APQP(stabilizer bar)Advanced Product Quality Planning and Control Plan
APQP产品质量先期策划(PPT 110页)

)
2021/11/9
第一页,共109页。
什么(shén me)是〝APQP〞
• APQP是Advanced Product Quality Planning 的英文缩写。它是由〝美国三大 公司〞即〝通用、福特和戴姆勒-克莱斯勒 〞共同发布的通用产品完成谋划方法指南。 它是一种结构化的方法,用来(yònɡ lái) 明白并树立确保产品使顾客满意所需的义 务步骤,即总体规那么了一个产品从概念 开发到批量消费所需阅历的各个阶段及每 个阶段的义务义务。
第九页,共109页。
小组(xiǎozǔ)组成
多功用小组〔包括但不限于以下职能〕 工程 质量 推销 制造 测试(cèshì) 物流 销售/营销等
外部成员(chéngyuán): 还能够包括顾客和供应商代表的参与
第十页,共109页。
确定(quèdìng)范围
• 任命一名项目小组组长 • 确定小组成员的作用和责任 • 确认和了解顾客〔内、外部〕及其希冀 • 评价项目可行性〔设计、功用要求(yāoqiú)和制造进程〕 • 确定本钱、时间布置和应思索的限制条件 • 确定需求从顾客那里失掉那些协助 • 确定报告的顺序和方法 • 制定文件化的新产品开发流程
• 义务—产品/项目、顾客和方法
• 范围—包括(bāokuò)与不包括(bāokuò)〔能否含有设计责任〕
• 目的—QCD〔质量、本钱和交付〕目的
• 需求—可交付的QCD目的
• 解释和说明—相关的法律、法规和规范
• 市场剖析—产量的预测,消费节拍,交付日期,目的价钱,
•
竞争对手剖析等
勇于开始,才能找到成功的路
PRCESS DESIGN AND DEVELOPMENT
apqp 产品质量先期策划
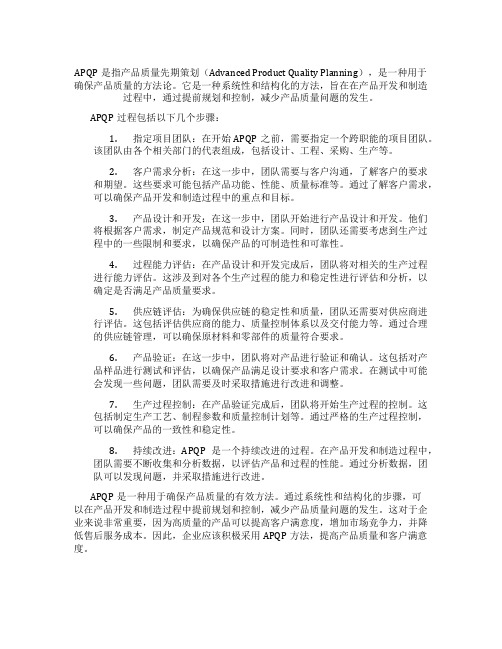
APQP是指产品质量先期策划(Advanced Product Quality Planning),是一种用于确保产品质量的方法论。
它是一种系统性和结构化的方法,旨在在产品开发和制造过程中,通过提前规划和控制,减少产品质量问题的发生。
APQP过程包括以下几个步骤:1.指定项目团队:在开始APQP之前,需要指定一个跨职能的项目团队。
该团队由各个相关部门的代表组成,包括设计、工程、采购、生产等。
2.客户需求分析:在这一步中,团队需要与客户沟通,了解客户的要求和期望。
这些要求可能包括产品功能、性能、质量标准等。
通过了解客户需求,可以确保产品开发和制造过程中的重点和目标。
3.产品设计和开发:在这一步中,团队开始进行产品设计和开发。
他们将根据客户需求,制定产品规范和设计方案。
同时,团队还需要考虑到生产过程中的一些限制和要求,以确保产品的可制造性和可靠性。
4.过程能力评估:在产品设计和开发完成后,团队将对相关的生产过程进行能力评估。
这涉及到对各个生产过程的能力和稳定性进行评估和分析,以确定是否满足产品质量要求。
5.供应链评估:为确保供应链的稳定性和质量,团队还需要对供应商进行评估。
这包括评估供应商的能力、质量控制体系以及交付能力等。
通过合理的供应链管理,可以确保原材料和零部件的质量符合要求。
6.产品验证:在这一步中,团队将对产品进行验证和确认。
这包括对产品样品进行测试和评估,以确保产品满足设计要求和客户需求。
在测试中可能会发现一些问题,团队需要及时采取措施进行改进和调整。
7.生产过程控制:在产品验证完成后,团队将开始生产过程的控制。
这包括制定生产工艺、制程参数和质量控制计划等。
通过严格的生产过程控制,可以确保产品的一致性和稳定性。
8.持续改进:APQP是一个持续改进的过程。
在产品开发和制造过程中,团队需要不断收集和分析数据,以评估产品和过程的性能。
通过分析数据,团队可以发现问题,并采取措施进行改进。
APQP是一种用于确保产品质量的有效方法。
质量体系五大工具七大手法定义及其详细解读
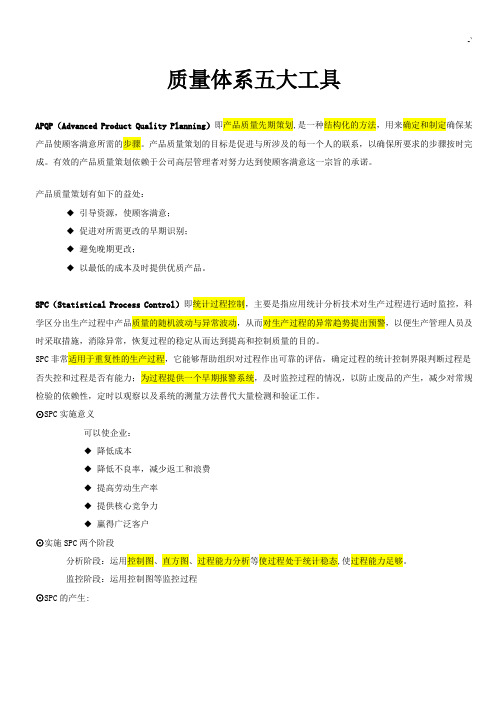
质量体系五大工具APQP(Advanced Product Quality Planning)即产品质量先期策划,是一种结构化的方法,用来确定和制定确保某产品使顾客满意所需的步骤。
产品质量策划的目标是促进与所涉及的每一个人的联系,以确保所要求的步骤按时完成。
有效的产品质量策划依赖于公司高层管理者对努力达到使顾客满意这一宗旨的承诺。
产品质量策划有如下的益处:◆ 引导资源,使顾客满意;◆ 促进对所需更改的早期识别;◆ 避免晚期更改;◆ 以最低的成本及时提供优质产品。
SPC(Statistical Process Control)即统计过程控制,主要是指应用统计分析技术对生产过程进行适时监控,科学区分出生产过程中产品质量的随机波动与异常波动,从而对生产过程的异常趋势提出预警,以便生产管理人员及时采取措施,消除异常,恢复过程的稳定从而达到提高和控制质量的目的。
SPC非常适用于重复性的生产过程,它能够帮助组织对过程作出可靠的评估,确定过程的统计控制界限判断过程是否失控和过程是否有能力;为过程提供一个早期报警系统,及时监控过程的情况,以防止废品的产生,减少对常规检验的依赖性,定时以观察以及系统的测量方法替代大量检测和验证工作。
⊙SPC实施意义可以使企业:◆ 降低成本◆ 降低不良率,减少返工和浪费◆ 提高劳动生产率◆ 提供核心竞争力◆ 赢得广泛客户⊙实施SPC两个阶段分析阶段:运用控制图、直方图、过程能力分析等使过程处于统计稳态,使过程能力足够。
监控阶段:运用控制图等监控过程⊙SPC的产生:工业革命以后,随着生产力的进一步发展,大规模生产的形成,如何控制大批量产品质量成为一个突出问题,单纯依靠事后检验的质量控制方法已不能适应当时经济发展的要求,必须改进质量管理方式。
于是,英、美等国开始着手研究用统计方法代替事后检验的质量控制方法。
1924年,美国的休哈特博士提出将3Sigma原理运用于生产过程当中,并发表了著名的“控制图法”,对过程变量进行控制,为统计质量管理奠定了理论和方法基础。
APQP产品质量先期策划方案
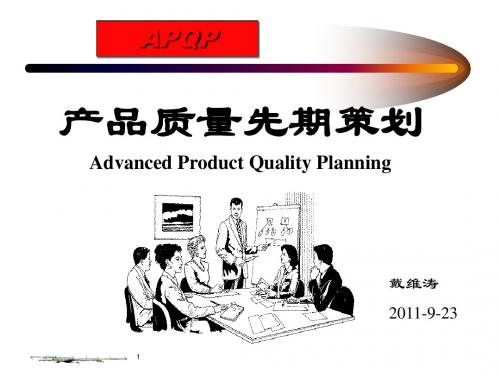
计划和确定 项目
产品设计 和开发
过程设计 和开发
产品和过程 确认
反馈,评价 和纠正措施
顾客 满意
任务: • 识别、确定顾客和产品要求,以及计划和规定项目, • 识别、确定类似产品和过程中存在的失效和不足。 输入:顾客呼声、顾客输入、产品的可靠性研究 输出:设计目标、可靠性和质量目标、初始材料清单、初始过程流程图、产品 和过程特殊特性清单、产品保证计划、管理者支持
7
APQP
7.1
注:
产品实现的策划
某些顾客把项目管理或先期产品质量策划看作产品实现的手段。
先期产品质量策划具体表现了缺陷预防和持续改进的概念,而并非发现
缺陷。
以跨部门的工作方法(Multidisciplinary approach)为基础。
8
APQP
什么是APQP?
• APQP是用来确定和制定确保产品让用户满意所需步骤的 组织方法。 • APQP的目标是促进与之有关的每一个人的沟通,以确保
a)目标明确:满足顾客要求,不 断改进。 b)按规定的方法和组织形式进行 策划。 c)应用各类分析工具: FMEA,MSA,SPC、流程图,QFD 等。 d)保证跨职能活动的效率:横向 协调小组。
• • • • •
5
APQP
产品实现核心过程
顾客要求
QFD
APQP
FMEA
CP
SOP
防错法
SPC
顾客反馈 交付 生产 PPAP
4
APQP
APQP特点:
理解要点: • • • • 结构化、系统化的方法; 确保使产品满足顾客的需要和期望; 团队的努力,(横向职能小组是重要方 法); 从产品的概念设计、设计开发、过程开 发、试生产到生产,以及全过程中的信 息反馈、纠正措施和持续改进活动; 不断采取防错措施降低产品风险 持续改进; 制定必要的程序、标准和控制方法; 控制计划是重要的输出; 制定、实施时间表。
产品建议书-APQP

产品建议书-APQP标题:产品建议书-APQP引言概述:APQP(Advanced Product Quality Planning)是一种产品质量管理工具,旨在确保在产品开发和生产过程中,质量标准得到满足。
本文将介绍APQP的五个主要部分,包括项目管理、质量计划、设计验证、过程验证和生产评估。
一、项目管理:1.1 项目目标的设定:明确产品的功能、性能和质量目标,确保团队对项目目标的一致理解。
1.2 项目计划的制定:制定详细的时间表和里程碑,确保项目按时交付。
1.3 项目资源的分配:合理分配人力、物力和财力资源,确保项目的顺利进行。
二、质量计划:2.1 质量标准的制定:制定产品质量标准和测试方法,确保产品符合客户需求。
2.2 过程流程图的绘制:绘制产品生产过程的流程图,明确每个环节的责任和流程。
2.3 产品检验计划的制定:制定产品的检验计划,明确检验点和检验标准。
三、设计验证:3.1 产品设计评审:对产品设计进行评审,确保设计满足功能和性能要求。
3.2 产品样品的制作:制作产品样品用于验证设计的可行性和质量。
3.3 产品测试和验证:进行产品的各项测试,包括性能测试、可靠性测试等,确保产品质量。
四、过程验证:4.1 生产工艺评审:对生产工艺进行评审,确保生产过程的可行性和质量。
4.2 生产线试运行:进行生产线的试运行,发现和解决潜在问题。
4.3 过程能力评估:评估生产过程的能力和稳定性,确保产品的一致性和可靠性。
五、生产评估:5.1 制造能力分析:分析制造能力,确保生产能够满足需求。
5.2 产品可靠性评估:评估产品的可靠性和寿命,确保产品质量和可靠性。
5.3 生产效率评估:评估生产效率,寻找提高生产效率的方法。
结论:APQP是一种有效的产品质量管理工具,通过项目管理、质量计划、设计验证、过程验证和生产评估等五个部分,可以确保产品在开发和生产过程中达到高质量标准。
通过严格遵循APQP流程,企业可以提高产品质量、减少生产风险,并满足客户的需求。
APQP-和PPAP过程专业术语
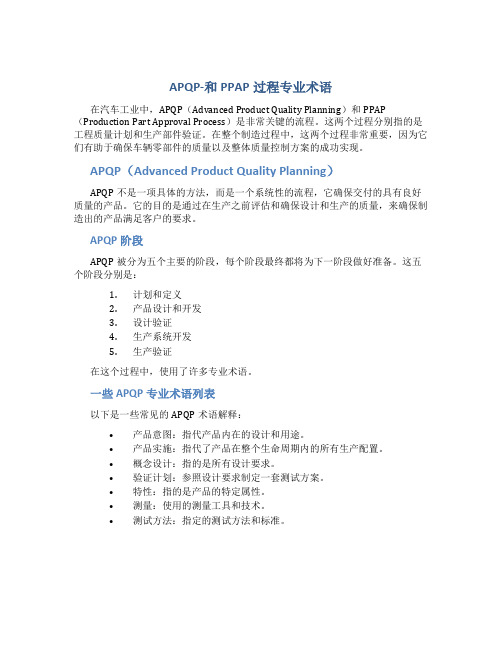
APQP-和PPAP过程专业术语在汽车工业中,APQP(Advanced Product Quality Planning)和PPAP (Production Part Approval Process)是非常关键的流程。
这两个过程分别指的是工程质量计划和生产部件验证。
在整个制造过程中,这两个过程非常重要,因为它们有助于确保车辆零部件的质量以及整体质量控制方案的成功实现。
APQP(Advanced Product Quality Planning)APQP不是一项具体的方法,而是一个系统性的流程,它确保交付的具有良好质量的产品。
它的目的是通过在生产之前评估和确保设计和生产的质量,来确保制造出的产品满足客户的要求。
APQP阶段APQP被分为五个主要的阶段,每个阶段最终都将为下一阶段做好准备。
这五个阶段分别是:1.计划和定义2.产品设计和开发3.设计验证4.生产系统开发5.生产验证在这个过程中,使用了许多专业术语。
一些APQP专业术语列表以下是一些常见的APQP术语解释:•产品意图:指代产品内在的设计和用途。
•产品实施:指代了产品在整个生命周期内的所有生产配置。
•概念设计:指的是所有设计要求。
•验证计划:参照设计要求制定一套测试方案。
•特性:指的是产品的特定属性。
•测量:使用的测量工具和技术。
•测试方法:指定的测试方法和标准。
PPAP(Production Part Approval Process)PPAP是一系列的评估过程,确保所涉及的部件在开始生产前是合格的。
这个过程的主要目的是确保在量产阶段,所生产的零件满足要求的质量标准。
这是实现全面质量控制方案的一部分。
PPAP阶段PPAP也分为五个主要的阶段,可以与APQP的五个阶段相对应。
这五个阶段分别是:1.部件计划2.材料评估3.制造过程评估4.部件评估5.PPAP批准一些PPAP专业术语列表以下是一些常见的PPAP术语解释:•过程登记:是指过程的过程记录和统计分析。
五大工具系列课程之APQP产品质量先期策划要求AdvancedProductQualityPlanning
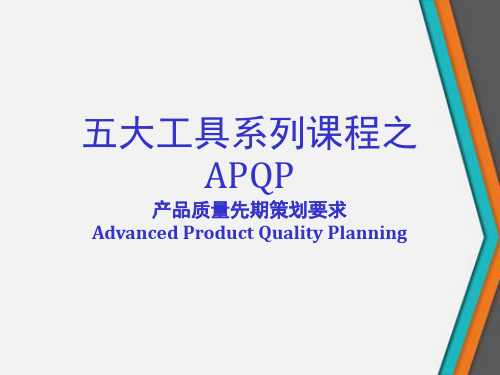
APQP的第一阶段
(1.2 业务计划和市场策略 )
顾客的业务计划和市场策略将成为产品质量策划 的框架。业务计划会对小组给出限制(例如:时间, 成本,投资、产品定位,研究 (R&D)资源),影响 其把握的方向。 市场策略会定义目标顾客,主要卖点,以及主要 的竞争对手。
APQP的第一阶段
( 1.3 产品/过程标竿数据 )
入,这些输入已在第一阶段-“计划和确定项目”中予以定义。
例子:
第一阶段:设计输入-孔的位置度公差+/- 1.0 mm
第二阶段:设计输出
图样
——规定孔的位置度公差为+/- 1.0 mm
的工程
34
APQP的第二阶段
• 设计评审
进行设计评审是为了监控项目相对于顾客要求的进 展。这些评审由横向职能小组进行,而且每次评审 的结果都必须以文件存档。
标竿管理的使用可以为产品/过程业绩目标的建立 提供输入,研发也可以带来标竿和创意概念。一个 成功标竿管理的实现方式是: 识别恰当的标竿,理解造成你的现状和标竿之间产 生差距的原因,开发计划来缩小差距,跟上标竿, 者超越标竿。
APQP的第一阶段
1.4 产品/过程设想 • 设想产品可能会有的固有特征,设计或过程概念,
APQP的基础知识
● 定义顾客的要求(适用时使用QFD)。 ● 选择必须加入到小组的规则,个人和供应 商,以 及那些不要求加入的。 ● 理解顾客的期望,即:设计测试数量。 ● 评估提议的设计,性能要求和制造过程的可
行性。 ● 识别必须考虑的成本﹑时间和限制。 ● 确定所需的顾客协助。 ● 识别文档过程和方法。
1.8 可靠性与质量目标 • 可靠性目标是建立在顾客的需求和期望,项目目标和
☆APQP英文培训教程

☆APQP英文培训教程APQP又叫做Advanced Product Quality Planning, 是新产品开发的一种高级质量规划技术。
这种技术的核心思想是在新产品的开发过程中,尽可能地发现并纠正问题,最大程度地提高产品的质量以及生产效率。
为了能够学会如何进行APQP,并为了在公司中实施该技术,我们需要进行APQP英文培训。
1. Introduction to APQPAdvanced Product Quality Planning (APQP) 是一种高级的质量规划技术,它是用于新产品开发的。
确保新产品的质量,并将产品生产和交付保持在要求的质量水平上。
APQP的目标是最大程度地减少产品生命周期中的成本,改善交付时间,提高产品质量,同时增强组织的竞争力。
2. Core Elements of APQPAPQP是基于五大核心元素的。
这些元素包括:- Plan and Define the Program在计划和定义项目时,APQP的目标是最大限度地满足顾客的需求,并确保产品质量和交付满足要求的目标指标。
从规定规范到开发项目经费以及资源,这个阶段的目标是确保确定可实现的计划。
- Design and Development在设计和开发阶段,重点是确保产品的功能性和性能。
为了做到这一点,需要确保必要的资源,设备,过程和技能,并根据项目方案实施相关的验证和测试。
- Validation在验证阶段,APQP的重点是验证产品是否符合各项指标。
为了做到这一点,需要根据验证计划执行相关的测试和确认。
- Production and Launch在生产和推出阶段,APQP的目标是确保产品可以按照要求的质量标准和时间表稳定地生产。
组织和资源的状况以及工艺设计的质量都是这一阶段的考虑因素。
- Feedback, Assessment and Improvement在回馈,评估和改进阶段,APQP的目标是检查产品在生命周期的不同阶段中的性能水平,收集数据并进行评估,以用于未来项目中的改进。
产品质量先期策划(31)(APQP)

第一章:計劃和確定項目(本章输入)
1.“顧客的呼聲”包括來自內部和/或外部顧 客們的報怨、建議、資料和信息。收集此信息 的方法有:
1.1市場研究:通過以下作法來獲取反映顧客 呼聲的市場研究資料和信息 ❖對顧客的採訪
❖顧客意見征詢與調查
:
第一章:計劃和確定項目(本章输入)
❖市場測試和定位報告 ❖新產品質量和可靠性研究 ❖競爭產品質量的研究 ❖運行情況良好報告
x
一.计划和确认 x
二.产品设计和开发 x
可行性
x
三.过程设计和开发 x
四.产品和过程确认 x
五.反馈评定和纠正
措施
x
六.控制计划方法论 x
仅限制造
x
x x x
x x
服务供方如热处理 贮存、运输等等 x
x x x
x x
初始決定(確定範圍)
阶段 项目与内容
输出的文件
预计开 始时间
预计完 成时间
实际完 成时间
品 备要求
单
设
计
小组可行性承诺
小组可行性承
诺和管理者支 设计信息检查清单 持
第二阶段总结报告
预计开 始时间
预计完 成时间
实际完 成时间
责任 人
备注
第二章:產品設計和開發
說明:本章討論的是策劃過程中設計特征和特性發展 到接近最終形式時的要素一個可行的設計應能滿足生 產量、工期和工程要求的能力,並滿足質量可靠性、 投資成本、重量、單件成本和進度目標等。(因我公 司QS9000 體系不包含設計,故設計評審,驗証等略過)
第一章:計劃和確定項目(本章输入)
1.3 小組經驗:小組適當時可利用包括如下內容 的任何信息來源: ❖來自更高層體系或過去質量功能開發項目的輸 入 ❖顧客的信件和建議 ❖現場服務報告 ❖合同評審等等 2 業務計劃/營銷戰略:顧客業務計劃和營銷策 略將成為產品質量計劃的設定框架。營銷戰略將 確定目標顧客、主要的銷售點和主要的競爭者。
产品质量先期策划五大工具培训课件(PPT 47页)

APQP的基本原则(六)
八、问题的解决: ----解决产品设计和/或加工过程中的问题,责任、时间
矩阵表的要求;Open issue list. 九、制订产品质量策划的进度计划:
----小组成立后的第一项工作:制定APQP计划; 十、与进度计划有关的计划-应符合顾客计划时间:
×
控制方法论
×
概念与TS一致有权制定 和更改产品规范
仅限制造 ×
服务组织如热处理 、储存、运输等等××××××
×
×
×
×
×
精品ppt模板供大家使用
什么是APQP? “质量策划”的定义 ▪ 质量管理的一部分,致力于制定质量目标并规定必要的运行过程和相关
资源以实现质量目标。 ▪ 质量策划是一种活动。 ▪ 就制造行业而言,质量策划可以理解为从概念到批量生产的整个过程。 ▪ 产品质量策划是一种结构化的方法,用来确定和制定确保某产品使顾客
五大工具的关系 :APQP是树干,其余为树枝
DFMEA
PFMEA
精品ppt模板供大家使用
SPC APQP
MSA
PPAP
ISO/TS标准的目标
❖
在供应链中建立
❖ 持续改进,
❖
强调缺陷预防,
❖
减少变差和浪费
❖ 的质量管理体系
精品ppt模板供大家使用
7.1 产品实现的策划
在对产品实现进行策划时,组织必须确定以下方面的适当内容: 产品的质量目标和要求; 针对产品确定过程、文件和资源的需求; 产品所要求的验证、确认、监测的试验活动,以及产品接收准则; 实现过程及其产品满足要求提供证据所需的记录 策划的输出形式必须适于组织的运作方式。
【质量】质量体系五大工具七大手法定义及详细解读

【关键字】质量质量体系五大工具APQP(Advanced Product Quality Planning)即产品质量先期策划,是一种结构化的方法,用来确定和制定确保某产品使顾客满意所需的步骤。
产品质量策划的目标是促进与所涉及的每一个人的联系,以确保所要求的步骤按时完成。
有效的产品质量策划依赖于公司高层管理者对努力达到使顾客满意这一宗旨的承诺。
产品质量策划有如下的益处:◆引导资源,使顾客满意;◆促进对所需更改的早期识别;◆避免晚期更改;◆以最低的成本及时提供优质产品。
SPC(Statistical Process Control)即统计过程控制,主要是指应用统计分析技术对生产过程进行适时监控,科学区分出生产过程中产品质量的随机波动与异常波动,从而对生产过程的异常趋势提出预警,以便生产管理人员及时采取措施,消除异常,恢复过程的稳定从而达到提高和控制质量的目的。
SPC非常适用于重复性的生产过程,它能够帮助组织对过程作出可靠的评估,确定过程的统计控制界限判断过程是否失控和过程是否有能力;为过程提供一个早期报警系统,及时监控过程的情况,以防止废品的产生,减少对常规检验的依赖性,定时以观察以及系统的测量方法替代大量检测和验证工作。
⊙SPC实施意义可以使企业:◆降低成本◆降低不良率,减少返工和浪费◆提高劳动生产率◆提供核心竞争力◆赢得广泛客户⊙实施SPC两个阶段分析阶段:运用控制图、直方图、过程能力分析等使过程处于统计稳态,使过程能力足够。
监控阶段:运用控制图等监控过程⊙SPC的产生:工业革命以后,随着生产力的进一步发展,大规模生产的形成,如何控制大批量产品质量成为一个突出问题,单纯依靠事后检验的质量控制方法已不能适应当时经济发展的要求,必须改进质量管理方式。
于是,英、美等国开始着手研究用统计方法代替事后检验的质量控制方法。
1924年,美国的休哈特博士提出将3Sigma原理运用于生产过程当中,并发表了著名的“控制图法”,对过程变量进行控制,为统计质量管理奠定了理论和方法基础。
APQP(全英文版)
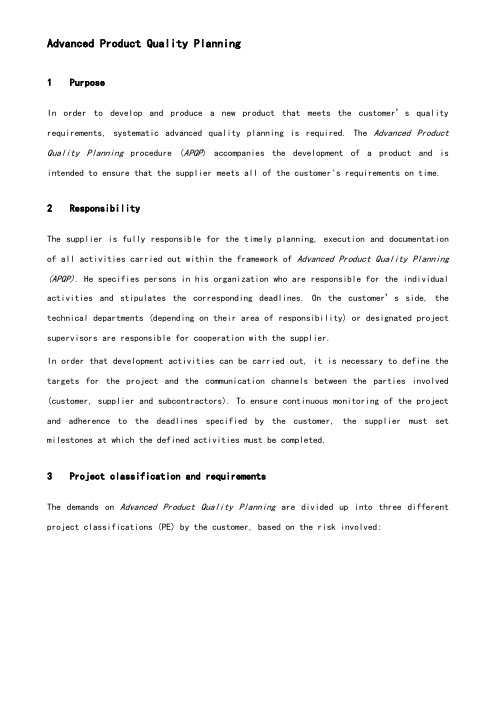
Advanced Product Quality Planning1PurposeIn order to develop and produce a new product that meets the customer’s quality requirements, systematic advanced quality planning is required. The Advanced Product Quality Planning procedure (APQP) accompanies the development of a product and is intended to ensure that the supplier meets all of the customer's requirements on time.2ResponsibilityThe supplier is fully responsible for the timely planning, execution and documentation of all activities carried out within the framework of Advanced Product Quality Planning (APQP). He specifies persons in his organization who are responsible for the individual activities and stipulates the corresponding deadlines. On the customer’s side, the technical departments (depending on their area of responsibility) or designated project supervisors are responsible for cooperation with the supplier.In order that development activities can be carried out, it is necessary to define the targets for the project and the communication channels between the parties involved (customer, supplier and subcontractors). To ensure continuous monitoring of the project and adherence to the deadlines specified by the customer, the supplier must set milestones at which the defined activities must be completed.3Project classification and requirementsThe demands on Advanced Product Quality Planning are divided up into three different project classifications (PE) by the customer, based on the risk involved:The supplier is informed of the project classification when the order is issued, at the latest. The customer may change the project classification during the course of the project as a result of unforeseen circumstances.Should any requirements change during the course of the project, all affected documents, e. g. Control Plan, FMEA, process flow diagram etc., must be changed accordingly.3.1 Project classification PE 1 – Increased riskThe supplier reports to the designated customer contact on his own responsibility using the APQP Status Report (see QAA Part 1, Appendix 3):No later than four weeks after order confirmationAt initial mass production samplingIn good time in the event of problems (APQP status of an element is "yellow “ or "red “)On additional dates which have been agreed between customer and supplier on an individual basis within the framework of the project work.The customer checks the progress of the project during project reviews held at either the supplier’s premises or the customer’s premises. Documents such as the Control Plan, FMEA, process flow chart etc. must be submitted as evidence.The customer releases the mass production process after carrying out a process review /audit at the supplier’s premises and, where necessary, at the subcontractor'sPE 1Increased risk PE 2 Medium risk Maximum requirementProject work in acc.with APQP methodAPQP Status Reports (increased number) Project Review(s)Medium requirement Project work in acc. with APQP method APQP Status Reports Project discussion(s), where required Standard requirement Simplified project work (e. g. time scheduling) Project discussion(s)where required PE 3 Standard productpremises. The date and scope of the on-site inspection are agreed between supplier and customer within the framework of the APQP.3.2Project classification PE 2 – Medium riskThe supplier reports to the designated customer contact on his own responsibility using the APQP Status Report (see QAA Part 1, Appendix 3):No later than four weeks after order confirmationAt initial mass production samplingIn good time in the event of problems (APQP status of an element is "yellow“ or "red“)The customer can check the progress of the project during project reviews held at either the supplier’s premises or the customer’s premises. Documents such as the Control Plan, FMEA etc. must be submitted as evidence.The customer can release the mass production process after carrying out a process review/audit at the supplier’s premises and, where necessary, at the subcontractor’s premises. The date and scope of the on-site inspection are agreed between supplier and customer within the framework of the APQP.3.3Project classification PE 3 – Standard productThe supplier reports to the designated customer contact on an informal basis (without the use of the APQP Status Report):In good time in the event of problemsThe customer can check the progress of the project during project discussions held at either the supplier’s premises or the customer's premises. Documents such as the Control Plan, FMEA etc. must be submitted as evidence.4Monitoring project progressThe supplier must monitor the progress of the project independently and report to the customer on the basis of the project classification.In order to plan the project and monitor dates, the target dates for the individual APQP elements must be entered in the APQP Status Report at the start of the project. The actual dates are entered to document the completion of the elements.If the date or individual elements are at risk of not being fulfilled, the supplier must introduce suitable corrective measures and monitor these on his own responsibility.A further course of action must be agreed jointly with the customer.The status of the individual elements must be indicated in the APQP Status Report using the following colour codes:Date / quality of the element are not at riskStart of production is not at riskDate / quality of the element are at riskStart of production is not at riskAppropriate corrective measures and responsible persons must be definedDate / quality of the element will not be observedStart of production is at riskAppropriate corrective measures and responsible persons must be definedand agreed with the customer5Product development processThe product development process (PEP) consists of consecutive phases that are separated by milestones. The current status of the project is reviewed when a milestone is reached. Additional activities must then be defined where necessary.The procedure proposed by the customer is shown in Appendix 1and represents the foundation for handling the project on a joint and structured basis.In specific cases, e. g. in the case of complex systems or at the request of the end customer, the customer can take the procedure VDA(Verband der Automobilindustrie) volume "New Part Maturity Level Assuredness" as a base and agree this with the supplier.6Applicable documentsApplicable appendices to S 296001Part 1(see / Suppliers / Quality / Production Material)Appendix 1 Product Development ProcessAppendix 2 APQP ElementsAppendix 3 APQP Status ReportAppendix 4 Feasibility ConfirmationAppendix 5 Capacity ConfirmationApplicable customer-specific standardS 102012-1 Classification of characteristics / Special required documentation。
- 1、下载文档前请自行甄别文档内容的完整性,平台不提供额外的编辑、内容补充、找答案等附加服务。
- 2、"仅部分预览"的文档,不可在线预览部分如存在完整性等问题,可反馈申请退款(可完整预览的文档不适用该条件!)。
- 3、如文档侵犯您的权益,请联系客服反馈,我们会尽快为您处理(人工客服工作时间:9:00-18:30)。
dd/mm/yy
07/11/20
dd/mm/yy
07/11/20
Hale Waihona Puke dd/mm/yy07/11/20
dd/mm/yy
SI
LR
07/11/20
dd/mm/yy
Team's Overall Rating of this Element ( G/Y/R )
31/08/04
G
05/02/14 05/06/27
G
<SI> <SC> <PH> <PA> (ST) <PR> (CP) <CC> <LR> <LS> (J1) <FS>
G G G G G G G G G G G G
2.
SI
PA
05/10/24
dd/mm/yy
3.
SI
PA
05/10/24
15/02/05
4.
SI
PA
05/10/24
15/02/05
5. 6. 7.
Copyright © 2003 Ford Motor Company All Rights Reserved Ver 3.2 August 2003 Macros Included by Ford Aust STA : 25-Oct-2004 by CSID: wgallop
Page 1 of 1 - Checklist: 8. Facilities, Tools, Gauges
If a particular "Expectations" item is not applicable, enter "N/A" in the Milestone/Team Event column. Additional lines have been left blank, and may be used by Teams to add additional Expectations. Light Aqua shaded cells are not required to be completed and are blocked from data entry. White Shaded cells under Milestones are available for APQP Status (G/Y/R) Entry. Item Ford Supplier Date Open Date Closed Issues / Comments / Risks Corrective Actions / Resolution Plan
SI SI SI
PA PA PA
05/10/24
dd/mm/yy
05/10/24
dd/mm/yy
05/10/24
dd/mm/yy
8.
SI
PA
05/10/24
15/02/05
9.
SI
PA
05/10/24
dd/mm/yy
10.
SI
PA
05/10/24
dd/mm/yy
11.
SI
PA
05/10/24
dd/mm/yy
Date Printed: 2016/12/1
9:20
12.
SI SI
PA CC
05/10/24
25/10/05
13.
07/06/12
dd/mm/yy
14.
SI
CC
07/06/12
dd/mm/yy
15. 16. 17. 18. 19. Other
Overall
SI SI SI SI SI
CC LR LR LR LR
07/06/12
dd/mm/yy
07/11/20
05/10/24 05/12/06 06/05/09 06/12/12
R
07/06/12
R
07/10/16 07/11/20 dd/mm/yy DD/MM/YY
Instructions: Overall Rating for the milestone is automatically determined. Enter open issues/comments/risks & resolution plans below. Rate this element based on the expectations that should be complete at the milestone (GREY shaded areas). Future Expectations should be considered when developing a Plan for completion of this Element.
Item
1.
Start
SI
Target
---
Program Supplier Timing Timing
05/02/14 dd/mm/yy
Expectations
There are NO major Facilities, Tooling, or Gauge issues/inhibitors, that will create an uncontainable risk now or in the foreseeable future. Define the appropriate cross-functional team and process to identify the Facility, Tooling, and Gauge requirements, necessary to manufacture the customer specified product at designated quantity and quality levels. (Ref. appropriate AIAG manuals) Identify Tooling and Equipment that will be required for the process with particular emphasis on SC/CC's (e.g. torque, welding, etc). Identify Test Equipment and Checking Fixtures that will be required for the process with particular emphasis on SC/CC's (e.g. torque, welding, etc) and develop a timing plan to support the vehicle program. Ensure Tooling and Equipment design has provided for a Flexible System, e.g. Cell Manufacturing, etc. Ensure that Tooling and Equipment design has provided for Synchronous Material Flow (SMF) and quick change over. Ensure that Tooling and Equipment design has provided for volume fluctuations. Ensure that Tooling and Equipment design incorporates the recommend actions from the Process FMEA. Ensure that Tooling and Equipment design has provided for mistake proofing. Obtain agreement of acceptance criteria for tooling and equipment between the customer and the supplier of the equipment. Obtain agreement of acceptance criteria for test and checking equipment between the customer and the supplier of the equipment. Establish gauge and test and checking equipment feasibility and accuracy. through Gauge R and R studies. Ensure that an FMEA has been conducted on all equipment and tooling that is new to the process. (Ref. appropriate AIAG manuals) Ensure capable gauges are available to run preliminary Process Capability Studies at the tooling and equipment supplier's facility. Conduct an initial preliminary Process Capability Study at the tooling and equipment supplier's facility, prior to shipment to the customer. (Ref. appropriate AIAG manuals) Conduct Preliminary Capability Studies at the customer's manufacturing facility. Develop a training plan that ensures training has been conducted on new/revised tooling and equipment. Ensure a preventative maintenance plan is complete for tooling and equipment. Ensure setup instructions for new tooling and equipment are complete and understandable to the user.