不良品分析流程图
制程不良品处理流程图
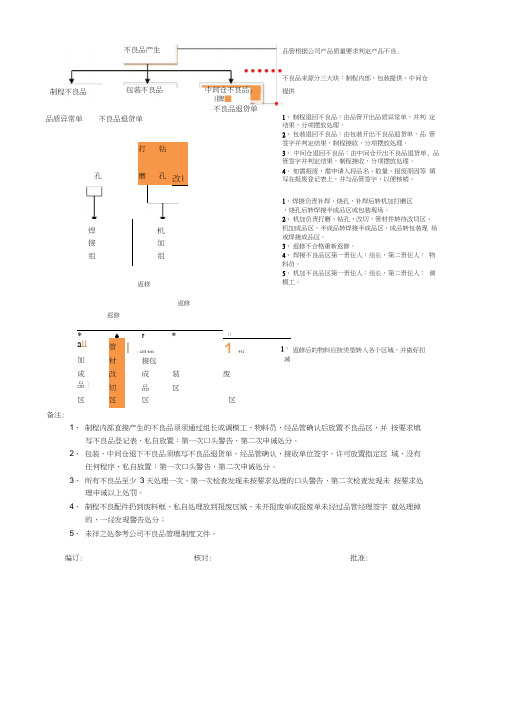
品管根据公司产品质量要求判定产品不良.
包装不良品
制程不良品
不良品退货单
品质异常单
孔
打
磨
钻
孔
改|
焊
机
接
加
组
组
返修
中间仓不良品
|牌■
不良品退货单
不良品来源分三大块:制程内部、包装提供、中间仓
提供
1、制程退回不良品:由品管开出品质异常单,并判 定结果,分项摆放处理。
2、包装退回不良品:由包装开出不良品退货单,品 管签字并判定结果,制程接收,分项摆放处理。
3、中间仓退回不良品:由中间仓开出不良品退货单, 品管签字并判定结果,制程接收,分项摆放处理。
4、如需报废,需申请人将品名、数量、报废原因等 填写在报废登记表上,并与品管签字,以便核销。1、焊接负补焊、烧孔,补焊后转机加打磨区
,烧孔后转焊接半成品区或包装现场。
2、机加负责打磨、钻孔,改切,管材件转待改切区、 机加成品区,半成品转焊接半成品区,成品转包装现 场或焊接成品区。
3、返修不合格重新返修。
4、焊接不良品区第一责任人:组长,第二责任人: 物料员。
5、机加不良品区第一责任人:组长,第二责任人: 调模工。
失效分析流程图

2.3.2 进一步用HF去除烧结玻璃,观察焊接件并拍照留证。 2.3.3 再用HNO3将引线、晶粒、焊片分开,观察晶粒状况(30倍显微镜)并拍照留证。
流程图及能力说明
流程说明
1.0 对不良品外观进行检查,采用20,30倍显微镜观察,电子数显卡尺对外观检测,并对材料进行
2.0 电性参数的不良,分别进行常规电性测试及试验测试,进一步确定不良状态,与相同类型的材 料做电性对比(留样及库存材料),收集各相关的实验资料,TK-168测试仪(VR/VF/DVR/IR/TRR) 4810示波器测试VR/VF;576示波器测试VR/VF/IR; 正向电压测试仪测试VF;反向电压测试仪测
研磨(2.1)
X-RAY(2.2)
化学(2.3)
试VR;TDS TRR测试仪测试TRR曲线状况。 2.1 研磨机采用快速固化剂将材料固化与此内,再用180、320、600目砂纸进行研磨,然后再用抛
纵/横切面 结深 结构 缺损 横截 面积
焊接偏位
焊接气 孔
晶粒位置
H2SO4 (2.3.1)
HF (2.3.2)
FA流程图及能力说明
FA流程图 外观观察(1.0) 流程说明
1.0 对不良品外观进行检查,采用20,30倍显微镜观察,电子数显卡尺对外观检测,并对材料进行 拍照留证,外观的不良需调查用户之使用方法及环境,并模拟作对比。
电性测试(2.0) 解剖分析
2.0 电性参数的不良,分别进行常规电性测试及试验测试,进一步确定不良状态,与相同类型的材 料做电性对比(留样及库存材料),收集各相关的实验资料,TK-168测试仪(VR/VF/DVR/IR/TRR) 4810示波器测试VR/VF;576示波器测试VR/VF/IR; 正向电压测试仪测试VF;反向电压测试仪测
不合格品处理流程图
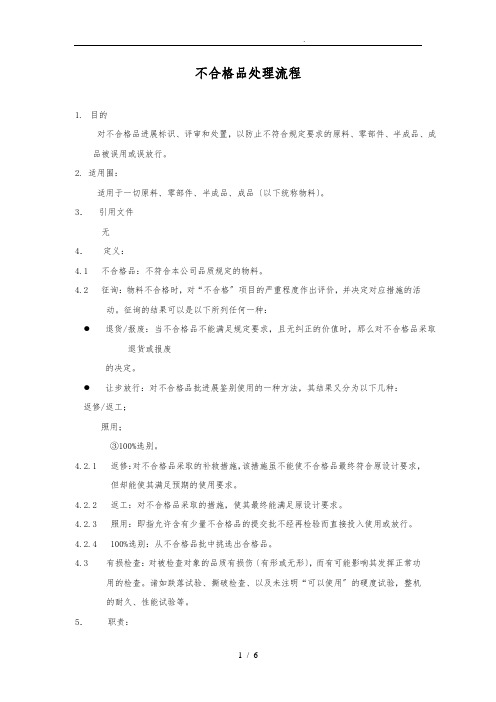
不合格品处理流程1.目的对不合格品进展标识、评审和处置,以防止不符合规定要求的原料、零部件、半成品、成品被误用或误放行。
2. 适用围:适用于一切原料、零部件、半成品、成品〔以下统称物料〕。
3.引用文件无4.定义:4.1不合格品:不符合本公司品质规定的物料。
4.2征询:物料不合格时,对“不合格〞项目的严重程度作出评价,并决定对应措施的活动。
征询的结果可以是以下所列任何一种:●退货/报废:当不合格品不能满足规定要求,且无纠正的价值时,那么对不合格品采取退货或报废的决定。
●让步放行:对不合格品批进展鉴别使用的一种方法,其结果又分为以下几种:返修/返工;照用;③100%选别。
4.2.1返修:对不合格品采取的补救措施,该措施虽不能使不合格品最终符合原设计要求,但却能使其满足预期的使用要求。
4.2.2返工:对不合格品采取的措施,使其最终能满足原设计要求。
4.2.3照用:即指允许含有少量不合格品的提交批不经再检验而直接投入使用或放行。
4.2.4100%选别:从不合格品批中挑选出合格品。
4.3有损检查:对被检查对象的品质有损伤〔有形或无形〕,而有可能影响其发挥正常功用的检查。
诸如跌落试验、撕破检查、以及未注明“可以使用〞的硬度试验,整机的耐久、性能试验等。
5.职责:5.1 品质部:●对不合格品进展标识、隔离;●对经返修/返工的物料进展再检验;并予以判断。
●参与“征询〞工作。
5.2 物控专员:●参与“征询〞工作;●安排返工/返修等事宜。
●将不适用的原料/零部件退回供给商;●安排供给商补料,对供给商进展经济等各方面约束。
●加强供给商管理、辅导、考核5.3 生产部门:对在制程中发现的不合格零部件、半成品进展回收隔离,并且以红色作明确的标注;●挑选、返修/返工遭品质检查人员(IQC\IPQC\FQC\QA)拒收之产品;●参与“征询〞;●针对本部门制造的不合格品申请进展征询。
5.5开发部:●参与“征询〞。
6.程序:6.1进料“不合格〞的处理〔IQC〕。
不良品分析流程图

不良品分析QC
不良分析及跟踪报告
不良品解析 批产品返 工 解 析
不良品分析作业指导书
每批 返工批
测量/ 解剖
不良品分析QC
不良分析及跟踪报告
不良品分析作业指导书
实物核对
作业员/QC
电子参数测试统计
不良品分析作业指导书
每批
综合原因
不良品分析QC
不良分析及跟踪报告 异常LOT处置报告书 异常产品处理单 异常产品处理单 异常LOT处置报告书
降级/ 报废
不良品分析作业指导书
每批
实物核对
QC/作业员
批产品正常流传
分选作业指导书
每批
实物核对
作业员/QC
电子参数测试统计
启动纠正预防 改
异常LOT处置报告书
降级/报
检查追踪
品管/生产
异常LOT处置报告书
原因分析、预防改 善措施
异常LOT处置报告书
改善效果
分析改善 结果跟踪
品管/生产
异常LOT处置报告书
分选不良品解析工作流程相关图
工作流程相关图
批产品上机前首检
管理项目/ 管理项目/标准
检查频次
检查方法
责任人
管理图表
分选作业标准/指导书
换批前
目视/核对
作业员/QC
电子参数测试统计
批产品正常生产
分选作业标准/指导书
每批上机分类取样
C、DF、ILC、短路、
开
每批
实物核对
OQC作业流程图
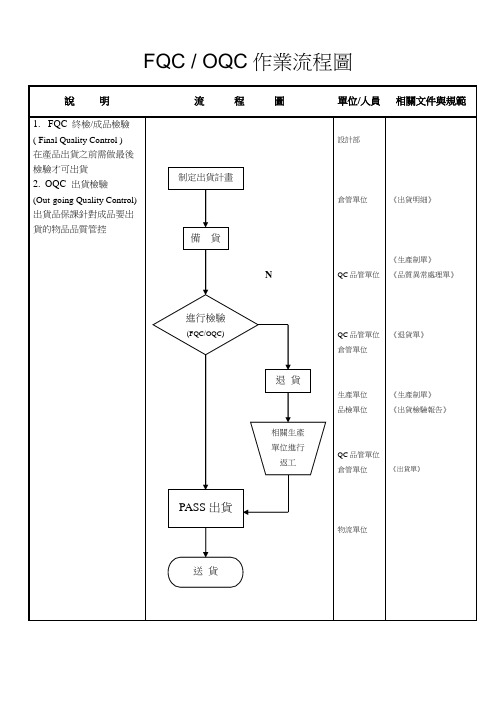
FQC / OQC作業流程圖製程巡檢作業辦法目的:落實品質意識在現場作業人員于制程過程中,實施檢驗或試驗以查證制程之合格性。
三〃範圍:凡本公司產品之各制程。
四、職責:生產部門:負責自製品自檢、送檢、重工、維修及入庫。
品保部門:負責自製品檢驗及記錄、標示。
五、內容:1、首件(產前樣/批版)、自主、巡迴檢驗:(1)品保部門IPQC人員在以下時段需做首件檢驗。
(1)每台機開始生產前開機需做首件檢驗。
(2)設計規格變更時需做首件檢驗。
(3)人員或材料更換時需做首件檢驗。
(2)生產部門作業人員應隨時注意生產產品品質狀況,並按照規定做好自主檢驗。
(3)品保部門IPQC人員應到現場做巡迴檢驗並做好記錄。
(4)品保部門檢驗管制程式,應按照規範和作業指導書之要求訂制(QC工程圖)。
(5)生產部門相關人員在制程中,發現不合格又無法矯正時,應及時停機報告主管,並通知品保部門,而品保部門應按照相關程式處理。
(6)品保部門IPQC人員按照實際檢驗情況記錄不合格品,並對制程式不良品作統計分析把結果回饋於相關部門,作糾正預防對策之依據。
(7)不合格品處理與標示(紅豆標&件投標):(1)、經判定為不合格品時,應在該批半成品貼上紅色圓點貼紙(故障貼紙)又稱紅豆,並加以區分,隨後將不合格批移至返工區或報廢區進行處理。
(2)、發生不合格品時,品保部門IPQC人員應填寫《IPQC服裝(巡廠)驗貨報告》加以記錄,並按照相關程序處理,並通知相關部門處理。
六〃使用表單:1、首件(制前樣/批版)吊卡2、特采申請單3、IPQC服裝(巡廠)驗貨報告4、返工\返修單5、報廢單6、制程異常備忘錄不合格品處理作業辦法一、目的:按照品質計畫及管制措施找出不合格品,採取各項管理及處理措施,並對不合格品進行分析,以防誤用。
二、範圍:供方之原材料、主輔料;廠內制程中之半成品、成品和庫存品;顧客之退貨品。
三、職責:生產、資材部門:負責不合格品標示、隔離及處理,必要時參與評審。
ISO9001不合格品控制程序(含流程图)
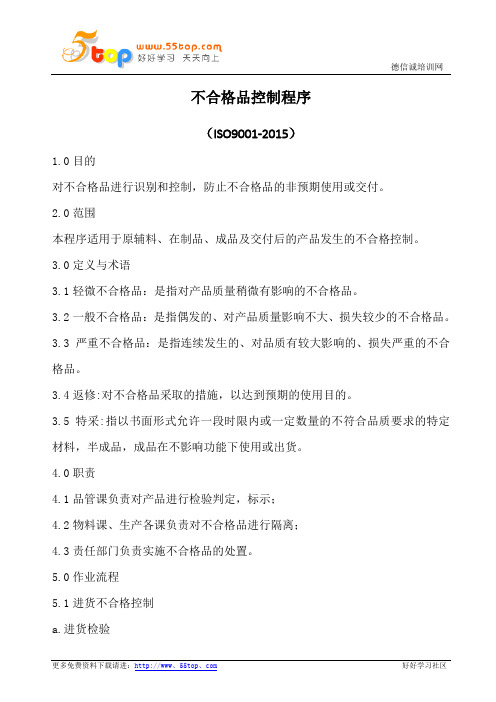
不合格品控制程序(ISO9001-2015)1.0目的对不合格品进行识别和控制,防止不合格品的非预期使用或交付。
2.0范围本程序适用于原辅料、在制品、成品及交付后的产品发生的不合格控制。
3.0定义与术语3.1轻微不合格品:是指对产品质量稍微有影响的不合格品。
3.2一般不合格品:是指偶发的、对产品质量影响不大、损失较少的不合格品。
3.3严重不合格品:是指连续发生的、对品质有较大影响的、损失严重的不合格品。
3.4返修:对不合格品采取的措施,以达到预期的使用目的。
3.5特采:指以书面形式允许一段时限内或一定数量的不符合品质要求的特定材料,半成品,成品在不影响功能下使用或出货。
4.0职责4.1品管课负责对产品进行检验判定,标示;4.2物料课、生产各课负责对不合格品进行隔离;4.3责任部门负责实施不合格品的处置。
5.0作业流程5.1进货不合格控制a.进货检验检验人员依据原物料检验标准、工程图纸、顾客要求等进行检验,判定为不合格品时开《品质异常处理单》并填写相关异常信息并附上不合格样品一并交给品管课长审核和管理部经理批准后扫描发邮件给采购课、生管课、物料课。
b.标示隔离进料不合格品由品管课检验人员进行标示,物料课人员将产品移至不合格品区域进行隔离。
c.不合格品处理1.退货:由物料课开具《退货单》,经品管、仓管确认后,经物料课长审核后通知采购课在7日内退货,若超出期限由我司自行处理。
当同一供应商因产品连续有2批因同样质量被拒收时,品管课开出《纠正和预防措施单》交采购课处理。
2.挑选使用:由采购课通知供应商,确定挑选方式:(1)由供应商进行挑选,挑选后的原物料须由品管课重新检验合格后方可入库使用;(2)由我公司安排物料课全检组人员进行挑选,挑选后的原物料须由品管课重新检验合格后方可入库使用;3.特采接收:在生产急需或紧急出货的情况下不影响安全,功能或结构的不合格品由采购课填写《品质异常处理单》交相关单位会审后由管理部经理核准后方可特采,同时品管员于该批产品上加贴“进料特采标签”;4.报废:制程中发现无法使用的来料不良品(含特采物料),由采购课与供应商沟通处理方式,物料课接收到可报废处理邮件或已扣款的财务部确认签署后开立《报废单》经资材部经理审核、副总核准后进行报废;5.不合格品的处理期限要求:采购课接单后需在24H内签回。
不合格品控制程序及处理流程图
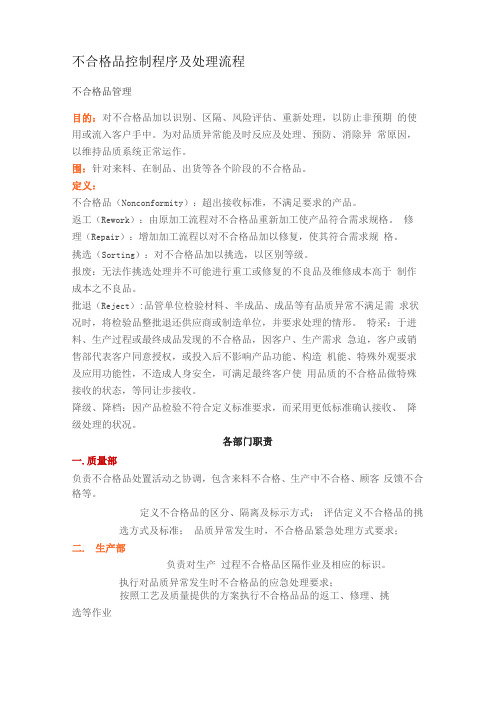
不合格品控制程序及处理流程不合格品管理目的:对不合格品加以识别、区隔、风险评估、重新处理,以防止非预期的使用或流入客户手中。
为对品质异常能及时反应及处理、预防、消除异常原因,以维持品质系统正常运作。
围:针对来料、在制品、出货等各个阶段的不合格品。
定义:不合格品(Nonconformity):超出接收标准,不满足要求的产品。
返工(Rework):由原加工流程对不合格品重新加工使产品符合需求规格。
修理(Repair):增加加工流程以对不合格品加以修复,使其符合需求规格。
挑选(Sorting):对不合格品加以挑选,以区别等级。
报废:无法作挑选处理并不可能进行重工或修复的不良品及维修成本高于制作成本之不良品。
批退(Reject):品管单位检验材料、半成品、成品等有品质异常不满足需求状况时,将检验品整批退还供应商或制造单位,并要求处理的情形。
特采:于进料、生产过程或最终成品发现的不合格品,因客户、生产需求急迫,客户或销售部代表客户同意授权,或投入后不影响产品功能、构造机能、特殊外观要求及应用功能性,不造成人身安全,可满足最终客户使用品质的不合格品做特殊接收的状态,等同让步接收。
降级、降档:因产品检验不符合定义标准要求,而采用更低标准确认接收、降级处理的状况。
各部门职责一.质量部负责不合格品处置活动之协调,包含来料不合格、生产中不合格、顾客反馈不合格等。
定义不合格品的区分、隔离及标示方式;评估定义不合格品的挑选方式及标准;品质异常发生时,不合格品紧急处理方式要求;二. 生产部负责对生产过程不合格品区隔作业及相应的标识。
执行对品质异常发生时不合格品的应急处理要求;按照工艺及质量提供的方案执行不合格品品的返工、修理、挑选等作业负责生产原因造成品质异常之分析与改善;三. 工艺部品质异常发生时之应急处理方案拟定。
对过程品质异常之分析与改善要求。
对修理、返工作业方式定义。
其他部门负责履行本部门的职责予以协助。
不合格品控制流程一. 进料品质异常控制质量部负责设计抽检方案,按照标准执行检验。
不合格品控制流程图
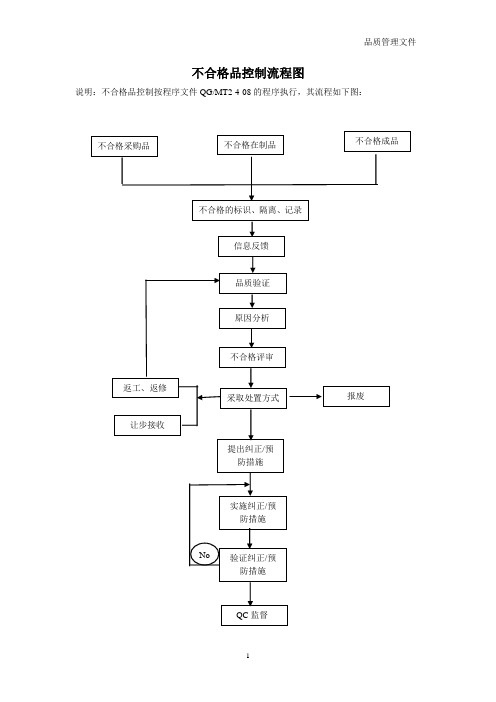
《零件不合格统计表(供应商)》
2
◆检验员应在进货检验记录上记录不合格的现象(含数据)、数量、规格、料号等信息。
◆检验员对不合格品,用不合格品标牌进行标识。
检验员
3
◆检验员通知仓库管理人员将不合格品或批次,移到不合格品区隔离。
依据检验标准分别进入“退/换货”程序或评审程序
检验员
仓库员
4
退货/换货
◆返工、返修:采购部负责组织供方或公司人员在返修区进行返工、返修,技品部负责返工、返修作业的指导和返工、返修后的重检(再次抽检),合格后标识入库。
采购部
技品部
采购部
技品部
《进货检验单》
序号
流程
工作说明
责任部门
使用表单
6
◆让步接收:技品部贴“让步接收”标识入库。
◆整批退货:由采购部负责处理退回,技品部贴“退货”标识。
◆技品部对纠正和预防措施的效果进行验证。
◆技品部对各车间的不合格品,每月进行量化分析,并跟踪和验证计划的实施效果。
生产车间
技品部
《品质异常处置单》
4、客户退货的不合格品处置流程:
序号
流程
工作说明
责任部门
使用表单
1
◆客户的退货产品到公司后,销售部通知仓管员核对退货产品型号和数量,将退货产品隔离存放并做好标识。
◆评审判定为全检由生产车间执行,经检验人员复检合格后才能出货。
◆评审判定为报废则由生产副总指定人员报废。
技品部
生产车间
5
纠正和预防措施及验证
◆属技术问题由技品部组织《品质异常处置单》的制定和实施,由车间进行跟踪验证。
◆属过程控制问题由生产车间组织《品质异常处置单》制定和实施,技品部对纠正和预防措施的效果进行验证。
失效分析流程图

2.1 研磨机采用快速固化剂将材料固化与此内,再用180、320、600目砂纸进行研磨,然后再用抛 光纸进行抛光使之更清晰,再用显微镜观察(15倍)数显微镜测试纵、横截面积及测量结深之
2.2 X-RAY了解到烧结件或焊接件之异常点,若详细观察内部结构还要采用 化学方式解剖分析。
2.3.1 采用H2SO4每次倒200ml左右在烧杯中,再将烧杯放到功率400W的电炉上进行加热,加热到30
2.3.2 进一步用HF去除烧结玻璃,观察焊接件并拍照留证。 2.3.3 再用HNO3将引线、晶粒、焊片分开,观察晶粒状况(30倍显微镜)并拍照留证。
流程图及能力说明
流程说明
1.0 对不良品外观进行检查,采用20,30倍显微镜观察,电子数显卡尺对外观检测,并对材料进行
2.0 电性参数的不良,分别进行常规电性测试及试验测试,进一步确定不良状态,与相同类型的材 料做电性对比(留样及库存材料),收集各相关的实验资料,TK-168测试仪(VR/VF/DVR/IR/TRR) 4810示波器测试VR/VF;576示波器测试VR/VF/IR; 正向电压测试仪测试VF;反向电压测试仪测
电性测试(2.0) 解剖分析
2.0 电性参数的不良,分别进行常规电性测试及试验测试,进一步确定不良状态,与相同类型的材 料做电性对比(留样及库存材料),收集各相关的实验资料,TK-168测试仪(VR/VF/DVR/IR/TRR) 4810示波器测试VR/VF;576示波器测试VR/VF/IR; 正向电压测试仪测试VF;反向电压测试仪测
1研磨机采用快速固化剂将材料固化与此内再用180320600目砂纸进行研磨然后再用抛焊接偏位焊接气孔晶粒位置光纸进行抛光使之更清晰再用显微镜观察15倍数显微镜测试纵横截面积及测量结深之结深深度
质量异常处理流程图

零(合)检检验记录(专检)质量记录台帐
产品标识卡
质量问题通知单
退修品通知单
质量问题通知单
紧急/例外放行申请单
退修品通知单
质量问题通知单
紧急/例外放行申请单
退修品通知单
质量问题通知单
紧急/例外放行申请单退修品通知单
质量问题通知单
紧急/例外放行申请单
十你想过普通的生活,就会遇到普通的挫折。你想过最好的生活,就一定会遇上最强的伤害。
质量异常处理基准
异常
发生时流程
1、停止生产2、隔离标识3、报告班长4、等待指示
1首次发现的不合格
2初物不合格
3关键工序的不合格
4性能项目的不合格
5不良品的连续发生
6其它不合格
责任者
操作工
上序操作工、班长
检查员
工艺员
车间主任
质量部长
技术部长
主管经理
处置对策
内容
异常定义:连续三件不合格以及控制图出现异常。
车间主任:组织追溯不合格品;向质量部报告。
不合格品处置;停产或再生产指示
对不合格进行评审,对工程进行确认,向质量部报告。
对不合格进行评审,对工程进行确认,明确处理方法。
对不合格进行评审。
再生产品质
确认
品质确认后作业开始。
追溯无误后恢复生产。
确认生产的产品无误。
对不合格进行功能性能试验。
记录
零(合)检检验记录(自检)
处置方式:停机、隔离、标识、向上序操作工、班长、检验员报告,等待作业。异常排除后再作业。
上序操作工:自检追溯确认,返工返修后再检验。
班长:互检、追溯、确认,向车间主任报告。处置不合格。
不合格品( HSF)处理流程图ppt课件

工厂内部出现环 境管理物质不合格
负责单位 品保/仓库/制造
库存品的处理
材料向供应商退货替代 合格品/成品直接报废
发生异常
原材料或部件中含 有禁止使用物质 异常连络书的发行
★报告品保部经理/总经理 ★与客户进行联络并报告 ★处理时需注意模向展开其 它料号与追踪上一批物料质 量状况
原因调查
工厂内部混入
纠正预防措施单的发行
ppt课件完整
5
4.0 权责
• 4.1 MRB﹙物料审查委员会﹚:负责不合格 品处理之审核,以决定不合格品之挑选、 返修、重工、退回供应商或予以裁定报废 或特采。
• 4.2不合格品发现/发生部门:负责对不合 格品做适当的识别、隔离及通知。
• 4.3品保:负责产品检验判定及标示区隔, 通知相关单位处置。
从客户反馈环境管理物质不合格信息工厂内部出现环境管理物质不合格供应商提供环境管理物质不合格材料报告品保部经理总经理与客户进行联络并报告处理时需注意模向展开其它料号与追踪上一批物料质量状况原因调查库存品的处理原材料或部件中含有禁止使用物质工厂内部混入异常工序纠正预防措施单的发行异常连络书的发行供应商材料向供应商退货替代合格品成品直接报废不合格对策处理确认会议库存品处理的确认防止再次发生的确认向其它部门或工序的水平推广模向展开标准化对策实施批量产品的进货出货发生异常品保仓库制造负责单位品保品保资料制造供应商业务品保仓库制造品保制造9ppt课件53重工作业流程图此流程不适用于hsf不合格处理流程挑选重工作业重工作业申请批退报废作业流程包装入库保存作业不良状况所费工时记录不合格批产生mrb审查可否重工检验业务
不合格批产生
MRB审查 可否挑选?
NG
报废作业申请
OK
SMT不良品处理流程图

查证是否有代用料 N N
IPQC复核生产线上料正确性 Y
IPQC签名确认
工程科
提供工程样机 PE确认
SMT首件样机确认流程
品质科
SMT科
IPQC元件实物测量 Y
OQC对焊接质量进行复检
生产调试合格首部机芯
N 核对工程样机
Y Y
元件贴装效果确认
N N
通知技术员调试
Y
N
回流焊接或固化并确认质量
填写样机卡并签名
对照样机进行生产、检查
SMT科
SMT首件样机测量流程
品质科
通知技术员调整
转机调试已贴元件合格机芯
N 检查所有极性元件方向 Y
参照丝印图从机芯上取下元件
将仪表调至合适档位进行测量
将实测值记录到首件测量记录表
检查元件实物或通知技术员调整 更换物料或调试后再次确认 将机芯标识并归还生产线
SMT总流程图
N PCB来料检查
Y Y
网印锡膏/红胶
通知IQC处理
N IPQC确认
N 印锡效果检查
Y
贴片
清洗 夹下已贴片元件
N 炉前QC检查
Y
过回流炉焊接/固化
通知技术人员改善
N
校正 Y
N 焊接效果检查
Y 后焊(红胶工艺先进行波峰
效果检查)
N 后焊效果检查
Y N
功能测试 Y
成品机芯包装送检
向上级反馈改善
交修理维修
向上级反馈改善 交修理员进行修理
SMT品质控制流程图
品质科
IPQC在线工艺监督、物料/首件确认 IQC来料异常跟踪处理
OQC外观、功能抽检
Y
N
质量异常处理流程图(1)

异常
发生时流程
1、停止生产2、隔离标识3、报告班长4、等待指示
1首次发现的不合格
2初物不合格
3关键工序的不合格
4性能项目的不合格
5不良品的连续发生
6其它不合格
责任者
操作工
上序操作工、班长
检查员
工艺员
车间主任
质量部长
技术部长
主管经理
处置对策
内容
异常定义:连续三件不合格以及控制图出现异常。
处置方式:停机、隔离、标识、向上序操作工、班长、检验员报告,等待作业。异常排除后再作业。
产品标识卡
质量问题通知单
退修品通知单
质量问题通知单
紧急/例外放行申请单
退修品通知单
质量问题通知单
紧急/例外放行申请单
退修品通知单
质量问题通知单
紧急/例外放行申请单退修品通知单
质量问题通知单
紧急/例外放行申请单互检、追溯、确认,向车间主任报告。处置不合格。
检查员:检查确认判定,隔离、标识,填写“质量问题通知单”向车间、质量部报告,有权停止生产。返工返修后再检验。
工艺员:确认,明确处理方法,考虑其它同类产品,修改工艺。
车间主任:组织追溯不合格品;向质量部报告。
不合格品处置;停产或再生产指示
对不合格进行评审,对工程进行确认,向质量部报告。
对不合格进行评审,对工程进行确认,明确处理方法。
对不合格进行评审。
再生产品质
确认
品质确认后作业开始。
追溯无误后恢复生产。
确认生产的产品无误。
对不合格进行功能、性能试验。
记录
零(合)检检验记录(自检)
产品标识卡
零(合)检检验记录(专检)质量记录台帐
制程不良品处理流程图
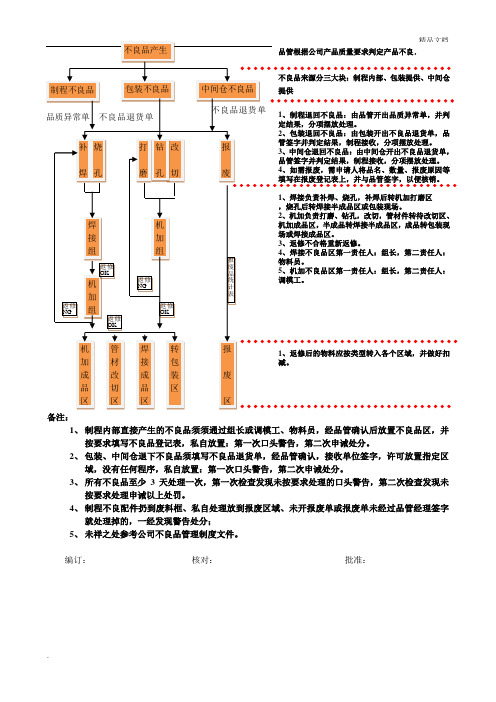
1、制程内部直接产生的不良品须须通过组长或调模工、物料员,经品管确认后放置不良品区,并
按要求填写不良品登记表,私自放置:第一次口头警告,第二次申诫处分。
2、包装、中间仓退下不良品须填写不良品退货单,经品管确认,接收单位签字,许可放置指定区
域,没有任何程序,私自放置:第一次口头警告,第二次申诫处分。
3、所有不良品至少3天处理一次,第一次检查发现未按要求处理的口头警告,第二次检查发现未
按要求处理申诫以上处罚。
4、制程不良配件扔到废料框、私自处理放到报废区域、未开报废单或报废单未经过品管经理签字
就处理掉的,一经发现警告处分;
5、未祥之处参考公司不良品管理制度文件。
编订:核对:批准:
.。
品质不良品的管理流程图
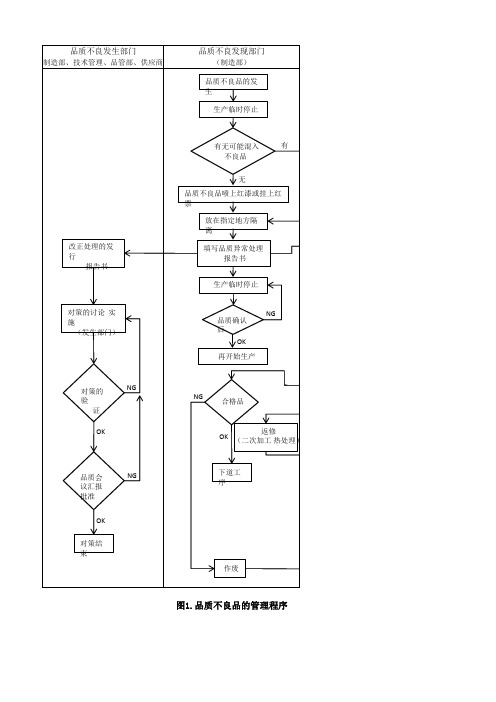
品质不良发生部门 (制造部、技术管理、品管部、供应商)
品质不良发现部门 (制造部)
品质不良品的发 生
生产临时停止
改正处理的发 行
报告书
对策的讨论 实 施
(发生部门)
对策的
NG
验
证
OK
品质会
NG
议汇报
批准
OK
对策结 束
有无可能混入
有
不良品
无 品质不良品喷上红漆或挂上红 票
放在指定地方隔 离
填写品质异常处理 报告书生产临时停止来自品质确认NG后
OK
再开始生产
NG
合格品
返修 OK (二次加工 热处理)
下道工 序
作废
图1.品质不良品的管理程序
品质管理部
追记
确认 过去的品质记 录
品质不良品
品质不良品的识 别
品质不良
NG
品的处理
决定
(品管部)
OK
挑
返修 特采使
退
作废
选
用
货
热处理)
向客户提交特
NG
殊采用申请书
(品管部)
返修件 的检查
OK 下道工 序
OK NG
根据客户要求生 产
出货
不良品处理流程
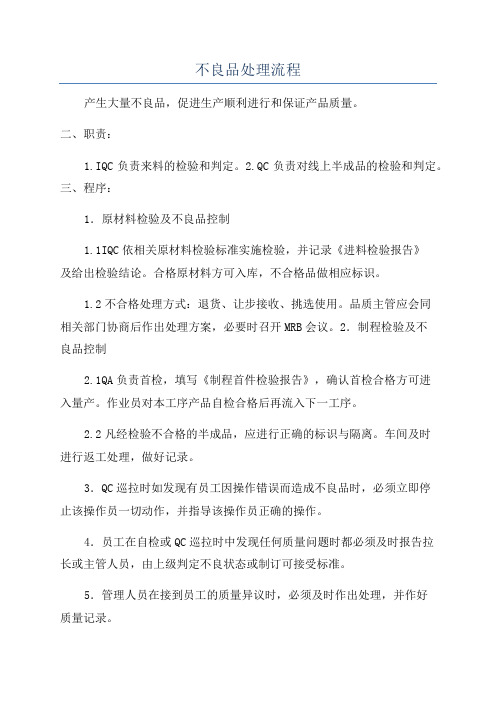
不良品处理流程产生大量不良品,促进生产顺利进行和保证产品质量。
二、职责:1.IQC负责来料的检验和判定。
2.QC负责对线上半成品的检验和判定。
三、程序:1.原材料检验及不良品控制1.1IQC依相关原材料检验标准实施检验,并记录《进料检验报告》及给出检验结论。
合格原材料方可入库,不合格品做相应标识。
1.2不合格处理方式:退货、让步接收、挑选使用。
品质主管应会同相关部门协商后作出处理方案,必要时召开MRB会议。
2.制程检验及不良品控制2.1QA负责首检,填写《制程首件检验报告》,确认首检合格方可进入量产。
作业员对本工序产品自检合格后再流入下一工序。
2.2凡经检验不合格的半成品,应进行正确的标识与隔离。
车间及时进行返工处理,做好记录。
3.QC巡拉时如发现有员工因操作错误而造成不良品时,必须立即停止该操作员一切动作,并指导该操作员正确的操作。
4.员工在自检或QC巡拉时中发现任何质量问题时都必须及时报告拉长或主管人员,由上级判定不良状态或制订可接受标准。
5.管理人员在接到员工的质量异议时,必须及时作出处理,并作好质量记录。
6.管理人员在巡查过程中如发现因来料不良或工艺缺陷导致产生不良品时,应立即停工并及时报告生产主管,由主管人员牵头查找问题根源,并制订相关解决方案后再进行生产。
7.QC负责每日对不良品放置场内的不良品进行判定和常规处理,并作相关记录。
不良品数量较大或不良原因较为突出时,应立刻报告生产主管,由主管负责制订处理方案8.由生产通知相关部门,召开MRB会议,制订不良品的解决方案(退货、加工使用、降级11.物料员对生产现场流入不良品堆放区而又没有不良原因标识的不良品有权拒绝并不予以退换和处理,拉长对因此造成货期延误的事件负责;物料员对有标识但因自身工作疏忽没有及时退换料件造成延误货期事件负责。
12.仓库对生产退换的不良品必须接收,并做好标识,按MRB会议的解决方案进行处理。
13.因不良品产生的欠料,由生产作出统计,如库存不能满足生产时,向计划部出具《物料欠料单》,计划员负责制定《采购申请单》,交采购部安排物料采购。
- 1、下载文档前请自行甄别文档内容的完整性,平台不提供额外的编辑、内容补充、找答案等附加服务。
- 2、"仅部分预览"的文档,不可在线预览部分如存在完整性等问题,可反馈申请退款(可完整预览的文档不适用该条件!)。
- 3、如文档侵犯您的权益,请联系客服反馈,我们会尽快为您处理(人工客服工作时间:9:00-18:30)。
不良分析及跟踪报告
不良品解析 批产品返 工 解 析
不良品分析作业指导书
每批
返工批
测量/ 解剖
不良品分析QC
不良分析及跟踪报告
不良品分析作业指导书
实物核对
作业员/QC
电子参数测试统计
不良品分析作业指导书
每批
综合原因
不良品分析QC
不良分析及跟踪报告 异常LOT处置报告书 异常产品处理单 异常产品处理单 异常LOT处置报告书
降级/ 报废
不良品分析作业指导书
每批
实物核对
QC/作业员
批产品正常流传
分选作业指导书
每批
实物核对
作业员/QC
电子参数测试统计
启动纠正预防 改
异常LOT处置报告书
降级பைடு நூலகம்报
检查追踪
品管/生产
异常LOT处置报告书
原因分析、预防改 善措施
异常LOT处置报告书
改善效果
分析改善 结果跟踪
品管/生产
异常LOT处置报告书
分选不良品解析工作流程相关图
工作流程相关图
批产品上机前首检
管理项目/标准
检查频次
检查方法
责任人
管理图表
分选作业标准/指导书
换批前
目视/核对
作业员/QC
电子参数测试统计
批产品正常生产
分选作业标准/指导书
每批
目视/核对
作业员/QC
对批不良品 上机分类取样
C、DF、ILC、短路、
开
每批
实物核对
不良品分析QC