硅锰合金生产中入炉锰矿的优化搭配
硅锰合金生产工艺流程
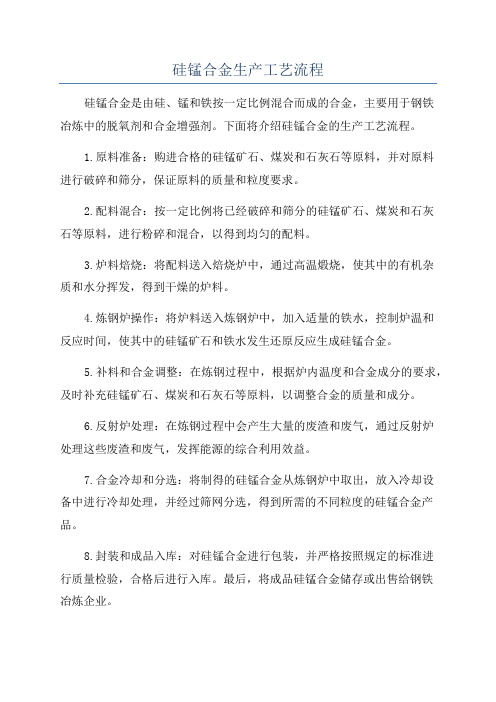
硅锰合金生产工艺流程
硅锰合金是由硅、锰和铁按一定比例混合而成的合金,主要用于钢铁
冶炼中的脱氧剂和合金增强剂。
下面将介绍硅锰合金的生产工艺流程。
1.原料准备:购进合格的硅锰矿石、煤炭和石灰石等原料,并对原料
进行破碎和筛分,保证原料的质量和粒度要求。
2.配料混合:按一定比例将已经破碎和筛分的硅锰矿石、煤炭和石灰
石等原料,进行粉碎和混合,以得到均匀的配料。
3.炉料焙烧:将配料送入焙烧炉中,通过高温煅烧,使其中的有机杂
质和水分挥发,得到干燥的炉料。
4.炼钢炉操作:将炉料送入炼钢炉中,加入适量的铁水,控制炉温和
反应时间,使其中的硅锰矿石和铁水发生还原反应生成硅锰合金。
5.补料和合金调整:在炼钢过程中,根据炉内温度和合金成分的要求,及时补充硅锰矿石、煤炭和石灰石等原料,以调整合金的质量和成分。
6.反射炉处理:在炼钢过程中会产生大量的废渣和废气,通过反射炉
处理这些废渣和废气,发挥能源的综合利用效益。
7.合金冷却和分选:将制得的硅锰合金从炼钢炉中取出,放入冷却设
备中进行冷却处理,并经过筛网分选,得到所需的不同粒度的硅锰合金产品。
8.封装和成品入库:对硅锰合金进行包装,并严格按照规定的标准进
行质量检验,合格后进行入库。
最后,将成品硅锰合金储存或出售给钢铁
冶炼企业。
整个硅锰合金生产工艺流程中,需要严格控制每个步骤的工艺参数,如原料的质量和粒度、炉温、反应时间等,以保证生产过程的稳定和最终产品的质量。
同时,还需要加强能源利用效率,减少废渣和废气的排放,注重环境保护,实现可持续发展。
硅锰合金冶炼对入炉原料、辅料的要求

1、锰矿石锰矿石是指可供工业提取锰或直接用于工业上的含锰矿物。
根据一成条件可分为沉积矿床、变质矿床和风化层矿床,按化学结构可分为氧化锰矿、碳酸盐锰矿、硅酸盐锰矿等。
我国锰矿资源大部分集中在中南和西南地地区,类型以氧化锰矿和碳酸锰矿为主。
在锰硅合金生产中,对锰矿石的要求有以下几个方面:1.1含Mn高:含锰量是锰矿石的主要质量指标,锰含量越高,越有益于各项经济技术指标的改善。
1.2含Fe适中:由于铁在冶炼过程中95%以上进入合金,因此对锰矿中铁含量随生产品种不同要求也不一样,在实际生产中,常使用锰矿石和含铁低的富锰渣搭配入炉,得到合格的产品。
1.3SiO2不作严格限制:锰矿石中含有一定的SiO2对锰硅合金生产是有益的,但也不是越高越好,一般以料批中不须配入硅石即能生产出合格产品为益。
1.4CaO和MgO不予限制。
1.5P、Al2O3要低:锰矿中的P、Al2O3对所有锰系合金冶炼来说都是无益组分,但适量Al2O3的对冶炼过程有一定的促进作用。
1.6物理特征:锰矿石要求有一定的粒度、抗压强度和低的含水量。
粉矿会降低炉料的透气性,抗压强度低的矿石在炉内易粉化,也会降你炉料透气性,锰挥发多,不利于化学反应和热交换,锰回收率低;含水量高的矿石入炉后会使热损耗增大,降低化料速度。
2、焦炭在锰硅合金生产中对焦炭的要求一般为:固定碳含量80%以上,灰分低于18%,挥发分不作限制(4~5%),水分越低越好,电阻率高,反应活性好,粒度合适,有一定的机械强度。
3、辅料3.1硅石:要求SiO2含量在97%以上,粒度适合,具有良好的抗爆性能。
3.2白云石:要求CaO%≧30%,MgO≧20%,粒度合适。
3.3石灰:要求CaO%≧82%,使用前无粉化。
3.4萤石:要求CaF2%≧50%,粒度合适。
硅锰合金生产工艺

硅锰合金生产工艺
硅锰合金是以硅、锰为主要原料,经过选矿、破碎、混合、煅烧、冷却、粉碎、筛分等工艺制成的一种合金产品。
下面是硅锰合金生产工艺的主要步骤:
1. 选矿:首先对硅锰矿石进行选矿处理,去除其中的杂质,获得含锰、含硅较高的矿石。
2. 破碎:将选矿后的矿石进行粉碎,将矿石破碎成符合工艺要求的颗粒大小。
3. 混合:将经过破碎的矿石与适量的高纯氧化锰粉、高纯氧化硅粉等原料进行混合,保持适当的比例。
4. 煅烧:将混合后的原料放入电炉或其他煅烧设备中进行煅烧,提高矿石中锰和硅的含量,进一步获得合格的硅锰合金。
5. 冷却:待煅烧完成后,将烧结块进行冷却处理,使其温度降至适宜的操作温度。
6. 粉碎:将冷却后的烧结块进行粉碎,使其成为符合产品要求的颗粒。
7. 筛分:对粉碎后的硅锰合金进行筛分,将颗粒按照不同粒度进行分类,以满足不同客户的需求。
以上就是硅锰合金生产工艺的主要步骤。
在整个生产过程中,
需要严格控制各个环节的工艺参数,如煅烧温度、持续时间、原料配比等,以确保产品质量的稳定性和一致性。
此外,还需要进行定期的检测和分析,对产品进行质量评估,以满足市场的需求。
硅锰合金矿热炉原料系统介绍

硅锰合金矿热炉原料系统介绍内容摘要:硅锰合金炉的原料按各自的配比进行自动称量、计量、配料并输送进矿热炉,配料室的配比计算。
关键词:硅锰矿热炉、锰矿、烧结锰矿、焦炭、皮带输送机、称量斗,减量计量。
硅锰合金生产原料的质量在很大程度上决定着工艺过程的技术经济指标好坏,原料的各项指标稳定,特别是化学成份和粒度组成的稳定,是保证冶炼制度稳定顺行的重要条件,可以使原料以及电力资源得以有效利用。
传统硅锰合金矿热炉因规模小,原料需要量少,原料回厂后堆放到简易棚内,用铲车造堆堆料及大致铲车配比后输送进矿热炉中进行冶炼,自动化程度不高,随着硅锰合金矿热炉规模的扩大,产品质量要求的提高,对原料的堆存及配比要求越来越严,环保和自动化程度也越来越高。
特别对进矿热炉原料的化学成份和粒度组成的稳定配比要求越来越严格,为了保证矿热炉冶炼出合格的高精度产品,进矿热炉的每炉料都要求比较严格的配比,比如硅锰合金矿热炉,要求从配料站配料的每批料不超过200kg,误差不超过2kg。
某公司建设8台铁合金矿热炉工程,建成后实际生产48.7万吨锰系合金,其中锰硅合金40.2万吨,高碳锰铁8.5万吨;配套1台65m2锰矿焙烧机、给排水系统、供配电系统、通风除尘系统以及余热发电系统、空压站等公辅设施。
硅锰合金矿热炉的原料系统设计范围是从外购锰矿(块矿)、锰矿粉、焦炭等原料进厂卸车开始至铁合金电炉顶层环形加料车为止;包括锰矿卸车堆场、锰矿筛分破碎室、锰矿烘干系统、锰矿粉矿棚(含焙烧用熔剂和燃料)、成品块矿棚(含矿热炉用白云石、硅石)、焦炭干燥棚、焦炭烘干系统、成品焦炭棚、配料室、转运站及皮带机等。
硅锰矿热炉所需主要原料有锰矿(块矿)、富锰渣、焦炭、烧结锰矿、硅石及白云石。
锰矿(块矿)主要购自海外南非锰矿,部分来自国内采购,入炉粒度10~80mm,并进行烘干。
富锰渣外购,经破碎筛分后入炉粒度10~80mm。
焦炭国内就近采购。
入炉粒度15~30mm,根据工艺要求入炉焦炭含水量要尽可能低一些,需进行烘干。
12-硅锰冶炼操作规程
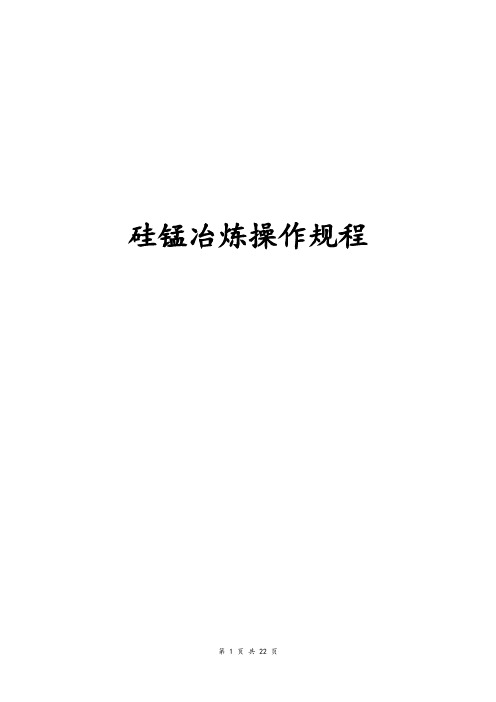
硅锰冶炼操作规程前言为了有效地进行生产和确保产品质量,改善技术经济指标,特制定该标准,作为本企业12500KVA锰硅合金冶炼操作的依据。
本操作规程由张开赋总经理提出制定;本操作规程由生产管理中心归口;本操作规程主要起草单位:XXX本操作规程主要起草人:XXX本操作规程审核人:XXX本操作规程批准人:XXX12500KVA半封闭电炉锰硅合金冶炼操作规程1、范围本标准规定了公司12500KVA电炉锰硅合金生产的冶炼操作,原材料技术要求,遵循标准,电极使用,用电制度,设备维护等工艺要领。
本标准适用于本企业12500KVA电炉锰硅合金生产的操作过程。
1.1电炉参数二分厂各炉炉台参数二分厂电炉变压器参数型号:HKSSPZ-14500/1102、产品技术标准GB/T4008-1996标准及用户要求3、技术要求(内控)3.1锰硅合金主要生产的产品为:MnSi6014;MnSi6517;MnSi7016;MnSi7216。
3.2原料技术要求3.2.1锰矿石3.2.1.1锰矿石作为锰硅合金(含半成品)生产的主要原料,其入炉化学成分应符合:MnSi6014:∑Mn%≥24%,∑Mn/Fe≥3、8,∑P≤0、10%MnSi6517:Mn%≥∑28%,∑Mn/Fe≥6.0,∑P≤0.06%MnSi7016:∑Mn%≥35%,∑Mn/Fe≥10MnSi7216:∑Mn%38%,∑Mn/Fe≥13、2,∑P≤0、06%3.3.1.2入炉锰矿石的物理状态应达到以下要求:粒度不大于80mm,水分不大于6%。
3.2.2萤石萤石作为锰硅合金生产的辅助原料,其理化性质应符合:CaF2≥80%,S≤1%;粒度:20~80mm之间。
3.2.3焦炭3.2.3.1焦炭作为锰硅合金冶炼的还原剂,其化学成分应符合:∑C≥78%,∑灰份≤18%,∑S≤2%(MnSi6014),∑S≤1、5%(MnSi6517),∑S≤1%(MnSi7016)∑S≤1.5%(MnSi7216);3.2.3.2为了焦炭能充分发挥效用,其物理性质应符合:粒度不大于60mm。
锰硅电炉(矿热炉)炉况控制工艺措施

锰硅电炉(矿热炉)炉况控制工艺措施锰硅电炉(矿热炉)炉况控制工艺措施2019.12.281、电极的生成、使用维护在电炉中依靠电极把经过炉用变压器输送的低电压大电流传到炉内,通过电极端部的电弧、炉料电阻及炉内熔体把电能转化为热能进行高温冶炼,形象的被称为炉体的“心脏”,保持好电极的工作状态,减少电极不良变化对炉况的稳定至关重要。
1.1、电极的生成理想自焙电极应具有良好的导电、导热性,抗氧化及抗振等性质,能最大限度的避免在使用过程中出现“蜂腰”、脱块、削尖、和软硬断事故。
1.1.1电极生成送电工艺送电工艺对电极的生成质量起着决定性作用,集中表现在电流的大小和电流的梯度。
新开电炉或热停炉电极在供电的过程中,电极糊随着焙烧温度逐渐升高,粘结剂软化,煤沥青分解开始,挥发份排出,继续升温分解逐渐加快。
热分解在500℃~800℃是发生碳氢化合物的缩聚反应,是粘结剂生产沥青焦,此时的电极糊的导热系数还不高,过快的升温将造成沥青分解速度过快,挥发量过快导致结焦成碳率下降,使得电极的内外温差增大而引起热应力,是电极的强度降低,结构不致密,形成大量的裂纹。
熔融的电极糊与电极壳的不良接触使局部电阻过大,而易将其击穿,漏糊。
当温度升至1500℃~2000℃时导热系数增大,线性膨胀系数减少,挥发分减少,电极的内外温差度减少。
此时可以逐渐送满负荷。
建议在可送满负荷之后再用一定时间的低负荷焙烧,使其均热充分,减少和释放各种应力。
1.1.2电极糊的选择、使用电极糊的好坏与厂商的配方及工艺有密切的关系,不同炉台或不同品牌的生产都应摸索其适合的电极糊成分。
应根据环境温度的变化控制不同糊柱的高度及糊块的大小,使电极糊融化产生的气体顺利排出,避免电极糊“夹生”产生气泡、局部电阻过大、偏析等。
1.1.3电极壳作为电极焙烧的模子,在铜瓦以上承受着大部分的电流,根据电极直径和炉子负荷采用不同厚度的钢板和筋片数量。
实践表明电极壳钢板的厚度、筋片的数量及其高度对电极的焙烧有很大影响1.2、合理热停炉维护在生产过程中由于受到限电、设备检修等因数常需要热停炉,而热停炉电极维护不当,在送电后最易发生硬断或送不起负荷现象。
31500KVA硅锰炉生产工艺、质量标准

31500KV A硅锰炉生产工艺操作规程1.总则1.1产品1.1.1名称、符号硅锰合金:M nSi1.1.2.用途:主要用于做炼钢脱氧剂和合金的和添加剂,生产中低碳硅铁的原料。
1.1.3产品质量标准:注:①硅锰合金以块状或粒状交货,其粒度范围及允许偏差符合下表规定。
②硅锰合金呈块状交货,每块不得超过20Kg,粒度小于20mm的数量不超过总量的8%.③硅锰合金的内部及表面不得带有明显非金属杂物。
1.2主要原材料标准:1.2.1.锰矿石:1.2.1.1.粒度:10-80,小于10 mm粉矿不大于10%。
1.2.1.2.堆放:硅矿进厂后按不同种类、不同品位分别堆放,不得混杂,更不得混入泥土等其它有害杂物。
1.2.2.焦炭:冶金焦,固定碳不小于80%,粒度10-28mm,小于10 mm的不大于10%。
1.2.3.硅石:Sio2≥98%/Ae2o3≤0.5%/Cao≤0.20%/P2O5≤0.02%、粒度20-40mm,小于20mm不大于10%,大于40mm不大于8%,不得带入泥土和杂物。
1.2.4.白云石:Cao≥30%Mgo≥19%Sio2≤3.5%粒度20-40mm.1.2.5.其它:凡进厂的各种原料,入炉前必须有化验结果。
1.3生产工艺流程图:硅石锰矿焦炭白云石硅石萤石↓破碎↓筛分↓料仓↓配料↓冶炼↓渣厂→炉渣→铁水包→扒渣浇注→分析→脱模→入库1.4主要冶金原理及化学反应方程式:1.4.10锰的高价氧化物受热分解或被CO还原:2Mno=Mn2o3+o2 570℃3Mn2o3=2Mn3o4+o2 900℃Mn3o4+CO=3Mno+CO21.4.2.Mno、Feo 、p2o5、Sio2、被碳还原:Mno+C=Mn+CO↑ 1420℃Mno+4/3C=1/3Mn3C+CO↑ 1220℃FeO+C=Fe+CO↑Sio2+2C=Si+2CO↑ MnSi14 1475℃MnSi17 1490℃P2O5+5C=2p+5CO↑1.4.3炉内总反应式及高硅排碳:.MnSiO3+3C=MnSi+3CO↑3MnSiO3+4C=Mn3C+3SiO2+3CO↑SiO2+2C=Si+2CO↑Mn3C+3Si=3MnSi+C2.工艺技术操作规程:2.1.原料工序技术操作规程:2.1.1.生产前准备工作:①各种原材料加工成合格的料,并加到贮料仓中。
硅锰合金生产技术及工艺优化探析

硅锰合金生产技术及工艺优化探析摘要:在社会经济水平快速发展的背景下,工业生产也迎来了全新的变革机会,社会各界在工业产量需求上提升到了全新的高度水平。
而在工业生产流程下,硅锰合金就属于较为普遍的国金原料,而市面上的需求也在逐渐增长。
硅锰合金生产中普通存在渣铁分离不好、翻渣、电流送不上、产量低、电耗高等问题,在很大程度上导致了能耗较高、污染难以控制。
本文通过阐述硅锰合金生产工艺及其存在的问题,以问题为基础提出了针对性的对策。
关键词:硅锰合金;节能技术;高硅硅锰合金;生产工艺一、主要元素功能介绍在实际的炼钢工作流程中,锰元素更多是作用于脱氧剂。
锰元素能够借助自身化学性质,将氧化物的熔点调低,从而使其漂浮在钢水表面。
除此之外,通过锰元素的应用,硅铝制品的脱氧性能可以得到进一步优化。
所以绝大部分工业炼钢流程,都会在熔炼过程中加入合适的锰元素以提升最终的锻造性能,增强刚才的韧性强度,防止在使用过程中出现断裂问题。
而在整个生铁锻造或者碳钢生产环节中,硅元素的重要作用也不容忽视,其实部分钢材熔炼,也会选择将硅元素作为脱氧剂应用,同时这种元素也能够有效增强碳钢结构的稳定程度和韧性,实现钢材性能的全方位优化。
除此之外,硅元素,还具备特殊的石墨化介质属性,可以将生铁中的碳元素转化为对应的石墨碳。
二、硅锰合金生产节能技术分析及应用(一)冶炼周期控制技术冶炼周期控制技术,根据其字面意思,就是通过加热矿热炉实现硅锰合金演练周期的合理管控,适当增加冶炼时间,同时要注意不能超标。
而在此前提下,矿炉内的熔炼反应区会逐渐针对各个元素进行重新控制,从而有效降低渣比。
而在实际操作过程中,冶炼矿热炉的操作手法更加困难,同时炉内有功功率和温度的提升也不容忽视,可能会引发相应的焦炭层反应区,并以此增强部分元素的还原率,生产工作节约大量能源。
不过要注重对冶炼时间延长的控制标准,从而预防时间过长引发的铁温度超标,导致合金内部锰元素大量流失,并且mn回收率也会受到严重影响。
浅谈硅锰合金生产中原料合理搭配

浅谈硅锰合金生产原料的合理搭配及高铝炉渣的合理利用陈渊(锰系铁合金公司)摘要对冶炼硅锰合金原料配比的进行分析后,对冶炼硅锰合金的原料的合理搭配,原料的配比存在的缺陷进行进一步的探讨,同时浅析了冶炼硅锰合金的合理渣型选择,对炉渣成分进行了分析,对炉渣中的Al2O3成的作用进行了浅析。
关键词原料合理搭配渣型硅锰合金一概述在硅锰合金生产中锰矿选择搭配和选择合理的渣型,是硅锰合金工艺操作的关键环节和改善各项生产技术指标的重要措施。
针对国内锰矿质量差、成分波动大的状况,就需要在生产中合理搭配锰矿和充分利用资源,是公司目前生产工艺技术人员的工作重点。
在硅锰合金生产中,锰矿石合理搭配,选择合理的炉渣渣型,既可取得高产品的质量,又可以使炉况能稳定、生产正常,同时改善了各项生产技术指标,降低了生产成本,充分提高公司的经济效益。
现在硅锰生产企业对硅锰生产中怎样合理搭配锰矿和炉渣选择合理优化的炉渣渣型,进行大量探讨和实践摸索,总结经验,使硅锰合金得生产收到了一定的效果。
现在公司对硅锰合金的生产还有一定的差距,需要工艺技术人员进一步的实践摸索、总结经验。
在生产中如何对硅锰合金炉渣中的Al2O3进行合理利用、调节,根据国内多家知名铁合金厂家对硅锰合金炉渣中的Al2O3的摸索和探讨后,总结得出在硅锰合金炉渣中合理利用Al2O3,可以使硅锰合金生产中的渣铁比降低,冶炼电耗降低,产量比较稳定,电极下插稳定,有利于炉况的维护。
锰系公司目前生产硅锰合金中出现了渣量大、渣型不合理,造成电耗高、电极下插差、炉况不稳定、锰回收率低、生产指标差,现在公司硅锰合金的生产,原料的合理搭配、调整渣型、降低渣量已经成为我们当务之急。
二、原料的搭配首先我们对冶炼硅锰合金锰矿合理搭配进行探讨,锰系公司自生产以来,对硅锰合金如炉锰矿石的搭配思路主要是满足硅锰合金的锰、硅、磷、硫、碳的含量控制,在配料时主要控制锰铁比、磷锰比。
在生产中主要遵循高入炉锰来改善生产指标。
冶炼硅锰合金最合理配方

冶炼硅锰合金最合理配方1. 硅锰合金的魅力嘿,朋友们!今天咱们来聊聊硅锰合金。
这玩意儿可是冶炼行业里的宝贝,像极了烹饪中的调味品,没了它,铁铝合金的味道就差多了。
你可能会问,硅锰合金到底是什么?简单来说,它是一种由硅、锰和其他元素组成的合金,主要用于钢铁的冶炼。
可以说,它的存在为钢铁的强度和韧性提供了保障,真是不可或缺。
2. 合理配方的奥秘接下来,咱们得聊聊这合金的配方。
配方嘛,就像是调配鸡尾酒,必须得掌握好比例才能出好酒。
硅锰合金的关键成分就是硅和锰,通常硅的含量在15%到30%之间,锰的含量则在70%到85%之间。
你想想,如果你把这两样东西放在一起,嘿,那就能产生神奇的反应,让金属更结实、更耐磨!可别小看这比例哦,稍微多了点或者少了点,效果都能差天差地。
2.1 硅的作用硅在这个合金里可不是打酱油的角色。
它能提高合金的强度,增加抗氧化性,真是个小英雄。
而且,硅还能改善铸造性能,帮助金属更好地流动,简直是冶炼界的小能手。
2.2 锰的作用至于锰,它的作用同样重要,像是合金里的调皮捣蛋鬼。
锰能显著提高金属的硬度和韧性,防止脆性破坏,让铁的结构更加稳定,简直就是个“防护神”。
3. 配方的实际操作那么,如何把这些理论变成现实呢?这就需要一些技巧和经验了。
首先,你得准备好高纯度的硅和锰,最好是在冶炼厂里进行操作,毕竟安全第一嘛。
接着,把硅和锰按比例混合在一起,放入电炉中加热。
这时候可得注意温度,控制在1600℃到1800℃之间,太高了可能会导致成分的分离,太低又不够熔化。
3.1 注意事项在熔炼的过程中,要时刻观察熔体的状态,确保它均匀混合,像搅拌一锅浓汤一样。
还有,咱们可得避免一些杂质的混入,比如硫、磷等,它们可是合金的大敌,会影响成品的质量。
3.2 最终结果一旦熔炼完成,最后要进行铸造。
等合金冷却后,就能得到一块块闪闪发亮的硅锰合金了。
把它们拿去测试,看看强度、韧性,保证一切正常,心里才会踏实。
好了,朋友们,今天咱们就聊到这儿,硅锰合金的配方就像人生,有时候得调整比例,才能让生活变得更加美好!希望你们在冶炼的道路上都能如鱼得水,找到那个最合理的配方!。
硅锰合金的生产工艺
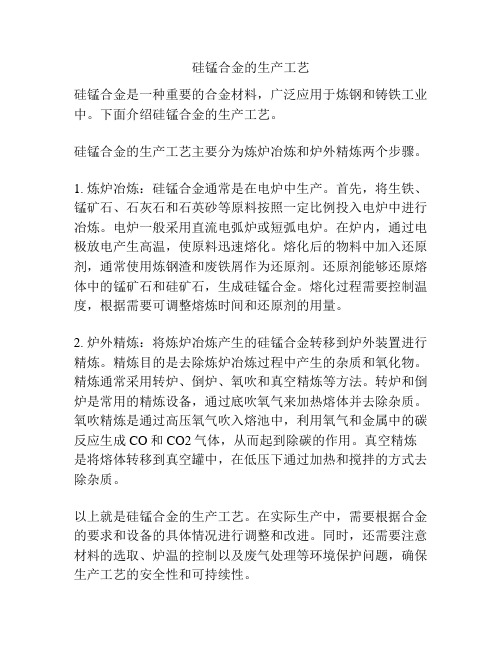
硅锰合金的生产工艺
硅锰合金是一种重要的合金材料,广泛应用于炼钢和铸铁工业中。
下面介绍硅锰合金的生产工艺。
硅锰合金的生产工艺主要分为炼炉冶炼和炉外精炼两个步骤。
1. 炼炉冶炼:硅锰合金通常是在电炉中生产。
首先,将生铁、锰矿石、石灰石和石英砂等原料按照一定比例投入电炉中进行冶炼。
电炉一般采用直流电弧炉或短弧电炉。
在炉内,通过电极放电产生高温,使原料迅速熔化。
熔化后的物料中加入还原剂,通常使用炼钢渣和废铁屑作为还原剂。
还原剂能够还原熔体中的锰矿石和硅矿石,生成硅锰合金。
熔化过程需要控制温度,根据需要可调整熔炼时间和还原剂的用量。
2. 炉外精炼:将炼炉冶炼产生的硅锰合金转移到炉外装置进行精炼。
精炼目的是去除炼炉冶炼过程中产生的杂质和氧化物。
精炼通常采用转炉、倒炉、氧吹和真空精炼等方法。
转炉和倒炉是常用的精炼设备,通过底吹氧气来加热熔体并去除杂质。
氧吹精炼是通过高压氧气吹入熔池中,利用氧气和金属中的碳反应生成CO和CO2气体,从而起到除碳的作用。
真空精炼是将熔体转移到真空罐中,在低压下通过加热和搅拌的方式去除杂质。
以上就是硅锰合金的生产工艺。
在实际生产中,需要根据合金的要求和设备的具体情况进行调整和改进。
同时,还需要注意材料的选取、炉温的控制以及废气处理等环境保护问题,确保生产工艺的安全性和可持续性。
硅锰生产工艺流程

COMPULSORY WINDING-UP
硅锰生产工艺流程
锰矿石、焦粒、辅料经过破碎到生产指定的粒度大小且干燥后进入配料系统,经工艺人员计算配比告知车间中控操作人员后经配料系统合理入炉,进行冶炼,按规定电量进行出铁(有渣)。
产生的渣进行水淬,产生的水淬渣存放于水淬渣临时存放区后外售到水泥厂,出铁产生的液态硅锰合金进行浇铸(池铸),待合金池达到指定高度后使用铲车铲到成品库经砸铁工人进行精整、破碎、装袋进行外销。
生产过程中所产生的烟气经过除尘系统(布袋除尘)进行有毒有害气体的二次利用(气柜)。
除尘系统所产生的除尘灰经收集进入供料机压密后制球,按配料要求计算配比合理入炉。
页脚内容。
锰硅合金生产节能措施
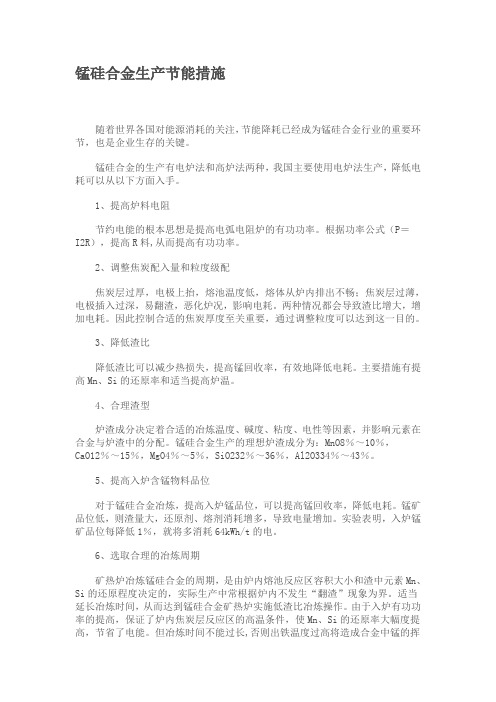
锰硅合金生产节能措施随着世界各国对能源消耗的关注,节能降耗已经成为锰硅合金行业的重要环节,也是企业生存的关键。
锰硅合金的生产有电炉法和高炉法两种,我国主要使用电炉法生产,降低电耗可以从以下方面入手。
1、提高炉料电阻节约电能的根本思想是提高电弧电阻炉的有功功率。
根据功率公式(P=I2R),提高R料,从而提高有功功率。
2、调整焦炭配入量和粒度级配焦炭层过厚,电极上抬,熔池温度低,熔体从炉内排出不畅;焦炭层过薄,电极插入过深,易翻渣,恶化炉况,影响电耗。
两种情况都会导致渣比增大,增加电耗。
因此控制合适的焦炭厚度至关重要,通过调整粒度可以达到这一目的。
3、降低渣比降低渣比可以减少热损失,提高锰回收率,有效地降低电耗。
主要措施有提高Mn、Si的还原率和适当提高炉温。
4、合理渣型炉渣成分决定着合适的冶炼温度、碱度、粘度、电性等因素,并影响元素在合金与炉渣中的分配。
锰硅合金生产的理想炉渣成分为:MnO8%~10%,CaO12%~15%,MgO4%~5%,SiO232%~36%,Al2O334%~43%。
5、提高入炉含锰物料品位对于锰硅合金冶炼,提高入炉锰品位,可以提高锰回收率,降低电耗。
锰矿品位低,则渣量大,还原剂、熔剂消耗增多,导致电量增加。
实验表明,入炉锰矿品位每降低1%,就将多消耗64kWh/t的电。
6、选取合理的冶炼周期矿热炉冶炼锰硅合金的周期,是由炉内熔池反应区容积大小和渣中元素Mn、Si的还原程度决定的,实际生产中常根据炉内不发生“翻渣”现象为界。
适当延长冶炼时间,从而达到锰硅合金矿热炉实施低渣比冶炼操作。
由于入炉有功功率的提高,保证了炉内焦炭层反应区的高温条件,使Mn、Si的还原率大幅度提高,节省了电能。
但冶炼时间不能过长,否则出铁温度过高将造成合金中锰的挥发损失,降低Mn的回收率。
此外,MnO含量已接近还原平衡的“乏渣”,留在炉内,会使冶炼电耗增加。
因而,根据具体的操作条件,通过实践决定合理的冶炼时间。
论硅锰指标提高与生产管理

论电炉硅锰技术经济指标的提高与生产管理硅锰冶炼的各项技术经济指标与原料结构、设备参数、操作参数与基础管理密切相关,众多生产厂家在生产实践中针对上述因素进行了广泛探索和研究,积累了不少先进的生产经验。
硅锰合金冶炼要想获得良好的技术经济指标,必须寻求合理的原料结构,高品位高金属量精料入炉,选择合理的操作参数与先进的设备参数有机结合,强化炉前基础生产管理,保持炉况的长期稳定顺行。
下面作者就从“人、机、料、法”几个方面论述如何提高硅锰技术经济指标:一、合理的原料结构是提高硅锰技术经济指标的基础生产硅锰合金的原料有:锰矿石、富锰渣、硅石、焦碳、白云石和萤石等。
生产硅锰合金可使用一种锰矿或几种锰矿(包括富锰渣)的混合矿,为保证炼出合格的产品,矿石中的锰铁比和锰磷比要满足一定的要求。
所用锰矿含锰越高(从某种意义上讲Mn+Fe金属量越高),各项指标越好。
锰矿中二氧化硅通常不受限制,采用含二氧化硅较高的锰矿(30%~40%SiO2)来冶炼硅锰合金在技术上是受欢迎的,在资源利用上是合理的。
原、燃料的物理化要求:对锰矿的要求,P2O5含量要低,锰矿粒度一般控制在10~60mm,小于10mm的不超过总量的10%富锰渣Mn/Fe要高,P/Mn要低,粒度10~80mm。
对硅石的要求,SiO2≥97%,P2O5<0.02%,粒度10~40mm,不带泥土及杂物。
对白云石的要求,(CaO+MgO)≥60%,粒度10~40mm。
对萤石的要求,CaF2≥75%,粒度10~40mm。
对焦碳的要求,固定碳≥84%,灰分≤14%,焦碳粒度,一般中小电炉5~15mm,大电炉使用5~25mm。
入炉料应该筛分彻底,尽量降低含粉率,含粉率低可以改善炉料的透气性,减少料面翻渣和频繁趟生料现象,减少炉外吹损,但还应讲究生熟料的合理搭配。
桂康公司使用如下原料结构取得了良好的技术指标,料面火苗均匀,基本无刺白火现象,出炉整体炉料均匀下沉,冶炼电耗3850~4000kwh/t,锰金属回收率≥87%。
硅锰合金生产工艺流程
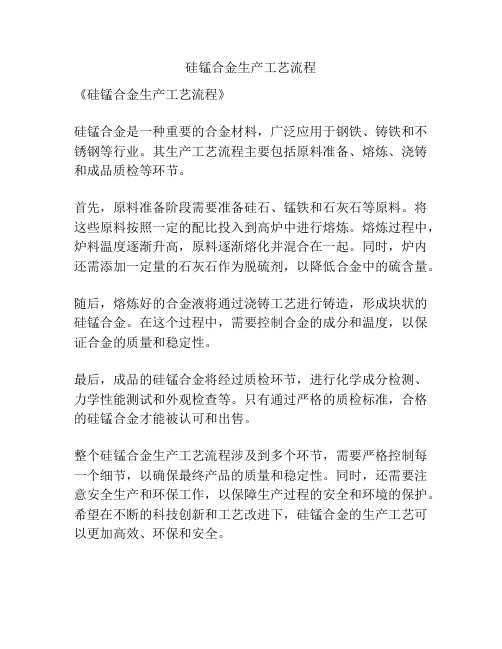
硅锰合金生产工艺流程
《硅锰合金生产工艺流程》
硅锰合金是一种重要的合金材料,广泛应用于钢铁、铸铁和不锈钢等行业。
其生产工艺流程主要包括原料准备、熔炼、浇铸和成品质检等环节。
首先,原料准备阶段需要准备硅石、锰铁和石灰石等原料。
将这些原料按照一定的配比投入到高炉中进行熔炼。
熔炼过程中,炉料温度逐渐升高,原料逐渐熔化并混合在一起。
同时,炉内还需添加一定量的石灰石作为脱硫剂,以降低合金中的硫含量。
随后,熔炼好的合金液将通过浇铸工艺进行铸造,形成块状的硅锰合金。
在这个过程中,需要控制合金的成分和温度,以保证合金的质量和稳定性。
最后,成品的硅锰合金将经过质检环节,进行化学成分检测、力学性能测试和外观检查等。
只有通过严格的质检标准,合格的硅锰合金才能被认可和出售。
整个硅锰合金生产工艺流程涉及到多个环节,需要严格控制每一个细节,以确保最终产品的质量和稳定性。
同时,还需要注意安全生产和环保工作,以保障生产过程的安全和环境的保护。
希望在不断的科技创新和工艺改进下,硅锰合金的生产工艺可以更加高效、环保和安全。
硅锰合金冶炼生产中炉渣成分、分类、特性与原料粒度、搭配、电阻要求及冶炼操作技术

硅猛合金冶炼生产中炉渣成分、分类、特性与原料粒度、搭配、电阻要求及冶炼操作技术硅锚合金的冶炼中,猛的还原是在成渣过程中依靠炉渣的对流运动来完成的,其渣量约占总量的50%左右。
碳素猛铁、硅镭合金的冶炼均为有渣冶炼,因此研究炉渣的性质,有助于冶炼过程中矿物的互相搭配,改善炉料的适应性,使还原更充分,对合金高产有着极其重要的意义。
一、炉渣成分及分类按冶炼产品不同或加入的溶剂不同,炉渣的化学成分也就不同。
炉渣主要由氧化物组成,不同氧化物有不同的化学性质,一般铁合金生产中常见的氧化物可分为碱性氧化物、酸性氧化物和两性氧化物。
炉渣的形成主要是碱性氧化物与酸性氧化物中和而产生的盐,即硅酸盐、铝酸盐和三重化合物。
冶炼硅猛时MnO与Si02结合成MnO・Si02,使MnO还原不充分,渣中MnO高。
故需要加入与Si02化学亲和力较强的碱性氧化物CaO参加反应:CaO+MnO ・ SiO2=MnO+CaO ・ Si02;使MnO活度提高,并充分还原。
通过炉渣的置换反应使金属氧化物活度提高,有利于氧化物的还原,达到提高产量,降低消耗的目的。
碱性氧化物的加入量是由冶炼品种、冶炼条件、以及炉渣性质决定的。
炉渣的碱度就是渣中碱性氧化物与酸性氧化物之比,用R表/J'* o当R VI称酸性渣,如硅猛合金R二0.6〜0.8;当R >1. 2称弱碱性渣,如生产碳素镭铁R二1. 2〜1. 4;当R>2叫强碱性渣,如中碳铭铁、锐铁。
二、炉渣性质1、熔点:炉渣的熔点主要与炉渣组成有关,SiO2熔点1723°C, A1203 熔点2050°C,纯00熔点2615°C,在冶炼碳素猛铁时炉渣所依据的成分主要有Si02、CaO、MgO、A1203,几种氧化物在相互反应时,能在冶金温度下生成液体化合物或共晶,使熔点低于其单独氧化物的熔点。
2、粘度:冶炼硅猛时碱度过低,硅易还原,炉渣粘度增加,熔池不活跃,冶炼不能顺利进行,渣与合金未能完全分离,金属混在渣中损失大;碱度过高,渣流动性好,严重侵蚀炉衬,降低炉衬寿命,因此合适的粘度对猛铁冶炼至关重要。
硅锰合金生产中入炉锰矿的优化搭配0001

硅锰合金生产中入炉锰矿的优化搭配通过对以往配矿思路的缺陷分析,弓I入炉料含锰的概念和配矿思路,相应补充和推导部分配矿参数,浅谈了这些参数的应用方法及步骤,以达到合理配矿和优化配比的目的及效果。
长时间以来,对锰硅合金入炉锰矿石的优劣评价和搭配思路,与冶炼高碳锰铁的用、配矿相类似,即为满足所炼产品的质量要求而严格控制入炉矿石的锰铁比和磷锰比。
在合理搭配矿石来改善生产的技术经济指标上,基本遵循矿石锰含量高则技术经济指标好的思路,对提高入炉锰矿石的品位非常注重,相反对矿石所含的炉渣成分(SQ2、AI2Q、CaO MgO考虑较少或只有定性而无定量的考虑。
这势必会产生以下问题:1)入炉矿石锰含量高,而矿石所含SiO2低时,为满足产品硅含量的质量要求或工艺规律,必须配加的硅石也多。
2)入炉矿石的锰含量高,而造渣物质的含量不理想,配人的熔剂(CaO、MgO以及上述的硅石等辅助原料多,不仅会改变炉内反应的热力学条件,而且会增大渣量或渣比,导致冶炼的单位电耗上升,不利于指标改善。
3)追求矿石锰品位,忽视了矿石所含对于锰硅合金冶炼有用的成份,导致部分锰品位偏低而综合成分较适于该品种冶炼的锰矿石得不到利用,浪费了锰矿资源。
1入炉锰矿石的合理搭配从以上分析可知,以矿石锰含量高低作为锰硅合金入炉锰矿石优劣评价和在矿石搭配上追求入炉矿石锰含量是不全面的,也不尽合理和科学。
要达到合理搭配锰硅合金入炉锰矿石的目的,除了注重锰矿这一重要品位指标外,更为重要的是确立以炉料含锰量来评价和搭配锰矿石,且分析预测其经济效果, 确定最佳矿石配比的配矿思路。
1、1炉料含锰的概念、含义及相关系数推导所谓炉料含锰量就是包括入炉料比中的还原剂、附加硅石、熔剂、添加剂等在内的锰含量,可用下式表达:Mn料=100X Mn矿/ (100 + A+ B+ C) (1)式中,Mn料一入炉炉料含锰量,%; Mn矿一入炉锰矿石含锰量,%; A —以100kg入炉矿石所算料比需补充的硅石量,kg ;B—以100kg入炉矿石所算料比需补充的熔剂量,kg;C—以100kg入炉矿石所算料比的焦炭量,kg。
优化工艺提高锰硅合金生产中锰的回收率

优化工艺提高锰硅合金生产中锰的回收率近年来,国内外众多铁合金厂家就如何在硅锰冶炼中提高锰元素回收率,进行了深入的研究和实践。
虽然在工艺配比、渣型选择、配送电制度等方面存在不尽相同的观点,但这些厂家均通过实践提高了回收率。
“精料入炉,优化配料”是铁合金生产的发展方向之一,不同理化性能原料的搭配在很大程度上影响着铁合金的各项经济技术指标。
提高入炉有效功率。
电炉设备参数和电气操作制度对炉内冶炼熔池温度影响较大,温度差异直接影响化学反应速率。
根据设备参数及实际原料条件合理地选择供电制度,确定合适的二次电压、二次电流、有功功率,使电炉熔池功率和极心圆功率密度达到最理想状态,电炉甚至可以通过超负荷运行来确保熔池达到足够高的冶炼温度。
温度越高,MnO和SiO2还原进入合金的程度越大,其中SiO2比MnO对还原温度的要求更高。
在铁合金电炉内,主要存在由电能向热能的转化,即提高有效入炉功率有利于提高炉膛温度,同时有利于促进Mn和Si的还原。
选择合理的工艺制度。
锰硅合金炉料配比以精料入炉为原则,入炉原料的有效成分应包括Mn、Fe、SiO2的总和(下文提到的有效成分皆同上),有效成分越高,即主要元素的富集度越高,越利于增大锰矿石还原反应速率,MnO和SiO2还原形成合金的程度越深。
以某企业冶炼锰硅合金FeMn68Si18牌号为例,锰矿石700公斤/批,配比中富锰渣占主料的30%以上,白云石30公斤/批,综合有效成分占51.5%,生产过程中硅的回收率不到50%,锰回收率为85%,渣铁比大于1。
选择低渣铁比生产工艺以后,该企业碱度控制由0.4提高到0.55以上,配料有效成分明显提高:富锰渣使用量一般控制在6%~11%,另外配入10%的高自然碱度矿石(平均含CaO15%),可以减少甚至不加白云石,综合有效成分占53.67%。
经过实践,采用该方法后硅的回收率明显提高,达到60%以上,锰回收率达到91%以上,渣铁比小于0.8。
硅锰配料计算及分析201205210

50 8.15 0.18
97
1
85 0.015
50 37.5 2.3
97
7
97
7.5
97
1.5
0
0
85 0.12
50
24
1
85 0.02
50
25 7.5
85 0.06
50
16 3.5
0
0
50
92
0
Al2O3 灰度
1.2 50.142 1.7
1 47.87 1.7 5 47.551 6.2
3 49.822 3.18
铁板
b11
0 c11
0 d11
93.1 e11
0.000 f11
g11
铁板
0
0
平均回收率
0.7892
0
6.400
锰含量≥65% 磷含量≤0.25%
限额系 数: m1 m2
1吨矿石入炉品味及其回收率的乘积 0 0
0.000
锰铁比 = 磷锰比 =
合计
6.2788 0.0023
铁含量≤16.4% m3
0
硅含量≥17% m4
最优取值
0 Kg 100 Kg
0 Kg 0 Kg 130 Kg 250 Kg
工艺取值范围
M1<x1≤M2 M1<x2≤M2 M1<x3≤M2 M1<x4≤M2 M1<x5≤M2 M1<x6≤M2
1234.2
下限M1
0 0 0 0 0 0
上限M2
0 0 0 0 0 0
元/吨
吨矿耗= 2.96
烧结矿 a7 原生矿 a8
锰铁比 磷锰比
278.15
- 1、下载文档前请自行甄别文档内容的完整性,平台不提供额外的编辑、内容补充、找答案等附加服务。
- 2、"仅部分预览"的文档,不可在线预览部分如存在完整性等问题,可反馈申请退款(可完整预览的文档不适用该条件!)。
- 3、如文档侵犯您的权益,请联系客服反馈,我们会尽快为您处理(人工客服工作时间:9:00-18:30)。
硅锰合金生产中入炉锰矿的优化搭配【字体:大中小】本文通过对以往配矿思路的缺陷分析,引入炉料含锰的概念和配矿思路,相应补充和推导部分配矿参数,浅谈了这些参数的应用方法及步骤,以达到合理配矿和优化配比的目的及效果。
长时间以来,对锰硅合金入炉锰矿石的优劣评价和搭配思路,与冶炼高碳锰铁的用、配矿相类似,即为满足所炼产品的质量要求而严格控制入炉矿石的锰铁比和磷锰比。
在合理搭配矿石来改善生产的技术经济指标上,基本遵循矿石锰含量高则技术经济指标好的思路,对提高入炉锰矿石的品位非常注重,相反对矿石所含的炉渣成分(SiO2、Al2O3、CaO、MgO)考虑较少或只有定性而无定量的考虑。
这势必会产生以下问题:1)入炉矿石锰含量高,而矿石所含SiO2低时,为满足产品硅含量的质量要求或工艺规律,必须配加的硅石也多。
2)入炉矿石的锰含量高,而造渣物质的含量不理想,配人的熔剂(白云石)以及上述的硅石等辅助原料多,不仅会改变炉内反应的热力学条件,而且会增大渣量或渣比,导致冶炼的单位电耗上升,不利于指标改善。
3)追求矿石锰品位,忽视了矿石所含对于锰硅合金冶炼有用的成分,导致部分锰品位偏低而综合成分较适于该品种冶炼的锰矿石得不到利用,浪费了锰矿资源。
1 入炉锰矿石的合理搭配从以上分析可知,以矿石锰含量高低作为锰硅合金入炉锰矿石优劣评价和在矿石搭配上追求入炉矿石锰含量是不全面的,也不尽合理和科学。
要达到合理搭配锰硅合金入炉锰矿石的目的,除了注重锰矿这一重要品位指标外,更为重要的是确立以炉料含锰量来评价和搭配锰矿石,且分析预测其经济效果,确定最佳矿石配比的配矿思路。
1、1炉料含锰的概念、含义及相关系数推导所谓炉料含锰量就是包括入炉料比中的还原剂、附加硅石、熔剂、添加剂等在内的锰含量,可用下式表达:Mn料=100×Mn矿/(100+A+B+C) (1)式中,Mn料—入炉炉料含锰量,%;Mn矿—入炉锰矿石含锰量,%;A—以100kg入炉矿石所算料比需补充的硅石量,kg;B—以100kg入炉矿石所算料比需补充的熔剂量,kg;C—以100kg入炉矿石所算料比的焦炭量,kg。
从(1)式可看出,即使入炉矿石锰含量高,如果补充配入的硅石、白云石等辅料多,说明该炉料入炉锰含量并不高,必将影响冶炼效果。
相反矿石锰含量适当,矿石所含SiO2、Al2O3、CaO、MgO 等合理,不需补充或少量补充硅石、白云石等辅料,表明入炉炉料含锰量高。
炉料含锰量高,不仅说明矿石锰品位高,而且弥补了前述以矿石锰品位评价的不足,还表明入炉原料的有用成分多,成渣和无用成分少,渣比下降,电能利用率和合金有用元素的收得率相应提高,单位功率和时间内电炉熔化和还原的炉料多,生产效率和冶炼的技术经济指标也就相应改善。
因此,在搭配锰硅合金入炉锰矿石上,不只是考虑产品质量要求和矿石锰含量高低的问题,更重要的是从利于工艺控制、炉况顺行和生产稳定,以及能改善综合技术经济指标的角度出发,以炉料含锰量的高低作为入炉锰矿石选择搭配的依据。
依据以上分析和以炉料含锰配矿的思路要求,我们在锰硅合金入炉硅石的选择搭配上,除了根据所炼产品的质量要求,充分利用锰铁比、磷锰比和硫含量控制值等常规参数外,还根据锰硅合金冶炼的特点,补充了SiO2/Mn、(CaO+MgO)/Mn、Al2O3/Mn等计算参数。
1.1.1锰铁比、磷锰比及硫含量锰铁比、磷锰比分别是指锰矿石的锰、铁、磷三种元素含量的比值。
根据资料〔1〕,锰铁比、磷锰比的控制可用以下公式计算:Mn矿/Fe矿≥[Mn]×ηFe/[Fe]×ηMn (2) P矿/Mn矿≤[P]×ηMn/[Mn]×ηP (3)式中,Mn矿、Fe矿、P矿—分别表示入炉锰矿石中的锰、铁、磷含量,%;[Mn]、[Fe]、[P]—分别表示所炼产品牌号的锰、铁、磷含量要求,%;ηMn、ηFe、ηP—分别表示锰、铁、磷入合金率,%。
在锰铁合金的冶炼中,硫元素入合金的比率不到1%,且还原剂带入的硫量占炉料总硫量的比例较大,故对矿石的含硫量一般不作具体要求。
1.1.2 SiO2矿/Mn矿(CaO+MgO)矿/Mn矿依据(1)式可知,当补充配入硅石和熔剂最少(即A、B都等于零),而含锰量最高的矿石,才是最理想的入炉锰矿石,即炉料含锰最高。
根据锰硅合金冶炼中锰、硅、铁等元素的主要还原反应可推导出如下参数式(均以100kg入炉锰矿石为基准):合金产量G=Mn矿×ηMn/[Mn] (4)硅石配比A={(G×[Si]×60/28)/ηSi-SiO2矿-C×SiO2焦}/SiO2石(5)熔剂配比B={(G×[Si]×60/28)×(ηSi渣/ηSi)×R-(CaO+MgO)矿-C×(CaO+MgO)焦}/(CaO+MgO)熔剂(6)式中,[Si]—表示所炼产品牌号的硅含量要求,%;ηSi、ηSi渣—分别表示硅入合金和入渣的比率,%;SiO2矿、SiO2焦、SiO2石—分别表示矿石、焦炭和硅石的二氧化硅含量,%;(CaO+MgO)矿、(CaO+MgO)焦、(CaO+MgO)熔—分别表示矿石、焦炭、熔剂的氧化钙和氧化镁含量,%;R—表示炉渣碱度,一般控制在0.6~0.8之间。
其余与(1)、(2)、(3)式相同。
根据国内铁合金生产所用还原剂焦炭化学成分的普遍情况,焦炭带入的SiO2、Al2O3、CaO、MgO主要来源于灰分,其数量相对较少,含量比例类似或接近该品种冶炼的炉渣成分。
因而可将(5)、(6)两式中焦炭带入部分忽略不计。
通过前述的假设(A=0和B=0),将(4)式分别代入(5)、(6)两式整理得:SiO2矿/Mn矿=2.14×([Si]×ηMn)/([Mn]×ηSi)(7)(CaO+MgO)矿/Mn矿=2.14×([Si]×ηMn×ηSi渣×R)/([Mn]×ηSi)(8)1.1.3 Al2O3矿/Mn矿在锰硅合金冶炼中,进入炉内的Al2O3一般不被还原,也不会挥发,几乎全部入渣。
且因Al2O3属中性氧化物,对炉渣的熔点、流动性,以及锰、硅二元素在炉渣金属液相间的分配和回收率,都有较大的影响和作用,是决定炉渣性质,影响渣比及锰硅合金技术经济指标的主要因素。
为此用低Al2O3矿石,造高Al2O3炉渣,一直是科技人员长期研究的课题和目标。
然而实践证明,由于工艺、设备参数和所炼牌号的炉温区别,渣中Al2O3含量也不尽一致。
因而在实际生产当中,要结合实际情况来确定炉渣的渣型和渣中Al2O3的含量。
通过锰硅合金炉渣的普遍物质组元和上述定义可得出:Al2O3入渣/(SiO2入渣+CaO入渣+MgO入渣)≤(Al2O3)/[(SiO2)+(CaO)+(MgO)] (9)通过代入和整理可得到:Al2O3矿/Mn矿≤2.14×{[Si]×ηMn×ηSi渣×(Al2O3)×(1+R)}/{[Mn]×ηSi×[(SiO2)+(CaO)+(MgO)]} (10)式中,Al2O3入渣、Al2O3矿、(Al2O3)—分别表示Al2O3入渣量和在锰矿石、炉渣中的含量;SiO2入渣、(SiO2)—分别表示SiO2入渣量和在炉渣中的含量;CaO入渣、(CaO)—分别表示CaO入渣量和在炉渣中的含量;MgO入渣、(MgO)—分别表示MgO入渣量和在炉渣中的含量;从上几式可知,对入炉锰矿石的锰铁比、磷锰比、硅锰比、铝锰比以及(CaO+MgO)/Mn的具体要求,都与所炼产品的化学成分和各元素入合金的比率有关,而元素入合金率又受渣型、还原剂、炉型及设备参数等因素的影响。
因此,上述参数的计算,要综合产品质量、原料条件、矿热炉特性和炉渣渣型的选择来确定。
2 参数的应用利用上述参数计算式,可确定入炉锰矿石的最佳工艺配比,达到合理配矿和改善指标的目的,其具体步骤如下:1)根据所炼品种牌号的化学成分要求,矿热炉特性、回收率、入渣率、挥发率和适宜渣型等条件,代入上述公式计算出该品种牌号的理想配矿参数值。
2)根据锰矿石的化学成分,初步确定出若干满足锰铁比、磷锰比要求的矿石配比。
3)计算出上述各配比混合矿的硅锰比、铝锰比及(CaO+MgO)/Mn等的比值,与第一步算出的理想参数值进行比较,得出与各理论参数值最为接近的几个配矿比例,并计算出各配比的炉料含锰量,以最高炉料含锰量的锰矿搭配比例为最佳工艺配比。
由该比例构成的入炉料,在实际冶炼过程中,工艺易于控制,炉况较为稳定,炉渣渣型合理,且渣铁比较小,生产的技术经济指标比较理想。
3 选择确定最经济的配矿方案前已说明,合理搭配矿石的目的,不只是为稳定生产出合格产品和获取较好技术指标,更为重要的是充分利用锰矿资源,用最低的原料成本,创造较好的经济效益,也就是选择最经济的配矿方案。
根据单位重量锰矿石所产铁合金量、辅配料比及各矿石原料的价格,其单位原料成本可按如下公式计算:吨混合矿成本=ΣXiJi (11)吨矿石所配辅料成本=A×JA+B×JB+C×JC(12)吨混合矿的锰含量Mn矿=ΣXi×Mn矿i (13)吨矿合金产量(吨)=Mn矿×ηMn/[Mn] (14)综合整理得:单位原料成本=[Mn]×(ΣXiJi+A×JA+B×JB+C×JC)/(ηMn×ΣXi×Mn矿i)(15)式中,Xi—第i种锰矿石的搭配比例,%,i为自定序号;Ji—第i种锰矿石的单位价格,元/吨;JA、JB、JC—分别为硅石、熔剂、焦炭的单位价格,元/吨;Mn矿i—第i种锰矿石的含锰量,%;A、B、C—分别为1吨入炉锰矿石所需配入的硅石、熔剂、焦炭量,吨;其余与前面公式相同。
利用前述得出的最接近各理论配矿参数的矿石配比,通过(15)式进行单位原料成本的预算,以成本最低的方案用于实际生产,即是最经济的配矿方案。