磨削参数对硬质合金磨削力和温度的影响
硬质合金刀具切削金属材料的刀具磨损机理研究
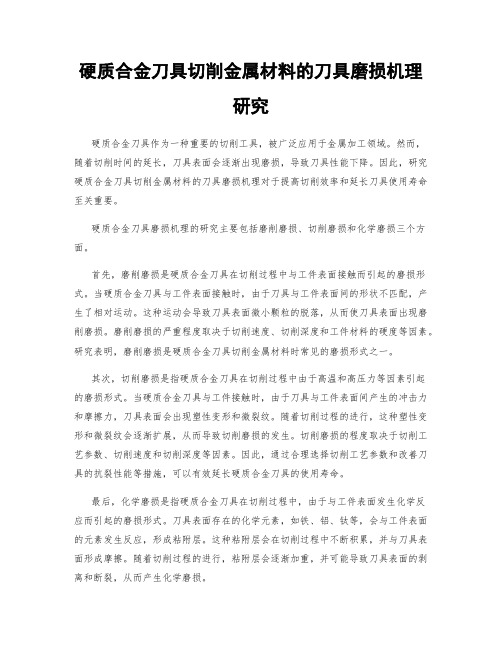
硬质合金刀具切削金属材料的刀具磨损机理研究硬质合金刀具作为一种重要的切削工具,被广泛应用于金属加工领域。
然而,随着切削时间的延长,刀具表面会逐渐出现磨损,导致刀具性能下降。
因此,研究硬质合金刀具切削金属材料的刀具磨损机理对于提高切削效率和延长刀具使用寿命至关重要。
硬质合金刀具磨损机理的研究主要包括磨削磨损、切削磨损和化学磨损三个方面。
首先,磨削磨损是硬质合金刀具在切削过程中与工件表面接触而引起的磨损形式。
当硬质合金刀具与工件表面接触时,由于刀具与工件表面间的形状不匹配,产生了相对运动。
这种运动会导致刀具表面微小颗粒的脱落,从而使刀具表面出现磨削磨损。
磨削磨损的严重程度取决于切削速度、切削深度和工件材料的硬度等因素。
研究表明,磨削磨损是硬质合金刀具切削金属材料时常见的磨损形式之一。
其次,切削磨损是指硬质合金刀具在切削过程中由于高温和高压力等因素引起的磨损形式。
当硬质合金刀具与工件接触时,由于刀具与工件表面间产生的冲击力和摩擦力,刀具表面会出现塑性变形和微裂纹。
随着切削过程的进行,这种塑性变形和微裂纹会逐渐扩展,从而导致切削磨损的发生。
切削磨损的程度取决于切削工艺参数、切削速度和切削深度等因素。
因此,通过合理选择切削工艺参数和改善刀具的抗裂性能等措施,可以有效延长硬质合金刀具的使用寿命。
最后,化学磨损是指硬质合金刀具在切削过程中,由于与工件表面发生化学反应而引起的磨损形式。
刀具表面存在的化学元素,如铁、铝、钛等,会与工件表面的元素发生反应,形成粘附层。
这种粘附层会在切削过程中不断积累,并与刀具表面形成摩擦。
随着切削过程的进行,粘附层会逐渐加重,并可能导致刀具表面的剥离和断裂,从而产生化学磨损。
综上所述,硬质合金刀具在切削金属材料时会发生磨削磨损、切削磨损和化学磨损等多种磨损形式。
刀具磨损的机理与切削工艺参数、工件材料的硬度以及刀具自身的材料和制造工艺等因素密切相关。
因此,我们在实际应用中,应根据具体情况选择合适的刀具材料和加工工艺,以减少刀具的磨损,提高切削效率和刀具的使用寿命。
Y2O3对硬质合金晶粒尺寸和摩擦磨损性能的影响
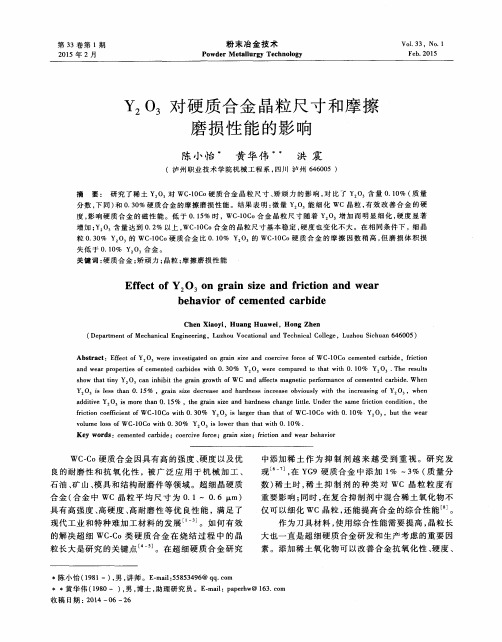
Abs t r a c t : Ef f e c t o f Y2 O3 we r e i n v e s t i g a t e d o n g r a i n s i z e a n d c o e r c i v e f o r c e o f W C一 1 0Co c e me n t e d c a r bi d e,f r i c t i o n
a nd we a r pr o pe r t i e s o f c e me n t e d c a r bi de s wi t h 0. 3 0% Y2 O3 we r e c o mpa r e d t o t ha t wi t h 0.1 0% Y2 O3 . The r e s ul t s
Ke y wo r ds:c e me nt e d c a r bi d e;c o e r c i v e f o r o e; g r a i n s i z e;f ri c t i o n an d we a r b e h av i o r
失低 于 0 . 1 0 % Y , 0 合 金 。
关键词 : 硬质合金 ; 矫顽力 ; 晶粒 ; 摩 擦 磨 损 性 能
Ef f e c t o f Y2 O3 o n g r a i n s i z e a n d f r i c t i o n a nd we a r b e ha v i o r o f c e me n t e d c a r b i d e
硬质合金切削工具材料性能研究
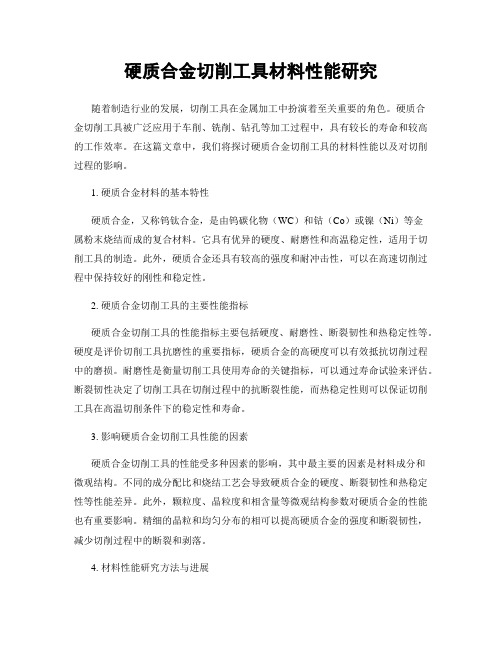
硬质合金切削工具材料性能研究随着制造行业的发展,切削工具在金属加工中扮演着至关重要的角色。
硬质合金切削工具被广泛应用于车削、铣削、钻孔等加工过程中,具有较长的寿命和较高的工作效率。
在这篇文章中,我们将探讨硬质合金切削工具的材料性能以及对切削过程的影响。
1. 硬质合金材料的基本特性硬质合金,又称钨钛合金,是由钨碳化物(WC)和钴(Co)或镍(Ni)等金属粉末烧结而成的复合材料。
它具有优异的硬度、耐磨性和高温稳定性,适用于切削工具的制造。
此外,硬质合金还具有较高的强度和耐冲击性,可以在高速切削过程中保持较好的刚性和稳定性。
2. 硬质合金切削工具的主要性能指标硬质合金切削工具的性能指标主要包括硬度、耐磨性、断裂韧性和热稳定性等。
硬度是评价切削工具抗磨性的重要指标,硬质合金的高硬度可以有效抵抗切削过程中的磨损。
耐磨性是衡量切削工具使用寿命的关键指标,可以通过寿命试验来评估。
断裂韧性决定了切削工具在切削过程中的抗断裂性能,而热稳定性则可以保证切削工具在高温切削条件下的稳定性和寿命。
3. 影响硬质合金切削工具性能的因素硬质合金切削工具的性能受多种因素的影响,其中最主要的因素是材料成分和微观结构。
不同的成分配比和烧结工艺会导致硬质合金的硬度、断裂韧性和热稳定性等性能差异。
此外,颗粒度、晶粒度和相含量等微观结构参数对硬质合金的性能也有重要影响。
精细的晶粒和均匀分布的相可以提高硬质合金的强度和断裂韧性,减少切削过程中的断裂和剥落。
4. 材料性能研究方法与进展研究硬质合金切削工具材料性能的方法主要包括实验测试和数值模拟。
实验测试可以通过切削试验、硬度测试、显微镜观察等手段来获取硬质合金的性能数据。
数值模拟则通过计算机模拟切削过程中的材料应力、变形和热传导等物理过程,预测硬质合金切削工具的性能。
近年来,基于人工智能和机器学习的模型也逐渐应用于硬质合金材料性能研究中,提高了研究效率和准确性。
5. 切削工具性能改善的途径为了改善硬质合金切削工具的性能,研究人员采取了多种途径。
整体硬质合金刀具磨削裂纹的原因分析及其工艺改进

整体硬质合金刀具磨削裂纹的原因分析及其工艺改进1 引言整体硬质合金刀具在航空航天业、模具制造业、汽车制造业、机床制造业等领域得到越来越广泛的应用,尤其是在高速切削领域占有越来越重要的地位。
在高速切削领域,由于对刀具安全性、可靠性、耐用度的高标准要求,整体硬质合金刀具内在和表面的质量要求也更加严格。
而随着硬质合金棒材尤其是超细硬质合金材质内在质量的不断提高,整体硬质合金刀具表面的质量情况越来越受到重视。
众所周知,硬质合金刀具的使用寿命除了与其耐磨性有关外,也常常表现在崩刃、断刃、断裂等非正常失效方面,磨削后刀具的磨削裂纹等表面缺陷则是造成这种非正常失效的重要原因之一。
这些表面缺陷包括经磨削加工后暴露于表面的硬质合金棒料内部粉末冶金制造缺陷(如分层、裂纹、未压好、孔洞等)以及磨削过程中由于不合理磨削在磨削表面造成的磨削裂纹缺陷,而磨削裂纹则更为常见。
这些磨削裂纹,采用肉眼、放大镜、浸油吹砂、体视显微镜和工具显微镜等常规检测手段往往容易造成漏检,漏检的刀具在使用时尤其是在高速切削场合可能会造成严重的后果,因此整体硬质合金刀具产品磨削裂纹缺陷的危害很大。
因此对整体硬质合金刀具磨削裂纹的产生原因进行分析和探讨,并提出有效防止磨削裂纹的工艺改进措施具有很重要的现实意义。
2 整体硬质合金刀具磨削裂纹的原因分析1.整体硬质合金刀具的磨削加工特点硬质合金材料由于硬度高,脆性大,导热系数小,给刀具的刃磨带来了很大困难,尤其是磨削余量很大的整体硬质合金刀具。
硬度高就要求有较大的磨削压力,导热系数低又不允许产生过大的磨削热量,脆性大导致产生磨削裂纹的倾向大。
因此,对硬质合金刀具刃磨,既要求砂轮有较好的自砺性,又要有合理的刃磨工艺,还要有良好的冷却,使之有较好的散热条件,减少磨削裂纹的产生。
一般在刃磨硬质合金刀具时,温度高于600℃,刀具表面层就会产生氧化变色,造成程度不同的磨削烧伤,严重时就容易使硬质合金刀具产生裂纹。
硬质合金刀具的镜面磨削
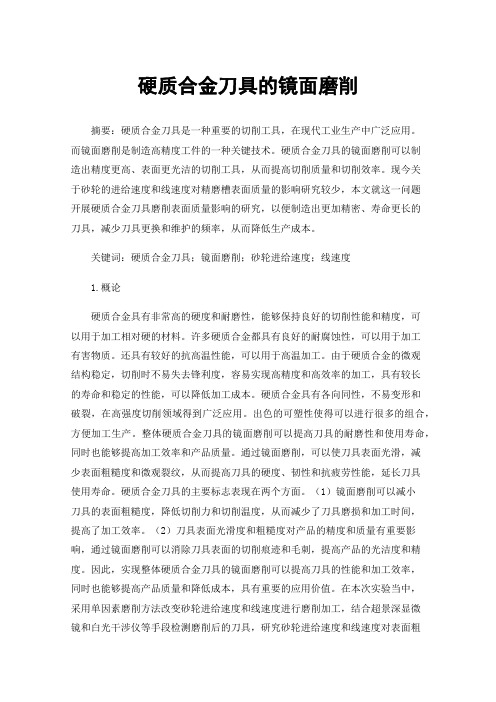
硬质合金刀具的镜面磨削摘要:硬质合金刀具是一种重要的切削工具,在现代工业生产中广泛应用。
而镜面磨削是制造高精度工件的一种关键技术。
硬质合金刀具的镜面磨削可以制造出精度更高、表面更光洁的切削工具,从而提高切削质量和切削效率。
现今关于砂轮的进给速度和线速度对精磨槽表面质量的影响研究较少,本文就这一问题开展硬质合金刀具磨削表面质量影响的研究,以便制造出更加精密、寿命更长的刀具,减少刀具更换和维护的频率,从而降低生产成本。
关键词:硬质合金刀具;镜面磨削;砂轮进给速度;线速度1.概论硬质合金具有非常高的硬度和耐磨性,能够保持良好的切削性能和精度,可以用于加工相对硬的材料。
许多硬质合金都具有良好的耐腐蚀性,可以用于加工有害物质。
还具有较好的抗高温性能,可以用于高温加工。
由于硬质合金的微观结构稳定,切削时不易失去锋利度,容易实现高精度和高效率的加工,具有较长的寿命和稳定的性能,可以降低加工成本。
硬质合金具有各向同性,不易变形和破裂,在高强度切削领域得到广泛应用。
出色的可塑性使得可以进行很多的组合,方便加工生产。
整体硬质合金刀具的镜面磨削可以提高刀具的耐磨性和使用寿命,同时也能够提高加工效率和产品质量。
通过镜面磨削,可以使刀具表面光滑,减少表面粗糙度和微观裂纹,从而提高刀具的硬度、韧性和抗疲劳性能,延长刀具使用寿命。
硬质合金刀具的主要标志表现在两个方面。
(1)镜面磨削可以减小刀具的表面粗糙度,降低切削力和切削温度,从而减少了刀具磨损和加工时间,提高了加工效率。
(2)刀具表面光滑度和粗糙度对产品的精度和质量有重要影响,通过镜面磨削可以消除刀具表面的切削痕迹和毛刺,提高产品的光洁度和精度。
因此,实现整体硬质合金刀具的镜面磨削可以提高刀具的性能和加工效率,同时也能够提高产品质量和降低成本,具有重要的应用价值。
在本次实验当中,采用单因素磨削方法改变砂轮进给速度和线速度进行磨削加工,结合超景深显微镜和白光干涉仪等手段检测磨削后的刀具,研究砂轮进给速度和线速度对表面粗糙度和锯齿量的影响。
机械制造技术基础(第2版)第二章课后习题答案

机械制造技术基础(第2版)第二章课后习题答案编辑整理:尊敬的读者朋友们:这里是精品文档编辑中心,本文档内容是由我和我的同事精心编辑整理后发布的,发布之前我们对文中内容进行仔细校对,但是难免会有疏漏的地方,但是任然希望(机械制造技术基础(第2版)第二章课后习题答案)的内容能够给您的工作和学习带来便利。
同时也真诚的希望收到您的建议和反馈,这将是我们进步的源泉,前进的动力。
本文可编辑可修改,如果觉得对您有帮助请收藏以便随时查阅,最后祝您生活愉快业绩进步,以下为机械制造技术基础(第2版)第二章课后习题答案的全部内容。
《机械制造技术基础》部分习题参考解答第二章 金属切削过程2-1 什么是切削用量三要素?在外圆车削中,它们与切削层参数有什么关系? 答:切削用量三要素是指切削速度v 、进给量f 、背吃刀量a p (切削深度)。
在外圆车削中,它们与切削层参数的关系是:2—2 确定外圆车刀切削部分几何形状最少需要几个基本角度?试画图标出这些基本角度。
答:确定外圆车刀切削部分几何形状最少需要7个基本角度:前角、后角、主偏角、副偏角、副前角、副后角和刃倾角,这些基本角度如下图所示(其中副前角、副后角不做要求)。
2—3 试述刀具标注角度和工作角度的区别。
为什么车刀作横向切削时,进给量取值不能过大?答:刀具标注角度是在静态情况下在刀具标注角度参考系中测得的角度;而刀具工作角度是在刀具工作角度参考系中(考虑了刀具安装误差和进给运动影响等因素)确定的刀具角度。
车刀作横向切削时,进给量取值过大会使切削速度、基面变化过大,导致刀具实际工作前角和工作后角变化过大,可能会使刀具工作后角变为负值,不能正常切削加工(P23).2—4 刀具切削部分的材料必须具备哪些基本性能?答:(P24)(1) 高的硬度和耐磨性;(2) 足够的强度和韧性;(3) 高耐热s i n /s i n D rD p rD ph f b a A f a κκ===切削层公称厚度: 切削层公称宽度: 切削层公称横截面积:性;(4) 良好的导热性和耐热冲击性能;(5)良好的工艺性.2—5 常用的硬质合金有哪几类?如何选用?答:(P26)常用的硬质合金有三类:P类(我国钨钴钛类YT),主要用于切削钢等长屑材料;K类(我国钨钴类YG),主要用于切削铸铁、有色金属等材料;M类(我国通用类YW),可以加工铸铁、有色金属和钢及难加工材料。
硬质合金刀具加工的基本知识
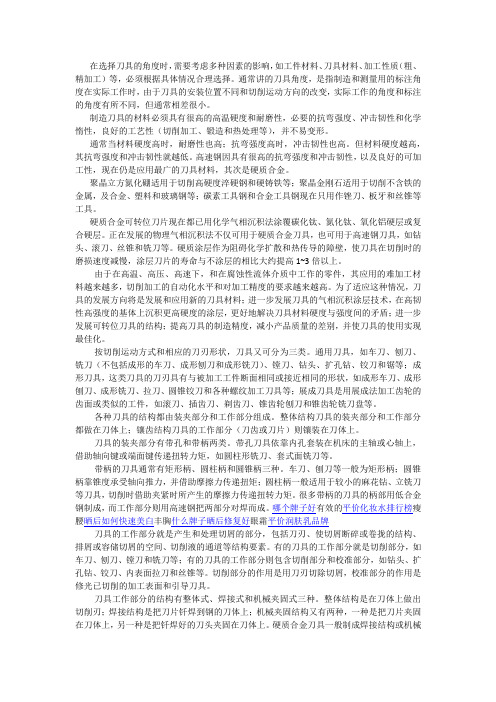
在选择刀具的角度时,需要考虑多种因素的影响,如工件材料、刀具材料、加工性质(粗、精加工)等,必须根据具体情况合理选择。
通常讲的刀具角度,是指制造和测量用的标注角度在实际工作时,由于刀具的安装位置不同和切削运动方向的改变,实际工作的角度和标注的角度有所不同,但通常相差很小。
制造刀具的材料必须具有很高的高温硬度和耐磨性,必要的抗弯强度、冲击韧性和化学惰性,良好的工艺性(切削加工、锻造和热处理等),并不易变形。
通常当材料硬度高时,耐磨性也高;抗弯强度高时,冲击韧性也高。
但材料硬度越高,其抗弯强度和冲击韧性就越低。
高速钢因具有很高的抗弯强度和冲击韧性,以及良好的可加工性,现在仍是应用最广的刀具材料,其次是硬质合金。
聚晶立方氮化硼适用于切削高硬度淬硬钢和硬铸铁等;聚晶金刚石适用于切削不含铁的金属,及合金、塑料和玻璃钢等;碳素工具钢和合金工具钢现在只用作锉刀、板牙和丝锥等工具。
硬质合金可转位刀片现在都已用化学气相沉积法涂覆碳化钛、氮化钛、氧化铝硬层或复合硬层。
正在发展的物理气相沉积法不仅可用于硬质合金刀具,也可用于高速钢刀具,如钻头、滚刀、丝锥和铣刀等。
硬质涂层作为阻碍化学扩散和热传导的障壁,使刀具在切削时的磨损速度减慢,涂层刀片的寿命与不涂层的相比大约提高1~3倍以上。
由于在高温、高压、高速下,和在腐蚀性流体介质中工作的零件,其应用的难加工材料越来越多,切削加工的自动化水平和对加工精度的要求越来越高。
为了适应这种情况,刀具的发展方向将是发展和应用新的刀具材料;进一步发展刀具的气相沉积涂层技术,在高韧性高强度的基体上沉积更高硬度的涂层,更好地解决刀具材料硬度与强度间的矛盾;进一步发展可转位刀具的结构;提高刀具的制造精度,减小产品质量的差别,并使刀具的使用实现最佳化。
按切削运动方式和相应的刀刃形状,刀具又可分为三类。
通用刀具,如车刀、刨刀、铣刀(不包括成形的车刀、成形刨刀和成形铣刀)、镗刀、钻头、扩孔钻、铰刀和锯等;成形刀具,这类刀具的刀刃具有与被加工工件断面相同或接近相同的形状,如成形车刀、成形刨刀、成形铣刀、拉刀、圆锥铰刀和各种螺纹加工刀具等;展成刀具是用展成法加工齿轮的齿面或类似的工件,如滚刀、插齿刀、剃齿刀、锥齿轮刨刀和锥齿轮铣刀盘等。
成形磨齿工艺参数对磨削温度影响规律的研究苏建新J

成形磨齿工艺参数对磨削温度影响规律的研究*苏建新胡海峰任小中王建生董后云(河南科技大学机电工程学院,河南洛阳471003)摘要:基于矩形移动热源理论分析了成形磨齿工艺参数对磨削温度的影响。
根据有限元离散化原理,建立了干式磨削瞬态温度场数学模型。
根据热量分配关系,导出了磨削区热流密度的理论计算公式。
在磨削区施加由不同磨削工艺参数计算得到的热流密度,进行了瞬态温度场的三维有限元仿真,从而得出了不同工况下齿面温度场的变化规律。
关键词:成形磨齿;磨削温度;热流密度;磨削工艺参数中图分类号:TG616文献标识码:AStudy on the influence of gear form grinding parameters on grinding temperature SU Jianxin,HU Haifeng,REN Xiaozhong,WANG Jiansheng,DONG Houyun(College of Mechatronical Engineering,Henan University of Science&Technology,Luoyang471003,CHN)Abstract:Based on the rectangular moving heat source theory,the influence of gear form grinding parameters on the grinding temperature is analyzed.According to the finite element discretization principle,the mathe-matical model of transient temperature field in dry grinding is established.According to the heat distri-bution relationship,the theoretical formula calculating heat flux is derived.3-D finite element simula-tion of transient temperature field is carried out through applying the heat flux density calculated underthe different grinding parameters to grinding zone,and the distribution law of tooth surface temperaturefield is achieved finally.Keywords:gear form grinding;grinding temperature;heat flux;grinding parameter成形磨削过程中砂轮在短时间内去除材料时会产生很高的温度且只有小部分被带走,这些集中在齿面表层的热量达到一定程度时,会造成齿面材料金相组织变化,导致磨削烧伤、残余应力和裂纹等热损伤问题,这将严重影响齿轮的使用性能[1]。
硬质合金各项参数之间的关系
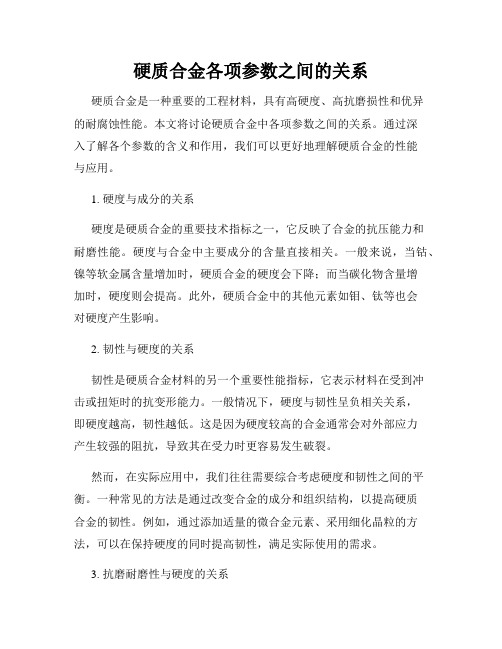
硬质合金各项参数之间的关系硬质合金是一种重要的工程材料,具有高硬度、高抗磨损性和优异的耐腐蚀性能。
本文将讨论硬质合金中各项参数之间的关系。
通过深入了解各个参数的含义和作用,我们可以更好地理解硬质合金的性能与应用。
1. 硬度与成分的关系硬度是硬质合金的重要技术指标之一,它反映了合金的抗压能力和耐磨性能。
硬度与合金中主要成分的含量直接相关。
一般来说,当钴、镍等软金属含量增加时,硬质合金的硬度会下降;而当碳化物含量增加时,硬度则会提高。
此外,硬质合金中的其他元素如钼、钛等也会对硬度产生影响。
2. 韧性与硬度的关系韧性是硬质合金材料的另一个重要性能指标,它表示材料在受到冲击或扭矩时的抗变形能力。
一般情况下,硬度与韧性呈负相关关系,即硬度越高,韧性越低。
这是因为硬度较高的合金通常会对外部应力产生较强的阻抗,导致其在受力时更容易发生破裂。
然而,在实际应用中,我们往往需要综合考虑硬度和韧性之间的平衡。
一种常见的方法是通过改变合金的成分和组织结构,以提高硬质合金的韧性。
例如,通过添加适量的微合金元素、采用细化晶粒的方法,可以在保持硬度的同时提高韧性,满足实际使用的需求。
3. 抗磨耐磨性与硬度的关系硬质合金的抗磨性能是其在工程领域得到广泛应用的重要原因之一。
抗磨耐磨性与硬度之间存在着密切的关系。
一般来说,硬度越高的硬质合金,在受到磨擦和磨粒冲击时,损耗的材料越少,抗磨性能越好。
此外,硬质合金的抗磨耐磨性还与材料中碳化物的类型和分散程度有关。
硬质合金中主要的碳化物有钨碳化物、钼碳化物、钛碳化物等。
一般来说,碳化物颗粒尺寸越小、分散越均匀,抗磨耐磨性能就越好。
4. 导热性与硬度的关系硬质合金的导热性能是其在高速切削等工艺中受到关注的一个参数。
导热性与硬度之间存在着反比关系。
硬度较高的硬质合金通常具有较低的导热性,这是因为在硬质合金中,碳化物的高硬度会对热的传导产生阻碍。
然而,硬质合金的导热性也受到其他因素的影响,如合金中金属相的含量、晶粒大小等。
金属切削工艺参数优化及其对刀具寿命的影响

金属切削工艺参数优化及其对刀具寿命的影响概述:金属切削是制造业中常见的加工工艺,因为其高效、准确性以及广泛的应用领域而受到广泛关注。
刀具寿命是金属切削工艺中一个重要的指标,它直接关系到生产效率和成本。
本文将探讨金属切削工艺参数的优化方法,并分析这些参数对刀具寿命的影响。
金属切削工艺参数的优化方法:1. 切削速度:切削速度是指刀具在切削过程中与金属工件相对运动的速度。
切削速度的选取要根据具体的材料和加工情况来决定。
通常情况下,选取较高的切削速度能够提高加工效率,但可能会增加刀具磨损和损坏的风险。
因此,在确定切削速度时,需要综合考虑加工效率和刀具寿命,通过试验和经验来确定最佳切削速度。
2. 进给速度:进给速度是指切削刀具在切削过程中沿着工件表面移动的速度。
进给速度的选择要综合考虑加工表面质量、切削力和刀具寿命等因素。
通常情况下,选取较高的进给速度可以提高加工效率,但可能会增加切削力并缩短刀具寿命。
因此,在确定进给速度时,需要综合考虑多个参数,并进行试验和调整以找到最佳值。
3. 切削深度:切削深度是指刀具在每次切削中与工件接触的距离。
切削深度的选取要根据具体的刀具和材料来决定。
一般来说,较小的切削深度可以减小切削力和刀具磨损,但可能会降低加工效率。
在确定切削深度时,需要综合考虑加工效率、刀具寿命和切削质量等方面的因素。
切削工艺参数对刀具寿命的影响:1. 切削速度对刀具寿命的影响:较高的切削速度可能会导致刀具表面温度升高,增加刀具磨损和损坏的风险。
因此,在确定切削速度时,需要平衡加工效率和刀具寿命,并根据具体材料和刀具来进行调整。
2. 进给速度对刀具寿命的影响:较高的进给速度可能会增加切削力和切削温度,从而加速刀具磨损和损坏。
因此,在确定进给速度时,需要综合考虑加工效率、刀具寿命和切削质量等因素,选择一个合适的值。
3. 切削深度对刀具寿命的影响:较大的切削深度可能会增加切削力和切削温度,导致刀具磨损加剧。
机械制造业磨削基本知识.

等级
超软
软
中软
中
中硬
硬
超硬
代号
D
E
F
G
H
J
K
L
M
N
P
Q
R
S
T
Y
选择
磨淬硬钢选用L~N,磨淬火合金钢选用H~K,高表面质量磨削时选用K~L,刃磨硬质合金刀具选用H~J
表5-1 砂轮特性及用途选择4—硬度
5.1.5 砂轮的组织
砂轮结构的紧密或疏松程度
用颗粒、结合剂和气孔三者体积的比例关系来表示
5.1.2 粒度
表示磨料颗粒的大小
1.一般磨粒
粒度号---磨粒刚好可通过的筛网每英寸长度上(25.4mm)上的孔眼数。单位称为“目”。 粒度号越大,磨粒的实际尺寸越小
类别
粒度号
适 用 范 围
磨粒
8# 10# 12# 14# 16# 20# 22# 24# 30# 36# 40# 46# 54# 60# 70# 80# 90# 100# 120# 150# 180# 220# 240#
双斜边砂轮
OSX
磨齿轮及螺纹
双面凹砂轮
PSA
磨外圆,刃磨刀具,无心磨
切断砂轮 (薄片砂轮)
PB
切断及切槽
筒形砂轮
N
端磨平面
杯形砂轮
B
磨平面、内圆,刃磨刀具
碗形砂轮
BW
刃磨刀具,磨导轨
碟形砂轮
D
磨齿轮,刃磨铣刀、拉刀、铰刀
表5-2 常用砂轮的形状、代号及用途举例
有效磨粒切削刃
无效磨粒切削刃
有效磨粒切削刃只为静态切削刃总数的5%~12%; 一个磨粒可能有几个有效切削刃与工件接触,有60%的有效切削刃分布在不同磨粒上面。
磨削加工中的磨削表面质量

磨削加工中的磨削表面质量磨削作为一种高精度加工方法,被广泛应用于各种工件的制造。
它可以将工件表面磨削至极高的精度与光洁度,从而获得较好的表面质量。
然而,磨削加工中的磨削表面质量却受到许多因素的影响,如磨削工具、工件材料、磨削参数等等。
本文旨在探讨磨削加工中磨削表面质量的影响因素及其改善方法。
1. 磨削工具对表面质量的影响磨削工具是决定磨削加工结果的关键因素之一。
常用的磨削工具有金刚石、氧化铝等硬质磨料、砂轮等。
其中,金刚石磨削工具是应用最为广泛的一种。
磨削工具的形状和尺寸对砂轮的切削性能和磨削表面质量都有直接影响。
刀头的尺寸、尖角和切削边缘的几何形状,都会影响切削力、加工质量和表面粗糙度。
因此,在选择磨削工具时,要根据工件的形状、材料、加工要求等因素选用适当的刀头形状、尺寸和配合角。
2. 工件材料的影响磨削加工中常用的工件材料有金属、陶瓷、非金属等。
不同的工件材料对磨削表面质量的影响不同。
钢是一种常见的金属材料,但是其机械性能与磨削表面质量之间的关系却十分复杂。
一些研究表明,较硬的金属工件往往需要更细小的磨削颗粒,才能获得更好的表面质量。
陶瓷材料因其硬度大、强度高、耐磨性能好等特点而被广泛应用于磨削加工中。
但是,陶瓷材料往往在磨削过程中易产生裂纹和碎裂,因此在磨削过程中需要采取适当的磨削工具和磨削参数。
对于非金属材料,如玻璃、聚合物等,其表面质量往往受到磨削颗粒的大小、形状和密度的影响。
因此,在选择磨削工具和磨削参数时应注意控制磨削颗粒的大小和密度,以获得满足要求的表面质量。
3. 磨削参数的作用除了磨削工具和工件材料外,磨削参数也对磨削表面质量起着重要的作用。
磨削参数包括切削速度、进给量、切削深度等。
切削速度是指砂轮转速与砂轮半径的乘积。
过高的切削速度会导致砂轮表面温度过高,磨削表面质量差,进而烧伤工件表面。
因此,在选择磨削速度时应根据工件材料及其硬度来决定。
进给量是指工件在单位时间内移动的距离。
磨刀器对刀具切削表面质量的影响分析

磨刀器对刀具切削表面质量的影响分析切削表面质量是衡量刀具性能的重要指标之一,而磨刀器作为刀具磨削的工具,对刀具切削表面质量有着重要的影响。
本文将对磨刀器对刀具切削表面质量的影响进行详细分析。
首先,磨刀器的刀具磨削技术对切削表面质量有直接影响。
对于不同的刀具材料和刀具类型,磨刀器需要选择合适的磨削工艺和磨削参数。
比如,对于高硬度刀具材料如硬度超过HRC60的刀具,磨削时需要选择较低的磨削速度和为刀具提供足够的冷却润滑剂,以免导致刀具表面温度过高和刀具磨削面的氧化等问题,从而影响切削表面质量。
其次,磨刀器的刀具磨削精度也会直接影响切削表面质量。
刀具的磨削精度包括磨削精度和磨削粗糙度两个方面。
磨削精度是指刀具的精细度和几何形状的精确度,包括刀具的刃角、刃尖半径、刃腰排列等参数。
磨削粗糙度则是指刀具表面的粗糙度,这直接影响刀具与工件间的摩擦和切削力,进而影响切削表面质量。
对于要求高精度切削表面的工艺,磨刀器需要具备高度的精确度和稳定性,同时要注意控制磨削粗糙度,保证刀具表面的光洁度和精细度。
在刀具磨削过程中,刀具与磨刀器之间的磨削力也会影响切削表面质量。
刀具磨削过程中的磨削力包括正向磨削力和切削力两个方向的力。
正向磨削力是指磨削过程中刀具与磨刀器之间的垂直方向的力,而切削力则是指磨削过程中刀具与磨刀器之间的切向力。
这两个力的大小和方向会影响刀具的稳定性和切削表面质量。
磨刀器需要合理调整磨削参数和磨刀器结构,以减小磨削力对刀具表面的影响,并保持稳定性和一致性。
另外,磨刀器的材料也对切削表面质量有一定的影响。
磨刀器材料的选择应根据刀具的材料和刀具的磨削要求来确定。
常见的磨刀器材料有高速钢、硬质合金、陶瓷等。
不同材料的磨刀器对刀具表面的磨削效果和切削表面质量有着不同的影响。
选择适合的磨刀器材料可以提高刀具的磨削效率和切削表面质量。
此外,刀具和磨刀器的配合度也会影响切削表面质量。
刀具与磨刀器之间的配合度主要包括刀具安装精度和磨刀器结构尺寸与刀具尺寸的匹配度。
硬质合金刀具铣削GFRP_材料加工特性的研究

第51卷㊀第2期2023年2月㊀㊀林业机械与木工设备FORESTRYMACHINERY&WOODWORKINGEQUIPMENTVol51No.2Feb.2023研究与设计硬质合金刀具铣削GFRP材料加工特性的研究宋宇翔1ꎬ㊀袁向东2ꎬ㊀林雨斌2ꎬ㊀伍占文1ꎬ㊀贾㊀翀1ꎬ㊀丁建文1∗(1.南京林业大学材料科学与工程学院ꎬ江苏南京210037ꎻ2.乐客精密工具(太仓)有限公司ꎬ江苏苏州215400)摘㊀要:为了获得硬质合金刀具加工玻璃纤维增强复合材料(GFRP)的理想铣削参数ꎬ为实际生产提供参考ꎬ使用硬质合金柄铣刀对GFRP进行开料铣削加工ꎬ以进给速度及主轴转速为铣削因素ꎬ以铣削力㊁铣削温度㊁表面粗糙度及表面损伤形貌为评价指标ꎬ对硬质合金铣刀开料铣削加工GFRP材料的加工特性进行探究ꎮ结果表明ꎬ随着进给速度的增加ꎬ铣削力F(x)与F(y)均呈上升趋势ꎬ铣削温度呈下降趋势ꎬ表面粗糙度随着温度的下降也呈下降趋势ꎻ随着刀具转速的增加ꎬ铣削力F(x)与F(y)呈先下降后上升的趋势ꎬ并在14000r/min时达到谷值ꎮ同时ꎬGFRP开料加工时顺铣端的表面损伤程度要低于逆铣端ꎬ即顺铣可以得到更好的表面质量ꎮ因此ꎬ在选择GFRP材料的开料加工参数时ꎬ应根据刀具参数ꎬ在计算出合适的每齿进给量的基础上ꎬ尽可能选用较大的进给速度与主轴转速ꎬ从而提高加工效率ꎬ并在一定程度上减小刀具磨损ꎬ提高表面质量ꎬ降低成本ꎮ关键词:硬质合金刀具ꎻ玻璃纤维增强复合材料(GFRP)ꎻ开料ꎻ加工特性中图分类号:TS643㊀㊀文献标识码:A㊀㊀文章编号:2095-2953(2023)02-0043-07StudyonefficientmillingofGFRPmaterialswithcementedcarbidetoolSONGYu ̄xiang1ꎬ㊀YUANXiang ̄dong2ꎬ㊀LINYu ̄bin2ꎬ㊀WUZhan ̄wen1ꎬ㊀JIAChong1ꎬ㊀DINGJian ̄wen1∗(1.CollegeofMaterialsScienceandEngineeringꎬNanjingForestryUniversityꎬNanjingJiangsu210037ꎬChinaꎻ2.LEUCOPrecisionTooling(Taicang)Co.ꎬLtdꎬSuzhouJiangsu215400ꎬChina)Abstract:Inordertoobtaintheidealmillingparametersofglassfiberreinforcedcomposites(GFRP)processedbycementedcarbidetoolsꎬanalyzethesurfacedamageformandfailuremechanismꎬandprovidereferenceforpracticalproductionꎬthispapercarriedthemillingexperimentalwithcarbideshankmillingcutterandtakingthefeedspeedandspindlespeedasthemillingfactorsꎬandtakingthemillingforceꎬmillingtemperatureꎬsurfaceroughnessandsurfacedamagemorphologyastheevaluationindexesꎬthemachiningcharacteristicsofGFRPmaterialswereinvesti ̄gated.TheresultsshowthatwiththeincreaseofthefeedspeedꎬthemillingforceF(x)andF(y)bothincreasesꎬthemill ̄ingtemperaturedecreasesꎬandthesurfaceroughnessalsodecreaseswiththedecreaseoftemperature.WiththeincreaseoftoolspeedꎬthemillingforcesF(x)andF(y)decreasefirstandthenincreaseꎬandreachthepeakvalueat14000r/min.Atthesametimeꎬthesurfacequalityoftheup-millingendishigherthanthatofthereversemillingend.㊀㊀收稿日期:2022-09-15基金项目:南京林业大学2021年自制实验教学仪器项目(nlzzyq202113)第一作者简介:宋宇翔ꎬ硕士研究生ꎬ研究方向为木材加工装备ꎬE-mail:457833753@qq.comꎮ∗通讯作者:丁建文ꎬ副教授ꎬ硕士ꎬ研究方向为木材加工装备工程ꎬE-maill:dingjianwen@njfu.edu.cnꎮ林业机械与木工设备第51卷ThereforeꎬwhenselectingtheprocessingparametersofGFRPmaterialsꎬthefeedingspeedandspindlespeedshouldbeselectedaslargeaspossibleonthebasisofcalculatingtheappropriatefeedamountofeachtoothaccordingtothetoolparametersꎬsoastoimprovetheprocessingefficiencyꎬreducethetoolweartoacertainextentꎬimprovethesur ̄facequalityandreducethecost.Keywords:CementedcarbidetoolꎻGlassfiberreinforcedcomposite(GFRP)ꎻCuttingꎻProcessingproperties随着科学技术发展与时代的进步ꎬ我国工业快速发展ꎬ各行各业对于材料的要求越来越高ꎬ在很多领域新型材料逐渐取代大部分传统材料ꎬ复合材料的发展也愈发迅速ꎬ并开始被广泛应用于交通㊁航空航天㊁建筑㊁风力发电以及休闲等领域[1ꎬ2]ꎮ根据增强材料种类的不同ꎬ又可分为玻璃纤维增强复合材料㊁碳纤维增强复合材料以及芳纶纤维增强复合材料等ꎬ其中玻璃纤维增强复合材料(GFRP)是指由二氧化硅㊁氧化硼㊁氧化铝㊁氧化钙等组成的玻璃纤维材料与环氧树脂融合后热压成型的一种复合材料ꎮGFRP相较于其他传统材料有更加优异的性能ꎬ主要有质量轻㊁电绝缘性好㊁热均匀性佳㊁使用寿命长㊁高强度㊁高模量㊁隔热性好㊁阻燃性强等优点ꎮ另外值得一提的是ꎬ玻璃纤维是一种性能优异的无机非金属材料ꎬ它是以玻璃球或废旧玻璃为原料经高温熔制㊁拉丝㊁络纱㊁织布等工艺制造而成的ꎬ所以它可有效解决玻璃废弃物的污染及回收处理问题ꎬ在一定意义上保护了自然环境ꎬ提高了玻璃制品的附加价值ꎮ因此ꎬ玻璃纤维材料现在已经被广泛应用且愈受重视ꎬ发展前景广阔[3-7]ꎮ玻璃纤维增强复合材料一般为一次性整体成型ꎬ不需再进行机械加工ꎬ但因装配与精度的需要ꎬ在实际生产中ꎬ需要对其进行一定的加工ꎮ相对于金属材料而言ꎬ复合材料的加工要更加困难ꎮGFRP中分布有纤维ꎬ其为各向异性㊁非均质性的材料[8ꎬ9]ꎬ在加工过程中难免会出现纤维破坏㊁撕裂的现象ꎬ这样的加工缺陷往往会使得材料在装配及实际使用中产生不适ꎬ所以对GFRP的加工特性进行研究ꎬ对其制造环节的发展有较大的意义ꎮ在对复合材料进行机械加工中ꎬ切削是较为重要的二次加工方式ꎬ常用的切削方式有铣削[10]㊁锯切㊁钻削[11]㊁车削等ꎬ而在GFRP加工中ꎬ对钻削与车削的研究较多ꎬ与铣削相关的研究并不多见ꎬ本文主要是对GFRP进行铣削加工ꎬ铣削加工是指刀具沿预定工件表面铣削玻璃纤维材料ꎬ获得要求的尺寸㊁形状及粗糙度的过程ꎮ铣削加工中ꎬ刀具与工件的相对运动ꎬ会产生较大切削力ꎬ较高切削温度ꎬ不同的表面粗糙度ꎬ以及不同的加工质量ꎮ它们取决于铣削参数(进给速度㊁切削深度㊁刀具转速)与刀具参数(前后角㊁切削刃数量及分布)的变化ꎬ这些切削性能指标都能直接或间接地对产品质量㊁生产效率㊁生产成本及能耗产生较大的影响[12-15]ꎮ而通过试验及数据分析得出的结论ꎬ能够为玻璃纤维材料在工厂实际生产提供理论指导依据ꎬ并为玻璃纤维材料的制造加工及更深远的发展奠定一定的理论基础ꎮ1㊀材料与方法1.1㊀材料1.1.1㊀加工刀具鉴于GFRP材料具有硬度高㊁散热差等特性ꎬ高速钢刀具的磨损较快ꎬ加工质量较差ꎬ所以本次试验采用赛诚精密工具有限公司提供的高硬度㊁耐高温的硬质合金柄铣刀ꎬ其在复合材料如CFRP㊁GFRP等加工中已经被广泛应用ꎮ硬质合金铣刀如图1所示ꎬ铣刀参数见表1ꎮ图1㊀硬质合金柄铣刀1.1.2㊀加工工件以临安普力电子材料有限公司生产的6mm玻璃纤维增强复合材料板为试验对象ꎬ实际试件尺寸(长㊁宽㊁厚)为140mmˑ8mmˑ6mmꎮGFRP复合材料板由树脂和电子级玻璃布组成ꎬ材料成分及板件物理性能检测报告如表2所示:44第2期宋宇翔ꎬ等:硬质合金刀具铣削GFRP材料加工特性的研究表1㊀硬质合金柄铣刀参数刀齿数量刀刃直径/mm最大转速/r min-1刀柄直径/mm总长度/mm282400012.770表2㊀GFRP材料成分表树脂成分占比(%)玻璃纤维布成分占比(%)溴化环氧树脂99.97MgO0~5B2O3.5~10Na2O㊁K2O0~2Fe2O30.05~0.4水解氯0.02~0.035F20~1.0SiO252~56CaO16~25Al2O312~161.2㊀试验方法本次试验场所为南京林业大学材料工程学院ꎬ试验设备使用南兴MGK01加工中心ꎬ刀具材料为8mm硬质合金柄铣刀ꎬ工件材料尺寸为80mmˑ140mmˑ6mmꎮ加工工件为玻璃纤维增强复合材料ꎬ加工方式为开料加工ꎬ试验如图2所示ꎬ试验流程如图3所示ꎮ图2㊀铣削试验示意图图3㊀试验流程图本次试验采用控制变量法ꎬ通过设定不同的进给速度(100~500mm/min)及主轴转速(10000~18000r/min)ꎬ对玻璃纤维增强复合材料进行开料加工ꎬ以加工时产生的铣削力㊁铣削温度及加工后试件的表面粗糙度及表面形貌为评价指标ꎮ其中ꎬ铣削力采用kistler公司9257B型号测力仪进行采集ꎬ如图3(a)所示ꎻ铣削温度采用红外热成像仪进行拍摄ꎬ如图3(b)所示ꎻ表面粗糙度采用探针式轮廓仪进行测量ꎬ如图3(c)所示ꎻ表面损伤形貌采用Quanta200扫描电镜拍摄并进行对比分析ꎮ2㊀结果与分析本次试验为高效开料加工ꎬ采用了较大的主轴转速及进给速度ꎬ铣削试验共获得15种不同铣削参数组合下的F(x)和F(y)ꎬ试验结果如表3所示ꎮ2.1㊀铣削力的分析铣削力是评判材料铣削性能的重要指标之一ꎬ它是铣削层材料在刀具的作用下发生变形的结果ꎬ直接影响到加工稳定性ꎬ对铣削热生成㊁刀具磨损㊁工件表面质量及设备损耗有着重要的影响ꎮ因此ꎬ对铣削力的研究一直是铣削加工中的研究重点ꎮ深入研究不同铣削参数对铣削力的影响ꎬ对提高GFRP加工质量与加工性能有显著价值ꎮ在开料过程中ꎬ机床的振动及刀具的振动和轴向跳动均会导致Z轴铣削力的波动ꎬ致使误差出现ꎬ因此试验只对F(x)及F(y)的变化情况进行研究ꎬ在铣削力相对平稳阶段取平稳值进行研究ꎮ(1)进给速度对铣削力的影响分析不同进给速度对铣削力的影响ꎬ如图4所示ꎬ其结果表明ꎬ铣削力F(x)与F(y)均随进给速度的增大而增大ꎬ这是因为随着铣刀进给速度的增加ꎬ每齿进给量也在不断变大ꎬ单位时间内铣削刃需要切54林业机械与木工设备第51卷除更多的材料ꎬ并且随着进给速度的增大ꎬ切屑也更难排出ꎬ汇聚在铣削加工的中心ꎬ在增加铣削量的同时也会增加相应的刀具/工件及刀具/切屑间的摩擦ꎬ使得铣削力进一步增大ꎮ表3㊀硬质合金刀具在不同参数下的试验结果主轴转速/r∙min-1进给速度/mm∙min-1铣削力F(x)/N铣削力F(y)/N温度T/ħ表面粗糙度Ra/μm左侧面(顺铣)右侧面(逆铣)1800010076.9738.28123.81.7372.05620095.6060.20117.81.6451.871300116.3074.95115.81.3881.621400114.2078.40102.50.8551.196500174.1092.99100.80.6141.0141400010030.9833.10131.21.5431.83020031.9733.48128.21.5031.67230038.0534.94125.11.4211.52740041.2234.68123.11.3611.43150046.9936.89119.31.3691.4151000010032.9428.66125.91.3571.53620038.7244.70113.81.3211.51230053.8458.38112.91.2311.39840067.7672.79111.31.2761.33750076.6776.03108.21.1371.295图4㊀进给速度及主轴转速对铣削力的影响㊀㊀(2)主轴转速对铣削力的影响如图4所示ꎬ其结果表明ꎬ随着主轴转速的不断增大ꎬ铣削力F(x)与F(y)均呈现先下降再上升的趋势ꎬ随着主轴转速从10000r/min增至14000r/minꎬ刀具与工件的摩擦加剧ꎬ产生大量铣削热ꎬ软化树脂ꎬ使得工件表面结合力下降ꎬ较小的铣削力即可切除材料ꎮ而在转速从14000r/min增加至18000r/min时ꎬ铣削力反而呈快速上升趋势ꎬ可能是当转速达到相应临界点时所发生的变化ꎬ规律尚不明确ꎬ需后续进一步探究ꎮ2.2㊀铣削温度的分析在铣削加工过程中ꎬ铣削层材料在刀具的挤压作用下形成切屑ꎬ并沿着刀具回转方向排出ꎮ在该过程中ꎬ除了刃口前端的材料发生塑性变形做功之外ꎬ刀具还会与切屑和已加工表面接触摩擦做功产生铣削热ꎬ特别是对于产生粉末状切屑的GFRP铣削过程ꎬ摩擦做功现象更加显著ꎬ产生的铣削热提高64第2期宋宇翔ꎬ等:硬质合金刀具铣削GFRP材料加工特性的研究了铣削区域的温度ꎬ而铣削温度也是一个重要的衡量指标ꎬ对加工表面的质量和刀具磨损都有着直接或间接性的影响ꎮ本次试验的铣削温度数据采集为最大温度ꎮ以主轴转速为18000r/minꎬ进给速度为500mm/min为例ꎬ铣削温度于铣刀切出工件时取得最大温度100.8ħꎬ铣削温度取值如图5所示ꎮ图5㊀铣削温度取值结果表明ꎬ随着进给速度的增大ꎬGFRP的铣削温度呈现明显下降的趋势ꎬ如图6所示ꎬ这主要是因为GFRP材料本身的导热性能较差ꎬ且硬质合金刀具的导热性能也不强ꎬ在开料过程中ꎬ粉状GFRP切削大量积聚在刀具铣削刃处ꎬ并与刀具产生摩擦ꎬ进一步减弱了热传导能力ꎬ促使温度升高ꎬ并且开料过程一般最大温度是在刀具切出工件处取得ꎬ这与热累积效应相关ꎬ即铣削完成后ꎬ下一次铣削时温度无法降低至常温ꎬ热量不断累积ꎬ致使温度不断升高ꎬ本次试验为开料试验ꎬ刀具行程为80mmꎬ在低进给速度条件下ꎬ热累积的时间较长ꎬ而在高进给速度条件下ꎬ加工时长较短ꎬ热量累计时长短ꎬ所以最高温度较低ꎮ而从试验数据可知主轴转速对温度的影响规律与铣削力相反ꎬ并且主轴转速的变化对温度的影响较进给速度而言并不明显ꎮ图6㊀进给速度及主轴转速对铣削温度的影响2.3㊀表面质量的分析表面质量作为产品的一项重要评价指标ꎬ一般以表面粗糙度及表面损伤形貌作为判定标准ꎮ2.3.1㊀表面粗糙度的分析表面粗糙度是评价铣削质量的一项重要指标ꎬ它表征了加工后表面的光洁度与质量ꎬ影响到后续的加工及使用ꎬ本文试验数据中的表面粗糙度取值均为顺铣端数值ꎮ进给速度及主轴转速对表面粗糙度的影响如图7所示ꎬ随着进给速度的增大ꎬGFRP的表面粗糙度呈现下降趋势ꎬ这主要是取决于开料加工的特殊性ꎬ加工距离较短ꎬ切屑大量堆积ꎬ铣削温度随进给速度的下降而不断升高ꎬ随着温度的升高ꎬ材料表面的树脂软化ꎬ使得玻璃纤维与树脂间结合力大大下降ꎬ在加工过程中纤维更易被拉扯ꎬ产生材料表面的毛刺与撕裂ꎬ致使表面粗糙度增大ꎮ而随着转速的变化ꎬ表面粗糙度无明显规律ꎬ但在18000r/min的条件下ꎬ表面粗糙度的变化幅度加大ꎮ同时ꎬ由于本次试验为开料加工ꎬ加工方式分为顺铣和逆铣两种ꎬ顺铣得到的左表面与逆铣得到的右表面进行对比ꎬ顺铣与逆铣对表面粗糙度的影响如图8所示ꎬ同加工参数下ꎬ顺铣端的工件表面粗糙度明显小于逆铣端ꎬ这主要与加工过程中刀具的回转方式相关ꎬ在开料铣削加工中ꎬ顺铣与逆铣所产生的铣削力的方向相反ꎬ在加工GFRP这类复合材料时ꎬ由于其各向异性与非均质性等特点ꎬ顺铣所产生的力与热量就会明显小于逆铣ꎬ顺铣表面在热力耦合作用下的纤维损伤程度也会小于逆铣表面ꎬ所以其结果表明ꎬ在开料铣削加工中ꎬ顺铣的表面较逆铣的表面更加平滑ꎮ图7㊀进给速度及主轴转速对表面粗糙度的影响74林业机械与木工设备第51卷图8㊀顺铣与逆铣对表面粗糙度的影响2.3.2㊀加工表面损伤机理的分析试验所用GFRP材料为编织成型ꎬ其结构原理如图9(a)所示ꎬ本次试验采用SEM扫描电镜对加工后工件的表面形貌进行分析研究ꎬ如图9(b)所示ꎬ箭头所指区域为材料铣削后的纵向编织纤维的横截面ꎬ可见扫描电镜下GFRP结构也清晰可见ꎮ图9㊀GFRP成型结构㊀㊀在GFRP铣削开料加工中ꎬ损伤多位于材料表层且分布不规则形状无规律ꎬ在开料过程中由于刀具的回转方式不同导致铣削力方向不同ꎬ因而顺铣表面与逆铣表面损伤程度往往不同ꎬ其主要以表层纤维撕裂及表面毛刺为主ꎬGFRP开料加工材料破坏特征如图10所示ꎬ在扫描电镜2000倍放大下ꎬ可看到图10(a)顺铣表面表层纤维多为完整纤维ꎬ图10(b)逆铣表面表层纤维撕裂程度较大ꎬ且顺铣表面以零星的细小树脂颗粒为主ꎬ而逆铣表面存在较大块的树脂碎块并交杂着撕裂的纤维ꎬ但同时裸露纤维处上方纵向切断的纤维横截面并未看出顺铣与逆铣加工下的明显差异ꎬ综上可明显看出顺铣下的左表面质量要高于逆铣下的右表面质量ꎬ尽管损伤类型相似ꎬ但逆铣的表面质量较顺铣会明显较低ꎬ这与分析表面粗糙度得出的结果是一致的ꎮ图10㊀GFRP开料加工材料破坏特征84第2期宋宇翔ꎬ等:硬质合金刀具铣削GFRP材料加工特性的研究3㊀结论本文使用硬质合金铣刀对GFRP材料进行开料加工ꎬ试验设计采用控制变量法ꎬ以刀具进给速度及机床主轴转速为因素ꎬ加工时采集的铣削力及铣削温度与加工后GFRP表面粗糙度及扫描电镜下的工件损伤形貌作为具体评价指标ꎬ对GFRP的开料加工特性进行分析与评价ꎬ结果如下:(1)在较短距离的开料加工中ꎬ随着进给速度的不断增大ꎬ单位时间内的材料去除量增大ꎬ铣削力F(x)与F(y)均呈明显上升趋势ꎬ同时因为热累积效应以及刀具及材料的热传导能力均较差ꎬ较高的进给速度所需加工时间较短ꎬ铣削温度反而呈下降趋势ꎬ同时表面粗糙度也因温度的下降而呈下降趋势ꎬ这与以往的结论并不相似ꎮ(2)随着主轴转速的增加ꎬ铣削力F(x)与F(y)均呈现先减后增的趋势ꎬ在14000r/min时铣削力达到谷值ꎮ同时ꎬ在18000r/min时ꎬ表面粗糙度的下降幅度大大增加ꎮ(3)从表面粗糙度的结果对比可知ꎬ在开料加工中顺铣的表面质量较逆铣要更高ꎬ扫描电镜显微图中也可清晰看到ꎬ顺铣与逆铣损伤形式类似ꎬ但逆铣加工纤维的损伤较顺铣加工纤维损伤更加明显ꎮ参考文献:[1]㊀ChawlaKK.Compositematerials:scienceandengineering[M].NewYork:Springerꎬ2012.[2]㊀陈祥宝ꎬ张宝艳ꎬ邢丽英.先进树脂基复合材料技术发展及应用现状[J].中国材料进展ꎬ2009ꎬ28(6):2-12.[3]㊀徐敏东.玻璃纤维增强玻璃复合材料研究[D].上海:东华大学ꎬ2011.[4]㊀YahyaHışmanÇelikꎬCihatTürkan.InvestigationofmechanicalcharacteristicsofGFRPcompositesproducedfromchoppedglassfi ̄berandapplicationoftaguchimethodstoturningoperations[J].SNAppliedSciencesꎬ2020ꎬ2(5).[5]㊀AnjanaJainꎬShivkumarMina ̄jagiꎬEnoosDangeꎬSushmaUBhoverꎬYTDharanendra.Impactandacousticemissionperformanceofpolyvinylidenefluoridesensorem ̄beddedinglassfiber-reinforcedpolymercompositestructure[J].PolymersandPolymerCompositesꎬ2020ꎬ29(5): [6]㊀NgoTuanT.ꎬPhamThongM.ꎬHaoHongꎬChenWensuꎬElchalakaniMohamed.PerformanceofmonolithicanddryjointswithGFRPboltsreinforcedwithdifferentfibresandGFRPbarsunderimpactloading[J].EngineeringStructuresꎬ2021ꎬ240.[7]㊀朱殿功.高强度GFRP纤维筋与耐久性[C].贵阳:2021第八届海洋材料与腐蚀防护大会暨2021第二届钢筋混凝土耐久性与设施服役安全大会ꎬ2021.[8]㊀WANGDHꎬRAMULUMꎬAROLAD.Orthogonalcuttingmecha ̄nismsofgraphite/epoxycomposite.PartII:multi-directionallami ̄nate[J].InternationalJournalofMachineTools&Manufactureꎬ1995ꎬ35(12):1639-1648.[9]㊀周井文ꎬ黄久超ꎬ杨叶ꎬ等.玻璃纤维增强复合材料端铣加工刀具磨损与表面质量研究[J].工具技术ꎬ2021ꎬ55(11):45-48. [10]㊀PalanikumarK.Mathematicalmodeltopredictthesurfaceroughnessonthemachiningofglassfiberreinforcedpolymercomposites[J].JournalofReinforcedPlastics&Compos-itesꎬ2006ꎬ25(25):407-419.[11]㊀宋中权.玻璃纤维增强复合材料钻削加工试验研究[D].南京:南京理工大学ꎬ2010.[12]㊀郑凯.玻璃纤维增强复合材料铣磨槽加工工艺研究[D].南京:南京航空航天大学ꎬ2020.[13]㊀ChangChungShin.Turningofglass–fiberreinforcedplasticsmaterialswithchamferedmaincuttingedgecarbidetools[J].Jour ̄nalofMaterialsProcessingTech.ꎬ2006ꎬ180(1).[14]㊀张秀丽ꎬ张振国ꎬ魏凤春.高强玻璃纤维复合材料的铣削加工性能研究[J].材料导报ꎬ2009ꎬ23(8):84-87.[15]㊀ShenXuehongꎬZhangDinghuaꎬTanLiang.Effectsofcutterpatho ̄rientationsonmillingforceꎬtemperatureꎬandsurfaceintegritywhenballendmillingofTC17alloy[J].ProceedingsoftheInsti ̄tutionofMechanicalEngineersꎬPartB:JournalofEngineeringManufactureꎬ2021ꎬ235(6-7).94。
轧辊磨床磨削工艺参数选择对磨削质量的影响
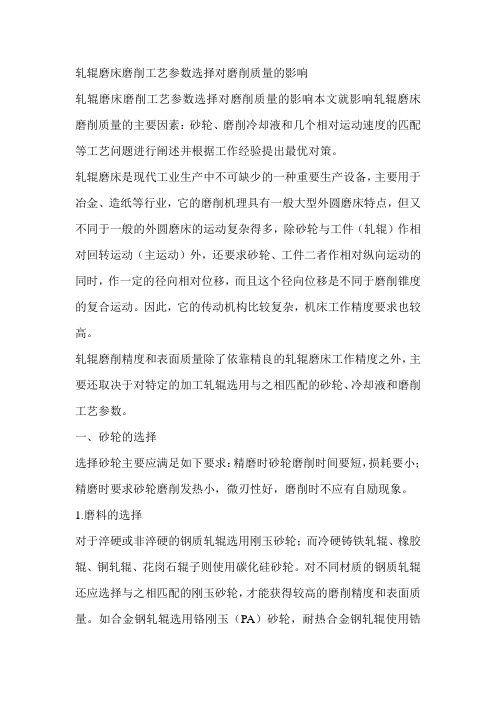
轧辊磨床磨削工艺参数选择对磨削质量的影响轧辊磨床磨削工艺参数选择对磨削质量的影响本文就影响轧辊磨床磨削质量的主要因素:砂轮、磨削冷却液和几个相对运动速度的匹配等工艺问题进行阐述并根据工作经验提出最优对策。
轧辊磨床是现代工业生产中不可缺少的一种重要生产设备,主要用于冶金、造纸等行业,它的磨削机理具有一般大型外圆磨床特点,但又不同于一般的外圆磨床的运动复杂得多,除砂轮与工件(轧辊)作相对回转运动(主运动)外,还要求砂轮、工件二者作相对纵向运动的同时,作一定的径向相对位移,而且这个径向位移是不同于磨削锥度的复合运动。
因此,它的传动机构比较复杂,机床工作精度要求也较高。
轧辊磨削精度和表面质量除了依靠精良的轧辊磨床工作精度之外,主要还取决于对特定的加工轧辊选用与之相匹配的砂轮、冷却液和磨削工艺参数。
一、砂轮的选择选择砂轮主要应满足如下要求:精磨时砂轮磨削时间要短,损耗要小;精磨时要求砂轮磨削发热小,微刃性好,磨削时不应有自励现象。
1.磨料的选择对于淬硬或非淬硬的钢质轧辊选用刚玉砂轮;而冷硬铸铁轧辊、橡胶辊、铜轧辊、花岗石辊子则使用碳化硅砂轮。
对不同材质的钢质轧辊还应选择与之相匹配的刚玉砂轮,才能获得较高的磨削精度和表面质量。
如合金钢轧辊选用铬刚玉(PA)砂轮,耐热合金钢轧辊使用锆刚玉(ZA)砂轮,对不锈钢轧辊要采用单晶刚玉(SA)。
2.粒度的选择粗磨时选用粗粒度(24~60)砂轮;精磨时选用细粒度(60~100)砂轮;精密磨削时采用150粒度砂轮;超精磨削或镜面磨削时,一般使用微粉(W63~W14)砂轮。
3.硬度的选择磨削辊面越硬,砂轮硬度应当选择越软。
(1)如果砂轮磨损太快,说明对于特定加工的轧辊所选用的砂轮太软,可采取以下改善措施:A.提高砂轮的线速度;B.提高拖板纵向进给速度,即工件每转拖板纵向进给量增加到砂轮宽度的2/3~3/4;C.降低轧辊的速度。
如果采取上述措施后尚未取得明显的磨削效果,说明砂轮太软,不适用,应选择硬一点的砂轮。
切削参数变化对加工表面质量的影响—
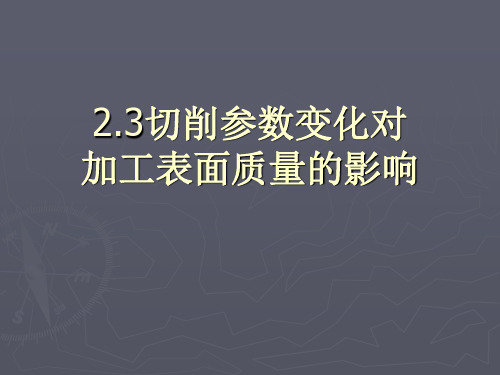
第一变形区(剪切滑移) 第二变形区(挤压摩擦) 第三变形区(挤压摩擦回弹)
1. 切削速度增加时,塑性变形减小,塑性变形区也缩小,因 此,硬化层深度减小。
2. 另一方面,且由于切削速度的增加,切削温度升高,回复 作用增大,冷硬层随之减小。
3. 但切削速度增加,切削热在工件表面层上的作用时间也缩 短了。
► 切削参数包括:
1、切削速度v。2、进给量ƒ。3、切削深度ap。
1、切削速度对表面质量的影响
在不使用切削液的条件下,切削速度增大到一定值后,表面 粗糙度随着切削速度增大而降低。
在实际生产中,切削液的使用很好的改善了加工表面质量。 切削速度增大一定值时,其变化对表面粗糙度的影响不明显。 较大的切削速度下,都可以得到镜面。
22淬火烧伤当磨削区温度超过相变温度时工件表层局淬火烧伤当磨削区温度超过相变温度时工件表层局部区域就会变成奥氏体随后受到冷却液及工件自身导热部区域就会变成奥氏体随后受到冷却液及工件自身导热的急速冷却作用而在表面极薄层内出现二次淬火马氏体的急速冷却作用而在表面极薄层内出现二次淬火马氏体次表层为硬度大为降低的回火索氏体这就是二次淬火烧次表层为硬度大为降低的回火索氏体这就是二次淬火烧33退火烧伤当工件表面层温度超过相变临界温度时则退火烧伤当工件表面层温度超过相变临界温度时则马氏体转变为奥氏体
从图可以看出,残留应力在切削速度方向和进给方向呈现 出不同的变化规律。在切削速度方向随着切削速度增大, 残留应力由残留压应力逐渐变为残留拉应力;在进给方向, 改变切削速度时,残留应力一直是残留压应力。
改变切削速度时,相应地改变了已加工表面所承受的塑性 变形、切削温度的大小与分布情况,因而影响己加工表面 的残留应力。提高切削速度时,切削温度引起的热应力所 占比重增大,因而切削速度方向的残留压应力减小而残留 拉应力增大。
硬质合金刀具刃磨工艺的研究
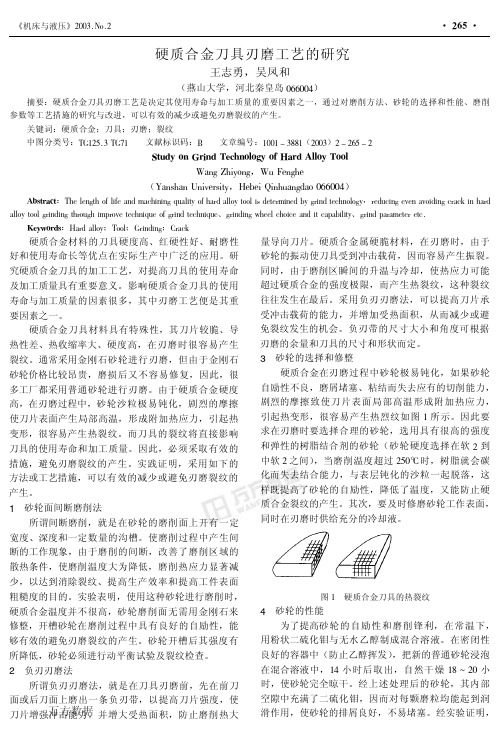
《机床与液压》/##!, ?<,/
轮在工作中如轴向和径向跳动过大,砂轮的旋转方向 与刃口的磨削受力方向不对,刃磨刀具前角与后角的 顺序不妥,都将使刃口产生崩刃如图 / 所示,在主副 切刃、刀尖圆弧上和前刀面上都可能产生细微碎裂状 崩刃。所以要控制砂轮的轴向窜动和径向跳动,砂轮 的旋转方向应使刀片压向刀杆。刃磨时先磨前面负倒 棱、断屑槽,其次磨主后面,最后磨刀尖圆弧及修光 刃。同时采用合理的刃磨步骤,一般要先粗磨、精磨 再研磨的工序。
万方数据 刀片增强冲击能力,并增大受热面积,防止磨削热大
・ "!! ・
利用浸过二硫化钼的砂轮磨削硬质合金刀片,磨削锋 利,砂轮颗粒不易钝化;排屑流畅,切屑的形状基本 呈带状。且工件的变形小,磨削中产生的磨削热,大 部分由切屑带走,提高了磨削效果,并大大提高了刀 片的成品率。 为了获得较高的表面粗糙度和锋利的刃口,要采 用降低磨削速度和软化砂轮的磨削方法。软化砂轮的 方法是用按体积 !:" 的苛性钠和水进行混合,将砂轮 放到该液体中进行煮沸,粒度高的时间为 !# 分钟左 右,粒度低的 $# 分钟左右,每多降一级硬度多煮 !# 分钟左右。 ! 合理的磨削用量 如果刃磨过程中用力过猛,摩擦力过大,使温度 急剧上升,或刃磨时急剧冷却、断续冷却、温度突变、 收缩压力过大,都将导致刀片产生爆裂。因此,在刃 磨时,必须选择合理的磨削用量。通常选用的磨削用 量为:圆 周 速 度 ! % &# ’ &() * +,进 给 量 " 纵 % #,( ’ &,#) * )-.," 横 % #,#& ’ #,#/)) * 行程。对于 01 类的硬质 合金采用 &2 ’ &3) * + 的磨削速度,04 类的硬质合金采 用 &# ’ &/) * + 磨削速度,04!# 及 01! 类的硬质合金采 用 3) * + 磨削速度。手工刃磨时,纵向和横向进给量不 宜太大。 " 其他工艺措施 如果刀杆刚性不足,刀具夹持不稳,机床主轴有 跳动,这些都会造成刃磨裂纹。因此,要求机床、砂 轮、夹具和刀具所组成的系统应具有一定的刚性。砂 (上接第 /"5 页) 出版社名,出版年月,页码(如有两个以上作者,作 者间用逗号分开) 。 !期刊:作者姓名 7 文章名 7 期刊名,年份,卷 (期) 、页码。 (()作者简介附在参考文献下方。 “作者简介”四 字请用小 ( 号黑体字左起顶格排,后空一格,接排简 介内容。作者简介 (# 字以内,包括姓名、出生年月、 工作单位、职务职称、专业领域、地址、邮编、电话、 传真、8 6 )9-:。 (2)如在学术刊物上公开发表过的文章请在简介 下面加注,注明文章发表日期、题目、刊物名称、出 版单位。注文字体用 2 号宋体。 ( 征文截止日期及投递方式 论文作者需填写论文摘要登记表,连同软盘和清 样稿各 & 份,于 /##! 年 $ 月 !# 日前直接送交学术年会 各个会场牵头组织单位(各个会场牵头单位地址及联 系人见附件 2 ) 。各牵头单位将经审定后所推荐的所有 论文摘要软盘 & 张、文章清样稿各一份及录用论文摘 万方数据 # 结论
硬质合金刀具刃磨质量的研究

图 2 切削速度与粗糙度的关系
这是由于砂轮的线速度越高,单位时间内磨粒
图 3 粒度和表面粗糙度的关系
4 . 3 材料与 !zmax之关系 从图 2 和图 3 的曲线中不难看出,在相同的条 件下,YT14 的表面粗糙度均小于 YG6 的表面粗糙 度。这是由于在同样的磨削条件下,由于刀具材料 的导热系数不同(即 YT14 的导热系数小于 YG6 的 导热系 数),即 使 是 单 位 时 间 内 产 生 的 热 量 相 同, YT14 较 YG6 散热慢,磨削区的温度相对较高,材料 软化程度就较大,在磨粒的碾平和推抹作用下,刀具 表面的粗糙度下降。 4.4 粒度、速度和表面裂纹的关系 本试验所用刀具在刃磨前,均用 M10 放大镜进 行了观察,并将有裂纹的刀具剔除。刃磨后将其放
日本在发展 数 控 机 床 的 过 程 中,特 别 注 意 发 展 关 键 技 术,开发核心产品。日本政府重点扶植发那克公司开发数控 机床的数控系统,其他厂家则重点研发机械加工部分。日本 政府引导政策使发那克公司逐步发展成为世界上最大的数 控机床的数控系统供应商,该公司生产的数控系统在日本市 场的占有率达到 80% 以上。即使在世界市场,该公司的数 控系统的销售额也达到了约 50% 。这种合作分工关系提高 了日本数控机床行业效率,避免了美国数控机床行业由于各 厂家都希望 自 己 的 标 准 成 为 行 业 标 准,导 致 产 品 相 互 不 兼 容,而削弱了竞争力的问题。
CNC机床加工中的加工刀具磨损与切削力与切削温度关系研究

CNC机床加工中的加工刀具磨损与切削力与切削温度关系研究随着制造业的不断发展和进步,CNC机床加工已经成为现代机械切削加工领域中的重要技术手段之一。
在CNC机床加工过程中,加工刀具是一个关键的因素,它的磨损情况直接影响到加工质量和效率。
同时,切削力和切削温度也是影响加工刀具寿命和表面质量的重要因素。
因此,研究加工刀具磨损与切削力以及切削温度之间的关系,对于提高CNC机床加工的效率和质量具有重要意义。
1. 加工刀具磨损与切削力关系的研究在CNC机床加工中,加工刀具的磨损是一个不可避免的问题。
随着加工时间的增加,刀具的磨损会导致切削力的增加,从而影响加工质量和效率。
研究发现,刀具磨损与切削力之间存在着紧密的关系。
当刀具磨损较小的时候,切削力主要由刀具的几何形状和材料性质决定;而当刀具磨损达到一定程度时,切削力的增加主要是由刀具磨损形成的刃口变形和堆积效应引起的。
2. 加工刀具磨损与切削温度关系的研究刀具的磨损不仅会影响切削力,还会导致切削温度的升高。
在CNC 机床加工过程中,切削温度的升高会导致刀具的热膨胀和表面氧化,进而加剧刀具的磨损。
因此,研究刀具磨损与切削温度之间的关系对于延长刀具寿命具有重要意义。
研究表明,切削温度的升高是导致刀具磨损的主要原因之一,而刀具磨损又会进一步提高切削温度,从而形成了一个恶性循环。
3. 切削力与切削温度关系的研究切削力和切削温度是CNC机床加工过程中的两个重要参数,它们之间存在着密切的关系。
切削力的大小会直接影响刀具的磨损情况,而切削温度的升高则会增加切削力。
研究表明,切削力与切削温度之间存在着非线性关系,即切削温度的增加会导致切削力的非线性增加。
此外,切削力和切削温度还受到工件材料、切削参数等因素的影响,需要进一步深入研究。
综上所述,CNC机床加工中的加工刀具磨损与切削力以及切削温度之间存在着紧密的关系。
加工刀具的磨损会导致切削力的增加和切削温度的升高,而切削力和切削温度又会进一步加剧加工刀具的磨损。