仓库来料收货系统操作流程
1.仓库收货流程及注意事项
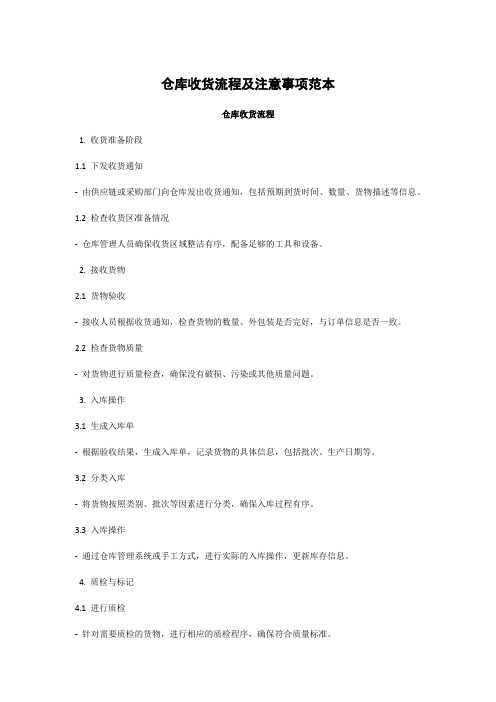
仓库收货流程及注意事项范本仓库收货流程1. 收货准备阶段1.1 下发收货通知-由供应链或采购部门向仓库发出收货通知,包括预期到货时间、数量、货物描述等信息。
1.2 检查收货区准备情况-仓库管理人员确保收货区域整洁有序,配备足够的工具和设备。
2. 接收货物2.1 货物验收-接收人员根据收货通知,检查货物的数量、外包装是否完好,与订单信息是否一致。
2.2 检查货物质量-对货物进行质量检查,确保没有破损、污染或其他质量问题。
3. 入库操作3.1 生成入库单-根据验收结果,生成入库单,记录货物的具体信息,包括批次、生产日期等。
3.2 分类入库-将货物按照类别、批次等因素进行分类,确保入库过程有序。
3.3 入库操作-通过仓库管理系统或手工方式,进行实际的入库操作,更新库存信息。
4. 质检与标记4.1 进行质检-针对需要质检的货物,进行相应的质检程序,确保符合质量标准。
4.2 标记货物-对已完成验收和质检的货物进行标记,例如打上标签、贴上标识,以便后续的查找和管理。
5. 更新库存和通知相关部门5.1 更新库存信息-确保库存系统中的信息与实际入库情况一致,包括数量、状态等。
5.2 通知相关部门-向相关部门发送入库通知,以便及时更新相关记录和通知其他相关方。
注意事项1. 准确性确保验收过程准确无误,货物信息与订单信息一致。
2. 质量检查对于需要质检的货物,严格执行质检标准,确保货物质量符合要求。
3. 安全操作在搬运、入库过程中,确保操作人员遵循安全操作规程,防止货物损坏和人员受伤。
4. 记录完整性入库单和其他记录要详细完整,以便后续追溯和管理。
5. 及时通知及时向相关部门通知入库情况,保持信息畅通。
6. 环境整洁保持收货区域和入库区域的整洁有序,方便操作和管理。
家具原料仓库收发货流程,收货、发货、销售类出库流程

家具原料仓库收发货流程,收货、发货、销售类出库流程家具原料仓库收发货流程1. 收货流程为确保家具原料仓库的有效管理和及时补充库存,以下是家具原料仓库收货流程的步骤:步骤一:接收货物当供应商将原料运送到仓库时,仓库管理员应在货车到达的同时进行接收。
确保在货物到达之前,仓库管理员已准备好所有必要的文件和记录。
步骤二:验收货物仓库管理员应对收到的货物进行验收,以确保货物的数量和质量与订单相匹配。
验收过程包括:- 检查货物的数量,与订单或提货单上的数量进行对比。
- 检查货物的包装是否完好,以确保在运输过程中没有受到损坏。
- 检查货物的质量和规格,以确认其符合预期标准。
步骤三:记录货物信息管理员在验收后应立即记录货物信息。
这些信息包括:- 货物名称和型号- 货物数量- 生产日期和批次号(如果适用)- 供应商名称和联系信息- 货物的存放位置步骤四:入库操作一旦货物验收并记录完毕,管理员将货物发往合适的存放位置。
在仓库中,货物应分门别类、有序地存放,并确保易于查找和管理。
2. 发货流程为了满足客户需求并及时处理订单,以下是家具原料仓库发货流程的步骤:步骤一:接收订单家具原料仓库应定期检查订单系统以接收新的出货请求。
一旦收到新的订单,仓库管理员应确认其有效性,并准备相应的发货流程。
步骤二:备货准备管理员应在发出货物之前,检查库存以确保有足够的原料进行发货。
如果库存不足,管理员应尽快与采购部门联系,以补充所需的原料。
步骤三:打包和标记管理员应在发货前,正确地打包和标记货物。
这包括使用耐用的包装材料,并在包装上标注有关货物名称、数量、收件人信息和任何其他必要的标识。
步骤四:出库操作一旦货物准备就绪,管理员将货物发出。
在进行出库操作时,管理员应记录出库的货物信息,包括货物名称、数量、接收人和出库日期。
3. 销售类出库流程在家具原料仓库发生销售类出库时,应遵循以下流程:步骤一:接收销售订单家具原料仓库应根据销售订单系统,接收销售类出库的请求。
仓储配送sop操作流程
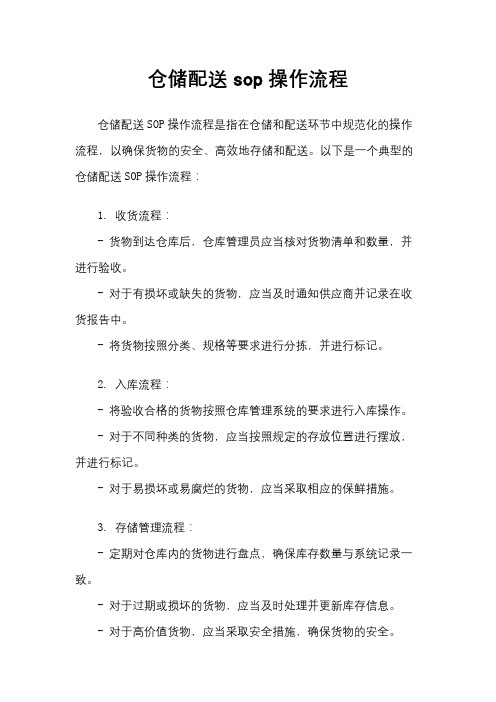
仓储配送sop操作流程仓储配送SOP操作流程是指在仓储和配送环节中规范化的操作流程,以确保货物的安全、高效地存储和配送。
以下是一个典型的仓储配送SOP操作流程:1. 收货流程:- 货物到达仓库后,仓库管理员应当核对货物清单和数量,并进行验收。
- 对于有损坏或缺失的货物,应当及时通知供应商并记录在收货报告中。
- 将货物按照分类、规格等要求进行分拣,并进行标记。
2. 入库流程:- 将验收合格的货物按照仓库管理系统的要求进行入库操作。
- 对于不同种类的货物,应当按照规定的存放位置进行摆放,并进行标记。
- 对于易损坏或易腐烂的货物,应当采取相应的保鲜措施。
3. 存储管理流程:- 定期对仓库内的货物进行盘点,确保库存数量与系统记录一致。
- 对于过期或损坏的货物,应当及时处理并更新库存信息。
- 对于高价值货物,应当采取安全措施,确保货物的安全。
4. 出库流程:- 根据客户订单,仓库管理员应当按照要求进行货物的拣选和打包。
- 对于不同客户的订单,应当进行分类处理,并进行标记。
- 出库前应当进行货物的质量检查,确保货物完好无损。
5. 配送流程:- 根据订单要求,选择合适的配送方式和车辆。
- 对于不同地区的配送,应当进行路线规划,并确保配送时间准确。
- 配送过程中应当及时更新客户信息,并保持与客户的沟通。
通过以上的仓储配送SOP操作流程,可以有效地提高仓储和配送的效率,减少错误和损失,确保货物的安全和及时到达客户手中。
同时,规范化的操作流程也有助于提升仓储配送的管理水平,提高客户满意度。
仓储收货作业的流程
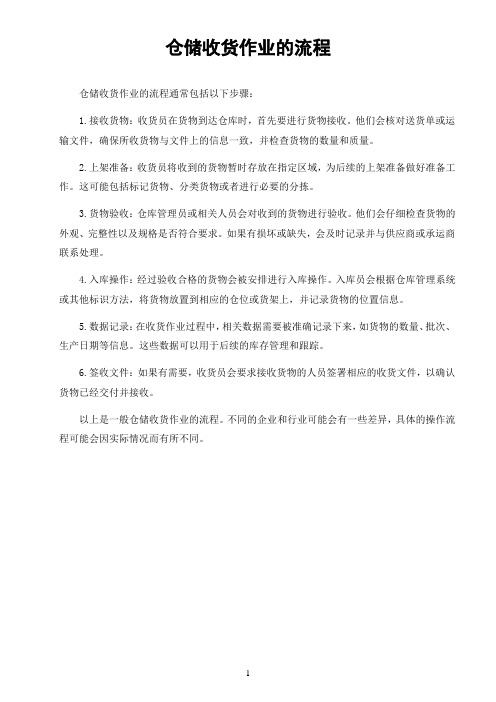
仓储收货作业的流程
仓储收货作业的流程通常包括以下步骤:
1.接收货物:收货员在货物到达仓库时,首先要进行货物接收。
他们会核对送货单或运输文件,确保所收货物与文件上的信息一致,并检查货物的数量和质量。
2.上架准备:收货员将收到的货物暂时存放在指定区域,为后续的上架准备做好准备工作。
这可能包括标记货物、分类货物或者进行必要的分拣。
3.货物验收:仓库管理员或相关人员会对收到的货物进行验收。
他们会仔细检查货物的外观、完整性以及规格是否符合要求。
如果有损坏或缺失,会及时记录并与供应商或承运商联系处理。
4.入库操作:经过验收合格的货物会被安排进行入库操作。
入库员会根据仓库管理系统或其他标识方法,将货物放置到相应的仓位或货架上,并记录货物的位置信息。
5.数据记录:在收货作业过程中,相关数据需要被准确记录下来,如货物的数量、批次、生产日期等信息。
这些数据可以用于后续的库存管理和跟踪。
6.签收文件:如果有需要,收货员会要求接收货物的人员签署相应的收货文件,以确认货物已经交付并接收。
以上是一般仓储收货作业的流程。
不同的企业和行业可能会有一些差异,具体的操作流程可能会因实际情况而有所不同。
1。
仓库sop怎么操作流程
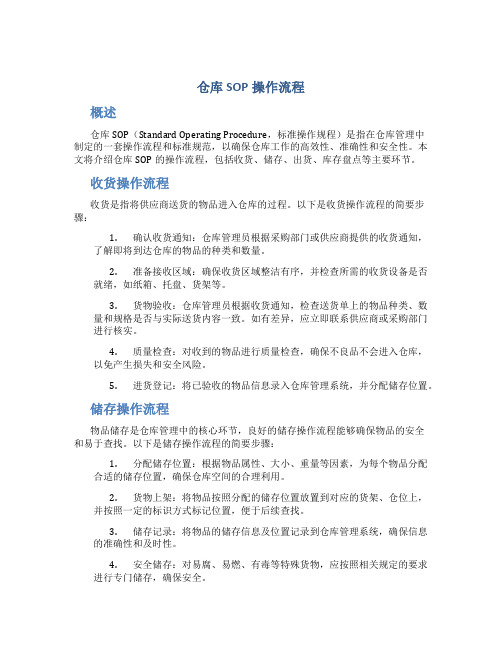
仓库SOP操作流程概述仓库SOP(Standard Operating Procedure,标准操作规程)是指在仓库管理中制定的一套操作流程和标准规范,以确保仓库工作的高效性、准确性和安全性。
本文将介绍仓库SOP的操作流程,包括收货、储存、出货、库存盘点等主要环节。
收货操作流程收货是指将供应商送货的物品进入仓库的过程。
以下是收货操作流程的简要步骤:1.确认收货通知:仓库管理员根据采购部门或供应商提供的收货通知,了解即将到达仓库的物品的种类和数量。
2.准备接收区域:确保收货区域整洁有序,并检查所需的收货设备是否就绪,如纸箱、托盘、货架等。
3.货物验收:仓库管理员根据收货通知,检查送货单上的物品种类、数量和规格是否与实际送货内容一致。
如有差异,应立即联系供应商或采购部门进行核实。
4.质量检查:对收到的物品进行质量检查,确保不良品不会进入仓库,以免产生损失和安全风险。
5.进货登记:将已验收的物品信息录入仓库管理系统,并分配储存位置。
储存操作流程物品储存是仓库管理中的核心环节,良好的储存操作流程能够确保物品的安全和易于查找。
以下是储存操作流程的简要步骤:1.分配储存位置:根据物品属性、大小、重量等因素,为每个物品分配合适的储存位置,确保仓库空间的合理利用。
2.货物上架:将物品按照分配的储存位置放置到对应的货架、仓位上,并按照一定的标识方式标记位置,便于后续查找。
3.储存记录:将物品的储存信息及位置记录到仓库管理系统,确保信息的准确性和及时性。
4.安全储存:对易腐、易燃、有毒等特殊货物,应按照相关规定的要求进行专门储存,确保安全。
出货操作流程出货是指从仓库中将货物发运给客户的过程。
以下是出货操作流程的简要步骤:1.接收出货通知:仓库管理员根据销售部门或客户提供的出货通知,了解需要出货的物品种类、数量和出货时间等要求。
2.准备出货单:根据出货通知,填写出货单并确认物品的储存位置,方便后续的查找和装载。
3.物品拣选:根据出货单的要求,仓库人员按照货位上的物品信息进行拣选,确保出货物品的准确性。
仓库收货、发货、退货、领料流程

仓库收货、发货、退货、领料流程仓库是企业的重要组成部分,对于企业的物流运作起着至关重要的作用。
其中,仓库的收货、发货、退货、领料流程是核心环节,直接影响到企业的产品生产和市场销售。
本文将从以下四个方面详细介绍仓库的收货、发货、退货、领料流程。
一、仓库收货流程1. 物料预定收货环节的第一步是接收到客户的预订或销售订单,并将订单信息录入到仓库管理系统中。
2. 准备收货在确认订单后,仓库管理员需要开始准备收货。
这通常包括检查货物数量和准备接收货物的空间。
3. 检查货物在收到货物之前,需要进行外观检查以确定货物是否符合规格和订单要求。
如果有任何瑕疵或问题,应及时与客户沟通。
4. 货物记录对于每一批货物,都需要进行详细记录,包括货物数量、重量、生产批次、生产日期等信息,并更新仓库管理系统。
5. 存储质量控制收到货物后,需要将货物放置在适当的区域,并按照规定的温度、湿度和其他条件进行存储,以确保货物质量。
6. 关注库存在货物存放之后,需要监控库存情况,及时更新库存信息并进行调整。
二、仓库发货流程1. 接收出货指令在收到出货指令后,仓库管理员需要在仓库管理系统中查找相应的订单。
2. 准备包装和配送仓库管理员需要准备包装材料并对货物进行包装,将货物交付给承运商并跟踪货物的运送过程。
3. 打印标签和运单在出货前,需要打印标签和运单,并将其附在相关货物上。
标签和运单上应列出货物名称、数量、批次号和出货日期等信息。
4. 货物出库在出货时,对货物进行确认,确保货物的数量和质量符合订单要求,同时在仓库管理系统中更新库存信息。
5. 客户签收在货物到达客户手中之后,需要进行客户签收,并将签收单返还给仓库管理人员,作为出库的最终记录。
三、仓库退货流程1. 了解客户要求在接到客户退货请求后,需要了解退货原因和退货商品的数量。
2. 记录相关信息针对每个退货请求,需要进行详细的记录,包括客户姓名、退货原因、退货商品数量和生产批次等信息,更新仓库管理系统。
简述仓库收料入库流程及内容

简述仓库收料入库流程及内容英文版A Brief Overview of the Warehouse Receipt and Storage ProcessThe warehouse receipt and storage process is a crucial aspect of supply chain management, ensuring the efficient and organized handling of goods. Here, we outline the key steps involved in this procedure.Receiving the Goods: The first step involves the receipt of goods from suppliers or other sources. This involves checking the quantity, quality, and condition of the items.Documentation Verification: Documents such as invoices, delivery notes, and purchase orders are verified against the received goods. This ensures accuracy and traceability.Quality Inspection: A quality check is performed to ensure that the goods meet the specified standards. This may involve physical inspection, sampling, or testing.Inventory Recording: The received goods are then recorded in the warehouse management system, updating inventory levels and stock locations.Storage Allocation: Based on the nature and requirements of the goods, suitable storage locations are allocated. This ensures that the goods are stored safely and accessibly.Labeling and Marking: Goods are labeled and marked to facilitate easy identification and tracking. This includes barcodes, SKU numbers, and other relevant information.Maintenance and Monitoring: Regular maintenance and monitoring of stored goods are performed to ensure their integrity and condition. This may involve temperature control, humidity monitoring, and pest control measures.By following this structured process, the warehouse can ensure the smooth and efficient handling of goods, maintaining high levels of accuracy, traceability, and safety.简述仓库收料入库流程及内容仓库收料入库是供应链管理中的关键环节,确保了货物的高效和有组织处理。
仓库收货流程

仓库收货流程仓库收货流程涉及到多个环节,包括货物到仓、验收、入库等。
下面是一个较为详细的仓库收货流程。
一、货物到仓1.当货物到达仓库前,负责接收货物的仓库管理员应提前做好准备工作,如准备好收货工具(如搬运工具、测量工具等)和收货记录表。
2.货物运抵仓库后,仓库管理员应及时与供货商核对货物数量和品质是否与订货单一致。
如果发现有问题,应及时与供货商沟通并解决。
3.确认货物数量和品质无误后,仓库管理员应将货物进行分拣,以便后续的验收工作。
二、验收货物1.验收人员应按照仓库规定的流程和标准进行验收工作。
首先,对货物进行外观检查,包括检查货物包装是否完好无损、标签是否清晰可辨认等。
2.验收人员还应对货物进行计量和称重,以确保货物的数量和重量与供货商的记录一致。
3.对于特殊货物(如易碎品、危险品等),验收人员应按照相关安全规定进行操作,并记录相关信息。
4.如果在验收过程中发现货物有质量问题或数量不符,验收人员应及时记录并与供货商联系,协商解决方案。
三、入库货物1.经过验收合格的货物应及时进行入库操作。
仓库管理员应根据不同种类和属性的货物分门别类地进行入库,便于后续的仓储管理。
2.在入库操作中,仓库管理员应按照仓库的存储规则和标准进行操作,确保货物放置整齐、稳固,并利用好仓储空间。
3.在入库过程中,仓库管理员应对货物进行二次核对,以确保入库的货物与验收的货物一致。
同时,应将货物的信息录入到仓库管理系统中,便于日后的查询和管理。
四、记录和报告1.在收货流程中,仓库管理员应及时记录相关信息,如货物的收货时间、供货商等信息。
2.将货物的收货信息整理成报告,上报给上级领导或相关部门。
这些报告可以作为仓库运营情况的参考依据,也可以作为与供货商沟通和纠纷处理的依据。
以上是一个标准的仓库收货流程,不同企业的仓库收货流程可能会有所不同,具体的操作步骤和标准应根据企业的实际情况进行调整。
仓库收货流程的规范化和有效执行,对于保证货物质量和数量一致,提高仓储管理效率和准确性,具有重要的意义。
sop仓库管理操作流程

SOP仓库管理操作流程
一、仓库入库操作流程
1.收货确认:收到货物后,核对物料清单,确保无误。
2.分类登记:将货物按照分类进行登记,标明货物名称、数量、生产日
期等信息。
3.入库存放:将货物按照分类、尺寸等特征放置到指定位置,并记录存
放位置信息。
4.入库盘点:完成入库后,进行盘点确认,确保库存信息准确无误。
二、仓库出库操作流程
1.领料申请:根据需求部门需求,填写领料申请单,并核对申请物料信
息。
2.出库操作:按照领料单信息,到仓库取货,核对物料信息,并记录出
库数量。
3.物料发放:发放物料给领料部门,确认领料部门签收。
4.出库记录:记录出库信息,包括出库数量、日期、领料部门等。
三、库存管理操作流程
1.定时盘点:每日对仓库进行盘点,核对实际库存与系统库存是否一致。
2.库存调整:发现库存异常时,及时调整库存信息,确保库存准确。
3.超期处理:定期检查库存中的物料是否超期,做好超期物料的处理工
作。
4.库存报表:定期生成库存报表,分析库存情况,为后续采购和管理提
供参考依据。
以上即为SOP仓库管理操作流程,通过严谨的操作和规范流程,能有效提高仓库管理效率,降低出错率。
纺织原料仓库收发货流程,收货、发货、销售类出库流程
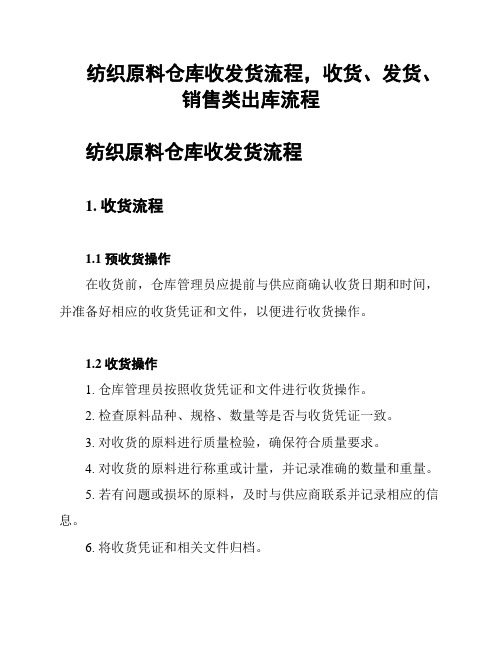
纺织原料仓库收发货流程,收货、发货、销售类出库流程纺织原料仓库收发货流程1. 收货流程1.1 预收货操作在收货前,仓库管理员应提前与供应商确认收货日期和时间,并准备好相应的收货凭证和文件,以便进行收货操作。
1.2 收货操作1. 仓库管理员按照收货凭证和文件进行收货操作。
2. 检查原料品种、规格、数量等是否与收货凭证一致。
3. 对收货的原料进行质量检验,确保符合质量要求。
4. 对收货的原料进行称重或计量,并记录准确的数量和重量。
5. 若有问题或损坏的原料,及时与供应商联系并记录相应的信息。
6. 将收货凭证和相关文件归档。
1.3 入库操作1. 按照收货凭证和文件,将原料送至相应库区。
2. 仓库管理员将原料按照规定的标识码放置于指定位置。
3. 对入库的原料进行登记,包括品种、规格、数量、重量等信息。
4. 更新库存管理系统中的相应信息。
5. 若有特殊要求的原料,需按照要求进行分类和标识。
2. 发货流程2.1 发货准备1. 仓库管理员根据销售订单或发货通知单进行发货准备,并准备好相应的出库凭证和文件。
2. 检查库存情况,确保所需发货的原料充足。
2.2 发货操作1. 仓库管理员按照出库凭证和文件进行发货操作。
2. 针对出库的原料进行称重或计量,并记录准确的数量和重量。
3. 对发货的原料进行质量检验,确保符合质量要求。
4. 对发货的原料进行包装,确保在运输过程中不受损。
5. 若有问题或损坏的原料,及时与销售部门联系并记录相应的信息。
6. 将发货凭证和相关文件归档。
2.3 出库操作1. 按照出库凭证和文件,将原料从库区中取出。
2. 根据发货单上的信息,将原料装载到相应的运输工具上。
3. 更新库存管理系统中的相应信息。
4. 根据发货方式,完成相应的运输操作。
3. 销售类出库流程3.1 销售类出库准备1. 销售部门提供发货通知单或销售订单。
2. 仓库管理员根据发货通知单或销售订单准备出库凭证和文件。
3.2 销售类出库操作1. 仓库管理员按照出库凭证和文件进行出库操作。
仓库各环节运作流程图PPT

清点归位 记录料卡
入账 分发单据
送货单 送货单 报检单 退货单 特采标签
台账 料卡
2.发货作业流程图
部门 PMC 仓库
生产部仓库 生产部仓库
仓库 仓库 仓库
仓库
流程图演示 生产套料单 备料 清点数量 单据签字 料卡记录 分发单据 系统扣帐 单据归档
使用表单 生产套料单 生产套料单 生作业流程 三.退货作业流程 四.成品入库流程 五.成品出库流程 六.单据整理 七.盘点作业流程 八.仓库重要注意事项
1.收货作业流程图
部门
流程图演示
使用表单
采购部
采购订单
采购订单
供应商 收货组
品管采购 仓库
供应商交货 清点收货
记录报检
检验 OK
物料入库
退回 特采
出库单
6.单据整理作业流程图
单据类型
送货单
收货人核对单据 确认签字
录单员录单编号
调拨单 加工厂点数签字 录单员录单编号
退货单 录单员录单 供应商签字确认
按供应商及单号 顺序整理
按加工厂、单号 及日期顺序整理
按供应商及单 号顺序整理
摆放整齐按单据分类归档
7.盘点作业流程
①仓库接到财务部盘点通知后,按照盘点计划从ERP 系统导出数据组织盘点人员进行库存的初盘工作 ②初盘完成后,各库存管理部门的主盘人组织复盘人 员,进行库存的复盘工作。 ③复盘完成后,复盘人和初盘人将复盘和初盘的结果 进行比对,对有差异的库存要双方一起重盘,确定最 终盘点结果,并将复盘结果输入电子档,和复盘盘点 表一并发给财务部。 ④财务部主盘人,按照盘点计划,组织财务部监盘人 员对库存进行抽盘,抽盘完成后,双方在盘点表上签 字确认。 ⑤盘点差异处理:各仓位负责人需在一周核查差异原 因,并制定相应的处理方法。财务部根据反馈情况核 查后交领导层批准进行差异的调整。
仓库收发料作业流程
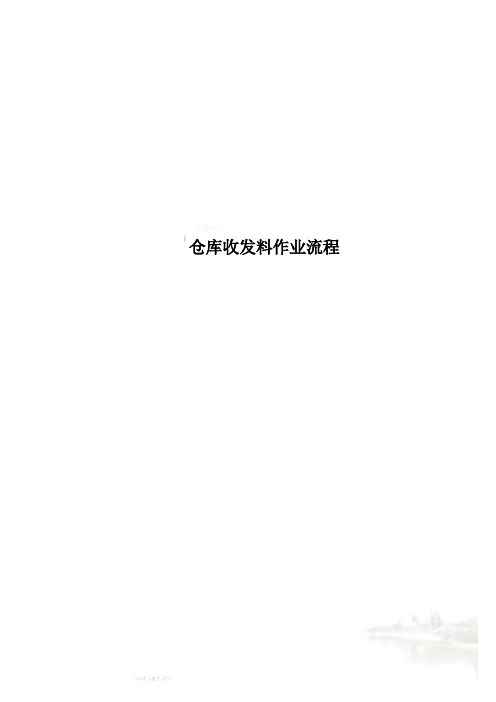
仓库收发料作业流程仓库收退货作业流程4.实物/K3/入库/退货1.送货1.1供应商根据采购订单进行送货,送货单必须具备物料编码、采购单号、数量等相关要素,且所交货物在交期之内;供应商、外协加工厂、客户(包括客供品)等送货到公司卸货后将“送货单”(“送货单”最少一式三联,签收后收货员留两联);1.2首先收货仓管员使用送货单与系统采购单进行核对,如有异常(指送货数量大于采购数量时)需与采购员针对异常部分进行确认,对于多送货部分,如需仓库收下,需物控经理、厂长总经理批准方可收货,确认无误后,送货人员即可与对应仓管员进行收料作业;2.收货2.1送货人员将所送货物料拉至收货员指定位置摆放整齐,需要核对包装标示是否与送货单一致,包装是否有破损、潮湿等状况,检查是否依照产品防护要求进行包装防护;2.2收料仓管员须对来料数量进行清点,根据送货单各项内容与实务进行核对,100pcs以下必须全点,尾数需要进行全点,针对定量包装、整箱、整件货物根据比例进行抽点,点收过程中发现不一致内容时需要做出标记,如发现一箱货物有少时,应要求送货方将所有货物当面清点,否则拒收同时并报组长、主管、相关物控、采购等人处理;2.3点收无误需在送货单上盖公司“收货章”(细数未点、品质未检)交一联记账员处打制《来料检验入库单》;2.4 对来料明细在《来料登记表》做登记,用于与仓管员之间的交接以及相关部门对来料状况的了解;3.(送)检验3.1收料人员将打好的《来料检验入库单》签字注明送检日期/时间交IQC(任意人员)在最后一联上签接收人名字、日期/时间,收料员用于存底以及查询送检时间与IQC接收时间;3.2日常物料送检时间不得晚于收料后2H,紧急物料应在收料后0.5H内送检,特急物料应在10分钟内送检;(对于紧急物料采购、物控等相关人员应通知至仓库组长或主管),贵重物料禁止在收料区存放过夜;3.3 IQC检验完成的物料应知会收料人员;3.4 对于主板、硬盘、内存、CF卡等需要上机测试周期较长的物料交对应区域仓管员自行送检,仓管员对于不能当天测完或者测试周期较长的物料除了交《来料检验入库单》给IQC应填写《转仓单》经IQC签字后系统做账转仓至IQC仓;3.5检验合格的物料需在产品单个包装上面贴合格标示;3.6检验经确认不合格的物料需在单个包装上贴红色不良标示;3.7经确认不良公司领导确认可以特采的物料贴黄色特采标示;3.8素材需外发加工的贴白色标签;3.9自制半成品需贴蓝色标签;3.10检验完成的物料IQC在《来料检验入库单》上注明检验完成日期/时间,留下第五联作为留底,其余四联交送检人;4.交接、入仓、归位4.1收料人员根据IQC判定结果进行交仓、转仓作业;4.2 良品交对应区域的仓管员(详见《仓储部岗位职责指导书》);4.3 良品仓管员接收后在《来料检验入库单》签字确认,收货员将此四联交制单人,(其中仓库留底一联,采购两联,财务一联);4.4 仓管员收到货物后,清点大致数量后在《来料登记表》上签收;4.5 区域仓管员在归位时对来料物料进行细致清点,数量与定量包装有异常时,须及时告知收料员,收料员确认属实需于3日内以邮件方式反馈至采购员处,由采购知会送货厂商并予以补货或做退货扣数(自反馈之日起3日内厂商未将短数物料补到即做退货处理),数量清点无误后,4.6 仓管员归位时需对物料进整理、尾数合并、登卡并及时记录帐目明细;5.放行1.退货申请1.1 仓库针对采购回复在库不良品退货明细,(包括来料不良、产线生产过程中发生的不良)在系统中打制《退货单》;1.2同一产品为两个以上供应商的需由品质判定来料供货商;1.3零星采购物料退货时仍沿用以上办法,不同的只是零星采购员作为接收人签字;1.4对于电源、硬盘等物料出现的不良由仓管员提供数据给采购,由采购决定是否由供应商提供良品换取不良品或作退货处理2.品质判定2.1对于不良原因判定不清楚的请IQC重新判定;2.2对于供应商有争议的物料需IQC判定;2.3经IQC重新判定可特采或属于良品的部分填写《转仓单》,转良品仓;3.物控采购会签3.1物控签核退货单注明是否需要补货留一联;3.2采购会签并留一联,通知供应商及时拉走退货;4.交接4.1供应商来取退货时当面对数量进行清点;4.2确认无误仓管员、供货商需签名确认并开具放行条签核完成交供应商;5.放行5.1警卫对放行的物品依照退货单进行清点,清点的内容包括品名、数量等;5.2清点数量异常时仓管员需及时处理,或返回第一环节重新处理,确认无误警卫准予放行。
库房收货流程和步骤
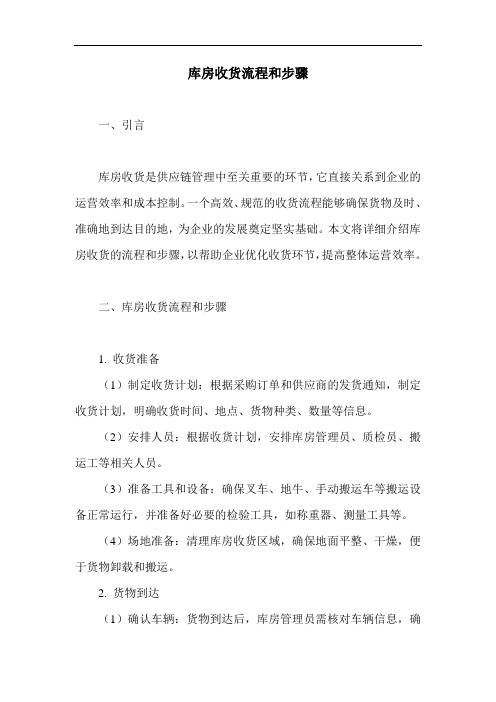
库房收货流程和步骤一、引言库房收货是供应链管理中至关重要的环节,它直接关系到企业的运营效率和成本控制。
一个高效、规范的收货流程能够确保货物及时、准确地到达目的地,为企业的发展奠定坚实基础。
本文将详细介绍库房收货的流程和步骤,以帮助企业优化收货环节,提高整体运营效率。
二、库房收货流程和步骤1. 收货准备(1)制定收货计划:根据采购订单和供应商的发货通知,制定收货计划,明确收货时间、地点、货物种类、数量等信息。
(2)安排人员:根据收货计划,安排库房管理员、质检员、搬运工等相关人员。
(3)准备工具和设备:确保叉车、地牛、手动搬运车等搬运设备正常运行,并准备好必要的检验工具,如称重器、测量工具等。
(4)场地准备:清理库房收货区域,确保地面平整、干燥,便于货物卸载和搬运。
2. 货物到达(1)确认车辆:货物到达后,库房管理员需核对车辆信息,确认与采购订单一致。
(2)货物卸载:搬运工按照库房管理员的指示,将货物从车辆上卸载至指定地点。
(3)货物核对:库房管理员对照采购订单,核对货物的种类、数量、规格等信息,确保无误。
3. 质量检验(1)初验:质检员对货物进行初步检查,包括外包装、外观、数量等,确保货物无明显损坏、短缺。
(2)复验:对初验合格的货物,进行详细的质量检验,包括性能、尺寸、功能等,确保货物符合企业要求。
(3)记录:质检员将检验结果记录在验收单上,对不合格的货物进行标记,并拍照留证。
4. 货物入库(1)系统录入:库房管理员根据验收单,将货物信息录入库存管理系统,确保库存数据的准确性。
(2)货物上架:搬运工按照库房管理员的指示,将合格货物上架至指定库位。
(3)库位调整:库房管理员根据库存情况,调整库位,确保库房空间利用率。
5. 文件归档(1)验收单:验收单需由库房管理员、质检员、供应商代表共同签字,一式三份,分别留存。
(2)采购订单:将采购订单与验收单进行匹配,归档保存。
(3)送货单:供应商提供的送货单需与验收单进行核对,无误后归档保存。
仓库收货流程
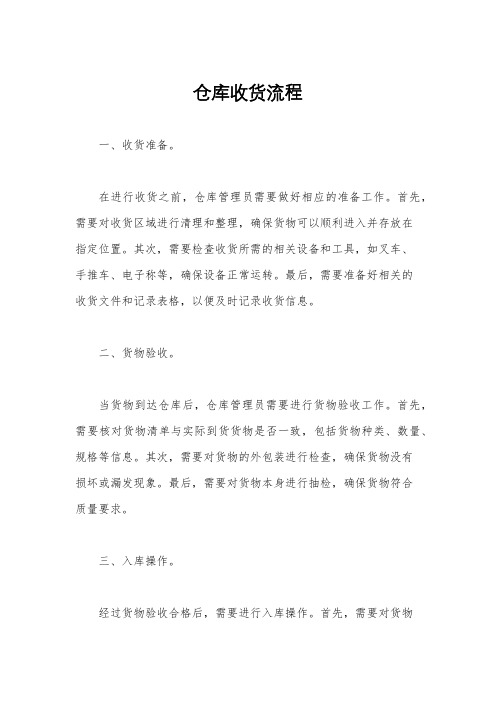
仓库收货流程一、收货准备。
在进行收货之前,仓库管理员需要做好相应的准备工作。
首先,需要对收货区域进行清理和整理,确保货物可以顺利进入并存放在指定位置。
其次,需要检查收货所需的相关设备和工具,如叉车、手推车、电子称等,确保设备正常运转。
最后,需要准备好相关的收货文件和记录表格,以便及时记录收货信息。
二、货物验收。
当货物到达仓库后,仓库管理员需要进行货物验收工作。
首先,需要核对货物清单与实际到货货物是否一致,包括货物种类、数量、规格等信息。
其次,需要对货物的外包装进行检查,确保货物没有损坏或漏发现象。
最后,需要对货物本身进行抽检,确保货物符合质量要求。
三、入库操作。
经过货物验收合格后,需要进行入库操作。
首先,需要对货物进行分类和编号,以便于后续的存储和管理。
其次,需要填写入库记录,包括货物名称、数量、生产日期、供应商信息等,确保入库信息准确无误。
最后,需要将货物按照分类和编号放置到指定的存储位置,并做好相应的标识。
四、信息录入。
在完成入库操作后,需要将相关的入库信息录入到电脑系统中。
首先,需要在仓库管理系统中录入货物的基本信息,包括货物名称、规格、数量、生产日期、保质期等。
其次,需要更新库存信息,确保系统中的库存数据与实际库存保持一致。
最后,需要生成入库报告和相应的统计分析,以便后续的库存管理和业务分析。
五、收货记录。
在完成收货流程后,需要对整个收货过程进行记录和总结。
首先,需要对收货过程中的问题和异常情况进行记录,以便后续的问题处理和改进。
其次,需要对收货数据进行分析,包括货物种类、数量、供应商质量等方面的统计分析。
最后,需要总结收货过程中的经验和教训,以便提高日后的收货效率和质量。
六、收货流程优化。
在完成收货记录后,需要对收货流程进行优化和改进。
首先,需要分析收货过程中存在的问题和瓶颈,找出改进的方向和措施。
其次,需要制定相应的改进计划和措施,包括流程优化、设备更新、人员培训等方面的措施。
最后,需要实施改进计划,并对改进效果进行评估和总结,以确保收货流程的持续改进和提高。
仓库来料收货流程

仓库来料收货流程
以下是店铺为大家整理的关于仓库来料收货流程图,给大家作为参考,欢迎阅读!
仓库来料收货流程图
仓库收货清点程序
1,是源头上进行控制,尽量杜绝供应商少数的事情发生。
这个需要与采购部进行沟通,在签定供货合同的时候,需要在合同中加入条款,如果发生到厂点数少数的情况。
将处以惩罚性质的扣数(如同一批次送货,点数时如果包装数量标称100个,实际点数5包分别为98个、99个、101个、103个、95个,则所有包装均按95个包计算。
)这样供应商在送货前就会更加用心做好核查工作,保证来料数量。
同时也减轻了自己的工作量。
2,来料点数制度一定要落实,不管合作多久,以前从来没有出现问题的供应商,每批货都必须抽点,并且建立抽点登记本。
(记录好相关数据,如总来料包数,抽点包数,抽点的包号,数量)并由仓管员的上级人员或财务人员不定时去核查抽点情况,
3,严格控制生产用料,严格执行按BOM表和订单领料,超领料的一定要高级别管理人员核准后才可以领料,杜绝仓库管理人员与车间领料人员联合作弊,每批生产单结束后,需核查所有领料与仓库出料是否一致,以及与订单所需材料是否一致。
这样仓管员才会有压力,努力保证收料与发料数据的准确性。
不至于收料时不细致,待盘点时或平时核查时发现实物与账不相符时,通过假领料平账。
4,建立好常用材料的单重,包重,包装数量等数据库。
方便来料清点以及平时核查。
来料检验与仓库收货退货操作流程

及时反馈问题:一旦发现来料或仓库收货退货存在问题,应立即向相关部门或人员反馈
沟通协调:与相关部门或人员保持密切沟通,确保问题得到及时解决
解决方案:针对不同问题,制定相应的解决方案,并确保方案得到有效执行
持续改进:不断总结经验教训,对流程进行持续改进,提高工作效率和质量
定期沟通与协调会议
退货跟进:销售代表或客户对退货处理结果进行跟进
信息系统更新
退货信息录入系统
更新后的库存信息同步到各个部门
定期对系统进行维护和升级
系统自动更新库存信息
05
来料检验与仓库收货退货的协调与沟通
信息共享与传递
沟通技巧和注意Biblioteka 项来料检验与仓库收货退货的协调与沟通的重要性
信息共享的方式和渠道
协调与沟通的实践案例
添加标题
对于需要上架的货物,需要按照货架的编号和货物的编号进行匹配,确保货物放置在正确的位置。
添加标题
如果货物数量较多,需要进行分类、分区存放,以便后续的查找和取货。
信息系统录入
信息系统录入:将收货信息录入信息系统,包括货物名称、数量、规格、生产日期等
实物核对:对收到的货物进行实物核对,确保与信息系统录入信息一致
准备检验工具和设备
了解来料的基本信息和规格要求
检验实施
检验准备:明确检验目的、范围和标准
检验实施:按照检验计划进行来料检验,记录检验结果
问题处理:对不合格的来料进行处理,包括退货、返工等
总结与改进:对来料检验流程进行总结,提出改进意见
检验记录
检验方法:目视、测量、试验等
检验记录填写:详细记录检验过程、结果及异常情况
小无名,a click to unlimited possibilities
- 1、下载文档前请自行甄别文档内容的完整性,平台不提供额外的编辑、内容补充、找答案等附加服务。
- 2、"仅部分预览"的文档,不可在线预览部分如存在完整性等问题,可反馈申请退款(可完整预览的文档不适用该条件!)。
- 3、如文档侵犯您的权益,请联系客服反馈,我们会尽快为您处理(人工客服工作时间:9:00-18:30)。
系统登录选择RII仪控生产账套进入,选择登陆人员,录入登陆口令,进入系统界面库存管理模块
物料出入单据操作指引:
1.仓库来料验收收货入库
来料收货验收入库分以下两种情况进行单据流转;
免检物料:来料验收收货(制单)-来料收货审批(仓库确认)
需检物料:来料验收收货(制单)-来料收货审批(仓库确认、质检信息确认)- 质量检验领料(制单)-质检领料审批(仓库确认)-质量检验入库(制单)-质检入库审批(仓库确认)
1.1来料验收收货:进入系统来料入库-来料验收收货即如图1所示单据界面,此处正常收货入库需选择蓝字单据,根据物料基本属性(是否免检)选择对应流转类型,同时选择对应仓库,注意针对免检物料只能选择原材料仓库,需检物料需选择收货待处理库,通过选择录入供应商信息、来料类型信息,手工填入供应商送货单号、物料对应采购使用项目、收货人、收货时间,然后根据物料信息选择物料进行录入物料信息、物料编号、数量、厂家批号(按需录入)、生产/到货日期(按需录入默认到货日期)、采购合同号等信息;点击保存后此单据记录保存系统自动依据物料生成来料物料批号,如对应物料属性有S/N序列号管理,此处必须依据物料行信息点击鼠标右键进入条码管理,通过物料S/N序列标签条码扫码或手工录入S/N序列号方式录入条码信息,同时对应物料信息通过鼠标右键上传录入供应商对应物料提供的供应商质量检验文件(合格证明文件)、质量保证文件,完成后提交单据,点击打印单据按钮打印物料来料收货单、物料信息标签,粘贴物料标签。
图1
1.2来料验收收货审批:来料验收收货单据与物料实物共同流转至仓库收货确认/质检信息确认,仓库依据单据流转类型分类流转物料与单据,将免检物料按收货上架入库处理,记录物料库位信息,确认物料信息与实物,需检物料数量信息核实后物料暂存收货待检区,记录区域库位信息,系统通过系统来料入库-来料收货审批如下图2所示单据界面,根据单据流转方向,依据系统权限,根据单据号双击进入对应单据进入图3,录入物料库位信息,依据单据与物料信息进行系统确认点击审核,如单据为需检物料,需仓库流转审核确认后流转至质检审核环节,相同方式进行审批流转,直至单据审批完成,单据信息发现错误时可以点击返退,信息将按流转反方向一流转返退,直至制单人,制单人修改错误信息后重新按如上流程提交流转单据。
图2
图3
质量检验领料:依据来料收货内容,质量人员或计划人员根据待检物料进行任务编制,生成任务分配制作质量检验领料单,进入系统如图4,根据来料收货单进行状态检验领料完成筛选,选择未完成任务内容物料生成领料单,选择
领料任务人员,保存提交单据。