Residual stresses due to gas arc welding of aluminum alloy
ASME压教材力容器常用词汇中英文对照1

ASME常用词汇Abrasion,allowance for磨损,裕量Accessibility,pressure vessels压力容器可达性Access openings通道孔Allowance for corrosion,erosion,or abrasion腐蚀裕量侵蚀或/磨损裕量Applied linings,tightness应用衬里密封性Approval of new materials,新材料的批准Articles in Section V第V卷中的各章Article1,T-150第1章T150Article2第2章Attachments附件lugs and fitting支耳和配件lugs for platforms,ladders,etc.平台,梯子等的支耳nonpressure parts非受压件nozzles接管pipe and nozzle necks to vessel walls在器壁上的管子和接管颈stiffening rings to shell壳体上的刚性环Backing strip垫板Bending stress,welded joints弯曲应力,焊接接头Bend test弯曲试验Blind flanges盲板法兰Bolted flange connections螺栓法兰连接bolt lands螺栓载荷bolt stress螺栓应力design of关于设计flange moments法兰力矩flange stresses法兰应力materials材料studs双头螺栓tightness of紧密性types of attachment附件类型Bolts螺栓Braced and stayed surfaces支持和支撑面Brazed connections for nozzles接管的钎焊连接Brazed joints,efficiency of钎焊接头,焊缝系数maximum service temperature最高使用温度strength of强度Brazing,cleaning of brazed surfaces钎焊,钎焊的表面清理fabrication by用……制造filler metal填充金属fluxes钎焊剂heads into shells封头接入壳体operating temperature操作温度Buttstraps,curvature对接盖板,曲率forming ends of成型端thickness and corrosion allowance厚度和腐蚀裕量welding ends of焊接端Carbon in material for welding焊接用材料中的碳Cast ductile iron vessels,design可锻铸铁容器,设计pressure-temperature limitations压力-温度界限service restrictions使用限制Castings铸件carbon steel碳钢defects缺陷impact test冲击试验inspection检查quality factor质量系数specifications标准Cast iron circular dished heads铸铁碟形封头Cast iron standard parts,small铸铁标准部件,小件Cast iron pipe fittings铸铁管件Cast iron vessels铸铁容器corners and fillets圆角和倒角head design封头设计hydrostatic test水压试验nozzles and fittings接管和配件pressure-temperatures limitations压力-温度界限Certificate of Authorization for Code Symbol Stamp规范符号标志的认可证书Certification of material材料证明书Certification of Nondestructive Personnel无损检验人员证明书Magnetic Particle Examination磁粉检验Liquid Penetrant Examination液体渗透检验Radiographic Examination射线超声检验Ultrasonic Examination超声检验Chip marks on integrally forged vessels整体锻造容器上的缺口标志Circumferential joints alignment tolerance环向连接,组对公差assembling装配brazing钎焊vessels subjected to external pressure承受外压的容器Clad material,inserted strips覆层材料,嵌条examination检查Clad plate复合板Cleaning,of brazed surfaces钎焊表面清理of welded surfaces焊接表面Clearance between surfaces to be brazed钎焊表面间的间隙Combination,of different materials不同材料组合of methods of fabrication制造方法Computed working pressure from hydrostatic tests由水试验计算的工作压力Conical heads锥形封头Conical sections圆锥截面Connections,bolted flange(see Bolted flange connections)连接,螺栓法兰(见螺栓法兰连接)brazed钎焊clamp卡箍expanded胀接from vessels to safety valves由容器至安全阀studded双头螺栓threaded螺纹welded焊接Cooling,after postweld heat treating冷却,焊后热处理Corrosion allowance腐蚀裕度Corrosion resistant linings防腐蚀衬里Corrugated shells波纹形壳体Corrugating Paper Machinery波纹板机械Cover plates盖板on manholes and handholes在人孔和手孔上的spherically dished球形封头Cracking,stress corrosion应力腐蚀裂缝Cutting plates板材切割Cylindrical shells,supplementary loading柱状壳体,附加载荷thickness厚度transition in过渡段Data report,guide for preparation准备数据报告的指南Defects in welded vessels,repair修理焊接容器中的缺陷Definitions定义Design,brazed vessels设计钎焊容器carbon and low alloy steel vessels碳钢及低合金钢容器cast ductile iron vessels可锻铸铁容器cast iron vessels铸铁容器clad vessels覆层容器ferritic steel vessels with properutsenhanced by heat treatment经热处理后提高抗拉性能的铁素体钢容器forged vessels锻造容器high-alloy steel vessels高合金钢容器loadings载荷multichamber vessels多受压室容器nonferrous vessels非铁金属容器welded vessels焊接容器design pressure设计压力Diameter exemption直径的豁免Dimensions,checking of尺寸,校核Discharge of safety valves安全阀泄放Dished heads(see formed heads)碟形封头(见成形封头)Disks,rupture防爆膜Dissimilar weld metal不同金属的焊接Distortion,of welded vessels大变形、焊接容器supports to prevent用支撑防止Drainage,discharge from safety and relief valves排放,由安全阀和泄压阀泄放Drop weight tests落锤试验Eccentricity of shells壳体的偏心度Edges of plates,metal removal from由加工板边去除金属tapered锥度Efficiency,around openings for welded attachments焊缝系数,环绕焊接附件孔口Elasticity,modulus of弹性模量Electric resistance welding电阻焊Ellipsoidal heads椭圆封头Erosion,allowance for侵蚀裕量Etching,of sectioned speciments侵蚀,关于截面试样solutions for examination for materials检验材料的溶液Evaporators蒸发器Examination,of sectioned speciments剖面试样的检验of welded joints焊接接头的检验Exemptions diameter and volume直径和容积的豁免Expanded connections胀接连接External pressure,tube and pipe外压管External pressure vessels外压容器allowable working pressure for许用工作压力charts算图design of heads for封头设计joints in shells of壳体上的接头reinforcement for openings开孔补强stiffening rings in shells壳体上的刚性环supports for支承thickness of shell壳体厚度reducers变径段Fabrication,brazed vessels制造,钎焊容器Ferritic steels vessels with tensile properties enhanced by heat treatment,design经热处理后提高抗拉性能的铁素体钢容器,设计fabrication制造head design封头设计heat treatment热处理heat treatment verification tests热处理验证试验marking标志materials材料stamping标记welded joints焊接接头Field assembly of vessels容器的现场安装Filler plugs for trepanned holes锥孔的管塞Fillet welds角焊Fired process tubular heaters直接火管式加热炉Fitting attachments附件装配Flange connections法兰连接Flange contact facings法兰接触面Flanges法兰bolted design螺柱法兰设计of formed heads for welding用于焊接成型封头type of attachment附件的类型Flat heads and covers,unstayed无支撑平封头和盖板reinforcement of openings开孔补强Flat spots on formed heads成型封头上的平坦部分Flued openings翻边开孔Forged parts,small锻造部件,小的Forged vessels锻造容器heat treatment热处理localized thin areas局部薄壁区welding焊接Forgings锻件identification of识别Ultrasonic Examination超声检验Formmanufacturer’s data report制造厂数据报告格式partial report零部件数据报告Formed heads成型封头flued openings in封头上翻边开孔insertion of,welded vessels插入,焊接容器joint efficiency接头系数knuckle radius转角半径length of skirt直边长度on welded vessels在焊接容器上reinforcement for openings开孔补强Forming成型ends of shell plates and buttstraps壳体板和对接搭板端forged heads锻造封头shell sections and heads筒节和封头Furnaces炉子temperatures for postweld head treatment焊后热处理温度Furnaces for heat treating热处理炉temperature control of炉温控制Galvanized vessels镀锌容器Gasket materials垫片材料Girth joints(see circumferential joints)环缝接头(见环向接头)Handhole and manhole openings手孔和人孔开孔Head flange(skirt)length封头翻边(直边)长度Head joints封头接头brazing钎焊welded焊接Head openings封头开孔entirely in spherical portion全部在球体部分Head joints封头接头concave and convex凹面和凸面flat(see flat heads)平板(见平封头)forged锻造的formed(see Formed heads)成型的(见成形封头)forming面型thickness,after forming厚度,成型之后Heads,design,conical封头,设计,锥形ellipsoidal椭圆形hemispherical半球形spherically dished球状碟形toriconical带折边的锥形torispherical带折边的球形torispherical,knuckle radius带折边的球形,转角半径Heads and shells封头和壳体external pressure,out-of-roundness外压,不圆度openings through or near welded joints通过或靠近焊缝处的开孔roundness tolerance不圆度公差Heat exchangers热交换器Heat treatment热处理by fabricator由制造厂进行carbon and low-alloy steel vessels碳钢和低合金钢容器ferritic steel vessels with tensile properties enhanced by heat treatment经过热处理后提高抗拉性能的铁素体的容器forged vessels锻造容器furnaces炉子high-alloy vessels高合金容器of test specimens试样的热处理verification tests of热处理验证试验Hemispherical heads半球形封头High pressure vessels高压封头Holes小孔for screw stays用于螺丝固定for trepanning plug sections,refilling用于穿孔螺塞部分,再填充telltale指示孔unreinforced,in welded joints不补强,在焊缝上Hubs,on flanges高颈,在法兰上Hydrostatic proof tests水压验证试验destructive破坏性prior pressure application在升压之前Hydrostatic test水压试验cast iron vessels铸铁容器combined with pneumatic与气压试验混合的enameled vessels搪玻璃容器external pressure vessels外压容器galvanized vessels镀锌容器standard标准welded vessels焊接容器Identification识别of forging锻件of plates平板of welds焊接Identification markers,radiographs识别标志,射线照相Impact test冲击试验certification证明properties性能specimens试样temperature温度Inspection检查before assembling组装之前carbon and low-alloy steel碳钢和低合金钢cast ductile iron vessels可锻铸铁容器cast iron vessels铸铁容器clad vessels覆层容器during fabrication在制造期间ferritic steel vessels with tensile properties enhanced by heat treatment经过热处理后提高抗拉性能的铁素体的容器fitting up组对forged vessels锻造容器heat treatment,forgings热处理,锻件high-alloy steel vessels高合金钢容器magnetic particle磁粉material材料nonferrous vessels非铁金属容器plate板材postweld heat treatment焊后热处理pressure vessels,accessibility压力容器,可达性quality control质量管理sectioning of welded joints焊接接头的剖面检验spot examination抽样检查steel castings铸钢件surfaces exposed and component parts暴露的表面和元件部分test specimens试样vessels容器vessels exempted from免检容器welded vessels焊接容器Inspection openings检查孔Inspectors检查师access to plant在厂内应有的便利control of stamping打印管理duties职责facilities装备qualification资格reports报告Installation安装pressure-relieving devices泄压装置pressure vessel压力容器Integral cast iron dished heads整体铸铁碟形封头integrally finned tubes整体翅片管Internal structures内部构件Jacketed vessels夹套容器Joints接头brazed钎焊circumferential(see Circumferential joints)efficiency,brazed环缝(见环向接头)系数,钎焊welded焊接electric resistance,butt welding电阻,对接焊in cladding and applied linings在覆层及衬里in vessels subjected to external pressure在承受外压的容器lap(see Lap joints)搭接(见搭接接头)longitudinal(see Longitudinal joints)纵向(见纵向接头)tube-to-tubesheet管子对管板Jurisdictional Review权限审查Knuckles过渡圆角radius半径transition section变径段Lap joints搭接接头amount of overlap搭接量brazed钎焊longitudinal under external pressure在外压作用下纵向的welded焊接Laws Covering Pressure Vessels涉及压力容器的法规Lethal gases or liquids致命的气体或液体Ligaments,efficiency of孔带,系数Limitation on welded vessels焊接容器的限制Limit of out-of-roundness of shells壳体不圆度的限制Linings衬里corrosion resistant抗腐蚀Liquid penetrant examination液体渗透检验Loadings载荷Local postweld heat treatment局部焊后热处理Longitudinal joints纵向接头alignment tolerance对准公差brazing钎焊vessels subjected to external pressure承受外压的容器Low-temperature operation低温操作Low-temperature vessels brazed低温容器,钎焊for gases and liquids用于气体和液体impact test requirements冲击试验要求impact test,when not required冲击试验,当不要求时marking标志materials材料testing of materials材料试验Lugs for ladders,platforms,and other梯子,平台及其它附件的支耳Magnetic particle inspection磁粉检查Manholes,and handholes人孔,手孔cover plate for盖板minimum vessel diameter requiring所需最小容器直径Manufacture,responsibility of制造者,职责Manufacturer’s Data Report(see Data Report)制造厂数据报告(见数据报告) Manufacturer’s stamps制造厂的印记Marking castings标志,铸件materials材料plates板材standard pressure parts标志受压件valves and fittings阀门和配件with Code symbol带有规范符号Markings,transfer after cutting plates标志,板材切割以后的转移Materials,approval of new材料,新材料的批准approval of repairs修补的批准brazed vessels钎焊容器carbon and low-alloy steel vessels碳钢和低合金钢容器cast ductile iron可锻铸铁castings铸铁cast iron vessels铸铁容器certification合格证clad vessels覆层容器combination of组合材料ferritic steel vessels with tensile properties enhanced by heat treatment经热处理后提高抗拉性能的铁素体钢容器forged vessels锻造容器for nonpressure parts非受压元件heat treatment of热处理high-alloy steel vessels高合金钢容器inspection of检查nonferrous vessels非铁金属容器pipe and tube管子plate板rods and bars杆和棒specification for标准standard pressure,parts标准受压元件unidentified未鉴别的use of over thickness listed in SectionⅡ采用超过列于第Ⅱ卷表中的厚度welded vessels焊接容器Measurement,测量dimensional尺寸of out-of-roundness of shells壳体不圆度Metal temperature determination金属温度,确定control of控制Mill undertolerance钢厂负公差控制Minimum thickness of plate板材的最小厚度控制Miscellaneous pressure parts其它受压件控制Multichamber vessels design多承压室容器,设计Multiple duplicate vessels多个相同的容器Multiple safety valves多个安全阀Nameplates铭牌New materials新材料Noncircular vessels非圆形容器ligament efficiency孔带系数nomenclature术语obround design长圆形设计rectangular design矩形设计reinforcement补强examples实例Nonpressure parts,attachment of非受压元件的连接Notch ductility test缺口韧性试验Nozzle openings,reinforced接管开孔,补强的unreinforced非补强的vessels subjected to external pressure承受外压得容器Nozzles attachment of to shell接管,与壳体的连接minimum thickness of neck缩颈的最小厚度(see also Connections)(也可见连接件)Nuts and washers螺母和垫圈Offset of edges of plates at joints在接头处板边的偏差Openings adjacent to welds开孔,邻近焊缝closure of封闭for connections to brazed vessels用于对钎焊容器的连接for drainage用于排放head(see Openings head and shell)封头(见开孔,封头和壳体)in flat heads在平板封头上inspection检查manhole(see Manholes)人孔(见人孔)nozzle(see Nozzle opening)接管(见接管开孔)shell(see Openings,head and shell)壳体(见开孔,封头和壳体) through welded joints通过焊接接头Openings,head and shell,computation of开孔,封头和壳体,计算not requiring additional reinforcement不需要附加补强reinforced,size补强,尺寸reinforcement for adjacent openings邻近开孔的补强reinforcement of补强requiring additional reinforcement需要附加补强shapes permissible许用形式unreinforced,size不补强的,尺寸Outlets,discharge,pressure relieving devices排放口,出料,泄压装置Out-of-roundness不圆度Overpressure limit for vessels容器的超压极限Partial data report,manufacturer’s零部件数据报告,制造厂的Parts,miscellaneous部件,各种各样的Peening捶击Pipe connections openings for管子的连接,用于开孔Pipe fittings vessels built of管子配件,制造的容器Pipe and tubes各类管子Pipe used for shells用作壳体的管子piping external to vessel容器外的管子Plate,curvature板,曲率measurement,dimensional check测量,尺寸校核Plate edges cutting板边,切割exposed left unwelded留下不予焊接的显露部分inspection of检查Plates平板alignment找准cover盖板cutting切割forming成型heat treatment热处理identification标志impact test冲击试验inspection检查laying out划线less than6mm thickness厚度小6mmmarkings transfer after cutting标志,在切割以后的转移minimum thickness最小厚度repair of defects缺陷修理specifications标准structural carbon steel结构碳钢Plug welds塞焊Pneumatic test气压试验pressure压力yielding屈服Porosity welded joints气孔,焊接接头Porosity charts气孔图Postheat treatment后热处理connections for nozzles and attachments用于接管和附件的连接cooling after随后的冷却furnace temperature炉温inspection检查local局部requirements要求temperature range温度范围welded vessels焊接容器Preheating预热Preparation of plates for welding焊接板材的准备pressure,design压力,设计limits极限(see also Working pressure,allowable)(也可见工作压力,许用)Pressure parts miscellaneous受压件,其它的Pressure relieving devices泄压装置discharge排放installation and operation安装和运转rupture disks防爆模setting整定Pressure vessels压力容器exempted from inspection免检Produce form of Specification产品技术条件Proof test hydrostatic(see Hydrostatic proof test)验证试验,水压(见水压试验) Qualification评定of brazers钎焊工of welders焊工of welding procedure焊接工艺Quality Control System质量保证体系Quenching and tempering淬火及回火Quick-actuating closures快开盖Radiograph factor射线照相系数Radiographing射线照相examination by检查partial部分quality factors质量系数requirements要求spot examination抽样检查retests重新试验thickness,mandatory minimum规定最小厚度Radiographs,acceptance by inspector射线照相,由检查员认为合格gamma rays,radium capsuleγ射线,装镭的盒子interpretation by standard procedure由标准程序的说明rounded indications圆形显示Reaming holes for screw stays为固定螺钉用的铰孔Reducer sections,rules for变径段,规程Reinforcement补强defined limits规定的范围head and shell openings封头及壳体开孔large openings大开孔multiple openings多个开孔nozzle openings接管开孔of openings in shells,computation of壳体上开孔,计算openings subject to rapid pressure fluctuation经受压力突然波动的开孔Fluctuation经受压力突然波动的开孔strength强度Relief devices泄放装置(see also Pressure relieving devices,Safety and relief Valves)(也可见泄压装置,安全阀和泄压阀)Relieving capacity of safety valves安全阀排量Repairs,approval of defects in material修理,材料中缺陷的认可defective Brazing有缺陷的钎焊defects in forgings锻件中的缺陷defects in welds焊缝中的缺陷Responsibility of manufacturer制造者的职责Retention of Records记录的保存Radiographs射线照相Manufacturer’s Data Reports制造厂的数据报告Retests,frogings复试,锻件impact specimens冲击试样joints,welded接头,焊接Rods,bars,and shapes杆棒喝型材Rolled parts,small轧制件,小件Rupture disks爆破模Safety安全性safety relief,and pressures relief valves,adjustable blow down,capacity certification安全泄放和泄压阀,可调节的泄放,排放量证明capacity,conversion排量,换算connection to vessels连接至容器construction结构discharge pipe排放管indirect operation间接操作installation安装installation on vessels in service容器在役时的安装liquid relief液体泄放marking标志minimum requirements最低要求pressure setting压力整定spring loaded受载弹簧springs,adjustment弹簧,调节stop valves adjacent to邻近的截止阀test试验protective devices防护装置for unfired steam boiler对非直接火蒸气锅炉Scope适用范围sectioning,closing holes left by解剖,解剖孔的封闭etching plugs taken解剖样的侵蚀examination by检查Service restriction使用限制Shapes,special形状,特殊Shell plates,forming ends of壳体用材料,封头成型Shells壳体allowable working pressure许用工作压力computation of openings in开孔计算forming成型made from pipe由管子制造的stiffening rings刚性环thickness厚度Transition section过渡段Sigma-phase formationσ相的形成Skirts length on heads直边、封头上的长度support of vessels裙座,容器支撑Slag inclusion welds焊缝中的夹渣Special constructions特殊结构Specification for materials材料标准Spherical sections of vessels容器的球形部分Spot examination of welded joints焊接接头的抽样检查Springs for safety valves安全阀的弹簧Stamping location of打印位置multipressure vessels多重压力容器omission of省略safety valves安全阀with Code symbol带有规范标记Stamps,certificate of authorization钢印,授权low stress低压力not to be covered不应覆盖to be visible on plates在板上可见Static head,in setting safety valves,effect of on limiting stresses静压头,在整定安全阀时,影响,对极限应力Stayed surfaces支撑表面Staying formed heads成型封头的支撑Stays and staybolts,adjacent to edges of staybolted surface支撑件及拉撑螺栓,邻近用螺栓拉撑得表面周边处allowable stress许用应力area supported支撑面dimensions尺寸ends端部location位置pitch节距screw,holes for螺孔upset for threading为车制螺纹的镦粗welded焊接的Steam generating vessels,unfired蒸汽锅炉,非直接火Steel,carbon content钢,含碳量Stenciling plates for identification在板材上打印标志Stiffening rings,attachment to shell刚性环,和壳体的装配for vessels under external pressure用于外压容器Stiffness,support of large vessels for刚性,大容器支座Stop valves截止阀adjacent to safety and relief valves邻近于安全和泄压阀Strength of brazed joints钎焊接头的强度Stress corrosion cracking应力腐蚀裂缝Stress values,attachment weld应力值,连接焊缝basis for establishing确定的基础carbon and low-alloy steel碳钢和低合金钢cast iron铸铁ferritic steels with tensile properties enhanced by heat treatment经热处理后提高抗拉性能的铁素体刚high-alloy steel高合金钢nonferrous metals非铁金属Stud bolt threads双头螺栓螺纹Studded connections双头螺纹连接Supplementary design formulas补充设计公式Supports,design支座,设计pressure vessels压力容器temperature free movement under在温度下活动不受约束types of steel permissible for容许的钢材类型vessels subjected to external pressure承受外压的容器Surface Weld Metal Buildup金属堆焊表面Tables,effective gasket width b表,有效垫片宽度bgasket materials and contact facings垫片材料和接触面maximum allowable efficiencies for arc and gas welded joints电弧焊和气焊接头的最大许用系数minimum number of pipe threads for connections管螺纹连接的最少螺纹牙数molecular weights of gases and vapors气体和蒸汽的分子量of stress values,carbon and low-alloy steel应力值,碳钢和低合金钢cast iron铸铁cast ductile iron可锻铸铁ferritic steels with tensile properties enhanced by heat treatment经热处理后提高抗拉性能的铁素体钢high-alloy steel高合金钢nonferrous metals非铁金属welded carbon low-alloy pipe and tubes焊接低合金碳钢管of values factorK系数K值factor M系数Mfactor系数postweld heat treatment requirements焊后热处理要求recommended temperature ranges for heat treatment推荐的热处理温度范围spherical radius factor K1球半径系数K1Telltale holes指示孔in opening reinforcement开孔补强Temperature,definitions温度,定义design设计determination确定free movement of vessel on supports支座上的容器活动不受约束heat treatment热处理limitations,of brazed vessels限制,钎焊容器of cast ductile iron可锻铸铁of postweld heat treating焊后热处理metal,control of金属,控制operating or working,definitions操作或工作,定义zones of different不同区域Termination point of a vessel容器的界限点Test coupons试样Test gages requirements试验仪表,要求Test plates heat treatment试板,热处理impact test冲击试验production生产Tests,hydrostatic proof试验,水压验证pneumatic(see pneumatic test)气压,见气压试验vessels whose strength cannot be calculated不能由计算求得强度的容器calculated不能由计算求得强度的容器Thermal buffers热缓冲器Thermocouples attachment热电偶,安装Thickness gages,details厚度量规,细节Thick shells,cylindrical厚壳体,圆柱形spherical球形Thin plates marking薄板,标志Threaded connection螺纹连接Threaded inspection openings螺纹检查孔Threads,stud bolts螺纹,双头螺栓Tolerances,forged shells and heads公差,锻造容器及封头Toriconical heads带折边的锥形封头Torispherical heads带折边的球形封头Transfering marking on plates板上标志的移植Transition in cylindrical shells柱状壳体的过渡Trays and baffles,acting as partial shell stiffeners塔盘及挡板,作为部分壳体加强圈Tubes and pipe管子Tube-to-tubesheet joints管子与管板的连接Ultrasonic examination of welds焊缝的超声检验UM vessels UM容器Unfired steam boiler非直接火蒸汽锅炉Unidentified materials未识别的材料Valves,connections阀,连接safety and relief(see safety and relief valves)安全和泄压装置Valves and fittings,marking阀及其配件,标志Verification tests,heat treatment验证试验,热处理V olume exemption容器的免检Weld deposits,cleaning焊接熔敷金属,清理peening捶击Welded joints,category焊接接头,类别description of types类型的描述efficiency焊缝系数impact test,across冲击试验,横向postweld heat treating焊后热处理radiographic examination,complete射线照相检查,整个的rounded indications圆形显示sectioning,etch test解剖,侵蚀试验spot examination抽样检查staggered,longitudinal错开,轴向taper,plates of unequal thicknesses锥度,不等厚板types around openings类型,环绕开孔ultrasonic examination of超声检验Welded reinforcement of nozzle openings接管开孔的焊缝补强Welded vessels焊接容器holes in joints of接头处的孔inspection检查limitations on限制tests of试验Welders and welding operators焊工和自动焊工identifying stamps识别标记records of,by manufacturers由制造厂所作的记录test of qualification评定试验Welding焊接cleaning of welded surfaces焊件表面清理details,limitations细节,限制forged vessels锻造容器materials材料materials having different coefficients of expansion膨胀系数不同的材料of attachment around openings开孔周围的连接plate,fitting up joints平板,连接处的装配plate edges,matching板边,匹配preparation of plates钣材的制备procedure qualification工艺评定processes工艺test requirement试验要求Weld metal,composition焊缝金属,成分Welds acceptability,when radiographed焊缝合格,用射线照相时when sectioned解剖时fillet填角identification of识别plug塞焊reinforcement,butt welds补强,对接焊repairs of defects in焊缝中缺陷的修补sharp angles,avoid at weld edges尖角,避免在焊缝边上structural结构tack定位焊types,description类型,描述ultrasonic examination of超声检验Working pressure allowable,braced and stayed surfaces许用工作压力,有拉撑和支撑表面by proof test验证性试验definition of定义。
RESIDUALSTRESSES...

D. NOVOSELOVIĆ, I. BUDIĆ, I. SAMARDŽIĆRESIDUAL STRESSES IN CASTINGSPRODUCED BY PRESS DIE CASTING TECHNOLOGYReceived – Prispjelo: 2013-12-20Accepted – Prihvaćeno: 2014-06-20Preliminary Note – Prethodno priopćenjeISSN 0543-5846METABK 54(1) 119-122 (2015)UDC – UDK 621.746:669.083:620.16=111D. Novoselovi ć, I. Budi ć, I. Samardži ć, Mechanical Engineering Fac-ulty in Slavonski Brod, University of Osijek, CroatiaThe influence of technological parameters on residual stresses in pressure die castings is analysed in this paper. In order for the residual stresses to be as low as possible the optimization of technological parameters is necessary. The centrally composed plan of experiment 24cs is used in the investigation. Technologically influencing parameters are changed according to the mentioned plan of experiment and they are: temperature of pouring, rate of die cavity filling with the melt, post pressure in already filled die and the casting cooling time along with the pouring system.Key words : casting technology, pressure die casting, residual stresses, the influential technological parametersINTRODUCTIONA common cause of defects in castings is residual stresses that can cause cracks and deformations of cast-ings. In order to reduce the amount of residual stresses, it is necessary to know the reason of their occurrence, to determine the technological parameters that influence the occurrence of residual stresses, to determine the relative importance of each of the technological param-eters, and to conduct testing of the influence of techno-logical parameters in which the amount of residual stresses will be minimal in order to avoid the occur-rence of casting defects.Residual stresses in castings being affected by vari-ous parameters, they cannot be avoided but can be re-duced to the least possible value.Residual stresses can be reduced if the corresponding technological parameters in the casting fabrication are used. They can also be reduced by heat treatment (an-nealing for stress reduction) as well as by natural ageing.Residual stresses occur frequently in pressure die casting and can cause defects on castings (cracks and deformations).They have not been investigated in detail and are therefore a frequent subject of current investigations.Residual stresses depend on a number of technolog-ical parameters, some of them acting simultaneously.With the increased need for alluminium alloy cast-ings (particularly in automobile industry) a need has also been shown for investigating the influence of tech-nological parameters in reducing casting defects and increasing production quality and productivity.A review of literature [1 - 7] has shown that until now the on mechanical and structural characteristics has been most often investigated while the parametersaffecting residual stresses in pressure die casting have not been systematically studied. The reason for that is the fact that under operating conditions they are very difficult to determine.To calculate residual stresses computer programs are often used (e.g. MAGMAsoft and ProCast) which simulate the casting process and approximately deter-mine the residual stresses. The programs are based on theoretical assumptions that are within certain limits different from real operating conditions.EXPERIMENTAL PROCEDUREAt pressure die casting various technological param-eters affect the occurence of residual stresses in cast-ings, some of the parameters acting simultaneously. Pressure die casting technological parameters are:∙ melt pouring temperature∙ rate of filling the pouring system with the melt ∙ cross-section and form of the pouring system ∙ rate of filling die cavity with the melt ∙ post pressure in a filled up die ∙ start of the casting second phase ∙ dimensions of pressure cylinder ∙ pressure cylinder rate of filling ∙ type and quantity of lubricant ∙ dimensions of the venting system ∙ dimensions of the cooling system ∙ composition of the melt.In order for the residual stresses to be as low as pos-sible the optimization of technological parameters is necessary. Only some of the technological parameters of influence will be investigated in the paper while the other parameters will be constant.The centrally composed plan of experiment 24cs is used in the investigation.D. NOVOSELOVIC et al.: RESIDUAL STRESSES IN CASTINGS PRODUCED BY PRESS DIE CASTING TECHNOLOGYTechnologically influencing parameters are changedaccording to the mentioned plan of experiment (Table1) and they are given as follows:ϑu - temperature of pouring,vII faze - rate of die cavity filling with the melt,pIII faze - post pressure in already filled die,t ods - t he casting cooling time along with the pouring system, upon withdrawal from the die, min.Table 1 Centrally composed plan of experiment 24csThe test casting (Figure 1) was cast according to the centrally composed plan of experiment 24cs in the Lipo-vica Foundry d.o.o. on compression machine with cold chamber type ItalPresse 250 t.The alloy (EN 46100) was used for casting. It was molten in a gas furnace from the firm Botta – Italy. Pre-vious to pouring into the mould the melt temperature was measured by a digital thermometer DT 02 (ther-mosteam Fe - Cu Ni).Upon the casting removal from the mould its cool-ing time along with the pouring system was measured by a measuring watch (stop-watch).Figure 2 shows the cast castings and their measured cooling time according to the plan of experiment 24cs.The method of measuring used to determine the re-sidual stresses is a method of drilling, belonging to the partly destructive methods.To calculate residual stresses in linear elastic materi-als in which the stress does not change with the depth of drilling a method is used that is described in terms of the standard ASTM E837-08.For some general purpose strain gauge rosette ac-cording to Figure 3 [8] normal stresses σx, σy, τxyare measured from the measured deformations. Based on normal stresses the main stresses σ1= σmax, σ2= σminand their direction b are measured.Calculation of residual stresses in terms of ASTM E837-08 for uniformly distributed stress is carried out based on measured deformations ε1, ε2, ε3on strain gauges. Based on measured deformations the main i.e. equivalent stresses are calculated according to:dop212221ekvσσσσσσ≤⋅-+= (1)σekv- equivalent stress,σ1, 2- main stresses,σdop- design stress of material.The firm HBM (Figure 4a) measuring equipment was used for deformation measuring. Drilling control and data collection are performed by computer (main se-lector of the RESTAN software (Figure 4b), I/O card and electric device). Upon deformation measurement, for separate strain gauges, obtained data are entered into the program …SINT_RSM.EXE“, where the residual stresses are calculated based on the measured results [8].The results of measuring obtained according to the centrally composed plan of experiment 24cs are shown in Table 2.Graphical presentation of the function dependance of the calculated residual stresses depending on two technological parameters is shown in Figure 5. One technological parameter is tous– cooling time of thecasting along with the pouring system upon removal Figure 1 Test casting with pouring systemFigure 2 T he cast castings measured according to the plan ofexperimentFigure 3 S chematic presentation of a general purpose straingauge rosetteD. NOVOSELOVIC et al.: RESIDUAL STRESSES IN CASTINGS PRODUCED BY PRESS DIE CASTING TECHNOLOGYfrom the mould, the second technological parameter is the melt pouring temperature (Figure 5).It can be concluded from the diagram that the equiv-alent residual stresses increase with the cooling time prolongation of the casting along with the pouring sys-tem (upon removal from the mould). This means that the shape and dimensions of pouring system cause re-sidual stresses in castings.CONCLUSIONThe investigation has demonstrated that equivalent residual stresses increase with prolonged cooling of the casting together with the pouring system outside the mould. This can be explained by the fact that at cooling the casting cools off earlier than the pouring system (due to a thinner wall).Based on the investigations it can be concluded that they should be continued in the following direction: ∙ perform computer simulations and compare them with the residual stresses computed based on the measured deformations∙ carry out pressure die casting on a machine provided with the possibility of computer adjusting the influ-encing technological parameters for a more precise analysis∙ study also the influence of other technological pa-rameters on residual stresses at pressure die casting.a) b)Figure 4 M easuring equipment for determination of residual stresses a) device for drilling, b) measuring software RESTAN Table 2 R esults of measuring obtained according to thecentrally composed plan of experiment 24csFigure 5 C alculated equivalent residual stressesσekv = f (t ods, ϑu ) at υII phase = const. i p III phase = const.D. NOVOSELOVIC et al.: RESIDUAL STRESSES IN CASTINGS PRODUCED BY PRESS DIE CASTING TECHNOLOGYREFERENCES[1] A. Maleki, B. Niroumand, A. Shafyei, Materials Scienceand Engineering, 428 (2006), 135-140.[2] S. G. Lee, A. M. Gokhale, G. R. Patel, M. Evans, MaterialsScience and Engineering, 427 (2006), 99-111.[3] P. K. M. Rui, M. A. Rossi, Journal of Materials ProcessingTechnology, 179 (2006), 190-195.[4] M. Okayasu, Y. Ohkura, S. Takeuchi, S. Takasub, H.Ohfuji, T. Shiraishi, Materials Science and Engineering,543 (2012), 185-192.[5] S. A. Sajjadi, H. R. Ezatpour, M. Torabi Parizi, Materialsand Design 34 (2012) 106-111.[6] M. Rübner, M. Günzl, C. Körner*, R.F. Singer MaterialsScience and Engineering A 528 (2011) 7024-7029.[7] Z. Hu, L. Wan, S. Wu, H. Wu, X. Liu, Materials and De-sign, 46 (2013) 451-456.[8] ASTM E 837-08e1, Standard Test Method for Determi-ning Residual Stresses by the Hole-Drilling Strain-Gage Method, SAD, 2008.Note:T he responsible translator for English language is S. Setina, Slavonski Brod, Cro a tia。
[中学教育]焊接技术与工程专业英语
![[中学教育]焊接技术与工程专业英语](https://img.taocdn.com/s3/m/68a6e7b9dc3383c4bb4cf7ec4afe04a1b071b08d.png)
激光切割laser cutting(LC); laser beam cutting电子束切割electron beam cutting喷气激光切割gas jet laser cutting碳弧切割carbon arc cutting水下切割underwater cutti ng喷水式水下电弧切割waterjet method underwater arc cutting氧矛切割oxygen lancing; oxygen lance cutting溶剂氧切割powder lanci ng手工气割manual oxygen cutting碳弧气割carbon arc air gouging火焰气刨flame gouging火焰表面清理scarfing氧熔剂表面修整powder washing预热火焰preheat flame预热氧preheat oxygen切割氧cutting oxygen/ cutting stream切割速度cutting speed切割线lone of cut/ cut l i ne切割面face of cut/ cut face切口kerf切口上缘cutting shoulder切口宽度kerf width后拖量drag切割面平面度evenness of cutting surface/ planeness of cutti ng surface割纹深度depth of cutting veins/ stria depth 切割面质量quality of cut fac e上缘熔化度shoulder meltability/ melting degree of shoulder切口角kerf angle缺口notch割枪cutting gun割嘴cutting nozzle/ cutting tip快速割嘴divergent nozzle/ high-speed nozzle 表面割炬gouging blowpi pe水下割炬under-water cutting blowpipe水下割条electrode for under-water cutting粉剂罐powder dispenser焊接部件weld assembl y组装件built-up member接头设计joint design焊接应力welding stress焊接瞬时应力transient welding stress焊接残余应力welding residual stress热应力thermal stress收缩应力contraction stress局部应力local stress拘束应力constraint stress固有应力inherent stress固有应变区inherent strain zone残余应力测定residual stress analysis逐层切割法Sach’s methodX射线衍射法X-ray stress analysis小孔释放法Mathar method固有应变法inherent strain method消除应力stress relievi ng局部消除应力local stress relievi ng应力重分布stress redistribution退火消除应力stress relieving by annealing温差拉伸消除应力low temperature stress relieving机械拉伸消除应力mechanical stress relieving应力松弛stress relaxation焊接变形welding deformati on焊接残余变形welding residual deformation 局部变形local deformati on角变形angular distortion自由变形free deformati on收缩变形contraction deformation错边变形mismatching deformation挠曲变形deflection deformation波浪变形wave-like deformation火焰矫正flame straighteni ng反变形backward deformati on焊接力学welding mechani cs 断裂力学fracture mechanic s弹塑性断裂变形elasto-plastic fracture mechanics线弹性断裂力学linear elastic fracture mechanics延性断裂ductile fracture脆性断裂brittle fracture应力腐蚀开裂stress corrosion cracking热应变脆化hot straining embrittlement临界裂纹尺寸critical crack size裂纹扩展速率crack propagation rate裂纹张开位移(COD)crack opening displacement拘束度restraint intensi tyintensity factor of stress corrosion crackingJ积分J-integration罗伯逊止裂试验Robertson crack arrest testESSO试验ESSO test双重拉伸试验doucle tension test韦尔斯宽板拉伸试验Well’s wide plate test帕瑞斯公式Paris formula断裂分析图fracture analysis diagram焊接车间welding shop焊接工作间welding booth焊接工位welding post/ welding station焊接环境welding surroundi ngs焊工welder电焊工manual arc welder气焊工gas welder焊接检验员weld inspector焊工培训welders training焊工模拟训练器trainer of syntheti c wel d焊工考试welder qualification test焊工合格证welder qualification/ welder qualified certification钢板预处理steel plate pretreatment喷沙sand blast喷丸shot blast矫正straighten开坡口bevelling (of the edge)/ chanfering装配assembly/ fitting安装erect刚性固定rigid fixing装配焊接顺序sequence of fitting and welding焊接工艺评定welding procedure qualification焊接工艺试验welding procedure test焊接工艺卡welding procedure card工序operational sequence焊接材料消耗定额welding consumables quota焊接工时定额welder-hour quota清渣slag removal清根back gouging/ back chipping锤击peening返修次数number of rewelding焊接工作台welding benc h 装焊平台welding platen电磁平台electromagnetic platen焊接翻转机welding tilter焊接回转台floor turnable positi oner焊接变位机positioner焊接滚轮架turning rol l s焊接操作机manpulator焊工升降台welder’s lifting platform焊接夹具welding jig/ fixture焊丝盘绕机welding wire coiler焊条压涂机welding electrode extrusion press 红外线加热器infra-red heater干燥箱dryer焊条保温筒thermostat for electrodeCO2预热器CO2 heaterCO2干燥器CO2 desiccator焊接电缆welding cable电缆夹头welding connector地线earth lead地线夹头earth clamp焊接参数记录仪welding parameter recorder焊缝检测规weld gauge喷嘴通针tip cleaner测温笔tempil stick敲渣锤chipping hammer焊接衬垫backing/ welding backing保留垫板fusible backing/ permanent backing临时垫板temporary backing焊剂垫flux backing惰性气体衬垫inert-gas backi ng引弧板run-on tab/ end tab/ starting weld tab 引出板run-off tab/ end tab定位板strong-back加强勒stiffener嵌条insert套环ferrule焊接烟尘weld fume焊接发尘量total amount of fumes焊接烟尘浓度weld fume concentration焊接烟尘容限浓度threshold limit values of weld fume (TLV)焊接发尘速率weld fume emission rate焊接有害气体welding toxic gases/ weld harmful gases标定卫生空气需要量nominal hygienic air requirement焊工尘肺pheumocomsis of welder焊工锰中毒chronic occupational manganese poisoning of welder护脚welding spats防护鞋shielding shoes焊接欠缺welding imperfection焊接缺陷weld defect气孔blowhole/ gas pore针尖状气孔pinhole密集气孔porosity条虫状气孔wormhole裂纹crack表面裂纹surface crack咬边undercut焊瘤overlap凹坑pit 烧穿burn through塌陷excessive penetration未焊透incomplete penetration/ lack of penetration未熔合lack of fusion/ incomplete fusion未焊满incompletely filled weld根部凹陷root concavi ty电弧擦伤arc scratch夹渣slag inclusion夹杂物inclusion夹钨tungsten inclusion白点fish eye/ flake错边misalignment/ dislocati on试件test piece试样test specimen无损检验nondestructive test破坏检验destructive test外观检查visual examinatio n超声波探伤ultrasonic inspection射线探伤radiographic inspection/ radiographyX射线探伤X-ray radiographic inspectionγ射线探伤gamma-ray inspectionX射线工业电视探伤X-ray industrial television inspection磁粉探伤magnetic particle inspecti on电磁探伤electromagnetic inspection/ eddy current test耐压检验pressure test水压检验hydraulic test气压检验pneumatic test液晶检验liquid crystal test声发射检测acoustic emission testing面弯试验face bend testi ng背弯试验root bend test侧弯试验side bend test横弯试验horizontal bend test纵弯试验axial bend test压扁试验squeezing testH焊接welding, weld航空材料aerial material合成纤维synthetic fiber合金钢alloy steel合金化alloying合金结构钢structural alloy steel红硬性red hardness滑移slip, glide滑移方向glide direction, slip direction 滑移面glide plane, slip plane滑移系slip system化合物compound化学气相沉积chemical vapour eposition(CVD)化学热处理chemical heat treatmentJ基体matrix机械混合物mechanical mixture机械性能mechanical property激光热处理heat treatment with a laser beam激光laser激光熔凝laser melting and consolidation 激光表面硬化surface hardening by laserbeam加工硬化work hardening加热heating胶粘剂adhesive结构材料structural material结晶crystallize, crystallization结晶度crystallinity金属材料metal material金属化合物metallic compound金属键metallic bond金属组织metal structure金属结构metallic framework金属塑料复合材料plastimets 金属塑性加工metal plastic?working金属陶瓷metal ceramic金相显微镜metallographic microscope,metalloscope金相照片metallograph晶胞cell晶格crystal lattice晶格常数lattice constant晶格空位lattice vacancy晶粒crystal grain晶粒度grain size晶粒细化grain refining晶体结构crystal structure抗拉强度tensilestrength抗压强度compression strength颗粒复合材料particle composite扩散diffusion, diffuseL老化aging莱氏体ledeburite冷变形cold deformation冷加工cold work, cold working冷却cool, cooling冷作硬化cold hardening离子ion粒状珠光体granular pearlite连续转变曲线continuous coolingtransformation(CCT) curve孪晶twin crystal孪生twinning, twin螺旋位错helical dislocation洛氏硬度Rockwell hardnessM马氏体martensite (M)密排六方晶格close-packed xagonal lattice(C.P.H.)面心立方晶格face-centred cubic lattice(F.C.C.)摩擦friction磨损wear, abrade, abrasion模具钢die steelMf 点martensite finishing pointMs点martensite starting pointN纳米材料nanostructured materials耐磨钢wear-resisting steel耐磨性wearability, wear resistance耐热钢heat resistant steel , high temperature steel 扭转疲劳强度torsional fatiguestrengthP泡沫塑料foamplastics, expanded plastics 配位数coordination number喷丸硬化shot-peening疲劳强度fatigue strength疲劳寿命fatigue life片状马氏体lamellar martensite, plate typemartensite普通碳钢ordinary steel, plain carbon steelQ气体渗碳gas carburizing切变shear切削cut, cutting切应力shearing stress球化退火spheroidizing annealing屈服强度yielding strength, yield strength 屈强比yielding-to-tensile ratio屈氏体troolstite (T)去应力退火relief annealingR热处理heat treatment热加工hot work, hot working热喷涂thermal spraying热固性thermosetting热塑性hot plasticity热硬性thermohardening柔顺性flexibility人工时效artificial ageing刃具cutting tool刃型位错edge dislacation, blade dislocation韧性toughness溶质solute溶剂solvent蠕变creep蠕墨铸铁quasiflake graphite cast iron软氮化soft nitriding金属材料专业英语Material Science 材料科学Material Science Definition 材料科学定义Machinability [məʃi:nə'biliti] 加工性能Strength .[streŋθ] 强度Corrosion & resistance durability.[kə'rəʊʒən] &[ri'zistəns] .[ 'djʊrə'bɪlətɪ] 抗腐蚀及耐用Special metallic features 金属特性Allergic, re-cycling & environmental protection 抗敏感及环境保护[ə'lə:dʒik] Chemical element 化学元素'elimənt] Atom of Elements 元素的原子序数Atom and solid material 原子及固体物质Atom Constitutes 原子的组织图['kɔnstitju:t]Periodic Table 周期表[,piəri'ɔdik] adj. 周期的;定期的Atom Bonding 原子键结合Metal and Alloy 金属与合金['ælɔi, ə'lɔi]Ferrous & Non Ferrous Metal 铁及非铁金属['ferəs] adj. [化]亚铁的;铁的,含铁的Features of Metal 金属的特性Crystal Pattern 晶体结构['kristəl] n. 水晶;结晶,晶体;水晶饰品adj. 水晶的;透明的,清澈的分析法[,ænə'litik,-kəl]Metal space lattice 金属结晶格子Metal Phase and Phase Rule金相及相律Solid solution 固熔体Substitutional type solid solution 置换固熔体[,sʌbstitju:ʃənəl]Interstitial solid solution 间隙固熔体[,intə'stiʃəl] n. 填隙原子;节间adj. 间质的;空隙的;填隙的Intermetallic compound 金属间化合物[,intəmi'tælik] ['kɔmpaund, kəm'paund] vt. 混合;合成;和解妥协;搀合vi. 妥协;和解n. 化合物;复合词;混合物adj. 复合的;混合的Transformation 转变Transformation Point 转变点Magnetic Transformation 磁性转变[mæɡ'netik]Allotropic Transformation 同素转变[mæɡ'netik] adj. [化]同素异形的Thermal Equilibrium 热平衡['θə:m əl] adj. 热的,热量的 Degree of freedom 自由度Critical temperature 临界温度Eutectic 共晶[ju:'tektik] n. 共熔合金Peritectic [.peri’tektik] Temperature 包晶温度Peritectic Reaction 包晶反应Peritectic Alloy 包晶合金Hypoeutectic Alloy 亚共晶体[,haip əuju'tektik] n. 低级低共熔体adj. 亚共晶的Hypereutectic Alloy 过共晶体PlasticDeformation 金属塑性[,di:f ɔ:'mei ʃən] n. 变形Slip Plan 滑动面Distortion 畸变[dis't ɔ:ʃən]Work Hardening 硬化Annealing 退火Crystal Recovery 回复柔软Recrystallization 再结晶[ri:,krist əlai'zei ʃən]Properties & testing of metal 金属材料的性能及试验Chemical Properties 化学性能['pr ɔp əti ]Physical Properties 物理性能Magnetism 磁性['mæɡnitizəm]Specific resistivity & specific resistance 比电阻Specific gravity & specific density 比重Specific Heat 比热热膨胀系数 Coefficient of thermal expansion['mæɡnitizəm] n. 协同因素;[数]系数;[物]率 adj. 合作的;共同作用的 ['θə:m əl] adj. 热的,n. 上升暖气流导热度 Heat conductivity屈服强度(降伏强度) (Yield strength)伸长度[,i:l ɔŋ'ɡei ʃən, i,l ɔŋ-]断面缩率 Reduction of area [ri'd ʌk ʃən]破坏性检验 destructive inspections渗透探伤法 Penetrate inspecti on磁粉探伤法 Magnetic particle inspection放射线探伤法 Radiographic inspection[,reidi əu'græfik] adj. 射线照相术的超声波探伤法 Ultrasonic inspection[,ʌltr ə's ɔnik] adj. 超音速的;超声的n. 超声波显微观察法 Microscopic inspection [,maikr ə'sk ɔpik]破坏的检验 Destructive Inspection冲击测试 Impact Test疲劳测试 Fatigue Test [f ə'ti:ɡ] n. 疲劳,疲乏;杂役vt. 使疲劳;使心智衰弱vi. 疲劳adj. 疲劳的 蠕变试验Creep Test [kri:p]vi. 爬行潜变强度 Creeps Strength第一潜变期 Primary Creep第二潜变期 Secondary Creep第三潜变期 Tertiary Creep主要金属元素之物理性质Physical properties of major Metal El ements工业标准及规格–铁及非铁金属Industrial Standard – Ferrous & Non – ferrous Metal磁力Magnetic简介General软磁Soft Magnetic硬磁Hard Magnetic磁场Magnetic Field磁性感应Magnetic Inducti on导磁率[系数,性] Magnetic Permeability [,pə:miə'biliti] n. 弥漫;渗透性;[物]透磁率,导磁系数磁化率Magnetic Susceptibility (Xm) [sə,septə'biləti]磁力(Magnetic Force)铁磁体Ferromagnetism转变元素Transition element交换能量Positive energy exchange磁畴Magnetic domain [dəu'mein] n. 领域;产业;地产;[计]域名相反旋转Opposite span ['ɔpəzit, -si t]反铁磁体Antiferromagnetism亚铁磁体Ferrimagnetism磁矩magnetic moment净磁矩Net magnetic moment钢铁的主要成份The major element of steel钢铁用"碳"之含量来分类Classification of Steel according to Carbon contents铁相Steel Phases ['feisi:z] n. 阶段,时期(phase的复数形式)v. 逐步实行(phase 的三单形式)钢铁的名称Name of steel铁素体Ferrite ['ferait]渗碳体Cementitle奥氏体Austenite珠光体及共析钢Pearlite &Eutectoid奥氏体碳钢Austenite Carbon Steel\;使…兴奋粗珠光体Coarse pearlite [kɔ:s] adj. 粗糙的;下等的;粗俗的中珠光体Medium Pearlite幼珠光体Fine pearlite磁性变态点Magnetic Transformati on钢铁的制造Manufacturing of Steel [,mænju'fæktʃər iŋ]连续铸造法Continuous casting process电炉Electric furnace均热炉Soaking pit ['səukiŋ] n. 浸湿,浸透adj. 湿透的,极湿的adv. 湿透地全静钢Killed steel半静钢Semi-killed steel沸腾钢(未净钢) Rimmed steel [rim] n. 边,边缘;轮辋;圆圈vi. 作…的边,装边于vt. 作…的边,装边于钢铁生产流程Steel Production Flow Chart钢材的熔铸、锻造、挤压及延轧The Casting, Fogging, Extrusion, Rolling & Steel熔铸Casting锻造Fogging挤压Extrusion延轧Rolling冲剪Drawing & stamping [sʌl'fjuərik]硬化性能Hardenability钢的脆性Brittleness of Steel ['britlnis] n.脆弱性;脆性,脆度低温脆性Cold brittleness回火脆性Temper brittleness硬度Hardness表面处理Surface fini sh冷辘钢捆片及张片制作流程图表Production flow chart cold rolled steel coil sheet冷辘钢捆片及张片的电镀和印刷方法Cold rolled steel coil & sheet electro-plating & painting method [kɔil] vt. n. 延长;伸长;延伸率;伸长率盘绕,把…卷成圈n. 卷;线圈vi. 成圈状\硬度及拉力Hardness & Tensile strength test ['tensail, -səl] adj. [物]拉力的;可伸长的;可拉长的拉伸测试(顺纹测试) Elongation test [,i:lɔŋ'ɡeiʃən, i,lɔŋ-]杯突测试(厚度: 0.4公厘至1.6公厘,准确至0.1公厘3个试片平均数) Erichsen test (Thickness: 0.4mm to 1.6mm, figure round up to 0.1mm)曲面(假曲率) Camber厚度及阔度公差Tolerance on Thickness & Width平坦度(阔度大于500公厘,标准回火) Flatness (width>500mm, temper: standard)弯度Camber冷辘钢片储存与处理提示General advice on handling & storage of cold rolled steel coil & sheet防止生锈Rust Protecti on生锈速度表Speed of rusting焊接Welding气焊Gas Welding埋弧焊Submerged-arc Welding [səb'mə:dʒd]\电镀锌钢片或电解钢片Electro-galvanized Steel Sheet/Electrolytic Zinc Coated Steel Sheet电镀锌钢片的焊接Welding of Electro-galvanized steel sheet ['ɡælvənaiz] vt. 通电;镀锌;刺激点焊Spot welding滚焊Seam welding [si:m] n. 缝;接缝vt. 缝合;接合;使留下伤痕Vi. 裂开;产生裂缝电镀锌(电解)钢片Electro-galvanized Steel Sheet生产流程Production Flow Chart常用的镀锌钢片(电解片)的基层金属、用途、锌镀层质量Zinc Coating Mass [ziŋk]表面处理Surface Treatment冷轧钢片Cold-Rolled Steel Sheet/Stri p热轧钢片Hot-Rolled Sheet/Strip电解冷轧钢片厚度公差Thickness Tolerance of Electrolytic Cold-rolled sheet热轧钢片厚度公差Thickness Tolerance of Hot-rolled sheet冷轧或热轧钢片阔度公差Width Tolerance of Cold or Hot-rol l ed sheet长度公差Length Tolerance理论质量Theoretical Mass [,θiə'retikəl, ,θi:ə-]锌镀层质量(两个相同锌镀层厚度) Mass Calculation of coating (For equal coating)/MM锌镀层质量(两个不同锌镀层厚度) Mass Calculation of coating (For differential coating)/MM\锡层质量Mass of Tin Coating (JIS G3303-1987)两面均等锡层Both Side Equally Coated Mass两面不均等锡层Both Side Different Thickness Coated Mass硬度Hardness单相轧压镀锡薄铁片(白铁皮/马口铁) Single-Reduced Tinplate双相辗压镀锡薄钢片(马口铁/白铁皮) Dual-Reduction Tinplate钢的种类Type of Steel常用尺寸Commonly Used Size电器用硅[硅] 钢片Electrical Steel Sheet简介General软磁材料Soft Magnetic Material滞后回线Narrow Hysteresis矫顽磁力Coercive Force [kəu'ə:siv] adj. 强制的;高压的;胁迫的硬磁材料Hard Magnetic Materi al最大能量积Maximum Energy Product硅含量对电器用的低碳钢片的最大好处The Advantage of Using Silicon low Carbon Steel晶粒取向(Grain-Oriented)及非晶粒取向(Non-Oriented) Grain Oriented & Non-Oriented ['ɔ:rientid, 'əu-] adj. 定向的;应力退火温度Stress –relieving Annealing Temperature绝缘表面Surface Insulation非晶粒取向电力用钢片的电力、磁力、机械性能及夹层系数Lamination Factors of Electrical, Magnetic & Mechanical Non-Grain Oriented Electrical电器及家电外壳用镀层冷辘[低碳] 钢片Coated (Low Carbon) Steel Sheets for Casing,Electricals & Home Appli ances镀铝硅钢片Aluminized Silicon Alloy Steel Sheet镀铝硅合金钢片的特色Feature of Aluminized Silicon Alloy Steel Sheet用途End Usages抗化学品能力Chemical Resistance焊接能力Weldability镀铝钢片的焊接状态(比较冷辘钢片) Tips on welding of Aluminized sheet in comparasion with cold rolled steel stri p钢板Steel Plate钢板用途分类及各国钢板的工业标准包括\钢板生产流程Production Flow Chart钢板订货需知Ordering of Steel Pl ate不锈钢Stainless Steel不锈钢的定义Definition of Stainless Steel马氏体不锈钢Martensite Stainless Steel低碳马氏体不锈钢Low Carbon Martensite Stainless Steel含铁体不锈钢Ferrite Stainless Steel镍铬系不锈钢Nickel Chrome Stainless Steel铬系耐热钢Chrome Heat Resistance Steel镍铬耐热钢Ni - Cr Heat Resi stance Steel超耐热钢Special Heat Resistance Steel抗热超级合金Heat Resistance Super Alloy\边缘处理Edge Finish硬度Hardness\高碳钢片High Carbon Steel Strip分类Classification用组织结构分类Classification According to Grain Structure\弹簧用碳钢片Carbon Steel Strip For Spring Use冷轧状态Cold Rolled Stri p回火状态Annealed Stri p淬火及回火状态Hardened & Tempered Strip/ Precision –Quenched Steel Stri p贝氏体钢片Bainite Steel Stri p弹簧用碳钢片材之边缘处理Edge Finished淬火剂Quenching Medi a碳钢回火Tempering回火有低温回火及高温回火Low & High Temperature Tempering高温回火High Temperature Temperi ng退火Annealing完全退火Full Annealing扩散退火Diffusion Annealing [di'fju:ʒən] n. 扩散,传播;[物]漫射低温退火Low Temperature Anneal i ng中途退火Process Annealing 球化退火Spheroidizing Annealing光辉退火Bright Anneali ng淬火Quenching [kwentʃ] vt. 结束;熄灭,淬火;解渴;冷浸vi. 熄灭;平息时间淬火Time Quenchi ng奥氏铁孻回火Austempering马氏铁体淬火Marquenching高碳钢片用途End Usage of High Carbon Steel Strip低碳钢或铁基层金属Iron & Low Carbon as Base Metal不锈钢基层金属Stainless Steel as Base Metal易溶合金Fusible All oy焊接合金Soldering and Brazing All oy硬焊Brazing Alloy机械性能Mechanical Properites易车(快削)不锈钢种类Type of steel加工方法Manufacturing Method应用材料Material Used特点CharacteristicMaterial Science物料科学定义Material Science Definition加工性能Machinability强度Strength抗腐蚀及耐用Corrosion & resistance durability金属特性Special metallic features抗敏感及环境保护Allergic, re-cycling & environmental protection化学元素Chemical element元素的原子序数Atom of Elements原子及固体物质Atom and solid material原子的组成、大小、体积和单位图表The size, mass, charge of an atom, and is particles (Pronton,Nentron and Electron)原子的组织图Atom Constitutes周期表金属与合金Metal and Alloy铁及非铁金属Ferrous & Non Ferrous Metal 金属的特性Features of Metal晶体结构Crystal Pattern金属间化物Intermetallic compound合金平衡状态Thermal Equilibrium相律Phase Rule自由度Degree of freedom临界温度Critical temperture共晶Eutectic包晶温度Peritectic Temperature包晶反应Peritectic Reacti on包晶合金Peritectic Al l oy亚共晶体Hypoeutetic Alloy过共晶体Hyper-ectectic All oy 金属塑性Plastic Deformation滑动面Slip Plan畸变Distortion硬化Work Hardening退火Annealing回复柔软Crystal Recovery再结晶Recrystallization金属材料的性能及试验Properties & testing of metal化学性能Chemical Properties物理性能Physical Properties磁性Magnetisum比电zu ific resistivity & specific resistance 比重Specific gravity & specific densi ty比热Specific Heat热膨胀系数Coefficient of thermal expansion 导热度Heat conductivity机械性能Mechanical properties屈服强度(降伏强度) (Yield strangth)弹性限度、阳氏弹性系数及屈服点elastic limit, Y eung's module of elasticity to yield point伸长度Elongation断面缩率Reduction of area金属材料的试验方法The Method of Metal inspection不破坏检验Non – destructive inspections渗透探伤法Penetrate inspecti on磁粉探伤法Magnetic particle inspection 放射线探伤法Radiographic inspection 超声波探伤法Ultrasonic inspection显微观察法Microscopic inspecti on破坏的检验Destructive Inspecti on冲击测试Impact Test疲劳测试Fatigue Test潜变测试Creep TestTertiary Creep磁力Magnetic简介General软磁Soft Magnetic硬磁Hard Magnetic磁场Magnetic Field磁性感应Magnetic Inducti on透磁度Magnetic Permeability磁化率Magnetic Susceptibility (Xm)顺磁体Paramagnetic正磁化率Positive magnetic susceptibility 铁磁体Ferromagnetism转变元素Transition element交换能量Positive energy exchange外价电子Outer valence electrons化学结合Chemical bond亚铁磁体Ferrimagnetism磁矩magnetic moment净磁矩Net magnetic moment 钢铁的主要成份The major element of steel钢铁用"碳"之含量来分类Classification of Steel according to Carbon contents铁相Steel Phases钢铁的名称Name of steel纯铁体Ferrite渗碳体Cementitle奥氏体碳钢Austenite Carbon Steel单相金属Single Phase Metal共释变态Eutectoid Transformation珠光体Pearlite亚铁释体Hyppo-Eutectoid初释纯铁体Pro-entectoid ferrite过共释钢Hype-eutectoid珠光体Pearlite粗珠光体Coarse pearlite中珠光体Medium pearli te幼珠光体Fine pearlite磁性变态点Magnetic Transformation钢铁的制造Manufacturing of Steel连续铸造法Continuous casting process电炉Electric furnace均热炉Soaking pit全静钢Killed steel半静钢Semi-killed stee l沸腾钢(未净钢) Rimmed steel钢铁生产流程Steel Production Flow Chart 钢材的熔铸、锻造、挤压及延轧The Casting, Fogging, Extrusion, Rolling & Steel熔铸Casting锻造Fogging挤压Extrusion延轧Rolling冲剪Drawing & stampi ng特殊钢Special Steel简介General特殊钢以原素分类Classification of Special Steel according to Element特殊钢以用途来分类Classification of Special Steel according to End Usage易车(快削)不锈钢Free Cutting Stainless Steel含铅易车钢Leaded Free Cutting Steel含硫易车钢Sulphuric Free Cutting Steel硬化性能Hardenability钢的脆性Brittleness of Steel低温脆性Cold brittleness回火脆性Temper brittleness材料的加工性能Drawing abilli ty硬度Hardness表面处理Surface fini sh冷辘钢捆片及张片制作流程图表Production flow chart cold rolled steel coil sheet冷辘钢捆片及张片的电镀和印刷方法Cold rolled steel coil & sheet electro-plating & painting method \\\\Rust Protection生锈速度表Speed of rusting焊接Welding气焊Gas Welding埋弧焊Submerged-arc Welding电阻焊Resistance Weldi ng冷辘钢片(拉力: 30-32公斤/平方米)在没有表面处理状态下的焊接状况Spot welding conditions for bared (free from paint, oxides etc) Cold rolled mild steel sheets(T/S:30-32 Kgf/ μ m2)时间效应(老化)及拉伸应变Aging & Stretcher Strains电镀锌钢片的焊接Welding of Electro-galvanized steel sheet点焊Spot welding滚焊Seam welding电镀锌(电解)钢片Electro-galvanized Steel Sheet生产流程Production Flow Chart锌镀层质量Zinc Coating Mass表面处理Surface Treatment冷轧钢片Cold-Rolled Steel Sheet/Stri p热轧钢片Hot-Rolled Sheet/Strip电解冷轧钢片厚度公差Thickness Tolerance of Electrolytic Cold-rolled sheet热轧钢片厚度公差Thickness Tolerance of Hot-rolled sheet冷轧或热轧钢片阔度公差Width Tolerance of Cold or Hot-rolled sheet 长度公差Length Tolerance理论质量Theoretical Massn Steel退火Annealing应力退火温度Stress –relieving Annealing TemperatureEnd Usages抗化学品能力Chemical Resistance钢板生产流程Production Flow Chart钢板订货需知Ordering of Steel Plate不锈钢Stainless Steel不锈钢的定义Definition of Stainless Steel不锈钢之分类,耐腐蚀性及耐热性Classification, Corrosion Resistant & Heat Resistance of Stainless Steel铁铬系不锈钢片Chrome Stainless Steel马氏体不锈钢Martensite Stainless Steel低碳马氏体不锈钢Low Carbon Martensite Stainless Steel含铁体不锈钢Ferrite Stainless Steel表面处理Surface fini sh 不锈钢薄片用途例End Usage of Thi nner Gauge不锈钢片、板用途例Examples of End Usages of Strip, Sheet & Plate不锈钢应力退火卷片常用规格名词图解General Specification of Tension Annealed Stainless Steel Strips耐热不锈钢Heat-Resistance Stainless Steel超耐热钢Special Heat Resistance Steel抗热超级合金Heat Resistance Super Alloy耐热不锈钢比重表Specific Gravity of Heat –resistance steel plates and sheets stainl ess steel不锈钢材及耐热钢材标准对照表Stainless and Heat-Resisting Steels发条片Power Spring Strip弹簧用碳钢片CarbonSteel Strip For Spri ng U se冷轧状态Cold Rolled Strip回火状态Annealed Stri p淬火及回火状态Hardened & Tempered Strip/ Precision –Quenched Steel Strip贝氏体钢片Bainite Steel Stri p弹簧用碳钢片材之边缘处理Edge Finished 淬火剂Quenching Media碳钢回火Tempering回火有低温回火及高温回火Low & High Temperature Temperi ng高温回火High Temperature Tempering退火Annealing完全退火Full Anneali ng扩散退火Diffusion Annealing低温退火Low Temperature Annealing中途退火Process Anneali ng球化退火Spheroidizing Anneali ng光辉退火Bright Anneali ng淬火Quenching时间淬火Time Quenchi ng奥氏铁孻回火Austempering马氏铁体淬火Marquenching高碳钢片用途End Usage of High Carbon Steel StripComparison of Tin base, Lead base and Zinc base alloy for Beari ng purpose易溶合金Fusible Alloy焊接合金Soldering and Brazing Alloy化学成份Chemical Compositi on易车碳钢Free Cutting Carbon Steels (to JIS G4804 )化学成份Chemical composition 应用材料Material Used特点Characteristic用途End Usages热导率thermal conductivity,应力和应变stress and strai n,弹性应变elastic strai n,塑性应变plastic strain,屈服强度yield strength,最大抗拉强度ultimate tensile strength, 最大强度ultimate strength,延展性ductility,伸长率elongation,断面收缩率reduction of area,颈缩necking,断裂强度breaking strength,韧性toughness,硬度hardness,疲劳强度fatigue strength,热脆性heat shortness,晶胞中的原子数atoms per cell,点阵lattice, 阵点lattice point,点阵参数lattice parameter,密排六方hexagonal close-packed,六方晶胞hexagonal unit cel l,体心立方body-centered cubic,面心立方face-centered cubic,晶面crystal plane,晶系crystal system,晶向crystal direction,相变机理Phase transformation mechanism:成核nucleation,成核机理nucleation mechanism,金属组织的)基体quay,基体,基块,基质,结合剂matrix,子晶,雏晶matted crystal,均质核化homogeneous nucleation,异质核化heterogeneous ucleation,均匀化热处理homogenization heat treatment,熟料grog,自恰场self-consistent fiel d固溶体Solid solution:有序固溶体ordered solid soluti on,无序固溶体disordered solid solution,有序合金ordered alloy,无序合金disordered alloy.无序点阵disordered lattice,分散,扩散,弥散dispersal,分散剂dispersant,分散剂,添加剂dispersant additive,分散剂,弥散剂dispersant agent缺陷defect, imperfection,点缺陷point defect,线缺陷line defect, dislocation,面缺陷interface defect, surface defect,体缺陷volume defect,位错排列dislocation arrangement,位错阵列dislocation array,位错气团dislocation atmosphere,位错轴dislocation axi s,位错胞dislocation cel l,位错滑移dislocation slip, dislocation movement by slip,回火tempering,退火annealing,退火的,软化的softened,软化退火,软化(处理)softening,淬火quenching,淬火硬化quenching hardening,正火normalizing, normalization,退火织构annealing texture,人工时效artificial aging,细长比aspect ratio,形变热处理ausforming,等温退火austempering,奥氏体austenite,奥氏体化austenitizing,贝氏体bainite,马氏体martensite,马氏体淬火marquench,马氏体退火martemper,马氏体时效钢maraging steel,渗碳体cementite,固溶强化solid solution strengthening,waterproofing agent,扩散diffusion,扩散系数diffusivity,相变phase transition,烧结sintering,固相反应solid-phase reaction,相图与相结构phase diagrams and phase structures ,相phase,组分component,自由度freedom,相平衡phase equilibrium,吉布斯相律Gibbs phase rule,吉布斯自由能Gibbs free energy,吉布斯混合能Gibbs energy of mixing,吉布斯熵Gibbs entropy,吉布斯函数Gibbs function,相平衡phase balance,相界phase boundary,相界线phase boundary l i ne,相界反应phase boundary reacti on,相变phase change,相组成phase composition,共格相phase-coherent,金相相组织phase constentuent,相衬phase contrast,相衬显微镜phase contrast microscope,相衬显微术phase contrast microscopy,相分布phase distribution,相平衡常数phase equilibrium constant,相平衡图phase equilibrium diagram,相变滞后phase transition lag, Al-Si-O-N系统相关系phase relationships in the Al-Si-O-N system,相分离phase segregation, phase separation, 玻璃分相phase separation in glasses,相序phase order, phase sequence,相稳定性phase stability,相态phase state,相稳定区phase stabile range,相变温度phase transition temperature,相变压力phase transition pressure,同质多晶转变polymorphic transformation, 相平衡条件phase equilibrium conditions,低共熔体eutectoid,crystallization,不混溶性immiscibility,固态反应solid state reaction,烧结sintering,相变机理Phase transformation mechanism: 成核生长相变nucleation–growth transition,。
06_ Weldability and defects in weldments

Weldability and defects in weldmentsSubjects of Interest•Reviews of weld design and weldability•Residual stresses and weld distortionWeld metal inhomogeneitiesmicro/macro segregations•Inclusion•Gas porosity•Weld cracking•Solidification cracking•Liquation cracking•Hydrogen crackingObjectivesThis chapter aims to:•Students are required to understand the causes ofresidual stresses,distortion and their remedies.Students are also required to differentiate weld defectsthat might occur during metal welding for example,solidification cracking, liquation cracking, distortion, weldembrittlement.Students can suggest possible remedies associatedwith individual weld defects.Weld design –joint typeFive basic joint types Welds are made at the junction of all the pieces that make up the weldment (assembled part).•A joint between two members alignedapproximately in the same plane.•A joint between two members locatedapproximately at right angles to each otherin the form of an L.•A joint between two members locatedapproximately at right angles to each otherin a form of a T.•A joint between two overlappingmembers located in parallel.A: Butt jointD: Lap jointD: Edge joint•A joint between the edges of two or moreparallel or nearly parallel members.Weld design –weld type •There are eight weld types:Fillet weld-On the jointGroove weld-In the joint-Made on the backside of theBack weldWithout prepared holesWelding a metal studWeld beads deposited on thebase metal or broken surfaceWeld design –Fillet weldDefinitions of different parts in fillet weldWeld design –Groove weld •There are seven basic groove welds:square, V, bevel, U, J, flare V and flarebevel.Groove weldTypes of groove weldsWeld approvalFor quality control Welding procedure sheet is approved and distributed to personnel concerned with its implementation.consumable used: filler, shielding gas, flux Inspection technique used•Weldability depends on various factors such as, nature of metals, weld designs, welding techniques, skills, etc.It has been stated that all metals are weldable some are more difficult than another.is readily weldable (in many ways) than aluminium and copper.•Copper is not easily welded due to its high thermal conductivity which makes it difficult to raise the parent metal to its melting point. require preheating ~300-400o C.•Some aluminium based die casting alloys give weld pool too large to control, and aluminium welds normally have oxide inclusions and porosity.DefinitionThe capability of a material to be welded under the imposed fabrication conditions into a specific, suitably designed structure and to perform satisfactorily in the intended service.Steels•Weldability of steels is inversely proportional to its hardenability,due to martensite formation during heat treatmentWeldabilityHardenabilityCarbon content•There is a trade-off between materials strength and weldability.tend to be the most weldable but suffer from distortion due to high thermal expansion. Cracking and reduced corrosion resistance.Ferritic and martensitic stainless steels are not easily welded, often to be preheated and use special electrodes.is susceptible to hot cracking if the ferrite amount is notAluminium and its alloys•Weldability of aluminium depends on chemical composition of the alloy.•Aluminium alloys are susceptible to hot cracking, oxide inclusions, dross, porosity (hydrogen).•Most of wrought series, 1xxx, 3xxx, 5xxx, 6xxx, and medium strength can be fusion welded by TIG, MIG while 2xxx and high strength are not readily welded due to liquation and solidification cracking.Cracks in aluminium weldsPorosity observed in aluminium welded specimen after fractured.PorosityCracksCopper and copper alloys•Weldability of copper depends onchemical composition of the alloy.Copper•High thermal conductivity required preheating tocounteract heat sink effect.•Can be TIG or MIG welded.Brasses•Volatilization (toxic) of zinc is the main problem, reducingLow zinc content brass can be TIG or MIG welded.Most are weldable, except gun metal or phosphor bronzes.Require careful cleaning and deoxidization to avoid porosity.improves weldability due to its deoxidizing and fluxing actions.causes porosity and reduce strength of welds.increases hot-cracked susceptibility during welding.Precipitation hardened alloys should be welded in the annealedcondition, and then precipitation hardening treatment.Titanium alloys•Weldability of titanium depends on chemical composition of the alloy.•Titanium alloys with low amounts of alloying elements are more readily welded. For example: CP titanium alloys, α, α, α+βα+βtitanium alloys.•Highly stabilised beta titanium alloys are difficult to weld due to segregation .•Welding at above 500-550o C requires special precaution .Fluxes are not normally used since they combine with titanium to cause : TIG, MIG, PAW, LBW, EBW, FW, RW.Ar, He or the mixture of the two (avoid contact with oxygen).grades should match the alloys being welded, normally with lower yield strength to retain ductility. (used unalloyed with lower βcontent to avoid martensite transformation and with minimised O, N, H contents).tungsten electrodes (EWTh-1 or EWTh-2) are used for TIG welding.Magnesium alloys•Weldability of titanium depends onchemical composition of the alloy.•Welding processes:Arc welding, RW as well as oxyacetylene welding, brazing. TIG and MIG are recommended.is lowered in the base metal, in the workand grain growth in the HAZ.Similar to welding of aluminium, magnesium has low melting point, high thermal conductivity, thermal expansion, oxide surface coating.alloys (AZxx), Al >10% improves weldability by refining grainZn > 1% increases hot shortness.Filler metals are selected by the composition of the base metals.•It is unusual for the weldments to be completely sound.•They normally contain small defects such as porosity, slag, oxide inclusions, lack of fusion, undercut, crack, distortion, etc.Cross sections of welds containing typical defectsUnderstandthe causeSolve/preventthe problem •Furthermore, different metals have different weldability so we need to understand the nature of the metal to be welded.Incomplete fusionRoot and joint penetrationsGroove welds andvarious defectsResidual stresses in weldmentResidual stresses(internal stresses) arestresses that would exist in a body afterremoving all external loads (normally dueto non uniform temperature change duringwelding in this case).•Weld metal and adjacent baseResidual tensilestressesResidualcompressivestressesThermally induced residual stresses in weld.Changes in temperature and stresses during welding•Zero temperature and stressdistribution at A-A.•Small compressive in theweld zone and small tensile inthe base metal at B-B duringduring cooling.Further contraction of themetal producing highertensile stress in the weld centreand compressive in the baseChanges in temperature and stresses during weldingTypical residual stress distribution in weldment (longitudinal)•Residual stress distribution across the weld shows tensile in the weld metal and the adjacent base metal and then goes compressive in the area further away from the weld metal.•Residual tensile stresses are notdesirable, which can cause problemsTensionzone Post weld heat treatment is oftenused to reduce residual stresses.Other techniques : preheating,peening, vibration have also beenused for stress relief.Typical residual stress (longitudinal)distribution in weldmentEffect of temperature and time on stress relief of steel weldsStress relief temperature% Relief of initial stressTypical thermal treatments for stress relieving weldmentsDistortion•Weld distortion is due to solidification shrinkage and thermal contraction of the weld metal during welding.Distortion in welded structureAngular distortionSingle-pass-single-V groove butt jointMultiple-pass-single-V groove butt joint usually occurs when the weld is made from the top of the workpiecewider at the than the bottom, causing more solidification shrinkage and thermal contractionInside filletcorner jointFabricated beamDistortion in fillet welding of T joint Thin platesThick platesThere are several techniques used to reduceangular distortion.•Reducing volume of weld metal•Using double-V joint and alternate welding•Placing welds around neutral axisControlling weld distortionReducing volume of weld metal andby using single-pass deepPlacing weld around neutral axispenetration welding.Using double-V joint and weld alternately on either side of joint.•Balancing the angular weld distortionon either side of the double V joint .•Double V-joints balance the shrinkage almostsame amount of contraction on each side (a).•Asymetrical double V : The first weld alwaysproduces more angular distortion the second sideis larger too pull back the distortion when the firstweld is made (b).•A single U joint gives a uniform weld with throughthe section (c).(a) Symmetricaldouble V (b) Asymmetricaldouble V(c) Single URemedies for angular distortionMethods for controlling weld distortion:•Presetting:by compensating the amount of distortion to occur in welding.•Elastic prespringing can reduce angular changes after restraint is removed.•Preheating and post weld treatment(a) Preseting(b) Springing(c) PerheatingLongitudinal distortionLongitudinal bowing of distortion in a butt joint RemediesSequences forwelding shortlengths of a joint toreduce longitudinalbowing•Heating and cooling cycles along the joint during welding build up a cumulative effect of longitudinal bowing.•Welding short lengths on a planned or randomdistribution are used to controlled this problem.Mechanical methods: straightening press,Thermal methods: local heating to relievestresses (using torches) but cannot be used forhighly conductive metal such as Al and Cu.Longitudinal distortion•Angular distortion and longitudinal bowing can also be observed in joints made with fillet welds such as fillet-welded T joint.Remedies•Back-step technique is also used. Eachsmall increment will have its own shrinkagepattern which then becomes insignificant tothe whole pattern of weldment. (But timeconsuming)•Using the smallest possible weld size. Longitudinal bowing in a fillet-Back step techniqueWeld metal chemical inhomogeneities•Micro segregationMacro segregationInclusions and gas porosity.Micro segregation•Lack of solid state diffusion might cause micro segregation in weldments. EX:Solid state diffusion in a moreclosely packed FCC structure(austenite) is more difficult than aacross columnardendrite near quenched weld pool ina martensitic stainless steel.Banding•Banding occurs due to fluctuations in welding speed and power input.Banding and rippling near centreline of as-welded top surfaceof a 304 stainless steel YAG laser welded.Inclusions and gas porosityRadiograph of a weld showing a large slag inclusion.Gas porosity and inclusions in multipass welding.•Gas-metal and slag-metal reactions produce slag inclusion and gas porosity.•Incomplete slag removal in multipass welding can cause slag inclusions trapped within the weld.SlaginclusionMacro segregation•Weld pool macro segregation occur by lack of weld pool mixing(by convection) especially in welding of dissimilar metals, or some special types of rapidly solidified power metallurgy alloys.•if the weld pool mixing is incomplete in single pass welding (greater extent) and even in multipass welding.the weld pool mixed better.Powder metallurgy Al-10Fe-5Ce GTAwelded with Al-5Si filler metal (a) AC,(b) DCENRemedies for macro segregation •Applying magnetic weld pool stirring to give a better mixing in the weld pool.•For GTAW, using DCEN for a deeper weld penetration and mixing.•Using proper filler metals.•Give enough time for the weld pool to be melt. Ex:EBW with a high welding speed might not give enough time for weld pool mixing inEffect of weld pool stirringWeld crackingThere are various types of weld cracking•Solidification cracking (hot cracking)Hydrogen cracking (cold cracking)Lamellar TearingSolidification cracking•Similar to casting, solidification cracking can also occur in welding.•It happens at the terminal stage of solidification due to contraction of solidifying metal and thermal contraction . (Intergranular crack)•Solidification cracking is intensified if the base metal is attached on to non moving parts (building up tensile stresses).•The less ductile the weld metal is, the more likely solidification cracking Solidification cracking in a GMAWSolidification cracking in an autogenous weld of 7075 aluminium at high magnification.Base metalWeld Solidification crackSolidification crack (intergranular)Factors affecting solidification cracking Grain structure•Coarse columnar grains aremore susceptible to solidificationcracking than equiaxed grains.Centreline cracking in a coarse-grainedCentreline crackingContraction stresses •Contraction stresses can be due to thermal contraction, solidification shrinkage.Ex:Austenitic stainless steels (high thermalexpansion) susceptible to solidificationcracking.Solidificationcracking in steel weldRestrainingFirst weld Second weld Solidification cracking •The weldment is restrained after the firstweld, causing solidification cracking in thesecond weld in T joints.Remedies for solidification cracking•Controlling composition of the metal to be welded.•Using filler metal with proper composition.•Controlling Mn and S content in carbon and low alloy steels.•Controlling solidification structure: grain refining, arc oscillation, arc pulsation, etc.: concave fillet weld suffers higher tensile stress on the face than the convex fillet weld, deep weld is more susceptible to solidification cracking.Hydrogen cracking (Cold cracking)Hydrogen cracking occurs when•Hydrogen in the weld metal sources: moisture from metal surface, tools, atmosphere, flux,•High stresses•Susceptible microstructure : martensite(HAZ of carbon steels due to lower diffusion coefficient of hydrogen in austenite than in ferrite),combination of hydrogen + martensite promotes hydrogen cracking.cold cracking or delayed cracking.crack in a low-alloy Hydrogen cracking in a fillet weld of 1040 steel.Remedies for hydrogen cracking•Controlling welding parameters: proper preheat and interpass temperature•Postweld treatment: stress relief.Use proper welding processes and Materials (consumables),Liquation crackingSegregation in PMZ liquation crackingRemedies for liquation cracking•Use proper filler metal.•Reducing the heat input to lower the size of PMZ.•Reducing the degree of restraint, lowering the level of tensilestresses.Controlling impurities, suppressing micro segregation at grainSmaller grain size is better (less concentration of impurities on grain boundaries. Also control grain orientation.Lamellar Tearing•Lamellar tearing occurs when tensile stresses are acting on fibred structure (stringers of nonmetallic materials), causing decohesion of nonmetallic inclusions.Lamellar tearing in steel Lamellar tearing near a C-Mn steel weld Avoid tensile stresses acting on transverse direction of the sample.References•Kou, S., Welding metallurgy, 2nd edition, 2003, John Willey andSons, Inc., USA, ISBN 0-471-43491-4.•Gourd, L.M., Principles of welding technology, 3rd edition, 1995, Edward Arnold, ISBN 0 340 61399 8.•Cary, H.B., Modern welding technology, 4th edition, 1998, Prentice 。
ASME压力容器常用词汇中英文对照
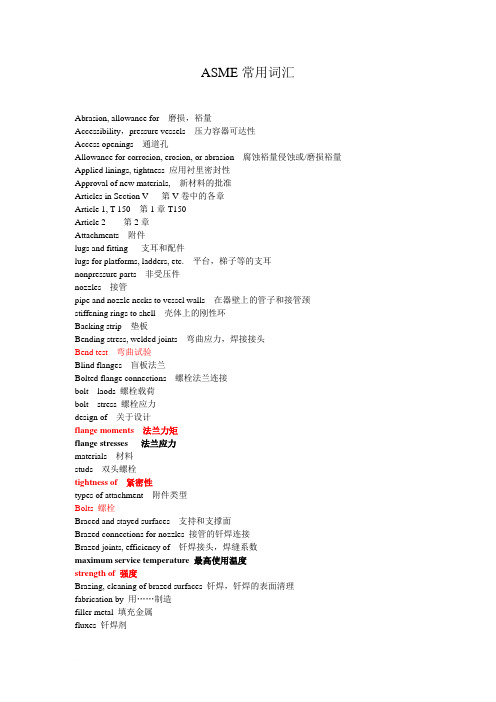
ASME常用词汇Abrasion, allowance for 磨损,裕量Accessibility,pressure vessels 压力容器可达性Access openings 通道孔Allowance for corrosion, erosion, or abrasion 腐蚀裕量侵蚀或/磨损裕量Applied linings, tightness 应用衬里密封性Approval of new materials, 新材料的批准Articles in Section V 第V卷中的各章Article 1, T-150 第1章T150Article 2 第2章Attachments 附件lugs and fitting 支耳和配件lugs for platforms, ladders, etc. 平台,梯子等的支耳nonpressure parts 非受压件nozzles 接管pipe and nozzle necks to vessel walls 在器壁上的管子和接管颈stiffening rings to shell 壳体上的刚性环Backing strip 垫板Bending stress, welded joints 弯曲应力,焊接接头Bend test 弯曲试验Blind flanges 盲板法兰Bolted flange connections 螺栓法兰连接bolt laods 螺栓载荷bolt stress 螺栓应力design of 关于设计flange moments 法兰力矩flange stresses 法兰应力materials 材料studs 双头螺栓tightness of 紧密性types of attachment 附件类型Bolts 螺栓Braced and stayed surfaces 支持和支撑面Brazed connections for nozzles 接管的钎焊连接Brazed joints, efficiency of 钎焊接头,焊缝系数maximum service temperature 最高使用温度strength of 强度Brazing, cleaning of brazed surfaces 钎焊,钎焊的表面清理fabrication by 用……制造filler metal 填充金属fluxes 钎焊剂heads into shells 封头接入壳体operating temperature 操作温度Buttstraps, curvature 对接盖板,曲率forming ends of 成型端thickness and corrosion allowance 厚度和腐蚀裕量welding ends of 焊接端Carbon in material for welding 焊接用材料中的碳Cast ductile iron vessels, design 可锻铸铁容器,设计pressure-temperature limitations 压力-温度界限service restrictions 使用限制Castings 铸件carbon steel 碳钢defects 缺陷impact test 冲击试验inspection 检查quality factor 质量系数specifications 标准Cast iron circular dished heads 铸铁碟形封头Cast iron standard parts, small 铸铁标准部件,小件Cast iron pipe fittings 铸铁管件Cast iron vessels 铸铁容器corners and fillets 圆角和倒角head design 封头设计hydrostatic test 水压试验nozzles and fittings 接管和配件pressure-temperatures limitations 压力-温度界限Certificate of Authorization for Code Symbol Stamp 规范符号标志的认可证书Certification of material 材料证明书Certification of Nondestructive Personnel 无损检验人员证明书Magnetic Particle Examination 磁粉检验Liquid Penetrant Examination液体渗透检验Radiographic Examination 射线超声检验Ultrasonic Examination 超声检验Chip marks on integrally forged vessels 整体锻造容器上的缺口标志Circumferential joints alignment tolerance环向连接,组对公差assembling装配brazing钎焊vessels subjected to external pressure 承受外压的容器Clad material, inserted strips 覆层材料,嵌条examination 检查Clad plate 复合板Cleaning ,of brazed surfaces 钎焊表面清理of welded surfaces 焊接表面Clearance between surfaces to be brazed 钎焊表面间的间隙2第 3 页共19 页Combination, of different materials 不同材料组合of methods of fabrication制造方法Computed working pressure from hydrostatic tests 由水试验计算的工作压力Conical heads 锥形封头Conical sections 圆锥截面Connections ,bolted flange (see Bolted flange connections)连接,螺栓法兰(见螺栓法兰连接)brazed 钎焊clamp 卡箍expanded 胀接from vessels to safety valves 由容器至安全阀studded 双头螺栓threaded 螺纹welded 焊接Cooling, after postweld heat treating 冷却,焊后热处理Corrosion allowance 腐蚀裕度Corrosion resistant linings 防腐蚀衬里Corrugated shells 波纹形壳体Corrugating Paper Machinery 波纹板机械Cover plates 盖板on manholes and handholes 在人孔和手孔上的spherically dished 球形封头Cracking, stress corrosion 应力腐蚀裂缝Cutting plates 板材切割Cylindrical shells, supplementary loading 柱状壳体,附加载荷thickness 厚度transition in 过渡段Data report, guide for preparation 准备数据报告的指南Defects in welded vessels, repair 修理焊接容器中的缺陷Definitions 定义Design, brazed vessels 设计钎焊容器carbon and low alloy steel vessels 碳钢及低合金钢容器cast ductile iron vessels 可锻铸铁容器cast iron vessels 铸铁容器clad vessels 覆层容器ferritic steel vessels with properutsenhanced by heat treatment 经热处理后提高抗拉性能的铁素体钢容器forged vessels 锻造容器high-alloy steel vessels 高合金钢容器loadings 载荷multichamber vessels 多受压室容器nonferrous vessels 非铁金属容器welded vessels 焊接容器design pressure 设计压力Diameter exemption 直径的豁免3Dimensions, checking of 尺寸,校核Discharge of safety valves 安全阀泄放Dished heads (see formed heads) 碟形封头(见成形封头)Disks, rupture 防爆膜Dissimilar weld metal 不同金属的焊接Distortion, of welded vessels 大变形、焊接容器supports to prevent 用支撑防止Drainage, discharge from safety and relief valves 排放,由安全阀和泄压阀泄放Drop weight tests 落锤试验Eccentricity of shells 壳体的偏心度Edges of plates, metal removal from 由加工板边去除金属tapered 锥度Efficiency, around openings for welded attachments 焊缝系数,环绕焊接附件孔口Elasticity, modulus of 弹性模量Electric resistance welding 电阻焊Ellipsoidal heads 椭圆封头Erosion, allowance for 侵蚀裕量Etching, of sectioned speciments 侵蚀,关于截面试样solutions for examination for materials 检验材料的溶液Evaporators 蒸发器Examination, of sectioned speciments 剖面试样的检验of welded joints 焊接接头的检验Exemptions diameter and volume 直径和容积的豁免Expanded connections 胀接连接External pressure, tube and pipe 外压管External pressure vessels 外压容器allowable working pressure for 许用工作压力charts 算图design of heads for 封头设计joints in shells of 壳体上的接头reinforcement for openings 开孔补强stiffening rings in shells 壳体上的刚性环supports for 支承thickness of shell 壳体厚度reducers 变径段Fabrication, brazed vessels 制造,钎焊容器Ferritic steels vessels with tensile properties enhanced by heat treatment, design经热处理后提高抗拉性能的铁素体钢容器,设计fabrication 制造head design 封头设计heat treatment热处理heat treatment verification tests 热处理验证试验marking 标志4第 5 页共19 页materials 材料stamping 标记welded joints 焊接接头Field assembly of vessels 容器的现场安装Filler plugs for trepanned holes 锥孔的管塞Fillet welds 角焊Fired process tubular heaters 直接火管式加热炉Fitting attachments 附件装配Flange connections 法兰连接Flange contact facings 法兰接触面Flanges 法兰bolted design 螺柱法兰设计of formed heads for welding 用于焊接成型封头type of attachment 附件的类型Flat heads and covers, unstayed 无支撑平封头和盖板reinforcement of openings 开孔补强Flat spots on formed heads 成型封头上的平坦部分Flued openings 翻边开孔Forged parts, small 锻造部件,小的Forged vessels 锻造容器heat treatment 热处理localized thin areas 局部薄壁区welding 焊接Forgings 锻件identification of 识别Ultrasonic Examination 超声检验Formmanufacturer’s data report 制造厂数据报告格式partial report 零部件数据报告Formed heads 成型封头flued openings in 封头上翻边开孔insertion of, welded vessels 插入,焊接容器joint efficiency 接头系数knuckle radius 转角半径length of skirt 直边长度on welded vessels 在焊接容器上reinforcement for openings 开孔补强Forming 成型ends of shell plates and buttstraps 壳体板和对接搭板端forged heads 锻造封头shell sections and heads 筒节和封头Furnaces 炉子temperatures for postweld head treatment 焊后热处理温度Furnaces for heat treating 热处理炉5temperature control of 炉温控制Galvanized vessels 镀锌容器Gasket materials 垫片材料Girth joints (see circumferential joints) 环缝接头(见环向接头)Handhole and manhole openings 手孔和人孔开孔Head flange (skirt) length 封头翻边(直边)长度Head joints 封头接头brazing 钎焊welded 焊接Head openings 封头开孔entirely in spherical portion 全部在球体部分Head joints 封头接头concave and convex 凹面和凸面flat (see flat heads) 平板(见平封头)forged 锻造的formed (see Formed heads) 成型的(见成形封头)forming 面型thickness, after forming 厚度,成型之后Heads, design, conical 封头,设计,锥形ellipsoidal 椭圆形hemispherical 半球形spherically dished 球状碟形toriconical 带折边的锥形torispherical 带折边的球形torispherical, knuckle radius 带折边的球形,转角半径Heads and shells 封头和壳体external pressure, out-of-roundness 外压,不圆度openings through or near welded joints 通过或靠近焊缝处的开孔roundness tolerance 不圆度公差Heat exchangers 热交换器Heat treatment 热处理by fabricator 由制造厂进行carbon and low-alloy steel vessels 碳钢和低合金钢容器ferritic steel vessels with tensile properties enhanced by heat treatment 经过热处理后提高抗拉性能的铁素体的容器forged vessels 锻造容器furnaces 炉子high-alloy vessels 高合金容器of test specimens 试样的热处理verification tests of 热处理验证试验Hemispherical heads 半球形封头High pressure vessels 高压封头Holes 小孔for screw stays 用于螺丝固定6第7 页共19 页for trepanning plug sections, refilling 用于穿孔螺塞部分,再填充telltale 指示孔unreinforced, in welded joints 不补强,在焊缝上Hubs, on flanges 高颈,在法兰上Hydrostatic proof tests 水压验证试验destructive 破坏性prior pressure application 在升压之前Hydrostatic test 水压试验cast iron vessels 铸铁容器combined with pneumatic 与气压试验混合的enameled vessels 搪玻璃容器external pressure vessels 外压容器galvanized vessels 镀锌容器standard 标准welded vessels 焊接容器Identification 识别of forging 锻件of plates 平板of welds 焊接Identification markers, radiographs 识别标志,射线照相Impact test 冲击试验certification 证明properties 性能specimens 试样temperature 温度Inspection 检查before assembling 组装之前carbon and low-alloy steel 碳钢和低合金钢cast ductile iron vessels 可锻铸铁容器cast iron vessels 铸铁容器clad vessels 覆层容器during fabrication 在制造期间ferritic steel vessels with tensile properties enhanced by heat treatment 经过热处理后提高抗拉性能的铁素体的容器fitting up 组对forged vessels 锻造容器heat treatment, forgings 热处理,锻件high-alloy steel vessels 高合金钢容器magnetic particle 磁粉material 材料nonferrous vessels 非铁金属容器plate 板材postweld heat treatment 焊后热处理pressure vessels, accessibility 压力容器,可达性7quality control 质量管理sectioning of welded joints 焊接接头的剖面检验spot examination 抽样检查steel castings 铸钢件surfaces exposed and component parts 暴露的表面和元件部分test specimens 试样vessels 容器vessels exempted from 免检容器welded vessels 焊接容器Inspection openings 检查孔Inspectors 检查师access to plant 在厂内应有的便利control of stamping 打印管理duties 职责facilities 装备qualification 资格reports 报告Installation 安装pressure-relieving devices 泄压装置pressure vessel 压力容器Integral cast iron dished heads 整体铸铁碟形封头integrally finned tubes 整体翅片管Internal structures 内部构件Jacketed vessels 夹套容器Joints 接头brazed 钎焊circumferential (see Circumferential joints) efficiency, brazed 环缝(见环向接头)系数,钎焊welded 焊接electric resistance, butt welding 电阻,对接焊in cladding and applied linings 在覆层及衬里in vessels subjected to external pressure 在承受外压的容器lap (see Lap joints) 搭接(见搭接接头)longitudinal (see Longitudinal joints) 纵向(见纵向接头)tube-to-tubesheet 管子对管板Jurisdictional Review 权限审查Knuckles 过渡圆角radius 半径transition section 变径段Lap joints 搭接接头amount of overlap 搭接量brazed 钎焊longitudinal under external pressure 在外压作用下纵向的welded 焊接Laws Covering Pressure Vessels 涉及压力容器的法规8第9 页共19 页Lethal gases or liquids 致命的气体或液体Ligaments, efficiency of 孔带,系数Limitation on welded vessels 焊接容器的限制Limit of out-of-roundness of shells 壳体不圆度的限制Linings 衬里corrosion resistant 抗腐蚀Liquid penetrant examination 液体渗透检验Loadings 载荷Local postweld heat treatment 局部焊后热处理Longitudinal joints 纵向接头alignment tolerance 对准公差brazing 钎焊vessels subjected to external pressure 承受外压的容器Low-temperature operation 低温操作Low-temperature vessels brazed 低温容器,钎焊for gases and liquids 用于气体和液体impact test requirements 冲击试验要求impact test, when not required 冲击试验,当不要求时marking 标志materials 材料testing of materials 材料试验Lugs for ladders, platforms, and other 梯子,平台及其它附件的支耳Magnetic particle inspection 磁粉检查Manholes, and handholes 人孔,手孔cover plate for 盖板minimum vessel diameter requiring 所需最小容器直径Manufacture, responsibility of 制造者,职责Manufacturer’s Data Report (see Data Report) 制造厂数据报告(见数据报告) Manufacturer’s stamps 制造厂的印记Marking castings 标志,铸件materials 材料plates 板材standard pressure parts 标志受压件valves and fittings 阀门和配件with Code symbol 带有规范符号Markings, transfer after cutting plates 标志,板材切割以后的转移Materials, approval of new 材料,新材料的批准approval of repairs 修补的批准brazed vessels 钎焊容器carbon and low-alloy steel vessels 碳钢和低合金钢容器cast ductile iron 可锻铸铁castings 铸铁cast iron vessels 铸铁容器certification 合格证9clad vessels 覆层容器combination of 组合材料ferritic steel vessels with tensile properties enhanced by heat treatment 经热处理后提高抗拉性能的铁素体钢容器forged vessels 锻造容器for nonpressure parts 非受压元件heat treatment of 热处理high-alloy steel vessels 高合金钢容器inspection of 检查nonferrous vessels 非铁金属容器pipe and tube 管子plate 板rods and bars 杆和棒specification for 标准standard pressure, parts 标准受压元件unidentified 未鉴别的use of over thickness listed in SectionⅡ采用超过列于第Ⅱ卷表中的厚度welded vessels 焊接容器Measurement, 测量dimensional 尺寸of out-of-roundness of shells 壳体不圆度Metal temperature determination 金属温度,确定control of 控制Mill undertolerance 钢厂负公差控制Minimum thickness of plate 板材的最小厚度控制Miscellaneous pressure parts 其它受压件控制Multichamber vessels design 多承压室容器,设计Multiple duplicate vessels 多个相同的容器Multiple safety valves 多个安全阀Nameplates 铭牌New materials 新材料Noncircular vessels 非圆形容器ligament efficiency 孔带系数nomenclature 术语obround design 长圆形设计rectangular design 矩形设计reinforcement 补强examples 实例Nonpressure parts, attachment of 非受压元件的连接Notch ductility test 缺口韧性试验Nozzle openings, reinforced 接管开孔,补强的unreinforced 非补强的vessels subjected to external pressure 承受外压得容器10第11 页共19 页Nozzles attachment of to shell 接管,与壳体的连接minimum thickness of neck 缩颈的最小厚度(see also Connections)(也可见连接件)Nuts and washers 螺母和垫圈Offset of edges of plates at joints 在接头处板边的偏差Openings adjacent to welds 开孔,邻近焊缝closure of 封闭for connections to brazed vessels 用于对钎焊容器的连接for drainage 用于排放head (see Openings head and shell) 封头(见开孔,封头和壳体)in flat heads 在平板封头上inspection 检查manhole (see Manholes) 人孔(见人孔)nozzle (see Nozzle opening) 接管(见接管开孔)shell (see Openings, head and shell) 壳体(见开孔,封头和壳体) through welded joints 通过焊接接头Openings, head and shell, computation of 开孔,封头和壳体,计算not requiring additional reinforcement 不需要附加补强reinforced, size 补强,尺寸reinforcement for adjacent openings 邻近开孔的补强reinforcement of 补强requiring additional reinforcement 需要附加补强shapes permissible 许用形式unreinforced, size 不补强的,尺寸Outlets, discharge, pressure relieving devices 排放口,出料,泄压装置Out-of-roundness 不圆度Overpressure limit for vessels 容器的超压极限Partial data report, manufacturer’s 零部件数据报告,制造厂的Parts, miscellaneous 部件,各种各样的Peening 捶击Pipe connections openings for 管子的连接,用于开孔Pipe fittings vessels built of 管子配件,制造的容器Pipe and tubes 各类管子Pipe used for shells 用作壳体的管子piping external to vessel 容器外的管子Plate, curvature 板,曲率measurement, dimensional check 测量,尺寸校核Plate edges cutting 板边,切割exposed left unwelded 留下不予焊接的显露部分inspection of 检查Plates 平板alignment 找准cover 盖板cutting 切割forming 成型heat treatment 热处理identification 标志impact test 冲击试验inspection 检查laying out 划线less than 6 mm thickness 厚度小6mmmarkings transfer after cutting 标志,在切割以后的转移minimum thickness 最小厚度repair of defects 缺陷修理specifications 标准structural carbon steel 结构碳钢Plug welds 塞焊Pneumatic test 气压试验pressure 压力yielding 屈服Porosity welded joints 气孔,焊接接头Porosity charts 气孔图Postheat treatment 后热处理connections for nozzles and attachments 用于接管和附件的连接cooling after 随后的冷却furnace temperature 炉温inspection 检查local 局部requirements 要求temperature range 温度范围welded vessels 焊接容器Preheating 预热Preparation of plates for welding 焊接板材的准备pressure, design 压力,设计limits 极限(see also Working pressure, allowable) (也可见工作压力,许用)Pressure parts miscellaneous 受压件,其它的Pressure relieving devices 泄压装置discharge 排放installation and operation 安装和运转rupture disks 防爆模setting 整定Pressure vessels 压力容器exempted from inspection 免检Produce form of Specification 产品技术条件Proof test hydrostatic (see Hydrostatic proof test) 验证试验,水压(见水压试验) Qualification 评定of brazers 钎焊工第13 页共19 页of welders 焊工of welding procedure 焊接工艺Quality Control System 质量保证体系Quenching and tempering 淬火及回火Quick-actuating closures 快开盖Radiograph factor 射线照相系数Radiographing 射线照相examination by 检查partial 部分quality factors 质量系数requirements 要求spot examination 抽样检查retests 重新试验thickness, mandatory minimum 规定最小厚度Radiographs, acceptance by inspector 射线照相,由检查员认为合格gamma rays, radium capsule γ射线,装镭的盒子interpretation by standard procedure 由标准程序的说明rounded indications 圆形显示Reaming holes for screw stays 为固定螺钉用的铰孔Reducer sections, rules for 变径段,规程Reinforcement 补强defined limits 规定的范围head and shell openings 封头及壳体开孔large openings 大开孔multiple openings 多个开孔nozzle openings 接管开孔of openings in shells, computation of 壳体上开孔,计算openings subject to rapid pressure fluctuation 经受压力突然波动的开孔Fluctuation 经受压力突然波动的开孔strength 强度Relief devices 泄放装置(see also Pressure relieving devices, Safety and relief Valves)(也可见泄压装置,安全阀和泄压阀)Relieving capacity of safety valves 安全阀排量Repairs, approval of defects in material 修理,材料中缺陷的认可defective Brazing 有缺陷的钎焊defects in forgings 锻件中的缺陷defects in welds 焊缝中的缺陷Responsibility of manufacturer 制造者的职责Retention of Records 记录的保存Radiographs 射线照相Manufacturer’s Data Reports 制造厂的数据报告Retests, frogings 复试,锻件impact specimens 冲击试样joints, welded 接头,焊接Rods, bars, and shapes 杆棒喝型材Rolled parts, small 轧制件,小件Rupture disks 爆破模Safety 安全性safety relief, and pressures relief valves, adjustable blow down, capacity certification 安全泄放和泄压阀,可调节的泄放,排放量证明capacity, conversion 排量,换算connection to vessels 连接至容器construction 结构discharge pipe 排放管indirect operation 间接操作installation 安装installation on vessels in service 容器在役时的安装liquid relief 液体泄放marking 标志minimum requirements 最低要求pressure setting 压力整定spring loaded 受载弹簧springs, adjustment 弹簧,调节stop valves adjacent to 邻近的截止阀test 试验protective devices 防护装置for unfired steam boiler 对非直接火蒸气锅炉Scope 适用范围sectioning, closing holes left by 解剖,解剖孔的封闭etching plugs taken 解剖样的侵蚀examination by 检查Service restriction 使用限制Shapes, special 形状,特殊Shell plates, forming ends of 壳体用材料,封头成型Shells 壳体allowable working pressure 许用工作压力computation of openings in 开孔计算forming 成型made from pipe 由管子制造的stiffening rings 刚性环thickness 厚度Transition section 过渡段Sigma-phase formation σ相的形成Skirts length on heads 直边、封头上的长度support of vessels 裙座,容器支撑Slag inclusion welds 焊缝中的夹渣Special constructions 特殊结构第15 页共19 页Specification for materials 材料标准Spherical sections of vessels 容器的球形部分Spot examination of welded joints 焊接接头的抽样检查Springs for safety valves 安全阀的弹簧Stamping location of 打印位置multipressure vessels 多重压力容器omission of 省略safety valves 安全阀with Code symbol 带有规范标记Stamps, certificate of authorization 钢印,授权low stress 低压力not to be covered 不应覆盖to be visible on plates 在板上可见Static head, in setting safety valves, effect of on limiting stresses 静压头,在整定安全阀时,影响,对极限应力Stayed surfaces 支撑表面Staying formed heads 成型封头的支撑Stays and staybolts, adjacent to edges of staybolted surface 支撑件及拉撑螺栓,邻近用螺栓拉撑得表面周边处allowable stress 许用应力area supported 支撑面dimensions 尺寸ends 端部location 位置pitch 节距screw, holes for 螺孔upset for threading 为车制螺纹的镦粗welded 焊接的Steam generating vessels, unfired 蒸汽锅炉,非直接火Steel, carbon content 钢,含碳量Stenciling plates for identification 在板材上打印标志Stiffening rings, attachment to shell 刚性环,和壳体的装配for vessels under external pressure 用于外压容器Stiffness, support of large vessels for 刚性,大容器支座Stop valves 截止阀adjacent to safety and relief valves 邻近于安全和泄压阀Strength of brazed joints 钎焊接头的强度Stress corrosion cracking 应力腐蚀裂缝Stress values, attachment weld 应力值,连接焊缝basis for establishing 确定的基础carbon and low-alloy steel 碳钢和低合金钢cast iron 铸铁ferritic steels with tensile properties enhanced by heat treatment 经热处理后提高抗拉性能的铁素体刚high-alloy steel高合金钢nonferrous metals 非铁金属Stud bolt threads 双头螺栓螺纹Studded connections 双头螺纹连接Supplementary design formulas 补充设计公式Supports, design 支座,设计pressure vessels 压力容器temperature free movement under 在温度下活动不受约束types of steel permissible for 容许的钢材类型vessels subjected to external pressure 承受外压的容器Surface Weld Metal Buildup 金属堆焊表面Tables, effective gasket width b 表,有效垫片宽度bgasket materials and contact facings 垫片材料和接触面maximum allowable efficiencies for arc and gas welded joints 电弧焊和气焊接头的最大许用系数minimum number of pipe threads for connections 管螺纹连接的最少螺纹牙数molecular weights of gases and vapors 气体和蒸汽的分子量of stress values, carbon and low-alloy steel 应力值,碳钢和低合金钢cast iron 铸铁cast ductile iron 可锻铸铁ferritic steels with tensile properties enhanced by heat treatment经热处理后提高抗拉性能的铁素体钢high-alloy steel 高合金钢nonferrous metals 非铁金属welded carbon low-alloy pipe and tubes 焊接低合金碳钢管of values factor K系数K值factor M 系数Mfactor 系数postweld heat treatment requirements 焊后热处理要求recommended temperature ranges for heat treatment 推荐的热处理温度范围spherical radius factor K1球半径系数K1Telltale holes 指示孔in opening reinforcement 开孔补强Temperature, definitions 温度,定义design 设计determination 确定free movement of vessel on supports 支座上的容器活动不受约束heat treatment 热处理limitations, of brazed vessels 限制,钎焊容器of cast ductile iron 可锻铸铁of postweld heat treating 焊后热处理metal, control of 金属,控制operating or working, definitions 操作或工作,定义zones of different 不同区域第17 页共19 页Termination point of a vessel 容器的界限点Test coupons 试样Test gages requirements 试验仪表,要求Test plates heat treatment 试板,热处理impact test 冲击试验production 生产Tests, hydrostatic proof 试验,水压验证pneumatic (see pneumatic test) 气压,见气压试验vessels whose strength cannot be calculated 不能由计算求得强度的容器calculated 不能由计算求得强度的容器Thermal buffers 热缓冲器Thermocouples attachment 热电偶,安装Thickness gages, details 厚度量规,细节Thick shells, cylindrical 厚壳体,圆柱形spherical 球形Thin plates marking 薄板,标志Threaded connection 螺纹连接Threaded inspection openings 螺纹检查孔Threads, stud bolts 螺纹,双头螺栓Tolerances, forged shells and heads 公差,锻造容器及封头Toriconical heads 带折边的锥形封头Torispherical heads 带折边的球形封头Transfering marking on plates 板上标志的移植Transition in cylindrical shells 柱状壳体的过渡Trays and baffles, acting as partial shell stiffeners 塔盘及挡板,作为部分壳体加强圈Tubes and pipe 管子Tube-to-tubesheet joints 管子与管板的连接Ultrasonic examination of welds 焊缝的超声检验UM vessels UM 容器Unfired steam boiler 非直接火蒸汽锅炉Unidentified materials 未识别的材料Valves, connections 阀,连接safety and relief (see safety and relief valves) 安全和泄压装置Valves and fittings, marking 阀及其配件,标志Verification tests, heat treatment 验证试验,热处理V olume exemption 容器的免检Weld deposits, cleaning 焊接熔敷金属,清理peening 捶击Welded joints, category 焊接接头,类别description of types 类型的描述efficiency 焊缝系数impact test, across 冲击试验,横向postweld heat treating 焊后热处理radiographic examination, complete 射线照相检查,整个的rounded indications 圆形显示sectioning, etch test 解剖,侵蚀试验spot examination 抽样检查staggered, longitudinal 错开,轴向taper, plates of unequal thicknesses 锥度,不等厚板types around openings 类型,环绕开孔ultrasonic examination of 超声检验Welded reinforcement of nozzle openings 接管开孔的焊缝补强Welded vessels 焊接容器holes in joints of 接头处的孔inspection 检查limitations on 限制tests of 试验Welders and welding operators 焊工和自动焊工identifying stamps 识别标记records of, by manufacturers 由制造厂所作的记录test of qualification 评定试验Welding 焊接cleaning of welded surfaces 焊件表面清理details, limitations 细节,限制forged vessels 锻造容器materials 材料materials having different coefficients of expansion 膨胀系数不同的材料of attachment around openings 开孔周围的连接plate, fitting up joints 平板,连接处的装配plate edges, matching 板边,匹配preparation of plates 钣材的制备procedure qualification 工艺评定processes 工艺test requirement 试验要求Weld metal, composition 焊缝金属,成分Welds acceptability, when radiographed 焊缝合格,用射线照相时when sectioned 解剖时fillet 填角identification of 识别plug 塞焊reinforcement, butt welds 补强,对接焊repairs of defects in 焊缝中缺陷的修补sharp angles, avoid at weld edges 尖角,避免在焊缝边上structural 结构tack 定位焊types, description 类型,描述ultrasonic examination of 超声检验Working pressure allowable, braced and stayed surfaces 许用工作压力,有拉撑和支撑表面第19 页共19 页by proof test 验证性试验definition of 定义。
铸造名词术语(中英对照,GB5611-85)

3.5.23. 旧砂 floor sand
3.5.24. 枯砂(焦砂) burnt sand
3.5.25. 废砂 waste sand
3.5.26. 热砂 hot sand
3.5.27. 松砂 aeration , sand-cutting
2.9. 凝固温度范围 solidification range
2.10. 定向凝固(顺序凝固) directional
solidification
2.11. 液态收缩(液体收缩) liquid
contraction
2.12. 凝固收缩 solidification contraction
4.1.16. 铁素体可锻铸铁 ferritic malleable cast iron
4.1.17. 白心可锻铸铁 white heart malleable cast iron
4.1.18. 团絮石墨 tempered graphite
4.1.19. 冷硬铸铁(激冷铸铁) chilled iron
2.3. 吸气 gas absorption
2.4. 过冷 undercooling, supercooling
2.5. 过冷度 degree of undercooling
2.6. 成核 nucleation
2.7. 自发成核(均质成核) homogeneous
nucleation
2.8. 非自发成核(非均质成核)heterogeneous nucleation
2.13. 固态收缩(固体收缩) solid contraction
2.14. 凝固时间 solidification time
稀有金属学报英文版关于残余应力的文章

稀有金属学报英文版关于残余应力的文章Title: Residual Stress Analysis in Advanced Materials: A ReviewResidual stress, a prevalent phenomenon in advanced materials, plays a crucial role in determining their mechanical properties and performance characteristics. Understanding and controlling residual stress have become imperative for optimizing the reliability and functionality of various engineering components. In this review, we delve into recent advancements in residual stress analysis methodologies, focusing on their applications in the field of rare metals.X-ray diffraction (XRD) techniques have emerged as powerful tools for quantifying residual stresses in metallic materials. By analyzing the diffraction patterns produced by X-rays interacting with the crystalline lattice, researcherscan accurately determine the magnitude and distribution of residual stresses within a material. Moreover, synchrotron X-ray sources have enabled high-resolution mapping of residual stresses in intricate microstructures, providing valuable insights for material design and process optimization.Neutron diffraction represents another indispensable technique for residual stress characterization, particularly in materials with large penetration depths or complex geometries. Neutrons, being highly penetrating and non-destructive, can interrogate bulk materials without significant sample preparation. Recent developments in neutron scattering instrumentation have facilitated in-situ stress monitoring during material processing, offering unprecedented opportunities for real-time quality control and defect detection.Furthermore, finite element analysis (FEA) has become indispensable for simulating and predicting residual stressdistributions in advanced materials. By discretizing the material domain into finite elements and solving the equilibrium equations iteratively, FEA can accurately model the thermo-mechanical processes involved in residual stress generation. Incorporating advanced material models and boundary conditions, researchers can simulate various manufacturing scenarios to optimize processing parameters and minimize residual stress-induced defects.In addition to experimental and numerical techniques, analytical models provide valuable insights into the underlying mechanisms governing residual stress formation. The superposition principle, plasticity theory, and phase transformation kinetics are commonly employed to formulate closed-form expressions for residual stress prediction in specific material systems. Although analytical models may lack the predictive accuracy of experimental and numerical methods, they offer valuable qualitative understanding and insights for guiding subsequent investigations.Moreover, advancements in material synthesis and processing techniques have enabled tailored manipulation of residual stresses in rare metal alloys. Additivemanufacturing processes, such as selective laser melting (SLM) and electron beam melting (EBM), offer unprecedented control over thermal gradients and cooling rates, thereby allowing precise adjustment of residual stress distributions within printed components. Furthermore, post-processing treatments, including shot peening and annealing, can alleviate residual stresses and enhance the mechanical properties of rare metal alloys.In conclusion, residual stress analysis remains acritical aspect of material characterization and process optimization in the field of rare metals. By leveraging advanced experimental techniques, numerical simulations, and analytical models, researchers can gain deeper insights into the origins and implications of residual stresses in advanced materials. Moreover, synergistic integration of materialsynthesis and processing techniques enables precise manipulation of residual stress distributions, thereby unlocking new opportunities for enhancing the performance and reliability of rare metal components in diverse engineering applications.。
燃气专业外语翻译

1.1工程热力学基础Thermodynamics is a science in which the storage, transformation, and transfer of energy are studied. Energy is stored as internal energy (associated with temperature), kinetic energy (due to motion), potential energy (due to elevation) and chemical energy (due to chemical composition); it is transformed from one of these forms to another; and it is transferred across a boundary as either heat or work.热力学是一门研究能量储存、转换及传递的科学。
能量以内能(与温度有关)、动能(由物体运动引起)、势能(由高度引起)和化学能(与化学组成相关)的形式储存。
不同形式的能量可以相互转化,而且能量在边界上可以以热和功的形式进行传递。
In thermodynamics, we will derive equations that relate the transformations and transfers of energy to properties such as temperature, pressure, and density. Substances and their properties, thus, become very important in thermodynamics. Many of our equations will be based on experimental observations that have been organized into mathematical statements or laws; the first and second laws of thermodynamics are the most widely used.在热力学中,我们将推导有关能量转化和传递与物性参数,如温度、压强及密度等关系间的方程。
焊接残余应力与变形(II)_李晓峰-96

Prediction versus Measurements – TRAINSS Mock Up Weld
预测与测量-TRAINSS模拟焊接
Inter-pass temp. = 25C ( assumed)
层间 温度=25C(假设)
Inter-pass temp. = 200C
固态焊接工艺的残余应力 Resistance welding
电阻焊
Friction/inertia welding
摩擦/惯性焊接
Friction stir welding
搅拌摩擦焊
Residual Stresses from Friction/Inertia Welding Processes
3D残余应力特征和OD的发展
3D Residual Stress Characteristics in a Multi-Pass Girth Weld
多道环焊中3D残余应力的特征
Example: SS Pipe Girth Weld
举例:SS管环形焊
Understanding the Need in a Specific Application is Important
举例:铝锂合金板(2195)上的VPPA对接焊缝
Full Field Residual Stress Distributions are Required for Appropriate Interpretation
全域残余应力分布的适当解释
3D Residual Stress Features and Development -OD
Heat and Material Flow
Residual Stresses from Friction Stir Welding –– SS 304 (03)
锅炉小词典

锅炉小词典水循环试验circulation test:查明锅炉在启动、停炉和各种运行工况下水循环可靠性的试验。
负荷试验load test:为确定锅炉的经济负荷、最低负荷以及相应于机组各种出力的负荷所进行的试验。
风压试验pressure decay test:按规定的压力和保持时间对炉瞠或烟道用空气进行的压力试验,以检查其严密性是否符合要求。
漏风试验air leakage test:检查锅炉和烟风道漏风的试验验证性水压试验hydrostatic deformati:对没有相应规定并且不能以合理的准确度计算其强度的受压元件等用水进行的压力试验,以求得最高允许工作压力。
水压试验hydrostatic test:按规定的压力和保持时间对锅炉受压元件、受压部件或整台锅炉机组用水进行的压力试验,以检查其有无泄漏和残余变形。
锅炉效率试验;锅炉热效率试验boiler efficiency test:确定锅炉效率的试验,包括正平衡法和反平衡法。
排放置;排汽能力discharge capacity:按有关规程规定通过试验所确定的安全阀或安全泄压阀排汽量。
回座压差blowdown::安全阀起座压力与回座压力之差,一般以整定压力的百分数表示。
回座压力reseating pressure::安全阀阀瓣重新与阀座接触、升程为零时的进口侧静压。
起座压力popping pressure:安全阀起跳,蒸汽开始强烈泄放时的进口侧静压。
前泄压力start-to-discharge pressure:安全阀动作前已有微量蒸汽流出时的进口侧静压。
整定压力set pressure:按有关规程规定所整定的安全阀起座压力。
漏风系数air leakage factor:烟气通道进出口处烟气中过量空气系数之差或空气通道进出口处空气量差值与理沦空气量之比。
燃烧器调节比turndown ratio:单只燃烧器的最大燃料量与最小燃料量之比。
锅炉负荷调节范围load range of boiler:锅炉在规定工况下安全运行所允许的最小负荷与最大负荷的范围。
表面质量对疲劳强度的影响英语

• Stress concentration occurs easily at the troughs of surface roughness ,especially the groove and fillet corner ,which can lead to fatigue crack and accelerate the fatigue failure .
These data are measured by the blind hole drilling method. It shows residual stress increases with the depth .
We can see that an increase of feed rate causes an increase of compressive stresses in both directions. On the other hand, an increase of the nose radius of the insert causes a decrease of the compressive residual stresses.
Residual stress
• After the turning operation, the residual stresses were measured using the blind hole drilling method. The machining of round samples was carried out with different feed rates and nose radius .
机械制造技术英文PPT25

(3) Arrange the process of eliminating internal stress.
One is to the blank or in the large workpiece rough processing, let the workpiece stay under natural conditions for a period of time to process, using the natural change of temperature to make it many times hot expansion and cold contraction, natural aging. The second is through artificial aging heat treatment process, such as casting, forging, welding parts for annealing or tempering; Parts are tempered after quenching; For high precision parts, such as bed, screw, or precision spindle box, making low temperature tempering after rough machining, even for screw cold processing, precision spindle after finishing, etc. Third, some casting, forging, welding parts in the form of vibration will be added to the mechanical energy on the workpiece, vibration aging treatment, causing the internal lattice creep of the workpiece, so that the metal internal structure stability, the elimination of internal stress.
残余应力对搅拌摩擦焊接头裂纹扩展速率的影响
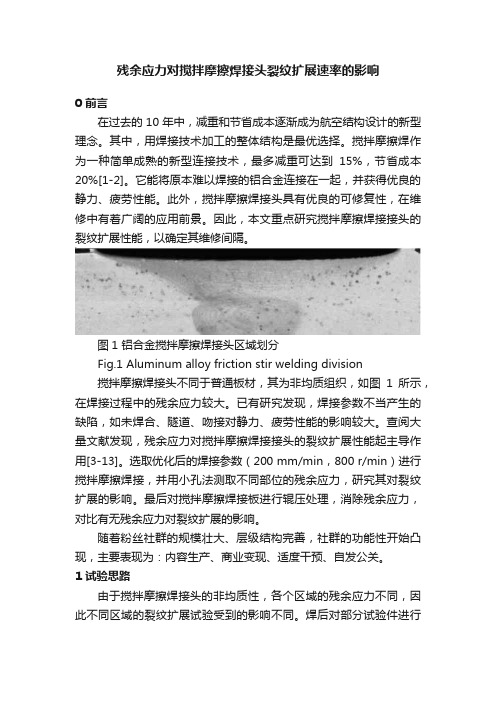
残余应力对搅拌摩擦焊接头裂纹扩展速率的影响0 前言在过去的10年中,减重和节省成本逐渐成为航空结构设计的新型理念。
其中,用焊接技术加工的整体结构是最优选择。
搅拌摩擦焊作为一种简单成熟的新型连接技术,最多减重可达到15%,节省成本20%[1-2]。
它能将原本难以焊接的铝合金连接在一起,并获得优良的静力、疲劳性能。
此外,搅拌摩擦焊接头具有优良的可修复性,在维修中有着广阔的应用前景。
因此,本文重点研究搅拌摩擦焊接接头的裂纹扩展性能,以确定其维修间隔。
图1 铝合金搅拌摩擦焊接头区域划分Fig.1 Aluminum alloy friction stir welding division搅拌摩擦焊接头不同于普通板材,其为非均质组织,如图1所示,在焊接过程中的残余应力较大。
已有研究发现,焊接参数不当产生的缺陷,如未焊合、隧道、吻接对静力、疲劳性能的影响较大。
查阅大量文献发现,残余应力对搅拌摩擦焊接接头的裂纹扩展性能起主导作用[3-13]。
选取优化后的焊接参数(200 mm/min,800 r/min)进行搅拌摩擦焊接,并用小孔法测取不同部位的残余应力,研究其对裂纹扩展的影响。
最后对搅拌摩擦焊接板进行辊压处理,消除残余应力,对比有无残余应力对裂纹扩展的影响。
随着粉丝社群的规模壮大、层级结构完善,社群的功能性开始凸现,主要表现为:内容生产、商业变现、适度干预、自发公关。
1 试验思路由于搅拌摩擦焊接头的非均质性,各个区域的残余应力不同,因此不同区域的裂纹扩展试验受到的影响不同。
焊后对部分试验件进行辊压处理消除残余应力,对比有无残余应力对裂纹扩展速率的影响。
在静力、疲劳试验中,试验断口容易出现在前进侧和后退侧热影响区处,因此在平行于焊缝的裂纹扩展试验中,分别选取焊核区中心(见图2)、前进侧热影响区边缘(见图3)、后退侧热影响区(见图4)边缘预制裂纹,进行裂纹扩展试验。
选用MT型试验件,如图5所示。
试验前用小孔法测量搅拌摩擦焊接头残余应力,并在试验完全结束后分析残余应力对裂纹扩展速率的影响。
practical residual stress measurement methods

practical residual stress measurementmethodsResidual stress is defined as the stress that remains in a material even when no external force is applied to it. It can have a significant impact on the mechanical properties of the material, and as such, it is important to accurately measure residual stress. Fortunately, there are a variety of practical residual stress measurement methods available to engineers and materials scientists.One commonly used method is X-ray diffraction (XRD). XRD measures the changes in the diffraction pattern of X-rays when they interact with the material being tested. These changes provide information about the crystallographic orientation and lattice spacing of the material, which inturn can be used to calculate residual stress.Another common method is the hole-drilling technique. This involves drilling a small hole into the material, and then measuring the change in strain around the hole. From this, the residual stress can be calculated. This method can be used on a variety of materials, including metals, composites, and ceramics.Ultrasonic testing is another practical method for measuring residual stress. Ultrasonic waves are sent through the material, and the time it takes for them to reflect back is measured. The speed of the waves is affected by the presence of residual stress, and this can be used tocalculate the stress.Other methods for measuring residual stress include neutron diffraction, strain gauges, and hole-drilling with strain gauges. The choice of method depends on factors such as the material being tested, the required accuracy, and the availability of equipment.In conclusion, there are a variety of practical methods for measuring residual stress in materials. These methods are important for ensuring the mechanical properties of the material are known, and for predicting the behavior of the material in specific applications. The choice of method will depend on a variety of factors, but engineers and materials scientists have a range of options at their disposal.。
钢管氩弧焊焊缝裂纹

钢管氩弧焊焊缝裂纹英文回答:I have encountered a problem with cracks in the weld seam of steel pipe during argon arc welding. This is a common issue in welding, and it can be caused by various factors such as improper welding techniques, poor joint preparation, and high levels of residual stress.One possible reason for the cracks is the use of excessive heat during welding. When the heat input is too high, it can lead to rapid cooling and contraction of the metal, resulting in cracks. To avoid this, it is important to control the heat input by adjusting the welding parameters such as the welding current and travel speed.Another possible cause of the cracks is the presence of impurities or contaminants in the weld area. These impurities can weaken the weld and make it more susceptible to cracking. It is crucial to properly clean and preparethe joint before welding to remove any dirt, grease, or oxide layers that may be present.Additionally, the use of improper filler material can also contribute to the formation of cracks. The filler material should have similar properties to the base metal to ensure proper fusion and minimize the risk of cracks. Using a filler material with a high hydrogen content can increase the likelihood of cracking, so it is important to select the appropriate filler material for the specific application.Furthermore, the design and fit-up of the joint can also play a role in crack formation. If the joint is not properly aligned or if there are gaps between the pieces being welded, it can create stress concentrations that can lead to cracking. It is essential to ensure proper fit-up and alignment of the joint to minimize the risk of cracks.To address the issue of cracks in the weld seam, I would first assess and adjust the welding parameters to control the heat input. I would also thoroughly clean andprepare the joint to remove any impurities. Additionally, I would carefully select the appropriate filler material and ensure proper fit-up and alignment of the joint.中文回答:我在钢管氩弧焊过程中遇到了焊缝裂纹的问题。
制冷剂气相检测不合格

制冷剂气相检测不合格英文回答:As a professional in the field of refrigeration, I have encountered situations where the gas phase of refrigerants did not meet the required standards. This can be a serious issue as it affects the efficiency and safety of the refrigeration system.When the gas phase of a refrigerant is found to be non-compliant, it means that the composition or concentration of the refrigerant is not within the acceptable range. This can be due to various reasons such as contamination, improper handling, or even a manufacturing defect.For example, let's say I am working on a refrigeration system in a restaurant. The system is using a commonly used refrigerant known as R-134a. During routine maintenance, I decide to check the gas phase of the refrigerant using a gas analyzer. To my surprise, the readings indicate thatthe refrigerant is not within the specified composition range.In such a situation, it is important to take immediate action to rectify the issue. This may involve purging the system of the non-compliant refrigerant and replacing it with a fresh supply that meets the required standards. It is also necessary to identify the root cause of the problem and take steps to prevent it from happening again in the future.Furthermore, it is crucial to communicate the issue to the relevant stakeholders, such as the restaurant owner or manager, and explain the potential consequences of using non-compliant refrigerants. This can help them understand the importance of maintaining the refrigeration system and using only approved refrigerants.中文回答:作为制冷领域的专业人士,我曾遇到过制冷剂气相不合格的情况。
- 1、下载文档前请自行甄别文档内容的完整性,平台不提供额外的编辑、内容补充、找答案等附加服务。
- 2、"仅部分预览"的文档,不可在线预览部分如存在完整性等问题,可反馈申请退款(可完整预览的文档不适用该条件!)。
- 3、如文档侵犯您的权益,请联系客服反馈,我们会尽快为您处理(人工客服工作时间:9:00-18:30)。
ORIGINAL RESEARCHResidual stresses due to gas arc welding of aluminum alloy joints by numerical simulationsM.Ahmadzadeh&B.Farshi&H.R.Salimi&A.Hoseini FardReceived:21April2011/Accepted:27October2011#Springer-Verlag France2011Abstract This study deals with the numerical simulation of the gas arc welding process of Aluminum tee joints using finite element analysis and evaluation of the effect of welding parameters on residual stress build up.The3D simulations are performed using ABAQUS code for thermo-mechanical analyses with moving heat source, material deposition,solid-liquid phase transition,tempera-ture dependent material properties,metal elasticity and plasticity,and transient heat transfer.Quasi Newton method is used for the analysis routine and thermo-mechanical coupling is assumed;i.e.the thermal analysis is completed before performing a separate mechanical analysis based on the thermal history.The residual stress build up and temperature history state in a three-dimensional analysis of the tee joint is then compared to experimental results. Hole drilling method is used for measuring the residual stress,while temperature history is measured by thermo-couples.After carrying out numerical simulations,the effects of voltage/current,welding speed,material thickness and size of electrode on residual stress build-up and resulting distortions are evaluated.Keywords Finite element.Aluminum alloys.Residual stresses.Gas arc welding.Welding parameters IntroductionWelding is commonly used for permanently joining metals in the manufacturing industries.Highly non-uniform field temperature,phase transfer and plastic deformation pro-duced during welding process give rise to residual stresses and distortions in the final product.Tensile residual stresses adversely influence fatigue,creep strength,stress corrosion cracking,brittle fracture and reduction of ultimate strength. Compressive residual stresses also adversely affect the behavior of metal products such as yield and buckling strength;Therefore prediction and control of residual stresses is important in the production of metal products.The prediction of welding residual stresses has been studied by many researchers.Finite element analysis(FEA) has been the main tool used by several authors[1–4,12–26] to perform welding simulations in order to predict welding residual stresses in different types of joints and materials. Main difficulty in prediction is the complex variations of temperature,thermal contraction,expansion and changes of material properties with time and space in the model. Furthermore,modeling of the welding process must be accounted for the specialized effects of the practical aspects of welding such as movement of welding arc,material deposition,and metallurgical transformations.Oddy et al.[6]stated that prediction of the temperature field requires a nonlinear transient3D analysis.Studies by Chao and Qi[5]concluded that3D modeling of the welding process is essential for practical problems to provide accurate residual stress and distortion predictions that cannot be obtained from2D simulations.McDill et al.[10]also stated that some2D predictions of residual stresses for materials exhibiting phase transformations show large differences with experimental measurements,leading to their choice of a3D finite element model.Due tothe M.Ahmadzadeh(*):B.FarshiDepartment of Mechanical Engineering,Iran University of Science&Technology,Narmak16846,Tehran,Irane-mail:Mohsen.ahmadzade@H.R.Salimi:A.Hoseini FardDepartment of Marine Structures,Iran Air Naval Research Center,Chamran7194915685,Shiraz,IranInt J Mater FormDOI10.1007/s12289-011-1081-4above prior conclusions,a 3D simulation model is also adopted in this research.Most of the researchers have reported the coupling of thermal and structural model in their analysis procedures [2,4–9,13–16,18–21],using the three dimensional double ellipsoid proposed by Goldak et al.[12]to model the heat source;Therefore in this study both the coupling method and double ellipsoid heat source are also employed.Karlsson and Josefson [4]utilize the so-called element “birth ”facility of ADINAT software to keep weld elements ahead of the welding arc inactive in the thermal analysis,until the front of the heat source reaches those elements.In the mechanical analysis reported in their research,the elements are kept inactive until the front of the source has passed the element by about an additional element length.In this study however,the elements are kept inactive by means of a subroutine,until the front of the source has passed the inactive element by three element length.Most of the researchers [4,7,11,15,23]have reported that the effect of radiation is typically much smaller than the effect of convection in the heat transfer,which is also followed herein.The effects of some welding parameters on residual stresses have been studied by Ribycki et al.[27];who studied the effect of wall thickness and pipe diameter using axisymmetric FEA model with lateral symmetry for multi-pass welding of stainless steel pipes.Dong et al.[3]used a shell model with lateral symmetry to inspect the effect of pipe wall thicknessand welding speed for pipes of various thicknesses.Fricke et al.[28]used a full 3D model for pipe welding and presented residual stresses on two different pipe diameters.In this study the effects of voltage/current,speed of welding,thickness of welding pieces,and electrode sizes on residual stresses are also evaluated by finite element models.As Tee joint welding is widely used in different application fields such as buildings,bridges,aerospace structures and etc.it is also examined here.Experimental procedureThe base metal used in the experiments here is aluminum alloy 2519-T87and the filler metal is aluminum alloy 2319.Table 1contains the chemical compositions of both 2519and 2319aluminum alloys [29].The designed process experiment is the welding of a tee joint with just one fillet weld on one side of the joint.The welding parameters are listed as below:Current:300–400A,voltage:33–37V and electrode speed:6mm/s.There was no pre or post-weld heat treatment and the welding process was performed in temperature of 27°C.By heating the plates to 250°C temperature and decreasing to ambient temperature very slowly Stress relief procedure was done on platesTable 1Chemical composition of aluminum alloys 2519-T87and 2319(mass%)[29]ElementZn Fe Si Mg Zr Ag V Ti Mn Cu Base metal (Aluminum alloy 2519-T87)0.10.30.250.05–0.40.1–0.25–0.05–0.150.02–0.10.01–0.05 5.3–6.4Filler metal (aluminum alloy 2319)0.10.030.20.02–0.40.1–0.25–0.05–0.150.1–0.20.2–0.45.6–6.8Fig.1Tee joint configurationInt J Mater Formbefore welding.The dimensions and configuration of the tee joint are shown in Fig.1.After welding,hole drilling method is to be adopted for measurement of the welding residual stresses,while the temperature history is to be monitored by thermocouples placed on the thin plate side that usually has the critical stresses.In these experiments,the strain gauges with designa-tion of EA-XX-031RE-120and .031(IN)length are used.Six strain gauges were used to measure the residual stresses and one thermocouple was used to monitor the temperature history,whose locations on the welded piece are shown in Fig.2.The RS-200Milling Guide was used for accurate positioning of the drilling bit for a hole through the center of the strain gauge rosette.The hole diameters were in range of 0.03to 0.04in,and the holes ’depth was 0.03in.There was limitation in experiment method to set up the thermocouple near the melting zone due to high temperature [30].Strain gauges are not mounted near the welding area due to restriction caused by tee joint shape for drilling holes near welding joint with RS-200Milling Guide.The specified mechanical boundary conditions are those which are just sufficient to prevent rigid body motion of the model.Those are explained in boundary condition section in details.Finite element modeling Model geometryDue to the wide spread use of tee joints in metal industries it is adopted in this resrearch as the physical model.Overall dimensions of the 3D model of the experimental piece are shown in Fig.1.It ’s corrected that double side of welding modeled but elements of one side were just active during simulation.As stated earlier,a 3D modeling of the welding process is essential for practical problems as it can provide accurate residual stress and distortion results which cannot be obtained from 2D simulations.In 2D models transverse stresses and 3D effect of electrode movement are all neglected.The only problem of a 3D model analysis is its time consuming due to its domain size;which in this case it took about 19h on a quad (four core)CPU with 4Gigabyte RAM Pc to be run.After evaluating the accuracy of finite element model and comparing it with experimental results,three models of connecting plates with different thicknesses were designed to study the effect of thickness variation.The choices of plate thicknesses were 12,10,8,mm.Fig.2Strain gauge and thermocouple positions on platepieceFig.3Phase diagram of aluminum alloy 2519-T87[29]Fig.4Yield stress versus temperature for aluminum alloy 2519-T87and 2319[29]Int J Mater FormAnother parameter that influences residual stress build up is electrode size.Effect of this parameter relates to theeffect of molten pool size that electrode creates on the piece during welding.To study the effect of this parameter,10 separate models with different molten pool sizes were designed whose molten pools sizes were6.58,6.20,6.00, 5.73,5.49,4.77,4.58,4.39,3.82and3.05mm.Material propertiesThe phase diagram for the base metal i.e.aluminum alloy 2519-T87is shown in Fig.3.[29]As temperature increases, material phase changes fromα+θtoαin520°C.The next phase isα+L at which point the material is melting.As material’s phase changes fromαtoα+L very fast,first phase transfer is neglected with a good approximation in this study,but the second phase transition is modeled with the help of material library of ABAQUS elements.By including the user specified material annealing or melting temperature, when the material temperature exceeds it,ABAQUS would assume that the material at that point loses its hardening memory.The effect of prior work hardening is removed by setting the equivalent plastic strain to zero.For kinematic and combined hardening models the back-stress tensor is also reset to zero.If the temperature of the material falls below the annealing temperature at a subsequent point in time,the material is allowed to work harden again.Therefore depending on the temperature history,a material may lose and accumulate memory several times which would simply correspond to repeated melting and re-solidification.The material model has been used for this research is a plasticity model utilizing von Mises criterion with isotropic strain hardening.Due to the thermal loading and large strains which develop,a strain hardening model is more appropriate than an elastic-perfectly plastic model.Yield stress of aluminum2519-T87and2319are plotted versus temperature in Fig.4.The hardening curves used for Aluminum alloy2519-T87and2319are depicted in Figs.5 and6respectively.The mass density of both materials is taken as2823Kg/m3.The melting temperature range for Al 2519-T87is555°C−668°C,and for Al2319is543–643°C. Fig.6Strain hardening of aluminum alloy2319[29]Fig.7Young’s modulus and coefficient of thermal expansion ofaluminum alloys2519-T87and2319as a function of temperature[29]Fig.8Specific heat and thermal conductivity of aluminum alloys2519-T87and2319as a function of temperature[29]Fig.5Strain hardening of aluminum alloy2519-T87[29]Int J Mater FormDue to lack of all required data for Al 2519and Al 2319and their similar chemical compositions,their data were used alternatively.Coefficients of thermal expansion and young ’s modulus are shown in Fig.7,while thermal conductivity and specific heat as a function of temperature are shown in Fig.8.The thermal effect caused by solidification of the welding pool was modeled by considering the latent heat of fusion,which was assumed to be 374J/g [29].Mesh and analysis methodElement C3D8T from ABAQUS is used which is an 8node brick element that has the ability of being used in coupled thermo-structural analysis.Due to complicated material properties and nonlinear geometry and etc.,welding process simulation is a tedious task which is also very sensitive to number of element used;so it is imperative that a minimum number of elements be chosen that are capable of producing acceptable results compared to experiments data.By increasing element number more than 18000elements,variation of maximum residual stress is negligible.Conver-gence trend of the results (maximum residual stress)obtained versus the choice of different number of elements used,is shown in Fig.9and their corresponding meshes are shown in Fig.10.A total number of 50solution steps are enacted in ABAQUS to model element birth and heat source move-ment.In every step 3elements are added to the model with initial temperature of 550°C based of melting temperature and heat source move 3elements forward as shown in Fig.11.Size of elements in welding direction is 1mm so in each step heat source moves 3mm forward.The inactive elements have no mechanical properties but possessing thermal properties same as the surrounding air.Similarly 50steps are included for the welding process with the final step done for cooling the model to the ambient temperature.To evaluate the effect of welding speed,three different speeds of 5,6and 7mm/s are assumed for the various employed models.Different speeds are simply included by changing the time increment of each step.Finally,quasi Newton method is used for the thermo-mechanical coupling analysis.When the stress analysis is dependent on the temperature distribution and the temper-ature distribution depends on the stress solution,coupled thermo-mechanical analysis is used.In ABAQUS the temperatures are integrated using a backward-difference scheme,and the nonlinear coupled system is solved using quasi-Newton ’s method.ABAQUS offers an exact as well as an approximate implementation of Newton ’s method for coupled temperature-displacement analysis.Boundary conditionsA welding heat source is usually arc plasma radiating intense heat outwardly with decreasing temperature [25,26],which the mathematical model of it can be represented by a Gaussiandistribution.Fig.10Tee joint finite elementmeshFig.9Convergence of maximum residual stress versus the number of elements used in the meshInt J Mater FormFor modeling of the heat source,many authors[7,12, 20],utilized the3D double ellipsoid proposed by Goldak et al.[25].The double ellipsoid geometry is used so that the size and shape of the heat source can be easily changed to model both the shallow penetration arc welding processes. The power or heat flux distribution is Gaussian along the longitudinal axis.The front half of the source is the quadrant of one ellipsoidal source while the rear half is the quadrant of another ellipsoidal source.Four character-istic lengths must be determined which physically corre-spond to the radial dimensions of the molten zone.If the cross-section of the molten zone is known from experiment, this information can be used to set the heat source dimensions.If precise data does not exist,Goldak et al.[25]suggest that is reasonable to take the distance in front of the source equal to one half the weld widths and the distance behind the source equal to two times the weld width.A double ellipsoidal heat source consists of two different concentric single ellipsoids suitable as a more advanced heat source as compared to the single ellipsoidal due to its greater flexibility in modeling shapes of moving heat sources realistically.Referring to Fig.12,the heat density at an arbitrary point(x,y,z)within each one-half ellipsoid is described by the following equations.q f¼6ffiffiffi3pQf fpffiffiffippc f baeÀ3z2a2þy2b2þx2c f2h ið1Þq r¼6ffiffiffi3pQf rpffiffiffippc b baeÀ3z2a2þy2b2þx2c b2h ið2ÞQ¼h IVð3Þf fþf r¼2ð4ÞIn the above relations,x is the welding direction,a,b,c f,c b are the ellipsoidal heat source parameters,ηis the efficiency,V and I are the arc voltage/current,and f f,f r are the proportional coefficients at the front and the back of the heat source.Since the heat source moves at a constant speed along a straight line,and the heat input Q from the source is constant,experience shows that such conditions lead to a fused zone of constant width.Moreover,zones of temperatures below the melting point also remain at constant width[31].The heat source parameters that used in this study are given in Table2.To study the effects of voltage/current on residual stresses three heat inputs are created in different models such that the heat inputs be equal to11.5,8.625,5.25KW. Assuming a transient solution for the convection,heat transfer in the surrounding temperature of20°C gives the coefficient of convection as a function of temperature for Aluminum2519-T87and2319as shown in Fig.13.TheFig.13Convection coefficient of aluminum alloys2519-T87and 2319as a function of temperature[29]Table2Strain hardening of aluminum alloys2519-T87and2319[29] a,mm b,mm C f,mm C b,mm f f f r n 30302482.60.45 1.5585% Fig.12Double ellipsoidal heat source modelparametersFig.11Elements birth in the modelInt J Mater Formradiation effects are neglected since they are typically much smaller than the convection effects.In the first 50steps of welding process boundary conditions 1and 2are assumed,and in the final step (cooling)only boundary condition 2is assumed while condition 1is relaxed;these boundary condition are shown in Fig.14.Results and discussionThe simulation was run for a time period of 68700s,i.e.,more than 19h,allowing for the complete thermo-structural cycle,including heating and subsequent air cooling to take place.The temperature profiles obtained at 25s is shown in Fig.15.Figure 16shows temperature history measured by the thermocouple and also evaluated by finite element analysis.The welding condition for Fig.16is:Welding speed:6mm/s,heat input:11.5KW,Thickness:10mm,Molten pool size:6mm.It shows that the thermal analysis is sufficiently accurate and finite element model gives good results for temperature distribution,and that neglected radiation heat transfer seems to be a reasonable assumption.The difference between experiment and simulation result is caused by rapid evaluations of temperatures that cannot have been regis-tered by the thermocouple due to its thermal inertia and thermal resistance phenomena.In accordance to the temperature diagrams,temperature in the parts increases to 550°C in the welding direction.Figure 17shows the temperature history of some points from beginning to middle of welding direction (molten pool center).Except two first points other points seem to have the same temperature history which suggests the heat transfer rate can be assumed as a steady state process in a short time after the welding is started.Figure 18shows V on Mises residual stress contours after welding is completed.It shows that the maximum stress occurs at the center of the molten pool zone since thermal strains in this zone have increased intensively withsolidifica-Fig.16Temperature variation by time for finite element andexperimentFig.15Temperature contours of the model at t=25sFig.14Boundary condition for different steps of solution procedureInt J Mater Formtion.Stresses at physical boundary zones are not significant since the boundary conditions are selected to allow free movement there.The dominant tensile stresses occur in the Z direction,e.g.S33component which emphasizes that the probability of crack growth normal to Z direction is more than other directions(S33is principal stress in the Z direction). Figure19shows a comparison of experimental and finite element results.It also shows that the finite element results exhibit good agreement with experimental ones on positions of strain gauges.The differences between these results are possibly due to ignoring phase change fromα+βtoαat the start,and/or the measurement and/or truncation errors in numerical analysis at the end.The FEA results show that the longitudinal high tensile residual stresses occur in the region near the weld line and drop in value when moving away up to the middle of the plate,but near the boundaries the residual stresses increase again.The analysis results also show that the transverse and normal stresses are small in magnitude(nearing zero)in the region close to the centre line,and tend to increase towards the outer edges of the plate,in agreement with experimental results(Fig.19).Residual stresses are produced by an uneven distribution of nonelastic strains including Plastic and thermal strains. Large local plastic strains in the solidified weld metal and the heat affected zone originate from the very non-uniform temperature field around the weld pool[4].During the welding thermal cycle,complex transient thermal stresses are produced in the weldment and the surrounding joint. Beneath the welding arc,stresses are close to zero because molten metal does not support shear loading.As the expansion of metal surrounding the weld pool is restrained by the base metal,stresses become compressive adjacent to the welding arc and moving away from the welding arc. These compressive stresses are as high as the yield strength of the base metal at corresponding temperatures.The temperatures of the metal surrounding the weld pool are very high and therefore cause the yield strength of the material to become quite low[32].Stresses occurring in regions farther away from the welding arc are tensile and balance with these compressive stresses near the weld pool.As the weld-metal and base metal regions cool and shrink the regions in and adjacent to the weld,experience tensile stresses.As the distance from the weld increases,the stresses become compressive.High tensile residual stresses in areas near the weld can cause premature failures of welded structures under certain pressive residual stresses in the base plate can reduce the buckling strength of a structural member subjected to compressive loading[32].To study the relative effects of input parameters on the residual stresses,a total of84finite element models with combinations of different input parameters are tested as depicted schematically in Fig.20.Three weldingspeeds, Fig.18Residual stress contours afterweldingFig.17Temperature history for some points in welding directionInt J Mater Formten electrode sizes,three voltage/current (heat input)values,and three plate thicknesses are chosen in combination with one another.Figure 21(a),(b),and (c)show maximum residual stresses as a function of heat input (voltage/current)for different electrode sizes,plate thicknesses and welding speeds of:7,6,and 5(mm/s)respectively.The residual stresses due to welding of an aluminum tee joint of 2519alloy with given different welding parameters can be obtained from charts 21-(a),21-(b),and 21-(c).Further-more,for tee joint welding of plates of different thicknesses the best combination of welding parameters (electrode size,welding current/voltage and welding speed)for minimum residual stresses also can be selected from those charts.Effect of welding speedCase C-1in Table 3is designed to study the effect of welding speed on residual stresses.Results of longitudinal and transverse residual stresses for case C-1are plotted along gage line 1,as a function of the distance from the center of weld bead (see Fig.2),and are shown in Fig.22(a)and (b)respectively.Higher welding speeds have beneficial effect in reducing residual stresses.Low welding speeds result inhigh heat input per unit length of the weld,producing relatively larger weld puddle and HAZ (heat affected zone)causing an increase in residual stresses in the plates around the welding line;thus closer to the weld centerline,lower welding speeds cause higher tensile stresses.Further away from the HAZ the stress profile remains less affected by any changes in the welding speed.Effect of voltage/currentCase C-2in Table 3is designed to study the effect of current/voltage on residual stresses.Results of longitudinal and transverse residual stresses for case C-2are plotted along gage line 1,as a function of the distance from the center of weld bead (see Fig.2),and are shown in Fig.23(a)and (b)respectively.The change in heat input per unit length of welding is directly proportional to the change in the welding current/voltage (see Eq.3)provided the other welding parameters are kept unchanged.It is observed that welding current/voltage has opposite effect compared to welding speed.The effect of welding speed on residual stress is higher than the effect of current/voltage as shown in Figs.22(a),(b),23(a),and (b).Welding current/voltage has a direct algebraic relation to the heat input of weldment (see Eq.3);while welding speed has an exponential relation to the heat input of weldment (see Eq.1).Effect of thicknessCase-3in Table 3is designed to study the effect of thickness on residual stresses.Results of longitudinal and transverse residual stresses for case C-3are plotted along gage line 1,as a function of the distance from the center of weld bead (see Fig.2),and are shown in Fig.24(a)and (b)respectively.Strength of the plate and the heat flow function are dependent upon the thickness whereby increasing itwouldFig.20Schematic flow of input parameters for the finite elementmodelFig.19Residual stresses measured by experimental and finite element methodsInt J Mater FormFig.21Maximum residual stresses as a function of heat input for different electrode (molten pool)size and thickness:a7mm/s welding speed b6mm/s welding speed b5mm/s welding speed Int J Mater Formincrease the strength and change the heat flow,causing the thermal strains to drop off with reduction of plastic areas which consequently lead to a decrease in residual stresses.The effect of thickness on residual stresses near the welding line are little different from those located far from it,since anincrease in the thickness causes the strength of whole model to increase.The effect of thickness on the residual stress variations between points near and far from the center of welding line is due to its effect on the heat flow affected by it.The effect of thickness on residual stress change is moreTable 3Cases designed to study the effect of geometry and other welding parameters on residual stress build up Case Model Welding speed (mm/s)Heat input (kW)Molten pool size (mm)Thickness (mm)Effect of welding speed C-15,6,711.56.0012Effect of voltage/current C-26 5.25,8.625,11.5 6.0012Effect of plate thickness C-3611.5 6.008,10,12Effectofelectrode sizeC-4611.56.58,6.20,6.0012Fig.22Effect of welding speed on residual stresses in welding line:a Longitudinal residual stress b Transverse residual stressthan welding current but is less than welding speed as can be concluded from the presented figures.Effect of electrode sizesCase-4in Table 3is designed to study the effect of electrode size on residual stresses.Results of longitudinal and transverse residual stresses for case C-4are plotted along gage line 1,as a function of the distance from the center of weld bead (see Fig.2),and are shown in Fig.25(a)and (b)respectively.Decreasing the electrode size causes a decrease in the heat input to the plates and the size of the molten pool,which causes a reduction in the residual stresses.The effect of electrode size around the welding line is more than the outlying areas of the welding zone.So near the welding line an increase in the electrode size,results in an increase of molten pool size and HAZ as well as the amount of heat input,as the most significant parameters causing an increase in residual stresses.The sensitivity of residual stress to electrode size is more than other parameters as shown in the presented figures.This is because of electrode size influencing boththeFig.23Effect of welding current or voltage (heat input)on residual stresses in welding line:a Longitudinal residual stress.b Transverse residual stress。