不锈钢的车削加工方法
分析不锈钢的机械加工方法

分析不锈钢的机械加工方法不锈钢是一种耐腐蚀的金属材料,广泛应用于制造行业中。
机械加工是对不锈钢进行形状加工和表面处理的重要方法之一,本文将分析常用的不锈钢机械加工方法。
1.铣削加工:铣削是将刀具在工件上旋转切削的一种加工方法。
不锈钢的硬度相对较高,因此在铣削过程中需要选用高硬度的刀具,并采用适当的切削速度和进给速度。
对于精密加工,还可采用数控铣床进行精确控制。
2.车削加工:车削是通过旋转车刀将工件宽度修整到设计尺寸的加工方法。
不锈钢的硬度高,具有很高的切削难度。
为了保证加工质量,需要选用刀具的刀片材料具有良好的切削性能,经常更换刀片,并且适当选择进给速度和切削速度。
3.钻削加工:钻削是通过旋转刀具在工件上切削孔洞的加工方法。
在不锈钢的钻削中,由于工件硬度高,钻头容易损坏。
因此,应选择硬质合金钻头,采用较低的切削转速,并进行冷却润滑剂的切削润滑。
4.磨削加工:磨削是通过磨料颗粒对工件进行磨削的一种加工方法。
不锈钢硬度高,适合采用砂轮进行磨削。
在磨削过程中,应选用适当的磨具和磨削磨粒,并保证切削液的良好冷却和润滑。
5.锻造加工:锻造是通过对不锈钢材料施加压力,使其发生塑性变形并改变形状的一种加工方法。
不锈钢具有较好的锻造性能,适合进行锻造加工。
通过锻造可以获得高强度和良好的耐腐蚀性能的零件。
6.激光切割:激光切割是通过高能激光束对不锈钢表面进行烧蚀,达到切割的目的。
激光切割具有高精度、高速度的特点,可用于制造复杂形状的零件。
7.电火花加工:电火花加工是通过电脉冲在工件表面产生高能量火花,使工件表面产生微小的氧化腐蚀,从而实现对不锈钢进行精细加工和切割的一种方法。
以上是常见的不锈钢机械加工方法,每种方法都具有适用的情况和要求。
在实际应用中,需要根据具体的加工需求和工件材料特性进行选择,以获得最佳的加工效果。
车削奥氏体不锈钢的加工要点

(r t gad d e gpa t i h u i nn 2 0 0 hn ; h nagA rnui lP leh i Istt h nag Pi i n y i l ,J z o, a i 1 10 , ia S ey oa ta o t nc ntu ,Se yn, nn n n n Lo g C n e c yc i e Lan g 1O 3,hn) i i l0 4C ia on
不锈钢 归为难加工材料。 关键词 : 奥氏体不锈钢 ; 车削加 工; 材料 中圈分类号 :Q 2 . + T 3 06 7 6 文献标识码 : A
文章编 号 :0 7 8 2 (0 2 0— 0 2 0 10 — 30 2 1 ) 10 7 — 2
Bre a y i f t e t r i g o u t n tc sa n e s se l p o e sng p i t if An l ss o h u n n f a se ii t i ls te r c s i o n s
象。
量 、 具 参 数 、 削 条 件 。 些 对 于 奥 氏体 不 锈 钢 的 加 工 就 显 刀 切 这
得 极 为 重要 。
( ) 氏体 不锈钢 的综合 性能优 良, 2奥 塑性 和韧性高 , 的 它
延 伸 率 、 面 收缩 率 和 冲 击 值 都 较 高 。C 8 i i 氏 体 不 锈 断 1 d N9 奥 T
() 4奥氏体不锈钢 中存在较多的碳化钛( i) TC 颗粒 , 硬度相
对 :我 们 选 择 的 f 硬度 商 。这种 颗 粒 枉 奥 氏体 小 锈 钢 什 j L, } 中, 会增 大对 于刀 具 的 冲击 , 剧 加
不锈钢加工 技术要求
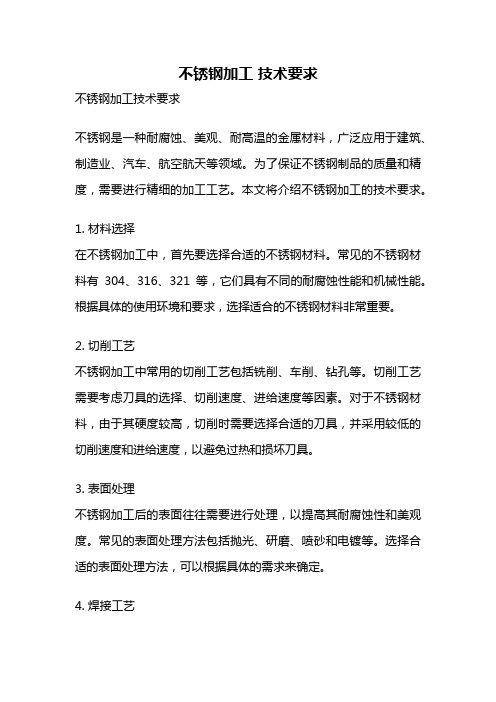
不锈钢加工技术要求不锈钢加工技术要求不锈钢是一种耐腐蚀、美观、耐高温的金属材料,广泛应用于建筑、制造业、汽车、航空航天等领域。
为了保证不锈钢制品的质量和精度,需要进行精细的加工工艺。
本文将介绍不锈钢加工的技术要求。
1. 材料选择在不锈钢加工中,首先要选择合适的不锈钢材料。
常见的不锈钢材料有304、316、321等,它们具有不同的耐腐蚀性能和机械性能。
根据具体的使用环境和要求,选择适合的不锈钢材料非常重要。
2. 切削工艺不锈钢加工中常用的切削工艺包括铣削、车削、钻孔等。
切削工艺需要考虑刀具的选择、切削速度、进给速度等因素。
对于不锈钢材料,由于其硬度较高,切削时需要选择合适的刀具,并采用较低的切削速度和进给速度,以避免过热和损坏刀具。
3. 表面处理不锈钢加工后的表面往往需要进行处理,以提高其耐腐蚀性和美观度。
常见的表面处理方法包括抛光、研磨、喷砂和电镀等。
选择合适的表面处理方法,可以根据具体的需求来确定。
4. 焊接工艺不锈钢材料的焊接需要注意选择合适的焊接方法和焊接材料。
常见的焊接方法有TIG焊、MIG焊和电弧焊等。
在焊接过程中,需要注意保护焊接区域免受氧化和污染,以保证焊接接头的质量。
5. 尺寸精度控制不锈钢加工中,尺寸精度是非常重要的。
根据具体的产品要求,需要控制不同的尺寸公差。
在加工过程中,需要采用合适的测量工具和精度控制方法,确保产品的尺寸精度符合要求。
6. 表面质量控制不锈钢制品的表面质量对于美观度和耐腐蚀性非常重要。
在加工过程中,需要注意避免表面划伤、瑕疵和氧化。
对于表面质量要求较高的产品,可以采用抛光、喷砂等方法进行处理,以提高表面质量。
7. 清洁和防护不锈钢制品在加工完成后,需要进行清洁和防护工作。
清洁可以采用清洗剂和纯净水进行,以去除加工过程中产生的油污和颗粒。
防护可以采用防锈剂、包装膜等方法,避免不锈钢制品在储存和运输过程中受到腐蚀和损坏。
总结:不锈钢加工技术要求包括材料选择、切削工艺、表面处理、焊接工艺、尺寸精度控制、表面质量控制、清洁和防护等方面。
不锈钢车削加工特点及加工工艺
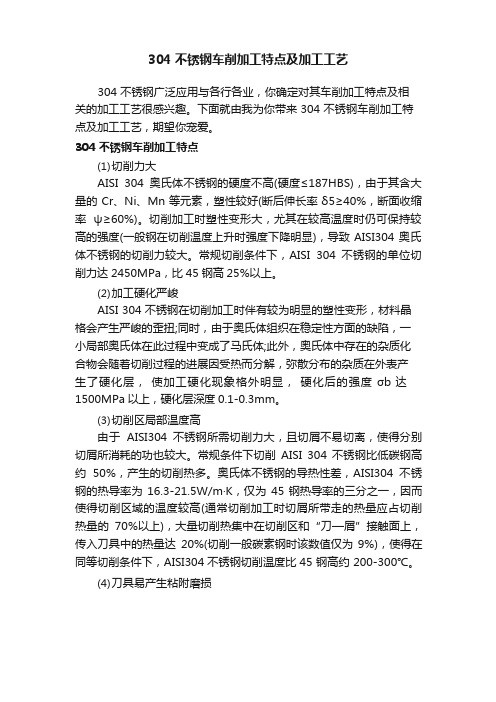
304 不锈钢车削加工特点及加工工艺304 不锈钢广泛应用与各行各业,你确定对其车削加工特点及相关的加工工艺很感兴趣。
下面就由我为你带来 304 不锈钢车削加工特点及加工工艺,期望你宠爱。
304 不锈钢车削加工特点(1)切削力大AISI 304 奥氏体不锈钢的硬度不高(硬度≤187HBS),由于其含大量的 Cr、Ni、Mn 等元素,塑性较好(断后伸长率δ5≥40%,断面收缩率ψ≥60%)。
切削加工时塑性变形大,尤其在较高温度时仍可保持较高的强度(一般钢在切削温度上升时强度下降明显),导致 AISI304 奥氏体不锈钢的切削力较大。
常规切削条件下,AISI 304 不锈钢的单位切削力达 2450MPa,比 45 钢高 25%以上。
(2)加工硬化严峻AISI 304 不锈钢在切削加工时伴有较为明显的塑性变形,材料晶格会产生严峻的歪扭;同时,由于奥氏体组织在稳定性方面的缺陷,一小局部奥氏体在此过程中变成了马氏体;此外,奥氏体中存在的杂质化合物会随着切削过程的进展因受热而分解,弥散分布的杂质在外表产生了硬化层,使加工硬化现象格外明显,硬化后的强度σb达1500MPa 以上,硬化层深度 0.1-0.3mm。
(3)切削区局部温度高由于AISI304 不锈钢所需切削力大,且切屑不易切离,使得分别切屑所消耗的功也较大。
常规条件下切削AISI 304 不锈钢比低碳钢高约50%,产生的切削热多。
奥氏体不锈钢的导热性差,AISI304 不锈钢的热导率为 16.3-21.5W/m·K,仅为 45 钢热导率的三分之一,因而使得切削区域的温度较高(通常切削加工时切屑所带走的热量应占切削热量的70%以上),大量切削热集中在切削区和“刀—屑”接触面上,传入刀具中的热量达20%(切削一般碳素钢时该数值仅为9%),使得在同等切削条件下,AISI304 不锈钢切削温度比 45 钢高约 200-300℃。
(4)刀具易产生粘附磨损由于奥氏体不锈钢的高温强度高,加工硬化倾向大,因此,切削负荷重,奥氏体不锈钢与刀具和切屑之间会由于切削过程中其与刀具之间的亲合趋势显著增加,从而不行避开地产生粘结、集中等现象,并生成“切屑瘤”,造成刀具粘附磨损。
浅谈不锈钢材料的车削加工
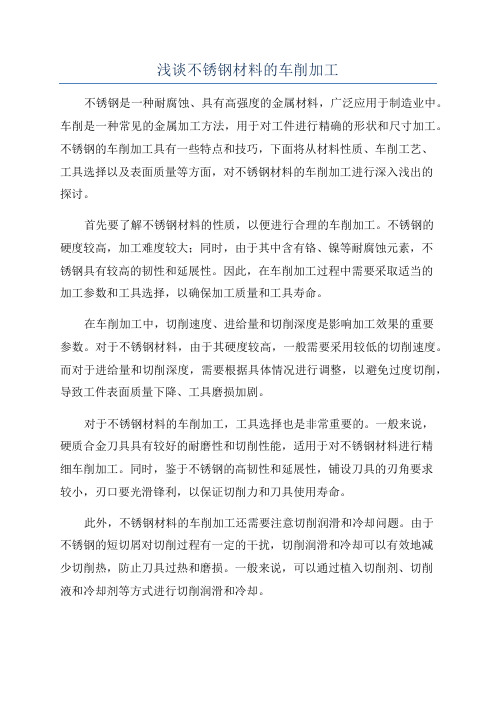
浅谈不锈钢材料的车削加工不锈钢是一种耐腐蚀、具有高强度的金属材料,广泛应用于制造业中。
车削是一种常见的金属加工方法,用于对工件进行精确的形状和尺寸加工。
不锈钢的车削加工具有一些特点和技巧,下面将从材料性质、车削工艺、工具选择以及表面质量等方面,对不锈钢材料的车削加工进行深入浅出的探讨。
首先要了解不锈钢材料的性质,以便进行合理的车削加工。
不锈钢的硬度较高,加工难度较大;同时,由于其中含有铬、镍等耐腐蚀元素,不锈钢具有较高的韧性和延展性。
因此,在车削加工过程中需要采取适当的加工参数和工具选择,以确保加工质量和工具寿命。
在车削加工中,切削速度、进给量和切削深度是影响加工效果的重要参数。
对于不锈钢材料,由于其硬度较高,一般需要采用较低的切削速度。
而对于进给量和切削深度,需要根据具体情况进行调整,以避免过度切削,导致工件表面质量下降、工具磨损加剧。
对于不锈钢材料的车削加工,工具选择也是非常重要的。
一般来说,硬质合金刀具具有较好的耐磨性和切削性能,适用于对不锈钢材料进行精细车削加工。
同时,鉴于不锈钢的高韧性和延展性,铺设刀具的刃角要求较小,刃口要光滑锋利,以保证切削力和刀具使用寿命。
此外,不锈钢材料的车削加工还需要注意切削润滑和冷却问题。
由于不锈钢的短切屑对切削过程有一定的干扰,切削润滑和冷却可以有效地减少切削热,防止刀具过热和磨损。
一般来说,可以通过植入切削剂、切削液和冷却剂等方式进行切削润滑和冷却。
最后,不锈钢材料的车削加工后还需要进行相应的表面处理,以提高工件的表面质量和防锈性能。
一般可以采用研磨、抛光等方式进行表面处理,以增加工件的光洁度和美观度。
总之,不锈钢材料的车削加工是一项综合性的任务,需要考虑材料性质、车削工艺、工具选择以及表面质量等多个方面的因素。
只有合理选择加工参数和工具,严格控制加工过程,才能获得满意的加工效果和产品质量。
同时,注重切削润滑和冷却、以及后续表面处理,也是保证不锈钢材料车削加工成功的关键。
不锈钢的车削技巧

不锈钢的车削技巧主要包括以下几个方面:1.刀具选择:选择适合不锈钢车削的刀具非常重要。
通常,选择具有较高耐热性、耐磨性和与不锈钢亲和作用小的刀具材料,如高碳、高钒或钼系的高速钢。
此外,刀具的几何形状和角度也需要根据具体加工要求进行选择。
2.切削用量选择:切削用量包括切削速度、进给量和切削深度。
对于不锈钢的车削,切削速度通常较低,一般为普通碳钢切削速度的40%~60%。
进给量和切削深度也需要根据具体情况进行选择,以避免刀具过度磨损和工件表面质量下降。
3.冷却液选择:使用合适的冷却液可以有效降低切削温度,减少刀具磨损和提高工件表面质量。
对于不锈钢的车削,通常选择具有较好冷却和润滑性能的冷却液。
4.操作技巧:在车削不锈钢时,需要注意以下几点操作技巧:首先,保持刀具的锋利,及时更换磨损的刀具;其次,避免使用过大的切削用量,以减少刀具的受力;最后,注意工件的装夹方式和切削力的方向,以避免工件变形或振动。
此外,还需要注意以下几点:1.由于不锈钢的塑性大、韧性高,车削时容易产生积屑瘤和鳞刺,这不仅影响工件的表面粗糙度,还会使刀具的磨损加快。
因此,需要选择合适的刀具材料和几何角度,以及合理的切削用量来避免这些问题的产生。
2.不锈钢的导热性差,导致切削热无法及时散出,使刀具的刃口温度升高,加剧刀具磨损。
为了降低切削温度,可以采用浇注冷却液的方法。
3.在车削过程中,应随时注意观察切削情况,如发现异常现象(如振动、噪声、温度升高等),应及时采取措施进行调整。
4.对于不同种类和规格的不锈钢材料,其车削性能也会有所不同。
因此,在实际加工前,最好先进行一些试验性切削,以确定最佳的切削参数和工艺方案。
总之,掌握不锈钢的车削技巧需要综合考虑多个因素,包括刀具选择、切削用量、冷却液和操作技巧等。
通过合理的选择和调整这些参数,可以提高加工效率、降低生产成本并获得高质量的工件。
不锈钢薄板类工件的车削工艺

2
2 5 。 ;后 角选 用 5 。 ~8 。 ;主 偏 角选 用7 5 。 或6 0 。 ;
.
拦 旦主 持 楚. 宝 . 垄 .
嘉
不锈钢薄板类工件的车削工艺
天津赛 瑞机 器设备有 限公 司 ( 3 0 0 3 0 1 ) 刘 天津 菱云刀 具设计有 限公 司 ( 3 0 0 3 8 4 ) 王 鹏 毅
薄 ,只有 ( 1 5 ±0 . 1 )mm,工件在机床上无法一次 装夹完成加工。采用常规的装夹方式 ,工件装夹无 论夹外 圆或是撑 内圆,个别处在装夹时受 力稍有不
式普车 ( 型号为C 5 1 1 6 A)。由于设备使用时 间较
长 ,设 备 的 回转 工 作 台 和卡 爪 均 有 一 定磨 损 老化 。 工 件 直接 装夹 在 设 备 上 ,加 工 误 差 较大 ,精 度很 难 保证。
3 . 材料分析
此 密封环材 质为 1 Cr l 8 Ni 9 ,按 不 锈 钢 成 分 分 类 ,属于 铬 镍 不 锈 钢 ;按 不 锈 钢 金相 组 织 分 类 ,属 于 奥 氏体 不 锈 钢 ;从切 削加 工 性 能 方面 来 说 ,属 于
圆 一 三次倒个撑 内圆 ,精车外 圆及 下端面 一 成
品。
经过 上 述 反 复 翻 面 加 工 工艺 过 程 ,加 工试 制 出 两 件 产 品 。检 验 发 现 ,端 面 厚 度 不 均匀 ,无 法保 证 在 公 差范 围之 内 ,平行 度达 不 到要 求 , 出现加 工变
使 切 削力 增 加 。 同时 ,加 工 硬 化严 重 ,热 强 度高 , 进 一 步 增 大 了切 削抗 力 ,切 屑 的卷 曲折 断 也 比较 困
不锈钢车削加工工艺

不锈钢车削加工工艺1 什么是不锈钢?通常,人们把含铬量大于12%或含镍量大于8%的合金钢叫不锈钢。
这种钢在大气中或在腐蚀性介质中具有一定的耐蚀能力,并在较高温度(>450℃)下具有较高的强度。
含铬量达16%~18%的钢称为耐酸钢或耐酸不锈钢,习惯上通称为不锈钢。
钢中含铬量达12%以上时,在与氧化性介质接触中,由于电化学作用,表面很快形成一层富铬的钝化膜,保护金属内部不受腐蚀;但在非氧化性腐蚀介质中,仍不易形成坚固的钝化膜。
为了提高钢的耐蚀能力,通常增大铬的比例或添加可以促进钝化的合金元素,加Ni、Mo、Mn、Cu、Nb、Ti、W、Co等,这些元素不仅提高了钢的抗腐蚀能力,同时改变了钢的内部组织以及物理力学性能。
这些合金元素在钢中的含量不同,对不锈钢的性能产生不同的影响,有的有磁性,有的无磁性,有的能够进行热处理,有的则不能热处理。
由于不锈钢所具有的上述特性,越来越广泛地应用于航空、航天、化工、石油、建筑和食品等工业部门及日常生活中。
所含的合金元素对切削加工性影响很大,有的甚至很难切削。
2 不锈钢可分为哪几类?不锈钢按其成分,可分为以铬为主的铬不锈钢和以铬、镍为主的铬镍不锈钢两大类。
工业上常用的不锈钢一般按金相组织分类,可分为以下五大类:1. 马氏体不锈钢:含铬量12%~18%,含碳量0.1%~0.5%(有时达1%),常见的有1Cr13、2Cr13、3Cr13、4Cr13、1Cr17Ni2、9Cr18、9Cr18MoV、30Cr13Mo等。
2. 铁素体不锈钢:含铬量12%~30%,常见的有0Cr13、0Cr17Ti、0Cr13Si4NbRE、1Cr17、1Cr17Ti、1Cr17M02Ti、1Cr25Ti、1Cr28等。
3. 奥氏体不锈钢:含络量12%~25%,含镍量7%~20%(或20%以上),最典型的代表是1Cr18Ni9Ti,常见的还有00Cr18Ni10、00Cr18Ni14Mo2Cu2、0Cr18Ni12Mo2Ti、0Cr18Ni18Mo2Cu2Ti、0Cr23Ni28M03Cu3Ti、1Cr14Mn14Ni、2Cr13Mn9Ni4、1Cr18Mn8Ni5N等。
不锈钢工件加工工艺简介

不锈钢工件加工工艺简介不锈钢是一种耐腐蚀、耐高温、耐磨损的金属材料,因其具有优良的物理和化学性能,在工程领域中得到广泛应用。
不锈钢工件的加工是指对不锈钢材料进行切削、成形、焊接等加工工艺,以满足工程应用的需要。
不锈钢工件加工工艺包括车削、铣削、磨削、钻孔、焊接、抛光等工艺步骤,下面将对不锈钢工件加工工艺进行简要介绍。
一、车削加工工艺车削是一种常用的加工不锈钢工件的方法,通过车床对工件进行旋转切削,使工件表面得到精密加工。
在车削加工中,不锈钢工件通常采用硬质合金刀具,利用切削原理对工件表面进行切削,以得到所需尺寸和形状。
车削加工不锈钢工件需要注意刀具的选择、切削速度和进给量的控制,以确保工件表面光洁度和尺寸精度。
对于不锈钢工件,由于其硬度和韧性较高,车削过程中需要保持合理的切削参数,避免刀具损坏和工件变形。
铣削是一种使用铣刀进行切削的加工方法,适用于不锈钢工件的平面加工、凹槽加工和轮廓加工等。
在不锈钢工件的铣削加工中,需要选择合适的刀具类型、切削参数和切削方式,以保证工件加工表面粗糙度和尺寸精度。
铣削加工可以采用立式铣床、卧式铣床、数控铣床等设备进行加工,根据不同的工件形状和要求选择合适的设备和工艺路线。
磨削是一种利用磨具对不锈钢工件进行加工的方法,能够获得精密的表面质量和尺寸精度。
磨削加工常用于不锈钢工件的表面精加工、内外圆孔加工和平面磨削等。
在磨削加工中,需要选择合适的磨具类型、磨削参数和冷却润滑方式,以避免工件表面产生热裂纹和变形。
焊接是将金属材料通过加热熔化和冷却凝固的方式连接在一起的加工方法,适用于不锈钢工件的连接和结构加工。
在焊接加工中,需要选择合适的焊接方法、焊接材料和焊接参数,以确保焊缝质量和连接强度。
不锈钢材料具有一定的焊接难度,焊接过程中需要控制温度和避免氧化,以减少焊接变形和气孔等缺陷。
抛光是一种通过摩擦和磨擦使不锈钢工件表面得到光滑和亮度的加工方法。
抛光加工可以采用机械抛光、化学抛光和电化学抛光等方式进行,以获得不同表面粗糙度和光洁度的要求。
不锈钢螺栓制造工艺

不锈钢螺栓制造工艺一、引言不锈钢螺栓在工业生产中扮演着重要的角色,它们被广泛应用于建筑、机械、航空航天等领域。
不锈钢螺栓具有耐腐蚀、耐高温、强度高等特点,因此备受青睐。
本文将介绍不锈钢螺栓的制造工艺。
二、原材料选择不锈钢螺栓的制造首先要选择合适的原材料。
常见的不锈钢材料有304、316、321等。
根据螺栓的使用环境和要求,选择合适的不锈钢材料非常重要。
三、冷镦成型不锈钢螺栓的制造过程通常从冷镦成型开始。
冷镦成型是指将钢材通过模具加工成所需形状的工艺。
在冷镦成型过程中,将经过预处理的不锈钢原料锤击压制,使其逐渐变形成螺栓的形状。
四、热处理冷镦成型后的不锈钢螺栓需要进行热处理。
热处理是通过加热和冷却的方式改变材料的组织结构和性能。
这一步的目的是增加螺栓的硬度和强度,提高其耐腐蚀性。
五、车削加工经过热处理的不锈钢螺栓需要进行车削加工。
车削是通过旋转工件并使用刀具切削的工艺。
通过车削加工,可以使螺栓的直径、长度和螺纹尺寸达到标准要求。
六、螺纹加工螺纹是不锈钢螺栓的重要组成部分,它能够让螺栓与螺母紧密连接。
螺纹加工是将螺栓表面进行切割或滚动,形成螺纹纹理的过程。
螺纹加工需要精确的控制参数,以确保螺纹质量达到要求。
七、表面处理不锈钢螺栓的表面处理非常重要,可以提高其耐腐蚀性和美观度。
常见的表面处理方法有镀锌、电镀和喷涂等。
镀锌可以在螺栓表面形成一层锌层,提供耐腐蚀的保护。
电镀可以在螺栓表面形成一层金属镀层,提高其外观和耐腐蚀性能。
喷涂是将特殊的涂料喷涂在螺栓表面,提供良好的防腐蚀性能。
八、质量检验制造完成的不锈钢螺栓需要进行质量检验。
质量检验包括外观检查、尺寸检验和性能检验等。
外观检查主要是检查螺栓的表面是否有缺陷和污染物。
尺寸检验包括测量螺栓的直径、长度和螺纹尺寸是否符合标准要求。
性能检验主要是测试螺栓的强度和耐腐蚀性能是否达到要求。
九、包装和运输经过质量检验合格的不锈钢螺栓需要进行包装和运输。
包装通常采用纸箱、木箱或塑料袋等包装材料,以保护螺栓免受损坏。
简述不锈钢的加工工艺

简述不锈钢的加工工艺
不锈钢是一种耐腐蚀、抗氧化的金属材料,常用于制造各种产品,包括厨具、建筑材料、化工设备等。
不锈钢的加工工艺通常包括以下几个步骤:
1.切割:针对不同的产品需求,不锈钢通常需要进行切割,以获得所需的形状和尺寸。
常用的切割方法包括机械切割、火焰切割、等离子切割等。
2.弯曲和成形:在制造过程中,需要将不锈钢板材弯曲成特定的形状。
这可以通过机械弯曲、滚轮弯曲或液压弯曲等方法实现。
3.焊接:不锈钢制品通常需要通过焊接来连接零部件。
电弧焊、氩弧焊和激光焊等是常用的不锈钢焊接方法。
焊接后可能需要进行表面处理,以保持不锈钢的耐腐蚀性。
4.表面处理:不锈钢的表面处理可以包括抛光、酸洗、电镀等步骤,以提高其表面光洁度、耐腐蚀性和美观度。
抛光可以使不锈钢表面更光滑,酸洗可以去除氧化层,电镀则可以改变不锈钢的表面颜色和质感。
5.机械加工:不锈钢零部件通常需要进行机械加工,例如车削、铣削、钻孔等,以获得精确的尺寸和表面质量。
6.装配:在加工完成后,不锈钢零部件可能需要进行组装,形成最终的产品。
这可能涉及到螺栓连接、焊接、胶合等方式。
06cr18ni11ti奥氏体不锈钢 加工工艺
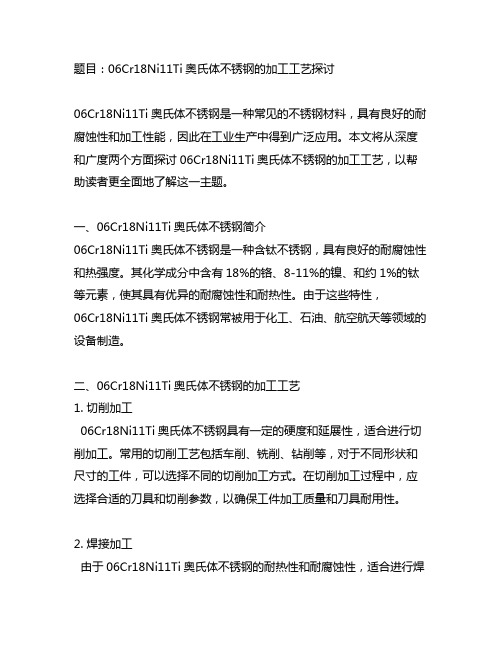
题目:06Cr18Ni11Ti奥氏体不锈钢的加工工艺探讨06Cr18Ni11Ti奥氏体不锈钢是一种常见的不锈钢材料,具有良好的耐腐蚀性和加工性能,因此在工业生产中得到广泛应用。
本文将从深度和广度两个方面探讨06Cr18Ni11Ti奥氏体不锈钢的加工工艺,以帮助读者更全面地了解这一主题。
一、06Cr18Ni11Ti奥氏体不锈钢简介06Cr18Ni11Ti奥氏体不锈钢是一种含钛不锈钢,具有良好的耐腐蚀性和热强度。
其化学成分中含有18%的铬、8-11%的镍、和约1%的钛等元素,使其具有优异的耐腐蚀性和耐热性。
由于这些特性,06Cr18Ni11Ti奥氏体不锈钢常被用于化工、石油、航空航天等领域的设备制造。
二、06Cr18Ni11Ti奥氏体不锈钢的加工工艺1. 切削加工06Cr18Ni11Ti奥氏体不锈钢具有一定的硬度和延展性,适合进行切削加工。
常用的切削工艺包括车削、铣削、钻削等,对于不同形状和尺寸的工件,可以选择不同的切削加工方式。
在切削加工过程中,应选择合适的刀具和切削参数,以确保工件加工质量和刀具耐用性。
2. 焊接加工由于06Cr18Ni11Ti奥氏体不锈钢的耐热性和耐腐蚀性,适合进行焊接加工。
常用的焊接工艺包括氩弧焊、氩气保护焊、电阻焊等,其中氩弧焊是最常用的一种。
在焊接过程中,需要注意控制焊接电流和电压,以避免产生氧化皮和焊缝不良。
3. 热处理工艺06Cr18Ni11Ti奥氏体不锈钢的热处理工艺包括固溶处理和时效处理。
固溶处理可以改善材料的塑性和韧性,时效处理则可以提高材料的硬度和强度。
在热处理过程中,需要控制加热温度和保温时间,以确保材料的组织结构和性能达到设计要求。
4. 表面处理工艺06Cr18Ni11Ti奥氏体不锈钢的表面处理工艺包括抛光、喷丸、酸洗等。
这些工艺可以改善材料表面的光洁度和耐腐蚀性,同时也可以提高涂层的附着力和耐磨性。
在表面处理过程中,应根据具体要求选择合适的工艺流程和化学药剂,以确保材料表面的质量和性能。
基于Deform3D的不锈钢车削加工仿真研究

基于Deform3D的不锈钢车削加工仿真研究作者:韦辽来源:《现代商贸工业》2019年第22期摘要:不锈钢是典型的难加工材料。
为了更详细地了解金属材料的切削加工,采用CAE 仿真软件Deform 3D为平台,根据有限元法对304不锈钢的切削加工过程进行建模和仿真。
同时采用正交试验法对304不锈钢进行车削加工试验,并对试验结果和有限元仿真模拟结果进行了对比分析,为实际生产工艺选择参数提供合理的参考。
关键词:切削加工;Deform 3D;正交试验;有限元仿真中图分类号:TB ; ; 文献标识码:A ; ; ;doi:10.19311/ki.1672-3198.2019.22.0920 引言切削加工是机械制造行业中应用广泛的零件金属成形工艺,是国内外研究的重点课题。
在实际生产应用中,304不锈钢广泛用于制造需要良好性能的设备和零件上。
硬质合金硬度比较高,是加工304不锈钢常用的刀具材料之一。
硬质合金因为超高硬度、高红硬性、高强度和韧性广泛地应用于切削刀具、矿用工具和耐磨零件中。
随着计算机技术和有限元方法理论的飞跃发展,有限元已被广泛应用于分析切削加工领域中。
常用的CAE仿真软件有MARC、DEFORM、AdvantEdge、ABAQUS等。
Deform 3D可以随着刀具的几何形状、切削速度和切削深度来预测一些参数的情况,如切削力大小、应力应变、切削温度高低、磨损大小、磨损形式等。
采用CAE仿真软件Deform 3D为平台,根据有限元法对304不锈钢的切削加工过程进行建模和仿真。
同时采用正交试验法对304不锈钢进行车削加工试验,并对试验结果和有限元仿真模拟结果进行了对比分析,为实际生产工艺选择参数提供合理的参考。
1 基于Deform 3D的不锈钢车削加工仿真1.1 Deform 3D简介Deform 3D是基于有限元分析方法的专业工艺仿真软件,可以综合建模、网格划分、成形、热传导等进行模拟仿真分析,适用于热、冷、温成形,可以得到详细和有益的工艺数据。
耐磨球生产流程

耐磨球生产流程
耐磨球的生产流程一般包括原料采购、制造铸件母体、车削加工
成型、质量检验、表面处理等六个过程。
1、原料采购:主要从几家厂家采购耐磨球材料,通常采用不锈钢
材料或高强度耐磨合金,要求采购材料满足动力传递部件的特殊要求,特别是强度、硬度和疲劳寿命等。
2、制造铸件母体:根据要求,将不锈钢或高强度耐磨合金材料熔
炼成铸件,然后在连铸机上装入模具,冷却室内的温度控制在要求的
范围内,得到的铸件母体,可以根据要求的外型尺寸和性能指标经过
加工制作成耐磨球。
3、车削加工成型:车削加工是耐磨球成形生产过程中很重要的环节,其主要工艺步骤是:定位→切削→ 抛光→放料→模压→ 完成。
在车削加工过程中,引进先进数控技术,实现了全自动化操作,使车
削成型的过程具有较高的加工质量。
4、质量检验:所生产的耐磨球在经过半成品或成品加工完成后,
应经过严格的检验,检验项目的检测标准一般按照表中的要求,主要
检测外形尺寸、表面光洁度、硬度、机械强度、抗磨损性能等。
5、表面处理:耐磨球在生产前,主要有清洗、橡胶包覆、表面抛光、涂漆等工艺,在这些工艺流程后,可以使耐磨球的通气性能得到
改善,提高表面的光泽度,同时还可以防止耐磨球的表面受到腐蚀,
延长耐磨球的使用寿命。
6、包装:最后,经过质量检验和表面处理完成的耐磨球,要进行
专业包装,防止损坏,确保耐磨球安全交付使用。
不同的金属材料切削
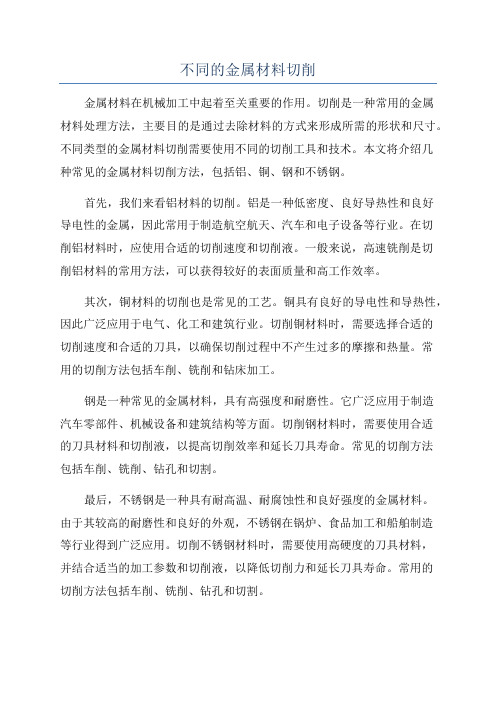
不同的金属材料切削金属材料在机械加工中起着至关重要的作用。
切削是一种常用的金属材料处理方法,主要目的是通过去除材料的方式来形成所需的形状和尺寸。
不同类型的金属材料切削需要使用不同的切削工具和技术。
本文将介绍几种常见的金属材料切削方法,包括铝、铜、钢和不锈钢。
首先,我们来看铝材料的切削。
铝是一种低密度、良好导热性和良好导电性的金属,因此常用于制造航空航天、汽车和电子设备等行业。
在切削铝材料时,应使用合适的切削速度和切削液。
一般来说,高速铣削是切削铝材料的常用方法,可以获得较好的表面质量和高工作效率。
其次,铜材料的切削也是常见的工艺。
铜具有良好的导电性和导热性,因此广泛应用于电气、化工和建筑行业。
切削铜材料时,需要选择合适的切削速度和合适的刀具,以确保切削过程中不产生过多的摩擦和热量。
常用的切削方法包括车削、铣削和钻床加工。
钢是一种常见的金属材料,具有高强度和耐磨性。
它广泛应用于制造汽车零部件、机械设备和建筑结构等方面。
切削钢材料时,需要使用合适的刀具材料和切削液,以提高切削效率和延长刀具寿命。
常见的切削方法包括车削、铣削、钻孔和切割。
最后,不锈钢是一种具有耐高温、耐腐蚀性和良好强度的金属材料。
由于其较高的耐磨性和良好的外观,不锈钢在锅炉、食品加工和船舶制造等行业得到广泛应用。
切削不锈钢材料时,需要使用高硬度的刀具材料,并结合适当的加工参数和切削液,以降低切削力和延长刀具寿命。
常用的切削方法包括车削、铣削、钻孔和切割。
总之,不同类型的金属材料切削需要选用不同的切削工具和技术,并结合合适的加工参数和切削液。
通过正确选择和应用切削方法,可以获得理想的切削效果,并提高生产效率和产品质量。
因此,在进行金属材料切削时,必须根据具体材料的性质和要求进行选择和操作,以获得最佳的切削效果。
不锈钢材料的车削技巧
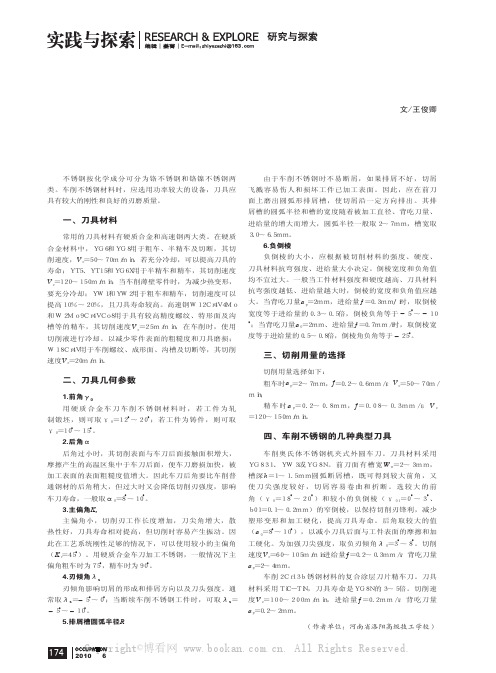
OCCUPATION1742010 6不锈钢按化学成分可分为铬不锈钢和铬镍不锈钢两类。
车削不锈钢材料时,应选用功率较大的设备,刀具应具有较大的刚性和良好的刃磨质量。
一、刀具材料常用的刀具材料有硬质合金和高速钢两大类。
在硬质合金材料中,YG6和YG8用于粗车、半精车及切断,其切削速度,V c=50~70m/min,若充分冷却,可以提高刀具的寿命;YT5、YT15和YG6X用于半精车和精车,其切削速度V c=120~150m/min,当车削薄壁零件时,为减少热变形,要充分冷却;YW1和YW2用于粗车和精车,切削速度可以提高10%~20%,且刀具寿命较高。
高速钢W12Cr4V4Mo和W2Mo9Cr4VCo8用于具有较高精度螺纹、特形面及沟槽等的精车,其切削速度V c=25m/min,在车削时,使用切削液进行冷却。
以减少零件表面的粗糙度和刀具磨损;W18Cr4V用于车削螺纹、成形面、沟槽及切断等,其切削速度V c=20m/min。
二、刀具几何参数1.前角γ0用硬质合金车刀车削不锈钢材料时,若工件为轧制锻坯,则可取γ0=12˚~20˚;若工件为铸件,则可取γ0=10˚~15˚。
2.后角α后角过小时,其切削表面与车刀后面接触面积增大,摩擦产生的高温区集中于车刀后面,便车刀磨损加快,被加工表面的表面粗糙度值增大。
因此车刀后角要比车削普通钢材的后角稍大,但过大时又会降低切削刃强度,影响车刀寿命,一般取α0=8˚~10˚。
3.主偏角K r主偏角小,切削刃工作长度增加,刀尖角增大,散热性好,刀具寿命相对提高,但切削时容易产生振动。
因此在工艺系统刚性足够的情况下,可以使用较小的主偏角(K r=45˚)。
用硬质合金车刀加工不锈钢,一般情况下主偏角粗车时为75˚,精车时为90˚。
4.刃倾角λs刃倾角影响切屑的形成和排屑方向以及刀头强度。
通常取λs =﹣5˚~0˚;当断续车削不锈钢工件时,可取λs =﹣5˚~﹣10˚。
5.排屑槽圆弧半径R由于车削不锈钢时不易断屑,如果排屑不好,切屑飞溅容易伤人和损坏工件已加工表面。
3Crl3不锈钢零件批量数控车削加工技巧
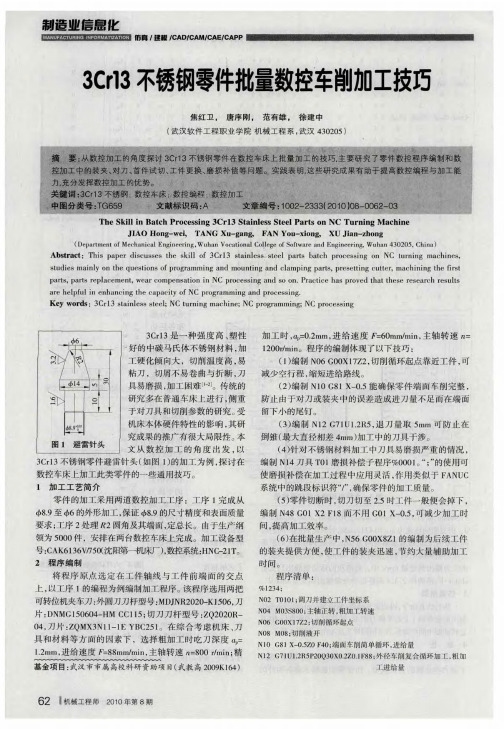
,
主轴转速
n
=
好 的 中碳 马 氏 体 不 锈 钢 材 料 加
工
12 0 0 r / m in
。
程 序 的编 制体 现 了 以 下 技 巧
,
硬 化倾 向大
,
,
切 削温 度 高 易
,
,
( 1 )编 制 N 0 6 G 0 0 X 1 7 2 2 切 削 循 环 起 点 靠 近 工 件 可
,
粘刀
切 屑 不 易 卷 曲与 折 断 刀
N 10
:
可 转 位 机 夹 车刀 :外 圆 刀 刀 杆 型 号 :M D J N R 2 0 2 0 K 1 5 0 6 刀
.
T 0 1 0 1 ;调 刀 并建 立 工
M0 3S800
;
,
件坐 标 系
片 :D N M G
04
in NC p r
a m m
in g
a n
S O
o n
Pr
.
a c t
ic
e
ha
s
pr
o v e
d tha
t the
s e
r e s e a r c
h
r e s u
lts
he lp fu l in
y
w o r
ha
n c
in g
ta in
t
he
s s
c a
p
e
a c
f NC pro gr
tu
r n
in g
留下 小 的尾 钉
(3
。
机 床本 体 硬 件 特性 的 影 响 其 研
,
)编 制
N 12 G 7 l u l 2 R 5
不锈钢数控车削加工工艺
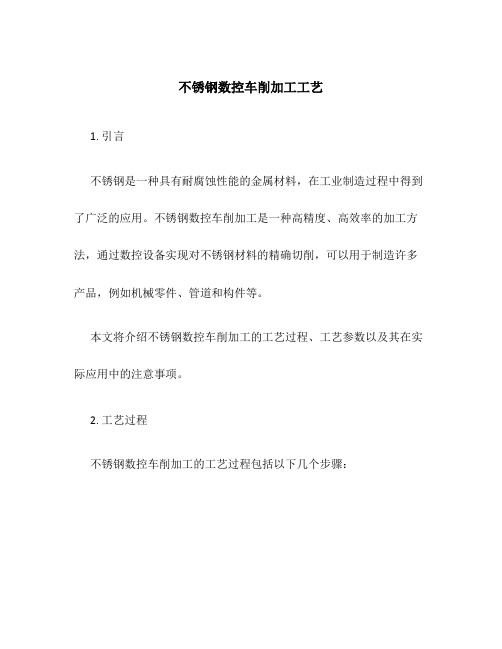
不锈钢数控车削加工工艺1. 引言不锈钢是一种具有耐腐蚀性能的金属材料,在工业制造过程中得到了广泛的应用。
不锈钢数控车削加工是一种高精度、高效率的加工方法,通过数控设备实现对不锈钢材料的精确切削,可以用于制造许多产品,例如机械零件、管道和构件等。
本文将介绍不锈钢数控车削加工的工艺过程、工艺参数以及其在实际应用中的注意事项。
2. 工艺过程不锈钢数控车削加工的工艺过程包括以下几个步骤:2.1 零件准备在进行车削加工之前,首先需要准备好要加工的不锈钢零件。
清洁表面,并确保其表面没有明显的凹陷和磨损。
2.2 工艺规划在进行数控车削加工之前,需要进行工艺规划。
工艺规划包括确定零件的加工顺序、选择合适的刀具和切削参数等。
2.3 加工装夹将不锈钢零件安装在数控车床上,进行加工装夹。
确保零件固定牢固且位置准确。
使用合适的夹具和固定装置,以避免零件在加工过程中发生移动或变形。
2.4 加工参数设置根据零件的要求和刀具的特性,设置合适的加工参数。
包括切削速度、进给速度和切削深度等。
合理的加工参数可以提高加工效率和加工质量。
2.5 车削加工根据工艺规划和加工参数,使用数控设备进行车削加工。
通过控制刀具的运动轨迹和加工参数,将不锈钢材料逐渐切削,得到所需形状和尺寸的零件。
2.6 质量检验在完成车削加工后,进行质量检验。
检查零件的尺寸、表面质量和精度等。
确保加工的零件符合要求。
3. 工艺参数不锈钢数控车削加工的工艺参数对加工质量和效率有着重要影响。
以下是一些常用的工艺参数:•切削速度:通常以米/分钟为单位。
根据不锈钢材料的硬度和刀具的材质来确定合适的切削速度。
•进给速度:刀具在单位时间内在工件上的移动速度。
根据不同的切削工况和加工精度要求,选择合适的进给速度。
•切削深度:刀具每次切削所去除的材料层厚度。
根据零件的要求和刀具的稳定性,选择合适的切削深度。
•刀具半径补偿:在车削过程中,考虑到刀具的几何特性和零件的轮廓,需要进行刀补。
2507不锈钢机加工工艺
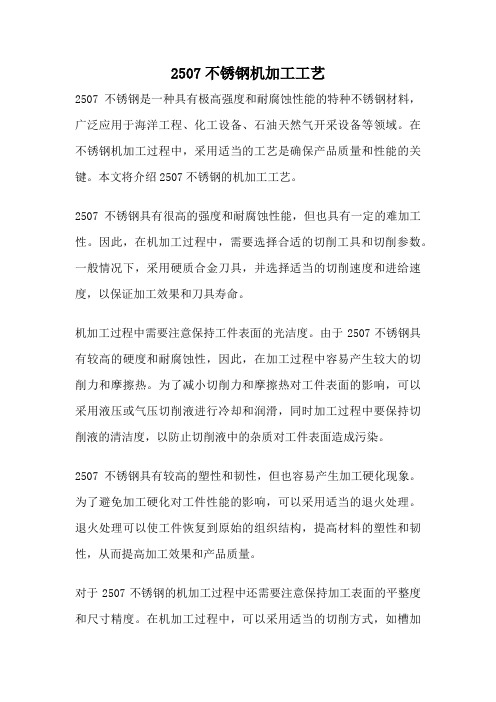
2507不锈钢机加工工艺2507不锈钢是一种具有极高强度和耐腐蚀性能的特种不锈钢材料,广泛应用于海洋工程、化工设备、石油天然气开采设备等领域。
在不锈钢机加工过程中,采用适当的工艺是确保产品质量和性能的关键。
本文将介绍2507不锈钢的机加工工艺。
2507不锈钢具有很高的强度和耐腐蚀性能,但也具有一定的难加工性。
因此,在机加工过程中,需要选择合适的切削工具和切削参数。
一般情况下,采用硬质合金刀具,并选择适当的切削速度和进给速度,以保证加工效果和刀具寿命。
机加工过程中需要注意保持工件表面的光洁度。
由于2507不锈钢具有较高的硬度和耐腐蚀性,因此,在加工过程中容易产生较大的切削力和摩擦热。
为了减小切削力和摩擦热对工件表面的影响,可以采用液压或气压切削液进行冷却和润滑,同时加工过程中要保持切削液的清洁度,以防止切削液中的杂质对工件表面造成污染。
2507不锈钢具有较高的塑性和韧性,但也容易产生加工硬化现象。
为了避免加工硬化对工件性能的影响,可以采用适当的退火处理。
退火处理可以使工件恢复到原始的组织结构,提高材料的塑性和韧性,从而提高加工效果和产品质量。
对于2507不锈钢的机加工过程中还需要注意保持加工表面的平整度和尺寸精度。
在机加工过程中,可以采用适当的切削方式,如槽加工、铣削、车削等,以保持工件表面的平整度。
同时,需要对加工尺寸进行严格控制,可以使用适当的测量工具和检测设备进行尺寸测量和检验。
2507不锈钢的机加工过程中还需要注意保护环境和安全。
在加工过程中,产生的切屑和废液应进行合理的处理,以防止对环境造成污染。
同时,操作人员要严格遵守安全操作规程,佩戴好相应的防护用品,确保人身安全。
2507不锈钢的机加工工艺是一个综合性的过程,需要选择合适的切削工具和切削参数,保持工件表面的光洁度,注意加工硬化和尺寸精度的控制,同时要注重环境保护和安全。
只有在合理的工艺控制下,才能够确保2507不锈钢产品的质量和性能,满足各种工程领域的需求。
- 1、下载文档前请自行甄别文档内容的完整性,平台不提供额外的编辑、内容补充、找答案等附加服务。
- 2、"仅部分预览"的文档,不可在线预览部分如存在完整性等问题,可反馈申请退款(可完整预览的文档不适用该条件!)。
- 3、如文档侵犯您的权益,请联系客服反馈,我们会尽快为您处理(人工客服工作时间:9:00-18:30)。
不锈钢的车削加工
关键词:刀具材料、刀具参数、切削用量、涂层刀具
目前应用的不锈钢,按其组织状态主要分为马氏体不锈钢、铁素体不锈钢和奥氏体不锈钢,常把含鉻量超过11.7%或含镍量大于8%的合金钢,叫不锈钢,在合金钢种加入较多的金属元素(Cr和Ni),而改变了合金的物理性质和化学性质。
增强了抗腐蚀能力,无论在空气中还是在酸盐的溶液中,均不易氧化生锈并在较高温度(>450℃)下仍具有较高的强度,因此被广泛应用于航空,航天、化工、石油、建筑和食品等工业部门及日常生活中。
1不锈钢的主要切削特点
(1)切削力大
其中奥氏体不锈钢尤为突出,这种材料虽然硬度不高,以牌号1Cr18Ni9Ti 为例,其硬度≤187HBW,但塑性很好(断后伸长率δ=40%,断面收缩率Ψ=60%),因此在切削过程中塑性变形大,使切削力增加。
在切削用量相同时,切奥氏体不锈钢耗能比低碳钢约高50%。
(2)加工硬化严重
在不锈钢中,以奥氏体和奥氏体铁素体不锈钢的加工硬化现象最为突出。
他们塑性大,塑性变形时晶格产生强烈歪扭;同时奥氏体稳定性差,在切削力的作用下,部分奥氏体会转变为马氏体;再加上化合物杂质在切削热的作用下,易于分解呈弥散分布,使切削加工时产生硬化层。
这一切均使加工硬化现象更为明显。
(3)刀具易产生粘附磨损
不锈钢材料在切削过程中产生高温下,与刀具材料的亲和性较大,使刀具与切削间产生粘结、扩散,易形成“刀瘤”,而造成刀具粘附磨损,降低刀具的使用寿命。
(4)切削区局部温度高
这类材料所需切削力大,分离切削消耗的功率也大,产生的切削热也就多,传入刀具的热量可达20%,而加工碳素钢时仅占9%,同时由于不锈钢的导热性不好(不锈钢的导热系数约为碳钢的1/3左右),大量切削热都集中在切削区和刀-屑接触的界面上,从而是切削区局部温度很高。
2.刀具材料的选择
根据前述不锈钢的切削特点,要求刀具材料应具有耐热性好、耐磨性高、与不锈钢的亲和作用小等特点。
目前常用的刀具材料有硬质合金、高速钢和涂层刀具。
(1)硬质合金
通常情况下,多数难加工材料都宜选用YG类硬质合金加工。
最好不选用YT 类硬质合金,尤其是在加工1Cr18Ni9Ti奥氏体不锈钢时,应绝对避免选用YT
类硬质合金。
因为不锈钢中的钛(Ti)和YT类硬质合金中的Ti产生亲和作用,切削容易把合金中的Ti带走,促使刀具磨损加剧。
YG类硬质合金的韧性较好,有较高的耐磨性和红硬性,更适合不锈钢材料的加工,可采用较大的前角,使切削轻快;导热性也好;同时切屑与刀具间不易粘接。
(2)高速钢
当工件的形状、尺寸、结构不便使用硬质合金刀具或或硬质合金刀具易于损坏时,需选用高性能高速钢刀具。
普通高速钢(如W18Cr4V等)的刀具寿命很低,不符合要求,可采用新型高速钢刀具如含钴高速钢(W2Mo9Cr4Vco8)、含铝超硬高速钢(W6Mo5Cr4V2Al)、含氮高速钢(W12Mo3Cr4V3N)等。
(3)新型刀具材料涂层刀具
采用化学气相沉积(CVD)或物理气相沉积(PVD)法,在硬质合金或其他材料刀具基本上涂覆一薄层耐磨性高的难溶金属(或非金属)化合物而得到的刀具材料。
涂层刀具的镀膜可以防止切屑和刀具直接接触,减小摩擦,降低各种机械热应力。
使用涂层刀具,可缩短切削时间,降低成本,减少换刀次数,提高加工精度,且刀具寿命长。
涂层刀具可减少或取消切削液的使用。
3 刀具参数的确定
合理选择道具参数,对提高刀具的寿命和工件的加工质量非常重要。
在保证刀具有足够强度,力求不蹦刃的前提下,应选用较大前角,不仅能降低切削力和切削温度,而且也将使硬化深度降低。
车削各种不锈钢的前角一般为12°-13°。
在保证刀具足够的前提下,宜选较大的后角。
一般取10°-20°,还可采用在主刀刃上负倒棱等措施来强化到头,以提高刀具的耐磨能力。
由于不锈钢韧性、塑性大,切削时断屑困难,应用强迫变形的方法,主要是合理地选择前刀面上断屑槽的参数和切削用量。
我们在合理选择切削用量基础上,一般采用双刃倾角加外斜式卷屑槽的办法。
对外圆车刀磨出双刃倾角,使切屑面呈棱面形,刀具前刀面上刃磨出外斜式圆弧卷屑槽,使切屑沿卷屑槽导流卷曲成宝塔状卷屑或短紧螺旋卷屑。
加工不锈钢时,切屑对刀具的粘附性强,容易产生积屑瘤,因此刀具的前、后刀面及刃口要有较小的表面粗糙度值,以降低切削阻力。
减小切削粘附、提高刀具寿命。
4.切削用量
(1)切削速度v
为了保证合理的刀具寿命,可降低切削速度。
一般切削不锈钢时切削速度可按车削普通碳钢的40%-60%。
(2)进给量f
为提高加工表面质量,给进量宜采用较小值。
(3)背吃刀量ap
(4)一般粗加工时可选ap=2—5mm,精加工时可选ap=0/2—0.5mm。
5,切削液
由于不锈钢的切削加工性较差,切削区温度高,要求切削液具有较高的冷却性能、润滑性能和渗透性。
为强化冷却效果,可采用高压喷住或油雾冷却。
常用的切削液有:
(1)硫化油:具有一定的冷却性能和润滑性能,而且来源丰富,成本较低。
(2)四氯化碳+矿物油或其他油类:矿物油或其他油类添加四氯化碳后,大大提高了切削液的渗透性,特备由于不锈钢材料的精加工。
6实例
在数控车床粗工1Cr18Ni9Ti不锈钢轴类零件(直径为60mm)。
采用涂层刀具,切削速度n=800r/min背吃刀量ap=0.7-1mm,进给量f=0.2-0.3mm/r,切削轻快,断屑良好。
刀具磨损较少,一个刀片能够连续加工4个小时以上,节约了更换到片的时间,同时我采用精车用过的刀片进行粗加工,可以节约刀具成本,对刀片进行二次利用节约能源,达到同样的效果。
7结束语
基于以上所述,不锈钢材料车削的基本原则是:刀具材料应用坚韧好、强度高的硬质合金或涂层刀具,刀具参数应尽可能的合理并尽可能将刀具刃磨得锋利些,便于切屑的卷曲、折断,还应使切削用量适当和切削液供应充足。
相关措施方法应尽量配合使用。
使用涂层刀具时,合理选用车削要素,通过多次试验,批量加工涂层刀具更胜一筹,比以往在普通车床加工效率提高五倍以上。