浅谈烧结点火器与节能途径
浅谈降低烧结工序能耗的措施
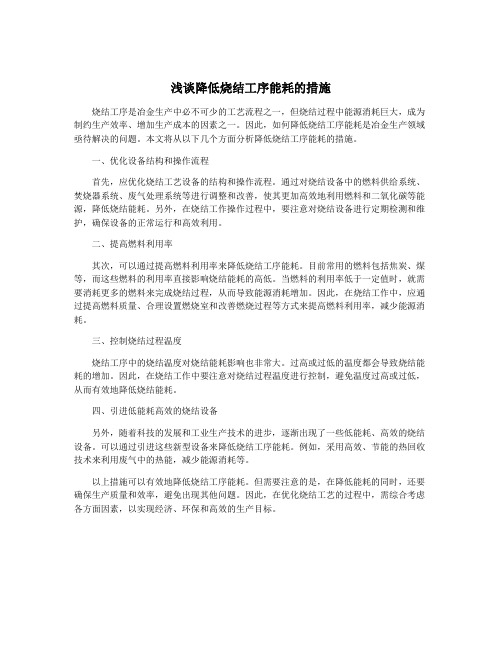
浅谈降低烧结工序能耗的措施烧结工序是冶金生产中必不可少的工艺流程之一,但烧结过程中能源消耗巨大,成为制约生产效率、增加生产成本的因素之一。
因此,如何降低烧结工序能耗是冶金生产领域亟待解决的问题。
本文将从以下几个方面分析降低烧结工序能耗的措施。
一、优化设备结构和操作流程首先,应优化烧结工艺设备的结构和操作流程。
通过对烧结设备中的燃料供给系统、焚烧器系统、废气处理系统等进行调整和改善,使其更加高效地利用燃料和二氧化碳等能源,降低烧结能耗。
另外,在烧结工作操作过程中,要注意对烧结设备进行定期检测和维护,确保设备的正常运行和高效利用。
二、提高燃料利用率其次,可以通过提高燃料利用率来降低烧结工序能耗。
目前常用的燃料包括焦炭、煤等,而这些燃料的利用率直接影响烧结能耗的高低。
当燃料的利用率低于一定值时,就需要消耗更多的燃料来完成烧结过程,从而导致能源消耗增加。
因此,在烧结工作中,应通过提高燃料质量、合理设置燃烧室和改善燃烧过程等方式来提高燃料利用率,减少能源消耗。
三、控制烧结过程温度烧结工序中的烧结温度对烧结能耗影响也非常大。
过高或过低的温度都会导致烧结能耗的增加。
因此,在烧结工作中要注意对烧结过程温度进行控制,避免温度过高或过低,从而有效地降低烧结能耗。
四、引进低能耗高效的烧结设备另外,随着科技的发展和工业生产技术的进步,逐渐出现了一些低能耗、高效的烧结设备。
可以通过引进这些新型设备来降低烧结工序能耗。
例如,采用高效、节能的热回收技术来利用废气中的热能,减少能源消耗等。
以上措施可以有效地降低烧结工序能耗。
但需要注意的是,在降低能耗的同时,还要确保生产质量和效率,避免出现其他问题。
因此,在优化烧结工艺的过程中,需综合考虑各方面因素,以实现经济、环保和高效的生产目标。
烧结降低点火煤气单耗的措施
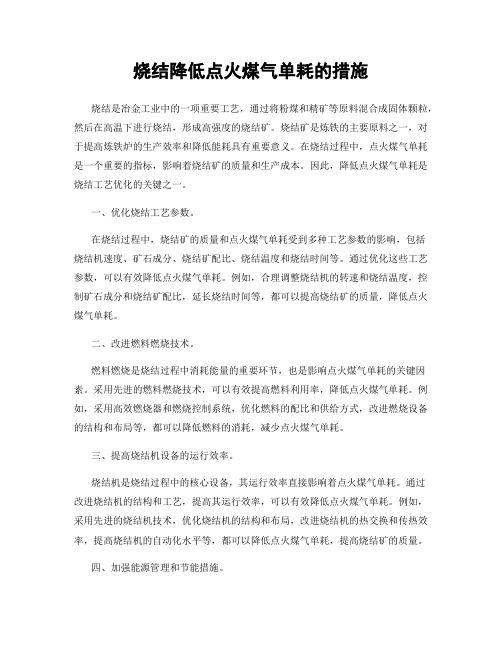
烧结降低点火煤气单耗的措施烧结是冶金工业中的一项重要工艺,通过将粉煤和精矿等原料混合成固体颗粒,然后在高温下进行烧结,形成高强度的烧结矿。
烧结矿是炼铁的主要原料之一,对于提高炼铁炉的生产效率和降低能耗具有重要意义。
在烧结过程中,点火煤气单耗是一个重要的指标,影响着烧结矿的质量和生产成本。
因此,降低点火煤气单耗是烧结工艺优化的关键之一。
一、优化烧结工艺参数。
在烧结过程中,烧结矿的质量和点火煤气单耗受到多种工艺参数的影响,包括烧结机速度、矿石成分、烧结矿配比、烧结温度和烧结时间等。
通过优化这些工艺参数,可以有效降低点火煤气单耗。
例如,合理调整烧结机的转速和烧结温度,控制矿石成分和烧结矿配比,延长烧结时间等,都可以提高烧结矿的质量,降低点火煤气单耗。
二、改进燃料燃烧技术。
燃料燃烧是烧结过程中消耗能量的重要环节,也是影响点火煤气单耗的关键因素。
采用先进的燃料燃烧技术,可以有效提高燃料利用率,降低点火煤气单耗。
例如,采用高效燃烧器和燃烧控制系统,优化燃料的配比和供给方式,改进燃烧设备的结构和布局等,都可以降低燃料的消耗,减少点火煤气单耗。
三、提高烧结机设备的运行效率。
烧结机是烧结过程中的核心设备,其运行效率直接影响着点火煤气单耗。
通过改进烧结机的结构和工艺,提高其运行效率,可以有效降低点火煤气单耗。
例如,采用先进的烧结机技术,优化烧结机的结构和布局,改进烧结机的热交换和传热效率,提高烧结机的自动化水平等,都可以降低点火煤气单耗,提高烧结矿的质量。
四、加强能源管理和节能措施。
能源管理和节能是降低点火煤气单耗的重要手段。
通过加强能源管理,优化能源结构,提高能源利用率,可以有效降低点火煤气单耗。
例如,采用高效节能设备,改进能源供应和利用系统,加强能源监测和控制,实施能源管理和节能政策等,都可以降低能耗,降低点火煤气单耗。
五、加强运行管理和技术培训。
运行管理和技术培训是保证烧结工艺稳定运行和降低点火煤气单耗的重要保障。
浅谈降低烧结工序能耗的措施
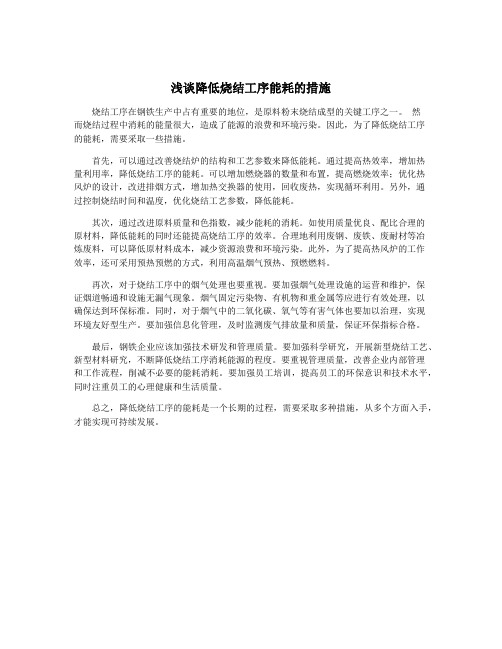
浅谈降低烧结工序能耗的措施烧结工序在钢铁生产中占有重要的地位,是原料粉末烧结成型的关键工序之一。
然而烧结过程中消耗的能量很大,造成了能源的浪费和环境污染。
因此,为了降低烧结工序的能耗,需要采取一些措施。
首先,可以通过改善烧结炉的结构和工艺参数来降低能耗。
通过提高热效率,增加热量利用率,降低烧结工序的能耗。
可以增加燃烧器的数量和布置,提高燃烧效率;优化热风炉的设计,改进排烟方式,增加热交换器的使用,回收废热,实现循环利用。
另外,通过控制烧结时间和温度,优化烧结工艺参数,降低能耗。
其次,通过改进原料质量和色指数,减少能耗的消耗。
如使用质量优良、配比合理的原材料,降低能耗的同时还能提高烧结工序的效率。
合理地利用废钢、废铁、废耐材等冶炼废料,可以降低原材料成本,减少资源浪费和环境污染。
此外,为了提高热风炉的工作效率,还可采用预热预燃的方式,利用高温烟气预热、预燃燃料。
再次,对于烧结工序中的烟气处理也要重视。
要加强烟气处理设施的运营和维护,保证烟道畅通和设施无漏气现象。
烟气固定污染物、有机物和重金属等应进行有效处理,以确保达到环保标准。
同时,对于烟气中的二氧化碳、氧气等有害气体也要加以治理,实现环境友好型生产。
要加强信息化管理,及时监测废气排放量和质量,保证环保指标合格。
最后,钢铁企业应该加强技术研发和管理质量。
要加强科学研究,开展新型烧结工艺、新型材料研究,不断降低烧结工序消耗能源的程度。
要重视管理质量,改善企业内部管理和工作流程,削减不必要的能耗消耗。
要加强员工培训,提高员工的环保意识和技术水平,同时注重员工的心理健康和生活质量。
总之,降低烧结工序的能耗是一个长期的过程,需要采取多种措施,从多个方面入手,才能实现可持续发展。
烧结机节能降耗措施

烧结机节能降耗措施在建筑材料、化工等行业中,烧结机是一种常用的设备,用于将粉状或粒状原料加热至一定温度后烘干、烧结成固体,制成块状产品。
然而,烧结机的运行过程中会产生大量的能源消耗和环境污染。
因此,烧结机节能降耗已经成为了当前行业中的一个重要问题。
本文将介绍烧结机节能降耗的几种措施。
1. 采用高效热交换技术烧结机内部的热量分布不均,导致了很大一部分热量的浪费。
此时,可以采用高效的热交换技术,将一部分废热收集起来,用于预热后续的原料,从而提高了热能的利用率。
例如,可以在烧结机的烟囱上安装烟囱热交换器,将烟气中的热量通过水的循环来直接回收利用。
另外,还可以在烧结机的废气出口处安装余热回收设备,将排放的热量再利用起来。
2. 降低热损失烧结机在运行过程中会产生大量的热损失,这也是造成能源浪费的重要因素。
因此,降低热损失是节能降耗的重要措施之一。
可以在烧结机的内部加装热防护材料,减少热量的散失,从而提高了热能的利用效率。
此外,还可以在烧结机的内部加装隔热板,减少热量的传导和散失,降低能源的消耗。
3. 优化燃料燃烧燃料燃烧是烧结机中能源消耗的主要来源之一。
因此,优化燃料燃烧也是节能降耗的重要措施。
可以采用合理的燃烧方式,如改善燃烧空气调节和混合方式,从而提高燃烧效率。
此外,还可以采用节能型的燃烧设备,例如采用带有预热功能的燃烧系统,利用废气回收设备对未燃烧的燃料进行再次燃烧,从而降低了能源的消耗。
4. 减少机械损失烧结机在运行过程中,机械损失也会导致能源消耗。
因此,减少机械损失也是节能降耗的重要措施。
可以采用精密的机件和材料,提高烧结机的精度和韧性。
此外,还可以加强运行维护和保养,定期检查和更换机件,避免机件的磨损和损坏,从而降低了运行时的能源消耗。
5. 提高运行效率在烧结机的运行过程中,提高运行效率也是一种节能降耗的重要措施。
可以采取以下方法:•加强设备的操作培训和技能提升,提高员工对设备的理解和操作技能;•采用自动化控制系统,利用先进技术对烧结机的运行进行监测和控制,提高了运行效率;•合理规划烧结机的生产计划,避免重复性操作和浪费。
浅谈降低烧结工序能耗的措施

浅谈降低烧结工序能耗的措施1. 引言1.1 烧结工序对能源消耗的重要性烧结工序是冶金工业重要的炼铁生产工序之一,其能源消耗对整个生产过程的能耗影响极为重要。
烧结工序主要是通过将铁矿石等原料在高温下加热,使其在烧结炉中发生一系列物理化学反应,最终形成高强度的铁制品。
烧结工序的能源消耗占据了整个冶金生产的重要比重,对于企业的生产成本和环境影响都具有重要的意义。
烧结工序所需能源包括燃料能源和电力能源,其中以燃料消耗较大。
在烧结工序中,煤炭、焦炭等燃料被用来提供高温热能,使原料得以烧结。
传统的烧结工序存在能源利用率低、排放浪费等问题,导致能源消耗较高。
降低烧结工序的能源消耗具有重要意义。
通过优化烧结工艺参数、采用先进的设备和技术、加强热能回收利用、提高烧结燃料的利用率以及应用节能技术等措施,可以有效降低烧结工序的能源消耗,提高生产效率,减少生产成本,实现可持续发展。
节能减排也是当前社会发展的重要趋势,降低烧结工序的能源消耗,不仅符合环保要求,也能提升企业的竞争力。
2. 正文2.1 优化烧结工艺参数优化烧结工艺参数是降低烧结工序能耗的重要措施之一。
通过调整烧结工艺中的各项参数,可以实现更高效的烧结过程,减少能源的消耗。
优化烧结工艺参数可以提高烧结的热效率。
合理调节烧结温度、烧结时间等参数,可以使烧结过程中的热能更加充分利用,减少能源的浪费。
优化参数还可以提高烧结矿的燃烧效率,减少燃料的使用量,降低能耗。
优化烧结工艺参数还可以改善产品质量。
通过精确控制烧结过程中的各项参数,可以确保产品的成分和性能达到要求,避免因为工艺参数不合理导致的质量问题,减少了产品的废品率,提高了资源利用率。
优化烧结工艺参数还可以减少设备运行时的能耗。
通过合理设置烧结设备的工作参数,有效控制能源的消耗,延长设备的使用寿命,减少了能源的浪费,降低了生产成本。
优化烧结工艺参数是降低烧结工序能耗的有效途径之一,可以提高烧结热效率,改善产品质量,减少设备能耗,从而实现节能减排的目标。
烧结降能耗具体方式分析
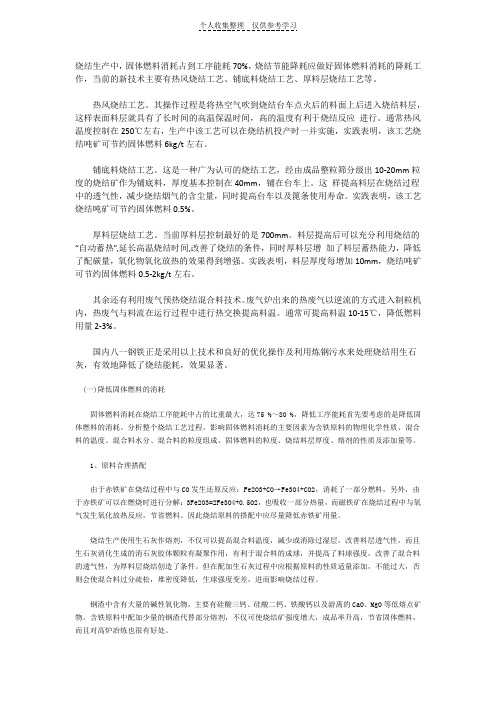
烧结生产中,固体燃料消耗占到工序能耗70%,烧结节能降耗应做好固体燃料消耗的降耗工作,当前的新技术主要有热风烧结工艺、铺底料烧结工艺、厚料层烧结工艺等。
热风烧结工艺。
其操作过程是将热空气吹到烧结台车点火后的料面上后进入烧结料层,这样表面料层就具有了长时间的高温保温时间,高的温度有利于烧结反应进行。
通常热风温度控制在250℃左右,生产中该工艺可以在烧结机投产时一并实施,实践表明,该工艺烧结吨矿可节约固体燃料6kg/t左右。
铺底料烧结工艺。
这是一种广为认可的烧结工艺,经由成品整粒筛分级出10-20mm粒度的烧结矿作为铺底料,厚度基本控制在40mm,铺在台车上。
这样提高料层在烧结过程中的透气性,减少烧结烟气的含尘量,同时提高台车以及篦条使用寿命。
实践表明,该工艺烧结吨矿可节约固体燃料0.5%。
厚料层烧结工艺。
当前厚料层控制最好的是700mm。
料层提高后可以充分利用烧结的“自动蓄热”,延长高温烧结时间,改善了烧结的条件,同时厚料层增加了料层蓄热能力,降低了配碳量,氧化物氧化放热的效果得到增强。
实践表明,料层厚度每增加10mm,烧结吨矿可节约固体燃料0.5-2kg/t左右。
其余还有利用废气预热烧结混合料技术。
废气炉出来的热废气以逆流的方式进入制粒机内,热废气与料流在运行过程中进行热交换提高料温。
通常可提高料温10-15℃,降低燃料用量2-3%。
国内八一钢铁正是采用以上技术和良好的优化操作及利用炼钢污水来处理烧结用生石灰,有效地降低了烧结能耗,效果显著。
(一)降低固体燃料的消耗固体燃料消耗在烧结工序能耗中占的比重最大,达75 %~80 %,降低工序能耗首先要考虑的是降低固体燃料的消耗。
分析整个烧结工艺过程,影响固体燃料消耗的主要因素为含铁原料的物理化学性质、混合料的温度、混合料水分、混合料的粒度组成、固体燃料的粒度、烧结料层厚度、熔剂的性质及添加量等。
1、原料合理搭配由于赤铁矿在烧结过程中与CO发生还原反应:Fe2O3+CO→Fe3O4+CO2,消耗了一部分燃料,另外,由于赤铁矿可以在燃烧时进行分解:3Fe2O3=2Fe3O4+0.5O2,也吸收一部分热量,而磁铁矿在烧结过程中与氧气发生氧化放热反应,节省燃料。
浅谈降低烧结工序能耗的措施

浅谈降低烧结工序能耗的措施
烧结是粉煤灰等煤屑燃烧后生成的产物,具有一定的热值和热能,因此在其烧结过程中能耗较高。
为了降低烧结工序的能耗,需要采取以下措施:
1. 优化燃料选择和使用:燃料的选择和使用在烧结过程中起着重要作用。
合理选择和使用高热值、低硫、低灰分的燃料,以减少燃料消耗,降低烟气排放,提高烧结效率。
2. 热能回收利用:在烧结过程中,热能可以通过余热锅炉等方式回收利用,以减少能量损失,提高能源利用率。
3. 优化烧结过程控制参数:通过优化烧结温度、温度梯度、气体流速等控制参数,可以提高烧结质量,降低能耗。
4. 选用高效节能设备:采用高效节能设备,如高效烧结机、省电烘干设备等,可以有效降低能耗,提高工艺效率和产品质量。
5. 建立能源管理体系:建立能源管理体系,对能源消耗进行监测和管理,对关键环节进行能耗分析和优化,制定科学合理的能源管理措施,可以有效降低烧结工序的能耗。
综上所述,通过优化燃料选择和使用、热能回收利用、优化烧结过程控制参数、选用高效节能设备以及建立能源管理体系等措施,可以有效降低烧结工序的能耗,提高能源利用效率和企业经济效益。
浅谈烧结节能降耗的技术途径和措施
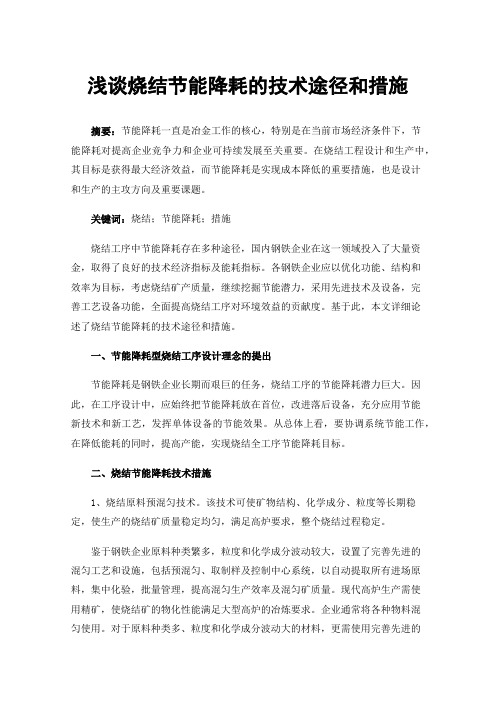
浅谈烧结节能降耗的技术途径和措施摘要:节能降耗一直是冶金工作的核心,特别是在当前市场经济条件下,节能降耗对提高企业竞争力和企业可持续发展至关重要。
在烧结工程设计和生产中,其目标是获得最大经济效益,而节能降耗是实现成本降低的重要措施,也是设计和生产的主攻方向及重要课题。
关键词:烧结;节能降耗;措施烧结工序中节能降耗存在多种途径,国内钢铁企业在这一领域投入了大量资金,取得了良好的技术经济指标及能耗指标。
各钢铁企业应以优化功能、结构和效率为目标,考虑烧结矿产质量,继续挖掘节能潜力,采用先进技术及设备,完善工艺设备功能,全面提高烧结工序对环境效益的贡献度。
基于此,本文详细论述了烧结节能降耗的技术途径和措施。
一、节能降耗型烧结工序设计理念的提出节能降耗是钢铁企业长期而艰巨的任务,烧结工序的节能降耗潜力巨大。
因此,在工序设计中,应始终把节能降耗放在首位,改进落后设备,充分应用节能新技术和新工艺,发挥单体设备的节能效果。
从总体上看,要协调系统节能工作,在降低能耗的同时,提高产能,实现烧结全工序节能降耗目标。
二、烧结节能降耗技术措施1、烧结原料预混匀技术。
该技术可使矿物结构、化学成分、粒度等长期稳定,使生产的烧结矿质量稳定均匀,满足高炉要求,整个烧结过程稳定。
鉴于钢铁企业原料种类繁多,粒度和化学成分波动较大,设置了完善先进的混匀工艺和设施,包括预混匀、取制样及控制中心系统,以自动提取所有进场原料,集中化验,批量管理,提高混匀生产效率及混匀矿质量。
现代高炉生产需使用精矿,使烧结矿的物化性能满足大型高炉的冶炼要求。
企业通常将各种物料混匀使用。
对于原料种类多、粒度和化学成分波动大的材料,更需使用完善先进的混匀工艺和设施作为技术支持,通过自动制样系统,对所有进场原料进行自动取料及集中化验,并根据不同品种、成分和定量进行堆放,实现原料的批次管理。
2、超厚料层烧结自动蓄热技术。
在烧结工艺中,蓄热量会随着料层厚度的不断增加而逐渐积累,当厚度达到180~220mm时,蓄热率为35~45%,厚度为400mm,蓄热率可达65%。
浅谈降低烧结工序能耗的措施
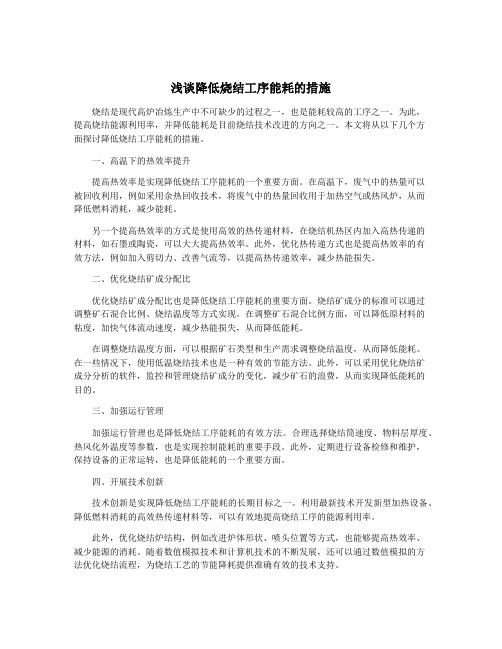
浅谈降低烧结工序能耗的措施烧结是现代高炉冶炼生产中不可缺少的过程之一,也是能耗较高的工序之一。
为此,提高烧结能源利用率,并降低能耗是目前烧结技术改进的方向之一。
本文将从以下几个方面探讨降低烧结工序能耗的措施。
一、高温下的热效率提升提高热效率是实现降低烧结工序能耗的一个重要方面。
在高温下,废气中的热量可以被回收利用,例如采用余热回收技术,将废气中的热量回收用于加热空气或热风炉,从而降低燃料消耗,减少能耗。
另一个提高热效率的方式是使用高效的热传递材料,在烧结机热区内加入高热传递的材料,如石墨或陶瓷,可以大大提高热效率。
此外,优化热传递方式也是提高热效率的有效方法,例如加入剪切力、改善气流等,以提高热传递效率,减少热能损失。
二、优化烧结矿成分配比优化烧结矿成分配比也是降低烧结工序能耗的重要方面。
烧结矿成分的标准可以通过调整矿石混合比例、烧结温度等方式实现。
在调整矿石混合比例方面,可以降低原材料的粘度,加快气体流动速度,减少热能损失,从而降低能耗。
在调整烧结温度方面,可以根据矿石类型和生产需求调整烧结温度,从而降低能耗。
在一些情况下,使用低温烧结技术也是一种有效的节能方法。
此外,可以采用优化烧结矿成分分析的软件,监控和管理烧结矿成分的变化,减少矿石的浪费,从而实现降低能耗的目的。
三、加强运行管理加强运行管理也是降低烧结工序能耗的有效方法。
合理选择烧结筒速度、物料层厚度、热风化外温度等参数,也是实现控制能耗的重要手段。
此外,定期进行设备检修和维护,保持设备的正常运转,也是降低能耗的一个重要方面。
四、开展技术创新技术创新是实现降低烧结工序能耗的长期目标之一。
利用最新技术开发新型加热设备、降低燃料消耗的高效热传递材料等,可以有效地提高烧结工序的能源利用率。
此外,优化烧结炉结构,例如改进炉体形状、喷头位置等方式,也能够提高热效率、减少能源的消耗。
随着数值模拟技术和计算机技术的不断发展,还可以通过数值模拟的方法优化烧结流程,为烧结工艺的节能降耗提供准确有效的技术支持。
浅谈降低烧结工序能耗的措施
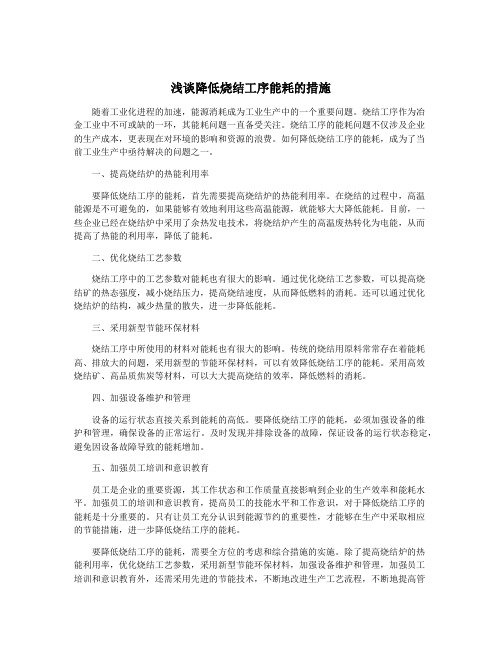
浅谈降低烧结工序能耗的措施随着工业化进程的加速,能源消耗成为工业生产中的一个重要问题。
烧结工序作为冶金工业中不可或缺的一环,其能耗问题一直备受关注。
烧结工序的能耗问题不仅涉及企业的生产成本,更表现在对环境的影响和资源的浪费。
如何降低烧结工序的能耗,成为了当前工业生产中亟待解决的问题之一。
一、提高烧结炉的热能利用率要降低烧结工序的能耗,首先需要提高烧结炉的热能利用率。
在烧结的过程中,高温能源是不可避免的,如果能够有效地利用这些高温能源,就能够大大降低能耗。
目前,一些企业已经在烧结炉中采用了余热发电技术,将烧结炉产生的高温废热转化为电能,从而提高了热能的利用率,降低了能耗。
二、优化烧结工艺参数烧结工序中的工艺参数对能耗也有很大的影响。
通过优化烧结工艺参数,可以提高烧结矿的热态强度,减小烧结压力,提高烧结速度,从而降低燃料的消耗。
还可以通过优化烧结炉的结构,减少热量的散失,进一步降低能耗。
三、采用新型节能环保材料烧结工序中所使用的材料对能耗也有很大的影响。
传统的烧结用原料常常存在着能耗高、排放大的问题,采用新型的节能环保材料,可以有效降低烧结工序的能耗。
采用高效烧结矿、高品质焦炭等材料,可以大大提高烧结的效率,降低燃料的消耗。
四、加强设备维护和管理设备的运行状态直接关系到能耗的高低。
要降低烧结工序的能耗,必须加强设备的维护和管理,确保设备的正常运行。
及时发现并排除设备的故障,保证设备的运行状态稳定,避免因设备故障导致的能耗增加。
五、加强员工培训和意识教育员工是企业的重要资源,其工作状态和工作质量直接影响到企业的生产效率和能耗水平。
加强员工的培训和意识教育,提高员工的技能水平和工作意识,对于降低烧结工序的能耗是十分重要的。
只有让员工充分认识到能源节约的重要性,才能够在生产中采取相应的节能措施,进一步降低烧结工序的能耗。
要降低烧结工序的能耗,需要全方位的考虑和综合措施的实施。
除了提高烧结炉的热能利用率,优化烧结工艺参数,采用新型节能环保材料,加强设备维护和管理,加强员工培训和意识教育外,还需采用先进的节能技术,不断地改进生产工艺流程,不断地提高管理水平,从而才能够全面降低烧结工序的能耗,实现可持续发展的目标。
探究降低烧结工艺能耗的措施
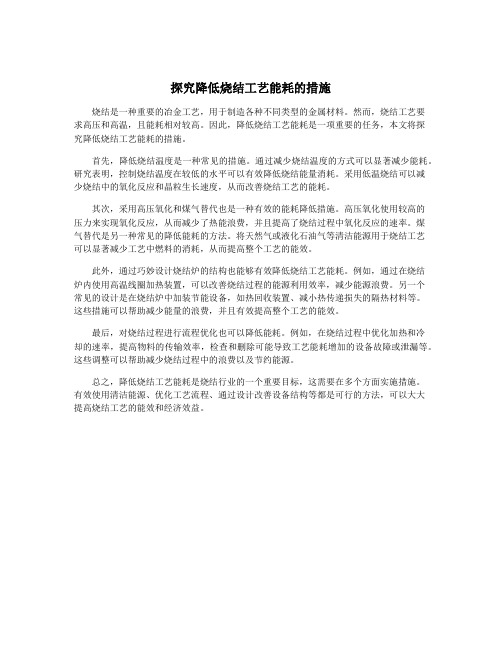
探究降低烧结工艺能耗的措施烧结是一种重要的冶金工艺,用于制造各种不同类型的金属材料。
然而,烧结工艺要求高压和高温,且能耗相对较高。
因此,降低烧结工艺能耗是一项重要的任务,本文将探究降低烧结工艺能耗的措施。
首先,降低烧结温度是一种常见的措施。
通过减少烧结温度的方式可以显著减少能耗。
研究表明,控制烧结温度在较低的水平可以有效降低烧结能量消耗。
采用低温烧结可以减少烧结中的氧化反应和晶粒生长速度,从而改善烧结工艺的能耗。
其次,采用高压氧化和煤气替代也是一种有效的能耗降低措施。
高压氧化使用较高的压力来实现氧化反应,从而减少了热能浪费,并且提高了烧结过程中氧化反应的速率。
煤气替代是另一种常见的降低能耗的方法。
将天然气或液化石油气等清洁能源用于烧结工艺可以显著减少工艺中燃料的消耗,从而提高整个工艺的能效。
此外,通过巧妙设计烧结炉的结构也能够有效降低烧结工艺能耗。
例如,通过在烧结炉内使用高温线圈加热装置,可以改善烧结过程的能源利用效率,减少能源浪费。
另一个常见的设计是在烧结炉中加装节能设备,如热回收装置、减小热传递损失的隔热材料等。
这些措施可以帮助减少能量的浪费,并且有效提高整个工艺的能效。
最后,对烧结过程进行流程优化也可以降低能耗。
例如,在烧结过程中优化加热和冷却的速率,提高物料的传输效率,检查和删除可能导致工艺能耗增加的设备故障或泄漏等。
这些调整可以帮助减少烧结过程中的浪费以及节约能源。
总之,降低烧结工艺能耗是烧结行业的一个重要目标,这需要在多个方面实施措施。
有效使用清洁能源、优化工艺流程、通过设计改善设备结构等都是可行的方法,可以大大提高烧结工艺的能效和经济效益。
浅谈降低烧结工序能耗的措施
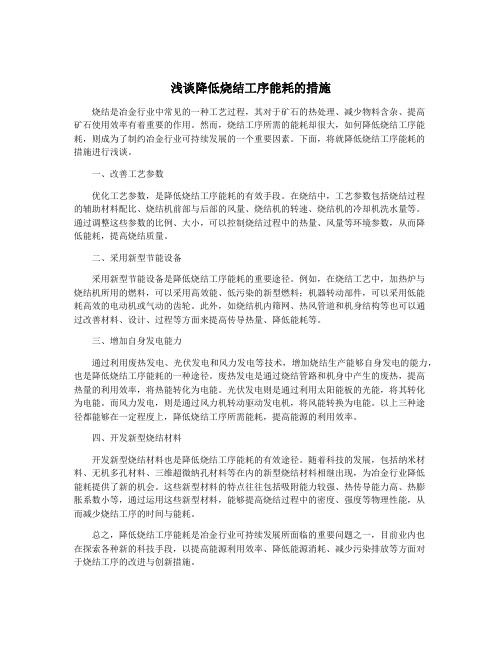
浅谈降低烧结工序能耗的措施烧结是冶金行业中常见的一种工艺过程,其对于矿石的热处理、减少物料含杂、提高矿石使用效率有着重要的作用。
然而,烧结工序所需的能耗却很大,如何降低烧结工序能耗,则成为了制约冶金行业可持续发展的一个重要因素。
下面,将就降低烧结工序能耗的措施进行浅谈。
一、改善工艺参数优化工艺参数,是降低烧结工序能耗的有效手段。
在烧结中,工艺参数包括烧结过程的辅助材料配比、烧结机前部与后部的风量、烧结机的转速、烧结机的冷却机洗水量等。
通过调整这些参数的比例、大小,可以控制烧结过程中的热量、风量等环境参数,从而降低能耗,提高烧结质量。
二、采用新型节能设备采用新型节能设备是降低烧结工序能耗的重要途径。
例如,在烧结工艺中,加热炉与烧结机所用的燃料,可以采用高效能、低污染的新型燃料;机器转动部件,可以采用低能耗高效的电动机或气动的齿轮。
此外,如烧结机内筛网、热风管道和机身结构等也可以通过改善材料、设计、过程等方面来提高传导热量、降低能耗等。
三、增加自身发电能力通过利用废热发电、光伏发电和风力发电等技术,增加烧结生产能够自身发电的能力,也是降低烧结工序能耗的一种途径。
废热发电是通过烧结管路和机身中产生的废热,提高热量的利用效率,将热能转化为电能。
光伏发电则是通过利用太阳能板的光能,将其转化为电能。
而风力发电,则是通过风力机转动驱动发电机,将风能转换为电能。
以上三种途径都能够在一定程度上,降低烧结工序所需能耗,提高能源的利用效率。
四、开发新型烧结材料开发新型烧结材料也是降低烧结工序能耗的有效途径。
随着科技的发展,包括纳米材料、无机多孔材料、三维超微纳孔材料等在内的新型烧结材料相继出现,为冶金行业降低能耗提供了新的机会。
这些新型材料的特点往往包括吸附能力较强、热传导能力高、热膨胀系数小等,通过运用这些新型材料,能够提高烧结过程中的密度、强度等物理性能,从而减少烧结工序的时间与能耗。
总之,降低烧结工序能耗是冶金行业可持续发展所面临的重要问题之一,目前业内也在探索各种新的科技手段,以提高能源利用效率、降低能源消耗、减少污染排放等方面对于烧结工序的改进与创新措施。
浅谈烧结节能降耗的技术途径和措施

收稿日期:2003-03-25 联系人:张瑞年(410007)湖南 长沙冶金设计研究总院烧结分院浅谈烧结节能降耗的技术途径和措施张瑞年(长沙冶金设计研究总院) 摘 要 分析了我国烧结节能降耗现状,结合国内外先进的烧结节能降耗技术,从烧结工艺设计的角度提出了节能降耗的方向和技术措施。
关键词 烧结设计 节能降耗 途径 措施1 前 言节能降耗始终是冶金工作的重点,尤其是在当前市场经济条件下,节能降耗无论是对增加企业的竞争力,还是对企业的持续发展来说,都具有十分重大的意义。
就烧结工程设计、生产而言,其目标就是获取最大经济效益,而节能降耗是实现成本降低的重要措施,亦是设计、生产的主攻方向和重要课题。
2 我国烧结节能降耗现状我国重点和地方骨干企业,平均每吨烧结矿消耗的固体燃料分别比国内、外先进企业高1014kg 、1119kg 标煤和1218kg 、1413kg 标煤,工序能耗分别比宝钢高1517kg 和1715kg 标煤,若按我国每年生产116亿t 烧结矿计算,每年工序能耗要多消耗约265万t 标煤。
由此可以看出,我国烧结节能的潜力是很大的。
所以,在设计、生产中采取有效措施,最大幅度地降低烧结过程中的固体燃料消耗,对降低烧结成本具有重大意义。
3 烧结节能降耗的主要途径和措施311 向大型烧结机发展,是节能降耗的方向从近几年国内情况看,烧结生产发展的特点就是建设大型烧结机,继我国宝钢450m 2烧结机、武钢四烧435m 2等大型烧结机投产后,又有鞍钢二烧360m 2、东烧360m 2、武钢四烧435m 2等大型烧结机相继建成。
这是因为,大型烧结机与多台小型烧结机相比,具有投资少、质量好、能耗低、成本低,易于环保治理,便于实现烧结过程自动化的优点。
其中,能耗低的优点是显而易见的,如宝钢450m 2烧结机的工序能耗在57~60kg/t ,而一般小型烧结机的工序能耗大多在80kg/t 左右。
312 在设计中采用新工艺、新技术,是实现节能降耗的根本途径31211 建设原料场和强化原料混匀作业现代化高炉生产需要精料,这就要求烧结矿的物化性能均要满足大型高炉冶炼的需要。
探究降低烧结工艺能耗的措施
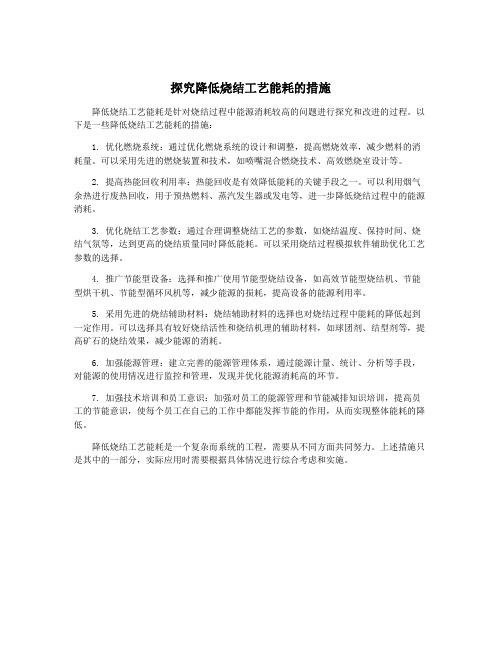
探究降低烧结工艺能耗的措施
降低烧结工艺能耗是针对烧结过程中能源消耗较高的问题进行探究和改进的过程。
以下是一些降低烧结工艺能耗的措施:
1. 优化燃烧系统:通过优化燃烧系统的设计和调整,提高燃烧效率,减少燃料的消耗量。
可以采用先进的燃烧装置和技术,如喷嘴混合燃烧技术、高效燃烧室设计等。
2. 提高热能回收利用率:热能回收是有效降低能耗的关键手段之一。
可以利用烟气余热进行废热回收,用于预热燃料、蒸汽发生器或发电等,进一步降低烧结过程中的能源消耗。
3. 优化烧结工艺参数:通过合理调整烧结工艺的参数,如烧结温度、保持时间、烧结气氛等,达到更高的烧结质量同时降低能耗。
可以采用烧结过程模拟软件辅助优化工艺参数的选择。
4. 推广节能型设备:选择和推广使用节能型烧结设备,如高效节能型烧结机、节能型烘干机、节能型循环风机等,减少能源的损耗,提高设备的能源利用率。
5. 采用先进的烧结辅助材料:烧结辅助材料的选择也对烧结过程中能耗的降低起到一定作用。
可以选择具有较好烧结活性和烧结机理的辅助材料,如球团剂、结型剂等,提高矿石的烧结效果,减少能源的消耗。
6. 加强能源管理:建立完善的能源管理体系,通过能源计量、统计、分析等手段,对能源的使用情况进行监控和管理,发现并优化能源消耗高的环节。
7. 加强技术培训和员工意识:加强对员工的能源管理和节能减排知识培训,提高员工的节能意识,使每个员工在自己的工作中都能发挥节能的作用,从而实现整体能耗的降低。
降低烧结工艺能耗是一个复杂而系统的工程,需要从不同方面共同努力。
上述措施只是其中的一部分,实际应用时需要根据具体情况进行综合考虑和实施。
烧结工序节能降耗的技术措施
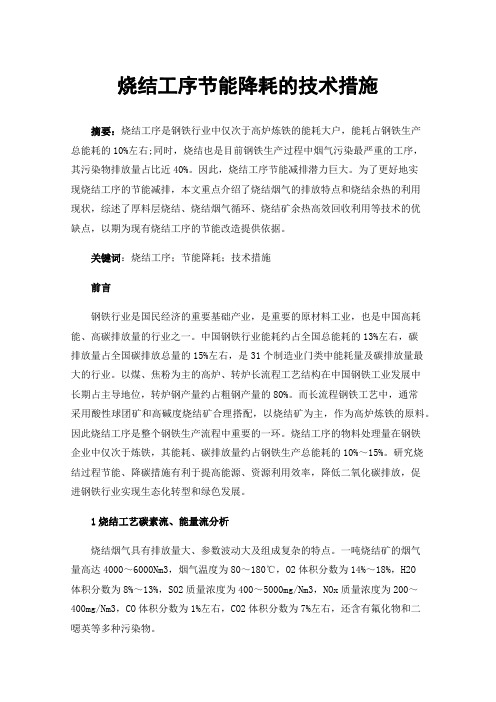
烧结工序节能降耗的技术措施摘要:烧结工序是钢铁行业中仅次于高炉炼铁的能耗大户,能耗占钢铁生产总能耗的10%左右;同时,烧结也是目前钢铁生产过程中烟气污染最严重的工序,其污染物排放量占比近40%。
因此,烧结工序节能减排潜力巨大。
为了更好地实现烧结工序的节能减排,本文重点介绍了烧结烟气的排放特点和烧结余热的利用现状,综述了厚料层烧结、烧结烟气循环、烧结矿余热高效回收利用等技术的优缺点,以期为现有烧结工序的节能改造提供依据。
关键词:烧结工序;节能降耗;技术措施前言钢铁行业是国民经济的重要基础产业,是重要的原材料工业,也是中国高耗能、高碳排放量的行业之一。
中国钢铁行业能耗约占全国总能耗的13%左右,碳排放量占全国碳排放总量的15%左右,是31个制造业门类中能耗量及碳排放量最大的行业。
以煤、焦粉为主的高炉、转炉长流程工艺结构在中国钢铁工业发展中长期占主导地位,转炉钢产量约占粗钢产量的80%。
而长流程钢铁工艺中,通常采用酸性球团矿和高碱度烧结矿合理搭配,以烧结矿为主,作为高炉炼铁的原料。
因此烧结工序是整个钢铁生产流程中重要的一环。
烧结工序的物料处理量在钢铁企业中仅次于炼铁,其能耗、碳排放量约占钢铁生产总能耗的10%~15%。
研究烧结过程节能、降碳措施有利于提高能源、资源利用效率,降低二氧化碳排放,促进钢铁行业实现生态化转型和绿色发展。
1烧结工艺碳素流、能量流分析烧结烟气具有排放量大、参数波动大及组成复杂的特点。
一吨烧结矿的烟气量高达4000~6000Nm3,烟气温度为80~180℃,O2体积分数为14%~18%,H2O体积分数为8%~13%,SO2质量浓度为400~5000mg/Nm3,NOx质量浓度为200~400mg/Nm3,CO体积分数为1%左右,CO2体积分数为7%左右,还含有氟化物和二噁英等多种污染物。
1.1烧结工艺主要功能烧结的生产过程是把精矿粉、燃料(焦粉、无烟煤)和熔剂(石灰石、白云石、生石灰)按一定比例配料混匀后,在烧结机上点火燃烧,利用燃料和铁氧化物氧化反应放出热量,使混合料局部熔化,并将散粒颗粒黏结成块状烧结矿,作为炼铁原料。
烧结工序生产工艺的节电措施

烧结工序生产工艺方面可以采取的节电措施。
1.在正常生产过程中尽量减少设备的空载运行时间。
控制好风机的风门是关键,并要做好烧结终点的控制工作,根据终点的提前或延后及时控制风机风门。
根据烧结过程情况及季节变化,选择合适的冷却风机台数及冷却风机的风门开度以节约电耗;
2.减少抽风系统的漏风率,增加通过料层的有效风量,对节约电耗意义重大。
烧结台车和首尾风箱(密封板)、台车与滑道、台车与台车之间的漏风占烧结机总漏风量的80%以上,因此改进台车与滑道之间的密封形式,特别是首尾风箱端部的密封结构形式,可以显著地减少有害漏风,增加通过料层的有效风量,提高烧结矿产量,节约电能;
3.及时更换、维护台车,改善布料方式,减少台车挡板与混合料之间存在的边缘漏风等,有效地减少有害漏风;
4.通过改造机头机尾密封装置,加强设备的维护、管理,使烧结机的漏风率明显降低,增加通过料层的有效风量,提高了烧结矿产质量,降低电耗;
5.减少设备空转时间,降低电耗;
6.严格控制各工段的操作时间,以便在出现生产事故停机时控制好各段的运行时间,减少不必要的停机。
提高设备的运转率及作业率,达到降低烧结工序能耗的目的。
钢铁厂烧结工艺的节能降耗设计探讨

钢铁厂烧结工艺的节能降耗设计探讨烧结工艺是钢铁厂能量消耗最大的环节,其消耗量将直接影响钢铁厂的经济效益,制约钢铁厂的发展。
为促进钢铁厂的快速发展,对钢铁厂烧结工艺进行节能降耗设计显得越来越重要。
论文就钢铁厂烧结工艺的节能降耗设计进行分析。
【Abstract】Sintering process is the most important part of energy consumption in iron and steel works. The part of the energy consumption will directly affect the economic benefits of steel plants,restrict the development in iron and steel plants. In order to promote the rapid development of iron and steel plants,it is more and more important to carry out energy saving design of sintering process of steel plants. This paper analyzes the energy saving design of the sintering process in iron and steel pants.标签:钢铁厂;烧结工艺;节能降耗1 引言钢铁厂降低烧结工艺的能量消耗,提高烧结工艺的生产效率,已经成为促进发展的核心部分。
保障生产产品质量同时,降低能量消耗,实现节能降耗的目的,将是钢铁厂长远发展的关键。
2 钢铁厂烧结工艺的概述根据钢铁相关原材料的不同特点,选择与之相应的加工程序,就是钢铁厂的烧结工艺。
钢铁厂烧结的过程中,烧结工艺的重要性不容忽视。
钢铁烧结过程影响生产产品质量。
浅谈钢铁厂烧结工艺的节能环保设计

浅谈钢铁厂烧结工艺的节能环保设计摘要:近几年来,钢铁行业产能过剩严重,整个行业的竞争环境日益恶劣,经济效益大幅滑坡,影响了行业的进一步发展,同时也给国家的节能环保造成重大压力。
钢铁厂的烧结部分是能量消耗的主要环节之一,通过技术创新,积极改进钢铁厂烧结工艺是钢铁厂实现节能环保的重要途径之一。
文章对烧结工艺的节能环保设计进行了介绍。
关键词:钢铁厂;烧结工艺;节能环保设计1 钢铁厂烧结工艺钢铁厂的烧结是原材料加工成钢铁的重要步骤,它通过烧结机将各种矿石依据高炉的需要加入一定的熔剂、燃料,通过点火燃料燃烧,在抽风作用下,在燃料提供热量下,将各种矿石通过液相粘结形成具有一定粒度的烧结矿,供高炉使用。
一般来说,钢铁厂的烧结工艺流程主要包括烧结前原料的预混处理,配料、混合加水、布料、点火、烧结、冷却、整粒等环节。
通过烧结工艺的创新设计,使得烧结工艺更加适应原材料的特性,保证烧结过程中产品的质量以及更进一步的节能、环保。
2 烧结工艺节能设计我国大部分钢铁厂都是以烧结矿作为高炉的主要炉料,烧结能耗是钢铁工业耗能的重要部分,主要包括固体燃料、点火燃料、电能消耗等。
所以,烧结环节要真正做到节能环保,就需要在以下几个方面进行设计。
2.1 降低固体燃料消耗一是实施厚料层烧结技术。
由于烧结过程中,厚料层烧结自动蓄热效果更高,可以有效降低燃料配比;烧结过程的边缘效应的比例降低,有利于烧结成品率的提高,单位产品消耗的燃料降低。
所以应该在机器设备允许的范围内逐步增高烧结机结料层的厚度。
二是科学回收利用生产过程中的含碳粉尘。
钢铁企业在烧结以及其它环节中会产生大量的含铁、含碳粉尘,通过控制粉尘中的有害杂质,在烧结环节采用混匀矿、小球烧结等方式加以利用,既代替了一部分固体燃料(例如焦粉),又回收了铁、碳等原材料。
三是采取措施改善固体燃料的燃烧效果和性能。
固体燃料的不完全燃烧是烧结热能损失的重要原因,可以通过控制燃料粒度以及粒度分布来改善烧结过程中的传热和燃烧速度,从而有效减少不完全燃烧比例。
- 1、下载文档前请自行甄别文档内容的完整性,平台不提供额外的编辑、内容补充、找答案等附加服务。
- 2、"仅部分预览"的文档,不可在线预览部分如存在完整性等问题,可反馈申请退款(可完整预览的文档不适用该条件!)。
- 3、如文档侵犯您的权益,请联系客服反馈,我们会尽快为您处理(人工客服工作时间:9:00-18:30)。
损失 , 以及开展 余热 利用 等节 能 问题 大有 文章 可做 。
2 传 统 型顶 喷 式 点 火器 在 我 厂 一烧 、 二 烧车 间的应用
2 1 点 火 器 结 构 型 式 .
点 火 器 安装 在烧 结 机 机 头 布 料 器 的后 面 , 构 结 较简 单 。在 我 国各 烧 结 厂使 用 的 点火 器 型式 大概 有 两种 : A传统 型 点火 器 , 是 一 个用 耐 火 材 料砌 筑 成 这 的炉 膛 , 由耐热 梁 支撑 悬 挂 于烧 结 机 的上 方 , 台车 可
ቤተ መጻሕፍቲ ባይዱ
我 厂 一 烧 、 烧 共 有 6台 烧 结 机 , 烧 结 机 机 头 二 在
安装 的 六 台点 火 器 结 构 型 式 是 一样 的 , 采 用 顶 喷 都 式传 统 型 结构 。其 简 图如 图 1 。
以上 。我厂 点火 器 向混 合 料 提 供 热量 占整 个 烧 结 过 程 所需 热量 的 8 。因此 , 好点 火器 结构 , 计高 效 % 选 设 率的燃 烧器 , 降低 单 位 面 积 的供 热 量 , 少 炉 体 的 热 减
维普资讯
9 0
包 钢 科 技
第 2 卷 8
台车 与 点火 器 炉 体 间 起 密 封 作 用 , 防止 了 冷 风 进 即 入 叉提 高 了热 利用 效 率 。 炉顶 采 用预 热 段 、 火段 、 点 保 温段 , 各段 各 成 一体 , 段 损 坏 都 能单 独 检 修 , 每 每 次节 省 2 3的检修 费 用 。 /
侧墙 长 度 方 向下 面安 装 3 0 5 MM 宽 的 白钢 密 封 板 , 对
收 稿 日期 :0 20 —0 2 0 —2 1 作 者 简 介 : 春 贵 (9 5 ) , 西 大 余 县 人 , 9 7年 毕 业 于 沈 阳大 学 北 院 工 业 炉 及 热 能 利 用 专 业 , 工 炉 窑 助 理 工 程 师 高 17一男 江 19 热 现从事热工 炉窑与 能源管理工 作。
,
文 章 编 号 :0 9—5 3 ( 0 2 0 —0 8 —0 10 4 820 )3 0 9 3
l 前 言
烧 结 点 火 器 担 负 着 的 主 要 任 务 是 把 台 车 上 的 表
热 合 金钢 做 成 , 特点 是 体 积小 , 量轻 , 构 简单 , 其 重 结 能 耗 低 , 点 是 烧 嘴寿 命 短 , 缺 检修 频 繁… 。
Jn 2 0 u e, 0 2
浅 谈 烧 结 点 火 器 与 节 能 途 径
高 春 贵
( 包钢 ( 团) 司炼 铁 厂 , 集 公 内蒙 古 包头 04 1) 10 0
摘 要 : 文论 述 了烧 结 点 火 器 结 构 与 烧 结 有 关 的 节 能 途 径 本 关 键 词 : 结 ; 火 器 ; 能 ; 径 烧 点 节 途 中 图分 类 号 : K 7 T 15 文 献 标 识 码 : B
矿 物结 晶条件 变 好 。 晶 度 提 高 , 结 矿 强 度 上 升 , 结 烧 成 品率 增加 , 次 , 其 料层 升 高 , 料层 蓄 热 量 增加 , 料层 高度 为 10 2 MM 时 , 热 量 只 点 燃 烧 带 总 收 入 8 —2 0 蓄
维普资讯
第 2 8卷 第 3期 20 0 2年 6月
包 钢 科 技
S in e& T c n lg fB oo te Gru )Co oa o ce c e h ooyo atuSe l( o p r rt n p i
Vo . 8. 1 2 No. 3
热量 散 失 多 , 体 使 用 寿命 短 。 为改变 以 上缺 点 , 炉 我
厂选 用 低水 泥 耐火 防爆高 强 度 浇注 料 , 炉两 侧 、 顶 炉 全部 浇 注而 成 , 温 效 果 好 , 量 散 失 少 , 体 使 用 保 热 炉
寿命 明显增 长 ( 以前延 长 两 年时 间检 修 ) 比 。沿 炉两
22 点 火 器 材 料 的 选 用 及 烧 结 的 改 进 和 节 能 效 果 .
2. 1 材 料 的 选 用 2.
层混合 料点燃 , 也就 是说 烧结 矿所 需 的热量 是 从点 火 器点火 开始 的 。一般 点 火 器 向混合 料提 供 的热 量 是
整 个 生 产 过 程 所 需 热 量 的 5 ~1 % , 者 可 达 1 % % 0 高 0
混合 料 稍加 预 热 , 高点 火 效 果 ; 点 火 器 后 部 , 提 在 一
般设 有保 温 罩 , 的 保 温 罩 安 装有 烧 嘴 起 继 续 加 热 有 作 用 , 的不设 烧 嘴 , 有 只起 防止 热 损 失和 表层 烧 结 矿 急 冷作 用 。B简 单 型 点 火 器 , 是 从 国 外 引 进 的先 这 进技 术 , 种点 火 器 实质 上 是 一个 高 效燃 烧 器 , 这 由耐
2. 2 烧 嘴 的 改 进 2.
3 1 厚 料 层 烧 结 节 能 途 径 . 国 外 烧 结 工 作 者 都 在 努 力 采 取 措 施 , 加 料 层 增 厚 度 , 到 节 能 与 增 产 的 目 的 , 理 由 是 , 先 厚 料 达 其 首 层烧 结 时 , 温 带 宽 度 相 应 地 增 加 , 结 速 度 减 慢 , 高 烧
图 1 顶 喷 式 点 火 器 结 构
台车
自由通过 炉 膛 的 底 部 。烧 嘴 有 的 安 装 在 炉 膛 两 侧 ,
称为侧 喷 式 ; 的安 装 在 炉 膛 的 顶 部 , 为 顶 喷 式 。 有 称 这种 结 构 的点 火器 , 部 一般 没有 预 热段 , 前 目的 是把 这 种 结 构 的 点 火 器 , 九 十年 代 初 两 侧 墙 都 采 在 用砖砌 筑 , 顶 用 预 制块 构 成 , 点 是 保 温效 果 差 , 炉 缺