氧化锌烟尘中氟氯脱除方法的研究进展
锌氧化物杂料中氯的脱除工艺研究

等, 这些物料成分复杂, 杂质含量高 , 尤其是含氯较 高对 后续 锌 回收工 艺 选 择 的影 响 较 大 , 研究 其 脱 除
氯 的技术 对再 生锌 回收 至关重 要 。
2 水洗除氯工艺 的深入探索
2 1 实验 室试 验 .
2 1 1 试 验 目的 ..
1 国内脱氯工艺技术现状
试验原 料 为阴极 锌 铸 型 渣 , 4 目筛 网筛 分 , 用 0 筛下 部分 留做实 验 , 分情况 如表 1 筛 所示 , 筛下 部 分 铸 型渣 的化学成 分如 表 2所 示 。
表 1 阴极 锌 铸 型 渣 粒 度 分 布 表
洗涤 使氯 离子进 入溶 液通 过过 滤与不 溶 的氧化锌 分
碱洗 法 : 洗是 基 于 原料 中的氯 化 锌 和其 它氯 碱
化物, 与碱 或弱 碱性 碳 酸 盐反 应 生 成难 溶 的氢 氧化 锌 或碱式 碳酸锌 , 氯 化 物溶 入 溶 液 中通 过 过 滤 实 而 现 氯 的脱 除 。碱 洗 除 氯 , 受设 备 防腐 限制 建 设 投 资 高 于 水 洗 法 , 试 剂 消 耗 高 致 使 成 本 高 , 氯 率 且 脱
离 。水洗 除氯 , 能耗 较低 , 建设 投资 少 , 作简单 , 操 但
文献 … 报 道 , 氯率 不理 想 , 脱 只有 8 % ~ 5 。 0 8%
表 2 阴极 锌 铸 型 渣 化 学 成 分 表
2 13 试验及 结 果分析 ..
中 、 三档 四个实 验 因子安排 正交 实验 , 高 正交 实验结
关键词 : 铸型渣 ; 熔铸 电炉烟尘 ; 焦结烟尘 ; 多膛炉除氯烟尘 ; 水洗除氯
中图 分 类 号 : 7 1 1 X8. 文献 标 识 码 : A
氧化锌烟尘脱氯技术研究进展
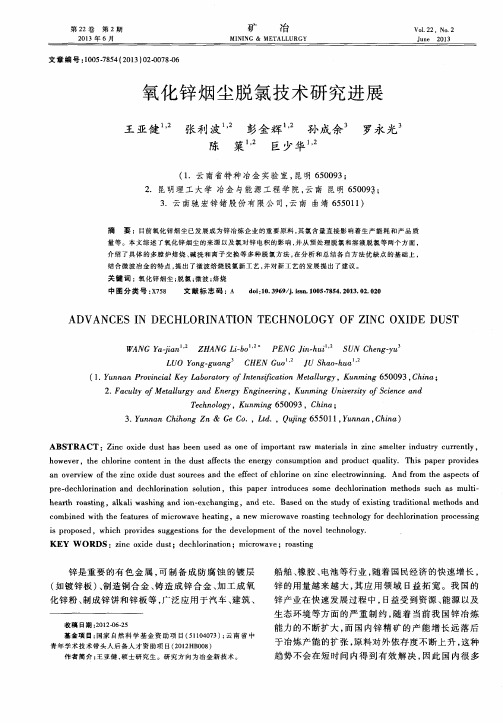
2 . F a c u l t y f o Me t a l l u r g y a n d E n e r g y E n g i n e e r i n g , K u n m i n g U n i v e r s i t y f o S c i e n c e a n d
WA NG Y a - j i a n , ZH A NG L i . b o ’
L U O Y o n g - g u a n g
P E NG in f . h u i 。 ’ S U N C h e n g . y u
. , U S h a o - h u a
ABSTRAC T :Zi n c o x i de d u s t h a s b e e n u s e d a s o n e o f i mp o r t a n t r a w ma t e r i a l s i n z i n c s me l t e r i nd u s t r y c u r r e n t l y, h o we v e r,t h e c h l o r i n e c o n t e n t i n t h e d u s t a f f e c t s t h e e n e r g y c o n s ump t i o n a n d p r o d uc t q u a l i t y .T hi s p a p e r p r o v i d e s a n o v e r v i e w o f t h e z i n c o x i d e d u s t s o u r c e s a n d t h e e f f e c t o f c h l o r i n e o n z i n c e l e c t r o wi n ni n g . An d f r o m t h e a s p e c t s o f p r e — d e c h l o r i n a t i o n a n d d e c h l o r i n a t i o n s o l u t i o n, t h i s p a p e r i n t r o d u c e s s o me d e c h l o r i na t i o n me t h o ds s u c h a s mu l t i — h e a r t h r o a s t i n g,a l ka l i wa s h i n g a nd i o n— e x c h a n g i ng,a n d e r e . Ba s e d o n t h e s t ud y o f e x i s t i n g t r a d i t i o n a l me t h o d s a n d c o mbi n e d wi t h t he f e a t u r e s o f mi c r o wa v e he a t i n g,a ne w mi c r o wa v e r o a s t i n g t e c h n o l o g y f o r d e c h l o r i n a t i o n p r o c e s s i n g i s pr o po s e d,whi c h p r o v i de s s u g g e s t i o n s or f t h e de v e l o p me n t o f t he n o v e l t e c hn o l o g y . K EY W OR DS :z i n c o x i d e d u s t ;d e c h l o r i n a t i o n; mi c r o wa v e; r o a s t i n g
湿法炼锌体系除氟技术研究

湿法炼锌体系除氟技术研究摘要:随着我国二次锌资源的规模化利用,湿法炼锌脱氟技术的发展趋势日益明显。
目前常用的除氟方法有:针铁矿法、沉淀法、萃取法、离子交换法、吸附法等。
其中,吸附法以其高效、廉价、无二次污染等优点得到了广泛的应用。
本文将在已有的活性氧化铝、铝基复合材料、金属基吸附剂、天然矿物及活性炭等方面,通过对其作用机制及影响因素的分析,提出湿法炼锌过程中氟的来源及对环境的影响,并建立相应的脱除吸附剂设计方法,为湿法炼锌技术的开发及应用奠定理论基础。
关键词:湿法炼锌体系;除氟技术;氟化物产生和危害;现状研究前言:锌及它的合金在现代工业中有着广泛的应用,锌的冶炼工艺可以分成两种类型,一种是火法,另一种是湿法。
在这两种类型中,湿法炼锌是最主流的一种锌冶炼方法,它的主要内容包括了焙烧、浸出、净化和电积等工艺流程。
由于二次锌资源的大量存在,使得湿法炼锌过程中的氟化物含量一直居高不下。
但是,氟的存在会对锌电积工艺造成严重的危害,所以,在目前湿法炼锌过程中,氟的脱除是一个迫切需要解决的问题。
1、湿法精炼过程中氟化物的产生和危害在湿法炼锌工艺中,湿法炼锌技术省去了锻烧、烟气制酸等工序,在降低环境污染、降低投资成本的同时,也不能将含氟元素以烟气制酸的方式排放出去。
在全湿法炼锌过程中,大量的氟将随浸出过程而流入体系,从而使全湿法炼锌过程的含氟量进一步升高。
氟化物对不锈钢的钝化膜有很强的破坏作用,但由于湿法炼锌装置主要由不锈钢制成,高浓度的氟化物会加速装置的腐蚀。
此外,氟化物还可抑制Pb-Ag薄膜(PbO2)的生长,促进PbSO4的产生,进而导致薄膜致密化,加速腐蚀。
另外,氟化物还会破坏阳极铝材表面的氧化膜,导致电化学析出的Zn和Al形成固溶体,加大了电解锌在阳极铝材上的剥离难度,从而提高了操作成本和电解锌质量。
在湿法炼锌工艺中,通常采用50mg/L以下的氟化物溶液,因为氟化物的浓度高于50mg/L,会使阴极铝片表面产生明显的蚀坑。
湿法炼锌中氟氯去除方法的研究

湿法炼锌中氟氯去除方法的研究苏莎;陈海清【摘要】分析了湿法炼锌体系中氟、氯的来源及氟、氯的存在对生产设备和电积的危害,从火法和湿法两个方面阐述了湿法炼锌中氟、氯的去除方法,火法中重点介绍了多膛炉和回转炉焙烧脱氟氯;湿法中重点介绍了吸附法、沉淀法、絮凝沉淀法脱氟和铜渣、氧化铋、离子交换法脱氟氯.【期刊名称】《湖南有色金属》【年(卷),期】2013(029)001【总页数】4页(P40-43)【关键词】湿法炼锌;氟;氯【作者】苏莎;陈海清【作者单位】湖南有色金属研究院,湖南长沙410015【正文语种】中文【中图分类】TF813目前世界精锌的总产量中大约五分之四由湿法冶炼技术生产,即焙烧-浸出-净化-电积。
随着工业生产的飞速发展,矿产资源的日趋短缺,目前国内矿业界所产锌精矿杂质含量越来越高,对锌冶炼系统的适应性提出了更高的要求。
近年来,由于原料中氟、氯含量的上升,资源综合利用最大化逐步实施和环保要求的更加严格,很多大型湿法炼锌厂系统中氟、氯水平呈上升趋势[1,2]。
而氟氯的存在对制酸系统及湿法系统设备的危害都相当大,因此湿法炼锌中氟氯的去除成为目前亟待解决的问题。
1 湿法炼锌中氟氯的来源在湿法炼锌工艺中,氟与氯的主要来源于焙砂和回转窑挥发的次氧化锌。
据资料显示,在湿法炼锌工序中,含氟、氯的锌精矿在沸腾焙烧过程中,70%氟与氯以HF 和HCl的形式进入到烟气制酸系统中,30%氟与氯(氯含量应高些)则随着焙砂、次氧化锌烟尘而进入湿法系统。
焙砂中氟氯的含量与锌精矿中氟氯含量成正比,即锌精矿氟氯含量高时,焙砂氟氯含量也高。
来自于回转炉的氧化锌与浸出渣一起经多膛炉脱除氟氯,一部分氟、氯随炉气和烟尘进入烟气系统,一部分随酸浸进入湿法工序,由于有浸出渣的加入,这部分氟、氯含量不稳定[2,3]。
2 湿法炼锌中氟氯的危害2.1 对设备的危害氟、氯的存在对设备会产生严重的危害,对搅拌机的影响主要体现在浆叶上,湿法炼锌系统搅拌机使用广泛,浆叶材质大多数为不锈钢,氟氯离子浓度升高,使搅拌机浆叶的使用周期缩短。
湿法碱洗脱除及净化氧化锌烟尘
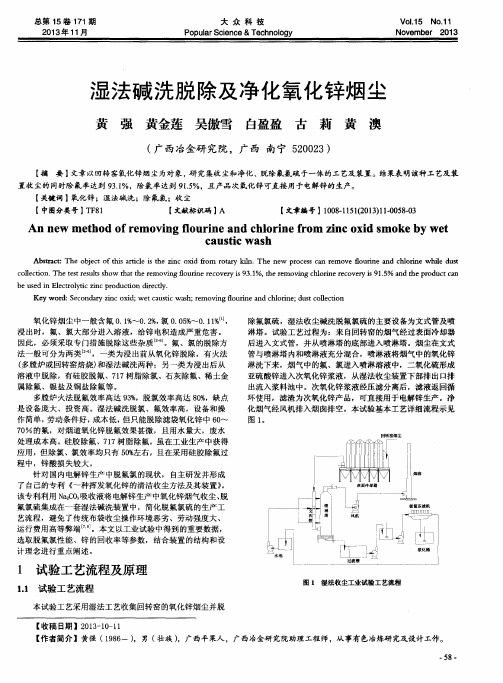
除氟氯硫 ,湿法收尘碱洗脱氟氯硫 的主要设备为文式管及 喷 淋塔 。试验工艺过程为:来 自回转窑的烟 气经过 表面冷却器 后进入文式管,并从喷淋 塔的底 部进入 喷淋塔 。烟尘在文式
管与喷淋塔 内和喷淋液充分混合,喷淋 液将烟气 中的氧化锌 淋洗下来,烟气中的氟、氯进入 喷淋溶液 中,二氧化硫形成 亚硫酸锌进 入次氧化锌浆 液,从湿法 收尘装 置下部排 出口排
氧化锌烟尘 中一般含氟 0 . 1 % ~0 . 2 % , 氯0 . 0 5 %  ̄0 . 1 1 % , 浸 出时 ,氟 、氯大部分进入溶液 , 给锌 电积造成严重危害 。 因此,必须采取专 门措施脱除这些杂质 。氟 、氯 的脱 除方 法一般可分为两类 ,一类为浸 出前从氧化锌脱 除,有火法 ( 多膛炉或回转窑焙烧) 和湿法碱洗两种 ;另一类为浸 出后从 溶 液中脱除 ,有硅胶脱氟 、7 1 7树脂除氯 、石灰除氟 、稀 土金 属除氟、银盐及铜盐除氟等 。 多膛炉 火法 脱氟效率高达 9 3 % ,脱氯效率高达 8 0 % ,缺 点 是设备庞 大、投 资高 。湿 法碱洗脱氯、氟效率高 ,设备和操 作 简单, 劳动条件好 , 成本低 , 但只能脱除滤袋氧化锌 中 6 O ~ 7 0 %的氟,对烟 道氧 化锌 脱氟效果甚微 ,且用水量大 ,废水 处 理成本 高。硅胶 除氟、7 1 7 树脂除氟 ,虽在工业生产 中获得 应用 ,但除 氯、氯效率 均只 有 5 0 % 左右 ,且在采用硅胶除氟过 程 中,锌酸损 失较大 。 针对 国内电解锌 生产 中脱氟氯的现 状, 自主研发并形成 了 自己的专利 《 ~种挥发氧化锌 的清洁 收尘 方法及其 装置》 。 该专利利用 N a z C 0 吸收液将 电解锌 生产 中氧化锌烟气 收尘 、 脱 氟氯硫集成在一套湿法碱洗装 置中,简化脱氟氯硫 的生产工 艺流程 ,避免 了传统布袋 收尘操作环境恶劣 、劳动 强度大 、 运行 费用高等弊端 。本文 以工业试 验中得到的重要数据, ’
湿法碱洗脱除氧化锌烟尘中的氟氯新工艺
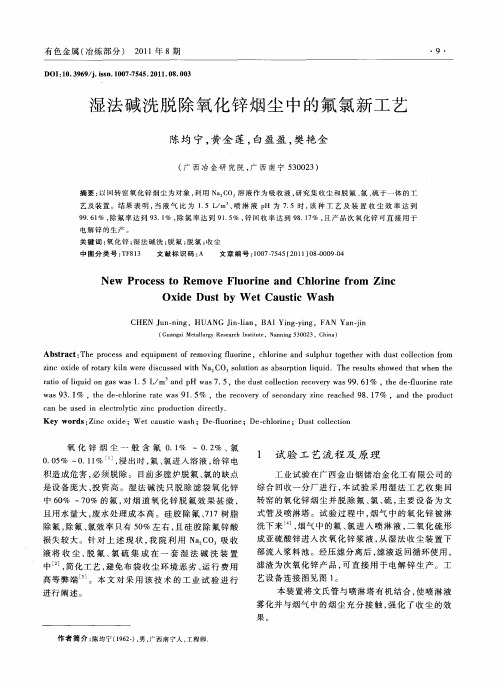
式 管及 喷 淋塔 。试 验 过 程 中 , 气 中的氧 化 锌 被 淋 烟
洗 下来 , 气 中 的氟 、 烟 氯进 入 喷淋 液 , 氧 化 硫 形 二
损失 较 大 。针 对 上 述 现 状 , 院利 用 N , O 我 aC 吸 收 液将 收 尘 、 氟 、 硫 集 成 在 一 套 湿 法 碱 洗 装 置 脱 氯 中 , 简化 工艺 , 免布 袋 收 尘 环境 恶 劣 、 行 费用 避 运
zn xd fr tr in we edic s e t 2 o u in a bs r in lq i T e u t h we h twh n t e i c o i e o o ay k l r s u s d wih Na O3s l t sa opto i u d. her s lss o d t a e h C o r t flq i n g swa . /m a d p wa . ai o i u d o a s1 5 L o n H s7 5,t e d s olc in r c v r s99 61 ,t e fu rner t h u tc le to e o e wa . % y hed — o i ae l
中 6 % ~ 0 的氟 , 烟 道 氧化 锌 脱 氟 效 果 甚 微 , 0 7% 对 且用 水 量大 , 废水 处理 成 本 高 。硅胶 除氟 、 1 7 7树 脂 除氟 , 除氟 、 氯效 率只有 5 % 左 右 , 硅胶 除氟 锌 酸 0 且
综 合 回收一 分 厂进 行 , 试 验 采 用 湿法 工 艺 收集 回 本
( 西冶金研 究院 , 西 南 宁 5 0 2 ) 广 广 3 0 3
次氧化锌氟氯脱出方法探讨

次氧化锌氟氯脱出方法探讨次氧化锌(ZnO)是一种重要的无机化合物,具有广泛的应用领域,如橡胶工业、橡塑制品、涂料和油墨等。
然而,在催化剂或其他材料的制备过程中,由于次氧化锌中可能存在的氯、氟等杂质,需要进行脱除,以提高其纯度和性能。
本文将探讨次氧化锌氟氯脱出方法的相关研究进展。
首先,目前的次氧化锌氟氯脱出方法主要包括物理法和化学法两种。
物理法主要利用高温热解和高温蒸馏等方法,通过升温过程中氯、氟的脱出差异实现目标。
例如,一些研究表明,在1100-1200℃的高温条件下,次氧化锌中氟的脱出速率较快,而氯的脱出速率较慢,从而实现了氟氯的分离。
此外,高温蒸馏法也被广泛应用于次氧化锌氟氯脱出过程中,通过汽化和冷凝的方式,将氟、氯分离出来,从而提高次氧化锌的纯度。
其次,化学法在次氧化锌氟氯脱出中也具有重要的应用。
例如,氯在酸性介质中易于被还原为氯离子,因此,可以通过酸洗的方法将次氧化锌中的氯脱除。
一些研究表明,采用浓硫酸和高温的方式进行酸洗,可以有效地去除次氧化锌中的氯,并提高其纯度。
此外,一些研究还尝试了氟化物的沉淀法,通过加入适量的氟化物溶液,可以将次氧化锌中的氟沉淀下来,然后通过离心的方式分离,从而实现次氧化锌脱氟的目的。
除了物理法和化学法之外,也有研究尝试了其他方法,如酸碱中和法和水煮法等。
酸碱中和法是指通过酸碱反应将次氧化锌中的氟氯中和,并通过沉淀或溶解的方式分离出来。
水煮法则是将次氧化锌与水在高温条件下进行反应,通过水蒸气的作用将氟氯从次氧化锌中脱出。
然而,这些方法的应用还需要进一步的研究和优化,以实现高效、低成本的次氧化锌氟氯脱出。
综上所述,次氧化锌氟氯脱出方法的研究尚处于起步阶段,当前主要集中在物理法和化学法两个方面。
其中,物理法主要包括高温热解和高温蒸馏等方法,而化学法主要包括酸洗和沉淀等方法。
此外,还有一些其他方法,如酸碱中和法和水煮法等。
然而,这些方法还需要进一步的研究和优化,以提高脱出效率和降低成本,并实现工业化应用。
用氧化铋从锌冶炼废水中除氯试验研

第41卷第6期(总第186期)2022年12月湿法冶金H y d r o m e t a l l u r g y ofC h i n a V o l .41N o .6(S u m.186)D e c .2022用氧化铋从锌冶炼废水中除氯试验研究周正华(株洲冶炼集团股份有限公司,湖南株洲 412007)摘要:研究了以氧化铋为脱氯剂,采用酸化㊁吸附㊁碱洗工艺从锌冶炼废水中去除氯㊂结果表明:在温度40ħ㊁氧化铋用量为10倍氯离子质量㊁溶液初始p H=1.5㊁反应时间1h 条件下,氯去除率为93.37%,溶液中残留氯质量浓度24.85m g /L ;对吸氯渣碱洗脱氯,在温度90ħ㊁N a O H 质量浓度80g /L ㊁反应时间60m i n ㊁液固体积质量比5/1条件下,氯脱除率达93.64%,碱洗液中氯质量浓度20.07g /L ㊂脱氯后铋化合物经酸化处理可重复利用㊂该工艺实际上只消耗氢氧化钠,生产成本低,操作简单㊂关键词:氧化铋;湿法炼锌;废水;氯;去除中图分类号:T F 803.25;X 703 文献标识码:A 文章编号:1009-2617(2022)06-0548-05D O I :10.13355/j .c n k i .s f y j.2022.06.014收稿日期:2022-07-19作者简介:周正华(1977 ),男,本科,M B A ,高级工程师,主要研究方向为湿法炼锌㊂引用格式:周正华.用氧化铋从锌冶炼废水中除氯试验研究[J ].湿法冶金,2022,41(6):548-552.锌冶炼过程中产生大量含氟㊁氯等有害杂质的冶炼废水,需进行脱氟脱氯处理[1-3]㊂从溶液中除氯主要有萃取法㊁针铁矿法㊁离子交换法㊁化学沉淀法和吸附法等[4]㊂萃取法主要采用二-(2-乙基己基)磷酸及三烷基叔胺㊁正辛醇等溶剂萃取脱除氯离子[5]㊂针铁矿法主要用F e2+作配合体,通过其与氟离子㊁氯离子形成针铁矿共沉淀而脱除氯离子[6]㊂离子交换法主要是利用选择性离子交换树脂交换溶液中的氯离子,使氯离子吸附到树脂上,实现脱氯[7-8]㊂吸附法高效清洁,常用吸附材料有铝基㊁铁基和铋基[9-10]㊂沉淀法则是利用铜离子或银离子与溶液中的氯离子生成难溶氯化亚铜或氯化银沉淀实现脱氯[11-12]㊂总体来说,溶剂萃取法和离子交换法处理量较小,而氯化银法成本较高,针铁矿法实施有一定难度,因而研发一种经济㊁高效的废水中氯开路工艺具有重要意义㊂试验借助氯化铋稳定性强的特性[13-14],研究了以氧化铋为除氯剂从废水中去除氯,并对除氯渣进行碱洗再生,以期为含氯废水的高效处理提供参考㊂1 试验部分1.1 试验原料㊁试剂废水:取自湖南株冶有色金属有限公司,C l-质量浓度375m g /L ,p H=1.5㊂试剂:氧化铋㊁氧化钙㊁氢氧化钠,均为分析纯;硫酸,工业纯㊂1.2 试验原理氧化铋经酸化处理后得到酸化物,其物相转变成B i (O H )S O 4(式(1)):B i 2O 3+2H 2S O 4 2B i (O H )S O 4+H 2O ㊂(1)B i (O H )S O 4与氯离子结合形成氯氧铋难溶物进而将氯离子从溶液中去除(式(2))㊂氯氧铋在高浓度N a O H 溶液中转化为B i 2O 3或Bi O O H (式(3)㊁(4)),B i 2O 3或Bi O O H 酸化后转化为B i (O H )S O 4脱氯剂(式(5)㊁(6))㊂B i (O H )S O 4+Cl - B i O C l ˌ+H ++S O 2-4;(2)2B i O C l +2N a O H B i 2O 3+2N a C l +H 2O ;(3)B i O C l +N a O H B i O O H+N a C l ;(4)B i 2O 3+2H 2S O 4 2B i (O H )S O 4+H 2O ;(5)B i O O H+H 2S O 4 B i (O H )S O 4+H 2O ㊂(6)1.3 试验方法从废水中除氯:废水体积200m L ,加入酸化Copyright ©博看网. All Rights Reserved.第41卷第6期周正华:用氧化铋从锌冶炼废水中除氯试验研究后的氧化铋,在一定温度㊁氧化铋用量㊁废水p H 下反应一定时间,之后过滤得到滤液和滤渣,分析滤液氯质量浓度,滤渣为除氯渣㊂除氯渣碱洗脱氯:除氯渣20g,与一定量氢氧化钠溶液混合,在一定温度㊁N a O H 浓度和液固体积质量比条件下反应一定时间,之后过滤得滤液和滤渣,分析滤液中氯质量浓度,计算氯脱除率;滤渣为碱洗脱氯后的氧化铋酸化物㊂2 试验结果与讨论2.1 废水除氯2.1.1 温度的影响反应时间1h ,氧化铋用量为废水中氯离子质量的10倍,溶液初始p H=1.5,温度对除氯的影响试验结果如图1所示㊂图1 温度对氯去除率的影响由图1看出:随温度升高,氯去除率升高,至40ħ时达最高,为93.37%,之后随温度升高,氯去除率逐渐降低㊂温度较低时,溶液中离子扩散速度较慢,反应不充分,除氯效果不佳;温度过高,则氯氧铋不稳定,容易解离出游离态C l-,影响氯的实际去除效果㊂综合考虑,确定温度以40ħ为宜㊂2.1.2 氧化铋用量的影响反应时间1h ,温度40ħ,溶液初始p H=1.5,氧化铋用量对氯去除率的影响试验结果如图2所示㊂可以看出:随氧化铋用量增大,B i (O H )S O 4与氯的反应更加充分,有利于氯的去除,因此氯去除率升高;氧化铋用量增至废水中氯离子质量的10倍后,氯去除率趋于稳定,维持在93%左右,残氯质量浓度在20m g /L 左右㊂综合考虑,确定氧化铋用量以氯离子质量的10倍为宜㊂图2 氧化铋用量对氯去除率的影响2.1.3 溶液初始p H 的影响反应时间1h ,温度40ħ,氧化铋用量为废水中氯离子质量的10倍,以C a O 调溶液p H ,溶液初始p H 对氯去除率的影响试验结果如图3所示㊂图3 溶液初始p H 对氯去除率的影响由图3看出:随溶液初始p H 升高,氯去除率降低㊂这是由于铋离子极易水解,在弱酸环境中直接转化为B i O (O H ),从而降低对氯的去除能力㊂溶液p H=1.5时,氯去除效果最好,去除率达93.37%㊂废水p H 即为1.5左右,所以不必调p H ,原始p H 即可㊂2.1.4 反应时间的影响溶液初始p H=1.5,反应温度40ħ,氧化铋用量为废水中氯离子质量的10倍,反应时间对氯去除率的影响试验结果如图4所示㊂可以看出:氯去除反应速度较快,1h 后反应基本达到平衡,氯去除率趋于稳定,维持在92%左右㊂氧化铋除氯虽属于吸附法脱氯,但铋盐与氯结合生成氯氧铋沉淀物也具沉淀反应特点,反应速度较快㊂综合考虑,确定反应时间以1h 为宜㊂㊃945㊃Copyright ©博看网. All Rights Reserved.湿法冶金 2022年12月图4 反应时间对氯脱除率的影响2.2 除氯渣碱洗脱氯2.2.1 除氯渣的组成除氯渣的X R D 和S E M 分析结果如图5所示㊂可以看出,除氯渣呈针状和片状,形貌与氧化铋的颗粒形貌[15]完全不同,说明除氯过程中发生了物相转变和晶型重构,氯与铋反应生成了新的物相B i O C l ,表明废水中的氯主要以B i O C l 形式被去除㊂图5 除氯渣的S E M (a )㊁X R D (b)分析结果2.2.2 温度对除氯渣碱浸脱氯的影响N a O H 质量浓度80g /L ,反应时间1h ,液固体积质量比5/1,温度对除氯渣碱洗脱氯的影响试验结果如图6所示㊂可以看出,温度对碱洗脱氯影响较大:随温度升高,氯脱除率提高;温度升至90ħ时,氯脱除率达最大㊂随温度升高,反应动力学速度加快,反应更趋完全,脱氯效果更好㊂综合考虑能耗㊁成本等因素,确定温度以90ħ为宜㊂图6 温度对碱洗脱氯率的影响2.2.3 氢氧化钠质量浓度对除氯渣碱浸脱氯的影响温度90ħ,反应时间1h ,液固体积质量比5/1,氢氧化钠质量浓度对除氯渣碱洗脱氯的影响试验结果如图7所示㊂图7 N a O H 质量浓度对碱洗脱氯的影响由图7看出:随N a O H 质量浓度升高,氯脱除率提高,至N a O H 质量浓度为80g /L 后,氯脱除率趋于稳定㊂N a O H 质量浓度过高,即溶液呈强碱性,会导致铋生成氢氧化铋胶体,吸附部分氯,从而影响脱氯效果;另外,N a O H 质量浓度越高,溶液黏度越大,也不利于溶液与渣的分散,不利于反应充分进行,进而影响脱氯效果㊂综合考虑,确定N a O H 质量浓度以80g /L 为宜㊂2.2.4 反应时间对除氯渣碱浸脱氯的影响温度90ħ,N a O H 质量浓度80g /L ,液固体积质量比5/1,反应时间对除氯渣碱洗脱氯的影响试验结果如图8所示㊂㊃055㊃Copyright ©博看网. All Rights Reserved.第41卷第6期周正华:用氧化铋从锌冶炼废水中除氯试验研究图8 反应时间对碱洗脱氯的影响由图8看出:碱洗时间对脱氯影响不大,反应30m i n 脱氯率即可达82%,反应60m i n 后基本达到平衡㊂在强碱作用下,除氯渣可快速脱氯,氯渣本身得到再生㊂综合考虑,确定脱氯反应时间以60m i n 为宜㊂2.2.5 液固体积质量比对除氯渣碱浸脱氯的影响温度90ħ,反应时间1h ,N a O H 质量浓度80g /L ,液固体积质量比对除氯渣碱洗脱氯的影响试验结果如图9所示㊂图9 液固体积质量比对碱洗脱氯的影响由图9看出:增大液固体积质量比有利于氯的脱除㊂更多碱液的参与可使脱氯反应更充分,脱氯效果更好;但液固体积质量比过大,碱液耗量增加,同时也使后续碱洗液的处理难度加大㊂综合考虑,确定液固体积质量比以5/1为宜㊂2.2.6 脱氯渣的S E M 和X R D 分析在上述试验确定的适宜条件(温度90ħ,N a O H 质量浓度80g /L ,反应时间60m i n ,液固体积质量比5/1)下对除氯渣碱洗脱氯,脱氯率为93.64%,碱洗液中氯质量浓度为20.07g /L ,相较于废水中的氯质量浓度375m g /L ,富集了50倍以上㊂脱氯渣的S E M 和X R D 分析结果如图10所示㊂可以看出,脱氯渣呈棒状和三角锥状,与除氯渣的针片状有明显不同,表明碱洗过程中发生了系列反应使物相重组,生成了均匀的化合物B i 2O 3,且物相组成单一,可返回酸化处理后再次用于除氯㊂图10 脱氯渣的S E M (a )㊁X R D (b)分析结果3 结论氧化铋经酸化处理后从冶炼废水中去除氯是可行的,在废水初始p H=1.5㊁温度40ħ㊁氧化铋用量为废水中氯离子质量的10倍㊁反应时间1h 条件下,废水中氯去除率在90%以上,除氯后液中残留氯质量浓度低于30m g /L ㊂除氯渣形貌呈针状和片状,物相组成为B i O C l ㊂除氯渣用碱液洗涤可脱除氯,在反应温度90ħ㊁N a O H 质量浓度80g /L ㊁反应时间60m i n㊁液固体积质量比5/1条件下,脱氯率达93.64%,碱洗液中氯质量浓度为20.07g /L ,富集了50倍以上㊂脱氯渣呈棒状和三角锥状,主要物相为B i 2O 3,可返回酸化处理后再次用于废水除氯㊂参考文献:[1] 梅光贵.湿法炼锌学[M ].长沙:中南工业大学出版社,2001:23-45.[2] 凡杰,谢刚,田林,等.闪锌矿加压酸浸工艺及动力学试验研究[J ].湿法冶金,2020,39(6):483-489.[3] Z H A N G X R ,L I U Z H ,L I W S ,e t a l .A l k a l i n e㊃155㊃Copyright ©博看网. All Rights Reserved.湿法冶金2022年12月p r e t r e a t m e n t f o r c h l o r i n e r e m o v a l f r o m h i g h-c h l o r i n e r h o d o c h r o s i t e[J].I n t e r n a t i o n a l J o u r n a l o f M i n e r a l s, M e t a l l u r g y a n d M a t e r i a l s,2016,23(11):1252-1257. [4]谭青,李启厚,刘志宏,等.湿法炼锌过程中氟氯脱除技术研究现状[J].湿法冶金,2015,34(4):264-269.[5]路永锁,宁建平,阮海丰,等.从次氧化锌烟尘中湿法回收锌及去除氟氯[J].湿法冶金,2016,35(5):422-426. [6]何醒民,左小红.针铁矿部分沉铁除锌电解液中氟氯的工艺研究[J].铜业工程,2016(4):62-64.[7] C A R MO N A M,PÉR E ZA,L U C A SA D,e t a l.R e m o v a l o fc h l o r ide i o n sf r o ma n i n d u s t r i a l p o l y e t h y l e n i m i n e f l o c c u l a n ts h i f t i n g i ti n t o a n a d h e s i v e p r o m o t e r u s i n g t h e a n i o ne x c h a n g e r e s i n A m b e r l i t e I R A-420[J].R e a c t i v e a n dF u n c t i o n a l P o l y m e r s,2008,68(8):1218-1224.[8] L I H S,C H E N Y H,L O N G J Y,e ta l.S i m u l t a n e o u sr e m o v a l o ft h a l l i u m a n d c h l o r i d e f r o m a h i g h l y s a l i n ei n d u s t r i a lw a s t e w a t e r u s i n g m o d i f i e da n i o ne x c h a n g e r e s i n s[J].J o u r n a l o fH a z a r d o u sM a t e r i a l s,2017,333:179-185.[9]杨晓冬,徐俊忠,马先春,等.从湿法炼锌硫酸锌溶液中去除氯试验研究[J].湿法冶金,2021,40(1):68-71. [10] HU A N G S Q,L I L,Z HU N W,e ta l.R e m o v a la n dr e c o v e r y o f c h l o r i d e i o n s i n c o n c e n t r a t e d l e a c h a t e b yB i(Ⅲ)c o n t a i n i n g o x i d e s q u a n t u m d o t s/t w o-d i m e n s i o n a lf l a k e s[J].J o u r n a lo f H a z a r d o u s M a t e r i a l s,2020,382.D O I:10.1016/j.j h a z m a t.2019.121041.[11] WA N GLP,L E E W H,T S E N G S M,e ta l.R e m o v a lo fc h l o r ide i o n sf r o m a na q u e o u ss o l u t i o nc o n t a i n i ng ahi g hc h l o r id ec o n ce n t r a t i o nt h r o u g ht h ec h e m i c a l p r e c i p i t a t i o no f f r i e d e l s s a l t[J].M a t e r i a l sT r a n s a c t i o n s,2018,59(2): 297-302.[12]张阳,史丙丁,马保中,等.酸性溶液除氯技术研究现状及进展[J].有色金属科学与工程,2021,12(5):10-17. [13]唐谟堂.三氯化铋水解体系的热力学研究[J].中南矿冶学院学报,1993,24(1):45-51.[14]郑国渠,唐谟堂,赵天从.氯盐体系中铋湿法冶金的基础理论研究[J].中南工业大学学报,1997,28(1):34-36. [15]王晓静,边超群.电泳沉积制备氧化铋涂层的研究[J].功能材料,2020,51(6):6120-6126.R e m o v a l o fC h l o r i n eF r o mZ i n c S m e l t i n g W a s t e w a t e rW i t hB i s m u t hO x i d eZ H O UZ h e n g h u a(Z h u z h o uS m e l t e rG r o u p C o.,L t d.,Z h u z h o u412007,C h i n a)A b s t r a c t:T h e r e m o v a l o f c h l o r i n e f r o mz i n c s m e l t i n g w a s t e w a t e r b y a c i d i f i c a t i o n,a d s o r p t i o n a n d a l k a l i w a s h i n g w i t hb i s m u t ho x i d ea sd e c h l o r i n a t i o na g e n tw a ss t u d i e d.T h er e s u l t ss h o wt h a tu n d e rt h e c o n d i t i o n s o f t e m p e r a t u r eo f40ħ,b i s m u t ho x i d ec o n t e n to f10t i m e s t h ea m o u n to f c h l o r i d e,i n i t i a l s o l u t i o n p Ho f1.5a n d r e a c t i o n t i m eo f1h,t h e r e m o v a l r a t eo f c h l o r i n e i s93.37%,a n d t h e r e s i d u a l c h l o r i n e m a s sc o n c e n t r a t i o ni n w a s t e w a t e ri s24.85m g/L.D e c h l o r i n a t i o nf r o m c h l o r i n ea s p i r a t e r e s i d u eb y a l k a l iw a s h i n g,t h ed e c h l o r i n a t i o nr a t e i s93.64%a n dt h ec h l o r i d em a s sc o n c e n t r a t i o n i n a l k a l i w a s h i n g s o l u t i o ni s20.07g/L u n d e rt h ec o n d i t o n s o ft e m p e r a t u r eo f90ħ,N a O H m a s s c o n c e n t r t i o no f80g/L,r e a c t i o nt i m eo f60m i na n dl i q u i dv o l u m e/s o l i d m a s so f5/1.T h eb i s m u t h c o m p o u n da f t e rd e c h l o r i n a t i o nc a nb er e u s e db y a c i d i f i c a t i o n.T h e p r o c e s sa c t u a l l y c o n s u m e so n l y s o d i u mh y d r o x i d e a n dh a s l o w p r o d u c t i o nc o s t a n d s i m p l e o p e r a t i o n.K e y w o r d s:b i s m u t ho x i d e;z i n c h y d r o m e t a l l u r g y;w a s t e w a t e r;c h l o r i n e;r e m o v a l㊃255㊃Copyright©博看网. All Rights Reserved.。
钢铁行业含锌烟尘回收利用技术研究进展

钢铁行业含锌烟尘回收利用技术研究进展摘要:目前,部分企业采用固化/玻化填埋法处理无回收价值的钢铁烟尘,通过加热使重金属被稳定的包裹在粘土等物质中不易被浸出,或采用高温熔融、改变有害金属元素的化学形态,从而在后续填埋处置中防止造成环境污染,但处理成本高、效益差,且没有有效回收利用烟尘中的铁、锌等有价金属,造成巨大的资源浪费。
部分钢铁企业则将含锌烟尘按照一定比例配入烧结混合料直接返回烧结,回收烟尘中的铁和碳,综合利用资源、降低烟尘数量,但由于钢铁烟尘未进行预处理,烟尘中的锌在循环烧结利用过程中不断富集,会降低烧结矿的质量和品位,加快炉衬腐蚀,减少高炉寿命,直接返回处理仅适用于处理含锌、铅等杂质元素较低的钢铁烟尘,且配比不可过多。
关键词:含锌烟尘;湿法冶金;火法冶金;钢铁行业引言通常钢铁企业对生产过程中产生的大部分烟尘经直接或间接处理后返烧结、球团、炼铁或炼钢等生产工序利用。
但其中含锌烟尘有800~1000万吨,其大部分仍没得到“高效”的处理利用。
对于含锌钢铁烟尘的回收处理工艺主要有:1含锌烟尘成分特点湿法炼锌产氧化锌烟尘通常含有较高的氟和氯,在直接进行酸性浸出时氟和氯几乎全部进入硫酸锌溶液,使锌电解液中氟、氯的含量超过标准。
因此,在浸出之前必须将氧化锌中的氟、氯进行脱除预处理。
高锌含量的含锌烟尘是获取锌的重要来源,具有较高的回收利用价值,但其成分复杂,杂质元素较多,且杂质元素如硅、钙、铁、氟和氯等含量相对较高,在综合回收利用这类二次资源时需考虑杂质对金属回收工艺的影响。
2钢铁行业含锌烟尘回收利用技术研究进展2.1物理法物理法锌回收技术是采用机械分离(离心、重选等)或磁性分离(磁选)的方式富集钢铁烟尘中的锌元素。
常用的机械分离方法有浮选一重选工艺、水力旋流脱锌工艺等;常用磁性分离方法有弱磁、强磁联合工艺。
经过处理后可以得到中高锌含铁料和低锌含铁料两类物质,分别用于提锌和回用烧结。
目前国内绝大多数的钢铁企业采用此方法,虽回收效率低,但投资也相对少。
铜渣脱氯工艺实验研究

外排
图 1 铜渣脱氯工艺流程图
3 实验结果 3.1 反应温度对脱氯效率的影响
取氧化锌烟灰浸出液 200ml,在反应 pH=1,反应时间 2h, 搅拌器转速 230r/min,温度 20℃、30℃、40℃、50℃、60℃条件 下进行实验,考察反应温度对脱氯效率的影响。试验结果见图 2。
收稿日期 :2020-04 作者简介 :廖天鹏,男,生于 1985 年,汉族,甘肃甘谷人,硕士,助理工程师, 研究方向 :冶金固废资源化与无害化处理。
M 冶金冶炼 etallurgical smelting
铜渣脱氯工艺实验研究
廖天鹏1,李彦龙2,李银丽2
(1. 甘肃工业职业技术学院,甘肃 天水 741025 ;2. 西北矿冶研究院,甘肃 白银 730900)
摘 要 :本文对氧化锌烟灰酸浸液进行铜渣脱氯实验研究,通过单因素试验考察实验浓度、温度、时间、pH 等因素对脱氯效率
3.3 反应时间对氯脱除率的影响 取氧化锌烟灰浸出液 200ml,在 pH=1.5,反应温度 40℃,搅
拌 器 转 速 230r/min,反 应 时 间 1.0h、1.5h、2.0h、2.5h、3.0h 条 件 下进行试验。考察不同反应时间对氯脱除率的影响,试验结果见 表 4。
于平稳,再增加反应时间,脱氯效率几乎不变,说明在反应时间 为 2.0h 时,反应完全,氯脱除效率为 79.12%。因此确定反应时间
的影响,对温度、时间、pH 三因素进行 33 的正交试验并进行极差分析,确定影响脱氯效率的主要因素。实验结果表明 :反应温
度为 40℃、pH 为 1.5、反应时间为 2h 的条件下,氯脱除率可达 79% 以上。通过极差分析,确定 pH 是影响脱氯效率的主要因素,
反应温度次之,反应时间影响最小。
湿法炼锌过程中脱除F、Cl的生产实践

湿法炼锌过程中脱除F、Cl的生产实践作者:黄开胤陈志明王军路鹏贾兆霖牛文敏来源:《中国科技博览》2019年第07期[摘要]在湿法炼锌过程中,系统的F、Cl含量过高,对锌的电机造成较大影响,腐蚀阴阳极板,析出锌难剥离等。
某炼锌厂在生产过程中针对系统的F、Cl离子含量过高问题,采用氯化亚铜沉淀及钙法沉淀脱除系统中过量的F、Cl,保证了锌电积生产的稳定运行。
[关键词]湿法炼锌铜渣脱氯钙法沉淀 F、Cl中图分类号:C912 文献标识码:A 文章编号:1009-914X(2019)07-0002-01前言在湿法炼锌过程中,氟、氯的存在对系统设备和环境都影响较大。
氟氯含量达一定值后会使电解阴阳极消耗和作业环境恶化。
在硫酸锌电积过程中,氟离子破坏阴极铝板表面的氧化铝膜,使析出锌与铝板新鲜表面形成锌铝合金,导致锌皮难以剥离,阴极铝板消耗增加。
氯离子氧化成氯酸盐后与阳极铅反应,增加电解液含铅,降低析出锌质量,同时缩短阳极寿命;另外氯离子在酸性环境中被二氧化锰氧化产生氯气,污染作业环境。
为此在湿法炼锌中,国内外各生产企业对电积液中的氟、氯含量都提出了严格限定,一般要求氟离子小于50 mg /L,氯离子小于100 mg /L。
1、湿法系统F、Cl的来源在某厂的锌冶炼生产中过程中,F、Cl的来源多样,主要是因为原料短缺,采用其它含锌杂料生产带进系统的F、Cl,以及回转窑氧化锌、铟回收萃余液、氧化锌法尾气脱硫后液进入系统带进的F、Cl,这部分带进系统的F、Cl量占系统F、Cl含量的60%以上。
在某厂的生产过程控制中,一般要求含F≤30mg/l,含Cl≤0.5g/l,在此范围内,析出锌的剥离、极板的腐蚀及生产现场的环境都处在正常水平。
而当系统F、Cl超出此范围时,析出锌开始出现难剥离、极板腐蚀加剧、现场环境变坏,严重影响生产的正常进行。
2、F、Cl的脱除方法F的脱除方法主要有吸附法、化学沉淀法、离子交换树脂法等。
Cl的脱除方法主要有氯化亚铜沉淀法、氯氧化铋沉淀法、电化学法、氧化法等。
脱氯技术现状与研究进展

化应用。本文介绍了一些现行脱氯技术的原理、特 点及研究进展,同时对炼厂催化重整装置的腐蚀防 护提出相应的建议。
!
!" !
催化脱氯
有机氯的脱除
有机氯脱除技术主要有 ! 类。 * # + 催化加氢脱氯。催化加氢脱氯的反应机理
分为 " 步: 第一步, 氢气在催化剂的表面吸附。氢气 分子首先吸附在催化剂的活性金属颗粒表面上并均 裂成氢原子,然后从金属表面逸出至催化剂的表 面。氢原子在催化剂表面微弱 , 酸的作用下失去一 个电子而变为 - . ,形成了催化剂表面的 / 酸中心; 第二步,有机氯化物在催化剂载体表面上吸附。有 机氯化物的氯原子由于强的吸电子诱导效应而带负 电荷,并吸附在已形成 / 酸中心 - . 的催化剂载体 表面上; 第三步, 表面反应。吸附的氢和有机氯化物 生成 -01 和相应的烃类; 第四步, 产物脱附。反应生 成的烃类和氯化氢从脱氯催化剂表面脱附。 * ! + 催化氢转移脱氯。反应机理如下:第一步, 催化剂与氯代烃接触形成络合物 ! ; 第二步, 供氢剂 与生成的络合物之间发生氢转移反应,将氯离子替 代后形成新的络合物 " ,氯离子以游离态脱离络合 物" ; 第三步, 新的络合物发生分解, 又形成了新络 合物 #; 第四步, 新络合物 #发生分解之后, 形成了 催化剂和对应的烃类。 对于有机氯化物一般采用二元金属体系催化剂 作为脱氯催化剂。目前用铁系金属化合物作为主催
氯的危害比硫更大,氯中毒后催化剂中会有新相生 成,使催化剂的结构遭到破坏,促使催化剂中铜晶 粒迅速长大, 活性急剧下降, 无法再生。近年来, 各 油田为了提高原油的产量,广泛使用各种采油助 剂, 如破乳剂、 清蜡剂、 酸化剂等, 其中不少采油助 剂含有各种类型的有机氯化物,这些有机氯化物不 溶于水, 热稳定性好, 很难用电脱盐的方法脱除, 大 部分存在于常减压产品的直馏石脑油馏分。在重整 加工过程中,原料经过预加氢处理,有机氯化物将 转化为氯化氢,氯化氢与水和氨分别形成盐酸和氯 化铵,对设备造成严重的腐蚀并阻塞管道,严重时 会导致装置被迫停工检修,给企业造成巨大的经济 损失。 在已有的脱氯技术中催化脱氯技术比较成熟, 应用最为广泛。电化学脱氯技术的应用有较大的局 限性,而生物脱氯技术尚未成熟,目前未实现工业
p204萃取脱除锌浸出液中氟氯

随着锌富矿资源的不断减少,低品位难处理锌 矿及锌二次资源越来越受到重视口司。次氧化锌烟 尘的主要成分为锌和铅,同时含有锢、铤等有价金
属⑹。铅锌矿和次氧化锌中常含有氟、氯等杂质,随 着生产的持续进行,锌冶炼系统中的氟、氯不断累 积,浓度越来越高,对锌电解产生危害,锌冶炼企业
收稿日期=2019-08-22 基金项目:广西科技厅重点研发计划项目(桂科AB16380013) 作者简介:罗远辉(1968-),男,河南罗山人,教授级高级工程师
等问题。串级试验萃余液含锌2. 42 g/L、氟0.52 g/L、氯1.42 g/L,经沉氟、沉氯处理后,氟、氯浓度分
别降低到0.042 g/L.0.079 g/L,可返回锌冶炼系统配入浸出、净化使用。
关键词:P204;萃取;反萃;氟;氯;锌浸出液
中图分类号:TF813
文献标志码:A
文章编号:1007-7545(2020)03-0012-05
2020年第3期
有色金属(冶炼部分)(http://ysyl. bgrimm. cn)
・13・
一般要求新电解液中的氟离子浓度低于50 mg/L, 氯离子浓度低于100 mg/LUZ。
目前,脱除锌浸出液中氟、氯的方法有火法和湿 法工艺[7切。火法工艺主要有多膛炉锻烧法和回转 窑锻烧法,多膛炉设备庞大,投资高,生产作业中维 护复杂[⑹;回转窑锻烧法氟、氯脱除率优于多膛炉, 但回转窑易“结圈”,需要停炉清理。湿法脱除氟氯 方法主要有:1)碱洗法,以碱液洗涤,使冶炼原料中 的氟、氯溶入碱洗液中口口 ;2)硫酸洗涤法,以浓硫酸 洗涤,使氟、氯形成氟化氢、氯化氢挥发;3)热水洗涤 法;4)吸附法,包括针铁矿沉淀吸附法(吸附除氟、 氯)阴、焙烧水滑石吸附法(吸附除氟、氯)、离子交 换树脂吸附法(脱氟)等;5)沉淀法,包括氟化钙沉淀 脱氟、氯化亚铜沉淀脱氯、氯氧化铤沉淀脱氯等;6) 卤化氢挥发法,使溶液变为酸性,形成氟化氢和氯化 氢挥发;7)萃取法,萃取锌或萃取氟、氯,使锌与氟、 氯分离[烁⑷泮)电解法,电解溶液形成氯化亚铜沉 淀除氯;9)氧化法,加入氧化剂,使氯离子氧化成氯 气挥发除去。这些方法各有其优点和适应性,但也 存在氟、氯脱除率低、作业成本高的问题。
n235萃取脱除锌溶液中氟氯

・8・有色金属(冶炼部分)(http://)2020 4 doi:10.3969力・issn1007-7545.2020.04.002N235萃取脱除锌溶液中氟氯楚立军】,苏秋琼】,罗远辉2,袁学韬2,莫毅1,李晓彤1(1.南丹县南方有色金属有限责任公司,广西南丹547204;2.有研工程技术研究院有限公司,北京100088)摘要:采用N235萃取含氟、氯的锌浸出液,氟、氯被萃取到有机相中,锌留存于萃余液中,锌萃取率低于5%,氟脱除率高于80%,氯脱除率高于94%。
在N235有机相中加入异辛醇,萃取、水洗、反萃温度控制在40〜45C,可避免出现有机相乳化和分相时间长的问题。
萃余液中锌、氟、氯浓度分别为55.54、0.011,0.082g/L,可返回锌冶炼系统配入浸出、净化或送锌电解配液。
关键词:N235;萃取;反萃;氟;氯中图分类号:TF813文献标志码:A7章编号:1007-7545(2020)04-0008-04Removal of Fluorine and Chlorine from Zinc LeachingSolution by N235ExtractionCHU Li-jun1,SU Qiu-qiong1,LUO Yuan-hui2,YUAN Xuetao2,MO Yi1,LI Xiao-tong1(1.Nandan Southern Nonferrous Metals Co.,Ltd.,Nandan547204,Guangxi,China;2.GRIMAT Engineering Institute Co.,Ltd.,Beijing100088,China)Abstract:N235was used to extract zinc and remove fluorine and chlorine from zinc leaching solution. Fluorine and chlorine were extracted into organic phase.Zinc extraction rate is lower than5%,fluorine extraction rate is over80%,and chlorine extraction efficiency is over94%.Organic phase emulsification and long time phase separation can be avoided when sooctanol is added to N235organic phase,and temperature of extraction,washing and stripping is controlled at40一45°C.Concentrations of Zn,F,Cl in raffinate is55.54,0.011and0.082g/L respectively,which can be reused in zinc leaching,purification, andelectrolytepreparaton.Key words:N235;extraction;stripping;fluorine;chlorine在锌的湿法冶炼中,锌精矿中的氟、氯会在浸出时进入浸出液、净化液和电解液卩2],电积锌后的电解废液中一般含有40〜60g/L的锌,可返回浸出、净化或新电解液的配制。
锌溶液中氟氯脱除技术研究

锌溶液中氟氯脱除技术研究王洪刚;刘三平【摘要】铜渣可有效去除锌溶液中的氯离子,在10 g/L硫酸浓度,60℃,反应时间1h,铜渣加入量3.38 g/L条件下,除氯效率可达90%,氯离子含量降低到100 mg/L 以下.针铁矿法吸附氟氯结果表明,氟、氯的脱除率可以分别达到60%和35%;时间越长,已经吸附的氟氯离子又解除吸附,重新回到溶液中.%Copper residue can remove chlorine ions in zinc solution effectively.The removal efficiency of chlorine is over 90% under the conditions of 10 g/L sulfuric acid concentration,60 ℃,1 hour retention time and 3.38 g/L copper residue dosage.The concentration of fluorine ions can be lower than 100 mg/L after purification.The absorption method by goethite have shown that the removal of F and Cl can be reached 60% and 35%,respectively.With extension of the time,the absorbed F and Cl ions are desorbed and released into the solution again.【期刊名称】《矿冶》【年(卷),期】2017(026)004【总页数】5页(P49-52,58)【关键词】锌溶液净化;铜渣;针铁矿;除氟;除氯【作者】王洪刚;刘三平【作者单位】北京矿冶研究总院,北京100160;北京矿冶研究总院,北京100160【正文语种】中文【中图分类】TF813在锌冶炼系统中,氟氯离子浓度的上升给生产工艺造成了许多不利影响,会加速叶轮、反应釜、管道等的腐蚀,增加断裂和泄漏的风险。
次氧化锌生产电锌工艺的氟氯脱出

次氧化锌生产电锌工艺中氟氯脱出方法探讨一、现有次氧化锌生产电锌工艺过程中氟氯脱除工艺概述次氧化锌生产电解锌工艺中,一般采用传统湿法流程,但是氟氯的脱出问题一直没有比较好的解决办法,目前国内利用次氧化锌生产电锌的从流程布局来看,一般分成两种,一种是次氧化锌作为辅助回收流程,只进行浸出过程,在对浸出液中的铟锗进行回收后,浸出液与焙砂浸出流程的浸出液汇合,进行后续工序的联合流程。
另一种是次氧化锌单独浸出处理的流程。
相对来说,联合流程中,次氧化锌处理量比例比较小,一般不超过电解锌产量的20%,对次氧化锌的脱氟氯预处理采用多膛炉煅烧工艺,相对产量比较大。
氟、氯在和大系统混合后浓度相对较低,而且由于蒸发、化合等作用,系统氟氯的积累不严重,所以只要多膛炉控制好,一般不会产生严重危害。
次氧化锌的单独处理流程一般是中小企业采用,由于系统的氟氯积累速度快,起始浓度高,导致氟氯的危害比较严重,脱氟氯主要采用火法和湿法两种方法,表述如下:(1)多膛炉预处理;该方法在国内得到了广泛应用,但是脱除的效果有限,一般来看,氟的脱除效率为80-90%,氯的脱除效率为80%,而且通过我们自己的生产实践认为,这种处理方法还存在明显的地域影响因素,在南方地区脱除率相对较高,而在北方脱除率比较低,鑫大公司的氟脱除率只能达到70%,而氯的脱除率只能达到60%。
多膛炉脱除氟氯的工艺方法在联合法中应用基本上能控制住系统氟氯的浓度,但是在纯粹用次氧化锌生产电锌的流程中应用并不多见。
(2)回转窑处理:该方法和多膛炉基本一样,缺点是烟尘率高,直收率比较低,为了提高直收率,必须对原料制粒,增加了流程的复杂性。
国内一些小厂采用该方法。
(3)水洗预处理:采用碱性水洗涤次氧化锌也是国内中小企业生产的一个方法,该方法在小规模生产中(5000吨电锌/年)应用比较多,但是洗涤效果仍然不能满足生产要求,氟氯在湿法系统中的积累也导致生产困难,如果推广到大规模生产,则预处理系统比较庞大,而且由此带来水消耗和水处理的问题。
- 1、下载文档前请自行甄别文档内容的完整性,平台不提供额外的编辑、内容补充、找答案等附加服务。
- 2、"仅部分预览"的文档,不可在线预览部分如存在完整性等问题,可反馈申请退款(可完整预览的文档不适用该条件!)。
- 3、如文档侵犯您的权益,请联系客服反馈,我们会尽快为您处理(人工客服工作时间:9:00-18:30)。
2 0 1 3年 1 2月
云南 冶 金
YUNNAN MET ALL URGY
De c .2 Ol 3
第4 2卷 第 6期 ( 总第 2 4 3期 )
V o 1 . 4 2 .No . 6( 的研 究 进展
森 维 ,孙红 燕 ,李正永 ,林 大志 ,宋兴诚 ,杨继生
t h e m i s d i f ic f u l t a n d S O o n,t h i s p a p e r p r o v i d e s t h e r e f e r e n c e s t o c h l o r i d e a n d l f u o i r d e r e mo v a l p r o c e s s i n z i n c h y d r o me t a l l u r g y p l a n t .F C O B -
( 1 . 云南 锡业 股份 有 限公 司 ,云南 2 .红 河学 院理学 院 ,云南
摘
个旧 6 6 1 0 0 0 ;
蒙自 6 6 1 1 0 0 )
要 :本 文针 对 氧 化 锌 烟尘 含 氟 氯 高 ,脱 氟氯 难 等 问题 ,综 合 论 述 了 国内 外 各 种 脱 氟 氯 方 法 和 最 新 进 展 情
t e n t i n z i n c o x i d e d u s t r e a c h u p t o 0 . 2 % ~0 . 3% ,C1 c o n t e n t r e a c h u p t o 0. 3 % 一0. 4% ,a t p r e s e n t ,s e v e r a l F a n d CI r e mo v a l me t h o d s
关键 词 :湿 法 炼锌 ;氧 化 锌 烟尘 ;除 氟 氯
中 图分 类 号 :T F 8 1 3 文 献标 识 码 :A 文 章 编 号 :1 0 0 6 - 0 3 0 8( 2 0 1 3 )0 6 — 0 0 4 2 — 0 4
Re s e a r c h Pr o g r e s s o n t h e Re mo v a l Me t h o d s f o r Chl o r i de a n d Fl u o r i d e i n Zi n c Ox i d e Du s t
mu s t b e a p p l i e d j o i n t l y t o r e a c h d e e p p u i r i f c a t i o n a i m a n d m e e t t h e e l e c t r o l y t e r e q u i r e m e n t s .
K EY W O RD S: z i n c h y d r o me t a l l u r g y;z i n c o x i d e d u s t ;c h l o id r e a n d l f u o id r e r e mo v a l
u a t i o n s a r e c o mp r e h e n s i v e l y d i s c u s s e d a c c o r d i n g t h e p r o b l e ms ,s u c h a s c h l o r i d e a n d l f u o r i d e c o n t e n t i s h i g h i n z i n c o x i d e d u s t ,r e mo v i n g o f
S EN We i ,S UN Ho n g—y a n ,L I Zh e n g—y o n g ,L I N Da—z h i 。 S o n g Xi n g— c h e n g ,YANG J i — s h e n g
,
( 1 .Y u n n a n T i n C o m p a n y L i mi t e d , G e j i u , Y u n n a n 6 6 1 0 0 0 ,C h i n a ; 2 .C o l l e g e o f s c i e n c e ,H o n g h e U n i v e r s i t y , Me n g z i , Y u n n a n 6 6 1 1 0 0 ,C h i n a )
况 ,可为 湿 法 炼锌 厂 的脱 氟 氯 工 艺选 择 提 供 参 考 。氧 化 锌 烟 尘 含 F高 达 0 . 2 %~ 0 . 3 % ,含 c l 高达 0 . 3 %~ 0 . 4 %,
要使 氧化锌烟尘中的氟氯脱除达到电解液要求 ,目前必须将几种除氟氯方法联合应用 ,才能达到深度 净化 目的 。