涡轮叶片精铸模具辅助机构参数化研究
航空发动机涡轮叶片精密成形技术分析
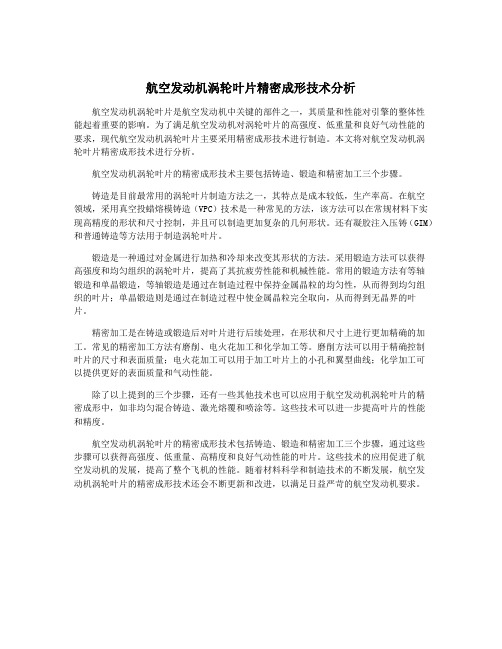
航空发动机涡轮叶片精密成形技术分析航空发动机涡轮叶片是航空发动机中关键的部件之一,其质量和性能对引擎的整体性能起着重要的影响。
为了满足航空发动机对涡轮叶片的高强度、低重量和良好气动性能的要求,现代航空发动机涡轮叶片主要采用精密成形技术进行制造。
本文将对航空发动机涡轮叶片精密成形技术进行分析。
航空发动机涡轮叶片的精密成形技术主要包括铸造、锻造和精密加工三个步骤。
铸造是目前最常用的涡轮叶片制造方法之一,其特点是成本较低,生产率高。
在航空领域,采用真空投蜡熔模铸造(VPC)技术是一种常见的方法,该方法可以在常规材料下实现高精度的形状和尺寸控制,并且可以制造更加复杂的几何形状。
还有凝胶注入压铸(GIM)和普通铸造等方法用于制造涡轮叶片。
锻造是一种通过对金属进行加热和冷却来改变其形状的方法。
采用锻造方法可以获得高强度和均匀组织的涡轮叶片,提高了其抗疲劳性能和机械性能。
常用的锻造方法有等轴锻造和单晶锻造,等轴锻造是通过在制造过程中保持金属晶粒的均匀性,从而得到均匀组织的叶片;单晶锻造则是通过在制造过程中使金属晶粒完全取向,从而得到无晶界的叶片。
精密加工是在铸造或锻造后对叶片进行后续处理,在形状和尺寸上进行更加精确的加工。
常见的精密加工方法有磨削、电火花加工和化学加工等。
磨削方法可以用于精确控制叶片的尺寸和表面质量;电火花加工可以用于加工叶片上的小孔和翼型曲线;化学加工可以提供更好的表面质量和气动性能。
除了以上提到的三个步骤,还有一些其他技术也可以应用于航空发动机涡轮叶片的精密成形中,如非均匀混合铸造、激光熔覆和喷涂等。
这些技术可以进一步提高叶片的性能和精度。
航空发动机涡轮叶片的精密成形技术包括铸造、锻造和精密加工三个步骤,通过这些步骤可以获得高强度、低重量、高精度和良好气动性能的叶片。
这些技术的应用促进了航空发动机的发展,提高了整个飞机的性能。
随着材料科学和制造技术的不断发展,航空发动机涡轮叶片的精密成形技术还会不断更新和改进,以满足日益严苛的航空发动机要求。
基于收扩叶型的涡轮叶片参数化造型方法与分析
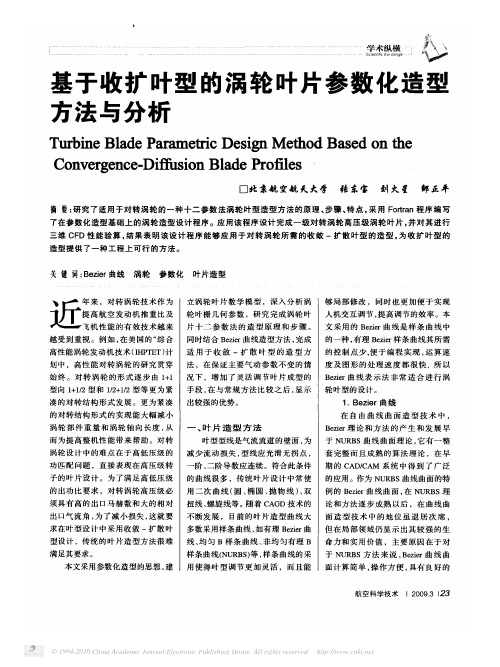
,
鑫
图
个 关 键 点 及 其 切
个
特
征 点
条 分 段
曲
叶 型 形
状
线
带有 次
个 控制 点的 三 曲线
可 以 合 理 地 控 制 型 线 以获 得 满 足 预
期 气 动性 能 的 叶 片
。
十 二 参数 法 叶 型 造型 流 程 图
曰 则 仃们 ℃人 《
还
浇
册
。 ,
© 1994-2010 China Academic Journal Electronic Publishing House. All rights reserved.
中 气 流 实 现 加 速 过程 以达 到较 高 的 马赫 数
。
为 叶栅几 何 形状 的后 续 优化 提 供 了
图
中给 出 了 调 整 叶 盆 压 力
曲线 控 制 点 之 后 叶 型 的变
与传统 叶 型 比 较 气 流 只
,
在 叶栅 通道 尾 缘 三 角 区 域 部 分 实现
化情 况
。
由 图 中 可 以 看 出 曲 线调 节
曲线
书 币
,
。
趾
由速 度 三 角 形 提 供 了 叶 栅 角 度 信 工 程 实 际 中 有 两种 典 型 的 叶 栅 一种 是 在
,
第 三 组 涉及 叶 型厚 度 分 布及 前 尾 缘 尖 角 等 一 些 信 息 的 参数 包 括 几何 出 口 角 热
前 缘楔 形 角 安装 角
以上
。
、
造型思 路 动反设计
、
。
,
轮 叶型 的 设 计
。
凑 的对 转结 构 形式 发 展
精铸涡轮叶片的误差分析技术
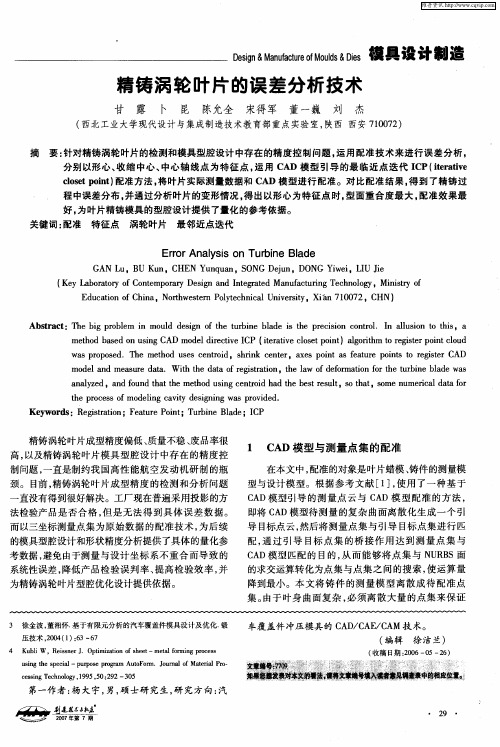
G N L , U K n H N Y n un O G D jn O G Y w i LU J A u B u ,C E u q a 。S N e ,D N ie, I i u e ( e a oa r o otm oayD s na dItg t n f tr gT c nlg , ii r o K yL b r oy f ne p r ei n er e Ma ua u n eh o y M ns f t C r g n ad ci o t y E u a o f hn , ot et nP l eh i l nvr t, in7 0 7 C N) d ct no i N r w s r o t nc ie i X h 10 2, H i C a h e yc aU sy
程 中误差分 布 , 通过 分析 叶片 的变 形情 况 。 出 以形心 为特 征 点 时 , 面 重合 度最 大 , 准效 果最 并 得 型 配 好, 为叶片精 铸模 具的 型腔设计 提供 了量 化的参 考依据 。
关键词 : 配准 特征点 涡轮 叶片 最邻 近点迭 代
Er r ay i o u bn a e r o An l s n T r ie Bld s
m to ae nuigC D m dl i c v C i rt ec st o t a o tm t rgs r on co d ehdb sdo s A o e dr t eI P( ea v l e pi ) l rh ie it l n ei t i o n gi oe t p u
法检验 产 品是 否 合 格 , 是 无 法 得 到具 体 误 差 数 据 。 但 而 以三 坐标测 量点 集为 原 始 数据 的配 准技 术 , 后 续 为
的模具型腔设计 和形状精度分析提供了具体的量化参 考数据 , 避免 由于测量与设计坐标 系不重合 而导致 的 系统性误差 , 降低产 品检验误判率、 提高检验效率 , 并 为精铸涡轮叶片型腔优化设计提供依据。
大型涡轮叶片精密铸造尺寸精度控制研究_反变形技术

Table 1 List of characteristic parameters
位置参数
构造参数
前缘圆心
P1Leabharlann 内弦长b弦倾角
β
叶背控制点
…,Ci,…
叶片控制点
…,Ki,…
图4 位置参数示意图 Fig. 4 Sketch of position parameters
图5 构造参数示意图 Fig. 5 Sketch of structure parameters
Abstract:A simple and efficient reversing methodology of adjusting wax-pattern was proposed for compensating the deformation of turbine blade in investment casting. Basing on measured data by 3D coordinate measuring machine, the characteristic parameters were designed to characterize the model. The average deviations of parameters between theory-model and measure-model of blade were calculated and then the reverse deformation model was restructured according to the average deviations. Finally, the adjusting mould of wax pattern was designed and fabricated. The research indicates that adopting reverse deformation technology based on the measure and the statistic data to solve the size-of-tolerance problem of 4th turbine blade casting is effective. Key words:large-size turbine blades; investment casting; reverse deformation; adjusting mould of
导向器叶片精铸模具外围辅助机构参数化设计

2 .山东新 华 医疗器 械股份 有限公 司 , 山东 淄博 2 5 8 ; 5 0 6 3 .西安航空 计算技 术研究所 , 陕西 西安 7 0 6 1 0 5)
摘要 :导 向器类零件分 体式精铸 的关键技 术之 一就 是 叶 片模 具 的设计 。利 用 专 家知识 , 结合
知 识推 理 , 实现 了导 向器 叶片精 铸模具 的 外围辅助机 构 的智能化 生成 , 并与 实例库 中的实例进 行 匹 配、 比较 , 通过 参数化进 行修 改 , 高 了设计 效率 , 提 缩短 了生产周期 。 关键词 : 家知识 ; 专 知识 推理 ; 例库 ; 数化 实 参
新 型航空发 动 机不 断 追求 高 推 重 比 , 导 向器 使
结构 日趋 复杂 , 向器 类零 件 的 叶 片 向薄壁 、 曲、 导 扭
多 、 量大 、 发 动机性 能影 响 大 、 计 制造 周 期 长 数 对 设 等特 点 。因此 , 向器 叶 片的设计 、 导 制造技 术水平对 提高航 空发 动机性 能 、 短研 制 周期 和 降低 制 造 费 缩 用起 着重 要的作用 。如何快 捷地 制造 出此类零 件成 为制约发 动机研制 和生产周 期 的瓶 颈之 一。
Ab ta t On f t e k y tc n lg e fg i i g d v c n e t n a t g i d s n n l f sr c : e o h e —e h oo is o ud n e ie i v sme t c si s e i i g mo d o n g ba e u i.Th sp p rr aiec e t n o x e i r u i a yb d fc si g mo d o u d n e i ld ld n t i a e e l ra i f tr x l r o yo a t l f i i g d v c ba e z o e o a i n g e u i i tl g n il ,u i g e p r n wl d e a d k o e g e s n n ; t e o p r h m t n n t n el e t y sn x e t k o e g n n wld e ra o i g h n c m a e t e wi i — i z h
涡轮叶片精铸模具CAD系统实例库的设计与研究
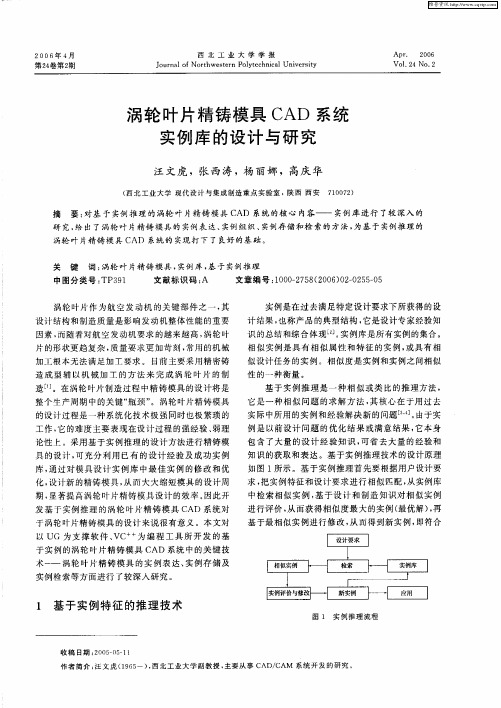
求 , 实例特 征和 设计 要求 进行 相似 匹配 , 实例库 把 从
中检 索相 似 实例 , 于 设计 和制 造 知识 对 相 似实例 基 进 行评 价 , 而获 得相 似度 最 大 的实 例 ( 优解 )再 从 最 , 基 于最 相似 实例 进行 修改 , 而得 到新实例 , 从 即符合
涡 轮叶 片作 为 航 空 发动 机 的关键 部 件 之 一 , 其 设计 结构 和制造 质量 是影 响发 动机 整体 性能 的重要
因素 , 而随 着对航 空 发动机 要求 的越 来越 高 , 涡轮 叶
实 例是在 过 去满 足特定 设计 要求 下所获得 的设
计 结果 , 也称 产品 的典 型结 构 , 是设计 专家 经验知 它 识 的总 结和综 合 体现口 。 例库 是所有 实例 的集合 。 ]实 相 似 实例 是具 有 相 似属 性 和 特 征 的实例 , 具有 相 或 似 设计 任务 的实 例 。相 似度 是 实例和 实例之 间相似
工 作 , 的难度 主要 表现在 设计 过 程 的强经验 、 它 弱理 论性 上 。采用基 于实 例推 理 的设 计 方法 进行精 铸模
具 的设计 , 可充 分 利用 已有 的设 计 经 验 及成 功 实例
库, 通过 对模 具设 计 实 例 库 中最 佳 实 例 的修 改 和优 化, 设计新 的精铸 模 具 , 而 大大缩 短模 具 的设 计周 从 期, 显著提 高涡 轮叶 片精铸 模 具设 计 的效率 。 因此 开 发 基 于实例 推理 的涡 轮 叶片 精铸 模 具 C D 系 统对 A 于涡轮 叶片精铸模 具 的设 计 来说很 有 意义 。本 文对 以 UG 为支 撑 软 件 、 为 编 程 工 具 所 开 发 的 基 VC
航空发动机涡轮叶片精密成形技术分析
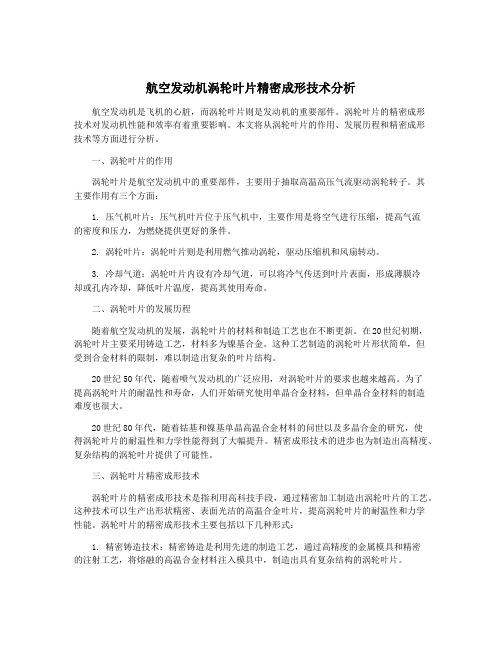
航空发动机涡轮叶片精密成形技术分析航空发动机是飞机的心脏,而涡轮叶片则是发动机的重要部件。
涡轮叶片的精密成形技术对发动机性能和效率有着重要影响。
本文将从涡轮叶片的作用、发展历程和精密成形技术等方面进行分析。
一、涡轮叶片的作用涡轮叶片是航空发动机中的重要部件,主要用于抽取高温高压气流驱动涡轮转子。
其主要作用有三个方面:1. 压气机叶片:压气机叶片位于压气机中,主要作用是将空气进行压缩,提高气流的密度和压力,为燃烧提供更好的条件。
2. 涡轮叶片:涡轮叶片则是利用燃气推动涡轮,驱动压缩机和风扇转动。
3. 冷却气道:涡轮叶片内设有冷却气道,可以将冷气传送到叶片表面,形成薄膜冷却或孔内冷却,降低叶片温度,提高其使用寿命。
二、涡轮叶片的发展历程随着航空发动机的发展,涡轮叶片的材料和制造工艺也在不断更新。
在20世纪初期,涡轮叶片主要采用铸造工艺,材料多为镍基合金。
这种工艺制造的涡轮叶片形状简单,但受到合金材料的限制,难以制造出复杂的叶片结构。
20世纪50年代,随着喷气发动机的广泛应用,对涡轮叶片的要求也越来越高。
为了提高涡轮叶片的耐温性和寿命,人们开始研究使用单晶合金材料,但单晶合金材料的制造难度也很大。
20世纪80年代,随着钴基和镍基单晶高温合金材料的问世以及多晶合金的研究,使得涡轮叶片的耐温性和力学性能得到了大幅提升。
精密成形技术的进步也为制造出高精度、复杂结构的涡轮叶片提供了可能性。
三、涡轮叶片精密成形技术涡轮叶片的精密成形技术是指利用高科技手段,通过精密加工制造出涡轮叶片的工艺。
这种技术可以生产出形状精密、表面光洁的高温合金叶片,提高涡轮叶片的耐温性和力学性能。
涡轮叶片的精密成形技术主要包括以下几种形式:1. 精密铸造技术:精密铸造是利用先进的制造工艺,通过高精度的金属模具和精密的注射工艺,将熔融的高温合金材料注入模具中,制造出具有复杂结构的涡轮叶片。
2. 精密锻造技术:精密锻造是通过将金属加热至塑性变形温度,再施加压力,使金属产生塑性变形,从而制造出精密的涡轮叶片。
%91动机涡轮叶片精铸模具集成设计系统

以模具智能主模型为核心,实现涡轮叶片精铸模具 的设计数据库、位移场数据库、实例库、设计规范/知 识库、标准组件库等复杂数据的统一管理,彻底改变以 往设计流程多数据源的混乱局面;在此基础上以模具设 计智能主模型技术实现叶片模型到各从模型(铸件模 型、铸件工艺模型、型腔模型等)之间的映射和主、从 模型间可变复杂度的转换;通过连续的一系列转换模型 的关联,建立基于典型特征的模型关联矩阵。
The generaI structure iS presented and the related WOrk iS mainly focus on the realization of key
modules such as integration system framework.master model building and designing information management, anti.deformation design of mould cavity. intelligent mould design。 blade nondestructive testing and evaluation.The system can manage the data flow of mould design and blade test effectively.optimize the mould design process and achieve the goal of integration design. Key WOrds:turbo blade;investment casting mould design;integration design;product master modeI
China Northwestern Polytechnical University,Xi’an 71 0072,Shanxi,China)
涡轮叶片参数化建模技术研究与系统

涡轮叶片参数化建模技术研究与系统开发TechnologyResearchandSystemDevelopmentofParametricDesignSoftwareforTurbineBlade戴 禹1 王成恩1 柳 伟2(1上海交通大学机械与动力工程学院,上海 200240;2上海交通大学材料科学与工程学院,上海 200030) 摘 要牶航空发动机涡轮叶片具有复杂的外形和冷却结构,造型设计周期长、可复用性低。
本文开发了一款涡轮叶片参数化建模专用软件,并以榫头结构为例,介绍了参数化设计功能模块的开发流程。
先进行特征分析提取参数和约束后,求取草图截面的点列,并以组合NURBS表示和存储几何数据,进行实体造型。
软件可实现涡轮叶片外形结构的参数化建模,提高设计效率。
关键词牶参数化设计 涡轮叶片 工业软件DOI牶10.16413/j.cnki.issn.1007080x.2022.z2.005Abstract牶Aero engineturbinebladeshaveacomplexshapeandcoolingstructure,leadingtoalongmodelingdesignperiodandlowreusability.Aspecializedsoftwareforparametricmodelingofturbinebladesisdeveloped,andthedevelopmentprocessoftheparametricdesignfunctionmodulewasintroducedtakingthetenonstructureasanexample.Afterperformingfeatureanalysistoextracttheparametersandconstraints,thepointsequenceofthesketchsectionisobtained.ThegeometricdataisexpressedandstoredinNURBS,thenusedforsolidmodeling.Thesoftwareiscapableofparametricmodelingofexternalstructureoftheturbineblade,whichcanimprovedesignefficiency.Keywords牶parametricdesign turbineblade industrialsoftware0 引 言航空发动机涡轮叶片的外形通常是扭曲的变截面实体,并具有诸多复杂特征。
M951合金高压涡轮导向叶片组合件熔模精密铸造工艺研究_李杨

,
采用
,
M9
5
1
合 金 无余 量 精 密
巾
2 8
1
.
铸造工 艺 铸造而 成
心叶片 数多 达
3 5
。
该部件 由
,
内环
、
外环 和 空 心 叶 片 三 部 分 组 成
1
最 大 直径
,
4 mm
,
空
,
有 效 的解 决 了 空 心 叶 片 的偏 芯 儿 问 题
了
。
设计 采 用 顶
。
注 侧 注 相 结合 的 浇 注 系 统
改善 凝 固 条 件 有 效 地 解 决
,
叶 根 疏松 和 叶 片缩裂 的 问 题
,
采用
。
适当 的模 壳温度和浇注温度
浇 注 出 的 铸件 冶 金 质 量 优 良
1
7 6
G
第 十 夂躺 屮 W 高 温 介 金 午 会 人 摘 要 文 *
魏
—
M9 5
1
合金 高 压 涡 轮 导 向 叶 片 组 合件 熔 模精 密 铸 造 工 艺 研 宄
李 杨
刘浩然 李 培佳
谢秋峰
,
刘富宇
1
孔胜 国
1
李俊涛
钢 铁研 宄 总 院
北京
0 0 0 8
摘要
,
:
采用 模具分体压制
精 密 夹 具 组合 定 位
,
熔模 拼 装 组 合 成 型 的 工 艺 方 案
,
航空发动机涡轮叶片精密成形技术分析
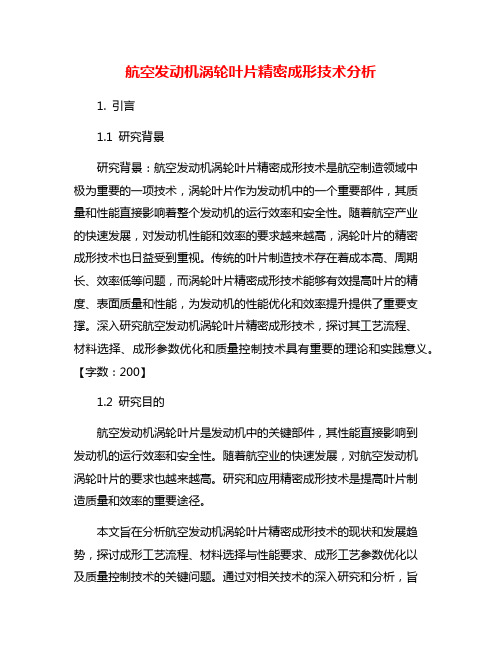
航空发动机涡轮叶片精密成形技术分析1. 引言1.1 研究背景研究背景:航空发动机涡轮叶片精密成形技术是航空制造领域中极为重要的一项技术,涡轮叶片作为发动机中的一个重要部件,其质量和性能直接影响着整个发动机的运行效率和安全性。
随着航空产业的快速发展,对发动机性能和效率的要求越来越高,涡轮叶片的精密成形技术也日益受到重视。
传统的叶片制造技术存在着成本高、周期长、效率低等问题,而涡轮叶片精密成形技术能够有效提高叶片的精度、表面质量和性能,为发动机的性能优化和效率提升提供了重要支撑。
深入研究航空发动机涡轮叶片精密成形技术,探讨其工艺流程、材料选择、成形参数优化和质量控制技术具有重要的理论和实践意义。
【字数:200】1.2 研究目的航空发动机涡轮叶片是发动机中的关键部件,其性能直接影响到发动机的运行效率和安全性。
随着航空业的快速发展,对航空发动机涡轮叶片的要求也越来越高。
研究和应用精密成形技术是提高叶片制造质量和效率的重要途径。
本文旨在分析航空发动机涡轮叶片精密成形技术的现状和发展趋势,探讨成形工艺流程、材料选择与性能要求、成形工艺参数优化以及质量控制技术的关键问题。
通过对相关技术的深入研究和分析,旨在揭示精密成形技术在航空发动机涡轮叶片制造领域的重要性,并为未来的发展提供参考和借鉴。
在探讨研究目的的过程中,希望能够全面了解航空发动机涡轮叶片精密成形技术的关键问题,为提高叶片制造质量、减少生产成本和优化生产效率提供理论指导和技术支持。
通过该研究,为航空发动机涡轮叶片制造技术的进一步发展和提升质量水平提供理论基础和实践经验。
2. 正文2.1 叶片精密成形技术概述叶片精密成形技术是航空发动机制造中关键的工艺之一,它直接影响着发动机的性能和可靠性。
叶片是发动机中的重要部件,起着承受高温、高压气流的作用。
叶片的精密成形技术至关重要。
叶片精密成形技术是指利用精密模具和高精度设备对叶片进行成形加工的技术。
这种技术可以确保叶片的几何形状和表面质量达到设计要求,从而提高发动机的性能和寿命。
面向精锻叶片的模具计算机辅助设计研究
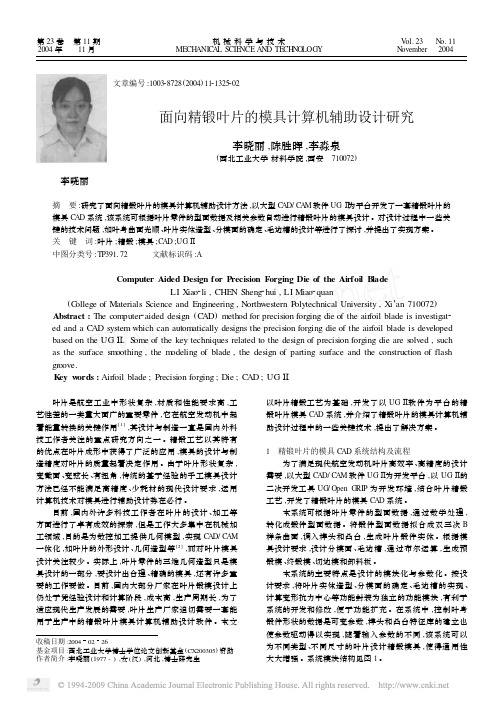
收稿日期:20040226基金项目:西北工业大学博士学位论文创新基金(CX200305)资助作者简介:李晓丽(1977-),女(汉),河北,博士研究生李晓丽文章编号:100328728(2004)1121325202面向精锻叶片的模具计算机辅助设计研究李晓丽,陈胜晖,李淼泉(西北工业大学材料学院,西安 710072)摘 要:研究了面向精锻叶片的模具计算机辅助设计方法,以大型C AD/C AM 软件UG Ⅱ为平台开发了一套精锻叶片的模具C AD 系统,该系统可根据叶片零件的型面数据及相关参数自动进行精锻叶片的模具设计。
对设计过程中一些关键的技术问题,如叶身曲面光顺、叶片实体造型、分模面的确定、毛边槽的设计等进行了探讨,并提出了实现方案。
关 键 词:叶片;精锻;模具;C AD ;UG Ⅱ中图分类号:TP391172 文献标识码:AComputer Aided Design for Precision Forging Die of the Airfoil B ladeLI X iao 2li ,CHE N Sheng 2hui ,LI Miao 2quan(C ollege of Materials Science and Engineering ,N orthwestern P olytechnical University ,X i ′an 710072)Abstract :The com puter 2aided design (C AD )method for precision forging die of the airfoil blade is investigat 2ed and a C AD system which can automatically designs the precision forging die of the airfoil blade is developed based on the UG Ⅱ.S ome of the key techniques related to the design of precision forging die are s olved ,such as the surface sm oothing ,the m odeling of blade ,the design of parting surface and the construction of flash groove.K ey w ords :Airfoil blade ;Precision forging ;Die ;C AD ;UG Ⅱ 叶片是航空工业中形状复杂,材质和性能要求高,工艺性差的一类量大面广的重要零件,它在航空发动机中起着能量转换的关键作用[1],其设计与制造一直是国内外科技工作者关注的重点研究方向之一。
某发动机涡轮导向器精密整体叶盘铸造工艺研究
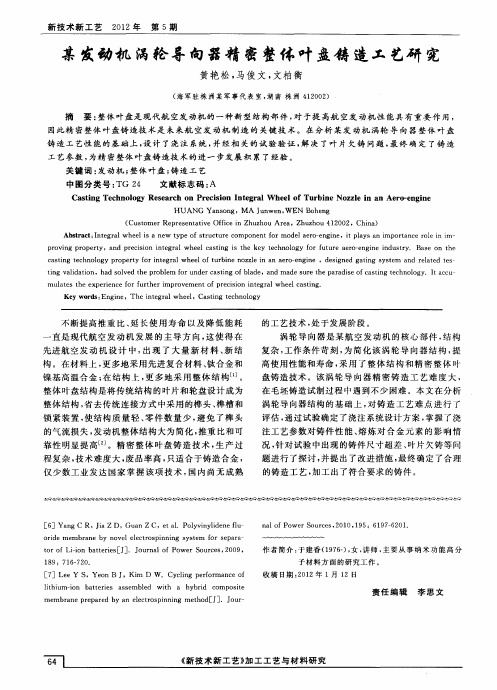
具 , 因铸 件结 构上 下厚 薄不 均 、 会 浇注 系统设 计 不 同
及收 缩不 同而 导致 尺 寸 超 差 , 同时 如 浇 注方 案 设 计
不合 理 , 铸件 冶金 质量 和 内环 圆度也 无法 保证 , 该 因 此必 须合 理设 计浇 注系 统和铸 造模 具 。
Ca tn c si g Te hnoo y Re e r h o e ii n I t g a h e fTu bi e No ze i n Ae o e g n lg s a c n Pr cso n e r lW e lo r n z l n a r - n i e
n lo we our e , 01 1 a fPo r S c s 2 0, 95: 6 7 62 19 — 01
tr f io atr s J .J un l fP we o re, 0 9 o — nb t i [] o ra o o rS ucs 20 , oLi ee
Ke r E n ne,The i e a y wo ds: gi ntgr lwhe l e ,Ca tn e hno o s ig t c l gy
不 断提 高推重 比 、 长 使 用 寿命 以及 降低 能 耗 延
一
的工艺技 术 , 于发展 阶段 。 处 涡轮 导 向器 是 某航 空 发动 机 的 核心 部 件 , 构 结
程度 进行 验证 。 验证 方 法是 分 别 采 用这 2种 方 案 , 相 同浇 注 以
压气 机一 级转 子轴 机匣 、 燃烧 室外 套 、 安装 边和 支承 座等 。 。此 次 在涡 轮 导 向 器 上应 用 , 。 ] 尚无 可 供 参 考 的精 密铸 造工 艺 , 因此其 精 密铸造 性 能 尚需 摸 索 。 3 )铸 件 叶 片 薄 , 易 产 生欠 铸 等 缺 陷 , 任 一 容 且 叶片 上微 小 的疏松 缺 陷 都 将 导 致整 个 铸 件 报 废 , 因
基于事例推理技术的涡轮叶片精铸模分模设计研究与应用
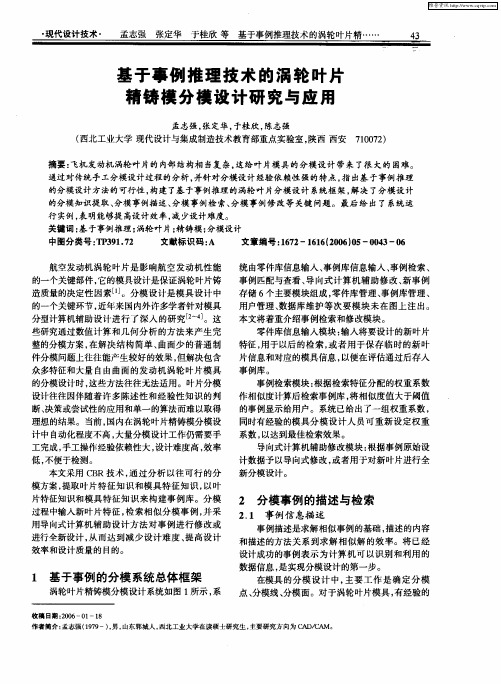
・
现代设计技术 ・
孟志强
张定华
于桂欣 等
基于事例推理技术的涡轮叶片精……
4 3
基 于 事例 推 理 技 术 的涡 轮 叶 片 精 铸 模 分 模设 计 研 究与应 用
孟志 强 , 定华 , 张 于桂欣 , 志强 陈
( 西北工业大学 现代设计与集成制造技术教育部重点实验室 , 陕西 西安 70 7 ) 10 2
片特征知识和模具特征知识来构建 事例库。分模 过程中输入新叶片特征 , 检索相似分模事例 , 并采 用导向式计算机辅助设计方法对事例进行修改或 进行全新设计 , 从而达到减少设计难度 、 提高设计 效率和设计质量的目的。
2 分模事例 的描述与检 索
2 1 事例 信 息描 述 .
事例描述是求解相似事例的基础 , 描述的内容 和描述的方法关系到求解 相似解 的效率。将 已经 设计成功的事例表示 为计算机可 以识别和利用 的 数据信息, 是实现分模设计的第一步。 在模具的分模设计 中, 主要工 作是确定 分模 点、 分模线 、 分模面。对于涡轮叶片模具 , 有经验的
事例匹配与查看 、 向式计算 机辅 助修改 、 导 新事例 存储 6 个主要模块组成 , 零件库管理 、 事例库管理 、 的一个 关键 环节 , 近年来 国内外许 多学 者针对模 具 用户管理 、 数据库维护等次要模块 未在 图上注出。 分型计算机辅助设计进行 了深入 的研究[ 4 2 ] - 。这 本文将着重介绍事例检索和修改模块 。 些研究通过数值计算和几何分析 的方法来产生完 零件库信息输入模块 : 输入将要设计的新叶片 用于以后 的检索 , 或者用于保存临时的新 叶 整的分模方案 , 在解决结构简单 、 曲面少的普通制 特征 , 件分模问题上往往能产生较好 的效果, 但解决包含 片信息和对应的模具信息 , 以便在评估通过后存人
航空发动机涡轮叶片精密成形技术分析

航空发动机涡轮叶片精密成形技术分析1. 引言1.1 研究背景航空发动机是飞机的心脏,而航空发动机涡轮叶片作为发动机的关键部件,对发动机的性能和效率起着至关重要的作用。
随着航空业的快速发展和飞行器对性能要求的不断提高,涡轮叶片的精密成形技术也日益受到重视。
传统涡轮叶片成形技术存在着一些问题,如成形周期长、成形精度低、材料利用率低等,难以满足现代航空发动机对涡轮叶片性能的要求。
研究和探索先进的涡轮叶片精密成形技术成为当前的热点之一。
通过采用先进的数控加工技术、材料工程技术以及仿真分析技术,可以有效提高涡轮叶片的成形精度和生产效率,从而满足航空发动机对涡轮叶片的高性能要求。
在这样一个背景下,本文旨在对航空发动机涡轮叶片精密成形技术进行深入分析,探讨其作用和重要性,比较传统成形技术和先进成形技术的优缺点,展示精密成形技术在航空发动机涡轮叶片中的应用以及影响成形精度的因素。
通过研究,为航空发动机涡轮叶片的精密成形提供技术支持,并为未来的研究方向提供参考。
1.2 研究目的研究目的是通过分析航空发动机涡轮叶片精密成形技术,探讨其在航空发动机性能提升中的作用和价值。
具体包括了对传统涡轮叶片成形技术和先进涡轮叶片精密成形技术的比较分析,以及精密成形技术在航空发动机涡轮叶片制造中的应用现状和发展趋势。
研究旨在揭示精密成形技术对提高航空发动机涡轮叶片成形精度和性能的影响,以及探讨成形精度的影响因素,为提高航空发动机燃烧效率、降低燃油消耗、延长涡轮叶片使用寿命等方面提供参考和借鉴。
通过深入研究航空发动机涡轮叶片的精密成形技术,旨在促进我国航空发动机产业的发展,并为全球航空工业的进步提供技术支持和保障。
1.3 研究意义航空发动机涡轮叶片精密成形技术的研究意义是非常重要的。
航空发动机是飞机的“心脏”,涡轮叶片是航空发动机的核心部件之一,直接影响着发动机的性能和效率。
提高涡轮叶片的制造工艺和精度可以大大提升航空发动机的整体性能。
涡轮冷却叶片参数化建模及多学科设计优化

第22卷第8期2007年8月航空动力学报Journal of Aerospace Pow erVol.22No.8Aug.2007文章编号:100028055(2007)0821346206涡轮冷却叶片参数化建模及多学科设计优化虞跨海,岳珠峰(西北工业大学力学与土木建筑学院,西安710072)摘 要:建立了一个涉及结构、气动、传热、振动、强度和寿命等学科的涡轮冷却叶片多学科设计优化系统,进行了单孔薄壁冷却叶片的多学科设计优化.提出了单孔薄壁冷却叶片的参数化造型方法,叶片叶型采用5次多项式构造,气动与传热为三维耦合分析;叶片体积平均温度与最高温度为优化目标,强度、振动和寿命等学科相关参数为约束,模拟退火与序列二次规划组合算法进行叶片参数空间寻优,在保持冷却气体流量不变的条件下,优化提高了冷却效果,降低了叶片材料的性能要求.关 键 词:航空、航天推进系统;冷却叶片;多学科设计优化;参数化建模;耦合分析中图分类号:V232 文献标识码:A收稿日期:2006208208;修订日期:2006211203基金项目:国家自然科学基金(50375124,10472094),航空科学基金(03B53003)作者简介:虞跨海(19822),男,浙江义乌人,博士生,主要从事多学科设计优化、结构设计与优化方面工作.Parametric modeling and multidisciplinary designoptimization for cooling turbine bladeYU Kua 2hai ,YU E Zhu 2feng(School of Mechanics ,Civil Engineering and Architect ure ,Nort hwesternPolytechnical U niversity ,Xi ’an 710072,China )Abstract :A multidisciplinary design optimization system for gas t urbine blade ,which involves st ruct ure ,aerodynamic ,heat transfer ,vibration and service life ,etc ,has been devel 2oped ,serving t he p urpose of multidisciplinary design optimization of single 2hole t hin wall cooling blade.A paramet ric modeling met hod was also proposed for single 2hole t hin wall cooling blade.The blade surface geomet ry is defined by five 2order polynomials ,while 32D coupling analysis was made for aerodynamic and heat t ransfer.The average temperat ure and maximum temperat ure of blade volume were optimized ,wit h aerodynamic ,vibration and serv 2ice life as t he const raint s.A combined algorit hm of annealing simulation and SQ P (SequentialQuadratic Programming )was used to optimize t he blade parameters.While t he flow rate of cooling air was kept unchanged ,t he cooling effect was improved and t he performance require 2ment on t he blade materials was reduced.K ey w ords :aero space p rop ulsion system ;cooling t urbine blade ;multidisciplinary de 2sign optimization (MDO );paramet ric modeling design ;coupling analysis 航空发动机涡轮入口温度的不断提高,对涡轮叶片的材料与结构提出了挑战,目前涡轮叶片主要采用以空气为冷却介质的冷却方式,但是冷却气体的引入又降低了涡轮的热能效率,因此如何提高冷却气体的冷却效率是涡轮叶片结构设计的重要内容.国内外许多学者在涡轮冷却叶片的设计优化方面做了许多的工作,取得了一定的进展,Carlo 第8期虞跨海等:涡轮冷却叶片参数化建模及多学科设计优化Carcasci[1]等人进行了燃气涡轮静子叶片内冷却设计的研究,但是只分析了一维冷却叶片模型;Shuye Teng[2]等人研究了气膜孔形状对涡轮叶片传热系数分布的影响问题;Louis[3]等人进行了涡轮叶片冷却通道内部传热、流动和压力分布的数值测试;Talya[4,5]等人进行了二维、三维冷却叶片优化.但是这些研究基本上都是基于单学科的,气动与传热的分析是分离的,在三维叶片的温度场计算上采用由二维到三维扩展的方法.涡轮叶片设计是一个典型的多学科设计问题,涉及气动、传热、结构、强度、振动和寿命等多个学科,必须采用多学科设计优化的方法才能获得叶片的最佳设计方案.1 涡轮冷却叶片参数化建模涡轮叶片参数化过程中,叶栅的压力面与吸力面型线的选择对叶片的气动性能有很大的影响.5次多项式作为叶片压力面和吸力面型线可以减少流动损失,文献[6]中给出了叶栅几何参数与多项式系数之间的关系.压力面和吸力面均为5次多项式y=a0+a1x+a2x2+a3x3+a4x4+a5x5(1) 如图1所示为叶型及中弧线示意图,根据中弧线的定义得到叶片中弧线求解方程组(y0-f(x1))f′(x1)=x1-x0(y0-g(x2))g′(x2)=x2-x 0(x1-x0)2+(f(x1)-y0)2= (x2-x0)2+(g(x2)-y0)2(2)其中,[x1,f(x1)]与[x2,g(x2)]分别是压力面和吸力面上相对应的任意的一对内切圆切点,(x0, y0)是与x1和y1相对应的内切圆的圆心坐标.图1 叶型及中弧线示意图Fig.1 Blade profile and camber line直接求解方程组(2)比较困难,通过数值迭代方法求解得到中弧线上一系列离散点,再用5次多项式进行最小二乘方法拟合得到各项系数:‖r(y3)‖2=min‖r(y)‖2(3)在{1,x,x2,x3,x4,x5}空间范围内,有:A T A C=A T y(4)式中C为5次多项式系数向量,图2所示为求解得到的叶片两个不同截面的中弧线.图2 叶型型面中弧线Fig.2 Camber line of blade cascade计算得到中弧线方程之后,沿中弧线给出壁面厚度分布函数,可以建立单孔薄壁冷却叶片参数化模型(图3(a));通过圆心在中弧线上的定位,给出相应的圆半径,可以建立多孔直流冷却叶片参数化模型(图3(b)).本文选取单孔薄壁冷却叶片进行了多学科设计优化.2 各学科分析及优化策略涡轮冷却叶片的优化涉及结构、气动、传热、强度、振动和寿命等多个学科,求解学科之间的耦合关系,是实现多学科设计优化的关键.本文的研究是建立在对叶片外形进行设计优化并获得理想气动外形的基础之上[7],针对前述参数化方法建立的单孔薄壁冷却叶片,以冷却效果为优化目标7431航 空 动 力 学 报第22卷图3 冷却叶片参数化模型Fig.3 Parametric cooling blade models进行优化,优化过程中保持叶身外形不变,只改变叶片冷却内腔形状. 气动与传热实现了三维耦合分析计算,并根据计算结果将叶片内部温度载荷及叶片表面气压载荷传递到结构分析模型当中,强度分析的结果为寿命预测提供依据,振动分析考虑了温度与转动对固有频率的影响.2.1 叶片三维流固耦合分析涡轮叶片内外流场的三维流固耦合计算,可以更准确地得到叶片内部的温度场分布情况,为强度分析提供更可靠的计算数据.采用Fluent计算软件进行流固耦合分析,流体域计算采用三维稳态可压缩气体N2S方程和k2ε湍流模型进行求解;流体与固体之间的热交换采用标准壁面函数方法求解能量方程.分析过程中考虑了叶片温度对材料性能的影响,如表1所示.表1 材料热导率及比热容随温度变化情况T able1 V ariation of heat conductivity and specif ic heat with temperature changes温度/℃100200300400500600700800900热导率/(W/cm・K)13.3915.0716.3217.5819.2520.5721.7723.0224.70比热容/(J/kg・K)638661668654654662668673721 冷却叶片几何结构复杂,包含叶片内冷通道、主流通道、叶片固体区域,在网格的划分上难度较大,文中流体域与固体域均采用四面体非结构网格划分,网格总数约100万.流固耦合分析的结果,通过数据信息的传递应用于结构分析.由于流场与结构分析采用不同的计算软件,可能导致其分析模型网格划分的不一致,需要通过网格节点线性插值的方法进行温度与气压载荷的传递;为了提高精度,本文通过保持叶片气动分析与结构分析网格的一致性来保证载荷信息传递的高精度.如图4所示为载荷信息传递前后叶片温度分布情况,温度载荷在两个不同分析模型上的传递具有很高的精度.图4 温度信息传递Fig.4 Transfer of temperature data 2.2 强度、振动和寿命分析采用有限元方法对涡轮叶片进行强度和振动分析.强度分析考虑了温度分布不均引起的应力应变以及叶片高速旋转产生的离心力,要求叶片内最大当量应力小于材料的屈服拉伸应力.叶片振动分析采用了叶根固支和叶尖自由的悬臂梁式振动[829],由于叶片的温度以及叶片转速对振动频率的影响,振动分析时在模型上施加了温度载荷以及叶片转速,确保分析结果更加准确可靠.利用强度计算的结果,采用基于Manson2 Coffin方程的经验公式方法对涡轮叶片低循环疲劳寿命进行近似预测,预测模型[10]为σ=2E×[010417(2Nf)-017013+010129(2N f)-011976](5)式中σ为强度分析求得的等效应力,N f为预测低循环疲劳寿命,E为材料的平均弹性模量.2.3 冷却叶片多学科设计优化策略标准优化方法能较全面地反映问题的各个方面,可保证求解过程收敛到全局最优解,是目前用得最多的优化方法.根据各学科分析模型,本文采用标准优化方法进行了单孔薄壁冷却叶片的多学科设计优化,实现了各学科分析软件在多学科优化平台下的集成,图5所示为叶片多学科设计优8431 第8期虞跨海等:涡轮冷却叶片参数化建模及多学科设计优化化(MDO )流程.图5 冷却叶片多学科设计优化流程图Fig.5 MDO flow chart for cooling blade design 优化设计以叶片内部体积平均温度与最高温度的加权值最小为目标T =λ1T average +λ2T max (6)式中λ1+λ2=1,文中取λ1=λ2=015.优化设计变量、约束条件以及优化算法的选取规则如下:(1)设计变量的选取涡轮叶片参数化造型时,只采用叶根与叶尖两个截面来构造三维模型,因此在优化过程中只选取叶根与叶尖截面的壁面厚度作为设计变量.(2)约束条件的选取叶片的设计必须考虑其在使用过程中的安全性与可靠性,设计时必须满足强度、寿命、振动等各方面的综合要求,这些要求体现在优化模型中就是满足一定的约束条件.对于各学科约束条件的规定如下:(a )叶片中的各项应力值必须满足应力指标规定的要求;(b )叶片激振频率根据转子叶片的实际工作情况(20000r/min 转速)和叶轮的叶片数为36,计算叶轮激振频率F 激振=(2000/60)・36・n =12000n (7)即对于本文中涡轮转子叶片而言,其激振频率为12000,24000,….衡量叶片是否避开共振区的的指标是共振裕度K ,其定义如下:K =|叶片频率-f 激振|f 激振×100%(8)本文中要求叶片各阶频率裕度值不小于10%;(c )根据Manson 2Coffin 公式计算结果,规定叶片的低循环疲劳寿命最少循环数为6000次,考虑到材料的分散性,在设计中取材料的分散系数为6,则最少循环数不能少于36000次.(3)优化算法采用模拟退火算法(SA )与序列二次规划(SQ P )算法的组合进行设计参数空间的综合寻优,模拟退火算法全局搜索最优之后使用序列二9431航 空 动 力 学 报第22卷次规划算法达到快速收敛,这样既保证能取得全局最优解又能提高计算效率,降低计算成本.3 优化计算与结果前述方法建立的冷却叶片多学科设计优化模型,通过学科间信息的传递实现了强度、寿命与气动及传热学科之间的解耦.利用各学科分析软件的二次开发接口,在Isight优化平台下实现了各学科分析软件的集成,对单孔薄壁冷却叶片进行了优化设计计算.优化结果表明:在满足各学科约束的条件下,较大的降低了叶片体积平均温度,获得了目标函数的最优解,改善了叶片的性能.优化设计变量与约束变量优化前后的变化情况如表2和表3所示,表4为目标函数优化前后变化情况.表2 设计变量表T able2 List of optimized variables变量名设计初值优化上限优化下限优化终值叶尖壁面厚度/mm0.3200.5000.2500.401叶根壁面厚度/mm0.4600.6000.3000.552表3 约束变量表T able3 List of bounded variables变量物理意义设计初值优化上限优化下限优化终值σmax 最大当量应力/MPa572.1600—560.9K44阶振动频率裕度/%38.3—1030.9K55阶振动频率裕度/%32.9—1023.76K66阶振动频率裕度/%16.6—1011.7N f低循环疲劳寿命循环数81156—3600085226表4 优化目标变化情况T able4 Object function values beforeand after optimization变量名优化前优化后优化量温度值加权/K1164.5911161.1505 3.4405平均温度/K1042.3161035.488 6.828最大温度/K1286.8661286.8130.053如图6所示为叶片优化前后在90mm高度与110mm高度温度分布情况比较.在优化设计前后,叶片内部体积平均温度降低约7K,而最高温度的降低量较少.图6 叶片优化前后温度分布Fig.6 Temperature distribution of blade cascadebefore and after optimization0531 第8期虞跨海等:涡轮冷却叶片参数化建模及多学科设计优化4 结 论本文主要研究了涡轮冷却叶片的参数化建模方法以及涡轮冷却叶片多学科设计优化的实现,主要工作如下:(1)提出了一种涡轮冷却叶片参数化建模方法.采用5次多项式构造叶片型线,求解各叶型面中弧线方程,通过沿叶片中弧线厚度分布或圆心的定位,建立了冷却叶片模型;(2)实现了涡轮叶片的三维流固耦合分析,更准确地得到叶片内部温度分布;(3)考虑了多个学科以及学科间的耦合,学科间耦合信息的传递具有较高精度;(4)开发软件数据接口程序,在优化平台下实现了涡轮冷却叶片多学科设计优化系统的集成,完成了叶片冷却结构的优化,提高了冷却效率.优化改善了涡轮叶片冷却结构的性能,在相同冷气流量的条件下,通过优化设计计算,提高了冷气的冷却效果,降低了叶片内部体积平均温度与最高温度,从而可以降低对叶片材料性能的要求,提高叶片工作的安全性与可靠性,因此具有良好的工程应用价值.参考文献:[1] Carcasci C,Facchini B.A numerical procedure to design in2ternal cooling of gas turbine stator blades[J].Rev CenTherm,1996,35:2572268.[2] Teng S,Han J C.Effect of film2hole shape on t urbine bladeheat transfer coefficient distribution[R].AIAA2200021035.[3] Russell L M,Thurman D R.Measurement s of heat trans2fer,flow and pressure in a simulated turbine blade internal cooling passage[R].NASA TP23646,1997.[4] Talya S S,Rajadas J N.Multidisciplinary optimization ofGas turbine blade design[R].A IAA2199824864.[5] Talya S S,Rajadas J N.An integrated multidisciplinary de2sign optimization procedure for cooled gas turbine blades [R].AIAA2200021664.[6] 冯进,符达良.涡轮钻具涡轮叶片造型设计新方法[J].石油机械,2000,28(11):9213.FEN G Jin,FU Daliang.New design met hod of turbine blade shape of turbodrill[J].China Petroleum Machinery,2000, 28(11):9213.[7] 虞跨海,李立州,王婧超,等.涡轮叶片三维气动优化[J].机械设计,2005,22(11):31233.YU Kuahai,L I Lizhou,WAN G Jingchao,et al.Aerodynam2 ic3D optimization design for turbine blade[J].Journal of Machine Design,2005,22(11):31233.[8] 林垲,高庆,黄维娜.I级涡轮叶片振动特性研究[J].燃气涡轮试验与研究,2002,15(3):28233.L IN Kai,GAO Qing,HUAN G Weina.Study on vibration characteristics of1st stage t urbine rotor blade[J].Gas Tur2 bine Experiment and Research,2002,15(3):28233.[9] 张锦,刘晓平.叶轮机振动模态分析理论及数值方法[M].北京:国防工业出版社,2001.[10] 苏清友.航空涡喷、涡扇发动机主要零部件定寿指南[M].北京:航空工业出版社,2004.1531。
- 1、下载文档前请自行甄别文档内容的完整性,平台不提供额外的编辑、内容补充、找答案等附加服务。
- 2、"仅部分预览"的文档,不可在线预览部分如存在完整性等问题,可反馈申请退款(可完整预览的文档不适用该条件!)。
- 3、如文档侵犯您的权益,请联系客服反馈,我们会尽快为您处理(人工客服工作时间:9:00-18:30)。
c si gd e a d i u i ay me h n s w r xr c e h u h ma y a ay e b u h t cu a h r ce sis o r i e b a e a d a t i n t a x l r c a im e e e t td t o g n n ls sa o tt e sr t r lc a a t r t ft b n ld n n s i a u i c u p e iin c sig d e o r i e b a e tt e s me t ,t e p r merc la xl r c a im fp e iin c sig d e t r i e ba e rc s a t i f u b n l d ,a a i o n t h me h a a t a u i a me h n s o r cso a t i o t bn ld i iy n u wa e in d b s d o l t r b sn t o f u l i gt mp ae d tb s .T e d sg f ce c si r v d a d p o u t n sd sg e a e n UG p af m y u ig a meh d o i n e l t aa a e h e i n e in y i o b d i mp o e n rd ci o
21 0 2年 1 月
机床与液压
MACHI NE T0OL & HYDRAUL CS I
J n 01 a .2 2
Vo. 0 No 1 14 .
第4 0卷 第 1 期
D I 1 .99 ji n 10 — 8 12 1. 109 O : 0 36 /.s .0 1 3 8 .0 20 . 2 s
涡轮叶片精铸模具辅助机构参数化研究
李海滨 ,高天宇 ,周长军 ,唐 小波 ,廖善联
( 西北工业大学现代设计与集成制造技术教育部重点实验室,陕西西安 7 07 ) 102
摘要 :涡轮叶片精铸模具是航空发动机涡轮 叶片类零件精密铸造过程 中的关键工装 ,其设 计过程繁琐 ,使得采 用现有 通用软件系统进行模 具设计 时 ,只能依靠设计经 验丰 富的人员手工 操作实 现 ,自动化程 度不高 ,严 重制约 了其设计 周期 。 通过分析涡轮叶片的结构特征以及现有涡轮叶片精铸模具 的结 构特点 ,提取精铸模 具 的设计方 案及模具辅助机 构生成 的设 计 知识 ,采用构建精铸模具模板库的方法 ,基于 U G平 台对 涡轮 叶片精铸模具辅助机构进行参数化设计 ,提高 了设计 效率 ,
ba e t d s npo e s sS eb s a t o l ei s gc r n e e l o w r ytm cn js b p rt y sao e l .I e i r s i Ov ro et t h m ud d s u i ur t n r f a ss a ut eo ea d b e sn d d s g c h e n g n e g de et bn a
L abn G O Ta y , HO h njn T N i b , I O S al n I ii , A inu Z U C a g , A G X a o LA hni H u o a
( ’ e aoa r f o t oa ei n tga d M n f tr , nsyo E u a o , r eK yLb rt yo ne rr D s na dI ert a ua ue Miir f d ct n I h o C mp y g n e c t i
缩短 了生产周期。
关键词 :涡轮叶片 ;模板库 ;参数化设计 ;精铸模具辅助机构
中图分类号 :T 3 17 P9.3 文献标 识码 :A 文章编 号:10 3 8 2 1 )1 0 4 0 1— 8 1(0 2 —16—
Pa a e r c lRe e r h b u x l r e ha i m fPr c so s i r m ti a s a c a o t Au ii y M c n s o e ii n Ca tng a
NotwetP lte ne lU ies y,X ,n S a n i 0 2, C ia r h s oye h ia nv ri t i h a x 1 7 a 70 hn )
Ab ta t P e iin c s n is t r i eb a e i ak yfo k b t e h o h s c t d c sig p o e s so eo n ie t r i e s r c : r c s a t g de o t b n ld e rc ewe n t e s p it ae a t r c s e fa re g n b n o i u s i n u