压铸铸造不良要因分析
压铸件不良品原因及对策
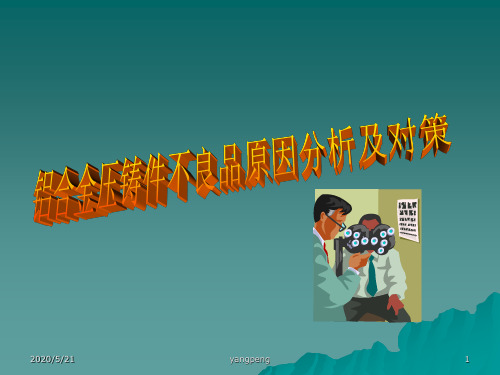
错 模
20122012-2-1
yangpeng
24
20122012-2-1
yangpeng
11
3.压铸型主要由动模、静(定) 模两部分组成,改变铸造方案, 就要变更铸型的分型面。因此铸 造方案不能作很大的变动,在变 动较大的情况下,有非重作铸型 的危险性。
20122012-2-1
yangpeng
12
4. 因为压铸件的尺寸精度 很高,即使是很小的变形, 也往往导致不能装配,或因 加工余量不足而成为不良品。 大多数会发生尺寸不合格。
厚壁中心部 位的气孔
20122012-2-1
在厚壁中心部位出现的球状小孔
yangpeng
6
缺陷的分类
缺陷的种类
缺陷的特征
硬点
在铸件中出现的硬度高,并妨碍正常加工的颗粒
材质缺陷
材质不良
铸件的化学成分不符合规定,有杂质
氧化物
铸件里混有氧化物
20122012-2-1
yangpeng
7
缺陷的分类
缺陷的种类
缺陷的特征 由于种种原因造成铸件不符合原设计的尺寸 因铸型错位造成铸件错模
尺寸缺陷
因铸型涨开 因铸型涨开,型芯后退,在铸件局部铸出厚的飞 使型芯后 边,不符合制品的原定尺寸 退 变形 多肉,欠铸 掉肉 铸件变形改变了原来的形状 铸件局部过厚或太薄以及有局部缺损 去掉浇口和飞边时造成铸件局部缺损
yangpeng 3
20122012-2-1
yangpeng
20
分类 原因 对策 尺 尺寸不 铸型的组装不 1.检查铸型装配有无错误,如有应予 合格 合理 纠正。 寸 2.检查螺栓有无松动,装配是否正 确,并加以修理。 不 3.检查垫板和铸型安装面上有无凹凸 不平,并加以修理。 合 4.检查铸型按装面的表面状态是否良 格 好,调整垫板的间隙。
压铸铸造不良要因分析课件

压铸铸造的应用领域
01
02
03
汽车工业
压铸铸造广泛应用于汽车 零部件制造,如发动机缸 体、气瓶等。
电子工业
压铸铸造用于制造电子产 品中的精密零件,如手机 外壳、电视框架等。
五金工具
压铸铸造用于制造各种五 金工具,如剪刀、钳子等 的手柄部件。
缩孔和气孔
缩孔
压铸过程中,金属冷却收缩时未 能得到足够的金属补充,导致在 铸件内部形成孔洞。
冷隔
由于金属液在冷却过程中流动性不足,导致铸件表面形成不规则的冷凝区,呈 现出一种“断层”状的结构。
欠铸和飞边
欠铸
铸件未能完全填充模具型腔,导致铸件部分缺失或不完全。
飞边
铸件与模具型腔接触的部分出现多余的金属边,通常是由于 金属液溢出模具型腔所致。
材料因素
材料成分不均Βιβλιοθήκη 原材料成分不均或含有杂质,导致压铸件性能不 稳定。
造不良要分析 件
目 录
• 压铸铸造简介 • 压铸铸造不良现象 • 压铸铸造不良要因分析 • 压铸铸造不良改善措施 • 案例分析
contents
压铸铸造的定义
01
压铸铸造是一种金属铸造工艺, 利用高压将液态金属注入模具中, 冷却后形成铸件。
02
压铸铸造适用于各种金属材料, 如铝、锌、镁等轻质合金,具有 生产效率高、尺寸精度高、表面 质量好等优点。
国际知名品牌压铸产品不良分析
01
案例概述
国际知名品牌在进行压铸产品生产时,也经常面临铸造不良的问题,影
响了品牌形象和市场竞争力。
02 03
要因分析
通过对多个国际知名品牌的压铸产品不良案例进行分析,发现主要问题 包括设计缺陷、原材料选用不当、生产设备精度不足以及质量控制不严 格等。
压铸缺陷产生原因及解决方案

1.降低浇注温度,减小收缩量 2.提高铸造压力,提高致密性 3.修改内浇口,使压力更好传递,利于金属液补缩 4.改变铸件结构,消除金属集聚部位,壁厚尽可能均匀 5.加快壁厚部位冷却 6.加厚料饼,增加补缩的效果
压铸缺陷产生的原因及分析
缩陷形成的原因:
缩孔缩松位于铸件表皮下时产生表面凹陷。
1.压铸件结构设计不当,壁厚差太大 2.合金收缩大 3.浇道位置不当 4.压射比压低 5.模具局部温度过高。 6.由憋气引起: 填充型腔时,局部气体未排出,被压缩 在 改型善腔措表施面:与金属液界面之间。
改善措施: 1.提高模具温度,特别提高产生缺陷处模具的温度。 2.改进工艺,包括浇铸温度、充填时间、压力。 3.改进内浇口和流道设计,以改善不同股的金属液流动。 4.此外,还要检查: 对于铝合金: -Si 元素含量在要求范围内尽可能高 -金属液尽可能干净 对于锌合金: -铝含量在范围内尽可能高
5.结构设计缺陷
3.经常检查分型面并清理干净;
4. 模具设计时模具厚度及大小应正确计算并校核;
5.检查滑块和镶块,红丹研配修复。
6. 红丹研配配模具,分型面红丹贴合面积≥90%
压铸缺陷产生的原因及分析
机械性能不符合要求:
形成的原因:
1.合金的化学成分不符合标准; 2.铸件内部有较多的气孔、缩孔缩松、夹渣等缺陷; 3.铸件结构设计不合理,限制了铸件达到标准; 4.合金的熔炼工艺不当。
压铸缺陷产生的原因及分析
产生原因:
1.当压力不足、活动前沿的金属凝固过早,造成转角、深凹、 薄壁、柱形孔壁等部位产生欠铸。压铸加工模具温度过低; 合金浇入温度过低;内浇口位置不好,形成大的活动阻力。 2、气体阻碍,欠铸部位表面润滑,但形状不规则,难以开设 排溢系统的部位,气体积累;熔融金属的活动时,湍流剧烈,包 卷气体。
压铸件不良及原因分析

一、 氧化夹渣
A. B.
C.
缺陷特征:氧化夹渣多分布在铸件的上表面,在铸型不通 气的转角部位。断口多呈灰白色或黄色,经x光透视或在 机械加工时发现,也可在碱洗、酸洗或阳极化时发现 产生原因: 1.炉料不清洁,回炉料使用量过多 2.浇注系统设计不良 3.合金液中的熔渣未清除干净 4.浇注操作不当,带入夹渣 5.精炼变质处理后静置时间不够 防止方法: 1.炉料应经过吹砂,回炉料的使用量适当降低 2.改进浇注系统设计,提高其挡渣能力 3.采用适当的熔剂去渣 4.浇注时应当平稳并应注意挡渣 5.精炼后浇注前合金液应静置一定时间
八、冷裂纹(拉模)
A. 缺陷特征: 當推杆顶出铸時,铸件未能順利與模具分离所产 生之不良現象 。 B. 主要影响因素及需改良项目: 推杆頂出時需確保同步前进(Ejector Pin)。 合金温度( Molten Metal Temperature)。 模温( Mould Temp.)。 拔模斜度(Greater Draft Angle)。 模具硬度(Require Hardness 44-48度)。
二、气孔/气泡
A.
B.
C.
缺陷特征:三铸件壁内气孔一般呈圆形或椭圆形,具有光滑的 表面,一般是发亮的氧化皮,有时呈油黄色。表面气孔、气泡 可通过喷砂发现,内部气孔 气泡可通过X光透视或机械加工发 现气孔 气泡在X光底片上呈黑色 产生原因: 1.浇注合金不平稳,卷入气体 2.型(芯)砂中混入有机杂质(如煤屑、草根 马粪等) 3.铸型和砂芯通气不良 4.冷铁表面有缩孔 5.浇注系统设计不良 防止方法 : 1.正确掌握浇注速度,避免卷入气体。 2.型(芯)砂中不得混入有机杂质以减少造型材料的发气量 3.改善(芯)砂的排气能力 4.正确选用及处理冷铁 5.改进浇注系统设计
压铸件缺陷产生原因及对应措施

1.降低浇注温度,减少收缩量 2.提高压射比压及增压压力,提高致密 性 3.修改内浇口,使压力更好传递,有利 于液态金属补缩作用 4.改变铸件结构,消除金属积聚部位, 壁厚尽可能均匀 5.加快厚大部位冷却 6.加厚料柄,增加补缩的效果
3
夹杂
1.炉料不洁净,回炉料太多 混入压铸件内的金属或非金属 2.合金液未精炼 杂质,加工后可看到形状不规 3.用勺取液浇注时带入熔渣 则,大小、颜色、亮度不同的 4.石墨坩埚或涂料中含有石墨脱落混 点或孔洞 入金属液中 5.保温温度高,持续时间长 1.铝合金中杂质锌、铁超过规定范围 铸件基体金属晶粒过于粗大或 2.合金液过热或保温时间过长,导致 极小,使铸件易断裂或磁碎 晶粒粗大 3.激烈过冷,使晶粒过细 1.压力不足,基体组织致密度差 2. 内部缺陷引起,如气孔、缩孔、渣 压铸件经耐压试验,产生漏气 孔、裂纹、缩松、冷隔、花纹 、渗水 3.浇注和排气系统设计不良 4.压铸冲头磨损,压射不稳定 机械加工过程或加工后外观检 查或金相检查:铸件上有硬度 高于金属基体的细小质点或块 状物使刀具磨损严重,加工后 常常显示出不同的亮度 一、非金属硬点: 1.混入了合金液表面的氧化物 2.合金与炉衬的反应物 3.金属料混入异物 4.夹杂物
铸件缺陷产生原因及应对措施
一、表面缺陷
序号 缺陷名称 特征
沿开模方向铸件表面呈现条状 的拉伤痕迹,有一定深度,严 重时为一面状伤痕;另一种是 金属液与模具产生焊合、粘附 而拉伤,以致铸件表面多肉或 缺肉
产生原因
1.型腔表面有损伤 2.出模方向斜度太小或倒斜 3. 顶出时偏斜 4.浇注温度过高或过低、模温过高 导 致合金液产生粘附 5.脱模剂使用效果不好 6. 铝合金成分铁含量低于 7.冷却时间过长或过短 1.合金液在压室充满度过低,易产生 卷气,压射速度过高 2. 模具排气不良 3. 熔液未除气,熔炼温度过高 4.模温过高,金属凝固时间不够,强 度不够,而过早开模顶出铸件,受压 气体膨胀起来 5.脱模剂太多 6.内浇口开设不良,充填方向不顺
压铸件铸造缺陷不良改善对策

压铸件铸造缺陷不良改善对策缺陷名称特征产生原因防止方法拉伤沿开模方向铸件表面呈现条状的拉伤痕迹,有一定深度,严重时为一面状伤痕。
另一种是金属液与模具产生焊合、粘附而拉伤,以致铸件表面多肉或缺肉。
1、型腔表面有损伤、出模方向斜度太小或倒斜 23、顶出时偏斜4、浇注温度过高或过低,模温过高导致合金液产生粘附5、脱模剂使用效果不好6、铝合金成分含铁量低于0.6%7、冷却时间过长或过短1、修理模具表面损伤处,修正斜度,600细油石顺磨提高光洁度2、调整或更换顶杆,使顶出力平衡3、更换离型剂4、调整合金含铁量5、控制合适的浇注温度,控制模具温度6、修改内浇口,避免直冲型芯型壁或对型芯表面进行特殊处理气泡铸件表面有米粒大小的隆起表皮下形成的空洞 1、合金液在压室充满度过低,易产生卷气,压射速度过高2、模具排气不良3、溶液未除气,熔炼温度过高4、模温过高,金属凝固时间不够,强度不够,而过早开模顶出铸件,受压气体膨胀起来5、脱模剂太多6、内浇口开设不良,充填方向不顺 1、提高金属液充满度 2、降低第一阶段压射速度,改变低速与高速压射切换点3、降低模温4、增设排气槽、溢流槽、充分排气5、调整熔炼工艺,进行除气处理6、留模时间延长7、减少脱模剂用量裂纹 1. 铸件表面有呈直线状或波浪形的纹路,狭小而长,在外力作用下有发展趋势2. 冷裂,开裂处金属没有被氧化3. 热裂,开裂处金属已经被氧化 1. 合金中含铁量过高或硅含量过低 2. 合金中有害杂质的含量过高,降低了合金的可塑性3. 铝硅合金:铝硅铜合金含锌或含铜量过高;铝镁合金中含镁量过多4. 模具:特别是型芯温度太低5. 铸件壁存有剧烈变之处,收缩受阻,尖角位形成应力6. 留模时间过长,应力大7. 顶出时受力不均匀 1. 正确控制合金成分,在某种情况下可在合金中加纯铝锭以降低合金中含镁量;或在合金中加铝硅中间合金以提高硅含量 2. 改变铸件结构,加大圆角,加大出模斜度,减少壁厚差3. 变更或增加顶出位置,使顶出受力均匀4. 缩短开模及抽芯时间5. 提高模温,保持模温稳定变形 1. 铸件几何形状与图纸不符2. 整体变形或局部变形 1. 铸件结构设计不良,引起不均匀收缩 2. 开模过早,铸件刚性不够3. 顶杆设置不当,顶出时受力不均匀4. 切除浇口方法不当5. 由于模具表面粗糙造成举报阻力大而引起顶出时变形 1. 改进铸件结构 2. 调整开模时间3. 合理设置顶杆位置及数量4. 选择合适的切除浇口方法5. 加强模具型腔表面抛光,减少托模阻力流痕、花纹 1. 铸件表面上有与金属液流动方向一致的条纹,有明显可见的与金属体颜色不一样的无方向性的纹路,无发展趋势 1. 首先进入型腔的金属液形成一个极薄的而又不完全的金属层后,被后来的金属液所弥补而留下的痕迹 2. 模温过低,模温不均匀3. 内浇道截面积过小及位置不当产生喷溅4. 作用于金属液的压力不足5. 花纹:涂料用量过多 1. 提高金属液温度2. 提高模温3. 调整内浇道截面积或位置4. 调整充填速度及压力5. 选用合适的涂料及调整用量冷隔 1. 铸件表面有明显的、不规则的、下陷线性纹路(有穿透与不穿透两种)形状细小而狭长,有的交接边缘光滑,在外力作用下有发展的可能 1. 两股金属流相互对接,但未完全熔合而又无夹杂存在其间,两股金属流结合力很薄弱 2. 浇注温度或压铸模温度偏低3. 选择合金不当,流动性差4. 浇道位置不对或流路过长5. 充填速度低6. 压射比压低 1. 适当提高浇注温度和模具温度 2. 提高压射比压,缩短充填时间3. 提高压射速度,同时加大内浇口截面积4. 改善排气、充填条件5. 正确选用合金,提高合金流动性变色、斑点 1. 铸件表面呈现出不同的颜色及斑点 1. 不合适的脱模剂2. 脱模剂用量过多,局部堆积3. 含有石墨的润滑剂中的石墨落入铸件表层4. 模温过低,金属液温度过低导致不规则的凝固引起 1. 更换优质脱模剂 2. 严格喷涂量及喷涂操作3. 控制模温4. 控制金属液温度网状毛翅 1. 压铸件表面上有网状发丝一样凸起或凹陷的痕迹,随压铸次数增加而不断扩大和延伸 1. 压铸模型腔表面龟裂2. 压铸模材质不当或热处理工艺不正确3. 压铸模冷热温差变化大4. 浇注温度过高5. 压铸模预热不足6. 型腔表面粗糙 1. 正确选用压铸模材料及热处理工艺 2. 浇注温度不易过高,尤其是高熔点合金3. 模具预热要充分4. 压铸模要定期或压铸一定次数后退火,消除内应力5. 打磨成型部分表面,减少表面粗糙度6. 合理选择模具冷却方法凹陷 1、铸件平滑表面上出现凹陷部位 1. 铸件壁厚相差太大,凹陷多产生在厚壁处2. 模具局部过热,过热部分凝固慢3. 压射比压低4. 由憋气引起型腔气体排不出,被压缩在型腔表面与金属液界面之间 2. 铸件壁厚设计尽量3. 模具局部领却调整4. 提高压射比压5. 改善型腔排气条件欠铸(缺料) 1、铸件表面有浇不足部位 1、流动性差原因: 1) 合金液吸气、氧化夹杂物,含铁量高,使其质量差而降低流动性 2) 浇注温度低或模温低2、充填条件不良:1) 比压过低2) 卷入气体过多,型腔的背压变高,充型受阻3、操作不良,喷涂料过度,涂料堆积,气体挥发不掉 1、提高合金液质量2、提高浇注温度或模具温度3、提高比压、充填速度4、改善浇注系统金属液的导流方式,在欠铸部位加开溢流槽、排气槽5、检查压铸机能力是否足够毛刺飞边 1. 压铸件在分型面边缘上出现金属薄片 1. 锁模力不够 2. 压射速度过高,形成压力冲击峰过高3. 分型面上杂物未清理干净4. 模具强度不够造成变形5. 镶块、滑块磨损与分型面不平齐 1. 检查合模力和增压情况,调整压铸工艺参数2. 清洁型腔及分型面3. 修理模具4. 最好是采用闭合压射结束时间控制系统,可实现无飞边压铸气孔(内部缺陷) 1. 解剖后外观检测或探伤检查,气孔具有光滑的表面、形状为圆形 1. 合金液导入方向不合理或金属液流动速度太高,产生喷射;过早堵住排气道或正面冲击壁而形成漩涡包住空气,这种气孔多产生排气不良或深腔处2. 由于炉料不干净或熔炼温度过高,使金属液中较多的气体没除净,在凝固时析出没能充分排出。
压铸不良原因分析

缺陷名称特征产生原因防止方法气泡铸件表面有米粒大小的隆起表皮下形成的空洞1、合金液在压室充满度过低,易产生卷气,压射速度过高2、模具排气不良3、溶液未除气,熔炼温度过高4、模温过高,金属凝固时间不够,强度不够,而过早开模顶出铸件,受压气体膨胀起来5、脱模剂太多6、内浇口开设不良,充填方向不顺1、提高金属液充满度2、降低第一阶段压射速度,改变低速与高速压射切换点3、降低模温4、增设排气槽、溢流槽、充分排气5、调整熔炼工艺,进行除气处理6、留模时间延长7、减少脱模剂用量气孔(内部缺陷) 1. 解剖后外观检测或探伤检查,气孔具有光滑的表面、形状为圆形 1. 合金液导入方向不合理或金属液流动速度太高,产生喷射;过早堵住排气道或正面冲击壁而形成漩涡包住空气,这种气孔多产生排气不良或深腔处2. 由于炉料不干净或熔炼温度过高,使金属液中较多的气体没除净,在凝固时析出没能充分排出。
3. 涂料发气量大或使用过多,在浇注前未浇净,使气体卷入铸件,这种气孔多呈暗灰色表面4. 高速切换点不对 1. 采用干净炉料,控制熔炼温度,进行排气处理。
2. 选择合理工艺参数、压射速度、高速切换点3. 引导金属液平衡,有序充填型腔,有利气体排出4. 排气槽、溢流槽要有足够的排气能力5. 选择发气量小的涂料及控制排气量缩孔、缩松(内部缺陷) 1. 解剖或探伤检查,空洞形状不规则、不光滑、表面呈暗色2. 大而集中为缩孔小而分散为缩松 1. 铸件在凝固过程中,因产生收缩而得不到金属液补偿而造成孔穴2. 浇注温度过高,模温梯度分布不合理3. 压射比压低,增压压力过低4. 内浇口较薄,面积过小,过早凝固,不利于压力传递和金属液补缩5. 铸件结构上有热节部位或截面积变化剧烈6. 金属液浇注量偏小,余料太薄,起不到补缩作用 1. 降低浇注温度,较少收缩量2. 提高压射比压及增压压力,提高致密性3. 修改内浇口,使压力更好传递,有利于液态金属补缩作用4. 改变铸件结构,消除铸件积聚部位,壁厚尽可能均匀5. 加快厚大部位冷却6. 加厚料柄,增加补缩效果夹杂(内部缺陷) 1. 混入压铸件内的金属或非金属杂质,加工后可看道形状不规则、大小、颜色、亮度不同的点或空洞 1. 炉料不洁净,回炉料太多2. 合金液未精练3. 用勺取液浇注时带入熔渣4. 石墨坩锅或涂料中含有石墨脱落混入金属液中5. 保温温度高,持续时间长 1. 使用清洁的合金料,特别是回炉料炉上脏物必须清理干净2. 合金溶液须精练除气,将熔渣清干净3. 用勺取液浇注时,仔细拨开液面避免混入熔渣和氧化皮4. 清理型腔、压室5. 控制保温温度和减少保温时间。
压铸件缺陷原因分析

三、砂孔(有气孔和缩孔之分,为铸件表面或截面上出现不规则的小孔,我们统称为 “砂孔”)
原因分析:
1、进浇口过厚,填充方式不当,造成浇口与铸件断面处形成砂孔。 2、使用原材料质量差,杂质及水口料所占比例过大。 3、浇口位置不当造成金属液流动混乱,在型腔里形成涡流,此种状态形成的气孔在铸件表面看
3、成型时间不够长,即冷却时间过短,铸件没有完全定型硬化,铸件脱模后,留在铸件内的气 体膨胀而形成气泡。
4、脱模剂配比过多,生产时喷的脱模剂配比太浓、太多,造成模具温度过低,析出的气体不易 蒸发排出,形成气泡缺陷原因分析
一、披锋,又称毛刺、飞边,是在铸件的分型面或滑块、镶件、顶针等处凸出过多的 金属薄片。
原因分析:
1、压铸机的安装调整不良,压铸机必须安装在水平的地面上,安装好以后,动模板与定模板要 平行,各种压力调整完成,方能用于生产。
2、模具制造不良,配合不严密,定模与动模闭合后在两者之间不能留有空隙,否则生产时必有 多余合金飞出形成披锋。
四、起泡(在铸件表面有光滑的凸起的鼓包,形成位置不固定,有明泡、暗泡、水纹 泡之分)
原因分析:
1、模具排气不良,排气位置不当,合金溶液充填模腔后,铸件某些部位的排渣包、排气槽等排 溢系统开得不够大、不够深、位置不当而使得留在模腔内的气体不能顺利排出,留在铸件中 形成起泡。
2、进浇口过多,由于有两条以上的液流同时充型,因液流方向、速度等不同,容易使两股液流 产生对撞,在碰撞出形成涡流,产生气泡。
3、浇注系统不合理,如流程长、流道曲折,且流道四周产生大的披锋,所有这些会损耗填充压 力而导致水纹。
4、排气溢流系统不良,渣包位置设置不合理或不够大,模腔里面的空气排出不充分,影响溶液 填充。
压铸常见缺陷、原因及改进措施

渗漏
水、
合金选择不当
提高比压 改进浇注系统 选用良好合金
排气不良
改进排气系统
二十四、 化学成分 不符合要
求
经化学分析,铸件合 金不符要求或杂质太
多
配料不正确 原材料及回炉料未加分析即行投入使用
炉料应经化学分析后才能配用
炉料应严格管理,新旧料要按一定比例 配用 严格遵守熔炼工艺,熔炼工具应刷涂料
编制:
涂料不纯或用量过多 涂料中石墨含量过多
充型过程中由于模具 填充时金属分散成密集液滴,高速撞击
十四、麻 面
温度或合金液温度过 低,在近似于欠压条 件下铸件表面形成的
型壁
细小麻点状分布区域 内浇口厚度偏小
涂料使用应薄而均匀,不能堆积,要用 压缩空气吹散
减少涂料中的石墨含量或选用无石墨水 基涂料
正确设计浇注系统,避免金属液产生喷 溅,改善排气条件,避免液流卷入过多 气体,降低内浇口速度并提高模具温度
合金收缩率大 内浇口截面积太小
比压偏低
模具温度过高
合理设计浇注系统,避免合金液直接冲 击型芯、型壁,适当降低填充速度
修正模具
打光表面,保证粗糙度符合要求 涂料使用薄而均匀,不能漏喷涂料
适当增加含铁量至0.8-1%
改善铸件结构,使壁厚稍为均匀,厚薄 相差较大的连接处应逐步缓和过渡,消 队热节
选择收缩率较小的合金
合金液过热或保温时间过长
合金不宜过热,避免合金长时间保温
二十二、 碎性
铸件基本金属粒过于 粗大或细小,使铸件
易断裂或碰碎
激烈过冷,结晶过细 铝合金中杂质锌、铁等含量太多
铝合金中含铜量超出规定范围
提高模具温度,降低浇注温度
严格控制合金化学成分
十大铸件不良现象及原因教育资料
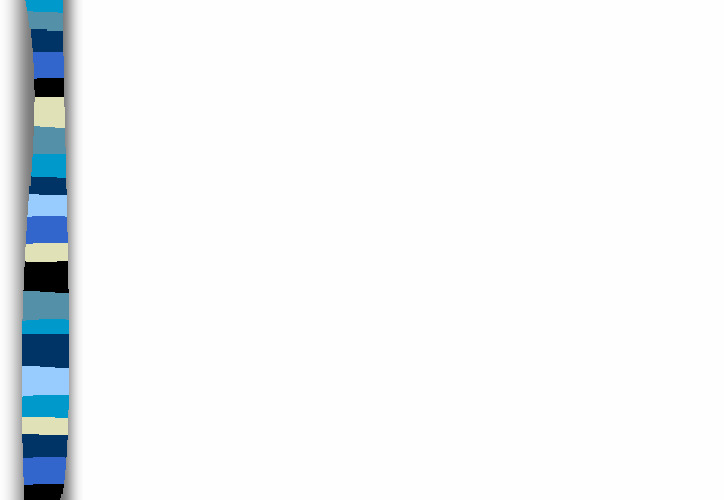
铸件不良现象及产生的原因2.成因:1)铁水浇注温度太低或浇注不足。
2)模型设计中,如水口太小,入水慢。
3)浇注之铁水压力不足,薄壁处或拐角处铁水不易成形。
4)浇注分层,多次浇注。
5)液流流头产生了凝固堵塞或流头氧化造成两股流头不能融合在一起第一种:冷隔3.对策:①提高浇注温度,增强铁水的流动性。
②合理的设置入水口的位置,避免距离浇口较远部位因铁水氧化和降温出现冷隔。
③保证排气通畅,降低冲型阻力。
④提高冲型速度,增加冲型力。
⑤避免铁水氧化。
⑥避免断续浇注。
⑦多处入水时,保证铁水交汇处铁液具有较高温度。
1. 现象:铸件主体有裂纹状的间隙或断流,不完整的位置多呈现冷硬的圆弧面,外观较为光洁。
第二种:砂(渣)眼1.原因:流路或模具的表面光洁度或拔模斜度小对策:1、避免生产使用的模板表面生锈。
2、提高模具的质量,减少补土的使用;模具上的补土应完整、平滑。
3、模具的使用和存放要小心,避免模具表面的碰伤。
4、增加拔模斜度。
现象:在铸件表面上出现分布不均匀的小空洞,通常呈现不规整,深浅不一且内部较不光洁,无冷口现象。
2 原因——流路设计不合理,浇注时铁水的冲刷形成砂眼。
对策:1、改变入水位置,避免入水严重冲击砂型。
2、改变入水口面积,降低铁水的冲刷力。
3、制作压边或采用综合式浇注系统,提高浇注系统的挡渣效果。
3 原因——流路设计不合理,冲型时间过长,长时间的烘烤及“水份迁移”造成局部型砂强度低形成砂眼。
对策:流路设计保证快速冲型,同时冲型。
现象:在铸件表面上出现分布不均匀的小空洞,通常呈现不规整,深浅不一且内部较不光洁,无冷口现象。
4 原因——型砂含水量低。
对策:1、调整型砂水份。
2、长时间停机后,要将皮带上的型砂排掉。
3、长时间未浇注的型砂要报废。
5 原因——浇口杯的位置向下偏移,造型时在浇口杯上积存的型砂在脱模时落入型腔。
对策:1、将浇口杯锁紧。
2、必要时去除反板浇口杯的上缘部分,以防止反板抬起后,DISA衡量挤压浇口杯造成浇口杯下移。
压铸件的缺陷及产生的原因

压铸生产中遇到的质量问题很多,其原因也是多方面。
生产中必须对产生的质量问题作出正确的判断。
找出真正的原因,才能提出相应切实可行的有效的改进措施,以便不断提高铸件质量。
压铸件生产所出现的质量问题中,有关缺陷方面的特征、产生的原因(包括改进措施)分别叙述于后。
一、欠铸压铸件成形过程中,某些部位填充不完整,称为欠铸。
当欠铸的部位严重时,可以作为铸件的形状不符合图纸要求来看待。
通常对于欠铸是不允许存在的。
造成欠铸的原因有:1)填充条件不良,欠铸部位呈不规则的冷凝金属当压力不足、不够、流动前沿的金属凝固过早,造成转角、深凹、薄壁(甚至薄于平均壁厚)、柱形孔壁等部位产生欠铸。
模具温度过低合金浇入温度过低内浇口位置不好,形成大的流动阻力2)气体阻碍,欠铸部位表面光滑,但形状不规则难以开设排溢系统的部位,气体积聚熔融金属的流动时,湍流剧烈,包卷气体3)模具型腔有残留物涂料的用量或喷涂方法不当,造成局部的涂料沉积成型零件的镶拼缝隙过大,或滑动配合间隙过大,填充时窜入金属,铸件脱出后,并未能被完全带出而呈现片状夹在缝隙上。
当之种片状的金属(金属片,其厚度即为缝隙的大小)又凸于周围型面较多,便在合模的情况下将凸出的高度变成适为铸件的壁厚,使以后的铸件在该处产生穿透(对壁厚来说)的沟槽。
这种穿透的沟槽即成为欠铸的一种特殊形式。
这种欠铸现象多在由镶拼组成的深腔的情况下出现。
浇料不足(包括余料节过薄)。
立式压铸机上,压射时,下冲头下移让开喷嘴孔口不够,造成一系列的填充条件不良。
二、裂纹铸件的基体被破坏或断开,形成细长的缝隙,呈现不规则线形,在外力作用下有发展的趋势,这种缺陷称为裂纹。
在压铸件上,裂纹是不允许存在的。
造成裂纹的原因有:1.铸件结构和形状铸件上的厚壁与薄壁的相接处转变避剧烈铸件上的转折圆角不够铸件上能安置推杆的部位不够,造成推杆分布不均衡铸件设计上考虑不周,收缩时产生应力而撕裂。
2.模具的成型零件的表面质量不好,装固不稳成型表面沿出模方向有凹陷,铸件脱出撕裂凸的成型表面其根部有加工痕迹未能消除,铸件被成型零件装固有偏斜,阻碍铸件脱出。
压铸常见不良及改善对策

气泡
1、排气道堵塞。
2、模温过高,脱模剂喷涂不够。
3、流通过快,铝液推进卷入空气。
1、清理模面排气道。
2、依据产品结构调整料温,防止模温过高。
3、调机改善射程及射速,调整开模时间
编制:
审核:
核准
冷料
1、料温过低,铝液流动性差。
2、喷水时间过长,导致模温过低影响铝液 流动性。
3、调机不良(压力、行程)。
1、检查料温,根据产品结构调整。
2、喷涂脱模剂手法改善,特别是径位较深产品,
需增加吹气时间(特别是模具带行位的)。
3、调机改善。
冷隔、冷纹
1、调机射程不良。
2、打汤过多、过少,影响二次射程远近。
崩缺
1、检查产品调机外观有无冷纹,造成进浇 崩缺。
2、敲渣包水口方向错误。
1、增加进浇及渣包口R角,增加强度。
2、调整敲包水口方向。
变形
1、压铸件拉模。
2、模具断顶针。
3、压型时间不够。
1、拉模省模处理。
2、更换顶针。
3、调整开模时间。
砂孔
1、压铸成型压力不够。
2、渣包堵塞未出模。
1、调机改善成型压力。
1、控制颗粒油。
2、调整脱模剂浓度,改善喷水手法。
积碳
1、脱模剂配比不良,喷涂不均匀。
2、模温过高,导致脱模剂粘附模面。
1、模具省模处理,注意省模方式,不可造成产 品尺寸变异。
2、调整脱模剂浓度,改善喷水手法。
断差
1、检查导柱有无变形。
2、检查滑块位有无飞料。
1、更换导柱。
2、清理滑块,重新锁模调紧,适当调整压力, 降低料温,防止滑块飞料。
压铸过程缺陷及简要分析

编制:张敬修
日期:2017-6-6
1 ,压铸部分
1,冷隔: 压铸件表面有明显的、不 规则的、下陷线性型纹路(有 穿透与不穿透两种)形状细小 而狭长,有时交接边缘光滑, 在外力作用下有断相互对接,但未完全熔合而又无夹杂存在其间; 2,浇注温度或模具温度偏低; 3,填充速度低。 预防及改善方法: 1,适当提高浇注温度; 2,提高压射比压缩短填充时间,提高压射速度; 3,改善排气、渣包、填充条件。
预防及改善方法: 1,顶杆长短合理配置; 2,模温偏高处降低模温,多喷水; 3,省修出模困难处。
1 ,压铸部分
12,断销子: 销子孔孔底变浅,且孔底 不平(除非磨平)。
产生的可能原因: 1,销子硬度不够; 2,销子较长或较细,易变形,在外力作用下易断裂; 3,销子老化。 预防及改善方法: 1,选择合适的材料,提高硬度; 2,合理选择销子直径及长短; 3,易断销子处多喷水; 4, 定期更换销子。
1 ,压铸部分
10,级位(段差/台阶): 压铸件表面出现阶梯痕迹。
产生的可能原因: 1,动定模错位; 2,滑块错位、松动后退; 3,披锋厚导致。
预防及改善方法: 1,紧固滑块及其他活动部位; 2,配合面调整合适。
1 ,压铸部分
11,顶杆高/低: 顶杆位凸出或凹入。
产生的可能原因: 1,顶杆配置长短不合理; 2,模具局部温度过高,顶杆易被卡住; 3,模具局部出模困难。
1 ,压铸部分
7,气泡: 压铸件表面有气体聚集, 甚至在铸件表面鼓泡。 产生的可能原因: 1,有卷入性气体; 2,铝料中气体较多; 3,局部模温过高,料温过高。
预防及改善方法: 1,改善内浇道,提高压射压力; 2,除去铝料中气体和杂质; 3,局部模温过高处多喷水,控制好模温。
铸件发生不良的原因及解决方法

压铸件发生不良的原因1:于压铸件的设计有关(1)压铸件的肉厚设计不良。
(2)压铸件的形状太复杂。
(3)太铸件的脱模斜度不当。
2:于太铸机的性有关者(1)锁模力、射出力的太小。
(2)压铸机射出量不足或太多。
(3)压铸速度不正当。
3:于太铸模具有关者(1)模具制作精度不合及脱模斜不良。
(2)顶出方式的先择不当(3)流道系统设计不良(4)气孔及溢流槽数目太少(5)模具先择材料不良(6)冷却水道的位置及大小等设计制作不当4:于压铸作业有关者(1)合金熔液的温度控制不当(2)模温的控制不当(3)离型剂的使用不发(4)合金熔液处理不发,混进杂物(5)合金原料的管制不当压铸件缺陷及其对策1:铸件表面冷纹(流纹)表面冷纹是不同的固化区之间的细接合线,铸件表面形成难看的细纹,这种缺陷的形成,主要是模温太低,离型剂涂布过量或模具于合金熔液的温差太大,冷纹旦形成则对铸件的镀层或著漆均不利,使表面涂层失去保护作用,在浇口处也易产生内应力。
其防止的方法为:(1)提高模温。
(2)增设溢流槽(3)注意离型剂的使用。
(4)必要时加大流道系统。
2:缩裂发生缩裂是由于铸件的内应力,脱模斜度过小或顶出不良所影响。
基防止方法为加在铸件脱模斜度,检讨顶出及铸件的形状各射出条件。
3:缩陷铸件较厚处于模穴局部过热点,该处冷却凝固缓慢,且常发生表面凹陷现象,其预防方法为:(1)注意模具的设计于铸件的形状设计肉厚就均匀。
(2)增高熔液的射出压力。
(3)注意浇口的位置形状及大小4:隔层或冷界金属熔液由于射出速度太慢,射出压力不足或模温过低,其前端在模穴内形成氧化膜,而使熔液未能完全熔合,所产生的残留交界。
其预防方法:(1)增大射出速度及射出压力。
(2)提高合金液温及模温。
(3)增大横浇道及浇口断面积。
(4)改变浇口的位置(止法一般不可行)(5)增加溢流槽的设置。
5:表面砂眼(气泡)砂眼或气泡是铸件表面的残存空气囊,当开模时,若铸件的强度无法防止在射出的压力状态下的空气膨胀,就会出现气泡,尤其厚度低于1mm的薄件更易发生。
压铸件常见缺陷及改善对策
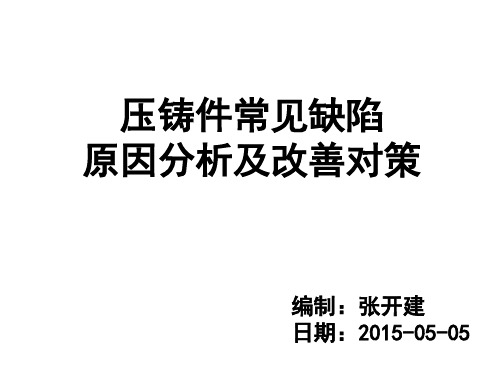
喷涂工艺:使用量过多,造成气体挥发量大, 冲头润滑剂太多,或被烧焦,都是气体的来源。
气孔-防止方法: 1、干燥、干净的合金料。 2、控制熔炼温度,避免过热,进行除气处理。 3、合理选择压铸工艺参数,特别是压射速度。调 整高速切换起点。
4、顺序填充有利于型腔气体排出,直浇道和横浇 道有足够的长度(>50mm),以利于合金液平稳流 动和气体有机会排出。可改变浇口厚度、浇口方向、 在形成气孔的设置溢流槽、排气槽。
溢流品截面积总和不能小于内浇口截面总和的 60%,否则排渣效果差。
5、选择性能好的涂料及控制喷涂量。
二、粘模、拉模图片
缺陷名称:粘模 英文名称: solder
缺陷名称:扣模,拉模 英文名称: drags
二、粘模(拉模)
特征及检验方法:沿开模方向铸件表面呈现条状的拉伤痕 迹,有一定深度,严重时为面状伤痕。另一种是金属液与模具 产生粘合,粘附而拉伤,以致铸件表面多料或缺料。目视检查 可以识别
产生原因: 1、型腔表面有损伤(压塌或敲伤)。 2、脱模方向斜度太小或倒斜。 3、顶出时不平衡,顶偏斜。 4、浇注温度过高、模温过高导致合金液产生粘附。 5、脱模剂效果不好。 6、铝和金成份含铁量低于0.6%。 7、型腔粗糙不光滑,模具硬度偏低。
粘模(拉模)-预防措施: 1、修复模具表面损伤部位,修正脱模斜度,提高 模具硬度(HRC45°~48°),提高模具光洁度。 2、调整顶杆,使顶出平衡。 3、更换脱模效果好的脱模剂。 4、调整合金含铁量。 5、降低浇注温度,控制模具温度平稳、平衡。 6、调整内浇口方向,避免金属液直冲型芯、型壁。
目录
九、缩水的产生原因及改善对策 十、欠铸的产生原因及改善对策 十一、毛刺的产生原因及改善对策 十二、夹渣的产生原因及改善对策 十三、夹层的产生原因及改善对策 十四、解决压铸缺陷的思路
压铸件不良及原因分析
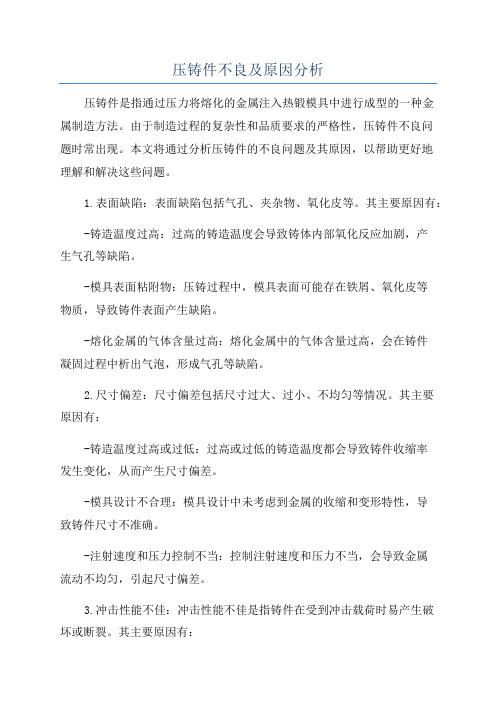
压铸件不良及原因分析压铸件是指通过压力将熔化的金属注入热锻模具中进行成型的一种金属制造方法。
由于制造过程的复杂性和品质要求的严格性,压铸件不良问题时常出现。
本文将通过分析压铸件的不良问题及其原因,以帮助更好地理解和解决这些问题。
1.表面缺陷:表面缺陷包括气孔、夹杂物、氧化皮等。
其主要原因有:-铸造温度过高:过高的铸造温度会导致铸体内部氧化反应加剧,产生气孔等缺陷。
-模具表面粘附物:压铸过程中,模具表面可能存在铁屑、氧化皮等物质,导致铸件表面产生缺陷。
-熔化金属的气体含量过高:熔化金属中的气体含量过高,会在铸件凝固过程中析出气泡,形成气孔等缺陷。
2.尺寸偏差:尺寸偏差包括尺寸过大、过小、不均匀等情况。
其主要原因有:-铸造温度过高或过低:过高或过低的铸造温度都会导致铸件收缩率发生变化,从而产生尺寸偏差。
-模具设计不合理:模具设计中未考虑到金属的收缩和变形特性,导致铸件尺寸不准确。
-注射速度和压力控制不当:控制注射速度和压力不当,会导致金属流动不均匀,引起尺寸偏差。
3.冲击性能不佳:冲击性能不佳是指铸件在受到冲击载荷时易产生破坏或断裂。
其主要原因有:-金属组织不均匀:熔化金属在快速冷却过程中,易产生晶粒过大、晶界异常等问题,导致冲击性能下降。
-含气量过高:熔化金属中的气体含量过高,会在铸件凝固过程中析出气泡,降低冲击性能。
-金属材料的不合理选择:选择不合适的金属材料,其化学成分和机械性能可能不满足冲击性能要求。
4.裂纹:裂纹是指铸件表面或内部出现的细小或明显的裂缝。
其主要原因有:-材料内部应力过大:熔化金属在凝固过程中,由于收缩等原因会产生内部应力,过大的应力会导致铸件出现裂纹。
-注射速度和压力控制不当:控制注射速度和压力不当,使得金属充实不充分或过量,都会导致铸件的裂纹。
-模具温度不均匀:模具温度不均匀会导致铸件冷却速率不均匀,产生应力过大而发生裂纹。
5.金属疲劳:金属疲劳是指铸件在循环载荷下产生的微裂纹最终引起断裂。
压铸常见缺陷原因及改善方法
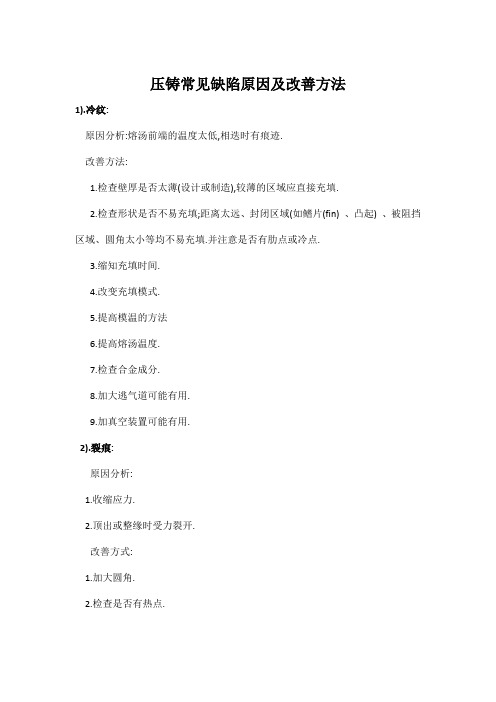
压铸常见缺陷原因及改善方法1).冷纹:原因分析:熔汤前端的温度太低,相迭时有痕迹.改善方法:1.检查壁厚是否太薄(设计或制造),较薄的区域应直接充填.2.检查形状是否不易充填;距离太远、封闭区域(如鳍片(fin) 、凸起) 、被阻挡区域、圆角太小等均不易充填.并注意是否有肋点或冷点.3.缩知充填时间.4.改变充填模式.5.提高模温的方法6.提高熔汤温度.7.检查合金成分.8.加大逃气道可能有用.9.加真空装置可能有用.2).裂痕:原因分析:1.收缩应力.2.顶出或整缘时受力裂开.改善方式:1.加大圆角.2.检查是否有热点.3.增压时间改变(冷室机).4.增加或缩短合模时间.5.增加拔模角.6.增加顶出销.7.检查模具是否有错位、变形.8.检查合金成分.3).气孔:原因分析:1.空气夹杂在熔汤中.2.气体的来源:熔解时、在料管中、在模具中、离型剂.改善方法:1.适当的慢速.2.检查流道转弯是否圆滑,截面积是否渐减.3.检查逃气道面积是否够大,是否有被阻塞,位置是否位于最后充填的地方.4.检查离型剂是否喷太多,模温是否太低.5.使用真空.4).空蚀:原因分析:因压力突然减小,使熔汤中的气体忽然膨胀,冲击模具,造成模具损伤. 改善方法:1.流道截面积勿急遽变化5).缩孔:原因分析:当金属由液态凝固为固态时所占的空间变小,若无金属补充便会形成缩孔.通常发生在较慢凝固处.改善方法:1.增加压力.2.改变模具温度.局部冷却、喷离型剂、降低模温、.有时只是改变缩孔位置,而非消缩孔.6).脱皮:原因分析:1.充填模式不良,造成熔汤重迭.2.模具变形,造成熔汤重迭.3.夹杂氧化层.改善方法:1.提早切换为高速.2.缩短充填时间.3.改变充填模式,浇口位置,浇口速度.4.检查模具强度是否足够.5.检查销模装置是否良好.6.检查是否夹杂氧化层.7).波纹:原因分析:第一层熔汤在表面急遽冷却,第二层熔汤流过未能将第一层熔解,却又有足够的融合,造成组织不同.改善方法:1.改善充填模式.2.缩短充填时间.8).流动不良产生的孔:原因分析:熔汤流动太慢、或是太冷、或是充填模式不良,因此在凝固的金属接合处有孔.改善方法:1.同改善冷纹方法.2.检查熔汤温度是否稳定.3.检查模具温充是否稳定.9).在分模面的孔:原因分析:可能是缩孔或是气孔.改善方法:1.若是缩孔,减小浇口厚度或是溢流井进口厚度.2.冷却浇口.3.若是气孔,注意排气或卷气问题.10).毛边:原因分析:1.锁模力不足.2.模具合模不良.3.模具强度不足.4.熔汤温度太高.11).缩陷:原因分析:缩孔发生在压件表面下面.改善方法:1.同改善缩孔的方法.2.局部冷却.3.加热另一边.12).积碳:原因分析:离型剂或其他杂质积附在模具上.改善方法:1.减小离型剂喷洒量.2.升高模温.3.选择适合的离型剂.4.使用软水稀释离型剂.13).冒泡:原因分析:气体卷在铸件的表面下面.改善方式:1.减少卷气(同气孔).2.冷却或防低模温.14).黏膜:原因分析:1.锌积附在模具表面.2.熔汤冲击模具,造成模面损坏. 改善方法:1.降低模具温度.2.降低划面粗糙度.3.加大拔模角.4.镀膜.5.改变充填模式.6.降氏浇口速度.。
压铸不良原因发生与对策

压铸不良原因发生与对策一、流痕◎定义产品表面形成的褶皱。
多发生在产品薄肉部,袋形部分(气孔易残留,排气不畅处)◎特点沟槽处的浅褶皱在产品表面广泛形成◎原因1.模温低,溶汤温度低时,易发生2.脱模剂使用量过多3.排气性不好时◎对策1-1提升模温T℃↑1-2提升铝汤温度T℃↑1-3提升易产生不良处的温度T℃↑2-1少量使用脱模剂2-2吹气徹底3-1防止气体无法排出3-2 防止气体堵产品内部3-3适当调整射出速度V,高速切换时间二、流动不顺◎定义由于铝汤在完全充填之前,便发生凝固而产生的不良缺陷。
轻微时,前端直角部产生欠肉,或平面处有孔洞产生。
◎特征产品的边角部位铝汤未填充満,而产生的带圆形缺肉状◎原因1.铝液温度低而导致凝固。
2.排气性不好。
◎对策1-1提高模具温度。
1-2提高铝汤温度1-3调节射出速度、鋳造圧力到合适值1-4浇品位置,厚度,宽度的合适化2-1 防止气体堵塞三、缩孔◎定义在产品的角部,R角部,由于铝汤在凝固收缩时而产生的凹坑现象。
◎特征在产品壁厚部或薄厚很不均的产品壁内侧产生的收缩空洞◎原因1.局部过热2.铝汤供给不充分时3.有必要调查模温的分布◎对策1-1 在过热部分,加强冷却1-2 改变产品形状2-1 改变铸造条件2-2 采用适当的铸造方案四、收缩裂纹◎定义在铸造凝固过程中,沿着结晶粒界,缝隙中产生的裂纹。
◎特征由于凝固收缩产生了不规则形状的裂纹,龟裂部位有细小树枝状结晶呈现出来。
◎原因1凝固収縮造成铝汤不足2产品形状不均等3凝固速度缓慢,确认模温分布。
◎对策1-1铸造方案变更(提高汤流性)浇道速度增加填充时间缩短铸造压力增加(确认氮气量)模具温度最适化溶汤温度最适化2-1产品形状变更产品壁厚R部,角部形状V形盗肉追加3-1模温管理检讨在壁厚部追加点冷强化壁厚部的脱模剂量五、冷隔◎定义产品表面上,当铝液合流时,未能完全融合,形成的隔层。
隔层边缘呈圆滑状◎特征在铸造物表面的垂直方向上产生冷隔,其两侧完全分离开,间隔一定距离◎原因1铝汤温度低,在合流处不能完全溶合,铝液前端形成氧化膜,相互间的氧化膜不能溶合从而产生冷隔。
铸件十大不良现象及原因
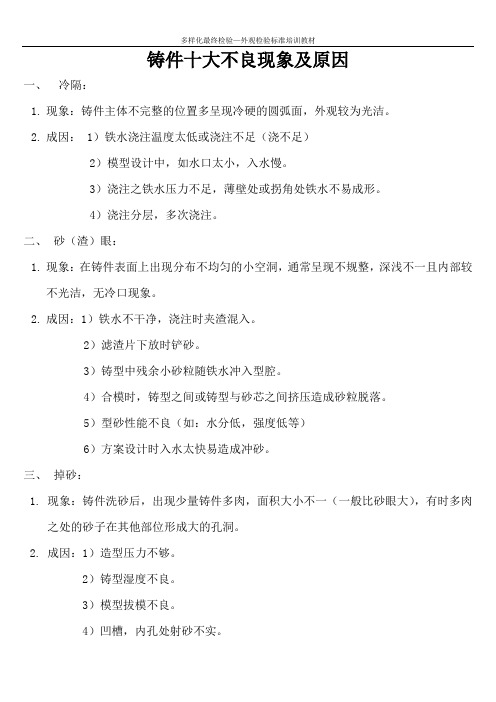
铸件十大不良现象及原因一、冷隔:1.现象:铸件主体不完整的位置多呈现冷硬的圆弧面,外观较为光洁。
2.成因: 1)铁水浇注温度太低或浇注不足(浇不足)2)模型设计中,如水口太小,入水慢。
3)浇注之铁水压力不足,薄壁处或拐角处铁水不易成形。
4)浇注分层,多次浇注。
二、砂(渣)眼:1.现象:在铸件表面上出现分布不均匀的小空洞,通常呈现不规整,深浅不一且内部较不光洁,无冷口现象。
2.成因:1)铁水不干净,浇注时夹渣混入。
2)滤渣片下放时铲砂。
3)铸型中残余小砂粒随铁水冲入型腔。
4)合模时,铸型之间或铸型与砂芯之间挤压造成砂粒脱落。
5)型砂性能不良(如:水分低,强度低等)6)方案设计时入水太快易造成冲砂。
三、掉砂:1.现象:铸件洗砂后,出现少量铸件多肉,面积大小不一(一般比砂眼大),有时多肉之处的砂子在其他部位形成大的孔洞。
2.成因:1)造型压力不够。
2)铸型湿度不良。
3)模型拔模不良。
4)凹槽,内孔处射砂不实。
四、粘板:1.现象:铸件出现大量之多肉,且同一模具位置较为一致,多在拐角不易拔模处。
2.成因:1)造型时,模板未预热。
2)分型液喷洒不良(或不适量)3)模型拔模不良4)铸砂稳定性不够,一般在较干时易粘板五、押入(挤砂):1.现象:铸件表面上呈现落沉现象,边缘明显。
2.成因:1)合模压力过大,造成铸型破裂,裂成的表面移动。
2)造模之参数选定不良等。
3)浇注后,不良异物重压铸件(铁水尚未凝固时)4)砂芯位置跑偏或芯头与型腔配合不好。
六、错模:1.现象:铸件之分型部位出现不吻合,或上下或左右移动。
2.成因:1)正反板模型位置不统一。
2)DISA跑偏。
3)砂型跑偏(漏铁水时常见)七、粘砂:1.现象:铸件表面参差不齐,粗糙。
2.成因:1)铸砂性能不良。
2)离型液喷洒不良。
3)模板温度低于型砂温度。
八、气孔:1.现象:铸件表面呈现数量不等的小孔洞,比砂眼小且深孔洞一般比砂眼较为圆整。
2.成因:1)型砂的透气型不好。
- 1、下载文档前请自行甄别文档内容的完整性,平台不提供额外的编辑、内容补充、找答案等附加服务。
- 2、"仅部分预览"的文档,不可在线预览部分如存在完整性等问题,可反馈申请退款(可完整预览的文档不适用该条件!)。
- 3、如文档侵犯您的权益,请联系客服反馈,我们会尽快为您处理(人工客服工作时间:9:00-18:30)。
收縮孔要因分析圖表
局部容易過熱形狀
sle e v e 內 徑 太 粗 糙
產品設計
金屬模
澆口襯套尺寸不合格 澆口襯套有磨損 冷卻水孔不足 澆口位置有缺陷 型蕊停止器有缺陷(漏壓) 型蕊嵌合有缺陷 剛性不足(漏壓) 模具精度不合格(漏壓)
鑄造技術
條件的設定有缺陷 調整金屬液量有缺陷 調整冷卻水有缺陷 金屬液溫變化大 模具溫度變化大 周期不均一
作業員
溶解
素材缺陷不良要因圖例子
金屬模
型腔配置有缺陷 冷卻水有泄漏 溫度分佈不均勻
作業員
調整冷卻水有缺陷 脫模劑噴塗有缺陷 沒有知識 注金屬液量不足
溶融金屬
新舊配合有錯誤 脫氧脫氣體有缺陷 分配金屬液溫度有缺陷 混有夾雜物 原材料材質不合格 金屬液量不足
冷卻孔有缺陷
澆口方案有缺陷 溢流有缺陷 排氣孔有缺陷 發生毛刺 金屬模精度不合格 澆口襯套有磨損 澆口襯套偏蕊 壓射壓力不足(N2不足)
鋁合金材料不合格 柱塞潤滑有缺陷 冷卻水不足.停水 QC活動不足(機前檢查) 作業標準書有缺陷 檢查標準不充分
壓射柱塞冷卻பைடு நூலகம்缺陷
機械
鑄造條件
其他
特性主要因素圖例子(氣泡孔)
金屬模
剛性不足 型蕊漏油 模具精度不合格 冷卻孔有缺陷(位置,大小) 冷卻水有泄漏 排氣孔有缺陷(位置,大小) 溢流有缺陷(位置,大小) 澆口方案有缺陷
金屬液溫變動大 錯誤的材料
材料補充法有缺陷 溫度調節器有缺陷
脫模劑太多 脫模劑噴塗有缺陷 送風有缺陷 柱塞潤滑油太多
材料的配合有缺陷 成份不合格(混有鐵質) 脫氧脫氣有缺陷 除去氧化物有缺陷 金屬液溫太低,太高
速度轉換位置有缺陷 模具溫度太低 預熱不足 注金屬液量不足
調整合模力有缺陷 柱塞冷卻有缺陷
作業員
周期 調整金屬模溫度 柱塞潤滑油量
調整金屬液溫度 噴塗位置 脫膜劑量,濃度 低高速轉換位置
調整柱金屬液動作
注金屬液量 壓射速度 鑄造條件的設定有缺陷 壓射壓力 金屬模清掃不充足(毛剌、溢流、水印) 作業標準書不充足 鑄造條件的設定有缺陷 研究不充分 教育指導不充分 質量管理活動不足 處理溶融金屬有缺陷 機械維修有缺陷 金屬模維修有缺陷 副資材質量不合格 附帶設備有缺陷 金屬料錠材質不合格
在厚壁部不能安裝澆口 厚壁差距很大 局部的壁很大
收縮孔
N2氣體不足 增壓時間不良 澆套筒徑太粗 澆套筒卡住 壓射柱塞卡住 維修有缺陷
壓射力太小 不能增壓 壓射蕊偏位 柱塞嵌合有缺陷 柱塞有磨損 澆套筒有磨損 加工尺寸不合格+_
金屬液溫太高 模具溫度分布不均勺 模具溫度太高 注金屬液量不足 增壓時期太慢 澆口襯套太冷
模具溫度 變動大
作業員不習慣
金屬模精度不合格 溶融金屬溫度太高 壓射壓力太高 壓射速度太高 清掃模具有缺陷
注金屬液時期不好 計器時的設定有缺陷 調整合模力有缺陷
特性主要因素圖例子(膨脹)
金屬模 作業員 溫度管理及加工
研磨加工有缺陷 加熱方法有缺陷 (參閱氣泡孔) (參閱氣泡孔) 熱處理時間太長 DT設定有缺陷 產品取出溫度太高
其他
嵌入物形狀有缺陷 氣壓變動 空氣含有水分 副資材有缺陷(柱塞潤滑油,脫模劑 作業標準書有缺陷
澆口襯套偏心 漏壓, 排氣孔有缺陷 模具表面有缺陷 溢流, 排氣孔有缺陷 澆口方案有缺陷
表面有 缺陷
模具溫度變動太大 調整壓射壓力有缺陷 調整壓射速度有缺陷
冷卻水壓變動 周期不一定 發生毛刺 作業員偷懶 其他 調整冷卻水有缺陷
無活動
壓射速度不足
作業員教育不充分 質量管理活動不足 實行力不充足 材料管理有缺陷 模具調整有缺陷
副資材有缺陷(脫膜劑
、柱塞潤滑油) 學習、研究不充分
機械
管理員
其他
模具溫度變動大要因圖例子
調整冷卻水有缺陷 水道堵塞 供水泵發生故障 供水能力不足 水溫變化很大 水量變化很大 水壓變化很大 周期不一定 調整脫模劑量有缺陷 調整送風有缺陷 脫模劑噴塗有缺陷 氣壓變動很大 氣體含有水分 溶融金屬溫度變化大 分配金屬液溫度有缺陷 發生毛刺 嵌入物尺寸不合格 金屬模熱粘 反常壓射 作業員偷懶 造型有缺陷 造型作業有缺陷 箱容量不足 冷卻機有缺陷 機械發生故障 金屬模有問題 管理員教育不充分 作業員教育不充分 作業員技術水平低 作業標準書有缺陷
鑄造條件的設定有錯誤 脫膜劑太多,太濃 送風不足 周期不一定 金屬液溫變動大 模具溫度變動大 預熱不足 作業標準書有缺陷
素材有缺 陷
調整,維修有缺陷
金屬模維修有缺陷 機械維修有缺陷 嵌入物形狀有缺陷 情報交流不足 氣體含有水分(排水有缺陷 質量管理界限不明確 業務負責人不明確
模板平行度不合格 柱塞有磨損 壓射套筒有磨損 壓射中心有缺陷 發生故障(反常)
水泡
(參閱氣泡孔)
(參閱氣泡孔)
(參閱氣泡孔)
機械
管理員
其他
氣泡孔
柱塞漏冷卻水 壓射壓力不足(N2氣體不足) 壓射速度不足 低高速轉換有缺陷 澆套簡有磨損 壓射柱塞有磨損 增壓有缺陷 精度不合格,功能有缺陷
機械
管理員
其他
素材外觀不良要因圖例子(表面缺陷)
金屬模
定位銷,襯套鬆動 脫模斜度不足 模具表面燒結 冷卻水有泄漏
型蕊澆口塞 有缺陷
機械
機械維修有缺 同下嵌合有缺陷 套筒有磨損 柱塞漏水 柱塞有磨損(漏壓) 壓射速度不足 機械 壓射力不足 能力 合模力不足 澆口襯套偏心 模具剛性不足 模具精度不合格