生产稼动率与OEE
OEE公式

在TnPM体系里,除了生产现场操作员工参与的规范化活动之外,精心设计的检维修系统解决方案具有重要的实践意义。
这个体系我们称为SOON体系,即"Strategy--On-site-information--Organizing--Normalizing":其中S代表维修策略,可以根据故障的特征起因、役龄、特点,按照费用最小化原则,选择不同的维修策略或者组合策略;第一个O代表现场的信息检查、监测和诊断体系设计;第二个O代表组织和维修资源的配置安排;N代表维修规范,即维修流程的规范和维修技术标准的制定。
——TPM 的作用以及与TPS 的关系:作为TPS 管理系统的一个设备管理子系统
——TQM (全员质量管理)——TPM 是一种维修程序
——TPM 的目标可以概括为四个“零”,即停机为零、废品为零、事故为零、速度损失为零
五阶:TPM 第一阶段—初期清扫;TPM 第二阶段—困难点/发生源对策;TPM 第三阶段—总点检;TPM 第四阶段—提高点检效率(目视化管理); TPM 第五阶段—自主管理体制建立。
稼动率与设备总合效率(OEE)分析
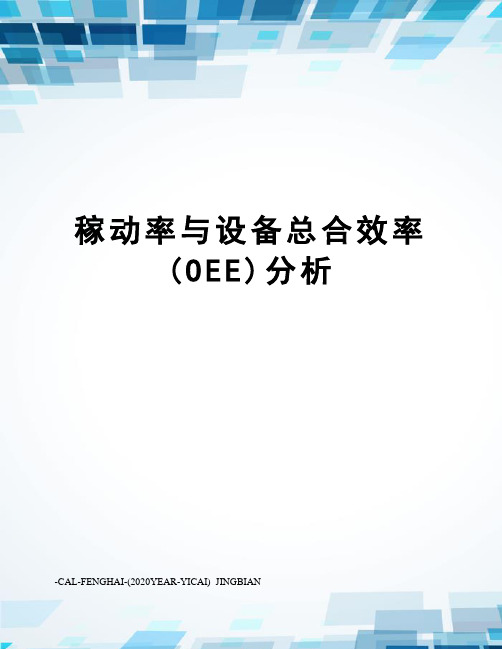
稼动率与设备总合效率(O E E)分析-CAL-FENGHAI-(2020YEAR-YICAI)_JINGBIAN稼动率与设备综合效率分析如果您被问到「我们部门的稼动率为90%,你们厂里是多少」,您可知道其所谓的稼动率定义为何90%这数字代表的是好是坏呢基本上稼动率有数种不同的定义,在此略加解释:1、时间稼动率首先定义最大操作时间,指的是设备可用的最大时间,若设备本身为厂内自购,且可完全由厂内自主使用,则最大操作时间一般为日历时间;而负荷时间则为设备可稼动的时间,乃是最大操作时间扣除停机(Shutdown, SD)损失,停机损失乃是计画上的休止时间,如休假、教育训练、保养等。
而稼动时间则是负荷时间扣除停止时间,而停止时间包括批次转换及制程异常、设备异常停止及修复时间。
最大操作时间:设备可用的最大时间负荷时间:最大操作时间扣除停机(Shutdown, SD)损失;这里的停机损失是计划是可预见的为客观实际的事实:如班前后会,保养、吃饭时间,日历时间或法定假日等。
停机(Shutdown, SD)损失:计画上的休止时间,如休假、教育训练、保养等稼动时间:负荷时间扣除停止时间停止时间:包括批次转换及制程异常、设备异常停止及修复时间。
由以上的定义,即可算出最常用的稼动率定义-设备稼动率(也称为时间稼动率),其公式为时间稼动率=稼动时间 / 负荷时间也可等于(操作时间/计划工作时间)目的:减少停止时间!!!通过资源整合,管理优化,进行资源充分利用,降低成本,提高效率。
2、性能稼动率/实质稼动率/速度稼动率时间稼动率并无法完全表现设备对生产的贡献程度;例如,相同的设备,相等的稼动时间,可能因效率的不同,而有不同的产能,此类效率降低的损失则称为性能损失。
在此定义速度稼动率如下:速度稼动率=基准周期时间/ 实际周期时间其中,基准周期时间:设备原设计产出单位产量所需的时间。
实际周期时间:目前设备实际产出单位产量所需的时间。
oee时间构成及计算公式

*价值时间=良品工时=良品数X单件工时
二﹑OEE计算公式4.缺料休息
5.计划保养
一﹑OEE 时间构成
1.预定节假日休息与班次休息
2.预定用餐时间与工间休息
3.缺订单休息
OEE = = X X
OEE=可用率×稼动率×性能效率×良率= 负荷时间/(总时间 ) ×作业时间/负荷时间×净作业时间/作业时间×价值时间/净作业时间
*价值时间=良品工时=良品数X单件工时
二﹑OPE公式
一﹑OPE时间构成
1.设备故障
2.换线
3.调机
4.物料异常(待料﹑错料﹑混料等)
OPE =管理效率×操作效率×平衡率×良率= 作业时间/(负荷时间 ) ×净作业时间/作业时间×产品作业时间/净作业时间×价值时间/产品作业时间。
设备综合效率OEE的定义及计算示例
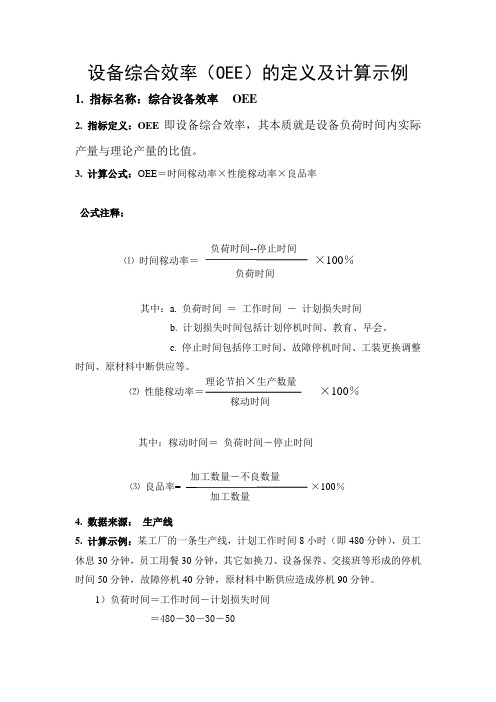
设备综合效率(OEE)的定义及计算示例1. 指标名称:综合设备效率OEE2. 指标定义:OEE即设备综合效率,其本质就是设备负荷时间内实际产量与理论产量的比值。
3. 计算公式:OEE=时间稼动率×性能稼动率×良品率公式注释:负荷时间--停止时间⑴时间稼动率=×100%负荷时间其中:a. 负荷时间=工作时间-计划损失时间b. 计划损失时间包括计划停机时间、教育、早会。
c. 停止时间包括停工时间、故障停机时间、工装更换调整时间、原材料中断供应等。
理论节拍×生产数量⑵性能稼动率=×100%稼动时间其中:稼动时间=负荷时间-停止时间加工数量-不良数量⑶良品率= ×100%加工数量4. 数据来源:生产线5. 计算示例:某工厂的一条生产线,计划工作时间8小时(即480分钟),员工休息30分钟,员工用餐30分钟,其它如换刀、设备保养、交接班等形成的停机时间50分钟,故障停机40分钟,原材料中断供应造成停机90分钟。
1)负荷时间=工作时间-计划损失时间=480-30―30―50=370(分钟)停止时间为:40分钟+90分钟=130分钟时间稼动率=(370-130)÷370=0.649(64.9%)2)性能稼动率理论节拍是0.85分钟/件,日产量(加工数量)为270件,其中不良品为30件性能稼动率=0.85×270÷240=0.956(95.6%)3)良品率良品率=(270-30)÷270=0.889(88.9%)由上,则:OEE=64.9%×95.6%×88.9% =55.2%6. 指标目的:1)利用OEE进行损失分析;2)OEE可以准确反映设备本身的问题,也能够客观评价企业的精益生产的实施水平,同时也不会使企业之间的OEE因理解与算法不同而不可比。
IE改善与提高OEE、稼动率:提升生产效率和竞争力
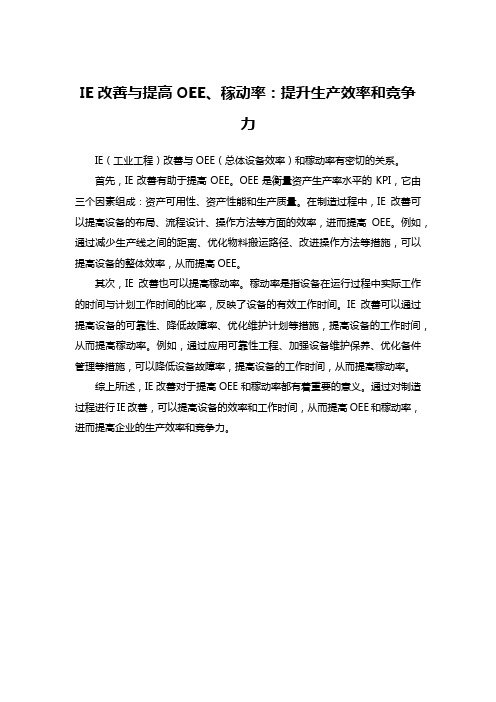
IE改善与提高OEE、稼动率:提升生产效率和竞争
力
IE(工业工程)改善与OEE(总体设备效率)和稼动率有密切的关系。
首先,IE改善有助于提高OEE。
OEE是衡量资产生产率水平的KPI,它由三个因素组成:资产可用性、资产性能和生产质量。
在制造过程中,IE改善可以提高设备的布局、流程设计、操作方法等方面的效率,进而提高OEE。
例如,通过减少生产线之间的距离、优化物料搬运路径、改进操作方法等措施,可以提高设备的整体效率,从而提高OEE。
其次,IE改善也可以提高稼动率。
稼动率是指设备在运行过程中实际工作的时间与计划工作时间的比率,反映了设备的有效工作时间。
IE改善可以通过提高设备的可靠性、降低故障率、优化维护计划等措施,提高设备的工作时间,从而提高稼动率。
例如,通过应用可靠性工程、加强设备维护保养、优化备件管理等措施,可以降低设备故障率,提高设备的工作时间,从而提高稼动率。
综上所述,IE改善对于提高OEE和稼动率都有着重要的意义。
通过对制造过程进行IE改善,可以提高设备的效率和工作时间,从而提高OEE和稼动率,进而提高企业的生产效率和竞争力。
OEE分析与管理
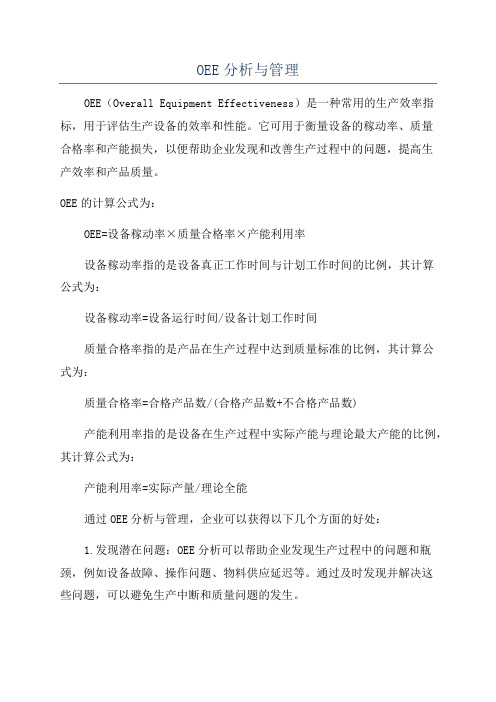
OEE分析与管理OEE(Overall Equipment Effectiveness)是一种常用的生产效率指标,用于评估生产设备的效率和性能。
它可用于衡量设备的稼动率、质量合格率和产能损失,以便帮助企业发现和改善生产过程中的问题,提高生产效率和产品质量。
OEE的计算公式为:OEE=设备稼动率×质量合格率×产能利用率设备稼动率指的是设备真正工作时间与计划工作时间的比例,其计算公式为:设备稼动率=设备运行时间/设备计划工作时间质量合格率指的是产品在生产过程中达到质量标准的比例,其计算公式为:质量合格率=合格产品数/(合格产品数+不合格产品数)产能利用率指的是设备在生产过程中实际产能与理论最大产能的比例,其计算公式为:产能利用率=实际产量/理论全能通过OEE分析与管理,企业可以获得以下几个方面的好处:1.发现潜在问题:OEE分析可以帮助企业发现生产过程中的问题和瓶颈,例如设备故障、操作问题、物料供应延迟等。
通过及时发现并解决这些问题,可以避免生产中断和质量问题的发生。
2.提高设备利用率:OEE分析可以帮助企业识别设备非生产时间(例如停机、换模、调机等),并优化生产计划以减少这些时间。
这将提高设备的稼动率,降低生产成本,提高生产效率。
3.提高产品质量:OEE分析可以帮助企业识别生产中的质量问题,并采取相应措施进行改进。
提高质量合格率将减少废品和返工的数量,提高产品的完整性和可靠性。
4.优化生产计划:OEE分析可以帮助企业确定生产的瓶颈和瓶颈,以优化生产计划和资源调度。
通过合理调整生产顺序、提高关键设备的利用率等措施,可以实现更高的产量和更好的资源利用效率。
5.设定目标和监控绩效:OEE分析可以帮助企业设定合理的生产目标,并对实际绩效进行监控和评估。
通过与目标进行比较,可以识别绩效差距并寻找改进之处,确保生产过程保持良好状态。
综上所述,OEE分析与管理是一个重要的管理工具,可以帮助企业提高生产效率和产品质量,降低成本,实现可持续发展。
OEE及嫁动率

OEEOEE是一个独立的测量工具,它用来表现实际的生产能力相对于理论产能的比率。
国际上对OEE的定义为:OEE是Overall Equipment Effectiveness(全局设备效率)的缩写,它由可用率(Availability time),表现性(Performance)以及质量指数(Quality)三个关键要素组成。
目录OEE的定义详细解释OEE计算实例OEE数据采集方法OEE计算实例设备综合效率(OEE)一、OEE的实质一般,每一个生产设备都有自己的最大理论产能,要实现这一产能必须保证没有任何干扰和质量损耗。
当然,实际生产中是不可能达到这一要求,由于许许多多的因素,车间设备存在着大量的失效: 例如除过设备的故障,调整以及设备的完全更换之外,当设备的表现非常低时,可能会影响生产率,产生次品,返工等。
二、详细解释OEE=可用率X 表现性 X质量指数。
其中:可用率(稼动率)=操作时间 / 计划工作时间它是用来考虑停工所带来的损失,包括引起计划生产发生停工的任何事件,例如设备故障,原料短缺以及生产方法的改变等。
表现性=(总产量/操作时间)/理想周期时间=(总产量 / 操作时间)/ 生产速率表现性考虑生产速度上的损失。
包括任何导致生产不能以最大速度运行的因素,例如设备的磨损,材料的不合格以及操作人员的失误等。
质量指数=良品/总产量质量指数考虑质量的损失,它用来反映没有满足质量要求的产品(包括返工的产品)。
利用OEE的一个最重要目的就是减少一般制造业所存在的六大损失:停机损失、换装调试损失、暂停机损失、减速损失、启动过程次品损失和生产正常运行时产生的次品损失。
下面表格是六大损失的说明及其与OEE的关系:三、OEE计算实例我们举一个例子来说明OEE的计算方法:设某设备某天工作时间为8h, 班前计划停机15min, 故障停机30min,设备调整25min, 产品的理论加工周期为0.6 min/件, 一天共加工产品450件, 有20件废品, 求这台设备的OEE。
oee设备综合效率目标值

oee设备综合效率目标值一、OEE设备综合效率的定义OEE(Overall Equipment Efficiency),即设备综合效率,是一种用于衡量设备运行效率的指标。
它综合考虑了设备的稼动率、性能效率和质量合格率三个方面,通过计算得出一个综合的效率值。
OEE的计算公式为:OEE = 稼动率× 性能效率× 质量合格率。
通过OEE指标的监控和分析,企业可以评估设备的运行状态和效率水平,为提高生产线的综合效率提供依据。
二、提高设备稼动率设备稼动率是指设备运行时间与总时间之比,反映了设备的利用率。
提高设备稼动率是提高设备综合效率的基础。
要提高设备稼动率,首先需要对设备进行定期维护保养,确保设备处于良好的工作状态。
其次,要合理安排生产计划,避免设备闲置或过度负荷运行。
此外,采用先进的设备监控系统,及时发现并解决设备故障,也是提高稼动率的关键。
三、优化设备性能效率设备性能效率是指设备在单位时间内完成工作量的能力。
提高设备性能效率可以通过多种方式实现。
首先,要对设备进行有效的培训和操作指导,提高操作人员的技能水平。
其次,要进行设备参数的优化调整,确保设备在最佳状态下运行。
另外,采用先进的自动化技术和设备改进措施,也能有效提高设备的性能效率。
四、提高产品质量合格率产品质量合格率是指产品合格数量与总产量之比,反映了产品质量的水平。
提高产品质量合格率可以通过加强质量管理和控制来实现。
首先,要建立完善的质量管理体系,包括从原材料采购到生产过程的全程质量控制。
其次,要加强对生产过程的监控和检测,及时发现并纠正质量问题。
此外,要进行持续的质量改进,通过分析和解决质量问题的根本原因,提高产品质量合格率。
五、综合考虑实现最优化要实现生产线的最优化,除了提高设备综合效率外,还需要综合考虑其他因素。
首先,要合理安排生产计划和调度,确保生产线的平衡运行。
其次,要进行供应链的优化管理,确保原材料和零部件的及时供应。
OEE定义和计算方式解析

➢返修率递减活动
各单位OEE月度协调会议
提 升 OEE
OEE数据记录系统 ➢准确把握现场情况 ➢精确记录相关数据 ➢反映客观实际
减少等待 ➢物料等待 ➢车体等待 ➢在制品等待 ➢满载停止
提升 OEE
故障零化 ➢严格执行点检表制度 ➢提升保养人员的技能 ➢对故障的彻底分析与对策 ➢改进设计上的缺陷
提高品质 ➢提高良品率 ➢返修率的低减
教育训练 ➢个别改善能力提高 ➢保养技能训练 ➢技能员技能的提升 ➢RTC培训(制造、保 全)
减少短暂停线 ➢三现主义的想法 ➢PM分析 ➢改善课题 ➢小暂停管控
系统水准
消退
超出管制
OEE管制 保持
TPM改善
改善系统
保持 OEE管制
时间
流程设计
有3位大学生一起合租了某个旅馆的房间作为住宿。每人交了1000元 作为房费。招待员刚要把这3000元入帐时,旅店经理说:“由于看他 们都是大学生,现在还没有独立工作赚钱,就少收一些吧。退他们 500元好了。”于是从这些钱里拿出5张100元的钞票,叮嘱招待员给 学生送回去。
= 良品数×量100 (%) 投入数量
设备
负荷时间
停
开动时间
止 损
失
净开 性
动时
能 损
间
失
价值 不
开动
良 损
时间 失
七大损失
1)故障 2)换模换线时间 3)刀具调整 4)开机暖机 5)短暂停机,空转 6)速度降低
7)不良返工
设备综合效率 时间稼动率
性能稼动率 良品率
停线时间
停线时间 : 由于以下的缘由而引起的设备不能稼动的时间 机器故障 : 因机器故障引起的设备不能生产的时间 机种变更 : 因资材不良, 品质等偶然发生的因素,依据生
OEE计算公式

完全有效生产率=设备综合效率×利用率 =0.7799×0.862×100% 3 =67.2%
■练习
• 某生产线共有10台设备,单班出勤时间为11H,当班生产实绩1800台,不良率为5%, 设计C/T为18秒,例行的早晚会30分钟,设备清扫点检15分钟,在生产过程中一台设 备停止30分钟,刀具交换、型号更换及设备调整30分钟,请问此生产线的综合效率是 多少,完全有效生产率是多少?
4
2
■OEE的计算实例
某生产线作业一天的生产状况:
勤务时间 580分 计划内停机时间 早晚会/教育 60分 其它 20分 计划外停机 故障 30分 调整 30分 200个 2.50% 2分 生产数 不良率 理论C/T
稼动时间 时间稼动率= 负荷时间 理论C/T×生产数 性能稼动率= 稼动时间 良品数 良品率= 生产数 负荷时间
■OEE与TEEP的计算方式
·设备综合效率(OEE)=时间稼动率×性能稼动率×良品率 ·=(稼动时间/负荷时间×100%) ×(性能稼动时间/稼动时间×100%)
×(生产台数-不良台数/生产台数×100%)
·完全有效利用率(TEEP)=设备利用率×OEE ·设备利用率=负荷时间/勤务时间 ·负荷时间=勤务时间-计划停机时间-非设备因素停机时间
这里,非设备因素停机时间指:停水、停电、停气、停汽、等待计划排产、等待定单、 等待上、下工序等所有不是本台设备因素造成的停机损失
1
■OEE与TEEP的计算方式
·时间稼动率=稼动时间/负荷时间×100% =(负荷时间-停机时间)/负荷时间×100% 即负荷时间与设备扣除停机后实际稼动之比率
·性能稼动率=速度稼动率×实质稼动率×100% =(基准C/T/实际C/T) ×(生产量×实际C/T/稼动时间)×100% = 基准C/T×生产量/稼动时间×100% = 性能稼动时间/稼动时间×100%
OEE介绍及计算方法

OEE定义及计算公式
五﹑速度损失定义
速度损失时间分为两部分﹕ 1﹑速度降低 2﹑空转和小停顿 分别定义如下﹕ • 速度降低
机器操作中与理论速度的差异造成的损 失时间。 • 空转和小停顿损失
制程中由于小的停顿(比如断料)导致的 生产损失。
稼动时间(=负荷时间-停机时间)
时间稼动率 =
出勤时间
性能稼动率 = 理论周期*加工数量
稼动时间
为了区分速度降低﹑小停顿对性能稼动率的影响﹐将性能稼动率 拆分为纯稼动率和速度稼动率﹐分别表达速度降低的影响和小停顿的 影响。
OEE定义及计算公式
纯稼动率是指设备在稼动时间内﹐以一定速度保持稳定﹑连续运 转的程度。以一定之速度运转这并不是与理论速度比快或慢﹐即 使本身速度比较慢﹐但要看是否能在长时间内保持安定的速度运 转。所以可以衡量因小停顿引起的损失﹐或在每日报表上看不出 来之微缺损失。
性能 稼动 率
纯稼动率 =(实际周期时间×加工数量)/稼动时间×100%
=×
速度稼动率 =理论周期/实际周期×100%
速度稼动率是指速度的差﹐对设备应具备的能力﹐与实 际速度比率。也就是判断是否以规定的速度进行运转。如 果设备的速度降低﹐会有多少损失。
良品数
良品率 = 总产出量
OEE定义及计算公式
= 时间稼动率 ×性能稼动率 ×良品率
OEE三大
设 备
模换暖 具线机
空速 转度
不 良
要素对应 故 故 调 损 与 降
件
的损失 障 障 整 失 小 低
停
顿
综合设备效率是从上述的时间性﹑性能﹑良率观察后得到的使 用有效率﹐来整体性进行设备评估的标准。
稼动率的计算方法

稼动率的计算方法稼动率(Utilization Rate)是指生产设备、工作人员、生产线或整个生产系统在一段时间内实际运行的时间与可运行的时间之比,也就是工作时间的利用率。
在生产管理中,稼动率是一个重要的指标,反映了生产资源的有效利用程度。
稼动率计算方法主要根据不同的生产对象和时间粒度有所差异,以下是几种常见的计算方法:1.设备稼动率的计算方法:设备稼动率是指一台或多台设备实际运行时间与可运行时间之比。
设备稼动率可以按照设备运行情况分为两种:- 总稼动率(Overall Equipment Effectiveness,OEE):OEE是指设备在一定时间内实际生产数量与理论最大生产能力之比。
计算公式为:OEE=设备实际运行时间/(设备理论运行时间×设备设计生产能力)设备实际运行时间是指设备在一定时间内真正处于生产状态的时间,不包括设备运行中的停机、换模、维修等非生产时间。
设备理论运行时间是指设备在一定时间内能够连续运行的最长时间,通常以24小时为基准。
设备设计生产能力是指设备在理论运行状态下能够达到的最大产能。
- 开动率(Running Rate):开动率是指设备实际运行时间与可运行时间之比。
计算公式为:开动率=设备实际运行时间/可运行时间可运行时间是指设备在一定时间内应该处于运行状态的时间,包括除停机、换模、维修外的所有时间。
2.人工稼动率的计算方法:人工稼动率是指生产线上工人实际工作时间与可工作时间之比。
计算公式为:人工稼动率=工人实际工作时间/可工作时间工人实际工作时间是指工人在一定时间内实际从事生产工作的时间,不包括工人的休息、用餐、集合、培训等非工作时间。
可工作时间是指工人在一定时间内应该从事生产工作的时间,包括除非工人休息、用餐、集合、培训等以外的所有时间。
3.生产线稼动率的计算方法:生产线稼动率是指生产线实际运行时间与可运行时间之比。
生产线稼动率可以按照不同的计算方法分为两种:-连续开动率:连续开动率是指生产线在一定时间内连续运行的时间与可运行时间之比。
机加线稼动率及OEE

机加设备生产线,设备综合效率(OEE)及稼动时间计算方式:设备总体效率(OEE)=时间稼动率X性能稼动率X直通率时间稼动率=稼动时间/负荷时间X100%性能稼动率=标准CT X 生产数/稼动时间X100%直通率=良品数/生产数X100%OEE指标范围:卓越:OEE》80%,优秀:70%《OEE《79%,良好:55%《OEE《69%,一般:OEE《55%。
时间稼动率计算:最大操作时间A:设备理论上可以使用的最大时间;负荷时间B:最大操作时间扣除停机时间B=A-C;停机时间C:计划上的停机休息时间,例如休假、培训学习、设备保养等时间;稼动时间D:负荷时间扣除设备停止时间D=B-E;停止时间E:包括设备在生产批次之间的转换停止时间,现场生产过程中的异常处理时间,设备故障引起的异常停止及修复时间稼动率定义/设备稼动率(也称为时间稼动率)其计算公式:时间稼动率S=稼动时间D/负荷时间B=1-E/B=1-E/A-C(最大操作时间-停机损失时间-停止时间)最大操作时间-停机损失时间(概括起来说就是设备本身具备的最大生产时间扣除因为计划停机时间和生产过程异常引起的时间损失与设备最大理论生产时间扣除计划停机时间的比值百分比)。
在评价设备生产效率时,可能因为生产时间相同,计划停机时间相同但是设备生产效率不同而带来的设备整体生产效率评价上的不准确,所以引入了设备性能稼动率作为意向评价标准。
性能稼动率/实质稼动率/速度稼动率速度稼动率=基准周期时间/实际周期时间基准周期时间=设备原设计产出单位产量产品所需要的时间时间周期时间=目前设备时间生产单位产量产品所实际需要的时间实质稼动率=生产量X实际周期时间/稼动时间性能稼动率=速度稼动率X实质稼动率性能稼动时间=稼动时间X性能稼动率=稼动时间-性能损失时间产品直通率,既是单位产量的产品在设备生产加工过程中,在各个工序的质量检查中都OK,一次性通过整条生产线所占的比率,是用来衡量生产线生产性能及质量稳定性的指标。
OEE公式

在TnPM体系里,除了生产现场操作员工参与的规范化活动之外,精心设计的检维修系统解决方案具有重要的实践意义。
这个体系我们称为SOON体系,即"Strategy--On-site-information--Organizing--Normalizing":其中S代表维修策略,可以根据故障的特征起因、役龄、特点,按照费用最小化原则,选择不同的维修策略或者组合策略;第一个O代表现场的信息检查、监测和诊断体系设计;第二个O代表组织和维修资源的配置安排;N代表维修规范,即维修流程的规范和维修技术标准的制定。
——TPM 的作用以及与TPS 的关系:作为TPS 管理系统的一个设备管理子系统
——TQM (全员质量管理)——TPM 是一种维修程序
——TPM 的目标可以概括为四个“零”,即停机为零、废品为零、事故为零、速度损失为零
五阶:TPM 第一阶段—初期清扫;TPM 第二阶段—困难点/发生源对策;TPM 第三阶段—总点检;TPM 第四阶段—提高点检效率(目视化管理); TPM 第五阶段—自主管理体制建立。
OEE及嫁动率

OEEOEE是一个独立的测量工具,它用来表现实际的生产能力相对于理论产能的比率。
国际上对OEE的定义为:OEE是Overall Equipment Effectiveness(全局设备效率)的缩写,它由可用率(Availability time),表现性(Performance)以及质量指数(Quality)三个关键要素组成。
目录OEE的定义详细解释OEE计算实例OEE数据采集方法OEE计算实例设备综合效率(OEE)一、OEE的实质一般,每一个生产设备都有自己的最大理论产能,要实现这一产能必须保证没有任何干扰和质量损耗。
当然,实际生产中是不可能达到这一要求,由于许许多多的因素,车间设备存在着大量的失效: 例如除过设备的故障,调整以及设备的完全更换之外,当设备的表现非常低时,可能会影响生产率,产生次品,返工等。
二、详细解释OEE=可用率X 表现性 X质量指数。
其中:可用率(稼动率)=操作时间 / 计划工作时间它是用来考虑停工所带来的损失,包括引起计划生产发生停工的任何事件,例如设备故障,原料短缺以及生产方法的改变等。
表现性=(总产量/操作时间)/理想周期时间=(总产量 / 操作时间)/ 生产速率表现性考虑生产速度上的损失。
包括任何导致生产不能以最大速度运行的因素,例如设备的磨损,材料的不合格以及操作人员的失误等。
质量指数=良品/总产量质量指数考虑质量的损失,它用来反映没有满足质量要求的产品(包括返工的产品)。
利用OEE的一个最重要目的就是减少一般制造业所存在的六大损失:停机损失、换装调试损失、暂停机损失、减速损失、启动过程次品损失和生产正常运行时产生的次品损失。
下面表格是六大损失的说明及其与OEE的关系:三、OEE计算实例我们举一个例子来说明OEE的计算方法:设某设备某天工作时间为8h, 班前计划停机15min, 故障停机30min,设备调整25min, 产品的理论加工周期为0.6 min/件, 一天共加工产品450件, 有20件废品, 求这台设备的OEE。
什么是OEE

课程思路: 1、OEE是什么? 2、OEE怎么使用? 3、OEE有什么好处? ※我们日常生产数据问题?
前言
场景—— 下班了!主管在生产现场,找到班组长 主管:今天生产如何? 班组长:不怎么样,产量没达标。 主管:什么情况?怎么没达标? 班组长:我们看一下OEE的各项数据,就清楚了。
项目
结果1
稼动率
75%
可动率
89%
设备故障停线率
6%
品质异常停线率
5%
待料停线率
0%
其他停线率
3%
表现性
88%
质量指数
96%
4
它由可动率(Availability time),表现性(Performance) 以及质量指数(Quality)三个关键要素组成。
公式: 稼动率(OEE)=可动率× 表现性 ×质量指数
可动率=可动时间/负荷时间×100% 表现性=实绩产量/理论产量×100% 质量指数=合格品数量/生产数量×100%
OEE是什么?
OEE是什么?
生产 达成率
稼动率
OEE
可动率
表现性
质量指数
设备故障 品质异常
待料 其他
新员工操作 设备磨损 材料不良
其他
产品不良
产品返工
1
OEE是一个独立的测量工具,它用来表现实际的生产能力相对
于理论产能的比率。OEE的定义为:OEE是Overall Equipment Effectiveness(综合稼动率)的缩写。
2
OEE怎么使用?
1、设定各项数据的管理目标 2、计算各项数据 3、记录、统计 4、目标管理 5、异常分析、对策
3
OEE实践运用ቤተ መጻሕፍቲ ባይዱ
OEE计算公式来历
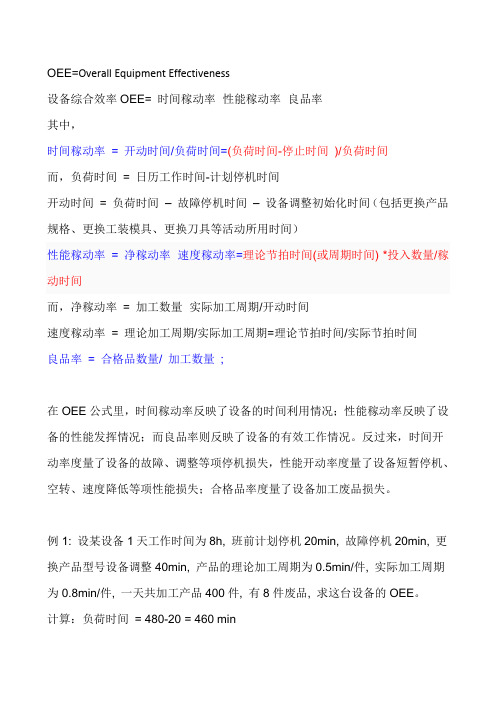
OEE=Overall Equipment Effectiveness设备综合效率OEE= 时间稼动率×性能稼动率×良品率其中,时间稼动率= 开动时间/负荷时间=(负荷时间-停止时间)/负荷时间而,负荷时间= 日历工作时间-计划停机时间开动时间= 负荷时间–故障停机时间–设备调整初始化时间(包括更换产品规格、更换工装模具、更换刀具等活动所用时间)性能稼动率= 净稼动率×速度稼动率=理论节拍时间(或周期时间) *投入数量/稼动时间而,净稼动率= 加工数量×实际加工周期/开动时间速度稼动率= 理论加工周期/实际加工周期=理论节拍时间/实际节拍时间良品率= 合格品数量/ 加工数量;在OEE公式里,时间稼动率反映了设备的时间利用情况;性能稼动率反映了设备的性能发挥情况;而良品率则反映了设备的有效工作情况。
反过来,时间开动率度量了设备的故障、调整等项停机损失,性能开动率度量了设备短暂停机、空转、速度降低等项性能损失;合格品率度量了设备加工废品损失。
例1: 设某设备1天工作时间为8h, 班前计划停机20min, 故障停机20min, 更换产品型号设备调整40min, 产品的理论加工周期为0.5min/件, 实际加工周期为0.8min/件, 一天共加工产品400件, 有8件废品, 求这台设备的OEE。
计算:负荷时间= 480-20 = 460 min开动时间= 460 – 20 – 40 = 400 min时间稼动率= 400/460 = 87%速度稼动率= 0.5/0.8 = 62.5%净稼动率= 400×0.8/400 = 80%性能稼动率= 62.5%×80% = 50%良品率= (400-8)/400 = 98%于是得到OEE = 87%×50%×98% = 42.6%。
有些企业还可以根据生产的实际, 用便于统计的数据来推算TPM[2]。
- 1、下载文档前请自行甄别文档内容的完整性,平台不提供额外的编辑、内容补充、找答案等附加服务。
- 2、"仅部分预览"的文档,不可在线预览部分如存在完整性等问题,可反馈申请退款(可完整预览的文档不适用该条件!)。
- 3、如文档侵犯您的权益,请联系客服反馈,我们会尽快为您处理(人工客服工作时间:9:00-18:30)。
例:某生产线一天生产三种机型,三种机型节拍分别为100s、120s、150s,产量分别为60、50、40件, 生产线当天的负荷时间为7h。则该生产线当天的稼动率=【(100*60+120*50+150*40)/(7*3600)】 *100%=71.43%
三、OEE与稼动率的区别
OEE定义:OEE是Overall Equipment Effectiveness(全局设备效率)的缩写。一般,每一个生产设备都有 自己的理论产能,要实现这一理论产能必须保证没有任何干扰和质量损耗。OEE就是用来表现实际的生产能 力相对于理论产能的比率,它是一个独立的测量工具。
OEE计算实例:
设某设备某天工作时间为8H,班前计划停机10min,故障停机30 min,设备调整35 min,产品的理论加工 周期为1min/件,一天共加工产品400件,有20件废品,求这台设备的OEE。
根据上面可知: 计划运行时间=8*60-10=470(min) 实际运行时间=470-30-35=405(min) 时间利用率=405/470=0.86(86%) 性能利用率=400/405=0.98(98%) 良品率=(400-20)/400=0.95(95%)OEE=有效率*表现性*质量指数=80%
生产线稼动率与OEE
一、定义
稼动率是指设备在所能提供的时间内为了创造价值而占用的时间所占的比重。是指一台机器设备可能的 生产数量与实际生产数量的比值。
二、基本公式
单机型CT相同:
稼动率=【稼动时间/负荷时间】*100%=(总加工数*实际CT)/负荷时间 *100%
稼动时间=实绩CT*总生产数
实绩CT=设备加工时间+辅助时间=连续线的设定CT或产出一个或一箱产品的时间
OEE=时间稼动率*性能稼动率*合格品率=时间稼动率*净开动率*速度开动率*合格品率 =稼动时间*【(总加工数*实际CT*理论)/负荷时间 * 理论CT/实际CT】*100%*合格品率 =(合格品数*理论CT)/负荷时间
主要区别:OEE重视合格品数,即生产的有效性。两者主要区别在于计算时分别用了理论CT和实际CT。
总生产数=合格品数+不良品总数
例:某生产线实绩(瓶颈)节拍为120s,每天的负荷时间为7h,当天的产量为130件(其中不合格件数 为2),则该生产线这一天的稼动率=【(120*130)/(7*3600)】=61.9% 生产多种机型CT不同的情况:
稼动率=(A机型CT*A总生产数+B机型CT*B生产总数