过程评审表
CQI-9特殊过程:热处理评审(第二版)评审表
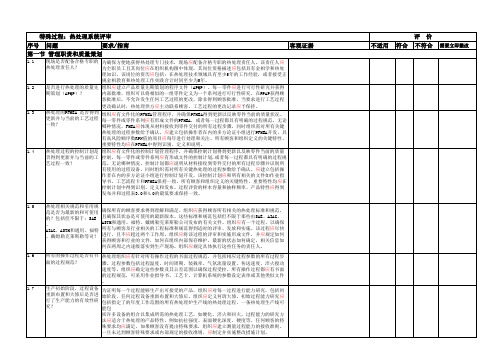
1.7
序号
1.8
特殊过程: 特殊过程:热处理系统评审 问题 要求/指南 要求/
是否针对整个热处理过程 热处理产品及全过程的数据分析能提供缺陷预防(防错)的重要信息。组织应建立相应的系 定期收集和分析数据,并 统用于持续地收集、分析产品和过程的数据并对其作出反应。分析方法应包括重要产品和 对数据分析结果作出应? 重要过程参数的现行趋势或历史数据的分析。组织应确定哪些重要参数需要列入分析范围 。 管理者是否每24小时检查 管理者检查热处理监控系统的间隔应不超过24小时。热处理监控系统包括但不限于:温度 热处理监控系统? 纸带记录、气氛纸带记录、计算机数据日志、热处理炉及操作者日志等。管理者检查应包 括对失控状态或报警状态的探测。热处理炉数据的检查过程应予记录存档,此要求也适用 于计算机数据。 是否按AIAG的热处理系统 组织应按AIAG的热处理系统评审要求每年至少进行一次内部评审,应及时发布审核发现的 评审要求每年至少进行一 问题。 次内部评审? 现场是否有一个文件化的 质量管理体系应有一个文件化的返工(重新热处理)处理过程,该过程应包括对指定责任人 返工处理过程? 的授权。返工处理程序应规定哪些产品特性允许返工,哪些产品特性不允许返工。 任何返 工操作应由有资格的技术人员编制新的过程控制表,以注明所需热处理的更改事项。应清 晰地记录何时、哪种材料进行了返工处理。返工产品的放行应经质量经理或指派的授权人 批准。 质量部门是否对与顾客相 关的重大事项和组织内部 质量管理体系应对与顾客相关的重大事项和组织内部的重大事项进行评审、处理并形成文 的重大事项进行评审、处 件。应采用成熟规范的解决问题的方式。 理并形 是否针对热处理评审范围 内的每个过程,建立了适 组织应针对热处理系统评审范围内的每个热处理过程建立持续改进过程。这些过程的设计 应促使产品质量和生产率的持续改进。采取的措施应体现优先顺序并应包括日期要求(预 用的持续改进计划? 计完成时间)。组织应提供该项目运行有效性的证据。 质量经理或指定的责任人 是否批准对隔离材料进行 质量经理负责批准并以文件规定适当的人员对隔离材料进行处置。 处置? 是否建立覆盖整个热处理 过程适用于操作者的程序 应建立覆盖整个热处理过程(从接收到发运)并适用于操作人员的程序文件或作业指导书 。该程序文件或作业指导书应包括处置潜在紧急情况(如停电)、设备启动及停止、产品 文件或作业指导书? 隔离封存(见2.8)、产品检验和基本操作程序。这些程序文件或作业指导书应覆盖从原 材料接收到产品发运的所有操作步骤,且车间操作人员应易于得到和理解。 管理者是否始终为热处理 组织应提供所有热处理作业的操作培训,所有员工包括后备工和临时工均应参加。应保持 员工(包括后备工、临时 员工培训的文件记录,以表明员工得到了培训并进行了培训有效性的评价。管理者应规定 工)提供培训? 每一岗位的资格要求,同时还应确定现在和将来的培训需求。 是否建立责任矩阵表,以 确保由有资质的人员履行 组织应建立所有关键管理职责和监控职责的责任矩阵表,并确保这些岗位职责由有资质的 所有关键的管理职责和监 人员履行。同时还应识别这些关键职责的主要人员和后备人员。这些关键职责由组织规 定,无论何时管理层应能方便地看到该责任矩阵表。 控职责?
文件评审表模板

文件评审表模板评审概述本文档旨在提供一个通用的文件评审表模板,用于评审各种类型的文件。
评审表的目的是帮助评审人员系统地检查文件的内容、格式和准确性,以确保文件达到预期的质量标准。
文件信息- 文件名称:- 文件版本号:- 评审日期:评审内容在评审过程中,请针对以下内容进行评价、点评和记录。
1. 文件格式- 文件命名规范是否符合要求?- 文字排版是否清晰、统一和易于阅读?- 是否包含必要的页眉、页脚和页码?- 是否使用合适的字体和字号?- 是否使用了正确的标点符号和缩进?2. 文件内容- 内容是否准确、完整和清晰表达?- 所使用的术语和表达是否准确和易于理解?- 是否遵循相关的规范、法规和标准?- 是否包含足够的支持性材料和参考资料?3. 文章结构- 是否具有逻辑和连贯的结构?- 是否包含了必需的部分,如引言、正文、结论等?- 段落是否组织有序且内容连贯?- 是否使用了适当的标题和子标题?4. 图表和图像- 图表和图像是否清晰、易于理解和正确标注?- 是否包含了必要的图例、单位和标题?- 是否有必要对图表和图像进行进一步的解释和说明?5. 语法和拼写- 是否有任何语法错误、拼写错误或标点符号错误?- 是否使用了正确的语法结构和词汇?6. 其他事项- 是否有任何其他需要特别关注的事项?结论根据对以上评审内容的评价和记录,提出评审结论,包括对文件的优点、问题和改进建议。
评审人员- 评审人员1:- 评审人员2:- 评审人员3:- 评审人员4:注释在完成对文件的评审后,请在此处添加任何其他需要记录的注释或建议。
附件- 附件1:文件原本- 附件2:评审结果记录表。
26个过程内审检查表(问题应用清单)
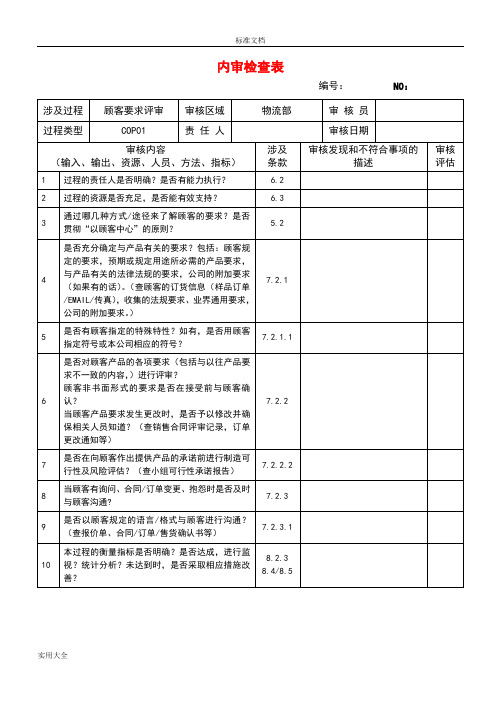
内审检查表
编号:NO:
江阴成澄佳机械制造有限公司内审检查表
江阴成澄佳机械制造有限公司内审检查表
江阴成澄佳机械制造有限公司内审检查表
内审检查表
内审检查表
内审检查表
江阴成澄佳机械制造有限公司内审检查表
江阴成澄佳机械制造有限公司内审检查表
内审检查表
内审检查表
内审检查表
内审检查表
内审检查表
内审检查表
内审检查表
内审检查表
江阴成澄佳机械制造有限公司内审检查表
内审检查表
内审检查表
江阴成澄佳机械制造有限公司内审检查表
江阴成澄佳机械制造有限公司内审检查表
内审检查表
内审检查表
内审检查表
内审检查表
内审检查表
内审检查表
江阴成澄佳机械制造有限公司内审检查表
江阴成澄佳机械制造有限公司内审检查表
江阴成澄佳机械制造有限公司内审检查表
江阴成澄佳机械制造有限公司内审检查表
江阴成澄佳机械制造有限公司内审检查表
江阴成澄佳机械制造有限公司内审检查表。
IATF16949过程方法审核检查表(全面)
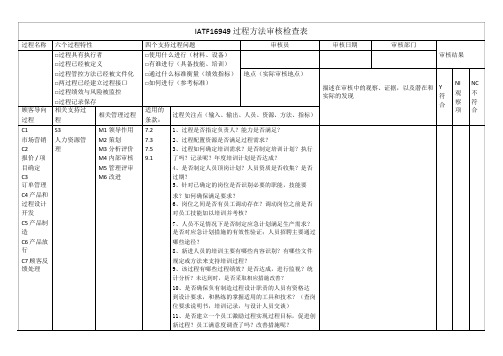
过程名称六个过程特性四个支持过程问题审核员审核日期审核部门□过程具有执行者 □使用什么进行(材料、设备)审核结果□过程已经被定义□有谁进行(具备技能、培训)□过程管控方法已经被文件化 □通过什么标准衡量(绩效指标) 地点(实际审核地点)□两过程已经建立过程接口 □如何进行(参考标准)描述在审核中的观察、证据,以及潜在和 YNI NC□过程绩效与风险被监控观 不实际的发现符□过程记录保存察 符合顾客导向 相关支持过相关管理过程 适用的过程关注点(输入、输出、人员、资源、方法、指标)项合过程程条款:C1 S3M1 领导作用 7.2 1、过程是否指定负责人?能力是否满足?市场营销 人力资源管 M2 策划7.3 2、过程配置资源是否满足过程需求?C2理M3 分析评价 7.5 3、过程如何确定培训需求?是否制定培训计划?执行报价 / 项 M4 内部审核 9.1了吗?记录呢?年度培训计划是否达成?目确定 M5 管理评审 4、是否制定人员顶岗计划?人员资质是否收集?是否C3M6 改进 过期?订单管理 5、针对已确定的岗位是否识别必要的职能,技能要C4 产品和 求?如何确保满足要求?过程设计 6、岗位之间是否有员工调动存在?调动岗位之前是否开发 对员工技能加以培训并考核?C5 产品制 7、人员不足情况下是否制定应急计划满足生产需求? 造 是否对应急计划措施的有效性验证;人员招聘主要通过C6 产品放 哪些途径?行 8、新进人员的培训主要有哪些内容识别?有哪些文件C7 顾客反 规定或方法来支持培训过程?馈处理9、该过程有哪些过程绩效?是否达成,进行监视?统计分析?未达到时,是否采取相应措施改善?10、是否确保负有制造过程设计职责的人员有资格达 到设计要求,和熟练的掌握适用的工具和技术?(查岗位要求说明书,培训记录,与设计人员交谈)11、是否建立一个员工激励过程实现过程目标,促进创过程名称六个过程特性四个支持过程问题审核员审核日期审核部门□过程具有执行者 □使用什么进行(材料、设备)审核结果□过程已经被定义□有谁进行(具备技能、培训)□过程管控方法已经被文件化 □通过什么标准衡量(绩效指标) 地点(实际审核地点)□两过程已经建立过程接口 □如何进行(参考标准)描述在审核中的观察、证据,以及潜在和 YNI NC□过程绩效与风险被监控观 不实际的发现符□过程记录保存察 符合顾客导向 相关支持过相关管理过程 适用的过程关注点(输入、输出、人员、资源、方法、指标)项合过程程条款:C1 S4M1 领导作用5.3 1、过程的责任人是否明确?是否有能力执行?市场营销 文件记录管 M2 策划7.5 2、过程的资源是否充足?是否能有效支持?C2理M3 分析评价 7.3 3、质量管理体系文件是否包括以下方面:报价 / 项 M4 内部审核 7.1.3 a)质量方针和质量目标是否文件化?目确定 M5 管理评审 7.1.6 b)质量手册是否编制?C3M6 改进 8.2.1 c)IATF16949:2016 所要求的文件化程序?订单管理 8.5.2 d)为确保其过程有效规则、运作和控制所需文件?C4 产品和 8.5.3e) IATF16949:2016 所要求的记录?过程设计 (查质量手册,质量方针和目标,程序文件及记录样开发式)C5 产品制4、是否规定本过程需要遵守的规则?是否按规则对造文件按进行管理?(查一查文件发放记录、现场文件 C6 产品放格式、编号等)是否确定组织的知识并收集知识清 行单?针对必要的知识是否内部培训(知识:通常从其 C7 顾客反经验中获得,知识产权;从经验获得的知识;从失败 馈处理和成功项目吸取的经验教训,标准;学术交流;专业会议,从顾客或外部供方收集的知识)5、是否对质量记录也进行适当控制?是否规定其保 存期限?期限设定合理吗?所有的记录是否被标示、易于查找、得到适当保护、编号?6、是否有外来文件按照文件控制合理管控?(查外过程名称六个过程特性四个支持过程问题审核员审核日期审核部门□过程具有执行者 □使用什么进行(材料、设备)审核结果□过程已经被定义□有谁进行(具备技能、培训)□过程管控方法已经被文件化 □通过什么标准衡量(绩效指标) 地点(实际审核地点)□两过程已经建立过程接口 □如何进行(参考标准)描述在审核中的观察、证据,以及潜在和 YNI NC□过程绩效与风险被监控观 不实际的发现符□过程记录保存察 符合顾客导向 相关支持过相关管理过程 适用的过程关注点(输入、输出、人员、资源、方法、指标)项合过程程条款:7、本过程的衡量指标是否明确?是否达成,进行监视?统计分析?未达到时,是否采取相应措施改善?过程名称六个过程特性四个支持过程问题审核员审核日期审核部门□过程具有执行者 □使用什么进行(材料、设备)审核结果□过程已经被定义□有谁进行(具备技能、培训)□过程管控方法已经被文件化 □通过什么标准衡量(绩效指标) 地点(实际审核地点)□两过程已经建立过程接口 □如何进行(参考标准)描述在审核中的观察、证据,以及潜在和 YNI NC□过程绩效与风险被监控观 不实际的发现符□过程记录保存察 符合顾客导向 相关支持过相关管理过程 适用的过程关注点(输入、输出、人员、资源、方法、指标)项合过程程条款:C2 S5M1 领导作用 5.3 1、过程的责任人是否明确?是否有能力执行?报价 / 项 采购过程M2 策划6.1 2、过程的资源是否充足,是否能有效支持?目确定M3 分析评价 6.2 3、是否确定供应商选择准则并有效执行?查看记录 C3 M4 内部审核 7.1 选择准则里是否包含:汽车业务量(绝对值,以及占订单管理 M5 管理评审 7.2 总业务量的百分比) ;C4 产品和 M6 改进 7.4 — 账务稳定性;过程设计 7.5 — 采购的产品、材料或服务的复杂性;开发8.2 — 所需技术(产品或过程)C5 产品制 8.4 — 可用资源(如:人员、基础设施)的充分性;造8.5.2 — 设计和开发能力(包括项目管理);8.5.3 — 制造能力;8.5.4 — 更改管理过程;8.6 — 业务连续性规划(如:防灾准备、应急计划);8.7 — 物流过程;9.1 — 顾客服务;10.2 4、是否对供方进行现场/资料评审,是否对新进供方 10.3的PPAP 进行批准?是否规定各类供方的管控类型和程 度?(查物料分类明细、合格供方清单、PPAP 一套资料)5、所有采购物料的信息如何获得?整个过程是否建立过程规则加以规范?哪些文件?过程名称六个过程特性四个支持过程问题审核员审核日期审核部门□过程具有执行者 □使用什么进行(材料、设备)审核结果□过程已经被定义□有谁进行(具备技能、培训)□过程管控方法已经被文件化 □通过什么标准衡量(绩效指标) 地点(实际审核地点)□两过程已经建立过程接口 □如何进行(参考标准)描述在审核中的观察、证据,以及潜在和 YNI NC□过程绩效与风险被监控观 不实际的发现符□过程记录保存察 符合顾客导向 相关支持过相关管理过程 适用的过程关注点(输入、输出、人员、资源、方法、指标)项合过程程条款:C2 S5M1 领导作用 5.3 6、是否有顾客指定的供方?如如何管理的?记录呢 报价 / 项 采购过程M2 策划6.1 7、是否与供方签订必要的协议?比如采购合同、品 目确定M3 分析评价 6.2 质协议?在这些协议里是否包含顾客要求?或通过 C3 M4 内部审核 7.1 其他形式传递了顾客要求?协议是否规定必要的包 订单管理 M5 管理评审 7.2 装规范,PPM 指标等?这些要求是否监督供方执行?C4 产品和 M6 改进 7.4 记录过程设计 7.5 8、是否制定供方定期评价的准则?是否按照准则执 开发8.2 行?对于不能满足准则要求的供方是否采取必要措C5 产品制 8.4 施?造8.5.2 9、对于交付时的放行是否制定放行准则?是否与供8.5.3 方沟通达成一致?8.5.4 10、本过程的衡量指标是否明确?是否达成,进行监 8.6 视?统计分析?未达到时,是否采取相应措施改善?8.7 9.1 10.210.3过程名称六个过程特性四个支持过程问题审核员审核日期审核部门□过程具有执行者 □使用什么进行(材料、设备)审核结果□过程已经被定义□有谁进行(具备技能、培训)□过程管控方法已经被文件化 □通过什么标准衡量(绩效指标) 地点(实际审核地点)□两过程已经建立过程接口 □如何进行(参考标准)描述在审核中的观察、证据,以及潜在和 YNI NC□过程绩效与风险被监控观 不实际的发现符□过程记录保存察 符合顾客导向 相关支持过相关管理过程 适用的过程关注点(输入、输出、人员、资源、方法、指标)项合过程程条款:C2S6M1 领导作用 5.31、过程的责任人是否明确?是否有能力执行?报价 / 项 生产设备管 M2 策划6.1.2.2 2、过程的资源是否充足?是否能有效支持?目确定 理M3 分析评价 6.1.2.33、如何确定所需配置的设备?设备的验收是否按照C4 产品和 M6 改进7.1.3 规则执行?记录呢?过程设计7.1.5 4、验收合格的设备在交付前是否建立设备履历,编 开发7.2 号?是否识别关键设备?是否是被关键的备品备C5 产品制7.3 件?对此是否建立管理原则?对于关键设备的使用造7.4 是否建立应急计划,计划是否进行有效性验证?7.5 5、设备是否建立预防性维护计划?达成情况?(查8.2 年度保养计划、关键设备清单、维修记录、点检记录、8.4 对维护目标的达成)8.3.5 6、对于存在安全隐患的设备是否设定隔离栏?安全9.1 警示标示等?10.3 7、本过程的衡量指标是否明确?是否达成,进行监视?统计分析?未达到时,是否采取相应措施改善?过程名称六个过程特性四个支持过程问题审核员审核日期审核部门□过程具有执行者 □使用什么进行(材料、设备)审核结果□过程已经被定义□有谁进行(具备技能、培训)□过程管控方法已经被文件化 □通过什么标准衡量(绩效指标) 地点(实际审核地点)□两过程已经建立过程接口 □如何进行(参考标准)描述在审核中的观察、证据,以及潜在和 YNI NC□过程绩效与风险被监控观 不实际的发现符□过程记录保存察 符合顾客导向 相关支持过相关管理过程 适用的过程关注点(输入、输出、人员、资源、方法、指标)项合过程程条款:C2S7 M1 领导作用 5.3 1、过程的责任人是否明确?是否有能力执行?报价 / 项 工装管理M2 策划6.1.2.2 2、过程的资源是否充足?是否能有效支持?目确定 M3 分析评价 6.1.2.3 3、如何确定必要的工装模具?是否为工具和量具的 C4 产品和 M6 改进 7.1.3 设计、制造和验证活动提供适当的技术资源?(查相 过程设计 7.1.5 关开模申请单、图纸,数据的设计资料、验收记录)开发7.2 4、是否建立和实施生产工装管理的系统,包括: C5 产品制 7.3 --维护、修理设施与人员?(查 培训资料)造7.4 --储存与修复?(储存环境、维修/保养记录)7.5 --工装准备?(模夹具制造申请单,模具开制计划,8.2 模/夹具检验报告)8.4 --易损工具的更换计划?(查易损件的更换计划或寿8.3.5 命规定)9.1 --工具设计修改的文件,包括工程变更等级?(查更10.3改记录必要的验证记录比如 CPK 统计)--工具的修改和文件的修订?(查更改记录)--工装确认,明确其状态,如生产、修理或处置?(查模具状态标识)5、如果工装模具的开发被外包,是否对外包过程实 施控制(查模夹具制造申请单,模具制造商调查表/ 评审表,合格模具制造商一览表,工装模具验收记录等)过程名称六个过程特性四个支持过程问题审核员审核日期审核部门□过程具有执行者 □使用什么进行(材料、设备)审核结果□过程已经被定义□有谁进行(具备技能、培训)□过程管控方法已经被文件化 □通过什么标准衡量(绩效指标) 地点(实际审核地点)□两过程已经建立过程接口 □如何进行(参考标准)描述在审核中的观察、证据,以及潜在和 YNI NC□过程绩效与风险被监控观 不实际的发现符□过程记录保存察 符合顾客导向 相关支持过相关管理过程 适用的过程关注点(输入、输出、人员、资源、方法、指标)项合过程程条款:C2S7 M1 领导作用 5.3 6、是否有顾客或外部供方提供的工装模具,如何实 报价 / 项 工装管理M2 策划6.1.2.2 施控制?是否对工装模具也应进行永久性标识? 目确定 M3 分析评价 6.1.2.3 7、工装模具的维修过程是否被定义?过程记录是否 C4 产品和 M6 改进7.1.3 被合理管控?模具履历卡是否按照维修时间进行更 过程设计 7.1.5 新?维修合格的是否被再次验收?验收记录呢? 开发7.2 8、模具库房是否被隔离,模具领用回收被记录吗?C5 产品制 7.3 9、本过程的衡量指标是否明确?是否达成,进行监 造7.4 视?统计分析?未达到时,是否采取相应措施改善? 7.5 8.2 8.4 8.3.5 9.110.3过程名称六个过程特性四个支持过程问题审核员审核日期审核部门□过程具有执行者 □使用什么进行(材料、设备)审核结果□过程已经被定义□有谁进行(具备技能、培训)□过程管控方法已经被文件化 □通过什么标准衡量(绩效指标) 地点(实际审核地点)□两过程已经建立过程接口 □如何进行(参考标准)描述在审核中的观察、证据,以及潜在和 YNI NC□过程绩效与风险被监控观 不实际的发现符□过程记录保存察 符合顾客导向 相关支持过相关管理过程 适用的过程关注点(输入、输出、人员、资源、方法、指标)项合过程程条款:C4 产品和 S8 M2 策划4.3.2 1、过程的责任人是否明确?是否有能力执行?过程设计 产品防护M3 分析评价 5.3 2、过程的资源是否充足?是否能有效支持?开发M6 改进 7.2 3、产品过程设计开发时是否考虑顾客要求?提供顾C5 产品制 8.2 客要求清单?造8.4 4、生产现场的产品防护是否按照程序规定执行?生C6 产品交 8.3.3 产车间是否规定具体的原材料半成品、成品防护要付8.5.4 求?8.5.4.15、进料区、待转区、仓库、化学物品产品防护是否 保持产品标识、考虑存放环境?尤其是化学品仓库是 否设定消防类器具?化学物品的存放条件是否按照 MSDS 要求?是否按适当计划的时间间隔来检查库存品状况,以便及时侦测变质情况?6、仓库物料的收发存是否保持账物卡一致?对于过 程出现的超领,退库产品、呆滞物料如何定义?是否 形成必要的文件支持?查一查记录是否符合流程规定7、本过程的衡量指标是否明确?是否达成,进行监视?统计分析?未达到时,是否采取相应措施改善?过程名称六个过程特性四个支持过程问题审核员审核日期审核部门□过程具有执行者 □使用什么进行(材料、设备)审核结果□过程已经被定义□有谁进行(具备技能、培训)□过程管控方法已经被文件化 □通过什么标准衡量(绩效指标) 地点(实际审核地点)□两过程已经建立过程接口 □如何进行(参考标准)描述在审核中的观察、证据,以及潜在和 YNI NC□过程绩效与风险被监控观 不实际的发现符□过程记录保存察 符合顾客导向 相关支持过相关管理过程 适用的过程关注点(输入、输出、人员、资源、方法、指标)项合过程程条款:C4 产品和 S9M2 策划5.3 1、过程是否定义责任人?能力具备吗?过程设计 产品和服务 M3 分析评价 7.2 2、过程配置资源符合要求吗?开发放行M6 改进 7.4 3、进料检验、过程检验、成品检验的接收是否制定 C5 产品制 7.5 接收准则?成品是否有顾客规定的接收准则?对于 造8.1 技术型抽样的接收准则是否定义为零缺陷?查看执C6 产品交 8.2 行记录、检验指导书付8.5.1 4、对于原材料需要实验室检测的特性,是否按要求8.5.2 记录结果并对结果进行评审?8.65、供方样品接收准则是否满足顾客要求?查供方样品承认书6、对于特采的过程是否定义接收、批准、追踪流程? 生产过程中有关半成品、成品的接收准则是否定义? 是否进行产品检验,以验证产品要求已得到满足?并保持验证的记录且记录签名齐全?7、以上接收准则是否与控制计划要求保持一致,比 如产品的检验试验标准、过程巡检频次、过程配置的计量器具是否完整有效等8、是否定义最终检验标准?是否按照要求进行记录检验结果?9、但最终检验出现不合格时,需要放行的是否得到顾客批准?、过程名称六个过程特性四个支持过程问题审核员审核日期审核部门□过程具有执行者 □使用什么进行(材料、设备)审核结果□过程已经被定义□有谁进行(具备技能、培训)□过程管控方法已经被文件化 □通过什么标准衡量(绩效指标) 地点(实际审核地点)□两过程已经建立过程接口 □如何进行(参考标准)描述在审核中的观察、证据,以及潜在和 YNI NC□过程绩效与风险被监控观 不实际的发现符□过程记录保存察 符合顾客导向 相关支持过相关管理过程 适用的过程关注点(输入、输出、人员、资源、方法、指标)项合过程程条款:10、本过程的衡量指标是否明确?是否达成,进行监视?统计分析?未达到时,是否采取相应措施改善?过程名称六个过程特性四个支持过程问题审核员审核日期审核部门□过程具有执行者 □使用什么进行(材料、设备)审核结果□过程已经被定义□有谁进行(具备技能、培训)□过程管控方法已经被文件化 □通过什么标准衡量(绩效指标) 地点(实际审核地点)□两过程已经建立过程接口 □如何进行(参考标准)描述在审核中的观察、证据,以及潜在和 YNI NC□过程绩效与风险被监控观 不实际的发现符□过程记录保存察 符合顾客导向 相关支持过相关管理过程 适用的过程关注点(输入、输出、人员、资源、方法、指标)项合过程程条款:C5 产品制 S10 M1 领导作用 5.3 1、过程是否定义责任人?能力具备吗?造不合格输出 M3 分析评价 7.4 2、处理不合格品过程配置的资源符合要求吗?C6 产品交 控制M6 改进 7.5 3、是否建立文件化的程序,对不合格品控制与不合 付8.7 格品相关职责和权限做出规定? (查看程序文件) C7 顾客反 9.1.3 4、现场不合格品是否按照该流程处理?(抽查不合 馈处理10.2 格品的处理案件,查看是否结案,记录是否清晰明确) 10.35、对于顾客退回的产品是否组织评审?并按要求记录评审结果6、返工后的产品是否再经检验验证其是否为合格 品?(查看不合格品报告,纠正措施记录,让步记录,返工返修的记录)7、生产现场是否建立不合格品区域,以隔离不合格 品防止流转其他工序?是否建立不良品台账有效管理 不良品的进出、返修?8、针对历来发生的质量问题是否总结事故原因,组 织对质量问题的预防展开培训或制定不良品限度样本悬挂现场?9、针对返工、返修的产品公司制定相应的作业指导 书,是否被适当的人易于得到和使用?(查看相关指导书)10、本过程的衡量指标是否明确?是否达成,进行监过程名称六个过程特性四个支持过程问题审核员审核日期审核部门□过程具有执行者 □使用什么进行(材料、设备)审核结果□过程已经被定义□有谁进行(具备技能、培训)□过程管控方法已经被文件化 □通过什么标准衡量(绩效指标) 地点(实际审核地点)□两过程已经建立过程接口 □如何进行(参考标准)描述在审核中的观察、证据,以及潜在和 YNI NC□过程绩效与风险被监控观 不实际的发现符□过程记录保存察 符合顾客导向 相关支持过相关管理过程 适用的过程关注点(输入、输出、人员、资源、方法、指标)项合过程程条款:C7 S11 M3 分析评价 9.1.2 1、过程是否定义责任人?能力具备吗?顾客反馈 客户满意度 M4 内部审核 9.1.32、处理不合格品过程配置的资源符合要求吗? 处理测量M5 管理评审 3、是否定义顾客满意度测评的时间、频次要求? M6 改进 4、是否按时间进行顾客满意调查,是否出具分析报 告?是否对内部交付绩效进行统计以证明顾客满 意?规定了哪些属于内部交付绩效?是否实施统计?5、对回收的调查表是否进行分析汇总并形成满意度 调查报告?满意度指标不达标的顾客是否采取针对性的措施来提高满意度?过程名称六个过程特性四个支持过程问题审核员审核日期审核部门□过程具有执行者 □使用什么进行(材料、设备)审核结果□过程已经被定义□有谁进行(具备技能、培训)□过程管控方法已经被文件化 □通过什么标准衡量(绩效指标) 地点(实际审核地点)□两过程已经建立过程接口 □如何进行(参考标准)描述在审核中的观察、证据,以及潜在和 YNI NC□过程绩效与风险被监控观 不实际的发现符□过程记录保存察 符合顾客导向 相关支持过相关管理过程 适用的过程关注点(输入、输出、人员、资源、方法、指标)项合过程程条款:C3 S1M1 领导作用 7.5.3 1、过程是否定义责任人?能力具备吗?订单管理 标识与可追 M2 策划8.2.2 2、处理不合格品过程配置的资源符合要求吗? C4溯性M3 分析评价 8.5.23、是否定义过程中产品标识与可追溯性的方法? 产品过程 M6 改进 实际操作于规定是否相符合?设计开发 4、对于监视测量的产品是否策划标识方法?如进料 C5退货产品、过程判定不良产品、客退产品、返工返修生产制造后产品、特采产品的标识、报废品标识C6 5、现场模拟可追溯性,查看是否有效? 产品交付过程名称六个过程特性四个支持过程问题审核员审核日期审核部门□过程具有执行者 □使用什么进行(材料、设备)审核结果□过程已经被定义□有谁进行(具备技能、培训)□过程管控方法已经被文件化 □通过什么标准衡量(绩效指标) 地点(实际审核地点)□两过程已经建立过程接口 □如何进行(参考标准)描述在审核中的观察、证据,以及潜在和 YNI NC□过程绩效与风险被监控观 不实际的发现符□过程记录保存察 符合顾客导向 相关支持过相关管理过程 适用的过程关注点(输入、输出、人员、资源、方法、指标)项合过程程条款:C2 S3 M1 领导作用 4.1M1 领导作用报价及项 人力资源 M24.2 1、最高管理者是否知晓本部门在产品实现过程里担 目确定 S4策划4.3 负的职责?是否定义影响产品符合性和质量管理体 C1 市场开 文件记录管4.4 系有效性人员职责?(查岗位说明书、管理职责程序) 发理5.1 2、是否为产品实现提供相关资源?(人力资源、培5.2 训教育资源、设备工装、工具等查部门是否有人员补5.3 充计划、针对性的培训计划)6.1 3、是否积极参与质量改进的过程当中?是否理解本6.2 部门过程绩效如何达成?过程绩效制定是否考察了过程的有效性和过程的效率?4、是否理解公司质量方针的含义?并在内部宣导质量方针M2 策划最高管理者是否组织策划过程风险与机遇,并确保过程拥有者知晓其过程存在风险和机遇机器应对措施?是否组织策划管理评审或内部审核?。
外包过程-评审表
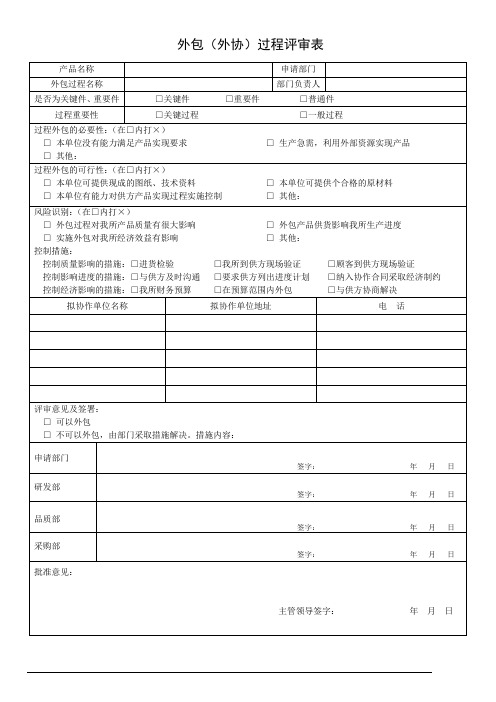
拟协作单位名称
拟协作单位地址
电 话
评审意见及签署:
□ 可以外包
□ 不可以外包,由部门采取措施解决。措施内容:
申请部门
签字: 年 月 日
研发部
签字: 年 月 日
品质部
签字: 年 月 日
采购部
签字: 年 月 日
批准意见:
主管领导签字: 年 月 日
□ 本单位有能力对供方产品实现过程实施控制 □ 其他:
风险识别:(在□内打×)
□ 外包过程对我所产品质量有很大影响 □ 外包产品供货影响我所生产进度
□ 实施外包对我所经济效益有影响 □ 其他:
控制措施:
控制质量影响的措施:□进货检验 □我所到供方现场验证 □顾客到供方现场验证
控制影响进度的措施:□与供方及时沟通 □要求供方列出进度计划 □纳入协作合同采取经济制约
外包(外协)过程评审表
产品名称
申请部门
外包过程名称
部门负责人
是否为关键件、重要件□关键Βιβλιοθήκη □重要件 □普通件过程重要性
□关键过程 □一般过程
过程外包的必要性:(在□内打×)
□ 本单位没有能力满足产品实现要求 □ 生产急需,利用外部资源实现产品
□ 其他:
过程外包的可行性:(在□内打×)
□ 本单位可提供现成的图纸、技术资料 □ 本单位可提供个合格的原材料
CQI-9第3版过程表和评审表 中文

Version 2, Issue 8/07
特殊过程:热处理系统评估
工厂名称: 地址:
电话: 传真: 工厂热处理员数量: 自有热处理企业(是/否): 商业热处理企业(是/否):
评估日期: 以往评估日期:
职位:
电话:
邮箱:
审核员/评估员: 姓名:
ห้องสมุดไป่ตู้
公司:
电话:
邮箱:
“不满意”项目数:
“需要立即纠正”项目数:
作业审核中“不合格”项目数:
工厂热处理工艺类型: 过程表 A - 亚铁 渗碳 碳氮共渗 碳修复 中性淬火 (淬火和回火) 奥氏体等温淬火 / 马氏体等温淬 火 回火 脱溶硬化 / 时效
过程表 B - 亚铁 渗氮 (气体) 铁素体碳氮共渗(气体或盐浴) 过程表 C - 铝合金 铝合金热处理 过程表 D - 亚铁 感应热处理 过程表 E 退火 正火 应力消除 过程表 F 低压渗碳 过程表 G 烧结硬化 过程表 H 离子氮化 现有质量认证体系: 再次评估日期(如果需要): 人员联系方式: 姓名:
过程评审表
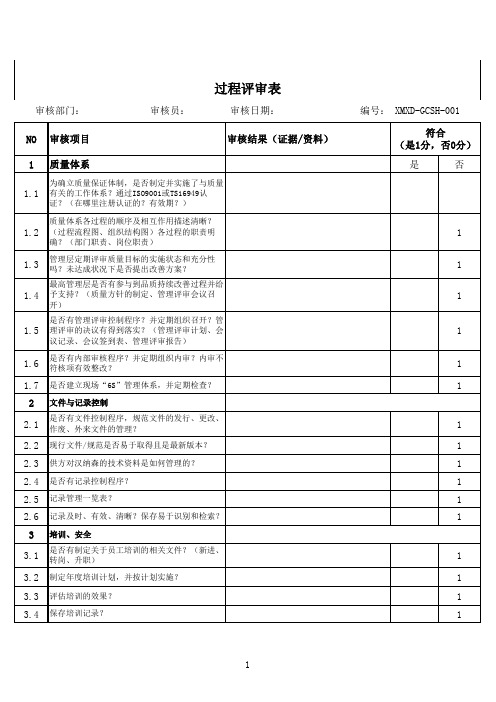
2
符合 (是1分,否0分)
0 1 0
1 1
1
1 1
1 1 1 1 1 1 1 1 1 1 1 0
NO 审核项目
审核结果(证据/资料)
是否有供应商管理规定?有选择供应商的流程或
6.1 新供应商的选择标准是否明确?(调查、评审、
资质等)
6.2
是否有合格供方名录?是否有合格供方再次评审 的机制?如交货及时率、进料合格率等
7.3
每个工位是否都有最新版本的作业指导书?以确 保每个员工都能正确操作?
7.4
制程是否定义关键过程,并对关健过程实行SPC 管制?
7.5
操作员是否按照作业指导书或CP的要求,进行首 件确认?
7.6
操作员是否对生产过程的主要参数进行监控,并 作记录?如温度、压力等。
7.7
制程中的原材料、半成品、成品是否明确标识且 可追溯?防护符合要求?
12.1 是否有检验、测量和测试设备的一览表?
12.2 是否有量检具的保养、校准、操作作业指导书?
12.3
现场使用的量检具是否都在有效期内,有状态标 识?
12.4
新仪器投入使用前或原有仪器经过搬动、维修 后,有重新校准?
12.5 现场是否有足够的检测设备保证符合规格要求?
12.6
仪器出现异常后,是否可追溯到前一批检测的产 品?
是否有制定定期可靠性验证计划,并依计划实
8.5 施,以确认产品在客户端的品质及减少隐患性风
险?
不合格品在交货后或开始使用后才被发现,供方
8.6 对不符合的影响或潜在影响是否有采取适当的措
施?
8.7 让步放行的产品是否有经过客户批准?
9 不合格品控制
4
CQI-9特殊过程:热处理评审(第二版)评审表(1)

客观证据
不适用
符合
评 价 不符合
需要立即整改
1.9
1.10
Байду номын сангаас
1.11
1.12
1.13
1.14
1.15
1.16
1.17
序号
1.18
特殊过程:热处理系统评审 问题 要求/指南
是否有预防性维护程序? 组织应建立关键过程设备(由组织识别)的预防性维护程序,该程序应是从维护申请到实 并利用其数据形成预见性 施再到有效性评价的整个维护工作的闭环。设备操作者应有机会报告问题并应在闭环中解 维护计划? 决问题。组织的数据资料,如停机时间、质量拒收(QR)、初始过程能力、重新维修指令 和操作者问题报告均应用于改进预防性维护程序。热处理炉和各类发生器应按规定的频率 制定相应的燃尽计划(详见过程表1.0)。应收集并分析维护保养工作的数据,作为预见性 维护计划的一部分。 热处理组织是否建立了关 键零部件备件清单,以保 热处理组织应建立并保持关键零部件备件清单,并应确保每一个零部件是适用的,以保证 证最小程度的生产中断? 最小程度的生产中断时间。
2.2
2.3
2.4
2.5
2.6
2.7
序号
2.8
特殊过程:热处理系统评审 问题 要求/指南
操作者是否接受当设备出 现紧急情况包括停电时如 何进行材料处理、实施遏 制措施和隔离产品的培 训? 计划外或紧急情况停工在很大程度上会增加不恰当的过程风险。操作者应接受针对设备出 现紧急情况包括停电时如何进行材料处理、实施遏制措施和隔离产品的培训,培训应形成 文件记录。明确规定设备出现紧急情况和潜在失效的作业指导书操作者应易于得到并理解 。该作业指导书应规定所有与热处理过程如装炉、奥氏体化、淬火、回火等有关的遏制措 施。
47试生产过程评审表

试生产过程评审表
表单编号:ZW-07-024 A1
制定部门: 工程部 制定日期: 2019年 4 月28 日 产 品 名 称
采集线束1 规格/型号 102200302210 产 品 代 号
102200302210 顾客名称/代号 广州鹏辉新能源 评审项目
□ 设计输入 ☑ 制样过程 评
审
内
容
1. 制造过程中,图纸是否符合制样需求。
2. 制造过程中,产品验证记录是否齐全。
评 审 结 果
1. 产品制作过程中,图纸符合要求,裁线尺寸符合图纸要求。
2. 产品制作过程中,各接点依据图纸要求,清晰明确。
3. 产品尺寸有进行全检。
4. 产品制作过程中,端子压接拉力、剖面分析、电压降实验已完成。
5. 产品制作完成后,有进行100%电气性能测试,符合要求。
备 注。
CQI-9热处理过程评审表

2.2
·在热处理全过程中产 品是否清楚地标识并实 施?
2.3
在热处理全过程中是否 完整地维护的批次追踪 和完整性?
2.4
·必须对可疑品或不合格品进行控制,以防止错误的发运和污染其它产 ·是否有足够的程序规 品 ·应有足够的程序规定用于防止不合格产品流入到生产系统 定以防止不合格产品流 ·应有文件规定适当的处理、产品标识以及原材料进出指定区域的跟踪 入到生产系统? ·应指定不合格存放区,以保持这类材料的隔离 在整个热处理过程中是 否有一个系统用于识别 死角区,以减少零件混 淆的风险(包括外来的 、合格件、和不正确处 理的零件)? ·在整个热处理过程中应有一个系统用于识别死角区,以减少零件混淆 的风险(包括外来的、合格件、和不正确处理的零件 ·应建立文件对每一个热处理过程/设备的死角区(trap points)进行识 别和监控 ·当每个零件的生产方法或装备改变时应识别潜在的死角区(trap poi有顾客产品的容器内应无外来材料的影响 容器内是否摆脱了外来 ·必须检查容器中的外来材料并通报其来源 材料的影响? ·在容器空出或再使用后应检查是否还有未经热处理的零件,以防污染 已完工产品 是否建立装炉操作规范 ·应建立装炉操作规范、作业文件并加以控制 、作业文件并加以控 ·装炉参数包括:进料速度、传动带速度、每筐的零件数、装裁重量, 制? 检查频率参见过程表3.0 ·操作者是否得到有关 当设备出现紧急情况 (包括动力中断时)如 何进行材料处理、围堵 措施和隔离产品的培 训? ·非计划或紧急情况停工在很大程度上来引起不恰当过程的风险 ·操作者应得到有关当设备出现紧急情况(包括动力中断时)如何进行 材料处理、围堵措施和隔离产品的培训 ·应形成培训文件,表明设备出现紧急情况或失效的潜在类型的作业指 导书易于被设备操作者接受和理解,这类指导应规定所有与热处理过程 有关的围堵措施,应覆盖整个热处理过程:装炉、奥氏体化、淬火和回 火
工程施工标准化评审表

工程施工标准化评审表一、评审项目基本信息1. 项目名称:XXXX工程施工项目2. 项目地点:XXXX3. 施工单位:XXXX建筑工程有限公司4. 工程规模:XXXX5. 工程总投资:XXXX6. 工程进度:XXXX7. 评审日期:XXXX二、评审内容1. 施工组织管理(1)施工组织设计:是否符合工程特点和施工要求,是否有明确的施工方案和进度计划。
(2)施工现场管理:施工现场是否整洁有序,安全防护设施是否到位,施工人员是否持证上岗。
(3)质量管理体系:是否建立完善的质量管理体系,是否有质量检测和验收标准。
(4)环境保护措施:是否采取有效措施保护环境,减少施工对周边环境的影响。
2. 工程质量(1)工程实体质量:是否存在质量问题,如裂缝、空鼓、平整度等。
(2)施工工艺:施工工艺是否符合规范要求,是否有技术创新和优化。
(3)工程材料:工程材料是否符合设计要求,是否有合格证和检测报告。
(4)工程验收:验收程序是否合规,验收结果是否符合标准要求。
3. 工程施工安全(1)施工现场安全:施工现场是否存在安全隐患,是否定期进行安全检查。
(2)施工人员安全:施工人员是否接受过安全培训,是否佩戴安全防护用品。
(3)机械设备安全:机械设备是否符合安全要求,操作人员是否具备相应资质。
(4)应急预案:是否制定应急预案,是否定期进行应急演练。
4. 工程进度与成本控制(1)工程进度:工程进度是否符合计划要求,是否存在延期情况。
(2)成本控制:成本控制是否有效,是否存在超预算情况。
三、评审结论与建议1. 综合考虑施工组织管理、工程质量、工程施工安全以及工程进度与成本控制等方面,本次工程施工标准化评审得分如下:施工组织管理:XX分工程质量:XX分工程施工安全:XX分工程进度与成本控制:XX分总分:XX分2. 评审结论:根据评审得分,本次工程施工标准化评审结果为“合格”或“不合格”。
3. 建议:针对评审过程中发现的问题,提出以下建议:(1)加强施工组织管理,完善施工现场管理制度,提高施工效率。
设计过程评审表
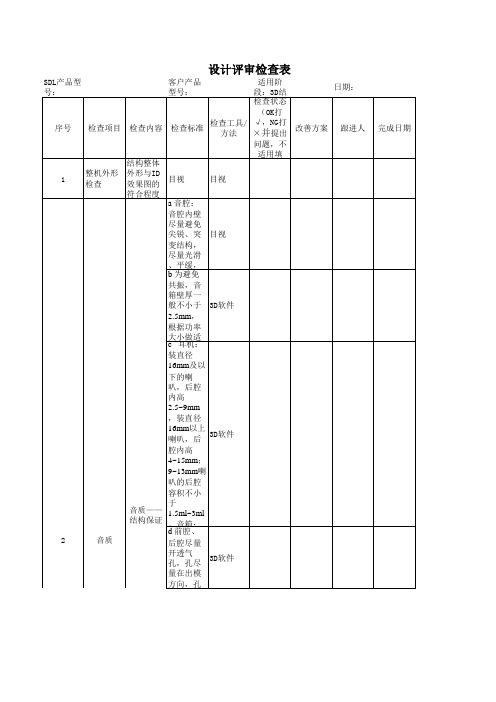
3D软件
目视
目视
3D软件
3D软件
3D软件
3
4
入耳式: 人体工程 导音管外 人体工程 径一般取 学 5.2~5.8mm ,最大不 超过 7.0mm, 导音管总 长度不小 耳塞式: 面盖直径 15~17.5m 耳罩式耳 套:内孔 尺寸长度 不小于 50mm,宽 度不小于 头带有拉 伸结构, 耳壳部分 可自动迎 合耳朵方 向减小佩 与耳朵或 头部接触 部分结构 光滑,不 可有尖锐 a 零件与 静态干涉 零件是否 检查 存在干涉 b 卡扣在 滑动的行 程中有无 与其他周 边零件干 c 模拟翻 盖部分在 绕转轴轴 心于工作 结构整体 角度范围 干涉检查 整机动态 内旋转动 干涉检查 全过程有 d 模拟整 机在工作 角度内转 动时FPC与 其他周边 零件有无 e 电池插 入和取出 过程中是 否有干涉
3D软件 3D软件
3D软件
3D软件 3D软件
3D软件
3D软件
按键配合
6
关键尺寸及 配合问题
侧键配合
电池部分
b.Rubber厚 度0.35~ 0.4mm c.Rubber按 键钉直径2 ~2.5, 高度0.35~ 0.4mm d.按键钉与 PCB板间隙 0.35mm e.OK按键钉 高出数字键 0.05,与主 PCB板间隙 0.3mm f.P+R式按 键与壳体周 边配合 间隙0.15mm G.按键表面 高出壳平面 0.05~0.1mm H.按键 Rubber须紧 壳体,配合 间隙为0 I.为增加按 键手感, Rubber须做 一些加固钉 等结构 a.侧键表面 高出壳体 0.6mm b.与壳体配 合单边 0.1mm间隙 c.侧键的设 计须考虑装 配的可性 是否有做一 些得于装配 的结构 a.厚度方 向:电池与 主机间隙 0.15~ 0.25mm b.长度方 向:固定端 间隙为0- 0.05mm与电 池 固定端间隙 为0.1mm
安全操作规程评审表
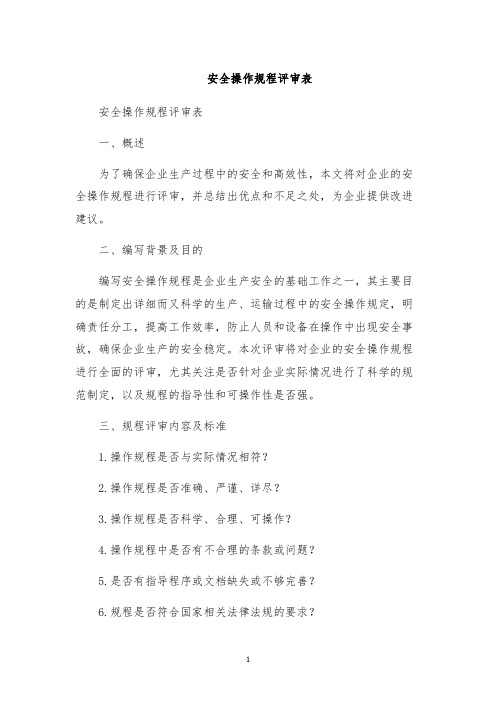
安全操作规程评审表安全操作规程评审表一、概述为了确保企业生产过程中的安全和高效性,本文将对企业的安全操作规程进行评审,并总结出优点和不足之处,为企业提供改进建议。
二、编写背景及目的编写安全操作规程是企业生产安全的基础工作之一,其主要目的是制定出详细而又科学的生产、运输过程中的安全操作规定,明确责任分工,提高工作效率,防止人员和设备在操作中出现安全事故,确保企业生产的安全稳定。
本次评审将对企业的安全操作规程进行全面的评审,尤其关注是否针对企业实际情况进行了科学的规范制定,以及规程的指导性和可操作性是否强。
三、规程评审内容及标准1.操作规程是否与实际情况相符?2.操作规程是否准确、严谨、详尽?3.操作规程是否科学、合理、可操作?4.操作规程中是否有不合理的条款或问题?5.是否有指导程序或文档缺失或不够完善?6.规程是否符合国家相关法律法规的要求?7.规程是否支持和保障企业的全面发展?8.规程是否有利于提高工作效率和生产效益?四、评审结果1.操作规程与实际情况相符程度高,但还存在与实际情况不符的内容。
2.操作规程准确、严谨、详尽度较高,但还需进一步明确责任分工。
3.操作规程科学、合理、可操作性强,但还需加强业务指导并考虑更多操作细节。
4.操作规程中无不合理的条款或问题。
5.指导程序或文档较为完善,但还需进一步完善。
6.操作规程符合国家相关法律法规的要求。
7.规程支持和保障企业的全面发展,但还需进一步完善和改进。
8.规程有利于提高工作效率和生产效益,但还需进一步深挖潜力和优化管理方法。
五、评审结论和建议本次评审表明,企业的安全操作规程已经得到了相应的制定和实施,但还存在一些不足之处。
为进一步提高规程的效果和效益,建议采取以下措施:1.进一步对规程内容进行科学的修订和完善,使其更加贴合实际,有利于提高操作的效率。
2.加强对员工的培训和指导,提高员工素质和操作技能,以避免因人力不足或工作不当而导致的事故。
3.制定出更具体、更细致的指导程序、模板和文档,将规程中的操作细节详细化,以方便员工实际操作。
IATF16949-2016最新的VDE6.3过程审核要素说明及评审表
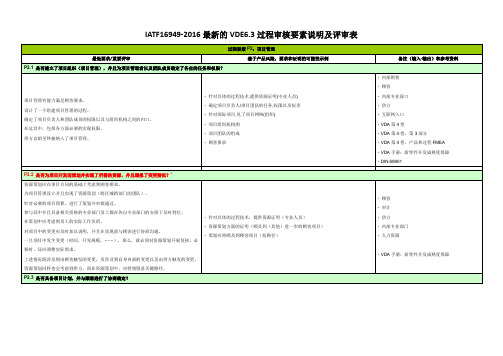
针对变更的规模制定了规定(分发,处理时间,事态升级路径)。
必须满足顾客就变更管理的要求,或者对此开张了特定的管理并加以记录。
为变更的负责人定义了一套规定。
-时间表
-变更管理过程描述
-责权的确定
-变更表单
-变更历史
-变更评价
-变更认可
-顾客
确定了项目负责人和团队成员的权限以及与组织机构之间的归口。
在这其中,包括各方面必要的实现权限。
供方自始至终被纳入了项目管理。
-针对具体的过程技术,提供资源证明(专业人员)
-确定项目负责人/项目团队的任务,权限以及权责
-针对国际项目,见了项目网络(组织)
-项目组织机构图
-项目团队的组成
-顾客要求
-内部销售
针对变更,应及时加以说明,并做好相关记录。
应在一道定义的过程的基础上,对所有变更开展记录。
对于不是由顾客触发的变更,应同顾客协商沟通。
对于影响到产品质量的变更,必须和顾客一起对风险开展评价。
在变更管理中,应确保供方(关键群体)能够主动参与。
对变更停止的时间点有明确的定义,因而必须遵守。
如果不能遵守,则在顾客和供方之间必须以书面形式加以记录。
SOP之间的变更时间段不会影响到产品质量。
变更的实现应考虑到SOP之间剩余的时Fra bibliotek,综合加以评价。
-时间表
-变更管理过程描述
-变更表单
-变更历史
-变更评价
-变更许可
-顾客
-供方
-内部专业部门
- VDA第1卷
- VDA第4卷,第3部分
- VDA手册:新零件开发成熟度保障
IATF16949-2016最新的VDE6.3过程审核要素说明及评审表
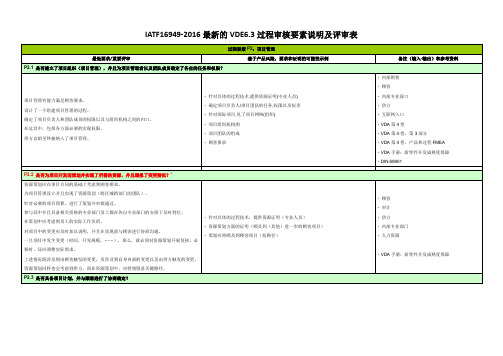
-顾客要求
-时间安排,时间框架
-针对下级供方权责关系的定义
-规范,标准,法律,环保
-顾客规范
-产品责任要求
-产能
-原材料到位情况
-负责开发的有资格的人员
-生产制造可能,生产地点
-建筑,空间
-设备,模具,生产/检验设备,辅助工具,实验室设备,运输工具,容器,仓库
- CAM,CAQ
标准化生产系统的方法:
这些假话中包含有特定开发和策划活动的具体时间点/持续时间,里程碑,生产测试等相关信息。
里程碑应和顾客的里程碑协调一致。为各里程碑确定考量指标,并且确定关键路径。
内部开发计划应与对应的项目事件表协调一致。尤其是针对各个里程碑的考量指标。必须确保开发计划始终处于更新状态。
在开发计划中,应包括一套质量管理策划,期内容应涉及检验策划,检验设备策划以及风险分析。
供方自始至终被纳入了项目管理。
-针对具体的过程技术,提供资源证明(专业人员)
-确定项目负责人/项目团队的任务,权限以及权责
-针对国际项目,见了项目网络(组织)
-项目组织机构图
-项目团队的组成
-顾客要求
-内部销售
-顾客
-内部专业窗口
-供方
-互联网入口
- VDA第4卷
- VDA第4卷,第3部分
- VDA第4卷,产品和过程FMEA
在策划中应考虑到员工的实际工作负荷。
对项目中的变更应及时加以说明,并且在实现前与顾客进行协商沟通。
一旦项目中发生变更(时间,开发规模,……),那么,就必须对资源策划开展复核。必要时,还应调整实际需求。
上述情况既涉及到由顾客触发的变更,页涉及到自身内部的变更以及由供方触发的变更。
- 1、下载文档前请自行甄别文档内容的完整性,平台不提供额外的编辑、内容补充、找答案等附加服务。
- 2、"仅部分预览"的文档,不可在线预览部分如存在完整性等问题,可反馈申请退款(可完整预览的文档不适用该条件!)。
- 3、如文档侵犯您的权益,请联系客服反馈,我们会尽快为您处理(人工客服工作时间:9:00-18:30)。
审核部门: NO 1 1.1 审核项目 质量体系
为确立质量保证体制,是否制定并实施了与质量 有关的工作体系?通过ISO9001或TS16949认 证?(在哪里注册认证的?有效期?) 质量体系各过程的顺序及相互作用描述清晰? (过程流程图、组织结构图)各过程的职责明 确?(部门职责、岗位职责) 管理层定期评审质量目标的实施状态和充分性 吗?未达成状况下是否提出改善方案? 最高管理层是否有参与到品质持续改善过程并给 予支持?(质量方针的制定、管理评审会议召 开) 是否有管理评审控制程序?并定期组织召开?管 理评审的决议有得到落实?(管理评审计划、会 议记录、会议签到表、管理评审报告) 是否有内部审核程序?并定期组织内审?内审不 符核项有效整改? 是否建立现场“6S”管理体系,并定期检查? 文件与记录控制 是否有文件控制程序,规范文件的发行、更改、 作废、外来文件的管理? 现行文件/规范是否易于取得且是最新版本? 供方对汉纳森的技术资料是如何管理的? 是否有记录控制程序? 记录管理一览表? 记录及时、有效、清晰?保存易于识别和检索? 培训、安全 是否有制定关于员工培训的相关文件?(新进、 转岗、升职) 制定年度培训计划,并按计划实施? 评估培训的效果? 保存培训记录?
1 1 1 0
6
12.1 是否有检验、测量和测试设备的一览表? 12.2 是否有量检具的保养、校准、操作作业指导书? 12.3 识?
现场使用的量检具是否都在有效期内,有状态标 新仪器投入使用前或原有仪器经过搬动、维修
1 1 1 1 1 0
12.4 后,有重新校准?
12.5 现场是否有足够的检测设备保证符合规格要求? 12.6 品?
NO 3.5 3.6 3.7 4 4.1 4.2 4.3 4.4 4.5 5 5.1 5.2 5.3 5.4 5.5 5.6 5.7 5.8 5.9
审核项目
特殊岗位,如司机、电工、内审员等持证上岗? 是否制定员工的激励政策? 是否制定应急计划?如供应中断、劳动力短缺、 关键设备故障等 合同评审 是否有文件规定顾客合同评审要求? 是否识别顾客的特殊特性和特殊要求,并进行传 达? 供应商是否确认,当产品要求被改变,组织应确 保相关文件已被修订,且变更的要求知会相关人 员? 对客户提供的图纸有无经评审并转化为自已的图 纸?客户的要求转化为内部要求? 客户资料和项目资料是否保存安全? 工程技术 供方是否具备设计开发的能力? 建立设计开发过程的管理文件,如APQP? 设计和开发过程的每个阶段都有进行评审,并保 持记录? 新产品开发有作FMEA分析?(DFMEA,PFMEA)或 建立失效模式分析的方法? 设计过程的变更有经过再评审,并通知到相关人 员处? 如变更涉及到客户,是否有取得客户同意后才执 行变更?是否有客户书面确认的记录? 产品量产前是否已制定出工艺流程图,QC工程图 或控制计划? 产品量产前制程是否对重要性能或参数做CPK? 产品量产前是否进行小批量试产或试模,并对试 产过程中的不良率进行统计、分析、验证,用来 分析和改善过程。
审核结果(证据/资料)
符合 (是1分,否0分) 1 1 1 1 1 1 1 1 1 1
6.1 6.2 6.3 6.4 6.5 6.6 6.7 6.8 6.9
6.10 件,并得到充分验证? 7 7.1 7.2 7.3 7.4 7.5 7.6 7.7 7.8 7.9
1 0 1 1 1 1 1 1 1
3
NO
审核结果(证据/资料)
符合 (是1分,否0分) 1 1 1 1 1
10.1 仓库是否整齐有序?实物与标签上的内容一致? 10.2 仓库存储环境符合产品特性要求? 10.3 否按照先进先出的原则发放使用? 10.4 整性和可追溯性?
原材料是否可以追溯到材质证明或检验记录?是
1 1 1 1 1
整个制程中,批标识是否得到保持以保证批的完
审核结果(证据/资料)
符合 (是1分,否0分) 0 1 0
1 1 1 1 1 1 1 1 1 1 1 1 1 1 1 1 0
5.10 样品出给客户前是否经过检验并保存检验记录? 5.11 产品量产前是否有得到客户的批准? 5.12 向客户提供PPAP资料? 6
采购与进料检验控制
2
NO
审核项目
是否有供应商管理规定?有选择供应商的流程或 新供应商的选择标准是否明确?(调查、评审、 资质等) 是否有合格供方名录?是否有合格供方再次评审 的机制?如交货及时率、进料合格率等 定期对供方进行评审,保存评审记录? 是否有制定供应商或外包商的审核计划? 是否按计划实施审核,保持审核记录?审核问题 点有做改善确认? 是否有进料检验作业指导书?原料检验标准? 原材料检验合格后才入库按排生产? 特采的原材料是有明确标识?以便发现不合格时 立即召回? 是否有不合格原材料的处置流程?(隔离、标识 、反馈供方整改、加严检验) 新材料是否要求供方提交PPAP?或样品承认文 制程控制 生产现场是否有生产产品所必须的信息?如工程 规范、工艺流程图、PFMEA、CP、操作作业指导 书等。 操作员及验验员都有持证上岗?各工序操作员都 熟悉该工位? 每个工位是否都有最新版本的作业指导书?以确 保每个员工都能正确操作? 制程是否定义关键过程,并对关健过程实行SPC 管制? 操作员是否按照作业指导书或CP的要求,进行首 件确认? 操作员是否对生产过程的主要参数进行监控,并 作记录?如温度、压力等。 制程中的原材料、半成品、成品是否明确标识且 可追溯?防护符合要求? 制程中对于特殊材料或溶济存储是否依据其本身 的特性或安全进行特定管制和防护? 有过程检验作业指导书或CP?
审核员:
审核日期: 审核结果(证据/资料)
编号: XMXD-GCSH-001 符合 (是1分,否0分) 是 否
1.2 1.3 1.4
1 1 1
1.5 1.6 1.7 2 2.1 2.2 2.3 2.4 2.5 2.6 3 3.1 3.2 3.3 3.4
1 1 1
1否可追溯到前一批检测的产
5
NO
审核项目
审核结果(证据/资料)
符合 (是1分,否0分) 1
12.7 是否有对检测设备的主要特性定期做MSA分析? 13
设备保养
13.1 是否有设备、工装的一览表? 13.2 是否有设备的保养、操作作业指导书? 13.3 按要求进行保养,并保存记录? 13.4 是否有易损件清单,并备有必要的易损件?
1 1 1 1 1
8.6 8.7 9
1 1
4
NO 9.1 9.2 9.3 9.4 9.5 10
审核项目
是否建立不合格品控制文件? 规定让步接收/放行的批准权限? 不合格品的标识、隔离、处置符合文件要求? (包括进料、制程中、成品、客退品等) 有运用QC七大手法等对不合格的根本原因进行分 析? 查各阶段不合格品处理的记录,是否得到有效跟 进与改善?(进料检验不良记录、制程不良记录 、成品不良记录、客诉记录等) 重点审核! 仓库、标识与可追溯性
审核项目
PQC按照作业指导书或CP要求,进行巡检,并保
审核结果(证据/资料)
符合 (是1分,否0分) 1 1 1 1 1 1 0 1 1 1 1 1
7.10 存记录?
7.11 制程中的不合格品有明确标识、隔离? 7.12 有制程出现异常的处理流程?谁有权停线待命? 7.13 取纠正预防措施?
有对制程中的不合格品进行根本原因分析,并采
7.14 过程变更是否受控并文件化? 7.15 是否有文件化的返工/挑选程序? 7.16 度、防尘要求? 7.17 命、编号等) 7.18
生产现场的环境符合生产产品的要求?温度、湿 是否制定模具管理文件?(模具储存、修复、寿 模具寿命、五金冲压寿命是否进行评估?并定期 更新寿命记录、达到寿命时及时处理?(模具寿 命评估值、模具使用次数记录)
10.5 是否有不合格品的隔离区域? 11
纠正预防措施
11.1 是否建立纠正预防措施管理文件? 11.2
目标未达标,内/外审不符合,制程的不符合, 客户投诉是否进行根本原因分析,并制定纠正预 防措施;重点审核!
1 1 1 1
11.3 预防措施有进行验证? 11.4 训? 12
确认措施可行时,是否修订相关文件,并进行培 量具管理
7.19 是否建立模具履历卡,记录修模、维修状况? 7.20 保存记录?
修模或维修后的模具,是否有进行首件确认,并 对客户提供的模具进行修模或报废,是否得到客
7.21 户同意,有书面确认? 8 8.1 8.2 8.3 8.4 8.5
成品检验
有成品检验作业指导书?成品检验标准?(明确 检验项目、判定、抽样方法) 检验员是否知道汉纳森产品的品质要求? 出货检验报告是否批准后才被放行?并保存记 录? 出货检验不合格时,出货检验记录是否有相关处 理过程记录? 是否有制定定期可靠性验证计划,并依计划实 施,以确认产品在客户端的品质及减少隐患性风 险? 不合格品在交货后或开始使用后才被发现,供方 对不符合的影响或潜在影响是否有采取适当的措 施? 让步放行的产品是否有经过客户批准? 不合格品控制