摆线切削
摆线走刀方式下高速铣削淬硬钢的切削力研究
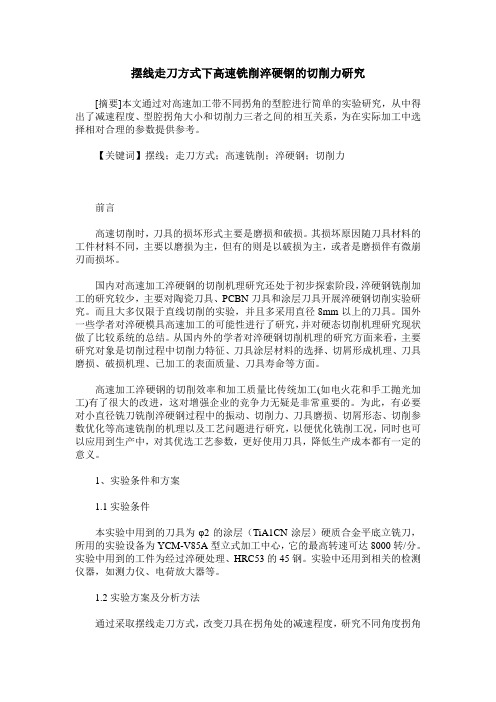
摆线走刀方式下高速铣削淬硬钢的切削力研究[摘要]本文通过对高速加工带不同拐角的型腔进行简单的实验研究,从中得出了减速程度、型腔拐角大小和切削力三者之间的相互关系,为在实际加工中选择相对合理的参数提供参考。
【关键词】摆线;走刀方式;高速铣削;淬硬钢;切削力前言高速切削时,刀具的损坏形式主要是磨损和破损。
其损坏原因随刀具材料的工件材料不同,主要以磨损为主,但有的则是以破损为主,或者是磨损伴有微崩刃而损坏。
国内对高速加工淬硬钢的切削机理研究还处于初步探索阶段,淬硬钢铣削加工的研究较少,主要对陶瓷刀具、PCBN刀具和涂层刀具开展淬硬钢切削实验研究。
而且大多仅限于直线切削的实验,并且多采用直径8mm以上的刀具。
国外一些学者对淬硬模具高速加工的可能性进行了研究,并对硬态切削机理研究现状做了比较系统的总结。
从国内外的学者对淬硬钢切削机理的研究方面来看,主要研究对象是切削过程中切削力特征、刀具涂层材料的选择、切屑形成机理、刀具磨损、破损机理、已加工的表面质量、刀具寿命等方面。
高速加工淬硬钢的切削效率和加工质量比传统加工(如电火花和手工抛光加工)有了很大的改进,这对增强企业的竞争力无疑是非常重要的。
为此,有必要对小直径铣刀铣削淬硬钢过程中的振动、切削力、刀具磨损、切屑形态、切削参数优化等高速铣削的机理以及工艺问题进行研究,以便优化铣削工况,同时也可以应用到生产中,对其优选工艺参数,更好使用刀具,降低生产成本都有一定的意义。
1、实验条件和方案1.1实验条件本实验中用到的刀具为φ2的涂层(TiA1CN涂层)硬质合金平底立铣刀,所用的实验设备为YCM-V85A型立式加工中心,它的最高转速可达8000转/分。
实验中用到的工件为经过淬硬处理、HRC53的45钢。
实验中还用到相关的检测仪器,如测力仪、电荷放大器等。
1.2实验方案及分析方法通过采取摆线走刀方式,改变刀具在拐角处的减速程度,研究不同角度拐角加工时的切削力和振动,进行拐角处的走刀方式和减速的参数优选,并得出刀具受力和振动随拐角角度的变化而变化的情况。
摆线加工
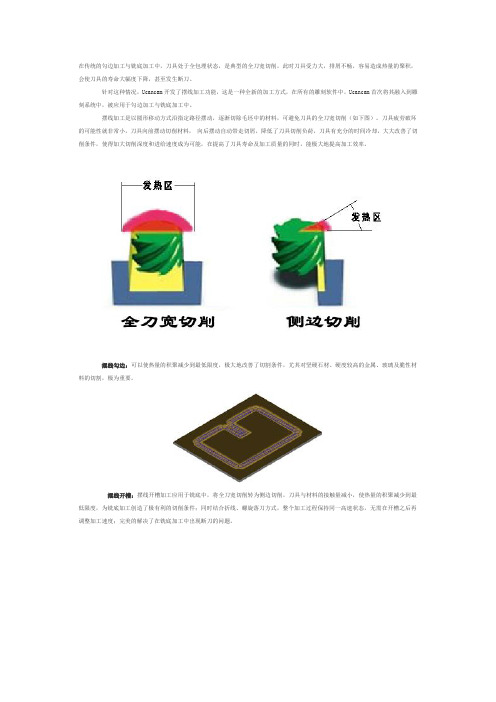
在传统的勾边加工与铣底加工中,刀具处于全包埋状态,是典型的全刀宽切削,此时刀具受力大,排屑不畅,容易造成热量的聚积,会使刀具的寿命大幅度下降,甚至发生断刀。
针对这种情况,Ucancam开发了摆线加工功能,这是一种全新的加工方式,在所有的雕刻软件中,Ucancam首次将其融入到雕刻系统中,被应用于勾边加工与铣底加工中。
摆线加工是以圆形移动方式沿指定路径摆动,逐渐切除毛坯中的材料,可避免刀具的全刀宽切削(如下图)。
刀具疲劳破坏的可能性就非常小,刀具向前摆动切削材料,向后摆动自动带走切屑,降低了刀具切削负荷,刀具有充分的时间冷却,大大改善了切削条件,使得加大切削深度和进给速度成为可能,在提高了刀具寿命及加工质量的同时,能极大地提高加工效率。
摆线勾边:可以使热量的积聚减少到最低限度,极大地改善了切割条件,尤其对坚硬石材、硬度较高的金属、玻璃及脆性材料的切割,极为重要。
摆线开槽:摆线开槽加工应用于铣底中,将全刀宽切削转为侧边切削,刀具与材料的接触量减小,使热量的积聚减少到最低限度,为铣底加工创造了极有利的切削条件;同时结合折线、螺旋落刀方式,整个加工过程保持同一高速状态,无需在开槽之后再调整加工速度;完美的解决了在铣底加工中出现断刀的问题。
ug摆线加工参数计算
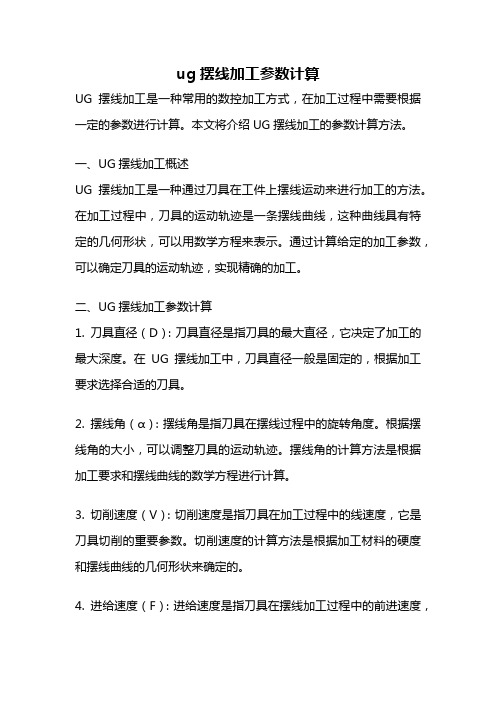
ug摆线加工参数计算UG摆线加工是一种常用的数控加工方式,在加工过程中需要根据一定的参数进行计算。
本文将介绍UG摆线加工的参数计算方法。
一、UG摆线加工概述UG摆线加工是一种通过刀具在工件上摆线运动来进行加工的方法。
在加工过程中,刀具的运动轨迹是一条摆线曲线,这种曲线具有特定的几何形状,可以用数学方程来表示。
通过计算给定的加工参数,可以确定刀具的运动轨迹,实现精确的加工。
二、UG摆线加工参数计算1. 刀具直径(D):刀具直径是指刀具的最大直径,它决定了加工的最大深度。
在UG摆线加工中,刀具直径一般是固定的,根据加工要求选择合适的刀具。
2. 摆线角(α):摆线角是指刀具在摆线过程中的旋转角度。
根据摆线角的大小,可以调整刀具的运动轨迹。
摆线角的计算方法是根据加工要求和摆线曲线的数学方程进行计算。
3. 切削速度(V):切削速度是指刀具在加工过程中的线速度,它是刀具切削的重要参数。
切削速度的计算方法是根据加工材料的硬度和摆线曲线的几何形状来确定的。
4. 进给速度(F):进给速度是指刀具在摆线加工过程中的前进速度,它决定了加工的进给量。
进给速度的计算方法是根据加工要求和摆线曲线的数学方程进行计算。
5. 加工深度(h):加工深度是指刀具在加工过程中的切削深度,它决定了加工的精度和加工时间。
加工深度的计算方法是根据加工要求和摆线曲线的数学方程进行计算。
6. 切削力(Fc):切削力是指刀具在切削过程中对工件的作用力,它是刀具切削的重要参数。
切削力的计算方法是根据切削速度、进给速度和刀具结构等参数进行计算。
三、UG摆线加工参数计算实例以一个具体的UG摆线加工实例来说明参数的计算方法。
假设需要加工一个直径为100mm的摆线曲线工件,刀具的直径为10mm,摆线角为60度,切削速度为200m/min,进给速度为0.1mm/r,加工深度为0.5mm。
根据给定的摆线角和工件直径,可以计算出摆线曲线的数学方程。
然后,根据切削速度和摆线曲线的几何形状,可以计算出刀具的线速度。
摆线齿轮磨削加工产生龟裂原因分析

比如现代钟表、 仪表中就广泛地采用
摆线齿轮, 而其变化形式——摆线针 轮传动也获得越来越广泛的应用。
某厂采 用 GC 1 制 造摆 线 齿 r5
接成网状 ,裂纹方向多与磨削方向
垂直 。
磨削裂纹的成因
磨削裂纹是多种应力的叠加,
轮,加工工艺流程为:备料一锻造
一
尤其是拉应力的产物。磨削裂纹与
6 左右 O 大干6 2
将同样的材料经过同样的锻造一球化退火一粗加工之后,采用 40 预 0 ̄ C 热,80 保温 1 n 5 ̄ C 5 油冷, mi 随后加热到 20 保温 6mn 2 ̄ C, 0 i空冷,其硬度达 到规定要求5 ~ 2 R , 8 6H C 经磨削加工后表面未出现龟裂现象 , 这说明适当提
显微组织分析
针对以上原因分析 , 我们沿裂纹齿廓上取样, 用金相显微镜进行微观组
织是马氏体和一定数量的残余奥氏
体,处于膨胀状态 ( 未经回火处理
织观察。金相组织为隐晶状马氏体+ 碳化物 + 残余奥氏体,奥氏体含量约为
1%, 5 超出规定的5 %~1%允许值 , 0 裂纹四周无脱碳现象, 表面组织与心部
磨削应力和热处理应力密切相关。
球化退火一机械加工一淬火、低
温 回火、喷丸 一磨 齿 ,要求热处 理
后硬度定为5 ~6 H C 其尺寸如 8 2R ,
图l 所示 。
1 . 磨削应力
磨削过程实质是磨粒切削刃切
削金属的过程 , 刃具 切削一样 , 与 被
磨削的金属也经受了弹性变形、塑
图 2
热处理工艺作了些改进 。第一 种方案: 将回火温度提高到20 保温时间6r n 2 ̄ C, 0 i。第二种方案:回火温度 a 不变 ,将保温时间延长到 10 i。 2m n
摆线齿轮加工方法
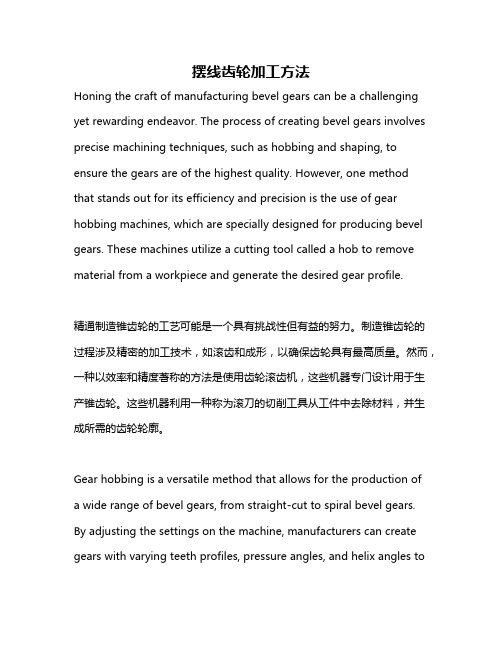
摆线齿轮加工方法Honing the craft of manufacturing bevel gears can be a challenging yet rewarding endeavor. The process of creating bevel gears involves precise machining techniques, such as hobbing and shaping, to ensure the gears are of the highest quality. However, one method that stands out for its efficiency and precision is the use of gear hobbing machines, which are specially designed for producing bevel gears. These machines utilize a cutting tool called a hob to remove material from a workpiece and generate the desired gear profile.精通制造锥齿轮的工艺可能是一个具有挑战性但有益的努力。
制造锥齿轮的过程涉及精密的加工技术,如滚齿和成形,以确保齿轮具有最高质量。
然而,一种以效率和精度著称的方法是使用齿轮滚齿机,这些机器专门设计用于生产锥齿轮。
这些机器利用一种称为滚刀的切削工具从工件中去除材料,并生成所需的齿轮轮廓。
Gear hobbing is a versatile method that allows for the production of a wide range of bevel gears, from straight-cut to spiral bevel gears. By adjusting the settings on the machine, manufacturers can create gears with varying teeth profiles, pressure angles, and helix angles tosuit different applications. This flexibility makes gear hobbing a popular choice for producing custom bevel gears that meet specific design requirements.齿轮滚齿是一种多功能方法,可以生产各种锥齿轮,从直齿到螺旋锥齿轮。
摆线铣削在硬零件槽铣加工中的应用技术
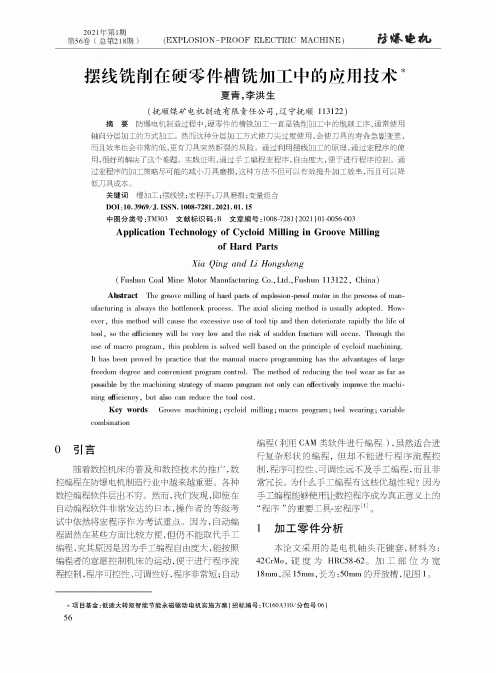
20211期第56卷(218期)(EXPLOSION-PROOF ELECTRIC MACHINE)摆线”削在硬零件槽”加工中的应用技术',李洪生(抚顺煤矿电机制造有限责任公司,辽宁抚顺113122)摘要防爆电机制造过程中,硬零件的槽铳加工一直是X中的序,通常使用轴向分的方。
然而这种分方式使刀尖过度使用,会使刀具的差,而且效率也会非常的低,更有刀具突然断裂的风险。
通过线的原理,通过序的使用,的决了这个。
实践证明,通过手工编程宏程序,自由度大,便于进行程序控制。
通过序的策略尽可能的减小刀损,这种方法不但可以有效提率,而且可以降低刀具成本。
关键词槽加工;摆线X;宏程序;刀具磨损;变量组合DO【:10.3969/J.ISSN.1008-7281.2021.01.15中图分类号:TM303文献标识码:B文章编号:1008-281(2021)01试056试03Application Technology of Cycloin Milling c Groove Millingof Hard PadsXia Qing and L'Hongsheng%Fushun Coat Mine Motor Manufacturing Co.,Ltd.,Fushun113122,China) Abttract Thegeoovemi e ingofhaed pa ets of e cp eosion-p eoof moto ein thepeoce s ofman-uOcturing is always the bottleneck process.The axiai slicing method is usually adopted.However,this method wili cause the excessive use of tooi tip and then deteriorate/pidly the life of tooe,sothee f iciencswi e beveeseowand theeisk ofsudden feactueewi e occue.Theough the use of macro program,this problem is solved weli based on the p/nciple of cycloid machining.It has been proved by practice that the manuai macro programming has the advantaaes of la/e Oeedom de-ree and convenient program controi.The method of reducing the tooi wear as far as po s ibeebsthemachiningstategsofmacop ogamnotonescan e f ectieeesimp oeethemachi-ninge f iciencs,butaesocan educethetooecost.Key wo U s Groove machining;cycloid milling;macro program;tooi wearing;va7ab1e combination0引言随着数控机床的和数控的,数控编程在防爆电机制造行业中越来越重要。
数学摆线在车床上进行多边形切削的应用
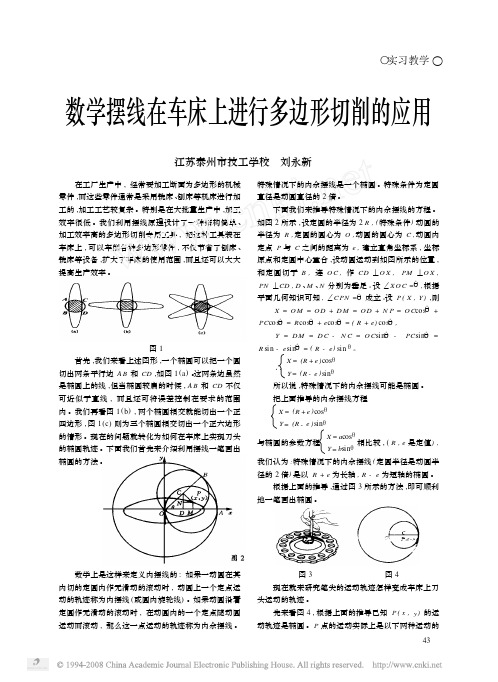
工件的转速比为 2 ∶1 ,所以当刀盘中心 A o 绕 O 按逆
时针方向转过θ角而到达 A 点时 ,刀尖 M o 在刀盘上
按顺时针方向转过 2θ角 , 到达点 M ( x , y) (即自转了
2θ角) 。根据图 6 可以看出
X = B A- CA = | O A | co sθ- | A M | co s ( 2θ-θ)
普通车床上车削多边形零件与车削普通的圆形零 件相比较 ,其共同点都是工件以一定的转速旋转 ,其不 同点是 ,在车削多边形零件时车刀不是固定不动的 ,而 是以 K ( = nc ∶no) 于工件的转速作相同方向的旋转 , 这就是多边形切削的主要特点 。
现在我们先以 K = 2 为例来说明普通车床车削多 边形零件的工作情况 。如图 5 所示 ,车刀固定在刀盘
取工件中心 O 为原点 , 射线 OA o 为 X 轴的半 轴 ,建立固定在工件上的直角坐标系 ,设刀盘和工件都 按顺时针方向转动 。我们把刀盘和工件之间的相对运 动看成工件固定不动 , 而刀盘中心以工件转速绕工件
44
中心反方向转动 (即按逆时针方向) , 同时刀盘还绕它
自己的中心转动 (按顺时针方向 ,如图 6) 。由于刀盘与
O 不在一条直线上 , 则车削出来的就是平行四边形 ,
图形的形状决定于车刀的多少及刀盘上各车刀之间的
角度和长短 。如果装三把车刀 (彼此间的夹角为 120°,
到刀盘中心的距离 r 均相等) , 那么工件就被车削成
近似的正六边形 (如图 1 中的 c 图) 。多边形切削实际
上就是在一定的条件下“以曲代直”, 用一种便于加工
特殊情况下的内余摆线是一个椭圆 。特殊条件为定圆
直径是动圆直径的 2 倍 。
下面我们来推导特殊情况下的内余摆线的方程 。
配速法处理摆线运动问题
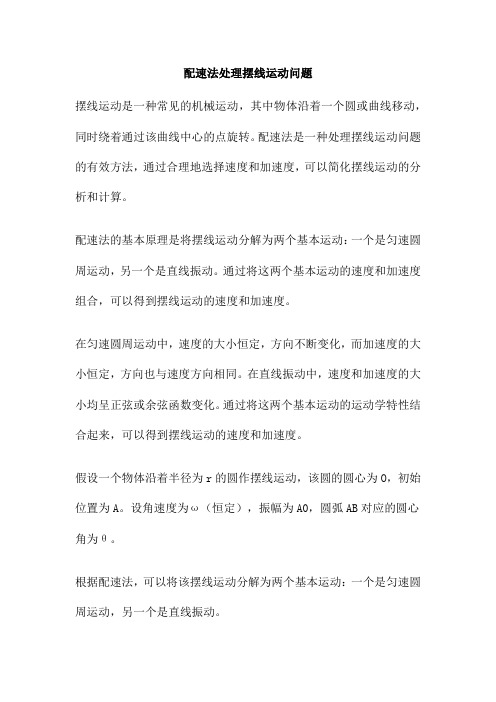
配速法处理摆线运动问题摆线运动是一种常见的机械运动,其中物体沿着一个圆或曲线移动,同时绕着通过该曲线中心的点旋转。
配速法是一种处理摆线运动问题的有效方法,通过合理地选择速度和加速度,可以简化摆线运动的分析和计算。
配速法的基本原理是将摆线运动分解为两个基本运动:一个是匀速圆周运动,另一个是直线振动。
通过将这两个基本运动的速度和加速度组合,可以得到摆线运动的速度和加速度。
在匀速圆周运动中,速度的大小恒定,方向不断变化,而加速度的大小恒定,方向也与速度方向相同。
在直线振动中,速度和加速度的大小均呈正弦或余弦函数变化。
通过将这两个基本运动的运动学特性结合起来,可以得到摆线运动的速度和加速度。
假设一个物体沿着半径为r的圆作摆线运动,该圆的圆心为O,初始位置为A。
设角速度为ω(恒定),振幅为A0,圆弧AB对应的圆心角为θ。
根据配速法,可以将该摆线运动分解为两个基本运动:一个是匀速圆周运动,另一个是直线振动。
在匀速圆周运动中,速度的大小恒定,方向不断变化。
因此,物体在圆弧AB上的速度大小为v=rωθ,方向沿圆弧切线方向。
加速度的大小恒定,方向也与速度方向相同,因此物体在圆弧AB上的加速度大小为a=rω²θ,方向沿圆弧切线方向。
在直线振动中,速度和加速度的大小均呈正弦或余弦函数变化。
因此,物体在圆弧AB上的速度大小为v=A0sin(ωt),方向沿直线OA方向。
加速度的大小为a=A0ω²cos(ωt),方向沿直线OA方向。
通过将这两个基本运动的运动学特性结合起来,可以得到物体在圆弧AB上的速度和加速度。
将角度θ代入得到:v=rωθ+A0sin[ω(t-θ/r)]a=rω²θ+A0ω²cos[ω(t-θ/r)]其中,第一项是匀速圆周运动的贡献,第二项是直线振动的贡献。
通过调整振幅A0和角速度ω可以得到不同的摆线运动形式。
配速法是一种处理摆线运动问题的有效方法,通过将摆线运动分解为匀速圆周运动和直线振动并组合它们的速度和加速度,可以得到摆线运动的速度和加速度。
摆线针原理
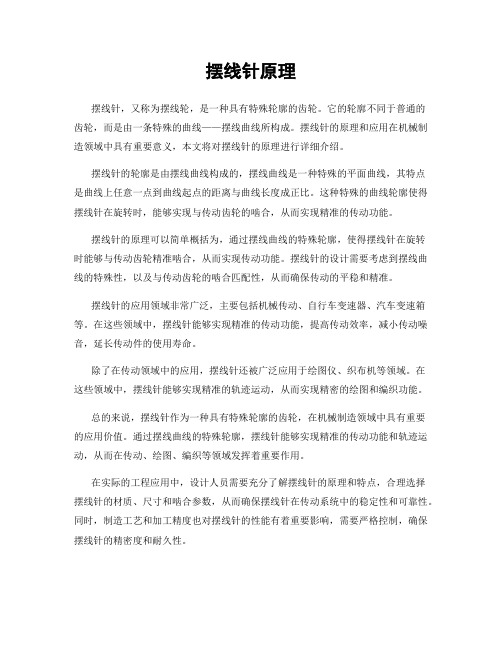
摆线针原理摆线针,又称为摆线轮,是一种具有特殊轮廓的齿轮。
它的轮廓不同于普通的齿轮,而是由一条特殊的曲线——摆线曲线所构成。
摆线针的原理和应用在机械制造领域中具有重要意义,本文将对摆线针的原理进行详细介绍。
摆线针的轮廓是由摆线曲线构成的,摆线曲线是一种特殊的平面曲线,其特点是曲线上任意一点到曲线起点的距离与曲线长度成正比。
这种特殊的曲线轮廓使得摆线针在旋转时,能够实现与传动齿轮的啮合,从而实现精准的传动功能。
摆线针的原理可以简单概括为,通过摆线曲线的特殊轮廓,使得摆线针在旋转时能够与传动齿轮精准啮合,从而实现传动功能。
摆线针的设计需要考虑到摆线曲线的特殊性,以及与传动齿轮的啮合匹配性,从而确保传动的平稳和精准。
摆线针的应用领域非常广泛,主要包括机械传动、自行车变速器、汽车变速箱等。
在这些领域中,摆线针能够实现精准的传动功能,提高传动效率,减小传动噪音,延长传动件的使用寿命。
除了在传动领域中的应用,摆线针还被广泛应用于绘图仪、织布机等领域。
在这些领域中,摆线针能够实现精准的轨迹运动,从而实现精密的绘图和编织功能。
总的来说,摆线针作为一种具有特殊轮廓的齿轮,在机械制造领域中具有重要的应用价值。
通过摆线曲线的特殊轮廓,摆线针能够实现精准的传动功能和轨迹运动,从而在传动、绘图、编织等领域发挥着重要作用。
在实际的工程应用中,设计人员需要充分了解摆线针的原理和特点,合理选择摆线针的材质、尺寸和啮合参数,从而确保摆线针在传动系统中的稳定性和可靠性。
同时,制造工艺和加工精度也对摆线针的性能有着重要影响,需要严格控制,确保摆线针的精密度和耐久性。
综上所述,摆线针作为一种特殊的齿轮,在机械制造领域中具有重要的应用价值。
通过摆线曲线的特殊轮廓,摆线针能够实现精准的传动功能和轨迹运动,为机械传动、绘图、编织等领域提供了重要的技术支持。
对摆线针的原理和应用进行深入研究,将有助于推动相关领域的技术进步和产品创新。
以退为进,看看摆线铣削是怎么解决航空制造中大麻烦的
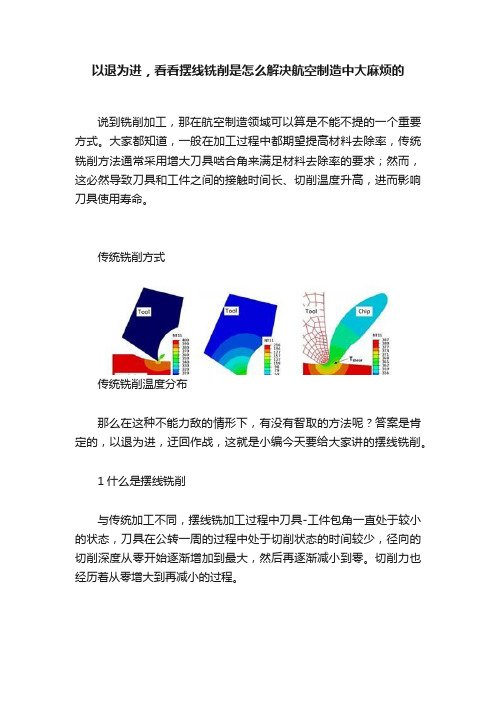
以退为进,看看摆线铣削是怎么解决航空制造中大麻烦的说到铣削加工,那在航空制造领域可以算是不能不提的一个重要方式。
大家都知道,一般在加工过程中都期望提高材料去除率,传统铣削方法通常采用增大刀具啮合角来满足材料去除率的要求;然而,这必然导致刀具和工件之间的接触时间长、切削温度升高,进而影响刀具使用寿命。
传统铣削方式传统铣削温度分布那么在这种不能力敌的情形下,有没有智取的方法呢?答案是肯定的,以退为进,迂回作战,这就是小编今天要给大家讲的摆线铣削。
1什么是摆线铣削与传统加工不同,摆线铣加工过程中刀具-工件包角一直处于较小的状态,刀具在公转一周的过程中处于切削状态的时间较少,径向的切削深度从零开始逐渐增加到最大,然后再逐渐减小到零。
切削力也经历着从零增大到再减小的过程。
摆线铣削加工(1)摆线铣削切削力的变化摆线铣削主要目的是在充分满足径向切深的情况下避免槽铣等全浸入式铣削,这对于减少刀具的磨损、延长刀具的使用寿命非常有利。
在摆线铣技术中,可以采用比常规铣削方法更大的轴向切深以提高材料去除率。
摆线铣削加工(2)摆线铣削与传统切削刀具运动对比2摆线铣削的原理摆线铣的轨迹形式通常采用的摆线刀具轨迹有两种模型:圆形模型和次摆线模型。
其中,圆形模型轨迹由圆和直线段组成,刀具公转运行轨迹为圆形,旋转一周后沿圆弧一侧的直线移动一个步长再进行公转。
这种加工轨迹的计算较为简单,但是会产生加速度的不连续。
圆形模型次摆线模型轨迹与圆形模型轨迹相比,主要差别在于刀具进给方向上的运动不单纯是直线运动。
这种摆线轨迹在切向和曲率上都是连续的,更容易满足数控机床的运动学要求。
一般常用的轨迹是次摆线模型轨迹的改进版,这种轨迹在次摆线轨迹的基础上缩短非切削部分的轨迹长度,采用直线进行连接,从而有助于提高加工效率。
次摆线模型3摆线铣削的优点摆线铣加工中,刀具沿摆线轨迹进行切削,可以适应各种加工余量的变化,从而降低加工余量突变对刀具的破坏;特别适合难加工材料的切削加工,如高温合金、钛合金、耐热不锈钢等材料;摆线铣加工技术可以采用较大的轴向切削深度,从而可以代替传统加工中需要进行多次分层的情况。
ug摆线加工增强
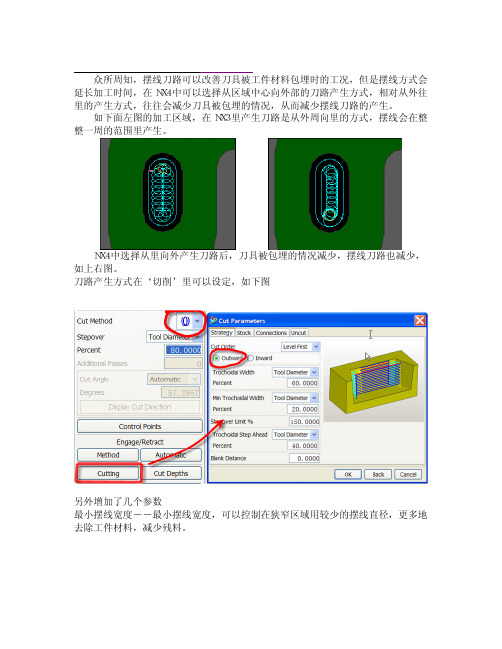
摆线加工增强
众所周知,摆线刀路可以改善刀具被工件材料包埋时的工况,但是摆线方式会延长加工时间,在NX4中可以选择从区域中心向外部的刀路产生方式,相对从外往里的产生方式,往往会减少刀具被包埋的情况,从而减少摆线刀路的产生。
如下面左图的加工区域,在NX3里产生刀路是从外周向里的方式,摆线会在整整一周的范围里产生。
NX4中选择从里向外产生刀路后,刀具被包埋的情况减少,摆线刀路也减少,如上右图。
刀路产生方式在‘切削’里可以设定,如下图
另外增加了几个参数
最小摆线宽度――最小摆线宽度,可以控制在狭窄区域用较少的摆线直径,更多地去除工件材料,减少残料。
步距限制%--这是一个百分数,介于100到200之间,它和Operation对话框上Stepover数值相乘的结果应该小于刀具直径尺寸。
当刀路的步距大于这个结果的时候,就产生摆线刀路。
这个极限百分数太大可能导致刀具被工件材料包埋,太小可能产生不必要的摆线刀路。
摆线向前――摆线前后相邻圆弧的中心距离,这个数值应该大于零。
。
- 1、下载文档前请自行甄别文档内容的完整性,平台不提供额外的编辑、内容补充、找答案等附加服务。
- 2、"仅部分预览"的文档,不可在线预览部分如存在完整性等问题,可反馈申请退款(可完整预览的文档不适用该条件!)。
- 3、如文档侵犯您的权益,请联系客服反馈,我们会尽快为您处理(人工客服工作时间:9:00-18:30)。
摆线切削是一种切削模式,此模式采用回环控制嵌入的刀具。
当需要限制过大的步距以防止刀具在完全嵌入切口时折断,且需要避免过量切削材料时,需使用此功能。
在进刀过程中的岛和部件之间、形成锐角的内拐角以及窄区域中,几乎总是会得到内嵌区域。
摆线切削可消除这些区域。
刀以小的回环切削模式来加工材料。
也就是说,刀在以回环切削模式移动的同时,也在旋转。
向外摆线切削是首选模式,它将圆形回环和流畅的跟随移动有效地组合在一起。
下面的示例对向外摆线切削进行了说明。
请注意回环切削模式。
将这种模式与常规切削方法进行比较,在后一种情况下,刀以直线刀轨向前移动,其各个侧面都被材料包围。
摆线切削模式
向外摆线切削
摆线切削的切削方向设置为向外,这种切削模式适合进行高速粗加工。
这种模式包括摆线铣削、拐角倒圆和其他拐角及嵌入区域处理,以确保达到指定的步距。
它是跟随部件和向内摆线切削模式的组合,可用于型腔铣、平面铣和面铣削操作。
向外摆线切削:
•通过引入摆线刀轨,防止刀具开槽或超出指定的步距限制。
•对尖角倒圆,使其成为圆滑的转角。
•通常从远离部件壁处开始,向部件壁方向行进。
•仅在必要时才引入摆线切削。
•提供可变摆线宽度,以便加工槽和尖角。
您指定一个最小宽度,软件根据需要逐步减小实际摆线宽度以避免过切。
注意:最小摆线宽度值必须大于0。
•
在典型的腔体加工例程中,刀具首次进入封闭型腔或沟槽时,就被完全嵌入进去了。
刀具在拐角处承受的载荷也将超出预期的。
金属切削率的峰值会导致刀具过早损坏。
这迫使机械师减小加工参数,进而导致生产力丧失。
恒定的金属切削率是高效加工的一个非常重要的准则。
经过优化的摆线刀轨可确保在整个刀轨中保持预期的金属切削率。
1. 选择型腔铣、平面铣或面铣削操作中主要参数页面上的摆线作为切削方法。
2. 接受默认参数,生成刀轨并检查结果。
3. 如有必要,可进行小的调整。
o在操作对话框中可调整步距值。
o调整摆线宽度、最小摆线宽度、步距限制%和摆线向前步长值(从切削参数对话框)。
a. 单击切削。
b. 单击策略。
所有相互作用的摆线参数有五个。
一开始最好使用默认参数,然后返回并一次对一个参数进行小的调整。
在更改其他参数之前查看每次调整的结果。
参考向外摆线选项,了解对每个参数的限制。
刀轨结果调整
环太宽。
使摆线宽度略微小些。
刀轨进入尖角的深度不够,或未进入狭窄区域。
使最小摆线宽度略微小些。
摆线切削不足。
使步距限制%略微小些。
摆线切削过量。
使步距限制%略微大些。
环相隔太远。
使摆线向前步长略微小些。
刀轨样本
向外摆线切削通常从远离部件壁处开始,向部件壁方向行进。
摆线设置(在切削参数对话框的策略选项卡上,前提是切削方向设置为向外时)如下:
选项最小
值
最大值默认值
摆线宽度
这就是在刀轨中心线处测量的摆线圆的直径。
0
无限制,但最好
不超过刀具直径
刀具直径
的60%
最小摆线宽度
这就是允许的摆线圆的最小直径。
使用可变宽度可加大在尖角和狭槽中对刀轨的控制。
> 0 < 摆线宽度刀具直径的20%
步距限制%
输入实际步距可超过在主操作页面上指定的步距的最大数
量。
摆线环可防止出现更大的步距。
100% 200% 150%
摆线向前步长
这就是摆线圆沿刀轨相互间隔的距离值。
> 0 <= 步距刀具直径的40%
注意:步距限制(计算的距离)必须小于刀具直径。
默认向外摆线参数基于默认的步距值的50%。
对于硬铣削,步距大约为10%。
推荐的摆线设置为:
•步距限制%= 150%
•摆线向前步长= 刀轨步距的80-100%。
•摆线宽度= 步距的1.5 倍。
对于简单槽,推荐值为:
•步距限制%= 150%
•摆线向前步长= 与刀轨步距相同。
•摆线宽度= 槽加工区域的宽度、刀轨步距。
摆线切削方向设置为向内后,刀按圆形回环模式移动,同时圆心沿轨迹(1) 移动。
在外观上看起来就像伸长的弹簧。
光顺的跟随模式(2) 向内切削区域。
这是原有的模式,已很少使用,因为向外摆线切削有更多的优点。
摆线宽度
输入摆线宽度(在切削参数对话框上,策略页面中)。
下面的摆线切削模式的宽度较小。
向内摆线切削模式
下面的摆线切削模式显示了更大的刀轨宽度:
摆线切削模式,大刀轨宽度对于向内摆线模式,步距必须小于刀轨宽度的三分之二。
向内模式的摆线宽度(2) 和步距(1)
最大移刀
最大移刀(切削参数对话框,连接页面)是在区域内移动时,沿部件表面以步距进给率移动时的最大允许移动距离。
如果移动距离大于此值,则系统会生成内部退刀以重新定位刀具。
最大移刀关闭时,NX 总是会尝试以步距进给率沿直线方向移动。
使用摆线切削后,其他的刀路都与光顺的跟随周边向内模式相似。
自动进刀移动
使用向内摆线切削时,沿线和沿外形进刀具有特殊的行为。
沿线将跟随摆线切削的中心,如下所示。
沿线进刀
沿外形在斜削进部件时将跟随摆线切削的所有环,如下图所示。
沿外形进刀
螺旋线进刀具有常见的行为,如下图所示。
螺旋进刀
拐角对话框
选择向内切削顺序(摆线)时,拐角和进给率控制对话框上的以下项可用:
•圆周进给率补偿
•拐角角度确定应该应用圆角加工的时间。
•角环确定是否应添加环。
•减速
对于摆线切削,不要使用圆角或拐角角度。
但确实要使用环。
区域
软件会在向内摆线模式不适合的位置(狭长的区域)改变切削类型。
使用跟随部件模式对要采用摆线模式的非常小的区域进行加工。