出了IE的正式定义。
精益生产培训系列课件

18
IE七大手法
丰田生产模式TPS学习
动作改善原则:有关人体运用的原则 1﹑双手并用原则:两手同时开始及完成动作
❖ 用一只手:插完30只销子需30S
❖ 用双手:插完30只销子只需23S,节约时间29%
19
IE七大手法
丰田生产模式TPS学习
动作改善原则:有关人体运用的原则
2﹑除休息时间外,两手不应同时空闲: 不必要的动作会浪费操作时间,使动作效率下降,必须
4、使动作轻松: 如,汽车装配时车轮由自动提升设备,自动提升到与车轴高 度,操作人员只需要用开关进行控制就可以了
15
IE七大手法
丰田生产模式TPS学习
动作经济的四个基本原理:
4、使动作轻松: 如,操作人员的装配零部件时必须将零部件转向,但零部件 过大、过重时,可使用带转向的工装台。
16
IE七大手法
10
IE七大手法
丰田生产模式TPS学习
动作经济的四个基本原理:
2、同时进行动作: 不管是工具的改善,方法的改善或零件摆放方法改善等,
想办法使两手能同时使用,或脚也能同时使用。 例, 打麻将动两手;开汽车;打鼓、弹钢琴;两手同时拿取 2个部件;两手同时上两个螺丝; 在制品槽移动时拿取配件;走动 中按开关等。
排除。而即使必要的动作,通过改变动作的顺序、重整操作 环境等也可以减少。
20
IE七大手法
丰田生产模式TPS学习
动作改善原则:有关人体运用的原则
3﹑对称反向原则:两只手臂的动作应反向同时对称 大多数人均惯一手拿着东西另一手去工作,这是动作浪
费。应当使双手用对称方式一起工作,同时开始和结束。工 作要适当地分布在双手的工作区域,使双手能同时发挥。
单手操作容易使人体产生心理上及生理上不平衡感,为 克服此种不平衡就必须用身体的应力去反制,因而使我们容 易身心疲劳。对称的动作方式,使操作者的身体部位产生平 衡感,而减少了身体运用应力的机会,使工作者较轻松愉快 而不容易疲劳。
现场改善的利器IE七大手法(推荐)
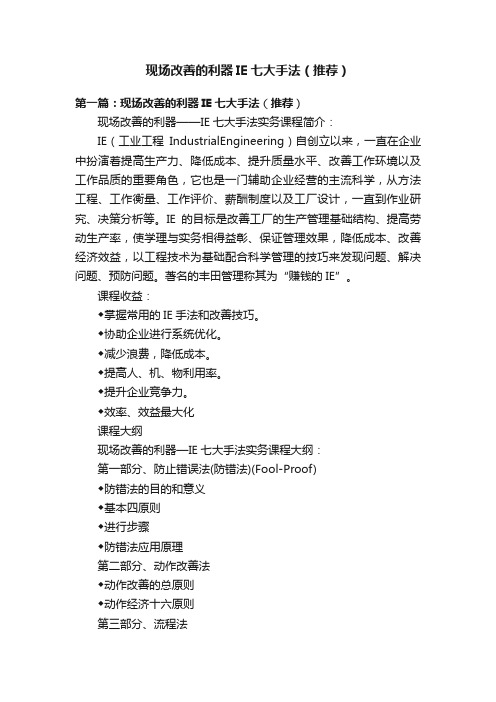
现场改善的利器IE七大手法(推荐)第一篇:现场改善的利器IE七大手法(推荐)现场改善的利器——IE七大手法实务课程简介:IE(工业工程IndustrialEngineering)自创立以来,一直在企业中扮演着提高生产力、降低成本、提升质量水平、改善工作环境以及工作品质的重要角色,它也是一门辅助企业经营的主流科学,从方法工程、工作衡量、工作评价、薪酬制度以及工厂设计,一直到作业研究、决策分析等。
IE的目标是改善工厂的生产管理基础结构、提高劳动生产率,使学理与实务相得益彰、保证管理效果,降低成本、改善经济效益,以工程技术为基础配合科学管理的技巧来发现问题、解决问题、预防问题。
著名的丰田管理称其为“赚钱的IE”。
课程收益:◆掌握常用的IE手法和改善技巧。
◆协助企业进行系统优化。
◆减少浪费,降低成本。
◆提高人、机、物利用率。
◆提升企业竞争力。
◆效率、效益最大化课程大纲现场改善的利器—IE七大手法实务课程大纲:第一部分、防止错误法(防错法)(Fool-Proof)◆防错法的目的和意义◆基本四原则◆进行步骤◆防错法应用原理第二部分、动作改善法◆动作改善的总原则◆动作经济十六原则第三部分、流程法◆目的和应用范围◆流程法的功用◆流程释义◆流程法范例第四部分、五五法◆五五法的目的和意义◆五五法与创意思考第五部分、人机分析法◆人机分析的目的与意义◆人机分析的应用范围与功用◆人机法名词释义◆人机分析图◆人机法案例分享第六部分、双手法◆双手法的目的与意义◆双手法的运用范围与功用◆双手法名词释义◆双手法应用范围介绍◆绘图注意事项◆双手法案例分享第七部分、工作抽样◆工作抽样的意义◆工作抽样之实验◆工作抽查之应用◆抽样及工作抽查之好处◆抽样的技巧◆工作抽查之要点◆不同的对象进行分类◆标准时间设定应用案例◆工作绩效衡量应用案例师资介绍专家简介:黄杰国内著名生产管理顾问、现场管理专家。
生产管理高级咨询师;多家国际国内知名培训咨询公司高级培训师、咨询顾问。
经典与实务的NPS(新产品开发与生产技能)与IE 手法 於改善作业之运用
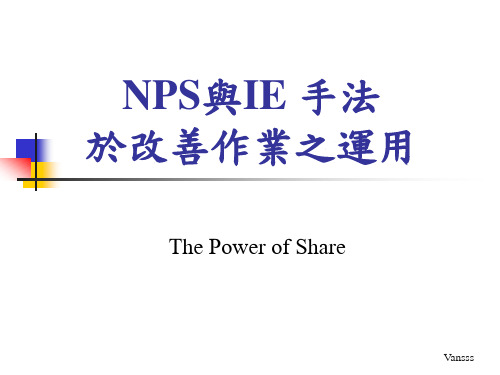
The Power of Share
Vansss
前言
改善是企業維持成長及達到永續經營的重要項 目之一;所以若從經營決策者至基層之作業人 員皆有改善意識時,改善之活動將可事半功倍 的順利被推展,幫助企業節省成本。故不論使 用之方法而何,只要持續不斷進行,相信最終 皆可嚐到改善後甜美的果實。
Vansss
二、IE 的基本職能
4.系統創新功能 : 創新是企業發展的根本源泉,通過對系統的分 析評價、完善改造以達到促進系統不斷創新的 目標,是IE的功能之一。這裏主要包括產品 改進、工藝改進、設施改進、系統組織改進、 工作方式改進、技術創新的激勵與組織、新產 品新技術的工作開發等。
Vansss
三、IE 工作改善的步驟
1.認清問題並設定目標,生產工廠的問題有: P (Productivity) :生產量 Q (Quality) :品質 C (Cost) :成本 D (Delivery) :交期 S (Safety) :員工的安全 M (Morale) :員工的士氣
Vansss
三、IE 工作改善的步驟
Vansss
三、IE 工作改善的步驟
4.把對策移諸實施 人都是厭惡改變現狀的。因此在工作改善時, 應該要讓與這個變化有關的人(作業員及領班) 共同參與,在實施時上才會有成效。
Vansss
三、IE 工作改善的步驟
5.結果評估 把實施的結果與當初的預定比較,如未能達 到預期效果時,便回到第1步驟再度加以檢 討。
Vansss
二、NPS 的好處
1.縮短交貨期. 2.降低庫存. 3.減少不良品與重工品. 4.提升勞働生產力. 5.節約空間. 6.減少人員需求. 7.提升設備整體效率.e 技 skill 心 concept
IE改善手法:五五法
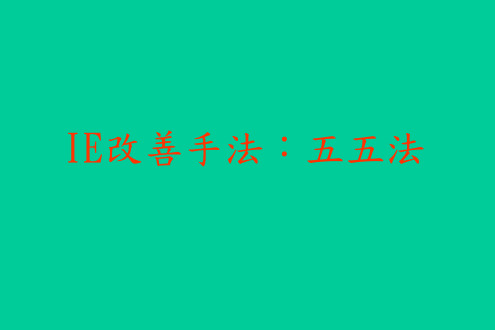
10.
放锯于柜台上
V
(因此经常下次找不到Fra bibliotek子)V
11.
再量试尺寸
1.有无其他更合适的时间 锯?
答:似可以最初于铁架处 选取管子时锯,或事先锯 好最常用的各种尺寸管 子.
2.如何做(他是如何锯的).
答:他用左手握住管子,用 拇指按住管子锯切的地 方作为锯片下切处.
3.有无其他更合适的办法?
答:如何使用一个简单的 设备夹住管子,则既可保 持正确平整的锯缝,又可 不致锯伤手指.
2).把其它4W1H用Why来质问.检讨,并找出最好的改善方案.
3).为何要如此做? 4).为何要用目前的机器.人来做这 种工作?
(六).How(如何)
1).如何使方法`手段更简单? 2).情形到底如何? 3).如何使作业方法简化,以减少劳力`降低成本? 4).要如何来做?
现行方法
步 骤
情况
距 改善要点
情况
步骤 操 运 检 等 储 作 送 验 待存
工作说明
距 改善要点
离 (米)
删 除
合 并
排 列
简 化
12.
发给领料人
13.
在领料单上签字
14.
放领料单上
于匣中
15.
带余料至
铁架中
16.
放余料在
V
铁架上
17.
回柜
1.5 V
台
改良方法
步
情况
骤 操作 运送 检验 等待 储存
工作说明
距离 (米)
1.
审阅领料单
6.
带橡皮管至 0.2
答:因为铁锯可能在铁架A
铁架A处.
处.
7.
从箱内取
TPS现场改善-OK(共75张PPT)

把我寄托在别人门下做事,我的工作能力受到了限制 操作员要学会维护他们的设备. 我的产品不好,如果给了别人我是“骗子”所以我不传递 現場改善的三項基本活動
3. 当场采取暂行处置措施 大家应该发挥团队合作精神
不良品的影响(附下图) (三)不要解释不能做的理由,要想出能做下去的方法 藉由環境維持,員工學習和實踐到 自律 ~让事情向正确的方向发展~
10. 建立系统 多咨询,多聆听以达致信息反馈,谋求连接性 的改善。
11. Takt Time 每件产品生产频率,通常以秒计,Takt time = 一天的有效工作时间/一天要求的生产量。
12. 目视管理 (6S) 13. 整理、整顿、清洁、清扫、素养、安全。
目视管理
有了目视看板,现场 的情况一目了然,操
4. 標准的特征:A. 最好,最易,最安全 的 工作方法
5.
B.保存及共享
6.
C.衡量積效的基准
7.
D.因果之間關系
8.
E.提供維持及改善的基准
9.
F.目標及培訓
10.
G.稽核及診斷基礎
11.
H. 防止錯誤最發生及減 少變異
12种现场改善工具
1. 灯箱报警
2.
灯箱报警是一种可视形式的管理,当生产出现异常时,
而坚持己见,各行其是了。
(七)打破沙锅问到底,找出问题的真因
碰到问题时要想办法,找出造成问题的真 正原因所在,只有找出真正的原因才能对 症下药,彻底解决。
(八)用智慧来改善,不要用金钱来改善
改善要以不花钱为原则来进行,不要
一碰到问题,就马上花钱买设备,或请外
面的人来做,这样的投资就大了,应该动
IE七大手法五五法OKP14
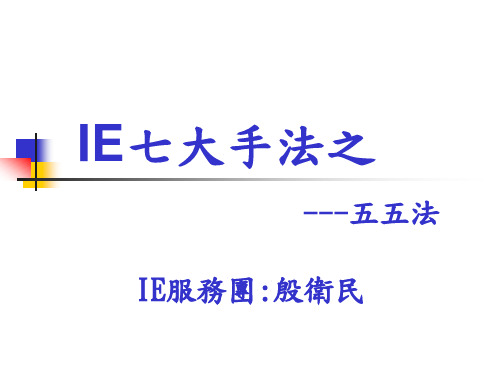
宁 可 千 日 不 松无事 ,不可 一日不 防酿祸 。20.12.2320.12.2318:31:0418:31:04December 23, 2020
老 毛 病 , 要 根治; 小问题 ,要重 视。2020年 12月 23日 下午 6时31分 20.12.2320.12.23
秤 砣 不 大 压 千斤安 全帽小 救人命 。2020年 12月 23日 星期三 下午6时 31分 4秒18:31:0420.12.23
五五法概念
4. 應用範圍 :
改善的前提---發現問題---懷疑的態度。 懷疑為改善之母, 懷疑應是有系統的,循序漸進的,而且是有具體的方向。 5WIH是一種找尋問題之根源及尋求改善的系統化的質問工
具。防止疏漏了某些值得去改善的地方。
5. 功用 : 5WIH功力無限大,可適用於任何行業不同地點
品 质 第 一 , 顾客满 意。20.12.232020年 12月 23日 星 期 三6时 31分 4秒20.12.23
谢谢大家!
減少,故清潔乾燥器時間不能大幅 否
減少
8
無預乾燥系統不能進行中 間轉換
與 A 座供料系統進行對 比
A 座的熱風乾燥器配有預乾燥系 統,停機換料時間僅為 13 分鐘/ 次。
是
結論
要因:無預干燥系統﹐ 不能進行中間轉換。
現在可以 確定目標了!
安 全 就 是 效 益,安 全就是 幸福。 20.12.2320.12.23Wednesday, December 23, 2020
FD
揭下
硬式保護膜
保護
FV
膜
OQC
案例2
換料停機時間長﹐平均為
150分鐘/次.
柏拉圖分析
影響換料停機時間因素排列圖
IE改善手法与技巧综述
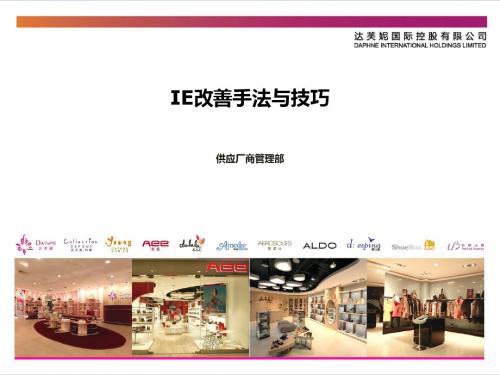
强作业有危险时,设法安装无法马虎或无法勉强作业的装置。
D.自动化原则——依赖像眼睛,耳朵等感官进行业时,容易发生失误。制作治具或使 之机械化,减少用人的感官来判断的作业。一定要依赖感官的作业,譬如:当信号一 红即同时有声音出现,设法使之能够二重三重的判断。
18
三、IE七大手法-防错法
例
19
三、IE七大手法-动改法
12
三、IE七大手法-流程法
例:
13
三、IE七大手法-人机法
1、手法:人机配合法(Man-Machine Chart),简称为“人机法” 2、目的:学习如何记录人与机器配合工作时之过程。 3、意义:以图表的方式,记录操作者与一部机器或多部机器之操作关系, 并以此记录来做进一步之分析与改善。 4、应用范围 (1)1人操作1部机器或多部机器。 (2)数人操作1部机器或多部机器。 (3)数人操作一共同之工作。 人机作业图的记录符号 ––––表示工作 ––––表示空闲
30
备注
10、 抽样法
抽样调查是一种非全面调查,它是从全部调查研究对象中,抽选一部分单位进行 调查,并据以对全部调查研究对象作出估计和推断的一种调查方法。
3
二、解决问题的九大步骤及改善方法
步骤 发掘问题 选定题目 追查原因 分析资料 提出办法 选择对策 草拟行动 成果比较 标准化 相关改善方法 脑力激荡法、查检表、 5W1H、 5S、统计表、流程图 改善流程、消除异常、提升产能、缩短交期﹐确保质量、降 低成本、保障工安 鱼骨图、层别法、 5W1H、流程图、作业分析表 抽样法、差异分析、相关性分析(散布图)、趋势图、直方图、 柏拉图 脑力激荡法、系统图、5W1H、 ECRS、鱼骨图、时间/方法研究 、动作分析 决策矩阵法、多数表决法、控制图 甘特图、性能评审技术、实验验证、推移图 推移图、效果评估、现值法 标准化、系统化、模式化、质量履历、改善成果通报
现场改善及IE手法
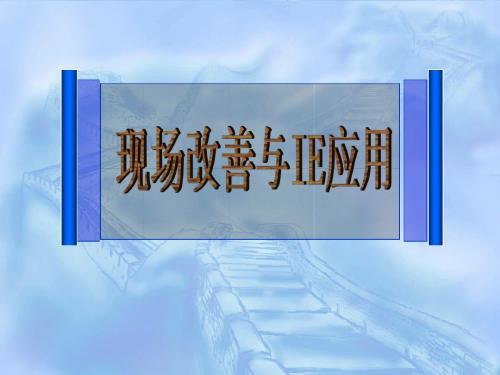
---
IE 用途
客户要求 15H 1H 1 2H 3 4H 4 5H 2H 6 8H 2 3H 5 8H 7
17H
12H
IE用途举例
搬运距离减少,提高效率
改善前
装盘部 装盘部 手 推 车 小 汽 车 总库 总库 日用库
改善后
四、 IE手法在现场改善中应用
1生产流程分析与作业程序分析—价值流图 2布局与搬运效率分析与改善 3人机程序分析—防呆手法,合理配置 4线平衡与时间研究—找到瓶劲,取得突破 5动作经济原则—提高效率,降低强度
即为劳累,指作业一 员、机器以及工作的流 程,处在一种费力气的 状态下
对策:
1.员工的技能训练,使其成为一名熟练工
2.利用夹治具或机器来替代人力作业
3.利用动作经济原则来改善作业的劳动强度
本节总结
七大浪费? 三无工程? 现场浪费认识?
三、IE是什么?能做什么?
IE ----工业工程,industrial engineering ---- 改善效率 Improve efficiency
3.U型布局 4.综合式
1 2 3
直线式与U型布局比较
搬运距离
省人化
并列式,
1人多机
半流线 与 流线式
实例:
去半成品库
来自料堆
磨床 6
磨床 5
铣床 2
磨床 4
车床 1
搓丝 8
磨床 7
车床 3
车床 1
改进:
去半成品库 车床1
来自料堆
车床 3 磨床4 磨床5
铣床 2
节约面积 车床1
磨床 6
1.整理生产工序流程;
2.工序流程中是否存在不经济,停滞现象;