第3章 钢的热处理和表面改性
3第三章 钢的热处理和表面改性

下料→ 锻造→ 正火→ 粗加工→ 调质 ( 淬火 + 高温回火 ) → 局部表面淬火+ 低温回火→ 精磨→ 成品; (6)组织:表面:回火马氏体 心部:回火索氏体
2、齿轮(低碳钢、表面渗碳)
(1)工作条件: 齿轮根部承受交变弯曲应力;(传递扭矩时); 齿啮合时齿面承受较大的接触压应力并受强烈的摩擦和磨损; 换挡、气动、制动时齿轮承受一定的冲击。 (2) 失效形式:齿的折断(疲劳断裂和冲击过载断裂);齿 表面磨损。 (3)性能要求:高的疲劳强度和表面硬度,心部具有足够的塑 性韧性。
四、表面化学热处理(表层与心部的成分、组织都不同)
1
工艺: 将工件置于某种化学介质中,通过 加热、保温和冷却使介质中的某些元素渗入 工件表层以改变工件表层的化学成分和组织,
从而达到“表硬心韧”的性能特点。
2 可渗的元素: 渗碳、氮、碳氮共渗(C、N、C\N) 渗硼 、铬 (B、Cr 渗铝、硅 渗硫(S) )
五 典型零件工艺路线的制定
1 轴类零件(传动轴)
(1)分析工作条件:承受中等交变扭矩载荷、交变弯曲载荷 或者是拉压载荷;局部(轴颈、花键)承受摩擦和磨损。 (2)失效形式:疲劳断裂,轴颈处磨损(主要方式);冲击 过载断裂等(偶尔发生)
(3)性能要求:高的疲劳强度;良好的综合性能; 局部高硬度;
(4)中碳钢或者中碳合金钢: 45 (5)工艺路线: (40Cr)
火焰加热表面淬火 2 分类 感应加热表面淬火 激光加热表面淬火 3 材料及典型零件
中碳钢(Wc 0.4—0.5%), 如40Cr、45钢机床齿轮、轴等零 件。
常用的表面淬火方法
火焰加热表面淬火 淬硬层深度:2—6mm 优点:方法简便;无需特殊设备;适用于单件、小批量生产零 件;
金属材料的表面改性与热处理实现材料表面性能的提升

金属材料的表面改性与热处理实现材料表面性能的提升金属材料在工业和制造领域中广泛应用,其表面性能对材料整体性能和使用寿命起着至关重要的作用。
为了提高金属材料的表面性能,表面改性和热处理技术被广泛采用。
本文将介绍金属材料表面改性的常用方法和热处理对材料表面性能提升的作用。
一、金属材料的表面改性1.化学表面改性化学表面改性是通过在金属材料表面形成一层化学活性的物质或化合物,从而改变其表面性能。
常用的化学表面改性方法包括电化学处理、溶液浸渍和化学沉积等。
通过这些方法,可以实现金属材料表面的腐蚀耐久性、摩擦性能、润滑性能等的提高。
2.物理表面改性物理表面改性是通过物理手段对金属材料表面进行改良,包括机械处理、喷涂涂层和磁场处理等。
其中,机械处理如切削、打磨和抛光可以提高金属材料的光洁度和平滑度,从而降低表面粗糙度并增加强度。
喷涂涂层技术可以在金属表面形成一层保护性膜,提高耐磨性和耐腐蚀性。
磁场处理可以通过调控磁场对金属表面进行改性,改善其力学性能和磁性能。
二、金属材料的热处理热处理是一种通过对金属材料进行加热和冷却的工艺,以改变材料的组织结构和性能。
常用的热处理方法包括退火、淬火、回火和固溶处理等。
1.退火退火是将金属材料加热至一定温度,然后缓慢冷却的过程。
退火可以消除金属材料中的应力和缺陷,提高其塑性和可加工性。
此外,退火还可以改变材料的晶粒结构,从而调节材料的硬度和强度。
2.淬火淬火是将金属材料加热至临界温度,然后迅速冷却至常温的过程。
淬火可以使金属材料形成超饱和固溶体或马氏体组织,从而提高材料的硬度、强度和耐磨性。
淬火还可以产生残余应力,使材料表面形成压应力层,提高抗拉应力的能力。
3.回火回火是将淬火后的金属材料加热至较低温度,然后适当冷却的过程。
回火可以降低金属材料的脆性和残余应力,提高其韧性和可靠性。
回火还可以调节材料的硬度,使其适应不同的工作条件。
4.固溶处理固溶处理是将合金的固溶元素加热至高温区,然后迅速冷却的过程。
第3章 金属热处理及表面改性

TEM
②针状马氏体 立体形态为双凸透镜形的片 状。显微组织为针状。 在电镜下,亚结构主要是孪 晶,又称孪晶马氏体。
电镜形貌
光镜形貌
电镜形貌
37
(3) 马氏体的形态主
马氏体形态与含碳量的关系
要取决于其含碳量
C%小于0.2%C时,
组织几乎全部是板条 马氏体。
C%大于1.0%C时几
乎全部是针状马氏体。
高硬度是马氏体性能的主要特点。马氏体的硬度主要取 决于其含碳量。含碳量增加,其硬度增加。当含碳量大 于0.6%C时,其硬度趋于平缓。合金元素对马氏体硬度 的影响不大。
C%
马氏体硬度、韧性与含碳量的关系
40
马氏体的碳含量与性能的关系
41
马氏体强化的主要原因是过饱和碳引起的固溶强化。
此外,马氏体转变产生的组织细化也有强化作用。
晶粒粗大。
(2) 加热速度:加热速度越快,过热度越大,形核率越高, 晶粒越细。
(3) 合金元素:
阻碍奥氏体晶粒长大的元素:Ti、V、Nb、Ta、Zr、W、 Mo、Cr、Al等碳化物和氮化物形成元素,会形成难熔的
碳化物和氮化物颗粒,弥散分布于奥氏体晶界上,阻碍 奥氏体晶粒的长大。
促进奥氏体晶粒长大的元素:Mn、P、C、N。
光镜形貌
电镜形貌
珠光体显微组织图
20
②索氏体 形成温度为650~600℃,是片层的铁素体与渗碳体的双 相混合组织,其层片间距较小(80~150nm),800~1000 倍光镜下可辨,用符号S表示。
光镜形貌
电镜形貌
索氏体显微组织图
21
③托氏体 形成温度为600~550℃,是铁素体与片状渗碳体的机械 混合物,片层极薄,电镜下可辨,用符号T表示。
第3章 钢的热处理和表面改性

TTT:Time-Temperature-Transformation
共 析
P
钢
过
冷
贝氏体
A
的
等
温
转
变
曲
线
图
马氏体
1. 高温转变区(P转变区)(A1~550℃)
适宜保温时间
2.含碳量:在一定范围内,随含碳量的增加,奥氏体晶粒长大
的倾向增大,但是当含碳量超过某一限度,晶粒变细小
3. 合金元素
➢ 本质细晶粒钢:添加Al, Ti, W, Mo, V, Zr, Nb, Ta等元素, 晶粒长大倾向小;
➢ 本质粗晶粒钢:添加Si, Mn等元素,晶粒长大倾向大;
3.1.2 钢在冷却时的组织转变
从宏观上看A的转变:晶格发生变化;晶体含碳量变化
相图上组织和相的转变是可逆的
以共析钢为例:加热到727oC(A1)以上,珠 光体转变成奥氏体。(三个阶段)
奥氏体形核与 长大
残余渗碳体溶 解
奥氏体成分均 匀化
(a)
(b)
(c)
(d)
三. 影响奥氏体形成速度的因素
1. 加热温度与加热速度
同一个奥氏体化状态,较低温度较长时间的加热得到; 较高温度较短时间的加热得到
组织特点:渗碳体分布于条状铁素体之间,显微镜下的整体
形貌呈羽毛状
350℃~Ms区间内形成的称为下贝氏体(针状贝氏体) 组织特点:渗碳体以细小颗粒分布于针状铁素体的内部,显
微镜下的整体形貌呈针状组织
3. 低温转变区(Ms230~Mf-50oC) (马氏体转变区)
金属热处理及表面改性

钢加热(冷却)时各临界点的位置
由于过冷和过热现象的存在
3.1.1 钢在加热时的组织转变
1.奥氏体的形成(共析钢)
四个阶段:
奥氏体形核
晶核的长大 残留渗碳体的溶解
P(F+Fe3C)→A
两相→单相的过程 晶格改组和铁原子扩散的 过程
奥氏体的均匀化
2. 奥氏体晶粒大小及影响因素
3.1 钢的热处理原理
钢在固态下,通过加热、保温和冷却,以改变钢的 组织,从而获得所需性能的工艺方法。
45钢 退火 正火 淬火 σb(MPa) 650~700 700~800 1500~1700 δ(%) 15~20 15~20 1~ 2 αk(J/cm2) 40~60 50~80 15~20
钢的热处理分类
3.2.1 钢的退火与正火
一、钢的退火 将钢加热到适当温度,保持一定时间,然后在炉中缓慢地冷 却的热处理工艺。 根据钢的成分和处理目的的不同,可分为完全退火、球化退 火和去应力退火。 1、完全退火 定义:将钢加热Ac3以上30~50º C,完全奥氏体后,保温 一定时间随之缓慢冷却到500º C以下,出炉空冷。 目的:细化晶粒,消除内应力,降低硬度,以利于切削加 工。 适用范围:亚共析钢型材。
起始晶粒
是指珠光体刚刚全部转变成奥氏体时的晶粒。一般很细小。
实际晶粒
是指钢在某个具体热处理或热加工条件下所获得的奥氏体晶粒。直接 影响热处理后“小晶粒→大晶粒”将使合金总的晶界面积减少, 从而减少了界面能,使合金的总能量下降,因此 高温下A晶粒的长大是一个自发的过程。 钢的成分和冶炼条件:C和难溶第二相微粒 加热温度和保温时间
临界冷却速度
钢的热处理和表面处理(共30张PPT)

气电氛极::氨工气件、气-氮阴气极氛和容氢:器氨气-阳混极气合气、氮气和氢气混合气
渗碳材料 0、1-0、25%C 碳钢或低合金钢
压力:133-1333Pa 影响因素:温度、时间、合金元素、原始组织。
功率 30-400kW
1大气压=101300Pa
电压:—500V 4、相变特点:扩散型相变
将加钢热铁 温零度件浸93入0 几℃待±镀1种金0 ℃属元盐溶素液中渗并入接负零电极件,加表一定层直,流电以压使改零件变表面其形表成一面层所化需金学属的成镀分层。、组织和性能
工艺。 1、上B 550-350 ℃
无扩散、切变共格和表面浮凸、变温形成、高速长大、转变不完全性。
分类 渗碳 第四节 钢的退火与正火
2.固体渗碳
设备 箱式电阻炉
渗碳气氛 木炭+碳酸钠
加热温度 930 ℃±10 ℃
加热时间 3-7h
渗层深度
表面碳浓度: 0.85-1.05%
渗后不能直接淬火
适合小件和单件
3真空渗碳 比气体渗碳节约时间2/3. 4.渗碳后热处理 预冷直接淬火
缓冷一次淬火
缓冷二次淬火
二.钢的渗氮
目的:提高硬度\耐磨性\疲劳性能\抗咬合性 渗氮用钢38CrMoAl 渗氮方法:气体\离子
四、过冷奥氏体转变曲线
1、过冷奥氏体等温转变曲线
A建立 金相法 热分析法 膨胀法 B分析 C影响 碳、合金元素、加热温度、保温时间
2、过冷奥氏体连续冷却转变曲线
第四节 钢的退火与正火
一、退火 (炉冷)
1、完全退火
2、球化退火
3、等温退火
4、均匀化退火
5、去应力退火
二、正火
AC3+30-50℃ 空冷
钢的热处理表面热处理【共48张PPT】

3)用钢:
低碳钢和低碳合金钢。
4)方法: 固体、气体、液体渗碳。
程晓宇
固体渗碳法示意图
—程晓宇
气体渗碳法示意图
程晓宇
5)工艺: 加热温度为900~950℃; 渗碳时间一般为3~9小时;
二) 性质:是一种不改变钢表层分,但改变 表层组织的局部热处理工艺。
工程材料与热加工基础—程晓宇
五)表面淬火用钢:
选用中碳或中碳低合金钢。40、45、40Cr、40MnB等。
六)表面淬火加工的方法: 感应加热( 高、中、工频 )、火 焰加热、电接触加热法等。
第三章钢的热处理表面热处理
工程材料与热加工基础程晓宇
一) 定义:指将工件表面快速加热到淬火温度,迅速冷却,使工件表面得到一定深度的淬硬层,而心部仍保持未淬火状态组织的热处理工艺
三) 工艺特征:通过快速加热使钢的表层奥氏体化,然后急冷,使表层形成马氏体组织,而心部仍保持不变。四) 工艺要求:淬火前—工件应正火或调质 淬火后—应低温回火 目的
M回+Fe3C+A残
低碳钢
9)常用的钢种: 15、20、20Cr、20Mn2、 20CrMnTi、18Cr2Ni4WA等。
工程材料与热加工基础—程晓宇
2.钢的渗氮 ( Nitridation of steel )
1)定义:向钢的表面渗入氮原子的过程。
2)目的:获得具有表硬里韧及抗蚀性能 的零件。
工程材料与热加工基础—
越王勾践剑
春秋晚期越国青铜兵器,出土于湖北江陵楚墓。 长厘米, 剑锷锋芒犀利,锋能割断头发。
工程材料与热加工基础程晓宇
渗碳与渗氮的工艺特点
工程材料与热加工基础—
第3章-热表处理工艺
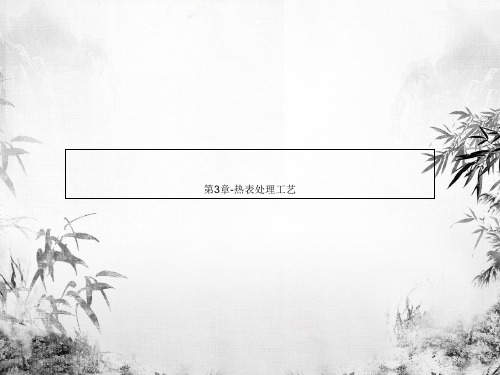
(3) 阳极化
所谓阳极化是指用电化学的方法在铝及铝 合金表面获得一层氧化膜的方法,由于在 处理时零件为阳极,所以称为阳极氧化处 理(阳极化)。
氧化膜的性质: a.多孔:b.硬度高 c.化学稳定性好
d.绝缘性好:e.结合能力好:f.耐高温:
几乎所有的铝合金零件都能氧化。如机械 加工、钣金、部分铸造和焊接等铝制零件。 因此在航空工业、电气工业、各种机械制 造业、日用品工业获得了广泛的应用。
(3) 渗氮
(1)表面淬火
工件
表面淬火是将钢件 表面进行快速加热, 使其表面组织转变 为奥氏体,然后快 速冷却,表面层转 变为马氏体的一种 局部淬火的方法。
冷却水 感应线圈
冷却水
淬火喷水套 进水
图3-17 感应加热淬火示意图
(2)渗碳
( Carburize of steel )
液体渗碳剂 废气 沙封
20钢渗碳缓冷组织 ( 化染 )
580
表层珠光体 + 网状渗碳体; 中层珠光体; 内层铁素体 + 珠光体
(3) 渗氮( Nitridation of steel )
渗氮是将氮原子渗入钢 件表面,形成以氮化物 为主的渗氮层,以提高 渗层的硬度、耐磨性、 抗蚀性、疲劳强度等多 种性能。渗氮种类很多, 有气体渗氮法、盐浴氮 化法、软氮化、离子氮 化等。
(2)钢的磷化处理
钢铁零件在含有锰、铁、锌的磷酸盐溶液中,进 行化学处理,使其表面生成一层难溶于水的磷酸 盐保护膜的方法,叫做磷化处理。
磷化膜的外观由于基体材料及磷化工艺的不同可 由暗灰到黑灰色。磷化膜的主要成分由磷酸盐 Me3(PO4)2或磷酸氢盐(MeHPO4)的晶体组成。 用于涂漆前打底,提高漆膜层的附着力与防腐蚀 能力。
钢的热处理和表面改性资料.pptx

(a)光学显微照片 1300×
(b) 电子显微照片 5000×
第26页/共28页
<=中温转变区
下贝氏体
• 组织特点是渗碳体以细 小颗粒分布于针状铁素 体的内部,显微镜下的 整体形貌呈针状组织
• 铁素体针状细小,没有 方向性,位错密度大, 碳化物分布均匀
• 具有较好的综合机械性 能,热处理中常常用等
钢在加热时的组织转变
• 实际转变温度与相图有所区别
加热时相变温度=>
• 相图只是平衡状态的情况,就是在及其缓慢的冷却或者加热过程中才能达到的状态,在实际钢铁生产 和热冷加工过程中的温度变化较快的条件下
• 实际加热温度都偏高、冷却温度都偏低,加热和冷却速度越大,这种差别越大,这使得钢在热处理时 的临界点偏离了相图中的临界点
• 淬硬性指钢淬火能够达到的最高硬度,主要取决于马氏体的含碳量
• “鼻尖”离纵坐标越远,淬透性越好
• 合金元素
• 含碳量
• 加热温度
淬火温度
第17页/共28页
冷却介质
淬透性及影响因素
温 度
时间
(a)完全淬透; (b)淬透较大厚度; (c)淬透较小厚度
第18页/共28页
钢的回火
• 钢件淬火后, 为了消除内应力并获得所要求的组织和性能, 将其加热到Ac1以下某一温度, 保温一定时间, 然 后冷却到室温 • 低温回火(150~250℃) • 中温回火(350~500℃) • 高温回火(500~650℃)
• 影响奥氏体形成速度的因素
• 加热速度与加热温度:温度;速度 温
奥氏体化越快
度
• 含碳量和合金元素:C 转变
• 合金元素不影响基本过程,但影响转变速 度
机械制造基础12_金属的热处理及材料改性

机械制造基础12_金属的热处理及材料改性金属的热处理是指通过控制金属的温度和加热和冷却速率来改善其物理和机械性能的过程。
金属的热处理可以通过改变金属的晶体结构、颗粒结构和相变来实现。
金属的热处理主要包括退火、正火、淬火、回火和低温处理等过程。
退火是将金属加热至恰当的温度,然后在适当的速率下冷却,以使金属的晶体结构发生变化,消除应力和硬化。
退火可以提高金属的塑性和韧性。
正火是将金属加热至适当温度,然后在空气中冷却。
正火可以提高金属的硬度和强度。
淬火是将金属加热到一定温度,然后迅速以较快的速度冷却至室温。
淬火可以使金属产生硬脆性,提高金属的硬度和强度,但会减少其韧性。
回火是将金属在淬火后加热至一定温度,然后在适当速率下冷却。
回火可以消除金属的内应力,改善其硬度和韧性的平衡。
低温处理是将金属在低于室温的温度下处理一段时间。
低温处理可以提高金属的硬度和强度,改善金属的耐磨和耐腐蚀性。
金属的热处理可以在一定程度上改变其物理、化学和机械性能。
例如,通过退火处理,过热退火可以使金属的晶体粗大化,提高金属的塑性和韧性;通过正火处理,可以使金属的组织细化,提高金属的硬度和强度;通过淬火处理,可以使金属产生马氏体,提高金属的硬度和强度,但会降低其韧性;通过回火处理,可以消除金属的内应力,提高金属的韧性和抗冲击性。
材料改性是指利用各种物理和化学方法,通过改变材料的结构和组织,使其获得更好的性能和适应特定应用的过程。
材料改性主要包括合金化、快速凝固、化学改性等方法。
合金化是将两种或两种以上的金属或非金属元素混合在一起,并经过一系列的加热、冷却和处理工序,形成合金。
合金化可以改变金属的晶体结构、晶粒大小和相变,以提高金属的硬度、强度和耐腐蚀性。
快速凝固是将金属液体迅速冷却至较低温度,使其形成非晶态结构或细小的晶体结构。
快速凝固可以提高金属的硬度、韧性和磁、电等性能。
化学改性是通过在材料表面形成化学层或化学反应,使材料获得新的性能。
金属表面化学热处理

第三节金属表面化学热处理1、什么叫金属表面化学热处理?表面热处理是指仅对零部件表层加热、冷却,从而改变表层组织和性能而不改变成分的一种工艺,是最基本、应用最广泛的材料表面改性技术之一。
金属表面化学热处理是利用元素扩散性能,使合金元素渗入金属表层的一种热处理工艺。
2、工艺过程首先将工件置于含有渗入元素的活性介质中加热到一定温度,使活性介质通过分解并释放出欲渗入元素的活性原子、活性原子被表面吸附并溶入表面、溶入表面的原子向金属表层扩散渗入形成一定厚度的扩散层,从而改变表层的成分、组织和性能。
3、化学热处理的基本过程化学热处理包括三个基本过程,即①化学渗剂分解为活性原子或离子的分解过程;②活性原子或离子被钢件表面吸收和固溶的吸收过程;③被渗元素原子不断向内部扩散的扩散过程。
4、金属表面化学热处理的特点?和表面淬火不同,化学热处理后的工件表面不仅有组织的变化,而且也有化学成分的变化。
5、金属表面化学热处理的目的?一、提高金属表面的强度、硬度和耐磨性。
如渗氮、渗硼等. 渗氮硬度可达950HV~~1200HV,渗硼硬度可达1400HV~~2000HV.常用的硬度单位有布氏硬度、洛氏硬度和维氏硬度等.什么叫渗氮?渗氮,就是把工件置于含有氮原子的介质中加热到一定温度,保温一段时间后,在工件表面形成一层坚硬的渗氮层。
说白了就是在一定温度下一定介质中使氮原子渗入工件表层。
二、提高材料疲劳强度。
如渗氮、渗硼、渗铬。
三、使金属表面具有良好的抗粘着、抗咬合的能力和降低摩擦系数。
如渗硫等。
四、提高金属表面的耐蚀性。
如渗氮、渗铝等。
5、金属表面化学热处理的性能?化学热处理后的钢件表面可以获得比表面淬火所具有的更高的硬度、耐磨性和疲劳强度;心部在具有塑性和韧性的同时,还可获得较高的强度。
6、化学热处理的种类i.固体法。
(粉末填充法、膏剂涂覆法、电热旋流法、覆盖层扩散法)ii.液体法(包括盐浴法、电解盐浴法、水溶液电解法等)iii.气体法(固体气体法、间接气体法、流动粒子炉法)iv.等离子法。
金属热处理及表面改性优秀课件

钢坯加热
第一步 奥氏体晶核形成:首先在与Fe3C相界形核。 第二步 奥氏体晶核长大: 晶核通过碳原子的扩散向
和Fe3C方向长大。
第三步 残余Fe3C溶解: 铁素体的成分、结构更接近于 奥氏体,因而先消失。残余的Fe3C随保温时间延长继 续溶解直至消失。
金属热处理及表面改性优秀课件
3.1 钢的热处理原理
1、热处理:是指将钢在固态下加热、保温和冷却, 以改变钢的组织结构,获得所需要性能的一种工艺.
为简明表示热处理 的基本工艺过程, 通常用温度—时间 坐标绘出热处理工 艺曲线。
热处理是一种重要的加工工艺. 在机床制造中约60-70%的零
件要经过热处理。 在汽车、拖拉机制造业中需
热处理的零件达70-80%。
模具、滚动轴承100%需经过 热处理。
总之,重要零件都需适当热处 理后才能使用。
2、热处理特点: 热处理区 别于其他加工工艺如铸造、 压力加工等的特点是只通
过改变工件的组织来改变
性能,而不改变其形状。
铸造
3、热处理适用范围: 只适用于固态下发生
相变的材料,不发生
两线之间及Ms 与Mf之间为转 变区。
温 度
A1
A
过
A→P
冷
P
奥
转变终了线
氏
B
体
A→B
转变开始线
MS
A→M
Mf
M 时间
2、C 曲线的分析 ⑴ 转变开始线与纵
坐标之间的距离为 孕育期。
孕育期越小,过冷 奥氏体稳定性越小.
孕育期最小处称C 曲线的“鼻尖”。 碳钢鼻尖处的温度 为550℃。
在鼻尖以上, 温度较 高,相变驱动力小.
耐候钢的稳定化处理方式
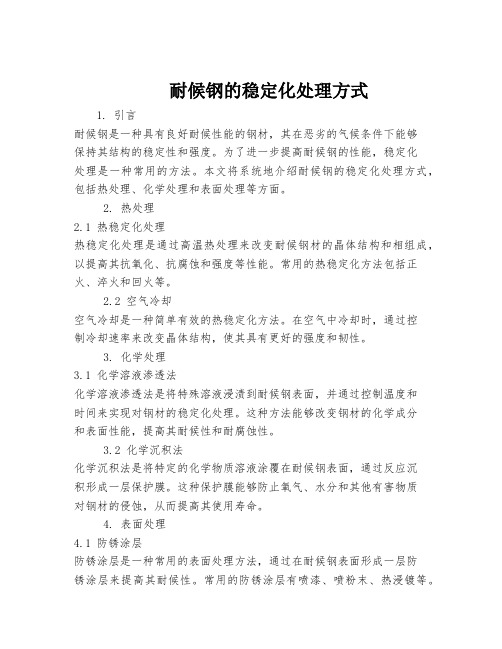
耐候钢的稳定化处理方式1. 引言耐候钢是一种具有良好耐候性能的钢材,其在恶劣的气候条件下能够保持其结构的稳定性和强度。
为了进一步提高耐候钢的性能,稳定化处理是一种常用的方法。
本文将系统地介绍耐候钢的稳定化处理方式,包括热处理、化学处理和表面处理等方面。
2. 热处理2.1 热稳定化处理热稳定化处理是通过高温热处理来改变耐候钢材的晶体结构和相组成,以提高其抗氧化、抗腐蚀和强度等性能。
常用的热稳定化方法包括正火、淬火和回火等。
2.2 空气冷却空气冷却是一种简单有效的热稳定化方法。
在空气中冷却时,通过控制冷却速率来改变晶体结构,使其具有更好的强度和韧性。
3. 化学处理3.1 化学溶液渗透法化学溶液渗透法是将特殊溶液浸渍到耐候钢表面,并通过控制温度和时间来实现对钢材的稳定化处理。
这种方法能够改变钢材的化学成分和表面性能,提高其耐候性和耐腐蚀性。
3.2 化学沉积法化学沉积法是将特定的化学物质溶液涂覆在耐候钢表面,通过反应沉积形成一层保护膜。
这种保护膜能够防止氧气、水分和其他有害物质对钢材的侵蚀,从而提高其使用寿命。
4. 表面处理4.1 防锈涂层防锈涂层是一种常用的表面处理方法,通过在耐候钢表面形成一层防锈涂层来提高其耐候性。
常用的防锈涂层有喷漆、喷粉末、热浸镀等。
4.2 表面改性表面改性是通过在耐候钢表面进行物理或化学处理来改变其表面特性。
常见的方法包括阳极氧化、电镀等,这些方法能够增加钢材的硬度、抗磨损性和抗腐蚀性。
5. 结论耐候钢的稳定化处理是提高其耐候性能的重要手段。
热处理、化学处理和表面处理是常用的稳定化处理方式。
热稳定化处理能够改变钢材的晶体结构和相组成,提高其抗氧化、抗腐蚀和强度等性能。
化学处理和表面处理则通过改变钢材的化学成分和表面特性,形成保护膜或防锈涂层,提高其耐候性。
在实际应用中,可以根据具体要求选择适合的稳定化处理方式来提高耐候钢材的性能。
- 1、下载文档前请自行甄别文档内容的完整性,平台不提供额外的编辑、内容补充、找答案等附加服务。
- 2、"仅部分预览"的文档,不可在线预览部分如存在完整性等问题,可反馈申请退款(可完整预览的文档不适用该条件!)。
- 3、如文档侵犯您的权益,请联系客服反馈,我们会尽快为您处理(人工客服工作时间:9:00-18:30)。
(b) 索氏体 8000×
(c)屈氏体 8000 ×
二. 中温转变区(550℃ ~Ms230oC,贝氏体转变区) 贝氏体(B)是细小碳化物分布在碳过饱和的铁 B
素体基体上的混合物
奥氏体向贝氏体的转变属于半扩散型转变,
铁原子不扩散而碳原子有一定扩散能力
350~550℃区间形成的称为上贝氏体(羽毛状贝氏体)
冷却方式
¤ 等温冷却:钢由加热温度迅速冷却到临界点Ac1以下的既定
温度,保温一段时间,进行恒温转变,然后再冷却至室温
¤ 连续冷却:钢由加热温度连续冷却到室温,在临界点Ac1
以下进行连续转变
过冷奥氏体:在A1( 727 °C )温度下尚未发生转变
的奥氏体。
等温转变曲线(C曲线或TTT图):钢在不同温
组织特点:渗碳体分布于条状铁素体之间,显微镜下的整体
形貌呈羽毛状
B
350℃~Ms区间内形成的称为下贝氏体(针状贝氏体) 组织特点:渗碳体以细小颗粒分布于针状铁素体的内部,显
微镜下的整体形貌呈针状组织
B
三. 低温转变区(Ms230~Mf-50oC) (马氏体转变区) B
马氏体(M):碳在α-Fe中的过饱和间隙固溶体。过饱 和碳使α-Fe 的晶格发生很大畸变, 产生很强的固溶强 化;
从宏观上看A的转变:晶格发生变化;晶体含碳量变化
相图上组织和相的转变是可逆的
以共析钢为例:加热到727oC(A1)以上,珠 光体转变成奥氏体。(三个阶段)
奥氏体形核与 长大
残余渗碳体溶 解
奥氏体成分均 匀化
(a)
(b)
(c)
(d)
三. 影响奥氏体形成速度的因素
1. 加热温度与加热速度
同一个奥氏体化状态,较低温度较长时间的加热得到; 较高温度较短时间的加热得到
温度升高,加热速度增大´奥氏体化越快 2.含碳量和合金元素
含碳量增加´奥氏体转变速度增加 合金元素不影响奥氏体转变的基本过程,但影响
转变速度:Co和Ni加快,Cr、Mo、V减慢,Si、Mn、 Al基本不影响
四. 影响奥氏体晶粒度的因素
1. 加热温度与速度和保温时间
¾ 加热温度升高,A晶粒急剧长大;有利于A的形成和均匀化; ¾ 加热速度越快,晶粒越细; ¾ 保温时间延长,A晶粒粗大;只需使材料均匀化的最短时间-
3.1.1 钢在加热时的组织转变
一.相图和实际转变温度
实际转变温度与相图有所区别
¤ 相图只是平衡状态的情况,就是在及其缓慢的冷 却或者加热过程中才能达到的状态,在实际的钢铁 生产和热冷加工过程中,温度变化较快 ¤ 实际加热温度都偏高、 冷却温度都偏低,加热 和冷却速度越大,这种 差别越大,这使得钢在 热处理时的临界点偏离 了相图中的临界点
第3章 钢的热处理 和表面改性
教学目标 1. 熟悉钢在热处理过程中的组织转变及转变产物的形 态和性能,等温转变动力学曲线; 2. 掌握退火、正火、淬火和回火常规热处理工艺的特 点、目的及应用; 3. 理解钢的表面热处理强化、化学热处理强化; 4. 了解钢的表面处理改性。
重点 1. 等温转变动力学曲线(C曲线)的意义和应用。
2) 变温转变:在Ms~Mf范围内完成,只有在不 断降温条件下才能使M转变继续进行
3) 转变不完全性:通常情况下,即使降到Mf 下,也不能得到100%M,留有未转变的残余A, 塑性、韧性增加,硬度下降;但不稳定,可能 引起尺寸的变化
Байду номын сангаас
2 . 马氏体的形态
根据钢中的含碳量不同,马氏体可分为高碳马氏 体和低碳马氏体
适宜保温时间
2.含碳量:在一定范围内,随含碳量的增加,奥氏体晶粒长大
的倾向增大,但是当含碳量超过某一限度,晶粒变细小
3. 合金元素
¾ 本质细晶粒钢:添加Al, Ti, W, Mo, V, Zr, Nb, Ta等元素, 晶粒长大倾向小;
¾ 本质粗晶粒钢:添加Si, Mn等元素,晶粒长大倾向大;
3.1.2 钢在冷却时的组织转变
Á 高碳马氏体:主要是在高碳钢和高碳合金钢 中,显微形貌呈针状(或者竹叶状),故又称针 状马氏体; 性能:高碳马氏体的硬度高、塑性和韧性很差
Á 低碳马氏体:主要是在低碳钢和低碳合金钢
中,显微形貌呈板条状,故又称板条马氏体。
度下的等温转变动力学曲线,通过实验绘制。共析钢的过冷奥 氏体在不同温度下发生等温转变时,按转变温度的高低可以得 到珠光体、索氏体、屈氏体、上贝氏体、下贝氏体和马氏体等
TTT:Time-Temperature-Transformation
共
析
钢
P
过
冷
A
的
贝氏体
等
温
转
变
曲
线
图
马氏体
一. 高温转变区(P转变区)(A1~550℃) B
3.1 钢在热处理时的组织转变
热处理:将固态金属以一定的升温速度加热 到既定的温度,保温一定时间,再以一定的降温 速度冷却的工艺方法 目的:通过改变钢的组织结构来改善金属零 件的使用性能和工艺性能 工况:过程装备中的许多构件和零部件要进 行热处理,提高制品质量,延长使用寿命,改善 加工性能
¾ 铁和碳原子都不能进行扩散,仅发生晶格改变,非 扩散型转变。
¾ 铁原子沿奥氏体一定晶面, 集体地(不改变相互位置 关系)作一定距离的移动(不超过一个原子间距), 使面心 立方晶格改组为体心正方晶格,碳原子原地不动,过 饱和地留在新组成的晶胞中,增大了其正方度c/a ;
1. 马氏体转变特点
1) 非扩散型转变:仅仅是点阵的改组,没有化 学成分的改变与扩散,无孕育期,晶粒度取决 于A的晶粒度
A1~650 : 珠光体(P) 650~600℃:索氏体(S) 600~550℃:屈氏体(T)
片层逐渐变细 硬度、强度、塑性上升
渗碳体呈层片状分布在铁素体基体上,转变温度越 低,层间距越小 奥氏体向珠光体的转变为扩散型的形核、长大过程, 是通过碳、铁的扩散和晶体结构的重构来实现的
(a)珠光体 3800×
二. 奥氏体的形成
1.形核与长大:晶核优先形成在铁素体与渗碳体的界 面处,因为界面处成分较不均匀,原子排列最不规 则,为产生A准备了浓度起伏、结构起伏的有利条件
2.剩余渗碳体溶解:部分没有溶解的渗碳体在继续保 温过程中逐渐溶入奥氏体A而消失
3.奥氏体成分的均匀化:渗碳体完全溶解时,奥氏体A 中碳的浓度很不均匀,要进一步延长保温时间,使 碳充分扩散从而达到奥氏体A的成分均匀化