DTY加工常见问题及解决方法
影响涤纶DTY染色均匀性的问题分析

影响涤纶DTY染色均匀性的问题分析涤纶DTY是一种化学纤维,具有强度高、耐磨损、耐化学腐蚀等优点。
在纺织行业中得到了广泛应用,尤其是在纺织品染色中。
然而,涤纶DTY染色的过程中,容易出现染色不均匀的问题。
这个问题对于生产和加工而言是非常棘手的,因为它会降低染色品质、裸露出白点和色差,影响产品的美观度。
本文将会探讨影响涤纶DTY染色均匀性的问题的原因和解决方法。
原因分析1.染料选择不当染色剂是染色过程中最关键的部分之一,选择不当可能会导致染色不均匀。
染色剂的颜色浓度、温度和染液的PH值等都会影响染色剂的效果。
若染色剂不配合涤纶DTY的物理特性,如硬度和垂度的差异等,就很容易引起染色不均匀的问题。
2.预处理不当涤纶DTY染色前,需要对其进行预处理,包括脱油、漂白、Mercerizing等处理。
如果预处理的时间不够、浓度不够导致残留等情况,都有可能影响涤纶DTY染色的均匀性。
3.工艺参数不精确染色工艺是非常复杂的,染色温度、染液比例、染色机器的转速等都会影响涤纶DTY的染色效果。
如果工艺参数不精确,就可能导致染色不均匀。
4.设备问题涤纶DTY的染色需要使用染色机器,如果机器性能有问题,比如旋转不稳定,或染色流程出现问题等都有可能导致涤纶DTY染色的不均匀性。
解决方法1.染料选择合适在选择染料时,需要考虑到其颜色浓度、温度,以及和涤纶DTY物理特性的配合。
在选取染料剂之前,建议通过试验检测,选择一种性能稳定的染料。
2.加强预处理在涤纶DTY染色之前,要对其进行足够充分的预处理,确保清洁度、柔软度、可染性等,防止残留导致染色不均匀。
3.精确控制工艺参数在染色过程中,需要精确控制染色温度、染液比例、染色机器转速等参数,防止其偏差导致染色不均匀。
4.设备维护对涤纶DTY染色过程中的设备进行维护和保养,比如清理机器、保持相对湿度等可以有效防止设备偏差影响染色均匀性。
结语涤纶DTY染色不均匀对于纺织企业生产和加工都是非常不利的,因此需要重视该问题的解决。
DTY生产过程问题类型及排查规范
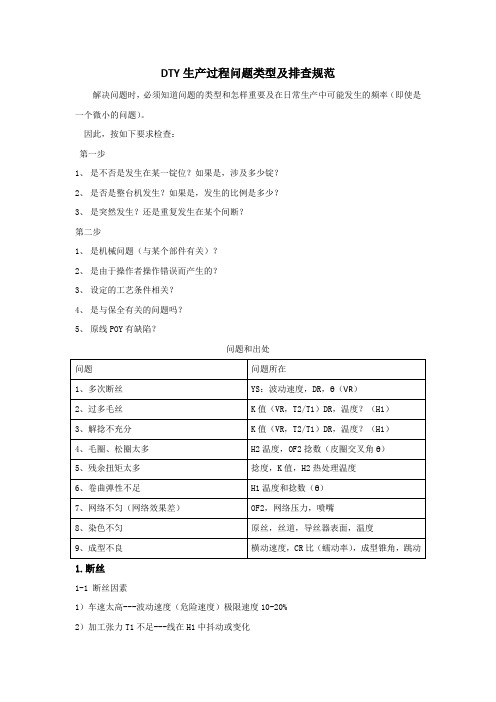
DTY生产过程问题类型及排查规范解决问题时,必须知道问题的类型和怎样重要及在日常生产中可能发生的频率(即使是一个微小的问题)。
因此,按如下要求检查:第一步1、是不否是发生在某一锭位?如果是,涉及多少锭?2、是否是整台机发生?如果是,发生的比例是多少?3、是突然发生?还是重复发生在某个间断?第二步1、是机械问题(与某个部件有关)?2、是由于操作者操作错误而产生的?3、设定的工艺条件相关?4、是与保全有关的问题吗?5、原线POY有缺陷?问题和出处1.断丝1-1断丝因素1)车速太高---波动速度(危险速度)极限速度10-20%2)加工张力T1不足---线在H1中抖动或变化3)POY退绕不良、毛丝、成型不良(如蛛网丝)4)生头错误,包括丝路不正和过尾丝5)诸如皮圈磨损而造成拉伸不足(保养不周)1-2 断头的防止为了避免丝的断头,做如下的一种改变:1)稍为增加DR---以增加T1→检查最终纤度2)减少皮圈交叉角θ,减少捻数→必须随即调整张力比T2/T1,用VR(VR也下降)。
·随着捻数的下降,丝的运行更加稳定(有更大的调整范围)。
在这方面,蓬松性(卷曲弹性)将变小。
3)降低YS50---10m/min(但会牺牲产量)。
1-3 机台各个部件的检查1)加工条件是否合适?YS、DR、VR、CP、θ。
2)所有的陶瓷导丝器都正常吗?3)POY损伤?各个罗拉皮圈是否磨损?运行正常吗?丝在H1内抖动吗?假捻器前后张力不足或有变化?网络喷嘴会倒吹丝吗?卷绕张力恰当和稳定吗?是否由于成型不良(脱边)丝被切断。
2.毛丝2-1 毛丝原因1)解捻张力太高(K值太高)。
2)H1温度太高,引起丝的燃烧。
3)DR太高,丝被过分拉伸。
4)捻数太低,在运行中对丝产生损害并产生毛丝和松圈(T1太大)。
5)由于丝路上的导丝器的磨损、裂缝、或抛光不良造成对丝的伤害。
---必须仔细检查。
6)POY油剂不匹配(包括摩擦系数、耐热性能等等)。
DTY生产过程中网丝、毛丝产生原因及解决办法
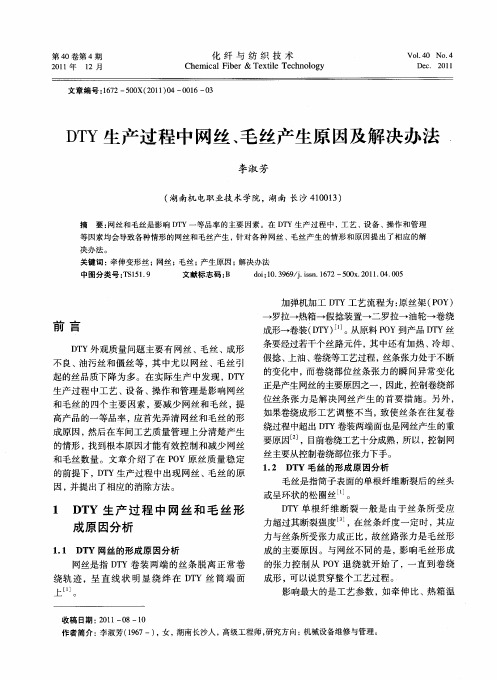
李淑芳 : T D Y生产 过程 中网丝 、毛丝产 生原因及解决办法
1 7
度、 假捻器的配置 、 喂率等 , 超 故工艺参数调整 是质量的首要保障 , 丝路张力的控制是减少毛丝 的有效 途径 。
因后即更换筒管, 并将信息反馈给筒管厂家 ; 另 外, 检修 时对筒管夹及其轴承应定期检查 , 如发
成原 因分析
1 1 DT 网丝 的形成 原 因分路张力是毛丝形
成 的主要原 因 。与 网丝 不 同 的是 , 响毛 丝形 成 影
网丝是指 D Y卷装两端 的丝条脱离正常卷 T 绕轨 迹 , 直线 状 明显 绕 绊在 D Y丝 筒端 面 呈 T
的张力控制从 P Y退绕就开始了, O 一直到卷绕
可 能 没有 放 到位 ,没 被筒 管夹 牢 牢 卡住 , 筒 管 使 与 卷 绕 黑 辊 不 平 行 ,卷 装 在 卷 绕 过 程 中跳 动 严
决办法。
关键词 : 牵伸变形丝 ;网丝 ; 毛丝 ; 生原 因 ; 产 解决办法
中图 分 类 号 :S 5 . T 1 19 文 献标 志 码 : B d i1 .99 ji n 17 o:0 3 6 /.s .62—50 .0 10 .0 s 0 x2 1.4 0 5
加弹机加 工 D Y工 艺 流程 为 : 丝 架 ( O T 原 P Y)
1 2 DT 毛丝 的形成 原 因分析 . Y
毛 丝是 指筒子 表 面的单根 纤维 断裂后 的丝 头 或 呈环 状 的松圈丝 。
1 DT 生 产 过 程 中 网 丝 和 毛 丝 形 Y
D Y单 根 纤 维 断 裂 一 般 是 由于 丝 条 所 受 应 T 力 超过 其断 裂强度 j ,在丝 条 纤 度一 定 时 , 应 其
涤纶DTY质量对织造的影响及改进

涤纶DTY质量对织造的影响及改进涤纶长丝以其独特的风格被广泛应用于服装、装饰等领域,随着纺丝技术的不断改进以及人们对服装要求的多样性与个发货舒适性的追求,对涤纶长丝的质量要求也越来越高。
由于DTY生产过程控制及检测手段的局限性,DTY的一些质量问题只有到织造过程中才显现出来。
跟踪某公司最近三年的售后服务情况,客房反馈比较多的质量问题主要有色差或横条、僵丝、毛丝、织造效率低(退绕)、网络及其他,它们所占的比重如图1。
这些质量缺陷除了由织造、染整工艺或者设备的因素造成外,主要是从DTY原料中带来的。
随着用户对织造效率、成品率和染色均匀性能的要求更加严格,尤其是随着DTY市场竞争日趋白热化以及新投产厂家的设备优势,涤纶DTY生产厂家都在不断提升DTY 的质量,加大检测力度,提供客户满意的产品。
分析与讨论1色差或横条1疵点现象及原因从图1可以看出,布面色差或横条是DTY在织造过程中最常见的质量缺陷,同时也是造成损失最大的质量问题。
它是在织物上出现的并轴整数倍的有色差经纱,或者在纬向上反映出来的条状色差,或者经纬向色差不一致;在针织物中会在间隔等于总筒子数生产一圈的宽度距离(俗称一个纱线循环)上出现等距横条。
色差和横条现象主要是某一些锭的线密度、吸色性、卷曲收缩率与同批号丝锭之间存在差异,以至在织成的坯布上出现横条或疵布,经染整后出现色差横条,经过贴胶海棉或者磨毛等后整理以后,色差变得更加明显。
线密度差异会使织物粗糙或者透光异常、异经;着色差异产生色差;卷曲收缩率差异,经染整高温处理后会使织物局部尺寸稳定性差,由于收缩差异造成横条。
2解决办法要解决线密度、吸色性和卷曲收缩率这三个影响染色的问题,必须要从POY原料开始着手进行全流程管理。
在生产过程中必须保证线密度的均匀性,及时处理漏浆组件、计量泵,飘丝要严格分流。
加强管理,避免混批、错位丝的生产,切片或者熔体质量、组件周期、侧吹风冷却条件要稳定;生产工艺参数中压力、压差、温度、速度必须保持稳定,制定严格的波动分流标准;加强锭位管理,减少锭位差异;对到期的DTY设备部件如假捻盘、皮圈、罗拉等整批更换,保持所有锭位加工条件一致;DTY加工过程丝道必须保持一致;采用更严格的判色标准,实践证明采用国标所使用的灰卡标准判色越来越难以满足用户日益严格的染色需求,往往造成小色差情况,目前很多厂家已经采用4.5级的标准,并且以加织标样作为参考的形式对产品颜色进行深、中、浅三色细分,进一步提高产品的染色均匀性;另外可根据客户织物的特点加工,如纬编织物,可提高DTY的卷曲收缩率,这样DTY的弹性好且丰满,织物染色整理后可掩盖一些轻微条纹。
DTY常见疵点成因分析

常见疵点的成因分析毛丝A、局部性1、原丝受机械损伤;2、导丝器(瓷件)损伤;3、丝路不正,与非接触部件接触;4、POY原丝少油或无油;5、第一或二热箱不干净,有积垢;6、假捻器摩擦盘损伤;7、卷绕筒管轴上的废丝触及卷装中丝束;8、导丝器位置不正。
B、整机性1、牵伸倍数太高;2、温度过高或过低;3、加工速度太高;4、D/Y比太低;5、摩擦盘(数或材质)不适用于丝的品种和纤度;6、静电的影响,尤以定型区为甚;7、原丝的上油率太低;8、油剂类型不当。
断头率高A、局部性1、卷绕筒管严重磨损;2、原丝受机械性磨损;3、压辊磨损或调校不准;4、卷绕筒管不平行;5、假捻器摩擦盘损伤;6、导丝器位置不正。
B、整机性1、加工速度太高,不适合原丝种类;2、牵伸倍数不适当;3、张力太低;4、张力比太高;5、摩擦盘(数或材质)不适用于丝的品种和纤度;6、原丝油剂不当;7、检测器误动作;8、定型超喂(OF2)过高;9、第一热箱温度太高。
紧点A、局部性1、W1或W2皮圈损伤、跑偏;2、W1或W2皮圈轮坏;3、W1或W2皮圈握持力太小;4、丝路不正或有缠丝。
B、整机性1、牵伸倍数太低;2、D/Y比没有按纤度调校到最佳;3、加工速度太高导致生产过程不稳定;4、第一热箱温度太高。
绊丝、蛛网丝A、局部性1、筒管架不平行(一侧发生);2、动程太大;3、横动导丝器松脱或磨损。
B、整机性1、卷绕张力太高;2、卷绕角太小;3、轴向干扰幅度太高;4、在最大动程时,轴向静止角太低;5、锥体角度太低;6、径向干扰太高。
筒子退绕性能差A、局部性1、动程长度太长;2、丝束自横动导丝器逃出;3、蛛网丝。
B、整机性1、卷绕张力太低(卷装松软);2、卷绕角度太高;3、径向干扰太低;4、锥体角度太低;5、轴向干扰幅度太低;6、含油太低;7、毛丝。
涤纶短纤维后加工操作要点和故障处理
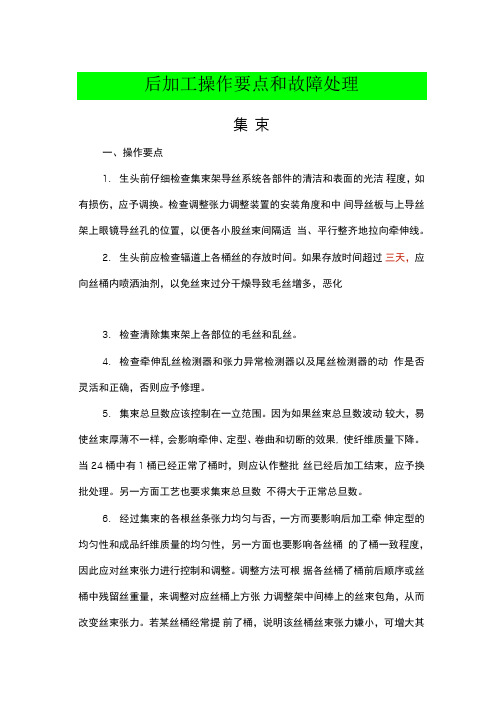
集束一、操作要点1.生头前仔细检查集束架导丝系统各部件的清洁和表面的光洁程度,如有损伤,应予调换。
检查调整张力调整装置的安装角度和中间导丝板与上导丝架上眼镜导丝孔的位置,以便各小股丝束间隔适当、平行整齐地拉向牵伸线。
2.生头前应检查辐道上各桶丝的存放时间。
如果存放时间超过三天,应向丝桶内喷洒油剂,以免丝束过分干燥导致毛丝增多,恶化3.检查清除集束架上各部位的毛丝和乱丝。
4.检查牵伸乱丝检测器和张力异常检测器以及尾丝检测器的动作是否灵活和正确,否则应予修理。
5.集束总旦数应该控制在一立范围。
因为如果丝束总旦数波动较大,易使丝束厚薄不一样,会影响牵伸、定型、卷曲和切断的效果, 使纤维质量下降。
当24桶中有1桶已经正常了桶时,则应认作整批丝已经后加工结束,应予换批处理。
另一方面工艺也要求集束总旦数不得大于正常总旦数。
6.经过集束的各根丝条张力均匀与否,一方而要影响后加工牵伸定型的均匀性和成品纤维质量的均匀性,另一方面也要影响各丝桶的了桶一致程度,因此应对丝束张力进行控制和调整。
调整方法可根据各丝桶了桶前后顺序或丝桶中残留丝重量,来调整对应丝桶上方张力调整架中间棒上的丝束包角,从而改变丝束张力。
若某丝桶经常提前了桶,说明该丝桶丝束张力嫌小,可增大其张力调整架的丝束包角,反之,若某丝桶的桶脚丝一直较多,说明该桶位丝束张力嫌大,这时可减小其张力调整架的丝束包角。
通过调整,可控制各丝束张力均匀一致,从而防止集朿后的大股丝朿中出现“荡丝”、“拖尾丝”等现象。
7.按照操作规程进行集束生头,要求剪去丝端硬头,丝条在导丝架各部件上穿丝位置正确,无扭结、交叉现象。
8.正常生产过程中,应加强巡回检查,发现荡丝、吊丝以及丝条缠结时,可采取停车或不停车处理。
当集束架各导丝罗拉上存有毛丝、乱丝时,应及时清除,以免被丝束带入后加工生产线,形成疵点。
9.集束采用整批换桶,一般中途不补加丝束,但如遇特殊情况处理半桶丝时,可补加丝束,应避免打结,而只需将补加丝头嵌入其它丝束之中即可(待卷曲前将未拉伸部分剪去)。
DTY生产产生僵丝原因分析与解决对策

初始浓度100mg·L-1时,改性木质纤维素对Cr(VI)的去除率大于98%[14]。
4 结语木质纤维素作为地球上最丰富的可再生资源,对作物秸秆及废弃纸张和木材废料纤维回收开发利用,既减少了丢弃废弃物对环境污染的负面影响,又提高了废物的再利用。
另一方面,通过对纤维素的微生物降解或化学改性,应用于重金属废水处理,方法简单、价格便宜、环境友好,为重金属废水的处理提供一种新型、高效吸附剂,有望将来应用到实际生产中。
参考文献:[1]P. Tan, Y. Jiang, X.Q. Liu, D.Y. Zhang,L.B. Sun. Magnetically Responsive Core-Shell Fe3O4@C Adsorbents for Efficient Capture of Aromatic Sulfur and Nitrogen Compounds. ACS Sustainable Chem. Eng.2016,4,2223-2231. [2]王莉.植物废弃原料纤维素提取技术研究进展[J].广州化工,2018,46(12):24-25.[3]杨阳,李春露,崔志芳.两种化学预处理方法对小麦秸秆纤维素的影响[J].化学与生物工程,2017,3(10):61-64.[4]蒋艺,苏宁,方诩.木质纤维素降解酶生产菌株的遗传改造及应用[J].微生物学报,2017,57(8):1235-1248. [5]何水清,艾士奇,王建豪,等.木质纤维素分解复合菌系的分解特性与细菌组成多样性分析[J].江苏农业科学, 2017,45(16):241-246.[6]李淼淼,沈飞,张庆华.纤维素降解复合菌系的微生物多样性及关键功能菌解析[J].环境科学学报,2018, 38(7):2690-2695.[7]国巍,燕红,裴蕾.可降解木质纤维素的双菌共生菌丝球的制备[J].哈尔滨理工大学学报,2018,23(4):127-132.[8]林青雯,赵琪,高梦凡,等. Fe3O4/纤维素纳米复合材料的制备及其对亚甲基蓝的吸附[J].环境工程学报,2016,10 (11):6451-6556.[9]商文婷,盛占武,谷满囤,等.丁二酰化香蕉纤维素对Pb2+的吸附性能及其结构表征[J].中国食品学报,2017, 17(7):25-33.[10]叶满辉,王丽,杜慧琴.聚天冬氨酸/木质纤维素水凝胶对Pb(Ⅱ)的吸附及脱附性能[J].2016,32(11):63-68.[11]史艳茹,薛振华,王喜明,等.木质纤维素-g-丙烯酸/蒙脱土水凝胶制备及吸附性能研究[J].功能材料,2014, 44(4):502-506.[12]谷军,周冠成,吴伟兵,等.改性纤维素微球的制备及其对Pb2+吸附性能的研究[J].纤维素科学与技术,2014, 22(3):8-13.[13]黄沅清,杨春平,孙志超,等.氨三乙酸酐改性纤维素对Cd2+的吸附性能[J].环境科学学报,2015,(6):1792-1799.[14]李晨,王培丽.改性木质纤维素对水溶液中Cr(VI)的吸附性能研究[J].河南工业大学学报,2014,35(3):68-71.作者简介:韦燕婷(1995-),女,汉族,海南白沙人,西北民族大学本科生,化工学院化学工程与工艺专业。
【百科】涤纶纺纱各工序常见问题的处理
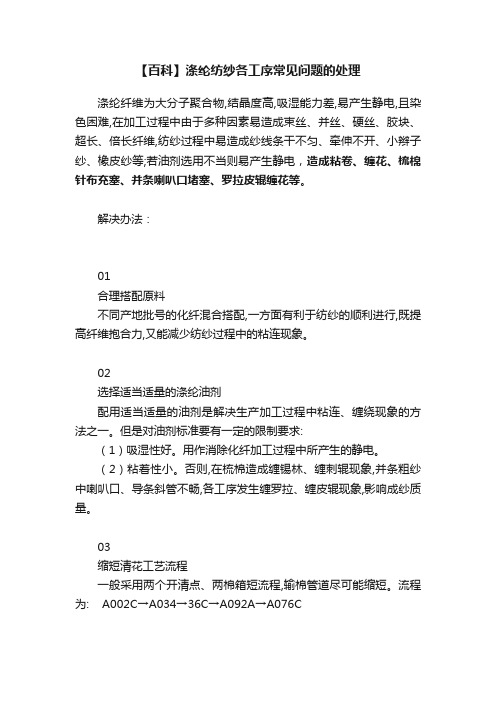
【百科】涤纶纺纱各工序常见问题的处理涤纶纤维为大分子聚合物,结晶度高,吸湿能力差,易产生静电,且染色困难,在加工过程中由于多种因素易造成束丝、并丝、硬丝、胶块、超长、倍长纤维,纺纱过程中易造成纱线条干不匀、牵伸不开、小辫子纱、橡皮纱等;若油剂选用不当则易产生静电,造成粘卷、缠花、梳棉针布充塞、并条喇叭口堵塞、罗拉皮辊缠花等。
解决办法:01合理搭配原料不同产地批号的化纤混合搭配,一方面有利于纺纱的顺利进行,既提高纤维抱合力,又能减少纺纱过程中的粘连现象。
02选择适当适量的涤纶油剂配用适当适量的油剂是解决生产加工过程中粘连、缠绕现象的方法之一。
但是对油剂标准要有一定的限制要求:(1)吸湿性好。
用作消除化纤加工过程中所产生的静电。
(2)粘着性小。
否则,在梳棉造成缠锡林、缠刺辊现象,并条粗纱中喇叭口、导条斜管不畅,各工序发生缠罗拉、缠皮辊现象,影响成纱质量。
03缩短清花工艺流程一般采用两个开清点、两棉箱短流程,输棉管道尽可能缩短。
流程为: A002C→A034→36C→A092A→A076C开清棉工序中各部打手速度不宜过高,各部落杂区隔距宜小。
但是若原料中粗硬丝、并丝、倍粗倍长纤维胶块含量较高时,各部打手速度可适当提高,各落杂区隔距可适当放大,以争取最大限度的排除异形纤维。
04清花工序中产生的棉卷膨松、粘连现象处理方法(1)加装积极回转的凹凸防粘罗拉,对棉层上下压紧刻出印痕,以起到防粘作用。
(2)采用单尘笼吸棉。
关闭下尘笼可减少粘层结合而单尘笼吸棉,在打手到尘棒间通道两侧加装边长50mm及190mm外包铁皮的直角三角形木块,可解决棉层两侧厚边现象。
(3)增大紧压罗拉压力,使纤维集聚紧密。
(4)缩短棉卷长度,加重棉卷定量。
棉卷长度以25~30mm为宜,棉卷定量以350g/m为宜。
(5)采用5~7根粗纱夹入花卷外层。
05解决梳理静电缠绕问题在梳棉工序中,涤纶易与分梳元件摩擦产生静电,且不易消除,易造成缠绕锡林、道夫、盖板、刺辊等,且棉条膨松易堵塞喇叭口。
锦纶(PA6)DTY僵丝成因分析

锦纶(PA6)DTY僵丝成因分析DTY长丝又称拉伸假捻变形丝,具有一定的蓬松性、伸缩性、手感柔和、保暖、衣着舒适、抗疲劳(耐磨)、染色好、色牢度高等优点。
因此,DTY长丝在纺织及航天军工领域得到广泛应用,纺织方面主要用于经编、纬编、混纺、包纱(芯为橡根、氨纶等)、织带、无缝内衣、运动服装、服装面料、手套、花边等,航天军工领域主要用于降落伞、绳索、作战训练服等。
在DTY长丝生产过程中,多种原因会导致拉伸假捻状态不稳定而产生僵丝,对其下游产业造成不良影响,织物染色后出现色斑、横条、织物表面产生麻感,甚至下游客户加工过程中发生断纱。
为此,因僵丝问题时常会引起下游客户不满意,产生质量投诉甚至索赔。
1、DTY生产工艺流程简介:POY→第一罗拉→止捻器→热箱→冷却板→假捻器→第二罗拉→(网络喷嘴)→断丝传感器→上油→卷绕→DTY2、僵丝的外观特点及在织袜染色检验时袜带上的表象:无论哪种僵丝,外观表象具有卷曲蓬松性不足,在织袜染色时袜带上表现出颜色较深的色点或条纹(与正常色比较)。
3、僵丝的种类有:长段僵丝、紧捻僵丝、紧点僵丝、叠捻僵丝。
3.1、长段僵丝:卷曲蓬松性不足或基本无卷曲蓬松性,长度通常在1厘米以上,甚至几十厘米。
与POY性状相近,袜带透明,且染色后出现横纹甚至有规律性。
3.2、紧点僵丝:单丝直接发生黏连形成结点,手感发硬,在一定外力作用下不易打开结点,一般情况下在同一锭位发生后会反复出现,多为原料POY的质量问题引起。
3.3、紧捻僵丝:在丝条上形成瘦弱状的细节,与正常丝条部分相比蓬松性差,手感偏硬,在一定外力作用下可以拉开,织物或袜带表面纹理不清,有色斑。
3.4、叠捻僵丝:又称复捻丝,在加捻过程中产生捻度重叠,自然状态下丝条不匀称不光滑,带刺状,袜带透薄,表面不平整带绒感(较烂)。
4、僵丝的成因(表现在假捻张力不稳定):4.1、原料(POY)的质量问题:4.1.1、松圈(单纤凸起):因POY加工工艺问题或设备原因产生松圈丝,在DTY加工过程中导致假捻张力波动而产生僵丝,严重的松圈丝会导致DTY加工时断头大,僵丝多发且长段。
化纤知识(涤纶短纤)
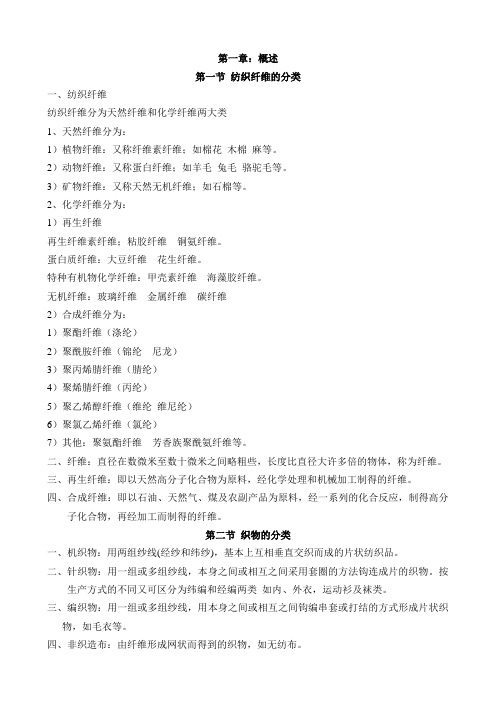
第一章:概述第一节纺织纤维的分类一、纺织纤维纺织纤维分为天然纤维和化学纤维两大类1、天然纤维分为:1)植物纤维:又称纤维素纤维;如棉花木棉麻等。
2)动物纤维:又称蛋白纤维;如羊毛兔毛骆驼毛等。
3)矿物纤维:又称天然无机纤维;如石棉等。
2、化学纤维分为:1)再生纤维再生纤维素纤维;粘胶纤维铜氨纤维。
蛋白质纤维:大豆纤维花生纤维。
特种有机物化学纤维:甲壳素纤维海藻胶纤维。
无机纤维:玻璃纤维金属纤维碳纤维2)合成纤维分为:1)聚酯纤维(涤纶)2)聚酰胺纤维(锦纶尼龙)3)聚丙烯腈纤维(腈纶)4)聚烯腈纤维(丙纶)5)聚乙烯醇纤维(维纶维尼纶)6)聚氯乙烯纤维(氯纶)7)其他:聚氨酯纤维芳香族聚酰氨纤维等。
二、纤维:直径在数微米至数十微米之间略粗些,长度比直径大许多倍的物体,称为纤维。
三、再生纤维:即以天然高分子化合物为原料,经化学处理和机械加工制得的纤维。
四、合成纤维:即以石油、天然气、煤及农副产品为原料,经一系列的化合反应,制得高分子化合物,再经加工而制得的纤维。
第二节织物的分类一、机织物:用两组纱线(经纱和纬纱),基本上互相垂直交织而成的片状纺织品。
二、针织物:用一组或多组纱线,本身之间或相互之间采用套圈的方法钩连成片的织物。
按生产方式的不同又可区分为纬编和经编两类如内、外衣,运动衫及袜类。
三、编织物:用一组或多组纱线,用本身之间或相互之间钩编串套或打结的方式形成片状织物,如毛衣等。
四、非织造布:由纤维形成网状而得到的织物,如无纺布。
五、其他特种织物:如由两组(或多组)经纱,一组纬纱用梭织方法生产三向织物,三维织物。
第三节纤维分类一、长丝:包括单丝、复丝和帘子丝。
1、单丝:指用单孔喷丝板纺制而成的一根连续单纤维。
但在实际应用中,往往也包括3---6孔喷丝板纺制的3---6根单纤维组成的少孔丝。
较粗的合成纤维单丝(直径0.02—2mm)称为鬃毛,用作绳索毛刷日用网兜鱼网等,细的用作透明丝袜等其他用品。
DTY僵丝产生原因的探讨

DTY僵丝产生原因的探讨DTY加工中僵丝经常不同程度影响DTY染色一等品率及外观降等,从而影响DTY最终的一等品率、合格品率及单耗,在POY质量不稳定时表现尤为明显。
僵丝对后道工序的加工质量影响也较大,常引起用户的质量反馈。
现根据多年的生产经验从产生僵丝现象入手,分析其形态特征、产生原因,以便将生产中的僵丝降到最低程度。
1僵丝形态特征 DTY僵丝在实际生产中表现在DTY卷装外观上为长短不一的、不膨松的点(1~5cm),反应在试验袜筒上为深色点状或条纹,具体主要存在以下几种形态:1.1单丝粘连深色点状型(僵丝长度在1cm以下且在袜筒上呈深色点状) 若将袜筒剪开,小心抽出相应的DTY丝条时即会发现产生深色点处的DTY单纤维呈粘连状态,无法分开。
这种僵丝的形成主要发生在受热过程中,纤维某处薄弱环节(即分子间力强度、大分子链的刚性、单体单元位置的规整性较正常低)熔点较低,受热时单丝融合在一起,即使解捻后纤维也不能够分开,染色僵点上呈深色点。
1.2单丝未粘连的深色点状型(僵丝长度在1cm以下) 若将袜筒剪开,小心抽出相应的DTY丝条时即会发现产生深色点处的DTY丝条的膨松性差,单纤维扭结在一起,形状如网络节,握紧丝条两端用一定的力,深色点处的单丝松开,单丝有明显的丝圈和丝辫,与1.1不同的是DTY单纤维并没有粘连在一起,这是单纤维扭结在一起没能顺利解捻嘭松造成的。
丝条在受热变形时,由于受不利因素影响发生捻度传递不匀,丝条在迁移过程中受到扭矩不均匀形成特异点,解捻后,特异扭矩作用使复丝缠绕在一起,造成嘭松性差。
染色时,这些不良部位反应在袜筒上为深色点。
1.3长短不一的深色条纹在试验袜筒上表现为长短不一而纤细的深色条纹,将丝条抽出后观察同1.2类型相差不多,只是有色差处单纤维纠缠稍长一些(1~5cm)或在几十厘米范围内出现连续不断的点状僵丝,说明不利因素变化不定,不象1.2类型不利因素变化不大。
1.4有规律的深色条纹在试验袜筒上表现有规律的深色条纹,将丝条抽出后观察同1.2类型相差不多,只是有色差的丝条长度一致,比较有规律,说明不利因素是某个固定因素。
涤纶DTY染色不良原因分析及预防措施

涤纶DTY 染色不良原因分析及预防措施陈伟群,陈杰,杨剑飞,刘春福,崔利(桐乡市中维化纤有限公司,浙江桐乡314513)摘要:通过对DTY 染色不良的种类分析,结合聚酯、POY 纺丝工艺条件、DTY 工艺参数设定等因素,对造成DTY 染色不良的各原因进行分析,并对相应的解决办法进行分析探讨。
关键词:条干不匀率;拉伸变形丝;染色不良;风速;拉伸比;D/Y 比中图分类号:TS193文献标志码:Bdoi:10.3969/j.issn.1672-500x.2019.01.004收稿日期:2018-12-03作者简介:陈伟群(1981-),女,浙江桐乡人,工程师,主要从事涤纶长丝检验。
文章编号:1672-500X (2019)01-0014-04第48卷第1期化纤与纺织技术Vol.48No.12019年3月Chemical Fiber &Textile TechnologyMar.20190前言涤纶DTY (Draw texturing yarn),即拉伸变形丝,是在加弹机上进行连续或同时拉伸、经过假捻变形加工后的成品丝,可直接用于织造,因此DTY 的染色均匀性直接影响成品面料质量。
其中染色M 率是检验DTY 品质的重要指标之一,染色的均匀性会直接反应在织造的面料上,如果染色M 率较低,说明染色均匀性差,染色不良纱较多,不仅造成DTY 生产厂家的优等率降低,DTY 染色不良纱会造成几十万米的面料降等,严重影响企业经济效益。
分析并解决造成DTY 染色不良的产生原因有助于提升产品质量,减少不必要损失。
1DTY 染色不良的形态特征DTY 染色均匀性直接影响DTY 的等品率,影响生产厂家的经济效益。
生产上常用染色M 率来表示,根据染色后的袜筒颜色深浅、段斑的长短等判定不良丝。
染色不良形态主要有以下几种。
1.1F 丝,又称段斑丝F 丝(段斑丝)是横向条纹丝(见图1),是指同一试样染色袜带中夹杂着带有明显色差的条纹。
涤纶DTY僵丝形成原因及其利用

文献识别码 { B
文章编号 :10—0120)305 3 0104 (030 050
涤 纶 D Y 生 产 中有 时会 遇 到 大 量僵 丝 , T 且 采 取各种措 施也很难 有效 解决 。这 种含有 大量僵 丝 的 DT Y织 物 染色 后 有 明显 色斑 , 麻感 显 著 , 外 观有提 花风格 . 如果人 为控 制其规律 , 生产 出这 种 别有 风格的长丝 . 失为 一种 好的选择 。 不 竹节 丝就
是这种 含有大量 僵丝的 长丝 。
3 产 生僵 丝 的 原 因
3 1 D Y工 艺参数的影 响 . T
3L 1 拉伸 比 ( . DR )
拉 伸过 程 中 , 由于 取 向和结 晶效 应 使 内能 增 加, 其弹性 回复力 也增大 。另一 方面 , 由于 DR与 张 力 的 比值 K ( T ) 正 比 , DR增 大 . T/ 成 而 加 捻张 力 7 增 加较小 , 捻张 力 r。 加较大 , 且 ’ 解 厂增 并 丁 的增大量 大于弹性 回复力 的增 大量 。因此 DR 增大 , 僵丝减 少 , 反之则 解捻 张力的减 少量也大 于 弹性 回复 力 的减 少量 , 使解捻 张 力不 足 于克服 致 弹性 回复力 , 随即出现僵丝 。
许 文 珠
( 海 裕 华股 份有 限 公 司 . 东 珠 海 5 98 ) 珠 广 1 00 摘 要: 从工艺、 设备、 原丝、 操作等方面分析了潦培 D Y瑁墼的形成原因, T 井通过工艺调整 使僵丝间 D Y 僵丝 T 竹节丝
隔 出现 生产 出竹 节 丝 ,
关键调 : 涤纶长丝中圉分类 Nhomakorabea : Q 4. T 322
j 型垫塑』 室 一
j 丝J 塑三 一
DTY品质管理培训
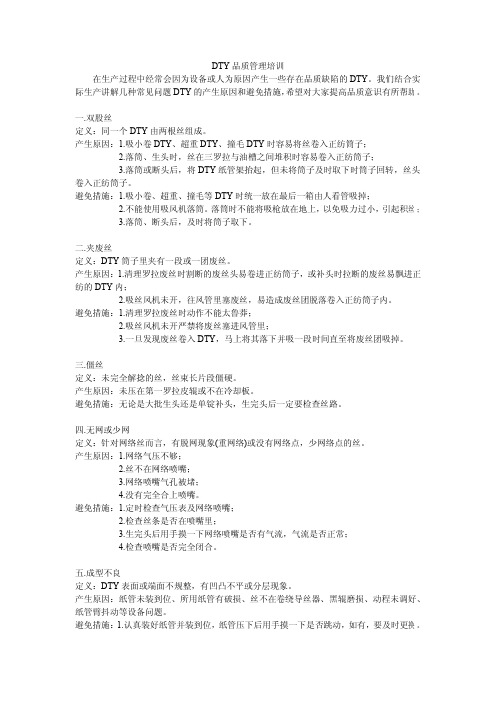
DTY品质管理培训在生产过程中经常会因为设备或人为原因产生一些存在品质缺陷的DTY。
我们结合实际生产讲解几种常见问题DTY的产生原因和避免措施,希望对大家提高品质意识有所帮助。
一.双股丝定义:同一个DTY由两根丝组成。
产生原因:1.吸小卷DTY、超重DTY、撞毛DTY时容易将丝卷入正纺筒子;2.落筒、生头时,丝在三罗拉与油槽之间堆积时容易卷入正纺筒子;3.落筒或断头后,将DTY纸管架抬起,但未将筒子及时取下时筒子回转,丝头卷入正纺筒子。
避免措施:1.吸小卷、超重、撞毛等DTY时统一放在最后一箱由人看管吸掉;2.不能使用吸风机落筒。
落筒时不能将吸枪放在地上,以免吸力过小,引起积丝;3.落筒、断头后,及时将筒子取下。
二.夹废丝定义:DTY筒子里夹有一段或一团废丝。
产生原因:1.清理罗拉废丝时割断的废丝头易卷进正纺筒子,或补头时拉断的废丝易飘进正纺的DTY内;2.吸丝风机未开,往风管里塞废丝,易造成废丝团脱落卷入正纺筒子内。
避免措施:1.清理罗拉废丝时动作不能太鲁莽;2.吸丝风机未开严禁将废丝塞进风管里;3.一旦发现废丝卷入DTY,马上将其落下并吸一段时间直至将废丝团吸掉。
三.僵丝定义:未完全解捻的丝,丝束长片段僵硬。
产生原因:未压在第一罗拉皮辊或不在冷却板。
避免措施:无论是大批生头还是单锭补头,生完头后一定要检查丝路。
四.无网或少网定义:针对网络丝而言,有脱网现象(重网络)或没有网络点,少网络点的丝。
产生原因:1.网络气压不够;2.丝不在网络喷嘴;3.网络喷嘴气孔被堵;4.没有完全合上喷嘴。
避免措施:1.定时检查气压表及网络喷嘴;2.检查丝条是否在喷嘴里;3.生完头后用手摸一下网络喷嘴是否有气流,气流是否正常;4.检查喷嘴是否完全闭合。
五.成型不良定义:DTY表面或端面不规整,有凹凸不平或分层现象。
产生原因:纸管未装到位、所用纸管有破损、丝不在卷绕导丝器、黑辊磨损、动程未调好、纸管臂抖动等设备问题。
DTY生产工艺及参数设定 (2)

DTY生产工艺及参数设定DTY是有POY(预取向丝)通过假捻而形成的,我们公司的DTY设备是TMT公司的ATF-1500SZ加弹机,加弹机是由拉伸变形区、定型区、卷绕区所组成的。
整个流程是:原丝架→切丝器→第一罗拉(FR1)→生头杆导丝器→第一加热箱(H1)→冷却板→假捻器→张力器→第二罗拉(FR2)→网络喷嘴→第二罗拉A(FR2A)→第二加热箱(H2)→第三罗拉(FR3)→探丝器(感应器)→上油轮→卷绕成型装置。
一、设备简述?????第一罗拉为喂入罗拉,其装置有两种组成方式。
一个是喂丝罗拉和皮圈,另一个是喂丝罗拉和皮辊,皮圈的优点接触面积大、握持力大、可减少轴承磨损,其缺点是易损坏。
而皮辊的优点是耐磨且可多次使用,其缺点是握持力不足,须在辊上绕圈弥补。
我司设备是由喂丝罗拉和皮辊组成的,在FR2上必须绕两圈,在加工细旦时还需在FR1上绕两圈(移丝间距一般为5-10mm)来弥补张力不足。
丝条通过第一罗拉到升头杆,升头杆顶部有个止捻器装置,作用是将丝条固定在第一热箱顶部,起到防止丝逃捻或回捻。
?第一热箱又叫变形热箱,它是接触式加热方式(与第二热箱不同),其作用是加热丝条呈塑化状态,更容易拉伸变形,它的温度越高蓬松性和卷曲性越好,染色变浅。
其长度为 2.5m (加弹机分为两种型,“M”型和“V”型,我司的加弹机属于“M”型,而“V”型的长度为2m)。
它是由真空密封联苯蒸汽和电加热复合加热。
定型区主要是第二热箱又叫定型热箱,是非接触型空气加热,它是由热媒加热的。
?第二罗拉A与第三罗拉之间的超喂比,即定型超喂,主要控制丝条在相对松驰状态下定型。
? 假捻器(叠盘式摩擦假捻器)是整个加弹机的核心部位,它是通过摩擦盘的转向对丝条进行加捻和解捻从而形成一个假捻的作用(我们公司一般做“Z”捻)。
一般摩擦盘分软盘(聚氨酯PU盘等)和硬盘(陶瓷盘、砂盘等),软盘摩擦系数高、表面柔软、对丝条损伤小、“雪花少”?但使用寿命短成本贵;而硬盘与软盘反之。
涤纶短纤维后加工操作要点和故障处理

后加工操作要点和故障处理集束一、操作要点1.生头前仔细检查集束架导丝系统各部件的清洁和表面的光洁程度,如有损伤,应予调换。
检查调整张力调整装置的安装角度和中间导丝板与上导丝架上眼镜导丝孔的位置,以便各小股丝束间隔适当、平行整齐地拉向牵伸线。
2.生头前应检查辊道上各桶丝的存放时间。
如果存放时间超过三天,应向丝桶内喷洒油剂,以免丝束过分干燥导致毛丝增多,恶化拉伸性能。
3.检查清除集束架上各部位的毛丝和乱丝。
4.检查牵伸乱丝检测器和张力异常检测器以及尾丝检测器的动作是否灵活和正确,否则应予修理。
5.集束总旦数应该控制在一定范围。
因为如果丝束总旦数波动较大,易使丝束厚薄不一样,会影响牵伸、定型、卷曲和切断的效果,使纤维质量下降。
当24桶中有1桶已经正常了桶时,则应认作整批丝已经后加工结束,应予换批处理。
另一方面工艺也要求集束总旦数不得大于正常总旦数。
6.经过集束的各根丝条张力均匀与否,一方面要影响后加工牵伸定型的均匀性和成品纤维质量的均匀性,另一方面也要影响各丝桶的了桶一致程度,因此应对丝束张力进行控制和调整。
调整方法可根据各丝桶了桶前后顺序或丝桶中残留丝重量,来调整对应丝桶上方张力调整架中间棒上的丝束包角,从而改变丝束张力。
若某丝桶经常提前了桶,说明该丝桶丝束张力嫌小,可增大其张力调整架的丝束包角,反之,若某丝桶的桶脚丝一直较多,说明该桶位丝束张力嫌大,这时可减小其张力调整架的丝束包角。
通过调整,可控制各丝束张力均匀一致,从而防止集束后的大股丝束中出现“荡丝”、“拖尾丝”等现象。
7.按照操作规程进行集束生头,要求剪去丝端硬头,丝条在导丝架各部件上穿丝位置正确,无扭结、交叉现象。
8.正常生产过程中,应加强巡回检查,发现荡丝、吊丝以及丝条缠结时,可采取停车或不停车处理。
当集束架各导丝罗拉上存有毛丝、乱丝时,应及时清除,以免被丝束带入后加工生产线,形成疵点。
9.集束采用整批换桶,一般中途不补加丝束,但如遇特殊情况处理半桶丝时,可补加丝束,应避免打结,而只需将补加丝头嵌入其它丝束之中即可(待卷曲前将未拉伸部分剪去)。
DTY生产工艺及参数设定
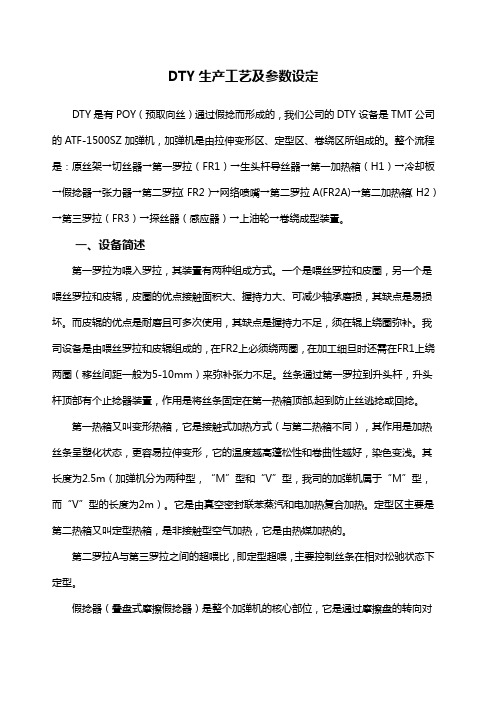
DTY生产工艺及参数设定DTY是有POY(预取向丝)通过假捻而形成的,我们公司的DTY设备是TMT公司的ATF-1500SZ加弹机,加弹机是由拉伸变形区、定型区、卷绕区所组成的。
整个流程是:原丝架→切丝器→第一罗拉(FR1)→生头杆导丝器→第一加热箱(H1)→冷却板→假捻器→张力器→第二罗拉(FR2)→网络喷嘴→第二罗拉A(FR2A)→第二加热箱(H2)→第三罗拉(FR3)→探丝器(感应器)→上油轮→卷绕成型装置。
一、设备简述第一罗拉为喂入罗拉,其装置有两种组成方式。
一个是喂丝罗拉和皮圈,另一个是喂丝罗拉和皮辊,皮圈的优点接触面积大、握持力大、可减少轴承磨损,其缺点是易损坏。
而皮辊的优点是耐磨且可多次使用,其缺点是握持力不足,须在辊上绕圈弥补。
我司设备是由喂丝罗拉和皮辊组成的,在FR2上必须绕两圈,在加工细旦时还需在FR1上绕两圈(移丝间距一般为5-10mm)来弥补张力不足。
丝条通过第一罗拉到升头杆,升头杆顶部有个止捻器装置,作用是将丝条固定在第一热箱顶部,起到防止丝逃捻或回捻。
第一热箱又叫变形热箱,它是接触式加热方式(与第二热箱不同),其作用是加热丝条呈塑化状态,更容易拉伸变形,它的温度越高蓬松性和卷曲性越好,染色变浅。
其长度为2.5m(加弹机分为两种型,“M”型和“V”型,我司的加弹机属于“M”型,而“V”型的长度为2m)。
它是由真空密封联苯蒸汽和电加热复合加热。
定型区主要是第二热箱又叫定型热箱,是非接触型空气加热,它是由热媒加热的。
第二罗拉A与第三罗拉之间的超喂比,即定型超喂,主要控制丝条在相对松驰状态下定型。
假捻器(叠盘式摩擦假捻器)是整个加弹机的核心部位,它是通过摩擦盘的转向对丝条进行加捻和解捻从而形成一个假捻的作用(我们公司一般做“Z”捻)。
一般摩擦盘分软盘(聚氨酯PU盘等)和硬盘(陶瓷盘、砂盘等),软盘摩擦系数高、表面柔软、对丝条损伤小、“雪花少”但使用寿命短成本贵;而硬盘与软盘反之。
毛丝产生要因分析及解决方案

3、导丝器
丝路上导丝器使用时间长有磨损或者位置不对,造成丝束磨 损大,单丝断裂形成毛丝,这种情况形成的毛丝细密,应检 查导丝器的质量及位置是否正常。
13
4、分丝辊、热辊
分丝辊位置调整不当,使丝束在热辊 上跳动较严重,造成毛丝和染色的问 题,要调整分丝辊的位置使丝束运行 稳定。
14
5、卫生
16
三、改正方法
管理者引导
现场管理者首先自己应熟知并严格执行这些规则,同时以身作则起
示范作用,要不断检查要求,不断改善,抓反复、反复抓。改善,永无止尽!
对下属交代工作应清楚明确
向部下交代该做什么,为什么这样做,在什么时间
之前完成,在什么地方做,怎么做,员工没做好,是因为我们没教好! 。 一般采用TWI培训方法,说给他听,做给他看,他说给我听,他做给我看。
我们的情况:油轮上油。
6
4、预网络,主网络压力设定过高。
一般情况下生产FDY预网络压力不要超过0.8bar,主网 络压力一般控制在2.7bar―3.0bar之间。网络压力过高 极易产生毛丝,出现这种情况一般通过观看FDY丝卷出 现的毛丝情况就知道是否该原因造成的,网络器造成毛 丝一般是圈毛。
网络器位置安装不到位,丝条不在网络器中心位置,这 样会造成严重毛丝。
9
二、个别位及个别锭位某个丝卷出现的 毛丝,这种情况主要有如下几个可能原
因
10
1、组件
个别锭位上某锭组件上机质量不好(喷丝 板不清洁、组装问题,出现弱丝,细丝带 入丝束,弱丝或细丝在挂伸时断裂产生毛 丝,或过滤网被击穿。如果由于组件因素 造成的毛丝是粗长的双面毛丝。
11
2、上油的均匀性
某锭位上由于有油垢影响上油效果丝束上 油少且不均。在拉伸过程中出现单丝断裂, 造成毛丝,这种情况通过观察丝卷就能确 定是否该原因造成的毛丝。一般表现为细 小的圈毛,同时观察两热相间有毛羽。 (要因)
- 1、下载文档前请自行甄别文档内容的完整性,平台不提供额外的编辑、内容补充、找答案等附加服务。
- 2、"仅部分预览"的文档,不可在线预览部分如存在完整性等问题,可反馈申请退款(可完整预览的文档不适用该条件!)。
- 3、如文档侵犯您的权益,请联系客服反馈,我们会尽快为您处理(人工客服工作时间:9:00-18:30)。
加捻器后面的转向导丝器轴承旋转不良
(规格不同,转角导丝器亦不同)
检查转角导丝器是否被废丝缠住,并检查是否由于轴承自身不良旋转不良
5.卷装筒子发生毛丝
问题
操作
(a)特定锭位连续发生毛丝时:
(1)导丝器损伤
(2)输送皮带损伤
(3)喂入罗拉表面损伤
(4)加捻器皮带的转速设定过低
3.加捻张力太低
问题
操作
用于第一喂入罗拉的皮圈的接触压力过低
检查罗拉皮圈的接压机构正常与否
4.解捻张力过高
问题
操作
加捻器皮带轮的转速太低
查看切线皮带和导轮之间是否有油,引起打滑
加捻器皮圈磨损
调换新皮圈
丝偏离加捻器的夹持中心
调整半捻器导丝器的位置
加捻器皮圈的接压设定过低,捻数施加困难
首先,检查提供接压给加捻皮圈的空气软管,连接是否适当。
(5)加捻器皮圈的接触压力设定过低
更换导丝器
调换皮圈
调换罗拉
检查皮圈和导轮之间是否被一些油粘住,造成打滑
首先,检查加捻器皮圈的空气软管是否连接好
(b)锭位无规则地产生毛丝时:
(1)第一热箱的丝槽过脏
(2)POY原丝不良(POY或FOY)
清洗第一热箱丝槽
向POY的质量管理部门和POY纺丝部门反映
6.卷装筒子中发生未解捻丝时
操作
纸筒管没有牢牢夹住
重新准确固定筒管
纸了,用布擦拭干净,如果轧头刹车坏了,进行调换
纸筒管不平行于卷绕罗拉
使用规矩管筒进行调整
接触压力太高
改变钩接弹簧的位置,降低接触压力
全部锭位的卷绕张力太高,引起筒子振动
参考7卷装筒子绕外
固定锭位的卷绕张力太高,造成纸筒管变形而引起振动
被卷绕的卷装筒子振动
参照8,卷装筒子振动
全部锭位卷绕张力过高引起绕外
升高OF3,降低TW
固定锭位卷绕张力过高,引起绕外
检查到卷绕为止的全部丝道
卷绕角过小
(在这种情况时,卷绕拱凸趋大)
设定卷绕角为13~14之间
蠕动凸轮停止位置不正确
纠正蠕动凸轮的停止位置,如果链条松弛需进行紧固
8.卷装筒子产生振动时
问题
1.挂丝困难
问题
操作
原丝
不良
原丝表面上的丝紊乱
剥去外层丝
原丝成形不良
(特别边缘有塌边)
剥去不良部分
原丝筒子出口处有破口和毛刺
处理掉这些破口和毛刺
原丝筒子中心没有与丝架导丝器中心对准
偏离中心的锭位调整
挂丝
操作
不良
导丝器通丝不良
检查导丝器
在丝未加捻时,丝碰撞到第一热箱表面
夹紧生头杆的导轨,稍上升生头杆的位置
向POY的质量管理部门和POY纺丝部门进行反映
11.异常丝的产生
问题
操作
加捻器皮圈表面异常
更换皮圈
加捻皮带轮转速变化
加查加捻器装置和驱动皮带
加捻器皮圈的接触压力变动
使用设定器检查加捻器的实际接触压力
检查到卷绕为止的全部丝道
9.卷装拱凸
问题
操作
全部锭位的卷绕张力太高,引起卷装拱凸
升高OF3,降低TW
固定锭位的卷绕张力太高,引起卷装拱凸
检查全部丝道是否正常
卷绕角度太小
把卷绕角设定为13~14之间
10.染色后M率过低
问题
操作
(a)断丝的发生:
(1)第一热箱丝槽污染
(2)第一热箱温度不良
(b)如果无规则地发生断斑:
则是原丝(POY,FOY)不良
清洗第一热箱沟槽
按需要对热箱进行排净
向POY的质量管理部门和POY纺丝部门进行反映
亮丝的发生
(a)某些锭位连续产生亮丝:
(1)第一热箱温度表面温度过高
(2)由于导丝器异常,造成加捻力异常升高
(b)如果亮丝无规则地发生:
则是原丝(POY,FOY)不良
检查温度调控器
检查导丝器,如果损坏,调换新的
问题
操作
(a)在卷装筒子表面有许多不完全解捻的点:
解捻张力设定值过低(T2)
降低加捻器速度比升高T2
(b)固定锭位产生未解捻时:
(1)原丝纤度不匀(POY或FOY
(2)原丝上油(OPU)不匀
(这时易产生绕外现象)
向质量管理部门和纺丝部门反映
7.卷装筒子上发生绕外时
问题
操作
横动导丝器中心位置不良
调整导丝器位置
当压上第一喂入罗拉时,丝从罗拉皮圈中逃出
减慢第一喂入罗拉压上的速度
半捻或全捻时丝道不良
调整半捻器导丝器的位置
加工
条件
不良
加工条件不良
检查加工条件和修正设定条件
压上第一喂入罗拉的同时发生断丝时,这是由于加捻张力过高
设定较小DR,降低加捻张力
挂丝后,第一热箱内丝抖动时,即加捻张力过低
设定较大DR,提高加捻张力,或将丝速下降50~100m/min
下面三个因素,对挂丝成功有很大影响:
(1)YS,(2)DR,(3)加捻角,即捻数,上述这些因素,彼此间密切相关,如果它们中间有一个设定不正确,就会发生丝的断裂问题
机
械
故
障
加捻罗拉转速过低
切线皮和导轨之间是否有油,引起打滑
加捻皮圈不良
更换皮圈
罗拉皮圈不良(裂缝、磨损等)
更换皮圈
加捻皮圈无接触压力
检查提供接压的空气软管,连接是否适当
2.加捻张力太高
问题
操作
丝条逃出,丝架或加捻区的导丝器
检查丝条是否进入导丝器
由于第一和第二喂入的罗拉上缠丝导致转动不良
除去卷绕在罗拉上的丝
加捻器皮带的转速太低捻数不足
查看切线皮带和导轮之间是否有油,引起打滑
在加捻器皮圈破损,捻施加受影响
更换皮圈
加捻器皮圈的接压太低,影响捻数施加
首先,检查提供接压给加捻皮圈的空气软管,连接是否适当