φ33.25m环形炉设计特点
平均直径18m的管坯环形加热炉设计

()炉顶 。炉 顶砌 筑从 炉 内向炉外 依 次为 :低 2
水 泥浇 注 料 ( 度 2 0 mm) 厚 3 ,轻 质浇 注 料 ( 度 7 厚 0 a ,磷 酸盐珍 珠岩 砖 ( rm) 厚度 6 m) 0r 。 a
De a l d i h r i l st e d sg ft e f r a e i v l i g t u n c o y t e c mb s i n s s e , t e me t ie n t e a t e i h e i n o u n c , n o v n hef r a e b d , h o u to y t m c h h — c a i a q i me t a d t e a t ma i n r l t d t h l c rc la d i sr me t ls s e .T e o e a i n o h h n c le u p n , n h u o to e a e o t e e e ti a n n t u n a y t ms h p r t ft e o
4 7
烧 嘴 的加热 一段 、加热二 段 和均 热段 几部 分组 成 。 平 均 直径 1 的管 坯 环形 加 热 炉 的供 热 能 力 m 8 和各段 热 量分 配情 况 见 表 1 ,加 热炉 的平焰 烧 嘴 的 设 置见 表 2 。
1 )天然气平焰烧嘴分配 该环 形加 热炉 的供 热 由不设烧 嘴 的预 热段 ,设
10 ) .5
最大烟气量
空气 预热 温度
2 4 /( 气 过 量 系 数 54 0m3 空 h
o 1 5 t . ) = 0
4 ~50 50 0
管式加热炉的基本知识

管式加热炉的基本知识一、管式加热炉的分类与特征各种管式加热炉通常可按外形或用途来分类。
1.按外形大致可分为四类:箱式炉、立式炉、圆形炉、大型方炉。
这种划分方法是按辐射室的外观形状区分,而与对流室无关。
例如:所谓箱式炉,顾名思义其辐射室为一箱子状的六面体。
所谓立式炉,其辐射室为直立状的六面体,其宽度要窄一些,两侧墙的间距与炉膛高度之比约为1:2。
1.1箱式炉1.1. 1横管和立管大型箱式炉如图2.5.1、图2.5.2所示,这两种炉型结构基本一致,只是一为横管、一为立管。
它们的优点是只要增加中央的隔墙数目,可在炉膛体积热强度图2.5.1 横管大型箱式炉图2.5.2 立管大型箱式炉图2.5.3 顶烧式炉图2.5.4 斜顶炉错误!未指定书签。
不变的前提下,“积木组合式”地把炉子放大。
该炉型适合于大型炉,其主要缺点是敷管率低,炉管需要合金吊挂,造价高,需设独立烟囱等。
1.1. 2顶烧式炉图2.5.3为顶烧式炉。
这种炉子的燃烧器和辐射炉管交错排列,单排管双面辐射,管子沿整个圆周的热分布均匀,燃烧器顶烧,对流室和烟囱在地面。
它的缺点是炉子体积大,造价较高,用于单纯加热不经济。
目前,在合成氨厂常用它作为大型烃蒸汽转化炉的炉型。
1.1. 3斜顶炉图2.5.4为斜顶炉,它由箱式炉演变而来,砍去其炉膛烟气流动死区而变成斜顶炉。
常用的是双斜顶炉。
由于改成斜顶,使箱式炉受热不均匀性有所改善,处理量也可加大。
其对流室在中间,烟气下行经地下或地面烟道排入烟囱内,也可在烟道处加装空气预热器,提高炉子热效率。
这种炉子没有克服箱式炉的其它缺点,除老装置原有使用外,新建装置很少采用。
1.2立式炉1.2.1底烧横管立式炉图2.5.5为底烧横管立式炉,传热方式与箱式炉相似,辐射室保持了立式炉特点。
炉管布置在两侧,中间是一列底烧的燃烧器,烟气由辐射室经对流室、烟囱一直上行。
其燃烧器能量小,数量多,在炉子中央形成一道火焰膜,以提高辐射传热效果。
高炉炉型设计

制钢铁/年
(万吨)
W2
70 40 60 65 50 30
铸造生铁/年
(万吨)
这种两头小中间大的准圆筒型,符合炉料
下降时受热膨胀、松动和软化熔化的要求
,同时也与煤气上升过程中温度下降、体
积收缩相适应。随着精料和高压操作等新 技术的发展,高炉炉型进一步向着“矮胖” 、“大型横向”发展。
世界高炉之王——沙钢5860立方米炼铁高炉
日本第二大钢铁集团——日本JFE钢铁福山厂 。
(左起)第2高炉、第3高炉、第4高炉、第5高炉,4号高炉 2006年5月扩容到5000立方米,5号高炉扩容到5500立方米
•
=(W1+1.1W2)/ 350
• 若设计n座高炉:
• 单座高炉日产P=(W1+1.1W2)/ 350n
p
•
利用系数
v
=
单座高炉日产/单座高炉有效容积=
V
' u
•
V
' u
p v
• 取 v =2― 2.25 t / m3 •d
五、按计算法Ⅰ进行炉型设计 • 1、大型高炉: Hu 6.4V 4u0.2; H u ― 有效高度
图1 高炉炉型示意图
三、炉型设计的要求
• 高炉炉型的合理性,是高炉能实现高产、优质、 低耗、长寿的重要条件。实践证明,合理的设计 炉型能促进高炉冶炼指标的改善,利于寿命的延 长。因此,炉型是高炉最基本的要素。合理炉型 应该是使炉型能够很好的适应于炉料的顺利下降 和煤气流的上升运动。既要符合高炉冶炼规律, 又要和原燃料、设备和生产技术等条件所达到的 水平相适应。
铁 ― 铁水密度,可取7.1 t/m3
d ― 炉缸直径,m
3、死铁层厚度ho :铁口中心线到炉底砌砖 表面之距离
几种固定床煤气炉结构与工艺分析

几种固定床煤气炉结构与工艺分析作者/来源:赵乐群 (江西昌昱实业有限公司南昌 330032) 日期:2007-2-130 前言目前固定床间歇气化煤气炉技术改造气氛非常活跃。
成功的技术改造与劳而无功甚至是效果适得其反的技术改造交织混杂,构成一个纷纷绕绕、令人眼花缭乱的局面。
怎样才能用一双慧眼,看透这杂乱无章的技术改造,使企业少走弯路,以最短的时间取得最好的效益?我们必须对几种煤气炉从基本结构和工艺进行综合对比分析。
我国固定床间歇气化煤气炉的炉型很多。
φ1980、φ2240、φ2400、φ2610、φ2650、φ2800、φ 2740、φ3000、φ3200、φ3300、φ3600、φ3800mm,等等,但是基本炉型只有3种:即φ1980、φ2745、φ3600mm,其它炉型都是从这3种基本炉型改造派生的。
1 从炉膛直径与灰盘直径的结构关系看工艺操作φ1980mm煤气炉的灰盘直径为φ2820mm,两者的关系:(2820-1980)÷2=420mm,φ2740mm煤气炉的灰盘直径为φ3520mm,两者的关系:(3520-2740)÷2=390mm,φ3600mm煤气炉的灰盘直径为φ4440 mm,两者的关系:(4440-3600)÷2=420 mm,为什么几种煤气炉的灰盘比炉膛一边都多出400mm?这是因为:几种煤气炉的物料、工艺原理、气化中产生的灰碴程度基本是相同的,排灰口按300mm设计可以满足生产。
根据物料灰碴的“堆积安息角”35°角的要求,灰盘应比炉膛一边宽出400mm左右。
可以清楚地看出,几种基本炉型原始设计是科学、严谨的。
但是,随着时间的推移,几种基本炉型在生产实践中进行了技术改造。
φ1980mm的煤气炉扩大炉膛,扩至φ2240、φ2400、φ2610、φ2650mm,直至扩至φ2800mm。
因为在扩径改造中,灰盘、炉底基本没有加大。
为了防止流炭、垮炭的现象发生,就出现“梯形破碴条”、“防流板”、“假灰盘”等相应的技术改造。
环形加热炉设计浅析

环形加热炉烘炉时需要转动炉底, 使炉底耐火 材料和炉盘框架被均匀加热。 合理的烘炉设计方案 对环形加热炉砌筑结构的烘烤效果和使用寿命至关 重要。
如果烘炉时用天然气作燃料, 烘炉管比较细而 且短, 常规的烘炉方法是将几段烘炉管架在内、 外 环炉墙的凸台上, 烘炉时就不会影响炉底转动。 需 要指出的是, 有些设计将烘炉管布置在侧墙烧嘴开 孔上, 笔者认为这种做法不可取。 因为高温时烧嘴 的高温火焰会直接冲刷炉顶, 而此时的炉底温度却 偏低, 炉墙、 炉顶、 炉底耐火材料温度很不均匀。
1 — 抗渣浇注料 2 — 绝热材料 3 — 炉底钢板 4 — 上层框架 图 2 环形加热炉非对称炉底砌筑结构示意
值得一提的是, 该环形加热炉使用 8 个月后, 内环局部的炉底表层浇注料出现了开裂拱起现象。 用户单位技术人员经过对其他生产厂的几座环形加 热炉考察后发现, 使用一段时间后, 在内环或外环 炉底表层浇注料开裂拱起的现象普遍存在。 分析认 为, 这种现象与炉底的膨胀结构设计不合理有关, 期待有新的炉底设计结构, 解决炉底耐火材料开裂 拱起问题, 提高炉底耐火材料的使用寿命。
关键词: 环形加热炉; 设计; 布料角; 炉底砌筑; 烘炉 中图分类号: TG155.1 %%文献标志码: B %文章编号: 1001-2311(2011)03-0031-04
A Brief Analysis of Designing of Rotary Hearth Heating Furnace
α — 布料角 β — 装出料炉门夹角 D — 环形炉平均直径 1 — 装料炉门中心线 2 — 出料炉门中心线
图 1 环形加热炉布料示意
(1) 炉底没有布料槽或支架。 在这种情况下,
环形加热炉的布料角通常要求满足:
6m转底式环形炉技术方案文件

目录一、技术要求 (2)二、环形炉技术参数 (2)三、概述及方案特点 (3)四、炉子本体 (3)五、环形炉报价 (9)一、技术要求1.1.设备用途:工件连续锻造加热1.2.装炉温度:常温;1.3.加热温度:1250℃;Kcal);1.4.燃料:天然气(83003m吨;1.5.生产能力:~6.5小时1.6.炉子中径:Φ5.6m;1.7.炉子内宽:1.5m1.8.最快出钢节奏:0.5支/min;二、环形炉技术参数2.1.加热钢种:连铸坯;2.2.钢坯尺寸(mm):矩形工件:L=300~900mm,B=300~700mm, H=60~150mm,圆形工件:约Φ250~600mm,H=60~150mm;2.3.钢坯典型规格(mm):方形工件以正方形为主,约占60%。
2.4.钢坯加热温度:~1250℃;2.5.钢坯入炉温度:常温;t;2.6.典型工件额定产量:6.5hkJ;2.7.燃气低位发热量:8300×4.183NmNm3;2.8.额定燃料消耗量:270hNm3;2.9.助燃空气消耗量:2900hNm3;2.10.烟气生成量:3200h2.11.燃烧器种类及数量:蓄热烧嘴18个.三、概述及方案特点环形加热炉的设计、制造、检验和验收都将在满足有关规范和标准的基础上进行;其各部件都选用优质材料制作,保证整套设备能够安全、可靠长寿运行;炉子主要由炉体(包括炉衬)、炉门、转底、炉底传动装置、燃烧系统、各种管路系统、排烟余热回收系统、密封装置、控制系统及记录系统和计算机系统等主要部分组成。
为满足该环形加热炉加热工艺的要求以及使工人操作简便,在保证运行可靠性的基础上具有很高的自动化程度,使之整体达到国际先进水平。
该炉的控制系统采用了计算机多媒体集散式控制技术,全中文画面生动直观、简单实用,实现了上位工控机、自动控制(PLC)和手控三种兼容控制方式,可做到无忧操作和无忧转换,且可保证在脱机状态下,炉子仍能实现自动控温操作。
铸造冶金炉的所有知识点

铸造冶金炉的所有知识点本文以铸造冶金炉为例,简要介绍铸造炉的构造、工作原理、主要设备和主要特点,对铸造炉有全面深入系统介绍。
铸造炉是指铸造铁水的设备,包括铸造球墨铸铁炉(简称球墨铸铁炉)和铸钢炉等。
铸造炉是一种熔炼、冶炼过程中进行机械加工后使铁水形成球状(铸球状)铸锭并用熔融金属从熔池中浇注到铸件表面实现铸造操作和冶炼作业后经冷却、加工而成的冶金设备。
在我国铸造行业中应用最广、技术最先进的铸造冶金炉是 QTL (铸铁)铸造球墨铸铁炉(以下简称球墨铸铁炉)和 SMD (铸铁)铸造球墨铸铁炉(以下简称 SMD炉)。
其主要优点是:铸件内部结构紧凑、操作方便、设备简单、制造容易、生产率高、成本低;其特点是:使用寿命长(一般为10-15年)和消耗低;对环境污染小。
铸造球墨铸铁炉是以优质耐火材料为主,同时辅以机械加工零部件或采用其他工艺方法制成造型各异的铸件产品的现代化冶金炉;它能够提高钢的可铸性和韧性以及冶炼操作技术性能(耐火材料寿命)和钢种适应性(适钢性和适切度)。
目前我国铸造工业发展迅速,已成为国民经济中重要的基础工业之一。
一、铸造炉的组成铸造炉由炉体、炉盖、浇注系统和冷却系统组成。
铸件生产工艺过程主要分为:铁水铸造、浇注系统和冷却设施。
其中浇注系统是铸造炉的核心,它包括进料口、入口管道、出料口及出料管道与钢液循环管道等。
在实际生产中,需要增加出钢口处的进料口和出钢口处的冷却水阀或控制系统。
铁水铸造又分为:球墨铸铁炉和铸钢炉,如图1所示。
铸铁炉熔炼温度为850℃~950℃,有金属液从出料口流出或浇注到钢液循环管道的流动过程,浇注时需控制进料量以及浇注速度、质量和出钢温度。
铸钢炉熔炼冷却方式有金属直接冷却和机械冷却两种方式。
它主要包括水冷系统和电热系统两大类,常用的有以下几种方式:用水直接冷却;用电热管直接冷却;用电热管夹式冷却器等电-热耦合方式冷却塔(俗称电热管)冷却机来作为热源。
1、水冷系统铸钢炉在熔炼过程中,由于金属液被冷却到较低的温度(约70~80℃),从而减少了金属与热源的接触,因此金属冷却器),如冷却塔或冷却水器(循环水)是铸钢炉上水冷系统的核心设备。
Φ26.408m环形加热炉的设计特点

Φ26.408m环形加热炉的设计特点摘要从炉型结构、燃烧方式等方面简单介绍了Φ26.408m环形加热炉的设计特点。
关键词环形加热炉;炉型结构;设计特点1概述攀钢集团成都钢铁有限责任公司A-R轧管机组重建工程新建1座环形加热炉,主要生产品种有普碳钢、中低合金钢和不锈钢,年加热连铸圆管坯24.7万吨。
受工厂条件限制,该加热炉采用了高炉煤气和天然气两种燃料,采用了蓄热燃烧和常规燃烧两种燃烧方式。
2环形加热炉主要技术参数炉型:单面加热、多段供热的环形连续加热炉;炉子用途:管坯穿孔前加热;原料:连铸圆管坯;管坯规格:直径:Φ180mm,Φ220mm,Φ280mm,Φ310mm;长度:1 200mm~4 500mm;最大单重:2 666kg;管坯装炉温度:20℃;管坯加热温度:1240℃~1 280℃;出炉管坯温度均匀性:纵向±10℃,径向±5℃;炉子产量:最大135t/h;出料节奏:最快125支/h;燃料及发热值:天然气,热值8 300×4.18kJ/Nm3;高炉煤气,热值800×4.18 kJ/Nm3;单位热耗:1.46GJ/t(低合金钢、最大产量,出炉温度为1 250℃时) ;烧咀形式:预热段及加热段采用蓄热式烧嘴;均热段采用炉顶平焰烧嘴;炉底机械型式:双层框架梯形结构;炉内布料:单排:长度>2 200mm;双排:长度≤2 200mm;并采用可变布料角;炉子尺寸:炉底中心线平均直径:26 408mm;炉底宽度:4 930mm;炉膛内宽:5 280mm;装出料炉门中心线夹角:15°。
3环形加热炉主要设计特点3.1燃烧方式的确定根据工厂所给定的燃料条件,结合本生产线无缝钢管生产的加热工艺特点,在预热段、加热I段、加热II段、加热III段选用空煤气蜂窝体双蓄热的蓄热式燃烧方式,以满足钢坯加热温度的要求。
在均热I段、均热II段选用天然气平焰烧嘴的常规燃烧技术以保证钢坯长度方向的温度均匀性。
环形炉和步进炉对比

1)连铸机和加热炉之间匹配由于采用热装热送,炼钢连铸设备和轧管机之间需要紧凑布置,原来的环形加热炉面积较大,无法做到紧凑布置,另外一般的环形加热炉都是采用定尺加热,如果采用直接热装热送的话,会影响连铸机的生产效率。
除此之外步进式加热炉和环形加热炉相比,也具有以下优点:(1)步进梁式可以加热定尺和倍尺长度的连铸圆坯,最长可达10m,环形炉也可以加热定尺和倍尺长度的连铸圆坯,但不合适加热长度达10m的连铸圆坯。
(2)步进梁式炉单位炉底面积产量大约500kg/m2.h,而环形路单位炉底面积产量大约250~300 kg/m2.h,也就是说,在连铸圆坯加热起始温度和加热小时产量相同的条件下,步进梁式炉的炉底面积是环形炉的约50%~60%,尽管步进梁式炉单位面积的投资比环形炉高,但总体上步进梁式炉投资比环形炉的低很多。
(3)为了真正达到节约燃料和减少炉温的波动的目的,对连铸圆坯热装加热,要求采用两座加热炉,一座高温炉,一座预热炉。
两座步进梁式炉便于布置,占地面积小,节省厂房面积,而两座环形炉占地面积达,也不好布置。
(4)连铸圆坯在步进梁式炉中加热时,连铸圆坯四面受热,目前已克服金属梁对圆坯温度的影响,加热温度均匀,而环形炉在加热圆坯时,底面有一长条面积和炉底接触不受热,均热时间要长一些,温度才均匀。
(5)在步进梁式炉内连铸圆坯的间距是相同的,环形炉装、出料机的夹角一般为10°~14°,在环形炉内连铸圆坯长度方向的间距是不同的,炉底面积利用率低,燃料消耗比步进梁式炉高约10%。
国内外用步进梁式炉加热连铸圆坯有很成熟的经验,在上世纪1977年到1997年期间,不完全统计国外共建成9套采用步进式加热炉加热圆(方)管坯的热轧钢管机组。
这些热轧钢管机组的圆管坯直径为90~360mm,管坯长度为1500~12000mm。
热轧钢管轧机有自动轧管机、半限动芯棒连轧管机、限动芯棒连轧管机和狄赛尔轧管机。
近年来国内建设的4-5套棒材轧机,采用连铸圆坯生产圆钢和方钢,其加热设备是采用步进式加热炉,如江阴、淮安、无锡和大连特殊钢厂等棒材轧机,其加热设备都是步进梁式加热炉,其中江阴特殊钢和大连钢厂的步进梁式加热炉加热连铸圆坯的规格(直径×长度)是:Φ500mm×6000mm、Φ350mm×4000~8000mm、Φ500mm×4000~8000mm和Φ280mm×4000~8000mm和Φ500mm×4000~6000mm。
浅述环形炉设备基础清水混凝土施工工艺

浅述环形炉设备基础清水混凝土施工工艺一、工程概况本工程为环形加热炉基础施工工程,基础占地面积约为2600m2,环形炉为板式环形基础,烟道为板式基础。
烟道底板标高-7.4米,局部为-7.67米,底板厚0.93米,侧壁0.8米厚,烟道顶部标高±0.000米.环形炉底板标高-1.5米、-1.7米局部-2.7米,环形炉基础外径R=28.6米,内径R=19.4米,环形炉上部外径29.9米,内径18.1米,上部顶板最厚1.6米,最薄0.4米。
1.工程特点及难点:1)环形路所在区域主厂房钢结构基本完成,屋面挂瓦已封闭,设备基础施工必须采用闭式施工法。
2)烟道基础埋深较深,且与柱基础较近,施工时加强对柱基、钢柱的位移检测。
3)环形炉机组设备基础直径达57.2m,工程量大,施工精度要求高,务必提高精品意识,提升施工技术水平,强化施工质量意识,注重施工安全文明.4)环形加热炉设备基础地脚螺栓(直埋螺栓)数量多直埋螺栓。
设备基础施工时,要认真做好地脚螺栓的中心控制及标高控制,并做好螺栓的成品保护。
5)设备基础中心和各环同心度、圆弧度圆滑控制难度较大,必须采取周全、可行的措施和方法,统筹安排,严格控制。
6)环形炉设备基础直径大,实体厚,一次性浇筑混凝土量大,控制大体积混凝土的浇筑至关重要,必须采取科学、可行的措施控制大体积混凝土裂缝的产生,确保混凝土质量和美观,达到无渗漏。
7)环形炉上部结构中间与两边高差较大,临边安全防护措施应及时落到实处,加强施工现场安全管理工作,确保安全无事故8)本工程后期施工进入冬季施工,应做好冬期施工技术措施和安全措施,保证结构实体质量和现场安全。
二、环形炉清水混凝土施工技术该工程清水混凝土是以混凝土的自然质感作为饰面的混凝土,一次成型,不做任何装饰,要求表面平整光滑,色泽均匀,棱角分明,无碰损和污染,最终效果取决于模板工程,钢筋工程,混凝土工程的施工工艺技术。
环形炉烟道采用的是组合钢模板,环形炉设备基础主体结构由于对饰面效果较高,采用的是芬兰进口的18mm WISA模板。
φ33.25m环形炉设计特点
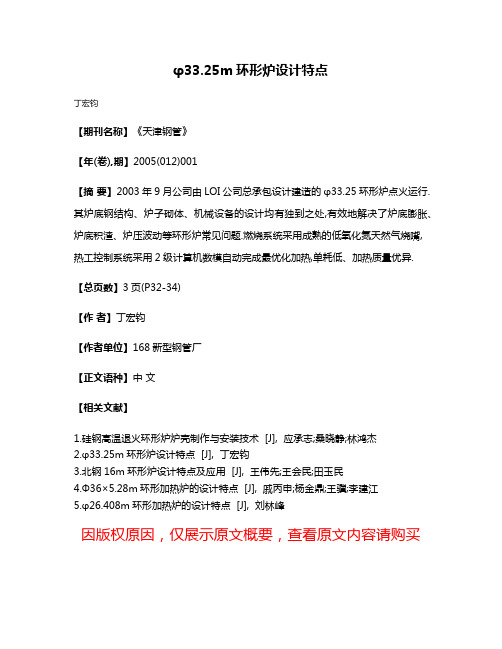
φ33.25m环形炉设计特点
丁宏钧
【期刊名称】《天津钢管》
【年(卷),期】2005(012)001
【摘要】2003年9月公司由LOI公司总承包设计建造的φ33.25环形炉点火运行.其炉底钢结构、炉子砌体、机械设备的设计均有独到之处,有效地解决了炉底膨胀、炉底积渣、炉压波动等环形炉常见问题.燃烧系统采用成熟的低氧化氮天然气烧嘴,
热工控制系统采用2级计算机数模自动完成最优化加热,单耗低、加热质量优异.【总页数】3页(P32-34)
【作者】丁宏钧
【作者单位】168新型钢管厂
【正文语种】中文
【相关文献】
1.硅钢高温退火环形炉炉壳制作与安装技术 [J], 应承志;桑晓静;林鸿杰
2.φ3
3.25m环形炉设计特点 [J], 丁宏钧
3.北钢16m环形炉设计特点及应用 [J], 王伟先;王会民;田玉民
4.Φ36×
5.28m环形加热炉的设计特点 [J], 戚丙申;杨金鼎;王骥;李建江
5.φ2
6.408m环形加热炉的设计特点 [J], 刘林峰
因版权原因,仅展示原文概要,查看原文内容请购买。
环形炉分区加热技术的应用与研究
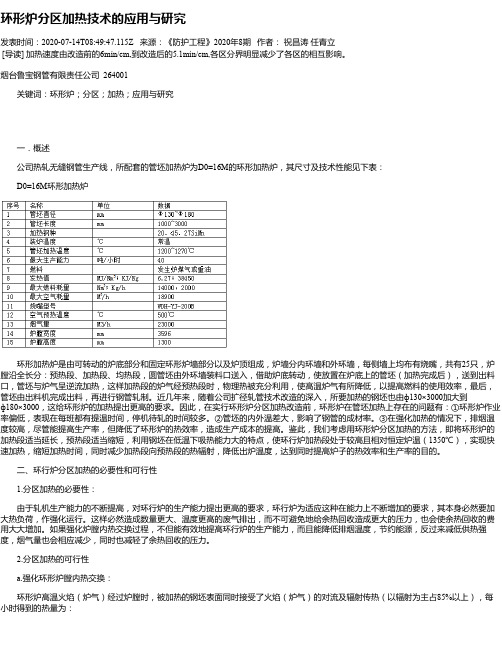
环形炉分区加热技术的应用与研究发表时间:2020-07-14T08:49:47.115Z 来源:《防护工程》2020年8期作者:祝昌涛任青立[导读] 加热速度由改造前的6min/cm,到改造后的5.1min/cm,各区分界明显减少了各区的相互影响。
烟台鲁宝钢管有限责任公司 264001关键词:环形炉;分区;加热;应用与研究一.概述公司热轧无缝钢管生产线,所配套的管坯加热炉为D0=16M的环形加热炉,其尺寸及技术性能见下表:D0=16M环形加热炉环形加热炉是由可转动的炉底部分和固定环形炉墙部分以及炉顶组成,炉墙分内环墙和外环墙,每侧墙上均布有烧嘴,共有25只,炉膛沿全长分:预热段、加热段、均热段,圆管坯由外环墙装料口送入,借助炉底转动,使放置在炉底上的管坯(加热完成后),送到出料口,管坯与炉气呈逆流加热,这样加热段的炉气经预热段时,物理热被充分利用,使高温炉气有所降低,以提高燃料的使用效率,最后,管坯由出料机完成出料,再进行钢管轧制。
近几年来,随着公司扩径轧管技术改造的深入,所要加热的钢坯也由ф130×3000加大到ф180×3000,这给环形炉的加热提出更高的要求。
因此,在实行环形炉分区加热改造前,环形炉在管坯加热上存在的问题有:①环形炉作业率偏低,表现在每班都有提温时间,停机待轧的时间较多。
②管坯的内外温差大,影响了钢管的成材率。
③在强化加热的情况下,排烟温度较高,尽管能提高生产率,但降低了环形炉的热效率,造成生产成本的提高。
鉴此,我们考虑用环形炉分区加热的方法,即将环形炉的加热段适当延长,预热段适当缩短,利用钢坯在低温下吸热能力大的特点,使环行炉加热段处于较高且相对恒定炉温(1350℃),实现快速加热,缩短加热时间,同时减少加热段向预热段的热辐射,降低出炉温度,达到同时提高炉子的热效率和生产率的目的。
二、环行炉分区加热的必要性和可行性1.分区加热的必要性:由于轧机生产能力的不断提高,对环行炉的生产能力提出更高的要求,环行炉为适应这种在能力上不断增加的要求,其本身必然要加大热负荷,作强化运行。
环形加热炉——精选推荐

第四节环形加热炉一、环形加热炉特点环形加热炉具有以下特点:(1)可以加热圆形或异形钢坯;(2)根据需要可以改变钢坯在炉内的分布,从而改变加热制度,在生产中有较大的灵活性;(3)钢坯在整个加热过程中,随炉底的转动没有相对摩擦和振动,氧化铁皮不易脱落;(4)钢坯在炉底上相互间隔放置,三面受热,加热时间短,温度均匀,没有水冷"黑印",加热质量较好(温度差≤±10℃);(5)与推钢式连续加热炉比较,炉子容易排空,可避免钢坯在炉内长时间停留,同时便于更换钢坯规格;(6)环形炉的机械化与自动化程度较高,装出料与钢坯在炉内运送均可自动运行.另外,燃烧及管理可自控;(7)环形炉的转动炉底与固定的内外环墙之间的环缝,由环状水封槽进行水封.由于环状炉底钢结构高温时向外热膨胀,冷态的内外环缝大小是不同的,一般根据炉子的中径大小不同相差约40~70mm,故活动的炉底中心与固定的炉膛中心在冷态是不一致的,而热态则趋向一致.环形炉尺寸是以炉膛的平均直径(中径)和炉膛的内宽来表示的.环形加热路属特殊工艺所要求的加热设备,与长形连续加热炉相比有其自身缺点:1)炉子是圆环形的,特别是大直径的环形炉,占用厂房面积较大;2)环形炉一经建成,改建或扩建都比较困难,因此发展的余地、潜力都较小;3)钢坯在炉内呈辐射状间隔分布,炉底面积利用较差.特别是炉膛较宽的炉子,炉底外半环利用更低.环形加热炉的炉子有效长度内的利用率(根据装出料机夹钳夹钢所要求的不了间距与料长等有关)仅为30%~50%.二、钢坯的加热与加热时间环形加热炉相当于一座头尾相接的长形连续加热炉,所以炉子的热工制度及分段(预热段、加热段、均热段)原则,均与推钢式连续加热炉等类似.但环形炉内的钢坯加热有其自身特点. (一)间隔布料的影响由于装出料机夹钳操作的需要,炉底上钢坯与钢坯之间必须留有一定间隙,其大小视夹钳操作所必需的空间而定.钢坯三面加热,加热时间较单纯上加热可大大缩短,钢坯内外温差较少.但炉内的单位炉底过钢面积的产量却很低,一般管坯在300kg/m2²h左右.(二)热炉底的影响环形炉炉底由高温的均热段过度到预热段时,由于他积蓄的热量只散失很少一部分,所以它的温度仍高于预热段炉膛的温度约200℃左右,对刚入炉的冷坯有明显的加热作用.(三)加热时间据有关文献统计,环形加热炉内管坯的加热由于间隔布料和热炉底影响,加热速度约5.5~6.5min/cm,普通钢取5.5~5.7min/cm,合金钢取6.0~6.5min/cm,.低碳钢管坯的加热时间可按有关计算手册进行计算,也可按式3.5-3的经验公式计算:τ=(5.1+0.034d)d (3.5-3)式中τ-加热时间,min;D-管坯直径,cm.三、炉子产量和装载量的确定环形炉的装载量按式3.5-4确定:P=Gτ 1 (3.5-4)式中 P-炉子装载量,t;G-炉子产量,t/h;τ-加热时间,h.1炉子生产能力(G)应与轧机的产量相配合.由于环形炉一经建成,改建或扩建都很困难,因此炉子产量要充分满足轧机的需要.但也不能过大,一面炉子长期在低负荷下工作.四、炉膛尺寸的确定环形炉炉内钢坯是呈辐射状布置,钢坯在环形炉炉底上的布料,见图3.5-13所示.(一)炉子直径的确定根据小时产量、钢坯单重、钢坯的布料间距与排放及相应的加热时间,以及装出料夹角来确定.单排布料按公式3.5-5,双排布料按公式3.5-6和公式3.5-7计算.D= Pd (3.5-5)gk(π-0.5α)式中 D-炉底平均直径,m;P-炉子装钢量,t;d-钢坯直径,m;g-钢坯单重,t;π-圆周率;α-装料机与出料机轴线的中心角,rad(弧度).1°=π÷180=0.0174533rad(或1rad=57.2958°)中心角的大小与环形炉的直径D大小有光,一般大中型环形炉为均0.17~0.26rad(10°~15°),而小型环形炉可达0.44rad(25°);;k-炉子有效长度内的填充系数,k=d/S2-相邻钢坯的布料间距,m.S2D1= Pd (3.5-6)ngk(π-0.5α)式中D1-双排布料时,那排钢坯中心在炉底所占平均直径,m;n-钢坯在炉底径向上的排数.D=D1+S1 (3.5-7)式中S1-双排钢坯中心的径向间距,m.由公式3.5-5或公式3.5-6和公式3.5-7计算所得D,是环形炉炉底的平均直径,初定时可视为环形炉炉膛的平均直径(D).均(二)环形炉的炉膛高度环形炉的炉膛高度一般为1.5~2m,而非供热段炉膛高度有时降到0.8~0.9m.(三)环形炉有效炉底长度有效炉底长度是使钢坯沿着炉底总长度移动的那一部分,即装了口和出料口中心外侧轴线之间的炉底长度.有效长度L(m)有式3.5-8确定:L=D(π-0.5α) (3.5-8) (四)环形炉布料角为了把沿炉直径方向排列的钢坯从环形炉炉底上一次轮流取出,环形炉每次转过的角度β(rad,弧度)等于相邻钢坯的布料角,由式3.5-9确定:2S2β= πD (3.5-9) 式中β-每次取料转过的角度,rad(弧度).(h)(五)炉底转一圈的平均时间τ周炉底转一圈的平均时间τ(h)按式3.5-10确定:周τ周=βτ 12(π-0.5α) (3.5-10)。
高炉炉型选择以及炉容计算
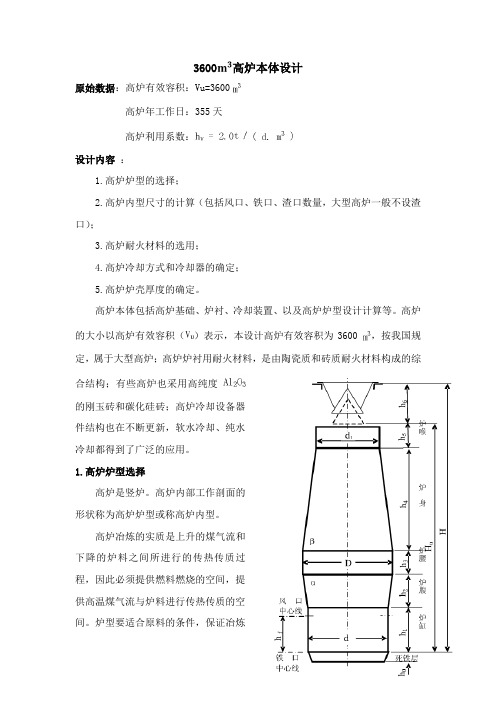
3600高炉本体设计原始数据:高炉有效容积:Vu=3600高炉年工作日:355天高炉利用系数:设计内容:1.高炉炉型的选择;2.高炉内型尺寸的计算(包括风口、铁口、渣口数量,大型高炉一般不设渣口);3.高炉耐火材料的选用;4.高炉冷却方式和冷却器的确定;5.高炉炉壳厚度的确定。
高炉本体包括高炉基础、炉衬、冷却装置、以及高炉炉型设计计算等。
高炉的大小以高炉有效容积()表示,本设计高炉有效容积为3600,按我国规定,属于大型高炉;高炉炉衬用耐火材料,是由陶瓷质和砖质耐火材料构成的综合结构;有些高炉也采用高纯度的刚玉砖和碳化硅砖;高炉冷却设备器件结构也在不断更新,软水冷却、纯水冷却都得到了广泛的应用。
1.高炉炉型选择高炉是竖炉。
高炉内部工作剖面的形状称为高炉炉型或称高炉内型。
高炉冶炼的实质是上升的煤气流和下降的炉料之间所进行的传热传质过程,因此必须提供燃料燃烧的空间,提供高温煤气流与炉料进行传热传质的空间。
炉型要适合原料的条件,保证冶炼过程的顺行。
近代高炉炉型为圆断面五段式,是两头小中间大的准圆筒形。
高炉内型如图1。
高炉有效高度(炉腰直径(D)与有效高度()之比值是表示高炉“细长”或“矮胖”的一个重要指标,在我国大型高炉Hu/D =—,随着有效容积的增加,这一比值在逐渐降低。
在该设计中,。
炉缸高炉炉型下部圆筒部分为炉缸,炉缸的上、中、下部位分别装有风口、渣口、铁口。
炉缸下部容积盛液态渣铁,图1 高炉内型上部空间为风口燃烧带。
铁口位于炉缸下水平面,铁口数目依炉容或产量而定,对于3000的高炉,设置3—4个铁口,以每个铁口日出铁量1500—3000t设置铁口数目。
在该设计中,设置4个铁口。
渣口与铁口中心线的距离称为渣口高度(),它取决于原料条件,即渣量的大小。
渣口高度的确定参照下式计算:= =式中:P——生铁日产量,t;B——生铁产量波动系数,取;N——昼夜出铁次数,取9;——铁水密度,取;C——渣口以下炉缸容积利用系数,一般为,在该设计中,取;d——炉缸直径m。
环形炉
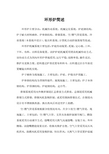
环形炉简述环形炉主要分由:机械传动系统、机械定位系统,炉底钢结构,炉子耐火材料砌体、炉体钢结构、排烟系统、空/燃气管道系统、冷却系统(本系统不设计)、装出料系统、计算机自动控制系统等组成。
环形炉机械系统主要包括:炉底传动装置、托辊、定心辊、上环、下环、布料、出料设备装置。
该炉炉底机械采用销齿机械传动方式,该传动方式为国内环形炉普遍采用,运行平稳,故障率低,操作灵活,维护及更换方便。
进料通过炉顶设置布料料斗,出料通过在台车面设置螺旋出料机实现。
炉子砌体为现场施工,主要包括:炉底、炉墙及炉顶施工。
炉体钢结构均为型钢焊接件,属现场施工,主要包括:炉子本体钢结构、炉顶钢结构、炉底钢结构,走台等。
排烟系统采用内外侧多烟道汇总排放方式排放,总烟道采用机械排烟方式排烟,排烟风机变频控制。
或采用烟囱排烟方式。
在烟道内设计有不锈钢换热器,换出热风后再送至炉上助燃。
空/燃气管道系统根据分组情况布局,共分3组空/燃气管道,现场施工,主要包括:空/燃气主管、支管及各级控制调节阀门。
燃烧系统采用自动调节方式,烧嘴采用天然气高速烧嘴,安装于内、外环侧墙,该烧嘴燃烧效果良好,检修及维护方便。
空气主管采用高压风机供风,助燃风机采用变频控制,恒压供风;天然气主管设置炉前减压稳压站,减压稳压站包括减压稳压阀、旁路阀、电磁阀、安全放散阀、高低压开关等。
冷却系统采用直接风冷方式,主要包括冷却风系统和抽热系统。
冷却风由高压风机、相应的管路和多组喷口组成;抽热系统由锅炉引风机、相应的管路和多个吸风口组成。
(本系统不设计)。
计算机自动控制系统控制该炉所有电器设备运行、连锁及报警等;仪表控制系统手、自动控制该炉温度、压力及设备转速等物理量。
具备手动/自动无扰切换功能,计算机具备参数设定、记录、储存及报表功能,主要元器件采用进口名牌产品。
1.2.1排烟段结构在砖底炉的排烟段设计五对排烟口,每个排烟口的尺寸为348x268,经侧墙排出后在炉顶混合,再经烟囱或排烟机排出,选用烟囱时,烟囱为:45米高,直径为1.2米,并设计一烟囱闸板,自动调节炉内压力;选用排烟机时,排烟机电机功率为30KW,并用变频仪调节炉内压力,排烟机前还设计有兑冷风装置,以调节排烟温度。
6圆形竖炉与矩形竖炉对比
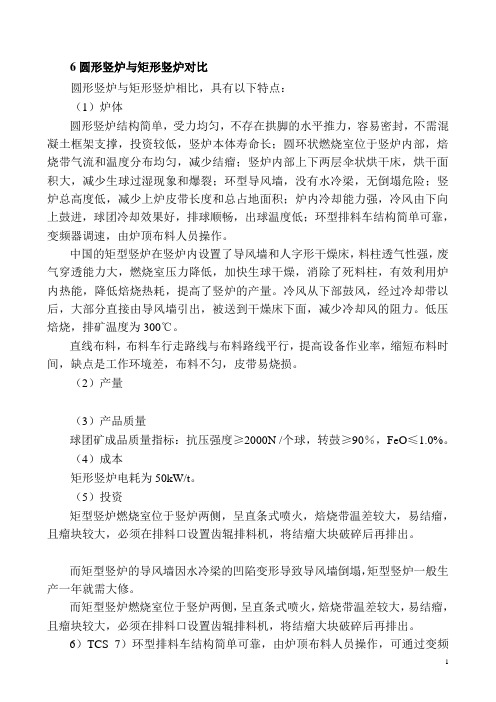
6圆形竖炉与矩形竖炉对比圆形竖炉与矩形竖炉相比,具有以下特点:(1)炉体圆形竖炉结构简单,受力均匀,不存在拱脚的水平推力,容易密封,不需混凝土框架支撑,投资较低,竖炉本体寿命长;圆环状燃烧室位于竖炉内部,焙烧带气流和温度分布均匀,减少结瘤;竖炉内部上下两层伞状烘干床,烘干面积大,减少生球过湿现象和爆裂;环型导风墙,没有水冷梁,无倒塌危险;竖炉总高度低,减少上炉皮带长度和总占地面积;炉内冷却能力强,冷风由下向上鼓进,球团冷却效果好,排球顺畅,出球温度低;环型排料车结构简单可靠,变频器调速,由炉顶布料人员操作。
中国的矩型竖炉在竖炉内设置了导风墙和人字形干燥床,料柱透气性强,废气穿透能力大,燃烧室压力降低,加快生球干燥,消除了死料柱,有效利用炉内热能,降低焙烧热耗,提高了竖炉的产量。
冷风从下部鼓风,经过冷却带以后,大部分直接由导风墙引出,被送到干燥床下面,减少冷却风的阻力。
低压焙烧,排矿温度为300℃。
直线布料,布料车行走路线与布料路线平行,提高设备作业率,缩短布料时间,缺点是工作环境差,布料不匀,皮带易烧损。
(2)产量(3)产品质量球团矿成品质量指标:抗压强度≥2000N /个球,转鼓≥90%,FeO≤1.0%。
(4)成本矩形竖炉电耗为50kW/t。
(5)投资矩型竖炉燃烧室位于竖炉两侧,呈直条式喷火,焙烧带温差较大,易结瘤,且瘤块较大,必须在排料口设置齿辊排料机,将结瘤大块破碎后再排出。
而矩型竖炉的导风墙因水冷梁的凹陷变形导致导风墙倒塌,矩型竖炉一般生产一年就需大修。
而矩型竖炉燃烧室位于竖炉两侧,呈直条式喷火,焙烧带温差较大,易结瘤,且瘤块较大,必须在排料口设置齿辊排料机,将结瘤大块破碎后再排出。
6)TCS 7)环型排料车结构简单可靠,由炉顶布料人员操作,可通过变频器调速,以实现布料与排料的良好配合。
8)TCS竖炉回收了干燥系统的废气余热以预热助燃风,使助燃风平均温度达到250~300℃,并且燃烧室压力仅为6~8kPa可保证生产。
- 1、下载文档前请自行甄别文档内容的完整性,平台不提供额外的编辑、内容补充、找答案等附加服务。
- 2、"仅部分预览"的文档,不可在线预览部分如存在完整性等问题,可反馈申请退款(可完整预览的文档不适用该条件!)。
- 3、如文档侵犯您的权益,请联系客服反馈,我们会尽快为您处理(人工客服工作时间:9:00-18:30)。
炉 子 钢结 构 由定心 辊 、 撑 辊 、 底 框 架 、 底 钢 支 炉 炉 板、 炉墙立 柱 、 炉墙 钢 板及 炉顶 钢 梁组 成 。这 座 炉子 在 钢结 构 方 面最 突 出的 设计 特 点 是 , 底框 架 和 炉 底 钢 炉 板 冷 态 时有 4 m 偏 心 , 态 时 . 底 钢 板 随 炉 底 耐 1m 热 炉 火 材 料 膨 胀至 中心 重叠 。也 就 是说 . 计 中预 先 考 虑 设
加热 系统
设计特 点 分析
1 前言 2 0 年天津钢管公司筹建第二套轧管生产线项 目 02
中 ,由德 国 L I 司 总 承 包 设计 建 造 3 . 环 形 O 公 32 m 5 炉 。换热 器 、 嘴 、 压 站 等关 键 设 备 由德 国进 口 , 烧 液 耐
炉膛 高度 fm)180 m : 0
图 3 两路 。线 路 2通余 热 锅 炉 , 此 时闸 门 1 闭 , 门 2 闸 门 3打开 。另一 线 路 直接 关 闸 、 通 至 烟 囱 . 时 闸 门 2闸 门 3关 闭 , 门 1 开 . 图 此 闸 打 如
规则偏心 。即 : 炉子工作状态下炉底框架并不是均衡
3 9 N : 89 1( m)
该环形炉设计特点做简单介绍。
设计单位燃耗 ( m/ : 9 N S 3 t ) 3 动作描述
如图 1 所示 管 坯 由装 料机 A送入 炉 底 上 , 炉底 随
一
2 基本参数
21 加 热 能 力 : . 设计 10t (5 2 h 10支/ ) / h 最 大 10t (8 4 h 10支,) / h
为 了保 证 炉 底运 转 良好 . 底 和 侧墙 的 内外 环 之 炉
间留有一定 的缝隙, 即环缝。冷态时内环缝为 8 m, 0m
外环 缝 为 12 6 mm。 态 时 , 底膨 胀 内外环 缝 均达 到 热 炉
1 1 mm 。 2
n n/ l Q
墙C/ /
/ l
炉底 和 炉 墙 之 间 的环 缝 采用 水 封 . 封 系统 由水 水 封槽 、 动 刀 、 活 固定 刀 组 成 。活 动 刀 安 装 在 炉墙 上 不 动 。在 活 动刀 底部 装有 刮 板 , 样炉 底在 转 动时 , 这 通过
) 烟1 排 2 1
/
墙 隔B / , A 墙 ‘ \ /
环形炉炉 内烟气按照与炉底转 动相反的方 向流 动. 加热管坯后废气经 由装料端 内环侧墙上的排烟 口
排 除 炉外 。
最大单重(g : 1 4 k) 0 o 注: 管坯材质为低合金钢 、 合金钢和碳素钢 。
炉 内有 效料 位 :1 32 布料 方 式 : 排 、 单 交错 管坯 加热 温度 ℃ : 20 1 8 1 6 ~ 0 2
门负 责 随 时清 理 炉底 积 渣 ,有 效 地 解决 了这 个 难 题 .
成倍的提高 了炉子的使用周期 ,提高了加热质量 、 降 低 了能耗。
432 装 、 - . 出料 门
5 结束语 经过一年多 的使用 , 此环形炉 运转可靠 、 自动化
水平 高 。 只需 两 名工 人 即可 操 做 , 员 比 19 定 92年全 套 引进 意大 利 的  ̄ 8I环形 炉少 一半 : 4 I T 平均单 耗 3 m3 5N /
释风机 、 炉底液压马达。其 中以双系统炉底定位 为基 础的物料跟踪准确可靠 , 2 为 级控制的投用提供了有 力保障。
453 过 程计 算 机 系统 ( .. 2级 ) 有炉 子 操 作过 程 优 化 . 热工 工 程 的 自动 化 数 学模 型 。 为炉 子 加 热最 优 化 提 供
版 社 .9 4 18
频电机的调速范围时 , 计算卷取机功率时应考虑增大 电机 的计算功率 Ⅳ 。以满足卷取过程中的张力及 - 速度 的工艺要求 。
( 稿 20 — 0 1 责编 苗 龙 军 ) 收 0 4 1— 8
[1 连家 创, 满 - 钢设 备及工 艺. 东北重 型机 械学 院 ,9 5 3 李春 车 L 原 18
作者简 介 吴永 杰 . . 男 助理 工程 师 。现 在西 安重 型机 械研究 所工 作 :
参 考文献
[ 周 国盈 . 钢卷 取设 M】 京 : 金工业 出版 社 ,9 2 1 】 带 . 北 冶 19
t@y jt j y j j 舢 — .研 I弭 — t zj —_ 穷 — j @ j .,应 硼 与鲥 用 y 当. j t咖 z y
口. 形 设 特 32 35 环 炉 计 点
全 自动 ; 自动化装置控制下列 系统部分 : 出料 门及 装
扒 渣 门 、 出 料机 及 扒 渣机 、 装 液压 系统 、 燃 风 机 和 稀 助
环 形炉 一个 非 常难 以解 决 的 问题是 炉底 积渣 。由 于 加 热 坯 料 过 程 中不 可 避 免 地产 生 氧 化 铁 皮 积 留 于
体 、 械设 备 的设 计均 有独 到之处 , 机 有效 地解决 了炉 底膨 胀 、 积渣 、 压波 动等 环形 炉常见 问题 。燃烧 系统 采用 成熟 的低 炉底 炉
氧化氮天然气烧嘴 , 热工控制系统采用 2 级计算机数模 自动完成最优化加热 , 单耗低 、 加热质量优异。
关键词 环 形炉 烧嘴
的 支撑 着 炉 底运 转 , 利 于 炉 底钢 结 构 的长 期 稳 定 运 不 行 。而在冷 态 就 预 留膨 胀 量并 在钢 结构 设计 上 作相 应 考虑 的做 法 . 炉子 在 工 作 状态 下 炉 底 框架 均 衡 的 支 使 撑着 炉 底 运 转 ,利 于 炉底 钢 结 构 的长 期 稳 定运 行 , 加
如图 3 。
了炉底膨胀的情况。对于环形炉这种炉型来说 , 其最
大 的一 个 特 点 就 是 炉 底 耐火 材 料 在 由冷 态 升 温 至 热 态 时 发生 膨 胀 , 动 炉 底 钢板 发 生位 移 。传 统 的环 形 拖 炉 设 计 中冷 态 时 炉底 框 架 和炉 底 钢 板 没有 偏 心 . 温 升 过 程 中 由于 炉 底 耐 火 材 料 受 热 膨 胀 拖 动 炉 底 钢 板 发 生 位 移 , 由于炉 底 各部 位 耐 火 材料 及 钢结 构 施 工 质 且 量 存在 差 异,此 位 移使 炉底 框 架 和炉 底 钢板 间 产生 无
3 线路 1 所示( 在锅炉停炉时用 ) 。其耐火材料设计特
点 是 换热 器 前 部 分选 用 喷 涂 浇注 料 , 热 器 后 部分 采 换 用 陶 瓷纤维 内衬 。这 样在 换热 器 前侧 重对 高 温烟 气 的
耐热 . 在换热器后注重减少烟气温降提高烟气 回收价
值 节约 能源 。较 之传 统 的全部 用 浇注 料砌 筑 的烟道 有 明显 的节 能 优 势 。运 行 中其 换 热 器 后 烟 气 温 度 达 到 30℃时烟 道 外表 面 温度 仅 有 3 9 0℃左 右 . 传统 设 计 而 烟道 外表 面 在 同等烟 气 温度 下高 达 10℃。 0
加热质量 ,同时使炉膛压力受炉门开闭的影 响减小 ,
图 4 环缝 水封 示意 图
t j
— ・研 与 用 — — 究 应 —
拦 《 瘪 写
维普资讯
⑥ 第星 总 @ ⑨ 年 期 第 霪期
43 机械设 备 .
431 扒 渣 机 ..
维普资讯
⑨ 第霪 总 @ ⑨ 年 期 第霪期
p. 32 形 设 特 35 环 炉 计 点
0 3 5m 环形 炉 设计 特点 3. 2
丁宏钧 ( 津钢 管公 司 18厂, 00) 天 6 3 31 0
[ 摘要] 对天津钢管公司由德国 L I O 公司总承包设计建造的 3 5m环形炉设计特点做了分析。其炉底钢结构 、 3. 2 炉子砌
维普资讯
『髓A EI G 嚅TL Y 篡J R U
JN I
2 @第 期总第 U 期 @ - ⑤ y @, 星 1 期 - 矛
4 设计 特点
4 1 钢 结 构 方 面 .
利于 炉 压的稳 定 。 422 炉体 耐火 材料 .. 采 用复 合结 构 . 根据 不 同部 位 情 况选 用不 同 的耐 火 材料 组合 , 到最 佳 使用 效果 和经 济 效益 。 达
为液压驱动侧开式 , 节奏慢时(7s 2 以上 ) 与装 出 料机联动 , 节奏快时常开 。其侧开式的设计使炉 门驱 动设备有效避开 了炉门 口的高温烟气 , 提高了设备的 可靠性和使用寿命 。
炉底耐火材料表面 . 形成炉底积渣 。久而久之越积越
多 使 炉 底 标 高 上 升 ,直 至 影 响正 常装 料 被 迫 停 炉 检 修, 严重影 响 生产 。同时 , 随着 积渣 增 多还 严重 影 响加 热质 量 和能耗 指标 。以往环 形 炉 的传 统 设 计 中无 法 解
了计算最优 化的加热条件 ,并作为控 制系统 的设定 值 。可实现预设定常规的 、 与坯料相关 的和可重复的
起转动 , 在转 动 过程 中 , 安 装 在 炉 子 内外 墙 上 的 被
22 管坯规格及 布料方式 .
管坯 规 格 : 直径 ( mm)20 20 10 ;0 1 5
长度 ( mm) 112 42 0 : 2 ~ 0
烧 嘴 和炉 顶 的烧 嘴加 热 , 动 一 圈 后, 转 由出料 机 B将 被 加热 好 的管坯 取 出 。
42 水 封 系统 .. 4
强 了炉底钢结 构的工作稳定性 .提高 了设备使 用寿
命 。当然这一技术进步是在精确计算耐火材料膨胀量
的基 础上 实现 的。 42 炉 体 部 分 . 环 形 炉 炉 体 由转 动 炉 底 和 固定 的 炉墙 、炉 顶 、 炉 内隔墙 、 道 、 囱组成 。 烟 烟 421 独特 的三 道 隔墙设 计 . . 这座炉 子 设计 有三 道 隔墙 如 图 2所 示 。