复合白点问题解决及分析
干式复合的常见问题及处理方法

干式复合的常见问题及处理方法浏览次数:603 发布日期:2011-8-11 20:14:411、复合膜剥离强度不够分以下几种情况:胶水固化不完全,剥离开来的时候在胶水面还有粘性。
原因:1)粘合剂的配比错误,固化剂的比例不足导致固化不完全。
在配制粘合剂时要按粘合剂生产厂家规定的配比参数进行配制;2)溶剂的纯度不够,溶剂中含有水或醇类超标,水或醇类与胶水中的固化剂发生反应,降低的固化剂的比例导致胶水固化不完全。
用于干复的溶剂是乙酯,所以乙酯在进厂时每一批都要抽检,如发现纯度不够时不可使用;3)印刷膜中油墨的残留溶剂高引起胶水固化不够。
油墨(特别是PET油墨)的残留溶剂有一部分会与胶水中的固化剂发生反应,从而消耗了固化剂导致胶水固化不够。
对策:①薄膜印刷好后最好不要立即复合,如果时间允许的话可先放置1—2天后再进行复合;②印刷膜下机后检测残留溶剂,如残留溶剂高,在复合时可适当增加固化剂的比例;③选用快速固化的胶水。
4)复合膜熟化温度低、熟化时间不够,出现交联不充分,固化不完全。
对策:提高熟化温度或选用快速固化的胶水。
2、复合薄膜的表观问题1)小墨点。
一般复膜后马上出现的可能性较小,除非是渣浑杂质等。
复膜后一段时间的镀铝膜有可能出现这种现象,原因是因为油墨对铝的腐蚀,当油墨呈现一定的酸性或碱性,而上胶量又小,不能形成连接的一层时,就可能发生这种情况。
2)小灰点。
出现小灰点的可能性有两种,一是辊筒不均匀造成胶的斑点,二是油墨的不均匀造成的油墨没有压实的斑点。
两种可能性都和工艺有关,可以通过调整工艺解决,提高上胶量的厚度。
3)小白点。
一般表面的油墨变色的情况下容易出现。
多出现在镀铝膜的复合中。
出现原因有二:一是油墨本色的遮盖力不强或遮盖不均匀,尤其是白油墨,使铝的颜色渗透出来,没有铝颜色渗透的地方形成小白点;二是工艺原因,烘道温度(特别是一级烘道)太高或上胶量太厚,导致在一级烘道内胶层表面凝结,乙酯在二、三级烘道中冲出来的时候,挤起胶水,显出油墨本色。
造成印刷白点问题的原因及解决方案
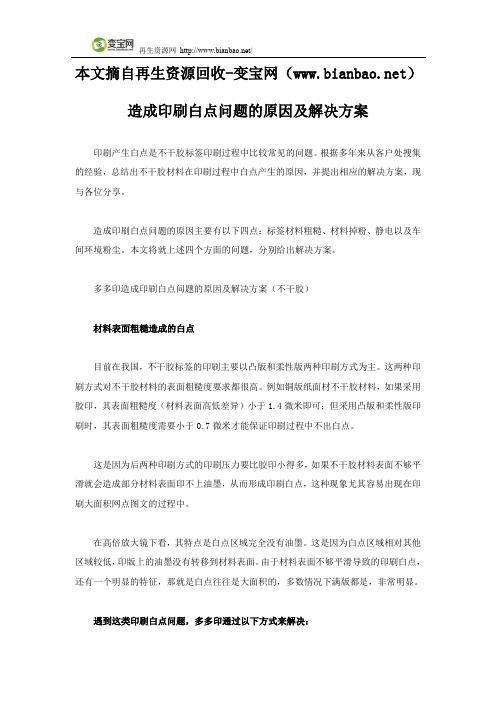
本文摘自再生资源回收-变宝网()造成印刷白点问题的原因及解决方案印刷产生白点是不干胶标签印刷过程中比较常见的问题。
根据多年来从客户处搜集的经验,总结出不干胶材料在印刷过程中白点产生的原因,并提出相应的解决方案,现与各位分享。
造成印刷白点问题的原因主要有以下四点:标签材料粗糙、材料掉粉、静电以及车间环境粉尘。
本文将就上述四个方面的问题,分别给出解决方案。
多多印造成印刷白点问题的原因及解决方案(不干胶)材料表面粗糙造成的白点目前在我国,不干胶标签的印刷主要以凸版和柔性版两种印刷方式为主。
这两种印刷方式对不干胶材料的表面粗糙度要求都很高。
例如铜版纸面材不干胶材料,如果采用胶印,其表面粗糙度(材料表面高低差异)小于1.4微米即可;但采用凸版和柔性版印刷时,其表面粗糙度需要小于0.7微米才能保证印刷过程中不出白点。
这是因为后两种印刷方式的印刷压力要比胶印小得多,如果不干胶材料表面不够平滑就会造成部分材料表面印不上油墨,从而形成印刷白点,这种现象尤其容易出现在印刷大面积网点图文的过程中。
在高倍放大镜下看,其特点是白点区域完全没有油墨。
这是因为白点区域相对其他区域较低,印版上的油墨没有转移到材料表面。
由于材料表面不够平滑导致的印刷白点,还有一个明显的特征,那就是白点往往是大面积的,多数情况下满版都是,非常明显。
遇到这类印刷白点问题,多多印通过以下方式来解决:1、更换合格的材料。
不干胶材料表面不够平滑属于材料质量问题,我们可以要求材料供应商更换达标的材料来进行生产。
2、在多数情况下,更换材料就无法保证工期,因为不干胶标签印刷企业的生产周期相当紧凑。
况且印刷厂更换活件需要一系列的准备工作,一旦材料有问题不能印刷,那么准备工作就是白做,这对于印刷厂来说严重影响生产效率。
如果遇到这种情况,我们可以考虑先在材料表面印刷一层底涂油或是冲淡剂(撤淡剂)。
这两种印刷助剂基本上是无色的,不会对印刷品的颜色造成太大影响。
印刷这两种助剂后材料表面会被填平,人为提高材料的平滑度,印刷白点现象会大大减少。
复合镀铝膜白点现象的产生及解决
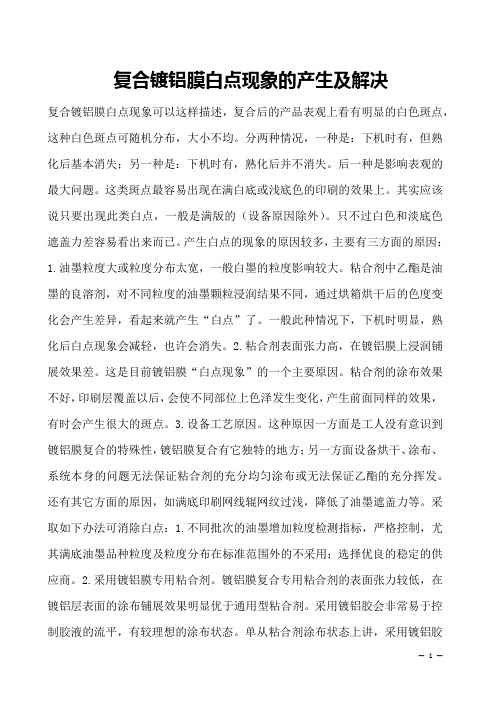
复合镀铝膜白点现象的产生及解决复合镀铝膜白点现象可以这样描述,复合后的产品表观上看有明显的白色斑点,这种白色斑点可随机分布,大小不均。
分两种情况,一种是:下机时有,但熟化后基本消失;另一种是:下机时有,熟化后并不消失。
后一种是影响表观的最大问题。
这类斑点最容易出现在满白底或浅底色的印刷的效果上。
其实应该说只要出现此类白点,一般是满版的(设备原因除外)。
只不过白色和淡底色遮盖力差容易看出来而已。
产生白点的现象的原因较多,主要有三方面的原因:1.油墨粒度大或粒度分布太宽,一般白墨的粒度影响较大。
粘合剂中乙酯是油墨的良溶剂,对不同粒度的油墨颗粒浸润结果不同,通过烘箱烘干后的色度变化会产生差异,看起来就产生“白点”了。
一般此种情况下,下机时明显,熟化后白点现象会减轻,也许会消失。
2.粘合剂表面张力高,在镀铝膜上浸润铺展效果差。
这是目前镀铝膜“白点现象”的一个主要原因。
粘合剂的涂布效果不好,印刷层覆盖以后,会使不同部位上色泽发生变化,产生前面同样的效果,有时会产生很大的斑点。
3.设备工艺原因。
这种原因一方面是工人没有意识到镀铝膜复合的特殊性,镀铝膜复合有它独特的地方;另一方面设备烘干、涂布、系统本身的问题无法保证粘合剂的充分均匀涂布或无法保证乙酯的充分挥发。
还有其它方面的原因,如满底印刷网线辊网纹过浅,降低了油墨遮盖力等。
采取如下办法可消除白点:1.不同批次的油墨增加粒度检测指标,严格控制,尤其满底油墨品种粒度及粒度分布在标准范围外的不采用;选择优良的稳定的供应商。
2.采用镀铝膜专用粘合剂。
镀铝膜复合专用粘合剂的表面张力较低,在镀铝层表面的涂布铺展效果明显优于通用型粘合剂。
采用镀铝胶会非常易于控制胶液的流平,有较理想的涂布状态。
单从粘合剂涂布状态上讲,采用镀铝胶可消除了白点现象产生的可能。
3.胶液的粘度与网线辊线数有一定的匹配关系,超出匹配区间太大会破坏胶的涂布状态,造成“白点”的产生和更严重的其它方面的影响,但在镀铝膜上似乎主要还是“白点”的产生更令人关注。
无溶剂复合外观问题解决办法,气泡、白点、隧道、褶皱、异物

无溶剂复合外观问题解决办法,气泡、白点、隧道、褶皱、异物无溶剂复合包括无溶剂复合设备、无溶剂复合粘合剂、无溶剂复合工艺均与传统的干式复合有较大区别。
无溶剂复合常见外观问题如:气泡、白点、白斑、涂布效果差、隧道、褶皱、异物等。
以上外观问题在溶剂胶干式复合中也有出现,但无溶剂复合表现得更为明显。
(1)无溶剂复合比干式复合更容易出现白点、白斑或者气泡问题。
这是因为无溶剂复合上胶量低于干式复合,更容易出现涂胶不足的情况,此时没有足够的粘合剂渗透到油墨中,导致白点或气泡。
特别是在白墨的地方,由于白墨与色墨相比,相同的遮盖力下需要添加更多的填料,这导致白墨处更容易出现白点、白斑和气泡。
(2)无溶剂复合比干式复合更容易出现隧道和褶皱问题。
由于无溶剂复合初粘力很低,需要精确控制好设备张力、压力、上胶量等才能达到良好的复合效果。
以下将外观问题分门别类进行分析:1、气泡(1)气泡与复合用薄膜材料相关薄膜表面电晕处理不好或储存时间过长,造成表面润湿性差,复合膜易出现气泡。
应提高基材薄膜的表面张力,并在复合前应对基材进行检测,PE和PP 薄膜的表面张力应不小于40mN/m,PA和PET薄膜的表面张力均应不小于50mN/m,镀铝薄膜镀铝面的表面张力均应不小于40 mN/m。
薄膜中的添加剂析出,也会造成表面润湿性差,复合膜易出现气泡。
薄膜不平滑,使粘合剂涂布不均匀或不足,应选用优质薄膜或适当增加涂布量。
薄膜本身温度低,粘合剂涂布后流动不良造成阻塞而润湿性差。
粘合剂在熟化过程中与油墨或基材薄膜中的水分发生反应产生气泡。
在夏季,加工尼龙复合膜时易出现该问题,大面积白墨以及专色墨印刷时易出现该问题。
(2)气泡与印刷油墨相关油墨颗粒粗,使粘合剂涂布不均匀或不足。
对此应选用优质油墨或适当增加涂布量。
(3)气泡与粘合剂相关粘合剂涂布量不足,易造成气泡。
粘合剂流动性差、粘度大导致涂布效果不佳。
可适当提高固定辊和上胶辊温度以增加粘合剂的流动性。
无论什么样的无溶剂复合白点,看完这篇你就全懂了!

无论什么样的无溶剂复合白点,看完这篇你就全懂了!无溶剂复合过程中,出现白点或者气泡是最常见的质量问题之一,造成原因也是多方面的。
1、上胶量不足引起现象:无规则、不同油墨区域情况不一样;严重时可以观察到“雪花”的形状。
原因分析:上胶量太小,涂布的胶水层不能够填平材料(油墨及薄膜)表面的凹凸不平,产生气泡,该气泡实际是因为“没有胶水”而形成的空隙。
控制关键点:上胶量是一个相对的概念,不同的基材、不同油墨上胶量都不一样。
一般情况下透明材料上胶量最小,一般为1.0~1.3 g/m2;而镀铝材料以及满版印刷的材料所需上胶量较大,视具体情况可以控制在1.3~2.0 g/m2之间。
2、灰尘、异物、间隙/压力不一或机械破损引起现象:有规律的、周期性的重复出现在某个位置,某一边或者中间位置。
原因分析:涂布部分不干净或者有机械破损;或者两边与中间间隙不一样;或者涂胶辊长时间使用后周长发生变化等;需要根据具体情况进行判断。
举例:曾有长时间使用后,发现胶辊中间周长和两边周长存在明显差异造成每次复合时,中间位置有白点,后经过胶辊重新打磨和更换胶辊后,解决了这一问题。
控制关键点:每次生产前都需要将各单元辊筒彻底擦干净,及时清理附着的异物;并且认真检查涂布单元格辊筒的情况,发现有缺损、裂纹等异常情况时及时更换;经常观察胶槽中胶粘剂的状态,是否有异常情况。
3、湿度太大引起现象:分布面广、无规则;“白点”大小虽然不一,但往往都呈现为圆形。
在潮湿天气复合阻隔性好的材料,特别是尼龙材料时容易出现。
原因分析:无溶剂复合所用的胶粘剂是聚氨酯类型,聚氨酯胶粘剂中的异氰酸酯组分非常容易与空气中的水汽发生反应。
少量的水即可消耗大量的异氰酸酯组分,并产生大量的气体,在熟化期间会将复合的两层基材胀起,在无溶剂胶粘剂完全固化后留下气泡。
控制关键点:严格控制环境湿度,对尼龙和镀铝材料的复合时更要特别注意。
4、油墨干燥不良引起现象:气泡往往出现在油墨叠印率高的部分,叠印率低的地方气泡很少。
智能电视的屏幕出现白色斑点该怎么处理

智能电视的屏幕出现白色斑点该怎么处理智能电视作为现代家庭中常见的家电设备,给我们提供了丰富多样的娱乐和信息服务。
然而,有时候我们可能会遇到一些问题,比如智能电视屏幕出现白色斑点,这对于我们的使用体验来说是非常不友好的。
那么,当我们遇到这个问题时,该如何处理呢?本文将就如何处理智能电视屏幕出现白色斑点的问题进行探讨。
1. 了解白色斑点的可能原因首先,我们需要了解白色斑点出现的可能原因,这样才能更好地处理问题。
智能电视屏幕出现白色斑点可能是由于以下几个方面引起的:(1) 像素点故障:像素点是组成屏幕图像的基本单元,如果有些像素点出现故障,就会导致白色斑点的出现。
(2) 显示芯片问题:显示芯片是控制屏幕显示的关键组件,如果出现问题,也有可能导致屏幕出现白色斑点。
(3) 信号干扰:如果电视信号出现干扰,也可能导致屏幕出现白色斑点。
2. 检查和调整连接线当发现智能电视屏幕出现白色斑点时,我们首先应该检查和调整连接线。
连接线是将电视和外部设备连接的关键,如果连接线出现松动或者损坏,就可能导致电视屏幕显示异常。
我们可以按照以下步骤进行检查和调整:(1) 确保连接线插头与电视和外部设备的接口连接牢固。
(2) 检查连接线是否有损坏或者老化,如果有,及时更换。
(3) 尝试重新插拔连接线,以保证连接的质量。
3. 调整屏幕设置如果检查和调整连接线后,问题仍然存在,我们可以尝试调整屏幕设置来解决。
以下是一些常见的屏幕设置调整方法:(1) 亮度和对比度:调整亮度和对比度可以改变屏幕的显示效果,有时候适当调整可以减少白色斑点的出现。
(2) 色彩和色温:调整色彩和色温可以改变屏幕的色彩表现,有时候合理调整可以减少白色斑点的显现。
(3) 清洁屏幕:有时候屏幕的白色斑点可能是由于灰尘或者污渍导致的,我们可以使用专业的屏幕清洁剂和柔软的布进行清洁,看是否能够消除斑点。
4. 寻求专业维修帮助如果以上方法都无法解决问题,智能电视屏幕仍然出现白色斑点,那么我们需要考虑寻求专业维修帮助。
深入浅出复合事件处理

CEP关键过程
格式化 预处理 模式侦测 事件发派 报警
CEP关键模块
3 件接入 模块
4 预处理 模块
1 EPL 解析器
6 据模型 模块
5 EP规则 引擎
2 则管理 模块
7 件发派 模块
8 动模块
CEP辅助工具
规则制作工具 报表输出工具 实时仪表板
事件接入 模块
EPL解析器
预处理 模块
EPL 解析器
对内外:防止资损 银行、商户、用户错帐;内部错帐
对内:业务状况监控 趋势因应、营销决策、风险规避
商业CEP产品
难得有微软没做的领域? 微软即将推出StreamInsight
CEP关键技术
CEP 关键字
• Streaming - 连续不间断 - 实时处理
• Base - 资料量大 -数据库
• Insight - 有用的信息 -智能
分「总督系统」都能做到!
这么强大?不会只是 宣传噱头吧?
冤枉呀!大人。 总督系统通过状态机引擎运行监 控规则,只要编写各式各样的总 督规则,就可做各种不同的监控。 而这总督规则就是程序,可以做 任何的事,任何数学计算与逻辑
运算都难不倒它。
这么强大,给本府一 套玩玩。
大人你有所不知,因为小的编程能 力有限,所以系统现在还有很多 BUG,不太稳定。加上人力短缺, 开发进度一直快不起来,估计最快 还要两三季才能完善整个系统。
ORDER BY INSERT INTO
…
CEP
CEP-EPL
RETAIN MATCHING
OUTPUT …
无误报警,但漏网之鱼很多…
有误报警,但无漏网之鱼
有误报警,漏网之鱼很少
无误报警,无漏网之鱼… YA!
TFT-LCD白点不良机理研究及改善

第36卷第3期2021年3月液晶与显示Chinese Journal of Liquid Crystals and Display;Vol.36 No.3Mar. 2021文章编号:1007-2780(2021)03-0405-06TFT-LCD 白点不良机理研究及改善刘 信",高玉杰1,郭 坤1,杨 志1,程 石:,林鸿涛2,毛大龙:,盛子沬:,赵 剑1,吴 伟:,郭会斌江 鹏1(1.武汉京东方光电科技有限公司,湖北武汉430040;2.北京京东方显示技术有限公司,北京100176)摘要:TFT 基板四道掩膜版工艺可提升产能,但其带来的产品品质困扰着各工厂,白点不良即为四道掩膜版工艺产生°本文通过直流实验探究了白点产生的原因;采用光照实验和高温实验,研究了白点产生的机理,同时利用工艺调整来改善白点不良°结果表明,有源层膜质存在异常,其导电性不同导致了反冲电压(A V p)的差异,最佳公共电压的不同形成白点不良°栅极和源极耦合电容越小,即硅边宽度越小,白点越少,直至消失°子像素存储电容越大,钝化层厚度(PVX) 由600 nm 减小到400 nm,白点不良程度可减轻1个等级°通过工艺调整,将硅边宽度降低到1.2 y m ,可解决四道掩膜版工艺导致的白点问题。
该研究对于产品品质和收益的提升以及后续产品开发提供了有效的解决方法及参考° 关 键 词:白点;反冲电压;Staebler-Wronski 效应中图分类号:TN873+.93;TN321+.5 文献标识码:A doi :10.27188/CJLCD.2020-0153Mechanism research and improvement ofTFT-LCD white dotLIU Xin 1 * , GAO Yu-ie 1 , GUO Kun 1 , YANG Zhi 1 , CHENG Shi 1 , LIN Hongtao 2 , MAO Da-long 1 , SHENG Zi-mo 1 , ZHAO Jian 1 , WU Wet , GUO Hui-bin 1 , JIANG Peng 1收稿日期:202-06-13 ;修订日期:20201007.* 通信联系人,E-mail : liuxin_cq@ (1. Chongqing BOE Optoelectronics Technology Co . ? Ltd . , Wuhan 430040 , China ;2. Beijing BOE Display Technology Co ., Ltd ., Beijing 100176 , China )Abstract : The 4 mask process of TFT substrate can improve production capacity , but it also bringsthe problemsin product quality. For example , the 4 mask process can generate white dot defects. The causes of white dots is explored through DC experiment. The mechanism of white dots is studied by il lumination experiment and high temperature experiment , and the white dots defects are improved byprocess adjustment. The mechanism of white dots defects is that the conductivity of active layer is dif ferent due to SW effect, resulting in different feedthrough voltage (A V p ) , and the difference of opti mal V com leads to white dots defects. With the gate and drain electrode signal coupling capacitance C gs becaming smaller (i.e . the smaller active tail width) , the white dots gradually decrease until they dis-406液晶与显示第36卷appear.With the pixel storage capacitor C st becoming larger,the insulation layer thickness(PVX)is reduced from600nm to400nm,and the degree of white dots defects can be reduced by1level.After the process adjustment,the width of active tail is reduced to1.2“m,which can solve the white dots problem caused by4mask process.This work provides effective solutions and references for the improvement of product quality and benefits as well as subsequent product development.Key words:white dot;feedthrough voltage;SW effect1引言随着生活水平提升,人们对显示器的品质需求越来越高,高分辨率、高刷新频率、高对比度、高亮度等高端产品逐渐占领市场。
无溶剂复合常见问题-白斑产生原因详细介绍
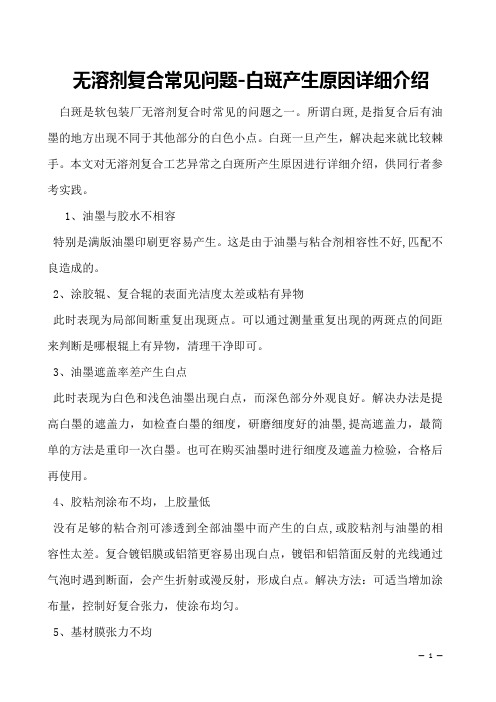
无溶剂复合常见问题-白斑产生原因详细介绍白斑是软包装厂无溶剂复合时常见的问题之一。
所谓白斑,是指复合后有油墨的地方出现不同于其他部分的白色小点。
白斑一旦产生,解决起来就比较棘手。
本文对无溶剂复合工艺异常之白斑所产生原因进行详细介绍,供同行者参考实践。
1、油墨与胶水不相容特别是满版油墨印刷更容易产生。
这是由于油墨与粘合剂相容性不好,匹配不良造成的。
2、涂胶辊、复合辊的表面光洁度太差或粘有异物此时表现为局部间断重复出现斑点。
可以通过测量重复出现的两斑点的间距来判断是哪根辊上有异物,清理干净即可。
3、油墨遮盖率差产生白点此时表现为白色和浅色油墨出现白点,而深色部分外观良好。
解决办法是提高白墨的遮盖力,如检查白墨的细度,研磨细度好的油墨,提高遮盖力,最简单的方法是重印一次白墨。
也可在购买油墨时进行细度及遮盖力检验,合格后再使用。
4、胶粘剂涂布不均,上胶量低没有足够的粘合剂可渗透到全部油墨中而产生的白点,或胶粘剂与油墨的相容性太差。
复合镀铝膜或铝箔更容易出现白点,镀铝和铝箔面反射的光线通过气泡时遇到断面,会产生折射或漫反射,形成白点。
解决方法:可适当增加涂布量,控制好复合张力,使涂布均匀。
5、基材膜张力不均基膜张力不均,进入复合辊之前打折,造成局部复合效果差,出现气泡,宏观表现为白斑。
6、复合和涂胶压力复合部位或涂胶部位压力设置不当,呈大小头。
压力不均使得胶液中的空气不能在复合过程被排出。
另外,复合时第二基材与复合压辊夹角不能太大,否则容易夹杂空气形成气泡。
7、两基材膜面粗糙度太大,添加剂上浮以往基材膜面粗糙度一般在0.08~0.16um(用无溶剂胶膜表面粗糙度应更低些)。
若高于这个粗糙度,那么膜表面凹凸严重,高低不平,油墨及胶粘剂很难将凹凸穴填平,从而造成复合气泡。
若基膜添加剂质量偏劣或受热上浮,也会产生白斑。
透明复合膜出现斑点或气泡”,该如何解决呢
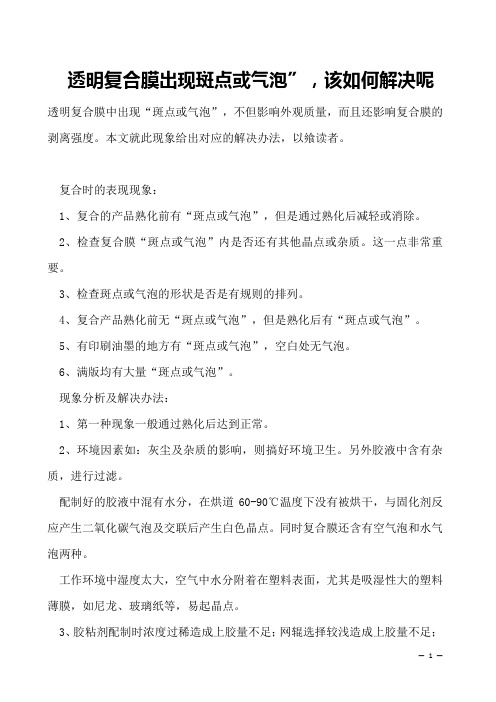
透明复合膜出现斑点或气泡”,该如何解决呢透明复合膜中出现“斑点或气泡”,不但影响外观质量,而且还影响复合膜的剥离强度。
本文就此现象给出对应的解决办法,以飨读者。
复合时的表现现象:1、复合的产品熟化前有“斑点或气泡”,但是通过熟化后减轻或消除。
2、检查复合膜“斑点或气泡”内是否还有其他晶点或杂质。
这一点非常重要。
3、检查斑点或气泡的形状是否是有规则的排列。
4、复合产品熟化前无“斑点或气泡”,但是熟化后有“斑点或气泡”。
5、有印刷油墨的地方有“斑点或气泡”,空白处无气泡。
6、满版均有大量“斑点或气泡”。
现象分析及解决办法:1、第一种现象一般通过熟化后达到正常。
2、环境因素如:灰尘及杂质的影响,则搞好环境卫生。
另外胶液中含有杂质,进行过滤。
配制好的胶液中混有水分,在烘道60-90℃温度下没有被烘干,与固化剂反应产生二氧化碳气泡及交联后产生白色晶点。
同时复合膜还含有空气泡和水气泡两种。
工作环境中湿度太大,空气中水分附着在塑料表面,尤其是吸湿性大的塑料薄膜,如尼龙、玻璃纸等,易起晶点。
3、胶粘剂配制时浓度过稀造成上胶量不足;网辊选择较浅造成上胶量不足;网辊堵版造成有规则的“斑点或气泡”现象。
4、由于残留溶剂的影响造成,适当提高烘道温度;由于初粘力不足造成二层薄膜间离位,可以更换初粘力更高的胶粘剂或适当提高热合辊的温度;薄膜表面张力差也会造成初粘力不足。
5、印刷油墨与胶粘剂不匹配,造成印刷油墨处与胶粘剂粘合不良;印刷油墨层假干现象,复合后通过熟化,残留溶剂侵蚀印刷及复合层。
6、薄膜质量差即基膜表面张力太差,造成胶粘剂流平性差或没有胶的地方产生气泡。
复合时刮刀角度及胶液落差较大,冲击产生气泡。
复合机高速运转时,气泡不能及时消散,致胶盘内产生大量气泡,然后被夹带入转移到薄膜上;复合压力不足,复合辊表面温度太低,胶粘剂活化不足,流动性小,使胶液网点与网点间的间隙无法填补,产生有微小的空隙,造成气泡;胶粘剂质量问题;水分及醇类的影响,在复合时尽量避免。
复合过程中的白点和气泡

复合过程中的白点和气泡复合产品的白点、气泡形状各异,人们对气泡、白点的概念不尽相同。
虽然都叫白点、气泡,但细究起来大多数不是同一现象,形成机理更是千差万别。
下面分情况分别讲解:一镀铝膜复合印刷基材,如产生气泡,在印刷膜浅色部分看起来就是白点。
气泡部分两层基材未密切贴合,不一定是圆鼓鼓地凸起状。
但严重的干燥不良形成的气泡倒是鼓起的,大的象芝麻粒。
产生这类气泡的原因有的是胶粘剂未干透,有的却是油墨溶剂干燥不充分造成,经常出现在大面积迭印部分。
某些小印刷机还在使用红外线干燥箱,大面积迭印时残留溶剂量高达100毫克。
轻微的干燥不良虽没有鼓起的大气泡,只形成细微的小气泡,却影响膜的透明性。
当气泡足够小时,能透过某些薄膜释放溶剂。
如同样的工艺条件,PET复铝箔有气泡,而BOPP复铝箔熟化后气泡会消失。
二干燥不良形成的小气泡和上胶量不足产生的气泡用放大镜观察区别不大,这时需要作理性分析。
任何看起来很光滑的表面,用放大镜观察都是凹凸不平的。
胶粘剂把表面抹平需要一定厚度——也就是上胶量。
普通透明复合膜用低粘度胶粘剂,每平方米上胶量需1.8~2.2克,低于这水平就是上胶量不足。
印刷膜涂胶要厚点,如白墨厚度一般在0.7~0.9微米,色块下托白墨厚度就更大。
里印复合墨树脂含量少于表印白墨,所以复合白墨表面较粗糙。
粗糙本来是复合白墨的优点,有利于胶粘剂渗透产生足够的剥离强度。
反过来却需要较多的上胶量。
为了保证油墨部分有足够的胶粘剂厚度,上胶量需要3~3.5克,少于这标准也是上胶量不足。
因堵版造成上胶量不足容易理解。
堵版分二种:一种是突发性的,因涂料复溶性差和操作中转移率不断下降造成。
这类堵版如未找出原因及时排除,仅靠停车擦版只能维持一时,马上又故态复萌。
另一种堵版是渐变型的,严格地说不能算故障,因为每次复合后不可能把网纹辊中的残胶完全清洗干净,残胶日复一日地在网孔底部沉积并固化。
上胶量慢慢变小、小气泡也渐渐产生、由少变多、由小变大。
复合膜产生斑点的原因分析
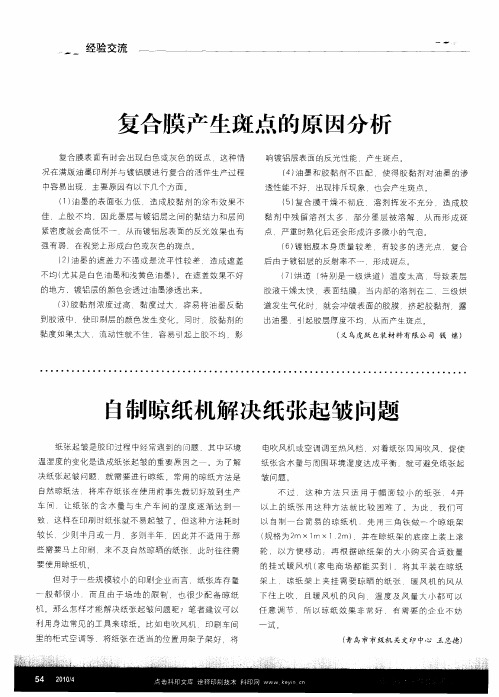
车 间 ,让 纸 张 的 含 水 量 与 生 产 车 间 的 湿 度 逐 渐 达 到 ~ 致 ,这 样在 印刷 时纸 张就 不 易起皱 了。但 这种 方法 耗 时
较长 ,少则 半月 或
月 ,多则 半年 ,因此 并不适 用于那
电吹风 机 或 空调 调至 热风 档 ,对 着纸 张 四周吹 风 ,促使 纸 张含 水 量与 周 围环境 湿 度达 成平 衡 .就 可避 免纸张 起 皱 问题 。 不 过 ,这 种 方 法 只 适 用 于 幅 面较 小 的纸 张 .4 开 以 上 的 纸张 用 这 种 方 法 就 比 较 困难 了 。 为 此 ,我 们 可 以 自制一 台 简 易 的 晾纸 机 :先 用三 角铁 做 一 个 晾 纸 架
经验 交流
~
复合膜产生斑 点的原 因分析
复 合膜 表 面有 时会 出现 白色或 灰色 的斑 点 ,这种 情
况 在满 版油 墨 印刷并 与 镀铝膜 进 行 复合 的活件 生产 过 程
中容易 出现 主要原 因有 以下几 个方 面 。
响镀 铝层 表面 的反光 性能 ,产 生斑 点 。 ( 油 墨和 胶 黏 剂不 匹配 使得 胶 黏 剂对 油 墨 的渗 4) 透 性 能不好 出现排 斥现 象 也 会产 生斑点 。
பைடு நூலகம்
些需要 马 上 印刷 来不 及 自然 晾晒 的纸 张 ,此 时往 往 需
要使 用晾纸机 。
轮 ,以 方 便 移 动 ;再 根 据 晾 纸 架 的 大 小 购 买 合 适 数 量
的 挂 式 暖风 机 ( 电商 场 都 能 买 到 ) 家 ,将 其 平 装 在 晾纸 架上 .晾纸 架 上 夹挂 需要 晾 晒 的纸 张 暖风 机 的风 从 下 往 上 吹 ,且 暖 风 机 的风 向 、温 度 及 风 量 大 小 都 可 以 任 意 调 节 ,所 以 晾 纸 效 果 非 常 好 有 需 要 的 企 业 不妨
复合白点问题解决及分析

白点问题分析及解决软包装干式复合膜出现气泡的故障很常见,导致其产生的原因也有多种,下面将逐一讨论.一、薄膜方面的因素1.薄膜表面的张力复合用薄膜的表面张力必须达到一定的数值(如聚乙烯薄膜的表面张力必须大于3.8×10—2N/m),如果薄膜的表面张力太小,则胶少或没胶的地方就会产生气泡。
此外,薄膜的表面张力应当是均匀一致的,如果表面张力不均匀,则涂胶也就不均匀,容易产生空洞和气泡。
因此,塑料薄膜在复合前一般都要进行表面处理,以提高其表面张力值,保证复合工艺的顺利进行。
在生产之前,一定要对薄膜的表面张力进行认真仔细的检查,一旦发现其表面张力达不到要求,就必须重新进行表面处理。
2.薄膜平均厚度误差及误差分布复合用薄膜的厚度应当尽可能均匀一致,平均厚度误差应控制在误差范围之内,越小越好。
而且平均误差的分布也应当均匀,如果分布不均,厚度太大的地方就会出现凸筋,造成复合压力的不均衡,压力小的地方就会出现空档,从而形成气泡。
3.薄膜的表面清洁度在干式复合工艺中,要进行复合的薄膜表面必须干燥、清洁。
如果塑料薄膜表面不太清洁,黍附了灰尘、油脂等污物,就会使复合膜的两层基材之间无法紧密贴合。
中间夹的这些异物,也会导致空档和气泡的形成.薄膜表面不清洁,除了用干净的棉布进行清洁外,还可以对薄膜重新进行电晕处理.电晕处理既可以去除薄膜表面吸附的灰尘、水分及其他油垢,提高薄膜的表面张力,还可使薄膜表面有良好的粗糙度,从而能够减少气泡等故障的发生率,并进一步提高复合牢度. 4.薄膜的含水量对于一些吸湿性较强的薄膜:如PT、NY等,如果保管不当致使其吸收了大量的水分而又未加处理就直接使用,在复合或熟化过程中水分就会逐步向外蒸发,也可能使复合膜产生气泡。
因此,对于吸湿性强的薄膜一定要注意防潮,如果发现薄膜已经吸潮,可以先预热烘干,然后再进行复合。
二、油墨及印刷工艺方面的因素1.油墨的类型和质量正确选用油墨也可以从一定程度上控制和减少复合膜气泡的产生。
复合膜白斑点的形成原因分析.
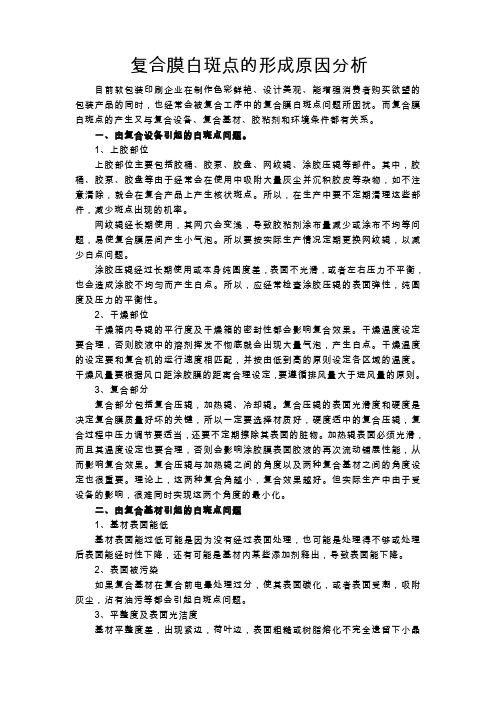
复合膜白斑点的形成原因分析目前软包装印刷企业在制作色彩鲜艳、设计美观、能增强消费者购买欲望的包装产品的同时,也经常会被复合工序中的复合膜白斑点问题所困扰。
而复合膜白斑点的产生又与复合设备、复合基材、胶粘剂和环境条件都有关系。
一、由复合设备引起的白斑点问题。
1、上胶部位上胶部位主要包括胶桶、胶泵、胶盘、网纹辊、涂胶压辊等部件。
其中,胶桶、胶泵、胶盘等由于经常会在使用中吸附大量灰尘并沉积胶皮等杂物,如不注意清除,就会在复合产品上产生核状斑点。
所以,在生产中要不定期清理这些部件,减少斑点出现的机率。
网纹辊经长期使用,其网穴会变浅,导致胶粘剂涂布量减少或涂布不均等问题,易使复合膜层间产生小气泡。
所以要按实际生产情况定期更换网纹辊,以减少白点问题。
涂胶压辊经过长期使用或本身纯圆度差,表面不光滑,或者左右压力不平衡,也会造成涂胶不均匀而产生白点。
所以,应经常检查涂胶压辊的表面弹性,纯圆度及压力的平衡性。
2、干燥部位干燥箱内导辊的平行度及干燥箱的密封性都会影响复合效果。
干燥温度设定要合理,否则胶液中的溶剂挥发不彻底就会出现大量气泡,产生白点。
干燥温度的设定要和复合机的运行速度相匹配,并按由低到高的原则设定各区域的温度。
干燥风量要根据风口距涂胶膜的距离合理设定,要遵循排风量大于进风量的原则。
3、复合部分复合部分包括复合压辊,加热辊、冷却辊。
复合压辊的表面光滑度和硬度是决定复合膜质量好坏的关键,所以一定要选择材质好,硬度适中的复合压辊,复合过程中压力调节要适当,还要不定期擦除其表面的脏物。
加热辊表面必须光滑,而且其温度设定也要合理,否则会影响涂胶膜表面胶液的再次流动铺展性能,从而影响复合效果。
复合压辊与加热辊之间的角度以及两种复合基材之间的角度设定也很重要。
理论上,这两种复合角越小,复合效果越好。
但实际生产中由于受设备的影响,很难同时实现这两个角度的最小化。
二、由复合基材引起的白斑点问题1、基材表面能低基材表面能过低可能是因为没有经过表面处理,也可能是处理得不够或处理后表面能经时性下降,还有可能是基材内某些添加剂释出,导致表面能下降。
复合膜白斑点现象分析及解决
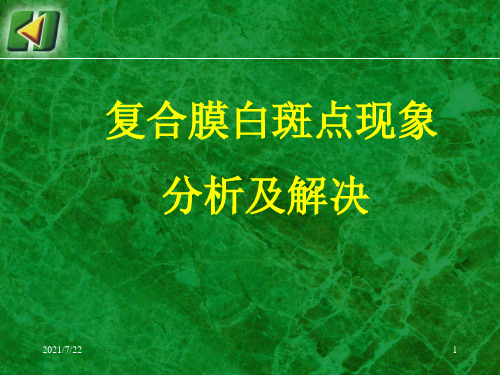
2021/7/22
18 4
基材有三个方面:
表面张力低 表面污染 其它
2021/7/22
19
基
表面张力低:
1 基材没经电晕处理
2 下机基材表面张力低
处理机车速太快: 处理机电压、频率太低: 处理机火花咀与基材距离太大:
2021/7/22
20
1
3 使用时表面张力不够 存放时间过长: 存放环境恶劣:温度高、湿度大 基材内添加剂太多:
热效率低
风管:过滤、洁净
2021/7/22
8
复合部位:
1 复合热辊 表面温度:
表面状况:原始加工、后天污染
2 复合压辊 材质:硬度、耐性
表面状况:
同心度:
压力: 2021/7/22
9
3
3 包角 基材与复合辊: 基材之间:
2021/7/22
10
导辊:
转动不灵: 表面缺陷:
2021/7/22
11
4
复合膜白斑点现象 分析及解决
2021/7/22
1
复合膜的白斑点通常出现在
浅色油墨(白、黄、灰等)印刷的塑/ 铝箔、塑/镀铝膜复合膜
深色油墨(兰、绿等)印刷的塑/乳白膜 等复合膜(反面看较明显)
产生这种现象的原因很复杂,下面从
设备、基材、胶水、油墨、溶剂等方面进
行分析
2021/7/22
2
机械设备有四个方面:
涂胶部位
干燥部位
复合部位 导辊部位
2021/7/22
3
机
涂胶部位:
1 涂布网纹辊 网眼深度 (μ) :
上胶量(g/㎡) ﹦(1/4~1/6)× h (μ) ×工作液浓度(%)
网眼线数(目/英寸):越大网眼可做得越深
白点问题分析

复合常见故障白点和气泡的剖析所谓气泡是指两层薄膜未完全贴合,两层复合薄膜之间有空档、有气体存在。
所谓白点也是指两层薄膜未完全贴合,复合成品内有空档,但没有气体存在。
复合产品中常见的白点和气泡形状各异且不易区分,产生白点和气泡的原因也往往不容易判断。
复合产品的白点和气泡给许多软包装企业带来了极大的损失。
对白点和气泡产生的原因以及解决的方法,至今许多软包装企业还常处在困惑、头痛、甚至无奈之中。
复合薄膜常见的的气泡或白点有三种不完全相同的表现:第一种:下机时有,但熟化后消失或基本消失;第二种:下机时有,熟化后并不消失。
这类斑点最容易出现在满版白或大面积浅黄色的颜色中。
第三种,下机时没有,熟化后出现。
气泡和白点产生的原因之一上胶量不足任何看起来很光滑的表面(如PET、BOPP、NY、PE、CPP、镀铝薄膜、铝箔等),但用放大镜观察,可以发现都是凹凸不平的。
尤其是印刷后的油墨表面更是凹凸不平且多孔隙。
第一基材油墨胶水第二基材复合时,首先要将粘合剂填平复合基材本身的凹凸不平和填平油墨表面的凹凸不平和众多的孔隙、同时还要在油墨的表面形成一定厚度的粘合剂层,这样才能将二层需复合的基材牢固地粘合在一起。
用于里印的复合白墨中的树脂含量通常少于表印白墨,所以复合白墨的表面更为粗糙和有更多的孔隙。
粗糙的表面本来是复合白墨的优点,有利于胶粘剂渗透产生足够的剥离强度,但反过来由于要将凹凸不平和众多孔隙的油墨填平,因此遇到满版白墨的印刷膜复合时往往需要更多的上胶量。
胶少或没胶的地方就容易出现气泡或白点现象。
选择涂布量,既要考虑到产品对剥离强度的要求,同时也要考虑到产品的表观。
不同的产品、不同的油墨甚至不同的复合基材对上胶量都有不同的要求。
如果我们对此缺乏起码的认识,常常就会对产生气泡或白点的现象疑惑不解。
复合膜上胶量的常规要求 结 构 上胶量(g/m2) 塑/塑(无印刷) 2.0g/m2左右 塑/塑(油墨少) 2.5g/m2左右 塑/塑(油墨多) 3.0g/m2左右 塑/铝(无印刷) 3.0g/m2左右 塑/铝(油墨少) 3.3g/m2左右 塑/铝(油墨多)3.5g/m2左右油墨复合薄膜粘合剂印刷薄膜 上胶量不足示意图油墨复合薄膜粘合剂印刷薄膜塑/铝(抗酸辣) 3.8g/m2左右塑/铝(耐蒸煮) 4.5g/m2左右塑/纸 5.0g/m2左右判断涂布量不足的简易方法因刚复合完的复合薄膜,尚未固化的双组分聚氨酯胶像热熔胶,在熟化室内会再次被融熔而流动,熟化温度越高流动性越大,我们称为“二次流平”。
光学玻璃产生白点问题解决方法及工业清洗剂的选用

在日常生产手机盖板玻璃和光学玻璃的厂家的工作人员都知道,手机玻璃盖板和光学玻璃经常会出现白点问题,另外在清洗过程中也会出现白点问题。
那么造成手机盖板玻璃和光学玻璃产生的白点是什么原因呢?对此,光学玻璃清洗剂厂家“联诺化工”通过了解分析发现造成手机盖板玻璃和光学玻璃产品出现白点的原因有很多种,比如常见的有清洗水质量环境没保养好,超声波清洗机的调式不当,也有生产车间环造成等原因。
但往往的是在使用光学玻璃清洗剂中出现问题,如光学玻璃清洗剂去污力度不够等原因。
一、光学玻璃清洗剂配方造成和解决方法光学玻璃清洗剂的去污能力是否足够强,取净于光学玻璃清洗剂的配方,手机盖板玻璃和光学玻璃对于干净度要求是非常高的,而且光学玻璃和手机盖玻璃板丝印后的油墨对强碱性非常的敏感,光学玻璃清洗剂碱性过强会对油墨水产生伤害,而光学玻璃清洗剂碱性不强对清洗去污力又不够强。
由于这些产品的要求非常高,所以手机盖板玻璃和光学玻璃在选择光学玻璃清洗剂产品的时候要选择优质光学玻璃清洗剂厂家,如“联诺化工”。
“联诺化工”除了有成熟的光学玻璃清洗剂配方和专业研发团队外,还有一套为客户解决清洗难的清洗方案。
“联诺化工”正是因为有优质的产品和成熟的配方才能在市场上受到众多客户的喜爱和成功合作达上万客户。
二、烤炉造成白点和水印问题出现和解决方法如果清洗白片玻璃排除水质、漂洗水槽、振动最大、光学玻璃清洗剂等,光学玻璃盖板在平磨下来擦架都更换以后等原因,还出现白点和水印,基本可以确定是烤炉内清洁卫生造成的。
最常见的是烤炉内部最底部四面角落有脏污或过滤器寿命到了,所以可以用干净的无尘布粘纯水或工业酒精擦拭干净各个烤炉角落里的脏污,另外要用一盘纯水放置烤炉内,开启烤炉风机进行水吸附烤炉内空气流动的灰尘。
通过这样的方法换不同的位置吸附灰尘(一般吸附时间5-15分钟)。
在这个过程中溢流水开大一点,注意慢拉槽的慢拉速度,调节好速度后进行下快上慢的原则。
要注意的是慢拉附近不能有太大的气流流动,只有这样才能彻底清洗干净。
油墨复合不牢的几点
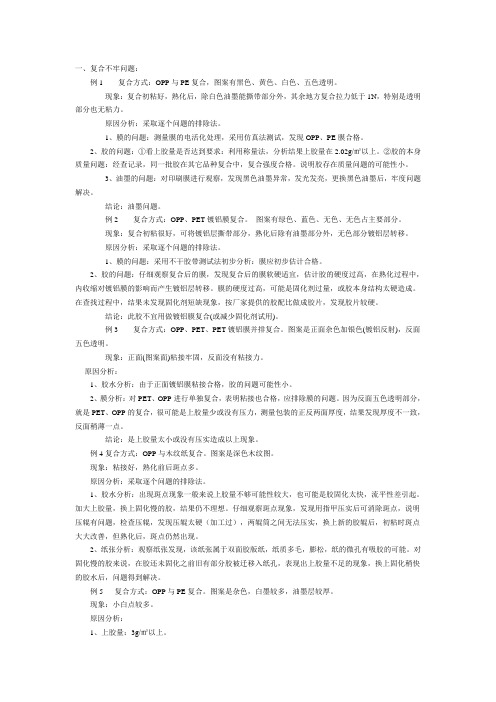
一、复合不牢问题:例1 复合方式:OPP与PE复合,图案有黑色、黄色、白色、五色透明。
现象:复合初粘好,熟化后,除白色油墨能撕带部分外,其余地方复合拉力低于1N,特别是透明部分也无粘力。
原因分析:采取逐个问题的排除法。
1、膜的问题:测量膜的电活化处理,采用仿真法测试,发现OPP、PE膜合格。
2、胶的问题:①看上胶量是否达到要求:利用称量法,分析结果上胶量在2.02g/㎡以上。
②胶的本身质量问题:经查记录,同一批胶在其它品种复合中,复合强度合格。
说明胶存在质量问题的可能性小。
3、油墨的问题:对印刷膜进行观察,发现黑色油墨异常,发光发亮,更换黑色油墨后,牢度问题解决。
结论:油墨问题。
例2 复合方式:OPP、PET镀铝膜复合。
图案有绿色、蓝色、无色、无色占主要部分。
现象:复合初粘很好,可将镀铝层撕带部分,熟化后除有油墨部分外,无色部分镀铝层转移。
原因分析:采取逐个问题的排除法。
1、膜的问题:采用不干胶带测试法初步分析:膜应初步估计合格。
2、胶的问题:仔细观察复合后的膜,发现复合后的膜软硬适宜,估计胶的硬度过高,在熟化过程中,内收缩对镀铝膜的影响而产生镀铝层转移。
膜的硬度过高,可能是固化剂过量,或胶本身结构太硬造成。
在查找过程中,结果未发现固化剂短缺现象,按厂家提供的胶配比做成胶片,发现胶片较硬。
结论:此胶不宜用做镀铝膜复合(或减少固化剂试用)。
例3 复合方式:OPP、PET、PET镀铝膜并排复合。
图案是正面杂色加银色(镀铝反射),反面五色透明。
现象:正面(图案面)粘接牢固,反面没有粘接力。
原因分析:1、胶水分析:由于正面镀铝膜粘接合格,胶的问题可能性小。
2、膜分析:对PET、OPP进行单独复合,表明粘接也合格,应排除膜的问题。
因为反面五色透明部分,就是PET、OPP的复合,很可能是上胶量少或没有压力,测量包装的正反两面厚度,结果发现厚度不一致,反面稍薄一点。
结论:是上胶量太小或没有压实造成以上现象。
例4复合方式:OPP与木纹纸复合。
加气混凝土坯体中有白点处理方法

加⽓混凝⼟坯体中有⽩点处理⽅法
我们在加⽓混凝⼟⽣产过程中,经常会碰到坯体上有⽩点。
我们该如何解决这个问题呢?
我们先看看这个⽩点在什么位置。
加⽓混凝⼟设备如果在坯体底部有⽩点。
那么原因⽆⾮有两个。
⼀,那是沉降的磷⽯膏颗粒。
我们只需要把磷⽯膏过磨或滤去粗颗粒。
⼆,搅拌机中粘着陈⽯灰掉⼊。
那么我们就需要及时清理搅拌机。
如果是坯体中部多处出现未消解的⽯灰团块。
出现这种现象的原因有4种:1,搅拌不均。
怎么解决?第⼀,延长搅拌时间。
第⼆,更换搅拌机叶轮。
2,⽯灰⽤量⼤。
减少⽯灰⽤量就好了。
3,⽯灰过烧。
更换⽯灰就⾏了。
4,⽯灰太粗。
降低⽯灰筛余量。
多处拉伸⽯灰点。
那是因为搅拌不均。
我们需要及时更换搅拌机叶轮。
以上是可以解决⽩点的3种现象原因及解决⽅法。
其实⽩点也就是⽯灰,我们需要做的就是找出⽯灰在坯体上出现的原因,出现在不同部位的⽯灰就有不同的原因,找出原因,然后对症下药。
软包装复合膜白点的分类
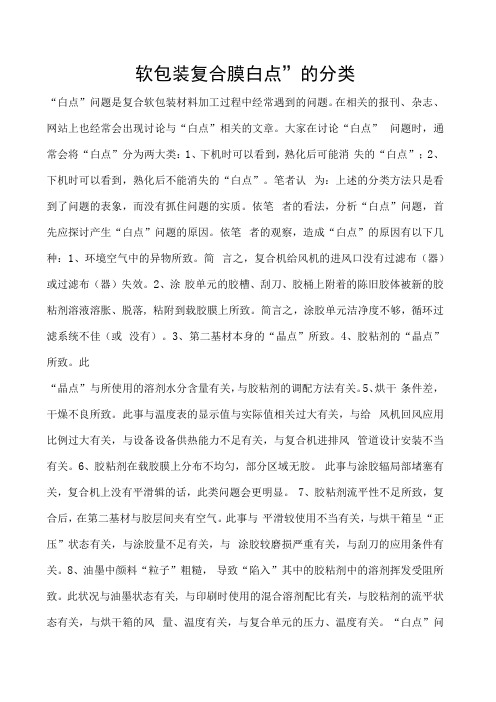
软包装复合膜白点”的分类“白点”问题是复合软包装材料加工过程中经常遇到的问题。
在相关的报刊、杂志、网站上也经常会出现讨论与“白点”相关的文章。
大家在讨论“白点” 问题时,通常会将“白点”分为两大类:1、下机时可以看到,熟化后可能消失的“白点”;2、下机时可以看到,熟化后不能消失的“白点”。
笔者认为:上述的分类方法只是看到了问题的表象,而没有抓住问题的实质。
依笔者的看法,分析“白点”问题,首先应探讨产生“白点”问题的原因。
依笔者的观察,造成“白点”的原因有以下几种:1、环境空气中的异物所致。
简言之,复合机给风机的进风口没有过滤布(器)或过滤布(器)失效。
2、涂胶单元的胶槽、刮刀、胶桶上附着的陈旧胶体被新的胶粘剂溶液溶胀、脱落, 粘附到载胶膜上所致。
简言之,涂胶单元洁净度不够,循环过滤系统不佳(或没有)。
3、第二基材本身的“晶点”所致。
4、胶粘剂的“晶点”所致。
此“晶点”与所使用的溶剂水分含量有关,与胶粘剂的调配方法有关。
5、烘干条件差,干燥不良所致。
此事与温度表的显示值与实际值相关过大有关,与给风机回风应用比例过大有关,与设备设备供热能力不足有关,与复合机进排风管道设计安装不当有关。
6、胶粘剂在载胶膜上分布不均匀,部分区域无胶。
此事与涂胶辐局部堵塞有关,复合机上没有平滑辑的话,此类问题会更明显。
7、胶粘剂流平性不足所致,复合后,在第二基材与胶层间夹有空气。
此事与平滑较使用不当有关,与烘干箱呈“正压”状态有关,与涂胶量不足有关,与涂胶较磨损严重有关,与刮刀的应用条件有关。
8、油墨中颜料“粒子”粗糙,导致“陷入”其中的胶粘剂中的溶剂挥发受阻所致。
此状况与油墨状态有关, 与印刷时使用的混合溶剂配比有关,与胶粘剂的流平状态有关,与烘干箱的风量、温度有关,与复合单元的压力、温度有关。
“白点”问题主要反映在镀铝膜复合产品上,其实,在透明的复合产品同样存在,只是大家对其关注得不够,或者说,对于透明或不透明的复合产品,大家的关注点不一样。
- 1、下载文档前请自行甄别文档内容的完整性,平台不提供额外的编辑、内容补充、找答案等附加服务。
- 2、"仅部分预览"的文档,不可在线预览部分如存在完整性等问题,可反馈申请退款(可完整预览的文档不适用该条件!)。
- 3、如文档侵犯您的权益,请联系客服反馈,我们会尽快为您处理(人工客服工作时间:9:00-18:30)。
白点问题分析及解决软包装干式复合膜出现气泡的故障很常见,导致其产生的原因也有多种,下面将逐一讨论。
一、薄膜方面的因素1.薄膜表面的张力复合用薄膜的表面张力必须达到一定的数值(如聚乙烯薄膜的表面张力必须大于3.8×10-2N/m),如果薄膜的表面张力太小,则胶少或没胶的地方就会产生气泡。
此外,薄膜的表面张力应当是均匀一致的,如果表面张力不均匀,则涂胶也就不均匀,容易产生空洞和气泡。
因此,塑料薄膜在复合前一般都要进行表面处理,以提高其表面张力值,保证复合工艺的顺利进行。
在生产之前,一定要对薄膜的表面张力进行认真仔细的检查,一旦发现其表面张力达不到要求,就必须重新进行表面处理。
2.薄膜平均厚度误差及误差分布复合用薄膜的厚度应当尽可能均匀一致,平均厚度误差应控制在误差范围之内,越小越好。
而且平均误差的分布也应当均匀,如果分布不均,厚度太大的地方就会出现凸筋,造成复合压力的不均衡,压力小的地方就会出现空档,从而形成气泡。
3.薄膜的表面清洁度在干式复合工艺中,要进行复合的薄膜表面必须干燥、清洁。
如果塑料薄膜表面不太清洁,黍附了灰尘、油脂等污物,就会使复合膜的两层基材之间无法紧密贴合。
中间夹的这些异物,也会导致空档和气泡的形成。
薄膜表面不清洁,除了用干净的棉布进行清洁外,还可以对薄膜重新进行电晕处理。
电晕处理既可以去除薄膜表面吸附的灰尘、水分及其他油垢,提高薄膜的表面张力,还可使薄膜表面有良好的粗糙度,从而能够减少气泡等故障的发生率,并进一步提高复合牢度。
4.薄膜的含水量对于一些吸湿性较强的薄膜:如PT、NY等,如果保管不当致使其吸收了大量的水分而又未加处理就直接使用,在复合或熟化过程中水分就会逐步向外蒸发,也可能使复合膜产生气泡。
因此,对于吸湿性强的薄膜一定要注意防潮,如果发现薄膜已经吸潮,可以先预热烘干,然后再进行复合。
二、油墨及印刷工艺方面的因素1.油墨的类型和质量正确选用油墨也可以从一定程度上控制和减少复合膜气泡的产生。
如果印刷所用的胶黏剂的亲和性比较差,就会造成油墨表面上的涂胶量少,甚至有漏涂的地方,这就容易形成气泡。
如果是生产蒸煮包装膜(袋),则必须采用耐蒸煮的复合里印油墨。
否则包装经过蒸煮后可能会产生气泡,甚至发生有油墨处的两层薄膜剥离,脱开的现象。
因此,在实际生产中应当根据承印材料的类型,内容物的性质、后加工的条件等具体情况和要求来选择适当类型的复合里印油墨,这也是保证复合膜黏结强度的一个方面。
2.油墨的干燥性能。
油墨的干燥性能是油墨的一个主要印刷适性,如果油墨干燥不良,特别是当油墨中大量地使用了甲笨、丁醇等沸点较高的溶剂时,就会有许多溶剂残留在油墨层中,经过复合工艺之后,这些残留溶剂就可能产生许多小气泡,影响复合膜的剥离强度。
因此,在印刷过程中一定要对油墨的干燥性能进行严格的控制,保证油墨充分干燥。
3.印刷工艺在印刷过程中,印刷速度和干燥温度等工艺条件也会对油墨中溶剂的挥发干燥产生一定的影响。
一般来说,在设定干燥箱的温度时,必须综合考虑印刷速度、油墨和干燥速度、承印材料种类以及印刷图案的大小等因素。
如果印刷速度较快,且印刷机干燥箱的温度比较低,则油墨中的溶剂可能无法完全挥发掉,这些残留的溶剂就会形成一些小泡,从而使复合膜中夹杂气泡,此时,应当降低印刷速度,并适当提高干燥温度。
三、胶黏剂方面的因素1.胶黏剂的黏度胶黏剂的黏度对胶黏剂的流动性、润湿性、涂胶均匀度等有着十分重要的影响。
干式复合中应当将胶黏剂的黏度值控制在适当的范围内,如果胶黏剂的黏度太高,分散性和流平性可能比较差,影响其在复合基材表面的润湿性,在涂胶过程中就可能会发生涂漏和气泡等故障。
2.胶黏剂的类型和质量胶黏剂的选择必须综合考虑基材的的种类、性能、后加工条件以及复合材料的最终用途等实际情况,否则就可能影响到复合产品的质量。
例如,当包装内容物具有比较强的碱性、酸性或刺激性时,所用的胶黏剂必须具有较强的抗介质性,否则就可能影响黏结牢度,局部产生小气泡,并最终引起复合膜的分层、脱胶。
3.胶液的配制在配制双组分胶黏剂时一定要充分搅拌,使其均匀分散,这样有利于在复合膜上润湿和黏合,减少气泡的发生。
此外,配制好的胶液还要充分静置脱气,然后再倒入胶盘中使用,而且倒胶时要沿着胶盘边缘慢慢地倒下,不能剧烈搅动胶盘内的胶液,以免由于空气的混入而在复合膜中形成气泡。
4.稀释剂目前,干式复合聚氨酯胶黏剂所用的稀释剂一般为乙酸乙酯,而且要求乙酸乙酯中水分含量不能超过0.2%。
如果稀释剂的纯度不高,含有水、醇等活性物质,聚氨酯所含的-NCO基团就会与水或醇中的活泼氢原子发生反应,反应的同时会放出CO2气体,从而生成气泡。
因此,一定要做好稀释剂检测工作,保证其纯度,控制CO2气体的产生。
四、干式复合工艺及工装方面的因素1.涂胶量涂胶量太少也是产生气泡的原因。
涂胶量不足,空隙处就会夹杂小气泡。
在实际工作生产中应根据包装内容物的不同要求来确定合适的涂胶量。
调整涂胶量主要从以下3个方面进行考虑:一是涂胶用的网纹辊,其网线数、网穴深浅都影响着涂胶量的大小;二是胶液的浓度;三是涂布胶辊的软硬程度、压力大小、刮刀的角度及压力大小。
2.烘道干燥温度、排风量干燥温度太低、胶黏剂干燥不够充分,溶剂挥发不彻底,就会产生小气泡。
而干燥温度太高,又会使胶黏剂起泡,或者使胶层表皮结膜,影响涂层内部溶剂的挥发,也会造成溶剂的残留和微小气泡的形成。
总的来说,在实际生产中,应根据基材的耐热性、复合线速度、胶液中溶剂的含量等具体情况来综合考虑和设置干复机3段烘道的温度,使溶剂充分干燥,严格控制溶剂的残留量,减少气泡的发生率。
一般来说,3段干燥烘道的干燥温度分别控制在50~60℃、60~70℃、70~80℃较适合。
3.复合线的速度复合线速度快慢直接影响着胶黏剂中溶剂的挥发。
复合线速度过快,基材通过烘道的时间短,不利于溶剂的挥发,胶黏剂干燥不充分,造成残余溶剂量过多,从而可能使复合膜产生气泡。
因此,在实际生产中应当掌握好复合线速度和溶剂的挥发速度。
4.复合钢辊表面的温度如果复合钢锟表面温度太低,就会影响胶黏剂的活化程度,胶黏剂活化不足,流平性差,形成微小的空隙,就会导致小气泡的产生。
一般将复合钢辊表面的温度控制在50~90℃。
具体还应考虑到复合基材的性质、复合膜的厚度以及复合线速度等因素。
5.复合压力如果复合压力太小,则复合基材之间贴合不紧密,就会导致小气泡的产生。
一般将复合压力控制在40~50N。
6.复合夹角如果复合夹角过大,两层复合膜中间就很容易夹入空气,从而导致气泡和隧道现象,特别是当薄膜材料比较厚,比较硬时更容易产生气泡。
因此复合夹角越小越好。
7.熟化程度双组分聚氨酯胶黏剂在复合后一般要在40~50℃的温度下熟化24~28小时,如果熟化时间不够,也会有微小气泡产生。
8.残留溶剂复合后的产品在烘道内干燥的过程中,要求胶黏剂中的溶剂挥发越干净越好。
溶剂若没有挥发干净,残留溶剂的逐渐积累会在冷却后的复合膜上形成微小的气泡。
而且,胶中的残留溶剂乙酸乙酯还是油墨连结料的良好溶剂,也会逐步渗透到油墨层并使油墨发生软化,从而在有油墨处形成气泡。
如果残留溶剂比较多,应当适当提高烘道的干燥温度,降低复合线速度,并加大排风量,以使溶剂充分挥发。
9.干复机工装在干复机工装中,涂布辊、涂布胶辊和复合胶辊是最重要的三大部件,这里仅介绍这三者对复合膜气泡成因的影响。
(1)涂布辊涂面辊的作用是在一定的压力作用下将胶黏剂转移到薄膜表面,它与复合膜气泡的产生有一定的关系。
由于涂布辊的网穴深度直接影响涂胶量的大小,因此,如果涂布辊的网穴被堵塞,或者有的网穴损坏了,就会直接影响涂布胶量的大小以及涂胶的均匀度,给复合膜产生气泡制造机会。
尤其是在炎热的夏季,更容易发生涂布辊网穴堵塞现象,因此一定要及时清洗涂布辊。
(2)涂布胶辊涂布胶辊的作用是给涂布辊一定的压力,将涂布辊上的黏合剂转移到薄膜上去。
涂布胶辊的软硬程度,压力大小对涂布量也有一定的影响。
如果涂布胶辊的表面的损坏、凹痕、砂眼等现象,或者表面橡胶层的硬度不一致,就会造成涂胶压力和涂胶量不均匀,导致气泡产生。
因此,涂布胶辊表面要光滑,无压痕、划伤、凹坑等弊病。
(3)复合胶辊复合胶辊的作用是在一定的温度,压力下,将两层薄膜相互贴合在一起。
如果复合胶辊表面有缺陷,如有划道、凹痕、砂眼等,复合时这些部位就会形成空档,压不实,从而使复合膜产生小气泡。
此外,如果复合胶辊表面老化程度不一,硬度不一致,也容易导致气泡产生。
五、车间环境方面因素1.环境温度和相对湿度环境温湿度过高,过低都不利于复合膜的生产。
如果车间的温度和相对湿度过高,会使已经配制发好的胶液中混入水分,并产生气泡。
此外,相对湿度过高,则塑料薄膜容易吸附空气中的水分,尤其是吸湿性大的塑料薄膜,如尼龙和玻璃纸等,致使复合后形成气泡。
相反,如果车间内的温度和相对湿度都比较低(如在寒冷干燥的冬季),而且车间内没有安装空调,胶黏剂分散就不好,对薄膜的润湿和黏附性都不太好,也会导致气泡的产生。
一般来说,将车间温度控制在18~25℃,相对湿度保持在60%~70%为宜。
2.车间内环境卫生状况车间内环境卫生状况对复合产品的质量也有很大的影响。
如果空气中含有大量的灰尘、杂质等粒子,那么这些粒子被吸附到塑料薄膜上,或者落到涂布辊、复合辊、胶液中,都会影响两层复合基材贴合的紧密程度。
当将两层膜顶起时,就形成了小气泡。
因此,一定要保持车间内清洁、卫生,减少空气中的浮尘,且应经常清扫烘道,并尽量使车间保持良好的密封状态。
六、结束语针对上述导致影响复合膜产生气泡的几大因素,在实际生产中可以采取积极的预防和应对措施,减少复合膜气泡的发生率,并进一步提高复合膜的质量。
1.加强对各种原辅材料的(包括薄膜、油墨、胶黏剂、各种溶剂等)的检测工作,严把质量关,从源头上降低复合膜气泡及其他故障的发生几率,提高复合膜质量。
2.在实际生产中应当根据不同的印刷工艺、薄膜的类型和特点、包装内容物的性能和要求以及以后加工条件等具体情况来选择合适的印刷油墨和复合用胶黏剂,并根据具体的生产情况调整和控制印刷和复合工艺参数,保证复合膜的质量。
3.在日常操作过程中,对工装要倍加爱护,并要注意工装的保养和维护,每次开车前及停车后要及时清洁工装,用浸有少量溶剂的干净柔软的棉布擦净黏附在涂布辊和胶辊表面的黏附剂或其他污物,避免这些黏附物干固后影响涂胶的均匀度,从而减少气泡的发生率。
此外,对于涂布辊还要用毛刷或铜刷反复刷其网穴部份,尽可能彻底地清除网穴内残存的胶黏剂,以免造成网穴堵塞,影响涂胶量及涂胶均匀度。
在保存涂布辊,涂布胶辊和复合胶辊时,应当将其放置在专用的支架上,绝不允许直接置于地上,以防硌伤而影响复合产品的质量。