铬酸检测钢铁磷化膜重的方法
重铬酸钾外加热滴定法

重铬酸钾外加热滴定法重铬酸钾外加热滴定法,是一种常用的化学检测方法。
本文将从以下几个方面进行讲解。
一、实验原理重铬酸钾外加热滴定法是通过滴定重铬酸钾溶液来测定样品中可滴定物质的含量。
具体实验原理如下:将待测样品溶解于水中,然后加入过量的硝酸银溶液反应,产生氯化银沉淀,并将剩余的硝酸银滴定。
之后,将滴过硝酸银的溶液与硝酸钾和硫酸混合加热,使其产生的硝酸还原为氮气,并把氯化银溶解为氯离子。
然后再滴定产生的氯离子,直到硝酸银完全被滴定为止。
根据滴定所用的重铬酸钾溶液的体积和浓度,就能够计算出待测样品中可滴定物质的含量。
二、实验流程1.将待测样品溶解在少量水中,加入过量的硝酸银溶液反应,产生氯化银沉淀。
2.将剩下的硝酸银滴定,得出滴定的初值。
3.将滴过硝酸银的溶液与硝酸钾和硫酸混合加热,使其产生的硝酸还原为氮气,并把氯化银溶解为氯离子。
4.再滴定产生的氯离子,直到硝酸银完全被滴定为止。
5.根据滴定所用的重铬酸钾溶液的体积和浓度,计算出待测样品中可滴定物质的含量。
三、实验注意事项1.样品溶解应尽可能彻底,以免影响后续的滴定结果。
2.硝酸银应用非金属容器保存,避免与其他物质反应。
3.在钛合金或石英反应器中加热反应液,避免产生金属离子影响滴定结果。
4.实验操作应仔细、安全,确保使用合适的防护设备。
四、实验应用重铬酸钾外加热滴定法广泛应用于环境监测、食品卫生、医药、冶金等领域。
例如,可以用来测定环境中重金属物质的含量,确定食品中的营养成分含量等。
总之,重铬酸钾外加热滴定法是一种简单、准确、广泛应用的化学检测方法,具有重要的现实应用价值。
在进行实验时,需要严格按照实验流程和注意事项操作,以确保实验结果准确、可靠。
磷化膜的缺陷及解决办法
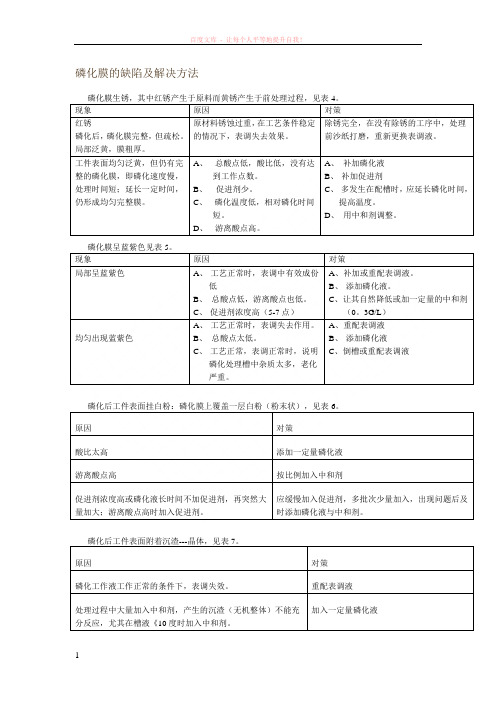
磷化膜的缺陷及解决方法磷化膜生锈,其中红锈产生于原料而黄锈产生于前处理过程,见表4。
现象原因对策红锈磷化后,磷化膜完整,但疏松。
局部泛黄,膜粗厚。
原材料锈蚀过重,在工艺条件稳定的情况下,表调失去效果。
除锈完全,在没有除锈的工序中,处理前沙纸打磨,重新更换表调液。
工件表面均匀泛黄,但仍有完整的磷化膜,即磷化速度慢,处理时间短;延长一定时间,仍形成均匀完整膜。
A、总酸点低,酸比低,没有达到工作点数。
B、促进剂少。
C、磷化温度低,相对磷化时间短。
D、游离酸点高。
A、补加磷化液B、补加促进剂C、多发生在配槽时,应延长磷化时间,提高温度。
D、用中和剂调整。
磷化膜呈蓝紫色见表5。
现象原因对策局部呈蓝紫色A、工艺正常时,表调中有效成份低B、总酸点低,游离酸点也低。
C、促进剂浓度高(5-7点)A、补加或重配表调液。
B、添加磷化液。
C、让其自然降低或加一定量的中和剂(0。
3G/L)均匀出现蓝紫色A、工艺正常时,表调失去作用。
B、总酸点太低。
C、工艺正常,表调正常时,说明磷化处理槽中杂质太多,老化严重。
A、重配表调液B、添加磷化液C、倒槽或重配表调液磷化后工件表面挂白粉:磷化膜上覆盖一层白粉(粉末状),见表6。
原因对策酸比太高添加一定量磷化液游离酸点高按比例加入中和剂促进剂浓度高或磷化液长时间不加促进剂,再突然大量加大;游离酸点高时加入促进剂。
应缓慢加入促进剂,多批次少量加入,出现问题后及时添加磷化液与中和剂。
磷化后工件表面附着沉渣---晶体,见表7。
原因对策磷化工作液工作正常的条件下,表调失效。
重配表调液处理过程中大量加入中和剂,产生的沉渣(无机整体)不能充分反应,尤其在槽液《10度时加入中和剂。
加入一定量磷化液磷化处理槽中沉渣太多倒槽排渣酸比高于30以上,或总酸点低,游离酸点正常。
补加磷化液水洗不充分,水洗槽受到污染。
更换水结疤:磷化膜形成不完全,见表8。
原因对策除油未尽表调液中混入过多杂质磷化槽中沉渣太多游离酸点高重新除油重配表调液倒槽除渣用中和剂处理磷化膜出现水锈斑,见表9。
钢铁磷化实验报告
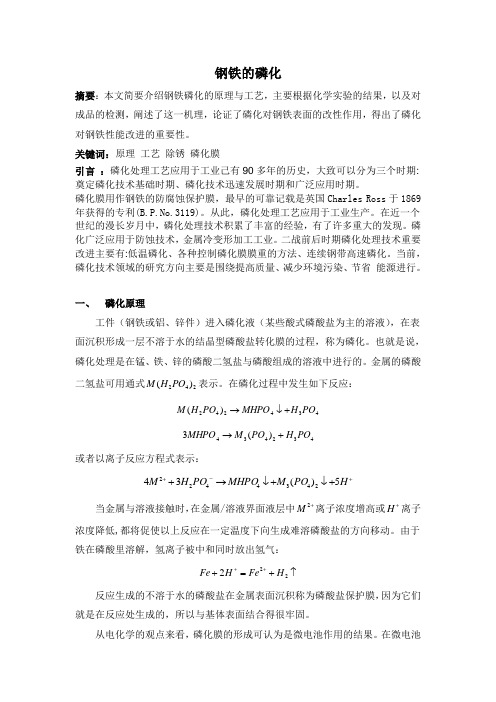
钢铁的磷化摘要:本文简要介绍钢铁磷化的原理与工艺,主要根据化学实验的结果,以及对成品的检测,阐述了这一机理,论证了磷化对钢铁表面的改性作用,得出了磷化对钢铁性能改进的重要性。
关键词:原理 工艺 除锈 磷化膜引言 :磷化处理工艺应用于工业己有90多年的历史,大致可以分为三个时期:奠定磷化技术基础时期、磷化技术迅速发展时期和广泛应用时期。
磷化膜用作钢铁的防腐蚀保护膜,最早的可靠记载是英国Charles Ross 于1869年获得的专利(B.P.No.3119)。
从此,磷化处理工艺应用于工业生产。
在近一个世纪的漫长岁月中,磷化处理技术积累了丰富的经验,有了许多重大的发现。
磷化广泛应用于防蚀技术,金属冷变形加工工业。
二战前后时期磷化处理技术重要改进主要有:低温磷化、各种控制磷化膜膜重的方法、连续钢带高速磷化。
当前,磷化技术领域的研究方向主要是围绕提高质量、减少环境污染、节省 能源进行。
一、 磷化原理工件(钢铁或铝、锌件)进入磷化液(某些酸式磷酸盐为主的溶液),在表面沉积形成一层不溶于水的结晶型磷酸盐转化膜的过程,称为磷化。
也就是说,磷化处理是在锰、铁、锌的磷酸二氢盐与磷酸组成的溶液中进行的。
金属的磷酸二氢盐可用通式242)(PO H M 表示。
在磷化过程中发生如下反应:434242)(PO H MHPOPO H M +↓→432434)(3PO H PO M MHPO+→或者以离子反应方程式表示:+-++↓+↓→+H PO M MHPOPO H M5)(342434422当金属与溶液接触时,在金属/溶液界面液层中+2M 离子浓度增高或+H 离子浓度降低,都将促使以上反应在一定温度下向生成难溶磷酸盐的方向移动。
由于铁在磷酸里溶解,氢离子被中和同时放出氢气:↑+=+++222H FeHFe反应生成的不溶于水的磷酸盐在金属表面沉积称为磷酸盐保护膜,因为它们就是在反应处生成的,所以与基体表面结合得很牢固。
从电化学的观点来看,磷化膜的形成可认为是微电池作用的结果。
45钢磷化处理-南京工程学院实验报告解析

表面工程综合实验周
实验报告
学年学期2016/2017学年第 1学期
学生系部材料工程学院
学生班级复合材料XXX班
学生姓名 XXX 学生学号 205XXXXXX 实验日期 2016.11.28-2016.12.2
南京工程学院
实验报告
课程名称表面工程综合实验
实验项目名称 45钢的磷化处理
实验学生班级复合材料XXX班
实验学生姓名 XXX
实验学生学号 205XXXXXX
同组学生姓名 XXXXXX
实验指导教师 XXXXXX
实验时间 2016.11.28-2016.12.2 实验地点基础实验楼XXXX
六、实验结论与分析
(1)镀层宏观形貌分析
(1#磷化时间20min、2#磷化时间30min、3#磷化时间40min、4#磷化时间50min)观察镀层的宏观形貌,可以发现,随着磷化处理时间加长,45钢表面颜色越黑且越均匀,说明延长磷化时间可以使表层所形成的磷化膜越完整。
(2)膜厚测试(膜厚测量仪测得)
序号
膜厚
(μm)
膜厚
(μm)
膜厚
(μm)
膜厚
(μm)
膜厚
(μm)
平均
膜厚
1#8.8 9.1 13.4 9.9 9.3 10.1 2# 10.1 7.6 12.7 8.3 11.9 10.12 3# 8.6 7.5 10.7 9.4 9.1 9.06 4# 11.4 10.7 9.2 8.9 8.4 9.72 (1#磷化时间20min、2#磷化时间30min、3#磷化时间40min、4#磷化时间50min)。
磷化膜厚度或膜重

磷化膜厚度或膜重Company Document number:WUUT-WUUY-WBBGB-BWYTT-1982GT磷化(Ⅵ)——质量控制及检测方法磷化后的工件,根据其用途,对其质量指标进行分项检验。
主要质量控制指标,包括磷化膜外观、磷化膜厚度或膜重、磷化膜或后处理以后的耐蚀性三大共性指标。
根据磷化用途有时还要检测:磷化与漆膜配套性、磷化膜硬度、摩擦系数、抗擦伤性等指标。
关于磷化的三共性指标,可参照如下标准及方法。
磷化膜外观:采用目测法,相关标准GB 11376-89《金属的磷酸盐转化膜》和GB 6807-86《钢铁工件涂漆前磷化处理技术条件》。
磷化膜厚度或膜重:膜厚度测量采用GB 6462《金属的氧化覆盖层横断面厚度显微镜测量法》,也可采用测厚仪,按照GB 4956《磁性金属基体上非磁性覆盖层厚度测量磁性方法》或GB 4957《非磁性金属基体上非导电覆盖层测量涡流方法》。
膜重测量采用重量法,可依照GB 6807《钢铁工件涂漆前磷化处理技术条件》或GB 9792《金属材料上的转化膜单位面积上膜层质量的测定》。
耐蚀性:检测磷化膜本身的耐蚀性可采用硫酸铜点滴法,氯化钠盐水浸泡法和盐雾试验法。
点滴法和盐水浸泡法可依照GB 6807-86《钢铁件涂漆前磷化处理技术条件》,磷化膜经过后处理如涂油,涂蜡,涂漆后一般进行盐雾试验检验。
盐雾试验可依照GB 1771-79《漆膜耐盐雾测定法》或GB 6458《金属覆盖层中性盐雾性试验》。
1 涂漆前打底用磷化用于漆前打底的磷化处理,其主要目的是提高漆膜的附着力和涂层系统的耐蚀性,因此重点在于与漆膜的配合性能方面。
一般对磷化质量检测指标包括膜外观、膜厚度和与漆膜配套后的性能。
膜外观应为均匀细密完整的磷化膜,对轻铁系磷化,其外观应为均匀细密完整的磷化膜,对轻铁系磷化,其外观应为完整的红蓝彩色膜。
磷化膜不宜过厚,一般膜重应小于m2,最佳为~m2,对于轻铁系磷化膜重~m2为宜,过厚和粗糙的磷化膜是不利涂漆的。
磷化膜质量评定项目与方法
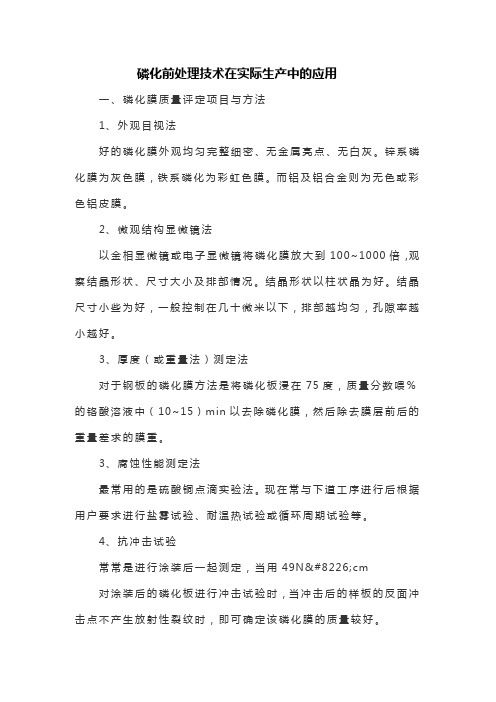
磷化前处理技术在实际生产中的应用一、磷化膜质量评定项目与方法1、外观目视法好的磷化膜外观均匀完整细密、无金属亮点、无白灰。
锌系磷化膜为灰色膜,铁系磷化为彩虹色膜。
而铝及铝合金则为无色或彩色铝皮膜。
2、微观结构显微镜法以金相显微镜或电子显微镜将磷化膜放大到100~1000倍,观察结晶形状、尺寸大小及排部情况。
结晶形状以柱状晶为好。
结晶尺寸小些为好,一般控制在几十微米以下,排部越均匀,孔隙率越小越好。
3、厚度(或重量法)测定法对于钢板的磷化膜方法是将磷化板浸在75度,质量分数喂%的铬酸溶液中(10~15)min以去除磷化膜,然后除去膜层前后的重量差求的膜重。
3、腐蚀性能测定法最常用的是硫酸铜点滴实验法。
现在常与下道工序进行后根据用户要求进行盐雾试验、耐温热试验或循环周期试验等。
4、抗冲击试验常常是进行涂装后一起测定,当用49N•cm对涂装后的磷化板进行冲击试验时,当冲击后的样板的反面冲击点不产生放射性裂纹时,即可确定该磷化膜的质量较好。
5、二次附着力测定磷化膜涂装后测定的附着力为一次附着力。
在一定条件下进行耐温水实验后测定的附着力称为二次附着力。
一般是在耐水试验后的样板上用划格法作附着力的测定,以胶带剥离后观察涂膜脱落等级,一般均为平行比较实验。
6、磷化膜孔隙率的测定取14%的NaCL和3%的铁氰化钾溶液,表面活性剂的质量分数为0.1%的蒸馏水溶液,保存在褐色瓶中24小时,用滤纸过滤。
使用时将滤纸切成长、宽均为 2.5厘米的纸片,用塑料镊子将纸片浸入上述溶液中,提出滴净多余试液,将他覆盖在戴测的磷化膜表面,经过一段时间(1分钟)后将试纸拿掉,观察膜层表面,有兰色斑点处表示有孔隙部分。
6、磷化膜的耐碱性比较磷化膜在浸碱液0.1mol/L的氢氧化钠,25度,5分钟前后的质量差,可以得到磷化膜在碱液中的溶解量。
7、磷化膜的耐酸性比较磷化膜在PH值位为2的酸液中的溶解量来评价磷化膜的耐酸性。
磷化膜快速鉴别
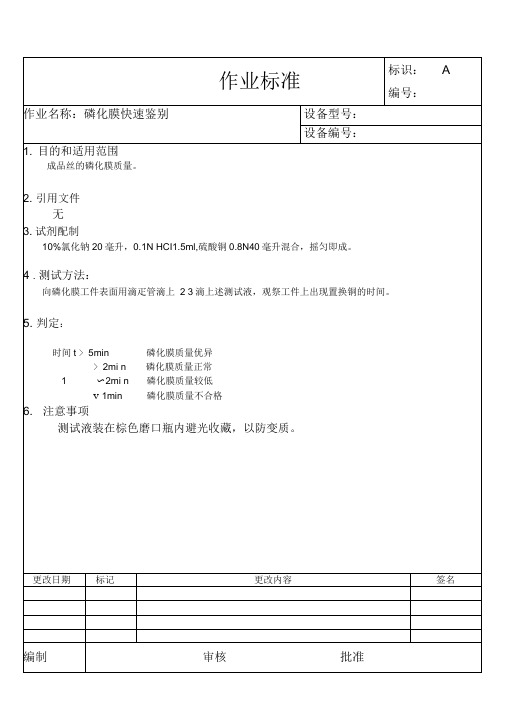
>2mi n磷化膜质量正常
1〜2mi n磷化膜质量较低
v1min磷化膜质量不合格
6.注意事项
测试液装在棕色磨口瓶内避光收藏,以防变质。
更改日期
标记
更改内容
签名
编制
审核批准
作业标准
标识:A
编号:
作业名称: 硅的测定(硅钼蓝光度法)
设备型号:
设备编号:
1.目的和适用范围
测定钢材中硅
4注意事项
更改日期
标记
更改内容
签名
编制
审核批准
作业标准
标识:A
编号:
作业名称:钼的测定(硫氰酸盐光度法)
设备型号:
设备编号:
1.目的和适用范围
2.引用文件
3.使用规定: 所需试剂:
(1)硫酸-硫酸钛混合酸 取15僦酸钛溶液10ml于1+1硫酸130ml中以水稀释至500毫升。
(2)硫氰酸钠溶液10%
PAR溶液发生沉淀可滤后继续使用,对测定结果没有影响。
4注意事项
更改日期
标记
更改内容
签名
编制
审核批准
作业标准
标识:A
编号:
作业名称:磷的测定(Vc-铋盐光度法)
设备型号:
设备编号:
1.目的和适用范围
2.引用文件
3.使用规定: 所需试剂:
(1)抗坏血酸
(2)钼酸铵溶液5%
(3)磷显色溶液1000ml1+4硫酸溶液中含2克硝酸铋,取等量含硝酸铋溶液和 钼酸铵溶液混匀。按每100ml此溶液中加入3克抗坏血酸溶解即为磷的显色溶液。 操作方法;
(2)过硫酸铵溶液15%操作方法
磷化 质量控制及检测方法
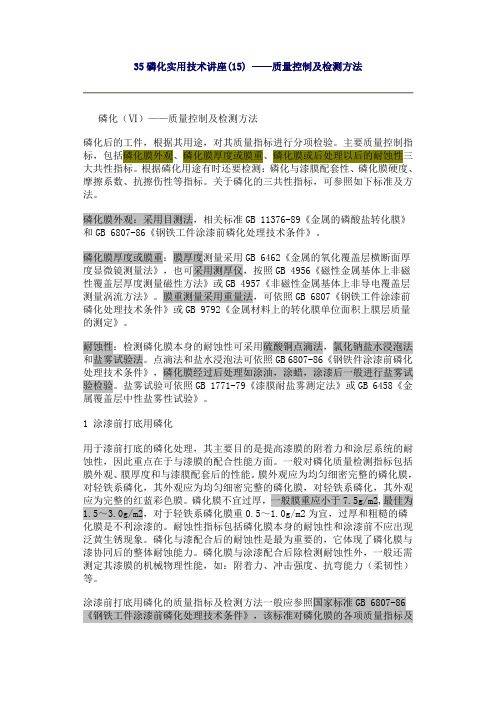
35磷化实用技术讲座(15) ——质量控制及检测方法磷化(Ⅵ)——质量控制及检测方法磷化后的工件,根据其用途,对其质量指标进行分项检验。
主要质量控制指标,包括磷化膜外观、磷化膜厚度或膜重、磷化膜或后处理以后的耐蚀性三大共性指标。
根据磷化用途有时还要检测:磷化与漆膜配套性、磷化膜硬度、摩擦系数、抗擦伤性等指标。
关于磷化的三共性指标,可参照如下标准及方法。
磷化膜外观:采用目测法,相关标准GB 11376-89《金属的磷酸盐转化膜》和GB 6807-86《钢铁工件涂漆前磷化处理技术条件》。
磷化膜厚度或膜重:膜厚度测量采用GB 6462《金属的氧化覆盖层横断面厚度显微镜测量法》,也可采用测厚仪,按照GB 4956《磁性金属基体上非磁性覆盖层厚度测量磁性方法》或GB 4957《非磁性金属基体上非导电覆盖层测量涡流方法》。
膜重测量采用重量法,可依照GB 6807《钢铁工件涂漆前磷化处理技术条件》或GB 9792《金属材料上的转化膜单位面积上膜层质量的测定》。
耐蚀性:检测磷化膜本身的耐蚀性可采用硫酸铜点滴法,氯化钠盐水浸泡法和盐雾试验法。
点滴法和盐水浸泡法可依照GB 6807-86《钢铁件涂漆前磷化处理技术条件》,磷化膜经过后处理如涂油,涂蜡,涂漆后一般进行盐雾试验检验。
盐雾试验可依照GB 1771-79《漆膜耐盐雾测定法》或GB 6458《金属覆盖层中性盐雾性试验》。
1 涂漆前打底用磷化用于漆前打底的磷化处理,其主要目的是提高漆膜的附着力和涂层系统的耐蚀性,因此重点在于与漆膜的配合性能方面。
一般对磷化质量检测指标包括膜外观、膜厚度和与漆膜配套后的性能。
膜外观应为均匀细密完整的磷化膜,对轻铁系磷化,其外观应为均匀细密完整的磷化膜,对轻铁系磷化,其外观应为完整的红蓝彩色膜。
磷化膜不宜过厚,一般膜重应小于7.5g/m2,最佳为1.5~3.0g/m2,对于轻铁系磷化膜重0.5~1.0g/m2为宜,过厚和粗糙的磷化膜是不利涂漆的。
钢铁磷化膜重测量方法

一、钢铁件磷化膜重丈量方法LFWI-008-01-01 1.合用范围:本标准规定了测定铁及其合金资料上单位面积磷化膜质量的方法。
磷化是指锰系磷化、锌系磷化。
本方法仅合用于没有任何附带覆盖层(如油膜、蜡膜、水基或溶剂型聚合物膜)的转变膜。
本方法未指明丈量区的裸斑存在与否或转变膜厚度低于规定最低厚度的部位,别的,每个丈量面所获得的一些单个数值是该丈量面范围内的变换膜的均匀厚度,不行能对这类单个的丈量值作进一步的数学剖析,比如为统计数目目的的剖析。
2.引用标准:GB/T9792-2003《金属资料上的转变膜单位面积膜质量的测定—重量法》。
3.仪器:器皿玻璃或其余不被所用试液腐化的适合资料制成,试件在此器皿中退除磷化剖析天平感量为,用于称量转变膜溶解前和溶解后的试件。
4.试件:试件的最大质量应为200g,总表面积应大到足以使退膜前后的质量损失能以知足要求的感量称量出来,并且应切合有关资料或产品规范的要求(如与工件同样材质,同样的热办理方式等)为使丈量结果有满意的正确度,试件总表面积应切合表 1 规定。
表 1:试验总表面积计的单位面积转变膜层质量 (m A) /( g/m 2)试件的最低总表面积( A ) /cm 2m A < 1 400 1≤ m A ≤ 10 200 10≤ m A ≤ 25 100 25< m A ≤ 5050 m > 5025A注:为使综合测定的不确立度不超出5﹪,表面积丈量的不确立度不该超出1﹪膜重应不低于表2 的规定值或依据客户要求两方磋商。
表 2:膜重范围磷化钢铁基体材膜层标准膜层主要成份种类料上的膜重g/m 2Zn Fe(PO ) · 4H 2O,Zn (PO ) · 4H O锌系ZnPh24 23 4 2 21~ 15树脂状,针状,缝隙许多 .锌钙Zn 2Ca(PO 4)2·4H 2O,Zn 2 Fe(PO 4)2· 4H 2OZnCa · PhZn (PO ) ·4H 2O 密切颗粒状,有时有1~ 15系34 2大的针状颗粒,缝隙较少 .锰系Mn · Ph(Mn ·Fe)5H 2(PO 4)4· 4H 2O,Mn 3(PO 4)2· 3H 2O8~ 20 密切颗粒状 ,缝隙少 .黑色 B-Zn · Ph8~ 20磷化B-Mn · Ph5.试液和程序 :总则除非还有说明,配制试液均采纳剖析纯试剂,配制所用水为蒸馏水或纯度相当的去离子水,取样程序应切合产品标准的规定。
磷化处理
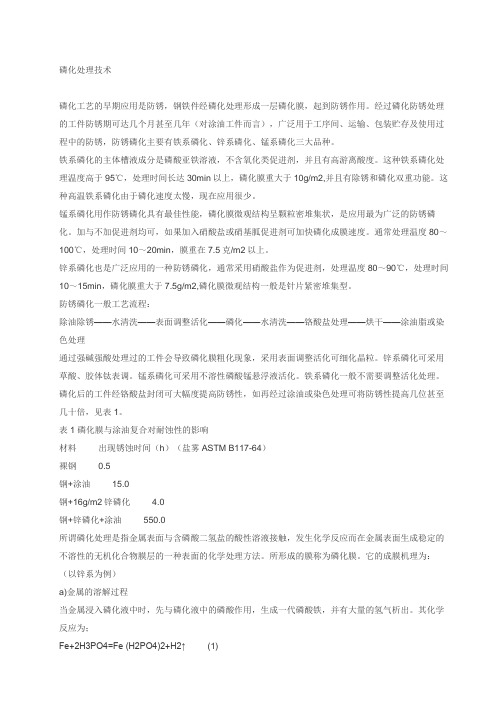
磷化处理技术磷化工艺的早期应用是防锈,钢铁件经磷化处理形成一层磷化膜,起到防锈作用。
经过磷化防锈处理的工件防锈期可达几个月甚至几年(对涂油工件而言),广泛用于工序间、运输、包装贮存及使用过程中的防锈,防锈磷化主要有铁系磷化、锌系磷化、锰系磷化三大品种。
铁系磷化的主体槽液成分是磷酸亚铁溶液,不含氧化类促进剂,并且有高游离酸度。
这种铁系磷化处理温度高于95℃,处理时间长达30min以上,磷化膜重大于10g/m2,并且有除锈和磷化双重功能。
这种高温铁系磷化由于磷化速度太慢,现在应用很少。
锰系磷化用作防锈磷化具有最佳性能,磷化膜微观结构呈颗粒密堆集状,是应用最为广泛的防锈磷化。
加与不加促进剂均可,如果加入硝酸盐或硝基胍促进剂可加快磷化成膜速度。
通常处理温度80~100℃,处理时间10~20min,膜重在7.5克/m2以上。
锌系磷化也是广泛应用的一种防锈磷化,通常采用硝酸盐作为促进剂,处理温度80~90℃,处理时间10~15min,磷化膜重大于7.5g/m2,磷化膜微观结构一般是针片紧密堆集型。
防锈磷化一般工艺流程:除油除锈——水清洗——表面调整活化——磷化——水清洗——铬酸盐处理——烘干——涂油脂或染色处理通过强碱强酸处理过的工件会导致磷化膜粗化现象,采用表面调整活化可细化晶粒。
锌系磷化可采用草酸、胶体钛表调。
锰系磷化可采用不溶性磷酸锰悬浮液活化。
铁系磷化一般不需要调整活化处理。
磷化后的工件经铬酸盐封闭可大幅度提高防锈性,如再经过涂油或染色处理可将防锈性提高几位甚至几十倍,见表1。
表1 磷化膜与涂油复合对耐蚀性的影响材料出现锈蚀时间(h)(盐雾ASTM B117-64)裸钢 0.5钢+涂油 15.0钢+16g/m2锌磷化 4.0钢+锌磷化+涂油 550.0所谓磷化处理是指金属表面与含磷酸二氢盐的酸性溶液接触,发生化学反应而在金属表面生成稳定的不溶性的无机化合物膜层的一种表面的化学处理方法。
所形成的膜称为磷化膜。
磷化工艺及检验
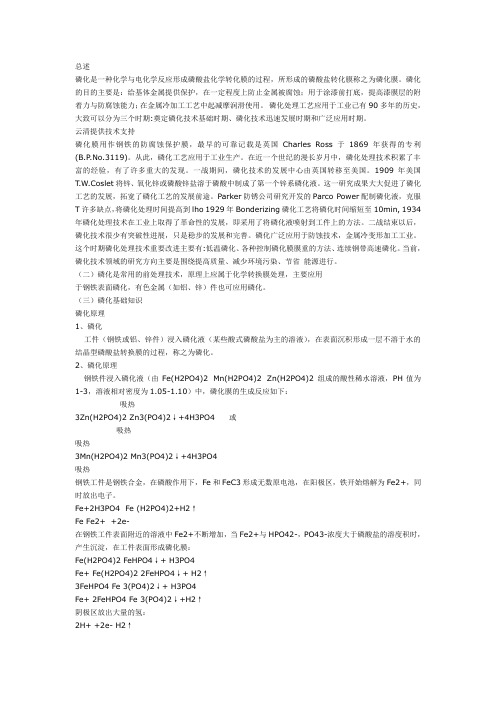
总述磷化是一种化学与电化学反应形成磷酸盐化学转化膜的过程,所形成的磷酸盐转化膜称之为磷化膜。
磷化的目的主要是:给基体金属提供保护,在一定程度上防止金属被腐蚀;用于涂漆前打底,提高漆膜层的附着力与防腐蚀能力;在金属冷加工工艺中起减摩润滑使用。
磷化处理工艺应用于工业己有90多年的历史,大致可以分为三个时期:奠定磷化技术基础时期、磷化技术迅速发展时期和广泛应用时期。
云清提供技术支持磷化膜用作钢铁的防腐蚀保护膜,最早的可靠记载是英国Charles Ross于1869年获得的专利(B.P.No.3119)。
从此,磷化工艺应用于工业生产。
在近一个世纪的漫长岁月中,磷化处理技术积累了丰富的经验,有了许多重大的发现。
一战期间,磷化技术的发展中心由英国转移至美国。
1909年美国T.W.Coslet将锌、氧化锌或磷酸锌盐溶于磷酸中制成了第一个锌系磷化液。
这一研究成果大大促进了磷化工艺的发展,拓宽了磷化工艺的发展前途。
Parker防锈公司研究开发的Parco Power配制磷化液,克服T许多缺点,将磷化处理时间提高到lho 1929年Bonderizing磷化工艺将磷化时间缩短至10min, 1934年磷化处理技术在工业上取得了革命性的发展,即采用了将磷化液喷射到工件上的方法。
二战结束以后,磷化技术很少有突破性进展,只是稳步的发展和完善。
磷化广泛应用于防蚀技术,金属冷变形加工工业。
这个时期磷化处理技术重要改进主要有:低温磷化、各种控制磷化膜膜重的方法、连续钢带高速磷化。
当前,磷化技术领域的研究方向主要是围绕提高质量、减少环境污染、节省能源进行。
(二)磷化是常用的前处理技术,原理上应属于化学转换膜处理,主要应用于钢铁表面磷化,有色金属(如铝、锌)件也可应用磷化。
(三)磷化基础知识磷化原理1、磷化工件(钢铁或铝、锌件)浸入磷化液(某些酸式磷酸盐为主的溶液),在表面沉积形成一层不溶于水的结晶型磷酸盐转换膜的过程,称之为磷化。
国标 钢铁工件涂漆前磷化处理技术条件 UDC62

国标钢铁工件涂漆前磷化处理技术条件 UDC62.9.032009-06-02 10:09本标准适用于钢铁工件涂漆前的磷化处理. 经处理所形成的磷化膜用作油漆底层, 以增强漆膜与钢铁基体的附著力及防护性, 提高钢铁工件的涂漆质量.1. 磷化膜分类2.1 待处理的工件应符合下列要求:2.1.1 无特别规定时, 工件的机械加工, 成型, 焊接和打孔应在处理前完成.2.1.2 工件的表面质量应符合技术文件的规定.2.2 工件的热处理特殊用途的零件, 应在磷化处理前消除应力及处理后消除氢脆.2.3 前处理2.3.1 工件表面的油污, 锈及氧化皮可用一种或几种方法清理.2.3.2 脱脂后的工件, 不应有油脂, 乳浊液等污物, 其表面应能被水完全润湿.2.3.3 酸洗后工件, 不应有目视可见的氧化物, 锈及过腐蚀现象, 其表面应色泽均匀.2.3.4 喷抛丸清理后的工件, 不应有漏喷, 磨料粘附,锈蚀及油污, 其表面应露出金属本色.2.4 磷化处理2.4.1 磷化处理的主要施工方法可采用浸渍法, 喷淋法或浸喷组合的方法进行.2.4.2 对于轻度油污或锈蚀的工件, 可以采用前处理和磷化或采用脱脂, 除锈, 磷化和钝化一步法进行.2.4.3 磷化处理可以在以锌, 锰, 锌钙, 碱金属, 其他金属或氨的磷酸二氢盐为主要成分的溶液中进行.2.4.4 磷化槽液的配制, 调整及管理应按工艺规定的要求进行.2.4.5 盛装磷化液的槽体材料或衬里材料应耐磷酸盐腐蚀, 所有制作磷化设备的材料或接触槽液的材料应不影响磷化液及损害磷化膜质量.2.4.6 工件表面生成的磷化膜应符合2.6, 2.7, 2.8 ,2.9条的技术要求.2.5 后处理2.5.1 为了提高磷化膜的耐腐蚀性能, 水洗后磷化工件建议在铬酸, 重铬酸盐或其他类型的钝化液中进行钝化.2.5.2 磷化或钝化后的工件, 一般情况下应进行水洗, 为了提高工件表面的清洗质量, 可采用脱离子水作最终水洗.2.5.3 最终水洗后的工件, 一般需干燥后方可涂漆.2.5.4 为了防止工件表面被污染或重新锈蚀, 干燥后应尽快的涂漆.2.5.5 磷化与涂漆间隔一般不超过16H, 对特殊的加工工序及特殊的零件可适当延长间隔时间, 但此期间的工件表面不得被污染或重新锈蚀.2.6 磷化膜外观2.6.1 磷化后工件的颜色应为浅灰色到深灰色或彩色, 膜层应结晶致密, 连续和均匀.2.6.2 磷化后的工件具有下列情况或其中之一时, 均为允许缺陷.2.6.2.1 轻微的水迹, 重铬酸盐的痕迹, 擦白及挂灰现象.2.6.2.2 由于局部热处理, 焊接以及表面加工状态的不同而造成颜色和结晶不均匀.2.6.2.3 在焊缝的气孔和夹渣处无磷化膜.2.6.3 磷化后的工件具有下列情况之一时, 均为不允许缺陷.2.6.3.1 疏松的磷化膜层.2.6.3.2 有锈蚀或绿斑.2.6.3.3 局部无磷化膜(焊缝的气孔和夹渣处除外).2.6.3.4 表面严重挂灰.2.7 磷化膜重量按附录A(补充件)测定的磷化膜重量, 应符合表1.所列数值, 磷化膜厚度与重量的换算关系参考附录C(参考件).2.8 磷化膜耐蚀性能按3.3条规定的方法检验磷化膜耐蚀性能时:2.8.1 浸渍法: 经1H, 基体金属不应现出锈蚀(棱边, 孔, 角及焊缝处除外).2.8.2 点滴法: 可作为工序间磷化膜质量的快速检验.2.9 漆膜耐蚀性能按3.4条规定的方法检验漆膜耐蚀性能时: 锌盐, 锰盐, 锌钙盐磷化膜涂漆试样经24H耐盐雾试验后, 铁盐磷化膜的涂漆试样8H耐盐雾试验收后, 除划痕部位处, 漆膜应无起泡, 脱落及生锈等现象.注: 划痕部位系指划痕任何一测的附近宽度0.5MM内.3. 检验方法3.1 外观检验在天然光或混合照明条件下, 用目视检查, 天然光照度要求不小于100lx, 采光系数最低值为2%, 混合照明的光照度要求不小于500lx.3.2 磷化膜重量测定法经过2.3, 2.4条及2.5.1款处理并干燥的试样, 按附录A规定的方法测定膜层重量.3.3 磷化膜耐蚀性能检验3.3.1 浸渍法: 将工件或试样(已降至室温)浸入3%的氯化钠(NaCl)的水溶液中, 在15-25℃下, 保持规定的时间, 取出工件或试样, 随时之洗净, 吹干, 目视检查磷化表面是否出现锈蚀.3.3.3 点滴法: 磷化膜耐蚀性能的点滴法检验见附录D(参考件)3.4 漆膜耐蚀性能检验.3.4.1 经2.3 2.4条及2.5.1款处理并干燥后的磷化试样, 按 GB1765-79<<测定耐湿热,耐盐雾, 耐候性(入工加速)的漆膜制备法>>中第3条制板方法的规定, 喷涂一层厚度为25-35um的A04-9白色氨基烘漆, 室温干燥30min, 再放入恒温鼓风烘箱中, 要温度102-107℃下烘2h, 干燥后的试样, 用石蜡和松香1:1的混合物或性能较好的自干漆封边, 封孔, 在室外温下置放24h, 待试.3.4.2 制备后的试样, 用18号缝纫机针将漆膜划成长2cm的交叉对角线(划痕深至钢铁基体, 对角线不贯穿对角, 对角线端点与对角成等到距离), 取试样三片, 划痕面朝上, 而后的将试样置于符合GB-1771-79<<漆膜耐盐雾测定法>>的盐雾试验箱中, 按其规定的试验条件连续试验.3.4.3 检查时, 取出试样, 用自来水冲净试样表面上所沉积的盐分, 冷风快速吹干(或毛巾, 滤纸吸干), 目视检查试样表面.4 验收规则4.1 工件磷化后的质量检验包括外观, 磷化膜重量, 磷化膜耐蚀性能及漆膜耐蚀性能检验.4.2 外观检验验收按下列规定:4.2.1 大工件和重要工件应100%进行检验并逐一验收 .4.2.2 一般工件(包括小工件或小零件)可按GB 2828-81<逐批检查度数抽样程序及抽样表>抽样检验验收, 检验规则见附录B(补充件).4.3 测定磷化膜重量时, 在受试的三个平行试样的平均值不合格, 则再取三件进行复验, 若其平均值仍不合格, 则该批产品为不合格.4.4 磷化工件由于数量, 尺寸及形状不能按规定的方法进行耐蚀性能检验时, 应按下列方法之一制作试样.4.4.1 从实际工件切取一部分.4.4.2 用与工件相同的材料长宽为70*150mm的试样与工件同时进行处理.4.5 磷化膜耐蚀性检验时,应从每批工件中抽取三件试样进行检验, 其中有一件不合格则再取双倍试样进行复验.若仍有一件不合格, 则采用4.7条的规定进行检验并以其结果为准.4.6 磷化膜重量及漆膜耐蚀性能检验为抽验,应在下列情况之一时进行:4.6.1 新设计投产的产品.4.6.2 企业规定的周期检验.4.6.3 设备, 工艺或槽液配方改变.4.6.4 其他认为必要时的检验.4.7 漆膜耐蚀性能检验时, 在受试的三个试样中, 其中有一个试样不合格, 则再取双倍试样复验,若仍有一个试样不合格, 则该批产品为不合格.国标钢铁工件涂漆前磷化处理技术条件 UDC62.9.03 补充2009-06-02 10:10附录A 磷化膜重量测定法 (补充件)本方法适用于钢铁表面生成的磷化膜单位面积重量的测定.A.1 一般规定A.1.1 仪器1. 容器: 玻璃的或其他适当材料的容器.2. 分析天平: 感量为0.1mg.3. 加热设备: 用于控制退膜液的温度.A.1.2 试样试样的总表面积应尽可能的大, 膜重小于1g/m2的试样的总表面积不应小于300cm2, 膜重1-10g/m2的试样的总表面积不应小于200cm2.A.1.3 试剂退膜溶液, 应由分析纯试剂和蒸馏水制备.A.2测定方法将试样用分析天平称量准确0.1mg, 再浸入下表规定的退膜溶液中, 取出后立即用自来水冲洗, 然后用蒸馏水冲洗, 迅速干燥再称重.重复本操作, 直至得到A.3 计算方法磷化膜单位面积膜层重量W 按下式计算:W={(P2-P1)/S}*10式中: W----膜重量,g/m2.P1--------退除磷化膜后试样的重量, mg.P2---------磷化后试样的重量,mg.S----------磷化试样的总表面积, cm2.取三个平行测定试样的平均值.附录B 磷化膜外观检验规则(补充件)本规则适用于一般工件磷化后外观检验.B.1 磷化膜的外观检验应符合GB 2828-81<<逐批检查计数抽样程序及抽样表>>的有关规定.B.2 缺陷分类: 磷化膜的外观缺陷分为轻缺陷及重缺陷. 2.6.2款中允许缺陷属于轻缺陷, 而2.6.3款式中的缺陷属于重缺陷 .B.3 外观检查时, 一般根据磷化膜的外观颜色及膜层质量进行验收, 以有无重缺陷来判断合格或不合格, 轻缺陷一般不用于判断合格或不合格.B.4逐批检查采用一次抽样方案, 初次检查为正常检查, 其缺陷类型 , 合格质2. 轻量级磷化膜重量与厚度之比1-2.3. 磷化膜重量与厚度之比一般在1-3之间.附录D点滴法(参考件)本方法适用于稳定性生产中, 工序间磷化膜耐蚀性能的快速检验.D.1` 检验溶液的成份和含量.硫酸铜 CuSO4.5H2O 41g/l.氯化钠 NaCl 35g/l0.1N盐酸 HCl 13ml/l注: 1. 检验溶液应使用化学纯试剂和蒸馏水配制.2. 溶液在5-35℃下有效期限为一周.D.2 检验方法在15-23℃下, 磷化表面滴一滴检验溶, 同时启动秒表, 观察滴液从天兰变为浅黄色或淡红色的时间.D.3 验收标准点滴法用作工序间磷化膜质量的快速检验, 其变色时间由供需双方商定.。
一种磷化膜深度测定方法

一种磷化膜深度测定方法磷化膜是一种广泛应用于金属表面的保护膜,可以起到防腐蚀、增加硬度和耐磨性的作用。
为了确保磷化膜的质量和性能,需要对其深度进行精确测定。
本文将介绍一种常用的磷化膜深度测定方法,并对其原理和操作步骤进行详细说明。
磷化膜深度测定方法主要有金相显微镜法、激光剥蚀法、微胶囊法等多种。
其中,金相显微镜法是一种常用的方法,具有操作简便、成本低廉等优点。
金相显微镜法是通过对待测样品进行金相显微观察,利用显微镜的放大功能,测定磷化膜的厚度。
其原理是通过显微镜对样品进行放大观察,测量其显微图像中磷化膜的厚度,然后通过图像处理软件进行分析和计算,得出磷化膜的深度。
操作步骤如下:1. 准备样品:首先需要准备待测样品,将其进行磷化处理后,进行清洗和抛光处理,使其表面平整光滑,便于观察和测量。
2. 制备显微图像:将样品放置在金相显微镜下,调整放大倍数和对焦距离,使显微图像清晰可见。
然后通过显微镜将待测样品的显微图像投射到荧光屏上,形成一个放大、清晰的图像。
3. 测量磷化膜厚度:利用显微镜放大的功能,通过目镜和物镜对样品表面进行测量,测量磷化膜的厚度,记录下其显微图像中的尺寸。
4. 图像处理和计算:将显微图像导入图像处理软件,对磷化膜的厚度进行测量和分析,计算出其深度值。
金相显微镜法测定磷化膜深度的优点在于操作简便、成本低廉,而且可以对不同类型的磷化膜进行测定。
但是,由于显微镜放大倍率有限,只能对局部区域进行测定,不能全面了解整个磷化膜的厚度。
综上所述,金相显微镜法是一种常用的磷化膜深度测定方法,其原理简单,操作方便,成本低廉。
然而,需要注意的是,测量过程中要保证样品表面平整光滑,避免因为表面不平整导致测量误差。
同时,对于不同类型的磷化膜,需要选择合适的显微镜放大倍率进行测定。
希望本文的介绍能对磷化膜深度测定方法有所帮助。
紧固件磷化常见问题及解决

紧固件磷化常见问题及解决(2009-12-25)紧固件磷化常用有两种,锌系磷化和锰系磷化,锌系磷化润滑性能比锰系磷化好,锰系磷化抗腐蚀性,耐磨性较锌系好。
它的使用温度可达105~205℃(华氏225F°-400F°)。
机械工业用紧固件很多用磷化涂油处理。
因为它扭矩-预紧力一致性很好,装配时能保证达到设计所预期的紧固要求,所以在机械工业中使用较多。
特别是一些重要零部件的连接。
如:钢结构连接副、发动机的连杆螺栓、螺母,缸盖、主轴承、飞轮螺栓、车轮螺栓螺母等。
高强度螺栓采用磷化,还可以避免氢脆问题,所以在机械工业领域10.9级以上的螺栓一般采用磷化表面处理。
紧固件磷化常见缺陷、产生原因及改进对策如下:常见磷化故障的解决办法类别:技术问题发布时间:2010/5/31 10:32:00浏览数:3862近年来,表面处理中转化膜技术发展较快。
在汽车摩托车的紧固件上采用较多的是磷酸盐(磷化)和氧化(发黑)。
虽然它们的防腐性能耐久性等级属于轻度保护,由于成本低廉,使用方便在表面防护领域还占有一席之地。
磷化是借磷化溶液在紧固件表面上人为地造成一层厚约10μm保护膜,这层膜是难溶的磷酸盐的混合物。
根据磷化液用的磷酸盐分类有:磷酸锌系、磷酸铁系、磷酸锰系。
此外,还有在磷酸锌中加钙的锌钙系,在磷酸锌中加铜、加镍的三元体系磷化等。
一、常见磷化故障的解决办法故障1:工件表面均匀泛黄,均匀疏松的磷化膜主要原因:⑴总酸度低、酸比低;⑵促进剂浓度低;⑶磷化温度低、时间短。
解决方法:⑴补加磷化液和碱;⑵补加促进剂;⑶提高温度,延长时间。
故障2:磷化成膜速度慢,但延长磷化时间仍可形成均匀完整膜主要原因:⑴表面调整能力不强;⑵促进剂溶度不够;⑶酸比低;⑷磷化温度低。
解决方法:⑴改进表调或换槽;⑵补加促进剂;⑶补加碱;⑷提高温度。
故障3:㈠磷化膜局部块状条状挂灰;㈡挂灰处磷化膜不均匀;㈢时有彩色膜。
主要原因:⑴工件在进入磷化槽前已经形成二次黄绿锈;⑵表面调整能力差;⑶磷化液中杂质多。
磷化膜的性能检测

磷化膜性能检测外观外观检测主要指颜色与结晶状态。
磷化膜干燥后按Q/XG 217-89标准检测。
对涂装磷化膜而言,颜色允许变化范围大,无严格规定。
其中灰色磷化膜在浅灰-深灰一灰黑范围内变化,取决槽液成分及钢铁种类;彩色磷化膜在纯蓝一金黄一彩虹范围内变化,取决槽液成分、磷化时间、水洗条件(热水与冷水)、干燥条件(水洗干燥与不水洗干燥)等,通常认为金黄色磷化膜的耐蚀性最佳;铬磷化膜在浅绿色一深湖绿色范围内变化。
功能磷化膜除黑色外,均无颜色要求,其中黑色磷化膜在浅黑色一深黑色一纯黑色范围内变化,取决于钢材品种(含碳量与合金元素)、预处理方法、槽液成分(发黑剂为主)、工作条件、油封处理等。
只能通过试验,确定黑度范围。
目前国内能真正达到纯黑色的磷化剂不多见(借助磷化前预黑化的除外)。
磷化膜结晶视磷化工艺不同而异。
涂装磷化膜结晶细致均匀;功能磷化膜结晶较粗糙。
允许磷化缺陷:轻微的水迹、钝化痕迹、擦白及挂灰(只允许涂装磷化膜轻微挂灰,涂装前需擦净);由于热处理、焊接以及表面机加工状态的不同而造成颜色和结晶不均匀;在焊缝处无磷化膜。
不允许缺陷:疏松的磷化膜层;有锈蚀和绿斑;局部无磷化膜;表面严重挂灰。
膜重涂装磷化膜膜重1-5g/m2(其中静电喷涂和电泳漆的磷化膜重1.2-2. 5g/rn2最佳);功能磷化膜膜重≥6. 5g/m2 膜重按Q/XG 217-89标准检测。
测试方法是将25一 400cm2干燥的磷化膜样板在天平上称量(精度士0. lmg),然后在化学退膜溶液中退除膜、水洗、干燥后称重,从第二次差值中即可算出磷化膜单位质量,允许误差士3%。
W=p1-p2/s*10式中,W为磷化膜单位质量,g/m2;p1为磷化后试样重,Mg; p2为退膜后试样重,mg; S为磷化试样的总面积, cm2。
取三块试样的平均值为膜重。
所用试样的面积可根据磷化膜单位质量选择。
膜重小于lg/m的试样,总面积不应小于300cm2;膜重1-log/m2的试样总面积不应小于200cm2 。
磷化膜厚度或膜重
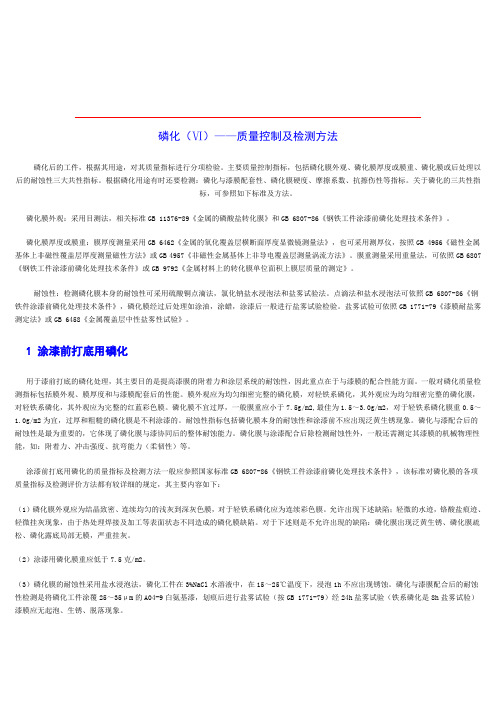
磷化(Ⅵ)——质量控制及检测方法磷化后的工件,根据其用途,对其质量指标进行分项检验。
主要质量控制指标,包括磷化膜外观、磷化膜厚度或膜重、磷化膜或后处理以后的耐蚀性三大共性指标。
根据磷化用途有时还要检测:磷化与漆膜配套性、磷化膜硬度、摩擦系数、抗擦伤性等指标。
关于磷化的三共性指标,可参照如下标准及方法。
磷化膜外观:采用目测法,相关标准GB 11376-89《金属的磷酸盐转化膜》和GB 6807-86《钢铁工件涂漆前磷化处理技术条件》。
磷化膜厚度或膜重:膜厚度测量采用GB 6462《金属的氧化覆盖层横断面厚度显微镜测量法》,也可采用测厚仪,按照GB 4956《磁性金属基体上非磁性覆盖层厚度测量磁性方法》或GB 4957《非磁性金属基体上非导电覆盖层测量涡流方法》。
膜重测量采用重量法,可依照GB 6807《钢铁工件涂漆前磷化处理技术条件》或GB 9792《金属材料上的转化膜单位面积上膜层质量的测定》。
耐蚀性:检测磷化膜本身的耐蚀性可采用硫酸铜点滴法,氯化钠盐水浸泡法和盐雾试验法。
点滴法和盐水浸泡法可依照GB 6807-86《钢铁件涂漆前磷化处理技术条件》,磷化膜经过后处理如涂油,涂蜡,涂漆后一般进行盐雾试验检验。
盐雾试验可依照GB 1771-79《漆膜耐盐雾测定法》或GB 6458《金属覆盖层中性盐雾性试验》。
1 涂漆前打底用磷化用于漆前打底的磷化处理,其主要目的是提高漆膜的附着力和涂层系统的耐蚀性,因此重点在于与漆膜的配合性能方面。
一般对磷化质量检测指标包括膜外观、膜厚度和与漆膜配套后的性能。
膜外观应为均匀细密完整的磷化膜,对轻铁系磷化,其外观应为均匀细密完整的磷化膜,对轻铁系磷化,其外观应为完整的红蓝彩色膜。
磷化膜不宜过厚,一般膜重应小于7.5g/m2,最佳为1.5~3.0g/m2,对于轻铁系磷化膜重0.5~1.0g/m2为宜,过厚和粗糙的磷化膜是不利涂漆的。
耐蚀性指标包括磷化膜本身的耐蚀性和涂漆前不应出现泛黄生锈现象。
磷化膜质量检验111003

九、磷化膜质量检验
①外观检验
肉眼观察磷化膜应是均匀、连续、致密的晶体结构。
表面不应有未磷化德的残余空白或锈渍。
由于前处理的方法及效果的不同,允许出现色泽不一的磷化膜,但不允许出现褐色。
②耐蚀性检查
⑴浸入法
将磷化后的样板浸入3%的氯化钠溶液中,经两小时后取出,表面无锈渍为合格。
出现锈渍时间越长,说明磷化膜的耐蚀性越好。
②点滴法
室温下,将蓝点试剂滴在磷化膜上,观察其变色时间。
磷化膜厚度不同,变色时间不同。
厚膜>5分钟,中等膜>2分钟,薄膜>1分钟。
十、游离酸度及总酸度的测定。
1、游离酸度的测定
用移液管吸取10 ml试液于250ml锥形瓶中,加50ml蒸馏水,加2—3滴甲基橙指示剂(或溴酚蓝指示剂)。
用0.1mol/l氢氧化钠标准液滴定至溶液呈橙色(或用溴酚蓝指示剂滴定至由黄变蓝紫色)即为终点,记下的耗氢氧化钠标准液毫升数即为滴定的游离酸度点数。
2、总酸度的测定
用移液管吸取10 ml试液于250ml锥形瓶中,加50ml蒸馏水,加2—3滴酚酞指示剂。
用0.1mol/l氢氧化钠标准液滴定至粉红色即为终点,记下的耗氢氧化钠标准液毫升数即为滴定的总酸度点数。
磷化了的零件是有磷化膜的,它的技术指标如下:
(1)外观:黑色,灰黑色,深灰色,浅灰色,均匀致密,不挂灰。
(2)膜厚:3~15µm
(3)抗腐蚀能力: A.硫酸铜检验液点滴试验:≥5min(滴定实验)
B.中性盐雾试验:≥4h(盐雾试验)
C.3%NaCl溶液浸渍试验: ≥8h
1 / 1。
铬酸检测钢铁磷化膜重的方法
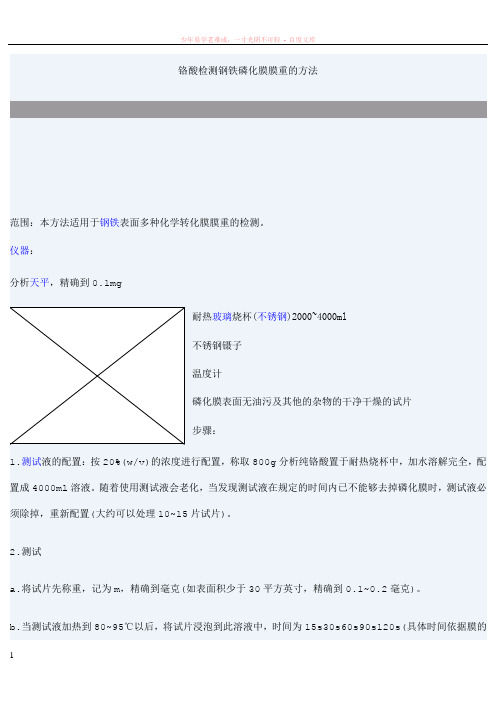
铬酸检测钢铁磷化膜膜重的方法
范围:本方法适用于钢铁表面多种化学转化膜膜重的检测。
仪器:
分析天平,精确到0.1mg
耐热玻璃烧杯(不锈钢)2000~4000ml
不锈钢镊子
温度计
磷化膜表面无油污及其他的杂物的干净干燥的试片
步骤:
1.测试液的配置:按20%(w/v)的浓度进行配置,称取800g分析纯铬酸置于耐热烧杯中,加水溶解完全,配置成4000ml溶液。
随着使用测试液会老化,当发现测试液在规定的时间内已不能够去掉磷化膜时,测试液必须除掉,重新配置(大约可以处理10~15片试片)。
2.测试
a.将试片先称重,记为m,精确到毫克(如表面积少于30平方英寸,精确到0.1~0.2毫克)。
b.当测试液加热到80~95℃以后,将试片浸泡到此溶液中,时间为15s30s60s90s120s(具体时间依据膜的
类型及预计的膜重而定)。
c.时间到达后,取出试片在流动的自来水中冲洗,吹干,再次称重,记为n(mg)。
d.计算:膜重(毫克/平方英尺)=144×(m-n)(毫克)/试片表面积(平方英寸)
注意事项:
1.操作时,注意穿戴好防护用品,防止测试液溅到眼睛及皮肤衣服上。
2.加热测试液时,防止液体溅出。
铬酸必须于易燃物隔离。
- 1、下载文档前请自行甄别文档内容的完整性,平台不提供额外的编辑、内容补充、找答案等附加服务。
- 2、"仅部分预览"的文档,不可在线预览部分如存在完整性等问题,可反馈申请退款(可完整预览的文档不适用该条件!)。
- 3、如文档侵犯您的权益,请联系客服反馈,我们会尽快为您处理(人工客服工作时间:9:00-18:30)。
a.将试片先称重,记为m,精确到毫克(如表面积少于30平方英寸,精确到0.1~0.2毫克)。
b.当测试液加热到80~95℃以后,将试片浸泡到此溶液中,时间为15s30s60s90s120s(具体时间依据膜的类型及预计的膜重而定)。
c.时间到达后,取出试片在流动的自来水中冲洗,吹干,再次称重,记为n(mg)。
铬酸检测钢铁磷化膜膜重的方法
范围:本方法适用于钢铁表面多种化学转化膜膜重的检测。
仪器:
分析天平,精确到0.1mg
耐热玻璃烧杯(不锈钢)2000~4000ml
不锈钢镊子
温度计
磷化膜表面无油污及其他的杂物的干净干燥的试片
步骤:
1.测试液的配置:按20%(w/v)的浓度进行配置,称取800g分析纯铬酸置于耐热烧杯中,加水溶解完全,配置成4000ml溶液。随着使用测试液会老化,当发现测试液在规定的时间内已不能够去掉磷化膜时,测试液必须除掉,重新配置(大约可以处理10~15片试片)。
d.计算:膜重(毫克/平方英尺)=144×(m-n)(毫克)/试片表面积(平方英寸)
注意事项:
1.操作时,注意穿戴好防护用品,防止测试液溅到眼睛及皮肤衣服上。
2.加热测试液时,防止液体溅出。铬酸必须于易燃物隔离。