低碳低硅生产
济钢低碳低硅钢增硅原因分析及对策

Si 含量超标炉次改判为普通热轧商品卷原料, 改判后
经济损失约达 50 美元/吨钢, 如果 Si 含量超过 0.05%
则直接判废, 影响了济钢冷轧厂正常生产, 降低了集
团公司的经济效益。
3 理论分析
3.1 增硅的热力学条件
工 艺 路 线 : KR 铁 水 预 处 理 →BOF 转 炉 →LF 精
炼→连铸机。一般情况下精炼过程温度处在 1 580 ℃ ̄
后 降 为 1.93% , SiO2 含 量 也 从 精 炼 前 的 8.0% 下 降 到 期的实际生产数据也证实了这一点。精炼时间与增硅
7.3%。这表明精炼后炉渣已经从转炉终点时的强氧化 量的对应关系如图 3 所示, 随着精炼时间的延长, 增硅
性转变为精炼后的较强还原性, 由此也 可 判 断 出 LF 量也逐渐变大。因精炼时间过长导致硅含量超标炉次
1 600 ℃之间, 由氧势图可知在此温度区间 FeO、P2O5、 MnO、SiO2、Al2O3 化合物稳定性依次增强。因此, 在还原 性气氛下 FeO、P2O5、MnO、SiO2 等不稳态化合物很容易 被 Al 置换出来。由于其它元素对本钢种成分合格率无
明显影响, 故本文只讨论 SiO2 的反应问题。其化学反 应式为:
成 为 SiO2 的 主 要 来 源 。 出 钢 时 及 LF 精 炼 初 期 加 入 CaO、CaF2 及 MgO 等造渣料一定程度稀释了 SiO2 的浓
因 LF 精 炼 脱 硫 任 务 过 重 ( 精 炼 进 站 硫 含 量 大 于 0.025%) 占超标总炉数的 81.1% 。
度。随着精炼过程的继续进行, 渣 中 FeO、P2O5、MnO、 SiO2 含 量 呈 下 降 趋 势 , Al2O3 呈 上 升 趋 势 。 精 炼 末 期
高硅铝固废基胶凝材料低碳制备关键技术及产业化

高硅铝固废基胶凝材料低碳制备关键技术及产业化随着社会的发展和工业化进程的加速,固废排放量不断增加,给生态环境带来了严重的压力。
高硅铝固废作为一种重要的工业固废资源,其合理利用和无害化处理已成为当前环保领域的热点问题。
为了充分利用高硅铝固废资源,降低CO2排放,实现低碳生产,开展高硅铝固废基胶凝材料的低碳制备关键技术及产业化研究具有重要的意义。
一、高硅铝固废基胶凝材料的研究意义高硅铝固废指的是含有较高硅、铝氧化物的固体废物,通常来源于铝冶炼、硅冶炼、陶瓷制造等过程。
高硅铝固废不仅含有大量的SiO2和Al2O3等有机物质,还具有较好的矿物质结构和活性,适合用于胶凝材料的生产。
通过对高硅铝固废基胶凝材料的研究,可以实现对固废资源的合理利用,降低对天然资源的开采,减少固体废物的堆放和排放,符合循环经济和可持续发展的要求。
二、高硅铝固废基胶凝材料的低碳制备关键技术1. 材料的配方设计高硅铝固废基胶凝材料的配方设计是实现低碳制备的关键环节。
通过合理选择高硅铝固废原料和外加剂,确定适合的配比和工艺参数,可以实现胶凝材料在制备过程中的低碳化。
2. 碱活化技术碱活化技术是高硅铝固废基胶凝材料低碳制备的重要方法,通过高碱度激发高硅铝固废的活性,提高材料的强度和耐久性,达到低碳环保的目的。
3. 绿色烧结技术传统的胶凝材料烧结过程会消耗大量的能源,造成二氧化碳的排放。
绿色烧结技术采用高温固化和微波烧结等技术,降低烧结温度,减少能耗,实现胶凝材料的低碳制备。
4. 降碳减排技术在高硅铝固废基胶凝材料的制备过程中,可以通过优化工艺流程、减少废气和废水排放等措施,实现降碳减排,减少对环境的影响。
三、高硅铝固废基胶凝材料低碳制备的产业化进展在高硅铝固废基胶凝材料低碳制备的产业化进程中,必须克服以下几个关键问题:1. 技术标准与规范需要制定相关的技术标准与规范,明确高硅铝固废基胶凝材料的生产要求和质量控制标准,促进产业化进程的有序进行。
方坯低碳低硅钢水口结瘤

控制在适当的程度(既防止气孔产生,又利于钢
水可浇性的控制)。使整个脱氧过程使用的总铝 量控制在1kg/t钢以内,减少在脱氧过程中Al2O3夹 杂物的生成量。
• 5.3 合理控制到站温度和节奏,确保出站软吹氩 时间≥5min。
• 5.4中包烘烤时间≥120分钟;中包上水口使用锆质 水口。
• 5.5 优化连铸保护浇注,采用密封环,中包执行 先上大包保护浇注管后再开浇的浇注工艺,大包 后期的敞浇时间控制在3min以内。
(3)中包钢样中夹杂物分析
• 金相检验结果:
• 在200倍目镜下对各炉次各样品进行观 察100个视场,每个视场直径为在1mm。金 相检验表明,钢中夹杂物多数是小于50μm 的 Al2O3 、 SiO2 、 硫 化 物 夹 杂 , 尤 以 5 ~ 10μm居多。该类夹杂很难在中间包中上浮、 排除,浇注过程中极易附着在水口壁,成为 水口的结瘤物,影响浇注顺行。
从图2可见:转炉终点氧含量高,平均为1024ppm, 且波动大( 331.2 ~1970ppm )。
(2)吹氩站进站氧、出站氧与终脱氧喂铝量见: 表2和图3
• 表2 进站氧、出站氧与终脱氧喂铝量情况
项目
炉数 最大 最小 平均
进站α o,ppm 出站α o,ppm
31 77.1 10.1 43.72
采取冲棒操作时,还会导致结晶器液面翻卷,增加结 晶器卷渣和漏钢的几率。 2.3 水口结瘤实物
对水口堵塞严重的中包浇次结束,取水口实物样
观察发现中包水口存在严重的结瘤物,且水口结瘤物 断面层次清晰,见图1。
图1 水口内部结瘤物结构图
• 3、水口结瘤的相关调查
• 3.1 调查方法
• 由于12LW除碳低、硅低外,锰也较低, 钢水中[O]含量相对较高,通常使用Al作脱 氧剂。为此,在调查水口结瘤原因时,采取 如下方法:
低硅低温铁水去磷冶炼生产实践

出江, l } 舍
3 5
低 硅 低 温 铁 水 去 磷 冶 炼 生产 实 践
任海 军 吴辉 强2 李 军辉
( 1 . 杭 州钢 铁 集 团公 司转 炉炼钢 厂 ; 2 . 杭 州钢铁 集 团公 司技 术 中心 摘 3 1 0 0 2 2 )
浇 注
依据 脱磷 的热 力学 条件 ¨ j , 去磷 的基本 条 件是 高( F e O) 、 高( C a O ) 和较低 的温度 。从 冶炼 时期 的特 性 上看 , 吹炼 前期 [ s i ] 、 [ M n ] 大 量氧 化 , 炉 渣 中氧 化 铁高、 碱度高、 温 度 相对 较 低 均 可 以 满 足脱 磷 的条
化 渣 的同 时减缓 C—O反应 速度 , 提 高 渣 中氧化 铁 含量 , 保持 炉渣 具有 良好 的流 动性 。
表 1 杭钢 转 炉入 炉铁 水成 分要 求 %
注: ① 冶 炼优 碳 钢 时 , 要 求 入 炉铁 水含 硫 量 不超 过 0 . 0 3 5 %。
2 . 1 铁水 硅 含量低 对脱 磷 的影 响
关键 词 : 转炉; 低硅 低 温铁 水 ; 脱磷
2 ) 入 炉铁 水温 度不 小 于 1 2 5 0  ̄。 3 ) 入 炉铁 水带 渣量 小于 0 . 冶 炼 是 一 个 复 杂 多 变 的 过 程 , 受 铁 水 条
件、 废 钢结 构 、 造渣材 料 质量 等 多种 因素 的影 响 , 冶
一 一
② 当铁 水成分 、 温度 达不到要 求 时 , 在 不影 响品种质 量 的情况下 , 由公司总调协调处理。
,
铁水 中 的 硅 , 是 转 炉 炼 钢 的 主 要 发 热 元 素 之 般铁 水含 硅量 以 0 . 5 %~ 0 . 8 %为 宜 。
硅钢生产(简易版)

硅钢基础知识硅钢带的生产1903年美国和德国首先生产了热轧硅钢。
美国阿姆柯钢公司于1935年开始生产冷轧取向硅钢,20世纪40年代初生产无取向硅钢。
50年代主要工业发达国家陆续引进阿姆柯技术专利。
70年代前,世界约80%取向硅钢都按此专利生产。
1968年日本新日铁正式生产高磁感取向硅钢(Hi-B钢)。
从1971年开始,美国等6个国家引进了日本H i—B钢专利。
从1968年开始,日本在冷轧电工钢产品质量、制造技术和装备、开发新产品和新技术、科研和测试技术各方面都远超过美国,处于领先地位。
我国太原钢铁(集团)公司于1954年首先生产热轧硅钢。
1957年钢铁研究总院研制成功冷轧取向硅钢,到197 3年已掌握阿姆柯技术专利要点。
1974年武汉钢铁(集团)公司从日本新日铁引进冷轧硅钢制造装备和专利,1979年正式生产11个牌号的冷轧取向及无取向硅钢。
4.1 电工钢的分类及性能4.1.1 电工钢的分类电工钢按其成分分为低碳低硅(碳含量很低,硅的质量分数小于0.5%)电工钢和硅钢两类;按最终加工成形的方法分为热轧硅钢和冷轧硅钢两大类;按其磁各向异性分为取向电工钢和无取向电工钢。
热轧硅钢板均系无取向硅钢,硅钢的磁各向异性是在冷轧后通过二次再结晶过程发展而成的,因此只有冷轧电工钢才有取向与无取向之分。
由于产品的用途不同对磁各向异性的要求不同。
在旋转状态下工作的电机要求电工钢磁各向同性,用无取向电工钢制造;变压器在静止状态下工作,要求沿一个方向磁化(轧制方向),用冷轧取向硅钢制造,因此取向硅钢又称变压器钢。
我国电工用热轧硅钢薄板的国家标准号为GB5212—85;从20世纪60年{BANNED}始,主要工业发达国家陆续停止了热轧硅钢板的生产。
我国冷轧晶粒取向、无取向磁性钢带(片)的国家标准号为GB2521—1996。
(现新标准GB2521—2008)标准中的牌号表示方法为:以字母W表示无取向钢带(片);以字母Q表示取向钢带(片);以字母G表示取向钢中的高磁感材料。
SPHC钢的冶炼实践

用 挡渣锥 挡渣 , 少 下 渣 , 减 减少 转 炉 渣 向 钢水 传 氧 ,
并避 免精 炼 回硅 或 回磷 。出钢过 程 中加适量 小 颗粒 石灰 、 石造渣 , 证熔化 并有 良好 的流动性 。 萤 保 出钢 过程 中随 钢水 流加入 中碳锰 铁 和铝锭 预脱 氧, 先加 中碳锰 铁 , 再加铝 锭 , 出钢 2 3时 加完 , 据 / 根 残 锰配加 中碳 锰铁 。 喂铝线前 适 当控制氩 气 流量 保 证 化渣 并有 良好 的流动 性 。喂线后 吹氩 采用 弱搅 拌
qu lt f c t le e c d t e sa dad a d m e t h e ie e t or c so e s a i o asi biltr a he h tn r n y ng est e r qur m n sf m u t m r . K e o d lw — c r n lw — sl on aum ium le te ;ca tn r p ry;c m p ii n c nto ;p a tc y W r s:o abo o ii c l n kild se l si g p o e t o osto o r l r ci e
少 回硅 。精 炼炉 渣主要 成 分见 表 3 与 普通 钢 种 比 , , 渣 中 SO i 降低 了而 A : 增 加 了 , 渣没 有 完全 脱 1 O, 炉
氧 , 化性 相对 较强 。 氧
表 3 L F精 炼 渣 样 成 分
Ta 3 Co p st n o lg s m p e i e i i g b. m o i o f sa a l n LF r f n i n
性 问题 。由于 钢 中碳 含量 要求 低 , 钢水 氧化 性 强 , 钢 中铝 含量 要 求 高 , 易 出 现 钢 水 流 动 性 差 , 响 浇 容 影
济钢低碳低硅钢冶炼工艺的开发与应用

第2卷 第6 8 期
20 0 6年 1 2月
山 东 冶 金
S a d n Meal r y hn o g tl g u
V0 . 8. . 1 2 No6 De e e o 6 c mb r 2 o
・
生产 技 术 ・
济钢低碳低 硅钢冶炼 工艺 的开发与应用
1 1
冶金学 院炼钢专业 。现为济钢第三炼钢厂高级工程师 , 从事炼钢 工 艺 研究 和品种钢 的开发 工作 。
维普资讯
20 年 1 月 06 2
山
东
冶
金
第 2 卷 8
不同, 保证一次加 足 , 喂线速度 2O / i 0rr n ea 。喂线毕 3 n 即测温 取样 吊包 。 mi立 3 . 精炼控制 吹氩控制:第一批造渣材料熔化 .3 2 前可适当控制氩气流量保证化渣 良好 ,化渣后采用 弱搅拌( 不裸露钢水为原则) 。加造渣材料前用铁锨
钢水可浇性。由于钢中 C控制低 , 钢水氧化性强 , 钢 中铝含量要求高 , 非常容易出现钢水粘度大 , 导致连
3 生产 实践
31 成分 控制 ‘ .
铸机停机的现象 。 二是钢中 S 的控制。由于钢中 S i i 要求低 , A 要求不小于 0 2 %, 而 l . 0 精炼还原容易发 0
生回 S 现象 。随着冶炼技术的进步 , i 尤其是钢水氧
为 了保证钢材有 良好的冲压性能 ,低碳低硅钢 的冶炼成分要求严格 , S C 以 P C为例 , 其化学成分见
表1 。济钢确定的内控成分范围较窄 , 且化学成分稳
化性及 s、、 、l i c A 成分控制等关键技术的成熟 , s 产 品质量不断提高 , 为济钢开拓市场 , 实现做强做精 的
高品质硅铁的生产方法

高品质硅铁的生产方法目前国内高品质硅铁的生产方法,主要有5种,一是采用精选炉料生产高纯硅铁,二是采用炉外吹氯精炼的方法生产高纯及低碳硅铁,三是采用炉外顶吹氧气的方法生产高纯及低铝硅铁,四是采用热冲渣洗的方法生产高纯及低碳硅铁,五是采用精选炉料的方法生产低铝、低碳硅铁。
采用精选炉料的方法生产高纯硅铁主要是通过精选石英石和石油焦、木块、木炭以及硅钢片原材料进行冶炼生产、以达到降低产品中杂质元素含量的目的。
该方法由于存在着原材料质量波动较大,冶炼生产过程中难免带入一部分杂质,从而产品中杂质含量的降低率受到限制,产品质量不高,成品率较低,而且生产炉况较难维护、炉口操作难度较大,产品的生产成本和能耗较大,经济指标较差。
炉方法脱除钙、铝效果较好,但尾气较多、且生产中常常产生泄漏和吹氯石墨管折断而中止精炼等情况,从而严重地污染了环境,危害工人的身体健康,而且对生产设备腐蚀较大。
炉外顶吹氧的方法进行炉外精炼,对产品中杂质钙、铝、碳元素脱除也较好。
但在使用过程中,由于铁水翻腾剧烈、喷溅损失较大,铁水温度迅速下降,造成粘包、铁损失较大,资料统计损失在12%-20%。
吹氧用石墨管也经常发生折断事故而中止精炼、成品率低,经济上也很不合算。
精选炉料的方法生产低铝、低碳硅铁主要是通过精选还原剂,如兰碳、气煤焦等原材料进行冶炼生产,以达到降低产品中杂质元素,主要是铝含量的目的。
该方法由于存在着原材料成份波动较大,冶炼过程中难免带入一部分杂质,从而产品中的杂质含量的降低率有限,铝含量一般可降至1.6%,最多只能降至1.2%, 碳含量0.2%,只能生产部分品牌的产品。
本发明的目的是要克服上述几种方法的不足,提供一种高品质硅铁的生产方法,该方法实用于系列高品质硅铁的生产。
本发明的高品质硅铁的生产方法包括如下步骤:(1)筛选原料硅石、还原剂、钢悄或/硅钢屑,硅石为石英石或白硅石、黑硅石、还原剂为冶金焦和气煤焦,或者兰炭和气煤焦,兰炭和石油焦及木块、根据各种原料的准确成份含量和所要生产的品种对所有元素成份要求,按公知技术进行计算各原料量、配料混合后填入矿热炉内按通常冶炼硅铁合金的条件和操作进行冶炼。
低碳低硅钢流动性控制
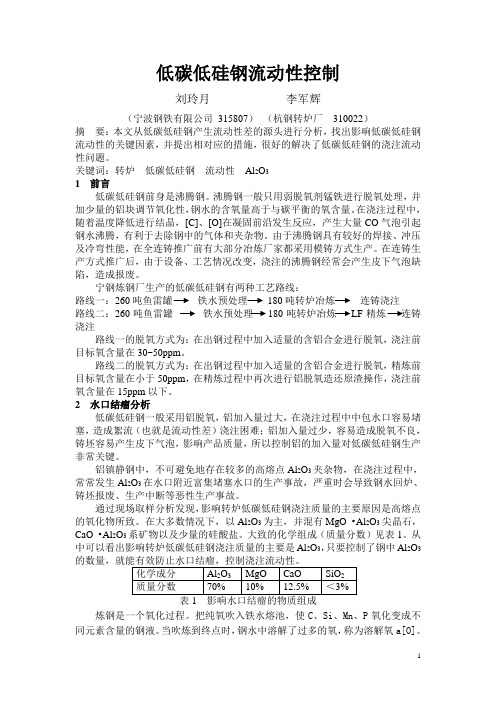
低碳低硅钢流动性控制刘玲月李军辉(宁波钢铁有限公司315807)(杭钢转炉厂310022)摘要:本文从低碳低硅钢产生流动性差的源头进行分析,找出影响低碳低硅钢流动性的关键因素,并提出相对应的措施,很好的解决了低碳低硅钢的浇注流动性问题。
关键词:转炉低碳低硅钢流动性Al2O31 前言低碳低硅钢前身是沸腾钢。
沸腾钢一般只用弱脱氧剂锰铁进行脱氧处理,并加少量的铝块调节氧化性,钢水的含氧量高于与碳平衡的氧含量。
在浇注过程中,随着温度降低进行结晶,[C]、[O]在凝固前沿发生反应,产生大量CO气泡引起钢水沸腾,有利于去除钢中的气体和夹杂物。
由于沸腾钢具有较好的焊接、冲压及冷弯性能,在全连铸推广前有大部分冶炼厂家都采用模铸方式生产。
在连铸生产方式推广后,由于设备、工艺情况改变,浇注的沸腾钢经常会产生皮下气泡缺陷,造成报废。
宁钢炼钢厂生产的低碳低硅钢有两种工艺路线:路线一:260吨鱼雷罐铁水预处理180吨转炉冶炼连铸浇注路线二:260吨鱼雷罐铁水预处理180吨转炉冶炼LF精炼连铸浇注路线一的脱氧方式为:在出钢过程中加入适量的含铝合金进行脱氧,浇注前目标氧含量在30~50ppm。
路线二的脱氧方式为:在出钢过程中加入适量的含铝合金进行脱氧,精炼前目标氧含量在小于50ppm,在精炼过程中再次进行铝脱氧造还原渣操作,浇注前氧含量在15ppm以下。
2 水口结瘤分析低碳低硅钢一般采用铝脱氧,铝加入量过大,在浇注过程中中包水口容易堵塞,造成絮流(也就是流动性差)浇注困难;铝加入量过少,容易造成脱氧不良,铸坯容易产生皮下气泡,影响产品质量,所以控制铝的加入量对低碳低硅钢生产非常关键。
铝镇静钢中,不可避免地存在较多的高熔点Al2O3夹杂物,在浇注过程中,常常发生Al2O3在水口附近富集堵塞水口的生产事故,严重时会导致钢水回炉、铸坯报废、生产中断等恶性生产事故。
通过现场取样分析发现,影响转炉低碳低硅钢浇注质量的主要原因是高熔点的氧化物所致。
硅钢发展现状及生产工艺

硅钢片平 均单耗t/ 万kW
-
硅钢片 消耗量 t/a
-
1500 1200 300 700 150
75
-
7 15 16.5 15
-
26010 6750 9900 2250 31500
2)小型
水电制造量 核能发电
-
20 5 100
小计
2150
2.7 我国变压器用取向硅钢发展很快。特 别是近几年来的农网,城网改造对取向硅钢 的需求不断增加,在取向硅钢的厚度上已全 部淘汰了0.35㎜的使用。目前已大量生产 S9、S10等系列节能变压器和干湿变压器。 HiB的需求量在不断增加,该行业朝着体积 小、薄规格、噪音小、使用期长的方向发展。 表4为国内大、中型变压器企业生产及硅钢 需求(不含小型变压器厂及三资企业)。
2005年产 量/万台
硅钢片 需量/万 t
备注
以热轧矽钢片为主
以热轧、冷板为主 以热轧矽钢片为主 热轧+冷轧 热轧+冷轧 热轧+冷轧 冷轧硅钢片 冷轧硅钢片 冷轧硅钢片
4000
8000
45.000
39.000
3
1.5
6.0 3.5 2.5 11.0 5.0 5.0 4.0
9000.00
1443.00 1010.00 366.15 1827.00 1278.00
2.1 我国中、小型电机容量一般界定在0.75~ 100kW之间,电压≤380V,形成Y系列产品。 目前国内主要生产企业约300多家,生产电机 ,国内中、 小型电机生产能力达6000万kW,主要用热轧 矽钢片DR510~50制作铁芯。从电机台数、耗 电量上看占电机总量的70%。因此,如何提高 中、小型电机对高效节能有着十分重要的意义, 也是推行电工钢“以冷代热”的重点。
低碳低硅钢SPHC精炼工艺实践

图 1 同脱 氧工艺 R 不 H精炼结束后 T. O含量
3- . 2降低 R 1 H铝氧加热率 R H真空精炼过程 , 若钢包蓄热不饱和 , 真空槽 烘烤温度得不到保证 、 转炉出钢时间提前而延长 R H
・
3 ・ O
《 碳低 硅钢 S H 低 P C精 炼工 艺实践 》
工 序 时 间 、钢水 循 环 流量 控 制 不 当 等 因素 ,钢水 精
种属于低碳低硅铝镇静钢 ,该钢种成分设计见表 1 。
表1 S H P C化学成分设计 ( ) %
・
2 ・ 9
《 低碳低硅钢 S H P C精炼工艺实践 》
从 表 1 以看 出S HC 可 P 钢种 的主要 特 点 :
B F L + C O + H C 生产 工艺 , 工艺 效果 见 O + F C 、B F R + C 其 表2 。不 同生 产工 艺实 绩表 明 ,C S A 精炼 结束 后钢 中 TO 量较 高 ,连铸 浇注过 程 中A , 塞 中包 水 口 , .含 1 堵 O 连 续浇 注仅 4 7炉而 被迫 中断 生产 ,打破 “ ~ 一罐 制 ” 钢 铁界 面 平衡 。L 精 炼 过程 中 ,钢 水增 硅 、碳 得 不 F 到有 效控 制 ,硅或碳 成分 出格 综合 炼成 率仅 7.%, 5 6 因钢种 改 炼 而 中断铸 坯 热 送 ,严 重 时轧 钢 断坯 料 , 依 然打破 “ 一罐 制 ”钢 铁界 面平 衡 。R H精炼 结束 后 , 钢 中TO 定控 制在 3 .稳 5×1 0 以下 ,彻底 解决 了中包
专. 敞 黾
CI E SC T CHN L O OG Y
低 碳低 硅钢 S H P C精 炼工艺实践
何 宏侠 高祝 兵 陈露 涛
鞍钢RH轻处理钢种生产工艺实践

( eea Sel a igPat f n a gSel o Ld, n hn 14 2 , io i , hn G n rl t m kn l gn t . t.A sa 0 1 Lann C ia) e n oA eC , 1 g
Absr c t a t:Th s pa r n r d c s h p o e s p a tc o p o u i g a u n i pe i to u e t e r c s r ci e f r r d c n l mi um il d t e k le se l wih l w c r o a d ii o b h i e r t d r c s c nssi g o e r ame t f h t t o a b n n slc n y t e ntg a e p o e s o itn f pr te t n o o mea , tl c mbi e o n o v re t e ma i g n r fn n i RH.Op r t p a tc s o t a t e o n d blwi g c n e tr se l k n a d e i g‘n i eai ng r ci e h ws h t h
周 期 , 高 了钢 水的 洁净度 , 提 有效缓 解 了 R L H— F双联 工 艺对 吊车 和 L F精 炼 的压 力 , 证 了生 保
产 组 织 的 平 稳 顺 行 ‘
关键 词 : 铝镇静 钢 ; 低碳低 硅钢 ; H精 炼 ; 处理 R 轻 中图分 类号 : F 0 T T3 文 献标识 码 : A 文章 编号 : 0 6 4 1 (0 2 0 — 0 6 0 1 0 — 6 3 2 1 )4 0 4 — 3
Op r t n P a t ef r Tr a i g S e l y RH g tT e t e ti g n e a i r c i o e t tesb o c n Lih r a m n An a g n
冷轧基板SPHC钢转炉直上规模化生产

2020年第2期典型冷轧基板钢种SPHC 钢属低碳、低硅、低硫铝镇静钢,具有较强的延展性及冷加工性能,用途广需求量大。
钢种特性要求决定了其基本的冶炼任务为深脱氧、深脱硫、控铝、控硅、夹杂物控制。
生产实践表明,该类钢种冶炼工艺的复杂性和难点还比较突出,传统工艺为了实现低硫目标往往采用铁水预处理工艺;为实现精确控铝、深脱氧、深脱硫、夹杂物及流动性控制往往必须采用精炼处理工艺,从而形成了铁水预处理→转炉冶炼→LF (RH )精炼→连铸的典型生产工艺流程。
传统工艺流程已经很成熟稳定了,不论在生产的稳定性和连续性、质量控制已经没有太多问题,但存在工艺流程复杂、工序多、生产成本高、效率低等问题。
在行业产能过剩、市场竞争激烈、成本控制压力大的背景下,很多冶金工作者热衷于研究精简化的生产工艺流程。
传统工艺流程中铁水预处理和精炼工序趋于省略。
SPHC 钢转炉直上浇铸的生产工艺,近年来在国内也初步取得了一定的成果,但存在的问题是生产不稳定,钢水流动性不好(絮流)、钢中Al 和S 成分控制不稳定、连浇炉数低等。
笔者在柳州钢铁集团公司柳钢转炉炼钢厂120t 转炉作业区,通过研究摸索优化工艺,解决了上述难题,实现了冷轧基板SPHC 钢转炉直上连续规模化批量生产的目的,生产过程控制稳定、钢的质量控制接近或等同于原走精炼工艺流程的水平。
因简化了生产工序,提升了生产效率,降低了生产成本。
炼钢工序工艺简介柳钢为华南地区特大型钢铁联合企业。
柳钢转炉炼钢厂为柳钢钢铁制造流程上极其重要的工序,近年来通过技术改造,已装备了目前国内主流先进的炼钢工艺装备,在产量、品种、质量上面已达到国内同类企业先进水平。
2019年钢产量达到1367万吨,品种涵盖了建筑、造船、桥梁、汽车、及其他工业用材。
采用SPHC 转炉直上工艺的主要生产现状如下:生产条件柳钢转炉炼钢厂第二作业区装备2套颗粒镁喷吹脱硫装置,3座120t 顶底复吹转炉,2台120t LF 精炼炉,1台120t RH 精炼,3台断面220mm ×(1000~1810)mm 板坯连铸机,2台断面165mm ×165mm7机7流方坯连铸机。
碳氧平衡在低碳低硅钢RH轻处理工艺中的应用

2U21 年 2 月炼钢Feb.2021第 37 卷第 1 期 Steelmaking Vol. 37 No. 1•39 •碳氧平衡在低碳低硅钢RH轻处理工艺中的应用朱坦华,颜慧成,汤海明•程迪,王现周(河北钢铁集团邯钢公司,河北邯郸()56()15)摘要:通过对低碳低硅钢炼钢过程碳氧平衡进行系统计算,结合RH轻处理工艺要求,详细分析了过程碳、氧含量的控制要点,结果表明:C0分压对碳氧积的影响比钢水温度更加显著;RH生产超低碳钢时要求极限真空度和较高的平衡氧含量;RH轻处理生产低碳低硅钢的适宜条件是进站初始碳质量分数().()3 %〜().()4 %、初始氧质量分数().()4 %〜().()5 %、真空度5 kPa,研究规律在生产中得到了应用与验证。
关键词:碳氧平衡;RH轻处理;低碳低硅钢中图分类号:T F769.4文献标志码:A文章编号:1()()2-1043(2()21)()1-()039-05Application of carbon-oxygen equilibrium in RH soft-treating process for lowcarbon and low silicon steelZHU Tanhua.YAN Huicheng,TANG Haiming,CHENG Di.WANG XianzhouHansteel Branch.HBIS Group. Handan 056015,ChinaAbstract:Carbon-oxygen equilibrium in steelmaking process was systemically calculated. Controlpoints of carbon and oxygen content were analyzed in detail based on the technological requirement ofRH soft treating process. The results showed that the effect of CO partial pressure on carbon-oxygenequilibrium was more significant than that of molten steel temperature. The ultrahigh vacuum andsuitable mass fraction of equilibrium oxygen were needed for RH process to produce ultra-low carbonsteel. It was suitable for production of low carbon and low silicon steel with RH soft treating atvacuum degree 5 kPa,initial carbon mass fraction 0.03 % -0.04% and initial oxygen mass fraction0.04 % - 0.05 %. The result was applied and verified in actual production of low carbon and lowsilicon steel.Key words:carbon-oxygen equilibrium:RH soft treating process;low carbon and low silicon steel碳氧平衡是炼钢反应的重要现象,碳氧积作 为基本参数,是炼钢终点控制的一个特征指标,碳 氧平衡在真空脱碳工艺中得到重要应用。
生产SWRM6优质低碳低硅钢盘条工艺实践
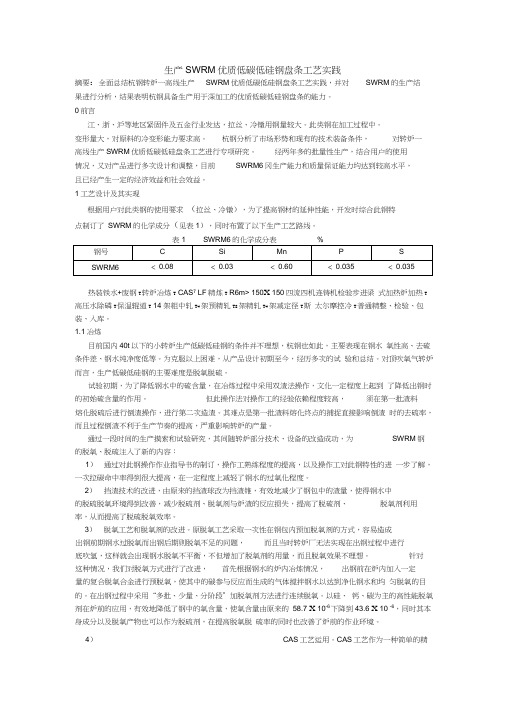
生产SWRM优质低碳低硅钢盘条工艺实践摘要:全面总结杭钢转炉一高线生产SWRM优质低碳低硅钢盘条工艺实践,并对SWRM的生产结果进行分析,结果表明杭钢具备生产用于深加工的优质低碳低硅钢盘条的能力。
0前言江、浙、沪等地区紧固件及五金行业发达,拉丝、冷镦用钢量较大。
此类钢在加工过程中。
变形量大,对原料的冷变形能力要求高。
杭钢分析了市场形势和现有的技术装备条件,对转炉一高线生产SWRM优质低碳低硅盘条工艺进行专项研究。
经两年多的批量性生产,结合用户的使用情况,又对产品进行多次设计和调整,目前SWRM6冈生产能力和质量保证能力均达到较高水平,且已经产生一定的经济效益和社会效益。
1工艺设计及其实现根据用户对此类钢的使用要求(拉丝、冷镦),为了提高钢材的延伸性能,开发时综合此钢特点制订了SWRM的化学成分(见表1),同时布置了以下生产工艺路线。
热装铁水+废钢T转炉冶炼T CAS7 LF精炼T R6m> 150X 150四流四机连铸机检验步进梁式加热炉加热T 高压水除磷T保温辊道T 14 架粗中轧T4架预精轧T8架精轧T4架减定径T斯太尔摩控冷T普通精整、检验、包装、入库。
1.1冶炼目前国内40t以下的小转炉生产低碳低硅钢的条件并不理想,杭钢也如此,主要表现在钢水氧性高、去硫条件差、钢水纯净度低等。
为克服以上困难,从产品设计初期至今,经历多次的试验和总结。
对顶吹氧气转炉而言,生产低碳低硅钢的主要难度是脱氧脱硫。
试验初期,为了降低钢水中的硫含量,在冶炼过程中采用双渣法操作,文化一定程度上起到了降低岀钢时的初始硫含量的作用。
但此操作法对操作工的经验依赖程度较高,须在第一批渣料熔化脱硫后进行倒渣操作,进行第二次造渣。
其难点是第一批渣料熔化终点的捕捉直接影响倒渣时的去硫率,而且过程倒渣不利于生产节奏的提高,严重影响转炉的产量。
通过一段时间的生产摸索和试验研究,其间随转炉部分技术、设备的改造成功,为SWRM钢的脱氧、脱硫注入了新的内容:1)通过对此钢操作作业指导书的制订,操作工熟练程度的提高,以及操作工对此钢特性的进一步了解,一次拉碳命中率得到很大提高,在一定程度上减轻了钢水的过氧化程度。
无取向硅钢片生产技术要点

无取向硅钢片生产技术要点一、无取向硅钢片生产技术要点首先要求钢水纯净,经真空处理后碳含量降至0.01~0.005%,氧<0.005%,保护浇铸成厚板坯,低温热送,加热到1100~1200℃,保温3~4h,使AlN粗化,若轧机能力强,最好是1050~1100℃加热,防止铸坯中较粗的AlN、MnS析出物再固溶,使热轧及退火后晶粒细化,组分增多,磁性变坏。
终轧温度要高些,以防止晶粒变粗,铁损降低。
对无取向的Si>1.7%的硅钢,由于变形抗力显著提高,导热性降低,并且连铸后柱状晶粗大,产品表面易产生瓦垅状缺陷,铸坯易产生内、外裂纹,故需慢热慢冷,加热温度也可略高一些,达1 200℃。
这更便于热轧而且使终轧温度提高,热轧板晶粒粗化,可改善磁性。
加热到1200℃,Mn S不会固溶,而AlN可能部分固溶,但由于钢中碳含量降低(如<0.01%,至0.004%),可使AlN固溶度明显减小,亦即使固溶温度提高。
则≤1200℃加热仍可使AlN粗化,P15降低。
通常开轧温度1180±20℃,终轧温度850±20℃。
应注意含Si<1.7%或Si<2.5%而C>0.01%的硅钢在约1 000℃时存在明显的α+γ两相区,热轧塑性显著降低,γ相与α相变形抗力之差易引起不均匀变形,使板形不好,易出现裂边,成材率下降。
故应尽量降低碳含量,使热轧精轧基本处于α相区或避开α+γ两相区,C≤0.003%的1.5%Si钢,热轧时由于γ相数量减少,也不裂边。
碳量低,以后退火也不需要脱碳。
二、无取向硅钢片和取向硅钢片的关系:1、二者都是冷轧硅钢片,但含硅量不同。
冷轧无取向硅钢片含硅量0.5%-3.0%,冷轧取向硅钢片含硅量在3.0%以上。
2、生产工艺及性能的不同:无取向硅钢片较取向硅钢片工艺要求相对较低。
无取向硅钢片是将钢坯或连铸坯热轧成厚度约2.3mm带卷。
制造低硅产品时,热轧带卷酸洗后一次冷轧到0.5mm厚。
- 1、下载文档前请自行甄别文档内容的完整性,平台不提供额外的编辑、内容补充、找答案等附加服务。
- 2、"仅部分预览"的文档,不可在线预览部分如存在完整性等问题,可反馈申请退款(可完整预览的文档不适用该条件!)。
- 3、如文档侵犯您的权益,请联系客服反馈,我们会尽快为您处理(人工客服工作时间:9:00-18:30)。
Science乙Technology,W uhan4 30081,China)
Abstract;T hep orductionp rocesso fl ow carbona ndl ow silicons teelQ 195-1i si ntro- duceda ndf actorsa ffectingc ompositionso fth es teela ndc ounterm easuresa nalyzeda nd itis p ointedo utt hatt hek eyt oc ontrolt hec ompositionso ft hes teelis t oc ontrolw (C)
硅钢的终点碳都较低,这时钢水残锰也很低,可以
忽略不计。但当在一次倒炉出钢或冶炼 HRB335
钢种的回炉钢时,终点的残锰量可能较高,这时在 确定锰铁合金加人量时应该考虑残锰的影响。
3.3.2 出钢量的影响
在加 人 同 样锰铁合金量的条件下,随着出钢 量的增加,钢中锰含量降低,因此稳定转炉装人量
是重要的。
由于 装 人 量不准、石灰用量过大等不正常操 作所造成的终点钢水含碳量过低,主要影响脱氧 铝块和 Si-AI-Ca-Ba的回收率和钢水的脱氧状 况,而吹炼过程中因枪位控制过高,尤其是终点前
20^30s 枪位控制过高造成炉内钢水温度和成分 不均匀导致终点钢水 zv(C)过高(>0.05 %),将
会影响碳的准确控制,甚至会因碳高而报废。 因此 , 应 通过采用合理的装人制度、正确控制
3.1.1 终点碳含量
吹炼 终 点 钢水含碳量对碳成分的准确控制影 响较大,Q195-1钢生产要求钢水终点 w(C)必须 小于0.05%。但钢中的w(C)G0.06 %后,随着 碳含量的降低,钢水的氧化性就迅速增强。因此, 在保证成品钢 w(C)镇0.08%的前提下,尽可能 地提高终点碳含量是十分必要的。
摘 要:介绍了Q195-1低碳低硅钢的生产工艺,分析了影响其成分的因素及控制措施,指出将终点钢水 w(C)准确控制在0.04 Y o- 0.05 %和保证成品中W(Si))0.05 %是其成分控制的关键。通过钢包喂 Si- AI-Ca-Ba线,可以增加钢中Ca和Ba含量、减少夹杂物含量以及改变夹杂物形态,改善钢的力学性能。 关键词:低碳低硅钢;成分控制;热带性能 中图分类号:TF761 文献标识码:B 文章编号:1002-1043(2005)01-0029-03
3.2.2 下渣情况的影响
生产 实 践 发现:未采用任何挡渣措施的炉次, 钢包内渣量约 80%为出钢过程下渣,其中一次下
万方数据
第 1期
陈 晋,等:Q195-1低碳低硅钢的生产实践
31
渣量约占5%,二次下渣量约为95%,因此防止
转炉出钢时的二次下渣是挡渣操作的重点。一次 下渣可以用挡渣帽防止,其效果稳定可靠,二次下
渣可以用挡渣球(塞)挡渣,挡渣成功率达90%以
上,效果显著。挡渣的炉次,包内渣层厚度波动在 30^-60m m,比未挡渣炉次减少 70-110m m,脱
氧合金 Si和 Mn的收得率分别提高约 10%和
5%,同时成品成分(尤其是 Si)更趋稳定。 因此 出 钢 时采用挡渣帽及挡渣球挡渣对于稳
定 Al块和 Si-AI-Ca-Ba的收得率,稳定成品中 Si 元素含量是极其重要的。
contentin s teela tt hee nd-pointw ithint hel imito f0 .04 % to0 .05 % andw (Si)) 。.05%int hefi nishp roducts.I tis p rovedt hatth ein clusionsin s teelca nb er educed,
3.2.3 喂线量的影响
钢包 喂 Si-AI-Ca-Ba时,因 Si-AI-Ca-Ba线中
w(SI)= 45.45 %,所以在补充脱氧的同时还有增 Si的作用。当钢中w(Sl)小于临界值0.05%时,
除了正常喂 Si-Al-Ca-Ba线 100m 以外,还必须
增加喂线量确保成品w(Si)>0.05 %的临界值,
钢锭翻皮缺陷,钢锭表面质量较好;沸腾钢碳、硅 含量较低,具有较好的焊接、冲压及冷弯性能;沸 腾钢的金属收得率高,脱氧剂和耐材消耗少,其成
本也低〔’」。由于沸腾钢具有这些优点,大多数国 家沸腾钢的产量曾经都 占钢产量的 40%一 50%,广泛用于板材、线材等大宗产品。
随着 全 连 铸生产厂(车间)的不断涌现,这些 企业就需要利用连铸设备来生产沸腾钢的替代 品— 低碳低硅钢,以继续占领市场。鄂城钢铁 股份有限公 司 (以下简称鄂钢)转炉炼钢厂于
2000^-2001年在其30t 转炉上进行了 NQ195低 碳低硅钢热带的试制工作,所试制热带的伸长率
大部分达到了8)36%的预期性能Cz1。但就强度
而言,试制钢仍比沸腾钢高,且铸坯皮下气泡时有 发生,废品量过大。为此,鄂钢转炉炼钢厂在此基 础上,通过进一步控制化学成分、调整脱氧制度、 规范转炉和连铸操作等手段,生产出一种性能指 标全部达到沸腾钢标准的 Q195-1低碳低硅钢。
X1 0-6,从而使硅成分的稳定控制相当困难,因此
Si-AI-Ca-Ba的加人时机相当重要,应在出钢中期
加人,不应加人过早或过晚。 当终 点 钢 水含碳量较高或一次倒炉出钢时,钢
水中氧含量相对较低,此时所加入的硅铝钙钡合金 的回收率大幅度提高且稳定,Q195-1低碳低硅钢
成品中常出现碳高硅高的现象,其原因正是如此。
毛0.08 0.20^-0.40 毛0.10 毛0.035 (().035 (0.025 235^ 300
330-v345
> 36
表 2 Q195-1低碳低硅钢生产主要工艺参数
出钢温度/℃ 氢后温度/0C 开浇温度/℃
16 40- 16 60 16 00- 16 20 1 590^-16 10
Keyw ords:lo wc arbona ndlo ws ilicons teel;co mpositionc ontrol;h otrc >llcds tripp roperty
沸腾 钢 一 般只用弱脱氧剂锰铁脱氧,并加少 量的铝块调节氧化性,钢水的含氧量高于与碳平
衡的氧含量。在浇铸过程中,随着温度降低和进 行结晶,[C]和[()」在凝固前沿发生液析和浓聚, 并进行反应,大量 CO气泡引起模内钢水沸腾。 钢水在模内沸腾,有利于去除气体和夹杂物,减少
毛0.10%,控制范围较窄。理论上认为,对于一 定 Si,M n,O 含量的钢来讲,具有临界的 C-Si含 量。在临界含量以上,凝固时不形成 CO,在临界 C-Si含量以下,形成 co,即有气孔形成。鄂钢转 炉炼钢厂生产实践发现,当zv(Si)<0.05%时铸 坯易产生皮下气泡,即凡发现产生皮下气泡的铸 坯其对应的成品中w(Si)一般都小于0.05%。
碳低硅钢时采用低碳锰铁是非常必要的。
3.1. 3 出钢量的影响
在锰 铁 加 人量相同的条件下 ,出钢量增大 ,由 锰铁合金所产生的增碳量减少。所以稳定转炉装 人量,规范转炉的操作稳定出钢量不仅对碳成分 控制极其重要,而且对其他成分的控制也是重要
的。
3.2 硅成分的控制
这种 钢 的 另一个特点是 Si含量低,即 w(Si)
3.3.3 合金含锰量的影响
在 出钢 量 、合金用量、合金收得率等相同的条
件下 ,合金含锰量越高 ,成品中锰含量越高 。
3.3.4 锰铁收得率的影响
在出 钢 量 、合金用量、锰铁含锰量等相同的条 件下,合金收得率越高,成品中锰含量越高。但在 一般条件下,锰铁的收得率比较稳定,波动不大, 通常为 880 0-93%。
年 卷 第 2月
1期
炼 钢 Steelmaking
Fe b.2 005
Vol.2 1 No.1 ·29 ·
Q195-1低碳低硅钢的生产实践
陈 晋‘,黄道昌‘,倪红卫2
(1.鄂城钢铁股份公司 转炉炼钢厂,湖北 鄂城 436000;2 .武汉科技大学 材料与冶金学院,湖北 武汉 430081)
以防止铸坯产生皮下气泡。
3.3 锰成分的控制
由于 锰 铁 的收得率比较稳定,所以锰成分的 控制相对较简单些,主要受钢水残锰量、出钢量、 合金含锰量及锰铁收得率等因素的影响。
3.3.1 钢水残锰量的影响
鄂 钢 转 炉炼钢厂所 用铁水 w (Mn)= 0.20%一0.40%,在一般条件下,Q195-1低碳低
thein clusions hapeim proveda ndt hem echanicalp ropertieso fst eelin creasedb yf eeding
Si-AI-Ca-Bac ladw irei ntot hel iquids teelto i ncreaset heC aa ndB ac ontentin s teel.
万方数据
炼钢
第 21卷
表 1 Q195-1低碳低硅钢化学成分和热带性能要求
ze,B / % 力 学 性 能
C M n Si P S C u a ,/M Pa ah /M Pa a /% o
枪位、在终点前20-30s 枪位适当降低 50.100
mm、精心操作保证终点碳一温协调等措施来控
制终点碳含量,确保 w( C)控制在0.04%一 0.05%。
3.1.2 合金含碳量的影响
鄂钢 转 炉 炼 钢厂 使 用 的锰 铁 w( C)= 5.02% -^-6.60%,用量一般在 150一170k g/炉,当 采用二(C)= 5 .02%的锰铁时,可以在终点 w(C) =0 .05 % -0.06 %时 出钢,而 采 用 w(C)= 6.60%的锰铁时,必须在终点w(000.05 %时出 钢,否则将会造成碳成分超标。故冶炼 Q195-1低