氨酸法
氨酸法工艺技术简述

氨酸法(稀酸法)复合肥工艺技术简介1、工艺技术概述氨酸法(料床反应)工艺生产复合肥,从原理上介于团粒法和料浆法之间,具有两者的优点,可显著提高生产产量。
生产的产品,颗粒圆润光滑、强度高、不易结块。
生产中,对原料、配方的适应性强,产品适应性广,对土壤副作用小。
液氨与硫酸在工艺中,是硫酸喷在物料的表面,这是化肥生产氨化造粒中多孔固体中酸的氨化问题。
液氨通过埋在料床中的分布器,沿造粒机轴向均匀喷出。
生产实践表明,氨通过料床的流态可分为两种:一种是滤过式,氨通过颗粒之间的缝隙连续流过,几乎不影响粒子的运动;一种是喷射式,氨通过喷嘴流速较大,在颗粒床形成空间或喷舌,引起颗粒作剧烈的旋转运动,大大强化了传质和传热过程。
良好的设计可使氨的吸收率达到95%以上。
氨分布器是氨化造粒机的重要部件。
从国内外常年运行的状况看,该技术是成熟安全可靠的。
2、工艺流程2.1原料预处理与计量结块磷铵和氯化铵,影响输送和计量,需对其进行预处理,生产高氮肥尿素需粉碎1/3,上述三种原料经人工解包后,送入各自的破碎机,破碎后直接落入各自的原料计量贮料斗。
原料计量采用电子皮带秤,电子秤分别用于原料磷铵、氯化钾、氯化铵、固体尿素、微量元素配方计量,并采用工控机控制,以实现原料计量报表、历史记录、配方自动调节等功能。
2.2 造粒来自酸站的浓硫酸和水按比例稀释到一定质量分数后,经流量计计量喷入造粒物料料床;氨站液氨进入埋在料床中的反应器与稀硫酸产生中和反应,生成温度较高的硫酸铵料浆。
粉状物料与硫酸铵料浆混合,形成一定液相的固溶体,在转鼓造粒机内滚动成粒;磷酸一铵与过量的氨发生中和反应,在适宜的温度和PH值环境下溶融,利用磷铵自身溶融的溶液粘结其他物料成粒,同时在高温下各物料间发生复分解反应生成复盐,在造粒机不断的转动下,使物料处于流动状态,相互摩擦、翻动、挤压粘附成粒。
成球率可达95%,成品率达80%以上。
2.3 干燥与冷却造粒物料由皮带机送入干燥机进行干燥,干燥机出料进入第一冷却器,冷却后的物料进入中间筛,筛上物料进入第二冷却机,细粉进入返料,以回收返料热量,降低装置的能耗。
氨酸法复合肥项目技术简介
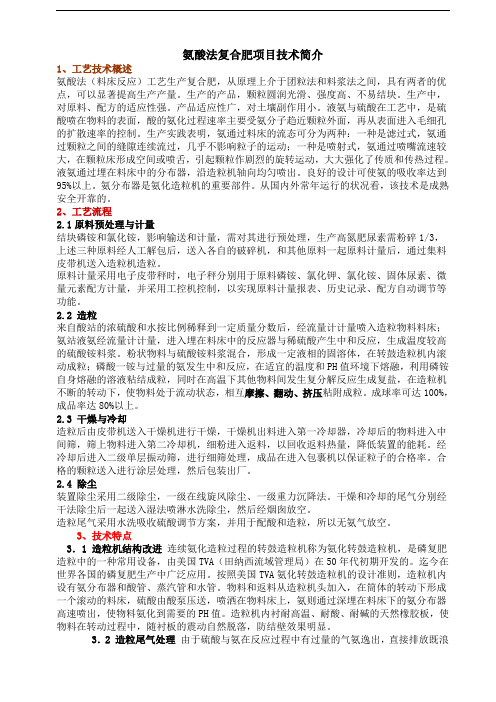
氨酸法复合肥项目技术简介1、工艺技术概述氨酸法(料床反应)工艺生产复合肥,从原理上介于团粒法和料浆法之间,具有两者的优点,可以显著提高生产产量。
生产的产品,颗粒圆润光滑、强度高、不易结块。
生产中,对原料、配方的适应性强。
产品适应性广,对土壤副作用小。
液氨与硫酸在工艺中,是硫酸喷在物料的表面,酸的氨化过程速率主要受氨分子趋近颗粒外面,再从表面进入毛细孔的扩散速率的控制。
生产实践表明,氨通过料床的流态可分为两种:一种是滤过式,氨通过颗粒之间的缝隙连续流过,几乎不影响粒子的运动;一种是喷射式,氨通过喷嘴流速较大,在颗粒床形成空间或喷舌,引起颗粒作剧烈的旋转运动,大大强化了传质和传热过程。
液氨通过埋在料床中的分布器,沿造粒机轴向均匀喷出。
良好的设计可使氨的吸收率达到95%以上。
氨分布器是氨化造粒机的重要部件。
从国内外常年运行的状况看,该技术是成熟安全开靠的。
2、工艺流程2.1原料预处理与计量结块磷铵和氯化铵,影响输送和计量,需对其进行预处理,生产高氮肥尿素需粉碎1/3,上述三种原料经人工解包后,送入各自的破碎机,和其他原料一起原料计量后,通过集料皮带机送入造粒机造粒。
原料计量采用电子皮带秤时,电子秤分别用于原料磷铵、氯化钾、氯化铵、固体尿素、微量元素配方计量,并采用工控机控制,以实现原料计量报表、历史记录、配方自动调节等功能。
2.2 造粒来自酸站的浓硫酸和水按比例稀释到一定质量分数后,经流量计计量喷入造粒物料料床;氨站液氨经流量计计量,进入埋在料床中的反应器与稀硫酸产生中和反应,生成温度较高的硫酸铵料浆。
粉状物料与硫酸铵料浆混合,形成一定液相的固溶体,在转鼓造粒机内滚动成粒;磷酸一铵与过量的氨发生中和反应,在适宜的温度和PH值环境下熔融,利用磷铵自身熔融的溶液粘结成粒,同时在高温下其他物料间发生复分解反应生成复盐,在造粒机不断的转动下,使物料处于流动状态,相互摩擦、翻动、挤压粘附成粒。
成球率可达100%,成品率达80%以上。
氨酸法工艺在复合肥料生产中的应用分析
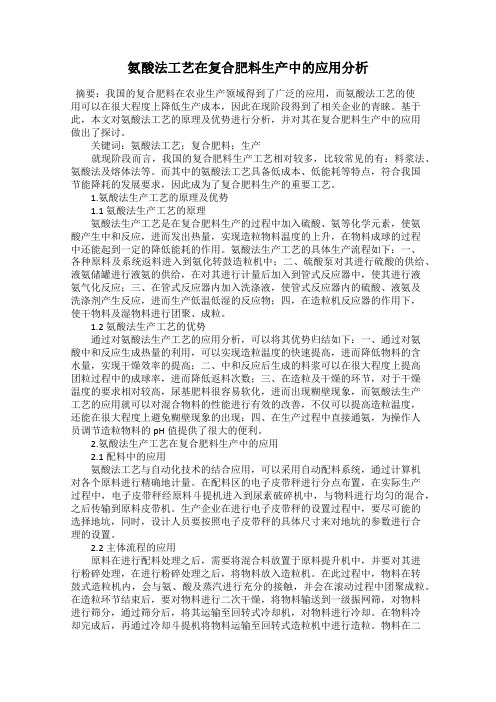
氨酸法工艺在复合肥料生产中的应用分析摘要:我国的复合肥料在农业生产领域得到了广泛的应用,而氨酸法工艺的使用可以在很大程度上降低生产成本,因此在现阶段得到了相关企业的青睐。
基于此,本文对氨酸法工艺的原理及优势进行分析,并对其在复合肥料生产中的应用做出了探讨。
关键词:氨酸法工艺;复合肥料;生产就现阶段而言,我国的复合肥料生产工艺相对较多,比较常见的有:料浆法、氨酸法及熔体法等。
而其中的氨酸法工艺具备低成本、低能耗等特点,符合我国节能降耗的发展要求,因此成为了复合肥料生产的重要工艺。
1.氨酸法生产工艺的原理及优势1.1氨酸法生产工艺的原理氨酸法生产工艺是在复合肥料生产的过程中加入硫酸、氨等化学元素,使氨酸产生中和反应,进而发出热量,实现造粒物料温度的上升,在物料成球的过程中还能起到一定的降低能耗的作用。
氨酸法生产工艺的具体生产流程如下:一、各种原料及系统返料进入到氨化转鼓造粒机中;二、硫酸泵对其进行硫酸的供给、液氨储罐进行液氨的供给,在对其进行计量后加入到管式反应器中,使其进行液氨气化反应;三、在管式反应器内加入洗涤液,使管式反应器内的硫酸、液氨及洗涤剂产生反应,进而生产低温低湿的反应物;四,在造粒机反应器的作用下,使干物料及湿物料进行团聚、成粒。
1.2氨酸法生产工艺的优势通过对氨酸法生产工艺的应用分析,可以将其优势归结如下:一、通过对氨酸中和反应生成热量的利用,可以实现造粒温度的快速提高,进而降低物料的含水量,实现干燥效率的提高;二、中和反应后生成的料浆可以在很大程度上提高团粒过程中的成球率,进而降低返料次数;三、在造粒及干燥的环节,对于干燥温度的要求相对较高,尿基肥料很容易软化,进而出现糊壁现象,而氨酸法生产工艺的应用就可以对混合物料的性能进行有效的改善,不仅可以提高造粒温度,还能在很大程度上避免糊壁现象的出现;四、在生产过程中直接通氨,为操作人员调节造粒物料的pH值提供了很大的便利。
2.氨酸法生产工艺在复合肥料生产中的应用2.1配料中的应用氨酸法工艺与自动化技术的结合应用,可以采用自动配料系统,通过计算机对各个原料进行精确地计量。
氨酸法——精选推荐

(一)酸氨管式反应器造粒技术的工艺过程工艺流程简述来自配料工序的各固体原料(氯化钾、磷酸一磷、固体尿素、氯化铵、普钙、填充剂等)和系统的返料进入转鼓造粒机,由硫酸贮罐来的浓硫酸和尾气洗涤系统的洗涤液,经计量后加入到特制的管式反应器的混和段进行混和稀释;来自氨站的液氨经计量后分为两路,一路通过液氨蒸发器和混和器A与少量蒸汽混和气化,经管式反应器混和段进入反应段,通过特制的分布器快速与混和后的稀硫酸反应,生成的高温硫酸铵溶液经雾化喷头均匀喷涂到造粒机料床上。
另一路液氨通过液氨蒸发器和混和器B与蒸汽混和气化后,由混和分布器进入料层与料层中的磷酸一铵、普钙等继续在造粒机内进入化学反应,同时释放出化学反应热,干湿物料在造粒机的转动作用下团聚成粒,如有尿液等液体原料喷入,则氨、酸及洗涤水量适当降低,以保证造粒的液相与热量平衡。
管式反应器排出的水蒸汽以及料层中排出的水蒸汽随造粒尾气排出,造料尾气经复喷管和洗涤塔进行洗涤吸收,经洗涤后的净化尾气经尾气风机烟囱排空,洗涤液用泵送至洗涤塔和管式反应器,洗涤水通过管式反应器后形成过热蒸汽及高温料浆予以回收。
出造粒机的物料经干燥、筛分、冷却、筛分、包膜处理后进入成品库进行包装,大粒返料经破碎后与细粉返料一起返回造粒系统,干燥、冷却尾气以及吸尘尾气分别经旋风除尘器、重力沉降和水浴洗涤三级处理后达标排放。
(二)氨酸管式反应器喷浆造粒新技术的主要特征1、造粒工况明显改善和稳定造粒部分利用气氨与硫酸、磷酸一铵的化学反应热来提高造粒物料温度和改善物料特性,提温幅度可达15-30℃,而并非主要靠蒸汽和尿液来提高造粒温度,造粒温度可高达75-85℃,物料水份小于2.5%,成球率高达60%以上。
2、实现一段干燥工艺、简化工艺过程由于造粒物料温度较高,水份较低,一段干燥便于使产品水份降至1.5%以下,实现了一段干燥工艺生产高氮尿基复合肥工艺过程,简化了工艺过程。
3、实现热筛分、热破碎工艺、提高能源利用率由于干燥后产品水份较低(小于1.5%)可满足热筛分和热大粒破碎工艺,同时也提高了热返料的热量利用效率,以及降低了冷却负荷,缓解了产品的热结块倾向。
氨酸法复合肥生产工艺

氨酸法复合肥生产工艺氨酸法复合肥是将氨基酸、氮磷钾等营养元素有机结合,制成颗粒状或粉末状的肥料。
下面介绍氨酸法复合肥的生产工艺。
首先,氨酸法复合肥的生产工艺主要分为原料处理、发酵、压球造粒、干燥和包装等几个步骤。
原料处理是指将各种原料进行加工,以提高其可发酵性。
一般来说,氨酸法复合肥的原料包括有机氮源、无机氮源、磷酸盐和钾肥等。
这些原料需要经过破碎、筛分和配比等工艺处理,以保证各种原料的比例合理、均匀。
发酵是指将处理好的原料进行发酵,使之转化为有机氮源。
一般来说,发酵工艺采用固态发酵或液态发酵。
固态发酵一般是将原料放入发酵罐中,通过控制温度、湿度和通风量等参数,使之发生微生物的发酵作用,转化为有机氮源。
液态发酵一般是将原料放入发酵罐中,加入适量的水和发酵菌种,通过控制温度、搅拌和通气等参数,使之发生液态发酵作用,转化为有机氮源。
压球造粒是指将发酵好的原料进行造粒,制成颗粒状的肥料。
一般来说,压球造粒工艺采用双辊压球机,通过辊式压制的方式,将发酵好的原料进行挤压和成形,制成颗粒状的肥料。
干燥是指将压球造粒好的肥料进行干燥,使其含水率达到标准要求。
一般来说,干燥工艺采用旋转干燥机,通过加热和风力作用,将肥料的含水率降低到标准范围内。
包装是指将干燥好的肥料进行包装和贮存,以便运输和销售。
一般来说,包装工艺采用自动包装机,将肥料装入袋子中,并进行称重、封口和码垛等操作,最终成品肥料可以直接投放市场。
总之,氨酸法复合肥的生产工艺包括原料处理、发酵、压球造粒、干燥和包装等几个步骤。
通过科学的生产工艺和技术手段,可以生产出高质量的氨酸法复合肥,满足农业生产的需求。
氨酸法与水汽法工比较
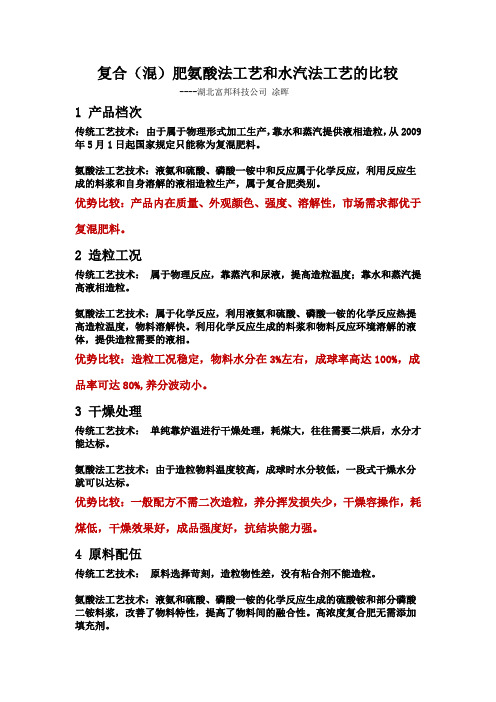
复合(混)肥氨酸法工艺和水汽法工艺的比较----湖北富邦科技公司凃晖1 产品档次传统工艺技术:由于属于物理形式加工生产,靠水和蒸汽提供液相造粒,从2009年5月1日起国家规定只能称为复混肥料。
氨酸法工艺技术:液氨和硫酸、磷酸一铵中和反应属于化学反应,利用反应生成的料浆和自身溶解的液相造粒生产,属于复合肥类别。
优势比较:产品内在质量、外观颜色、强度、溶解性,市场需求都优于复混肥料。
2 造粒工况传统工艺技术:属于物理反应,靠蒸汽和尿液,提高造粒温度;靠水和蒸汽提高液相造粒。
氨酸法工艺技术:属于化学反应,利用液氨和硫酸、磷酸一铵的化学反应热提高造粒温度,物料溶解快。
利用化学反应生成的料浆和物料反应环境溶解的液体,提供造粒需要的液相。
优势比较:造粒工况稳定,物料水分在3%左右,成球率高达100%,成品率可达80%,养分波动小。
3 干燥处理传统工艺技术:单纯靠炉温进行干燥处理,耗煤大,往往需要二烘后,水分才能达标。
氨酸法工艺技术:由于造粒物料温度较高,成球时水分较低,一段式干燥水分就可以达标。
优势比较:一般配方不需二次造粒,养分挥发损失少,干燥容操作,耗煤低,干燥效果好,成品强度好,抗结块能力强。
4 原料配伍传统工艺技术:原料选择苛刻,造粒物性差,没有粘合剂不能造粒。
氨酸法工艺技术:液氨和硫酸、磷酸一铵的化学反应生成的硫酸铵和部分磷酸二铵料浆,改善了物料特性,提高了物料间的融合性。
高浓度复合肥无需添加填充剂。
优势比较:原料选择范围广成本低,产品洁白、光滑圆润,无不溶性残渣,避免了填料颜色不稳定影响产品外观,溶解性能好,作为易吸收。
5 生产条件传统工艺技术:造粒受天气湿度和原料特性影响大,操作弹性小,设备不能长周期稳定运行,限制了多品种开发生产。
氨酸法工艺技术:由于有化学反应,改善物料配伍特性,保证不同原料、配方、季节的造粒效果,能有效提高装置操作弹性。
优势比较:不受原料和季节限制,可生产多品种、多系列产品,实现装置长周期稳定运行。
氨酸法处理二氧化硫原则流程图及原理

英文回答:The use of amino acids in the treatment of sulfur dioxide is grounded in their capacity to chemically react with the gas and produce stablepounds. This approach ismonly employed in the mitigation of industrial emissions containing heightened concentrations of sulfur dioxide, such as those stemming from power generation facilities or industrial operations. The method entails the utilization of an aqueous solutionprised of amino acids, which effectively absorbs and neutralizes the sulfur dioxide present within the emissions. Consequently, this process yields the formation of stablepounds that can be readily separated from the gas stream, thereby curtailing the release of sulfur dioxide into the atmosphere.在二氧化硫的处理中使用氨基酸是基于其与气体发生化学反应并产生稳定磅的能力。
这种方法仅用于减少二氧化硫浓度升高的工业排放,例如来自发电设施或工业作业的排放。
这种方法需要利用氨基酸的水溶液,有效吸收和中和排放中的二氧化硫。
氨酸法氨站设计技术方案
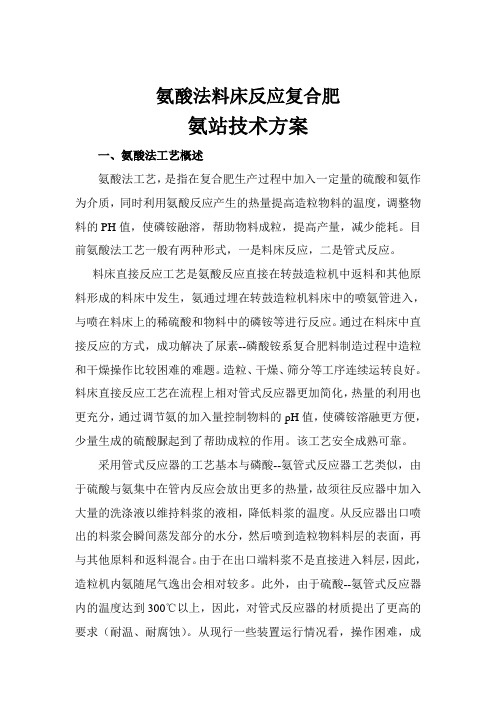
氨酸法料床反应复合肥氨站技术方案一、氨酸法工艺概述氨酸法工艺,是指在复合肥生产过程中加入一定量的硫酸和氨作为介质,同时利用氨酸反应产生的热量提高造粒物料的温度,调整物料的PH值,使磷铵融溶,帮助物料成粒,提高产量,减少能耗。
目前氨酸法工艺一般有两种形式,一是料床反应,二是管式反应。
料床直接反应工艺是氨酸反应直接在转鼓造粒机中返料和其他原料形成的料床中发生,氨通过埋在转鼓造粒机料床中的喷氨管进入,与喷在料床上的稀硫酸和物料中的磷铵等进行反应。
通过在料床中直接反应的方式,成功解决了尿素--磷酸铵系复合肥料制造过程中造粒和干燥操作比较困难的难题。
造粒、干燥、筛分等工序连续运转良好。
料床直接反应工艺在流程上相对管式反应器更加简化,热量的利用也更充分,通过调节氨的加入量控制物料的pH值,使磷铵溶融更方便,少量生成的硫酸脲起到了帮助成粒的作用。
该工艺安全成熟可靠。
采用管式反应器的工艺基本与磷酸--氨管式反应器工艺类似,由于硫酸与氨集中在管内反应会放出更多的热量,故须往反应器中加入大量的洗涤液以维持料浆的液相,降低料浆的温度。
从反应器出口喷出的料浆会瞬间蒸发部分的水分,然后喷到造粒物料料层的表面,再与其他原料和返料混合。
由于在出口端料浆不是直接进入料层,因此,造粒机内氨随尾气逸出会相对较多。
此外,由于硫酸--氨管式反应器内的温度达到300℃以上,因此,对管式反应器的材质提出了更高的要求(耐温、耐腐蚀)。
从现行一些装置运行情况看,操作困难,成球率低。
故本项目采用料床直接反应工艺。
二、氨站技术指标氨酸法工艺的基本介质是硫酸和液氨。
目前氨的使用有两种,一是直接使用液氨,二是将液氨蒸发成气氨使用(国家生产许可证现场审核要求,实际生产中使用液氨多)。
本项目拟采用直接使用液氨,省去液氨蒸发设备投资、蒸发液氨耗用大量蒸汽能源,同时避免了液氨蒸发的高危操作。
根据项目装置设计要求,氨站采用设计压力2.2MPa,工作压力1.8MPa,工作温度45℃,设计温度53℃,设计储存量25400kg,装量系数0.85,容器类别三的50立方米的氨液储槽2个。
复合肥氨酸法造粒工艺
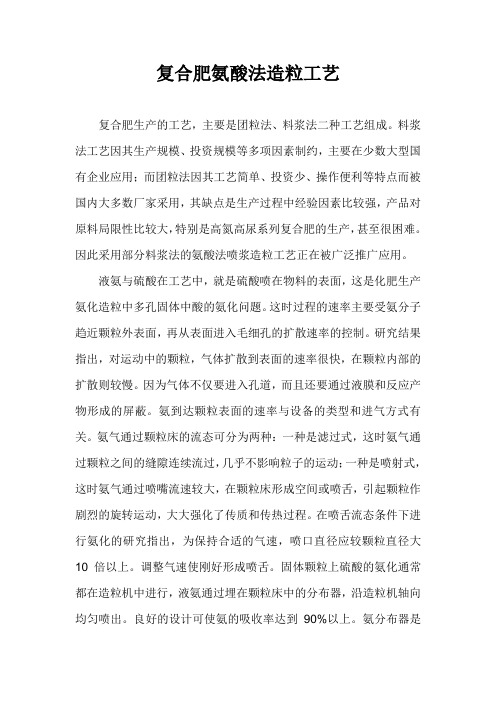
复合肥氨酸法造粒工艺复合肥生产的工艺,主要是团粒法、料浆法二种工艺组成。
料浆法工艺因其生产规模、投资规模等多项因素制约,主要在少数大型国有企业应用;而团粒法因其工艺简单、投资少、操作便利等特点而被国内大多数厂家采用,其缺点是生产过程中经验因素比较强,产品对原料局限性比较大,特别是高氮高尿系列复合肥的生产,甚至很困难。
因此采用部分料浆法的氨酸法喷浆造粒工艺正在被广泛推广应用。
液氨与硫酸在工艺中,就是硫酸喷在物料的表面,这是化肥生产氨化造粒中多孔固体中酸的氨化问题。
这时过程的速率主要受氨分子趋近颗粒外表面,再从表面进入毛细孔的扩散速率的控制。
研究结果指出,对运动中的颗粒,气体扩散到表面的速率很快,在颗粒内部的扩散则较慢。
因为气体不仅要进入孔道,而且还要通过液膜和反应产物形成的屏蔽。
氨到达颗粒表面的速率与设备的类型和进气方式有关。
氨气通过颗粒床的流态可分为两种:一种是滤过式,这时氨气通过颗粒之间的缝隙连续流过,几乎不影响粒子的运动;一种是喷射式,这时氨气通过喷嘴流速较大,在颗粒床形成空间或喷舌,引起颗粒作剧烈的旋转运动,大大强化了传质和传热过程。
在喷舌流态条件下进行氨化的研究指出,为保持合适的气速,喷口直径应较颗粒直径大10倍以上。
调整气速使刚好形成喷舌。
固体颗粒上硫酸的氨化通常都在造粒机中进行,液氨通过埋在颗粒床中的分布器,沿造粒机轴向均匀喷出。
良好的设计可使氨的吸收率达到90%以上。
氨分布器是氨化造粒机的重要部件。
用在需连续氨化造粒过程的转鼓造粒机称为氨化转鼓造粒机,是磷复肥造粒中的一种常用设备,是美国TVA(田纳西流域管理局)在50年代初期开发的。
迄今在世界各国的磷复肥生产中广泛应用。
按照美国TVA氨化转鼓造粒机的设计准则,在造粒机靠筒体轴线的上方设有一管梁,以便安装氨分布器和酸管、蒸汽管,返料从造粒机头加入,在筒体的转动下形成一滚动的物料床,硫酸由酸泵压送,从硫酸喷洒管的喷嘴喷洒在物料床上进行造粒。
氨酸法项目说明
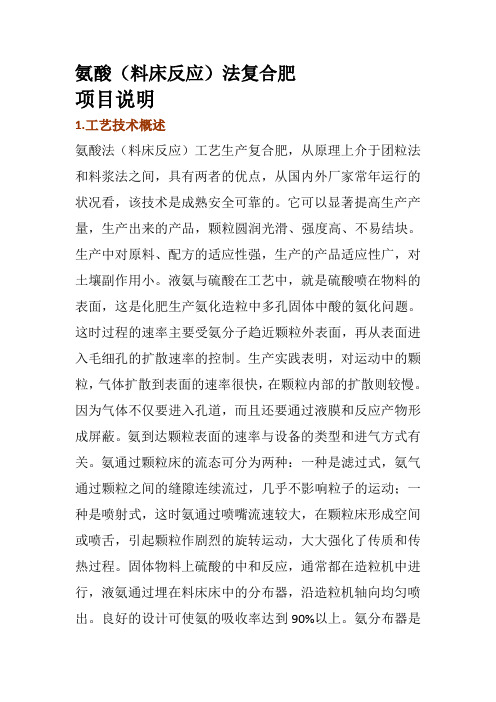
氨酸(料床反应)法复合肥项目说明1.工艺技术概述氨酸法(料床反应)工艺生产复合肥,从原理上介于团粒法和料浆法之间,具有两者的优点,从国内外厂家常年运行的状况看,该技术是成熟安全可靠的。
它可以显著提高生产产量,生产出来的产品,颗粒圆润光滑、强度高、不易结块。
生产中对原料、配方的适应性强,生产的产品适应性广,对土壤副作用小。
液氨与硫酸在工艺中,就是硫酸喷在物料的表面,这是化肥生产氨化造粒中多孔固体中酸的氨化问题。
这时过程的速率主要受氨分子趋近颗粒外表面,再从表面进入毛细孔的扩散速率的控制。
生产实践表明,对运动中的颗粒,气体扩散到表面的速率很快,在颗粒内部的扩散则较慢。
因为气体不仅要进入孔道,而且还要通过液膜和反应产物形成屏蔽。
氨到达颗粒表面的速率与设备的类型和进气方式有关。
氨通过颗粒床的流态可分为两种:一种是滤过式,氨气通过颗粒之间的缝隙连续流过,几乎不影响粒子的运动;一种是喷射式,这时氨通过喷嘴流速较大,在颗粒床形成空间或喷舌,引起颗粒作剧烈的旋转运动,大大强化了传质和传热过程。
固体物料上硫酸的中和反应,通常都在造粒机中进行,液氨通过埋在料床床中的分布器,沿造粒机轴向均匀喷出。
良好的设计可使氨的吸收率达到90%以上。
氨分布器是氨化造粒机的重要部件。
2. 氨酸法工艺流程经配料岗位计量、混合、粉碎后的固相物料被输送到转鼓造粒机内。
浓硫酸和水按比例稀释到一定质量分数后,经流量计计量喷入造粒物料料床,液氨经流量计计量,进入埋在料床中的反应器与稀硫酸产生中和反应,生成温度较高的硫酸铵料浆。
粉状物料与硫酸铵料浆混合,形成一定液相的固溶体,在转鼓造粒机内滚动成粒;磷酸一铵与过量的氨发生中和反应,在适宜的温度和PH值环境下熔融,利用磷铵自身熔融的溶液粘结成粒,同时在高温下各物料间发生复分解反应生成复盐,在造粒机不断的转动下,使物料处于流动状态,相互摩擦、翻动、挤压粘附成粒。
造粒过程中产生的尾气,经文丘里洗涤器洗涤后放空。
氨酸法技改方案323

氨酸法复合肥技术改造方案一、氨酸造粒复合肥生产原理1、液氨与稀硫酸中和反应工业浓硫酸经稀释后与定量的液体无水氨(液氨)通过悬埋管式反应器在造粒机中进行中和反应,生成硫酸铵料浆并放出热量,其化学反应方程式:H2SO4(稀)+2NH3=(NH4)2SO4+Q2、氯化钾、磷酸一铵与硫酸铵间的复分解反应从配料岗位输送到造粒机内的氯化钾和磷酸一铵在低温下可进行复分解反应生成磷酸二氢钾和氯化铵,但该反应在温度低时反应缓慢生成的磷酸二氢钾量较低;当硫酸与液氨进行中和反应放出大量的热量时,物料温度升高,进而加快了该反应速度。
同时液氨与硫酸进行中和反应生成的高温硫酸铵又与物料中的氯化钾发生复分解反应,生成硫酸钾和氯化铵。
KCl+ NH4 H2PO4= KH2PO4+ NH4Cl(NH4)2SO4 +2 KCl= K2SO4+2NH4Cl3、复盐固溶体的形成该物料中氯化钾和磷酸一铵发生复分解反应生成的氯化氨与原料中的氯化钾将形成氯化铵钾复盐固溶体[(NH4,K)Cl]。
硫酸与液氨进行中和反应生成的硫酸铵又与氯化钾复分解反应所产生的硫酸钾形成硫酸铵钾固溶体[(NH4,K) 2SO4]。
氯化钾和磷酸一铵反应生成的磷酸二氢钾与原料中的磷酸一铵又形成磷酸铵钾固溶体[(NH4,K) H2PO4]。
这些固溶体将是该肥料的主要成分,并在造粒过程中起到粘结成球的作用。
其化学反应式如下:(1~ p)NH4Cl+ p KCl=(NH4,K)Cl p=0~1(1~q) (NH4)2SO4+q K2SO4=(NH4,K) SO4 q =0~1(1~n) NH4 H2PO4+nk H2PO4=(NH4,K)H2PO4 n=0~1二、工艺改造路线的选择原转鼓蒸汽造粒复混肥生产工艺,生产过程中尚存在如下问题:(1)原工艺在造粒时需消耗大量蒸汽进行预热,造成了成球后的物料水分高,需消耗大量的无烟煤进行烘干,从而增加了成本,降低了产能。
(2)原工艺由于在生产过程中一次成球率低,使生产系统余料返料量大,从而出现了装置产量低,电耗高,物料损耗大,粉尘污染严重,生产成本直线上升等问题。
氨酸法处理二氧化硫方程式

氨酸法处理二氧化硫方程式哎呀,说到氨酸法处理二氧化硫,这可是个很有意思的话题啊!你知道二氧化硫吧,那玩意儿可不是什么好东西,常常是工业排放的“产物”。
闻着可刺鼻了,有点像你在路边嗅到的过期臭豆腐,真是让人受不了。
可别小看这个二氧化硫,它可是大气污染的罪魁祸首之一。
想想看,霾天里,空气那么糟糕,呼吸都像是在吞云吐雾,怎么能让人高兴呢?这时候,氨酸法就显得格外重要了,简直像是空气清新剂中的“超级英雄”。
氨酸法到底是什么呢?简单来说,就是用氨酸来处理二氧化硫,打个比方,就像你用香皂洗手,把手上的脏东西洗干净。
氨酸,听起来有点高大上,但其实它就是氨基酸中的一员,咱们日常生活中常见的东西。
你知道的,蛋白质啊、营养啊,这些东西里都少不了它。
氨酸就像是那种能和各种“坏家伙”打交道的好手,遇到二氧化硫,直接上阵,形成一种新东西,顺便把空气弄得清新点。
你想想啊,氨酸和二氧化硫的化学反应,就好比是两位搭档,默契得很。
一来一往,二氧化硫被氨酸抓住,经过一番“对话”,它们就转变成了更无害的化合物。
哇,这可真是“山穷水尽疑无路,柳暗花明又一村”啊。
原本在空中横行霸道的二氧化硫,经过氨酸的“调教”,变得乖巧多了。
这么一来,不仅空气变得清新,呼吸起来也像是在深山老林里游荡,心情都随之变好。
说到氨酸法,其实这背后还有很多科学原理。
你可能会想,化学反应听起来好复杂,其实就是一堆小分子在那儿“打交道”。
氨酸像个热心肠的调解人,给二氧化硫找到了个“出路”。
他们之间的互动,就像老朋友聚会时聊得火热,讨论着生活、工作,最终都找到各自的方向。
虽然反应过程中有点小麻烦,但大方向绝对是为了改善空气质量,真是值得为之奋斗。
氨酸法不仅简单有效,还能让环境变得更友好,真是一举多得。
不过,咱们也不能光靠这种方法,得多方面入手。
比如,减少工业排放、倡导绿色生活、推广清洁能源,都是重要的一环。
想要根本解决问题,单靠氨酸法可不够,要综合治理,才能把二氧化硫这样的“坏家伙”打得落花流水。
氨酸法脱硫的工作原理

氨酸法脱硫的工作原理
氨酸法脱硫是一种常见的烟气脱硫方法,其工作原理如下:
1. 氨酸(NH2CH2COOH)与SO2反应生成硫代硫酸胺
(NH2CH2COONH4),即氨酸与硫酸气体反应生成盐。
2. 这一反应通常在低温下进行,通常在100℃以下,以确保高
反应选择性和高脱硫效率。
在反应过程中,氨酸作为合适的还原剂用于与SO2发生氧化还原反应。
3. 反应后的烟气中产生的硫酸气体通过吸收塔或吸收剂吸收后,形成硫酸溶液。
硫酸为强酸,可以与氨酸中的NH3发生酸碱
中和反应,生成硫酸铵。
4. 硫酸铵可以被进一步处理,如结晶、干燥、再利用等。
也可以通过氨酸法脱硝设备、混凝剂和过滤剂进行处理,使其回收利用。
总之,氨酸法脱硫利用氨酸与SO2发生反应,生成硫酸胺盐,将SO2从烟气中去除,达到脱硫的目的。
通过处理后,脱硫
烟气变得更环保,减少了空气污染物的排放。
氨酸法处理二氧化硫方程式
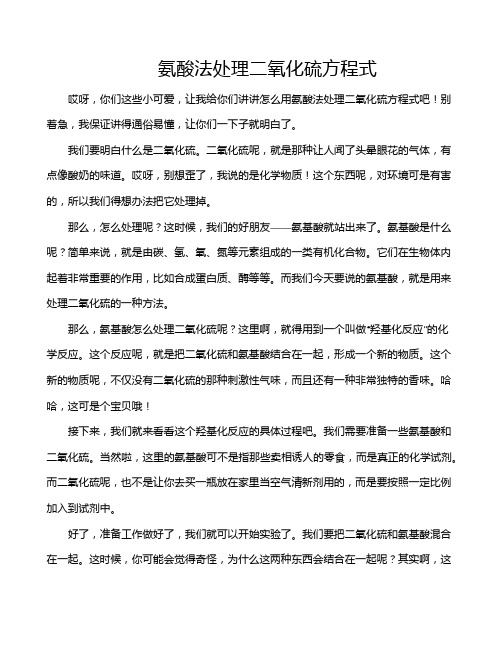
氨酸法处理二氧化硫方程式哎呀,你们这些小可爱,让我给你们讲讲怎么用氨酸法处理二氧化硫方程式吧!别着急,我保证讲得通俗易懂,让你们一下子就明白了。
我们要明白什么是二氧化硫。
二氧化硫呢,就是那种让人闻了头晕眼花的气体,有点像酸奶的味道。
哎呀,别想歪了,我说的是化学物质!这个东西呢,对环境可是有害的,所以我们得想办法把它处理掉。
那么,怎么处理呢?这时候,我们的好朋友——氨基酸就站出来了。
氨基酸是什么呢?简单来说,就是由碳、氢、氧、氮等元素组成的一类有机化合物。
它们在生物体内起着非常重要的作用,比如合成蛋白质、酶等等。
而我们今天要说的氨基酸,就是用来处理二氧化硫的一种方法。
那么,氨基酸怎么处理二氧化硫呢?这里啊,就得用到一个叫做“羟基化反应”的化学反应。
这个反应呢,就是把二氧化硫和氨基酸结合在一起,形成一个新的物质。
这个新的物质呢,不仅没有二氧化硫的那种刺激性气味,而且还有一种非常独特的香味。
哈哈,这可是个宝贝哦!接下来,我们就来看看这个羟基化反应的具体过程吧。
我们需要准备一些氨基酸和二氧化硫。
当然啦,这里的氨基酸可不是指那些卖相诱人的零食,而是真正的化学试剂。
而二氧化硫呢,也不是让你去买一瓶放在家里当空气清新剂用的,而是要按照一定比例加入到试剂中。
好了,准备工作做好了,我们就可以开始实验了。
我们要把二氧化硫和氨基酸混合在一起。
这时候,你可能会觉得奇怪,为什么这两种东西会结合在一起呢?其实啊,这是因为它们的分子结构非常相似,就像一对亲兄弟一样。
当它们结合在一起的时候,就会发生一些神奇的化学反应。
这个化学反应的过程呢,就像是一场精彩的舞蹈表演。
二氧化硫会像一个小丑一样,跳上舞台,然后和氨基酸一起跳舞。
这时候,它们会互相碰撞、融合,形成一个新的物质。
这个新的物质呢,就像是一个美丽的公主,散发着迷人的香气。
接下来,我们就要看看这个新的物质到底是什么样子的了。
这时候,我们就需要用到一个叫做“色谱分析”的实验方法。
氨酸法造粒工艺流程

氨酸法造粒工艺流程The granulation process using the ammoniation method is a critical step in producing high-quality fertilizer. 氨酸法造粒工艺是生产高质量肥料的关键步骤。
This method involves combining ammonium nitrate solution with other ingredients to create granules that are ready for distribution and application in the agricultural sector. 这种方法包括将硝酸铵溶液与其他成分结合,制成颗粒,以便在农业领域分发和应用。
It is essential to understand the detailed procedure involved in the ammoniation granulation process to ensure efficiency and effectiveness in fertilizer production. 了解氨酸法造粒工艺中的详细程序是确保肥料生产效率和有效性的关键。
One of the key steps in the ammoniation granulation process is the preparation of the core materials, which will form the basis of the final granules. 氨酸法造粒工艺中的关键步骤之一是准备核心材料,这些材料将构成最终颗粒的基础。
The core materials typically include ammonium nitrate solution, phosphoric acid, and other additives such as binders and fillers. 核心材料通常包括硝酸铵溶液、磷酸和其他添加剂,如粘合剂和填充剂。
氨酸法造粒工艺及岗位操作规程

氨酸法造粒工艺及岗位操作规程一、前言氨酸法造粒工艺是一种常见的药品制剂工艺。
该工艺主要采用氨酸为溶剂,将固体药品制剂喷雾成小颗粒,以适应不同的用药需求。
本文将详细介绍氨酸法造粒工艺及岗位操作规程。
二、氨酸法造粒工艺概述氨酸法造粒工艺是一种湿法造粒工艺,其主要原理是通过喷雾器将氨酸和制剂混合,形成小颗粒,然后通过干燥装置将其干燥固化。
氨酸法造粒工艺常用于制备药品的微、小颗粒。
这些颗粒可以轻松地组合成胶囊、丸剂或直接制成口服溶液。
总体而言,氨酸法造粒工艺包括以下几个步骤:1. 药品混合。
将需要制备成颗粒的药品加入氨酸中混合均匀。
2. 喷雾成颗粒。
将药品混合液通过喷雾器喷出,形成小颗粒。
3. 干燥固化。
将喷出的小颗粒通过干燥装置干燥,使其成为坚硬的颗粒。
4. 筛分。
将干燥后的颗粒进行筛分,以去除不必要的细颗粒和杂质。
5. 包装。
最后将筛分后的颗粒包装成所需的制剂。
三、岗位操作规程作为一个行业工作者,在执行任何任务之前,必须遵守制定的操作规程。
下面是氨酸法造粒工艺的操作规程。
1. 工具和设备准备在进行氨酸法造粒工艺之前,必须检查和准备所需的工具和设备。
2. 工作区准备操作人员应确保工作区域干净整洁,并有足够的净化和通风系统,以确保在操作中尽量减少空气中的污染物。
3. 安全保障在进行任何实验室操作之前,必须遵循安全标准,包括穿戴个人防护装备如口罩、手套等,并在使用化学品时要注意保护眼睛和皮肤。
在必要的情况下,应对药品进行排气、灭菌等处理。
4. 药品加入将所需的药品主要成分逐一加入氨酸中,并使用搅拌器确定其充分混合。
5. 摇匀将所需的辅料逐一加入氨酸混合物中,利用搅拌器按预定比例摇匀。
在摇匀时,搅拌头必须保持在混合液中,以确保混合均匀。
6. 造粒调节喷雾器的操作参数,根据药品需求逐步调整氨酸流量和喷雾器压力,逐渐喷雾出小颗粒。
在造粒时,操作者必须注意氨酸的量,确保其满足制作颗粒的要求。
7. 干燥和筛分将喷出的小颗粒通过干燥装置进行干燥固化。
氨酸法工艺简介

氨酸法工艺简介氨酸法工艺是近两年来国内出现的一种最新的复肥生产技术,传统复混肥生产工艺相比,氨酸法工艺以其低成本,低能耗,高产量等特点得到了迅速发展,代表了复工艺发展的一个方向。
传统复肥生产为团粒法转鼓造粒,利用蒸气提供热量和水分,而氨酸法造粒则是利用氨酸反应时产生的大量反应热来加热物料,2NH3+H2SO4=(NH4)2SO4+热量与传统复复肥蒸汽受热方式相比,由于受热面以及受热方式的不同,氨酸造粒可以加热物料至80-100度,而传统工艺只有60度左右,这就进一步提高了化学盐类的溶解度,在同相的液相比例下造粒物料水分可以降低2-3%,同时成球率明显提高。
也就是说,在同等规模烘干系统设备规格下,可以大大提高烘高能力。
在氨酸反应过程控制中,氨是略过量的,这一方面是为了保证硫酸的充分反应,确保成品PH值在合理范围,另一方面略微过量的氨还可以进一步中和原料中磷酸一铵的酸性,改善物料的成球物性,大大提高了物造粒成球率。
据测算,氨酸工艺的造粒成球率可以达到60-90%,而按常规工艺只有40-60%。
返料比的改变直接提高了装置的生产能力,一般而言,常规设计的复肥生产线能力如果改为氨酸工艺生产,一般产量可以提高30%-50%,每吨成品能耗可以降低40%左右,这也体现了集约型社会的发展理念。
由于造粒过程成球物性的改善,对于常规15-15-15,16-16-16等配方,生产时无需再加入任何粘结剂便可以达到良好的成球状况,就当前市场行情,氮源中氯化铵与尿素单位养分价格存在较大差距的前提下,可以大量使用低价氮源,从而最大程度的降低了产品的原料成本。
就目前原料市场价格而言,氨酸法工艺生产成本平均可比传统工艺降低50-100元/吨。
在市场竞争如此激烈的今天,这无疑是一个重大利好,由此可见,氨酸法工艺确实代表了复肥发展的一个方向。
5-30万吨/年氨酸法(尿基)复合肥生产技术一.氨酸法工艺特点:①将化工原料硫酸、液氨引入到复合肥生产中,将简单的复混肥生产提升到了复合化的程度,提升了产品的质量。
氨酸法工艺技术简述
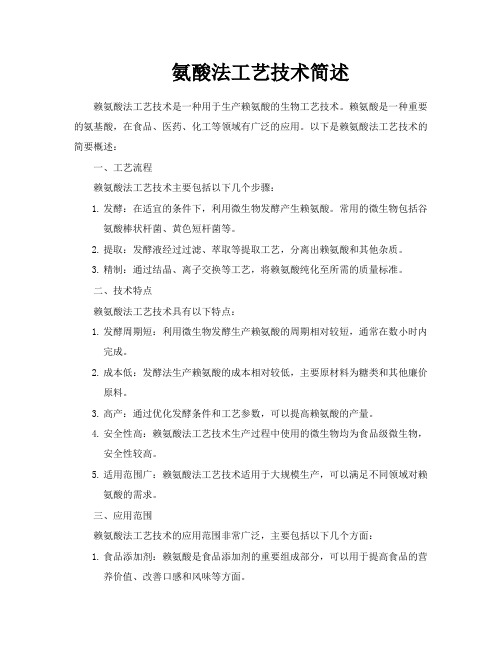
氨酸法工艺技术简述赖氨酸法工艺技术是一种用于生产赖氨酸的生物工艺技术。
赖氨酸是一种重要的氨基酸,在食品、医药、化工等领域有广泛的应用。
以下是赖氨酸法工艺技术的简要概述:一、工艺流程赖氨酸法工艺技术主要包括以下几个步骤:1.发酵:在适宜的条件下,利用微生物发酵产生赖氨酸。
常用的微生物包括谷氨酸棒状杆菌、黄色短杆菌等。
2.提取:发酵液经过过滤、萃取等提取工艺,分离出赖氨酸和其他杂质。
3.精制:通过结晶、离子交换等工艺,将赖氨酸纯化至所需的质量标准。
二、技术特点赖氨酸法工艺技术具有以下特点:1.发酵周期短:利用微生物发酵生产赖氨酸的周期相对较短,通常在数小时内完成。
2.成本低:发酵法生产赖氨酸的成本相对较低,主要原材料为糖类和其他廉价原料。
3.高产:通过优化发酵条件和工艺参数,可以提高赖氨酸的产量。
4.安全性高:赖氨酸法工艺技术生产过程中使用的微生物均为食品级微生物,安全性较高。
5.适用范围广:赖氨酸法工艺技术适用于大规模生产,可以满足不同领域对赖氨酸的需求。
三、应用范围赖氨酸法工艺技术的应用范围非常广泛,主要包括以下几个方面:1.食品添加剂:赖氨酸是食品添加剂的重要组成部分,可以用于提高食品的营养价值、改善口感和风味等方面。
2.医药领域:赖氨酸在医药领域也有广泛的应用,如合成抗生素、抗癌药物等。
3.化工领域:赖氨酸在化工领域的应用主要包括合成香料、助剂等。
4.其他领域:赖氨酸还可以应用于畜牧业、农业等领域,如作为饲料添加剂等。
四、未来发展方向随着科技的不断进步和应用领域的不断拓展,赖氨酸法工艺技术也在不断发展和改进。
未来,赖氨酸法工艺技术的研究和发展方向主要包括以下几个方面:1.发掘新菌种:寻找新的高效产赖氨酸的菌种,提高赖氨酸的产量和效率。
2.优化发酵条件:进一步优化发酵条件和工艺参数,提高赖氨酸的生产效率和产品质量。
3.联合其他技术:将赖氨酸法工艺技术与其他技术相结合,如基因工程技术、膜分离技术等,以实现更高效的生产和分离纯化。
- 1、下载文档前请自行甄别文档内容的完整性,平台不提供额外的编辑、内容补充、找答案等附加服务。
- 2、"仅部分预览"的文档,不可在线预览部分如存在完整性等问题,可反馈申请退款(可完整预览的文档不适用该条件!)。
- 3、如文档侵犯您的权益,请联系客服反馈,我们会尽快为您处理(人工客服工作时间:9:00-18:30)。
本人先介绍下团粒法造粒生产工艺与氨酸法造粒生产工艺的区别。团粒法造粒生产工艺就是将需要的原料按照一定的配比加入,经破碎后达到一定的细度,与返料混合后进入造粒机,通过加入一定量的蒸汽和水达到造粒所需的温度与湿度,经造粒后得到2~4mm的粒子达到一定的量,再经过干燥,筛分、冷却、包装等工序后,得到合格的产品。氨酸法造粒生产工艺是在团粒法造粒生产工艺的基础上,增加一套氨酸反应喷入造粒系统,并增加尾气洗涤系统,进行尾气中气体氨的回收。
硫酸铵 硫酸钾 氯化钾 尿素 二铵 一铵
配比% 46.8 4 10 3 6.9 29.3
另外,在造粒中按20KgH2SO4/t原料加入硫酸,气氨用量按造粒出口物料PH一定进行调节,在出口物料PH值的控制上,不宜太高,太高说明气氨过饱和,会造成浪费,使生产成本升高,太低说明气氨加入量不够,会造成(CNH4)2SO4量不够,而使成球率低,①从配方来看,沙性物料硫酸铵、硫酸钾、氯化钾占的比例达60.8%,而粘性物料尿素、二铵、一铵的比例只有39.2%,用团粒法造粒工艺是无法生产的,另外,料浆态的(CNH4)2SO4具有很强的粘性,在造粒中不需要加太多的水来提高物料粘性就可以有很好的成球率,因此在造粒出口物料的含水量能控制在3~4%,因此可以减少干燥负荷,保证产品质量,数据表明,氨酸法造粒工艺可比团粒法造粒工艺省煤10~20kg/t产品,节约了成本,并且能很好地控制住产品中含水量,防止结块现象产生;②而且也不用担心沙性物料与粘性物料失衡,而添加一种纯粘性、没有养份的白泥来调节生产,从生产的数据来看,氨酸法造粒成球率能达到70~80%,有时调节得好还能达到90%的成球率,而产品与系统返料的比例可少至只有1:(1.1~1.5),因此可以大大减少系统负荷,减少了设备因为负荷高而跳停的机率,并节约了电能,并且价格较贵的尿素、二铵用量仅占9.9%,而相对便宜的一铵用量占到29.3%,减少了成本。尤其是振动筛,基本上没有因为糊筛而导致产品粉料多的情况发生,而且在造粒中,气氨与一铵的反应一般是从表面开始的,因此颗粒表面光滑圆整,色泽明亮,大小如一,出来的产品外观非常好看,手摸有圆润的感觉,基本上没有团粒法造粒生产工艺中的所谓“三角六耳”,细长扁平等粒子的现象,因此,从造粒工序上来看,氨酸法造粒工艺远远优于团粒法造粒工艺,一是节能,如果氨酸法造粒比团粒法造粒每小时少用1吨蒸汽,蒸汽按80元/t来计算,那么一年如果只算300天,则省下80×24×300=576000,一年下来就省了57.6万元,氨酸法比团粒法生产少用煤按15kg/t来计算,煤按400元/t计算,一小时上20t台产,则省下0.015×20×24×300×400=86.4万元,两样相加一年则可省下一百四十多万元费用,另外还可以减低系统负荷、节约电能,减少设备因堵塞造成的停车等优点,并且因为成球率大大高于团粒法,所以产量都比团粒法生产工艺高出许多,年产十万吨的生产线,创造过日产660吨的记录,班产曾达到过256吨的记录.
氨酸法造粒生产工艺的生产原理就是在团粒法造粒工艺的基础上增加一套氨酸反应系统,利用硫酸与气氨进行反应:H2SO4+2NH3==(NH4)2SO4+热量,产生硫酸铵料浆和热量,并将料浆均匀的涂布在造粒物料上,由于料浆态的硫酸铵具有很强的粘性和结合力,因此为生产高浓度高氮复合肥提供了有力的保证。氨酸法造粒生产工艺也是按需要将原料按配比加入造粒机,在造粒机头部加入蒸汽、洗涤液以及将氨酸反应后的料浆均匀在喷入,但是在这里氨酸法造粒工艺与团粒法造粒工艺有很大的差别,首先团粒法造粒工艺是利用物料自身的粘性进行粘合造粒成球,这只是一个简单的物理过程,没有任何的化学反应,并且在原料的选择上有较严的要求,粘性物料、沙性物料都要求>40%,但氨酸法造粒工艺则基本上克服这些弱点。第一,他有化学反应,能将低附加值的H2SO4以及气氨转化成高附加值的复合肥,成为产品养份中的一部分,另一个化学反应是气氨与磷酸一铵的反应:NH3+NH4PO4==(NH4)2PO4+热量。从反应方程式中可以看到,也是能将附加值低的一铵,其中和度约是0.9(N/P)与气氨反应,生成中和度约是1.6(N/P)的磷铵(因其是一铵与二铵的中间体,因此称其为磷铵),并且在有水的情况下,将呈粘性好的料浆态,而且也提高了原料的附加值,节约了成本。第二,因为有化学反应,并且能放出大量的反应热,因此,能节约蒸汽用量,并且因为是在物料之间发生化学反应放出热量,而一铵是均匀地分散在物料里的,省去了传热过程也减少了蒸汽损耗。从生产数据来看,同样是生产20吨产品/小时,团粒法造粒需要蒸汽约2.5t/h才能将造粒出口物料温度提升至70℃,而氨酸法造粒工艺只需要蒸汽1.5t/h就可以了,极大的节约成本。第三,因气氨和硫酸反应生成的硫酸铵具有很强的粘性和结合力,当它均匀地涂布在造粒进口物料上时,就可以将他们粘合在一起,并随着造粒机的转动长大成球,得到我们需要的粒子。因此,氨酸法造粒工艺可以不太苛刻物料的粘性就可以造粒成球。我们也试举一例鹿化公司复合肥厂新试验成功的肥种,16-16-8-13(N:P:K:S),总养份为40%,其中含S≥13%,这是一种出口肥,在东南亚国家极受欢迎,因为东南亚国家大面积种植橡胶树,提取的橡胶中含S越高则其价值越高,因为S能大幅度地提高橡胶的耐磨能力,在之前我国能生产出来的含S最高的复合肥也只达到8%,因此此肥种的试验成功将具有很广阔的市场前景。配方如下:
氯化铵 普钙 磷酸一铵 白泥 氯化钾 磷酸二铵 尿素
配比% 35.7 8.3 4.2 23 12.9 12.9 3.0
从资料可知,普钙、磷酸一铵、白泥、磷酸二铵、尿素是粘性物料,它们的总合占到51.4%,那么沙性物料占到48.6%,其中磷酸一铵、磷酸二铵、尿素都是粘性很好的物料,但是我们在选择这些物料时一方面要考虑生成成本,因为磷酸一铵、磷酸二铵、尿素都是价格比较高的肥料,因此,我们在适量的使用一铵、二铵、尿素使造粒工序能保证成球率,同时使用普钙、白泥等粘性不是很好的物料,但价钱相对较便宜的物料,当然,控制几种物料的配比有个先决条件,就是生产出来的产品能够达到我们希望得到的养份,即,总养份达到30%,N:P:K为14:8:8(百分比)。另一方面,我们不能一味地追示提高粘性物料的配比,否则原料粘性太大,则造粒机出口物料容易出大粒子,甚至会产生“和面团”现象,生产出一大堆大大个的物料团,因此造粒成球率反而下降,同时会造成造粒出口很多粉料,使系统负荷加重,也是不利于生产的,因此在生产中,我们总结出一条经验,即沙性物料。及粘性物料都应大于40%,另外,控制造粒成球率的两个关键的因素,一个是造粒温度,一个是造粒湿度,造粒的温度从生产经验来看,控制在大于70℃是适宜的,在此温度下,一方面可以得到最佳的造粒效果,另一方面可以提高产品的强度,我们要控制好造粒温度,一方面要控制好进造粒温度,一般要控制大于45℃,另一方面则控制好加入造粒的蒸汽量,使造粒温度保持在70℃左右,另一个关键因素是加入造粒洗涤水的用量,一般我们控制出造粒机物料水份约4~5%。如果控制太高则一方面加重干燥负荷,甚至使产品含水量指标不合格,另一方面则有可能出潮料,或者是大团物料增多,俗称“和泥糊”。如果加水太少,则有可能使造粒物料粘性不够,出造粒细粉量多,合格粒子少。同时也增加后工序的负荷,另外,在团粒法生产工艺中,在造粒与干燥过程中,尿素、二铵等粘性物料受热易呈熔融状态,而使颗粒外部软化,熔融态的物料易粘结在一起,俗称“和泥糊”现象,而使造粒成球率下降,并容易粘住造粒机、干燥机等设备的外壁,形成结垢,造成清理困难,并影响产量,特别是在生产高氮复混肥、尿素、二铵用量较大的时,情况尤甚,所以团粒法造粒生产工艺生产复混肥时,不宜生产高氮品种的复混肥,一般N含量不高于15%,从生产的数据来看,造粒成球率一般在35~50%之间,较少能超过60%的成球率,产品与返料的比例一般在1:2.5左右,但如果造粒或筛分工况差时,这一比例甚至将达到1:(3~4),那么将在一段时间内看到只见投料,不见产出的情况。在系统返料量大的情况下还将出现振动筛糊筛,致使产品粉料量大,有时<1mm的粒子量能达到30%,严重影响产品质量,并且系统设备负荷过重的情况下,对生产是不利的,经常会导致设备过负荷跳停的情况发生,而致使全线停车。
在工艺流程上,两套系统是大同小异,首先原料经过称量皮带,按需要的配比加入系统,然后进入到原料破碎机,将原料粉碎到80%的粒度后,与返料一起进入造粒机,在造粒机里加入适量的水、蒸汽,新系统则增加气氨与H2S04的反应后的物料进行喷浆。通过造粒机后物料温度控制在75℃左右,然后进入干燥机,与热风炉来的约350℃的热风进行换热后,将物料中的水分干燥至≤2.0%。干燥出来的物料进入振动筛,共将物料分为三层,第一层是分离出≥4mm的物料,这些物料通过大粒破碎机破碎到0.8mm左右的颗粒与原料一起进入造粒机,第二层是2~4mm的颗粒,这部分颗粒将做为产品,经过冷却机冷却,包裹系统后进入包装得到合格的产品。第三层物料是<2mm的物料,将与原料混合进入造粒机,重新造粒. 新系统除了在旧系统的基础上,还增加了一套氨酸喷入系统及造粒尾气吸收系统,具体流程包括:浓酸酸贮槽贮存外界来的浓度为98%的浓酸,因为生产中不能将浓度为98%的硫酸直接与气氨反应,否则将会产生大量的酸雾污染厂房空气及造成能源浪费,因此需要将其稀释,所以增设一个稀释盒,先加入部分水,然后加入合适的浓硫酸,稀释到一定的浓度,通过泵打到稀酸贮槽中,在造粒开车时,便将稀酸通过泵打到造粒系统,并加入外界来的气氨,即可进行氨酸反应并喷浆。在造粒尾气中,由于气氨扩散速度快,与酸反应不完全,气氨占有一定的比例,如不进行回收,一方面造成能源损耗过大,生产成本大幅提高,一方面严重污染环境,并且空气中气氨浓度达到一定量时遇火会发生爆炸事故,因此,在尾气吸收系统中增加两个洗涤塔,四台循环洗涤泵,共八组喷头,用稀酸进行循环洗涤尾气中的气氨进行循环再利用,并增设风机一台,作为尾气的抽风动力源,而旧系统的团粒造粒工艺则不需要进行造粒尾气处理,新系统在氨酸系统、尾气处理系统方面共投资约两百多万元,也就是说新系统共比旧系统多花两百多万元的投资。
本人2004年3月起在**公司复合肥厂二车间任职,该厂共有两套不同的生产工艺流程,但年产能力都是十万吨/年,一套是团粒法造粒生产工艺,称作旧十万吨车间,一套是氨酸法造粒生产工艺,称作新十万吨车间。两套生产线都有他们的优缺点和共同点,在此,本人通过从他们的几个方面进行阐述,即:工艺流程、控制要点、工艺指标、实际生产水平、产品结构、市场情况、销售情况,进行综合对比,最终对两套装置进行评判优劣优劣情况,即可知晓,并提出一些整改措施。