A Shape Metric for Design-for-Assembly
ASME-BPE-中英对照
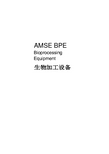
AMSE BPE Bioprocessing Equipment生物加工设备生物加工设备GR部分一般要求GR-1简介INTRODUCTION此标准所规定的要求,在生物处理﹑制药和个人保健品行业设备的设计非常实用,所涉及方面包括灭菌﹑清洁﹑材质﹑尺寸﹑公差﹑表面抛光﹑材料接合和密封等。
主要应用于:This Standard provides the requirements applicable to the design of equipment used in the bioprocessing,pharmaceutical,and personal care product industries,including aspects related to sterility and cleanability,materials,dimensions and tolerances, surface finish,material joining,and seals.These apply to:(a)在制造﹑改进和提高过程中与产品﹑原料﹑产品介质直接接触的关键部件;(b)产品制造中主要部件系统(如WFI,清洁蒸汽,过滤和半成品贮存等)(a)components that are in contact with the product,raw materials,or productintermediates during manufacturing,development,or scale-up;(b)systems that are a critical part of product manufacture[e.g.,water-for-injection(WFI),clean steam,filtration,and intermediate product storage].此标准不能应用于以下部分:不与成品或制造阶段介质部分直接接触的系统(如计算机系统,电气导管以及外部系统支撑结构)。
水系封闭解决方案潮水NSF标准61列出材料ISO9001 QS9000认证目录PSG5025A-US

Water System Sealing Solutions Potable Water NSF Standard 61 Listed MaterialsISO 9001 / QS 9000CertifiedCatalog PSG 5025A-USA(Revised September 2000)NSF®Parker Hannifin CorporationTechSeal Division/O-Ring Division Spartanburg, SC/Lexington, KY /sgBuild With The Best!Potable Water Sealing SolutionsPSG 5025AIntroductionBuild With The Best!Parker Hannifin CorporationTechSeal Division/O-Ring Division Spartanburg, SC/Lexington, KY/sgPotable Water Sealing Solutions PSG 5025AParker Seal Group produces a wide range of “standard” and “custom” seal products for potable water applications fabricated from a wide variety of approved NSF Standard 61 materials as well as many non-NSF Standard 61 materials.Seal materials used to produce these parts are guaranteed via Parker’s “C.B.I.” (controlled batch identification) system. This is a system of batch numbering, physical property testing, and traceability which ties the entire quality control system together from the master batch to finished seals.Parker TechSeal Division Extruded & Cut Parts have been manufactured for a large variety of high volume applications for over 35 years. Our unique process for producing precision extrusion and cut static seals provides customers tremendous design flexibility, typically with no tooling charges for any ID/OD combination from .040” to 3.000” outside diameters. T echSeal uses only “sealing grade” material formulations with the highest possible percentage of polymer for the most effective long-term sealing solutions.Extruded and cut products are primarily supplied as ID/OD tubing type cross-sections, but are also supplied in a variety of different cross-sections such as: square, rectangular, triangular and many other profiles.FEATURES - ADVANTAGES - BENEFITS•Custom designed seals can be produced for specific applications with no tooling required for ID/OD cross-sections, saving the customer time and money.•Maximum sealing surface contact area can be obtained because of flat, smooth edges with no hourglassing or mold flash.For more information regarding TechSeal Extruded & Cut Parts, please reference Parker’s TOTAL inPHorm Design Software.Parker O-Rings are offered in EPDM and Nitrile NSF 61 ap-proved elastomeric materials, ranging from 65 to 90 durometer, for use in sealing potable water applications.In addition to being NSF approved, these materials also minimize the potential for concentration of leachable contaminants in potable water.Parker O-Rings are available in AS568A Standard, DIN, JIS metric or custom sizes, as the application warrants. Parker technical support associates are available to address design considerations such as temperature, pressure, gland design, surface finish, etc., and can propose several design alternatives. In addition, Parker can support unique testing requirements or work with customers to develop the appropriate test protocol.FEATURES - ADVANTAGES - BENEFITS •Ongoing material development to respond to changes in the potable water systems industry.•Consistent physical properties to assure sealing integrity.•State-of-the-art equipment to ensure consistent process control.•In-house tooling design and fabrication capability allows for quick turnaround and delivery of prototypes and pro duction requirements.For additional information on all Parker O-Rings, please reference Parker’s TOTAL inPHorm Design Software. Or ask for a copy of the O-Ring Reference Guide (ORD5703).Product Lines - Extruded & Cut Parts & O-Rings Typical Parker TechSeal Extruded and Cut Parts used inPotable Water ApplicationsTypical Parker O-Ring Seals used in Potable WaterApplicationsPotable Water Sealing SolutionsPSG 5025AParFab Extruded Profiles are typically used for fabrication into spliced rings, 4-Corner Spliced Picture Frame Gaskets or custom parts cut to specific lengths. However , these profiles can also be supplied in bulk footage. T echSeal offers many standard extruded profiles in many configurations, such as:Solid & Hollow-O, Solid & Hollow D, U-Channel, Rectangular ,Solid & Hollow Square and Hollow-Dart configurations.Spliced/Fabricated Parts are made using a hot vulcanization process to provide spliced rings and custom gaskets from either “standard ” or “custom ” cross-sectional profiles. These products offer an ideal, cost-effective sealing solution for many applications. These include low-closure force seals, large diameter profiles that cannot be molded, or requirements for hollow O-rings, non-standard solid O-rings, and other ex-truded profiles with an inside diameter larger than 2.500.”FEATURES - ADVANTAGES - BENEFITS•Suitable for use in either traditional grooves or may be applied directly to any flat surface.•Superior hot vulcanization technology providesstronger, more reliable joints.•Finite Element Analysis (FEA) available to optimize seal design.•Ease of adjusting closure force by adjustment ofcross-section design, cross-section I.D. or durometer.•Hollow cross-sections are excellent replacements for foam or sponge gaskets and offer superior compres-sion set resistance.•Interference fit designs with asymmetrical solid or hollow cross-sections allow for ease of assembly.For more information on TechSeal ParFab ExtrudedProfiles and Spliced Seals and Gaskets, please reference the ParFab Catalog (JBL-5420).Parker Custom Molded Shapes are designed to meet customer-specific requirements, and incorporate a wide range of NSF approved Parker materials. These seals are homogenous rubber parts functioning as sealing devices in both dynamic and static applicationsthey are available in sizes up to 32 inches outside diameter with a cross section thickness up to 1.5 inches.Parker maintains a highly qualified staff of engineering professionals supported by a technical group using the latest CAD technology to assist customers during the critical early design phase of a project.Parker technical associates will work with customers on function,shape and material requirements, to design the best sealing solution for their application.Through value analysis, Parker can assist in selecting the most cost effective sealing solution, while maintaining full sealing integrity and quality control.FEATURES - ADVANTAGES - BENEFITS•Finite Element Analysis (FEA) available to shorten seal design time and provide the best sealing solution for the application.•Produced in NSF61 materials as well as other elas-tomer families, offering a wide selection of materials.•Designed to meet customer specific requirements to ensure compliance with all specifications.•Perfect fitting parts can result in less installation time and ultimately reduce assembly cost.For additional information or assistance in designing a custom molded seal or shape, please contact a TechnicalSupport Representative.Product Lines - Molded Shapes & Spliced SealsParker Hannifin CorporationTechSeal Division/O-Ring Division Spartanburg, SC/Lexington, KY /sgBuild With The Best!Typical Parker Custom Molded SealsTypical TechSeal ParFab Extruded and Spliced PartsParker Hannifin CorporationTechSeal Division/O-Ring Division Spartanburg, SC/Lexington, KYBuild With The Best!Potable Water Sealing SolutionsPSG 5025ANSF Standard 61 Listed MaterialsBuild With The Best!Parker Hannifin CorporationTechSeal Division 3025 West Croft Circle Spartanburg, SC 29302Phone: (864) 573-7332Fax: (864) 583-4299For the latest information on all Parker Hannifin products, visit our website at O-Ring Division 2360 Palumbo drive Lexington, KY 40509Phone: (859) 269-2351Fax: (859) 335-5128• O-Rings • Static Seals• Composite Sealing Products • Hydraulic & Pneumatic Seals• EMI Shielding & Thermal Management ProductsFor fast, easy and accurate seal design assistance, ask for a copy of Parker’s TOTAL inPHorm TM Seal Design and Material Selection Software. Now avail-able for:。
公司名:Parker,产品:Parkrimp系统,型号:无说明书
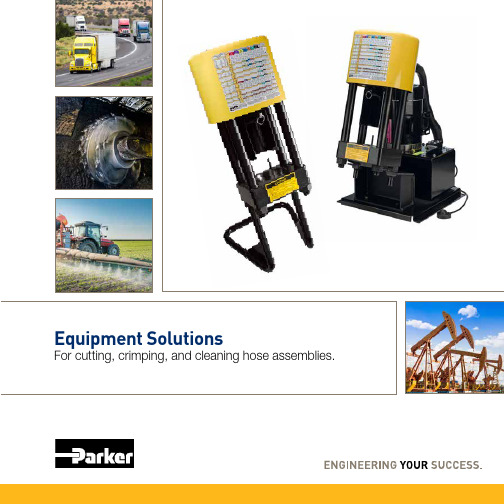
EQUIPMENT SOLUTIONS Every step of the way.With the largest selection of hose, and more fitting sizes andconfigurations than any other manufacturer, Parker has exactlywhat you need. Parker also delivers exceptional quality and reliabilitywhen it comes to equipment and tooling. Factory-quality hoseassemblies can be quickly, easily, and cost effectively manufacturedwith Parker’s industry leading equipment. For example, Parker’sParkrimp system provides users with several key advantages:n P erfect alignment: Our exclusive Parkalign systempositions the fitting in the die for a perfect crimp every time.n E fficient design: Bottom loading crimpers make iteasier for operators to manage long hose lengths.n C olor-coded linked dies: Our linked dies arecolor-coded by size for easy identification.n D urability: Parkrimp crimpers have been designed andmanufactured to provide years of reliable service.A complete line of equipment and tooling from hose saws, topush-on stands, to crimpers, to cleaning and capping systemsare available to help you every step of the way while fabricatinghose assemblies.Parker has a multiple hose cut-off machines that offer industry leading performance. They are engineered to cut single and multiple wire reinforced hose easily and efficiently. Our cut-off machines are easy to operate and assure clean, square hose cuts. These machines require very little work space due to their compact design. We offer three different cut-off machines in order to deliver what you need for your fabrication requirements.Part No. 332T-115Vn C uts spiral reinforced hose up to1¼" I.D.n8" scalloped cutting bladen1.5 HP, 3450 RPM, 115/230V singlephase electric motor wired for 115VLET PARKER HELP YOU select the appropriate materialsand tooling.CrimpSource is Parker’s exclusive online software applicationthat supplies you with the necessary crimp specifications inorder to adhere to our strict safety standards. It is the industry’smost complete resource for crimper technical information.It provides easy access to all the specifications necessaryto correctly fabricate a factory-quality hose assembly.With a series of dropdown menus, users are able to choosea crimper, the type of hose, and compatible fittings. Once thecrimper is selected, the user is provided with crimp specs,crimper die recommendations, technical manuals, and crimperdecals available for immediate printing.For complete product information on all of Parker’s crimpers,please visit:/crimpsourcePart No. 631075n C uts multi-braided wire reinforced hose including 4-wire spiral up to 1¼" I.D.n7" scalloped cutting bladen115V, 13 amp, universal AC motorn P ortable saw for cutting on the job with universal clamp attachment Part No. 239 & 339n C uts multi-braided wire reinforced hose including 6-wire spiral up to 2" I.D.n 10" scalloped cutting bladen Model 239 – 230V, single phase motor n M odel 339 – 3 HP motor 230V,3 phase, 60 cycleIn order to make a proper hose assembly, hoses must be pushedcompletely onto the fitting. If the hose is not inserted into the shell ofthe fitting per the recommended length, the fitting can blow off, makingfor extremely dangerous situations. Hose insertion depth blocks are away to quickly and easily mark proper hose insertion depth for guaranteedvalidity each and every time and reducing the risk of failure.In addition to hose insertion depth blocks, Parker offers a fitting push-onstand which quickly and easily pushes fittings onto hose, in order to boostproductivity and quality of hose assemblies. This stand eliminates the needfor rubber mallets and oils to get fittings onto the end of the hose and canbe used for crimped fittings as well as field attachable fittings.crimping is simple.Karrykrimp & Karrykrimp Bench MountParker’s Karrykrimp modular design comes in both bench mount and portable styles. This gives users the flexibility of aportable crimper with the advantages of increased productivity when connected to the stationary power unit. The increasedheight enables longer bent tube fittings to be crimped with Parker’s 25, 26, 43, 81 and HY Series Parkrimp fittings.Parker’s Karrykrimp models can crimp straight or bent-stem steel fittings from 5/8" to 1-1/4" in diameter.n C ompatible with 2-wire braided hoses up to 1-1/4" I.D. and 4-wire spiral hoses up to 5/8" I.D.n P ivoting pusher design for easy die change outn F or use with 25, 26, 43, 81, and HY series steel fittingsO ptional Tooling: Die Kit 43K-KDA (Includes 43 Series dies in sizes 1/4", 3/8", 1/2", 3/4", 1", 1-1/4" only)Karrykrimp 2 & Karrykrimp 2 Bench MountThe Karrykrimp 2 is a portable or bench mount, compact and ruggedly built crimper that is an economic alternative for the self-assembly of Parker’s hose and fittings. Parker’s Karrykrimp 2 models can easily crimp Parkrimp style straight or bent-stem stainless and stainless steel fittings up to 1-1/4" in diameter including 25, 26, 43, 70, 71, 73, 77, 78, 81 and HY series.n C ompatible with 2-wire braided hoses up to 1-1/4" I.D., 4-wire spiral hose up to 1-1/4" I.D., and 6-wire spiral hose up to 1" I.D.n P ivoting pusher design for easy die change outn F or use with 25, 26, 43, 70, 71, 73, 77, 78, 81 and HY series fittingsParkrimp 2The Parkrimp 2 is Parker’s largest and most versatile crimper that comes in either single phase or three phase electric. Parker’s Parkrimp 2 models can crimp straight or bent-stem steel and stainless steel fittings from 1/4" to 2" in diameter including 25, 26, 43, 70, 71, 73, 76, 77*, 78, 79, 81 S6, and HY series.n C ompatible with 2-wire braided hose up to 2" I.D., and 4- and 6-wire spiral hose up to 2" I.D.n C rimps both steel and stainless steel fittingsn For use with 25, 26, 43, 70, 71, 73, 76, 77*, 78, 79, 81 S6, and HY series fittings*Can crimp 77 series stainless steel fittings up to 1-1/2"Optional Tooling: D ie Kit PK2-KDA (Includes 43 Series dies in sizes 1/4", 3/8", 1/2", 3/4", 1", 1-1/4" and77 Series dies in sizes 1/2", 5/8", 3/4", 1", 1-1/4", 1-1/2", and 2" only) or Die Kit 77K-KDA(includes 77 Series dies in sizes 1/2", 5/8", 1", 1-1/4", 1-1/2", and 2" only)O ptional Tooling: D ie Kit KK2-KDA (Includes 43 Series dies in sizes 1/4", 3/8", 1/2", 3/4", 1", 1-1/4" and77 Series dies in sizes 1/2", 5/8", 3/4", and 1" only)the way you want.Production CrimperThe TH8-380 sets a new standard for high quality and cost effective production crimpers. The electronic controls come preloaded with Parker hose part numbers and crimp specifications to make hose selection quick and easy. Furthermore, the greaseless die design of the TH8-380 requires less maintenance and provides a cleaner work environment due to the revolutionary slide bearing technology.n C ompatible with 2-wire braided hose up to 3" I.D., 4- and 6-wire spiral hose up to 3" I.D., and up to 4" industrial hoses n G reaseless die designUltra Clean Hose Cleaning Kit .ORGANIZATION IS KEYto reducing labor costs.After your hose assembly is complete, the final step is to rid the assembly of any possible contamination. Tiny particles could be stuck inside the hose from the fabrication process, so Parker offers several products to help make sure your hose assemblies are contamination free – reducing costly downtime and hose failures. Parker offers two hose cleaning kits that will ensure your hose assemblies are contamination free. These kits include a pellet flushing system, which fires a Styrofoam pellet through the hose assembly dragging out any debris that may be stuck in the hose. It takes only seconds to clean, greatly reducing the chance of a hydraulic system failure.Along with the pellet flushing system, Parker offers an innovative capping system. Clean Seal is a quick, easy, and clean alternative to cap your hose and fitting assemblies. This reduces contamination, capping time, and cap inventory as one cap may fit many different end configurations and sizes. Simply place the cap on the end of your hose or fitting, place in the Clean Seal System for a few seconds, and remove. The caps enable a secure fit due to the heat shrink technology. Caps can just as easily be removed by pulling the tab that sticks up once heated.Parker offers stock bins and die racks in order to keep hoses, fittings, and dies organized so you can easily and efficiently find what you are looking for. Storing and selecting the right materials is made easy and simple, which can boost productivity and quality of fabricating hose assemblies.Economy Hose Cleaning KitClean Seal© 2016 Parker Hannifin Corporation BUL.4480-B188 10/16Your complete source for quality tube fittings, hose & hose fittings, brass & composite fittings, quick-disconnect couplings, valves, and assembly tools, locally available from a worldwide network of authorized distributors.Fittings:Available in inch and metric sizes covering SAE, BSP , DIN, GAZ, JIS, and ISO thread configurations, manufactured from steel, stainless steel, brass, aluminum, nylon, and thermoplastic.Hose, Tubing, and Bundles:Available in a wide variety of sizes and materials including rubber, wire-reinforced, thermoplastic, hybrid and custom compounds.Worldwide Availability:Parker operates Fluid Connectors manufacturing locations and sales offices throughout North America, South America, Europe, and Asia-Pacific.For information, call toll-free:1-800-C-PARKER (1-800-272-7537)Parker Fluid Connectors GroupNorth American Divisions & Distribution Service CentersNorth American DivisionsFluid System Connectors Division Otsego, MIphone 269 694 9411fax 269 694 4614Hose Products Division Wickliffe, OHphone 440 943 5700fax 440 943 3129Industrial Hose Division Wickliffe, OHphone 440 833 2120fax 440 833 2230Parflex Division Ravenna, OHphone 330 296 2871fax 330 296 8433Quick Coupling Division Minneapolis, MNphone 763 544 7781fax 763 544 3418Tube Fittings Division Columbus, OHphone 614 279 7070fax 614 279 7685Distribution Service CentersBuena Park, CAphone 714 522 8840fax 714 994 1183Conyers, GAphone 770 929 0330fax 770 929 0230Louisville, KYphone 502 937 1322fax 502 937 4180Portland, ORphone 503 283 1020fax 503 283 2201Toledo, OHphone 419 878 7000fax 419 878 7001fax 419 878 7420 (FCG Kit Operations)CanadaGrimsby, ONTphone 905 945 2274fax 905 945 3945(Contact Grimsby for other Service Center locations.)Parker Hannifin Corporation Fluid Connectors Group 30240 Lakeland Blvd.Wickliffe, OH 44092phone 440 943 5700fax 440 943 3129。
常用机械制图英语
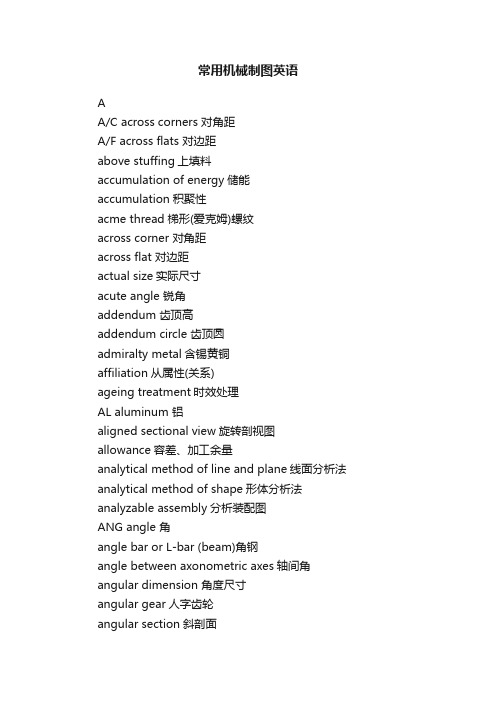
常用机械制图英语AA/C across corners 对角距A/F across flats 对边距above stuffing上填料accumulation of energy储能accumulation积聚性acme thread梯形(爱克姆)螺纹across corner 对角距across flat 对边距actual size实际尺寸acute angle 锐角addendum 齿顶高addendum circle 齿顶圆admiralty metal含锡黄铜affiliation从属性(关系)ageing treatment时效处理AL aluminum 铝aligned sectional view旋转剖视图allowance容差、加工余量analytical method of line and plane线面分析法analytical method of shape形体分析法analyzable assembly分析装配图ANG angle 角angle bar or L-bar (beam)角钢angle between axonometric axes轴间角angular dimension 角度尺寸angular gear人字齿轮angular section斜剖面angularity倾斜度anneal退火anti-clockwise逆时针方向的arrow or arrowheads 箭头asbestos packing石棉填料ASM assembly 装配(图)、部件assembly drawing number装配图图号assembly drawings装配(组装)图assembly for installation安装图assembly parts装配组合零件assembly sketches装配草图auxiliary circle辅助圆auxiliary plane辅助平面auxiliary sectional view斜(辅助)剖视图 aligned and developed 展开视图AVG average 平均axial coefficients of foreshortening轴向变形系数axis line 轴线axis of rotation转轴axis轴线axonometric axes轴测轴axonometric drawing轴测图axonometric projection轴测投影BBAB Babbitt 巴氏(轴承)合金back (rear) view后(背)视图bar杆base line 基准线base parts机座base plane底平面basic deviation基本偏差basic hole基准孔basic shaft基准轴basic size基本尺寸BB ball bearing 滚动轴承bearing cover轴承盖bearing set轴承座 bearing轴承bell metal青铜(锡铜)合金belt wheel带轮bevel gear斜齿轮BHN Brinell hardness number 布氏硬度值bisector 平分线blade spring板簧blind hole 盲孔(不通的孔)blind hole盲孔blind threaded hole螺纹盲孔blunt angle 钝角body of revolution回转体bolt joint螺栓连接bolt螺栓border 图框border line 图框线boring machine or boring镗床boring镗孔boss club凸台bottom shell 下轴瓦box箱体brazing metal铜锌合金bright washer平垫圈Brinell hardness布氏(HB)硬度broacher拉床、绞孔机broaching拉床、扩孔机broach拉光broken line 断裂线broken view (local view)局部视图BRS brass 黄铜BRZ bronze 青铜burnish or polishing磨光butterfly valve蝶形阀buttress (screw) thread锯齿形(枪膛)螺纹caliper卡尺(钳)cap screw带帽螺钉(栓)capital letters 大写字母carburizing (carbon infiltration)渗碳case hardened硬化、表面淬火casting defect铸件缺陷casting processes铸造工艺casting铸造、铸件castle nut内六角圆螺母cavity空腔(穴)CBORE counterbore 沉孔、埋头孔center to center distance 中心距centerline (central line) 中心线center-to-center spacing中心距central projection中心投影CH HD cheese head 开槽圆柱头CHAM chamfer 倒角chamfer倒角channel bar槽钢characteristics of projection 投影特性CHD checked (by) (由) …校对check drawings校(核)图cheese head圆柱头Chinese characters 汉字chrome plating镀铬CI cast iron 铸铁CIR circular 圆的circular arc 圆弧、弧circular pitch 齿距circular pitch周节circular runout圆跳动CL or centerline 中心线clamping夹紧clearance fit间隙配合clockwise顺时针方向的CM centimeter 厘米coarse pitch thread粗牙普通螺纹coarse wheel粗砂轮加工coating涂覆coincidence (revolved) section重合断面coincident point重影(合)点color-hardening着色硬化、发蓝、发黑combination solids组合体commom tangent公切线common axis公共轴线common point 共有点compass 圆规component构件compound sectional view复合剖视图concave millstone凹面磨盘concentric circle同心圆concentricity and coaxiality同轴(心)度conic (miter) gear圆锥(伞)齿轮connecting bar连杆construction line 作图线contact surfaces接触表面continuous straight thin line with zig zags 折线continuous thick line 粗实线continuous thin irregular line 波浪线continuous thin line 细实线contour arithmetic mean deviation轮廓算术平均偏差contour element外形素线conventional breaks折断规定画法conventional representation规定画法converge聚为一点convex millstone凸面磨盘coordinate axis坐标轴COP copper 铜copper plating镀铜corrosion腐蚀cotter (split) pin 开口(尾)销counterbore hole 阶梯沉孔、埋头孔counterboring tool 平底扩孔钻counter-drill 阶梯钻countersunk hole锥形沉孔、埋头孔coupling or union连轴器covering external thread套扣CP circular pitch 周节crank摇把cross rib十字肋cross section shape横断面形状crossing line交叉线crossing point交叉点CRS (C to C) centers 中心距CSK countersunk 锥孔、埋头孔CU cubic 立方的CU FT cubic foot 立方英尺CU IN cubic inch 立方英寸CU YD cubic yard 立方码cube立方体cuboid长方体cup packing皮碗密封curve template 曲线板curved line of intersection曲交线curved slot 曲线槽cutting plane symbol剖切平面符号cutting plane剖切平面cut断面图cycloidal gear摆线齿轮CYL cylinder (cylindrical) 圆柱、圆柱体的cylindricity圆柱度Ddashed thin lines 虚线datum feature基准要素datum line基准线datum plane基准面datum point基准点datum symbo基准代号 ldeburring去毛刺dedendum circle 齿根圆dedendum 齿根高DEG or ? degree 度delineator制图者descriptive geometry 画法几何descriptive geometry solution 图解法design datum设计基准DET DWG detail drawing 零件图detail drawing零件图detailing (an assembly drawing) (由装配图)拆画零件图deviation尺寸偏差(偏差)DIA or φ diameter 直径DIAG diagonal 对角线(的)diagonal line 对角线diagram assembly drawing装配工作图diagrammatic drawing示意图diameter 直径diamond knurling网纹滚花dimension 尺码dimension figure 尺寸数字dimension form 尺寸格式dimension line 尺寸线dimension text 尺寸数值dimension tolerance尺寸公差dimetric drawing正二轴测图dividers 分规dome圆顶状double-start thread双线螺纹dowel pin 圆柱销draft or draught起模斜度drafting paper 绘图纸drafting tape 胶带纸drawing board 图板drawing number图号DRG drawing 制图、图样drilling钻孔drive gear主动齿轮driven gear从动齿轮driven shaft从动轴DRN drawn (by) (由) …绘图ductile cast iron球墨铸铁dynamometry测力Eedge line棱线effective diameters弹簧中径effective length有效长度EI or ei 来自法文ecart inferieur 下偏差代号elbow肘形弯管(头) element circle素线圆element symbol基本符号elementary unit基本体ellipse椭圆elongated hole延长孔、拉伸孔end cover端盖end face端面end point端点engineering requirements技术要求enlarged partial view局部放大图enlargement scale 放大比例EQUI SP or EQS equally spaced 均布erasing shield 擦图片ES or es 来自法文ecart superieur 上偏差代号EXT external 外部的extension line 尺寸界线external (male) thread外(阳)螺纹external diameter弹簧外径external dimension外形尺寸external tangency 外切external thread lathing车外螺纹external view外形视图extreme position of moveable part 活动极限位置extruding挤压FFAB fabricate 制造、装配faucet旋塞、水龙头feed spiral送料螺旋felt ring毡圈ferrous metal黑色金属FIG. figure 附图、插图FIL fillister 凹槽file锉filing margin 装订边fill in填写fillet铸造(内)圆角fine boring精镗fine broaching精拉fine grinding精磨fine milling精铣fine pitch thread细牙普通螺纹fine planning精刨fine turning精车finish all over全部加工fissure裂纹fit symbol配合代号fit system配合制fit配合55? non sealing pipe thread 55?非密封管螺纹55? sealing pipe thread 55?密封管螺纹fixed body固定钳身flange法兰盘、凸缘flat bar扁钢flat heads平顶flat or plane平面flatness平面度follower从动(大齿)轮font 字体font cavity缩孔、铸口forging锻压fork拨叉form error形状误差forth quadrant第四象限four quadrants四个象限45? mitre line 45?斜线free hand 徒手(画)free height自由高度frontal line正平线frontal plane (or V-plane)正投影面frontal plane正平面frustum of a cone圆锥台frustum of a cone截头圆锥frustum of a pyramid棱锥台FT or ′foot 英尺full sectional view全剖视图full size 原值比例full thread全螺纹functional dimensions功能尺寸Ggasket密封垫(圈)gauge calipers卡(量)规gear box (case)齿轮箱gear train齿轮传动gear齿轮general fit class配合种类general-plane 一般位置平面general-position line一般位置直线generating circle母线圆generator (generation) line母线Geometric construction 几何作图geometrical solid几何体geometrical tolerance symbol形位公差符号geometrical tolerance形状位置公差GI galvanized iron 马口铁、镀锌铁gib-head key钩头楔键gland压盖gland密封压盖globe valve球阀good-quality carbon steel优质碳素钢grade 坡度grade A and grade B of type one hexagon nutI 型六角螺母A 级和B级graduated scale 比例(分度)尺graphical representation 图示法Graphics 图学GRD grind 磨削grey cast iron灰口铸铁grinding machine磨床grinding研磨grinding磨削groove 凹槽、沟纹guard valve安全阀guide pin定位销guide screw丝杠Hhalf sectional view半剖视图half view半视图hand valve手压阀hard casting白口铁hard metal硬质合金hardened and tempered调质的harden淬火hardness number硬度值Hatching 剖面线heat-treatment热处理heavy lines 加深图线heavy metal重金属helical compression spring圆柱螺旋压缩弹簧helical spring螺旋弹簧helical spur gear斜齿圆柱齿轮helical tension spring圆柱螺旋拉伸弹簧herringbone gear人字形圆柱齿轮HEX hexagon 六角(边)形HEX HD hexagon head 六角头hex nut六角螺母hex slotted nut六角开槽螺母hexagon head 六角头hexagon head bolt六角头螺栓hexagon head bolt六角头螺栓hexagon socket cap screw内六角圆柱头螺钉hexagon thin nut 六角薄螺母hidden edges 不可见轮廓线high-carbon steel高碳钢high-speed steel高速钢hole-basis system of fits基孔制配合horizontal (level) plane水平面horizontal line水平线horizontal projection plane (H-plane)水平投影面hot-rolled steel热轧钢HP horsepower 马力H-perpendicular line铅垂线H-perpendicular plane铅垂面HR hour 小时hub轮毂hub轮毂、中心hyperbola双曲线Ihypotenuse直角三角形之斜边(弦)I/D inside diameter 内径、内形尺寸I-beam工字钢imaginary line 假想线IN or ″ inch 英寸incenter 内(切圆)心included angle夹角inflexion拐点ingot iron低碳钢(工业纯铁)initial outline 初始轮廓线inlet side入口端inner race内圈inside diameter内径instruction book说明书instrumental drawing 用仪器画的图INT internal 内部的interchangeability互换性interference fit过盈配合internal (female) thread内(阴)螺纹internal (inside) caliper内卡尺(钳)internal diameters弹簧内径internal tangency 内切internal thread lathing车内螺纹interpenetration相贯intersecting plane截平面intersection line截交线intersection of plane surfaces平面之交线intersection of surfaces表面之交线intersection point交点Intersection相交Intuitive illustrations直观图involute gear渐开线齿轮iron铁ISO standards ISO国际标准ISO=International Standardization Organization国际标准化组织isometric drawing (diagram)正等轴测图isometric projection正等测投影isometric sectional view正等轴测剖视图Italic font 斜体Jjack千斤顶、起重器jig body夹具体junction surface结合面Kkey diagram原理草图key joint键连接key seat键座key types键的型式key way (slot)键槽key键knobbled (wrought) iron熟(锻)铁knurling 滚花knurling nut滚花螺帽Llamp plank钳口板LAT lateral 侧(横)向的lathe车床LB pound 磅lead distance导程leader line 指引线lead导程leaf spring叶(薄)片弹簧left hand-thread左旋螺纹left-hand side (end) view左(端)视图length of thread engagement螺纹旋合长度letter 字母lever arm长臂杠杆LG long .length 长度、长的LH left hand 左旋、左方向light metal轻金属limit size极限尺寸limiting deviations极限偏差limiting element转向轮廓素线LIN linear 线性的、直线的line segment 线段line styles 线型linearity直线性lines in planes线在面上L-iron角铁local (broken-out) sectional view局部剖视图location by dimension 定位尺寸location dimension尺寸定位lock nut防松螺母lock screw锁紧螺钉locking device锁紧装置LONG longitude 经度(线)long dashed dotted thin line 点画线long dashed double dotted thin line 双点画线lower-case letters 小写字母lower deviation下偏差lower limit下限(值)lubricant pump齿轮油泵。
ASTM钢铁标准.F432
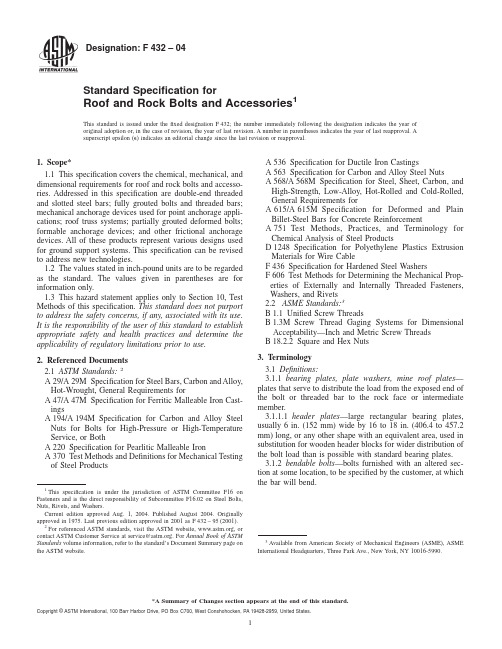
Designation:F432–04Standard Specification forRoof and Rock Bolts and Accessories1This standard is issued under thefixed designation F432;the number immediately following the designation indicates the year of original adoption or,in the case of revision,the year of last revision.A number in parentheses indicates the year of last reapproval.A superscript epsilon(e)indicates an editorial change since the last revision or reapproval.1.Scope*1.1This specification covers the chemical,mechanical,and dimensional requirements for roof and rock bolts and accesso-ries.Addressed in this specification are double-end threaded and slotted steel bars;fully grouted bolts and threaded bars; mechanical anchorage devices used for point anchorage appli-cations;roof truss systems;partially grouted deformed bolts; formable anchorage devices;and other frictional anchorage devices.All of these products represent various designs used for ground support systems.This specification can be revised to address new technologies.1.2The values stated in inch-pound units are to be regarded as the standard.The values given in parentheses are for information only.1.3This hazard statement applies only to Section10,Test Methods of this specification.This standard does not purport to address the safety concerns,if any,associated with its use. It is the responsibility of the user of this standard to establish appropriate safety and health practices and determine the applicability of regulatory limitations prior to use.2.Referenced Documents2.1ASTM Standards:2A29/A29M Specification for Steel Bars,Carbon and Alloy, Hot-Wrought,General Requirements forA47/A47M Specification for Ferritic Malleable Iron Cast-ingsA194/A194M Specification for Carbon and Alloy Steel Nuts for Bolts for High-Pressure or High-Temperature Service,or BothA220Specification for Pearlitic Malleable IronA370Test Methods and Definitions for Mechanical Testing of Steel ProductsA536Specification for Ductile Iron CastingsA563Specification for Carbon and Alloy Steel NutsA568/A568M Specification for Steel,Sheet,Carbon,and High-Strength,Low-Alloy,Hot-Rolled and Cold-Rolled, General Requirements forA615/A615M Specification for Deformed and Plain Billet-Steel Bars for Concrete ReinforcementA751Test Methods,Practices,and Terminology for Chemical Analysis of Steel ProductsD1248Specification for Polyethylene Plastics Extrusion Materials for Wire CableF436Specification for Hardened Steel WashersF606Test Methods for Determining the Mechanical Prop-erties of Externally and Internally Threaded Fasteners, Washers,and Rivets2.2ASME Standards:3B1.1Unified Screw ThreadsB1.3M Screw Thread Gaging Systems for Dimensional Acceptability—Inch and Metric Screw ThreadsB18.2.2Square and Hex Nuts3.Terminology3.1Definitions:3.1.1bearing plates,plate washers,mine roof plates—plates that serve to distribute the load from the exposed end of the bolt or threaded bar to the rock face or intermediate member.3.1.1.1header plates—large rectangular bearing plates, usually6in.(152mm)wide by16to18in.(406.4to457.2 mm)long,or any other shape with an equivalent area,used in substitution for wooden header blocks for wider distribution of the bolt load than is possible with standard bearing plates. 3.1.2bendable bolts—bolts furnished with an altered sec-tion at some location,to be specified by the customer,at which the bar will bend.1This specification is under the jurisdiction of ASTM Committee F16on Fasteners and is the direct responsibility of Subcommittee F16.02on Steel Bolts, Nuts,Rivets,and Washers.Current edition approved Aug.1,2004.Published August2004.Originally approved st previous edition approved in2001as F432–95(2001).2For referenced ASTM standards,visit the ASTM website,,or contact ASTM Customer Service at service@.For Annual Book of ASTMStandards volume information,refer to the standard’s Document Summary page on the ASTM website.3Available from American Society of Mechanical Engineers(ASME),ASME International Headquarters,Three Park Ave.,New York,NY10016-5990.1*A Summary of Changes section appears at the end of this standard. Copyright©ASTM International,100Barr Harbor Drive,PO Box C700,West Conshohocken,PA19428-2959,United States.3.1.2.1Discussion—Bending is necessary to permit instal-lation of bars longer than the mine opening height.This altered section may be produced by hot or cold forging,or by shearing, sawing,trimming,machining,grinding,or a combination of these processes.3.1.3beveled washers—washers whose faces are at an angle permitting a headed bolt or threaded bar to be installed at a slight angle to the rock face and yet maintained the face of the bolt head perpendicular to the bolt axis.3.1.4chemical anchors—chemical materials that provide anchorage between the bolt or bar and the drilled hole.3.1.5expansion shells—anchorage devices that expand to grip the sides of a drilled hole mechanically and transfer load from the location of the anchor to the bar or bolt.3.1.6extensions—threaded bars used to extend the length of threaded or threaded slotted bars.3.1.7formable anchorage devices—any roof support de-vices that provide anchorage through some means of physical interference and engagement of the surface of a bar or bolt with any formable material,other than chemical grout,in a bore-hole.3.1.8frictional anchorage devices—roof support devices that are designed so that the holding force acts over the full contact length.3.1.9fully grouted bolts and threaded bars—deformed bars or plain bars used with full-length grouting and having special deformations or other design features to provide interlocking between the steel and the grout.3.1.10hardened washers—washers that have been hard-ened by heat treatment to provide consistency to the torque tension relation necessary to control installation tension of bolts and threaded bars.3.1.11minimum non-seizure load(MNSL)—the load level in pounds through which bolt/plug thread seizure must not occur.3.1.12minimum ultimate load(MUL)—the load level in pounds through which bolt/plug thread failure must not occur.3.1.13rollers,cams—moving devices that,when used with internally threaded cylinders containing external tapered slots, provide expansion to grip the sides of a drilled hole mechani-cally and transfer load from the location of the anchor to the bar or bolt.3.1.14roof and rock bolts—headed hot-rolled bars with cold-rolled or machine-cut threads at the end,to be used with anchorage devices to hold up mine roofs,hold back walls,or hold down equipment or foundations.3.1.15roof truss system—a roof support system incorporat-ing bolts that are joined together by crossmember(s)that is (are)tensioned by design.3.1.16spherical washers or seats—washers that areflat on one side and have a spherical face on the other side.The combination of spherical washer together with a depression in the bearing plate produces a ball-and-socket joint permitting bolts to be installed at a slight angle to the rock face while still maintaining the face of the bolt head perpendicular to the bolt axis.3.1.17tapered wedges—plain wedges that provide the expansion for threaded slotted bars.3.1.18tension nuts—nuts that are intended to induce and maintain tension in a bolt.3.1.19threaded bars—bars that are used with a nut on one end and an anchorage device on the other.They are used in a manner similar to the bolts described in3.1.14.3.1.20threaded couplings—couplings used to permit the assembly of additional externally threaded items.3.1.21threaded slotted bars—bars threaded at one end each with a forged,burned,or sawed slot at the other,into which a tapered wedge can be inserted.When each assembly is driven into a bottomed hole,the wedge spreads the slot and an anchorage is produced.3.1.22threaded tapered plugs—threaded wedge that ex-pands the expansion shell by the movement of the threaded plug within the shell as tightening progresses.4.Ordering Information4.1Orders for material under this specification shall include at least the following information:4.1.1Quantity(number of pieces),4.1.2Name of product together with description of acces-sories,4.1.3Dimensions,4.1.4ASTM designation and year of issue,including strength grade,4.1.5Special requirements,if any,including packaging and thread protection instructions,and4.1.6Certifications,if required.4.2The products covered by this specification are currently produced by many manufacturers to a wide variety of designs. It is necessary for the user and the manufacturer to establish the requirements of the individual installation and to agree as to the type of assembly to be employed.See Annex A1and Appendix X1for additional information.5.Manufacturing Processes5.1Materials for Bolts,Extensions,and Threaded or Threaded Slotted Bars:5.1.1Steel shall conform to the requirements shown in Table1and in Specification A29/A29M for plain bars or TABLE1Chemical RequirementsProduct Carbon,max,%Sulfur,max,%Phosphorus,max,%Heat Product Heat Product Heat Product Bolts,threadedbars,and threadedslotted bars A0.750.790.13B0.0500.058 Steel tapered wedges0.800.840.13B0.0500.058 Hardened spherical,flat,or beveledwashers0.800.840.0500.0580.0500.058 Spherical or beveledwashers0.800.840.0500.0580.0500.058 Bearing and headerplates 1.00 1.040.0500.0580.0500.058 Steel threaded taperedplugs0.600.640.13B0.0500.058 Steel expansion shells0.300.330.0500.0580.0500.058 A Bars furnished in accordance with Specification A615/A615M may be substitutedfor these requirements.B Check analysis for sulfur if a resulfurized steel is not technically appropriate.Specification A615/A615M for plain or deformed bars unless otherwise specified.5.1.1.1Threaded slotted bars may have the slot produced by forging,burning,or sawing.Burned slots of Grades55and75 threaded slotted bars must have the slotted end normalized by heating to a minimum of1600°F(870°C)and air coolingsubsequent to burning.5.1.1.2Threads on bolts or threaded bars may be cold rolled or machine cut on the hot-rolled bars.5.2Materials for Tapered Wedges for Use With Threaded Slotted Bars:5.2.1Malleable iron casting shall conform to Specification A47/A47M.5.2.2Pearlitic malleable iron castings shall conform to Specification A220,Grades45006or50005.5.2.3Steel shall conform to the requirements shown in Table1.5.3Materials for Expansion Shells:5.3.1Malleable iron castings shall conform to Specification A47/A47M.5.3.2Steel shall conform to the requirements shown in Table1.5.3.3Ductile iron castings shall conform to Specification A536,Grades60-40-18.5.4Materials for threaded tapered plugs used with expan-sion shells shall conform to the test specifications in10.8. 5.5Materials for Bearing and Header Plates,Also Known As Plate Washers or Mine Roof Plates:5.5.1Steel shall conform to the requirements shown in Table1.5.5.1.1Bearing and header plates may be strengthened by cold forming or may be hardened by quenching in a liquid medium from above the austenitizing temperature and temper-ing at a temperature of not less than650°F(345°C).5.6Materials for Spherical,Flat,or Beveled Hardened Washers:5.6.1Steel shall conform to the requirements shown in Table1.5.6.1.1Hardened steel washers shall be through hardened by quenching in a liquid medium from above the austenitizing temperature and tempering at a temperature of not less than 650°F(345°C).Case-hardened washers are not permitted. 5.7Materials for Spherical or Beveled Washers:5.7.1Malleable iron castings shall conform to Specification A47/A47M.5.7.2Pearlitic malleable iron castings shall conform to Specification A220,Grades45006,50005,or60004.5.7.3Steel shall conform to the requirements shown in Table1.5.8Nuts shall be in accordance with Specifications A194/ A194M or A563.Appropriate nuts for each grade of threaded bar are shown in Table2.Higher strength nuts conforming to Specifications A194/A194M or A563may be substituted. When specified on the order or contract,nuts with external dimensions of nominal3⁄4-in.heavy hex or heavy square size may be supplied with5⁄8-in.threads for use with5⁄8-in.threaded bars.5.9Chemical grouting materials are covered in Annex A3of this specification.5.10Materials for threaded couplings shall be selected by the manufacturer to ensure compliance with7.6and8.7.5.11Materials for Bolts and Threaded Bars for Use in Grouted Systems—Plain or deformed steel bars shall conform to Table1or Specification A615/A615M.5.12Materials for Frictional Anchorage Devices—Sheet steel shall conform to Specification A568/A568M.5.13Components of roof truss systems shall be manufac-tured in accordance with the appropriate paragraph(s)of Section5of this specification.5.14Materials for Formable Anchors:5.14.1Materials for formable anchor tubes are as follows: 5.14.1.1Polyethylenes used for formable anchor tubes shall conform to ASTM D1248Classification Type III,Class A or B,Category5.N OTE1—All shapes,compositions,and properties of formable anchor materials are not covered by this specifiers must ensure that the formable anchor material offered is suitable for its intended use.6.Chemical Composition6.1Materials used for bolts,threaded bars,threaded slotted bars,spherical,flat,or beveled washers,threaded tapered plugs,tapered wedges,expansion shells,bearing plates and roof truss components shall be as specified in Table1and Section5.6.2Materials for all cast or wrought metallic items other than those covered in6.1shall conform to the requirements as specified in Section5.6.3Individual heats of steel or cast iron are not identified in any of thefinished products.6.4Chemical analyses for steel products shall be performed in accordance with Test Methods,Practices,and Terminology A751.6.5Materials for formable anchors shall conform to the requirements,if applicable,specified in Section5.6.6Chemical analyses shall be performed in accordance with Test Methods,Practices,and Terminology A751.7.Mechanical Properties7.1Mechanical properties of steel bars,for the manufacture of bolts,threaded bars,or threaded slotted bars shall be as specified in Table3for the required grade.7.2Mechanical properties of steel bolts,threaded bars,and threaded slotted bars whose slots have been produced without material removal shall be as specified in Table4for the required grade.7.3Expansion shells,threaded tapered plugs,tapered wedges,and spherical washers shall conform to the applicable specification of Section5and shall successfully perform the required purpose as described in Annex A1.TABLE2Appropriate NutsBolt,Threaded Bar,or Threaded SlottedBar GradeNut Specification30(regular strength)A194,Grade1;A563,Grade B55(high strength)A194,Grade1;A563,Grade B75(extra high strength)A194,Grade2;A563,Grade C7.4Bearing plates and header plates that are strengthened by quenching and tempering shall have a maximum hardness of 45HRC.7.4.1Bearing plates and header plates shall be provided in 10000-lbf (44.5-kN)grade increments.The minimum grade rating permitted shall be 20000lbf (89.0kN).7.5Hardened washers shall have a hardness range from 35to 45HRC.7.6Threaded couplings must be capable of developing the actual yield and tensile values of the bolt,threaded bar,or threaded slotted bar with which they are to be used.7.7Extensions must be in accordance with 7.1and 7.2for the grade of item specified.7.8Mechanical properties for bolts and threaded bars for use in grouted systems shall be as specified in Table 3for plain bars;and Table 3or Specification A 615/A 615M for deformed bars.Bolts and threaded bars made from plain material must contain some design feature to provide interlocking between the steel and the grout.These items can be supplied threaded or headed.7.9Threaded slotted bars whose slots have been produced by burning shall be heat treated by normalizing in accordance with 5.1.1.The normalizing heat treatment and the removal of material from the slot,whether it be by burning or sawing,will result in lower test values.When either the burning or sawing or other methods involving metal removal are used,the mechanical properties of threaded slotted bolts shall be as specified in Table 5.7.10Threaded tapered plugs for expansion anchors must be capable of withstanding the minimum nonseizure load (MNSL)and minimum ultimate load (MUL),in accordance with Table 6.7.11Tension nuts must be capable of withstanding the ultimate tensile strength of the bolt or rebar of the highest grade with which they are to be used.7.12The mechanical properties of components of roof truss systems shall be in accordance with the appropriate para-graph(s)of this section.7.12.1Truss brackets shall be provided in 10000-lbf (44.5-kN)grade increments.7.13Formable anchor materials shall conform to the appli-cable specifications of Section 5.8.Dimensions,Mass,and Permissible Variations8.1Threaded bolts shall conform to the dimensions shown in Fig.1.8.1.1Deformed bar bolts are bars that have been forged to produce one of the standard heads described in Fig.1.8.2Threaded and threaded slotted bars shall conform to the dimensions shown in Fig.2.8.3Thread Requirements :N OTE 2—Thread size variations can be expected due to bar diameter and out-of-round variations.These special requirements reflect practices for external and internal threads that have been found to provide adequate strength and interchangeability.8.3.1External threads shall be in accordance with ASME B 1.1UNC 1A except that the minimum pitch diameter has been reduced by 0.003in.(0.08mm)and the minimum major diameter has been reduced 0.010in.(0.25mm)to reflect the normal variations expected on hot-rolled bars due to the combined effect of bar diameter and out-of-round rmation on this increased tolerance is described in Note 3.The modified requirements are listed in Table 7.N OTE 3—External threads that are to be used with threaded tapered plugs in expansion anchors are permitted to have somewhat increased pitch and major diameter tolerance.As bolt load is increased,the tendency for thread failure through nut diametrical expansion normally increases;however,in the case of threaded tapered plugs,increased load is accompanied by an increasing compression of the internal threads onto the external threads.This compensation for decreased major diameter is further augmented by the length of engagement which is longer than for standard nuts.Nuts to be used with threaded bars and threaded slotted bars shall be selected to provide adequate strength under these thread condi-tions.8.3.2Internal threads in threaded tapered plugs and threaded couplings shall be in accordance with ASME B 1.1UNC 1B except that the threads shall be tapped oversize.This oversize is an increase in the pitch diameter of 0.003in.(0.08mm)to allow for handling damage on the external thread and dirt and long engagement in the internal thread.The maximum minor diameters are standard 1B for 11⁄2to 3diameter length of engagement.The modified requirements are listed in Table 7.8.3.3Internal threads in nuts shall be tapped standard UNC 2B size in accordance with ASME.1or may be tapped oversize in accordance with 8.3.2with agreement of producer and purchaser.8.3.4Gaging of threads shall be performed in accordance with System 21,ASME B 1.3M.Pitch diameter and thread crest diameter limits are specified in Table 7.8.3.5Threaded tapered plugs shall have a tapped length at least equal to one times the nominal bolt diameter with which they are to be used.8.3.6Threaded couplings shall have a tapped length at least equal to two times the nominal bolt diameter with which they are to be used.8.4Round and square hardened washers shall be as shown in Fig.3.8.4.1There are two types of hardened flat washers avail-able.Type 1is to be furnished unless otherwise specified.8.4.1.1Type 1is either circular or square as shown in Fig.3.It is designed for use with plate washers containing 13⁄8-in.(35-mm)holes,but may be used for all smaller hole sizes.TABLE 3Mechanical Properties of Steel Bars for the Manufacture of Bolts,Threaded Bars,and Threaded SlottedBars ABGradeNominal Diameter,in.C Yield Point min,psi (MPa)Tensile Strength min,psi (MPa)Elongation in 8in.or 200mm Minimum,%40D 3⁄4–11⁄240000(276)70000(483)12555⁄8–11⁄255000(379)85000(586)1260D 5⁄8–11⁄260000(414)90000(621)9755⁄8–11⁄275000(517)100000(688)81005⁄8–11⁄2100000(689)125000(862)6A Test of bars shall be performed full size.BHigher grades would be produced in 20000-psi increments.The minimum tensile strength shall be 25000psi above the minimum yield strength.The minimum elongation shall be 4%for all grades above 100.CActual bar diameters are somewhat less than nominal,especially when roll threading methods are employed.DGrade 40and 60only apply to deformed bar.8.4.1.2Type2is the hardenedflat washer in accordance with Specification F436.It may be used only when sufficient clearance is available between the threaded-bar or threaded-rolled-bar body diameter near the head and the washer hole. This washer is not suitable for use with plate washers that contain holes that are more than3⁄8in.(9.5mm)greater in diameter than the nominal bolt diameter.8.5Bearing and header plates may be of any thickness that successfully meets the test requirements in accordance with 10.4.The maximum hole size for use with bolts up to3⁄4-in. nominal diameter shall be13⁄8in.(35mm)except that hole size may be11⁄2in.(38mm)when spherical washers or seats are used.Tolerance on hole diameter shall be−0,1⁄8in.(−0,+3.2 mm).Bearing plates for direct bearing applications shall be6 by6in.(152by152mm)with tolerances for length and width of61⁄rger bearing plates may be furnished,dimensionsTABLE4Load Support Requirements of Steel Bolts,Threaded Bars,(see Annex A2)Threaded Deformed Bars, and Threaded Slotted Bars Whose Slot Has Been Produced Without Metal Removal AN=NewtonkN=kiloNewton1lb=4.448N or0.004448kNNominal Diameter (in.)/Thread /in.ThreadStress Area,in.2(mm2)Grade40B5560B75100 Yield lbs(kN)CUltimate lbs(kN)CYield lbs(kN)CUltimate lbs(kN)CYield lbs(kN)CUltimate lbs(kN)CYield lbs(kN)CUltimate lbs(kN)CYield lbs(kN)CUltimate lbs(kN)C5⁄8–110.226(1.46)D D12400(55.16)19200(85.4)13600(60.50)20300(90.30)17000(75.6)22600(100.5)22600(100.5)26300(130.8)3⁄4–100.334(2.65)13400(59.60)23400(104.08)18400(81.8)28400(126.3)20000(89.0)30100(133.9)25100(111.6)33400(148.6)33400(146.6)41800(193.5)7⁄8–90.462(2.96)18500(82.3)32300(143.7)25400(113.0)39300(174.8)27700(123.2)41600(185.0)34700(154.3)46200(205.5)46200(205.5)57800(267.3)1–80.606(3.91)24200(107.6)42400(188.6)33300(148.1)51500(229.0)36400(161.9)54500(242.4)45500(202.4)60600(269.5)60600(269.5)75800(350.5)11⁄6–70.763(4.92)30500(135.7)53400(237.5)42000(186.8)64900(286.7)45800(203.7)68700(305.6)57200(254.4)76300(339.4)76300(339.4)95400(441.2)11⁄4–70.969(6.25)38800(172.6)67800(301.6)53300(237.1)82400(366.5)58100(258.4)87200(387.9)72700(323.4)96900(431.0)96900(431.0)121100(560.4)13⁄8–6 1.155(7.45)46200(205.5)80900(359.8)63500(282.4)96200(436.8)69300(308.2)104000(462.6)86600(385.2)115500(513.7)115500(513.7)144400(668.1)11⁄2–6 1.405(9.06)56200(250.0)98400(437.7)77300(343.8)119400(531.1)84300(375.0)126500(562.7)105400(468.8)140500(624.9)140500(624.9)175600(814.6)A Tests of bolts and threaded bars shall be performed using full-diameter products.B Information for Gr40and60only applies to deformed bars.C Required yield and tensile loads shown are calculated by multiplying thread stress areas times the yield point and tensile strength values shown in Table3.Thread stress area is calculated from the mean root and pitch diameters of adrenal threads as follows:A s50.7854S D20.9743n D2where:A s=stress area,in.2D=nominal diameter,in.,andn=number of threads per inch.D5⁄8in.Gr40products are not covered.TABLE5Load Support Requirements for Threaded Slotted BarsWhose Slot Has Been Produced by Methods Involving MetalRemoval ANominal Diameter, in.Thread StressArea,min,in.2(mm2)Grade55Yield Load,min,lbf(kN)BUltimate TensileLoad,min,lbf(kN)B10.606(3.91)30000(133.3)46400(206.2) 11⁄40.969(6.25)48000(213.4)74200(329.9) 13⁄8 1.155(7.45)57200(254.2)88400(393.1) 11⁄2 1.405(9.06)69600(309.4)107500(478.0) A Tests of bolts,threaded bars,and threaded slotted bars shall be performed using full-diameter products.B Required yield and tensile loads shown are calculated by multiplying thread stress areas times the yield point and tensile strength values shown in Table2. Thread stress area is calculated from the mean of the mean root and pitch diameters of Class3external threads as follows:A s50.7854S D20.9743n D2where:A s=stress area,in.2D=nominal diameter,in.,andn=number of threads per inch.TABLE6Plug Grade Rating SystemNominalDiameter,in.Grade1Grade2Grade3Grade4 MNSL A MUL B MNSL A MUL B MNSL A MUL B MNSL A MUL B 1⁄27.014.210.717.013.519.916.322.7 5⁄812.422.617.027.121.531.626.036.1 3⁄418.433.425.1†40.131.746.8†38.453.4†7⁄825.4†46.234.755.440.064.740.073.9 133.360.640.072.740.084.840.096.9 11⁄840.076.340.091.640.0106.840.0122.0 11⁄440.096.940.0116.340.0135.740.0155.0†13⁄840.0115.5†40.0138.640.0161.740.0184.8 11⁄240.0140.5†40.0168.640.0196.740.0224.8A MNSL—Minimum Non-Seizure Load(1000lb).B MUL—Minimum Ultimate Load(1000lb).†Editorially corrected.and tolerances to be by agreement between the producer and the purchaser.Smaller bearing plates may be used in conjunc-tion with steel channels,with other accessories,or in hard rock areas by agreement between the producer and the purchaser.Header plates are typically 6in.(152mm)wide by 16to 18in.(406.4to 457.2mm)long,or any other shape with an equivalent area.8.6Bearing and header plates used with frictional anchor-age devices shall meet the test requirements in 10.4.TheholeNominal Bolt Size,5⁄8to 1in.(Note 1)H Head Height,min.,in.(mm)0.476(12.09)F Head Across Flats,in.(mm) 1.088to 1.125(27.64to 28.58)G Head Across Corners,in.(mm) 1.425to 1.591(36.19to 40.41)EBody diameter is controlled by the roll threading operation.Note 1—When specified by the customer on the order or contract,the 5⁄8-in.diameter bolt may be supplied at:H—0.400(10.16)F—0.906to 0.938(23.01to 23.83)G—1.244to 1.326(31.60to 33.68)Note 2—When specified by the customer on the order or contract,a shoulder,collar,or swell equal to the body diameter of a 3⁄4-in.diameter bolt may be applied under the head of a 5⁄8-in.diameter bolt for a length of approximately 3⁄16in.Note 3—Pinched ears may be provided to support the expansion shell during installation.Note 4—Bolt head may have depressed center.Note 5—See Table 7for head markings.Note 6—See Paragraph 8.3.1for threads.Note 7—Forging flash is permitted.FIG.1Roof and RockBoltsN OTE 1—Pinched ears may be provided to support the expansion shell during installation.N OTE 2—See 8.3.1for threads.N OTE 3—E Body diameter is established by the method of threading.N OTE 4—Body diameter is controlled by the roll threading operation.FIG.2Threaded Bars and Slotted ThreadedBars。
Solidworks术语中英文对照

cavity
型腔
Seemold.
请参阅模具
center mark
中心符号线
A cross that marks the center of a circle or arc.
标记圆或圆弧中心的十字
centerline
中心线
在所选的项目下显示面、特征、实体和零件的颜色和纹理的标注,是一种编辑颜色和纹理的快捷方式
area hatch
区域剖面线
A crosshatch pattern or fill applied to a selected face or to a closed sketch in a drawing. Seecrosshatch.
A centerline marks, in phantom font, an axis of symmetry in a sketch or drawing.
中心线以双点画线标记草图或工程图中的对称轴。
(1) 附加到注释、块、或其它注解的引线端点。另请参阅附加点。(2) 图纸格式包含材料明细表、孔表、修订表、以及焊件切割清单的定位点。
annotation
注解
A text note or a symbol that adds specificdesign intent to a part, assembly, or drawing. Specific types of annotations include note, hole callout, surface finish symbol, datum feature symbol, datum target, geometric tolerance symbol, weld symbol, balloon, and stacked balloon. Annotations that apply only to drawings include center mark, annotation centerline, area hatch, and block.
丹福斯高标准钢管适配器产品简介说明书

Welcome to the higher standard for steel adapters BrochureWelcome to the higher standard for steel adaptersHigher pressure.Higher performance.Beyond SAE certified.Danfoss expands your possibilities.With more than 3000 steel adapter part numbers globally, Danfoss has a wide variation of configurations with large portfolio of ORFS, JIC, BSPP , NPTF, and manyother terminal ends.Expand the equation.Same exceptional Danfoss adapters —now with outstanding corrosion resistance.Achieve operating pressures up to 125% more than SAE.Dura-Kote plating technology.Danfoss Competitor B Competitor Pan assembly that can perform up to 125% greater operating pressureCarbon steel corrosion protection This is a comparison of current carbon steel adaptersafter 650-hours of exposure to salt spray testing which far exceeds the SAE standard of 72-hours. Carbon steelfluid conveyance products protected with Danfoss’Dura-Kote plating technology resist rust longer than other carbon steel products available today.Discover the additional value of using a Danfoss system of products designed to work together to achieve even higher operating pressures. When Danfoss hoses are combined with Danfoss 1A or 4S/6S fittings and Danfoss adapters, assemblies can perform up to 125% higher pressures than the SAE rating.Danfoss adapters now come with Dura-Kote ® plating, which gives you up to 1,000 hours of corrosion resistance. Dura-Kote is an innovative plating technology for steel adapters, offering more corrosive protection for longer life, lower replacement costs, and improved appearance. This corrosion protection decreases the likelihood of leaking, meaning less equipment downtime and greater productivity. Plus, there are no compatibility issues with Dura-Kote plating. The Danfoss adapters you rely on today will look, feel, and perform exactly the same.Many companies offer extra plating services and special requests to enhance corrosion resistance. Requesting extra services can delay your order, complicate delivery, and add significantly to your costs. That is why Danfoss has responded to the needs of the market and simplified the entire process. With Dura-Kote plating now standard on Danfoss adapters, you’ll get products that look better, last longer, and cost less to maintain, which gives you and your customers one less thing to worry about. ++=Same form and functional capabilities Same torque values and pressure ratings Same silver appearance Same procedures for assemblyFor over 90 years, Danfoss has continued to manufacture and supply the highest performing quick disconnect couplings for customers globally. Danfoss’ quality and performance are never compromised when it comes to engineering and manufacturing its full line of quick disconnect couplings. From traditional industry standards to custom couplings for the next generation of emerging markets and new advanced technologies, Danfoss continues to provide quick disconnect coupling solutions to meet your demands. Quick Disconnect Coupling applications:• Hydraulic applications in construction, agriculture, etc. • Fluid transfer • Liquid cooling • Pneumatic • Chemical • Oil and Gas • Aerospace • Medical • Food and Beverage • Law enforcement/rescueCheck out our complete portfolio of Quick Disconnect Couplings found in our catalog at .Literature number: AF435258198969en-000101Patented STC Snap-To-Connect products are threadless connectors that keep equipment up and running longer with simple, leak-free connections.Danfoss has the broadest range of threadless connectors in the industry. Our patented STC technology excels in rigorous mobile application in agriculture, construction, forestry, transportation, utility, and lawn and turf. Because of their easy installation — even in confined spaces — and virtually zero-leak performance (per SAE J1176), more than 25 million STC connections are currently in use worldwide.STC benefits:• Fast reliable one-hand connections requiring no assembly tools • Eliminates cross-threading, over or undertorquing, and hose twisting • Virtually zero leak performance • Direct porting eliminates adapters to maximize cost savings • Resists external contamination • Allows easy disconnection with release toolA full list of available STC products can be found in our catalog at .Literature number: AF444058468933en-000101Making the right connections is easy with Danfoss’ Waltech metric tube fittings. A variety of available sizes and configurations make Danfoss’ metric tube fittings a simple, flexible and cost-effective solution for many applications. With three unique systems — including Walpro ®, WalringPlus ®, and Walform ® — each tube fitting is manufacturered to meet DIN 2353 and ISO 8434-1 standards and withstand pressure and corrosion with best-in-class performance. Metric tube fitting applications:• Harvester/balers • Machine tool • Hydraulic presses • Excavators • Loaders • Mining equipment • Mining equipment • Concrete pumpers • Off-shore equipmentLearn more about Danfoss’ entire line of metric tube fittings by reviewing our Waltech Metric Tube Fittings catalog at .Literature number: AF403661682130en-000201Regardless of the job, Danfoss has the right products to meet the challenge every time.Additional products available from Danfoss.Danfoss Quick Disconnect CouplingsWaltech Metric Tube FittingsDanfoss STC Snap-To-ConnectWalpro WalformWalringPlusAD440177948096en-000101© Danfoss | Power Solutions | April 2023Any information, including, but not limited to information on selection of product, its application or use, product design, weight, dimensions, capacity or any other technical data in product manuals, catalogues descriptions, advertisements, etc. and whether made available in writing, orally, electronically, online or via download, shall be considered informative, and is only binding if and to the extent, explicit reference is made in a quotation or order confirmation. Danfoss cannot accept any responsibility for possible errors in catalogues, brochures, videos and other material. Danfoss reserves the right to alter its products without notice. This also applies to products ordered but not delivered provided that such alterations can be made without changes to form, fit or function of the product. All trademarks in this material are property of Danfoss A/S or Danfoss group companies. Danfoss and the Danfoss logo are trademarks of Danfoss A/S. All rights reserved.Danfoss Power Solutions, Nordborgvej 81, 6430 Nordborg, Denmark, Tel. +45 74 88 22 22, Fax +45 74 65 25 80,E-mail:****************。
常用机械制图英语
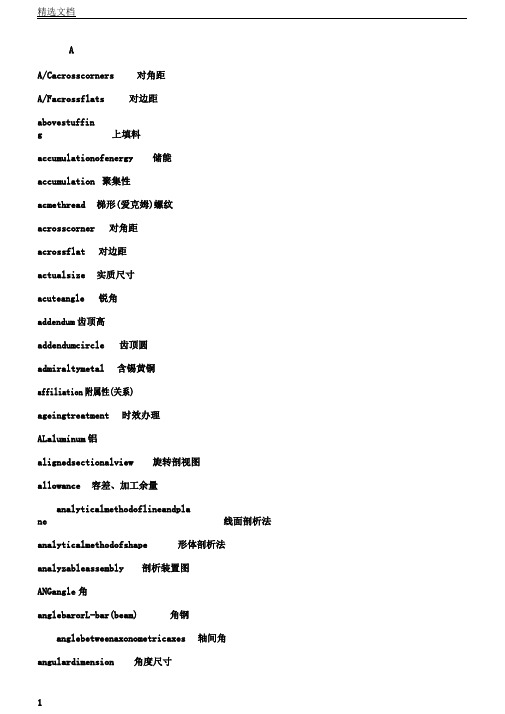
AA/Cacrosscorners对角距A/Facrossflats对边距abovestuffing上填料accumulationofenergy储能accumulation聚集性acmethread梯形(爱克姆)螺纹acrosscorner对角距acrossflat对边距actualsize实质尺寸acuteangle锐角addendum齿顶高addendumcircle齿顶圆admiraltymetal含锡黄铜affiliation附属性(关系)ageingtreatment时效办理ALaluminum铝alignedsectionalview旋转剖视图allowance容差、加工余量analyticalmethodoflineandplane线面剖析法analyticalmethodofshape形体剖析法analyzableassembly剖析装置图ANGangle角anglebarorL-bar(beam)角钢anglebetweenaxonometricaxes轴间角angulardimension角度尺寸angulargear人字齿轮angularsection斜剖面angularity倾斜度anneal退火anti-clockwise逆时针方向的arroworarrowheads箭头asbestospacking石棉填料ASMassembly装置(图)、零件assemblydrawingnumber装置图图号assemblydrawings装置(组装)图assemblyforinstallation安装图assemblyparts装置组合零件assemblysketches装置草图auxiliarycircle协助圆auxiliaryplane协助平面auxiliarysectionalview斜(协助)剖视图alignedanddeveloped睁开视图AVGaverage均匀axialcoefficientsofforeshortening轴向变形系数axisline轴线axisofrotation转轴axis轴线axonometricaxes轴测轴axonometricdrawing轴测图axonometricprojection轴测投影BBABBabbitt巴氏(轴承)合金back(rear)view后(背)视图bar杆baseline基准线baseparts机座baseplane底平面basicdeviation基本偏差basichole基准孔basicshaft基准轴basicsize基本尺寸BBballbearing转动轴承bearingcover轴承盖bearingset轴承座bearing轴承bellmetal青铜(锡铜)合金beltwheel带轮bevelgear斜齿轮BHNBrinellhardnessnumber布氏硬度值bisector均分线bladespring板簧blindhole盲孔(不通的孔)blindhole盲孔blindthreadedhole螺纹盲孔bluntangle钝角bodyofrevolution展转体boltjoint螺栓连结bolt螺栓border图框borderline图框线boringmachineorboring镗床boring镗孔bossclub凸台bottomshell下轴瓦box箱体brazingmetal铜锌合金brightwasher平垫圈Brinellhardness布氏(HB)硬度broacher拉床、绞孔机broaching拉床、扩孔机broach拉光brokenline 断裂线brokenview(localview) 局部视图BRSbrass黄铜BRZbronze青铜burnishorpolishing 磨光butterflyvalve 蝶形阀buttress(screw)thread 锯齿形(枪膛)螺纹caliper 卡尺(钳)capscrew带帽螺钉(栓)capitalletters 大写字母carburizing(carboninfiltration) 渗碳casehardened硬化、表面淬火castingdefect 铸件缺点castingprocesses 锻造工艺casting 锻造、铸件castlenut 内六角圆螺母cavity 空腔(穴)CBOREcounterbore沉孔、用心孔centertocenterdistance中心距centerline(centralline)中心线center-to-centerspacing中心距centralprojection中心投影CHHDcheesehead开槽圆柱头CHAMchamfer倒角chamfer倒角channelbar槽钢characteristicsofprojection投影特征CHDchecked(by)(由)校正checkdrawings校(核)图cheesehead圆柱头Chinesecharacters汉字chromeplating镀铬CIcastiron铸铁CIRcircular圆的circulararc圆弧、弧circularpitch齿距circularpitch周节circularrunout圆跳动CLorcenterline中心线clamping夹紧clearancefit空隙配合clockwise顺时针方向的CMcentimeter厘米coarsepitchthread粗牙一般螺纹coarsewheel粗砂轮加工coating涂覆coincidence(revolved)section重合断面coincidentpoint重影(合)点color-hardening着色硬化、发蓝、发黑combinationsolids组合体commomtangent公切线commonaxis公共轴线commonpoint共有点compass圆规component构件compoundsectionalview 复合剖视图concavemillstone 凹面磨盘concentriccircle 齐心圆concentricityandcoaxiality 同轴(心)度conic(miter)gear 圆锥(伞)齿轮connectingbar 连杆constructionline 作图线contactsurfaces 接触表面continuousstraightthinlinewithzigzags continuousthickline 粗实线continuousthinirregularline 波涛线折线continuousthinline 细实线contourarithmeticmeandeviation 轮廓算术均匀偏差contourelement外形素线conventionalbreaks折断规定画法conventionalrepresentation规定画法converge聚为一点convexmillstone凸面磨盘coordinateaxis坐标轴COPcopper铜copperplating镀铜corrosion腐化cotter(split)pin张口(尾)销counterborehole阶梯沉孔、用心孔counterboringtool平底扩孔钻counter-drill阶梯钻countersunkhole锥形沉孔、用心孔couplingorunion连轴器coveringexternalthread套扣周节CPcircularpitchcrank摇把crossrib十字肋crosssectionshape横断面形状crossingline交错线crossingpoint交错点CRS(CtoC)centers中心距CSKcountersunk锥孔、用心孔CUcubic立方的CUFTcubicfoot立方英尺CUINcubicinch立方英寸CUYDcubicyard立方码cube立方体cuboid长方体cuppacking皮碗密封curvetemplate曲线板curvedlineofintersection曲交线curvedslot曲线槽cuttingplanesymbol剖切平面符号cuttingplane剖切平面cut断面图cycloidalgear摆线齿轮CYLcylinder(cylindrical)圆柱、圆柱体的cylindricity圆柱度Ddashedthinlines虚线datumfeature基准因素datumline基准线datumplane基准面datumpoint基准点datumsymbo基准代号ldeburring去毛刺dedendumcircle齿根圆dedendum齿根高DEGor?degree度delineator制图者descriptivegeometry画法几何descriptivegeometrysolution图解法designdatum设计基准DETDWGdetaildrawing零件图detaildrawing零件图detailing(anassemblydrawing)(由装置图)拆画零件图deviation尺寸偏差(偏差)DIAorφdiameter直径DIAGdiagonal对角线(的)diagonalline对角线diagramassemblydrawing装置工作图diagrammaticdrawing表示图diameter直径diamondknurling网纹滚花dimension尺码dimensionfigure尺寸数字dimensionform尺寸格式dimensionline尺寸线dimensiontext尺寸数值dimensiontolerance尺寸公差dimetricdrawing正二轴测图dividers分规dome圆顶状double-startthread双线螺纹dowelpin圆柱销draftordraught起模斜度draftingpaper画图纸draftingtape胶带纸drawingboard图板drawingnumber图号DRGdrawing制图、图样drilling钻孔drivegear主动齿轮drivengear从动齿轮drivenshaft从动轴DRNdrawn(by)(由)画图ductilecastiron球墨铸铁dynamometry测力Eedgeline棱线effectivediameters弹簧中径effectivelength有效长度EIorei 来自法文ecartinferieur下偏差代号elbow肘形弯管(头)elementcircle素线圆elementsymbol基本符号elementaryunit基本体ellipse椭圆elongatedhole延伸孔、拉伸孔endcover端盖endface端面endpoint端点engineeringrequirements技术要求enlargedpartialview局部放大图enlargementscale放大比率EQUISPorEQSequallyspaced均布erasingshield擦图片ESores 来自法文ecartsuperieur上偏差代号EXTexternal外面的extensionline尺寸界限external(male)thread外(阳)螺纹externaldiameter弹簧外径externaldimension外形尺寸externaltangency外切externalthreadlathing车外螺纹externalview外形视图extremepositionofmoveablepart活动极限地点extruding挤压FFABfabricate制造、装置faucet旋塞、水龙头feedspiral送料螺旋feltring毡圈ferrousmetal黑色金属FIG.figure附图、插图FILfillister凹槽file锉filingmargin装订边fillin填写fillet锻造(内)圆角fineboring精镗finebroaching精拉finegrinding精磨finemilling精铣finepitchthread细牙一般螺纹fineplanning精刨fineturning精车finishallover所有加工fissure裂纹fitsymbol配合代号fitsystem配合制fit配合55?nonsealingpipethread55?非密封管螺纹55?sealingpipethread55?密封管螺纹fixedbody固定钳身flange法兰盘、凸缘flatbar扁钢flatheads平顶flatorplane平面flatness平面度follower从动(大齿)轮font字体fontcavity缩孔、铸口forging锻压fork拨叉formerror形状偏差forthquadrant第四象限fourquadrants四个象限45?mitreline45?斜线freehand徒手(画)freeheight自由高度frontalline正平线frontalplane(orV-plane)正投影面frontalplane正平面frustumofacone圆锥台frustumofacone截头圆锥frustumofapyramid棱锥台FTor′foot英尺fullsectionalview全剖视图原值比率fullsizefullthread 全螺纹functionaldimensions 功能尺寸Ggasket密封垫(圈)gaugecalipers卡(量)规gearbox(case)齿轮箱geartrain齿轮传动gear齿轮generalfitclass配合种类general-plane一般地点平面general-positionline一般地点直线generatingcircle母线圆generator(generation)line母线Geometricconstruction几何作图geometricalsolid几何体geometricaltolerancesymbol形位公差符号geometricaltolerance形状地点公差GIgalvanizediron马口铁、镀锌铁gib-headkey钩头楔键gland压盖gland密封压盖globevalve球阀good-qualitycarbonsteel优良碳素钢grade坡度gradeAandgradeBoftypeonehexagonnutI型六角螺母A级和B级graduatedscale比率(分度)尺图示法graphicalrepresentationGraphics图学GRDgrind磨削greycastiron灰口铸铁grindingmachine磨床grinding研磨grinding磨削groove凹槽、沟纹guardvalve安全阀guidepin定位销guidescrew丝杠Hhalfsectionalview半剖视图halfview半视图handvalve手压阀hardcasting白口铁hardmetal硬质合金hardenedandtempered调质的harden淬火hardnessnumber硬度值Hatching剖面线heat-treatment热办理heavylines加深图线heavymetal重金属helicalcompressionspring圆柱螺旋压缩弹簧helicalspring螺旋弹簧helicalspurgear斜齿圆柱齿轮helicaltensionspring圆柱螺旋拉伸弹簧herringbonegear人字形圆柱齿轮HEXhexagon六角(边)形HEXHDhexagonhead六角头hexnut六角螺母hexslottednut六角开槽螺母hexagonhead六角头hexagonheadbolt六角头螺栓hexagonheadbolt六角头螺栓hexagonsocketcapscrew内六角圆柱头螺钉hexagonthinnut六角薄螺母hiddenedges不行见轮廓线high-carbonsteel高碳钢high-speedsteel高速钢hole-basissystemoffits基孔制配合horizontal(level)plane水平面horizontalline水平线horizontalprojectionplane(H-plane)水平投影面hot-rolledsteel热轧钢HPhorsepower马力H-perpendicularline铅垂线H-perpendicularplane铅垂面HRhour小时hub轮毂hub轮毂、中心hyperbola 双曲线Ihypotenuse直角三角形之斜边(弦) I/Dinsidediameter 内径、内形尺寸I-beam工字钢imaginaryline设想线INor″inch英寸incenter内(切圆)心includedangle夹角inflexion拐点ingotiron低碳钢(工业纯铁) initialoutline初始轮廓线inletside进口端innerrace内圈insidediameter内径instructionbook说明书instrumentaldrawing用仪器画的图INTinternal内部的interchangeability交换性interferencefit过盈配合internal(female)thread内(阴)螺纹internal(inside)caliper内卡尺(钳)internaldiameters弹簧内径internaltangency内切internalthreadlathing车内螺纹interpenetration相贯intersectingplane截平面intersectionline截交线intersectionofplanesurfaces平面之交线intersectionofsurfaces表面之交线intersectionpoint交点Intersection订交Intuitiveillustrations直观图involutegear渐开线齿轮iron铁ISOstandardsISO国际标准ISO=InternationalStandardizationOrganization国际标准化组织正等轴测图isometricdrawing(diagram)isometricprojection正等测投影isometricsectionalview正等轴测剖视图Italicfont斜体Jjack千斤顶、起重器jigbody 夹详细junctionsurface 联合面Kkeydiagram 原理草图keyjoint 键连结keyseat 键座keytypes 键的型式keyway(slot) 键槽key键knobbled(wrought)iron 熟(锻)铁knurling 滚花knurlingnut 滚花螺帽LlampplankLATlatera l 钳口板侧(横)向的lathe 车床LBpound磅leaddistance导程leaderline引导线lead导程leafspring叶(薄)片弹簧lefthand-thread左旋螺纹left-handside(end)view左(端)视图lengthofthreadengagement螺纹旋合长度letter字母leverarm长臂杠杆LGlong.length长度、长的LHlefthand左旋、左方向lightmetal轻金属limitsize极限尺寸limitingdeviations极限偏差limitingelement转向轮廓素线LINlinear线性的、直线的linesegment线段linestyles线型linearity直线性linesinplanes线在面上L-iron角铁local(broken-out)sectionalview局部剖视图locationbydimension定位尺寸locationdimension尺寸定位locknut防松螺母lockscrew锁紧螺钉lockingdevice锁紧装置LONGlongitude经度(线)longdasheddottedthinline点画线longdasheddoubledottedthinline双点画线lower-caseletters小写字母lowerdeviation下偏差lowerlimit下限(值)lubricantpump齿轮油泵。
图纸常用英语模板
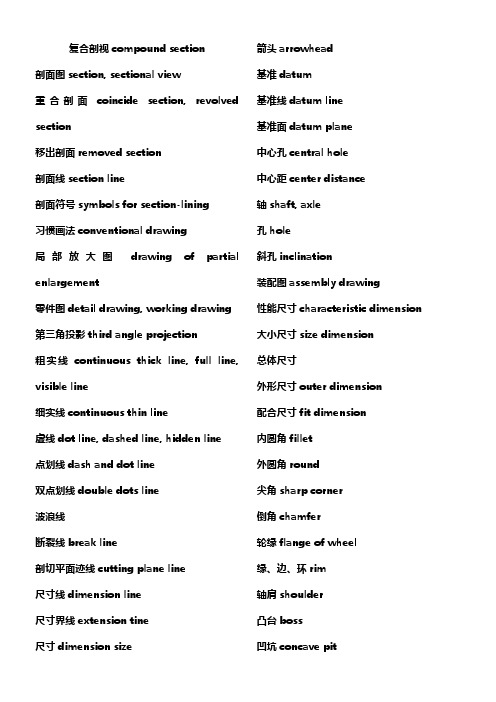
复合剖视compound section剖面图section, sectional view重合剖面coincide section, revolved section移出剖面removed section剖面线section line剖面符号symbols for section-lining习惯画法conventional drawing局部放大图drawing of partial enlargement零件图detail drawing, working drawing 第三角投影third angle projection粗实线continuous thick line, full line, visible line细实线continuous thin line虚线dot line, dashed line, hidden line点划线dash and dot line双点划线double dots line波浪线断裂线break line剖切平面迹线cutting plane line尺寸线dimension line尺寸界线extension tine尺寸dimension size 箭头arrowhead基准datum基准线datum line基准面datum plane中心孔central hole中心距center distance轴shaft, axle孔hole斜孔inclination装配图assembly drawing性能尺寸characteristic dimension 大小尺寸size dimension总体尺寸外形尺寸outer dimension配合尺寸fit dimension内圆角fillet外圆角round尖角sharp corner倒角chamfer轮缘flange of wheel缘、边、环rim轴肩shoulder凸台boss凹坑concave pit轴颈shaft neck轮毂hub轮辐spoke, spoke of wheel 直纹滚花straight knurling s 网纹滚花hatching knurling 键槽key-way退刀槽escape拔模斜度pattern draft填料盒gland box油槽oil groove油封oil seal标准件standard parts螺纹thread外螺纹external thread内螺纹internal thread大径major diameter小径minor diameter螺距pitch of thread牙型form of thread旋向direction of turning 右旋螺纹right-hand thread 左旋螺纹left-hand thread 头数number of thread导程lead 粗牙coarse thread细牙fin thread螺栓bolt螺钉screw螺柱stud螺母nut垫片washer公差tolerance公差带tolerance zone零线zero line标准公差standard tolerance公差等级tolerance grade基本偏差fundamental deviation配合fit间隙配合clearance fit过盈interference过盈配合interference fit过渡配合transition fit基孔制hole-basic system of fits基轴制shaft-basic system of fits间隙clearance形状公差tolerance in form, form tolerance直线度straightness平面度flatness圆度roundness圆柱度cylindricity线轮廓度profile of any line面轮廓度profile of any plane位置公差tolerance in position, position tolerances平行度parallelism齿轮gear圆柱齿轮cylindrical gear正齿轮spur gear斜齿轮spiral gear轮齿gear tooth节圆pitch circle齿顶圆addendum circle, outside circle 齿根圆root circle, addendum circle模数modulus齿数number of teeth齿高tooth height齿顶高height of addendum齿根高height of addendum齿厚circular thickness齿间tooth space齿宽tooth width 压力角angle of pressure弹簧spring销pin圆柱销round pin圆锥销taper pin开口销cotter pin, split键key平键flat key半圆键half round key, woodruff key 轴承bearing滚动轴承rolling bearing向心铀承radial bearing密封装置sealing equipment锁紧装置locking equipment粗糙度roughness基本尺寸basic size实际尺寸actual size极限尺寸limits size最大极限尺寸maximum limit of size 最小极限尺寸minimum limit of size 偏差deviation上偏差upper deviation下偏差lower deviation垂直度perpendicularity倾斜度angularity同轴度concentricity对称度symmetry位置度true position跳动run-out圆跳动cycle run-out全跳动total run-out轴测投影axonometric projection轴测投影面plane of axonometric projection轴测图axonometric drawing正等轴测投影isometric projection正二测bimetric projection斜二测oblique bimetric projection轴测轴axonometric axis轴间角axis angle, angle between ales缩短foreshortened轴向缩短率coefficient of axial deformation ratio offore shortening for any axis切割法cutting method, by cutting方箱法boxing method坐标法coordinate method方框法enclosing-square method 四心近似法four-center approximate method机械工程图中常用的英语词汇Abbreviation 缩写Accuracy 精度、准确性Acme thread 梯形螺纹(29°) Addendum 齿顶高Addendum angle 齿顶角Addendum circle 齿顶圆Addendum of mating gear 啮合齿轮的齿顶高Adjacent-part lines 相邻零件线Aligned sections 旋转剖视Aligned view旋转视图Allowance 容差、加工余量Alloy 合金Alloy steel 合金钢Alphabet 字母Alteration 变更、更改Alternate-position views 位置改变的视图Alternator 交流发电机Induction alternator 感应(交流)发电机Motor alternator 电动(交流)发电机Single-phase alternator 单向(交流)发电机Synchronous alternator 同步(交流)发电机Three-phase alternator 三相(交流)发电机Amount 总量、总计Analyzable assembly 分析装配图Anchor bolt 地脚螺栓Angles 角Acute angle 锐角Blunt angle 钝角Right angle 直角Sliding angle 摩擦角Spiral angle 螺旋角Taper angle 锥角Angular 有角的Angular bearing 径向止推轴承Angular bevel gears 斜交伞齿轮Angular gear人字齿轮Angular section斜剖面Anneal 退火Approval 批准、许可Arc 弧、圆弧Arc thickness 弧长厚度(齿厚)Arc welding 弧焊Arrangement 布置、装置Arrangement of views 视图的布置Clamping arrangement 夹紧装置Cramping arrangement 紧固装置General arrangement 总体布置Arrow 箭头Arrowheads 箭头Assembly 装配图、组装图Assembly drawing 装配图Assembly drawing number 装配图图号Assembly for installation 安装图Assembly parts 组装配合零件Assembly sections 装配图剖视Assembly sketches 装配草图Auxiliary elevation 辅助立面图Auxiliary line辅助线Auxiliary section 辅助剖视Auxiliary surface 辅助面Auxiliary view 辅助视图Average 平均数Axial 轴的、轴向的Axial pitch 轴向节距Axial plane 轴向平面Axial thickness 轴向厚度Axis 轴线、中心线Axis of revolution 回转轴线Axis of rotation 旋转轴线Axis of symmetry 对称轴线Horizontal axis 水平轴Major axis 长轴Minor axis 短轴Vertical axis 垂直轴X axis X轴Y axis Y轴Axle 轴Axle bearing 轴向(止推)轴承Axle sleeve 轴向(止推)套筒Axonometric drawing 轴测图Babbitt 巴氏合金Back cone 背锥Back cone radius 背锥半径Back elevation 后视图Backstop 托架、棘爪Ball bearing 球轴承Bar 杆Angle bar 角钢Channel bar 槽钢Flat bar 扁钢Round bar 圆棒、圆钢Base 基础、底座、基线、基面、基准Base circle 基圆Base circular thickness 基圆弧线齿厚Base cylinder 基圆柱Base helix angle 基圆上的螺旋角Base plane 基平面Base point 基点Key base 键座Basic circle 基准圆Basic hole system 基孔制Base shaft system 基轴制Basic size 基本尺寸、公称尺寸、标称直径Basis 基础、基准、基线Battery 电池、蓄电池Bearing 轴承、支撑、方位Bearing accuracy 定位精度Bearing box 轴承箱Bearing brass 铜轴衬Bearing bridge 轴承支架Bearing oil seal 轴承油封圈Bearing support 轴承架Bearing unit 轴承组合件Anti-friction bearing 减摩轴承Ball and socket bearing 球窝轴承Conical bearing 锥形轴承Journal bearing 径向轴承Needle bearing 滚针轴承Plain bearing 滑动轴承Roller bearing 滚柱轴承Self-aligning bearing 自位轴承Thrust bearing 止推轴承Belt 带、皮带Bench 工作台Work bench 工作台Bend 弯头、接头Elbow bend 肘形弯管Normal bend 正弯管(90°) Bender 弯曲机Bending 挠曲Bending strength 抗弯强度Bent axle 曲轴Bevel 倾斜的、斜角的、斜面Bevel gear 圆锥齿轮、伞齿轮Bevel pinion 小圆锥齿轮Bevel washer 斜垫圈Bevel wheel 伞齿轮、斜摩擦齿轮Bilateral tolerance 双向公差Bill of materials 送料单Block in、block out 画草图Blue paper 蓝晒纸Blueprint 蓝图、设计图Board 板、(管理)局、厅Bottom board 底板Moulding board 模板Body 机体、机身Boiler 锅炉Bolt 螺栓、插销Adjusting bolt 调整螺栓Assembling bolt 装配螺栓Binding bolt 连接螺栓Bright blot 光制螺栓Captive bolt 固定螺栓Double-screw bolt 双头螺栓Fitter bolt 装配螺栓Foundation bolt 地脚螺栓Hexagonal head bolt 六角头螺栓Hook bolt 钩形螺栓Screw bolt 全螺纹螺栓Snap bolt 圆头螺栓Tension bolt 拉紧螺栓Bolted joints 螺栓连接Book 书、册Hand book 手册Instruction book 说明书Bore face machine 镗孔端面加工机床Borer 镗床Jig borer 坐标镗床Table borer 台式镗床Boring 镗孔Boring machine 镗床Boring mill 镗床Bottom case 底座Bottom clearance 径向间隙Bottom view 底视图Bracket 托架、支柱Brake 制动器、闸Brass 黄铜、铜轴衬Braze 铜焊Brazing 铜焊Breadth 宽度、厚度Break line 断裂线Brinell figure (number) 布氏硬度Brinell hardness 布氏硬度Broacher 拉床、绞孔机Broaching 扩孔机、拉床、拉削Broken circle 虚线圆Broken out section 断裂剖面Broken view 局部视图Bronze 青铜Burnishing 抛光、磨光Burr 三角矬、毛刺、去毛刺Bush 衬套、轴瓦Bushing 轴衬、衬套、套管Butt joint 对接焊Butterfly nut 蝶形螺母Butterfly valve 蝶形阀Button 按钮Push button 控制按钮Cable 电缆Cage 盒、罩、箱Caliper 卡尺、卡钳Gauge caliper 卡规、量规Internal caliper 内卡钳Sliding (vernier) caliper 游标卡尺Cam 凸轮Cam design 凸轮设计Cam shaft 凸轮轴Actuating cam 主动凸轮Adjustable cam 可调凸轮Control cam 控制凸轮Cap 盖、帽、罩Cap screw 带帽螺钉Capital 大写字母Carburizing 渗碳Card 卡片Cartographer 制图员Cartography 制图学、制图法Case 箱、盒、容器、表面Case hardened 表面淬火、硬化Nitrogen case hardening 渗氮硬化Casing箱、盒、壳Oil pump casing 油泵(壳) Casting 铸造、铸件Defect casting 铸件缺陷Die casting 压铸Sand casting 砂型铸造Spun casting 离心铸造Steel casting 铸钢Cast-iron 铸铁Castle circular nut 六角圆螺母Castle nut 蝶形螺母Catalogue data 表列数据Cave 凹槽、内腔Centre 中心、圆心Centre distance 中心距Centre hole 中心孔Centre line 中心线Centre-section 中心剖面Centre to centre 中心距Centesimal 百分的、百分之一的Centimeter 厘米、公分Central hole 中心孔Central plane 中心平面Central projection 中心投影Chafe 摩擦、磨损Chain 链Drive chain 主动链Transmission chain 传动链Chamfer 倒角、倒棱、斜面Dimensioning of chamfer 倒角的尺寸注法Changes on drawing 图的更改Channel 沟槽Chapter 章Chart 图表、计算图Chart of symbols 符号图表Auxiliary chart 辅助图Dimensions chart 外廓尺寸图Graphical chart 图表Process chart 工艺程序图Progress chart 工艺程序表、工作进度表Charting 制图(表)、填图Check 校验、校核、制动装置Check drawings 校图Check nut 防松螺母Check ring 挡圈Check test校核试验Chief draftsman 主任制图员Chromium 铬Chromizing 镀铬处理Circle 圆、圆周Circle of reference 参考圆Addendum circle 齿顶圆Base circle 基圆Graduated circle 分度圆Imaginary circle 虚圆Outside circle 齿顶圆、外圆Pitch circle 节圆Rack circle 平面齿轮、扇形齿轮Root circle 根圆Top circle齿顶圆Circular cylinder 圆柱Circular pitch 弧线节距Circular thickness 弧线(齿)厚度Circumference 圆周长Clamp 夹紧、夹板Class 种类Class of fit 配合级别Classification 分类Claw 爪、钩、卡爪Clearance fit 间隙配合Clevice /clevis U形钩、U形夹Clevis bolt 套环(插销)螺栓Clevis pin U形夹销Clockwise 顺时针方向Clutch 离合器、联轴器Coat 外层、涂镀层Coat of metal 金属镀层First coat 底漆Coating 镀、覆盖Electrodeposited coating 电镀层Coaxial circle 共轴圆Cock 旋塞Coil 蛇形管、螺管、线圈Coil spring 盘簧Coincident line 重叠线Cold-rolled steel 冷轧钢Collet 夹头Collet chuck 弹簧夹头Color-harden 着色硬化、发蓝、煮黑Common difference 公差Company 公司Joint company 股份公司Limited company 有限公司Compass 圆规Compass of proportion 比例规Component 零件、构件Compression spring 压力弹簧Compressor 压缩机Computer 计算机Concave face 凹面Concentricity 同心度Cone 圆锥Cones development 锥面展开Cone pulley 锥形轮、塔轮Conical spring 锥形弹簧Connection 联接Bolt-on connection 螺栓联接Flange connection 法兰联接Rivet connection 铆钉联接Screw connection 螺钉联接Contact 接触、接合、啮合Contact angle 啮合角Angular contact ball bearing 向心止推球轴承Contour 外形、轮廓线Contracted drawing 缩图Contrast 对比、对照、比较Convention 惯例、常规、习惯Convention for materials 材料的习惯表示法Conventional break 习惯断裂画法Conventional diagram 习惯画法Conventional intersection 习惯交线(画法)Conventional practice 习惯画法Conventional sign 图例、习惯符号|Convex 凸面Conveyer 输送机、传送机Cooler 冷冻机Coordinate axis 坐标轴Coordinate paper 方格纸、坐标纸Copper 铜Copy 抄本、样板Correction 校正、修正Cotter pin 开口销Split cotter 开口销Counterbore 埋头孔、锥口孔Counterclockwise 逆时针方向Countersink 埋头孔、沉孔Countersink drill 中心钻、钻Countersunk 钻埋头孔、钻锥口孔Countersunk bolt 埋头螺钉Countersunk head 埋头Countersunk hole 锥坑Coupling 联轴节Cover 盖、罩Cylinder cover 汽缸盖Dust cover 防尘罩Cowl 壳、套、盖Crane 起重机Crank 曲柄、曲轴Crankshaft 曲轴Crest 峰、尖、牙尖Cross head 十字头Cross section 横剖面、横断面Crown gear 冕状齿轮Cube 立方形体、正六面体Current 电流Curvature 曲率Curvature radius 曲率半径Curve 弯曲、曲线、曲线板Curve plotter 绘图仪Curve ruler 曲线板French curve 曲线板Moment curve 力矩曲线、力矩图Cutter 刀、刀具Cutting plane 截平面Cutting plane symbols 剖切(迹线)平面符号Cycloid 摆线Cycloidal gear 摆线齿轮Cylinder 圆柱体Cylinder base 汽缸座Pump cylinder 泵缸Cylindrical cam 圆柱凸轮Cylindrical fit 圆柱配合Cylindrical roller bearing 圆柱滚子轴承Dash 短划线、虚线、破折号Dash and dot line 点划线Broken dash 断裂线Data 数据、资料Engineering data工程数据Master data 主要数据Date 日期、年代Datum 基准(点、线、面)、资料Datum line 基准线Datum point 基准点Datum plane 基准面Decade 十进制、十进位Decelerator 减速器、制动器、缓动装置Decimal 小数的、十进位小数的Decimal fraction 十进制分数Decimal fraction system 十进小数制Decimal scale 十进位比例尺Decimeter 分米、公分Dedendum angle 齿根角Dedendum circle 齿根圆Definition 定义Deformation 变形、扭曲Degree 度、程度Degree of accuracy 精度Degree of freedom 自由度Degree of hardness 硬度Degree scale 刻度Circular degree 圆度Delineation 轮廓、草图Delineator 制图者Department 科、处、系、车间Draft department 设计科Engineering department 技术科Fitting department 装配车间Heat treatment department 热处理车间Mechanical department 机加工车间Processing department 工艺科Depth 深度、高度Depth dial gauge 深度千分表Depth of engagement 啮合深度Depth of thread 螺纹深度Depth of tooth 齿高Contact depth of tooth 啮合高度Working depth of tooth 齿工作高度Derivation 偏差Standard derivation 标准偏差Description 描述、作图、绘制Design 设计、计划Design activity 设计机关(组织) Design assembly 设计装配图Design drawing 设计图Design layout 设计草图、初步设计图Preliminary design 初步设计Standard design 标准设计Technical design 技术设计Designation 符号、标志Designation strip 铭牌Designer 设计员、制图者、设计师Desk 桌、控制台Drawing desk 绘图桌Detail 细目、细节、详图、零件Detail drawing 详图、零件工作图Detail paper底图纸、描图纸Detail specification 详细规格Detent 棘爪、扳手、制动器Developable surface 可展曲面Developed view 展开图Development inner port 内表面展开图Development of surface 表面展开图Deviation 偏差、偏移Angular deviation 角偏差Average deviation 平均偏差Standard deviation 标准偏差Tolerance deviation 允许偏差Device 装置、设备Diagram 示意图、图解Diagram drawing 图解图、结构图Arrangement diagram 布置图Assembly diagram 装配示意图Block diagram 方框图Schematic diagram 原理图、简图Diagrammatic drawing 草图、示意图Dial gauge 千分表Dial inside micrometer 内径千分表Diameter 直径Diameter of aperture 孔径Diameter of pitch circle 节圆直径Diameter pitch (齿轮)径节Diameter run-out径向跳动Major diameter 大直径、螺纹外径Minor diameter 小直径、螺纹内径Nominal diameter 公称直径Pitch diameter of screw thread 螺纹中径Thread diameter 螺纹外径(直径) Diametral pitch 齿轮径节Die 模具、扳牙Diesel 柴油机、内燃机Dimension 尺寸Dimension line 尺寸线Limiting dimension 极限尺寸Nominal dimension 公称尺寸Outer dimension 外形尺寸、轮廓尺寸Direction 方位、方向Clockwise direction 顺时针方向Disc = disk 圆盘、原板Disk cam 圆盘凸轮Dismount 拆卸Dismountable 可拆卸的Displacement 移位、变位Distance 距离、路程Distortion 变形、歪扭Distribution 分配、分布、配置Ditto machine 复印机Diversion 变更、转换Dividing head 分规Dot line 虚线Dotted line 虚线Double dots line 双点划线Double helical pinion 人字小齿轮Double helical spur gear 人字齿轮Double thread 双头螺柱Dowel thread 定位销、圆柱销Dozer 推土机Draft = draught (拔模)斜度、草图、制图Drafting 制图Drafting board 制图板Drafting machine 制图机Drafting tape 制图带、胶带Draftsman 绘图员Drawer 制图员Drawing 绘图、图样Drawing board 绘图纸Drawing control 图样管理Drawing free-head 草图Drawing instrument 绘图仪器Drawing number 图号Drawing pencil 绘图铅笔Drawing pin 图钉Drawing size 图纸尺寸Drawing table 制图桌Drawing with compass 用圆规画图Blue print drawing 蓝图Free hand drawing 徒手图Full size drawing 原大图Skeleton drawing 草图、结构图Working drawing 施工图、制造图、工作图Drill 钻孔、穿孔、穿孔器Drive 传动、驱动Drive fit 打入配合Air drive 气动Belt drive 带传动Chain drive 链传动Friction drive 摩擦传动Gear drive 齿轮传动Hydromatic drive 液压传动Speed-reducer drive 减速器传动Variable-speed drive 变速传动Worm-wheel drive 蜗轮传动Driven gear 从动齿轮Driven shaft 从动轴Driving gear 主动齿轮Driving shaft 主动轴Drum cam 凸轮轴Ductile iron 球墨铸铁Duplicating tracing 复制描图Durometer (钢轨)硬度计Dusting cloth 抹灰布、撒粉布Eccentricity 偏心距Edge iron 角铁Edge round 外圆角Edge view 边视图Effective diameter 有效直径Effective face width 有效齿宽Efficiency 效率、性能Mechanical efficiency 机械效率Elastic deformation 弹性变形Elasticity 弹性Elbow 肘形弯管、弯头Electric current 电流Electric element 电池Elephant 绘图纸(28X23英寸) Elevation 正面图、立视图End 末端、头Ball end 秋端Butt end 平端、端面Tail end 尾端Top end 顶端Engagement 啮合Engineer 工程技术人员、工程师Engineer-in-chief 总工程师Equipment 设备Eraser 橡皮Erasing shield 擦图片Erection diagram 安装图、装配图Error 误差Accumulated error 累积误差Allowance error 容许误差Average error 平均误差Permissible error 容许误差Relative error 相对误差Exterior 外表面External 外部External diameter 外径External dimension 外形尺寸External fillet 外圆角External thread 外螺纹Extra fine(screw)特细牙螺纹Eyelet = eyelet-hole 小孔Fabrication 建造、制造Face 面、正面、表面、端面Face cam 平面凸轮Face gear 平面齿轮Face hardening 表面硬化Inner face 里面Outer face 外面Face off 倒角Factor of safety 安全系数Factory 工厂、制造厂Factory made 工厂制造的Fastener 接合件、紧固件Fastening 连接件、紧固件Fatigue 疲劳Faucet 旋塞、龙头、开关Feather 滑键、冒口Feather key 滑键Feature 特征、特性、性能Basic mechanical design feature 主要机械设计性能Mechanical feature 机械性能(特性) Feed-pump 供油泵、供水泵Feet 英尺Ferrous metal 黑色金属Field 工场、现场Figure 形状、图样、插图、数字File 锉刀、锉平Filler 填料、垫片Fillet (内)圆角、填角、嵌条Fillet radius 内圆角半径Filter 过滤器Fine thread series 细螺纹级(系列) Finish 完工、加工、磨光Finish all over 全部加工Finish marks 加工符号Machine finish 机器光制Fit 配合Clearance fit 间隙配合Free fit 自由配合Interference fit 静配合Light press fit 轻压配合Light running fit 轻传动配合Loose fit 松配合Normal-running fit 传动配合Running fit 动配合Shrink fit 冷缩配合Slide fit 滑动配合Transition fit 过渡配合Fix 安装、装配、调整、修理、固定Flange 法兰盘、凸缘Flank 边、侧面、齿侧、后面Flat 扁头、平面Flat key 平键Flat spring 板弹簧Flat surface 平面Flexible disk coupling 挠性盘形联轴节Flexible gear-type coupling 挠性齿轮联轴节Flywheel 飞轮Foot 英尺Foot screw 地脚螺钉Force 力Fore word 序、前言Forge 锻Forge steel 锻钢Former 样板、模型、量规Wooden former 木模Formula 公式Foundation 基础、基座Foundation bolt 地脚螺栓Foundry 铸件、铸工车间Fraction 分数、小数Front view 前视图、主视图Full diameter 大直径、主直径Full line 实线Full size 原大Full scale 原大Full section 全剖视Full section view 全剖视图Furbish 研磨、擦光Fuse 保险丝、熔断器Gage = gauge 量规Gallon 加仑Galvanize 镀锌、电镀Gasket 垫圈、密封垫Gasket material 填料Gasoline engine 汽油(内燃)机Gate 门、阀门Gear 齿轮Gear addendum angle 齿顶角Gear box(case) 齿轮箱Gear centre 齿轮中心Gear dedendum angle 齿根角(圆锥齿轮) Epicyclic gear 行星齿轮Herringbone gear 人字齿轮Ratchet gear 棘轮General drawing 总图Geometry 几何学Gland 压盖、填料盖、密封装置Glass 玻璃Glasscloth 砂布、玻璃布Glossary 词汇(表)Grade 等级、斜度Steel grade 钢号Graduated hardening 分级淬火Graduated scale 比例尺、分度尺Gram 克Graph 图(表、解、形)、曲线图Graph paper 方格纸Graphic图示、制图学Grease 滑脂Grind 磨削、抛光Grinding machine 磨床Grinding wheel 砂轮Groove cam 槽凸轮Groove pulley 槽轮、三角带轮Guide 手册、指南Guide bar 导杆Guide pin 定位销、导向销Guide screw 丝杠Guidebook 参考手册、指南、入门Half 二分之一、一部分Half bearing 轴瓦Half section 半剖视Half section view 半剖视图Hammer 锤子Handbook 手册、指南Hand-made 手工制造的Hand-operated 手控的Handle 手柄Hand wheel 手轮Hard casting 白口铁Hard drawn 冷拔Hard rolled 冷轧的Hard surfacing 表面硬化Harden 淬火、硬化Hardened and tempered 调质的Hardened-steel 淬火钢Hardening 硬化Hardness 硬度Hardometer 硬度计Hatch 剖面线H-beam 工字梁、H形梁Heat–treatment 热处理Heavy force fit 重压配合Height 高度Helical bevel gear 螺旋伞齿轮Helical gear 螺旋齿轮、圆柱斜齿轮Helical rack 斜齿齿条Helical spring 螺旋弹簧Hex nut 六角螺母Hexagon jam nut 六角锁紧螺母Hexagon socket head 内六角头Hidden line 虚线Hidden outline 看不见的轮廓线High-carbon steel 高碳钢High-duty 重型的、大型的、优产的High-speed steel 高速钢Hosting jack 千斤顶Hole 孔Horizontal datum plane 水平基准面Horizontal line 水平线Horizontal projection 水平投影Horizontal projection plane 水平投影面Horse-power 马力、功率Hose 软管Hose coupling 软管接头Hot-rolled steel 热轧钢Hot-work 热加工Hour 小时Housing 机座Housing of pump 泵体Bearing housing 轴承箱Gear housing 齿轮箱Hub 轮、中心、衬套I-beam 工字钢Illustration 插图、实例Inaccuracy 不精确、不准确Incenter 内(切圆)心Inch 英寸Incline 斜度、斜面Index plate 分度盘Indicator 指示计、百分表Industrial 工业公司Industrial drawing 工业制图Industry 工业Inertia 惯性Ink 墨水、油墨Ink holder 钢笔杆China ink 墨汁Inscription 标题Inside diameter 内径Inspection 检修、检查Inspection machine 检修机器Inspector 检查员Installation 装置、设备、安装Installation diagram 安装图Institute 研究所、协会、学院、学会Instruction 说明、指示Instrument 仪器、仪表、工具Instrument drawing 仪器图Intensity 强度Interchangeability 互换性1 Interconnection 互相连接Interference fit 静配合Interior view 内部(的)视图Internal combustion engine 内燃机Internal fillet 内圆角Internal gear 内齿轮Introduction 引言、介绍、序言Invisible line 虚线Involute 渐(伸)开线Involute gear 渐开线齿轮Involute rack 渐开线齿条Involute spline 渐开线花键Involute teeth 渐开线齿形Iron 铁Ingot iron 低碳铁、工业纯铁Knobbled iron 熟铁Magnetic iron 磁铁Malleable iron 可锻铁、韧性铁Plate iron 铁板、钢板Quadrant iron 方钢Rod iron 圆铁、棒钢Round iron 圆铁、圆钢Rustless iron 不锈铁Section iron 型钢Structural iron 结构钢White iron 白口铁Wrought iron 熟铁、锻铁Isometric diagram 等轴测图Isometric drawing 等轴测图Jack-screw 螺旋千斤顶Job sheet 零件图纸Joint 结合、连接、焊接Bolt joint 螺栓连接Riveted joint 铆钉连接Welded joint 焊接Journal 轴径Journal bearing 径向轴承Keeper 保持器(片)、架、定位件卡箍Keep-ring 保持环Key diagram 键、按钮Key way(seat、seating、slot)键槽Key wrench 套筒扳手Gib-head taper key 钩头斜键Square key 方形键Tightening key 斜扁键Woodruff key 半圆键Key-bolt 键螺栓Kilogram(me)公斤、千克Kilogram-meter 公斤米、千克米Kilometer 公里、千米Kilovolt 千瓦Kilowatt 千伏Kit 一套工具Knee 弯头、升降台Knee bend 弯管Knob 捏手、按钮Knuckle thread 圆形螺纹Knurl 滚花、压花Knurled nut滚花螺母L-bar = L-beam 角钢Laboratory 实验室、研究室Lamp 灯Alarm lamp 信号灯Daylight lamp 日光灯Incandescent lamp 白炽灯Indicating lamp 信号灯、指示灯Lantern 游环、套环Large compasses 大圆规Lathe 车床Lathe-hand 车工Lattin = Latten 金属薄板、黄铜片Law 规律、定律Lay 布置、安排、放置Layer 层Carburized layer 渗碳层Layout 计划、方案、草图Layout design 草图设计、方案设计Layout drawing 方案草图Lead angle 螺旋升角Lead line 指引线Leaf spring 板弹簧Left hand 左方向Left hand thread 左旋螺纹Legend 图例、图表符号、代号、说明书Length 长度、距离Length gauge 长度规Length of normal 法线长Length of side 边长Effective length 有效长度Lens 透镜、镜片Letter 字、字母Capital letter 大写字母Level surface 水平面Lift 升降机、电梯Light alloy 轻合金Light beam 光束Light series 轻系列Light-duty 轻型Lighting installation 照明装置Lightning switch 照明开关Liquid 液体Limit 极限尺寸Limit switch 限位开关Line 线Line of action (齿轮)压力线Line of contact (齿轮)接触线Line of shaft轴线Line of thickness 线型的粗度Line weight线的粗细程度Actual line实线Addendum line齿顶线Broken line断裂线Center line = central line中心线Continuous line实线Dash(ed) line虚线Diagonal line 对角线Imaginary line 假想线Generation line 母线Pitch line 节线Real line 实线Reference line 基准线、参考线Right line 直线Skeleton line 轮廓线Solid line 实线Straight line 直线Vertical line 垂直线Liner 衬套Bearing line 轴瓦Link 连接环、链节Line assembly 连杆装配图Chain link 链节L-iron 角铁List 注册、记录、名册、目录Load 符合Actual load 有效载荷、实际载荷Allowable load 容许载荷Full load 满载(荷)、全负载(荷) Local view 局部视图Localization 定位\固定Locating pin 定位销Location by angle 角度定位Location by dimension 定位尺寸Location pin 定位销Location tolerance 定位公差Lock 锁\阀Lock nut 防松螺母Lock screw 锁紧螺钉Lock washer 弹簧垫圈Valve lock 阀簧抵座销、气门制销Loco 机车、火车头Logarithm 对数Long break 长断裂线Long radius 长半径Longitudinal key 长方键Lower limit 下限Lubricant pump 润滑油泵Lubricating ring 润滑油环Lubrication 润滑Bath lubrication 油浴润滑Bearing lubrication 轴承润滑Ring lubrication 油环润滑Shot lubrication 油枪润滑Splash lubrication 飞溅润滑Lubricator 润滑器Lubro-pump 油泵Luminaire 光源Machine 机器、切割Machine building (manufacturing) 机械制造Machine drawing 机械制图Machine finish 机械加工Machine maker 机械工厂(制造者) Machine part 机械零件Machine shop 机工车间Drawing machine 绘图机Tracing machine 描图机Machining allowance 加工余量Machinist 机械工人\机械师Magazine 杂志Magnetic-particle clutch 电磁离合器Magnitude 数量、长度、大小Major type of slotted nut 大型锁母Make 制造、构造Malleable cast iron 可锻铸铁Malleable casting 韧铸件Malleable steel 软钢、展性钢Manual 手册、说明书Manual control 手控Manufacture 加工、制造业Manucturing engineering 制造工艺(技术) Manucturing machine 生产机械Manucturing tolerance 制造公差Master check 校正、校对Master drawing 样图Master gauge 标准规、校准规Master gear 主齿轮、标准齿轮Master making 手工Master screw 标准螺纹Match 匹配、配合Mate 啮合部分Material 物质、材料Fibre material 纤维材料Insulating material 绝缘材料Plastic material 塑料Maximal valve 极大值Maximum 极点、极限、最大量Maximum admitted diameter of work 工件最大许可直径Mean axis 中间轴Measure 量度、大小、尺寸Measure of precision 精确度Measurement 测定、尺寸、大小Measuring device 量具Measuring tools 量具Mechanical bolt 螺钉Mechanical drawing 机械制图Mechanical engineering’s scale 机械工程比例尺Mechanical properties 机械性能Mechanical reduction gear 齿轮减速装置Mechanism 机械结构、机械装置Medium series 中系列Mating member 配合件Meshing gear 啮合齿轮Metal 金属Admiralty metal 含锡黄铜Bell metal 青铜合金、种铜、铜锡合金Brazing metal 铜锌合金Hard metal 硬质合金Heavy metal 重金属Light metal 轻金属Monel metal 铜镍合金Power(ed) metal 粉末合金Wear-resistant metal 耐磨金属White metal 白合金(铅锑锡合金)Yellow metal 黄金、黄色金属Metallized 镀金属的、喷涂金属的Meter 米、公尺。
design_for_manufacture_and_assembly

2.1Design for Manufacture and AssemblyDesign for Manufacture andAssemblyA set of guidelines developed to ensurethat a product is designed so that it can beeasily and efficiently manufactured andassembled with a minimum of effort,time, and cost.Products designed using DFMA principles should have higher quality and reliability than those developed using traditional design methods. DFMA also ensures that the transition from the design phase to the production phase is as smooth and rapid as possible.Why Use DFMA?•Lower Assembly Cost•Shorter Assembly Time•Increased Reliability•Shorter Total Time-To-MarketLower Assembly CostDFMA lowers assembly costs by using fewer parts, eliminating unique parts wherever possible, and decreasing the amount of labor required for assembly.Shorter Assembly TimeDFMA shortens assembly time by utilizing standard assembly practices such as vertical assembly and self-aligning parts.Increased ReliabilityDFMA increases reliability by lowering the number of parts, thus decreasing the chance of failure. Shorter Total Time-To-MarketSince products developed using DFMA make the quickest and smoothest transition into the production phase, the time for a product to go from conception to the consumer (total time-to market) is reduced. The result is a more complete and workable design the first time.Design for Manufacturability ConsiderationsMaterials1.Is material available in standard stock configurations (e.g., bar stock, sheet, standardextrusion)?2.Is material compatible with the most desirable manufacturing process (e.g., ease of forming,casting, machining)?3.Is the material available from reliable sources?4.Do material prices fluctuate widely over time?5.Are special alloys and exotic materials used only for environmental or functional demands? Fabricated parts1.Are specified tolerances reasonable for functional requirements?2.Are tolerances attainable within normal capability of the manufacturing process to be used?3.Are data points, surfaces, and tooling points clear and accessible?4.Does parts configuration minimize the need for special processes and special tooling? Product Assembly1.Are tolerance dimensions realistic?2.Is marking and stenciling defined and visible?3.Are assembly notes complete and definitive?4.Is internal wiring layout critical? If so, is the location and routing specified?5.Is harness development required? If so, can the harness be fabricated outside the unit andinstalled as a subassembly?6.Does the design lend itself to automated assembly?7.Are component parts accessible for assembly?8.Can testing be performed without disassembling the unit?9.Are standard connectors and assembly hardware used?10.Are circuit cards, if used, designed to plug in?11.Has the assembly been analyzed to meet electrical, thermal, vibration, and shockspecifications?12.Can printed circuit flex cable or molded ribbon be used in place of hard wiring?13.Can plastic tie-wraps be used in place of lacing or spot ties?[Source: Practical Engineering Guides for Managing Risk: Design for Reduce Technical Risk,AT&T, McGraw-Hill, Inc., New York, New York pp. 503-528]Principles of DFMA forMechanical Design•Minimize Part Count•Make Parts Multi-Functional•Reduce the Number of Screws and Screw Types•Facilitate Parts Handling•Use Standard Parts and Hardware•Encourage Modular Assembly•Use Stack Assemblies/Don’t Fight GravityPrinciples of DFMA forMechanical Design•Design Parts with Self-Locating Features•Minimize Number of Surfaces•Assemble in the Open•Simplify and Optimize the ManufacturingProcess•Eliminate Interfaces•Design for Part Interchangeability•Design Tolerances to Meet Process CapabilityMinimize Part CountThe final cost of a product is directly proportional to the number of parts. As the number of parts is reduced, product quality and reliability typically increase. This comes about because fewer parts are present to break or work loose and reduces the chances of misalignment. The following three questions can be used to determine the necessity of a particular part.A Simple Test to Determine if a PartCan Be Eliminated•Must the part move relative to other partsin performing its function?•Must the part be made of differentmaterial?•Must the part be a separate component?If the answer to these three questions is "NO", then the possibility of combining the part with other parts should be considered.Make Parts Multi-FunctionalMulti-functional parts combine several functions into one part and reduce complexity.Reduce The Number of Screws and Screw TypesDecreasing the number of fasteners reduces assembly weight, cost, and complexity. The alternative to fasteners is to incorporate self-aligning features into parts design. If fasteners are necessary then use a common size and/or self-tapping screws.Facilitate Parts HandlingParts should be designed with handling in mind. They should be designed to minimize the potential for becoming tangled or stuck together. The goal is quick and easy parts handling that does not require special tooling or fixturing for assembly. Making parts easily identifiable also speeds handling. Where possible we would like to make parts symmetric so that orientation is not an issue. However, if a specific orientation is necessary, the use of asymmetric features will force correct alignment, eliminating the potential of incorrect assembly.Use Standard Parts and HardwareThe use of standard components in a design reduces the number of tools required for assembly and lowers assembly cost. Unfortunately, standardization requires increased communication between the multiplicity of design teams working on complex products and systems. Often the best way to handle this is to create a list of standard parts for each project. Generally, fasteners and hardware can quickly get out of hand. A good rule of thumb is to never design a part that you can get out of a catalog. In order to facilitate the use of standard parts, the design team should utilize various resources such as the preferred parts lists, standard parts manuals, vendor catalogs, trade magazines, etc.Encourage Modular AssemblyModular designs simplify assembly operations and make problem identification easier by reducing the number of parts. Modular assembly also simplifies inventory and improves maintenance and serviceability. By designing parts as separate, self-contained modules, disassembly time is reduced, fewer tools are required, and overall repair time is reduced.Use Stack AssembliesAssembly operations should use, not fight, gravity. One way to do this is to design parts for stack assembly (i.e., assembly components from the bottom up). This makes automatic assembly possible. Stack assemblies require less reorientation of the components which speeds the assembly process. Not using gravity generally requires the use of additional tooling and fixturing.Design Parts With Self-Locating FeaturesSelf aligning parts can be placed into an exact location with no adjustment required. This makes assembly easier and faster for the assembly workers. Examples of self-locating features include projections, indentations, chamfers, molded keyways, etc.Minimize Number of SurfacesMinimizing the number of surfaces can reduce the manufacturing and assembly requirements of a system or subsystem. This is realized by minimizing the number of times that an item must be picked up and repositioned.Assemble in the OpenAssemblies should be designed so that assembly operations are accessible and in the open. Blind assembly can increase assembly time, cost, complexity and can contribute to quality problems. Simplify and Optimize the Manufacturing ProcessSimplification and optimization of the manufacturing process reduces recurring direct and overhead costs. In designing the production process the focus should be on: smoothing material flow; minimizing the number of material moves; using processes that are easily controllable; avoiding, where possible, processes that are difficult to control (i.e., welding, brazing, etc.); performing like operations simultaneously; and separating manual and mechanized operations. Eliminate InterfacesInterfaces increase the cost of an assembly. Each interface doubles the amount of information required and increases overall assembly time (i.e., “2 sets of dimensions, 2 sets of tolerances, 2 sets of interface features, assembly labor, assembly materials, etc.”).Design for Part InterchangeabilityUsing interchangeable parts is a simple way to reduce part numbers, simplify the assembly operation (i.e., part orientation is not an issue) and ultimately minimize assembly time and cost. In particular, left-handed and right-handed parts should be avoided; they often, unnecessarily, increase the potential for confusion and complexity of assembly.Design Tolerances to Meet Process CapabilityManufacturability is enhanced when part designs take into consideration process capabilities. Specification of unnecessarily tight tolerances is a significant waste of time and money. Overly tight tolerances may require additional fixturing, processes, and/or inspections. Therefore, designers must consider manufacturing and supplier capability when specifying tolerances to ensure that tight tolerances are truly necessary.Principles of DFMA forElectronics Assembly•Use Standard Parts and Material Whenever Possible•Determine Capabilities of Each Process Step•Design for Ease of Part Orientation for Assembly•Eliminate Multiple Solder and Cleaning Steps•Eliminate Adjustments•Minimize the Number of Parts•Publish and Maintain Up-To-Date Design Guidelines•Design for Component Variability•Identify Defect Rates by CauseUse Standard Parts and Material whenever PossibleUse of standard parts and material reduces the cost, delay, and risk of processing problems. The primary advantage of standard parts and materials is that these are known quantities. As such they should minimize the potential for problems.Determine Capabilities of each Process StepProcess capability defines the ability of the process to produce within acceptable specification limits. By documenting process capabilities we can provide the design team with useful information for choosing processing technologies and the appropriate processing sequences. Design for Ease of Part Orientation for AssemblyUsing uniform part orientations eases inspection and assembly tasks. Maintaining the correct orientation is important because of potential impact on quality, particularly the quality of solder joints. Orientation can be facilitated by using notched packages, chamfered packages or special markings to ensure correct placement.Eliminate Multiple Solder and Cleaning StepsWe would like to minimize the processing technologies utilized. The greater the number of technologies used, the greater the chance for errors and reduction in process yield. Likewise, each additional processing step increases cost, risk, and potential for delays.Eliminate AdjustmentsAdjustments are costly and complicate processing. Process controls should be in place to minimize misalignments. Note, however, that not all misalignments must be repaired. In particular, minor misalignments may only affect the look of the product and not its functionality.Elimination of adjustments could also include replacement of potentiometers and manual switches with phase lock loops, feedback loops, voltage regulators, etc.Minimize the Number of PartsMinimizing the number and sizes of parts makes assembly (particularly automated assembly) easier. A potential strategy is to consider combining part functions. Reductions in part counts can also have a positive impact on system reliability. In addition, it can reduce machine requirements (i.e., placement machines have a finite number of feeders).Publish and Maintain Up-To-Date Design for Manufacturing GuidelinesAn organization utilizing IPD should establish Design for Manufacturing (DFM) guidelines. These guidelines should address reliability, quality, and manufacturing requirements of the company. They should also include: board parameters (i.e., coating, plating, materials, etc.), critical process steps, process capabilities, and important machine parameters that impact component design. Design for Component VariabilityWe cannot address every aspect of variability but the designer should realize and make allowances for uncontrollable variations (i.e., what Deming would call common cause variation) that are inherent to any system. For example, the lead-width of fine pitch packages is controlled but still varies from item to item. Knowing this we should design pads that are large enough to reliably hold the leads regardless of width.Benefits of DFMA•Reduced part number and part counts•Reduced assembly operation•Reduced product lead-time•Reduced packaging costs•Increased productivity and efficiency•Reduced material cost•Reduction in overall system/product cost•Improved product quality and reliabilityMany companies have used DFMA with great success. One example is Digital Equipment Corporation. Digital used DFMA principles when it decided to re-design its mouse. Some of the improvements realized because of DFMA were:• The number of parts used was reduced by 50%.• The number of assembly steps was reduced by 33%.• The amount of time required for assembly was reduced by 53%.• The volume of material required was reduced by 47%.• The cost of packaging was reduced by 41%.In addition, the project was completed in half the average time normally required.Design for Manufacture/Assembly SoftwareBoothroyd Dewhurst, Inc. has developed a software package that allows engineers to implement DFMA techniques within a user friendly, graphical environment. The software can quickly calculate the costs involved for different materials and manufacturing processes as well as identify areas where the number of parts can be reduced.The software allows engineers who are not familiar with the DFMA process to reap the benefits of implementing DFMA. Engineers can change the materials or processes used and quickly determine if the costs are reduced or not. The system incorporates databases of parts and subassemblies with Design for Assembly (DFA) information associated with the manufacturing site. Subassemblies are graphically represented along with information on unnecessary parts, estimated assembly times, and approximate cost data. The system also provides an accurate cost estimate for a variety of materials and associated manufacturing processes including: injection molding, machining, sheet metal work, die casting, and powder metal parts.Potential users of the Boothroyd Dewhurst software should note that they must have a detailed knowledge of their manufacturing process plan before they begin using the software. The software is not knowledge-based, and does not aid the user in developing a process plan. This drawback can be frustrating to new users of the tool; however, it does not diminish the importance of the software as it relates to DFMA. The primary benefit of the system is that it allows design engineers to quickly and easily consider the impact of using alternative materials and manufacturing processes. Boothroyd and Dewhurst, Inc. have documented significant reductions in parts count and cost (51% and 37%), time to market (50% faster), assembly time (62%), and manufacturing cycle time (57%) as well as improved quality and reliability (68%) by system users.(Illustrations in Section 2.1 were adapted from Machine Design Magazine)。
DIN946(中英文版)
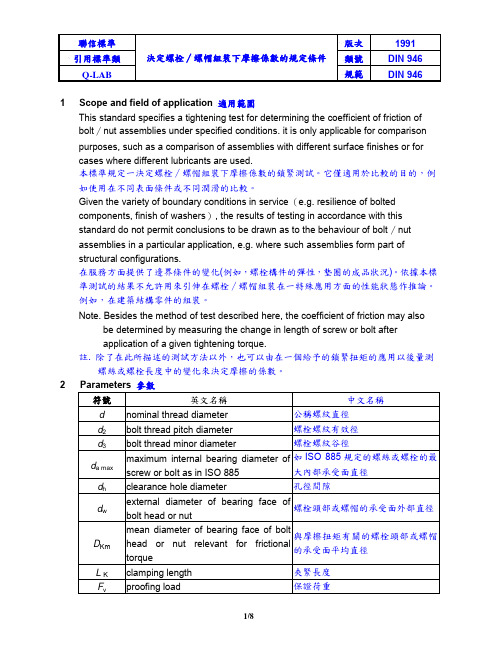
版次 類號 規範
1991 DIN 946 DIN 946
This standard specifies a tightening test for determining the coefficient of friction of bolt∕nut assemblies under specified conditions. it is only applicable for comparison purposes, such as a comparison of assemblies with different surface finishes or for cases where different lubricants are used. 本標準規定一決定螺栓∕螺帽組裝下摩擦係數的鎖緊測試。它僅適用於比較的目的,例 如使用在不同表面條件或不同潤滑的比較。 Given the variety of boundary conditions in service (e.g. resilience of bolted components, finish of washers ), the results of testing in accordance with this standard do not permit conclusions to be drawn as to the behaviour of bolt ∕nut assemblies in a particular application, e.g. where such assemblies form part of structural configurations. 在服務方面提供了邊界條件的變化(例如,螺栓構件的彈性,墊圈的成品狀況)。依據本標 準測試的結果不允許用來引伸在螺栓∕螺帽組裝在一特殊應用方面的性能狀態作推論。 例如,在建築結構零件的組裝。 Note. Besides the method of test described here, the coefficient of friction may also be determined by measuring the change in length of screw or bolt after application of a given tightening torque. 註. 除了在此所描述的測試方法以外,也可以由在一個給予的鎖緊扭矩的應用以後量測 螺絲或螺栓長度中的變化來決定摩擦的係數。 Parameters 參數 符號 d d2 d3 da max dh dw 英文名稱 nominal thread diameter bolt thread pitch diameter bolt thread minor diameter 中文名稱 公稱螺紋直徑 螺栓螺紋有效徑 螺栓螺紋谷徑
AIAG-Cqi-14-Warranty-Key-Terms

AUTOMOTIVE WARRANTY MANAGEMENTKEY TERMSAUTOMOTIVE INDUSTRY ACTION GROUPINTRODUCTIONThe warranty management project was formed by our members to facilitate a change from a cost-transfer system to a problem prevention system to benefit end users, as well as carmakers and their suppliers. AIAG partnered with OESA to develop a common approach to promote consumer satisfaction and continuous warranty improvement by providing a recommended, robust warranty management program that instills a consumer-centric approach to warranty management.The output of this group is the newly launched 3rd Edition of the Automotive Warranty Management Guideline. These are the key terms you’ll want to be familiar with when taking the CQI-14 Automotive Warranty Assessment Training or Pre-Assessment, or when implementing the CQI-14 processes.TABLE OF CONTENTSA (1)Adaptive Control, Advanced Product Quality Planning (APQP), Aftermarket, Anti-lock Brake System (ABS), Axiomatic DesignB (1)BenchmarkingC (1)Claim Data, Claims per 1,000 vehicles (C/1000), Component,Consumer, Consumer Concern Not Duplicated (CCND), Consumer -Centric Warranty, Control Plans, Corrective Action, Cost Per Unit (CPU) or Cost Per Vehicle (CPV), Critical to Quality (CTQ),Cross- Functional T eam (CFT), CultureD (2)Dealer, Deep Dive, Design Failure Mode and Effects Analysis (DFMEA), Design for Assembly (DFA), Design for Manufacture (DFM), Design for Serviceability, Design for Six Sigma (DFSS), Design Of Experiments (DOE), Design Release Engineer (DRE OR DR), Design Review Based On Failure Mode (DRBFM), Design Review Based On Test Results (DRBTR), Design Validation Plan And Report (DVP&R OR DVP), Detection, Detection-T o-Correction Measure, Diagnostic Trouble Code (DTC), Directed SourceE (4)Early Warning Tracking (EWT), End of Life (EOL), Error DetectionF (4)Failure Mode, Failure Modes and Effects Analysis (FMEA), Fault Tree Analysis (FTA), Federal Motor Vehicle Safety Standard (FMVSS), FrequencyH (4)Hypothesis TestingI (4)Ideal FunctionK (5)Key Performance Indicators (KPI)L (5)Labor Operation Codes (Labor Op), Lessons Learned, Look-AcrossM (5)Mahalanobis-Taguchi System (MTS), Measurement Systems N (5)Noise, National Highway Traffic Safety Administration (NHTSA), No Fault Found (NFF), No Trouble Found (NTF)O (6)Original Equipment Manufacturer (OEM)P (6)Paynter Chart, Parametric Design, Pareto Chart, Part, Partner Organization, Parts Return Center (Returned Parts Center), Plan, Do, Check, Action (PDCA), Poka-Yoke, Product Service Manual, Production Part Approval Process (PPAP), Production Preparation Process (3P), Production Validation Test (PV), Pugh AnalysisQ (7)Quality Function Deployment (QFD)R (7)Read-Across or Replication, Regression Analysis, Repair Codes, Risk Priority Number (RPN), Road Maps, Robustness, Root CauseS (8)Sub-system, Supplier, Supplier Quality Assurance (SQA), Supplier Quality Engineer (SQE), Supplier Technical Assistance (STA), Supply Chain, Swim Lanes, SystemT (9)Technical Service Bulletin (TSB), Test to Failure, Things-Gone-Right (TGR), Things-Gone-Wrong (TGW) , Tier Supplier, Time-to-Detection, Transportation Recall Enhancement, Accountability and Documentation Act (TREAD), Trend (Run) Chart, TRIZ , Trouble Not Found (TNF)V (10)Value Analysis (VA), Value Engineering (VE), Value StreamMapping, Vehicle Identification Number (VIN), Verbatims, Voice of the Customer (VOC)W (10)Weibull Analysis# (10)8 D, 5 Phase, 5 S [Methodology], 5 Why, 7 StepAADAPTIVE CONTROL: The ability of a system to measure, identify, decide and adjust to changes in the operation or environment to provide the desired output.ADVANCED PRODUCT QUALITY PLANNING (APQP): A structured method of defining and establishing the steps necessary to assure that a product satisfies the customer.AFTERMARKET: The part of the automotive industry concerned with the manufacturing, remanufacturing, distribution, retailing, and installation of all vehicle parts, chemicals, tools, equipment and accessories for light and heavy vehicles after the initial sale of the vehicle.ANTI-LOCK BRAKE SYSTEM (ABS): A braking system that prevents wheels from locking while braking.AXIOMATIC DESIGN: A systems design methodology using matrix methods to systematically analyze the transformation of customer needs into functional requirements, design parameters, and process variables. The method gets its name from the use of design principles or design axioms governing the analysis and decision making process in developing high quality product or system designs.BBENCHMARKING: Systematic approach to identifying standards for comparison. It provides input to the establishment of measurable performance targets, as well as ideas for product design and process design.CCLAIM DATA: Record of data associated with vehicle repairs and claims.CLAIMS PER 1,000 VEHICLES (C/1000): Metric equivalent to 1000 ppm and used in association with exposure to measure quality of vehicles in service.COMPONENT: A constituent element of a system on the vehicle.CONSUMER: The end customer who leases/purchases and uses the vehicle.CONSUMER CONCERN NOT DUPLICATED (CCND): The designation applied to a consumer concern that, when investigated by the dealer service organization, cannot be reproduced. This does not discount the concern; rather, it indicates that the condition(s) that caused the concern was not reproduced and/or no data was captured by the in-vehicle diagnostic system indicating such a concern.CONSUMER-CENTRIC WARRANTY: A claim rate reduction focus that aligns all value chain members to collaboratively and continuously approach warranty improvement through best practices, recommended tools and a root cause culture.CONTROL PLANS: Written descriptions of the systems for controlling parts and processes. Control plans provide a written summary description of the systems used in minimizing process and product variation.CORRECTIVE ACTION: Any action taken by an organization that is designed to permanently prevent the occurrence of the failure mode, detect when the failure mode or effect occurs, and to plan for the failure mode and its risk.COST PER UNIT (CPU) OR COST PER VEHICLE (CPV): The calculated cost of warranty related repairs by totaling the sum of the repair costs divided by the number of vehicles produced to determine a per vehicle cost.CRITICAL TO QUALITY (CTQ): The key measurable characteristics of a product or process whose performance standards or specification limits must be met in order to satisfy the customer.CROSS-FUNCTIONAL TEAM (CFT): A group that contains people with different skill sets all working together toward a common goal. This team could include operations, finance, quality, design engineering, process engineering, supply chain management, commercial, legal, warranty, etc.CULTURE: Refers to norms of behavior and shared values among a group of people. Culture is behavioral change over time.DDEALER: The retail organization that sells the vehicle to the consumer; also can be referred to as Retailer.DEEP DIVE: A technique used to rapidly and deeply immerse a team into a situation for problem-solving or idea creation.DESIGN FAILURE MODE AND EFFECTS ANALYSIS (DFMEA): An analytical methodology used to ensure that potential problems have been considered and addressed throughout the product design and development phase.DESIGN FOR ASSEMBLY (DFA): The process of considering how the product will be assembled, potential problems that could occur and simplifying by revising the design and assembly procedure to reduce the risk of these problems, lowering costs and making it easier to assemble.DESIGN FOR MANUFACTURE (DFM): The process of considering how the product will be manufactured and potential problems that could occur and then optimizing the design to be easier to produce, have higher throughput and improved quality.DESIGN FOR SERVICEABILITY: Engineering process used to optimize the serviceability of a design.DESIGN FOR SIX SIGMA (DFSS): A design philosophy of systematic methodology, tools, and techniques which enables the ability to design products and processes that meet customer expectations and can be produced at a six sigma quality level.DESIGN OF EXPERIMENTS (DOE): A test or sequence of tests where potentially influential process variables are systematically changed according to a prescribed design matrix.DESIGN RELEASE ENGINEER (DRE OR DR): The engineer that approves and releases a component, sub-system or system design for use.DESIGN REVIEW BASED ON FAILURE MODE (DRBFM): A philosophy of reviewing the potential impactof a design change based on 1) how can an unintended function occur as a result of the change, 2) cross-functional discussion regarding the details of the design change, controls to mitigate an unintended function and 3) design review to determine additional improvement actions that would prevent the change from causing an unintended function.DESIGN REVIEW BASED ON TEST RESULTS (DRBTR): A formal process for conducting proactive design reviews when tests results are available or with field returns. The review assesses performance on various tests or field conditions, review of actual end of test or field return component conditions, potential cause(s) of resultant conditions and improvements that can be made as well as tracking implementation and verificationof these improvements. The intent is to uncover all hidden problems and can work either independently or in conjunction with Design Review Based on Failure Modes (DRBFM).DESIGN VALIDATION PLAN AND REPORT (DVP&R OR DVP): A method to plan and document testing activity through each phase of product/process development from inception to ongoing refinement.DETECTION: An assessment of how well the product or process controls detect the cause of the failure or failure mode.DETECTION-TO-CORRECTION MEASURE: The time it takes to correct an unintended condition after it has been detected.DIAGNOSTIC TROUBLE CODE (DTC): A code number generated by a vehicle’s onboard computer that corresponds to a specific fault. Most computerized engine control systems have a certain amount of self-diagnostic capability. When the engine is running and the computer detects a problem in one of its sensor or output circuits, or even within itself, it triggers a trouble code. In some systems, the code number is retainedin memory. In others, the code is not stored but is regenerated when a mechanic runs the system through a special self-diagnostic test. The only indication of trouble is when the “Check Engine” light on the instrument panel lights up.DIRECTED SOURCE: A supplier in a supply chain that is identified by a vehicle manufacturer (or higher tier supplier, e.g., Tier 1 supplier) as an essential member of the supply chain for a particular part or component. Generally, when a supplier is awarded business, it is able to select its own lower tier suppliers. However, in this case, the inclusion of a “directed source” supplier is dictated by the vehicle manufacturer or higher tier supplier.EEARLY WARNING TRACKING (EWT): FCA US LLC’s process for tracking early field returns for new vehicle launches.END OF LIFE (EOL): Condition or state of the product system at the end of the vehicle service life.ERROR DETECTION: Refers to any devices and practices that prevent a failure mode from being passed along in the process once it has occurred.FFAILURE MODE: The way or manner in which a product or process could fail to meet design intent or process requirements.FAILURE MODES AND EFFECTS ANALYSIS (FMEA): An analytical methodology used to ensure that potential problems have been considered and addressed throughout the product and process development process.FAULT TREE ANALYSIS (FTA): Technique for system analysis where system faults are analyzed from a single potential failure to identify all possible causes.FEDERAL MOTOR VEHICLE SAFETY STANDARD (FMVSS): Federal mandate defined by the U.S. Department of Transportation’s National Highway Traffic Safety Administration that motor vehicle manufactures and equipment manufacturers must comply.FREQUENCY: The rate at which a problem is occurring or is being experienced by the customer.HHYPOTHESIS TESTING: An evaluation of two mutually exclusive statements about a population to determine which statement is best supported by the sample data.IIDEAL FUNCTION: The information or energy transformation that occurs to the input signal to achieve the desired output response.KKEY PERFORMANCE INDICATORS (KPI): Financial and non-financial metrics used to help an organization define and measure progress toward organizational goals.LLABOR OPERATION CODES (LABOR OP) : Code used to describe a specific repair, alignment, adjustment, replacement, or reinstallation done on a vehicle to a specific part or assembly.LESSONS LEARNED: The collection of knowledge for an organization based on past successes, failures, and experiences. The form of this knowledge can take many forms; databases, paper records, suggestion programs, etc.LOOK-ACROSS: The process of applying lesson’s learned across similar processes, products or systems in the organization as a preventive measure to reduce risk and improve performance and customer satisfaction.MMAHALANOBIS-TAGUCHI SYSTEM (MTS) : A measuring or evaluating tool used to recognize a pattern from multidimensional data by applying the Mahalanobis Distance, a process of distinguishing one group from another, into a process of defining a reference group and measuring individual subsets. MEASUREMENT SYSTEMS ANALYSIS (MSA): A collection of tools which seek to identify the components of variation in measurement devices.MONTHS-IN-SERVICE (MIS): Measurement of the time interval in which a vehicle is exposed to consumption. Approximately 30 days = 1.0 MIS, also commonly referred to as Time-In-Service (TIS).NNOISE: A consistent level of reported failure performance that cannot be attributed to one single cause or defect.NATIONAL HIGHWAY TRAFFIC SAFETY ADMINISTRATION (NHTSA): The agency within the Department of Transportation that is responsible for establishing and enforcing safety standards for passenger vehicles.NO FAULT FOUND (NFF): See “No Trouble Found”.NO TROUBLE FOUND (NTF): The designation applied to a part (component, system or module), replaced during a service event that, when analyzed by the vehicle or parts manufacturer, meets all requirements ofa “good part.” This does not discount the concern; rather, it indicates that the condition(s) that caused the concern was not reproduced or identified in the statement of requirements, qualification tests did not challenge the component sufficiently and/or no data was captured by the in-vehicle diagnostic system or part intelligence system indicating such a concern. (Also see “No Fault Found” or “Trouble Not Found.”)OORIGINAL EQUIPMENT MANUFACTURER (OEM): Typically a company that uses a component made by a second company in its own product, or sells the product of the second company under its own brand. The specific meaning of the term varies in different contexts. In the automotive industry, OEMs are the industry’s brand name auto manufacturers, such as General Motors, Ford and Toyota.PPAYNTER CHART: A long-term validation tool that displays the history of a problem. It is used to monitor and track multiple problems and occurrences of failure and validate the impact of containment and corrective actions over an extended period of time.PARAMETRIC DESIGN: A technique based on Design of Experiments that provides a low cost way of achieving product robustness i.e., making the product insensitive to the effect of noise. P-Diagrams are a means of reducing complex systems to understandable elements in order to capture potential internal and external influences on system, sub-system, assembly or component functionality. Parametric design is applied to reduce the impact of these influences.PARETO CHART: Shows the frequency of occurrence of items and arranges them from the most frequent to the least frequent. Pareto Charts are a visually effective means of displaying the relative importance of causes, problems, or other conditions.PART: An individual automobile component; an essential element or constituent that can be separated from or attached to a system; a detachable piece which can be replaced.PARTNER ORGANIZATIONS: Includes all members of a specific supply chain plus the dealers orother organizations involved in the sale or servicing as well as manufacturing of a vehicle manufacturer’s automobiles. (Also see “Supply Chain” and “Original Equipment Manufacturers (OEM).”)PARTS RETURN CENTER (RETURNED PARTS CENTER): Area where warranty parts are returned to. Here they are evaluated and/or tested and made available or sent out to the supplying party for investigation.PLAN, DO, CHECK, ACTION (PDCA): Deming continuous four step quality problem-solving process cycle of plan, doing the planned activity, checking/verifying the results met expectations and the action of implementing the improvement.POKA-YOKE: The practice of designing products or processes in a manner that prevents or minimizes the probability of human or mechanical error. This is also called Error-Proofing or Mistake-Proofing and prevents defects by detecting and correcting the errors that cause them before they occur.PRODUCT SERVICE MANUAL: A set of instructions that defines the components in the sub-system or system of the vehicle, diagnostic steps, disassembly and assembly steps of the component when it needs tobe serviced or replaced.PRODUCTION PART APPROVAL PROCESS (PPAP): A generic requirement for production part approval, including production and bulk material. PPAP’s purpose is to provide the evidence that all customer engineering design record and specification requirements are properly understood by the organization and that the manufacturing process has the potential to produce product consistently meeting these requirements during an actual production run at the quoted production rate.PRODUCTION PREPARATION PROCESS (3P): A clean sheet tool for designing production processes that facilitates a lean culture, eliminating waste.PRODUCTION VALIDATION TEST (PV): Engineering tests that validate that products made from production tools and processes meet customer engineering standards including appearance requirements.PUGH ANALYSIS: Charts similar to pros vs. cons lists. These are used for evaluating multiple options against each other, in relation to a baseline option.QQUALITY FUNCTION DEPLOYMENT (QFD): A systematic tool for translating customer requirements into appropriate company requirements at each phase from concept to engineering development to manufacturing to sales and distribution.RREAD-ACROSS OR REPLICATION: Reproducing the improvements in other areas of the organization and updating the corporate knowledge base. (Also see “Look-Across.”)REGRESSION ANALYSIS: A correlation measure of the strength of the relationship or association between variables.REPAIR CODES: Trouble codes used to classify repairs in the warranty data system and / or trouble codes stored in the cars computer system, when tripped a service light often comes on letting the driver know the vehicle needs to be taken in for repair.RISK PRIORITY NUMBER (RPN): The product of the severity (S), occurrence (O), and detection (D) rankings. (S) x (O) x (D) = RPN. Within the scope of the individual FMEA, this value (between 1 and 1000) can be used to assist the team in ranking the concerns in the design of the product and process.ROAD MAPS: The defining and documentation of activities in sequential process steps, typically through diagrams, that helps the understanding of how an objective or end result is to be achieved.ROBUSTNESS: The quality of being able to withstand stresses, pressures, or changes in the procedure, environment or circumstances. A system or design may be said to be “robust” if it is capable of coping well with variations (sometimes unpredictable or unplanned variations) in its operating environment with minimal damage, alteration or loss of functionality.ROOT CAUSE: The underlying cause(s) of the problem. Root cause is what is happening that results in the failure mode and effect on the product.SSUB-SYSTEM: Any system that is part of a larger system; component system on the vehicle.SUPPLIER: A Company engaged primarily in the manufacture of components, systems or modules for use in light duty (passenger car and light truck) automobiles.SUPPLIER QUALITY ASSURANCE (SQA): Organization to assist supply partners with quality and launch performance as well as problem-solving activity.SUPPLIER QUALITY ENGINEER (SQE): The functional position within the Supplier Quality Assurance organization that interfaces with the supply chain.SUPPLIER TECHNICAL ASSISTANCE (STA): This is another term used for the functional position within the Supplier Quality Assurance organization.SUPPLY CHAIN: All suppliers and the vehicle manufacturer that represent the flow of raw materials and finished products that go into the vehicles sold by the vehicle manufacturers.SWIM LANES: Method of displaying a process flow with the responsibilities organized into vertical organizational/functional lanes.SYSTEM: A set or arrangement of things so related or connected as to form a unity or whole. Typically, an integration of a number of components on the vehicle to perform the desired function such as braking, steering, fuel delivery as examples.TTECHNICAL SERVICE BULLETIN (TSB): Recommended repair procedure issued to dealers for specific problems. These are issued when there are several occurrences of the same issue.TEST TO FAILURE: A test in which the system being assessed is subjected to sufficient stress for a long enough time or large enough number of cycles to cause it to fail.THINGS-GONE-RIGHT (TGR): Product attributes or characteristics that produce a positive reaction from customers. Usually expressed as a rate: TGR/100.THINGS-GONE-WRONG (TGW): Product attributes or characteristics that produce a negative reaction from customers. Includes both component malfunctions and “correct” component functions that don’t meet customer expectations.TIER SUPPLIER: Suppliers are, at times, referred to as Tier n suppliers, where n is a number from 1 to 3 and represents the closeness of the supplier to the vehicle manufacturer when tracking the supply of parts. For example, a Tier 2 supplier supplies parts to a Tier 1 supplier, which in turn adds value and suppliers the parts to the OEM. (Also see “Supplier.”)TIME-TO-DETECTION: The time between the occurrence of an undesirable condition until the detection of that undesirable condition.TRANSPORTATION RECALL ENHANCEMENT, ACCOUNTABILITY AND DOCUMENTATION ACT (TREAD): The TREAD Act was enacted on November 1, 2000, as a direct consequence of hearings before the Committee on Energy and Commerce on the safety of tires and related matters. The TREAD Act contains provisions requiring vehicle and equipment manufacturers to report periodically to NHTSA on a wide variety of information that could indicate the existence of a potential safety defect and to advise NHTSA of foreign safety recalls and other safety campaigns.TREND (RUN) CHART: A simple graphic representation of a characteristic of a process. A Trend Chart combines the information on a Run Chart with a calculated “best fit” line to track the magnitude of change in a characteristic (whether it is improving, remaining stable, or deteriorating over time).TRIZ: A Russian acronym for the “Theory of Inventive Problem-Solving.” A methodology, tool set, knowledgebase, and model-based technology for generating innovative ideas and solutions for problem-solving. TRIZ provides tools and methods for use in problem formulation, system analysis, failure analysis, and patterns of system evolution (both “as-is” and “could be”).TROUBLE NOT FOUND (TNF) : See “No Trouble Found.”VVALUE ANALYSIS (VA): A systematic, cross-functional team approach to maximize product/process value by identifying functions and their related costs.VALUE ENGINEERING (VE): See “Vaule Analysis”VALUE STREAM MAPPING: Data resulting from the measurement of a parameter or a variable.VEHICLE IDENTIFICATION NUMBER (VIN): A unique serial number used by the motor vehicle industry to identify individual motor vehicles.VERBATIMS: A text associated with a claim detailing a consumer’s concern or the technician’s diagnosis and repair process.VOICE OF THE CUSTOMER (VOC): Customer feedback both positive and negative including likes, dislikes, problems and suggestions.WWEIBULL ANALYSIS: A probability plot of failures versus time measured (in time to failure, cycles to failure, miles to failure, etc.).#8 D: 8D is a problem-solving methodology for product and process correction and improvement that is structured into eight disciplines (D1–D8), plus one preparation step (D0).5 PHASE: The name of a General Motors problem-solving tool.5 S [METHODOLOGY]: A lean philosophy method for creating and maintaining an organized, clean, safe and standardized work place. The English terminology is roughly taken from the Japanese five steps of: Seiri (separate), Seiton (straighten or simplify), Seiso (sanitize or shine), Seiketsu (standardize), Shitsuke (sustain).5 WHY: The name of a problem-solving tool.7 STEP: T he name of a FCA US LLC problem-solving tool.AUTOMOTIVE WARRANTY MANAGEMENT KEY TERMS。
ANSI B92.1-1970(R1993) SAE美国渐开线花键-中文翻译完整版0429解读
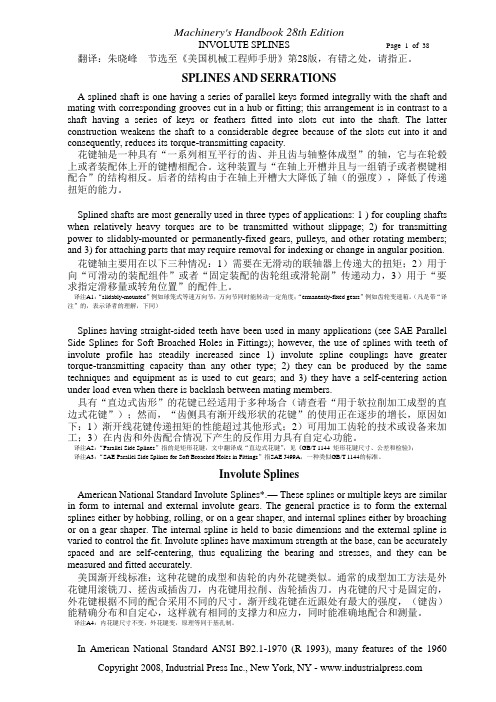
翻译:朱晓峰节选至《美国机械工程师手册》第28版,有错之处,请指正。
SPLINES AND SERRATIONSA splined shaft is one having a series of parallel keys formed integrally with the shaft and mating with corresponding grooves cut in a hub or fitting; this arrangement is in contrast to a shaft having a series of keys or feathers fitted into slots cut into the shaft. The latter construction weakens the shaft to a considerable degree because of the slots cut into it and consequently, reduces its torque-transmitting capacity.花键轴是一种具有“一系列相互平行的齿、并且齿与轴整体成型”的轴,它与在轮毂上或者装配体上开的键槽相配合。
这种装置与“在轴上开槽并且与一组销子或者楔键相配合”的结构相反。
后者的结构由于在轴上开槽大大降低了轴(的强度),降低了传递扭矩的能力。
Splined shafts are most generally used in three types of applications: 1 ) for coupling shafts when relatively heavy torques are to be transmitted without slippage; 2) for transmitting power to slidably-mounted or permanently-fixed gears, pulleys, and other rotating members; and 3) for attaching parts that may require removal for indexing or change in angular position. 花键轴主要用在以下三种情况:1)需要在无滑动的联轴器上传递大的扭矩;2)用于向“可滑动的装配组件”或者“固定装配的齿轮组或滑轮副”传递动力,3)用于“要求指定滑移量或转角位置”的配件上。
图纸常用英语.
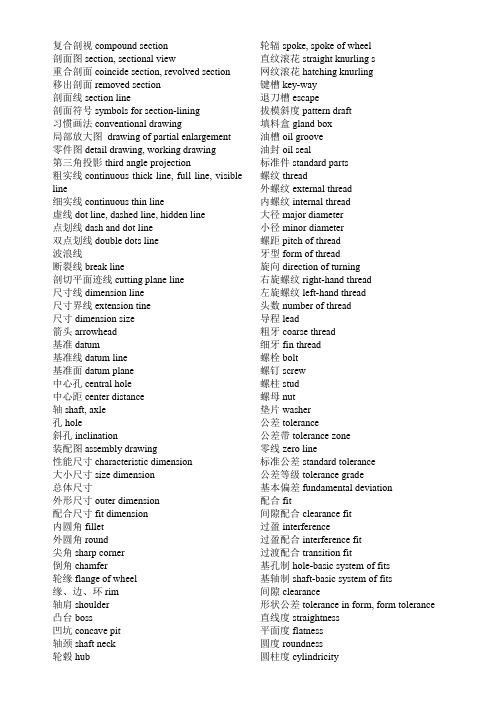
复合剖视compound section剖面图section, sectional view重合剖面coincide section, revolved section移出剖面removed section剖面线section line剖面符号symbols for section-lining习惯画法conventional drawing局部放大图drawing of partial enlargement零件图detail drawing, working drawing第三角投影third angle projection粗实线continuous thick line, full line, visible line细实线continuous thin line虚线dot line, dashed line, hidden line点划线dash and dot line双点划线double dots line波浪线断裂线break line剖切平面迹线cutting plane line尺寸线dimension line尺寸界线extension tine尺寸dimension size箭头arrowhead基准datum基准线datum line基准面datum plane中心孔central hole中心距center distance轴shaft, axle孔hole斜孔inclination装配图assembly drawing性能尺寸characteristic dimension大小尺寸size dimension总体尺寸外形尺寸outer dimension配合尺寸fit dimension内圆角fillet外圆角round尖角sharp corner倒角chamfer轮缘flange of wheel缘、边、环rim轴肩shoulder凸台boss凹坑concave pit轴颈shaft neck轮毂hub 轮辐spoke, spoke of wheel直纹滚花straight knurling s网纹滚花hatching knurling键槽key-way退刀槽escape拔模斜度pattern draft填料盒gland box油槽oil groove油封oil seal标准件standard parts螺纹thread外螺纹external thread内螺纹internal thread大径major diameter小径minor diameter螺距pitch of thread牙型form of thread旋向direction of turning右旋螺纹right-hand thread左旋螺纹left-hand thread头数number of thread导程lead粗牙coarse thread细牙fin thread螺栓bolt螺钉screw螺柱stud螺母nut垫片washer公差tolerance公差带tolerance zone零线zero line标准公差standard tolerance公差等级tolerance grade基本偏差fundamental deviation配合fit间隙配合clearance fit过盈interference过盈配合interference fit过渡配合transition fit基孔制hole-basic system of fits基轴制shaft-basic system of fits间隙clearance形状公差tolerance in form, form tolerance 直线度straightness平面度flatness圆度roundness圆柱度cylindricity线轮廓度profile of any line面轮廓度profile of any plane位置公差tolerance in position, position tolerances平行度parallelism齿轮gear圆柱齿轮cylindrical gear正齿轮spur gear斜齿轮spiral gear轮齿gear tooth节圆pitch circle齿顶圆addendum circle, outside circle齿根圆root circle, addendum circle模数modulus齿数number of teeth齿高tooth height齿顶高height of addendum齿根高height of addendum齿厚circular thickness齿间tooth space齿宽tooth width压力角angle of pressure弹簧spring销pin圆柱销round pin圆锥销taper pin开口销cotter pin, split键key平键flat key半圆键half round key, woodruff key轴承bearing滚动轴承rolling bearing向心铀承radial bearing密封装置sealing equipment锁紧装置locking equipment粗糙度roughness基本尺寸basic size实际尺寸actual size极限尺寸limits size最大极限尺寸maximum limit of size最小极限尺寸minimum limit of size偏差deviation上偏差upper deviation下偏差lower deviation垂直度perpendicularity倾斜度angularity同轴度concentricity对称度symmetry 位置度true position跳动run-out圆跳动cycle run-out全跳动total run-out轴测投影axonometric projection轴测投影面plane of axonometric projection 轴测图axonometric drawing正等轴测投影isometric projection正二测bimetric projection斜二测oblique bimetric projection轴测轴axonometric axis轴间角axis angle, angle between ales缩短foreshortened轴向缩短率coefficient of axial deformation ratio offore shortening for any axis切割法cutting method, by cutting方箱法boxing method坐标法coordinate method方框法enclosing-square method四心近似法four-center approximate method机械工程图中常用的英语词汇Abbreviation 缩写Accuracy 精度、准确性Acme thread 梯形螺纹(29°)Addendum 齿顶高Addendum angle 齿顶角Addendum circle 齿顶圆Addendum of mating gear 啮合齿轮的齿顶高Adjacent-part lines 相邻零件线Aligned sections 旋转剖视Aligned view旋转视图Allowance 容差、加工余量Alloy 合金Alloy steel 合金钢Alphabet 字母Alteration 变更、更改Alternate-position views 位置改变的视图Alternator 交流发电机Induction alternator 感应(交流)发电机Motor alternator 电动(交流)发电机Single-phase alternator 单向(交流)发电机Synchronous alternator 同步(交流)发电机Three-phase alternator 三相(交流)发电机Amount 总量、总计Analyzable assembly 分析装配图Anchor bolt 地脚螺栓Angles 角Acute angle 锐角Blunt angle 钝角Right angle 直角Sliding angle 摩擦角Spiral angle 螺旋角Taper angle 锥角Angular 有角的Angular bearing 径向止推轴承Angular bevel gears 斜交伞齿轮Angular gear人字齿轮Angular section斜剖面Anneal 退火Approval 批准、许可Arc 弧、圆弧Arc thickness 弧长厚度(齿厚)Arc welding 弧焊Arrangement 布置、装置Arrangement of views 视图的布置Clamping arrangement 夹紧装置Cramping arrangement 紧固装置General arrangement 总体布置Arrow 箭头Arrowheads 箭头Assembly 装配图、组装图Assembly drawing 装配图Assembly drawing number 装配图图号Assembly for installation 安装图Assembly parts 组装配合零件Assembly sections 装配图剖视Assembly sketches 装配草图Auxiliary elevation 辅助立面图Auxiliary line辅助线Auxiliary section 辅助剖视Auxiliary surface 辅助面Auxiliary view 辅助视图Average 平均数Axial 轴的、轴向的Axial pitch 轴向节距Axial plane 轴向平面Axial thickness 轴向厚度Axis 轴线、中心线Axis of revolution 回转轴线Axis of rotation 旋转轴线Axis of symmetry 对称轴线Horizontal axis 水平轴Major axis 长轴Minor axis 短轴Vertical axis 垂直轴X axis X轴Y axis Y轴Axle 轴Axle bearing 轴向(止推)轴承Axle sleeve 轴向(止推)套筒Axonometric drawing 轴测图Babbitt 巴氏合金Back cone 背锥Back cone radius 背锥半径Back elevation 后视图Backstop 托架、棘爪Ball bearing 球轴承Bar 杆Angle bar 角钢Channel bar 槽钢Flat bar 扁钢Round bar 圆棒、圆钢Base 基础、底座、基线、基面、基准Base circle 基圆Base circular thickness 基圆弧线齿厚Base cylinder 基圆柱Base helix angle 基圆上的螺旋角Base plane 基平面Base point 基点Key base 键座Basic circle 基准圆Basic hole system 基孔制Base shaft system 基轴制Basic size 基本尺寸、公称尺寸、标称直径Basis 基础、基准、基线Battery 电池、蓄电池Bearing 轴承、支撑、方位Bearing accuracy 定位精度Bearing box 轴承箱Bearing brass 铜轴衬Bearing bridge 轴承支架Bearing oil seal 轴承油封圈Bearing support 轴承架Bearing unit 轴承组合件Anti-friction bearing 减摩轴承Ball and socket bearing 球窝轴承Conical bearing 锥形轴承Journal bearing 径向轴承Needle bearing 滚针轴承Plain bearing 滑动轴承Roller bearing 滚柱轴承Self-aligning bearing 自位轴承Thrust bearing 止推轴承Belt 带、皮带Bench 工作台Work bench 工作台Bend 弯头、接头Elbow bend 肘形弯管Normal bend 正弯管(90°)Bender 弯曲机Bending 挠曲Bending strength 抗弯强度Bent axle 曲轴Bevel 倾斜的、斜角的、斜面Bevel gear 圆锥齿轮、伞齿轮Bevel pinion 小圆锥齿轮Bevel washer 斜垫圈Bevel wheel 伞齿轮、斜摩擦齿轮Bilateral tolerance 双向公差Bill of materials 送料单Block in、block out 画草图Blue paper 蓝晒纸Blueprint 蓝图、设计图Board 板、(管理)局、厅Bottom board 底板Moulding board 模板Body 机体、机身Boiler 锅炉Bolt 螺栓、插销Adjusting bolt 调整螺栓Assembling bolt 装配螺栓Binding bolt 连接螺栓Bright blot 光制螺栓Captive bolt 固定螺栓Double-screw bolt 双头螺栓Fitter bolt 装配螺栓Foundation bolt 地脚螺栓Hexagonal head bolt 六角头螺栓Hook bolt 钩形螺栓Screw bolt 全螺纹螺栓Snap bolt 圆头螺栓Tension bolt 拉紧螺栓Bolted joints 螺栓连接Book 书、册Hand book 手册Instruction book 说明书Bore face machine 镗孔端面加工机床Borer 镗床Jig borer 坐标镗床Table borer 台式镗床Boring 镗孔Boring machine 镗床Boring mill 镗床Bottom case 底座Bottom clearance 径向间隙Bottom view 底视图Bracket 托架、支柱Brake 制动器、闸Brass 黄铜、铜轴衬Braze 铜焊Brazing 铜焊Breadth 宽度、厚度Break line 断裂线Brinell figure (number) 布氏硬度Brinell hardness 布氏硬度Broacher 拉床、绞孔机Broaching 扩孔机、拉床、拉削Broken circle 虚线圆Broken out section 断裂剖面Broken view 局部视图Bronze 青铜Burnishing 抛光、磨光Burr 三角矬、毛刺、去毛刺Bush 衬套、轴瓦Bushing 轴衬、衬套、套管Butt joint 对接焊Butterfly nut 蝶形螺母Butterfly valve 蝶形阀Button 按钮Push button 控制按钮Cable 电缆Cage 盒、罩、箱Caliper 卡尺、卡钳Gauge caliper 卡规、量规Internal caliper 内卡钳Sliding (vernier) caliper 游标卡尺Cam 凸轮Cam design 凸轮设计Cam shaft 凸轮轴Actuating cam 主动凸轮Adjustable cam 可调凸轮Control cam 控制凸轮Cap 盖、帽、罩Cap screw 带帽螺钉Capital 大写字母Carburizing 渗碳Card 卡片Cartographer 制图员Cartography 制图学、制图法Case 箱、盒、容器、表面Case hardened 表面淬火、硬化Nitrogen case hardening 渗氮硬化Casing箱、盒、壳Oil pump casing 油泵(壳) Casting 铸造、铸件Defect casting 铸件缺陷Die casting 压铸Sand casting 砂型铸造Spun casting 离心铸造Steel casting 铸钢Cast-iron 铸铁Castle circular nut 六角圆螺母Castle nut 蝶形螺母Catalogue data 表列数据Cave 凹槽、内腔Centre 中心、圆心Centre distance 中心距Centre hole 中心孔Centre line 中心线Centre-section 中心剖面Centre to centre 中心距Centesimal 百分的、百分之一的Centimeter 厘米、公分Central hole 中心孔Central plane 中心平面Central projection 中心投影Chafe 摩擦、磨损Chain 链Drive chain 主动链Transmission chain 传动链Chamfer 倒角、倒棱、斜面Dimensioning of chamfer 倒角的尺寸注法Changes on drawing 图的更改Channel 沟槽Chapter 章Chart 图表、计算图Chart of symbols 符号图表Auxiliary chart 辅助图Dimensions chart 外廓尺寸图Graphical chart 图表Process chart 工艺程序图Progress chart 工艺程序表、工作进度表Charting 制图(表)、填图Check 校验、校核、制动装置Check drawings 校图Check nut 防松螺母Check ring 挡圈Check test校核试验Chief draftsman 主任制图员Chromium 铬Chromizing 镀铬处理Circle 圆、圆周Circle of reference 参考圆Addendum circle 齿顶圆Base circle 基圆Graduated circle 分度圆Imaginary circle 虚圆Outside circle 齿顶圆、外圆Pitch circle 节圆Rack circle 平面齿轮、扇形齿轮Root circle 根圆Top circle齿顶圆Circular cylinder 圆柱Circular pitch 弧线节距Circular thickness 弧线(齿)厚度Circumference 圆周长Clamp 夹紧、夹板Class 种类Class of fit 配合级别Classification 分类Claw 爪、钩、卡爪Clearance fit 间隙配合Clevice /clevis U形钩、U形夹Clevis bolt 套环(插销)螺栓Clevis pin U形夹销Clockwise 顺时针方向Clutch 离合器、联轴器Coat 外层、涂镀层Coat of metal 金属镀层First coat 底漆Coating 镀、覆盖Electrodeposited coating 电镀层Coaxial circle 共轴圆Cock 旋塞Coil 蛇形管、螺管、线圈Coil spring 盘簧Coincident line 重叠线Cold-rolled steel 冷轧钢Collet 夹头Collet chuck 弹簧夹头Color-harden 着色硬化、发蓝、煮黑Common difference 公差Company 公司Joint company 股份公司Limited company 有限公司Compass 圆规Compass of proportion 比例规Component 零件、构件Compression spring 压力弹簧Compressor 压缩机Computer 计算机Concave face 凹面Concentricity 同心度Cone 圆锥Cones development 锥面展开Cone pulley 锥形轮、塔轮Conical spring 锥形弹簧Connection 联接Bolt-on connection 螺栓联接Flange connection 法兰联接Rivet connection 铆钉联接Screw connection 螺钉联接Contact 接触、接合、啮合Contact angle 啮合角Angular contact ball bearing 向心止推球轴承Contour 外形、轮廓线Contracted drawing 缩图Contrast 对比、对照、比较Convention 惯例、常规、习惯Convention for materials 材料的习惯表示法Conventional break 习惯断裂画法Conventional diagram 习惯画法Conventional intersection 习惯交线(画法) Conventional practice 习惯画法Conventional sign 图例、习惯符号|Convex 凸面Conveyer 输送机、传送机Cooler 冷冻机Coordinate axis 坐标轴Coordinate paper 方格纸、坐标纸Copper 铜Copy 抄本、样板Correction 校正、修正Cotter pin 开口销Split cotter 开口销Counterbore 埋头孔、锥口孔Counterclockwise 逆时针方向Countersink 埋头孔、沉孔Countersink drill 中心钻、钻Countersunk 钻埋头孔、钻锥口孔Countersunk bolt 埋头螺钉Countersunk head 埋头Countersunk hole 锥坑Coupling 联轴节Cover 盖、罩Cylinder cover 汽缸盖Dust cover 防尘罩Cowl 壳、套、盖Crane 起重机Crank 曲柄、曲轴Crankshaft 曲轴Crest 峰、尖、牙尖Cross head 十字头Cross section 横剖面、横断面Crown gear 冕状齿轮Cube 立方形体、正六面体Current 电流Curvature 曲率Curvature radius 曲率半径Curve 弯曲、曲线、曲线板Curve plotter 绘图仪Curve ruler 曲线板French curve 曲线板Moment curve 力矩曲线、力矩图Cutter 刀、刀具Cutting plane 截平面Cutting plane symbols 剖切(迹线)平面符号Cycloid 摆线Cycloidal gear 摆线齿轮Cylinder 圆柱体Cylinder base 汽缸座Pump cylinder 泵缸Cylindrical cam 圆柱凸轮Cylindrical fit 圆柱配合Cylindrical roller bearing 圆柱滚子轴承Dash 短划线、虚线、破折号Dash and dot line 点划线Broken dash 断裂线Data 数据、资料Engineering data工程数据Master data 主要数据Date 日期、年代Datum 基准(点、线、面)、资料Datum line 基准线Datum point 基准点Datum plane 基准面Decade 十进制、十进位Decelerator 减速器、制动器、缓动装置Decimal 小数的、十进位小数的Decimal fraction 十进制分数Decimal fraction system 十进小数制Decimal scale 十进位比例尺Decimeter 分米、公分Dedendum angle 齿根角Dedendum circle 齿根圆Definition 定义Deformation 变形、扭曲Degree 度、程度Degree of accuracy 精度Degree of freedom 自由度Degree of hardness 硬度Degree scale 刻度Circular degree 圆度Delineation 轮廓、草图Delineator 制图者Department 科、处、系、车间Draft department 设计科Engineering department 技术科Fitting department 装配车间Heat treatment department 热处理车间Mechanical department 机加工车间Processing department 工艺科Depth 深度、高度Depth dial gauge 深度千分表Depth of engagement 啮合深度Depth of thread 螺纹深度Depth of tooth 齿高Contact depth of tooth 啮合高度Working depth of tooth 齿工作高度Derivation 偏差Standard derivation 标准偏差Description 描述、作图、绘制Design 设计、计划Design activity 设计机关(组织) Design assembly 设计装配图Design drawing 设计图Design layout 设计草图、初步设计图Preliminary design 初步设计Standard design 标准设计Technical design 技术设计Designation 符号、标志Designation strip 铭牌Designer 设计员、制图者、设计师Desk 桌、控制台Drawing desk 绘图桌Detail 细目、细节、详图、零件Detail drawing 详图、零件工作图Detail paper底图纸、描图纸Detail specification 详细规格Detent 棘爪、扳手、制动器Developable surface 可展曲面Developed view 展开图Development inner port 内表面展开图Development of surface 表面展开图Deviation 偏差、偏移Angular deviation 角偏差Average deviation 平均偏差Standard deviation 标准偏差Tolerance deviation 允许偏差Device 装置、设备Diagram 示意图、图解Diagram drawing 图解图、结构图Arrangement diagram 布置图Assembly diagram 装配示意图Block diagram 方框图Schematic diagram 原理图、简图Diagrammatic drawing 草图、示意图Dial gauge 千分表Dial inside micrometer 内径千分表Diameter 直径Diameter of aperture 孔径Diameter of pitch circle 节圆直径Diameter pitch (齿轮)径节Diameter run-out径向跳动Major diameter 大直径、螺纹外径Minor diameter 小直径、螺纹内径Nominal diameter 公称直径Pitch diameter of screw thread 螺纹中径Thread diameter 螺纹外径(直径) Diametral pitch 齿轮径节Die 模具、扳牙Diesel 柴油机、内燃机Dimension 尺寸Dimension line 尺寸线Limiting dimension 极限尺寸Nominal dimension 公称尺寸Outer dimension 外形尺寸、轮廓尺寸Direction 方位、方向Clockwise direction 顺时针方向Disc = disk 圆盘、原板Disk cam 圆盘凸轮Dismount 拆卸Dismountable 可拆卸的Displacement 移位、变位Distance 距离、路程Distortion 变形、歪扭Distribution 分配、分布、配置Ditto machine 复印机Diversion 变更、转换Dividing head 分规Dot line 虚线Dotted line 虚线Double dots line 双点划线Double helical pinion 人字小齿轮Double helical spur gear 人字齿轮Double thread 双头螺柱Dowel thread 定位销、圆柱销Dozer 推土机Draft = draught (拔模)斜度、草图、制图Drafting 制图Drafting board 制图板Drafting machine 制图机Drafting tape 制图带、胶带Draftsman 绘图员Drawer 制图员Drawing 绘图、图样Drawing board 绘图纸Drawing control 图样管理Drawing free-head 草图Drawing instrument 绘图仪器Drawing number 图号Drawing pencil 绘图铅笔Drawing pin 图钉Drawing size 图纸尺寸Drawing table 制图桌Drawing with compass 用圆规画图Blue print drawing 蓝图Free hand drawing 徒手图Full size drawing 原大图Skeleton drawing 草图、结构图Working drawing 施工图、制造图、工作图Drill 钻孔、穿孔、穿孔器Drive 传动、驱动Drive fit 打入配合Air drive 气动Belt drive 带传动Chain drive 链传动Friction drive 摩擦传动Gear drive 齿轮传动Hydromatic drive 液压传动Speed-reducer drive 减速器传动Variable-speed drive 变速传动Worm-wheel drive 蜗轮传动Driven gear 从动齿轮Driven shaft 从动轴Driving gear 主动齿轮Driving shaft 主动轴Drum cam 凸轮轴Ductile iron 球墨铸铁Duplicating tracing 复制描图Durometer (钢轨)硬度计Dusting cloth 抹灰布、撒粉布Eccentricity 偏心距Edge iron 角铁Edge round 外圆角Edge view 边视图Effective diameter 有效直径Effective face width 有效齿宽Efficiency 效率、性能Mechanical efficiency 机械效率Elastic deformation 弹性变形Elasticity 弹性Elbow 肘形弯管、弯头Electric current 电流Electric element 电池Elephant 绘图纸(28X23英寸) Elevation 正面图、立视图End 末端、头Ball end 秋端Butt end 平端、端面Tail end 尾端Top end 顶端Engagement 啮合Engineer 工程技术人员、工程师Engineer-in-chief 总工程师Equipment 设备Eraser 橡皮Erasing shield 擦图片Erection diagram 安装图、装配图Error 误差Accumulated error 累积误差Allowance error 容许误差Average error 平均误差Permissible error 容许误差Relative error 相对误差Exterior 外表面External 外部External diameter 外径External dimension 外形尺寸External fillet 外圆角External thread 外螺纹Extra fine(screw)特细牙螺纹Eyelet = eyelet-hole 小孔Fabrication 建造、制造Face 面、正面、表面、端面Face cam 平面凸轮Face gear 平面齿轮Face hardening 表面硬化Inner face 里面Outer face 外面Face off 倒角Factor of safety 安全系数Factory 工厂、制造厂Factory made 工厂制造的Fastener 接合件、紧固件Fastening 连接件、紧固件Fatigue 疲劳Faucet 旋塞、龙头、开关Feather 滑键、冒口Feather key 滑键Feature 特征、特性、性能Basic mechanical design feature 主要机械设计性能Mechanical feature 机械性能(特性)Feed-pump 供油泵、供水泵Feet 英尺Ferrous metal 黑色金属Field 工场、现场Figure 形状、图样、插图、数字File 锉刀、锉平Filler 填料、垫片Fillet (内)圆角、填角、嵌条Fillet radius 内圆角半径Filter 过滤器Fine thread series 细螺纹级(系列)Finish 完工、加工、磨光Finish all over 全部加工Finish marks 加工符号Machine finish 机器光制Fit 配合Clearance fit 间隙配合Free fit 自由配合Interference fit 静配合Light press fit 轻压配合Light running fit 轻传动配合Loose fit 松配合Normal-running fit 传动配合Running fit 动配合Shrink fit 冷缩配合Slide fit 滑动配合Transition fit 过渡配合Fix 安装、装配、调整、修理、固定Flange 法兰盘、凸缘Flank 边、侧面、齿侧、后面Flat 扁头、平面Flat key 平键Flat spring 板弹簧Flat surface 平面Flexible disk coupling 挠性盘形联轴节Flexible gear-type coupling 挠性齿轮联轴节Flywheel 飞轮Foot 英尺Foot screw 地脚螺钉Force 力Fore word 序、前言Forge 锻Forge steel 锻钢Former 样板、模型、量规Wooden former 木模Formula 公式Foundation 基础、基座Foundation bolt 地脚螺栓Foundry 铸件、铸工车间Fraction 分数、小数Front view 前视图、主视图Full diameter 大直径、主直径Full line 实线Full size 原大Full scale 原大Full section 全剖视Full section view 全剖视图Furbish 研磨、擦光Fuse 保险丝、熔断器Gage = gauge 量规Gallon 加仑Galvanize 镀锌、电镀Gasket 垫圈、密封垫Gasket material 填料Gasoline engine 汽油(内燃)机Gate 门、阀门Gear 齿轮Gear addendum angle 齿顶角Gear box(case) 齿轮箱Gear centre 齿轮中心Gear dedendum angle 齿根角(圆锥齿轮) Epicyclic gear 行星齿轮Herringbone gear 人字齿轮Ratchet gear 棘轮General drawing 总图Geometry 几何学Gland 压盖、填料盖、密封装置Glass 玻璃Glasscloth 砂布、玻璃布Glossary 词汇(表)Grade 等级、斜度Steel grade 钢号Graduated hardening 分级淬火Graduated scale 比例尺、分度尺Gram 克Graph 图(表、解、形)、曲线图Graph paper 方格纸Graphic图示、制图学Grease 滑脂Grind 磨削、抛光Grinding machine 磨床Grinding wheel 砂轮Groove cam 槽凸轮Groove pulley 槽轮、三角带轮Guide 手册、指南Guide bar 导杆Guide pin 定位销、导向销Guide screw 丝杠Guidebook 参考手册、指南、入门Half 二分之一、一部分Half bearing 轴瓦Half section 半剖视Half section view 半剖视图Hammer 锤子Handbook 手册、指南Hand-made 手工制造的Hand-operated 手控的Handle 手柄Hand wheel 手轮Hard casting 白口铁Hard drawn 冷拔Hard rolled 冷轧的Hard surfacing 表面硬化Harden 淬火、硬化Hardened and tempered 调质的Hardened-steel 淬火钢Hardening 硬化Hardness 硬度Hardometer 硬度计Hatch 剖面线H-beam 工字梁、H形梁Heat–treatment 热处理Heavy force fit 重压配合Height 高度Helical bevel gear 螺旋伞齿轮Helical gear 螺旋齿轮、圆柱斜齿轮Helical rack 斜齿齿条Helical spring 螺旋弹簧Hex nut 六角螺母Hexagon jam nut 六角锁紧螺母Hexagon socket head 内六角头Hidden line 虚线Hidden outline 看不见的轮廓线High-carbon steel 高碳钢High-duty 重型的、大型的、优产的High-speed steel 高速钢Hosting jack 千斤顶Hole 孔Horizontal datum plane 水平基准面Horizontal line 水平线Horizontal projection 水平投影Horizontal projection plane 水平投影面Horse-power 马力、功率Hose 软管Hose coupling 软管接头Hot-rolled steel 热轧钢Hot-work 热加工Hour 小时Housing 机座Housing of pump 泵体Bearing housing 轴承箱Gear housing 齿轮箱Hub 轮、中心、衬套I-beam 工字钢Illustration 插图、实例Inaccuracy 不精确、不准确Incenter 内(切圆)心Inch 英寸Incline 斜度、斜面Index plate 分度盘Indicator 指示计、百分表Industrial 工业公司Industrial drawing 工业制图Industry 工业Inertia 惯性Ink 墨水、油墨Ink holder 钢笔杆China ink 墨汁Inscription 标题Inside diameter 内径Inspection 检修、检查Inspection machine 检修机器Inspector 检查员Installation 装置、设备、安装Installation diagram 安装图Institute 研究所、协会、学院、学会Instruction 说明、指示Instrument 仪器、仪表、工具Instrument drawing 仪器图Intensity 强度Interchangeability 互换性1 Interconnection 互相连接Interference fit 静配合Interior view 内部(的)视图Internal combustion engine 内燃机Internal fillet 内圆角Internal gear 内齿轮Introduction 引言、介绍、序言Invisible line 虚线Involute 渐(伸)开线Involute gear 渐开线齿轮Involute rack 渐开线齿条Involute spline 渐开线花键Involute teeth 渐开线齿形Iron 铁Ingot iron 低碳铁、工业纯铁Knobbled iron 熟铁Magnetic iron 磁铁Malleable iron 可锻铁、韧性铁Plate iron 铁板、钢板Quadrant iron 方钢Rod iron 圆铁、棒钢Round iron 圆铁、圆钢Rustless iron 不锈铁Section iron 型钢Structural iron 结构钢White iron 白口铁Wrought iron 熟铁、锻铁Isometric diagram 等轴测图Isometric drawing 等轴测图Jack-screw 螺旋千斤顶Job sheet 零件图纸Joint 结合、连接、焊接Bolt joint 螺栓连接Riveted joint 铆钉连接Welded joint 焊接Journal 轴径Journal bearing 径向轴承Keeper 保持器(片)、架、定位件卡箍Keep-ring 保持环Key diagram 键、按钮Key way(seat、seating、slot)键槽Key wrench 套筒扳手Gib-head taper key 钩头斜键Square key 方形键Tightening key 斜扁键Woodruff key 半圆键Key-bolt 键螺栓Kilogram(me)公斤、千克Kilogram-meter 公斤米、千克米Kilometer 公里、千米Kilovolt 千瓦Kilowatt 千伏Kit 一套工具Knee 弯头、升降台Knee bend 弯管Knob 捏手、按钮Knuckle thread 圆形螺纹Knurl 滚花、压花Knurled nut滚花螺母L-bar = L-beam 角钢Laboratory 实验室、研究室Lamp 灯Alarm lamp 信号灯Daylight lamp 日光灯Incandescent lamp 白炽灯Indicating lamp 信号灯、指示灯Lantern 游环、套环Large compasses 大圆规Lathe 车床Lathe-hand 车工Lattin = Latten 金属薄板、黄铜片Law 规律、定律Lay 布置、安排、放置Layer 层Carburized layer 渗碳层Layout 计划、方案、草图Layout design 草图设计、方案设计Layout drawing 方案草图Lead angle 螺旋升角Lead line 指引线Leaf spring 板弹簧Left hand 左方向Left hand thread 左旋螺纹Legend 图例、图表符号、代号、说明书Length 长度、距离Length gauge 长度规Length of normal 法线长Length of side 边长Effective length 有效长度Lens 透镜、镜片Letter 字、字母Capital letter 大写字母Level surface 水平面Lift 升降机、电梯Light alloy 轻合金Light beam 光束Light series 轻系列Light-duty 轻型Lighting installation 照明装置Lightning switch 照明开关Liquid 液体Limit 极限尺寸Limit switch 限位开关Line 线Line of action (齿轮)压力线Line of contact (齿轮)接触线Line of shaft轴线Line of thickness 线型的粗度Line weight线的粗细程度Actual line实线Addendum line齿顶线Broken line断裂线Center line = central line中心线Continuous line实线Dash(ed) line虚线Diagonal line 对角线Imaginary line 假想线Generation line 母线Pitch line 节线Real line 实线Reference line 基准线、参考线Right line 直线Skeleton line 轮廓线Solid line 实线Straight line 直线Vertical line 垂直线Liner 衬套Bearing line 轴瓦Link 连接环、链节Line assembly 连杆装配图Chain link 链节L-iron 角铁List 注册、记录、名册、目录Load 符合Actual load 有效载荷、实际载荷Allowable load 容许载荷Full load 满载(荷)、全负载(荷) Local view 局部视图Localization 定位\固定Locating pin 定位销Location by angle 角度定位Location by dimension 定位尺寸Location pin 定位销Location tolerance 定位公差Lock 锁\阀Lock nut 防松螺母Lock screw 锁紧螺钉Lock washer 弹簧垫圈Valve lock 阀簧抵座销、气门制销Loco 机车、火车头Logarithm 对数Long break 长断裂线Long radius 长半径Longitudinal key 长方键Lower limit 下限Lubricant pump 润滑油泵Lubricating ring 润滑油环Lubrication 润滑Bath lubrication 油浴润滑Bearing lubrication 轴承润滑Ring lubrication 油环润滑Shot lubrication 油枪润滑Splash lubrication 飞溅润滑Lubricator 润滑器Lubro-pump 油泵Luminaire 光源Machine 机器、切割Machine building (manufacturing) 机械制造Machine drawing 机械制图Machine finish 机械加工Machine maker 机械工厂(制造者) Machine part 机械零件Machine shop 机工车间Drawing machine 绘图机Tracing machine 描图机Machining allowance 加工余量Machinist 机械工人\机械师Magazine 杂志Magnetic-particle clutch 电磁离合器Magnitude 数量、长度、大小Major type of slotted nut 大型锁母Make 制造、构造Malleable cast iron 可锻铸铁Malleable casting 韧铸件Malleable steel 软钢、展性钢Manual 手册、说明书Manual control 手控Manufacture 加工、制造业Manucturing engineering 制造工艺(技术) Manucturing machine 生产机械Manucturing tolerance 制造公差Master check 校正、校对Master drawing 样图Master gauge 标准规、校准规Master gear 主齿轮、标准齿轮Master making 手工Master screw 标准螺纹Match 匹配、配合Mate 啮合部分Material 物质、材料Fibre material 纤维材料Insulating material 绝缘材料Plastic material 塑料Maximal valve 极大值Maximum 极点、极限、最大量Maximum admitted diameter of work 工件最大许可直径Mean axis 中间轴Measure 量度、大小、尺寸Measure of precision 精确度Measurement 测定、尺寸、大小Measuring device 量具Measuring tools 量具Mechanical bolt 螺钉Mechanical drawing 机械制图Mechanical engineering’s scale 机械工程比例尺Mechanical properties 机械性能Mechanical reduction gear 齿轮减速装置Mechanism 机械结构、机械装置Medium series 中系列Mating member 配合件Meshing gear 啮合齿轮Metal 金属Admiralty metal 含锡黄铜Bell metal 青铜合金、种铜、铜锡合金Brazing metal 铜锌合金Hard metal 硬质合金Heavy metal 重金属Light metal 轻金属Monel metal 铜镍合金Power(ed) metal 粉末合金Wear-resistant metal 耐磨金属White metal 白合金(铅锑锡合金)Yellow metal 黄金、黄色金属Metallized 镀金属的、喷涂金属的Meter 米、公尺。
Design for Manufacturing and Assembly

Design for Manufacturing and Assembly Design for Manufacturing and Assembly (DFMA) is a critical engineering methodology that focuses on simplifying product design to optimize both the manufacturing process and the subsequent assembly operations. This approach aimsto reduce production costs, improve product quality, and shorten lead times by addressing design aspects from the very beginning. Essentially, DFMA encourages engineers to think like manufacturers and assemblers during the design phase, fostering a holistic approach to product development. One of the core principles of DFMA is reducing the number of parts in a product. By simplifying the designand eliminating unnecessary components, manufacturers can streamline theproduction process, reducing material costs and assembly time. Fewer parts also translate to fewer potential points of failure, leading to improved product reliability and reduced warranty claims. This principle aligns with the broader objective of minimizing complexity and enhancing efficiency throughout the entire product lifecycle. Another crucial aspect of DFMA is the selection of appropriate materials and manufacturing processes. Choosing materials that are readily available, cost-effective, and compatible with existing manufacturing technologies can significantly impact production efficiency and final product cost. Similarly, opting for readily available manufacturing processes like injection molding or stamping, instead of more complex methods, can lead to faster production times and lower overall expenses. This emphasis on practicality and manufacturability ensures that the design is not only conceptually sound but also realistically producible. DFMA also emphasizes the importance of designing for ease of assembly. This involves creating components that are easy to handle, align, and secure, minimizing the risk of errors during the assembly process. The use of modular design, where sub-assemblies are created independently and then combined into the final product, is a common DFMA strategy. This approach allows for greaterflexibility in the assembly line, facilitates parallel processing, and simplifies troubleshooting should problems arise. Furthermore, DFMA promotes the use of standardized components whenever possible. By utilizing readily available fasteners, bearings, and other common parts, manufacturers can leverage economies of scale and reduce procurement costs. Standardization also simplifies inventorymanagement, as fewer unique components need to be stocked. This focus on practicality and resource optimization underscores the pragmatic approach that DFMA brings to product design. In conclusion, DFMA is a powerful methodology that encourages a holistic, practical approach to product development. By considering manufacturing and assembly constraints from the outset, DFMA leads to productsthat are not only functional and innovative but also cost-effective and efficient to produce. This approach, therefore, represents a crucial strategy for businesses striving for competitive advantage in a global marketplace.。
模具专业英语试题及答案
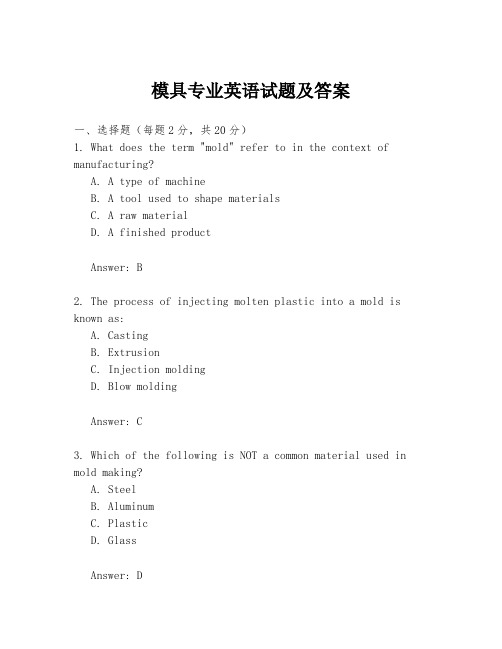
模具专业英语试题及答案一、选择题(每题2分,共20分)1. What does the term "mold" refer to in the context of manufacturing?A. A type of machineB. A tool used to shape materialsC. A raw materialD. A finished productAnswer: B2. The process of injecting molten plastic into a mold is known as:A. CastingB. ExtrusionC. Injection moldingD. Blow moldingAnswer: C3. Which of the following is NOT a common material used in mold making?A. SteelB. AluminumC. PlasticD. GlassAnswer: D4. The term "ejection system" in molds refers to:A. The system that heats the moldB. The system that cools the moldC. The system that removes the finished part from the moldD. The system that guides the mold into placeAnswer: C5. What is the purpose of the "runner system" in an injection mold?A. To cool the moldB. To eject the partC. To guide the material into the mold cavityD. To support the moldAnswer: C6. The "draft angle" in mold design is used to:A. Increase the strength of the moldB. Facilitate the removal of the part from the moldC. Improve the aesthetics of the partD. Control the flow of material into the moldAnswer: B7. What is the role of "shrinkage" in mold design?A. To increase the size of the partB. To decrease the size of the partC. To prevent warpingD. To improve the surface finishAnswer: B8. The "cavity" in a mold is the space that:A. Houses the moldB. Contains the cooling channelsC. Shapes the partD. Stores the raw materialAnswer: C9. "Flash" in molding is:A. A desirable feature for part aestheticsB. The thin layer of material that forms between the mold partsC. A type of mold release agentD. The process of cutting the part from the runner system Answer: B10. The term "gating system" refers to the part of the mold that:A. Controls the flow of material into the moldB. Supports the mold during productionC. Provides access for maintenanceD. Ejects the finished partAnswer: A二、填空题(每题1分,共10分)11. The _______ is the process of cutting away excessmaterial to form a part.Answer: machining12. In mold making, the term "plastic" refers to a material that can be _______.Answer: molded13. The _______ is the part of the mold that opens and closes to release the part.Answer: ejector14. A _______ mold is one that is used to produce multiple parts in a single cycle.Answer: multi-cavity15. The _______ is the process of creating a three-dimensional model from a two-dimensional drawing.Answer: prototyping16. The _______ is the process of making a mold from a solid block of material.Answer: machining17. A _______ is a tool used to cut threads into a hole.Answer: tap18. The _______ is the process of applying heat and pressure to shape a material.Answer: thermoforming19. The _______ is the process of removing material from aworkpiece to achieve the desired shape.Answer: milling20. The _______ is the process of joining two or more pieces of material together.Answer: welding三、简答题(每题5分,共30分)21. Explain the difference between a "hot runner" and a "cold runner" mold system.Answer: A hot runner mold system maintains the temperature of the plastic melt throughout the entire runner system, allowing for continuous flow and reducing waste. A cold runner mold system, on the other hand, cools the plastic in the runner system, resulting in a solidified runner thatis typically considered waste.22. What are the main factors to consider when designing a mold for injection molding?Answer: The main factors include material selection, part geometry, shrinkage, draft angles, gating and runner system design, cooling and heating requirements, ejection system design, and cycle time.23. Describe the role of a "core pin" in a mold.Answer: A core pin is a component。
空分常用英文单词
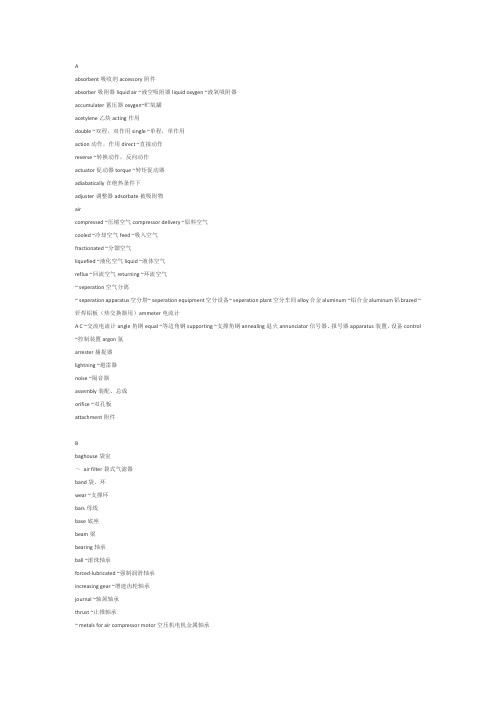
Aabsorbent吸收剂accessory附件absorber吸附器liquid air ~液空吸附器liquid oxygen ~液氧吸附器accumulater蓄压器oxygen~贮氧罐acetylene乙炔acting作用double ~双程,双作用single ~单程,单作用action动作,作用direct ~直接动作reverse ~转换动作,反向动作actuator促动器torque ~转矩促动器adiabatically在绝热条件下adjuster调整器adsorbate被吸附物aircompressed ~压缩空气compressor delivery ~原料空气cooled ~冷却空气feed ~吸入空气fractionated ~分馏空气liquefied ~液化空气liquid ~液体空气reflux ~回流空气returning ~环流空气~ seperation空气分离~ seperation apparatus空分塔~ seperation equipment空分设备~ seperation plant空分车间alloy合金aluminum ~铝合金aluminum铝brazed ~钎焊铝板(热交换器用)ammeter电流计A C ~交流电流计angle角钢equal ~等边角钢supporting ~支撑角钢annealing退火annunciator信号器、报号器apparatus装置、设备control ~控制装置argon氩arrester捕捉器lightning ~避雷器noise ~隔音器assembly装配、总成orifice ~双孔板attachment附件Bbaghouse袋室~air filter袋式气滤器band袋、环wear ~支撑环bars母线base底座beam梁bearing轴承ball ~滚珠轴承forced-lubricated ~强制润滑轴承increasing gear ~增速齿轮轴承journal ~轴颈轴承thrust ~止推轴承~ metals for air compressor motor空压机电机金属轴承~metals for oxygen compressor motor氧压机电机金属轴承bellow吹风机、皮老虎bias偏压blade叶片backward ~反向叶片block部件terminal ~接线板blower风机brake ~制动风机deforsting air ~解冻风机Roots ~罗茨风机single flow ~单级风机~ impeller风机叶轮board板ceiling ~顶板front ~前板semigraphic ~半模拟板side ~侧板switching ~切换板body体main ~主体bolt螺栓anchor ~地脚螺栓coupling ~ set称套的联接螺栓foundation ~地脚螺栓bonnet阀帽box箱盒check valve ~自动阀箱(交换器)cold ~冷箱relay ~继电器箱switch ~开关箱terminal ~分线盒bracket托架breaker断路器no-fuse circuit ~无熔断器的断路器oil immersed circuit ~油浸断路器brush电刷~ holder电刷架~ spring电刷弹簧buffer缓冲~ plate缓冲板bulb玻璃泡、测温仪表、外壳resistance ~电阻温度计bulk支架~ head上部支架buna-N布纳-N、丁晴橡胶bush衬套neck ~轴套、轴瓦button钮push ~按钮push ~ with lamp带灯按钮butyl rubber丁基橡胶buzzer蜂鸣器Ccable电缆extention ~补偿导线external ~外部电缆power ~电力电缆calibration校准cam凸轮cantileveredly悬臂地capacity容量interrupting ~遮断容量rupturing ~遮断容量casing箱、盒bearing ~轴承箱1st ~一级外壳turbine ~透平机壳casting铸造、铸件precision ~精密铸件spheroidal graphite iron ~球墨铸铁件channel槽钢base ~槽钢基础chart图、表、记录纸chiller过冷器chiller-liquefier过冷液化器liquid air-liquid nitrogen ~液空-液氮过冷器chipping凿circuit线路、电路electric ~电路high tension ~高压线路interlocking ~连锁线路printed ~印刷电路clutch离合器cock旋塞,旋阀code规范、符号、编号coil线圈tripping ~跳闸线圈、解扣线圈~ for trip跳闸线圈、解扣线圈column塔lower ~下塔rectifier ~精馏塔upper ~上塔compressor压缩机air ~空压机balanced opposed type ~相对平衡式压缩机centrifugal ~离心式压缩机instrument air ~仪表空压机integral speed-up gear type isothermal centrifugal ~整体增速齿轮式等温离心压缩机loop-sketch for oxygen ~氧压机线路系统图multi-stage ~多级压缩机one-shaft ~单轴压缩机one-shaft multi-stage ~单轴多级压缩机reciprocating ~活塞式压缩机turbo ~透平压缩机concentric同心的condenser冷凝器、电容器the main ~-reboiler主冷凝蒸发器evaporator ~冷凝蒸发器conduit导管、线管connection接头、接管conspectus大纲、概要consumptionpower ~电耗contact接头、触头alarming ~警报接头fixed ~固定触头moving ~滑动触头contactor接触器magnetic ~电磁接触器controllerlevel indicating ~液位指示控制器pressure indicating ~压力指示控制器cooler冷却器after ~后冷却器evaporator ~蒸发冷却器inter ~中间冷却器liquid air super ~液空过冷器liquid nitrogen super ~液氮过冷器oil ~油冷却器spray ~喷淋冷却器trickling ~水淋冷却器core芯子cold ~冷单元,冷端warm ~热单元,热端coupling联轴节rubber ~橡皮联轴节shaft ~轴接手联轴器cover盖end ~端盖sealing ~密封盖sound insulating ~隔音罩~ for lamp灯罩crankshaft曲轴、曲柄轴cubicle柜、小房间local electric control ~机旁电控柜motor ~电动机柜receiving ~受电柜static exciter ~静止励磁柜cutout截口panel ~盘上装仪表的洞cylinder气缸pneumatic ~气动气缸single ~单缸~ cover气缸盖~ gasket气缸垫圈~ liner气缸内衬Ddamper蝶阀、开闭器motorized ~电动蝶阀piston ~活塞阀~ for switching valve切换阀的蝶阀defrosting解冻~ air解冻空气~ air blower解冻风机deriming去霜detector检验器revolution ~转数检验器deviation 偏差~ and tolerances公差与配合devicecleaning ~净化装置delivery control ~输出(压力)控制装置discharge pressure control ~排出(压力)控制装置safety ~安全装置sampling ~取样分析装置silicon control rectifier ~可控硅正流装置suction pressure control ~吸入压力控制装置switching ~切换装置tripping ~断路装置wind up ~上弦装置、调整旋组dial标度盘diaphragm薄片disk盘cover ~盖盘hub ~壳盘distance~ piece距离块distillation column精馏塔drawingoutline ~外形图、布置总图driver驱动机~ tripped驱动机跳闸drum罐back pressure ~反压力罐surge ~缓冲罐dryer干燥器air ~空气干燥器defrosting air ~解冻空气干燥器duct槽wiring ~配线槽wiring & piping ~导线和管道槽Eelbow肘管、弯管、弯头enamel珐琅、搪瓷wrinkled ~皱纹珐琅endcold ~冷端energyabsorbed ~吸收能equipmentelectric ~电气设备liners for ~设备衬垫erection安装exchangerreversing heat ~可逆式换热器exciter激磁器exciting激励expansion~ joint膨胀接头~ turbine透平膨胀机Ffactor系数、因数power ~功率因数~ of safety安全系数fan风扇film膜oil ~油膜filter过滤器air ~空气过滤器defrosting air ~解冻空气过滤器liquid air ~液空过滤器multi-duty automatic air ~高效自动空气过滤器oil ~primary oil ~初级油过滤器secondary oil ~二级油过滤器sintered metallic ~烧结金属过滤器suction air ~吸入空气过滤器~ before turbine透平前过滤器fin翅片、波纹板cooling ~冷却片fitting配件、零件flange法兰、法兰盘flicker闪光float浮标floor楼板、层first ~一楼second ~flow流量air ~空气流量radial inward ~径向内流reflux ~回流流量~ rate流量速度flowmeter流量计flow-sheet流程、流程图general ~总流程图~ of cooling water line冷却水流程图~ of gas line气体流程图fluid流体flux焊剂、溶剂forcehorizontal ~水平力inertia ~forging锻件foundationgeneral ~基础总图oxygen compressor ~氧压机基础oxygen compressor general ~氧压机基础总图~ bolt and liner地脚螺栓和垫板frame框架、架子freeze致冷、冷冻fully-open全开furnaceflame ~火焰炉shaft ~竖炉blast ~高炉open hearth ~平炉cupola ~熔铁炉、冲天炉continuous ~连续加热炉travelling-bottom ~步进底式炉pusher-type ~推钢式加热炉rotary hearth ~转底炉electric-arc ~电弧炉electric ~电炉coke oven~焦炉converter~转炉fuse保险丝、熔断器Ggasdry ~干燥气generated ~返回气体impure nitrogen ~污氮sealing ~密封气gauge表、计level ~液位表oil level ~pressure ~gasket垫片、衬special ~特殊垫圈~ for transmitter and receiver变压器和记录器的垫圈gearbevel ~斜齿轮、伞形齿轮helical ~螺旋齿轮pinion ~小齿轮speed-up ~增速齿轮gel胶silica ~硅胶general概述glasshard ~硬质玻璃organic ~有机玻璃grinding磨光grounding接地grout灌浆~ bond灌浆结合grouting混凝土浇灌guarantee保证guide导板cross head ~十字头导板guide-vane导向叶片remote control of ~遥控导向叶片Hheader集管、集管箱heaterdefrosting ~解冻加热器heat-exchangerreversing ~可逆式热交换器helium氦housing室、罩insulating ~绝热室、绝热罩noise arresting ~隔音罩humidityrelative ~相对湿度hydrocarbon碳氢化合物~ absorber碳氢化合物吸收器I impeller叶轮blower ~风机叶轮high pressure stage ~高压级叶轮turbine ~透平叶轮~ of first stage一级叶轮impurities杂质indicatordamper opening ~蝶阀开度指示器different pressure ~阻力指示器fault ~故障指示器flow ~流量指示器level ~opening ~开度指示器pressure ~temperature ~thermal ~温度指示器inlet进口reference gas ~工作气体入口sample gas ~取样气体instrument仪表loop sketch of ~仪表连续表insulation绝缘、绝热~ over wrenching绝缘过热intake吸入air at the ~吸入之空气integrator积算器~ assembly积算器总成introduction引言ironcast ~铸铁iron-constantan铁-镍铜isothermal等温的Jjoint接头、接管、连接expansion ~膨胀接头、异径管Kkit工具箱Llabyrinth迷宫、曲径~ case迷宫盒~ cover迷宫盖~ packing迷宫填料~ sleeve迷宫套管lampannouncement ~指示灯announciator ~(报警)信号灯completion ~完成灯fluorometric ~ with glow lamps带辉光放电管的荧光灯green ~绿灯illumination ~照明灯pilot ~起动信号灯semigraphic ~半模拟盘灯signal ~信号灯layout布置(图)lineaerial ~架空线air ~空气管线defrost air ~解冻空气管道drain ~排出管道liquid air ~液空管线liquid nitrogen ~液氮管线liquid oxygen ~液氧管线liquid oxygen recirculating ~液氧循环线路waste nitrogen ~废氮管liner垫板liquefier液花器liquidlean ~贫液(poor ~)rich ~富液list清单instrument ~仪表清单load载荷、负荷braking ~ of blower风机的制动负荷dynamic ~动载荷full ~满负荷static ~静负荷loop sketch线路系统~ for oxygen compressor氧压机线路系统图lubricant润滑油lubrication润滑force feed ~强迫润滑、压油润滑forced ~强迫润滑pressure feed ~强迫润滑Mmagnesium镁manifold歧管manometer压力计manual指南、手册、手动mechanism机构driving ~传动机构、驱动机构metal金属、合金瓦white ~轴承合金、白色合金、钨金瓦~ case合金瓦套meter测量仪表frequency ~周波表over flow rotor ~溢流转子流量计3 phase indicating watt三相瓦特指示表3 phase power-factor ~三相功率因素表3 phase watt-hour ~三相瓦特-小时表set-~阀位指示计metric system公制micro-switch微型开关molecular sieve 分子筛motor电动机、马达chart ~记录纸传送电机induction ~感应电动机main ~主电动机synchronous ~同步电动机multi-stage多级的Nname名称~ plate名牌neon氖neoprene氯丁橡胶nipple螺纹接头、螺纹接嘴nitrogengenerated impure ~返回污氮liquid ~液氮pure ~纯氮noise噪音~ arresting housing隔音罩nozzle喷嘴~ ring喷嘴环nut螺母Ooillube ~润滑油lubricating ~润滑油transformer ~变压器油viscosine ~粘性油、精制残油~ free无油~ head tank高位油箱~ reservior贮油箱~ whip油抖动~ whirl油涡流orifice孔~ plate孔板~ plate assembly双孔板overhung悬臂地overspeed过速oxygenhigh purity ~高纯氧~ accumulator贮养器~ ion dry cell氧离子电池Ppacking填料gland ~压盖填料piston rod ~活塞杆填料seat ~座圈填料wiper ~擦油填料panel盘、板air compressor ~空压机表盘center ~中心盘general service ~公用表盘high tension ~高压盘instrument ~仪表板、仪表盘local ~机旁盘、机侧盘oxygen delivery device ~氧气输送装置仪表sub-~副线板part部件、零件、部分main ~主要部件middle ~中部spare ~备件P.B.(push button)按钮perlite 珠光砂pick-up传感器tachometer ~转速计传感器pin针、销crank ~曲柄销cross head ~十字头销pinion小齿轮pipeflexible ~软管、挠性管siphon ~弯管、虹吸管pit 坑、孔planning计划、布置plate板、牌、片bed ~底板checkered ~花纹(钢)板name ~名称牌orifice ~孔板plug塞子vent ~通风塞plunger柱塞point liquefaction ~液化点pointerred ~红指针positioner位置控制器potentiometer电位表press压力、阻力absorber ~吸附器阻力cold core different ~冷端各种压力delivery ~输出压力evaporator condenser ~冷凝蒸发器压力feed air ~吸入空气压力inlet air ~入口空气压力lubricating oil ~润滑油压力rectifier ~精馏塔压力recycle air ~循环空气压力surge tank ~缓冲罐压力pressurecompressor delivery ~压缩机输出压力compressor suction ~压缩机吸入压力lubricating oil ~润滑油压力max working ~最大工作压力normal ~标准压力test ~试验压力~ of input进口压力~ switch压力开关pressure-gauge压力表differential ~压差计~ with alarmer带报警器的压力计pressure-meter压力表differential ~压差计printing印,记录~ assembly for 3 points三点记录仪product成品、产品~ nitrogen产品氮project设计premilinary ~初步设计psychometer湿度计pumpaxial ~径流泵circulating ~循环泵gear ~齿轮泵liquid circulating ~液体循环泵motor driven oil lubricating ~电动机传动的润滑油泵screw ~螺旋泵stand-by ~备用泵suction ~抽气泵turbine oil ~透平油泵water circulating ~水循环泵purge清洗purificationair ~空气净化raw mixture argon ~原氩混合物净化Qquantity数量Rradial inward flow径向内流rating定额receiver接受器recorderflow ~流量记录器1-pen ~1笔记录器rectificationfinishing ~最后精馏rectifierupper ~上精馏塔~ column精馏塔recycle反流、回流(气体)air ~反流空气reducer减压阀、减压器、减速器、异径接头reflux回流(液)regeneration再生~ heater再生加热器regulation规则regulatorpress ~压力调整器reinforce加固relayannunciator ~警报器继电器auxiliary ~辅助继电器delay ~延迟继电器flow ~流量继电器interlocking ~连锁继电器oil pressure ~油压继电器over current ~过电流继电器over-speed ~过速继电器over voltage ground ~过电压接地继电器protective ~保护继电器selective ground ~选择性接地继电器under voltage ~低电压继电器water flow ~水流量继电器~ box继电器箱remark备注reservoirpressurized oil ~压力油箱reset重调、回零位without ~无零位、不能重调、不回零位resistor电阻器return回路R.H.E(reversing heat exchanger)可逆式换热器ringnozzle ~喷嘴环oil wiper ~刮油环piston ~活塞环Raschig ~拉西环Raschig ~ air filter拉西环式空气过滤器seal ~密封环seat ~座环、座圈ripple脉动、波动amperes ~电流波动rock wool岩棉rod杆connecting ~连杆rotator旋转器rotorassembled ~ 转子总成roughness粗糙度route流路flowing ~流动线路r.p.m(revolution per minute)转/分ruby红宝石runningcontinuous ~连续运转normal ~正常运转SS.A.C.E.(single acting crank end)单作用曲柄侧S.A.H.E.(single acting head end)单作用头端部sampling取样saturated~ state饱和状态scope~ of supply供应范围scraper刮刀screw螺丝scroll外壳、壳体seal密封dust ~尘土密封grease ~油脂密封oil ~ for piston rod活塞杆的油密封~ ring密封环~ing cover密封盖section截面manual selector手动选择器seperator分离器drain ~水分离器liquid air ~液空分离器service 服务、操作cold ~冷操作general ~公用仪表盘set装置、组、套air ~气动定值器three-valve ~平衡阀shaft轴crank ~曲柄轴imput ~大齿轮轴、输入轴pinion ~小齿轮轴turbine ~透平轴~ sealing device轴密封装置sheet板corrugated ~波纹板shell外壳shift(作业)班shrunk-fitted冷缩配合side 侧high-pressure ~高压侧sieve tray塞板塔sight glass观察玻璃signalpneumatic ~气动信号~ on信号指示signalization信号装置silica gel硅胶site位置sleeve套管、套垫shaft ~轴套slinger甩子oil ~甩油子、油吊环space距离liner ~二次浇注厚度spacer隔离物,垫片spare-parts备品、备件speedrated ~额定速度spindle心轴drive ~主动心轴spring~ for safety valve安全阀弹簧stack塔、烟囱air intake ~空气吸入塔stanchion 支柱stand架、台local ~机旁座、机旁台架local gauge ~机旁仪表台架stator定子motor ~电机定子steam蒸汽saturated ~饱和蒸汽steelangle ~角钢carbon ~碳钢channel ~槽钢cold rolled ~冷轧钢板equal angle ~等边角钢forged ~锻钢high finished ~高光洁度钢mild ~软钢stainless ~不锈钢stop停车emergency ~紧急停车strainer过滤器air ~空气过滤器strip带stroke行程structured packing填料塔subpane副板push button ~按钮副板support支座、支架switch开关ball float ~浮球开关change over ~转换开关、换向开关handle interlock ~手柄连锁开关level ~液位开关measure ~测量开关selector ~选择开关torque ~转矩开关~board配电盘、配电板switchgear开关机构、开关装置high tension ~高压开关metal-clad ~金属外壳开关symbol符号、记号system系统、方式braking ~制动方式、制动系统metric ~公制shell and coil ~盘管式Ttachometer测速计turbine ~透平测速计tag.标签~ No.位号图、标图tangentially切向tank槽、罐blow down ~排放槽cushion ~缓冲箱、缓冲罐oxygen surge ~氧气缓冲罐teflon聚四氟乙烯~ wear ring聚四氟乙烯支撑环temperatureambient ~环境温度packing gas ~充填气温度tempering回火tension电压hign ~高压terminal端子cable ~电缆接头grounding ~接地端子testbend ~弯曲测试tension ~张力测试、拉伸测试thermometer测温计dial ~盘式温度计electronic type auto-balance recording ~电子管式自动平衡记录温度计indicating resistance ~电阻温度指示计indicating thermoelectric ~热电温度指示计moving coil type point system recording ~动圈式多点温度记录仪recording ~记录温度计~ low pressure flat type扁平型低压测温计thread螺纹coarse screw ~粗螺纹fine screw ~细螺纹timerating ~定额时间response ~作用时间start up ~起动时间transformer变压器current ~电流互感器potential ~电压互感器transmission传送、传送装置electrical singal ~电动信号传送器transmitter变送器、传送器trap阱drain ~排水阀trouble事故、故障unforeseen~意外事故tubeflexible ~软管、挠性管trident ~三叉形管turbine透平centrifugal expension ~离心透平膨胀机expension ~透平膨胀机(ET)~ runner透平转子typebalanced opposed ~对称平衡式low pressure ~全低压型magnetic operated draw-out ~电磁脱扣型multi-plate ~多板式radial inward-flow~径向内流式Uunion联管节half ~半联管节(连接件)tee ~三通管alarm ~报警装置up-scaleburn out ~烧完的向上刻度Vvacuum真空valuelimited ~规定值、限定值valveadditional air slide ~补给空气分气阀air ~空气平衡阀angle ~角阀blow-off ~排气阀by-pass ~旁通阀check ~止回阀control ~ single seated单座式控制阀diaphragm ~隔膜阀drain ~放洩阀discharge ~排气阀emergency shut-off ~紧急切断阀flanged angle ~法兰角阀flange gate ~法兰闸阀flange globe ~法兰球阀gas change ~气体切换阀insulation type angle ~绝热式角阀main suction ~主吸入阀miniature ~微型阀needle ~针(形)阀non-return ~止回阀on-off ~双位阀(开关阀)pilot ~导阀reducing ~减压阀reflux ~回流阀regulating ~调节阀safety ~安全阀sampling ~取样阀screwed gate ~螺旋闸阀screwed angle ~螺旋角阀screwed globe ~螺旋球阀screwed lift check ~螺旋升降逆止阀screwed swing check ~螺旋摆动逆止阀slide ~滑阀solenoid ~电磁阀switching ~切换阀tap ~ for orifice孔板用内螺纹截止阀three way ~三通阀three-way switching ~三通切换阀turbine shut off ~透平关闭阀~ body阀体~ buffer plate阀缓冲板~ cap阀盖~ gasket阀垫圈~ guard阀防护盖~ positioner阀定位器~ rod阀杆~ seat阀座~ spring阀弹簧~ stand阀座vane叶片guide ~导向叶片variation变动、波动frequency ~频率波动voltage ~电压波动vent气孔、出口oil ~油出口vertical立式的vessel容器air ~空气罐vibration amplitude振幅vibration-proof防震的view图rear ~后面图、背视图voltmeter电压表AC ~交流电压表Wwasher垫圈locking ~锁紧垫圈spring ~弹簧垫圈wheel轮gear ~叶轮radial turbine ~径向透平叶轮wire钢丝、线notch ~凹形线圈、凹形钢丝圈notch ~ type oil filter element凹形线圈式滤油元件wiring接线、配线wool毛glass ~玻璃毛glass ~ element assembly玻璃毛元件work功external ~对外做功worm蜗杆~ wheel蜗轮补充:sieve tray塞板塔structured packing填料塔。
格林内尔机械产品安装 组装说明书

Grinnell Mechanical ProductsInstallation / Assembly Instructions, Couplings Page 1 of 4 DECEMBER 2017 G901General DescriptionThese installation instructions do not take the place of nor do they elimi-nate the need for the installer to fully read and understand the com-plete GRINNELL Mechanical Prod-ucts Installation Handbook (refer to IH-1000M). Always review the GRIN-NELL Mechanical Products Instal-lation Handbook and individual product tech data sheets for the latest instructions, techniques, and care and maintenance information. Current documentation can be obtained by contacting GRINNELL Mechanical Products or visiting .Installation GuidelinesNOTICEThe following instructions are a guide-line for the proper installation of GRIN-NELL grooved products.Always read and understand the instructions including the “Installation Guidelines”. Failure to follow these instructions may result in imp rop er p roduct installation, joint failure, leakage, serious personal injury, and/or property damage.To avoid serious personal injury, wear safety glasses, hard hat and foot protection.Never remove any piping component without verifying that the system is de-pressurized and drained. Failure to do so may result in serious personal injury.Torque values are supplied as a guide-line and may be used when setting the torque on p ower imp act wrenches. Always refer to the p ower imp act wrench manufacturer’s instructions for settings.Exceeding the suggested torque values may cause damage to the cou-pling and/or result in pipe-joint failure. Minimum bolt torque is required for the coupling to meet the published perfor-mance parameters.Couplings (1 - 24 Inch)Figures 772, 577, 472, 705, 707, 405, and 774The installation is based on pipe grooved in accordance with Standard Cut Groove or Roll Groove Specifica-tions. Refer to tech data sheet G710 for more information.Step 1. Inspect exterior groove and ends of the pipe to verify all burrs, loose debris, dirt, chips, paint and any other foreign material such as grease are removed. Pipe end sealing sur-faces must be free from sharp edges, projections, indentations, and/or other defects.Step 2. Verify that the coupling and gasket grade are correct for the appli-cation intended. Refer to tech data sheet G610 for additional gasket information.For dry pipe and freezer applications, use the EPDM Tri-Seal freezer gasket with a petroleum free silicone lubri-cant is recommended. Reducing Cou-plings are not recommended for freezer applications.The sealing edges and outer surfaces of the gasket should be covered with a fine layer of lubricant. To prevent dete-rioration of the gasket material, a petro-leum lubricant should never be used on Grade “E” “EPDM”. For assembly below 40°F (4°C), a petroleum-free sili-cone lubricant must be used to prevent freezing of the lubricant. Silicone based lubricant should not be used on Grade “L ” silicone gaskets.For Flexible Couplings Only:Figures 705, 707, and 405 Coupling Housing bolt pads must be in metal to metal contact. For Flexible Coupling deflection data refer to individual tech data sheets.For Rigid Couplings Only:Figure 772, 577, 472, and 774 Rigid Couplings have an intended gap of up to 1/16 of an inch at each pad to allow for positive rigid gripping onto the pipe. The patented tongue and groove design provides protection to the back of the gasket during installation.Bolt Size ANSI InchesBolt Torque Rangeft-lbs.Bolt Size Metric Bolt Torque RangeNm 3/830-40M1040-601/290-110M12120-1505/8a 100-130M16a 135-1753/4150-200M20200-2707/8180-220M22245-3001200-250M24270-3401-1/8225-275NOTESa. For 8 inch Figure 577, the bolt torque range is 150 to 180 ft.-lbs. for a 5/8 inch bolt (200 to 245 Nm for an M16 bolt).Coupling TypeCoupling Figure NumberData Sheet NumberRigid Figure 772G140, G141Rigid Figure 577TFP1854Rigid Figure 472G560Rigid Figure 774G142Flexible Figure 705G110Flexible Figure 707G130FlexibleFigure 405G565TABLE ABOLT TORQUE SPECIFICATIONSTABLE BCOUPLING DATA SHEET NUMBERSG901Page 2 of 4Couplings (1 to 12 Inch)Figures 772, 577, 472, 705, 707, 405, and 774Perform Steps 1 and 2 from Couplings (1 - 24 Inch) section prior to continuing with the following procedure.Step 3. Install the gasket by placing it over the pipe so that the gasket lip does not extend beyond the end of the pipe.Bring both pipe endstogether ensuringvertical and horizontal alignment. Slide the gasket into position centering it between the grooves of each pipe end.Step 4. With one nut and bolt removed, “swing” the cou-pling housing over the gasket. Verify that the housings areover the gasket andthat the housing keys are fully engaged into the grooves.Step 5. Insert the other bolt and nut into the coupling and rotate both nuts until finger tight. Verify that the bolt headsare fully recessed inthe housing.Step 6. Tighten nuts uniformly to the rec-ommended bolt torque per Table A. U neven tightening can cause the gasketto pinch or bind.Couplings (14 - 24 Inch) Figure 772 and 707 (Large Diameter)EDPM Tri-Seal gaskets are recom-mended for applications below 40°F (4°C).Installation / Assembly Instructions The following instructions apply to the 3 segment and 4 segment configurations for the Figure 772 (G140) Rigid Cou-plings, and the Figure 707 (G130) Heavy Duty Flexible Couplings. For additional information refer to the individual tech data sheet. The installation is based on pipe grooved in accordance with Stan-dard Cut Groove or Roll Groove Speci-fications. Refer to tech data sheet G710 for more information.Perform Steps 1 and 2 from Couplings (1 - 24 Inch) section prior to continuing with the following procedure.Step 3. Install the gasket by placing it over the end of the first pipe section. For larger pipe diame-ters, it may be easierto roll the gasketinside out, then onto the pipe end. Ensure that the gasket does not extend beyond the end of the pipe.Step 4. Bring both pipe ends together, ensure proper align-ment and slide the gasket into position. (If gasket was turnedinside out per step 3roll the gasket overinto position.) Center it between the grooved portions of each pipe.The gasket should not protrude into the grooves on either pipe segment or extend between the pipe ends.Step 5. Place the assembly over the gasket and verify that the housing keys are fully engaged into the pipe grooves.Step 6. Assemble two sections of the housing by inserting a bolt into the cou-pling and loosely engaging the nut.(For four segmentcouplings it may be easier to assemble two halves first.)Step 7. Bring the next section of the housing into posi-tion. Insert a bolt into the coupling and finger tighten the nut.Step 8. Tighten nuts uniformly to the rec-ommended bolt torque per Table A.Flexible Reducing Coupling Figure 716Reducing Couplings are not recom-mended for applications below 40°F (4°C).Installation / Assembly Instructions The following instructions apply to Figure 716 Flexible Reducing Cou-plings. For additional information refer to the tech data sheet G120.GRINNELL Reducing Couplings, when properly installed, will have pad to pad contact between the housings. U se an optional Type 304 metal insert to prevent pipe telescoping when install-ing the Figure 716 in the vertical posi-tion. Prior to Step 2 place the insert inside the gasket aligning the insert slots with the ribs on the gasket.Perform Steps 1 and 2 from Couplings (1 - 24 Inch) section prior to continuing with the following procedure.Step 3. Install the gasket by placing the gasket over the pipe that has the larger diameter. Bring the smaller pipe endinto alignment andslide the pipe intoposition. Slide the gasket into posi-tion, properly centering it between the grooved portions of each pipe.The gasket should not protrude into the grooves on either pipe segment.Step 4. With both bolts removed, place the coupling hous-ings over the gasket. Verify that the hous-ings are over thegasket and that thehousing keys are fully engaged into the pipe grooves.Step 5. Insert the bolts into the cou-pling and rotate the nuts until finger tight. Verify that the bolt heads arefully recessed in thehousing.Step 6. Tighten nuts uniformly to the rec-ommended bolt torque per Table A.Always tighten the nut and bolt setevenly. Uneven tight-ening can cause the gasket to pinch or bind.Step 3Step 3Step 3Step 6Step 7Step 8Step 4Step 4Step 4Step 5Step 6Step 5Step 6G901 Page 3 of 4Copyright © 2018 Tyco Fire Products, LP. All rights reserved.GLOBAL HEADQUARTERS | 1400 Pennbrook Parkway, Lansdale, PA 19446 | Telephone +1-215-362-0700G901Page 4 of 4。
伊顿螺纹插装阀插孔
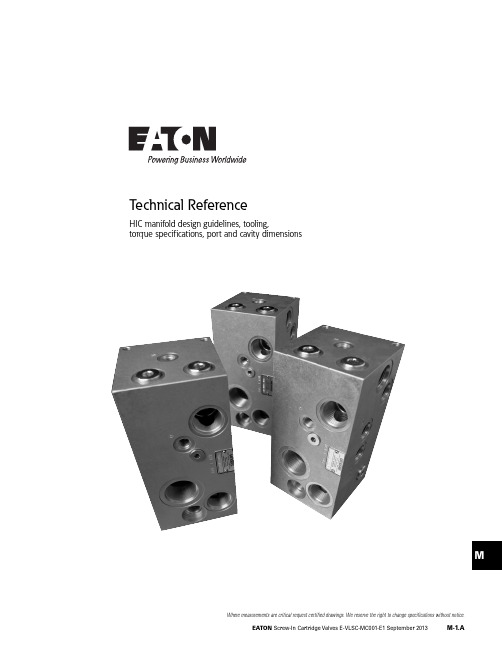
MTechnical ReferenceHIC manifold design guidelines, tooling,torque specifications, port and cavity dimensionsT echnical Reference Section ContentsMReviewing CircuitAll designs begin with a sche-matic circuit design inspired by the application. Before the planning stage, review the design utilizing the following steps:• Match schematic symbols to model codes.• Note size and cavity of each valve and write it on schematic.• Note port numbers of the valves and write them on schematic.• Note manifold port types and sizes specified by customer.• Note pressure, flow and material of manifold block (steel or aluminum).Circuit questions should be answered by the customer before beginning a design. It is also recommended that schematic hydraulic regions or networks be color coded using color pens. Regions or net-works may be broken down in individual colors (pressure, tank, pilot, etc.) but it may be easier to design if regions are broken down into sub-regions such as pressure from port one of a solenoid valve to port two of a relief valve. Colored layers may be assigned later to match schematic circuit coloring.Initial DesignOnce the circuit is fully under-stood, it is advisable to lay the design out by hand first. Things to consider while plan-ning the design are:• Block size is often specified by customer.• Specify an overallenvelope size, in addition to the specified block size. Overall envelope size includes block size and any valves or fittings protruding from the manifold block.• Restrictions specified for a mounting surface of the manifold block. Valves and ports may be restrictedfrom a particular surface.• Specify mounting holes, threaded holes and thru holes (if necessary).• Arrange valves in a logical manner. Valves and ports in the same regions should be located in close proximity to each other.• Eliminate as many turns in the regions as possible to reduce the number of cross drill holes or construction lines. This helps keep pressure drops ( D P) andmanufacturing costs down.Material SizesTo obtain an optimal cost man-ifold it is desirable to select a standard material size for the manifold, compare the block size with the standard mate-rial size table. See Standard Material Sizes (page M-5). If a standard size is not available, a cut plate may be used. Hydraulic SchematicIf a schematic is desired on the assembly, it may be cre-ated from existing symbols. As an alternative, the entire circuit may be created outside of an assembly and imported as a symbol (block). All of the Vickers screw-in cartridge valves have schematic sym-bols which can be found in the SICV Cartridge Valve Library of Symbols CD, used in conjunc-tion with AutoCad software. Schematic symbols not found in the library may be created on an “as needed” basis.Accurate DesignAll dimensions on CAD design must be accurate and to scale in order to be utilized by CAM software in conjunction with CNC machine tools. Manually or interactively modifieddimension cannot be tolerated.Example:Note: Failure to ensure thatCAD dimensions are accurate and to scale may result in improper machinery by CNC Machine Tools.Datum PointThe datum point or origin point (0,0,0) on machining drawings is the upper left corner when facing the front view.Assembly Dimensioning Dimension all ports, mount-ing holes and overall envelope size.External ClearancesAllow enough room for clear-ance around solenoid coils, handknobs, levers and wrench clearance for fittings. If 90° elbow fittings are to be used, some may be required to swing a full 360 arc.Assembly NotesNotes are added for standard or special assembly, handling, or shipping instructions, as well as special stampings.Port T ableInclude a port table with names and sizes of all ports.Standard T oolingIn order to obtain fastturnaround on designs, limit the tooling used to that listed in the standard tooling table. See Preferred Tooling for Machining Manifolds (page M-6).General Guidelines forHydraulic Integrated Circuits (HIC)professional in the design of manifold blocks and related hydraulic systems. It is the designer’s responsibility to verify the adequacy of thedesign through approporate verifications, review and test-ing of the final design.Always “square up” the raw block before machining the cavities, ports and holes. This is to eliminate any potential “drill walk” which leads to scrapped manifolds. When squaring up a block, remove approximately 0.015” of material from each face for Aluminum blocks and 0.030” of material from each face for steel blocks. This is done to ensure that all six faces are parallel or perpendicular. Finished machining shouldreflect the squared up dimen-sions. See Standard Material Sizes (Table 1).Example: 4.0” x 5.0” x 6.0” (101.6 mm x 127 mm x 152.4 mm) block will be dimen-sioned to 3.97” x 4.97” x 5.97” (100.8 mm x 126.2 mm x 151.6 mm)Creation of MachiningT able Create a machining operation table or bore chart. Machining depths are given from the sur-face of the block. List all drill depths, mills, taps and form tools in the machining table. Call out drill depths at the shoulder depth of the drill, not to the drill point depth.All machining depths are to the corner of the full diameter as opposed to the drill point. All depths are measured from the face plane (surface) of a manifold block.Avoid any drill depths greater than 25 diameters.Additional line lengths may result in increasing pressure drops.Machining NotesMachining notes are to beadded for standard or special machining, handling and ship-ping instructions.DrillingsDrillings that go completely through a cavity port area should be on the center axis of the cavity wherever possi-ble; see Figure (a). Otherwise it should intersect the cavity tangent to the outside diam-eter of the bore it connects with; see Figure (b).Note: Breaking into a cavity at some point in between these recommended areas will lead to drill walk and can result in a high scrap rate, as well as premature drill breakage.All SAE ports and cavities have spotface depths of .031” (.8 mm) unless otherwise speci-fied. BSPP ports have spotface depths of .060” (1.5 mm) unless otherwise specified.CounterboresIn counterbore cases, the actu-al cavity spotface is located at the depth of the counterbore. When counterbore depths are greater than 0.125”, the follow-ing diameters should be used:Use of Expander Plugs and Zero Leak Gold SAE O-Ring PlugsOn small HIC packages, expander plugs can be used to block off construction drill-ing at the surface of a face. Larger than a 12mm expander plug are not recommended in aluminum. Any construction drillings larger than 0.4” (10 mm) are plugged with zero leak gold SAE O-Ring plugs (internal hex type). The machin-ing callout for these plugs can be either the industry standard SAE straight thread O-ring boss port configuration or the straight thread O-ring boss short port configuration. Refer to Port Dimensions (page M-9 and M-10).Surface T reatmentsAny manifold face that calls for a surface mounted (gas-ket mounted) valve such as a DG4V type directional control valve, or a pump or motor interface, should have a mini-mum roughness callout of 63 microinches (.0016mm) and a flatness callout of .002”(.05mm). See examples below.To prevent corrosion, steel manifolds are oil dipped or coated with rust protec-tive fluid, unless otherwise specified. To prevent oxidation, aluminum manifold blocks are gold anodize, unless oth-erwise specified. Aluminum manifolds where the internally grounded coil is used should not be anodized. Prototypes are supplied without surface treatment.Datum Point Example in orthographic third angle projection:General Guidelines forHydraulic Integrated Circuits (HIC)MWall ThicknessFor pressures up to 3000 psi (210 bar), aluminum may be used, for pressures above 3000 PSI (210 bar). Dura-Bar cast iron manifold material is recommended.Larger cavities or bores require a greater wall thick-ness.The table below shows recommended minimum wall thicknesses for Aluminum and Dura-Bar.general guidelines will notguarantee the manifold will survive any finite number of cycles. The only way to properly assure a specified life is to run a thorough testing of both burst and endurance in the actual application circuit.T able 1Standard Material SizesGeneral Guidelines forHydraulic Integrated Circuits (HIC)Creating Bill of Material – BOMDevelop a BOM that includes quantity, model codes, part numbers and descriptions of the HIC. Model codes of some valves require pressure settings. A machining opera-tion table or bore chart should be created. All plugs, orifice plugs, disks, check valves, pistons, and any other part should be included in the BOM.2 x 2 2 x3 2 x4 2 x5 2 x 62.5 x 2.5 2.5 x 3 2.5 x3.5 2.5 x 42.5 x 4.5 3 x 33 x3.53 x 43 x4.53 x 53.5 x 3.53.5 x 43.5 x 4.54 x 44 x 4.54 x 54 x 64.5 x 4.55 x 55 x 65.5 x 5.56 x 6lead to manifold failure.Preferred T ooling for Machiningof Custom ManifoldsFlat Bottom Reamer Reamer Slot BallPreferred T ooling for Machining Custom ManifoldsSense Check Took SC-4-2-75SC-4-2-88Counter Sink2" x 902" x 5"1/4" x 90Drill1/4" x 90Center Drill#5Press Tap#6-32 X#10-24 X1/4"-20 X1/4"-20 5/16"-18 5/16"-24 3/8"-16 3/8"-24 7/16"-14 7/16"-20 1/2"-13 1/2"-20 9/16"-185/8"-115/8"-183/4"-167/8"-141"-141-1/16"-121-3/16"-121-5/16"-121-5/8"-121-7/8"-121/8"-28 BSPP1/4"-19 BSPP3/8"-19 BSPP1/2"-14 BSPP3/4"-14 BSPP1"-11 BSPP1/16"-27 NPTF1/8"-27 NPTF1/4"-18 NPTF3/8"-14 NPTF1/2"-14 NPTF3/4"-14 NPTF1"-11 1/2 NPTFM10 x 1.5 MetricM10 x 1.25 MetricTap Pulley Tap1/4" - 205/16" - 247/16" - 209/16" - 183/4" - 16MT orque Specifications For Cartridge Valves and FittingsSAE and BSPP PortsSpotfaceMheighta Diameter U shall be concentric with thread pitch diameter within 0.0005 in. (0.13mm) FIR, and shall be free from longitudinal and spiral tool marks. Annular tool marks up to 100 mu in. max. are allowedb If face of boss is on a machined surface, dim. Y and S need not applyc Tap drill depths given require use of bottoming taps to produce the specified full thread lengths. Where standard taps are used, the tap drill depths must be increased accordingly.d Nominal tubing O.D. is shown for the standard inch sizes and the conversion to equivalent to mm sizes. Figures are for reference only, as any boss can be used for a tubing size, depending upon other design criteriaShort SAE portsPort DimensionsShort Port – Straight Thread O–Ring Boss – SP–**Note : To be used for SAE plugged construction holes only. Not intended to be used for external porting with standard fittings.Roughing T oolsRoughers are basically step drills which leave .030” per cutting diameter and .015” above all radii for the finish-ing reamer, with an additional .015” depth in the cavity bot-tom as clearance. The rough-ing tool is necessary to prepare the cavity for the fin-ishing reamer, which has not been designed for the primary forming or bottom cutting.Cavity For Material Model Code Part Number 2–WayC-4-2 Aluminum / Steel RT-4-2-AS-8306 02-173997C–8–2 Aluminum / Steel RT1–8–2–AS–8028 02–165580C–10–2 Aluminum RT–10–2–A–8030 889509C–10–2 Steel RT–10–2–S–8035 889510C–12–2 Aluminum / Steel RT–12–2–AS–8213 02–160625C–16–2 Aluminum RT–16–2–A–8031 889515C–16–2 Steel RT–16–2–S–8036 889516C–20–2 Aluminum RT–20–2–A–8032 565822C–20–2 Steel RT–20–2–S–8037 8895193–WayC-4-3 Aluminum / Steel RT-4-3-AS-8304 02-173271C–8–3 Aluminum / Steel RT1–8–3–AS–8291 02–162384C–10–3 Aluminum RT–10–3–A–8038 889511C–10–3 Steel RT–10–3–S–8043 889512C–12–3 Aluminum / Steel RT–12–3–AS–8217 02–153261C–16–3 Aluminum RT–16–3–A–8039 565825C–16–3 Steel RT–16–3–S–8044 889517C–20–3 Aluminum RT–20–3–A–8041 02–165581C–20–3 Steel RT–20–3–S–8046 5667063–Way ShortC–10–3S Aluminum RT–10–3S–A–8099 565824C–10–3S Steel RT–10–3S–S–8209 566703C–12–3S Aluminum / Steel RT–12–3S–AS–8220 02–113178C–16–3S Aluminum RT–16–3S–A–8040 02–165582C–16–3S Steel RT–16–3S–S–8045 566704C–20–3S Aluminum RT–20–3S–A–8042 889520C–20–3S Steel RT–20–3S–S–8047 5667054–WayC–8–4 Aluminum / Steel RT–8–4–AS–8292 02–172803C–10–4 Aluminum RT–10–4–A–8072 889513C–10–4 Steel RT–10–4–S–8073 889514C–12–4 Aluminum RT–12–4–A–8313 02-176377C–16–4 Aluminum RT–16–4–A–8074 889518C–16–4 Steel RT–16–4–S–8075 565828C–20–4 Aluminum RT–20–4–A–8076 565829C–20–4 Steel RT–20–4–S–8077 5667075–Way ShortC–12–5S Aluminum RT–12–5–A–8350 02-187301C–12–5S Steel RT–12–5–S–8358 02-187309C–16–5S Aluminum RT–16–5–A–8352 02-187303C–16–5S Steel RT–16–5–S–8360 02-187311C–20–5S Aluminum RT–20–5–A–8354 02-187305C–20–5S Steel RT–20–5–S–8356 02-187307Cavity For Material Model Code Part Number 2–WayC–4–2 Aluminum FT–4–2–A–8297 02–182339C–8–2 Aluminum / Steel FT1–8–2–AS–8070 02–112933C–10–2 Aluminum / Steel FT–10–2–AS–8048 566235C–12–2 Aluminum / Steel FT–12–2–AS–8214 02–162162C–16–2 Aluminum / Steel FT–16–2–AS–8078 565832C–20–2 Aluminum / Steel FT–20–2–AS–8079 5658333–WayC–4–3 Aluminum FT–4–3–A–8275 02–172006C–8–3 Aluminum / Steel FT–8–3–AS–8295 02–171292C–10–3 Aluminum / Steel FT–10–3–AS–8050 565834C–12–3 Aluminum / Steel FT–12–3–AS–8244 02–163001C–16–3 Aluminum / Steel FT–16–3–AS–8080 565836C–20–3 Aluminum / Steel FT–20–3–AS–8082 8893583–Way ShortC–10–3S Aluminum / Steel FT–10–3S–AS–8210 566708C–12–3S Aluminum / Steel FT–12–3S–AS–8242 02–162998C–16–3S Aluminum / Steel FT–16–3S–AS–8081 889356C–20–3S Aluminum / Steel FT–20–3S–AS–8083 8893594–WayC–8–4 Aluminum / Steel FT–8–4–AS–8296 02–171291C–10–4 Aluminum / Steel FT–10–4–AS–8052 565838C–12–4 Aluminum / Steel FT–12–4–AS–8312 02-175596C–16–4 Aluminum / Steel FT–16–4–AS–8084 566571C–20–4 Aluminum / Steel FT–20–4–AS–8085 889360.5–Way ShortC–12–5S Aluminum FT–12–5–A–8351 02-187302C–12–5S Steel FT–12–5–S–8359 02-187310C–16–5S Aluminum FT–16–5–A–8353 02-187304C–16–5S Steel FT–16–5–S–8361 02-187312C–20–5S Aluminum FT–20–5–A–8355 02-187306C–20–5S Steel FT–20–5–S–8357 02-187308Finishing Form T oolsSpeed & Feed for Aluminum 6061–T6 (T651) This information is recommended as a good starting point. Speeds and/ or feeds may be increased or decreased depending on actual machining conditions.Note: Finish form tools may require 1/2 to 1 1/2 second dwell to obtain necessary finish.Finishing T oolsThese finishing tools have been designed as preci-sion reamers for finishing operations only. They are not intended for primary forming or bottom cutting operations. Vickers recommends that a finishing tool only be used in a properly roughed hole. Failure to conform to this practicewill produce unsatisfactory size and finishes and possibly break the tool.MC–**–2(P)Dimensionsmm (inch)Cavity bores can be machined accurately in aluminum or steel. The necessary UNF , or UN threads may be machined using standard small tools, possibly already in yourmachine shop or from a local tool supplier.Either you, our customer, or Eaton can design and manufacture customized manifolds or housings dedicated to indi-vidual applications. We call the resulting valve packages Hydraulic Integrated Circuits (HIC). Cartridges selected for your application can be accom-modated in one or more HICs, according to your require-ments.WARNING For EPV-10 &CV16-10, thecavity should bemachined to the 14,29 (0.562) max diameter (dimension X) and to the maximum depth of 36,0 (1.417) (dimension J)Dimensions mm (inch)Cavity bores can be machinedaccurately in aluminum orsteel. The necessary UNF, orUN threads may be machinedusing standard small tools,possibly already in yourmachine shop or from a localtool supplier.Either you, our customer, orEaton can design and manufacture customized manifoldsor housings dedicated to indi-vidual applications. We callthe resulting valve packagesHydraulic Integrated Circuits(HIC). Cartridges selected foryour application can be accom-modated in one or more HICs,according to your require-ments.WARNINGFor EPV-10 &CV16-10, thecavity should bemachined to the 14,29 (0.562)max diameter (dimension X)and to the maximum depth of36,0 (1.417) (dimension J)C-**-2 CavityDimensions(0.0625) Runless otherwise specifiedunless otherwise specified2-way cavity with undercut (u)MC-**-3 Cavity Dimensionsunless otherwise specified unless otherwise specifiedDimensionsmm (inch)MDimensionsmm (inch)MC-**-5SCavityDimensionsDimensionsmm (inch)Cartridge Cavities IndexMOur cavities have beendesigned to achieve standard-ization based on each thread size to reduce the amount of tooling required to cover the valve range. All new designs of cartridge are made to fit the ISO recommendations forstandard cavities. The diagram below shows the sequence of tooling using tools specified in the following pages. Note: a pilot drill may be required before the form drill.Great care must be taken to ensure that the tools are inserted along the same machining axis to maintain correct concentricities, hence bodies should not be moved between operations.Operation 1Form Drill Operation 2Form Reamer Operation 3Plug T apIndexCavity A877Cavity T ools Form Drill A1161Form Reamer A1162Plug Tap 1 5/16-12 UNFCavity A879 Cavity T ools Form Drill A1040Form Reamer A1041Plug Tap3/4-16 UNFCavity A878 Cavity T ools Form Drill A885Form Reamer A1173Plug Tap7/8-14 UNFCavity A880Cavity T ools Form Drill A1302Form Reamer A1303Plug Tap1-14 UNS45.0028.00Ø26.00ØMCavity A881Cavity T ools Form Drill A1183Form Reamer A1036Plug Tap1 -14 UNFCavity A1126 Cavity T ools Form Drill AT422Form Reamer AT488Plug Tap1 5/8-12 UNFCavity A893Cavity T ools Form Drill A894Form Reamer AT491Plug Tap7/8-14 UNFCavity A3145Cavity T oolsForm Drill A3226 Form Reamer A3227 Plug Tap 1 5/16-12 UNCavity A3531Cavity T oolsForm Drill A3538 Form Reamer A3539 Plug Tap 3/4-16 UNF Cavity A3146Cavity T oolsForm Drill A3315 Form Reamer A3316 Plug Tap 1 1/8-12 UNFCavity A5302Cavity T oolsForm Drill A5668 Form Reamer A5669 Plug Tap 7/8-14 UNFMCavity A6610 Cavity T ools Form Drill AT447Form Reamer AT448Plug TapM20 x 1.5Cavity T ools Form Drill A6933Form Reamer A6934Plug Tap 1 5/16-12 UNFCavity A6701 Cavity T ools Form Drill AT482Form Reamer AT483Plug Tap3/4-16 UNF30.0Ø 26.0012.704)Cartridge CavitiesCavity A6935Cavity T oolsForm Drill AT501 Form Reamer AT502 Plug Tap 1 5/8-12 UN Cavity A7447Cavity T oolsForm Drill A8115 Form Reamer A8117 Plug Tap M27 X 2MCavity A12088Cavity T ools Form Drill A3315Form Reamer A3316Plug Tap1 1/8-12 UNFCavity A12336 Cavity T ools Form Drill A12337Form Reamer A12338Plug TapM27 X 1.5Cavity A12370Cavity T ools Form Drill A12439Form Reamer A12440Plug Tap7/8-14 UNFCavity A12196Cavity T ools Form Drill A12197Form Reamer A12198Plug TapM27 X 1.530.00Cavity A12743Cavity T ools Form Drill A12802Form Reamer A12803Plug Tap7/8”-14 UNFCavity A13098 Cavity T ools Form Drill A13099Form Reamer A13100Plug Tap1 5/8”-12 UNCavity A12744Cavity T ools Form Drill A12804Form Reamer A12805Plug Tap7/8-14 UNF34.00Ø34.00MCavity A13245Cavity T ools Form Drill A13246Form Reamer A13247Plug Tap 1 5/8”-12UNF -2BCavity A16102Cavity T ools Form Drill A3226Form Reamer A3227Plug Tap 1 5/16-12UNF -2BCavity A16927Cavity T ools Form Reamer AT1097Plug TapM10 x 1.0Cavity A20081Cavity T ools Form Drill AT2369/1Form Reamer AT2369/2Plug TapM38 x 2-6H58.00Ø51.00NOTE: T hese cavity dimensions are for installation purposes only.Cavity CVA- 22- 06- 0Cavity T ools Form Drill A8966Form Reamer A8967Plug TapM22 X 1.5Cavity CVA- 27- 04- 0Cavity T ools Form Drill A12784Form Reamer A496Cavity C-I-M18-3Cavity CVA- 20- 01- 0Cavity T ools Form Drill A8961Form Reamer A8962Plug TapM20 X 1.534.00 32.00EATON Screw-In Cartridge Valves E-VLSC-MC001-E1 September 2013M-32.A Where measurements are critical request certified drawings. We reserve the right to change specifications without notice.Cavity CVB- 22- 06- 0Cavity T ools Form Drill A8966Form Reamer A8967Plug TapM22 X 1.5ISO StandardNOTE: These cavity dimensions are for installation purposes only.CVB- 42- 04- 0Cavity T ools Form Drill BT499Form Reamer AT498Plug TapM42 X 234.00EATON Screw-In Cartridge Valves E-VLSC-MC001-E1 September 2013M-33.AMWhere measurements are critical request certified drawings. We reserve the right to change specifications without notice.- Additional products, product lines, and services offered by Eaton -Sectional Design for Multiple ConfigurationsEaton’s MDG mobile directional control valve uses a modular, versatile design based on our proven Vickers ® DG4V3 design. Eaton ® MDG valves, trulydesigned for mobile applications, offer the traditional benefits of a stackable mobile valve and provide further value as circuit options for mobile manifoldsystems. T his same versatility and flexibility applies to system applications, making it your best value for customized, multi-functional circuits.For more information, contact your local Eaton distributor, call us at 800-547-7805 or visit us on the web at: /hydraulics.MDG Mobile ValveVersatile, Proven, Best ValueSame day solutions with our Build Kit Program!。
Schedule 80 CPVC技术产品数据页1,CPVC管筒数据与信息,Spears制造有限公司说
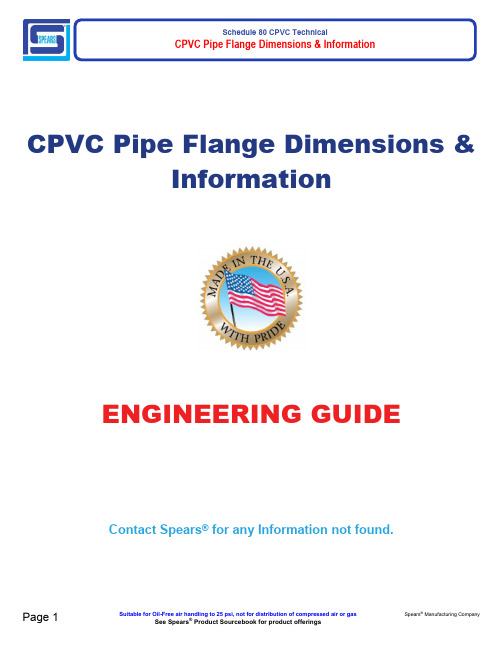
CPVC Pipe Flange Dimensions & InformationCPVC Pipe Flange Dimensions &InformationENGINEERING GUIDEContact Spears® for any Information not found.CPVC Pipe Flange OverviewThe information contained in this publication is based on current information and Product design at the time of publication and is subject to change without notification. Our ongoing commitment to product improvement may result in some variation. No representations, guarantees or warranties of any kind are made as to its accuracy, suitability for particular applications or results to be obtained therefrom. For verification of technical data or additional information not contained herein, please contact Spears® Technical Services Department [West Coast: (818) 364-1611 - East Coast: (678) 985-1263].GENERAL INFORMATIONRecommendations For Installers And UsersPlastic piping systems should be ENGINEERED, INSTALLED, and OPERATED in accordance with ESTABLISHED DESIGN AND ENGINEERING STANDARDS AND PROCEDURES for plastic piping systems. Suitability for the intended service application should be determined by the installer and /or user prior to installation of a plastic piping system. PRIOR TO ASSEMBLY, all piping system components should be inspected for damage or irregularities. Mating components should be checked to assure that tolerances and engagements are compatible. Do not use any components that appear irregular or do not fit properly. Contact the appropriate manufacturer of the component product in question to determine usability.Solvent Weld Connections - Use quality solvent cements and primers formulated for the intended service application, pipe size and type of joint. While the pipe and fitting materials may be compatible with the intended medium, the solvent cement may not be. Consult the manufacturer for suitability of use. Read and follow the cement and primer manufacturers' applications and cure time instructions thoroughly. Be sure to use the correct size applicator.Threaded Connections - Use a quality grade thread sealant. WARNING: SOME PIPE JOINT COMPOUNDS OR PTFE PASTES MAY CONTAIN SUBSTANCES THAT COULD CAUSE STRESS CRACKING TO PLASTIC. Spears® Manufacturing Company recommends the use of Spears®BLUE 75™ thread sealant which has been tested for compatibility with Spears® products. Please follow the sealant manufacturer's application/installation instructions. Choice of an appropriate thread sealant other than those listed above is at the discretion of the installer. 1 to 2 turns beyond FINGER TIGHT is generally all that is required to make a sound plastic thread connection. Unnecessary OVERTIGHTENING will cause DAMAGE TO BOTH PIPE AND FITTING."Lead Free" low lead certification - unless otherwise specified, all Spears® Thermoplastic Flanges specified here-in are certified by NSF International to ANSI/NSF® Standard 61, Annex G and is in compliance with California's Health & Safety Code Section 116825 (commonly known as AB1953) and Vermont Act 193. Weighted average lead content <=0.25%.CPVC Pipe Flange Overview Bolt Kit Selection GuideBolt Hardware Kits AvailableFor Connection of 2-Spears® FlangesIncludes Bolts, Nuts & Flat Washers for Specified Flange Size• Order Gaskets & Bolt Kits Separately• Pre-coated, Anti-seize Lubricated Bolts• Available in Zinc Coated Steel, Type 316 Stainless Steel or Type 304 Stainless SteelBolt TorqueRecommended Bolt Torque is shown in Table 1. Threadsshould be clean and well lubricated. Actual field conditions mayrequire variations in these recommendations. CAUTION:UNNECESSARY OVER TORQUING WILL DAMAGE THEFLANGE.Table 1Flange Size (in.)Recommended Torque(ft. lbs.)1/2 - 1-1/212 2 - 425530 6 - 8401064 1295 14 - 24110Torque SequenceBolt Torque sequence is shown Below in Table 2.Table 2Flange Size Bolts*Per KitDiameter(in.-TPI)Length(in.)Kit Part NumberZinc316 SS304 SS1/23/4 & 11-1/4 & 1-1/222-1/2345 & 6810 & 12444444888121/2 - 131/2 - 131/2 - 135/8 - 115/8 - 115/8 - 115/8 - 113/4 - 103/4 - 107/8 - 922-1/42-1/233-1/43-1/23-1/244-1/26HK-005HK-010HK-015HK-020HK-025HK-030HK-040HK-060HK-080HK-120HK1-005HK1-010HK1-015HK1-020HK1-025HK1-030HK1-040HK1-060HK1-080HK1-120HK2-005HK2-010HK2-015HK2-020HK2-025HK2-030HK2-040HK2-060HK2-080HK2-120* Each Bolt Includes Nut & Two (2) Flat WashersTemperature Pressure RatingCPVC Pipe Flange OverviewGasket Selection GuideFollowing Gasket Numbers Available from Spears ®• Order Gaskets & Bolt Kits Separately• 1/8" Full-Face design with ANSI Class 150 Bolt Patterns • Pressure rated to 150 psi @ 73°F • Available in Buna-N, EPDM, or FKMFlange Size Bolts Per Kit Gasket Part NumberBuna-N EPDM FKM 1/23/411-1/41-1/222-1/23456810124444444488881212GK1-005GK1-007GK1-010GK1-012GK1-015GK1-020GK1-025GK1-030GK1-040GK1-050GK1-060GK1-080GK1-100GK1-120GK2-005GK2-007GK2-010GK2-012GK2-015GK2-020GK2-025GK2-030GK2-040GK2-050GK2-060GK2-080GK2-100GK2-120GK3-005GK3-007GK3-010GK3-012GK3-015GK3-020GK3-025GK3-030GK3-040GK3-050GK3-060GK3-080GK3-100GK3-120GasketsFull faced, 1/8" thick elastomer gaskets with a Shore "A" Durometer of approximately 70 is recommended.Flange Make-upOnce a flange is joined to pipe, the method for joining two flanges is as follows:1.Piping runs joined to the flanges must be installed in a straight line position to the flange to avoid stress at the flange due tomisalignment. Piping must also be secured and supported to prevent lateral movement which can create stress and damage the flange.2.With gasket in place, align the bolt holes of the mating flanges by rotating the ring into position.3.Insert all bolts, washers (two standard flat washers per bolt), and nuts.4.Make sure the faces of the mating surfaces are flush against gasket prior to bolting down the flanges.5.Tighten the nuts by hand until they are snug. Establish uniform pressure over the flange face by tightening the bolts in 5 ft.-lbs. increments according to the sequence shown in Table 2 following a 180° opposing sequence.6.Care must be taken to avoid "bending" the flange when joining a Spears ® flange to a "raised face" flange, or a wafer-style valve. Do not use bolts to bring together improperly mated flanges.Configuration TerminologyMulti-Bolt Pattern Ring - Bolt hole drilling accepts ANSI and Metric Flanges Socket - Slip socket connection for solvent cement welding Spigot - Pipe O.D. connection for solvent welding Fipt - Female Iron Pipe ThreadSR Fipt - Spears ® patented Special Reinforced (SR) plastic thread IPS - Iron Pipe SizePIP - Plastic Irrigation PipeCPVC Pipe Flange OverviewMolded Flange Technical InformationApplicationMolded CLASS 150 Flange fittings are coupling devices designed for joining IPS (Iron Pipe Size) plastic piping systems, where frequent disassembly may be required, and can be used as a transitional fitting for joining plastic to metal piping systems.Suitability of application is at the discretion of the user.Pressure Rating150 psi, water at 73°F.Flange TypesOne Piece - Available in socket configuration, sizes 1/2" through 8"; threaded and SR threaded (Special Reinforced) configuration sizes 1/2" through 4".Van Stone Style - Two-piece design with rotating flange ring, available in socket configurations, sizes 1/2" through 18"; threaded configurations, sizes 1/2" through 4" and spigot configurations, sizes 1/2" through 12".Blind - Closed ring design for capping off a mating flange, flanged fitting or flanged valve, available in sizes 1/2" through 12".MaterialsAll injection molded flanges are produced from CPVC materials approved for potable water use by the NSF International (NSF®).Glass-filled CPVC materials may be used in certain Van Stone Style flange rings and large diameter Blind flanges where additional reinforcement is deemed necessary.Conformance StandardsSocket I.D. & Spigot O.D. - ASTM F 439 (CPVC).Threads - ASTM F 1498.Bolt Hole Pattern - ANSI B16.5; ASTM D 4024.Material - ASTM D 1784 (CPVC Cell Classification 23447-B).Weights & DimensionsSpecified minimum bolt lengths are based on the use of two Spears® Flanges, two standard flat washers, standard nut and 1/8"thick elastomer full face gasket. Mating with other brands or accessories may require variation. Bolts and gaskets are not supplied with flanges.Dimension references:L = Overall length of hub, ± 1/16 inch.M = Outside diameter of socket hub, ± 1/16 inch.N = (Laying Length) socket/spigot bottom to seal-ring face of flange, ± 1/16 inch.R = Height (thickness) of flange ring, ± 1/16 inch.Max O.D. = Outside diameter of ring, ± 1/16 inch.Bolt Circle Diameter = ANSI B 16.5 Standard; ASTM D 4024, ± 1/16 inch.5/8191-13/1615-3/4CPVC Pipe Flange Dimensions & InformationPage 11Suitable for Oil-Free air handling to 25 psi, not for distribution of compressed air or gas Spears ® Manufacturing CompanySee Spears ® Product Sourcebook for product offeringsFabricated Flange Technical InformationApplicationFabricated IPS and PIP Flange fittings are coupling devices designed for joining IPS (Iron Pipe Size) or PIP (Plastic Irrigation Pipe) plastic piping systems, where frequent disassembly may be required. These flanges can be used as transitional fittings for joining IPS-to-IPS, PIP-to-PIP, IPS-to-PIP, or plastic to metal piping systems. Suitability of application is at the discretion of the user.Pressure RatingAll standard fabricated flanges are Van Stone Style (except blind flange) - two piece design with rotating flange ring.Class 150 IPS Flanges (with steel ring): 150 psi, water at 73°F.IPS Flanges 18" - 24" (with plastic ring): 50 psi, water at 73°F.IPS Flanges, Class 300 Bolt Pattern (with plastic ring): 1/2" - 16" 150 psi, 18" - 24" 50 psi, water at 73°F.Blind Flanges, 14" - 24": 50 psi, water at 73°F.PIP Flanges, 6" - 16" (with plastic ring & molded IPS flanges w/PIP Adapters): 125 psi, water at 73°F.PIP Flanges, 18" - 24" (with steel ring): 125 psi, water at 73°F.Flange TypesVan Stone Style Class 150 IPS (with steel ring) - Fabricated CPVC body with steel flange ring, available in sizes 18" through 24", slip socket and 14" through 24", spigot.Van Stone Style IPS (with plastic ring) - Fabricated CPVC body with PVC flange ring, available in sizes 18" through 24", slip socket and 14" through 24", spigot.Van Stone Style PIP (with plastic ring) - PIP adapter fabricated to injection molded CPVC Van Stone Style IPS flange, available in sizes 6" through 16", slip socket.Van Stone Style PIP (with steel ring) - Fabricated CPVC body with steel flange ring, available in sizes 14" through 24", slip socket.Blind - Closed ring design for capping off a mating flange; fabricated CPVC available in sizes 5" and 14" through 24".Special Note On PIP Flange SizesIn order to facilitate connections between IPS and PIP systems, all Plastic Irrigation Pipe flanges are fabricated with PIP sockets using standard IPS Flange Rings. These are indicated in dimension tables under "Size" as (nominal IPS flange size) x (actual PIP O.D.), such as: 6" x 6.140".To better meet user needs, Spears ® offers flanges for 15.300" O.D. PIP with either 14" or 16" IPS Flange Rings. In addition, both 18.360" and 18.701" O.D. PIP are offered with 18" IPS Flange Rings.MaterialsAll fabricated flanges are produced from CPVC materials approved for potable water use by the National Sanitation Foundation (NSF ®).Steel flange rings are carbon steel.Conformance StandardsMaterials - ASTM D 1784 (CPVC Cell Classification 23447-B).Weights & DimensionsSpecified minimum bolt lengths are based on the use of two Spears ® Flanges, two standard flat washers, standard nut and 1/8" thick elastomer full face gasket. Mating with other brands or accessories may require variations.Note: Bolts and gaskets are not supplied with flanges.Dimension references:L = Overall length of hub, ± 1/2 inch.M = Outside diameter of socket hub, ± 1/4 inch.N = (Laying Length) socket bottom to seal-ring face offlange, ± 1/2 inch.R = Height (thickness) of flange ring, ± 1/16 inch.Max O.D. = Outside diameter of ring, ± 1/16 inch.Bolt Circle Diameter = ANSI B 16.5 Standard; ASTM D 4024, ± 1/16 inch.Made in the U.S.A.Suitable for Oil-Free air handling to 25 psi, not for distribution of compressed air or gasPage 12See Spears® Product Sourcebook for product offeringsPage 13Suitable for Oil-Free air handling to 25 psi, not for distribution of compressed air or gas Spears® Manufacturing CompanySee Spears® Product Sourcebook for product offerings。
- 1、下载文档前请自行甄别文档内容的完整性,平台不提供额外的编辑、内容补充、找答案等附加服务。
- 2、"仅部分预览"的文档,不可在线预览部分如存在完整性等问题,可反馈申请退款(可完整预览的文档不适用该条件!)。
- 3、如文档侵犯您的权益,请联系客服反馈,我们会尽快为您处理(人工客服工作时间:9:00-18:30)。
1 Introduction
\Design-for-Assembly"(DFA) is a process of improving product designs for easy and low cost assembly. An assembly-conscious design is desirable because it could result in signi cant savings in capital costs and assembly time. For example, the IBM Corporation has successfully applied the concept of DFA to one of its printer models, by redesigning and reducing the number of parts, which drastically lowered the printer's assembly cost, and price 3]. An assembly-conscious design is di cult, in general, because designers tend to focus only on the functionality of the product. Considering \assemblability" concurrently with the functionality of a product seems to be a major source of distraction that most traditional designers would like to avoid. This is especially
This project is supported in part by the Institute for Manufacturing and Automation Research (IMAR) Project No. 4 and by the National Science Foundation. Support for Dr. Goldberg is provided in part by a 1991 USC Faculty Research Initiation Fund (FRIF) grant.
Abstract
\Design-for-Assembly" (DFA) is a process of improving product designs for easy and low cost assembly. DFA often involves an analysis of an existing design according to qualitative criteria that are di cult to analyze. This paper introduces a quantitative shape metric for planar parts, called feedability, based on a stochastic parts feeding algorithm reported in 7] 8]. Although feedability is only one possible metric for DFA, it relates one aspect of assembly cost directly to part geometry. Therefore, based on feedability, one can produce a set of geometric redesign strategies. The application of feedability (or Design-for-Feedability) to DFA is illustrated and compared with other DFA methods.
apparent when there exist many parts exerting various constraints upon one other. Therefore, there is a desire to automate the DFA process, at least partially, through the use of computers. The purpose of this paper is to introduce a quantitative metric for part shapes, called feedability, and demonstrate its use. Although feedability is only one possible metric for DFA, it relates DFA cost directly to part geometry. Therefore, various redesign strategies are possible by manipulating the geometric parameters of the part and their constraints to improve the feedability. In a previous paper 10], we proposed a model for the DFA process that consists of iterations of three successive stages: analysis, suggestion, and veri cation. The actual implementation revealed some fundamental problems. One of the most important problems was that the current methods of DFA analysis lack a scienti c foundation that can associate DFA cost to a particular set of low level or geometrical design actions. Therefore, current DFA methods can only produce redesign strategies in terms of high level design axioms or design rules: for example, \make part A symmetric", \add a gripping feature to part B", \redesign part C to avoid tangling", etc. The geometric details for achieving above objectives have to made by the humans. One of the goal of this paper is to introduce low level redesign strategies by introducing a metric that can relate assembly cost to part geometry. Then, geometric redesign advice would be possible: for example, \change the length of part A from 3 inches to 5 inches in order to make it symmetror Design-for-Assembly
Gerard J. Kim, George A. Bekey and Kenneth Y. Goldberg Center for Manufacturing and Automation Research Computer Science Department University of Southern California, LA, CA 90089-0782, USA E-mail: gkim@, bekey@, goldberg@
2 Other Methods of DFA
Currently, there exist two main types of DFA methods. The most popular method is typi ed by the one pioneered by Boothroyd and Dewhurst 4]. In their approach, a product is analyzed according to various
\ease of assembly" criteria (such as symmetry, dimension, mating direction, number of parts, etc), organized with charts of scores, and a tabulated score is used to calculate a \design e ciency ratio". The scoring system (or the DFA metric) is empirically based on an engineering time study method 16]. Then, a redesign is proposed manually with the help of the score table which, more or less, pinpoints the source of the design problem. Many other commercial systems or in-house methods 11] 14] 15] are based on this approach partly because the table lookup and the arithmetic procedure is easily computerizable. The second type of approach is called the \axiomatic method". The axiomatic method is simply a set of design guidelines that have been empirically derived from years of experiences in design and assembly operations. If correctly applied either during the initial design phase or the redesign phase, they should result in a product that has an inherently low assembly cost 9]. Many such DFA axioms have been identi ed by a number of researchers 2] 3] 9]. In particular, in an e ort to make the axiomatic method more evaluative, Hoekstra has assigned scores to each of the design axioms in a subjective manner (for example, in a scale of 1 to 5). The rst method is suited for a comparative analysis of nished designs, but can not be applied to evolving designs. In practice, the score tables are very useful in analyzing and evaluating designs in terms of DFA. Nevertheless, such tools still have the drawback that they lack a capability of helping designers to explore new possibilities 6]. The second method allows the designer to consider assemblability from the initial design phase. However, in general, the second method lack quantitative measures for analysis and evaluation of nal or evolving designs 16]. Although Hoekstra's scoring system for the design axioms improved upon the evaluating capability of the axiomatic method, it is based on a subjective point of view, and can not relate its scores directly to part geometry. Suh has also cautioned against the handbook approach for the lack of theoretical conception and scienti c basis for the design axioms 17]. A more objective and analytic metric with a scienti c basis, which relates assembly cost directly to the design, could provide a systematic method of making geometric redesigns. Hoekstra best illustrated the need of such a metric by citing part of the following round table discussion on \Design for Assembly" reported in a recent Assembly Engineering Magazine 5] 9]. Among the panelists were G. Boothroyd, W. Morill (Manager, Design for Manufacturability, Digi-