水性涂料在汽车涂装中的应用研究.
汽车涂装的最新工艺技术及发展趋势
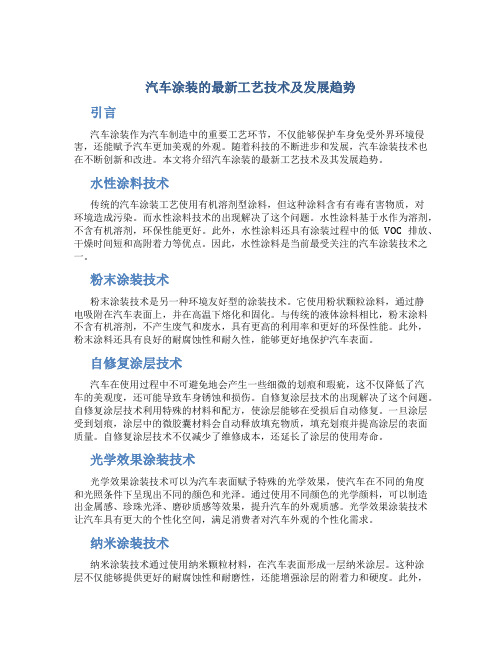
汽车涂装的最新工艺技术及发展趋势引言汽车涂装作为汽车制造中的重要工艺环节,不仅能够保护车身免受外界环境侵害,还能赋予汽车更加美观的外观。
随着科技的不断进步和发展,汽车涂装技术也在不断创新和改进。
本文将介绍汽车涂装的最新工艺技术及其发展趋势。
水性涂料技术传统的汽车涂装工艺使用有机溶剂型涂料,但这种涂料含有有毒有害物质,对环境造成污染。
而水性涂料技术的出现解决了这个问题。
水性涂料基于水作为溶剂,不含有机溶剂,环保性能更好。
此外,水性涂料还具有涂装过程中的低VOC排放、干燥时间短和高附着力等优点。
因此,水性涂料是当前最受关注的汽车涂装技术之一。
粉末涂装技术粉末涂装技术是另一种环境友好型的涂装技术。
它使用粉状颗粒涂料,通过静电吸附在汽车表面上,并在高温下熔化和固化。
与传统的液体涂料相比,粉末涂料不含有机溶剂,不产生废气和废水,具有更高的利用率和更好的环保性能。
此外,粉末涂料还具有良好的耐腐蚀性和耐久性,能够更好地保护汽车表面。
自修复涂层技术汽车在使用过程中不可避免地会产生一些细微的划痕和瑕疵,这不仅降低了汽车的美观度,还可能导致车身锈蚀和损伤。
自修复涂层技术的出现解决了这个问题。
自修复涂层技术利用特殊的材料和配方,使涂层能够在受损后自动修复。
一旦涂层受到划痕,涂层中的微胶囊材料会自动释放填充物质,填充划痕并提高涂层的表面质量。
自修复涂层技术不仅减少了维修成本,还延长了涂层的使用寿命。
光学效果涂装技术光学效果涂装技术可以为汽车表面赋予特殊的光学效果,使汽车在不同的角度和光照条件下呈现出不同的颜色和光泽。
通过使用不同颜色的光学颜料,可以制造出金属感、珍珠光泽、磨砂质感等效果,提升汽车的外观质感。
光学效果涂装技术让汽车具有更大的个性化空间,满足消费者对汽车外观的个性化需求。
纳米涂装技术纳米涂装技术通过使用纳米颗粒材料,在汽车表面形成一层纳米涂层。
这种涂层不仅能够提供更好的耐腐蚀性和耐磨性,还能增强涂层的附着力和硬度。
水性涂料的研究进展
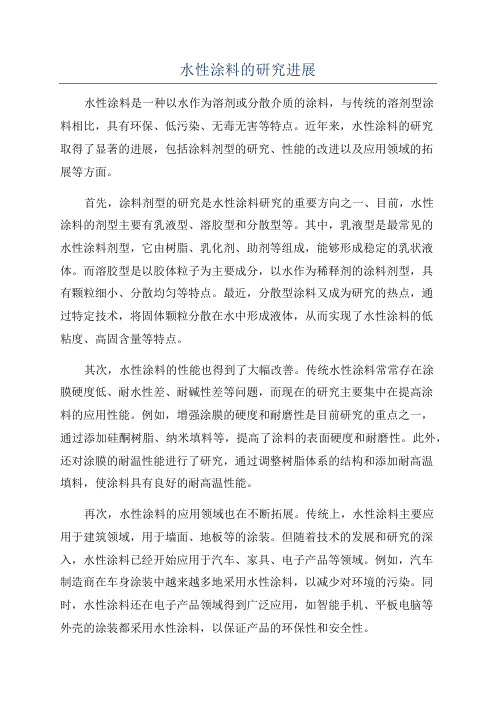
水性涂料的研究进展水性涂料是一种以水作为溶剂或分散介质的涂料,与传统的溶剂型涂料相比,具有环保、低污染、无毒无害等特点。
近年来,水性涂料的研究取得了显著的进展,包括涂料剂型的研究、性能的改进以及应用领域的拓展等方面。
首先,涂料剂型的研究是水性涂料研究的重要方向之一、目前,水性涂料的剂型主要有乳液型、溶胶型和分散型等。
其中,乳液型是最常见的水性涂料剂型,它由树脂、乳化剂、助剂等组成,能够形成稳定的乳状液体。
而溶胶型是以胶体粒子为主要成分,以水作为稀释剂的涂料剂型,具有颗粒细小、分散均匀等特点。
最近,分散型涂料又成为研究的热点,通过特定技术,将固体颗粒分散在水中形成液体,从而实现了水性涂料的低粘度、高固含量等特点。
其次,水性涂料的性能也得到了大幅改善。
传统水性涂料常常存在涂膜硬度低、耐水性差、耐碱性差等问题,而现在的研究主要集中在提高涂料的应用性能。
例如,增强涂膜的硬度和耐磨性是目前研究的重点之一,通过添加硅酮树脂、纳米填料等,提高了涂料的表面硬度和耐磨性。
此外,还对涂膜的耐温性能进行了研究,通过调整树脂体系的结构和添加耐高温填料,使涂料具有良好的耐高温性能。
再次,水性涂料的应用领域也在不断拓展。
传统上,水性涂料主要应用于建筑领域,用于墙面、地板等的涂装。
但随着技术的发展和研究的深入,水性涂料已经开始应用于汽车、家具、电子产品等领域。
例如,汽车制造商在车身涂装中越来越多地采用水性涂料,以减少对环境的污染。
同时,水性涂料还在电子产品领域得到广泛应用,如智能手机、平板电脑等外壳的涂装都采用水性涂料,以保证产品的环保性和安全性。
总的来说,水性涂料的研究进展可分为剂型研究、性能改进和应用领域拓展三个方面。
在剂型研究方面,乳液型、溶胶型和分散型涂料成为主要研究对象。
在性能改进方面,涂料的硬度、耐磨性和耐温性能得到了明显提升。
在应用领域方面,除了建筑领域外,水性涂料还在汽车、家具、电子产品等领域得到广泛应用。
随着研究的不断深入,相信水性涂料将在未来展现更广阔的应用前景。
汽车保险杠水性漆涂装过程控制及应用
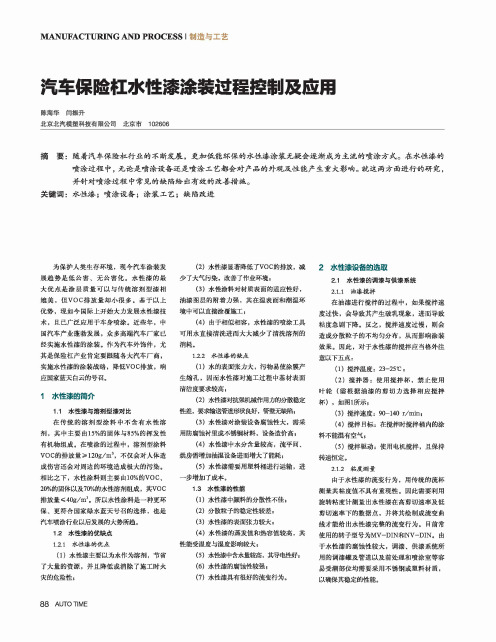
MANUFACTURING AND PROCESS I卸造与工艺汽车保险杠水性漆涂装过程控制及应用陈海华闫振升北京北汽模塑科技有限公司北京市102606摘要:随着汽车保险杠行业的不断发展,更加低能环保的水性漆涂装无疑会逐渐成为主流的喷涂方式。
在水性漆的喷涂过程中,无论是喷涂设备还是喷涂工艺都会对产品的外观及性能产生重大影响。
就这两方面进行的研究,并针对喷涂过程中常见的缺陷给出有效的改善措施。
关键词:水性漆;喷涂设备;涂装工艺;缺陷改进为保护人类生存环境,现今汽车涂装发 展趋势是低公害、无公害化。
水性漆的最 大优点是涂层质量可以与传统溶剂型漆相 媲美,但V0C排放量却小很多。
基于以上 优势,现如今国际上开始大力发展水性漆技 术,且已广泛应用于车身喷涂。
近些年,中国汽车产业蓬勃发展,众多高端汽车厂家已 经实施水性漆的涂装。
作为汽车外饰件,尤 其是保险杠产业肯定要跟随各大汽车厂商,实施水性漆的涂装战略,降低V0C排放,响应国家蓝天白云的号召。
1水性漆的简介1.1水性漆与溶剂型漆对比在传统的溶剂型涂料中不含有水性溶 剂,其中主要由15%的固体与85%的挥发性 有机物组成。
在喷涂的过程中,溶剂型涂料 V0C的排放量>120g/m3,不仅会对人体造 成伤害还会对周边的环境造成极大的污染。
相比之下,水性涂料则主要由10%的V0C、20%的固体以及70%的水性溶剂组成,其V0C 排放量<40g/m3。
所以水性涂料是一种更环 保、更符合国家绿水蓝天号召的选择,也是 汽车喷涂行业以后发展的大势所趋。
1.2水性漆的优缺点1.2.1水性漆的优点(1)水性漆主要以为水作为溶剂,节省 了大量的资源,并且降低或消除了施工时火 灾的危险性;(2)水性漆显著降低了V0C的排放,减少了大气污染,改善了作业环境;(3)水性涂料对材质表面的适应性好,油漆图层的附着力强,其在湿表面和潮湿环境中可以直接涂覆施工;(4)由于相似相容,水性漆的喷涂工具可用水直接清洗进而大大减少了清洗溶剂的消耗。
SUV车身水性免中涂工艺研究
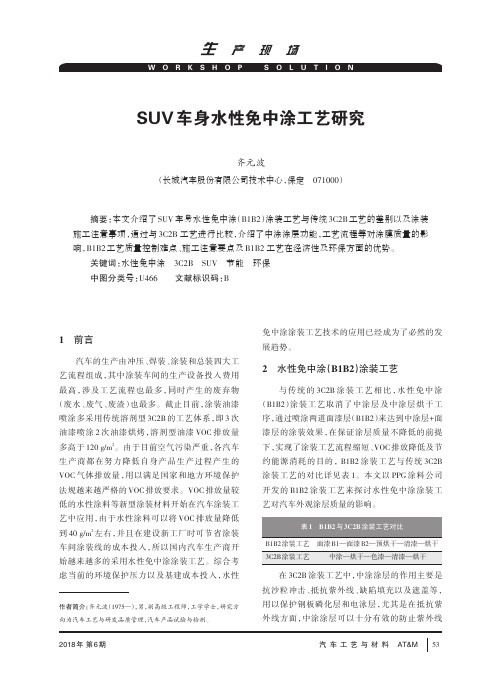
摘要:本文介绍了SUV 车身水性免中涂(B1B2)涂装工艺与传统3C2B 工艺的差别以及涂装施工注意事项,通过与3C2B 工艺进行比较,介绍了中涂涂层功能,工艺流程等对涂膜质量的影响,B1B2工艺质量控制难点、施工注意要点及B1B2工艺在经济性及环保方面的优势。
关键词:水性免中涂3C2B SUV节能环保中图分类号:U466文献标识码:BSUV 车身水性免中涂工艺研究齐元波(长城汽车股份有限公司技术中心,保定071000)作者简介:齐元波(1975—),男,副高级工程师,工学学士,研究方向为汽车工艺与研发品质管理,汽车产品试验与检测。
1前言汽车的生产由冲压、焊装、涂装和总装四大工艺流程组成,其中涂装车间的生产设备投入费用最高,涉及工艺流程也最多,同时产生的废弃物(废水、废气、废渣)也最多。
截止目前,涂装油漆喷涂多采用传统溶剂型3C2B 的工艺体系,即3次油漆喷涂2次油漆烘烤,溶剂型油漆VOC 排放量多高于120g/m 2。
由于目前空气污染严重,各汽车生产商都在努力降低自身产品生产过程产生的VOC 气体排放量,用以满足国家和地方环境保护法规越来越严格的VOC 排放要求。
VOC 排放量较低的水性涂料等新型涂装材料开始在汽车涂装工艺中应用,由于水性涂料可以将VOC 排放量降低到40g/m 2左右,并且在建设新工厂时可节省涂装车间涂装线的成本投入,所以国内汽车生产商开始越来越多的采用水性免中涂涂装工艺。
综合考虑当前的环境保护压力以及基建成本投入,水性免中涂涂装工艺技术的应用已经成为了必然的发展趋势。
2水性免中涂(B1B2)涂装工艺与传统的3C2B 涂装工艺相比,水性免中涂(B1B2)涂装工艺取消了中涂层及中涂层烘干工序,通过喷涂两道面漆层(B1B2)来达到中涂层+面漆层的涂装效果,在保证涂层质量不降低的前提下,实现了涂装工艺流程缩短、VOC 排放降低及节约能源消耗的目的,B1B2涂装工艺与传统3C2B 涂装工艺的对比详见表1。
水性汽车涂料的研究现状及发展趋势

主 某
。
2。
, . ~ … , . , .. . , . . , .
,
醛 汽 壁 瓮 油 璧 ? 季 要 c ,石 性 。性 策 耐 往 ; 暑 乏 漆 底 一 强 抗 击 好水 、 ; 兰 警 漆 阳离子型 苎 阴极 粉末底漆等几次 泳 + 有 面 同化 。 。 …树’ … ) 二 电泳底漆( _ 尊 和 二 = I = ‘ 性 睡 主 色 的 性 … 。。。 重 并 与 漆 极 电泳漆)
,
阴 电底 之 以 到车 业 青 ,要 因 水含基烯树 应提表干速, 极 泳 漆 所 受 汽行 的昧 主原 性羟丙酸脂薰奔舞,高面燥度
烘性等性 而具涂效高经、全污 水含基氨树 譬 提机性,高 托能特 ,且有装率 、济安、 性羟聚酯脂盖蓄磊每高械能提 底 鼍 动等 点 ! 用 阴 电 妻莴萎 奎 妻 自化 呈 特 。 作 极 泳 水性不含 藿 参交反,高度提外 与联应提硬,高观 漆的成膜物质很多 ,主要包括丙烯酸树脂 、环氧树脂、 没有参与交联反应
2 水性汽车涂料的研究现状
汽车车身的典型配套涂层及涂装工艺如图1 。完整的 22 水 性汽 车中涂 漆 .
汽车涂 层包括 电泳涂层 、中涂层、底色漆层和 罩光涂层 。 涂料的水性化也是 由底到面逐步发展的底漆已经 水性化 , 必 然趋 势。 中涂漆是介于底漆和面漆之间的一种涂 料 ,主要功能 是进一步改善工件已涂装底漆的表面 ,作进 一步 的填补 、 度提高 ,而且中涂漆还可以吸收一定 的 击能量 ,对提高 中
能的要求及 有利 于施 工涂装 的目的 ,阴极 电泳底漆 的开发
~
三聚氰胺
NK ̄ ,提高度 t' J
。
)
含有害重金属及有害金属(b n等) D、s 、降低溶 23 -
汽车涂装水性免中涂工艺的应用探究
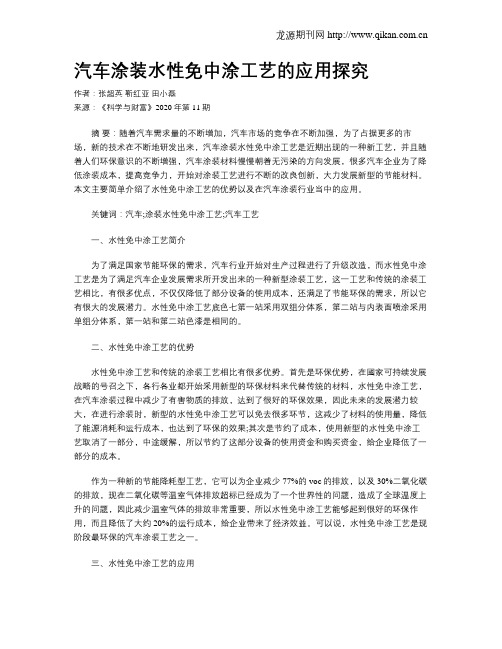
汽车涂装水性免中涂工艺的应用探究作者:张超英靳红亚田小磊来源:《科学与财富》2020年第11期摘要:随着汽车需求量的不断增加,汽车市场的竞争在不断加强,为了占据更多的市场,新的技术在不断地研发出来,汽车涂装水性免中涂工艺是近期出现的一种新工艺,并且随着人们环保意识的不断增强,汽车涂装材料慢慢朝着无污染的方向发展,很多汽车企业为了降低涂装成本,提高竞争力,开始对涂装工艺进行不断的改良创新,大力发展新型的节能材料。
本文主要简单介绍了水性免中涂工艺的优势以及在汽车涂装行业当中的应用。
关键词:汽车;涂装水性免中涂工艺;汽车工艺一、水性免中涂工艺简介为了满足国家节能环保的需求,汽车行业开始对生产过程进行了升级改造,而水性免中涂工艺是为了满足汽车企业发展需求所开发出来的一种新型涂装工艺,这一工艺和传统的涂装工艺相比,有很多优点,不仅仅降低了部分设备的使用成本,还满足了节能环保的需求,所以它有很大的发展潜力。
水性免中涂工艺底色七第一站采用双组分体系,第二站与内表面喷涂采用单组分体系,第一站和第二站色漆是相同的。
二、水性免中涂工艺的优势水性免中涂工艺和传统的涂装工艺相比有很多优势。
首先是环保优势,在國家可持续发展战略的号召之下,各行各业都开始采用新型的环保材料来代替传统的材料,水性免中涂工艺,在汽车涂装过程中减少了有害物质的排放,达到了很好的环保效果,因此未来的发展潜力较大,在进行涂装时,新型的水性免中涂工艺可以免去很多环节,这减少了材料的使用量,降低了能源消耗和运行成本,也达到了环保的效果;其次是节约了成本,使用新型的水性免中涂工艺取消了一部分,中途缓解,所以节约了这部分设备的使用资金和购买资金,给企业降低了一部分的成本。
作为一种新的节能降耗型工艺,它可以为企业减少77%的voc的排放,以及30%二氧化碳的排放,现在二氧化碳等温室气体排放超标已经成为了一个世界性的问题,造成了全球温度上升的问题,因此减少温室气体的排放非常重要,所以水性免中涂工艺能够起到很好的环保作用,而且降低了大约20%的运行成本,给企业带来了经济效益。
汽车用水性涂料的特征及其涂装技术

2 水 性涂装 的关 键工艺条 件
基 于水 性 涂 料 ( 中涂 漆 和底 色 漆 ) 特 性 , 特 的 如 殊 的流变 性 、 分难 挥 发 和润 湿性 差 等 , 获得 优 质 水 为
力。 水的表面张力较有机溶剂高得多 , 如醇类 、 酯类 、
酮类 溶 剂 的表 面张 力 为 ( 0 2 ×1~Nm;二 甲苯 、 2 — 5) 0 /
恒温 恒 湿 , 随气 侯条 件 变 化 , 而 随季 节 分别 设 定温 湿
煤焦油溶剂等芳香族碳氢化合物 的表面张力为 ( 8 2~
3 ×1 Nm;20溶 剂 油那样 的直链状 碳 氢化 合物 2) 0 / 0#
的表面张力为 2 ×1 / 5 0 Nm左右。 广泛采用 的高沸点
溶 剂 , 丁基溶纤 剂 的表面 张力 为( 7 2 ×1~N m, 如 2 ~ 8) 0 /
F g r T ei fu n e f e e a u e a d h mi i n iu e3 h n l e c so mp r t r n u d t o t y n nv lt ec ne t f tr on o t g o — a a i o t n e b r ec a i s l o wa n
RH7 %~ 5 5 8 %;其 它 2 ~ 5 , 0 8 %。 4 2 ℃ RH7 %~ 0
( ) 对 被 涂 面不 易 润湿 ,ቤተ መጻሕፍቲ ባይዱ易 渗入 小 细 缝 中 ; 1 不
度 值 范 围 。如 以下 3 温湿 度 控制 状 况 : 种
① 全年 2 ℃, H7 %( 5 R 0 恒定 ) ; ② 冬季 2 0 , H7 %;夏季 2 ℃, H 8%, 2( R 0 2 8 R 0 其
水性免中涂涂装工艺研究_邢汶平

were analyzed. A scheme for realization of optimal
automobile appearance by using the water-based midcoat-
free coating process was obtained.
Keywords: automobile coating; waterborne paint; midcoat-
橘皮(外观)
BYK 橘皮仪
水平面:长波(LW)<5,短波(SW)<20。垂直面:LW<10,SW<20
传统工艺中,中涂层主要起防紫外线辐射及抗石 击作用。在防紫外线辐射方面,中涂层保护钢板表面 的磷化、电泳涂层,防止紫外线透过表面涂层达到电 泳层,使电泳漆膜中的环氧树脂吸收能量后发生粉化。 能引起电泳涂层粉化的光谱主要集中在 280 ~ 400 nm 波长范围内的紫外区域以及 400 nm 以上的可见光区 域。在抗石击性能方面,有一定膜厚的中涂层对石击 等硬体撞击有一定的吸能及缓冲作用,起到保护整体 涂层附着力的作用。
关于水性免中涂工艺,不同的涂料厂商其命名不 同。巴斯夫称为 IPⅡ集成工艺,PPG 称为 B1B2 紧凑 型工艺,杜邦称为 Eco-concept 工艺。从技术路线上分 析:IPⅡ集成工艺与 B1B2 紧凑型工艺具有较强的相似 性,可以实现混线生产。从工艺布局及工艺流程的角度 而言,IPⅡ集成工艺、B1B2 紧凑型工艺与 Eco-concept 工艺之间都有所区别。本文主要探讨 B1:B2 工艺对汽 车外观质量的影响。
free process; film appearance
First-author’s address: Technological Center, Anhui Jianghuai Automobile Co., Ltd., Hefei 230601, China
水性涂料在汽车工业中的应用

映象度均能提高, 使车身更加美观。 二道浆虽然 目前 仍在使用 中、 固体分涂料 , 高 但水性化是必然趋势 ,
欧美水性中涂已达 4%。 0 () 1水性二道浆的组成 典型的水性二道浆 以聚脂为基材 ,以氨基树脂
交链 固化 ,聚脂 以所含 有 的羧 基被 胺 中和而 溶解 或
C D将 向超厚膜型、 E 高耐侯型、 低温 固化型 、 边棱防
蚀型、 底面合一型、 复合彩色型等方面发展[ 2 1 。
2 水性二道 浆
汽车车身涂料经常采用二道浆 , 目的有两个 : 其
一
是增加耐腐蚀性 、 耐水 、 耐潮湿性 , 增强漆膜的附
车身的保护能力 ; 二是使漆膜更加平整丰满 , 光泽和
湿漆 膜 的流 变 问题极 为 复杂 ,开发 水性 底 色所
尽管水性二道浆 已达 到降低有机溶剂的散发 ,
但 实际仅有 少数 ( 主要在 德 国 ) 的生产 线在使 用 。
大 多数 汽车制造厂还在评价水 性二道浆体 系 。有
的在计划 中 ,有 的刚 刚开始建 立水性二道 浆施工
生产线 。
留 的水 分 和防止 产 生针孔 。
( ) 展状 况 3发
金属闪光底色漆通常涂两道 ,两个涂膜的厚度 约 1: 。两涂膜都可气动喷涂 , 1 或第一道静 电和第 二道气动喷涂。 第一道以静 电高速杆施工 , 其转移效 率很高 , 比气动喷涂约高 5 %, 0 静电高速喷涂不能用
来喷第二道 , 因为雾化较差 , 漆滴大小分布不均 , 而 且漆滴冲击底材速度较低 ,于是金属闪光效果大为
降低 , 而与气动喷涂外观差别很大。 在闪干区 , 除空气的流速外 , 温度与湿度都是决
汽车涂装水性免中涂工艺的应用探讨_邢汶平

粗糙度 Ra 值在 0.2 ~ 0.3 μm 范围内,按照 B1B2 工艺
1.2 1.0 0.8 0.6 0.4 0.2 0 250 300 350
!"a
8.0#m
!"b
10.7#m 11.0#m 12.2#m 15.4#m
400
450
500
550
$%/nm
)3 *+,-.B1/01234&’(
表2 2 种工艺涂料基本参数对比 3C2B 水性工艺 涂层 清漆 色漆/B2 中涂/B1 膜厚 /μm 40 ~ 45 12 ~ 15 30 施工固体 含量/% 42 20 56
3C2B 100
B1B2 水性工艺 膜厚 /μm 40 ~ 45 9 ~ 12 12 ~ 15
B1B2 100 86
施工固体 含量/% 50 20 36
XING Wen-ping, GE Fei, PI Qin (Technological Centre, Anhui Jianghuai Automobile Co., Ltd, Anhui Hefei, 230601, China) Abstract: The application background and the process route of waterborne free intermediate coating technology were described, and the mechanisms and characteristics of waterborne free intermediate coating technologies (B1B2 ) which were verified by laboratory authentication and real vehicle spray verification were introduced in detail. Key words: waterborne coatings; painting; intermediate coating-free technology
汽车涂装水性“3C1B”工艺简介及其在国内的使用情况

汽车涂装水性“3C1B”工艺简介及其在国内的使用情况【涂料工业】一、“3C1B”工艺简介在电泳漆涂层后以“湿碰湿”的方式喷涂中涂、金属色漆和罩光清漆,并一次性烘干的工艺称为三涂一烘(“3C1B”)工艺。
“3C1B”工艺已被福特公司采用,国内南京福特马自达涂装线也即将采用此工艺。
与传统的汽车涂装工艺相比,该工艺取消了中涂烘干工序,从而减少中涂打磨、擦净和烘干等涂装设备的投资和占地面积,提高生产效率、降低能源消耗。
同时,由于无中涂打磨工序,因而节约了打磨所需的人员和辅料费用。
在“3C1B”工艺材料配方中采用了特殊的丙烯酸树脂和高韧性聚酯树脂,通过调整中涂的树脂结构及溶剂来优化固化速率,使之与面漆有良好的湿碰湿涂装性能。
同时,涂料粘度和触变性要求尽可能增大,保证在溶剂挥发时产生的湍流对铝粉片定位取向影响程度不致变差。
在施工过程中,“3C1B”工艺对喷漆室环境温度和湿度要求较高。
“3C1B”工艺的技术发展趋势是采用高固体分中涂、高固体分色漆和高固体分清漆,可提高涂装线速度,减少VOC的排放,降低中涂、色漆和清漆涂层之间的混溶。
高固体分中涂采用不透明的颜料防止紫外线的辐射,同时由于中涂膜厚高可防止电泳漆受紫外线辐射的影响。
二、水性“3C1B”涂装工艺的开发和运用我国的汽车OEM厂家从2003年开始在引入水性汽车涂装线以来,短短10年间,水性涂装线目前已经在整个汽车涂装线中占了半壁江山。
如何进一步减少汽车涂装过程中产生的VOC,也就成为了汽车制造业的重点课题。
所以,在溶剂型涂装线中曾引起重点关注的三涂一烘工艺顺理成章地成为了今后水性涂装线工艺中考虑的重点。
1、水性“3C1B”体系的分类(1)水性中涂涂装后有预热:(2)水性中涂涂装后无预热(俗称“免中涂”):三、水性“3C1B”涂装体系的涂料构成及膜厚变化1、涂料体系分类目前现有的中涂无预热型的水性“3C1B”工艺的涂料体系基本上可分为2大类:(1)以欧系车厂为主使用的“聚氨酯—聚酯体系”该涂料技术的主要特点是:A 第一层色漆中加入着色成分用以改善机械特性和抗紫外线问题的应用;B 第一道色漆B1与第二道色漆B2可以使用同色底漆。
水性色漆工艺在汽车涂装的应用与问题解决

水性色漆工艺在汽车涂装的应用与问题解决作者:陈兆波来源:《时代汽车》 2017年第9期陈兆波上汽通用五菱汽车股份有限公司广西柳州市545007摘要:介绍了水性色漆的特性、工艺特点以及对应的设备要求,结合具体的工艺调试,阐述了水性色漆在实际应用中的一些问题解决。
关键词:汽车涂装;水性漆;水性工艺应用问题1引言在汽车整车工厂工艺中,涂装是设备投资成本最高,生产工艺最多,同时也是三废排放最多的。
目前在涂装面漆工艺段,通常采用的是3C2B工艺体系,即3个涂层2次烘烤,较为经典的即是采用溶剂型油漆(溶剂型中涂、色漆及清漆),其VOC排放一般大于120g/m2。
随着社会环保意识的提高,国家环保法规越来越严格,水性色漆等新材料技术等开始在汽车涂装使用,通过在面漆工艺中采用水性色漆,可将vOc的排放降低到40g/m2,达到国家环保法规要求,因此国内汽车厂家越来越多开始采用水性漆工艺,成为了面漆工艺技术的必然趋势。
2水性色漆工艺流程宝骏基地作为SGMW乘用车基地,追求成为绿色、节能、环保汽车工厂的标杆,涂装车间即是以水性色漆工艺进行规划、设计和建设。
工艺流程为:前处理→电泳→电泳烘干→电泳打磨→焊缝密封→UBC→裙边喷涂→擦净→中涂(溶剂型)→中涂烘干→中涂打磨→擦净→色漆(水性)→色漆热闪干→清漆(溶剂)→面漆烘干,与溶剂型色漆相比,增加了“色漆闪干”工艺。
3水性色漆喷漆室要求宝骏涂装采用的是关西公司,型号为L2-08的水性色漆,结合色漆水性涂料与溶剂型涂料的组成对比(如下图所示),可以看出水性色漆对喷房的温湿度控制稳定性要求较高,一般控制在温度:25℃±1℃,湿度:夏季,75%±5%;冬季,65%±5%以便获得较好的外观质量。
4水性色漆热闪干要求4.1 热闪干工艺色漆与清漆仍然是湿碰湿工艺,在进行清漆喷涂之前,色漆表面的溶剂或者水含量要挥发降低到一定的程度,以便得到好的性能和外观质量。
水性漆的特点以及应用

水性漆的特点以及应用摘要:随着人们对生活质量越来越高的要求,健康环保的生活理念已经作为装修或者粉饰施工过程中的重要依据。
尤其是对油漆这类挥发性高的涂料,不当使用会对人体造成极大的危害。
现阶段人们大都选取水性漆作为优质健康的涂料来进行施工,因其以水为介质,与之前使用的溶剂型的漆相比其VOC排量较低,而且能够保持建筑体或板面较好的防腐及装饰性能,较好的施工性能,可谓是具有良好性能的新型材料和工艺技术。
因此在建筑装饰领域中被广泛采用。
相关人员要对水性漆的使用工艺和特点予以充分的把握,从而让其发挥更大的效用。
关键词:水性漆;特点分析;应用研究引言水性漆以水为溶剂或是稀释剂,不人为添加有机溶剂,特别是不人为添加苯、甲苯、二甲苯、甲醛、游离TDI、有毒重金属等,无毒无刺激气味,对人体无害,不污染环境,这是水性漆最优良的品质。
家居建材行业“低碳环保”的理念已经在消费者中深入人心,“要买就要买健康”的消费观念现在已经非常普遍。
按照当前的消费观念,健康压倒一切,水性漆和油漆相比,就有这方面的优势,水性漆健康环保,是绿色产业,是漆类未来发展的方向,油性漆必然为水性漆所淘汰。
1.水性漆的特点分析去离子水是水性漆的主要溶剂,其中存在少量的挥发性有机化学物,对于人体和环境产生的危害较小,是当前涂装中最受欢迎的环保涂料。
水性底色漆和水性电泳底漆等在汽车涂装行业的应用越来越广泛,这也是促进产业结构转型升级的重要渠道。
在汽车修补漆中,底色漆会产生大量的 VOC,将高固体含量 HS 清漆与水性底色漆进行配合使用,能够有效降低 VOC 的排放量。
另一方面,人体的造血系统、呼吸道黏膜、中枢神经系统、肝肾功能和皮肤等,也会受到挥发性有机化合物的影响,水性漆的应用降低了对钣金车间人员的损害,降低了职业病产生的概率。
喷漆室湿度与温度的控制,是控制水性漆中水分挥发程度的有效措施,溶剂型漆涂着固体份的调整,主要是通过稀释剂蒸发速率的调整而实现。
汽车车身涂装新技术及其应用

汽车车身涂装新技术及其应用
随着汽车工业的不断发展,汽车车身涂装技术也在不断更新换代。
新技术的应用不仅提高了汽车的外观质量,还能够提高汽车的耐久性和安全性。
本文将介绍几种汽车车身涂装新技术及其应用。
1. 电泳涂装技术
电泳涂装技术是一种利用电化学原理进行涂装的技术。
它可以使涂料在车身表面形成均匀、致密的涂层,提高涂层的附着力和耐腐蚀性。
电泳涂装技术广泛应用于汽车制造业中,特别是在汽车车身的底漆涂装中。
2. 粉末涂装技术
粉末涂装技术是一种无溶剂涂装技术,它可以使涂料在车身表面形成均匀、致密的涂层,提高涂层的耐磨性和耐腐蚀性。
粉末涂装技术广泛应用于汽车制造业中,特别是在汽车车身的中层涂装中。
3. 水性涂料技术
水性涂料技术是一种环保型涂装技术,它可以减少有害气体的排放,保护环境。
水性涂料技术广泛应用于汽车制造业中,特别是在汽车车身的面漆涂装中。
4. 纳米涂料技术
纳米涂料技术是一种利用纳米技术制造的涂料技术,它可以使涂料在车身表面形成均匀、致密的涂层,提高涂层的耐磨性和耐腐蚀性。
纳米涂料技术广泛应用于汽车制造业中,特别是在汽车车身的面漆涂装中。
汽车车身涂装新技术的应用不仅提高了汽车的外观质量,还能够提高汽车的耐久性和安全性。
未来,随着科技的不断进步,汽车车身涂装技术也将不断更新换代,为汽车工业的发展带来更多的机遇和挑战。
水性汽车涂料的研究进展

病, 降低了返修率 。 与溶剂型涂料相 比, 水性 中涂漆
可 增 加 底 漆 与 面 漆 的附 着 力 , 高 面 漆 的 鲜 映 性 和 提 丰 满度 , 整 车装饰 效 果 更佳 。 使 目前 ,国外 汽 车 用 水 性 中涂 漆 主要 采 用 水 性 聚 酯 氨 基 树 脂 和 封 闭 聚 氨 酯 树 脂 两 种 , 备 的涂 料 固 制
外 C D已发 展 到第 5 , 新 一 代 的产 品 已经 在 实 E 代 更
验 室取 得 成 功 。 E C D的发 展 方 向是 开 发 无 铅 、 锡 、 无
低 温 固化 的涂 料 新 品 种 。美 国 P G公 司 C D产 品 的 P E 发 展 方 向是 向 4 零 ( 发 性有 机 化 合 物 含 量 、 滤 个 挥 超 液 排 放量 、 重金 属 含量 、 料 含 量均 为零 ) 向发 展 , 颜 方 同 时进 一 步 提 高 抗 石 击 性 和节 约 能 源 , 低 烘 干 温 降 度。 P P G公 司成 功 开发 了双 层 电泳 系 统 , 幅度 降低 大
蒸 发速度缓慢 , 使水性涂料 在涂装过程 中对环境 的
温 湿 度 变化 比较 敏感 , 易 产 生气 泡 、 边 、 挂 等 容 缩 流
等 几类 。发 展 到 7 年 代 开 始 使 用 水 性 阴 极 电泳 底 漆 0 ( E , AD C D) 与 E相 比 , E C D在 防腐 性 、 理 力 学性 能 物
涂 料 在 浸 涂 槽 中 由于有 机溶 剂 的大 量 挥 发 导 致 着 火 爆 炸 。目前 尚存 的 浸 涂 漆 几 乎 都 是 水 性 丙 烯 酸 和 环
氧 酯类 。
车涂料不仅环保 , 同时还拥有更多不可替代的优势 ,
水性涂料的化学配方应用

水性涂料的化学配方应用摘要:现阶段,虽然我国经济取得了非常好的发展,但由于我国在早期发展经济的过程中,未重视环保问题,导致生态环境遭到严重破坏。
像在我国化工行业中,涂料是一种常见的化学材料,但由于其会对环境造成污染,影响我国的生态环境。
而水性涂料的出现,正好弥补了常规涂料的不足,因此,文章重点对水性涂料化学配方应用进行了分析,以供参考。
关键词:水性;涂料;化学;配方1.水性涂料的概念、种类及应用优势1.1水性涂料的概念在科学技术不断发展的背景下,先后有研究人员研究出各种类型的水性涂料,弥补了传统涂料的不足。
水性涂料即通过将水作为一种分散介质,形成的一种水性涂料。
通过按照涂料中含有的黏合剂类型对其进行划分,可以将水性涂料分为以下几种,即人工合成树脂型水性涂料,如丙烯酸树脂;天然水性涂料,如硅酸钾。
1.2水性涂料的优势1.2.1具备较强的安全性水性涂料顾名思义即将水作为一种稀释剂,其不具备易燃易爆的风险,在其运输生产过程中具备较高的安全性,不会威胁相关人员的生命财产安全,因此可以看出水性涂料具备较高的安全性。
1.2.2具备较强的实用性由于水性涂料的成膜方式较为特殊,导致其在延展性、透气性和耐黄性方面具有一定的优势,且在应用时手感非常好,附着力较强,不存在开裂脱落等问题,进而大大提高了产品的美观性,因此可以看出该材料具备较强的实用性。
1.2.3具备较强的环保性水性涂料是一种主要以水为稀释剂的涂料,在涂料中,大部分原材料为水,在生产该材料时无需添加类似于甲醛、铅等的有毒有害物质,在使用过程中可以最小化对人体的伤害,因此,可以看出水性材料具备较强的环保性。
1.3水性涂料的种类1.3.1水性环氧树脂涂料水性环氧树脂涂料主要是将环氧树脂作为原材料,并将其均匀分散在水中,形成一种水性环氧树脂涂料,由于该种水性涂料不含有机溶剂,且有机化合物含量非常低,具备绿色环保的优点。
在使用方面,具备方便施工和固化性强的优点,可以与其它水性聚合物体同时应用,经济价值相对较高。
我国水性涂料的研究现状

我国水性涂料的研究现状一、概述水性涂料作为一种环保、节能的涂料产品,近年来在我国得到了广泛的关注和研究。
水性涂料以水为分散介质,不含有害溶剂,具有低挥发性有机化合物(VOC)排放、安全环保、施工性能好等优点,符合我国绿色发展的战略需求。
随着国家环保政策的日益严格和消费者对健康环保意识的提高,水性涂料在建筑、汽车、家具等领域的应用越来越广泛。
同时,我国水性涂料行业在技术创新、产业升级等方面也取得了显著进展,一批具有自主知识产权的水性涂料产品不断涌现,为我国涂料产业的可持续发展注入了新的活力。
与发达国家相比,我国水性涂料的研究和应用水平仍存在一定差距。
主要表现在产品性能、涂装工艺、生产设备等方面。
加强水性涂料的基础研究和应用开发,提升我国水性涂料行业的整体竞争力,成为当前亟待解决的问题。
本文旨在综述我国水性涂料的研究现状,分析水性涂料的技术特点、应用领域及发展趋势,并探讨我国水性涂料行业面临的挑战和机遇,以期为我国水性涂料产业的进一步发展提供参考和借鉴。
1. 水性涂料的定义与特点水性涂料,顾名思义,是一种以水为分散介质的涂料。
其主要由水、树脂、颜料、填料、助剂等物质组成,通过特定的工艺将树脂分散或乳化在水中,形成稳定的涂料体系。
与传统的溶剂型涂料相比,水性涂料在环保、健康、安全等方面具有显著优势。
水性涂料的最大特点在于其环保性。
由于使用水作为分散介质,水性涂料在生产和施工过程中减少了有机溶剂的使用,从而降低了挥发性有机化合物(VOC)的排放,有助于改善空气质量和减少环境污染。
水性涂料还具有优良的施工性能。
其粘度适中,易于喷涂、滚涂或刷涂,且干燥速度快,提高了施工效率。
水性涂料还具有较好的附着力和耐候性,能够满足不同基材和环境的涂装需求。
再者,水性涂料在健康和安全方面也表现出色。
由于其低VOC含量,水性涂料在施工和使用过程中对人体无害,降低了职业健康风险。
同时,水性涂料不易燃爆,提高了生产和使用过程的安全性。
水性底盘装甲涂料在客车上的应用

层 。为 延长 汽 车车 身的使 用寿 命 、
12 第2 橡胶型油 性抗石击 防锈涂 好 、抗 石击 性 能也 较 强 的符 合 环保 . 代 要 求的 高分 子 型水 性 涂 料 .并 已 普 该 涂 料 防锈 性能 和 抗 石 击 性能 遍 采 用 。我 国 国内也 已经 出现 了 防
沥 青 型油 性 抗 石击 防 锈 涂料 ,后来
国产 客 车应 用很 早 的 水性 阻尼 采 用 水 性 阻尼 胶 ,发 现 水性 阻 尼胶
高 ,作业环境恶劣 ,不符合未来汽 车 胶 属于 高 分 子型 水 性涂 料 早 期 国 的 防锈 性 能达 不 到要 求时 ,也 曾 经 涂装生产线清洁生产 的要 求 因此开 产 的 水 性 阻 尼 胶 质 量 差 ,弹 性 不 采 用喷 涂 防护 蜡 的 方法 。但 喷涂 防
提高 汽 车 的舒 适 性和 车 身缝 隙间 的 料
耐腐 蚀 性 .在 车 身底 板 下 表面 ( 尤
其 是 易 受 石 击 的 轮 罩 、挡 泥 板 表 很 好 ,欧美 国 家早 已使 用 多年 .国 锈 及 抗 石击 性 能优 异 的高 分子 型 水 面 )增 涂 1 2 mm厚 的 具 有抗 石 击 产 客 车很 少 使 用 ,只 有 少部 分 中外 性涂料 。 -
1 客车底盘装 甲涂料的发展 过程
11 第1 . 代沥 青型油性抗 石击 防锈 涂 国外 特 别重 视底 盘 的防 锈及 抗 石 击 部 的锈 蚀 问题 , 同时也 有 减振 隔
料
性 能 所 以这 种初 期 的 水 性阻 尼胶 热 、防锈 和抗石击 的作 用。
沥 青 型油 性抗 石 击 防锈 涂 料 防 已不 能 满足 国际市 场 的 要 求 。有 的 21A 9 8 . B 5 水性底盘装甲涂料的特点
水性3C1B工艺在汽车涂装中的应用
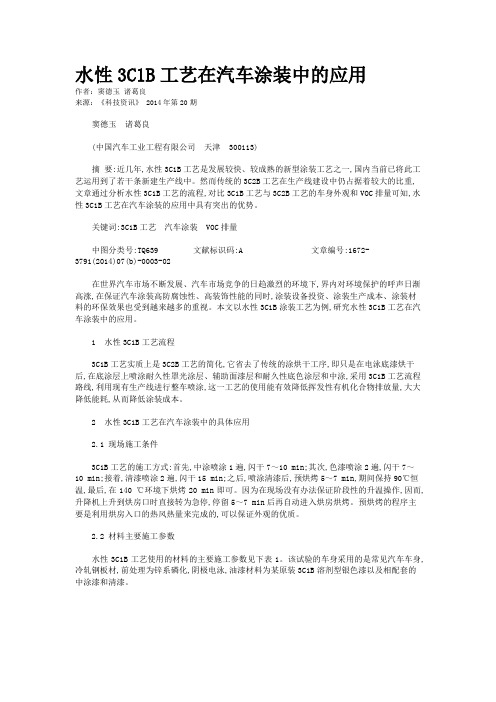
水性3C1B工艺在汽车涂装中的应用作者:窦德玉诸葛良来源:《科技资讯》 2014年第20期窦德玉诸葛良(中国汽车工业工程有限公司天津 300113)摘要:近几年,水性3C1B工艺是发展较快、较成熟的新型涂装工艺之一,国内当前已将此工艺运用到了若干条新建生产线中。
然而传统的3C2B工艺在生产线建设中仍占据着较大的比重,文章通过分析水性3C1B工艺的流程,对比3C1B工艺与3C2B工艺的车身外观和VOC排量可知,水性3C1B工艺在汽车涂装的应用中具有突出的优势。
关键词:3C1B工艺汽车涂装 VOC排量中图分类号:TQ639 文献标识码:A 文章编号:1672-3791(2014)07(b)-0003-02在世界汽车市场不断发展、汽车市场竞争的日趋激烈的环境下,界内对环境保护的呼声日渐高涨,在保证汽车涂装高防腐蚀性、高装饰性能的同时,涂装设备投资、涂装生产成本、涂装材料的环保效果也受到越来越多的重视。
本文以水性3C1B涂装工艺为例,研究水性3C1B工艺在汽车涂装中的应用。
1 水性3C1B工艺流程3C1B工艺实质上是3C2B工艺的简化,它省去了传统的涂烘干工序,即只是在电泳底漆烘干后,在底涂层上喷涂耐久性罩光涂层、辅助面漆层和耐久性底色涂层和中涂,采用3C1B工艺流程路线,利用现有生产线进行整车喷涂,这一工艺的使用能有效降低挥发性有机化合物排放量,大大降低能耗,从而降低涂装成本。
2 水性3C1B工艺在汽车涂装中的具体应用2.1 现场施工条件3C1B工艺的施工方式:首先,中涂喷涂1遍,闪干7~10 min;其次,色漆喷涂2遍,闪干7~10 min;接着,清漆喷涂2遍,闪干15 min;之后,喷涂清漆后,预烘烤5~7 min,期间保持90℃恒温,最后,在140 ℃环境下烘烤20 min即可。
因为在现场没有办法保证阶段性的升温操作,因而,升降机上升到烘房口时直接转为急停,停留5~7 min后再自动进入烘房烘烤。
- 1、下载文档前请自行甄别文档内容的完整性,平台不提供额外的编辑、内容补充、找答案等附加服务。
- 2、"仅部分预览"的文档,不可在线预览部分如存在完整性等问题,可反馈申请退款(可完整预览的文档不适用该条件!)。
- 3、如文档侵犯您的权益,请联系客服反馈,我们会尽快为您处理(人工客服工作时间:9:00-18:30)。
水性涂料在汽车涂装中的应用研究(中国表面工程协会涂装分会秘书处,上海200001)摘要:概述了国内外水性涂料的发展、应用概况。
介绍了水性涂料的施工设备、施工条件和施工实例。
认为在水性涂料推广应用的同时,对涂料价格、施工工艺、设备投资等方面应有创新和突破。
关键词:水性涂料;汽车涂料;汽车涂装0 引言溶剂型涂料中含有溶剂,在生产和施工过程中排放大量的VOC(挥发性有机化合物),危害人类健康,造成环境污染。
据统计,目前全球每年向大气排放的VOC为500~600万t。
自20世纪60年代初,美国率先开发成功水性涂料,采用电泳涂装用于汽车车身以来,在工业发达国家逐渐推广。
我国在60年代中期由上海市涂料研究所开发,随后由振华造漆厂研制成醇酸、环氧酯以及浅色丙烯酸阳极电泳涂料投入工业化生产;80年代初上海造漆厂又相继研制成功水性丙烯酸清漆,用于硅钢片的表面防腐防锈;90年代开发出双组分环氧类和无机富锌类防锈底漆,但水性面漆的应用因受限于当时的施工条件,进展缓慢。
相比西欧、北美汽车制造发达国家,在90年代已在汽车车身成功采用水性底色漆和水性中涂漆而言,我国仍存在较大差距。
1 涂料水性化的驱动随着人类环保意识的增强,工业发达国家相继制订保护环境的法规,限制VOC排入大气。
我国在2002年6月公布了《中华人民共和国清洁生产促进法》,并于2003年1月1日起实施。
国家环保局于2006年8月发布了《HJ/T293—2006清洁生产标准汽车制造业(涂装)》标准,规定了汽车涂装中有机废气产生量排放指标,并于2006年12月1日起实施。
在该标准中按不同涂装层数规定了VOC排放量指标:1级,国际清洁生产先进水平30~60g/m2;2级,国内清洁生产先进水平50~80g/m2;3级,国内清洁生产基本水平70~100g/m2。
当前,发达国家轿车车身制造新生产线VOC排放量的限值为:美国、欧盟经委会35g/m2;日本45g/m2;加拿大(2005年)55g/m2;英国60g/m2;世界先进水平15~20g/m2。
在汽车涂装中的VOC排放量随配套涂料体系不同而各异,见表1。
采用水性涂料配套体系的VOC排放量,能达到或低于欧盟经委会规定的35g/m2的排放限值。
表1 不同涂料体系VOC排放量(g/m2)点击此处查看全部新闻图片2 汽车涂料产量及其需求汽车制造是我国的支柱工业,2008年汽车产销量为934.5万辆,汽车保有量为6467.21万辆。
2008年我国涂料产量为638万t,其中汽车涂料为48万t,占涂料产量的7.5%;其他工业水性涂料为34.5万t,占涂料产量的5.4%。
汽车涂料用量约42~60万t(在此尚无确实可靠数据),占当年涂料总产量的4.5%~6.5%。
其中轿车用漆量(按25~30kg/辆计),2008年为23~28万t;修补用涂料(按3~5kg/辆计),2008年为19~32万t。
2009年1~11月我国涂料产量已超过822万t,国产汽车产销量突破1300万辆,其涂料用量虽无统计数据,按汽车产量增加比例估计应在60~80万t(包括修补用涂料),约达到当年涂料总产量的6.8%~8.8%。
在涂料市场中汽车涂料占有相当份额,有资料统计,在发达国家,汽车涂料约占本国涂料总产量的20%。
3 水性涂料的发展历程自20世纪90年代起,欧美汽车涂装已进入水性化、高固体分化和粉末化。
早在2005年,全球水性涂料产量已占涂料总产量的34.5%。
在工业发达国家,汽车涂装100%底漆、80%以上的中涂漆和60%以上的金属底色漆均采用水性涂料,水性罩光漆正在使用中。
3.1 水性底色漆水性底色漆使用方面,德国已达到100%,处于领先位置;日本70%;美国40%。
近几年来,我国新建的汽车涂装生产线中也很重视水性涂料的应用。
上海通用南厂及东岳厂已先后建造和使用水性涂料涂装生产线。
到目前为止,我国已有水性中涂生产线12条,水性底色漆喷涂线17条。
我国主要涂料合资公司(如上海BASF、DuPont)已率先将水性涂料国产化,天津PPG已开始进行水性涂料的生产。
3.2 水性涂料应用实例涂料市场已经商品化可提供生产应用的水性涂料有环氧、醇酸、丙烯酸、聚氨酯、有机硅改性和氟碳等涂料,以及各类防锈、耐高温、无机富锌和底面合一丙烯酸烤漆等功能性水性涂料。
汽车传动轴采用手工喷涂的水性醇酸涂料,有的零部件采用浸涂水性聚酯涂料。
铁道车辆和机车的修补采用双组分环氧底漆(厚度60μm)和双组分水性聚氨酯涂料(厚度40μm)。
AkzoNobel涂料公司在6年前提供名为Durasoft的双组分水性聚氨酯涂料,被GM公司指定用于汽车内部仪表板的涂装。
DaimlerChrysler也要求另一家仪表生产商Lear为ChryslerNeon汽车内饰件选用水性聚氨酯内饰涂料。
欧洲汽车涂装100%的底漆、70%以上的中涂漆和60%以上的金属底色漆均采用水性涂料,水性罩光漆也已开始使用。
西门子机车采用3层水性涂料涂装:水性环氧底漆+双组分水性聚氨酯底漆+双组分聚氨酯面漆。
干燥条件:60℃/2h,干膜厚度80μm。
欧洲的瑞典和芬兰等国水性涂料的比例超过90%。
拜耳公司在多年前提供用于塑料表面涂覆的双组分水性聚氨酯涂料,已用于福特、德国大众、宝马等汽车公司的内饰件涂装,使塑料件表面具有柔软触感,与底材的附着力和弹性,以及低光泽度、低VOC和雾化值都能获得满意效果。
4 水性涂料涂装对设备的要求4.1 输调漆系统由于水是腐蚀介质,会造成金属腐蚀,引起设备损坏和产生金属离子,不仅会使漆膜色泽泛黄,而且降低漆膜的防蚀能力。
为此,水性涂料的贮漆容器和输送管路需用不锈钢制作,并应经过化学钝化处理。
对涂装线中的调漆系统和搅拌机、背压调节阀均应选用低剪切力类型。
输漆管路连接应避免死角,输送系统以采用二线为佳,管路要加大,以增加循环供料泵的压力和流量。
调漆罐搅拌机的循环速度应在0.15m/s。
调漆间温度控制在低于涂料(3±1)℃。
水性涂料的贮存稳定条件:5~30℃/6个月。
4.2 静电喷涂设备水性涂料电阻小于0.1MΩ,有高压电泄漏,应采用专用的静电喷涂设备,通常采用外加电输漆系统,其优点为供输漆系统和换色与传统方式相同。
日本本田汽车公司在前些年开发成功和采用内加电的杯型静电喷枪,其优点是能提高涂料的利用率。
机器人弹匣式旋杯喷涂系统,将中转涂料容器做成独立的涂料容器(称为弹匣),可与旋杯进行快速组合,压送涂料。
其优点为:节省换色时清洗溶剂,可同时适用于溶剂型和水性涂料的静电喷涂。
4.3 喷漆室喷漆室的材质应采用不锈钢,喷漆室的新风补充__需配置除湿装置,防止涂膜流挂。
4.4 烘干室水性涂料中水的蒸发率低,其闪蒸或晾干的时间与湿度有关,应采取措施,防止涂层产生弊病,而在喷涂溶剂型罩光面漆前,要控制底色漆膜中残留溶剂<10%,以防止涂膜产生弊病。
降低闪蒸或晾干、烘干段湿度,提高水的蒸发率。
进行低温加热,吹风闪干,防止流挂。
采用红外加热60~80℃,保温2~3min。
采用冷却降湿法,降低闪蒸室循环空气的湿度,将闪干室空气温度升高。
5 水性涂料施工要求水性涂料的施工方法与溶剂型涂料没多大差别,但对涂装前的表面处理和对作业环境及施工条件等均有更高要求和严格规定。
作业环境条件:采用喷涂方法的场合,对环境的温度、湿度和空调系统流速有要求。
最佳相对湿度RH(65±5)%,温度(23±3)℃,空调系统流速0.3~0.5m/s。
水质要求:去离子水pH7,电导率<20μS/cm;自来水pH7,电导率<170μS/cm。
6 水性涂料在汽车涂装中的应用6.1 电泳底漆自20世纪60年代使用阳极电泳涂料以来,经过40年的发展,在阴极电泳涂料方面也已更新换代,汽车底漆已达到100%水性化,并开发出低毒无毒、环保友好型、高渗透、高质量、低温固化电泳涂料。
第5代阴极电泳涂料在世界各大汽车厂60多条生产线上广泛应用,VOC为0.048kg/L,改善表面缩孔,浮漆带出少。
PPG公司开发的第6代高泳透力阴极电泳涂料ED-6,已在奇瑞、上海和烟台的通用、神龙等汽车厂应用。
它将使用量减少12.8%,烘干温度由原先的170~180℃/30min降为现在的160~170℃/25min。
施工三段电压由原来100V-200V-270V降为现在的50V-100V-180V。
第7代阴极电泳涂料采用无铬、无铅、无锡的有机颜料。
该涂料为低温固化型、边角覆盖型,无亚硝盐,减少水耗,已在使用。
6.2 水性中涂漆、底色漆及清漆在欧洲,水性中涂漆的使用已达31%,面漆的水性化比率为57%。
水性罩光清漆已在使用,其中德国水性中涂漆的使用近80%,早在2006年水性底色漆已占100%(50%以上为水性闪光底色漆)。
日本本田、日产等汽车公司已有40%~50%的涂装线采用水性丙烯酸聚酯型涂料,固体分为60%。
涂料黏度(涂-4)40s,固化条件140℃/30min。
2002年,DuPont 公司已为Volvo汽车公司开发了一种白色水性珍珠涂料,采用湿碰湿工艺,可在标准喷漆线上完成3层涂料一次固化的喷涂作业。
6.3 免水性中涂漆的涂装工艺取消中涂漆工艺是通过采用特殊的水性底色漆,如杜邦公司的EcoConcept双组分水性底色漆,以及BASF、PPG等公司的产品,在喷涂后直接喷涂面漆来实现相关功能。
工艺举例:单色漆前处理:电泳底漆(20μm)+双组分水性单色漆(25~30μm)+双组分清漆(40μm)。
金属闪光漆前处理:电泳底漆(20μm)+双组分水性金属闪光底色漆(15μm)+水性底色漆(5~8μm)+双组分清漆(35~40μm)。
优点:简化工艺,提高生产率,减少VOC排放,节省设备投资费用,减少占地面积,降低能耗,节省材料。
7 施工举例举例1:水性底色漆主要有丙烯酸类和聚氨酯类漆,60~80℃辐射固化1min,对流烘干2~3min,在喷罩光漆前,底色漆涂膜中水分<10%,高固体分罩光漆固化条件:135~145℃/20~22min。
举例2:水性中涂漆→闪干(60℃/5~8min)→烘烤(140~150℃/20min)→水性底色漆→流平1~2min→闪干(60~80℃/5min)→保温3min(相对湿度RH<20%)→冷却→溶剂型罩光清漆→烘烤(140~160℃/30min)。
举例3:电泳漆→热空气吹干→水性中涂漆→晾干→烘干(70℃/5min~165℃/15min)→水性金属闪光底漆→闪蒸辐照1~3min→热空气吹(85℃/2~7min,使车身温度达65℃)→冷却2~3min,<35℃→溶剂型罩光清漆→晾干→烘干(140℃/30min)。
8 结语近年全球汽车制造行业受金融危机影响,生产大幅下滑,而中国汽车制造业进入高速发展期。