engine calibration
calibration 翻译

calibration 翻译calibration 在中文中可以翻译为“校准”或“标定”,是指通过调整或校验仪器、设备或系统的精确性和准确性,以确保其测量结果符合预期标准的过程。
以下是一些常见的用法和中英文对照例句:1. Calibration of instruments:- 仪器的校准:- The laboratory technician performed the calibration of the weighing scale. (实验室技术人员对称重秤进行了校准。
)- The temperature gauge needs to undergo calibration before it can be used for accurate measurements. (温度计在进行准确测量之前需要进行校准。
)2. Calibration of equipment:- 设备的校准:- The mechanic carried out the calibration of the machine to ensure its precise functioning. (机械师对机器进行了校准,以确保其精确运行。
)- The laser leveler requires regular calibration to maintain its accuracy. (激光水平仪需要定期校准以保持准确性。
)3. Calibration of systems:- 系统的校准:- The satellite navigation system underwent calibration to improve its positioning accuracy. (卫星导航系统进行了校准,以提高其定位精度。
)- The sound system in the concert hall was meticulously calibrated to ensure optimal audio quality. (音响系统在音乐厅中经过精心校准,以确保最佳音质。
汽车发动机英文参考文献(精选120个最新))

汽车发动机是为汽车提供动力的装置,是汽车的心脏,决定着汽车的动力性、经济性、稳定性和环保性。
下面是搜索整理的汽车发动机英文参考文献,欢迎借鉴参考。
汽车发动机英文参考文献一:[1]Barouch Giechaskiel,Ricardo Suarez-Bertoa,Tero L?hde,Michael Clairotte,Massimo Carriero,Pierre Bonnel,Maurizio Maggiore. Evaluation of NO x emissions of a retrofitted Euro 5 passenger car for the Horizon prize “Engine retrofit”[J]. Environmental Research,2018,166.[2]Shixuan Wang,Ying Liu,Carla Di Cairano-Gilfedder,Scott Titmus,Mohamed M. Naim,Aris A. Syntetos. Reliability Analysis for Automobile Engines: Conditional Inference Trees[J]. Procedia CIRP,2018,72.[3]Kévin Rosset,Violette Mounier,Eliott Guenat,Jürg Schiffmann. Multi-objective optimization of turbo-ORC systems for waste heat recovery on passenger car engines[J]. Energy,2018,159.[4]Mohamed Kamal Ahmed Ali,Hou Xianjun,Mohamed A.A. Abdelkareem,M. Gulzar,A.H. Elsheikh. Novel approach of the graphene nanolubricant for energy saving via anti-friction/wear in automobile engines[J]. Tribology International,2018,124.[5]Shweta Tripathi,K.A. Subramanian. Control of fuel spray wall impingement on piston bowl in palm acid oil biodiesel fueled direct injection automotive engine using retarded injection timing, EGR and increased compression ratio[J]. Applied Thermal Engineering,2018,142.[6]Gianfranco Gagliardi,Francesco Tedesco,Alessandro Casavola. A LPV modeling of turbocharged spark-ignition automotive engine oriented to fault detection and isolation purposes[J]. Journal of the Franklin Institute,2018.[7]Gritsada Sua-Iam,Natt Makul. Innovative utilization of foundry sand waste obtained from the manufacture of automobile engine parts as a cement replacement material in concrete production[J]. Journal of Cleaner Production,2018.[8]Kanhu Charan Nayak,Prashant P. Date. Manufacturing of light automobile engine piston head using sheet metal[J]. Procedia Manufacturing,2018,15.[9]Yisong Chen,Jinqiu Ma,Bin Han,Peng Zhang,Haining Hua,Hao Chen,Xin Su. Emissions of automobiles fueled with alternative fuels based on engine technology: A review[J]. Journal of Traffic and Transportation Engineering (English Edition),2018.[10]Xinfeng Zhang,Minghui Luo,Wei Dai,Chuanqi Yao,Jiwen Wang,DaojinHuang,Chunyang Wang. Automotive fuel cell engine test cell design and its thermal flow analysis[J]. International Journal of Hydrogen Energy,2018.[11]K. Sato,T. Sadahiro,M. Yamazaki,M. Iwase. Throttle Valve Control of Automotive Engine based on Boundary Model[J]. IFAC PapersOnLine,2018,51(13).[12]Ajay Kumar Maddineni,Dipayan Das,Ravi Mohan Damodaran. Numerical Investigation of Pressure and Flow characteristics of Pleated Air Filter System for Automotive Engine Intake Application[J]. Separation and Purification Technology,2018.[13]Masahiro Yamazaki,Kotoru Sato,Katsuya Shinozaki,Masami Iwase. Boundary Modeling and Identification of Normal Operation for Automobile Engine[J]. IFAC PapersOnLine,2018,51(31).[14]Guo Bin,Chen Hong,Song Dafeng. Research on Fast Matching Method of Power System Parameters of Parallel Hybrid Electric Vehicles[J]. IFAC PapersOnLine,2018,51(31).[15]Natália de Assis Brasil Weber,Bárbara Pacheco da Rocha,Paulo Smith Schneider,Luiz Carlos Daemme,Renato de Arruda Penteado Neto. Energy and emission impacts of liquid fueled engines compared to electric motors for small size motorcycles based on the Brazilian scenario[J]. Energy,2019,168.[16]Francesco Del Pero,Massimo Delogu,Marco Pierini. Life Cycle Assessment in the automotive sector: a comparative case study of Internal Combustion Engine (ICE) and electric car[J]. Procedia Structural Integrity,2018,12.[17]Shan Lin,Li Zhao,Shuai Deng,Jiaxin Ni,Ying Zhang,Minglu Ma. Dynamic performance investigation for two types of ORC system driven by waste heat of automotive internal combustion engine[J]. Energy,2019,169.[18]Zhang Jian,Piao Zhong-yu,Liu Shi-ying,Su Sheng-wei,Deng Li-jun. Investigation of wear behavior of graphite coating on aluminum piston skirt of automobile engine[J]. Engineering Failure Analysis,2019.[19]Karsten Wittek,Frank Geiger,Jakob Andert,Mario Martins,Vitor Cogo,Thompson Lanzanova. Experimental investigation of a variable compression ratio system applied to a gasoline passenger car engine[J]. Energy Conversion and Management,2019,183.[20]Adnan Kadhim Rashid,Mohd Radzi Abu Mansor,Alexandru Racovitza,Radu Chiriac. Combustion Characteristics of Various Octane Rating Fuels for Automotive Thermal Engines Efficiency Requirements[J]. Energy Procedia,2019,157.[21]Marlon Cadrazco,Alexander Santamaría,John R. Agudelo. Chemical and nanostructural characteristics of the particulate matter produced by renewable diesel fuel in an automotive diesel engine[J]. Combustion and Flame,2019,203.[22]Kenneth Holmberg,Ali Erdemir. The impact of tribology on energy use and CO 2 emission globally and in combustion engine and electric cars[J]. Tribology International,2019,135.[23]Hongli Gao,Fujun Zhang,Sufei Wang,Hao Wu,Zhengkai Wang. Effect of Characteristic Parameters on the Magnetic Properties of Voice Coil Motor for Direct Fuel Injection in Gasoline Engine[J]. Energy Procedia,2019,158.[24]Xunan Gao,Bojan Savic,Roland Baar. A numerical procedure to model heat transfer in radial turbines for automotive engines[J]. Applied Thermal Engineering,2019,153.[25]Senthil Kumar Kandasamy,Arun Saco Selvaraj,Thundil Karuppa Raj Rajagopal. Experimental investigations of ethanol blended biodiesel fuel on automotive diesel engine performance, emission and durability characteristics[J]. Renewable Energy,2019,141.[26]Ganesh Duraisamy,Murugan Rangasamy,Nagarajan Govindan. A comparative study on methanol/diesel and methanol/PODE dual fuel RCCI combustion in an automotive diesel engine[J]. Renewable Energy,2020,145.[27]Nosratollah Izadiamoli,Hoseyn Sayyaadi. Conceptual design, optimization, and assessment of a hybrid Otto-Stirling engine/cooler for recovering the thermal energy of the exhaust gasses for automotive applications[J]. Energy Conversion and Management,2018,171.[28]Federico Millo,Pranav Arya,Fabio Mallamo. Optimization of automotive diesel engine calibration using genetic algorithm techniques[J]. Energy,2018,158.[29]Yonggyu Lee,Seungmook Oh,Changup Kim,Junsun Lee,Kanghun Lee,Junghwan Kim. The dual-port fuel injection system for fuel economy improvement in an automotive spark-ignition gasoline engine[J]. Applied Thermal Engineering,2018,138.[30]S. d'Ambrosio,A. Ferrari,D. Iemmolo,A. Mittica. Dependence of combustion noise on engine calibration parameters by means of the response surface methodology in passenger car diesel engines[J]. Applied Thermal Engineering,2019.汽车发动机英文参考文献二:[31]Ivan Bortel,Ji?í Vávra,Michal Takáts. Effect of HVO fuel mixtures onemissions and performance of a passenger car size diesel engine[J]. Renewable Energy,2019,140.[32]Jaeho Cho,Kangjin Kim,Sungha Baek,Cha-Lee Myung,Simsoo Park. Abatement potential analysis on CO 2 and size-resolved particle emissions from a downsized LPG direct injection engine for passenger car[J]. Atmospheric Pollution Research,2019.[33]Jamie Sleigh,Catherine E. Warnaby. Finding the starter motor for the engine of consciousness[J]. British Journal of Anaesthesia,2019,123(3).[34]S. Prakash,M. Prabhahar,S. Sendilvelan,R. Venkatesh,Sanjay Singh,K. Bhaskar. Experimental studies on the performance and emission characteristics of an automobile engine fueled with fish oil methyl ester to reduce environmental pollution[J]. Energy Procedia,2019,160.[35]Sabino Caputo,Federico Millo,Giulio Boccardo,Andrea Piano,Giancarlo Cifali,Francesco Concetto Pesce. Numerical and experimental investigation of a piston thermal barrier coating for an automotive diesel engine application[J]. Applied Thermal Engineering,2019,162.[36]Nicole D?rr,Adam Agocs,Charlotte Besser,Andjelka Risti?,Marcella Frauscher. Engine Oils in the Field: A Comprehensive Chemical Assessment of Engine Oil Degradation in a Passenger Car[J]. Tribology Letters,2019,67(3).[37]Sumanchandran Devendran,Rajeshkumar Ramasamy,Varatharaj Neelakandan,Thulasirajan Ganesan,Praveen Chakrapani Rao. Failure assessment using accelerated testing on IC engine’s starter motor for reliability improvement[J]. Life Cycle Reliability and Safety Engineering,2019,8(2).[38]Jaegu Choi,Jongmin Lee,Namgyu Jun,Chang-Sung Seok,Sunghwan Park,Gayeon Kim. Development of Laboratory Fatigue Testing Apparatus for Automotive Vehicle Engine Valve Simulating Actual Operating Conditions[J]. International Journal of Precision Engineering and Manufacturing,2019,20(7).[39]Pavel Nicolaie,Chiriac Radu,Birtas Adrian,Draghici Florin,Dinca Mihai. On the improvement by laser ignition of the performances of a passenger car gasoline engine.[J]. Optics express,2019,27(8).[40]Ahmadipour Fatemeh,Esmaeili Sari Abbas,Bahramifar Nader. Characterization, concentration and risk assessment of airborne particles using car engine air filter (case study: Tehran metropolis).[J]. Environmental geochemistry and health,2019.[41]Sleigh Jamie,Warnaby Catherine E. Finding the starter motor for the engine of consciousness.[J]. British journal of anaesthesia,2019,123(3).[42]Derry Matthew J,Smith Timothy,O'Hora Paul S,Armes Steven P. Block Copolymer Nanoparticles Prepared via Polymerization-Induced Self-Assembly Provide Excellent Boundary Lubrication Performance for Next-Generation Ultralow-Viscosity Automotive Engine Oils.[J]. ACS applied materials & interfaces,2019.[43]. Hyundai Motor Company; Patent Issued for Continuous Variable Valve Duration Apparatus And Engine Provided With The Same (USPTO 10,060,307)[J]. Journal of Engineering,2018.[44]. Mazda Motor Corporation; Patent Issued for Engine Control Device (USPTO 10,060,372)[J]. Journal of Engineering,2018.[45]. Automotive Engine Market 2018 Global Industry Outlook By Size, Key Players, Trends, Share, Suppliers, Statistics, Sales, Growth, And Regional Forecast To 2023[J]. M2 Presswire,2018.[46]. Mathematics - Applied Mathematics; Researchers at University of Calabria Report New Data on Applied Mathematics (A LPV modeling of turbocharged spark-ignition automotive engine oriented to fault detection and isolation purposes)[J]. Journal of Transportation,2018.[47]. Ford Global Technologies LLC; "Hybrid Module, Hybrid Unit And Motor Vehicle As Well As Starting Process For An Internal Combustion Engine" in Patent Application Approval Process (USPTO 20180238291)[J]. Politics & Government Week,2018.[48]. Mazda Motor Corporation; Patent Application Titled "Engine Control Device" Published Online (USPTO 20180245529)[J]. Energy Weekly News,2018.[49]. Hitachi Automotive Systems Ltd.; "Cooling Device For Internal Combustion Engine Of Vehicle And Control Method Thereof" in Patent Application Approval Process (USPTO 20180245504)[J]. Journal of Transportation,2018.[50]. Automotive Engine Valves Market 2018 Global Industry Size, Key Player, Share, Mergers, Acquisition, Growth Analysis By Valves Type, Technology, Fuel Type, Vehicle And Region To 2023[J]. M2 Presswire,2018.[51]. Litens Automotive Partnership; Patent Issued for Isolator For Use With Engine That Is Assisted Or Started By An MGU Or A Motor Through An Endless Drive Member (USPTO 10,060,502)[J]. Journal of Engineering,2018.[52]. Honda Motor Co. Ltd.; Patent Issued for Supercharged Engine (USPTO 10,060,337)[J]. Journal of Engineering,2018.[53]. Hyundai Motor Company; Patent Issued for Method Of And System For Generating Virtual Engine Sound (USPTO 10,059,260)[J]. Journal of Engineering,2018.[54]. Suzuki Motor Corporation; Researchers Submit Patent Application, "Lubrication Structure For Internal Combustion Engine", for Approval (USPTO 20180238203)[J]. Politics & Government Week,2018.[55]. Energy; Studies from Brunel University in the Area of Energy Described (Expander Technologies for Automotive Engine Organic Rankine Cycle Applications)[J]. Journal of Engineering,2018.[56]. Hitachi Automotive Systems Ltd.; Patent Application Titled "Cooling Device For Internal Combustion Engine Of Vehicle And Control Method Thereof" Published Online (USPTO 20180245503)[J]. Journal of Transportation,2018.[57]. Honda Motor Co.Ltd.; Patent Application Titled "Internal Combustion Engine For Vehicle" Published Online (USPTO 20180245509)[J]. Politics & Government Week,2018.[58]. Honda Motor Co. Ltd.; Patent Issued for V Engine Having Valve Property Varying Mechanism (USPTO 10,066,553)[J]. Journal of Engineering,2018.[59]. Nissan Motor Co. Ltd.; Patent Issued for Vehicle Engine Stop Control Device (USPTO 10,065,646)[J]. Journal of Transportation,2018.[60]. Yamaha Motor Power Products Kabushiki Kaisha; Patent Issued for Engine (USPTO 10,066,522)[J]. Journal of Engineering,2018.汽车发动机英文参考文献三:[61]. Continental Automotive Systems Inc.; Patent Application Titled "Connected Energy Management And Autonomous Driving Strategy For Engine Cylinder Deactivation" Published Online (USPTO 20180238249)[J]. Journal of Transportation,2018.[62]. Honda Motor Co. Ltd.; Patent Issued for Variable Valve Mechanism For Internal Combustion Engine (USPTO 10,066,518)[J]. Journal of Engineering,2018.[63]. Suzuki Motor Corporation; Patent Issued for Engine For Outboard Motor (USPTO 10,059,416)[J]. Journal of Engineering,2018.[64]. MAHLE International GmbH; "Internal Combustion Engine For A Motor Vehicle" in Patent Application Approval Process (USPTO 20180216583)[J]. Energy Weekly News,2018.[65]. Hyundai Motor Company; "Engine Cooling System" in Patent Application Approval Process (USPTO 20180163608)[J]. Energy Weekly News,2018.[66]Jedd Cole. Grinder Simplifies Automotive Engine Part Production[J]. Modern Machine Shop,2018,91(3).[67]. Energy; Reports Outline Energy Study Results from Swiss Federal Institute of Technology in Lausanne (Multi-objective optimization of turbo-ORC systems for waste heat recovery on passenger car engines)[J]. Energy Weekly News,2018.[68]. Science - Applied Sciences; Researchers from Inha University Provide Details of New Studies and Findings in the Area of Applied Sciences (A New Method for Active Cancellation of Engine Order Noise in a Passenger Car)[J]. Science Letter,2018.[69]. Honda Motor Co. Ltd.; Researchers Submit Patent Application, "Engine Generator", for Approval (USPTO 20180283340)[J]. Energy Weekly News,2018.[70]. Mazda Motor Corporation; Patent Application Titled "Control Device Of Compression Self-Ignition Engine" Published Online (USPTO 20180283296)[J]. Energy Weekly News,2018.[71]. Continental Automotive GmbH; "High-Pressure Fuel Pump And Fuel Supply Device For An Internal Combustion Engine, In Particular Of A Motor Vehicle" in Patent Application Approval Process (USPTO 20180283336)[J]. Energy Weekly News,2018.[72]. Kia Motors Corporation; "Hybrid Vehicle And Method Of Controlling Engine Start" in Patent Application Approval Process (USPTO 20180297578)[J]. Energy Weekly News,2018.[73]. Mazda Motor Corporation; Patent Issued for Fuel Injection Control Device For Direct-Injection Engine (USPTO 10,119,492)[J]. Energy Weekly News,2018.[74]. Nissan Motor Co. Ltd.; Patent Issued for Engine Control Device And Engine Control Method (USPTO 10,119,486)[J]. Energy Weekly News,2018.[75]. Johnson Electric S.A.; "Motor, Circuit Board, And Engine Cooling Module Including The Motor" in Patent Application Approval Process (USPTO 20180337578)[J]. Electronics Business Journal,2018.[76]. Mazda Motor Corporation; Patent Application Titled "Structure Of Mounting Intake Air Temperature Sensor Of Engine With Supercharger" Published Online (USPTO 20180340496)[J]. Energy Weekly News,2018.[77]. Kia Motors Corporation; "System And Method For Controlling Engine Clutch" in Patent Application Approval Process (USPTO 20180335096)[J]. Energy Weekly News,2018.[78]. Kia Motors Corporation; "Method For Starting Engine For Hybrid Electric Vehicle" in Patent Application Approval Process (USPTO 20180340503)[J]. Energy Weekly News,2018.[79]. Kia Motors Corporation; "Piston For Engine" in Patent Application Approval Process (USPTO 20180340491)[J]. Energy Weekly News,2018.[80]Maniatis P,Wagner U,Koch T. A model-based and experimental approach for the determination of suitable variable valve timings for cold start in partial load operation of a passenger car single-cylinder diesel engine[J]. International Journal of Engine Research,2019,20(1).[81]Tauzia Xavier,Maiboom Alain,Karaky Hassan,Chesse Pascal. Experimental analysis of the influence of coolant and oil temperature on combustion and emissions in an automotive diesel engine[J]. International Journal of Engine Research,2019,20(2).[82]. Kia Motors Corporation; Patent Issued for Engine Idle Operation Control Method And System For Heating Of Hybrid Electric Vehicle (USPTO 10,220,828)[J]. Energy Weekly News,2019.[83]. Suzuki Motor Corporation; Patent Issued for Engine Control Device And Engine Control Method (USPTO 10,232,924)[J]. Computers, Networks & Communications,2019.[84]. Kia Motors Corporation; "Gasoline Direct Injection Engine" in Patent Application Approval Process (USPTO 20190078500)[J]. Energy Weekly News,2019.[85]. Proposed Information Collection Request; Comment Request; Motor Vehicle and Engine Compliance Program Fees (Renewal), EPA ICR 2080.07, OMB Control No. 2060-0545[J]. The Federal Register / FIND,2019,84(070).[86]. Energy; Findings from Federal University of Santa Maria in the Area of Energy Reported (Experimental Investigation of a Variable Compression Ratio System Applied To a Gasoline Passenger Car Engine)[J]. Energy Weekly News,2019.[87]. Energy; Studies from Federal University in the Area of Energy Described (Energy and Emission Impacts of Liquid Fueled Engines Compared To Electric Motors for Small Size Motorcycles Based On the Brazilian Scenario)[J]. Energy Weekly News,2019.[88]. Central Motor Wheel Co. Ltd.; Patent Application Titled "Thermoacoustic Engine, And Designing Method For Thermoacoustic Engine" Published Online (USPTO 20190085833)[J]. Energy Weekly News,2019.[89]. Kia Motors Corporation; Researchers Submit Patent Application, "Apparatus For Improving Efficiency Of Turbocharger Engine", for Approval (USPTO 20190093548)[J]. Energy Weekly News,2019.[90]. Engineering - Automobile Engineering; University of Birmingham Reports Findings in Automobile Engineering (On-board Thermochemical Energy Recovery Technology for Low Carbon Clean Gasoline Direct Injection Engine Powered Vehicles)[J]. Energy Weekly News,2019.汽车发动机英文参考文献四:[91]. Kia Motors Corporation; "Method And Device For Controlling Engine During Idle Purge Of Canister" in Patent Application Approval Process (USPTO 20190112993)[J]. Energy Weekly News,2019.[92]. Hitachi Automotive Systems Ltd.; Patent Issued for Fuel Injection System For Internal Combustion Engine (USPTO 10,267,253)[J]. Energy Weekly News,2019.[93]Song Kang,Upadhyay Devesh,Xie Hui. A physics-based turbocharger model for automotive diesel engine control applications[J]. Proceedings of the Institution of Mechanical Engineers,2019,233(7).[94]. Hitachi Automotive Systems Ltd.; Patent Issued for Engine Control Device (USPTO 10,309,366)[J]. Energy Weekly News,2019.[95]. Continental Automotive GmbH; "Gas Internal Combustion Engine With Auxiliary Starting System" in Patent Application Approval Process (USPTO 20190162123)[J]. Energy Weekly News,2019.[96]. Fuel Research; Studies from Volvo Car Group Add New Findings in the Area of Fuel Research (Impact of Closely-coupled Triple-pilot and Conventional Double-pilot Injection Strategies In a Ld Diesel Engine)[J]. Energy Weekly News,2019.[97]. Kia Motors Corporation; Patent Issued for Engine Start Control Method (USPTO 10,316,814)[J]. Biotech Business Week,2019.[98]. Kia Motors Corporation; "Apparatus And Method For Starting Engine Of Mild Hybrid Electric Vehicle" in Patent Application Approval Process (USPTO 20190184972)[J]. Energy Weekly News,2019.[99]. Energy; Findings from K.N. Toosi University of Technology Provides New Data on Energy (Conceptual design, optimization, and assessment of a hybrid Otto-Stirling engine/cooler for recovering the thermal energy of the exhaust gasses for automotive ...)[J]. Energy Weekly News,2019.[100]. Toyota Jidosha Kabushiki Kaisha; "Automotive Engine Coolant Composition, Automotive Engine Concentrated Coolant Composition, And Method Of Operating Internal Combustion Engine" in Patent Application Approval Process (USPTO 20190194516)[J]. Energy Weekly News,2019.[101]. Kia Motors Corporation; "Engine Control Method For Heating Of Hybrid Electric Vehicle" in Patent Application Approval Process (USPTO 20190193516)[J]. Energy Weekly News,2019.[102]. Kia Motors Corporation; "Vehicle And Method For Controlling Engine Startup Reference Power" in Patent Application Approval Process (USPTO 20190202432)[J]. Energy Weekly News,2019.[103]. Energy; Technical University Details Findings in Energy (A fully automated smooth calibration generation methodology for optimization of latest generation of automotive diesel engines)[J]. Energy Weekly News,2019.[104]. Black &Decker Inc.; "Battery And Motor System For Replacing Internal Combustion Engine" in Patent Application Approval Process (USPTO 20190238083)[J]. Energy Weekly News,2019.[105]. Mazda Motor Corporation; "Exhaust Gas Control Device, Method, And Computer Program Product For An Engine" in Patent Application Approval Process (USPTO 20190234330)[J]. Energy Weekly News,2019.[106]Dongha Kim,JongRoul Woo,Jungwoo Shin,Jongsu Lee,Yongdai Kim. Can search engine data improve accuracy of demand forecasting for new products? Evidence from automotive market[J]. Industrial Management & Data Systems,2019,119(5).[107]R. Ellappan,S. Arumugam. The effect of corrosion inhibitor on corrosion of automotive materials in Biodegradable engine oil[J]. IOP Conference Series: Materials Science and Engineering,2018,390(1).[108]P. Wi?niowski,M ?l?zak,A Niewczas,T Szczepański. Method for synthesizing the laboratory exhaust emission test from car engines based on road tests[J]. IOP Conference Series: Materials Science and Engineering,2018,421(4).[109]J Kaszkowiak,M Markiewicz-Patalon. The impact on the manner of loading theengines powered with biogas and natural gas on the selected parameters of the motor oil[J]. IOP Conference Series: Materials Science and Engineering,2018,421(4).[110]A Wolff. Numerical analysis of gas flow through the labyrinth seal of piston rings of an automotive IC engine[J]. IOP Conference Series: Materials Science and Engineering,2018,421(4).[111]Z Kneba. Research on the phenomena of warming up and free cooling down the car engine[J]. IOP Conference Series: Materials Science and Engineering,2018,421(4).[112]N C Nutu,C Pana,N Negurescu,A Cernat,D Fuiorescu,L Nemoianu. An experimental approach on fuelling a passenger car diesel engine with LPG[J]. IOP Conference Series: Materials Science and Engineering,2018,444(7).[113]T Ulian,V Vornicu,E Rakosi,G Manolache,S Talif,I Agape. The study of the performance improvement possibilities by using the principle of zonal cooling for the automotive engine[J]. IOP Conference Series: Materials Science and Engineering,2018,444(7).[114]V Serevina,A A Azhar,T Sutandi,K Sumeru. Effect Of Engine Speed On The Performance Of Automotive Air Conditioning System Using R134a And R152a As Refrigerants[J]. Journal of Physics: Conference Series,2019,1150(1).[115]Willyanto Anggono,Sutrisno,Fandi D Suprianto,Muji Setiyo,Rendy Wibisono,Gabriel Jeremy Gotama. Experimental investigation of the effect of Nephelium Lappaceum seed biodiesel to the automotive diesel engine performance[J]. IOP Conference Series: Earth and Environmental Science,2019,257(1).[116]Guorui Jia,Huanhuan Ren,Dongchang Zhao,Chuan Chen,Rujie Yu,Peng Ge,Shaohui Liu. Numerical Simulation of Multiple Injections on the Combustion of Reactivity Distribution in Automotive Engine[J]. IOP Conference Series: Earth and Environmental Science,2019,252(3).[117]Xitong Zhang,Tao Peng,Fuxin Mao,Ming Cheng. Research on Key Technologies of Integrated Teaching Platform for Automotive Engine ECU Control System[J]. Journal of Physics: Conference Series,2019,1237(4).[118]Huanhuan Ren,Guorui Jia,Dongchang Zhao,Chuan Chen,Rujiex Yu,Peng Ge,Shaohui Liu. Simulation Study of Injection Strategy on the Emission in Automotive Engine[J]. IOP Conference Series: Earth and Environmental Science,2019,252(3).[119]Olufemi Sylvester Bamisaye,Anthony Yinka Oyerinde,Ubong Akpan Essien. Investigation of the Effects of Air-Conditioning System on the Temperature and Speed of Automobile Engine Using Paired T-Test and Regression Analysis[J]. Open AccessLibrary Journal,2019,06(01).[120]Huali Guo,Jia Cui,Guofu Wang,Hongwang Zhao. Analysis and Research on the Teaching Principle of Automotive Engine Based on CDIO Concept[P]. Proceedings of the 2018 International Conference on Sports, Arts, Education and Management Engineering (SAEME 2018),2018.以上就是关于汽车发动机英文参考文献的分享,希望对你有所帮助。
calibration 翻译

calibration 翻译Calibration的中文翻译是"校准"。
校准是指通过比较和调整仪器或设备的度量结果,以确保其准确性和可靠性。
以下是一些关于calibration的用法和中英文对照例句:1. The technician performed a calibration on the thermometer to ensure accurate temperature readings. (技术人员对温度计进行了校准,以确保准确的温度读数。
)2. The laboratory regularly conducts calibrations on their measuring equipment to maintain their precision. (实验室定期对测量设备进行校准,以保持精确度。
)3. The calibration of the scales was necessary to ensure the correct weight measurements. (对秤的校准是为了确保正确的重量测量。
)4. It is important to calibrate the pH meter before conducting any experiments in the chemistry lab. (在化学实验室进行任何实验之前,对pH计进行校准是很重要的。
)5. The calibration of the sound system was adjusted to provide optimal audio quality for the concert. (音响系统的校准被调整以提供音乐会的最佳音质。
)6. The calibration process involves comparing the measuring device to a known standard and making necessaryadjustments. (校准过程涉及将测量设备与已知标准进行比较,并进行必要的调整。
整车开发过程中的英文缩写-汽车行业的你一定要知道的
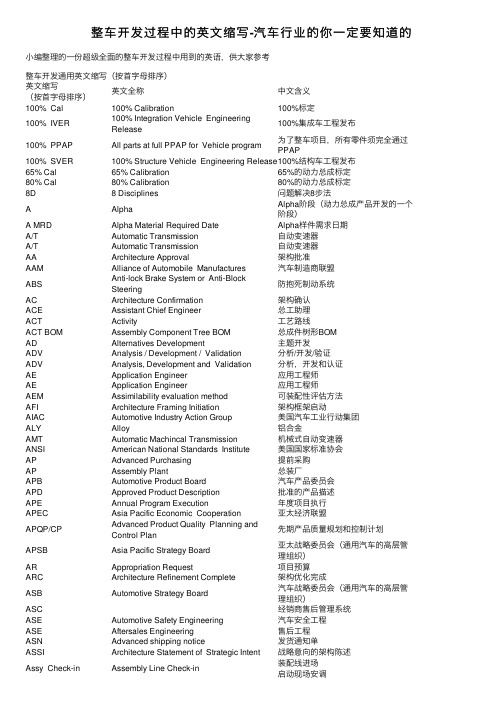
整车开发过程中的英⽂缩写-汽车⾏业的你⼀定要知道的⼩编整理的⼀份超级全⾯的整车开发过程中⽤到的英语,供⼤家参考整车开发通⽤英⽂缩写(按⾸字母排序)英⽂缩写英⽂全称中⽂含义(按⾸字母排序)100% Cal100% Calibration100%标定100% IVER 100% Integration Vehicle EngineeringRelease100%集成车⼯程发布100% PPAP All parts at full PPAP for Vehicle program为了整车项⽬,所有零件须完全通过PPAP100% SVER100% Structure Vehicle Engineering Release100%结构车⼯程发布65% Cal65% Calibration65%的动⼒总成标定80% Cal80% Calibration80%的动⼒总成标定8D8 Disciplines问题解决8步法A Alpha Alpha阶段(动⼒总成产品开发的⼀个阶段)A MRD Alpha Material Required Date Alpha样件需求⽇期A/T Automatic Transmission⾃动变速器A/T Automatic Transmission⾃动变速器AA Architecture Approval架构批准AAM Alliance of Automobile Manufactures汽车制造商联盟ABS Anti-lock Brake System or Anti-BlockSteering防抱死制动系统AC Architecture Confirmation架构确认ACE Assistant Chief Engineer总⼯助理ACT Activity⼯艺路线ACT BOM Assembly Component Tree BOM总成件树形BOMAD Alternatives Development主题开发ADV Analysis / Development / Validation分析/开发/验证ADV Analysis, Development and Validation分析,开发和认证AE Application Engineer应⽤⼯程师AE Application Engineer应⽤⼯程师AEM Assimilability evaluation method可装配性评估⽅法AFI Architecture Framing Initiation架构框架启动AIAC Automotive Industry Action Group美国汽车⼯业⾏动集团ALY Alloy铝合⾦AMT Automatic Machincal Transmission机械式⾃动变速器ANSI American National Standards Institute美国国家标准协会AP Advanced Purchasing提前采购AP Assembly Plant总装⼚APB Automotive Product Board汽车产品委员会APD Approved Product Description批准的产品描述APE Annual Program Execution年度项⽬执⾏APEC Asia Pacific Economic Cooperation亚太经济联盟APQP/CP Advanced Product Quality Planning andControl Plan先期产品质量规划和控制计划APSB Asia Pacific Strategy Board亚太战略委员会(通⽤汽车的⾼层管理组织)AR Appropriation Request项⽬预算ARC Architecture Refinement Complete架构优化完成ASB Automotive Strategy Board汽车战略委员会(通⽤汽车的⾼层管理组织)ASC经销商售后管理系统ASE Automotive Safety Engineering汽车安全⼯程ASE Aftersales Engineering售后⼯程ASN Advanced shipping notice发货通知单ASSI Architecture Statement of Strategic Intent战略意向的架构陈述Assy Check-in Assembly Line Check-in装配线进场启动现场安调Assy PPAP Assembly Line PPAP装配线通过PPAP Assy PPAP Assembly Line PPAP装配线通过PPAPAssy PPV Assembly Line Products and ProcessValidation装配线交付后的产品⼯艺验证Assy PPV Assembly Line Production and ProcessValidation装配线交付后产品⼯艺验证Assy Run-Off Assembly Line Run-Off装配线试装交样⽇期Assy Run-off Assembly Line RUN-Off装配线整线打通,启动试装,允许⼿⼯装配Assy Run-off MRD Assembly Line RUN-Off Material RequiedDate装配线ATC Auto Temperature Controller⾃动空调控制器ATF Automatic Transmission Fluid⾃动变速箱油ATT Attachment附件ATT Actual takt time实际单件⼯时AVD Advanced Vehicle Development先期车辆开发AVDC Advance Vehicle Development Center先期车辆开发中⼼AVD-LT Advanced Vehicle Development-LeadershipTeam前期整车开发-领导⼩组AVDP Advanced Vehicle Development Process(Time between DSI and VPI)先期车辆开发流程(在DSI与VPI之间)AVPM Advanced Vehicle Planning Manager先期车辆计划经理B Beta Beta阶段(动⼒总成产品开发的⼀个阶段)B Build制造B MRD Beta Material Required Date Beta样件需求⽇期B+U Building and Utility⼟建公⽤BAD Build Authorization Document试制授权⽂档BC Business Case业务计划BCM Body Control Module车⾝控制器BDC Body Distributon Central车辆调配中⼼BESC Base Engine Steering Committee发动机总成战略转向委员会BIQ Building in Quality制造质量BIR Prototype Build Issue Report试制问题报告BIR Build Issues Resolution试制问题BIR Build Incident Report装车问题报告BIR Bulding issue report造车问题报告BIW Body-In-White⽩车⾝BIW Body in White⽩车⾝BOD Bill of Design设计清单BOE Bill of Equipment设备清单BOM Bill of Material物料清单BOM Bill of Material物料清单BOM Bill of Material物料清单BOM Bill Of Material物料清单BOM Bill Of Material物料清单BOM Bill of Material物料清单BOP Bill of Process⼯艺清单BOP Bill Of Process⼯艺清单BP Break Point断点BPD Business Plant Deployment业务计划实施BPP Best people practices最佳⼈员准则BPR Business plan recompose业务流程重组BS Body Shop车⾝车间BSD Build Site Direction试制现场指导书BUFFER Buffer线边缓存区C/CAP Construction/Conversion and AccelerationPlan⼟建/改造和⽣产提速计划CAB Change Approval Board更改审批会CAC服务热线专员CAFE Corporate Average Fuel Economy公司平均油耗Cal Calibration动⼒总成标定CARE Customer acceptance review evaluation整车报交检查CARE Customer Acceptance & Review Evaluation⽤户接受度和审查评估CC Concept Confirmation验证概念CC Consolidation Center集散中⼼CC Confirmation Clinic确认临床Cert LSO Certification Lift Stop Order通过排放认证通知CET Cold Environment Test寒区试验CH Chassis Department底盘部CI Concept Initiation提出项⽬概念CIM Customer Interface Manager客户服务经理CIP Continue Improve Process持续改进CIP Continue Improve Process持续改进CIT Continuous Improvement Team不断改进⼩组CIT Compartment Integration Team车厢集成⼩组CMC Container Management Center空箱管理中⼼CME Change Management Engineer更改管理⼯程师Cmk N/A临界机器能⼒指数Cmk Capability Machine Index机器设备能⼒CMM三坐标测量C-NCAP China New CAR Assessment Process中国标准新车评估体系COC Centre of Competence能⼒中⼼COE Center of Expertise经验总结中⼼CP Control Plan控制计划CPIT Current Product Improvement Team现有产品改进⼩组Cpk Complex Process Capability过程能⼒指数Cpk Process Capability Index稳定过程的能⼒指数CPQE Current Product Quality Engineer现有产品质量⼯程师CPV Cost per Vehicle单车成本CR/DN Change Request / Decision Notice更改决议CR/DN Change Request/Decision Notice变更申请/决议通知CRB Change Review Board更改评审⼩组CS Contract Signing动⼒总成签署项⽬合同CS Contract Signing合同签订CS1Controled Shipping 1⼀级受控发运CS2Controled Shipping 2⼆级受控发运CSC Controls Steering Committee控制模块战略转向委员会CSI Customer Satisfaction Index⽤户满意度指标CSI Customer Satisfaction Index售后满意度CSN Current Sequence Number流⽔号CSO Contract Sign-Off合同签署CSO Contract Sign-Off (VDP)整车签署项⽬合同(VDP术语)CSO HC Contract Sign-Off Health Check合同签署健康检查CSO HC Contract Sign-Off Health Check合同签署健康检查CT Cycle Time制程周期CT Cycle time周期时间CT Creativity Teams创造性⼯作⼩组CT Critical Test关键试验CTS Component Technical Specification零部件技术标准CTT Common Timing Template标准2级进度模板CVER Concept Vehicle Engineering Release概念车⼯程发布CVER LL Concept Vehicle Engineering Release LongLead概念车⼯程发布--长周期CVIS Completed Vehicle Inspection Standards整车检验标准CVQC Completed vehicle quality ceter整车质量中⼼CVQCB Completed vehicle quality ceter board整车质量⽬视板CVT Continuously Variable Transmission⽆级变速器D.Q.R合格率概况DAS Design & Analysis Section设计分析科DC Deliver Charter递交项⽬章程DCN Design Change Notice设计更改通知DCN Design Change Notice设计更改通知DCP Dimension Control Plan尺⼨控制计划DCS Design Concept Sheet概念设计表DCT Double Clutch Transmission双离合器变速箱DD Direct Delivery直接投线DDSP Driver Door Switch Pack驾驶席门控开关DEI Die Engineering Integration模具⼯程集成DFA Design for Assembly装配⼯艺性设计DFM Design for Manufacturability制造⼯艺性设计DFMEA Design failure mode and effects analysis设计失效模式和效果分析DFMEA Design FMEA设计失效模式分析DIFF Differential差速器DL 3b Design Level 3b设计阶段3bDMS Dealer Manage System经销商管理系统DOL Dealer On Line经销商在线系统DP Demand Plan需求计划DPV Defects per vehicle单车缺陷数DPV Defect per Vehicle单车缺陷数DQ&V Design Quality & Validation设计质量和验证DR Direct run直接通过率DRC Design Review Committee设计评审委员会DRE Design Responsible Engineer设计和发布⼯程师DRE Design Release Engineer设计发布⼯程师DRE Design release engineer设计发布⼯程师DRL Direct run loss直接通过损失率Drop Off Drop Off停产DS44HIGH SPEED DURABILITY TEST⾼速耐久试验(MGRES 标准)DSG Direct shift gearbox双离合器变速箱DSI Document of Strategic Intent战略意向书DSM Driver Seat Module驾驶席座椅控制模块DSO Design Sign Off设计签署DTA Design Theme Alternatives设计主题选项DTC Diagnostic Trouble Code诊断故障码DV Design Validation设计验证DV Design Validation产品设计验证DVP Design Validation Plan设计验证计划DVT Dynamic vehicle test整车综合动态测试E/T/C Engine/Transmission/Controller发动机/变速器/控制模块EBA Emergency Brake Assistant紧急制动辅助系统EBD Electronical Brake Distribute电⼦制动⼒分配系统EBOM Engineering BOM⼯程BOMEC Embedded Controller控制模块ECC ERP Central Component ERP核⼼组建ECR Engineering Change Request⼯程更改请求ECR Engineering Change Request⼯程更改请求ECR Engineering Change Request⼯程更改申请ECR Engineering Change Request⼯程项⽬变更申请ECS Engineering Change Summary⼯程变更摘要ECT Emission Control System电⼦控制⾃动变速器EDS Electronic Data Systems电⼦数据系统EEVC European Enhanced Vehicle-SafetyCommittee欧洲提⾼车辆安全性委员会EFEO Emissions & Fuel Economy排放和燃料经济EGM Engineering Group Manager产品⼯程⼩组经理EI&S Electronics Integration & Software电器零件集成和软件ELV End of life vehicle整车寿命结束EMlS Emission排放EMS Engine Management System发动机管理系统ENB Build-Test Section试制试验科E-NCAP Euro New Car Assessment Process欧洲标准新车评估体系ENG Engineer⼯程师EOA End of Acceleration⽣产提速的完成EOLT End of Line Test⽣产线试验结束EP Engineering Prototype⼯程样车(件)EPA Environmental Protection Agency环境保护厅EPC Engineering Program Committee⼯程项⽬委员会EPN Engineering Project Number⼯程项⽬数⽬ERD Early Requirement Document早期的要求⽂件ESB European Strategy Board欧洲战略委员会(通⽤汽车的⾼层管理组织)ESO Engineering Sign Off发动机整机⼯程签署ESO Engineering Sign Off⼯程签署ESO Engineering Sign-off⼯程签署ET Engineering Technology⼯程技术EV Engineering Vehicle⼯程样车EWO Engineering Work Order⼯程⼯作指令EWO Engineering Work Order⼯程更改号EWO Engineering workorder⼯程更改流程Exp Cal Experimental Calibration尝试性标定FA Final Approval批准正式⽣产FAC集团销售经理FATG Final Approval to Grain⽣产最终批准FBIW First Body in White Complete第⼀轮⽩车⾝完成FE Functional Evaluation功能评估FE LSO Fuel Economy Label Lift Stop Order通过油耗认证的通知FIVC First Integration Vehicle Complete第1辆集成车制造完毕FIVC First Integration Vehicle Complete第⼀轮集成车完成FLO Factory Layout⼯⼚布局FM功能尺⼨FM Finance Manager财务经理FMC First Mule Complete第⼀轮骡⼦车完成FMC区域售后⽀持FMEA Failure model effectiveness analysis失效模式分析FMEA Failure model effectiveness analysis失效模式分析FMEA Failure Mode and Effects Analysis潜在失效模式及后果分析FMEA Failure mode and effects analysis失效模式和后果分析FMEA Failure Mode and Effect Analysis失效模式和影响分析FMS Flexible manufacturing systems柔性制造系统FMVSS Federal Motor Vehicle Safety Standards联邦汽车安全标准FPPV BIW First Product/Process Body in WhiteComplete第⼀轮产品/⼯艺⽩车⾝完成FPPVC First Product/Process Validation VehicleComplete第⼀轮产品/⼯艺验证车辆完成FPS Fixed Point Stop固定停⽌位置FTC First Time Capability⾸次能⼒FTP/FTQ First time pass/quality⼀次通过合格率FTQ First time quality下线合格率FWD Four Wheel Drive四轮驱动G Gamma Gamma阶段(动⼒总成产品开发的⼀个阶段)G MRD Gamma Material Required Date Gamma样件需求⽇期G/L Group leader⼯段长GA General Assembly总装GA General Assembly总装GADT Global Architecture Development Team全球架构开发⼩组GBOM Global Bill of Material全球物料清单GMNA General Motors North America通⽤汽车北美分部GMPT General Motors Powertrain通⽤汽车动⼒总成分部GPDC Global Product Development Council全球产品开发理事会GPDP Global Powertrain Development Process全球动⼒总成开发流程GPDS Global Product Description System全球产品管理系统GSD Global Segment Director全球细分主管GSS Global Sales and Service全球销售和服务GVDP Global Vehicle Development Process全球整车开发流程GVDP Global Vehicle Development Process整车开发流程GVDP Global Vehicle Development Process整车开发流程GVDP Global Vehicle Development Process全球汽车开发流程GVDP Global Vehicle Development Process全球整车开发流程GVDP Global Vehicle Development Process整车开发流程GVLE Global Vehicle Line Executive整车平台执⾏GVW Gross Vehicle Weight车辆总重GW Gateway⽹关HET Hot Environment Test热带试验HRC Hardware Release Center硬件发布中⼼ICD Interface Control Document接⼝控制⽂件IDR Initial Data Release初始数据发布IDSR Integration Driven Subsystem Requirement集成驱动⼦系统要求ILP Inbound Logistic Planning⼊⼚物流规划IMES Integration Manufacturing Executive System⽣产执⾏系统Initial Cal Initial Calibration初始标定IOM Inspection operator method检验操作⽅法IOS Inspection operator summary检验操作概要IPPE integrated Product and Process Engineering集成产品与⼯艺⼯程IPTV Incident per Thousand Vehicles每千辆车的故障率IPTV Incidents Per Thousand Vehicles每⼀千台车事故率IPTV Incidents Per Thousand Vehicles每千辆车的故障率IPTV Incidents Per Thousand Vehicles千辆车故障率IR Incident Report事故报告IRP Issue Resolution Process问题解决流程IRR Internal Rate of Return内含报酬率ISO International Standard Organization国际标准化组织IV Integration Vehicle集成车IV MRD Integration Vehicle Material Required Date集成车的物料需求⽇期IVBR Integration Vehicle Build Readiness Review集成车制造准备评审IVER Integration Vehicle Engineering Release集成车⼯程发布JIS Just In Sequence排序供货JIS Just In Sort供应商排序供货⽅式JIS Job Instruction Sheet岗位指导书JIT Just In Time及时供货JIT Just In Time供应商及时供货⽅式JPH Job per Hour⽣产节拍JRS Joint Ride Session联合评审JSC⽣产采购委员会JSC-GP Joint Sourcing Committee - General purchase联合采购委员会-⼀般采购Kcc Key Control Characteristic关键过程控制特性KCC Key Control Character关键控制特性KCDS Key Characteristic Designation System产品关键特性定义系统KO Kick-Off启动Kpc Key Product Characteristic关键产品特性KPC Key Product Characteristic关键产品特性KPC Key product characteristic主要产品特性KPC Key product characteristic主要产品特性KPC Key process control关键过程控制KPC Key process control关键过程控制LAAMSB Latin America, Africa, Middle East StrategyBoard通⽤的拉美,⾮洲,中东战略委员会LCL Lower Control Limit管制下限LCS Logistic Confirmation Sheet物流确认单LL Learning Loop学习周期LL Long Lead长周期LLPR Long Lead Production Release长周期的产品发布LM Launch Manager启动经理LOU Line of Usage BOM整车BOM⾏LSL Lower Specification Limit规格下限LSP Lean sales and marketing prograne精宜营销LTR Launch Team Release启动⼩组释放LWO Logistic Work Order物流属性更改号M+E Machine & Equipment机器设备MAC区域经理MBOM Manufacturing BOM制造BOMMDS Materiel Data Sheet物料数据单ME Manufacture Engineer样车试制⼯程师或⽣产线制造⼯程师ME Machine and Electronic电器设备ME Manufacturing Engineering制造⼯程ME Manufacturing Engineering制造⼯程MEC区域市场⽀持MEIS Manufacturing Engineering Info System制造⼯程信息系统MES Manufacturing Execution System制造执⾏系统MES Manufacturing Execution System制造执⾏系统MFG Site Dec Manufacturing Site Decision确定⽣产⼚址MIC Marketing Information Center市场信息中⼼MILKRUN Milkrun循环取货MKT Marketing营销MMR Manufacturable Math Release制造数模发布MO Manufacturing Operations⽣产管理部门MP OTS 100%100% Made Parts in OTS100%⾃制件达到OTS状态MP OTS 100%100% Made Parts in OTS100%⾃制件达到OTS状态MP PPAP Made Parts PPAP⾃制件通过PPAPMP PPAP Made Parts PPAP⾃制件通过PPAPMP PPV Made Parts Production and ProcessValidation⾃制件⽣产线交付后的产品⼯艺验证MP PPV Made Parts Production and ProcessValidation⾃制件⽣产线交付后的产品⼯艺验证MPS Master Planning System主计划系统MPV Multi-Purpose Vehicle多⽤途轿车MR Manufacturing Requirements制造要求MRD Material Required Date交样⽇期MRD Material Requirement Date物料需求⽇期MRD Material Required Date (for physical builds)物料需求⽇期(⽤于制造样机)MRD Math Required Date (for virtual builds)数模需求⽇期(⽤于虚拟制造)MRE Manufacturing Responsible Engineer制造⼯程师MS Manufacturing Studies制造车间MSA Measurement System Analysis测量系统分析⼿册MSA Measurement System Analysis测量系统分析MSA Measure System Analyse测量系统分析MSA Measurement system analysis测量系统分析MSS Market Segment Specification市场细分规范MSS区域销售⽀持MSS Market Segment Specification市场分割规范MT Manual Transmission⼿动变速箱MT&E Machines, Tools and Equipment机床,⼯装和设备MTS Manufacturing Technical Specification制造技术标准MVB Manufacturing Validation Build⽤于认证制造⼯艺的整车制造MVB Manufacturing Validation Build制造验证造车MVB (ns)Manufacturing Validation Build (nonsaleable)⽤于认证制造⼯艺的整车制造(不可销售的)MVB (s)Manufacturing Validation Build (saleable)⽤于认证制造⼯艺的整车制造(可销售的)MVBns Manufacturing Validation Build Non-Salable⾮销售制造验证造车MVBs Manufacturing Validation Build Salable销售制造验证造车MVSS Motor Vehicle Safety Standards汽车安全标准MWO Manufacture Work Order制造属性更改号MY Model Year年度款MYM Model Year Manager车型年经理NAO North American Operations通⽤的北美分部NEO New Employee Orientation新员⼯培训NOA Notice of Authorization授权书NOD Notice of Decision决议NOD Notice of Decision决议通知NPV Net Present Value净现值NRD Normal Road⼀般公路NSB North American Strategy Board通⽤的北美传略委员会(通⽤的⾼层管理组织)OBD On Board Diagnostics车载诊断系统OEM Original Equipment manufacturers原始设备制造商(主机⼚)OEM Run-Off Original Equipment Manufacturer Run-Off零件供应商⼯装设备具备试⽣产条件OEM Run-off Original Equipment Manufacturer Run-off零件供应商⼯装设备具备试⽣产条件OJT On Job Training在岗培训OPO Office of Product Operations产品⾼层管理组织ORS Occupant Restraint System乘员约束系统OT Overtime加班OTD Order to Delivery订单到货时间OTP On Time Performance及时性能OTS装车评审OTS Off-tool Sample⼯装样件OTS Off-tool Sample⼯装样件OTS Off-tool Sample⼯装样件OTS OFF-TOOL-SAMPLE⼯装样件OTS QV OTS Quality Valve OTS质量阀OTS交付状态满⾜质保的开阀要求OTS QV OTS Quality Valve OTS质量阀,OTS交付状态满⾜质保的开阀要求OTS TG2Off Tooling Samples Tooling Go Level 2OTS设计达到TG2阶段,发布图纸⽤于供应商启动⼯装和设备投⼊OTS TGL2Off Tooling Samples Tooling Go Level 2OTS设计达到TG2阶段P Pilot批量试⽣产P Pilot⼩批量⽣产PA Production Approval批准正式⽣产PA Program Administrator项⽬管理专员PaC Physical Alpha for Customer提交客户的Alpha样机PACK Packaging包装规划PAD Product Assembly Documentation产品装配⽂件PAM Product Assemble Manual样车装配指南PAM Product Assemble Manual产品装配⼿册PAPIR Product and Process Integration Review产品和⼯艺集成会议PAS Packaging Approval Sheet包装确认单PAS Parking Aid System泊车辅助系统PAS Parking Aid System泊车辅助系统PbC Physical Beta for Customer提交客户的Beta样机PBS Painted Body Store油漆车⾝存储区PC Deliver Pilot to Customer向客户提交Pilot产品PC Pullcord拉环PC Problem Communication问题信息PC&L Production Control and Logistics PC&L部门(GM的⼀个部门)PCL Production Control Manager⽣产控制与⽀持PCM Powertrain Control Module动⼒总成控制模块PCM Process Control Manager⼯艺控制负责⼈PCN Project Cost Change Notice项⽬更改通知单PCN Project Costbook Change Notice项⽬Costbook更改通知单PCR Problem communication report问题交流报告PCR Problem communication report问题交流报告PCR Problem Communication Report问题交流报告PCR Problem Communication Report问题交流报告PDC Parking Distance Control泊车距离控制PDC Parking Distance Control泊车距离控制PDCA Plan、Do、Check、Action计划、实施、检查、⾏动PDCA Plan-Do-Check-Action计划,实施,检查,⾏动PDI Product delivery inspection产品交付检查PDI Preliminary Data Indicator初步数据指⽰器PDI Pre-delivery Inspection车辆⾏运“零公⾥”检查报告PDS Product Data Structure 产品数据结构,在SCM中⽤到的数据对象,集成了BOM、⼯艺和⼯⼚布局信息PDT Product Development Team产品开发组PDT Product Development Team产品开发⼩组PDT Product Development Team产品开发⼩组PDT Product Development Team产品开发⼩组PDT Product Development Team产品开发⼩组PE Product Engineering产品⼯程PET Program Executive Team项⽬执⾏⼩组PET Program Execution Team项⽬组PET Program Execution Team项⽬执⾏⼩组PFI Program Framing Initiated项⽬框架启动PFMEA Process failure mode and effectsanalysis过程失效模式和后果分析PFMEA Process FMEA⼯艺失效模式分析PFMEA Process failure mode & effects analysis过程失效模式分析PFSE Product Focus Systems Engineer产品系统⼯程师PG3Powertrain Gateway关键⾥程碑节点PgC Physical Gamma for Customer向客户发运Gamma样机PGM Program Management / Project Management项⽬管理PGM Program Management项⽬管理PGM Program Management项⽬管理Pilot Pilot试⽣产Pilot Pilot试⽣产Pilot QV Pilot Quality Valve试⽣产质量阀满⾜启动试⽣产的开阀要球Pilot MRD Pilot Material Requied Date Pilot交样⽇期Pilot MRD Pilot Material Required Date Pilot的物料需求⽇期Pilot QV Pilot Quality Valve试⽣产质量阀满⾜启动试⽣产的开阀要求PIM Powertrain Interface Manager动⼒总成接⼝经理PLM Production Launch Manager⽣产启动经理PLP单车利润表PM Programme Manager项⽬⼯程经理PM Program Manager项⽬经理PM Program Manager项⽬经理PM Plan maintain计划维护PM Prevention Maintenance预防性维护PM Program Manager项⽬经理PMO Program Management Office项⽬管理办公室(通⽤的⼀个部门)PMP常规尺⼨PMT Product Management Team产品管理⼩组PN Part NO.零件号PP Pre-pilot前期试⽣产PP Pre-Pilot预试⽣产PP Pre-pilot试⽣产P-P Pre-Pilot试⽣产PP PPAP Purchased Parts Production Parts ApprovalProcess外购件完成⽣产件批准程序PP Appr.Purchased Parts Approved外购件批准SQE开具⼊库许可单PP ESO Purchased Parts Engineering Sign Off外购件⼯程签署,完成OTS认可/阶段认可PP OTS 100%100% Purchased Parts in OTS外购件的OTS交样率达到100%PP OTS 80%80% Purchased Parts in OTS外购件的OTS交样率达到80%PP OTS 80%80% Purchased Parts in OTS外购件的OTS交样率达到80%PP PPAP Purchased Parts PPAP外购件完成PPAPPPA Product Planning Approval产品规划批准PPAP Production Parts Approval Process⽣产件批准程序PPAP Production Part Approval Process⽣产零部件批准程序PPAP Production Part Approval Process⽣产件批准程序PPAP Production Part Approval Process⽣产件批准程序PPAP Production Parts Approval Process⽣产件批准程序PPAP Production Part Approval Process⽣产件批准流程PPAP PPAP Production Part Approval Process产品零部件批准流程PPAP Production Part Approval Process⽣产零部件批准程序PPC Deliver Pre-Pilot to Customer向客户发运Pre-pilot动⼒总成PPC Product Program Content项⽬任务书。
大陆西门子新尼杰特电喷标定教程

Engine characterisation1 / 25Originator A. BENNE / Y. DUPOUYModified by E. CALMELS Date 01/10/2009 Reviewed by:Calibration guideEngine characterisation1 - OBJECTIVESThe aim of this document is to describe the test to be performed to characterise the engine in terms of performance, volumetric efficiency, ignition advance, emissions.GlossaryECU: E ngine C ontrol U nit, M3A moduleEMS: E ngine M anagement S ystem, ECU + sensors and actuators °BTDCF: degrees B efore T op D ead C enter F iringDocuments and files related to engine characterisationThis document is linked to other documents and files such as:_ Engine_Characterisation_Report : It must be filled along the engine characterisation process in order to store the results from the tests_ INCA experiment : All the tests described in Engine Characterisation are linked to INCA experiment. This experiment is configured according to each test with important parameters, measured values etc..._xx.a2l and xx.mot : This file permits the communication between INCA and the ECUMake sure you have all of these documents / files before to sart the tests.Engine characterisation2 / 25CONTENTS1 - OBJECTIVES .................................................................................................... 12 - ENGINE INSTRUMENTATION ......................................................................... 4 2.1 - Instrumentation listing ............................................................................................... 4 2.2 -Installation drawing (5)3 - ENGINE TESTS (6)IMPORTANT NOTES (6)3.1 - PRELIMINARY CHECKING ......................................................................................... 8 3.1.1 - EMS components conformity ................................................................................... 8 3.1.2 - Mechanical components conformity ......................................................................... 8 3.1.3 - Wiring harness conformity ....................................................................................... 8 3.1.3.1 - M3A module PINOUT ...................................................................................... 8 3.1.3.2 - Power ground / sensor ground checking .......................................................... 9 3.1.3.3 - Wiring harness pin to pin continuity checking (ECU disconnected) .................. 9 3.1.4 - Inputs / outputs ........................................................................................................ 9 3.1.4.1 - First communication with the ECU ................................................................... 9 3.1.4.2 - Crankshaft sensor signal checking................................................................... 9 3.1.4.3 - Inputs ............................................................................................................... 9 3.1.4.3.1- Engine coolant sensor ECT ....................................................................... 9 3.1.4.3.2- O2 sensor .................................................................................................. 9 3.1.4.3.3- Air temperature sensor ............................................................................ 10 3.1.4.3.4- Throttle position sensor............................................................................ 10 3.1.4.3.5- Manifold pressure sensor ......................................................................... 10 3.1.4.4 - Outputs .......................................................................................................... 10 3.1.4.4.1- Spark advance ......................................................................................... 10 a First method: with a non-adjustable stroboscopic lamp .................................. 10 b Second method: with an adjustable stroboscopic lamp .................................. 10 3.1.4.4.2- Dwell time ................................................................................................ 11 3.1.4.4.3- Tests with engine running ........................................................................ 11 3.1.4.4.4- Fuel supply capability . (11)3.2 - ENGINE RUN-IN ........................................................................................................ 13 3.3 - ENGINE CHARACTERISATION generalities ............................................................ 13 3.3.1 - Recording method recommendations .................................................................... 13 3.3.2 - EMS setting manually ............................................................................................ 13 3.4 - ENGINE CHARACTERISATION tasks ...................................................................... 14 3.4.1 - Engine daily checking ............................................................................................ 14 3.4.1.1 - Parameters to be measured and recorded ..................................................... 14 3.4.1.2 - Test conditions ............................................................................................... 14 3.4.1.3 - Warnings ....................................................................................................... 14 3.4.1.4 - Measurements ............................................................................................... 15 3.4.1.4.1- Points to be measured ............................................................................. 15 3.4.1.4.2- Testing ..................................................................................................... 15 3.4.2 - Full load ................................................................................................................. 15 3.4.2.1 - Parameters to be measured and recorded ..................................................... 15 3.4.2.2 - Test conditions ............................................................................................... 15 3.4.2.3 - Warnings ....................................................................................................... 16 3.4.2.4 - Measurements ............................................................................................... 16 3.4.2.4.1- Points to be measured ............................................................................. 16 3.4.2.4.2- Testing ..................................................................................................... 16 3.4.3 - SOI optimization .................................................................................................... 17 3.4.3.1 - Parameters to be measured and recorded .. (17)Engine characterisation3 / 253.4.3.2 - Test conditions ............................................................................................... 17 3.4.3.3 - Warnings ....................................................................................................... 17 3.4.3.4 - Measurements .. (18)a Points to be measured ................................................................................... 18 b Testing ........................................................................................................... 18 c Optional: optimisation of SOI at Tmax and Pmax points .. (18)3.4.4 - Air path .................................................................................................................. 18 3.4.4.1 - Parameters to be measured and recorded ..................................................... 18 3.4.4.2 - Test conditions ............................................................................................... 19 3.4.4.3 - Warnings ....................................................................................................... 20 3.4.4.4 - Measurements ............................................................................................... 20 3.4.4.4.1- Points to be measured ............................................................................. 20 3.4.4.4.2- Testing ..................................................................................................... 20 3.4.5 - Ignition advance..................................................................................................... 21 3.4.5.1 - Parameters to be measured and recorded ..................................................... 21 3.4.5.2 - Test conditions ............................................................................................... 21 3.4.5.3 - Warnings ....................................................................................................... 21 3.4.5.4 - Measurements ............................................................................................... 21 3.4.5.4.1- Points to be measured ............................................................................. 21 3.4.5.4.2- Testing First step: .................................................................................... 22 3.4.6 - Catalyst efficiency tests .. (23)3.4.6.1.1- Parameters to be measured and recorded............................................... 23 3.4.6.1.2- Test conditions......................................................................................... 23 3.4.6.1.3- Warnings ................................................................................................. 23 3.4.6.1.4- Measurements ......................................................................................... 24 a Points to be measured ................................................................................... 24 b Testing .. (24)3.4.7 - Engine photo (24)3.4.7.1.1- Parameters to be measured and recorded............................................... 24 3.4.7.1.2- Test conditions......................................................................................... 24 3.4.7.1.3- Warnings ................................................................................................. 24 3.4.7.1.4- Measurements ......................................................................................... 25 a Points to be measured ................................................................................... 25 b Testing .. (25)Engine characterisation4 / 252 - ENGINE INSTRUMENTATION2.1 - Instrumentation listingThe following table lists the minimum instrumentation necessary for the tests.Engine characterisation5 / 252.2 - Installation drawing EMS communication facility:1st option: bananas connectors 4mm to be installed corresponding to EMS pin-out A3, A4and D12nd option: Lemo connectors2 134 6 5Engine characterisation6 / 253 - ENGINE TESTSIMPORTANT NOTES1. For each test described in the following parts, information and results from the testshave to be reported in the Engine_Characterization_Report document.2. Everyday, recorded data from tests must be sent to Synerject so as to be archivedand analysed.3. As shown in the planning array above, all the steps of this documentation are not tobe achieved in the first phase of the engine characterization :Some of them are needed for the "Preliminary Phase": this phase allows tobuild a first calibration, so as to check if pollution and performance goals could be achieved, and so as to make vehicles running safe.The others are needed for the 'Industrial Phase": this phase allows to check thevehicle and the system as accurate as possible, and to build a final "basic calibration", that means to obtain some engine characterization calibrations which should not be modified during the following steps: it's the first "productive" phase.The array below is making a sum-up of these steps.Engine characterisation Array7 / 25Engine characterisation8 / 253.1 - PRELIMINARY CHECKINGSpecific equipment is required in this part:_ Oscilloscope (with recording function if possible) _ Stroboscopic lamp _ Multimetre _ Current probeHowever, the most important tests could be done only with a multimetre.3.1.1 - EMS components conformityThe aim is to check that all the components are conformed according to their specifications. Compare the reference of each components with the specified reference (refer to the TAS). 3.1.2 - Mechanical components conformityThe aim is to be sure of the engine configuration. See the engine characterisation report. 3.1.3 - Wiring harness conformityEngine characterisation9 / 253.1.3.2 - Power ground / sensor ground checkingECU disconnected, the power ground and the sensor ground should be separated. Check with a multimetre there is no continuity between the pin D1 and H1 of the wiring harness, the test should be done with all the sensor and actuators connected.3.1.3.3 - Wiring harness pin to pin continuity checking (ECU disconnected)With a multimetre check the continuity and the resistance between the ECU connector pins and the actuator or sensors connector pins. The resistance between 2 points must be inferior to 0.2 Ω. 3.1.4 - Inputs / outputs3.1.4.1 - First communication with the ECUWith all the actuators and sensors disconnected and ECU connected, try to get the communication between the ECU and INCA under key-on. INCA should be well configured to perform this part, make sure of using the good software / calibration as well as good ETAS cables and PCMCIA card. Check the calibration and software inside the ECU.3.1.4.2 - Crankshaft sensor signal checkingConnect the crankshaft sensor, and with the help of an oscilloscope check the signal shape from the crank sensor at the engine speed value of the application under cranking( 400-500 rpm) :_ The signal should have amplitude around 800mV peak to peak._ Check the value of the engine speed (N) with INCA, this value has to correspond to the value measured by the engine test bench._ Check if the crankshaft sensor (CPS) is well connected by displaying CPS+ and CPS- on an oscilloscope:CPS + : Signal rises after long tooth detection : SIGNAL OKCPS + : Signal falls after long tooth detection : SIGNAL INVERTED3.1.4.3 - InputsWith INCA connected and under key-on. All the actuators disconnected at the moment.3.1.4.3.1- Engine coolant sensor ECTConnect the sensor, and check the value TCO displayed with INCA. TCO must equal the engine temperature measured by the thermocouple +/- 1°C. 3.1.4.3.2- O2 sensorIf the O2 Sensor is a ZFAS one, no test should be done.Engine characterisation10 / 25If not, note the INCA value VLS_UP_1 (should be around 0.4V)3.1.4.3.3- Air temperature sensorThe air temperature TIA displayed with INCA must equal the air temperature measured by the thermocouple inside the air box +/- 1°C.3.1.4.3.4- Throttle position sensorCheck the value of TPS with INCA at minimum and maximum opening of the throttle. The value should be respectively 0° closed throttle and around 80° or 65° (if the application is without ISA) at maximum opening.3.1.4.3.5- Manifold pressure sensorThe manifold pressure MAP displayed with INCA must be equal to the atmospheric pressure in the engine test cell +/- 20 mbar.3.1.4.4 - Outputs 3.1.4.4.1-Spark advanceaFirst method: with a non-adjustable stroboscopic lampUnplug the injector so as the engine doesn't start.Verify that a TDC indicator exists on the crankcase and a mark exists on the flywheel in order to be able to detect Top Dead Center.Make mark on the flywheel, using a reflective sticker for example, to locate the Top Dead Center. With INCA:- set LC_IGA_MAN_ACT to 1 so as to work under bench mode -set C_IGA_MAN to fix an ignition value at 0°.With the stroboscopic lamp, check the respective mark alignment with the crankcase TDC indicator.The difference should not be greater than 1 degree crank angle.b Second method: with an adjustable stroboscopic lampUnplug the injector so as the engine doesn't start.Verify that a TDC indicator exists on the crankcase and a mark exists on the flywheel in order to be able to detect Top Dead Center.With INCA:- set LC_IGA_MAN_ACT to 1 so as to work under bench mode-set C_IGA_MAN to fix an ignition offset during cranking: -10, -5, 0°, 5, 10 degrees.For each value applied, adjust the stroboscopic lamp so as to align the mark on the flywheel and the crankcase indicator.Engine characterisation11 / 25 Note the value of the phase shifting on the stroboscopic lamp. The difference between the offset applied and the read value on the lamp should not be greater than 1 degree crank angle.3.1.4.4.2- Dwell time Unplug the injector so as the engine doesn't start. Connect a current probe across the positive lead to the primary ignition coil and display the current signal on an oscilloscope. (Pay attention to the direction of the current) Make the engine cranking, and record the current by an oscilloscope, and system values by INCA. On the oscilloscope record, measure the duration the primary coil is switched on in cranking (Dwell Time = TD). Note TD and the maximum value reached by the current in the report. Look at the INCA record, and note the value of TD_1 and CUR_IGC_DIAG_CYL_1 in the report. TD_1 should be equal or close to the value of Dwell Time measured by the oscilloscope,.Figure 1 : Oscilloscope signal In addition, check during cranking that the current value measured does not exceed the specified maximum value corresponding to the used coil. (6.5A for the coil furnished by Synerject)3.1.4.4.3- Tests with engine running Make the same tests (spark advance and dwell time) with engine running at middle speed (4000rpm) and at fast speed (8000rpm).3.1.4.4.4- Fuel supply capability Equipment: Digital oscilloscope Breakout box Fuel circuit equipped with pressure sensorTDEngine characterisation 12 / 25Detail the fuel circuit (hoses dimensions and components from the fuel tank to the injector) and detail the pressure measurement in the fuel circuit. Trace and record Fuel pressure, INJ (pin G1) and CRANK_OUT signals in addition to main software variables during a test which consists in start phase, IS, slow and continuous acceleration until Nmax, back to idle, WOT until Nmax, back to idle, stop. (add MAP record if the regulator reference is connected at the intake) Comment any anomaly: fuel pressure should be ensured at Pref with a +/- 50mbar tolerance and note the pressure keeping capability when engine is stopped.Engine characterisation13 / 253.2 - ENGINE RUN-IN The aim is to run the engine in order to stabilise it in terms of friction. The engine has to be run at different engine speed and loads for a certain duration. If possible and if a carburettor vehicle version exists, this step could be done with a carburettor mounted on the engine. If it is not possible, at this stage the calibration might not be able to assure a good running of the engine at every speed and loads, consequently the operator has to adjust manually the richness on each point of the run-in in order to be at richness 1 or more rich to stay under 850°C of exhaust gas temperature. Look at the RUN-IN table in the report document to see the run-in procedure. 3.3 - ENGINE CHARACTERISATION generalities3.3.1 - Recording method recommendations Principle: 1 point - 1 file -1 tracking in the report Naming convention: Task name _ EMS setting linked to task For example: for daily checking test of the 6th of May 2009 Daily_Checking _20090506.dat (INCA file) and Daily_Checking _20090506.xls (Dyno file) for full load test at 6000 rpm and IGA sweep at 20°CRk (next step at 25°CRK) Full_load _6000_20.dat (INCA file) and Full_load _6000_20.xls (Dyno file) for airpath Speed Throttle test at 5500 rpm and TPS 25° Airpath_ST _5500_25.dat and Airpath_ST _5500_25.xls (Dyno file) INCA file: Contains EMS data during 20s and if possible engine dyno data Dyno file (if it is not possible to make acquisition on INCA): Main sheet with dyno data (Torque, Power, Thermocouple info, Atmospheric pressure, Humidity) If engine ratio changed, check the gear ratio computation of the bench Second sheet: emission data written by "hand": HC, CO, NOx,O2 and CO2, Lambda 3.3.2 - EMS setting manually IGA change: Use C_IGA_MAN to set a constant value & LC_IGA_MAN_ACT to activate this value in EMS.Engine characterisation 14 / 25 Richness change: Use C_TI_HOM_MAN to set a constant value & LC_TI_HOM_MAN_ACT . 3.4 - ENGINE CHARACTERISATION tasks 3.4.1 - Engine daily checking This test has to be done every day before starting the tests as soon as the engine is warm. The aim is to check the good running of the engine by running it on 3 speed / load point. 3.4.1.1 - Parameters to be measured and recorded EMS data: Use INCA experiment Dyno bench data: _ Torque _ Temperatures (all temperatures from thermocouples) _ Richness _ Atmospheric pressure _ Hygrometry IMPORTANT NOTE: If dyno bench data recording is not possible, please contact Synerject. 3.4.1.2 - Test conditions _ Engine temperature regulated at 90°C for liquid cooled engine and between 150°C and 160°C for air cooled engine _ Hygrometry regulated at 50% _ Air temperature regulated at 25°C at the inlet of the air box3.4.1.3 - WarningsEngine Temperature: do not go beyond 110°C for liquid cooled engine and 190°C for air cooled engine. An alarm will occur in the top right hand corner of the screen if the threshold is exceeded. Exhaust gas temperature: Do not go beyond 850°C of exhaust gas temperature; regulate it by enrichment of the air fuel mixture (the richer the air fuel mixture, the colder the exhaust gas temperatures). An alarm will occur in the top right hand corner of the screen if the threshold is exceeded. Knocking: Pay attention to knocking, as soon as knocking is detected retard the spark advance by 5 degrees, never stay more than few seconds with knocking. Richness : Do not go behind 0.9 of richness. An alarm will occur in the top right hand corner of the screen if the threshold is exceeded. Engine synchronisation : pay attention that LV_SYN_VLD should always be equal to 1 during tests.3.4.1.4.1- Points to be measured_ First point in idle_ Partial load, 6000 rpm and TPS at 25°_ Full load at the engine speed where the maximum power is reached (this point has to be done only after full load characterisation)3.4.1.4.2- Testing1. Fill the tank2. Check injector mounting (no rotation)3. Check that module ECU connector is OK (not melted)4. Get ECU communication5. Warm-up the engine by perform 1st point measurement Run the engine at 1st point 5° TPS/ 4000rpm / 6 IGA / 50°C OIL check if the value TI_LAM_COR is between -30% and +30%, then record all EMS and dyno bench parameters after stabilisation. Fill the report.6. Perform 2nd point of measurement. Mid Power 20°TPS / 4000rpm / 19° IGA /55°C OIL.check if the value TI_LAM_COR is between -30% and +30%, then record all EMS and dyno bench parameters after stabilisation7. Run the engine in full load at the engine speed where the maximum power is reached,make set manually the spark advance and the richness at the full load settings (defined after full load characterisation) then record all EMS and dyno bench parameters after stabilisation3.4.2 - Full loadThe aim is to characterise the engine in terms of performance and volumetric efficiency.3.4.2.1 - Parameters to be measured and recordedEMS data: Use INCA experimentDyno bench data:_ Torque_ Temperatures (all temperatures from thermocouples)_ RichnessIMPORTANT NOTE: If dyno bench data recording is not possible, please contact Synerject.3.4.2.2 - Test conditions_ Engine temperature regulated at 90°C for liquid cooled engine and between 150°C and 160°C for air cooled engine_ Hygrometry regulated at 50%_ Air temperature regulated at 25°C at the inlet of the air box_Be careful to use the pre-calibration sent by Synerject Toulouse:Engine_Bench_PreCalibration.mot15 / 25Engine Temperature: do not go beyond 110°C for liquid cooled engine and 190°C for air cooled engine. An alarm will occur in the top right hand corner of the screen if the threshold is exceeded.Exhaust gas temperature: Do not go beyond 850°C of exhaust gas temperature; regulate it by enrichment of the air fuel mixture (the richer the air fuel mixture, the colder the exhaust gas temperatures). An alarm will occur in the top right hand corner of the screen if the threshold is exceeded.Knocking: Pay attention to knocking, as soon as knocking is detected retard the spark advance by 5 degrees, never stay more than few seconds with knocking.Richness: Do not go behind 0.9 of richness. An alarm will occur in the top right hand corner of the screen if the threshold is exceeded.Stability of the measurement point: Be careful to check during the whole measurement on a fixed point, that bench controlled parameters (engine speed and load) stay constants.Stability of measured parameters: Be careful of the stability of both EMS and dyno bench parameters before to start the recording. Depending on the case it might be necessary to wait few seconds especially for pollutant measurement.Injection time range:The alert TI_RANGE (with the other alerts n the full load experiment) is activated as soon as the injection time is at maximum possible value. If this alert occurs it means the injector has a too low static flow and has to be changed.Engine synchronisation: pay attention that LV_SYN_VLD should always be equal to 1 during tests.3.4.2.4 - Measurements3.4.2.4.1- Points to be measured_ Performance characterisation: Every 250 rpm at full open throttle from 2000 rpm (if possible) to maximum engine speed._ Richness characterisation in full load: Richness sweep from 1 to 1.3 every 0.05, at N of max power at full open throttle and ignition advance = 30° (or If you want to do something more optimized, you could perform it at N of max power with IGA opti taken form the sweep result)._Optional: Power and Torque optimization: every 250 rpm at full open throttle from 2000 rpm (if possible) to maximum engine speed, at each engine speed, make a Richness sweep from 1 to 1.3 every 0.05, and then look for IGA nominal value._ Break points determination: Measure Engine performance at Richness 1 every 100 rpm at PQ_AMP_COR = 0.6 from 2000 rpm (if possible) to maximum engine speed.3.4.2.4.2- Testing_ Performance characterisation:On each point of engine speed, carry on the following steps:16 / 25Engine characterisation 17 / 25 1. Adjust the richness to 1.1, if exhaust gas temperature goes beyond 850°C with richness 1.1, enrich (put more fuel) to stay under 850°C. 2. Ignition advance sweep from 10° to 50° (or knocking limit – 2°) every 5°, on each ignition advance point record EMS and dyno bench parameters, and fill the testing grid. With ignition retard pay attention to the exhaust gas temperatures, do not exceed 850°C, enrich if necessary. When knocking is detected retard the spark advance by 5degrees, then put spark advance again only by step of 2 degrees until you reach the knocking limit, record the optimum point at knocking limit -2°. 3. Go on to the next engine speed point, take care of exhaust gas temperature and engine knocking. _ Richness in full load characterisation: Richness sweep from 1 to 1.3 every 0.05, at 4500 rpm full open throttle and ignition advance = 30°. For each richness point, record all EMS and dyno bench parameters. _ Break points determination: Keep a constant value of PQ_AMP_COR = 0.6. On each point of engine speed: 1. Adjust the richness to 1. 2. Make an acquisition of EMS variables and bench data. 3. Go on to the next engine speed point; take care of exhaust gas temperature and constant PQ_AMP_COR. 3.4.3 - SOI optimization3.4.3.1 - Parameters to be measured and recorded EMS data: Use INCA experiment Dyno bench data: _ Torque _ Temperatures (all temperatures from thermocouples) _ Richness _ Emissions, NOx, HC, CO, CO 2, O 2 before catalyst IMPORTANT NOTE: If dyno bench data recording is not possible, please contact Synerject. 3.4.3.2 - Test conditions _ Engine temperature regulated at 90°C for liquid cooled engine and between 150°C and 160°C for air cooled engine _ Hygrometry regulated at 50% _ Air temperature regulated at 25°C at the inlet of the air box _Be careful to use the last calibration sent by Synerject Toulouse, and resulting from the Ignition advance tests: Engine_Bench_Ignition_Advance.mot3.4.3.3 - Warnings Engine Temperature: do not go beyond 110°C for liquid cooled engine and 190°C for air cooled engine. An alarm will occur in the top right hand corner of the screen if the threshold is exceeded. Richness : Do not go behind 0.9 of richness. An alarm will occur in the top right hand corner of the screen if the threshold is exceeded.。
汽车标定和环境舱

Calibration Development Using Climatic Chamber通过环境仓完成系统标定Traditional calibration process uses territory vehicle trips to calibrate various engine and vehicle functions. The goal is to expose the energy management system (EMS) to extreme temperature and environment. This ensures the system will operate appropriately under stressed conditions. The vehicle test trips often compose of hot, cold, and altitude conditions. Because the test trips are sensitive to suitable weather conditions, using climatic chambersfor extreme temperature testing has been used to supplement calibration process when seasonal constraints and production timing do not line up. In order to meet the F-series Euro II SOP in July, the process is to use exclusively climatic chamber for calibration and validation instead of territory test trips.要标定全面的引擎和汽车性能参数,传统的方法是通过驾驶被测车辆进行一次道路三高试验来完成测试.目的是为了把汽车的发动机管理系统暴露在极端条件下(温度和环境).这保证了所有的系统在比较恶劣的环境下能够正常有效的运行.而这样的旅行常常包含高温,低温,高海拔条件.由于这样的旅行测试对气候条件非常敏感,因此当标定工作被季节或者产品开发时间所限制的时候,我们把环境仓测试当作普通标定过程的一种补充形式.为了达到7月份F 系列发动机欧II排放的标准,这次标定完全由环境仓来代替传统的自然环境标定过程.While territory test trips have certain benefits such as lower cost and expose vehicles to greater range of conditions, there are benefits to using climatic chamber. The benefits are:和传统旅行标定方式拥有低成本,参数广泛全面等优点一样,环境仓标定方法也有自己的好处:1)Controllability 可控性It is easier to adjust the temperature/barometric pressure to the exact conditionthat is not always possible in actual vehicle test trip. In test trips, you are at themercy of the weather conditions. Sometimes it may not be at the extremeconditions you are looking for.能够精确调节大气压力和温度,并且还能模拟一些自然中不太可能存在的天气状况.传统测试过程往往受自然气候条件的限制,而且有些时候寻找一些理想的极端天气状况会非常困难.2)Repeatability 可重复性For calibration, repeatable environment is critical to resolve issues. Being able toset up the chamber to the exact condition removes the ambiguity from day-to-daydifferences in weather conditions.在标定工作中,对解决问题来说,可重复性的环境参数非常重要.通过环境仓,我们可以把每次测试都保证在一个精确的模拟天气条件下,这样消除了自然环境下每天测试天气参数无法完全相同的问题.3)Speed 迅速的Since the climatic chamber is located on site near the engineering center, there isa greater support staff on site to help with any development problem. This iscontrary to territory trip where the team must bring everything they need on thetrip. Any uncompleted tasks during a territory test trip will need to be repeatedlater if the weather does cooperate.由于环境仓位于工程开发中心的旁边,当我们遇到任何问题时,都能够从工程师或技术人员那里获得迅速而及时有效的技术支持或帮助.而传统旅行标定往往一开始就需要把所有的技术团队和工具都带在身边,并且任何由于天气状况不符合测试要求而造成的任务未完成都需要整个标定工作重新开始.For the above reasons, climatic chambers have been used as part of the calibration process.基于以上原因,环境仓被作为整个标定过程的一部分.Engine and vehicle calibrations are not an exact science due to the complex nature of the powertrain, vehicle, and legal interactions. The goal of the calibration process is to find optimal points of the system to meet functional requirements, robustness assurance, and government regulations. The calibration engineers often make trade off to satisfy all three criteria. The decision process is based on knowledge and experience.由于动力系统,汽车与法律的相互干涉和交互作用,发动机和汽车的标定无法成为一门精确的科学.因此标定工作就是为了在系统中寻求一个最优点,能使产品能够满足功能需求, 鲁棒性保证和政府相关法规的要求.标定工程师们常常设法同时满足这三个要求.而得出结论的过程是同时基于知识和经验..The following sections are not meant to be an all encompassing description of the climatic calibration procedure but an overview the calibration tasks using climatic chambers.以下的章节将给大家总体介绍一下使用环境仓的标定过程,而不是一个完整,详细的环境标定过程的描述.1) Cold start and drive testing 冷车启动和驾驶测试2) Hot start & drive testing 热车启动和驾驶测试3) Hot fuel Handling 热燃油处理The goal of the hot fuel handling test is to evaluate the accuracy of the model in the strategy to compensate for the effect of hot injector. Typically, during a hot soak with engine off, the injector tip becomes hotter as fuel flow stop and less air flow to cool the injector. During this engine-off period, with lower fuel pressure, and hotter injector, the chance for fuel vapour is much greater, especially for returnless fuel system which can cause lean fuel if not compensated by the strategy.热燃油处理测试是为了评估热喷油嘴效果补偿模型的精确度. 典型的情况是,当发动机在高温状态下停止以后, 由于燃油流动的停止,没有新鲜的空气进来冷却喷油嘴,喷油嘴顶部温度会升高.在这个期间,油压降低,喷油嘴高温,产生燃油蒸汽的可能性大大增加,特别是没有燃油回收系统的发动机,如果没有这类的补偿策略,便更会出现稀燃油的情况.The following tests are to verify that the system accounts for fuel vaporization in the fuel rail and does not cause failure to start or lean excursions.以下的测试目的是证实这个系统解决了油轨中燃油蒸汽的问题,并不会导致车辆启动失败或过稀Drivability is evaluated for different hot fuelling scenario, primarily, through different hot-soak times and driving profile. For detail on drivability test, please see the tab “Manual Drivability” i n the calibration sign-off document for list of different driving conditions at the end of the document.驾驶性能常常由不同的热油情况,特别是通过不同的热浸时间和驾驶风格来评估..为了获得更多关于驾驶性能测试的细节,请阅读在本文档最后,不同驾驶情况列表的标定签发文档”手动驾驶性能’表格4) Canister Purge 碳罐净化Canister purge system is used to capture generated fuel vapour inside the fuel tank in a carbon canister. Through the control of vapour management valve, the fuel vapour captured in the carbon canister can be empty back into the fuel charging assembly. The calculation of the purged fuel into the fuel system needs to be properly calculated to ensure the engine operates at the proper stoichiometric air/fuel ratio. Improper compensation can cause either too lean or too rich fuel operations. The worst case scenario is during hot test where vaporization of the fuel is more likely. 碳罐净化系统的作用是通过碳罐捕获油箱内产生的燃油蒸汽.通过对蒸汽管理阀门的控制,被碳罐捕获的燃油蒸汽能返回到喷油总成中去.为了使发动机工作在合适的空燃比状态下,被净化的燃油量应该被精确计算.不适当的回油补偿会造成燃油混合物过稀或过浓.最坏的情况会发生在容易产生燃油蒸汽的高温测5) AC & CoolingCheck to ensure good AC and cooling operation at elevated temperatures.检查和确保好的空调和冷却运行在提高的温度下。
976-2024透射式烟度计检定规程

976-2024透射式烟度计检定规程1.透射式烟度计检定规程是指对透射式烟度计进行检定的程序和要求。
The transmission smoke meter calibration procedure refers to the procedure and requirements for calibrating transmission smoke meters.2.透射式烟度计是一种用于测量柴油机废气排放浓度的仪器。
The transmission smoke meter is an instrument used to measure the concentration of diesel engine exhaust emissions.3.检定规程旨在确保透射式烟度计的准确性和可靠性。
The calibration procedure aims to ensure the accuracy and reliability of the transmission smoke meter.4.检定规程包括校准、维护、记录等内容。
The calibration procedure includes calibration, maintenance, and record-keeping.5.透射式烟度计检定应由具有相应资质和设备的检定机构进行。
The calibration of transmission smoke meter should be carried out by a calibration institution with the corresponding qualification and equipment.6.在进行检定前,应检查透射式烟度计的外观和功能是否正常。
Before calibration, the appearance and function of the transmission smoke meter should be checked for normality.7.应使用标准气体对透射式烟度计进行校准。
ABNT_NBR6601_2005en

BRAZILIAN STANDARD ABNT NBR6601 Second edition30.09.2005 Effective as from31.10.2005Light Road Motor Vehicles – Determination of hydrocarbons, carbon monoxide, nitrogen oxides, carbon dioxide and particulate matter in exhaust gasKeywords: Exhaust gas, road vehicleDescriptors: Exhaust gas. Road vehiclesICS 43.020; 13.040.50ABNT - Associação Brasileira de Normas Técnicas (Brazilian Association of Technical Standards)Reference number ABNT NBR 6601:200544 PAGES©ABNT 2005© ABNT 2005All rights reserved. Unless specified otherwise, no portion of this publication may be reproduced by any means, electronic or mechanical, including photocopy and microfilm, without ABNT’s written permission. ABNT HeadquartersAv. Treze de Maio, 13 – 26o. andar20031-901 – Rio de Janeiro – RJPhone: +55 21 3974-2300Fax: +55 21 2220-1762abnt@.br.brPrinted in Brazil.SummaryForeword (iv)1 Purpose (1)2 StandardReferences (1)3 Definitions (1)4 Apparatus (3)4.1 Chassisdynamometer (3)4.2 Sampling system for testing vehicle with spark ignition (3)4.3 Sampling system for Diesel vehicle testing (5)4.4 Equipment for analysing particulate matter gas and filter (7)heater (11)4.5 Fuel4.6 Temperature recorder (11)4.7 Drainage and feeding apparatus (11)cooling fan (12)4.8 Engineverification of apparatus (12)4.9 Calibrationand4.9.1 Calibrations gases (12)4.9.2 Frequencycalibrations and verifications (12)ofdynamometer calibration and performance checking (13)4.9.3 Chassisverificationconstant volume sampling (CVS) (124)ofand4.9.4 Calibrationverification of analysers 17 and4.9.5 Calibration5Performing the test (20)5.1 Fuels (20)requirements (20)5.2 General5.3 Vehiclepreparation (20)vehicle (21)5.4 Preconditioningthe5.5 Vehicle operation and exhaust gas sampling (24)5.6 Analysis of the exhaust gas sample (31)5.7 Weighing and handling particulate filter of the Diesel (31)6 Results (32)6.1Calculation procedure (32)for the calculations (32)6.1.1 Readingsrequired6.1.2 Calculations of the correction coefficients and of the general parameters (33)mass 33 6.1.3 Pollutantof final results (33)6.1.4 Calculation6.1.5 Calculation of emissions of particulate matter by diesel vehicles (34)6.2. Report (35)ATTACHMENT A (Informational)– Determination of the tractive effort on the roll at the speed of 80.5 km (TE80)38 ATTACHMENT B (Informational) ATTACHMENT B (Informational) Coordinates of the Urban Driving Cycle41ForewordThe Brazilian Association of Technical Standards – ABNT is a National Forum for Standardisation. The Brazilian Standards, the content of which is the responsibility of the Brazilian Committees (ABNT/CB), of the Sectoral Standardisation Organisms (ABNT/ONS) and of the Temporary Special Study Commissions (ABNT/CEET) are prepared by Study Commissions (CE) formed by representatives of the involved industries including: producers, consumers and neutral parties (universities, laboratories and other).ABNT NBR 6601 was written by the Brazilian Automotive Committee (ABNT/CB-05), by the Committee of Study of Emissions in Light Vehicles (CE-05:102.02). This Project was circulated for National Examination in accordance with Invitation No. 12, dated 12/30/2004, under ABNT NBR 6601 Project.This second edition cancels and replaces the prior edition (ABNT NBR 6601:2001), which has been technically revised. This Standard includes Attachments A and B, which are of an informational nature.Light Road Motor Vehicles – Determination of hydrocarbons, carbon monoxide, nitrogen oxides, carbon dioxide and particulate matter in exhaust gas1 Purpose1.1 This Standard prescribes a method for the determination of total hydrocarbons (THC) and non-methane hydrocarbons (NMHC), carbon monoxide (CO), nitrogen oxides (NO x), carbon dioxide (CO2) and particulate matter emitted by the engine through the exhaust tailpipe of light road motor vehicles, under simulated conditions of average regular use in urban traffic.1.2 This Standard also establishes the minimum characteristics of the equipment and materials and also the driving cycle for performing the tests.References2 StandardThe standards listed below include provisions, which, whenever cited herein, are applicable to this Standard. The issues listed herein were in force at the time of this publication. Since any standard is subject to revision, it is recommended that, when executing an agreement based on this standard, the parties review the convenience of using more recent issues of the standards cited below. ABNT can inform which standards are in force on a given date.ABNT NBR 6070:2002 – Masses of road motor vehicles, their trailers and combiners – Definitions and symbolsABNT NBR 8689:2000 – Light road motor vehicles – Fuel for testing – Gasoline, alcohol and their mixturesABNT NBR 10312:1991 – Light Road Motor Vehicles – Determination of resistance to displacement by free deceleration on a driving track and simulation in a dynamometerABNT NBR 11481:2002 – Light Road Motor Vehicles – Measurement of evaporative emission3 DefinitionsFor the purposes of this Standard, the definitions in ABNT NBR 6070 and the definitions below are applicable:3.1 engine feeding:Group of fuel reservoirs, pipelines, pumps, pressure regulators, feeding valve, filters, vapour return lines, mixture generators and all vents and control of evaporative emissions in the vehicle.3.2 evaporative emission control: It includes all vehicle components for controlling or reducing the quantity of fuel vapour emitted.3.3 canister: a reservoir for absorbing vehicle fuel vapours.3.4 measurement accuracy: Proximity between the value of a magnitude obtained by measurement and the actual conventional value of such magnitude.ABNT NBR-6601:20053.5 calibration gas: Gas of known concentration, used to determine the response curve of an analyser.3.6 exhaust gas: A group of substances released by any opening in the tail pipe exhaust, emitted into the atmosphere.3.7 reference gas: Gas of known concentration, used in checking during testing of the analyser response. 3.8 zero gas: Gas used in setting the analyser to zero.3.9 total Hydrocarbons (THC): Total hydrocarbons, including methane, contained in a gas sample.3.10non-methane hydrocarbons (NMHC): hydrocarbons, excluding methane (CH 4), contained in a gas sample.3.11 measurement uncertainty: Part of the expression of a result from a measurement that indicates the value range among which the actual value of the measured magnitude is included.3.12 equivalent inertia: Sum of all rotational inertia masses, in kilograms (or pounds) that, connected to the chassis dynamometer rolls, produces a dynamic effect equivalent to the inertia mass in a vehicle in linear movement. Equivalent inertias observe a discrete staggering according to the vehicle mass under testing, as per 5.5.1.1. 3.13 total gross vehicle mass (TGVM): Mass corresponding to maximum total vehicle weight as specified by NBR6070. 3.14 curb weight: The corresponding mass of a vehicle curb weight as specified by NBR 6070. 3.15 mass of a vehicle used in tests: The curb weight, increased by 136 kilograms.3.16particulate matter: Solid particles emitted by the Diesel engine and resulting from combustion.3.17 micromol/mol (μmol/mol): Ratio between the number of moles of the component and the number of total moles of a gaseous mixture. For the purposes of this Standard, the μmol/mol unit is considered as equivalent to the ppm unit.3.18 nitrogen oxides (NOx): Sum of nitric oxide and nitrogen dioxide contained in a sample.3.19 Parts per million (ppm): Number of volume of units in a determined gas, contained in a million of units of volume of a gaseous mixture.3.20 Parts per million of carbon (ppmC): Hydrocarbons concentration, in ppm, expressed as equivalent to methane. Thus, 1 ppm of methane is indicated as being 1 ppmC. To convert concentrations in ppm from any HC into an equivalent value in ppmC, multiply the concentration in ppm by the number of carbon atoms in each gas molecule. For example, 1 ppm of hexane is equal to 6 ppmC.3.21 Friction power (P f ): Power inherent to the chassis dynamometer through its internal frictions, measured at the speed of 80.5 km/h.3.22 Indicated power (IP 80): Power indicated on the chassis dynamometer controls, at the speed of 80.5 km/h, in such a way that the sum of this power plus the machine friction power results in the tractive effort value on the rolls at 80.5 km/h (TE 80).3.23 Tractive effort (braking force) on the rolls (TE 80): Net power corresponding to the force and to the tangential speed applied to the roll surface on the chassis dynamometers, at a speed of 80.5 km/h.Main fuel tank of the vehicle, i.e., the tank that contains the predominant fuel used to make the tank:3.24 fuelengine function.3.25 light road motor vehicles: Light road passenger vehicle, cargo or all purpose, with carrying capacity up to 12 passengers including the engine or total maximum mass lower than 2800 kilograms.Speed at which the vehicle is regularly driven, according to various convenience factors.speed:3.26 cruising4 ApparatusThe necessary apparatus for conducting the tests is described in items 4.1 to 4.8.4.1 Chassis dynamometerThe chassis dynamometer must have an electric or hydraulic power absorption unit, to simulate the laden condition of the vehicle on the track, as specified by ABNT NBR 10312 or Attachment A. It should also have a group of inertia flywheels and/or other means to simulate the equivalent inertia of the vehicle (see 3.12). Twin roll chassis dynamometers must have rated roll diameters greater than or equal to 219 mm. Single roll chassis dynamometer must have a rated dynamometer greater than or equal to 1200 mm.4.2 Sampling system for vehicle testing with spark ignition4.2.1 This system must be a constant volume sampler type (CVS) and it should permit to measure the actual masses of the substances released by the engine through the tail pipe exhaust. For this, the following is required:a) measurement of the total volume of the mixture of exhaust gas / dilution air.b) ongoing collection for analysis of an amount of this mixture, proportional to that volume.4.2.2The system must have sufficient capacity to eliminate the water condensation in the system. A flow of 0.10 m3/s to 0.20 m3/s is enough in most cases.4.2.2.1The static pressure in the tail pipe(s) exhaust of the vehicle connected to the CVS, verified during the driving cycle should not have variations higher than ± 1.2 kPa in relation to the same conditions, however with the tail pipe(s) exhaust under free exhaustion. The connections used should not have leaks.4.2.3The system must be equipped with sample collecting bags, for the dilution air and for the diluted exhaust gas, with sufficient volumetric capacity so that it will not restrict the flow of the sample being collected. It should be of a special material to prevent quantitative and qualitative changes in the composition of the stored samples.4.2.4The sampling system may be critical venturi (CV), called CVS-CV sampling system. Other sampling systems may be used, provided that the equivalence of results is demonstrated and proven.4.2.4.1The CVS-CV sampling system works based on the fluid dynamics principles associated to a critical flow. In this kind of system, the total flow of diluted gas is kept at a sonic velocity, which is proportional to the square root of the absolute gas temperature, continuously computed. Proportional sampling is performed through another VC system, installed in the same gas flow. Since the pressure and temperature are the same for the inlet of the respective venturis, the sampling volume is proportional to the total volume of the mixture. This system, according to Figure 1, is formed by the following components:a) mixture chamber with filter in the dilution air inlet;b) cyclone-type collection for particulate matter;c) critical venturi for the establishment of total flow;sampling;venturid) criticalsystem;e) samplingf) valves and sensors of temperature and pressure;g) temperature measuring device for the diluted gas at the CV inlet, with a resolution lower than or equal to 1o C;g) integrating electronic circuit for the establishment of the total volume sampled;h) pressure meter with a resolution lower than or equal to 0.40% kPa.Ambient air inletTo the air dilution sample bagSampling Venturi; To the diluted gas pipe sample bagPulse absorberAbsolute pressure transducerAbsolute manifold Critical venturi Tail pipe gas inlet Pressure gauge CVS exhausting unitSampling unit CVSExhaustDischargeSymbolsFlow control valveParticulate filterPumpPressure meterFlow meterTemperature sensor Figure 1- Sampling system of the exhaust gas (CVS-CV)4.2.4.2 Other sampling systems may be used, provided that the equivalence of results is demonstrated and proven. 4.3 Sampling system for testing Diesel vehiclesThis system, according to figure 2, is formed by the components described in 4.3.1 to 4.3.7.4.3.1 The CVS-VC must be equipped with a measurement system for particulate matter, so as to provide sufficientflow/volume to keep the diluted sample at a temperature lower than 52oC at the intake point of the particulate sample. If gas temperature is increased due to the heated points, the use of a heat exchanger after the sampling point of the particulate matter, as well as filters and cyclone separator to withdraw particulate matter before reaching the CV is optional.4.3.2 The dilution air must be between 20o C and 30oC during testing.FID = Flame Ionising DetectorFigure 2 – Sampling system for Diesel testing4.3.3 The dilution tunnel must be:a) sized so as to permit a turbulent flow and a thorough mixing of the exhaustion gas with the dilution gas before the point where sample is collected;b) built with a minimum diameter of 203 mm;c) built with an electricity –conducting material which does not react to the components of the vehicle exhaust gas;d) grounded.4.3.4 The sampling collection point (probe) of particulate matter must be:a) installed in front of the flow, at the point where the exhaust gas and the dilution gas are well mixed (near the tunnel centreline and approximately 10 times the tunnel diameter, as from the point where the gas enters in the dilution tunnel).b) sufficiently far (radially) from the sample collection to the heated flame ionising detector (HFID) for the determination of hydrocarbons so as to be free from influences such as vacuum produced by the probe;c) minimum internal diameter of 12.7 mm;d) such that the distance from the probe to the filter support is not less than 5 times the diameter of the sampler (for filters located inside the tunnel), but no more than 1,020 mm distant, for filters located outside the dilution tunnel;e) free from live edges;f) configured in a way that a pair of clean particulate filters (primary and secondary) may be selected, at the same time as the selection of the set of empty bags for gas emissions, for each phase of the measurement process.4.3.5To pass through the particulate probe, the adjusted flow must be kept at a constant value within +- 5%.4.3.6The sampling pump and the volume measuring devices must be far enough away from the dilution tunnel, so that the temperature of the gas may be kept constant at about +-2.8ºC.4.3.7The sampling point for HFID shall be:a) installed facing the flow, at a distance of about 10 times the diameter of the tunnel, as from its inlet;b) installed at a sufficient radial distance from the particulate probe, to remain free from the influence of such factors as vacuums produced by the probe;c) through a heated line with an internal diameter of at least 4.8 mm with filter, insulated along its whole length, in order to keep the temperature at 191ºC ± 11ºC at its wall.4.4 Equipment for gas analysis and filters for particulate matter4.4.1 The equipment for gas analysis shall consist essentially of an analytical system as that shown in Figure 3. The exact conformity to this scheme is by no means necessary, provided that it is possible to obtain satisfactory results within the specified accuracy of measurements. In order to obtain further information or to co-ordinate the functions of some of the subsystems, other components may be added, including instruments, valves, solenoids, pumps, and so forth, as long as they do not in any way affect the results.4.4.2 The equipment for gas analysis, as shown in Figure 3, consists of flame detector by ionisation, to establish the total hydrocarbon content; a flame detector by ionisation equipped with a selective catalytic converter (cutter), or a chromatographic column in gaseous phase, to establish the methane content; analysing devices by absorption of non-dispersive infrared rays (IND) to establish the content of carbon monoxide and carbon dioxide; and a chemical luminescence analyser (CL) to establish the quantity of nitrogen oxides present. All these analysing devices shall always be operated in full compliance with the manufacturer’s instructions.4.4.3After the initial setting up of the equipment for gas analysis, a check shall be carried out, to see if the analysing devices meet the requirements set forth in 4.4.3.1 to 4.4.3.5 below.4.4.3.1In all analysing devices, the stability of the “zero” and “reference” points over a period of 24 hours shall show deviation of no more than 3% of the maximum showing of the scale.4.4.3.2The FID must show a response to oxygen (O2) of no more than 2% of the maximum showing of the scale, in the case of mixtures of nitrogen (N2) and O2, within a band from 0% to 21% of O2 by volume.4.4.3.3 A CO analyser is considered free from interference caused by CO2 and water vapour when it supplies a response of less than 1% of the maximum showing of the scale (when the maximum showing of the scale is 300 ppm or more) or 3 ppm (when the maximum showing of the scale is less than 300 ppm), for a mixture containing between 3% and 5% of N2 bubbling in water at room temperature, analysed using the equipment’s most sensitive scale.4.4.3.4The maximum response of the CO2 analyser for concentrations between 3,000 ppm and 5,000 ppm of CO, at room temperature and water vapour saturation conditions, should be no more than 1% of the maximum showing of the scale.4.4.3.5The analysing device for NOx by CL requires that the nitrous acid (NO2) present in the sample be converted into nitric oxide (NO) before the analysis, with an efficiency rate of above 90%.4.4.4 The particulate material sampling filters should meet the criteria set forth in items 4.4.4.1 to 4.4.4.4 below.4.4.4.1.1 Acceptance Criterion for the filters:a) During each phase of the conduction cycle, the diluted exhaustion gas shall be collected, simultaneously by a pair offilters (primary and secondary);b) The secondary filter shall be located between 76 mm and 102 mm after the primary filter;c) The net weight of the particulate materials collected from each primary filter shall be established as set forth in item5.7;d) The net weight ratio shall be calculated using the following equation:R pl = MP fp / (MP fp + MP fs)Where: Rpl is the net weight ratio;MPfp is the mass of particulates in the primary filter, in micrograms;MPfs is the mass of particulates in the secondary filter, in micrograms.e) If the ratio is greater than 0.95, the calculations of emissions of particulates shall be based only on the net weight ofthe primary filter;f) If the ratio is less than 0,95, then the calculations of emissions of particulates shall be based on the combination ofthe net weights of the primary and secondary filters.4.4.4.2 – The filter for the collection of particulate materials shall have a diameter of at least 47 mm (a minimum of 37 mmdiameter in the retention and deposit area).4.4.4.3 - The recommended minimum load on the primary filter 47 mm in diameter is 0.05 g. Equivalent loads (i.e.,deposition mass/diameter) are recommended when setting the size for larger filters.4.4.4.4 - The filters for the collection of particulate materials shall be made of glass fibre coated with fluorocarbon or othermembrane of the fluorocarbon type.Ambient(openingtoairinletAtmosphere)Zero gas Fuel gasgasesCalibrationGas Fuel gasCalibration GasesHighZero gasFrom gas sample ConditioningBags ColumnCalibrationGases LowZero GasCalibration GasesAir or O2Zero GasTo externalOutletCalibration gasesSymbolsFlow control valve PumpvalvemeterPressureselectorTwo-wayFlowmetervalveselectorThree-wayFilter Recorder ParticulateFigure 3 – Analytical System for exhaust gas4.4.5For the system for the analysis of exhaust gas emitted by diesel engines, proceed as stated in sections 4.4.5.1 and 4.4.5.2 below.4.4.5.1 The schematic drawings and the descriptions of the main components for the analysis of CO, NOx and CO2 are the same as described for the Otto cycle (spark ignition) as shown in Figure 3.4.4.5.2 To carry out measurements on Diesel vehicles, THC levels should be sampled and measured continuously through HFID, using a heated set of equipment, with analyser, line, filter and pump. Flow control shall be according to Figure 2 or 4.The response time of this instrument shall be less than 1.5 seconds for a response of 90% of the main scale.The set of equipment for the continuous collection of THC can have an overflow system for the zero point calibration gas and also for the gas at the end of the scale (span), as shown in Figure 4. In this case, the gases for the overflow shall enter the heated line as close as possible to the outside face of the dilution tunnel.No other system shall drain the sample of the THC continuous collection line.The sampling line and the filter shall be heated, to keep the gas at a temperature of 191ºC ± 6ºC before the filter and the HFID.Other equipment and analysing devices may be used, provided it has been proven that they produce similar results.4.4.6 The specifications of the weighing chamber (or room) and scales for particulate materials are described in items 4.4.6.1 to 4.4.6.7 below.4.4.6.1 The temperature of the room where the particulate materials filters are made and weighed shall be recorded, and kept between 20ºC and 30ºC during the whole production and weighing process.4.4.6.2 The relative humidity of the room where the particulate materials filters are made and weighed shall be recorded, and kept between 30% and 70% during the whole production and weighing process.4.4.6.3 The site must be free from any contaminant (dust) that could settle on the particulate filters during their stabilisation period.4.4.6.4 It is necessary that two reference filters remain in the weighing room, and that these filters are weighed every 24 hours, when in trial mode.4.4.6.5 If the weight of one of the reference filters deviates by more than ±2% off the filter’s nominal tare (the minimum recommended tare for the 47 mm filter is 0.05 g) during a period of 24 hours, then all filter weighings carried out over this period shall be rendered invalid. The filters that are undergoing a stabilisation process over this period shall be disposed of.4.4.6.6 The reference filters shall be changed at least once a month.4.4.6.7 The scales used in establishing the weights of all the filters shall have a resolution of 1 μg.Zero Span HC Integrator CounterCounterHeated FID3-way valve ExhaustRecorderFigure 4 – HFID Optional configuration with overflow schematic4.5 Fuel heater4.5.1This consists of a heat source and a temperature regulating device. An electric heating mat, with enough power to accompany the fuel heating curve, as set forth in 5.4.10.7, equipped with a transformer for electrical voltage variations, to regulate the amount of heat supplied, is appropriate for most vehicles.4.5.2Alternative heating methods may be used, provided they show the performance necessary for the carrying out of the trials, as stated in 5.4.10.7. All methods shall avoid hot points on the wet surface of the reserve tank, that could bring about local overheating of the fuel. Heating may not be applied directly onto the fuel vapour, within the reserve tank.4.6 Temperature recorder4.6.1 A continuous recorder should be employed to record the fuel temperature in the tank of the vehicle. The temperature should be recorded at least every minute.4.6.2The recorder should have a time resolution of not more than 15 s and a temperature of 0.5°C or less. As for time, it shall have a measurement accuracy of 15 s in the period under testing.4.6.3The sensor of the temperature meter in the fuel tank shall be placed in such a way that the fuel temperature can be measured at about half of the fuel film quota as measured in the region where the buoy/pump grouping has been assembled.4.7 Drainage and supply apparatusThe fuel tank of the vehicle should be totally drained by gravity or by a transfer pump. Fuel should be supplied by an apparatus that, when the fuel is finished, enables the temperature of the tank to go lower than 14°C.NOTE: The fuel heater, the temperature registration and the fuel temperature below 14ºC apply to the measurement of evaporating emissions or in the canister saturation test in vehicles with spark ignition.4.8 Engine cooling fanA fan with constant speed and a capacity not greater than 2.50 m3/s, under normal conditions of temperature and pressure.4.9 Calibration and verification of apparatus4.9.1 Calibration gases4.9.1.1 Gases for calibration of CO and CO2 analysers must be plain CO and CO2 mixtures, respectively, using N2 as the dilution medium.4.9.1.2Gases for calibration of HC analysers must be plain propane mixtures using air as the dilution medium.4.9.1.3The calibration gases of the NO x analysers must be NO mixtures (denominated NO x with a maximum NO2 concentration of 5% of the nominal value), using N2 as the dilution medium.4.9.1.4The gases for the calibration of the CH4 analysers should be simple mixtures of methane, using air as the dilution medium.4.9.1.5In order to obtain the calibration curve, there is a need to use at least six concentrations distributed along the whole of the scale used. The use of proportioning and mixing equipment is allowed, and such equipment should operate with gases at concentrations between 90% and 100% of the maximum readings of each scale used. This equipment shall have an accuracy of ± 0,5% of the maximum reading of the scale.4.9.1.6The fuel used for the FID and HFID must be a mixture of (40 ± 2)% of hydrogen, using helium or nitrogen as a dilution medium. The mixture must have a response lower than 1 ppmC. A fuel gas with 98% to 100% of hydrogen may be used, provided that the requirements of item 4.4.3 are complied with.4.9.1.7The zero gas impurity concentration (air or nitrogen) must not exceed the requirements of ABNT NBR 12857for synthetic and nitrogen.4.9.1.8The calibration gases must be specified within ± 1% of their actual value.4.9.2 Frequency of calibrations and verifications4.9.2.1 The chassis dynamometer and the HC, CH4, CO, NO x and CO2 analysers must be calibrated at least once a month and after any maintenance service that may affect them. In the case of the dynamometer, this monthly calibration may be dispensed with if, at the weekly checking according to item 4.9.3.1.2 or 4.9.3.2.2, it is verified that it remained calibrated.4.9.2.2The performance of the chassis dynamometer and the constant volume sampler system must be verified at least once a week and after any maintenance service that may affect them.4.9.2.3The constant volume sampler must be calibrated after the initial installation during the main check-ups or when the weekly check indicates such need (as according to 4.9.4.4).。
整车开发通用英文缩写

APEC
Asia Pacific Economic Cooperation
APQP/CP APSB
Advanced Product Quality Planning aAnsdiaCoPnatcrioflicPlSatnrategy Board
AR
Appropriation Request
ARC
Architecture Refinement Complete
Assembly Component Tree BOM
AD
Alternatives Development
ADV
Analysis / Development /
ADV
VAanlaildyastiiso,nDevelopment and
AE
VAaplpildiactaitoinon Engineer
AE
Assy PPAP
Assembly Line PPAP
Assy Assy Assy Assy
PPAP PPV PPV Run-Off
Assembly Line PPAP
Assembly Line Products and Process VAaslsiedmabtliyonLine Production and PArsosceemsbslyVaLliindeatRiuonn-Off
ccp协议使用

ccp协议使用一、数据读取与测量CCP协议(CAN Calibration Protocol)主要用于汽车行业的标定和诊断。
它提供了一种标准化的方式来读取和测量ECU(Engine Control Unit)中的数据。
通过使用CCP协议,工程师可以获取发动机、变速器和其他汽车系统的实时数据,从而进行精确的测量和标定。
这些数据可以帮助工程师优化车辆性能,提高燃油经济性,并解决任何潜在的故障。
二、ECU系统处理在汽车中,ECU是控制各种系统(如发动机、变速器、刹车系统等)的关键组件。
CCP协议允许工程师直接与ECU进行通信,以读取和修改其内部的数据和配置。
这使得工程师能够更加精确地控制和调整ECU的行为,以满足特定的性能要求或解决特定的故障。
三、通信方式CCP协议基于CAN总线通信,这是一种广泛用于汽车行业的通信协议。
通过使用CAN总线,CCP协议可以在汽车内部的各种ECU之间进行高速、实时的数据传输。
这使得工程师可以从任何支持CCP协议的设备上远程访问和控制ECU。
四、系统结构CCP协议的系统结构相对简单。
它主要包括以下几个部分:1.硬件接口:用于连接CAN总线和ECU的硬件设备。
2.软件工具:用于读取、写入和测量ECU数据的软件应用程序。
3.数据传输协议:定义了如何通过CAN总线传输数据的规则和格式。
4.诊断和标定协议:定义了如何通过CCP协议对ECU进行诊断和标定的规则和格式。
五、应用领域由于CCP协议在汽车行业中广泛使用,因此其应用领域非常广泛。
以下是一些常见的应用领域:1.发动机标定:工程师可以使用CCP协议来读取和测量发动机的实时数据,然后使用这些数据来优化发动机的性能。
2.故障诊断:通过使用CCP协议,工程师可以诊断和解决汽车中的各种故障,从而提高车辆的可靠性和耐久性。
3.研发和测试:在汽车研发和测试阶段,工程师可以使用CCP协议来验证新设计的性能和功能。
Atlas data sheet

Robust Flexible Tool forAutomated Engine CalibrationThe Atlas Real-Time Mapping and Optimization Tool automates the process of mapping and optimizing an engine. It does this byconnecting to a test bed through the data acquisition and control (DAC) system, and to the ECM through an interface tool such as ATI Vision, ETAS Inca or a proprietary application tool. It also incorporates the modeling and analysis capabilities of widely used products from The MathWorks, such as MATLABand the Model-Based Calibration Toolbox, to the running test bed.The combination of Atlas and the MBC Toolbox provides an extremely powerful environment for cost-effective engine calibration. It is robust, yet flexible and easy to use. The modular design allows you to configure it to a specific set of requirements, rather than having to adhere to rigid methodologies dictated by other prescriptive software tools.Atlas with the MBC Toolbox provides an extremely powerful, easy-to-use environment for cost-effective engine calibration.Copyright 2006 A&D Technology, Inc. All rights reserved. All products and brand names are trademarks or registered trademarks of their respective holders.In keeping with our commitment to continuous product improvement, information contained herein is subject to change. Printed in the U.S.A.Design of Experiment (DoE)Data CollectionData ModelingCalibrationImplementationThe aim of DoE is to determine the most statistically useful data, but only the minimum required to fit the desired model. This resulting reduction in experiment time yields a signifi-cant cost savings. The output of the DoE conforms to the standard MATLAB .csv format.The Atlas DoE Import Wizard uses the .csv file to generate a schedule suitable for running the experiment. The Atlasruntime interface communicates with the test bed controller, and monitors performance limits to safely identify boundary conditions for the specimen.The data logged by Atlas is imported into the MBC Toolbox for further analysis. MATLAB is used to validate the data and build the resulting model. At this point either the model fit is determined to be adequate, or the user returns to the DoE step to generate a new experiment with the revised data.Steps 1 - 3 can be repeated as necessary until the model fit meets the design goal.The MATLAB calibration generation (CAGE) tool uses the new data model to generate ECU tables that are utilized by the ECU strategy.The resulting ECU tables are then ready for download to a prototype or production ECU.。
主机缸套测量报告

缸号 cylinder No.
主机缸套测量报告 Main Engine Cylinder Liner Calibration Report
测量日期 calibrate date 测量地点 calibrate place
主机制造厂及型号 M/E manufacturer & type
缸套制造厂及标记 cylinder liner manufacturer & mark
缸套安装日期 cylinder liner installation date
缸套安装后运转小时 runnning hrs from installation
上次吊缸日期 ast overhaul date 标准缸套内径 liner bore dia.
气口 scavenge port
缸壁布油槽 cyl.wall oil groove
缸壁注油状况 cyl.wall lubricating condition
பைடு நூலகம்
吊缸原因 overhaul reason
备注 remark
上次吊缸后运转小时 running hrs from last overhaul
磨损极限 limit of wear
测量者: calibrate person
轮机长C/E
机务主管审核: superintendent verify
审核人: verifier
机务主管意见 superintendent view
注:主机吊缸时测量并填报,缸套内径的测量点数及位置应以船上标尺为准; 本报告一式两份,一份报公司主管部门,一份轮机长存,保存期为3年。Calibration and report when M/E overhaul, measuring p
修改发动机排量和喷油器参数

1.单击菜单栏“calibrations”,选择“System Parameters”,之后选择“Engine Displacement”。
2.ProCAL软件会弹出Engine Displacement窗体。
标定量VAL_vEng是发动机每个汽缸的排量,单位:cc。
3.双击数值,即可修改排量,之后敲击回车,数值变成红色。
注:通常如果是双缸或多缸发动机,则需要填写单个气缸的排量,而不是发动机总排量。
4.刷写到ECU中,修改完毕。
1.单击菜单栏“calibrations”,选择“Fuel system”,选择“Fuel injector characteristic”。
2.ProCAL会弹出Fuel injector characteristics窗体。
VAL_Qstat 是喷油器的静态流量,单位:克每分钟(g/min)。
3.双击数值,即可修改喷油器静态流量,之后敲回车,数值变成红色。
4.刷写到ECU中,修改完毕。
最后,另存为一个新的cal文件,以备下次使用。
点击菜单栏“File”,选择“Save as”,生成一个新的cal文件。
ECE R85 第5次修订

GE.10-AGREEMENTCONCERNING THE ADOPTION OF UNIFORM TECHNICAL PRESCRIPTIONSFOR WHEELED VEHICLES, EQUIPMENT AND PARTS WHICH CAN BE FITTED AND/OR BE USED ON WHEELED VEHICLES AND THE CONDITIONS FOR RECIPROCAL RECOGNITION OF APPROVALS GRANTED ON THE BASIS OF THESE PRESCRIPTIONS *(Revision 2, including the amendments which entered into force on 16 October 1995)Addendum 84: Regulation No. 85Revision 1 - Amendment 5Supplement 5 to the original version of the Regulation: Date of entry into force: 17 March 2010UNIFORM PROVISIONS CONCERNING THE APPROVAL OF INTERNAL COMBUSTION ENGINES OR ELECTRIC DRIVE TRAINS INTENDED FOR THE PROPULSION OF MOTOR VEHICLES OF CATEGORIES M AND N WITH REGARD TO THE MEASUREMENT OF THE NET POWER AND THE MAXIMUM 30 MINUTES POWER OF ELECTRIC DRIVE TRAINS_________UNITED NATIONS* Former title of the Agreement: Agreement Concerning the Adoption of Uniform Conditions of Approval and Reciprocal Recognition of Approval for Motor Vehicle Equipment and Parts, done at Geneva on 20 March 1958.E /ECE/324/Rev.1/Add.84/Amend.5−E /ECE/TRANS/505/Rev.1/Add.84/Amend.510 May 2010E/ECE/324/Rev.1/Add.84/Amend.5E/ECE/TRANS/505/Rev.1/Add.84/Amend.52Content - Annexes, amend to read:"Annex 1 - Essential characteristics of the internal combustion engine and information concerning the conduct of testsAnnex 2 - Essential characteristics of the electric drive train and information concerning the conduct of testsAnnex 3a - Communication concerning the approval or extension or refusal or withdrawal of approval or production definitely discontinued of a drive train type pursuant to Regulation No. 85Annex 3b - Communication concerning the approval or extension or refusal or withdrawal of approval or production definitely discontinued of a vehicle type with regard to the drive train type pursuant to Regulation No. 85Annex 4 - Arrangements of approval marksAnnex 5 - Method for measuring internal combustion engine net powerAnnex 6 - Method for measuring net power and the maximum 30 minutes power of electric drive trainsAnnex 7 - Checks on conformity of production"The text of the Regulation,Paragraph 1.2., amend to read:"1.2. The internal combustion engines belong to one of the following categories:Reciprocating piston engines (positive-ignition or compression-ignition),but excluding free piston engines;Rotary piston engines (positive-ignition or compression ignition).Naturally aspirated or supercharged engines."Insert new paragraph 2.4., to read:"2.4. "Maximum net power" means the maximum value of the net power measured at full engine load."Paragraphs 2.4. to 2.5.3. (former), renumber as paragraphs 2.5. to 2.6.3.Insert a new paragraph 2.7., to read:"2.7. "Standard-production equipment" means equipment provided by the manufacturer for a particular application."Paragraph 4.3., amend to read:"4.3. Notice of approval or of extension or of refusal of approval of a drive train type pursuant to this Regulation shall be communicated to the Partiesto the 1958 Agreement applying this Regulation by means of a formconforming to the model in Annex 3a to this Regulation."Insert a new paragraph 4.4., to read:"4.4. Notice of approval or of extension or of refusal of approval of vehicle type with regard to the drive train type pursuant to this Regulation shall becommunicated to the Contracting Parties to the 1958 Agreement applyingthis Regulation by means of a form conforming to the model in Annex 3bto this Regulation."E/ECE/324/Rev.1/Add.84/Amend.5E/ECE/TRANS/505/Rev.1/Add.84/Amend.5Paragraphs 4.4. to 4.8. (former), renumber as paragraphs 4.5. to 4.9.Paragraph 5.2.2., amend to read:"5.2.2. Measurements shall be taken at a sufficient number of engine speeds todefine correctly the power curve between the lowest and the highestengine speeds recommended by the manufacturer. This range of speedsshall include the speeds of revolution at which the engine produces itsmaximum power and its maximum torque. For each speed, the average ofat least two stabilized measurements is to be determined."Paragraph 5.2.3.3.2., amend to read:"5.2.3.3.2. In the case of an engine without self-adaptive fuelling:The fuel used shall be the one available on the market with a Wobbeindex at least 52.6 MJm-3(4°C, 101.3 kPa). In case of dispute the fuelused shall be the reference fuel G20 specified in Annex 8, i.e. the fuelwith the highest Wobbe Index, or"Paragraph 5.2.3.3.3., amend to read:"5.2.3.3.3. In the case of an engine labelled for a specific range of fuels:The fuel used shall be the one available on the market with a Wobbeindex at least 52.6 MJm-3 (4°C, 101.3 kPa) if the engine is labelled for theH-range of gases, or at least 47.2 MJm-3 (4°C, 101.3 kPa) if the engine islabelled for the L-range of gases. In case of dispute the fuel used shall bethe reference fuel G20 specified in Annex 8 if the engine is labelled forthe H-range of gases, or the reference fuel G23 if the engine is labelled forthe L-range of gases, i.e. the fuel with the highest Wobbe Index for therelevant range, or"Insert a new paragraph 5.2.3.5., to read:"5.2.3.5. Positive ignition engines of vehicles that can run either on petrol or on agaseous fuel, are to be tested with both fuels, in accordance with theprovisions in paragraphs 5.2.3.1. to 5.2.3.3. The vehicles that can befuelled with both petrol and a gaseous fuel, but where the petrol system isfitted for emergency purposes or starting only and of which the petroltank cannot contain more than 15 liters of petrol will be regarded for thetest as vehicles that can only run a gaseous fuel."Paragraph 5.2.5., amend to read:"5.2.5. The test report shall contain the results and all the calculations required tofind the net power, as listed in the appendix to Annex 5 to this Regulationtogether with the characteristics of the engine listed in Annex 1 to thisRegulation. In order to draw up this document, the competent authoritymay use the report prepared by an approved or recognized laboratorypursuant to the provisions of this Regulation."3E/ECE/324/Rev.1/Add.84/Amend.5E/ECE/TRANS/505/Rev.1/Add.84/Amend.54Annex 1, amend to read:"Annex 1Essential characteristics of the internal combustion engine and information concerning the conduct of testsThe following information, if applicable, shall be supplied in triplicate and include a list of contents. Any drawings shall be supplied in appropriate scale and in sufficient detail on size A4 or on a folder of A4 format. Photographs, if any, shall show sufficient detail. If the systems, components or separate technical units have electronic controls, information concerning their performance shall be supplied.0. GENERAL IDENTIFICATION OF THE VEHICLE...............................................................................0.1. Make (trade name of manufacturer): ........................................................................................................0.2. Type and general commercial description(s): ..........................................................................................0.3. Means of identification of type, if marked on the vehicle: .......................................................................0.3.1. Location of that marking: .........................................................................................................................0.4. Category of vehicle: .................................................................................................................................0.5. Name and address of manufacturer: .........................................................................................................0.8. Address(es) of assembly plant(s): ............................................................................................................1. GENERAL CONSTRUCTION CHARACTERISTICS OF THE VEHICLE1.1. Photographs and/or drawings of a representative vehicle: .......................................................................1.2. Hand of drive: left/right: 1 ........................................................................................................................2.0. POWER PLANT2.1. Manufacturer: ...........................................................................................................................................2.2. Manufacturer's engine code (as marked on the engine, or other means of identification): ......................2.3. Working principle: positive ignition/compression ignition, four stroke/two stroke 12.4. Number and arrangement of cylinders: ....................................................................................................2.5. Bore: ………… mm2.6. Stroke: …………mm2.7. Firing order: .............................................................................................................................................2.8. Engine capacity: ………… cm32.9. Volumetric compression ratio: .................................................................................................................2.10. Drawings of combustion chamber, piston crown and, in the case of positive ignition engines, pistonrings:2.11. Maximum net power: …………kW at ………… min-1(manufacturer's declared value)2.12. Maximum permitted engine speed as prescribed by the manufacturer: …………min-12.13. Maximum net torque 1: …………Nm at …………min-1(manufacturer's declared value)3.0. Fuel: diesel oil/petrol/LPG/NG 13.1. RON, leaded: ............................................................................................................................................3.2. RON, unleaded: ........................................................................................................................................3.3. Fuel feed3.3.1. By carburettor(s): yes/no 13.3.1.1. Make(s): ...................................................................................................................................................3.3.1.2. Type(s): ....................................................................................................................................................3.3.1.3. Number fitted: ..........................................................................................................................................E/ECE/324/Rev.1/Add.84/Amend.5E/ECE/TRANS/505/Rev.1/Add.84/Amend.5 3.3.1.4. Adjustments3.3.1.4.1. Jets: ........................................................................................................................................................... 3.3.1.4.2. Venturis: ................................................................................................................................................... 3.3.1.4.3. Float-chamber level: ................................................................................................................................. 3.3.1.4.4. Mass of float: ............................................................................................................................................ 3.3.1.4.5. Float needle: .............................................................................................................................................Or the curve of fuel delivery plotted against the air flow and settings requiredto keep to the curve3.3.1.5. Cold start system: manual/automatic 13.3.1.5.1. Operating principle(s): ............................................................................................................................. 3.3.1.5.2. Operating limits/settings: 1 ....................................................................................................................... 3.3.2. By fuel injection (compression ignition only): yes/no 13.3.2.1. System description: .................................................................................................................................. 3.3.2.2. Working principle: direct injection/pre-chamber/swirl chamber 13.3.2.3. Injection pump3.3.2.3.1. Make(s): ................................................................................................................................................... 3.3.2.3.2. Type(s): .................................................................................................................................................... 3.3.2.3.3. Maximum fuel delivery: 1………… mm3/stroke or cycle at a pump speed of: ………… min-1 or,alternatively, a characteristic diagram: …………3.3.2.3.4. Injection timing: ....................................................................................................................................... 3.3.2.3.5. Injection advance curve: ........................................................................................................................... 3.3.2.3.6. Calibration procedure: test bench/engine 13.3.2.4. Governor3.3.2.4.1. Type: ........................................................................................................................................................ 3.3.2.4.2. Make: ....................................................................................................................................................... 3.3.2.4.3. Cut-off point3.3.2.4.3.1. Cut-off point under load: ………… min-13.3.2.4.3.2. Cut-off point without load: ………… min-13.3.2.4.4. Maximum speed without load: …………min-13.3.2.4.5. Idle speed: ................................................................................................................................................ 3.3.2.5. Injection piping3.3.2.5.1. Length: ………… mm3.3.2.5.2. Internal diameter: ………… mm3.3.2.6. Injector(s)3.3.2.6.1. Make(s): ................................................................................................................................................... 3.3.2.6.2. Type(s): .................................................................................................................................................... 3.3.2.6.3. Opening pressure: ………… kPa or characteristic diagram: …………3.3.2.7. Cold start system3.3.2.7.1. Make(s): ................................................................................................................................................... 3.3.2.7.2. Type(s): .................................................................................................................................................... 3.3.2.7.3. Description: .............................................................................................................................................. 3.3.2.8. Electronic control unit3.3.2.8.1. Make(s): ................................................................................................................................................... 3.3.2.8.2. Description of the system: ........................................................................................................................ 3.3.3. By fuel injection (positive ignition only): yes/no 13.3.3.1. Working principle: intake manifold (single-/multi-point 1) direct injection/other (specify): 1 ................. 3.3.3.2. Make(s): ................................................................................................................................................... 3.3.3.3. Type(s): .................................................................................................................................................... 3.3.3.4. System description3.3.3.4.1. Type or number of the control unit: ......................................................................................................... 3.3.3.4.2. Type of fuel regulator: .............................................................................................................................. 3.3.3.4.3. Type of air-flow sensor: ........................................................................................................................... 3.3.3.4.4. Type of fuel distributor: ...........................................................................................................................5E/ECE/324/Rev.1/Add.84/Amend.5E/ECE/TRANS/505/Rev.1/Add.84/Amend.53.3.3.4.5. Type of pressure regulator: ......................................................................................................................3.3.3.4.6. Type of throttle housing: ..........................................................................................................................In the case of systems other than continuous injection give equivalent details.3.3.3.5. Injectors: opening pressure: ……… kPa or characteristic diagram: …………3.3.3.6. Injection timing: .......................................................................................................................................3.3.3.7. Cold start system3.3.3.7.1. Operating principle(s): .............................................................................................................................3.3.3.7.2. Operating limits/settings: 1........................................................................................................................4.0. Feed pump4.1. Pressure: ………… kPa or characteristic diagram: …………5.0. Electrical system5.1. Rated voltage: ………… V, positive/negative ground 15.2. Generator5.2.1. Type: ........................................................................................................................................................5.2.2. Nominal output: ………… VA6.0. Ignition6.1. Make(s): ...................................................................................................................................................6.2. Type(s): ....................................................................................................................................................6.3. Working principle: ...................................................................................................................................6.4. Ignition advance curve: ............................................................................................................................6.5. Static ignition timing ………… degrees before TDC6.6. Contact-point gap: ………… mm6.7. Dwell-angle: ………… degrees7.0. Cooling system (liquid/air) 17.1. Nominal setting of the engine temperature control mechanism: ..............................................................7.2. Liquid7.2.1. Nature of liquid: .......................................................................................................................................7.2.2. Circulating pump(s): yes/no 17.2.3. Characteristics ………………………………, or7.2.3.1. Make(s): ...................................................................................................................................................7.2.3.2. Type(s): ....................................................................................................................................................7.2.4. Drive ratio(s): ...........................................................................................................................................7.2.5. Description of the fan and its drive mechanism: ......................................................................................7.3. Air7.3.1. Blower: yes/no 17.3.2. Characteristics: …………, or7.3.2.1. Make(s): ...................................................................................................................................................7.3.2.2. Type(s): ....................................................................................................................................................7.3.3. Drive ratio(s): ...........................................................................................................................................8.0. Intake system8.1. Pressure charger: yes/no 18.1.1. Make(s): ...................................................................................................................................................8.1.2. Type(s): ....................................................................................................................................................8.1.3. Description of the system (e.g. maximum charge pressure: ………… kPa, wastegate if applicable): ....8.2. Intercooler: yes/no 18.3. Description and drawings of inlet pipes and their accessories (plenum chamber, heating device,additional air intakes, etc.): ......................................................................................................................8.3.1. Intake manifold description (include drawings and/or photos): (6)E/ECE/324/Rev.1/Add.84/Amend.5E/ECE/TRANS/505/Rev.1/Add.84/Amend.5 8.3.2. Air filter, drawings: …………, or8.3.2.1. Make(s): ................................................................................................................................................... 8.3.2.2. Type(s): .................................................................................................................................................... 8.3.3. Intake silencer, drawings: …………, or8.3.3.1. Make(s): ...................................................................................................................................................8.3.3.2. Type(s): ....................................................................................................................................................9.0. Exhaust system9.1. Description and/or drawing of the exhaust manifold: .............................................................................. 9.2. Description and/or drawing of the exhaust system: ..................................................................................9.3. Maximum allowable exhaust back pressure at rated engine speed and at 100 per cent load: ……… kPa10.0. Minimum cross-sectional areas of inlet and outlet ports: .........................................................................11.0. Valve timing or equivalent data11.1. Maximum lift of valves, angles of opening and closing, or timing details of alternative distributionsystems, in relation to dead-centres: .........................................................................................................11.2. Reference and/or setting ranges: 1 ............................................................................................................12.0. Measures taken against air pollution12.1. Additional anti-pollution devices (if any, and if not covered by another heading)12.2. Catalytic converter: yes/no 112.2.1. Number of catalytic converters and elements: ......................................................................................... 12.2.2. Dimensions, shape and volume of the catalytic converter(s): .................................................................. 12.3. Oxygen sensor: yes/no 112.4. Air injection: yes/no 112.5. Exhaust gas recirculation: yes/no 112.6. Particulate trap: yes/no 112.6.1. Dimensions, shape and capacity of the particulate trap: ...........................................................................12.7. Other systems (description and operation): ..............................................................................................13.0. LPG fuelling system: yes/no 113.1. Approval number according Regulation No. 67: ...................................................................................... 13.2. Electronic engine management control unit for LPG fuelling:13.2.1. Make(s): ................................................................................................................................................... 13.2.2. Type(s): .................................................................................................................................................... 13.2.3. Emission-related adjustment possibilities: ............................................................................................... 13.3. Further documentation: ............................................................................................................................ 13.3.1. Description of the safeguarding of the catalyst at switch-over from petrol to LPG or back: ................... 13.3.2. System lay-out (electrical connections, vacuum connections compensation hoses, etc.): ........................13.3.3. Drawing of the symbol: ............................................................................................................................14.0. NG fuelling system: yes/no 114.1. Approval number according to Regulation No. 110: ............................................................................... 14.2. Electronic engine management control unit for NG fuelling:14.2.1. Make(s): ................................................................................................................................................... 14.2.2. Type(s): .................................................................................................................................................... 14.2.3. Emission-related adjustment possibilities: ............................................................................................... 14.3. Further documentations: ........................................................................................................................... 14.3.1. Description of the safeguarding of the catalyst at switch-over from petrol to NG or back: ..................... 14.3.2. System lay-out (electrical connections, vacuum connections compensation hoses, etc.): ........................ 14.3.3. Drawing of the symbol: ............................................................................................................................7E/ECE/324/Rev.1/Add.84/Amend.5E/ECE/TRANS/505/Rev.1/Add.84/Amend.515.0. Temperatures permitted by the manufacturer15.1. Cooling system15.1.1. Liquid coolingMaximum temperature at outlet: ………… °C15.1.2. Air cooling15.1.2.1. Reference point: .......................................................................................................................................15.1.2.2. Maximum temperature at reference point: ………… °C15.2. Maximum outlet temperature of the inlet intercooler: ………… °C15.3. Maximum exhaust temperature at the point in the exhaust pipe(s) adjacent to the outer flange(s) of theexhaust manifold: …………°C15.4. Fuel temperatureminimum: …………°Cmaximum: …………°C15.5. Lubricant temperatureminimum: …………°Cmaximum: …………°C16.0. Lubrication system16.1. Description of the system16.1.1. Position of the lubricant reservoir: ...........................................................................................................16.1.2. Feed system (by pump/injection into intake/mixing with fuel, etc.) 1: .....................................................16.2. Lubricating pump16.2.1. Make(s): ...................................................................................................................................................16.2.2. Type(s): ....................................................................................................................................................16.3. Mixture with fuel16.3.1. Percentage: ...............................................................................................................................................16.4. Oil cooler: yes/no 116.4.1. Drawing(s): …………, or16.4.1.1. Make(s): ...................................................................................................................................................16.4.1.2. Type(s): ....................................................................................................................................................Other auxiliary equipment driven by the engine (as per item 2.3.2. of Annex 5) (list and briefdescription if necessary): …………17.0. Additional information on test conditions (for positive ignition engines only)17.1. Spark plugs17.1.1. Make: .......................................................................................................................................................17.1.2. Type: ........................................................................................................................................................17.1.3. Spark-gap setting: .....................................................................................................................................17.2. Ignition coil17.2.1. Make: .......................................................................................................................................................17.2.2. Type: ........................................................................................................................................................17.3. Ignition condenser17.3.1. Make: .......................................................................................................................................................17.3.2. Type: ........................................................................................................................................................17.4. Radio interference suppression equipment17.4.1. Make: .......................................................................................................................................................17.4.2. Type: ........................................................................................................................................................………………………………(Date, file) 1Delete where not applicable."8。
CALIBRATION OF ENGINE CONTROL SYSTEMS

专利名称:CALIBRATION OF ENGINE CONTROL SYSTEMS发明人:STEWART, Gregory, E.,SHAHED, Sved, M.,KOLAVENNU, Soumitri, N.申请号:EP06845171.5申请日:20061208公开号:EP1969430A2公开日:20080917专利内容由知识产权出版社提供摘要:A system for automatic multivariable calibration of an engine controller. The system may take inputs which include actuator setpoints, sensor measurements, performance requirements, and so forth. There may be an algorithm to compute engine calibration parameters for the controller. Each of the actuators may be separately stepped through to experimentally obtain actuator input and sensor output data. Algorithmic processing of the experimentally obtained data may be performed to calculate parameters of a model of an engine. A model based control design algorithm may then be invoked to obtain the calibration parameters for a controller. The calibrated controller may be tested with real or simulated engine conditions. The performance related to the parameters may be analyzed and determination of the acceptability of the data be made. If not acceptable, the parameters may be reprocessed. If acceptable, the calibration parameters may be downloaded to the engine controller for application and use.申请人:Honeywell International Inc.地址:101 Columbia Avenue P.O. Box 2245 Morristown NJ 07960 US国籍:US代理机构:Buckley, Guy Julian 更多信息请下载全文后查看。
发动机控制器开发流程

发动机控制器开发流程Developing an engine controller is a complex process that involves designing, testing, and refining the software and hardware components that regulate an engine's performance. 发动机控制器的开发是一个复杂的过程,涉及设计、测试和改进软件和硬件组件,以规范发动机的性能。
Developing an engine controller requires a strong understanding of engine dynamics, control theory, and software development. 发动机控制器的开发需要对发动机动力学、控制理论和软件开发有深刻的理解。
Engine controllers play a crucial role in optimizing engine performance, fuel efficiency, and emissions control. 发动机控制器在优化发动机性能、燃油效率和排放控制方面发挥着关键作用。
Effective engine controller development involves a multidisciplinary approach that combines engineering, computer science, and automotive technology. 有效的发动机控制器开发涉及多学科方法,结合工程学、计算机科学和汽车技术。
Collaboration between engineers, software developers, and testing teams is essential for successful engine controller development. 工程师、软件开发人员和测试团队之间的合作对于成功的发动机控制器开发至关重要。
康明斯引擎-环境空气温度传感器故障、位置和故障排除说明书

Less InfoCountries : CANADA, TAIWAN, UNITED STATES, MEXICO, GUAM, KOREA, SOUTH KOREA Document ID : IK0800284Availability : ISIS, FleetISIS, NotSIRRevision : 25Major System : ELECTRICAL SYSTEMCreated : 5/16/2011Current Language : EnglishLastModified : 7/28/2020OtherLanguages : Fran çais , Espa ñol , Author :Charles SchroederViewed :22083Hide Details CodingInformationCopy LinkCopy Relative LinkBookmarkAdd to FavoritesPrintProvide FeedbackHelpfulNot Helpful(Return to Top )Symptom(s)Diagnostic Trouble Code(s) & Dashboard Indicator Light(s):DTC / Light Cummins Fault DescriptionSPN 171 FMI 22389AAT signal does not agree with other sensorsSPN 171 FMI 3249AAT signal out of range HIGHSPN 171 FMI 4256AAT signal out of range LOWCustomer Observations or Concerns:•MIL•Engine performance may be reduced•Unable to perform regen(Return to Top )Special Tool(s) / SoftwareTool Description Tool Number Comments Instructions Navistar Engine Diagnostics™EZ-Tech SoftwareCummins INSITE EZ-Tech Software(Return to Top )Service Parts InformationKit Description Part Number Quantity RequiredNotesSender, Ambient Temperature3561562C11(Return to Top )Engine Sensor TroubleshootingThere are two ambient temperature sensors. The sensor located behind the cab along the left frame rail is the sensor the engine uses. To confirm this, unplug the sensor and observe the cluster LCD display, it the reading stays the same, the correct sensor is unplugged. There is also a sensor located at the front of the chassis that the gauge cluster uses for the temp display.This article begins and discusses the Engine AAT Sensor, prior to and first. After August 23, 2013, Some SCR engines have the Engine AAT sensor mounted in the driver side mirror head and alternatively the sensor could be mounted to the horn bracket. The location depends on build date.2013 Navistar N13 DiagnosticsFAULT CODE 171-2 ONLYStep Action Decision1Update ECM Calibration•Check Engine Calibration using NavKal.•Use Electronic Service Tool (EST) to clear the fault code.This code has been corrected with an ECM CalibrationRepair Complete.2010 MaxxForce 11/13L DiagnosticsFAULT CODE 171-2 ONLYNOTE: If the ECM is setting/logging code 171-2 and the sensor tests good DO NOT replace the sensor, there is a new calibration available as of March 7, 2014 for EGR engines.Step Action Decision1Update ECM Calibration•Check Engine Calibration using NavKal.•Use Electronic Service Tool (EST) to clear the fault code.This code has been corrected with an ECM Calibration as of March 7, 2014Repair Complete.All Engines with Ambient Air Temp SensorFAULT CODE(s) 171-3 and 171-4 ONLYRefer to the appropriate Engine or Chassis wiring schematic manual to ensure you are on the proper ECM connector and terminal. Step Action Decision1Measure Resistance of the sensor and compare tothe chart shown in Figure 1•SPEC: Based on Ambient TempIs resistance measurement in spec?Yes: Go to step 2No: Replace AAT SensorStep Action Decision2Measure voltage between ambient temperaturesensor connector cavity A and GND•SPEC: 5 +/- 0.5 VdcIs voltage measurement in spec?Yes: Go to step 3No: Inspect wire from ECM to AAT sensor pin A foropen or shortStep Action Decision3Measure voltage between ambient temperaturesensor connector cavity A and cavity B•SPEC: 5 +/- 0.5 VdcIs voltage measurement in spec?Yes: Restore back to operational condition andretest for fault code 171-3 or 171-4No: Inspect ZVR wire from ECM to AAT sensor pinB for open or short(Return to Top )Cluster Sensor TroubleshootingFAULT CODE(s) 171-3 and 171-4 ONLYThe instrument cluster, connector 1501 pin 9, sends a 5-volt source to the temperature sensor. As the voltage goes across the temperature sensor it decreases, the amount of voltage drop depends on outside temperature. The reduced voltage then returns to the instrument cluster on pin 8 of connector 1500. The instrument cluster turns the received signal into to the temperature shown on the display.NOTE: The Electronic Gage Cluster display will replace temperature reading with two dashes (- -) if a fault is present with the Ambient Temperature Sensor circuit.Step Action Decision1Measure Resistance of the sensor and compare tothe chart shown in Figure 1•SPEC: Based on Ambient TempIs resistance measurement in spec?Yes: Go to step 2No: Replace AAT SensorStep Action Decision2Measure voltage between ambient temperaturesensor connector cavity A and GNDYes: Go to step 3•SPEC: 5 +/- 0.5 VdcIs voltage measurement in spec?No: Inspect wire from cluster 1501-9 to AAT sensor pin A for open or shortStep Action Decision3Measure voltage between ambient temperaturesensor connector cavity A and cavity B•SPEC: 5 +/- 0.5 VdcIs voltage measurement in spec?Yes: Restore back to operational condition andretest for fault code 171-3 or 171-4No: Inspect ZVR wire from cluster 1500-8 to AATsensor pin B for open or shortAAT Sensor Temperature VS. Resistance ChartFigure 1•Return to Troubleshooting Engine Sensor•Return to Cluster Sensor Troubleshooting(Return to Top )Cluster Circuit Diagram(s)IMPORTANT: Due to variations during vehicle production, be sure to select the most current wiring schematic manual, specific to the year and model of the vehicle being serviced.•ProStar / LoneStar wiring for Cab Sensor•ProStar / LoneStar wiring for Cab Sensor with Front Axle Load Sensor•HPV wiring for Cab Sensor•HPV wiring for Cab Sensor with Front Axle Load Sensor•TerraStar wiring for Cab SensorThe Cab Temperature Sensor is typically mounted near the front bumper or on the cooling package. If the sensor cannot be found verify the wiring to the gauge cluster is present or that the outside air temp monitor feature as ordered on the truck.Figure 2Medium Duty Chassis Standard Mounting Location for Cluster SensorFigure 3TerraStar Chassis only: The AAT sensor was relocated to the ABS ECU bracket May 2012 (Return to Top )Sensor Location - Big Bore EnginesBig Bore PreSCR Engines and SCR Engine prior to August 2013:The engine sensor is located on the left frame rail midway between the back of cab and front drive axle, or near the front drive axle. The two photos below show both possible mounting locations (Figure 4 and Figure 5).Figure 4Figure 5Big Bore Post August 2013 build w/SCR engine, driver's side mirror head (Figure 6):Figure 6ISX15 and N13 Alternate Location (Figure 7):Figure 7ISX15 and N13 Alternate Location PayStar / 9900i (Figure 8):Figure 8(Return to Top )Sensor Location - Medium Duty EnginesN9/10 and ISB engine platforms moved the Engine AAT to the driver mirror on August 8, 2014 (Figure 9):Figure 9Location prior to August 8, 2014 on CE BusFigure 10(Return to Top )Sensor Location - HXHX Location - Driver's Side Mirror HeadFor circuit diagram information, refer to the HX circuit diagram manualFigure 11Figure 12Hide DetailsFeedbackInformation( Return to Top )Engine Sensor Circuit Diagram(s)( Return to Top )Warranty InformationWarranty Claim Coding:Refer to the Warranty Coding Manual for Group and Noun Codes.Standard Repair Time(s):Refer to the SRT Manual for Repair Times ( Return to Top )Other Resource(s)•IK0800369 - 2006-2009 Cummins Active Fault 249 / 256 Ambient Air Temperature Sensor 1 Circuit ( Return to Top )Viewed:22082Helpful:157Not Helpful:55 No Feedback FoundCopyright©2020Navistar, Inc.Page11 of 11IK0800284 -Ambient Air Temperature (AAT) Sensor Faults/Location/Diagnostics8/3/2020 https:///service_kb/DocTool/ArticleViewer.aspx?ControlID...。
Calibrationengineer标定工程师JD

Calibration engineer 标定工程师4 missions assigned to this position :Handle car specific instrumentation for calibration work1.Installation of temperature and pressure sensors on engine, exhaust, fuel pump,battery2.Installation of etas device to connect record all these sensors (measuring andrecording devices)Handle car maintenance, part exchange, car modernization with new components1.For each car of the proto pool plan the maintenance2.Make himself the car parts changing (starter, exhaust manifold, etc…)3.Manage the invest of tooling needed and the subcontratcting he may do to PSA 4slocal dealersManage all instrumentation devices and car equipment1.Record in database all ETAS measuring tools, make the planning of usage andsharing for all project2.Manage the budget of investment of sensors (pressure, temperature, Air fuellambda)Manage the car pool and follow up of temporary police plate1.Manage who use the car when, handle the checking of the car before and after test2.Manage for each car the temporary police plate licensesTools: ETAS, INCA处置汽车专用仪器校准工作1.发动机,排气,燃料泵,电池的温度和压力传感器上的安装2.ETAS设备的安装,连接所有这些传感器(测量和记录装置记录)处置汽车维修,部份兑换,汽车现代化的新组件1.关于每一个汽车原池打算的保护2.让自己的汽车零部件改变(起动器,排气歧管,等...)3.治理的投资所需的工具subcontratcting的,他可能会做PSA4S本地经销商治理所有的仪器设备和车载设备1.记录在数据库中的所有ETAS测量工具的利用和共享,使计划的所有项目2.治理的预算投资的传感器(压力,温度,空气燃料的lambda)治理拼车的临时警方板的跟进1.治理利用的汽车时,汽车的检查处置前后测试2.每节车箱板许可证的临时警察治理工具:ETAS INCA1. KNOWLEDGE in AUTOMOBILE COMPOSANT or SYSTEMa)Knowledge power train can be better. Experience in emission chassis dynobench will be appropriate.SPECIFIC COMPETENCETests Data Management knowledgeTo realize an operation of benchmark vehicles for fuel consumption tests on emissions chassis dyno bench. Application of the French standard (testprotocol, standard) and improvement proposals.To have a good synthesis ability for tests reporta)Writing of training support adapted to Chinese activities.b)Need to get good relationship (link with suppliers)Regular Business trips1.EXPERIENCE in VEHICLE DEVELOPMENTa)Work experience in planning team1.知识的汽车COMPOSANT或系统1.知识动力传动系可能会更好。
- 1、下载文档前请自行甄别文档内容的完整性,平台不提供额外的编辑、内容补充、找答案等附加服务。
- 2、"仅部分预览"的文档,不可在线预览部分如存在完整性等问题,可反馈申请退款(可完整预览的文档不适用该条件!)。
- 3、如文档侵犯您的权益,请联系客服反馈,我们会尽快为您处理(人工客服工作时间:9:00-18:30)。
3.3标定实验工作流程
3.4标定工具
标定工具是标定试验中使用的重要因素,标定工具的先进程度直接决定标定数据 的准确性以及标定试验的进度。
标定试验使用的基本工具有以下部分: 硬件 1,发动机测试设备: ●用于测试和监控发动机运转的测功机,燃烧分析仪,排放分析仪,烟度计等 ●用于采集温度,压力,LAMBDA等信号的传感器及采集设备。 2,发动机标定专用ECU,如BOSCH带ETK的ECU 3,串行通讯接口设备,用于PC与ECU的通讯 4,安装了应用软件的个人PC
标定
1概念介绍
• 1.3标定: 通常同一型号的发动机ECU内部的控制算法软件是固定的,但其包含 的数千个自由参数是可调的,对于不同的车型这些参数都需要通过发 动机匹配标定进行调试优化,使得整车通过各种排放与驾驶性能指标。 对于一个新机型的标定大概需要18个月左右.
2.标定过程
概念设计 根据整车属性参数,确定发动机基本动力性能,排放,及经济性需 概念设计 求.发动机设计部门确立发动机基本技术路线,确定发动机性能、 排放关键性部件,及发动机管理系统软硬件。
…… 路试验证\三高标定验证 OBD文档编制
概念设计
模拟计算
发动机台架标 定 整车标定 OBD标定
标定验证
2.标定过程
标定验证
确定零部件散差对排放及EOBD的影响 整车性能验证 发动机台架性能验证
概念设计
模拟计算
发动机台架标 定 整车标定 OBD标定
标定验证
3.标定方法
3.标定方法
• 在发动机标定过程中获得数据大致有以下两种路径: 一,发动机模拟计算:基于现有的发动机数据库建立发动机模型,通过模拟
…….
概念设计
模拟计算
发动机台架标 定 整车标定 OBD标定
标定验证
2.标定过程
整车标定Байду номын сангаас
把发动机搭载在整车上对发动机 各系统功能的动态优化,完善发 动机管理系统与整车附件功能管 理,有利于增强发动机对整车的 适应性,实现发动机在整车上的 动力性、经济性、排放各项指标 的良好表现。 扭矩管理 喷油脉宽优化 轨压管理 轨压控制 空气系统管理 EGR,VGT整车标定 大气压力修正 空调系统标定 整车排放及后处理标定
3.4标定工具
AVL自动标定软件CAMEO应用
软件进行计算如AVL WORKSPACE,GT SUITE, 二, 标定试验.
3.1发动机模拟计算
• 一,根据设计目标需求建立数学模型,再通过模拟软件进行计算如AVL WORKSPACE,GT SUITE, 获得大量基于数学模型的预测数据,再通过优化形成前期标定初始数据。当然该初始数据必 须建立在大量的实验基础之上,同时也必须经过一个实验‐优化‐再实验的反复过程以获得发 动机的最佳性能。通过大量的发动机模拟计算可以给后期的发动机标定试验提供了准确的方 向,节省了开发成本及时间。
……
概念设计
模拟计算
发动机台架标 定 整车标定 OBD标定
标定验证
2.标定过程
发动机基础MAPPING 为了进一步达到设计目标,必须在发动机台架进行测试试
验,确定关键零部件特性,精确寻找发动机各工况最优运行参 数MAP。 发动机硬件确认,如油嘴,油嘴突出高度,增压器特性等 曲轴、凸轮轴同步标定 喷油脉宽MAPPING 轨压MAPPING 轨压控制 喷油量、喷油正时稳态、瞬态MAPPING 发动机过热,转速,扭矩限制标定 多次喷射标定 EGR ,VGT MAPPING 可变涡流MAPPING 发动机排放标定 后处理标定
瞬态喷油正时,喷油量及油轨压 力标定
冷启动 噪音优化Combustion noise optimization 黑烟、蓝烟优化 诊断标定 默认运行模式标定 发动机三高环境修正补偿 喷油系统低压油路检查
……..
概念设计
模拟计算
发动机台架标 定 整车标定 OBD标定
标定验证
整车驾驶性标定
档位识别标定 稳态怠速标定 各档位怠速标定 整车动力性标定 加速踏板MAPPING 主动减震功能标定 整车限制功能标定 ………
模拟计算
控制器选择
燃油系统部件设计
EGR,增压器,涡流控制阀,节流阀等硬件确定 后处理方案确定
发动机台架标 定
整车特殊功能要求
确定软件子功能列表 ……
整车标定
OBD标定
标定验证
2.标定过程
发动机初始基础数据准备 通过对整车及发动机系统建模计算,获得发动机台架试验的准备 数据,也可以采用类似机型数据经过少量调整获得。该数据可 满足发动机基本功能需求,可支持发动机第一次点火。 整车模拟计算 定义发动机限制,如排温,最大扭矩,最高转速等 喷油脉宽定义 发动机同步与启动标定 轨压管理标定 油量标定,确定发动机喷油 空气系统标定:EGR,VGT 自诊断标定
2.标定过程
概念设计
模拟计算
发动机台架标 定 整车标定 OBD标定
标定验证
2.标定过程
OBD标定 由于国家法规要求,自2007年7月1日起申请型式认证的轻型车 必须装备EOBD(N1类车目前可不装).即当整车排放超出法规要 求时,EOBD必须指出造成排放超标的部件. 主要标定工作如下:
零部件和系统故障诊断标定 排放影响关键零部件确认及故障诊断标定 ‐‐‐EGR系统 ‐‐‐空气流量传感器 ‐‐‐轨压传感器 ‐‐‐老化催化剂
3.4标定工具
软件 1,通讯软件,用于PC与ECU通讯及工程师可视化操作,如INCA,ATI VISUAL。 标定工程时通过通讯软件可以监测发动机运行状态,对ECU内参数、MAP可以 直接通过键盘操作更改。 2,自动标定软件。采集大范围发动机工况点数据时,为了提高工作效率及准确 性,可以通过自动标定软件建立合适的实验计划,自动标定软件既可按照即定的 实验计划同时控制发动机测试设备及ECU,实现大量数据的同步采集。 3,数据处理软件。基于大量的实验数据,需经过一定的数据处理后才能形成最 可靠最优化的MAP。如对数据进行统计学可靠性检查,通过遗传算法工具进行 优化计算,通过神经网络工具实现由部分工况点计算出整张MAP等等。
• 举例说明使用AVL BOOST软件预测发动机外特性,从而获得发动机外特性喷油量、提前角、 增压压力的一些基础数据。
3.2标定实验
发动机的标定试验是指在发动机不同的工作状态和气候环境下,对发动机管理系 统的参数进行不断调试,找到发动机最佳工作状态下一组参数的测试技术。标定 试验按实验地点不同大致有发动机台架标定试验,整车转毂标定试验,野外道路 试验,三高标定试验等。 1 ,发动机台架标定试验:主要用于发动机基础数据标定,是整个标定过程中最 为重要的一部分,是后期标定工作的基础。在这期间形成的发动机基本MAP可以 基本上满足发动机基本性能指标和排放指标。 2,整车转毂标定试验:主要用于轻型车排放标定验证及优化;OBD标定; 3,野外道路试验:用于标定车辆的驾驶特性标定及发动机与整车匹配后的精细 标定。 4,三高试验:高原,高温,高寒试验,简称三高试验。由于我国环境和气候的 多样性,为了使我们的产品在各个地区都有很好的性能表现,我们就必须在一些 典型的环境区域进行气候适应性试验。根据不同的气候发动机管理系统将作出相 应的补偿修正,如在高寒高原冷启动时增大提前角、降低轨压,在高温情况下验 证由于水温偏高喷油量如何限制等。