不锈钢车削方法
3Cr13不锈钢零件批量数控车削技巧

3Cr13不锈钢零件批量数控车削加工技巧3Cr13是一种强度高、塑性好的中碳马氏体不锈钢材料,加工硬化倾向大、切削温度高、易粘刀、切屑不易卷曲与折断、刀具易磨损,加工困难。
[1] [2]传统的研究多在普通车床上进行,侧重于对刀具和切削参数的研究。
受机床本体硬件特性的影响,其研究成果的推广有很大局限性。
本文从数控加工的角度出发,以3Cr13不锈钢零件避雷针头(见图1)的加工为例,图1 避雷针头1 加工工艺简介零件的加工采用两道数控加工工序:工序1完成从8.9至6的外形加工,保证8.9的尺寸精度和表面质量要求;工序2处理R2圆角及其端面,定总长。
由于生产纲领为5000件,安排在两台数控车床上完成。
加工设备型号:CAK6136V/750 (沈阳第一机床厂),数控系统:HNC-21T。
2程序编制将程序原点选定在工件轴线与工件前端面的交点上,以工序1的编程为例编制加工程序如下(见程序清单)。
该程序选用两把可转位机夹车刀:外圆刀刀杆型号:MDJNR2020-K1506 ,刀片:DNMG150604-HM CC115;切刀刀杆型号:ZQ2020R-04,刀片:ZQMX3N11-1E YBC251。
在综合考虑机床、刀具和材料等方面的因素下,选择粗加工时吃刀深度ap=1.2 mm,进给速度F=88 mm/min ,主轴转速n=800 r/min;精加工时,ap=0.2 mm,进给速度F=60mm/ min,主轴转速n=1200r/min。
程序的编制体现了以下技巧:(1)编制N06 G00X17Z2,切削循环起点靠近工件,可减少空行程,缩短进给路线。
(2)编制N10 G81 X-0.5能确保零件端面车削完整,防止由于对刀或装夹中的误差造成进刀量不足而在端面留下小的尾钉。
(3)编制N12G71U1.2R5,退刀量取5mm可防止在倒锥(最大直径相差4mm)加工中的刀具干涉。
(4)针对不锈钢材料加工中刀具易磨损严重的情况,编制N14刀具T01磨损补偿子程序%0001。
1Cr18Ni9Ti不锈钢的切削加工

( 1) 切削速度 Vc 为了保证合理的刀具耐用度, 可适当降低切削 速度。切削不锈钢时, 切削速度通常可按切削普通 碳钢的 40% - 60% 来选取。 ( 2) 背吃刀量 ap 粗加工时余量较大, 应选用较大的背吃刀量, 以 减少走刀次数, 同时可避免刀尖与工件毛坯表皮接 触, 以减轻刀具磨损。但背吃刀量也不宜过大, 否则 会引起振动。粗加工时, 可选取 ap= 2- 5mm。精加 工时, 可选 取较小的背吃刀量, 同时还 要避开硬化 层, 一般可选取 ap= 0 2- 0 5mm。 ( 3) 进给量 f 增大进给量会使切削残留高度和积屑瘤高度加 大, 通常选取 f = 0 1- 0 8mm。为了提高加工表面 质量, 精加 工时应采用较小的 进给量, 但不得小于 0 1mm, 以免在加工硬化区进行切削。还应注意, 进 给量 f 与背吃刀量 ap 成反比。 3 4 切削液的选择
一般来说不锈钢被认为是切削加工性能较差的金属材料1cr18ni9ti不锈钢尤为突出45钢相比其相对可切削性仅为013015属于典型的难加工材料不锈钢的主要切削特点不锈钢的切削加工具有以下特点切削力大奥氏体不锈钢表现尤为突出这种材料虽然硬度不高例如1cr18ni9ti的硬度hb187但塑性很好断后伸长率因此在切削过程中塑性变形大使切削力增加合理选择切削加工工艺由于1cr18ni9ti不锈钢切削加工性差因此必须合理选择切削加工工艺以获得良好的加工效果收稿日期
收稿日期: 2008 年 11 月
相同加工条件下, 1Cr18Ni9T i 的单位切削力比 45 钢 大 25% 以上。
车削奥氏体不锈钢的加工要点

(r t gad d e gpa t i h u i nn 2 0 0 hn ; h nagA rnui lP leh i Istt h nag Pi i n y i l ,J z o, a i 1 10 , ia S ey oa ta o t nc ntu ,Se yn, nn n n n Lo g C n e c yc i e Lan g 1O 3,hn) i i l0 4C ia on
不锈钢 归为难加工材料。 关键词 : 奥氏体不锈钢 ; 车削加 工; 材料 中圈分类号 :Q 2 . + T 3 06 7 6 文献标识码 : A
文章编 号 :0 7 8 2 (0 2 0— 0 2 0 10 — 30 2 1 ) 10 7 — 2
Bre a y i f t e t r i g o u t n tc sa n e s se l p o e sng p i t if An l ss o h u n n f a se ii t i ls te r c s i o n s
象。
量 、 具 参 数 、 削 条 件 。 些 对 于 奥 氏体 不 锈 钢 的 加 工 就 显 刀 切 这
得 极 为 重要 。
( ) 氏体 不锈钢 的综合 性能优 良, 2奥 塑性 和韧性高 , 的 它
延 伸 率 、 面 收缩 率 和 冲 击 值 都 较 高 。C 8 i i 氏 体 不 锈 断 1 d N9 奥 T
() 4奥氏体不锈钢 中存在较多的碳化钛( i) TC 颗粒 , 硬度相
对 :我 们 选 择 的 f 硬度 商 。这种 颗 粒 枉 奥 氏体 小 锈 钢 什 j L, } 中, 会增 大对 于刀 具 的 冲击 , 剧 加
不锈钢车削参数
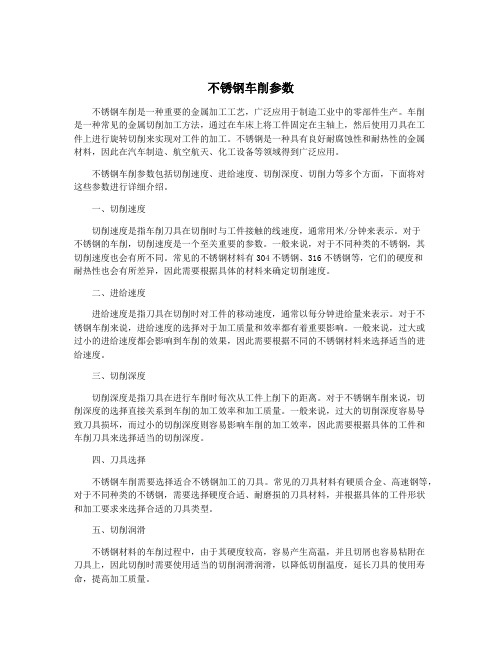
不锈钢车削参数不锈钢车削是一种重要的金属加工工艺,广泛应用于制造工业中的零部件生产。
车削是一种常见的金属切削加工方法,通过在车床上将工件固定在主轴上,然后使用刀具在工件上进行旋转切削来实现对工件的加工。
不锈钢是一种具有良好耐腐蚀性和耐热性的金属材料,因此在汽车制造、航空航天、化工设备等领域得到广泛应用。
不锈钢车削参数包括切削速度、进给速度、切削深度、切削力等多个方面,下面将对这些参数进行详细介绍。
一、切削速度切削速度是指车削刀具在切削时与工件接触的线速度,通常用米/分钟来表示。
对于不锈钢的车削,切削速度是一个至关重要的参数。
一般来说,对于不同种类的不锈钢,其切削速度也会有所不同。
常见的不锈钢材料有304不锈钢、316不锈钢等,它们的硬度和耐热性也会有所差异,因此需要根据具体的材料来确定切削速度。
二、进给速度进给速度是指刀具在切削时对工件的移动速度,通常以每分钟进给量来表示。
对于不锈钢车削来说,进给速度的选择对于加工质量和效率都有着重要影响。
一般来说,过大或过小的进给速度都会影响到车削的效果,因此需要根据不同的不锈钢材料来选择适当的进给速度。
三、切削深度切削深度是指刀具在进行车削时每次从工件上削下的距离。
对于不锈钢车削来说,切削深度的选择直接关系到车削的加工效率和加工质量。
一般来说,过大的切削深度容易导致刀具损坏,而过小的切削深度则容易影响车削的加工效率,因此需要根据具体的工件和车削刀具来选择适当的切削深度。
四、刀具选择不锈钢车削需要选择适合不锈钢加工的刀具。
常见的刀具材料有硬质合金、高速钢等,对于不同种类的不锈钢,需要选择硬度合适、耐磨损的刀具材料,并根据具体的工件形状和加工要求来选择合适的刀具类型。
五、切削润滑不锈钢材料的车削过程中,由于其硬度较高,容易产生高温,并且切屑也容易粘附在刀具上,因此切削时需要使用适当的切削润滑润滑,以降低切削温度,延长刀具的使用寿命,提高加工质量。
通过对不锈钢车削参数的合理选择,在保证车削加工效率的还能够得到尺寸精确、表面光滑的加工零件。
不锈钢车削加工特点及加工工艺
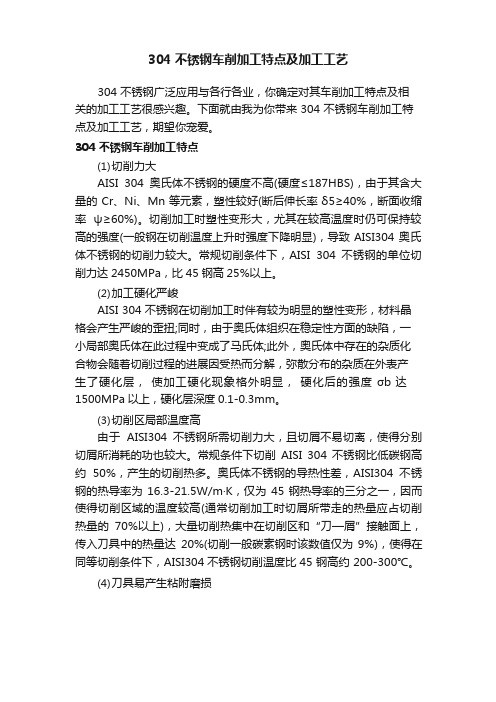
304 不锈钢车削加工特点及加工工艺304 不锈钢广泛应用与各行各业,你确定对其车削加工特点及相关的加工工艺很感兴趣。
下面就由我为你带来 304 不锈钢车削加工特点及加工工艺,期望你宠爱。
304 不锈钢车削加工特点(1)切削力大AISI 304 奥氏体不锈钢的硬度不高(硬度≤187HBS),由于其含大量的 Cr、Ni、Mn 等元素,塑性较好(断后伸长率δ5≥40%,断面收缩率ψ≥60%)。
切削加工时塑性变形大,尤其在较高温度时仍可保持较高的强度(一般钢在切削温度上升时强度下降明显),导致 AISI304 奥氏体不锈钢的切削力较大。
常规切削条件下,AISI 304 不锈钢的单位切削力达 2450MPa,比 45 钢高 25%以上。
(2)加工硬化严峻AISI 304 不锈钢在切削加工时伴有较为明显的塑性变形,材料晶格会产生严峻的歪扭;同时,由于奥氏体组织在稳定性方面的缺陷,一小局部奥氏体在此过程中变成了马氏体;此外,奥氏体中存在的杂质化合物会随着切削过程的进展因受热而分解,弥散分布的杂质在外表产生了硬化层,使加工硬化现象格外明显,硬化后的强度σb达1500MPa 以上,硬化层深度 0.1-0.3mm。
(3)切削区局部温度高由于AISI304 不锈钢所需切削力大,且切屑不易切离,使得分别切屑所消耗的功也较大。
常规条件下切削AISI 304 不锈钢比低碳钢高约50%,产生的切削热多。
奥氏体不锈钢的导热性差,AISI304 不锈钢的热导率为 16.3-21.5W/m·K,仅为 45 钢热导率的三分之一,因而使得切削区域的温度较高(通常切削加工时切屑所带走的热量应占切削热量的70%以上),大量切削热集中在切削区和“刀—屑”接触面上,传入刀具中的热量达20%(切削一般碳素钢时该数值仅为9%),使得在同等切削条件下,AISI304 不锈钢切削温度比 45 钢高约 200-300℃。
(4)刀具易产生粘附磨损由于奥氏体不锈钢的高温强度高,加工硬化倾向大,因此,切削负荷重,奥氏体不锈钢与刀具和切屑之间会由于切削过程中其与刀具之间的亲合趋势显著增加,从而不行避开地产生粘结、集中等现象,并生成“切屑瘤”,造成刀具粘附磨损。
304不锈钢车削的高压断屑技术研究

304不锈钢车削的高压断屑技术研究
戚远大;周永胜;崔成林
【期刊名称】《组合机床与自动化加工技术》
【年(卷),期】2022()2
【摘要】针对304不锈钢的车削过程中铁屑折断难,经常导致铁屑缠刀、加工表面划伤、排屑困难、影响自动化生产线的稳定运行等问题,设计开发7 MPa高压供液系统为车削过程提供高压冷却液。
在高压冷却环境下,试验比较304不锈钢在粗、精加工的不同车削参数、刀片情况下的铁屑状态。
研究结果表明,7 MPa高压冷却可以解决304不锈钢精加工铁屑不易折断的问题。
铁屑的长度与冷却压力、切削参数、刀片有关,通过匹配适当的切削参数和刀片,铁屑长度可以被控制在较短的范围内。
在此基础上,提出了一套针对304不锈钢车削加工的高压断屑方案,实现铁屑的可靠折断。
【总页数】4页(P112-114)
【作者】戚远大;周永胜;崔成林
【作者单位】沈阳机床集团有限责任公司
【正文语种】中文
【中图分类】TH161;TG51
【相关文献】
1.车削中三维复杂断屑槽刀具断屑仿真研究
2.简易车削断屑装置及其断屑规律研究
3.车削加工切屑形状分析及合理断屑方法
4.不锈钢车削刀片槽型断屑仿真研究
5.伊斯卡推出适合切断不锈钢的新型断屑槽及IC5400牌号
因版权原因,仅展示原文概要,查看原文内容请购买。
浅谈不锈钢材料的车削加工
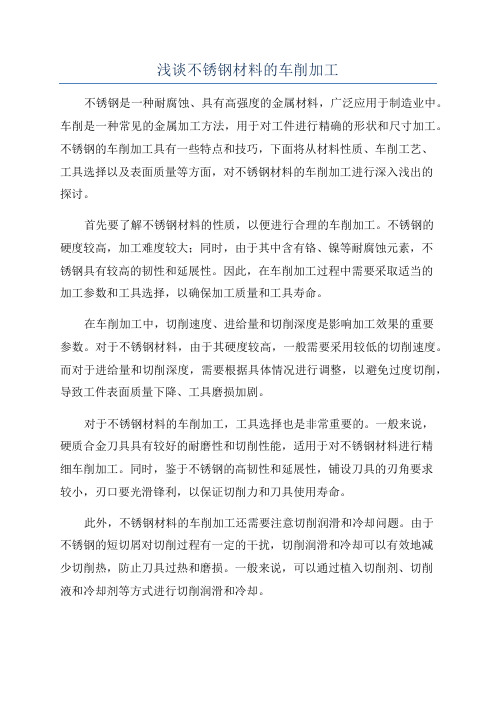
浅谈不锈钢材料的车削加工不锈钢是一种耐腐蚀、具有高强度的金属材料,广泛应用于制造业中。
车削是一种常见的金属加工方法,用于对工件进行精确的形状和尺寸加工。
不锈钢的车削加工具有一些特点和技巧,下面将从材料性质、车削工艺、工具选择以及表面质量等方面,对不锈钢材料的车削加工进行深入浅出的探讨。
首先要了解不锈钢材料的性质,以便进行合理的车削加工。
不锈钢的硬度较高,加工难度较大;同时,由于其中含有铬、镍等耐腐蚀元素,不锈钢具有较高的韧性和延展性。
因此,在车削加工过程中需要采取适当的加工参数和工具选择,以确保加工质量和工具寿命。
在车削加工中,切削速度、进给量和切削深度是影响加工效果的重要参数。
对于不锈钢材料,由于其硬度较高,一般需要采用较低的切削速度。
而对于进给量和切削深度,需要根据具体情况进行调整,以避免过度切削,导致工件表面质量下降、工具磨损加剧。
对于不锈钢材料的车削加工,工具选择也是非常重要的。
一般来说,硬质合金刀具具有较好的耐磨性和切削性能,适用于对不锈钢材料进行精细车削加工。
同时,鉴于不锈钢的高韧性和延展性,铺设刀具的刃角要求较小,刃口要光滑锋利,以保证切削力和刀具使用寿命。
此外,不锈钢材料的车削加工还需要注意切削润滑和冷却问题。
由于不锈钢的短切屑对切削过程有一定的干扰,切削润滑和冷却可以有效地减少切削热,防止刀具过热和磨损。
一般来说,可以通过植入切削剂、切削液和冷却剂等方式进行切削润滑和冷却。
最后,不锈钢材料的车削加工后还需要进行相应的表面处理,以提高工件的表面质量和防锈性能。
一般可以采用研磨、抛光等方式进行表面处理,以增加工件的光洁度和美观度。
总之,不锈钢材料的车削加工是一项综合性的任务,需要考虑材料性质、车削工艺、工具选择以及表面质量等多个方面的因素。
只有合理选择加工参数和工具,严格控制加工过程,才能获得满意的加工效果和产品质量。
同时,注重切削润滑和冷却、以及后续表面处理,也是保证不锈钢材料车削加工成功的关键。
不锈钢的车削技巧

不锈钢的车削技巧主要包括以下几个方面:1.刀具选择:选择适合不锈钢车削的刀具非常重要。
通常,选择具有较高耐热性、耐磨性和与不锈钢亲和作用小的刀具材料,如高碳、高钒或钼系的高速钢。
此外,刀具的几何形状和角度也需要根据具体加工要求进行选择。
2.切削用量选择:切削用量包括切削速度、进给量和切削深度。
对于不锈钢的车削,切削速度通常较低,一般为普通碳钢切削速度的40%~60%。
进给量和切削深度也需要根据具体情况进行选择,以避免刀具过度磨损和工件表面质量下降。
3.冷却液选择:使用合适的冷却液可以有效降低切削温度,减少刀具磨损和提高工件表面质量。
对于不锈钢的车削,通常选择具有较好冷却和润滑性能的冷却液。
4.操作技巧:在车削不锈钢时,需要注意以下几点操作技巧:首先,保持刀具的锋利,及时更换磨损的刀具;其次,避免使用过大的切削用量,以减少刀具的受力;最后,注意工件的装夹方式和切削力的方向,以避免工件变形或振动。
此外,还需要注意以下几点:1.由于不锈钢的塑性大、韧性高,车削时容易产生积屑瘤和鳞刺,这不仅影响工件的表面粗糙度,还会使刀具的磨损加快。
因此,需要选择合适的刀具材料和几何角度,以及合理的切削用量来避免这些问题的产生。
2.不锈钢的导热性差,导致切削热无法及时散出,使刀具的刃口温度升高,加剧刀具磨损。
为了降低切削温度,可以采用浇注冷却液的方法。
3.在车削过程中,应随时注意观察切削情况,如发现异常现象(如振动、噪声、温度升高等),应及时采取措施进行调整。
4.对于不同种类和规格的不锈钢材料,其车削性能也会有所不同。
因此,在实际加工前,最好先进行一些试验性切削,以确定最佳的切削参数和工艺方案。
总之,掌握不锈钢的车削技巧需要综合考虑多个因素,包括刀具选择、切削用量、冷却液和操作技巧等。
通过合理的选择和调整这些参数,可以提高加工效率、降低生产成本并获得高质量的工件。
不锈钢薄板类工件的车削工艺

2
2 5 。 ;后 角选 用 5 。 ~8 。 ;主 偏 角选 用7 5 。 或6 0 。 ;
.
拦 旦主 持 楚. 宝 . 垄 .
嘉
不锈钢薄板类工件的车削工艺
天津赛 瑞机 器设备有 限公 司 ( 3 0 0 3 0 1 ) 刘 天津 菱云刀 具设计有 限公 司 ( 3 0 0 3 8 4 ) 王 鹏 毅
薄 ,只有 ( 1 5 ±0 . 1 )mm,工件在机床上无法一次 装夹完成加工。采用常规的装夹方式 ,工件装夹无 论夹外 圆或是撑 内圆,个别处在装夹时受 力稍有不
式普车 ( 型号为C 5 1 1 6 A)。由于设备使用时 间较
长 ,设 备 的 回转 工 作 台 和卡 爪 均 有 一 定磨 损 老化 。 工 件 直接 装夹 在 设 备 上 ,加 工 误 差 较大 ,精 度很 难 保证。
3 . 材料分析
此 密封环材 质为 1 Cr l 8 Ni 9 ,按 不 锈 钢 成 分 分 类 ,属于 铬 镍 不 锈 钢 ;按 不 锈 钢 金相 组 织 分 类 ,属 于 奥 氏体 不 锈 钢 ;从切 削加 工 性 能 方面 来 说 ,属 于
圆 一 三次倒个撑 内圆 ,精车外 圆及 下端面 一 成
品。
经过 上 述 反 复 翻 面 加 工 工艺 过 程 ,加 工试 制 出 两 件 产 品 。检 验 发 现 ,端 面 厚 度 不 均匀 ,无 法保 证 在 公 差范 围之 内 ,平行 度达 不 到要 求 , 出现加 工变
使 切 削力 增 加 。 同时 ,加 工 硬 化严 重 ,热 强 度高 , 进 一 步 增 大 了切 削抗 力 ,切 屑 的卷 曲折 断 也 比较 困
不锈钢的车削加工方法
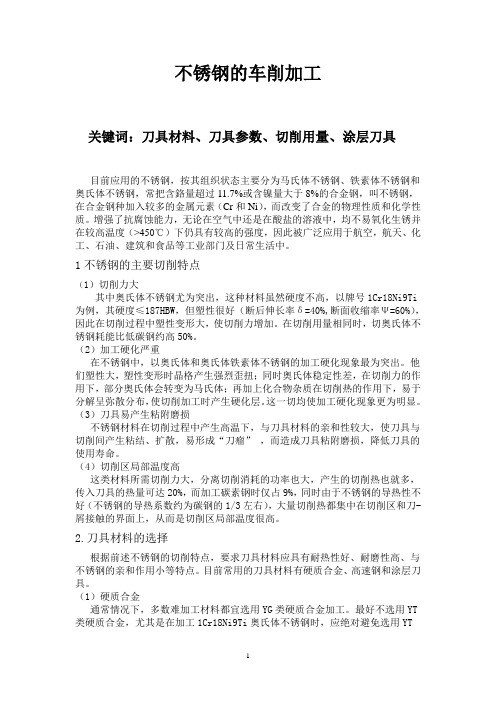
不锈钢的车削加工关键词:刀具材料、刀具参数、切削用量、涂层刀具目前应用的不锈钢,按其组织状态主要分为马氏体不锈钢、铁素体不锈钢和奥氏体不锈钢,常把含鉻量超过11.7%或含镍量大于8%的合金钢,叫不锈钢,在合金钢种加入较多的金属元素(Cr和Ni),而改变了合金的物理性质和化学性质。
增强了抗腐蚀能力,无论在空气中还是在酸盐的溶液中,均不易氧化生锈并在较高温度(>450℃)下仍具有较高的强度,因此被广泛应用于航空,航天、化工、石油、建筑和食品等工业部门及日常生活中。
1不锈钢的主要切削特点(1)切削力大其中奥氏体不锈钢尤为突出,这种材料虽然硬度不高,以牌号1Cr18Ni9Ti 为例,其硬度≤187HBW,但塑性很好(断后伸长率δ=40%,断面收缩率Ψ=60%),因此在切削过程中塑性变形大,使切削力增加。
在切削用量相同时,切奥氏体不锈钢耗能比低碳钢约高50%。
(2)加工硬化严重在不锈钢中,以奥氏体和奥氏体铁素体不锈钢的加工硬化现象最为突出。
他们塑性大,塑性变形时晶格产生强烈歪扭;同时奥氏体稳定性差,在切削力的作用下,部分奥氏体会转变为马氏体;再加上化合物杂质在切削热的作用下,易于分解呈弥散分布,使切削加工时产生硬化层。
这一切均使加工硬化现象更为明显。
(3)刀具易产生粘附磨损不锈钢材料在切削过程中产生高温下,与刀具材料的亲和性较大,使刀具与切削间产生粘结、扩散,易形成“刀瘤”,而造成刀具粘附磨损,降低刀具的使用寿命。
(4)切削区局部温度高这类材料所需切削力大,分离切削消耗的功率也大,产生的切削热也就多,传入刀具的热量可达20%,而加工碳素钢时仅占9%,同时由于不锈钢的导热性不好(不锈钢的导热系数约为碳钢的1/3左右),大量切削热都集中在切削区和刀-屑接触的界面上,从而是切削区局部温度很高。
2.刀具材料的选择根据前述不锈钢的切削特点,要求刀具材料应具有耐热性好、耐磨性高、与不锈钢的亲和作用小等特点。
目前常用的刀具材料有硬质合金、高速钢和涂层刀具。
如何解决不锈钢螺纹车削问题

如何解决不锈钢螺纹车削问题如何解决不锈钢螺纹车削问题螺纹是机械工程中常见的几何特征之一, 应用广泛。
螺纹的加工工艺较多, 如基于塑性变形的滚丝与搓丝, 基于切削加工的车削、铣削、攻螺纹与套螺纹、螺纹磨削、螺纹研磨等。
不同种类的不锈钢由于机械性能和化学成分的不同,其数控切削的难度也不相同。
有的不锈钢在切削加工时,很难达到满意的加工表面粗糙度;而有的不锈钢,虽容易达到要求的加工表面粗糙度,但在切削加工过程中刀具却特别容易磨损。
经总结,各类不锈钢很难切削的主要原因有以下几个方面:1 热强度高、韧性大奥氏体类不锈钢与马氏体类不锈钢其硬度和抗拉强度不高,只相当于40号钢,但延伸率、断面收缩率和冲击值却比较高,这样在数控高速切削过程中就不容易被切断,切削变形时所消耗的功相当大。
相对来说,不锈钢在高温下的强度降低较少,如45号钢在500°时其持久强度为7kg/mm2,而1Cr18Ni9Ti在550°时其持久强度仍保持在19——24kg/mm2。
实践证明,在相同切削温度的作用下,不锈钢切削比普通碳素钢难加工,其热强度高是一个极其重要的因素。
2 加工硬化趋势强在数控高速车削的过程中,由于刀尖对工件材料挤压的结果使切削区的金属产生变形,晶内发生滑移,晶格畸变,组织致密,机械性能也随着发生变化,一般切削硬度也能增加2——3倍。
数控切削后加工硬化层深度可以从几十微米到几百微米不等,因此前一次走刀所产生的加工硬化现象又妨碍了下一次走刀时的切削,并且加工硬化层的高硬度导致刀具特别容易磨损。
3 切屑的粘附性强、导热差在数控切削过程中,切削碎屑很容易牢固地粘附或熔着在刀尖和刀刃上,形成积屑瘤,造成工件加工表面的表面粗糙度恶化,同时增加切削过程中的振动,加速刀具磨损。
而且大量的切削热无法及时传导出来,甚至切削产生的热量也无法传导到切屑的整体上,造成传入刀具总热量比普通碳素钢多3——5倍,使切削刃在高温下失去切削性能。
不锈钢工件加工工艺简介

不锈钢工件加工工艺简介不锈钢是一种耐腐蚀、耐高温、耐磨损的金属材料,因其具有优良的物理和化学性能,在工程领域中得到广泛应用。
不锈钢工件的加工是指对不锈钢材料进行切削、成形、焊接等加工工艺,以满足工程应用的需要。
不锈钢工件加工工艺包括车削、铣削、磨削、钻孔、焊接、抛光等工艺步骤,下面将对不锈钢工件加工工艺进行简要介绍。
一、车削加工工艺车削是一种常用的加工不锈钢工件的方法,通过车床对工件进行旋转切削,使工件表面得到精密加工。
在车削加工中,不锈钢工件通常采用硬质合金刀具,利用切削原理对工件表面进行切削,以得到所需尺寸和形状。
车削加工不锈钢工件需要注意刀具的选择、切削速度和进给量的控制,以确保工件表面光洁度和尺寸精度。
对于不锈钢工件,由于其硬度和韧性较高,车削过程中需要保持合理的切削参数,避免刀具损坏和工件变形。
铣削是一种使用铣刀进行切削的加工方法,适用于不锈钢工件的平面加工、凹槽加工和轮廓加工等。
在不锈钢工件的铣削加工中,需要选择合适的刀具类型、切削参数和切削方式,以保证工件加工表面粗糙度和尺寸精度。
铣削加工可以采用立式铣床、卧式铣床、数控铣床等设备进行加工,根据不同的工件形状和要求选择合适的设备和工艺路线。
磨削是一种利用磨具对不锈钢工件进行加工的方法,能够获得精密的表面质量和尺寸精度。
磨削加工常用于不锈钢工件的表面精加工、内外圆孔加工和平面磨削等。
在磨削加工中,需要选择合适的磨具类型、磨削参数和冷却润滑方式,以避免工件表面产生热裂纹和变形。
焊接是将金属材料通过加热熔化和冷却凝固的方式连接在一起的加工方法,适用于不锈钢工件的连接和结构加工。
在焊接加工中,需要选择合适的焊接方法、焊接材料和焊接参数,以确保焊缝质量和连接强度。
不锈钢材料具有一定的焊接难度,焊接过程中需要控制温度和避免氧化,以减少焊接变形和气孔等缺陷。
抛光是一种通过摩擦和磨擦使不锈钢工件表面得到光滑和亮度的加工方法。
抛光加工可以采用机械抛光、化学抛光和电化学抛光等方式进行,以获得不同表面粗糙度和光洁度的要求。
不锈钢的车削加工

一切削难加工材料的综合分析不锈钢简介通常,人们把含铬量大于12%或含镍量大于8%的合金钢叫不锈钢。
这种钢在大气中或在腐蚀性介质中具有一定的耐蚀能力,并在较高温度(>450℃)下具有较高的强度。
含铬量达16%~18%的钢称为耐酸钢或耐酸不锈钢,习惯上通称为不锈钢。
钢中含铬量达12%以上时,在与氧化性介质接触中,由于电化学作用,表面很快形成一层富铬的钝化膜,保护金属内部不受腐蚀;但在非氧化性腐蚀介质中,仍不易形成坚固的钝化膜。
为了提高钢的耐蚀能力,通常增大铬的比例或添加可以促进钝化的合金元素,加Ni、Mo、Mn、Cu、Nb、Ti、W、Co等,这些元素不仅提高了钢的抗腐蚀能力,同时改变了钢的内部组织以及物理力学性能。
这些合金元素在钢中的含量不同,对不锈钢的性能产生不同的影响,有的有磁性,有的无磁性,有的能够进行热处理,有的则不能热处理。
由于不锈钢所具有的上述特性,越来越广泛地应用于航空、航天、化工、石油、建筑和食品等工业部门及日常生活中。
所含的合金元素对切削加工性影响很大,不锈钢的分类不锈钢按其成分,可分为以铬为主的铬不锈钢和以铬、镍为主的铬镍不锈钢两大类。
工业上常用的不锈钢一般按金相组织分类,可分为以下五大类:1)马氏体不锈钢:含铬量12%~18%,含碳量%~%(有时达1%),常见的有1Cr13、2Cr13、3Cr13、4Cr13、1Cr17Ni2、9Cr18、9Cr18MoV、30Cr13Mo等。
2)铁素体不锈钢:含铬量12%~30%,常见的有0Cr13、0Cr17Ti、0Cr 13Si4NbRE、1Cr17、1Cr17Ti、1Cr17M02Ti、1Cr25Ti、1Cr28等。
3)奥氏体不锈钢:含络量12%~25%,含镍量7%~20%(或20%以上),最典型的代表是1Cr18Ni9Ti,常见的还有00Cr18Ni10、00Cr18Ni14M o2Cu2、0Cr18Ni12Mo2Ti、0Cr18Ni18Mo2Cu2Ti、0Cr23Ni28M03Cu3Ti、1Cr14Mn14Ni、2Cr13Mn9Ni4、1Cr18Mn8Ni5N等。
不锈钢材料的车削技巧
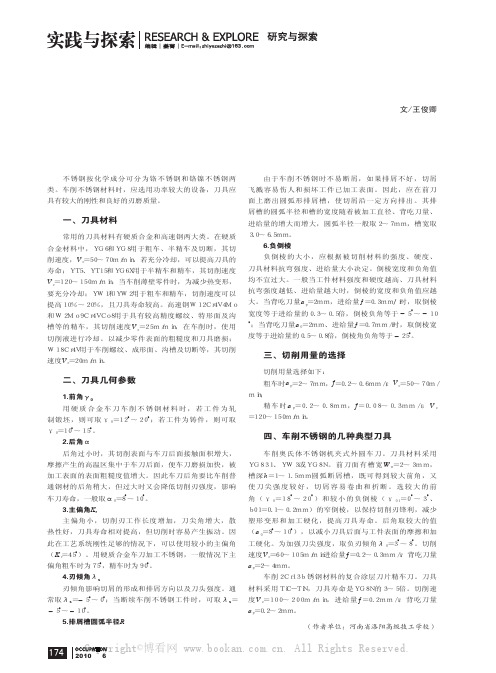
OCCUPATION1742010 6不锈钢按化学成分可分为铬不锈钢和铬镍不锈钢两类。
车削不锈钢材料时,应选用功率较大的设备,刀具应具有较大的刚性和良好的刃磨质量。
一、刀具材料常用的刀具材料有硬质合金和高速钢两大类。
在硬质合金材料中,YG6和YG8用于粗车、半精车及切断,其切削速度,V c=50~70m/min,若充分冷却,可以提高刀具的寿命;YT5、YT15和YG6X用于半精车和精车,其切削速度V c=120~150m/min,当车削薄壁零件时,为减少热变形,要充分冷却;YW1和YW2用于粗车和精车,切削速度可以提高10%~20%,且刀具寿命较高。
高速钢W12Cr4V4Mo和W2Mo9Cr4VCo8用于具有较高精度螺纹、特形面及沟槽等的精车,其切削速度V c=25m/min,在车削时,使用切削液进行冷却。
以减少零件表面的粗糙度和刀具磨损;W18Cr4V用于车削螺纹、成形面、沟槽及切断等,其切削速度V c=20m/min。
二、刀具几何参数1.前角γ0用硬质合金车刀车削不锈钢材料时,若工件为轧制锻坯,则可取γ0=12˚~20˚;若工件为铸件,则可取γ0=10˚~15˚。
2.后角α后角过小时,其切削表面与车刀后面接触面积增大,摩擦产生的高温区集中于车刀后面,便车刀磨损加快,被加工表面的表面粗糙度值增大。
因此车刀后角要比车削普通钢材的后角稍大,但过大时又会降低切削刃强度,影响车刀寿命,一般取α0=8˚~10˚。
3.主偏角K r主偏角小,切削刃工作长度增加,刀尖角增大,散热性好,刀具寿命相对提高,但切削时容易产生振动。
因此在工艺系统刚性足够的情况下,可以使用较小的主偏角(K r=45˚)。
用硬质合金车刀加工不锈钢,一般情况下主偏角粗车时为75˚,精车时为90˚。
4.刃倾角λs刃倾角影响切屑的形成和排屑方向以及刀头强度。
通常取λs =﹣5˚~0˚;当断续车削不锈钢工件时,可取λs =﹣5˚~﹣10˚。
5.排屑槽圆弧半径R由于车削不锈钢时不易断屑,如果排屑不好,切屑飞溅容易伤人和损坏工件已加工表面。
不锈钢车削参数
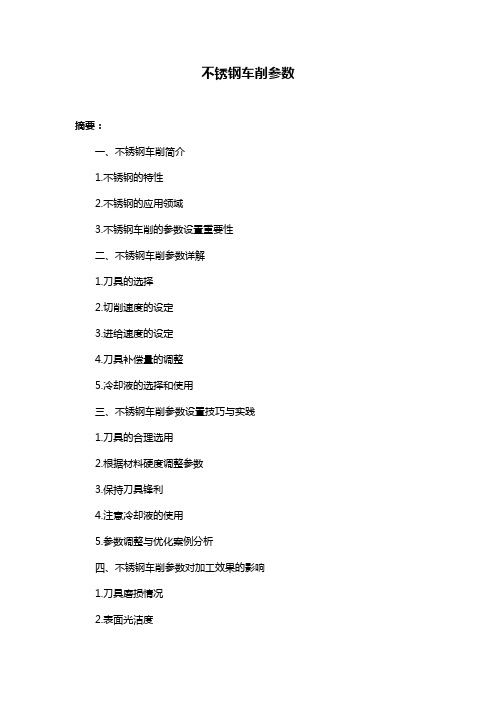
不锈钢车削参数摘要:一、不锈钢车削简介1.不锈钢的特性2.不锈钢的应用领域3.不锈钢车削的参数设置重要性二、不锈钢车削参数详解1.刀具的选择2.切削速度的设定3.进给速度的设定4.刀具补偿量的调整5.冷却液的选择和使用三、不锈钢车削参数设置技巧与实践1.刀具的合理选用2.根据材料硬度调整参数3.保持刀具锋利4.注意冷却液的使用5.参数调整与优化案例分析四、不锈钢车削参数对加工效果的影响1.刀具磨损情况2.表面光洁度3.加工效率4.零件尺寸精度正文:不锈钢是一种具有良好耐腐蚀性和耐磨性的合金材料,广泛应用于机械、航空、航天、石油化工、医疗器械等领域。
不锈钢车削是金属加工的一种重要方式,合理设置车削参数对于保证加工质量、提高生产效率具有重要意义。
本文将详细解析不锈钢车削参数的相关知识。
一、不锈钢车削简介不锈钢具有较高的硬度,加工难度相对较大。
因此,在车削过程中,需要根据不锈钢的特性选择合适的刀具、切削液以及调整切削参数。
正确设置参数能够保证不锈钢车削的顺利进行,提高加工质量。
二、不锈钢车削参数详解1.刀具的选择不锈钢车削应选用硬度高、韧性好的刀具材料,如硬质合金、陶瓷等。
同时,根据加工零件的形状、尺寸及加工要求选择合适的刀具类型。
2.切削速度的设定切削速度是影响不锈钢车削加工效果的重要参数。
一般情况下,切削速度要适当降低,以降低刀具磨损、提高加工质量。
切削速度的选择应根据不锈钢的材质、硬度以及刀具的材质等因素综合考虑。
3.进给速度的设定进给速度直接影响到不锈钢车削的效率和表面质量。
合理的进给速度能够降低刀具磨损,提高加工效率。
进给速度的设定要根据不锈钢的硬度、刀具的材质及加工要求综合考虑。
4.刀具补偿量的调整由于刀具的磨损、装配误差等原因,实际加工过程中,刀具的切削刃与理论切削刃存在一定的偏差。
因此,需要根据刀具的磨损情况及时调整刀具补偿量,以保证加工精度。
5.冷却液的选择和使用冷却液对于不锈钢车削具有重要作用,可以降低刀具磨损、冷却切削区域、冲刷切屑,有助于提高加工表面质量。
硬质合金刀具车削Cr12Mn5Ni4M03A不锈钢的试验研究

Z艺与检潮
a n d
硬质合金刀具车削 C 1 Mn N4 3 l r2 5 iMo A 不锈 钢 的试 验 研究
周建涛 邓建新 张 辉 颜 培
( 山东大学机械工程学院, 山东 济南 206 ) 50 1 摘 要: 使用硬质合金刀具 Y W2进行 c 1Ml N4 3 l r2 l i 5 M0A 不锈钢 的干车削试验。分析 了切削速度对车削
Z U Ja to E HO ina ,D NG in i Ja xn,Z NG i AN P i HA Hu ,Y e
( c ol f ca i l n ier g h n o gU i rt, i a 5 0 , H S ho o h nc gne n ,S ad n n esy j’n n2 0 6 C N) Me aE i v i 1
o a e fc ,a d c n h ia a e p e o n n w sa s u d o a e f c u o lw s e d n r k a e n o c od f k h n me o a lo f n n r k a e d e t o p e . l l o
n s s d c e s d frta d t e n r a e o g wi u t p e la k we r wa eaiey sih ; e swa e r a e s n h n i ce s d a n t c ti s e d;f n a s r ltv l lg t i l h ng
不锈钢的车削参数

不锈钢的车削参数不锈钢作为一种常见的材料,因其耐腐蚀、耐磨损、抗氧化等优异性能,在许多行业中广泛应用。
在机械加工领域,车削是一种常见的加工方法,本文将探讨不锈钢车削的参数。
1.选用合适的切削工具不锈钢的硬度较高,所以在车削过程中要选用硬度较高的切削工具。
常见的不锈钢车削刀具有硬质合金刀具、陶瓷刀具和PCD刀具等。
根据具体的车削任务和不锈钢的类型选择合适的切削工具,以获得最佳的切削效果。
2.合理选择切削速度切削速度是车削过程中一个重要的参数,它直接影响到加工效率和刀具的寿命。
针对不锈钢材料,由于其硬度较高,切削速度一般较低。
一般来说,切削速度不宜超过35m/min,以免造成刀具磨损过快或加工质量下降。
3.控制进给量进给量是指单位时间内工件在车床上行进的距离。
在车削不锈钢时,应适当减小进给量,以减小切削力,避免过度磨损刀具。
合理的进给量可以保证加工表面质量,提高生产效率。
4.选用适当的切削液切削液在车削过程中起到冷却和润滑的作用,能够减小切削温度、降低切削力、延长刀具寿命。
对于不锈钢的车削,应选用适合的切削液,并注意及时更换和清洗,以保证切削效果和安全生产。
5.控制切削深度切削深度是指刀具在一次进给中切削下去的距离。
在车削不锈钢时,一般建议控制较小的切削深度,避免过大切削深度导致切削力过大,影响刀具寿命和加工质量。
6.刀具角度选择刀具的刃角和主偏角的选择对车削效果具有重要影响。
对于不锈钢的车削,一般推荐采用大主偏角和大刃角,以减小刀具与工件的接触面积,减小切削力,降低刀具磨损。
7.注意刀具的使用情况刀具的磨损情况对车削效果和刀具寿命有着直接的影响。
应定期检查和更换刀具,确保刀具的良好状态。
此外,还要注意切削过程中刀具的冷却、润滑和清洁,以保证切削质量和刀具寿命。
总之,不锈钢车削的参数选择要根据具体的材料和车削任务来确定。
合理的切削工具、切削速度、进给量、切削液等参数的选择能够提高车削效率,优化切削质量,并最大限度延长刀具的使用寿命。
浅谈不锈钢材料的车削加工

浅谈不锈钢材料的车削加工不锈钢是一种耐腐蚀、耐热、耐高温的材料,广泛应用于机械制造、汽车制造、航空航天、建筑装饰等行业。
在不锈钢的车削加工中,需要特别注意材料的性质、工艺参数以及切削工具的选择。
不锈钢的性质决定了它的车削加工相对复杂。
首先,不锈钢的硬度较高,所以切削力比较大,对车削刀具的耐磨性提出了更高的要求。
其次,由于不锈钢具有较好的导热性,切削时容易产生热量,导致刀具快速磨损和加工表面产生尺寸偏差,因此需要采取合理的降温和冷却措施。
此外,不锈钢还具有较好的韧性和塑性,容易产生切削硬化,使切削加工更加困难。
在不锈钢的车削加工中,选择合适的车削工艺参数非常重要。
首先,应根据不锈钢的成分和硬度,选择合适的切削速度、进给速度和切削深度。
一般来说,低硬度的不锈钢适合选择较高的切削速度和进给速度,以提高生产效率;而高硬度的不锈钢则需要选择较低的切削速度和进给速度,以避免过度切削或切削过热。
此外,还需根据加工的具体要求和工件的尺寸,选择合适的刀具和切削方式。
切削工具的选择也对不锈钢的车削加工起着至关重要的作用。
不锈钢的硬度和耐热性,要求使用高强度、高耐磨性的刀具。
一般来说,硬质合金刀具可以满足这些要求,但也需要根据具体的加工情况选择合适的刀具材料和刀具几何形状。
此外,应根据切削参数和加工要求,合理选择切削润滑剂和冷却液,以降低切削温度、延长刀具使用寿命和提高加工质量。
总之,不锈钢材料的车削加工相对复杂,需要注意材料的性质、工艺参数和切削工具的选择。
在实际生产中,需要根据不锈钢的具体类型和加工要求,采取合适的加工工艺和切削方式,以提高加工效率和加工质量。
此外,还需加强刀具的研发和刀具涂层技术的应用,以适应不锈钢材料的车削加工需求。
304车削参数

304车削参数304车削参数是指在车削加工过程中所使用的一组参数,用来控制车床工件与刀具之间的相对运动关系,以达到满足工件加工要求的目的。
这些参数包括进给速度、主轴转速、切削深度、切削速度等。
进给速度是指车床工件在车削过程中的线速度,一般用mm/min表示。
进给速度的选择应根据工件材料、刀具材料和刀具结构等因素综合考虑。
进给速度过大会导致切削力增大、刀具磨损加剧,甚至引起刀具断裂;而进给速度过小又会导致产量降低、加工效率低下。
因此,在选择进给速度时需要根据具体情况进行合理调整。
主轴转速是指车削中主轴的转速,一般用r/min表示。
主轴转速的选择应根据工件材料、刀具材料和切削深度等因素综合考虑。
主轴转速过高会导致切削过程中温度升高,容易引起刀具磨损加剧;而主轴转速过低又会导致加工效率低下。
因此,在选择主轴转速时需要根据具体情况进行合理调整。
切削深度是指刀具在车削过程中每次接触工件的深度,一般用mm 表示。
切削深度的选择应根据工件材料、刀具材料和切削速度等因素综合考虑。
切削深度过大会导致切削力增大,容易引起刀具破裂;而切削深度过小又会导致加工效率低下。
因此,在选择切削深度时需要根据具体情况进行合理调整。
切削速度是指刀具在车削过程中相对于工件表面的速度,一般用m/min表示。
切削速度的选择应根据工件材料、刀具材料和切削深度等因素综合考虑。
切削速度过高会导致刀具磨损加剧、刀具寿命缩短;而切削速度过低又会导致加工效率低下。
因此,在选择切削速度时需要根据具体情况进行合理调整。
除了以上几个主要的车削参数外,还有一些次要的参数也需要考虑,比如切削角度、进给量、刀具前角和后角等。
切削角度是指刀具与工件表面的夹角,一般用度数表示。
切削角度的选择应根据工件材料和刀具材料等因素综合考虑。
进给量是指刀具在车削过程中每分钟进给的长度,一般用mm/rev表示。
进给量的选择应根据工件材料和切削速度等因素综合考虑。
刀具前角和后角是指刀具前端和后端的刀尖角度,一般用度数表示。
不锈钢数控车削加工工艺
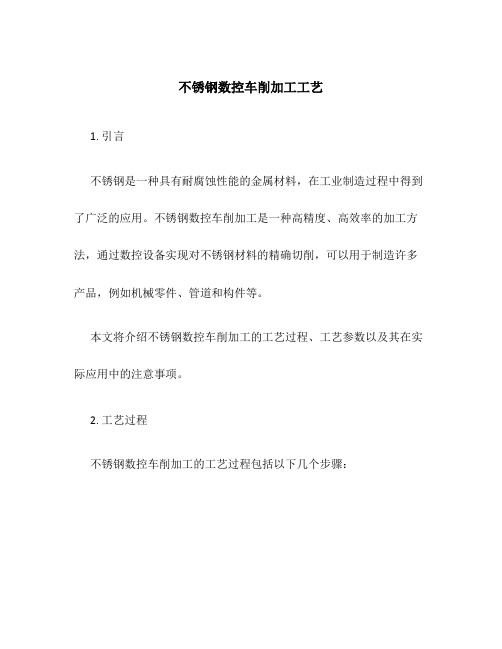
不锈钢数控车削加工工艺1. 引言不锈钢是一种具有耐腐蚀性能的金属材料,在工业制造过程中得到了广泛的应用。
不锈钢数控车削加工是一种高精度、高效率的加工方法,通过数控设备实现对不锈钢材料的精确切削,可以用于制造许多产品,例如机械零件、管道和构件等。
本文将介绍不锈钢数控车削加工的工艺过程、工艺参数以及其在实际应用中的注意事项。
2. 工艺过程不锈钢数控车削加工的工艺过程包括以下几个步骤:2.1 零件准备在进行车削加工之前,首先需要准备好要加工的不锈钢零件。
清洁表面,并确保其表面没有明显的凹陷和磨损。
2.2 工艺规划在进行数控车削加工之前,需要进行工艺规划。
工艺规划包括确定零件的加工顺序、选择合适的刀具和切削参数等。
2.3 加工装夹将不锈钢零件安装在数控车床上,进行加工装夹。
确保零件固定牢固且位置准确。
使用合适的夹具和固定装置,以避免零件在加工过程中发生移动或变形。
2.4 加工参数设置根据零件的要求和刀具的特性,设置合适的加工参数。
包括切削速度、进给速度和切削深度等。
合理的加工参数可以提高加工效率和加工质量。
2.5 车削加工根据工艺规划和加工参数,使用数控设备进行车削加工。
通过控制刀具的运动轨迹和加工参数,将不锈钢材料逐渐切削,得到所需形状和尺寸的零件。
2.6 质量检验在完成车削加工后,进行质量检验。
检查零件的尺寸、表面质量和精度等。
确保加工的零件符合要求。
3. 工艺参数不锈钢数控车削加工的工艺参数对加工质量和效率有着重要影响。
以下是一些常用的工艺参数:•切削速度:通常以米/分钟为单位。
根据不锈钢材料的硬度和刀具的材质来确定合适的切削速度。
•进给速度:刀具在单位时间内在工件上的移动速度。
根据不同的切削工况和加工精度要求,选择合适的进给速度。
•切削深度:刀具每次切削所去除的材料层厚度。
根据零件的要求和刀具的稳定性,选择合适的切削深度。
•刀具半径补偿:在车削过程中,考虑到刀具的几何特性和零件的轮廓,需要进行刀补。
- 1、下载文档前请自行甄别文档内容的完整性,平台不提供额外的编辑、内容补充、找答案等附加服务。
- 2、"仅部分预览"的文档,不可在线预览部分如存在完整性等问题,可反馈申请退款(可完整预览的文档不适用该条件!)。
- 3、如文档侵犯您的权益,请联系客服反馈,我们会尽快为您处理(人工客服工作时间:9:00-18:30)。
复合
°°
°
5 1 185
涂层
用) Ra~
刀片
5
Ra1.6
3.
刀具的几何角度和结构的选取
对于良好的刀具材料,选择合理的几何角度则显得尤为重要。
• 前角 γ:一般车削马氏体不锈钢刀具前角取10°~20°较为适宜。 • 后角 α:一般取5°~8°较合适,最大不过10°。 • 刃倾角 λ:一般选取 λ 为-10°~30°。 • 主偏角 Kr 应根据工件的形状、加工部位和装刀情况来选择。 • 刃口表面粗糙度应不大于 Ra0.4~Ra0.2。 • 在结构上,我们对外圆车刀采用外斜式圆弧断屑槽,靠刀尖处切屑卷曲半径大,靠 外缘处切屑卷曲半径小,切屑将翻向待加工表面而折断,断屑情况好。而对切断刀,我
5.
选用适当的冷却润滑液 车削不锈钢用的冷却润滑液,应该具有以下几个特点:
• 高的冷却性能,保证能带走大量的切削热。 • 不锈钢韧性大,切削时易产生刀瘤,恶化加工表面,这就要求冷却润滑液有高的润 滑性能,能起到较好的润滑作用。 • 渗透性好,对不易被切离的切屑,能起到较好的楔裂、扩散和内润滑作用。 常用的加工不锈钢的冷却润滑液有如下几种:硫化油、硫化豆油,煤油加油酸或植物油、四 氯化碳加矿物油、乳化液等。 考虑到硫对机床有一定的腐蚀作用,植物油(如豆油)容易附在机床上结痂和变质,我们选用 了四氯化碳与机油按重量比为1:9的混合物。其中四氧化碳渗透性好,机油的润滑性好。试 验证明,这种冷却润滑液适用于表面粗糙度要求小的不锈钢零件的半精加工和精加工工序, 特别适合于马氏体类不锈钢零件的车加工。
3结论
由于采取了一系列措施,我们对 3Cr13 不锈钢材料的加工已完全处于正常状态。磨刀次数 只有试生产时的 1/3,提高了生产效率,零件质量完全达到设计要求。
表1
切削用
量 刀具 加工表
3Cr13钢 ν s 耐用 面粗糙
材料 m/ m 度
度
mi m min
μm
n /r
HB240( 退火)
45 0 90~ Ra6.3~
~. 115 Ra3.2
55 1
45 0
HRC25~
95~
~.
30(调质)
110
55 1
Ra3.2
45 0
HRC35~
60~
~.
38(调质)
75
1切削过程中的难点及原因分析
在零件试生产时,我们按车削普通碳钢的工艺方法对3Cr13不锈钢进行了车削试验,结果是 刀具磨损非常严重,生产率极低,零件表面质量达不到要求。 比较3Cr13钢与40钢、45钢等碳素结构钢的机械性能可知,3Cr1 3钢的强度比40钢和45钢 高,它是一种强度高、塑性好的中碳马氏体不锈钢。由于切削时加工硬化严重,切削抗力大, 切削温度高,导致刀具磨损严重,磨刀次数增多,增加了停机时间和机床调整时间,降低了 生产率。同时又容易粘刀,产生积屑瘤,引起工件尺寸的变化并影响表面粗糙度,而且切屑 不易卷曲和折断,易损伤工件已加工表面,影响零件质量。所以,不能用切削45钢的工艺 来切削3Cr13,也不能把通用车床上的加工方法照搬到自动车床上来。因为一般自动车床装刀 较少,要求最好一次走刀就能使被加工表面达到要求的尺寸和表面粗糙度,以保证较高的生 产率。
55 1
Ra3.2
2.
刀具材料的选择
在自动车床上车削不锈钢,一般使用的硬质合金的刀具材料有:YG6、YG8、YT15、YT30、 YW1、YW2等材料。 常用的高速钢刀具有:W18Cr4V、W6M05Cr4V2AL 等材料。我们在切削参数相同的条件
下,对几种材料的刀具进行了车削对比试验,从表2可见:采用 TiC-TiCN-TiN 复合涂层刀片 的外圆车刀,耐用度比较高,切削速度可取高,工件表面质量好,生产率高。但是,没有这
种材料的切断刀片。通过表2的对比试验,YW2硬质合金的切削性能也不错,我们选用 YW2 材料的刀片作为切断刀。
表2不同刀具材料切削对比试验
刀具 材料
刀具的几何角度
主刃 前后
偏倾 角角
角角 γα
Kr λ
切削
用量 刀
νs 具
m
耐
/ m用
mm 度
i / min
加工 表面 粗糙
度 μm
nr
4
1
5 0 72
8 90 -1
YG8 5
~. ~
°° 0
°
5 1 82
3.2
5
4
1
5 0 80
8 90 -1
YT14 5
~. ~
°° 0
°
5 1 95
Ra3.2
5
4
1
5 0 90
8 90 -1
YW2 5
~ . ~ Ra3.2
°° 0
°
5 1 110
5
Tic-T
Ra6.3
iCN-
4 (切断
1
5 0 128
TiN
8 90
2
-4 ~ . ~
2主要技术措施
1.
通过热处理,改变材料的硬度
马氏体不锈钢在热处理后的不同硬度,对车削加工的影响很大。表1是用 YW2材料的车刀对 热处理后不同硬度的3Cr13钢的车削情况。可见,退火状0.10.10.1态的马氏体不锈钢虽然硬 度低,但车削性能差,这是因为材料塑性和韧性大,组织不均匀,粘附,熔着性强,切削过
程易产生刀瘤,不易获得较好的表面质量。而调质处理后硬度在 HRC30以下的3Cr13材料, 车削加工性较好,易达到较好的表面质量。用硬度在 HRC30以上的材料加工出的零件,表 面质量虽然较好,但刀具易磨损。所以,在条件允许的情况下,可以在材料进厂后,先进行
调质处理,硬度达到 HRC25~HRC30,然后再进行切削加工。
们将副偏角控制在1o 以内,这样可以改善排屑条件、延长刀具的使用寿命。
4.
合理选择切削用量 切削理论认为,切削速度 v 对切削温度和刀具耐用度的影响最大,走刀量 s 次之,吃刀量 t 最小,而在自动车床上一次走刀加工工件的表面,其吃刀量 t 是由零件尺寸与材料毛坯尺寸 来决定的,一般为0~3mm;难加工材料的切削速度往往比普通钢的切削速度低得多。 走刀量 s 对刀具耐用度影响不如切削速度大,但会影响断屑和排屑,拉伤、擦伤工件表面, 影响加工的表面质量,一般认为吃刀深度大时,走刀量应减小,而切断的走刀量又比车外圆 要小。在被加工表面粗糙度要求不高时,s 选用0.1mm/r~0.2mm/r。 总之,对于难加工材料,一般选用较低的切削速度、中等的走刀量。