售后千辆车故障率的算法模型和应用_IPTV
英文缩写词和概念
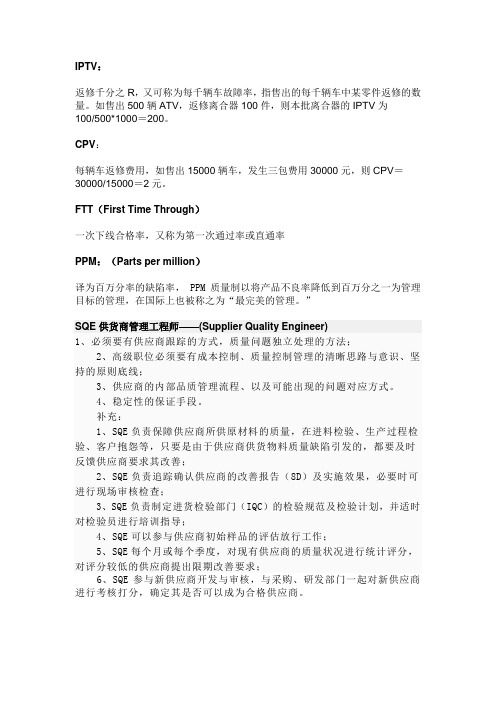
IPTV:
返修千分之R,又可称为每千辆车故障率,指售出的每千辆车中某零件返修的数量。如售出500辆ATV,返修离合器100件,则本批离合器的IPTV为
100/500*1000=200。
CPV:
每辆车返修费用,如售出15000辆车,发生三包费用30000元,则CPV=30000/15000=2元。
FTT(First Time Through)
一次下线合格率,又称为第一次通过率或直通率
PPM:(Parts per million)
译为百万分率的缺陷率, PPM质量制以将产品不良率降低到百万分之一为管理目标的管理,在国际上也被称之为“最完美的管理。”
SQE供货商管理工程师——(Supplier Quality Engineer)
1、必须要有供应商跟踪的方式,质量问题独立处理的方法;
2、高级职位必须要有成本控制、质量控制管理的清晰思路与意识、坚持的原则底线;
3、供应商的内部品质管理流程、以及可能出现的问题对应方式。
4、稳定性的保证手段。
补充:
1、SQE负责保障供应商所供原材料的质量,在进料检验、生产过程检验、客户抱怨等,只要是由于供应商供货物料质量缺陷引发的,都要及时反馈供应商要求其改善;
2、SQE负责追踪确认供应商的改善报告(8D)及实施效果,必要时可进行现场审核检查;
3、SQE负责制定进货检验部门(IQC)的检验规范及检验计划,并适时对检验员进行培训指导;
4、SQE可以参与供应商初始样品的评估放行工作;
5、SQE每个月或每个季度,对现有供应商的质量状况进行统计评分,对评分较低的供应商提出限期改善要求;
汽车故障率计算公式
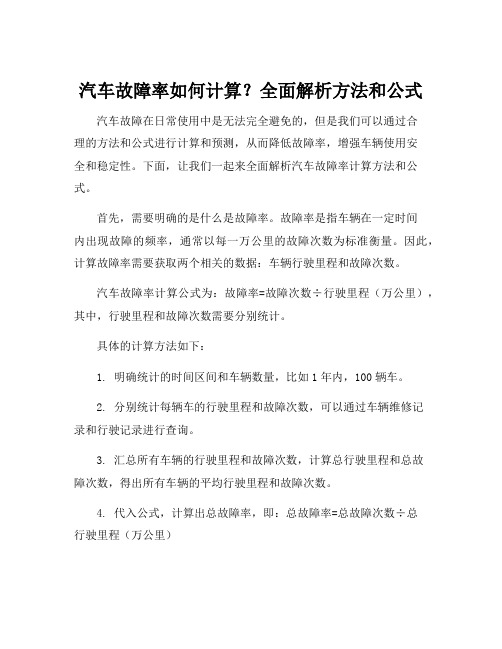
汽车故障率如何计算?全面解析方法和公式汽车故障在日常使用中是无法完全避免的,但是我们可以通过合
理的方法和公式进行计算和预测,从而降低故障率,增强车辆使用安
全和稳定性。下面,让我们一起来全面解析汽车故障率计算方法和公式。
首先,需要明确的是什么是故障率。故障率是指车辆在一定时间
内出现故障的频率,通常以每一万公里的故障次数为标准衡量。因此,计算故障率需要获取两个相关的数据:车辆行驶里程和故障次数。
汽车故障率计算公式为:故障率=故障次数÷行驶里程(万公里),其中,行驶里程和故障次数需要分别统计。
具体的计算方法如下:
1. 明确统计的时间区间和车辆数量,比如1年内,100辆车。
2. 分别统计每辆车的行驶里程和故障次数,可以通过车辆维修记
录和行驶记录进行查询。
3. 汇总所有车辆的行驶里程和故障次数,计算总行驶里程和总故
障次数,得出所有车辆的平均行驶里程和故障次数。
4. 代入公式,计算出总故障率,即:总故障率=总故障次数÷总
行驶里程(万公里)
经过计算,我们可以得出车辆的故障率,并作为参考数据和依据,进行维护和保养的决策。
除此之外,还可以通过比较不同车型、不同年份、不同工况等条
件下的故障率差异,分析并得出有效的故障预测和改进措施。
总之,科学的汽车故障率计算方法和公式,可以帮助我们更好的
掌握车辆安全运行的状态,提高维护和管理效率,减少故障和事故发
生的风险和损失。
上海通用常用术语
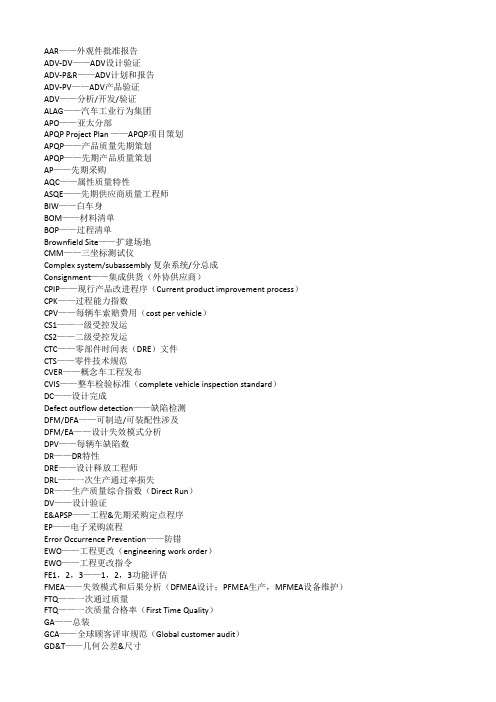
SQ——供应商质量 SSF——系统填充开始 SSTS——分系统技术规范 Sub contactor——分供方 Sub-Assembly/Sub-System SVER——结构车工程车 SVE——子系统验证工程师 Team feasibility commitment——小组可行性承诺 TKO——模具启动会议 UG——UG工程绘图造型系统 VAP——每辆车开发过程 VLE——车辆平台负责人 VTC——验证试验完成 WDPV——平均每辆车不符合项与权重乘积的综合(平均每辆车扣分值)weighted discrepancies per vehicle WO——工程工作质量 WWP——全球采购
MVBns(原NS)——非销售车制造验证 MVBs(原S)——销售车制造验证 N.O.D——决议通知 NAO——北美分部 NBH——停止新业务 OEM——主机客户 OTS——外购国产化零部件和/或系统工程认可程序 PAA——生产行动授权(Production action authorization) PAD——生产装配文件 PC&L——生产控制&物流 PCR——问题交流报告(Problem Communication Report) PDI——发运前检查(pre-delivery inspection)、 PDT——产品开发小组 PFMEA——过程失效模式和后果分析 PPAP——生产件批准程序 PPAP——生产件审批 PPK——过程能力指数 PPM——1)项目经理;2)每白万件的产品缺陷数 PPV——产品及过程验证 PQC——产品质量特性 PR/R——问题报告及解决 Pre-Production——预生产 PRR——问题报告和解决(problem report and resolution PRR——问题交流与解决程序(Problem resolution report) PSA——潜在供应商评审 PTR——零部件试生产 PTR——生产试运行(Production trial run) PVV——Trgout QSA——质量体系评审 QSB——质量体系基础、 QTC——工装报价能力 R&R——按节拍生产 RASIC——负责,批准,支持,通知,讨论 RFQ——报价要求 RPN reduction plan——降低RPN值计划 RPN——风险顺序数 S&R——车辆行驶时摩擦、振动噪音,泛指异响(Squeak&Rattle) S.T.E.P——采购定点小组评估过程 SDE——供应商开发工程师 SFMEA——系统失效模式分析 SIL——单一问题清单(Single issues list) SMT——系统管理小组 SOA——加速开始 SOR——(供应商质量)要求声明 SORP——正式生产 SOS——标准作业单(Standardized operation sheets) SPA——发运前检查(Shipping priority aduit) SPC——统计过程控制 SPO——(通用汽车)零件与服务分部 SQE——供应商质量工程师 SQIP——供应商质量改进过程
上海通用常用术语
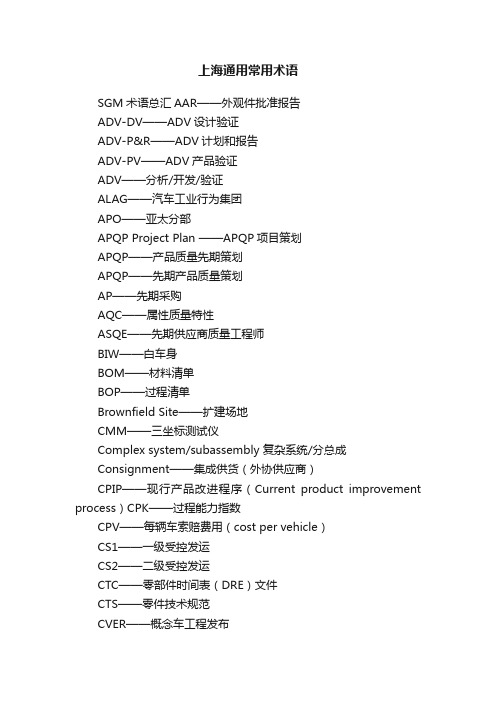
上海通用常用术语
SGM术语总汇AAR——外观件批准报告
ADV-DV——ADV设计验证
ADV-P&R——ADV计划和报告
ADV-PV——ADV产品验证
ADV——分析/开发/验证
ALAG——汽车工业行为集团
APO——亚太分部
APQP Project Plan ——APQP项目策划
APQP——产品质量先期策划
APQP——先期产品质量策划
AP——先期采购
AQC——属性质量特性
ASQE——先期供应商质量工程师
BIW——白车身
BOM——材料清单
BOP——过程清单
Brownfield Site——扩建场地
CMM——三坐标测试仪
Complex system/subassembly 复杂系统/分总成
Consignment——集成供货(外协供应商)
CPIP——现行产品改进程序(Current product improvement process)CPK——过程能力指数
CPV——每辆车索赔费用(cost per vehicle)
CS1——一级受控发运
CS2——二级受控发运
CTC——零部件时间表(DRE)文件
CTS——零件技术规范
CVER——概念车工程发布
CVIS——整车检验标准(complete vehicle inspection standard)
DC——设计完成
Defect outflow detection——缺陷检测
DFM/DFA——可制造/可装配性涉及
DFM/EA——设计失效模式分析
DPV——每辆车缺陷数
DR——DR特性
DRE——设计释放工程师
DRL——一次生产通过率损失
DR——生产质量综合指数(Direct Run)
IPTV计算方法.doc
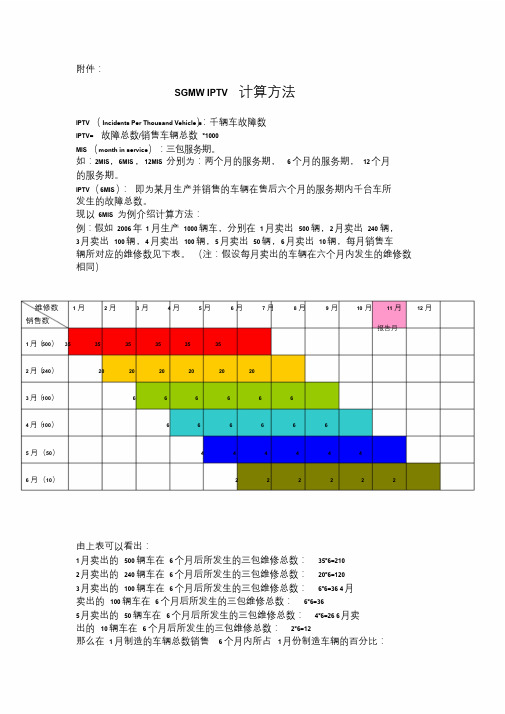
附件:
SGMW IPTV 计算方法
IPTV (Incidents Per Thousand Vehicle)s:千辆车故障数
IPTV= 故障总数/销售车辆总数*1000
MIS (month in service):三包服务期。
如:2MIS,6MIS ,12MIS 分别为:两个月的服务期, 6 个月的服务期,12 个月
的服务期。
IPTV(6MIS ):即为某月生产并销售的车辆在售后六个月的服务期内千台车所
发生的故障总数。
现以6MIS 为例介绍计算方法:
例:假如2006年1 月生产1000 辆车,分别在1 月卖出500辆,2 月卖出240 辆,
3 月卖出100辆,
4 月卖出100辆,
5 月卖出50 辆,
6 月卖出10 辆,每月销售车
辆所对应的维修数见下表。(注:假设每月卖出的车辆在六个月内发生的维修数
相同)
维修数 1 月 2 月 3 月 4 月 5 月 6 月7 月8 月9 月10 月11 月12 月销售数
报告月
1 月(500)35 35 35 35 35 35
2 月(240)20 20 20 20 20 20
3 月(100) 6 6 6 6 6 6
4 月(100) 6 6 6 6 6 6
5 月(50) 4 4 4 4 4 4
6 月(10) 2 2 2 2 2 2
由上表可以看出:
1 月卖出的500辆车在6 个月后所发生的三包维修总数:35*6=210
2 月卖出的240辆车在6 个月后所发生的三包维修总数:20*6=120
3 月卖出的100辆车在6 个月后所发生的三包维修总数:6*6=36
上海通用常用术语
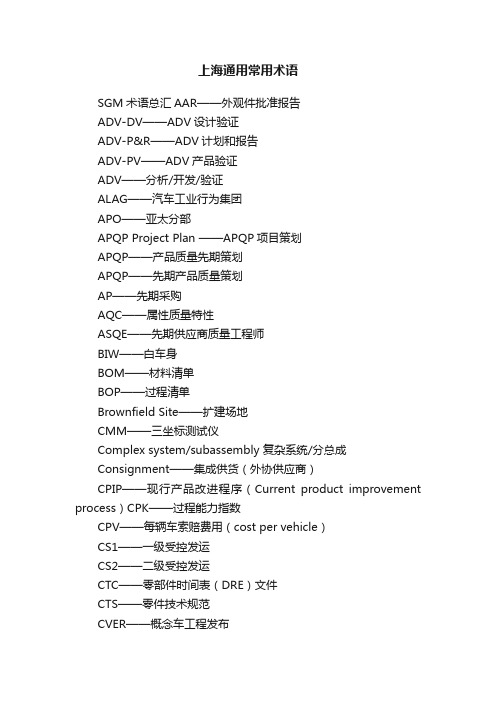
上海通用常用术语
SGM术语总汇AAR——外观件批准报告
ADV-DV——ADV设计验证
ADV-P&R——ADV计划和报告
ADV-PV——ADV产品验证
ADV——分析/开发/验证
ALAG——汽车工业行为集团
APO——亚太分部
APQP Project Plan ——APQP项目策划
APQP——产品质量先期策划
APQP——先期产品质量策划
AP——先期采购
AQC——属性质量特性
ASQE——先期供应商质量工程师
BIW——白车身
BOM——材料清单
BOP——过程清单
Brownfield Site——扩建场地
CMM——三坐标测试仪
Complex system/subassembly 复杂系统/分总成
Consignment——集成供货(外协供应商)
CPIP——现行产品改进程序(Current product improvement process)CPK——过程能力指数
CPV——每辆车索赔费用(cost per vehicle)
CS1——一级受控发运
CS2——二级受控发运
CTC——零部件时间表(DRE)文件
CTS——零件技术规范
CVER——概念车工程发布
CVIS——整车检验标准(complete vehicle inspection standard)
DC——设计完成
Defect outflow detection——缺陷检测
DFM/DFA——可制造/可装配性涉及
DFM/EA——设计失效模式分析
DPV——每辆车缺陷数
DR——DR特性
DRE——设计释放工程师
DRL——一次生产通过率损失
DR——生产质量综合指数(Direct Run)
IPTV计算方法
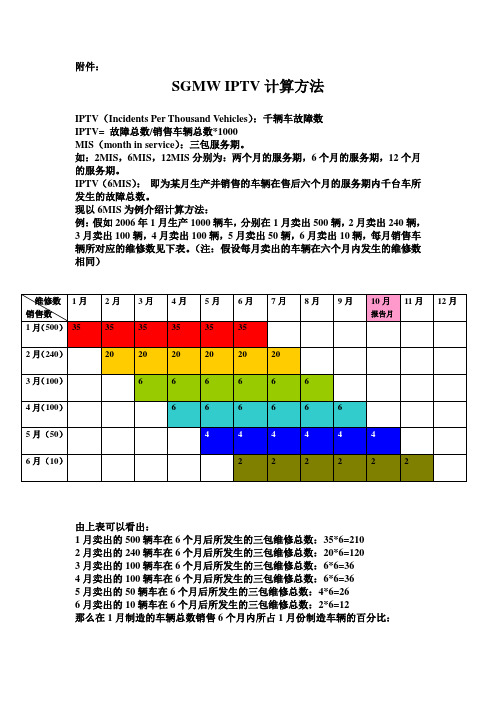
附件:
SGMW IPTV计算方法
IPTV(Incidents Per Thousand Vehicles):千辆车故障数
IPTV= 故障总数/销售车辆总数*1000
MIS(month in service):三包服务期。
如:2MIS,6MIS,12MIS分别为:两个月的服务期,6个月的服务期,12个月的服务期。
IPTV(6MIS):即为某月生产并销售的车辆在售后六个月的服务期内千台车所发生的故障总数。
现以6MIS为例介绍计算方法:
例:假如2006年1月生产1000辆车,分别在1月卖出500辆,2月卖出240辆,3月卖出100辆,4月卖出100辆,5月卖出50辆,6月卖出10辆,每月销售车辆所对应的维修数见下表。(注:假设每月卖出的车辆在六个月内发生的维修数相同)
由上表可以看出:
1月卖出的500辆车在6个月后所发生的三包维修总数:35*6=210
2月卖出的240辆车在6个月后所发生的三包维修总数:20*6=120
3月卖出的100辆车在6个月后所发生的三包维修总数:6*6=36
4月卖出的100辆车在6个月后所发生的三包维修总数:6*6=36
5月卖出的50辆车在6个月后所发生的三包维修总数:4*6=26
6月卖出的10辆车在6个月后所发生的三包维修总数:2*6=12
那么在1月制造的车辆总数销售6个月内所占1月份制造车辆的百分比:
那么在1月份制造的车辆在销售6个月后的故障总数:
那么我们在计算IPTV 6MIS 时取值到9月份底,那么我们10月初得出报告: (我们的计算忽略了最后两个月的索赔数,而实际的IPTV 值取值到11月底,这相当于我们的计算值低于实际值)
千车故障率模型

修正千车故障数
=
保修总次数 ×1000 迄今已售出的轿车总数 − 2004年3月对于0201批次的月销售量
3
C 题-李根,邓文平,唐小妹-一等奖
对于上式,各批次的月销售量附表一并未给出,根据假设 3 可以得到,该批 次在 26 个月的每个月销售量相等,都是 2457 ,因而可以进一步计算得到修正后
净故障发生数
使用月数
生产月份
1
...
当前月-出厂月
×
×
×. . . ×
ຫໍສະໝຸດ Baidu
×
(注:其中的第 i 个月的故障数表示的为,使用了 i 个月时发生故障的车数)
根据表 4.1 和表 4.2 的数据,可以准确简单的得出我们所需要的差分千车故 障数,具体的计算方法:
使用了第i个月的千车故障数
=
使用了第i个月的净故障发生数 i个月前的销售量之和
月千车故障数 生产月份
×
表 4.3
1 ×
先通过对表内数据的纵向最小二乘拟和与横向卡尔曼(Kalman)滤波方法的 联合预测对表格中的空表项进行预测,然后由完整的数据表得出 X -11的同一预 测模型。对模型进行检验,抽取原始数据报中已经存在的多个千车故障数,发现 预测值与原值能够很好地吻合。经计算得到,0205 批次使用月数 18 时的千车故 障数为 49.00;0306 批次使用月数 9 时的千车故障数 7.28;0310 批次使用月数 12 时的千车故障数 3.23。
上海通用常用术语

AAR——外观件批准报告
ADV-DV——ADV设计验证
ADV-P&R——ADV计划和报告
ADV-PV——ADV产品验证
ADV——分析/开发/验证
ALAG——汽车工业行为集团
APO——亚太分部
APQP Project Plan ——APQP项目策划
APQP——产品质量先期策划
APQP——先期产品质量策划
AP——先期采购
AQC——属性质量特性
ASQE——先期供应商质量工程师
BIW——白车身
BOM——材料清单
BOP——过程清单
Brownfield Site——扩建场地
CMM——三坐标测试仪
Complex system/subassembly 复杂系统/分总成
Consignment——集成供货(外协供应商)
CPIP——现行产品改进程序(Current product improvement process)CPK——过程能力指数
CPV——每辆车索赔费用(cost per vehicle)
CS1——一级受控发运
CS2——二级受控发运
CTC——零部件时间表(DRE)文件
CTS——零件技术规范
CVER——概念车工程发布
CVIS——整车检验标准(complete vehicle inspection standard)
DC——设计完成
Defect outflow detection——缺陷检测
DFM/DFA——可制造/可装配性涉及
DFM/EA——设计失效模式分析
DPV——每辆车缺陷数
DR——DR特性
DRE——设计释放工程师
DRL——一次生产通过率损失
DR——生产质量综合指数(Direct Run)
汽车故障率计算公式
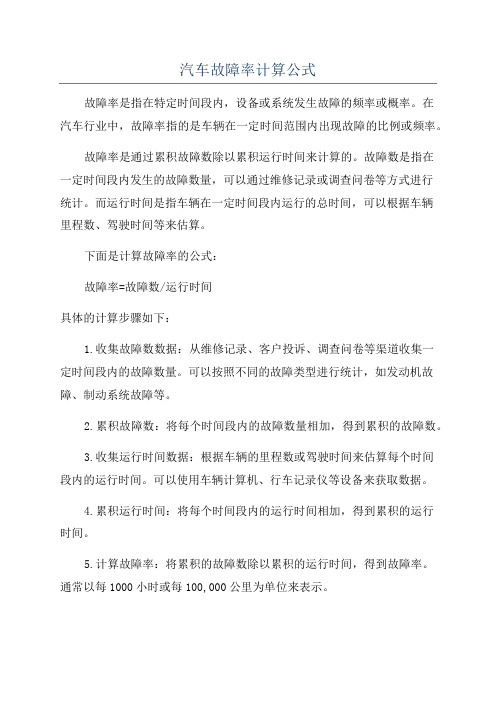
汽车故障率计算公式
故障率是指在特定时间段内,设备或系统发生故障的频率或概率。在
汽车行业中,故障率指的是车辆在一定时间范围内出现故障的比例或频率。
故障率是通过累积故障数除以累积运行时间来计算的。故障数是指在
一定时间段内发生的故障数量,可以通过维修记录或调查问卷等方式进行
统计。而运行时间是指车辆在一定时间段内运行的总时间,可以根据车辆
里程数、驾驶时间等来估算。
下面是计算故障率的公式:
故障率=故障数/运行时间
具体的计算步骤如下:
1.收集故障数数据:从维修记录、客户投诉、调查问卷等渠道收集一
定时间段内的故障数量。可以按照不同的故障类型进行统计,如发动机故障、制动系统故障等。
2.累积故障数:将每个时间段内的故障数量相加,得到累积的故障数。
3.收集运行时间数据:根据车辆的里程数或驾驶时间来估算每个时间
段内的运行时间。可以使用车辆计算机、行车记录仪等设备来获取数据。
4.累积运行时间:将每个时间段内的运行时间相加,得到累积的运行
时间。
5.计算故障率:将累积的故障数除以累积的运行时间,得到故障率。
通常以每1000小时或每100,000公里为单位来表示。
总结起来,汽车故障率的计算公式可以通过累积故障数除以累积运行时间来得到。通过统计和分析故障数据,可以帮助汽车制造商和维修服务提供商评估车辆的可靠性和性能,为用户提供更好的服务和产品。
上海通用常用术语
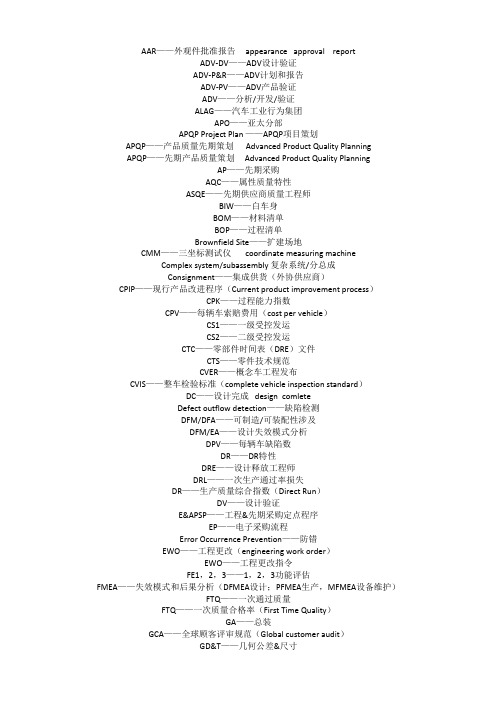
AAR——外观件批准报告 appearance approval report
ADV-DV——ADV设计验证
ADV-P&R——ADV计划和报告
ADV-PV——ADV产品验证
ADV——分析/开发/验证
ALAG——汽车工业行为集团
APO——亚太分部
APQP Project Plan ——APQP项目策划
APQP——产品质量先期策划 Advanced Product Quality Planning
APQP——先期产品质量策划 Advanced Product Quality Planning
AP——先期采购
AQC——属性质量特性
ASQE——先期供应商质量工程师
BIW——白车身
BOM——材料清单
BOP——过程清单
Brownfield Site——扩建场地
CMM——三坐标测试仪 coordinate measuring machine
Complex system/subassembly 复杂系统/分总成
Consignment——集成供货(外协供应商)
CPIP——现行产品改进程序(Current product improvement process)
CPK——过程能力指数
CPV——每辆车索赔费用(cost per vehicle)
CS1——一级受控发运
CS2——二级受控发运
CTC——零部件时间表(DRE)文件
CTS——零件技术规范
CVER——概念车工程发布
CVIS——整车检验标准(complete vehicle inspection standard)
DC——设计完成 design comlete
IPTV
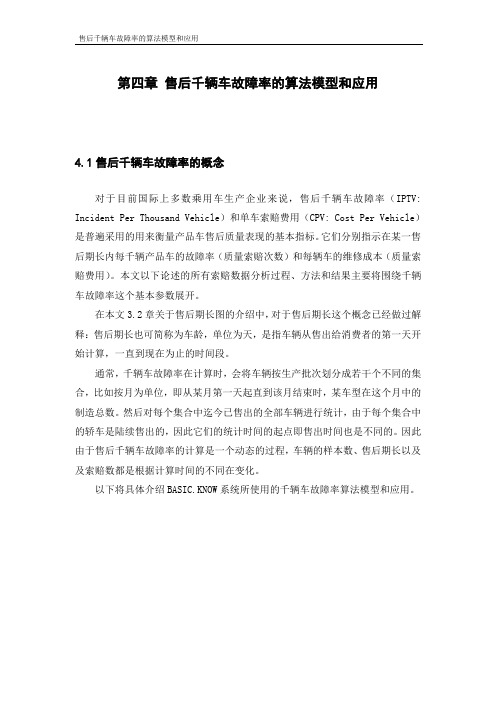
第四章售后千辆车故障率的算法模型和应用
4.1售后千辆车故障率的概念
对于目前国际上多数乘用车生产企业来说,售后千辆车故障率(IPTV: Incident Per Thousand Vehicle)和单车索赔费用(CPV: Cost Per Vehicle)是普遍采用的用来衡量产品车售后质量表现的基本指标。它们分别指示在某一售后期长内每千辆产品车的故障率(质量索赔次数)和每辆车的维修成本(质量索赔费用)。本文以下论述的所有索赔数据分析过程、方法和结果主要将围绕千辆车故障率这个基本参数展开。
在本文3.2章关于售后期长图的介绍中,对于售后期长这个概念已经做过解释:售后期长也可简称为车龄,单位为天,是指车辆从售出给消费者的第一天开始计算,一直到现在为止的时间段。
通常,千辆车故障率在计算时,会将车辆按生产批次划分成若干个不同的集合,比如按月为单位,即从某月第一天起直到该月结束时,某车型在这个月中的制造总数。然后对每个集合中迄今已售出的全部车辆进行统计,由于每个集合中的轿车是陆续售出的,因此它们的统计时间的起点即售出时间也是不同的。因此由于售后千辆车故障率的计算是一个动态的过程,车辆的样本数、售后期长以及及索赔数都是根据计算时间的不同在变化。
以下将具体介绍BASIC.KNOW系统所使用的千辆车故障率算法模型和应用。
4.2售后千辆车故障率的计算方法
4.2.1 非校准法(Unadjusted )
图16 非校准法图示
Fig.16 Unadjusted arithmetic illustration
非校准法算法条件: 1. 取所有车辆样本;
汽车故障率计算公式
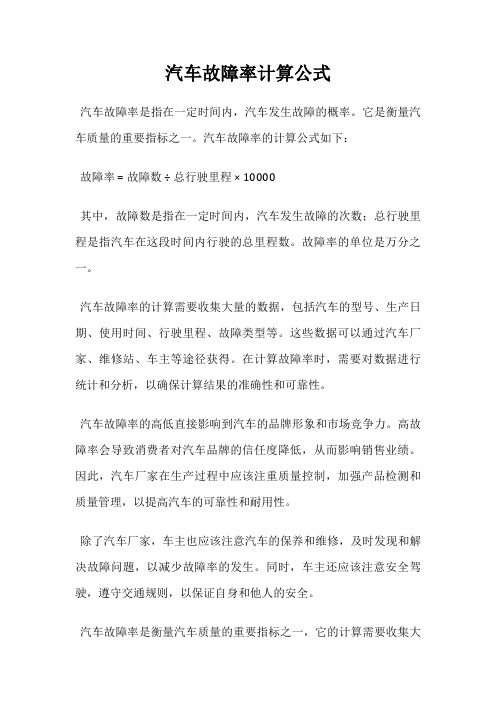
汽车故障率计算公式
汽车故障率是指在一定时间内,汽车发生故障的概率。它是衡量汽车质量的重要指标之一。汽车故障率的计算公式如下:
故障率 = 故障数 ÷ 总行驶里程 × 10000
其中,故障数是指在一定时间内,汽车发生故障的次数;总行驶里程是指汽车在这段时间内行驶的总里程数。故障率的单位是万分之一。
汽车故障率的计算需要收集大量的数据,包括汽车的型号、生产日期、使用时间、行驶里程、故障类型等。这些数据可以通过汽车厂家、维修站、车主等途径获得。在计算故障率时,需要对数据进行统计和分析,以确保计算结果的准确性和可靠性。
汽车故障率的高低直接影响到汽车的品牌形象和市场竞争力。高故障率会导致消费者对汽车品牌的信任度降低,从而影响销售业绩。因此,汽车厂家在生产过程中应该注重质量控制,加强产品检测和质量管理,以提高汽车的可靠性和耐用性。
除了汽车厂家,车主也应该注意汽车的保养和维修,及时发现和解决故障问题,以减少故障率的发生。同时,车主还应该注意安全驾驶,遵守交通规则,以保证自身和他人的安全。
汽车故障率是衡量汽车质量的重要指标之一,它的计算需要收集大
量的数据,并进行统计和分析。汽车厂家和车主都应该注重汽车的质量和安全,以提高汽车的可靠性和耐用性。
汽车行业术语大全
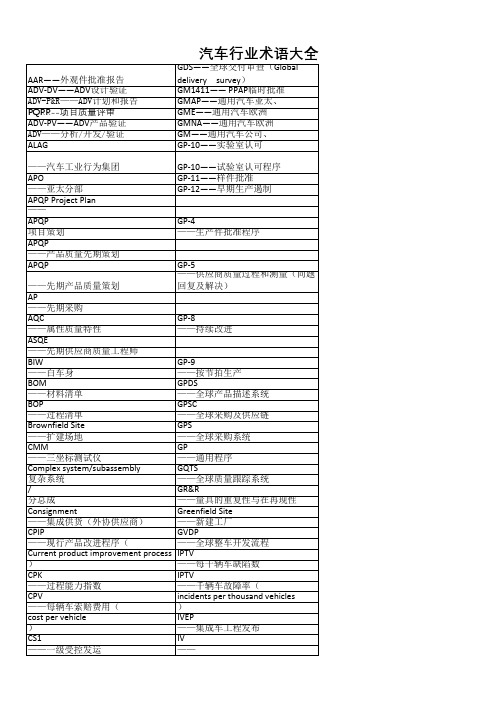
大全
MVBns(原NS)——非销售车制造验证 MVBs(原S)——销售车制造验证 N.O.D——决议通知 NAO——北美分部 NBH——停止新业务 OEM——主机客户 OTS——手工样件 PAA——生产行动授权Production action
authorization
SVER ——结构车工程车 SVE ——子系统验证工程师 Team feasibility commitment ——小组可行性承诺 TKO ——模具启动会议
GD&T ——几何公差
& 尺寸
——供应商质量改进过程 SQ ——供应商质量 SSF ——系统填充开始 SSTS ——分系统技术规范 Sub contactor ——分供方 Sub-Assembly/Sub-System
VLE ——车辆平台负责人 VTC ——验证试验完成 WDPV ——平均每辆车不符合项与权重乘 积的综合(平均每辆车扣分值) weighted discrepancies per vehicle WO ——工程工作质量 WWP ——全球采购
——防错 EWO ——工程更改( engineering work order )
EWO ——工程更改指令
OTS JIS ——作业指导书(
Job instruction sheets )
KCC ——关键控制特性
KCDS ——关键特性指示系统
Warranty
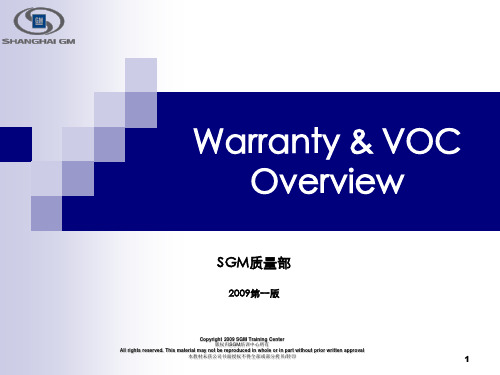
脱离使用时间(Exposure, 或称Age)谈Warranty指标没有意义!
若某车型60天IPTV为100,属于较差的表现; 但若360天IPTV为100,则是非常好的表现。
Copyright 2009 SGM Training Center 版权归SGM培训中心所有 All rights reserved. This material may not be reproduced in whole or in part without prior written approval 本教材未获公司书面授权不得全部或部分拷贝/转印
7
定义
即售后保修,指在一定使用时间和里程数内,属于保修范围的零 部件在客户正常使用的情况下出现问题,可以到4S店进行免费维 修或更换(索赔)
轮胎、雨刮片、皮带、 灯泡、刹车片、机油等 易损件不在保修范围内
有条件的 免费!
Copyright 2009 SGM Training Center 版权归SGM培训中心所有 All rights reserved. This material may not be reproduced in whole or in part without prior written approval 本教材未获公司书面授权不得全部或部分拷贝/转印