连铸坯热轧工艺及控制
热轧工艺流程及其设备
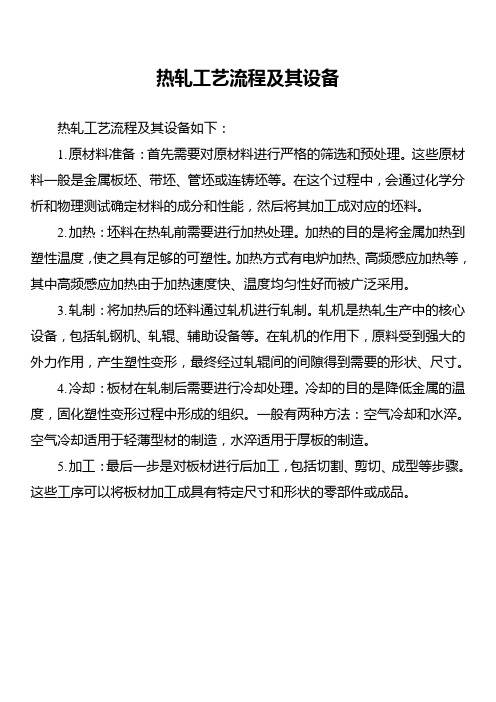
热轧工艺流程及其设备
热轧工艺流程及其设备如下:
1.原材料准备:首先需要对原材料进行严格的筛选和预处理。
这些原材料一般是金属板坯、带坯、管坯或连铸坯等。
在这个过程中,会通过化学分析和物理测试确定材料的成分和性能,然后将其加工成对应的坯料。
2.加热:坯料在热轧前需要进行加热处理。
加热的目的是将金属加热到塑性温度,使之具有足够的可塑性。
加热方式有电炉加热、高频感应加热等,其中高频感应加热由于加热速度快、温度均匀性好而被广泛采用。
3.轧制:将加热后的坯料通过轧机进行轧制。
轧机是热轧生产中的核心设备,包括轧钢机、轧辊、辅助设备等。
在轧机的作用下,原料受到强大的外力作用,产生塑性变形,最终经过轧辊间的间隙得到需要的形状、尺寸。
4.冷却:板材在轧制后需要进行冷却处理。
冷却的目的是降低金属的温度,固化塑性变形过程中形成的组织。
一般有两种方法:空气冷却和水淬。
空气冷却适用于轻薄型材的制造,水淬适用于厚板的制造。
5.加工:最后一步是对板材进行后加工,包括切割、剪切、成型等步骤。
这些工序可以将板材加工成具有特定尺寸和形状的零部件或成品。
热轧带钢生产工艺及工艺要求

钢往板往表 破面坏不钢• 得板有的成气物品泡理、性:结能厚疤或、成度拉为1裂产.、生2~刮破2伤裂5、和.4折锈m叠蚀、的m裂缺缝陷宽、源度夹,杂成6和为50压应~入力2氧集1化中3铁的0m皮薄等弱m缺环陷节,。因为这些缺陷不仅影响轧件的外观形象,而且
板坯:厚度135~180mm 宽度650~2080mm 长度6~17m
薄板坯连铸连轧热轧带钢工艺 Nhomakorabea对定于的重 化要学1用成.2途分.2的,结保设构证备钢良板好布,的置要焊求接2具性有能较、好常的温综或合低性温能冲,击即韧除性了或有一良定好的的冲工压艺性性能能,,保甚证至一除定了的有金一相定 组的织强及度各和向塑组性织以均外匀,性还等要。求保证一
薄板坯连铸连轧热轧带钢工艺 热轧带钢生产工艺及工艺要求
2、薄板坯连铸连轧工艺
薄板坯 连铸连轧 流程1
连铸
定尺坯剪切
定尺坯加热
精轧 轧后冷却
卷取
开卷检查 钢卷运输
钢卷打包 钢卷称重 钢卷打号 钢卷入库
薄板坯 连铸连轧 设备布置1 CSP
CSP连铸机
辊底式均热炉
除鳞机 事故剪
生产能力: - 单线: 150万吨/年 - 双线: 250万吨/年
铸坯厚度: 55~70 mm 成品宽度: 900.....1 680 mm
生产线:唐钢 UTSP 本钢连铸连轧线
3、中厚板坯连铸连轧热轧带钢工艺
工艺流程
连铸
定尺坯切割 定尺坯加热
热坯下线
冷坯装炉 板坯库
可逆 粗轧
热卷
精轧
轧后 冷却
卷取
开卷检查 钢卷运输
钢卷打包
钢卷称重 钢卷打号 钢卷入库
中厚板坯 连铸连轧 设备布置
除鳞 1 定宽压力机
热连轧过程及计算机控制(L-2)

(3) 半连续式热带轧机(Semi-continuous Hot Strip Mills)(图2-3a) 粗轧机有两个以上的可逆机座,或者全部为可逆机座。
(4) 3/4连续式热带轧机(3/4 Continuous Hot Strip Mills)(图2-3c) 4座粗轧机中有一个可逆机座。
生产效率提高。 (5)热加工变形可引起组织性能的变化,以满足对产品某些组织与性能的要求。
WUST
图1-1 铁碳合金相图
WUST
热加工变形除具有上述优点,使之在生产实践中得到广泛的应用外,同其 他加工方法相比较它也有如下的不足:
(1) 对薄或细的轧件由于散热较快,在生产中保持热加工的温度条件比较 困难;
(2) 热加工后轧件的表面不如冷加工生产的尺寸精确和光洁; (3) 热加工后产品的组织及性能不如冷加工时均匀; (4) 从提高钢材的强度来看,热加工不及冷加工。
热加工变形可以认为是加工硬化和再结晶两个过程的相互重叠。在此过 程中由于再结晶能充分进行和变形时靠三向压应力状态等因素的作用,可使:
(1) 铸态金属组织中的缩孔、疏松、空隙、气泡等缺陷得到压密或焊合。 (2) 在热加工变形中可使晶粒细化和夹杂物破碎。 (3)金属在热变形过程中产生带状组织。
(5) 带卷取箱的热带轧机(图2-4)
WUST
Left Furnace Coiler
FourHight Mill
Right Furnace Coiler
Slab Feed roll
Fig.2-1 Schematic diagram of Steckel mill
钢材轧制工艺及质量控制研究
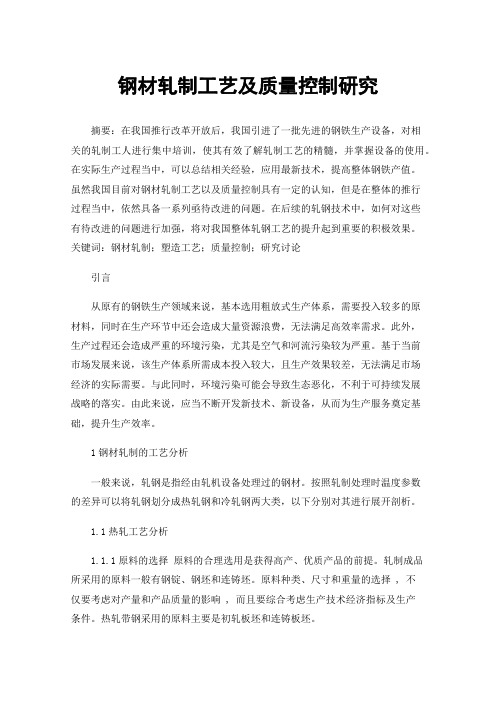
钢材轧制工艺及质量控制研究摘要:在我国推行改革开放后,我国引进了一批先进的钢铁生产设备,对相关的轧制工人进行集中培训,使其有效了解轧制工艺的精髓,并掌握设备的使用。
在实际生产过程当中,可以总结相关经验,应用最新技术,提高整体钢铁产值。
虽然我国目前对钢材轧制工艺以及质量控制具有一定的认知,但是在整体的推行过程当中,依然具备一系列亟待改进的问题。
在后续的轧钢技术中,如何对这些有待改进的问题进行加强,将对我国整体轧钢工艺的提升起到重要的积极效果。
关键词:钢材轧制;塑造工艺;质量控制;研究讨论引言从原有的钢铁生产领域来说,基本选用粗放式生产体系,需要投入较多的原材料,同时在生产环节中还会造成大量资源浪费,无法满足高效率需求。
此外,生产过程还会造成严重的环境污染,尤其是空气和河流污染较为严重。
基于当前市场发展来说,该生产体系所需成本投入较大,且生产效果较差,无法满足市场经济的实际需要。
与此同时,环境污染可能会导致生态恶化,不利于可持续发展战略的落实。
由此来说,应当不断开发新技术、新设备,从而为生产服务奠定基础,提升生产效率。
1钢材轧制的工艺分析一般来说,轧钢是指经由轧机设备处理过的钢材。
按照轧制处理时温度参数的差异可以将轧钢划分成热轧钢和冷轧钢两大类,以下分别对其进行展开剖析。
1.1热轧工艺分析1.1.1原料的选择原料的合理选用是获得高产、优质产品的前提。
轧制成品所采用的原料一般有钢锭、钢坯和连铸坯。
原料种类、尺寸和重量的选择 , 不仅要考虑对产量和产品质量的影响 , 而且要综合考虑生产技术经济指标及生产条件。
热轧带钢采用的原料主要是初轧板坯和连铸板坯。
1.1.2加热对热轧带钢的板坯加热 , 一般采用连续式加热炉。
为了适应热轧产量增大的需要,无论是热滑轨式还是步进式,一方面采用多段式供热方式,以延长炉子高温区,实现强化操作快速烧钢;另一方面尽可能加大炉宽和炉长,扩大炉子容量。
1.1.3粗轧热带钢轧制分为除鳞、粗轧和精轧几个阶段。
1.CSP连铸连轧的轧制工艺控制
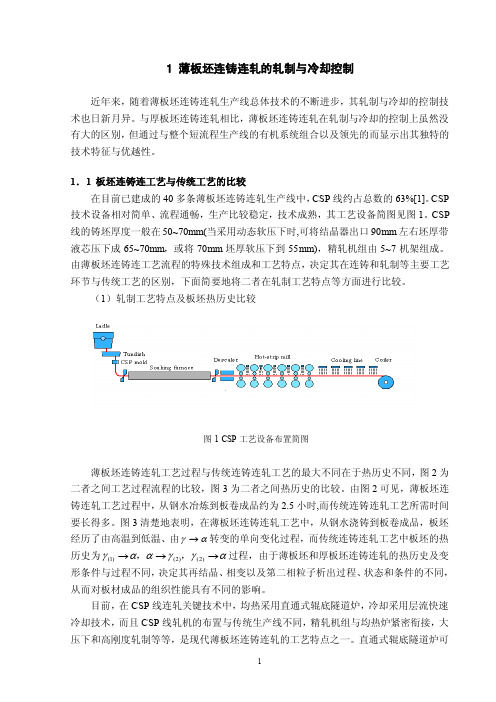
1 薄板坯连铸连轧的轧制与冷却控制近年来,随着薄板坯连铸连轧生产线总体技术的不断进步,其轧制与冷却的控制技术也日新月异。
与厚板坯连铸连轧相比,薄板坯连铸连轧在轧制与冷却的控制上虽然没有大的区别,但通过与整个短流程生产线的有机系统组合以及领先的而显示出其独特的技术特征与优越性。
1.1 板坯连铸连工艺与传统工艺的比较在目前已建成的40多条薄板坯连铸连轧生产线中,CSP 线约占总数的63%[1]。
CSP 技术设备相对简单、流程通畅,生产比较稳定,技术成熟,其工艺设备简图见图1。
CSP 线的铸坯厚度一般在50~70mm(当采用动态软压下时,可将结晶器出口90mm 左右坯厚带液芯压下成65~70mm ,或将70mm 坯厚软压下到55mm),精轧机组由5~7机架组成。
由薄板坯连铸连工艺流程的特殊技术组成和工艺特点,决定其在连铸和轧制等主要工艺环节与传统工艺的区别,下面简要地将二者在轧制工艺特点等方面进行比较。
(1)轧制工艺特点及板坯热历史比较薄板坯连铸连轧工艺过程与传统连铸连轧工艺的最大不同在于热历史不同,图2为二者之间工艺过程流程的比较,图3为二者之间热历史的比较。
由图2可见,薄板坯连铸连轧工艺过程中,从钢水冶炼到板卷成品约为2.5小时,而传统连铸连轧工艺所需时间要长得多。
图3清楚地表明,在薄板坯连铸连轧工艺中,从钢水浇铸到板卷成品,板坯经历了由高温到低温、由αγ→转变的单向变化过程,而传统连铸连轧工艺中板坯的热历史为αγγααγ→→→)2()2()1(,,过程,由于薄板坯和厚板坯连铸连轧的热历史及变形条件与过程不同,决定其再结晶、相变以及第二相粒子析出过程、状态和条件的不同,从而对板材成品的组织性能具有不同的影响。
目前,在CSP 线连轧关键技术中,均热采用直通式辊底隧道炉,冷却采用层流快速冷却技术,而且CSP 线轧机的布置与传统生产线不同,精轧机组与均热炉紧密衔接,大压下和高刚度轧制等等,是现代薄板坯连铸连轧的工艺特点之一。
薄板坯连铸连轧产品的质量控制
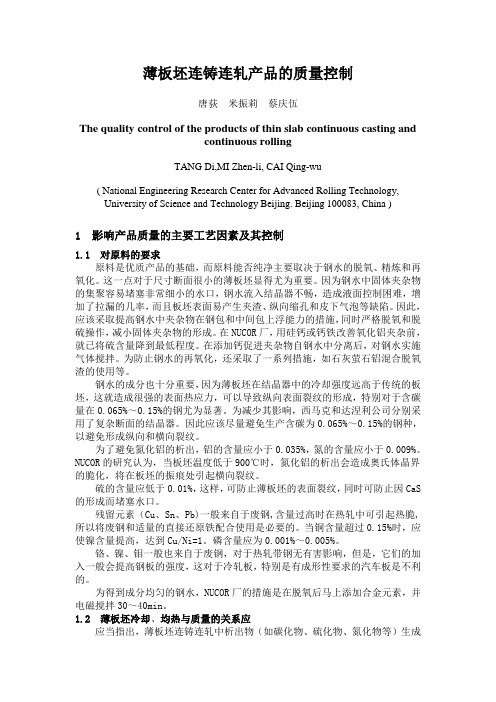
薄板坯连铸连轧产品的质量控制唐荻米振莉蔡庆伍The quality control of the products of thin slab continuous casting andcontinuous rollingTANG Di,MI Zhen-li, CAI Qing-wu( National Engineering Research Center for Advanced Rolling Technology,University of Science and Technology Beijing. Beijing 100083, China )1 影响产品质量的主要工艺因素及其控制1.1 对原料的要求原料是优质产品的基础,而原料能否纯净主要取决于钢水的脱氧、精炼和再氧化。
这一点对于尺寸断面很小的薄板坯显得尤为重要。
因为钢水中固体夹杂物的集聚容易堵塞非常细小的水口,钢水流入结晶器不畅,造成液面控制困难,增加了拉漏的几率,而且板坯表面易产生夹渣、纵向缩孔和皮下气泡等缺陷。
因此,应该采取提高钢水中夹杂物在钢包和中间包上浮能力的措施,同时严格脱氧和脱硫操作,减小固体夹杂物的形成。
在NUCOR厂,用硅钙或钙铁改善氧化铝夹杂前,就已将硫含量降到最低程度。
在添加钙促进夹杂物自钢水中分离后,对钢水实施气体搅拌。
为防止钢水的再氧化,还采取了一系列措施,如石灰萤石铝混合脱氧渣的使用等。
钢水的成分也十分重要,因为薄板坯在结晶器中的冷却强度远高于传统的板坯,这就造成很强的表面热应力,可以导致纵向表面裂纹的形成,特别对于含碳量在0.065%~0.15%的钢尤为显著。
为减少其影响,西马克和达涅利公司分别采用了复杂断面的结晶器。
因此应该尽量避免生产含碳为0.065%~0.15%的钢种,以避免形成纵向和横向裂纹。
为了避免氮化铝的析出,铝的含量应小于0.035%,氮的含量应小于0.009%。
NUCOR的研究认为,当板坯温度低于900℃时,氮化铝的析出会造成奥氏体晶界的脆化,将在板坯的振痕处引起横向裂纹。
连铸坯热送热装工艺热技术概述

连铸坯热送热装工艺热技术概述蒋扬虎肖坤伟王德仓肖世华丁翠娇(技术中心)摘要简要回顾了连铸坯热送热装工艺的历史,介绍了该项技术的应用现状及可取得的技术经济效果,并重点从“通用高温坯生产技术”和“温度均匀性保证技术”两个方面介绍了连铸坯热送热装工艺的各项“热技术”。
关键词连铸坯热送热装直接轧制加热炉1前言连铸坯热送热装工艺,是一项具有降低热轧加热炉燃耗、减少钢坯氧化烧损和提高热轧产量等多方面经济效益的技术。
该项工艺是连铸技术的一项重大突破,它不仅对节能有重要意义,而且对改革传统的钢铁工业结构有深远的意义,它涉及从炼钢到热轧之间各个生产环节,是一项系统工程。
目前世界许多钢铁企业根据自身的特点不同程度上采用了该项技术。
本文将对该项技术作一个初步的概括。
2连铸坯热送热装技术的历史及现状1968年美国麦克劳斯钢公司将连铸板坯装入感应加热炉,从而迈出了热装技术的第一步。
70年代初期,由于石油危机的冲击,日本钢铁工业面临严重的能源问题,日本钢铁界以此为契机,开始研究和应用连铸坯热送热装工艺,1973年日本钢管公司鹤见厂首先实现连铸坯热装轧制工艺(CC—HCR);1981年6月新日铁土界厂研究成功并在生产中实现了近程(连铸机终点和轧机始点之间距离为130m)连铸—直接轧制工艺(CC—DR);1987年6月新日铁八幡厂在生产中实现了远程CC—DR工艺(连铸机终点和轧机始点之间距离为620m)。
日本在该项技术上的成功,促进了世界各国对该项技术的研究和应用。
经过80年代世界各国钢铁界的努力,连铸坯热装和直接轧制工艺正日趋完善。
按照温度的高低,连铸坯热送工艺可分为三种情况。
(1)热装轧制HCR(Hot Charge Rolling)。
将经过(或不经过)表面处理的热板坯在大约400~700℃装入加热炉。
(2)直接热装轧制DHCR(Direct Hot Charge Rolling)。
按照和连铸同一序号,将经过(或不经过)表面处理的热板坯在大约700~1000℃装入加热炉。
连铸板坯热轧工艺参数优化及其对钢材质量的影响
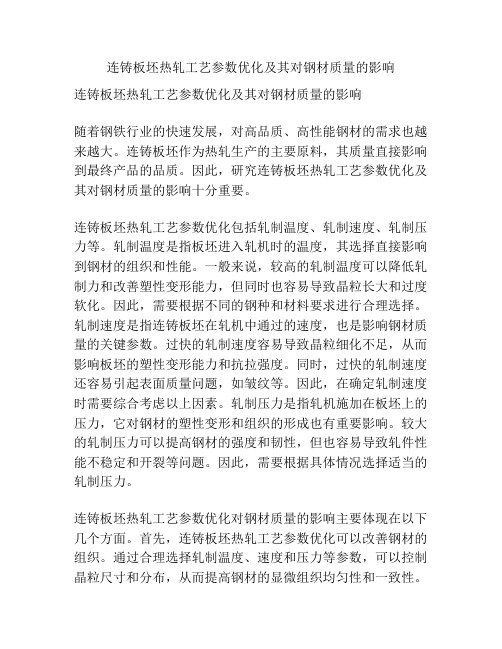
连铸板坯热轧工艺参数优化及其对钢材质量的影响连铸板坯热轧工艺参数优化及其对钢材质量的影响随着钢铁行业的快速发展,对高品质、高性能钢材的需求也越来越大。
连铸板坯作为热轧生产的主要原料,其质量直接影响到最终产品的品质。
因此,研究连铸板坯热轧工艺参数优化及其对钢材质量的影响十分重要。
连铸板坯热轧工艺参数优化包括轧制温度、轧制速度、轧制压力等。
轧制温度是指板坯进入轧机时的温度,其选择直接影响到钢材的组织和性能。
一般来说,较高的轧制温度可以降低轧制力和改善塑性变形能力,但同时也容易导致晶粒长大和过度软化。
因此,需要根据不同的钢种和材料要求进行合理选择。
轧制速度是指连铸板坯在轧机中通过的速度,也是影响钢材质量的关键参数。
过快的轧制速度容易导致晶粒细化不足,从而影响板坯的塑性变形能力和抗拉强度。
同时,过快的轧制速度还容易引起表面质量问题,如皱纹等。
因此,在确定轧制速度时需要综合考虑以上因素。
轧制压力是指轧机施加在板坯上的压力,它对钢材的塑性变形和组织的形成也有重要影响。
较大的轧制压力可以提高钢材的强度和韧性,但也容易导致轧件性能不稳定和开裂等问题。
因此,需要根据具体情况选择适当的轧制压力。
连铸板坯热轧工艺参数优化对钢材质量的影响主要体现在以下几个方面。
首先,连铸板坯热轧工艺参数优化可以改善钢材的组织。
通过合理选择轧制温度、速度和压力等参数,可以控制晶粒尺寸和分布,从而提高钢材的显微组织均匀性和一致性。
其次,连铸板坯热轧工艺参数优化可以提高钢材的机械性能。
通过选择适当的轧制参数,可以增加钢材的抗拉强度、屈服强度和延伸率等机械性能指标,从而提高钢材的耐久性和适用性。
最后,连铸板坯热轧工艺参数优化还可以改善钢材的表面质量。
通过控制轧制参数,可以减少皱纹、划痕和银色条纹等表面缺陷,提高钢材的外观质量。
总之,连铸板坯热轧工艺参数优化及其对钢材质量的影响是一个复杂的系统工程,需要综合考虑多个因素。
只有通过合理选择和优化热轧工艺参数,才能得到高品质、高性能的钢材产品。
热轧工艺
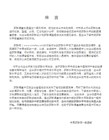
轧钢是指在旋转的轧辊间改变钢锭,钢坯形状的压力加工过程叫轧钢。轧钢的目的与其他压力加工一样,一方面是为了得到需要的形状,例如:钢板,带钢,线材以及各种型钢等;另一方面是为了改善钢的内部质量,我们常见的汽车板、桥梁钢、锅炉钢、管线钢、螺纹钢、钢筋、电工硅钢、镀锌板、镀锡板,包括火车轮都是通过轧钢工艺加工出来的。
冷轧工艺
与热轧相比,冷轧厂的加工线比较分散,冷轧产品主要有普通冷轧板、涂镀层板也就是镀锡板、镀锌板和彩涂板。经过热轧厂送来的钢卷,先要经过连续三次技术处理,先要用盐酸除去氧化膜,然后才能送到冷轧机组。在冷轧机上,开卷机将钢卷打开,然后将钢带引入五机架连轧机轧成薄带卷。从五机架上出来的还有不同规格的普通钢带卷,它是根据用户多种多样的要求来加工的。冷轧厂生产各种各样不同品质的产品,那飞流直下,似银河落九天的是镀锡板,那银光闪闪的是镀锌板,有红、黄、兰各种颜色的是彩色涂层钢板。镀锡板是制造罐头和易拉罐的原料,又叫马口铁,以前我国所需要的镀锡板全靠进口,自从武钢镀锡板大量生产后,部分替代了进口货。武钢生产镀锡板采取的是电镀锡工艺,这些镀锡板好像镜子一样,光鉴照人,就像诗人描写的:“轧钢工人巧手绘锦帐,千万面银镜送给心爱的姑娘,你知道不知道,在那爱妻牌洗衣机上,有我们汗水的芬芳”。镀锌板的生产工艺有两种,一种是热镀锌,一种是电镀锌。那貌不惊人包装特别的是硅钢片,它们用在发电设备、机电设备、轻工、食品和家电上。用镀锌板作为基材,在反面涂上各种涂料就成为彩色涂层钢板。由于工艺先进,涂层十分牢固,可以直接用于家电产品和作装饰材料。除了板材以外,轧钢厂也生产长材,如型钢、钢轨、棒材、圆钢和线材,它的生产过程和轧钢原理与板材类似,但是使用的轧辊辊型完全不同。
钢材的轧制工艺及质量控制
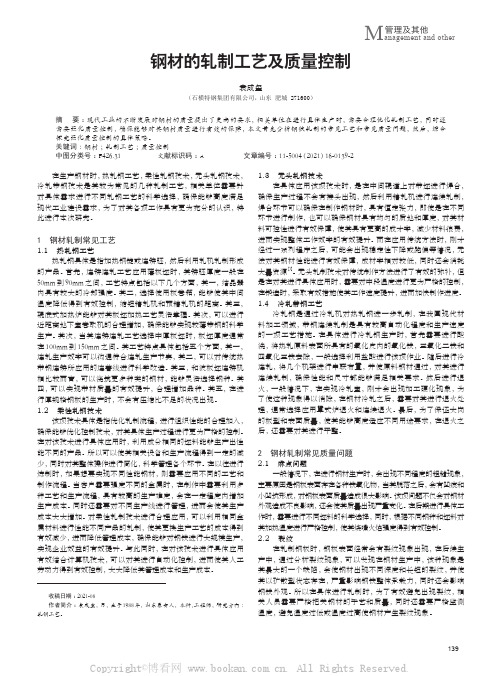
管理及其他M anagement and other在生产钢材时,热轧钢工艺,柔性轧钢技术,无头轧钢技术,冷轧带钢技术是其较为常见的几种轧制工艺,相关单位需要针对具体需求进行不同轧钢工艺的科学选择,确保能够高度满足现代工业建设需求,为了对其各项工作具有更为充分的认识,特此进行本次研究。
1 钢材轧制常见工艺1.1 热轧钢工艺热轧钢具体是指加热钢锭或连铸胚,然后利用轧机轧制形成的产品。
首先,连铸连轧工艺应用薄板坯时,其铸胚厚度一般在50mm到90mm之间,工艺特点包括以下几个方面,其一,结晶器内具有较大的冷却强度。
其二,选择使用板卷箱,能够使其中间温度降低得到有效控制,缩短精轧机和预精轧机的距离。
其三,辊底式加热炉能够对其板坯加热工艺灵活掌握。
其次,可以进行近距离地下室卷取机的合理增加,确保能够实现较薄带钢的科学生产。
其次,当其连铸连轧工艺选择中厚板坯时,板坯厚度通常在100mm到150mm之间。
其工艺特点具体包括五个方面,其一,连轧生产效率可以沟通符合连轧生产节奏,其二,可以对传统热带钢连铸所应用的连着线进行科学改造。
其三,和波板坯连铸机相比较而言,可以浇筑更多种类的钢材,能够灵活选择钢种。
其四,可以实现带材质量的有效提升,合理增加品种。
其五,在进行厚规格钢板的生产时,不会有压缩比不足的状况出现。
1.2 柔性轧钢技术该项技术具体是指优化轧制流程,进行组织性能的合理加入,确保能够优化控制技术,对其具体生产过程进行更为严格的控制。
在对该技术进行具体应用时,利用成分相同的坯料能够生产出性能不同的产品。
所以可以使其相关设备和生产流程得到一定的减少,同时对其整体操作进行简化,科学管理各个环节。
在以往进行炼制时,如果想要实现不同性能钢材,则需要应用不同的工艺和制作流程。
当客户需要强度不同的金属时,在制作中需要利用多种工艺和生产流程,具有较高的生产难度,会在一定程度内增加生产成本。
同时还需要对不同生产线进行管理,进而会使其生产成本大大增加。
热轧工艺流程

热轧工艺流程热轧工艺流程----初学必看1.主轧线工艺流程简述板坯由炼钢连铸车间的连铸机出坯辊道直接送到热轧车间板坯库,直接热装的钢坯送至加热炉的装炉辊道装炉加热,不能直接热装的钢坯由吊车吊入保温坑,保温后由吊车吊运至上料台架,然后经加热炉装炉辊道装炉加热,并留有直接轧制的可能。
连铸板坯由连铸车间通过板坯上料辊道或板坯卸料辊道运入板坯库,当板坯到达入口点前,有关该板坯的技术数据已由连铸车间的计算机系统送到了热轧厂的计算机系统,并在监视器上显示板坯有关数据,以便工作人员进行无缺陷合格板坯的核对和接收。
另外,通过过跨台车运来的人工检查清理后的板坯也需核对和验收,并输入计算机。
进入板坯库的板坯,由板坯库计算机管理系统根据轧制计划确定其流向。
常规板坯装炉轧制:板坯进入板坯库后,按照板坯库控制系统的统一指令,由板坯夹钳吊车将板坯堆放到板坯库中指定的垛位。
轧制时,根据轧制计划,由板坯夹钳吊车逐块将板坯从垛位上吊出,吊到板坯上料台架上上料,板坯经称量辊道称重、核对,然后送往加热炉装炉辊道,板坯经测长、定位后,由装钢机装入加热炉进行加热。
碳钢保温坑热装轧制:板坯进入板坯库后,按照板坯库控制系统的统一指令,由板坯夹钳吊车将板坯堆放到保温坑中指定的垛位。
轧制时,根据轧制计划,由板坯夹钳吊车逐块将板坯从保温坑取出,吊到板坯上料台架上上料,板坯经称量辊道称重、核对,然后送往加热炉装炉辊道,板坯经测长、定位后,由装钢机装入加热炉进行加热。
直接热装轧制:当连铸和热轧的生产计划相匹配时,合格的高温连铸板坯通过加热炉上料辊道运到称量辊道,经称重、核对,进入加热炉的装炉辊道,板坯在指定的加热炉前测长、定位后,由装钢机装入加热炉进行加热。
其中一部分通过卸料辊道运输的直接热装板坯需通过吊车吊运一次放到上料辊道后直接送至加热炉区。
如果炼钢厂可以实现直接热装板坯由上料辊道运送,则可减少部分吊车吊运作业。
板坯经加热炉的上料辊道送到加热炉后由托入机装到加热炉内,加热到设定温度后,按轧制节奏要求由出钢机托出,放在加热炉出炉辊道上。
(五)连铸坯热装与直接轧制
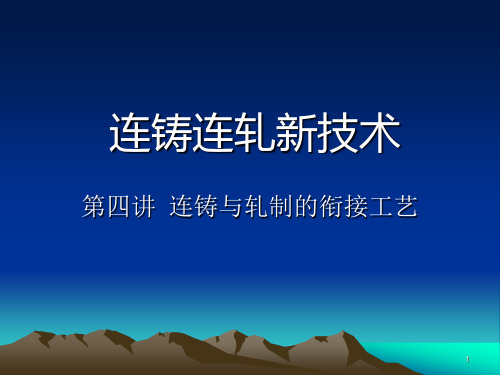
5、炼钢-连铸-热轧生产管理一体化 连铸坯热送热装工艺特别是直装工艺对各工 序的时间要求很严格,如果生产组织不当, 将 达不到热送热装应有的效果。因此,需要有一 个能够合理连接炼钢-连铸-热轧三大工序生产计 划管理一体化的系统,以实现三大工序时间上 的衔接及生产批量的协调。
17
三. 铸坯温度保证技术
• 提高铸坯温度主要靠充分利用其内部冶金 热能,其次靠外部加热。后者虽属常用手 段,但因时间短,其效果不太大,故一般 只用做铸坯边角部补偿加热的措施。 • 保证板坯温度的技术主要是在连铸机上争 取铸坯有更高更均匀的温度(保留更多的 冶金热源和凝固潜热)、在输送途中绝热 保温及补偿加热等,
18
谢谢!
6
二. 连铸与轧制衔接模式
• 从温度与热能利用着眼,钢材生产中连铸与轧制 两个工序的衔接模式一般有如下图所示的五种类 型
7
• 方式1为连续铸轧工艺,铸坯在铸造的同 时进行轧制。方式1称为连铸坯直接轧制工 艺(CC-DR),高温铸坯不需进加热炉加 热,只略经补偿加热即可直接轧制。 • 方式2称为连铸坯直接热装轧制工艺(CCDHCR或HDR),也可称为高温热装炉轧 制工艺,铸坯温度仍保持在A3线以上奥氏 体状态装入加热炉,加热到轧制温度后进 行轧制。
铸机的生产能力应与炼钢及轧钢的能力相匹配铸坯的断面和规格应与轧机所需原料及产品规格相匹配见表21及表22并保证一定的压缩比见表2aa55aa66为实现连铸与轧制过程的连续化生产应使连铸机生产能力略大于炼钢能力而轧钢能力又要略大于连铸能力例如约大10才能保证产量的匹配关系
连铸连轧新技术
第四讲 连铸与轧制的衔接工艺
13
2、连铸坯热送热装过程中的热技术 连铸坯热送热装全部热过程的数学模型是由四 个子模型组成:连铸坯凝固过程数学模型、连铸 坯辊道输送过程数学模型、连铸坯在保温坑内保 温过程数学模型和连铸坯在加热炉内加热过程数 学模型。这四个模型基本上包括了生产实际过程 中的各种情况。结果最大相对误差不超过5%。这 些模型除了用于生产控制外,还可用于分析、完 善设备和工艺过程。
热连轧不锈钢连铸坯加热工艺研究
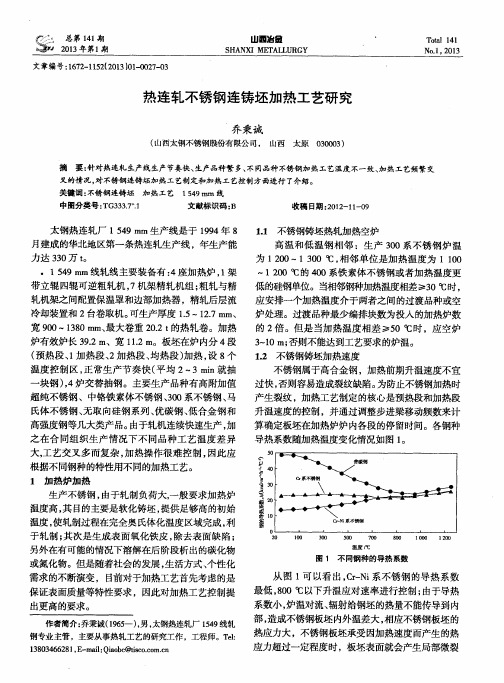
不锈钢属于高合金钢 ,加热前期升温速度不宜 过快 , 否则容易造成裂纹缺陷。 为防止不锈钢加热时
产生裂纹 ,加热工艺制定的核心是预热段和加热段
超纯不锈钢 、中铬铁素体不锈钢、 3 0 0 系不锈钢 、 马 氏体不锈钢 、 无取 向硅钢系列、 优碳钢、 低合金钢和 高强度钢等几大类产品。 由于轧机连续快速生产 , 加 之在合 同组织生产情况下 不同品种 工艺温度差异 大, 工艺交叉多而复杂 , 加热操作很难控 制 , 因此应
另外在有可能的情况下溶解在后阶段析出的碳化物 或氮化物。但是随着社会 的发展 , 生活方式 、 个性化
韫 ,
图1 不同钢种的导热系数
需求的不断演变 ,目 前对于加热工艺首先考虑的是 保证表面质量等特性要求 ,因此对加热工艺控制提
出更高的要求。
作者简介 : 乔秉诚 ( 1 9 6 5 一) , 男, 太钢热连轧厂 1 5 4 9 线轧 钢专业 主管 ,主要从事热轧工艺 的研 究工作 ,工程师 。T e l :
1 . 3 . 1 硫
的底层逐渐富集为稳定 的氧化物 的膜层 ,形成 以 c r 2 ( ) 。 , A 1 2 0 , , S i O 为主的氧化膜, 这类氧化膜形成后 ,
铁、 氧通 过膜 的扩 散严重 受 阻 , 氧化性 显 著提 高 。
一
般情况下 , 1 5 4 9 m m线不锈钢铸坯加热均为
太钢热连轧厂 1 5 4 9 m m生产线是于 1 9 9 4年 8 月建成的华北区第一条热连轧生产线 ,年生产能
力达 3 3 0万 t 。
1 . 1 不锈钢铸坯热轧加热空炉 高温 和低 温钢相邻 :生产 3 0 0系不锈钢 炉温 为1 2 0 0—1 3 0 0 o C, 相邻单位是加热温度为 1 1 0 0
连铸坯热装热送

蔡 开 科 北京科技大学冶金与生态工程学院 2004年11月
目录
1 2 3 4 前言 生产高温连铸坯技术 生产无缺陷铸坯技术 结语
前言
连铸坯热送热装工艺 主要有连铸坯直接热装轧制和连铸坯热送热装两种工艺 连铸坯直接热装轧制:典型工艺是薄板坯连铸连轧流程 (如CSP、FTSR),其优点: 液芯长度短,减轻了铸机重量,简化了铸机结构 完全凝固时间短(1min) 拉速高(4~6m/min) 冷却快,枝晶细化,铸坯质量好 板坯温度高,节能,不会产生第二相质点沉淀(AlN, Nb(CN)),减少裂纹
无缺陷铸坯生产-铸坯表面纵裂纹
(9) 结晶器变形 对于小方坯常出现角部纵裂纹(靠近角部棱边或离开角部1015mm),它是与凝固前沿热撕裂有关的。它的产生决定于: 方坯菱变; 结晶器圆角半径R(R大,纵裂沿棱角;R小,纵裂离开角部); 结晶器变形与磨损。 保持结晶器合适锥度,较大的圆角半径(R=6-8mm),准确对弧 和支承,防止结晶器磨损,均匀的冷却等可消除小方坯角部纵裂。 (10)出结晶器下口的冷却 足辊和零段二冷水过强,板坯宽面纵裂加剧,如水流密度由 110l/m2· min 降到60 l/m2 ·min,纵裂指数由纵裂指数的影响
无缺陷铸坯生产-铸坯表面纵裂纹
250×1400mm板坯,结晶的宽面平均热流与板坯纵裂指数如图2-11。 结晶的侧面热流与纵裂纹指数如图2-12。由图可知:结晶器的宽面 铜板平均热流为1.4- 1.6MW/m2 ,侧面平均热流为1.1-.3MW/ m2, 板坯表面纵裂纹发生率最小。
前言
连铸坯热送热装工艺 是传统的板坯和方坯普遍采用的。它的主要优点是: 节能。500℃热装,减少燃耗30%;800℃热装,可 降燃耗50%。 提高金属收得率2~3% 缩短生产周期(板坯→热轧卷节约1小时左右) 降低生产成本(节约生产费用8~10%)
第六讲 连铸坯表面质量控制

◆ 横裂纹可位于铸坯面部或角部
◆ 横 裂 纹 与 振 痕 共 生 , 深 度 2 ~ 4mm , 可 达 7mm,裂纹深处生成FeO。不易剥落,热轧板 表面出现条状裂纹。振痕深,柱状晶异常,形 成元素的偏析层,轧制板上留下花纹状缺陷。
◆ 铸坯横裂纹常常被FeO覆盖,只有经过酸洗 后,才能发现。
-沿振痕波谷处元素呈正偏析。
这样,振痕波谷处,奥氏体晶界脆性增大,为裂纹产生提 供了条件。
(2) 铸坯运行过程中,受到外力(弯曲,矫直,鼓肚, 辊子不对中等)作用时,刚好处于低温脆性区(图1- 5)的铸坯表面处于受拉伸应力作用状态,如果坯壳所 受的ε临>1.3%,在振痕波谷处就产生裂纹。
3.3.3影响产生横裂纹因素
结晶器弱冷,有利于减少纵裂纹(图3- 11)。
图3-11 结晶器弱冷对小纵裂的影响
(6) 结晶器的锥度
图3-12 结晶器锥度和钢成分对皮下内裂的影响 (断面尺寸240x240mm,拉速0.7m/min)
◆ 锥度<0.8%/m,窄面凸出→角部纵裂; ◆ 锥度>0.8%/m,窄面凹入→无角部纵裂。
(7) 结晶器振动
3.3.2横裂纹产生原因
(1) 横裂纹产生于结晶器初始坯壳形成振痕的波谷处,振痕 越深,则横裂纹越严重,在波谷处,由于: -冷却速度降低,晶粒粗大(图3-13);
图3-13 铸坯内γ晶粒尺寸对裂纹的影响
-奥氏体晶界析出沉淀物(AlN,Nb(CN)),产生晶间断裂 (图3-14);
断裂前
断裂后
图3-14 钢在600~900℃区域内发生脆断示意图
(1) 结晶器初始坯壳均匀生长
◆ 热顶结晶器(弯月面区热流减少50~60%) ◆ 波浪结晶器(弯月面区热流减少17~25%) ◆ 结晶器弱冷 ◆ 合适结晶器锥度
铝材热轧生产工艺
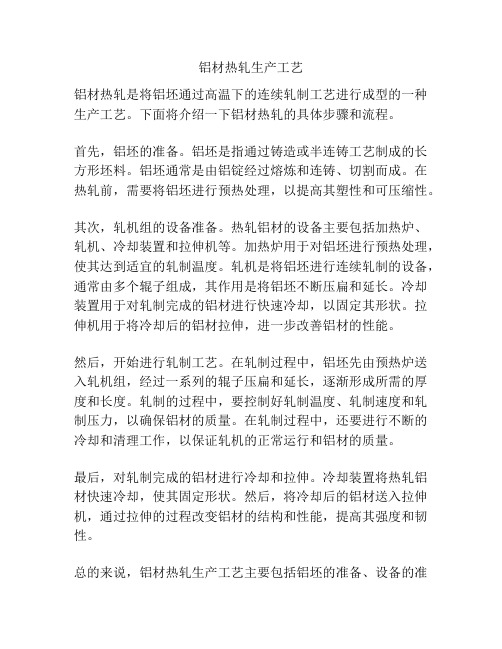
铝材热轧生产工艺
铝材热轧是将铝坯通过高温下的连续轧制工艺进行成型的一种生产工艺。
下面将介绍一下铝材热轧的具体步骤和流程。
首先,铝坯的准备。
铝坯是指通过铸造或半连铸工艺制成的长方形坯料。
铝坯通常是由铝锭经过熔炼和连铸、切割而成。
在热轧前,需要将铝坯进行预热处理,以提高其塑性和可压缩性。
其次,轧机组的设备准备。
热轧铝材的设备主要包括加热炉、轧机、冷却装置和拉伸机等。
加热炉用于对铝坯进行预热处理,使其达到适宜的轧制温度。
轧机是将铝坯进行连续轧制的设备,通常由多个辊子组成,其作用是将铝坯不断压扁和延长。
冷却装置用于对轧制完成的铝材进行快速冷却,以固定其形状。
拉伸机用于将冷却后的铝材拉伸,进一步改善铝材的性能。
然后,开始进行轧制工艺。
在轧制过程中,铝坯先由预热炉送入轧机组,经过一系列的辊子压扁和延长,逐渐形成所需的厚度和长度。
轧制的过程中,要控制好轧制温度、轧制速度和轧制压力,以确保铝材的质量。
在轧制过程中,还要进行不断的冷却和清理工作,以保证轧机的正常运行和铝材的质量。
最后,对轧制完成的铝材进行冷却和拉伸。
冷却装置将热轧铝材快速冷却,使其固定形状。
然后,将冷却后的铝材送入拉伸机,通过拉伸的过程改变铝材的结构和性能,提高其强度和韧性。
总的来说,铝材热轧生产工艺主要包括铝坯的准备、设备的准
备、轧制工艺和冷却拉伸等工艺步骤。
通过严格控制每个步骤的工艺参数,可以得到优质的铝材产品。
铝材热轧生产工艺具有高效、高质量的特点,广泛应用于航空航天、汽车、建筑等行业。
热轧工艺流程
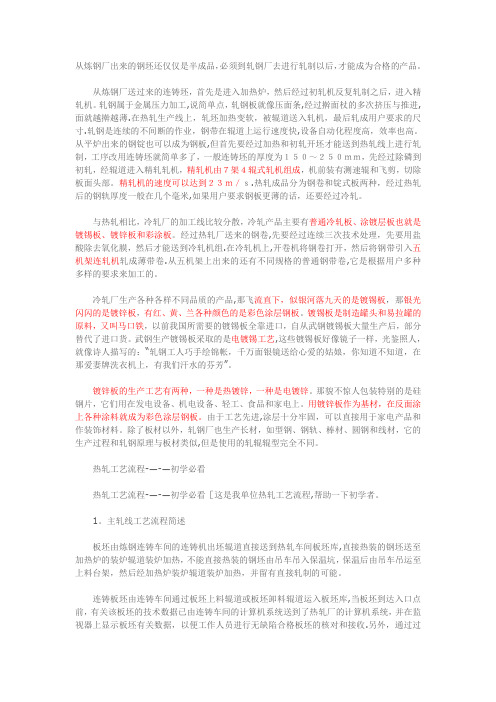
从炼钢厂出来的钢坯还仅仅是半成品,必须到轧钢厂去进行轧制以后,才能成为合格的产品。
从炼钢厂送过来的连铸坯,首先是进入加热炉,然后经过初轧机反复轧制之后,进入精轧机。
轧钢属于金属压力加工,说简单点,轧钢板就像压面条,经过擀面杖的多次挤压与推进,面就越擀越薄.在热轧生产线上,轧坯加热变软,被辊道送入轧机,最后轧成用户要求的尺寸.轧钢是连续的不间断的作业,钢带在辊道上运行速度快,设备自动化程度高,效率也高。
从平炉出来的钢锭也可以成为钢板,但首先要经过加热和初轧开坯才能送到热轧线上进行轧制,工序改用连铸坯就简单多了,一般连铸坯的厚度为150~250mm,先经过除磷到初轧,经辊道进入精轧轧机,精轧机由7架4辊式轧机组成,机前装有测速辊和飞剪,切除板面头部。
精轧机的速度可以达到23m/s.热轧成品分为钢卷和锭式板两种,经过热轧后的钢轨厚度一般在几个毫米,如果用户要求钢板更薄的话,还要经过冷轧。
与热轧相比,冷轧厂的加工线比较分散,冷轧产品主要有普通冷轧板、涂镀层板也就是镀锡板、镀锌板和彩涂板。
经过热轧厂送来的钢卷,先要经过连续三次技术处理,先要用盐酸除去氧化膜,然后才能送到冷轧机组.在冷轧机上,开卷机将钢卷打开,然后将钢带引入五机架连轧机轧成薄带卷.从五机架上出来的还有不同规格的普通钢带卷,它是根据用户多种多样的要求来加工的。
冷轧厂生产各种各样不同品质的产品,那飞流直下,似银河落九天的是镀锡板,那银光闪闪的是镀锌板,有红、黄、兰各种颜色的是彩色涂层钢板。
镀锡板是制造罐头和易拉罐的原料,又叫马口铁,以前我国所需要的镀锡板全靠进口,自从武钢镀锡板大量生产后,部分替代了进口货。
武钢生产镀锡板采取的是电镀锡工艺,这些镀锡板好像镜子一样,光鉴照人,就像诗人描写的:“轧钢工人巧手绘锦帐,千万面银镜送给心爱的姑娘,你知道不知道,在那爱妻牌洗衣机上,有我们汗水的芬芳”。
镀锌板的生产工艺有两种,一种是热镀锌,一种是电镀锌。
那貌不惊人包装特别的是硅钢片,它们用在发电设备、机电设备、轻工、食品和家电上。
铝热轧工艺流程
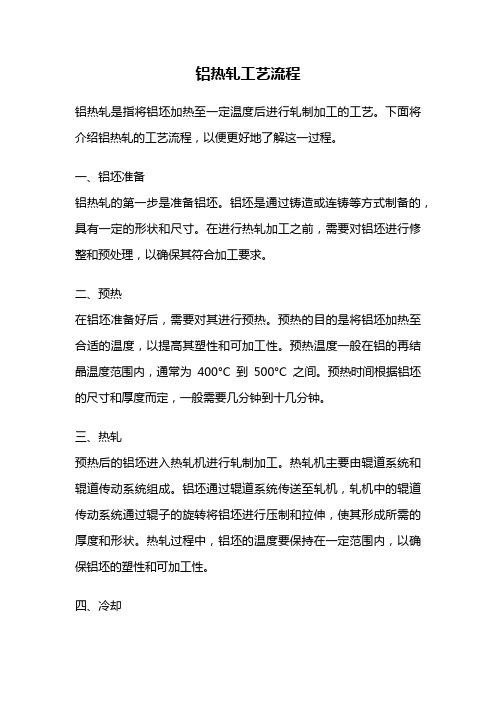
铝热轧工艺流程铝热轧是指将铝坯加热至一定温度后进行轧制加工的工艺。
下面将介绍铝热轧的工艺流程,以便更好地了解这一过程。
一、铝坯准备铝热轧的第一步是准备铝坯。
铝坯是通过铸造或连铸等方式制备的,具有一定的形状和尺寸。
在进行热轧加工之前,需要对铝坯进行修整和预处理,以确保其符合加工要求。
二、预热在铝坯准备好后,需要对其进行预热。
预热的目的是将铝坯加热至合适的温度,以提高其塑性和可加工性。
预热温度一般在铝的再结晶温度范围内,通常为400°C到500°C之间。
预热时间根据铝坯的尺寸和厚度而定,一般需要几分钟到十几分钟。
三、热轧预热后的铝坯进入热轧机进行轧制加工。
热轧机主要由辊道系统和辊道传动系统组成。
铝坯通过辊道系统传送至轧机,轧机中的辊道传动系统通过辊子的旋转将铝坯进行压制和拉伸,使其形成所需的厚度和形状。
热轧过程中,铝坯的温度要保持在一定范围内,以确保铝坯的塑性和可加工性。
四、冷却热轧后的铝板需要进行冷却处理。
冷却的目的是使铝板快速降温,增加其硬度和强度。
冷却方式可以采用自然冷却或水冷等方式,具体根据铝板的要求和工艺而定。
五、整平冷却后的铝板需要进行整平处理。
整平是指通过机械力对铝板进行拉伸和压制,以消除其内部应力,使其表面平整。
整平一般通过辊道系统和辊道传动系统来完成。
六、切割整平后的铝板需要根据需要进行切割。
切割可以采用剪切、切割机等方式进行,以得到所需的尺寸和形状。
七、表面处理切割后的铝板需要进行表面处理。
表面处理可以采用酸洗、抛光、喷涂等方式进行,以提高铝板的表面质量和光洁度。
八、检验和包装表面处理后的铝板需要进行质量检验,确保其符合要求。
检验可以包括外观检查、尺寸检查、化学成分分析等。
检验合格后,铝板经过包装后可以出厂销售或作为下一道工序的原材料使用。
以上就是铝热轧的工艺流程。
通过对铝坯的准备、预热、热轧、冷却、整平、切割、表面处理以及检验和包装等多个环节的处理,可以得到符合要求的铝板产品。
- 1、下载文档前请自行甄别文档内容的完整性,平台不提供额外的编辑、内容补充、找答案等附加服务。
- 2、"仅部分预览"的文档,不可在线预览部分如存在完整性等问题,可反馈申请退款(可完整预览的文档不适用该条件!)。
- 3、如文档侵犯您的权益,请联系客服反馈,我们会尽快为您处理(人工客服工作时间:9:00-18:30)。
铸—连轧) 短流程生产线。
!
前言 "
众所周知, 连续炼钢与传统炼钢—注锭—初轧
连铸坯热送热装工艺方案
主要工艺设备及性能参数 炼轧厂生产工艺流程见图 - 。
开坯相比, 以其减少金属损失和能源消耗所产生的 巨大经济效益, 在钢铁行业得到推广和应用。人们 在有效地利用高温连铸坯的显热, 实现了在炼钢— 连铸—轧钢过程中更大幅度的节省能源。为充分发 挥连铸坯热送热装工艺的优势、降低钢坯加热能 耗、 缩短加热时间, 减少连铸坯氧化烧损、 降低生产 成本和提升企业竞争力。韶钢于 !""" 年配套建成 了 #" $ %&’($))* 电炉炼钢生产线, 和原小型连轧厂 合并为 “四位一体” ( 即 %&’($))* 电弧炉—+, 炉—连
#"$ 设备改造 3A!A! 入炉前送钢地辊改造
原送钢地辊仅输送冷坯, 为适应热送热装的需 要, 将原地辊轴改为水冷, 并将原地辊辊面改为高 温耐磨材质, 以减少设备故障。为减少钢坯传输过 程中的温降, 所有地辊均安装了保温罩。
3A!A(
进钢上料系统改造 原 !(# , 8 F 步进梁式加热炉进钢上料采用液压
方坯连 铸机
技术参数 其它参数
!"!
热送热装工艺实施方案 韶钢炼轧厂采用连铸坯热直接轧制工艺技术,
连铸坯, 拉坯速度也较为稳定, 因此连铸机小时产 量较为稳定, 且作业率较高。而轧钢工序因受市场 影响需频繁更换品种规格, 生产中经常需要更换轧 辊和孔槽, 作业率相对较低。为充分挖掘轧钢工序
步进
热送热装工艺平面布置见图 (。
出坯辊道 连铸 机
!B
冷床
(B
冷床 冷坯上料台架
梁式 加热炉
的生产能力、 降低设备故障率、 减少停机时间、 提高 作业率, 在炼钢工序设备调试及试生产期间, 对轧 钢工序设备及工艺做了一定程度的改造和调整, 以 适应连铸坯热送热装的需要。
!B 提升机
(B 提升机
图(
钢坯剔除台架
热送辊道
热送热装工艺平面布置图
#
设备及工艺技术改造
由于炼钢工序生产线年设计能力为 73 万 ,, 实
际产钢能力可达 &% 万 , 8 9 。而轧钢工序年设计能力 仅为 #% 万 , , 且送热装, 对轧机本体结构也做了相应
(’
《工
业
炉》 第 #5 卷
第0期
#&&% 年 5 月
#$)4#$/ ##& 及以上 #$#4#$0
)&&4/&& 1
#$)4#$/ ##& 及以上 #$#4#$0
/&& 1 以上
#$)4#$/ ##& 及以上
#%
经验交流: 连铸坯热轧工艺及控制
理的重点。采用了一系列切实可行的措施, 取得了 较好的效果。
率及热装温度逐步提高而下降, 高温连铸坯的显热 得到了较为充分的利用。加热炉燃耗、 钢坯氧化烧 损及加热炉产量、 钢坯热装温度的关系曲线如图 & 、 图 ’ 所示。 具体经济效益有下几点: (% ) 节约了能源。热送热装后, 重油单耗下降了 重油单价按 %-. 元 ! +, 计算, * +, ! " 钢, ())& 年全年 轧材 /)-& 万 ",仅此一项年降低生产成本近 /’&-%. 万元。 (( ) 降低了钢坯氧化烧损。热送热装工艺实施 后, 钢坯氧化烧损显著降低, 轧钢工序成材率提高 年创经济效益 %)*-/’ 万元。 )-%.0, (& ) 节省了钢坯运输费用。以前电炉炼钢和轧 钢是两个不同的分厂, 各自独立。小型连轧所需连 铸坯要用汽车或火车运输, 且距离较远 (约 (-. +1) , 每 " 钢坯需运输费用 ( 元, ())% 年全年仅此一项节 约开支 %%)-2 万元。 以上三项合计: (万元) /’&-%.3%)*-/’3%%)-24% )2%-.5 这 一 技 改 措 施 创 造 的 总 经 济 效 益 为 % )2%-.5 万元。
>,=1)-%02. ?1%,2’(
文章编号 M-""-NO#PPQ!""1R"S?""!0?"S
U&*2!T V&2S WA*2!""1
连铸坯热轧工艺及控制
周 明, 谢志雄
(广东韶关钢铁集团有限公司, 广东 韶关 !"#"## )
摘 要: 介绍了韶钢炼轧厂连铸坯热轧工艺的实施方案, 总结了连铸坯热送、 热装、 热轧工艺及控制的一些经验。 实施这一
方案取得了缩短加热时间, 减少钢坯烧损, 降低能耗的效果。 关键词: 热送热装; 连铸坯; 温度 中图分类号: ./0012-文献标识码: 3
$%&’()) * +&,-%&. &/ +&,-0,&1) +2)-0,3 4&- +2%%50,3 +62%30,3 7&..0,3
4567 89’:, ;<= 4>9?@9&’: (!"#$%&#’ ()$’ * !+,,- .$ , !"#$%&#’ 1-!-!!, ."/’#) 89)-%2’-: .>) (&*A$9&’ &B CD($9’:?>&$ CDEEF9’: C>DE:9’: E&**9’: D$ ($))*?GDH9’: I E&**9’: J*D’$ &B (>D&:AD’ 9( 9’$E&KAC)K , D’K (&G) )@J)E9)’C) &B CD($9’:?>&$ CDEEF9’: C>DE:9’: E&**9’: D$ ($))* GDH9’: I E&**9’: J*D’$ &B L<L/ DE) C&’C*AK)K2 ;(5 <&%=): >&$ CDEEF9’: I C>DE:9’: ; C&’$9’&A( CD($9’:; $)GJ)ED$AE)
的改进。中轧和精轧机组增设了快速换辊、轧辊 导卫预调装置,并使用了导卫快速定位技术。水管、 液压管改为快速安装接头,尽可能减少换规格和换 轧辊的时间。
段下部两侧各布置 0 个高压重油烧嘴。炉子燃烧控 制采用双交叉限幅控制方式,炉温分均热段和加热 段两段控制。 #&&& 年炼钢工序投产后, 开始实施高 温连铸坯热送热装工艺, 随着炼钢工序的逐步稳产、 顺产,高温连铸坯的热送热装率有了较大幅度的提 高。在此基础上, 又在生产实践中不断摸索, 根据不 同温度条件下的连铸坯, 轧制不同规格棒材, 制订出 不同的温度制度和加热制度。当出现热—冷(冷— 热) 坯混装时, 以 第 0& 料 位 为 分 界 点 (本 加 热 炉 共 , 实施升降温加热制度。 当冷坯进至第 0& /& 个料位) 料位时, 均热段保持原加热制度不变, 加热段实施相 应的冷坯升温 (或热坯降温) 加热制度。 当冷坯 (或热 坯) 进至第 #& 料位时, 均热段再实施相应的冷坯升 温 (或热坯降温) 加热制度。 通过对各段燃料流量、 空 气流量、 炉压等进行控制和调节, 保证各段炉温在设 定范围。这样, 既保证了钢坯加热质量 (加热温度和 温度均匀性) ,又大幅度降低了加热炉重油单耗, 减 少了钢坯氧化烧损, 取得了良好的经济效益。 每一个炉号在入炉前, 均要用红外线测温仪测量 连铸坯温度并跟踪了解其在炉内的位置, 并及时实施 相应的温度和加热制度。各段温度控制参数如表 #。
-./0,112
电弧炉
炉容量 其它参数 冶炼钢种
;< 炉
炉容量 机型
! 台四机四流弧形两点渐进矫直 =>?>@ 连铸机
铸坯断面 !$% **+!$% ** (平均拉速 3A3 * 8 *:/ ) , 连铸机长度 (&A& *, 抛物线结晶器长度 ! %%% ** 浇注时间 ’$ *:/ 8 炉 73 万 , 坯 8 9 ,
!"# !"#"$
工艺技术改进 调整轧制工艺及参数 原 来小 型 连 轧 生 产 线 采 用 $%& ’’($%& ’’(
为增加轧机机时产量, $& &&& ’’ 连铸坯生产棒材, 缩短轧制过程中的间歇时间, 并与炼钢工序相匹配, 将原 $%& 方坯孔型系列改为 $)& 方坯孔型。并提高 了各不同规格之间孔型的共用性, 减少了换辊量。 采用无孔型轧制技术,将原 $ 、 ! 水平轧机由
规格和参数
连铸生产线主要设备性能参数
连续预热电弧炉、 并热装铁水 ! 座带连续装料、 装入量 !3# , , 出钢量 "% , ; 变压器功率 $%456 冶炼周期 #!*:/ 8 炉, 带除尘设备 7$ 万 , 钢水 8 9 , 低合金钢、 合金钢、 优质碳素结构钢、 普通碳素结构钢 国产 "% , ;< 炉 ! 座, 变压器容量 !$456
* *
单槽改为平辊轧制。换辊时, 由于对轧辊轴向相对 位置要求不严格, 导卫板既简单又好调整, 使换辊 时间大为缩短。 连铸冷装入炉时, 在加热过程发生的 !!" 相变 能够细化 " 组织。但装炉温度高于 +!时,在随后的 加热过程中没有或近乎没有 !!" 相变,钢的 " 组织 较为粗大。对于此类情况,在实际生产中增大粗轧 各机组的压下量,提高其延伸系数,使其在再结晶 区通过加大轧件变形量以细化晶粒,从而确保轧材 质量。