冷镦线材改制加工工艺
材料改制
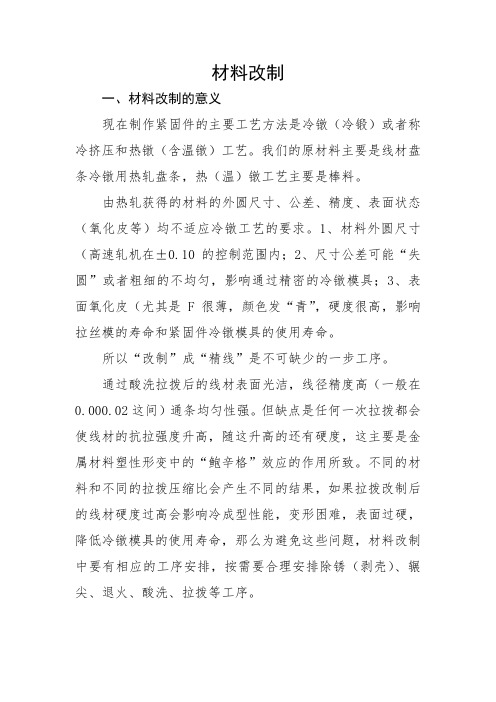
材料改制一、材料改制的意义现在制作紧固件的主要工艺方法是冷镦(冷锻)或者称冷挤压和热镦(含温镦)工艺。
我们的原材料主要是线材盘条冷镦用热轧盘条,热(温)镦工艺主要是棒料。
由热轧获得的材料的外圆尺寸、公差、精度、表面状态(氧化皮等)均不适应冷镦工艺的要求。
1、材料外圆尺寸(高速轧机在±0.10的控制范围内;2、尺寸公差可能“失圆”或者粗细的不均匀,影响通过精密的冷镦模具;3、表面氧化皮(尤其是F很薄,颜色发“青”,硬度很高,影响拉丝模的寿命和紧固件冷镦模具的使用寿命。
所以“改制”成“精线”是不可缺少的一步工序。
通过酸洗拉拨后的线材表面光洁,线径精度高(一般在0.000.02这间)通条均匀性强。
但缺点是任何一次拉拨都会使线材的抗拉强度升高,随这升高的还有硬度,这主要是金属材料塑性形变中的“鲍辛格”效应的作用所致。
不同的材料和不同的拉拨压缩比会产生不同的结果,如果拉拨改制后的线材硬度过高会影响冷成型性能,变形困难,表面过硬,降低冷镦模具的使用寿命,那么为避免这些问题,材料改制中要有相应的工序安排,按需要合理安排除锈(剥壳)、辗尖、退火、酸洗、拉拨等工序。
二、材料改制的基本工艺路线热轧 (盘圆) 除锈、碾尖酸洗、润滑 冷拨 检验 多置、重复①除锈(机械除锈、剥壳)酸洗、润滑拉拨②先进炉退火除锈、剥壳酸洗、润滑拉拨③除锈酸洗、润滑拉拨退火除锈酸洗拉拨(二拉一退) ④退火除锈酸洗、润滑拉拨退火除锈酸洗拉拨(二拉二退)A 只用①工艺步骤的俗称“生料拉”,主要用于外六角螺栓等;B 只用②工艺步骤一退一拉,适用中炭冷镦钢生产螺母大料小变形;C 用③工艺步骤二拉一退,适用中炭或低合金、内六角螺钉、法兰面螺栓、10级螺母、异型件;D 用④工艺步骤二拉二退,一般第一拉安排超过25~30%压缩比,第二拉仅0.2~0.4‟轻拉,主要是合金钢紧固件、法兰面、沉头内六角异型件,及需要在调质前调整好材料基本组织的线材。
冷镦成型工艺

紧固件冷镦成型工艺紧固件成型工艺中,冷镦(挤)技术是一种主要加工工艺。
冷镦(挤)属于金属压力加工范畴。
在生产中,在常温状态下,对金属施加外力,使金属在预定的模具内成形,这种方法通常叫冷镦。
实际上,任何紧固件的成形,不单是冷镦一种变形方式能实现的,它在冷镦过程中,除了镦粗变形外,还伴随有正、反挤压、复合挤压、冲切、辗压等多种变形方式。
因此,生产中对冷镦的叫法,只是一种习惯性叫法,更确切地说,应该叫做冷镦(挤)。
冷镦(挤)的优点很多,它适用于紧固件的大批量生产。
它的主要优点概括为以下几个方面: a .钢材利用率高。
冷镦(挤)是一种少、无切削加工方法,如加工杆类的六角头螺栓、圆柱头内六角螺钉,采用切削加工方法,钢材利用率仅在25%~35%,而用冷镦(挤)方法,它的利用率可高达85%~95%,仅是料头、料尾及切六角头边的一些工艺消耗。
b .生产率高。
与通用的切削加工相比,冷镦(挤)成型效率要高出几十倍以上。
c .机械性能好。
冷镦(挤)方法加工的零件,由于金属纤维未被切断,因此强度要比切削加工的优越得多。
d .适于自动化生产。
适宜冷镦(挤)方法生产的紧固件(也含一部分异形件),基本属于对称性零件,适合采用高速自动冷镦机生产,也是大批量生产的主要方法。
总之,冷镦(挤)方法加工紧固件、异形件是一种综合经济效益相当高的加工方法,是紧固件行业中普遍采用的加工方法,也是一种在国内、外广为利用、很有发展的先进加工方法。
因此,如何充分利用、提高金属的塑性、掌握金属塑性变形的机理、研制出科学合理的紧固件冷镦(挤)加工工艺,是本章的目的和宗旨所在。
1 金属变形的基本概念1.1 变形变形是指金属受力(外力、内力)时,在保持自己完整性的条件下,组成本身的细小微粒的相对位移的总和。
1.1.1 变形的种类a.弹性变形金属受外力作用发生了变形,当外力去掉后,恢复原来形状和尺寸的能力,这种变形称为弹性变形。
弹性的好坏是通过弹性极限、比例极限来衡量的。
冷镦成型工艺
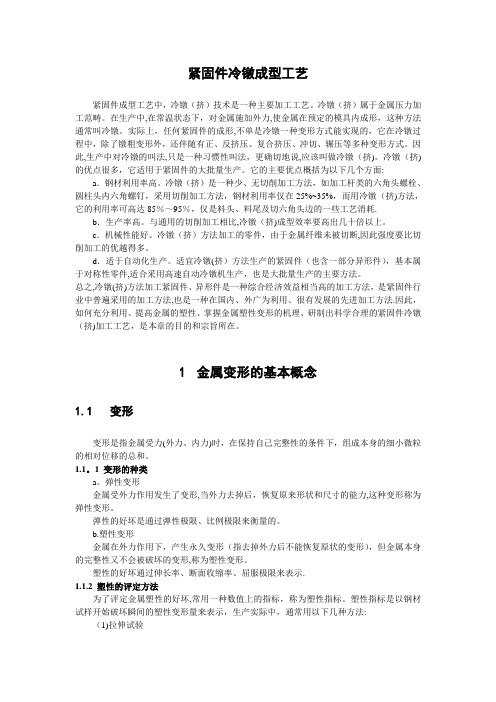
紧固件冷镦成型工艺紧固件成型工艺中,冷镦(挤)技术是一种主要加工工艺。
冷镦(挤)属于金属压力加工范畴。
在生产中,在常温状态下,对金属施加外力,使金属在预定的模具内成形,这种方法通常叫冷镦。
实际上,任何紧固件的成形,不单是冷镦一种变形方式能实现的,它在冷镦过程中,除了镦粗变形外,还伴随有正、反挤压、复合挤压、冲切、辗压等多种变形方式。
因此,生产中对冷镦的叫法,只是一种习惯性叫法,更确切地说,应该叫做冷镦(挤)。
冷镦(挤)的优点很多,它适用于紧固件的大批量生产。
它的主要优点概括为以下几个方面: a.钢材利用率高。
冷镦(挤)是一种少、无切削加工方法,如加工杆类的六角头螺栓、圆柱头内六角螺钉,采用切削加工方法,钢材利用率仅在25%~35%,而用冷镦(挤)方法,它的利用率可高达85%~95%,仅是料头、料尾及切六角头边的一些工艺消耗.b.生产率高。
与通用的切削加工相比,冷镦(挤)成型效率要高出几十倍以上。
c.机械性能好。
冷镦(挤)方法加工的零件,由于金属纤维未被切断,因此强度要比切削加工的优越得多。
d.适于自动化生产。
适宜冷镦(挤)方法生产的紧固件(也含一部分异形件),基本属于对称性零件,适合采用高速自动冷镦机生产,也是大批量生产的主要方法。
总之,冷镦(挤)方法加工紧固件、异形件是一种综合经济效益相当高的加工方法,是紧固件行业中普遍采用的加工方法,也是一种在国内、外广为利用、很有发展的先进加工方法.因此,如何充分利用、提高金属的塑性、掌握金属塑性变形的机理、研制出科学合理的紧固件冷镦(挤)加工工艺,是本章的目的和宗旨所在。
1 金属变形的基本概念1.1变形变形是指金属受力(外力、内力)时,在保持自己完整性的条件下,组成本身的细小微粒的相对位移的总和。
1.1。
1 变形的种类a。
弹性变形金属受外力作用发生了变形,当外力去掉后,恢复原来形状和尺寸的能力,这种变形称为弹性变形。
弹性的好坏是通过弹性极限、比例极限来衡量的。
冷镦钢的技术要求及主要工艺流程

冷镦钢的技术要求:冷镦钢盘条一般为低、中碳优质碳素结构钢和合金结构钢。
标准件对原材料尺寸精度要求比较严格,热轧钢材规格有限,尺寸精度也很难满足要求,所以标准件几乎全部采用冷拉钢丝作为原料,合格的冷镦钢丝必须满足以下要求。
(1)化学成分要求:O,P,S等元素对钢中夹杂物的形态及数量、大小有决定性影响,所以要求控制其含量;对合金钢而言,硅、铝、锰等元素控制在中下限为宜,避免造成冷顶锻裂纹。
(2)表面品质:标准件厂统计表明,冷镦开裂的80%是由钢丝表面缺陷造成的,如折迭、划伤、密集的发纹、局部微裂纹、结疤。
因此对线材表面品质要求很严,尺寸公差±0.20mm,不圆度<0.30mm,表面裂纹、划伤最深<0.07mm。
(3)脱碳:表面脱碳造成螺栓表面强度降低,疲劳寿命大幅下降。
(4)非金属夹杂物:钢中非金属夹杂物含量高、尺寸大是造成标准件冷镦开裂的一个重要原因,尤其是非金属夹杂中B类和D类脆性夹杂,距钢丝表面愈近危害性越大,所以要求B类夹杂物距表层2mm之内应不大于15μm。
(5)金相组织:冷镦钢的金相组织为铁素体+粒状珠光体,珠光体的晶粒尺寸和分布也是影响冷镦性能的因素,理想的组织是珠光体晶粒大小相近并均匀地分布在铁素体基体上。
珠光体不同显微组织冷镦性能从好到坏的排列次序为粒状珠光体、索氏体、细片状珠光体、片状珠光体。
(6)低倍组织:冷镦钢丝对钢的低倍组织要求比较严,低倍检查不应有缩孔、分层、白点、裂纹、气孔等缺陷,对中心疏松、方框偏析、中心增碳等缺陷,不同钢种都有明确的级别规定。
(7)晶粒度:冷镦钢丝内部组织不同于其它钢丝,晶粒度不是越细越好。
晶粒度太细,抗拉强度、屈服强度升高,变形抗力增大,对冷镦成型很不利。
除10.9级以上螺栓晶粒细、保证成品强度外,冷镦钢丝的晶粒度应控制在5~7级。
(8)冷镦性能:冷镦性能好是指钢丝具有较低的变形抗力,能经受很大程度的变形而不产生裂纹。
一般认为以断面收缩率和屈强比作为衡量冷镦性能指标比较可靠。
紧固件冷镦成型工艺,一文搞懂!
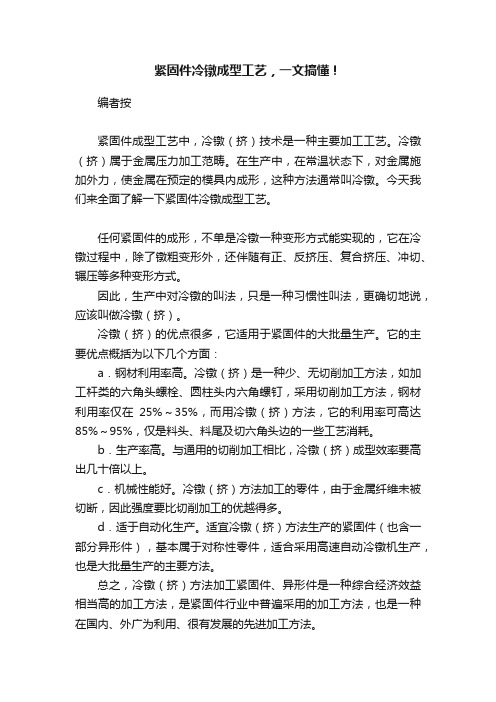
紧固件冷镦成型工艺,一文搞懂!编者按紧固件成型工艺中,冷镦(挤)技术是一种主要加工工艺。
冷镦(挤)属于金属压力加工范畴。
在生产中,在常温状态下,对金属施加外力,使金属在预定的模具内成形,这种方法通常叫冷镦。
今天我们来全面了解一下紧固件冷镦成型工艺。
任何紧固件的成形,不单是冷镦一种变形方式能实现的,它在冷镦过程中,除了镦粗变形外,还伴随有正、反挤压、复合挤压、冲切、辗压等多种变形方式。
因此,生产中对冷镦的叫法,只是一种习惯性叫法,更确切地说,应该叫做冷镦(挤)。
冷镦(挤)的优点很多,它适用于紧固件的大批量生产。
它的主要优点概括为以下几个方面:a.钢材利用率高。
冷镦(挤)是一种少、无切削加工方法,如加工杆类的六角头螺栓、圆柱头内六角螺钉,采用切削加工方法,钢材利用率仅在25%~35%,而用冷镦(挤)方法,它的利用率可高达85%~95%,仅是料头、料尾及切六角头边的一些工艺消耗。
b.生产率高。
与通用的切削加工相比,冷镦(挤)成型效率要高出几十倍以上。
c.机械性能好。
冷镦(挤)方法加工的零件,由于金属纤维未被切断,因此强度要比切削加工的优越得多。
d.适于自动化生产。
适宜冷镦(挤)方法生产的紧固件(也含一部分异形件),基本属于对称性零件,适合采用高速自动冷镦机生产,也是大批量生产的主要方法。
总之,冷镦(挤)方法加工紧固件、异形件是一种综合经济效益相当高的加工方法,是紧固件行业中普遍采用的加工方法,也是一种在国内、外广为利用、很有发展的先进加工方法。
因此,如何充分利用、提高金属的塑性、掌握金属塑性变形的机理、研制出科学合理的紧固件冷镦(挤)加工工艺,是研究的目的和宗旨所在。
一、金属变形的基本概念变形变形是指金属受力(外力、内力)时,在保持自己完整性的条件下,组成本身的细小微粒的相对位移的总和。
1 变形的种类a.弹性变形金属受外力作用发生了变形,当外力去掉后,恢复原来形状和尺寸的能力,这种变形称为弹性变形。
弹性的好坏是通过弹性极限、比例极限来衡量的。
紧固件冷镦工艺详解

冷镦:就是利用金属的塑性,采用冷态力学进行施压或冷拔,达到金属固态变形的目的。
(基本定义)在室温下把棒材或线材的顶部加粗的锻造成形方法.冷镦主要用於制造螺栓、螺母、铁钉、铆钉和钢球等零件.锻坯材料可以是铜、铝、碳钢、合金钢、不锈钢和钛合金等,材料利用率可达80~90%。
冷镦多在专用的冷镦机上进行,便於实现连续、多工位、自动化生产。
在冷镦机上能顺序完成切料、镦头、聚积、成形、倒角、搓丝、缩径和切边等工序。
生产效率高,可达300件/分以上,最大冷镦工件的直径为48毫米。
冷镦螺栓工序示意图为冷镦螺栓的典型工序.多工位螺母自动冷镦机为多工位螺母自动冷镦机。
棒料由送料机构自动送进一定长度,切断机构将其切断成坯料,然后由夹钳传送机构依次送至聚积压形和冲孔工位进行成形。
冷镦是指原材料在常温下进行冲压,热镦是指原材料在经过加温后进行冲压,具体的用途没有特别的要求,一般情况下都要求用冷镦,因为这样的表面光洁度,材料的组织成份会比较紧密些,还有就是较大的工件常采用热镦加工。
锻造头部,也叫热墩,把头部加热烧红,挤压成型;螺丝的六角头是墩出来的吗?绝大多数是墩出来的,因为这样可以节省材料.根据墩锻机吨位大小和螺栓直径,可以采用冷墩或热墩工艺。
小批量的专用或特殊螺栓的六角头是车削后铣成的.丝又是怎样制出的?单件小批量可以用板牙套丝、车床挑丝、旋风铣铣制等方法。
大批量生产中常采用搓丝机搓丝、滚丝机滚丝的方法,效率很高。
因为螺栓杆成形方法有冷拔和缩径,所以这种螺栓的没有螺纹的部分直径不一定略小。
采用冷拔时,略小;采用缩径时,可以与螺纹等径或稍大.螺栓整个是压铸造的吗?如果螺栓材料为铝合金、锌合金、铜合金等低熔点的合金或金属,也可以采用压铸成型的方法。
钢制的不采用压铸制造。
螺栓的六角头的成形不能一概而论,有冷墩的、有热墩的、有镦后直接出成品的,也有镦后再机加工的,也有全部机加工的。
镦制的螺栓头部是有加工痕迹的,在根部有模具的夹具痕迹。
冷镦锻工艺与模具设计

以GB5786-M8六角头螺栓为例来说明...冷镦锻工艺是一种少无切削金属压力加工工艺。
它是一种利用金属在外力作用下所产生的塑性变形,并借助于模具,使金属体积作重新分布及转移,从而形成所需要的零件或毛坯的加工方法。
冷镦锻工艺的特点:1.冷镦然是在常温条件进行的。
冷镦锻可使金属零件的机械性能得到改善。
2.冷镦锻工艺可以提高材料利率。
它是以塑性变形为基础的压力加工方法,可实现少切削或者无切削加工。
一般材料利用率都在85%以上,最高可达99%以上。
3.可提高生产效率。
金属产品变形的时间和过程都比较短,特别是在多工位成形机上加工零件,可大大提高生产率。
4.冷镦锻工艺能提高产品表面粗糙度、保证产品精度。
二、冷镦锻工艺对原材料的要求1.原材料的化学成份及机械性能应符合相关标准。
2.原材料必须进行球化退火处理,其材料金相组织为球状珠光体4-6级。
3.原材料的硬度,为了尽可能减少材料的开裂倾向,提高模具使用寿命还要求冷拔料有尽可能低的硬度,以提高塑性。
一般要求原材料的硬度在HB110~170(HRB62-88)。
4.冷拔料的尽寸精度一般应根据产品的具体要求及工艺情况而定,一般来说,对于缩径和强缩尺寸精度要求低一些。
5.冷拔料的表面质量要求有润滑薄膜呈无光泽的暗色,同时表面不得有划痕、折叠、裂纹、拉毛、锈蚀、氧化皮及凹坑麻点等缺陷。
6.要求冷拔料半径方向脱碳层总厚度不超过原材料直径的1-1.5%(具体情况随各制造厂家的要求而定)。
7.为了保证冷成形时的切断质量,要求冷拔料具有表面较硬,而心部较软的状态。
8.冷拔料应进行冷顶锻试验,同时要求材料对冷作硬化的敏感性越低越好,以减少变形过程中,由于冷作硬化使变形抗力增加。
三、紧固件加工工艺简述紧固件主要分两大粪:一类是螺纹类紧固件;另一类是非螺纹类紧固件或联接件。
这里仅针对螺纹类紧固件进行简述。
1. 螺纹类紧固件加工流程一般都是由剪断、冷镦、或者冷挤压、切削、螺纹加工、热处理、表面处理等生产工序组成的。
冷镦材料与热处理方法

冷镦材料与热处理方法一、冷镦工艺对金属材料的要求1、冷镦用金属材料的机械性能要求根据冷镦工艺特点,对钢材机械性能提出如下要求:1)屈服强度Re以及变形抗力尽可能低,这样可使单位变形力相应减小,以延长模具寿命;2)材料的冷变形性能要好,既材料应有较好的塑性,较低的硬度,在大的变形程度下不致引起开裂。
如冷镦高强度螺栓时,即可使用含碳量较高的碳素钢,又可使用含碳量较低的低合金钢。
如果增加含碳量,就会使硬度提高,塑性降低,使冷变形性能变坏。
但是在含碳量较低的钢中加入少量合金元素(如添加少量硼10B21、10B33钢),即可显著提高钢材强度,从而满足产品的使用性能要求,同时又不损害其冷变形性能;3)材料的加工硬化敏感性能越低越好,这样不致使变形过程中的变形力太大。
材料的加工硬化敏感性可用变形抗力--应变曲线的斜率来反映。
斜率越大,则加工硬化敏感性越高。
如不锈钢0Cr18Ni9(SUS304)的曲线斜率最大。
这种材料的加工硬化敏感性就比较剧烈,随着变形程度的增加,变形抗力急剧上升。
钢材的机械性能不但表现原始坯料的Rm、Re、A、Z 及硬度等指标,不但受原材料的化学成分、宏观组织、微观组织等方面的影响,还受到材料准备过程中的拉拔及各道工序之间的热处理影响。
2、化学成分的要求⑴碳(C)碳是影响钢材冷塑性变形的最主要元素。
含碳量越高,钢的强度越高,而塑性越低。
含碳量每提高0.1%,其屈服强度Re提高27.4MPa,抗拉强度Rm提高(58.8-78.4MPa),而伸长率A则降低4.3%,断面收缩率Z降低7.3%。
当钢的含碳量<0.5%、含锰量<1.2%、断面收缩率Z=80%时,单位冷变形力P与钢材含C、Mn量之间的近似关系如下:P=1950C+500Mn+1860(MPa) (1)可见,钢中含碳量对于钢材的冷塑性变形性能的影响是很大的。
在实际工艺过程中,冷镦挤压用钢的含碳量大于0.25%时,要求钢退火成具有最好的塑性组织——球状珠光体组织。
冷镦线材改制加工工艺

冷镦线材改制加工工艺1、序言紧固件制造业是现代工业的基础,而紧固件质量的优劣很大程度上取决于其所使用的冷镦材料的质量。
其中如成分偏析、疏松和夹杂物等材料的冶金质量,作为使用者的机械厂往往难以改变。
但材料的强度、硬度、塑性、组织结构和韧性,则与随后的材料加工过程有着密切的关系。
这些性能实际上就是材料的冷镦性能、切削性能、热处理性能的体现。
因此研究和掌握冷镦线材的加工工艺特性是制造优质冷镦线材和保证紧固件质量的基础。
2、冷镦线材的选择:2.1、钢材牌号选择钢材牌号应根据产品图纸和相关国家标准的要求进行选择,表1可供选材时参考(见表1)。
也可选择相应日本牌号的材料(见表2)。
表1 钢材牌号的选择注:当紧固件规格较大时为保证材料热处理性能,应选用较高一个档次的材料。
2.2、 拉丝车间应按生产计划领取经检验合格的原材料进行材料改制,检验不合格的钢材不能投产。
3、改制工艺:3.1、钢材(盘圆)改制工艺流程:在金相组织正常和拉拔减面率不大于35%的情况下,中低碳钢一般可不进行球化退火,而直接进行拉拔,但中碳合金钢应在退火后进行材料改制,当材料需要两次或两次以上拉拔时,第一次的拉拔比宜控制在20%~25%,最后一道拉拔前应进行中间退火处理,且拉拔比宜控制在15%~20%。
3.2、退火3.2.1、退火工艺a、球化退火:热轧盘条的首次退火一般在真空退火炉或井式炉中进行球化处理,其目的是使珠光体完全球化并均匀分布在铁素体的机体上,使材料获得最好的塑性和最低的硬度。
其工艺为750℃~780℃充分加热,然后在680℃~700℃等温转变。
具体的参数取决于炉型、材料的种类和装炉量,合适的工艺需要通过实验确定。
b、再结晶退火:经过加工的材料,第二次退火应采用再结晶退火处理,同样是在真空炉或井式炉中进行。
其目的是使产生了加工硬化的材料消除应力,使各向异性的铁素体组织重结晶,重新软化回复良好的塑性。
其工艺为680℃~700℃充分加热保温,随炉冷却到550℃出炉。
冷镦锻工艺简介

冷镦锻工艺简介一、冷镦锻工艺简介冷镦锻工艺是一种少无切削金属压力加工工艺。
它是一种利用金属在外力作用下所产生的塑性变形,并借助于模具,使金属体积作重新分布及转移,从而形成所需要的零件或毛坯的加工方法。
冷镦锻工艺的特点:1.冷镦然是在常温条件进行的。
冷镦锻可使金属零件的机械性能得到改善。
2.冷镦锻工艺可以提高材料利率。
它是以塑性变形为基础的压力加工方法,可实现少切削或者无切削加工。
一般材料利用率都在85%以上,最高可达99%以上。
3.可提高生产效率。
金属产品变形的时间和过程都比较短,特别是在多工位成形机上加工零件,可大大提高生产率。
4.冷镦锻工艺能提高产品表面粗糙度、保证产品精度。
二、冷镦锻工艺对原材料的要求1.原材料的化学成份及机械性能应符合相关标准。
2.原材料必须进行球化退火处理,其材料金相组织为球状珠光体4-6级。
3.原材料的硬度,为了尽可能减少材料的开裂倾向,提高模具使用寿命还要求冷拔料有尽可能低的硬度,以提高塑性。
一般要求原材料的硬度在HB110~170(HRB62-88)。
4.冷拔料的尽寸精度一般应根据产品的具体要求及工艺情况而定,一般来说,对于缩径和强缩尺寸精度要求低一些。
5.冷拔料的表面质量要求有润滑薄膜呈无光泽的暗色,同时表面不得有划痕、折叠、裂纹、拉毛、锈蚀、氧化皮及凹坑麻点等缺陷。
6.要求冷拔料半径方向脱碳层总厚度不超过原材料直径的1-1.5%(具体情况随各制造厂家的要求而定)。
7.为了保证冷成形时的切断质量,要求冷拔料具有表面较硬,而心部较软的状态。
8.冷拔料应进行冷顶锻试验,同时要求材料对冷作硬化的敏感性越低越好,以减少变形过程中,由于冷作硬化使变形抗力增加。
三、紧固件加工工艺简述紧固件主要分两大粪:一类是螺纹类紧固件;另一类是非螺纹类紧固件或联接件。
这里仅针对螺纹类紧固件进行简述。
1. 螺纹类紧固件加工流程一般都是由剪断、冷镦、或者冷挤压、切削、螺纹加工、热处理、表面处理等生产工序组成的。
冷镦成型工艺
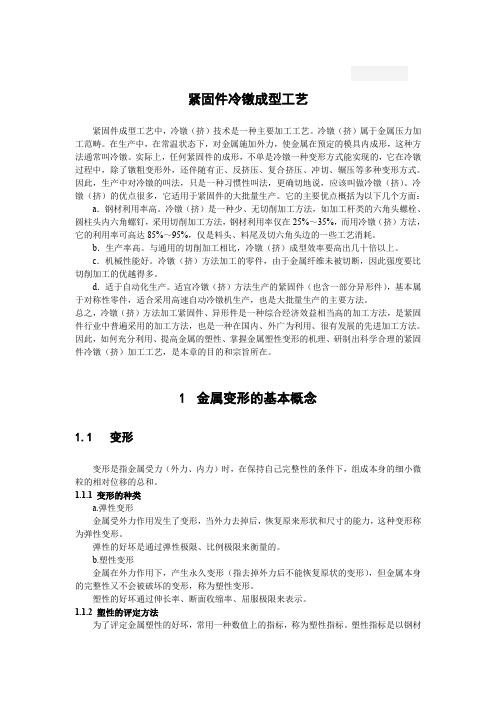
紧固件冷镦成型工艺紧固件成型工艺中,冷镦(挤)技术是一种主要加工工艺。
冷镦(挤)属于金属压力加工范畴。
在生产中,在常温状态下,对金属施加外力,使金属在预定的模具内成形,这种方法通常叫冷镦。
实际上,任何紧固件的成形,不单是冷镦一种变形方式能实现的,它在冷镦过程中,除了镦粗变形外,还伴随有正、反挤压、复合挤压、冲切、辗压等多种变形方式。
因此,生产中对冷镦的叫法,只是一种习惯性叫法,更确切地说,应该叫做冷镦(挤)。
冷镦(挤)的优点很多,它适用于紧固件的大批量生产。
它的主要优点概括为以下几个方面:a.钢材利用率高。
冷镦(挤)是一种少、无切削加工方法,如加工杆类的六角头螺栓、圆柱头内六角螺钉,采用切削加工方法,钢材利用率仅在25%~35%,而用冷镦(挤)方法,它的利用率可高达85%~95%,仅是料头、料尾及切六角头边的一些工艺消耗。
b.生产率高。
与通用的切削加工相比,冷镦(挤)成型效率要高出几十倍以上。
c.机械性能好。
冷镦(挤)方法加工的零件,由于金属纤维未被切断,因此强度要比切削加工的优越得多。
d.适于自动化生产。
适宜冷镦(挤)方法生产的紧固件(也含一部分异形件),基本属于对称性零件,适合采用高速自动冷镦机生产,也是大批量生产的主要方法。
总之,冷镦(挤)方法加工紧固件、异形件是一种综合经济效益相当高的加工方法,是紧固件行业中普遍采用的加工方法,也是一种在国内、外广为利用、很有发展的先进加工方法。
因此,如何充分利用、提高金属的塑性、掌握金属塑性变形的机理、研制出科学合理的紧固件冷镦(挤)加工工艺,是本章的目的和宗旨所在。
1 金属变形的基本概念1.1变形变形是指金属受力(外力、内力)时,在保持自己完整性的条件下,组成本身的细小微粒的相对位移的总和。
1.1.1 变形的种类a.弹性变形金属受外力作用发生了变形,当外力去掉后,恢复原来形状和尺寸的能力,这种变形称为弹性变形。
弹性的好坏是通过弹性极限、比例极限来衡量的。
冷镦材料与热处理方法

冷镦材料与热处理方法一、冷镦工艺对金属材料的要求1、冷镦用金属材料的机械性能要求根据冷镦工艺特点,对钢材机械性能提出如下要求:1)屈服强度Re以及变形抗力尽可能低,这样可使单位变形力相应减小,以延长模具寿命;2)材料的冷变形性能要好,既材料应有较好的塑性,较低的硬度,在大的变形程度下不致引起开裂。
如冷镦高强度螺栓时,即可使用含碳量较高的碳素钢,又可使用含碳量较低的低合金钢。
如果增加含碳量,就会使硬度提高,塑性降低,使冷变形性能变坏。
但是在含碳量较低的钢中加入少量合金元素(如添加少量硼10B21、10B33钢),即可显著提高钢材强度,从而满足产品的使用性能要求,同时又不损害其冷变形性能;3)材料的加工硬化敏感性能越低越好,这样不致使变形过程中的变形力太大。
材料的加工硬化敏感性可用变形抗力--应变曲线的斜率来反映。
斜率越大,则加工硬化敏感性越高。
如不锈钢0Cr18Ni9(SUS304)的曲线斜率最大。
这种材料的加工硬化敏感性就比较剧烈,随着变形程度的增加,变形抗力急剧上升。
钢材的机械性能不但表现原始坯料的Rm、Re、A、Z 及硬度等指标,不但受原材料的化学成分、宏观组织、微观组织等方面的影响,还受到材料准备过程中的拉拔及各道工序之间的热处理影响。
2、化学成分的要求⑴碳(C)碳是影响钢材冷塑性变形的最主要元素。
含碳量越高,钢的强度越高,而塑性越低。
含碳量每提高0.1%,其屈服强度Re提高27.4MPa,抗拉强度Rm提高(58.8-78.4MPa),而伸长率A则降低4.3%,断面收缩率Z降低7.3%。
当钢的含碳量<0.5%、含锰量<1.2%、断面收缩率Z=80%时,单位冷变形力P与钢材含C、Mn量之间的近似关系如下:P=1950C+500Mn+1860(MPa) (1)可见,钢中含碳量对于钢材的冷塑性变形性能的影响是很大的。
在实际工艺过程中,冷镦挤压用钢的含碳量大于0.25%时,要求钢退火成具有最好的塑性组织——球状珠光体组织。
冷镦成型工艺
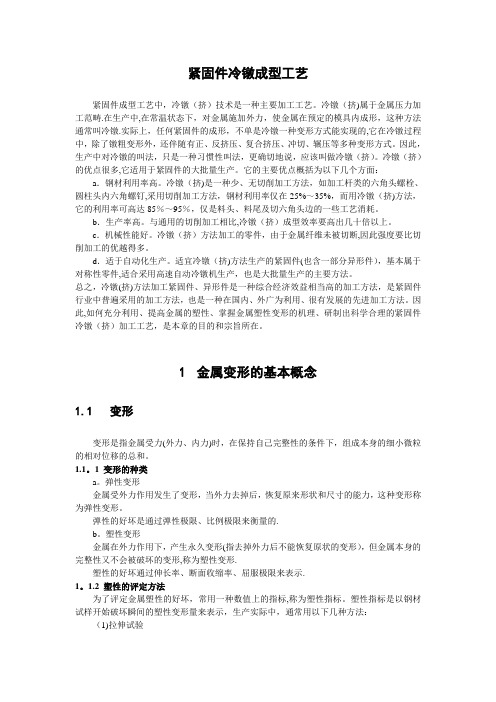
紧固件冷镦成型工艺紧固件成型工艺中,冷镦(挤)技术是一种主要加工工艺。
冷镦(挤)属于金属压力加工范畴.在生产中,在常温状态下,对金属施加外力,使金属在预定的模具内成形,这种方法通常叫冷镦.实际上,任何紧固件的成形,不单是冷镦一种变形方式能实现的,它在冷镦过程中,除了镦粗变形外,还伴随有正、反挤压、复合挤压、冲切、辗压等多种变形方式。
因此,生产中对冷镦的叫法,只是一种习惯性叫法,更确切地说,应该叫做冷镦(挤)。
冷镦(挤)的优点很多,它适用于紧固件的大批量生产。
它的主要优点概括为以下几个方面:a.钢材利用率高。
冷镦(挤)是一种少、无切削加工方法,如加工杆类的六角头螺栓、圆柱头内六角螺钉,采用切削加工方法,钢材利用率仅在25%~35%,而用冷镦(挤)方法,它的利用率可高达85%~95%,仅是料头、料尾及切六角头边的一些工艺消耗。
b.生产率高。
与通用的切削加工相比,冷镦(挤)成型效率要高出几十倍以上。
c.机械性能好。
冷镦(挤)方法加工的零件,由于金属纤维未被切断,因此强度要比切削加工的优越得多。
d.适于自动化生产。
适宜冷镦(挤)方法生产的紧固件(也含一部分异形件),基本属于对称性零件,适合采用高速自动冷镦机生产,也是大批量生产的主要方法。
总之,冷镦(挤)方法加工紧固件、异形件是一种综合经济效益相当高的加工方法,是紧固件行业中普遍采用的加工方法,也是一种在国内、外广为利用、很有发展的先进加工方法。
因此,如何充分利用、提高金属的塑性、掌握金属塑性变形的机理、研制出科学合理的紧固件冷镦(挤)加工工艺,是本章的目的和宗旨所在。
1 金属变形的基本概念1.1变形变形是指金属受力(外力、内力)时,在保持自己完整性的条件下,组成本身的细小微粒的相对位移的总和。
1.1。
1 变形的种类a。
弹性变形金属受外力作用发生了变形,当外力去掉后,恢复原来形状和尺寸的能力,这种变形称为弹性变形。
弹性的好坏是通过弹性极限、比例极限来衡量的.b。
冷镦成型工艺设计

目录1.形状、尺寸2. 坯料准备3. 自动锻压机的型号4. 凹模孔的直径5. 滚压螺纹坯径尺寸的确定6. 送料滚轮设计7. 切料模8. 送料与切料时常见的缺陷、产生的原因9. 初镦10. 终镦冲模11. 镦锻凹模12. 减径模13. 切边14. 常用模具材料及硬度要求15. 冷成形工艺对原材料的要求16. 切边时容易出现的缺陷、产生原因17. 化学成份对材料冷成形性能的影响18. SP.360设备参数19. 台湾设备参数20. 台湾搓丝机参数21. 国内搓丝机、滚丝机参数22. YC-420、YC-530滚丝机参数23. 磨床参数24. 单位换算25. 钻床参数形状、尺寸:1.圆角半径――取直径的1/20~1/5。
冷锻时圆角过大反而难锻造。
2.镦粗头部和法兰部尺寸――头部或法兰部体积V在2D3(D为坯料直径)以下时用单击镦锻机,3.5D3以下时可用双击镦锻机加工,而不会产生纵向弯曲。
如V为4.7D3必须经三道镦粗工序。
这部分的直径D1,(镦粗后直径)对于C<0.2%的碳素钢,不经中间退火能够镦粗到2.5D。
超过上述范围必须中间退火。
侧面尺寸由于难以控制,公差要尽可能放宽。
3.镦粗部分的形状――头部或头下部的高度比直径大时,侧壁上向上和向下设置2°左右的锥度,使材料填充良好。
球形头部顶上允许设计成小平面。
4.挤压件坯料和挤出部分断面积之比A0/A1,即挤压比R,对S10C、BSW1的实心、空心正挤压件,如在5~10以下,对反挤压杯形件,如在1.3~4间,能够一次成形。
自由挤压件的R如在1.25~1.4以下,能经一道工序加工。
杯形件反挤压时的冲头压力,当R约为1.7时最小。
5.挤压件断面变化部分的锥度如图1,但对于变形抗力高的材料,从模具强度上考虑,α(度)要取较大值。
6.反挤压杯形件的侧壁高度――侧壁高度H和冲头直径d的比H/d,对S10C、BSW1如在2~3以下,对更硬的材料如在1~2以下,均可一次成形。
- 1、下载文档前请自行甄别文档内容的完整性,平台不提供额外的编辑、内容补充、找答案等附加服务。
- 2、"仅部分预览"的文档,不可在线预览部分如存在完整性等问题,可反馈申请退款(可完整预览的文档不适用该条件!)。
- 3、如文档侵犯您的权益,请联系客服反馈,我们会尽快为您处理(人工客服工作时间:9:00-18:30)。
冷镦线材改制加工工艺
1、序言
紧固件制造业是现代工业的基础,而紧固件质量的优劣很大程度上取决于其所使用的冷镦材料的质量。
其中如成分偏析、疏松和夹杂物等材料的冶金质量,作为使用者的机械厂往往难以改变。
但材料的强度、硬度、塑性、组织结构和韧性,则与随后的材料加工过程有着密切的关系。
这些性能实际上就是材料的冷镦性能、切削性能、热处理性能的体现。
因此研究和掌握冷镦线材的加工工艺特性是制造优质冷镦线材和保证紧固件质量的基础。
2、冷镦线材的选择:
2.1、钢材牌号选择
钢材牌号应根据产品图纸和相关国家标准的要求进行选择,表1可供选材时参考(见表1)。
也可选择相应日本牌号的材料(见表2)。
表1 钢材牌号的选择
注:当紧固件规格较大时为保证材料热处理性能,应选用较高一个档次的材料。
表2几种材料牌号的选择
2.2、拉丝车间应按生产计划领取经检验合格的原材料进行材料改制,检验不
合格的钢材不能投产。
3、改制工艺:3.1、钢材(盘圆)改制工艺流程:
材料球化退火-酸洗清洗-磷化-皂化I 呻间退火丨
辗尖-拉拔■入库。
在金相组织正常和拉拔减面率不大于35%的情况下,中低碳
钢一般可不进行球化退火,而直接进行拉拔,但中碳合金钢应在
退火后进行材料改制,当材料需要两次或两次以上拉拔时,第一
次的拉拔比宜控制在20%〜25%,最后一道拉拔前应进行中间退火处理,且拉拔比宜控制在15%〜20%。
3.2、退火
3.2.1、退火工艺
a球化退火:热轧盘条的首次退火一般在真空退火炉或井式炉中进行球化处理,其目的是使珠光体完全球化并均匀分布在铁素体的机体上,使材料获得最好的塑性和最低的硬度。
其工艺为750C
〜780 C充分加热,然后在680C ~700 C等温转变。
具体的参数取决于炉型、材料的种类和装炉量,合适的工艺需要通过实验确定。
b、再结晶退火:经过加工的材料,第二次退火应采用再结晶退火处理,同样是在真空炉或井式炉中进行。
其目的是使产生了加工硬化的材料消除应力,使各向异性的铁素体组织重结晶,重新软化回复良好的塑性。
其工艺为680C
~700 C充分加热保温,随炉冷却到550C出炉。
具体的参数取决于炉型、材料的种类和装炉量,合适的工艺需要通过实验确定。
3.2.2退火作业
a、操作者应熟悉真空退火炉的安全操作规程,并按给定的球化退火工艺进行操作,每隔1 〜2 小时检查一次炉温,并作好记录。
b、退火装炉量应控制在真空退火炉的额定装载量范围内,不得超负荷生产。
待退火线材捆扎不宜过紧,以便于均热。
装炉要领:装出
炉时应注意勿使炉口密封受损、尽可能相同材质和状态的材料同炉处理、材料入炉不要阻碍炉内气流循环、潮湿的材料升温到
300C后提升炉盖排除水汽5分钟后在重新盖好盖升温。
c、炉子被抽真空后应回充氮气,真空度应达到1330〜133Pa如果
不回充氮气,则炉内真空度应达到133〜13.3P&充入炉子内氮气的纯度为
99.99%,低于此纯度的氮气不能使用。
d、炉子抽真空同时可开始升温,升温速度应不大于200C /小时。
炉子到温后,其温差不得超过土10C。
e、整个退火周期内,炉口应通冷却水以保护炉口密封材料,冷却
水流量应控制在1〜2m3/h,出水口的水温应小于55C。
f、出炉:出炉温度设置必须考虑热电偶与炉内实际温度的差异,炉子的控温热电偶通常在炉子的马佛罐外边,而炉内的温度,尤其是捆扎得很紧密的线卷的里层的材料的温度在降温阶段比仪表显示的温度高很多。
这一点在冬天尤其如此。
因此不能盲目的相信仪表的显示。
g、退火后的钢材应进行硬度检验(HB或HRB)、冷顶锻试验、表面脱碳层和金相组织检验。
①硬度:中碳结构钢退火后的硬度不大于133HB (或80HRB),中
碳合金结构钢退火后的硬度不大于151HB (或86HRB)。
②冷顶锻试验:冷顶锻后与冷顶锻前之比:对法兰面螺栓、内六
角螺钉等为1/4 合格,对六角头螺栓、螺母等为1/3 合格。
③表面脱碳层:表面不完全脱碳层w 1.0% d (d—材料直径),退火
后表面不允许有铁素体层。
④金相组织:对用于法兰面螺栓、内六角螺钉等冷镦变形大的材
料其球化退火后的组织应为5〜6 级;用于六角头螺栓等的材料其
球化退火后的组织应为4〜6 级;用于螺母等的材料其球化退火后的组织应为3〜6 级;金相组织的检验依据JB/T5074-2007 进行检验。
3.3酸洗
3.3.1 酸洗液的配制(见表2)
表2
注意:并非是新酸的腐蚀能力最强,而是新旧算混合使用时具有最强的腐
蚀能力。
332、上料
盘兀穿上吊架横梁后应去掉捆扎带,再将线卷吊起1米咼后快速
落下摔打线卷,同时向前滚动120°左右,换一个位置吊起材料再次摔打。
如此至少三次,直到线卷完全松散,注意:地面上垫一块厚钢板,并及时扫去氧化皮。
3.3.3酸洗
用吊车将线材平稳吊入酸洗槽中,在酸洗过程中应将材料上下串动2次左右,以保证各部位的线材与酸接触。
为防止氢脆或过酸洗,浸酸时间不宜过久,,室温酸洗一般不超过
十五分钟,视线材表面达到银灰色为止。
材料酸洗后表面呈银灰色,应无氧化皮,锈迹和黑斑。
3.4、清洗:经酸洗后的线材应迅速放入流动清水缸,并上下来回串动,然后用高压水冲洗材料表面残酸及附着物,冲洗后的线材表面不应有棕黄色。
3.5、磷化、皂化(见磷化、皂化工艺规程)。
3.6、干燥:经中和挂浆后的线材应立即干燥处理.一般采用阳光干燥法和炉火烘干法。
3.7、辗尖:拉拔前材料头部应辗尖,其长度为100〜150毫米左右直径控制在能顺利通过拉丝模。
3.8、拉拔
拉拔在拉丝机上进行。
根据不同产品的冷镦工艺选取拉丝模拉装好即可拉拔。
拉后的成品线材直径尺寸应符合冷镦工艺要求的直径尺寸,表面无影响使用的麻点、拉痕、裂纹等。
3.8.1、对采用马钢、邢钢SWRCH35K热轧线材生产的M6〜M12 规格的8.8级的六角头螺栓,不进行球化退火处理,一次性拉拔到
成品丝尺寸;对其它钢厂生产的SWRCH35K、35# 、ML35 热轧线材生产的
8.8 级六角头螺栓,应进行球化退火处理后,再一次性拉拔到成品丝尺寸,这两种情况的总拉拔比应小于25%;对采用SWRCH35K 、35#、ML35 热轧线材生产的8.8 级法兰面螺栓、内六角螺钉等变形量较大的产品应先按10%〜15%的拉拔比进行预
拉拔,再进行球化退火处理,然后再拉拔到成品丝尺寸,最后一次的拉拔比应小于10%。
原材料的规格选用参见附表A。
3.8.2、对采用40Cr、ML40Cr 热轧线材生产的10.9级六角头螺栓,应先进行球化退火处理,再一次性拉拔到成品丝尺寸,总拉拔比应小于20%;对采用40Cr、ML40Cr 热轧线材生产的1 0.9级法兰面螺栓、内六角螺钉等变形量较大的产品,应先按10%〜15%的拉拔比进行预拉拔,再进行球化退火处理,然后再拉拔到成品丝尺寸,最后一次的拉拔比应小于10%。
原材料的规格选用参见附表A。
3.8.3、对采用35CrMo、ML35CrMo 热轧线材生产的12.9级六角头
螺栓,应先进行球化退火处理,再一次性拉拔到成品丝尺寸,总拉拔比应小于20%;对采用35CrMo、ML35CrMo 热轧线材生产的12.9级法兰面螺栓、内六角螺钉等变形量较大的产品,应先进行球化退火处理,再按比成品丝尺寸大
0.3〜0.5mm 进行预拉拔,再
进行中间退火处理,然后再拉拔到成品丝尺寸。
原材料的规格选用参见附表
A 。
3.8.4、对采用中碳钢生产的六角螺母,先进行球化退火处理,再一
次性拉拔到成品丝尺寸。
原材料的规格选用参见附表B。
3.8.5、对双头螺柱产品,不进行球化退火处理,而一次性拉拔到成品尺寸。
3.8.6、对自攻螺钉产品,因原材料没有合适的规格,一般只有$
6.5mm 的规格,因此,需要二〜四次的拉拔,在最后一次拉拔前,应进行球化退火处理,再拉拔到成品丝尺寸。
可参见附表C。
特别注意:
经拉拔后再进行中间退火的线材,退火前的拉拔压缩比必须避开临界压缩比,以防止中间退火时晶粒胀大、塑性降低甚至报废。
不同材料的临界压缩比为:A3 钢7%〜16%、35 钢8%〜15%
压缩比计算公式:
原面积-拉拔后面积
x 100%
= ———————
原面积
2)、当螺杆较长时应适当缩小用料直径,螺杆较短时应取上限。
3)、头部用料较多时,应选较大的料。
4)、对于需要镦后磨削滚丝的产品,需选用较大料时根据冷镦工艺确定。
1
附表B 六角螺母冷镦用线材尺寸表
附表C 自攻螺钉拉拔次数和退火位置
2。