浅谈线路板图形电镀阻镀成因及解决之道
图形电镀线铜粒原因分析改善案例

打造世界级PCB企题分析(图形电镀工序)
3)微蚀槽的问题 ) 分析:因微蚀槽的蚀刻特性, 分析:因微蚀槽的蚀刻特性,故此缸不 可能存在残留金属颗粒的可能性, 可能存在残留金属颗粒的可能性,也 就不可能造成生产板板面沾上杂质。 就不可能造成生产板板面沾上杂质。
11
打造世界级PCB企业 打造世界级PCB企业 PCB
问题分析(外图工序) 问题分析(外图工序)
B. 显影线的影响 可能缺陷: 可能缺陷:干膜没有清洗干净 水洗不净 显影液残留…… 显影液残留 分析:所有以上的问题, 分析 : 所有以上的问题 , 均只是导致图性电镀时 镀铜不上,而不是导致产生铜粒。 镀铜不上,而不是导致产生铜粒。 结论: 结论:可不考虑此过程的影响
17
打造世界级PCB企业 打造世界级PCB企业 PCB
问题分析(加厚电镀工序电镀铜缸) 问题分析(加厚电镀工序电镀铜缸) 对应措施: 对应措施: 每次倒缸时, ②每次倒缸时,打磨缸体内的不锈钢支架 上的铁锈,清洗缸体; 上的铁锈,清洗缸体;规范镀铜缸盐酸的 加药方法, 加药方法,防止盐酸对不锈钢造成的腐蚀 ③保证拖缸板的储存环境 每次发现现场有烧板时, ④每次发现现场有烧板时,现象轻微的进 行拖缸处理, 行拖缸处理,现象严重的进行倒缸处理
15
打造世界级PCB企业 打造世界级PCB企业 PCB
问题分析(加厚电镀工序) 问题分析(加厚电镀工序)
2.2 加厚电镀工序 同样也采取从后往前推的思考方法。 同样也采取从后往前推的思考方法。 A. 出铜缸的后处理过程至卸板 现象:板件出铜缸,经过水洗,进入风干箱时板面 现象:板件出铜缸,经过水洗, 的颜色为均匀的亮黄色,但是一出风干箱后板面 的颜色为均匀的亮黄色, 有很明显的水流氧化印(顺着夹点方向) 有很明显的水流氧化印(顺着夹点方向)。 分析:这是因为夹具外层的包胶破损后, 分析:这是因为夹具外层的包胶破损后,铜缸内的 酸液藏在了胶里面, 酸液藏在了胶里面,经过风干箱内的风吹流了出 粘在板面造成腐蚀、氧化,造成板面粗糙。 来,粘在板面造成腐蚀、氧化,造成板面粗糙。 解决: 解决:定期重新包胶
电镀不良及对策
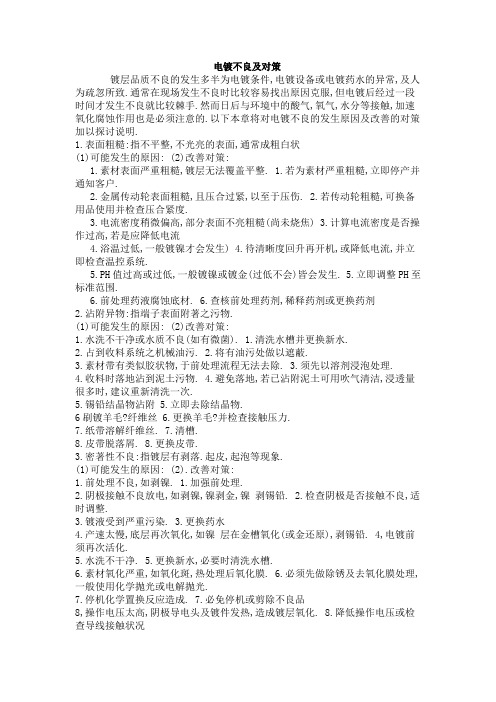
电镀不良及对策镀层品质不良的发生多半为电镀条件,电镀设备或电镀药水的异常,及人为疏忽所致.通常在现场发生不良时比较容易找出原因克服,但电镀后经过一段时间才发生不良就比较棘手.然而日后与环境中的酸气,氧气,水分等接触,加速氧化腐蚀作用也是必须注意的.以下本章将对电镀不良的发生原因及改善的对策加以探讨说明.1.表面粗糙:指不平整,不光亮的表面,通常成粗白状(1)可能发生的原因: (2)改善对策:1.素材表面严重粗糙,镀层无法覆盖平整. 1.若为素材严重粗糙,立即停产并通知客户.2.金属传动轮表面粗糙,且压合过紧,以至于压伤. 2.若传动轮粗糙,可换备用品使用并检查压合紧度.3.电流密度稍微偏高,部分表面不亮粗糙(尚未烧焦) 3.计算电流密度是否操作过高,若是应降低电流4.浴温过低,一般镀镍才会发生) 4.待清晰度回升再开机,或降低电流,并立即检查温控系统.5.PH值过高或过低,一般镀镍或镀金(过低不会)皆会发生. 5.立即调整PH至标准范围.6.前处理药液腐蚀底材. 6.查核前处理药剂,稀释药剂或更换药剂2.沾附异物:指端子表面附著之污物.(1)可能发生的原因: (2)改善对策:1.水洗不干净或水质不良(如有微菌). 1.清洗水槽并更换新水.2.占到收料系统之机械油污. 2.将有油污处做以遮蔽.3.素材带有类似胶状物,于前处理流程无法去除. 3.须先以溶剂浸泡处理.4.收料时落地沾到泥土污物. 4.避免落地,若已沾附泥土可用吹气清洁,浸透量很多时,建议重新清洗一次.5.锡铅结晶物沾附 5.立即去除结晶物.6刷镀羊毛?纤维丝 6.更换羊毛?并检查接触压力.7.纸带溶解纤维丝. 7.清槽.8.皮带脱落屑. 8.更换皮带.3.密著性不良:指镀层有剥落.起皮,起泡等现象.(1)可能发生的原因: (2).改善对策:1.前处理不良,如剥镍. 1.加强前处理.2.阴极接触不良放电,如剥镍,镍剥金,镍剥锡铅. 2.检查阴极是否接触不良,适时调整.3.镀液受到严重污染. 3.更换药水4.产速太慢,底层再次氧化,如镍层在金槽氧化(或金还原),剥锡铅. 4,电镀前须再次活化.5.水洗不干净. 5.更换新水,必要时清洗水槽.6.素材氧化严重,如氧化斑,热处理后氧化膜. 6.必须先做除锈及去氧化膜处理,一般使用化学抛光或电解抛光.7.停机化学置换反应造成. 7.必免停机或剪除不良品8,操作电压太高,阴极导电头及镀件发热,造成镀层氧化. 8.降低操作电压或检查导线接触状况9,底层电镀不良(如烧焦),造成下一层剥落. 9.改善底层电镀品质.10.严重.烧焦所形成剥落 10.参考NO12处理对策.4.露铜:可清楚看见铜色或黄黑色于低电流处(凹槽处)(1)可能发生原因: (2)改善对策:1.前处理不良,油脂,氧化物.异物尚未除去,镀层无法析出. 1.加强前处理或降低产速2.操作电流密度太低,导致低电流区,镀层无法析出. 2.重新计算电镀条件.3镍光泽剂过量,导致低电流区,镀层无法析出 3.处理药水,去除过多光泽剂或更新.4.严重刮伤造成露铜. 4.检查电镀流程,(查参考NO5)5.未镀到. 5.调整电流位置.5刮伤:指水平线条状,一般在锡铅镀层比较容易发生.(1)可能发生的原因: (2)改善对策:1.素材本身在冲压时,及造成刮伤. 1.停止生产,待与客户联系.2.被电镀设备中的金属制具刮伤,如阴极头,烤箱定位器,导轮等. 2.检查电镀流程,适时调整设备和制具.3.被电镀结晶物刮伤. 3.停止生产,立即去除结晶物.6.变形(刮歪):指端子形状已经偏离原有尺寸或位置.(1)可能发生的原因: (2)改善对策:1.素材本身在冲压时,或运输时,即造成变形. 1.停止生产,待与客户联系.2.被电镀设备,制具刮歪(如吹气.定位器,振荡器,槽口,回转轮) 2.检查电镀流程,适时调整设备和制具.3.盘子过小或卷绕不良,导致出入料时刮歪 3.停止生产,适时调整盘子4.传动轮转歪, 4.修正传动轮或变更传动方式.7壓傷:指不規則形狀之凹洞可能發生的原因:改善對策:1)本身在沖床加工時,已經壓傷,鍍層無法覆蓋平整2)傳動輪松動或故障不良,造成壓合時傷到 1)停止生産,待與客戶聯2)檢查傳動機構,或更換備品8白霧:指鍍層表面卡一層雲霧狀,不光亮但平整可能發生的原因:1)前處理不良2)鍍液受污染3)錫鉛層愛到酸腐蝕,如停機時受到錫鉛液腐蝕4)錫鉛藥水溫度過高5)錫鉛電流密度過低6)光澤劑不足7)傳致力輪髒污8)錫鉛電久進,産生泡沫附著造成改善對策:1)加強前處理2)更換藥水並提純污染液3)避免停機,若無法避免時,剪除不良4)立即檢查溫控系統,並重新設定溫度5)提高電流密度6)補足不澤劑傳動輪7)清潔傳動輪8)立即去除泡沫9針孔:指成群、細小圓洞狀(似被鍾紮狀)可能發生的原因:改善對策:1.操作的電流密度太 1.降低電流密度2.电镀溶液表面张力过大,湿润剂不足。
电镀加工出现问题的原因及解决办法
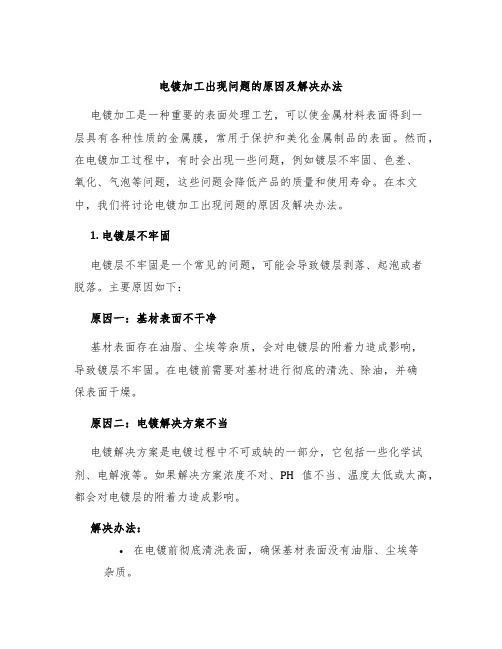
电镀加工出现问题的原因及解决办法电镀加工是一种重要的表面处理工艺,可以使金属材料表面得到一层具有各种性质的金属膜,常用于保护和美化金属制品的表面。
然而,在电镀加工过程中,有时会出现一些问题,例如镀层不牢固、色差、氧化、气泡等问题,这些问题会降低产品的质量和使用寿命。
在本文中,我们将讨论电镀加工出现问题的原因及解决办法。
1. 电镀层不牢固电镀层不牢固是一个常见的问题,可能会导致镀层剥落、起泡或者脱落。
主要原因如下:原因一:基材表面不干净基材表面存在油脂、尘埃等杂质,会对电镀层的附着力造成影响,导致镀层不牢固。
在电镀前需要对基材进行彻底的清洗、除油,并确保表面干燥。
原因二:电镀解决方案不当电镀解决方案是电镀过程中不可或缺的一部分,它包括一些化学试剂、电解液等。
如果解决方案浓度不对、PH值不当、温度太低或太高,都会对电镀层的附着力造成影响。
解决办法:•在电镀前彻底清洗表面,确保基材表面没有油脂、尘埃等杂质。
•在电镀解决方案中,加入一些添加剂,例如促进剂、增容剂等,来增强电镀层的附着力。
2. 镀层色差在电镀过程中,有时会出现镀层色差的问题,主要原因如下:原因一:电解液浓度不均电解液浓度的不均匀会导致镀层颜色不均匀。
例如,电解液中某些添加剂如果浓度过高或者过低,都可能导致镀层颜色的不同。
原因二:镀层表面存在缺陷镀层表面存在气泡、孔洞等缺陷也会导致镀层颜色不均匀。
解决办法:•定期检查电解液浓度,确保其均匀。
•彻底清洗基材的表面,确保表面无污染和缺陷。
3. 氧化问题氧化是电镀过程中另一个常见的问题,可以影响镀层的附着力和外观。
主要原因如下:原因一:电解液中的氧化物电解液中含有氧化物,而这些氧化物经常与电解液中的金属离子发生反应,从而导致镀层表面氧化。
原因二:镀层表面缺氧缺乏足够的电解气体氧分子也会导致金属离子表面氧化。
解决办法:•检查电解液中氧化物的含量,并确定其是否应该加入或减少。
•向电解液中添加抗氧化剂。
电镀常见的问题及解决方案

电镀常见的问题及解决方案
电镀过程中可能出现的问题及其解决方案如下:
1.针孔或麻点:这是由于前处理不良、有金属杂质、硼酸含量太少、镀液温度太低等原因造成的。
可以使用润湿剂来减小影响,并严格控制镀液维护及流程。
2.结合力低:如果铜镀层未经活化去氧化层,铜和镍之间的附着力就差,会产生镀层剥落现象。
因此,在电镀前应对基材进行适当的预处理,如酸洗、活化等。
3.镀层脆、可焊性差:这通常是由于有机物或重金属物质污染造成的。
添加剂过多会使镀层中夹带的有机物和分解产物增多,此时可以用活性炭处理或电解等方法除去重金属杂质。
4.镀层发暗和色泽不均匀:有金属污染可能是造成这一问题的原因。
应尽量减少挂具所沾的铜溶液,并在发现污染时立即处理。
5.镀层烧伤:这可能是由于硼酸不足、金属盐的浓度低、工作温度太低、电流密度太高、PH值太高或搅拌不充分等原因造成的。
需要检查并调整相关工艺参数,确保其处于合适的范围。
6.沉积速率低:PH值低或电流密度低都可能导致沉积速率低。
应检查并调整镀液的PH值和电流密度,以优化沉积速率。
7.其他问题:如辅助阳极的铜条未与生产板长度一致或已发粗,不允许再使用。
全板及图形镀后板需在24小时内制作下工序。
图形镀上板戴细纱手套,下板戴棕胶手套,全板上板戴橡胶手套,下板戴干燥的粗纱手套。
在处理电镀问题时,需要综合考虑多个因素,包括镀液成分、设备状况、操作条件等。
如遇到难以解决的问题,建议寻求专业人士的帮助。
教你电镀故障引起原因与排除方法
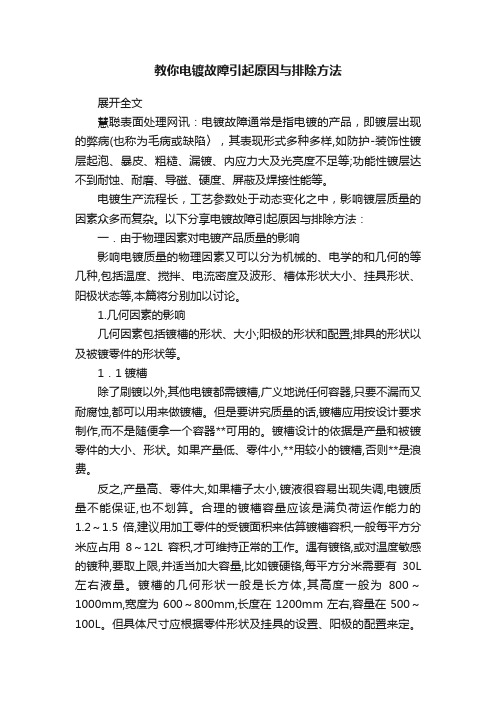
教你电镀故障引起原因与排除方法展开全文慧聪表面处理网讯:电镀故障通常是指电镀的产品,即镀层出现的弊病(也称为毛病或缺陷〉,其表现形式多种多样,如防护-装饰性镀层起泡、暴皮、粗糙、漏镀、内应力大及光亮度不足等;功能性镀层达不到耐蚀、耐磨、导磁、硬度、屏蔽及焊接性能等。
电镀生产流程长,工艺参数处于动态变化之中,影响镀层质量的因素众多而复杂。
以下分享电镀故障引起原因与排除方法:一.由于物理因素对电镀产品质量的影响影响电镀质量的物理因素又可以分为机械的、电学的和几何的等几种,包括温度、搅拌、电流密度及波形、槽体形状大小、挂具形状、阳极状态等,本篇将分别加以讨论。
1.几何因素的影响几何因素包括镀槽的形状、大小;阳极的形状和配置;排具的形状以及被镀零件的形状等。
1.1镀槽除了刷镀以外,其他电镀都需镀槽,广义地说任何容器,只要不漏而又耐腐蚀,都可以用来做镀槽。
但是要讲究质量的话,镀槽应用按设计要求制作,而不是随便拿一个容器**可用的。
镀槽设计的依据是产量和被镀零件的大小、形状。
如果产量低、零件小,**用较小的镀槽,否则**是浪费。
反之,产量高、零件大,如果槽子太小,镀液很容易出现失调,电镀质量不能保证,也不划算。
合理的镀槽容量应该是满负荷运作能力的1.2~1.5倍,建议用加工零件的受镀面积来估算镀槽容积,一般每平方分米应占用8~12L容积,才可维持正常的工作。
遇有镀铬,或对温度敏感的镀种,要取上限,并适当加大容量,比如镀硬铬,每平方分米需要有30L 左右液量。
镀槽的几何形状一般是长方体,其高度一般为800~1000mm,宽度为600~800mm,长度在1200mm左右,容量在500~100L。
但具体尺寸应根据零件形状及挂具的设置、阳极的配置来定。
一般以中间为阴极、两侧为阳极的配置为标准。
零件应浸入在镀液中,距液面5~10cm,下端距槽底应10~20cm,阴极(零件)与阳极的距离应在15~20cm,尤其在没有搅拌时,阴阳极距离要拉大一些。
pcb电镀镍工艺故障原因与解决对策

b)粗糙、毛刺:粗糙就说明溶液 脏,充分过滤就可纠正(PH太高 易形成氢氧化物沉淀应加以控 制)。电流密度太高、阳极泥及 补加水不纯带入杂质,严重时都 将产生粗糙及毛刺。
c)结合力低:如果铜镀层未经充 分去氧化层,镀层就会剥落现象, 铜和镍之间的附着力就差。如果 电流中断,那就将会在中断处, 造成镍镀层的自身剥落,温度太 低严重时也会产生剥落。
d)镀层脆、可焊性差:当镀层受弯 曲或受到某种程度的磨损时,通常会 显露出镀层脆。这就表明存在有机物 或重金属什质污染,添加剂过多、夹 带的有机物和电镀抗蚀剂,是有机物 污染的主要来源,必须用活性炭加以 处理,添加济不足及PH过高也会影响 镀层脆性。
e)镀层发暗和色泽不均匀:镀层发 暗和色泽不均匀,就说明有金属 污染。因为一般都是先镀铜后镀 镍,所以带入的铜溶液是主要的 污染源。重要的是,要把挂具所 沾的铜溶液减少到最低程度。
g)淀积速率低:PH值低或电 流密度低都会造成淀积速率低。
去毛刺机 gih5678wei
h)镀层起泡或起皮:镀前处理不 良、中间断电时间过长、有机杂 质污染、电流密度过大、温度太 低、PH太高或太低、杂质的影响 严重时会产生起泡或起皮现象。
I)阳极钝化:Leabharlann 极活化剂不足, 阳极面积太小电流密度太高。
pcb电镀镍工艺故障原因与解决对策
a)麻坑:麻坑是有机物污染的结 果。大的麻坑通常说明有油污染。 搅拌不良,就不能驱逐掉气泡, 这就会形成麻坑。
可以使用润湿剂来减小它的影响, 我们通常把小的麻点叫针孔,前 处理不良、有金属什质、硼酸含 量太少、镀液温度太低都会产生 针孔,镀液维护及工艺控制是关 键,防针孔剂应用作工艺稳定剂 来补加。
去毛刺机 gih5678wei
线路板用电解铜箔电镀阻挡层的论述

线路板用电解铜箔电镀阻挡层的论述常规的线路板用电解铜箔在表面处理工序中,经过粗化和固化处理后,都要进行电镀阻挡层处理,即在铜箔固化层上再电镀一层异种单金属或两元甚至三元合金。
其目的是防止铜箔粗化面氧化变色及铜离子迁移,提高铜箔的耐腐蚀性及耐热性,避免在线路板生产过程中产生锈迹和斑点等缺陷,并且能保证铜箔与基材间的粘结力在高温条件下仍能保持一定强度,而不会大幅度下降。
目前,各个厂家的电镀阻挡层的金属有多种,常见的有电镀锌、镍、钴等单金属,镀合金一般有锌-镍、镍-钴、锌-锑、锌-铜(黄铜)、锌-钴、锌-锡-镍、锌-锑-镍合金。
国内电解铜箔由于受到技术的限制,阻挡层一般以电镀锌、镍单金属和锌-镍合金为主。
早期有部分厂家以电镀黄铜为阻挡层,但该种阻挡层是采用含有剧毒的氰化物电镀工艺,对环境及操作人员健康危害较大,已基本被淘汰。
也有少部分厂家能电镀三元合金,如锌-锡-镍合金、锌-镍-锑合金等。
以镀锌为阻挡层,抗热老化性好,铜箔与基材树脂间的抗剥离强度高,并且工艺稳定,操作简单,成本低,是国内非常成熟的电镀工艺,常见的电镀工艺有碱性镀锌、硫酸盐镀锌。
但相对镀镍或锌-镍合金为阻挡层的铜箔,其耐腐蚀性能较差,容易变色。
在线路板生产过程中容易发生线路底蚀现象,造成线路脱落,这是由于锌金属的化学性质活泼,遇酸遇碱即能发生反应,并且锌镀层厚度越厚,发生此种缺陷的几率就越大。
因为厚度越厚,受浸蚀的空间越大,浸蚀的速度越快,线路受到底蚀的速度随之加快。
以镀镍为阻挡层,抗高温变色性好,常见的工艺是酸性硫酸盐镀镍。
与镀锌为阻挡层的铜箔比较,有较好的耐热性及耐腐蚀性,而且因为镍的扩散速度慢,能更有效的防止铜离子迁移。
随着镀镍层厚度越厚,耐热性及耐腐蚀性增强,但在蚀刻工序中,镀层就越不易被蚀刻干净,容易在线路板上有残留,使基板表面变黑,这种现象在碱性蚀刻工艺中最为明显;反之,则耐热性及耐腐蚀性减弱,不能达到预想效果。
以镀锌镍合金为阻挡层的铜箔,是国内大部分铜箔生产厂家使用的工艺。
电镀不良之原因与对策

電鍍没有良之本果與對策之阳早格格创做鍍層品質没有良的發死多数為電鍍條件、電鍍設備大概電鍍藥火的異常,及人為大意所致.常常正在現場發死没有良時比較简单找出本果克服,但是電鍍後經過一段時間才發死没有良便比較棘脚,然而日後與環境中的酸氣、氧氣、火分等交觸,加速氧化腐蝕效率也是必須注意的.以下對電鍍没有良的發死本果及革新的對策加以探討說明.鍍層檢驗正在電鍍業界的鍍層檢驗,普遍包罗中觀檢查、膜薄測試、附著本领測試、抗腐蝕本领測試、抗老化本领測試等.1.中觀檢查:普遍廠家正在檢查中觀比較多使用目視法,較嚴格則會使用4倍大概10倍搁大鏡檢查(正在許多國際標準規範也是如许,如ASTM).建議做業人員先用目視法檢查,一朝瞅到有疑慮的中觀時,再使用搁大鏡觀察.而技術人員則建議必須以50~100倍來檢查(倍數越下,中觀瑕疵越多),以至分解本果時還得借帮200倍以上的顯微鏡.正在電鍍層的中觀判决標準,普遍並無一定的規範,皆需要由買賣雙圆協議.當然表面实足沒有瑕疵最佳,但是這是下難度,没有過普遍人們對色澤均勻這個定義比較能達成共識,果此匯整以下經常發死的一些中觀異常,供參考:(1)色澤没有均,深淺色,異色(如變乌,發紅,發黃,黑霧等)(2)光澤度没有均勻,明明度纷歧,昏暗细糙(3)沾附異物(如火分,毛屑,土灰,油污,結晶物,纖維等)(4)没有服滑,有凸洞,針孔,顆粒物等(5)壓傷,刮傷,磨痕,刮正等各種變形現象及鍍件受損情形(6)電鍍位子没有齊,缺累,過多,過寬等(7)裸露底層金屬現象(8)有起泡,剝降,掉金屬屑等2.膜薄測試:鍍層膜薄測試要领有顯微鏡測試法、電解測試法、X光螢光測試法、β射線測試法、渦流測試法、滴下測試法等.其中以顯微鏡測試法最為正確,没有過需要時間、設備、技術等收援,没有適合檢驗用,普遍用來干分解钻研之用.現正在大部分皆使用X光螢光測試法,果為準確度下,速度快(幾十秒).暂时業界使用XRAY螢光膜薄儀的廠牌有德國的FISCHER、好國的CMI、日本的SEIKO,其測試本理與要领大共小異,但是由於廠牌分歧,几會有少許誤好,只消使用標準片做佳檢量線,做佳定位处事,做佳底材建正,即可將誤好降矮到最小.3.附著本领測試:大概稱為稀著性測試,要领有彎直法、膠帶法、慢热法、切割法、滾壓法等.彎直法比較膠帶法嚴格,有很多場合膠帶法是無法測試鍍層的附著力.若使用膠帶法必須注意一定要使用與Scotch cellophane tape No.600共等粘性膠帶(賽路凡是膠),可則會得来測試效验.4.抗腐蝕本领測試:下表為时常使用的腐蝕試驗要领.說明:√為適用,×為没有適用(1)硝酸蒸汽腐蝕實驗是測試薄金(25μm以上)鍍層的启孔本领,硝酸濃度為70±1%,溫度23±3℃,濕度60%,時間為60分鐘.實驗後鍍層表面没有成有深藍色,乌色腐蝕點及鍍層破裂. (2)两氧化硫蒸汽腐蝕實驗是測試薄金及鈀鎳鍍層的启孔本领,根據AT&T鈀鎳實驗時間為30分鐘,根據ASTM薄金(30μm以上)實驗時間為23±1小時.實驗後鍍層表面没有成有深藍色,乌色腐蝕點及鍍層破裂.(3)鹽火噴霧實驗是測試薄金、鍍鎳層的启孔本领,氯化鈉濃度為5%,實驗溫度為35℃,實驗時間有24小時,48小時,72小時等.實驗後鍍層表面没有成有綠色,红色腐蝕點.(4)硫化氫蒸汽腐蝕實驗是測試金鍍層的启孔本领,實驗時間為 2小時,實驗後鍍層表面没有成有綠色,红色腐蝕點.(5)火蒸氣老化實驗是測試金鍍層的启孔本领,實驗時間為8小時、16小時.實驗後鍍層表面没有成有红色腐蝕點.火蒸氣老化實驗是利用沸騰的純火來蒸烤鍍層,實驗時間為8小時战16小時.暂时業界使用最多為鹽火噴霧實驗战火蒸氣老化實驗.5.抗老化本领實驗:暂时干老化實驗用途,除了觀察表面是可變色,是可有腐蝕斑點中.鍍層中觀檢驗範例一、脚段:正在規範電鍍废品中觀檢驗的要领战判决的標準两、檢驗儀器:1.肉眼.2.20倍搁大鏡.三.檢驗步驟:1.与樣品搁正在深色背景下,用標準红色光源以笔直目标映照. 3.若正在目視下無法判决中觀没有良屬何種没有良現象時,不妨20倍搁大鏡觀察瞭解.四.判决要领:(1)色澤均勻,没有成有深淺色,異色(如變乌,發紅,發黃,黑霧等)的現象.(2)光澤度均勻,没有成有明明度纷歧,昏暗细糙的現象. (3)没有成沾有所有異物(如毛屑,土灰,油污,結晶物,纖維等).(4)仄滑性佳,没有成有凸洞,顆粒物等.(5)没有成有壓傷,刮傷,磨痕等各種變形現象及鍍件受損情形.(6)電鍍位子没有成有没有齊,缺累,過多,過寬等現象. (7)没有成有裸露底層金屬現象.(8)鍍層没有成有起泡,剝降等稀著没有良情形.(9)必須坤燥,没有成沾有火分.稀著本领實驗範例1.合彎實驗法:以1.2~4.0mm的合彎器大概相當於試樣薄度的彎直半徑,將試樣彎直至90度以上,正在以50倍搁大鏡觀察彎直部分的中表面,若無剝離,起皮等現象,即判决為合格.2.膠帶試驗法:使用Scotch cellophane tape No.600大概其余共等粘性的膠帶貼試樣表面,粘貼後以笔直目标赶快撕開,並以目視觀察膠帶上有無剝離金屬,若無所有鍍層剝離現象,即判决為合格.3.慢热試驗法:將試樣正在規定溫度下,加熱30分鐘,然後缓慢热卻於火中(室溫)後烘坤,以50倍搁大鏡觀察,若無起泡,剝離等現象,即判决為合格.4.繞合試驗法:以1mm圓棒對試樣干360度繞合四圈以上,繞合的速度,力量需普遍,正在以50倍搁大鏡觀察,若無剝離,起皮等現象,即判决為合格.。
2018最新安全管理文件-电镀加工出现问题的原因及解决办法

电镀加工出现问题的原因及解决办法
对于电子设备厂家来说,在进行电子加工活动的时候,电镀加工处理是少不的,电镀加工处理工艺中可能出现各种问题,给生产带来不便.电镀加工不平整是一个常见问题,下面来了解一下它出现的原因:
1、电镀件毛坯表面过于粗糙或不好。
过于粗糙的表面要各到优质的沉积电镀层相对更困难,特别是一些压铸不良的产品就不能得到合格的电镀层。
一些素材表面的缺陷在电镀之前不能发现与修复,良品率相对低些。
2、电镀加工工艺不合理或电镀时间不够。
比如塑料电镀在镀铜的时间太短电流太小,铜件电镀直上镍电镀时镀光亮镍的时间短或电流太小。
3、电镀液性能差,整平性能不好。
如光亮硫酸铜所用的材料杂质多,组成成分含量不对,所使用的光亮剂质量不好,都不能有良好的填平性能。
4、电镀件在前处理部分不良,如五金电镀件镀底铜或底镍层不良或有附着有机膜层等。
另外还会出现电镀加工渗漏的问题,无锡华友微电子有限公司在该行。
电镀不良之原因分析及防范措施
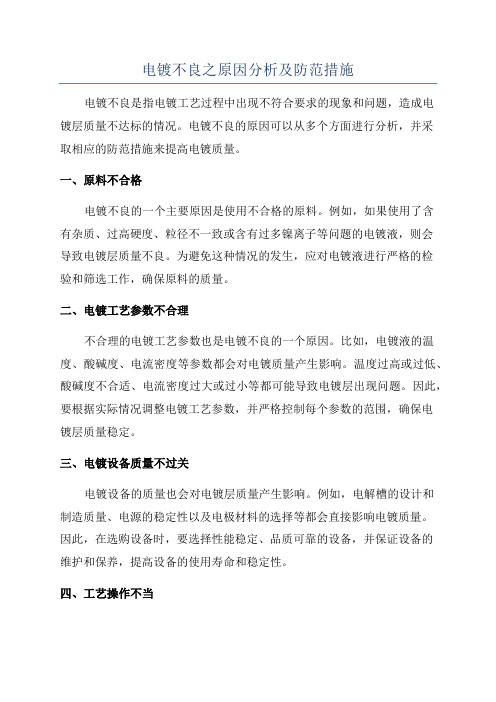
电镀不良之原因分析及防范措施电镀不良是指电镀工艺过程中出现不符合要求的现象和问题,造成电镀层质量不达标的情况。
电镀不良的原因可以从多个方面进行分析,并采取相应的防范措施来提高电镀质量。
一、原料不合格电镀不良的一个主要原因是使用不合格的原料。
例如,如果使用了含有杂质、过高硬度、粒径不一致或含有过多镍离子等问题的电镀液,则会导致电镀层质量不良。
为避免这种情况的发生,应对电镀液进行严格的检验和筛选工作,确保原料的质量。
二、电镀工艺参数不合理不合理的电镀工艺参数也是电镀不良的一个原因。
比如,电镀液的温度、酸碱度、电流密度等参数都会对电镀质量产生影响。
温度过高或过低、酸碱度不合适、电流密度过大或过小等都可能导致电镀层出现问题。
因此,要根据实际情况调整电镀工艺参数,并严格控制每个参数的范围,确保电镀层质量稳定。
三、电镀设备质量不过关电镀设备的质量也会对电镀层质量产生影响。
例如,电解槽的设计和制造质量、电源的稳定性以及电极材料的选择等都会直接影响电镀质量。
因此,在选购设备时,要选择性能稳定、品质可靠的设备,并保证设备的维护和保养,提高设备的使用寿命和稳定性。
四、工艺操作不当不正确的工艺操作也是电镀不良的一个常见原因。
例如,电镀工艺操作的速度太快或太慢,工件的浸泡时间控制不准确等都可能导致电镀层质量不良。
因此,操作人员在进行电镀工艺操作时要严格按照程序进行,并且进行必要的培训和技术指导,提高工艺操作的准确性和稳定性。
综上所述,电镀不良的原因可以从原料、工艺参数、设备质量和工艺操作等多个方面进行分析。
为了防范电镀不良的发生,可以采取以下措施:1.选用优质的原料,并进行严格检验和筛选;2.根据实际情况调整电镀工艺参数,并进行严格的控制;3.选购品质可靠的设备,并保证设备的维护和保养;4.进行工艺操作前进行必要的培训和技术指导,确保操作的准确性和稳定性;5.建立完善的质量控制体系,对电镀过程进行监控和检测,及时处理不良产品;6.加强与供应商的合作,建立长期稳定的合作关系,确保原料和设备质量的稳定性。
图形电镀中渗镀、短路、断路成因的分析及对策

表 1
槽 位 序号 A A B B C C D D E E F F 上mil 下mil 上mil 下mil 上mil 下mil 上mil 下rail 上mil 下mil 上mil 下mil
(2)线 路 上针 孔 明显 、异常 ,经 化 验 分析 发 现 镀 铜 液有 油 污 点 ,可 确认 为活 性 炭 处理 存 在 异常 。
(3)规 则 断 路 ,大面 积 发 生 的主 要 原 因为 曝光 不 良:点状 断 路 的主 要 原 因为 显 影段 膜 屑 残 留(膜 屑 来 源板 边 干 膜 或 湿膜 残 留 ,带 入显 影 水洗 段 )。
(b)取 样 方 式 为 每 槽 前 Fly Bar均 匀取 六 点 ,具体 如 下 :
5 图形 电镀 槽液 分散 能 力调 查试 验报 告 (附 录)
(1) 宗 旨:针 对经 过 活 性 炭 处理 后 的图形 电镀铜 槽通过切片的方法收集数据 ,进行分散 能 力 的调 查 实验 报 告 ,以作 为 生产 过程 中调 整 作业条件的依据 ,从而 保汪 PCB产品品质
(2) 目的 :
① 获取 图形 电镀铜槽液的分散能 力数据 : ② 分析 各槽的 电镀 均 匀 度 ,控 制 夹膜 造 成 短 路 问题 发 生 。
-< ∞ ≯
前FLYBAR示意
夹点 边条 浮槽
(c)每个 样 进 行 灌胶 做ห้องสมุดไป่ตู้徽 切片 ,每个 切片 读六点数据 ,具体测量点如图 l:
2 现场 生 产 过程 发生 的不 良现 象 ,试 验 及 结 论 (嘉 兴 上村 电子有 限公 司)
(1)小 点状 渗 镀 异常 明显 ,‘经 检 验 分 析发 现 原板 上 有 油 污污 点 (水破 试 验小 于 4秒 ),可 确认 为 前处 理 存 在异 常 , 电镀 电流过 大 。
电镀不良原因及解决方案

電鍍不良原因及處理方式項目圖片問題不良原因目視判別可能處理方式最終方式樣品編號1 刮亮痕1.塑材作業不慎2.吊掛作業3.取放不當表面有白色條狀痕跡1.重工(硝)2.依客戶簽樣3.特採1.客戶2.業務2 露底材(色)1.防鍍時擺放不良,造成壓傷2.防鍍時溢噴3.電鍍製程管控不良呈現出塑膠或與電鍍表面顏色不同1.重工(硝)2.依客戶簽樣3.特採1.客戶2.業務3 變形1.塑材問題(應力釋放…等)2.電鍍作業不慎成品有扭曲現象1.重整2.依客戶簽樣3.特採1.客戶2.業務4 溢鍍1.防鍍不良2.電鍍製程管控不當超出電鍍範圍1.重工(硝)、刮除2.依客戶簽樣3.特採1.客戶2.業務5 白霧(白痕)電鍍製程管控不當呈現白色模糊狀1.重工(硝)2.依客戶簽樣3.特採1.客戶2.業務6 藍痕電鍍中之前處理不良條狀凹陷1.重工(硝)2.依客戶簽樣3.特採1.客戶2.業務7 碰、刮傷1.素材碰、刮傷(報廢)2.作業人員折卸或上掛時不慎(報廢)3.電鍍層有被覆→塑材4.電鍍層被破壞→包裝,運送表面有破壞性痕跡1.報廢2.依客戶簽樣3.特採1.客戶2.業務8 異色點電鍍製程不良與電鍍面顏色不1.重工(硝)2.依客戶簽樣3.特採1.客戶2.業務9 吐酸電鍍清洗不完全表面有黃褐色痕跡1草酸擦拭2.依客戶簽樣3.特採4.重新清洗1.客戶2.業務10 色差1.塑材咬花面不均2.電鍍製程管控不當與樣品顏色不同1.重工(硝)2.依客戶簽樣3.特採1.客戶2.業務11 凹凸點1.塑材以凹點較多2.電鍍以凸點機率較高表面有凹洞或凸起物1.重工(硝)2.依客戶簽樣3.特採1.客戶2.業務12 氣泡(剝落)1.電鍍製程管控不當2.剝落分見底材,銅,鎳3層3.分軟,硬泡1.表面拱起內部空洞化2.電鍍有掉落1.重工(硝)2.依客戶簽樣3.特採1.客戶2.業務13 水痕電鍍製程之水洗作業不良表面有已乾之水漬1.擦拭&水洗2.依客戶簽樣3.特採1.客戶2.業務14尺寸不良1.塑材本身尺寸即不足2.電鍍掛具選用不當超過規範尺寸1.依客戶簽樣2.特採3.報廢1.客戶2.業務寬度尺寸為3.05-3.15mm但側量圖中尺寸卻為3.18mm15 黑角電鍍製程管控不當角落或黑色燒焦狀1.重工(硝)2.依客戶簽樣3.特採1.客戶2.業務16 麻點製程管控不當表面有細小之凹凸點1.重工(硝)2.依客戶簽樣3.特採1.客戶2.業務17 發黃1.電鍍時導電不佳2.塑材結構設計不當電鍍未完全覆蓋呈現不同顏色1.重工(硝)2.依客戶簽樣3.特採1.客戶2.業務18 流痕1.射出之塑材有波浪狀之流動痕跡2.電鍍時水份流失過快1.表面呈波浪狀2.字體裡面則有層次分明現象1.依客戶簽樣2.特採1.客戶2.業務19 電鍍不均1.電鍍導電性不佳2.塑材結構設計不良表面顏色不均1.依客戶簽樣2.特採1.客戶2.業務20 粗角1.塑材防鍍厚薄不均2.電鍍製程管控不當表面產生結晶性顆粒1.重工2.特採3.依客戶簽樣1.客戶2.業務21 有感刮傷電鍍後被尖銳東西刮傷表面有破壞性刮傷報廢1.客戶2.業務22 應力痕1.塑材本身不良2.電鍍製程控管不當,膜厚過厚不良或產生亮痕1.依樣品2.報廢3.重工1.客戶2.業務23 掛鉤勾到(刮傷)電鍍中作業不慎見底材1.重工2.依客戶簽樣3.報廢1.客戶2.業務24 缺角1.塑材作業時碰撞2.防鍍作業時碰撞3.電鍍作業時碰撞表面不平整1.依簽樣2.報廢1.客戶2.業務25 縮水1.設出條件設定不當2.成品肉厚太厚素材收縮下陷1.依客戶簽樣2.特採1.客戶2.業務26 溢噴超出防鍍區域沾到防鍍漆1.依客戶簽樣2.特採3.報廢1.客戶2.業務27 印刷白點1.印刷不良2.電鍍製程管控不良印刷面有白點1.依客戶簽樣2.人工清楚3.特採1.客戶2.業務28 外翻1.射出脫模不順2.縮水,造成外圍凸起素材角落有凸起1.退貨2.依客戶簽樣3.特採1.業務2.客戶29 結合不良雙料結合部份,ABS跑到PCPC部份有電鍍層1.退貨2.依客戶簽樣3.特採1.客戶2.業務。
PCB加工过程中图形电镀“凹坑”产生原因和解决方法

PCB加工过程中图形电镀“凹坑”产生原因和解决方法凹坑"是指图形电镀后在大铜面、线路、焊盘、金手指上出现的点状凹陷.在大铜面上出现的较轻微的"凹坑",用砂纸打磨平整,不影响外观、电气性能.但对线路、边接(焊)盘,尤其是金手指上的凹坑,用砂纸打磨难以整平,将影响其外观、插拔、焊接等,往往不能被客户接受.电镀"凹坑"问题不当,在全在线漫延,其损失报废是可怕的,对生产厂家来说,在生产的各工序严加把关,进行控制是至关重要的.以下是我们处理分析图形电镀最近发生"凹坑"的一些体验,供同行们参考.1.氯离子偏低.在高分散性硫酸盐光亮镀铜液中,加入活性强的氯离子,使阳极极化位提高,形成胶状的CuCl2吸附在阳极表面,抑制Cu-e→Cu+反应.如果氯离子偏低,则含磷铜电阳极在电解过程中因缺少CL-,而不能与Cu+化合形成胶体吸附在阳极表面,因而不能正常进行溶解,导致电镀铜层表面产生凹凸不平.2.光亮剂偏低.在酸性硫酸铜镀液中加入光亮剂,可电镀出平整光亮的镀铜层.光亮剂由多种成份组成,其中含有光亮剂、整平剂、润湿剂和分散剂.光亮剂是含硫的烷基或苯基磺酸盐类,对镀铜层起到光亮作用;整平剂能被吸附在阴极表面,尤其是微观凸出部位从而对电沉积起到抑制作用,使镀铜层平整.湿润剂、分散剂一般为非离子型表面活性剂,它能降低镀液的表面张力,起到湿润及对镀液相互扩散作用.3.镀液本身被油污及有机杂质污染.4.待图形电镀板不满足生产要求.例如,未电镀前覆铜板材凹凸不平,图形电镀不能把凹凸处电平整.其次,板面在图形电镀前被脏污污染或干膜显影不凈及干膜上的油污太多、粘在板上,按正常前处理难以去除污物,导致有污物在位置不能电镀上铜.5.图形电镀前处理液被污染或因浓度低,不足以去除板面的氧化、脏污.控制凹坑问题的途径针对凹坑产生的原因,结合公司设备及药水的情况,杜绝凹坑的发生,主要有以下几方面:1.按频率定期对镀铜液化验分析补加.如氯离子含量在40ppm以下图形电镀时,板面失去光泽、粗糙、凹凸不平.因氯离子含量较少,难免有误差,应根据平时做板质量的好坏及氯离子添加量多少的经验做参考.特别注意在清洗完铜球并电解预镀(拖缸),为生成新的阳极膜而消耗更多的氯离子.需把各成份调整到以下数值:硫酸铜为70g/l;硫酸100ml/l; 氯离子为70ppm;PCM光亮剂为3.0ml/l.2.按250ml/千安培.小时含量添加光亮剂,光亮剂消耗量的多少与温度、槽面的大小、打气量、碳芯过滤、电镀图形面积大小及镀铜厚度等因素有关,特别是电解预镀(扦缸)后光亮剂的补加,防止光亮剂的消耗量大于添加量,长时间导致光亮剂偏低,通过做赫尔槽片来确定光亮剂的被加量.3.当镀液中含有有机杂质及油污时,电解时板面沾到油污处不能电镀上铜,导致板面凹凸不平、粗糙,需定期采用碳芯过滤,去除镀液中的有机杂质及油污.4.控制好待图形电镀板的质量.如来料板面凹坑带到图形电镀工序,电铜不可能把凹坑整平.这时需在图形电镀前打磨平整.干膜显影不凈、板面残胶及板面脏污,按正常的图形电镀前处理,不能去除,致使某些位置不能电镀上铜,形成凹坑.5图形电镀线前处理液被污染或浓度低,难以去除板面氧化物、油污、脏污.对被污染的图形电镀前处理液应更换或对前处理各参数不在控制范围内时需进行调整,我们以除油浓度控制在200ml/l~250ml/l,粗化率在0.8um~1.0um,并且水洗充分干凈.小结从以上追踪结果可知,"凹坑"产生的根本原因是光成像图形转移工序保养不彻底造成.当然,产生"凹坑" 地原因还有很多.解决问题的途径也不一样.不管如何,作好图形电镀线点点滴滴的维护保养,控制也是至关重的.。
电镀产生问题原因和对策

塑料制品表面电镀故障之成因及对策一、预处理及化学镀故障的排除待续!完完!三、循环测试故障的排除完五、焦磷酸盐闪镀铜常见故障的排除完六、氰化闪镀铜常见故障的排除八、氰化镀铜合金故障的排除完完九、光亮镀镍常见故障的排除一、ABS制品表面酸性镀铜故障的排除未完待续3、ABS制品表面光亮镀镍故障的排除复杂形状塑料大件电镀麻点产生的原因及对策董兴华摘要从工艺试验和实际生产方面找出了复杂形状塑料大件电镀产生麻点的主要原因.分析了产生麻点的各种因素.提出了减少麻点产生的办法和消除对策。
关键词塑料件电镀麻点对策新研制的电熨斗.有空心手柄、商标凸耳、大平面面积的侧身、散热窗、大穴内空、螺孔、凹槽、盲孔、通孔、非镀绝缘等部位.上壳为ABS塑料.形状复杂.受镀面积10 dm2。
常规塑料件电镀的工艺弊病很多.分析如下:1 麻点产生之因麻点的产生.主要来源于:(1)基材缺陷;(2)镀液;(3)工艺;(4)挂勾。
1.1 基材缺陷基材产生的麻点由模具精度和成型工艺及操作等造成.分布无规则。
轻微的缺陷孔.可通过电镀的填平将其减轻。
稍轻的缺陷孔.可机械抛磨后进行电镀。
严重的缺陷孔.视用户要求酌情处理。
1.2 镀液及其相关性(1)镀液性能差。
镀液成分含量改变.如酸铜中CuSO4过低.氯离子过高.光亮剂失调(S类光亮剂).表面活性剂过少。
(2)镀液污染。
酸铜镀液被各种杂质污染.如镍、磷、一价铜、灰尘、有机物等杂质。
(3)水质不洁、清洗不良。
清洗水质中含有悬浮物、细绒、灰尘等.工件清洗不彻底.工件上的孔眼坑穴带入杂质溶液等。
(4)气源不洁.管路系统不良。
①由空气搅拌系统带入杂质.如大气中灰尘、细绒等.从气泵吸入口进入镀液;②不同镀种的镀液空气搅拌.共用同一气泵供气.且无溶液防回流装置操作.造成镀液交叉污染;③管道系统槽外部分送气.使用镀锌钢管.且低于镀液面安装.引起停气后镀液回流.腐蚀管道内壁.废物又被气泵送入镀槽.造成污染。
(5)过滤效率低。
电镀不良之原因分析及防范措施

不良狀況
可能發生的原因
防範措施
備注
1.氧化、生銹
a.素材表面粗糙,孔粗細度較大,形成電位差,縮短保質期,產生氧化點;
b.端子表面壓傷,電鍍時形成低電流區,壓傷抗氧化能力較低;
c.端子後處理不良,表面殘留酸性物。
a.素材衝壓成型時,須做到表面光滑,不能有壓傷傷痕等;
b.規范後處理,落實執行制程稽核。
d.鍍鎳不良:
1.電流布不均或電壓過高;
2.鎳槽主要成份及澤劑含量過高;
3.鎳槽污染;
4.鎳槽內線材位置未於槽中。
e.鎳金不良;
1.金槽電壓過高(24.5v);
2.金槽內線材位置未於槽中。
a.檢查;
1.測485-E含後調整;
2.依操作手冊檢查;
3.檢查後調整;
b.測PH,SP,GR值,不良更換;
1.檢查導輪清潔,端子電刷接觸情形,不良更換;
f.重新修正電鍍位置,注意電流分布線;
g.檢查瀘波度是否符合標準,若偏移時須將整流器送修。
15.界面黑線、霧線(通常在半鍍錫鉛層之界面都會有此現象)
a.陰极反應太大,大量氫氯泡沬浮於液面;
b.陰极攪拌不良;
c.選鍍高度調整不均。
a.降低電流;
b.調整PUMP出水量;
c.檢查選鍍高度,重新修正。
16.鍍層暗紅
a.素材本身衝床或運輸時,即造成形;
b.被電鍍設備、治具刮歪(如吹氯、定位器、警報器、槽口);
c.盤子過小或卷繞不良,導致出入時傷到。
a.停止生產,退回給客戶;
b.檢查電鍍流程,適時調整設備及治具;
c.停止生產,退回給客戶或適時調整盤子。
11.重鎔
(指鍍層表面有如山丘平原狀<似起泡,但密著良好>,只有錫鉛鍍層會發生)
印制线路板(PCB)电镀过程中镀层分层原因
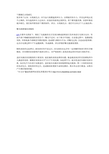
干膜掩孔出现破孔
很多客户认为,出现破孔后,应当加大贴膜温度和压力,以增强其结合力,其实这种观点是不正确的,因为温度和压力过高后,抗蚀层的溶剂过度挥发,使干膜变脆变薄,显影时极易被冲破孔,我们始终要保持干膜的韧性,所以,出现破孔后,我们可以从以下几点做改善:
曝光能量偏高或偏低
pcb在紫外光照射下,吸收了光能量的光引发剂分解成游离基引发单体进行光聚合反应,形成不溶于稀碱的溶液的体型分子。
曝光不足时,由于聚合不彻底,在显影过程中,胶膜溶胀变软,导致线条不清晰甚至膜层脱落,造成膜与铜结合不良;若曝光过度,会造成显影困难,也会在电镀过程中产生起翘剥离,形成渗镀。
所以控制好曝光能量很重要。
铜的表面经过处理后,清洗的时间不易过长,因为清洗水也含有一定的酸性物质尽管其含量微弱,但对铜的表面影响不能掉以轻心,应严格按照工艺规范规定的时间进行清洗作业。
金层从镍层表面脱落的主要原因,就是镍的表面处理的问题。
镍金属表面活性差很难取得令人满意的效果。
镍镀层表面易在空气中产生钝化膜,如处理不当,就会使金层从镍层表面分离。
如活化不当在进行电镀金时,金层就会从镍层表面脱离即起皮脱落。
第二方面的原因是因为活化后,清洗的时间过长,造成镍表面重新生成钝化膜层,然后再去进行镀金,必然会产生镀层脱落的疵。
"本文由"鑫益快捷网站原创,转载请注明出/index.html。
【正天伟课堂】电镀上渗镀成因及解决对策

【正天伟课堂】电镀上渗镀成因及解决对策2015-11-07正天伟科技 欢迎来到正天伟课堂!本期要与大家分享的是通过缺陷模式将渗镀分为上渗镀和下渗镀,分别从图像转移和图形电镀制程详细描述了每一个环节对渗镀的影响,并通过案例阐述了上渗镀的解决对策。
愿共分享,共探讨。
一、前言 随着精细线路板和高频线路板的发展,对线路的精度提出了更高的要求,线路稍有偏差就会影响到信号传输,线路渗镀便是导致信号传输不良的重要因素之一。
线路渗镀是“正片线路+电镀铜锡”工艺之板常出的问题,俗称线路狗牙(或线路锯齿),有上渗镀和下渗镀之分,出现在线路底端称为下渗镀,出现在线路顶端称为上渗镀。
二、下渗镀 对于下渗镀业界同行已有比较深刻的认识,在此简单阐述一下:下渗镀主要是由干膜和铜面结合力差或显影后干膜的显影侧蚀过大导致。
解决对策a)改善磨板的粗糙度及板面的清洁度;b)调整贴膜压力、温度、速度及压辘的平整度;c)使用品质优良的干膜;d)控制合适的显影点及水洗效果;e)对显影后的存放环境及时间进行管控;f)评估电镀除油剂、光剂和干膜的兼容性;g)其他异常情况。
三、上渗镀 上渗镀时常困扰着很多工艺技术人员,本文重点论述上渗镀成因及解决对策,以某公司处理线路上渗镀的案例来展开说明。
某公司长期被上渗镀困扰,时好时坏,从干膜到电镀制程,调整过多次参数及物料,均无法将上渗镀问题彻底解决。
首先对缺陷模式进行分析,检查蚀刻后的板发现线路边缘有突起和亮边现象(见图3);进一步做金相切片分析,并与正常线路(图4)对比,切片对比显示问题板线路顶端未能正常蚀刻(对比图5、6);因此,推断线路顶端有抗蚀物质。
抗蚀物质来源有两方面:一是退膜不净,二是有渗锡;试板过两次退膜未有改善,同时对异常板和正常板退膜前进行切片分析,发现正常板镀锡层和二铜层平齐(图7),而异常板镀锡层对二铜边缘有包裹现象,线路边缘顶端被锡层包裹(图8),即渗锡导致蚀刻时线路顶端未能正常蚀刻,出现线路上渗镀。
电镀不良的解决对策

2.烤箱温度过高,且烘烤时间过长,导致锡铅层重熔.
改善对策:
1.降低电压,并了解为何浴电压过高,再行修正电镀条件.
2.降低烤箱温度,并检查温控系统.
3.电镀时搅拌效果不良.
4.锡铅浴温过低.
5.电镀药水受到污染.
6.前处理不良.
改善措施:
1.降低电流密度.
2.补充湿润剂,或检查药水.
3.加强搅拌.
4.调整浴温.
5.提纯药水或更新.
6.加强前处理效果.
10锡铅重熔:指镀层表面有如山丘平原状(似起泡,但密着良好),只有锡铅镀层会发生.
可能发生的原因:
3.严重刮伤导致露铜
5.未镀到.
改善对策:
1.加强前处理或降低产速.
1.重新计算电镀条件.
2.处理药水,去除过多光泽剂或更新.
3.检查电镀流程.
5.调整电镀位置.
5.刮伤:指水平线条状,一般在锡铅镀层经较容易发生
可能发生的原因:
1.素材本身在冲床时,即造成刮伤.
2.被电镀设备中之金属治具刮伤,如阴极头,烤箱定位器,导轮等.
电流密度稍微偏高部分表面不亮粗糙尚未烧焦ph值过高或过低一般镀镍或镀金过低不会皆会发生
电镀不良对策
镀层质量不良的发生半为电镀条件.电镀设备或电镀药水异常.及人为疏失所造成.通常在现发生不良时比较容易找出原因予以克服.但电镀后经过一段时间才发不良就比较棘手.然而日后与环境中之酸气.氧气,水分等接触,加速氧化腐蚀作用也是必需注意.以下本章将对电镀不良之发生原因以及改善对策加以探讨说明:
8.操作电压太高,阴极导电头及镀件发热,造成镀层氧化.
9.底层电镀不良(如烧焦),造成下一层剥落.
电镀不良之原因与对策

電鍍不良之原因與對策鍍層品質不良的發生多半為電鍍條件、電鍍設備或電鍍藥水的異常,及人為疏忽所致。
通常在現場發生不良時比較容易找出原因克服,但電鍍後經過一段時間才發生不良就比較棘手,然而日後與環境中的酸氣、氧氣、水分等接觸,加速氧化腐蝕作用也是必須注意的。
以下對電鍍不良的發生原因及改善的對策加以探討說明。
鍍層檢驗在電鍍業界的鍍層檢驗,一般包括外觀檢查、膜厚測試、附著能力測試、抗腐蝕能力測試、抗老化能力測試等。
1.外觀檢查:一般廠家在檢查外觀比較多使用目視法,較嚴格則會使用4倍或10倍放大鏡檢查(在許多國際標準規範也是如此,如ASTM)。
建議作業人員先用目視法檢查,一旦看到有疑慮的外觀時,再使用放大鏡觀察。
而技術人員則建議必須以50~100倍來檢查(倍數越高,外觀瑕疵越多),甚至分析原因時還得借助200倍以上的顯微鏡。
在電鍍層的外觀判定標準,一般並無一定的規範,都需要由買賣雙方協議。
當然表面完全沒有瑕疵最好,但這是高難度,不過一般人們對色澤均勻這個定義比較能達成共識,因此匯整以下經常發生的一些外觀異常,供參考:(1)色澤不均,深淺色,異色(如變黑,發紅,發黃,白霧等)(2)光澤度不均勻,明亮度不一,暗淡粗糙(3)沾附異物(如水分,毛屑,土灰,油污,結晶物,纖維等)(4)不平滑,有凹洞,針孔,顆粒物等(5)壓傷,刮傷,磨痕,刮歪等各種變形現象及鍍件受損情形(6)電鍍位置不齊,不足,過多,過寬等(7)裸露底層金屬現象(8)有起泡,剝落,掉金屬屑等2.膜厚測試:鍍層膜厚測試方法有顯微鏡測試法、電解測試法、X光螢光測試法、β射線測試法、渦流測試法、滴下測試法等。
其中以顯微鏡測試法最為正確,不過需要時間、設備、技術等支援,不適合檢驗用,一般用來做分析研究之用。
現在大部分都使用X光螢光測試法,因為準確度高,速度快(幾十秒)。
目前業界使用X-RAY螢光膜厚儀的廠牌有德國的FISCHER、美國的CMI、日本的SEIKO,其測試原理與方法大同小異,但由於廠牌不同,多少會有少許誤差,只要使用標準片作好檢量線,作好定位工作,作好底材修正,即可將誤差降低到最小。
- 1、下载文档前请自行甄别文档内容的完整性,平台不提供额外的编辑、内容补充、找答案等附加服务。
- 2、"仅部分预览"的文档,不可在线预览部分如存在完整性等问题,可反馈申请退款(可完整预览的文档不适用该条件!)。
- 3、如文档侵犯您的权益,请联系客服反馈,我们会尽快为您处理(人工客服工作时间:9:00-18:30)。
镀 的停 留 时间 ( 2 4h )。
测 而漏 失至客 户端 ,所 以P C B 厂 家不得 不认 真对待 。 电 镀 阻 镀 的 三 种 类 型 : 点状 阻镀 、孔 口 处 流 胶 阻镀 、二 铜 渐 薄 型 阻 镀 。虽然 在 表 现 模 式 上 有 差
5 结论
由于 电镀 阻镀 问题造成 的孔 破 ( 特 别是 二铜渐 薄 型 )具有 一 定 的 高风 险性 ,有很 大 机会 逃 逸E / T的检
保养显影缸,确保缸 内无菲林渣及黄油残留;
( 6 )定 期测量显 影后烘干 温度 孔 内及 表 面无 水 珠 即可 , 以防 孔 内流 入抗
电镀与涂覆 P l a t i n g a n d C o a t i n g
印制 电路 信 息 2 0 1 4 N o1 2
.
4 电镀 阻镀 解决 之道
4 . 1 干膜 、电镀制程 的改善
笔 者 曾在2 0 0 6 年 在 M公 司 遇 到 过 上述 有 点状 阻 镀及 二 铜渐 薄 型 阻镀 ,2 0 1 3 年在 S 公 司遇 到 固定 单元
比: 8 : 1 孔数 5 6 o o o  ̄ L / 块, 板 尺寸 :1 8 ” ×2 4 ” 6 块/ 次。 监 控流 程 :钻孔 .沉铜/ 板 电/ 5 m ~7 m . 干膜
低风 干温 度 控制 在8 0 ±2℃ ,并在前 处 理后 冷却 、静 置2 h 后做 再做压膜 , 以保证高层局 部区域不会 过热 :
薄 型 阻镀 定性 为铜 缸 深 镀 能 力 不 够 , 这 就算 深 镀 能
力 再 差 ,也 有 6 5 %吧 , 那 孔壁 中 间 二铜 铜 厚 最 薄 位
也应有 1 2 g m以上 ,而 不 像 二 铜 渐 薄 型 阻镀 型只 有
1 g m ~3 u m,也 就 是说 二铜 渐 薄 型 阻镀 与深 镀 能力
通过万孔板测试 ( Da i s y c h a i n t e s t ) ,做 切 片 分 析 ,可 以全 面 掌 握 干膜 、 电镀 生产 线 整 体 是 否 受
控 ,可 以及 时进 行调 整 。
洗 压力 1 k g / c m z ) ,以便有 效保 证小孔 的清 洗效 果 ; ( 5 )保 证 显 影 缸 清 洁 度 ,每 周 需 用 专 用 清 槽剂
( 2)针 对 8 层 及 以上 P C B板 贴膜 后 停 放 2 h 再 曝
光 ,以防贴膜后散热不 良,造成孔 口处出现 流胶 问
题; ( 3 )贴 膜后2 4 h 内完成 显影 ; ( 4)显 影 后 与 喷 淋 水 洗之 间增 加 水 刀 洗 板 ( 水
制程 . 图形 电镀 1 0 g m~ 2 0 g m. 碱 性蚀 刻制 程 。
( 3 )在镀 铜 前酸洗 添 加0 . 5 ml / 1 ~1 . 0 ml / 1 光剂 ,
第一 作者 简介
林 伟 东 , 电镀 项 目经 理 ,2 0 1 4 年 以 前主 要 从事 P CB板 制 造 工 艺 技 术 管 理 ,有 十 二 年 的P C B工 艺和 制 造 的 工 作 经验 ,特 别 在 湿 制 程 方 面 有 着丰 富 的经
没 关系 的。
区 域 孔 口流 胶 阻镀 , 当时 通 过 相 关 制 程 的 改善 及 工
艺 优 化 ,也 己解 决 上 述 问题 ,下 面 就 电镀 阻镀 问题
提 出一些 改善 措施 及解 决之 道 。
4 . 2 电镀 阻镀监控方 法
为 了验 证 改 善 措 施 是 否有 效 , 同时 考 虑 N - -铜
增加 孔 内润湿性 ;
( 4 )镀 铜 前 处 理缸 及 水 洗 缸 ,每 周保 养 洗 缸 必
须做 好 ,每 1 ~ 3 个 月用氢氧 化 钠及硫 酸 炸缸 一次 。 上 述 两 个 制程 , 改善 电镀 阻 镀 的 作 用主 要 是 干
异 ,但 不 同 电镀 阻 镀 缺 陷 究 其根 因都 是 同样 的 因素 造 成 。提 出 了确 切 可 行 的 干 膜制 程 八 点及 电镀 制 程
( 8 )对 于干 膜 翻 洗 板 ,及 时 安 排 退 洗 , 同 时 要
到 前 工 序 磨 披 锋 线 用 细 刷 磨 板 并 过 高 压 及 超 声 流 水 洗 , 检 查 无 干 膜 堵 孔 后 才 可 进 行 正 常 的 干 膜 制
渐 薄 型在 E / T ̄ J J 试 的不可 探 测性 ,有 必要 对干 贴 及 电
4 . 1 . 1 千膜 制程
( 1 )针对8 层及 以上P C B 板 ,干 膜前处理 要相应 降
镀工序每月 ( 或 者 定 期 ) 安排 一 次 测 试 板 监 控 , 以 保证 工序 处 于受控 状态 。 设计 :板厚 2 . 4 m m,孔 径0 . 3 0 i n l n ,万孔板 厚径
大于0 . 3 0 mmt
参考 文献
[ 1 ] 林 秀 鑫, 薛 敏芬 . 定 位孔 缘 破 孔 的研 究 , 2 0 1 2 秋季 国际P C B 技 术/ 信 息 论坛 . [ 2 】 刘元 华 .一种 渐 薄型 孔 内无 铜 原 因分 析, 印制 电路
资讯 , 2 0 1 4 , 1 .
程操 作。
四点 改善 方法 ,基本 上 可 以清 除 电镀 阻镀 问题 。
以上 为 笔 者 的过 往 的经 验 汇 总 及心 得 ,仅 供 业
界 同行参 考 。团
4 . 1 . 2 电镀 制 程
( 1 )提 高 除 油 缸 及 微 蚀 缸 浓 度 及 温 度 至 中 上 限 ,加强 前处理 效果 ; ( 2 )每 6 h 检 查 前 处理 缸 ,铜 缸 震动 器 震 幅务 必