不锈钢加工参数
不锈钢加工参数表

不锈钢加工参数表【原创实用版】目录一、引言二、不锈钢的概述三、不锈钢加工的常用方法四、不锈钢加工参数表的详细内容五、不锈钢加工参数表的应用六、结语正文一、引言不锈钢以其耐腐蚀、抗氧化、耐磨损等特性被广泛应用于建筑、化工、医疗等各个领域。
在加工不锈钢制品时,参数的选择和控制至关重要,直接影响到产品的质量。
因此,针对不锈钢的加工参数进行系统性的整理,对于提高生产效率和产品质量具有重要意义。
二、不锈钢的概述不锈钢是一种具有较高耐腐蚀性的合金钢,主要成分是铁、铬、镍等。
其中,铬作为主要合金元素,能提高钢的耐腐蚀性。
根据铬含量的不同,不锈钢可分为高铬不锈钢、中铬不锈钢和低铬不锈钢。
不锈钢的耐腐蚀性与其组织结构、化学成分、加工工艺等多种因素有关。
三、不锈钢加工的常用方法不锈钢的加工方法包括但不限于:切割、焊接、冷弯、热处理、抛光等。
其中,切割方法有激光切割、等离子切割、水刀切割等;焊接方法有氩弧焊接、电阻焊接、焊条焊接等;冷弯方法有冷弯成型、滚圆等;热处理方法有退火、正火、调质等;抛光方法有手动抛光、机械抛光、电解抛光等。
四、不锈钢加工参数表的详细内容不锈钢加工参数表主要包括以下内容:1.切割参数:切割速度、切割气压、切割功率等;2.焊接参数:焊接电流、焊接电压、焊接速度等;3.冷弯参数:冷弯半径、冷弯角度、冷弯力等;4.热处理参数:加热温度、保温时间、冷却方式等;5.抛光参数:抛光速度、抛光液浓度、抛光时间等。
五、不锈钢加工参数表的应用在实际生产中,根据不锈钢的材质、厚度、规格等因素,参照不锈钢加工参数表,选择合适的加工参数,可保证产品的加工质量。
同时,不锈钢加工参数表也为生产者提供了一个依据,便于优化生产过程,提高生产效率。
六、结语不锈钢加工参数表对于保证产品质量、提高生产效率具有重要作用。
不锈钢加工参数表

不锈钢加工参数表【最新版】目录一、引言二、不锈钢的概述三、不锈钢加工的常用方法四、不锈钢加工参数表的内容五、不锈钢加工参数表的应用六、结语正文一、引言在工业生产中,不锈钢以其耐腐蚀、抗氧化、耐磨损等特性被广泛应用。
为了更好地对不锈钢进行加工,我们需要了解不锈钢的性质以及加工方法,以便在实际操作中能够选择合适的参数。
本文将介绍不锈钢加工参数表,帮助大家更好地理解和应用这一工具。
二、不锈钢的概述不锈钢是一种含有 17% 以上的铬的合金钢,具有较高的耐腐蚀性能。
根据其组织结构和性能特点,不锈钢可分为两大类:奥氏体不锈钢和马氏体不锈钢。
其中,奥氏体不锈钢具有较好的耐腐蚀性、抗氧化性和可焊性,广泛应用于化工、建筑、食品等工业领域。
马氏体不锈钢具有较高的强度、硬度和耐磨性,主要用于制造轴承、刀具等耐磨零件。
三、不锈钢加工的常用方法不锈钢加工的常用方法包括切割、焊接、打磨、钻孔等。
这些方法在不同的加工阶段和工艺要求下,需要选用不同的设备和参数。
为了确保加工质量,操作者需要对不锈钢的性质和加工方法有充分的了解。
四、不锈钢加工参数表的内容不锈钢加工参数表主要包括以下内容:1.切割:切割速度、切割气体、切割功率等;2.焊接:焊接方法、焊接电流、焊接电压、焊接速度等;3.打磨:打磨速度、打磨砂纸号数、打磨液等;4.钻孔:钻孔速度、钻孔深度、钻孔孔径等。
五、不锈钢加工参数表的应用在实际加工过程中,操作者可以根据不锈钢加工参数表选择合适的参数,以达到最佳的加工效果。
同时,参数表还可以作为参考,帮助操作者分析和解决加工过程中可能出现的问题。
六、结语不锈钢加工参数表是针对不锈钢这一特殊材料制定的加工指南,对于保证加工质量、提高生产效率具有重要意义。
加工中心304 不锈钢光面参数

加工中心304 不锈钢光面参数英文版Machining Center 304 Stainless Steel Smooth Surface Parameters304 stainless steel, a common material in the machining industry, is widely used due to its corrosion resistance, ductility, and weldability. When working with this material on a machining center, achieving a smooth surface finish is crucial to ensure the quality of the final product. Here are some key parameters to consider when machining 304 stainless steel to achieve a smooth surface:Tool Material Selection: When machining 304 stainless steel, it's essential to choose a tool material that can withstand the high temperatures and wear resistance required. Carbide tools coated with titanium nitride (TiN) or aluminum titanium nitride (AlTiN) are commonly used for this purpose.Cutting Speed: The cutting speed plays a vital role in achieving a smooth surface. Lower cutting speeds can help reduce friction and heat generation, resulting in a finer surface finish. However, it's crucial to avoid extremely low speeds as they can lead to increased tool wear.Feed Rate: The feed rate determines the speed at which the tool moves across the workpiece. Higher feed rates can promote a smoother surface by reducing the time the tool spends in contact with the material. However, excessive feed rates can lead to tool wear and poor surface quality.Depth of Cut: The depth of cut affects the amount of material removed during each pass of the tool. Shallower depths of cut can lead to a smoother surface by reducing the amount of force exerted on the tool. However, this may require multiple passes to achieve the desired material removal.Coolant Usage: The application of coolant during machining can help reduce heat generation and improve surface finish.Water-based coolants are commonly used for 304 stainless steel, as they provide effective cooling and lubrication.Post-Machining Processes: Achieving a smooth surface may also require additional processes such as polishing or buffing after machining. These processes can remove any residual roughness or marks left by the machining process.By carefully selecting the right tool material, adjusting cutting parameters, and implementing post-machining processes, it is possible to achieve a smooth surface finish when machining 304 stainless steel on a machining center.中文版加工中心304不锈钢光面参数304不锈钢是加工行业中常见的材料,因其耐腐蚀、延展性和可焊性而被广泛使用。
不锈钢车削参数

不锈钢车削参数不锈钢车削参数是指在车削加工过程中,针对不锈钢材料的特性和要求所设定的一系列切削参数。
这些参数对于保证加工质量和提高生产效率具有重要意义。
以下是一些建议的不锈钢车削参数:1. 切削速度(Vc):切削速度是刀具在旋转时与工件接触点的速度。
对于不锈钢材料,切削速度应适当降低,以防止刀具过热和磨损。
一般推荐切削速度为20-60m/min。
2. 进给量(f):进给量是指刀具在每次切削行程中沿工件轴向移动的距离。
对于不锈钢材料,进给量应适当降低,以减小刀具磨损和切削力。
一般推荐进给量为0.1-0.3mm/r。
3. 切削深度(ap):切削深度是指刀具在每次切削行程中切入工件的深度。
对于不锈钢材料,切削深度应适当降低,以减小刀具磨损和切削力。
一般推荐切削深度为0.1-0.5mm。
4. 刀具前角(γo):刀具前角是指刀具主切削刃与工件表面的夹角。
对于不锈钢材料,刀具前角应适当增大,以提高切削性能和减少刀具磨损。
一般推荐前角为10-20°。
5. 刀具后角(αo):刀具后角是指刀具主切削刃与工件表面的夹角。
对于不锈钢材料,刀具后角应适当增大,以提高切削性能和减少刀具磨损。
一般推荐后角为8-12°。
6. 切削液:不锈钢车削过程中,应使用适当的切削液来冷却和润滑刀具和工件,以降低切削温度和减少刀具磨损。
常用的切削液有水溶性切削液、油溶性切削液和乳化液等。
7. 刀具材质:不锈钢车削过程中,应选择具有良好耐磨性和抗腐蚀性的刀具材质,如硬质合金、陶瓷和高速钢等。
8. 机床刚性:不锈钢车削过程中,应选择具有较高刚性的机床,以保证加工精度和表面质量。
9. 工艺路线:不锈钢车削过程中,应根据工件的形状和尺寸选择合适的工艺路线,以减少切削力和热量对加工质量的影响。
总之,不锈钢车削参数的选择应根据具体的工件材料、形状和尺寸以及加工要求进行综合考虑,以达到最佳的加工效果。
钨钢钻头加工不锈钢参数

钨钢钻头加工不锈钢参数【原创版】目录一、钨钢钻头加工不锈钢的优点二、钨钢钻头加工不锈钢的参数设置三、加工过程中需要注意的事项四、总结正文一、钨钢钻头加工不锈钢的优点钨钢钻头是一种具有高硬度、高耐磨性和高韧性的切削工具,因此在加工不锈钢这类高硬度、高韧性的材料时表现出优异的性能。
相较于其他材料的钻头,钨钢钻头在加工不锈钢时具有以下优点:1.高硬度:钨钢钻头的硬度可以达到 HRC55 以上,这意味着它在加工不锈钢时可以承受更大的切削力和热量,降低磨损程度。
2.高耐磨性:钨钢钻头的耐磨性能好,可以在加工不锈钢时保持刃口的锋利,减少换刀次数,提高生产效率。
3.高韧性:钨钢钻头具有较高的韧性,可以抵御加工过程中产生的冲击和振动,避免钻头断裂。
二、钨钢钻头加工不锈钢的参数设置在钨钢钻头加工不锈钢时,需要合理设置加工参数,以保证加工效率和加工质量。
以下是一些建议的参数设置:1.线速度:线速度是切削过程中重要的参数之一。
过高的线速度会导致切削温度升高,加剧刀具磨损;过低的线速度则会导致切削效果不佳,加工效率低下。
一般来说,钨钢钻头加工不锈钢的线速度应该控制在 200米/分钟(即 s5500 左右)。
2.进给速度:进给速度是指钻头在加工过程中沿刀具进给方向的移动速度。
进给速度过快会导致切削力增大,加剧刀具磨损;进给速度过慢则会导致加工效率低下。
合适的进给速度应该根据工件材料、刀具直径和加工深度等因素综合考虑。
3.切削深度:切削深度是指钻头在加工过程中每次切削的深度。
切削深度过深会导致切削力增大,加剧刀具磨损;切削深度过浅则会导致加工效率低下。
合适的切削深度应该根据刀具直径、刀具材料和加工条件等因素综合考虑。
三、加工过程中需要注意的事项1.刀具的刃磨:在加工过程中,刀具的刃口可能会磨损,导致切削效果不佳。
因此,需要定期对刀具进行刃磨,以保证刀具的锋利度。
2.冷却液的使用:在加工过程中,使用合适的冷却液可以降低切削温度,减少刀具磨损,提高加工质量。
不锈钢加工参数表

不锈钢加工参数表1. 切削速度:切削速度是指在切削过程中,刀具与工件接触点处的线速度。
不锈钢的切削速度通常在20-60m/min之间,具体数值取决于刀具材料、刀具几何形状、工件材料和加工要求等因素。
切削速度过高可能导致刀具磨损加快,切削力增大,加工精度降低;切削速度过低则可能导致刀具寿命降低,加工效率降低。
2. 进给速度:进给速度是指刀具在切削过程中沿工件进给方向的移动速度。
不锈钢的进给速度通常在0.1-0.5mm/r之间,具体数值取决于刀具材料、刀具几何形状、工件材料和加工要求等因素。
进给速度过高可能导致刀具磨损加快,切削力增大,加工精度降低;进给速度过低则可能导致刀具寿命降低,加工效率降低。
3. 切削深度:切削深度是指刀具在一次切削过程中切入工件的深度。
不锈钢的切削深度通常在0.1-0.5mm之间,具体数值取决于刀具材料、刀具几何形状、工件材料和加工要求等因素。
切削深度过大可能导致刀具磨损加快,切削力增大,加工精度降低;切削深度过小则可能导致刀具寿命降低,加工效率降低。
4. 切削宽度:切削宽度是指刀具在一次切削过程中切入工件的宽度。
不锈钢的切削宽度通常在2-10mm之间,具体数值取决于刀具材料、刀具几何形状、工件材料和加工要求等因素。
切削宽度过大可能导致刀具磨损加快,切削力增大,加工精度降低;切削宽度过小则可能导致刀具寿命降低,加工效率降低。
5. 切削油或冷却液:不锈钢加工过程中,为了降低切削温度,减少刀具磨损,提高加工精度和表面质量,通常需要使用切削油或冷却液。
切削油或冷却液的选择应根据不锈钢材料、刀具材料、加工条件等因素进行。
常用的切削油或冷却液有矿物油、乳化液、水溶性切削液等。
6. 刀具材料:不锈钢加工过程中,常用的刀具材料有高速钢、硬质合金、陶瓷、金刚石等。
不同材料的刀具对不锈钢的加工性能和加工效果有很大影响。
选择合适的刀具材料可以提高加工效率,延长刀具寿命,提高加工精度和表面质量。
不锈钢的铣削加工参数

不锈钢的铣削加工参数不锈钢是一种常用的金属材料,广泛应用于工业制造和建筑领域。
铣削加工是一种常见的金属加工方法,通过切削工具在工件表面进行旋转切削,从而得到所需形状和尺寸的工件。
在不锈钢的铣削加工过程中,需要考虑多个参数,以确保加工质量和效率。
以下将介绍一些常见的不锈钢铣削加工参数。
1. 铣削切削速度(Cutting Speed)铣削切削速度是指刀具在工件表面的切削速度。
对于不锈钢材料,由于其硬度较高,切削速度应相对较低。
通常,不锈钢的切削速度范围为30-60m/min,具体数值需要根据具体材料和刀具来确定。
2. 进给速度(Feed Rate)进给速度是指刀具在横向方向上的移动速度,即每刀齿每转所移动的距离。
对于不锈钢材料,进给速度应适中,过低容易造成切削过热,过高则会降低切削效率。
通常,不锈钢材料的进给速度范围为0.1-0.3mm/tooth。
3. 刀具转速(Spindle Speed)刀具转速是指刀具在加工过程中的旋转速度。
对于不锈钢材料,刀具转速应较低,避免因过高的转速导致切削过热。
通常,不锈钢材料的刀具转速范围为500-3000rpm。
4. 切削深度(Cutting Depth)切削深度是指每次切削时刀具进入工件的深度。
对于不锈钢材料,切削深度应适中,过深容易导致切削过热和刀具磨损加剧。
通常,不锈钢材料的切削深度范围为0.5-3mm,具体数值需要根据具体材料和刀具来确定。
5. 切削润滑方式(Coolant)切削润滑是指在铣削加工过程中使用润滑剂来降低切削温度和减少切削力。
对于不锈钢材料,由于其导热性较低,应使用润滑剂来改善切削状况。
常见的切削润滑方式包括湿式切削和干式切削。
湿式切削可以通过冷却剂或润滑油来降低切削温度,减少刀具磨损;干式切削则需要通过空气或其他方式来冷却切削区域。
6.刀具材料和刀具形状选择合适的刀具材料和刀具形状也是不锈钢铣削加工的关键。
不锈钢材料的硬度高,切削性能差,因此需要采用高硬度和高耐磨抗热的刀具材料,如硬质合金刀具。
不锈钢的铣削加工参数
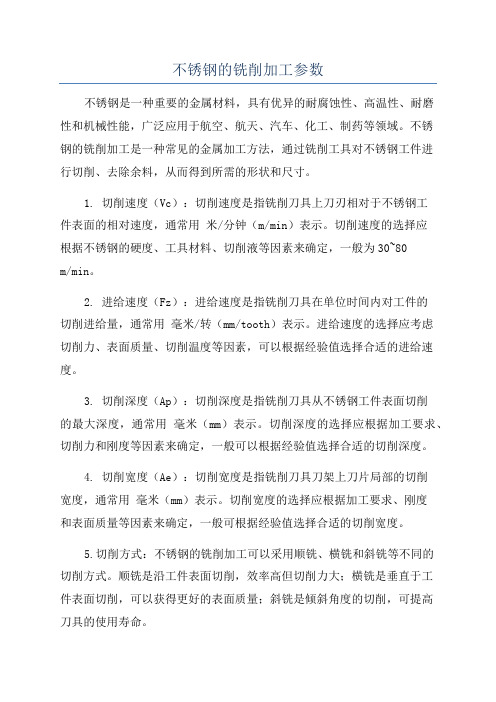
不锈钢的铣削加工参数不锈钢是一种重要的金属材料,具有优异的耐腐蚀性、高温性、耐磨性和机械性能,广泛应用于航空、航天、汽车、化工、制药等领域。
不锈钢的铣削加工是一种常见的金属加工方法,通过铣削工具对不锈钢工件进行切削、去除余料,从而得到所需的形状和尺寸。
1. 切削速度(Vc):切削速度是指铣削刀具上刀刃相对于不锈钢工件表面的相对速度,通常用米/分钟(m/min)表示。
切削速度的选择应根据不锈钢的硬度、工具材料、切削液等因素来确定,一般为30~80m/min。
2. 进给速度(Fz):进给速度是指铣削刀具在单位时间内对工件的切削进给量,通常用毫米/转(mm/tooth)表示。
进给速度的选择应考虑切削力、表面质量、切削温度等因素,可以根据经验值选择合适的进给速度。
3. 切削深度(Ap):切削深度是指铣削刀具从不锈钢工件表面切削的最大深度,通常用毫米(mm)表示。
切削深度的选择应根据加工要求、切削力和刚度等因素来确定,一般可以根据经验值选择合适的切削深度。
4. 切削宽度(Ae):切削宽度是指铣削刀具刀架上刀片局部的切削宽度,通常用毫米(mm)表示。
切削宽度的选择应根据加工要求、刚度和表面质量等因素来确定,一般可根据经验值选择合适的切削宽度。
5.切削方式:不锈钢的铣削加工可以采用顺铣、横铣和斜铣等不同的切削方式。
顺铣是沿工件表面切削,效率高但切削力大;横铣是垂直于工件表面切削,可以获得更好的表面质量;斜铣是倾斜角度的切削,可提高刀具的使用寿命。
6.刀具选择:不锈钢的铣削刀具应选择高硬度、高耐磨性的刀具材料,如硬质合金、高速钢等。
刀具的形状和刃数也应根据加工要求选择合适的类型。
在铣削不锈钢时,还需要注意以下几点:1.选择合适的切削液:切削液能够冷却刀具和工件,并降低切削温度,减少切削力和摩擦,改善表面质量。
常用的切削液有油基切削液和水溶性切削液,应根据切削工艺和加工要求选择合适的切削液。
2.注意切削力和切屑排除:不锈钢的铣削容易产生较大的切削力和切屑,需要加强刀具的刚度和排屑能力,避免卡刀和切削过程中产生的振动和噪声。
不锈钢的车削参数

不锈钢的车削参数不锈钢是一种耐腐蚀、耐高温的金属材料,常用于制造机械零件、压力容器、航空航天器械等领域。
在进行车削加工时,需要根据不锈钢的特性和要求选择合适的车削参数,以达到理想的加工效果。
一、切削速度(vc)切削速度是车刀在工件表面移动的速度,也是车削过程中最基本的参数。
不锈钢的切削速度较低,一般在30-60m/min之间。
过高的切削速度会导致刀具过热、磨损加剧,影响切削质量和加工效率;过低的切削速度则会造成切削力增大,刀具负荷过大,甚至造成刀具断裂。
二、进给速度(f)进给速度是指车刀在单位时间内向工件进给的量。
在车削不锈钢时,进给速度一般在0.05-0.15mm/r之间。
进给速度过高会造成刀具磨损加剧、表面质量下降;进给速度过低则会导致车削效率低下。
需要根据具体材料硬度和刀具的质量要求来确定合适的进给速度。
三、切削深度(ap)切削深度是指车刀在一次切削过程中,刀尖与工件表面的距离。
不锈钢的切削深度一般在0.5-4mm之间,具体取决于工件的硬度和刀具的强度。
切削深度过大会增加切削力,容易造成刀具断裂;切削深度过小则会导致车削效率低下。
四、切削角度(γ)切削角度是指车刀主切削刃与工件表面的切削角。
在车削不锈钢时,一般选择切削角较小的刀具,如30度左右。
切削角较小的刀具可以减小切削力,提高刀具的切削性能和寿命。
五、冷却液由于不锈钢的切削过程会产生较高的温度,因此在车削不锈钢时需要使用冷却液进行冷却和润滑。
冷却液的选择应根据不锈钢的材质和车削过程的具体要求来确定,以保证切削效果和刀具的使用寿命。
六、切削工具选择不锈钢的切削难度较大,对切削工具的要求也比较高。
一般采用硬质合金或散热钨钢制成的切削工具。
此外,还可以通过涂覆刀具和刀具几何形状的优化来提高不锈钢的切削效果。
总结起来,车削不锈钢需要根据不锈钢的特性和要求选择适当的车削参数,包括切削速度、进给速度、切削深度、切削角度等。
同时还需要选择合适的切削工具和冷却液,以保证切削效果和刀具的使用寿命。
不锈钢nc加工参数
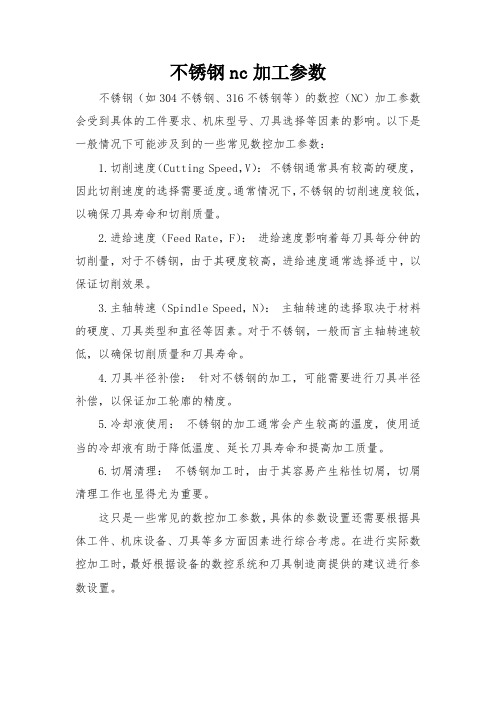
不锈钢nc加工参数
不锈钢(如304不锈钢、316不锈钢等)的数控(NC)加工参数会受到具体的工件要求、机床型号、刀具选择等因素的影响。
以下是一般情况下可能涉及到的一些常见数控加工参数:
1.切削速度(Cutting Speed,V):不锈钢通常具有较高的硬度,因此切削速度的选择需要适度。
通常情况下,不锈钢的切削速度较低,以确保刀具寿命和切削质量。
2.进给速度(Feed Rate,F):进给速度影响着每刀具每分钟的切削量,对于不锈钢,由于其硬度较高,进给速度通常选择适中,以保证切削效果。
3.主轴转速(Spindle Speed,N):主轴转速的选择取决于材料的硬度、刀具类型和直径等因素。
对于不锈钢,一般而言主轴转速较低,以确保切削质量和刀具寿命。
4.刀具半径补偿:针对不锈钢的加工,可能需要进行刀具半径补偿,以保证加工轮廓的精度。
5.冷却液使用:不锈钢的加工通常会产生较高的温度,使用适当的冷却液有助于降低温度、延长刀具寿命和提高加工质量。
6.切屑清理:不锈钢加工时,由于其容易产生粘性切屑,切屑清理工作也显得尤为重要。
这只是一些常见的数控加工参数,具体的参数设置还需要根据具体工件、机床设备、刀具等多方面因素进行综合考虑。
在进行实际数控加工时,最好根据设备的数控系统和刀具制造商提供的建议进行参数设置。
不锈钢加工对刀具材质和参数的要求

不锈钢加工对刀具材质和参数的要求济南钢铁集团张文周谭承峰1 不锈钢加工对刀具的基本要求对刀具几何参数的要求加工不锈钢时,刀具切削部分的几何形状,一般应从前角、后角方面的选择来考虑。
在选择前角时,要考虑卷屑槽型、有无倒棱和刃倾角的正负角度大小等因素。
不论何种刀具,加工不锈钢时都必须采用较大的前角。
增大刀具的前角可减小切屑切离和清出过程中所遇到的阻力。
对后角选择要求不十分严格,但不宜过小,后角过小容易和工件表面产生严重摩擦,使加工表面粗糙度恶化,加速刀具磨损。
并且由于强烈摩擦,增强了不锈钢表面加工硬化的效应;刀具后角也不宜过大,后角过大,使刀具的楔角减小,降低了切削刃的强度,加速了刀具的磨损。
通常,后角应比加工普通碳钢时适当大些。
对刀具切削部分表面粗糙度的要求提高刀具切削部分的表面光洁度可减少切屑形成卷曲时的阻力,提高刀具的耐用度。
与加工普通碳钢相比较,加工不锈钢时应适当降低切削用量以减缓刀具磨损;同时还要选择适当的冷却润滑液,以便降低切削过程中的切削热和切削力,延长刀具的使用寿命。
对刀杆材料的要求加工不锈钢时,由于切削力较大,故刀杆必须具备足够的强度和刚性,以免在切削过程中发生颤振和变形。
这就要求选用适当大的刀杆截面积,同时还应采用强度较高的材料来制造刀杆,如采用调质处理的45号钢或50号钢。
对刀具切削部分材料的要求加工不锈钢时,要求刀具切削部分的材料具有较高的耐磨性,并能在较高的温度下保持其切削性能。
目前常用的材料有:高速钢和硬质合金。
由于高速钢只能在600°C以下保持其切削性能,因此不宜用于高速切削,而只适用于在低速情况下加工不锈钢。
由于硬质合金比高速钢具有更好的耐热性和耐磨性,因此用硬质合金材料制成的刀具更适合不锈钢的切削加工。
硬质合金分钨钴合金(YG)和钨钴钛合金(YT)两大类。
钨钴类合金具有良好的韧性,制成的刀具可以采用较大的前角与刃磨出较为锋利的刃口,在切削过程中切屑易变形,切削轻快,切屑不容易粘刀,所以在一般情况下,用钨钴合金加工不锈钢比较合适。
不锈钢加工参数表

不锈钢加工参数表摘要:一、不锈钢加工概述1.不锈钢的定义和特性2.不锈钢的分类和应用领域二、不锈钢加工参数表介绍1.参数表的构成和作用2.常见不锈钢加工参数及其意义三、不锈钢加工参数表的使用1.如何选择合适的加工参数2.加工参数对不锈钢加工效果的影响四、不锈钢加工过程中的注意事项1.加工前的准备工作2.加工过程中的操作技巧3.加工后期的处理与保养五、总结1.不锈钢加工参数表的重要性2.如何提高不锈钢加工效果正文:不锈钢是一种具有良好耐腐蚀性、耐磨性和美观性的合金材料,广泛应用于建筑、化工、医疗、食品加工等领域。
为了确保不锈钢制品的质量和性能,不锈钢加工过程中的参数选择尤为重要。
不锈钢加工参数表正是为了指导加工者正确选择加工参数而设计的。
不锈钢加工参数表主要包括材料牌号、硬度、加工方法、刀具材料、刀具几何参数、切削参数、冷却液等栏目。
通过对这些参数的合理选择,可以确保不锈钢加工顺利进行,提高加工效率和产品质量。
在选择不锈钢加工参数时,首先要根据材料的牌号和硬度选择合适的加工方法。
例如,对于硬度较高的奥氏体不锈钢,应选择采用磨削、铣削等加工方法;对于马氏体不锈钢,可选择车削、钻孔等加工方法。
其次,要选择合适的刀具材料和几何参数。
不锈钢加工中常用的刀具材料包括硬质合金、陶瓷和金属陶瓷等。
根据加工方法和零件要求,合理选择刀具的几何参数,如刀尖角、前角、后角等,以提高刀具的耐磨性和加工性能。
此外,切削参数和冷却液的选择也对不锈钢加工效果产生重要影响。
切削参数包括切削速度、进给速度和背吃刀量等,应根据加工方法和刀具材料合理设定。
冷却液的选择要考虑其冷却性能、润滑性能以及对不锈钢的腐蚀性等因素。
总之,不锈钢加工参数表是指导加工者正确选择加工参数,确保不锈钢制品质量和性能的重要工具。
在加工过程中,应根据参数表进行操作,并结合实际情况进行调整,以提高不锈钢加工效果。
合金铣刀加工不锈钢参数
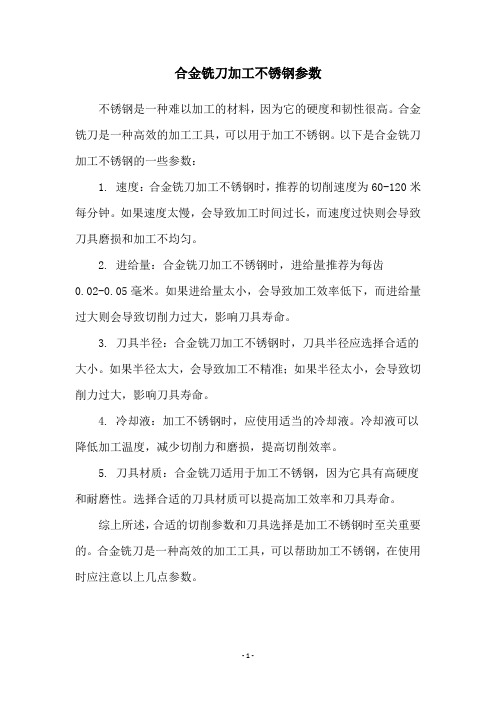
合金铣刀加工不锈钢参数
不锈钢是一种难以加工的材料,因为它的硬度和韧性很高。
合金铣刀是一种高效的加工工具,可以用于加工不锈钢。
以下是合金铣刀加工不锈钢的一些参数:
1. 速度:合金铣刀加工不锈钢时,推荐的切削速度为60-120米每分钟。
如果速度太慢,会导致加工时间过长,而速度过快则会导致刀具磨损和加工不均匀。
2. 进给量:合金铣刀加工不锈钢时,进给量推荐为每齿
0.02-0.05毫米。
如果进给量太小,会导致加工效率低下,而进给量过大则会导致切削力过大,影响刀具寿命。
3. 刀具半径:合金铣刀加工不锈钢时,刀具半径应选择合适的大小。
如果半径太大,会导致加工不精准;如果半径太小,会导致切削力过大,影响刀具寿命。
4. 冷却液:加工不锈钢时,应使用适当的冷却液。
冷却液可以降低加工温度,减少切削力和磨损,提高切削效率。
5. 刀具材质:合金铣刀适用于加工不锈钢,因为它具有高硬度和耐磨性。
选择合适的刀具材质可以提高加工效率和刀具寿命。
综上所述,合适的切削参数和刀具选择是加工不锈钢时至关重要的。
合金铣刀是一种高效的加工工具,可以帮助加工不锈钢,在使用时应注意以上几点参数。
- 1 -。
不锈钢加工参数表

不锈钢加工参数表摘要:一、不锈钢加工概述二、不锈钢加工参数分类1.材料参数2.设备参数3.工艺参数4.环境参数三、不锈钢加工参数应用与调整1.材料选择与加工性能2.设备选型与加工效率3.工艺流程与加工质量4.环境因素与安全生产四、不锈钢加工参数的优化与实践1.提高加工性能2.提升加工效率3.确保加工质量4.保障安全生产正文:一、不锈钢加工概述不锈钢加工是指利用机械设备对不锈钢材料进行各种形状、尺寸和表面质量的改变,以满足各类制品的生产需求。
不锈钢具有良好的耐腐蚀性、耐磨性和美观性,广泛应用于建筑、厨具、化工、能源等领域。
在进行不锈钢加工时,合理选择和调整加工参数至关重要。
二、不锈钢加工参数分类1.材料参数:包括不锈钢的品种、规格、硬度、厚度等,这些参数直接影响加工的难易程度和制品性能。
2.设备参数:包括加工设备的类型、功率、转速等,合理选择设备参数可提高加工效率和加工质量。
3.工艺参数:包括加工速度、进给量、切削深度等,这些参数决定了加工过程中的切削力和切削温度,直接影响制品的表面质量和加工效率。
4.环境参数:包括加工环境温度、湿度、通风等,合理控制环境参数有利于提高加工性能和安全生产。
三、不锈钢加工参数应用与调整1.材料选择与加工性能:根据制品用途和性能要求,选择合适不锈钢品种和规格,以确保加工性能和制品质量。
2.设备选型与加工效率:根据加工需求,选择合适的设备类型和参数,提高加工效率,降低生产成本。
3.工艺流程与加工质量:制定合理的工艺流程,调整加工参数,确保制品的加工质量。
4.环境因素与安全生产:确保加工环境温湿度适宜,通风良好,降低事故风险,保障安全生产。
四、不锈钢加工参数的优化与实践1.提高加工性能:通过改进材料性能、优化设备选型和工艺参数,提高不锈钢加工性能。
2.提升加工效率:采用高效加工设备和技术,提高加工速度和进给量,实现生产效益最大化。
3.确保加工质量:严格控制加工过程中的工艺参数,提高制品的表面质量和尺寸精度。
4.2钻头钻不锈钢参数

4.2钻头钻不锈钢参数
钻不锈钢的钻头参数是非常重要的,因为钻不锈钢需要特殊的钻头来完成。
以下是钻不锈钢常见的钻头参数:
1. 钻头材质,钻不锈钢通常需要使用高速钢或钴钨合金等硬质材料制成的钻头,以确保足够的硬度和耐磨性。
2. 刃部设计,钻不锈钢的钻头通常具有特殊的刃部设计,例如螺纹刀头或者特殊的刃角,以便更好地切削不锈钢材料。
3. 冷却方式,钻不锈钢时,通常需要配合冷却润滑剂,因此钻头的设计可能会考虑冷却润滑系统,或者需要有排屑槽设计。
4. 钻头直径和长度,钻不锈钢时,钻头的直径和长度需要根据具体的工件和加工要求来选择,通常直径较小的钻头更适合钻不锈钢。
5. 螺纹规格,如果是用于螺纹加工,钻头的螺纹规格也是非常重要的参数,需要根据实际需要进行选择。
6. 螺纹锥度,如果是用于钻螺纹孔,钻头的锥度也是需要考虑
的参数,不同规格的螺纹需要不同的锥度设计。
总的来说,钻不锈钢的钻头参数需要根据具体的加工要求来选择,包括材质、刃部设计、冷却方式、直径和长度、螺纹规格以及
锥度等因素。
合适的钻头参数可以有效提高钻不锈钢的效率和质量。
激光切割2mm不锈钢工艺参数
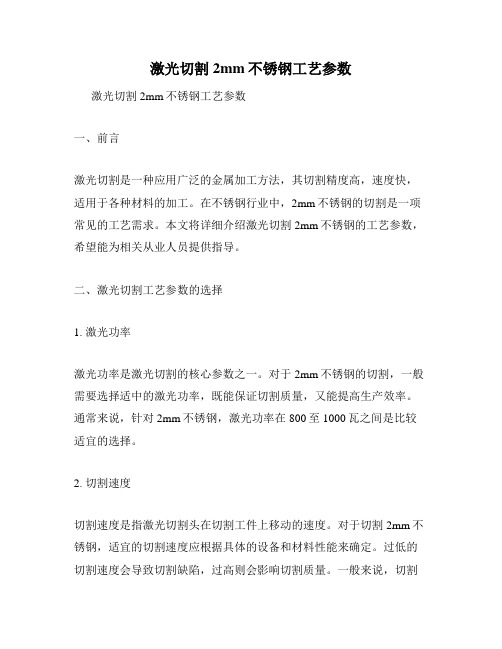
激光切割2mm不锈钢工艺参数激光切割2mm不锈钢工艺参数一、前言激光切割是一种应用广泛的金属加工方法,其切割精度高,速度快,适用于各种材料的加工。
在不锈钢行业中,2mm不锈钢的切割是一项常见的工艺需求。
本文将详细介绍激光切割2mm不锈钢的工艺参数,希望能为相关从业人员提供指导。
二、激光切割工艺参数的选择1. 激光功率激光功率是激光切割的核心参数之一。
对于2mm不锈钢的切割,一般需要选择适中的激光功率,既能保证切割质量,又能提高生产效率。
通常来说,针对2mm不锈钢,激光功率在800至1000瓦之间是比较适宜的选择。
2. 切割速度切割速度是指激光切割头在切割工件上移动的速度。
对于切割2mm不锈钢,适宜的切割速度应根据具体的设备和材料性能来确定。
过低的切割速度会导致切割缺陷,过高则会影响切割质量。
一般来说,切割速度在400至600毫米/分钟范围内是较为合适的选择。
3. 气体喷嘴直径气体喷嘴直径决定了切割过程中的气体流速。
对于2mm不锈钢的切割,喷嘴直径一般在1.5至2.5毫米之间选择。
较小的喷嘴直径可以提供较高的气体速度,有助于将熔融物质吹离切割区域,提高切割质量。
4. 气体种类在激光切割过程中,常用的气体有氮气和氧气。
在切割2mm不锈钢时,氧气可作为切割气体使用,具有较高的切割速度和质量,但容易产生氧化边。
而氮气可以避免氧化边的产生,但切割速度略低。
切割过程中应根据具体需求选择合适的气体。
5. 焦点位置焦点位置的选择对于切割质量有着重要影响。
针对2mm不锈钢,一般将焦点位置放在工件表面附近,以确保较好的切割效果。
三、激光切割2mm不锈钢的注意事项1. 预热处理对于较薄的不锈钢,预热处理可以缓解材料在切割过程中产生的热应力,减少变形和裂纹的发生。
预热温度一般在200至300℃范围内。
2. 板材质量不锈钢板材的质量直接影响到切割效果和工艺参数的选择。
在进行切割之前,应检查板材的平整度、表面状态等,确保其满足切割要求。
不锈钢的铣削加工参数
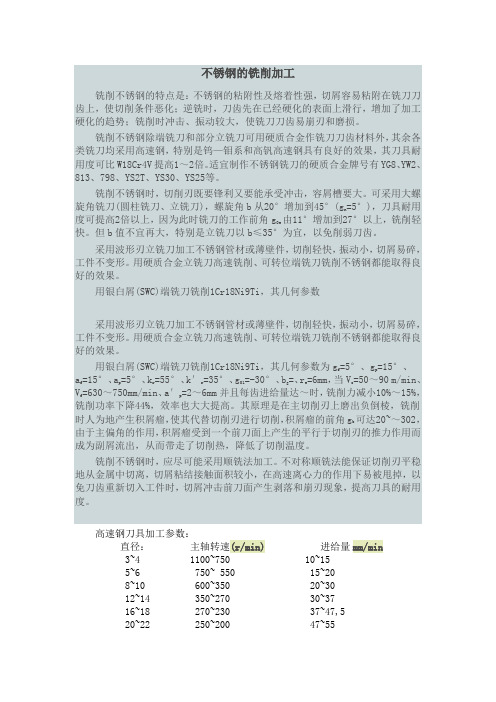
不锈钢的铣削加工铣削不锈钢的特点是:不锈钢的粘附性及熔着性强,切屑容易粘附在铣刀刀齿上,使切削条件恶化;逆铣时,刀齿先在已经硬化的表面上滑行,增加了加工硬化的趋势;铣削时冲击、振动较大,使铣刀刀齿易崩刃和磨损。
铣削不锈钢除端铣刀和部分立铣刀可用硬质合金作铣刀刀齿材料外,其余各类铣刀均采用高速钢,特别是钨—钼系和高钒高速钢具有良好的效果,其刀具耐用度可比W18Cr4V提高1~2倍。
适宜制作不锈钢铣刀的硬质合金牌号有YG8、YW2、813、798、YS2T、YS30、YS25等。
铣削不锈钢时,切削刃既要锋利又要能承受冲击,容屑槽要大。
可采用大螺旋角铣刀(圆柱铣刀、立铣刀),螺旋角b从20°增加到45°(gn=5°),刀具耐用度可提高2倍以上,因为此时铣刀的工作前角g0e由11°增加到27°以上,铣削轻快。
但b值不宜再大,特别是立铣刀以b≤35°为宜,以免削弱刀齿。
采用波形刃立铣刀加工不锈钢管材或薄壁件,切削轻快,振动小,切屑易碎,工件不变形。
用硬质合金立铣刀高速铣削、可转位端铣刀铣削不锈钢都能取得良好的效果。
用银白屑(SWC)端铣刀铣削1Cr18Ni9Ti,其几何参数采用波形刃立铣刀加工不锈钢管材或薄壁件,切削轻快,振动小,切屑易碎,工件不变形。
用硬质合金立铣刀高速铣削、可转位端铣刀铣削不锈钢都能取得良好的效果。
用银白屑(SWC)端铣刀铣削1Cr18Ni9Ti,其几何参数为gf =5°、gp=15°、a f =15°、ap=5°、kr=55°、k′r=35°、g01=-30°、bg=、re=6mm,当Vc=50~90 m/min、V f =630~750mm/min、a′p=2~6mm并且每齿进给量达~时,铣削力减小10%~15%,铣削功率下降44%,效率也大大提高。
其原理是在主切削刃上磨出负倒棱,铣削时人为地产生积屑瘤,使其代替切削刃进行切削,积屑瘤的前角gb可达20~~302,由于主偏角的作用,积屑瘤受到一个前刀面上产生的平行于切削刃的推力作用而成为副屑流出,从而带走了切削热,降低了切削温度。
- 1、下载文档前请自行甄别文档内容的完整性,平台不提供额外的编辑、内容补充、找答案等附加服务。
- 2、"仅部分预览"的文档,不可在线预览部分如存在完整性等问题,可反馈申请退款(可完整预览的文档不适用该条件!)。
- 3、如文档侵犯您的权益,请联系客服反馈,我们会尽快为您处理(人工客服工作时间:9:00-18:30)。
不锈钢切削加工不锈钢切削加工摘要:螺纹类零件10的数控车床加工编程NUM公司力推新一代Axium Power 数控系统数控铣削的编程与工艺分析基于细胞神经网络刀具磨损图像处理的研究中国最大乙烯装置的裂解气压缩机试车成功发动机盲孔除切屑机的研制与应用在不断变化时代的工具钢加工什么是智能变送器?机械故障的形成及其特性分析数控车间(机床)集成管理技术及产品浅谈CAD的特征造型技术轴承钢的表面强化方法如何进行电话销售?拉刀齿距及同时工作齿数的确定大型水轮机叶片的多轴联动数控加工编程技术张晓静:计算机在冲压领域的应用 PLC位控单元在精密磨削控制中的应用硬质材料铣削技术 CAD技术发展趋势数控机床软件界面人的因素分析 [标签:tag] 1 什么是不锈钢?通常,人们把含铬量大于12%或含镍量大于8%的合金钢叫不锈钢。
这种钢在大气中或在腐蚀性介质中具有一定的耐蚀能力,并在较高温度(450℃)下具有较高的强度。
含铬量达16%~18%的钢称为耐酸钢或耐酸不锈钢,习惯上通称为不锈钢。
钢中含铬量达12%以上时,.1?什么是不锈钢?通常,人们把含铬量大于12%或含镍量大于8%的合金钢叫不锈钢。
这种钢在大气中或在腐蚀性介质中具有一定的耐蚀能力,并在较高温度(>450℃)下具有较高的强度。
含铬量达16%~18%的钢称为耐酸钢或耐酸不锈钢,习惯上通称为不锈钢。
钢中含铬量达12%以上时,在与氧化性介质接触中,由于电化学作用,表面很快形成一层富铬的钝化膜,保护金属内部不受腐蚀;但在非氧化性腐蚀介质中,仍不易形成坚固的钝化膜。
为了提高钢的耐蚀能力,通常增大铬的比例或添加可以促进钝化的合金元素,加Ni、Mo、Mn、Cu、Nb、Ti、W、Co等,这些元素不仅提高了钢的抗腐蚀能力,同时改变了钢的内部组织以及物理力学性能。
这些合金元素在钢中的含量不同,对不锈钢的性能产生不同的影响,有的有磁性,有的无磁性,有的能够进行热处理,有的则不能热处理。
由于不锈钢所具有的上述特性,越来越广泛地应用于航空、航天、化工、石油、建筑和食品等工业部门及日常生活中。
所含的合金元素对切削加工性影响很大,有的甚至很难切削。
2?不锈钢可分为哪几类?不锈钢按其成分,可分为以铬为主的铬不锈钢和以铬、镍为主的铬镍不锈钢两大类。
工业上常用的不锈钢一般按金相组织分类,可分为以下五大类:马氏体不锈钢:含铬量12%~18%,含碳量0.1%~0.5%(有时达1%),常见的有1Cr13、2Cr13、3Cr13、4Cr13、1Cr17Ni2、9Cr18、9Cr18MoV、30Cr13Mo等。
?铁素体不锈钢:含铬量12%~30%,常见的有0Cr13、0Cr17Ti、0Cr13Si4NbRE、1Cr17、1Cr17Ti、1Cr17M02Ti、1Cr25Ti、1Cr28等。
?奥氏体不锈钢:含络量12%~25%,含镍量7%~20%(或20%以上),最典型的代表是1Cr18Ni9Ti,常见的还有00Cr18Ni10、00Cr18Ni14Mo2Cu2、0Cr18Ni12Mo2Ti、0Cr18Ni18Mo2Cu2Ti、0Cr23Ni28M03Cu3Ti、1Cr14Mn14Ni、2Cr13Mn9Ni4、1Cr18Mn8Ni5N等。
?奥氏体铁素体不锈钢:与奥氏体不锈钢相似,仅在组织中含有一定量的铁素体,常见的有0Cr21Ni5Ti、1Cr21Ni5Ti、1Cr18Mn10Ni5M03N、0Cr17Mn13Mo2N、1Cr17Mn9Ni3M03Cu2N、Cr2bNi17M03CuSiN、1Cr18Ni11Si4AlTi等。
?沉淀硬化不锈钢:含有较高的铬、镍和很低的碳,常见的有0Cr17Ni4Cu4Nb、0Cr17Ni7Al、0Cr15Ni7M02Al等。
前两类为铬不锈钢,后三类为铬镍不锈钢。
3?不锈钢有哪些物理、力学性能?马氏体不锈钢:能进行淬火,淬火后具有较高的硬度、强度和耐磨性及良好的抗氧化性,有的有磁性,但内应力大且脆。
经低温回火后可消除其应力,提高塑性,切削加工较困难,有切屑擦伤或粘结的明显趋向,刀具易磨损。
当钢中含碳量低于0.3%时,组织不均匀,粘附性强,切削时容易产生积屑瘤,且断屑困难,工件已加工表面质量低。
含碳量达0.4%~0.5%时,切削加工性较好。
马氏体不锈钢经调质处理后,可获得优良的综合力学性能,其切削加工性比退火状态有很大改善。
铁素体不锈钢:加热冷却时组织稳定,不发生相变,故热处理不能使其强化,只能靠变形强化,性能较脆,切削加工性一般较好。
切屑呈带状,切屑容易擦伤或粘结于切削刃上,从而增大切削力,切削温度升高,同时可能使工件表面产生撕裂现象。
?奥氏体不锈钢:由于含有较多的镍(或锰),加热时组织不变,故淬火不能使其强化,可略改善其加工性。
通过冷加工硬化可大幅度提高强度,如果再经时效处理,抗拉强度可达2550~2740 MPa。
奥氏体不锈钢切削时的带状切屑连绵不断,断屑困难,极易产生加工硬化,硬化层给下一次切削带来很大难度,使刀具急剧磨损,刀具耐用度大幅度下降。
奥氏体不锈钢具有优良的力学性能,良好的耐蚀能力,较突出的是冷变形能力,无磁性。
奥氏体铁素体不锈钢:有硬度极高的金属间化合物析出,强度比奥氏体不锈钢高,其切削加工性更差。
?沉淀硬化不锈钢:含有能起沉淀硬化的铊、铝、钼、钛等合金元素,它们在回火时时效析出,产生沉淀硬化,使钢具有很高的强度和硬度。
由于含碳量低保证了足够的含铬量,因此具有良好的耐腐蚀性能。
4?不锈钢有哪些切削特点?不锈钢的切削加工性比中碳钢差得多。
以普通45号钢的切削加工性作为100%,奥氏体不锈钢1Cr18Ni9Ti的相对切削加工性为40%;铁素体不锈钢1Cr28为48%;马氏体不锈钢2Cr13为55%。
其中,以奥氏体和奥氏体铁素体不锈钢的切削加工性最差。
不锈钢在切削过程中有如下几方面特点:加工硬化严重:在不锈钢中,以奥氏体和奥氏体铁素体不锈钢的加工硬化现象最为突出。
如奥氏体不锈钢硬化后的强度sb达1470~1960MPa,而且随sb的提高,屈服极限ss升高;退火状态的奥氏体不锈钢ss不超过的σb30%~45%,而加工硬化后达85%~95%。
加工硬化层的深度可达切削深度的1/3或更大;硬化层的硬度比原来的提高1.4~2.2倍。
因为不锈钢的塑性大,塑性变形时品格歪扭,强化系数很大;且奥氏体不够稳定,在切削应力的作用下,部分奥氏体会转变为马氏体;再加上化合物杂质在切削热的作用下,易于分解呈弥散分布,使切削加工时产生硬化层。
前一次进给或前一道工序所产生的加工硬化现象严重影响后续工序的顺利进行。
?切削力大:不锈钢在切削过程中塑性变形大,尤其是奥氏体不锈钢(其伸长率超过45号钢的1.5倍以上),使切削力增加。
同时,不锈钢的加工硬化严重,热强度高,进一步增大了切削抗力,切屑的卷曲折断也比较困难。
因此加工不锈钢的切削力大,如车削1Cr18Ni9Ti的单位切削力为2450MPa,比45号钢高25%。
?切削温度高:切削时塑性变形及与刀具间的摩擦都很大,产生的切削热多;加上不锈钢的导热系数约为45号钢的?~?,大量切削热都集中在切削区和刀—屑接触的界面上,散热条件差。
在相同的条件下,1Cr18Ni9Ti的切削温度比45号钢高200℃左右。
?切屑不易折断、易粘结:不锈钢的塑性、韧性都很大,车加工时切屑连绵不断,不仅影响操作的顺利进行,切屑还会挤伤已加工表面。
在高温、高压下,不锈钢与其他金属的亲和性强,易产生粘附现象,并形成积屑瘤,既加剧刀具磨损,又会出现撕扯现象而使已加工表面恶化。
含碳量较低的马氏体不锈钢的这一特点更为明显。
?刀具易磨损:切削不锈钢过程中的亲和作用,使刀—屑间产生粘结、扩散,从而使刀具产生粘结磨损、扩散磨损,致使刀具前刀面产生月牙洼,切削刃还会形成微小的剥落和缺口;加上不锈钢中的碳化物(如TiC)微粒硬度很高,切削时直接与刀具接触、摩擦,擦伤刀具,还有加工硬化现象,均会使刀具磨损加剧。
线膨胀系数大:不锈钢的线膨胀系数约为碳素钢的1.5倍,在切削温度作用下,工件容易产生热变形,尺寸精度较难控制。
5?切削不锈钢时怎样选择刀具材料?合理选择刀具材料是保证高效率切削加工不锈钢的重要条件。
根据不锈钢的切削特点,要求刀具材料应具有耐热性好、耐磨性高、与不锈钢的亲和作用小等特点。
目前常用的刀具材料有高速钢和硬质合金。
高速钢的选择:高速钢主要用来制造铣刀、钻头、丝锥、拉刀等复杂多刃刀具。
普通高速钢W18Cr4V使用时刀具耐用度很低已不符合需要,采用新型高速钢刀具切削不锈钢可获得较好的效果。
在相同的车削条件下,用W18Cr4V和95w18Cr4V两种材料的刀具加工1Cr17Ni2工件,刀具刃磨一次加工的件数分别为2~3件和12件,用95w18Cr4V的刀具耐用度提高了几倍。
这是由于提高了钢的含碳量,从而增加了钢中碳化物含量,常温硬度提高2HRC红硬性更好,600℃时由W18Cr4V的HRC48.5上升到HRC51~52,耐磨性比W18Cr4V提高2~3倍。
应用高钒高速钢W12Cr4V4Mo制作型面铣刀加工1Cr17Ni2可以获得较高的刀具耐用度。
因为含钒量增加,可在钢中形成硬度很高的VC,细小的VC存在于晶介,可以阻止晶粒长大,提高钢的耐磨性;W12Cr4V4Mo的红硬性很好,600℃时硬度可达HRC51.7,因此适合于制作切削不锈钢的各种复杂刀具。
但其强度(sb=3140 MPa)及冲击韧性(ak=2.5 J/cm3)略低于W18Cr4V,使用时要稍加注意。
随着刀具制作技术的不断发展,对于批量大的工件,采用硬质合金多刃、复杂刀具进行切削加工效果会更好。
硬质合金的选择:YG类硬质合金的韧性较好,可采用较大的前角,刀刃也可以磨得锋利些,使切削轻快,且切屑与刀具不易产生粘结,较适于加工不锈钢。
特别是在振动的粗车和断续切削时,YG类合金的这一优点更为重要。
另外,YG类合金的导热性较好,其导热系数比高速钢高将近两倍,比YT类合金高一倍。
因此YG类合金在不锈钢切削中应用较多,特别是在粗车刀、切断刀、扩孔钻及铰刀等制造中应用更为广泛。
较长时期以来,一般都采用YG6、YG8、YG8N、YW1、YW2等普通牌号的硬质合金作为切削不锈钢的刀具材料,但均不能获得较理想的效果;采用新牌号硬质合金如813、758、767、640、712、798、YM051、YM052、YM10、YS2T、YD15等,切削不锈钢可获得较好的效果。
而用813牌号硬质合金刀具切削奥氏体不锈钢效果很好,因为813合金既具有较高的硬度(≥HRA91)、强度(sb=1570MPa),又具有良好的高温韧性、抗氧化性、抗粘结性,其组织致密耐磨性好。
6?切削不锈钢时怎样选择刀具几何参数?前角g0:不锈钢的硬度、强度并不高,但其塑性、韧性都较好,热强性高,切削时切屑不易被切离。