BC6818EM_assemble_language_guide_V11(正式版)
matlab2018部分中文部分英文

matlab2018部分中文部分英文如果您在MATLAB 2018中遇到部分中文部分英文的情况,可能是由于某些因素导致中文字符和英文字符混合在一起。
以下是一些可能的原因和解决方法:1. 字体问题:确保您使用的字体支持中文字符。
如果您的编辑器或系统默认字体不支持中文,您需要更改字体设置。
在MATLAB编辑器中,选择“工具”>“选项”>“字体”,选择支持中文字符的字体,例如“宋体”或“微软雅黑”。
2. 语言环境设置:检查您的MATLAB语言环境设置。
在MATLAB命令窗口中输入以下命令:```matlabsetenv('MATLAB_LANG','zh_CN')```这将设置MATLAB语言环境为中文。
如果您想设置为英文,可以将'zh_CN'替换为'en_US'。
3. 文件编码:确保您的MATLAB脚本或代码文件使用正确的编码格式。
如果文件编码不正确,可能会导致中文字符和英文字符混合在一起。
使用文本编辑器(如Notepad++)打开文件,并检查并更改文件编码为UTF-8。
4. MATLAB版本问题:确保您使用的是支持中文的MATLAB版本。
MATLAB的不同版本可能对中文支持有所不同。
如果您的MATLAB版本不支持中文,您可以考虑升级到较新的版本。
5. 操作系统语言环境:确保您的操作系统语言环境设置为中文。
如果您的操作系统语言环境设置为英文,可能会导致MATLAB中的中文字符显示为乱码。
您可以进入操作系统设置,将语言环境更改为中文。
尝试以上方法,并检查是否可以解决您的问题。
如果问题仍然存在,请考虑寻求技术支持或与MATLAB社区联系以获得帮助。
Elatec TWN4 MultiTech M User Manual
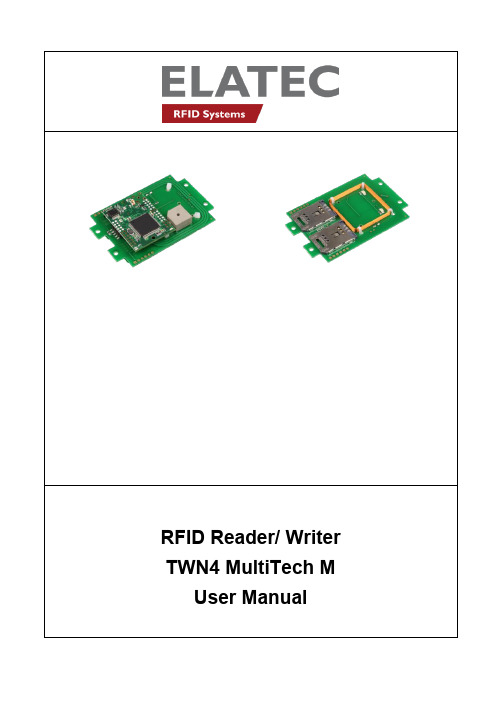
1. IntroductionThe transponder reader module TWN4 MultiTech M is a device for reading and writing RFID transponders. There are different versions of TWN4 devices available, which cover a large range of transponder types both in the frequency range of 125kHz and 13.56MHz.2. Getting Started2.1 Cable ConnectionIn order to start operating a TWN4 transponder reader, it simply has to be connected to a host.2.2 EnumerationOnce the device has been powered up, it is waiting for completion of the enumeration by the USB host. As long as the device is not enumerated, it is entering a minimum power consumption mode, where both LEDs are turned off.2.3 InitializationAfter powering up and enumeration, the device is turning on the built-in transponder reader logic. The green LED is turned on permanently. Some transponder readers need some kind of initialization, which is performed inthis step. After successful initialization, the device sounds a short sequence, which consists of a lower tone followed by a higher tone.2.4 Normal OperationAs soon as the device has completed the initialization, it is entering normal operation. During normal operation the device is searching for a transponder continuously.Detection of a TransponderIf a transponder is detected by the reader, following actions are performed ∙Send the ID to the host. By default, the USB device sends by emulating keystrokes of a keyboard.∙Sound a beep∙Turn off the green LED∙Blink the red LED for two seconds∙Turn on the green LEDWithin the two seconds timeout, where the red LED is blinking, the transponder, which just has been recognized will not be accepted again. This prevents the reader from sending identical IDs more than one time to the host.If during the two seconds timeout of the red LED a different transponder is detected, the complete sequence restarts immediately.Suspend ModeThe transponder reader supports the USB suspend mode. If the USB host is signaling suspend via the USB bus, the transponder reader is turning off most of its power consuming peripherals. During this operation mode, no detection of transponders is possible and all LEDs are turned off.Once the host is resuming to normal operation mode, this is also signaled via the USB bus. Therefore, the transponder reader will resume to normal operation, too.3. List of Antennas HF antennaLF antenna4. Compliance statementsFCC(RF module)Compliance statement:This device complies with Part 15 of the FCC Rules. Operation is subject to the following two conditions: (1) this device may not cause harmful interference, and (2) this device must accept any interference received, including interference that may cause undesired operation.Modification of equipment:The instruction manual of the host shall include the following statement: Changes or modifications made to this equipment not expressly approved by the party responsible for compliance may void the FCC authorization to operate this equipment.Information to the user:(The instruction manual of the host shall include the following statement) A compliance statement as applicable, e.g., for devices subject to part 15 of CFR 47 as specified in §15.19(a)(3), that the product complies with the rules; and the identification, by name, address and telephone number or Internet contact information, of the responsible party, as defined in §2.909. The responsible party for Supplier’s Declaration of Conformity must be located within the United States.Host devicesFCC notes for a host subject to verification or SDoC:For a host device assembled with the certified module and subject to 47 CFR Part 15 verification of class A digital devices, the following statements have to be included in the user manual and the host device has to be labelled as noted below. If the host device is subject to other authorization procedures or parts the appropriate requirements of these authorization procedures or parts apply.Important note:OEM integrator is still responsible for the FCC compliance requirements of the end product, which integrates this module. Appropriate measurements (e.g. 15B compliance) and if applicable additional equipment authorization of the host device to be addressed by the integrator/ manufacturerThe end device must be labeled with:Contains FCC ID: WP5TWN4F17Contains IC: 7948A-TWN4F17HVIN: EL20208Example for SDoC:The compliance information statement shall be included in the user's manual or as a separate sheet. In cases where the manual is provided only in a form other than paper, such as on a computer disk or over the Internet, the information required by this section may be included in the manual in that alternative form, provided the user can reasonably be expected to have the capability to access information in that form. The information may be provided electronically as permitted in §2.935.NOTE: The Commission does not have a required SDoC format. This is an example only and is provided to illustrate the type of information that may be supplied with the product at the time of marketing or importation for meeting the FCC SDoC requirement.For class B devices:FCC §15.105 (b):Note: This equipment has been tested and found to comply with the limits for a Class B digital device, pursuant to part 15 of the FCC Rules. These limits are designed to provide reasonable protection against harmful interference in a residential installation. This equipment generates, uses and can radiate radio frequency energy and, if not installed and used in accordance with the instructions, may cause harmful interference to radio communications. However, there is no guarantee that interference will not occur in a particular installation. If this equipment does cause harmful interference to radio or television reception, which can be determined by turning the equipment off and on, the user is encouraged to try to correct the interference by one or more of the following measures:- Reorient or relocate the receiving antenna.- Increase the separation between the equipment and receiver.- Connect the equipment into an outlet on a circuit different from that to which the Receiver is connected.- Consult the dealer or an experienced radio/TV technician for help.For class A devices:FCC §15.105 (b):NOTE: This equipment has been tested and found to comply with the limits for a Class A digital device, pursuant to part 15 of the FCC Rules. These limits are designed to provide reasonable protection against harmful interference when the equipment is operated in a commercial environment. This equipment generates, uses, and can radiate radio frequency energy and, if not installed and used in accordance with the instruction manual, may cause harmful interference to radio communications. Operation of this equipment in a residential area is likely to cause harmful interference in which case the user will be required to correct the interference at his own expense.CANADA:This device complies with Industry Canada’s license-exempt RSSs. Operation is subject to the following two conditions:(1) This device may not cause interference; and(2) This device must accept any interference, including interference that may cause undesired operation of the device.Le présent appareil est conforme aux CNR d’Industrie Canada applicables aux appareils radio exempts de l icence. L’exploitation est autorisée aux deux conditions suivantes:1) l’appareil ne doit pas produire de brouillage;2) l’utilisateur de l’appareil doit accepter tout brouillage radioélectrique subi, même si le brouillage est susceptible d’en compr omettre le fonctionnement. Special accessories:Where special accessories such as shielded cables and/or special connectors are required to comply with the emission limits, the instruction manual shall include appropriate instructions on the first page of the text describing the installation of the device.Simultaneous transmission:When the host product supports simultaneous-transmission operations the host manufacturer needs to check if there are additional RF exposure filing requirements due to the simultaneous transmissions. When additionalapplication filing for RF exposure compliance demonstration is not required (e. g. the RF module in combination with all simultaneously operating transmitters complies with the RFexposure simultaneous transmission SAR test exclusion requirements), the host manufacturer may do his own evaluation without any filing, using reasonable engineering judgment and testing for confirming compliance with out-of-band, restricted band, and spurious emission requirements in the simultaneous-transmission operating modes. If additional filing is required please contact the person at ELATEC GmbH responsible for certification of the RF module.5. Service AddressIn case of any technical questions, please contact: Elatec GmbHZeppelinstr. 182178 PuchheimGermanyPhone: +49 (0) 89 5529961 0Fax: +49 (0) 89 5529961 29Email: ********************6. TrademarksAll referenced brands, product names, service names and trademarks mentioned in this document are the property of their respective owners.。
模组说明书:Modicon M258 TM258LF66DT4L
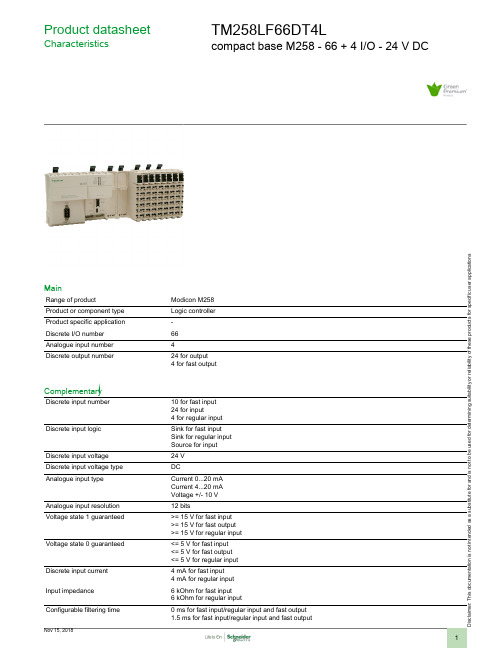
i s c la i me r : T h i s d o c u m e n t a t i o n i s n o t i n t e n d e d a s a s u b s t i t u t ef o r a n d i s n o t t o b e u s e d f o r d e t e r m i n i ng s u i t a b i l i t y o r r e l i a b i l i t y o f th e s e p r o d u c t s f o r s p e ci f i c u s e r a p p l i c a t i o n sProduct datasheetCharacteristicsTM258LF66DT4Lcompact base M258 - 66 + 4 I/O - 24 V DCMainRange of productModicon M258Product or component type Logic controller Product specific application -Discrete I/O number 66Analogue input number 4Discrete output number24 for output 4 for fast outputComplementaryDiscrete input number10 for fast input 24 for input4 for regular input Discrete input logicSink for fast input Sink for regular input Source for input Discrete input voltage 24 V Discrete input voltage type DCAnalogue input typeCurrent 0...20 mA Current 4...20 mA Voltage +/- 10 V Analogue input resolution 12 bitsVoltage state 1 guaranteed>= 15 V for fast input >= 15 V for fast output >= 15 V for regular input Voltage state 0 guaranteed<= 5 V for fast input <= 5 V for fast output <= 5 V for regular input Discrete input current 4 mA for fast input 4 mA for regular input Input impedance 6 kOhm for fast input 6 kOhm for regular inputConfigurable filtering time0 ms for fast input/regular input and fast output 1.5 ms for fast input/regular input and fast output12 ms for fast input/regular input and fast output4 ms for fast input/regular input and fast outputAnti bounce filtering 2 µs...4 ms (configurable) fast input/regular input and fast outputCable distance between devices30 m for fast input30 m for fast output30 m for regular input500 Vrms ACIsolation between channels andinternal logicIsolation between channels NoneDiscrete output logic SourceDiscrete output voltage24 V DCOutput voltage limits19.2...28.8 VDiscrete output current 4 mA for fast output[Us] rated supply voltage24 V DC for embedded expert modules power24 V DC for I/O power segment24 V DC for main supplySupply voltage limits20.4...28.8 V[In] rated current0.04 A for embedded expert modules power0.31 A for main supply10 A for I/O power segmentPeak current<= 100 kA during <= 70 s main supply<= 25 kA during <= 500 s I/O power segment<= 50 kA during <= 150 s embedded expert modules power<= 1.2 kA during > 70 s main supplyPower consumption in W<= 18.11 WExecution time per instruction22 ns : BooleanMemory description Flash 128 MBInternal RAM 64 MBRealtime clock With user calibration realtime clock, drift: <= 6 s/monthWithout any user calibration realtime clock, drift: < 30 s/month at 25 °CData backed up Variables of type retain and retain persistent CR2477M Renata, 1.5 years autonomy Integrated connection type 1 CANopen male SUB-D 9, CANopen master1 isolated serial link female RJ45, Ethernet Modbus TCP/IP slave (10BASE-T/100BASE-TX)2 free slots PCI1 isolated serial link female RJ45, Modbus master/slave RTU/ASCII or character mode ASCII(RS232/RS485), 300...115200 bps1 isolated serial link mini B USB, 480 Mbit/s1 isolated serial link USB type A, 480 Mbit/sTransmission rate125 kbit/s for bus length of 500 m, CANopen250 kbit/s for bus length of 250 m, CANopen50 kbit/s for bus length of 1000 m, CANopen500 kbit/s for bus length of 100 m, CANopen10 kbit/s for bus length of 5000 m, CANopen1000 kbit/s for bus length of 4 m, CANopen20 kbit/s for bus length of 2500 m, CANopen800 kbit/s for bus length of 25 m, CANopenCounting input number8 counting input(s) 200 kHzLocal signalling 1 LED per channel for I/O state1 LED for CAN0 STS1 LED for MBS COM1 LED green/red for APP01 LED green/red for APP11 LED green/red for Eth NS (Ethernet network status)1 LED green/red for Eth ST (Ethernet status)1 LED green/red for RUN/MS (module status)1 LED green/red for USB host1 LED green/yellow for Eth LA (Ethernet activity)1 LED red for BATT (battery status)Marking CEMounting support Symmetrical DIN railWidth262.5 mmHeight99 mmDepth85 mmProduct weight0.8 kgEnvironmentStandardsCSA C22.2 No 142IEC 61131-2UL 508CSA C22.2 No 213Product certificationsCSA C-Tick cULus GOST-RAmbient air temperature for operation0...55 °C without derating factor horizontal installation 0...60 °C with derating factor horizontal installation 0...50 °C vertical installation Ambient air temperature for storage -25...70 °CRelative humidity 5...95 % without condensation IP degree of protection IP20 conforming to IEC 61131-2Pollution degree 2 conforming to IEC 60664Operating altitude 0...2000 m Storage altitude 0...3000 mVibration resistance 1 gn 8.4...150 Hz DIN rail 3.5 mm 5...8.4 Hz DIN rail Shock resistance15 gn for 11 msResistance to electrostatic discharge 4 kV on contact conforming to EN/IEC 61000-4-28 kV in air conforming to EN/IEC 61000-4-2Resistance to electromagnetic fields 1 V/m 2...2.7 GHz conforming to EN/IEC 61000-4-310 V/m 80...2000 MHz conforming to EN/IEC 61000-4-3Resistance to fast transients1 kV I/O conforming to EN/IEC 61000-4-41 kV shielded cable conforming to EN/IEC 61000-4-42 kV power lines conforming to EN/IEC 61000-4-4Surge withstand0.5 kV differential mode conforming to EN/IEC 61000-4-51 kV common mode conforming to EN/IEC 61000-4-5Disturbance radiated/conductedCISPR 11Offer SustainabilitySustainable offer status Green Premium productRoHS (date code: YYWW)Compliant - since 1039 - Schneider Electric declaration of conformity Schneider Electric declaration of conformity REAChReference not containing SVHC above the threshold Reference not containing SVHC above the threshold Product environmental profile AvailableProduct environmental Product end of life instructionsAvailableEnd of life manualContractual warrantyWarranty period18 monthsDimensions DrawingsControllerDimensionsTM5 System Wiring RecommendationsWire Sizes to Use with Removable Spring Terminal BlocksExternal Power SuppliesWiring Diagram of the Controller Power Distribution Module(1)Internal electronics(2)24 Vdc I/O power segment integrated into the bus bases (3)PS1/PS2: External isolated SELV power supply 24 Vdc (4)External fuse, Type T slow-blow, 3 A 250 V (5)External fuse, Type T slow-blow, 2 A 250 V(6)External fuse, Type T slow-blow, 10 A max., 250 V。
Dell OpenManage IT Assistant 8.8 用户指南说明书

Dell OpenManage IT Assistant 版本 8.8 用户指南注和小心本出版物中的信息如有更改,恕不另行通知。
© 2010 Dell Inc. 版权所有,翻印必究。
未经 Dell Inc. 书面许可,严禁以任何形式复制这些材料。
本文中使用的商标:Dell ™、DELL 徽标、Dell Precision ™、OpenManage ™、OptiPlex ™、PowerEdge ™、PowerVault ™、PowerConnect ™、EqualLogic ™、KACE ™、FlexAddress ™ 和 Vostro ™ 是 Dell Inc. 的商标。
Intel ®、Pentium ®、Xeon ®、Core ® 和 Celeron ® 是 Intel Corporation 在美国 和其它国家/地区的商标或注册商标。
AMD ® 是注册商标并且 AMD Opteron ®、AMD Phenom ® 和 AMD Sempronyx 是 Advanced Micro Devices, Inc. 的商标。
VMware ®、Virtual SMP ®、vMotion ®、vCenter ®、vSphere ® 和 ESX ® Serveryx 是 VMware, Inc. 在美国和/或其他管辖区的注册商标或商标。
Microsoft ®、Windows ®、Windows NT ®、Windows Server ®、Microsoft Hyper-V Server 2008®、Windows Vista ®、Active Directory ®、Internet Explorer ®、SQL Server ® 和 Excel ® 是 Microsoft Corporation 在美国和/或其他国家/地区的商标或注册商标。
Clonezilla Basics for Windows Embedded说明书

Clonezilla Basics for Windows EmbeddedBy Sean D. Liming and John R. MalinAnnabooks –August 22, 2014Cloning a master image for mass production is an important step for Windows Embedded Standard and Windows Embedded Industry. First, the image must be rolled back to create the master, which is accomplished using sysprep. Here is an example command:Sysprep /generalize /oobe /shutdown /unattend:c:\myunattend.xmlThe unattended XML file is a small answer file that handles several of the Out-of-Box Experience (OOBE) screens as well as accounts, run–time key, computer names, etc. There are those that say you don’t need sysprep, but failure to run sysprep and just copy the image can run into technical consequences. In short, one must run sysprep to duplicate the image.Once the image has been rolled back, the next step is to capture the master image for deployment to other systems. The books: Starter Guide for Windows® System Image Manager, Professional's Guide To Windows® Embedded 8 Standard, and Professional's Guide To Windows® Embedded Standard 7 - 2nd Edition cover creating the unattended file and running sysprep, but what is not covered is an actual full disk capture utility. There are several hardware disk duplication solutions for hard drive and compact flash cards. International Microsystems I nc. and Logicube are two companies that offer hardware duplication products. . There are also software solutions, but some of the most popular like Norton Ghost are going end-of-life in favor of licensed server-based solutions. Microsoft has solutions to capture partitions into WIM files, but when multiple partitions need to be captured, the WIM file solution is very cumbersome. Simple and inexpensive software image capture solutions are becoming hard to find. Luckily, the Linux community has developed a solution called Clonezilla that captures full disk images; and best of all, it is a free solution that can be used to capture a Windows Embedded master image.This paper walks through the steps to create a Clonezilla disk to capture and deploy a Windows Embedded master disk image. You will need two USB flash disks. One will hold the Clonezilla boot disk image (USB disk size 8 GB), and the other will hold the captured image (USB flash disk size 32 GB or greater recommended).Note: This paper is based on Clonezilla 2.2.3-25 live image. The steps and pictures will be different for later versions.Generate Clonezilla boot diskWe start on the development machine, and download a utility to help create the Clonezilla boot disk.1. Download Tuxboot from . The actual download comes from SourceForge.2. Format the smaller USB flash disk as FAT 32. Format the larger flash disk as exFAT.3. Plug the smaller USB flash disk into the development machine and run Tuxboot.4. The Tuxboot application will start. Make sure that clonezilla_live_stable is selected forthe On-Line Distribution. Also, point to the correct USB flash drive.5. Click OK to start the process. The Clonezilla ISO will be downloaded, mounted locally,and then copied over to the flash disk.6. Do not reboot when asked. Just Exit Tuxboot.7. Safely eject the USB flash drive.Capture Disk ImageNow, we move to the target system that holds the master image.1. Plug the Clonezilla boot disk that we just created into the target system.2. Boot the target and make sure the BIOS is set up to boot from the USB flash disk.3. The Clonezilla boot screen appears. Select Clonezilla Live (Default settings, VGAXXXxYYY) and hit Enter.4. The OS will load. Select English as the language to use and hit Enter.5. Keep the default Don’t touch keymap and hit Enter.6. The default Start_Clonezilla Start Clonezilla should be selected, hit Enter.7. In the next menu, select device-image work with disks or partitions using images asthe operation mode and hit Enter.8. The next menu is for the image directory. Keep the default, local_dev, and hit Enter.9. Insert the larger USB flash disk when prompted, wait about 5 seconds, and then hitEnter.10. The system will mount and prepare the UBS flash disk for the image. You will be askedfor the home directory to store the image. Select the USB flash disk image (sdx1) and hit Enter.11. The top directory is the default, hit Enter.12. A summary will appear, hit Enter.13. The clone wizard starts. Select Beginner and hit Enter.14. The Select Mode screen appears. Select save disk, and hit Enter.15. An image name with date has been started. Rename the image as you like. For example“Annabooks-2014-08-18-19-img”, hit Enter.16. The hard disk will be selected as the default source. Hit Enter.17. Select Skip checking/repairing source file system, hit Enter.18. Check save disk image option appears, the default is Yes, check the saved image. HitEnter.19. Hit Enter to continue.20. Click y at the prompt and hit Enter to begin the backup process.21. The capture and check process takes several minutes depending on image size. HitEnter when completed22. Select Poweroff to Power down the system, and hit Enter.23. Remove both flash disks after the target powers down.Deploy the Captured Disk ImageThe two USB disks to capture the image can now be used to deploy the image to other systems.1. Plug the Clonezilla boot disk into the target system.2. Boot the target and make sure the BIOS is setup to boot from the USB flash disk.3. The Clonezilla boot screen appears. Select Clonezilla Live (Default settings, VGAXXXxYYY) and hit Enter.4. The OS will load. Select English as the language to use and hit Enter.5. Keep the default Don’t touch keymap and hit Enter.6. The default Start_Clonezilla Start Clonezilla should be selected, hit Enter.7. In the next menu, select device-image work with disks or partitions using images asthe operation mode and hit Enter8. The next menu is for the image directory. The default is for local_dev, hit Enter.9. Insert the larger USB flash disk when prompted, wait about 5 seconds, and then hitEnter.10. The system will mount and prepare the UBS flash disk for the image. You will be askedfor the home directory to store the image. Select the USB flash disk image (sdx1) and hit Enter.11. The top directory is the default, hit Enter.12. A summary will appear, hit Enter.13. The clone wizard starts. Select Beginner and hit Enter.14. The Select Mode screen appears. Select restoredisk and hit Enter.15. The system will search the disk for an image. Since there is only one image on the disk, itis already select, so hit Enter.16. Select the hard drive and hit Enter.17. Hit Enter again.19. One more time, enter y at the prompt and hit Enter.20. The process can take several minutes. Hit Enter when completed.21. Select to Poweroff to power down the system, and hit Enter.22. Remove both flash disks after the target powers down.23. Boot the system again and let the Windows cloning process run on the system.Once the master Clonezilla image has been created, it can be deployed any number of times to identical target hardware systems. This could easily be incorporated as part of the manufacturing process for an embedded system product.。
戴尔存储库管理器版本 1.8 快速安装指南说明书

Dell Repository Manager Version 1.8 Quick Install GuideNotes, Cautions, and WarningsNOTE: A NOTE indicates important information that helps you make better use of your computer.CAUTION: A CAUTION indicates either potential damage to hardware or loss of data and tells you how to avoid the problem.WARNING: A WARNING indicates a potential for property damage, personal injury, or death.© 2013 Dell Inc. All Rights Reserved.Trademarks used in this text: Dell™, the Dell logo, Dell Boomi™, Dell Precision™ , OptiPlex™, Latitude™, PowerEdge™, PowerVault™, PowerConnect™, OpenManage™, EqualLogic™, Compellent™, KACE™, FlexAddress™, Force10™, Venue™ and Vostro™ are trademarks of Dell Inc. Intel®, Pentium®, Xeon®, Core® and Celeron® are registered trademarks of Intel Corporation in the U.S. and other countries. AMD® is a registered trademark and AMD Opteron™, AMD Phenom™ and AMD Sempron™ are trademarks of Advanced Micro Devices, Inc. Microsoft®, Windows®, Windows Server®, Internet Explorer®, MS-DOS®, Windows Vista® and Active Directory® are either trademarks or registered trademarks of Microsoft Corporation in the United States and/or other countries. Red Hat® and Red Hat®Enterprise Linux® are registered trademarks of Red Hat, Inc. in the United States and/or other countries. Novell® and SUSE® are registered trademarks of Novell Inc. in the United States and other countries. Oracle® is a registered trademark of Oracle Corporation and/or its affiliates. Citrix®, Xen®, XenServer® and XenMotion® are either registered trademarks or trademarks of Citrix Systems, Inc. in the United States and/or other countries. VMware®, vMotion®, vCenter®, vCenter SRM™ and vSphere® are registered trademarks or trademarks of VMware, Inc. in the United States or other countries. IBM® is a registered trademark of International Business Machines Corporation.2013 - 12Rev. A00Contents1 Introduction (5)Downloading Dell Repository Manager (5)Installing Dell Repository Manager (5)Running Repository Manager (6)To run Repository Manager from the Start menu: (7)To run Repository Manager from your desktop: (7)Launching DRM Using Command Line Options (7)4IntroductionThis guide describes how to quickly install the Dell Repository Manager (Repository Manager) on desktops, laptops, or servers running the supported version of Microsoft Windows operating systems. Repository Manager is available in two run-time modes:•Data Center Version — For managing repositories for Dell server and storage systems.•Business Client Version — For managing repositories for Dell Latitude, OptiPlex and Precision systems.Downloading Dell Repository ManagerYou can download Repository Manager directly from /us/en/enterprise/d/solutions/ repository-manager.aspx or from /support.To download Repository Manager from /support:1.Click Product Support tab.2.Chose Drivers & Downloads from the drop down list.3.In Choose by Service Tag, click Enter a Tag or in Choose a Model, click Select Model .4.If you select the Choose by Service Tag option, enter the service tag of the Dell system in Enter aservice tag, and then click Go.If you select the Select Model option, select the product type from the Select Your Product Family list.Select the product line and product model and then click Confirm.5.From the Operating System drop-down, select the operating system running on the system.6.Under the Results for <service_tag> section, expand the Systems Management category.7.Adjacent to Repository Manager, click Download File.8.In the File Title(s) column, click the .msi file, and then click Download.9.In the Download Options window, click the option for which you want to download RepositoryManager and then click Download.The Repository Manager is downloaded.Installing Dell Repository ManagerTo install Repository Manager:1.Double-click the Dell_Repository_Manager_1.8.<revision number>.msi, for example:Dell_Repository_Manager_1.8.0.msi, from the location on the system where you downloaded it.2.In the Dell Repository Manager - InstallShield Wizard, click Next.3.In the License Agreement, select I accept the terms in the license agreement, and then click Next.4.Enter your user name and the organization you belong to.5.Select an option to indicate who will use the application, and click Next. The options available are:–Anyone who uses this computer (all users)–Only for me (<name of the particular user>)6.The Destination Folder displays the default installation folder for Repository Manager. ClickChange to change the default location, and click Next.However, you can keep using the default location, click Next.5The default location for 32-bit Windows operating system is C:\Program Files\Dell\Dell Repository Manager v<version number of Repository Manager>.For example: C:\Program Files\Dell\Dell Repository Manager v1.8.0For 64-bit Windows operating system, the default location is C:\Program Files(x86)\Dell\DellRepository Manager v<version number of Repository Manager>. For example: C:\ProgramFiles(x86)\Dell\Dell Repository Manager v1.8.0.7.Click Install to begin the installation.NOTE: During an upgrade, ensure that the existing version of Repository Manager is closed.NOTE: During an upgrade, the existing repositories and settings are retained.8.After Repository Manager is installed successfully, click Finish.The installation creates two shortcuts on your desktop and a folder in the Start menu to launch Repository Manager in Data Center Version or Business Client Versions. The folder comprises the following shortcuts:•Dell Repository Manager Updater•Dell Repository Manager Business Client Version Online Help•Dell Repository Manager for Business Client Version systems•Dell Repository Manager for Data Centers Version•Dell Repository Manager Data Center Version Online HelpWhere, x.x indicates the version number of Repository Manager.The version number of the application installed appears as part of the short cuts, the folder name and folder options in the format:<(name of the application)>v<version number of Repository Manager>Once the installation is complete, you can access the Release Notes from the location where Repository Manager is installed. The Release Notes contains a brief of the new features and known issues. Running Repository ManagerYou can run Repository Manager from the desktop, from the Start menu or, from the folder location where you have installed it:To run Repository Manager from the folder location on the system:1.Start → All Programs→ Dell Repository Manager v<x.x> and double-click the desired option.2.Select one of the following modes:–Data Center Version–Business Client VersionsNOTE: By default, the mode in which you launched Repository Manager during theprevious run time, is selected.3.Click OK.NOTE: OME 1.0 and DRM 1.8 must be installed on the same system; however, OME 1.1 andhigher versions and DRM 1.8 can be installed and run on different systems. DRM 1.8 can access OME 1.1 and higher versions inventory data from a remote system. In DRM 1.8, you must clickConnect to obtain inventory data from OME irrespective of the version of OME it interacts.4.You can also navigate to the location where Repository Manager is installed. By default, DRM isinstalled at c:\Program Files (x86)\Dell\Dell Repository Manager v1.8.0.6To run Repository Manager from the Start menu:1.Click Start → All Programs → Dell Repository Manager v<version number of Repository Manager>.2.Click one of the following options:–Dell Repository Manager Business Client Version–Dell Repository Manager Data Center VersionTo run Repository Manager from your desktop:1.Double-click one of the following options:–(Data Center Version) Dell Repository Manager v<version number of Repository Manager>–(Business Client Version) Dell Repository Manager v<version number of Repository Manager> Launching DRM Using Command Line OptionsNavigate to the location where DRM is installed. By default, for 64–bit DRM is installed at c:\Program Files (x86)\Dell\Dell Repository Manager v1.8.0. For 32–bit the DRM is installed at c:\Program Files\Dell \Dell Repository Manager v1.8.0. Go to Start → Run , type cmd and press enter.Run the Dell Repository Manager using the following command:•RepositoryManager.exe -server — Launches the application in Data Center version.or•RepositoryManager.exe -client — Launches the application in Business Client version.7。
IAR SAM8 V3.10中文使用指南

IAR Embedded Workbench用户指南(翻译:老韦)版权声明版权所有1996–2006 IAR系统。
保留所有权利。
没有这个文件的一部分可能没有IAR事先书面同意转载系统。
本文档中描述的软件是提供一个许可下,只能使用或与这样的许可条款规定的复制。
免责声明本文档中的信息如有变更,恕不另行通知,不代表在IAR系统的任何部分的承诺。
而所包含的信息这里被认为是准确的,IAR系统的任何错误不承担任何责任或遗漏。
在任何情况下都不得IAR系统,其雇员,承包商,或该作者文档将承担特别的,直接的,间接的,直接或间接损害,损失,费用,费用,索赔,要求,主张对利润损失,费用,或任何种类或性质的费用。
商标IAR系统,从理念到目标,IAR Embedded Workbench,IAR编程能力makeapp和C-SPY通过IAR 系统拥有的商标的微软和Windows是微软公司的注册商标。
Adobe和Acrobat Reader是注册商标的Adobe系统incorporated.codewright是一个注册商标的母星公司。
所有其他产品名称是其各自的商标或注册商标业主。
版预告第六版:六月2006零件号:uew-6内部参考:4.7.0。
内容简介表..............................................................................................................................十九数字......................................................................................................................二十二前言.......................................................................................................................二十九1部分。
戴尔易安信OpenManage Ansible模块3.0.0安全配置指南说明书

Dell EMC OpenManage Ansible Modules 3.0.0 Security Configuration GuideNotes, cautions, and warningsA NOTE indicates important information that helps you make better use of your product.A CAUTION indicates either potential damage to hardware or loss of data and tells you how to avoidA WARNING indicates a potential for property damage, personal injury, or death.© 2018 - 2021 Dell Inc. or its subsidiaries. All rights reserved. Dell, EMC, and other trademarks are trademarks of Dell Inc. or its subsidiaries. Other trademarks may be trademarks of their respective owners.Chapter 1: Preface (4)Scope of the document (4)Document references (4)Chapter 2: Security Quick Reference (5)Deployment Model (5)Security Profiles (5)Chapter 3: Product and Subsystem Security (6)Security controls map (6)Authentication (6)Authentication with external systems (6)iDRAC authentication (7)OpenManage Enterprise Authentication (7)File server authentication (7)Data security (7)Serviceability (7)Security patches (7)Network security (7)Auditing and logging (8)Protecting sensitive data with 'no log' (8)Chapter 4: Miscellaneous configuration and management (9)OpenManage Ansible modules licensing (9)Protect authenticity and integrity (9)Ansible module security (9)Ansible vault (9)Contents3Preface Dell EMC OpenManage Ansible Modules(OMAM) allows data center and IT administrators to use RedHat Ansible to automate and orchestrate the configuration, deployment, and update of Dell EMC PowerEdge Servers and modular infrastructureby leveraging the management automation capabilities in-built into the Integrated Dell Remote Access Controller (iDRAC), OpenManage Enterprise, and OpenManage Enterprise Modular.OpenManage Ansible Modules simplifies and automates provisioning, deployment, and updates of PowerEdge servers and modular infrastructure. It allows system administrators and software developers to introduce the physical infrastructure provisioning into their software provisioning stack, integrate with existing DevOps pipelines and manage their infrastructure using version-controlled playbooks, server configuration profiles, and templates in line with the Infrastructure-as-Code (IaC) principles.As part of an effort to improve its product lines, Dell EMC periodically releases revisions of its software and hardware. Some functions that are described in this document might not be supported by all versions of the software or hardware currentlyin use. The product release notes provide the most up-to-date information about product features. Contact your Dell EMC technical support professional if a product does not function properly or does not function as described in this document.This document was accurate at publication time. To ensure that you are using the latest version of this document, go tohttps:///dell/dellemc-openmanage-ansible-modules/tree/devel.Topics:•Scope of the document•Document referencesScope of the documentThis document includes information about the security features and capabilities of OpenManage Ansible Modules (OMAM). Document referencesIn addition to this guide, you can access the associated OMAM guides available at https:///support:●OpenManage Ansible Modules Installation Guide●OpenManage Ansible Modules User's Guide.●OpenManage Ansible Modules Release Notes.4PrefaceSecurity Quick Reference Topics:•Deployment Model•Security ProfilesDeployment ModelOpenManage Ansible Modules release follows a monthly release cycle. Minor versions are released on the last week of each month and are posted to GitHub as well as to the Ansible-Galaxy (as collections). Once there are enough features, updates,and security fixes released over a series of minor releases and patches, a major version containing all these changes is eventually released to GitHub and Ansible Galaxy (as collections). To install the OMAM from Github or Ansible galaxy refer https:///dell/dellemc-openmanage-ansible-modules/tree/devel/guides.Security ProfilesOMAM has a default security profile for secure HTTP access.Security Quick Reference5Product and Subsystem Security Topics:•Security controls map•Authentication•Authentication with external systems•Data security•Serviceability•Network security•Auditing and loggingSecurity controls mapOpenManage Ansible Modules use Ansible Playbooks to run commands for interacting with iDRAC and Open Manage Enterprise. The system credentials are not stored by default. Some iDRAC modules use a file system to temporarily read and write files toa local Ansible control machine or a file server. The file server path is mounted on the Ansible control machine, and you must securely configure the file servers.iDRAC and OpenManage Enterprise communicate with Dell server for firmware updates over a HTTPS channel, facilitated by the Ansible control machine through modules and playbooks. The following figure displays the OMAM security controls map:AuthenticationAccess control settings provide protection of resources against unauthorized access. OMAM does not have any accesscontrol system of its own. It is dependent on the access control settings which are provided by Ansible, File Server, iDRAC, OpenManage Enterprise, and Redfish endpoints.For more information about the connection methods see the Ansible documentation.Authentication with external systemsThe OMAM modules communicate with iDRAC and OpenManage Enterprise over a secure HTTPS channel. OMAM supports session-based authentication for REST calls.Session-based authentication is used when issuing multiple Representational State Transfer (REST) requests.●Session login is initiated by accessing the Create session URI. The response to this request includes an X-Auth-Token headerwith a session token. Authentication for subsequent requests is made using the X-Auth-Token header.6Product and Subsystem Security●Session logout is performed by issuing a DELETE of the Session resource provided by the Login operation including theX-Auth-Token header.iDRAC authenticationThe Integrated Dell Remote Access Controller (iDRAC) is designed to make you more productive as a system administrator and improves the overall availability of Dell EMC servers. iDRAC alerts you on system issues, remotely manage your systems, and reduces the need for physical access to the system. See the latest iDRAC User Guide for more details on available methods of authentication.OMAM communicates with iDRAC using WSMan and REST. OMAM supports both session-based and basic authentication for iDRAC REST calls over HTTPS.OMAM supports standard Redfish endpoints as well. Both session-based and basic authentication are supported. OpenManage Enterprise AuthenticationOpenManage Enterprise is a simple-to-use, one-to-many systems management console. It is cost effective and facilitates comprehensive lifecycle management for Dell EMC PowerEdge servers through one console. OpenManage Enterprise supports basic authentication and X-Auth-Token Authentication for the REST calls. For more information, see the latest OpenManage Enterprise API guide.OMAM supports both session-based and basic authentication for OpenManage Enterprise over HTTPS.File server authenticationSome of the OMAM modules take the artifacts from CIFS or NFS shares as module parameters. These shares are accessed by iDRAC services to perform operations such as firmware update, system configuration exports or imports. It is recommended to configure the share folders securely with the required user access controls.Data securityOMAM does not store data. See Ansible Vault for details on securing credentials passed to external systems. ServiceabilityThe support website https:///support provides access to product documentation, advisories, downloads, and troubleshooting information. This information helps you to resolve a product issue before you contact the support team. Security patchesOMAM follows a monthly release cycle. On the last week of every month, the updated modules are posted on GitHub. The monthly OMAM releases include feature updates, defect fixes, and security only updates. Every major release is uploaded on the Dell support site. For a critical security issue, a security patch is released as soon as possible.Network securityOMAM uses HTTPS with a default security profile to communicate with OpenManage Enterprise and iDRAC. This release does not support SSL certificate validation.Product and Subsystem Security7Auditing and loggingOMAM does not have its own logging mechanism, and it depends on the default Ansible logging capability. By default, Ansible sends output about plays, tasks, and module arguments to your screen (STDOUT) on the control node see Logging Ansible Output for more details. Encryption with Ansible Vault only protects data at rest. Once the content is decrypted (data in use), play and plugin authors are responsible for avoiding any secret disclosure. For details on hiding output, see no_log. For security considerations on editors that you use with Ansible Vault, see Steps to secure your editor.Protecting sensitive data with 'no log'If you save Ansible output to a log, you expose any secret data in your Ansible output, such as passwords and usernames. To keep sensitive values out of your logs, mark tasks that expose them with the no_log: True attribute. However, the no_log attribute does not affect debugging output.8Product and Subsystem Security4Miscellaneous configuration andmanagement Topics:•OpenManage Ansible modules licensing•Protect authenticity and integrity•Ansible module securityOpenManage Ansible modules licensingOMAM is open source and licensed under the GNU General Public License v3.0+. For more details see COPYING.md. iDRAC and OpenManage Enterprise may require its own licenses for some functions in OMAM to work. Refer the User Guide for more details.Protect authenticity and integrityTo ensure the product integrity, the OMAM installation package is signed and uploaded to https:///support. The collection bundle uploaded to ansible-galaxy is also signed.Ansible module securityFor security guidelines for Ansible modules, see Module Best Practices. Any developer who wants to contribute to OMAM adhere to these guidelines, along with the UT and sanity requirements.Certain settings in Ansible are adjustable through a configuration file (ansible.cfg). The stock configuration should be sufficient for most users, but there may be reasons you would want to change them. Paths where the configuration file is searched are listed in the reference documentation.Ansible vaultAnsible Vault is a feature that allows users to encrypt values and data structures within the Ansible projects. This provides the ability to secure any sensitive data that is necessary to successfully run Ansible plays but should not be publicly visible, suchas passwords or private keys. Ansible automatically decrypts vault-encrypted content at runtime when the key is provided. See Vault documentation for more details.Miscellaneous configuration and management9。
MXview插件 дляMGate系列产品发布说明书

MXview Plugin for MGate Series Release NotesSupported Operating SystemsNotesChangesApplicable ProductsBugs FixedN/AN/AEnhancementsWindows 10, Windows 7, Windows 8, Windows Server 2008, Windows Server 2012, Windows Server 2012 R2MGate W5108, MGate W5108-T, MGate W5208, MGate W5208-T, MGate 5109, MGate 5109-T, MGate 5118, MGate 5118-T, MGate MB3180, MGate MB3280, MGate MB3480, MGate MB3170, MGate MB3170I, MGate MB3270, MGate MB3270I, MGate MB3170-T, MGate MB3170I-T, MGate MB3270-T,MGate MB3270I-T, MGate MB3170-M-SC, MGate MB3170-M-ST, MGate MB3170-S-SC, MGate MB3170I-M-SC, MGate MB3170I-S-SC, MGate MB3170-M-SC-T, MGate MB3170-M-ST-T, MGate MB3170-S-SC-T, MGate MB3170I-M-SC-T, MGate MB3170I-S-SC-T, MGate MB3660-8-J-2AC,MGate MB3660I-16-2AC, MGate MB3660-16-J-2AC, MGate MB3660-8-2AC, MGate MB3660-8-2DC,MGate MB3660I-8-2AC, MGate MB3660-16-2AC, MGate MB3660-16-2DC, MGate 5101-PBM-MN,MGate 5101-PBM-MN-T, MGate 5105-MB-EIP, MGate 5105-MB-EIP-T, MGate 5103, MGate 5103-T,MGate 5102-PBM-PN, MGate 5102-PBM-PN-T, MGate EIP3170, MGate EIP3170I, MGate EIP3270,MGate EIP3270I, MGate EIP3170-T, MGate EIP3170I-T, MGate EIP3270-T, MGate 5111, MGate 5111-T, MGate 5114, MGate 5114-T• Supports MGate 5114.• Added security view for MB3170, MB3170I, MB3170 fiber series, MB3270, MB3270I, MB3180,MB3280, MB3480, MB3660, MGate 5114.New FeaturesN/A• This version supports MXview v2.9.Supported Operating SystemsNotesChangesApplicable ProductsBugs Fixed• Supports MGate 5103, MGate 5111, MGate MB3660I-16-2AC, MGate MB3660-8-J-2AC, MGate MB3660-16-J-2AC.• Added security view for MGate 5101-PBM-MN, MGate 5102-PBM-PN, MGate 5105-MB-EIP, MGate W5108, MGate W5208, MGate 5103, MGate 5111.N/AEnhancementsWindows 7, Windows 8, Windows Server 2008, Windows Server 2012, Windows XPMGate W5108, MGate W5108-T, MGate W5208, MGate W5208-T, MGate 5109, MGate 5109-T, MGate 5118, MGate 5118-T, MGate MB3180, MGate MB3280, MGate MB3480, MGate MB3170, MGate MB3170I, MGate MB3270, MGate MB3270I, MGate MB3170-T, MGate MB3170I-T, MGate MB3270-T,MGate MB3270I-T, MGate MB3170-M-SC, MGate MB3170-M-ST, MGate MB3170-S-SC, MGate MB3170I-M-SC, MGate MB3170I-S-SC, MGate MB3170-M-SC-T, MGate MB3170-M-ST-T, MGate MB3170-S-SC-T, MGate MB3170I-M-SC-T, MGate MB3170I-S-SC-T, MGate MB3660-8-J-2AC,MGate MB3660I-16-2AC, MGate MB3660-16-J-2AC, MGate MB3660-8-2AC, MGate MB3660-8-2DC,MGate MB3660I-8-2AC, MGate MB3660-16-2AC, MGate MB3660-16-2DC, MGate 5101-PBM-MN,MGate 5101-PBM-MN-T, MGate 5105-MB-EIP, MGate 5105-MB-EIP-T, MGate 5103, MGate 5103-T,MGate 5102-PBM-PN, MGate 5102-PBM-PN-T, MGate EIP3170, MGate EIP3170I, MGate EIP3270,MGate EIP3270I, MGate EIP3170-T, MGate EIP3170I-T, MGate EIP3270-T, MGate 5111, MGate 5111-TN/ANew FeaturesN/A• This version supports MXview v2.9.Supported Operating SystemsNotesChangesApplicable ProductsBugs Fixed• Supports MGate 5118.• Added security view for MGate 5109, MGate 5118.• Added userid login for MGate 5109, MGate 5118.N/AEnhancementsWindows 7, Windows 8, Windows Server 2008, Windows Server 2012, Windows XPMGate MB3660I-16-2AC, MGate MB3660-16-J-2AC, MGate MB3660-8-2AC, MGate MB3660-8-2DC,MGate MB3660I-8-2AC, MGate MB3660-16-2AC, MGate MB3660-16-2DC, MGate 5101-PBM-MN,MGate 5101-PBM-MN-T, MGate 5105-MB-EIP, MGate 5105-MB-EIP-T, MGate 5102-PBM-PN, MGate 5102-PBM-PN-T, MGate EIP3170, MGate EIP3170I, MGate EIP3270, MGate EIP3270I, MGate EIP3170-T, MGate EIP3170I-T, MGate EIP3270-T, MGate W5108, MGate W5108-T, MGate W5208,MGate W5208-T, MGate 5109, MGate 5109-T, MGate 5118, MGate 5118-T, MGate MB3180, MGate MB3280, MGate MB3480, MGate MB3170, MGate MB3170I, MGate MB3270, MGate MB3270I,MGate MB3170-T, MGate MB3170I-T, MGate MB3270-T, MGate MB3270I-T, MGate MB3170-M-SC,MGate MB3170-M-ST, MGate MB3170-S-SC, MGate MB3170I-M-SC, MGate MB3170I-S-SC, MGate MB3170-M-SC-T, MGate MB3170-M-ST-T, MGate MB3170-S-SC-T, MGate MB3170I-M-SC-T, MGate MB3170I-S-SC-T, MGate MB3660-8-J-2ACN/ANew FeaturesN/A• This version supports MXview v2.8.Supported Operating SystemsNotesChangesApplicable ProductsBugs Fixed• Supports MGate 5109.N/AEnhancementsWindows 7, Windows 8, Windows Server 2008, Windows Server 2012, Windows XPMGate W5108, MGate W5108-T, MGate W5208, MGate W5208-T, MGate 5109, MGate 5109-T, MGate MB3180, MGate MB3280, MGate MB3480, MGate MB3170, MGate MB3170I, MGate MB3270, MGate MB3270I, MGate MB3170-T, MGate MB3170I-T, MGate MB3270-T, MGate MB3270I-T, MGate MB3170-M-SC, MGate MB3170-M-ST, MGate MB3170-S-SC, MGate MB3170I-M-SC, MGate MB3170I-S-SC, MGate MB3170-M-SC-T, MGate MB3170-M-ST-T, MGate MB3170-S-SC-T, MGate MB3170I-M-SC-T, MGate MB3170I-S-SC-T, MGate MB3660-8-J-2AC, MGate MB3660I-16-2AC,MGate MB3660-16-J-2AC, MGate MB3660-8-2AC, MGate MB3660-8-2DC, MGate MB3660I-8-2AC,MGate MB3660-16-2AC, MGate MB3660-16-2DC, MGate 5101-PBM-MN, MGate 5101-PBM-MN-T,MGate 5105-MB-EIP, MGate 5105-MB-EIP-T, MGate 5102-PBM-PN, MGate 5102-PBM-PN-T, MGate EIP3170, MGate EIP3170I, MGate EIP3270, MGate EIP3270I, MGate EIP3170-T, MGate EIP3170I-T,MGate EIP3270-TN/ANew FeaturesN/A• This version supports MXview v2.7.Supported Operating SystemsNotesChangesApplicable ProductsBugs Fixed• Supports MGate W5108/W5208, MGate MB3170 Fiber Series, MGate MB3660 Series.N/AEnhancementsWindows 7, Windows 8, Windows Server 2008, Windows Server 2012, Windows XPMGate W5108, MGate W5108-T, MGate W5208, MGate W5208-T, MGate MB3180, MGate MB3280,MGate MB3480, MGate MB3170, MGate MB3170I, MGate MB3270, MGate MB3270I, MGate MB3170-T, MGate MB3170I-T, MGate MB3270-T, MGate MB3270I-T, MGate MB3170-M-SC, MGate MB3170-M-ST, MGate MB3170-S-SC, MGate MB3170I-M-SC, MGate MB3170I-S-SC, MGate MB3170-M-SC-T, MGate MB3170-M-ST-T, MGate MB3170-S-SC-T, MGate MB3170I-M-SC-T, MGate MB3170I-S-SC-T, MGate MB3660-8-J-2AC, MGate MB3660I-16-2AC, MGate MB3660-16-J-2AC,MGate MB3660-8-2AC, MGate MB3660-8-2DC, MGate MB3660I-8-2AC, MGate MB3660-16-2AC,MGate MB3660-16-2DC, MGate 5101-PBM-MN, MGate 5101-PBM-MN-T, MGate 5105-MB-EIP,MGate 5105-MB-EIP-T, MGate 5102-PBM-PN, MGate 5102-PBM-PN-T, MGate EIP3170, MGate EIP3170I, MGate EIP3270, MGate EIP3270I, MGate EIP3170-T, MGate EIP3170I-T, MGate EIP3270-T N/ANew FeaturesN/A• This version supports MXview v2.6.Supported Operating SystemsNotesChangesApplicable ProductsBugs FixedN/AN/AEnhancementsWindows 7, Windows 8, Windows Server 2008, Windows Server 2012, Windows XPMGate MB3180, MGate MB3280, MGate MB3480, MGate MB3170, MGate MB3170I, MGate MB3270,MGate MB3270I, MGate MB3170-T, MGate MB3170I-T, MGate MB3270-T, MGate MB3270I-T, MGate 5101-PBM-MN, MGate 5101-PBM-MN-T, MGate 5105-MB-EIP, MGate 5105-MB-EIP-T, MGate 5102-PBM-PN, MGate 5102-PBM-PN-T, MGate EIP3170, MGate EIP3170I, MGate EIP3270, MGate EIP3270I, MGate EIP3170-T, MGate EIP3170I-T, MGate EIP3270-TN/ANew FeaturesN/A• This version supports MXview v2.4.Supported Operating SystemsNotesChangesApplicable ProductsBugs FixedN/AN/AEnhancementsWindows 7, Windows 8, Windows Server 2008, Windows Server 2012, Windows XPMGate MB3180, MGate MB3280, MGate MB3480, MGate MB3170, MGate MB3170I, MGate MB3270,MGate MB3270I, MGate MB3170-T, MGate MB3170I-T, MGate MB3270-T, MGate MB3270I-T, MGate 5101-PBM-MN, MGate 5101-PBM-MN-T, MGate 5105-MB-EIP, MGate 5105-MB-EIP-T, MGate 5102-PBM-PN, MGate 5102-PBM-PN-T, MGate EIP3170, MGate EIP3170I, MGate EIP3270, MGate EIP3270I, MGate EIP3170-T, MGate EIP3170I-T, MGate EIP3270-T• First release.New FeaturesN/AN/A。
BC6818 硬体开发说明

818 的 Pin.29 � VDD33 BC6818 的 Pin.30 � VDD18
是 BC6818 內建提供 3.3V 的 OUTPUT PIN; 是 BC6818 內建提供 1.8V 的 OUTPUT PIN
6 , BC6818 .37 ~ Pin.40 空接是沒有問題的, HPA & HPB 是兩個獨立分開的電路.
BC6818 硬体开发(PCB 制板)说明
1,如是使用 BC6818 內建的 3.3v & 1.8v Regulator, 就請不要使用外部穩壓 IC 對接在一起, 這樣會容易造成 IC 的燒燬. 這部份在新版的電路原理圖中都有附註. 2,BC6818 的 Internal Mode 控制腳中, 在應用時需請您注意 PROG.0(Pin.9)是最低位元(LSB); PROG.3(Pin.22)是最高位元(MSB) 所以下圖中的 1 為 MSB�PROG.3 ; 4 為 LSB�PROG.0
7,目前可以推到100mA, 使用 BC6818 同時去推外部 DAC & ADC 都是沒問題的。
附件2份最新原理图说明
.a.附件”BC6818_ctrl_board_20130322.pdf ”: 是開發套件板中關於 BC3250(MCU )的最新控制應用原理圖. b. 附件”BC6818_ 主板_20130322.pdf ”: 是開發套件板中關於 BC6818 周邊電路的最新應用原理圖.
依照上表(某种编码器规格)來看, 如 J3 的腳位是對照上表所示 , 那麼原理圖中可能是接 反的。 正確應為: J3- PROG.3(Pin.22); J3-2 PROG.2(Pin.21); J3-3 PROG.1(Pin.10); J3-4 PROG.0(Pin.09); 3,有關外部的 ADC & DAC 在新版的電路原理圖中都己經有些更正。 4,只要其輸出入腳能符合一般 8051 使用, 即可正常控制 BC6818 的內建 16 種音效基本操作. 5,
戴尔易安信刀片式服务器I O指南说明书

INFINIBAND
GbE M6220
3032
M6348
M8024 10GbE
FC4
FC4
FC8
M2401G
M3601Q
Pass
3130G
Pass
Pass M4424 M5424
DDR
QDR
DELTLhrCuONFIDENTIAL 3130X
Thru
Thru
Infiniband Infiniband
Cables CX4 cable, InfiniBand 4x connector
10GbE X2 Transceiver
Modules
MMF, dual SC
connector
10GbE X2 Transceiver
Modules
10GBASE-SR X2 Module
10GBASELRM X2 Module
4
POWERCONNECT M6220
PE server blade I/O
card
Uplinks
Uplinks
Transceivers XFP Optical Transceiver 10GBASE-LR, LC Connector XFP Optical Transceiver 10GBASE-SR, LC Connector
4 Copper
I/O bays
Fabric A1 &
A2
Fabric B1 &
B2
Fabric C1 &
C2
5
CISCO BLADE SWITCH
PE server blade I/O
card
Use Broadcom 5709 dual port server blade I/O Mezzanine Cards in PE blade servers for
ICP DAS I-7188EX 产品说明书
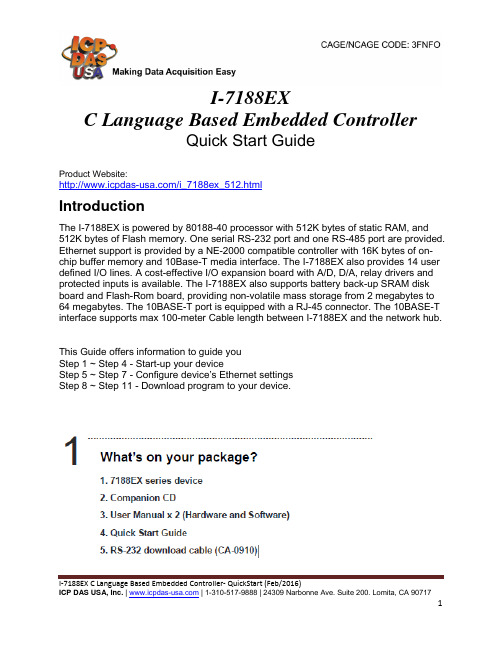
I-7188EXC Language Based Embedded ControllerQuick Start GuideProduct Website:/i_7188ex_512.htmlIntroductionThe I-7188EX is powered by 80188-40 processor with 512K bytes of static RAM, and 512K bytes of Flash memory. One serial RS-232 port and one RS-485 port are provided. Ethernet support is provided by a NE-2000 compatible controller with 16K bytes of on-chip buffer memory and 10Base-T media interface. The I-7188EX also provides 14 user defined I/O lines. A cost-effective I/O expansion board with A/D, D/A, relay drivers and protected inputs is available. The I-7188EX also supports battery back-up SRAM disk board and Flash-Rom board, providing non-volatile mass storage from 2 megabytes to 64 megabytes. The 10BASE-T port is equipped with a RJ-45 connector. The 10BASE-T interface supports max 100-meter Cable length between I-7188EX and the network hub. This Guide offers information to guide youStep 1 ~ Step 4 - Start-up your deviceStep 5 ~ Step 7 - Configure device’s Ethernet settingsStep 8 ~ Step 11 - Download program to your device.I-7188EX C Language Based Embedded Controller- QuickStart (Feb/2016)I-7188EX C Language Based Embedded Controller- QuickStart (Feb/2016)/vxcomm.htmlI-7188EX C Language Based Embedded Controller- QuickStart (Feb/2016)I-7188EX C Language Based Embedded Controller- QuickStart (Feb/2016)I-7188EX C Language Based Embedded Controller- QuickStart (Feb/2016)I-7188EX C Language Based Embedded Controller- QuickStart (Feb/2016)/minios7utility.html I-7188EX C Language Based Embedded Controller- QuickStart (Feb/2016)I-7188EX C Language Based Embedded Controller- QuickStart (Feb/2016)I-7188EX C Language Based Embedded Controller- QuickStart (Feb/2016)I-7188EX C Language Based Embedded Controller- QuickStart (Feb/2016)I-7188EX C Language Based Embedded Controller- QuickStart (Feb/2016)ICP DAS USA, Inc. | | 1-310-517-9888 | 24309 Narbonne Ave. Suite 200. Lomita, CA 90717 11。
Honeywell 7800 Series 221818A,C Extension Cable As
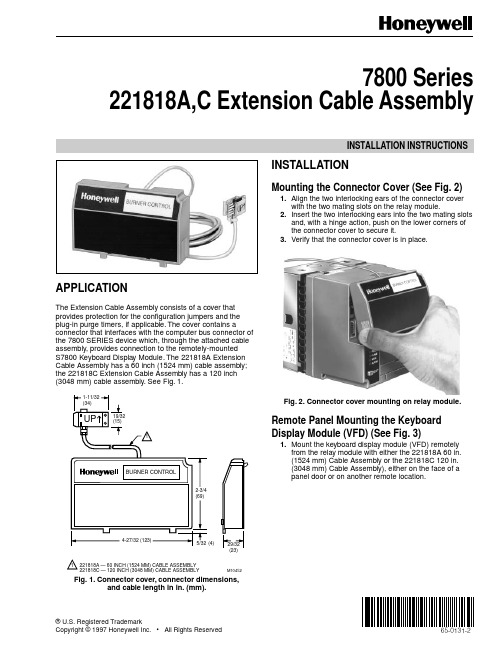
® U.S. Registered TrademarkCopyright © 1997 Honeywell Inc. • All Rights ReservedINSTALLATION INSTRUCTIONSX-XX UL65-0131-27800 Series221818A,C Extension Cable AssemblyAPPLICATIONThe Extension Cable Assembly consists of a cover that provides protection for the configuration jumpers and the plug-in purge timers, if applicable. The cover contains aconnector that interfaces with the computer bus connector of the 7800 SERIES device which, through the attached cable assembly, provides connection to the remotely-mounted S7800 Keyboard Display Module. The 221818A Extension Cable Assembly has a 60 inch (1524 mm) cable assembly;the 221818C Extension Cable Assembly has a 120 inch (3048 mm) cable assembly. See Fig. 1.Fig. 1. Connector cover, connector dimensions,and cable length in in. (mm).INSTALLATIONMounting the Connector Cover (See Fig. 2)1.Align the two interlocking ears of the connector cover with the two mating slots on the relay module.2.Insert the two interlocking ears into the two mating slots and, with a hinge action, push on the lower corners of the connector cover to secure it.3.Verify that the connector cover is in place.Fig. 2. Connector cover mounting on relay module.Remote Panel Mounting the Keyboard Display Module (VFD) (See Fig. 3)1.Mount the keyboard display module (VFD) remotely from the relay module with either the 221818A 60 in.(1524 mm) Cable Assembly or the 221818C 120 in.(3048 mm) Cable Assembly), either on the face of a panel door or on another remote location.M10452(4)(23)BURNER CONTROL221818A — 60 INCH (1524 MM) CABLE ASSEMBLY 221818C — 120 INCH (3048 MM) CABLE ASSEMBLYUP2-3/4 (69)5/3229/324-27/32 (123)19/32 (15)1-11/32 (34)117800 SERIES 221818A,C EXTENSION CABLE ASSEMBL Y65-0131—2Fig. 3. Flush panel mounting of keyboard display module.2.When mounting the keyboard display module on theface of the door panel, closely follow these instructions:a.Select the location on the door panel for flushmounting. Allow for the insertion dimension of theKeyboard Display Module two screws, twointerlocking ears and the two plug-in connectorsto assure sufficient clearance (1/4 inch minimumfrom the surface of the door panel).ing the keyboard display module or datacontrolbus module as a template, see Fig. 6,mark the two screw locations, two interlocking earlocations and the two plug-in connector locations.Drill the pilot holes for the mounting screws.Provide two holes on the door panel for theinterlocking ears and plug-in connector holes Aand B (shaded portions of Fig. 6).c.Insert the extension cable assembly connectorthrough the plug-in connector hole A. Use the208702 Retainer Bracket on the display to reducemovement and relieve strain on the connector.See Fig. 7. Be sure that the two flanges arebetween the keyboard display module and thepanel.d.Mount the keyboard display module, securing thetwo no. 4 screws.Remote Bracket Mounting the Keyboard Display Module (VFD) (See Fig. 4)1.When mounting the keyboard display module on a wallor remote location up to 120 in. (3048 mm) from therelay module, use the 2037656 Remote MountingBracket.ing the remote mounting bracket as atemplate, mark the four screw locations and drillthe pilot holes.b.Mount the remote mounting bracket by securingthe four no. 6 screws (see Fig. 4).c.On the extension cable assembly connector, witha pair of needle nose pliers, bend the two metalsides completely back and snap off the center ofthe connector at its score markings (see Fig. 5).d.Insert the extension cable assembly connector tothe keyboard display module connector A. SeeFig. 6.Fig. 4. Remote mounting of keyboard displaymodule using remote mounting bracket.Fig. 5. Modified connector for bracket mounting.e.Mount the keyboard display module by insertingthe two interlocking ears into the two mating slotson the remote mounting bracket; then push onthe lower corners to secure it.f.Assure that the keyboard display module is firmlyin place.27800 SERIES 221818A,C EXTENSION CABLE ASSEMBL YFig. 6. Flush mounting of keyboard display module.Fig. 7. Mounting 208702 Retainer Bracket.363-0131—2465-0131—265-0131—2 G.H. Rev. 2-97 Printed in Mexico Home and Building ControlHoneywell Limited-Honeywell Limitée 155 Gordon Baker Road North York, Ontario M2H 2C9Home and Building Control Honeywell Inc.Honeywell Plaza P.O. Box 524Minneapolis MN 55408-0524Helping You Control Your World ®。
TiWi-uB2 EM BOARD User Guide
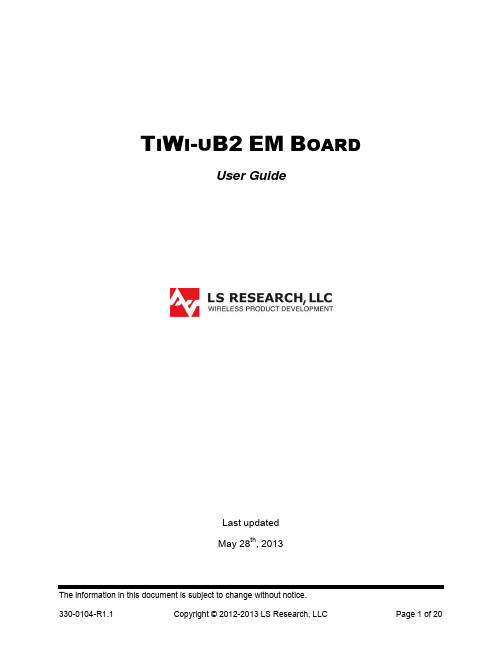
T I W I-U B2EM B OARDUser GuideLast updatedMay 28th, 2013Table of Contents1Introduction (3)1.1Purpose & Scope (3)1.2Applicable Documents (3)1.3Revision History (3)2TiWi-uB2 Module Description (4)3TiWi-uB2 EM Board Hardware (5)3.1Antenna (5)3.2Connectors (5)3.3Required Signals between EM Board and Host Device (6)3.4Connecting EM Board to Host Platform (7)3.5Power Supply (7)3.6Serial Interfaces (7)3.7HCI UART (8)3.8PCM Interface (8)3.9Option 1: Using EM Connectors (8)3.10Option 2: Using Single Row Headers (11)3.11Using J7 with USB to Serial Converter (12)4Schematic (13)4.1Bill Of Material (BOM) (14)5Application Development (15)5.1Overview (15)5.2Development Tools (15)6Contacting LS Research (20)1Introduction1.1 Purpose & ScopeThe purpose of this document is to provide details regarding the setup and use of theTiWi-uB2 module on an EM board. This document covers a description of the EM board and its features and a brief tutorial on how to operate the module EM board.1.2 Applicable Documents∙TiWi-uB2 Datasheet (330-0100)∙TiWi-uB2 Antenna Design Guide (330-0106)1.3 Revision HistoryTable 1 Revision History2TiWi-uB2 Module DescriptionThe TiWi-uB2 EM “Evaluation Module” Board is an evaluation platform for the LSResearch TiWi-uB2 Bluetooth and Bluetooth Low Energy (BLE) module.Communication between the TiWi-uB2 module, which is a slave, and the host device is through a UART interface.The TiWi-uB2 EM Board contains an on board chip antenna and U.FL connector. The EM board is intended for evaluation purposes when used in conjunction with variousTexas Instruments MSP430 and Stellaris development boards.Figure 1 TiWi-uB2 EM Board TopFigure 2 TiWi-uB2 EM Board Bottom3 TiWi-uB2 EM Board Hardware 3.1 AntennaThe TiWi-uB2 EM Board contains an on board chip antenna which is modular certified for FCC 15.247 and IC RSS-210, as well as compliant to the RF requirements for ETSI EN 300 328 and ETSI EN 301 489. The antenna layout and circuitry on the EM Board can be replicated on a custom designed PCB assembly. Assuming the design/layout is followed exactly as that which is on the EM Board, the custom PCB will retain the modular certification. Below are details on the certifications.FCC ID: TFB-BT1, 15.247 IC ID: 5969A-BT1, RSS 2103.2 ConnectorsThere are two primary connectors on the TiWi-uB2 EM Board (J1 & J2). These provide a standard interface to Texas Instruments development platforms (See Section 3.9). Two additional non populated connectors (J4 & J5) provide access to all of the significant signals on the module on a standard, single row 2mm pitch header.165423789Figure 3 TiWi-uB2 EM Board Top Side ConnectorsTable 2 TiWi-uB2 EM Board Top Side Connectors3.3 Required Signals between EM Board and Host DeviceIn addition to power and ground, there are three signals required for connecting a TiWi-uB2 module to a host device. See Table 3 below for details on these connections.Table 3 TiWi-uB2 Required Connections3.4 Connecting EM Board to Host PlatformThe TiWi-uB2 EM Board is intended to allow for evaluation of and early developmentwith a TiWi-uB2 module. The EM Board has two “EM” connectors on the bottom of the board that allows for easy connection to various Texas Instruments microcontrollerdevelopment platforms. The primary development platform is the MSP430F5438Experimenter Board.It is also possible to adapt the TiWi-uB2 EM Board to work with microcontroller platforms that do not have support for the EM connectors. Sections 3.9 and 3.10 describe the two options for adapting an EM Board to work with other microcontroller platforms.3.5 Power Supply3.5.1 VBATVBAT requires a 3.0V to 4.8V DC power supply.3.5.2 VDD_IOVDD_IO requires a 1.8V DC power supply.Figure 4 Power Supply3.6 Serial InterfacesThere are two serial interfaces to the module, HCI UART and PCM. Each interface isdescribed below.Figure 5 Serial Interfaces3.7 HCI UARTThis is the main interface between the host microcontroller and the module. TheBluetooth UART may also be used to download external patches from the host to theTiWi-uB2. The UART interface supports baud rates from 9600bps to 4Mbps.BT debug pin: The debug interface (TX_DBG) helps customers to debug the HW/SWissues for their application (not pictured).3.8 PCM InterfaceThe PCM Interface can connect to linear PCM Codec devices in master or slave mode.In master mode, the TiWi-uB2 generates the PCM_CLK and PCM_SYNC signals, and in slave mode, these signals are provided by another master on the PCM interface and are inputs to the TiWi-uB2.Figure 6 PCM Interface3.9 Option 1: Using EM ConnectorsEither build a PCB which has the EM Board mating connectors which will allow forplugging the TiWi-uB2 EM Board into, or solder wires to EM Board mating connectorsthat can then be wired into whatever development platform is being used.Below are two suggestions for the mating EM connectors.Through hole connector: Samtec TFM-110-01-S-D-WTSurface Mount connector: Samtec SFM-110-02-L-D-AIf building a PCB that has the mating EM Board connectors, the connectors need to be lined up and spaced 1.2” apart as shown in Figure 7.Figure 7 Host PCB EM Mating Connector Arrangement (Top View)Refer to Table 4 and Table 5 below for details on the signals brought out to the EM connectors J1 and J2.Table 4 EM Connector J1Table 5 EM Connector J2DI = Digital Input; DO = Digital Output; DIO = Digital Input/Output; PI = Power Input3.10 Option 2: Using Single Row HeadersSolder single row 12 pin 2mm headers into locations J4 and J5 on the EM Board, and then build a wiring harness between the headers on the EM Board and themicrocontroller development platform of interest.Below is a suggestion for the 12 pin 2mm headers.Sullins NRPN121PAEN-RCRefer to Table 6 and Table 7 below for details on the signals brought out to the single row headers J4 and J5.Table 6 Single Row Header J4DI = Digital Input; DO = Digital Output; PI = Power InputTable 7 Single Row Header J5DI = Digital Input; DO = Digital Output; DIO = Digital Input/Output; PI = Power Input3.11 Using J7 with USB to Serial ConverterJ7 is provided for interfacing the TiWi-uB2 Module to a USB-to-Serial converter, or similar serial device capable of providing 1.8V logic level data.Table 8 Single Row Header J7DI = Digital Input; DO = Digital Output; DIO = Digital Input/Output; PI = Power Input;4.1 Bill Of Material (BOM)Table 9 TiWi-uB2 EM Board BOM5Application Development5.1 OverviewThe TiWi-uB2 EM Board used in conjunction with a Bluetooth stack running on TI’sMSP430BT5438 or Stellaris LM3S9B96microcontroller (MCU) will reduce designbarriers and provides a highly flexible platform to enable customer’s early prototyping capabilities of embedded Bluetooth applications. The ready-to-go wireless platforms simplify the development process of pre-integrated and pre-validated Bluetooth serial link on an MSP430BT5438 or LM3S9B96system.For an overview of development platforms and software examples see CC256xBluetooth.5.2 Development Tools5.2.1 MSP430 HardwareHardware required for initial evaluation and development include:∙ 2 - TiWi-uB2 EM Boards∙ 1 - TI MSP430 USB Debugging Interface∙ 2 - TI MSP430F5438 Experimenter Boards5.2.2 Stellaris Hardware∙ 1 - TiWi-uB2 EM Board∙ 1 - TI MSP430 USB Debugging Interface∙ 1 - TI Stellaris LM3S9B96 EM2 Expansion Board∙ 1 - TI DK-LM3S9D965.2.3 SoftwareSoftware required for initial evaluation and development include:Stellaris∙Bluetopia®+LE SDK∙CC256x_Bluetopia_Stack∙Stellaris DK-LM3S9B96 SDKIntegrated BT Profiles∙Classic Bluetooth∙SPP∙A2DPFigure 9 TiWi-uB2 EM Board with Stellaris DK-LM3S9B96MSP430Bluetopia∙Bluetopia®+LE SDK∙CC256x_Bluetopia_Stack∙CC256x MSP430 Bluetopia Basic Demo APPSIntegrated BT Profiles∙Classic Bluetooth∙SPP∙Bluetooth Low Energy∙GATT∙ANP∙HRP∙HTP∙PASPThis Bluetooth software solution is licensed from Stonestreet One. The Bluetopia®+LE SDK is comprised of Single Mode and Dual Mode offering implementing the Bluetooth 4.0 specification. Bluetopia®+LE stack is built upon the solid foundation of the Bluetopia protocol stack that is currently being used in millions of consumer and industrial devices and that was first qualified in 2000 `TiWi-uB2 + MSP430 Bluetopia Basic Demo APPS allows users to evaluate TI's CC256x Bluetooth device by using the TiWi-uB2 EM board and the MSP-EXP430F5438 board. The CC256x+MSP430 Bluetooth sample applications code are provided to enable a rich out-of-box experience to the user. The application allows the user to use a console to send Bluetooth commands, setup a Bluetooth Device to accept connections, connect to a remote Bluetooth device and communicate over Bluetooth.Figure 10 TiWi-uB2 EM Board with MSP430F5438 Experimenter Board6Contacting LS ResearchHeadquarters LS Research, LLCW66 N220 Commerce CourtCedarburg, WI 53012-2636USATel: 1(262) 375-4400Fax: 1(262) 375-4248Website Wiki /products-wikiTechnical Support /products-forumSales Contact*************The information in this document is provided in connection with LS Research (hereafter referred to as “LSR”) products. No license, express or implied, by estoppel or otherwise, to any intellectual property right is granted by this document or in connection with the sale of LSR products. EXCEPT AS SET FORTH IN LSR’S TERMS AND CONDITIONS OF SALE LOCATED ON LSR’S WEB SITE, LSR ASSUMES NO LIABILITY WHATSOEVER AND DISCLAIMS ANY EXPRESS, IMPLIED OR STATUTORY WARRANTY RELATING TO ITS PRODUCTS INCLUDING, BUT NOT LIMITED TO, THE IMPLIED WARRANTY OF MERCHANTABILITY, FITNESS FOR A PARTICULAR PURPOSE, OR NON-INFRINGEMENT. IN NO EVENT SHALL LSR BE LIABLE FOR ANY DIRECT, INDIRECT, CONSEQUENTIAL, PUNITIVE, SPECIAL OR INCIDENTAL DAMAGES (INCLUDING, WITHOUT LIMITATION, DAMAGES FOR LOSS OF PROFITS, BUSINESS INTERRUPTION, OR LOSS OF INFORMATION) ARISING OUT OF THE USE OR INABILITY TO USE THIS DOCUMENT, EVEN IF LSR HAS BEEN ADVISED OF THE POSSIBILITY OF SUCH DAMAGES. LSR makes no representations or warranties with respect to the accuracy or completeness of the contents of this document and reserves the right to make changes to specifications and product descriptions at any time without notice. LSR does not make any commitment to update the information contained herein. Unless specifically provided otherwise, LSR products are not suitable for, and shall not be used in, automotive applications. LSR’s products are not intended, authorized, or warranted for use as components in applications intended to support or sustain life.Mouser ElectronicsAuthorized DistributorClick to View Pricing, Inventory, Delivery & Lifecycle Information:L S Research:450-0105。
戴尔易安信OpenManage版本端口信息指南说明书

Dell EMC OpenManage Version Port Information GuideVersion 9.1Notes, cautions, and warningsNOTE: A NOTE indicates important information that helps you make better use of your product.CAUTION: A CAUTION indicates either potential damage to hardware or loss of data and tells you how to avoid the problem.WARNING: A WARNING indicates a potential for property damage, personal injury, or death.Copyright © 2017 Dell Inc. or its subsidiaries. All rights reserved. Dell, EMC, and other trademarks are trademarks of Dell Inc. or its subsidiaries. Other trademarks may be trademarks of their respective owners.2017 - 12Rev. A001 Introduction (4)Accessing documents from the Dell EMC support site (4)Other Documents You May Need (4)Contacting Dell EMC (5)2 Ports (6)OpenManage Essentials (7)Management Stations (7)Managed Nodes (7)Dell Chassis Management Controller (8)OpenManage Integration for VMware vCenter (9)Virtual Appliance (9)Managed Nodes (10)OpenManage Server Administrator (11)OpenManage Storage Management (11)Dell Command Monitor OpenManage Client Instrumentation (12)OpenManage Baseboard Management Utility (12)Dell Management Console (13)OpenManage Power Center (15)Management Station (15)Managed Node (15)Dell Lifecycle Controller Integration for System Center Configuration Manager (16)Dell Lifecycle Controller Integration for System Center Virtualization Machine Manager (16)Dell Connections License Manager DCLM (17)Dell Management Pack for System Center Operation Manager (17)Dell Smart Plug-in SPI for HP Operations Manager for Microsoft Windows (18)OpenManage Connection for IBM Tivoli Network Manager (19)OpenManage Connection for IBM Tivoli Netcool OMNIbus (19)OpenManage Plug-in for Nagios (20)iDRAC Service Module (20)iDRAC7 and iDRAC8 (21)iDRAC6 for Rack and Tower Servers (21)iDRAC for Blade Servers (22)iDRAC6 Enterprise for Blade Servers (23)Dell Remote Access Configuration Tool DRACT (24)Digital KVM (25)DRAC 5 (25)DRAC 4 (26)Contents31Introduction The Dell EMC OpenManage Port Information document helps system administrators and technicians to identify the ports used by the Dell EMC OpenManage systems management software, standard operating system services, and other agent applications. Accessing documents from the Dell EMC support site You can access the required documents using the following links:•For Dell EMC Enterprise Systems Management documents — /SoftwareSecurityManuals•For Dell EMC OpenManage documents — /OpenManageManuals•For Dell EMC Remote Enterprise Systems Management documents — /esmmanuals•For iDRAC and Dell EMC Lifecycle Controller documents — /idracmanuals•For Dell EMC OpenManage Connections Enterprise Systems Management documents — /OMConnectionsEnterpriseSystemsManagement•For Dell EMC Serviceability T ools documents — /ServiceabilityT ools•a Go to /Support/Home.b Click Choose from all products.c From All products section, click Software & Security, and then click the required link from the following:•Enterprise Systems Management•Remote Enterprise Systems Management•Serviceability T ools•Dell Client Command Suite•Connections Client Systems Managementd To view a document, click the required product version.•Using search engines:•Type the name and version of the document in the search box.Other Documents You May NeedIn addition to this guide, you can access the following guides available at /support/home.•The Dell EMC Systems Software Support Matrix provides information about the various Dell systems, the operating systems supported by these systems, and the Dell EMC OpenManage components that can be installed on these systems.•The Dell EMC OpenManage Server Administrator Installation Guide contains instructions to help you install Dell EMC OpenManage Server Administrator.•The Dell EMC OpenManage Management Station Software Installation Guide contains instructions to help you install Dell EMC OpenManage management station software that includes Baseboard Management Utility, DRAC T ools, and Active Directory Snap-In.•The Dell EMC OpenManage Server Administrator SNMP Reference Guide documents the Simple Network Management Protocol (SNMP) management information base (MIB). The SNMP MIB defines variables that extend the standard MIB to cover the capabilities of systems management agents.•The Dell EMC OpenManage Server Administrator CIM Reference Guide documents the Common Information Model (CIM) provider, an extension of the standard management object format (MOF) file. The CIM provider MOF documents supported classes ofmanagement objects.•The Dell EMC OpenManage Server Administrator Messages Reference Guide lists the messages that are displayed in your Server Administrator home page Alert log or on your operating system’s event viewer. This guide explains the text, severity, and causes of each Instrumentation Service Alert message that Server Administrator issues.4Introduction•The Dell EMC OpenManage Server Administrator Command Line Interface User's Guide documents the complete command-line interface for Server Administrator, including an explanation of CLI commands to view system status, access logs, create reports, configure various component parameters, and set critical thresholds.•The Integrated Dell Remote Access Controller User’s Guide provides detailed information on configuring and using the iDRAC.•The Dell Chassis Management Controller User’s Guide provides detailed information on installing, configuring and using CMC.•The Dell Online Diagnostics User's Guide provides complete information on installing and using Online Diagnostics on your system.•The Dell EMC OpenManage Baseboard Management Controller Utilities User Guide provides additional information about using Server Administrator to configure and manage your system's BMC.•The Dell EMC OpenManage Server Administrator Storage Management User's Guide is a comprehensive reference guide for configuring and managing local and remote storage attached to a system.•The Dell Remote Access Controller RACADM User's Guide provides information about using the RACADM command-line utility.•The Dell Remote Access Controller 5 User’s Guide provides complete information about installing and configuring a DRAC 5 controller and using DRAC 5 to remotely access an inoperable system.•The Dell Update Packages User's Guide provides information about obtaining and using Dell Update Packages as part of your system update strategy.•The Dell EMC OpenManage Server Update Utility User's Guide provides information about obtaining and using the Server Update Utility (SUU) to update your Dell systems or to view the updates available for any systems listed in the Repository.•The Dell Management Console User’s Guide has information about installing, configuring, and using Dell Management Console. Dell Management Console is a Web-based systems management software that enables you to discover and inventory devices on your network. It also provides advanced functions, such as health and performance monitoring of networked devices and patchmanagement capabilities for Dell systems.•The Dell EMC OpenManage Essentials User’s Guide has information about installing, configuring, and using Dell EMC OpenManage Essentials. OpenManage Essentials is a hardware management application that provides a comprehensive view of Dell systems, devices, and components in the enterprise’s network.•The Dell Lifecycle Controller User Guide provides information on setting up and using the Unified Server Configurator to perform systems and storage management tasks throughout your system’s lifecycle. You can use the Unified Server Configurator to deploy an operating system, configure a Redundant Array of Independent Disks (RAID), and run diagnostics to validate the system and attached hardware. Remote Services capabilities enable automated system platform discovery by management consoles and enhance remote operating system deployment capabilities. These capabilities are exposed through the web services based hardware management interface provided by the Lifecycle Controller firmware.Contacting Dell EMCNOTE: If you do not have an active Internet connection, you can find contact information on your purchase invoice, packing slip,bill, or Dell EMC product catalog.Dell provides several online and telephone-based support and service options. Availability varies by country and product, and some services may not be available in your area. T o contact Dell EMC for sales, technical support, or customer service issues:1 Go to /support.2 Select your support category.3 Verify your country or region in the Choose a Country/Region drop-down list at the bottom of the page.4 Select the appropriate service or support link based on your need.Introduction5PortsThe following tables list the ports used by the OpenManage systems management software, standard operating system services and other agent applications.NOTE: Ports with the correct configuration are necessary to allow OpenManage systems management software to connect to a remote device throughfirewalls.NOTE: The systems management software version mentioned indicates the minimum version of the product required to use thatport.NOTE:CIM ports are dynamic. See the Microsoft knowledge base at for information on CIM port usage.NOTE: If you are using a firewall, you must open all ports listed in the following tables to ensure that OpenManage applicationsfunction correctly. Topics:•OpenManage Essentials•Dell Chassis Management Controller•OpenManage Integration for VMware vCenter •OpenManage Server Administrator •OpenManage Storage Management•Dell Command Monitor OpenManage Client Instrumentation •OpenManage Baseboard Management Utility •Dell Management Console •OpenManage Power Center•Dell Lifecycle Controller Integration for System Center Configuration Manager •Dell Lifecycle Controller Integration for System Center Virtualization Machine Manager •Dell Connections License Manager DCLM•Dell Management Pack for System Center Operation Manager•Dell Smart Plug-in SPI for HP Operations Manager for Microsoft Windows •OpenManage Connection for IBM Tivoli Network Manager •OpenManage Connection for IBM Tivoli Netcool OMNIbus •OpenManage Plug-in for Nagios •iDRAC Service Module •iDRAC7 and iDRAC8•iDRAC6 for Rack and T ower Servers •iDRAC for Blade Servers•iDRAC6 Enterprise for Blade Servers•Dell Remote Access Configuration T ool DRACT •Digital KVM •DRAC 5•DRAC 426PortsOpenManage EssentialsManagement StationsT able 1. Supported Protocols and Ports on Management StationsManaged NodesT able 2. Supported Protocols and Ports on Managed NodesPorts7* — If ports 443 and 623 are changed in iDRAC, ensure that you change these ports in the OME discovery wizard as well, so that OME can communicate with iDRAC on the new ports.Dell Chassis Management ControllerT able 3. Supported Protocols and Ports8Ports* — When a DHCP client connects to a DHCP server, the source port is 68 and the destination port is 67. When the DHCP server responds to the DHCP client, the source port is 67 and destination port is 68. The CMC acts as a DHCP client. OpenManage Integration for VMware vCenterNOTE: When deploying the Server Administrator agent using the Fix non-compliant vSphere hosts link available from the Compliance window in the Dell Management Center, the OpenManage Integration for VMware vCenter starts the http Client service and enables port 8080 on and releases after ESXi 5.0 to download OMSA VIB and install it. Once the OMSA installation is completed, the service automatically stops and the port is closed.Virtual ApplianceT able 4. Supported Protocols and Ports on Virtual AppliancePorts9Managed NodesT able 5. Supported Protocols and Ports on Managed Nodes10PortsOpenManage Server Administrator T able 6. Supported Protocols and PortsOpenManage Storage Management T able 7. Supported Protocols and PortsDell Command Monitor OpenManage Client InstrumentationT able 8. Supported Protocols and PortsOpenManage Baseboard Management UtilityT able 9. Supported Protocols and PortsDell Management Console T able 10. Supported Protocols and PortsOpenManage Power CenterManagement StationT able 11. Supported Protocols and Ports on Management StationsNOTE: The ports mentioned in the Management Station table are default ports in OpenManage Power Center. If required, you can change these default ports according to your requirements.Managed NodeT able 12. Supported Protocols and Ports on Managed NodesDell Lifecycle Controller Integration for System Center Configuration ManagerT able 13. Management StationNOTE: All other ports are as per SCCM. For more information, visit https:///en-us/library/hh427328.aspxT able 14. Managed NodeDell Lifecycle Controller Integration for System Center Virtualization Machine ManagerT able 15. Management StationT able 16. Managed NodeDell Connections License Manager DCLMT able 17. Management StationDell Management Pack for System Center Operation ManagerT able 18. Management StationNOTE: Other ports to be accessed or opened as perhttps:///en-in/library/jj656649.aspx#BKMK_FirewallT able 19. Managed NodeDell Smart Plug-in SPI for HP Operations Manager for Microsoft WindowsT able 20. Management StationT able 21. Managed NodeOpenManage Connection for IBM Tivoli Network ManagerT able 22. Management StationT able 23. Managed NodeOpenManage Connection for IBM Tivoli Netcool OMNIbusT able 24. Management StationT able 25. Managed NodeOpenManage Plug-in for Nagios T able 26. Management StationT able 27. Managed NodeiDRAC Service ModuleT able 28. Supported Protocols and PortsiDRAC7 and iDRAC8T able 29. Supported Protocols and Ports — Ports iDRAC Listens for ConnectionsT able 30. Supported Protocols and Ports — Ports iDRAC Uses as Client* — SNMP and SMTP ports can be configured, if the firmware version is 1.5x.5x or greater. iDRAC6 for Rack and Tower ServersT able 31. Supported Protocols and PortsiDRAC for Blade Servers T able 32. Supported Protocols and PortsiDRAC6 Enterprise for Blade Servers T able 33. Supported Protocols and PortsDell Remote Access Configuration T ool DRACT T able 34. Supported Protocols and PortsDigital KVMT able 35. Supported Protocols and PortsDRAC 5T able 36. Supported Protocols and PortsDRAC 4T able 37. Supported Protocols and Ports。
1794 FLEX I O 输入输出终端基单元及配件说明书

Technical Data1794 FLEX I/O Terminal Base UnitsStandard FLEX I/O Catalog Numbers 1794-TB2, 1794-TB3, 1794-TB3K, 1794-TB32, 1794-TB3G, 1794-TB3GK, 1794-TB3T, 1794-TB3TK, 1794-TB3S, 1794-TB3SK, 1794-TB32S, 1794-TB3GS, 1794-TB3GSK, 1794-TB3TS, 1794-TB3TSK, 1794-TBN, 1794-TBNF, 1794-TBNK, 1794-TBKD, 1794-TB37DS, 1794-TB62DSThe letter K in the last position of the catalog number, before the series designation, indicates a conformal coated versions of standard modules and can be used with extended temperature modules (modules ending in -XT).FLEX I/O Accessories Catalog Numbers 1794-CE1, 1794-CE3, 1794-NM1, 1794-LBL, 1794-N2, 1794-CJC2Each FLEX I/O™ module requires a terminal base unit that snaps onto the DIN rail to the right of the I/O adapter. The terminal bases provide terminal connection points for I/O wiring and plug together to form the backplane. They are available with cage, screw or spring - clamp terminations.Each FLEX I/O module has optional accessories available depending on the I/O module, field system set-up and requirements.Additional ResourcesThese documents contain additional information concerning related products from Rockwell Automation.Y ou can view or download publications at /literature/. T o order paper copies of technical documentation, contact your local Allen-Bradley® distributor or Rockwell Automation sales representative.TopicPageAdditional Resources1Available Terminal Base Units and Accessories2ResourceDescriptionIndustrial Automation Wiring and Grounding Guidelines, publication 1770-4.1Provides general guidelines for installing a Rockwell Automation industrial system.Product Certifications website, /products/certification/Provides declarations of conformity, certificates, and other certification details.1794 FLEX I/O Terminal Base UnitsAvailable Terminal Base Units and AccessoriesTypes of Terminal Base and AccessoriesType DescriptionTerminal Base Standard terminal base units which consist of different available temination types such as cage-clamp, spring-clamp and screw-clamp. D-Shell Terminal Base D-shell termination for both digital and analog modules, available with 37-pin or 62-pin.Accessories Accessories consist of panel kit, label kit, dummy filler module, cold junction compensation kit and extender cables.Catalog NumbersModule Type Catalog Numbers Page3Terminal Base Units1794-TB21794-TB31794-TB3K1794-TB321794-TB3G1794-TB3GK1794-TB3T1794-TB3TK1794-TB3S1794-TB3SK1794-TB32S1794-TB3GS1794-TB3GSK1794-TB3TS1794-TB3TSK1794-TBKD1794-TBN1794-TBNK1794-TBNF6D-Shell Terminal Base1794-TB37DS1794-TB62DS7Accessories1794-CE11794-CE31794-NM11794-LBL1794-N21794-CJC22Rockwell Automation Publication 1794-TD019A-EN-E - September 2013Rockwell Automation Publication 1794-TD019A-EN-E - September 201331794 FLEX I/O Terminal Base Units1794-TB2, 1794-TB3, 1794-TB3K, 1794-TB32, 1794-TB3G, 1794-TB3GK, 1794-TB3T, 1794-TB3TK, 1794-TB3S, 1794-TB3SK, 1794-TB32S, 1794-TB3GS, 1794-TB3GSK, 1794-TB3TS, 1794-TB3TSK, 1794-TBN, 1794-TBNF, 1794-TBNK, 1794-TBKD, 1794-TB37DS, 1794-TB62DSFLEX I/O T erminal Base UnitsTechnical SpecificationsCatalogTermination type ConnectionsUsed in applicationsCurrent capacity, max Wiring category Purpose1794-TB2Cage clamp16 I/O;18 common terminals;2 +V terminals Up to 125V AC/DC 10 A2A generic 2-wire version of the 1794-TB3.1794-TB31794-TB3K (1)(1)The letter K in the last position of the catalog number, before the series designation, indicates a conformal coated versions of standard modules and can be used with extended temperature modules(modules ending in -XT)16 I/O;18 common terminals;18 +V terminals2,3 or 4Primarily intended for use with input modules when using 3-wire input proximity switches – can also be used with output modules.1794-TB3S 1794-TB3SK Spring clamp A spring clamp version of the 1794-TB3 – provides faster, simpler wire installation.1794-TB32Cage clamp 32 I/O;8 common terminals;8 +V terminals Up to 31.2V DCA 32-point version of the 1794-TB3 to be used with 32-point digital modules and the 1794-IB16D module.1794-TB32S Spring clamp A spring clamp version of the 1794-TB32.1794-TB3G 1794-TB3GK Grounded screw clamp 36 I/O;2 common terminals;2 +V terminals;10 chassis ground terminals A screw clamp terminal base unit with individual grounding used with certain analog modules.1794-TB3GS 1794-TB3GSK Grounded spring clamp A spring clamp version of the 1794-TB3G.1794-TB3T 1794-TB3TK Cage clamp, temperature 16 I/O;10 common terminals; 4 +V terminals;8 chassis ground terminals;2 sets (6 terminals)of CJC for temperature modules Up to 125V AC/DCA cage clamp terminal base to be used with the 1794-IT8. It also provides chassis ground connections for 1794-IR8 (RTD module) and analog modules.1794-TB3TS 1794-TB3TSK Spring clamp, temperature A spring clamp version of the 1794-TB3T.1794-TBKDCage clamp, knife disconnect 16 I/O;18 common terminals;2 +V terminals Up to 132V AC A cage clamp terminal base with 16 knife disconnects.1794-TBN 1794-TBNK Screw clamp, NEMA-style 16 I/O;2 common terminals;2 +V terminals250V AC/DCA NEMA-style screw clamp terminal base for larger gauge wires with a cover for I/O wiring.1794-TBNF (2)(2)Contains eight 5 x 20 mm fuses (one for each even-numbered terminal – 0…14 on row B). Shipped with 1.6 A, 250V AC Slow Blow fuse suitable for the 1794-OA8 AC output module and 1794-OW8module with a replacement fuse. Refer to individual installation instructions for fusing recommendations for other modules.Screw clamp, fused NEMA-styleProvides eight 5 x 20 mm fused, screw terminals with a cover for I/O wiring.1794 FLEX I/O Terminal Base UnitsGeneral SpecificationsAttribute ValueTerminal screw torque1794-TB3TK, 1794-TB3G, 1794-TB3GK, 1794-TB2, 1794-TB32, 1794-TB3, 1794-TB3K, 1794-TB3T:0.56...0.79 Nm (5...7 lb-in)1794-TBKD:0.3...0.6 Nm (2.6...5.3 lb-in)1794-TBN, 1794-TBNF, 1794-TBNK:1.4 Nm (12 lb-in)Supply voltage range FLEXBUS: 5V DC, 640 mAI/O Terminals: 2 A max1794-TB3SK, 1794-TB3TK,1794-TB2, 1794-TB3, 1794-TB3K, 1794 -TB3S, 1794-TB3T, 1794-TB3TS:V/COM Terminals: 125V DC/AC, 50/60 Hz, 10 A1794-TB3GSK, 1794-TB3G, 1794-TB3GS, 1794-TB3GK, 1794-TB32, 1794-TB32S:V/COM Terminals: 31.2V DC/AC, 50/60 Hz, 10 A1794-TBN, 1794-TBNF, 1794-TBNK:V/COM Terminals: 250V DC/AC, 50/60 Hz, 10 A1794-TBKD only:Terminal Block: 120V AC, 50/60 Hz, 10 ADisconnecting Switch: 3 A, 20 mΩATTENTIONA disconnecting switch does not shut off the current. Make or break a circuit only under no-load conditions.Isolation voltage1794-TBN, 1794-TBNF, 1794-TBNK:Capable of 250V (continuous) maximum, Basic Insulation Type, Field Wiring Terminals to FLEXBUS, or the lesser of the installed module.1794-TB3SK, 1794-TB3TK, 1794-TB3T, 1794-TB3TSK, 1794-TB2, 1794-TB3, 1794-TB3K, 1794 -TB3S, 1794-TB3TS:Capable of 125V (continuous) maximum, Basic Insulation Type, Field Wiring Terminals to FLEXBUS, or the lesser of the installed module1794-TB3G, 1794-TB3GS, 1794-TB3GK, 1794-TB3GSK, 1794-TB32, 1794 -TB32S:Capable of 50V (continuous) maximum, Basic Insulation Type, Field Wiring Terminals to FLEXBUS, or the lesser of the installed module.Tested at 2121V DC/60s, Field Wiring Terminals to FLEXBUS.1794-TBKD:220V DC/s, Field Wiring Terminals to Functional Ground.Wire size1794-TB3SK, 1794-TB3GSK, 1794-TB3TSK, 1794-TB3GK, 1794-TB3GS, 1794-TB32S, 1794-TB3,1794-TB3K, 1794-TB3S, 1794-TB3TS, 1794-TBN, 1794-TBNF, 1794 -TBNK:0.34... 3.3 mm2 (22…12 AWG) solid or stranded copper wire rated at 75 °C (167 °F ) or greater, 1.2 mm (3/64 in.) insulation max. Strip Length: 5…6 mm (0.20...0.24 in.)1794-TBKD:0.34…2.1 mm2 (22...14 AWG) solid or stranded copper wire rated at 75 °C (167 °F) or greater, 1.2 mm (3/64 in.) insulation max1794-TB3TK, 1794-TB3G, 1794-TB2, 1794-TB32:0.21... 1.3 mm2 (24…16 AWG) stranded copper wire rated at 75 °C (167 °F) or greater, 1.2 mm (3/64 in.) insulation maxNorth American temp code1794-TB3G, 1794-TB3GS, 1794-TB3GSK, 1794-TB3GK, 1794-TB3, 1794-TB3K, 1794-TB3T, 1794-TB3TK, 1794-TB3S, 1794-TB3SK, 1794-TB3TS, 1794-TB3TSK, 1794-TBN, 1794-TBNK, 1794-TB32, 1794-TB32S:T4A1794-TB2:T6IEC temp code1794-TB3G, 1794-TB3GS, 1794-TB3GSK, 1794-TB3GK, 1794-TB3, 1794-TB3K, 1794-TB3T, 1794-TB3TK, 1794-TB3S, 1794-TB3SK, 1794-TB3TS, 1794-TB3TSK, 1794-TBN, 1794-TBNK:T41794-TB2:T694 x 94 x 69 mm (3.7 x 3.7 x 2.7 in.)Dimensions, HxWxD(with module installed interminal base)Publication,1794-IN092installation instructions4Rockwell Automation Publication 1794-TD019A-EN-E - September 2013Rockwell Automation Publication 1794-TD019A-EN-E - September 201351794 FLEX I/O Terminal Base UnitsEnvironmental (1)(1)EMC specifications determined by the installed modules.Attribute ValueTemperature, operating1794-TB3G, 1794-TB3GS, 1794-TB3GSK, 1794-TB3GK, 1794-TB3, 1794-TB3K, 1794-TB3T, 1794-TB3TK, 1794-TB3S, 1794-TB3SK, 1794-TB3TS, 1794-TB3TSK, 1794-TB32, 1794-TB32S, 1794-TBN, 1794-TBNK:IEC 60068-2-1 (Test Ad, Operating Cold),IEC 60068-2-2 (Test Bd, Operating Dry Heat),IEC 60068-2-14 (Test Nb, Operating Thermal Shock):-20…70 °C (-4…158 °F)1794-TBKD, 1794-TB37DS, 1794-TB62DS:0…55 °C (32…131 °F)1794-TBNF, 1794-TB2:-20…55 °C (-4…131 °F)Temperature, nonoperatingIEC 60068-2-1 (Test Ab, Unpackaged Non-operating Cold),IEC 60068-2-2 (Test Bb, Unpackaged Non-operating Dry Heat),IEC 60068-2-14 (Test Na, Unpackaged Non-operating Thermal Shock):-40…85 °C (-40…185 °F)1794-TBKD only:-20…85 °C (-4…185 °F)Relative humidity IEC 60068-2-30 (Test Db, Unpackaged Damp Heat):5…95% noncondensing Vibration IEC 60068-2-6 (Test Fc, Operating):5 g @ 10…500 HzShock, operatingAll catalogs except 1794-TBKD:IEC 60068-2-27 (Test Ea, Unpackaged Shock):30 gShock, nonoperatingAll catalogs except 1794-TBKD:IEC 60068-2-27 (Test Ea, Unpackaged Shock):50 gCertificationsCertifications (when product is marked)(1)DescriptionUL 1794-TB2:UL Listed Industrial Control Equipment. See UL File E65584.c-UL-us1794-TB3G, 1794-TB3GS, 1794-TB3GSK, 1794-TB3GK, 1794 -TB3, 1794-TB3K, 1794-TB3T, 1794-TB3TK, 1794-TB3S, 1794-TB3TS, 1794-TB3SK, 1794-TB3TSK, 1794-TBN, 1794 -TBNK, 1794-TB32, 1794-TB32S:UL Listed Industrial Control Equipment, certified for US and Canada. See UL File E65584.UL Listed for Class I, Division 2 Group A,B,C,D Hazardous Locations, certified for U.S. and Canada. See UL File E194810.1794 -TBKD, 1794-TBNF:UL Listed Industrial Control Equipment, certified for US and Canada. See UL File E65584.CSA1794-TB2, 1794-TB3, 1794-TB3K, 1794-TB3T, 1794-TB3S, 1794-TB3TS, 1794-TB3TK, 1794-TB3SK, 1794-TB3TSK, 1794-TBN, 1794-TBNK, 1794-TB3G, 1794-TB3GK, 1794-TB3GS, 1794-TB3GSK:CSA Certified Process Control Equipment. See CSA File LR54689C.CSA Certified Process Control Equipment for Class I, Division 2 Group A,B,C,D Hazardous Locations. See CSA File LR69960C.1794-TBNF:CSA Certified Process Control Equipment. See CSA File LR54689C.CEEuropean Union 2004/108/EC EMC Directive, compliant with:EN 61326-1; Meas./Control/Lab., Industrial Requirements EN 61000-6-2; Industrial Immunity EN 61000-6-4; Industrial EmissionsEN 61131-2; Programmable Controllers (Clause 8, Zone A & B)European Union 2006/95/EC LVD, compliant with:EN 61131-2; Programmable Controllers (Clause 11)C-TickAustralian Radiocommunications Act, compliant with:AS/NZS CISPR 11; Industrial Emissions6Rockwell Automation Publication 1794-TD019A-EN-E - September 20131794 FLEX I/O Terminal Base Units1794-TB37DS, 1794TB62DSFLEX I/O D-Shell T erminal Base UnitsEx1794-TB3G, 1794-TB3GS, 1794-TB3GSK, 1794-TB3GK, 1794-TB3, 1794-TB3K, 1794-TB3T, 1794-TB3S, 1794-TB3TS, 1794-TB3TK, 1794-TB3SK, 1794-TB3TSK, 1794-TBN, 1794-TBNK:European Union 94/9/EC ATEX Directive, compliant with:EN 60079-15; Potentially Explosive Atmospheres, Protection "n" EN 60079-0; General Requirements (Zone 2)II 3 G Ex nA IIC T4 Gc 1794-TB2:European Union 94/9/EC ATEX Directive, compliant with:EN 60079-15; Potentially Explosive Atmospheres, Protection "n"EN 60079-0; General Requirements (Zone 2)II 3 G Ex nA IIC T6 GcTÜV1794-TB3G, 1794-TB3GS, 1794-TB3GSK, 1794-TB3GK, 1794-TB3, 1794-TB3K, 1794-TB3T, 1794-TB3S, 1794 -TB3TS, 1794-TB3TK, 1794-TB3SK, 1794-TB3TSK, 1794-TBNF:TÜV Certified for Functional Safety:Capable of SIL 2KCKorean Registration of Broadcasting and Communications Equipment, compliant with:Article 58-2 of Radio Waves Act, Clause 3(1)See the Product Certification link at /products/certification/ for Declaration of Conformity, Certificates, and other certification details.Technical SpecificationsCatalogTermination type ConnectionsUsed in applicationsCurrent capacity, max Wiring category Purpose1794-TB37DS D-shell37 pin; digital and analog Up to 31.2 V DC10 AModule dependentA 37-pin D-shell termination for both digital and analog modules.1794-TB62DS62 pin; digitalA 62-pin D-shell termination for both digital and analog modules.General SpecificationsAttribute Value Terminal Screw Torque 0.6 Nm (5 lb-in.) Dimensions, HxWxD(with expansion module installed)127.0 x 94 x 69 mm (5.0 x 3.7 x 2.7 in.)Current Capacity1794-TB62DS:V1 - 8 A max V2 - 6 A max10 A max per module 5 A per pin 1794-TB37DS:10 A max per module 5 A per pinEnclosure type rating None (open style)Conductors wire size Category (1)(1)You use this category information for planning conductor routing as described in Allen-Bradley publication 1770-4.1, Industrial Automation Wiring and Grounding Guidelines12AWG (4 mm 2) stranded copper wire rated at 75 °C or higher 3/64 in.(1.2 mm) insulation maximum Established by installed module Isolation voltageEstablished by installed module Publication, installation instructions1794-IN107CertificationsCertifications (when product is marked)(1)DescriptionRockwell Automation Publication 1794-TD019A-EN-E - September 201371794 FLEX I/O Terminal Base Units1794-NM1, 1794-LBL, 1794-N2, 1794-CJC2, 1794-CE1, 1794-CE3FLEX I/O Accessory ProductsEnvironmental (1)AttributeValueTemperature, operatingIEC 60068-2-1 (Test Ad, Operating Cold),IEC 60068-2-2 (Test Bd, Operating Dry Heat),IEC 60068-2-14 (Test Nb, Operating Thermal Shock):0…55 °C (32…131 °F)Temperature, nonoperatingIEC 60068-2-1 (Test Ab, Unpackaged Nonoperating Cold),IEC 60068-2-2 (Test Bb, Unpackaged Nonoperating Dry Heat),IEC 60068-2-14 (Test Na, Unpackaged Nonoperating Thermal Shock):–40…85 °C (–40…185 °F)Relative humidity IEC 60068-2-30 (Test Db, Unpackaged Nonoperating Damp Heat):5…95% noncondensing Vibration IEC60068-2-6 (Test Fc, Operating):5 g @ 10…500 HzShock, operating IEC60068-2-27 (Test Ea, Unpackaged shock):30 gShock, nonoperatingIEC 60068-2-27 (Test Ea, Unpackaged Shock):50 g(1)EMC specifications determined by the installed modules.CertificationsCertifications (when product is marked)(1)DescriptionUL UL Recognized Component Industrial Control Equipment, certified for US and Canada. See UL File E65584CEEuropean Union 2004/108/EC EMC Directive, compliant with:EN 61326-1; Meas./Control/Lab., Industrial Requirements EN 61000-6-2; Industrial Immunity EN 61000-6-4; Industrial EmissionsEN 61131-2; Programmable Controllers (Clause 8, Zone A & B)C-Tick Australian Radiocommunications Act compliant with AS/NZS CISPR 11, Industrial Emissions KCKorean Registration of Broadcasting and Communications Equipment, compliant with:Article 58-2 of Radio Waves Act, Clause 3(1)See the Product Certification link at /products/certification/ for Declaration of Conformity, Certificates, and other certification details.ItemDescriptionPublication1794-CE1FLEX I/O 1 ft Extender Cable (0.3 m)to arrange your system in two rows or split your system into horizontal and vertical orientation 1794-IN0121794-CE3FLEX I/O 3 ft Extender Cable (0.9 m)to arrange your system in two rows or split your system into horizontal and vertical orientation 1794-IN0121794-NM1FLEX I/O Panel Mounting Kit to mount your FLEX I/O system on a panel without a DIN rail.1794-IN1351794-LBL FLEX I/O Label Kit to tailor the label on your FLEX I/O terminal base unit. Kit includes a diecut drawing and label sheet with five labels -1794-N2FLEX Dummy Filler Module - Slot Cover to fill a vacant slot, if desired-1794-CJC2Cold Junction Compensation Kit used as replacements for CJCs supplied with 1794-IT8 and 1794-IRT8-Allen-Bradley, FLEX I/O, RSLogix 5000, Rockwell Software, Rockwell Automation, and LISTEN. THINK. SOLVE are trademarks of Rockwell Automation, Inc.T rademarks not belonging to Rockwell Automation are property of their respective companies.Publication 1794-TD019A-EN-E - September 2013Copyright © 2013 Rockwell Automation, Inc. All rights reserved.Important User InformationSolid-state equipment has operational characteristics differing from those of electromechanical equipment. SafetyGuidelines for the Application, Installation and Maintenance of Solid State Controls (publication SGI-1.1 available from your local Rockwell Automation sales office or online at /literature/) describes some important differences between solid-state equipment and hard-wired electromechanical devices. Because of this difference, and also because of the wide variety of uses for solid-state equipment, all persons responsible for applying this equipment must satisfy themselves that each intended application of this equipment is acceptable.In no event will Rockwell Automation, Inc. be responsible or liable for indirect or consequential damages resulting from the use or application of this equipment.The examples and diagrams in this publication are included solely for illustrative purposes. Because of the many variables and requirements associated with any particular installation, Rockwell Automation, Inc. cannot assume responsibility or liability for actual use based on the examples and diagrams.No patent liability is assumed by Rockwell Automation, Inc. with respect to use of information, circuits, equipment, or software described in this manual.Reproduction of the contents of this manual, in whole or in part, without written permission of Rockwell Automation, Inc., is prohibited.Documentation FeedbackY our comments will help us serve your documentation needs better. If you have any suggestions on how to improve this document, complete this form, publication RA-DU002, available at /literature/.Rockwell Otomasyon Ticaret A.Ş., Kar Plaza İş Merkezi E Blok Kat:6 34752 İçerenköy, İstanbul, T el: +90 (216) 5698400。
Intel 8086 88 微处理器系统 SYSC3601 教学笔记说明书

8086/8088 Pin assignments & functions
• Pins to be discussed later:
– READY: Used to insert wait states (controlled by memory and IO for reads/writes) into the microprocessor.
entire 8086/8088 must be buffered.
SYSC3601
6
Microprocessor Systems
8086/8088 Pin assignments & functions
8086/8088 DIP pin assignments (max mode in brackets)
SYSC3601
4
Microprocessor Systems
8086/88 Hardware and Bus Structure
• General Characteristics
– Power:
• 8086 +5V ± 10%, 360mA (80C86 10mA) • 8088 +5V ± 10%, 340mA (80C86 10mA)
– lines carry status bits S6 - S3 whenever ALE is logic 0.
SYSC3601
9
Microprocessor Systems
8086/8088 Pin assignments & functions
• S6 always logic zero (not used). • S5 matches state of I flag bit (interrupt) • S4&S3 reports segment being accessed during
Bosch ESI[tronic] 2.0 Online Downloads FAQ’s说明书
![Bosch ESI[tronic] 2.0 Online Downloads FAQ’s说明书](https://img.taocdn.com/s3/m/69bf795d0812a21614791711cc7931b764ce7b6f.png)
1. How would one go about downloading intermediate update via online downloads?Answer: The Diagnostics Downloads Manager (DMM) that permits online updates will be installed while upgrading to ESI 2.0 2012/4. Once the customer logs-in to this application he will be enabled to access intermediate software updates online.The Process remains similar to the ESI [tronic] Classic online update process. Further information concerning the installation and login process can be found through the following support instructions:/update/ddm/en/manual.html2. How often would intermediate SD updates be available for online downloads?Answer: Online intermediate SD updates will be released every 2 weeks on average starting from 2012/4 ESI 2.0 releases and will be available on the DDM.3. Will the online updates be sequential (meaning all previous versions need to be downloaded in addition to the current one) or will each release include the previous updates?Answer: The updates are sequential. When downloading a particular version of the update, all previous versions need be downloaded prior to downloading the active version.Example: Joe has 2014/1.000 installed. Bosch releases Incremental updates 2014/1.001, 2014/1.002, and 2014/1.003, but Joe has not decided to allow his PC to be updated by the DDM function, or Joe’s PC has not been connected to the Internet for DDM to check for updates and notify Joe/update Joe’s PC. Now Joe decides to perform incremental updates and thinks he can go directly to downloading incremental update 2014/1.003 to get all the updates in one download.When he goes to the DDM, it will say that three ESI 2.0 updates are available. Once he clicks on it to start downloading, all three available updates will be downloaded automatically as long as he accepts. Joe will only be asked when setup of each updates starts whether he wants to install or not. If he says yes, download will proceed. At the end, Joe will be up to date with all of the three updates that is available to him.4. If enabled, does the DDM automatically check for and download updates? Can the user manually trigger/search for updates or must the DDM initiate contact with the update server automatically?Answer: By default, the DDM is configured to look for updates automatically. It can be changed to have the user check for updates manually.5. Where is the ESI[tronic] 2.0 SD intermediate content download server physically located?Answer: Intermedia Solutions which operates the server for the ESI 2.0 online downloads operates servers on a worldwide basis:Europe: Frankfurt, Munich, Karlsruhe, Cologne.USA: Washington D.C., Jacksonville.Asia: Singapore, Shanghai.6. What is the round trip (RT) time from a server to a client?Answer: <35ms7. From which server to which client does this RT time represent?Answer: This RT time represents a typical RT from an Intermedia Solutions server in “Frankfurt/Munich/Karlsruhe/ Cologne” to a client location in the country of GermanySimilarly, this RT time represents a typical RT from an Intermedia Solutions server in “Washington D.C./Jacksonville”to a client location in the country of USA.8. Has Bosch set up a server solution whereby the Bosch ESI[tronic] 2.0 package download is stored on anIntermedia Solutions server in Germany (Frankfurt/Munich/Karlsruhe/Cologne), or is the data mirrored/copied/or?to an Intermedia Solutions server in USA (Washington D.C./Jacksonville)?Answer: All ESI[tronic] 2.0 intermediate SD content will be copied to all available data centers worldwide. This means that US customers will download the ESI 2.0 intermediate downloads directly from US data centers.9. Are the downloads “resumable”? If a connection is broken, can the download be resumed or must it start againfrom the beginning?Answer: Yes10. Are the final downloads checked against an MD5 hash file for integrity?Answer: Yes11. Are the downloads “throttled” to prevent the DDM from saturating a users internet connection?Answer: The transfer will be managed by BITS (Background Intelligent Transfer Service). It uses only the freebandwidth.12. Can the update files be copied to a USB stick for transfer to another computer that is not connected to theinternet?Answer: Theoretically yes, but Bosch does not recommend it at this time.13. When an update is available – is it pushed to all users at once? (Potentially bringing the server to its knees, or arethey staggered by user ID / geographic area, etc.)Answer: When a update is available, it is pushed to all users at the same time and it can be downloaded by each customer immediately. There are no staggering issues. The server is able to handle this.14. Are updates pushed to ALL users of ESI 2.0, or only those with valid licenses?Answer: ESI 2.0 license is not checked for the download to be pushed. The only things that are needed are that the user should be logged into DDM with a valid ESI[tronic] customer no. and password and that the PC with the ESI 2.0 is connected to the internet.15. How big is the ESI2 download packages estimated to be ? Would this size stay constant or is it expected toincrease over time?Answer: Approximately 300 MB size. It’s expected to stay constant.16. How long would an ESI2 intermediate SD updates package of 300 MB take to download?Answer: Each intermediate update should take no more than 10 minutes to install.。
vivado中language templates的使用方法

vivado中language templates的使用方法
在Vivado软件中,Language Templates的使用方法如下:
1. 打开Vivado软件,并打开您的项目。
2. 在主界面上,点击“Tools”菜单。
3. 在下拉菜单中,选择“Language Templates”。
4. 此时将打开Language Templates界面。
您可以在此界面上查看可用的语言模板,并选择适合您项目的模板。
5. 选择模板后,您可以根据需要修改模板内容。
您可以使用Vivado提供的编辑器来编辑模板,或者手动添加代码。
6. 完成编辑后,您可以保存模板并在您的项目中重复使用。
需要注意的是,Vivado软件中的Language Templates主要用于帮助用户快速创建代码,而不是用于运行或仿真。
因此,在使用Language Templates时,您需要确保它们符合您的设计需求和目标。
- 1、下载文档前请自行甄别文档内容的完整性,平台不提供额外的编辑、内容补充、找答案等附加服务。
- 2、"仅部分预览"的文档,不可在线预览部分如存在完整性等问题,可反馈申请退款(可完整预览的文档不适用该条件!)。
- 3、如文档侵犯您的权益,请联系客服反馈,我们会尽快为您处理(人工客服工作时间:9:00-18:30)。
Assembly Language GuideAssembly Language GuideV1.1Date: 2014/07/19This document contains information on a new product. Specifications and information herein are subject to change without notice. WINBOY(HK) BC6818BC6818WINBOY(HK)TECHNOLOGY CO LTDWINBOY(HK) Assembly Language Guide Revision HistoryRev. Date Author DescriptionV10 2013/01/10 1. Initial Version.V11 2014/07/19 1. Modify P.5 red wordsContents IndexA. Introduction .…………………..………………………………..Page. 03B. General Information …………………………………………..Page. 03C. Address Format ………………………………..……………...Page. 03D. Coefficient Format …………………………………………….Page. 04E. LFO Setup Instruction Format ……………………………..Page. 05F. Chorus Instruction Format …………………………………Page. 06G. MEM Statement ……………………………………………….Page. 06H. ABS Statement ………………………………………………..Page. 08I. EQU Statement ………………………………………………..Page. 08 J. Read Instructions ……………………………………………..Page. 09 K. Write Instructions ……………………………………………..Page. 10 L. Chorus Controls ………………………………………………Page. 11PK ………………………………………………………………Page. 11PA ………………………………………………………………Page. 113.MASKA ………………………………………………………………Page. 12TCH ………………………………………………………………Page. 12PS ………………………………………………………………Page. 12M. Reserved Memory Labels ……………………………………Page. 13 N. Comments ………………………………………………………Page. 13Assembly Language GuideA. Introduction:Programs for the BC6818EM be written in machine code, as described in the BC6818EM data sheet, or written using the assembly language as described below.B. General Information:The assembler is not case-sensitive, ignores blank lines, does not differentiate between upper and lower case, and treats multiple tabs or spaces as a single space. Each instruction takes up one line.C. Address Format:Addresses may be entered in hexadecimal or decimal format. To specify a hexadecimal Address, prefix the number with a dollar sign ($) or “0x” or suffix it with an “H”. For example, the following instructions all specify the same Address:RZP $4 K=0.5 ; R ead A ddress 4 t imes 0.5RZP 004H K=0.5 ; R ead A ddress 4 t imes 0.5RZP 4 K=0.5 ; R ead A ddress 4 t imes 0.5RZP 0x04 K=0.5 ; R ead A ddress 4 t imes 0.5WINBOY(HK) BC6818Assembly Language GuideD. Coefficient Format:Coefficients may be entered in a variety of numerical formats, including binary, octal, hexadecimal, and real decimal. To specify a binary number, either use the percentage symbol prefix (%) or a “B” suffix. To specify an octal number, suffix the value with a “Q”. To specify a hexadecimal number, either prefix the number with a dollar sign ($), prefix it with a “0x”, or suffix it with an “H”. To specify a real decimal number, just enter the number. A real decimal number can have a decimal point, and it can be prefixed with a plus (+) or minus (-) sign.All MAC Instruction coefficients in the BC6818EM are stored as fixed-point,sign-magnitude values in the format S.7. The S signifies the sign bit, the period signifies the binary point, and the 7 signifies the number of fractional bits. When a number is written as binary, octal, or hexadecimal, it is written as a right-justified number with no separation between the integer and fractional bits, and unspecified leading bits are assumed to be zero. When a number is written as a decimal value, however, it can be written the same way as the other radices, or with the decimal point corresponding to the binary point of the S.7 value.For example, all of the following are ways of representing the number -0.34375 in S.7 format:Binary: %10101100 Hexadecimal: $AC10101100B 0xAC ACHOctal: 254Q Decimal: -0.34375-44172A simple way to convert a decimal into a hex, octal, or binary coefficient suitable for the compiler is to shift the binary point to the rightmost position for the calculation in order to make it an integer. For example, to see what the decimal value 0.1796875 looks like in the S.7 hex, octal, or binary value for the compiler:Multiply it by 27 (thus making the S.7 into S7):0.1796875 x 27 = 0.1796875 x 128 = 23 = 17H = 27Q = 10111BFor the value -0.1796875:-0.1796875 x 27 = -0.1796875 x 128 = -23 = 97H = 227Q = 10010111B*Note that the value is trimmed to be 8 bits.WINBOY(HK) BC6818E. LFO Setup Instruction Format:TheB C 6818 EM has four low frequency oscillators (LFOs) which must be set up before use. These instructions may occur anywhere in the assembly file. To set the parameters (amplitude, frequency, and waveshape), use the LFO Setup Instruction, formatted as follows:LFOn WAVESHAPE AMP=a FREQ=f [XFAD=x] [; COMMENTS]Note: Square brackets “[“ and “]” denote optional fields.Select LFOs 0-3 by setting n. WAVESHAPE can be either "SIN" for sinusoid, "TRI" for triangle wave, or "SAW" for sawtooth. The AMPlitude coefficient is a 15-bit unsigned number (a range of 0-32767 or $0-$7FFF), and gives a waveform amplitude of ±AMP/8 samples. The FREQuency coefficient is a 13-bit unsigned number (a range of 0-8191 or $0-$1FFF). XFAD selects the crossfade shape to use for pitch transposition algorithms. This setting is only valid when the waveshape is set to SAW. Valid crossfade settings are: 1, 1/2, 1/8, 1/16.To calculate the frequency produced by the oscillators, use the following formulae.f(Sinusoids) = (F/M) Fs/( 2)whereF = 13-bit frequency coefficient FREQ,Fs = Sample rate,M = 262143 (0x3FFFF, internal maximum 18 bit value).For a sample rate of 48kHz, f(Sinusoids) = 0.029142 Ff(Triangles) = (F*Fs*C)/(4*M*SIN)whereF = 13-bit frequency coefficient FREQ,Fs = Sample rate,C = 4194304 (0x400000, a constant used internally in the LFO),M = 262143 (0x3FFFF, internal maximum 18-bit value),SIN = 8388607 (0x7FFFFF, maximum positive 24-bit value).For a sample rate of 48kHz, f(Triangles) = 0.022888 FF(Sawtooths) = 2 F(Triangles)For a sample rate of 48kHz, f(Sawtooths) = 0. 045777 FFor example:LFO0 SIN AMP=0x3FFF FREQ=0x200 ; 14.9Hz, 1/2 amplitude sineF. Chorus Instruction Format:The Chorus Instruction format is generally as follows:[CHRn]OPCODE ADDRESS[CHORUS CONTROLS][; COMMENTS]Note: Square brackets “[“ and “]” denote optional fields.CHRn selects a chorus instruction, and the n selects the associated LFO to drive the instruction.The ADDRESS specifies an I/O (Address 0 is the left channel, Address 1 is the right), a relative Data RAM Address, or a memory label. CHORUS CONTROLS are an unordered list of parameters which activate certain functions for a chorus instruction.The following opcode mnemonics control the basic functions of the MAC. It defines a read or write operation, and selects which register (none, Acc, B, or C) is added to the multiplier output. Register B can store the current instruction’s multiplicand, and register C can store the same value as Acc.G. MEM Statement:The assembler provides the MEM statement as a means of declaring Address labels and allocating Data RAM usage. Address labels may be placed anywhere in the assembly file, as long as they are declared before their usage. The MEM statement format is as follows:MEM NAME SIZE [; COMMENTS]where NAME may be any unique alphanumeric string. The first character of a name must be a letter, and spaces are not permitted. SIZE is the size of the memory block, and is specified as the number of samples in decimal or hexadecimal. To specify a hexadecimal block size, prefix the number with a “0x” or suffix it with an “H”. Size may also be specified in milliseconds (assuming a 44.1kHz sample frequency) by suffixing the number with “ms”.For example:MEM L PF1;S pecifies a u nit d elay1s ample l ongMEM d elay100;S pecifies a d elay l ine100s amples l ongMEM F IR0x20;S pecifies a d elay l ine32s amples l ongMEM predelay 50.0ms ; Specifies a delay line 50.0ms longThe assembler will allocate the Data RAM beginning at Address 0 and work up to the higher Addresses.Note that since this declaration takes the memory offset counter into account, the actual number of memory locations allocated is 1 larger than specified. Also note that since the memory offset counter is a down-counter, writes should be done to lower Addresses and reads of delayed data done from higher Addresses.For example:WZP 0H K=0.5 ; Write data to be delayedRZP 4H K=0.5 ; Read 4-sample-delayed dataOnce you have defined your memory elements, you may access them in a number of ways.Simply using the name refers to the front of the delay line. Suffixing the name with an apostrophe (') refers to the back of the delay line. Suffixing the name with a quote (") refers to the middle of the delay line.For example, here is the code for a 100-sample delay:MEM delay100;S pecifies a d elay l ine100s amples l ongRZP INL127;G et L eft I nput i nto t he a ccumulatorWAP delay0;W rite a ccumulator t o f ront o f d elay l ineRZP delay’127;R ead f rom t he b ack o f t he d elay l ineWAP OUTL0;W rite t he a ccumulator t o L eft O utputYou can offset into a delay line by using the + or - modifiers.For example, to access the 512th tap of a long FIR filter:MEM FIR1023;U se1023l ocations o f D ata R AMRZP INR127;G et R ight I nput i nto t he a ccumulatorWAP FIR0;W rite a ccumulator t o t he f ront o f d elay l ineRZP FIR+512127;R ead t he512th t ap o f t he F IRWAP OUTR0;W rite t he a ccumulator t o R ight O utput The suffixes and offsets may be mixed in an instruction.Assembly Language GuideH. ABS Statement:The assembler provides the ABS statement as a means of declaring absolute Address labels. The ABS statement format is as follows:ABS LABEL [ADDRESS] [; COMMENTS]where LABEL can be any unique alpha-numeric string. The first character of a label must be a letter, and spaces are not permitted. ADDRESS is the absolute Address. TheAddress may be specified as a decimal or hexadecimal integer. To specify hexadecimal, prefix the number with a “0x” or suffix it with an “H”.For example:ABS param 0x0081 ; Use direct Address memory as a parameterMemory Address offsets and Addresses above 129 do not work with the ABS statement. Be sure that the code only accesses the exact Address below 130 specified by ABS.For example:ABS hparams 0x0082 ; This will give an errorABS params 0x0081 ; This will workRZP params +3 0.5 ; This will give an errorRZP p arams 0.5 ; T his w ill w orkI. EQU Statement:The assembler provides the EQU statement as a means of defining constants for coefficients. The EQU statement format is as follows:NAME EQU VALUE [; COMMENTS]where NAME can be any unique alpha-numeric string. The first character of a name must be a letter, and spaces are not permitted. VALUE is the numerical value for NAME, and must be a valid coefficient format.For example:gain EQU 0.5 ; Specifies a gain coefficient of -6dBRZP INL gain ; Get Left Input, gained down, in accumulatorWAP OUTL 0.0 ; Write the accumulator to Left OutputNote that EQU statements are not recursive. You may not equate a name to a value, and WINBOY(HK) BC6818J. Read Instructions:For read operations, Product = K*[ADDRESS], so register B stores either the Left Input, Right Input, or the Data RAM value specified by the Address or label.RZP Read, Acc = Zero + ProductRAP Read, Acc = Acc + ProductRBP Read, Acc = B Register + ProductRCP Read, Acc = C Register + ProductRZPB Read, Acc = Zero + Product, Load B registerRAPB Read, Acc = Acc + Product, Load B registerRBPB Read, Acc = B Register + Product, Load B registerRCPB Read, Acc = C Register + Product, Load B registerRZPC Read, Acc = Zero + Product, Load C registerRAPC Read, Acc = Acc + Product, Load C registerRBPC Read, Acc = B Register + Product, Load C registerRCPC Read, Acc = C Register + Product, Load C registerRZPBC Read, Acc = Zero + Product, Load B and C registersRAPBC Read, Acc = Acc + Product, Load B and C registersRBPBC Read, Acc = B Register + Product, Load B and C registersRCPBC Read, Acc = C Register + Product, Load B and C registersK. Write Instructions:For write operations, Product = k*Acc, so register B stores the Acc value from the last tick. Writes to memory stores the result of the previous instruction, while writes to outputs transfers the result of the current instruction.WZP Write, Acc = Zero + ProductWAP Write, Acc = Acc + ProductWBP Write, Acc = B Register + ProductWCP Write, Acc = C Register + ProductWZPB Write, Acc = Zero + Product, Load B registerWAPB Write, Acc = Acc + Product, Load B registerWBPB Write, Acc = B Register + Product, Load B registerWCPB Write, Acc = C Register + Product, Load B registerWZPC Write, Acc = Zero + Product, Load C registerWAPC Write, Acc = Acc + Product, Load C registerWBPC Write, Acc = B Register + Product, Load C registerWCPC Write, Acc = C Register + Product, Load C registerWZPBC Write, Acc = Zero + Product, Load B and C registersWAPBC Write, Acc = Acc + Product, Load B and C registersWBPBC Write, Acc = B Register + Product, Load B and C registersWCPBC Write, Acc = C Register + Product, Load B and C registersFor example:RZP delay” K=.500 ; Read (middle of delay)/2 into AccWAP delay+125 192 ; Write to 125th delay tap, Acc = -0.5*AccRAPB delay' K=128 ; Acc = -1*(end of delay)+Acc, B = end of delayWBPC delay’-1 ; Write to next-to-last delay tap, Acc & C = B + 0*AccRCP ADCL K=0x7F ; Read ~1*(Left Input) into Acc and CWCPB OUTR K=-0x40 ; B=Acc, write C-0.5*Acc into Right Output and AccAssembly Language Guide L. Chorus Controls:These statements define instructions as chorus commands. They redefine the coefficient bits to alternate meanings, and thus the lack of coefficients in chorusinstructions. Two adjacent commands are used to create chorusing, in order to interpolate to the exact fraction of a sample between two (integer) samples.The Chorus Controls consist of the following parameters:[+SIN|-SIN|+COS|-COS] [COMPK] [COMPA] [MASKA] [LATCH] [COMPS]+SIN Use +sine output of selected LFO.-SIN Use -sine output of selected LFO.+COS Use +cosine output of selected LFO.-COS Use -cosine output of selected LFO.The LFOs each have four taps: a ±sine output and a ±cosine output. The parameters described above indicate which tap to use. If this parameter is omitted, the default value used is +SIN. The sign is mandatory, "SIN" will be flagged as an error and prevent assembly.PK: One's complement the chorus interpolation coefficient.The LFO output is split into two parts: an offset Address and an interpolation coefficient.The offset Address is sent to the Address generator for the Data RAM, and is not accessible to the user. The interpolation coefficient should be applied to the value at the specified Address, the 1's complement of the coefficient then applied to the value at Address+1. The COMPK parameter will perform a one's complement on the coefficient.PA: One's complement the chorus interpolation Address.This parameter will perform a one's complement on the chorus interpolation Address, effectively shifting the phase of the chorus waveform by 180°. Specifying COMPA with +SIN is equal to specifying -SIN. In fact -SIN or -COS sets the same bit as COMPA. This statement is implemented for use in pitch transposition for increasing source code clarity. Proper use of the LFO output statements will make this command superfluous.WINBOY(HK) BC6818Assembly Language Guide3.MASKA: Mask chorus generator offset Address, select the crossfade coefficient. When the two interpolations required by pitch transposition are complete, they must be read back from memory and summed using the crossfade coefficient. In a chorus command, the Address generator will want to add the chorus offset Address when generating the absolute Address. This can be overridden with the MASKA parameter so that the offset is masked off, and the Address read from is as specified in the instruction. This parameter also indicates that the crossfade coefficients selected by the LFO Setup Instruction be used.TCH: Latch the data from selected LFO.When pairs of chorus commands are implemented, the LFO data must be latched; otherwise, the LFO could change during the execution of the commands, andunpredictable results could occur. This is required on the first chorus command, but must be omitted from the second.PS: One's complement the sign bit of the chorus offset Address.This parameter will perform a one's complement of the sign bit of the chorus offset Address. This is a leftover from a previous ASIC revision and is included here for informational purposes.For example:CHR0 RZP mem -COS COMPK LATCH ; Read fractional -COS chorus of mem CHR0 R AP m em+1 –COS ; S um w ith f ractional o f 2nd A ddress CHR1 RZP stor1 COMPK MASKA LATCH ; Read fractional crossfade of stor1 CHR1 R AP s tor2 M ASKA ; S um w ith f ractional c rossfade o f s tor2WINBOY(HK) BC6818WINBOY(HK) BC6818Assembly Language GuideM. Reserved Memory Labels:For your convenience, a number of memory labels have been pre-defined by the assembler. They may be accessed them just as any other memory element. They are: INL --------------------- Left Input (read only)ADCL ------------------ Left Input (read only)INR --------------------- Right Input (read only)ADCR ------------------ Right Input (read only)OUTL ------------------ Left Output (write only)OUTR ------------------ Right Output (write only)For example:RZP INL0.5;R ead L eft I nputRZP ADCL0.5;R ead L eft I nputRZP00.5;R ead L eft I nputN. Comments:Comments are delimited by the semicolon (;) character. The assembler ignores everything from the semicolon to the end of the line.For example:; ::::::::This is a valid comment::::::::RZP mem $5 ;This is also a valid comment; all text here is ignored.。