不同工艺乙烯产能
聚乙烯工艺技术的比较与选择
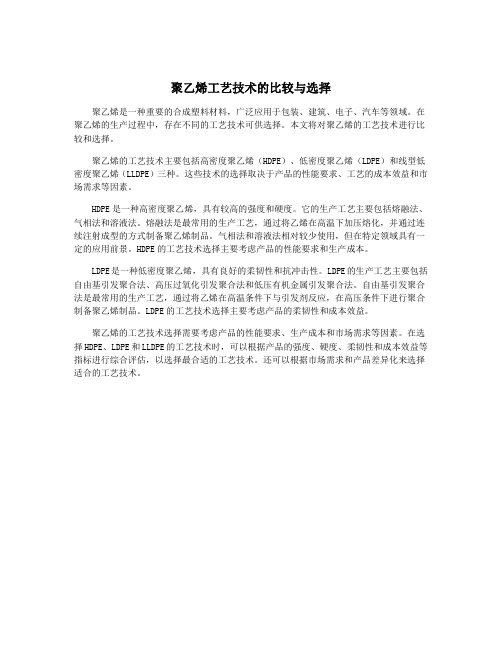
聚乙烯工艺技术的比较与选择
聚乙烯是一种重要的合成塑料材料,广泛应用于包装、建筑、电子、汽车等领域。
在聚乙烯的生产过程中,存在不同的工艺技术可供选择。
本文将对聚乙烯的工艺技术进行比较和选择。
聚乙烯的工艺技术主要包括高密度聚乙烯(HDPE)、低密度聚乙烯(LDPE)和线型低密度聚乙烯(LLDPE)三种。
这些技术的选择取决于产品的性能要求、工艺的成本效益和市场需求等因素。
HDPE是一种高密度聚乙烯,具有较高的强度和硬度。
它的生产工艺主要包括熔融法、气相法和溶液法。
熔融法是最常用的生产工艺,通过将乙烯在高温下加压熔化,并通过连续注射成型的方式制备聚乙烯制品。
气相法和溶液法相对较少使用,但在特定领域具有一定的应用前景。
HDPE的工艺技术选择主要考虑产品的性能要求和生产成本。
LDPE是一种低密度聚乙烯,具有良好的柔韧性和抗冲击性。
LDPE的生产工艺主要包括自由基引发聚合法、高压过氧化引发聚合法和低压有机金属引发聚合法。
自由基引发聚合法是最常用的生产工艺,通过将乙烯在高温条件下与引发剂反应,在高压条件下进行聚合制备聚乙烯制品。
LDPE的工艺技术选择主要考虑产品的柔韧性和成本效益。
聚乙烯的工艺技术选择需要考虑产品的性能要求、生产成本和市场需求等因素。
在选择HDPE、LDPE和LLDPE的工艺技术时,可以根据产品的强度、硬度、柔韧性和成本效益等指标进行综合评估,以选择最合适的工艺技术。
还可以根据市场需求和产品差异化来选择适合的工艺技术。
聚乙烯工艺技术的比较与选择
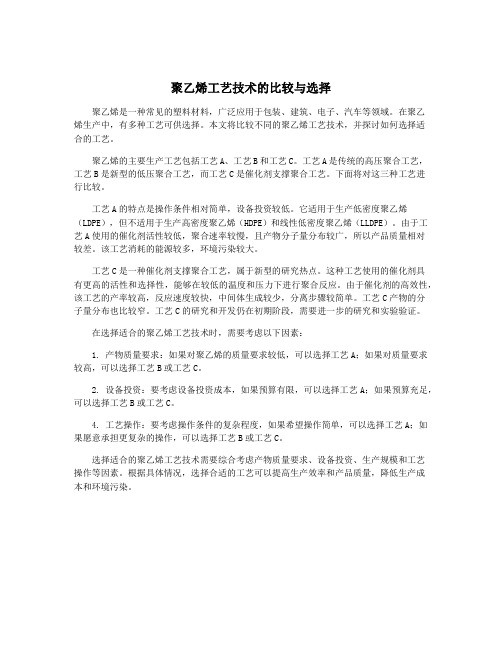
聚乙烯工艺技术的比较与选择聚乙烯是一种常见的塑料材料,广泛应用于包装、建筑、电子、汽车等领域。
在聚乙烯生产中,有多种工艺可供选择。
本文将比较不同的聚乙烯工艺技术,并探讨如何选择适合的工艺。
聚乙烯的主要生产工艺包括工艺A、工艺B和工艺C。
工艺A是传统的高压聚合工艺,工艺B是新型的低压聚合工艺,而工艺C是催化剂支撑聚合工艺。
下面将对这三种工艺进行比较。
工艺A的特点是操作条件相对简单,设备投资较低。
它适用于生产低密度聚乙烯(LDPE),但不适用于生产高密度聚乙烯(HDPE)和线性低密度聚乙烯(LLDPE)。
由于工艺A使用的催化剂活性较低,聚合速率较慢,且产物分子量分布较广,所以产品质量相对较差。
该工艺消耗的能源较多,环境污染较大。
工艺C是一种催化剂支撑聚合工艺,属于新型的研究热点。
这种工艺使用的催化剂具有更高的活性和选择性,能够在较低的温度和压力下进行聚合反应。
由于催化剂的高效性,该工艺的产率较高,反应速度较快,中间体生成较少,分离步骤较简单。
工艺C产物的分子量分布也比较窄。
工艺C的研究和开发仍在初期阶段,需要进一步的研究和实验验证。
在选择适合的聚乙烯工艺技术时,需要考虑以下因素:1. 产物质量要求:如果对聚乙烯的质量要求较低,可以选择工艺A;如果对质量要求较高,可以选择工艺B或工艺C。
2. 设备投资:要考虑设备投资成本,如果预算有限,可以选择工艺A;如果预算充足,可以选择工艺B或工艺C。
4. 工艺操作:要考虑操作条件的复杂程度,如果希望操作简单,可以选择工艺A;如果愿意承担更复杂的操作,可以选择工艺B或工艺C。
选择适合的聚乙烯工艺技术需要综合考虑产物质量要求、设备投资、生产规模和工艺操作等因素。
根据具体情况,选择合适的工艺可以提高生产效率和产品质量,降低生产成本和环境污染。
全国主要聚乙烯装置产能及工艺分布

全国主要聚乙烯装置产能及工艺分布在中国的聚乙烯产能及工艺分布方面,以下是一些重要的主要装置和工艺。
首先,中国的主要聚乙烯装置产能集中在东部沿海地区,特别是华东地区,包括上海、浙江、江苏等地。
这些地区拥有完善的基础设施和供应链网络,以及充足的原材料供应,使得聚乙烯装置的建设和运营更为便捷和高效。
其次,关于聚乙烯的工艺,中国主要采用乙烯在高压或中压条件下聚合的方法。
高压聚乙烯工艺是一种传统的工艺方法,具有简单、成熟和稳定的特点。
目前,中国约有60%的聚乙烯产能采用高压工艺。
中压聚乙烯工艺则是一种相对较新的工艺方法,该工艺具有较低的能耗和较高的产能,逐渐成为中国聚乙烯产能布局的趋势。
预计未来几年,中压聚乙烯产能将继续增加。
此外,中国的聚乙烯产能主要以线性低密度聚乙烯(LLDPE)和高密度聚乙烯(HDPE)为主。
LLDPE具有优异的机械性能和拉伸性能,适合用于薄膜、液体包装等领域;而HDPE具有出色的刚性和热稳定性,适用于制造容器、管道等产品。
至于产能规模,根据最新的数据,中国的聚乙烯总产能已经达到约4000万吨/年。
其中,约3000万吨/年是高压聚乙烯产能,约1000万吨/年是中压聚乙烯产能。
预计未来几年,中国的聚乙烯产能将保持稳定增长的态势。
总的来说,中国的聚乙烯产能主要集中在东部沿海地区,其中华东地区是最主要的聚乙烯生产基地。
聚乙烯的工艺主要以高压和中压聚合为主,其中高压聚乙烯占据绝大部分。
产能规模方面,中国的聚乙烯总产能已经达到4000万吨/年,预计未来仍将保持稳定增长。
世界上主要的11种聚乙烯PE生产技术
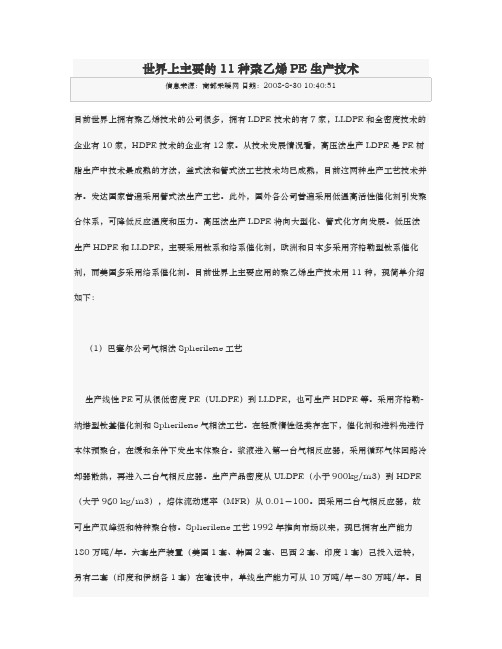
目前世界上拥有聚乙烯技术的公司很多,拥有LDPE技术的有7家,LLDPE和全密度技术的企业有10家,HDPE技术的企业有12家。
从技术发展情况看,高压法生产LDPE是PE树脂生产中技术最成熟的方法,釜式法和管式法工艺技术均已成熟,目前这两种生产工艺技术并存。
发达国家普遍采用管式法生产工艺。
此外,国外各公司普遍采用低温高活性催化剂引发聚合体系,可降低反应温度和压力。
高压法生产LDPE将向大型化、管式化方向发展。
低压法生产HDPE和LLDPE,主要采用钛系和络系催化剂,欧洲和日本多采用齐格勒型钛系催化剂,而美国多采用络系催化剂。
目前世界上主要应用的聚乙烯生产技术用11种,现简单介绍如下:(1)巴塞尔公司气相法Spherilene工艺生产线性PE可从很低密度PE(ULDPE)到LLDPE,也可生产HDPE等。
采用齐格勒-纳塔型钛基催化剂和Spherilene气相法工艺。
在轻质惰性烃类存在下,催化剂和进料先进行本体预聚合,在缓和条件下发生本体聚合。
浆液进入第一台气相反应器,采用循环气体回路冷却器散热,再进入二台气相反应器。
生产产品密度从ULDPE(小于900kg/m3)到HDPE (大于960 kg/m3),熔体流动速率(MFR)从0.01-100。
因采用二台气相反应器,故可生产双峰级和特种聚合物。
Spherilene工艺1992年推向市场以来,现已拥有生产能力180万吨/年。
六套生产装置(美国1套、韩国2套、巴西2套、印度1套)己投入运转,另有二套(印度和伊朗各1套)在建设中,单线生产能力可从10万吨/年-30万吨/年。
目前,中国没有这类技术的生产装置。
(2)北欧化工公司北星(Bastar)工艺北星PE工艺可生产双峰和单峰LLDPE、MDPE(中密度PE)和HDPE。
采用串联的回路、气相低压法反应器。
PE密度为918-970kg/m3,熔融指数0.1-100。
采用Z-N催化剂或SSC(单活性中心)催化剂。
国内乙烯工艺技术简介

脱乙烷
乙烯精馏
脱丙烷
顺序切割式脱丙烷
废碱氧化
低压湿式氧化方法(0.45~0.6MpaG)
四、林德、SW技术附件比较
装置主要消耗量及性能保证指标对比
主要产品收率和单耗比较(P/E=0.5)
工况一
LINDE 乙烯收率% 乙烯原料单耗 丙烯收率% 丙烯原料单耗 混合碳四收率% 混合碳四原料消耗 S&W LINDE
一、乙烯裂解工艺基本概况
装置原理图
裂解气压缩机碱洗
压 缩 NAP 加氢汽油 柴油 其它 乙 烯 装 置 裂 解 炉 深 冷 冷 分
酸性气体 H2
CH4
C2H4 C2H2 C2H6 C3H6 C3H8 MAPD 混合C4 裂解汽油
热 分
急 冷
裂解柴油 裂解重油
加 氢 装 置
C5 C6-C8 C9-200℃
四、林德、SW技术附件比较
工艺技术特点对比-裂解炉部分
专利商 裂解炉型 炉管排列 炉膛数量 辐射炉管长 辐射炉管尺寸 辐射炉管数? 急冷锅炉 炉管联接废锅 形式 裂解物在辐射 管内停留时间 林德(LINDE) PyroCrack1-1型 24-12(2-1) 2个 25米 入口:ID=51mm 出口:ID=73mm 96根 斯通-韦伯斯特(S&W) USC-176U型 U型,一进一出(变径) 2个 23米 入口:ID=45mm 出口:ID=51mm 176根 入口:ID=105mm 出口:ID=110mm 12根 12个双套管式(USX) USC-12M型
乙炔加氢系统
深冷分离
常规深冷分离
四、林德、SW技术附件比较
工艺技术特点对比-压缩分离部分
专利商 脱甲烷塔 林德(LINDE) 塔顶采用内回流方式,塔顶冷凝器、 回流罐与塔结合在一起。有深冷泵。 采用高低压前脱乙烷流程。高压塔顶 料进入碳二加氢,低压塔釜液送至脱 丙烷塔。 乙烯塔和乙烯制冷压缩机形成开始热 泵。没有中间再沸器。乙烯机用户采 用 U 形管釜式换热器。 斯通-韦伯斯特(S&W) 采用双塔脱甲烷技术, 约 40%的混合碳二 不经过脱乙烷塔直接进入乙烯精馏塔。没 有深冷泵。 部分顺序切割乙烷 乙烯塔和乙烯制冷压缩机形成开始热泵。 设有中间再沸器。乙烯机用户采用冷剂罐 与翅片式换热器组合方式。 高、 低压双塔脱丙烷, 约 50%的碳三在高 压塔随碳二以轻馏分进入碳二加氢及深 冷,50%的混合碳三在低压塔进入碳三加 氢。 中压压湿式氧化方法 (0.85~1.0MpaG)
2023年乙烯行业技术特点:石脑油裂解法为主流生产工艺

2023年乙烯行业技术特点:石脑油裂解法为主流生产工艺网讯,乙烯产量的大小可以衡量一个国家石油化工进展水平,我国乙烯产量近些年始终呈现增长的趋势进展,目前产能已经位居全球其次水平。
聚乙烯是乙烯需求消耗最大的。
以下是2023年乙烯行业技术特点。
我国乙烯行业仍处于产不足需状态,但供应状况已经得到极大改善,乙烯当量自给率已经从2022年的不足50%提高到了2022年的接近60%,估计将来自给率会进一步增加。
乙烯行业工艺技术分析乙烯生产工艺分为石油路线和非石油路线,以中石化CBL(北方炉)乙烯裂解技术的中国裂解技术不断进步,技术水平与国外先进裂解技术相比已相差甚微。
煤经甲醇制烯烃工艺具有较高的经济性,受中国多煤少油的资源分布影响,该工艺在中国得到广泛关注并快速进展。
此外,因乙烷裂解路线成本优势明显,且原料供应相对稳定。
乙烯生产工艺路线走向多元化。
在中国能源禀赋为“富煤、贫油、少气”的背景下,中国走出了独具特色的CTO/MTO乙烯路线,并成为现代煤化工的六大路线之一。
乙烯行业技术特点有关数据显示2022年,石脑油裂解法仍是中国生产乙烯的主流生产工艺,占比达73.95%,其次是CTO/MTO工艺,占比20.87%。
乙烯市场国有企业占据主要地位乙烯行业技术特点有关资料显示2022年,乙烯需求连续保持增长,乙烯表观消费量2349.16万吨,同比增长4.5%,当量消费量达到6450万吨,同比增长6.6%。
国内加大进口乙烯下游产品替代力度,进口增速放缓,当量自给率同比提高7.5个百分点,达到59%。
中国乙烯行业产能主要来自国有企业。
依据中国乙烯行业技术特点相关数据,2022年,中国石油、中国石化、中国海油等国有企业合计产能占比则从上年的74.9%降至57.1%;民营乙烯产能达873.5万吨/年,占比升至24.8%,同比提高2.4个百分点。
随着浙石化、盛虹炼化、恒力石化等民营大炼化企业加速入局后,“两桶油”市场份额被渐渐蚕食,央企新的扩能方案,势必会引发炼化行业新一轮洗牌。
乙烯的生产工艺流程

乙烯的生产工艺流程一、乙烯的概述乙烯是一种重要的有机化学品,广泛应用于塑料、橡胶、纤维等工业领域。
其化学式为C2H4,是一种无色、易燃气体,具有较强的还原性和不稳定性。
乙烯的生产工艺主要包括石油制乙烯和煤制乙烯两种方式。
二、石油制乙烯1. 原料准备石油制乙烯的原料主要是轻质裂解汽油(LPG)和液化天然气(LNG)。
这些原料需要经过脱硫、脱水等处理后才能用于生产。
2. 裂解反应将经过处理后的原料送入裂解器中进行裂解反应。
通常采用催化剂加热法进行反应。
反应温度一般在500℃左右,压力为0.5~1.5MPa。
反应生成的混合气体经过冷却后进入分离塔。
3. 分离塔分离在分离塔中,将混合气体进行分离,得到乙烯和其他副产物。
由于其他副产物的沸点不同,因此可以通过分馏的方式将其分离出来。
4. 纯化得到的乙烯需要进行纯化处理,以去除杂质和不纯物。
通常采用冷却凝固法进行纯化。
将乙烯冷却至-100℃左右,使其凝固后去除杂质和不纯物。
5. 储存经过纯化处理后的乙烯需要进行储存。
通常采用压缩气体储罐或液态储罐进行储存。
三、煤制乙烯1. 煤气化煤制乙烯的原料是煤。
首先需要对煤进行气化处理,将其转化为合成气。
合成气主要由一氧化碳、二氧化碳、氢等组成。
2. 合成反应将合成气送入反应器中进行合成反应。
在适当的温度和压力下,合成气会发生一系列反应,生成乙烯等有机物。
3. 分离塔分离与石油制乙烯类似,在分离塔中对混合气体进行分离,得到乙烯和其他副产物。
4. 纯化得到的乙烯需要进行纯化处理,以去除杂质和不纯物。
通常采用冷却凝固法进行纯化。
5. 储存经过纯化处理后的乙烯需要进行储存。
通常采用压缩气体储罐或液态储罐进行储存。
四、总结无论是石油制乙烯还是煤制乙烯,其生产工艺都包括原料准备、裂解反应、分离塔分离、纯化和储存等步骤。
在实际生产中,需要根据不同的原料和设备条件选择合适的工艺流程,并对其进行优化和改进,以提高生产效率和降低成本。
乙烯产能的发展历程

乙烯产能的发展历程乙烯是一种重要的化工原料,广泛应用于塑料、橡胶、纺织、包装等行业。
乙烯产能的发展历程可以追溯到20世纪初,经过近百年的发展,乙烯产能经历了较大的变化和提升。
20世纪初,乙烯的产能非常有限,主要依靠从煤炭、石油等资源中提取乙烯。
当时的乙烯产业还处于起步阶段,生产工艺相对简单,产能规模较小。
随着化工工艺的不断发展和技术的进步,乙烯的产能也逐渐增加。
到20世纪60年代,乙烯的生产工艺发生了重大变革,石油裂解法取代了传统的煤炭裂解法,大大提高了乙烯的产能。
同时,乙烯的生产规模也逐渐扩大,进入了工业化生产阶段。
20世纪70年代至80年代,乙烯的产能进一步提升。
在这一时期,乙烯的生产技术不断创新,新型催化剂的应用使得乙烯的生产更加高效和稳定。
此外,乙烯的生产工艺也得到了进一步改进和优化,使得乙烯的产能得到了进一步提高。
进入21世纪,随着经济的快速发展和社会需求的增加,乙烯的产能也得到了进一步的提升。
新型的乙烯生产技术不断涌现,例如乙烯裂解技术、乙烯蒸汽重整技术等,使得乙烯的产能不断突破新的纪录。
全球乙烯产能已经达到了数千万吨的规模,其中以中东和亚洲地区为主要生产基地。
中国作为全球最大的乙烯生产和消费国,乙烯的产能也在不断提升。
随着新型石化项目的投产和现有生产设施的升级改造,中国的乙烯产能已经超过了3000万吨。
未来,随着科技的不断进步和新型工艺的应用,乙烯的产能还将继续增加。
同时,环保和可持续发展的要求也将促使乙烯生产向更加清洁和高效的方向发展,以减少对环境的影响。
乙烯产能经过近百年的发展,从最初的小规模生产到如今的数千万吨规模,取得了巨大的进步和发展。
乙烯产能的提升离不开工艺技术的创新和优化,也离不开市场需求的推动。
相信在不久的将来,乙烯产能还将继续增加,并为人们的生活和工业发展提供更多的支持和便利。
干货详述三种乙烯制MMA工艺及未来发展方向
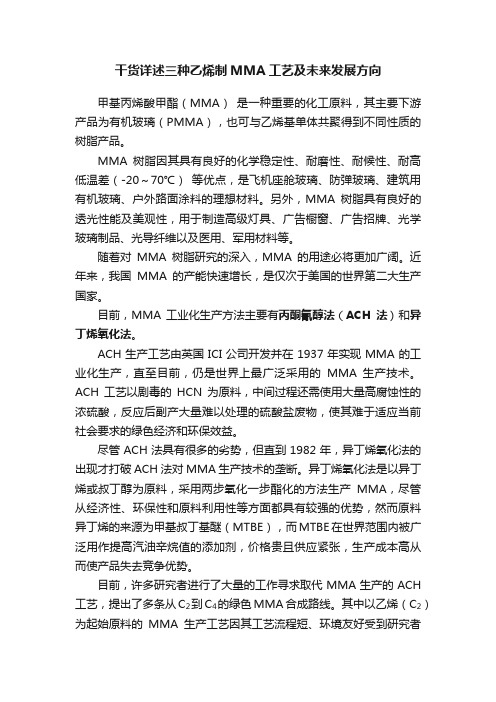
干货详述三种乙烯制MMA工艺及未来发展方向甲基丙烯酸甲酯(MMA)是一种重要的化工原料,其主要下游产品为有机玻璃(PMMA),也可与乙烯基单体共聚得到不同性质的树脂产品。
MMA树脂因其具有良好的化学稳定性、耐磨性、耐候性、耐高低温差(-20~70℃)等优点,是飞机座舱玻璃、防弹玻璃、建筑用有机玻璃、户外路面涂料的理想材料。
另外,MMA树脂具有良好的透光性能及美观性,用于制造高级灯具、广告橱窗、广告招牌、光学玻璃制品、光导纤维以及医用、军用材料等。
随着对MMA树脂研究的深入,MMA的用途必将更加广阔。
近年来,我国MMA的产能快速增长,是仅次于美国的世界第二大生产国家。
目前,MMA工业化生产方法主要有丙酮氰醇法(ACH 法)和异丁烯氧化法。
ACH生产工艺由英国ICI公司开发并在1937年实现MMA的工业化生产,直至目前,仍是世界上最广泛采用的MMA生产技术。
ACH工艺以剧毒的HCN为原料,中间过程还需使用大量高腐蚀性的浓硫酸,反应后副产大量难以处理的硫酸盐废物,使其难于适应当前社会要求的绿色经济和环保效益。
尽管ACH法具有很多的劣势,但直到1982年,异丁烯氧化法的出现才打破ACH法对MMA生产技术的垄断。
异丁烯氧化法是以异丁烯或叔丁醇为原料,采用两步氧化一步酯化的方法生产MMA,尽管从经济性、环保性和原料利用性等方面都具有较强的优势,然而原料异丁烯的来源为甲基叔丁基醚(MTBE),而MTBE在世界范围内被广泛用作提高汽油辛烷值的添加剂,价格贵且供应紧张,生产成本高从而使产品失去竞争优势。
目前,许多研究者进行了大量的工作寻求取代MMA生产的ACH 工艺,提出了多条从C2到C4的绿色MMA合成路线。
其中以乙烯(C2)为起始原料的MMA生产工艺因其工艺流程短、环境友好受到研究者的广泛关注。
另外,原料乙烯、甲醇、CO、甲醛等均可来自煤化工企业,低碳制烯烃、煤制稀烃工艺使烯烃来源更加丰富,这将为C2工艺提供充足的原料。
乙烯的生产工艺流程概述

乙烯的生产工艺流程概述乙烯是一种重要的有机化学品,在化工和塑料工业中具有广泛的应用。
乙烯的生产工艺流程通常包括石油炼制、蒸馏分离、烷烃裂化和乙烯分离等步骤。
本文将概述乙烯的生产工艺流程,介绍每个步骤的基本原理和关键操作。
1. 石油炼制:乙烯的生产通常从石油炼制开始。
石油是一种复杂的混合物,其中包含许多碳氢化合物。
通过石油炼制,可以将石油分离成不同碳数的烃类混合物,其中包括乙烯的前体物质。
2. 蒸馏分离:经过石油炼制得到的原料石油馏分将进行蒸馏分离,目的是将混合物中的乙烯前体物质分离出来。
蒸馏过程中,通过控制温度和压力,使得不同碳数的烃类在不同的蒸馏塔中分离出来。
得到含有乙烯前体物质的馏分。
3. 烷烃裂化:烷烃裂化是乙烯的主要生产方法之一。
在烷烃裂化过程中,乙烯前体物质(如丙烷、丁烷等)被分解成乙烯和其他副产物。
这一过程通常在高温和一定压力下进行,同时使用催化剂增加反应速率。
裂化反应后,产生的混合气体中含有乙烯。
4. 乙烯分离:乙烯分离是为了将乙烯从混合气体中分离出来,以便进一步的处理和应用。
乙烯分离通常采用吸附分离或者膜分离等方法。
其中,吸附分离是将混合气体通过吸附剂,使乙烯被吸附,进而实现分离的过程。
膜分离是利用聚合物膜的分离特性,根据不同化学物质穿过膜的速率不同,从而实现乙烯的分离。
总结回顾:乙烯的生产工艺流程可以从石油炼制开始,经过蒸馏分离、烷烃裂化和乙烯分离等步骤。
石油炼制将石油分离成不同碳数的烃类混合物,蒸馏分离将乙烯前体物质从原料中分离出来,烷烃裂化将乙烯前体物质分解成乙烯和其他副产物,乙烯分离将乙烯从混合气体中分离出来。
这些步骤相互配合,能够高效地生产乙烯。
对于乙烯的生产工艺流程,我认为可以进一步探讨以下几个方面:1. 各个步骤中的工艺条件和操作参数如何影响乙烯的产率和质量?2. 对于乙烯的分离过程,不同的分离方法有哪些优缺点?如何选择最适合的分离方法?3. 在烷烃裂化中产生的副产物有哪些?如何处理和利用这些副产物,以实现资源的高效利用和环境的可持续发展?通过这样的深入探讨,我们可以更全面、深刻地了解乙烯的生产工艺流程,以及相关的技术和环境问题。
乙烯生产工艺

Ⅱ.急冷技术
包括:急冷油塔、急冷水塔、稀释蒸汽发 生系统。
主要作用: ①使裂解气快速降温,防止聚合。 ②回收热量。 ③发生稀释蒸汽。
Ⅲ.压缩技术
包括:压缩机、碱洗、凝液汽提塔、 裂解气干燥
主要作用: ①提高裂解气压力 ②脱除酸性气 ③脱除裂解气中的水分,防止冷区堵塞
裂解气自 急冷水塔 1~3段
2005年乙烯生产能力排在前十位的国家如 下表(万吨):
美国 日本 中国 沙特 德国 韩国 加拿大 荷兰 俄罗斯 法国
2874. 1
730
698. 8
684. 5
556.7
544
541.8
395
367
338.3
我国乙烯增速
独山子石化 乙烯生产装置
兰州石化 乙烯生产装置
乙烯生产工艺
乙烯在石油化工中的地位 乙烯原料 乙烯生产技术 我国乙烯现状
一、乙烯在石油化工中的地位
乙烯是石油化工的“龙头”产品,作为三大合成材 料的基本化工原料,乙烯被称为“石化工业之母” 。
乙烯生产技术是石油化工的核心技术,乙烯装置是 石油化工的核心装置。
乙烯的生产技术、产量、规模标志着一个国家石油 化学工业发展水平。
210℃ 裂解气
原油闪蒸馏分油裂解工艺
原油
闪蒸炉
闪蒸塔
沸腾裂解炉
裂解气
石脑油裂解工艺
原油
闪蒸炉 70℃ 闪蒸塔 820~840℃
沸腾裂解炉 500~600℃ 急冷器 210℃ 裂解气
三、乙烯生产技术
工段:裂解、急冷、压缩、分离
原料预热
裂解炉
工艺蒸汽系统 急冷油/水系统
碱洗系统
裂解气 压缩系统
预冷和干燥
国外高密度聚乙烯生产工艺对比

2511 概述高密度聚乙烯(HDPE)是由德国化学家Karl Ziegler使用锆钛络合催化剂,在低温低压条件下将乙烯聚合成具有较高密度和线型结构的聚乙烯,故高密度聚乙烯也称低压聚乙烯[1]。
HDPE具有较高的强度、硬度和熔点,生产过程的操作危险性较低。
HDPE密度在0.940g/cm 3以上,结晶度高于65%,相较于LDPE和LLDPE,HDPE的拉伸强度最高,耐受强氧化剂的腐蚀,抗冲击性能更优越,防渗防腐性能佳。
世界HDPE主要用于生产薄膜与片材、吹塑制品以及注塑制品等[2]。
2 国外高密度聚乙烯生产工艺HDPE的生产工艺通常分为三种,即气相法工艺、淤浆法工艺和溶液法工艺。
根据聚合反应使用反应器的形式差别,又可分为气相流化床工艺、环管反应器工艺和搅拌釜式反应器工艺。
2.1 气相法工艺气相聚合法也称气相流化床法,具有代表性的生产工艺为UNIPOL PE工艺、Innovene G工艺以及Spherilene工艺。
2.1.1 UNIPOL PE工艺Univation公司是低压气相流化床生产聚乙烯技术的开发者,近年来较重视HDPE产品的开发。
Unipol PE工艺诞生于20世纪70年代末期,目前应用范围十分广泛。
该工艺通过使用单台反应器完成全密度聚乙烯的生产,产品牌号多,最大单线产能可达60万吨/年[1]。
该聚合技术的专利催化剂以固体粉末态或淤浆态的形式注入顶部呈扩大段的立式气相流化床反应器中。
Unipol PE工艺流程可分为三个主要部分:反应系统、上游精制系统和下游加工系统。
该工艺对原料杂质要求高,需对乙烯和共聚单体进行精制,固体/气相分离的设计减少了粉料树脂的夹带,反应循环气无需设置机械分离设备,反应操作条件温和,反应器内无需设置混合器、搅拌器等运转部件,反应器床层内优异的混合效果使得气相组成和温度都较为稳定,但反应器尺寸较大,产品切换时间较长。
Unipol PE工艺因工艺流程短、设备结构相对简单、反应系统转动设备台数少、产品品种范围宽且性能良好、操作安全灵活等优点在全球范围迅速发展,国内采用该技术生产聚乙烯的装置较多。
乙烯法电石法PVC工艺大比拼

乙烯法电石法PVC工艺大比拼乙烯法PVC由于原料来源于石油,产品利润与油价关系密切。
而电石法PVC所用原料及电力均来自国内,一般不会受国际市场冲击,仅取决国内市场情况。
由于前几年国际原油价格的上涨,使得电石法PVC在生产成本上占据明显优势,从而引发了产能的爆发式增长。
2006至2008年,原油价格高企,乙烯价格达到1400美元/吨以上,而电石价格持续徘徊在2500元/吨左右,当时电石法PVC的生产成本比乙烯法低2000元/吨以上。
乙烯法成本的主要因素有乙烯消耗量、氯气消耗、耗电量、加工助剂、管理人工费用等,每生产1吨PVC要消耗乙烯0.5吨,消耗氯气0.65吨,两者约占成本的60%左右。
近两年,由于原油价格下跌,乙烯等原料价格一度跌至1000美元/吨以下,而电石价格由于国家节能减排政策的影响,目前上涨到4200元/吨以上,电石法聚氯乙烯赖以生存的成本优势已丧失殆尽,未来电石法PVC行业前景不容乐观。
成本:乙烯法凸显1. 电石法PVC 和乙烯法PVC 生产成本分析电石法成本主要由电石费用、氯化氢费用和水电费构成。
国家标准规定:生产1 吨PVC 消耗电石约为1.45-1.5 吨(一般以1.5 计),消耗氯化氢气体0.75-0.85吨(一般以0.76 计),每吨耗电量约为450-500 度,另有其它项目开支,如包装费、引发剂、分散剂、电费、税费、管理人员费用等因生产厂家和生产规模的不同而不尽相同。
电石法生产成本的经验公式为:生产成本=[(电石成本+氯化氢成本)/0.8+其它费用]*1.17=[(1.5*电石价格+0.76*氯化氢单价)/0.8+其它费用]*1.17;其中大致的成本构成比例为:电石占65-70%,氯化氢占15%,电力占6%,其它制造费用占6%。
电石法一个显著特点是耗电量高,虽然国家标准规定的PVC 生产的每吨耗电量仅为450-500 度,但是生产电石过程中所消耗的电力是很大的,生产1 吨电石大约需消耗3450 度电。
乙烯生产技术和工艺流程介绍
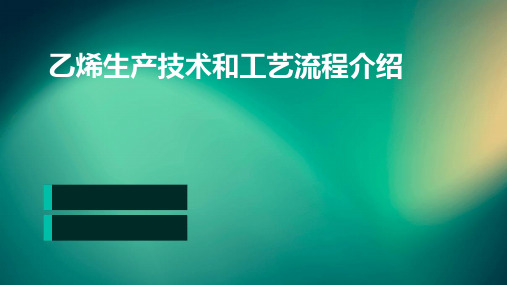
乙烯具有可燃性和麻醉性,常温下易 于聚合,因此需要避免长时间暴露于 空气中。
乙烯生产工艺简介
裂解工艺
01
通过高温裂解石油烃类或天然气等原料,生成含有乙烯的裂解
气。
分离工艺
02
裂解气经过急冷、压缩、深冷分离等步骤,将乙烯从其他气体
中分离出来。
精制工艺
03
对分离得到的乙烯进行进一步精制,以去除杂质和提高纯度。
安全联锁保护
定期安全检查
对关键设备和阀门设置安全联锁保护,避 免误操作导致的事故发生。
定期对装置进行安全检查和维护,确保各项 安全防护措施的有效性。
环保法规遵循及污染治理
废气治理
对裂解炉废气和压缩机尾气进行治理,采用干法 或湿法脱硫、脱硝技术,降低废气中的污染物排 放。
固体废弃物处理
对废催化剂、废保温材料等固体废弃物进行分类 收集和处理,避免对环境造成污染。
往复式压缩机
适用于高压比、小流量的场合,但易损件较多,维护成本较高。
螺杆式压缩机
运转平稳、可靠性高,适用于中等流量和压力范围,但制造成本 较高。
制冷原理及设备配置方案
制冷原理
设备配置方案
通过压缩机将制冷剂压缩成高温高压气体, 然后通过冷凝器将其冷却成高压液体,再通 过节流装置降压降温后进入蒸发器吸收热量, 实现制冷效果。
产品纯度提升措施
优化精馏塔操作条件
调整回流比、塔顶温度等参数,提高产品纯 度。
采用高效分离元件
如高效填料、新型塔板等,提高传质效率。
加强原料气预处理
如脱水、脱硫等,减少杂质对分离效果的影 响。
定期检测和维护设备
确保设备处于良好状态,减少因设备问题导 致的产品纯度下降。
- 1、下载文档前请自行甄别文档内容的完整性,平台不提供额外的编辑、内容补充、找答案等附加服务。
- 2、"仅部分预览"的文档,不可在线预览部分如存在完整性等问题,可反馈申请退款(可完整预览的文档不适用该条件!)。
- 3、如文档侵犯您的权益,请联系客服反馈,我们会尽快为您处理(人工客服工作时间:9:00-18:30)。
3.不同工艺路线乙烯产能构成,不同工艺路线的产品结构和成本差异。
乙烯的工艺路线主要有石脑油裂解制烯烃、乙烷裂解制烯烃、丙烷脱氢制烯烃、煤经甲醇制烯烃及重油催化裂解制烯烃等。
这些工艺各有特点,亚洲及欧洲以石脑油裂解制烯烃为主,中东及北美以乙烷裂解制烯烃为主,煤经甲醇制烯烃是近年来成为热点,主要在中国,重油催化裂解制烯烃产能很小。
2012年不同工艺路线乙烯产能构成见下表。
表 2012年不同工艺路线乙烯产能
不同工艺成本比较
北美地区将是未来全球乙烯产能新的增长点。
页岩气的大规模工业化开发使得北美地区的原料成本明显下降,2012年美国天然气价格甚至一度下跌到2美元/MMBtu以下。
低廉的原料成本使得北美地区成为仅次于中东地区的世界乙烯现金成本最低地区。
经济性比较的基准条件见下表1。
在相同的成本加回报值下,不同工艺路线的原料价格见表2。
从上表可见,当原油价格高于47美元/桶时,内蒙古地区MTO装置经济性东部沿海地区石脑油裂解装置好,但是不如中东地区乙烷裂解装置。
4.现在建和三年内规划建设的乙烯厂家情况
4.1 石脑油及轻烃裂解装置
从未来的发展趋势看,北美地区将是乙烯轻质化的代表。
从最新的资料看,美国页岩气的开发使得美国天然气产量大幅增加,到2011年页岩气产量达到1 800亿立方米,约占美国天然气总产量的25%以上。
按照目前了解的情况看,美国页岩气中C2和C3平均含量为8%~10%,同时优惠的定价策略使得美国页岩气在乙烯生产中极具竞争力。
按照美国页岩气定价原则,分离后的C2和C3产品价格仅为5美元/MMBtu。
正是由于以上原因,2008年后轻烃在美国乙烯原料中的比例不断增加,到2011年这一比例达到95%以上。
未来美国新建的乙烯装置也均以轻烃为原料设计的。
未来许多公司都将在北美地区规划建设乙烯项目,从目前了解的情况看,2012-2015年北美地区的乙烯扩能仍限于扩能改造或脱瓶颈,预计到2015年,包括巴斯夫、陶氏化学、帝斯曼、英力士等公司将对6套装置进行扩能,新增乙烯产能142万吨/年。
美国乙烯主要用于国内消费,其次是出口到中国及欧洲。
按照IHS咨询集团估计,2015年后北美大规模扩建的乙烯项目将逐步竣工,美国新建乙烯项目见下表。
美国新建乙烯项目
中国和中东也是新建乙烯装置的热点地区。
中东乙烯衍生物的90%供出口,主要目标市场是中国。
中国和中东正在建设及即将建设的乙烯装置见下表。
4.2 丙烷脱氢制丙烯
近年来,随着页岩气的发展及丙烯价格的高涨,全球特别是中国掀起了建设丙烷脱氢装置的热潮。
截止到2011年,全球共有约20套丙烷脱氢制丙烯(PDH)生产厂家,总生产能力约为654万吨/年。
全球已经投产的主要丙烷脱氢制丙烯装置见下表。
全球已经投产的主要丙烷脱氢制丙烯装置
由于美国页岩气的发展,美国掀起了新建丙烷脱氢制丙烯装置的热潮。
全球拟建丙烷脱氢装置见下表。
表全球拟建丙烷脱氢装置
在中国,有六套丙烷脱氢装置在建设,合计生产能力为335万吨/年,计划在2013年-2014年开车,至少还有六个丙烷脱氢项目在计划阶段。
中国拟建丙烷脱氢装置见下表。
表中国拟建丙烷脱氢装置
4.3 甲醇制烯烃
由于原油价格波动激烈,煤炭迅速成为聚烯烃及化工品的最佳替代原料。
中国快速发展的聚合物及聚脂工业导致对基础材料的需求激增,例如甲醇、烯烃及乙二醇。
作为对需求增长的响应,2010年中国甲醇行业产量大增。
但是传统产品增长缓慢,例如甲醛及甲酸,由于受到二甲醚增长限制,推动行业转向其它工艺/产品,例如甲醇制烯烃(MTO)、甲醇制丙烯(MTP)及甲醇制芳烃(MTA)。
估计有20多个MTO和MTP项目正处于计划或建设中,总产能达到1000万吨/年。
参与煤基MTO项目的中国公司有宁波禾元、大连福佳、浙江兴兴新能源技术、江苏盛虹集团、正大能源化工及神华宁夏煤炭集团。
此外,乙二醇的供不应求催生了煤制乙二醇(CTMEG)的发展。
有近20个CTMEG项目处于不同的阶段,总产能达到400万吨/年。
但是中国计划控制2015年甲醇总产能不超过5000万吨/年,生产商最多为150家。
中国煤化工业得到政府及跨国公司新一代技术的支持。
受到中国充裕的煤炭供应的吸引,道达尔、塞拉尼斯及陶氏化学等公司正在中国推广其先进技术。
下表提供了中国新项目的一些例子。
2012年90% PVC新增产能及85%甲醇新增产能由煤炭生产。
陶氏化学正在加紧推进煤化工项目,公司已经向中国政府提交了项目申请报告请求审批。
表中国最近的煤化工项目
4.4 重油催化裂解制烯烃
重油催化裂解制烯烃产能很小。
宁波科元塑胶有限公司采用重油催化裂解制烯烃,主要生产苯乙烯及丁苯橡胶等。