最新喷雾干燥优缺点整理
喷雾干燥原理及过程

喷雾干燥原理及过程
喷雾干燥是一种常用的干燥技术,其原理是将待干燥的液体物料通过雾化器分散成微小的雾滴,然后在高温下快速干燥。
该技术适用于大量液体的处理,常用于食品、药品和化工等行业。
喷雾干燥的过程主要包括以下步骤:
1. 液体物料通过管道进入雾化器,雾化器将其分散成微小的雾滴。
雾滴的大小和形状取决于雾化器的类型和操作条件。
2. 雾滴进入干燥塔,与热空气接触。
热空气将雾滴中的水分迅速蒸发,使雾滴变成干燥的固体颗粒。
3. 干燥后的颗粒通过重力或气力收集器收集,经过进一步处理后得到最终产品。
喷雾干燥的优点包括:
1. 处理量大,适用于大量液体的干燥。
2. 干燥速度快,可以在短时间内完成大量液体的干燥。
3. 干燥后的产品具有良好的分散性和流动性。
4. 可以根据需要调整产品的粒度和形状。
然而,喷雾干燥也存在一些缺点:
1. 干燥过程中需要消耗大量的热能,因此能耗较高。
2. 如果液体物料中含有易挥发成分,这些成分可能会在高温下挥发损失。
3. 干燥后的产品中可能会残留一些未挥发的溶剂或有害物质,
需要进行后续处理。
喷雾干燥与其他干燥方法比较具有许多的优点
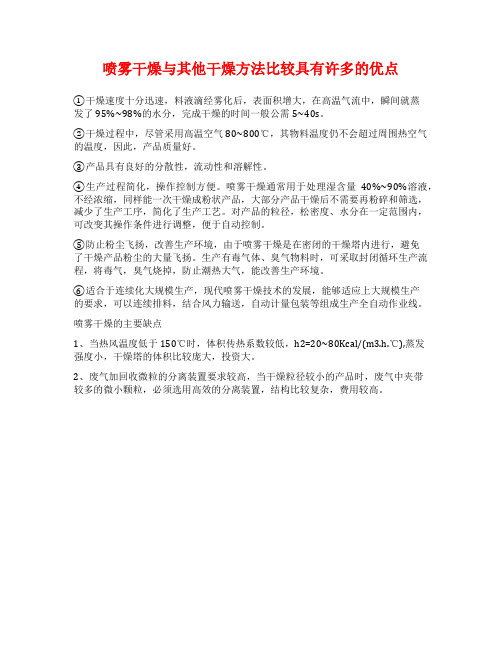
喷雾干燥与其他干燥方法比较具有许多的优点
①干燥速度十分迅速,料液滴经雾化后,表面积增大,在高温气流中,瞬间就蒸
发了95%~98%的水分,完成干燥的时间一般公需5~40s。
②干燥过程中,尽管采用高温空气80~800℃,其物料温度仍不会超过周围热空气的温度,因此,产品质量好。
③产品具有良好的分散性,流动性和溶解性。
④生产过程简化,操作控制方便。
喷雾干燥通常用于处理湿含量40%~90%溶液,不经浓缩,同样能一次干燥成粉状产品,大部分产品干燥后不需要再粉碎和筛选,减少了生产工序,简化了生产工艺。
对产品的粒径,松密度、水分在一定范围内,可改变其操作条件进行调整,便于自动控制。
⑤防止粉尘飞扬,改善生产环境,由于喷雾干燥是在密闭的干燥塔内进行,避免
了干燥产品粉尘的大量飞扬。
生产有毒气体、臭气物料时,可采取封闭循环生产流程,将毒气,臭气烧掉,防止潮热大气,能改善生产环境。
⑥适合于连续化大规模生产,现代喷雾干燥技术的发展,能够适应上大规模生产
的要求,可以连续排料,结合风力输送,自动计量包装等组成生产全自动作业线。
喷雾干燥的主要缺点
1、当热风温度低于150℃时,体积传热系数较低,h2=20~80Kcal/(m3.h.℃),蒸发
强度小,干燥塔的体积比较庞大,投资大。
2、废气加回收微粒的分离装置要求较高,当干燥粒径较小的产品时,废气中夹带
较多的微小颗粒,必须选用高效的分离装置,结构比较复杂,费用较高。
喷雾干燥技术总结
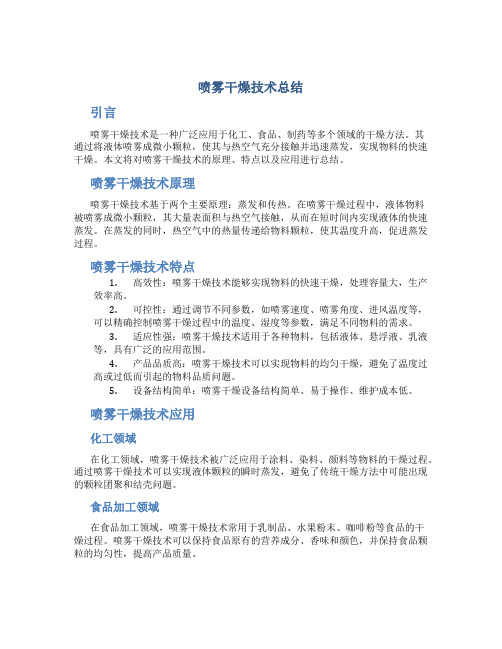
喷雾干燥技术总结引言喷雾干燥技术是一种广泛应用于化工、食品、制药等多个领域的干燥方法。
其通过将液体喷雾成微小颗粒,使其与热空气充分接触并迅速蒸发,实现物料的快速干燥。
本文将对喷雾干燥技术的原理、特点以及应用进行总结。
喷雾干燥技术原理喷雾干燥技术基于两个主要原理:蒸发和传热。
在喷雾干燥过程中,液体物料被喷雾成微小颗粒,其大量表面积与热空气接触,从而在短时间内实现液体的快速蒸发。
在蒸发的同时,热空气中的热量传递给物料颗粒,使其温度升高,促进蒸发过程。
喷雾干燥技术特点1.高效性:喷雾干燥技术能够实现物料的快速干燥,处理容量大,生产效率高。
2.可控性:通过调节不同参数,如喷雾速度、喷雾角度、进风温度等,可以精确控制喷雾干燥过程中的温度、湿度等参数,满足不同物料的需求。
3.适应性强:喷雾干燥技术适用于各种物料,包括液体、悬浮液、乳液等,具有广泛的应用范围。
4.产品品质高:喷雾干燥技术可以实现物料的均匀干燥,避免了温度过高或过低而引起的物料品质问题。
5.设备结构简单:喷雾干燥设备结构简单、易于操作、维护成本低。
喷雾干燥技术应用化工领域在化工领域,喷雾干燥技术被广泛应用于涂料、染料、颜料等物料的干燥过程。
通过喷雾干燥技术可以实现液体颗粒的瞬时蒸发,避免了传统干燥方法中可能出现的颗粒团聚和结壳问题。
食品加工领域在食品加工领域,喷雾干燥技术常用于乳制品、水果粉末、咖啡粉等食品的干燥过程。
喷雾干燥技术可以保持食品原有的营养成分、香味和颜色,并保持食品颗粒的均匀性,提高产品质量。
制药领域在制药领域,喷雾干燥技术被广泛应用于制造颗粒药物、药物包衣等工艺过程中。
通过喷雾干燥技术可以实现药物的快速干燥,并保持药物颗粒的均匀性和稳定性,提高药物的吸收率和生物利用度。
喷雾干燥技术的发展趋势随着科技的不断进步,喷雾干燥技术也得到了不断的发展和改进。
未来,喷雾干燥技术的发展趋势主要包括以下几个方面: 1. 提高干燥效率:通过改进喷雾器的结构和喷雾参数的调节,提高干燥效率,缩短干燥时间。
喷雾干燥的原理
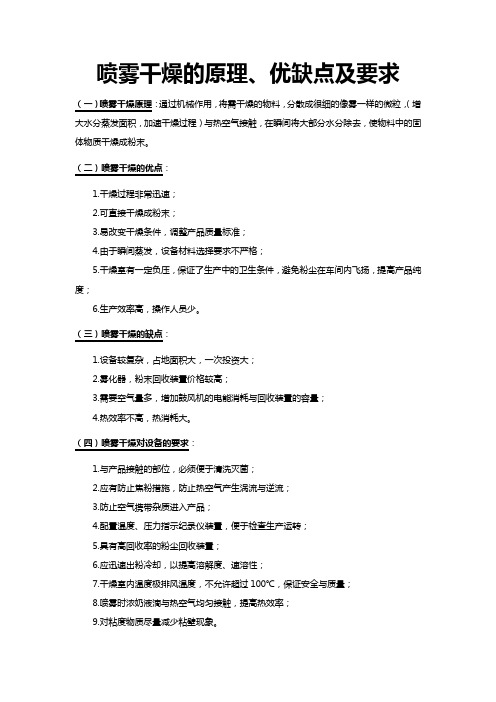
喷雾干燥的原理、优缺点及要求(一)喷雾干燥原理:通过机械作用,将需干燥的物料,分散成很细的像雾一样的微粒,(增大水分蒸发面积,加速干燥过程)与热空气接触,在瞬间将大部分水分除去,使物料中的固体物质干燥成粉末。
(二)喷雾干燥的优点:
1.干燥过程非常迅速;
2.可直接干燥成粉末;
3.易改变干燥条件,调整产品质量标准;
4.由于瞬间蒸发,设备材料选择要求不严格;
5.干燥室有一定负压,保证了生产中的卫生条件,避免粉尘在车间内飞扬,提高产品纯度;
6.生产效率高,操作人员少。
(三)喷雾干燥的缺点:
1.设备较复杂,占地面积大,一次投资大;
2.雾化器,粉末回收装置价格较高;
3.需要空气量多,增加鼓风机的电能消耗与回收装置的容量;
4.热效率不高,热消耗大。
(四)喷雾干燥对设备的要求:
1.与产品接触的部位,必须便于清洗灭菌;
2.应有防止焦粉措施,防止热空气产生涡流与逆流;
3.防止空气携带杂质进入产品;
4.配置温度、压力指示纪录仪装置,便于检查生产运转;
5.具有高回收率的粉尘回收装置;
6.应迅速出粉冷却,以提高溶解度、速溶性;
7.干燥室内温度极排风温度,不允许超过100℃,保证安全与质量;
8.喷雾时浓奶液滴与热空气均匀接触,提高热效率;
9.对粘度物质尽量减少粘壁现象。
干喷和湿喷工艺的优缺点
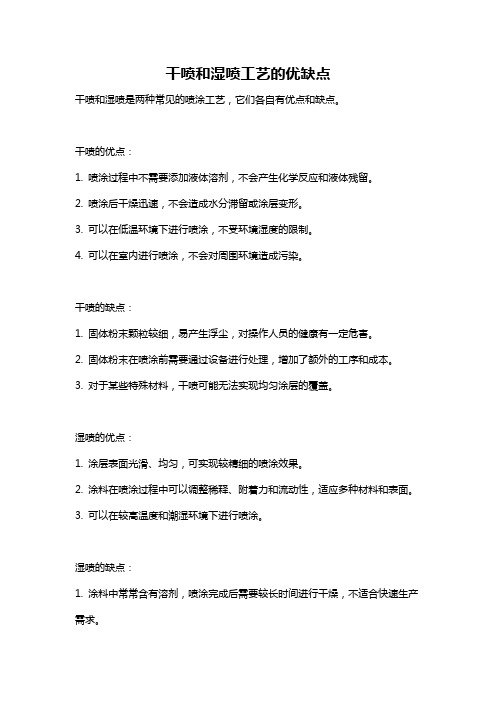
干喷和湿喷工艺的优缺点
干喷和湿喷是两种常见的喷涂工艺,它们各自有优点和缺点。
干喷的优点:
1. 喷涂过程中不需要添加液体溶剂,不会产生化学反应和液体残留。
2. 喷涂后干燥迅速,不会造成水分滞留或涂层变形。
3. 可以在低温环境下进行喷涂,不受环境湿度的限制。
4. 可以在室内进行喷涂,不会对周围环境造成污染。
干喷的缺点:
1. 固体粉末颗粒较细,易产生浮尘,对操作人员的健康有一定危害。
2. 固体粉末在喷涂前需要通过设备进行处理,增加了额外的工序和成本。
3. 对于某些特殊材料,干喷可能无法实现均匀涂层的覆盖。
湿喷的优点:
1. 涂层表面光滑、均匀,可实现较精细的喷涂效果。
2. 涂料在喷涂过程中可以调整稀释、附着力和流动性,适应多种材料和表面。
3. 可以在较高温度和潮湿环境下进行喷涂。
湿喷的缺点:
1. 涂料中常常含有溶剂,喷涂完成后需要较长时间进行干燥,不适合快速生产需求。
2. 喷涂过程中对周围环境有一定的污染风险,对操作人员的健康可能有一定危害。
3. 不适合用于涂饰较小的工件,由于涂料流动性较大,容易造成过度喷涂和浪费。
压力喷雾干燥和离心喷雾干燥

压力喷雾干燥和离心喷雾干燥一、压力喷雾干燥压力喷雾干燥是一种将液态物质通过喷嘴喷雾成小颗粒,并在高温高压的环境下快速蒸发的干燥方法。
其原理是通过将液体物料喷入干燥室,利用压缩空气将液滴雾化为微小颗粒,然后在干燥室中通过加热和通风使其迅速蒸发,最终得到干燥的粉末。
压力喷雾干燥具有以下优点:1. 干燥速度快:喷雾成小颗粒后,表面积大大增加,利于蒸发,从而实现快速干燥。
2. 适用范围广:适用于多种物料的干燥,包括液体、悬浮液、乳液等。
3. 干燥后的粉末颗粒均匀:喷雾干燥可获得均匀的颗粒尺寸,有利于产品的质量控制。
然而,压力喷雾干燥也存在一些缺点:1. 能耗较高:由于需要加热和通风,所以能耗相对较高。
2. 设备复杂:压力喷雾干燥设备需要具备喷雾、加热、通风等多种功能,设备复杂,维护成本较高。
二、离心喷雾干燥离心喷雾干燥是一种将液态物质通过离心力将其喷雾成小颗粒,并在高速旋转的离心机内迅速蒸发的干燥方法。
其原理是通过离心机的高速旋转将液体物料喷入旋转碟中,使其受到离心力的作用从而形成液滴雾化,然后在高温环境下迅速蒸发,最终得到干燥的粉末。
离心喷雾干燥具有以下优点:1. 干燥效果好:由于离心力的作用,液滴雾化更加均匀,干燥效果更好。
2. 适用范围广:适用于多种物料的干燥,包括液体、悬浮液、乳液等。
3. 设备相对简单:相比压力喷雾干燥,离心喷雾干燥设备相对简单,维护成本较低。
然而,离心喷雾干燥也存在一些缺点:1. 干燥速度较慢:相比压力喷雾干燥,离心喷雾干燥的干燥速度相对较慢。
2. 粉末颗粒不够均匀:由于离心力的作用,离心喷雾干燥得到的粉末颗粒尺寸分布相对不均匀。
压力喷雾干燥和离心喷雾干燥都是常见的干燥方法,各有优缺点。
在选择干燥方法时,需要根据物料的性质、干燥要求以及设备投资等方面进行综合考虑。
希望本文对读者有所帮助,增加对这两种干燥方法的了解。
超声喷雾干燥

超声喷雾干燥
超声喷雾干燥(Ultrasonic Spray Drying)是一种利用超声波产生的微小气泡将液体喷雾成微粒,然后通过干燥过程将其转化为粉末的技术。
这种技术通常用于制备粉末状的颗粒,例如在药物制剂、食品工业、化妆品等领域中。
超声喷雾干燥的基本原理是利用超声波产生的微小气泡将液体分散成微小颗粒,并将其喷雾到干燥室中。
在干燥室中,利用热气流或其他干燥方法将这些微粒进行干燥,从而得到粉末状的产物。
与传统的喷雾干燥技术相比,超声喷雾干燥具有以下优点:
1. 粒径均匀:利用超声波产生的微小气泡可以使液体喷雾成微粒,粒径分布较为均匀。
2. 保留活性成分:由于干燥过程中温度较低,可以有效保留颗粒中的活性成分,适用于制备药物、生物制品等需要保持活性的颗粒。
3. 高效节能:超声喷雾干燥过程中,喷雾和干燥同时进行,节省了能源和时间。
4. 操作简便:设备结构相对简单,操作方便,适用于规模较小的实验室和中小规模生产。
超声喷雾干燥技术在制备微粒状颗粒方面具有广泛的应用前景,尤其在制药、食品、化妆品等领域具有重要的意义。
离心喷雾干燥机的优缺点与使用时的检查
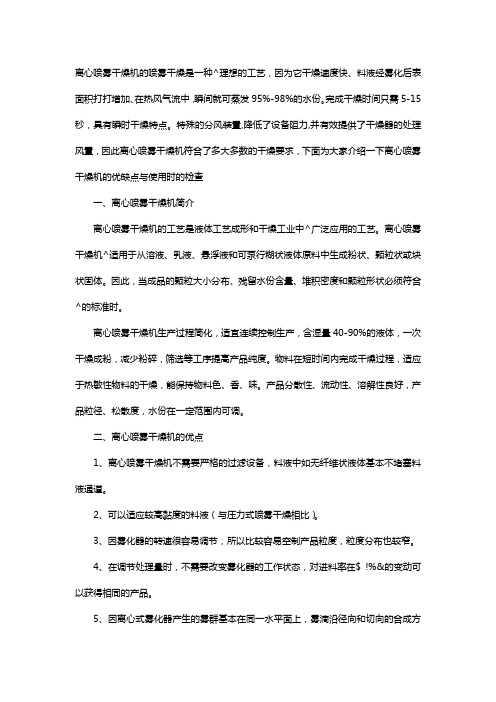
离心喷雾干燥机的喷雾干燥是一种^理想的工艺,因为它干燥速度快、料液经雾化后表面积打打增加、在热风气流中,瞬间就可蒸发95%-98%的水份。
完成干燥时间只需5-15秒,具有瞬时干燥特点。
特殊的分风装置,降低了设备阻力,并有效提供了干燥器的处理风置,因此离心喷雾干燥机符合了多大多数的干燥要求,下面为大家介绍一下离心喷雾干燥机的优缺点与使用时的检查一、离心喷雾干燥机简介离心喷雾干燥机的工艺是液体工艺成形和干燥工业中^广泛应用的工艺。
离心喷雾干燥机^适用于从溶液、乳液、悬浮液和可泵行糊状液体原料中生成粉状、颗粒状或块状固体。
因此,当成品的颗粒大小分布、残留水份含量、堆积密度和颗粒形状必须符合^的标准时。
离心喷雾干燥机生产过程简化,适宜连续控制生产,含湿量40-90%的液体,一次干燥成粉,减少粉碎,筛选等工序提高产品纯度。
物料在短时间内完成干燥过程,适应于热敏性物料的干燥,能保持物料色、香、味。
产品分散性、流动性、溶解性良好,产品粒径、松散度,水份在一定范围内可调。
二、离心喷雾干燥机的优点1、离心喷雾干燥机不需要严格的过滤设备,料液中如无纤维状液体基本不堵塞料液通道。
2、可以适应较高黏度的料液(与压力式喷雾干燥相比)。
3、因雾化器的转速很容易调节,所以比较容易空制产品粒度,粒度分布也较窄。
4、在调节处理量时,不需要改变雾化器的工作状态,对进料率在$ !%&的变动可以获得相同的产品。
5、因离心式雾化器产生的雾群基本在同一水平面上,雾滴沿径向和切向的合成方向运动,几乎没有轴向的初速度,所以干燥器的直径相对较大。
径、长比较小,可以^大限度地利用干燥室的空间。
三、离心喷雾干燥机的缺点1、离心喷雾干燥机当料液的进料量较少时,料液受离心力作用,迅速向分散盘的边缘移动,分散盘周边上隆起半球状液体环,形状取决于料液的粘度、表面张力、离心力及分散盘的形状和光滑程度。
当离心力大于表面张力时,分散盘边缘的球状液滴立即被抛出而分裂雾化,液滴中伴随有少量大液滴。
- 1、下载文档前请自行甄别文档内容的完整性,平台不提供额外的编辑、内容补充、找答案等附加服务。
- 2、"仅部分预览"的文档,不可在线预览部分如存在完整性等问题,可反馈申请退款(可完整预览的文档不适用该条件!)。
- 3、如文档侵犯您的权益,请联系客服反馈,我们会尽快为您处理(人工客服工作时间:9:00-18:30)。
对喷雾干燥的过程阶段及优缺点进行了分析, 综述了喷雾干燥技术的研究进展, 并对喷雾干燥技术的应用前景进行了分析, 最后给出了喷雾干燥技术在中药制药生产中的应用实例——中药液一步喷雾干燥造粒。
该项技术将中药稀药液直接喷雾干燥制成干颗粒, 将中药加工中药液的浓缩、多效浓缩、造粒、干燥四步合为一步, 大大简化并缩短了中药提取液到半成品或成品的工艺和时间, 提高了生产效率和产品质量。
可为喷雾干燥技术的推广应用以及提高中药制药水平提供借鉴与帮助。
关键词喷雾干燥雾化技术喷雾造粒中药制药一步造粒喷雾干燥是将原料液用雾化器分散成雾滴, 并用热空气(或其它气体) 与雾滴直接接触的方式而获得粉粒状产品的一种干燥过程。
原料液可以是溶液、乳浊液或悬浮液, 也可以是熔融液或膏状物。
干燥产品可以根据需要, 制成粉状、颗粒状、空心球状或团粒状。
喷雾干燥技术已有一百多年的历史。
自1865 年喷雾干燥最早用于蛋品处理以来, 这种由液态经雾化和干燥在极短时间直接变为固体粉末的过程, 已经取得了长足的进步。
它使许多有价值但不易保存的物料得以大大延长保质期, 使一些物料便于包装、使用和运输, 同时也简化了一些物料的加工工艺。
由于喷雾干燥具有“瞬时干燥”、“干燥产品质量好”、“干燥过程简单”等特点, 明显优于其它干燥方式, 到20 世纪三四十年代, 该技术已经被广泛地应用于乳制品、洗涤剂、脱水食品以及化肥、染料、水泥的生产, 目前常见的速溶咖啡、奶粉、方便食品汤料等就是由喷雾干燥得到的产品[ 1, 2 ]。
我国最早将喷雾干燥用于工业化规模生产的是乳品行业, 之后是洗涤剂和染料行业等, 目前应用已十分广泛, 遍及了以上所涉及的所有行业, 尤其在陶瓷和制药行业喷雾干燥的应用更为普遍。
对于中药制药行业, 喷雾干燥技术的应用有其独特的作用, 大大简化并缩短了中药提取液到制剂半成品或成品的工艺和时间, 提高了生产效率和产品质量。
本文对喷雾干燥的过程阶段及优缺点进行分析, 综述喷雾干燥技术的研究进展, 并对喷雾干燥技术的应用前景进行分析, 最后给出喷雾干燥技术在中药制药生产中的应用实例——中药液一步喷雾干燥造粒。
1 喷雾干燥的过程阶段及优缺点分析1.1 喷雾干燥的过程阶段喷雾干燥可分为三个基本过程阶段: 一是料液雾化成雾滴二是雾滴和干燥介质接触、混合及流动, 即进行干燥三是干燥产品与空气分离。
1.1.1 喷雾干燥的第一阶段——料液的雾化料液雾化为雾滴和雾滴与热空气的接触、混合, 是喷雾干燥独有的特征。
雾化的目的在于将料液分散成微细的雾滴, 使其具有很大的表面积, 当其与热空气接触时, 雾滴中水分迅速汽化而干燥成粉末或颗粒状产品。
雾滴的大小及其均匀程度对产品质量和技术经济指标影响很大, 特别是对热敏性物料的干燥尤为重要。
如果喷出的雾滴其大小很不均匀, 就会出现大颗粒还没达到干燥要求、小颗粒却已干燥过度而变质的现象。
因此料液雾化所用的雾化器是喷雾干燥的关键部件。
目前常用的雾化器有气流式、压力式、旋转式和声能雾化器等。
1.1.2 喷雾干燥的第二阶段——雾滴和空气的接触雾滴和空气的接触、混合及流动是同时进行的传热传质过程, 即干燥过程, 此过程在干燥塔内进行。
雾滴和空气的接触方式、混合与流动状态决定于热风分布器的结构型式、雾化器在塔内的安装位置及废气排出方式等。
在干燥塔内, 雾滴- 空气的流向有并流、逆流及混合流。
雾滴与空气的接触方式不同, 对干燥塔内的温度分布、雾滴(或颗粒) 的运动轨迹、颗粒在塔内的停留时间及产品性质等均有很大影响。
雾滴的干燥过程也经历着恒速和降速阶段。
研究雾滴的运动及干燥过程, 主要是确定干燥时间及干燥塔的主要尺寸。
1.1.3 喷雾干燥的第三阶段——干燥产品与空气分离喷雾干燥的产品大多采用塔底出料, 部分细粉夹带在排放的废气中, 废气在排放前必须将这些细粉收集下来, 以提高产品收率, 降低生产成本。
排放的废气必须符合环境保护的排放标准, 以防止环境污染。
1.2 喷雾干燥的优缺点分析1.2.1 喷雾干燥的优点只要干燥条件保持恒定, 干燥产品特性就保持恒定喷雾干燥的操作是连续的, 其系统可以是全自动控制操作喷雾干燥系统适用于热敏性和非热敏性物料的干燥, 适用于水溶液和有机溶剂物料的干燥原料液可以是溶液、泥浆、乳浊液、糊状物或熔融物, 甚至是滤饼等均可处理喷雾干燥操作具有非常大的灵活性,喷雾能力可达每小时几千克至200 吨[ 4 ]。
1.2.2 喷雾干燥的缺点喷雾干燥投资费用比较高喷雾干燥属于对流型干燥, 热效率比较低(除非利用非常高的干燥温度) ,一般为30%~ 40%。
2 喷雾干燥技术的研究进展喷雾干燥技术的核心是流化技术, 具有从流体到固体瞬时干燥的突出优势。
其设备一般是由雾化器(喷头) 、干燥塔、进出气及物料收集回收系统等组成。
其中使料液雾化所用的雾化器是喷雾干燥装置的关键部件。
2.1 雾化器的种类和雾化形式一般在生产中常用的雾化器有气流式雾化器、压力式雾化器和旋转式雾化器几种。
不同的雾化器可以产生不同的雾化形式, 按照不同的雾化形式可以将喷雾干燥分为气流式雾化、压力式雾化和旋转式雾化。
雾化形式的选择取决于料液的性质和最终产品所要求的特性。
对于液体的雾化机理, 基本上可分为三种类型, 即滴状分裂、丝状分裂和膜状分裂。
在喷雾干燥操作中, 雾化机理与雾化方法、操作条件、流体的物性等有关。
雾化机理可以指导我们进行合理的雾化器的设计和操作。
气流式雾化利用压缩空气(或水蒸气) 高速从喷嘴喷出并与另一通道输送的料液混合,借助空气(或水蒸气) 与料液两相间相对速度不同产生的摩擦力, 把料液分散成雾滴。
根据喷嘴的流体通道数及其布局, 气流式雾化器又可以分为二流体外混式、二流体内混式、三流体内混式、三流体内外混式以及四流体外混式、四流体二内一外混式等等[ 3 ]。
气流式雾化器的结构简单, 处理对象广泛, 但能耗大。
压力式雾化利用压力泵将料液从喷嘴孔内高压喷出, 直接将压力转化为动能, 使料液与干燥介质接触并被分散为雾滴。
压力式雾化器生产能力大, 耗能小细粉生成少, 能产生小颗粒, 固体物回收率高。
旋转式雾化利用高速旋转的盘或轮产生的离心力将料液甩出, 使之与干燥介质接触形成雾滴。
旋转式雾化器受进料影响(如压力) 变化小控制简单。
三种雾化器的比较见表1[ 3, 4, 5 ]。
三种雾化原理的理论研究, 主要围绕着喷雾器的关键参数与雾化性能而展开, 黄立新等[ 3 ]对此做了综述报道。
这方面的研究将有助于喷雾器性能的改进, 也有利于应用过程中根据喷雾料液及其产品要求对雾化器进行选择。
中药提取液的喷雾干燥, 基本上是以旋转式雾化和气流式雾化形式进行的, 而后者以小型试验设备多见。
从雾化的实现而言, 压力式雾化需要高压泵和较大的雾化空间, 气流式雾化能耗又很高, 这些都限制了它们的应用。
相对而言, 旋转式雾化器技术要求相对较低, 是最容易实现的。
2.2 喷雾干燥机理的研究影响喷雾干燥效果的因素很多, 除雾化器外, 还有干燥塔、进出气及物料收集回收系统以及整个干燥器系统。
国内外许多学者对喷雾干燥的数学模型进行了研究, 以期给出干燥塔内气体流动状态和各种热力学参数的分布信息, 这对喷雾干燥器的设计、优化以及干燥效果等的提高都具有很重要的意义。
吴中华等[ 6 ]应用气- 粒两相流理论和计算流体力学(CFD) , 结合喷雾干燥的特点, 建立了模拟喷雾干燥塔内气体- 颗粒两相湍流流动的CFD 模型, 并对实验室脉动燃烧喷雾干燥过程进行了数值模拟。
其结果具有详细、直观的特点模拟得到的喷雾干燥塔内气相流场和各种热力学参数的分布信息, 可以为喷雾干燥器的设计、干燥过程的优化等提供参考。
戴命和等[ 7 ]进行了喷雾干燥过程的热力学建模及仿真, 根据质量平衡原理、热平衡原理和牛顿定律推导了逆流喷雾干燥过程的一维双向静态热力学数学模型它包括了物料温度方程、热风温度方程、颗粒速度方程、热风湿含量方程、物料含水率方程, 用MA TLA 仿真后, 得到了增大空气量比提高空气温度更具技术经济性的结论。
2.3 喷雾工艺优化的研究在喷雾干燥的实验研究方面, 康智勇[ 8 ]研究了压力式喷雾干燥塔喷嘴孔径对粉料的影响, 认为大孔径更适于喷雾颗粒的分布向大颗粒集中。
王晓兰等[ 9 ]在工厂大生产的条件下研究了影响喷雾干燥粉粒粒度分布的因素, 分析了陶瓷坯料泥浆粘度、含水率、喷雾压力、喷雾器孔径与粉粒粒度分布之间的关系, 得出其影响系数由大至小分别为喷雾器孔径、压力、粘度、含水率等。
杨志生等[ 10 ]在对农药水分散性颗粒喷雾干燥过程的研究中, 分析了干燥进气温度、进料量对干燥产品的悬浮率、粒子密度、粒子形状等的影响。
喷雾干燥在越来越广泛的应用中, 已经不仅限于传统的干燥模式, 刘相东等[ 11 ]进行了脉动气流的喷雾干燥研究。
利用脉动燃烧产生的高频脉动气流对 aCl 溶液进行了喷雾干燥试验, 结果表明: 高温、高频振荡气流下的喷雾干燥比传统喷雾干燥的蒸发速率提高了 2.5倍。
2.4 喷雾干燥技术的发展趋势喷雾干燥技术应用广泛, 其优势明显, 但其理论仍然落后于实践, 突出表现在干燥理论的实践指导性差。
干燥动力学、非球形颗粒的干燥模拟、喷雾干燥等领域有待进行更深入的研究[ 3 ]。
喷雾干燥热效率低, 因此, 喷雾干燥的节能降耗问题就比较突出[ 1 ] 亚高温喷雾干燥(进风温度60~ 150 ℃) 、常温喷雾干燥(进风温度60℃以下) 、降低能耗与多级干燥等都将是今后的研究重点。
另外, 喷雾干燥技术与具体的应用领域结合还将用于喷雾冷却造型、喷雾反应、喷雾吸收、喷雾涂层和喷雾造粒等领域。
笔者认为, 在今后还应注意加强下述几方面的研究与开发。
(1) 采用组合干燥。
当喷雾干燥本身不能完成干燥任务时, 首先要想到组合干燥。
如喷雾干燥加流化床(干燥及冷却)、喷雾干燥加带式干燥等。
(2) 雾化器的改进。
当某种物料雾化很困难时, 可改进原有雾化器的结构, 以适应新物料的雾化要求。
例如, 对旋转雾化器已做了多种改进, 能够雾化粘性大的物料及喷雾造粒等。
(3) 静电雾化技术的研究与开发。
此项技术正处于研究与开发阶段, 它可以制造出微米及亚微米级粒子, 制造机能性粒子, 制造薄膜和喷涂等, 预测其将来有广阔的发展前景。
(4) 开发和完善在线测量系统。
使系统操作自动化, 确保产品的质量和产量。
(5) 开发过热蒸汽的喷雾干燥系统。
这是一个闭路循环系统, 可以节省能量, 省去氮气循环的操作。
(6) 利用计算流体力学(CFD) 的方法, 解决喷雾干燥器的设计问题。
将来可以利用一些可靠的实验数据(包括流动图形) , 利用CFD 的方法, 比较准确地算出干燥器尺寸及热风分布方式, 代替目前的半理论、半经验的方法(目前的方法误差太大)。