Development of three-axis desktop milling machine
三轴转台控制系统设计--优秀毕业论文

硕士学位论文三轴转台控制系统设计CONTROL SYSTEM DESIGN OF THREE-AXIS TURNTABLE陈丽娟哈尔滨工业大学2010年6月国内图书分类号:TP273.2 学校代码:10213 国际图书分类号:681.5 密级:公开硕士学位论文三轴转台控制系统设计硕士研究生:陈丽娟导师:伞冶教授申 请 学 位:工学硕士学科、专业:控制科学与工程所在单位:信息科学与工程学院答辩日期:2010年6月授予学位单位:哈尔滨工业大学Classified Index:TP273.2 School Number: 10213 U.D.C:681.5 Security: OpenDissertation for the Master Degree in EngineeringCONTROL SYSTEM DESIGN OFTHREE-AXIS TURNTABLECandidate: Chen LijuanSupervisor:Prof. San YeAcademic Degree Applied for:Master of Engineering Specialty: Control Science and Engineering Affiliation: School of Information Scienceand EngineeringDate of Defence:June, 2010Degree-Conferring-Institution:Harbin Institute of Technology哈尔滨工业大学工学硕士学位论文摘 要三轴转台是应用在半实物仿真系统中,模拟被测物体姿态变化的装置。
本文中,我们研究的主要内容为三轴转台。
本文以实际工程项目为背景,主要研究三轴转台的控制系统设计。
随着武器系统精度的不断提高,对其测试装置的要求也越来越高。
论文首先简要阐述了国内外三轴转台的研究现状,并简要总结了我国转台的发展方向、各类控制方法在该领域的应用情况以及转台控制系统存在的主要问题。
哈斯自动化GM-2大型平台3轴机器人铣制说明书
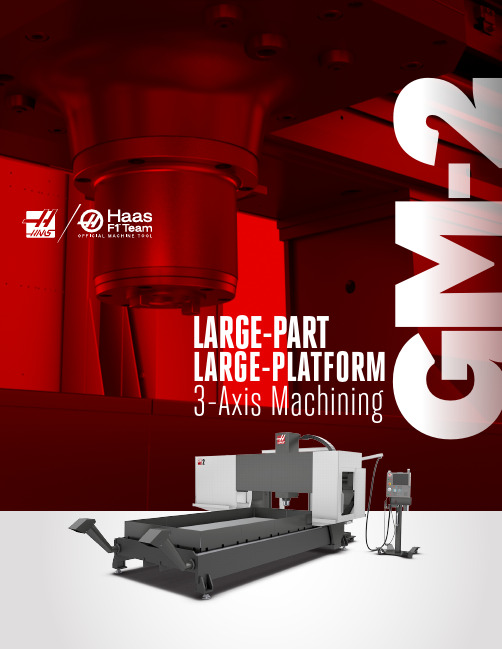
G M -2LARGE-PARTLARGE-PLATFORM 3-Axis MachiningHaas Automation, Inc.Large-Part, Large-Platform 3-axis MachiningThe GM-2 is a heavy-duty, 3-axis gantry mill designed for large-part machining, such as airframe components, large plates, and long extrusions. The machine’s rigid steel construction provides a very stable cutting platform, anda 1" thick aluminum table is standard. A traveling guard protects the operator from chips and coolant, and keeps the workspace clean.Dual Chip Augers while compressing them and wringing out the coolant. Ideal for both short runs and high-production environments, eliminating the downtime required for manual chip removal.to the cutting edge during machining operations. Increases tool life, allows for higher cutting speeds, and improves surface quality.Bring your machine tolife with the spindle that suits your needs.10,000-rpm Spindle 40 taper, 30 hp vector drive, inline direct-drive.15,000-rpm Spindle 40 taper, 30 hp vector drive, inline direct-driveNow with more X, Y , Z travels, andthe table space you need.GET MOREROOMTO T AKE ON LARGE P ARTSCOOLANT & CHIP MANAGEMENTMORE OPTIONS TO SUITYOUR SPECIFICA TRAVELS X Axis Y Axis Z AxisSpindle Nose to Table (~ max) Spindle Nose to Table (~ min) SPINDLE Max Rating Max Speed Max Torque Drive System TaperTABLELength 144" Length (Work Area) Thickness 1.0" Max Weight on Table (evenly distributed) Between Columns TOOL CHANGER Type / Capacity Max Tool Diameter (full) Max Tool Diameter (adjacent empty) Max Tool Length (from gage line ) Max Tool Weight 12 lb FEEDRATES Max Cutting 800 ipm Rapids on X 800 ipm Rapids on Y 2100 ipm Rapids on X1100 ipmDual-Ballscrew Drive SystemST ABILITY TWICE THE TORQUE Dual-Ballscrew Drive SystemTaking on those large parts needs greater stability. The GM-2’s dual-ballscrew design means more rigidity and power, for more accurate cutting and repeatability.Get your machine status notifications anywhere, on any device! The Haas Control has the ability to send you, and others you designate, email notifications about the operating status of your Haas machine. Set up is fast and easy through the MyHaas Portal and .HaasDrop is a fast and convenient method for sending images, videos, and even program files from a mobile device directly to a Haas NextGen Control. Download the free app, and start transferring files directly to the Haas control.MAKE THE CONNECTION WITH HAASCONNECTHAAS DROPMYHAAS MACHINE DET AILS P AGE View detailed information about your machines, including serial numbers,build dates, warranty start/end dates, product details, and machine option details. Sign up now at /myhaasFind out about the latest upgradesavailable for your machine, order parts, and quickly access service guides, manuals, and videos.Up-to-the-minute live eventtracking with HaasConnect remote monitoring.View detailed information about your machine, including serial number, machine build date, and warranty start /end dates.See how your machine isconfigured, with a detailed list of every option installed.MYHAAS Y OUR NEW FLEET MANAGEMENTHaas Automation, Inc. | | 800-331-6746 | Made in U.S.A.Specifications subject to change without notice. Not responsible for typographical errors. Machines shown with optional equipment.Actual product appearance may differ. Pricing subject to change without notice.39-20008B。
汽车变速器外文翻译

外文翻译Auto TransmissionFirst, an overview of automotive transmission and the development trendAutomobile available more than a century, especially from the mass production of motor vehicles and the automotive industry since the development of large, Car has been the economic development of the world for mankind to enter the modern life and have had a tremendous impact on the immeasurable, The progress of human society has made indelible contributions to the great, epoch-making set off arevolution. From From the vehicle as a power plant using internal combustion engine to start, auto transmission has become an important component. Is Generation is widely used in automotive reciprocating piston internal combustion engine with a small size, light weight, reliable operation and the use of The advantages of convenience, but its torque and speed range of smaller changes, and complex condition requires the use of motor vehicles Traction and the speed can be considerable changes in the scope. Therefore, its performance and vehicle dynamics and economy of There are large inter-contradictions, which contradictions of modern automotive internal combustion engine by itself is insoluble. Because Here, in the automotive power train set up the transmission and main reducer in order to achieve the purpose of deceleration by moment. Speed The main function of performance: ⑴ change gear ratio of motor vehicles, and expand the wheel drive torque and rotational speed of the Fan Wai, in order to adapt to constantly changing driving cycle, while the engine in the most favorable conditions within the scope of work; ⑵no change in the direction of engine rotation, under the premise of the realization of cars driving back; ⑶the realization of the free, temporary Interruption of power transmission, in order to be able to start the engine, idling, etc.. V ariable-speed drive transmission by the manipulation of institutions and agencies. Change the transmission ratio by way of transmission is divided into There are class-type, non-stage and multi-purpose three. Have class most widely used transmission. It uses gear drive, with a number of transmission ratio setting. Stepless transmission Continuously V ariable Transmission (CVT) transmission ratio of a certain The framework of multi-level changes may be unlimited, there is a common type of power and torque (dynamic fluid-type) and so on. Continuously V ariable Transmission Transmission development is the ultimate goal, because only it can make the most economical engine in working condition Can provide the best vehicle fuel economy and optimal power in order to provide the most comfortable By the feeling. Today's CVT is a typical representative of the CVTand IVT, however as a result of the reliability of Poor, non-durable materials and high cost issues, development is not very good. Comprehensive refers to transmission torque converter and the mechanical components have the level of transmission variable hydraulic mechanical Speed, the transmission ratio can be between the maximum and minimum range of a few discontinuous change for no class, but its Significantly lower transmission efficiency than the efficiency of gear drives. 2 By manipulation, transmission control type can be divided into mandatory, automatic and semi-automatic control to manipulate three - Species . Mandatory on the driver to manipulate the direct transmission gear shift control for the majority of motor vehicles used Also known as Manual Transmission Manual Transmission (MT). Automatic transmission control selection of the transmission ratio (transmission) is carried out automatically. Just add the driver to manipulate Speed pedal, you can control the speed, also known as Automatic Transmission Automatic Transmission (A T). It is According to the speed and load (throttle pedal travel) for two-parameter control, stall in accordance with the above two Parameters to automatically take-off and landing.A T and MT in common is that they are level transmission, but A T According to the speed of the speed shift automatically, you can eliminate the manual transmission "setback" of the shift feel. However, A T also have many drawbacks, such as body complex, mechanical efficiency is not high, high cost, reliability and control Sensitivity remains to be increasing . AMT (Automated Mechanical Transmission) is in the traditional dry clutch and manual transmission gear based on the transformation of form, mainly to change the part of the manual gearshift control. That is, the overall structure of the MT cases the same switch to electronically controlled automatic transmission to achieve. Semi-automatic control, there are two forms of transmission. A number of stalls is a common automatic control, and the remaining stalls manipulated by the driver; the other is pre-style, that is, pre-selected pilot stalls, the clutch pedal in the down or release the accelerator pedal, the for retirement or an electromagnetic device to shift the hydraulic device. In recent years, with advances in vehicle technology and road traffic density increased, the performance requirements of the transmission is also getting higher and higher. A large number of automotive engineers in improving the performance of automobile transmission study a great deal of effort devoted to the rapid transmission of technology development, such as A T, AMT, DCT, CVT and the emergence of IVT.2003 Hyundai A T, AMT, DCT, CVT forum reached a consensus on the following:in the next Development, MT will continue to be the most widely used automotive transmission, AMT will increase the proportion of the application, A T also Will occupy a large market share, CVT's use of certain limitations, can only be due to a number of small displacement Car, DCT (dual clutch transmission) will also be the budding growth. From 2003 to now, vehicle speed Thedevelopment of devices and the forum basically the consensus reached by consensus. By comparing the analysis, the traditional mechanical transmission is still the most widely used vehicle change Speed. Although it has many shortcomings, such as shifting the impact of large, bulky, cumbersome to manipulate and so on; however, it also There are many advantages, such as high transmission efficiency, reliable operation, long life, manufacturing processes mature and low cost. Therefore, if we can improve the mechanical transmission of the above-mentioned shortcomings, it still has great room for development.Second, Manual Transmission Fault DiagnosisManual transmission at the beginning of the fault diagnosis prior toFailure to confirm from other parts is not: to check the tire And wheels, to confirm the normal tire pressure, and the wheel is flat V alue of; to confirm instead of noise and vibration from the engine. Clutch , And steering and suspension, etc..(A), skip file1. PhenomenonV ehicle acceleration, deceleration, climbing or severe vehicle vibration, the gear lever neutral position automatically jump.2. Reasons① self-locking device of the ball did not enter the grooves or linked file does not meet the full-gear tooth meshing long;② self-locking device worn groove ball or serious, self-locking spring is too soft or broken fatigue;③ gear along the direction of tooth wear as a long cone-shaped;④ one or two too松旷shaft bearing, so that one or two three-axis and the crankshaft axis of the heart or different transmission and clutch shell shell bonding plane of the vertical axis the relative change in the crankshaft;⑤ Second Gear axis often axial or radial gap is too large;⑥ the axis of axial or radial gap is too large.3. Fault diagnosis and troubleshootingJump to file stalls Unascertained: After taking heat the entire vehicle, increase the use of continuous, slow approach to road test each file is determined.Will jump to the gear lever hanging file stalls the engine off, transmission cover removed carefully to observe the mating dance gear case file.① engagement does not meet the length, then the resulting fault;② to reach a total length of engagement, should continue to check;③ check mating wear parts: wear into a cone, then failure may be caused by;④ check b-axis of the gear profile and the axis of the axial and radial clearance, clearance is too large, then failure may be caused by;⑤ check self-locking devices, locking devices, if only a very small dynamic resistance, and even feel the ball is not plugged groove (the transmission cover caught in the vice, the hand-shaking shift stroke), the fault for the bad performance of self-locking ; Otherwise, the fault for the clutch and gearbox shell bonding plane and the vertical axis of the crankshaft caused by changes.(B), arbitrary files1. PhenomenonTechnical condition in the clutch normal circumstances, transmission at the same time put up or two files linked to the need to stall, the results linked to other stalls.2. Reasons① interlocking device failure: if the fork shaft, pin or interlocking interlocking ball too much wear and tear, etc.;② the bottom of the arc gear face wear and tear is too large or fork axis of the allocated blocks wear groove is too large;③ball pin gear lever broken or the ball-hole, ball松旷wear too. In short arbitrary file transmission is mainly due to institutional failure manipulation.3. Fault diagnosis and troubleshooting① linked to the need to stall, the results linked to the other stalls: rocking gear lever, to check their point of view before, if in excess of the normal range, while the lower end of failure by the gear lever ball pin and the positioning groove ball with or松旷, the ball is too large holes caused by wear and tear. Swung shift 360 °, compared with a broken pin.② If the pendulum angle to normal, still not on, or linked to more than picking file, then the lower end of failure by the gear lever away from the limitations arising from the groove in (due to break away from the bottom of the arc-shaped guide groove face wear and tear or wear).③ At the same time linked to the two files: the fault caused by the interlocking device failure.(C), the difficulties linked to files1. PhenomenonClutch technical condition, but can not be linked smoothly linked file into the stalls, often percussive sound gear.2. Reasons① synchronizer failure;② Bending fork shaft, locking the spring strong, ball injury, etc.;③ a shaft or a spline shaft bending injury;④ inadequate or excessive gear oil, gear oil does not meet the specifications.3. Fault diagnosis and troubleshooting①Synchronizer check whether the fall to pieces, cone ring is conical spiral groove wear, whether worn slider, spring is too soft, such as elastic.② If the Synchronizer normal, check whether the bending of a shaft, spline wear is severe.③ check whether the mobile axis normal fork.(D), abnormal sound transmission1. PhenomenonTransmission refers to transmission work abnormal sound when the sound is not normal.2. Reasons1) abnormal sound gearGear wear off very thin gap is too large, the impact of running in; bad tooth meshing, such as the repair did not replace the gear pairs. New and old gear with the gear mesh can not be correct; tooth metal fatigue spalling or damage to individual teeth broken; gear and the spline shaft with松旷, or the axial gear clearance is too large; axis caused by bending or bearing松旷space to change gears.2) Bearing ringSerious bearing wear; Bearing (outer) ring with the journal blocks (holes) with the loose; Ball Bearing Ma break-up or a point of ablation.3) ring made for other reasonsSuch as the transmission within缺油, lubricants have been thin, too thick or quality deterioration; transmission into the foreign body inside; some loose bolts fastening; odometer or the odometer shaft ring gear, such as fat.3. Troubleshooting①transmission issued metal dry friction sound, which is缺油and the poor quality of oil. Refueling and inspection should be the quality of oil, if necessary, replacement.② for moving into a file if the sound obvious, namely, the profile of gear tooth wear; If the occurrence of cyclical noise, while damage to individual teeth.③when the ring gap, and riding the clutch pedal under the noise disappeared after the general axis is a before and after the bearing or regular engagement ring gear; if any files are changed into the ring, after more than two-axis bearing ring.④transmission occurs when a sudden impact the work of sound, most of the tooth was broken and should be removed timely transmission inspection cover to prevent mechanicaldamage.⑤moving, only for transmission of a file into the ring gear made in the above-mentioned good premise, it should check with improper gear mesh, if necessary, should be re-assembling a pair of new gear. In addition, it may be synchronizer gear wear or damage should be repaired or replaced depending on the circumstances.⑥ when shifting gear ring made of impact, it may be the clutch or the clutch pedal can not be separated from stroke is incorrect, damaged synchronizer, excessive idling, gear improperly adjusted or tight-oriented, such as Bush. In such cases, to check whether the separation of the clutch, and then adjust the idle speed or the gear lever, respectively, the location, inspection-oriented with the bearing bushing and separation tightness.If excluded from the above examinations, the transmission is still made ring, should check the shaft bearings and shaft hole with the situation, bearing the state of their own technology, etc.; as well, and then view the odometer shaft and ring gear is made and, if necessary, be repaired or replacement.(E), transmission oil1. PhenomenonAround the transmission gear lubricants, transmission gear box to reduce the fuel can be judged as lubricant leakage.2. Reasons and troubleshooting① improper oil selection, resulting in excessive foam, or the volume too much oil, when in need of replacement or adjust the lubricant oil;② side cover is too loose, damaged gaskets, oil seal damage, damage to seals and oil seals should be replaced with new items;③ release and transmission oil tank and side cover fixed bolts loosening, tightening torque should be required;④ broken gear-housing shell or extended wear and tear caused by oil spills, must be replaced;⑤ odometer broken loose gear limit device must be locked or replaced; gear oil seal oil seal oil should be replaced.Third, the maintenance manual gearboxSantana is now as an example:Santana used to manually synchronize the entire, multi-stage gear transmission, there are four forward one block and reverse gear. Block are forward-lock synchronizer ring inertial, body-wide shift synchronizer nested engagement with a reasonable structure, the layout of a compact, reliable, long life and so on. However, if the use and maintenance is not the right way to do so, failure mayoccur at any time.The proper use of Synchronizer:1, the use of addition and subtraction block off both feet. Block addition and subtraction, if the clutch with one foot, then the speed at the time of addition and subtraction block must be correct, the timing should be appropriate and, if necessary, to addition and subtraction can be blocked off both feet, so that addition and subtraction method can reduce the block with Gear speed difference between the circumference, thereby reducing wear and tear Synchronizer to extend the life of Synchronizer.2, prohibited the use of tap-shift gear lever when the method (that is, a push of the operation of a song). Hand should always hold down the shift, this can greatly reduce the synchronizer sliding lock Moreton Central time and reduce wear and tear.3, no state in the gap off the use of force挂挡synchronizer start the engine. Moment of inertia as a great engine, the friction torque Synchronizer also small, so the time synchronization process is very long, so that lock ring temperature increased sharply, it is easy to burn synchronizer.4, is strictly prohibited by synchronizer clutch instead of the initial (that is, the use of non-use of the clutch friction synchronizer start挂挡role), control speed and braking.The correct use of lubricants:Santana at the factory, the transmission has been added to the quality of lubricating oil, under normal circumstances, the level of the transmission lubrication need to be checked. However, when normal travel 100,000 kilometers 10,000 kilometers -20 after the first lubricating oil must be replaced. Santana grade lubricants used in transmission as follows: Gear Oil API-GLA (MIL-L2105), SAE80 or SAE80W-90 grade汽车变速器一、汽车变速器概述及发展趋势汽车问世百余年来,特别是从汽车的大批量生产及汽车工业的大发展以来,汽车己为世界经济的发展、为人类进入现代生活,产生了无法估量的巨大影响,为人类社会的进步作出了不可磨灭的巨大贡献,掀起了一场划时代的革命。
《数控专业外语》期末复习.docx

2010学年度第一学期_________ 班《数控专业外语》课程期 末 考试试卷B 卷( )1 .Vertical mill machine ( )2.Right-hand Rule( )3.ATC automatic tool changer ()4.turning center( )5.wire EDM/ wire electrical discharge machine ( )6.axis framework ( )7.reference point ( )8.positioning mode ( )9.contouring control ( )lO.closed loop system ( )II.ball-nut lead screw\ballscrew ( )12.Point-to-Point control ( )13.manual programming ( )14.NC personnel ( )15.tooling system ( )16.end mill ( )I7.drilling machine ()18. tap1. 立式铳床2. 右手法则3. 白动换刀装置4. 车削屮心5.线切割电火花加工机床6. 坐标系7. 基准点&定位模式9.轮廓控制 10.闭环系统 11 •滚珠丝杠 12. 点位控制 13. 手工编程 14. 数控技术员 15. 刀具系统 16. 端铳刀 17. 钻床丝锥( )19.reamer 19.绞刀( )2O.taper shank 20.锥柄( )21.fixed cycle 21.固定循环( )22.variable type programming 22.变量编稈( )23.tool path 23.刀具路径( )C programming 24.数控编程( )25.holding mechanism 25.夹紧机构( )26.tool chaarm 26.换刀机械手( )27.boring tool 27.镣刀( )28.work piece 28.工件( )29.pallet 29.托盘( )3O.indexing head 30•分度头( )31 .rotary move me nt 31.旋转运动( )32.spindle 32.主轴( )33.feed rate 33.进给率( )34.AC servo 34.交流伺服系统( )35.machine table 35.工作台( )36.saddle 36.床鞍( )37.tolerance 37.公差( )38.repeatability 38.重复定位精度( )39.counterboring 39$忽孔( )4O.referenee plane 40參考平面( )41.tool length offset 刀具长度偏置( )42.zero preset 零点预置( )43.tool code刀具代码( )44.PRZ /Program Reference Zero 程序参考零点( )45.chuck 卡盘()46.tool radius compensation 刀具半径补偿( )47.tool nose radius compensation 刀尖圆弧半径补偿( )ling cutter 铳刀( )49.finish 精加T( )50.rough 粗加T( )51.CAD Computer-Aided Drafting 计算机辅助设计( )52.CAM Computer-Aided Manufacturing 计算机辅助制造()53.NC code数控代码()54.post-process 示置处理( )55.3-D solid models 三维实体模型( )56.conversational program 会话式程序( )57.CIM Computer-integrated Manufacturing 计算机集成制造( )58.DNC Direct Numerical Control 计算机直接数控( )59.postproduction 后处理( )60.GT group technology 成组技术( )6l.JITjust-in-time 准时制造( )62.FMS Flexible Manufacturing System 柔性制造系统( )63.raw stock 毛坯件( )64.casting 铸件( )65.band-saw 带锯( )66.erosion 腐蚀( )67.distortion 变形( )68.reset 重置( )69.1ead-in 导入( )70. lead-out 导出()71 .draft 草图( )72. three-dimensional space 三维空问( )73.simultaneous five-axis machining 五轴联动加匸( )74. surface machining ill]面加匸( )75. three-axis machining with fourth-axis positioning 四轴定位三轴联动加丁句子翻译:(每小题5分,共30分)1、Because no mechanical cutting forces are involved, lasers cut parts with a minimum of distortion, they have been very effective in machining slots and drilling holes.由于没有机械切削力,所以激光加工的工件变形非常小,激光切割机对加工窄槽和钻孔非常有效。
FANUC CNC 模拟器用户手册说明书

888-FANUC-USLearn More About Affordable & Portable Training Solution From The Leader in Factory AutomationFANUC CNC Simulator brings the world’s most popular CNCcontrol to the classroom, providing students with exposureto FANUC CNC controls without the need for a full machine.The FANUC CNC Simulator is based on the FANUC Series 0iMODEL F platform and can be operated in either milling orturning configurations. The FANUC CNC Simulator is an actu-al FANUC CNC control, so students will experience the look,feel and layout of the control as they navigate and program a fully functioning CNC. FANUC’s MANUAL GUIDE i conver-sational programming interface allows user to graphically generate programs that are simulated in 3D prior to being converted back to conventional NC programs and used on machine tools. Uploading and downloading (read and punch) functions are facilitated by means of the standard Flash ATA interface and USB interface, and DNC functions are supported by Ethernet and Flash ATA card. FANUC CNC SimulatorPart number: A02B-0158-B100#USFeatures•Switchable mill and lathe (turning) system in one simulator •3-axis milling / 2-axis turning system plus one spindle •Manual Guide i for conversational program creation and 3D simulation •USB, Flash ATA and Ethernet connectivity •Power: AC 100-240VProcess-orientated conversational programmingFor students advancing to a smaller job shop or tool room,MANUAL GUIDE i simplifies programming. Students learn howto get the job completed in the shortest time possible and focuson machine operations, rather than just G-code.MFA-081-EN_02_1602。
无人机三轴稳定云台智能控制算法的研究

学校编码
10390
学 号 2010539007
分类号 密级
TP391
硕士学位论文
无人机三轴稳定云台智能控制算法的研究
指 导 教 师: 陈水利 教授 作 者 姓 名: 郭炳坤 申 请 学位级别: 硕士 专 业 名 称: 应用数学 论 文 提交日期: 2013 年 4 月 15 日 论 文 答辩日期: 2013 年 6 月 8 日 学 位 授予单位: 集美大学 学 位 授予日期: 2013 年 6 月 21 日 答辩委员会主席: 李 军 教授 论 文 评 阅 人: 周武能 教授
(1) For small low-altitude UAV remote sensing system, the mathematical model of three axis self-stable Pan-tilt is established. Putting three-axis self-stable Pan-tilt as the research object, analyzed its structure in detail, built up the coordinate system of ground, the carrier, the sight and each frame rotation system, and established its mathematical model according to the Newtonian mechanics principle, analyzed its various disturbance factors. These established a foundation for subsequent precise control. And the classical PID was used to simulate system.
Sherline Jr. CNC Mill系列商品说明书
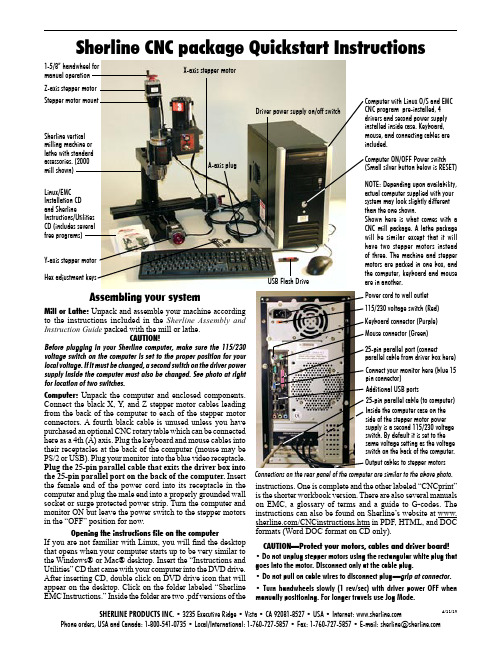
Z-axis stepper motor Y-axis stepper motor X-axis stepper motorA-axis plugDriver power supply on/off switchLinux/EMC Installation CD and SherlineInstructions/UtilitiesCD (includes severalfree programs)Sherline CNC package Quickstart InstructionsSherline vertical milling machine or lathe with standard accessories. (2000 mill shown)Computer with Linux O/S and EMC CNC program pre-installed, 4 drivers and second power supply installed inside case. Keyboard, mouse, and connecting cables are included.Additional USB portsKeyboard connector (Purple)Mouse connector (Green)25-pin parallel port (connectparallel cable from driver box here)Power cord to wall outlet Connect your monitor here (blue 15 pin connector)Connections on the rear panel of the computer are similar to the above photo.SHERLINE PRODUCTS INC. • 3235 Executive Ridge • Vista • CA 92081-8527 • USA • Internet: Phone orders, USA and Canada: 1-800-541-0735 • Local/International: 1-760-727-5857 • Fax: 1-760-727-5857 • E-mail:*********************4/11/13Output cables to stepper motors1-5/8” handwheel for manual operation Stepper motor mountHex adjustment keys115/230 voltage switch (Red)Inside the computer case on the side of the stepper motor power supply is a second 115/230 voltage switch. By default it is set to the same voltage setting as the voltage switch on the back of the computer.Assembling your systemMill or Lathe: Unpack and assemble your machine according to the instructions included in the Sherline Assembly and Instruction Guide packed with the mill or lathe.CAUTION!Before plugging in your Sherline computer, make sure the 115/230 voltage switch on the computer is set to the proper position for your local voltage. If it must be changed, a second switch on the driver power supply inside the computer must also be changed. See photo at right for location of two switches.Computer: Unpack the computer and enclosed components. Connect the black X, Y , and Z stepper motor cables leading from the back of the computer to each of the stepper motor connectors. A fourth black cable is unused unless you have purchased an optional CNC rotary table which can be connected here as a 4th (A) axis. Plug the keyboard and mouse cables into their receptacles at the back of the computer (mouse may be PS/2 or USB). Plug your monitor into the blue video receptacle. Plug the 25-pin parallel cable that exits the driver box into the 25-pin parallel port on the back of the computer. Insert the female end of the power cord into its receptacle in the computer and plug the male end into a properly grounded wall socket or surge protected power strip. Turn the computer and monitor ON but leave the power switch to the stepper motors in the “OFF” position for now.Opening the instructions file on the computerIf you are not familiar with Linux, you will find the desktop that opens when your computer starts up to be very similar to the Windows® or Mac® desktop. Insert the “Instructions and Utilities” CD that came with your computer into the DVD drive. After inserting CD, double click on DVD drive icon that will appear on the desktop. Click on the folder labeled “Sherline EMC Instructions.” Inside the folder are two .pdf versions of theinstructions. One is complete and the other labeled “CNCprint” is the shorter workbook version. There are also several manuals on EMC, a glossary of terms and a guide to G-codes. The instructions can also be found on Sherline’s website at /CNCinstructions.htm in PDF, HTML, and DOC formats (Word DOC format on CD only).CAUTION—Protect your motors, cables and driver board!• Do not unplug stepper motors using the rectangular white plug that goes into the motor. Disconnect only at the cable plug.• Do not pull on cable wires to disconnect plug —grip at connector.• Turn handwheels slowly (1 rev/sec) with driver power OFF when manually positioning. For longer travels use Jog Mode.USB Flash Drive25-pin parallel cable (to computer)NOTE: Depending upon availability, actual computer supplied with your system may look slightly different than the one shown.Shown here is what comes with a CNC mill package. A lathe package will be similar except that it will have two stepper motors instead of three. The machine and stepper motors are packed in one box, and the computer, keyboard and mouse are in puter ON/OFF Power switch (Small silver button below is RESET)Sherline CNC System SetupPlease read all of the instructions before attempting to use the EMC2 program. Machining with CNC is a complicated process, and you will be directed at the appropriate times to run the various features of the program once you have gained the knowledge you need to do so.Booting upBefore turning on your computer, make sure the 115/230 voltage switch on the computer is set to the proper voltage. If it must be changed, a second switch inside the computer must also be changed. Also make sure the ON/OFF switch for the stepper motor power supply is in the “OFF” (down) position. Once the EMC2 program is running, power to the stepper motors may be turned on.Opening the EMC Program–Login and Password When starting up, the computer will boot up without asking you to log in. If you log out of the desktop and log back in and get a login screen, enter sherline for the login (in lowercase letters) and sherline for the password. After completing the login, double click the [Go] button with your mouse, and the desktop will appear. To open EMC2, click on the lathe or mill, inch or metric icon for your machine on the desktop. If the icons don’t appear there, go to the top menu bar and navigate to Applications>CNC>EMC2. From that menu tree, choose either the inch or metric version for your machine and double click on it. This will open the “Axis GUI” version of EMC. Although this is slightly different version than the “Mini GUI” opened from the desktop icons you can still use it. Differences are explained in the EMC2 manual at Applications>CNC .Instruction filesThe instructions for use of your CNC system are pre-loaded on the Instructions and Utilities CD that came with your system. They are in .DOC (MS Word), PDF (Acrobat Viewer), and HTML formats. DOC files can be viewed on Windows® machines using MS Word or Wordpad. It will also open in OpenOffice on your Linux machine. HTML and PDF documents can be viewed on Windows, Mac® or Linux operating systems.Shutting down the computer when doneTo properly shut down your computer you should first exit all running programs. Then go to the menu bar at the top of the screen and navigate to System>Quit . After clicking on Quit , you have the choice to Log Off and leave the computer running or Turn off Computer which will log you off and shut down the computer. There is also a red power button icon in the upper right corner of the screen that will offer you several shut-down options. Finally, press and hold the power button on the front of the computer to turn off power to the computer.Emergency stopsIf you see a physical “crash” is about to occur, the fastest way to stop the stepper motors is to turn the driver board power switch on the side of the computer to OFF . The machine will have to be re-homed and the program restarted, but turning off power to the stepper motors while they are running will not cause damage. Running a slide until it hits a hard stop should not cause any physicalVersion 6.00 or higher (Ubuntu Linux)damage. Stop the motor as soon as possible by halting the program or by turning the stepper motor power supply switch to OFF to prevent possible overheating of the stalled motor.Transferring G-code files from another computer 1. Save your g-code text file to an appropriate media (DVD, CD, USB drive, etc.) in Plain Text (TXT) file format. Program files created in EMC will automatically be saved with the NGC extension. Either can be read by EMC. In other programs, limit your file name to eight characters or less in order to be able to transfer it to EMC.2. Insert the media containing your file into the appropriate drive or port on your Sherline Linux computer.3. On the desktop, click on the icon where your source file is located (DVD, USB, etc.) to open a window showing the contents of that media.4. On the desktop, double click the folder named G-Code .5. Drag the file from the selected media window and drop it into the G-Code folder window.Opening the file in EMC1. Open EMC2. Click the [AUTO] button along upper menu bar3. Click the [OPEN] button on lower menu bar4. Highlight the file by single clicking on it5. Click the [OPEN] buttonGetting answers to your questionsPlease read the instructions all the way through before calling Sherline with questions. Answers to questions relating to Linux or EMC can be found at . (Follow the links to the mailing list.) Using a Google search to ask a specific question often yields good results as well. Refer to the Sherline Assembly and Instruction Guide booklet that came with your machine for instructions on assembly, setup, adjustment and maintenance of your machine. If you have questions about assembly, missing or broken parts or other items relating to the machine, please call Sherline during business hours (M-F 8-5, Pacific) at 1-800-541-0735(USA)*****************************.From outside the USA call 1-760-727-5857.Minimum computer specifications for installation Successful installation of Linux/EMC2 v6.xx on your own computer requires at least the following:· Pentium III class processor or equivalent (800 MHz or faster)· 512 MB RAM (Sherline uses 1 Gb)· 20 GB hard drive or larger· CD/DVD drive (verify “Boot from DVD” is enabled before “Boot from HD” in the BIOS setting)· 25-pin parallel port to connect external driver boxNOTE: Sherline does not guarantee that the Linux operating system provided on the DVD enclosed with your CNC system or with the 8760 driver box will install on a non-Sherline computer. Sherline does not provide technical support for installation of Linux or EMC, but help is available on-line through the Linux group at or get subscription information on joining ****************************************************.For installations on another computer see /cgi-bin/wiki.pl?Hardware_Requirements for the latest requirements as specified by . Laptop computers are not recommended for CNC use.。
Geometric Modeling

Geometric ModelingGeometric modeling is a crucial aspect of computer graphics and design, allowing for the creation of three-dimensional representations of objects and scenes. It involves the use of mathematical equations and algorithms to define the shape, size, and position of objects in a virtual space. Geometric modeling isused in a wide range of applications, including animation, video games, architectural design, and engineering. One of the key benefits of geometric modeling is its ability to create realistic and detailed representations of objects. By accurately defining the geometry of an object, designers can create lifelike images that closely resemble the real world. This level of detail is essential for applications such as architectural design, where precise measurements and proportions are crucial. In addition to creating realistic images, geometric modeling also allows for the manipulation and transformation of objects in a virtual space. Designers can easily modify the size, shape, and position of objects, allowing for quick iterations and adjustments during the design process. This flexibility is particularly valuable in fields such as industrial design and engineering, where multiple design iterations are common. Another important aspect of geometric modeling is its ability to simulate physical phenomena and interactions. By accurately modeling the geometry of objects andtheir relationships, designers can simulate how objects will behave in different environments and under various conditions. This is essential for applications such as virtual prototyping and simulation, where designers need to test the performance of a design before it is physically built. Geometric modeling also plays a crucial role in computer-aided design (CAD) and computer-aided manufacturing (CAM) processes. By accurately defining the geometry of objects, designers can create detailed blueprints and specifications that can be used to manufacture physical objects. This level of precision is essential for industries such as aerospace and automotive, where small errors in design can havesignificant consequences. Overall, geometric modeling is a powerful tool that enables designers and engineers to create realistic, detailed, and accurate representations of objects in a virtual space. By leveraging mathematicalequations and algorithms, designers can create lifelike images, manipulate objects,simulate physical interactions, and generate detailed specifications for manufacturing. As technology continues to advance, geometric modeling will continue to play a crucial role in a wide range of industries and applications.。
PowerBox iGyro 三轴陀螺仪产品说明书

99 | Author:COLIN STRAUS Photographs:COLIN STRAUSPOWERBOXIGYROColin Straus takes a look at the new and much talked about iGyro from PowerBoxIfirst heard of the development of this new three-axis gyrosystem early in 2012, and keenly awaited its release, as Ihave been using PowerBox products for many years nowwith great success, and expected the new iGyro to be just aseffective as the other products I have used.The iGyro is purpose designed for use in fixed wing aircraft,and offers independently adjustable gyro stabilisation on roll,pitch and yaw axis, to both make the model much steadier inbumpy conditions and to make the overall flight path smootherand more realistic.WHAT WILL IT DO FOR ME?One of the main features of the iGyro is that it has dual functionality, both normal and heading modes being incorporated. Normal mode is operative when the transmitter sticks are moved even slightly from the neutral position and results in any deviation from the model’s flight path being damped. So for example any effects caused by gusts of wind, turbulence etc. will be damped out and made much less severe.Heading mode takes over when the sticks are at neutral and will maintain the model’s last commanded attitude, for example if the model is in knife edge flight the elevator will be trimmed by the iGyro to counteract any pitching moment caused by the rudderdeflection.Further to this, the iGyro will automatically compensatewhen flaps or airbrakes etc. are deployed, there is no need to have any mixing of functions, and in fact any such mixes should be disabled. Available as an optional extra is a GPS sensor, which is designed to be used in conjunction with the iGyro; primarily to enable the gyro gainto be varied depending upon theflying speed of the model.Packaged in the now familiar PowerBox two-tone blue boxing the iGyro is a neat and compact unit in an anodised aluminium case, and is fitted with a nice clear OLED display. It has inputs for most modern radio systems, including Futaba S-Bus, Spektrum, Multiplex M-Link, Jeti and Graupner HoTT , and single or twin receivers can be used as required, the use of twin receivers offering increased safety.Remaining inputs are forthe optional GPS sensor and a Bus 2 socket, whilst outputs total five, two aileron, two elevator and one rudder, there being one final connection for the SensorSwitch used during programming, this can then be disconnected as it is not required once set-up is completed. Further components included are four double-ended input leads, two for input and two for output, a USB interface adapter for software updates as well as servo tape to securely mount the iGyro. The optional GPS sensor is contained within a neatly moulded case, and has a single lead to connect to the The standard iGyro package includes the unit itself, as well as SensorSwitch for programming, USB interface andleads, tape etcThe compact nature and high quality finish of the iGyro are evident Reverse of the unit has all connections very clearly marked Optional GPS sensor is small and is very neatly packaged in this moulded case100 |iGyro, the sensor again being secured in the model with servotape. The supplied instruction manual is in both English andGerman and as per usual with PowerBox manuals is both clearand informative.ON TESTTo test out the iGyro I decided to install it into my FeiBao F9FPanther, as although this model flies superbly and is supersmooth in most flight regimes, the one weakness it suffers fromis its vulnerability to crosswinds when landing. If there is any significant crosswind the Panther can be a real handful during the approach, with aileron and rudder controls being used constantly to keep the wings level all the way to touchdown, this possibly being due to the amount of dihedral and the large tip tanks.I had previously fitted a single axis gyro for the ailerons and this had helped, but was still not a complete cure, so having a three axis gyro with the features of the iGyro would hopefully eliminate this less than welcome flying characteristic.Usefully the iGyro is quite flexible with regard to how it is installed as it can function as a standalone unit or in conjunction with a PowerBox power supply system, and this can be either a conventional unit such as the PowerBox Competition or an SRS unit such as the PowerBox Cockpit SRS.Installation of the unit into the Panther was verystraightforward, as the unit is nice and compact, asis the GPS module, and there is plenty of room in thelarge fuselage of the model. As I use Futaba radio an R7008SB (S-Bus) receiver was installed alongside aPowerBox Cockpit SRS system, these components all being compatible, and enabling very simple inter-connection as they all use serial bus communication. A single lead is used from the receiver to the iGyro, whilst two leads run from the iGyro to the Cockpit, offering a degree of redundancy, as only one lead is actually required for full operation. Note that if the iGyro is being used on a standalone basis or with a conventional PowerBox power supply system that up to five leads would be required, for ailerons, elevator and Initial programming screen enables the various menus to be accessedGyro setting screen provides information on direction of gyro effect, as well as the amount of gain in both normal and heading modes Airspeed setting screen enables the maximum airspeed reached to be read and then reset before the next flightThe first of four screens of the input mapping menu, where the functions, gain controls and flight mode switch are selectedInstallation into the Panther test model was very straightforward, using the double-sided tape supplied101 | FEBRUARY 2013rudder, but using the Cockpit SRS enables serial bus communication and the use of only two leads. The GPS unit was installed alongside the iGyro, and a single lead connects the two, whilst the SensorSwitch was only plugged in during set-up.Initial set-up was carried out following thecomprehensive instructions, initialling selecting the radio system being used and then going on to set the output to digital output for operation with the Cockpit SRS. This mode means that servos cannot be connecteddirectly to the outputs from the iGyro, as the output is in a serial digital format that the SRS system utilises. The exact positioning and orientation of the iGyro itself is not critical, apart from the requirement that it be mounted at 90 degrees to the models centreline, then the software within the iGyro is used to confirm the orientation of the iGyro within the model, this being quite straightforward.Selecting the wing type comes next as there is a Delta option in the software, if selected this removes theneed to have delta mixing in the transmitter – in fact any delta mixing in the transmitter must be switched off or theheading mode of the iGyro will not function correctly.The next section is the channel assignment, this allows thefive output channels (2 x aileron, 2 x elevator and 1 x rudder)to be assigned to the required radio channels, then the normaland heading gain set-up channels can be assigned to specificcontrols on the transmitter, after which the channel to be usedfor flight modes is selected.The direction of gyro on each axis is now set, this is a criticalstep as having the gyro operate in the reverse direction to thatrequired would cause a fright at best and a lost model at worst,so the settings here should be double checked for safety.The airspeed settings menu enables the effect of the GPSsystem to be adjusted, this system has been developed sothat the gyro gain is automatically changed as the airspeedof the model varies so that the gyro gain is higher when themodel is flying at lower airspeeds and the control surfacesneed more deflection to be effective, the gain then reducing asthe airspeed increases, to avoid any oscillation of the model atincreased airspeed due to the gain being too high.Before I started the in-flight adjustment and setting of theiGyro I carried out a test flight of the Panther with the gyrofunctions disabled to ensure all trims were correctly set, as thisis required to allow the gyro to operate at its optimum, and notto have to fight an out of trim model.With this complete the iGyro was programmed as per theinstructions with a three position switch being used to select the required flight mode, FM 1 being gyro disabled, FM 2 gyro enabled with rudder operating in normal mode only and FM 3 having the rudder gyro functioning both on normal and heading mode.The first set-up flight was made with only the aileron gyro able to function, with the right and left hand sliders on the transmitter being set to adjust normal and heading mode gain respectively. Take-off was made with the flight mode switch set to position 1, so that the gyro was inoperative, once at a safe height and at a steady and fairly slow cruise speed the switch was moved to position 2 and the right slider carefully moved to increase the gain of the gyro until I started to see the wings rock from side to side, signifying that the gain was now too high, at which point I reduced the gain slightly until the wings remained level. This completed setting the normal mode for aileron, but to check the effect of the GPS setting on the gain relating to airspeed I then carried out a couple of full power level passes, watching to see if the wings oscillated at this higher airspeed, which would have required adjustment when back on the ground to the change in sensitivity of the GPS speed compensation. Luckily the model stayed completely stable during these runs, confirming that the GPS setting recommended in the manual was correct. PRODUCT REVIEWGeneral settings screen enables the iGyro orientation to be set, as well as enabling delta or V tail mixing to be selectedReceiver setting screen where the radio being used can be set, and the output changed between analogue and digital (standard or serial bus)After the flight test session the iGyro confirms the maximum speed of the Panther at245 kmh, or just over 150 mph!102FEBRUARY 2013 |。
虚拟现实场景漫游系统设计与实现说明书
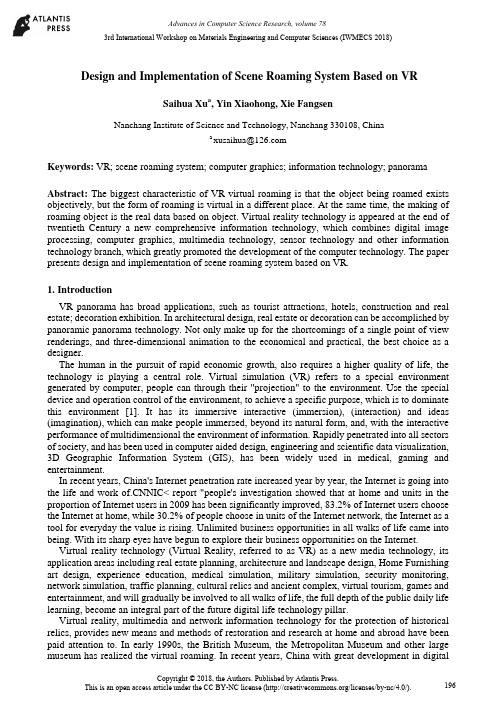
3rd International Workshop on Materials Engineering and Computer Sciences (IWMECS 2018) Design and Implementation of Scene Roaming System Based on VRSaihua Xu a, Yin Xiaohong, Xie FangsenNanchang Institute of Science and Technology, Nanchang 330108, Chinaa ****************Keywords: VR; scene roaming system; computer graphics; information technology; panoramaAbstract: The biggest characteristic of VR virtual roaming is that the object being roamed exists objectively, but the form of roaming is virtual in a different place. At the same time, the making of roaming object is the real data based on object. Virtual reality technology is appeared at the end of twentieth Century a new comprehensive information technology, which combines digital image processing, computer graphics, multimedia technology, sensor technology and other information technology branch, which greatly promoted the development of the computer technology. The paper presents design and implementation of scene roaming system based on VR.1.IntroductionVR panorama has broad applications, such as tourist attractions, hotels, construction and real estate; decoration exhibition. In architectural design, real estate or decoration can be accomplished by panoramic panorama technology. Not only make up for the shortcomings of a single point of view renderings, and three-dimensional animation to the economical and practical, the best choice as a designer.The human in the pursuit of rapid economic growth, also requires a higher quality of life, the technology is playing a central role. Virtual simulation (VR) refers to a special environment generated by computer, people can through their "projection" to the environment. Use the special device and operation control of the environment, to achieve a specific purpose, which is to dominate this environment [1]. It has its immersive interactive (immersion), (interaction) and ideas (imagination), which can make people immersed, beyond its natural form, and, with the interactive performance of multidimensional the environment of information. Rapidly penetrated into all sectors of society, and has been used in computer aided design, engineering and scientific data visualization, 3D Geographic Information System (GIS), has been widely used in medical, gaming and entertainment.In recent years, China's Internet penetration rate increased year by year, the Internet is going into the life and work NIC< report "people's investigation showed that at home and units in the proportion of Internet users in 2009 has been significantly improved, 83.2% of Internet users choose the Internet at home, while 30.2% of people choose in units of the Internet network, the Internet as a tool for everyday the value is rising. Unlimited business opportunities in all walks of life came into being. With its sharp eyes have begun to explore their business opportunities on the Internet.Virtual reality technology (Virtual Reality, referred to as VR) as a new media technology, its application areas including real estate planning, architecture and landscape design, Home Furnishing art design, experience education, medical simulation, military simulation, security monitoring, network simulation, traffic planning, cultural relics and ancient complex, virtual tourism, games and entertainment, and will gradually be involved to all walks of life, the full depth of the public daily life learning, become an integral part of the future digital life technology pillar.Virtual reality, multimedia and network information technology for the protection of historical relics, provides new means and methods of restoration and research at home and abroad have been paid attention to. In early 1990s, the British Museum, the Metropolitan Museum and other large museum has realized the virtual roaming. In recent years, China with great development in digitalcultural relics related areas, the Ministry of education established the "University Digital Museum Construction Engineering, Dunhuang Research Institute and Northwestern University jointly launched the" digital Dunhuang murals cooperative research ", the Imperial Palace Museum and Toppan Printing Company has developed a virtual the Imperial Palace in Beijing. The bid for the 2008 Olympic Games also put forward the" Virtual Olympic Museum "creative, has aroused great interest and concern of the International Olympic Committee, which host provides great help to get China Help.The research on virtual reality technology in the collection shows the application of practical task, the use of virtualization, virtual exhibition cultural digital technology, improve the display rate and the display effect of cultural relics and cultural relics protection entities, and further extended to break the constraints of time, the museum's collection, collection, exhibition and cultural dissemination function.2. Interactive roaming system based on VRAccording to the connotation and essential characteristics of virtual reality technology, it can be seen that its research and development is a relatively high technical requirements, it needs a corresponding software and hardware system environment to be matched. In addition to the perfect virtual reality software development platform and three-dimensional image processing system, according to the technical characteristics of virtual reality [2]. The system also requires a highly lifelike three-dimensional immersion, which is mainly realized by three-dimensional hearing, three-dimensional tactile or force sense and visual environment with high immersion. Stereo hearing is usually realized by three-dimensional surround stereo sound system, while highly immersive visual environment is usually realized by large screen stereoscopic projection display system.In addition, according to the technical characteristics of virtual reality, real-time interaction is the soul of virtual reality technology, which is different from other traditional media technology in essence. In virtual reality system, this kind of interaction is usually realized by virtual reality interactive device, and finally a complete virtual reality realization system is formed.This article from the modeling and rendering of 3D MAX baking technology to 3D campus roaming system using mature VRP-BUILDER virtual reality editor module to build a two development.The development of 3D and the method of 3D simulation roaming system based on VRP technology, Wuzhou University (North) to build the virtual scene, automatic roaming, manual roaming Campus navigation path, view the scenery of the campus, the campus information query, climate effect, dynamic effect of various entities, and do a detailed route according to the collision detection. At the same time according to the characteristics of 3D simulation roaming, roaming in the automatic and manual roaming process, based on the existing scene as the foundation, through the video, pictures, music. To the virtual reality system; provide convenience for the need to understand the Wuzhou University campus geographic information users [3].()1,,1,0,mod )()(10,−=−≡∑−=N k N l k x h k w j L l i l j j (1) The modeling method of Polygon+NURBS advanced modeling, each model using simplified model to the three-dimensional virtual campus architecture; using Bitmap bitmap +UVW Mapping mapping, VRAY real scene rendering method for reduction of the campus; using Max-for-VRP derived plug-in model into VRP-BUILDER virtual reality editor module, adding collision detection algorithm, VRP realize man-machine command line scripts the interactive function, to ensure the practicality of the system; the use of walking camera, dynamic roaming increase real 3D performance, multi angle view school environment; running from virtual reality editor module is derived for the EXE portable can run the executable file system.According to the real terrain data is used for terrain generation of a class of the most, at presentmost of the digital terrain model (Digital Terrain Model, DTM) to generate DTM data, by the sampling elevation in the grid map the value composition corresponding to the remote sensing image data captured texture plane or satellite.The texture image is mapped to the corresponding part in the reconstruction of terrain surface. Terrain rendering algorithm is simple, the DTM cell transformation of 4 adjacent grid points defined into 2 dimensional space of the triangle, then the optic internal area of pyramidal all such triangles sent to the graphics pipeline drawing.This algorithm can also be the image texture data to the highest resolution mapped to the corresponding polygon, but this is a very inefficient, because in general, triangle and remote sensing images The number of physical pixels is very large, and each individual triangle projection to the image space is very small, and a lot of texture pixels may be compressed to a pixel in the image, so that the effect is negligible [4]. Therefore, if directly generated by DTM terrain, even in high performance graphics hardware platform on real-time rendering, it is almost impossible, usually needs to be simplified to DTM. Data simplification methods will be discussed in detail in the next chapter.The biggest characteristic of this kind of virtual roaming is that the object being roamed is already objective and real, but the form of roaming is only fictitious in different places and at the same time. Roaming object making is real data based on object. It creates a virtual information environment in multidimensional information space, which can make users feel immersive and have perfect interaction ability with environment. And it helps to enlighten the idea that VR has not only been focused on computer graphics, it has been involved in a wider range of fields, such as videoconferencing, network technology and distributed computing technology. Virtual reality technology has become an important means of new product design and development.3.Design of 3D VR scene roaming systemThe virtual scene simulation technology is regarded as an important branch of virtual scene technology. Computer technology, image processing and graphics generation technology, multimedia technology, information synthesis technology, the integrated use of display technology and other high technology, its components include simulation modeling technology, animation technology and real-time visual technology at present domestic virtual scene technology market has not yet substantial development, but also has begun to take shape [5].The United States is in the leading position in the field, the basic research mainly focuses on perception, user interface, the four aspects of software and hardware. NASA (NASA) research focused on real time simulation of space station operation, they used a lot for the cockpit flight simulation technology [6]. The University of North Carolina (UNC) the computer department developed a help users in complex visual parallel processing system for real-time dynamic display of building landscape.Figure1. vehicle real-time 3D visual simulation and virtual environment Massachusetts Institute of Technology (Mrr) in 1985 to set up a media lab, a man named BOLIOtest environment for different graphic simulation experiment. University of Washington Washington Technology Center (HIT Lab) Interface Technology Laboratory of feeling, perception, cognition and motion control ability of.DaveSimS et al developed a virtual reality model to see how the system operates retreat in Illinois.The State University developed in vehicle design, system realization, distributed virtual remote collaboration support in different countries; different regions of the engineers can design through real-time collaboration computer network. George Mason University developed in a dynamic virtual environment in real-time fluid simulation system [7]. The California Graduate School of Naval Research Laboratory of NPS visualization the work in the virtual environment navigation and simulation.In order to achieve IEEE in distributed interactive simulation (Dls) network protocol under the support of the vehicle real-time 3D visual simulation and virtual environment. The Wright Patterson Air Force Base "3D image and Computer Graphics Lab" is S on GI4D/400 workstation built space satellite the virtual environment to simulate near space and describe the 3D graphical model of satellite earth's orbit and the running state of the simulation The information of the simulation object is more fully [8].Virtual reality (Virtual Reality VR) technology is appeared at the end of twentieth Century a new comprehensive information technology, which combines digital image processing, computer graphics, multimedia technology, sensor technology and other information technology branch, which greatly promoted the development of computer technology.The virtual technology of virtual reality technology (King) (such as virtual tour entity and Virtual Museum) virtual environment (landscape) technology (such as the restoration of generation Epang palace, Old Summer Palace has lost the building, construction has not yet been discovered Mausoleum of the First Qin Emperor) two categories. Application of virtual reality technology and cross field is very extensive. At present the successful use of the field of battlefield virtual reality technology the virtual reality simulation environment, combat command, aircraft, ship, vehicle virtual reality driving training, aircraft, missiles, ships and cars (virtual manufacturing virtual design system, including virtual reality construction) Display and visit of buildings, virtual reality surgery training, virtual reality game, virtual reality, film and television art, etc. so we can see that VR technology has strong market demand and technology drive [9].The construction of the integrated innovation of virtual reality system to realize the reconstruction of the product can be applied research and innovation training platform based on the overall goal is through the use of scientific, reasonable configuration, virtual laboratory system, the establishment of a virtual laboratory environment with the participants feel personally on the scene and real-time interactive capabilities, which will enhance the level of scientific research and teaching environment to a with the level of technological innovation platform. After the completion of the "integrated innovation based on reconfigurable product system virtual reality application of innovative research and training platform" should be a set of teaching, scientific research and demonstration functions, with immersive display and real-time interaction as the main function of the virtual reality laboratory environment and a new generation of digital media technology innovation platform.4.Design and implementation of scene roaming system based on VRThe mathematical model of distribution of Brown motion to generate realistic scenes from random fractal, many nonlinear phenomena he can express effectively in nature, is so far the best to describe the real terrain. Then he is a generalization of the Brown movement. The algorithm is: random fractal terrain generation technology of fractal geometry and FMB based on the method, used a Poisson step method (poissonfaulting), Fu Liye filter (fourierfiltersng), the midpoint displacement method (midpointdisplaeement), successive random additions (Suc.essiverandomadditions) and band limited noise accumulation method (summingbandlimit.dnoises) and other five categories. Among them, the random midpoint displacement method is the most simple and classic that is a direct application of FBM.A one-dimensional random midpoint displacement method for his own thought is: the known vertex elevation (or attribute) line, the midpoint of the elevation ( For the ends of attributes) or height (or attribute) the average value plus a random displacement, displacement of the two segment of the midpoint subdivision and recursive displacement, know that meet the resolution needed so far. The extension to the two-dimensional surface, according to the different pattern of the simulation can be divided into triangle grid simulation method, rectangular (square) grid simulation method, diamond square grid simulation method, parameter block grid simulation method, the thought and the one-dimensional similar. The square grid as an example the realization process of two-dimensional random midpoint displacement method.Good computer games, not only can achieve the purpose of work alternately, eliminate fatigue, and cultivate intelligence sentiment and inspire imagination. Computer game show is mainly virtual editing script under artificial scene behavior changes. So the application and effect of the virtual building scene roaming technology in the field of play a decisive role.The original delta game using a large number of indoor and outdoor architectural scenes, such as barracks, bunkers, tunnels, tower, armory, tower. Later the popular Quake, VR and other special police use the subway, train and ship building internal scene real-time strategy game has been more common. When this network game against the CS scene it is from 3D indoor and outdoor buildings. Even the sports games such as need for speed, FIFA, the stadium, bridge, tunnel and other buildings scene is also indispensable.Battlefield virtual simulation and command simulation training have all kinds of virtues of virtual simulation technology, such as safety, repeatability, economy, difficulty of battlefield environment adjustability, convenient against simulation, easy to achieve various tactical settings and so on.The virtual reality technology and multimedia technology, network technology is the application of computer technology in twenty-first Century three with the greatest development potential. Although the virtual reality technical difficulties still exist many unsolved theoretical problems have not yet overcome the impact on human life and work but also very little. However, it is foreseeable that in the near future, have a significant impact on the virtual reality technology is bound to human life and production.5.SummaryThe paper presents design and implementation of scene roaming system based on VR. Although all the countries have successfully developed some typical applications of virtual reality, but the application of high technology compared with other, is still in the initial stage of application development. Although it may not be able to clearly imagine, in the new century and new forms of popular virtual reality, but people can through the application of medium shape change the principle and extension of the field of medium main propagation characteristics, a reasonable conception of future scenarios.References[1] Wang Rui, the design and implementation of the money Xuelei.OpenSceneGraph 3D rendering engine. Beijing: Tsinghua University press, 2012.11.[2] Zhu Danchen, song Guiling. The realization of computer and modernization of virtual museum system based on Unreal3 and 2013, 34:48-52.[3] Duan Xinyu. The foundation of virtual reality and VRML programming. Beijing: Higher Education Press, 2014.3.[4] Xiao Peng, Liu Gengdai, Xu Mingliang.OpenSceneGraph 3D rendering engine programming guide. Beijing: Tsinghua University press, 2012.[5] Feng Yufen. Design and implementation of virtual cell roaming system based on Virtools.Computer simulation, 2015, 26 (6): 285-287.[6] Jiang Xuezhi, Li Zhonghua. Research status of virtual reality technology at home and abroad.Journal of Liaoning University of Technology, 2016.[7] Deng Zheng detailed translation of.OpenGL programming guide. Fourth edition. Beijing: people post and Telecommunications Press, 2015.[8] Yuan Haibo, Liu Houquan, and so on. 3D interactive. Microcomputer information based on scene semantics in virtual museums, 2012, 25 (9-3): 175-177.[9] Li Zhiwen, Han Xiaoling. Research status and future development of virtual reality technology and future development. Information technology and information technology (Human-ComputerInteraction Edition) 2015 (3): 94 - 96.。
PRO NC 3AXIS_mill

IntroductionThis document introduces the basic processes and techniques used to 1) Createa manufacturing model in Pro/NC 2) Define the setup required to efficientlycreate toolpaths. Although this document is intended for use by new users of Pro/NC, the information contained within could prove helpful for mature users also.The intent of this document is to provide users with a clear understanding of the various configuration and setup options available within Pro/NC. Not everything mentioned in this document is required to make toolpaths. However, to determine the optimal use of Pro/NC within one’s company, an understanding of the various functionalities mentioned in this document is key.The topics within this document are applicable for both Milling and Turningmodels.Note: Pro/ENGINEER Release 2001 will be used to demonstrate thefunctionalities listed below.· Model Definition/Creation· Operation Setup· Machine Tool Setup· Fixture Setup· Tool Definition/Setup· Site File Creation – “Tool Path Defaults”· PPRINT Setup – “Operator Messages”Estimated time to complete technique: 3 HoursSetupFor this technique, a previously created milling reference model is used in addition to a previously created fixture. Below are images of the above-mentioned models respectively.An NC-Assembly Model was used for this technique. The model contains a reference model, workpiece, and fixture assembly.Figure 1 - Reference Model: GEAR_HOUSINGFigure 2 - Fixture Assembly: VICEExample FilesThe example models used in this document can be downloaded at the following location:Example Part FilesFundamentalsThe Manufacturing ModelThe strategy used to machine a part within Pro/NC is to first define themanufacturing model. The manufacturing model is an assembly consisting of at least one reference part, and may include a workpiece (stock model) as well as fixtures used to hold the part while being machined. The Reference Modelrepresents the completely machined end product. The Workpiece represents the raw stock geometry from which the part will be machined. In some instances, the workpiece may be a casting and resemble the reference model. In otherinstances, the workpiece will be a billet or bar of material.Two types of manufacturing models can be defined in Pro/NC. The default model type is NC Assembly. The NC Assembly sub-type is used for machining more than one reference part or a reference model consisting of an assembly of parts.One, or many workpieces may be used in the manufacturing model or noworkpieces at all. The NC Assembly sub-type also allows for the use of both regular assemblies and manufacturing assemblies that have been previously created. Components of these previously defined assemblies can be classified as reference models, workpieces or fixtures. In an NC Assembly model, all of the features created in manufacturing mode are saved to the assembly (.asm) file.The second type of manufacturing model is NC Part. Multiple reference models can be used but there must be one and only one workpiece. The workpiece does not have to have solid geometry but does need to be present in themanufacturing assembly. Manufacturing features created during tool pathdevelopment will be placed into the workpiece model.Note: The ability to create an NC Part type of manufacturing model has been removed from Pro/ENGINEER Wildfire.Four different file types will be associated with the manufacturing model. The file types include the .prt (for the reference model and workpiece), .asm (theassembly containing the reference part and workpiece as components), the .mfg (contains the manufacturing specific information) and the .tph file (an encrypted file containing the computed toolpath geometry for the sequences within the*.mfg file.). These four file types are typically stored in the working directorywhere the manufacturing model is created.Sometimes, the complexity of a model can make feature and tool path creation difficult. Simplified representations enable the user to capture different states of the reference model during the machining process. Simplified representations can be used to 1.) Simplify the model, eliminating geometry not required for the current operation, 2.) Capture in-process geometry using the reference model.Refer to the online help for additional information regarding the creation and use of simplified representations.See the Additional Information section of this document for links regarding Simplified Representations.OperationsOperations are a series of NC sequences performed at a particular workcell and using a particular coordinate system for cutter location (CL) data output. The coordinate system used by an operation in Pro/NC is called Machine Zero and is synonymous with Program Zero, Part Zero or Zero Datum. Some parts will require more than one setup on the NC machine to reach all the surfaces where material is to be removed. These setups will typically require a new operation in Pro/NC because the part orientation changes in reference to the coordinate system used to generate the CL data.For instance, consider a square block with holes to be drilled on both the top face and one of the side faces. If the NC machine being used only has 3-axis capability, the machine operator would need to reposition the block, i.e. change the setup, in order to drill the holes on the second face. In Pro/NC, one operation would be defined for machining on the top face and another operation for the machining on the side face. Sometimes additional operations will be desirable even though the part setup has not changed.See the Additional Information section of this document for links regarding Operation setup.The NC MachineDuring the operation definition, the NC Machine is specified. The NC machine is often referred to as a Workcell in Pro/NC and in the Help documentation. The NC Machine is a feature that defines the machine tool attributes such as, the machine name, machine type, number of axes, associated tools, parameters, etc.The NC Machine types that can be defined are Mill, Lathe, Mill/Turn, and WEDM (Wire Electronic Discharge Machine). During the NC Machine definition, the user can also designate default values for settings related to the tool path creation. These default settings are stored in the form of a site file. Additional information regarding the machine tool is also defined such as spindle limitations, feed units, axis travel limits, workcell related comments, etc. Workcells can be saved to disk to be used in other operations or other manufacturing models.See the Additional Information section of this document for links regarding setup of the NC Machine setup.FixturesFixtures are defined in the Operation Setup dialog window. Fixtures are parts or assemblies that help orient and hold the workpiece during a manufacturing operation. In Pro/NC, Fixtures help to define tool paths such that the tool will not collide with positioning or fixturing equipment on the NC machine. Fixtures can be created and saved in Part or Assembly mode, prior to the manufacturing model creation, and then retrieved into manufacturing mode during fixture setup. They are assembled into the manufacturing model using standard component assembly procedures. Creating the fixture in Assembly mode is advantageous because fixtures can be created as needed, during the intermediate process steps, by referencing the workpiece. ,Fixtures can also be created from scratch within the Fixture Setup dialog or they can be retrieved from a library of existing models. The Pro/ENGINEER Tooling Library is an example of a library containing fixture and tooling models.See the Additional Information section of this document for links regarding Fixtures and Fixture Setup.ToolingTooling refers to the cutting tools used to remove material. Cutting tools consist of three different types, Parameter, Sketched, and Solid.Parameter tools are typically defined within the manufacturing model in the Tools Setup dialog window. Parameter tools are created by entering values for predefined parameters that describe the tool type and the tool shape. Parameter tools can be saved to disk to be later used in other manufacturing models or other workcells.Sketched tools are also defined in the Tools Setup dialog but instead of defining the tool shape by entering numerical values, a sketch of the tool is created. Sketched tools are only used in Trajectory type sequences.Solid tools are created outside of the manufacturing module. Solid tools can be either a single part or consist of multiple components in an assembly. Solid tool models must include user-defined parameters that will be used by Pro/NC for correct tool path generation. Once a solid tool is created, it can be retrieved into the Tools Setup dialog.See the Additional Information section of this document for links regarding tooling setup.DefaultsWithin Pro/NC, a Site file is created to specify the default parameters to be used in NC Sequences and tool paths. Sites can be created for the different NC sequence types such as Mill, Turn, Holemaking, WEDM, etc. Parameters are modifiable values, which control the tool motions during NC sequences. Some parameters are common to all or the majority of sequences. For these commonly used parameters, the Sites enable the user to automatically define these values for newly created sequences. In addition, relations can be used in Sites to drive NC sequence parameter values.See the Additional Information section of this document for links regarding Site setup.PPRINTS “Operator Messages”PPRINTS are used to output information about the manufacturing model to the CL files. When Post Processing a CL file, the PPRINTS are passed to the G-code file for the operator to view on the machine controller display (if applicable). Information output to the CL file from PPRINTS is typically used by the machine operator for tasks such as part and fixture setup and tool setup. In addition, PPRINTS can be used to pass special instructions, and general tool path information to the CL file.See the Additional Information section of this document for links regarding PPRINT usage.Procedure1.1 Creation of the Manufacturing ModelThe first step in creating any new Pro/NC Model is to select File, New fromthe drop down menus along the top of the main model window. The Newdialog window (in Figure 3 below) opens and selecting Manufacturingpopulates the Sub-type section with the various manufacturing options. Thevalid options for Pro/NC are NC Assembly and NC Part, which are defined in the Fundamentals section above and in the Glossary. Select NC Assemblyand enter an appropriate name for the new manufacturing model and pick the OK button. In this example, the manufacturing model is namedGEAR_HOUSING.Figure 3 - New Model Creation DialogNext, from the Menu Manager, select MFG Model, Assemble, Ref Model.When the Open dialog window appears, highlight the Pro/ENGINEER model that is to be used as the reference part and pick the Open button. If aworkpiece has been previously created, select Assemble from the menumanager. Otherwise, select Create to define a new model to be used as the workpiece. For this example, the Assemble option is used. After theworkpiece has been assembled, using standard assembly procedures, themodel will look like Figure 4 below.Figure 4 - Manufacturing ModelQuick TipTwo methods can be used to better view manufacturing models when using a workpiece. The two methods include: 1.) creating a component display 2.) assigning color and appearance to a component.For the model in this example (Figure 4 above), a component display was created to show the workpiece in wireframe while the reference model is shown as solid. To do this, select View from the main drop down menus and then select Model Setup, Component Display. From the Comp Display menu select Create, enter a descriptive name, Wireframe, Pick Mdl, and then pick the workpiece from the model window. Select Done from the Edit Display menu and Done/Return from the Comp Display menu. To change back to the original display with a solid workpiece, select View, Model Setup, Component Display, Set Current, Master Rep, Ok,Done/Return.To assign color and appearance to a component, first select View, Model Setup, Color and Appearance… In the Appearances dialog select Modify From Model and then pick any of the green surfaces of the workpiece. Select the Advanced tab and set the Transparency as desired (typically between 50 and 85). Click OK, Close. In shaded mode the manufacturing model appears as shown in Figure 5 below.Figure 5 - Workpiece Appearance Set to Be TranslucentAnother method used to clear up the model display is to Right Mouse clickon the workpiece in the Model Tree and select Hide. This will completelyblank the workpiece. To show the workpiece after it has been hidden, RightMouse click on it again in the model Tree and select Unhide.1.2 Creation of an OperationAfter the manufacturing model is created, the next step is to define anoperation. From the Manufacture menu, select Mfg Setup to open theOperation Setup dialog window as seen in Figure 6 below. The default name for the operation is OP010 but can be modified to be more descriptive. In the Operation Setup dialog window, red arrows appear next to the items that are required.Figure 6 - Operation Setup Dialog1.3 Creation of an NC MachineThe first required option in the Operation Setup dialog window is the NCMachine. Define the NC Machine or Workcell to be used for the operation by selecting the button. The Machine Tool Setup dialog opens as seen in Figure 7 below. In this dialog window, users can define the type of workcell, number of axes, post processor used to generate g-code files, tooling, axes limits, etc. For this example, the machine name has been changed from the default of MACH01to FADAL. A 3-axis Mill is defined. All other options in this dialog are optional.Figure 7 - Machine Tool Setup DialogSelect on the various tabs in the Machine Tool Setup dialog window to further define the NC Machine. Near the bottom of the dialog window is the section containing the Cutter Compensation options. To expand this section, pick on the blue right facing arrow next to the words “Cutter Compensation”.After all of the desired options have been defined, the workcell can be saved for future use in a different manufacturing model. When a workcell is saved, a .gph file, with the name of the workcell, is written to the directory specified by the configuration option pro_mf_workcell_dir. If this config option has not been set, the workcell file (fadal.gph in this example) will be saved to the current working directory. When a workcell is saved, any tools and parameter defaults (site) defined in the workcell are also saved in the .gph file. In contrast, PPRINTS defined in the workcell are not saved with the .gph file but can be retrieved into new workcells.Workcells, that have been saved, can be retrieved by selecting File, Open, in the Machine Tool Setup dialog or by picking the associated button. Since the tools and defaults are saved within the .gph file and the PPRINTS can be read into new workcells, users save a great deal of time (and in turn, money) when retrieving workcells into new operations. Once the NC Machine has been completely defined, pick OK to return to the Operation Setup dialog.For a reference with descriptions of the options in the Machine Tool Setupdialog, see the Additional Information section of this document.1.3.1 Tooling SetupThe cutting tools used in NC sequences can be defined using severaldifferent methods in Pro/NC. The first method is to select the Cutting Tools tab in the Machine Tool Setup dialog box when the NC machine is specified.The Machine Tool Setup dialog box can also be accessed by selecting, Mfg Setup, Workcell. In addition, selecting Mfg Setup, Tooling from the MenuManager, will cause the Tools Setup dialog to open. If the icon alongthe top of the main Pro/ENGINEER model window is selected, tools can bedefined for the active workcell. The final method is to define the tool to beused during the NC sequence creation. The Tools Setup dialog box is shown in Figure 8 below.Figure 8 - Tools Setup DialogWith the File menu option and associated buttons at the top of the Tools Setup dialog, new tools can be created from scratch, solid tools can be imported, tool parameters can be retrieved, and tools can be saved. When a tool is saved, the tool parameters are written to a text file called<name>.tpm, where <name> is the tool Name or toolid. This text file is saved in the directory defined by the pro_mf_tprm_dir configuration option. If the cutting data has been supplied, that is, the speeds and feeds for thetool, this data is stored in a <name>.tpm file in the appropriate Materialssubdirectory. If the pro_mf_tprm_dir configuration option has not been set,the .tpm files will be saved to the current working directory.The Edit menu option enables the user to delete tools from the tool list, editthe tool comments in the tool list, or create a new, sketched tool.Note: When defining a tool during the creation of an NC sequence, theSketch option will only be available for Trajectory type sequences.The View menu provides access to the information specific to each toolsuch as the tool parameters and sequences in which the tool is used.The tool Name, Type, Material, and Units can be defined for each tool. Thetool Type is important because the tool type is specific to the sequencetype. For example, a turning tool cannot be used in a milling sequence. TheMaterial option is used to define the material the tool is made of, such asCobalt or Carbide, and is only for information purposes. In other words,theCL output is not affected by the Material option value. The tool Units valuewill default to the manufacturing model units but the Units value is notrequired to be the same as the units for the model.Tab1.3.1.1 GeometryThe parameters on the Geometry tab are used to determine thedimensional shape of the tool. Parameters that are required arepopulated with default values. These dimension values are used incalculating the tool path and material removed, and should accuratelyreflect the actual tool dimensions and length units. The actualparameter names in this category depend on the tool type.Tab1.3.1.2 SettingsThe Settings tab contains the text boxes for specifying the tool tableelements and various optional parameters that define tool propertiesother than geometry. The options include, the tool number or pocketnumber, tool offsets, gauge lengths (for turning tools only), toolcomments and the Long Tool option.The Long Tool option is used if the tool is too long to retract to theRotation Clearance level during 4-axis machining. If the tool is markedas long, the tip of the tool moves to the Safe Rotary Point (specified inthe Operation Setup dialog box) during table rotations.1.3.1.3 Speeds & Feeds TabThe Speeds & Feeds tabbed page lets the user supply cutting data(feed, speed, axial and radial depths) for roughing and finishing withthis tool, based on the stock material type and condition.Note: In order to be able to specify the cutting data for a tool, youhave to first set up the Material directory structure. See Setting UpA Materials Directory Structure below in section 1.3.2.Tab1.3.1.4 BOMThe BOM tabbed page provides information about the Bill ofMaterials for the tool. When you retrieve a solid tool model, thesystem automatically includes all the parts and assemblies used inthe tool model into the Bill of Materials (BOM) for the tool.If the tool model is used By Reference, the tool BOM information isread-only. If you are using the tool model By Copy, you can edit thepart names, if needed, or change the type; you can also add orremove the BOM components.For all other types of tools, you can provide the BOM information bytyping the names of the components and specifying their type andquantity.1.3.2 Setting Up A Materials Directory StructureIn order to be able to specify the Stock Material for an Operation, import tools, retrieve tool parameters, or specify the cutting data for a tool, a Materialsdirectory structure must be defined.Pro/NC stores all the cutting tool data in a Tooling directory, which is specified by using the pro_mf_tprm_dir configuration option. The user determines thename of this directory. In the GEAR_HOUSING example, this configurationoption was set as follows:pro_mf_tprm_dir D:\ptc\toolingPro/NC then places all the tool parameter files (.tpm files) in theD:\ptc\tooing directory.The directory structure can further be defined to differentiate between inchtools and metric tools. When inch tools are being used, the config option isset to the corresponding directory. The config option is modified for the useof metric tools as in the example below.For inch tools pro_mf_tprm_dir D:\ptc\tooling\inch_toolsFor metric tools pro_mf_tprm_dir D:\ptc\tooling\metric_toolsTo set up the material directory structure, create a subdirectory called materials in your Tooling directory. The directory name must be spelled exactly as shown.Under the materials directory, create subdirectories corresponding to commonly used stock materials and conditions. For example, subdirectories such as aluminum, copper, stainless-hard, etc can be created. The directory structure created under D:\ptc for this example is shown below in Figure 9.Figure 9 - Materials Directory StructureWhen defining the Stock Material in an operation, the system lists the available material subdirectories from which the user can choose. See Figure 10.Figure 10 - Operation Setup Dialog with Materials DefinedIn addition, when a cutting tool is defined the Stock Material option on the Settings tab will also list the available material subdirectories from which the user can choose. See Figure 11.Figure 11 - Tools Setup Dialog with Materials DefinedAfter the materials directory structure has been set up, tools that include cutting data can be created and stored in an organized way. When you save the cutting tool data, the system stores two files. The tool geometry parameters are stored in a .tpm file, with the same name as the tool, in the Tooling directory. The system also creates another .tpm file, with the same file name, containing the feeds and speeds data, in the appropriate materialsubdirectory. This feeds and speeds data can be referenced to specify the manufacturing parameter values using relations.Note: If you do not use the pro_mf_tprm_dir configuration option, the system uses the current working directory as the Tooling directory.To retrieve saved tool parameters, use the File, Open Parameter File option and select the .tpm file associated with the tool to be used. Once the parameter values have been imported, the cutting data can be determined. To do this, go to the Settings tab and specify the Application (Roughing or Finishing) and the Stock Material. If a tool with the current name has been previously stored, the Read DB button can be picked to populate the Cutting Data values.If the tools name is not in the tooling directory structure for the Application and Stock Material defined, the cutting data can be entered and the tool saved. Saving the tool will add .tpm files to the corresponding locations in the tooling directory.For Example, to create a 2.25 inch High Speed Steel (HSS) flat end mill for machining aluminum and stainless steel, the following steps should be taken.Note: The tool does not currently exist in the Tooling directory.1. Open the Tooling Setup dialog box using one of the methods describedin section 3.1 (Tooling Setup) above.2. In the Tooling Setup dialog, select the button to create a new tool orFile, New.3. Type in the Name of the tool, FLT2250 in this example, keep thedefault Type as Milling and enter HSS for the Material.4. Fill in the values on the Geometry tab as shown Figure 12 below andApply the changes.Figure 12 - Tools Setup Dialog with Tool Parameters Defined 5. Next, enter the values for Rouging in Aluminum on theSpeeds_Feeds tab as shown in Figure 13 below.Figure 13 - Cutting Data for Roughing Aluminum6. Change the Application to Finishing and enter values for Finishing inAluminum.7. Now change the Stock Material to Stainless-Hard and enter thevalues for Roughing and Finishing as shown in Figures 14 and 15.Figure 14 - Cutting Data for Roughing Stainless SteelFigure 15 - Cutting Data for Finishing Stainless Steel8. Save the tool by highlighting the tool in the tool list and selecting File,Save Tool or the associated Save button.One .tpm file for this new tool is stored in the directory specified by thepro_mf_tprm_dir config option (i.e. D:\ptc\tooling\inch_tools). Two additional .tpm files are saved in the corresponding material directories(D:\ptc\tooling\inch_tools\materials\ALUMINUM andD:\ptc\tooling\inch_tools\materials\STAINLESS-HARD).The resulting .tpm files are shown in Figures 16 thru 18 below.Figure 16 - Parameters As Listed in the .tpm FileFigure 17 - Cutting Data for Aluminum As Listed in the .tpm FileFigure 18 - Cutting Data for Stainless Steel As Listed in the .tpm FileNote: The .tpm files are text files that can be modified in any text editor.1.3.3 PPRINT “Operator Comments”On the right side of the Output tab is the PPRINT button. Selecting this button allows the user to: 1.) Create a new set of PPRINTs 2.) Modify any PPRINTs currently assigned to the workcell 3.) Retrieve previously saved PPRINTsfrom disk 4.) Save currently assigned PPRINTs to disk or 5.) Show, in aninformation window, the current workcell PPRINTs.Selecting either the Create or Modify options opens the Acitvate PPRINTdialog as seen in Figure 19 below. If Save is selected, a .ppr text file will bewritten to the current working directory. Retrieve allows the user to read inPPRINT options from a previously saved .ppr file.Note: The directory specified by the pro_mf_param_dir config option does not affect where the .ppr file is saved. The .ppr is always saved to the current working directory. On the other hand, the system will retrieve .ppr files from the pro_mf_param_dir directory if this option is set.Figure 19 - Activate PPRINT Dialog for PPRINT DefinitionTo include a PPRINT item in the CL file, highlight the item in the table and pick the Yes button.Note: Multiple items can be highlighted before picking the Yes button.Comments can be entered for each PPRINT item/option to provide additional information, instruction, or clarification. PPRINT comments cannot consist of more than 69 characters. Users need to be aware that comments entered for PPRINT items are separate from the comments defined for operations, sequences, tools, workcells, etc.An example of a CL file before PPRINTs have been defined is shown below in Figure 20.Figure 20 CL File Prior to PPRINT DefinitionIn the GEAR_HOUSING example, the PPRINT options are set for the part name, operation, tool table, and sequence as shown in Figure 21 below.。
外文翻译-自定义一个3维数控机床

科技外文翻译翻译名称 VERICUT翻译原文系别专业班级姓名指导教师英文文献原文:Session 34- Modify a Generic 4-axis Mill to be a K&T MillThis session shows how to start with a generic "shapeless" 4-axis machine and modify it to become a K&T-type horizontal mill with a 5 inch "dead band"(偏心) and X table offset 12 inches from the spindle centerline (see below). To accomplish this task the X and B machine components must be modified to describe the kinematics of this specific machine. Machine location tables then set the initial machine location and tool change location for this machine.The machine zero is as follows: X-axis has 24 inches of travel, and B-axis centerline is at X=12. The Y-axis zero is located 3 inches above the rotary table surface. The Z-axis has 20 inches of travel, but the zerois 5 inches from the rotary table centerline. Using a tool length of 5.000, a command of "X12.0 Y0. Z0." places the tool tip on the rotary centerline in X and Z, and 3 inches above the table surface in Y.A Gemini D control interprets G-Code commands that are programmed to drive the spindle face, also known as "gage length" programming method.Session Steps:1. Start from a new Inch User file∙File > Properties∙Default Units=Inch, OK∙File > New SessionIf prompted, respond as follows:Reset cut model? Yes / Save changes? No2. Display Component axis systems∙View > Axes∙Component∙Close3. Open the Gemini D milling Control file∙Setup > Control > Open∙Shortcut=CGTECH_LIBRARY∙File Name=gemini_d.ctl, Open4. Open the generic Machine file representing a 4-axis horizontal mill with "B" rotary table∙Setup > Machine > Open∙Shortcut=CGTECH_LIBRARY∙File Name=g4hmtb.mch, Open∙5. Modify the "X" and "B" components to describe the K&T fixed home location∙Model > Component Tree∙In the Component Tree select "X"∙Model > Model Definition, Position Tab∙Position=12 0 0∙Apply∙In the Component Tree select "B"∙Model > Model Definition, Position Tab∙Position=0 0 -5∙OKComponent Tree after modifications:6. Set the initial machine location at Z full retract (X0 Y0 Z20)∙Setup > Machine > Settings: Tables tab∙Highlight the Subsystem:1, Value 0 0 0 0 0 0 0 0 record under Initial Machine Location∙Add/Modify∙Values(XYZABCUVWABC)=0 0 20∙Modify (unspecified axis values are automatically set to0)∙Close7. Set the tool change location at maximum X, Y, and Z (X24 Y20 Z20), then close the Tables window∙Add/Modify∙Table Name=Tool Change Location∙Values(XYZABCUVWABC)= 0 0 20∙Add∙Close∙OK∙Setup > Control > Settings: Tooling tab∙Tool Change Retract Method=Retract All Axes∙OK8. Save a "4axkt.mch" Machine file, then save a "4axkt.ctl" Control File∙In the Component Tree, choose File > Save As Machine (or Setup > Machine > Save As)∙Shortcut=Working Directory∙File Name=4axkt.mch, Save∙Setup > Control > Save As∙Shortcut=Working Directory∙File Name = 4axkt.ctl, Save9. Setup the User file with "gage length" programming method∙Setup > G-Code > Settings, Settings tab∙Programming Method=Gage Length∙OK10. Configure to process the "4axkt.mcd" G-Code tool path∙Setup > Toolpath∙Add∙Shortcut=CGTECH_SAMPLES∙File Name=4axkt.mcd, OK∙OKChange view to H-ISO:With the cursor in the view, right click to display the menu.∙Click Select View > H-ISOStock/fixture setup:∙Model > Model Definition: Model tab∙Active Component=Stock∙Type=Block∙Length(X)=4, Width(Y)=4, Height(Z)=4∙Add∙Position tab: Position= -2 0 -2∙Apply∙Component Attributes tab∙Visibility = Both Views∙Color = 6 Light goldenrod∙Apply∙Fit∙Active Component=Fixture∙Model Tab∙Type=Block∙Length(X)=6, Width(Y)=3, Height(Z)=6∙Add∙Component Attributes tab∙Visibility = Both Views∙Color = 6 Light goldenrod∙Apply∙Position tab: Position= -3 -3 -3∙OK∙Fit11. Configure to retrieve tool data from the "4axkt.tls" Tool Library file∙Setup > Tool Manager∙File > Open∙Shortcut=CGTECH_SAMPLES∙File Name=4axkt.tls, Open∙File > Close, Yes12. Reset the model to ensure VERICUT is aware of changes to the machine and control, then open the Status window to monitor the simulation∙Reset Model∙Info > Status∙Configure∙Select Machine Axes∙Select Tool Tip∙OKThe status window is configured to show machine axis and tool tip locations.13. Cut the model∙Play to End14. Save the user file∙File > Save As∙Shortcut=Working Directory∙File Name = r, SaveSession 35- Customize a 3-D NC Machine ToolThis session demonstrates how to customize an NC Machine file to simulate the kinematic properties and collision potential of an NC machining center. The "3vm.mch" default 3-axis vertical mill machine is retrofitted during this session to provide "A" axis rotary functionality. The shape of various machine components are also changed to support the A-axis addition and provide more accurate collision detection.The step at the end of the session shows how to save the machine configuration in a Machine file. A User file containing a reference to the Machine file is also saved enabling VERICUT to be easily configured to interpret the G-codes in this and similar tool path files destined for the machining center.Session Steps:1. Open the sample "r" User file∙File > Open∙Shortcut=CGTECH_SAMPLES∙File Name=r, OpenIf prompted, respond as follows:Reset cut model?Reset /Save changes? No2. Display all axis systems in a Machine/Cut Stock view∙Right mouse click in the VERICUT window, select Axes > Component∙Select Axes >Model∙View > Layout > Standard > 1 View∙Right mouse click in the VERICUT window, select View Type > Machine/Cut Stock3. Increase the "X" table width of the default 3-axis mill to 60 inches (centered about the machine "Y" axis)Desired "X" component shape:∙Model > Component Tree∙Highlight the X table block model∙Model > Model Definition: Model tab∙Length(X)=60∙Apply∙Position Tab∙Translate Tab∙From=highlight the field, then select the top center of the X table (10 0 0)∙To=0 0 0∙Move∙Cancel4. Add a 4 x 4 x 4 block model to represent an electrical box mounted on the left side of the "Z" componentDesired electrical box mounted to the "Z" component:∙In the graphics window select the "Z" axis housing to which the part electrical box is to be attached∙Model > Model Definition: Model tab ∙Type=Block∙Length(X)=4, Width(Y)=4, Height(Z)=4∙Add∙Position Tab∙Translate Tab∙From=highlight the field, then select the bottom front right corner of the block (4 0 15.2)∙To highlight the field, select the bottom left corner of the Z axis housing (-6 -4 20.2)∙Move5. Add an "A" rotary component (rotates about the X-axis) tothe "X" table; the center of rotation is located 2 inches abovethe "X" table and centered in X & Y (see below)Desired "A" rotary component configuration:∙In the Component Tree, select X∙Right-click > Append > A Rotary∙Model > Model Definition: Position tab∙Position=0 0 2∙Apply6. Modify the "Fixture" components to be connected to the new "A" componentThis action will make room for the "A" component shape that will be added during the next step. Note that the fixture mounting surface on "A" is 1 inch above the rotary center point, 3" above the "X" table.Modifying the "Fixture" to be connected to the "A" component:Fixture #1: vise jaws∙In the Component Tree, select Fixture∙Right-click > Component Attributes∙Connect To=A∙Apply∙Position Tab∙Position=0 0 1∙ApplyFixture #2: vise base∙In the Component Tree, select Fixture 2∙Component Attributes tab∙Connect To=A∙Apply∙Position Tab∙Position=0 0 1∙Apply7. Add the sample "a.stk" model file to the "A" component, orient the model Z-axis along the component X-axisAdding the "a.stk" model file to "A" component:∙In the Component Tree, select "A"∙Model > Model Definition: Model tab∙Type=Model File∙Browse∙Shortcut:CGTECH_SAMPLES∙File Name=a.stk, Open∙Add (the A-axis model is imported, but must be correctly oriented)∙Position Tab∙Rotate Tab∙Click to see the current center of rotation (click again later to erase the center of rotation symbol) ∙Center of Rotation=0 0 2∙Apply∙Increment=90, Y+∙OK8. Reset the machine & test the "A" component function using "MDI"∙Close the Modeling and Component Tree windows∙Reset Model∙Setup > Control > MDI∙Selection= A15, Apply - the A-axis rotates to the 15 degree position∙Selection= A-15, Apply - the A-axis rotates to the -15 degree position∙Cancel9. Save the new machine configuration in a "4axmill2.mch" Machine file∙Setup > Machine > Save As∙Shortcut=Working Directory∙File Name=4axmill2.mch, Save10. Save a "r" User file∙File > Save As∙Shortcut=Working Directory∙File Name=r, SaveThis session provided experience with configuring an NC Machine to simulate the kinematic properties and collision potential of an NC machining center. Modifications were made to machine components to alter their shape, and an "A" axis rotary component was added to the machine to give A-axis rotation functionality.The above changes were saved to a Machine file. A User file was also saved so that VERICUT could be quickly configured to with the new machine. Opening the User file automatically loads the Machine file, Control file, and all job related information required to simulate machine tool motions on this machining center.Session 36- Build and Model a 3-D Bridgeport 3-axis MillThis session shows how to start with a generic "shapeless" 3-axis machine and add 3D models to represent a Bridgeport-type vertical mill. Refer to the figure below for dimensions needed to define component models.Components and dimensions of a Bridgeport 3-axis vertical mill:Use a generic control to interpret G-Code commands that are programmed to drive the tool tip. After constructing this mill machine, VERICUT will be configured to simulate the cutting action of a G-Code tool path file.Session Steps:1. Start from a new Inch User file∙File > Properties∙Default Units= Inch∙OK∙File > New SessionIf prompted, respond as follows:Reset cut model? Yes / Save changes? No2. Display axis systems∙View > Axes∙Select Component, Model, Machine Origin, Workpiece Origin, and Driven Point Zero∙Close∙Right-click in the VERICUT window, View Type > Machine/Cut Stock3. Open the generic "Fanuc-like" Control file∙Setup > Control > Open∙Shortcut=CGTECH_LIBRARY∙File Name=generic.ctl, Open4. Open a generic Machine file representing a 3-axis vertical mill∙Setup > Machine > Open∙Shortcut=CGTECH_LIBRARY∙File Name=g3vm.mch, OpenThe following steps add 3D models to components to describe the Bridgeport 3-axis mill shapeRefer to the picture above for dimensions needed to define component models.Hint:A "V-ISO" view is great for visualizing this machine during construction.5. Add "X" model∙Model > Component Tree∙In the Component Tree, select "X"∙Model > Model Definition: Model tab∙Type=Block∙Length(X)=40, Width(Y)=10, Height(Z)=5∙Add∙Fit∙Position tab∙Translate tab∙From=Select top center of the block(value should be 20 5 5) ∙To=0 0 0∙Move∙Fit∙NOTE:Keep the Modeling and the Component Tree windows open6. Add "Y" model∙In the Component Tree, select "Y"∙Model tab∙Type=Block∙Length(X)=20, Width(Y)=20, Height(Z)=5∙Color=Aquamarine (or any available color except Red)∙Add∙Fit∙Position tab∙Translate tab∙From=Select top center of the new block (value should be 10 10 5)∙To=Select bottom center of the X component (value should be 0 0 -5)NOTE:The view needs to be rotated to select below the X component∙Fit7. Add "Base" models (3 blocks)∙In the Component Tree, select "Base"∙Model tab∙Type=Block∙Length(X)=20, Width(Y)=40, Height(Z)=20∙Color=Cornflower Blue (or any available color)∙Add∙Fit∙Position tab∙Translate tab∙From=On the new block: select on the top face, the forward left corner (value should be 0 0 20)∙To=On the Y component: select on the lower face, the forward left corner (value should be -10 -10 -10)∙∙Fit∙Model tab∙Type=Block∙Length(X)=20, Width(Y)=10, Height(Z)=30∙Add∙Fit∙Position tab∙Translate tab∙From=On the new block: select on the lower face, the back left corner (value should be 0 10 0)∙To=On the first Base block: select on the top face, the back left corner (value should be -10 30 -10)∙Move∙Fit∙Model tab∙Type=Block∙Length(X)=10, Width(Y)=25, Height(Z)=10 ∙Add∙Position tab∙Position=-5 5 20∙Apply∙∙Fit8. Add "Z" model∙In the Component Tree, select "Z"∙Model tab∙Type=Block∙Length(X)=10, Width(Y)=10, Height(Z)=25∙Color=Aquamarine (or any available color)∙Add∙Fit∙Position tab∙Position= -5 -5 0∙OKNote that when added, the machine Z-axis head is located such that the spindle face is flush with the "X" table (machine zero location). An initial machine location must be set to retract the Z-axis to a clear position for tool loading.9. Close the Component Tree window, then set the initial machine location at Z full retract (X0 Y0 Z20)∙In the Component Tree window, File > Close∙Setup > Machine > Settings: Tables tab∙Subsystem:1, Values:0 0 0 0 0 0 0 0 0∙Add/Modify∙Table Name=Initial Machine Location∙Values (XYZABCUVWABC) = 0 0 20∙Modify∙Close∙OK10. Reset the machine to verify the new initial machine location, then test machine kinematics as required∙Reset Model∙Setup > Control > MDI∙Selection - enter machine axis commands to test machine kinematics, e.g. "X10", etc.11. Save a "3axbridg.mch" Machine file∙Setup > Machine > Save As∙Shortcut=Working Directory∙File Name=3axbridg.mch, Save12. Configure to process the sample "cardhold.mcd" G-Code tool pathJob setup for sample "cardhold.mcd" tool path file:Stock:∙Model > Model Definition: Model tab∙Active Component=Stock∙Type=Block∙Length(X)=3, Width(Y)=2, Height(Z)=1.5∙Color=Light Goldenrod (or any available color)∙Add∙Component Attributes tab∙Visibility = Both Views∙OKTool path:∙Setup > Toolpath∙Add∙Shortcut=CGTECH_SAMPLES∙File Name=cardhold.mcd, OK, OK∙Right mouse click in the VERICUT window, View Type > Workpiece∙Fit∙Setup > G-Code > Settings; Tables tab∙Add/Modify∙Table Name = Program Zero∙Select From/To Locations∙From, Name = Tool∙To, Name = Stock∙Select the next to the Stock∙Move the cursor to the top center of the stock - when the arrow in the center of the part (see below), left-click to select this location. The value in the field should be (1.5 1 1.5).∙Add∙Close∙ OKTools:∙Setup > Tool Manager∙File > Open∙Shortcut=CGTECH_SAMPLES∙File Name=cardhold.tls, Open∙File > Close, Yes15. Save a "r" User file for use in VERICUT∙View > Axes > Clear all∙File > Save As∙Shortcut=Working Directory∙File Name=r, Save16. Cut the model∙Play to EndSession 38- Build a 5-axis Mill Using STL ModelsThis session describes how to define the same Cincinnati T30 5-axis milling machine demonstrated in Session 37- Build a 5-axis Mill Using Parametric Models, except using CAD generated Stereolithography (STL文件)model files to represent component shapes. The aforementioned session should be read prior to continuing as it describes basic machine definition principles. To save space, this session highlights differences from the above session.For education and instructional purposes, this session focuses on defining components and models to build a functional machine. Minimal consideration is given to display properties (e.g. color, draw mode, etc.). Component colors are chosen from the default "Shade Colors" provided via File > Colors: Define tab.The figure below shows the sample NC machine tool to be defined. The illustration identifies the machine coordinate system (XwYwZw axes), motion axes, and major components. A Fanuc 12M CNC milling control processes NC tool paths programmed in the gage length programming method.Components of a Cincinnati T30 5-axis milling machine tool:Session Steps:1. Start from a new Inch User file∙File > Properties∙Default units=Inch, OK∙File > NewIf prompted, respond as follows:Reset cut model? Yes / Save changes? No2. Display Component and Model axis systems in a Machine/Cut Stock view∙Right mouse click in the VERICUT window > Axes > Component, Model∙Right mouse click in the VERICUT window > View Type= Machine/Cut Stock3. Open the Fanuc 12M Control file∙Setup > Control > Open∙Shortcut=CGTECH_LIBRARY∙File Name=fan12m.ct l OpenThe following steps define the components from "Base" to "Tool"The components on the tool side of the machine are: Base > X > Y > A > Spindle > ToolThis session shows you how to set component colors that will be inherited by models attached to the components later.4. Display the Component Tree∙Model > Component Tree5. Set color for the "Base" component∙Select Base in the Component Tree then, right-click to pop up the menu > Component Attributes∙Color=Cornflower Blue∙Apply (leave the Modeling window open to set colors on components that will be added)5. Add "X" to "Base"∙With Base selected in the Component Tree,right-click > Append > X Linear∙In the Modeling window, Color=Light Steel Blue∙Apply6. Add "Y" to "X"∙With X selected in the Component Tree,right-click > Append > Y Linear∙In the Modeling window, Color=Light Steel Blue∙Apply7. Add "A" to "Y"∙With Y selected in the Component Tree,right-click > Append > A Rotary∙In the Modeling window, Color=Aquamarine∙Apply8. Add "Spindle" to "A"A Spindle component is often used in a mill machine to represent the pivot distance in multi-axis machines, as in this example.∙With A selected in the Component Tree,right-click > Append > Spindle∙In the Modeling window: Position tab∙Position=0 0 -12.5∙Apply∙Component Attributes tab∙Color=Light Steel Blue∙Apply9. Add "Tool" to "Spindle"∙With Spindle selected in the Component Tree, right-click > Append > Tool∙In the Modeling window, Color=White∙ApplyThe Tool component defines where cutting tools will be loaded. The Tool component must be defined prior to processing a tool path file, or attempting to move the machine via MDI. The Tool component origin is typically located at the intersection of the tool axis with the spindle face.Component Tree after adding "Tool side" components:The following steps define the components from "Base" to "Stock"The components on the tool side of the machine are: Base> Z > B > Fixture > Stock10. Add "Z" to "Base"∙Select Base in the Component Tree, thenright-click > Append > Z Linear∙In the Modeling window, Color=Light Steel Blue∙Apply11. Add "B" to "Z"∙With Z selected in the Component Tree,right-click > Append > B Rotary∙In the Modeling window, Color=Aquamarine∙OK12. Cut and Paste "Fixture" to "B"∙Select Fixture in the Component Tree, thenright-click > Cut∙Select the B in the Component Tree, then right-click > PasteThe Fixture component origin is the location where fixture models will be loaded. The presence of a fixture component in the machine definition does not affect how a tool path file is processed, however, is useful for detecting collisions between the fixture and other machine components.13. Cut and Paste "Stock" to "Fixture" (colors okay as is), delete the "Design" component∙Select Stock in the Component Tree, then right-click > Cut∙Select Fixture in the Component Tree, thenright-click > Paste∙Select Design in the Component Tree, thenright-click > Delete, YesThe Stock component origin is the origin in which stock (workpiece to be machined) is located. Every machine definition must include this component type. The Stock component is typically connected to a Fixture component, but this does not have to be the case. The Stock component can be connected to any other component, but must be defined prior to processing a tool path file or attempting to move the machine via MDI.Component Tree after adding "Stock side" components and deleting the Design component:15. Save a "5axcin.mch" Machine fileSave the machine configuration in a Machine file using the Component Tree window File menu. While working on your machine, update the Machine file periodically via the Save function.∙In the Component Tree, select File > Save As Machine∙Shortcut=Working Directory∙File Name=5axcin.mch, SaveNOTE: The Machine File can also be saved via:Setup > Machine > Save asAdd Models to "Tool side" ComponentsSample view setup for a horizontal mill:∙View > Orient∙XY∙Increment=30 ,Y-, Y-, X+∙Close16. Add "Base" model∙In the Component Tree, select "Base"∙Model > Model Definition: Model tab∙Type=Model File∙Browse∙Shortcut=CGTECH_LIBRARY∙File Name=cint30ba.stl, Open∙Color=Inherit (colors can be selected for individual models to highlight details on the machine)∙AddHint:Use Fit as needed throughout this session to see the entire machine.Note that the "cint30ba.stl" STL model file contains two shapes described in a single STL model file.17. Add "X" model∙In the Component Tree, select "X"∙Model > Model Definition: Model tab∙Type=Model File∙Browse∙Shortcut=CGTECH_LIBRARY∙File Name=cint30x.stl, Open∙Add18. Add "Y" model∙In the Component Tree, select "Y"∙Model > Model Definition: Model tab∙Type=Model File∙Browse∙Shortcut=CGTECH_LIBRARY∙File Name=cint30y.stl, Open∙Add19. Add "A" model∙In the Component Tree, select "A"∙Model > Model Definition: Model tab∙Type=Model File∙Browse∙Shortcut=CGTECH_LIBRARY∙File Name= cint30a.stl, Open∙Add20. Add "Spindle" model∙In the Component Tree, select "Spindle"∙Model > Model Definition: Model tab∙Type=Model File∙Browse∙Shortcut=CGTECH_LIBRARY∙File Name=cint30sp.stl, OK∙AddModel file shapes (STL or VERICUT) defined with the same origin as the machine are typically located correctly as imported. When acomponent's origin has been moved, such as often occurs with rotary components (or the Spindle component in this example), the model file shape must be moved in the reverse direction via the Model > Model Definition: Position tab features to restore the proper relationship with the machine.∙Position tab∙Position=0 0 12.5∙ApplyAdd Models to "Stock side" Components21. Add "Z" model∙In the Component Tree, select "Z"∙Model > Model Definition: Model tab∙Type=Model File∙Browse∙Shortcut=CGTECH_LIBRARY∙File Name=cint30z.stl, Open∙AddWith the machine located at machine zero, the "Y" and "Z" components appear in a collision state. Since VERICUT machines are constructed with all components located at their respective zero locations, collisions during machine definition are common. A step follows (after adding the "B" model) to define an Initial Machine Location table to move the machine out of the collision state to its start-up position.22. Add "B" model∙In the Component Tree, select "B"∙Model > Model Definition: Model tab∙Type=Model File∙Browse∙Shortcut=CGTECH_LIBRARY∙File Name=cint30b.stl, Open∙Add∙Cancel23. Set an "Initial Machine Location" table to locate the machine at X0 Y60 Z62The machine location tables describe where the machine is initially positioned, how the machine moves when changing tools or spindles, and the location of the machine's reference point.∙Setup > Machine > Settings: Tables tab∙Add/Modify∙Table Name=Initial Machine Location∙Values=0 60 62∙Add∙Close∙OK24. Reset the machine to verify the new initial machine location∙Reset ModelThe final machine configuration is shown below with the machine positioned at its initial spindle location of X0 Y60 Z62 A0 B0.Cincinnati T30 5-axis mill created from STL model file shapes:25. Use "MDI" to test for proper machine motions; when satisfied reset the machine∙Setup > Control > MDI∙Selection=A-45, Apply∙Selection=B-90, Apply, etc.∙Reset Model26. Save a "5axcin_m.mch" Machine file∙In the Component Tree window, select File > Save As Machine∙Shortcut=Working Directory∙File Name=5axcin_m.mch, SaveComplete Job Setup by Adding Stock & Fixture Models27. Add "Fixture" model∙In the Component Tree, select Fixture∙Model > Model Definition: Model tab∙Type=Model File∙Browse∙Shortcut=CGTECH_LIBRARY∙File Name=cint30fx.stl, Open∙Add28. Add "Stock" model∙In the Component Tree, select "Stock"∙Model > Model Definition: Model tab∙Type=Model File∙Browse∙Shortcut=CGTECH_LIBRARY∙File Name=cint30sk.stl, OK∙Add∙Close the Modeling window and the Component Tree window Note that the "cint30sk.stl" STL model file contains two shapes described in a single STL model file.29. Configure to simulate "gage length" programmed tool paths, save the job setup in a "5axcin_r" User fileThe Machine Simulation configuration for processing a tool path, or type of tool path, is saved in the User File using the File menu > Save As function. Opening the User file configures VERICUT for simulating tool path files destined for the machining center.∙Setup > G-Code > Settings: Settings Tab∙Programming Method=Gage Length∙OK∙File > Save As∙Shortcut=Working Directory∙File Name=5axcin_r, Save。
莱特兄弟发明飞机的英语作文

莱特兄弟发明飞机的英语作文English Answer:The Wright brothers, Orville and Wilbur, are widely recognized as the inventors of the first successful airplane. Their breakthrough achievement came on December 17, 1903, when they flew the Wright Flyer at Kitty Hawk, North Carolina.Prior to the Wright brothers' invention, numerous attempts had been made to develop flying machines. However, none were successful in achieving controlled, powered flight. The Wright brothers' innovation lay in their development of a three-axis control system that allowed the pilot to steer the aircraft in all three dimensions.The Wright brothers' groundbreaking invention revolutionized the field of aviation. It opened up new possibilities for transportation, exploration, and warfare. Today, airplanes are an indispensable part of modernsociety, connecting people and continents in ways that were once unimaginable.中文回答:莱特兄弟发明飞机。
CNC milling教程说明书

manufacturing.Practical Experience•Follow instructions to safely operate a mill and usecomputer software to program a mill.•Write a PART program and use industry-standard G andM operations.Mill various take home projects such as a desk•organizer, coaster, yo-yo, and name plate.Curriculum activities orequipment may change as Lab-Volt continually strives to providethe most up-to-date technology-education program.CLIENT WORKSTATION REQUIREMENTSOperating System:Windows XP or higherHardware Specifi cations:Personal computerMemory: 1 GB or higherSound: 16 Bit, full duplexCDRW/DVD combo: 48x or higherHard Drive Space: 30 GB with minimum of 10 GB free space Network Interface Card: 10 Mbps Card (recommended 100 Mbps) Software Specifi cations:Internet Explorer 8 or higher, Flash 10, .Net 3.0 Framework SKILLS AT A GLANCEMathematics Science3-D Modeling AD/DA Conversion Algebra Cause & Effect, Rate & Flow Arithmetic Computer Technology Boolean Logic, Charts Waste Management Coordinating Systems Thinking SkillsCurves & Angles, Sequencing Drawing Conclusions Positive/Negative Values Logical Reasoning Language Arts Problem SolvingNote TakingReading ComprehensionSpelling, Vocabulary, WritingCNC Mill 40070-70The curriculum is a complete learning unit containing work activities appropriate for students to cover a period of twelve lessons.Student Accomplishments:examine the history and development of CNC and CAM.•identify the benef i ts of using CAM software.•describe the main parts of a CNC mill.•explain the concept of Program Reference Zero.•understand CNC mill safety procedures.•discuss codes and instructions used in PART programs.•use CNC Mill software to prepare a CNC PART program •for execution.explore the history of design.•identify the relationship between CAD and CAM.•generate and view a PART program using an existing •design in Fabricus.compile and emulate the PART program using CNC Mill •software.implement a design change using CAD software.•modify the PART program to ref ect design changes.•examine the impact of manufacturing on the environment.•analyze basic instructions contained in PART programs.•prepare the new PART program for manufacturing.•decorate and customize the completed part.•study design geometries and options available in CAD •software.examine G&M codes used in CNC mill programs.•analyze the usage of the X-Y-Z coordinate system in CNC •Mill programs.create new design and emulate generated program code.•manufacture the part which was emulated before.•analyze vises.•explore programming subroutines and loops.•design a part in Fabricus and analyze the generated code.•complete CNC Mill software processing through emulation.•discuss problem determination and problem resolution.•examine Computer Integrated Manufacturing.•explore Flexible Manufacturing Systems.•explore careers in manufacturing.• Equipment, Course-Specifi c Software & Supplies: Mill: mid-size, three-axis milling machine, drilling and•engraving; offers spindle speeds up to 30,000 RPM;features on-board microprocessor and safety features.Mill Software software: provides direct compatibility with G •and M part programs; features onboard microprocessor,editor part program, fast syntax verif i cation, full 3D ToolPath Emulator, and graphical view tool editorCAD/CAM software: entry level CAD/CAM software used •to create GM code f i les; simultaneoulsy displays 4 screen views; design with grid; snap to grid and rulers; safetyglasses; rubber mat; Lexan milling stock; protofoam andwax engraving stock; hex key;Emery block; strings.Headphones (2) with a two-way adapter•Course plaque and mouse pad•Resources, Software & Courseware:Tech-Design eSeries courses contain the complete multimedia curriculum and resources. Supplementing the curriculum are resources such as Key Terms and Words, Timelines, Career Exploration, Environmental Impacts, Internet Link to age- and content-appropriate web sites for student research and T D-Quest projects. Instructor-enabled features such as: narration, electronic annotations, closed captioning, application launches, electronic student journal and lesson delivery options are integrated into the system.Tech Design is facilitated by the Mind-Sight eTraining System. Mind-Sight™ is a seamless integration of courseware delivery and classroom management. You can use the Mind-Sight eTraining System to manage student enrollment, schedule learning activities, customize courseware curriculum, and track performance objectives and assessments. Mind-Sight comes ready to “plug-and-play” on a fully-supported mini-server which has been pre-installed with the management and communication software.Instructional Resources: Instructor’s Guide (answer keys and other information to assist with class preparation), Mind-Sight Installation and User’s Guide (instructions for navigating through the curriculum and using interactive features), Supplemental Comprehensive Assessment Booklet.LAB-VOLT SYSTEMS, INC. • PO BOX 686 • FARMINGDALE NJ 07727 • 1-800-LAB-VOLT • • E-MAIL us@。
SINUMERIK CNC4you 3轴机器工具测量技术指南说明书

Machine-integrated workpiece measurement for 3-axis millingPrinciple and application with SINUMERIK Operate Restricted/cnc4youMachine-integrated workpiece measurement for 3-axis milling1SINUMERIK measurement functions–Overview1.1Measuring instruments1.2Measuring accuracy2Workpiece measurement2.1Workpiece measurement / Setup in JOG mode2.2Workpiece measurement in AUTOMATIC mode2.3Creating measuring reports3Practical part: SINUMERIK measuring cycles in the application 4SummaryMeasuring cycles are used in various measuring tasks.The measuring cycle for the measuring task is configured by setting various parameters in the input screen.Measuring the workpiece is used to define the position and alignment of the workpiece in the machine coordinate system .Workpiece measurement can take place in two modes:Introduction to workpiece measurement with SINUMERIKAutomated and repeated execution of workpiece programs requires the definition of reference points :Machine zero point•Located in the MCS machine coordinate system and defined by the machine manufacturer •Cannot be changed from end-user•Reference point for internal measuring systems in the machine•Limits the machine's working area Workpiece zero point•The basis of the WCS workpiece coordinate system -Zero point of the workpiece•Can be freely selected by the end-user•Is often positioned on a corner or in the center of the workpiece, a hole, a pin(to suit workpiece machining)Adaptation of MCS to WCS i.e.transformation of the machine zero point to the workpiece zero.Coordinate systems and reference pointsManual contacting / scratching Manual probe Switching probes•The operator manually moves an edge finder or a rotating tool to the workpiece•The operator determines thecurrent position on the basis ofvisual signals•The operator confirms the touching via a softkey•The workpiece zero point isautomatically saved by the CNC •The measuring instrument islocated in the spindle, which has itsprobe length and diameter stored inthe tool offset•The operator determines thecurrent position of the spindlecenter above an edge using a scale•The operator confirms the touchingvia a softkey•The operator positions a previouslycalibrated probe in the vicinity ofthe desired measuring object•The cycle is selected and themeasurement is started via NC-Start•The desired position isautomatically determined andsaved by the CNCManual contacting / scratching Manual probe Switching probes•The operator manually moves an edge finder or a rotating tool to the workpiece•The operator determines the current position on the basis of visual signals•The operator confirms the touching via a softkey•The workpiece zero point isautomatically saved by the CNC•The measuring instrument is located in the spindle, which has its probe length and diameter stored in the tool offset •The operator determines the current position of the spindlecenter above an edge using a scale •The operator confirms the touching via a softkey •The operator positions a previouslycalibrated probe in the vicinity of the desired measuring object •The cycle is selected and the measurement is started via NC-Start•The desired position isautomatically determined and saved by the CNCThe machine must be prepared on both the HW and SW side for the use of switching probes!ReceiverTransmitterCalibration = calibration of the probe before use•Set the radial eccentricity of the probe, see manufacturer's specifications •Radius alignment with calibration•Length alignment with internal or external length measuring deviceàDetermination of individual switching points (trigger points) in reference to the spindle center of each direction of the axis (e.g. +X,-X, +Y,-Y,-Z)Measurements must be made under the same conditions as for the calibration •Calibrations and measurements should be done in the same planes (G17, G18, G19).•The measuring feed must correspond to the calibration feed•At the start of the measurement, the probe should be located approximately in the center of the calibration ring (by eye)•In the best case, the probe will always be calibrated in the spindle (clamping tolerance)Calibration, the key factor in accurate measurementsInfluencing factors and measuring inaccuraciesThe following lead to measuring inaccuracies:•Geometric errors in the machine axes•Radial eccentricity of the spindle•A faulty calibration process (e.g. feedrate must be 100%!)•A faulty or dirty probe sphere•A dirty surface of the measuring object (e.g. due to chips)•Temperature fluctuations during the measurementThe obtainable measuring precision that can be obtained is dependent on the following factors:•Accuracy of the machine•Measuring precision of the calibrated probeWhen measuring workpieces, a measuring instrument similar to a tool is moved to the clamped workpiece.These measuring tasks can take place in two modes :JOG (set-up mode)AUTOMATIC (in-process measurement)•To prepare the machine for processing•The determination of the position and alignment of a workpiece•Definition of the zero point position of the workpiece in the machine space•Quality assurance in the machining process •For the correction of work offsets•Correction of thermally influenced changes to the machine•The creation and provision of measurement reports Workpiece measurementIn the JOG and AUTOMATIC modes2Partially automatic measurement, as interactive operation in the set-up mode of the machineFully automatic measurement by calling measuring cycles in the CNC machining programWorkpiece measurement / Setup in the JOG modeOverview of the measurement functionsEdge 1 hole 2 holes 3 holes 4 holes*)*)*)*)*)Distance 2 edges Any corner Rectangular spigot1 circular spigot2 circular spigots3 circular spigots4 circular spigots Plane*)Measuring variants for manual measuring instrumentsMeasuring variants forswitching probes2.1Selecting the desired measurement functionsAlignment on the workpiece edge•Saving the axis position in the rotary part of the zero point FRAME.•The twisting of the workpiece is compensated by rotating the coordinates of the workpiece coordinate systemWorkpiece measurement / Setup in JOG mode Aligning the workpiece on the workpiece edge2.1Workpiece measurement… with correction of the workoffset … with correction of the toolgeometry… measuring only•Checking the current clamping situation•Correction of the workpiece zero point offset resulting from themanual or automatic feeding ofworkpieces •Ensuring the adherence toworkpiece tolerances•Continuous correction of the toolwear or thermal expansions thatoccur during machining•Measurement of workpiecegeometries for individual reuse•Display of the workpiece geometryControl-internal correction of measured valuesEdgeHoleBallAlign edge Web Any corner Rectangular spigot Circular spigot Outer circle segment 3 ballsMeasuring variants only for switching probes3D probeMono probeL probeStar probeSpecial toolsOverview of the measurement functionsSINUMERIK makes a distinction between two kinds of measuring reports:•User measuring report (user-defined formatting of the contents)•Standard measuring report (pre-formatted form for each automatic measuring cycle)Creating measuring reportsQuality transparency can be achieved using standard reports2.3Meas. res. disp.: on/offDisplay mode: NC start, On alarm, autom. 8 s Log: on/offReport type: Standard report / User reportReport format: Text format (*.txt) / Table format (*.csv)Path: storage of the measuring report where the part program is locatedName of report file: name of the filePractical part: SINUMERIK measuring cycles in the application 3SummaryUser benefits•Time savings thanks to reduction in setup times •Increased process reliability due to cycle-driven applications•Integrated input support in ShopMill and programGUIDE workstep programming•Realistic display of the measuring process in the SINUMERIK simulation•Easy creation and output of measuring reports4Thank you for your attentionDigital Experience and Application Center Erlangen/cnc4you。
威力手三维数字化仪威力手三维数字化仪

业界领导者的用户 • Pixar • Industrial Light + Magic • PDI/Dreamworks • 迪斯尼
软件的合作伙伴 • discreet • Alias|wavefront • Form Z • Softimage
8
MicroScribe – M/CAD/CAM
MicroScribe 是适用于逆向工程、工业设计和 模具制造的低成本的设备
Thank You!
面对CAD和图形软件市场的数字化 系统
具有一个使用铰球连接的机械手 每个连接点都有一个光学编码器 基座的微处理器将连接点的角度数
据发送到主机 通过对物体表面的轨迹点追踪进行
数字化 精度可以达到 +/-0.009”
5
为什么要数字化?
为物理模型创建一个数字模型 测量和重新构建复杂的曲面 物理模型不能象数字模型那样进行操作和处理 应用案例
娱乐
计算机
3D
汽车
医学
3D Capture MicroScribe LightScribe
3D Interaction CyberGlove CyberTouch CyberGrasp CyberForce VirtualHand Studio VHX to World Toolkit
4
MicroScribe是什么?
业界领导者的用户 • 波音公司Boeing • 大众汽车Volkswagen of America • 耐克Nike • 阿迪达斯Adidas
• K2
• Fiskars
软件合作伙伴 • Delcam • SolidWorks • Pro/Engineer • Rhinoceros
PowerMill

It supports advanced technologies like high speed machining (HSM) and 5-axis simultaneous machining for complex geometry
Solution for special processing requirements
Creo
Wide range of application areas including aerospace, automotive, die&mold, and
general machining
Version updates and new features
01
Regular updates and new releases with enhanced functionality and performance improvements
01
02
03
04
Powerful 3-axis, 4-axis, and 5-axis machining
capabilities for milling, turning, and mill turn
operations
Comprehensive toolpath generation and verification tools for ensuring accuracy
03
Tool path generation and optimization
Tool path generation method and parameter settings
Methodology for Tool Path Generation
发明飞机英文作文

发明飞机英文作文英文:Inventing the airplane was a monumental achievement in human history. The Wright brothers, Orville and Wilbur, are credited with creating the world's first successful powered aircraft. Their invention revolutionized transportation and changed the way people travel and connect with one another.The idea of flight had fascinated humans for centuries, but it wasn't until the early 20th century that the Wright brothers made it a reality. They drew inspiration frombirds and their ability to soar through the sky, and they spent years experimenting with different designs and materials to create a machine that could achieve sustained, controlled flight.One of the key breakthroughs in their invention was the development of a three-axis control system, which allowed the pilot to steer the aircraft effectively. Thisinnovation set the stage for the modern aircraft design and laid the foundation for the aviation industry as we know it today.The impact of the airplane on society cannot be overstated. It has made the world a smaller place, allowing people to travel long distances in a fraction of the timeit would take by other means of transportation. It has also facilitated global trade and commerce, connecting people and cultures from all corners of the globe.Furthermore, the airplane has played a crucial role in shaping history, from military operations to humanitarian aid missions. It has enabled rapid response to emergencies and natural disasters, saving countless lives and providing essential supplies to those in need.In conclusion, the invention of the airplane has had a profound and far-reaching impact on the world. It has transformed the way we live, work, and interact with one another, and it continues to shape the course of human history.中文:发明飞机是人类历史上的一个重大成就。
CAM-POST Foundation:3轴铣机和2轴磨机的快速、易用的后处理器开发工具说明书

Why CAM-POST Foundation?CAM-POST Foundation is a fast and easy-to-use post-processor development tool specifically designed to give you control over the development of post-processors for your 3 axis milling and 2 axis lathe machines.Create unlimited 2-axis lathe and 3-axis mill post-processors for all machine tools & controls and for all popular CAD/CAM systems such as CATIA, NX and Mastercam Take Control and quickly make, modify & run posts yourself, whenever required Take advantage of Foundation’s advanced features such as Arc-fiing, High Speed Machining (HSM) and full Look-ahead functionality to make your parts better, cheaper and fasterIt’s easy-to-use, with full online “How-to” videos, a complete PDF user manual and it comes with a full library of ready-to-use default post-processors to get you into production even fasterIncludes extensive “Art-to-Part” examples that allow you to easily and quickly test your posts and CNC programsFreely borrow and share your posts with the CAM-POST Foundation user community while taking advantage of the collective knowledge and skill they have to offer Easily Migrate to all other ICAM Manufacturing Software Solutions2 &3 axis post-processor development software for multi-CAM applications TRY OUTCAM-POST Foundation for 30-days for FREE!As a Foundation user, you don’t need to rely on third party services to help you get (and keep) your machines up and running and to reach their maximum potential. Third party post suppliers rarely have the same unique knowledge about your machining environment as you do, or are as focused and flexible as you’d like.With CAM-POST Foundation at your fingertips, you can respond rapidly to your own machining environment’s unique needs by being in control of your post-processing needs on time and per your specifications.FANUC Oi-M HAAS Heidenhain 426 Cam-Post FOUNDATIONPost-Processor Generator for 2-Axis Lathes & 3-Axis MillsAre custom posts too expensive to buy and maintain? Now you can easily develop/modify them yourself and for a low cost.No need to pay extra costs or maintenance fees to get someone else to create/modify your posts. Create, modify, and manage your own post-processors for only $49.95 per month.All product updates are included in the lease program, as well as comprehensive video training tutorials and reference manuals.Pricing- Only $49.95/Month。
基于DMC1380三轴运动控制卡的软件系统开发研究_张延波

基于DMC1380三轴运动控制卡的软件系统开发研究_张延波第23卷第3期2010年6⽉⼭东科学SHANDONG SCIENCE Vol.23No.3Jun.2010收稿⽇期:2010-04-05作者简介:张延波(1976-),男,助理研究员,硕⼠,研究⽅向:⼯业⾃动化控制。
E-Mail :zhangyb@keylab.net ⽂章编号:1002-4026(2010)03-0038-03基于DMC1380三轴运动控制卡的软件系统开发研究张延波,解兆延,王忠民(⼭东省科学院⾃动化研究所,⼭东济南250014)摘要:采⽤PC 机+DMC1380运动控制卡模式,以VC ++6.0为开发⼯具,开发了具有通⽤性、开放性的三轴运动控制系统平台,实践证明该系统运⾏可靠、控制精度⾼。
关键词:DMC1380运动控制卡;运动控制;VC ++中图分类号:TP311⽂献标识码:ADevelopment of a DMC1380Based SoftwareSystem for a Three-Axis Motion Control CardZHANG Yan-bo ,XIE Zhao-yan ,WANG Zhong-min(Institute of Automation ,Shandong Academy of Sciences ,Jinan 250014,China )Abstract :We develop a three-axis motion control platform with an industrial computer ,a motioncontrol card (DMC1380)and VC ++6.0.It is public and general.Practice shows that the platformhas high control accuracy and credibility.Key words :DMC1380motion control card ;motion control ;VC ++PC-NC 是当前流⾏的数控系统开放化途径[1],是在PC 机硬件平台和操作系统的基础上,使⽤运动控制卡来实现运动控制系统的功能。
- 1、下载文档前请自行甄别文档内容的完整性,平台不提供额外的编辑、内容补充、找答案等附加服务。
- 2、"仅部分预览"的文档,不可在线预览部分如存在完整性等问题,可反馈申请退款(可完整预览的文档不适用该条件!)。
- 3、如文档侵犯您的权益,请联系客服反馈,我们会尽快为您处理(人工客服工作时间:9:00-18:30)。
Development of three-axis desktop milling machineQ.Y.Wang,F.Z.Fang,a͒and X.T.HuState Key Laboratory of Precision Measuring Technology and Instruments,Centre of MicroNanoManufacturing Technology,Tianjin University,92Weijin Road,Tianjin300072,China͑Received29September2008;accepted1December2008;published26May2009͒With a trend toward miniaturization,miniaturized machine tools turn to be more and more reasonable than conventional machine tools in fabricating scaled-down work parts with better quality,higher efficiency,and less expense.In the past20years,various miniaturized machine tools have been developed.For the purpose of studying machine tool miniaturization technology and micromachining mechanism,a three-axis desktop milling machine tool is presented in this article.Typical microfeatures such as microgears,microthin walls,and microelectrode made from copper alloy or aluminum alloy have been machined by end milling tools in diameters of0.1,0.2,and0.4mm.Meanwhile,the profile and roughness of these microstructures are also analysed.By theseexperiments,the machining performance of this three-axis desktop milling machine tool in aspect of three-dimensional complex microstructures is demonstrated.©2009American Vacuum Society.͓DOI:10.1116/1.3056173͔I.INTRODUCTIONAt present,there is an increasing need of smaller and smaller products both in industrial and commercial areas such as optical systems,semiconductors,sensors,biomedical devices,telecommunication appliances,consumer electron-ics,etc.1However,to fabricate miniaturized structures on conventional macroscale machine tools will cause many problems such as higher cost,more space and power con-sumption,etc.As the occurrence of relative novel precision technologies and components,miniaturized machine tools are becoming more and more superior to conventional mac-roscale machine tools in machining microparts with better quality,higher efficiency,and less expense.2As a result of this,thefirst microlathe with size of 32.0mm in length,25.0mm in width,30.5mm in height, and weigh of only100g was presented by the Mechanical Engineering Laboratory͑MEL͒of Japan in1990s.3After the presence of this lathe,a micromilling machine,a micropress machine,a microtransfer arm,and a two-fingered microhand were continuously developed by MEL.Consequently,the first portable microfactory was presented,which succeeded in manufacturing a microbearing assembly in diameter of only0.9mm.4,5Driven by the occurrence of thefirst micro-factory,more and more concern has been raised upon minia-turized machine tools over the world.In1999,a microturn-ing machine is presented by Lu and Yoneyama.Meanwhile, a microcutting experiment has been applied on a microwork-piece in this newly developed microturning machine.6Then, it was in2002that a microlathe in size of130ϫ160ϫ85mm3was produced by Kussul et al.Microstructures ranging from50m to5mm are allowed to be fabricated on this machine.7Recently,two micromachine tool proto-types were developed at the University of Illinois at Urbana-Champaign by Phillip et al.in2006as test vehicles for the new performance evaluation methodology.8Nevertheless,miniaturized machine tools should not be simply scaled down from conventional macroscale machine tools.Therefore,a better understanding of miniaturized ma-chine tools designing and micromachining mechanism should be researched deeply.II.DESIGN OF THREE-AXIS DESKTOP MILLING MACHINE TOOLIn order to study machine tool miniaturization technology and micromachining mechanism,a three-axis desktop mill-ing machine tool is developed͑Fig.1͒.This three-axis desk-top milling machine tool is in width of500mm,length of 800mm,and height of710mm,which can be set on a desk due to its small volume.The strokes of X,Y,and Z axes are 100,50,and50mm,respectively.The base board of the machine tool is made from cast iron,which has a good abil-ity of vibration isolation.As shown in Fig.1,the Y axis is orthogonally stacked on the X axis.Moreover the Z axis is perpendicular to the other two axes,which is supported by a cast iron bracket.For the purpose of reducing the load of the Z axis,a spindle mount made from aluminum alloy is de-signed to hold the spindle.To guarantee the accuracy of the work part,the accuracy of this three-axis desktop milling machine tool has been strictly adjusted while these compo-nents are assembled together,such as the squareness degree between X,Y,and Z axes,the parallelism between the spindle and the Z axis.A.Structure of three-axis desktop milling machine toolFor the purpose of building a three-axis desktop milling machine tool with the ability of machining three-dimensional complex microstructures,the close-looped motion control theory has been introduced͑Fig.2͒.In each axis of this mill-a͒Author to whom correspondence should be addressed;electronic mail:fzfang@12781278 J.Vac.Sci.Technol.B27…3…,May/Jun20091071-1023/2009/27…3…/1278/7/$25.00©2009American Vacuum Societying machine tool,a servomotor as the driving device,a pre-cision lead screw and a pair of precision guides as the trans-mission devices,and a precision grating with 0.1m resolution as the feedback system are equipped.Furthermore,as the numerical controller,a multiaxis control system which supports G-code programming,linear interpolation,circular interpolation is employed.In combination with the three-axis work stage driven by servomotor,the multiaxis control sys-tem and precision gratings,a close-looped precision motion control system has been set up to realize complex three-axis movements.Due to the small milling tool of which diameter is ranging from 100to 400m utilized for micromilling,an air turbine spindle with highest rotation speed up to 150000rpm,run-out within 1m but power consumption of only 21W is mounted on the Z axis to provide sufficient cutting speed for micromilling.Meanwhile,a microscope is equipped to facilitate tool and workpiece setup and to moni-tor the condition of the tool by magnifying the image.In addition,an air/mist cooling system is designed to decrease the temperature of the milling area as well as to providelubricant during the milling,which is capable of supplying air or mist according to the different requirements.B.Performance tests of servosystemDue to utilizing the precision driving device,transmission devices,and high resolution grating,each axis of this milling machine tool is able to realize microincremental movement and high repeatability.Taking Z axis,for example,a test result of microstepping of 0.2m is provided by a laser interferometer which shows the vibration of the work stage with amplitude about 0.2m ͓Fig.3͑a ͔͒.Moreover,another test shows the repeatability of the Z axis around position 0over a distance of 40mm is less than Ϯ0.3m ͓Fig.3͑b ͔͒.III.MACHINING TESTSAlthough the strokes of this three-axis milling machine tool are 50,50,and 100mm in the X ,Y ,and Z axes,respec-tively,it is recommended that the maximum size of the workpiece is within 10ϫ10ϫ2mm 3in the X ,Y ,and Zdi-F IG .1.͑Color online ͒Outlook of the three-axis desktop milling machinetool.F IG .2.͑Color online ͒Structure of the machinetool.F IG .3.͑Color online ͒Performance test results of the machine tool:͑a ͒0.2m stepping;͑b ͒repeatability.JVST B -Microelectronics and Nanometer Structuresrections,respectively.For the sake of machining microstruc-tures with size from tens of microns to hundreds of microns,the size of milling tools ranging from diameter of 100to 400m are employed on this three-axis desktop mill-ing machine tool.As a result,limited by the diameter of the milling tools,both the cutting depth and stepover are very small.Otherwise,the cutting force which is more than the tool load capacity will lead to a considerable tool wear.Therefore,taking the work efficiency into account,it is ob-vious that the size of the workpart should be limited.In addition,the general size of the flute length of these milling tools varies from 0.2m to 1.2mm as the diameter of the tool is increasing.Hence,it is a bottleneck of the maximum available workpart thickness.Evidently,if the thickness of the workpart is too large,the milling tool will not be capable of reaching the area to be machined.In the following part,three different workparts such as microgears,thin walls,and microelectrode are machined to demonstrate the machining performance of this three-axis desktop milling machine tool.The parameters of the tool used in these tests are listed in Table I .Depending on the material of the tools used in the follow-ing tests,aluminum alloys and copper alloys are the most suitable workpiece materials.During the cutting,spay mist as the lubricant is used to prevent the temperature of cutting area between tool and workpiece from increasing.Mean-while,the decreasing of the temperature as well as the lubri-cation action also has great impact on decreasing the forma-tion of build-up edge.According to the cutting tool materials and parameters in Table I ,the cutting parameters for every tool are shown in Table II .A.MicrogearTwo microgears machined by this three-axis desktop mill-ing machine tool are presented shown in Fig.4.Limited bythe diameter of the milling tool,only the gear of which thedistance between the two adjacent teeth is bigger than the tool diameter is possible to be machined.As shown in Fig.4͑a ͒,the bigger gear of which the base circle is in diameter of 5.4mm and thickness of 1mm is made from A16061͓Fig.4͑a ͔͒.Moreover the minimum dis-tance between each two adjacent teeth is 0.439mm from the designed gear model.Hence,in terms of both the tool diam-eter and machining efficiency,the tool with diameter of 0.4mm in Table I is chosen for finishing this workpart.The whole machining process is separated into three steps such as face milling,profile milling and deburring.First,the top face of the workpiece is made into a plane after the face milling.Second,the teeth of the gear are made by profile milling.Finally,as the finishing deburring cleans the burs on the edge of the gear.The smaller one of which the base circle is only in diam-eter of 1.35mm is made from copper ͓Fig.4͑b ͔͒.Due to the length limiation of the tool flute,the thickness of this gear is only 0.15mm.This gear is a scaling down of the bigger one.Therefore,the machining process for this gear is also divided into three steps which are the same as that of the bigger oneT ABLE I.Tool parameters.Tool diameter ͑mm ͒0.10.20.4Tool material Uncoated carbide Tool typeTwo-flute end milling toolFlute length ͑mm ͒0.20.51.2T ABLE II.Cutting parameters.Too diameter ͑mm ͒0.10.20.4Spindle speed ͑rpm ͒150000120000100000Maximumfeedrate ͑mm/min ͒303048Maximum cutting depth ͑m ͒81550V c ͑m/min ͒—surface speed47.1275.40125.67f z ͑m ͒—maximum feedrate per teeth 0.10.1250.24Workpiece materialAluminum alloys and copper alloys Spay mist pressure ͑bar ͒666F IG .4.͑Color online ͒Profile of the two microgears:͑a ͒⌽5.4mm gear and ͑b ͒⌽1.35mm gear.J.Vac.Sci.Technol.B,Vol.27,No.3,May/Jun 2009aforementioned.In terms of machining efficiency,the tool with diameter of 0.4mm in Table I is chosen for the face milling.Since the minimum distance between each two ad-jacent teeth is 0.110mm from the designed gear model,the tool with diameter of 0.1mm in Table I is chosen for both the profile milling and deburring.Generally,cutting parameters has a great impact on the surface roughness.For the purpose of testing the finishing quality of this three-axis desktop milling machine tool and studying how much effect the cutting parameters have on the surface roughness of the workpiece,two different stepovers have been chosen in this test.On condition that all the cut-ting parameters except for the stepover in the process of face milling for both gears are the same.The stepover for the gear in diameter of 5.4mm is 90%of the tool diameter,and the stepover for the gear in diameter of 1.35mm is 10%of the tool diameter.As a result,the roughness of the top face for the gear in diameter of 5.4mm is Ra223.84nm and Ra274.17nm for the gear in diameter of 1.35mm,respec-tively ͓Figs.5͑a ͒and 5͑b ͔͒.As we can see from Figs.5͑a ͒and 5͑b ͒,the roughness along the feeding direction is almost the same,but the roughness is not stable across the feeding direction.Moreover,this phenomenon becomes more evident as the stepover becoming larger.B.Microthin wallsTwo thin walls as well as a groove between the two thin wall are finished on this three-axis desktop milling machine tools by the tool in diameter of 0.2mm ͑Figs.6and 7͒on the workpiece of A16061.The width of the thin walls on the left side in Fig.6is 25m,and that of the other one is 20m.The height and length of both the two thin walls are 500m and 7.8mm,respectively.Limited by the length of tool flute,the largest available height of the thin wall is 500m.Oth-erwise,the tool tip is not capable of reaching a deeper dis-tance anymore.Calculating from the width and height,it is concluded that the aspect ratio of the two thin walls is 1:20and 1:25severally.In spite of such a big aspect ratio,there is almost no inclination occurred on these two thin walls.Ad-F IG .5.͑Color online ͒Surface rough-ness of the two gears:͑a ͒surface roughness of the top face for the ⌽5.4mm gear;͑b ͒surface roughness of the top face for the ⌽1.35mm gear.JVST B -Microelectronics and Nanometer Structuresditionally,there is also no longitudinal distortion in spite of the large length of the two thin walls.The width of the gap between the two thin walls is 250m which is 50m larger than the diameter of the milling tool used in this test.As a result of this,a groove in length of 7.8mm,width of 250m,and depth of 500m between the two thin walls is machined simultaneously.Inevitably,there always are some burrs formed on the workpart especially on the edge.How-ever,deburring for such kind of microstructures in size of tens of microns is an extremely hard work.In order to deburr around the thin wall,the tool path for a single thin wall has been well designed.Finally,burrs are minimized on the thin walls,as shown in both Figs.6and 7.Obviously,it is a challenge for the repeatability of the machine tool and the shape accuracy of the milling tool to succeed in machining such thin walls.As the height of each thin wall is 500m,the reasonal cutting depth should be taken into consideration.Consequentially,in this machining test the maximum cutting depth is fixed at 15m,which isno more than 7.5%of the tool diameter.Hence,the milling tool has to travel around the thin wall following the same path at different depth time and time again.Because of the small widths of 20and 25m,the two thin walls become weaker and easy to incline as the height increases.The re-peatability of the machine tool and tool shape accuracy turn into the key factors for this machining test.Although the result from the microscope in Figs.6and 7shows a great repeatability of this three-axis desktop milling machine tool and tool accuracy.However,from the result of roughness measurement for the flank of the thin walls,the tool path and the different cutting depth clearly show the effect of the re-peatability of the machine tool and the shape accuracy of the milling tool ͑Fig.8͒.In Fig.8,the horizontal axis stands for the depth of cut and the vertical axis stands for the feeding direction.It is clearly show that the roughness changes a lot as the cutting depth changes.Nevertheless,at a certain depth of cut,the roughness is smaller along the feeding direction than that of the whole area.As a result,the roughness is Ra360.97which is bigger than that of the face milling as shown in Fig.5.F IG .7.͑Color online ͒View of theflank.F IG .6.͑Color online ͒25and 20m thinwalls.F IG .8.͑Color online ͒Roughness of the flank of the thin wall.J.Vac.Sci.Technol.B,Vol.27,No.3,May/Jun 2009C.MicroelectrodeIn the field of aerospace,injection moulding and die cast-ing industries,electrical discharge machining ͑EDM ͒process is one of the most successful,applicable and economical technologies.EDM is a thermal process involving melting and vaporization between workpiece and electrode.Irrespec-tive of the hardness of workpiece materials,any electrically conductive materials can be machined by EDM process without deformation induced by mechanical stress.9For manufacturing precision components with microstruc-tures,micro-EDM with shaped electrode is highly regarded as a capable approach of machining three-dimensional mi-crostructure because of its special machining mechanism.However,it is always a difficulty to manufacture microelec-trodes.Because usually the size of the transverse section of the electrode used in micro-EDM is ranging from several microns to hundred of microns.Meanwhile,the length of the micro electrode is hundreds of microns even several milli-meters.Although there are already some methods available for making micro electrodes.10In contrast with these meth-ods,micro milling has many advantages in material removal rate,machining efficiency,and cost.For instance,a mi-crorectangular copper electrode in width of 90m,length of 810m,and height of 1mm is machined by this three-axis desktop milling machine tool ͑Fig.9͒.The total time for machining this electrode is less than 15min by utilizing the milling tool in diameter of 0.4mm.Then,an EDM experi-ment has been carried out with this electrode.In this EDM experiment,this electrode is used by die sinking into the stainless steel.As shown in Fig.7,a rectangular through hole in width of 110m,length of 840m,and depth of 300m is been machined within 10min ͑Fig.10͒.More-over the profile of the electrode is almost copied onto the workpiece.Meanwhile,the length wear of the electrode is only 60m.Undoubtedly,taking the hardness of the work-piece material into consideration,to machine the stainless steel by the milling tool made from carbide will cause a considerable tool wear and spend more time.Furthermore,due to the radius of the milling tool,the radius of everycorner of the rectangular hole will be almost the same as the tool radius.Hence,with the micro electrode machined by this three-axis desktop milling machine tool,workpieces with microstructures made from conductive materials such as hardened steel,molybdenum,and silicon can be machined.IV.CONCLUSIONTo study machine tool miniaturization technology and mi-cromachining mechanism,a three-axis desktop milling ma-chine tool is presented in this article.First,the design param-eter and the structure of the machine tool are described.Second,two motion performance tests,i.e.,microstepping of 0.2m and repeatability of Ϯ0.3m are provided by a laser interferometer with a measurement resolution of 1nm.Fi-nally,three microcomponents such as microgears,microthin walls and microelectrodes made from copper alloy or alumi-num alloy have been machined by end milling tools in diam-eter of 0.1,0.2,and 0.4mm.Meanwhile,themachining ability of this three-axis desktop milling ma-chine tool in aspect of three-dimensional complex micro-structures is verified by the machining tests,and the future work will be focussed on improving the workpiece surface roughness and micromachining mechanism.ACKNOWLEDGMENTSThe authors would like to acknowledge with thanks the support of the 111project and Scholar Exchange Base of Micro/Nano Science and Technology ͑SEBMNST, ͒from the Chinese Ministry of Education.1A.Bruno Frazier,Robert O.Warrington,and Craig Friedrich,IEEE Trans.Ind.Electron.42,423͑1995͒.2E.Kussul,T.Baidyk,L.Ruiz-Huerta,A.Caballero-Ruiz,G.Velasco,and L.Kasatkina,Proceedings of International Symposium on Micromecha-tronics and Human Science,2002͑unpublished ͒,pp.125–134.3T.Kitahara,Y .Ishikawa,T.Terada,N.Nakajima,and K.Furuta,b.50,117͑1996͒.F IG .9.͑Color online ͒Microelectrode.F IG .10.͑Color online ͒Through hole made by EDM.JVST B -Microelectronics and Nanometer Structures4Yuichi Okazaki,Nozomu Mishima,and Kiwamu Ashida,First Korea-Japan Conference on Positioning Technology,Daejeon,Korea,2002͑un-published͒.5Nozomu Mishima,Proceedings of the2006IEEE International Confer-ence on Mechatronics and Automation,Luoyang,China,25–28June2006͑unpublished͒.6Zinan Lu and Takeshi Yoneyama,Int.J.Mach.Tools Manuf.39,1171͑1999͒.7E.Kussul,T.Baidyk,L.Ruiz-Huerta,A.Caballero-Ruiz,and G.Velasco, J.Micromech.Microeng.12,795͑2002͒.8Andrew G.Phillip,Shiv G.Kapoor,and Richard E.DeV or,Int.J.Mach. Tools Manuf.46,1435͑2006͒.9J.C.Rebelo,A.MoraÄo Dias,Ruy Mesquita,Paolo Vassalo,and Mario Santos,Ind.Eng.Chem.Fundam.103,389͑2000͒.10Feng-Tsai Weng,R.F.Shyu,and Chen-Siang Hsu,J.Mater.Process. Technol.140,332͑2003͒.J.Vac.Sci.Technol.B,Vol.27,No.3,May/Jun2009。