M9346-RDW3T中文资料
20 cu ft WELDED STEEL ATV CART 3460SD-ATV 产品说明书

3460SD-ATV20 cu ft WELDED STEEL ATV CART1 (x1)3 (x1)4 (x1)6 (x2)19 (x1)5 (x2)16 (x4)17 (x2)9 (x2)8 (x1)18 (x2)14 (x2)15 (x2)10 (x8)11 (x14)12 (x1)13 (x3)2 (x1)7 (x1)38 (x4)37 (x1)TOOLS REQUIRED FOR ASSEMBLY:9/16" Wrench and Socket•Needle-Nose Pliers •Grease Gun•Carton Contents121011311373812413Attach undercarriage to body securely with hardware as shown.Attach front support to body securely with hardware as shown.Align holes in swivel clevis and undercarriage and install pin as shown.Secure pin on both ends with hairpins.132514151661617Press down on drawbar until it locks into place.Insert stub axles into undercarriage and secure with pins as shown.Slide washers and wheels onto stub axles as shown and install cotter pins. Bend legs of cotter pin to secure.46571181891913Attach tailgate to body as shown. No hardware is required, tailgate should move freely up or down.Attach ball hitch to drawbar with spacers and hardware as shown.Install hitch pin and hairpin to secure High Speed Safety Clevis.798Periodic Maintenance:Tighten fasteners as needed before each use •Check tire pressure before each use•Grease wheels annually (high temp red lithium grease recommended)•Before Using Dump Cart:Apply lithium grease to wheels using grease gun until grease can be seen 1.squeezing out from both sides of the wheel.Check tire pressure and inflate to 24 psi if needed.2.Read all Safety Rules found on page 1.3.How to Use Dump Cart:Attach Dump Cart to your ATV or UTV.1.Do not exceed 1500 pounds when loading material into the cart body.2.Distribute the weight of the load as evenly as possible in the cart body for3.best handling.When hauling heavy loads, verify that your vehicle has adequate towing and 4.braking capacity.Do not exceed 20 miles per hour when towing Dump Cart.5.Do not exceed 5 miles per hour without securing High Speed Safety Clevis.6.How to Empty Dump Cart:Step down the foot pedal to release the latch mechanism.1.Swivel as desired to guide the material to preferred location.2.Lower the body and guide the latch into the drawbar and relatch.3.WarrantyIf this product fails due to a defect in material or workmanship within THREE YEARS from the date of purchase, we will at our option repair or replace it free of charge. This warranty excludes tires and wheels, which are expendable and become worn during normal use.This warranty does not cover:•Repairs necessary because of operator abuse or negligence.Equipment used for commercial or rental purposes.•Paint that is worn or faded due to normal use or exposure.•To arrange for product repair call 1-800-652-2321, or return this product to place of purchase for replacement.This warranty gives you specific legal rights, and you may also have other rights which may vary from state to state. This warranty applies only while this product is in use in the United States.In the space below record the purchase date of your Dump Cart.Model Number 3460SD-ATVPurchase DateKeep this Owner's Manual and your receipt in a safe place for future reference.After the three year warranty period all replacement parts may be ordered by calling 1-800-652-2321.When ordering replacement parts, always give the following information:•Product 20 cu ft WELDED STEEL ATV CART•Model Number 3460SD-ATV•Part Number•Part Description1236161911131416155177111020291331122832212225242330272623229818114363738333435ITEM PART NO DESCRIPTION QTY ITEM PART NO DESCRIPTION QTY 16004183BODY, WELDED 34601206000369SHOULDER BOLT, 1/2" X 3/8"1 26004193UNDERCARRIAGE1213000720WASHER, 3/8" USS1 36004221FRONT SUPPORT122300061HEX NUT, 3/8-16 C-LOCK4 46004216DRAWBAR ASSEMBLY (incl. 20-32)1236000324BEARING2 56000523AXLE, STUB2246000370HEX BOLT, 3/8-16 X 3-1/2"2 66000727WHEEL, 18/950-8 X 1" (BLACK)225300055HEX BOLT, 3/8-16 X 3"1 7401042TAILGATE1266000305FOOT PEDAL1 8308301COUPLER, 1-7/8" BALL1276000309LATCH1 96004202SPACER, BALL HITCH228300075WASHER, 1/2" USS1 106001285HEX BOLT 3/8"-16 X 2-1/2"8296000368WASHER, SPRING1 11310061HEX NUT, 3/8-16 NYLOC14306000325SPRING, LATCH2 126000371PIN, 1/2" X 2-13/32"1316000321CLEVIS, SWIVEL1 136000372HAIRPIN COTTER, 0.080" X 1-9/16"3326004220DRAWBAR1 143000811CLEVIS PIN, 1/4" X 1-1/2"2336004215OWNER'S MANUAL1 153000812HAIRPIN COTTER, 0.080" X 1-3/16"2346004227HARDWARE BOLT BAG1 16300076WASHER, 1" SAE4356000162DECAL, OSI PRO2 17300087COTTER PIN, 3/16" X 1-1/2"2366000818KIT, 1" WHEEL BEARINGS1 186004260HEX BOLT, 3/8-16 X 4"2376004245ADAPTER PLATE1 196000533PIN, HITCH1386004259CARRIAGE BOLT, 3/8-16 X 1"4EXPLODED VIEWBefore you call…Please email our customer service team at **************** with:1. A description of the issue you are having2. Photos of the issue that include an overall view and detailed view from multiple angles3. If applicable, a short video showing the issueIf you believe this is a warranty related issue please see the warranty page in this manualReplacement Parts:If you are ordering replacement part(s) for your product, please note that some parts are only available as a repair kit.1. First locate the part on the Exploded View page (page 8)2. Take note of the part number3. If the part number is on the Repair Kits page, use the kit number to order your replacement parts4. If the part number is not on the Repair Kits page, use the part number to order your replacement part You can place your parts order online at /partsstore You can also reach our Customer Service Department at 1-800-652-2321KITKIT NUMBERPART NUMBER PART DESCRIPTIONQTY HARDWARE BOLT BAG60042276004259CARRIAGE BOLT, 3/8-16 X 1"46004202SPACER, BALL HITCH26001285HEX BOLT 3/8"-16 X 2-1/2"8310061HEX NUT, 3/8-16 NYLOC 146000371PIN, 1/2" X 2-13/32"16000372HAIRPIN COTTER, 0.080" X 1-9/16"33000811CLEVIS PIN, 1/4" X 1-1/2"23000812HAIRPIN COTTER, 0.080" X 1-3/16"2300076WASHER, 1" SAE4300087COTTER PIN, 3/16" X 1-1/2"26004260HEX BOLT, 3/8-16 X 4"26000533PIN, HITCH11" WHEEL BEARING KIT600081860008141" BEARING RETAINER 460008161" ROLLER BEARING 2DRAWBAR ASSEMBLY6004216300055HEX BOLT, 3/8-16 X 3"1300061HEX NUT, 3/8-16 C-LOCK 4300075WASHER, 1/2" USS 13000720WASHER, 3/8" USS 16000305FOOT PEDAL 16000309LATCH16000321CLEVIS, SWIVEL 16000324BEARING26000325SPRING, LATCH 26000368WASHER, SPRING16000369SHOULDER BOLT, 1/2" X 3/8"16000370HEX BOLT, 3/8-16 X 3-1/2"26004220WELDED DRAWBAR 1REPAIR KITSNotes10 (800)652-2321Designed And Tested In Columbus, OhioMODEL # 3460SD-ATV2575 Ferris Road Columbus, OH 43224(800)652-2321Manufactured In The U.S.A. From DomesticAnd Imported Components。
M93C86-RDW6中文资料

1/31August 2004M93C86, M93C76, M93C66M93C56, M93C4616Kbit, 8Kbit, 4Kbit, 2Kbit and 1Kbit (8-bit or 16-bit wide)MICROWIRE® Serial Access EEPROMFEATURES SUMMARYs Industry Standard MICROWIRE Bus sSingle Supply Voltage:– 4.5 to 5.5V for M93Cx6– 2.5 to 5.5V for M93Cx6-W – 1.8 to 5.5V for M93Cx6-Rs Dual Organization: by Word (x16) or Byte (x8) s Programming Instructions that work on: Byte, Word or Entire Memorys Self-timed Programming Cycle with Auto-Erases Ready/Busy Signal During Programming sSpeed:–1MHz Clock Rate, 10ms Write Time(Current product, identified by process identification letter F or M)–2MHz Clock Rate, 5ms Write Time (NewProduct, identified by process identification letter W or G or S) s Sequential Read Operations Enhanced ESD/Latch-Up Behaviour s More than 1 Million Erase/Write Cycles sMore than 40 Year Data RetentionTable 1. Product ListReferencePart Number ReferencePart Number M93C86M93C86M93C56M93C56M93C86-W M93C56-W M93C86-R M93C56-R M93C76M93C76M93C46M93C46M93C76-W M93C46-W M93C76-R M93C46-RM93C66M93C66M93C66-W M93C66-RM93C86, M93C76, M93C66, M93C56, M93C46TABLE OF CONTENTSFEATURES SUMMARY . . . . . . . . . . . . . . . . . . . . . . . . . . . . . . . . . . . . . . . . . . . . . . . . . . . . . . . . . . . . .1Table 1.Product List . . . . . . . . . . . . . . . . . . . . . . . . . . . . . . . . . . . . . . . . . . . . . . . . . . . . . . . . . . . .1 Figure 1.Packages. . . . . . . . . . . . . . . . . . . . . . . . . . . . . . . . . . . . . . . . . . . . . . . . . . . . . . . . . . . . . .1 Figure 2.Logic Diagram . . . . . . . . . . . . . . . . . . . . . . . . . . . . . . . . . . . . . . . . . . . . . . . . . . . . . . . . . .4 Table 2.Signal Names . . . . . . . . . . . . . . . . . . . . . . . . . . . . . . . . . . . . . . . . . . . . . . . . . . . . . . . . . .4 Table 3.Memory Size versus Organization. . . . . . . . . . . . . . . . . . . . . . . . . . . . . . . . . . . . . . . . . . .4 Table 4.Instruction Set for the M93Cx6 . . . . . . . . . . . . . . . . . . . . . . . . . . . . . . . . . . . . . . . . . . . . .4 Figure 3.DIP, SO, TSSOP and MLP Connections (Top View). . . . . . . . . . . . . . . . . . . . . . . . . . . . .5MEMORY ORGANIZATION . . . . . . . . . . . . . . . . . . . . . . . . . . . . . . . . . . . . . . . . . . . . . . . . . . . . . . . . . .5 POWER-ON DATA PROTECTION. . . . . . . . . . . . . . . . . . . . . . . . . . . . . . . . . . . . . . . . . . . . . . . . . . . ..5INSTRUCTIONS . . . . . . . . . . . . . . . . . . . . . . . . . . . . . . . . . . . . . . . . . . . . . . . . . . . . . . . . . . . . . . . . . . .6Table 5.Instruction Set for the M93C46 . . . . . . . . . . . . . . . . . . . . . . . . . . . . . . . . . . . . . . . . . . . . .6 Table 6.Instruction Set for the M93C56 and M93C66 . . . . . . . . . . . . . . . . . . . . . . . . . . . . . . . . . .7 Table 7.Instruction Set for the M93C76 and M93C86 . . . . . . . . . . . . . . . . . . . . . . . . . . . . . . . . . .7 Read . . . . . . . . . . . . . . . . . . . . . . . . . . . . . . . . . . . . . . . . . . . . . . . . . . . . . . . . . . . . . . . . . . . . . . . . .8 Erase/Write Enable and Disable. . . . . . . . . . . . . . . . . . . . . . . . . . . . . . . . . . . . . . . . . . . . . . . . . . .8 Figure 4.READ, WRITE, EWEN, EWDS Sequences. . . . . . . . . . . . . . . . . . . . . . . . . . . . . . . . . . . .8 Erase. . . . . . . . . . . . . . . . . . . . . . . . . . . . . . . . . . . . . . . . . . . . . . . . . . . . . . . . . . . . . . . . . . . . . . . . .9 Write . . . . . . . . . . . . . . . . . . . . . . . . . . . . . . . . . . . . . . . . . . . . . . . . . . . . . . . . . . . . . . . . . . . . . . . . .9 Figure 5.ERASE, ERAL Sequences . . . . . . . . . . . . . . . . . . . . . . . . . . . . . . . . . . . . . . . . . . . . . . . .9 Erase All. . . . . . . . . . . . . . . . . . . . . . . . . . . . . . . . . . . . . . . . . . . . . . . . . . . . . . . . . . . . . . . . . . . . .10 Write All . . . . . . . . . . . . . . . . . . . . . . . . . . . . . . . . . . . . . . . . . . . . . . . . . . . . . . . . . . . . . . . . . . . . .10 Figure 6.WRAL Sequence. . . . . . . . . . . . . . . . . . . . . . . . . . . . . . . . . . . . . . . . . . . . . . . . . . . . . . .10READY/BUSY STATUS . . . . . . . . . . . . . . . . . . . . . . . . . . . . . . . . . . . . . . . . . . . . . . . . . . . . . . . . . . . .11 COMMON I/O OPERATION . . . . . . . . . . . . . . . . . . . . . . . . . . . . . . . . . . . . . . . . . . . . . . . . . . . . . . . . .11CLOCK PULSE COUNTER . . . . . . . . . . . . . . . . . . . . . . . . . . . . . . . . . . . . . . . . . . . . . . . . . . . . . . . . .11 Figure 7.Write Sequence with One Clock Glitch . . . . . . . . . . . . . . . . . . . . . . . . . . . . . . . . . . . . . .11MAXIMUM RATING. . . . . . . . . . . . . . . . . . . . . . . . . . . . . . . . . . . . . . . . . . . . . . . . . . . . . . . . . . . . . . . .12 Table 8.Absolute Maximum Ratings. . . . . . . . . . . . . . . . . . . . . . . . . . . . . . . . . . . . . . . . . . . . . . .12DC AND AC PARAMETERS. . . . . . . . . . . . . . . . . . . . . . . . . . . . . . . . . . . . . . . . . . . . . . . . . . . . . . . . .13 Table 9.Operating Conditions (M93Cx6) . . . . . . . . . . . . . . . . . . . . . . . . . . . . . . . . . . . . . . . . . . .13 Table 10.Operating Conditions (M93Cx6-W) . . . . . . . . . . . . . . . . . . . . . . . . . . . . . . . . . . . . . . . . .13 Table 11.Operating Conditions (M93Cx6-R) . . . . . . . . . . . . . . . . . . . . . . . . . . . . . . . . . . . . . . . . .13 Table 12.AC Measurement Conditions (M93Cx6) . . . . . . . . . . . . . . . . . . . . . . . . . . . . . . . . . . . . .14 Table 13.AC Measurement Conditions (M93Cx6-W and M93Cx6-R) . . . . . . . . . . . . . . . . . . . . . .14 Figure 8.AC Testing Input Output Waveforms. . . . . . . . . . . . . . . . . . . . . . . . . . . . . . . . . . . . . . . .142/31M93C86, M93C76, M93C66, M93C56, M93C46Table 14.Capacitance. . . . . . . . . . . . . . . . . . . . . . . . . . . . . . . . . . . . . . . . . . . . . . . . . . . . . . . . . . .14 Table 15.DC Characteristics (M93Cx6, Device Grade 6). . . . . . . . . . . . . . . . . . . . . . . . . . . . . . . .15 Table 16.DC Characteristics (M93Cx6, Device Grade 7 or 3) . . . . . . . . . . . . . . . . . . . . . . . . . . . .15 Table 17.DC Characteristics (M93Cx6-W, Device Grade 6) . . . . . . . . . . . . . . . . . . . . . . . . . . . . .16 Table 18.DC Characteristics (M93Cx6-W, Device Grade 7 or 3). . . . . . . . . . . . . . . . . . . . . . . . . .17 Table 19.DC Characteristics (M93Cx6-R) . . . . . . . . . . . . . . . . . . . . . . . . . . . . . . . . . . . . . . . . . . .17 Table 20.AC Characteristics (M93Cx6, Device Grade 6, 7 or 3) . . . . . . . . . . . . . . . . . . . . . . . . . .18 Table 21.AC Characteristics (M93Cx6-W, Device Grade 6). . . . . . . . . . . . . . . . . . . . . . . . . . . . . .19 Table 22.AC Characteristics (M93Cx6-W, Device Grade 7 or 3). . . . . . . . . . . . . . . . . . . . . . . . . .20 Table 23.AC Characteristics (M93Cx6-R) . . . . . . . . . . . . . . . . . . . . . . . . . . . . . . . . . . . . . . . . . . .21 Figure 9.Synchronous Timing (Start and Op-Code Input). . . . . . . . . . . . . . . . . . . . . . . . . . . . . . .22 Figure 10.Synchronous Timing (Read or Write) . . . . . . . . . . . . . . . . . . . . . . . . . . . . . . . . . . . . . . .22 Figure 11.Synchronous Timing (Read or Write) . . . . . . . . . . . . . . . . . . . . . . . . . . . . . . . . . . . . . . .22PACKAGE MECHANICAL . . . . . . . . . . . . . . . . . . . . . . . . . . . . . . . . . . . . . . . . . . . . . . . . . . . . . . . . . .23Figure 12.PDIP8 – 8 pin Plastic DIP, 0.25mm lead frame, Package Outline . . . . . . . . . . . . . . . . .23 Table 24.PDIP8 – 8 pin Plastic DIP, 0.25mm lead frame, Package Mechanical Data. . . . . . . . . .23 Figure 13.SO8 narrow – 8 lead Plastic Small Outline, 150 mils body width, Package Outline . . . .24 Table 25.SO8 narrow – 8 lead Plastic Small Outline, 150 mils body width, Package Mechanical Data 24Figure 14.UFDFPN8 (MLP8) 8-lead Ultra thin Fine pitch Dual Flat Package No lead 2x3mm², Outline 25Table 26.UFDFPN8 (MLP8) 8-lead Ultra thin Fine pitch Dual Flat Package No lead 2x3mm², Data.25Figure 15.TSSOP8 3x3mm²– 8 lead Thin Shrink Small Outline, 3x3mm² body size, Package Outline 26Table 27.TSSOP8 3x3mm²– 8 lead Thin Shrink Small Outline, 3x3mm² body size, Mechanical Data 26Figure 16.TSSOP8 – 8 lead Thin Shrink Small Outline, Package Outline . . . . . . . . . . . . . . . . . . .27 Table 28.TSSOP8 – 8 lead Thin Shrink Small Outline, Package Mechanical Data. . . . . . . . . . . .27PART NUMBERING . . . . . . . . . . . . . . . . . . . . . . . . . . . . . . . . . . . . . . . . . . . . . . . . . . . . . . . . . . . . . . .28 Table 29.Ordering Information Scheme . . . . . . . . . . . . . . . . . . . . . . . . . . . . . . . . . . . . . . . . . . . . .28 Table 30.How to Identify Current and New Products by the Process Identification Letter. . . . . . .29REVISION HISTORY. . . . . . . . . . . . . . . . . . . . . . . . . . . . . . . . . . . . . . . . . . . . . . . . . . . . . . . . . . . . . . .30 Table 31.Document Revision History. . . . . . . . . . . . . . . . . . . . . . . . . . . . . . . . . . . . . . . . . . . . . . .303/31M93C86, M93C76, M93C66, M93C56, M93C464/31SUMMARY DESCRIPTIONThese electrically erasable programmable memo-ry (EEPROM) devices are accessed through a Se-rial Data Input (D) and Serial Data Output (Q)using the MICROWIRE bus protocol.Table 2. Signal NamesThe memory array organization may be divided into either bytes (x8) or words (x16) which may be selected by a signal applied on Organization Se-lect (ORG). The bit, byte and word sizes of the memories are as shown in Table 3..Table 3. Memory Size versus OrganizationThe M93Cx6 is accessed by a set of instructions,as summarized in Table 4., and in more detail in Table 5. to Table 7.).Table 4. Instruction Set for the M93Cx6A Read Data from Memory (READ) instruction loads the address of the first byte or word to be read in an internal address register. The data at this address is then clocked out serially. The ad-dress register is automatically incremented after the data is output and, if Chip Select Input (S) is held High, the M93Cx6 can output a sequential stream of data bytes or words. In this way, the memory can be read as a data stream from eight to 16384 bits long (in the case of the M93C86), or continuously (the address counter automatically rolls over to 00h when the highest address is reached).Programming is internally self-timed (the external clock signal on Serial Clock (C) may be stopped or left running after the start of a Write cycle) and does not require an Erase cycle prior to the Write instruction. The Write instruction writes 8 or 16 bits at a time into one of the byte or word locations of the M93Cx6. After the start of the programming cy-cle, a Busy/Ready signal is available on Serial Data Output (Q) when Chip Select Input (S) is driv-en High.S Chip Select Input D Serial Data Input Q Serial Data Output C Serial Clock ORG Organisation Select V CC Supply Voltage V SSGroundDevice Number of Bits Number of 8-bit Bytes Number of 16-bit Words M93C861638420481024M93C7681921024512M93C664096512256M93C562048256128M93C46102412864Instruction Description Data READ Read Data from Memory Byte or Word WRITEWrite Data to Memory Byte or WordEWEN Erase/Write Enable EWDS Erase/Write Disable ERASE Erase Byte or Word Byte or WordERAL Erase All Memory WRALWrite All Memory with same DataM93C86, M93C76, M93C66, M93C56, M93C46An internal Power-on Data Protection mechanism in the M93Cx6 inhibits the device when the supply is too low.Figure 3. DIP, SO, TSSOP and MLPNote: 1.See PACKAGE MECHANICAL section for package di-mensions, and how to identify pin-1.2.DU = Don’t Use.The DU (Don’t Use) pin does not contribute to the normal operation of the device. It is reserved for use by STMicroelectronics during test sequences. The pin may be left unconnected or may be con-nected to V CC or V SS. Direct connection of DU to V SS is recommended for the lowest stand-by pow-er consumption.MEMORY ORGANIZATIONThe M93Cx6 memory is organized either as bytes (x8) or as words (x16). If Organization Select (ORG) is left unconnected (or connected to V CC) the x16 organization is selected; when Organiza-tion Select (ORG) is connected to Ground (V SS) the x8 organization is selected. When the M93Cx6 is in stand-by mode, Organization Select (ORG) should be set either to V SS or V CC for minimum power consumption. Any voltage between V SS and V CC applied to Organization Select (ORG) may increase the stand-by current.POWER-ON DATA PROTECTIONTo prevent data corruption and inadvertent write operations during power-up, a Power-On Reset (POR) circuit resets all internal programming cir-cuitry, and sets the device in the Write Disable mode.–At Power-up and Power-down, the device must not be selected (that is, Chip Select Input (S) must be driven Low) until the supplyvoltage reaches the operating value V CCspecified in Table 9. to Table 11..–When V CC reaches its valid level, the device is properly reset (in the Write Disable mode) and is ready to decode and execute incominginstructions.For the M93Cx6 devices (5V range) the POR threshold voltage is around 3V. For the M93Cx6-W (3V range) and M93Cx6-R (2V range) the POR threshold voltage is around 1.5V.5/31M93C86, M93C76, M93C66, M93C56, M93C466/31INSTRUCTIONSThe instruction set of the M93Cx6 devices con-tains seven instructions, as summarized in Table 5. to Table 7.. Each instruction consists of the fol-lowing parts, as shown in Figure 4.:s Each instruction is preceded by a rising edgeon Chip Select Input (S) with Serial Clock (C) being held Low.s A start bit, which is the first ‘1’ read on SerialData Input (D) during the rising edge of Serial Clock (C).s Two op-code bits, read on Serial Data Input(D) during the rising edge of Serial Clock (C). (Some instructions also use the first two bits of the address to define the op-code).sThe address bits of the byte or word that is to be accessed. For the M93C46, the address is made up of 6 bits for the x16 organization or 7 bits for the x8 organization (see Table 5.). For the M93C56 and M93C66, the address is made up of 8 bits for the x16 organization or 9 bits for the x8 organization (see Table 6.). For the M93C76 and M93C86, the address is made up of 10 bits for the x16 organization or 11 bits for the x8 organization (see Table 7.).The M93Cx6 devices are fabricated in CMOS technology and are therefore able to run as slow as 0Hz (static input signals) or as fast as the max-imum ratings specified in Table 20. to Table 23..Table 5. Instruction Set for the M93C46Note: 1.X = Don ’t Care bit.Instruc tionDescriptionStart bit Op-Codex8 Origination (ORG = 0)x16 Origination (ORG = 1)Address 1DataRequiredClock CyclesAddress 1DataRequired Clock CyclesREAD Read Data from Memory 110A6-A0Q7-Q0A5-A0Q15-Q0WRITE Write Data to Memory101A6-A0D7-D018A5-A0D15-D025EWEN Erase/Write Enable 10011X XXXX 1011 XXXX 9EWDS Erase/Write Disable 10000X XXXX 1000 XXXX 9ERASE Erase Byte or Word 111A6-A010A5-A09ERAL Erase All Memory 10010X XXXX 1010 XXXX 9WRALWrite All Memory with same Data10001X XXXXD7-D01801 XXXXD15-D0257/31M93C86, M93C76, M93C66, M93C56, M93C46Table 6. Instruction Set for the M93C56 and M93C66Note: 1.X = Don ’t Care bit.2.Address bit A8 is not decoded by the M93C56.3.Address bit A7 is not decoded by the M93C56.Table 7. Instruction Set for the M93C76 and M93C86Note: 1.X = Don ’t Care bit.2.Address bit A10 is not decoded by the M93C76.3.Address bit A9 is not decoded by the M93C76.Instruc tionDescriptionStart bit Op-Codex8 Origination (ORG = 0)x16 Origination (ORG = 1)Address 1,2DataRequiredClock CyclesAddress 1,3DataRequired Clock CyclesREAD Read Data from Memory 110A8-A0Q7-Q0A7-A0Q15-Q0WRITE Write Data to Memory101A8-A0D7-D020A7-A0D15-D027EWEN Erase/Write Enable 100 1 1XXXXXXX 1211XX XXXX 11EWDS Erase/Write Disable 1000 0XXX XXXX 1200XX XXXX 11ERASE Erase Byte or Word 111A8-A012A7-A011ERAL Erase All Memory 100 1 0XXX XXXX 1210XX XXXX 11WRALWrite All Memory with same Data1000 1XXX XXXXD7-D02001XX XXXXD15-D027Instruc tionDescriptionStart bit Op-Codex8 Origination (ORG = 0)x16 Origination (ORG = 1)Address1,2DataRequiredClock CyclesAddress 1,3DataRequiredClock CyclesREAD Read Data from Memory 110A10-A0Q7-Q0A9-A0Q15-Q0WRITE Write Data to Memory101A10-A0D7-D022A9-A0D15-D029EWEN Erase/Write Enable 10011X XXXX XXXX 1411 XXXX XXXX 13EWDS Erase/Write Disable 10000X XXXX XXXX 1400 XXXX XXXX 13ERASE Erase Byte or Word 111A10-A014A9-A013ERAL Erase All Memory 10010X XXXX XXXX 1410 XXXX XXXX 13WRALWrite All Memory with same Data10001X XXXX XXXXD7-D02201 XXXX XXXXD15-D029M93C86, M93C76, M93C66, M93C56, M93C468/31ReadThe Read Data from Memory (READ) instruction outputs data on Serial Data Output (Q). When the instruction is received, the op-code and address are decoded, and the data from the memory is transferred to an output shift register. A dummy 0bit is output first, followed by the 8-bit byte or 16-bit word, with the most significant bit first. Output data changes are triggered by the rising edge of Serial Clock (C). The M93Cx6 automatically incre-ments the internal address register and clocks out the next byte (or word) as long as the Chip Select Input (S) is held High. In this case, the dummy 0 bit is not output between bytes (or words) and a con-tinuous stream of data can be read.Erase/Write Enable and DisableThe Erase/Write Enable (EWEN) instruction en-ables the future execution of erase or write instruc-tions, and the Erase/Write Disable (EWDS)instruction disables it. When power is first applied,the M93Cx6 initializes itself so that erase and write instructions are disabled. After an Erase/Write En-able (EWEN) instruction has been executed, eras-ing and writing remains enabled until an Erase/Write Disable (EWDS) instruction is executed, or until V CC falls below the power-on reset threshold voltage. To protect the memory contents from ac-cidental corruption, it is advisable to issue the Erase/Write Disable (EWDS) instruction after ev-ery write cycle. The Read Data from Memory (READ) instruction is not affected by the Erase/Write Enable (EWEN) or Erase/Write Disable (EWDS) instructions.M93C86, M93C76, M93C66, M93C56, M93C46EraseThe Erase Byte or Word (ERASE) instruction sets the bits of the addressed memory byte (or word) to 1. Once the address has been correctly decoded, the falling edge of the Chip Select Input (S) starts the self-timed Erase cycle. The completion of the cycle can be detected by monitoring the Ready/ Busy line, as described in the READY/BUSY STA-TUS section.WriteFor the Write Data to Memory (WRITE) instruction, 8 or 16 data bits follow the op-code and address bits. These form the byte or word that is to be writ-ten. As with the other bits, Serial Data Input (D) is sampled on the rising edge of Serial Clock (C).After the last data bit has been sampled, the Chip Select Input (S) must be taken Low before the next rising edge of Serial Clock (C). If Chip Select Input (S) is brought Low before or after this specific time frame, the self-timed programming cycle will not be started, and the addressed location will not be programmed. The completion of the cycle can be detected by monitoring the Ready/Busy line, as described later in this document.Once the Write cycle has been started, it is inter-nally self-timed (the external clock signal on Serial Clock (C) may be stopped or left running after the start of a Write cycle). The cycle is automatically preceded by an Erase cycle, so it is unnecessary to execute an explicit erase instruction before a Write Data to Memory (WRITE) instruction.9/31M93C86, M93C76, M93C66, M93C56, M93C4610/31Erase AllThe Erase All Memory (ERAL) instruction erases the whole memory (all memory bits are set to 1).The format of the instruction requires that a dum-my address be provided. The Erase cycle is con-ducted in the same way as the Erase instruction (ERASE). The completion of the cycle can be de-tected by monitoring the Ready/Busy line, as de-scribed in the READY/BUSY STATUS section.Write AllAs with the Erase All Memory (ERAL) instruction,the format of the Write All Memory with same Data (WRAL) instruction requires that a dummy ad-dress be provided. As with the Write Data to Mem-ory (WRITE) instruction, the format of the Write All Memory with same Data (WRAL) instruction re-quires that an 8-bit data byte, or 16-bit data word,be provided. This value is written to all the ad-dresses of the memory device. The completion of the cycle can be detected by monitoring the Ready/Busy line, as described next.While the Write or Erase cycle is underway, for a WRITE, ERASE, WRAL or ERAL instruction, the Busy signal (Q=0) is returned whenever Chip Se-lect Input (S) is driven High. (Please note, though, that there is an initial delay, of t SLSH, before this status information becomes available). In this state, the M93Cx6 ignores any data on the bus. When the Write cycle is completed, and Chip Se-lect Input (S) is driven High, the Ready signal (Q=1) indicates that the M93Cx6 is ready to re-ceive the next instruction. Serial Data Output (Q) remains set to 1 until the Chip Select Input (S) is brought Low or until a new start bit is decoded. COMMON I/O OPERATIONSerial Data Output (Q) and Serial Data Input (D) can be connected together, through a current lim-iting resistor, to form a common, single-wire data bus. Some precautions must be taken when oper-ating the memory in this way, mostly to prevent a short circuit current from flowing when the last ad-dress bit (A0) clashes with the first data bit on Se-rial Data Output (Q). Please see the application note AN394 for details. CLOCK PULSE COUNTERIn a noisy environment, the number of pulses re-ceived on Serial Clock (C) may be greater than the number delivered by the master (the microcontrol-ler). This can lead to a misalignment of the instruc-tion of one or more bits (as shown in Figure 7.) and may lead to the writing of erroneous data at an er-roneous address.To combat this problem, the M93Cx6 has an on-chip counter that counts the clock pulses from the start bit until the falling edge of the Chip Select In-put (S). If the number of clock pulses received is not the number expected, the WRITE, ERASE, ERAL or WRAL instruction is aborted, and the contents of the memory are not modified.The number of clock cycles expected for each in-struction, and for each member of the M93Cx6 family, are summarized in Table 5. to Table 7.. For example, a Write Data to Memory (WRITE) in-struction on the M93C56 (or M93C66) expects 20 clock cycles (for the x8 organization) from the start bit to the falling edge of Chip Select Input (S). That is:1 Start bit+ 2 Op-code bits+ 9 Address bits+ 8 Data bits11/3112/31MAXIMUM RATINGStressing the device above the rating listed in the Absolute Maximum Ratings" table may cause per-manent damage to the device. These are stress ratings only and operation of the device at these or any other conditions above those indicated in the Operating sections of this specification is not im-plied. Exposure to Absolute Maximum Rating con-ditions for extended periods may affect device reliability. Refer also to the STMicroelectronics SURE Program and other relevant quality docu-ments.Table 8. Absolute Maximum RatingsNote: pliant with JEDEC Std J-STD-020B (for small body, Sn-Pb or Pb assembly), the ST ECOPACK ® 7191395 specification, andthe European directive on Restrictions on Hazardous Substances (RoHS) 2002/95/EU 2.JEDEC Std JESD22-A114A (C1=100pF, R1=1500 Ω, R2=500 Ω)Symbol ParameterMin.Max.Unit T STG Storage Temperature–65150°C T LEAD Lead T emperature during Soldering See note 1°C V OUT Output range (Q = V OH or Hi-Z)–0.50V CC +0.5V V IN Input range –0.50V CC +1V V CC Supply Voltage–0.50 6.5V V ESDElectrostatic Discharge Voltage (Human Body model) 2–40004000V13/31DC AND AC PARAMETERSThis section summarizes the operating and mea-surement conditions, and the DC and AC charac-teristics of the device. The parameters in the DC and AC Characteristic tables that follow are de-rived from tests performed under the Measure-ment Conditions summarized in the relevant tables. Designers should check that the operating conditions in their circuit match the measurement conditions when relying on the quoted parame-ters.Table 9. Operating Conditions (M93Cx6)Table 10. Operating Conditions (M93Cx6-W)Table 11. Operating Conditions (M93Cx6-R)Symbol ParameterMin.Max.Unit V CCSupply Voltage4.55.5V T AAmbient Operating Temperature (Device Grade 6)–4085°C Ambient Operating Temperature (Device Grade 7)–40105°C Ambient Operating Temperature (Device Grade 3)–40125°CSymbol ParameterMin.Max.Unit V CCSupply Voltage2.5 5.5V T AAmbient Operating Temperature (Device Grade 6)–4085°C Ambient Operating Temperature (Device Grade 7)–40105°C Ambient Operating Temperature (Device Grade 3)–40125°CSymbol ParameterMin.Max.Unit V CC Supply Voltage1.8 5.5V T AAmbient Operating Temperature (Device Grade 6)–4085°C14/31Table 12. AC Measurement Conditions (M93Cx6)Note: 1.Output Hi-Z is defined as the point where data out is no longer driven.Table 13. AC Measurement Conditions (M93Cx6-W and M93Cx6-R)Note: 1.Output Hi-Z is defined as the point where data out is no longer driven.Table 14. CapacitanceNote:Sampled only, not 100% tested, at T A =25°C and a frequency of 1MHz.Symbol Parameter Min.Max.Unit C LLoad Capacitance 100pFInput Rise and Fall Times 50ns Input Pulse Voltages0.4V to 2.4V V Input Timing Reference Voltages 1.0V and 2.0V V Output Timing Reference Voltages0.8V and 2.0VVSymbol Parameter Min.Max.Unit C LLoad Capacitance 100pFInput Rise and Fall Times 50ns Input Pulse Voltages0.2V CC to 0.8V CC V Input Timing Reference Voltages 0.3V CC to 0.7V CC V Output Timing Reference Voltages0.3V CC to 0.7V CCVSymbol ParameterTest Condition MinMax Unit C OUT OutputCapacitance V OUT = 0V 5pF C INInputCapacitanceV IN = 0V5pF15/31Table 15. DC Characteristics (M93Cx6, Device Grade 6)Note: 1.Current product: identified by Process Identification letter F or M.2.New product: identified by Process Identification letter W or G or S.Table 16. DC Characteristics (M93Cx6, Device Grade 7 or 3)Note: 1.Current product: identified by Process Identification letter F or M.2.New product: identified by Process Identification letter W or G or S.Symbol ParameterTest Condition Min.Max.Unit I LI Input Leakage Current 0V ≤ V IN ≤ V CC±2.5 µA I LOOutput Leakage Current0V ≤ V OUT ≤ V CC , Q in Hi-Z ±2.5 µA I CCSupply CurrentV CC = 5V, S = V IH , f = 1 MHz, CurrentProduct 11.5 mA V CC = 5V, S = V IH , f = 2 MHz, NewProduct 22mAI CC1Supply Current (Stand-by)V CC = 5V , S = V SS , C = V SS ,ORG = V SS or V CC , Current Product 150 µA V CC = 5V , S = V SS , C = V SS , ORG = V SS or V CC , New Product 215 µA V IL Input Low Voltage V CC = 5V ± 10%–0.450.8 V V IH Input High Voltage V CC = 5V ± 10%2V CC + 1 V V OL Output Low Voltage V CC = 5V, I OL = 2.1mA 0.4 V V OHOutput High VoltageV CC = 5V , I OH = –400µA2.4VSymbol ParameterTest Condition Min.Max.UnitI LI Input Leakage Current 0V ≤ V IN ≤ V CC±2.5 µA I LOOutput Leakage Current0V ≤ V OUT ≤ V CC , Q in Hi-Z ±2.5 µA I CCSupply CurrentV CC = 5V, S = V IH , f = 1 MHz, CurrentProduct 11.5 mA V CC = 5V, S = V IH , f = 2 MHz, NewProduct 22 mA I CC1Supply Current (Stand-by)V CC = 5V , S = V SS , C = V SS ,ORG = V SS or V CC , Current Product 150 µA V CC = 5V , S = V SS , C = V SS , ORG = V SS or V CC , New Product 215 µA V IL Input Low Voltage V CC = 5V ± 10%–0.450.8 V V IH Input High Voltage V CC = 5V ± 10%2V CC + 1 V V OL Output Low Voltage V CC = 5V, I OL = 2.1mA 0.4 V V OHOutput High VoltageV CC = 5V , I OH = –400µA2.4V。
DW9T系列三相智能电量仪表说明书

该系列仪表可广泛应用于控制系统、SCADA系统和能源管理系统、变电站自动化、配电网自动化、小区电力监控、工业自动化、智能建筑、智能型配电盘、开关柜中;有安装方便、接线简单、维护方便、工程量小、现场可编程设置输入参数的特点。
警告 如果不按说明书操作会发生意外,而且会导致产品毁坏。
DW9T系列三相智能电量仪表说明书⊙测量项目:电压/电流/有功功率/无功功率/频率/功率因数/等,共28个电参数;⊙真有效值测量,电压、电流在0~420HZ时可保证测量精度;⊙最多四路开关量输入和最多三路开关量输出,输入/输出全隔离;⊙具有遥信、遥控功能;⊙具有可编程变送输出功能,可对电压/电流/有功功率/无功功率/频率/功率因数变送输出;⊙具有RS485通信接口,采用Modbus RTU通信协议;⊙具有二路电能脉冲输出,最多三路可编程报警输出;⊙对有功电度/无功电度有掉电保护功能;⊙可参考的双向有功电度/无功电度记录;⊙具有8时段,4种费率统计功能;⊙32条事件记录功能,可记录上电事件,清电能事件,修改参数以及报警动作等事件;⊙320×240像素彩色中英文液晶显示;特点一、仪表型号三、主要技术参数输入测量范围: B:5A×220V D:其它输入: 30:三相三线或三相四线输入 38:三相三线或三相四线输入带通讯 报警功能: C:表示两路报警 A:表示无报警 D:三路报警输出功能: R:表示无变送输出 D:表示变送输出 DC 4~20mA 2D:两路变送输出 DC:4~20mA DW系列三相电量表□□□□-DW9T 二、型号说明外形尺寸(mm): 9:96W×96H×104.6L L:表示段码LCD显示 T:表示TFT液晶显示 无:数码管 无RS485 无 RS485 无RS485无无 无 无 无 无报警方式脉冲输出功能变送功能 通讯功能 开关量输入 复费率DW9T-A30B DW9T-A38B DW9T-RC30B DW9T-RC38B DW9T-DD30B DW9T-DD38B 型 号22332路无无RS485 无 RS485 无RS485无无 无 无 无 无DW9T-A30BF DW9T-A38BF DW9T-RC30BF DW9T-RC38BF DW9T-2DC30BF DW9T-2DC38BF22222路有三相四线、三相三线3*220/380V 持续:1.2倍<1VA (每相)≥300K ΩRMS测量 精度0.2%F.S(作电工表应用时,电压可直接接入600V相电压进行测量),高达420HZ可以保证测量精度5A(经互感器接入)持续:1.2倍 瞬时:10倍/10S <0.4VA (每相)<20m Ω4~20mA 4~20mA 2×4~20mA 2×4~20mA一路有功电能脉冲一路无功电能脉冲一路有功电能脉冲一路无功电能脉冲电流阻抗电流功耗参比电压网络电流阻抗电压过负荷电压精度电压阻抗额定电流电流过负荷四、面板说明五、菜单修改说明查看测量值及仪表工作状态说明:复费率(使能情况下)等界面切换显示。
三汇示波器说明书(Ver1.0)
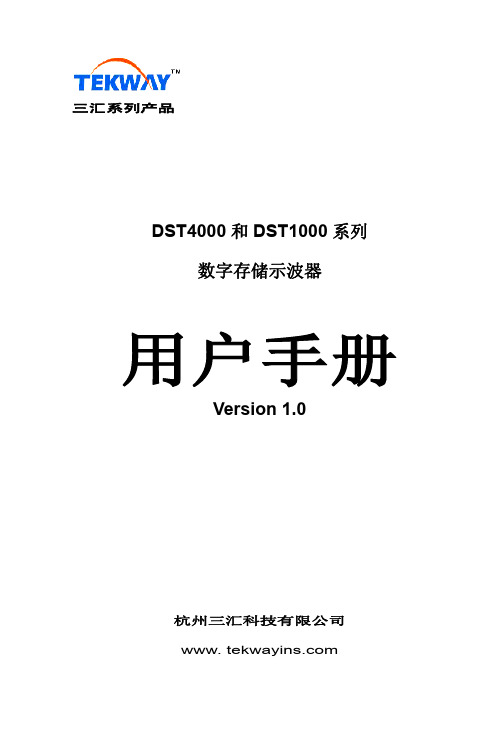
DST4000 和 DST1000 系列数字存储示波器用户手册
i
目录
5.1 显示区 ........................................................................................ 20 5.2 信息区域..................................................................................... 23 5.3 波形显示..................................................................................... 23
三汇系列产品
DST4000 和 DST1000 系列 数字存储示波器
Version 1.0
杭州三汇科技有限公司 www.
目录
目录
目 录 ...........................................................................................................i 版权申明 .......................................................................................................................................................................v 第 1 章 安全事项......................................................................................... 1
飞龙 wi
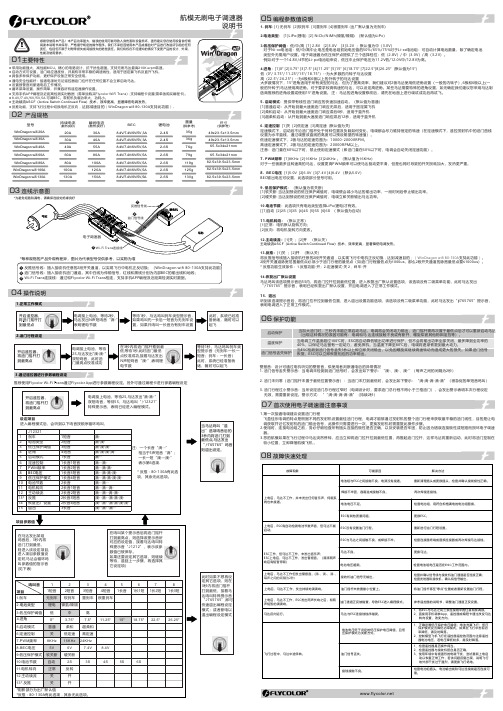
持续电流(散热良好)瞬间电流(散热良好)BEC尺寸(供参考)重量(供参考)20A 30A 40A 60A 30A 40A 55A 80A 锂电池型号79g 35g 36g 76g 49x23.5x13.5mm 65.5x34x21mm● 反推功能,支持飞行过程中切换电机正反向,达到减速目的(WinDragon wifi 80-130A 支持此功能)。
2-4S 2-4S 2-6S 2-6S 8.4V/7.4V/6V/5V ,5A 80A 100A 119g 2-6S 100A 120A 125g 2-6S 130A150A130g82.5x39.5x23.5mm2-6S航模无刷电子调速器WinDragon wifi 130AWinDragon wifi 100A WinDragon wifi 80A WinDragon wifi 60A WinDragon wifi 30A WinDragon wifi 40A WinDragon wifi 20A 8.4V/7.4V/6V/5V ,5A 8.4V/7.4V/6V/5V ,5A 8.4V/7.4V/6V/5V,5A8.4V/7.4V/6V/5V ,5A 82.5x39.5x23.5mm 82.5x39.5x23.5mm 65.5x34x21mm 49x23.5x13.5mm 02 产品规格04 操作说明1.正常工作模式2.油门行程设定3.通过遥控器进行参数编程设定推荐使用Flycolor Wi-Fi Trans 通过Flycolor App 进行参数编程设定。
另外可通过编程卡进行参数编程设定1. 刹车: [1] 无刹车 [2]软刹车 [3]重刹车 [4]很重刹车 (出厂默认值为无刹车)2.电池类型: [1]LiPo(锂电) [2] NiCb/NiMh(镍氢/镍隔) (默认值为Li Po )3.低压保护阈值:低/中/高 [1] 2.8V [2]3.0V [3]3.2V ;默认值为中(3.0V)对于Ni-xx电池组:低/中/高中止电压是电池组初始电压值的50%/65%/75%对于Li-xx电池组:可自动计算电池数量,除了确定电池 类型外无需用户设置。
2008年Ford自动变速箱组件目录说明书

1622008 AUTOMATIC TRANSMISSION KIT & COMPONENTS CATALOG ©2008 PARKER HANNIFIN CORP. ALL RIGHTS RESERVED3790103008397797405R55N / 5R55S / 5R55WRWD 5 SpeedA544510034070670Input ShaftO.Dr. Ring GearO.Dr. CenterShaft783Center SupportInterm. BandDirect DrumForward ClutchForward PlanetReverse BandReverse DrumLow Sprag310037179520036178530311914363912911913910896904896437490996V.B.Parts741E414494765-6370Case313321320Valve Body917747765746322420002OHK Kit004Master L/Steels Kit 006Master 030External Seal Kit1632008 AUTOMATIC TRANSMISSION KIT & COMPONENTS CATALOG ©2008 PARKER HANNIFIN CORP . ALL RIGHTS RESERVEDRWD 5 Speed5R55N / 5R55S / 5R55W862981971961560961971985879565126106146861*229964974877564285872962972104124552894Intermediate Sprag690074266Park Gear264847Park Pawl Assy995-1995-2995-3995916-2916-3919922915916-2916-3919922916263EDA181554770Ext. Hsg.781493305678Output ShaftO.Dr. Band StrutInterm. Band Strut268841Internal Linkage991-2991-3994799991-4761P-4991072410992Yoke1642008 AUTOMATIC TRANSMISSION KIT & COMPONENTS CATALOG©2008 PARKER HANNIFIN CORP. ALL RIGHTS RESERVED*Prefix Letter ‘T’ denotes Toledo-Trans Kit (TTK) Brand Transmission Kits *Prefix Letter ‘B’ denotes Bryco Brand Transmission Kits002.............T16002AP......Overhaul Kit, 5R55N (With Bonded Pistons) 1999-Up ..............................................................1..........002.............T16002GP......Overhaul Kit, 5R55S/5R55W (With Bonded Pistons) 2002-Up..................................................1..........004.............T16004AP......Master L/Steels Kit, 5R55N (With Bonded Pistons) 1999-Up ....................................................1..........004.............T16004GP......Master L/Steels Kit, 5R55S/5R55W (With Bonded Pistons) 2002-Up .......................................1..........006.............T16006AP......Master W/Steels Kit, 5R55N (With Bonded Pistons) 1999-Up...................................................1..........006.............T16006GP......Master W/Steels Kit, 5R55S/5R55W (With Bonded Pistons) 2002-Up ......................................1..........E300...........45019............Gasket, 5R55N Bottom Pan (Plastic With Silicon Bead) OE Style (With Large Holes) 1999-Up 1..........XW4Z-7A191CA D305...........45097668......Gasket, 5R55N/5R55S/5R55W Extension Housing To Case 1999-Up......................................1..........XW4Z-7086-AA A309..........41217............Gasket, 5R55N/5R55S/5R55W Pump Bolt Washer...................................................................AR ........A310..........45097667......Gasket, 5R55N/5R55S/5R55W Pump 1999-Up..........................................................................1..........XW4Z-7A136AB A311...........1988096........O-Ring, 5R55N/5R55S/5R55W Pump Cover 1999-Up ...............................................................1..........XW4Z-7A248AA A313..........1994747........O-Ring, 5R55N Inner Pump Gear 1999-Up.................................................................................1..........F77Z-7L323AA E320...........45097692......Gasket, 5R55N Valve Body Separator Plate To Case 1999-Up ................................................1..........XW4Z-7D100-BF E320...........45097738......Gasket, 5R55S/5R55W Valve Body Separator Plate To Case (Upper) 2002-Up......................1..........1L2Z-7Z490AB-1A070..........70243V..........Seal, 5R55N/5R55S/5R55W Front (No Flange) (Rubber Coated) 1999-Up ..............................1..........F77Z-7A248AA D072...........70083............Seal, 5R55N Linkage 1999-Up ..................................................................................................1..........D5AZ-7B498A D074...........70283............Seal, 5R55N Rear 2WD 2000-Up ...............................................................................................1..........XW4Z-7052AA D074...........70205............Seal, 5R55S/5R55W Rear (W/Long Boot) 2WD 2002-Up .........................................................1..........F6UZ-7052A D074...........70282............Seal, 5R55S/5R55W Extension Housing 4X4 2002-Up .............................................................1..........1L2Z-7052BA175.............6358..............Ring Kit, 5R55N/5R55S/5R55W (2 Metal 4PTFE 2 Torlon Rings) 1999-Up ...............................1..........A178..........45060279......Ring, 5R55N, 5R55W, 5R55S Pump Support (Lock-Up) 1999-Up .............................................1..........B181...........TAW- 2212....Ring, 5R55N, 5R55W, 5R55S Forward Clutch Cylinder 1999-Up .............................................2..........D184...........45060265......Ring, 5R55N, 5R55W, 5R55S Output Shaft 1999-Up.................................................................1..........A179..........30308............Ring, 5R55N, 5R55W, 5R55S Overdrive Brake Drum 1999-Up.................................................2..........B179...........30308P ..........Ring, 5R55N, 5R55W, 5R55S Direct Clutch (Center Support) 1999-Up Torlon .........................2..........119.............45082NR........Friction Module, 5R55N 1999-Up................................................................................................1..........119.............45082LR........Friction Module, 5R55S/5R55W 2002-Up...................................................................................1..........E010...........45040N ..........Filter, 5R55N (3/8” Tall Pick-up Tube) 1999-Up ..........................................................................1..........XW4Z-7A098BB E010...........F-340.............Filter, 5R55S/5R55W (2 1/4” Tall Pick-Up Tube) 2002-Up..........................................................1..........1L2Z-7A098AC5R55N / 5R55S / 5R55WRWD 5 Speed1652008 AUTOMATIC TRANSMISSION KIT & COMPONENTS CATALOG ©2008 PARKER HANNIFIN CORP. ALL RIGHTS RESERVEDB022...........45090............Band, 5R55N Overdrive/Intermediate (Hi-Energy) 1999-Up......................................................2..........XW4Z-7D034BA 030.............45030G..........Bushing Kit, 5R55N/5R55S/5R55W 1999-Up.............................................................................1..........A034..........31530............Bushing, 5R55N/5R55S/5R55W Pump Cover 1999-Up .............................................................1..........A036..........31531............Bushing, 5R55N/5R55S/5R55W Overdrive Sun Gear 1999-Up................................................1..........A036..........45039............Bushing, 5R55N/5R55S/5R55W Stator (Front) 1999-Up ...........................................................1..........A037..........31532............Bushing, 5R55N/5R55S/5R55W Stator (Rear) 1999-Up............................................................1..........A046..........31533............Bushing, 5R55N/5R55S/5R55W Coast Clutch Drum e 56036A................................................................................................................................1..........B211...........45176A..........Washer, 5R55N/5R55S/5R55W Pump To Coast Clutch Drum .063" (Plastic) 1999-Up.............1..........F7TZ-7D014TA B211...........45176B ..........Washer, 5R55N/5R55S/5R55W Pump To Coast Clutch Drum .071" (Plastic) 1999-Up.............1..........F7TZ-7D014MA B211...........45176C ..........Washer, 5R55N/5R55S/5R55W Pump To Coast Clutch Drum .075" (Plastic) 1999-Up.............1..........F7TZ-7D014NA B211...........45176D ..........Washer, 5R55N/5R55S/5R55W Pump To Coast Clutch Drum .079" (Plastic) 1999-Up.............1..........F7TZ-7D014PA B211...........45176E ..........Washer, 5R55N/5R55S/5R55W Pump To Coast Clutch Drum .083" (Plastic) 1999-Up.............1..........F7TZ-7D014RA B211...........45176F ..........Washer, 5R55N/5R55S/5R55W Pump To Coast Clutch Drum .087" (Plastic) 1999-Up.............1..........F7TZ-7D014SA C232...........45145............Washer, 5R55N/5R55S/5R55W Bearing to Forward Hub (Solid Bronze) 1999-Up .................1..........FOTZ-7D090A D263...........45077............Washer, 5R55N/5R55S/5R55W Parking Gear To Case 1999-Up ..............................................1..........D4ZZ-7B368-AD410...........D56955J ........Switch, 5R55N Neutral Safety (12 Prong Connector) 1999-Up ...............................................1..........XW4Z-7F293AA E922...........33991............Nut, 5R55N/S/W Band 1999-Up .................................................................................................2..........380850-SRWD 5 Speed5R55N / 5R55S / 5R55W。
LM346M中文资料

LM146/LM346Programmable Quad Operational AmplifiersGeneral DescriptionThe LM146series of quad op amps consists of four indepen-dent,high gain,internally compensated,low power,pro-grammable amplifiers.Two external resistors (R SET )allow the user to program the gain bandwidth product,slew rate,supply current,input bias current,input offset current and in-put noise.For example,the user can trade-off supply current for bandwidth or optimize noise figure for a given source re-sistance.In a similar way,other amplifier characteristics can be tailored to the application.Except for the two program-ming pins at the end of the package,the LM146pin-out is the same as the LM124and LM148.Features(I SET =10µA)n Programmable electrical characteristics n Battery-powered operationn Low supply current:350µA/amplifiern Guaranteed gain bandwidth product:0.8MHz min n Large DC voltage gain:120dB n Low noise voltage:28n Wide power supply range:±1.5V to ±22V n Class AB output stage–no crossover distortion n Ideal pin out for Biquad active filtersn Input bias currents are temperature compensated Connection DiagramPROGRAMMING EQUATIONSTotal Supply Current =1.4mA (I SET /10µA)Gain Bandwidth Product =1MHz (I SET /10µA)Slew Rate =0.4V/µs (I SET /10µA)Input Bias Current ≅50nA (I SET /10µA)I SET =Current into pin 8,pin 9(see schematic-diagram)Dual-In-Line PackageDS005654-1Top ViewOrder Number LM146J,LM146J/883,LM346M or LM346N See NS Package Number J16A,M16A or N16AMay 1999LM146/LM346Programmable Quad Operational Amplifiers©1999National Semiconductor Corporation Schematic DiagramDS005654-2 2Absolute Maximum Ratings(Notes1,5)If Military/Aerospace specified devices are required,please contact the National Semiconductor Sales Office/ Distributors for availability and specifications.LM146LM346Supply Voltage±22V±18V Differential Input Voltage(Note1)±30V±30VCM Input Voltage(Note1)±15V±15VPower Dissipation(Note2)900mW500mWOutput Short-Circuit Duration(Note3)Continuous Continuous Operating Temperature Range−55˚C to+125˚C0˚C to+70˚C Maximum Junction Temperature150˚C100˚CStorage Temperature Range−65˚C to+150˚C−65˚C to+150˚CLead Temperature(Soldering,10seconds)260˚C260˚CThermal Resistance(θjA),(Note2)Cavity DIP(J)Pd900mW900mWθjA100˚C/W100˚C/W Small Outline(M)θjA115˚C/WMolded DIP(N)Pd500mWθjA90˚C/WSoldering InformationDual-In-Line PackageSoldering(10seconds)+260˚C+260˚CSmall Outline PackageVapor Phase(60seconds)+215˚C+215˚CInfrared(15seconds)+220˚C+220˚CSee AN-450“Surface Mounting Methods and Their Effect on Product Reliability”for other methods of soldering surface mount de-vices.ESD rating is to be determined.DC Electrical Characteristics(V S=±15V,I SET=10µA),(Note4)Parameter Conditions LM146LM346UnitsMin Typ Max Min Typ MaxInput Offset Voltage V CM=0V,R S≤50Ω,T A=25˚C0.550.56mV Input Offset Current V CM=0V,T A=25˚C2202100nA Input Bias Current V CM=0V,T A=25˚C5010050250nA Supply Current(4Op Amps)T A=25˚C 1.4 2.0 1.4 2.5mA Large Signal Voltage Gain R L=10kΩ,∆V OUT=±10V,1001000501000V/mVT A=25˚CInput CM Range T A=25˚C±13.5±14±13.5±14VCM Rejection Ratio R S≤10kΩ,T A=25˚C8010070100dB Power Supply Rejection Ratio R S≤10kΩ,T A=25˚C,8010074100dBV S=±5to±15VOutput Voltage Swing R L≥10kΩ,T A=25˚C±12±14±12±14V Short-Circuit T A=25˚C5203552035mA Gain Bandwidth Product T A=25˚C0.8 1.20.5 1.2MHz Phase Margin T A=25˚C6060Deg Slew Rate T A=25˚C0.40.4V/µs Input Noise Voltage f=1kHz,T A=25˚C2828Channel Separation R L=10kΩ,∆V OUT=0V to120120dB±12V,T=25˚CAInput Resistance T A=25˚C 1.0 1.0MΩInput Capacitance T A=25˚C 2.0 2.0pF Input Offset Voltage V CM=0V,R S≤50Ω0.560.57.5mV3DC Electrical Characteristics(Continued)(V S=±15V,I SET=10µA),(Note4)Parameter Conditions LM146LM346UnitsMin Typ Max Min Typ MaxInput Offset Current V CM=0V2252100nA Input Bias Current V CM=0V5010050250nA Supply Current(4Op Amps) 1.7 2.2 1.7 2.5mA Large Signal Voltage Gain R L=10kΩ,∆V OUT=±10V501000251000V/mV Input CM Range±13.5±14±13.5±14V CM Rejection Ratio R S≤50Ω7010070100dB Power Supply Rejection Ratio R S≤50Ω,7610074100dBV S=±5V to±15VOutput Voltage Swing R L≥10kΩ±12±14±12±14V DC Electrical Characteristic(V S=±15V,I SET=10µA)Parameter Conditions LM146LM346UnitsMin Typ Max Min Typ MaxInput Offset Voltage V CM=0V,R S≤50Ω,0.550.57mVT A=25˚CInput Bias Current V CM=0V,T A=25˚C7.5207.5100nA Supply Current(4Op Amps)T A=25˚C140250140300µA Gain Bandwidth Product T A=25˚C8010050100kHzDC Electrical Characteristics(V S=±1.5V,I SET=10µA)Parameter Conditions LM146LM346UnitsMin Typ Max Min Typ MaxInput Offset Voltage V CM=0V,R S≤50Ω,0.550.57mV T A=25˚CInput CM Range T A=25˚C±0.7±0.7V CM Rejection Ratio R S≤50Ω,T A=25˚C8080dB Output Voltage Swing R L≥10kΩ,T A=25˚C±0.6±0.6V Note1:For supply voltages less than±15V,the absolute maximum input voltage is equal to the supply voltage.Note2:The maximum power dissipation for these devices must be derated at elevated temperatures and is dictated by T jMAX,θjA,and the ambient temperature, T A.The maximum available power dissipation at any temperature is P d=(T jMAX-T A)/θjA or the25˚C P dMAX,whichever is less.Note3:Any of the amplifier outputs can be shorted to ground indefinitely;however,more than one should not be simultaneously shorted as the maximum junction temperature will be exceeded.Note4:These specifications apply over the absolute maximum operating temperature range unless otherwise noted.Note5:Refer to RETS146X for LM146J military specifications.4Typical Performance CharacteristicsInput Bias Current vs I SETDS005654-44Supply Current vs I SETDS005654-45Open Loop Voltage Gain vs I SETDS005654-46Slew Rate vs I SETDS005654-47Gain Bandwidth Product vs I SETDS005654-48Phase Margin vs I SETDS005654-49Input Offset Voltage vs I SET DS005654-50Common-Mode Rejection Ratio vs I SETDS005654-51Power Supply Rejection Ratio vs I SET5Typical Performance Characteristics(Continued)Open Voltage Swing vs Supply VoltageDS005654-53Input Voltage Range vs Supply VoltageDS005654-54Input Bias Current vs Input Common-Mode VoltageDS005654-55Input Bias Current vs TemperatureDS005654-56Input Offset Current vs Temperature DS005654-57Supply Current vs TemperatureDS005654-58Open Loop Voltage Gain vs Temperature DS005654-20Gain Bandwidth Product vs Temperature DS005654-21Slew Rate vs TemperatureDS005654-22 6Typical Performance Characteristics(Continued)Application HintsAvoid reversing the power supply polarity;the device will mon-Mode Input Voltage:The negative common-mode voltage limit is one diode drop above the negative supply voltage.Exceeding this limit on either input will result in an output phase reversal.The positive common-mode limit is typically 1V below the positive supply voltage.No output phase reversal will occur if this limit is ex-ceeded by either input.Output Voltage Swing vs I SET :For a desired output voltage swing the value of the minimum load depends on the positive and negative output current capability of the op amp.The maximum available positive output current,(I CL+),of the de-vice increases with I SET whereas the negative output current (I CL−)is independent of I SET .Figure 1illustrates the above.Input Noise Voltage vs FrequencyDS005654-23Input Noise Current vs FrequencyDS005654-24Power Supply Rejection Ratio vs FrequencyDS005654-25Voltage Follower Pulse Response DS005654-26Voltage Follower Transient ResponseDS005654-27Transient Response Test CircuitDS005654-6DS005654-7FIGURE 1.Output Current Limit vs I SET7Application Hints(Continued)Input Capacitance:The input capacitance,C IN,of theLM146is approximately2pF;any stray capacitance,C S,(due to external circuit circuit layout)will add to C IN.Whenresistive or active feedback is applied,an additional pole isadded to the open loop frequency response of the device.For instance with resistive feedback(Figure2),this pole oc-curs at1⁄2π(R1||R2)(C IN+C S).Make sure that this pole oc-curs at least2octaves beyond the expected−3dB fre-quency corner of the closed loop gain of the amplifier;if not,place a lead capacitor in the feedback such that the timeconstant of this capacitor and the resistance it parallels isequal to the R I(C S+C IN),where R I is the input resistance ofthe circuit.Temperature Effect on the GBW:The GBW(gain band-width product),of the LM146is directly proportional to I SETand inversely proportional to the absolute temperature.When using resistors to set the bias current,I SET,of the de-vice,the GBW product will decrease with increasing tem-pensation can be provided by creating an I SETcurrent directly proportional to temperature(see typical ap-plications).Isolation Between Amplifiers:The LM146die is isother-mally layed out such that crosstalk between all4amplifiers isin excess of−105dB(DC).Optimum isolation(better than−110dB)occurs between amplifiers A and D,B and C;thatis,if amplifier A dissipates power on its output stage,ampli-fier D is the one which will be affected the least,and viceversa.Same argument holds for amplifiers B and C.LM146Typical Performance Summary:The LM146typicalbehaviour is shown in Figure3.The device is fully predict-able.As the set current,I SET,increases,the speed,the biascurrent,and the supply current increase while the noisepower decreases proportionally and the V OS remains con-stant.The usable GBW range of the op amp is10kHz to3.5−4MHz.Low Power Supply Operation:The quad op amp operatesdown to±1.3V supply.Also,since the internal circuitry is bi-ased through programmable current sources,no degrada-tion of the device speed will occur.Speed vs Power Consumption:LM146vs LM4250(singleprogrammable).Through Figure4,we observe that theLM146’s power consumption has been optimized for GBWproducts above200kHz,whereas the LM4250will reach aGBW of no more than300kHz.For GBW products below200kHz,the LM4250will consume less power.DS005654-9FIGURE2.DS005654-8FIGURE3.LM146Typical CharacteristicsDS005654-10FIGURE4.LM146vs LM42508Typical ApplicationsDual Supply or Negative Supply BlasingDS005654-39Single(Positive)Supply BlasingDS005654-11Current Source Blasingwith Temperature CompensationDS005654-40•The LM334provides an I SET directly proportional to absolutetemperature.This cancels the slight GBW product Temperature coefficientof the LM346.Blasing all4Amplifierswith Single Current SourceDS005654-41•For I SET1≅I SET2resistors R1and R2are not required if a slight errorbetween the2set currents can be tolerated.If not,then use R1=R2to create a100mV drop across these resistors.9Active Filters ApplicationsBasic (Non-Inverting “State Variable”)Active Filter Building BlockDS005654-12DS005654-33Note.All resistor values are given in ohms.DS005654-13DS005654-34 10Active Filters Applications(Continued)Circuit Synthesis EquationsDS005654-35A Simple-to-Design BP ,LP Filter Building BlockDS005654-14•If resistive biasing is used to set the LM346performance,the Q o of this filter building block is nearly insensitive to the op amp’s GBW product temperature drift;it has also better noise performance than the state variable filter.DS005654-36•For the eventual use of amplifier C,see comments on the previous page.11Active Filters Applications(Continued)Circuit Synthesis EquationsA 3-Amplifier Notch Filter (or Elliptic Filter Building Block)DS005654-15DS005654-37•For nothing but a notch output:R IN =R,C'=C.Capacitorless Active Filters (Basic Circuit)DS005654-16 12Active Filters Applications(Continued)Miscellaneous ApplicationsDS005654-381.Pick up a convenient value for b;(b <1)2.Adjust Q o through R53.Adjust H o(BP)through R44.Adjust f o through R SET .This adjusts the unity gain frequency (f u )of the op amp.A 4th Order Butterworth Low Pass Capacitorless FilterDS005654-17Ex:f c =20kHz,H o (gain of the filter)=1,Q 01=0.541,Q o2=1.306.•Since for this filter the GBW product of all 4amplifiers has been designed to be the same (z 1MHz)only one current source can be used to bias the circuit.Fine tuning can be further accomplished through R b .A Unity Gain Follower with Bias Current ReductionDS005654-18•For better performance,use a matched NPN pair.13Miscellaneous Applications(Continued)Circuit ShutdownDS005654-42•By pulling the SET pin(s)to V−the op amp(s)shuts down and its output goes to a high impedance state.According to this property,the LM346can be used as a very low speed analog switch.Voice Activated Switch and AmplifierDS005654-43 14Miscellaneous Applications(Continued)X10Micropower Instrumentation Amplifier with Buffered Input GuardingDS005654-19•CMRR:100dB(typ)•Power dissipation:0.4mW15Physical Dimensions inches(millimeters)unless otherwise notedCavity Dual-In-Line Package(J)Order Number LM146J,LM146J/883NS Package Number J16AS.O.Package(M)Order Number LM346MNS Package Number M16A 16Physical Dimensions inches(millimeters)unless otherwise noted(Continued)LIFE SUPPORT POLICYNATIONAL’S PRODUCTS ARE NOT AUTHORIZED FOR USE AS CRITICAL COMPONENTS IN LIFE SUPPORT DEVICES OR SYSTEMS WITHOUT THE EXPRESS WRITTEN APPROVAL OF THE PRESIDENT AND GENERAL COUNSEL OF NATIONAL SEMICONDUCTOR CORPORATION.As used herein:1.Life support devices or systems are devices orsystems which,(a)are intended for surgical implantinto the body,or(b)support or sustain life,andwhose failure to perform when properly used inaccordance with instructions for use provided in thelabeling,can be reasonably expected to result in asignificant injury to the user.2.A critical component is any component of a lifesupport device or system whose failure to performcan be reasonably expected to cause the failure ofthe life support device or system,or to affect itssafety or effectiveness.National SemiconductorCorporationAmericasTel:1-800-272-9959Fax:1-800-737-7018Email:support@National SemiconductorEuropeFax:+49(0)180-5308586Email:europe.support@Deutsch Tel:+49(0)180-5308585English Tel:+49(0)180-5327832Français Tel:+49(0)180-5329358Italiano Tel:+49(0)180-5341680National SemiconductorAsia Pacific CustomerResponse GroupTel:65-2544466Fax:65-2504466Email:sea.support@National SemiconductorJapan Ltd.Tel:81-3-5639-7560Fax:81-3-5639-7507 Molded Dual-In-Line Package(N)Order Number LM346NNS Package Number N16ALM146/LM346ProgrammableQuadOperationalAmplifiers National does not assume any responsibility for use of any circuitry described,no circuit patent licenses are implied and National reserves the right at any time without notice to change said circuitry and specifications.。
Samtec 微型抗摧断系统说明书

I N T E R C O N N E C T S O L U T I O N S G U I D ERugged contact systems, flexible power interconnects and rugged signal integrity create the foundation of Samtec’s micro rugged solutions for high cycle, high speed, high power and harshenvironment applications. Samtec’s rugged products are offered in conjunction with full engineering support, online tools and a service attitude that is unmatched in the connector industry.HIGH SPEEDS TO 56 Gbps PAM4EDGE RATE ®CONTACT DESIGN INCREASES WEAR LIFE EXPERTISE IN SIGNAL INTEGRITY DESIGN & ANALYSIS1,000+MATING CYCLES TIGER EYE ™ HEAT-TREATED BeCu CONTACTS MULTIPLE POINTS OF CONTACTFOR HIGH-RELIABILITY3 TO 60 AMPS CONFIGURABILITY OF POWER & SIGNAL SPACE-SAVING FORM FACTORRUGGED CONTACT SYSTEMFLEX POWERRUGGED SIGNAL INTEGRITY2RUGGED CONTACT SYSTEMSTiger Eye ™ contact system for high-reliability in rugged applications1,000+ mating cycles 0.80 mm to 2.00 mm pitchBoard-to-board, discrete wire and IDC cable assembliesRUGGED SIGNAL INTEGRITY SYSTEMSEdge Rate ® contact system for rugged signal integrity performance Performance to 56 Gbps PAM4 0.50 mm, 0.635 mm and 0.80 mm pitch Edge card and ultra-micro connectorsFLEXIBLE POWER SYSTEMSUltra-micro power to 17 A and incredible design flexibilityIndividually shrouded contactsSmall form factor, high power systems to 60 A Board-to-board and cable assembliesSEALED I/O SYSTEMSIP67 and IP68 rated for dust and water Variety of circular shell sizes with power, power/signal pinoutsRectangular designs for space savings Rugged latchingModified & Custom Solutions ...........................................................................................................................................Rugged Features .............................................................................................................................................................Power Integrity & Extended Life Product ™ .........................................................................................................................Severe Environment Testing ............................................................................................................................................Solutionator ®...................................................................................................................................................................Technology Centers .. (181920212223)4-78-1112-1516-17HIGH-RELIABILITY • MULTI-FINGER BeCu CONTACT • HIGH MATING CYCLESComponents (ISD2/CC81)& tooling available: /toolingEMI shielded 2.00 mmTiger Eye ™ discrete wire assembly(SS2SD/ST2M)2.00 mm PITCH TIGER EYE ™• Tiger Eye ™ is Samtec's most ruggedcontact system rated to 1,000+ mating cycles • Wide range of stack heights• Right-angle mating headers available • Optional screw downs, weld tabs and locking clips• Discrete wire assemblies available in 24-30 AWG PVC or Teflon ® wire 4/tigereyeOptional strain relief and variety of wiring optionsTCSD/EHTT2M/S2MTMM/SMMT2M/S2MMetal latching and screw down optionsS2SD/T2Mper pin3.8 ARight-angle availableVariety of stack heightsSurface mount or through-holeTFM/SFMSurface mount or through-hole tailsSFSST/TFMScrew down and retention latching options6-12 mm stack heightsHigh-density four row designMOLC/FOLC1.27 mm PITCH TIGER EYE ™• Screw down, locking clip, friction latching and weld tab ruggedizing options • Shrouded, polarized and keyed• Discrete wire assemblies available in single or double row, 28 and 30 AWG PVC or Teflon ® wire • Cable components (ISDF/CC03) and tooling availableLocking for increased unmating force (SFML/TFML)IDC cable assemblies withrugged strain relief (FFSD/FFMD, FFTP/FMTP)5Dupont ™ Teflon ® is a registered trademark of the E.I. du Pont de Nemours and Company or its affiliates./tigereyeTIGER EYE ™ CONTACT SYSTEM• Multi-finger design with several points of contact for high-reliability• Smooth, flat mating area increases mating cycles and lowers contact resistance • Heat-treated BeCu for the best combination of mechanical and electrical properties • Surface mount, micro slot tail increases solder surface area for higher joint strengthper pin3.2 ATEM/SEMVertical and right-angle mating headers0.80 mm PITCH TIGER EYE ™• Micro pitch and slim body for space-savings • 6 mm, 7 mm and 10 mm stack heights • Locking clip, alignment pins and weld tab ruggedizing features• Discrete wire assembly available with 32 AWG Teflon ® wire• Extended Life Product ™ testing availableRugged latching system for increased withdrawal forceSESDT/ TEM-L16HIGH-RELIABILITY • MULTI-FINGER BeCu CONTACT • HIGH MATING CYCLES/tigereyeComponents (ISDE/CC396) and tooling available: /toolingLocking for increased unmating force(SEML)TEMS/ SEMSCompatible with UMPT/UMPS for power/signal flexibilityper pin2.9 ATEM/ SEM1.00 mm PITCH CABLE SYSTEM• Crimp-style dual leaf contact system for reliable wire-to-board connection• 28 and 30 AWG cable options in PVC or Teflon®7/tigereye Components (ISS1, ISD1/CC09; T1SS, T1SD, T1PS, T1PD/T1M137-X) and tooling available: /tooling Dual leaf contact system for a reliable connectionT1PSTS1SDS1SS/ T1MT1SDS1SSTPanel-to-BoardCable-to-CableCable-to-BoardCustom solutions available (twisted pair cable shown):**************• Rugged positive latching for increased retention • Socket or terminal, single or double row assemblies • Vertical and right-angle mating headersOPTIMIZED FOR SI PERFORMANCE • INCREASED CONTACT WIPE • HIGH CYCLES 0.635 mm PITCH EDGE RATE®•Extremely slim 2.5 mm body width•Up to 120 positions in a 2-row design•5 mm stack height with others in development•Compatible with UMPT/UMPS for flexiblepower/signal solutions8ERX5ERX6ERX8 Sockets shown actual size at 40 total positions /edgerate0.50 mm PITCH EDGE RATE®•1.00 mm contact wipe for a reliable connection • Rugged friction locks and weld tabs available •Up to 40% PCB savings vs. ERM8/ERF8•Compatible with UMPT/UMPS for flexiblepower/signal solutionsStack Height Flexibility(Actual Size in mm)79101112ERM5/ERF5Right-angleavailable12 mmstack height7 mmstack heightERM6/ERF6Signal/power combinationwith UMPT/UMPSJ lead for easeof processingERM8/ERF87 mmstack heightRight-angle & edge mount available0.80 mm PITCH EDGE RATE ®• 1.50 mm extended wipe• Rugged metal latching for increased retention force • 360º shielding option reduces EMI • Compatible with UMPT/UMPS for flexible power/signal solutions• Cost-effective metal solder lock in development for a more secure connection to the boardStack Height Flexibility (Actual Size in mm)* In development 78*91011121314151618179Mating Cable Assemblies (ERCD/ERDP Series)360º shieldingSignal/power combination with UMPT/UMPS10 mmstack height with latching14 mmstack height with latching/edgerateEDGE RATE ® CONTACT SYSTEM• Smooth milled mating surface reduces wear and increases durability• Lower insertion and withdrawal forces • Robust when “zippered” during unmating• Minimized parallel surface area reduces broadside coupling and crosstalk • Designed, simulated and optimized for 50 Ω and 100 Ω systemsUP TO 56 Gbps PAM4 • CHOICE OF PITCH • EDGE RATE ® CONTACTS/edgecard0.80 mm & 1.00 mm PITCH SYSTEMS• High-speed Edge Rate ® contact system • Vertical, right-angle and edge mount • Power/signal combo to 60 A per power bank • Pass-through applicationHIGH-DENSITY EDGE CARD• Justification beam enables use of standard PCB tolerance • 0.50 mm ultra-fine pitch with up to 300 total I/Os • PCIe ® Gen 4 compatibleMICRO EDGE CARDS• 0.635 mm, 0.80 mm, 1.00 mm, 1.27 mm and 2.00 mm pitch • Optional rugged weld tabs, board locks and solder locks • Solutions for 1.60 mm (.062") and 2.36 mm (.093") thick cardsMisalignment mitigation(HSEC1-DV)56 Gbps with differentialpair (HSEC8-DP)PCI-SIG ® , PCI Express ® and the PCIe ® design marks are registered trademarks and/or service marks of PCI-SIG.HSEC8HSEC1-DVHSEC8-PV MEC5Beam ensures card and body are flushMEC1MEC6MECFHIGH-DENSITY • HIGH-RETENTION CONTACTS • SLIM ROW-TO-ROW DESIGNSLSSLSEMHERMAPHRODITIC RAZOR BEAM ™ INTERFACES• High-retention, high-speed Razor Beam ™ contacts • 0.50 mm, 0.635 mm and 0.80 mm pitch• EMI shielding available to limit signal degradation and optimize performanceRight-angle available formicro backplane applicationsFLOATING CONNECTORS• Provides 0.50 mm contact float in the X and Y axes to compensate for misalignment • 5 mm and 7 mm stack heights • Micro 0.50 mm pitchONE-PIECE INTERFACES• Robust design and mechanical hold-downs for high-shock and vibration applications • Optional rugged weld tabs and locking clips • 1.00 mm, 1.27 mm and 2.54 mm pitch designs5 - 12 mmstack height flexibilityLSHMFT5/FS5SEIFSISIBSIR1Profiles from1.65 mm to 10 mm11/micro17.1 A PER BLADE • MICRO 2.00 mm PITCH • DESIGN FLEXIBILITY MICRO 2.00 mm PITCH• Design flexibility as a power-only system or atwo-piece system for power/signal applications•Use with Samtec’s high-speed connector systemsfor a unique power/signal system (see chart)12SIGNAL CONNECTORMATED HEIGHT5 mm7 mm8 mm10 mmADM6/ADF6XBTE/BSE, BTH/BSH, BTS/BSS X XERM5/ERF5X XERM6/ERF6XERM8/ERF8X XLPAM/LPAF XQMS/QFS XQRM8/QRF8X XQTE/QSE, QTH/QSH,QTS/QSS X XSEAM/SEAF, SEAM8/SEAF8X XST4/SS4, ST5/SS5XTEM/SEM X XUMPT/UMPS/powerCREEPAGE CLEARANCEUMPT/UMPS 1.65 mm 2.20 mm•Tin or 10 µ" Gold plated power blades; 30 µ" Gold platingavailable to meet specific regulations•Selectively loading contacts achieves customer specificcreepage and clearance requirements; contact **************Choice of2, 3, 4 and 5position countsOptionalweld tabs5-10 mm stackheights available17.1 A/bladeUMPT/UMPS compared to othersmall form factor power solutions23 A/bladeper bladeTerminals shown actual size at 4 positions28.8 A/blade58.7 A/blade13P H A S E 15 Position,5 mm Stack HeightVertical UMPT & UMPS SeriesPOSITIONSSTACK HEIGHTS2, 3, 4, 55, 7, 8,10P H A S E 26 Position,9 mm Stack HeightVertical UMPT & UMPS SeriesPOSITIONSSTACK HEIGHTS6, 7, 8, 9, 106, 9, 11, 12, 14,16P H A S E 310 Position Right-AngleRight-Angle UMPT SeriesPOSITIONSOPTIONS2, 3, 4, 5, 6, 7, 8, 9, 10Latch for mating with cable assemblyP H A S E 44 Position Cable Assembly andUMPT Right-Angle with Staged BladesCable Assembly with LatchPOSITIONSMATES2, 3, 4, 5, 6, 7, 8, 9, 10UMPT Series vertical and right-angle with latch/powerLength, width and height shown actual sizeSamtec now offers power simulation that can calculate temperature increase in the connector area; contact *************************** for more details.SMALL FORM FACTORS • 10–60 A PER PIN/BLADE • INDIVIDUALLY SHROUDED CONTACTSMMSD/ IPL1MINI MATE ® & POWER MATE ®• Individually shrouded contacts for electrical and mechanical protection• .100" (2.54 mm) and .165" (4.19 mm) pitch • Discrete wire assemblies with 16-30 AWG PVC or Teflon ® cable• Selectively loading contacts achieves customer specific creepage and clearance requirements; contact **************14Metal or plasticrugged latching system/powerEXTREME POWER• AC or DC power, AC-DC combos and split power options (ET60T/ET60S)• High-density, double stacked power blades (LPHT/LPHS)• Selectively loading contacts achieves customer specific creepage and clearance requirements; contact **************3 or 5 signal rows in the same form factorLow 7.5 mm profile designCREEPAGECLEARANCE IPT1/IPS1MMSS(T)/MMSD(T) 2.55 mm 4.27 mm3.05 mm1.91 mm IPBT/IPBS PMSS(T)/PMSD(T)per pin10.3 ACREEPAGECLEARANCE LPHT/LPHS ET60T/ET60S5.63 mm 3.02 mm2.69 mm 1.87 mmET60T/ET60SLPHT/LPHSPMSDT/ IPBTIPT1/IPS1IPBT/IPBSRugged guide postsComponents and tooling availablePOWERSTRIP ™ SYSTEM• 23.5 A/blade to 58.7 A/blade (1 blade powered) • 5.00 mm and 6.35 mm pitch• Discrete wire assemblies with 10-16 AWG cable • Selectively loading contacts achieves customer specific creepage and clearance requirements; contact **************15MPT/MPSUPT/UPSMPTC/ MPSCPESS/PETMPSS/ MPTVertical and right-anglePower only or power/signal combinationsRugged latching system/power“Hinging” for 90º mating radius, ideal for blind mating (FMPT/FMPS)Discrete wire components (IMS5,IMSC5/CC46,CC81; IPS6/CC10) and tooling available: /toolingHermaphroditic power system with rugged screw downs (MPPT, UPPT)CREEPAGE CLEARANCE PET/PES/PETC/ PESC/PESS 3.66 mm 2.95 mm 5.80 mm2.71 mm 1.51 mm3.31 mm MPT/MPS/MPTC/ MPSC/MPSS/MPPT UPT/UPS/UPPTDual blade contactsCCP/CCRFLEXIBLE SEALED CIRCULAR SYSTEMS• Metal or plastic, 12 mm, 16 mm and 22 mm shells • Flexible pin configuration, gender and panel interface termination• Bayonet-style latching systems meet IP68 requirements • Cost-effective crimp version available• Mini push-pull latching system meets IP67 requirements for dust and waterproof sealing16Crimp 12 mm shellIP67 & IP68 • BAYONET/PUSH-PULL CIRCULARS • SPACE-SAVING RECTANGULARSKitted components for efficient field assembly/sealedMCP/MCRACP/ACRACP/ACRMini push-pull system16 mm size metal shell22 mm size plastic shell17SCPU25-45% panel area savings/sealedSEALED RECTANGULARS• Space saving design • Meets IP68 requirements • USB and Ethernet signal systems • Rugged dust caps available• 1 or 2-port vertical and right-angle panel mount socketsTHREADED CIRCULARS• Meets IP68 requirements for dust and waterproof sealing • Rugged overmold design• USB, Mini USB and Ethernet signal systems • 10 and 17 shell sizes• Rugged dust caps and panel-to-board termination availableRCERCUAudibleclick positive latching for quick connect/disconnectVertical or right-angleRPCURPBURPBEUSB type A and B10 or 17 shell sizeEthernet meets CAT3, CAT5 and CAT5eSCRESSCPESCRUSWILLINGNESS, SUPPORT & EXPERTISE18ExpressModificationsEngineeredCustoms23%5%Customs and Modifications make up about 28% of Samtec’s total sales92% do not require engineering or tooling chargesA substantial percentage of eachMicro Rugged product segment is customTiger Eye ™Edge Rate ®Edge Card PowerSealed I/O19%9%44%30%8%INDUSTRY LEADING CUSTOMER SERVICE FLEXIBLE IN-HOUSE MANUFACTURING SIGNAL INTEGRITYEXPERTISEEngineered CustomMulti-power staging, power/signal combo, header/socket combo, custom bodyExpress ModificationStandard PowerStrip ™ cable with non-standard end 2 optionFLEXIBLE SOLUTIONS• Full engineering, design and prototype support • Design, simulation and processing assistance • Quotes and samples turned around in 24 hours • Flexible, quick-turn manufacturing • Dedicated Application Specific Product engineers and technicians• Modified or custom options for board level connectors and cable assemblies including: contacts, bodies, stamping, plating, wiring, molding, ruggedizing features and much moreContact the Application Specific Products Group at ************** for express modifications or engineered customs.19OPTIONS FOR HIGH-RELIABILITY, HIGH-RETENTION AND HIGH-CYCLE LIFERUGGEDIZING OPTIONSWELD TABSSignificantly increase sheer resistance of connectorto PCBSHIELDING360° shielding reduces EMIGUIDE POSTSEasy and secure matingBOARD STANDOFFSPrecision machined standoffs for 5 mm to 25 mm board spacingSCREW DOWNS Secure mechanical attachment to the boardBOARD LOCKSBoards are mechanicallylocked togetherRETENTION PINSIncrease unmating forceby up to 50%FRICTION LOCKSMetal or plastic friction locks increase retention/withdrawal forcePOSITIVE LATCHINGManually activated latches increase unmating forceby up to 200%JACK SCREWS Ideal for high normal force, zippering and other ruggedapplicationsEDGE RATE ®Designed for Signal Integrity Superior Impedance Control Reduced Broadside CouplingTIGER BEAM ™Best CostReliable Performance Post & Beam ContactBLADE & BEAMMating/Alignment “Friendly”Cost-effectiveTIGER CLAW ™Dual Wipe Contact Pass-through ApplicationsUltra-low ProfileTIGER EYE ™High-reliability High Mating Cycles Multi-finger ContactCONTACT SYSTEMS20POWER INTEGRITY SERVICES• • • • • /powerintegrity EXTENDED LIFE PRODUCT ™• • • • /ELP**************POWER INTEGRITYCERTIFIEDCREEPAGECLEARANCEPITCHTYPECONTACTSERIES*0.50 mm Q Series ® Strip Blade & Beam QSH/QTH Basic Strip Blade & Beam BSH/BTH 0.635 mmQ Series ® Strip Blade & Beam QSS/QTS Basic Strip Blade & Beam BSS/BTS 0.80 mmEdge Rate ® Strip Edge Rate ®ERF8/ERM8Edge CardEdge Rate ®HSEC8Q Rate ®StripEdge Rate®QRM8/QRF8Q Series ® Strip Blade & Beam QSE/QTE Basic Strip Blade & Beam BSE/BTE StripTiger Eye ™SEM/TEM 1.00 mm StripTiger Claw ™CLM/FTMH 1.27 mmSEARAY ™ArrayEdge Rate®SEAF/SEAM Strip Tiger Eye ™SFM/TFM Strip Tiger Claw ™CLP/FTSH Strip Tiger Beam™FLE/FTSH 2.00 mm Strip Tiger Eye ™SMM/TMM Strip Tiger Claw ™CLT/TMMH 2.54 mmStrip Tiger Claw™SSM/TSM StripTiger Claw ™BCS/TSW* Tested socket/terminal combination shown. Other mating headers also available. Contact Samtec if header design you need is not shown.10 YEAR MFGEXTENDED LIFEPRODUCTHIGH MATINGCYCLES21Severe Environment Testing is a new Samtec initiative to test our products beyond typical industry standards and specifications, many set forth by common requirements for rugged industries. Several of our products will undergo additional testing to ensure they are more than suitable for industrial, military, automotive and other extreme applications.PRODUCTS TO BE TESTED:• Rugged Tiger Eye ™ connectors• Hermaphroditic Razor Beam ™ connectors• SEARAY ™ high-density arrays• Edge Rate ® rugged signal integrity connectors• AcceleRate ® HD ultra-micro connectors• Ultra Micro Power systems• High-speed coax and twinax cable assembliesPlease contact ************** for more information and test results when available.TESTING WILL INCLUDE:• Higher mating cycle testing• Intense shock and vibration• Altitude testing• ESD testing• Temperature cycling• And morePRND NETWORK vs. MIL-PRF-83401 PERFORMANCE TEST OR CONDITION MIL-PRF-83401VISHAY FOIL RESISTORS C Typical Resistance Temp Characteristic ppm/ºC ± 50± 2Tracking to Reference Element (-55 to +125 ºC)ppm/ºC ± 5± 2Max Ambient Temp at Rated Wattage ± 70 ºC Max Ambient Temp at Zero Power ± 125 ºC Thermal Shock and Power Conditioning ± 0.25 % ± 0.03 %± 0.015 % ± 0.015 %Low Temperature Operation ∆R ∆Ratio ± 0.10 % ± 0.02 %± 0.01 % ± 0.01 %Short Time Overload ∆R ∆Ratio ± 0.10 % ± 0.02 %± 0.01 % ± 0.01 %Terminal Strength ∆R ∆Ratio ± 0.10 % ± 0.03 %± 0.01 % ± 0.01 %Resistance to Soldering Heat ∆R ∆Ratio ± 0.10 % ± 0.02 %± 0.01 % ± 0.01 %Moisture Resistance ∆R ∆Ratio ± 0.20 % ± 0.02 %± 0.01 % ± 0.01 %Shock (Specified Pulse)∆R ∆Ratio ± 0.25 % ± 0.03 %± 0.01 % ± 0.01 %Vibration, High Frequency ∆R ∆Ratio ± 0.25 % ± 0.03 %± 0.01 % ± 0.01 %Load Life (Per EEE-INST-002) (+70 ºC, Full Power, 2000 hours)∆R ∆Ratio ± 0.10 % ± 0.03 %± 0.05 % ± 0.02 %+25 ºC Power Rating (1000 hours)∆R ∆Ratio ± 0.10 % ± 0.03 %± 0.01 % ± 0.01 %High Temperature Exposure (+125 ºC, 100 hours)∆R ∆Ratio ± 0.10 % ± 0.03 %± 0.01 % ± 0.01 %Low Temperature Storage ∆R ∆Ratio ± 0.10 % ± 0.02 %± 0.01 % ± 0.01 %Insulation Resistance 10,000 MΩResistance Tolerance and, when applicable, Resistance Ratio Accuracy ± 0.1 % (B)± 0.5 % (D) ± 1.0 % (F)± 0.1 % (B)± 0.5 % (D)22•Wide variety of search parameters and filters: creepage and clearance (power), pitch, stack height, etc. •Easily sort results to find the right mated set•Live chat with engineers for custom options•Immediately download models and open Specs KitQUICKLY BUILD MATED SETS ONLINETo build your mated set, visit /solutionatorSAMTEC TECHNOLOGY CENTERS ENABLE COMPLETE SYSTEM OPTIMIZATION FROM SILICON-TO-SILICON™HIGH–SPEEDCABLE MICROELECTRONICSADVANCEDINTERCONNECTSOPTICSSYSTEM SIGNALINTEGRITYPRECISION RFSamtec's Technology Centers offer high-level design and development of advanced interconnect systems and technologies, along with industry-leading signal integrity expertise which allows us to provide effective strategies and technical support for optimizing the entire serial channel of high-performance systems. Because Samtec's Technology Centers are not limited by the boundaries of traditional business units,we are able to work in a fully integrated capacity that enables true collaboration and innovation to support the demands of today, and the challenges of tomorrow.In-house R&D manufacturingof precision extruded cableand assembliesAdvanced IC packaging design, support and manufacturing capabilities R&D, design, developmentand support of micro opticalengines and assembliesRF interconnect design anddevelopment expertise, withtesting to 65 GHzHigh precision stamping,plating, molding andautomated assemblyFull channel signal and powerintegrity analysis, testing andvalidation services /tech-centers23UNITED STATES • NORTHERN CALIFORNIA • SOUTHERN CALIFORNIA • SOUTH AMERICA • UNITED KINGDOM GERMANY • FRANCE • ITALY • NORDIC/BALTIC • BENELUX • ISRAEL • INDIA • AUSTRALIA / NEW ZEALAND SINGAPORE • JAPAN • CHINA • TAIWAN • HONG KONG • KOREANOVEMBER 2018。
D-M9N系列、D-M9P系列、D-M9B系列自动开关(固态)安装与维护手册说明书
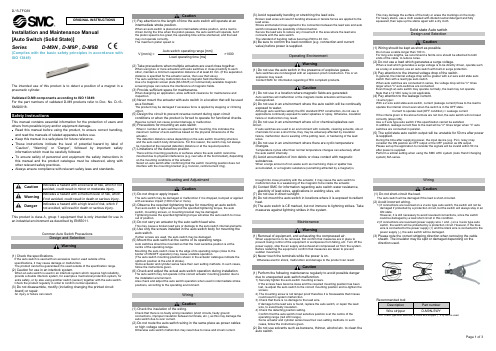
Installation and Maintenance Manual[Auto Switch (Solid State)]Series D-M9N , D-M9P , D-M9B(Complies with the basic safety principles in accordance withISO 13849)The intended use of this product is to detect a position of a magnet in a pneumatic cylinder.Validated D-M9 components according to ISO 13849:For the part numbers of validated D-M9 products refer to Doc. No. D-*S-SMQ0018.This manual contains essential information for the protection of users and others from possible injury and/or equipment damage.•Read this manual before using the product, to ensure correct handling, and read the manuals of related apparatus before use.•Keep this manual in a safe place for future reference.•These instructions indicate the level of potential hazard by label of “Caution”, “Warning” or “Danger”, followed by important safety information which must be carefully followed.•To ensure safety of personnel and equipment the safety instructions in this manual and the product catalogue must be observed, along with other relevant safety practices.•Always ensure compliance with relevant safety laws and standards.Caution Indicates a hazard with a low level of risk, which if notavoided, could result in minor or moderate injury.Warning Indicates a hazard with a medium level of risk, whichif not avoided, could result in death or serious injury.Danger Indicates a hazard with a high level of risk, which ifnot avoided, will result in death or serious injury.This product is class A, group 1 equipment that is only intended for use inan industrial environment as described by EN55011.Common Auto Switch PrecautionsDesign and SelectionWarning(1) Check the specifications.If the auto switch is used with an excessive load or used outside of thespecifications, it may cause damage or malfunction.The product cannot be guaranteed if is used outside of the specification range.(2) Caution for use in an interlock system.When an auto switch is used in an interlock system which requires high reliability,provide a double interlock system, for example a mechanical protection system, forextra safety, or by also using another switch (sensor) together with the auto switch.Check the product regularly in order to confirm normal operation.(3) Do not disassemble, modify (including changing the printed circuitboard) or repair.An injury or failure can result.Caution(1) Pay attention to the length of time the auto switch will operate at anintermediate stroke position.When an auto switch is placed at an intermediate stroke position, and a load isdriven during the time when the piston passes, the auto switch will operate, but ifthe piston speed is too great, the operating time will be shortened, and the loadmay not operate correctly.The maximum piston speed is:V [mm/s] =Auto switch operating range [mm]×1000Load operating time [ms](2) Take precautions when multiple actuators are used close together.When using two or more actuators with auto switches in close proximity to eachother, maintain a minimum separation distance of at least 40 mm. (If the separationdistance is specified for the actuator series, then use that value).The auto switches may malfunction due to magnetic field interference.Use of a magnetic screen plate (MU-S025) or commercially available magneticscreening tape can reduce the interference of magnetic fields.(3) Provide sufficient space for maintenance.When designing an application, allow sufficient clearance for maintenance andinspection.(4) Never mount the actuator with auto switch in a location that will be usedas a footrest.The product may be damaged if excessive force is applied by stepping or climbingonto it.(5) Design the circuit to prevent reverse current during open circuitconditions or when the product is forced to operate for functional checks.Reverse current can cause product damage or malfunction.(6) Precautions for mounting an auto switchWhen n number of auto switches is specified for mounting, this indicates themaximum number of auto switches based on the physical dimensions of theactuator.The detection distance varies depending on the auto switch mounting structureand the auto switch body dimensions. For this reason, the switch may not alwaysbe mounted at the required detection distance or at the required position.(7) Limitations of the detection position.There will be mounting positions or surfaces where the auto switch cannot bemounted due to physical interference (e.g. rear side of the foot bracket), dependingon the mounting conditions of the actuator.Select an auto switch after confirming that the switch mounting position does notinterfere with the mounting bracket (e.g. trunnion, reinforcement ring).Mounting and AdjustmentCaution(1) Do not drop or apply impact.The auto switch may be damaged or malfunction if it is dropped, bumped or appliedwith excessive impact (1000 m/s2 or more).(2) Observe the required tightening torque for mounting an auto switch.If an auto switch is tightened beyond the specified tightening torque, the autoswitch, mounting screws, or mounting bracket may be damaged.Tightening below the specified tightening torque will allow the auto switch to moveout of position.(3) Do not carry an actuator by the auto switch lead wire.This may cause a broken lead wire or damage to the auto switch internal elements.(4) Use only the screws installed in the auto switch body for mounting theauto switch.If other screws are used, the auto switch may be damaged.(5) Mount the auto switch at the centre of its operating range.Auto switches should be mounted so that the most sensitive position is at thecentre of the operating range.Mounting the auto switch close to the edge of its operating range (close to theborder of ON/OFF operation) may cause unstable operation.(The auto switch mounting positions shown in the actuator catalogue indicate theoptimum position at the end of stroke).Some actuator and cylinder series have their own setting methods. In such cases,follow the instructions given.(6) Check and adjust the actual auto switch operation during installation.The auto switch may not operate in the correct actuator mounting position due tothe installation environment.Also check and adjust the auto switch operation when used in intermediate strokepositions, according to the operating environment.WiringCaution(1) Check the insulation of the wiring.Check that there is no faulty wiring insulation (short circuits, faulty groundconnections, improper insulation between terminals, etc.), as this may damage theauto switch due to over current.(2) Do not route the auto switch wiring in the same place as power cablesor high voltage cables.Otherwise auto switch malfunction may result due to noise and inrush current.(3) Avoid repeatedly bending or stretching the lead wire.Broken lead wires will result if bending stresses or tensile forces are applied to thelead wires.Stress and tensile forces applied to the connection between the lead wire and autoswitch increases the possibility of disconnection.Secure the lead wire to reduce any movement in the area where the lead wireconnects with the auto switch.The standard of bending radius becomes R20 to 40 mm.(4) Be sure to confirm the load condition (e.g. connection and currentvalue) before power is supplied.Operating EnvironmentWarning(1) Do not use the auto switch in the presence of explosive gases.Auto switches are not designed with an explosion proof construction. Fire or anexplosion may result.Contact SMC for information regarding ATEX compliant products.Caution(1) Do not use in a location where magnetic fields are generated.Auto switches will malfunction or the magnets inside actuators will becomedemagnetized.(2) Do not use in an environment where the auto switch will be continuallyexposed to water.Although auto switches satisfy the IEC standard IP67 construction, do not use inapplications continually exposed to water splashes or spray. Otherwise, insulationfailure or malfunction may result.(3) Do not use in an environment where oil or chemical splashes canoccur.If auto switches are used in an environment with coolants, cleaning solvents, oils orchemicals for even a short time, they may be adversely affected by insulationfailure, malfunction due to swelling of the potting resin, or hardening of the leadwires.(4) Do not use in an environment where there are cyclic temperaturechanges.Temperature cycles other than normal temperature changes can adversely affectthe auto switch internally.(5) Avoid accumulation of iron debris or close contact with magneticsubstances.When a large amount of iron waste such as machining chips or spatter hasaccumulated, or a magnetic substance (something attracted by a magnet) isbrought into close proximity with the actuator, it may cause the auto switch tomalfunction due to a weakening of the magnetic force inside the actuator.(6) Contact SMC for information regarding auto switch water resistance,elasticity of lead wires, applications in welding sites, etc.(7) Do not use in direct sunlight.(8) Do not mount the auto switch in locations where it is exposed to radiantheat.(9) The auto switch is CE marked, but not immune to lightning strikes. Takemeasures against lightning strikes in the system.MaintenanceWarning(1) Removal of equipment, and exhausting the compressed air.When equipment is to be removed, first confirm that measures are in place toprevent losing control of the equipment or workpieces from falling, etc. Turn off thepower supply, stop the air supply and exhaust all compressed air from the system.Before restarting the equipment, confirm that measures are taken to preventsudden movement.(2) Never touch the terminals while the power is on.Otherwise electric shock, malfunction and damage to the product can result.Caution(1) Perform the following maintenance regularly to avoid possible dangerdue to unexpected auto switch malfunction.1) Securely tighten the auto switch mounting screws.If the screws have become loose and the required mounting position has beenlost, re-adjust the auto switch to the correct mounting position and re-tighten thescrews.2) The mounting screw is not tamper proof therefore it is foreseeable that misusecould result in system malfunction.3) Check that there is no damage to the lead wire.If damage to the lead wire is found, replace the auto switch, or repair the leadwire, to avoid faulty insulation.4) Check the detecting position setting.Confirm that the auto switch most sensitive position is at the centre of theoperating range (red LED range).Some actuator and cylinder series have their own setting methods. In suchcases, follow the instructions given.(2) Do not use solvents such as benzene, thinner, alcohol etc. to clean theauto switch.This may damage the surface of the body or erase the markings on the body.For heavy stains, use a cloth soaked with diluted neutral detergent and fullysqueezed, then wipe up the stains again with a dry cloth.Solid state Auto switchDesign and SelectionCaution(1) Wiring should be kept as short as possible.Do not use a cable longer than 100 m.For long wire lengths, we recommend a ferrite core should be attached to bothends of the cable, to reduce noise.(2) Do not use a load which generates a surge voltage.When a load which generates a surge voltage is to be directly driven, operate suchas a relay or solenoid, use an auto switch with built-in surge protection.(3) Pay attention to the internal voltage drop of the switch.In general, the internal voltage drop will be greater with a 2-wire solid state autoswitch than with a reed type auto switch.When auto switches are connected in series, the voltage drop will be "n" timeslarger when "n" auto switches are connected.Even though an auto switch may operate normally, the load may not operate.Note that a 12 VDC relay is not applicable.(4) Pay attention to the leakage current.<2-wire type>With a 2 wire solid state auto switch, current (leakage current) flows to the load tooperate the internal circuit even when the switch is in the OFF state.Current to operate load (OFF condition) > Leakage currentIf the criteria given in the above formula are not met, the auto switch will not resetcorrectly (stays ON).Use a 3 wire type auto switch if this specification cannot be satisfied.In addition, leakage current flow to the load will be "n" times larger when "n" autoswitches are connected in parallel.(5) The solid state auto switch output will be unstable for 50 ms after poweris supplied.During the time after supplying power, the input device (e.g. PLC, relay) mayconsider the ON position as OFF output or the OFF position as ON output.Please set up the application to consider the signals will be invalid within 50 msafter power is supplied.Perform a similar setting when using the SMC AHC system (Auto Hand Changingsystem) MA series.WiringCaution(1) Do not short-circuit the load.The auto switch will be damaged if the load is short-circuited.(2) Avoid incorrect wiring.1) If connections are reversed on a 2-wire type auto switch, the switch will not bedamaged if protected by a protection circuit, but the switch will always stay in anON state.However, it is still necessary to avoid reversed connections, since the switchcould be damaged by a load short circuit in this condition.2) If connections are reversed (power supply wire + and -) on a 3-wire type autoswitch, the switch will be protected by a protection circuit. However, if the bluewire is connected to the power supply (+) and the black wire is connected to thepower supply (-), the auto switch will be damaged.(3) Please note the correct stripping direction when removing the cablesheath. The insulator may be split or damaged depending on thedirection used.Recommended tool:Description Part numberWire stripper D-M9N-SWY*: For 2-wire type auto switches, a round wire stripper ( 2.0) can be used.ORIGINAL INSTRUCTIONSOperating EnvironmentCaution(1) Do not use in a location where surges are generated.When there are units (solenoid lifter, high frequency induction furnace, motor, etc.) which generate a large amount of surge in the area around the actuator with solid state auto switches, this may cause damage to the auto switch internal circuit.Switch modelNo.D-M9N D-M9P D-M9B Wiring 3 wire 2 wire Output NPN PNP -Application IC circuit / Relay / PLC24 VDC Relay / PLCPower voltage 5/12/24 VDC (4.5 to 28 VDC) - Currentconsumption10 mA or less -Load voltage 28 VDC or less - 24 VDC (10 to 28 VDC)Load current 40 mA or less2.5 to 40 mAInternal voltage drop 0.8 V or less at 10 mA load current (2V or less at 40 mA)4 V or lessCurrent leakage 100 A or less at 24 VDC0.8 mA orlessOperating time 1 ms or lessIndicator lightOperating position: Red LED lights up Optimum position: Green LED lights up (D-M9 W only)Electrical entrysystemGrommetLead wire Oil-proof heavy-duty vinyl cord 2.7 x 3.2 oval, 0.15 mm2, 2 wire (D-M9B), 3 wire (D-M9N/D-M9P)Impactresistance1000 m/s2Vibration resistance10 to 150 Hz, at the smaller amplitude,1.5 mm or 20 m/s2 in X,Y,Z directions for 2 hours each(De-energized)Insulationresistance50 M or more at 500 VDC megaWithstand voltage1000 VAC for 1 minute(between terminals and housing)Ambienttemperature-10o C to 60o CProtection structure IEC60529 standard IP67, JISC0920D-M9D-M9 VInstallationWarning•Do not install the product unless the safety instructions have been readand understood.MountingEach actuator has a specified mounting bracket for mounting the autoswitch."How to mount / Mounting bracket" depends on the actuator type and thetube I.D. Please refer to the actuator catalogue.When an auto switch is mounted for the first time, ensure that the actuatoris a type including a built in magnet, and select a bracket corresponding tothe actuator.• Setting the detecting position1) Set the actuator at the end of stroke.2) Mount the auto switch in the position where the red LED is ON(detecting position for the actuator end of stroke).3) Based on the A and B dimensions in the actuator catalogue, set theswitch.• HysteresisEnvironmentWarning•Do not use in an environment where corrosive gases, chemicals, saltwater or steam are present.•Do not install in a location subject to vibration or impact. Check theproduct specifications.*1: For the D-M9 (V) single colour auto switch the green LED is removed.The number shown in brackets [ ] indicates the connector pin number.D-M9D-M9 VExternal dimensions of Pre-wired connectorD-M9 A,BPCD-M9 DPCM2.5 mounting screwtightening torque shouldbe 0.05 to 0.15 NmWhen detection failure occurs (stay ON/OFF), please follow the flow chart below.A: Switch output parts failure (replace) B: Check wiring and correct faultC: Replace switch 2 wires --> 3 wires D: Switch failureE: Replace cylinder. Detectable magnet field inadequate (No magnet) F: Replace PLC input board or replace switch 2 wires --> 3 wiresLoad specification checks1) On voltage > Load voltage – Internal voltage drop 2) Off current > Leak currentLimitations of useAny use in an EN ISO 13849 system must be within the specified limits and application condition. The user is responsible for the specification, design, implementation, validation and maintenance of the safety system (SRP/CS)ContactsAUSTRIA (43) 2262 62280-0 LATVIA(371) 781 77 00 BELGIUM (32) 3 355 1464 LITHUANIA (370) 5 264 8126 BULGARIA (359) 2 974 4492 NETHERLANDS (31) 20 531 8888 CZECH REP. (420) 541 424 611 NORWAY (47) 67 12 90 20 DENMARK (45) 7025 2900 POLAND (48) 22 211 9600 ESTONIA (372) 651 0370 PORTUGAL (351) 21 471 1880 FINLAND (358) 207 513513 ROMANIA (40) 21 320 5111 FRANCE (33) 1 6476 1000 SLOVAKIA (421) 2 444 56725 GERMANY (49) 6103 4020 SLOVENIA (386) 73 885 412 GREECE (30) 210 271 7265 SPAIN (34) 945 184 100 HUNGARY (36) 23 511 390 SWEDEN (46) 8 603 1200 IRELAND (353) 1 403 9000 SWITZERLAND (41) 52 396 3131 ITALY(39) 02 92711UNITED KINGDOM(44) 1908 563888URL : http// (Global) http// (Europe) SMC Corporation,Akihabara UDX15F, 4-14-1, Sotokanda, Chiyoda-ku, Tokyo 101-0021 JAPAN Specifications are subject to change without prior notice from the manufacturer. © 2013 SMC Corporation All Rights Reserved.。
LT3469中文资料

LT3469
ABSOLUTE
(NoGE/ORDER I FOR ATIO
TOP VIEW OUT 1 FB 2 VIN 3 GND 4 8 –IN 7 +IN 6 VCC 5 SW
VIN Voltage ............................................................. 16V SW Voltage ............................................................. 40V VCC Voltage............................................................. 38V +IN, –IN Voltage ..................................................... 10V FB Voltage ................................................................ 3V Current Into SW Pin ................................................. 1A Operating Temperature Range (Note 2) .. – 40°C to 85°C Storage Temperature Range ................ – 65°C to 150°C Lead Temperature (Soldering, 10 sec)................. 300°C
The q denotes the specifications which apply over the full operating temperature range, otherwise specifications are at TA = 25°C. (Note 2) VIN = 5V, VCC = 35V, unless otherwise noted.
MAX3469中文资料
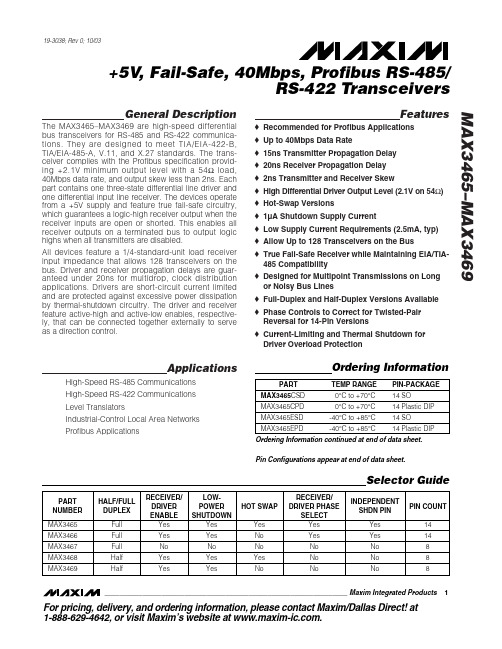
MAX3465–MAX3469
19-3038; Rev 0; 10/03
+5V, Fail-Safe, 40Mbps, Profibus RS-485/ RS-422 Transceivers
General Description
The MAX3465–MAX3469 are high-speed differential bus transceivers for RS-485 and RS-422 communications. They are designed to meet TIA/EIA-422-B, TIA/EIA-485-A, V.11, and X.27 standards. The transceiver complies with the Profibus specification providing +2.1V minimum output level with a 54Ω load, 40Mbps data rate, and output skew less than 2ns. Each part contains one three-state differential line driver and one differential input line receiver. The devices operate from a +5V supply and feature true fail-safe circuitry, which guarantees a logic-high receiver output when the receiver inputs are open or shorted. This enables all receiver outputs on a terminated bus to output logic highs when all transmitters are disabled.
WDJD-3多功能数字直流激电仪(最新版)

控放大送到A/D进行转换,电流信号则由标准电阻采样后,经隔放、滤波、 程控放大送A/D进行转换,由单片机从A/D取出电压与电流信号的转换结 果,送显示器显示。仪器采用人机对话方式来完成各种测量功能。
WDJD-3 多功能数字直流激电仪
常规电法
使用说明书
目
录
一、 仪器主要特点与功能·············································································2 二、 仪器主要技术指标·················································································2 三、 仪器工作原理··························································································3 四、 仪器结构···································································································4 五、 操作说明···································································································5
⑧ R地 :两芯电极接地电阻测试插座。
⑨ 报警 :出错报警蜂鸣器。
4
五、操作说明
WWII-M3系列枪支用户手册说明书
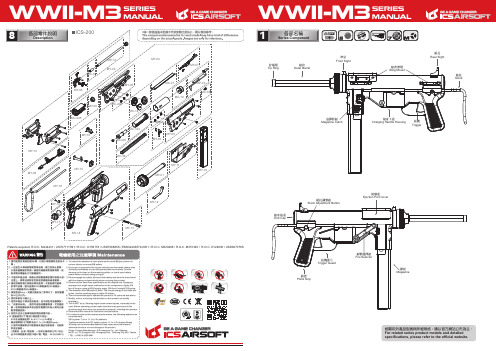
相關系列產品型號與詳細規格,請以官方網站公布為主。
For related series product models and detailed specifications, please refer to the official website.※使用非建議電池可能會造成產品效能低落、功能異常甚至損毀。
( 原產地 : 台灣 / 製造商 : 一芝軒企業有限公司 / 地址 : 台中市神岡區東洲路79巷67號 / 電話:04-25256461)※Using non-recommended batteries may cause poor performance, abnormal functions or even damage to the product.Origin: Taiwan/ Manufacturer: ICS enterprise Co., Ltd / Address:No.67, Ln. 79, Dongzhou Rd., Shengang Dist., Taichung City 429, Taiwan / TEL:(+886) 4-2525-64612-1裝BB彈方式Load BBs將彈匣上蓋依箭頭方向打開再倒入BB彈。
Open the cover to load BBs.建議使用 6mm BB彈。
6mm caliber BBs are recommended for optimum performance.依箭頭方向旋緊彈匣底下旋鈕,即可將BB彈順利送出。
To charge BB feed spring, please rotate the gear under the magazine.2彈匣使用方式Magazine Attachment 2-2裝卸彈匣Magazine Loading and Unloading1.直接將彈匣插入彈匣插槽。
2.按壓退彈匣鈕即可將彈匣卸下。
高血压左心室肥厚患者红细胞分布宽度、平均血小板体积、血小板分布宽度变化及其临床意义

山东医药2020年第60卷第33期高血压左心室肥厚患者红细胞分布宽度、平均血小板体积、血小板分布宽度变化及其临床意义,,,,徐州市中心医院,江苏徐州221009摘要:目的观察高血压左心室肥厚患者红细胞分布宽度(RDW)、平均血小板体积(MPV)、血小板分布宽度(PDW)变化,探讨其临床意义。
方法高血压患者161例,通过超声心动图检查计算左心室质量指数(LVMI),根据LVMI将患者分为左心室肥厚组(54例)和非左心室肥厚组(107例、。
收集并比较两组患者的年龄、性别、体质量、身高、吸烟史、糖尿病病史、口服降压药史等一般资料。
采集患者空腹外周静脉血,测定患者RDW、MPV、PDW、超敏C反应蛋白(hs-CRP)、空腹血糖、总胆固醇、甘油三酯、高密度脂蛋白胆固醇、低密度脂蛋白胆固醇治几1、尿酸等指标,计算估算的肾小球滤过率。
采用Spearman相关分析法分析RDW、MPV、PDW与LVMI的相关性。
采用Logistic回归分析法分析高血压患者发生左心室肥厚的危险因素。
采用受试者工作特征曲线(ROC)分析RDW, MPV、PDW对高血压患者左心室肥厚的诊断效能。
结果左心室肥厚组女性比例、RDW、MPV、PDW,s-CRP水平均高于非左心室肥厚组(P均<0.05)。
RDW、MPV、PDW与LVMI呈正相关关系((分别为0.182有.342,0.300,P 均<0.05)。
女性、RDW、MPV、PDW,s-CRP水平升高均为高血压患者发生左心室肥厚的独立危险因素。
RDW诊断高血压患者发生左心室肥厚的ROC下面积为0.619,取最佳截断值为13.55%时并寺异度为94.39%,敏感度为25.93%o MPV诊断高血压患者发生左心室肥厚的ROC下面积为0.725,取最佳截断值为11.55fL时并寺异度为89.72%,敏感度为46.30%。
PDW诊断高血压患者发生左心室肥厚的ROC下面积为0.715,取最佳截断值为13.35%时并寺异度为92.52%,敏感度为42.59%。
MC9S12_datasheet中文

目录 .................................................................................................................................................. I 第一章 PWM模块 ...........................................................................................................................1 第一节 PWM模块介绍 .........................................................................................................1 第二节 PWM寄存器简介 .......................................................................2 2.1 PWME寄存器 ........................................................................................................2 2.2 PWMPOL寄存器...................................................................................................2 2.3 PWMCLK寄存器 ..................................................................
98034计重秤

98134版高精度計重秤操作說明1.規格設定說明:1.1硬體需求開機前: 請將主板或A/D板上之SW A1的MINI JUMPER 插至ADJ方可進行校正。
1.2軟體校正說明:本機提供四種不同的校正模式,可依不同的精度及客戶而進行取捨,分別說明如下:a.線性校正模式:開機倒數前,按住“→O←”(零點)鍵至螢幕出現版號後再按“→O←”(零點)鍵即進入此模式。
此模式只用於1/10,000以上及認證規格機種之用,及當客戶只買電子頭未含秤台時(此時用DC STANDARD校正) (請依操作說明第2.項步驟操作)。
b.規格重量及重量單位設定模式:開機倒數前,按住“→O←”(零點)鍵至螢幕出現版號後再按“↵”(Enter)鍵, 即進入此模式。
此校正模式為生產或更改規格時之必要校正模式(請依操作說明第3.項步驟操作)。
c.溫度校正模式:開機倒數前按住“→O←”(零點)鍵至螢幕出現版號後再按“T”(扣重)鍵即進入此模式,此模式用於認證規機種之用,在A/D板上必需要加U8 , R27不要接才有此功能(請依操作說明第4.項步驟操作)。
d.廠外(使用者)校正模式:開機倒數前,按住“↵”(Enter)鍵即進入此模式。
此校正模式為當使用者發現重量準確有些許不準時進行校正之用。
當廠內生產時已做過a.中之規格,重量及重量單位設定模式後,可不必做此校正(請依操作說明第7.項步驟操作)。
1.3校正之先後順序為:1.3.1如要線性校正時順序為:(1)線性校正(請依操作說明第2.項步驟操作)(2)規格校正(請依操作說明第3.項步驟操作)(3)溫度校正(請依操作說明第4.項步驟操作)1.3.2如無線性校正時順序為:(1)規格校正(請依操作說明第3.項步驟操作)(2)溫度校正(請依操作說明第4.項步驟操作)2.線性校正模式2.1 開機,磅秤自動歸零倒數,倒數前,按住“→O←”(零點)鍵不放,即進入校正模式, 螢幕顯示版號。
(如為新磅秤未經校正此時記憶體內無資料,直接進入重量校正模式)。
威лен电子公司 SpitFire TIR3 LED控板仪说明书
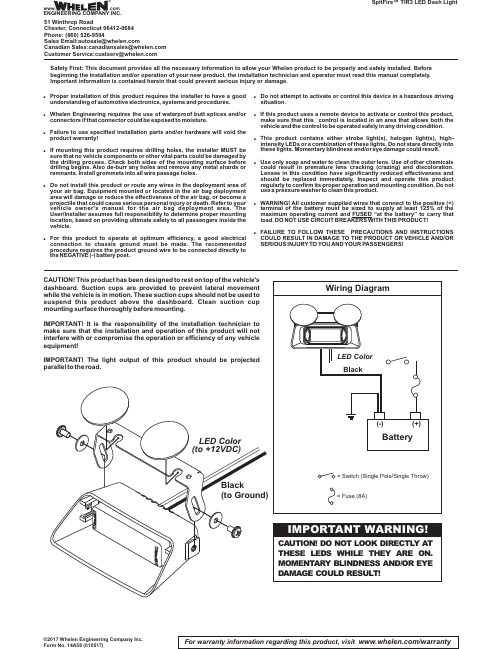
For warranty information regarding this product, visit /warranty©2017 Whelen Engineering Company Inc.Form No. 14A58 (010517)SpitFire™TIR3 LED Dash LightCAUTION!This product has been designed to rest on top of the vehicle'sdashboard.Suction cups are provided to prevent lateral movementwhile the vehicle is in motion.These suction cups should not be used tosuspend this product above the dashboard.Clean suction cupmounting surface thoroughly before mounting.IMPORTANT!It is the responsibility of the installation technician tomake sure that the installation and operation of this product will notinterfere with or compromise the operation or efficiency of any vehicleequipment!IMPORTANT!The light output of this product should be projectedparallel to the road.Safety First: This document provides all the necessary information to allow your Whelen product to be properly and safely installed. Beforebeginning the installation and/or operation of your new product, the installation technician and operator must read this manual completely.Important information is contained herein that could prevent serious injury or damage.!Proper installation of this product requires the installer to have a good understanding of automotive electronics,systems and procedures.!Whelen Engineering requires the use of waterproof butt splices and/or connectors if that connector could be exposed to moisture.!Failure to use specified installation parts and/or hardware will void theproduct warranty!!If mounting this product requires drilling holes,the installer MUST be sure that no vehicle components or other vital parts could be damaged by the drilling process.Check both sides of the mounting surface before drilling begins.Also de-burr any holes and remove any metal shards or remnants.Install grommets into all wire passage holes.!Do not install this product or route any wires in the deployment area of your air bag.Equipment mounted or located in the air bag deployment area will damage or reduce the effectiveness of the air bag,or become a projectile that could cause serious personal injury or death.Refer to your vehicle owner's manual for the air bag deployment area.The User/Installer assumes full responsibility to determine proper mounting location,based on providing ultimate safety to all passengers inside the vehicle.!For this product to operate at optimum efficiency,a good electrical connection to chassis ground must be made.The recommended procedure requires the product ground wire to be connected directly to the NEGATIVE (-)battery post.!Do not attempt to activate or control this device in a hazardous driving situation.!If this product uses a remote device to activate or control this product,make sure that this control is located in an area that allows both the vehicle and the control to be operated safely in any driving condition.!This product contains either strobe light(s),halogen light(s),high-intensity LEDs or a combination of these lights.Do not stare directly into these lights.Momentary blindness and/or eye damage could result.!Use only soap and water to clean the outer e of other chemicals could result in premature lens cracking (crazing)and discoloration.Lenses in this condition have significantly reduced effectiveness and should be replaced immediately.Inspect and operate this product regularly to confirm its proper operation and mounting condition.Do not use a pressure washer to clean this product.!WARNING!All customer supplied wires that connect to the positive (+)terminal of the battery must be sized to supply at least 125%of the maximum operating current and “at the battery”to carry that FUSED load.DO NOT USE CIRCUIT BREAKERS WITH THIS PRODUCT!!FAILURE TO FOLLOW THESE PRECAUTIONS AND INSTRUCTIONS COULD RESULT IN DAMAGE TO THE PRODUCT OR VEHICLE AND/OR SERIOUS INJURY TO YOU AND YOURPASSENGERS!®ENGINEERING COMPANY INC.51 Winthrop RoadChester, Connecticut 06412-0684Phone: (860) 526-9504SalesEmail:*******************CanadianSales:************************CustomerService:*******************Warnings to InstallersWhelen’s emergency vehicle warning devices must be properly mounted and wired in order to be effective and safe. Read and follow all of Whelen’s written instructions when installing or using this device. Emergency vehicles are often operated under high speed stressful conditions which must be accounted for when installing all emergency warning devices. Controls should be placed within convenient reach of the operator so that he can operate the system without taking his eyes off the roadway. Emergency warning devices can require high electrical voltages and/or currents. Properly protect and use caution around live electrical connections.Grounding or shorting of electrical connections can cause high current arcing, which can cause personal injury and/or vehicle damage, including fire. Many electronic devices used in emergency vehicles can create or be affected by electromagnetic interference.Therefore, after installation of any electronic device it is necessary to test all electronic equipment simultaneously to insure that they operate free of interference from other components within the vehicle. Never power emergency warning equipment from the same circuit or share the same grounding circuit with radio communication equipment.All devices should be mounted in accordance with the manufacturer’s instructions and securely fastened to vehicle elements of sufficient strength to withstand the forces applied to the device. Driver and/or passenger air bags (SRS) will affect the way equipment should be mounted.This device should be mounted by permanent installation and within the zones specified by the vehicle manufacturer, if any.Any device mounted in the deployment area of an air bag will damage or reduce the effectiveness of the air bag and may damage or dislodge the device. Installer must be sure that this device, its mounting hardware and electrical supply wiring does not interfere with the air bag or the SRS wiring or sensors. Mounting the unit inside the vehicle by a method other than permanent installation is not recommended as unit may become dislodged during swerving; sudden braking or collision. Failure to follow instructions can result in personal injury. Whelen assumes no liability for any loss resulting from the use of this warning device. PROPER INSTALLATION COMBINED WITH OPERATOR TRAINING IN THE PROPER USE OF EMERGENCY WARNING DEVICES IS ESSENTIAL TO INSURE THE SAFETY OF EMERGENCY PERSONNEL AND THE PUBLIC.Warnings to UsersWhelen’s emergency vehicle warning devices are intended to alert other operators and pedestrians to the presence and operation of emergency vehicles and personnel. However, the use of this or any other Whelen emergency warning device does not guarantee that you will have the right-of-way or that other drivers and pedestrians will properly heed an emergency warning signal. Never assume you have the right-of-way. It is your responsibility to proceed safely before entering an intersection, driving against traffic, responding at a high rate of speed, or walking on or around traffic lanes. Emergency vehicle warning devices should be tested on a daily basis to ensure that they operate properly. When in actual use, the operator must ensure that both visual and audible warnings are not blocked by vehicle components (i.e.: open trunks or compartment doors), people, vehicles, or other obstructions. It is the user’s responsibility to understand and obey all laws regarding emergency warning devices.The user should be familiar with all applicable laws and regulations prior to the use of any emergency vehicle warning device. Whelen’s audible warning devices are designed to project sound in a forward direction away from the vehicle occupants. However, because sustained periodic exposure to loud sounds can cause hearing loss, all audible warning devices should be installed and operated in accordance with the standards established by the National Fire Protection Association.。
- 1、下载文档前请自行甄别文档内容的完整性,平台不提供额外的编辑、内容补充、找答案等附加服务。
- 2、"仅部分预览"的文档,不可在线预览部分如存在完整性等问题,可反馈申请退款(可完整预览的文档不适用该条件!)。
- 3、如文档侵犯您的权益,请联系客服反馈,我们会尽快为您处理(人工客服工作时间:9:00-18:30)。
M93S66, M93S56M93S464Kbit, 2Kbit and 1Kbit (16-bit wide) MICROWIRE Serial Access EEPROM with Block ProtectionFEATURES SUMMARY■Industry Standard MICROWIRE Bus Array■Single Supply Voltage:– 4.5 to 5.5V for M93Sx6– 2.5 to 5.5V for M93Sx6-W– 1.8 to 5.5V for M93Sx6-R■Single Organization: by Word (x16)■Programming Instructions that work on: Wordor Entire Memory■Self-timed Programming Cycle with Auto-Erase■User Defined Write Protected Area■Page Write Mode (4 words)■■Speed:–1MHz Clock Rate, 10ms Write Time(Current product, identified by processidentification letter F or M)–2MHz Clock Rate, 5ms Write Time (NewProduct, identified by processidentification letter W or G)■Sequential Read Operation■Enhanced ESD/Latch-Up Behavior■More than 1 Million Erase/Write Cycles■More than 40 Year Data RetentionApril 20041/34M93S66, M93S56, M93S46TABLE OF CONTENTSFEATURES SUMMARY . . . . . . . . . . . . . . . . . . . . . . . . . . . . . . . . . . . . . . . . . . . . . . . . . . . . . . . . . . . . .1 Figure 1.Packages. . . . . . . . . . . . . . . . . . . . . . . . . . . . . . . . . . . . . . . . . . . . . . . . . . . . . . . . . . . . . .1SUMMARY DESCRIPTION. . . . . . . . . . . . . . . . . . . . . . . . . . . . . . . . . . . . . . . . . . . . . . . . . . . . . . . . . . .4Figure 2.Logic Diagram . . . . . . . . . . . . . . . . . . . . . . . . . . . . . . . . . . . . . . . . . . . . . . . . . . . . . . . . . .4 Table 1.Signal Names . . . . . . . . . . . . . . . . . . . . . . . . . . . . . . . . . . . . . . . . . . . . . . . . . . . . . . . . . .4 Figure 3.DIP, SO and TSSOP Connections . . . . . . . . . . . . . . . . . . . . . . . . . . . . . . . . . . . . . . . . . .4POWER-ON DATA PROTECTION. . . . . . . . . . . . . . . . . . . . . . . . . . . . . . . . . . . . . . . . . . . . . . . . . . . ..5INSTRUCTIONS . . . . . . . . . . . . . . . . . . . . . . . . . . . . . . . . . . . . . . . . . . . . . . . . . . . . . . . . . . . . . . . . . . .5Table 2.Instruction Set for the M93S46 . . . . . . . . . . . . . . . . . . . . . . . . . . . . . . . . . . . . . . . . . . . . .6 Table 3.Instruction Set for the M93S66, M93S56. . . . . . . . . . . . . . . . . . . . . . . . . . . . . . . . . . . . . .7 Figure 4.READ, WRITE, WEN and WDS Sequences. . . . . . . . . . . . . . . . . . . . . . . . . . . . . . . . . . .8 Read . . . . . . . . . . . . . . . . . . . . . . . . . . . . . . . . . . . . . . . . . . . . . . . . . . . . . . . . . . . . . . . . . . . . . . . . .9 Write Enable and Write Disable . . . . . . . . . . . . . . . . . . . . . . . . . . . . . . . . . . . . . . . . . . . . . . . . . . .9 Write . . . . . . . . . . . . . . . . . . . . . . . . . . . . . . . . . . . . . . . . . . . . . . . . . . . . . . . . . . . . . . . . . . . . . . . . .9 Figure 5.PAWRITE and WRAL Sequence. . . . . . . . . . . . . . . . . . . . . . . . . . . . . . . . . . . . . . . . . . .10 Page Write . . . . . . . . . . . . . . . . . . . . . . . . . . . . . . . . . . . . . . . . . . . . . . . . . . . . . . . . . . . . . . . . . . .10 Write All . . . . . . . . . . . . . . . . . . . . . . . . . . . . . . . . . . . . . . . . . . . . . . . . . . . . . . . . . . . . . . . . . . . . .11 Figure 6.PREAD, PRWRITE and PREN Sequences. . . . . . . . . . . . . . . . . . . . . . . . . . . . . . . . . . .12 Figure 7.PRCLEAR and PRDS Sequences. . . . . . . . . . . . . . . . . . . . . . . . . . . . . . . . . . . . . . . . . .13WRITE PROTECTION AND THE PROTECTION REGISTER . . . . . . . . . . . . . . . . . . . . . . . . . . . . . . .14Protection Register Read . . . . . . . . . . . . . . . . . . . . . . . . . . . . . . . . . . . . . . . . . . . . . . . . . . . . . . .14 Protection Register Enable. . . . . . . . . . . . . . . . . . . . . . . . . . . . . . . . . . . . . . . . . . . . . . . . . . . . . .14 Protection Register Clear. . . . . . . . . . . . . . . . . . . . . . . . . . . . . . . . . . . . . . . . . . . . . . . . . . . . . . .14 Protection Register Write. . . . . . . . . . . . . . . . . . . . . . . . . . . . . . . . . . . . . . . . . . . . . . . . . . . . . . .14 Protection Register Disable . . . . . . . . . . . . . . . . . . . . . . . . . . . . . . . . . . . . . . . . . . . . . . . . . . . . .14COMMON I/O OPERATION . . . . . . . . . . . . . . . . . . . . . . . . . . . . . . . . . . . . . . . . . . . . . . . . . . . . . . . . .15 Figure 8.Write Sequence with One Clock Glitch . . . . . . . . . . . . . . . . . . . . . . . . . . . . . . . . . . . . . .15CLOCK PULSE COUNTER . . . . . . . . . . . . . . . . . . . . . . . . . . . . . . . . . . . . . . . . . . . . . . . . . . . . . . . . .15MAXIMUM RATING. . . . . . . . . . . . . . . . . . . . . . . . . . . . . . . . . . . . . . . . . . . . . . . . . . . . . . . . . . . . . . . .16 Table 4.Absolute Maximum Ratings. . . . . . . . . . . . . . . . . . . . . . . . . . . . . . . . . . . . . . . . . . . . . . .16DC AND AC PARAMETERS. . . . . . . . . . . . . . . . . . . . . . . . . . . . . . . . . . . . . . . . . . . . . . . . . . . . . . . . .17Table 5.Operating Conditions (M93Sx6) . . . . . . . . . . . . . . . . . . . . . . . . . . . . . . . . . . . . . . . . . . .17 Table 6.Operating Conditions (M93Sx6-W) . . . . . . . . . . . . . . . . . . . . . . . . . . . . . . . . . . . . . . . . .17 Table 7.Operating Conditions (M93Sx6-R). . . . . . . . . . . . . . . . . . . . . . . . . . . . . . . . . . . . . . . . . .17 Table 8.AC Measurement Conditions (M93Sx6) . . . . . . . . . . . . . . . . . . . . . . . . . . . . . . . . . . . . .17 Table 9.AC Measurement Conditions (M93Sx6-W and M93Sx6-R). . . . . . . . . . . . . . . . . . . . . . .172/34M93S66, M93S56, M93S46Figure 9.AC Testing Input Output Waveforms. . . . . . . . . . . . . . . . . . . . . . . . . . . . . . . . . . . . . . . .18 Table 10.Capacitance. . . . . . . . . . . . . . . . . . . . . . . . . . . . . . . . . . . . . . . . . . . . . . . . . . . . . . . . . . .18 Table 11.DC Characteristics (M93Sx6, Device Grade 6). . . . . . . . . . . . . . . . . . . . . . . . . . . . . . . .19 Table 12.DC Characteristics (M93Sx6, Device Grade 3). . . . . . . . . . . . . . . . . . . . . . . . . . . . . . . .19 Table 13.DC Characteristics (M93Sx6-W, Device Grade 6). . . . . . . . . . . . . . . . . . . . . . . . . . . . . .20 Table 14.DC Characteristics (M93Sx6-W, Device Grade 3). . . . . . . . . . . . . . . . . . . . . . . . . . . . . .21 Table 15.DC Characteristics (M93Sx6-R) . . . . . . . . . . . . . . . . . . . . . . . . . . . . . . . . . . . . . . . . . . .21 Table 16.AC Characteristics (M93Sx6, Device Grade 6 or 3) . . . . . . . . . . . . . . . . . . . . . . . . . . . .22 Table 17.AC Characteristics (M93Sx6-W, Device Grade 6). . . . . . . . . . . . . . . . . . . . . . . . . . . . . .23 Table 18.AC Characteristics (M93Sx6-W, Device Grade 3). . . . . . . . . . . . . . . . . . . . . . . . . . . . . .24 Table 19.AC Characteristics (M93Sx6-R). . . . . . . . . . . . . . . . . . . . . . . . . . . . . . . . . . . . . . . . . . . .25 Figure 10.Synchronous Timing (Start and Op-Code Input). . . . . . . . . . . . . . . . . . . . . . . . . . . . . . .26 Figure 11.Synchronous Timing (Read or Write) . . . . . . . . . . . . . . . . . . . . . . . . . . . . . . . . . . . . . . .26 Figure 12.Synchronous Timing (Read or Write) . . . . . . . . . . . . . . . . . . . . . . . . . . . . . . . . . . . . . . .27PACKAGE MECHANICAL . . . . . . . . . . . . . . . . . . . . . . . . . . . . . . . . . . . . . . . . . . . . . . . . . . . . . . . . . .28Figure 13.PDIP8 – 8 pin Plastic DIP, 0.25mm lead frame, Package Outline . . . . . . . . . . . . . . . . .28 Table 20.PDIP8 – 8 pin Plastic DIP, 0.25mm lead frame, Package Mechanical Data. . . . . . . . . .28 Figure 14.SO8 narrow – 8 lead Plastic Small Outline, 150 mils body width, Package Outline . . . .29 Table 21.SO8 narrow – 8 lead Plastic Small Outline, 150 mils body width, Package Mechanical Data 29Figure 15.TSSOP8 3x3mm² – 8 lead Thin Shrink Small Outline, 3x3mm² body size, Package Outline 30Table 22.TSSOP8 3x3mm² – 8 lead Thin Shrink Small Outline, 3x3mm² body size, Mechanical Data 30Figure 16.TSSOP8 – 8 lead Thin Shrink Small Outline, Package Outline . . . . . . . . . . . . . . . . . . .31 Table 23.TSSOP8 – 8 lead Thin Shrink Small Outline, Package Mechanical Data. . . . . . . . . . . .31PART NUMBERING . . . . . . . . . . . . . . . . . . . . . . . . . . . . . . . . . . . . . . . . . . . . . . . . . . . . . . . . . . . . . . .32Table 24.Ordering Information Scheme . . . . . . . . . . . . . . . . . . . . . . . . . . . . . . . . . . . . . . . . . . . . .32 Table 25.How to Identify Current and New Products by the Process Identification Letter. . . . . . .32REVISION HISTORY. . . . . . . . . . . . . . . . . . . . . . . . . . . . . . . . . . . . . . . . . . . . . . . . . . . . . . . . . . . . . . .33 Table 26.Document Revision History. . . . . . . . . . . . . . . . . . . . . . . . . . . . . . . . . . . . . . . . . . . . . . .333/34M93S66, M93S56, M93S464/34SUMMARY DESCRIPTIONThis specification covers a range of 4K, 2K, 1K bit serial Electrically Erasable Programmable Memo-ry (EEPROM) products (respectively for M93S66,M93S56, M93S46). In this text, these products are collectively referred to as M93Sx6.Table 1. Signal NamesThe M93Sx6 is accessed through a serial input (D)and output (Q) using the MICROWIRE bus proto-col. The memory is divided into 256, 128, 64 x16bit words (respectively for M93S66, M93S56,M93S46).The M93Sx6 is accessed by a set of instructions which includes Read, Write, Page Write, Write Alland instructions used to set the memory protec-tion. These are summarized in Table 2. and Table 3.).A Read Data from Memory (READ) instruction loads the address of the first word to be read into an internal address pointer. The data contained at this address is then clocked out serially. The ad-dress pointer is automatically incremented after the data is output and, if the Chip Select Input (S)is held High, the M93Sx6 can output a sequential stream of data words. In this way, the memory can be read as a data stream from 16 to 4096 bits (for the M93S66), or continuously as the addresscounter automatically rolls over to 00h when the highest address is reached.Within the time required by a programming cycle (t W ), up to 4 words may be written with help of the Page Write instruction. the whole memory may also be erased, or set to a predetermined pattern,by using the Write All instruction.Within the memory, a user defined area may be protected against further Write instructions. The size of this area is defined by the content of a Pro-tection Register, located outside of the memory ar-ray. As a final protection step, data may be permanently protected by programming a One Time Programming bit (OTP bit) which locks the Protection Register content.Programming is internally self-timed (the external clock signal on Serial Clock (C) may be stopped or left running after the start of a Write cycle) and does not require an erase cycle prior to the Write instruction. The Write instruction writes 16 bits at a time into one of the word locations of the M93Sx6,the Page Write instruction writes up to 4 words of 16 bits to sequential locations, assuming in both cases that all addresses are outside the Write Pro-tected area. After the start of the programming cy-cle, a Busy/Ready signal is available on Serial Data Output (Q) when Chip Select Input (S) is driv-en High.Note:See PACKAGE MECHANICAL section for package dimen-sions, and how to identify pin-1.S Chip Select Input D Serial Data Input Q Serial Data Output C Serial ClockPRE Protection Register Enable W Write Enable V CC Supply Voltage V SSGroundM93S66, M93S56, M93S46An internal Power-on Data Protection mechanism in the M93Sx6 inhibits the device when the supply is too low.POWER-ON DATA PROTECTIONTo prevent data corruption and inadvertent write operations during power-up, a Power-On Reset (POR) circuit resets all internal programming cir-cuitry, and sets the device in the Write Disable mode.–At Power-up and Power-down, the device must not be selected (that is, Chip Select Input (S) must be driven Low) until the supplyvoltage reaches the operating value V CCspecified in Table 5. to Table 6..–When V CC reaches its valid level, the device is properly reset (in the Write Disable mode) and is ready to decode and execute incominginstructions.For the M93Sx6 devices (5V range) the POR threshold voltage is around 3V. For the M93Sx6-W (3V range) and M93Sx6-R (2V range) the POR threshold voltage is around 1.5V.INSTRUCTIONSThe instruction set of the M93Sx6 devices con-tains seven instructions, as summarized in Table 2. to Table 3.. Each instruction consists of the fol-lowing parts, as shown in Figure 4.:■Each instruction is preceded by a rising edge on Chip Select Input (S) with Serial Clock (C) being held Low.■ A start bit, which is the first ‘1’ read on Serial Data Input (D) during the rising edge of Serial Clock (C).■Two op-code bits, read on Serial Data Input(D) during the rising edge of Serial Clock (C).(Some instructions also use the first two bits of the address to define the op-code).■The address bits of the byte or word that is to be accessed. For the M93S46, the address is made up of 6 bits (see Table 2.). For theM93S56 and M93S66, the address is made up of 8 bits (see Table 3.).The M93Sx6 devices are fabricated in CMOS technology and are therefore able to run as slow as 0Hz (static input signals) or as fast as the max-imum ratings specified in Table 16. to Table 19..5/34M93S66, M93S56, M93S466/34Table 2. Instruction Set for the M93S46Note: 1.X = Don’t Care bit.InstructionDescription WPREStart bit Op-Code Address 1DataRequiredClock CyclesAdditional CommentsREAD Read Data from Memory X 0110A5-A0Q15-Q0WRITE Write Data to Memory10101A5-A0D15-D025Write is executed if the address is not inside the Protected areaPAWRITEPage Write to Memory 10111A5-A0N x D15-D09 + N x 16Write is executed if all the N addressesare not inside the Protected areaWRAL Write All Memory with same Data 1010001XXXXD15-D025Write all data if the Protection Register is clearedWEN Write Enable 1010011 XXXX 9WDSWrite Disable X10000 XXXX 9PRREAD Protection Register ReadX 1110XXXXXXQ5-Q0+ FlagData Output =Protection Register content + Protection Flag bitPRWRITEProtection Register Write 11101A5-A0 9Data above specified address A5-A0 are protectedPRCLEAR Protection Register Clear 11111111111 9Protect Flag is also cleared (cleared Flag = 1)PREN Protection Register Enable 1110011XXXX 9PRDS Protection Register Disable11100000000 9OTP bit is set permanently7/34M93S66, M93S56, M93S46Table 3. Instruction Set for the M93S66, M93S56Note: 1.X = Don’t Care bit.2.Address bit A7 is not decoded by the M93S56.InstructionDescription WPREStart bit Op-Code Address 1,2DataRequiredClock CyclesAdditional CommentsREAD Read Data from Memory X 0110A7-A0Q15-Q0WRITE Write Data to Memory10101A7-A0D15-D027Write is executed if the address is not inside theProtected areaPAWRITEPage Write to Memory10111A7-A0N xD15-D011 + N x 16Write is executed if all the Naddresses are notinside theProtected area WRALWrite All Memory with same Data 1010001XXXXXXD15-D027Write all data if the ProtectionRegister is clearedWEN Write Enable 1010011XXXXXX 11WDSWrite Disable X10000XXXXXX11PRREAD Protection Register ReadX 1110XXXXXXXX Q7-Q0+ FlagData Output = ProtectionRegister content + Protection Flag bit PRWRITEProtection Register Write11101A7-A0 11Data abovespecified address A7-A0 are protectedPRCLEARProtection Register Clear 1111111111111 11Protect Flag is also cleared (cleared Flag = 1)PREN Protection Register Enable 1110011XXXXXX 11PRDS Protection Register Disable1110000000000 11OTP bit is set permanentlyM93S66, M93S56, M93S468/34M93S66, M93S56, M93S46ReadThe Read Data from Memory (READ) instruction outputs serial data on Serial Data Output (Q). When the instruction is received, the op-code and address are decoded, and the data from the mem-ory is transferred to an output shift register. A dum-my 0 bit is output first, followed by the 16-bit word, with the most significant bit first. Output data changes are triggered by the rising edge of Serial Clock (C). The M93Sx6 automatically increments the internal address register and clocks out the next byte (or word) as long as the Chip Select In-put (S) is held High. In this case, the dummy 0 bit is not output between bytes (or words) and a con-tinuous stream of data can be read.Write Enable and Write DisableThe Write Enable (WEN) instruction enables the future execution of write instructions, and the Write Disable (WDS) instruction disables it. When power is first applied, the M93Sx6 initializes itself so that write instructions are disabled. After an Write En-able (WEN) instruction has been executed, writing remains enabled until an Write Disable (WDS) in-struction is executed, or until V CC falls below the power-on reset threshold voltage. To protect the memory contents from accidental corruption, it is advisable to issue the Write Disable (WDS) in-struction after every write cycle. The Read Data from Memory (READ) instruction is not affected by the Write Enable (WEN) or Write Disable (WDS) instructions.WriteThe Write Data to Memory (WRITE) instruction is composed of the Start bit plus the op-code fol-lowed by the address and the 16 data bits to be written.Write Enable (W) must be held High before and during the instruction. Input address and data, on Serial Data Input (D) are sampled on the rising edge of Serial Clock (C).After the last data bit has been sampled, the Chip Select Input (S) must be taken Low before the next rising edge of Serial Clock (C). If Chip Select Input (S) is brought Low before or after this specific time frame, the self-timed programming cycle will not be started, and the addressed location will not be programmed.While the M93Sx6 is performing a write cycle, but after a delay (t SLSH) before the status information becomes available, Chip Select Input (S) can be driven High to monitor the status of the write cycle: Serial Data Output (Q) is driven Low while the M93Sx6 is still busy, and High when the cycle is complete, and the M93Sx6 is ready to receive a new instruction. The M93Sx6 ignores any data on the bus while it is busy on a write cycle. Once the M93Sx6 is Ready, Serial Data Output (Q) is driven High, and remains in this state until a new start bit is decoded or the Chip Select Input (S) is brought Low.Programming is internally self-timed, so the exter-nal Serial Clock (C) may be disconnected or left running after the start of a write cycle.9/34M93S66, M93S56, M93S4610/34Page WriteA Page Write to Memory (PAWRITE) instruction contains the first address to be written, followed by up to 4 data words.After the receipt of each data word, bits A1-A0 of the internal address register are incremented, the high order bits remaining unchanged (A7-A2 for M93S66, M93S56; A5-A2 for M93S46). Users must take care, in the software, to ensure that the last word address has the same upper order ad-dress bits as the initial address transmitted to avoid address roll-over.The Page Write to Memory (PAWRITE) instruction will not be executed if any of the 4 words address-es the protected area.Write Enable (W) must be held High before and during the instruction. Input address and data, on Serial Data Input (D) are sampled on the rising edge of Serial Clock (C).After the last data bit has been sampled, the Chip Select Input (S) must be taken Low before the next rising edge of Serial Clock (C). If Chip Select Input (S) is brought Low before or after this specific time frame, the self-timed programming cycle will notbe started, and the addressed location will not be programmed.While the M93Sx6 is performing a write cycle, but after a delay (t SLSH) before the status information becomes available, Chip Select Input (S) can be driven High to monitor the status of the write cycle: Serial Data Output (Q) is driven Low while the M93Sx6 is still busy, and High when the cycle is complete, and the M93Sx6 is ready to receive a new instruction. The M93Sx6 ignores any data on the bus while it is busy on a write cycle. Once the M93Sx6 is Ready, Serial Data Output (Q) is driven High, and remains in this state until a new start bit is decoded or the Chip Select Input (S) is brought Low.Programming is internally self-timed, so the exter-nal Serial Clock (C) may be disconnected or left running after the start of a write cycle.Write AllThe Write All Memory with same Data (WRAL) in-struction is valid only after the Protection Register has been cleared by executing a Protection Reg-ister Clear (PRCLEAR) instruction. The Write All Memory with same Data (WRAL) instruction simul-taneously writes the whole memory with the same data word given in the instruction.Write Enable (W) must be held High before and during the instruction. Input address and data, on Serial Data Input (D) are sampled on the rising edge of Serial Clock (C).After the last data bit has been sampled, the Chip Select Input (S) must be taken Low before the next rising edge of Serial Clock (C). If Chip Select Input (S) is brought Low before or after this specific time frame, the self-timed programming cycle will not be started, and the addressed location will not be programmed.While the M93Sx6 is performing a write cycle, but after a delay (t SLSH) before the status information becomes available, Chip Select Input (S) can be driven High to monitor the status of the write cycle: Serial Data Output (Q) is driven Low while the M93Sx6 is still busy, and High when the cycle is complete, and the M93Sx6 is ready to receive a new instruction. The M93Sx6 ignores any data on the bus while it is busy on a write cycle. Once the M93Sx6 is Ready, Serial Data Output (Q) is driven High, and remains in this state until a new start bit is decoded or the Chip Select Input (S) is brought Low.Programming is internally self-timed, so the exter-nal Serial Clock (C) may be disconnected or left running after the start of a write cycle.11/34Note:For the meanings of An, Xn and Dn, please see Table 2. and Table 3.. 12/3413/34WRITE PROTECTION AND THE PROTECTION REGISTERThe Protection Register on the M93Sx6 is used to adjust the amount of memory that is to be write protected. The write protected area extends from the address given in the Protection Register, up to the top address in the M93Sx6 device.Two flag bits are used to indicate the Protection Register status:–Protection Flag: this is used to enable/disable protection of the write-protected area of theM93Sx6 memory–OTP bit: when set, this disables access to the Protection Register, and thus prevents anyfurther modifications to the value in theProtection Register.The lower-bound memory address is written to the Protection Register using the Protection Register Write (PRWRITE) instruction. It can be read using the Protection Register Read (PRREAD) instruc-tion.The Protection Register Enable (PREN) instruc-tion must be executed before any PRCLEAR, PRWRITE or PRDS instruction, and with appropri-ate levels applied to the Protection Enable (PRE) and Write Enable (W) signals.Write-access to the Protection Register is achieved by executing the following sequence:–Execute the Write Enable (WEN) instruction –Execute the Protection Register Enable (PREN) instruction–Execute one PRWRITE, PRCLEAR or PRDS instructions, to set a new boundary address in the Protection Register, to clear the protection address (to all 1s), or permanently to freezethe value held in the Protection Register. Protection Register ReadThe Protection Register Read (PRREAD) instruc-tion outputs, on Serial Data Output (Q), the con-tent of the Protection Register, followed by the Protection Flag bit. The Protection Enable (PRE) signal must be driven High before and during the instruction.As with the Read Data from Memory (READ) in-struction, a dummy 0 bit is output first. Since it is not possible to distinguish between the Protection Register being cleared (all 1s) or having been writ-ten with all 1s, the user must check the Protection Flag status (and not the Protection Register con-tent) to ascertain the setting of the memory protec-tion.Protection Register EnableThe Protection Register Enable (PREN) instruc-tion is used to authorize the use of instructions that modify the Protection Register (PRWRITE, PRCLEAR, PRDS). The Protection Register En-able (PREN) instruction does not modify the Pro-tection Flag bit value.Note: A Write Enable (WEN) instruction must be executed before the Protection Register Enable (PREN) instruction. Both the Protection Enable (PRE) and Write Enable (W) signals must be driv-en High during the instruction execution. Protection Register ClearThe Protection Register Clear (PRCLEAR) in-struction clears the address stored in the Protec-tion Register to all 1s, so that none of the memory is write-protected by the Protection Register. How-ever, it should be noted that all the memory re-mains protected, in the normal way, using the Write Enable (WEN) and Write Disable (WDS) in-structions.The Protection Register Clear (PRCLEAR) in-struction clears the Protection Flag to 1. Both the Protection Enable (PRE) and Write Enable (W) signals must be driven High during the instruction execution.Note: A Protection Register Enable (PREN) in-struction must immediately precede the Protection Register Clear (PRCLEAR) instruction. Protection Register WriteThe Protection Register Write (PRWRITE) instruc-tion is used to write an address into the Protection Register. This is the address of the first word to be protected. After the Protection Register Write (PRWRITE) instruction has been executed, all memory locations equal to and above the speci-fied address are protected from writing.The Protection Flag bit is set to 0, and can be read with Protection Register Read (PRREAD) instruc-tion. Both the Protection Enable (PRE) and Write Enable (W) signals must be driven High during the instruction execution.Note: A Protection Register Enable (PREN) in-struction must immediately precede the Protection Register Write (PRWRITE) instruction, but it is not necessary to execute first a Protection Register Clear (PRCLEAR).Protection Register DisableThe Protection Register Disable (PRDS) instruc-tion sets the One Time Programmable (OTP) bit. This instruction is a ONE TIME ONLY instruction which latches the Protection Register content, this content is therefore unalterable in the future. Both the Protection Enable (PRE) and Write Enable (W) signals must be driven High during the instruction execution. The OTP bit cannot be directly read, it can be checked by reading the content of the Pro-tection Register, using the Protection Register Read (PRREAD) instruction, then by writing this same value back into the Protection Register, us-14/34ing the Protection Register Write (PRWRITE) in-struction. When the OTP bit is set, the Ready/Busy status cannot appear on Serial Data Output (Q). When the OTP bit is not set, the Busy status ap-pears on Serial Data Output (Q).Note: A Protection Register Enable (PREN) in-struction must immediately precede the Protection Register Disable (PRDS) MON I/O OPERATIONSerial Data Output (Q) and Serial Data Input (D) can be connected together, through a current lim-iting resistor, to form a common, single-wire data bus. Some precautions must be taken when oper-ating the memory in this way, mostly to prevent a short circuit current from flowing when the last ad-dress bit (A0) clashes with the first data bit on Se-rial Data Output (Q). Please see the application note AN394 for details.CLOCK PULSE COUNTERIn a noisy environment, the number of pulses re-ceived on Serial Clock (C) may be greater than the number delivered by the Bus Master (the micro-controller). This can lead to a misalignment of the instruction of one or more bits (as shown in Figure 8.) and may lead to the writing of erroneous data at an erroneous address.To combat this problem, the M93Sx6 has an on-chip counter that counts the clock pulses from the start bit until the falling edge of the Chip Select In-put (S). If the number of clock pulses received is not the number expected, the WRITE, PAWRITE, WRALL, PRWRITE or PRCLEAR instruction is aborted, and the contents of the memory are not modified.The number of clock cycles expected for each in-struction, and for each member of the M93Sx6 family, are summarized in Table 2. to Table 3.. For example, a Write Data to Memory (WRITE) in-struction on the M93S56 (or M93S66) expects 27 clock cycles from the start bit to the falling edge of Chip Select Input (S). That is:1 Start bit+ 2 Op-code bits+ 8 Address bits+ 16 Data bits15/34。