FANUC机械臂原点设置
FANUC 机器人 ROBOT原点对位简易方法

FANUC ROBOT原点对位简易方法FANUC ROBOT 原点对位简易方法1、引言本文档旨在介绍 FANUC 的原点对位简易方法。
通过按照本文档,用户能够快速准确地进行的原点对位调整,确保运行的准确性和稳定性。
2、准备工作在进行 FANUC 的原点对位调整之前,请准备以下工具和设备:- FANUC 控制器- 原点对位专用工具- 操作手册- 坐标系设定程序3、原点对位调整步骤3.1 确定对位参考点- 根据实际需要,确定一个参考点作为原点的位置。
通常会选择一个稳定、易于测量的位置作为参考点。
- 在对位参考点上使用专用工具进行标记,以便后续调整时能够准确测量。
3.2 设置坐标系- 在控制器上运行坐标系设定程序。
- 按照程序提示,在对位参考点附近的位置上设置的坐标系。
3.3 进行原点对位调整- 在控制器上运行原点对位调整程序。
- 按照程序提示,使用专用工具将的示教点与对位参考点对准。
- 通过调整关节角度或位置实现对位调整,直至示教点与对位参考点完全对准。
3.4 验证调整结果- 运行测试程序,检查运动的准确性和稳定性。
- 如有需要,可进行微调以达到更高的精度要求。
4、附件本文档附带的附件包括:- 操作手册- 原点对位调整程序- 坐标系设定程序5、法律名词及注释- FANUC :由 FANUC 公司制造的工业,用于各种自动化工作任务。
- 原点对位:调整示教点与对位参考点完全对准的过程。
- 坐标系设定程序:用于设置坐标系的程序,确定工作空间的坐标系统。
fanuc原点的设定方法

fanuc原点的设定方法Fanuc原点的设定方法Fanuc原点的设定是CNC加工中非常重要的一步,它确定了工件坐标系与机床坐标系的关系,对于后续的加工操作具有决定性的影响。
下面将详细介绍Fanuc原点的设定方法。
一、Fanuc原点的概念Fanuc原点是指机床坐标系中的零点位置,也可以称之为零点坐标。
在Fanuc系统中,通常有三个原点,分别是X轴原点、Y轴原点和Z轴原点。
根据机床的不同类型和控制系统的不同,Fanuc原点的设定方法也有所区别。
二、Fanuc原点设定的准备工作在设定Fanuc原点之前,需要进行一些准备工作,以确保设定的准确性和安全性。
1. 确定机床的固定位置:机床在设定Fanuc原点时需要保持稳定的位置,确保不会发生移动或晃动。
2. 检查机床的零件状态:检查机床的各个零件是否完好,如导轨、螺杆等,确保没有松动或损坏的情况。
3. 清理机床工作台面:清理机床的工作台面,确保上面没有杂物或残留物。
三、Fanuc原点的设定方法1. 打开Fanuc控制面板:按下机床上的电源开关,打开Fanuc控制面板。
2. 进入原点设定界面:在控制面板上选择“参数设置”菜单,进入参数设置界面。
3. 选择轴向参数设定:在参数设置界面中选择“轴向参数设定”选项,进入轴向参数设定界面。
4. 选择原点设定功能:在轴向参数设定界面中选择“原点设定”功能,进入原点设定界面。
5. 选择需要设定的轴向:在原点设定界面中选择需要设定的轴向,如X轴、Y轴或Z轴。
6. 移动轴向到设定位置:根据实际需求,通过手动操作或使用机床的快速移动功能,将选定的轴向移动到设定位置。
7. 确定设定位置:当轴向移动到设定位置后,按下“确定”按钮,确认设定位置。
8. 完成设定:完成一个轴向的设定后,可以选择设定其他轴向的原点,或者退出设定界面。
四、Fanuc原点设定的注意事项在进行Fanuc原点设定时,需要注意以下几点,以确保设定的准确性和安全性。
1. 设定前确认坐标轴位置:在设定Fanuc原点之前,应该先确认坐标轴的起始位置,确保设定的位置不会超出机床的工作范围。
发那科、法兰克机器人单轴原点设置
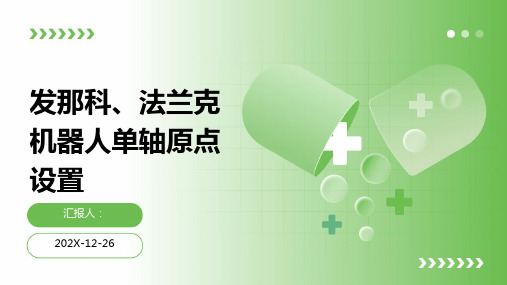
确认设置
在确认轴已经到达设定位置后 ,通过操作面板或示教器完成
原点设置。
注意事项和常见问题
安全注意事项
在设置原点过程中,要确保机 器人处于安全位置,避免发生
意外碰撞或损坏。
坐标系确认
在设置原点之前,要确保机器 人坐标系设置正确,以免影响 后续的编程和操作。
精度要求
在设置原点时,要保证对应轴 的移动精度,以免影响机器人 的运动轨迹和定位精度。
保存设置
完成参数修改后,保存设置并重新 启动机器人。
注意事项和常见问题
确保机器人处于安全状态
01
在设置原点前,应确保机器人处于安全位置,避免意外碰撞或
损伤。
参数设置错误
02
如果参数设置不正确,可能导致机器人无法正常工作或产生误
差。因此,在设置参数时务必仔细核对并确保准确性。
原点丢失
03
如果机器人发生故障或受到干扰,可能导致原点数据丢失。为
简化维护流程
单轴原点设置通常与特定 的机械部件相关,这使得 维护和故障诊断更为简单 。
案例分析
背景介绍
该汽车制造企业使用发那 科和法兰克机器人进行自 动化生产。
实施过程
为提高生产效率和设备可 靠性,企业决定对所有机 器人进行单轴原点设置。
效果评估
实施后,生产线的停机时 间减少了30%,生产效率 提高了20%。
常见问题解决
如果在设置原点过程中遇到问 题,可以通过查看机器人手册 或联系技术支持寻求解决方案
。
04
原点设置的实际应用和案 例分析
原点设置在生产线上的应用
01
02
03
提高生产效率
机器人单轴原点设置可以 快速定位,减少生产停机 时间,提高整体生产效率 。
FANUC原点及负载设置

单轴和多轴的原点设定CAUSEDEDIT EDIT EDIT图表1如果在system 菜单中没有master/cal 选项,如上图,选择上图中 EDIT EDIT EDIT EDIT rPIF-^149Mustcomplete [ip099LIKE4STATUS 54DGRAPHICSEDITEDIT EDITVariables 选项,切换到下图界面将上图344选项$MASTER_ENB后的值改为1切换到主菜单选择system,将光标移动到master/cal位置回车QUICKMASTERSINGLEAXISMASTERSETQUICKMASTEREtEF若机器人六个轴的原点全都丢失后,先将机器人手动调节至原点位:iTPIF-149^istcmrplece£專吃「nt:33曰firstBUP099tTNE J1PAUS-EIEBSSYSTEM>tast«r/亡住丄置(根据机器人本身的原点参照位置调节)调解完毕后将直接选择2,回车出现Masteratzeroposition?如下图选择yes原点设置完毕。
若机器人某个轴的原点丢失,则选择4,单轴变量的更改TYPt]回车后页面如下图先将机器人丢失原点的轴手动调节至原点位置(根据机器人本身的原点参照位置调节),光标切换到丢失原点轴的MSTRPOS选项下,将数值改为0,后光标切换到SEL 将数值改为1,回车,则ST数值直接生成2,(原点没有丢失的状态是ST的数值为2.)退出当前界面到下图回车后直接计算。
PAYLOAD(配重)目的:机器人给当前的工具(焊枪)或压盖陪相应的脉冲信号是机器人与之相对应,防止运动过程中发生危险选择系统菜单进入motion界面中进入后翻到下一页,点击F2IDEND进入如下页面0.0QE+00(1.33E+0.OOE+OO(1.41E+0.OOE+OO(1.41E+0.00E+00(7,84E+01210.000[ 翻到下一页F4进入到detail调整角度,shift+moveto试运行看是否有干涉最后退回到下图页面,打到自动,F4EXEC执行0,00E+00(l,33E+03)与PLC的安全信号信号固定为8入8出F-address为2状态DSBL为重启后有效。
FANUC系统原点设定

一、如何区分绝对位置编码器和相对位置编码器(增量 是 increase 的缩写,A 是 absolute 的缩写。
2 所有的βi 电机的编码器都是绝对的.
3 绝对位置编码器可以代替增量位置编码器。
1815#1 OPTx 为 1,使用全闭环。 为 0,使用半闭环。
三、电池电压及电池更换
以上三种电池,电压都是直流 6V,更换前测量电压,注意正负极! 必须在开机的情况下更换电池! 四、原点设定失败原因 1 把电机旋转半圈左右,重新设定。 2 编码器线无 6V 电线,或者线破损。 3 编码器坏。
二、1815 号参数意义
1815
#7 #6 #5 #4 #3 #2 #1 #0
APCx APZx
OPTx
1815#5 APCx 为 1,使用绝对位置编码器。 为 0,使用相对位置编码器。
1815#4 APZx 为 1,绝对位置编码器原点设定成功。 为 0,绝对位置编码器原点未设定。(会产生 300 号报警)
发那科、法兰克机器人单轴原点设置

发那科、法兰克单轴原点设置文档编号:XYZ-2021-001日期.2021年9月1日发那科、法兰克单轴原点设置1.概述本文档旨在详细描述发那科和法兰克单轴原点设置的步骤和注意事项。
单轴原点设置是操作中的重要步骤之一,确保在准确执行任务时能够正确定位。
2.前提条件在开始单轴原点设置之前,请确保以下条件已满足:a) 已接通电源并正常运行。
b) 各轴的电机和驱动器已正确安装。
c) 控制台已连接到,并已正确配置。
3.发那科单轴原点设置步骤a) 打开发那科控制台软件。
b) 进入系统设置菜单。
c) 选择轴配置选项。
d) 选择要设置原点的轴。
e) 根据制造商提供的指南,依次设置轴的原点位置。
f) 确认轴的原点设置是否成功。
g) 重复步骤d)至f),直到所有轴的原点都设置完成。
h) 保存设置并退出控制台软件。
4.法兰克单轴原点设置步骤a) 打开法兰克控制台软件。
b) 进入轴配置菜单。
c) 选择要设置原点的轴。
d) 根据制造商提供的指南,依次设置轴的原点位置。
e) 确认轴的原点设置是否成功。
f) 重复步骤c)至e),直到所有轴的原点都设置完成。
g) 保存设置并退出控制台软件。
附件:1.发那科用户手册.pdf2.法兰克操作指南.pdf法律名词及注释:1.原点位置:运动范围内的一个准确定点,用于参考和定位。
2.轴配置:对各轴进行设置的过程,包括原点设置等操作。
本文档涉及的法律名词及注释仅为参考,具体解释请参考相关法律条文和法规。
发那科、法兰克机器人单轴原点设置PPT演示
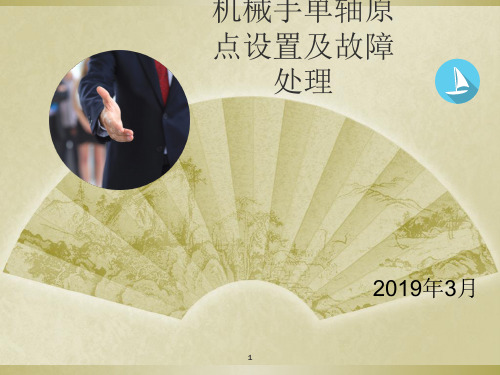
11
2.在系统变量中找到第307个选项“MCR”,选中后面的“MCR T”,按下 ENTER确定键
12
3、按下ENTER确定键,进入“MCR”菜单,选中第14个“SPC-RESET”, 再选择后面的“1”,然后按下“F4”设置成有效,至此报警消除。
13
谢谢聆听
14
9
四、更新零点标定结果
按下“PREV”返回键,返 回“零点标定/校准功能 ”页面,选择“更新零点标 定结果”,按下“ENTER” 键确认,再按“F5”完成。 至此,单轴零点设置完成。
10
五、更换减速机后的故障消除
1.按下示ห้องสมุดไป่ตู้器MENU键,选中系统选项,找到变量选项,按下ENTER键进入。
MENU键
机械手单轴原 点设置及故障
处理
2019年3月
1
目录
一、在系统设置中打开隐藏的原点设置功能 二、在系统中找到零点标定/校准功能 三、将所需设定原点的轴手动移至原点处设定 四、更新零点标定结果 五、更换减速机后的故障消除
2
一、在系统设置中打开隐藏的原点设置 功能
1.按下示教器MENU键,选中系统选项,找到变量选项,按下ENTER键进入。
MENU键
ENTER键
3
2.在系统变量中找到第304个选项SMASTER ENB,将后面设置的0改成1并按下 ENTER确定键
将0改成1
4
二、在系统中找到零点标定/校准功能
1、按下“MENU” 菜单键,选中“系统”菜单就会看到“零点标定/校准” 菜单,选中“零点标定/校准”菜单按下“ENTER”确定键进入
5
零点标定/校准界面
2.选择“单轴零点标定”并按下 “ENTER”确定键进入
FANUC车床原点设置步骤
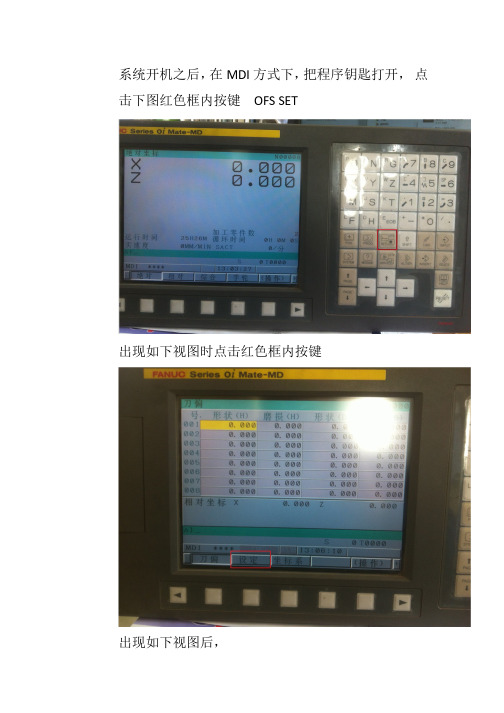
系统开机之后,在MDI方式下,把程序钥匙打开,点击下图红色框内按键OFS SET
出现如下视图时点击红色框内按键
出现如下视图后,
输入3208 然后号搜索。
出现下图
把3208最右面一位从1改成0
再把3299的最右面一位从1改成0
然后关系统再开系统如果系统报警的话,点击RESET+CAN ,可以消除报警
在手轮方式下把机床挪到如下图位置
机床到达位置后,在系统上把相对坐标清零,X,Z都清
然后点击
在参数设定界面
输入1321,然后号搜索,记住01321上X和Z的数值,例如X为-502,Z为-700
然后点击POS键(位置键),在手轮方式下,把X轴摇到相对坐标502处,把Z轴摇到相对坐标700处,再点击
输入1815,然后号搜索
把黄色处的0改为1,然后把Z 轴的相同参数也改成1(就是黄色下面的那个0,注意不是左面右面)。
、
改完之后关机,再开机,就可以了。
法那科原点设置参数

法那科原点设置参数法那科原点设置参数一、什么是法那科原点?在机床加工中,坐标系的起点被称为“原点”。
而法那科原点则是指在加工过程中,由控制器自动计算得出的机床工作台上的零点位置。
二、为什么需要设置法那科原点?在机床加工中,设置合理的原点位置可以保证加工精度和效率。
同时,在多次加工同一件产品时,通过保存原点位置可以减少重复调整的时间和劳动力成本。
三、如何设置法那科原点?1.找到“PARAM”菜单首先,在控制器界面上找到“PARAM”菜单,并进入该菜单。
2.选择“WORK COORDINATE SYSTEM”在PARAM菜单中,选择“WORK COORDINATE SYSTEM”选项,并进入该选项。
3.选择“SET WORK COORDINATE SYSTEM”在WORK COORDINATE SYSTEM选项中,选择“SET WORK COORDINATE SYSTEM”选项,并进入该选项。
4.输入坐标值在SET WORK COORDINATE SYSTEM选项中,输入需要设置的坐标值。
可以通过手动输入数值或使用机床上的定位装置来确定零点位置。
5.保存并退出确定好坐标值后,保存并退出SET WORK COORDINATE SYSTEM选项即可完成法那科原点的设置。
四、法那科原点设置参数的意义在设置法那科原点时,需要输入一些参数值,这些参数值的意义如下:1.G54~G59:表示工作坐标系的编号。
一个机床上可以设置多个工作坐标系,每个工作坐标系都有不同的编号。
2.X/Y/Z:表示在该工作坐标系下,机床工作台上X轴、Y轴、Z轴方向的偏移量。
3.A/B/C:表示在该工作坐标系下,旋转轴A、B、C方向的偏移量。
4.U/V/W:表示在该工作坐标系下,刀具补偿U、V、W方向的偏移量。
五、总结通过合理设置法那科原点参数值,可以大大提高加工精度和效率。
同时,在多次加工同一件产品时,保存原点位置也可以减少重复调整的时间和劳动力成本。
发那科原点复归的方法

原点复归一.准备工作开电后,将合模,推顶,螺杆相对应的马达旋转一周以上,关电再开电。
再按下急停按钮二.将机械位置置于零位a)模板打开合模侧后盖板,按图示方向拉动皮带(动模板向前),拉到无法再向前拉动为止,然后再反向回退,使皮带上的记号与皮带轮及机器本体上的记号第一次相对应起来。
假如皮带因跳齿而使得记号不可信的话,那么要使用以下方法。
使机构部的三个PIN在一直线上。
b)推顶器可按照类似模板的方法,即顶杆后退到最后,然后再向前至记号对上。
或者更简单的办法:使顶杆后退至不冒出模板即可。
c)螺杆升温到指定温度后,用手拉动皮带,使螺杆向前移动到最前端,然后后退1mm。
*在用手拉动皮带时,须按下紧急停止按钮,否则拉不动皮带。
在执行以上操作时请注意安全。
三.参数设定a)进入CNC画面:输入-9999然后按模开闭组键(下图)。
进入如下画面再按两下模具文件(有时也可能是别的按键(W-6#机是两下,这时要退到第一个画面再进行),到如下画面(SETTING画面)b)关闭写保护:将SETTING画面中的第一项PARAMETERWRITE改为1(使得参数允许被修改)。
c)按一下模开闭组键,进入PARAMETER画面;d)输入1815然后选择触摸屏上的NO.SRH(1815参数是原点位置记录的参数;按NO.SRH是表示搜寻1815号参数)其中列APC是表示电池的电量:1有,0无(即当外部电池电量过低时,会发生APC电池电量过低报警,此时此参数会自动变为0);列APZ表示原点位置的纪录:1记录,0丢失(电池电量过低时,丢失)。
e)将现在机械位置记为原点:将所需做原点复归的轴的APZ位先改为0,然后再改为1。
(X —射出,Y —模板,A —顶杆,C轴无原点)f)将写保护重新打开。
g)在黑色画面以外的部分点一下,退出CNC画面。
在操作画面的右上方检查一下校正过以后的原点位置。
h)关操作面板电源,关总电源。
i)再开机,再次确认位置后,原点复归结束。
FANUC绝对原点机床原点设定190919

FANUC绝对原点机床原点设定190919
图4
4.关电重启。
5.将模式开关选到“手轮”模式,用手轮摇动要设定绝对机械原点的轴,X或
Y或Z轴移动到正确的原点位置;或者在“JOG模式”,按对应轴的移动按钮,
将对应轴移动到正确的原点位置。
(若有原点标识,请摇到标识指示的正确
的原点位置为如图5所示箭头对齐的位置;没有标识,XY轴可以采用分中的
办法,或者看护罩的印迹进行设定;Z轴可以用卷尺量测机械手持刀爪下沿
平面到工作台面的距离A,主轴上装一把刀柄,将Z轴向上摇动,摇到刀柄
的V型槽下沿面到工作台面的距离也为A位置为准,再往上摇动到1241设
定的值取反位置,如1241设-10,则往上再摇10MM;1241设10,则往下摇-10MM,
设定为Z轴的机械原点)
轴(移动部分)
两箭头对齐
轴(不动部分)
图5
6.重新回到图4所示画面,将对应轴1815参数对应的APZ位依次再改为1。
7.找到图2所示画面,将“参数写入=1”改为“参数写入=0”。
8.关电重启。
9.重新对刀,确认机械位置正确后,重新找正工件原点及刀具长度补正后方可
加工。
10.对于Z轴,需要确认换刀点高度是否吻合,1241为Z轴第二原点设定参数。
(1320为轴向正行程设定,1321为轴向负行程设定)
作者:***20190919。
基本机床操作一 (FANUC O MATE-TD机床原点设置方法)

FANUC O MATE-TD机床原点设置方法
1、将准备设置原点的轴用HANDLE 或 JOG 方式使之移动到原点。
2、CRT UNIT 按 OFFSET,再按画面的SETTING(HANDY)软键使之被显
示。
3、MODE设置为 MDI ,修改PWE 为“1”,此时出现ALARM100,因为
打开了参数修改的保护。
4、将参数NO。
1815 的第4位修改为“0”
18150 0 0 1 1 0 0 0 (修改前)
18150 0 0 1 0 0 0 0 (修改后)
注意:仅修改第4位,其他不可修改,如果是2轴系统,请确认修改前都已经移动到原点.
5、出现ALARM000,内容为修改原点后要求重开电源。
将NC电源关闭,
5秒后再打开。
6、将参数NO。
1815 的第4位修改为“1”
7、修改PWE 参数为“0”
8、关闭NC电源 5秒后再开,CRT UNIT 按POS,显示机械坐标0.000,
原点设置完成.
相关参数说明。
发那科、法兰克机器人单轴原点设置

2.在系统变量 中找到第307 个选项 “MCR”,选 中后面的 “MCR T”, 按下ENTER确 定键
3、按下ENTER确 定键,进入 “MCR”菜单, 选中第14个 “SPC-RESET”, 再选择后面的 “1”,然后按下 “F4”设置成有 效,至此报警消除。
谢谢聆听
——
单击此处添加正文,文字是您思想的提炼,请尽量言简意赅的阐述观点。
四、更新零点标定 结果
按下“PREV”返回键,返回 “零点标定/校准功能 ”页面,选择“更新零点标定 结果”,按下“ENTER”键确 认,再按“F5”完成。 至此,单轴零点设置完成。
五、更换减速机后的故障消除
1.按下示教器MENU键,选中 系统选项,找到变量选项,按 下ENTER键进入。 MENU键 ENTER键
零点标定/校 准界面
2.选择“单轴零点标 定”并按下“ENTER” 确定键进入
单轴零 点标定 界面
三、将所需设 定原点的轴手 动移至原点处 设定
以此轴未例,刻度线互 相对齐,轴就到达零点
以J1轴为例,先将“零 点标定位置”设为 “0.000”,按下 “ENTER”键确认,然 后将“SEL”的值由“0” 改为“1”,再按下 “ENTER”键确认,最 后按“F5”键执行
机械手单轴原点设置及故障处理
——
2019年3月
目录
• 一、在系统设置中打开隐藏的原点设置功能
01.
单击此处添加标题
• 二、在系统中找到零点标定/校准功能 单击此处添加文本具体内容
02.
单击此处添加标题
单击此处添加文本具体内容
• 三、将所需设定原点的轴手动移至原点处设定
• 四、更新零点标定结果
一、在系统设置中打开隐藏的原ห้องสมุดไป่ตู้设置功能
FANUC数控机床机械原点的设置及回零常见故障分析

FANUC数控机床机械原点的设置及回零罕见故障分析之青柳念文创作当前大多数数控机床均采取通过减速档块的方式回零,但谊方式在日常使用中故障率却艰高,有时甚至出现机械原点的丢失.本文以FANUC系统的台中精机VCENTER-70加工中心为例浅析了数控机床机械原点的设置方法,并对该类数控机床罕见回零故障的各种形式式停止了分析与总结.机械原点是机床生产厂家在生产机床时任机床上设置的一个物理位置,可使节制系统和机床可以同步,从而建立起一个用于丈量机床运动坐标的起始位置点,通常也是程序坐标的参考点.大多数数控机床在开机后都需要回零即回机械原点的操纵.本文以FANUC系统的台中精机VCENTER-70加工中心为例浅析了数控机床机械原点的设置方法,并对此类数控机床罕见回零故障的各种形武停止了分析与总结.1 机械原点设置1.1 机械原点丢失的原因台中精机生产的VCENTER-70加工中心采取增量编码器作为机床位置的检测装置.系统断电后,工件坐标系的坐标值就会失去记忆,虽然靠电池可以维持坐标值的记忆,但只是记忆机床断电前的坐标值而不是机床的实际位置,所以机床首次开机后要停止返回参考点操纵.而当系统断电遇到电池没电或特殊情况失电时,就会造成机械原点的丢失.从而使机床回参考点失败而无法正常工作.此时机床会发生.#306 n轴电池电压0#的报警信息,而且还会发生机械坐标丢失报警.#300第n轴原点复位要求”(n代指X、Y、Z).1.2 机械原点的设置在通常情况下,设置数控机床机械原点的方法主要有以下两种:1)手动使X、Y、Z三轴超程印操纵三轴的极限位置选择机械原点.2)操纵各坐标轴的伺服检溯反馈系统提供相应基准脉冲来选择机床参考点即机械原点.由于第一种方法是机床厂家通常建议的也是较为简便和实用的方法.因此本文在此详细先容第1种做法.以X轴为例,设置步调如下:(1)将机床操纵面板上的方式选择开关设定为MDI方式.(2)按下机床MDI面板上的功能键[OFS/SET]数次,进入设定画面.(3)将写参数中的0改为1,由此,系统进入了参数可写状态.此时机床出现.SWO 100参数写入开关处于打开”的报警信息.忽略这条报警信息,设置完参数后改回为0即可.(4)按下功能键lsYSTEM】,进入系统参数键面.通过参数搜索找到参数1815(如表l所示)通常情况下,X轴的#4APZ或#5 APC会显示为0,若不为0就将其设定为0.(5)找到参数1320,此参数为存储各轴正向行程的坐标值.将其X轴的正向行程设定为最大值999999.目标是让X轴的正向软限位位置值大于其正向硬限位的位置值.(6)将方式选择开关打到手轮方式,然后摇动手轮使工作台碰及X轴的正向限位档块,此时机床会出现“#500+X过行程”报警.(7)按下MDI面板上的[POS]功能键.进入机床坐标显示键面.打开相对坐标显示键面,按下X+[起源]使X轴的相对坐标值变成0.(8)按下机床操纵面板上的【超程释放】并摇动手轮至X-6.5的位置.(9)再次找到参数1815,将X轴的#4APZ或#5 APC都设定为1.最后重启数控系统,完成X轴的机械原点设置.Y轴和Z轴的机械原点设置方法与X轴相同,三轴的机械原点都设定好后重新打开写参数设定键面,将其设定为0.此时机床的报警信息全部消失,完成了加工中心的机械原点设置.操纵基准脉冲设定机床零点.在通常情况下,闭环系统直线的光栅尺每隔50mm就会发生一个基准脉冲,但也会有一些特殊的直线光栅尺,它会每隔20mm就发生一个基准脉冲.对于闭环系统中的旋转编码器来讲,发生的基准脉冲间隔要比直线光栅尺小很多,比方只有6mm.由于这个基准脉冲在机床上常常会被选定为致控系统计数的基准.因此通过修改机床里的参数便可以将这个基准点的值设定为0,从而使这个点成为机床的参考点也就是机床的机械原点.1.3 设置机械原点时的注意事项(1)设置前要检查各坐标轴上要否装置有机床回零的微动开关,且各微动开关的位置是否适合.(2)在第一个基准脉冲验出之前,必顺包管该坐标轴到了需要降速的间隔上了.而这个降速间隔就是所选速度的滞后误差值.(3)由于使用的是编码器.故两个基准脉冲之间的间隔会很小,所以在回机床零点时,速度要低一些,从而使滞后误差不会高于这个值的500.(4)由于各坐标轴回机床机械原点时的速度是由机床的相应参效决议的.因此在设置这些参数时要注意.确保机床回零速度合适.(5)倘若机床在回零点时压住了微动开关,那末就必须通过手轮或是手动的方式操纵数控机床坐标轴,强制其退出微动开关并退到离微动开关较远的位置,然后再次执行各坐标轴回参考点的操纵.2 机床回零罕见故障分析及处理2.1 机床开机后不克不及回零故障分析及处理(1)可以系统参数设置有误.处理方法是仔细检查各个相关参数,需要时重设参数.(2)零脉冲不良导致的故障.零脉冲不良就会使回零时找不到零脉冲,引起的原因可以是系统轴板故障或是编码器及接线出现故障.处理方法是对编码器停止更换或清洗,检查线路及系统轴板是否有问题.(3)有可以减速开关短路或是已经损坏.这种故障会导致减速信号不克不及发生.处理方法是检查减速开关的线路,对减速开关停止维修,需要时更换减速开关.(4)可以检测元件已被污染.在全闭环节制的系统中,若光栅尺沾有油污,就不克不及收集到信号.处理方法是清洗光栅尺.2.2 机床回零时找不到零点位置故障分析及处理(1)减速开关有可以已经损坏或受污,也可以是线路短路或断路.处理方法就是及时对减速开关停止清理维修,需要时更换减速开关.检查线路毗连情况.及时发现问题并处理.(2)可以是减速档块所处位置不准确.处理方法是调整减速档块到限位开关的间隔,防止二者行程过小引发此故障.2.3 机床回零后的位置与零点位置发生螺距偏移故障分析及处理引起这一故障可以的原因是发生栅格信号的时刻与减速信号从断开到接通的时刻太接近了,再加上存在的传动误差,就使得机床回零过程中工作台碰到减速开关时,刚好错过了栅格信号,所以只能等到脉冲编码器再转过一周以后才干找到下一个栅格信号.故而出现了此类故障.详细分析如下:在减速开关的信号从断开恢复到接通状态时,随即便出现了栅格信号,也就是晚栅格信号处在门临界点上(如图1a所永).这样一来,机械部分的热变形,减速开关出现“通”、“断”信号的重复精度误差都会导致零点发生位置偏离的故障(如图1b所示).处理方法足可适当的阔整减速档块所处的位置,从而使零点位置与工作台停止的位置重合(如图1c所示).也可以采取修改栅格偏移量的方法,使发生栅格信号的时划离减速信号从断开到接通时刻的间隔是栅格信号发生周期的一半,便可消除此故障(如图1d 所示).图1故障分析及鳞决方法示意囤2.4 机床幽零位置随机性变更故障分析及处理(1)脉冲编码器的供电电压太低.处理方法是调整从主板上输出的电压值,同时检查编码器线路板上的电源电压是否已到了合适的范围.(2)伺服调节不良.从而引起跟踪误差偏大.处理方法足修改伺服参数.(3)滚珠丝杠间隙偏大或丝杠与电动机的联轴器出现了松动.处理的方法是对演珠丝杠螺母剐的间隙停止调整及优化,对联轴器停止紧周或更换.(4)零咏冲受到干扰.处理的方法是检查脉冲编码器的电缆安插是否合理,反馈电缆萍蔽是否毗连无误.3 结语掌握数拧机床原点的设置方法和罕见回零故障处理方式对于处理生产实践中的机床回零故障具有很好的指导作用.但值得说明的是故障观象与故障原因并不是是一一对应的,有可以是几种原困引起的.因此在维修时要根据机床的实际情况,连系实践经历和维修手册逐一检查解除假象,找到故障起因并予以解除.。
FANUC机器人ROBOT原点对位简易方法

FANUC机器人ROBOT原点对位简易方法
Fanuc 原点校准方法
1.正确接入机器人的电力,并将伺服上电.
2.移动机器各轴,到mark的位置并对准
3.示教器上按下MENU键再选择菜单0-NEXT
再选择6-SYSTEM后,按下F1(TYPE)键,再选择弹出菜单Master/CAL显示如下画面
此时按下F3对PCA进行复位.(注意,这一步只是复位了编码器数据)
4.重复前面的步骤,选中2 ZERO POSITION MASTER
5.进入ZERO POSITION MASTER 后按下F4(YES)按钮
6.完成零点对位后,还要进行机器人校准.(就是通知控制器对位
完成)步骤如下:
如画面1所示:选中6 CALIBRATE出现下面的画面:
选择F4(YES)后,再选择F5(DONE) 完成机器人校准.。
FANUC车床原点设置步骤
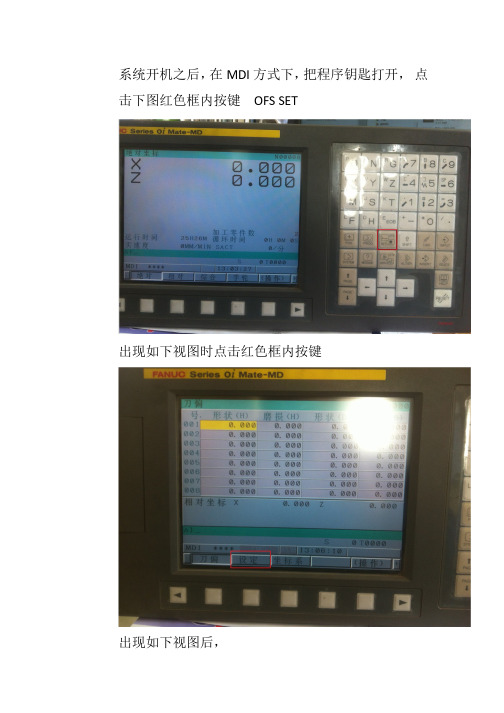
系统开机之后,在MDI方式下,把程序钥匙打开,点击下图红色框内按键OFS SET
出现如下视图时点击红色框内按键
出现如下视图后,
输入3208 然后号搜索。
出现下图
把3208最右面一位从1改成0
再把3299的最右面一位从1改成0
然后关系统再开系统如果系统报警的话,点击RESET+CAN ,可以消除报警
在手轮方式下把机床挪到如下图位置
机床到达位置后,在系统上把相对坐标清零,X,Z都清
然后点击
在参数设定界面
输入1321,然后号搜索,记住01321上X和Z的数值,例如X为-502,Z为-700
然后点击POS键(位置键),在手轮方式下,把X轴摇到相对坐标502处,把Z轴摇到相对坐标700处,再点击
输入1815,然后号搜索
把黄色处的0改为1,然后把Z 轴的相同参数也改成1(就是黄色下面的那个0,注意不是左面右面)。
、
改完之后关机,再开机,就可以了。
- 1、下载文档前请自行甄别文档内容的完整性,平台不提供额外的编辑、内容补充、找答案等附加服务。
- 2、"仅部分预览"的文档,不可在线预览部分如存在完整性等问题,可反馈申请退款(可完整预览的文档不适用该条件!)。
- 3、如文档侵犯您的权益,请联系客服反馈,我们会尽快为您处理(人工客服工作时间:9:00-18:30)。
FANUC机械臂原点设置
图1
图2
图3
图4
图5
图6
图7
图8
全轴原点设置:
1:更换电池如图1(正负极切记不能装反,电池为4节2号电池,原装电池品牌为松下)
2:选择“主菜单”按键(如图2)→“下页”(如图2)→选择“系统”(如图3)→选择“零点标定/校准”(如图3)→点击“RES_PCA”解除脉冲报警(如图4)→关机重启→手动关节把机械臂每个轴移到原点位置→选择“全轴零点位置标定”(如图4)点击“ENTER”(如图6)键→选择“更新零点标定结果”(如图5)点击“ENTER”(如图6)→点击“完成”(如图5)→关机重启(原点设置OK)
单轴原点设定(空间狭小,各轴不能完全回到原点位置,可先使可以回原点的几个轴回原点设置,进行全轴设置,剩余不在原点位置的轴可单独轴原点设置):
將需要设置原点的轴摇到零点,选择“简易零点标定(单轴)”(如图7),把“0改为1”(如图8)点击“执行”(如图8)则自动设置原点
注:设置原点时,每个轴需要旋转位置至少250mm,否则有可能原点设定不了,每个原点位置都有刻痕或标识牌
机械臂原点位置如下图:。