基于PLC的物料分拣控制系统的设计
基于PLC的物料分拣传送控制系统的设计与实现

基于PLC的物料分拣传送控制系统的设计与实现随着工业自动化的发展,PLC(可编程逻辑控制器)在物料分拣传送系统中的应用越来越广泛。
基于PLC的物料分拣传送控制系统可以实现对物料的高效分拣和传送,提高生产效率,降低人力成本,增强生产线的稳定性和可靠性。
本文将介绍基于PLC的物料分拣传送控制系统的设计与实现过程。
一、系统的需求分析在设计基于PLC的物料分拣传送控制系统之前,首先需要进行系统的需求分析。
系统需要具备以下几个基本功能:1. 物料分拣功能:根据既定的规则和逻辑,对到达传送线上的物料进行分拣,将不同种类的物料分别送往不同的目的地。
2. 物料传送功能:对已经分拣好的物料进行传送,确保物料能够按照预定的路线和速度送达目的地。
3. 系统监控功能:对整个系统进行实时监控,及时发现并处理异常情况,确保系统运行的稳定性和可靠性。
二、系统的设计与实现1. 系统的硬件设计系统的硬件设计包括传感器、执行机构、PLC等硬件设备的选型和布局。
传感器主要用于检测物料的到达、传送状态,执行机构用于对物料的分拣和传送,PLC则作为控制核心,负责对传感器和执行机构进行控制。
合理选型和布局能够有效提高系统的稳定性和可靠性。
2. 系统的软件设计系统的软件设计主要包括PLC编程、人机界面设计等内容。
PLC编程是系统的核心,通过对PLC进行程序设计,实现对传感器和执行机构的控制。
人机界面设计则是用户与系统交互的平台,需要具备直观、友好的操作界面,方便用户监控和控制系统运行状态。
3. 系统的通信设计在物料分拣传送控制系统中,各个设备之间需要进行通信,实现数据的传输和共享。
系统的通信设计是非常重要的一部分。
通过合理选择通信协议和网络拓扑结构,可以保证系统的数据传输稳定可靠。
三、系统的实施与调试系统的实施与调试是系统设计与实现的最后一步,通过此步骤可以验证系统设计的可行性和有效性。
在实施阶段,需要将系统的硬件设备进行安装和连接,并进行相关的调试和联调工作。
基于PLC的物料分拣控制系统设计

基于PLC的物料分拣控制系统设计一、引言随着工业自动化的发展和智能制造的推进,物料分拣是生产线上一个重要的环节。
物料分拣控制系统的设计和实施,将大大提高生产效率和质量。
本文将重点介绍基于PLC(可编程逻辑控制器)的物料分拣控制系统的设计。
二、系统需求分析物料分拣控制系统的设计旨在实现对多种不同物料的准确分拣和定位。
系统需要满足以下功能要求:1.可以识别并准确分辨多种不同物料的属性和特征,如尺寸、形状、颜色等。
2.可以通过PLC控制多个机械手和传送带等设备,实现物料的抓取和移动。
3.可以根据设定的优先级和规则,对物料进行分拣和分类,并且能够处理异常情况。
4.可以与其他系统集成,如上位机、仓储管理系统等,实现数据传输和互通。
三、系统设计方案基于上述需求,我们提出以下物料分拣控制系统的设计方案:1.硬件部分(1)传感器:利用视觉传感器和激光传感器等,获取物料的属性信息。
(2)执行器:采用电磁阀、气缸、伺服机械手等,实现物料的抓取和移动。
(3)PLC:选择合适的PLC进行控制,具备足够的输入输出点数、计算能力和通信功能。
(4)传送带:设置适当的传送带来实现物料的输送和分拣。
2.软件部分(1)PLC程序:通过Ladder Diagram或者Structured Text语言编写PLC程序,根据传感器信号来判断物料的属性,控制执行器对物料进行抓取和移动,实现分拣功能。
(2)图像处理算法:利用计算机视觉技术,对物料的图像进行处理和识别,提取出物料的特征信息。
(3)规则引擎:根据设定的规则和优先级,对物料进行分类和分拣。
(4)数据库:根据需要,设计数据库来存储物料的属性信息、分拣结果和异常情况等数据。
四、系统实施和测试在实施物料分拣控制系统之前,需要进行细致的系统测试和调试。
首先,通过对传感器和执行器的测试,验证其正常工作。
然后,编写PLC程序,并进行模拟仿真,验证分拣功能的正确性。
接下来,与其他系统进行集成测试,确保数据传输和互通的可靠性。
基于PLC的物料分拣传送控制系统的设计与实现

基于PLC的物料分拣传送控制系统的设计与实现1. 引言1.1 背景介绍物料分拣传送系统是现代生产线中必不可少的一部分,它可以有效地提高物料分拣的效率和准确性,降低人工成本和错误率。
传统的物料分拣传送系统多采用人工操作或简单的机械传送装置,存在着工作效率低、错误率高、适应性差等问题。
随着科技的不断发展和进步,基于PLC的物料分拣传送控制系统应运而生,它利用先进的电气控制技术和自动化技术,实现了传统系统无法实现的功能和优势。
基于PLC的物料分拣传送控制系统具有高性能、可靠性强、灵活性好等特点,可以根据不同的需求和物料特性进行个性化定制,能够满足现代生产线对物料分拣传送的高效、精准要求。
在自动化生产中,PLC已经成为控制系统的核心部件,广泛应用于各种领域,包括工业自动化、交通运输、能源设备等。
因此,研究基于PLC的物料分拣传送控制系统的设计与实现具有重要的意义和价值。
通过此研究,可以提高生产线的自动化水平,提升生产效率,降低成本,实现智能化生产,促进工业的发展和进步。
1.2 研究意义基于PLC的物料分拣传送控制系统能够实现对物料的高效分拣和传送,提高了生产效率和质量,降低了人力成本,使生产过程更加智能化。
这对于促进制造业转型升级,提高企业竞争力具有重要意义。
基于PLC的物料分拣传送控制系统能够实现物料的实时监测和数据采集,为生产过程提供了重要的数据支撑。
通过数据分析和处理,可以实现生产过程的优化和智能化管理,提高生产效率和质量。
基于PLC的物料分拣传送控制系统具有灵活性强、可靠性高、成本低等诸多优点,适用于各种规模和类型的制造企业。
研究基于PLC 的物料分拣传送控制系统的设计与实现,对于推动工业自动化发展,提高制造业水平,具有重要的理论和实践价值。
1.3 研究目的本文旨在设计和实现一种基于PLC的物料分拣传送控制系统,旨在解决传统物料分拣传送系统中存在的一些不足之处,提高物料分拣传送效率和准确性。
具体目的包括:1. 研究分析传统物料分拣传送系统的设计原理和工作流程,总结其优缺点;2. 提出基于PLC的物料分拣传送系统设计方案,探讨其适用性和优势;3. 进行PLC编程与控制逻辑设计,确保系统能够稳定运行并实现准确的物料分拣传送;4. 设计物料传送控制系统的硬件,选择合适的传感器、执行器等设备,保证系统可靠性和稳定性;5. 进行系统实验并对实验结果进行分析,评估系统的性能和可靠性;6. 评估设计与实现的效果,找出存在的问题并提出改进方向;7. 展望未来,探讨如何进一步完善基于PLC的物料分拣传送控制系统,提高其智能化和自动化水平。
基于PLC的物料分拣传送控制系统的设计与实现

3、调试与优化:在程序调试过程中,我们发现了一些问题,如传感器信号 干扰、机械臂运动不平滑等。针对这些问题,我们通过调整程序参数、优化机械 臂运动轨迹等方法进行了解决。
2、系统运行效果
经过调试后,系统运行稳定、可靠,实现了高效率、高精度的物料分拣传送。 在系统运行过程中,我们进行了可靠性测试和精度分析,结果如下:
基于PLC的物料分拣传送控制系统 的设计与实现
01 摘要
03 系统设计 05 结论
目录
02 引言 04 系统实现
摘要
本次演示主要介绍了基于PLC的物料分拣传送控制系统的设计与实现。在工 业生产中,物料分拣是一个重要的环节,涉及将物料根据种类、质量等因素进行 分类和传送。本次演示研究的控制系统主要涉及PLC(可编程逻辑控制器)的应 用,通过PLC与相关部件的连接和功能设计,实现了高效、准确的物料分拣传送 控制。
谢谢观看
结论
本次演示研究的基于PLC的物料分拣传送控制系统在设计、实现和应用方面 取得了显著的成果。通过PLC的应用,实现了系统的自动化控制和高效率、高精 度的物料分拣传送。在实际应用场景中,我们根据企业实际需求定制了个性化的 控制策略,进一步提高了系统的实用性和适应性。总结来说,基于PLC的物料分 拣传送控制系统为企业提供了高效、可靠的解决方案,具有广泛的应用前景和推 广价值。
1、可靠性测试:连续运行一个月,未出现任何故障或异常情况,证明系统 具有较高的可靠性;
2、精度分析:在测试过程中,我们对系统分拣传送的不同类型物料的准确 性进行了统计。结果表明,系统对不同类型物料的识别准确率均高于98%,证明 了系统具有较高的精度。
3、个性化控制策略实现
针对实际应用场景,我们实现了个性化的控制策略,满足不同需求的分拣传 送控制。例如,根据企业生产计划和工艺要求,我们定制了以下控制策略:
基于PLC控制的全自动物料分拣系统设计

基于PLC控制的全自动物料分拣系统设计目录1 引言 (1)2可编程序控制器 (2)2.1 PLC的发展历史 (2)2.2PLC的定义和特点 (2)2.3PLC的基本结构和工作原理 (3)3物料分拣系统的工作过程和设备选择 (4)3.1物料分拣系统的工作过程 (4)3.2物料分拣系统的设备选择 (4)4物料分拣系统的设计图 (10)4.1 PLC外部端子接线图 (10)4.2变频器端子接线图 (11)4.3步进梯形图 (12)4.4PLC梯形图 (13)5物料分拣系统的组态技术 (15)5.1组态技术概述 (15)5. 2组态技术功能和优点 (15)结论 (17)致谢 (18)参考文献 (19)第]页1引言自动分拣系统是指能够识别物品属性并对物品进行分类传输的自动系统。
自动分拣系统山传输供件同步导入装置、识别及控制系统、机械分拣机构及信息处理系统等组成。
自动分拣系统是二战后在美国、日本以及欧洲的大型物流中心广泛采用的一种分拣系统。
广泛应用在医药行业、生产制造业等行业。
国外的自动化程度很高,而在我国,曲于物流业起步晚,始于1980年代,自动化程度不高,大部分处于人工作业近期的市场兴起和技术发展始于1990年代。
一开始使用于机场行李处理和邮政处理,然后逐渐普及到其他行业。
近二十年来,特别是物流行业,随着经济发展,商品趋于短小轻薄。
分拣作业已成为工作的重要环节。
我国目前自动化程度不高,处于人工分拣阶段。
自动分拣的优点是能连续、大批量的分拣货物,分拣误差率低,分拣作业基本实现无人化。
虽然国内自动分拣系统使用还很少,但有关部门和企业正在做出努力。
自动分拣机是一个很成熟的产品,已成为当代物流技术发展的重要标志。
2可编程序控制器2.1 PLC的发展历史在可编程序控制器诞生之前•,是以继电器、接触器为主体的控制系统广泛应用于工业生产。
1968年,为适应生产需要,美国通用汽车公司提出一种新型工业控制器。
1969年, 美国数字设备公司研制出世界上第一台可编程逻辑控制器,U的是取代继电器,这打开了新的控制技术发展的大门。
基于PLC的物料分拣控制系统设计
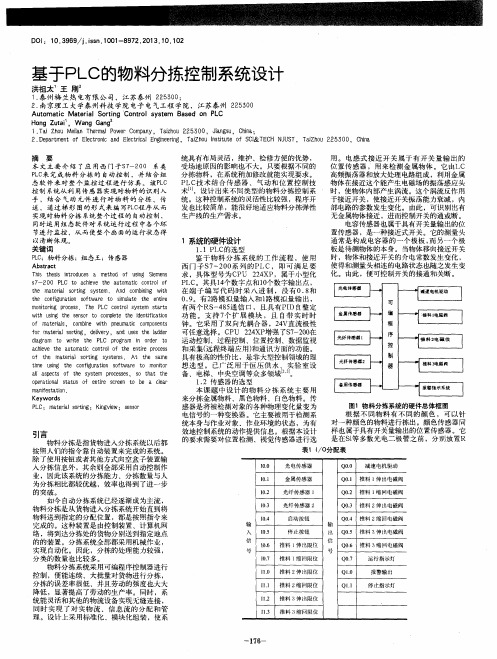
用 。 电 感 式 接 近 开 关 属 于 有 开 关 量 输 出 的 位 置传 感 器 ,用来 检 测 金 属物 体 。它 由LC 高频 振荡 器和 放大 处理 电路 组成 ,利 用金 属 物体 在接 近这 个能 产生 电磁 场 的振 荡感应 头 时 ,使物 体 内部产 生 涡流 。这 个涡流 反作 用 于接 近开 关 ,使接 近开 关振 荡能 力衰 减 ,内 部 电路 的参数 发生 变 化 。 由此 ,可 识 别出有 无 金属物 体接 近 ,进 而控 制开 关的 通或 断 。 电容传 感器也 属 于具 有开 关量输 出的位 置 传感 器 ,是 一种 接 近式 开关 。它 的测 量头 通 常是 构 成 电容 器的 一 个极 板 , 而 另一 个极 板是 待测 物体 的 本身 。 当物体 移 向接近 开关 时 ,物 体和接 近 开关 的介 电常 数发 生变 化 , 使 得和 测量 头相 连的 电路 状态 也随 之 发生 变 化 。 由此 ,便可控 制 开关 的接 通和 关断 。
Ab s t r a c t Th i s t h e s i s i n t r o d u c e s a me t h o d o f u s i n g s j e me n s
s 7 —2 0 O P L C t o a c h i e v e t h e a u t o m a t i c c o n t r o 』o f
D O I :1 0 . 3 9 6 9 / j . i s s n . 1 0 0 1 -8 9 7 2 . 2 0 1 3 . 1 0 . 1 0 2
基于P L C的物料分拣控制系统设计
洪祖太 王 刚 1 . 泰州梅 兰热 电有限公 司,江苏泰州 2 2 5 5 0 0 ; 2 . 南京理 工大学泰州科技 学院 电子 电气工程 学院,江苏泰州 2 2 5 3 0 0
基于PLC物料传送分拣控制系统设计
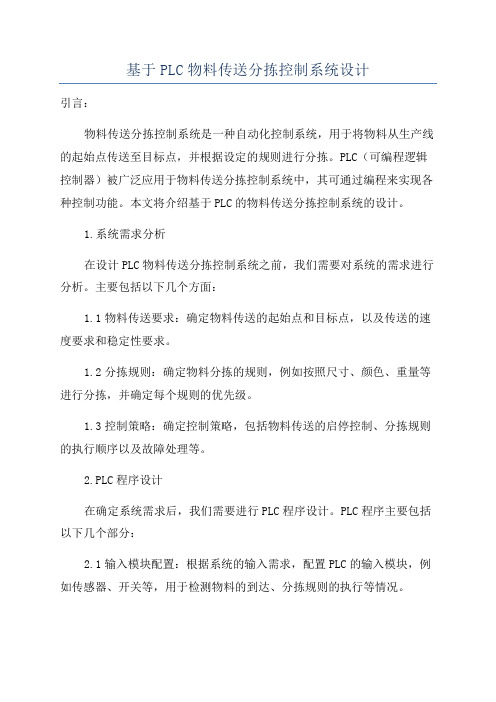
基于PLC物料传送分拣控制系统设计引言:物料传送分拣控制系统是一种自动化控制系统,用于将物料从生产线的起始点传送至目标点,并根据设定的规则进行分拣。
PLC(可编程逻辑控制器)被广泛应用于物料传送分拣控制系统中,其可通过编程来实现各种控制功能。
本文将介绍基于PLC的物料传送分拣控制系统的设计。
1.系统需求分析在设计PLC物料传送分拣控制系统之前,我们需要对系统的需求进行分析。
主要包括以下几个方面:1.1物料传送要求:确定物料传送的起始点和目标点,以及传送的速度要求和稳定性要求。
1.2分拣规则:确定物料分拣的规则,例如按照尺寸、颜色、重量等进行分拣,并确定每个规则的优先级。
1.3控制策略:确定控制策略,包括物料传送的启停控制、分拣规则的执行顺序以及故障处理等。
2.PLC程序设计在确定系统需求后,我们需要进行PLC程序设计。
PLC程序主要包括以下几个部分:2.1输入模块配置:根据系统的输入需求,配置PLC的输入模块,例如传感器、开关等,用于检测物料的到达、分拣规则的执行等情况。
2.2输出模块配置:根据系统的输出需求,配置PLC的输出模块,例如电机、气缸等,用于控制物料的传送和分拣。
2.3逻辑控制程序编写:根据系统需求和控制策略,编写逻辑控制程序。
程序主要包括启停控制、分拣规则的执行和故障处理等。
2.4HMI界面设计:为了方便系统操作和监视,可以设计人机界面(HMI),用于显示系统运行状态、设置参数等。
3.系统组态与调试在PLC程序设计完成后,需要进行系统组态与调试。
主要包括以下几个步骤:3.1确定输入输出映射关系:将PLC的输入输出模块与实际硬件设备进行映射,确保PLC能够正确读取传感器的信号和控制执行器的动作。
3.2参数设置与校准:根据实际情况,设置系统参数,例如物料传送速度、传感器的灵敏度等。
并进行校准,确保系统运行的准确性和稳定性。
3.3系统调试:进行系统的调试,测试物料传送、分拣和故障处理等功能的正确性和可靠性。
基于PLC的物料分拣传送控制系统的设计与实现

基于PLC的物料分拣传送控制系统的设计与实现一、引言随着现代工业的快速发展,物料分拣传送系统在生产中起着至关重要的作用。
目前,主流的物料分拣传送系统多采用了基于PLC(可编程逻辑控制器)的控制系统,它具有响应速度快、可靠性高、操作灵活等特点。
本文将介绍一个基于PLC的物料分拣传送控制系统的设计与实现过程。
二、系统设计1. 系统功能概述物料分拣传送控制系统主要用于对生产中的物料进行分拣和传送,以达到自动化生产的目的。
该系统包括物料传送带、传感器、执行机构和PLC控制器等组成部分。
2. 系统工作流程当物料被送上传送带时,传感器会检测到物料的到来并发送信号给PLC控制器。
PLC 控制器根据程序控制传送带的运行速度和方向,将物料送到指定的位置。
执行机构根据PLC控制器的指令,将物料分拣到不同的位置。
3. 系统硬件设计在硬件设计方面,需要选择适合的传感器、执行机构和传送带,并进行合理的布置和连接。
还需要选择适合的PLC控制器,并设计相应的电路连接。
4. 系统软件设计在软件设计方面,需要编写PLC程序,包括物料传送控制程序和物料分拣程序。
这些程序需要考虑传送带的运行速度、传感器的信号处理、执行机构的控制等方面,以实现物料的精准传送和分拣。
三、系统实现1. 硬件的组装和连接需要按照系统设计方案组装和连接好传感器、执行机构、传送带和PLC控制器等硬件设备,确保它们之间的良好连接和协调。
2. 软件的编写和调试根据系统设计方案编写PLC程序,并将其下载到PLC控制器中。
然后进行软件的调试,验证程序是否能够准确地控制传送带的运行和物料的分拣,并对程序进行优化和修改。
3. 系统的测试和运行对整个系统进行测试和调试,验证系统的稳定性和可靠性。
在确认系统可以正常运行后,即可投入生产使用。
四、系统优化在系统实现过程中,可能会遇到一些问题和挑战,需要对系统进行优化。
可能会存在传感器信号不稳定、执行机构控制不准确、传送带运行不稳定等问题。
基于PLC控制的物料自动检测与分拣系统设计共3篇

基于PLC控制的物料自动检测与分拣系统设计共3篇基于PLC控制的物料自动检测与分拣系统设计1基于PLC控制的物料自动检测与分拣系统设计随着工业化的不断推进和自动化技术的不断发展,物料自动检测与分拣系统在生产线上扮演着重要的角色。
物料自动检测与分拣系统一方面能够提高生产效率,另一方面还能保证产品的质量和安全性。
因此,为了满足企业生产的需求,本文将设计一种基于PLC控制的物料自动检测与分拣系统。
PLC即可编程逻辑控制器,是一种专业用于工业自动化控制的电子设备。
在设计物料自动检测与分拣系统时,经常使用PLC 控制其动作。
本文所设计的物料自动检测与分拣系统主要包括四大模块:传输模块、检测模块、分拣模块和控制模块。
首先,传输模块是将物料从一处到另一处的模块。
它包括物料传送带和物料传输驱动电机。
传输带通过驱动电机,将物料从输入端传到输出端。
因为传送带速度通常是固定不变的,所以驱动电机转速是最关键的因素,应该根据生产需要进行合理的调节。
其次,检测模块是用于检测物料所要包括的模块,可以检测物料的体积、形状、颜色等。
本系统所采用的检测装备是红外光电开关,这种检测装备具有反应快、稳定性高等优点。
第三,分拣模块是将合格和不合格的物料分别分类,以便于通过后续生产的加工。
在本系统中,合格品和不合格品分别通过不同的出口分拣出来。
当物料通过检测装备后,PLC控制系统将继续判断它是属于合格品还是不合格的品,由此决定其去向。
最后,PLC控制模块将控制整个系统的动作。
PLC通过将信号发送给传输模块、检测模块和分拣模块,协调这些模块中的行动以实现所需的功能。
PLC还能通过问题诊断和警报功能来警告操作人员有问题出现。
综上所述,本文设计了一个基于PLC控制的物料自动检测与分拣系统。
该系统具有高速、高效、高质的特点,能够提高生产效率和产品质量,同时也降低了公司的成本和投资风险。
该系统的应用将更好地满足生产需求,促进了企业的发展本文设计的基于PLC控制的物料自动检测与分拣系统具有高速、高效、高质的特点,能够提高生产效率和产品质量,同时也降低了公司的成本和投资风险。
基于PLC的物料分拣机械手自动化控制系统设计

基于PLC的物料分拣机械手自动化控制系统设计物料分拣是工业生产过程中常见的自动化操作之一,而机械手作为自动化设备的核心部件之一,在物料分拣中发挥着重要的作用。
本文将针对基于PLC的物料分拣机械手自动化控制系统的设计进行详细说明。
1.系统概述2.系统设计(1)PLC控制器选择:根据系统需求选择适合的PLC控制器,一般要求具有足够的输入输出端口以及较高的运算速度。
常见的PLC控制器有西门子、施耐德、欧姆龙等。
(2)机械手选择:根据物料的类型和分拣要求选择适合的机械手。
常见的机械手有直线式机械手、旋转式机械手等,可以根据需要组合使用。
(3)传感器选择:根据物料的特性和分拣要求选择适合的传感器。
常见的传感器有光电传感器、接近传感器、压力传感器等,用于检测物料的位置、重量、形状等参数。
(4)执行器选择:根据物料分拣的方式选择适合的执行器。
常见的执行器有气缸、电机、伺服驱动器等,用于实现机械手的运动。
3.系统实现(1)输入模块设置:将传感器的信号通过输入模块连接到PLC控制器的输入端口,实现对物料位置和状态的检测。
(2)处理模块编程:根据物料分拣的逻辑和要求进行PLC控制器的编程,包括控制机械手的运动、执行器的操作以及与传感器的通信等。
(3)输出模块设置:将PLC控制器的输出信号通过输出模块连接到执行器,实现对机械手和执行器的控制。
(4)系统调试和运行:将整个系统进行组装和调试,确保各个部件能够正常工作,并进行系统联调测试,验证系统的可靠性和稳定性。
4.系统优化在系统运行过程中,可以根据实际需求对系统进行优化和改进。
例如,可以通过增加传感器的数量和种类来提高物料分拣的准确性和效率;可以调整机械手的运动轨迹和速度,以适应不同的物料类型和分拣要求;可以改进控制算法,提高系统的响应速度和精度等。
总结:基于PLC的物料分拣机械手自动化控制系统的设计涉及到PLC控制器的选择、机械手的选择、传感器的选择、执行器的选择,以及输入模块设置、处理模块编程、输出模块设置等内容。
基于PLC的物料分拣传送控制系统的设计与实现
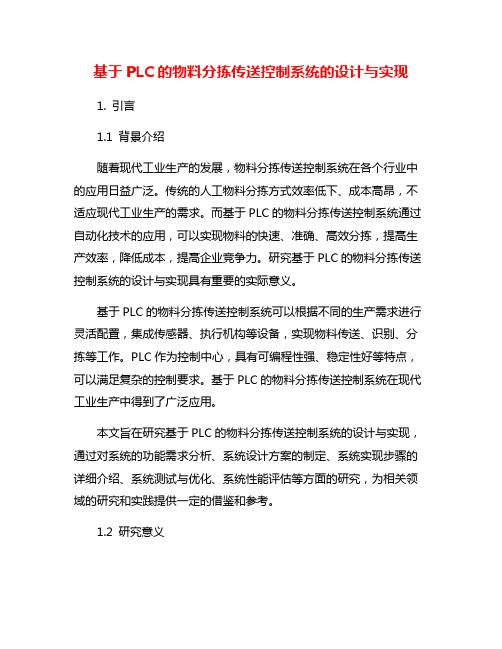
基于PLC的物料分拣传送控制系统的设计与实现1. 引言1.1 背景介绍随着现代工业生产的发展,物料分拣传送控制系统在各个行业中的应用日益广泛。
传统的人工物料分拣方式效率低下、成本高昂,不适应现代工业生产的需求。
而基于PLC的物料分拣传送控制系统通过自动化技术的应用,可以实现物料的快速、准确、高效分拣,提高生产效率,降低成本,提高企业竞争力。
研究基于PLC的物料分拣传送控制系统的设计与实现具有重要的实际意义。
基于PLC的物料分拣传送控制系统可以根据不同的生产需求进行灵活配置,集成传感器、执行机构等设备,实现物料传送、识别、分拣等工作。
PLC作为控制中心,具有可编程性强、稳定性好等特点,可以满足复杂的控制要求。
基于PLC的物料分拣传送控制系统在现代工业生产中得到了广泛应用。
本文旨在研究基于PLC的物料分拣传送控制系统的设计与实现,通过对系统的功能需求分析、系统设计方案的制定、系统实现步骤的详细介绍、系统测试与优化、系统性能评估等方面的研究,为相关领域的研究和实践提供一定的借鉴和参考。
1.2 研究意义物料分拣传送控制系统是现代生产线中重要的自动化设备之一,通过使用PLC作为核心控制器,可以实现对物料的高效分拣和传送,提高生产效率和降低人力成本。
在当前社会经济发展的背景下,工业自动化已成为提升企业竞争力的重要手段,而物料分拣传送控制系统作为其中的重要组成部分,具有重要的研究意义。
基于PLC的物料分拣传送控制系统可以实现物料分拣的自动化处理,能够快速、准确地对物料进行分类和分拣,避免了传统人工分拣中可能出现的误差和低效率问题,大大提高了生产效率。
该系统可以实现物料的自动传送,减少了人力搬运的劳动强度,提高了作业效率,减少了劳动成本,同时也提升了生产线的运行稳定性和可靠性。
基于PLC的物料分拣传送控制系统还具有较强的智能化和灵活性,能够根据不同的生产需求自由调整工作参数和作业流程,更好地适应不同生产场景的需求。
基于plc的物料分拣控制系统设计毕业设计

基于plc的物料分拣控制系统设计毕业设计
基于PLC的物料分拣控制系统是一种采用电气和电子设备实现物料自动分拣的控制系统。
它可以自动检测物料输入并将物料精准的分配到各类取料位置,实现省时省力的物料分拣服务。
基于PLC的物料分拣控制系统通常由一系列自动控制装置、传动机构和物料输送装置组成。
基于PLC的物料分拣控制系统主要包括:
一、控制系统
控制系统是整个物料分拣控制系统的核心部件,负责监控物料进出口、检测分拣位置物料变动情况等信息,对分拣装置进行自动控制。
它一般采用PLC控制系统,由控制器、I/O卡、传感器、显示屏和其他辅助设备组成。
二、传动机构
传动机构一般采用油膜离合器、减速机、电机及马达等设备,负责调节物料取料及分拣的位置,使物料可以更准确的定位。
三、物料输送装置
物料输送装置是基于PLC物料分拣控制系统的重要组成部件,一般采用输送带、滚筒等输送装置将物料从入口进行持续输送,取料时由传动机构实现各类物料取料位置的调节,从而实现物料的自动分拣。
基于PLC变频控制的物料分拣控制系统设计

3、变频器的认识、选择、安装、 设置
变频器是调节电机转速的重要设备,需根据实际需求选择合适的型号和规格。 在安装变频器时,应将其安装在干燥、通风良好、无尘的环境中,以确保其稳定 运行。设置变频器时,需要根据电机的实际负载和工艺要求进行参数设置,以确 保电机在最佳状态下运行。
4、相关传感器的选择、安装、 使用
三、系统设计
1、硬件设计
(1)电气控制系统:包括电源模块、输入模块、输出模块和通信模块。电 源模块为整个系统提供稳定的电源;输入模块接收操作人员输入的信号和传感器 采集的信号;输出模块根据PLC的处理结果控制变频器和执行机构;通信模块则 实现PLC与其他设备的数据交换。
(2)传感器选择:根据分拣要求选择相应的传感器,如重量传感器、颜色 传感器、尺寸传感器等,对物料进行检测和识别。
6、安全保护装置及其作用
安全保护装置是保障系统运行安全的重要设备,一般包括急停按钮、安全门、 光电保护等。这些装置可以有效地避免意外伤害和设备损坏,提高系统的安全性 能。在选择和使用安全保护装置时,需要根据实际情况进行选择和配置,以确保 其与系统整体的安全性相匹配。
系统运行
1、空载试运行
在系统空载试运行前,需要检查各设备连接是否正常,PLC程序是否正确等。 然后进行空载试运行,检查各设备是否正常运行,是否有异常噪音或发热等现象。 如有问题应及时排除,以确保系统正常运行。
(3)传感器数据处理:对传感器采集的信号进行处理和分析,识别物料类 型和位置。
四、系统优化
为提高系统的稳定性和可靠性,可采取以下优化措施:
1、采用高性能PLC:选择具有高速处理能力和稳定性的PLC,提高系统的响 应速度和抗干扰能力。
2、优化变频器调速:根据实际情况调整变频器的频率和电流极限值,实现 更精确的调速控制。
基于PLC物料传送分拣控制系统设计
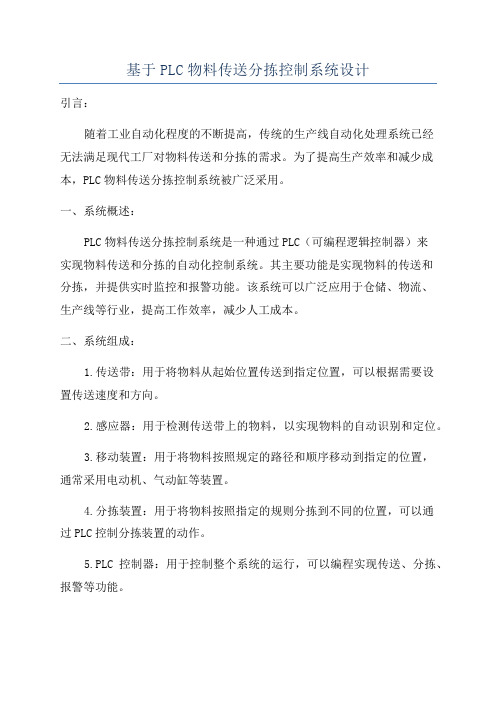
基于PLC物料传送分拣控制系统设计引言:随着工业自动化程度的不断提高,传统的生产线自动化处理系统已经无法满足现代工厂对物料传送和分拣的需求。
为了提高生产效率和减少成本,PLC物料传送分拣控制系统被广泛采用。
一、系统概述:PLC物料传送分拣控制系统是一种通过PLC(可编程逻辑控制器)来实现物料传送和分拣的自动化控制系统。
其主要功能是实现物料的传送和分拣,并提供实时监控和报警功能。
该系统可以广泛应用于仓储、物流、生产线等行业,提高工作效率,减少人工成本。
二、系统组成:1.传送带:用于将物料从起始位置传送到指定位置,可以根据需要设置传送速度和方向。
2.感应器:用于检测传送带上的物料,以实现物料的自动识别和定位。
3.移动装置:用于将物料按照规定的路径和顺序移动到指定的位置,通常采用电动机、气动缸等装置。
4.分拣装置:用于将物料按照指定的规则分拣到不同的位置,可以通过PLC控制分拣装置的动作。
5.PLC控制器:用于控制整个系统的运行,可以编程实现传送、分拣、报警等功能。
6.人机界面:用于操作和监控整个系统的运行状态,通常使用触摸屏、键盘等设备。
7.通信模块:用于与其他设备或上位机进行通信,可以实现数据传输和远程控制功能。
三、系统工作流程:1.启动PLC,接通传送带电源,传送带开始运行。
2.传送带上的物料经过感应器,系统开始检测物料的属性和位置。
3.PLC根据检测结果判断物料的目的地和排序规则。
4.PLC控制移动装置按照指定路径将物料移动到相应的位置。
5.分拣装置根据PLC的控制信号对物料进行分拣,将物料送到不同的位置。
6.PLC通过与人机界面的交互实现对整个系统的监控和控制。
7.当发生异常情况时,系统会进行相应的报警并停止运行。
四、系统特点:1.灵活性:PLC控制器可以通过编程来实现多种传送和分拣规则,可以根据实际需求进行调整和修改。
2.可靠性:PLC控制器具有较高的稳定性和可靠性,能够长时间稳定运行,减少系统故障的发生。
基于plc控制的物料分拣系统设计

基于plc控制的物料分拣系统设计物料分拣系统是一种自动化的系统,用于将不同类型的物料按照一定的规则进行分类和分拣。
基于PLC控制的物料分拣系统设计可以实现高效、准确地完成物料分拣任务。
首先,基于PLC控制的物料分拣系统需要通过传感器对待分拣的物料进行检测。
常用的传感器包括光电传感器、压力传感器和接近开关等。
通过传感器可以实时地获取物料的相关属性,如形状、大小和重量等。
其次,PLC控制器负责根据传感器的反馈信号来计算和判断物料的类型,并控制执行机构进行相应的分拣操作。
常用的执行机构包括电磁阀、气缸和电机等。
根据物料的性质和分拣规则的不同,可以选择合适的执行机构来实现分拣操作。
另外,为了提高分拣的速度和准确度,可以将物料分拣系统划分为多个工作区域,每个工作区域负责分拣一类物料。
这样可以同时进行多个物料的分拣,提高系统的效率。
同时,在设计分拣规则时,可以根据物料的属性和客户需求来设定优先级,以确保关键物料的优先分拣。
此外,为了确保系统的安全性和可靠性,可以在物料分拣系统中添加一些安全措施。
例如,设置急停开关、安全光幕和保护罩等设备,以防止工作人员或物料在操作过程中受伤或受损。
在系统设计过程中,还应考虑到系统的扩展性和可维护性。
通过合理的模块化设计,可以方便地对系统进行升级和维护。
同时,还可以通过合理的布线和避免过长的传输距离来降低系统的故障率。
总之,基于PLC控制的物料分拣系统设计需要考虑物料的检测、控制和执行等方面,以及系统的安全性、效率和扩展性等因素。
通过合理的设计和使用合适的设备,可以实现高效、准确地完成物料分拣任务。
基于PLC的物料分拣控制系统的设计

基于PLC的物料分拣控制系统的设计一、系统设计要点1.系统结构:基于PLC的物料分拣控制系统由物料传输系统、物料识别系统、分拣装置和PLC控制器组成。
2.物料传输系统:物料传输系统负责将待分拣物料从入口输送到分拣装置,并通过传感器确定物料当前位置和数量。
3.物料识别系统:物料识别系统采用视觉识别技术,通过摄像头获取物料图像,并通过图像处理算法进行特征提取和分类,以判断物料的种类和位置。
4.分拣装置:分拣装置根据物料识别结果,将物料分拣到相应的出口,可以采用气动执行机构、电磁执行机构等。
5.PLC控制器:PLC控制器是整个系统的核心,负责监控物料传输系统和物料识别系统的状态,根据识别结果控制分拣装置的动作,并与外部设备进行通信。
二、系统实施步骤1.确定需求:根据实际应用环境和需求,确定系统的功能要求、性能指标和工作流程。
2.确定硬件设备:选择适合的PLC型号和外围设备,如传感器、摄像头、执行机构等,并根据系统需求进行配置和连接。
3.编写程序:根据系统需求和设计要点,编写PLC程序,包括物料传输系统的控制逻辑、物料识别系统的图像处理算法和分拣装置的动作控制。
4.联调测试:将硬件设备和编写好的程序进行联调测试,验证系统的功能和性能指标。
根据测试结果进行调整和优化。
5.安装调试:将硬件设备和PLC控制器进行安装并进行调试,确保系统在实际工作环境下的正常运行。
6.系统应用:将系统投入实际应用,进行生产试运行和性能测试,根据实际需要进行调整和改进。
7.系统维护:定期对系统进行维护和检修,确保系统的稳定运行和长期可靠性。
三、总结基于PLC的物料分拣控制系统能够实现对物料的自动化分拣和转运,提高生产效率和准确性。
系统的设计要点包括系统结构、物料传输系统、物料识别系统、分拣装置和PLC控制器等。
系统的实施步骤包括确定需求、确定硬件设备、编写程序、联调测试、安装调试、系统应用和系统维护等。
通过合理的设计和实施,基于PLC的物料分拣控制系统可以在实际应用中取得良好的效果。
基于PLC的物料分拣传送控制系统的设计与实现

基于PLC的物料分拣传送控制系统的设计与实现1.系统架构设计系统采用四种传感器进行物料检测:激光传感器、红外线传感器、超声波传感器、触控传感器。
物料分拣传送控制系统由以下几部分组成:输入输出模块(I/O模块)、PLC、人机界面(HMI)、控制执行单元(CEU)。
其中,I/O模块用于采集设备控制状态;PLC 用于逻辑控制,实现物料分拣操作;HMI用于监视系统运行状态,显示控制信息;CEU用于执行PLC控制指令,实现物料传送操作。
2.系统实现2.1 硬件部分实现为实现物料分拣传送控制系统,需要选择相应的硬件设备进行关联搭建。
I/O模块选用通用型或专业型;PLC选用高效稳定的型号,配合编程软件实现编程流程;HMI选用触摸屏或触摸面板,对系统运行进行监视;CEU选用一体化或分布式模块,完成实际操作。
软件部分主要包括PLC程序的编写和HMI界面的设计,以及程序测试和调试等操作。
PLC程序主要指物料分拣控制程序,根据实际输入信号的不同来控制输出信号的类别,实现自动物料分拣;HMI界面主要负责监视系统运行状态,显示控制信息,用户可以通过界面对系统进行监测和控制。
3.系统测试对系统完成编写之后,需要对整个系统进行全面的测试,以保证系统运行正常。
测试主要包括软件测试和硬件测试。
软件测试主要包括逻辑错误、数值溢出等方面的测试,而硬件测试则主要是针对每个硬件模块进行测试,保证硬件的良好工作。
4.系统应用智能制造和信息化已经成为未来工业发展的主要方向之一,在此背景下,PLC技术的应用将会越来越广泛。
物料分拣传送控制系统能够实现物料自动分拣传送的目的,提高工作效率。
在物流、生产制造等领域得到了广泛应用。
总之,本文介绍了基于PLC的物料分拣传送控制系统的设计与实现。
通过对系统模块的选择、软件程序的编写和测试,实现了物料的自动分拣传送,可方便地应用于生产实践当中。
基于PLC的物料分拣控制系统的设计

PLC技术应用项目说明书产品自动分拣计数控制系统的设计学院机械工程学院专业机械电子工程班级 2012级机电1班学生姓名李钊指导老师王蕊2015 年 10 月 30 日课程设计任务书兹发给 2012级机电1 班学生李钊课程设计任务书,内容如下:1.设计题目:产品自动分拣计数控制系统的设计2.应完成的项目:(1)选题的背景和意义;(2)明确设计任务,拟定总体设计方案(有机械结构的要进行结构设计,三维软件建模);(3)硬件设计,传感器、PLC(和电机)选型,设计信号采集、转换电路,画出PLC端口分配图、接线控制端子连接图;(4)软件设计,编写控制程序流程图(或重要程序),设计人机界面;(5)课程设计说明书1份。
3.参考资料以及说明:(1)金发庆.传感器技术与应用(第二版)[M].北京:机械工业出版社,2004 (2)钟肇新.可编程控制器原理及应用[M].广州:华南理工大学出版社,2003 (3)常晓玲.电气控制系统与可编程控制器[M].北京:机械工业出版社,2004 (4)盖超会,阳胜峰.三菱PLC与变频器、触摸屏综合培训教程[M].北京:中国电力出版社,2011 (5)濮良贵,陈国定,吴立言.机械设计[M].北京:高等教育出版社,2013 4.本设计任务书于2015年10月12日发出,应于2015年10月30日前完成,然后进行答辩。
指导教师签发 2015 年 10 月 30 日课程设计评语:课程设计总成绩:指导老师签字:年月日目录摘要 (I)第一章绪论 (1)1.1分拣系统背景 (1)1.1.1分拣系统的发展前景 (1)1.1.2国内外分拣系统的对比 (2)1.2 研究分拣系统的意义 (3)1.3分拣系统的工作过程概述 (4)1.3.1 分拣系统结构图 (4)1.3.2 分拣系统的控制要求 (4)第二章分拣系统的硬件设计 (6)2.1 PLC及其组件的选型及控制原理 (6)2.1.1 PLC的型号选择 (6)2.1.2 I/O模块的选型 (7)2.2 传感器的选择 (9)2.2.1传感器的简介 (9)2.2.2传感器的选择 (10)2.3 驱动部分的分析与选择 (12)2.4 系统执行机构的分析与选择 (13)2.5 硬件设计及实际模型的建立 (15)2.6 其他元器件及其选择 (16)2.7 I/O接口的选择及PLC的接线 (17)第三章物料分拣系统软件设计 (21)3.1 可编程控制器(PLC)的简介 (21)3.2分拣系统的控制要求及其流程图 (25)3.3软件设计及编程 (27)第四章控制系统的安装接线及运行调试 (28)4.1 硬件调试 (28)4.2 软件调试 (28)4.3 整体调试 (29)第五章结论与展望 (30)附录 (32)摘要分拣控制系统在先进制造领域中扮演着极其重要的角色。
- 1、下载文档前请自行甄别文档内容的完整性,平台不提供额外的编辑、内容补充、找答案等附加服务。
- 2、"仅部分预览"的文档,不可在线预览部分如存在完整性等问题,可反馈申请退款(可完整预览的文档不适用该条件!)。
- 3、如文档侵犯您的权益,请联系客服反馈,我们会尽快为您处理(人工客服工作时间:9:00-18:30)。
PLC技术应用项目说明书产品自动分拣计数控制系统的设计学院机械工程学院专业机械电子工程班级 2012级机电1班学生姓名李钊指导老师王蕊2015 年 10 月 30 日课程设计任务书兹发给 2012级机电1 班学生李钊课程设计任务书,内容如下:1.设计题目:产品自动分拣计数控制系统的设计2.应完成的项目:(1)选题的背景和意义;(2)明确设计任务,拟定总体设计方案(有机械结构的要进行结构设计,三维软件建模);(3)硬件设计,传感器、PLC(和电机)选型,设计信号采集、转换电路,画出PLC端口分配图、接线控制端子连接图;(4)软件设计,编写控制程序流程图(或重要程序),设计人机界面;(5)课程设计说明书1份。
3.参考资料以及说明:(1)金发庆.传感器技术与应用(第二版)[M].北京:机械工业出版社,2004 (2)钟肇新.可编程控制器原理及应用[M].广州:华南理工大学出版社,2003 (3)常晓玲.电气控制系统与可编程控制器[M].北京:机械工业出版社,2004 (4)盖超会,阳胜峰.三菱PLC与变频器、触摸屏综合培训教程[M].北京:中国电力出版社,2011 (5)濮良贵,陈国定,吴立言.机械设计[M].北京:高等教育出版社,2013 4.本设计任务书于2015年10月12日发出,应于2015年10月30日前完成,然后进行答辩。
指导教师签发 2015 年 10 月 30 日课程设计评语:课程设计总成绩:指导老师签字:年月日目录摘要 (I)第一章绪论 (1)1.1分拣系统背景 (1)1.1.1分拣系统的发展前景 (1)1.1.2国内外分拣系统的对比 (2)1.2 研究分拣系统的意义 (3)1.3分拣系统的工作过程概述 (4)1.3.1 分拣系统结构图 (4)1.3.2 分拣系统的控制要求 (4)第二章分拣系统的硬件设计 (6)2.1 PLC及其组件的选型及控制原理 (6)2.1.1 PLC的型号选择 (6)2.1.2 I/O模块的选型 (7)2.2 传感器的选择 (9)2.2.1传感器的简介 (9)2.2.2传感器的选择 (10)2.3 驱动部分的分析与选择 (12)2.4 系统执行机构的分析与选择 (13)2.5 硬件设计及实际模型的建立 (15)2.6 其他元器件及其选择 (16)2.7 I/O接口的选择及PLC的接线 (17)第三章物料分拣系统软件设计 (21)3.1 可编程控制器(PLC)的简介 (21)3.2分拣系统的控制要求及其流程图 (25)3.3软件设计及编程 (27)第四章控制系统的安装接线及运行调试 (28)4.1 硬件调试 (28)4.2 软件调试 (28)4.3 整体调试 (29)第五章结论与展望 (30)附录 (32)摘要分拣控制系统在先进制造领域中扮演着极其重要的角色。
是工业控制及现代物流系统的重要组成部分,实现物料同时进行多口多层连续的分拣。
在社会各行业如:物流配送中心、邮局、仓库等行业得到广泛应用。
本文在对熟悉了自动及分拣系统的原理的基础上,根据一定的分拣要求,采用了整体化的设计思想,充分考虑了软、硬件各自的特点并进行互补优化,设计了一个物料传送及分拣系统。
此系统以PLC为主控制器,结合传感器技术,气动装置和位置控制等技术,并运用梯形图编程,实现对铁质、铝质和不同颜色的材料的自动分拣。
具有自动化程度高、容易控制、运行稳定、分拣精度高的特点,对不同的分拣对象,稍加修改本系统即可实现要求。
关键词:可编程控制器(PLC),传感器,气动控制,物料分I第一章绪论1.1分拣系统背景自动分拣系统(Automatic sorting system)在配送中心处于十分必要的地位。
具有非常高的效率,一般来说每小时所分拣商品的数量达6000-12000箱不等,可以说,自动分拣作为能够提高物流分配、发送效率重要因素之一。
也是二战后在许多国家例如日本等国家物流中心所广泛使用的一种自动分拣系统,目前,该系统已广泛的应用于发达国家的大中型物流中心。
关于自动分拣系统的作业流程的描述如下:物流中心吸收供应商送来的各种商品,并且在最短时间内这把上述商品卸下,然后根据商品的种类、供应商和发送地点来准确分类,并将上述商品送到指定目的地,同时,如果供应商通知物流中心按自己所要求的配送指示发送货物时,分拣系统能够在最短的时间内,从高层货存架存储系统中准确的找到要出库的商品及其所在位置,并按所需要求出库。
从不同储位上取出的不同数量的商品按配送地点的不同运送到不同的理货区域或配送站台集中,以便装车配送。
1.1.1分拣系统的发展前景最初的分拣系统是完全基于人力的作业系统, 通过人工搜索、承运货物完成货物的提取。
在这个系统中,书面文档生产和发现,如手动处理浪费了巨大的人力资源,效率很低,显然不能满足现代物流的速度、精度要求高的特点。
随着科学技术的飞速发展,分拣系统开始运用各种各样的自动化设备,计算机控制技术和信息技术成为信息传递和处理的重要手段。
虽然在大部分分拣系统中有些作业环节到目前为止需要有人工的参与,但作业强度越来越小。
完全由机械完成分拣作业的自动分拣系统也与之而生。
机械化、自动化、智能化成为现代分拣系统的主要特点与发展趋势。
现代物流配送中,高科技的应用为作业效率和质量的提高提供了坚实的技术保证。
现代化的分拣系统逐渐成为物流机械化系统、信息系统以及管理组织系统的有机组合。
物流机械化系统主要是各种物流设备的有效组合和配置,信息系统是分拣信息和控制信息等流动的载体,管理组织系统负责设备、人员的调度,控制系1统总体的运作模式。
计算机控制技术、信息技术以及物流自动化机械成为现代分拣系统的重要组成部分。
1.1.2国内外分拣系统的对比应用现状及趋势纵观国内外分拣系统的应用情况可以发现,国外的物流配送中心倾向于采用自动化程度很高的分拣系统。
而在我国,由于物流业起步晚,分拣系统中人工作业的比例也较高。
国外自动分拣系统的广泛使用以美国、日本及欧洲为代表的发达国家,在分拣系统的应用上体现出自动化程度越来越高的特点。
代表美国、日本和欧洲发达国家的应用分类系统反映的特点,自动化程度越来越高。
自动分拣系统已成为发达国家大中型物流中心、配送中心或一个配送中心是不可或缺的一部分。
自动分拣系统是二战后在美国,日本和其他国家的一个广泛应用于大中型物流中心分拣系统,参照邮局排序字母自动化经验配置。
一般包括控制装置、分类装置、传动装置和分拣道口,它们通过计算机网络联结在一起,配合人工控制及相应的人工处理环节构成一个完整的分拣系统。
其主要特点为: 能连续、大量的来给货物分类,分类错误率极低,基本实现无人操作排序。
自动分拣系统中人员的使用仅局限于进货时的接货、系统的控制、系统的经营、管理与维护等,这恰好达到了国外企业的下列要求:减少人员使用、减轻员工劳动强度、提高人员使用效率,所以受到了他们的广泛重视。
就国外进行配送业务的行业或企业来说,自动拣选系统已广泛应用在医药制造业和其他行业,比如日本,资生堂,如大木有限公司。
自动排序作为关键设备在自动分拣系统,因为它可以达到每小时5000 - 5000例排序的效率,也广泛用于日本和欧洲,日本,连锁经营企业(如西友、高岛屋等)和众议院JiBian(大和,佐川等等)是广泛使用的自动分选机;在日本唱片中心,CD及录像带的新出版品也利用高端的机器人自动分拣机拣货。
目前常用自动分拣系统2世界知名的自动化物流系统集成商德国德马泰克开发的自动分拣系统及相关系统;范德兰德;丹麦的克瑞斯普兰(德国伯曼机械)的全自动分拣系统;深圳市天和双力物流自动化设备有限公司的自动分拣系统;康大基业电子标签拣货系统;上海邮政通用技术设备公司的交叉带式分拣机控制系统;壹比多系列电子分拣系统等等。
1.2 研究分拣系统的意义1、可以连续的,大批量的货物进行分类。
由于使用自动用于大规模生产流水线、自动分拣系统不受气候、时间、身体条件的限制,如可以连续运行,同时由于数量的自动分拣系统单位时间排序,排序能力排序系统自动人工分拣系统能够连续运行100小时以上,每小时7000件包装商品,分类,比如使用人工分拣150件/小时左右,同时分拣工人无法工作8小时连续在这种劳动强度。
2、分类错误率极低。
自动分类系统的分类误差的大小主要取决于准确的信息输入订单,反过来取决于分类信息输入系统,如果使用手动键盘输入或语音识别方法,出错率超过3%,如使用条码扫描输入,除非条码印刷本身有错误,或者你不会出错。
因此,目前自动分拣系统主要使用条形码技术来识别商品。
3、基本实现无人整理活动的外国自动分拣系统的目的之一是为了减少人员的使用,降低了工人的劳动强度,提高使用效率的员工,因此自动分拣系统能减少人员,使用基本是无人驾驶的。
整理活动本身并不需要使用人员,人员使用限于以下工作: (1)、送货车辆到达结束自动分拣线进货,由工人来提货。
(2)、通过人工控制操作系统的分类。
(3)、排序,通过人工整理排在最后的负载、装载货物。
(4)、自动分拣系统,管理和维护业务。
如美国一家公司配送中心占地面积约100000平方米,每天近400000项排序,仅使用400名左右员工,这其中部分人员都在从事上述(1)、(3)、(4)项工作,自动分拣线作到了无人化作业对于分拣系统应用前景,主要着眼于分拣系统的可靠性,优越性,应用领域3的适用性以及系统的经济效益、成本等方而来考虑。
但是自动分拣系统对商品外包装要求也很高,自动分拣系统只适合于平坦和刚性包装底部的规则排序货物。
包装商品,柔软而不均匀的底部的包装,包装,容易变形,容易损坏,长、苗条、超重、超高、不能推翻的商品不能用正常的自动分类机进行排序,所以为了使大部分的货物已经完成了机械自动排序,可以采取两种措施:一是促进标准化的包装,使大部分的商品包装是符合国家标准的统一;二是基于排序的大部分商品的包装功能定制特定的分类机。
但是让所有供应商货物符合国家包装是非常困难的,自定义特性分类机,使硬件成本的上升,和它的普遍性是更糟更特殊。
所以公司应该根据操作和货物的包装决定建立或建立什么样的自动分拣系统[1]。
1.3分拣系统的工作过程概述1.3.1 分拣系统结构图指示灯图1-1 材料分拣系统的示意图1.3.2 分拣系统的控制要求4本课题是基于区分材料材质的不同而设计的材料分拣系统,主要是实现对铁质、铝质和不同颜色的材料的自动分拣,具体控制过程为:(1)接通电源,按下启动开关SB1,系统进入启动状态,指示灯绿灯L2亮。
(2)系统启动后,下料传感器SQ1(光电传感装置)检测到料槽无材料或各气缸未复位时,传送带须继续运行一个行程10S后自动停机,指示灯红灯L1亮。
(3)系统启动后,下料传感器(光电传感装置)检测到料槽有材料,出料气缸每隔2S动作一次,动作时间维持为1S,将待测材料推到传送带上,待测物体开始在传送带上运行,并对其进行计数。